HI5017 Managerial Accounting: Standard and Target Costing Report
VerifiedAdded on 2022/08/26
|12
|3325
|27
Report
AI Summary
This report delves into the intricacies of standard and target costing methods within managerial accounting. It begins by defining standard costing, highlighting its features, and illustrating its significance through a case study on manufacturing cost analysis. The report then explores target costing, explaining its role in market-driven pricing and product innovation, supported by a case study on technological product innovation. A detailed comparison of the two costing systems is provided, emphasizing their differences in approach, application, and suitability for various organizational contexts. The report concludes with recommendations, summarizing the advantages and disadvantages of each method and suggesting optimal implementation strategies to enhance cost management and achieve business objectives. The analysis is based on research papers, offering practical insights for informed decision-making in modern organizations.
Contribute Materials
Your contribution can guide someone’s learning journey. Share your
documents today.
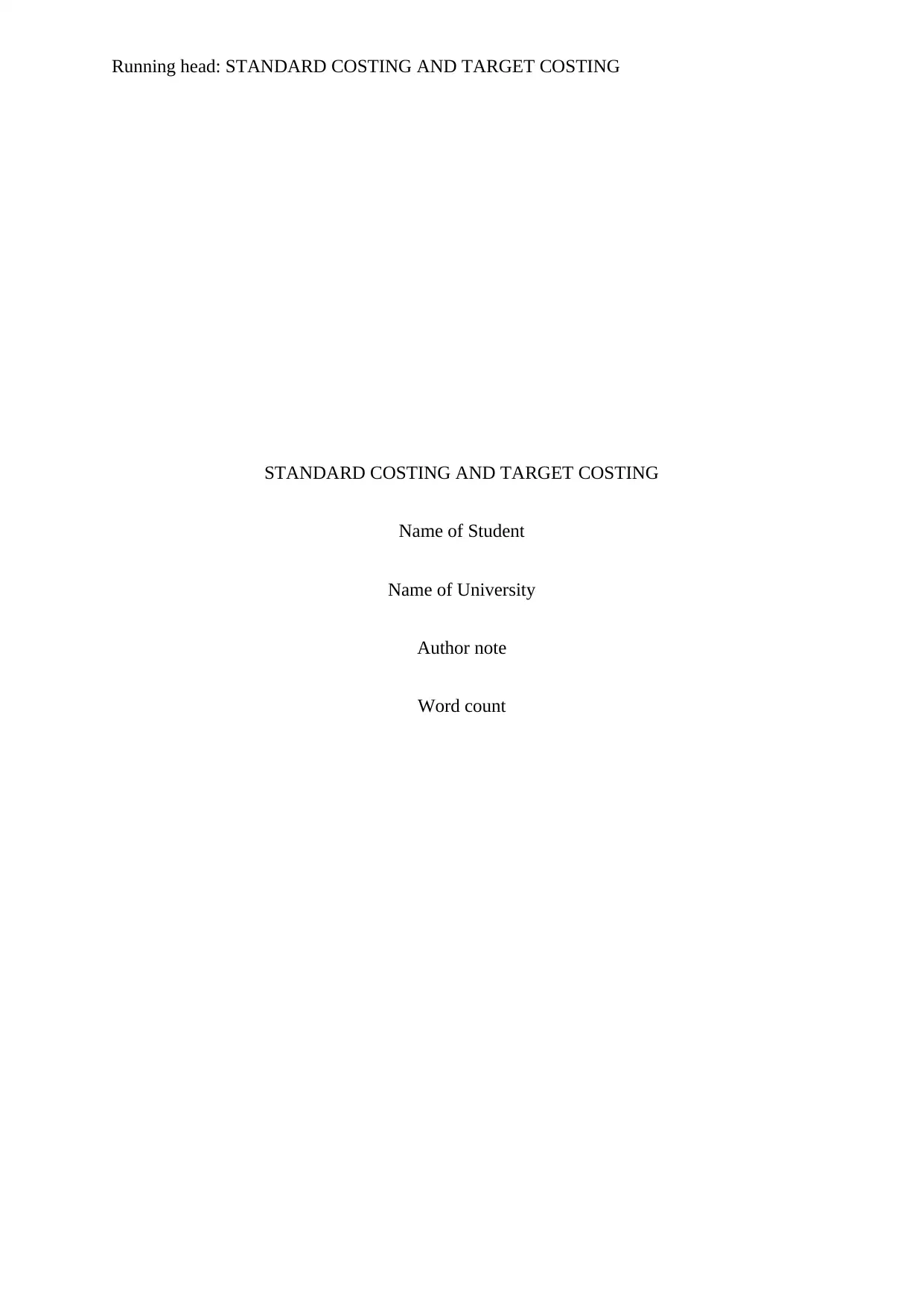
Running head: STANDARD COSTING AND TARGET COSTING
STANDARD COSTING AND TARGET COSTING
Name of Student
Name of University
Author note
Word count
STANDARD COSTING AND TARGET COSTING
Name of Student
Name of University
Author note
Word count
Secure Best Marks with AI Grader
Need help grading? Try our AI Grader for instant feedback on your assignments.
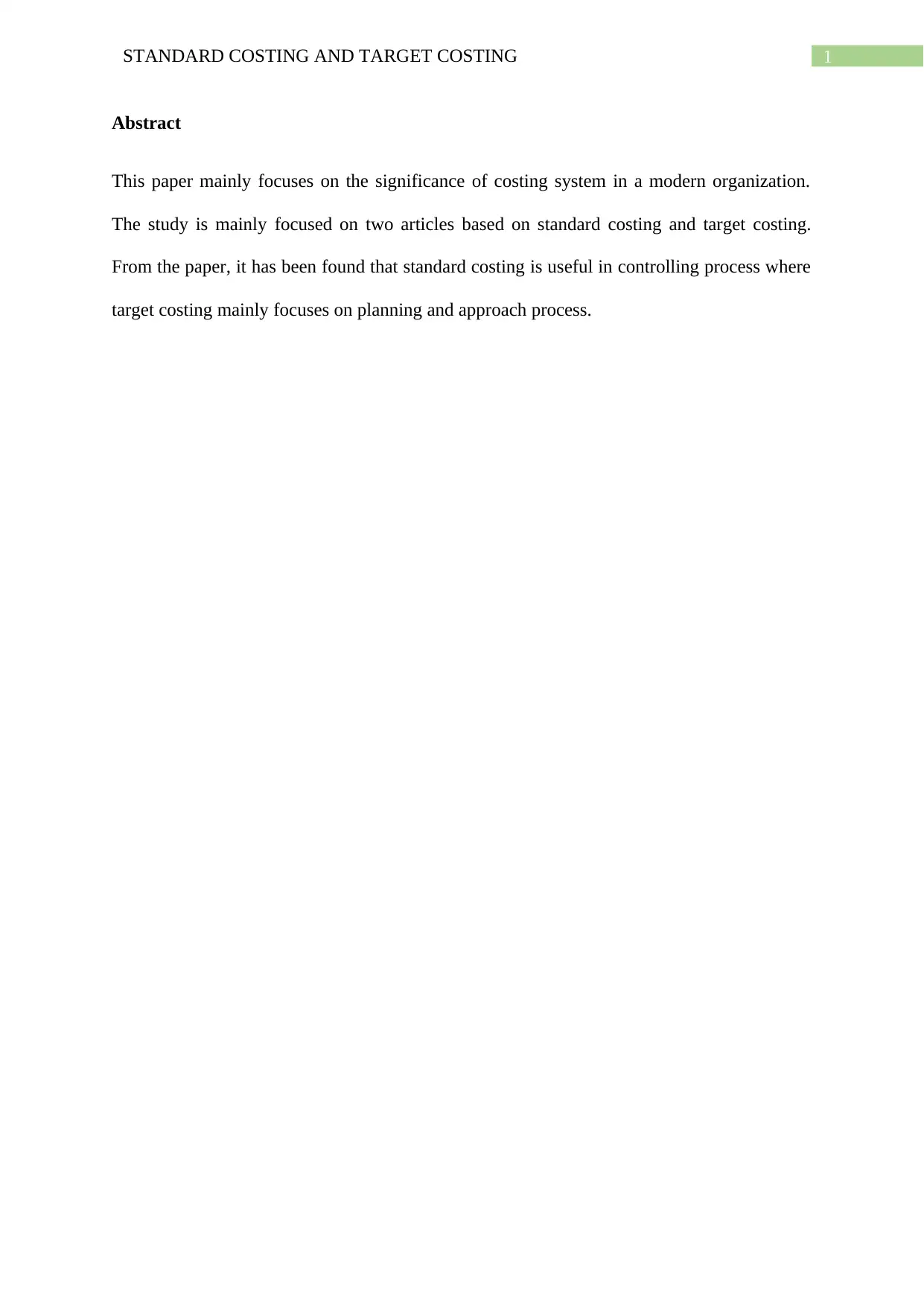
1STANDARD COSTING AND TARGET COSTING
Abstract
This paper mainly focuses on the significance of costing system in a modern organization.
The study is mainly focused on two articles based on standard costing and target costing.
From the paper, it has been found that standard costing is useful in controlling process where
target costing mainly focuses on planning and approach process.
Abstract
This paper mainly focuses on the significance of costing system in a modern organization.
The study is mainly focused on two articles based on standard costing and target costing.
From the paper, it has been found that standard costing is useful in controlling process where
target costing mainly focuses on planning and approach process.
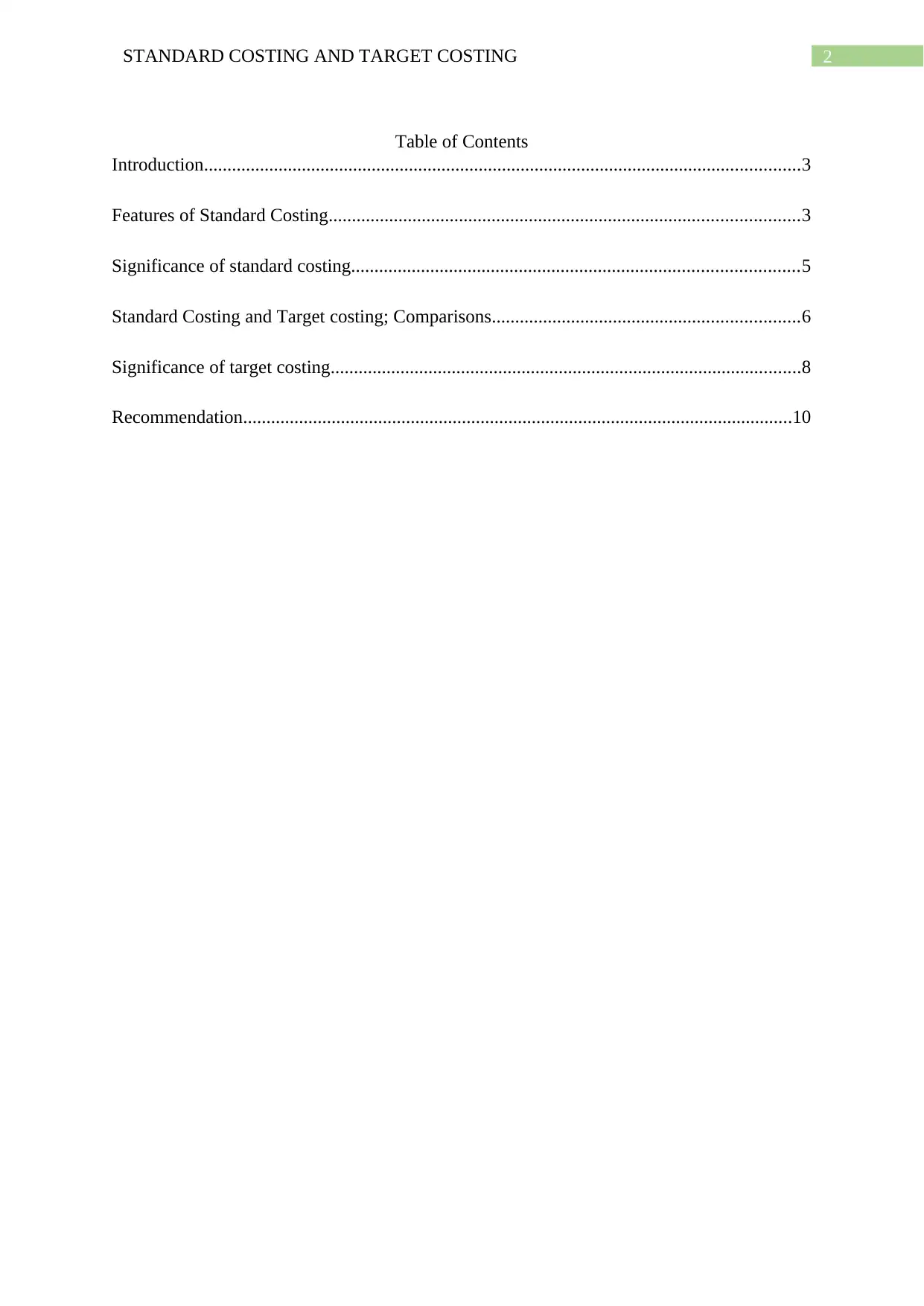
2STANDARD COSTING AND TARGET COSTING
Table of Contents
Introduction................................................................................................................................3
Features of Standard Costing.....................................................................................................3
Significance of standard costing................................................................................................5
Standard Costing and Target costing; Comparisons..................................................................6
Significance of target costing.....................................................................................................8
Recommendation......................................................................................................................10
Table of Contents
Introduction................................................................................................................................3
Features of Standard Costing.....................................................................................................3
Significance of standard costing................................................................................................5
Standard Costing and Target costing; Comparisons..................................................................6
Significance of target costing.....................................................................................................8
Recommendation......................................................................................................................10
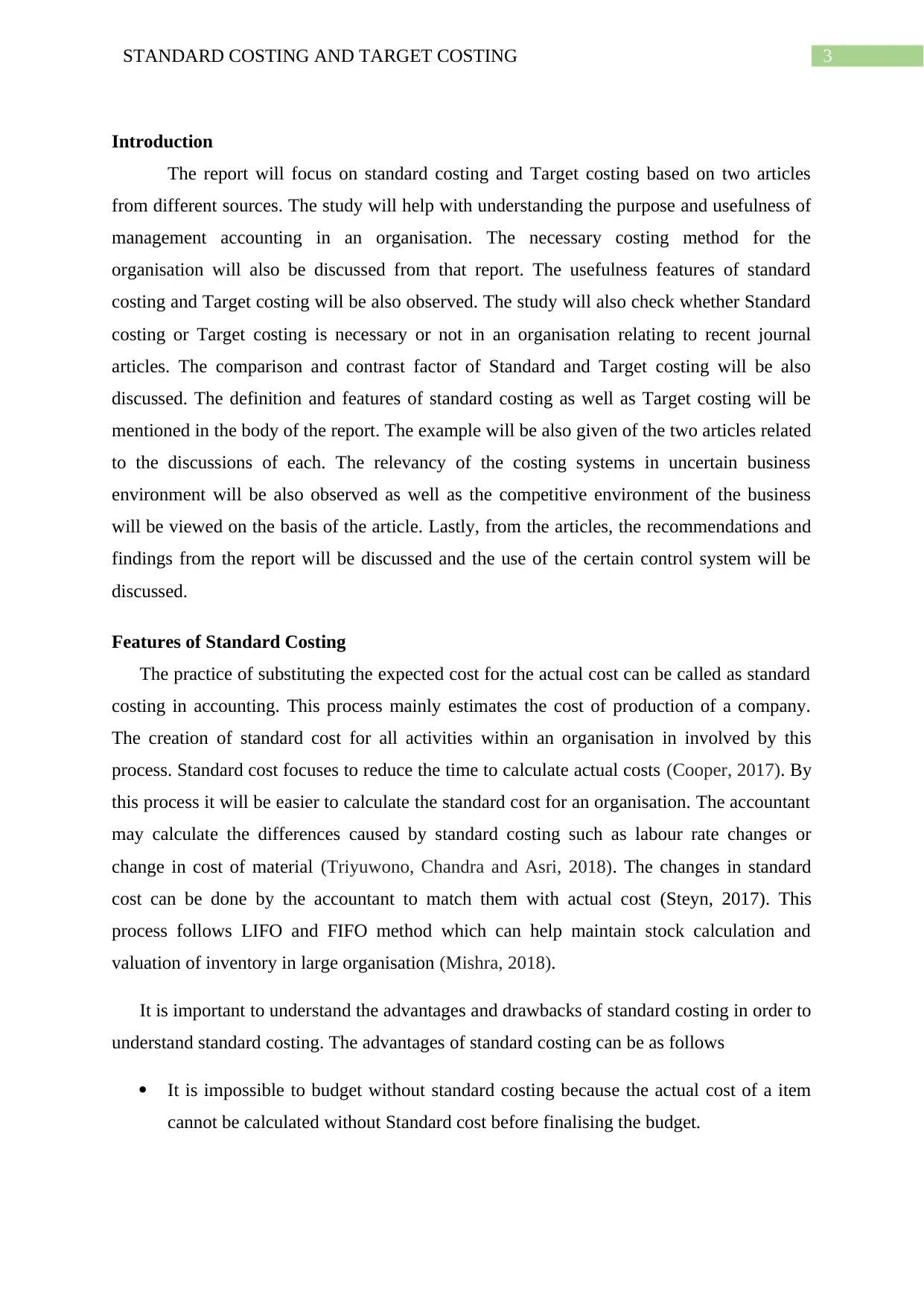
3STANDARD COSTING AND TARGET COSTING
Introduction
The report will focus on standard costing and Target costing based on two articles
from different sources. The study will help with understanding the purpose and usefulness of
management accounting in an organisation. The necessary costing method for the
organisation will also be discussed from that report. The usefulness features of standard
costing and Target costing will be also observed. The study will also check whether Standard
costing or Target costing is necessary or not in an organisation relating to recent journal
articles. The comparison and contrast factor of Standard and Target costing will be also
discussed. The definition and features of standard costing as well as Target costing will be
mentioned in the body of the report. The example will be also given of the two articles related
to the discussions of each. The relevancy of the costing systems in uncertain business
environment will be also observed as well as the competitive environment of the business
will be viewed on the basis of the article. Lastly, from the articles, the recommendations and
findings from the report will be discussed and the use of the certain control system will be
discussed.
Features of Standard Costing
The practice of substituting the expected cost for the actual cost can be called as standard
costing in accounting. This process mainly estimates the cost of production of a company.
The creation of standard cost for all activities within an organisation in involved by this
process. Standard cost focuses to reduce the time to calculate actual costs (Cooper, 2017). By
this process it will be easier to calculate the standard cost for an organisation. The accountant
may calculate the differences caused by standard costing such as labour rate changes or
change in cost of material (Triyuwono, Chandra and Asri, 2018). The changes in standard
cost can be done by the accountant to match them with actual cost (Steyn, 2017). This
process follows LIFO and FIFO method which can help maintain stock calculation and
valuation of inventory in large organisation (Mishra, 2018).
It is important to understand the advantages and drawbacks of standard costing in order to
understand standard costing. The advantages of standard costing can be as follows
It is impossible to budget without standard costing because the actual cost of a item
cannot be calculated without Standard cost before finalising the budget.
Introduction
The report will focus on standard costing and Target costing based on two articles
from different sources. The study will help with understanding the purpose and usefulness of
management accounting in an organisation. The necessary costing method for the
organisation will also be discussed from that report. The usefulness features of standard
costing and Target costing will be also observed. The study will also check whether Standard
costing or Target costing is necessary or not in an organisation relating to recent journal
articles. The comparison and contrast factor of Standard and Target costing will be also
discussed. The definition and features of standard costing as well as Target costing will be
mentioned in the body of the report. The example will be also given of the two articles related
to the discussions of each. The relevancy of the costing systems in uncertain business
environment will be also observed as well as the competitive environment of the business
will be viewed on the basis of the article. Lastly, from the articles, the recommendations and
findings from the report will be discussed and the use of the certain control system will be
discussed.
Features of Standard Costing
The practice of substituting the expected cost for the actual cost can be called as standard
costing in accounting. This process mainly estimates the cost of production of a company.
The creation of standard cost for all activities within an organisation in involved by this
process. Standard cost focuses to reduce the time to calculate actual costs (Cooper, 2017). By
this process it will be easier to calculate the standard cost for an organisation. The accountant
may calculate the differences caused by standard costing such as labour rate changes or
change in cost of material (Triyuwono, Chandra and Asri, 2018). The changes in standard
cost can be done by the accountant to match them with actual cost (Steyn, 2017). This
process follows LIFO and FIFO method which can help maintain stock calculation and
valuation of inventory in large organisation (Mishra, 2018).
It is important to understand the advantages and drawbacks of standard costing in order to
understand standard costing. The advantages of standard costing can be as follows
It is impossible to budget without standard costing because the actual cost of a item
cannot be calculated without Standard cost before finalising the budget.
Secure Best Marks with AI Grader
Need help grading? Try our AI Grader for instant feedback on your assignments.
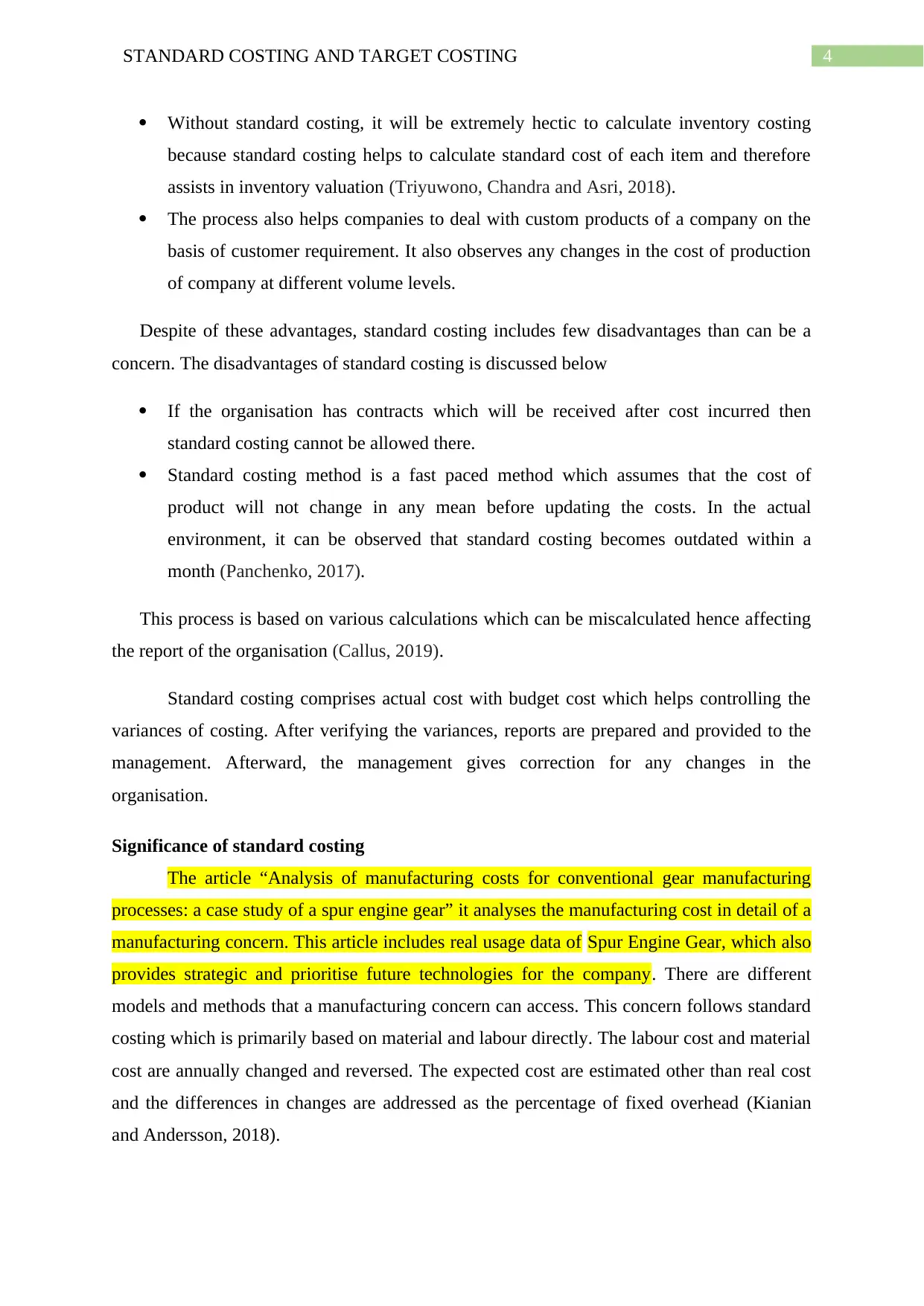
4STANDARD COSTING AND TARGET COSTING
Without standard costing, it will be extremely hectic to calculate inventory costing
because standard costing helps to calculate standard cost of each item and therefore
assists in inventory valuation (Triyuwono, Chandra and Asri, 2018).
The process also helps companies to deal with custom products of a company on the
basis of customer requirement. It also observes any changes in the cost of production
of company at different volume levels.
Despite of these advantages, standard costing includes few disadvantages than can be a
concern. The disadvantages of standard costing is discussed below
If the organisation has contracts which will be received after cost incurred then
standard costing cannot be allowed there.
Standard costing method is a fast paced method which assumes that the cost of
product will not change in any mean before updating the costs. In the actual
environment, it can be observed that standard costing becomes outdated within a
month (Panchenko, 2017).
This process is based on various calculations which can be miscalculated hence affecting
the report of the organisation (Callus, 2019).
Standard costing comprises actual cost with budget cost which helps controlling the
variances of costing. After verifying the variances, reports are prepared and provided to the
management. Afterward, the management gives correction for any changes in the
organisation.
Significance of standard costing
The article “Analysis of manufacturing costs for conventional gear manufacturing
processes: a case study of a spur engine gear” it analyses the manufacturing cost in detail of a
manufacturing concern. This article includes real usage data of Spur Engine Gear, which also
provides strategic and prioritise future technologies for the company. There are different
models and methods that a manufacturing concern can access. This concern follows standard
costing which is primarily based on material and labour directly. The labour cost and material
cost are annually changed and reversed. The expected cost are estimated other than real cost
and the differences in changes are addressed as the percentage of fixed overhead (Kianian
and Andersson, 2018).
Without standard costing, it will be extremely hectic to calculate inventory costing
because standard costing helps to calculate standard cost of each item and therefore
assists in inventory valuation (Triyuwono, Chandra and Asri, 2018).
The process also helps companies to deal with custom products of a company on the
basis of customer requirement. It also observes any changes in the cost of production
of company at different volume levels.
Despite of these advantages, standard costing includes few disadvantages than can be a
concern. The disadvantages of standard costing is discussed below
If the organisation has contracts which will be received after cost incurred then
standard costing cannot be allowed there.
Standard costing method is a fast paced method which assumes that the cost of
product will not change in any mean before updating the costs. In the actual
environment, it can be observed that standard costing becomes outdated within a
month (Panchenko, 2017).
This process is based on various calculations which can be miscalculated hence affecting
the report of the organisation (Callus, 2019).
Standard costing comprises actual cost with budget cost which helps controlling the
variances of costing. After verifying the variances, reports are prepared and provided to the
management. Afterward, the management gives correction for any changes in the
organisation.
Significance of standard costing
The article “Analysis of manufacturing costs for conventional gear manufacturing
processes: a case study of a spur engine gear” it analyses the manufacturing cost in detail of a
manufacturing concern. This article includes real usage data of Spur Engine Gear, which also
provides strategic and prioritise future technologies for the company. There are different
models and methods that a manufacturing concern can access. This concern follows standard
costing which is primarily based on material and labour directly. The labour cost and material
cost are annually changed and reversed. The expected cost are estimated other than real cost
and the differences in changes are addressed as the percentage of fixed overhead (Kianian
and Andersson, 2018).
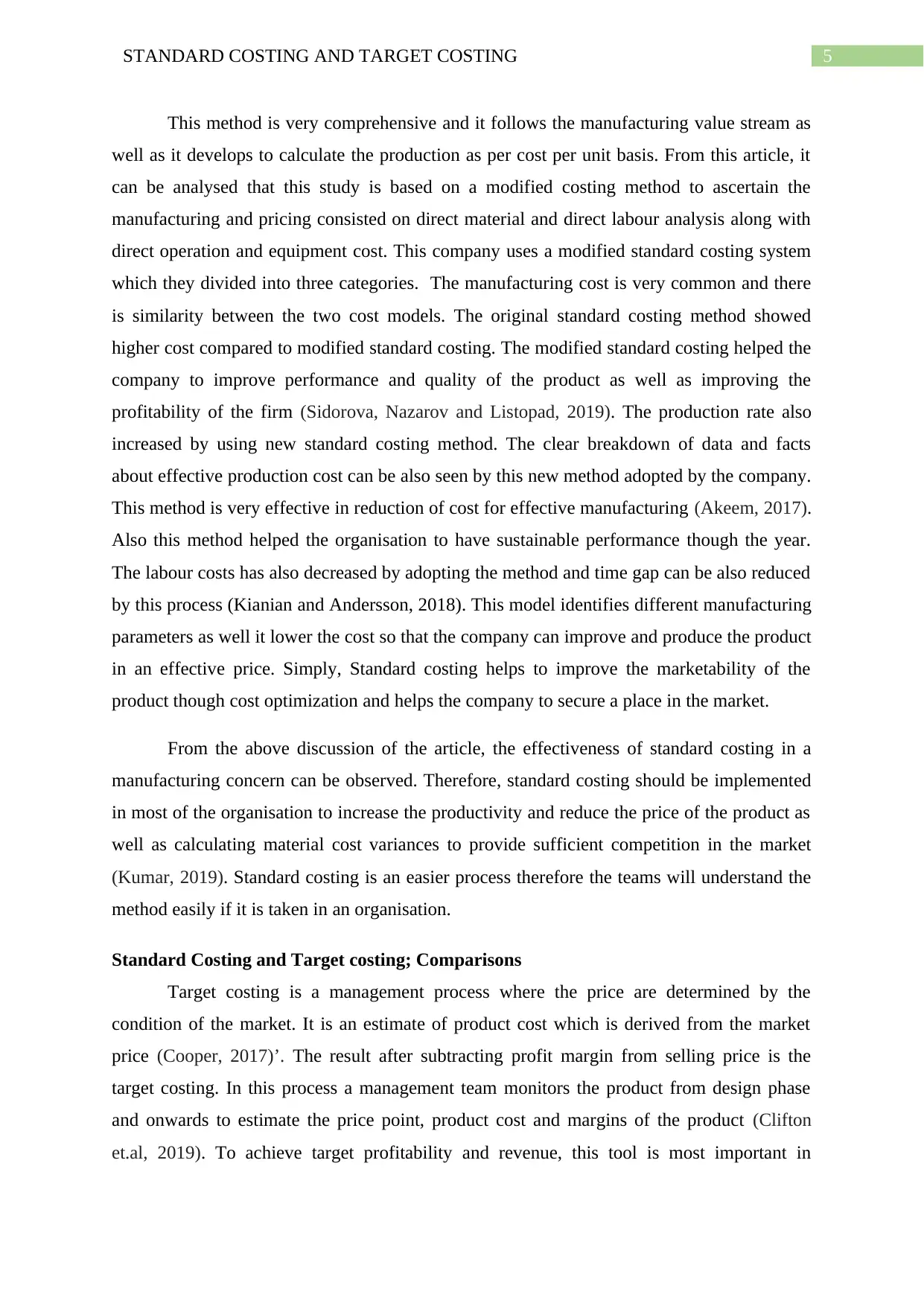
5STANDARD COSTING AND TARGET COSTING
This method is very comprehensive and it follows the manufacturing value stream as
well as it develops to calculate the production as per cost per unit basis. From this article, it
can be analysed that this study is based on a modified costing method to ascertain the
manufacturing and pricing consisted on direct material and direct labour analysis along with
direct operation and equipment cost. This company uses a modified standard costing system
which they divided into three categories. The manufacturing cost is very common and there
is similarity between the two cost models. The original standard costing method showed
higher cost compared to modified standard costing. The modified standard costing helped the
company to improve performance and quality of the product as well as improving the
profitability of the firm (Sidorova, Nazarov and Listopad, 2019). The production rate also
increased by using new standard costing method. The clear breakdown of data and facts
about effective production cost can be also seen by this new method adopted by the company.
This method is very effective in reduction of cost for effective manufacturing (Akeem, 2017).
Also this method helped the organisation to have sustainable performance though the year.
The labour costs has also decreased by adopting the method and time gap can be also reduced
by this process (Kianian and Andersson, 2018). This model identifies different manufacturing
parameters as well it lower the cost so that the company can improve and produce the product
in an effective price. Simply, Standard costing helps to improve the marketability of the
product though cost optimization and helps the company to secure a place in the market.
From the above discussion of the article, the effectiveness of standard costing in a
manufacturing concern can be observed. Therefore, standard costing should be implemented
in most of the organisation to increase the productivity and reduce the price of the product as
well as calculating material cost variances to provide sufficient competition in the market
(Kumar, 2019). Standard costing is an easier process therefore the teams will understand the
method easily if it is taken in an organisation.
Standard Costing and Target costing; Comparisons
Target costing is a management process where the price are determined by the
condition of the market. It is an estimate of product cost which is derived from the market
price (Cooper, 2017)’. The result after subtracting profit margin from selling price is the
target costing. In this process a management team monitors the product from design phase
and onwards to estimate the price point, product cost and margins of the product (Clifton
et.al, 2019). To achieve target profitability and revenue, this tool is most important in
This method is very comprehensive and it follows the manufacturing value stream as
well as it develops to calculate the production as per cost per unit basis. From this article, it
can be analysed that this study is based on a modified costing method to ascertain the
manufacturing and pricing consisted on direct material and direct labour analysis along with
direct operation and equipment cost. This company uses a modified standard costing system
which they divided into three categories. The manufacturing cost is very common and there
is similarity between the two cost models. The original standard costing method showed
higher cost compared to modified standard costing. The modified standard costing helped the
company to improve performance and quality of the product as well as improving the
profitability of the firm (Sidorova, Nazarov and Listopad, 2019). The production rate also
increased by using new standard costing method. The clear breakdown of data and facts
about effective production cost can be also seen by this new method adopted by the company.
This method is very effective in reduction of cost for effective manufacturing (Akeem, 2017).
Also this method helped the organisation to have sustainable performance though the year.
The labour costs has also decreased by adopting the method and time gap can be also reduced
by this process (Kianian and Andersson, 2018). This model identifies different manufacturing
parameters as well it lower the cost so that the company can improve and produce the product
in an effective price. Simply, Standard costing helps to improve the marketability of the
product though cost optimization and helps the company to secure a place in the market.
From the above discussion of the article, the effectiveness of standard costing in a
manufacturing concern can be observed. Therefore, standard costing should be implemented
in most of the organisation to increase the productivity and reduce the price of the product as
well as calculating material cost variances to provide sufficient competition in the market
(Kumar, 2019). Standard costing is an easier process therefore the teams will understand the
method easily if it is taken in an organisation.
Standard Costing and Target costing; Comparisons
Target costing is a management process where the price are determined by the
condition of the market. It is an estimate of product cost which is derived from the market
price (Cooper, 2017)’. The result after subtracting profit margin from selling price is the
target costing. In this process a management team monitors the product from design phase
and onwards to estimate the price point, product cost and margins of the product (Clifton
et.al, 2019). To achieve target profitability and revenue, this tool is most important in
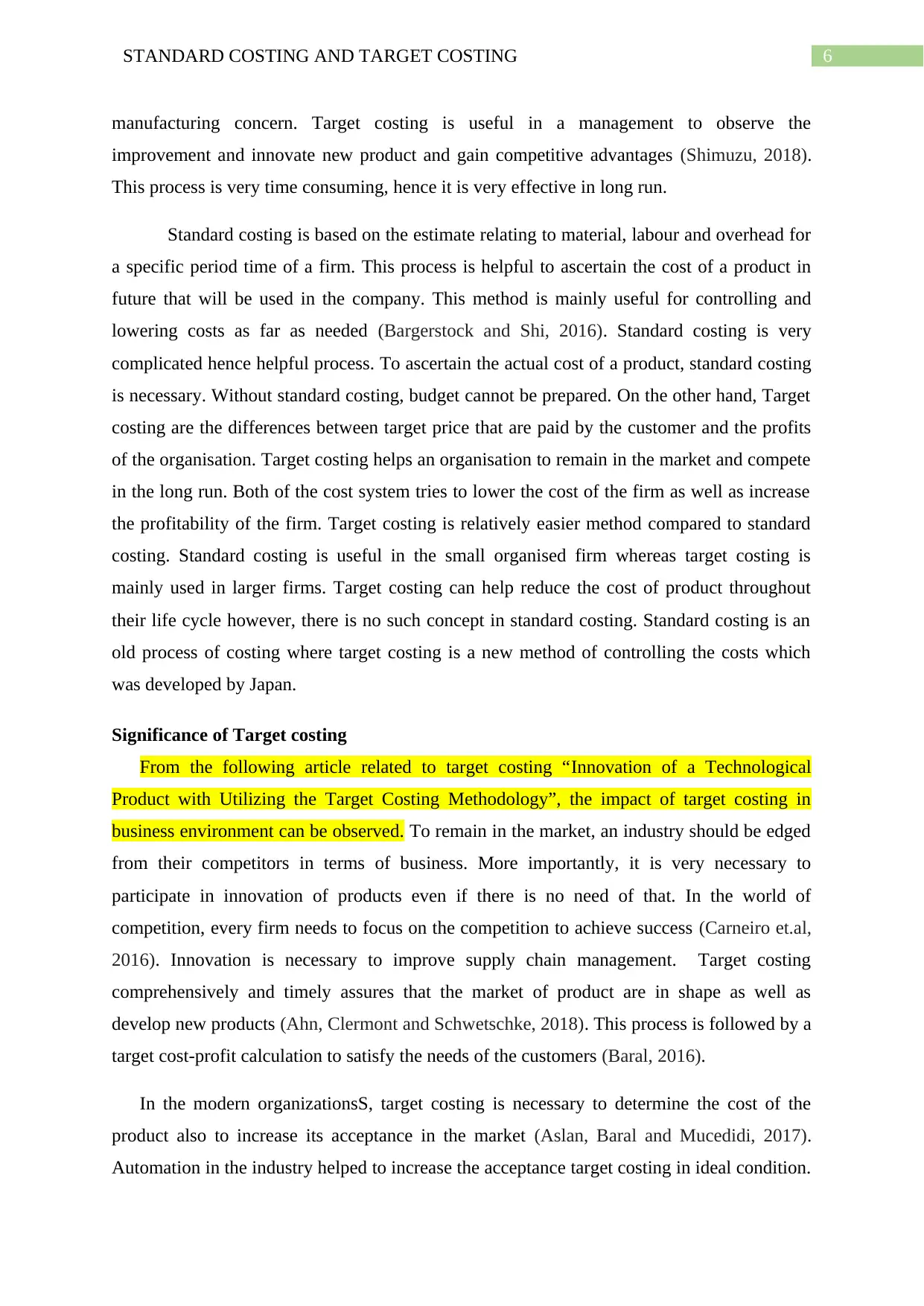
6STANDARD COSTING AND TARGET COSTING
manufacturing concern. Target costing is useful in a management to observe the
improvement and innovate new product and gain competitive advantages (Shimuzu, 2018).
This process is very time consuming, hence it is very effective in long run.
Standard costing is based on the estimate relating to material, labour and overhead for
a specific period time of a firm. This process is helpful to ascertain the cost of a product in
future that will be used in the company. This method is mainly useful for controlling and
lowering costs as far as needed (Bargerstock and Shi, 2016). Standard costing is very
complicated hence helpful process. To ascertain the actual cost of a product, standard costing
is necessary. Without standard costing, budget cannot be prepared. On the other hand, Target
costing are the differences between target price that are paid by the customer and the profits
of the organisation. Target costing helps an organisation to remain in the market and compete
in the long run. Both of the cost system tries to lower the cost of the firm as well as increase
the profitability of the firm. Target costing is relatively easier method compared to standard
costing. Standard costing is useful in the small organised firm whereas target costing is
mainly used in larger firms. Target costing can help reduce the cost of product throughout
their life cycle however, there is no such concept in standard costing. Standard costing is an
old process of costing where target costing is a new method of controlling the costs which
was developed by Japan.
Significance of Target costing
From the following article related to target costing “Innovation of a Technological
Product with Utilizing the Target Costing Methodology”, the impact of target costing in
business environment can be observed. To remain in the market, an industry should be edged
from their competitors in terms of business. More importantly, it is very necessary to
participate in innovation of products even if there is no need of that. In the world of
competition, every firm needs to focus on the competition to achieve success (Carneiro et.al,
2016). Innovation is necessary to improve supply chain management. Target costing
comprehensively and timely assures that the market of product are in shape as well as
develop new products (Ahn, Clermont and Schwetschke, 2018). This process is followed by a
target cost-profit calculation to satisfy the needs of the customers (Baral, 2016).
In the modern organizationsS, target costing is necessary to determine the cost of the
product also to increase its acceptance in the market (Aslan, Baral and Mucedidi, 2017).
Automation in the industry helped to increase the acceptance target costing in ideal condition.
manufacturing concern. Target costing is useful in a management to observe the
improvement and innovate new product and gain competitive advantages (Shimuzu, 2018).
This process is very time consuming, hence it is very effective in long run.
Standard costing is based on the estimate relating to material, labour and overhead for
a specific period time of a firm. This process is helpful to ascertain the cost of a product in
future that will be used in the company. This method is mainly useful for controlling and
lowering costs as far as needed (Bargerstock and Shi, 2016). Standard costing is very
complicated hence helpful process. To ascertain the actual cost of a product, standard costing
is necessary. Without standard costing, budget cannot be prepared. On the other hand, Target
costing are the differences between target price that are paid by the customer and the profits
of the organisation. Target costing helps an organisation to remain in the market and compete
in the long run. Both of the cost system tries to lower the cost of the firm as well as increase
the profitability of the firm. Target costing is relatively easier method compared to standard
costing. Standard costing is useful in the small organised firm whereas target costing is
mainly used in larger firms. Target costing can help reduce the cost of product throughout
their life cycle however, there is no such concept in standard costing. Standard costing is an
old process of costing where target costing is a new method of controlling the costs which
was developed by Japan.
Significance of Target costing
From the following article related to target costing “Innovation of a Technological
Product with Utilizing the Target Costing Methodology”, the impact of target costing in
business environment can be observed. To remain in the market, an industry should be edged
from their competitors in terms of business. More importantly, it is very necessary to
participate in innovation of products even if there is no need of that. In the world of
competition, every firm needs to focus on the competition to achieve success (Carneiro et.al,
2016). Innovation is necessary to improve supply chain management. Target costing
comprehensively and timely assures that the market of product are in shape as well as
develop new products (Ahn, Clermont and Schwetschke, 2018). This process is followed by a
target cost-profit calculation to satisfy the needs of the customers (Baral, 2016).
In the modern organizationsS, target costing is necessary to determine the cost of the
product also to increase its acceptance in the market (Aslan, Baral and Mucedidi, 2017).
Automation in the industry helped to increase the acceptance target costing in ideal condition.
Paraphrase This Document
Need a fresh take? Get an instant paraphrase of this document with our AI Paraphraser
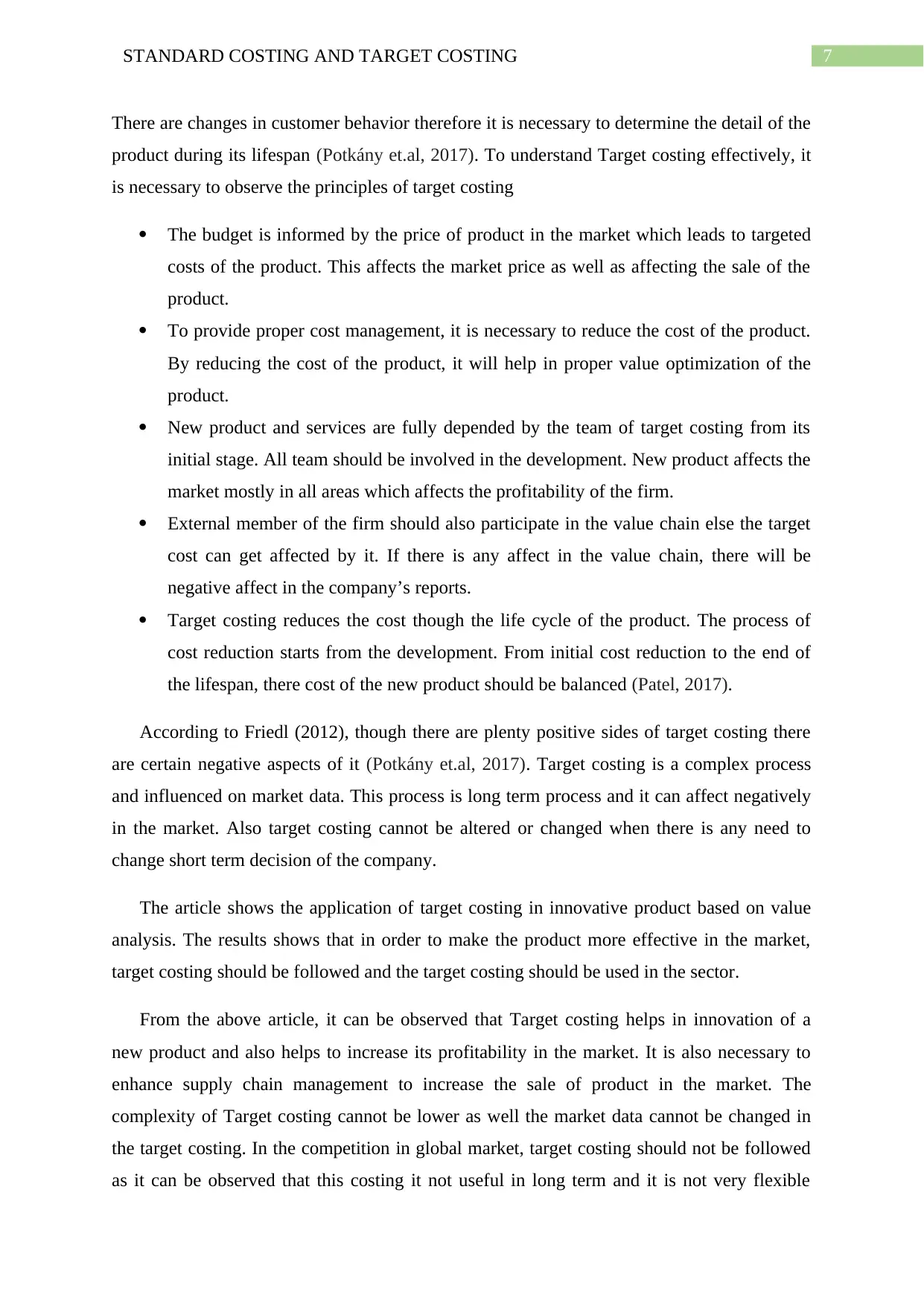
7STANDARD COSTING AND TARGET COSTING
There are changes in customer behavior therefore it is necessary to determine the detail of the
product during its lifespan (Potkány et.al, 2017). To understand Target costing effectively, it
is necessary to observe the principles of target costing
The budget is informed by the price of product in the market which leads to targeted
costs of the product. This affects the market price as well as affecting the sale of the
product.
To provide proper cost management, it is necessary to reduce the cost of the product.
By reducing the cost of the product, it will help in proper value optimization of the
product.
New product and services are fully depended by the team of target costing from its
initial stage. All team should be involved in the development. New product affects the
market mostly in all areas which affects the profitability of the firm.
External member of the firm should also participate in the value chain else the target
cost can get affected by it. If there is any affect in the value chain, there will be
negative affect in the company’s reports.
Target costing reduces the cost though the life cycle of the product. The process of
cost reduction starts from the development. From initial cost reduction to the end of
the lifespan, there cost of the new product should be balanced (Patel, 2017).
According to Friedl (2012), though there are plenty positive sides of target costing there
are certain negative aspects of it (Potkány et.al, 2017). Target costing is a complex process
and influenced on market data. This process is long term process and it can affect negatively
in the market. Also target costing cannot be altered or changed when there is any need to
change short term decision of the company.
The article shows the application of target costing in innovative product based on value
analysis. The results shows that in order to make the product more effective in the market,
target costing should be followed and the target costing should be used in the sector.
From the above article, it can be observed that Target costing helps in innovation of a
new product and also helps to increase its profitability in the market. It is also necessary to
enhance supply chain management to increase the sale of product in the market. The
complexity of Target costing cannot be lower as well the market data cannot be changed in
the target costing. In the competition in global market, target costing should not be followed
as it can be observed that this costing it not useful in long term and it is not very flexible
There are changes in customer behavior therefore it is necessary to determine the detail of the
product during its lifespan (Potkány et.al, 2017). To understand Target costing effectively, it
is necessary to observe the principles of target costing
The budget is informed by the price of product in the market which leads to targeted
costs of the product. This affects the market price as well as affecting the sale of the
product.
To provide proper cost management, it is necessary to reduce the cost of the product.
By reducing the cost of the product, it will help in proper value optimization of the
product.
New product and services are fully depended by the team of target costing from its
initial stage. All team should be involved in the development. New product affects the
market mostly in all areas which affects the profitability of the firm.
External member of the firm should also participate in the value chain else the target
cost can get affected by it. If there is any affect in the value chain, there will be
negative affect in the company’s reports.
Target costing reduces the cost though the life cycle of the product. The process of
cost reduction starts from the development. From initial cost reduction to the end of
the lifespan, there cost of the new product should be balanced (Patel, 2017).
According to Friedl (2012), though there are plenty positive sides of target costing there
are certain negative aspects of it (Potkány et.al, 2017). Target costing is a complex process
and influenced on market data. This process is long term process and it can affect negatively
in the market. Also target costing cannot be altered or changed when there is any need to
change short term decision of the company.
The article shows the application of target costing in innovative product based on value
analysis. The results shows that in order to make the product more effective in the market,
target costing should be followed and the target costing should be used in the sector.
From the above article, it can be observed that Target costing helps in innovation of a
new product and also helps to increase its profitability in the market. It is also necessary to
enhance supply chain management to increase the sale of product in the market. The
complexity of Target costing cannot be lower as well the market data cannot be changed in
the target costing. In the competition in global market, target costing should not be followed
as it can be observed that this costing it not useful in long term and it is not very flexible
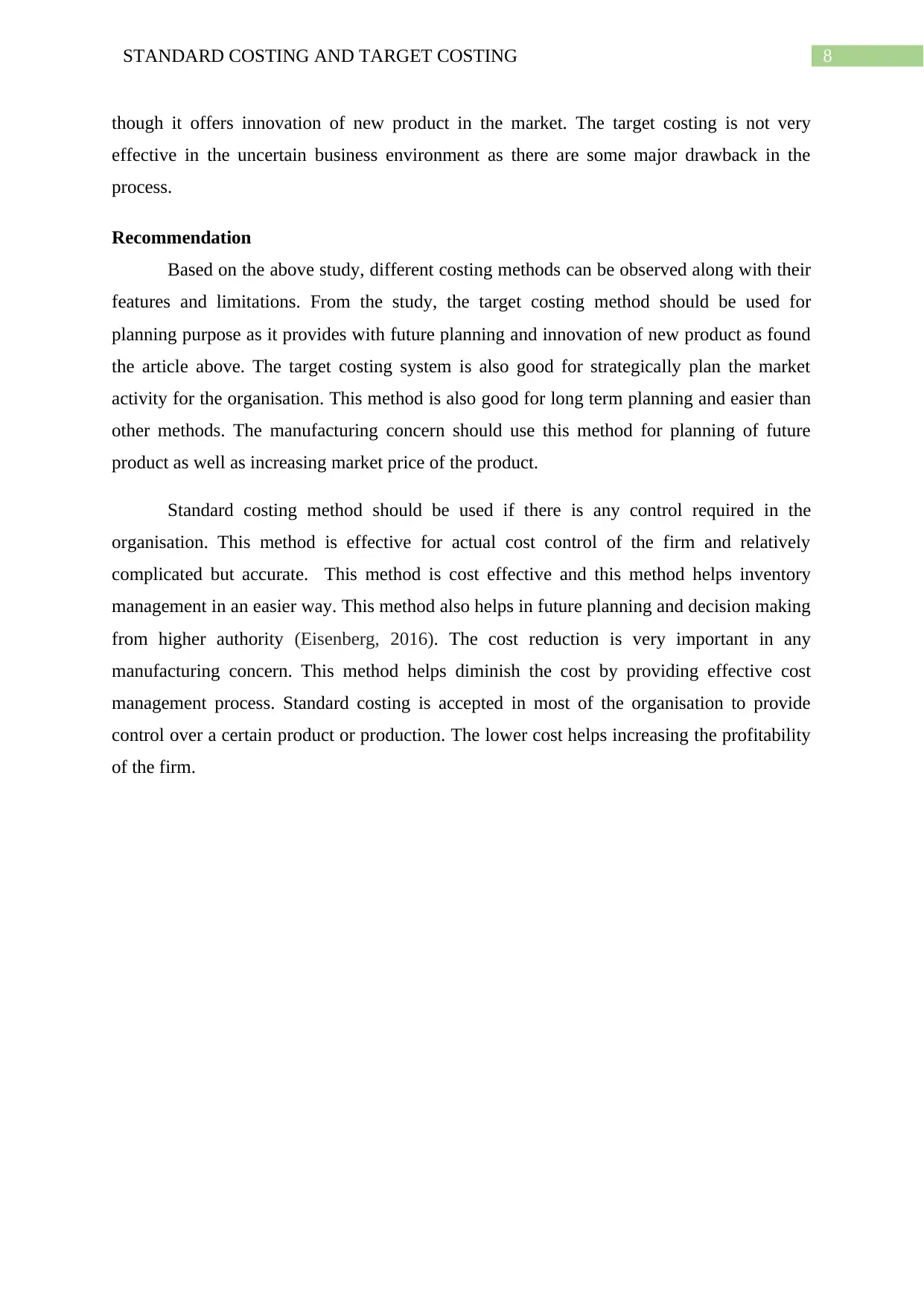
8STANDARD COSTING AND TARGET COSTING
though it offers innovation of new product in the market. The target costing is not very
effective in the uncertain business environment as there are some major drawback in the
process.
Recommendation
Based on the above study, different costing methods can be observed along with their
features and limitations. From the study, the target costing method should be used for
planning purpose as it provides with future planning and innovation of new product as found
the article above. The target costing system is also good for strategically plan the market
activity for the organisation. This method is also good for long term planning and easier than
other methods. The manufacturing concern should use this method for planning of future
product as well as increasing market price of the product.
Standard costing method should be used if there is any control required in the
organisation. This method is effective for actual cost control of the firm and relatively
complicated but accurate. This method is cost effective and this method helps inventory
management in an easier way. This method also helps in future planning and decision making
from higher authority (Eisenberg, 2016). The cost reduction is very important in any
manufacturing concern. This method helps diminish the cost by providing effective cost
management process. Standard costing is accepted in most of the organisation to provide
control over a certain product or production. The lower cost helps increasing the profitability
of the firm.
though it offers innovation of new product in the market. The target costing is not very
effective in the uncertain business environment as there are some major drawback in the
process.
Recommendation
Based on the above study, different costing methods can be observed along with their
features and limitations. From the study, the target costing method should be used for
planning purpose as it provides with future planning and innovation of new product as found
the article above. The target costing system is also good for strategically plan the market
activity for the organisation. This method is also good for long term planning and easier than
other methods. The manufacturing concern should use this method for planning of future
product as well as increasing market price of the product.
Standard costing method should be used if there is any control required in the
organisation. This method is effective for actual cost control of the firm and relatively
complicated but accurate. This method is cost effective and this method helps inventory
management in an easier way. This method also helps in future planning and decision making
from higher authority (Eisenberg, 2016). The cost reduction is very important in any
manufacturing concern. This method helps diminish the cost by providing effective cost
management process. Standard costing is accepted in most of the organisation to provide
control over a certain product or production. The lower cost helps increasing the profitability
of the firm.

9STANDARD COSTING AND TARGET COSTING
References
Potkány, M., Novák, P., Kováč, R. and Hitka, M., 2017. Innovation of a Technological
Product with Utilizing the Target Costing Methodology. International Review of
Management and Marketing, 7(2), pp.130-137.
Triyuwono, E., Chandra, F. and Asri, M., 2018. Costing Assignment Approaches. Available
at SSRN 3209974.
Panchenko, A., 2017. Standard Costing: Advantages and Disadvantages.
Callus, K., 2019. The relevance of standard costing and variance analysis in Maltese
bakeries (Master's thesis, University of Malta).
Steyn, E., 2017. An evaluation of a standard costing framework to manage transport costs
for a South African logistics company (Doctoral dissertation, North-West University (South
Africa), Potchefstroom Campus).
Mishra, C.R., 2018. The study on inventory valuation for a business; analysis of pricing issue
of materials fifo&lifo methods. International Journal of Management, IT and
Engineering, 8(7), pp.346-354.
Akeem, L.B., 2017. Effect of cost control and cost reduction techniques in organizational
performance. International Business and Management, 14(3), pp.19-26.
Bargerstock, A. and Shi, Y., 2016. Leaning away from standard costing. Инновации в
менеджменте, (2), pp.4-11.
Kumar, A., 2019. Standard Costing And Material Cost Variance. The Management
Accountant Journal, 54(1), pp.82-85.
References
Potkány, M., Novák, P., Kováč, R. and Hitka, M., 2017. Innovation of a Technological
Product with Utilizing the Target Costing Methodology. International Review of
Management and Marketing, 7(2), pp.130-137.
Triyuwono, E., Chandra, F. and Asri, M., 2018. Costing Assignment Approaches. Available
at SSRN 3209974.
Panchenko, A., 2017. Standard Costing: Advantages and Disadvantages.
Callus, K., 2019. The relevance of standard costing and variance analysis in Maltese
bakeries (Master's thesis, University of Malta).
Steyn, E., 2017. An evaluation of a standard costing framework to manage transport costs
for a South African logistics company (Doctoral dissertation, North-West University (South
Africa), Potchefstroom Campus).
Mishra, C.R., 2018. The study on inventory valuation for a business; analysis of pricing issue
of materials fifo&lifo methods. International Journal of Management, IT and
Engineering, 8(7), pp.346-354.
Akeem, L.B., 2017. Effect of cost control and cost reduction techniques in organizational
performance. International Business and Management, 14(3), pp.19-26.
Bargerstock, A. and Shi, Y., 2016. Leaning away from standard costing. Инновации в
менеджменте, (2), pp.4-11.
Kumar, A., 2019. Standard Costing And Material Cost Variance. The Management
Accountant Journal, 54(1), pp.82-85.
Secure Best Marks with AI Grader
Need help grading? Try our AI Grader for instant feedback on your assignments.
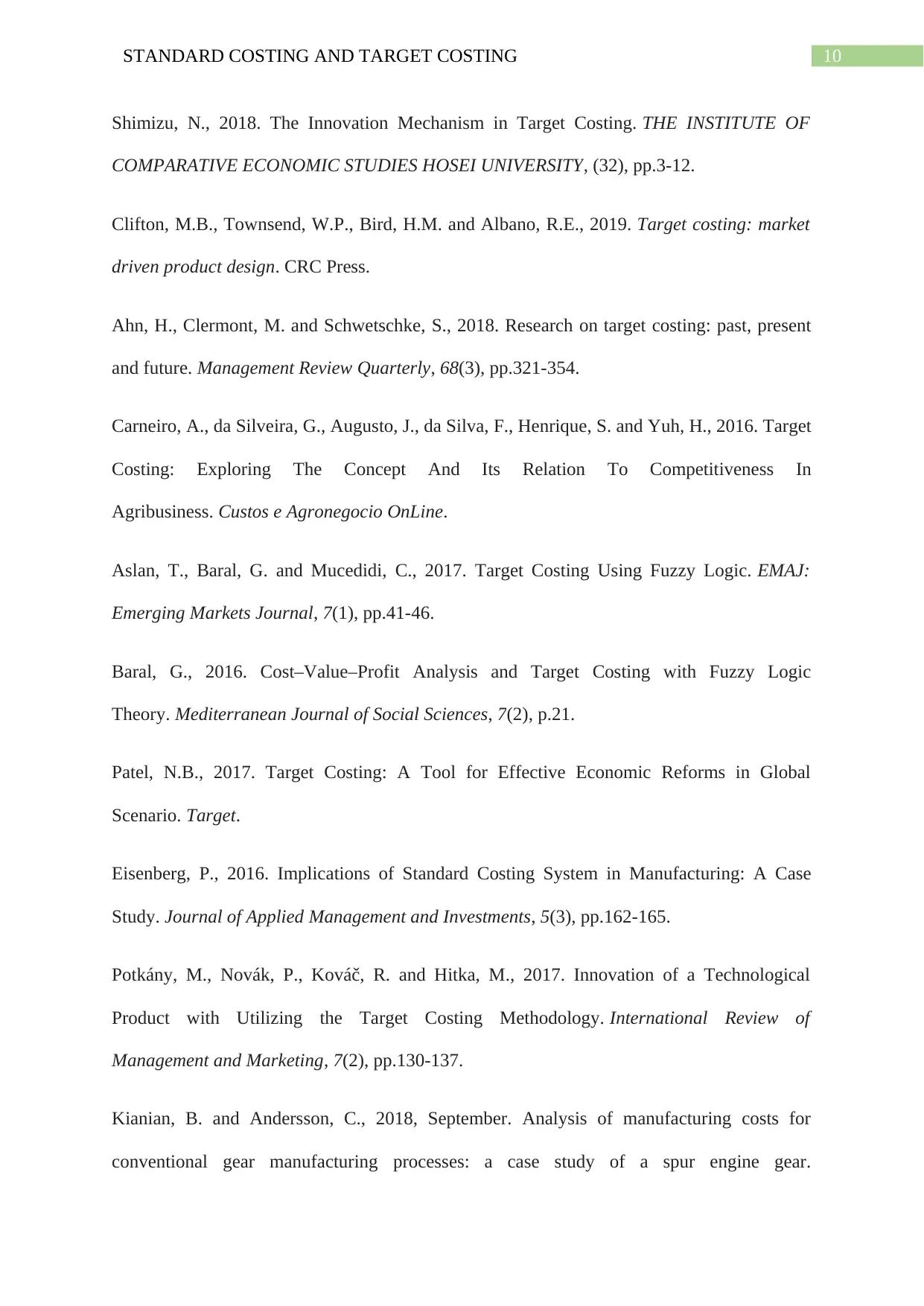
10STANDARD COSTING AND TARGET COSTING
Shimizu, N., 2018. The Innovation Mechanism in Target Costing. THE INSTITUTE OF
COMPARATIVE ECONOMIC STUDIES HOSEI UNIVERSITY, (32), pp.3-12.
Clifton, M.B., Townsend, W.P., Bird, H.M. and Albano, R.E., 2019. Target costing: market
driven product design. CRC Press.
Ahn, H., Clermont, M. and Schwetschke, S., 2018. Research on target costing: past, present
and future. Management Review Quarterly, 68(3), pp.321-354.
Carneiro, A., da Silveira, G., Augusto, J., da Silva, F., Henrique, S. and Yuh, H., 2016. Target
Costing: Exploring The Concept And Its Relation To Competitiveness In
Agribusiness. Custos e Agronegocio OnLine.
Aslan, T., Baral, G. and Mucedidi, C., 2017. Target Costing Using Fuzzy Logic. EMAJ:
Emerging Markets Journal, 7(1), pp.41-46.
Baral, G., 2016. Cost–Value–Profit Analysis and Target Costing with Fuzzy Logic
Theory. Mediterranean Journal of Social Sciences, 7(2), p.21.
Patel, N.B., 2017. Target Costing: A Tool for Effective Economic Reforms in Global
Scenario. Target.
Eisenberg, P., 2016. Implications of Standard Costing System in Manufacturing: A Case
Study. Journal of Applied Management and Investments, 5(3), pp.162-165.
Potkány, M., Novák, P., Kováč, R. and Hitka, M., 2017. Innovation of a Technological
Product with Utilizing the Target Costing Methodology. International Review of
Management and Marketing, 7(2), pp.130-137.
Kianian, B. and Andersson, C., 2018, September. Analysis of manufacturing costs for
conventional gear manufacturing processes: a case study of a spur engine gear.
Shimizu, N., 2018. The Innovation Mechanism in Target Costing. THE INSTITUTE OF
COMPARATIVE ECONOMIC STUDIES HOSEI UNIVERSITY, (32), pp.3-12.
Clifton, M.B., Townsend, W.P., Bird, H.M. and Albano, R.E., 2019. Target costing: market
driven product design. CRC Press.
Ahn, H., Clermont, M. and Schwetschke, S., 2018. Research on target costing: past, present
and future. Management Review Quarterly, 68(3), pp.321-354.
Carneiro, A., da Silveira, G., Augusto, J., da Silva, F., Henrique, S. and Yuh, H., 2016. Target
Costing: Exploring The Concept And Its Relation To Competitiveness In
Agribusiness. Custos e Agronegocio OnLine.
Aslan, T., Baral, G. and Mucedidi, C., 2017. Target Costing Using Fuzzy Logic. EMAJ:
Emerging Markets Journal, 7(1), pp.41-46.
Baral, G., 2016. Cost–Value–Profit Analysis and Target Costing with Fuzzy Logic
Theory. Mediterranean Journal of Social Sciences, 7(2), p.21.
Patel, N.B., 2017. Target Costing: A Tool for Effective Economic Reforms in Global
Scenario. Target.
Eisenberg, P., 2016. Implications of Standard Costing System in Manufacturing: A Case
Study. Journal of Applied Management and Investments, 5(3), pp.162-165.
Potkány, M., Novák, P., Kováč, R. and Hitka, M., 2017. Innovation of a Technological
Product with Utilizing the Target Costing Methodology. International Review of
Management and Marketing, 7(2), pp.130-137.
Kianian, B. and Andersson, C., 2018, September. Analysis of manufacturing costs for
conventional gear manufacturing processes: a case study of a spur engine gear.
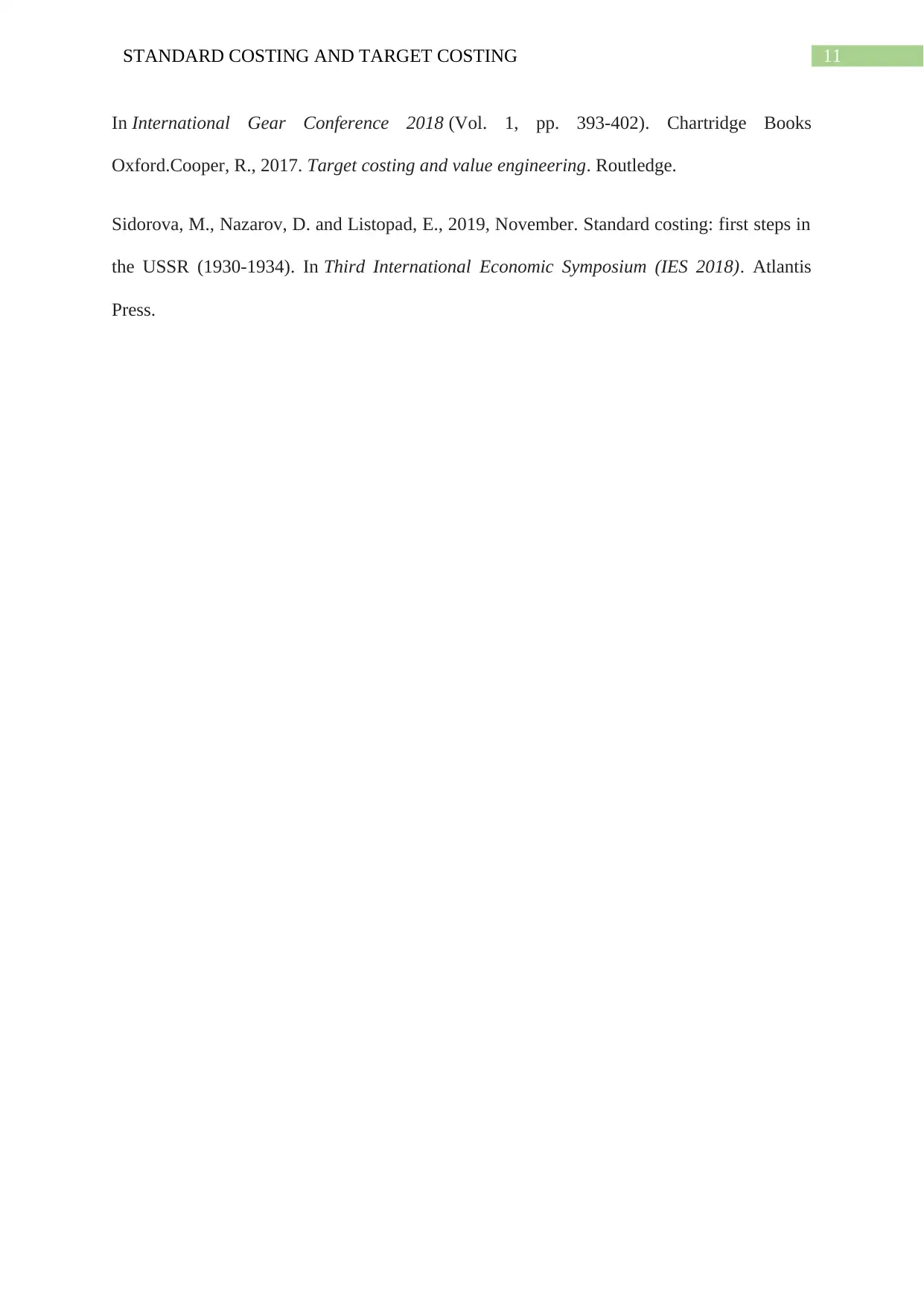
11STANDARD COSTING AND TARGET COSTING
In International Gear Conference 2018 (Vol. 1, pp. 393-402). Chartridge Books
Oxford.Cooper, R., 2017. Target costing and value engineering. Routledge.
Sidorova, M., Nazarov, D. and Listopad, E., 2019, November. Standard costing: first steps in
the USSR (1930-1934). In Third International Economic Symposium (IES 2018). Atlantis
Press.
In International Gear Conference 2018 (Vol. 1, pp. 393-402). Chartridge Books
Oxford.Cooper, R., 2017. Target costing and value engineering. Routledge.
Sidorova, M., Nazarov, D. and Listopad, E., 2019, November. Standard costing: first steps in
the USSR (1930-1934). In Third International Economic Symposium (IES 2018). Atlantis
Press.
1 out of 12
Related Documents

Your All-in-One AI-Powered Toolkit for Academic Success.
+13062052269
info@desklib.com
Available 24*7 on WhatsApp / Email
Unlock your academic potential
© 2024 | Zucol Services PVT LTD | All rights reserved.