MSc Operations Management: Analysis of Starbucks Production System
VerifiedAdded on 2023/01/13
|15
|4040
|30
Report
AI Summary
This report provides a comprehensive analysis of the Starbucks production system, examining its inventory management practices, including the use of Just-In-Time, safety stock, and lean manufacturing principles. It details the key operational functions within Starbucks, such as greener cups and packaging, coffee roasting processes, and maintenance of machinery. The report identifies areas where the delivery system may fail to align with operational performance measures, specifically in design and technical support and maintenance of equipment. Furthermore, it suggests how a lean approach can be utilized to address these failings and align operational performance measures, emphasizing the potential for improved efficiency and customer satisfaction. The report concludes with a discussion of how Starbucks can enhance its production system.
Contribute Materials
Your contribution can guide someone’s learning journey. Share your
documents today.
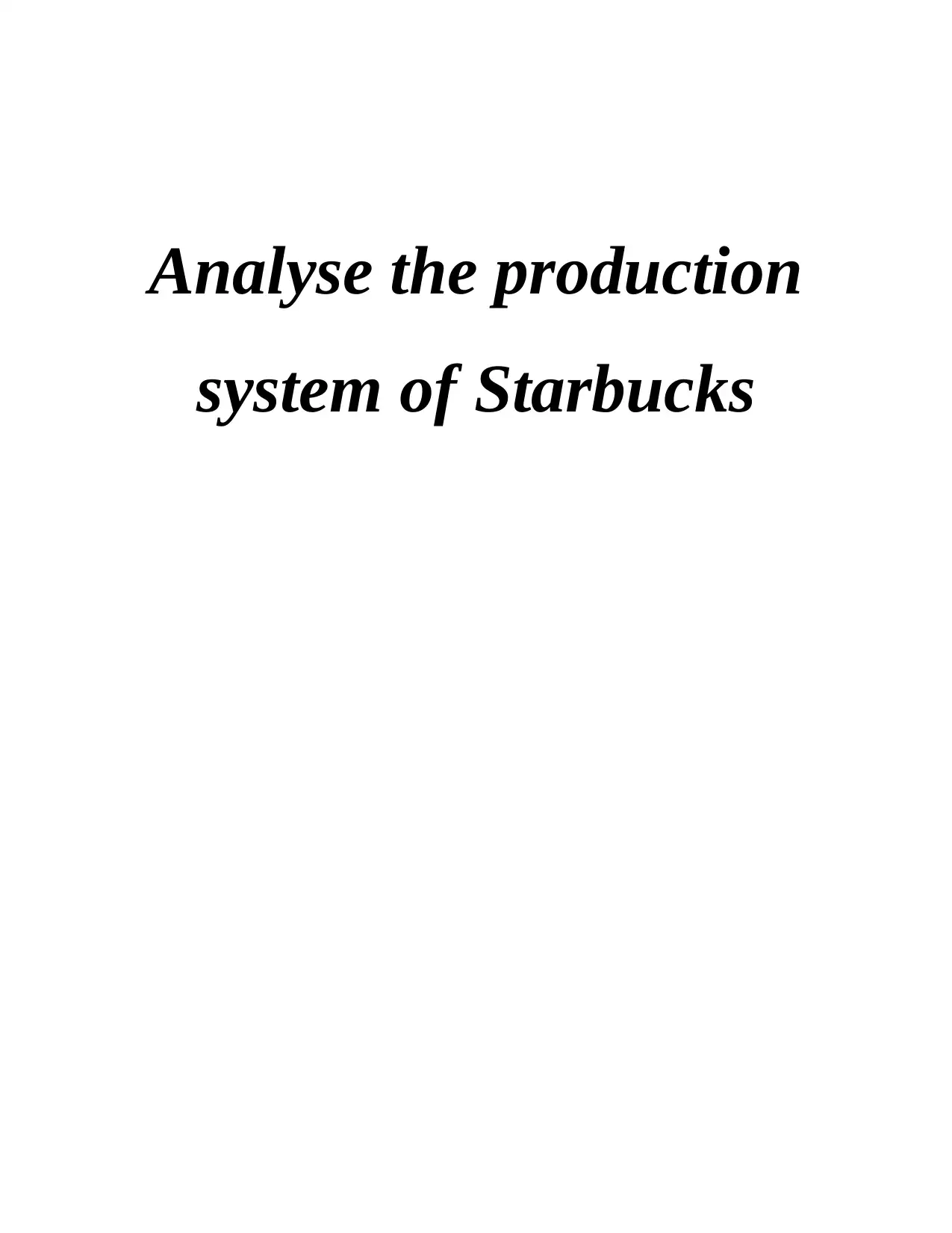
Analyse the production
system of Starbucks
system of Starbucks
Secure Best Marks with AI Grader
Need help grading? Try our AI Grader for instant feedback on your assignments.
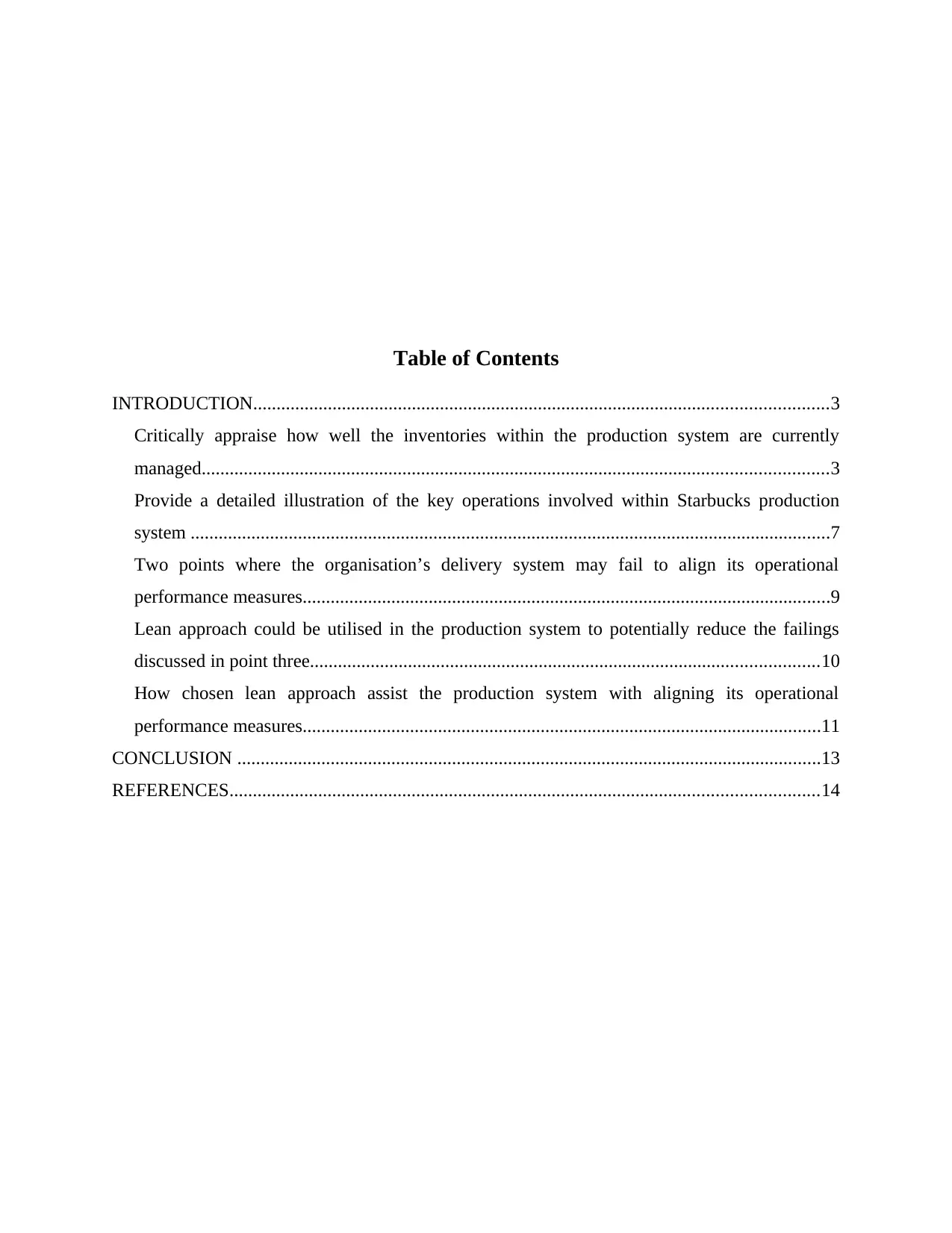
Table of Contents
INTRODUCTION...........................................................................................................................3
Critically appraise how well the inventories within the production system are currently
managed......................................................................................................................................3
Provide a detailed illustration of the key operations involved within Starbucks production
system .........................................................................................................................................7
Two points where the organisation’s delivery system may fail to align its operational
performance measures.................................................................................................................9
Lean approach could be utilised in the production system to potentially reduce the failings
discussed in point three.............................................................................................................10
How chosen lean approach assist the production system with aligning its operational
performance measures...............................................................................................................11
CONCLUSION .............................................................................................................................13
REFERENCES..............................................................................................................................14
INTRODUCTION...........................................................................................................................3
Critically appraise how well the inventories within the production system are currently
managed......................................................................................................................................3
Provide a detailed illustration of the key operations involved within Starbucks production
system .........................................................................................................................................7
Two points where the organisation’s delivery system may fail to align its operational
performance measures.................................................................................................................9
Lean approach could be utilised in the production system to potentially reduce the failings
discussed in point three.............................................................................................................10
How chosen lean approach assist the production system with aligning its operational
performance measures...............................................................................................................11
CONCLUSION .............................................................................................................................13
REFERENCES..............................................................................................................................14
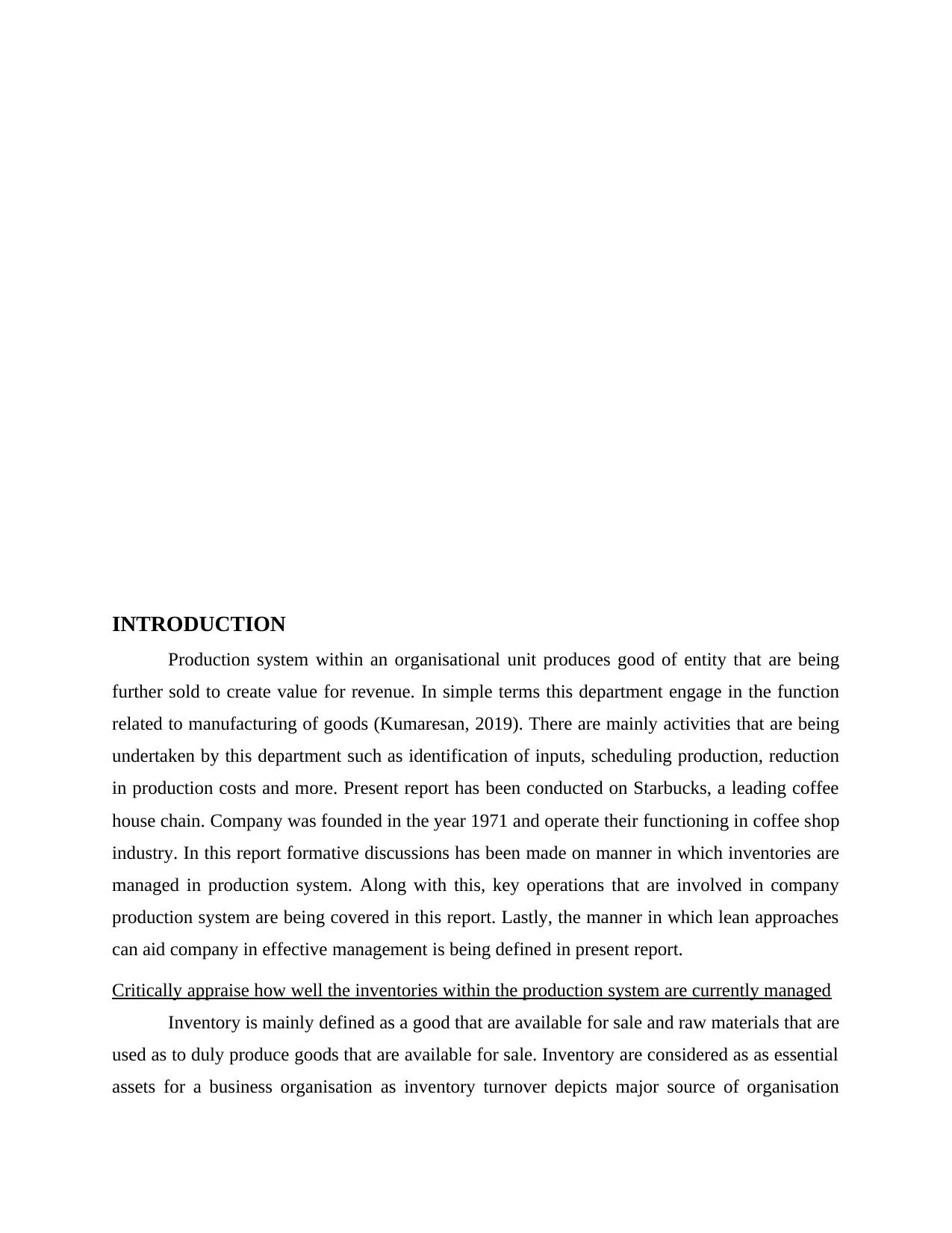
INTRODUCTION
Production system within an organisational unit produces good of entity that are being
further sold to create value for revenue. In simple terms this department engage in the function
related to manufacturing of goods (Kumaresan, 2019). There are mainly activities that are being
undertaken by this department such as identification of inputs, scheduling production, reduction
in production costs and more. Present report has been conducted on Starbucks, a leading coffee
house chain. Company was founded in the year 1971 and operate their functioning in coffee shop
industry. In this report formative discussions has been made on manner in which inventories are
managed in production system. Along with this, key operations that are involved in company
production system are being covered in this report. Lastly, the manner in which lean approaches
can aid company in effective management is being defined in present report.
Critically appraise how well the inventories within the production system are currently managed
Inventory is mainly defined as a good that are available for sale and raw materials that are
used as to duly produce goods that are available for sale. Inventory are considered as as essential
assets for a business organisation as inventory turnover depicts major source of organisation
Production system within an organisational unit produces good of entity that are being
further sold to create value for revenue. In simple terms this department engage in the function
related to manufacturing of goods (Kumaresan, 2019). There are mainly activities that are being
undertaken by this department such as identification of inputs, scheduling production, reduction
in production costs and more. Present report has been conducted on Starbucks, a leading coffee
house chain. Company was founded in the year 1971 and operate their functioning in coffee shop
industry. In this report formative discussions has been made on manner in which inventories are
managed in production system. Along with this, key operations that are involved in company
production system are being covered in this report. Lastly, the manner in which lean approaches
can aid company in effective management is being defined in present report.
Critically appraise how well the inventories within the production system are currently managed
Inventory is mainly defined as a good that are available for sale and raw materials that are
used as to duly produce goods that are available for sale. Inventory are considered as as essential
assets for a business organisation as inventory turnover depicts major source of organisation
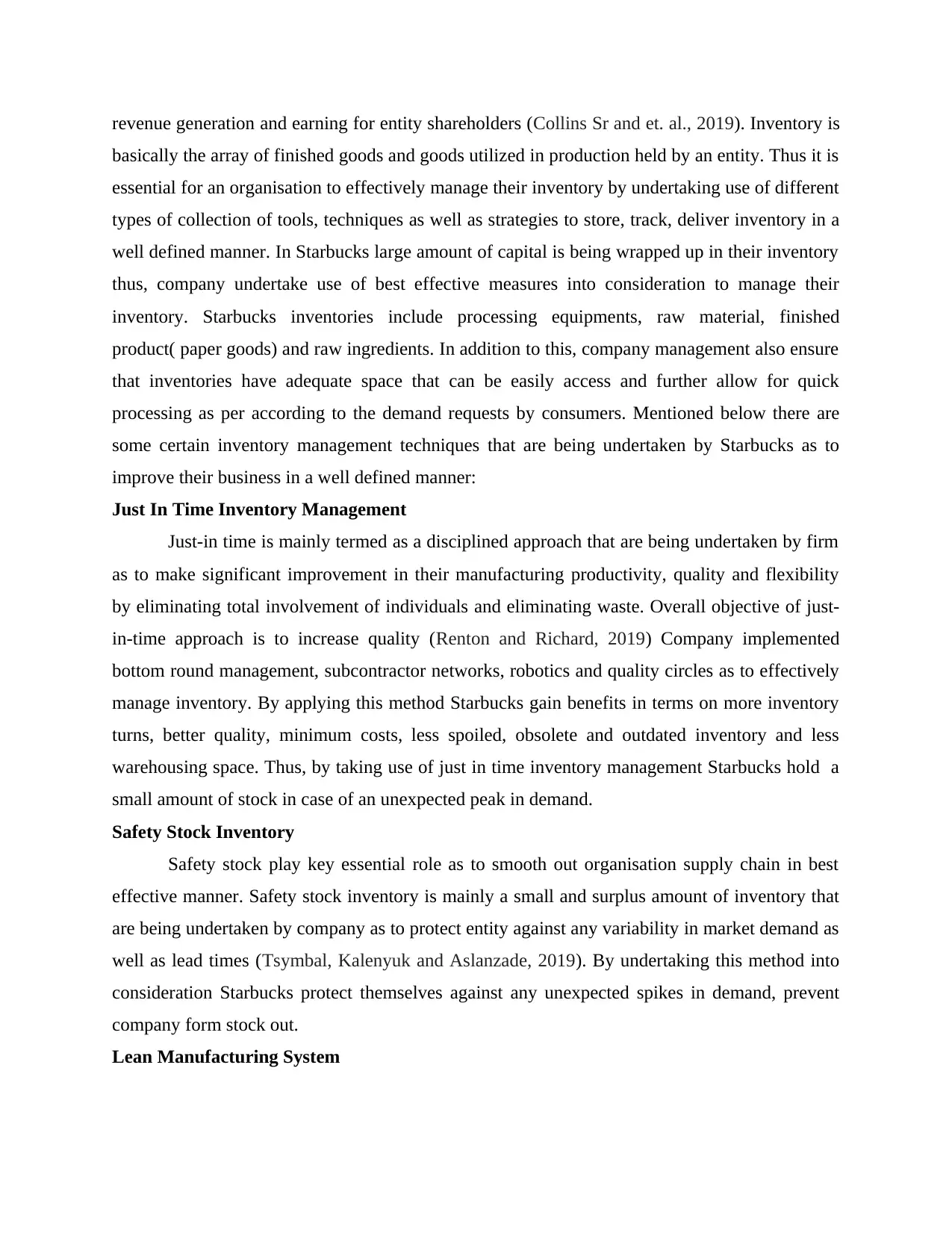
revenue generation and earning for entity shareholders (Collins Sr and et. al., 2019). Inventory is
basically the array of finished goods and goods utilized in production held by an entity. Thus it is
essential for an organisation to effectively manage their inventory by undertaking use of different
types of collection of tools, techniques as well as strategies to store, track, deliver inventory in a
well defined manner. In Starbucks large amount of capital is being wrapped up in their inventory
thus, company undertake use of best effective measures into consideration to manage their
inventory. Starbucks inventories include processing equipments, raw material, finished
product( paper goods) and raw ingredients. In addition to this, company management also ensure
that inventories have adequate space that can be easily access and further allow for quick
processing as per according to the demand requests by consumers. Mentioned below there are
some certain inventory management techniques that are being undertaken by Starbucks as to
improve their business in a well defined manner:
Just In Time Inventory Management
Just-in time is mainly termed as a disciplined approach that are being undertaken by firm
as to make significant improvement in their manufacturing productivity, quality and flexibility
by eliminating total involvement of individuals and eliminating waste. Overall objective of just-
in-time approach is to increase quality (Renton and Richard, 2019) Company implemented
bottom round management, subcontractor networks, robotics and quality circles as to effectively
manage inventory. By applying this method Starbucks gain benefits in terms on more inventory
turns, better quality, minimum costs, less spoiled, obsolete and outdated inventory and less
warehousing space. Thus, by taking use of just in time inventory management Starbucks hold a
small amount of stock in case of an unexpected peak in demand.
Safety Stock Inventory
Safety stock play key essential role as to smooth out organisation supply chain in best
effective manner. Safety stock inventory is mainly a small and surplus amount of inventory that
are being undertaken by company as to protect entity against any variability in market demand as
well as lead times (Tsymbal, Kalenyuk and Aslanzade, 2019). By undertaking this method into
consideration Starbucks protect themselves against any unexpected spikes in demand, prevent
company form stock out.
Lean Manufacturing System
basically the array of finished goods and goods utilized in production held by an entity. Thus it is
essential for an organisation to effectively manage their inventory by undertaking use of different
types of collection of tools, techniques as well as strategies to store, track, deliver inventory in a
well defined manner. In Starbucks large amount of capital is being wrapped up in their inventory
thus, company undertake use of best effective measures into consideration to manage their
inventory. Starbucks inventories include processing equipments, raw material, finished
product( paper goods) and raw ingredients. In addition to this, company management also ensure
that inventories have adequate space that can be easily access and further allow for quick
processing as per according to the demand requests by consumers. Mentioned below there are
some certain inventory management techniques that are being undertaken by Starbucks as to
improve their business in a well defined manner:
Just In Time Inventory Management
Just-in time is mainly termed as a disciplined approach that are being undertaken by firm
as to make significant improvement in their manufacturing productivity, quality and flexibility
by eliminating total involvement of individuals and eliminating waste. Overall objective of just-
in-time approach is to increase quality (Renton and Richard, 2019) Company implemented
bottom round management, subcontractor networks, robotics and quality circles as to effectively
manage inventory. By applying this method Starbucks gain benefits in terms on more inventory
turns, better quality, minimum costs, less spoiled, obsolete and outdated inventory and less
warehousing space. Thus, by taking use of just in time inventory management Starbucks hold a
small amount of stock in case of an unexpected peak in demand.
Safety Stock Inventory
Safety stock play key essential role as to smooth out organisation supply chain in best
effective manner. Safety stock inventory is mainly a small and surplus amount of inventory that
are being undertaken by company as to protect entity against any variability in market demand as
well as lead times (Tsymbal, Kalenyuk and Aslanzade, 2019). By undertaking this method into
consideration Starbucks protect themselves against any unexpected spikes in demand, prevent
company form stock out.
Lean Manufacturing System
Secure Best Marks with AI Grader
Need help grading? Try our AI Grader for instant feedback on your assignments.
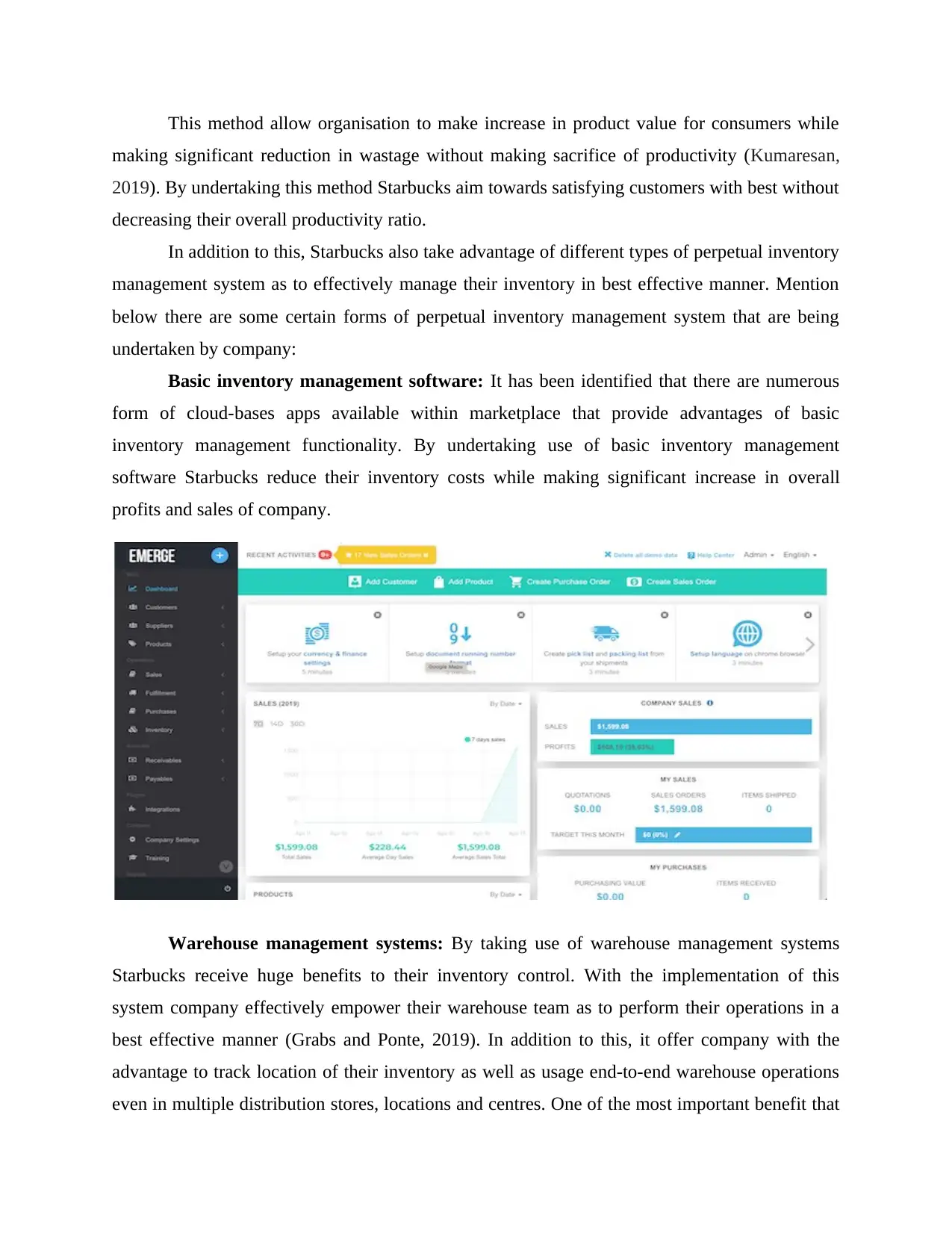
This method allow organisation to make increase in product value for consumers while
making significant reduction in wastage without making sacrifice of productivity (Kumaresan,
2019). By undertaking this method Starbucks aim towards satisfying customers with best without
decreasing their overall productivity ratio.
In addition to this, Starbucks also take advantage of different types of perpetual inventory
management system as to effectively manage their inventory in best effective manner. Mention
below there are some certain forms of perpetual inventory management system that are being
undertaken by company:
Basic inventory management software: It has been identified that there are numerous
form of cloud-bases apps available within marketplace that provide advantages of basic
inventory management functionality. By undertaking use of basic inventory management
software Starbucks reduce their inventory costs while making significant increase in overall
profits and sales of company.
Warehouse management systems: By taking use of warehouse management systems
Starbucks receive huge benefits to their inventory control. With the implementation of this
system company effectively empower their warehouse team as to perform their operations in a
best effective manner (Grabs and Ponte, 2019). In addition to this, it offer company with the
advantage to track location of their inventory as well as usage end-to-end warehouse operations
even in multiple distribution stores, locations and centres. One of the most important benefit that
making significant reduction in wastage without making sacrifice of productivity (Kumaresan,
2019). By undertaking this method Starbucks aim towards satisfying customers with best without
decreasing their overall productivity ratio.
In addition to this, Starbucks also take advantage of different types of perpetual inventory
management system as to effectively manage their inventory in best effective manner. Mention
below there are some certain forms of perpetual inventory management system that are being
undertaken by company:
Basic inventory management software: It has been identified that there are numerous
form of cloud-bases apps available within marketplace that provide advantages of basic
inventory management functionality. By undertaking use of basic inventory management
software Starbucks reduce their inventory costs while making significant increase in overall
profits and sales of company.
Warehouse management systems: By taking use of warehouse management systems
Starbucks receive huge benefits to their inventory control. With the implementation of this
system company effectively empower their warehouse team as to perform their operations in a
best effective manner (Grabs and Ponte, 2019). In addition to this, it offer company with the
advantage to track location of their inventory as well as usage end-to-end warehouse operations
even in multiple distribution stores, locations and centres. One of the most important benefit that
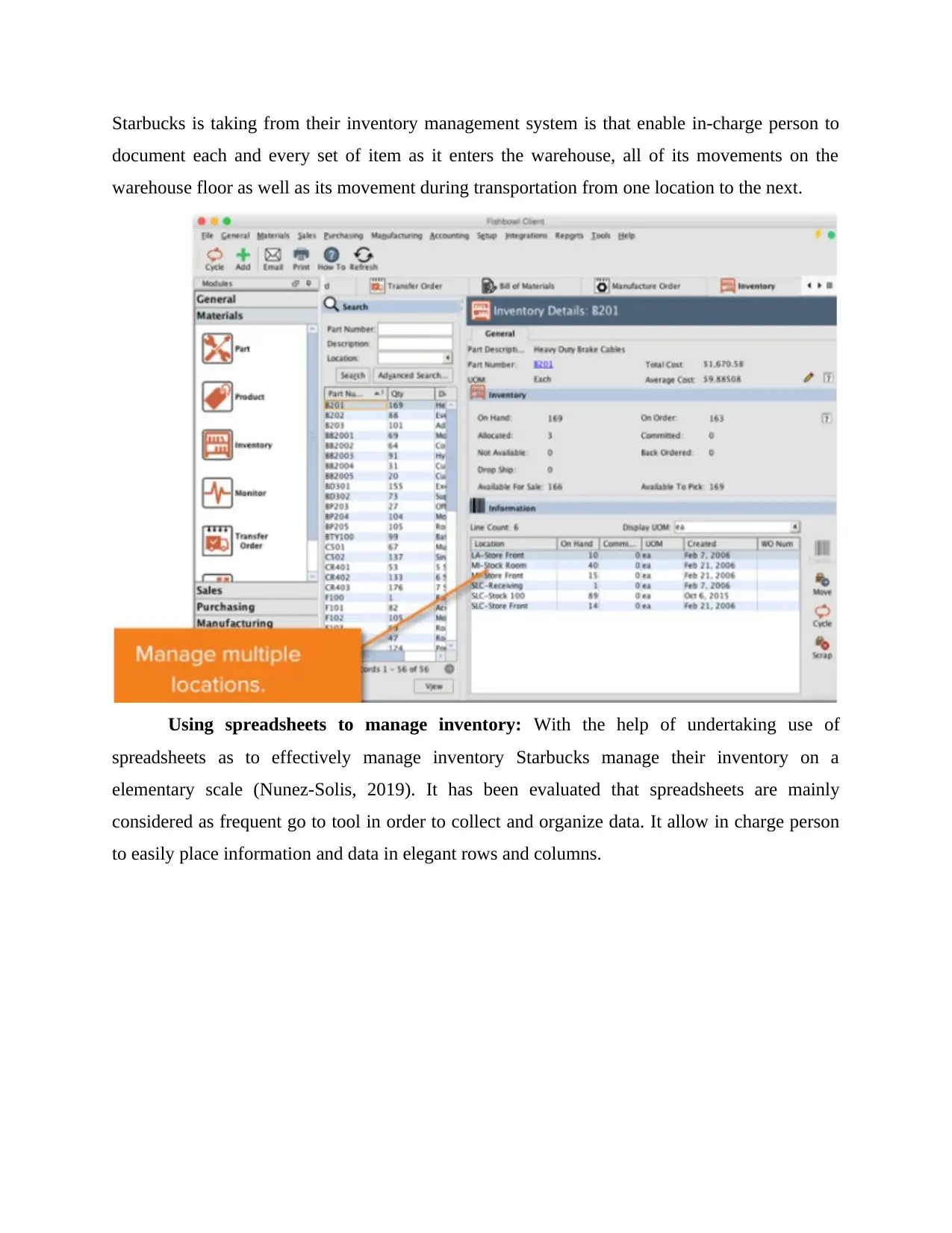
Starbucks is taking from their inventory management system is that enable in-charge person to
document each and every set of item as it enters the warehouse, all of its movements on the
warehouse floor as well as its movement during transportation from one location to the next.
Using spreadsheets to manage inventory: With the help of undertaking use of
spreadsheets as to effectively manage inventory Starbucks manage their inventory on a
elementary scale (Nunez-Solis, 2019). It has been evaluated that spreadsheets are mainly
considered as frequent go to tool in order to collect and organize data. It allow in charge person
to easily place information and data in elegant rows and columns.
document each and every set of item as it enters the warehouse, all of its movements on the
warehouse floor as well as its movement during transportation from one location to the next.
Using spreadsheets to manage inventory: With the help of undertaking use of
spreadsheets as to effectively manage inventory Starbucks manage their inventory on a
elementary scale (Nunez-Solis, 2019). It has been evaluated that spreadsheets are mainly
considered as frequent go to tool in order to collect and organize data. It allow in charge person
to easily place information and data in elegant rows and columns.
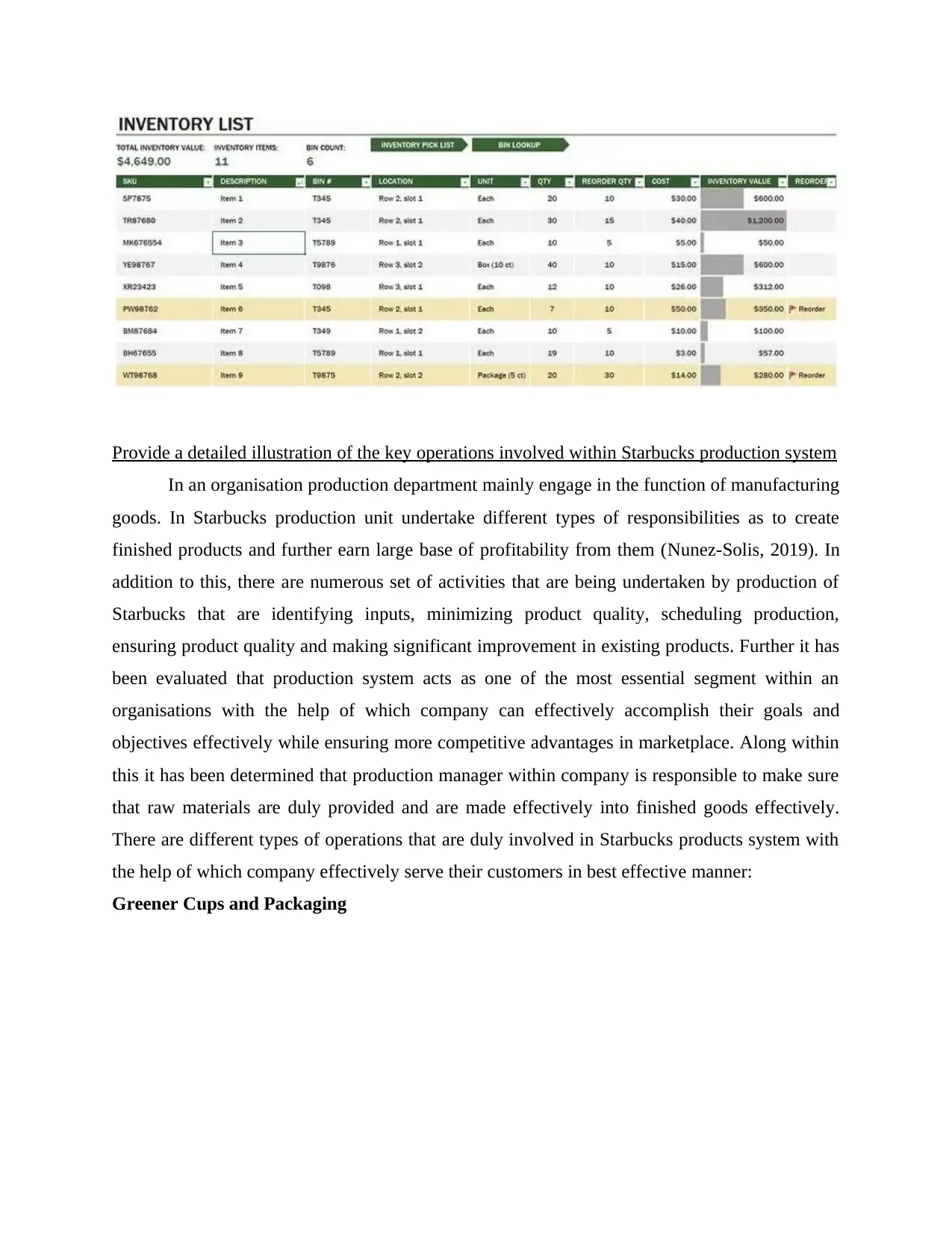
Provide a detailed illustration of the key operations involved within Starbucks production system
In an organisation production department mainly engage in the function of manufacturing
goods. In Starbucks production unit undertake different types of responsibilities as to create
finished products and further earn large base of profitability from them (Nunez-Solis, 2019). In
addition to this, there are numerous set of activities that are being undertaken by production of
Starbucks that are identifying inputs, minimizing product quality, scheduling production,
ensuring product quality and making significant improvement in existing products. Further it has
been evaluated that production system acts as one of the most essential segment within an
organisations with the help of which company can effectively accomplish their goals and
objectives effectively while ensuring more competitive advantages in marketplace. Along within
this it has been determined that production manager within company is responsible to make sure
that raw materials are duly provided and are made effectively into finished goods effectively.
There are different types of operations that are duly involved in Starbucks products system with
the help of which company effectively serve their customers in best effective manner:
Greener Cups and Packaging
In an organisation production department mainly engage in the function of manufacturing
goods. In Starbucks production unit undertake different types of responsibilities as to create
finished products and further earn large base of profitability from them (Nunez-Solis, 2019). In
addition to this, there are numerous set of activities that are being undertaken by production of
Starbucks that are identifying inputs, minimizing product quality, scheduling production,
ensuring product quality and making significant improvement in existing products. Further it has
been evaluated that production system acts as one of the most essential segment within an
organisations with the help of which company can effectively accomplish their goals and
objectives effectively while ensuring more competitive advantages in marketplace. Along within
this it has been determined that production manager within company is responsible to make sure
that raw materials are duly provided and are made effectively into finished goods effectively.
There are different types of operations that are duly involved in Starbucks products system with
the help of which company effectively serve their customers in best effective manner:
Greener Cups and Packaging
Paraphrase This Document
Need a fresh take? Get an instant paraphrase of this document with our AI Paraphraser
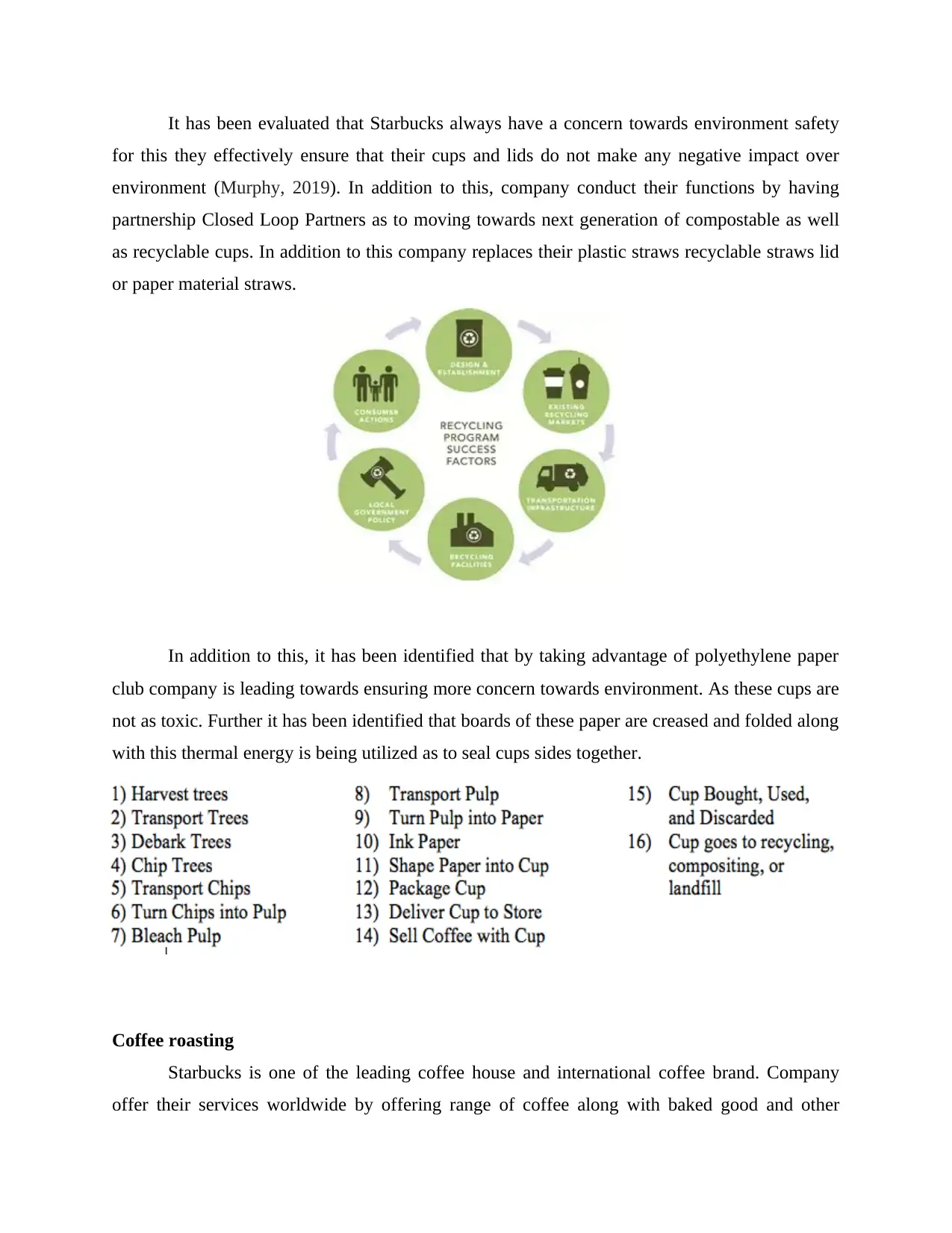
It has been evaluated that Starbucks always have a concern towards environment safety
for this they effectively ensure that their cups and lids do not make any negative impact over
environment (Murphy, 2019). In addition to this, company conduct their functions by having
partnership Closed Loop Partners as to moving towards next generation of compostable as well
as recyclable cups. In addition to this company replaces their plastic straws recyclable straws lid
or paper material straws.
In addition to this, it has been identified that by taking advantage of polyethylene paper
club company is leading towards ensuring more concern towards environment. As these cups are
not as toxic. Further it has been identified that boards of these paper are creased and folded along
with this thermal energy is being utilized as to seal cups sides together.
Coffee roasting
Starbucks is one of the leading coffee house and international coffee brand. Company
offer their services worldwide by offering range of coffee along with baked good and other
for this they effectively ensure that their cups and lids do not make any negative impact over
environment (Murphy, 2019). In addition to this, company conduct their functions by having
partnership Closed Loop Partners as to moving towards next generation of compostable as well
as recyclable cups. In addition to this company replaces their plastic straws recyclable straws lid
or paper material straws.
In addition to this, it has been identified that by taking advantage of polyethylene paper
club company is leading towards ensuring more concern towards environment. As these cups are
not as toxic. Further it has been identified that boards of these paper are creased and folded along
with this thermal energy is being utilized as to seal cups sides together.
Coffee roasting
Starbucks is one of the leading coffee house and international coffee brand. Company
offer their services worldwide by offering range of coffee along with baked good and other
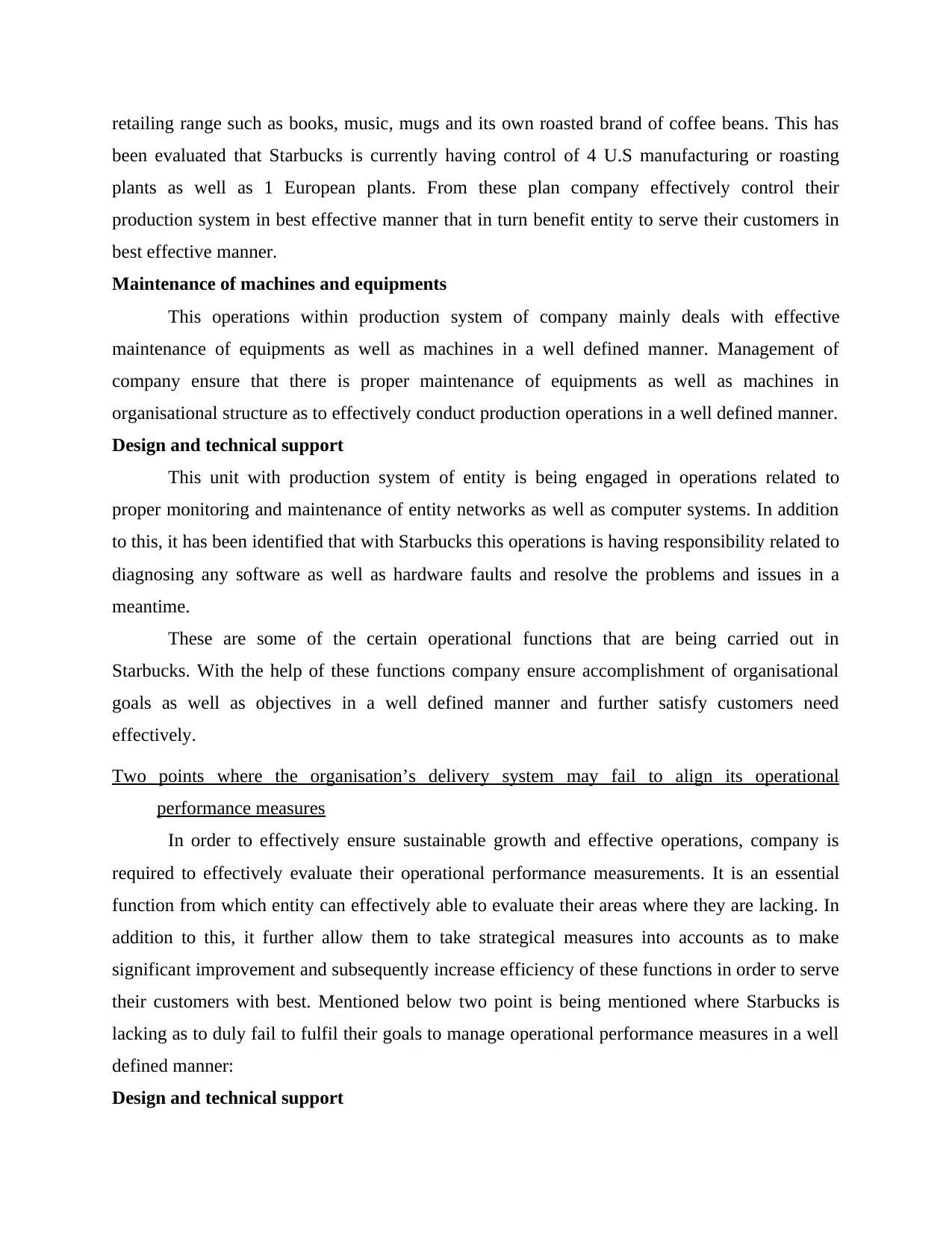
retailing range such as books, music, mugs and its own roasted brand of coffee beans. This has
been evaluated that Starbucks is currently having control of 4 U.S manufacturing or roasting
plants as well as 1 European plants. From these plan company effectively control their
production system in best effective manner that in turn benefit entity to serve their customers in
best effective manner.
Maintenance of machines and equipments
This operations within production system of company mainly deals with effective
maintenance of equipments as well as machines in a well defined manner. Management of
company ensure that there is proper maintenance of equipments as well as machines in
organisational structure as to effectively conduct production operations in a well defined manner.
Design and technical support
This unit with production system of entity is being engaged in operations related to
proper monitoring and maintenance of entity networks as well as computer systems. In addition
to this, it has been identified that with Starbucks this operations is having responsibility related to
diagnosing any software as well as hardware faults and resolve the problems and issues in a
meantime.
These are some of the certain operational functions that are being carried out in
Starbucks. With the help of these functions company ensure accomplishment of organisational
goals as well as objectives in a well defined manner and further satisfy customers need
effectively.
Two points where the organisation’s delivery system may fail to align its operational
performance measures
In order to effectively ensure sustainable growth and effective operations, company is
required to effectively evaluate their operational performance measurements. It is an essential
function from which entity can effectively able to evaluate their areas where they are lacking. In
addition to this, it further allow them to take strategical measures into accounts as to make
significant improvement and subsequently increase efficiency of these functions in order to serve
their customers with best. Mentioned below two point is being mentioned where Starbucks is
lacking as to duly fail to fulfil their goals to manage operational performance measures in a well
defined manner:
Design and technical support
been evaluated that Starbucks is currently having control of 4 U.S manufacturing or roasting
plants as well as 1 European plants. From these plan company effectively control their
production system in best effective manner that in turn benefit entity to serve their customers in
best effective manner.
Maintenance of machines and equipments
This operations within production system of company mainly deals with effective
maintenance of equipments as well as machines in a well defined manner. Management of
company ensure that there is proper maintenance of equipments as well as machines in
organisational structure as to effectively conduct production operations in a well defined manner.
Design and technical support
This unit with production system of entity is being engaged in operations related to
proper monitoring and maintenance of entity networks as well as computer systems. In addition
to this, it has been identified that with Starbucks this operations is having responsibility related to
diagnosing any software as well as hardware faults and resolve the problems and issues in a
meantime.
These are some of the certain operational functions that are being carried out in
Starbucks. With the help of these functions company ensure accomplishment of organisational
goals as well as objectives in a well defined manner and further satisfy customers need
effectively.
Two points where the organisation’s delivery system may fail to align its operational
performance measures
In order to effectively ensure sustainable growth and effective operations, company is
required to effectively evaluate their operational performance measurements. It is an essential
function from which entity can effectively able to evaluate their areas where they are lacking. In
addition to this, it further allow them to take strategical measures into accounts as to make
significant improvement and subsequently increase efficiency of these functions in order to serve
their customers with best. Mentioned below two point is being mentioned where Starbucks is
lacking as to duly fail to fulfil their goals to manage operational performance measures in a well
defined manner:
Design and technical support
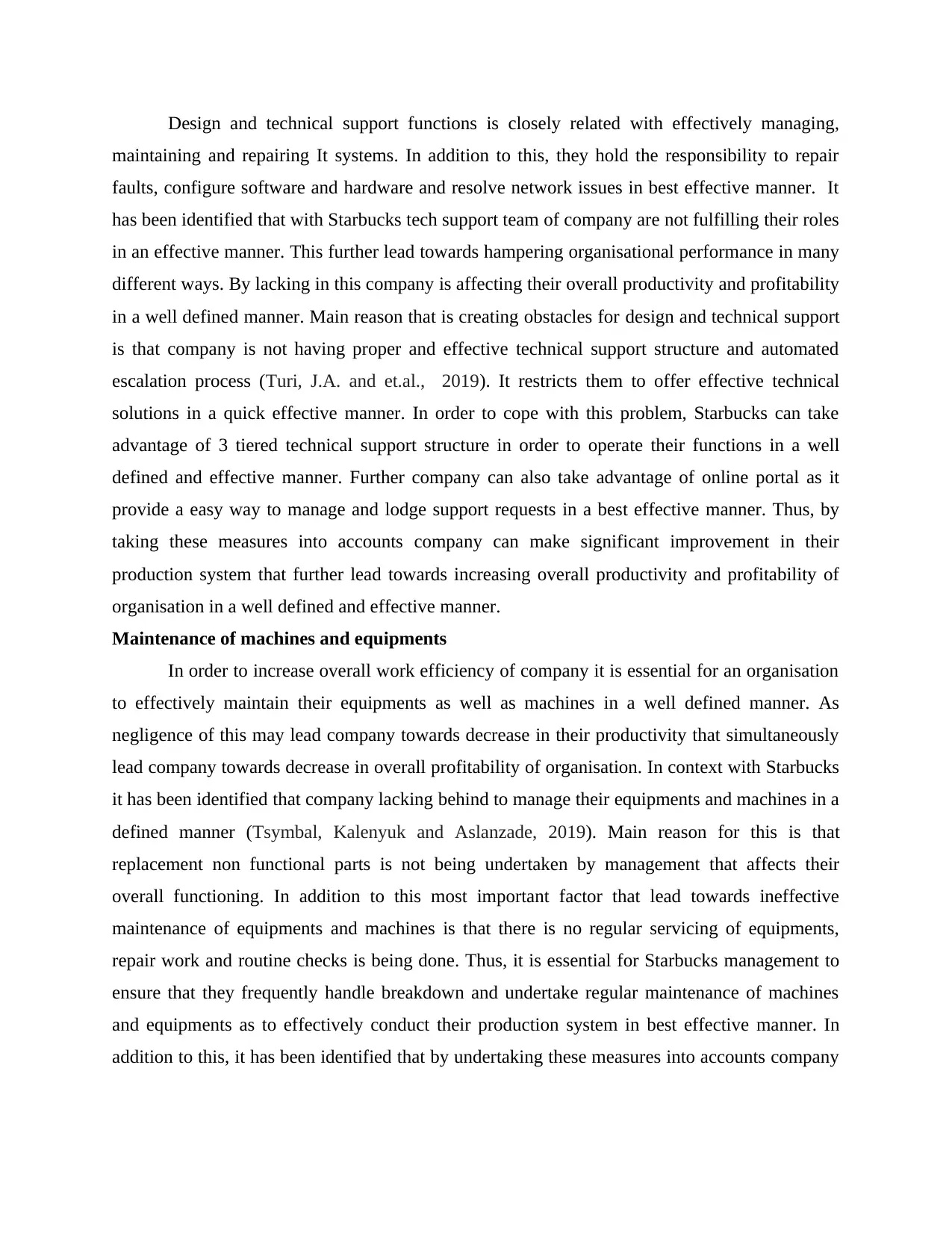
Design and technical support functions is closely related with effectively managing,
maintaining and repairing It systems. In addition to this, they hold the responsibility to repair
faults, configure software and hardware and resolve network issues in best effective manner. It
has been identified that with Starbucks tech support team of company are not fulfilling their roles
in an effective manner. This further lead towards hampering organisational performance in many
different ways. By lacking in this company is affecting their overall productivity and profitability
in a well defined manner. Main reason that is creating obstacles for design and technical support
is that company is not having proper and effective technical support structure and automated
escalation process (Turi, J.A. and et.al., 2019). It restricts them to offer effective technical
solutions in a quick effective manner. In order to cope with this problem, Starbucks can take
advantage of 3 tiered technical support structure in order to operate their functions in a well
defined and effective manner. Further company can also take advantage of online portal as it
provide a easy way to manage and lodge support requests in a best effective manner. Thus, by
taking these measures into accounts company can make significant improvement in their
production system that further lead towards increasing overall productivity and profitability of
organisation in a well defined and effective manner.
Maintenance of machines and equipments
In order to increase overall work efficiency of company it is essential for an organisation
to effectively maintain their equipments as well as machines in a well defined manner. As
negligence of this may lead company towards decrease in their productivity that simultaneously
lead company towards decrease in overall profitability of organisation. In context with Starbucks
it has been identified that company lacking behind to manage their equipments and machines in a
defined manner (Tsymbal, Kalenyuk and Aslanzade, 2019). Main reason for this is that
replacement non functional parts is not being undertaken by management that affects their
overall functioning. In addition to this most important factor that lead towards ineffective
maintenance of equipments and machines is that there is no regular servicing of equipments,
repair work and routine checks is being done. Thus, it is essential for Starbucks management to
ensure that they frequently handle breakdown and undertake regular maintenance of machines
and equipments as to effectively conduct their production system in best effective manner. In
addition to this, it has been identified that by undertaking these measures into accounts company
maintaining and repairing It systems. In addition to this, they hold the responsibility to repair
faults, configure software and hardware and resolve network issues in best effective manner. It
has been identified that with Starbucks tech support team of company are not fulfilling their roles
in an effective manner. This further lead towards hampering organisational performance in many
different ways. By lacking in this company is affecting their overall productivity and profitability
in a well defined manner. Main reason that is creating obstacles for design and technical support
is that company is not having proper and effective technical support structure and automated
escalation process (Turi, J.A. and et.al., 2019). It restricts them to offer effective technical
solutions in a quick effective manner. In order to cope with this problem, Starbucks can take
advantage of 3 tiered technical support structure in order to operate their functions in a well
defined and effective manner. Further company can also take advantage of online portal as it
provide a easy way to manage and lodge support requests in a best effective manner. Thus, by
taking these measures into accounts company can make significant improvement in their
production system that further lead towards increasing overall productivity and profitability of
organisation in a well defined and effective manner.
Maintenance of machines and equipments
In order to increase overall work efficiency of company it is essential for an organisation
to effectively maintain their equipments as well as machines in a well defined manner. As
negligence of this may lead company towards decrease in their productivity that simultaneously
lead company towards decrease in overall profitability of organisation. In context with Starbucks
it has been identified that company lacking behind to manage their equipments and machines in a
defined manner (Tsymbal, Kalenyuk and Aslanzade, 2019). Main reason for this is that
replacement non functional parts is not being undertaken by management that affects their
overall functioning. In addition to this most important factor that lead towards ineffective
maintenance of equipments and machines is that there is no regular servicing of equipments,
repair work and routine checks is being done. Thus, it is essential for Starbucks management to
ensure that they frequently handle breakdown and undertake regular maintenance of machines
and equipments as to effectively conduct their production system in best effective manner. In
addition to this, it has been identified that by undertaking these measures into accounts company
Secure Best Marks with AI Grader
Need help grading? Try our AI Grader for instant feedback on your assignments.
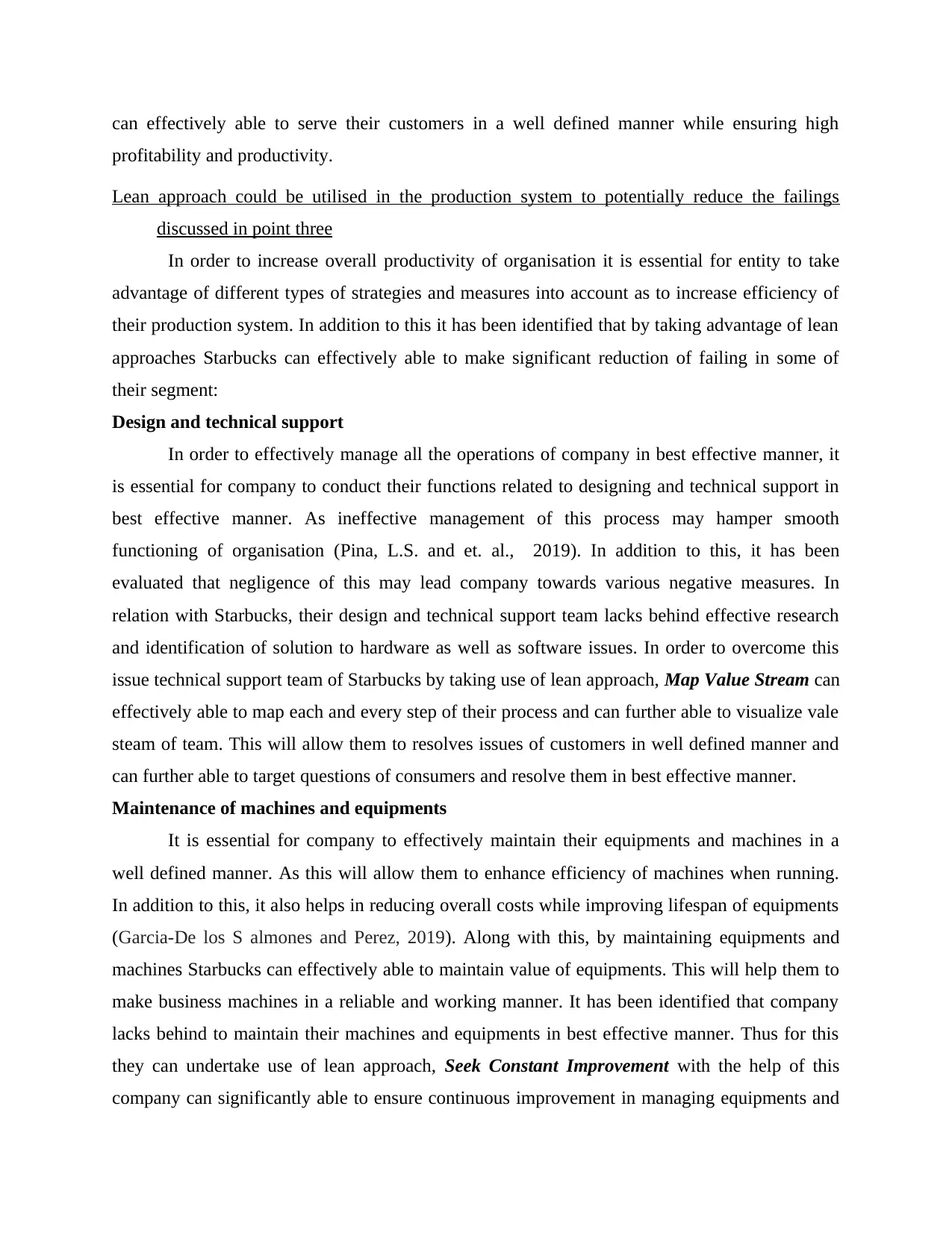
can effectively able to serve their customers in a well defined manner while ensuring high
profitability and productivity.
Lean approach could be utilised in the production system to potentially reduce the failings
discussed in point three
In order to increase overall productivity of organisation it is essential for entity to take
advantage of different types of strategies and measures into account as to increase efficiency of
their production system. In addition to this it has been identified that by taking advantage of lean
approaches Starbucks can effectively able to make significant reduction of failing in some of
their segment:
Design and technical support
In order to effectively manage all the operations of company in best effective manner, it
is essential for company to conduct their functions related to designing and technical support in
best effective manner. As ineffective management of this process may hamper smooth
functioning of organisation (Pina, L.S. and et. al., 2019). In addition to this, it has been
evaluated that negligence of this may lead company towards various negative measures. In
relation with Starbucks, their design and technical support team lacks behind effective research
and identification of solution to hardware as well as software issues. In order to overcome this
issue technical support team of Starbucks by taking use of lean approach, Map Value Stream can
effectively able to map each and every step of their process and can further able to visualize vale
steam of team. This will allow them to resolves issues of customers in well defined manner and
can further able to target questions of consumers and resolve them in best effective manner.
Maintenance of machines and equipments
It is essential for company to effectively maintain their equipments and machines in a
well defined manner. As this will allow them to enhance efficiency of machines when running.
In addition to this, it also helps in reducing overall costs while improving lifespan of equipments
(Garcia-De los S almones and Perez, 2019). Along with this, by maintaining equipments and
machines Starbucks can effectively able to maintain value of equipments. This will help them to
make business machines in a reliable and working manner. It has been identified that company
lacks behind to maintain their machines and equipments in best effective manner. Thus for this
they can undertake use of lean approach, Seek Constant Improvement with the help of this
company can significantly able to ensure continuous improvement in managing equipments and
profitability and productivity.
Lean approach could be utilised in the production system to potentially reduce the failings
discussed in point three
In order to increase overall productivity of organisation it is essential for entity to take
advantage of different types of strategies and measures into account as to increase efficiency of
their production system. In addition to this it has been identified that by taking advantage of lean
approaches Starbucks can effectively able to make significant reduction of failing in some of
their segment:
Design and technical support
In order to effectively manage all the operations of company in best effective manner, it
is essential for company to conduct their functions related to designing and technical support in
best effective manner. As ineffective management of this process may hamper smooth
functioning of organisation (Pina, L.S. and et. al., 2019). In addition to this, it has been
evaluated that negligence of this may lead company towards various negative measures. In
relation with Starbucks, their design and technical support team lacks behind effective research
and identification of solution to hardware as well as software issues. In order to overcome this
issue technical support team of Starbucks by taking use of lean approach, Map Value Stream can
effectively able to map each and every step of their process and can further able to visualize vale
steam of team. This will allow them to resolves issues of customers in well defined manner and
can further able to target questions of consumers and resolve them in best effective manner.
Maintenance of machines and equipments
It is essential for company to effectively maintain their equipments and machines in a
well defined manner. As this will allow them to enhance efficiency of machines when running.
In addition to this, it also helps in reducing overall costs while improving lifespan of equipments
(Garcia-De los S almones and Perez, 2019). Along with this, by maintaining equipments and
machines Starbucks can effectively able to maintain value of equipments. This will help them to
make business machines in a reliable and working manner. It has been identified that company
lacks behind to maintain their machines and equipments in best effective manner. Thus for this
they can undertake use of lean approach, Seek Constant Improvement with the help of this
company can significantly able to ensure continuous improvement in managing equipments and
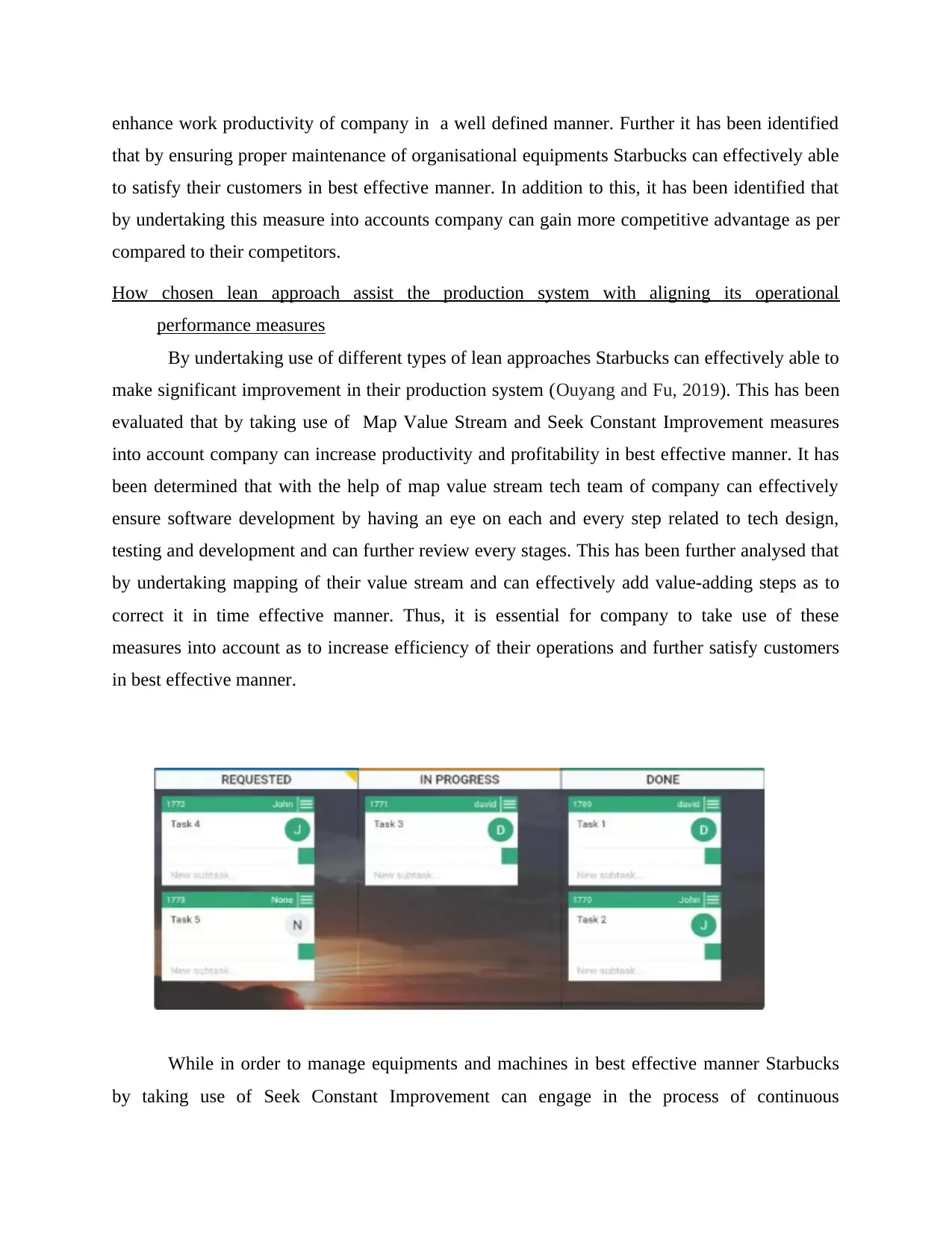
enhance work productivity of company in a well defined manner. Further it has been identified
that by ensuring proper maintenance of organisational equipments Starbucks can effectively able
to satisfy their customers in best effective manner. In addition to this, it has been identified that
by undertaking this measure into accounts company can gain more competitive advantage as per
compared to their competitors.
How chosen lean approach assist the production system with aligning its operational
performance measures
By undertaking use of different types of lean approaches Starbucks can effectively able to
make significant improvement in their production system (Ouyang and Fu, 2019). This has been
evaluated that by taking use of Map Value Stream and Seek Constant Improvement measures
into account company can increase productivity and profitability in best effective manner. It has
been determined that with the help of map value stream tech team of company can effectively
ensure software development by having an eye on each and every step related to tech design,
testing and development and can further review every stages. This has been further analysed that
by undertaking mapping of their value stream and can effectively add value-adding steps as to
correct it in time effective manner. Thus, it is essential for company to take use of these
measures into account as to increase efficiency of their operations and further satisfy customers
in best effective manner.
While in order to manage equipments and machines in best effective manner Starbucks
by taking use of Seek Constant Improvement can engage in the process of continuous
that by ensuring proper maintenance of organisational equipments Starbucks can effectively able
to satisfy their customers in best effective manner. In addition to this, it has been identified that
by undertaking this measure into accounts company can gain more competitive advantage as per
compared to their competitors.
How chosen lean approach assist the production system with aligning its operational
performance measures
By undertaking use of different types of lean approaches Starbucks can effectively able to
make significant improvement in their production system (Ouyang and Fu, 2019). This has been
evaluated that by taking use of Map Value Stream and Seek Constant Improvement measures
into account company can increase productivity and profitability in best effective manner. It has
been determined that with the help of map value stream tech team of company can effectively
ensure software development by having an eye on each and every step related to tech design,
testing and development and can further review every stages. This has been further analysed that
by undertaking mapping of their value stream and can effectively add value-adding steps as to
correct it in time effective manner. Thus, it is essential for company to take use of these
measures into account as to increase efficiency of their operations and further satisfy customers
in best effective manner.
While in order to manage equipments and machines in best effective manner Starbucks
by taking use of Seek Constant Improvement can engage in the process of continuous
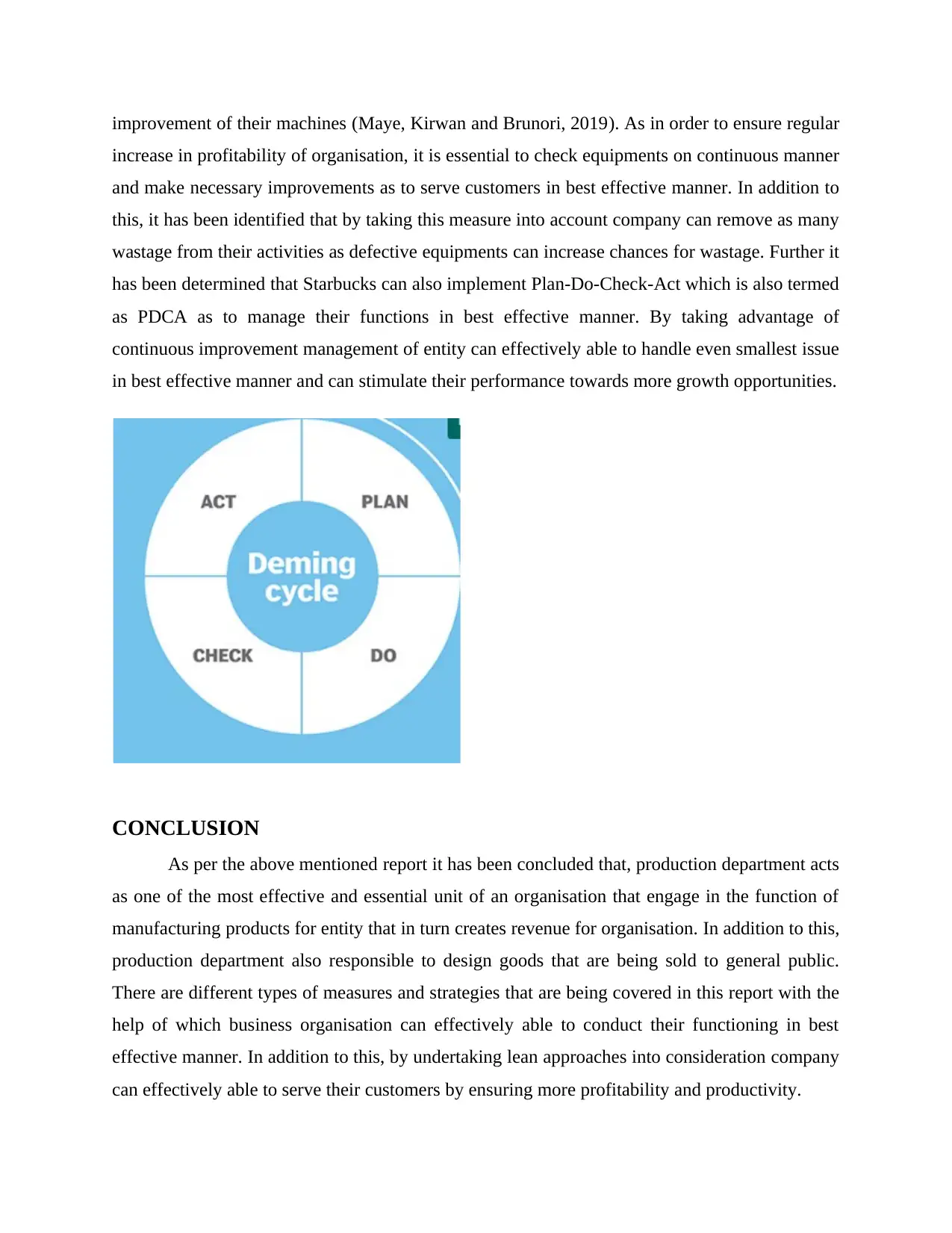
improvement of their machines (Maye, Kirwan and Brunori, 2019). As in order to ensure regular
increase in profitability of organisation, it is essential to check equipments on continuous manner
and make necessary improvements as to serve customers in best effective manner. In addition to
this, it has been identified that by taking this measure into account company can remove as many
wastage from their activities as defective equipments can increase chances for wastage. Further it
has been determined that Starbucks can also implement Plan-Do-Check-Act which is also termed
as PDCA as to manage their functions in best effective manner. By taking advantage of
continuous improvement management of entity can effectively able to handle even smallest issue
in best effective manner and can stimulate their performance towards more growth opportunities.
CONCLUSION
As per the above mentioned report it has been concluded that, production department acts
as one of the most effective and essential unit of an organisation that engage in the function of
manufacturing products for entity that in turn creates revenue for organisation. In addition to this,
production department also responsible to design goods that are being sold to general public.
There are different types of measures and strategies that are being covered in this report with the
help of which business organisation can effectively able to conduct their functioning in best
effective manner. In addition to this, by undertaking lean approaches into consideration company
can effectively able to serve their customers by ensuring more profitability and productivity.
increase in profitability of organisation, it is essential to check equipments on continuous manner
and make necessary improvements as to serve customers in best effective manner. In addition to
this, it has been identified that by taking this measure into account company can remove as many
wastage from their activities as defective equipments can increase chances for wastage. Further it
has been determined that Starbucks can also implement Plan-Do-Check-Act which is also termed
as PDCA as to manage their functions in best effective manner. By taking advantage of
continuous improvement management of entity can effectively able to handle even smallest issue
in best effective manner and can stimulate their performance towards more growth opportunities.
CONCLUSION
As per the above mentioned report it has been concluded that, production department acts
as one of the most effective and essential unit of an organisation that engage in the function of
manufacturing products for entity that in turn creates revenue for organisation. In addition to this,
production department also responsible to design goods that are being sold to general public.
There are different types of measures and strategies that are being covered in this report with the
help of which business organisation can effectively able to conduct their functioning in best
effective manner. In addition to this, by undertaking lean approaches into consideration company
can effectively able to serve their customers by ensuring more profitability and productivity.
Paraphrase This Document
Need a fresh take? Get an instant paraphrase of this document with our AI Paraphraser
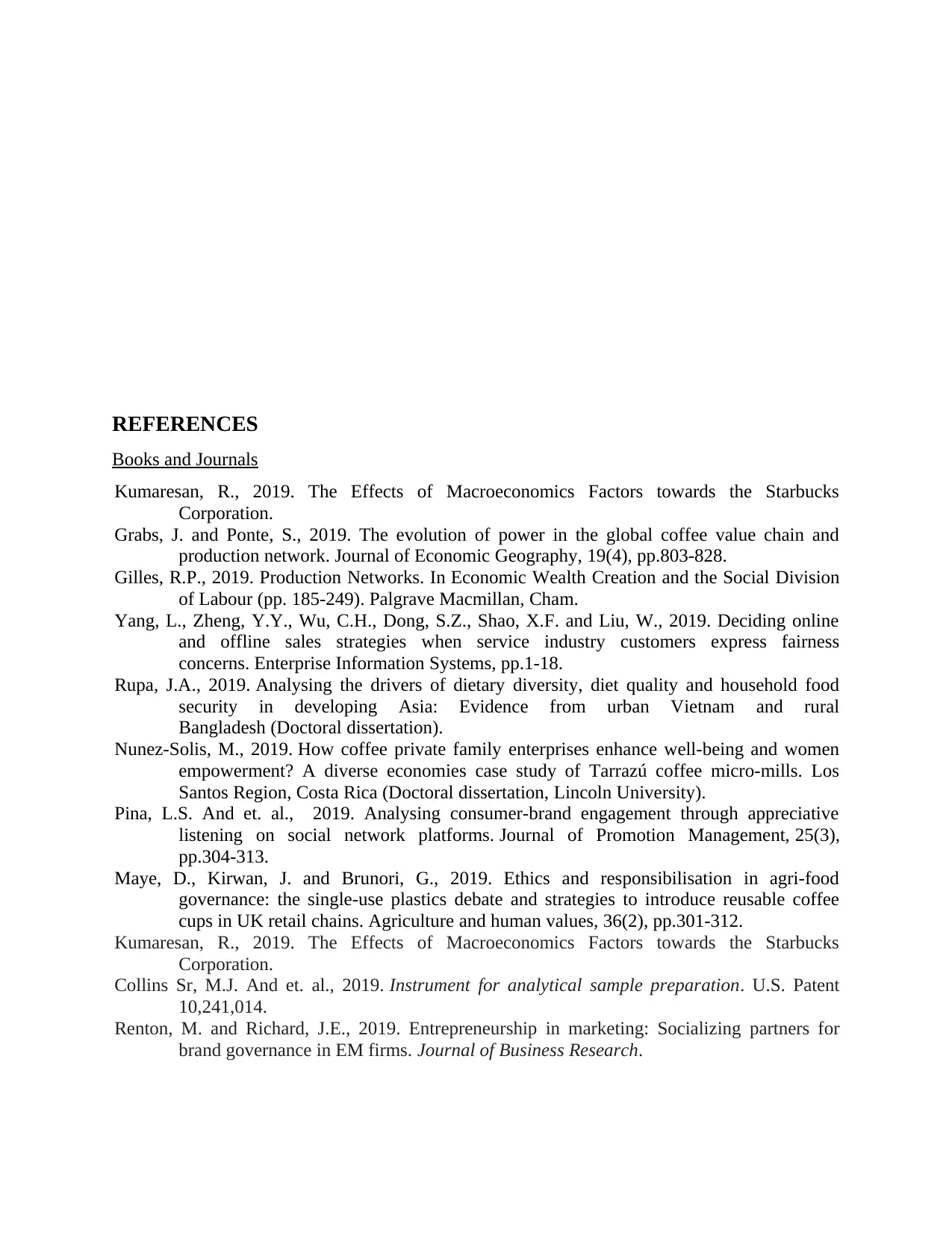
REFERENCES
Books and Journals
Kumaresan, R., 2019. The Effects of Macroeconomics Factors towards the Starbucks
Corporation.
Grabs, J. and Ponte, S., 2019. The evolution of power in the global coffee value chain and
production network. Journal of Economic Geography, 19(4), pp.803-828.
Gilles, R.P., 2019. Production Networks. In Economic Wealth Creation and the Social Division
of Labour (pp. 185-249). Palgrave Macmillan, Cham.
Yang, L., Zheng, Y.Y., Wu, C.H., Dong, S.Z., Shao, X.F. and Liu, W., 2019. Deciding online
and offline sales strategies when service industry customers express fairness
concerns. Enterprise Information Systems, pp.1-18.
Rupa, J.A., 2019. Analysing the drivers of dietary diversity, diet quality and household food
security in developing Asia: Evidence from urban Vietnam and rural
Bangladesh (Doctoral dissertation).
Nunez-Solis, M., 2019. How coffee private family enterprises enhance well-being and women
empowerment? A diverse economies case study of Tarrazú coffee micro-mills. Los
Santos Region, Costa Rica (Doctoral dissertation, Lincoln University).
Pina, L.S. And et. al., 2019. Analysing consumer-brand engagement through appreciative
listening on social network platforms. Journal of Promotion Management, 25(3),
pp.304-313.
Maye, D., Kirwan, J. and Brunori, G., 2019. Ethics and responsibilisation in agri-food
governance: the single-use plastics debate and strategies to introduce reusable coffee
cups in UK retail chains. Agriculture and human values, 36(2), pp.301-312.
Kumaresan, R., 2019. The Effects of Macroeconomics Factors towards the Starbucks
Corporation.
Collins Sr, M.J. And et. al., 2019. Instrument for analytical sample preparation. U.S. Patent
10,241,014.
Renton, M. and Richard, J.E., 2019. Entrepreneurship in marketing: Socializing partners for
brand governance in EM firms. Journal of Business Research.
Books and Journals
Kumaresan, R., 2019. The Effects of Macroeconomics Factors towards the Starbucks
Corporation.
Grabs, J. and Ponte, S., 2019. The evolution of power in the global coffee value chain and
production network. Journal of Economic Geography, 19(4), pp.803-828.
Gilles, R.P., 2019. Production Networks. In Economic Wealth Creation and the Social Division
of Labour (pp. 185-249). Palgrave Macmillan, Cham.
Yang, L., Zheng, Y.Y., Wu, C.H., Dong, S.Z., Shao, X.F. and Liu, W., 2019. Deciding online
and offline sales strategies when service industry customers express fairness
concerns. Enterprise Information Systems, pp.1-18.
Rupa, J.A., 2019. Analysing the drivers of dietary diversity, diet quality and household food
security in developing Asia: Evidence from urban Vietnam and rural
Bangladesh (Doctoral dissertation).
Nunez-Solis, M., 2019. How coffee private family enterprises enhance well-being and women
empowerment? A diverse economies case study of Tarrazú coffee micro-mills. Los
Santos Region, Costa Rica (Doctoral dissertation, Lincoln University).
Pina, L.S. And et. al., 2019. Analysing consumer-brand engagement through appreciative
listening on social network platforms. Journal of Promotion Management, 25(3),
pp.304-313.
Maye, D., Kirwan, J. and Brunori, G., 2019. Ethics and responsibilisation in agri-food
governance: the single-use plastics debate and strategies to introduce reusable coffee
cups in UK retail chains. Agriculture and human values, 36(2), pp.301-312.
Kumaresan, R., 2019. The Effects of Macroeconomics Factors towards the Starbucks
Corporation.
Collins Sr, M.J. And et. al., 2019. Instrument for analytical sample preparation. U.S. Patent
10,241,014.
Renton, M. and Richard, J.E., 2019. Entrepreneurship in marketing: Socializing partners for
brand governance in EM firms. Journal of Business Research.
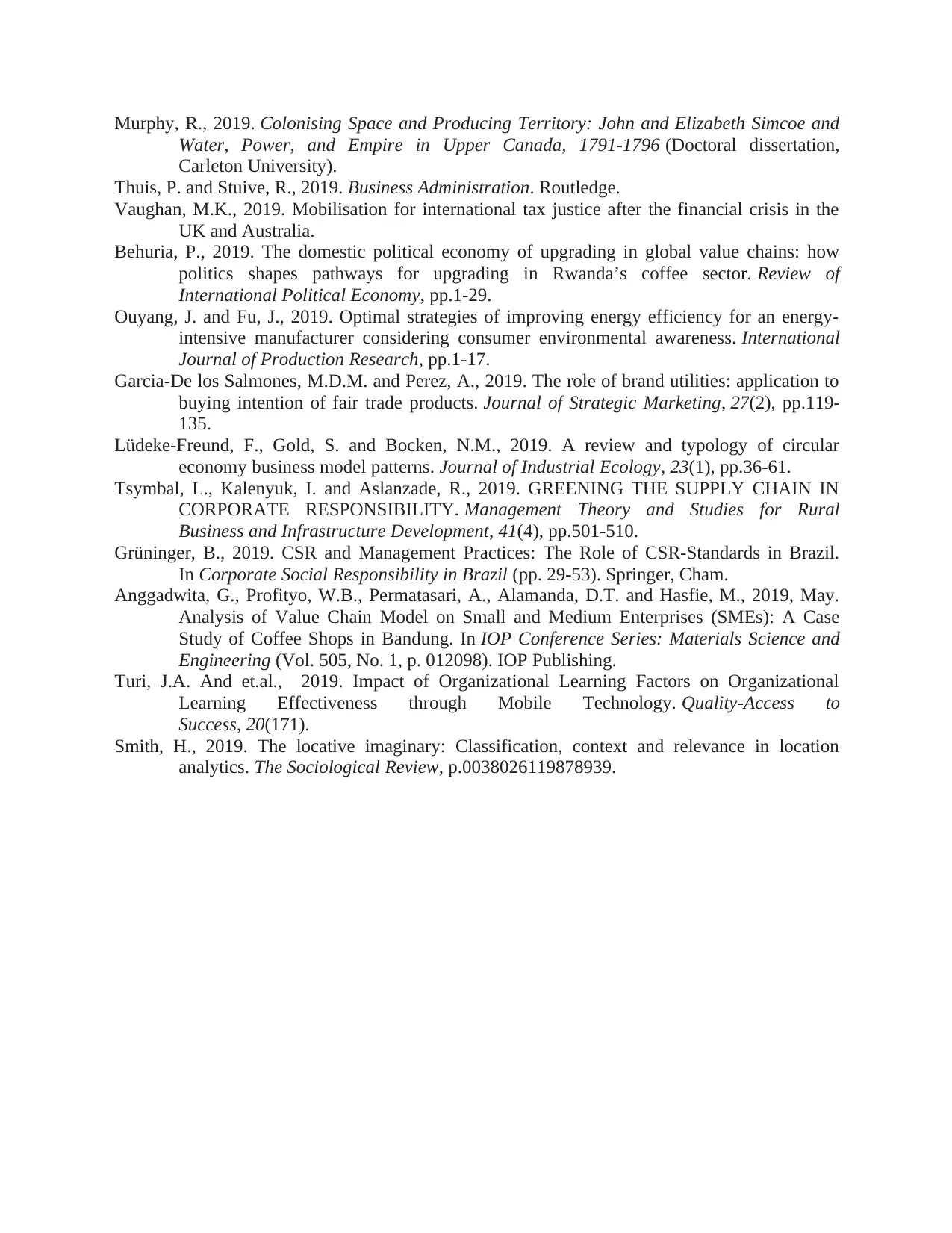
Murphy, R., 2019. Colonising Space and Producing Territory: John and Elizabeth Simcoe and
Water, Power, and Empire in Upper Canada, 1791-1796 (Doctoral dissertation,
Carleton University).
Thuis, P. and Stuive, R., 2019. Business Administration. Routledge.
Vaughan, M.K., 2019. Mobilisation for international tax justice after the financial crisis in the
UK and Australia.
Behuria, P., 2019. The domestic political economy of upgrading in global value chains: how
politics shapes pathways for upgrading in Rwanda’s coffee sector. Review of
International Political Economy, pp.1-29.
Ouyang, J. and Fu, J., 2019. Optimal strategies of improving energy efficiency for an energy-
intensive manufacturer considering consumer environmental awareness. International
Journal of Production Research, pp.1-17.
Garcia-De los Salmones, M.D.M. and Perez, A., 2019. The role of brand utilities: application to
buying intention of fair trade products. Journal of Strategic Marketing, 27(2), pp.119-
135.
Lüdeke‐Freund, F., Gold, S. and Bocken, N.M., 2019. A review and typology of circular
economy business model patterns. Journal of Industrial Ecology, 23(1), pp.36-61.
Tsymbal, L., Kalenyuk, I. and Aslanzade, R., 2019. GREENING THE SUPPLY CHAIN IN
CORPORATE RESPONSIBILITY. Management Theory and Studies for Rural
Business and Infrastructure Development, 41(4), pp.501-510.
Grüninger, B., 2019. CSR and Management Practices: The Role of CSR-Standards in Brazil.
In Corporate Social Responsibility in Brazil (pp. 29-53). Springer, Cham.
Anggadwita, G., Profityo, W.B., Permatasari, A., Alamanda, D.T. and Hasfie, M., 2019, May.
Analysis of Value Chain Model on Small and Medium Enterprises (SMEs): A Case
Study of Coffee Shops in Bandung. In IOP Conference Series: Materials Science and
Engineering (Vol. 505, No. 1, p. 012098). IOP Publishing.
Turi, J.A. And et.al., 2019. Impact of Organizational Learning Factors on Organizational
Learning Effectiveness through Mobile Technology. Quality-Access to
Success, 20(171).
Smith, H., 2019. The locative imaginary: Classification, context and relevance in location
analytics. The Sociological Review, p.0038026119878939.
Water, Power, and Empire in Upper Canada, 1791-1796 (Doctoral dissertation,
Carleton University).
Thuis, P. and Stuive, R., 2019. Business Administration. Routledge.
Vaughan, M.K., 2019. Mobilisation for international tax justice after the financial crisis in the
UK and Australia.
Behuria, P., 2019. The domestic political economy of upgrading in global value chains: how
politics shapes pathways for upgrading in Rwanda’s coffee sector. Review of
International Political Economy, pp.1-29.
Ouyang, J. and Fu, J., 2019. Optimal strategies of improving energy efficiency for an energy-
intensive manufacturer considering consumer environmental awareness. International
Journal of Production Research, pp.1-17.
Garcia-De los Salmones, M.D.M. and Perez, A., 2019. The role of brand utilities: application to
buying intention of fair trade products. Journal of Strategic Marketing, 27(2), pp.119-
135.
Lüdeke‐Freund, F., Gold, S. and Bocken, N.M., 2019. A review and typology of circular
economy business model patterns. Journal of Industrial Ecology, 23(1), pp.36-61.
Tsymbal, L., Kalenyuk, I. and Aslanzade, R., 2019. GREENING THE SUPPLY CHAIN IN
CORPORATE RESPONSIBILITY. Management Theory and Studies for Rural
Business and Infrastructure Development, 41(4), pp.501-510.
Grüninger, B., 2019. CSR and Management Practices: The Role of CSR-Standards in Brazil.
In Corporate Social Responsibility in Brazil (pp. 29-53). Springer, Cham.
Anggadwita, G., Profityo, W.B., Permatasari, A., Alamanda, D.T. and Hasfie, M., 2019, May.
Analysis of Value Chain Model on Small and Medium Enterprises (SMEs): A Case
Study of Coffee Shops in Bandung. In IOP Conference Series: Materials Science and
Engineering (Vol. 505, No. 1, p. 012098). IOP Publishing.
Turi, J.A. And et.al., 2019. Impact of Organizational Learning Factors on Organizational
Learning Effectiveness through Mobile Technology. Quality-Access to
Success, 20(171).
Smith, H., 2019. The locative imaginary: Classification, context and relevance in location
analytics. The Sociological Review, p.0038026119878939.
1 out of 15
Related Documents

Your All-in-One AI-Powered Toolkit for Academic Success.
+13062052269
info@desklib.com
Available 24*7 on WhatsApp / Email
Unlock your academic potential
© 2024 | Zucol Services PVT LTD | All rights reserved.