Strategic Quality and System Management Analysis for Unilever
VerifiedAdded on  2020/02/03
|19
|6681
|139
Report
AI Summary
This report provides a comprehensive analysis of strategic quality and system management within Unilever. It begins by exploring the importance of effective operations management in achieving organizational objectives, followed by an evaluation of Unilever's existing operations management processes. The report then delves into the significance of effective quality management, assessing the success of current quality management processes, including TQM and EFQM. A significant portion of the report focuses on developing a strategic quality change plan to enhance organizational performance, defining necessary resources, tools, and systems. It also examines the broader implications of the planned changes and designs a system for monitoring implementation. The final sections cover the implementation of strategic quality changes, embedding a quality culture, monitoring the changes, evaluating outcomes, and recommending areas for improvement to align with Unilever's objectives. The report utilizes supply chain models and discusses the impact of quality management on various aspects of Unilever's business, including product safety, employee motivation, and customer satisfaction.
Contribute Materials
Your contribution can guide someone’s learning journey. Share your
documents today.
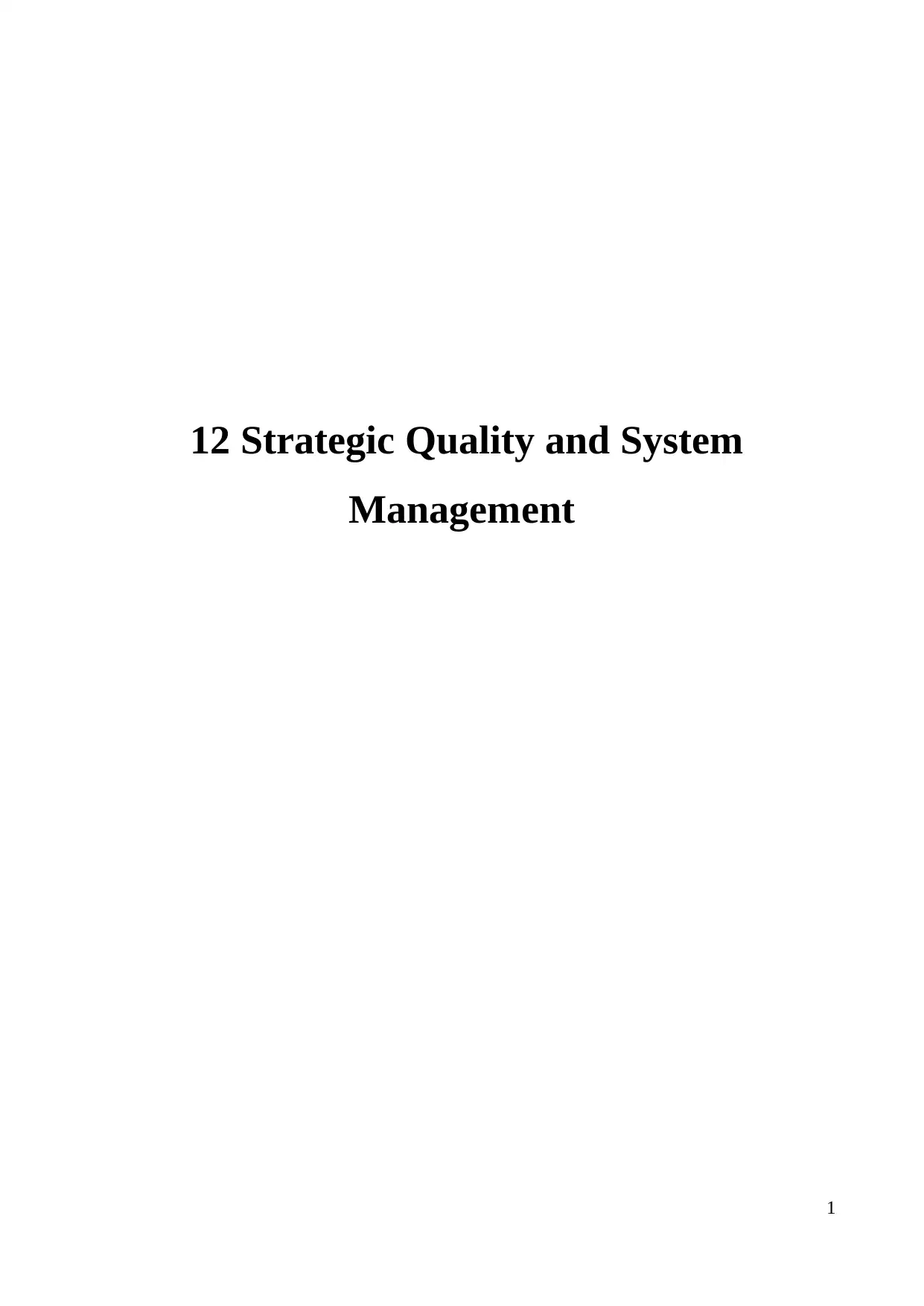
12 Strategic Quality and System
Management
1
Management
1
Secure Best Marks with AI Grader
Need help grading? Try our AI Grader for instant feedback on your assignments.
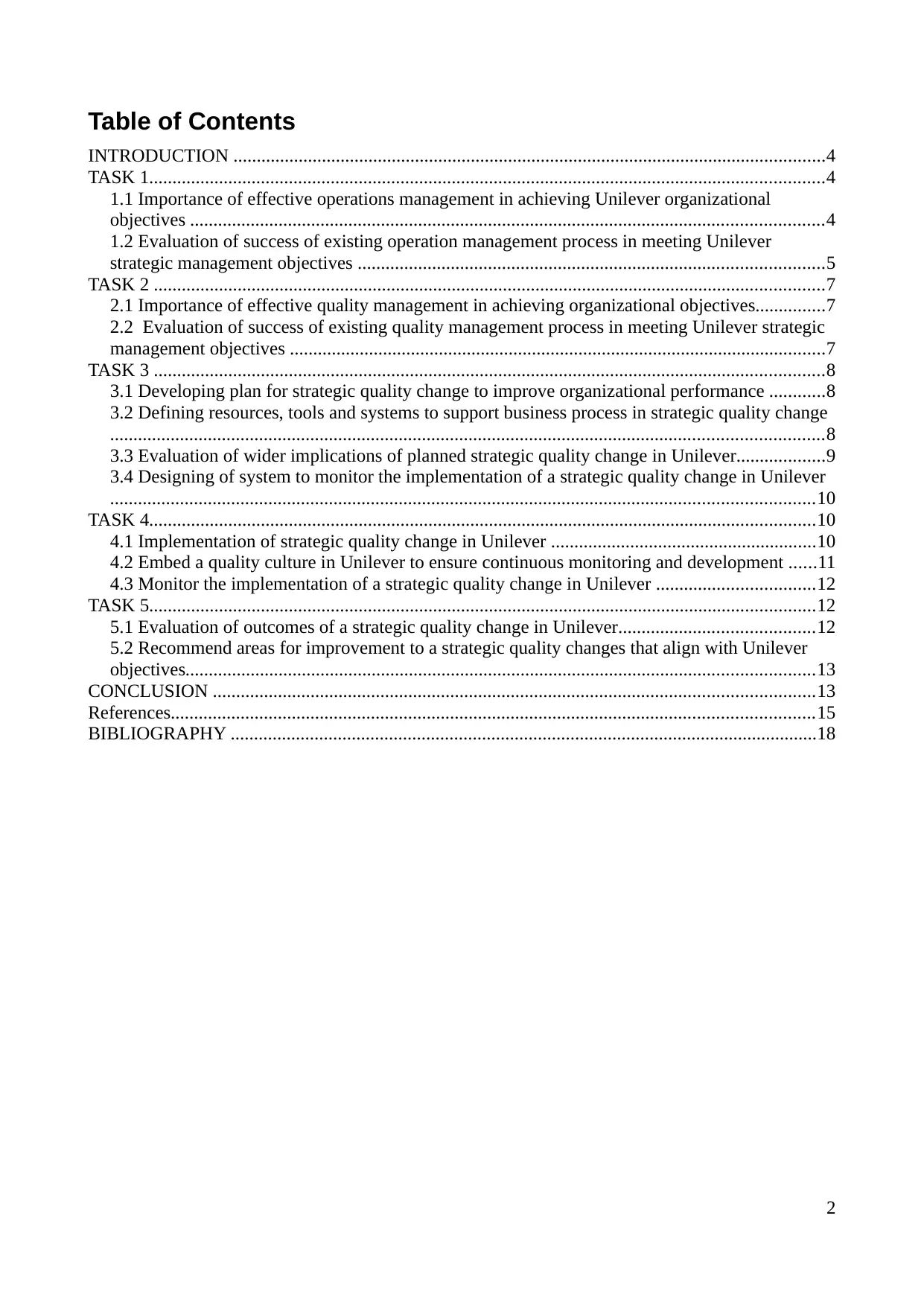
Table of Contents
INTRODUCTION ...............................................................................................................................4
TASK 1.................................................................................................................................................4
1.1 Importance of effective operations management in achieving Unilever organizational
objectives ........................................................................................................................................4
1.2 Evaluation of success of existing operation management process in meeting Unilever
strategic management objectives ....................................................................................................5
TASK 2 ................................................................................................................................................7
2.1 Importance of effective quality management in achieving organizational objectives...............7
2.2 Evaluation of success of existing quality management process in meeting Unilever strategic
management objectives ...................................................................................................................7
TASK 3 ................................................................................................................................................8
3.1 Developing plan for strategic quality change to improve organizational performance ............8
3.2 Defining resources, tools and systems to support business process in strategic quality change
.........................................................................................................................................................8
3.3 Evaluation of wider implications of planned strategic quality change in Unilever...................9
3.4 Designing of system to monitor the implementation of a strategic quality change in Unilever
.......................................................................................................................................................10
TASK 4...............................................................................................................................................10
4.1 Implementation of strategic quality change in Unilever .........................................................10
4.2 Embed a quality culture in Unilever to ensure continuous monitoring and development ......11
4.3 Monitor the implementation of a strategic quality change in Unilever ..................................12
TASK 5...............................................................................................................................................12
5.1 Evaluation of outcomes of a strategic quality change in Unilever..........................................12
5.2 Recommend areas for improvement to a strategic quality changes that align with Unilever
objectives.......................................................................................................................................13
CONCLUSION .................................................................................................................................13
References..........................................................................................................................................15
BIBLIOGRAPHY ..............................................................................................................................18
2
INTRODUCTION ...............................................................................................................................4
TASK 1.................................................................................................................................................4
1.1 Importance of effective operations management in achieving Unilever organizational
objectives ........................................................................................................................................4
1.2 Evaluation of success of existing operation management process in meeting Unilever
strategic management objectives ....................................................................................................5
TASK 2 ................................................................................................................................................7
2.1 Importance of effective quality management in achieving organizational objectives...............7
2.2 Evaluation of success of existing quality management process in meeting Unilever strategic
management objectives ...................................................................................................................7
TASK 3 ................................................................................................................................................8
3.1 Developing plan for strategic quality change to improve organizational performance ............8
3.2 Defining resources, tools and systems to support business process in strategic quality change
.........................................................................................................................................................8
3.3 Evaluation of wider implications of planned strategic quality change in Unilever...................9
3.4 Designing of system to monitor the implementation of a strategic quality change in Unilever
.......................................................................................................................................................10
TASK 4...............................................................................................................................................10
4.1 Implementation of strategic quality change in Unilever .........................................................10
4.2 Embed a quality culture in Unilever to ensure continuous monitoring and development ......11
4.3 Monitor the implementation of a strategic quality change in Unilever ..................................12
TASK 5...............................................................................................................................................12
5.1 Evaluation of outcomes of a strategic quality change in Unilever..........................................12
5.2 Recommend areas for improvement to a strategic quality changes that align with Unilever
objectives.......................................................................................................................................13
CONCLUSION .................................................................................................................................13
References..........................................................................................................................................15
BIBLIOGRAPHY ..............................................................................................................................18
2
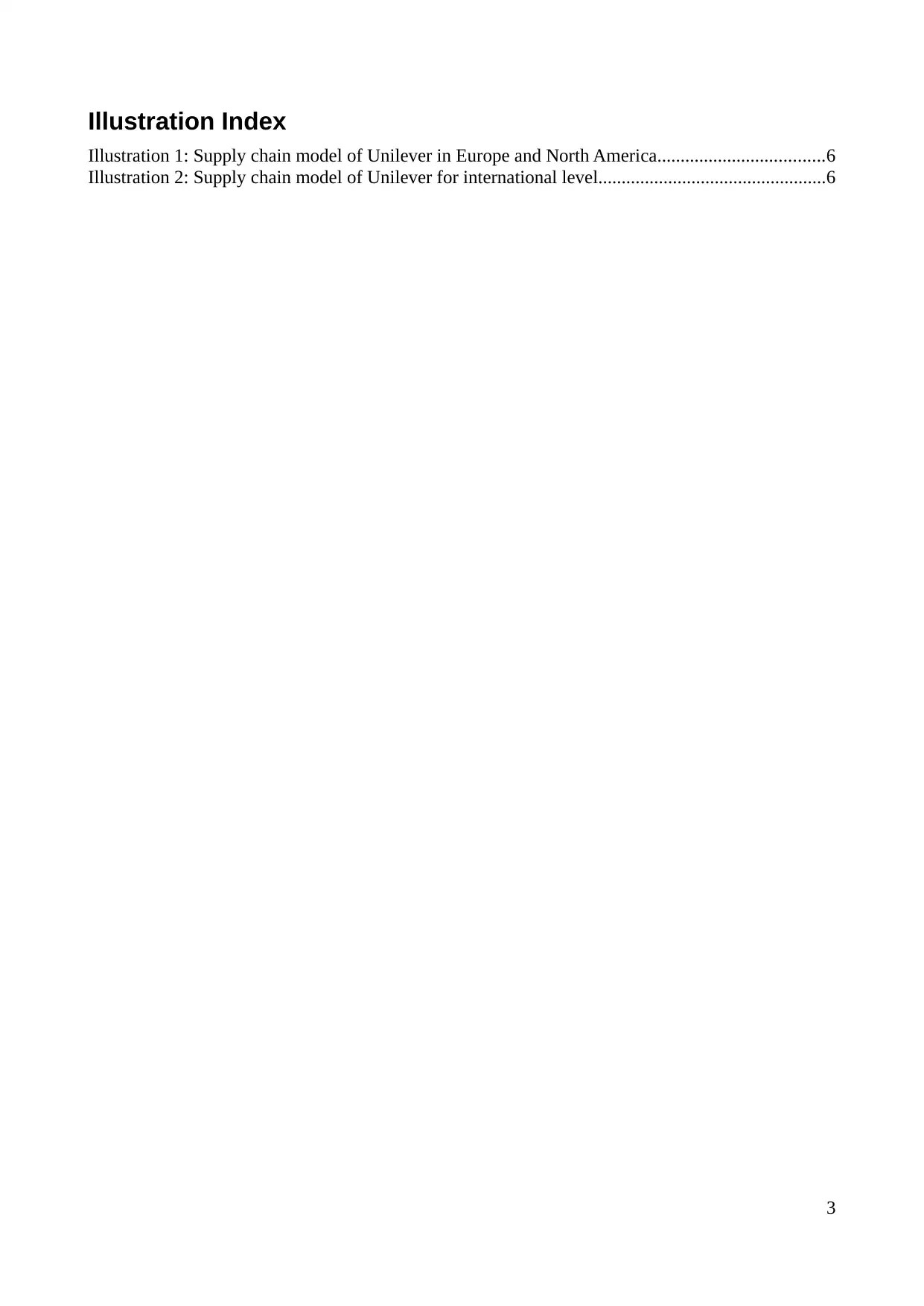
Illustration Index
Illustration 1: Supply chain model of Unilever in Europe and North America....................................6
Illustration 2: Supply chain model of Unilever for international level.................................................6
3
Illustration 1: Supply chain model of Unilever in Europe and North America....................................6
Illustration 2: Supply chain model of Unilever for international level.................................................6
3
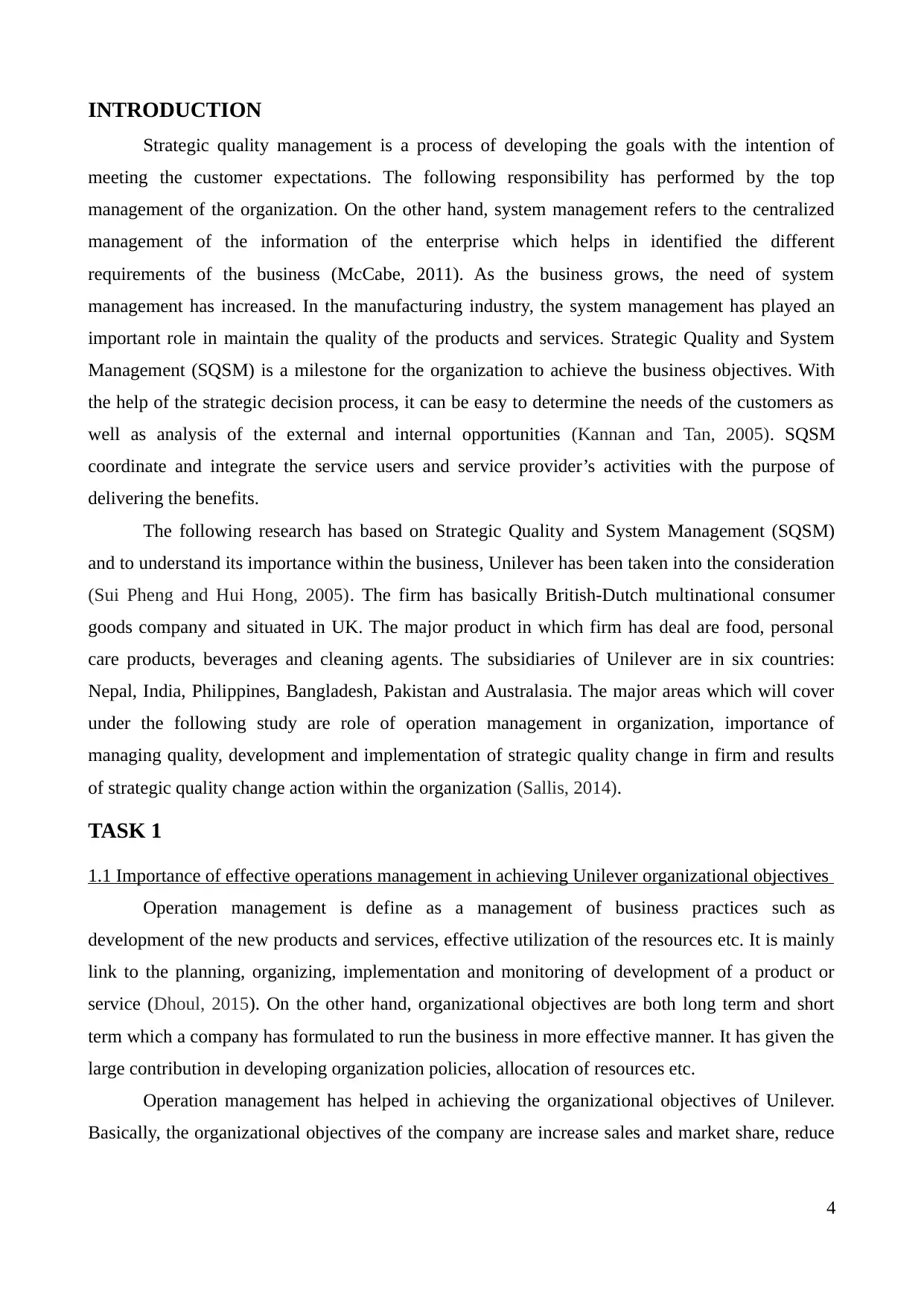
INTRODUCTION
Strategic quality management is a process of developing the goals with the intention of
meeting the customer expectations. The following responsibility has performed by the top
management of the organization. On the other hand, system management refers to the centralized
management of the information of the enterprise which helps in identified the different
requirements of the business (McCabe, 2011). As the business grows, the need of system
management has increased. In the manufacturing industry, the system management has played an
important role in maintain the quality of the products and services. Strategic Quality and System
Management (SQSM) is a milestone for the organization to achieve the business objectives. With
the help of the strategic decision process, it can be easy to determine the needs of the customers as
well as analysis of the external and internal opportunities (Kannan and Tan, 2005). SQSM
coordinate and integrate the service users and service provider’s activities with the purpose of
delivering the benefits.
The following research has based on Strategic Quality and System Management (SQSM)
and to understand its importance within the business, Unilever has been taken into the consideration
(Sui Pheng and Hui Hong, 2005). The firm has basically British-Dutch multinational consumer
goods company and situated in UK. The major product in which firm has deal are food, personal
care products, beverages and cleaning agents. The subsidiaries of Unilever are in six countries:
Nepal, India, Philippines, Bangladesh, Pakistan and Australasia. The major areas which will cover
under the following study are role of operation management in organization, importance of
managing quality, development and implementation of strategic quality change in firm and results
of strategic quality change action within the organization (Sallis, 2014).
TASK 1
1.1 Importance of effective operations management in achieving Unilever organizational objectives
Operation management is define as a management of business practices such as
development of the new products and services, effective utilization of the resources etc. It is mainly
link to the planning, organizing, implementation and monitoring of development of a product or
service (Dhoul, 2015). On the other hand, organizational objectives are both long term and short
term which a company has formulated to run the business in more effective manner. It has given the
large contribution in developing organization policies, allocation of resources etc.
Operation management has helped in achieving the organizational objectives of Unilever.
Basically, the organizational objectives of the company are increase sales and market share, reduce
4
Strategic quality management is a process of developing the goals with the intention of
meeting the customer expectations. The following responsibility has performed by the top
management of the organization. On the other hand, system management refers to the centralized
management of the information of the enterprise which helps in identified the different
requirements of the business (McCabe, 2011). As the business grows, the need of system
management has increased. In the manufacturing industry, the system management has played an
important role in maintain the quality of the products and services. Strategic Quality and System
Management (SQSM) is a milestone for the organization to achieve the business objectives. With
the help of the strategic decision process, it can be easy to determine the needs of the customers as
well as analysis of the external and internal opportunities (Kannan and Tan, 2005). SQSM
coordinate and integrate the service users and service provider’s activities with the purpose of
delivering the benefits.
The following research has based on Strategic Quality and System Management (SQSM)
and to understand its importance within the business, Unilever has been taken into the consideration
(Sui Pheng and Hui Hong, 2005). The firm has basically British-Dutch multinational consumer
goods company and situated in UK. The major product in which firm has deal are food, personal
care products, beverages and cleaning agents. The subsidiaries of Unilever are in six countries:
Nepal, India, Philippines, Bangladesh, Pakistan and Australasia. The major areas which will cover
under the following study are role of operation management in organization, importance of
managing quality, development and implementation of strategic quality change in firm and results
of strategic quality change action within the organization (Sallis, 2014).
TASK 1
1.1 Importance of effective operations management in achieving Unilever organizational objectives
Operation management is define as a management of business practices such as
development of the new products and services, effective utilization of the resources etc. It is mainly
link to the planning, organizing, implementation and monitoring of development of a product or
service (Dhoul, 2015). On the other hand, organizational objectives are both long term and short
term which a company has formulated to run the business in more effective manner. It has given the
large contribution in developing organization policies, allocation of resources etc.
Operation management has helped in achieving the organizational objectives of Unilever.
Basically, the organizational objectives of the company are increase sales and market share, reduce
4
Secure Best Marks with AI Grader
Need help grading? Try our AI Grader for instant feedback on your assignments.
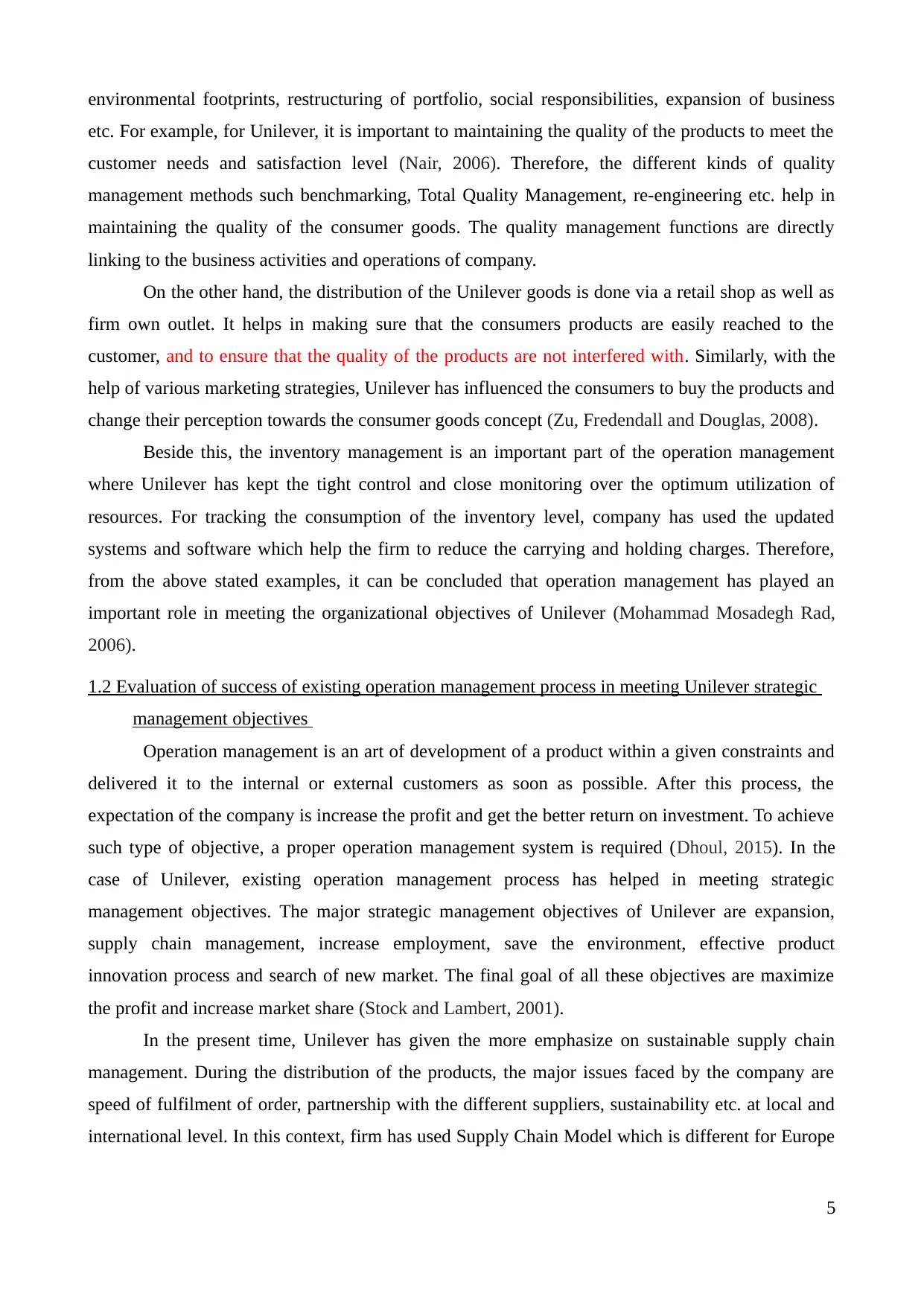
environmental footprints, restructuring of portfolio, social responsibilities, expansion of business
etc. For example, for Unilever, it is important to maintaining the quality of the products to meet the
customer needs and satisfaction level (Nair, 2006). Therefore, the different kinds of quality
management methods such benchmarking, Total Quality Management, re-engineering etc. help in
maintaining the quality of the consumer goods. The quality management functions are directly
linking to the business activities and operations of company.
On the other hand, the distribution of the Unilever goods is done via a retail shop as well as
firm own outlet. It helps in making sure that the consumers products are easily reached to the
customer, and to ensure that the quality of the products are not interfered with. Similarly, with the
help of various marketing strategies, Unilever has influenced the consumers to buy the products and
change their perception towards the consumer goods concept (Zu, Fredendall and Douglas, 2008).
Beside this, the inventory management is an important part of the operation management
where Unilever has kept the tight control and close monitoring over the optimum utilization of
resources. For tracking the consumption of the inventory level, company has used the updated
systems and software which help the firm to reduce the carrying and holding charges. Therefore,
from the above stated examples, it can be concluded that operation management has played an
important role in meeting the organizational objectives of Unilever (Mohammad Mosadegh Rad,
2006).
1.2 Evaluation of success of existing operation management process in meeting Unilever strategic
management objectives
Operation management is an art of development of a product within a given constraints and
delivered it to the internal or external customers as soon as possible. After this process, the
expectation of the company is increase the profit and get the better return on investment. To achieve
such type of objective, a proper operation management system is required (Dhoul, 2015). In the
case of Unilever, existing operation management process has helped in meeting strategic
management objectives. The major strategic management objectives of Unilever are expansion,
supply chain management, increase employment, save the environment, effective product
innovation process and search of new market. The final goal of all these objectives are maximize
the profit and increase market share (Stock and Lambert, 2001).
In the present time, Unilever has given the more emphasize on sustainable supply chain
management. During the distribution of the products, the major issues faced by the company are
speed of fulfilment of order, partnership with the different suppliers, sustainability etc. at local and
international level. In this context, firm has used Supply Chain Model which is different for Europe
5
etc. For example, for Unilever, it is important to maintaining the quality of the products to meet the
customer needs and satisfaction level (Nair, 2006). Therefore, the different kinds of quality
management methods such benchmarking, Total Quality Management, re-engineering etc. help in
maintaining the quality of the consumer goods. The quality management functions are directly
linking to the business activities and operations of company.
On the other hand, the distribution of the Unilever goods is done via a retail shop as well as
firm own outlet. It helps in making sure that the consumers products are easily reached to the
customer, and to ensure that the quality of the products are not interfered with. Similarly, with the
help of various marketing strategies, Unilever has influenced the consumers to buy the products and
change their perception towards the consumer goods concept (Zu, Fredendall and Douglas, 2008).
Beside this, the inventory management is an important part of the operation management
where Unilever has kept the tight control and close monitoring over the optimum utilization of
resources. For tracking the consumption of the inventory level, company has used the updated
systems and software which help the firm to reduce the carrying and holding charges. Therefore,
from the above stated examples, it can be concluded that operation management has played an
important role in meeting the organizational objectives of Unilever (Mohammad Mosadegh Rad,
2006).
1.2 Evaluation of success of existing operation management process in meeting Unilever strategic
management objectives
Operation management is an art of development of a product within a given constraints and
delivered it to the internal or external customers as soon as possible. After this process, the
expectation of the company is increase the profit and get the better return on investment. To achieve
such type of objective, a proper operation management system is required (Dhoul, 2015). In the
case of Unilever, existing operation management process has helped in meeting strategic
management objectives. The major strategic management objectives of Unilever are expansion,
supply chain management, increase employment, save the environment, effective product
innovation process and search of new market. The final goal of all these objectives are maximize
the profit and increase market share (Stock and Lambert, 2001).
In the present time, Unilever has given the more emphasize on sustainable supply chain
management. During the distribution of the products, the major issues faced by the company are
speed of fulfilment of order, partnership with the different suppliers, sustainability etc. at local and
international level. In this context, firm has used Supply Chain Model which is different for Europe
5
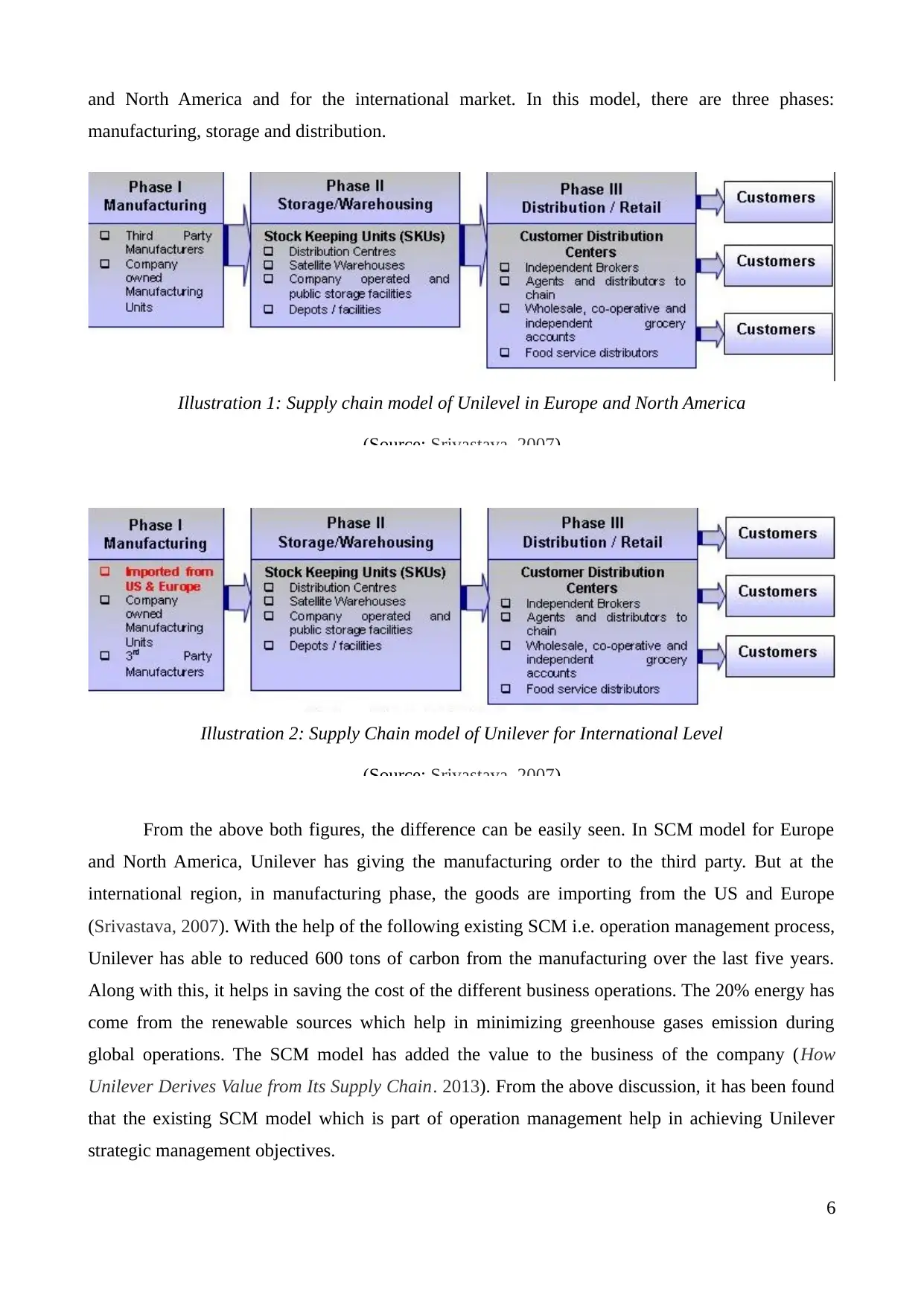
and North America and for the international market. In this model, there are three phases:
manufacturing, storage and distribution.
From the above both figures, the difference can be easily seen. In SCM model for Europe
and North America, Unilever has giving the manufacturing order to the third party. But at the
international region, in manufacturing phase, the goods are importing from the US and Europe
(Srivastava, 2007). With the help of the following existing SCM i.e. operation management process,
Unilever has able to reduced 600 tons of carbon from the manufacturing over the last five years.
Along with this, it helps in saving the cost of the different business operations. The 20% energy has
come from the renewable sources which help in minimizing greenhouse gases emission during
global operations. The SCM model has added the value to the business of the company (How
Unilever Derives Value from Its Supply Chain. 2013). From the above discussion, it has been found
that the existing SCM model which is part of operation management help in achieving Unilever
strategic management objectives.
6
Illustration 1: Supply chain model of Unilevel in Europe and North America
(Source: Srivastava, 2007)
Illustration 2: Supply Chain model of Unilever for International Level
(Source: Srivastava, 2007)
manufacturing, storage and distribution.
From the above both figures, the difference can be easily seen. In SCM model for Europe
and North America, Unilever has giving the manufacturing order to the third party. But at the
international region, in manufacturing phase, the goods are importing from the US and Europe
(Srivastava, 2007). With the help of the following existing SCM i.e. operation management process,
Unilever has able to reduced 600 tons of carbon from the manufacturing over the last five years.
Along with this, it helps in saving the cost of the different business operations. The 20% energy has
come from the renewable sources which help in minimizing greenhouse gases emission during
global operations. The SCM model has added the value to the business of the company (How
Unilever Derives Value from Its Supply Chain. 2013). From the above discussion, it has been found
that the existing SCM model which is part of operation management help in achieving Unilever
strategic management objectives.
6
Illustration 1: Supply chain model of Unilevel in Europe and North America
(Source: Srivastava, 2007)
Illustration 2: Supply Chain model of Unilever for International Level
(Source: Srivastava, 2007)
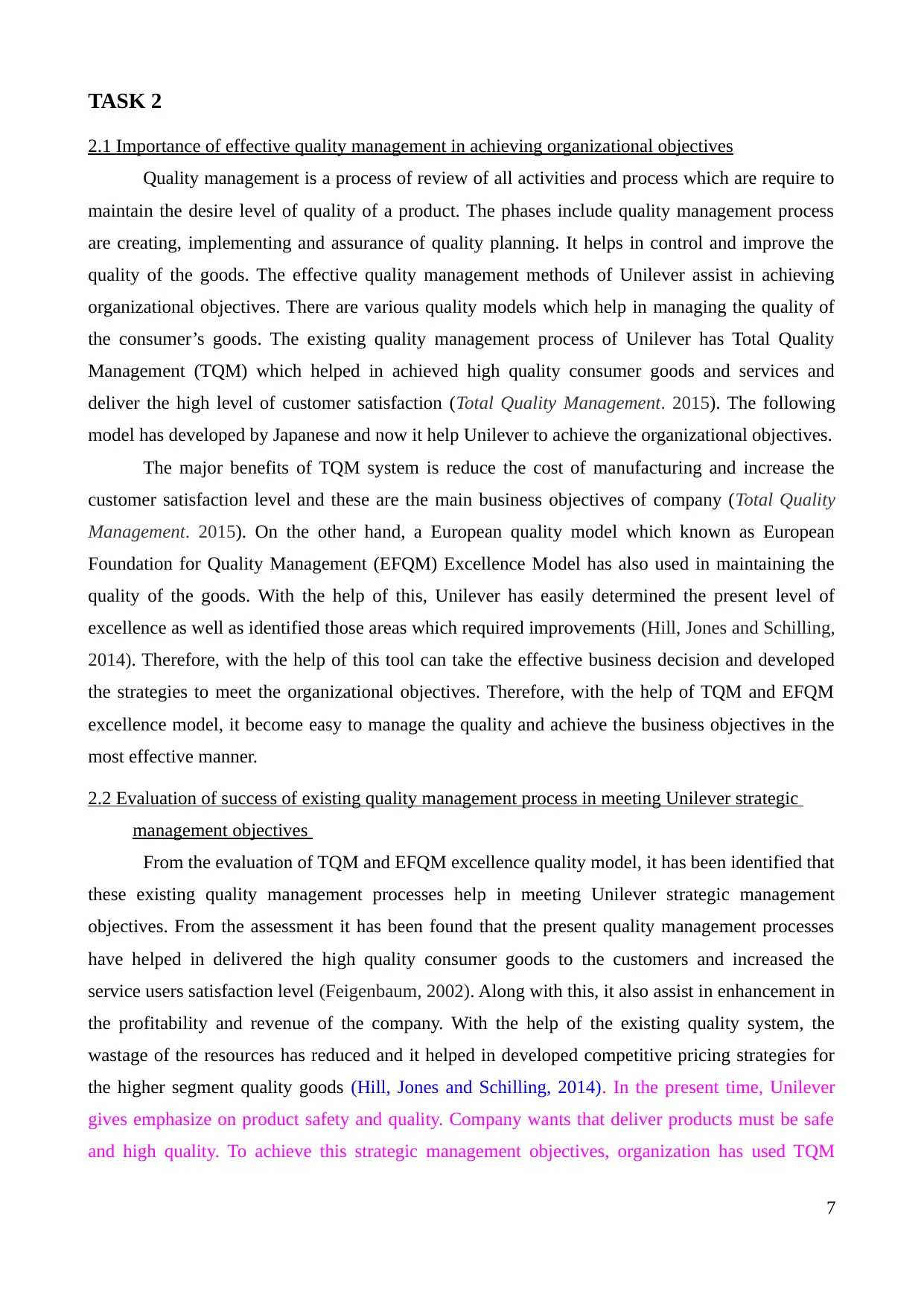
TASK 2
2.1 Importance of effective quality management in achieving organizational objectives
Quality management is a process of review of all activities and process which are require to
maintain the desire level of quality of a product. The phases include quality management process
are creating, implementing and assurance of quality planning. It helps in control and improve the
quality of the goods. The effective quality management methods of Unilever assist in achieving
organizational objectives. There are various quality models which help in managing the quality of
the consumer’s goods. The existing quality management process of Unilever has Total Quality
Management (TQM) which helped in achieved high quality consumer goods and services and
deliver the high level of customer satisfaction (Total Quality Management. 2015). The following
model has developed by Japanese and now it help Unilever to achieve the organizational objectives.
The major benefits of TQM system is reduce the cost of manufacturing and increase the
customer satisfaction level and these are the main business objectives of company (Total Quality
Management. 2015). On the other hand, a European quality model which known as European
Foundation for Quality Management (EFQM) Excellence Model has also used in maintaining the
quality of the goods. With the help of this, Unilever has easily determined the present level of
excellence as well as identified those areas which required improvements (Hill, Jones and Schilling,
2014). Therefore, with the help of this tool can take the effective business decision and developed
the strategies to meet the organizational objectives. Therefore, with the help of TQM and EFQM
excellence model, it become easy to manage the quality and achieve the business objectives in the
most effective manner.
2.2 Evaluation of success of existing quality management process in meeting Unilever strategic
management objectives
From the evaluation of TQM and EFQM excellence quality model, it has been identified that
these existing quality management processes help in meeting Unilever strategic management
objectives. From the assessment it has been found that the present quality management processes
have helped in delivered the high quality consumer goods to the customers and increased the
service users satisfaction level (Feigenbaum, 2002). Along with this, it also assist in enhancement in
the profitability and revenue of the company. With the help of the existing quality system, the
wastage of the resources has reduced and it helped in developed competitive pricing strategies for
the higher segment quality goods (Hill, Jones and Schilling, 2014). In the present time, Unilever
gives emphasize on product safety and quality. Company wants that deliver products must be safe
and high quality. To achieve this strategic management objectives, organization has used TQM
7
2.1 Importance of effective quality management in achieving organizational objectives
Quality management is a process of review of all activities and process which are require to
maintain the desire level of quality of a product. The phases include quality management process
are creating, implementing and assurance of quality planning. It helps in control and improve the
quality of the goods. The effective quality management methods of Unilever assist in achieving
organizational objectives. There are various quality models which help in managing the quality of
the consumer’s goods. The existing quality management process of Unilever has Total Quality
Management (TQM) which helped in achieved high quality consumer goods and services and
deliver the high level of customer satisfaction (Total Quality Management. 2015). The following
model has developed by Japanese and now it help Unilever to achieve the organizational objectives.
The major benefits of TQM system is reduce the cost of manufacturing and increase the
customer satisfaction level and these are the main business objectives of company (Total Quality
Management. 2015). On the other hand, a European quality model which known as European
Foundation for Quality Management (EFQM) Excellence Model has also used in maintaining the
quality of the goods. With the help of this, Unilever has easily determined the present level of
excellence as well as identified those areas which required improvements (Hill, Jones and Schilling,
2014). Therefore, with the help of this tool can take the effective business decision and developed
the strategies to meet the organizational objectives. Therefore, with the help of TQM and EFQM
excellence model, it become easy to manage the quality and achieve the business objectives in the
most effective manner.
2.2 Evaluation of success of existing quality management process in meeting Unilever strategic
management objectives
From the evaluation of TQM and EFQM excellence quality model, it has been identified that
these existing quality management processes help in meeting Unilever strategic management
objectives. From the assessment it has been found that the present quality management processes
have helped in delivered the high quality consumer goods to the customers and increased the
service users satisfaction level (Feigenbaum, 2002). Along with this, it also assist in enhancement in
the profitability and revenue of the company. With the help of the existing quality system, the
wastage of the resources has reduced and it helped in developed competitive pricing strategies for
the higher segment quality goods (Hill, Jones and Schilling, 2014). In the present time, Unilever
gives emphasize on product safety and quality. Company wants that deliver products must be safe
and high quality. To achieve this strategic management objectives, organization has used TQM
7
Paraphrase This Document
Need a fresh take? Get an instant paraphrase of this document with our AI Paraphraser
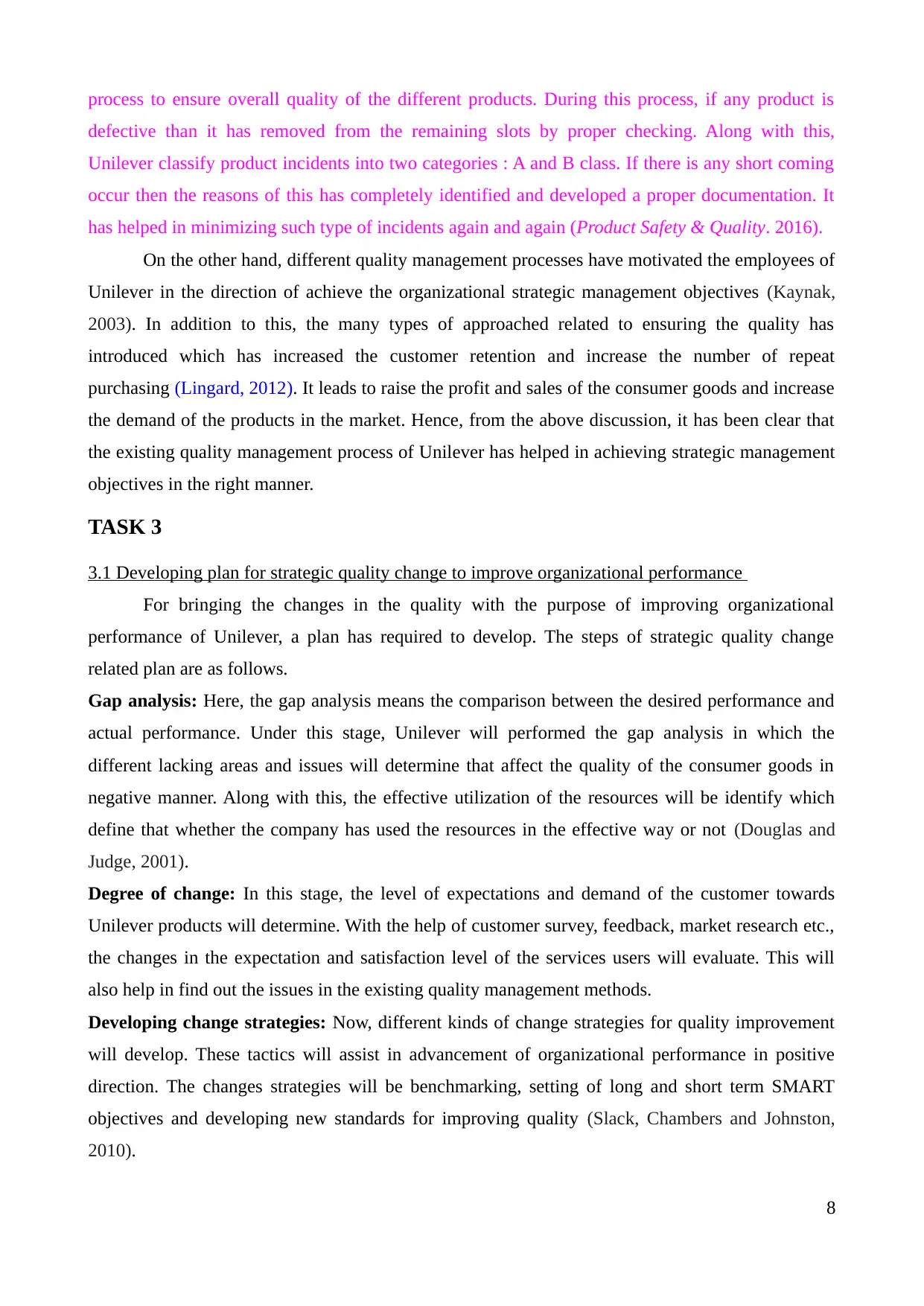
process to ensure overall quality of the different products. During this process, if any product is
defective than it has removed from the remaining slots by proper checking. Along with this,
Unilever classify product incidents into two categories : A and B class. If there is any short coming
occur then the reasons of this has completely identified and developed a proper documentation. It
has helped in minimizing such type of incidents again and again (Product Safety & Quality. 2016).
On the other hand, different quality management processes have motivated the employees of
Unilever in the direction of achieve the organizational strategic management objectives (Kaynak,
2003). In addition to this, the many types of approached related to ensuring the quality has
introduced which has increased the customer retention and increase the number of repeat
purchasing (Lingard, 2012). It leads to raise the profit and sales of the consumer goods and increase
the demand of the products in the market. Hence, from the above discussion, it has been clear that
the existing quality management process of Unilever has helped in achieving strategic management
objectives in the right manner.
TASK 3
3.1 Developing plan for strategic quality change to improve organizational performance
For bringing the changes in the quality with the purpose of improving organizational
performance of Unilever, a plan has required to develop. The steps of strategic quality change
related plan are as follows.
Gap analysis: Here, the gap analysis means the comparison between the desired performance and
actual performance. Under this stage, Unilever will performed the gap analysis in which the
different lacking areas and issues will determine that affect the quality of the consumer goods in
negative manner. Along with this, the effective utilization of the resources will be identify which
define that whether the company has used the resources in the effective way or not (Douglas and
Judge, 2001).
Degree of change: In this stage, the level of expectations and demand of the customer towards
Unilever products will determine. With the help of customer survey, feedback, market research etc.,
the changes in the expectation and satisfaction level of the services users will evaluate. This will
also help in find out the issues in the existing quality management methods.
Developing change strategies: Now, different kinds of change strategies for quality improvement
will develop. These tactics will assist in advancement of organizational performance in positive
direction. The changes strategies will be benchmarking, setting of long and short term SMART
objectives and developing new standards for improving quality (Slack, Chambers and Johnston,
2010).
8
defective than it has removed from the remaining slots by proper checking. Along with this,
Unilever classify product incidents into two categories : A and B class. If there is any short coming
occur then the reasons of this has completely identified and developed a proper documentation. It
has helped in minimizing such type of incidents again and again (Product Safety & Quality. 2016).
On the other hand, different quality management processes have motivated the employees of
Unilever in the direction of achieve the organizational strategic management objectives (Kaynak,
2003). In addition to this, the many types of approached related to ensuring the quality has
introduced which has increased the customer retention and increase the number of repeat
purchasing (Lingard, 2012). It leads to raise the profit and sales of the consumer goods and increase
the demand of the products in the market. Hence, from the above discussion, it has been clear that
the existing quality management process of Unilever has helped in achieving strategic management
objectives in the right manner.
TASK 3
3.1 Developing plan for strategic quality change to improve organizational performance
For bringing the changes in the quality with the purpose of improving organizational
performance of Unilever, a plan has required to develop. The steps of strategic quality change
related plan are as follows.
Gap analysis: Here, the gap analysis means the comparison between the desired performance and
actual performance. Under this stage, Unilever will performed the gap analysis in which the
different lacking areas and issues will determine that affect the quality of the consumer goods in
negative manner. Along with this, the effective utilization of the resources will be identify which
define that whether the company has used the resources in the effective way or not (Douglas and
Judge, 2001).
Degree of change: In this stage, the level of expectations and demand of the customer towards
Unilever products will determine. With the help of customer survey, feedback, market research etc.,
the changes in the expectation and satisfaction level of the services users will evaluate. This will
also help in find out the issues in the existing quality management methods.
Developing change strategies: Now, different kinds of change strategies for quality improvement
will develop. These tactics will assist in advancement of organizational performance in positive
direction. The changes strategies will be benchmarking, setting of long and short term SMART
objectives and developing new standards for improving quality (Slack, Chambers and Johnston,
2010).
8
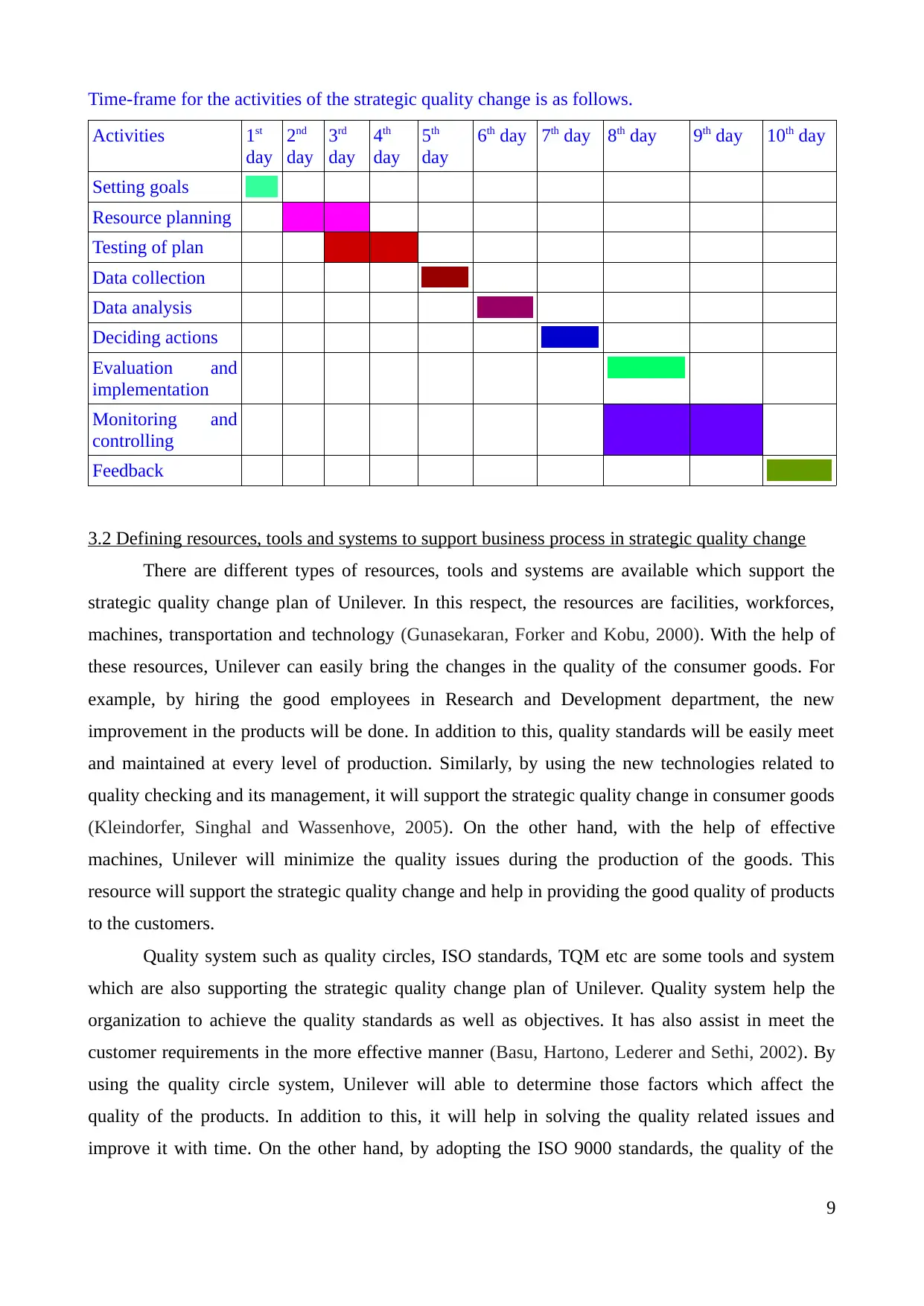
Time-frame for the activities of the strategic quality change is as follows.
Activities 1st
day
2nd
day
3rd
day
4th
day
5th
day
6th day 7th day 8th day 9th day 10th day
Setting goals
Resource planning
Testing of plan
Data collection
Data analysis
Deciding actions
Evaluation and
implementation
Monitoring and
controlling
Feedback
3.2 Defining resources, tools and systems to support business process in strategic quality change
There are different types of resources, tools and systems are available which support the
strategic quality change plan of Unilever. In this respect, the resources are facilities, workforces,
machines, transportation and technology (Gunasekaran, Forker and Kobu, 2000). With the help of
these resources, Unilever can easily bring the changes in the quality of the consumer goods. For
example, by hiring the good employees in Research and Development department, the new
improvement in the products will be done. In addition to this, quality standards will be easily meet
and maintained at every level of production. Similarly, by using the new technologies related to
quality checking and its management, it will support the strategic quality change in consumer goods
(Kleindorfer, Singhal and Wassenhove, 2005). On the other hand, with the help of effective
machines, Unilever will minimize the quality issues during the production of the goods. This
resource will support the strategic quality change and help in providing the good quality of products
to the customers.
Quality system such as quality circles, ISO standards, TQM etc are some tools and system
which are also supporting the strategic quality change plan of Unilever. Quality system help the
organization to achieve the quality standards as well as objectives. It has also assist in meet the
customer requirements in the more effective manner (Basu, Hartono, Lederer and Sethi, 2002). By
using the quality circle system, Unilever will able to determine those factors which affect the
quality of the products. In addition to this, it will help in solving the quality related issues and
improve it with time. On the other hand, by adopting the ISO 9000 standards, the quality of the
9
Activities 1st
day
2nd
day
3rd
day
4th
day
5th
day
6th day 7th day 8th day 9th day 10th day
Setting goals
Resource planning
Testing of plan
Data collection
Data analysis
Deciding actions
Evaluation and
implementation
Monitoring and
controlling
Feedback
3.2 Defining resources, tools and systems to support business process in strategic quality change
There are different types of resources, tools and systems are available which support the
strategic quality change plan of Unilever. In this respect, the resources are facilities, workforces,
machines, transportation and technology (Gunasekaran, Forker and Kobu, 2000). With the help of
these resources, Unilever can easily bring the changes in the quality of the consumer goods. For
example, by hiring the good employees in Research and Development department, the new
improvement in the products will be done. In addition to this, quality standards will be easily meet
and maintained at every level of production. Similarly, by using the new technologies related to
quality checking and its management, it will support the strategic quality change in consumer goods
(Kleindorfer, Singhal and Wassenhove, 2005). On the other hand, with the help of effective
machines, Unilever will minimize the quality issues during the production of the goods. This
resource will support the strategic quality change and help in providing the good quality of products
to the customers.
Quality system such as quality circles, ISO standards, TQM etc are some tools and system
which are also supporting the strategic quality change plan of Unilever. Quality system help the
organization to achieve the quality standards as well as objectives. It has also assist in meet the
customer requirements in the more effective manner (Basu, Hartono, Lederer and Sethi, 2002). By
using the quality circle system, Unilever will able to determine those factors which affect the
quality of the products. In addition to this, it will help in solving the quality related issues and
improve it with time. On the other hand, by adopting the ISO 9000 standards, the quality of the
9
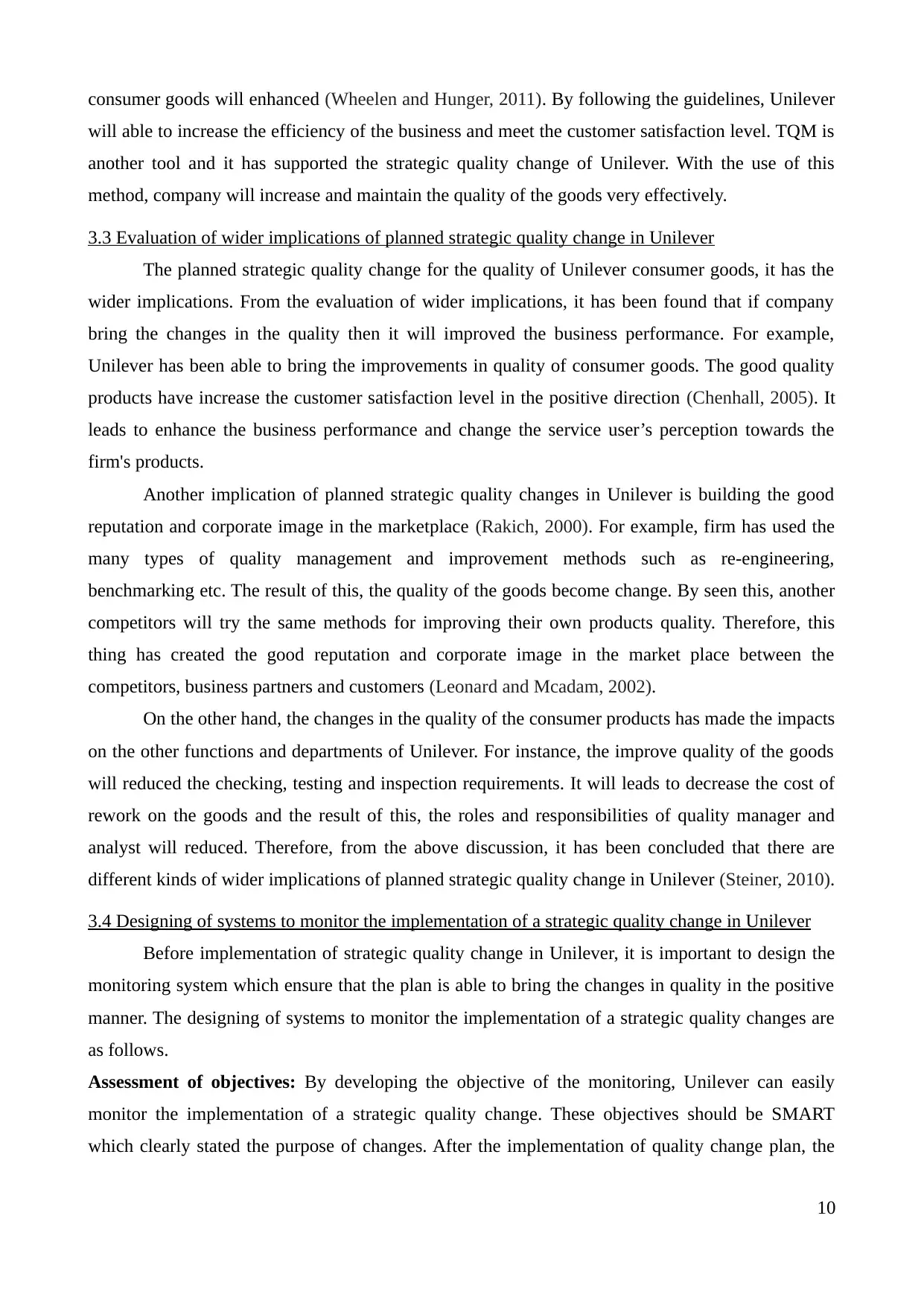
consumer goods will enhanced (Wheelen and Hunger, 2011). By following the guidelines, Unilever
will able to increase the efficiency of the business and meet the customer satisfaction level. TQM is
another tool and it has supported the strategic quality change of Unilever. With the use of this
method, company will increase and maintain the quality of the goods very effectively.
3.3 Evaluation of wider implications of planned strategic quality change in Unilever
The planned strategic quality change for the quality of Unilever consumer goods, it has the
wider implications. From the evaluation of wider implications, it has been found that if company
bring the changes in the quality then it will improved the business performance. For example,
Unilever has been able to bring the improvements in quality of consumer goods. The good quality
products have increase the customer satisfaction level in the positive direction (Chenhall, 2005). It
leads to enhance the business performance and change the service user’s perception towards the
firm's products.
Another implication of planned strategic quality changes in Unilever is building the good
reputation and corporate image in the marketplace (Rakich, 2000). For example, firm has used the
many types of quality management and improvement methods such as re-engineering,
benchmarking etc. The result of this, the quality of the goods become change. By seen this, another
competitors will try the same methods for improving their own products quality. Therefore, this
thing has created the good reputation and corporate image in the market place between the
competitors, business partners and customers (Leonard and Mcadam, 2002).
On the other hand, the changes in the quality of the consumer products has made the impacts
on the other functions and departments of Unilever. For instance, the improve quality of the goods
will reduced the checking, testing and inspection requirements. It will leads to decrease the cost of
rework on the goods and the result of this, the roles and responsibilities of quality manager and
analyst will reduced. Therefore, from the above discussion, it has been concluded that there are
different kinds of wider implications of planned strategic quality change in Unilever (Steiner, 2010).
3.4 Designing of systems to monitor the implementation of a strategic quality change in Unilever
Before implementation of strategic quality change in Unilever, it is important to design the
monitoring system which ensure that the plan is able to bring the changes in quality in the positive
manner. The designing of systems to monitor the implementation of a strategic quality changes are
as follows.
Assessment of objectives: By developing the objective of the monitoring, Unilever can easily
monitor the implementation of a strategic quality change. These objectives should be SMART
which clearly stated the purpose of changes. After the implementation of quality change plan, the
10
will able to increase the efficiency of the business and meet the customer satisfaction level. TQM is
another tool and it has supported the strategic quality change of Unilever. With the use of this
method, company will increase and maintain the quality of the goods very effectively.
3.3 Evaluation of wider implications of planned strategic quality change in Unilever
The planned strategic quality change for the quality of Unilever consumer goods, it has the
wider implications. From the evaluation of wider implications, it has been found that if company
bring the changes in the quality then it will improved the business performance. For example,
Unilever has been able to bring the improvements in quality of consumer goods. The good quality
products have increase the customer satisfaction level in the positive direction (Chenhall, 2005). It
leads to enhance the business performance and change the service user’s perception towards the
firm's products.
Another implication of planned strategic quality changes in Unilever is building the good
reputation and corporate image in the marketplace (Rakich, 2000). For example, firm has used the
many types of quality management and improvement methods such as re-engineering,
benchmarking etc. The result of this, the quality of the goods become change. By seen this, another
competitors will try the same methods for improving their own products quality. Therefore, this
thing has created the good reputation and corporate image in the market place between the
competitors, business partners and customers (Leonard and Mcadam, 2002).
On the other hand, the changes in the quality of the consumer products has made the impacts
on the other functions and departments of Unilever. For instance, the improve quality of the goods
will reduced the checking, testing and inspection requirements. It will leads to decrease the cost of
rework on the goods and the result of this, the roles and responsibilities of quality manager and
analyst will reduced. Therefore, from the above discussion, it has been concluded that there are
different kinds of wider implications of planned strategic quality change in Unilever (Steiner, 2010).
3.4 Designing of systems to monitor the implementation of a strategic quality change in Unilever
Before implementation of strategic quality change in Unilever, it is important to design the
monitoring system which ensure that the plan is able to bring the changes in quality in the positive
manner. The designing of systems to monitor the implementation of a strategic quality changes are
as follows.
Assessment of objectives: By developing the objective of the monitoring, Unilever can easily
monitor the implementation of a strategic quality change. These objectives should be SMART
which clearly stated the purpose of changes. After the implementation of quality change plan, the
10
Secure Best Marks with AI Grader
Need help grading? Try our AI Grader for instant feedback on your assignments.
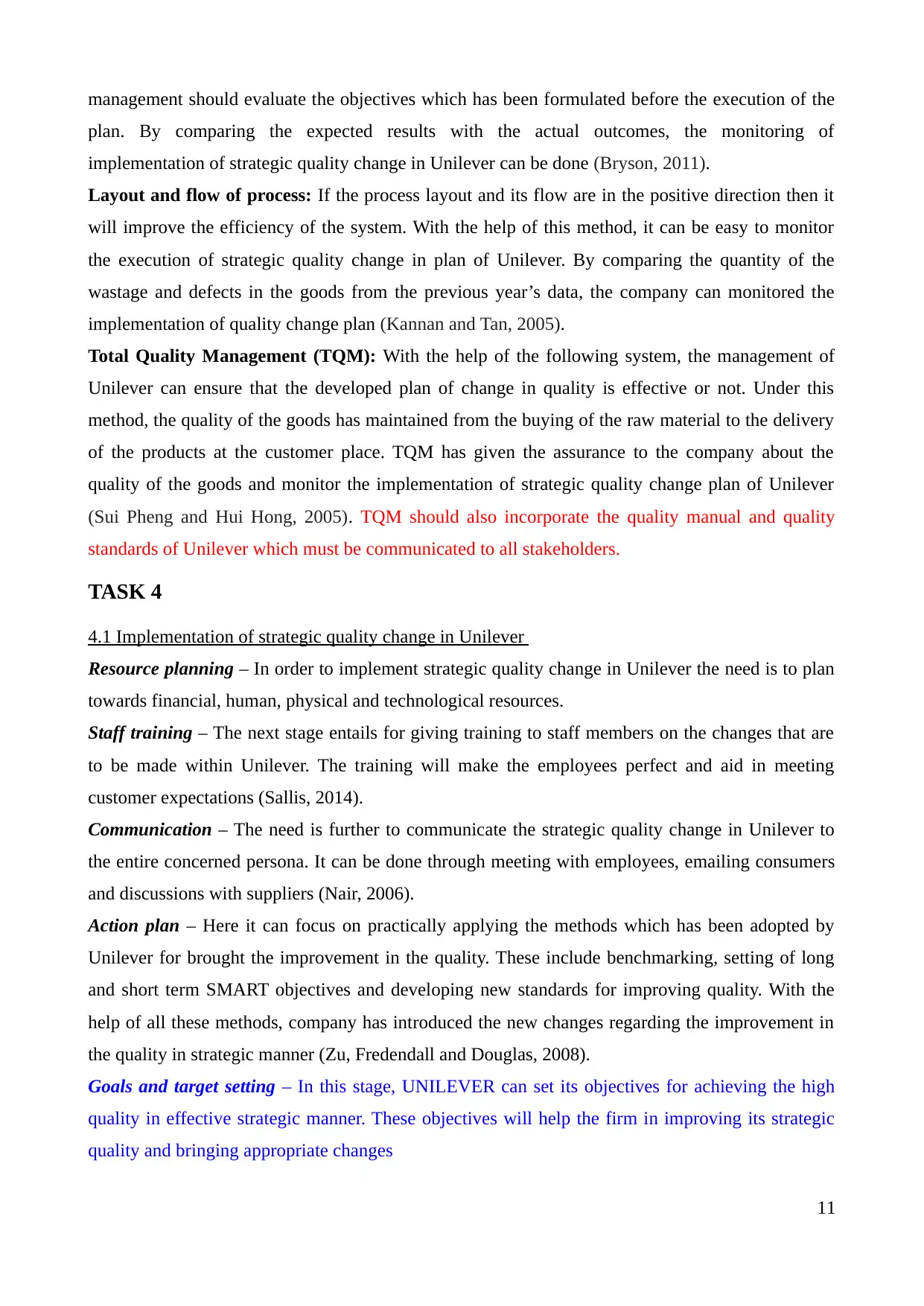
management should evaluate the objectives which has been formulated before the execution of the
plan. By comparing the expected results with the actual outcomes, the monitoring of
implementation of strategic quality change in Unilever can be done (Bryson, 2011).
Layout and flow of process: If the process layout and its flow are in the positive direction then it
will improve the efficiency of the system. With the help of this method, it can be easy to monitor
the execution of strategic quality change in plan of Unilever. By comparing the quantity of the
wastage and defects in the goods from the previous year’s data, the company can monitored the
implementation of quality change plan (Kannan and Tan, 2005).
Total Quality Management (TQM): With the help of the following system, the management of
Unilever can ensure that the developed plan of change in quality is effective or not. Under this
method, the quality of the goods has maintained from the buying of the raw material to the delivery
of the products at the customer place. TQM has given the assurance to the company about the
quality of the goods and monitor the implementation of strategic quality change plan of Unilever
(Sui Pheng and Hui Hong, 2005). TQM should also incorporate the quality manual and quality
standards of Unilever which must be communicated to all stakeholders.
TASK 4
4.1 Implementation of strategic quality change in Unilever
Resource planning – In order to implement strategic quality change in Unilever the need is to plan
towards financial, human, physical and technological resources.
Staff training – The next stage entails for giving training to staff members on the changes that are
to be made within Unilever. The training will make the employees perfect and aid in meeting
customer expectations (Sallis, 2014).
Communication – The need is further to communicate the strategic quality change in Unilever to
the entire concerned persona. It can be done through meeting with employees, emailing consumers
and discussions with suppliers (Nair, 2006).
Action plan – Here it can focus on practically applying the methods which has been adopted by
Unilever for brought the improvement in the quality. These include benchmarking, setting of long
and short term SMART objectives and developing new standards for improving quality. With the
help of all these methods, company has introduced the new changes regarding the improvement in
the quality in strategic manner (Zu, Fredendall and Douglas, 2008).
Goals and target setting – In this stage, UNILEVER can set its objectives for achieving the high
quality in effective strategic manner. These objectives will help the firm in improving its strategic
quality and bringing appropriate changes
11
plan. By comparing the expected results with the actual outcomes, the monitoring of
implementation of strategic quality change in Unilever can be done (Bryson, 2011).
Layout and flow of process: If the process layout and its flow are in the positive direction then it
will improve the efficiency of the system. With the help of this method, it can be easy to monitor
the execution of strategic quality change in plan of Unilever. By comparing the quantity of the
wastage and defects in the goods from the previous year’s data, the company can monitored the
implementation of quality change plan (Kannan and Tan, 2005).
Total Quality Management (TQM): With the help of the following system, the management of
Unilever can ensure that the developed plan of change in quality is effective or not. Under this
method, the quality of the goods has maintained from the buying of the raw material to the delivery
of the products at the customer place. TQM has given the assurance to the company about the
quality of the goods and monitor the implementation of strategic quality change plan of Unilever
(Sui Pheng and Hui Hong, 2005). TQM should also incorporate the quality manual and quality
standards of Unilever which must be communicated to all stakeholders.
TASK 4
4.1 Implementation of strategic quality change in Unilever
Resource planning – In order to implement strategic quality change in Unilever the need is to plan
towards financial, human, physical and technological resources.
Staff training – The next stage entails for giving training to staff members on the changes that are
to be made within Unilever. The training will make the employees perfect and aid in meeting
customer expectations (Sallis, 2014).
Communication – The need is further to communicate the strategic quality change in Unilever to
the entire concerned persona. It can be done through meeting with employees, emailing consumers
and discussions with suppliers (Nair, 2006).
Action plan – Here it can focus on practically applying the methods which has been adopted by
Unilever for brought the improvement in the quality. These include benchmarking, setting of long
and short term SMART objectives and developing new standards for improving quality. With the
help of all these methods, company has introduced the new changes regarding the improvement in
the quality in strategic manner (Zu, Fredendall and Douglas, 2008).
Goals and target setting – In this stage, UNILEVER can set its objectives for achieving the high
quality in effective strategic manner. These objectives will help the firm in improving its strategic
quality and bringing appropriate changes
11
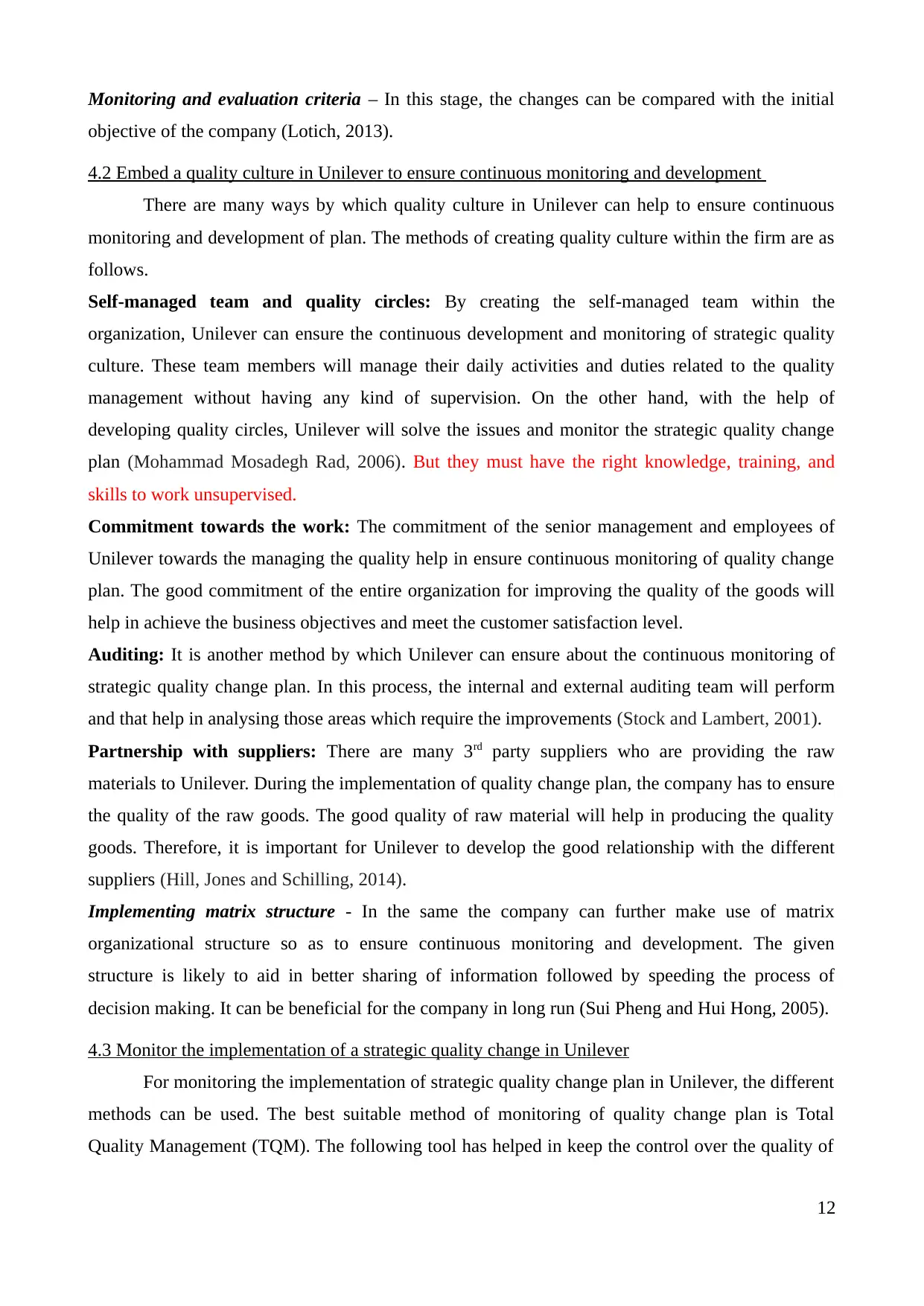
Monitoring and evaluation criteria – In this stage, the changes can be compared with the initial
objective of the company (Lotich, 2013).
4.2 Embed a quality culture in Unilever to ensure continuous monitoring and development
There are many ways by which quality culture in Unilever can help to ensure continuous
monitoring and development of plan. The methods of creating quality culture within the firm are as
follows.
Self-managed team and quality circles: By creating the self-managed team within the
organization, Unilever can ensure the continuous development and monitoring of strategic quality
culture. These team members will manage their daily activities and duties related to the quality
management without having any kind of supervision. On the other hand, with the help of
developing quality circles, Unilever will solve the issues and monitor the strategic quality change
plan (Mohammad Mosadegh Rad, 2006). But they must have the right knowledge, training, and
skills to work unsupervised.
Commitment towards the work: The commitment of the senior management and employees of
Unilever towards the managing the quality help in ensure continuous monitoring of quality change
plan. The good commitment of the entire organization for improving the quality of the goods will
help in achieve the business objectives and meet the customer satisfaction level.
Auditing: It is another method by which Unilever can ensure about the continuous monitoring of
strategic quality change plan. In this process, the internal and external auditing team will perform
and that help in analysing those areas which require the improvements (Stock and Lambert, 2001).
Partnership with suppliers: There are many 3rd party suppliers who are providing the raw
materials to Unilever. During the implementation of quality change plan, the company has to ensure
the quality of the raw goods. The good quality of raw material will help in producing the quality
goods. Therefore, it is important for Unilever to develop the good relationship with the different
suppliers (Hill, Jones and Schilling, 2014).
Implementing matrix structure - In the same the company can further make use of matrix
organizational structure so as to ensure continuous monitoring and development. The given
structure is likely to aid in better sharing of information followed by speeding the process of
decision making. It can be beneficial for the company in long run (Sui Pheng and Hui Hong, 2005).
4.3 Monitor the implementation of a strategic quality change in Unilever
For monitoring the implementation of strategic quality change plan in Unilever, the different
methods can be used. The best suitable method of monitoring of quality change plan is Total
Quality Management (TQM). The following tool has helped in keep the control over the quality of
12
objective of the company (Lotich, 2013).
4.2 Embed a quality culture in Unilever to ensure continuous monitoring and development
There are many ways by which quality culture in Unilever can help to ensure continuous
monitoring and development of plan. The methods of creating quality culture within the firm are as
follows.
Self-managed team and quality circles: By creating the self-managed team within the
organization, Unilever can ensure the continuous development and monitoring of strategic quality
culture. These team members will manage their daily activities and duties related to the quality
management without having any kind of supervision. On the other hand, with the help of
developing quality circles, Unilever will solve the issues and monitor the strategic quality change
plan (Mohammad Mosadegh Rad, 2006). But they must have the right knowledge, training, and
skills to work unsupervised.
Commitment towards the work: The commitment of the senior management and employees of
Unilever towards the managing the quality help in ensure continuous monitoring of quality change
plan. The good commitment of the entire organization for improving the quality of the goods will
help in achieve the business objectives and meet the customer satisfaction level.
Auditing: It is another method by which Unilever can ensure about the continuous monitoring of
strategic quality change plan. In this process, the internal and external auditing team will perform
and that help in analysing those areas which require the improvements (Stock and Lambert, 2001).
Partnership with suppliers: There are many 3rd party suppliers who are providing the raw
materials to Unilever. During the implementation of quality change plan, the company has to ensure
the quality of the raw goods. The good quality of raw material will help in producing the quality
goods. Therefore, it is important for Unilever to develop the good relationship with the different
suppliers (Hill, Jones and Schilling, 2014).
Implementing matrix structure - In the same the company can further make use of matrix
organizational structure so as to ensure continuous monitoring and development. The given
structure is likely to aid in better sharing of information followed by speeding the process of
decision making. It can be beneficial for the company in long run (Sui Pheng and Hui Hong, 2005).
4.3 Monitor the implementation of a strategic quality change in Unilever
For monitoring the implementation of strategic quality change plan in Unilever, the different
methods can be used. The best suitable method of monitoring of quality change plan is Total
Quality Management (TQM). The following tool has helped in keep the control over the quality of
12
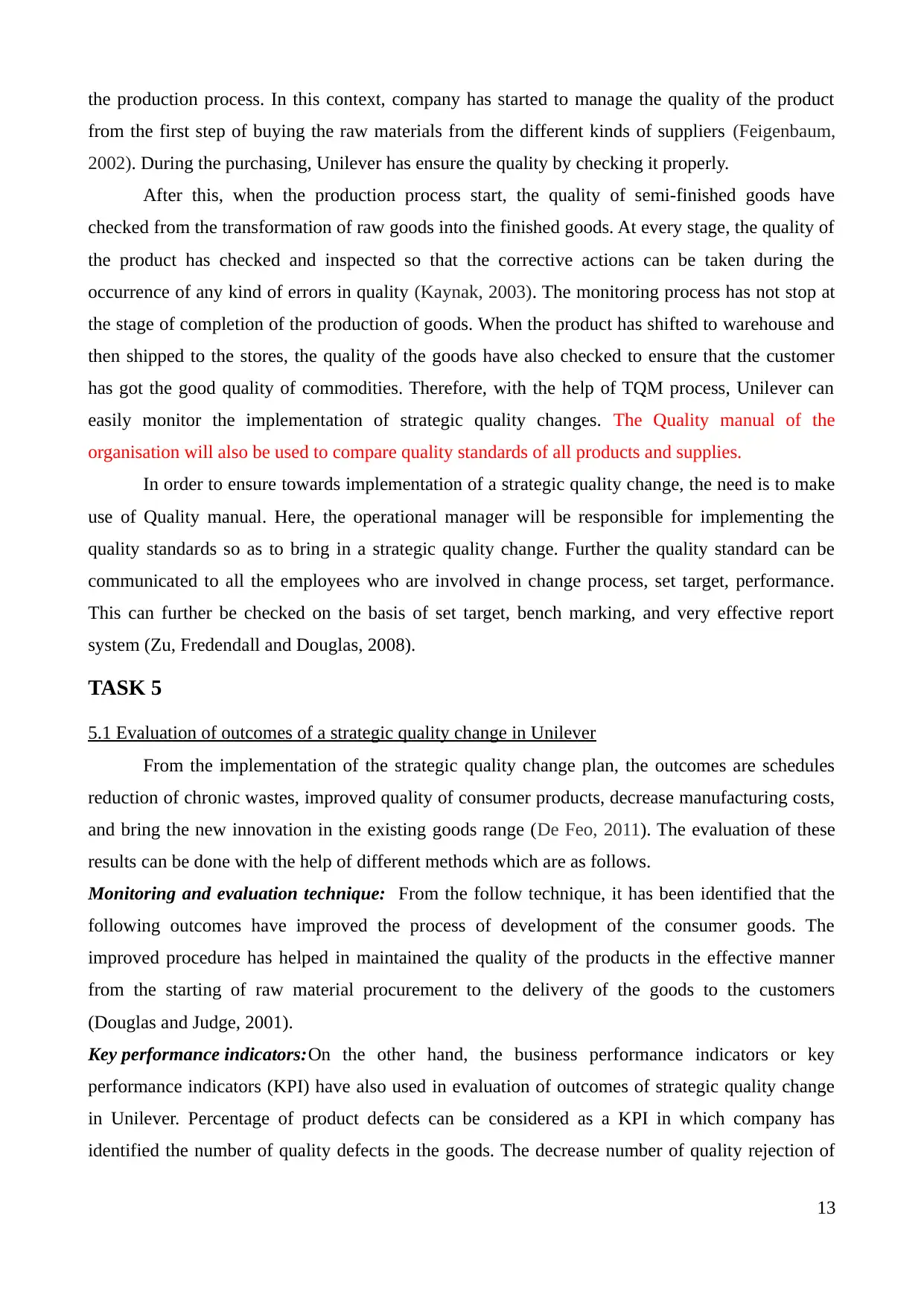
the production process. In this context, company has started to manage the quality of the product
from the first step of buying the raw materials from the different kinds of suppliers (Feigenbaum,
2002). During the purchasing, Unilever has ensure the quality by checking it properly.
After this, when the production process start, the quality of semi-finished goods have
checked from the transformation of raw goods into the finished goods. At every stage, the quality of
the product has checked and inspected so that the corrective actions can be taken during the
occurrence of any kind of errors in quality (Kaynak, 2003). The monitoring process has not stop at
the stage of completion of the production of goods. When the product has shifted to warehouse and
then shipped to the stores, the quality of the goods have also checked to ensure that the customer
has got the good quality of commodities. Therefore, with the help of TQM process, Unilever can
easily monitor the implementation of strategic quality changes. The Quality manual of the
organisation will also be used to compare quality standards of all products and supplies.
In order to ensure towards implementation of a strategic quality change, the need is to make
use of Quality manual. Here, the operational manager will be responsible for implementing the
quality standards so as to bring in a strategic quality change. Further the quality standard can be
communicated to all the employees who are involved in change process, set target, performance.
This can further be checked on the basis of set target, bench marking, and very effective report
system (Zu, Fredendall and Douglas, 2008).
TASK 5
5.1 Evaluation of outcomes of a strategic quality change in Unilever
From the implementation of the strategic quality change plan, the outcomes are schedules
reduction of chronic wastes, improved quality of consumer products, decrease manufacturing costs,
and bring the new innovation in the existing goods range (De Feo, 2011). The evaluation of these
results can be done with the help of different methods which are as follows.
Monitoring and evaluation technique: From the follow technique, it has been identified that the
following outcomes have improved the process of development of the consumer goods. The
improved procedure has helped in maintained the quality of the products in the effective manner
from the starting of raw material procurement to the delivery of the goods to the customers
(Douglas and Judge, 2001).
Key performance indicators:On the other hand, the business performance indicators or key
performance indicators (KPI) have also used in evaluation of outcomes of strategic quality change
in Unilever. Percentage of product defects can be considered as a KPI in which company has
identified the number of quality defects in the goods. The decrease number of quality rejection of
13
from the first step of buying the raw materials from the different kinds of suppliers (Feigenbaum,
2002). During the purchasing, Unilever has ensure the quality by checking it properly.
After this, when the production process start, the quality of semi-finished goods have
checked from the transformation of raw goods into the finished goods. At every stage, the quality of
the product has checked and inspected so that the corrective actions can be taken during the
occurrence of any kind of errors in quality (Kaynak, 2003). The monitoring process has not stop at
the stage of completion of the production of goods. When the product has shifted to warehouse and
then shipped to the stores, the quality of the goods have also checked to ensure that the customer
has got the good quality of commodities. Therefore, with the help of TQM process, Unilever can
easily monitor the implementation of strategic quality changes. The Quality manual of the
organisation will also be used to compare quality standards of all products and supplies.
In order to ensure towards implementation of a strategic quality change, the need is to make
use of Quality manual. Here, the operational manager will be responsible for implementing the
quality standards so as to bring in a strategic quality change. Further the quality standard can be
communicated to all the employees who are involved in change process, set target, performance.
This can further be checked on the basis of set target, bench marking, and very effective report
system (Zu, Fredendall and Douglas, 2008).
TASK 5
5.1 Evaluation of outcomes of a strategic quality change in Unilever
From the implementation of the strategic quality change plan, the outcomes are schedules
reduction of chronic wastes, improved quality of consumer products, decrease manufacturing costs,
and bring the new innovation in the existing goods range (De Feo, 2011). The evaluation of these
results can be done with the help of different methods which are as follows.
Monitoring and evaluation technique: From the follow technique, it has been identified that the
following outcomes have improved the process of development of the consumer goods. The
improved procedure has helped in maintained the quality of the products in the effective manner
from the starting of raw material procurement to the delivery of the goods to the customers
(Douglas and Judge, 2001).
Key performance indicators:On the other hand, the business performance indicators or key
performance indicators (KPI) have also used in evaluation of outcomes of strategic quality change
in Unilever. Percentage of product defects can be considered as a KPI in which company has
identified the number of quality defects in the goods. The decrease number of quality rejection of
13
Paraphrase This Document
Need a fresh take? Get an instant paraphrase of this document with our AI Paraphraser
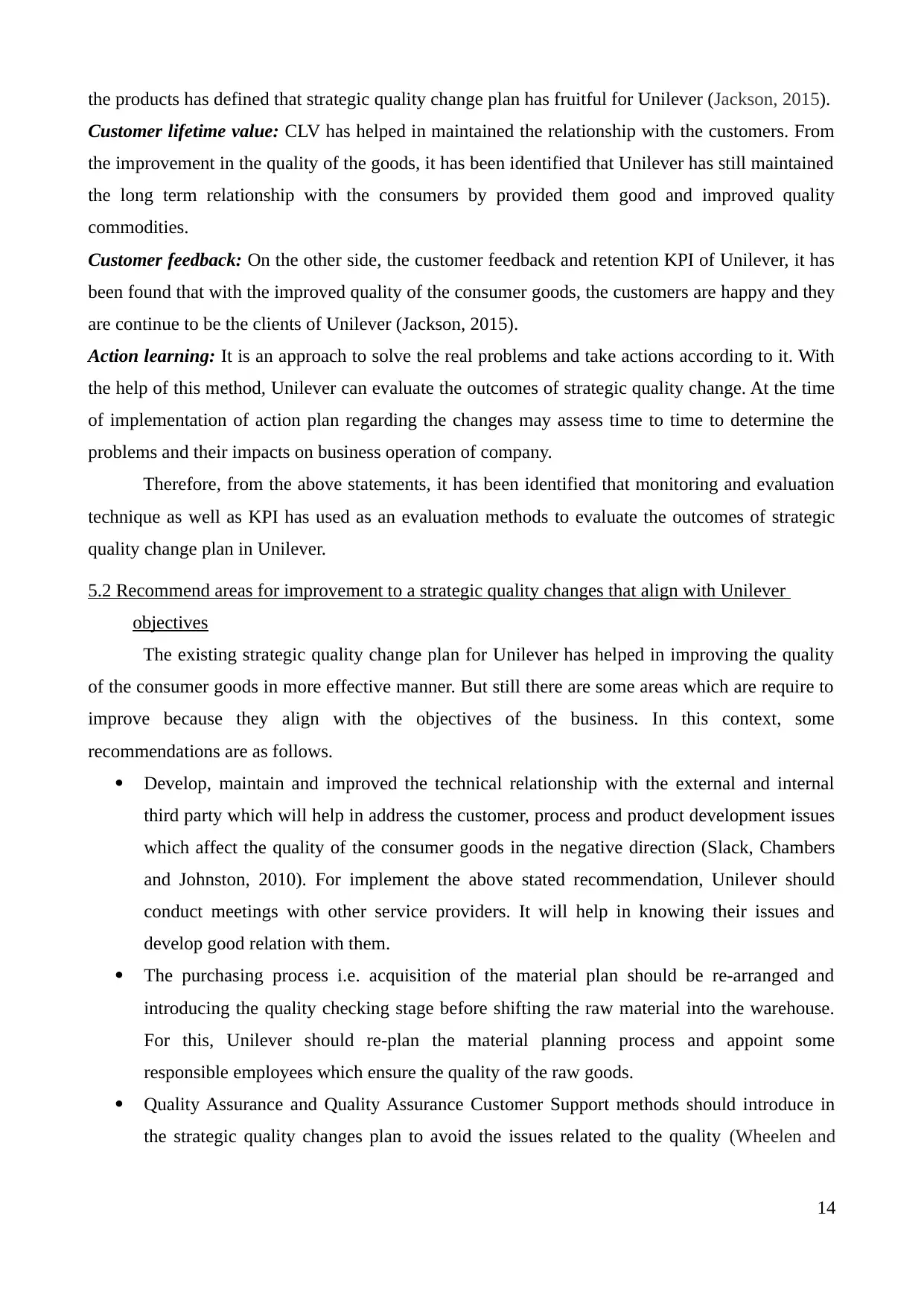
the products has defined that strategic quality change plan has fruitful for Unilever (Jackson, 2015).
Customer lifetime value: CLV has helped in maintained the relationship with the customers. From
the improvement in the quality of the goods, it has been identified that Unilever has still maintained
the long term relationship with the consumers by provided them good and improved quality
commodities.
Customer feedback: On the other side, the customer feedback and retention KPI of Unilever, it has
been found that with the improved quality of the consumer goods, the customers are happy and they
are continue to be the clients of Unilever (Jackson, 2015).
Action learning: It is an approach to solve the real problems and take actions according to it. With
the help of this method, Unilever can evaluate the outcomes of strategic quality change. At the time
of implementation of action plan regarding the changes may assess time to time to determine the
problems and their impacts on business operation of company.
Therefore, from the above statements, it has been identified that monitoring and evaluation
technique as well as KPI has used as an evaluation methods to evaluate the outcomes of strategic
quality change plan in Unilever.
5.2 Recommend areas for improvement to a strategic quality changes that align with Unilever
objectives
The existing strategic quality change plan for Unilever has helped in improving the quality
of the consumer goods in more effective manner. But still there are some areas which are require to
improve because they align with the objectives of the business. In this context, some
recommendations are as follows.
ï‚· Develop, maintain and improved the technical relationship with the external and internal
third party which will help in address the customer, process and product development issues
which affect the quality of the consumer goods in the negative direction (Slack, Chambers
and Johnston, 2010). For implement the above stated recommendation, Unilever should
conduct meetings with other service providers. It will help in knowing their issues and
develop good relation with them.
ï‚· The purchasing process i.e. acquisition of the material plan should be re-arranged and
introducing the quality checking stage before shifting the raw material into the warehouse.
For this, Unilever should re-plan the material planning process and appoint some
responsible employees which ensure the quality of the raw goods.
ï‚· Quality Assurance and Quality Assurance Customer Support methods should introduce in
the strategic quality changes plan to avoid the issues related to the quality (Wheelen and
14
Customer lifetime value: CLV has helped in maintained the relationship with the customers. From
the improvement in the quality of the goods, it has been identified that Unilever has still maintained
the long term relationship with the consumers by provided them good and improved quality
commodities.
Customer feedback: On the other side, the customer feedback and retention KPI of Unilever, it has
been found that with the improved quality of the consumer goods, the customers are happy and they
are continue to be the clients of Unilever (Jackson, 2015).
Action learning: It is an approach to solve the real problems and take actions according to it. With
the help of this method, Unilever can evaluate the outcomes of strategic quality change. At the time
of implementation of action plan regarding the changes may assess time to time to determine the
problems and their impacts on business operation of company.
Therefore, from the above statements, it has been identified that monitoring and evaluation
technique as well as KPI has used as an evaluation methods to evaluate the outcomes of strategic
quality change plan in Unilever.
5.2 Recommend areas for improvement to a strategic quality changes that align with Unilever
objectives
The existing strategic quality change plan for Unilever has helped in improving the quality
of the consumer goods in more effective manner. But still there are some areas which are require to
improve because they align with the objectives of the business. In this context, some
recommendations are as follows.
ï‚· Develop, maintain and improved the technical relationship with the external and internal
third party which will help in address the customer, process and product development issues
which affect the quality of the consumer goods in the negative direction (Slack, Chambers
and Johnston, 2010). For implement the above stated recommendation, Unilever should
conduct meetings with other service providers. It will help in knowing their issues and
develop good relation with them.
ï‚· The purchasing process i.e. acquisition of the material plan should be re-arranged and
introducing the quality checking stage before shifting the raw material into the warehouse.
For this, Unilever should re-plan the material planning process and appoint some
responsible employees which ensure the quality of the raw goods.
ï‚· Quality Assurance and Quality Assurance Customer Support methods should introduce in
the strategic quality changes plan to avoid the issues related to the quality (Wheelen and
14
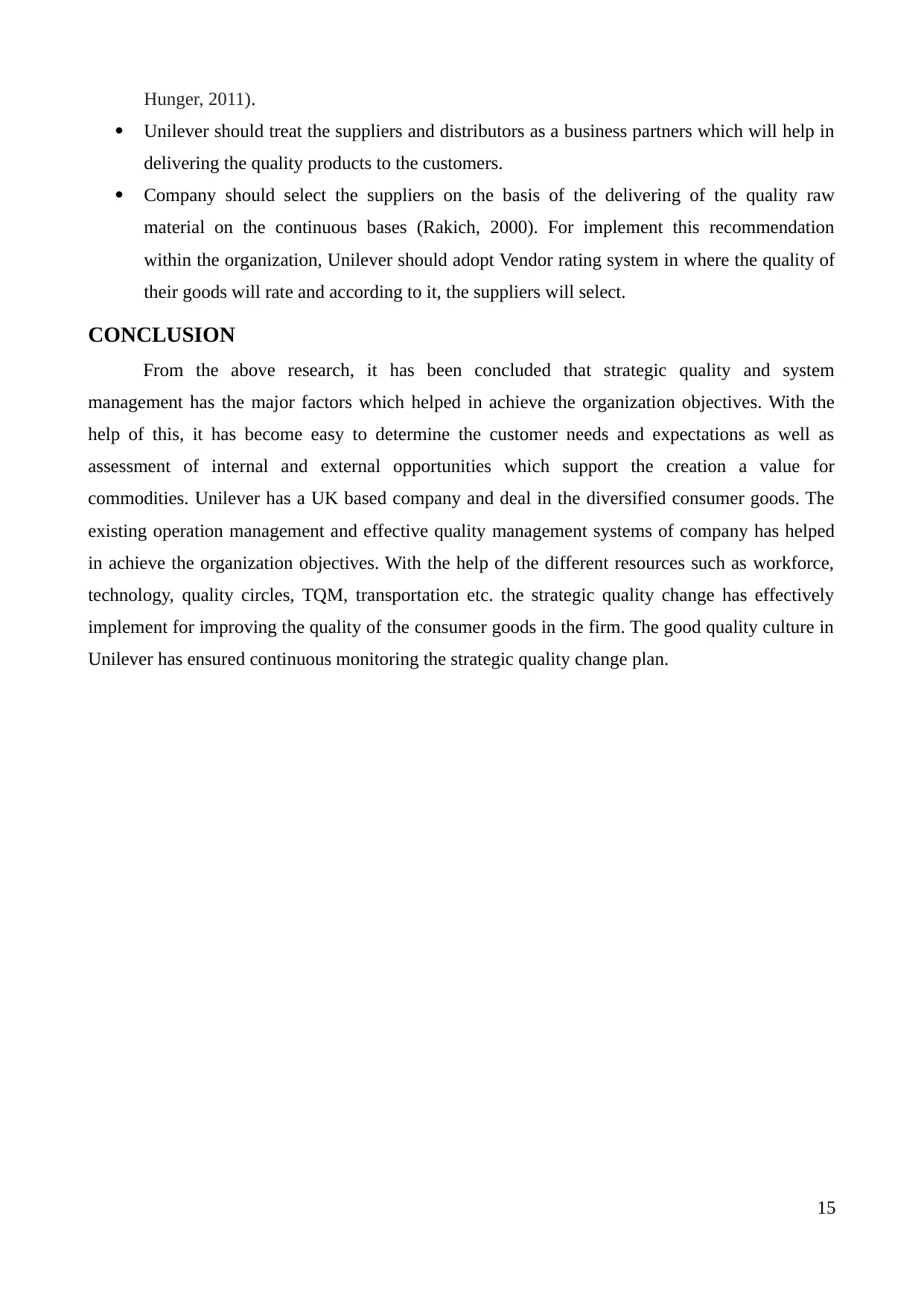
Hunger, 2011).
ï‚· Unilever should treat the suppliers and distributors as a business partners which will help in
delivering the quality products to the customers.
ï‚· Company should select the suppliers on the basis of the delivering of the quality raw
material on the continuous bases (Rakich, 2000). For implement this recommendation
within the organization, Unilever should adopt Vendor rating system in where the quality of
their goods will rate and according to it, the suppliers will select.
CONCLUSION
From the above research, it has been concluded that strategic quality and system
management has the major factors which helped in achieve the organization objectives. With the
help of this, it has become easy to determine the customer needs and expectations as well as
assessment of internal and external opportunities which support the creation a value for
commodities. Unilever has a UK based company and deal in the diversified consumer goods. The
existing operation management and effective quality management systems of company has helped
in achieve the organization objectives. With the help of the different resources such as workforce,
technology, quality circles, TQM, transportation etc. the strategic quality change has effectively
implement for improving the quality of the consumer goods in the firm. The good quality culture in
Unilever has ensured continuous monitoring the strategic quality change plan.
15
ï‚· Unilever should treat the suppliers and distributors as a business partners which will help in
delivering the quality products to the customers.
ï‚· Company should select the suppliers on the basis of the delivering of the quality raw
material on the continuous bases (Rakich, 2000). For implement this recommendation
within the organization, Unilever should adopt Vendor rating system in where the quality of
their goods will rate and according to it, the suppliers will select.
CONCLUSION
From the above research, it has been concluded that strategic quality and system
management has the major factors which helped in achieve the organization objectives. With the
help of this, it has become easy to determine the customer needs and expectations as well as
assessment of internal and external opportunities which support the creation a value for
commodities. Unilever has a UK based company and deal in the diversified consumer goods. The
existing operation management and effective quality management systems of company has helped
in achieve the organization objectives. With the help of the different resources such as workforce,
technology, quality circles, TQM, transportation etc. the strategic quality change has effectively
implement for improving the quality of the consumer goods in the firm. The good quality culture in
Unilever has ensured continuous monitoring the strategic quality change plan.
15
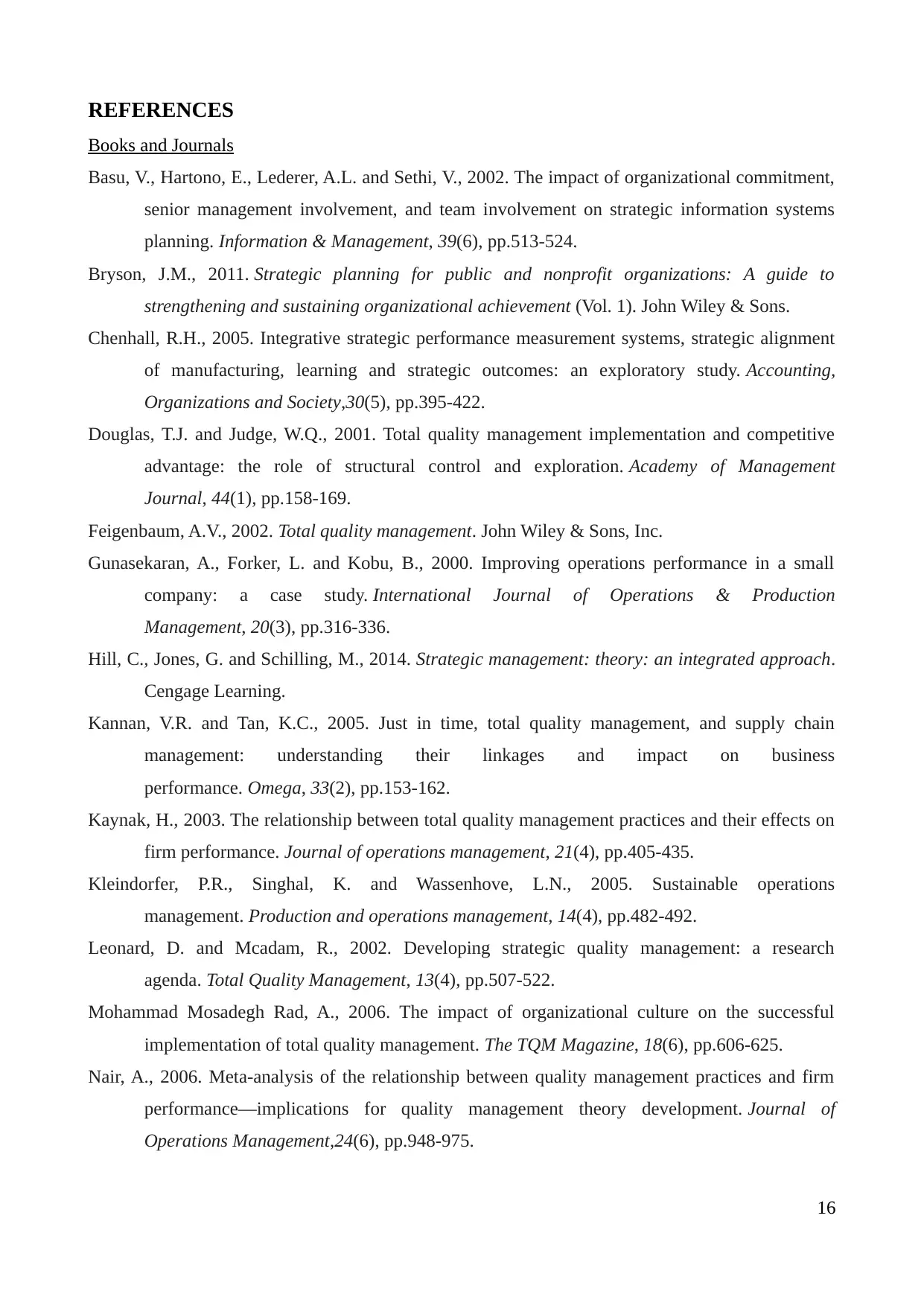
REFERENCES
Books and Journals
Basu, V., Hartono, E., Lederer, A.L. and Sethi, V., 2002. The impact of organizational commitment,
senior management involvement, and team involvement on strategic information systems
planning. Information & Management, 39(6), pp.513-524.
Bryson, J.M., 2011. Strategic planning for public and nonprofit organizations: A guide to
strengthening and sustaining organizational achievement (Vol. 1). John Wiley & Sons.
Chenhall, R.H., 2005. Integrative strategic performance measurement systems, strategic alignment
of manufacturing, learning and strategic outcomes: an exploratory study. Accounting,
Organizations and Society,30(5), pp.395-422.
Douglas, T.J. and Judge, W.Q., 2001. Total quality management implementation and competitive
advantage: the role of structural control and exploration. Academy of Management
Journal, 44(1), pp.158-169.
Feigenbaum, A.V., 2002. Total quality management. John Wiley & Sons, Inc.
Gunasekaran, A., Forker, L. and Kobu, B., 2000. Improving operations performance in a small
company: a case study. International Journal of Operations & Production
Management, 20(3), pp.316-336.
Hill, C., Jones, G. and Schilling, M., 2014. Strategic management: theory: an integrated approach.
Cengage Learning.
Kannan, V.R. and Tan, K.C., 2005. Just in time, total quality management, and supply chain
management: understanding their linkages and impact on business
performance. Omega, 33(2), pp.153-162.
Kaynak, H., 2003. The relationship between total quality management practices and their effects on
firm performance. Journal of operations management, 21(4), pp.405-435.
Kleindorfer, P.R., Singhal, K. and Wassenhove, L.N., 2005. Sustainable operations
management. Production and operations management, 14(4), pp.482-492.
Leonard, D. and Mcadam, R., 2002. Developing strategic quality management: a research
agenda. Total Quality Management, 13(4), pp.507-522.
Mohammad Mosadegh Rad, A., 2006. The impact of organizational culture on the successful
implementation of total quality management. The TQM Magazine, 18(6), pp.606-625.
Nair, A., 2006. Meta-analysis of the relationship between quality management practices and firm
performance—implications for quality management theory development. Journal of
Operations Management,24(6), pp.948-975.
16
Books and Journals
Basu, V., Hartono, E., Lederer, A.L. and Sethi, V., 2002. The impact of organizational commitment,
senior management involvement, and team involvement on strategic information systems
planning. Information & Management, 39(6), pp.513-524.
Bryson, J.M., 2011. Strategic planning for public and nonprofit organizations: A guide to
strengthening and sustaining organizational achievement (Vol. 1). John Wiley & Sons.
Chenhall, R.H., 2005. Integrative strategic performance measurement systems, strategic alignment
of manufacturing, learning and strategic outcomes: an exploratory study. Accounting,
Organizations and Society,30(5), pp.395-422.
Douglas, T.J. and Judge, W.Q., 2001. Total quality management implementation and competitive
advantage: the role of structural control and exploration. Academy of Management
Journal, 44(1), pp.158-169.
Feigenbaum, A.V., 2002. Total quality management. John Wiley & Sons, Inc.
Gunasekaran, A., Forker, L. and Kobu, B., 2000. Improving operations performance in a small
company: a case study. International Journal of Operations & Production
Management, 20(3), pp.316-336.
Hill, C., Jones, G. and Schilling, M., 2014. Strategic management: theory: an integrated approach.
Cengage Learning.
Kannan, V.R. and Tan, K.C., 2005. Just in time, total quality management, and supply chain
management: understanding their linkages and impact on business
performance. Omega, 33(2), pp.153-162.
Kaynak, H., 2003. The relationship between total quality management practices and their effects on
firm performance. Journal of operations management, 21(4), pp.405-435.
Kleindorfer, P.R., Singhal, K. and Wassenhove, L.N., 2005. Sustainable operations
management. Production and operations management, 14(4), pp.482-492.
Leonard, D. and Mcadam, R., 2002. Developing strategic quality management: a research
agenda. Total Quality Management, 13(4), pp.507-522.
Mohammad Mosadegh Rad, A., 2006. The impact of organizational culture on the successful
implementation of total quality management. The TQM Magazine, 18(6), pp.606-625.
Nair, A., 2006. Meta-analysis of the relationship between quality management practices and firm
performance—implications for quality management theory development. Journal of
Operations Management,24(6), pp.948-975.
16
Secure Best Marks with AI Grader
Need help grading? Try our AI Grader for instant feedback on your assignments.
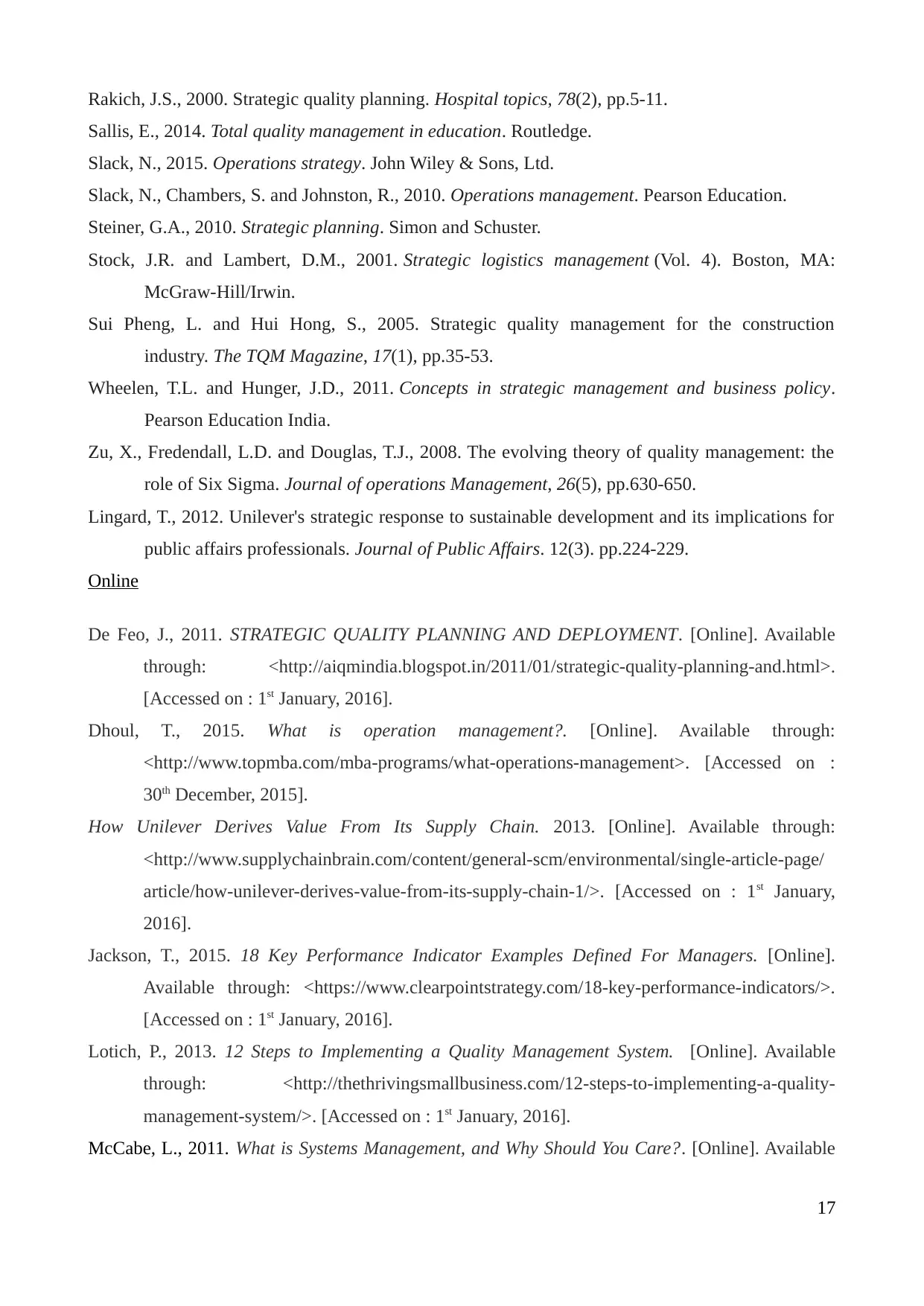
Rakich, J.S., 2000. Strategic quality planning. Hospital topics, 78(2), pp.5-11.
Sallis, E., 2014. Total quality management in education. Routledge.
Slack, N., 2015. Operations strategy. John Wiley & Sons, Ltd.
Slack, N., Chambers, S. and Johnston, R., 2010. Operations management. Pearson Education.
Steiner, G.A., 2010. Strategic planning. Simon and Schuster.
Stock, J.R. and Lambert, D.M., 2001. Strategic logistics management (Vol. 4). Boston, MA:
McGraw-Hill/Irwin.
Sui Pheng, L. and Hui Hong, S., 2005. Strategic quality management for the construction
industry. The TQM Magazine, 17(1), pp.35-53.
Wheelen, T.L. and Hunger, J.D., 2011. Concepts in strategic management and business policy.
Pearson Education India.
Zu, X., Fredendall, L.D. and Douglas, T.J., 2008. The evolving theory of quality management: the
role of Six Sigma. Journal of operations Management, 26(5), pp.630-650.
Lingard, T., 2012. Unilever's strategic response to sustainable development and its implications for
public affairs professionals. Journal of Public Affairs. 12(3). pp.224-229.
Online
De Feo, J., 2011. STRATEGIC QUALITY PLANNING AND DEPLOYMENT. [Online]. Available
through: <http://aiqmindia.blogspot.in/2011/01/strategic-quality-planning-and.html>.
[Accessed on : 1st January, 2016].
Dhoul, T., 2015. What is operation management?. [Online]. Available through:
<http://www.topmba.com/mba-programs/what-operations-management>. [Accessed on :
30th December, 2015].
How Unilever Derives Value From Its Supply Chain. 2013. [Online]. Available through:
<http://www.supplychainbrain.com/content/general-scm/environmental/single-article-page/
article/how-unilever-derives-value-from-its-supply-chain-1/>. [Accessed on : 1st January,
2016].
Jackson, T., 2015. 18 Key Performance Indicator Examples Defined For Managers. [Online].
Available through: <https://www.clearpointstrategy.com/18-key-performance-indicators/>.
[Accessed on : 1st January, 2016].
Lotich, P., 2013. 12 Steps to Implementing a Quality Management System. [Online]. Available
through: <http://thethrivingsmallbusiness.com/12-steps-to-implementing-a-quality-
management-system/>. [Accessed on : 1st January, 2016].
McCabe, L., 2011. What is Systems Management, and Why Should You Care?. [Online]. Available
17
Sallis, E., 2014. Total quality management in education. Routledge.
Slack, N., 2015. Operations strategy. John Wiley & Sons, Ltd.
Slack, N., Chambers, S. and Johnston, R., 2010. Operations management. Pearson Education.
Steiner, G.A., 2010. Strategic planning. Simon and Schuster.
Stock, J.R. and Lambert, D.M., 2001. Strategic logistics management (Vol. 4). Boston, MA:
McGraw-Hill/Irwin.
Sui Pheng, L. and Hui Hong, S., 2005. Strategic quality management for the construction
industry. The TQM Magazine, 17(1), pp.35-53.
Wheelen, T.L. and Hunger, J.D., 2011. Concepts in strategic management and business policy.
Pearson Education India.
Zu, X., Fredendall, L.D. and Douglas, T.J., 2008. The evolving theory of quality management: the
role of Six Sigma. Journal of operations Management, 26(5), pp.630-650.
Lingard, T., 2012. Unilever's strategic response to sustainable development and its implications for
public affairs professionals. Journal of Public Affairs. 12(3). pp.224-229.
Online
De Feo, J., 2011. STRATEGIC QUALITY PLANNING AND DEPLOYMENT. [Online]. Available
through: <http://aiqmindia.blogspot.in/2011/01/strategic-quality-planning-and.html>.
[Accessed on : 1st January, 2016].
Dhoul, T., 2015. What is operation management?. [Online]. Available through:
<http://www.topmba.com/mba-programs/what-operations-management>. [Accessed on :
30th December, 2015].
How Unilever Derives Value From Its Supply Chain. 2013. [Online]. Available through:
<http://www.supplychainbrain.com/content/general-scm/environmental/single-article-page/
article/how-unilever-derives-value-from-its-supply-chain-1/>. [Accessed on : 1st January,
2016].
Jackson, T., 2015. 18 Key Performance Indicator Examples Defined For Managers. [Online].
Available through: <https://www.clearpointstrategy.com/18-key-performance-indicators/>.
[Accessed on : 1st January, 2016].
Lotich, P., 2013. 12 Steps to Implementing a Quality Management System. [Online]. Available
through: <http://thethrivingsmallbusiness.com/12-steps-to-implementing-a-quality-
management-system/>. [Accessed on : 1st January, 2016].
McCabe, L., 2011. What is Systems Management, and Why Should You Care?. [Online]. Available
17
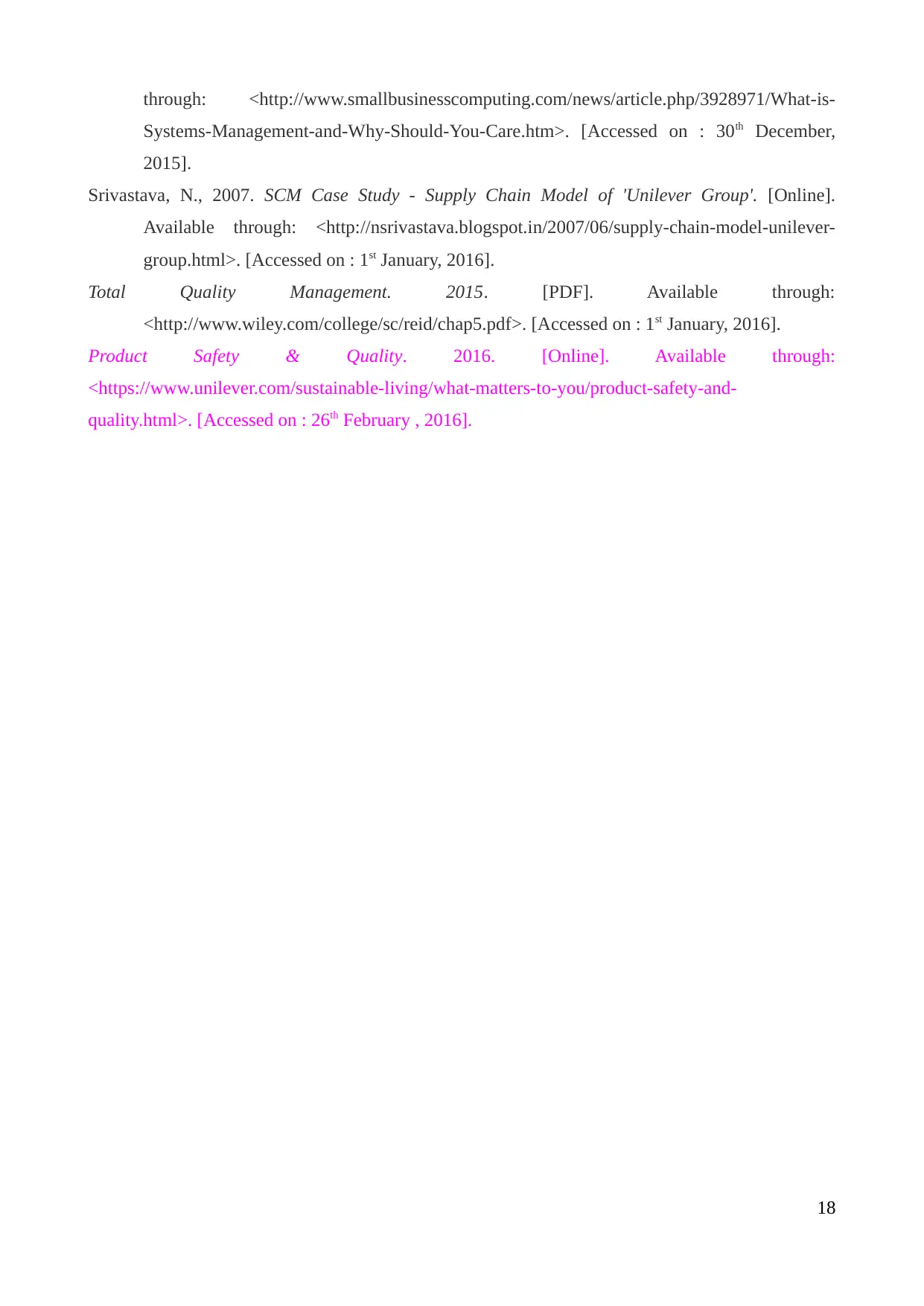
through: <http://www.smallbusinesscomputing.com/news/article.php/3928971/What-is-
Systems-Management-and-Why-Should-You-Care.htm>. [Accessed on : 30th December,
2015].
Srivastava, N., 2007. SCM Case Study - Supply Chain Model of 'Unilever Group'. [Online].
Available through: <http://nsrivastava.blogspot.in/2007/06/supply-chain-model-unilever-
group.html>. [Accessed on : 1st January, 2016].
Total Quality Management. 2015. [PDF]. Available through:
<http://www.wiley.com/college/sc/reid/chap5.pdf>. [Accessed on : 1st January, 2016].
Product Safety & Quality. 2016. [Online]. Available through:
<https://www.unilever.com/sustainable-living/what-matters-to-you/product-safety-and-
quality.html>. [Accessed on : 26th February , 2016].
18
Systems-Management-and-Why-Should-You-Care.htm>. [Accessed on : 30th December,
2015].
Srivastava, N., 2007. SCM Case Study - Supply Chain Model of 'Unilever Group'. [Online].
Available through: <http://nsrivastava.blogspot.in/2007/06/supply-chain-model-unilever-
group.html>. [Accessed on : 1st January, 2016].
Total Quality Management. 2015. [PDF]. Available through:
<http://www.wiley.com/college/sc/reid/chap5.pdf>. [Accessed on : 1st January, 2016].
Product Safety & Quality. 2016. [Online]. Available through:
<https://www.unilever.com/sustainable-living/what-matters-to-you/product-safety-and-
quality.html>. [Accessed on : 26th February , 2016].
18
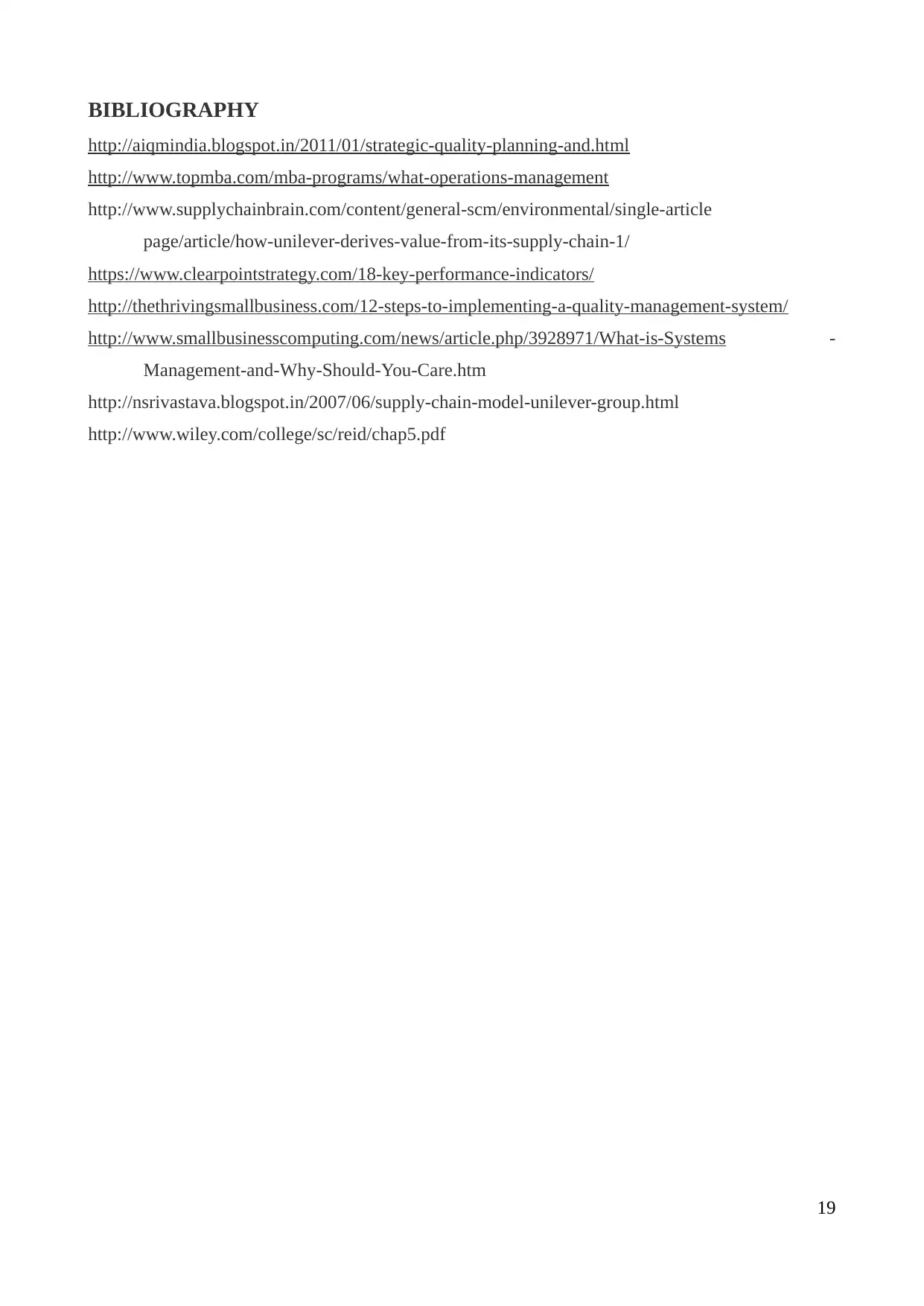
BIBLIOGRAPHY
http://aiqmindia.blogspot.in/2011/01/strategic-quality-planning-and.html
http://www.topmba.com/mba-programs/what-operations-management
http://www.supplychainbrain.com/content/general-scm/environmental/single-article
page/article/how-unilever-derives-value-from-its-supply-chain-1/
https://www.clearpointstrategy.com/18-key-performance-indicators/
http://thethrivingsmallbusiness.com/12-steps-to-implementing-a-quality-management-system/
http://www.smallbusinesscomputing.com/news/article.php/3928971/What-is-Systems -
Management-and-Why-Should-You-Care.htm
http://nsrivastava.blogspot.in/2007/06/supply-chain-model-unilever-group.html
http://www.wiley.com/college/sc/reid/chap5.pdf
19
http://aiqmindia.blogspot.in/2011/01/strategic-quality-planning-and.html
http://www.topmba.com/mba-programs/what-operations-management
http://www.supplychainbrain.com/content/general-scm/environmental/single-article
page/article/how-unilever-derives-value-from-its-supply-chain-1/
https://www.clearpointstrategy.com/18-key-performance-indicators/
http://thethrivingsmallbusiness.com/12-steps-to-implementing-a-quality-management-system/
http://www.smallbusinesscomputing.com/news/article.php/3928971/What-is-Systems -
Management-and-Why-Should-You-Care.htm
http://nsrivastava.blogspot.in/2007/06/supply-chain-model-unilever-group.html
http://www.wiley.com/college/sc/reid/chap5.pdf
19
1 out of 19
Related Documents

Your All-in-One AI-Powered Toolkit for Academic Success.
 +13062052269
info@desklib.com
Available 24*7 on WhatsApp / Email
Unlock your academic potential
© 2024  |  Zucol Services PVT LTD  |  All rights reserved.