Improvement of Supply Chain Management: A Case Study Analysis
VerifiedAdded on 2021/02/21
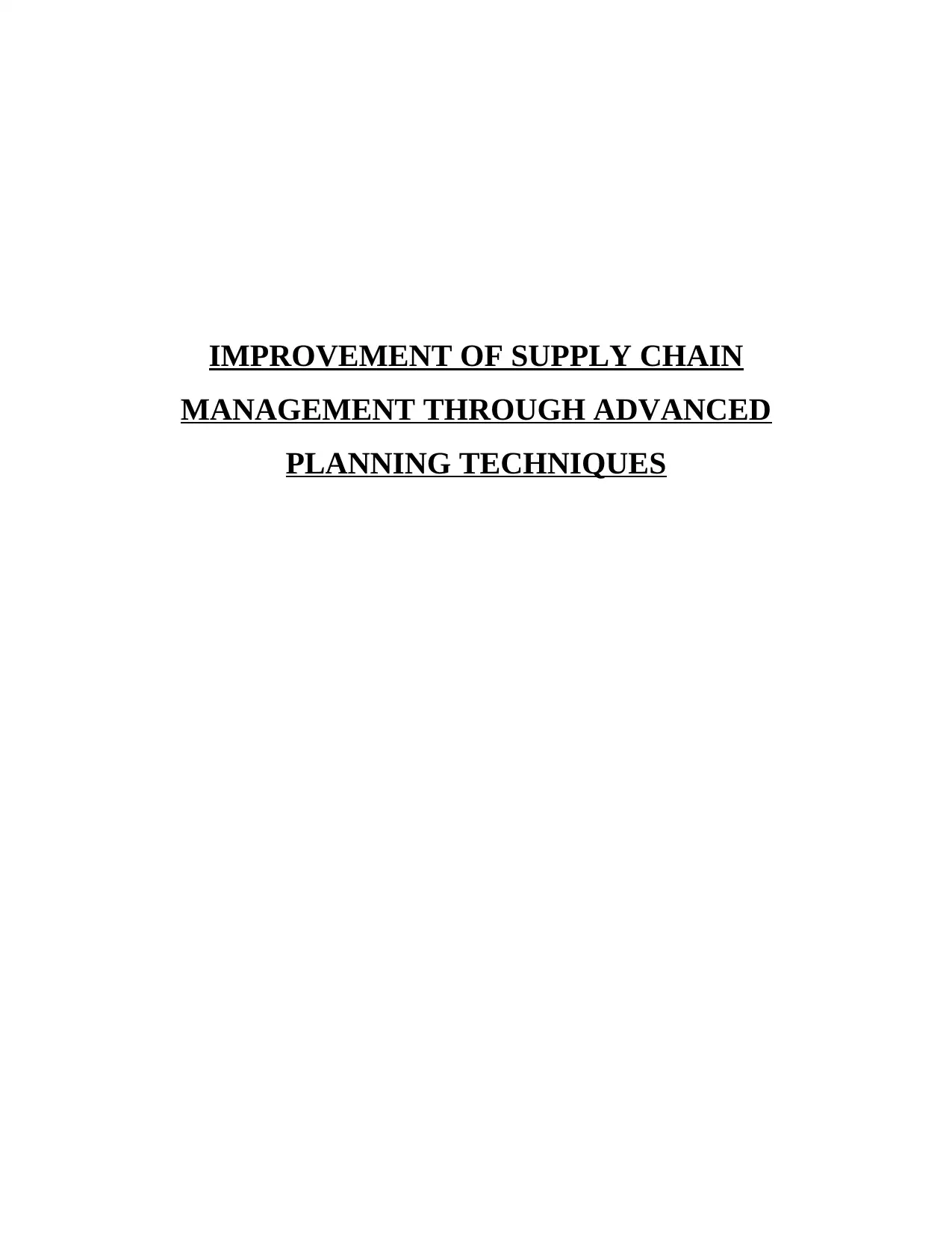
MANAGEMENT THROUGH ADVANCED
PLANNING TECHNIQUES
Paraphrase This Document
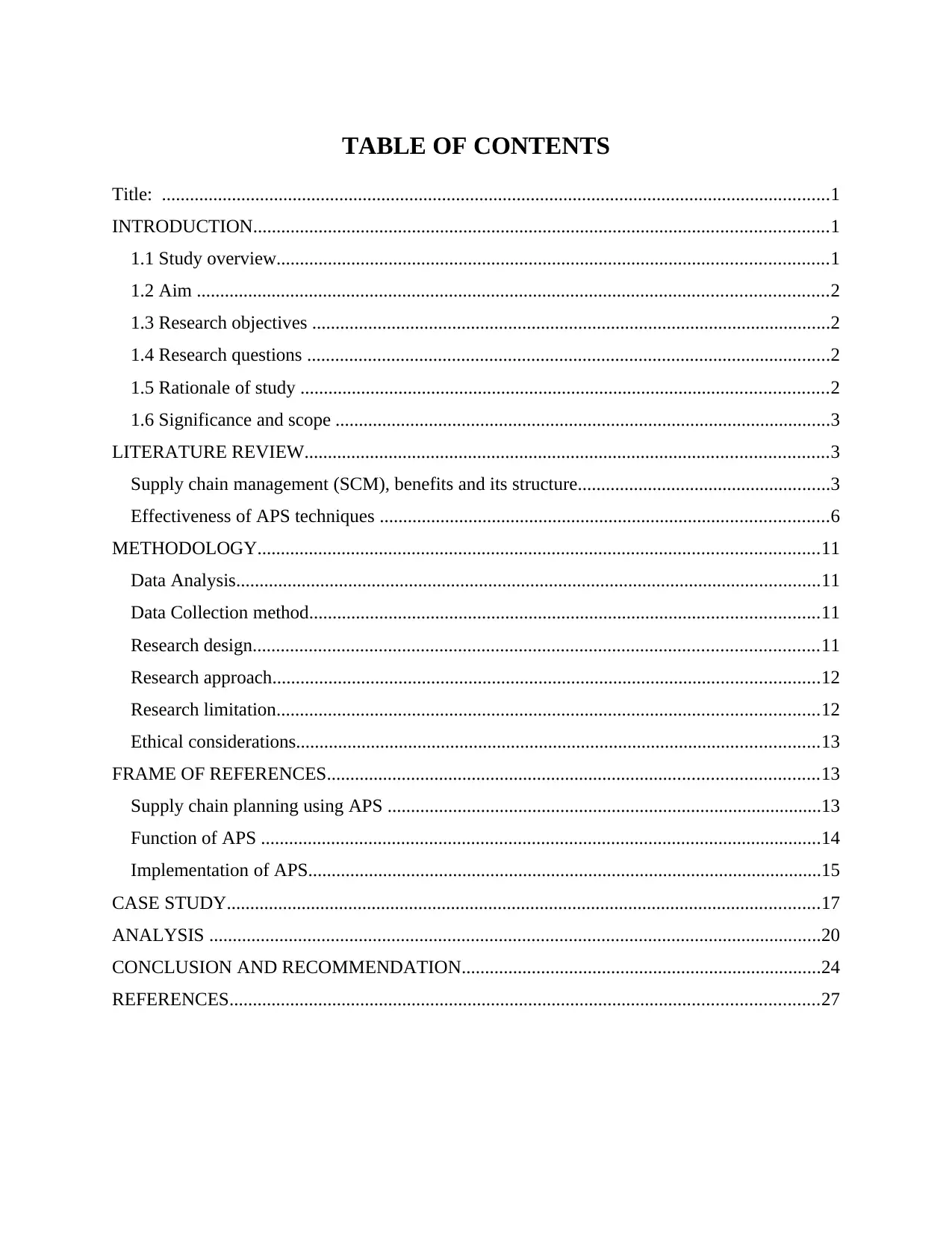
Title: ...............................................................................................................................................1
INTRODUCTION...........................................................................................................................1
1.1 Study overview......................................................................................................................1
1.2 Aim .......................................................................................................................................2
1.3 Research objectives ...............................................................................................................2
1.4 Research questions ................................................................................................................2
1.5 Rationale of study .................................................................................................................2
1.6 Significance and scope ..........................................................................................................3
LITERATURE REVIEW................................................................................................................3
Supply chain management (SCM), benefits and its structure......................................................3
Effectiveness of APS techniques ................................................................................................6
METHODOLOGY........................................................................................................................11
Data Analysis.............................................................................................................................11
Data Collection method.............................................................................................................11
Research design.........................................................................................................................11
Research approach.....................................................................................................................12
Research limitation....................................................................................................................12
Ethical considerations................................................................................................................13
FRAME OF REFERENCES.........................................................................................................13
Supply chain planning using APS .............................................................................................13
Function of APS ........................................................................................................................14
Implementation of APS..............................................................................................................15
CASE STUDY...............................................................................................................................17
ANALYSIS ...................................................................................................................................20
CONCLUSION AND RECOMMENDATION.............................................................................24
REFERENCES..............................................................................................................................27

Improvement of supply chain management through advanced planning techniques. A
case study on Pepsico.
INTRODUCTION
1.1 Study overview
Supply chain management (SCM) is defined as the interactive system which consist of
people, organisations, resources, actions and information so that products and services can be
moved from suppliers to consumers. The supply chain plays key role in transforming natural
resources and raw materials into finished products so that they can be delivered to the end users.
One of the key objective of SCM is to ensure that all needs of the consumers are fulfilled and
organisations are capable to make optimum use of their resources (Stadtler, 2015). It will help to
understand the needs of customers as well as to improve the inventory, labour and distribution.
The effective supply chain has significant impact on the overall performance of the
organisation. Thus, there is need to integrate supply chain with advanced planning systems
(APS) so that their effectiveness can be enhanced. APS are known as the systems which tracks
and monitor the cost of different organisational activities which drives the production and supply
process. APS systems regulates the resource allocation and focus on improving the production
capacity to the maximum level so that demand and organisational capacity can be balanced. APS
consists of vast range of techniques and tools to improve the manufacturing and supply process.
APS performs the planning and analysis of manufacturing and logistics process for both
long and short term goals. The use of highly advanced mathematical logics and algorithm helps
to simulate the resource planning, demand management and finance schedule. Supply chain
provides the detailed information regarding finance, material and information resources so that
resources and services can be delivered to various stakeholders (Dias and Ierapetritou, 2017).
The use of effective APS helps to balance the flow between finance, information and products.
For improving and generating the high performance supply chains, it is very essential for the
organisations to monitor the existing process flow and to address the flaws by using adequate
APS technology (Alicke, Rexhausen and Seyfert, 2017). The report will provide a case study of
Pepsico which is one of the leading multinational food, beverage and snack corporation. The
organisation has its headquarter in New York. The organisation is worldwide famous brand name
1
⊘ This is a preview!⊘
Do you want full access?
Subscribe today to unlock all pages.

Trusted by 1+ million students worldwide

long.
1.2 Aim
To explore how Advance Planning Systems (APS) help in improving supply chain in
production and planning at strategic level and to analyse the effects of using APS in supply chain
: A case study on Pepsico.
1.3 Research objectives
ï‚· To understand the structure and significance of supply chain.
ï‚· To evaluate the benefits of APS and their impact on SCM.
ï‚· To analyse the supply chain structure of Pepsico.
1.4 Research questions
ï‚· How supply chain management of organisation works?
ï‚· Analyse advanced planning techniques and how they are used in SCM?
ï‚· How supply chain structure of PepsiCo helps in sustaining its long term success?
1.5 Rationale of study
The use of APS techniques is very essential and important for making the business
process profitable. These approaches helps in identifying the real life constraints which
influences the real time business decisions, project scheduling and capabilities. Thus, it is very
essential that companies must manage their production, distribution and supply chain through
making the effective use of APS techniques. In order to survive in the competitive market
environment, it is necessary for the organisations to improve their supply chain (Garcia and You,
2015). This can be done by identifying the loop holes and operational deficient areas of business.
Most of the organisations which provide services globally needs to make their supply chain very
influential and impressive.
Thus, it is very essential to understand the different elements and structure of the supply
chain and its impact on overall business performance. APS techniques can help organisations to
achieve their long term goals and operational continuity. With the use of these techniques, it
becomes easy for the service providers to evaluate the implications of different decisions and
their possible consequences (Alicke, Rexhausen and Seyfert, 2017). Another reason for
conducting this study is to develop an understanding that how recommendations and
implementation of APS can helps managers to take better decisions. The report will also help to
2
Paraphrase This Document
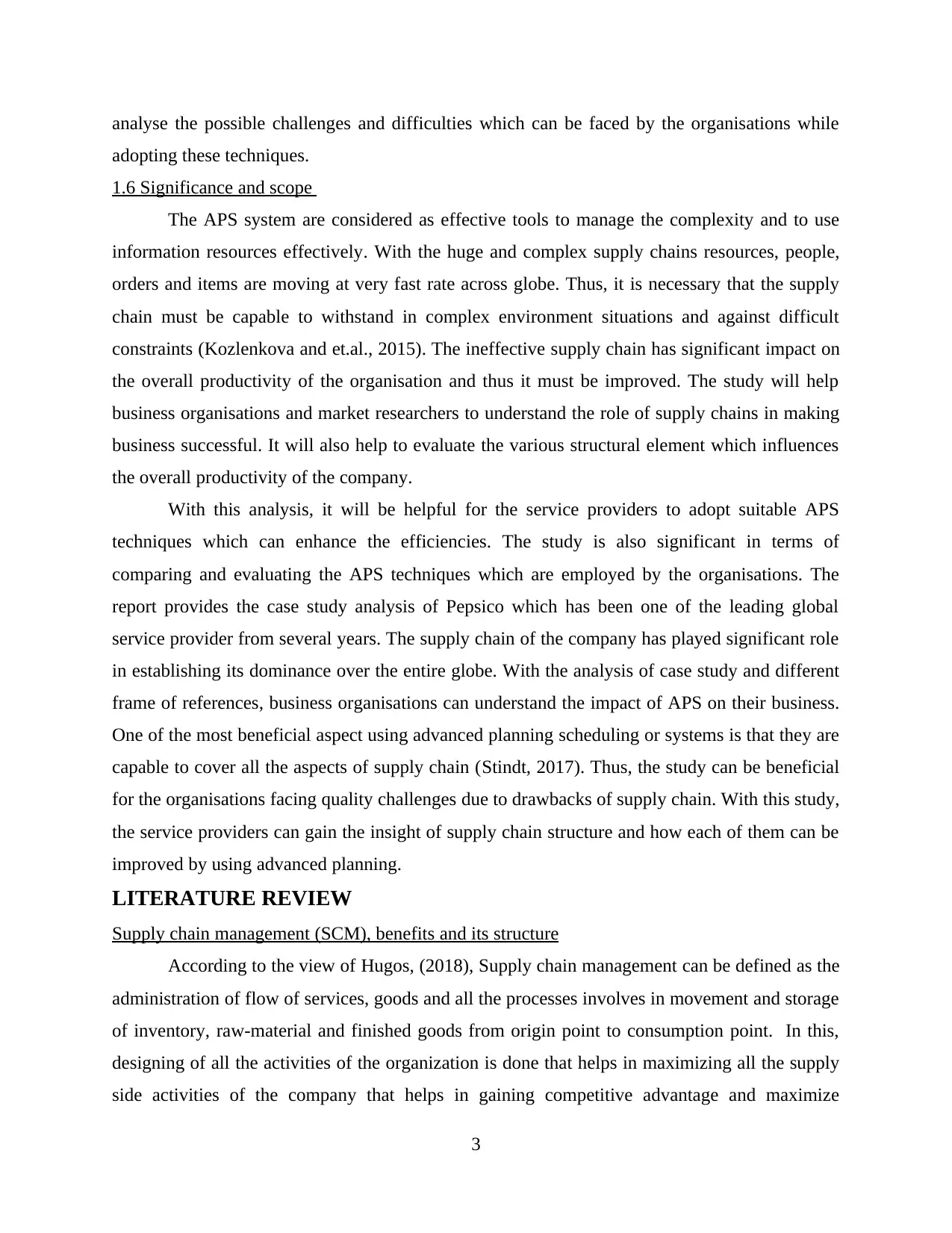
adopting these techniques.
1.6 Significance and scope
The APS system are considered as effective tools to manage the complexity and to use
information resources effectively. With the huge and complex supply chains resources, people,
orders and items are moving at very fast rate across globe. Thus, it is necessary that the supply
chain must be capable to withstand in complex environment situations and against difficult
constraints (Kozlenkova and et.al., 2015). The ineffective supply chain has significant impact on
the overall productivity of the organisation and thus it must be improved. The study will help
business organisations and market researchers to understand the role of supply chains in making
business successful. It will also help to evaluate the various structural element which influences
the overall productivity of the company.
With this analysis, it will be helpful for the service providers to adopt suitable APS
techniques which can enhance the efficiencies. The study is also significant in terms of
comparing and evaluating the APS techniques which are employed by the organisations. The
report provides the case study analysis of Pepsico which has been one of the leading global
service provider from several years. The supply chain of the company has played significant role
in establishing its dominance over the entire globe. With the analysis of case study and different
frame of references, business organisations can understand the impact of APS on their business.
One of the most beneficial aspect using advanced planning scheduling or systems is that they are
capable to cover all the aspects of supply chain (Stindt, 2017). Thus, the study can be beneficial
for the organisations facing quality challenges due to drawbacks of supply chain. With this study,
the service providers can gain the insight of supply chain structure and how each of them can be
improved by using advanced planning.
LITERATURE REVIEW
Supply chain management (SCM), benefits and its structure
According to the view of Hugos, (2018), Supply chain management can be defined as the
administration of flow of services, goods and all the processes involves in movement and storage
of inventory, raw-material and finished goods from origin point to consumption point. In this,
designing of all the activities of the organization is done that helps in maximizing all the supply
side activities of the company that helps in gaining competitive advantage and maximize
3
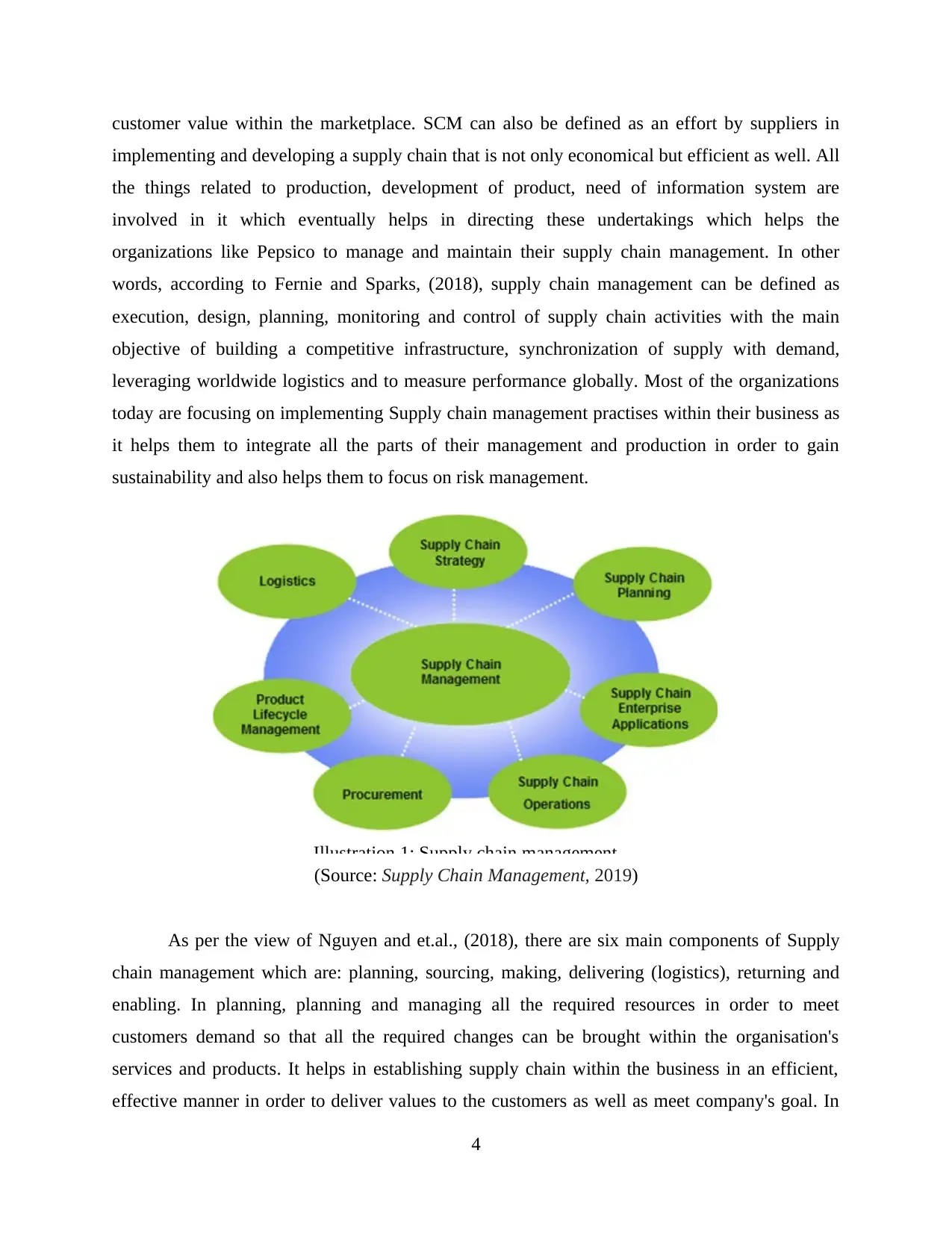
implementing and developing a supply chain that is not only economical but efficient as well. All
the things related to production, development of product, need of information system are
involved in it which eventually helps in directing these undertakings which helps the
organizations like Pepsico to manage and maintain their supply chain management. In other
words, according to Fernie and Sparks, (2018), supply chain management can be defined as
execution, design, planning, monitoring and control of supply chain activities with the main
objective of building a competitive infrastructure, synchronization of supply with demand,
leveraging worldwide logistics and to measure performance globally. Most of the organizations
today are focusing on implementing Supply chain management practises within their business as
it helps them to integrate all the parts of their management and production in order to gain
sustainability and also helps them to focus on risk management.
(Source: Supply Chain Management, 2019)
As per the view of Nguyen and et.al., (2018), there are six main components of Supply
chain management which are: planning, sourcing, making, delivering (logistics), returning and
enabling. In planning, planning and managing all the required resources in order to meet
customers demand so that all the required changes can be brought within the organisation's
services and products. It helps in establishing supply chain within the business in an efficient,
effective manner in order to deliver values to the customers as well as meet company's goal. In
4
Illustration 1: Supply chain management
⊘ This is a preview!⊘
Do you want full access?
Subscribe today to unlock all pages.

Trusted by 1+ million students worldwide
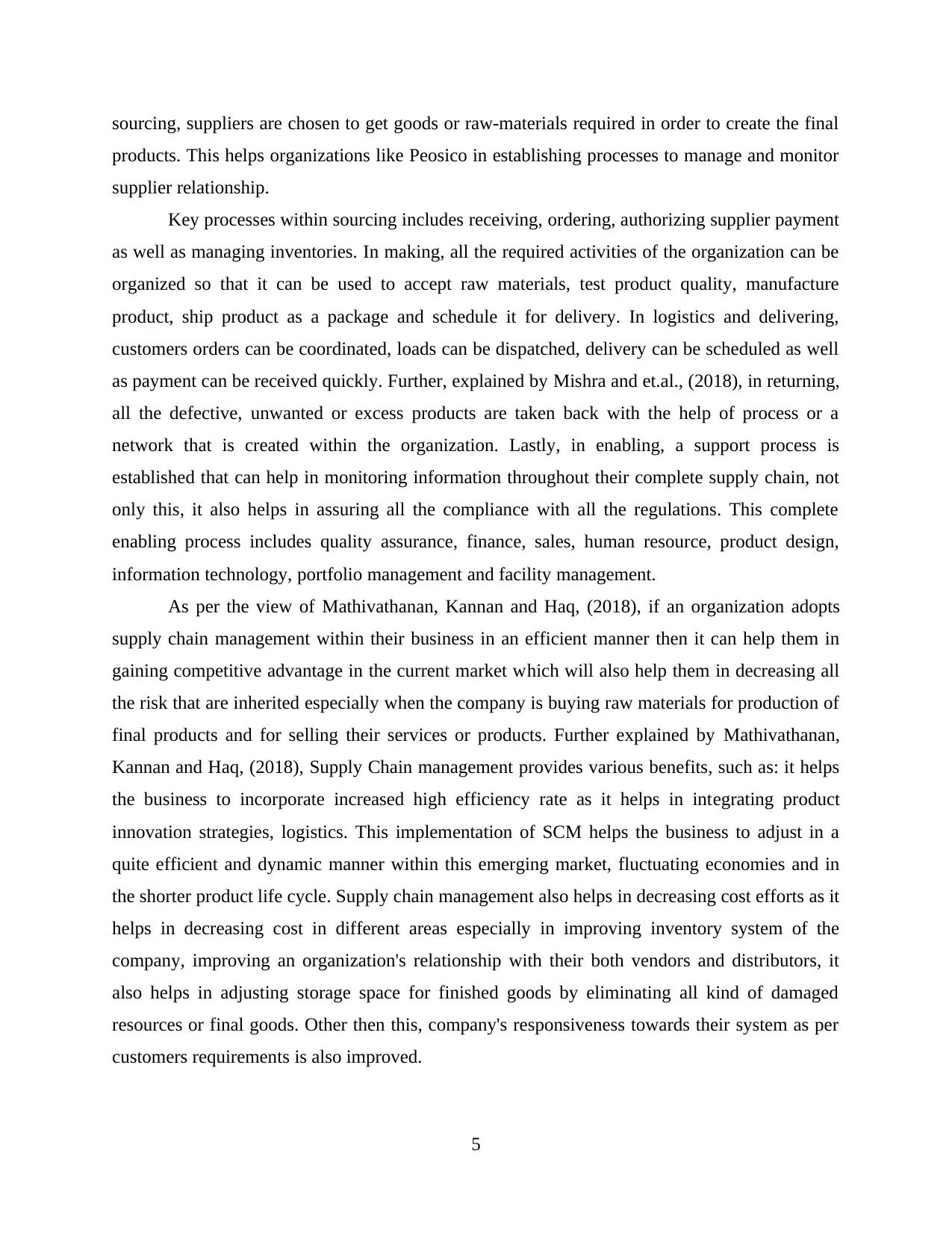
products. This helps organizations like Peosico in establishing processes to manage and monitor
supplier relationship.
Key processes within sourcing includes receiving, ordering, authorizing supplier payment
as well as managing inventories. In making, all the required activities of the organization can be
organized so that it can be used to accept raw materials, test product quality, manufacture
product, ship product as a package and schedule it for delivery. In logistics and delivering,
customers orders can be coordinated, loads can be dispatched, delivery can be scheduled as well
as payment can be received quickly. Further, explained by Mishra and et.al., (2018), in returning,
all the defective, unwanted or excess products are taken back with the help of process or a
network that is created within the organization. Lastly, in enabling, a support process is
established that can help in monitoring information throughout their complete supply chain, not
only this, it also helps in assuring all the compliance with all the regulations. This complete
enabling process includes quality assurance, finance, sales, human resource, product design,
information technology, portfolio management and facility management.
As per the view of Mathivathanan, Kannan and Haq, (2018), if an organization adopts
supply chain management within their business in an efficient manner then it can help them in
gaining competitive advantage in the current market which will also help them in decreasing all
the risk that are inherited especially when the company is buying raw materials for production of
final products and for selling their services or products. Further explained by Mathivathanan,
Kannan and Haq, (2018), Supply Chain management provides various benefits, such as: it helps
the business to incorporate increased high efficiency rate as it helps in integrating product
innovation strategies, logistics. This implementation of SCM helps the business to adjust in a
quite efficient and dynamic manner within this emerging market, fluctuating economies and in
the shorter product life cycle. Supply chain management also helps in decreasing cost efforts as it
helps in decreasing cost in different areas especially in improving inventory system of the
company, improving an organization's relationship with their both vendors and distributors, it
also helps in adjusting storage space for finished goods by eliminating all kind of damaged
resources or final goods. Other then this, company's responsiveness towards their system as per
customers requirements is also improved.
5
Paraphrase This Document
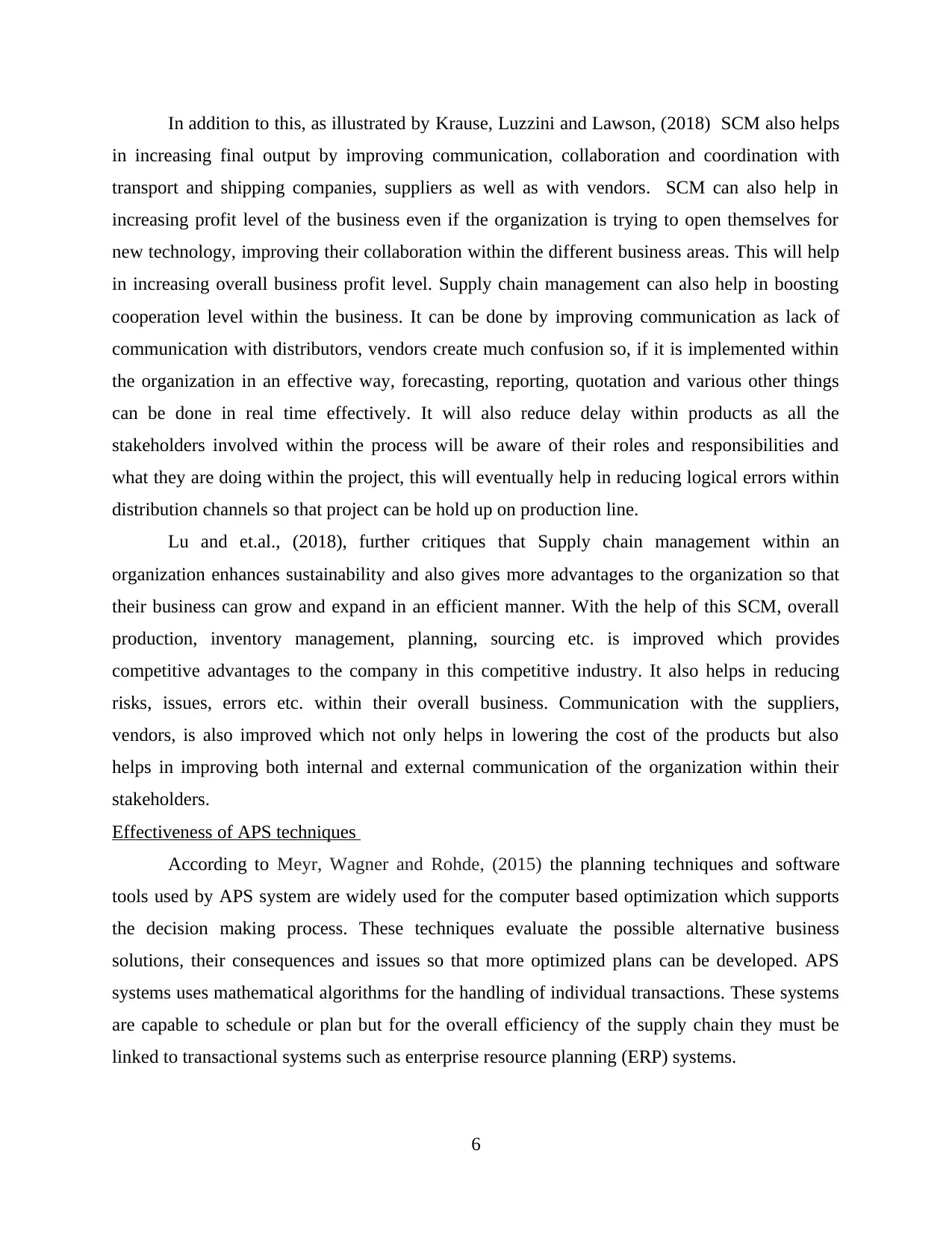
in increasing final output by improving communication, collaboration and coordination with
transport and shipping companies, suppliers as well as with vendors. SCM can also help in
increasing profit level of the business even if the organization is trying to open themselves for
new technology, improving their collaboration within the different business areas. This will help
in increasing overall business profit level. Supply chain management can also help in boosting
cooperation level within the business. It can be done by improving communication as lack of
communication with distributors, vendors create much confusion so, if it is implemented within
the organization in an effective way, forecasting, reporting, quotation and various other things
can be done in real time effectively. It will also reduce delay within products as all the
stakeholders involved within the process will be aware of their roles and responsibilities and
what they are doing within the project, this will eventually help in reducing logical errors within
distribution channels so that project can be hold up on production line.
Lu and et.al., (2018), further critiques that Supply chain management within an
organization enhances sustainability and also gives more advantages to the organization so that
their business can grow and expand in an efficient manner. With the help of this SCM, overall
production, inventory management, planning, sourcing etc. is improved which provides
competitive advantages to the company in this competitive industry. It also helps in reducing
risks, issues, errors etc. within their overall business. Communication with the suppliers,
vendors, is also improved which not only helps in lowering the cost of the products but also
helps in improving both internal and external communication of the organization within their
stakeholders.
Effectiveness of APS techniques
According to Meyr, Wagner and Rohde, (2015) the planning techniques and software
tools used by APS system are widely used for the computer based optimization which supports
the decision making process. These techniques evaluate the possible alternative business
solutions, their consequences and issues so that more optimized plans can be developed. APS
systems uses mathematical algorithms for the handling of individual transactions. These systems
are capable to schedule or plan but for the overall efficiency of the supply chain they must be
linked to transactional systems such as enterprise resource planning (ERP) systems.
6
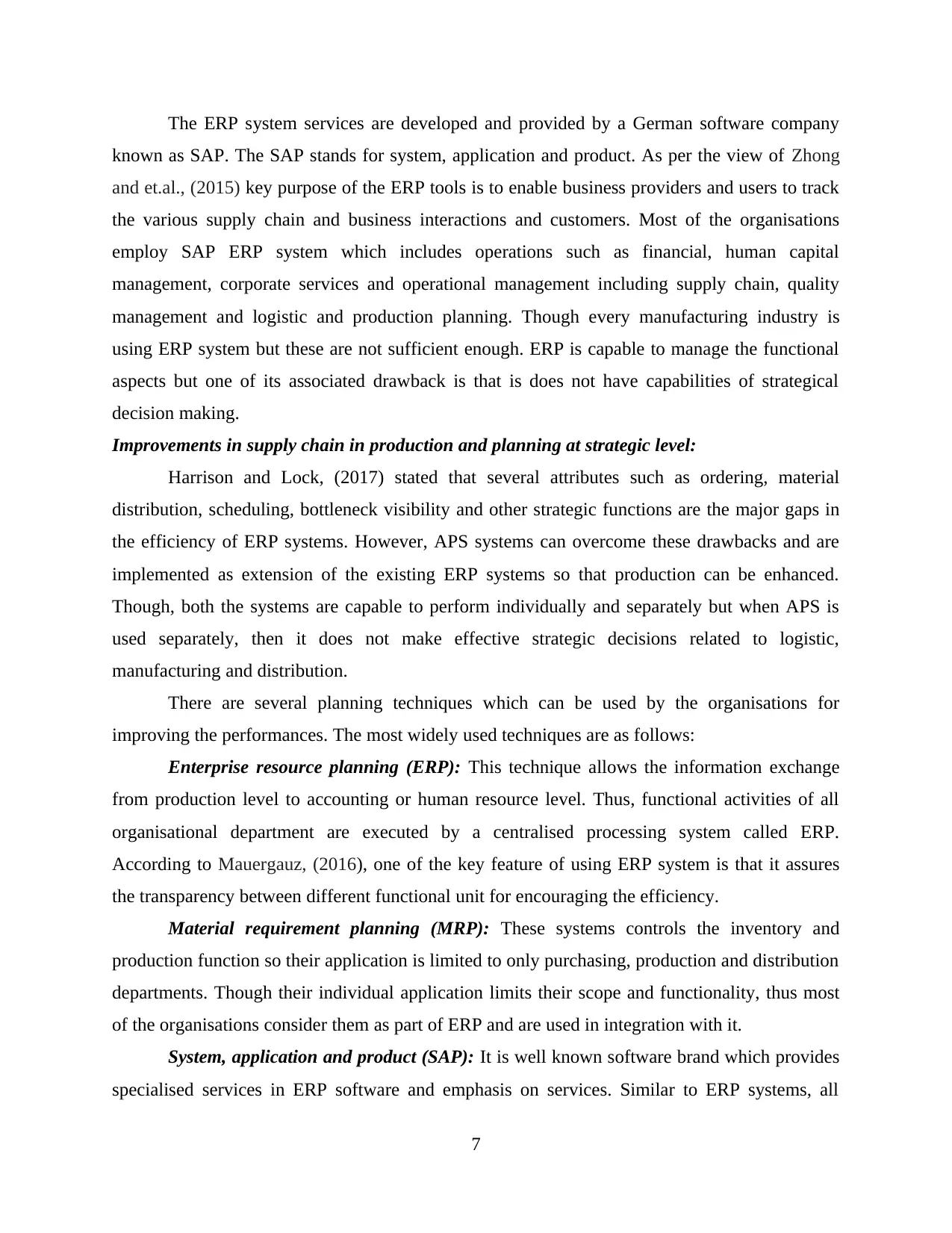
known as SAP. The SAP stands for system, application and product. As per the view of Zhong
and et.al., (2015) key purpose of the ERP tools is to enable business providers and users to track
the various supply chain and business interactions and customers. Most of the organisations
employ SAP ERP system which includes operations such as financial, human capital
management, corporate services and operational management including supply chain, quality
management and logistic and production planning. Though every manufacturing industry is
using ERP system but these are not sufficient enough. ERP is capable to manage the functional
aspects but one of its associated drawback is that is does not have capabilities of strategical
decision making.
Improvements in supply chain in production and planning at strategic level:
Harrison and Lock, (2017) stated that several attributes such as ordering, material
distribution, scheduling, bottleneck visibility and other strategic functions are the major gaps in
the efficiency of ERP systems. However, APS systems can overcome these drawbacks and are
implemented as extension of the existing ERP systems so that production can be enhanced.
Though, both the systems are capable to perform individually and separately but when APS is
used separately, then it does not make effective strategic decisions related to logistic,
manufacturing and distribution.
There are several planning techniques which can be used by the organisations for
improving the performances. The most widely used techniques are as follows:
Enterprise resource planning (ERP): This technique allows the information exchange
from production level to accounting or human resource level. Thus, functional activities of all
organisational department are executed by a centralised processing system called ERP.
According to Mauergauz, (2016), one of the key feature of using ERP system is that it assures
the transparency between different functional unit for encouraging the efficiency.
Material requirement planning (MRP): These systems controls the inventory and
production function so their application is limited to only purchasing, production and distribution
departments. Though their individual application limits their scope and functionality, thus most
of the organisations consider them as part of ERP and are used in integration with it.
System, application and product (SAP): It is well known software brand which provides
specialised services in ERP software and emphasis on services. Similar to ERP systems, all
7
⊘ This is a preview!⊘
Do you want full access?
Subscribe today to unlock all pages.

Trusted by 1+ million students worldwide
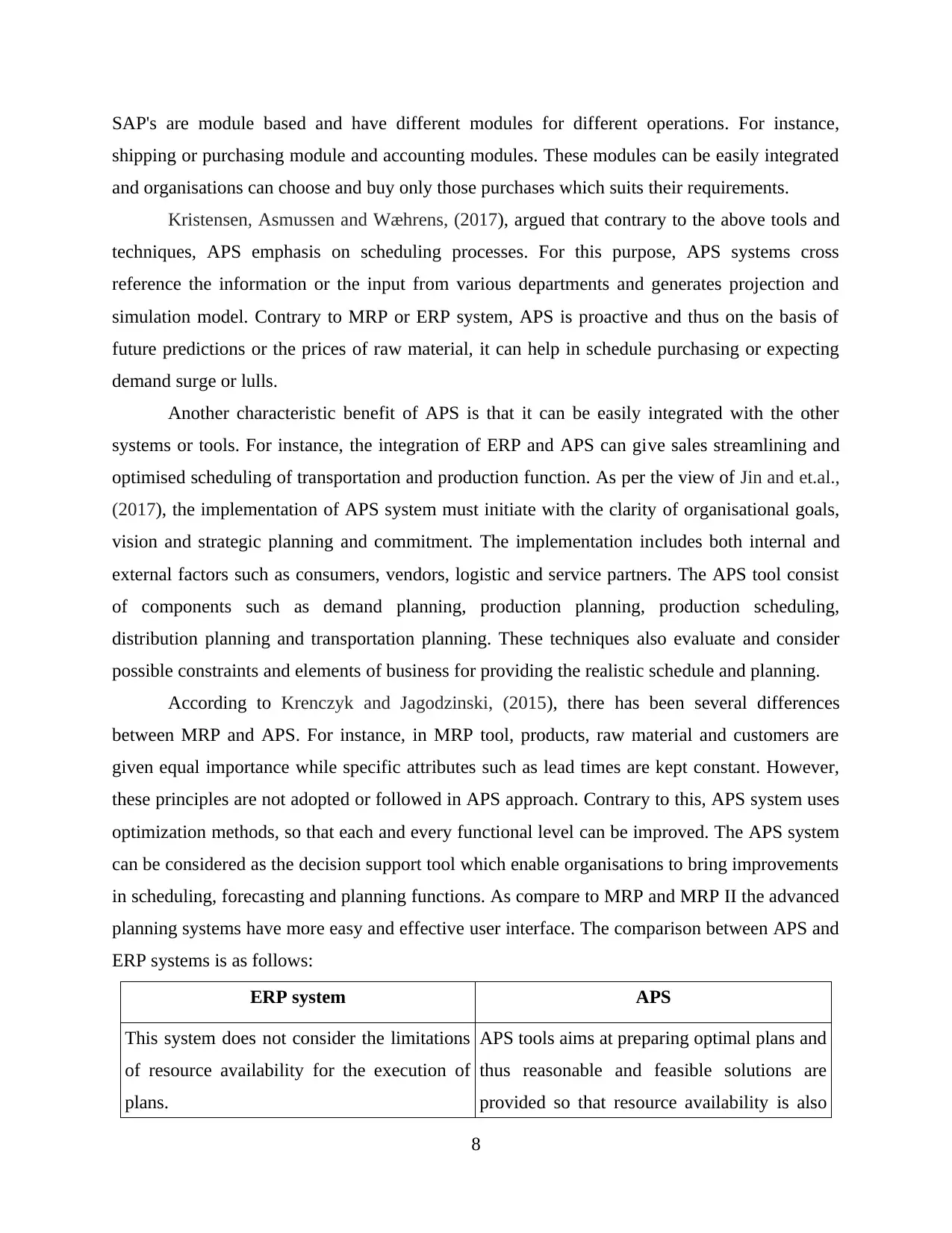
shipping or purchasing module and accounting modules. These modules can be easily integrated
and organisations can choose and buy only those purchases which suits their requirements.
Kristensen, Asmussen and Wæhrens, (2017), argued that contrary to the above tools and
techniques, APS emphasis on scheduling processes. For this purpose, APS systems cross
reference the information or the input from various departments and generates projection and
simulation model. Contrary to MRP or ERP system, APS is proactive and thus on the basis of
future predictions or the prices of raw material, it can help in schedule purchasing or expecting
demand surge or lulls.
Another characteristic benefit of APS is that it can be easily integrated with the other
systems or tools. For instance, the integration of ERP and APS can give sales streamlining and
optimised scheduling of transportation and production function. As per the view of Jin and et.al.,
(2017), the implementation of APS system must initiate with the clarity of organisational goals,
vision and strategic planning and commitment. The implementation includes both internal and
external factors such as consumers, vendors, logistic and service partners. The APS tool consist
of components such as demand planning, production planning, production scheduling,
distribution planning and transportation planning. These techniques also evaluate and consider
possible constraints and elements of business for providing the realistic schedule and planning.
According to Krenczyk and Jagodzinski, (2015), there has been several differences
between MRP and APS. For instance, in MRP tool, products, raw material and customers are
given equal importance while specific attributes such as lead times are kept constant. However,
these principles are not adopted or followed in APS approach. Contrary to this, APS system uses
optimization methods, so that each and every functional level can be improved. The APS system
can be considered as the decision support tool which enable organisations to bring improvements
in scheduling, forecasting and planning functions. As compare to MRP and MRP II the advanced
planning systems have more easy and effective user interface. The comparison between APS and
ERP systems is as follows:
ERP system APS
This system does not consider the limitations
of resource availability for the execution of
plans.
APS tools aims at preparing optimal plans and
thus reasonable and feasible solutions are
provided so that resource availability is also
8
Paraphrase This Document

The key purpose of ERP is to establish
coordination between manufacturing process.
On the other hand, this tools aims at satisfying
the customer demands.
Its simulation capabilities are low and
information flow is in top to down direction
only.
In APS system, information can flow from
both the directions and on the basis of high
simulation capabilities these are also capable
to optimize cost, profit and price which is not
possible with the ERP.
The ERP system provides constant
manufacturing lead times and there are no
choices for the incremental planning.
Contrary to the ERP systems, it is possible for
the organisations to adopt flexible lead times
and to adopt incremental plans.
In ERP system, data base is used and thus it
has low speed of replanning.
In case of APS system, memory resident data
storage choices provides high speed of
replanning.
According to Behnamian and Ghomi, (2016), there are several characteristics which
distinguishes APS from other systems. The most beneficial characteristic of this tool is that
ranging from the suppliers to customers this tools provides integral planning of entire
organisation. Another aspect which makes this tool dominating over ERP system is that it is
capable to identify the planning issues and by applying optimization techniques, it can evaluate
the possible solutions and constraints of the identified issue. Contrary to this, Rashidi and Tsang,
(2015), argued that features such as hierarchical planning and the use of algorithms in single
module does not make APS advanced. Instead, the use of APS characteristics in standard
software with reasonable planning and algorithms make them advance.
Sobeyko and Mönch, (2017) elucidated that APS architecture is organised at three levels
called strategic, tactical and operational level. The typical building blocks of APS architecture
are as follows:
Strategic network planning: This feature and the building block of APS tool provides a
strong support for making the strategical decisions. The long term plans of the organisation aims
at enhancing and improving the plant allocations and for the designing of physical distribution
9
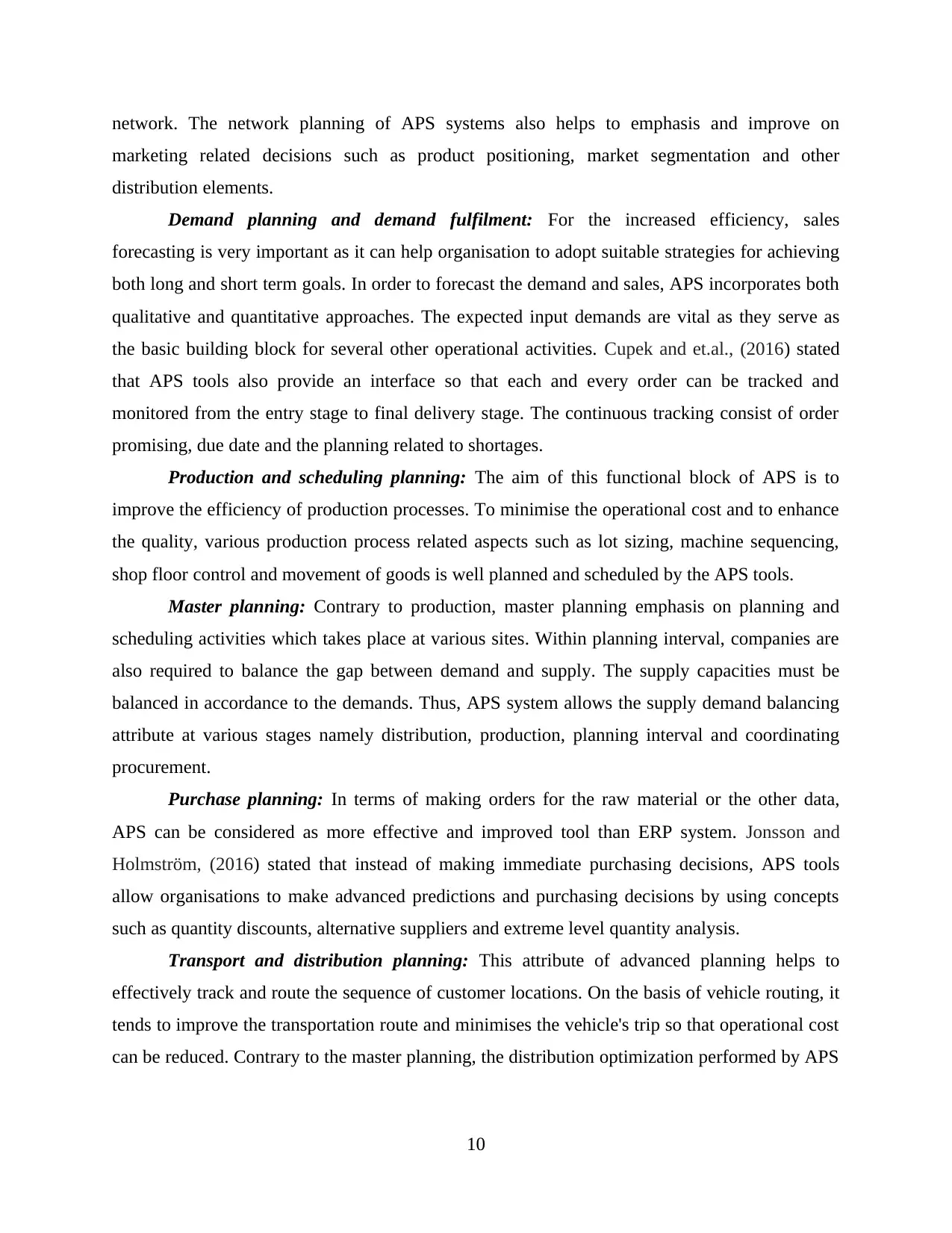
marketing related decisions such as product positioning, market segmentation and other
distribution elements.
Demand planning and demand fulfilment: For the increased efficiency, sales
forecasting is very important as it can help organisation to adopt suitable strategies for achieving
both long and short term goals. In order to forecast the demand and sales, APS incorporates both
qualitative and quantitative approaches. The expected input demands are vital as they serve as
the basic building block for several other operational activities. Cupek and et.al., (2016) stated
that APS tools also provide an interface so that each and every order can be tracked and
monitored from the entry stage to final delivery stage. The continuous tracking consist of order
promising, due date and the planning related to shortages.
Production and scheduling planning: The aim of this functional block of APS is to
improve the efficiency of production processes. To minimise the operational cost and to enhance
the quality, various production process related aspects such as lot sizing, machine sequencing,
shop floor control and movement of goods is well planned and scheduled by the APS tools.
Master planning: Contrary to production, master planning emphasis on planning and
scheduling activities which takes place at various sites. Within planning interval, companies are
also required to balance the gap between demand and supply. The supply capacities must be
balanced in accordance to the demands. Thus, APS system allows the supply demand balancing
attribute at various stages namely distribution, production, planning interval and coordinating
procurement.
Purchase planning: In terms of making orders for the raw material or the other data,
APS can be considered as more effective and improved tool than ERP system. Jonsson and
Holmström, (2016) stated that instead of making immediate purchasing decisions, APS tools
allow organisations to make advanced predictions and purchasing decisions by using concepts
such as quantity discounts, alternative suppliers and extreme level quantity analysis.
Transport and distribution planning: This attribute of advanced planning helps to
effectively track and route the sequence of customer locations. On the basis of vehicle routing, it
tends to improve the transportation route and minimises the vehicle's trip so that operational cost
can be reduced. Contrary to the master planning, the distribution optimization performed by APS
10
⊘ This is a preview!⊘
Do you want full access?
Subscribe today to unlock all pages.

Trusted by 1+ million students worldwide
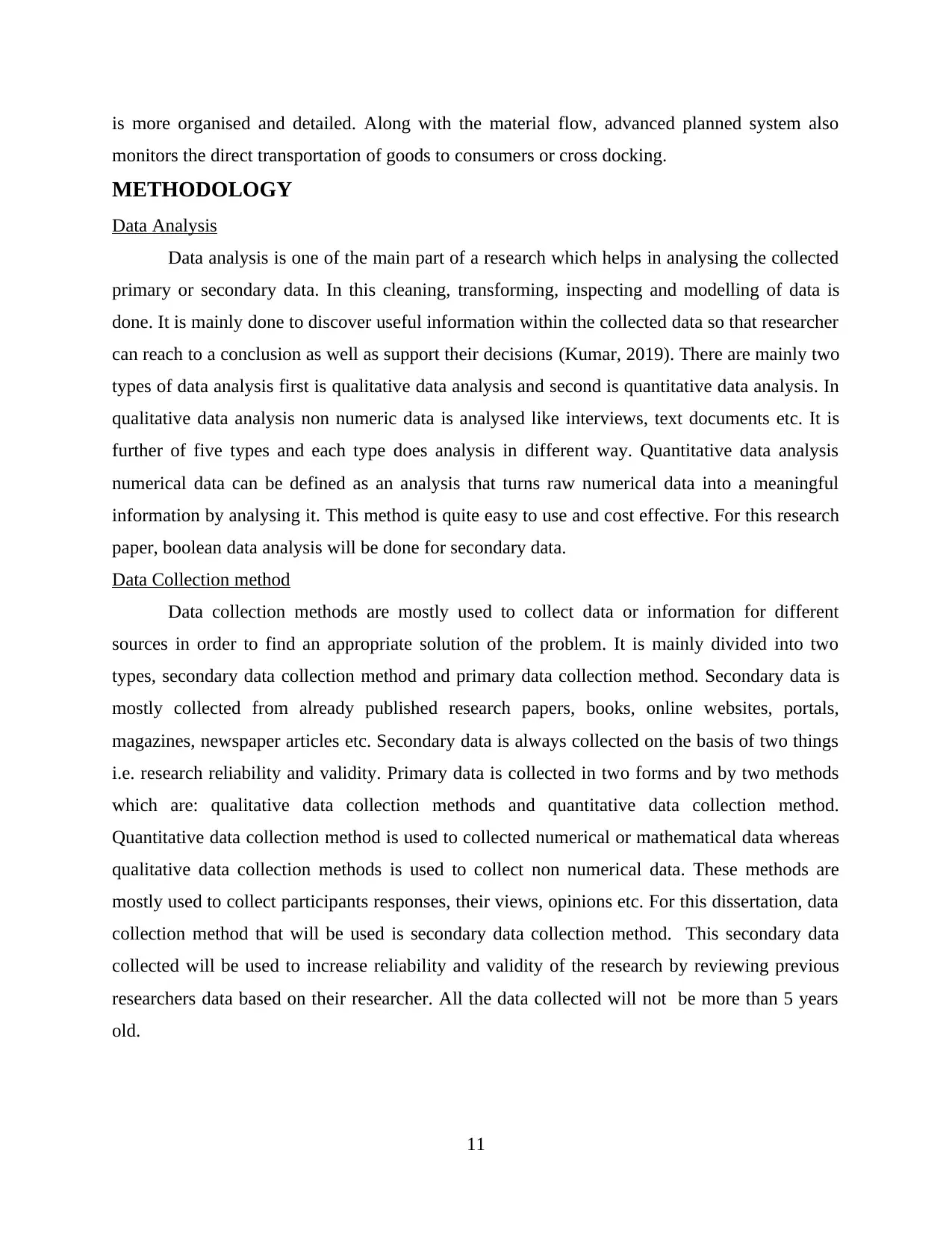
monitors the direct transportation of goods to consumers or cross docking.
METHODOLOGY
Data Analysis
Data analysis is one of the main part of a research which helps in analysing the collected
primary or secondary data. In this cleaning, transforming, inspecting and modelling of data is
done. It is mainly done to discover useful information within the collected data so that researcher
can reach to a conclusion as well as support their decisions (Kumar, 2019). There are mainly two
types of data analysis first is qualitative data analysis and second is quantitative data analysis. In
qualitative data analysis non numeric data is analysed like interviews, text documents etc. It is
further of five types and each type does analysis in different way. Quantitative data analysis
numerical data can be defined as an analysis that turns raw numerical data into a meaningful
information by analysing it. This method is quite easy to use and cost effective. For this research
paper, boolean data analysis will be done for secondary data.
Data Collection method
Data collection methods are mostly used to collect data or information for different
sources in order to find an appropriate solution of the problem. It is mainly divided into two
types, secondary data collection method and primary data collection method. Secondary data is
mostly collected from already published research papers, books, online websites, portals,
magazines, newspaper articles etc. Secondary data is always collected on the basis of two things
i.e. research reliability and validity. Primary data is collected in two forms and by two methods
which are: qualitative data collection methods and quantitative data collection method.
Quantitative data collection method is used to collected numerical or mathematical data whereas
qualitative data collection methods is used to collect non numerical data. These methods are
mostly used to collect participants responses, their views, opinions etc. For this dissertation, data
collection method that will be used is secondary data collection method. This secondary data
collected will be used to increase reliability and validity of the research by reviewing previous
researchers data based on their researcher. All the data collected will not be more than 5 years
old.
11
Paraphrase This Document
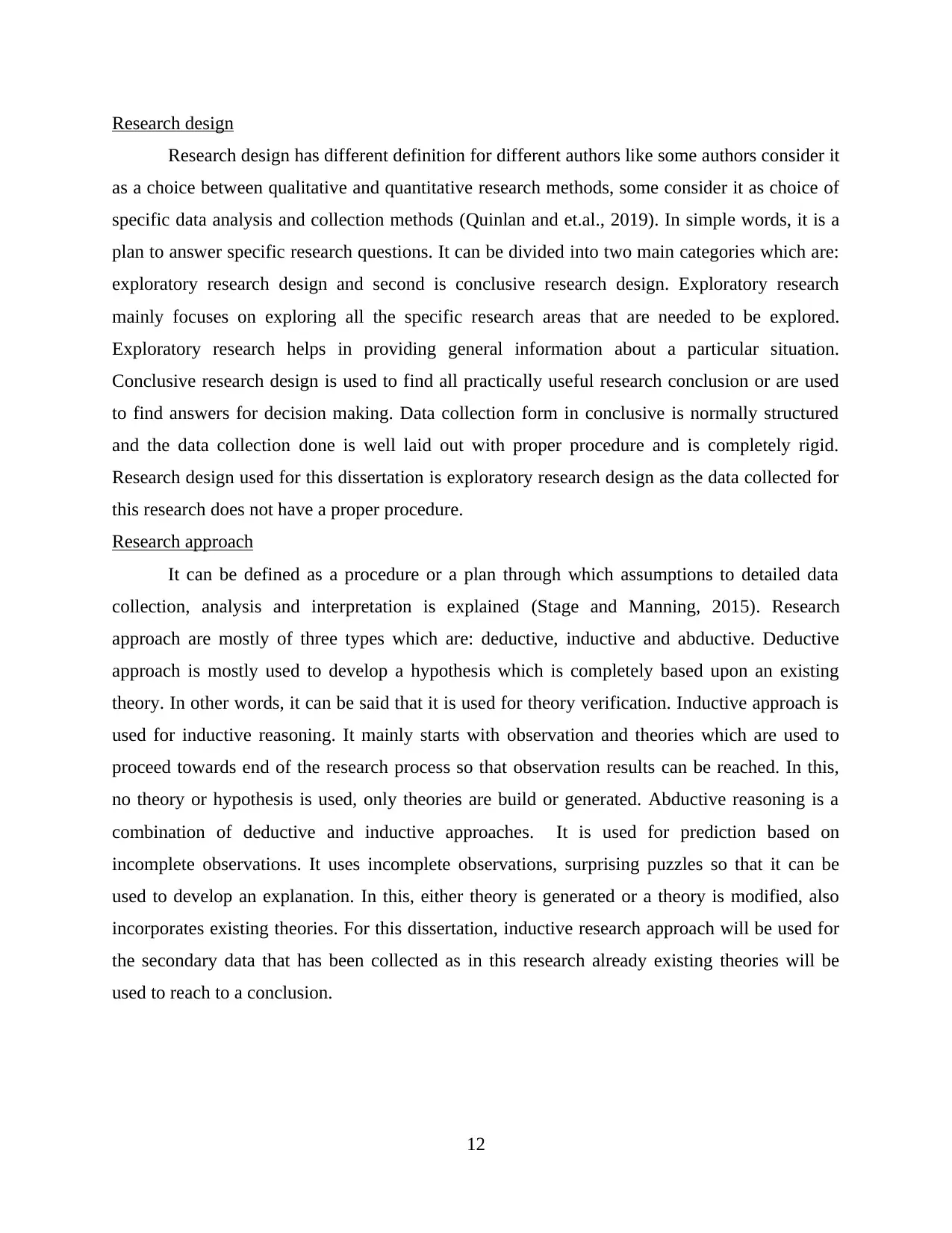
Research design has different definition for different authors like some authors consider it
as a choice between qualitative and quantitative research methods, some consider it as choice of
specific data analysis and collection methods (Quinlan and et.al., 2019). In simple words, it is a
plan to answer specific research questions. It can be divided into two main categories which are:
exploratory research design and second is conclusive research design. Exploratory research
mainly focuses on exploring all the specific research areas that are needed to be explored.
Exploratory research helps in providing general information about a particular situation.
Conclusive research design is used to find all practically useful research conclusion or are used
to find answers for decision making. Data collection form in conclusive is normally structured
and the data collection done is well laid out with proper procedure and is completely rigid.
Research design used for this dissertation is exploratory research design as the data collected for
this research does not have a proper procedure.
Research approach
It can be defined as a procedure or a plan through which assumptions to detailed data
collection, analysis and interpretation is explained (Stage and Manning, 2015). Research
approach are mostly of three types which are: deductive, inductive and abductive. Deductive
approach is mostly used to develop a hypothesis which is completely based upon an existing
theory. In other words, it can be said that it is used for theory verification. Inductive approach is
used for inductive reasoning. It mainly starts with observation and theories which are used to
proceed towards end of the research process so that observation results can be reached. In this,
no theory or hypothesis is used, only theories are build or generated. Abductive reasoning is a
combination of deductive and inductive approaches. It is used for prediction based on
incomplete observations. It uses incomplete observations, surprising puzzles so that it can be
used to develop an explanation. In this, either theory is generated or a theory is modified, also
incorporates existing theories. For this dissertation, inductive research approach will be used for
the secondary data that has been collected as in this research already existing theories will be
used to reach to a conclusion.
12
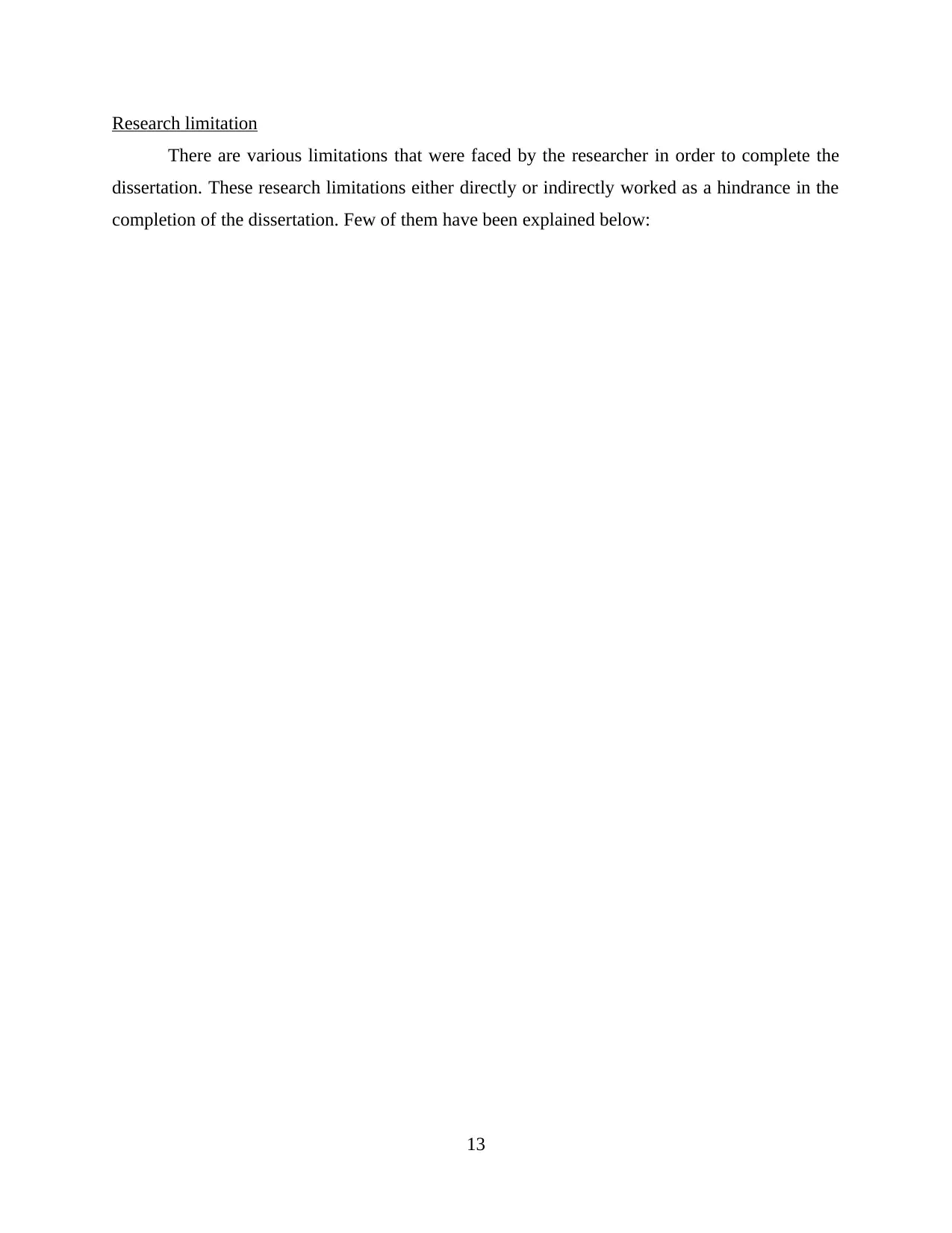
There are various limitations that were faced by the researcher in order to complete the
dissertation. These research limitations either directly or indirectly worked as a hindrance in the
completion of the dissertation. Few of them have been explained below:
13
⊘ This is a preview!⊘
Do you want full access?
Subscribe today to unlock all pages.

Trusted by 1+ million students worldwide
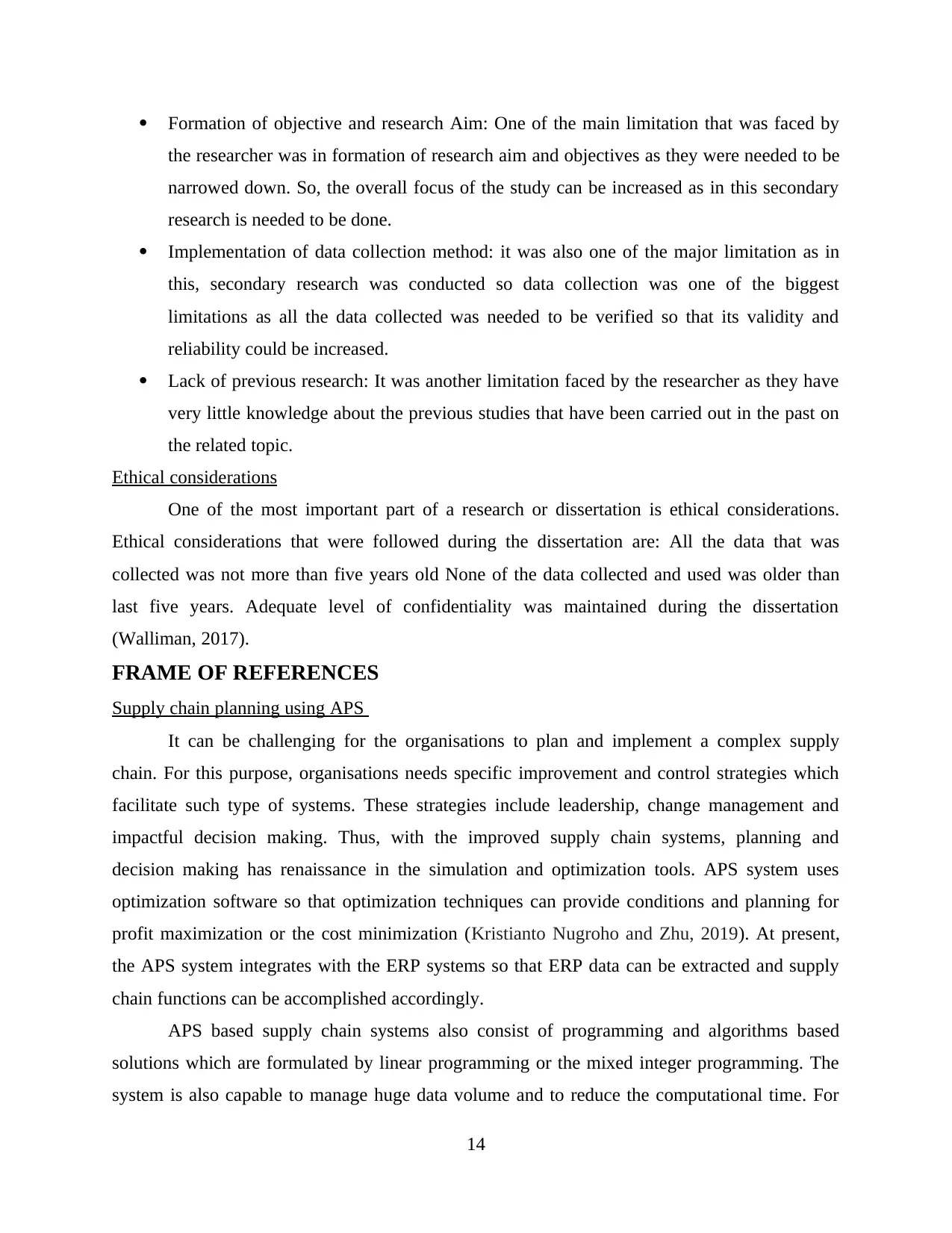
the researcher was in formation of research aim and objectives as they were needed to be
narrowed down. So, the overall focus of the study can be increased as in this secondary
research is needed to be done.
ï‚· Implementation of data collection method: it was also one of the major limitation as in
this, secondary research was conducted so data collection was one of the biggest
limitations as all the data collected was needed to be verified so that its validity and
reliability could be increased.
ï‚· Lack of previous research: It was another limitation faced by the researcher as they have
very little knowledge about the previous studies that have been carried out in the past on
the related topic.
Ethical considerations
One of the most important part of a research or dissertation is ethical considerations.
Ethical considerations that were followed during the dissertation are: All the data that was
collected was not more than five years old None of the data collected and used was older than
last five years. Adequate level of confidentiality was maintained during the dissertation
(Walliman, 2017).
FRAME OF REFERENCES
Supply chain planning using APS
It can be challenging for the organisations to plan and implement a complex supply
chain. For this purpose, organisations needs specific improvement and control strategies which
facilitate such type of systems. These strategies include leadership, change management and
impactful decision making. Thus, with the improved supply chain systems, planning and
decision making has renaissance in the simulation and optimization tools. APS system uses
optimization software so that optimization techniques can provide conditions and planning for
profit maximization or the cost minimization (Kristianto Nugroho and Zhu, 2019). At present,
the APS system integrates with the ERP systems so that ERP data can be extracted and supply
chain functions can be accomplished accordingly.
APS based supply chain systems also consist of programming and algorithms based
solutions which are formulated by linear programming or the mixed integer programming. The
system is also capable to manage huge data volume and to reduce the computational time. For
14
Paraphrase This Document
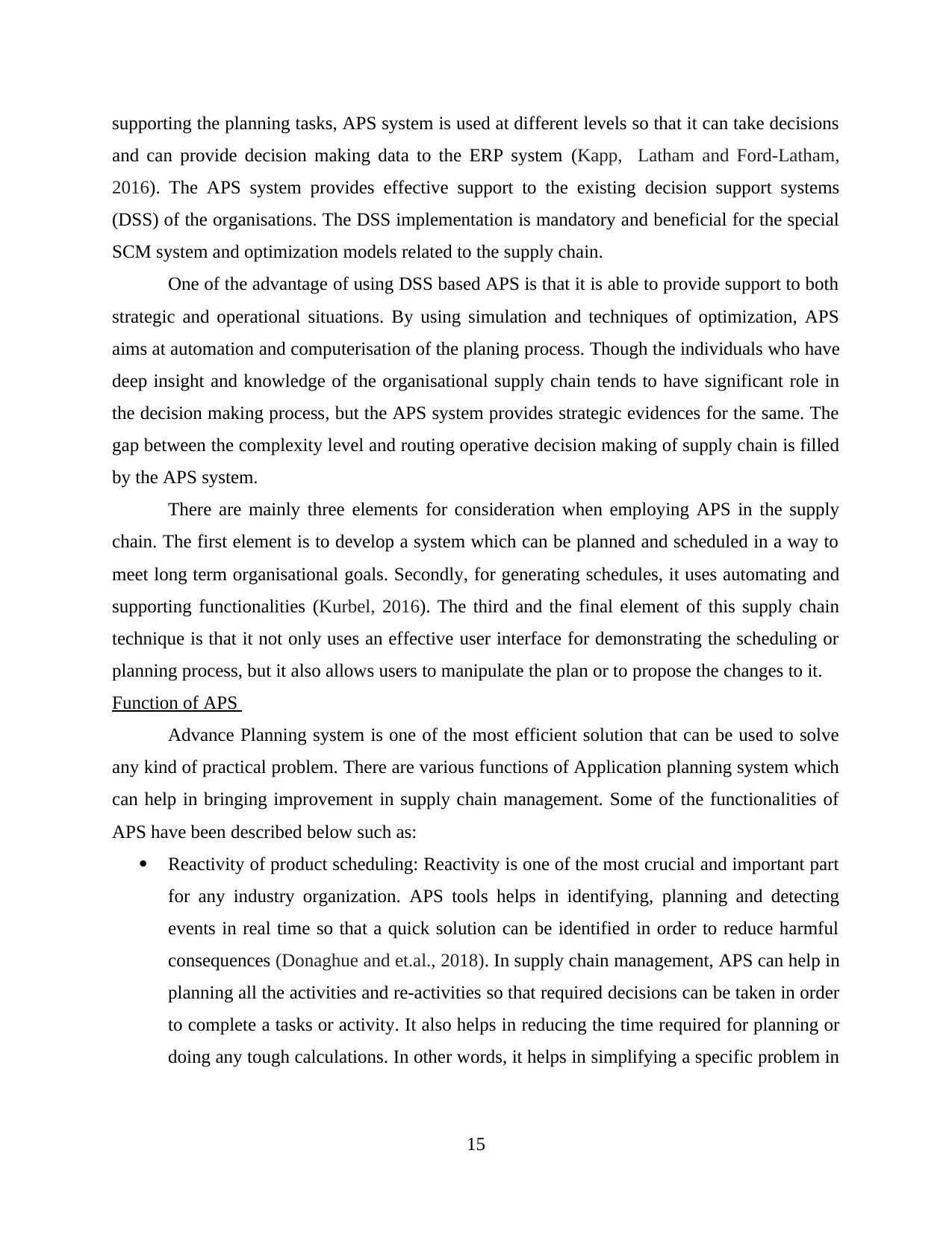
and can provide decision making data to the ERP system (Kapp, Latham and Ford-Latham,
2016). The APS system provides effective support to the existing decision support systems
(DSS) of the organisations. The DSS implementation is mandatory and beneficial for the special
SCM system and optimization models related to the supply chain.
One of the advantage of using DSS based APS is that it is able to provide support to both
strategic and operational situations. By using simulation and techniques of optimization, APS
aims at automation and computerisation of the planing process. Though the individuals who have
deep insight and knowledge of the organisational supply chain tends to have significant role in
the decision making process, but the APS system provides strategic evidences for the same. The
gap between the complexity level and routing operative decision making of supply chain is filled
by the APS system.
There are mainly three elements for consideration when employing APS in the supply
chain. The first element is to develop a system which can be planned and scheduled in a way to
meet long term organisational goals. Secondly, for generating schedules, it uses automating and
supporting functionalities (Kurbel, 2016). The third and the final element of this supply chain
technique is that it not only uses an effective user interface for demonstrating the scheduling or
planning process, but it also allows users to manipulate the plan or to propose the changes to it.
Function of APS
Advance Planning system is one of the most efficient solution that can be used to solve
any kind of practical problem. There are various functions of Application planning system which
can help in bringing improvement in supply chain management. Some of the functionalities of
APS have been described below such as:
ï‚· Reactivity of product scheduling: Reactivity is one of the most crucial and important part
for any industry organization. APS tools helps in identifying, planning and detecting
events in real time so that a quick solution can be identified in order to reduce harmful
consequences (Donaghue and et.al., 2018). In supply chain management, APS can help in
planning all the activities and re-activities so that required decisions can be taken in order
to complete a tasks or activity. It also helps in reducing the time required for planning or
doing any tough calculations. In other words, it helps in simplifying a specific problem in
15
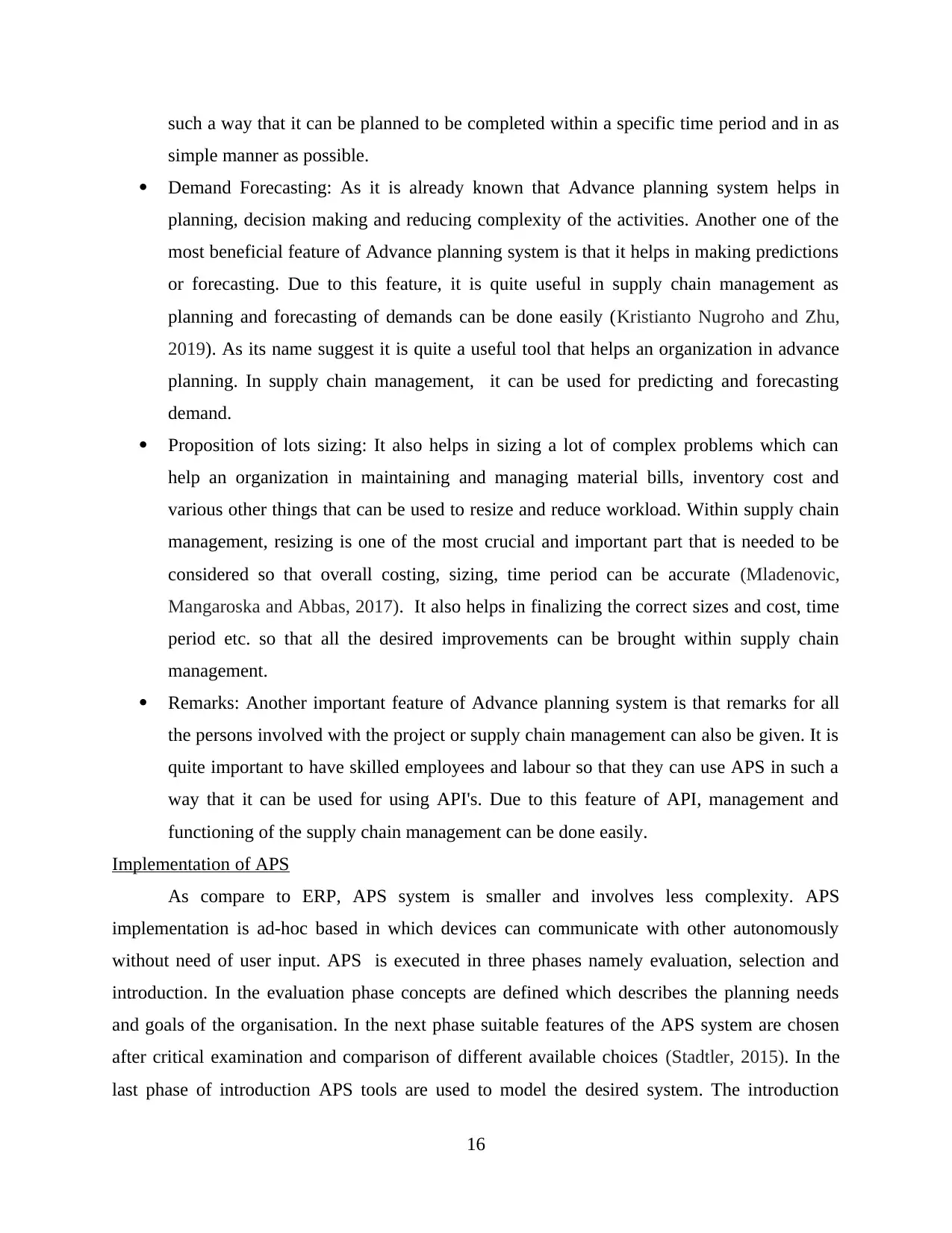
simple manner as possible.
ï‚· Demand Forecasting: As it is already known that Advance planning system helps in
planning, decision making and reducing complexity of the activities. Another one of the
most beneficial feature of Advance planning system is that it helps in making predictions
or forecasting. Due to this feature, it is quite useful in supply chain management as
planning and forecasting of demands can be done easily (Kristianto Nugroho and Zhu,
2019). As its name suggest it is quite a useful tool that helps an organization in advance
planning. In supply chain management, it can be used for predicting and forecasting
demand.
ï‚· Proposition of lots sizing: It also helps in sizing a lot of complex problems which can
help an organization in maintaining and managing material bills, inventory cost and
various other things that can be used to resize and reduce workload. Within supply chain
management, resizing is one of the most crucial and important part that is needed to be
considered so that overall costing, sizing, time period can be accurate (Mladenovic,
Mangaroska and Abbas, 2017). It also helps in finalizing the correct sizes and cost, time
period etc. so that all the desired improvements can be brought within supply chain
management.
ï‚· Remarks: Another important feature of Advance planning system is that remarks for all
the persons involved with the project or supply chain management can also be given. It is
quite important to have skilled employees and labour so that they can use APS in such a
way that it can be used for using API's. Due to this feature of API, management and
functioning of the supply chain management can be done easily.
Implementation of APS
As compare to ERP, APS system is smaller and involves less complexity. APS
implementation is ad-hoc based in which devices can communicate with other autonomously
without need of user input. APS is executed in three phases namely evaluation, selection and
introduction. In the evaluation phase concepts are defined which describes the planning needs
and goals of the organisation. In the next phase suitable features of the APS system are chosen
after critical examination and comparison of different available choices (Stadtler, 2015). In the
last phase of introduction APS tools are used to model the desired system. The introduction
16
⊘ This is a preview!⊘
Do you want full access?
Subscribe today to unlock all pages.

Trusted by 1+ million students worldwide
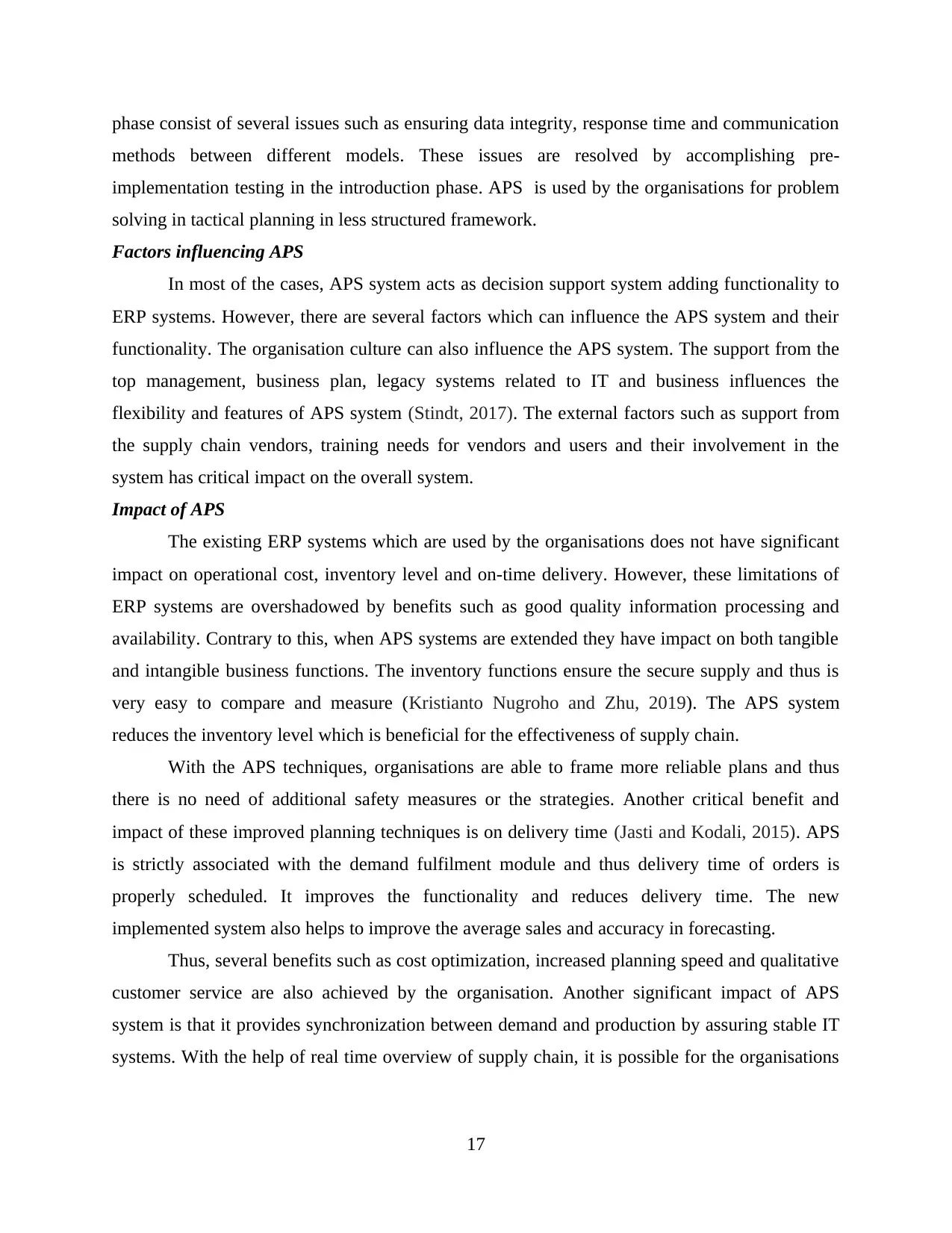
methods between different models. These issues are resolved by accomplishing pre-
implementation testing in the introduction phase. APS is used by the organisations for problem
solving in tactical planning in less structured framework.
Factors influencing APS
In most of the cases, APS system acts as decision support system adding functionality to
ERP systems. However, there are several factors which can influence the APS system and their
functionality. The organisation culture can also influence the APS system. The support from the
top management, business plan, legacy systems related to IT and business influences the
flexibility and features of APS system (Stindt, 2017). The external factors such as support from
the supply chain vendors, training needs for vendors and users and their involvement in the
system has critical impact on the overall system.
Impact of APS
The existing ERP systems which are used by the organisations does not have significant
impact on operational cost, inventory level and on-time delivery. However, these limitations of
ERP systems are overshadowed by benefits such as good quality information processing and
availability. Contrary to this, when APS systems are extended they have impact on both tangible
and intangible business functions. The inventory functions ensure the secure supply and thus is
very easy to compare and measure (Kristianto Nugroho and Zhu, 2019). The APS system
reduces the inventory level which is beneficial for the effectiveness of supply chain.
With the APS techniques, organisations are able to frame more reliable plans and thus
there is no need of additional safety measures or the strategies. Another critical benefit and
impact of these improved planning techniques is on delivery time (Jasti and Kodali, 2015). APS
is strictly associated with the demand fulfilment module and thus delivery time of orders is
properly scheduled. It improves the functionality and reduces delivery time. The new
implemented system also helps to improve the average sales and accuracy in forecasting.
Thus, several benefits such as cost optimization, increased planning speed and qualitative
customer service are also achieved by the organisation. Another significant impact of APS
system is that it provides synchronization between demand and production by assuring stable IT
systems. With the help of real time overview of supply chain, it is possible for the organisations
17
Paraphrase This Document
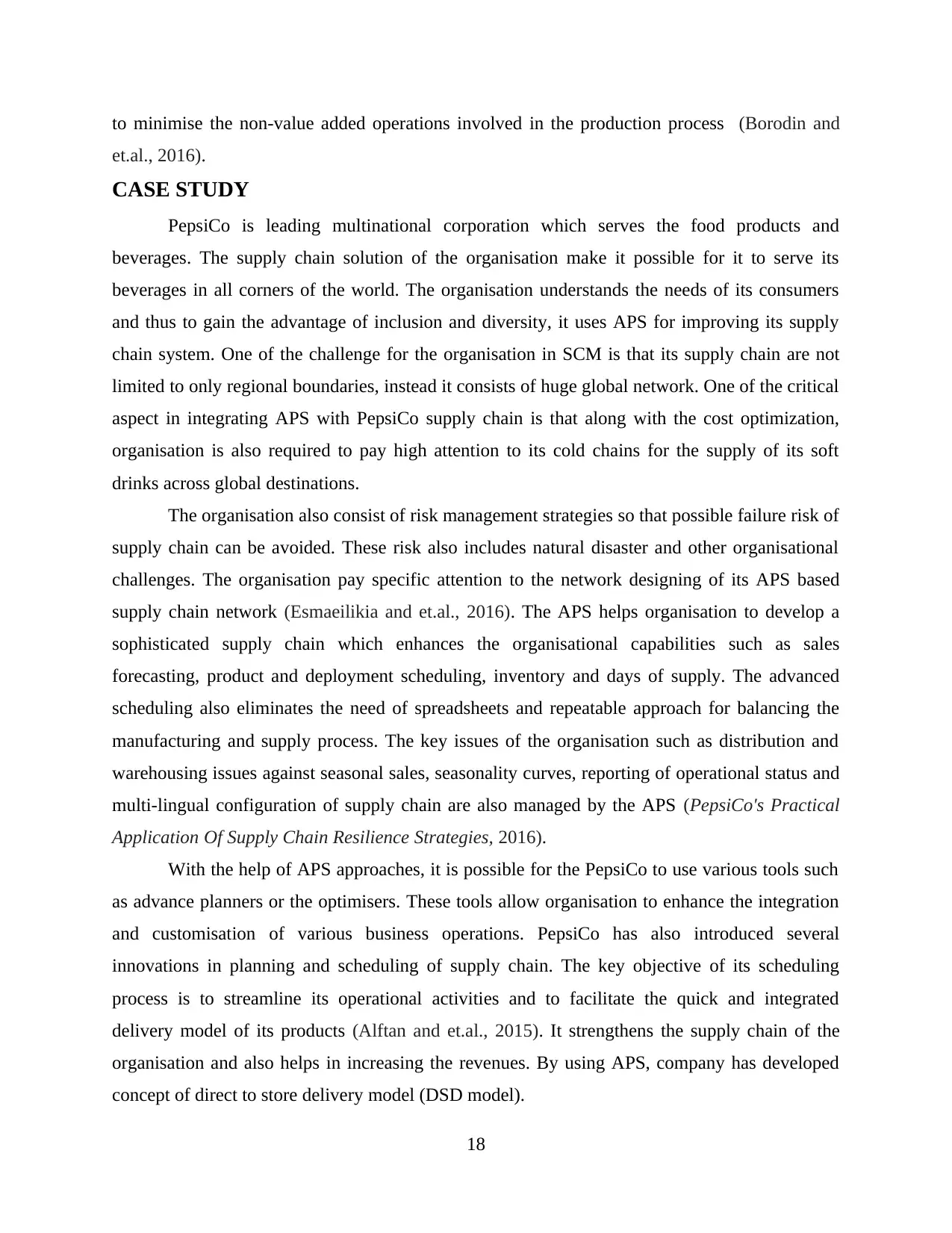
et.al., 2016).
CASE STUDY
PepsiCo is leading multinational corporation which serves the food products and
beverages. The supply chain solution of the organisation make it possible for it to serve its
beverages in all corners of the world. The organisation understands the needs of its consumers
and thus to gain the advantage of inclusion and diversity, it uses APS for improving its supply
chain system. One of the challenge for the organisation in SCM is that its supply chain are not
limited to only regional boundaries, instead it consists of huge global network. One of the critical
aspect in integrating APS with PepsiCo supply chain is that along with the cost optimization,
organisation is also required to pay high attention to its cold chains for the supply of its soft
drinks across global destinations.
The organisation also consist of risk management strategies so that possible failure risk of
supply chain can be avoided. These risk also includes natural disaster and other organisational
challenges. The organisation pay specific attention to the network designing of its APS based
supply chain network (Esmaeilikia and et.al., 2016). The APS helps organisation to develop a
sophisticated supply chain which enhances the organisational capabilities such as sales
forecasting, product and deployment scheduling, inventory and days of supply. The advanced
scheduling also eliminates the need of spreadsheets and repeatable approach for balancing the
manufacturing and supply process. The key issues of the organisation such as distribution and
warehousing issues against seasonal sales, seasonality curves, reporting of operational status and
multi-lingual configuration of supply chain are also managed by the APS (PepsiCo's Practical
Application Of Supply Chain Resilience Strategies, 2016).
With the help of APS approaches, it is possible for the PepsiCo to use various tools such
as advance planners or the optimisers. These tools allow organisation to enhance the integration
and customisation of various business operations. PepsiCo has also introduced several
innovations in planning and scheduling of supply chain. The key objective of its scheduling
process is to streamline its operational activities and to facilitate the quick and integrated
delivery model of its products (Alftan and et.al., 2015). It strengthens the supply chain of the
organisation and also helps in increasing the revenues. By using APS, company has developed
concept of direct to store delivery model (DSD model).
18
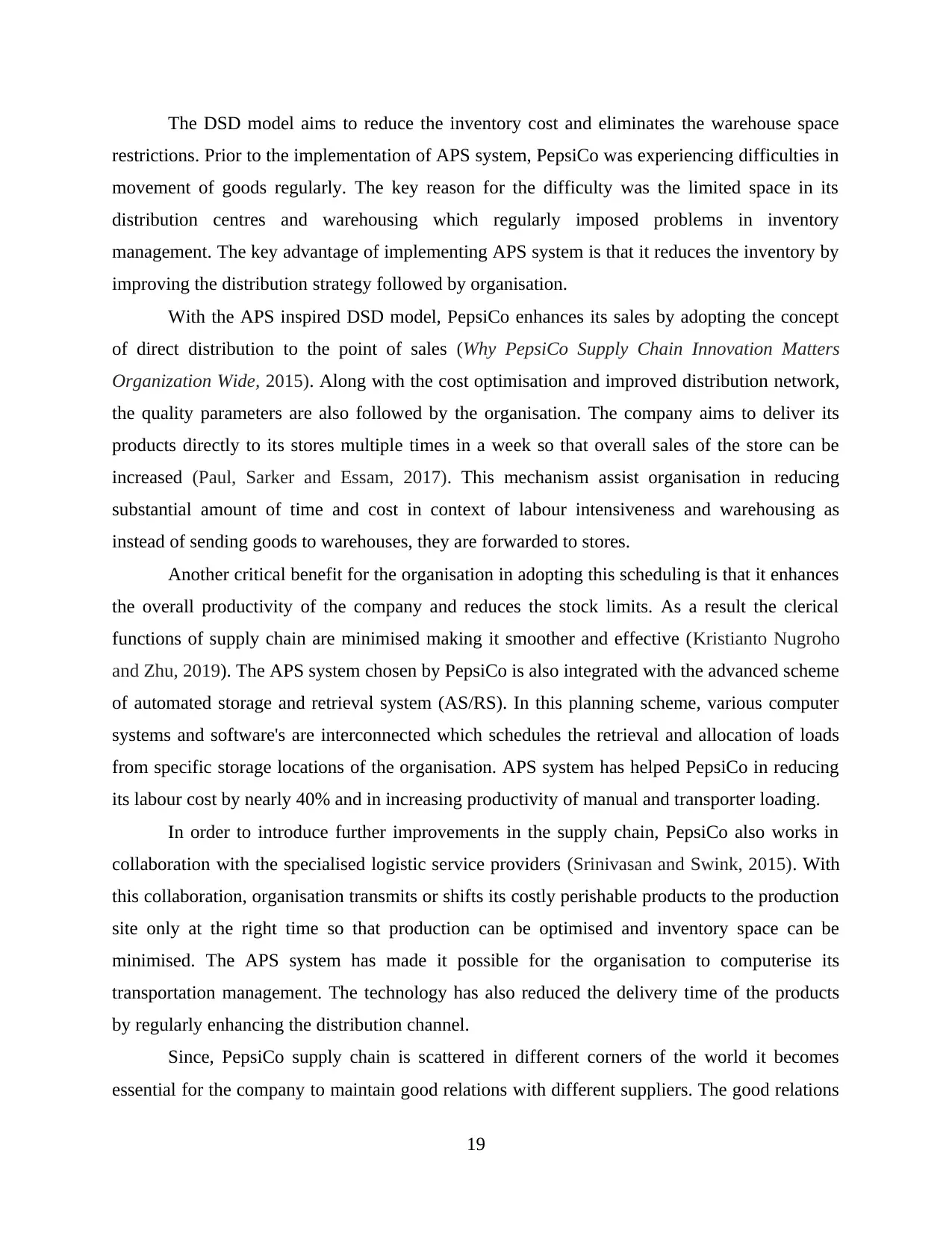
restrictions. Prior to the implementation of APS system, PepsiCo was experiencing difficulties in
movement of goods regularly. The key reason for the difficulty was the limited space in its
distribution centres and warehousing which regularly imposed problems in inventory
management. The key advantage of implementing APS system is that it reduces the inventory by
improving the distribution strategy followed by organisation.
With the APS inspired DSD model, PepsiCo enhances its sales by adopting the concept
of direct distribution to the point of sales (Why PepsiCo Supply Chain Innovation Matters
Organization Wide, 2015). Along with the cost optimisation and improved distribution network,
the quality parameters are also followed by the organisation. The company aims to deliver its
products directly to its stores multiple times in a week so that overall sales of the store can be
increased (Paul, Sarker and Essam, 2017). This mechanism assist organisation in reducing
substantial amount of time and cost in context of labour intensiveness and warehousing as
instead of sending goods to warehouses, they are forwarded to stores.
Another critical benefit for the organisation in adopting this scheduling is that it enhances
the overall productivity of the company and reduces the stock limits. As a result the clerical
functions of supply chain are minimised making it smoother and effective (Kristianto Nugroho
and Zhu, 2019). The APS system chosen by PepsiCo is also integrated with the advanced scheme
of automated storage and retrieval system (AS/RS). In this planning scheme, various computer
systems and software's are interconnected which schedules the retrieval and allocation of loads
from specific storage locations of the organisation. APS system has helped PepsiCo in reducing
its labour cost by nearly 40% and in increasing productivity of manual and transporter loading.
In order to introduce further improvements in the supply chain, PepsiCo also works in
collaboration with the specialised logistic service providers (Srinivasan and Swink, 2015). With
this collaboration, organisation transmits or shifts its costly perishable products to the production
site only at the right time so that production can be optimised and inventory space can be
minimised. The APS system has made it possible for the organisation to computerise its
transportation management. The technology has also reduced the delivery time of the products
by regularly enhancing the distribution channel.
Since, PepsiCo supply chain is scattered in different corners of the world it becomes
essential for the company to maintain good relations with different suppliers. The good relations
19
⊘ This is a preview!⊘
Do you want full access?
Subscribe today to unlock all pages.

Trusted by 1+ million students worldwide
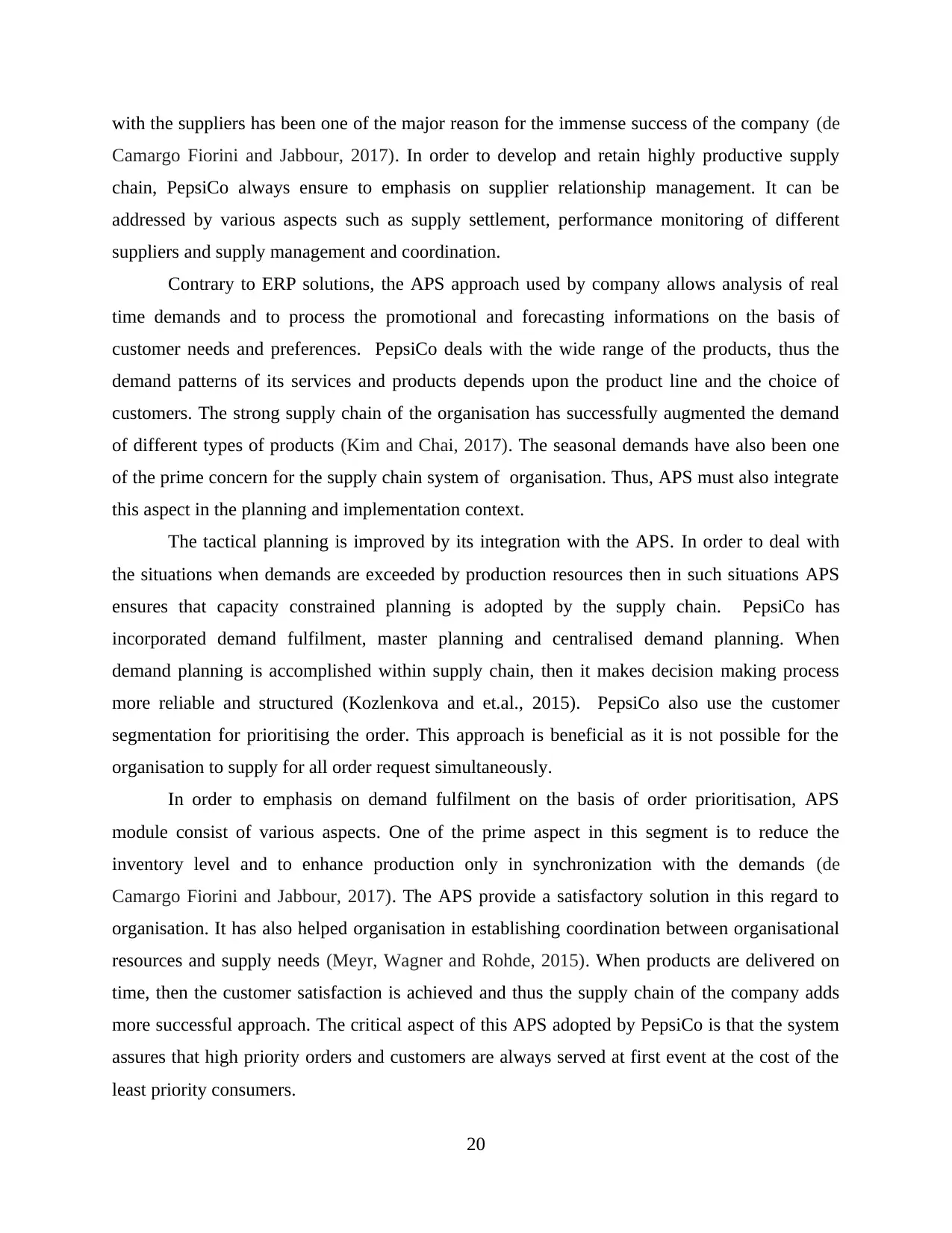
Camargo Fiorini and Jabbour, 2017). In order to develop and retain highly productive supply
chain, PepsiCo always ensure to emphasis on supplier relationship management. It can be
addressed by various aspects such as supply settlement, performance monitoring of different
suppliers and supply management and coordination.
Contrary to ERP solutions, the APS approach used by company allows analysis of real
time demands and to process the promotional and forecasting informations on the basis of
customer needs and preferences. PepsiCo deals with the wide range of the products, thus the
demand patterns of its services and products depends upon the product line and the choice of
customers. The strong supply chain of the organisation has successfully augmented the demand
of different types of products (Kim and Chai, 2017). The seasonal demands have also been one
of the prime concern for the supply chain system of organisation. Thus, APS must also integrate
this aspect in the planning and implementation context.
The tactical planning is improved by its integration with the APS. In order to deal with
the situations when demands are exceeded by production resources then in such situations APS
ensures that capacity constrained planning is adopted by the supply chain. PepsiCo has
incorporated demand fulfilment, master planning and centralised demand planning. When
demand planning is accomplished within supply chain, then it makes decision making process
more reliable and structured (Kozlenkova and et.al., 2015). PepsiCo also use the customer
segmentation for prioritising the order. This approach is beneficial as it is not possible for the
organisation to supply for all order request simultaneously.
In order to emphasis on demand fulfilment on the basis of order prioritisation, APS
module consist of various aspects. One of the prime aspect in this segment is to reduce the
inventory level and to enhance production only in synchronization with the demands (de
Camargo Fiorini and Jabbour, 2017). The APS provide a satisfactory solution in this regard to
organisation. It has also helped organisation in establishing coordination between organisational
resources and supply needs (Meyr, Wagner and Rohde, 2015). When products are delivered on
time, then the customer satisfaction is achieved and thus the supply chain of the company adds
more successful approach. The critical aspect of this APS adopted by PepsiCo is that the system
assures that high priority orders and customers are always served at first event at the cost of the
least priority consumers.
20
Paraphrase This Document
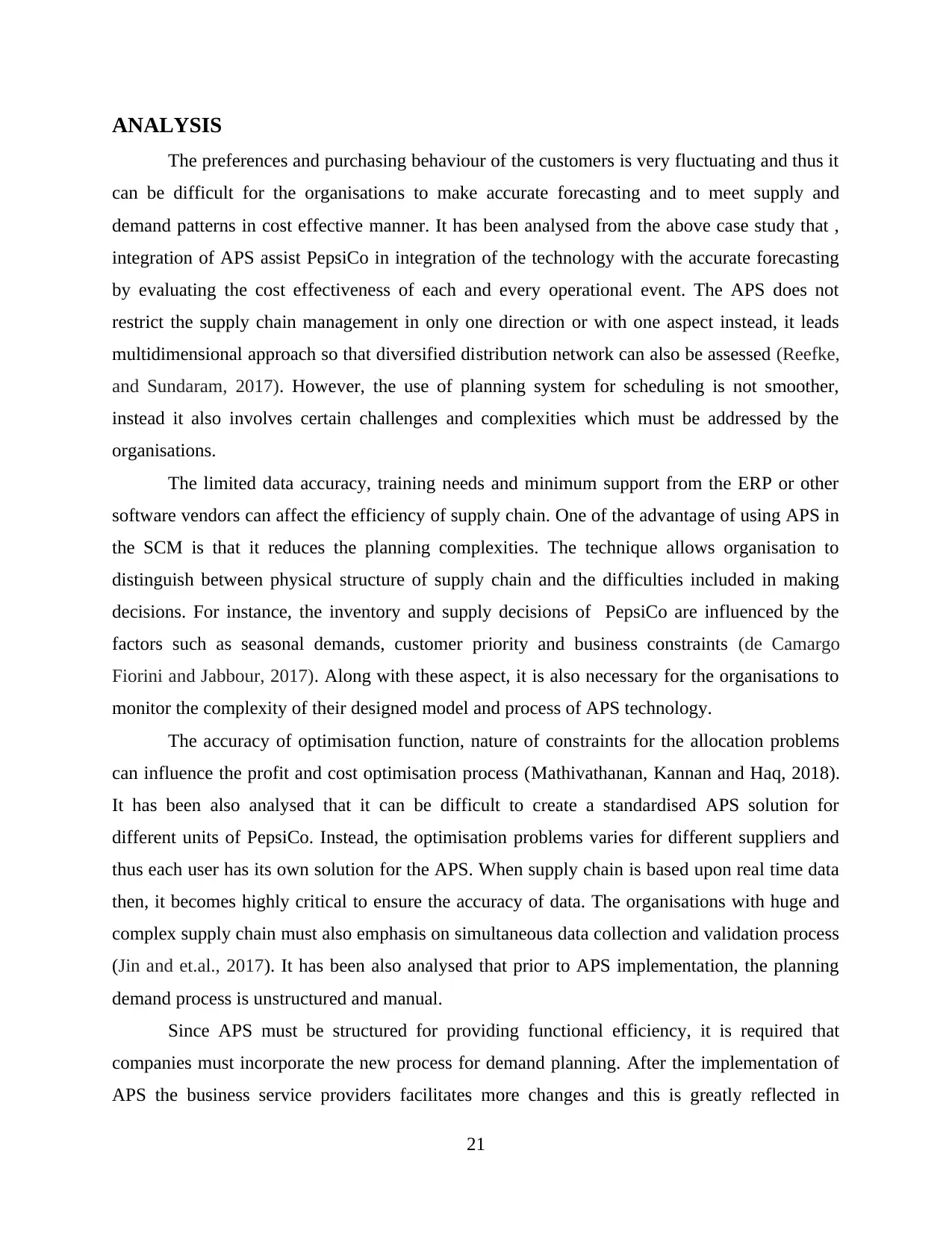
The preferences and purchasing behaviour of the customers is very fluctuating and thus it
can be difficult for the organisations to make accurate forecasting and to meet supply and
demand patterns in cost effective manner. It has been analysed from the above case study that ,
integration of APS assist PepsiCo in integration of the technology with the accurate forecasting
by evaluating the cost effectiveness of each and every operational event. The APS does not
restrict the supply chain management in only one direction or with one aspect instead, it leads
multidimensional approach so that diversified distribution network can also be assessed (Reefke,
and Sundaram, 2017). However, the use of planning system for scheduling is not smoother,
instead it also involves certain challenges and complexities which must be addressed by the
organisations.
The limited data accuracy, training needs and minimum support from the ERP or other
software vendors can affect the efficiency of supply chain. One of the advantage of using APS in
the SCM is that it reduces the planning complexities. The technique allows organisation to
distinguish between physical structure of supply chain and the difficulties included in making
decisions. For instance, the inventory and supply decisions of PepsiCo are influenced by the
factors such as seasonal demands, customer priority and business constraints (de Camargo
Fiorini and Jabbour, 2017). Along with these aspect, it is also necessary for the organisations to
monitor the complexity of their designed model and process of APS technology.
The accuracy of optimisation function, nature of constraints for the allocation problems
can influence the profit and cost optimisation process (Mathivathanan, Kannan and Haq, 2018).
It has been also analysed that it can be difficult to create a standardised APS solution for
different units of PepsiCo. Instead, the optimisation problems varies for different suppliers and
thus each user has its own solution for the APS. When supply chain is based upon real time data
then, it becomes highly critical to ensure the accuracy of data. The organisations with huge and
complex supply chain must also emphasis on simultaneous data collection and validation process
(Jin and et.al., 2017). It has been also analysed that prior to APS implementation, the planning
demand process is unstructured and manual.
Since APS must be structured for providing functional efficiency, it is required that
companies must incorporate the new process for demand planning. After the implementation of
APS the business service providers facilitates more changes and this is greatly reflected in
21
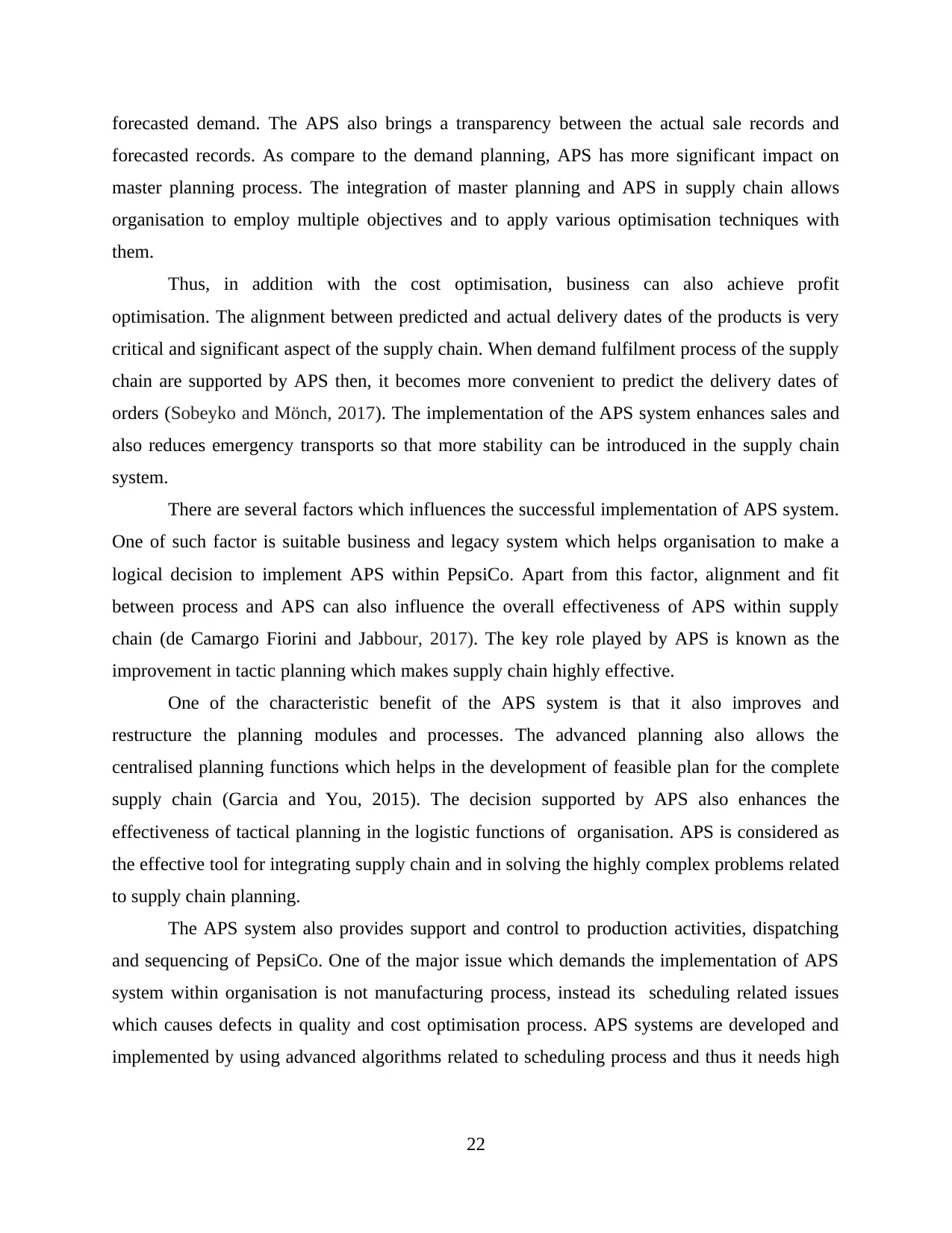
forecasted records. As compare to the demand planning, APS has more significant impact on
master planning process. The integration of master planning and APS in supply chain allows
organisation to employ multiple objectives and to apply various optimisation techniques with
them.
Thus, in addition with the cost optimisation, business can also achieve profit
optimisation. The alignment between predicted and actual delivery dates of the products is very
critical and significant aspect of the supply chain. When demand fulfilment process of the supply
chain are supported by APS then, it becomes more convenient to predict the delivery dates of
orders (Sobeyko and Mönch, 2017). The implementation of the APS system enhances sales and
also reduces emergency transports so that more stability can be introduced in the supply chain
system.
There are several factors which influences the successful implementation of APS system.
One of such factor is suitable business and legacy system which helps organisation to make a
logical decision to implement APS within PepsiCo. Apart from this factor, alignment and fit
between process and APS can also influence the overall effectiveness of APS within supply
chain (de Camargo Fiorini and Jabbour, 2017). The key role played by APS is known as the
improvement in tactic planning which makes supply chain highly effective.
One of the characteristic benefit of the APS system is that it also improves and
restructure the planning modules and processes. The advanced planning also allows the
centralised planning functions which helps in the development of feasible plan for the complete
supply chain (Garcia and You, 2015). The decision supported by APS also enhances the
effectiveness of tactical planning in the logistic functions of organisation. APS is considered as
the effective tool for integrating supply chain and in solving the highly complex problems related
to supply chain planning.
The APS system also provides support and control to production activities, dispatching
and sequencing of PepsiCo. One of the major issue which demands the implementation of APS
system within organisation is not manufacturing process, instead its scheduling related issues
which causes defects in quality and cost optimisation process. APS systems are developed and
implemented by using advanced algorithms related to scheduling process and thus it needs high
22
⊘ This is a preview!⊘
Do you want full access?
Subscribe today to unlock all pages.

Trusted by 1+ million students worldwide
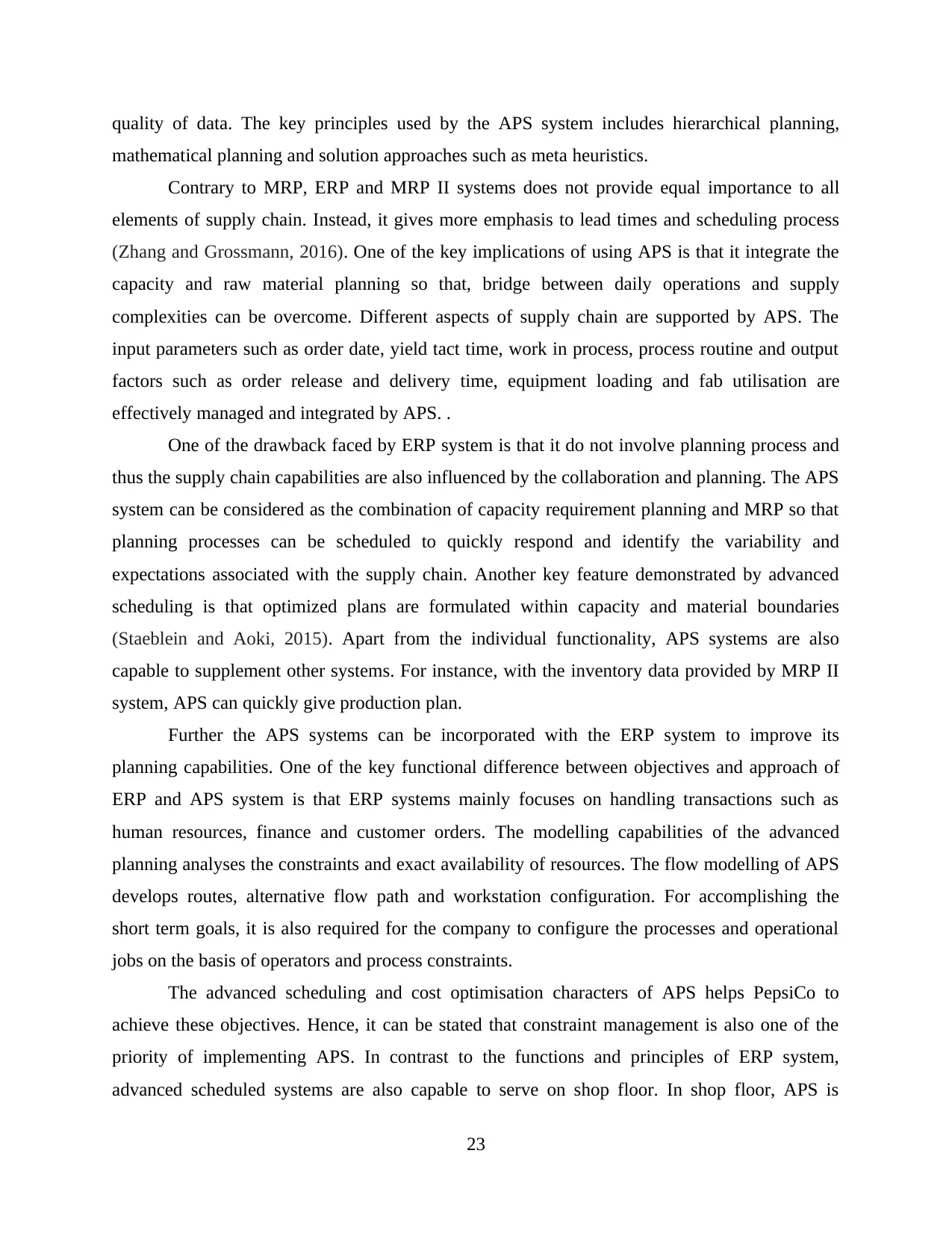
mathematical planning and solution approaches such as meta heuristics.
Contrary to MRP, ERP and MRP II systems does not provide equal importance to all
elements of supply chain. Instead, it gives more emphasis to lead times and scheduling process
(Zhang and Grossmann, 2016). One of the key implications of using APS is that it integrate the
capacity and raw material planning so that, bridge between daily operations and supply
complexities can be overcome. Different aspects of supply chain are supported by APS. The
input parameters such as order date, yield tact time, work in process, process routine and output
factors such as order release and delivery time, equipment loading and fab utilisation are
effectively managed and integrated by APS. .
One of the drawback faced by ERP system is that it do not involve planning process and
thus the supply chain capabilities are also influenced by the collaboration and planning. The APS
system can be considered as the combination of capacity requirement planning and MRP so that
planning processes can be scheduled to quickly respond and identify the variability and
expectations associated with the supply chain. Another key feature demonstrated by advanced
scheduling is that optimized plans are formulated within capacity and material boundaries
(Staeblein and Aoki, 2015). Apart from the individual functionality, APS systems are also
capable to supplement other systems. For instance, with the inventory data provided by MRP II
system, APS can quickly give production plan.
Further the APS systems can be incorporated with the ERP system to improve its
planning capabilities. One of the key functional difference between objectives and approach of
ERP and APS system is that ERP systems mainly focuses on handling transactions such as
human resources, finance and customer orders. The modelling capabilities of the advanced
planning analyses the constraints and exact availability of resources. The flow modelling of APS
develops routes, alternative flow path and workstation configuration. For accomplishing the
short term goals, it is also required for the company to configure the processes and operational
jobs on the basis of operators and process constraints.
The advanced scheduling and cost optimisation characters of APS helps PepsiCo to
achieve these objectives. Hence, it can be stated that constraint management is also one of the
priority of implementing APS. In contrast to the functions and principles of ERP system,
advanced scheduled systems are also capable to serve on shop floor. In shop floor, APS is
23
Paraphrase This Document
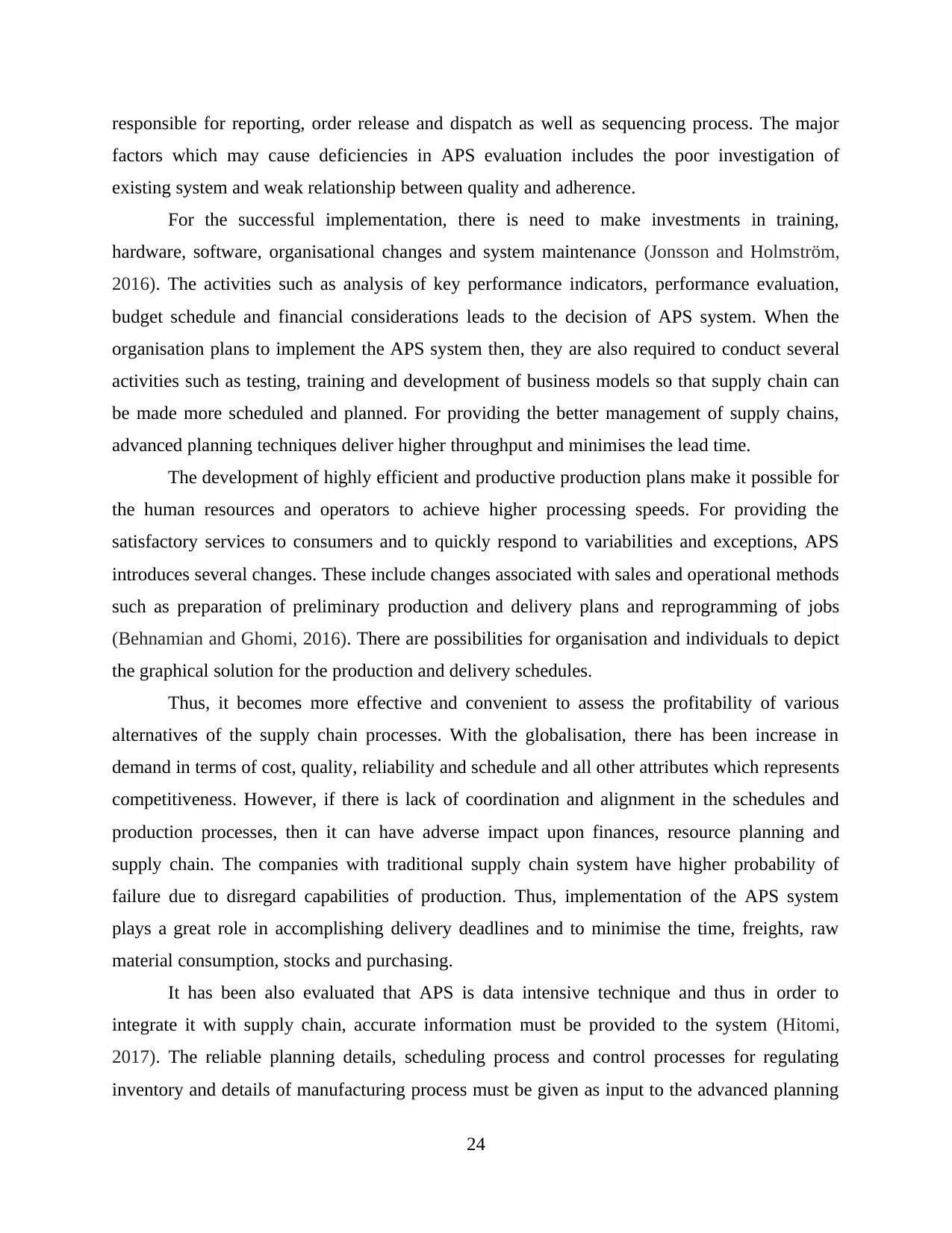
factors which may cause deficiencies in APS evaluation includes the poor investigation of
existing system and weak relationship between quality and adherence.
For the successful implementation, there is need to make investments in training,
hardware, software, organisational changes and system maintenance (Jonsson and Holmström,
2016). The activities such as analysis of key performance indicators, performance evaluation,
budget schedule and financial considerations leads to the decision of APS system. When the
organisation plans to implement the APS system then, they are also required to conduct several
activities such as testing, training and development of business models so that supply chain can
be made more scheduled and planned. For providing the better management of supply chains,
advanced planning techniques deliver higher throughput and minimises the lead time.
The development of highly efficient and productive production plans make it possible for
the human resources and operators to achieve higher processing speeds. For providing the
satisfactory services to consumers and to quickly respond to variabilities and exceptions, APS
introduces several changes. These include changes associated with sales and operational methods
such as preparation of preliminary production and delivery plans and reprogramming of jobs
(Behnamian and Ghomi, 2016). There are possibilities for organisation and individuals to depict
the graphical solution for the production and delivery schedules.
Thus, it becomes more effective and convenient to assess the profitability of various
alternatives of the supply chain processes. With the globalisation, there has been increase in
demand in terms of cost, quality, reliability and schedule and all other attributes which represents
competitiveness. However, if there is lack of coordination and alignment in the schedules and
production processes, then it can have adverse impact upon finances, resource planning and
supply chain. The companies with traditional supply chain system have higher probability of
failure due to disregard capabilities of production. Thus, implementation of the APS system
plays a great role in accomplishing delivery deadlines and to minimise the time, freights, raw
material consumption, stocks and purchasing.
It has been also evaluated that APS is data intensive technique and thus in order to
integrate it with supply chain, accurate information must be provided to the system (Hitomi,
2017). The reliable planning details, scheduling process and control processes for regulating
inventory and details of manufacturing process must be given as input to the advanced planning
24
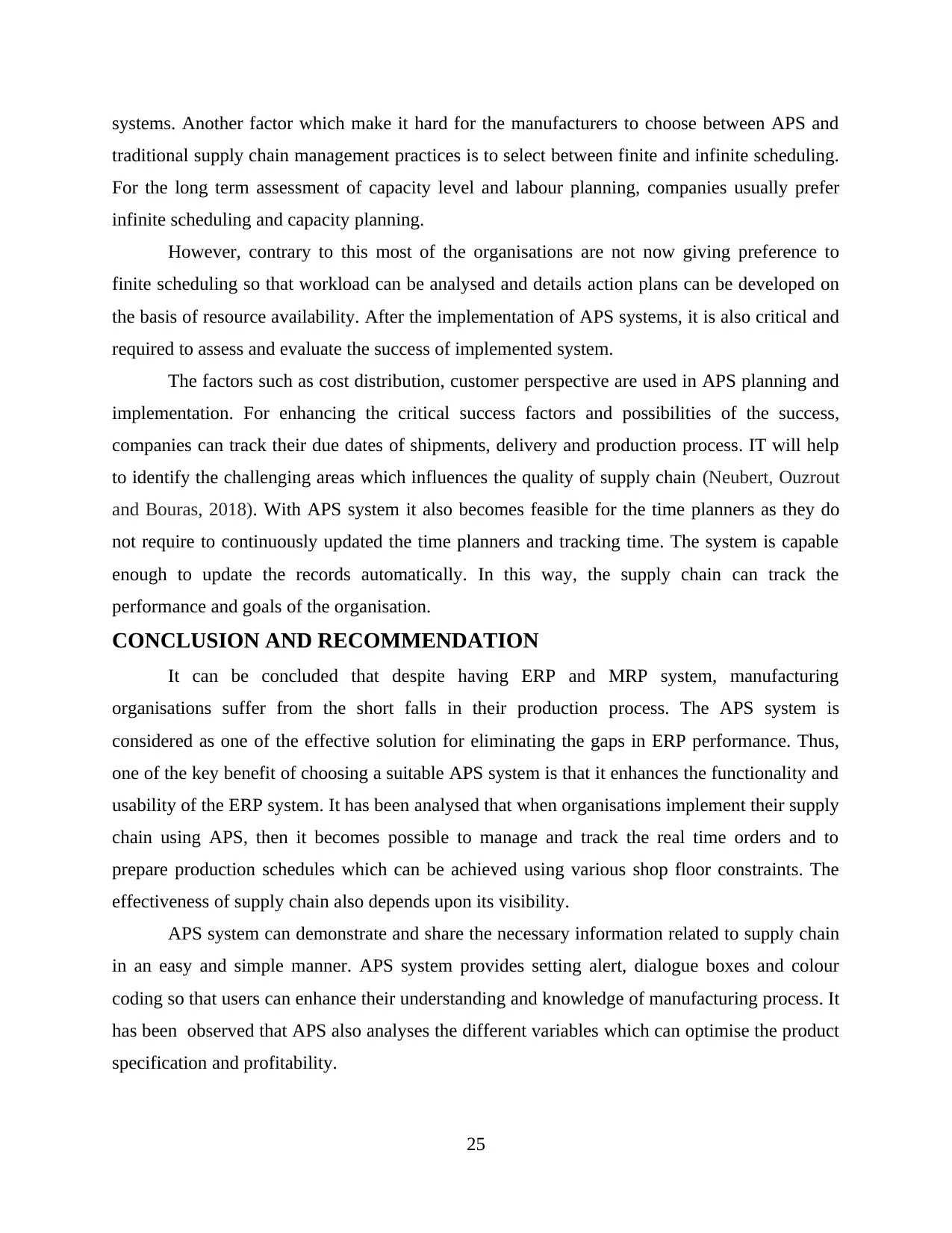
traditional supply chain management practices is to select between finite and infinite scheduling.
For the long term assessment of capacity level and labour planning, companies usually prefer
infinite scheduling and capacity planning.
However, contrary to this most of the organisations are not now giving preference to
finite scheduling so that workload can be analysed and details action plans can be developed on
the basis of resource availability. After the implementation of APS systems, it is also critical and
required to assess and evaluate the success of implemented system.
The factors such as cost distribution, customer perspective are used in APS planning and
implementation. For enhancing the critical success factors and possibilities of the success,
companies can track their due dates of shipments, delivery and production process. IT will help
to identify the challenging areas which influences the quality of supply chain (Neubert, Ouzrout
and Bouras, 2018). With APS system it also becomes feasible for the time planners as they do
not require to continuously updated the time planners and tracking time. The system is capable
enough to update the records automatically. In this way, the supply chain can track the
performance and goals of the organisation.
CONCLUSION AND RECOMMENDATION
It can be concluded that despite having ERP and MRP system, manufacturing
organisations suffer from the short falls in their production process. The APS system is
considered as one of the effective solution for eliminating the gaps in ERP performance. Thus,
one of the key benefit of choosing a suitable APS system is that it enhances the functionality and
usability of the ERP system. It has been analysed that when organisations implement their supply
chain using APS, then it becomes possible to manage and track the real time orders and to
prepare production schedules which can be achieved using various shop floor constraints. The
effectiveness of supply chain also depends upon its visibility.
APS system can demonstrate and share the necessary information related to supply chain
in an easy and simple manner. APS system provides setting alert, dialogue boxes and colour
coding so that users can enhance their understanding and knowledge of manufacturing process. It
has been observed that APS also analyses the different variables which can optimise the product
specification and profitability.
25
⊘ This is a preview!⊘
Do you want full access?
Subscribe today to unlock all pages.

Trusted by 1+ million students worldwide
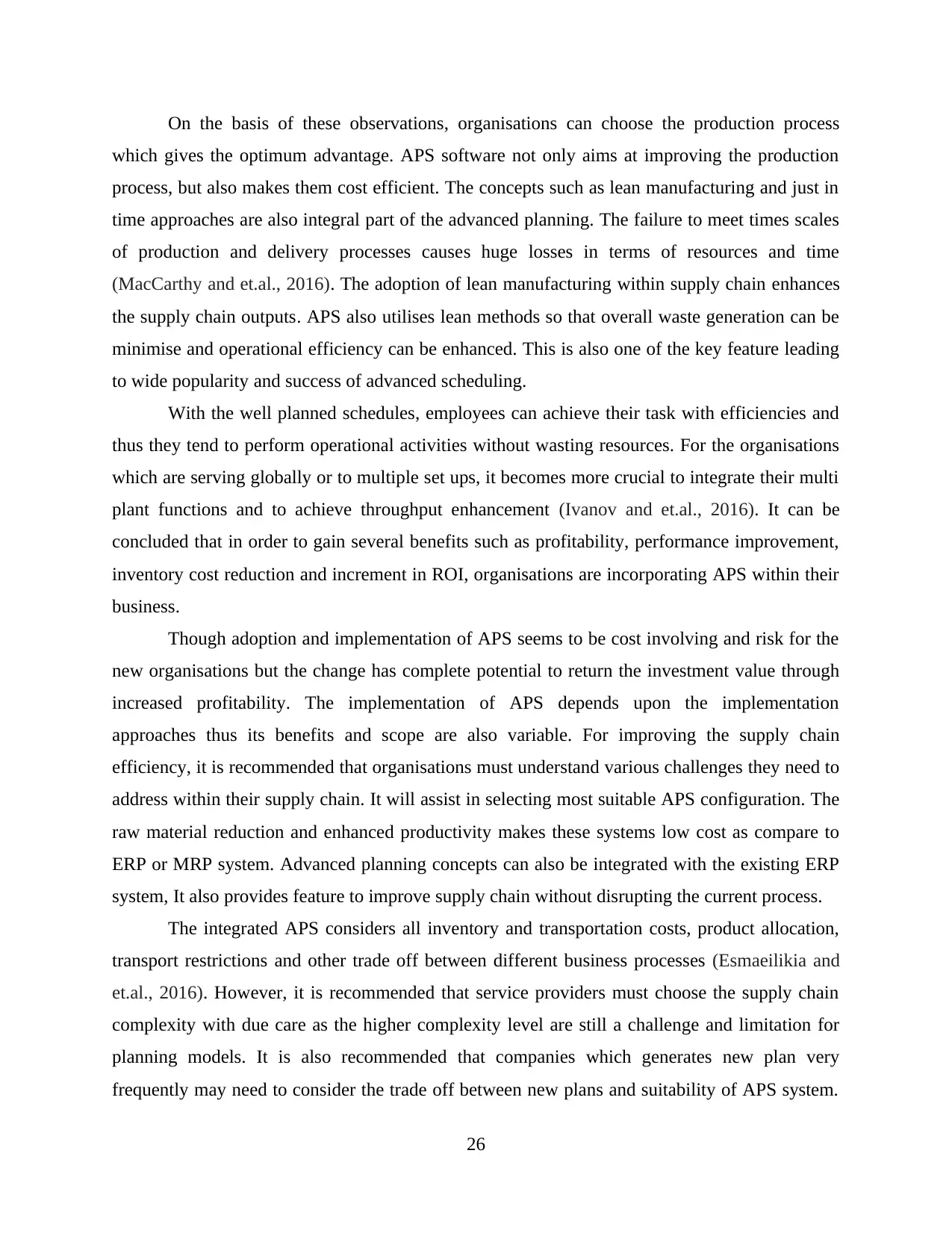
which gives the optimum advantage. APS software not only aims at improving the production
process, but also makes them cost efficient. The concepts such as lean manufacturing and just in
time approaches are also integral part of the advanced planning. The failure to meet times scales
of production and delivery processes causes huge losses in terms of resources and time
(MacCarthy and et.al., 2016). The adoption of lean manufacturing within supply chain enhances
the supply chain outputs. APS also utilises lean methods so that overall waste generation can be
minimise and operational efficiency can be enhanced. This is also one of the key feature leading
to wide popularity and success of advanced scheduling.
With the well planned schedules, employees can achieve their task with efficiencies and
thus they tend to perform operational activities without wasting resources. For the organisations
which are serving globally or to multiple set ups, it becomes more crucial to integrate their multi
plant functions and to achieve throughput enhancement (Ivanov and et.al., 2016). It can be
concluded that in order to gain several benefits such as profitability, performance improvement,
inventory cost reduction and increment in ROI, organisations are incorporating APS within their
business.
Though adoption and implementation of APS seems to be cost involving and risk for the
new organisations but the change has complete potential to return the investment value through
increased profitability. The implementation of APS depends upon the implementation
approaches thus its benefits and scope are also variable. For improving the supply chain
efficiency, it is recommended that organisations must understand various challenges they need to
address within their supply chain. It will assist in selecting most suitable APS configuration. The
raw material reduction and enhanced productivity makes these systems low cost as compare to
ERP or MRP system. Advanced planning concepts can also be integrated with the existing ERP
system, It also provides feature to improve supply chain without disrupting the current process.
The integrated APS considers all inventory and transportation costs, product allocation,
transport restrictions and other trade off between different business processes (Esmaeilikia and
et.al., 2016). However, it is recommended that service providers must choose the supply chain
complexity with due care as the higher complexity level are still a challenge and limitation for
planning models. It is also recommended that companies which generates new plan very
frequently may need to consider the trade off between new plans and suitability of APS system.
26
Paraphrase This Document
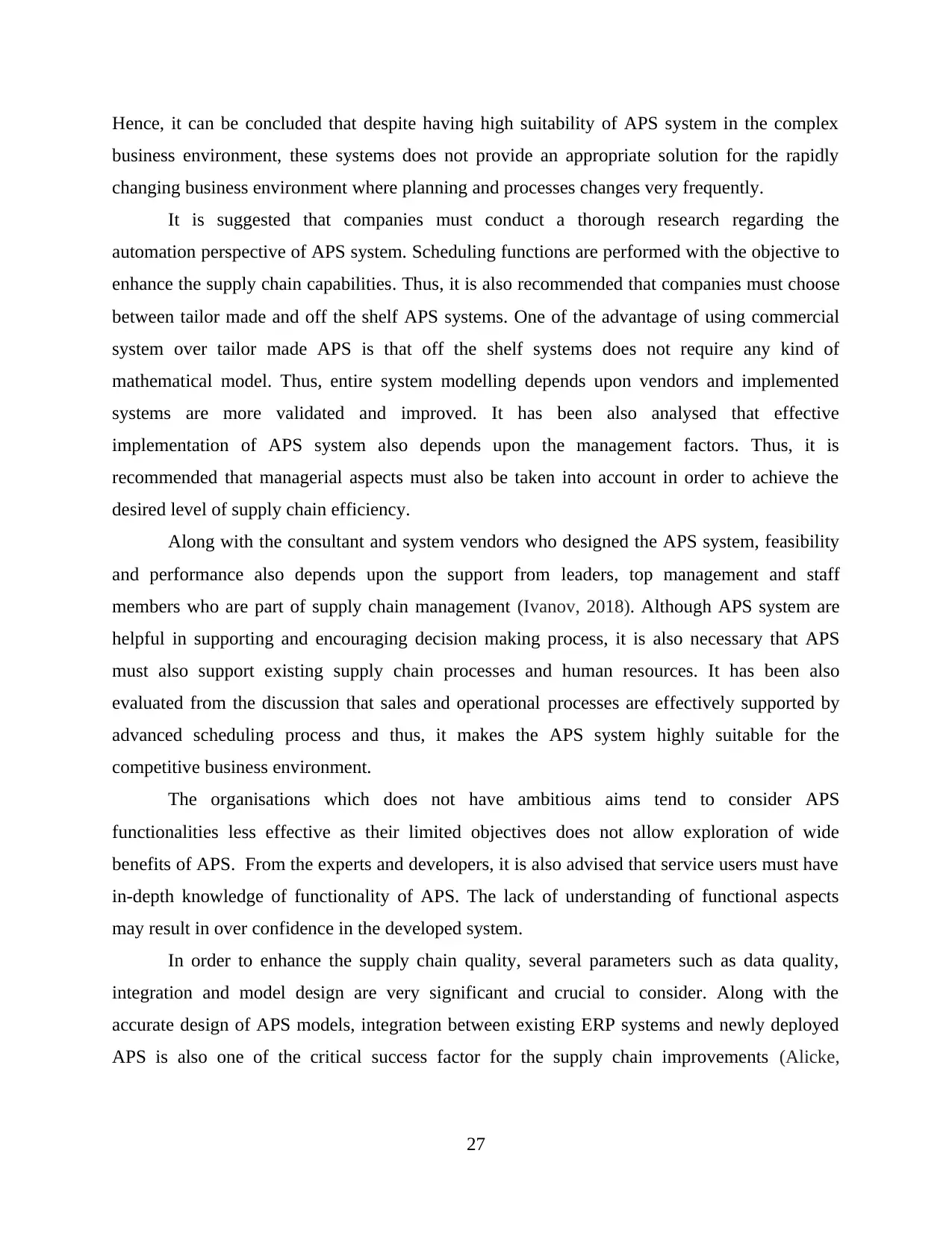
business environment, these systems does not provide an appropriate solution for the rapidly
changing business environment where planning and processes changes very frequently.
It is suggested that companies must conduct a thorough research regarding the
automation perspective of APS system. Scheduling functions are performed with the objective to
enhance the supply chain capabilities. Thus, it is also recommended that companies must choose
between tailor made and off the shelf APS systems. One of the advantage of using commercial
system over tailor made APS is that off the shelf systems does not require any kind of
mathematical model. Thus, entire system modelling depends upon vendors and implemented
systems are more validated and improved. It has been also analysed that effective
implementation of APS system also depends upon the management factors. Thus, it is
recommended that managerial aspects must also be taken into account in order to achieve the
desired level of supply chain efficiency.
Along with the consultant and system vendors who designed the APS system, feasibility
and performance also depends upon the support from leaders, top management and staff
members who are part of supply chain management (Ivanov, 2018). Although APS system are
helpful in supporting and encouraging decision making process, it is also necessary that APS
must also support existing supply chain processes and human resources. It has been also
evaluated from the discussion that sales and operational processes are effectively supported by
advanced scheduling process and thus, it makes the APS system highly suitable for the
competitive business environment.
The organisations which does not have ambitious aims tend to consider APS
functionalities less effective as their limited objectives does not allow exploration of wide
benefits of APS. From the experts and developers, it is also advised that service users must have
in-depth knowledge of functionality of APS. The lack of understanding of functional aspects
may result in over confidence in the developed system.
In order to enhance the supply chain quality, several parameters such as data quality,
integration and model design are very significant and crucial to consider. Along with the
accurate design of APS models, integration between existing ERP systems and newly deployed
APS is also one of the critical success factor for the supply chain improvements (Alicke,
27
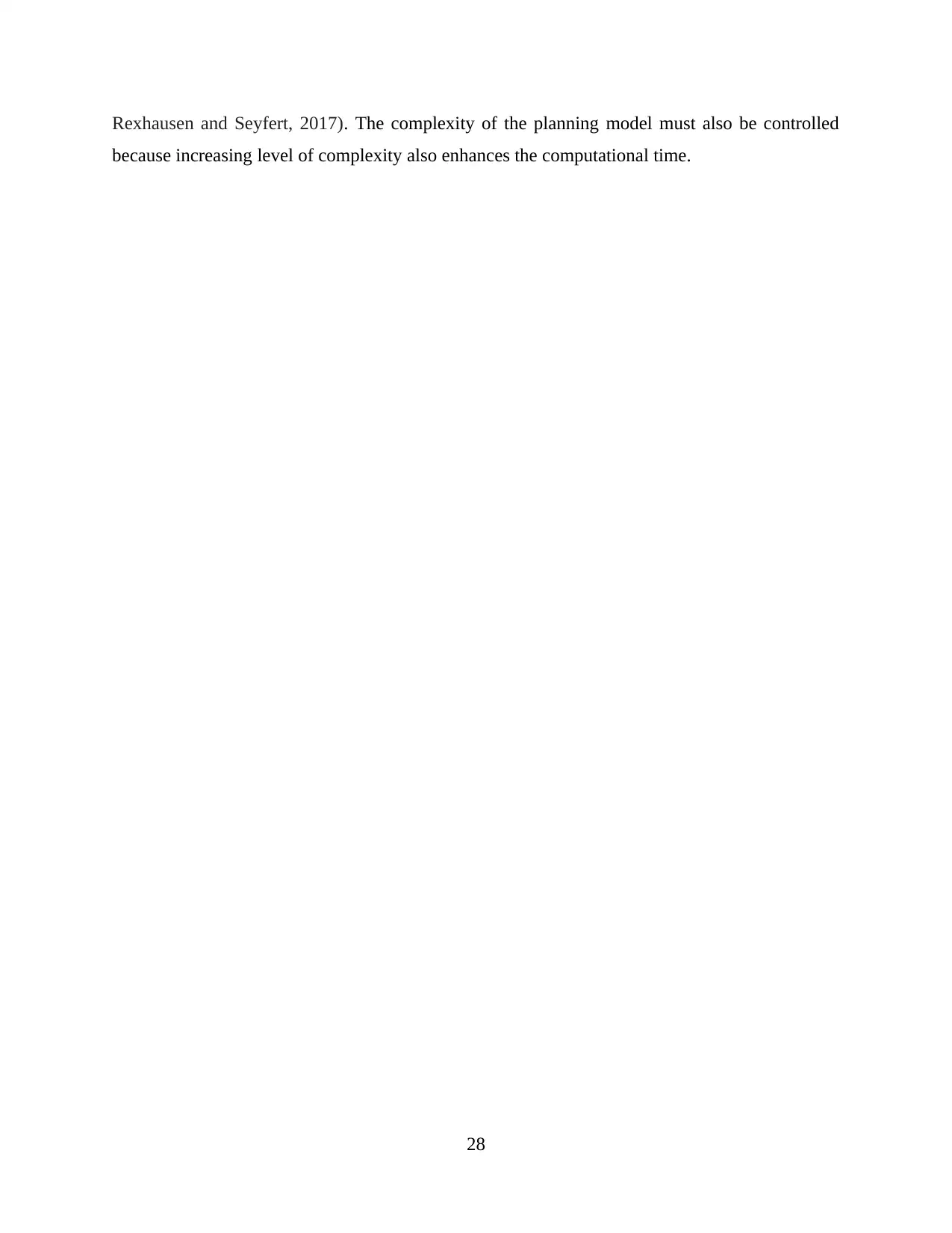
because increasing level of complexity also enhances the computational time.
28
⊘ This is a preview!⊘
Do you want full access?
Subscribe today to unlock all pages.

Trusted by 1+ million students worldwide
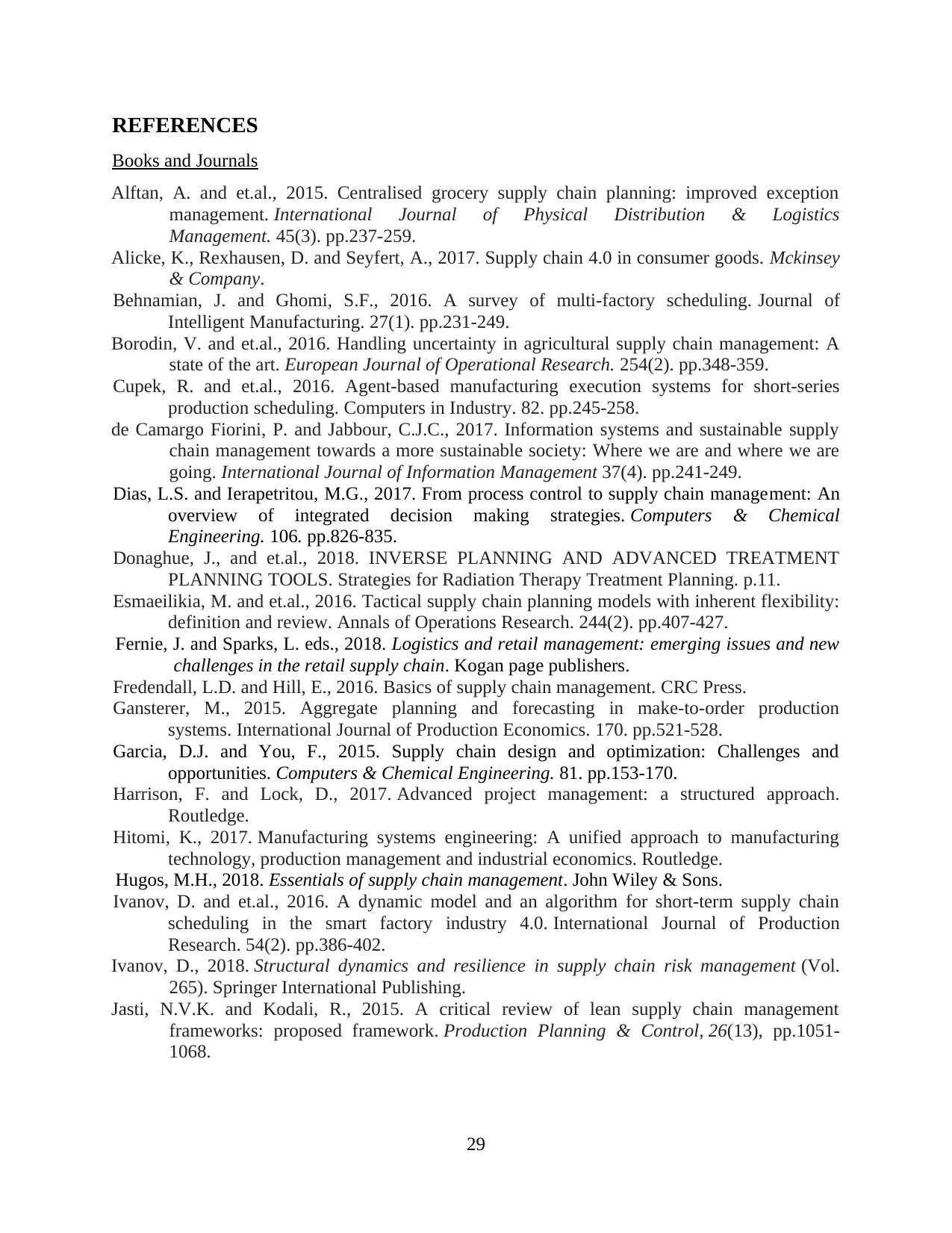
Books and Journals
Alftan, A. and et.al., 2015. Centralised grocery supply chain planning: improved exception
management. International Journal of Physical Distribution & Logistics
Management. 45(3). pp.237-259.
Alicke, K., Rexhausen, D. and Seyfert, A., 2017. Supply chain 4.0 in consumer goods. Mckinsey
& Company.
Behnamian, J. and Ghomi, S.F., 2016. A survey of multi-factory scheduling. Journal of
Intelligent Manufacturing. 27(1). pp.231-249.
Borodin, V. and et.al., 2016. Handling uncertainty in agricultural supply chain management: A
state of the art. European Journal of Operational Research. 254(2). pp.348-359.
Cupek, R. and et.al., 2016. Agent-based manufacturing execution systems for short-series
production scheduling. Computers in Industry. 82. pp.245-258.
de Camargo Fiorini, P. and Jabbour, C.J.C., 2017. Information systems and sustainable supply
chain management towards a more sustainable society: Where we are and where we are
going. International Journal of Information Management 37(4). pp.241-249.
Dias, L.S. and Ierapetritou, M.G., 2017. From process control to supply chain management: An
overview of integrated decision making strategies. Computers & Chemical
Engineering. 106. pp.826-835.
Donaghue, J., and et.al., 2018. INVERSE PLANNING AND ADVANCED TREATMENT
PLANNING TOOLS. Strategies for Radiation Therapy Treatment Planning. p.11.
Esmaeilikia, M. and et.al., 2016. Tactical supply chain planning models with inherent flexibility:
definition and review. Annals of Operations Research. 244(2). pp.407-427.
Fernie, J. and Sparks, L. eds., 2018. Logistics and retail management: emerging issues and new
challenges in the retail supply chain. Kogan page publishers.
Fredendall, L.D. and Hill, E., 2016. Basics of supply chain management. CRC Press.
Gansterer, M., 2015. Aggregate planning and forecasting in make-to-order production
systems. International Journal of Production Economics. 170. pp.521-528.
Garcia, D.J. and You, F., 2015. Supply chain design and optimization: Challenges and
opportunities. Computers & Chemical Engineering. 81. pp.153-170.
Harrison, F. and Lock, D., 2017. Advanced project management: a structured approach.
Routledge.
Hitomi, K., 2017. Manufacturing systems engineering: A unified approach to manufacturing
technology, production management and industrial economics. Routledge.
Hugos, M.H., 2018. Essentials of supply chain management. John Wiley & Sons.
Ivanov, D. and et.al., 2016. A dynamic model and an algorithm for short-term supply chain
scheduling in the smart factory industry 4.0. International Journal of Production
Research. 54(2). pp.386-402.
Ivanov, D., 2018. Structural dynamics and resilience in supply chain risk management (Vol.
265). Springer International Publishing.
Jasti, N.V.K. and Kodali, R., 2015. A critical review of lean supply chain management
frameworks: proposed framework. Production Planning & Control, 26(13), pp.1051-
1068.
29
Paraphrase This Document
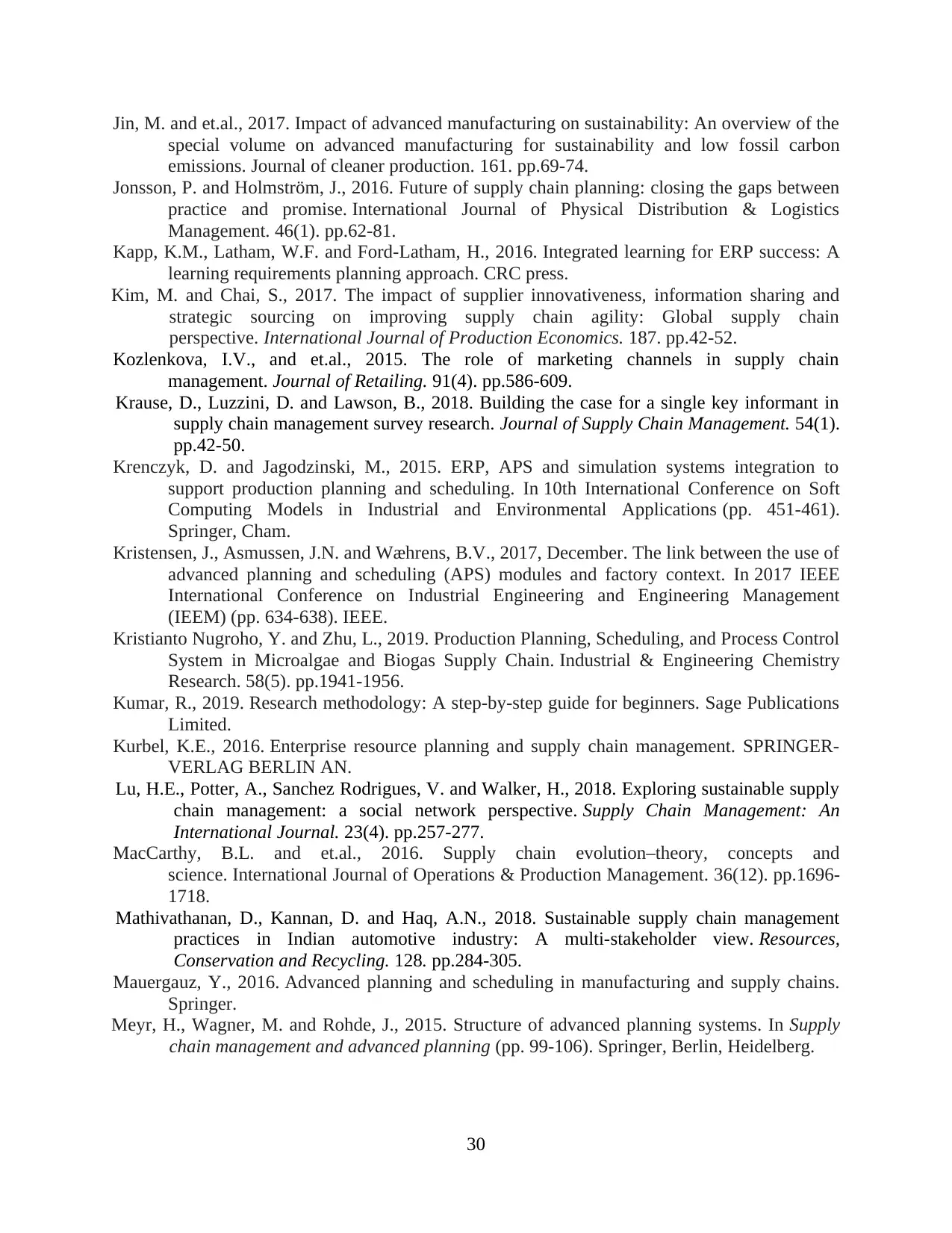
special volume on advanced manufacturing for sustainability and low fossil carbon
emissions. Journal of cleaner production. 161. pp.69-74.
Jonsson, P. and Holmström, J., 2016. Future of supply chain planning: closing the gaps between
practice and promise. International Journal of Physical Distribution & Logistics
Management. 46(1). pp.62-81.
Kapp, K.M., Latham, W.F. and Ford-Latham, H., 2016. Integrated learning for ERP success: A
learning requirements planning approach. CRC press.
Kim, M. and Chai, S., 2017. The impact of supplier innovativeness, information sharing and
strategic sourcing on improving supply chain agility: Global supply chain
perspective. International Journal of Production Economics. 187. pp.42-52.
Kozlenkova, I.V., and et.al., 2015. The role of marketing channels in supply chain
management. Journal of Retailing. 91(4). pp.586-609.
Krause, D., Luzzini, D. and Lawson, B., 2018. Building the case for a single key informant in
supply chain management survey research. Journal of Supply Chain Management. 54(1).
pp.42-50.
Krenczyk, D. and Jagodzinski, M., 2015. ERP, APS and simulation systems integration to
support production planning and scheduling. In 10th International Conference on Soft
Computing Models in Industrial and Environmental Applications (pp. 451-461).
Springer, Cham.
Kristensen, J., Asmussen, J.N. and Wæhrens, B.V., 2017, December. The link between the use of
advanced planning and scheduling (APS) modules and factory context. In 2017 IEEE
International Conference on Industrial Engineering and Engineering Management
(IEEM) (pp. 634-638). IEEE.
Kristianto Nugroho, Y. and Zhu, L., 2019. Production Planning, Scheduling, and Process Control
System in Microalgae and Biogas Supply Chain. Industrial & Engineering Chemistry
Research. 58(5). pp.1941-1956.
Kumar, R., 2019. Research methodology: A step-by-step guide for beginners. Sage Publications
Limited.
Kurbel, K.E., 2016. Enterprise resource planning and supply chain management. SPRINGER-
VERLAG BERLIN AN.
Lu, H.E., Potter, A., Sanchez Rodrigues, V. and Walker, H., 2018. Exploring sustainable supply
chain management: a social network perspective. Supply Chain Management: An
International Journal. 23(4). pp.257-277.
MacCarthy, B.L. and et.al., 2016. Supply chain evolution–theory, concepts and
science. International Journal of Operations & Production Management. 36(12). pp.1696-
1718.
Mathivathanan, D., Kannan, D. and Haq, A.N., 2018. Sustainable supply chain management
practices in Indian automotive industry: A multi-stakeholder view. Resources,
Conservation and Recycling. 128. pp.284-305.
Mauergauz, Y., 2016. Advanced planning and scheduling in manufacturing and supply chains.
Springer.
Meyr, H., Wagner, M. and Rohde, J., 2015. Structure of advanced planning systems. In Supply
chain management and advanced planning (pp. 99-106). Springer, Berlin, Heidelberg.
30
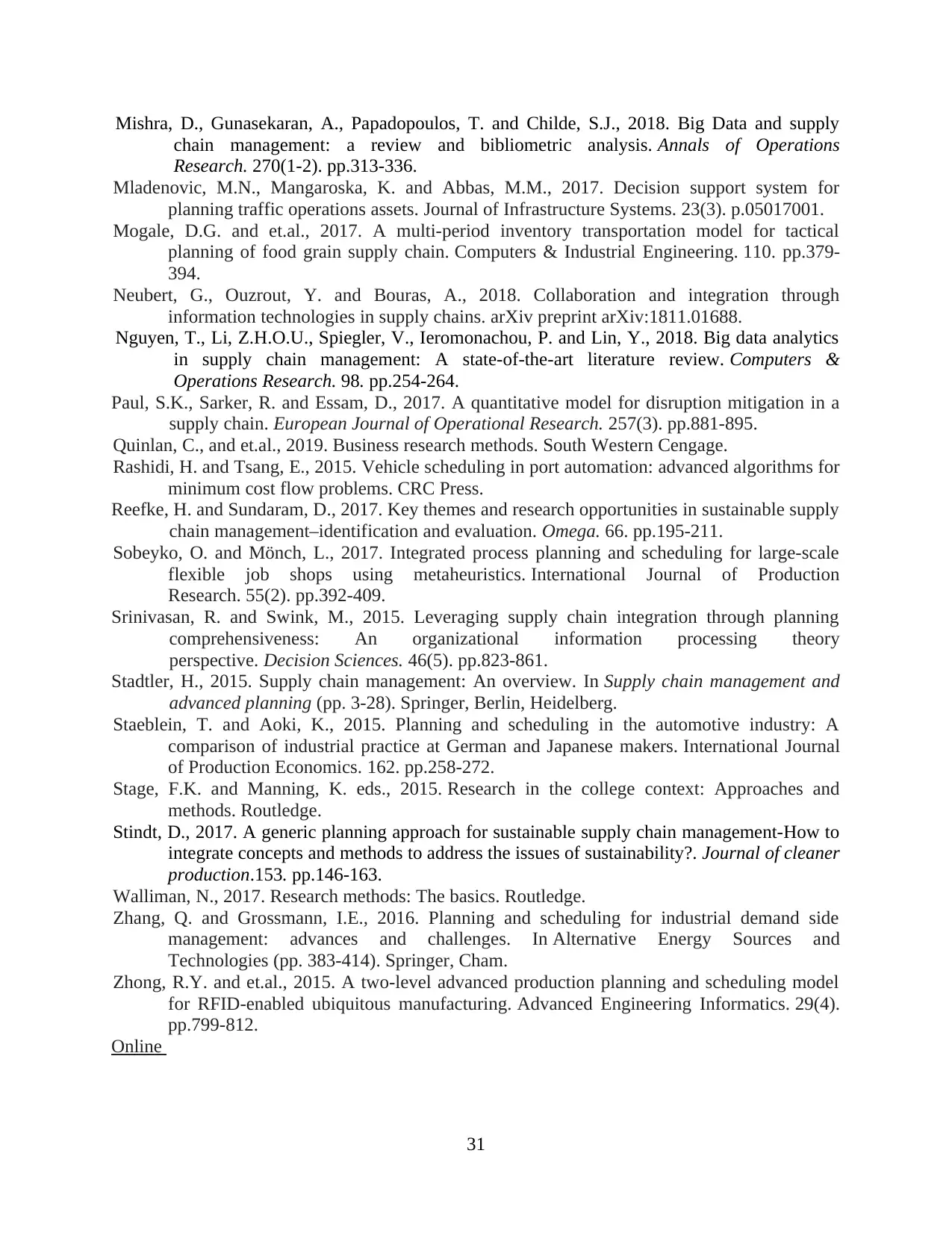
chain management: a review and bibliometric analysis. Annals of Operations
Research. 270(1-2). pp.313-336.
Mladenovic, M.N., Mangaroska, K. and Abbas, M.M., 2017. Decision support system for
planning traffic operations assets. Journal of Infrastructure Systems. 23(3). p.05017001.
Mogale, D.G. and et.al., 2017. A multi-period inventory transportation model for tactical
planning of food grain supply chain. Computers & Industrial Engineering. 110. pp.379-
394.
Neubert, G., Ouzrout, Y. and Bouras, A., 2018. Collaboration and integration through
information technologies in supply chains. arXiv preprint arXiv:1811.01688.
Nguyen, T., Li, Z.H.O.U., Spiegler, V., Ieromonachou, P. and Lin, Y., 2018. Big data analytics
in supply chain management: A state-of-the-art literature review. Computers &
Operations Research. 98. pp.254-264.
Paul, S.K., Sarker, R. and Essam, D., 2017. A quantitative model for disruption mitigation in a
supply chain. European Journal of Operational Research. 257(3). pp.881-895.
Quinlan, C., and et.al., 2019. Business research methods. South Western Cengage.
Rashidi, H. and Tsang, E., 2015. Vehicle scheduling in port automation: advanced algorithms for
minimum cost flow problems. CRC Press.
Reefke, H. and Sundaram, D., 2017. Key themes and research opportunities in sustainable supply
chain management–identification and evaluation. Omega. 66. pp.195-211.
Sobeyko, O. and Mönch, L., 2017. Integrated process planning and scheduling for large-scale
flexible job shops using metaheuristics. International Journal of Production
Research. 55(2). pp.392-409.
Srinivasan, R. and Swink, M., 2015. Leveraging supply chain integration through planning
comprehensiveness: An organizational information processing theory
perspective. Decision Sciences. 46(5). pp.823-861.
Stadtler, H., 2015. Supply chain management: An overview. In Supply chain management and
advanced planning (pp. 3-28). Springer, Berlin, Heidelberg.
Staeblein, T. and Aoki, K., 2015. Planning and scheduling in the automotive industry: A
comparison of industrial practice at German and Japanese makers. International Journal
of Production Economics. 162. pp.258-272.
Stage, F.K. and Manning, K. eds., 2015. Research in the college context: Approaches and
methods. Routledge.
Stindt, D., 2017. A generic planning approach for sustainable supply chain management-How to
integrate concepts and methods to address the issues of sustainability?. Journal of cleaner
production.153. pp.146-163.
Walliman, N., 2017. Research methods: The basics. Routledge.
Zhang, Q. and Grossmann, I.E., 2016. Planning and scheduling for industrial demand side
management: advances and challenges. In Alternative Energy Sources and
Technologies (pp. 383-414). Springer, Cham.
Zhong, R.Y. and et.al., 2015. A two-level advanced production planning and scheduling model
for RFID-enabled ubiquitous manufacturing. Advanced Engineering Informatics. 29(4).
pp.799-812.
Online
31
⊘ This is a preview!⊘
Do you want full access?
Subscribe today to unlock all pages.

Trusted by 1+ million students worldwide
Related Documents

Your All-in-One AI-Powered Toolkit for Academic Success.
+13062052269
info@desklib.com
Available 24*7 on WhatsApp / Email
© 2024 | Zucol Services PVT LTD | All rights reserved.