Supply Chain Management: Analyzing Performance Measures and Strategies
VerifiedAdded on 2020/04/01
|6
|1395
|104
Report
AI Summary
This report examines key performance measures in supply chain management, focusing on three critical areas: delivery reliability, damage in transit, and inventory holding costs. Delivery reliability is evaluated using the ratio of timely deliveries, highlighting the importance of accurate stock calculations and minimizing errors. The report provides a practical example using NTUC Fairprice Co-operative Ltd. to illustrate the impact of discrepancies. Damage in transit addresses insurance claims for goods, emphasizing the need for detailed record-keeping and the ability to claim for losses. Inventory holding cost is defined as the combined cost of inventory investment and physical space, including rent, depreciation, and taxes. The report illustrates how to calculate these costs. The conclusion recommends adopting these measures to maintain an efficient inventory system, particularly focusing on inventory holding costs to calculate gross profit and loss. References to relevant literature support the analysis.
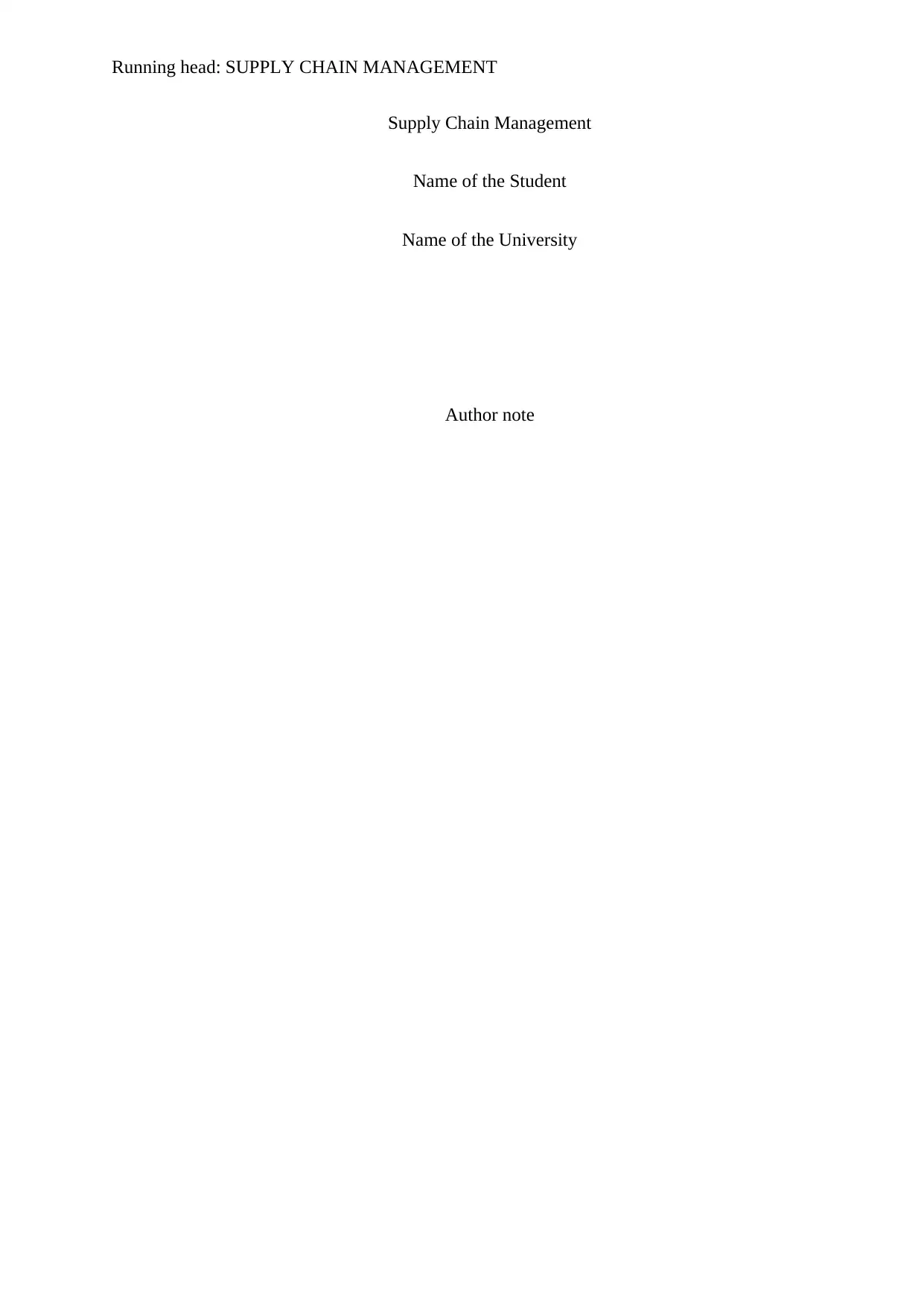
Running head: SUPPLY CHAIN MANAGEMENT
Supply Chain Management
Name of the Student
Name of the University
Author note
Supply Chain Management
Name of the Student
Name of the University
Author note
Paraphrase This Document
Need a fresh take? Get an instant paraphrase of this document with our AI Paraphraser
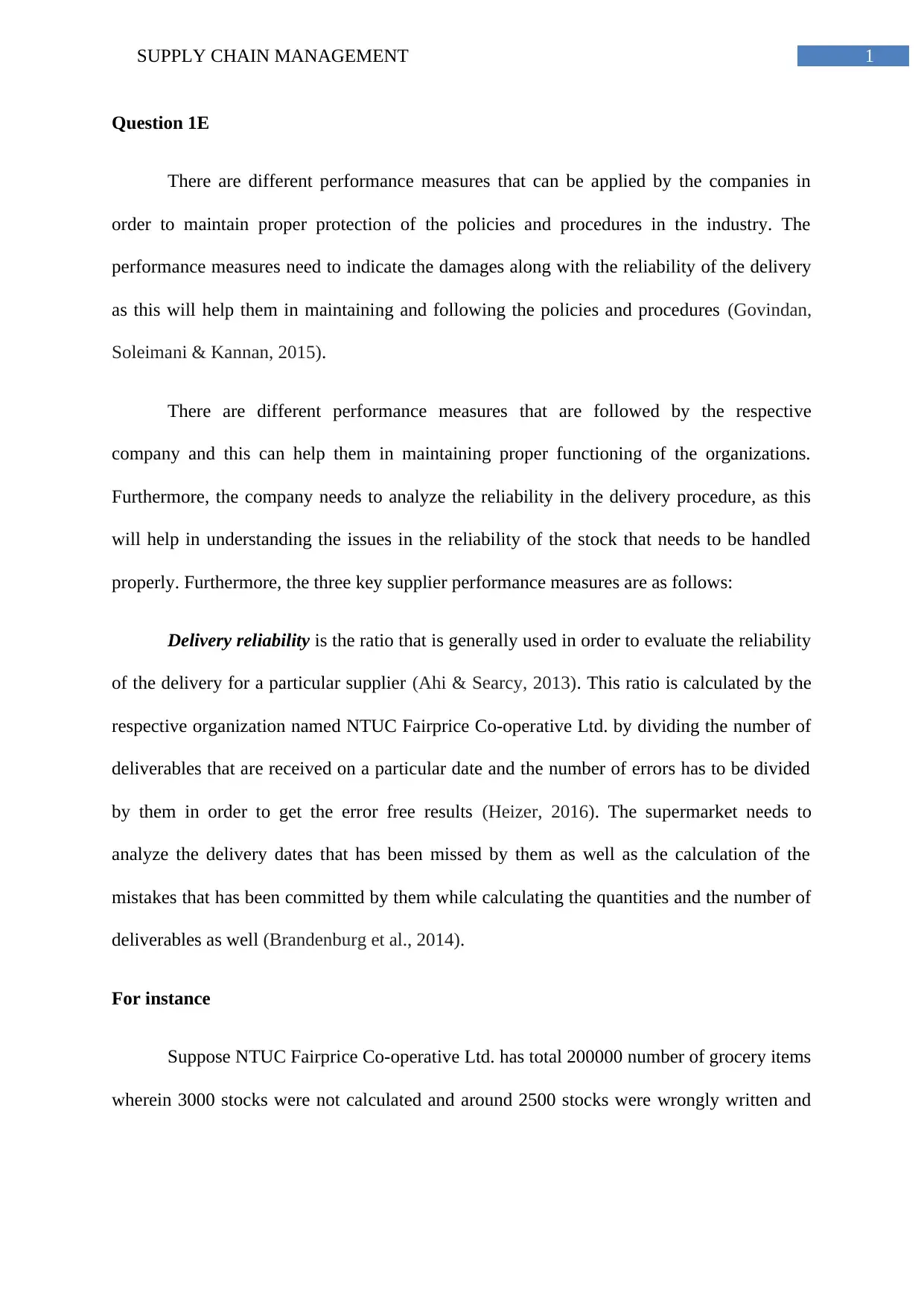
1SUPPLY CHAIN MANAGEMENT
Question 1E
There are different performance measures that can be applied by the companies in
order to maintain proper protection of the policies and procedures in the industry. The
performance measures need to indicate the damages along with the reliability of the delivery
as this will help them in maintaining and following the policies and procedures (Govindan,
Soleimani & Kannan, 2015).
There are different performance measures that are followed by the respective
company and this can help them in maintaining proper functioning of the organizations.
Furthermore, the company needs to analyze the reliability in the delivery procedure, as this
will help in understanding the issues in the reliability of the stock that needs to be handled
properly. Furthermore, the three key supplier performance measures are as follows:
Delivery reliability is the ratio that is generally used in order to evaluate the reliability
of the delivery for a particular supplier (Ahi & Searcy, 2013). This ratio is calculated by the
respective organization named NTUC Fairprice Co-operative Ltd. by dividing the number of
deliverables that are received on a particular date and the number of errors has to be divided
by them in order to get the error free results (Heizer, 2016). The supermarket needs to
analyze the delivery dates that has been missed by them as well as the calculation of the
mistakes that has been committed by them while calculating the quantities and the number of
deliverables as well (Brandenburg et al., 2014).
For instance
Suppose NTUC Fairprice Co-operative Ltd. has total 200000 number of grocery items
wherein 3000 stocks were not calculated and around 2500 stocks were wrongly written and
Question 1E
There are different performance measures that can be applied by the companies in
order to maintain proper protection of the policies and procedures in the industry. The
performance measures need to indicate the damages along with the reliability of the delivery
as this will help them in maintaining and following the policies and procedures (Govindan,
Soleimani & Kannan, 2015).
There are different performance measures that are followed by the respective
company and this can help them in maintaining proper functioning of the organizations.
Furthermore, the company needs to analyze the reliability in the delivery procedure, as this
will help in understanding the issues in the reliability of the stock that needs to be handled
properly. Furthermore, the three key supplier performance measures are as follows:
Delivery reliability is the ratio that is generally used in order to evaluate the reliability
of the delivery for a particular supplier (Ahi & Searcy, 2013). This ratio is calculated by the
respective organization named NTUC Fairprice Co-operative Ltd. by dividing the number of
deliverables that are received on a particular date and the number of errors has to be divided
by them in order to get the error free results (Heizer, 2016). The supermarket needs to
analyze the delivery dates that has been missed by them as well as the calculation of the
mistakes that has been committed by them while calculating the quantities and the number of
deliverables as well (Brandenburg et al., 2014).
For instance
Suppose NTUC Fairprice Co-operative Ltd. has total 200000 number of grocery items
wherein 3000 stocks were not calculated and around 2500 stocks were wrongly written and
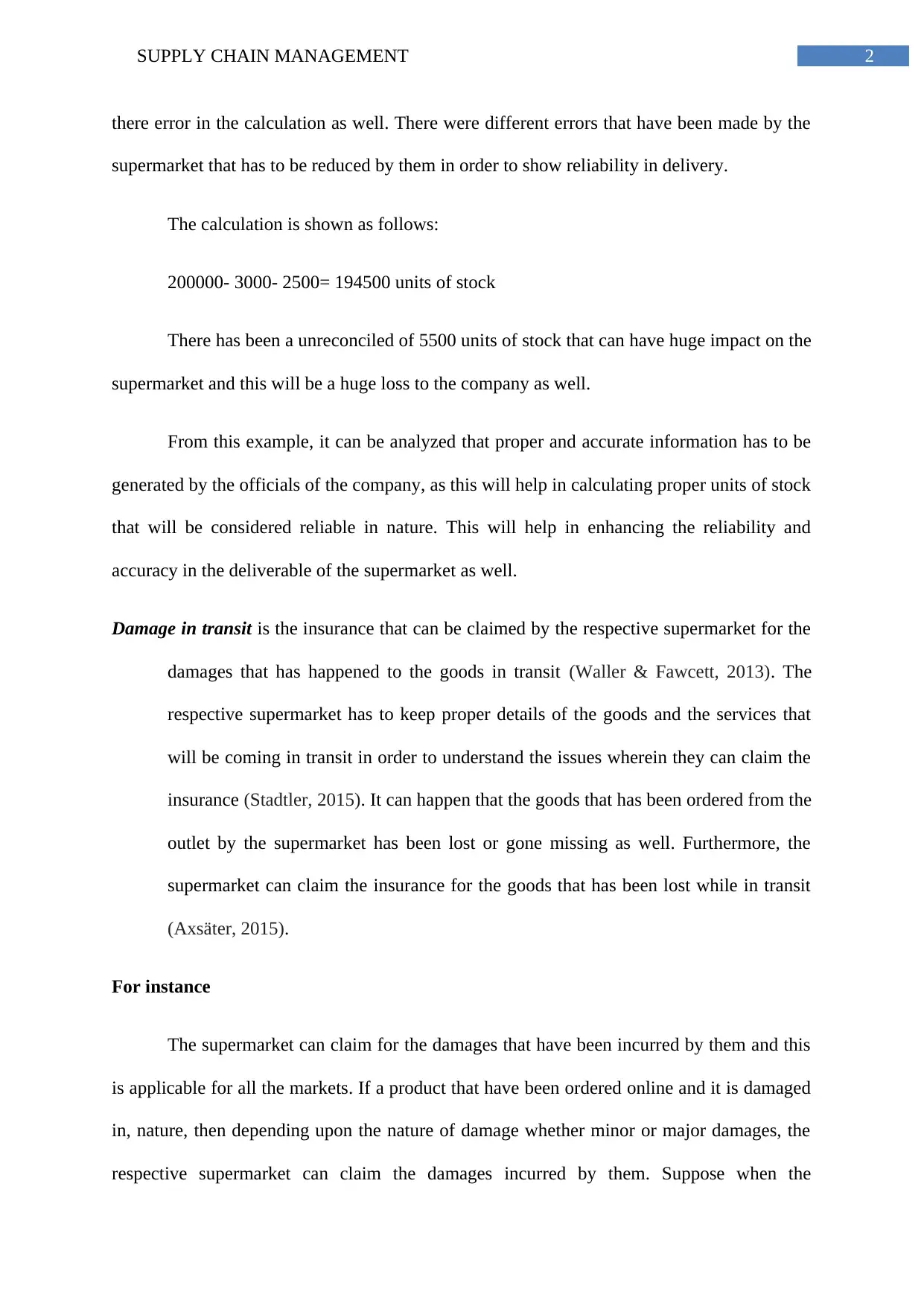
2SUPPLY CHAIN MANAGEMENT
there error in the calculation as well. There were different errors that have been made by the
supermarket that has to be reduced by them in order to show reliability in delivery.
The calculation is shown as follows:
200000- 3000- 2500= 194500 units of stock
There has been a unreconciled of 5500 units of stock that can have huge impact on the
supermarket and this will be a huge loss to the company as well.
From this example, it can be analyzed that proper and accurate information has to be
generated by the officials of the company, as this will help in calculating proper units of stock
that will be considered reliable in nature. This will help in enhancing the reliability and
accuracy in the deliverable of the supermarket as well.
Damage in transit is the insurance that can be claimed by the respective supermarket for the
damages that has happened to the goods in transit (Waller & Fawcett, 2013). The
respective supermarket has to keep proper details of the goods and the services that
will be coming in transit in order to understand the issues wherein they can claim the
insurance (Stadtler, 2015). It can happen that the goods that has been ordered from the
outlet by the supermarket has been lost or gone missing as well. Furthermore, the
supermarket can claim the insurance for the goods that has been lost while in transit
(Axsäter, 2015).
For instance
The supermarket can claim for the damages that have been incurred by them and this
is applicable for all the markets. If a product that have been ordered online and it is damaged
in, nature, then depending upon the nature of damage whether minor or major damages, the
respective supermarket can claim the damages incurred by them. Suppose when the
there error in the calculation as well. There were different errors that have been made by the
supermarket that has to be reduced by them in order to show reliability in delivery.
The calculation is shown as follows:
200000- 3000- 2500= 194500 units of stock
There has been a unreconciled of 5500 units of stock that can have huge impact on the
supermarket and this will be a huge loss to the company as well.
From this example, it can be analyzed that proper and accurate information has to be
generated by the officials of the company, as this will help in calculating proper units of stock
that will be considered reliable in nature. This will help in enhancing the reliability and
accuracy in the deliverable of the supermarket as well.
Damage in transit is the insurance that can be claimed by the respective supermarket for the
damages that has happened to the goods in transit (Waller & Fawcett, 2013). The
respective supermarket has to keep proper details of the goods and the services that
will be coming in transit in order to understand the issues wherein they can claim the
insurance (Stadtler, 2015). It can happen that the goods that has been ordered from the
outlet by the supermarket has been lost or gone missing as well. Furthermore, the
supermarket can claim the insurance for the goods that has been lost while in transit
(Axsäter, 2015).
For instance
The supermarket can claim for the damages that have been incurred by them and this
is applicable for all the markets. If a product that have been ordered online and it is damaged
in, nature, then depending upon the nature of damage whether minor or major damages, the
respective supermarket can claim the damages incurred by them. Suppose when the
You're viewing a preview
Unlock full access by subscribing today!
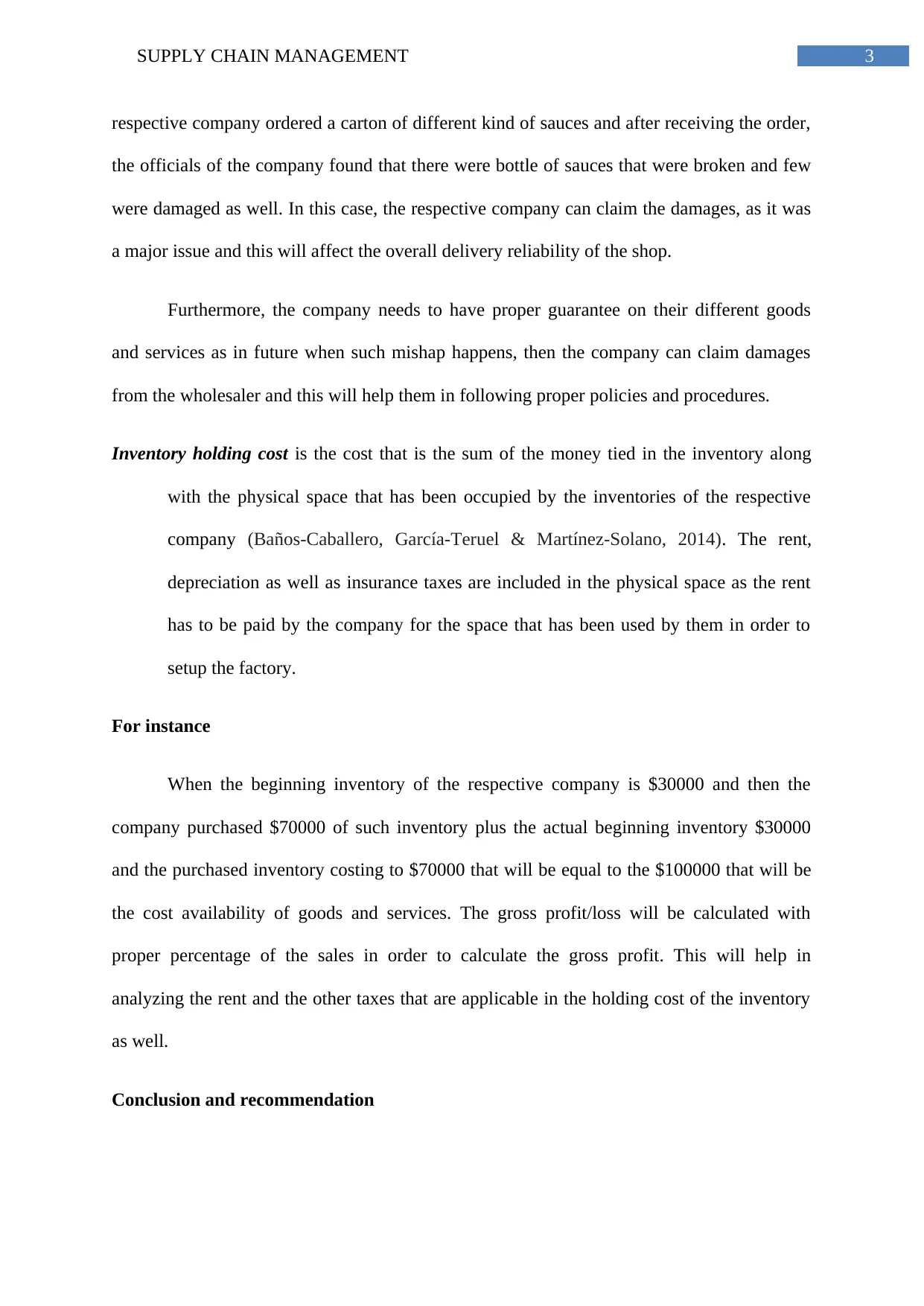
3SUPPLY CHAIN MANAGEMENT
respective company ordered a carton of different kind of sauces and after receiving the order,
the officials of the company found that there were bottle of sauces that were broken and few
were damaged as well. In this case, the respective company can claim the damages, as it was
a major issue and this will affect the overall delivery reliability of the shop.
Furthermore, the company needs to have proper guarantee on their different goods
and services as in future when such mishap happens, then the company can claim damages
from the wholesaler and this will help them in following proper policies and procedures.
Inventory holding cost is the cost that is the sum of the money tied in the inventory along
with the physical space that has been occupied by the inventories of the respective
company (Baños-Caballero, García-Teruel & Martínez-Solano, 2014). The rent,
depreciation as well as insurance taxes are included in the physical space as the rent
has to be paid by the company for the space that has been used by them in order to
setup the factory.
For instance
When the beginning inventory of the respective company is $30000 and then the
company purchased $70000 of such inventory plus the actual beginning inventory $30000
and the purchased inventory costing to $70000 that will be equal to the $100000 that will be
the cost availability of goods and services. The gross profit/loss will be calculated with
proper percentage of the sales in order to calculate the gross profit. This will help in
analyzing the rent and the other taxes that are applicable in the holding cost of the inventory
as well.
Conclusion and recommendation
respective company ordered a carton of different kind of sauces and after receiving the order,
the officials of the company found that there were bottle of sauces that were broken and few
were damaged as well. In this case, the respective company can claim the damages, as it was
a major issue and this will affect the overall delivery reliability of the shop.
Furthermore, the company needs to have proper guarantee on their different goods
and services as in future when such mishap happens, then the company can claim damages
from the wholesaler and this will help them in following proper policies and procedures.
Inventory holding cost is the cost that is the sum of the money tied in the inventory along
with the physical space that has been occupied by the inventories of the respective
company (Baños-Caballero, García-Teruel & Martínez-Solano, 2014). The rent,
depreciation as well as insurance taxes are included in the physical space as the rent
has to be paid by the company for the space that has been used by them in order to
setup the factory.
For instance
When the beginning inventory of the respective company is $30000 and then the
company purchased $70000 of such inventory plus the actual beginning inventory $30000
and the purchased inventory costing to $70000 that will be equal to the $100000 that will be
the cost availability of goods and services. The gross profit/loss will be calculated with
proper percentage of the sales in order to calculate the gross profit. This will help in
analyzing the rent and the other taxes that are applicable in the holding cost of the inventory
as well.
Conclusion and recommendation
Paraphrase This Document
Need a fresh take? Get an instant paraphrase of this document with our AI Paraphraser
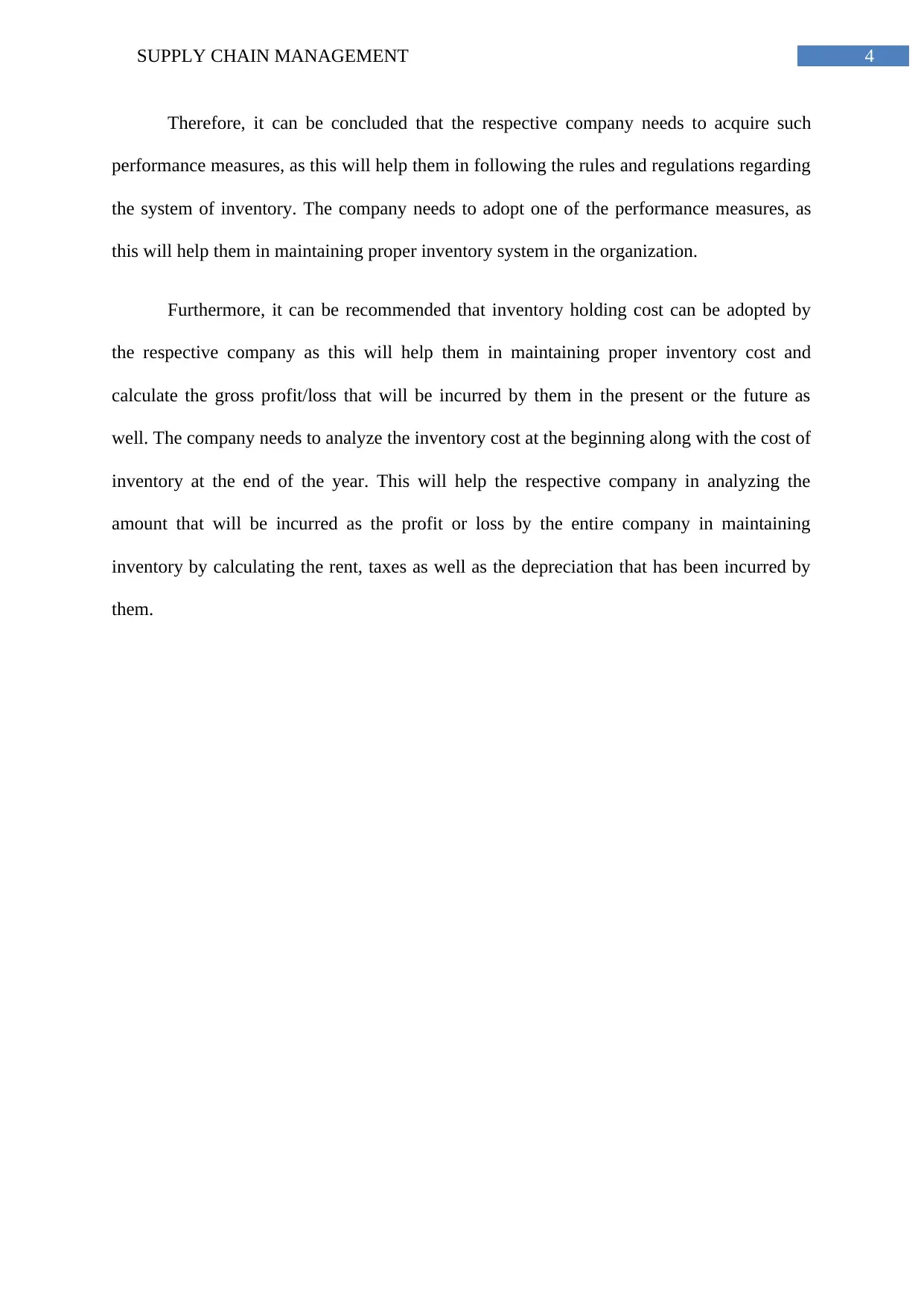
4SUPPLY CHAIN MANAGEMENT
Therefore, it can be concluded that the respective company needs to acquire such
performance measures, as this will help them in following the rules and regulations regarding
the system of inventory. The company needs to adopt one of the performance measures, as
this will help them in maintaining proper inventory system in the organization.
Furthermore, it can be recommended that inventory holding cost can be adopted by
the respective company as this will help them in maintaining proper inventory cost and
calculate the gross profit/loss that will be incurred by them in the present or the future as
well. The company needs to analyze the inventory cost at the beginning along with the cost of
inventory at the end of the year. This will help the respective company in analyzing the
amount that will be incurred as the profit or loss by the entire company in maintaining
inventory by calculating the rent, taxes as well as the depreciation that has been incurred by
them.
Therefore, it can be concluded that the respective company needs to acquire such
performance measures, as this will help them in following the rules and regulations regarding
the system of inventory. The company needs to adopt one of the performance measures, as
this will help them in maintaining proper inventory system in the organization.
Furthermore, it can be recommended that inventory holding cost can be adopted by
the respective company as this will help them in maintaining proper inventory cost and
calculate the gross profit/loss that will be incurred by them in the present or the future as
well. The company needs to analyze the inventory cost at the beginning along with the cost of
inventory at the end of the year. This will help the respective company in analyzing the
amount that will be incurred as the profit or loss by the entire company in maintaining
inventory by calculating the rent, taxes as well as the depreciation that has been incurred by
them.
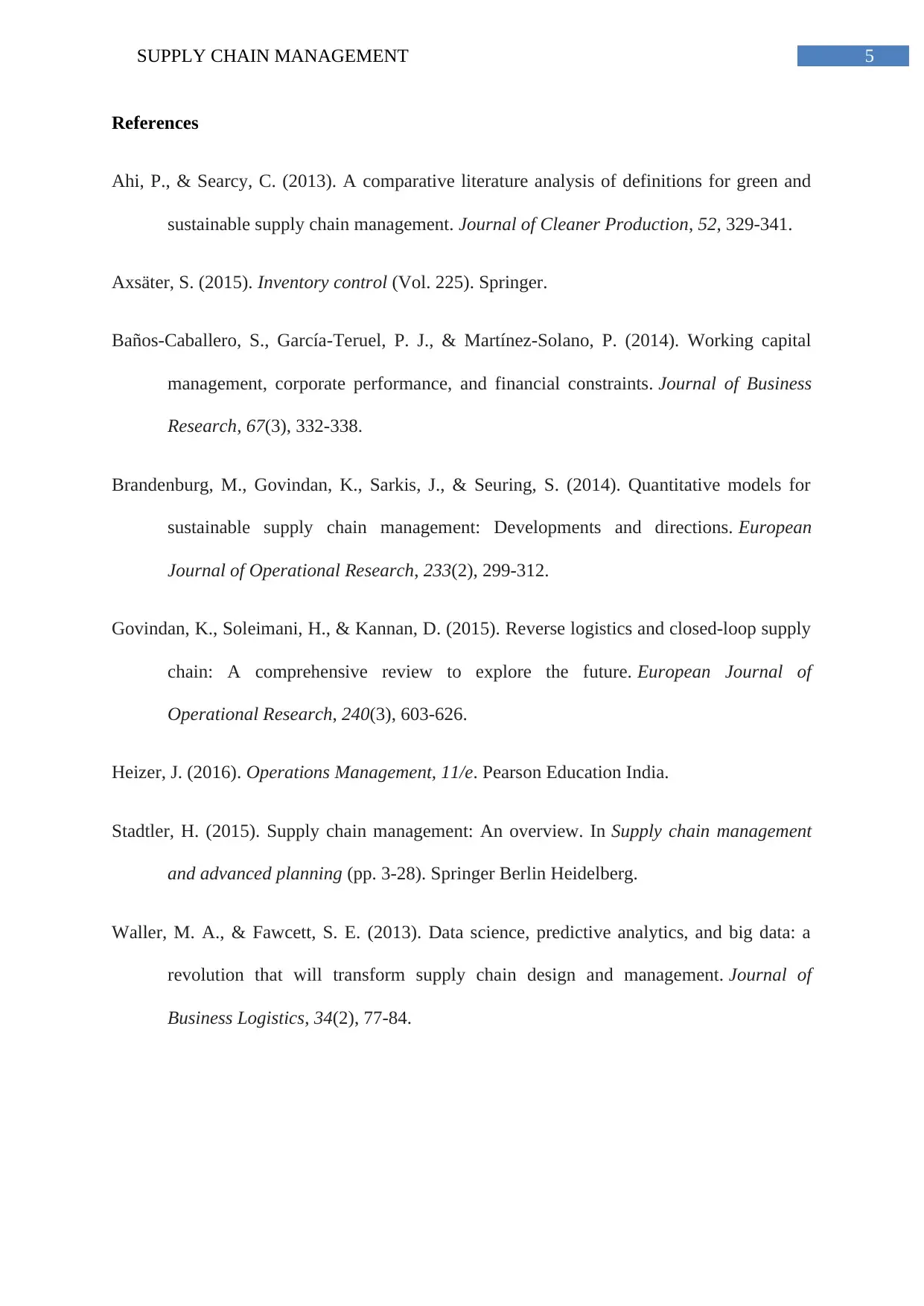
5SUPPLY CHAIN MANAGEMENT
References
Ahi, P., & Searcy, C. (2013). A comparative literature analysis of definitions for green and
sustainable supply chain management. Journal of Cleaner Production, 52, 329-341.
Axsäter, S. (2015). Inventory control (Vol. 225). Springer.
Baños-Caballero, S., García-Teruel, P. J., & Martínez-Solano, P. (2014). Working capital
management, corporate performance, and financial constraints. Journal of Business
Research, 67(3), 332-338.
Brandenburg, M., Govindan, K., Sarkis, J., & Seuring, S. (2014). Quantitative models for
sustainable supply chain management: Developments and directions. European
Journal of Operational Research, 233(2), 299-312.
Govindan, K., Soleimani, H., & Kannan, D. (2015). Reverse logistics and closed-loop supply
chain: A comprehensive review to explore the future. European Journal of
Operational Research, 240(3), 603-626.
Heizer, J. (2016). Operations Management, 11/e. Pearson Education India.
Stadtler, H. (2015). Supply chain management: An overview. In Supply chain management
and advanced planning (pp. 3-28). Springer Berlin Heidelberg.
Waller, M. A., & Fawcett, S. E. (2013). Data science, predictive analytics, and big data: a
revolution that will transform supply chain design and management. Journal of
Business Logistics, 34(2), 77-84.
References
Ahi, P., & Searcy, C. (2013). A comparative literature analysis of definitions for green and
sustainable supply chain management. Journal of Cleaner Production, 52, 329-341.
Axsäter, S. (2015). Inventory control (Vol. 225). Springer.
Baños-Caballero, S., García-Teruel, P. J., & Martínez-Solano, P. (2014). Working capital
management, corporate performance, and financial constraints. Journal of Business
Research, 67(3), 332-338.
Brandenburg, M., Govindan, K., Sarkis, J., & Seuring, S. (2014). Quantitative models for
sustainable supply chain management: Developments and directions. European
Journal of Operational Research, 233(2), 299-312.
Govindan, K., Soleimani, H., & Kannan, D. (2015). Reverse logistics and closed-loop supply
chain: A comprehensive review to explore the future. European Journal of
Operational Research, 240(3), 603-626.
Heizer, J. (2016). Operations Management, 11/e. Pearson Education India.
Stadtler, H. (2015). Supply chain management: An overview. In Supply chain management
and advanced planning (pp. 3-28). Springer Berlin Heidelberg.
Waller, M. A., & Fawcett, S. E. (2013). Data science, predictive analytics, and big data: a
revolution that will transform supply chain design and management. Journal of
Business Logistics, 34(2), 77-84.
You're viewing a preview
Unlock full access by subscribing today!
1 out of 6

Your All-in-One AI-Powered Toolkit for Academic Success.
+13062052269
info@desklib.com
Available 24*7 on WhatsApp / Email
Unlock your academic potential
© 2024 | Zucol Services PVT LTD | All rights reserved.