BPM Project Management Report: First Antenna Quality Analysis
VerifiedAdded on 2022/08/18
|31
|5985
|452
Report
AI Summary
This report provides a comprehensive analysis of the project management challenges faced by First Antenna Pty, a designer and supplier of communications hardware for the automotive industry. The company is experiencing quality issues with parts from a new factory, impacting the ...
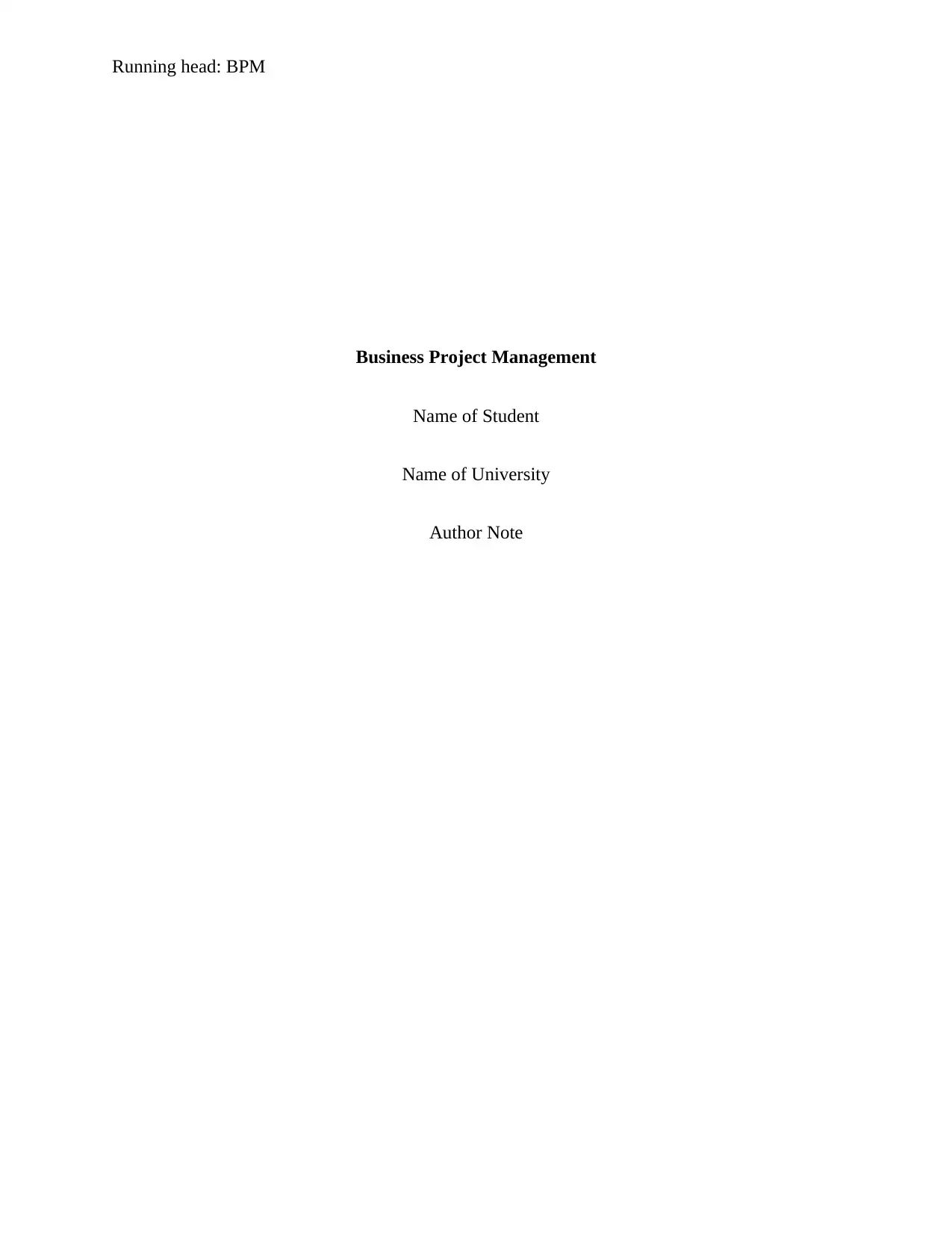
Running head: BPM
Business Project Management
Name of Student
Name of University
Author Note
Business Project Management
Name of Student
Name of University
Author Note
Secure Best Marks with AI Grader
Need help grading? Try our AI Grader for instant feedback on your assignments.
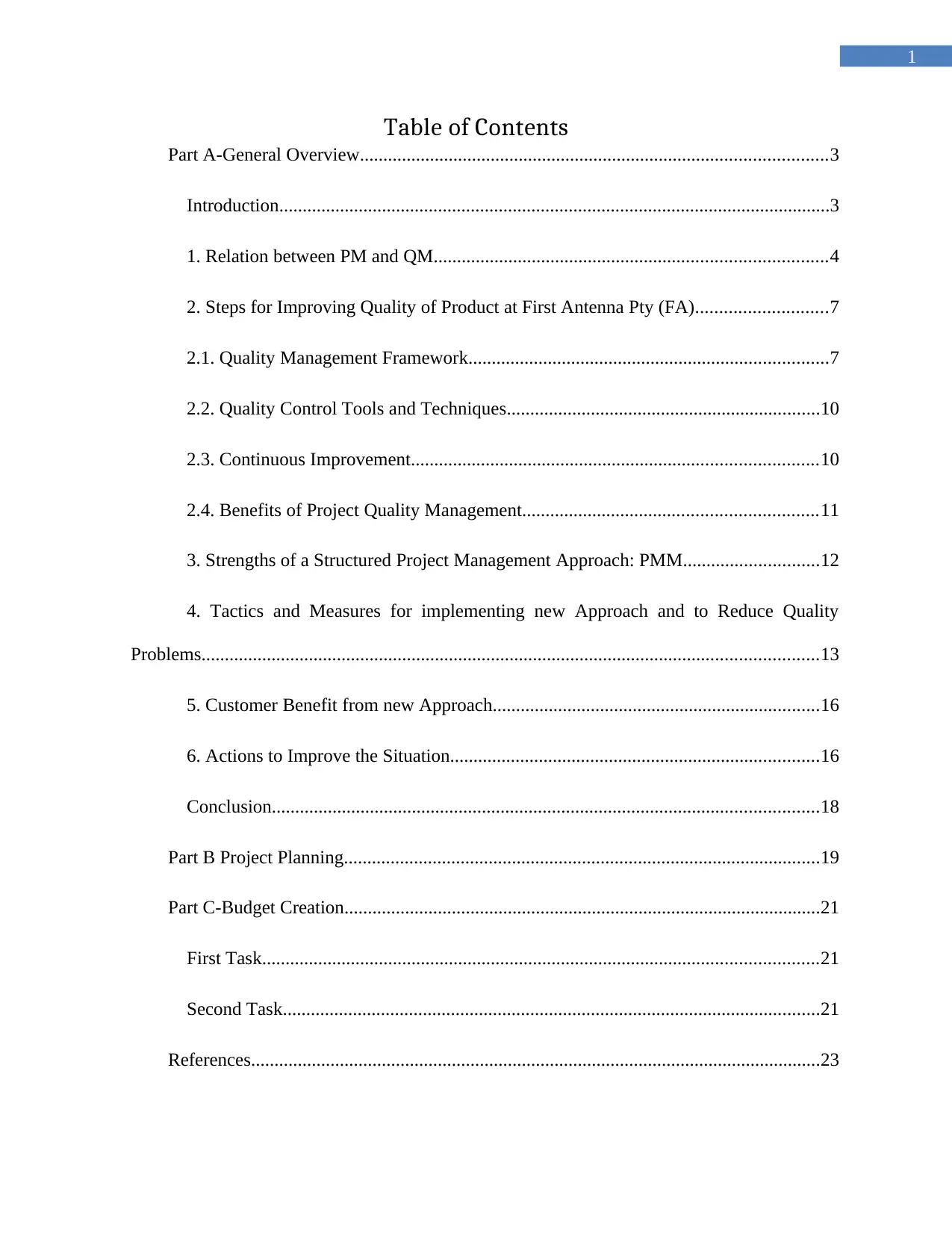
1
Table of Contents
Part A-General Overview....................................................................................................3
Introduction......................................................................................................................3
1. Relation between PM and QM....................................................................................4
2. Steps for Improving Quality of Product at First Antenna Pty (FA)............................7
2.1. Quality Management Framework.............................................................................7
2.2. Quality Control Tools and Techniques...................................................................10
2.3. Continuous Improvement.......................................................................................10
2.4. Benefits of Project Quality Management...............................................................11
3. Strengths of a Structured Project Management Approach: PMM.............................12
4. Tactics and Measures for implementing new Approach and to Reduce Quality
Problems....................................................................................................................................13
5. Customer Benefit from new Approach......................................................................16
6. Actions to Improve the Situation...............................................................................16
Conclusion.....................................................................................................................18
Part B Project Planning......................................................................................................19
Part C-Budget Creation......................................................................................................21
First Task.......................................................................................................................21
Second Task...................................................................................................................21
References..........................................................................................................................23
Table of Contents
Part A-General Overview....................................................................................................3
Introduction......................................................................................................................3
1. Relation between PM and QM....................................................................................4
2. Steps for Improving Quality of Product at First Antenna Pty (FA)............................7
2.1. Quality Management Framework.............................................................................7
2.2. Quality Control Tools and Techniques...................................................................10
2.3. Continuous Improvement.......................................................................................10
2.4. Benefits of Project Quality Management...............................................................11
3. Strengths of a Structured Project Management Approach: PMM.............................12
4. Tactics and Measures for implementing new Approach and to Reduce Quality
Problems....................................................................................................................................13
5. Customer Benefit from new Approach......................................................................16
6. Actions to Improve the Situation...............................................................................16
Conclusion.....................................................................................................................18
Part B Project Planning......................................................................................................19
Part C-Budget Creation......................................................................................................21
First Task.......................................................................................................................21
Second Task...................................................................................................................21
References..........................................................................................................................23
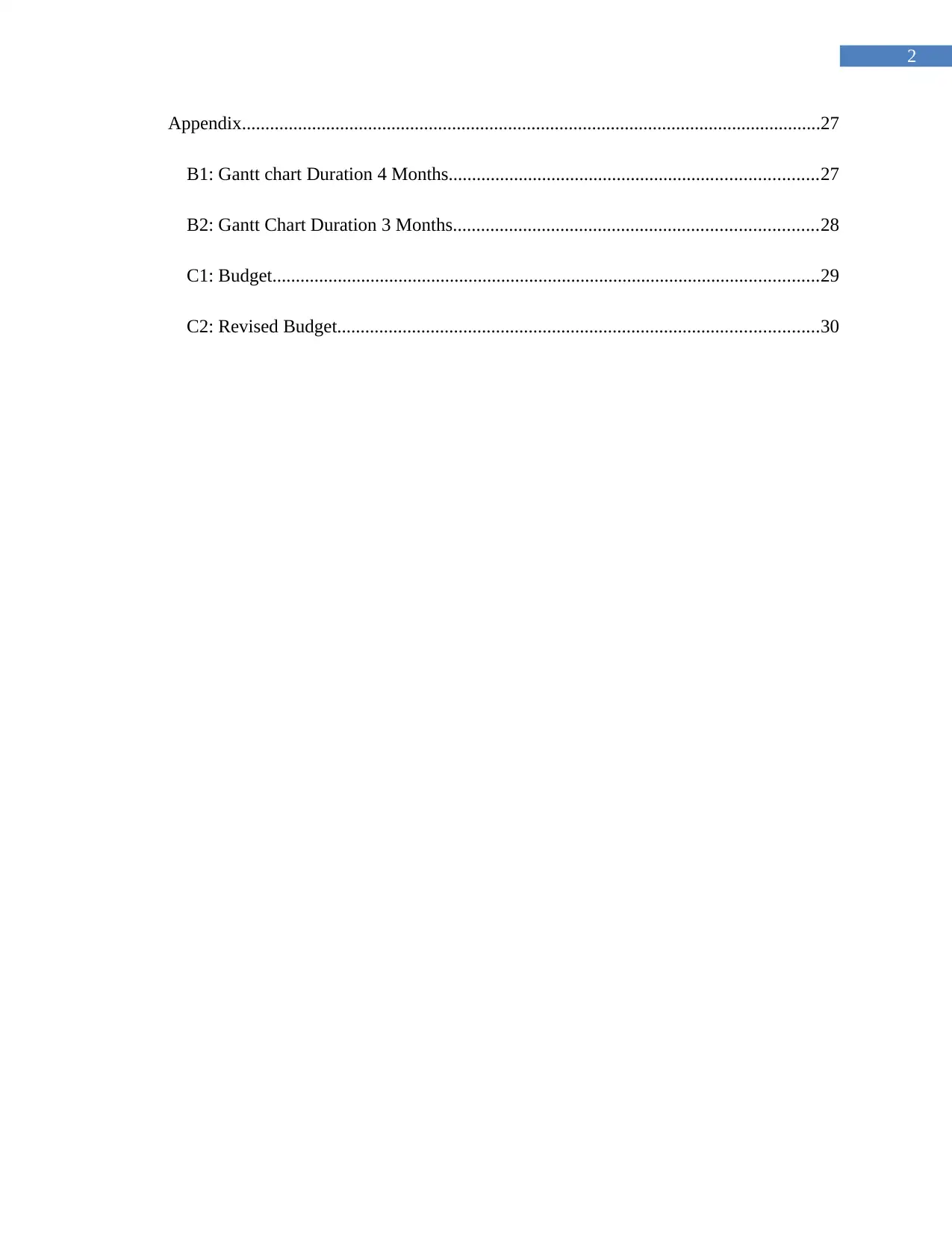
2
Appendix............................................................................................................................27
B1: Gantt chart Duration 4 Months...............................................................................27
B2: Gantt Chart Duration 3 Months..............................................................................28
C1: Budget.....................................................................................................................29
C2: Revised Budget.......................................................................................................30
Appendix............................................................................................................................27
B1: Gantt chart Duration 4 Months...............................................................................27
B2: Gantt Chart Duration 3 Months..............................................................................28
C1: Budget.....................................................................................................................29
C2: Revised Budget.......................................................................................................30
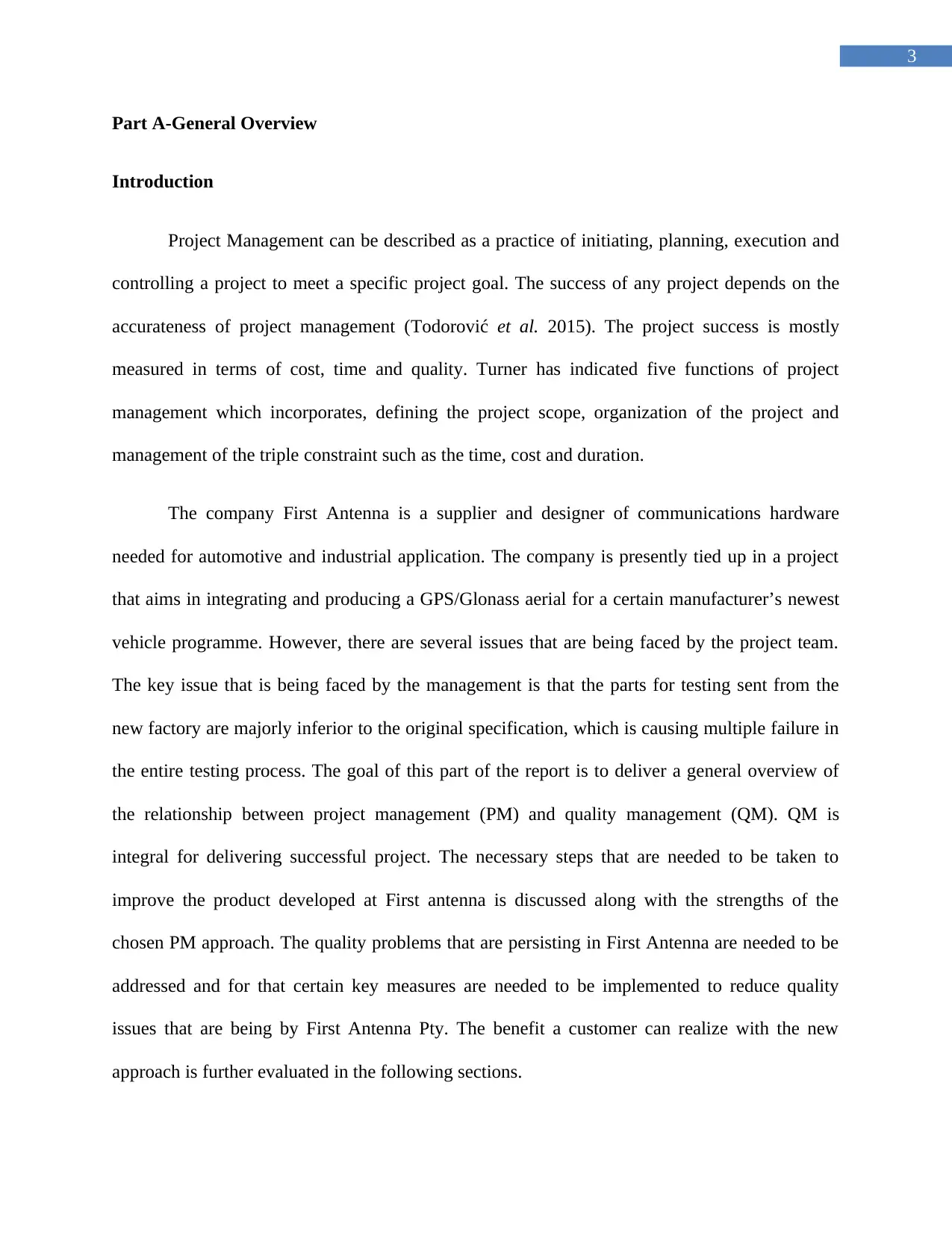
3
Part A-General Overview
Introduction
Project Management can be described as a practice of initiating, planning, execution and
controlling a project to meet a specific project goal. The success of any project depends on the
accurateness of project management (Todorović et al. 2015). The project success is mostly
measured in terms of cost, time and quality. Turner has indicated five functions of project
management which incorporates, defining the project scope, organization of the project and
management of the triple constraint such as the time, cost and duration.
The company First Antenna is a supplier and designer of communications hardware
needed for automotive and industrial application. The company is presently tied up in a project
that aims in integrating and producing a GPS/Glonass aerial for a certain manufacturer’s newest
vehicle programme. However, there are several issues that are being faced by the project team.
The key issue that is being faced by the management is that the parts for testing sent from the
new factory are majorly inferior to the original specification, which is causing multiple failure in
the entire testing process. The goal of this part of the report is to deliver a general overview of
the relationship between project management (PM) and quality management (QM). QM is
integral for delivering successful project. The necessary steps that are needed to be taken to
improve the product developed at First antenna is discussed along with the strengths of the
chosen PM approach. The quality problems that are persisting in First Antenna are needed to be
addressed and for that certain key measures are needed to be implemented to reduce quality
issues that are being by First Antenna Pty. The benefit a customer can realize with the new
approach is further evaluated in the following sections.
Part A-General Overview
Introduction
Project Management can be described as a practice of initiating, planning, execution and
controlling a project to meet a specific project goal. The success of any project depends on the
accurateness of project management (Todorović et al. 2015). The project success is mostly
measured in terms of cost, time and quality. Turner has indicated five functions of project
management which incorporates, defining the project scope, organization of the project and
management of the triple constraint such as the time, cost and duration.
The company First Antenna is a supplier and designer of communications hardware
needed for automotive and industrial application. The company is presently tied up in a project
that aims in integrating and producing a GPS/Glonass aerial for a certain manufacturer’s newest
vehicle programme. However, there are several issues that are being faced by the project team.
The key issue that is being faced by the management is that the parts for testing sent from the
new factory are majorly inferior to the original specification, which is causing multiple failure in
the entire testing process. The goal of this part of the report is to deliver a general overview of
the relationship between project management (PM) and quality management (QM). QM is
integral for delivering successful project. The necessary steps that are needed to be taken to
improve the product developed at First antenna is discussed along with the strengths of the
chosen PM approach. The quality problems that are persisting in First Antenna are needed to be
addressed and for that certain key measures are needed to be implemented to reduce quality
issues that are being by First Antenna Pty. The benefit a customer can realize with the new
approach is further evaluated in the following sections.
Secure Best Marks with AI Grader
Need help grading? Try our AI Grader for instant feedback on your assignments.
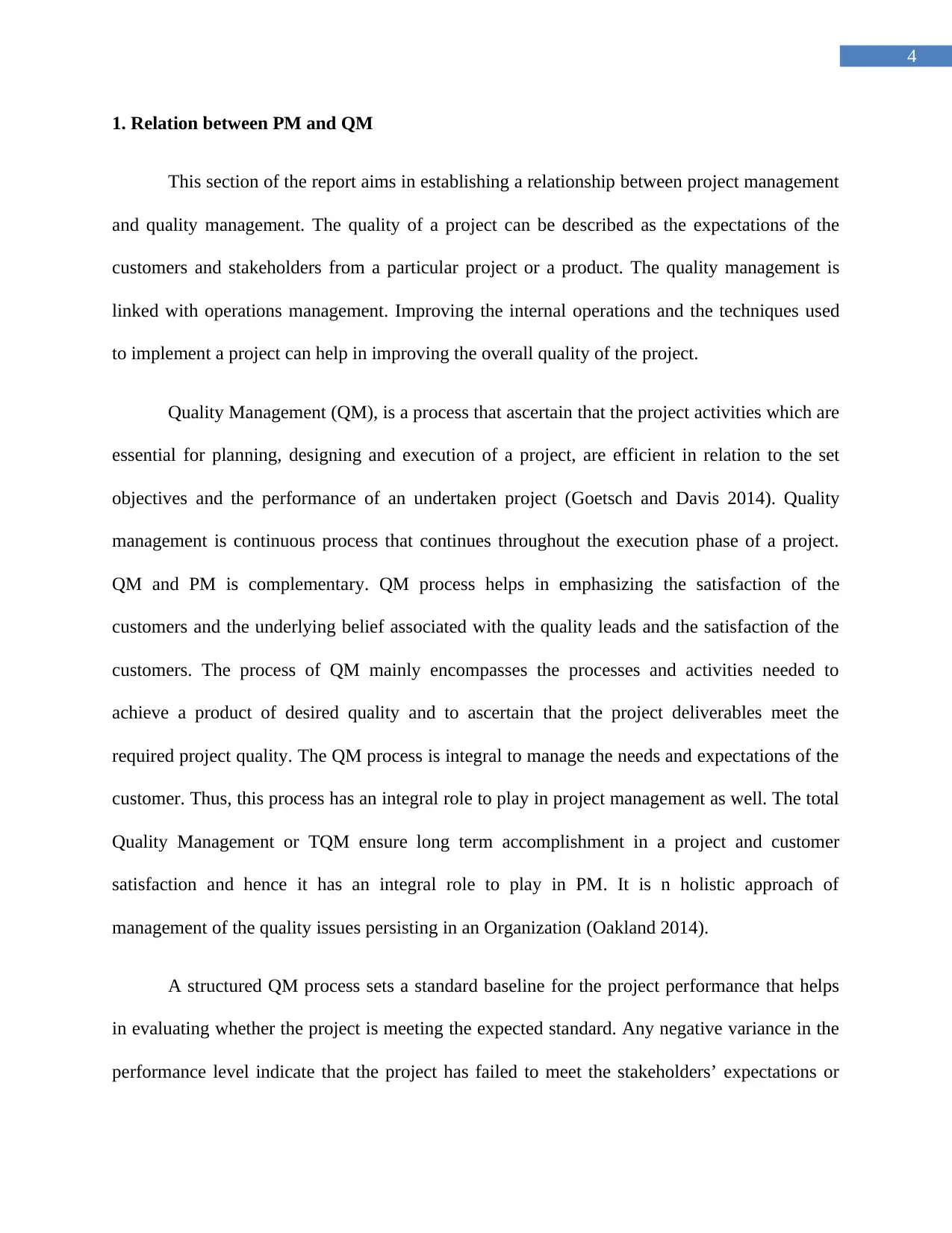
4
1. Relation between PM and QM
This section of the report aims in establishing a relationship between project management
and quality management. The quality of a project can be described as the expectations of the
customers and stakeholders from a particular project or a product. The quality management is
linked with operations management. Improving the internal operations and the techniques used
to implement a project can help in improving the overall quality of the project.
Quality Management (QM), is a process that ascertain that the project activities which are
essential for planning, designing and execution of a project, are efficient in relation to the set
objectives and the performance of an undertaken project (Goetsch and Davis 2014). Quality
management is continuous process that continues throughout the execution phase of a project.
QM and PM is complementary. QM process helps in emphasizing the satisfaction of the
customers and the underlying belief associated with the quality leads and the satisfaction of the
customers. The process of QM mainly encompasses the processes and activities needed to
achieve a product of desired quality and to ascertain that the project deliverables meet the
required project quality. The QM process is integral to manage the needs and expectations of the
customer. Thus, this process has an integral role to play in project management as well. The total
Quality Management or TQM ensure long term accomplishment in a project and customer
satisfaction and hence it has an integral role to play in PM. It is n holistic approach of
management of the quality issues persisting in an Organization (Oakland 2014).
A structured QM process sets a standard baseline for the project performance that helps
in evaluating whether the project is meeting the expected standard. Any negative variance in the
performance level indicate that the project has failed to meet the stakeholders’ expectations or
1. Relation between PM and QM
This section of the report aims in establishing a relationship between project management
and quality management. The quality of a project can be described as the expectations of the
customers and stakeholders from a particular project or a product. The quality management is
linked with operations management. Improving the internal operations and the techniques used
to implement a project can help in improving the overall quality of the project.
Quality Management (QM), is a process that ascertain that the project activities which are
essential for planning, designing and execution of a project, are efficient in relation to the set
objectives and the performance of an undertaken project (Goetsch and Davis 2014). Quality
management is continuous process that continues throughout the execution phase of a project.
QM and PM is complementary. QM process helps in emphasizing the satisfaction of the
customers and the underlying belief associated with the quality leads and the satisfaction of the
customers. The process of QM mainly encompasses the processes and activities needed to
achieve a product of desired quality and to ascertain that the project deliverables meet the
required project quality. The QM process is integral to manage the needs and expectations of the
customer. Thus, this process has an integral role to play in project management as well. The total
Quality Management or TQM ensure long term accomplishment in a project and customer
satisfaction and hence it has an integral role to play in PM. It is n holistic approach of
management of the quality issues persisting in an Organization (Oakland 2014).
A structured QM process sets a standard baseline for the project performance that helps
in evaluating whether the project is meeting the expected standard. Any negative variance in the
performance level indicate that the project has failed to meet the stakeholders’ expectations or
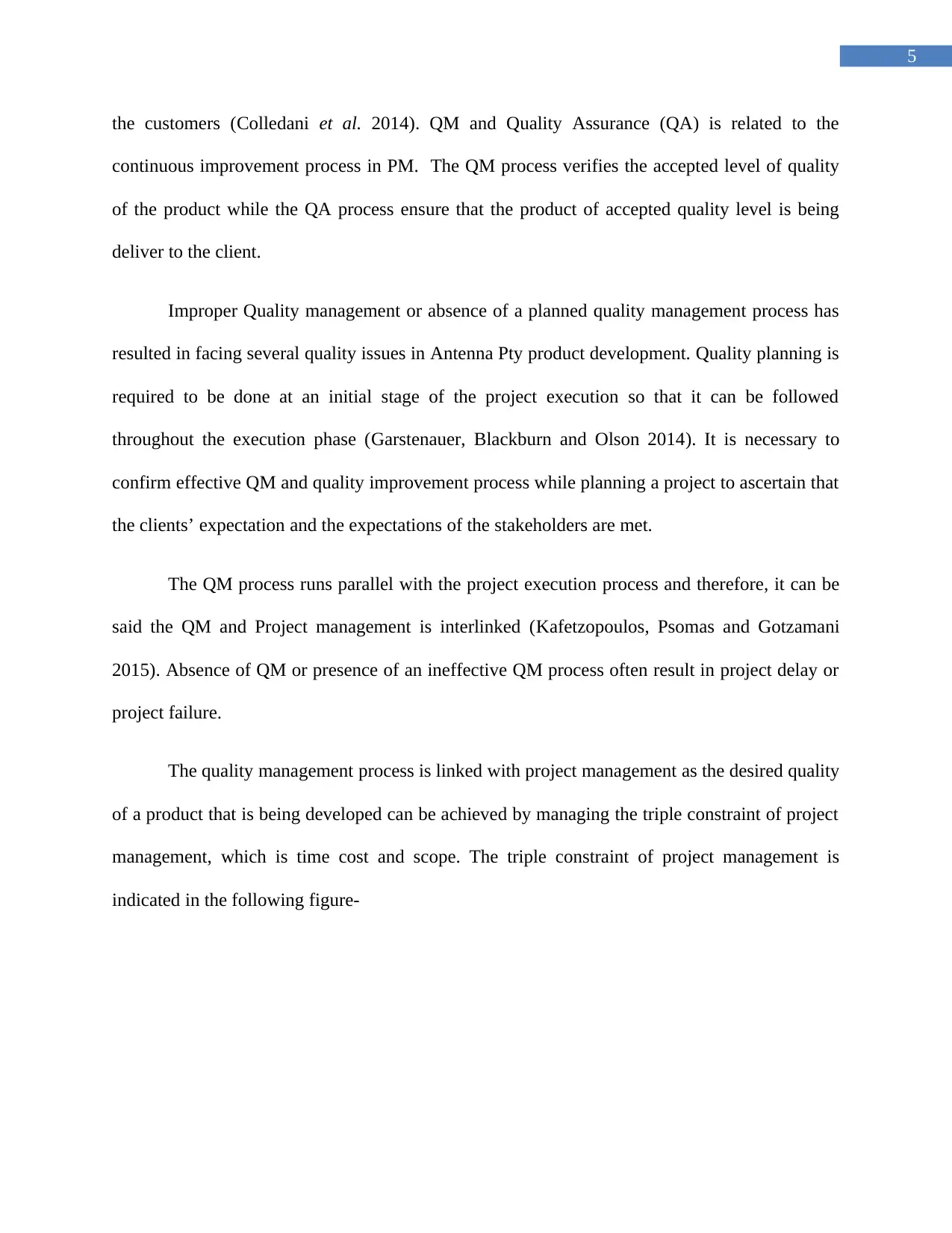
5
the customers (Colledani et al. 2014). QM and Quality Assurance (QA) is related to the
continuous improvement process in PM. The QM process verifies the accepted level of quality
of the product while the QA process ensure that the product of accepted quality level is being
deliver to the client.
Improper Quality management or absence of a planned quality management process has
resulted in facing several quality issues in Antenna Pty product development. Quality planning is
required to be done at an initial stage of the project execution so that it can be followed
throughout the execution phase (Garstenauer, Blackburn and Olson 2014). It is necessary to
confirm effective QM and quality improvement process while planning a project to ascertain that
the clients’ expectation and the expectations of the stakeholders are met.
The QM process runs parallel with the project execution process and therefore, it can be
said the QM and Project management is interlinked (Kafetzopoulos, Psomas and Gotzamani
2015). Absence of QM or presence of an ineffective QM process often result in project delay or
project failure.
The quality management process is linked with project management as the desired quality
of a product that is being developed can be achieved by managing the triple constraint of project
management, which is time cost and scope. The triple constraint of project management is
indicated in the following figure-
the customers (Colledani et al. 2014). QM and Quality Assurance (QA) is related to the
continuous improvement process in PM. The QM process verifies the accepted level of quality
of the product while the QA process ensure that the product of accepted quality level is being
deliver to the client.
Improper Quality management or absence of a planned quality management process has
resulted in facing several quality issues in Antenna Pty product development. Quality planning is
required to be done at an initial stage of the project execution so that it can be followed
throughout the execution phase (Garstenauer, Blackburn and Olson 2014). It is necessary to
confirm effective QM and quality improvement process while planning a project to ascertain that
the clients’ expectation and the expectations of the stakeholders are met.
The QM process runs parallel with the project execution process and therefore, it can be
said the QM and Project management is interlinked (Kafetzopoulos, Psomas and Gotzamani
2015). Absence of QM or presence of an ineffective QM process often result in project delay or
project failure.
The quality management process is linked with project management as the desired quality
of a product that is being developed can be achieved by managing the triple constraint of project
management, which is time cost and scope. The triple constraint of project management is
indicated in the following figure-
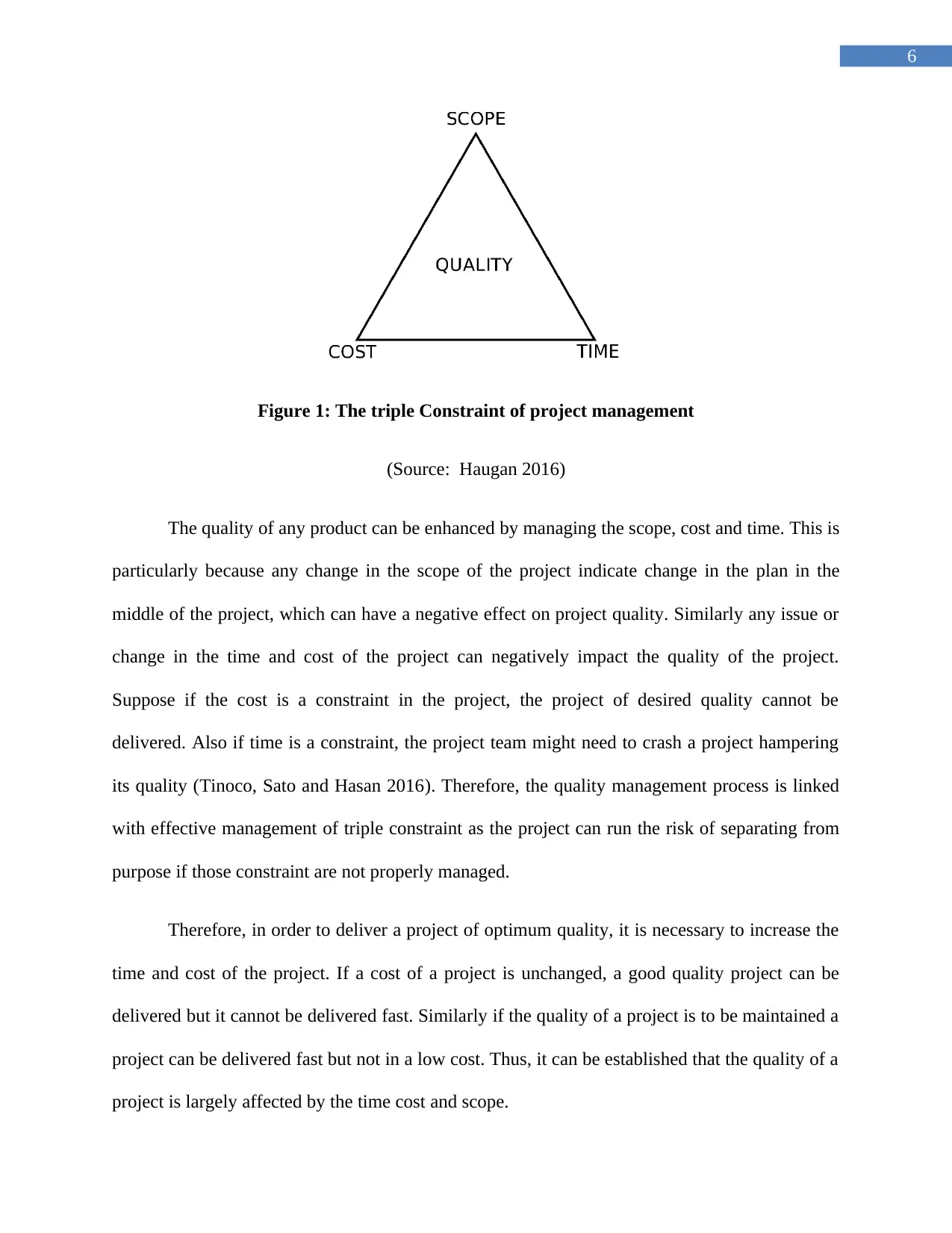
6
Figure 1: The triple Constraint of project management
(Source: Haugan 2016)
The quality of any product can be enhanced by managing the scope, cost and time. This is
particularly because any change in the scope of the project indicate change in the plan in the
middle of the project, which can have a negative effect on project quality. Similarly any issue or
change in the time and cost of the project can negatively impact the quality of the project.
Suppose if the cost is a constraint in the project, the project of desired quality cannot be
delivered. Also if time is a constraint, the project team might need to crash a project hampering
its quality (Tinoco, Sato and Hasan 2016). Therefore, the quality management process is linked
with effective management of triple constraint as the project can run the risk of separating from
purpose if those constraint are not properly managed.
Therefore, in order to deliver a project of optimum quality, it is necessary to increase the
time and cost of the project. If a cost of a project is unchanged, a good quality project can be
delivered but it cannot be delivered fast. Similarly if the quality of a project is to be maintained a
project can be delivered fast but not in a low cost. Thus, it can be established that the quality of a
project is largely affected by the time cost and scope.
Figure 1: The triple Constraint of project management
(Source: Haugan 2016)
The quality of any product can be enhanced by managing the scope, cost and time. This is
particularly because any change in the scope of the project indicate change in the plan in the
middle of the project, which can have a negative effect on project quality. Similarly any issue or
change in the time and cost of the project can negatively impact the quality of the project.
Suppose if the cost is a constraint in the project, the project of desired quality cannot be
delivered. Also if time is a constraint, the project team might need to crash a project hampering
its quality (Tinoco, Sato and Hasan 2016). Therefore, the quality management process is linked
with effective management of triple constraint as the project can run the risk of separating from
purpose if those constraint are not properly managed.
Therefore, in order to deliver a project of optimum quality, it is necessary to increase the
time and cost of the project. If a cost of a project is unchanged, a good quality project can be
delivered but it cannot be delivered fast. Similarly if the quality of a project is to be maintained a
project can be delivered fast but not in a low cost. Thus, it can be established that the quality of a
project is largely affected by the time cost and scope.
Paraphrase This Document
Need a fresh take? Get an instant paraphrase of this document with our AI Paraphraser
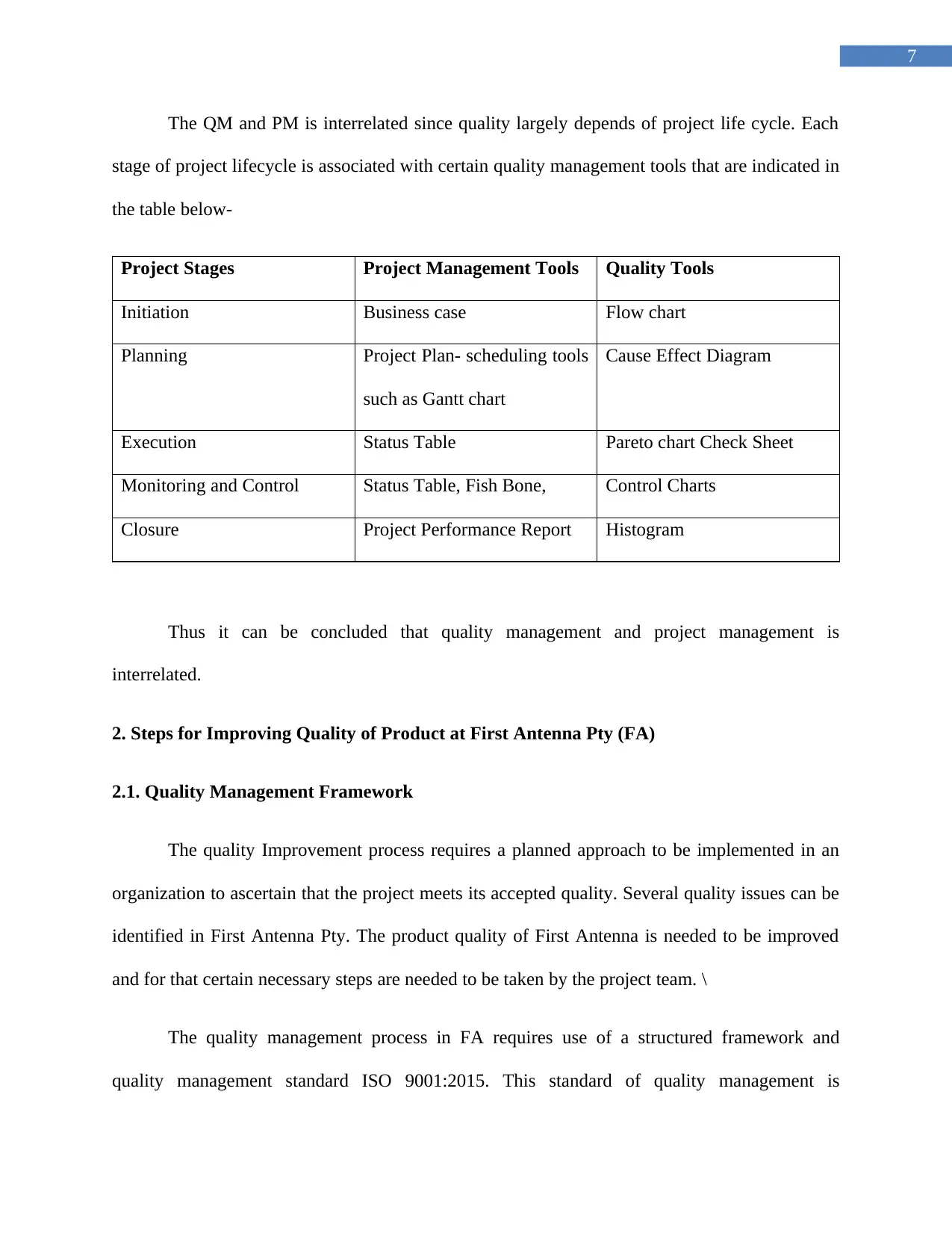
7
The QM and PM is interrelated since quality largely depends of project life cycle. Each
stage of project lifecycle is associated with certain quality management tools that are indicated in
the table below-
Project Stages Project Management Tools Quality Tools
Initiation Business case Flow chart
Planning Project Plan- scheduling tools
such as Gantt chart
Cause Effect Diagram
Execution Status Table Pareto chart Check Sheet
Monitoring and Control Status Table, Fish Bone, Control Charts
Closure Project Performance Report Histogram
Thus it can be concluded that quality management and project management is
interrelated.
2. Steps for Improving Quality of Product at First Antenna Pty (FA)
2.1. Quality Management Framework
The quality Improvement process requires a planned approach to be implemented in an
organization to ascertain that the project meets its accepted quality. Several quality issues can be
identified in First Antenna Pty. The product quality of First Antenna is needed to be improved
and for that certain necessary steps are needed to be taken by the project team. \
The quality management process in FA requires use of a structured framework and
quality management standard ISO 9001:2015. This standard of quality management is
The QM and PM is interrelated since quality largely depends of project life cycle. Each
stage of project lifecycle is associated with certain quality management tools that are indicated in
the table below-
Project Stages Project Management Tools Quality Tools
Initiation Business case Flow chart
Planning Project Plan- scheduling tools
such as Gantt chart
Cause Effect Diagram
Execution Status Table Pareto chart Check Sheet
Monitoring and Control Status Table, Fish Bone, Control Charts
Closure Project Performance Report Histogram
Thus it can be concluded that quality management and project management is
interrelated.
2. Steps for Improving Quality of Product at First Antenna Pty (FA)
2.1. Quality Management Framework
The quality Improvement process requires a planned approach to be implemented in an
organization to ascertain that the project meets its accepted quality. Several quality issues can be
identified in First Antenna Pty. The product quality of First Antenna is needed to be improved
and for that certain necessary steps are needed to be taken by the project team. \
The quality management process in FA requires use of a structured framework and
quality management standard ISO 9001:2015. This standard of quality management is
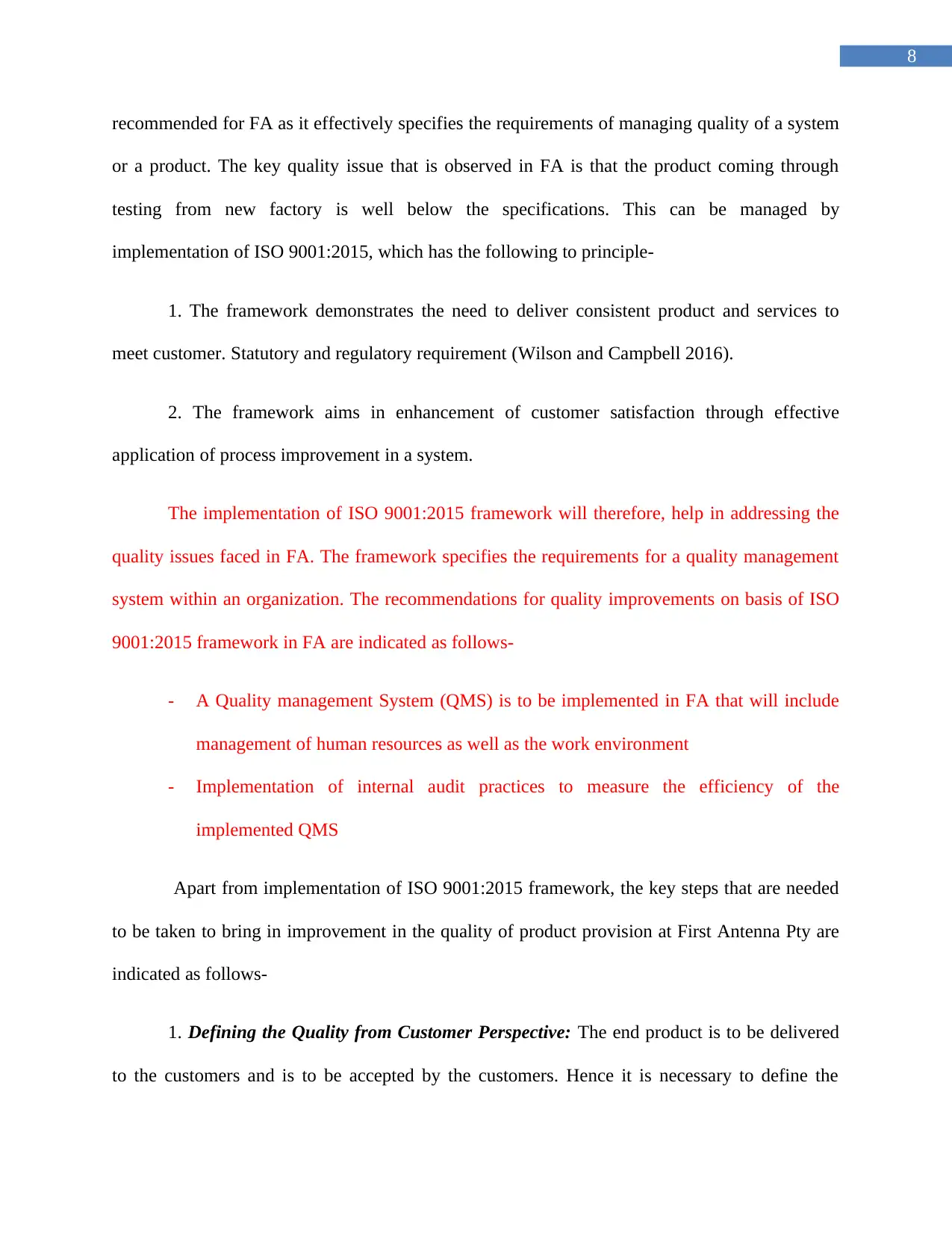
8
recommended for FA as it effectively specifies the requirements of managing quality of a system
or a product. The key quality issue that is observed in FA is that the product coming through
testing from new factory is well below the specifications. This can be managed by
implementation of ISO 9001:2015, which has the following to principle-
1. The framework demonstrates the need to deliver consistent product and services to
meet customer. Statutory and regulatory requirement (Wilson and Campbell 2016).
2. The framework aims in enhancement of customer satisfaction through effective
application of process improvement in a system.
The implementation of ISO 9001:2015 framework will therefore, help in addressing the
quality issues faced in FA. The framework specifies the requirements for a quality management
system within an organization. The recommendations for quality improvements on basis of ISO
9001:2015 framework in FA are indicated as follows-
- A Quality management System (QMS) is to be implemented in FA that will include
management of human resources as well as the work environment
- Implementation of internal audit practices to measure the efficiency of the
implemented QMS
Apart from implementation of ISO 9001:2015 framework, the key steps that are needed
to be taken to bring in improvement in the quality of product provision at First Antenna Pty are
indicated as follows-
1. Defining the Quality from Customer Perspective: The end product is to be delivered
to the customers and is to be accepted by the customers. Hence it is necessary to define the
recommended for FA as it effectively specifies the requirements of managing quality of a system
or a product. The key quality issue that is observed in FA is that the product coming through
testing from new factory is well below the specifications. This can be managed by
implementation of ISO 9001:2015, which has the following to principle-
1. The framework demonstrates the need to deliver consistent product and services to
meet customer. Statutory and regulatory requirement (Wilson and Campbell 2016).
2. The framework aims in enhancement of customer satisfaction through effective
application of process improvement in a system.
The implementation of ISO 9001:2015 framework will therefore, help in addressing the
quality issues faced in FA. The framework specifies the requirements for a quality management
system within an organization. The recommendations for quality improvements on basis of ISO
9001:2015 framework in FA are indicated as follows-
- A Quality management System (QMS) is to be implemented in FA that will include
management of human resources as well as the work environment
- Implementation of internal audit practices to measure the efficiency of the
implemented QMS
Apart from implementation of ISO 9001:2015 framework, the key steps that are needed
to be taken to bring in improvement in the quality of product provision at First Antenna Pty are
indicated as follows-
1. Defining the Quality from Customer Perspective: The end product is to be delivered
to the customers and is to be accepted by the customers. Hence it is necessary to define the
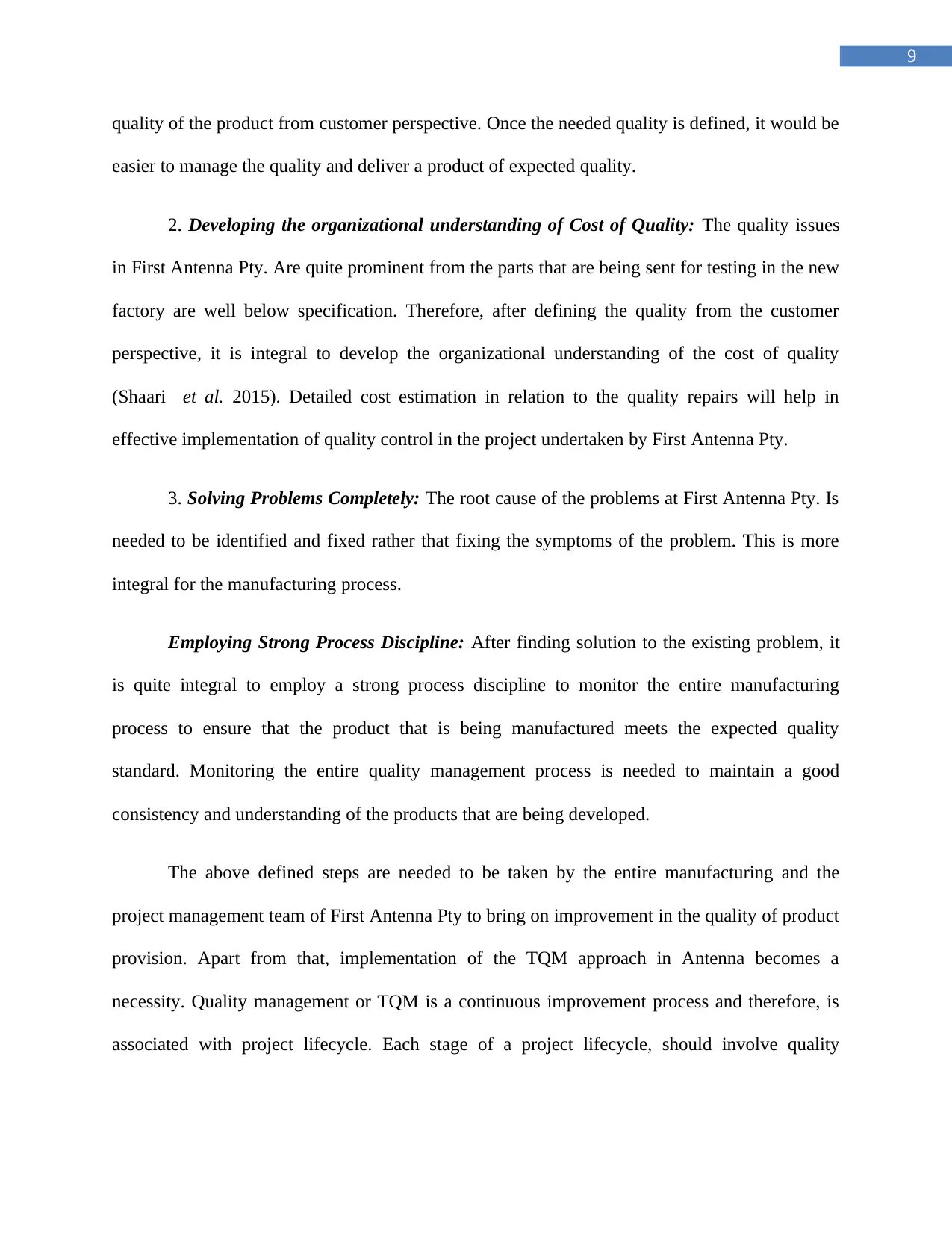
9
quality of the product from customer perspective. Once the needed quality is defined, it would be
easier to manage the quality and deliver a product of expected quality.
2. Developing the organizational understanding of Cost of Quality: The quality issues
in First Antenna Pty. Are quite prominent from the parts that are being sent for testing in the new
factory are well below specification. Therefore, after defining the quality from the customer
perspective, it is integral to develop the organizational understanding of the cost of quality
(Shaari et al. 2015). Detailed cost estimation in relation to the quality repairs will help in
effective implementation of quality control in the project undertaken by First Antenna Pty.
3. Solving Problems Completely: The root cause of the problems at First Antenna Pty. Is
needed to be identified and fixed rather that fixing the symptoms of the problem. This is more
integral for the manufacturing process.
Employing Strong Process Discipline: After finding solution to the existing problem, it
is quite integral to employ a strong process discipline to monitor the entire manufacturing
process to ensure that the product that is being manufactured meets the expected quality
standard. Monitoring the entire quality management process is needed to maintain a good
consistency and understanding of the products that are being developed.
The above defined steps are needed to be taken by the entire manufacturing and the
project management team of First Antenna Pty to bring on improvement in the quality of product
provision. Apart from that, implementation of the TQM approach in Antenna becomes a
necessity. Quality management or TQM is a continuous improvement process and therefore, is
associated with project lifecycle. Each stage of a project lifecycle, should involve quality
quality of the product from customer perspective. Once the needed quality is defined, it would be
easier to manage the quality and deliver a product of expected quality.
2. Developing the organizational understanding of Cost of Quality: The quality issues
in First Antenna Pty. Are quite prominent from the parts that are being sent for testing in the new
factory are well below specification. Therefore, after defining the quality from the customer
perspective, it is integral to develop the organizational understanding of the cost of quality
(Shaari et al. 2015). Detailed cost estimation in relation to the quality repairs will help in
effective implementation of quality control in the project undertaken by First Antenna Pty.
3. Solving Problems Completely: The root cause of the problems at First Antenna Pty. Is
needed to be identified and fixed rather that fixing the symptoms of the problem. This is more
integral for the manufacturing process.
Employing Strong Process Discipline: After finding solution to the existing problem, it
is quite integral to employ a strong process discipline to monitor the entire manufacturing
process to ensure that the product that is being manufactured meets the expected quality
standard. Monitoring the entire quality management process is needed to maintain a good
consistency and understanding of the products that are being developed.
The above defined steps are needed to be taken by the entire manufacturing and the
project management team of First Antenna Pty to bring on improvement in the quality of product
provision. Apart from that, implementation of the TQM approach in Antenna becomes a
necessity. Quality management or TQM is a continuous improvement process and therefore, is
associated with project lifecycle. Each stage of a project lifecycle, should involve quality
Secure Best Marks with AI Grader
Need help grading? Try our AI Grader for instant feedback on your assignments.
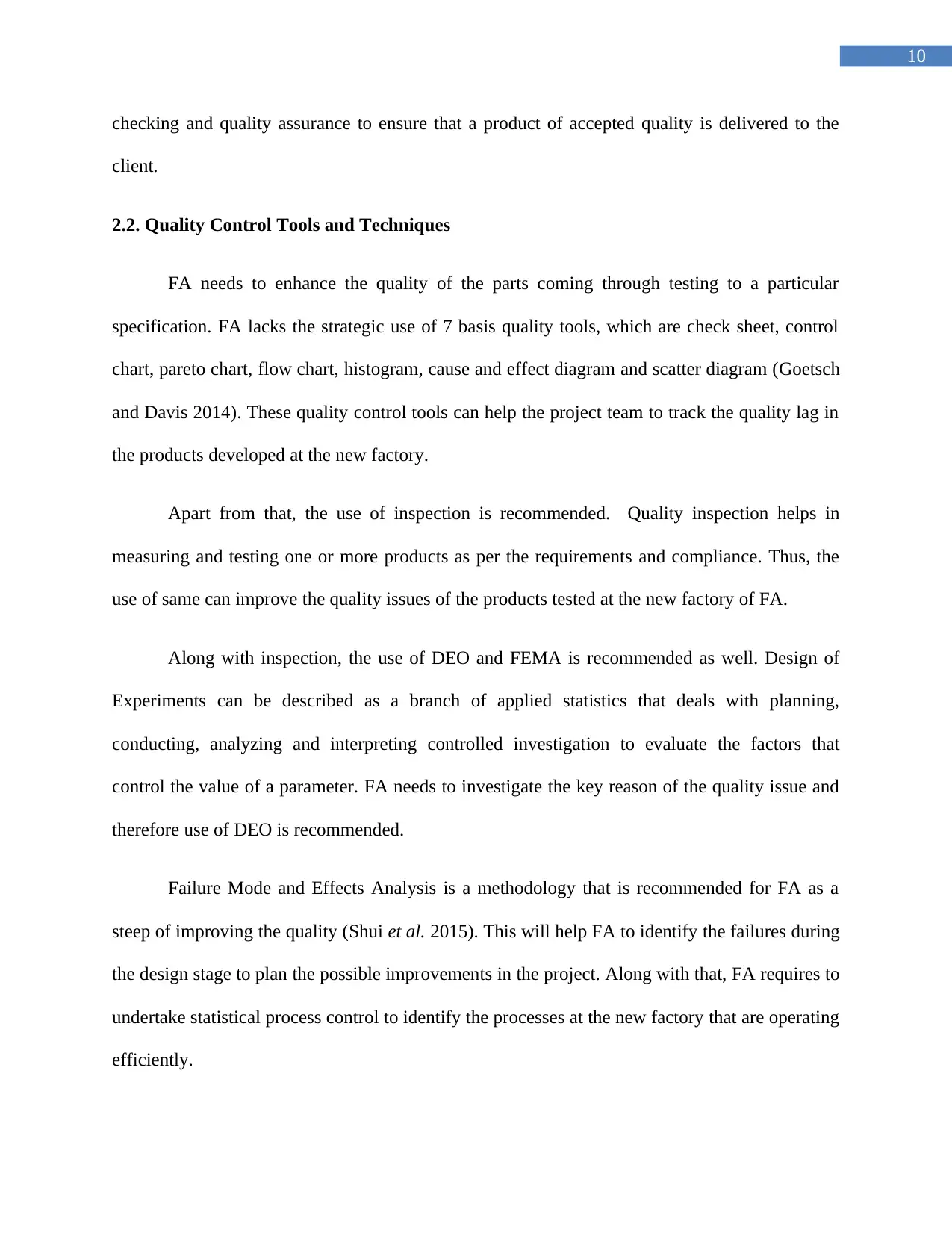
10
checking and quality assurance to ensure that a product of accepted quality is delivered to the
client.
2.2. Quality Control Tools and Techniques
FA needs to enhance the quality of the parts coming through testing to a particular
specification. FA lacks the strategic use of 7 basis quality tools, which are check sheet, control
chart, pareto chart, flow chart, histogram, cause and effect diagram and scatter diagram (Goetsch
and Davis 2014). These quality control tools can help the project team to track the quality lag in
the products developed at the new factory.
Apart from that, the use of inspection is recommended. Quality inspection helps in
measuring and testing one or more products as per the requirements and compliance. Thus, the
use of same can improve the quality issues of the products tested at the new factory of FA.
Along with inspection, the use of DEO and FEMA is recommended as well. Design of
Experiments can be described as a branch of applied statistics that deals with planning,
conducting, analyzing and interpreting controlled investigation to evaluate the factors that
control the value of a parameter. FA needs to investigate the key reason of the quality issue and
therefore use of DEO is recommended.
Failure Mode and Effects Analysis is a methodology that is recommended for FA as a
steep of improving the quality (Shui et al. 2015). This will help FA to identify the failures during
the design stage to plan the possible improvements in the project. Along with that, FA requires to
undertake statistical process control to identify the processes at the new factory that are operating
efficiently.
checking and quality assurance to ensure that a product of accepted quality is delivered to the
client.
2.2. Quality Control Tools and Techniques
FA needs to enhance the quality of the parts coming through testing to a particular
specification. FA lacks the strategic use of 7 basis quality tools, which are check sheet, control
chart, pareto chart, flow chart, histogram, cause and effect diagram and scatter diagram (Goetsch
and Davis 2014). These quality control tools can help the project team to track the quality lag in
the products developed at the new factory.
Apart from that, the use of inspection is recommended. Quality inspection helps in
measuring and testing one or more products as per the requirements and compliance. Thus, the
use of same can improve the quality issues of the products tested at the new factory of FA.
Along with inspection, the use of DEO and FEMA is recommended as well. Design of
Experiments can be described as a branch of applied statistics that deals with planning,
conducting, analyzing and interpreting controlled investigation to evaluate the factors that
control the value of a parameter. FA needs to investigate the key reason of the quality issue and
therefore use of DEO is recommended.
Failure Mode and Effects Analysis is a methodology that is recommended for FA as a
steep of improving the quality (Shui et al. 2015). This will help FA to identify the failures during
the design stage to plan the possible improvements in the project. Along with that, FA requires to
undertake statistical process control to identify the processes at the new factory that are operating
efficiently.
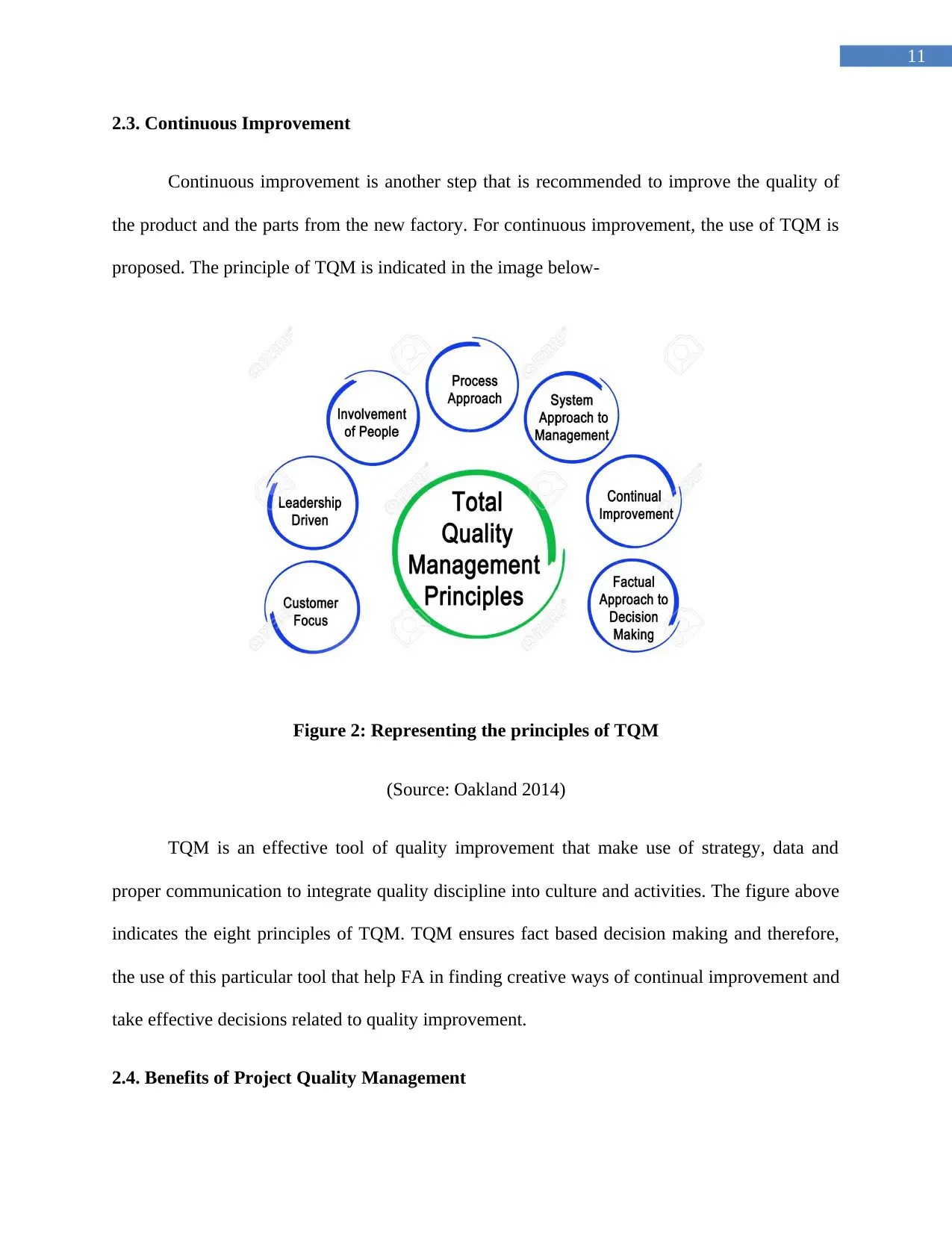
11
2.3. Continuous Improvement
Continuous improvement is another step that is recommended to improve the quality of
the product and the parts from the new factory. For continuous improvement, the use of TQM is
proposed. The principle of TQM is indicated in the image below-
Figure 2: Representing the principles of TQM
(Source: Oakland 2014)
TQM is an effective tool of quality improvement that make use of strategy, data and
proper communication to integrate quality discipline into culture and activities. The figure above
indicates the eight principles of TQM. TQM ensures fact based decision making and therefore,
the use of this particular tool that help FA in finding creative ways of continual improvement and
take effective decisions related to quality improvement.
2.4. Benefits of Project Quality Management
2.3. Continuous Improvement
Continuous improvement is another step that is recommended to improve the quality of
the product and the parts from the new factory. For continuous improvement, the use of TQM is
proposed. The principle of TQM is indicated in the image below-
Figure 2: Representing the principles of TQM
(Source: Oakland 2014)
TQM is an effective tool of quality improvement that make use of strategy, data and
proper communication to integrate quality discipline into culture and activities. The figure above
indicates the eight principles of TQM. TQM ensures fact based decision making and therefore,
the use of this particular tool that help FA in finding creative ways of continual improvement and
take effective decisions related to quality improvement.
2.4. Benefits of Project Quality Management
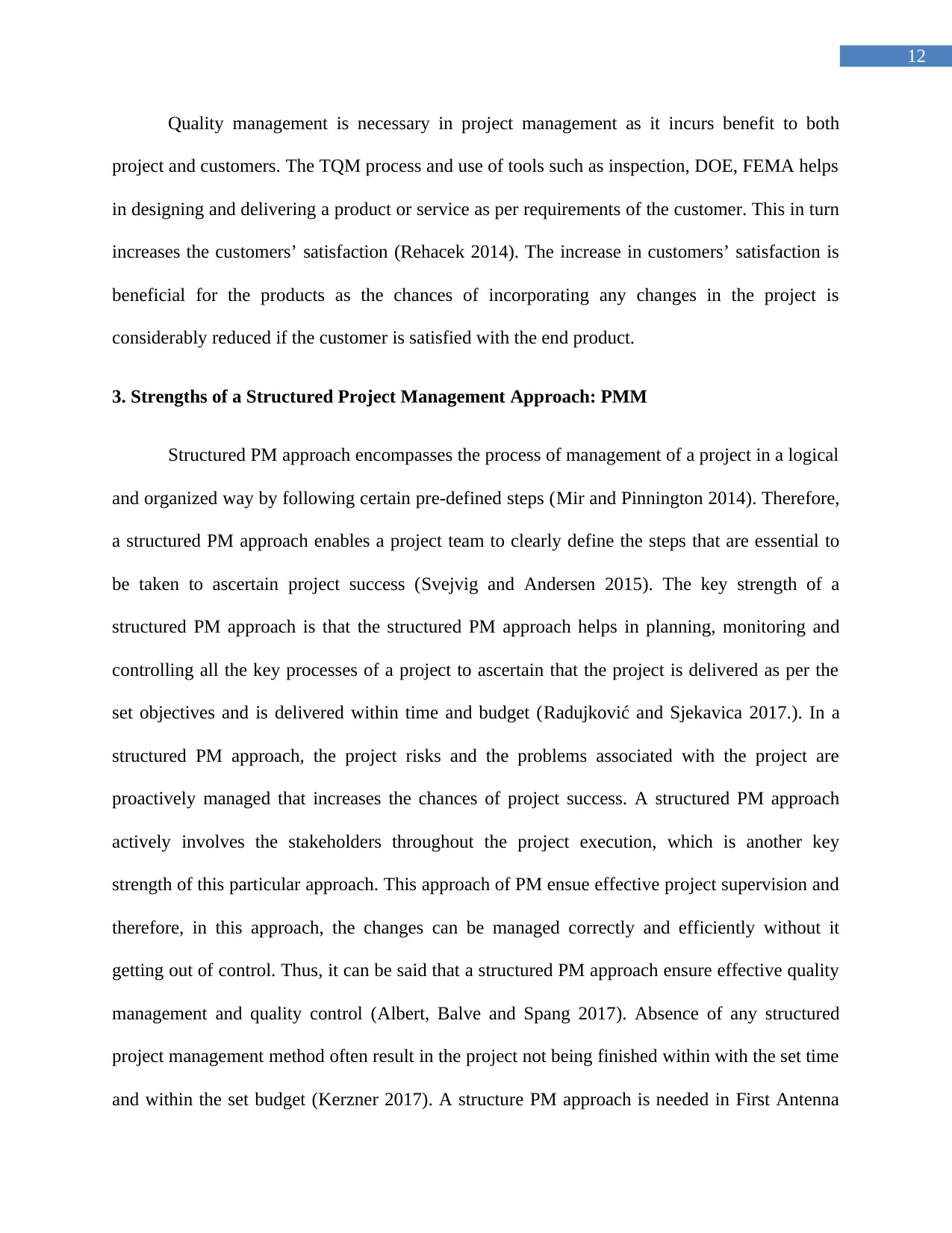
12
Quality management is necessary in project management as it incurs benefit to both
project and customers. The TQM process and use of tools such as inspection, DOE, FEMA helps
in designing and delivering a product or service as per requirements of the customer. This in turn
increases the customers’ satisfaction (Rehacek 2014). The increase in customers’ satisfaction is
beneficial for the products as the chances of incorporating any changes in the project is
considerably reduced if the customer is satisfied with the end product.
3. Strengths of a Structured Project Management Approach: PMM
Structured PM approach encompasses the process of management of a project in a logical
and organized way by following certain pre-defined steps (Mir and Pinnington 2014). Therefore,
a structured PM approach enables a project team to clearly define the steps that are essential to
be taken to ascertain project success (Svejvig and Andersen 2015). The key strength of a
structured PM approach is that the structured PM approach helps in planning, monitoring and
controlling all the key processes of a project to ascertain that the project is delivered as per the
set objectives and is delivered within time and budget (Radujković and Sjekavica 2017.). In a
structured PM approach, the project risks and the problems associated with the project are
proactively managed that increases the chances of project success. A structured PM approach
actively involves the stakeholders throughout the project execution, which is another key
strength of this particular approach. This approach of PM ensue effective project supervision and
therefore, in this approach, the changes can be managed correctly and efficiently without it
getting out of control. Thus, it can be said that a structured PM approach ensure effective quality
management and quality control (Albert, Balve and Spang 2017). Absence of any structured
project management method often result in the project not being finished within with the set time
and within the set budget (Kerzner 2017). A structure PM approach is needed in First Antenna
Quality management is necessary in project management as it incurs benefit to both
project and customers. The TQM process and use of tools such as inspection, DOE, FEMA helps
in designing and delivering a product or service as per requirements of the customer. This in turn
increases the customers’ satisfaction (Rehacek 2014). The increase in customers’ satisfaction is
beneficial for the products as the chances of incorporating any changes in the project is
considerably reduced if the customer is satisfied with the end product.
3. Strengths of a Structured Project Management Approach: PMM
Structured PM approach encompasses the process of management of a project in a logical
and organized way by following certain pre-defined steps (Mir and Pinnington 2014). Therefore,
a structured PM approach enables a project team to clearly define the steps that are essential to
be taken to ascertain project success (Svejvig and Andersen 2015). The key strength of a
structured PM approach is that the structured PM approach helps in planning, monitoring and
controlling all the key processes of a project to ascertain that the project is delivered as per the
set objectives and is delivered within time and budget (Radujković and Sjekavica 2017.). In a
structured PM approach, the project risks and the problems associated with the project are
proactively managed that increases the chances of project success. A structured PM approach
actively involves the stakeholders throughout the project execution, which is another key
strength of this particular approach. This approach of PM ensue effective project supervision and
therefore, in this approach, the changes can be managed correctly and efficiently without it
getting out of control. Thus, it can be said that a structured PM approach ensure effective quality
management and quality control (Albert, Balve and Spang 2017). Absence of any structured
project management method often result in the project not being finished within with the set time
and within the set budget (Kerzner 2017). A structure PM approach is needed in First Antenna
Paraphrase This Document
Need a fresh take? Get an instant paraphrase of this document with our AI Paraphraser
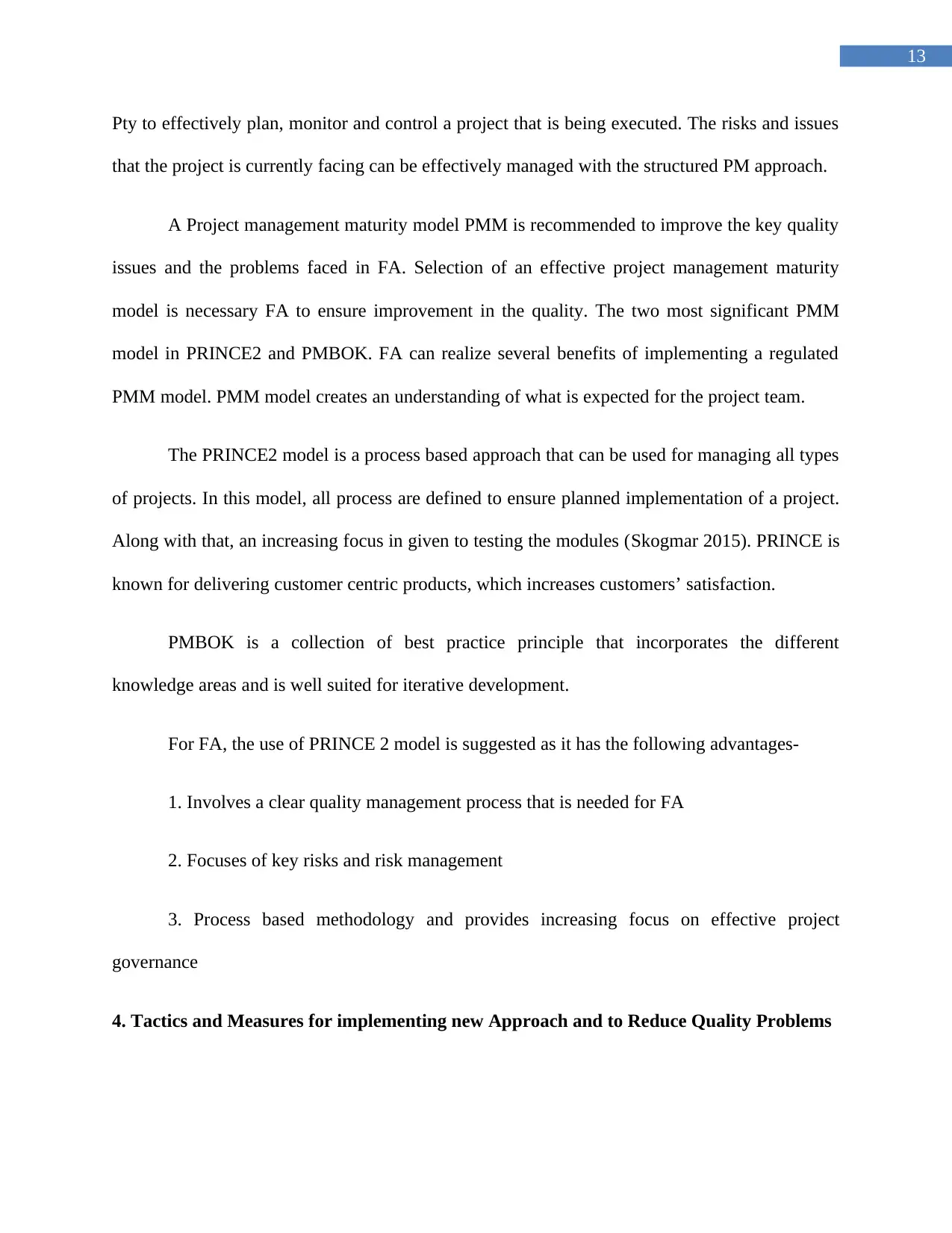
13
Pty to effectively plan, monitor and control a project that is being executed. The risks and issues
that the project is currently facing can be effectively managed with the structured PM approach.
A Project management maturity model PMM is recommended to improve the key quality
issues and the problems faced in FA. Selection of an effective project management maturity
model is necessary FA to ensure improvement in the quality. The two most significant PMM
model in PRINCE2 and PMBOK. FA can realize several benefits of implementing a regulated
PMM model. PMM model creates an understanding of what is expected for the project team.
The PRINCE2 model is a process based approach that can be used for managing all types
of projects. In this model, all process are defined to ensure planned implementation of a project.
Along with that, an increasing focus in given to testing the modules (Skogmar 2015). PRINCE is
known for delivering customer centric products, which increases customers’ satisfaction.
PMBOK is a collection of best practice principle that incorporates the different
knowledge areas and is well suited for iterative development.
For FA, the use of PRINCE 2 model is suggested as it has the following advantages-
1. Involves a clear quality management process that is needed for FA
2. Focuses of key risks and risk management
3. Process based methodology and provides increasing focus on effective project
governance
4. Tactics and Measures for implementing new Approach and to Reduce Quality Problems
Pty to effectively plan, monitor and control a project that is being executed. The risks and issues
that the project is currently facing can be effectively managed with the structured PM approach.
A Project management maturity model PMM is recommended to improve the key quality
issues and the problems faced in FA. Selection of an effective project management maturity
model is necessary FA to ensure improvement in the quality. The two most significant PMM
model in PRINCE2 and PMBOK. FA can realize several benefits of implementing a regulated
PMM model. PMM model creates an understanding of what is expected for the project team.
The PRINCE2 model is a process based approach that can be used for managing all types
of projects. In this model, all process are defined to ensure planned implementation of a project.
Along with that, an increasing focus in given to testing the modules (Skogmar 2015). PRINCE is
known for delivering customer centric products, which increases customers’ satisfaction.
PMBOK is a collection of best practice principle that incorporates the different
knowledge areas and is well suited for iterative development.
For FA, the use of PRINCE 2 model is suggested as it has the following advantages-
1. Involves a clear quality management process that is needed for FA
2. Focuses of key risks and risk management
3. Process based methodology and provides increasing focus on effective project
governance
4. Tactics and Measures for implementing new Approach and to Reduce Quality Problems
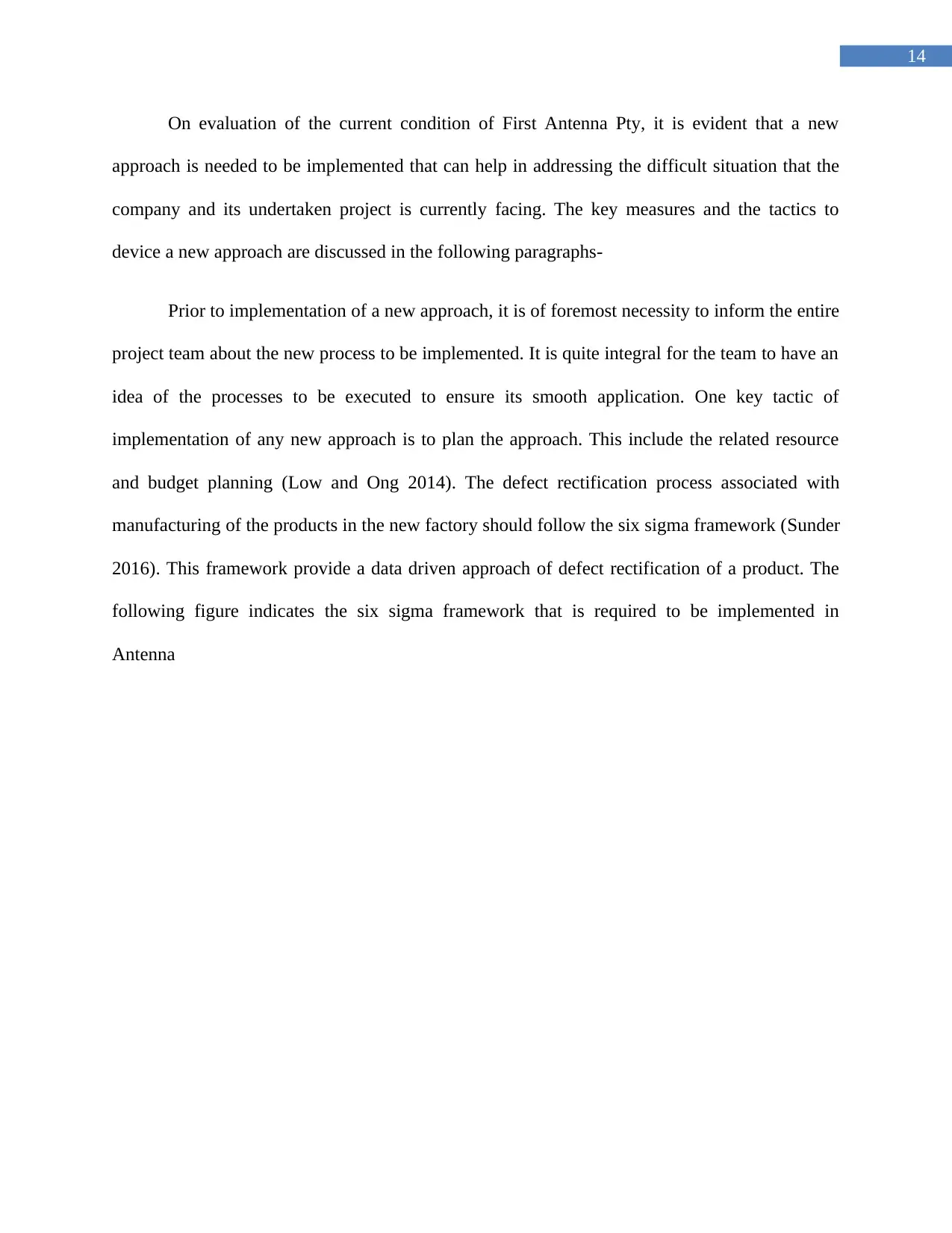
14
On evaluation of the current condition of First Antenna Pty, it is evident that a new
approach is needed to be implemented that can help in addressing the difficult situation that the
company and its undertaken project is currently facing. The key measures and the tactics to
device a new approach are discussed in the following paragraphs-
Prior to implementation of a new approach, it is of foremost necessity to inform the entire
project team about the new process to be implemented. It is quite integral for the team to have an
idea of the processes to be executed to ensure its smooth application. One key tactic of
implementation of any new approach is to plan the approach. This include the related resource
and budget planning (Low and Ong 2014). The defect rectification process associated with
manufacturing of the products in the new factory should follow the six sigma framework (Sunder
2016). This framework provide a data driven approach of defect rectification of a product. The
following figure indicates the six sigma framework that is required to be implemented in
Antenna
On evaluation of the current condition of First Antenna Pty, it is evident that a new
approach is needed to be implemented that can help in addressing the difficult situation that the
company and its undertaken project is currently facing. The key measures and the tactics to
device a new approach are discussed in the following paragraphs-
Prior to implementation of a new approach, it is of foremost necessity to inform the entire
project team about the new process to be implemented. It is quite integral for the team to have an
idea of the processes to be executed to ensure its smooth application. One key tactic of
implementation of any new approach is to plan the approach. This include the related resource
and budget planning (Low and Ong 2014). The defect rectification process associated with
manufacturing of the products in the new factory should follow the six sigma framework (Sunder
2016). This framework provide a data driven approach of defect rectification of a product. The
following figure indicates the six sigma framework that is required to be implemented in
Antenna
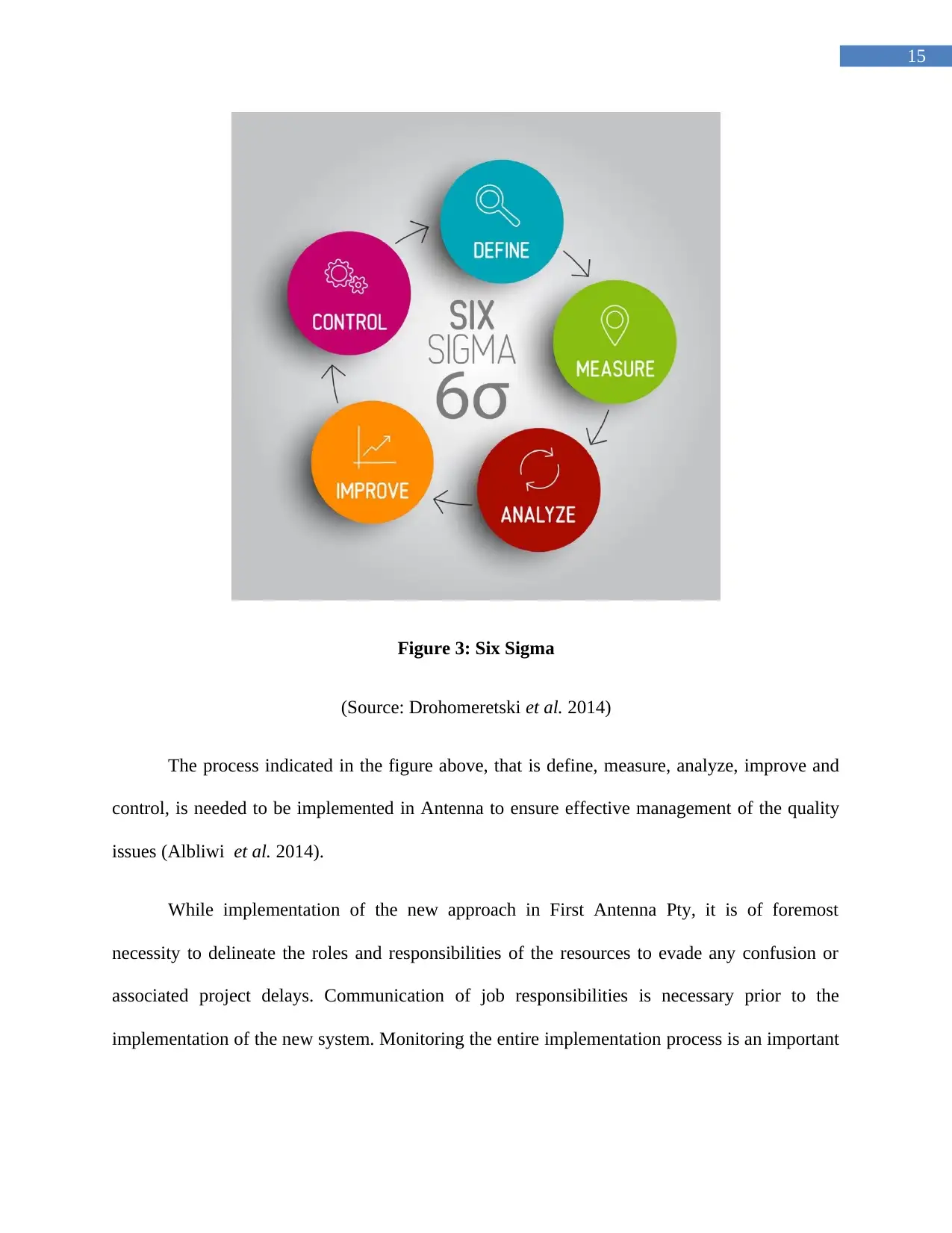
15
Figure 3: Six Sigma
(Source: Drohomeretski et al. 2014)
The process indicated in the figure above, that is define, measure, analyze, improve and
control, is needed to be implemented in Antenna to ensure effective management of the quality
issues (Albliwi et al. 2014).
While implementation of the new approach in First Antenna Pty, it is of foremost
necessity to delineate the roles and responsibilities of the resources to evade any confusion or
associated project delays. Communication of job responsibilities is necessary prior to the
implementation of the new system. Monitoring the entire implementation process is an important
Figure 3: Six Sigma
(Source: Drohomeretski et al. 2014)
The process indicated in the figure above, that is define, measure, analyze, improve and
control, is needed to be implemented in Antenna to ensure effective management of the quality
issues (Albliwi et al. 2014).
While implementation of the new approach in First Antenna Pty, it is of foremost
necessity to delineate the roles and responsibilities of the resources to evade any confusion or
associated project delays. Communication of job responsibilities is necessary prior to the
implementation of the new system. Monitoring the entire implementation process is an important
Secure Best Marks with AI Grader
Need help grading? Try our AI Grader for instant feedback on your assignments.
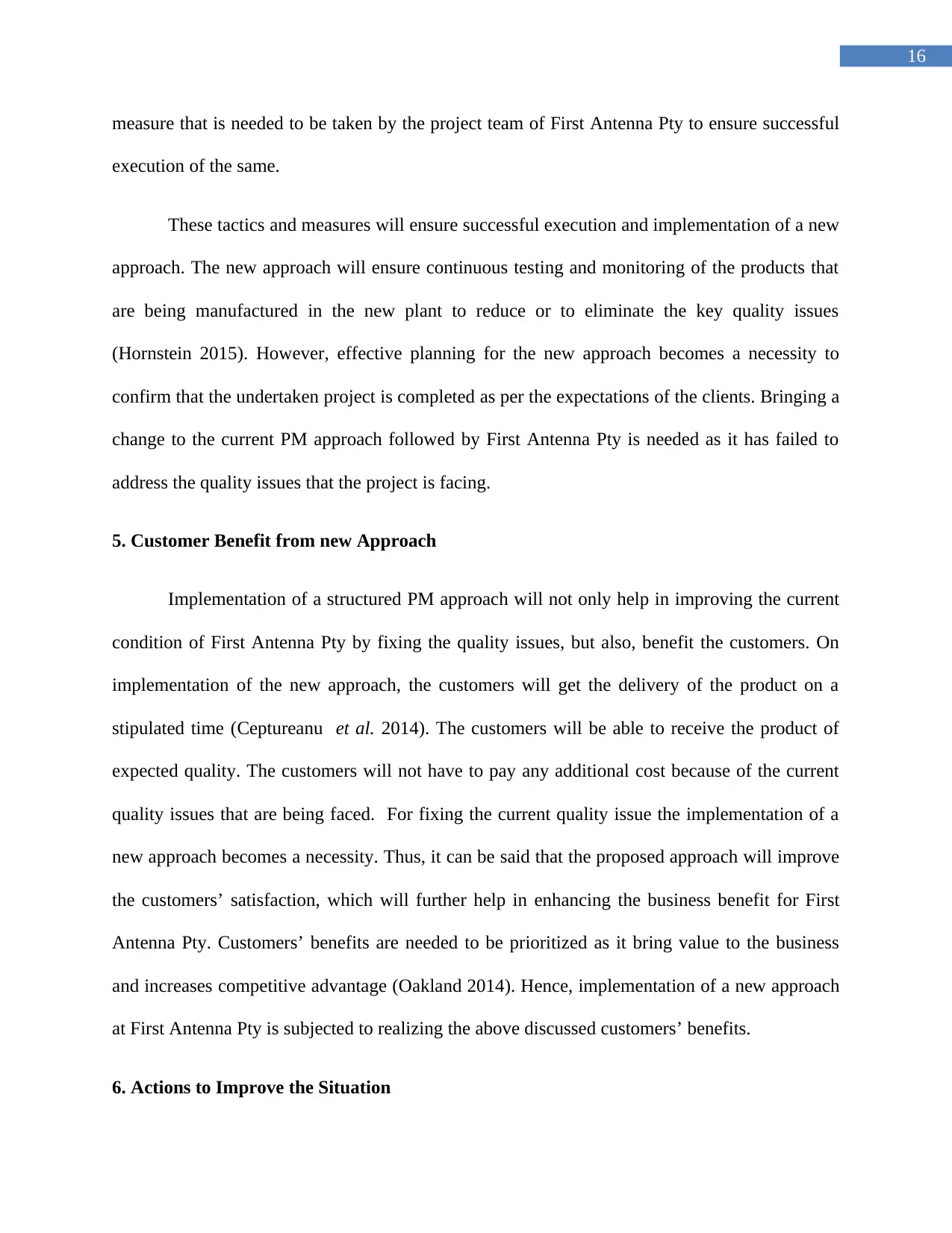
16
measure that is needed to be taken by the project team of First Antenna Pty to ensure successful
execution of the same.
These tactics and measures will ensure successful execution and implementation of a new
approach. The new approach will ensure continuous testing and monitoring of the products that
are being manufactured in the new plant to reduce or to eliminate the key quality issues
(Hornstein 2015). However, effective planning for the new approach becomes a necessity to
confirm that the undertaken project is completed as per the expectations of the clients. Bringing a
change to the current PM approach followed by First Antenna Pty is needed as it has failed to
address the quality issues that the project is facing.
5. Customer Benefit from new Approach
Implementation of a structured PM approach will not only help in improving the current
condition of First Antenna Pty by fixing the quality issues, but also, benefit the customers. On
implementation of the new approach, the customers will get the delivery of the product on a
stipulated time (Ceptureanu et al. 2014). The customers will be able to receive the product of
expected quality. The customers will not have to pay any additional cost because of the current
quality issues that are being faced. For fixing the current quality issue the implementation of a
new approach becomes a necessity. Thus, it can be said that the proposed approach will improve
the customers’ satisfaction, which will further help in enhancing the business benefit for First
Antenna Pty. Customers’ benefits are needed to be prioritized as it bring value to the business
and increases competitive advantage (Oakland 2014). Hence, implementation of a new approach
at First Antenna Pty is subjected to realizing the above discussed customers’ benefits.
6. Actions to Improve the Situation
measure that is needed to be taken by the project team of First Antenna Pty to ensure successful
execution of the same.
These tactics and measures will ensure successful execution and implementation of a new
approach. The new approach will ensure continuous testing and monitoring of the products that
are being manufactured in the new plant to reduce or to eliminate the key quality issues
(Hornstein 2015). However, effective planning for the new approach becomes a necessity to
confirm that the undertaken project is completed as per the expectations of the clients. Bringing a
change to the current PM approach followed by First Antenna Pty is needed as it has failed to
address the quality issues that the project is facing.
5. Customer Benefit from new Approach
Implementation of a structured PM approach will not only help in improving the current
condition of First Antenna Pty by fixing the quality issues, but also, benefit the customers. On
implementation of the new approach, the customers will get the delivery of the product on a
stipulated time (Ceptureanu et al. 2014). The customers will be able to receive the product of
expected quality. The customers will not have to pay any additional cost because of the current
quality issues that are being faced. For fixing the current quality issue the implementation of a
new approach becomes a necessity. Thus, it can be said that the proposed approach will improve
the customers’ satisfaction, which will further help in enhancing the business benefit for First
Antenna Pty. Customers’ benefits are needed to be prioritized as it bring value to the business
and increases competitive advantage (Oakland 2014). Hence, implementation of a new approach
at First Antenna Pty is subjected to realizing the above discussed customers’ benefits.
6. Actions to Improve the Situation
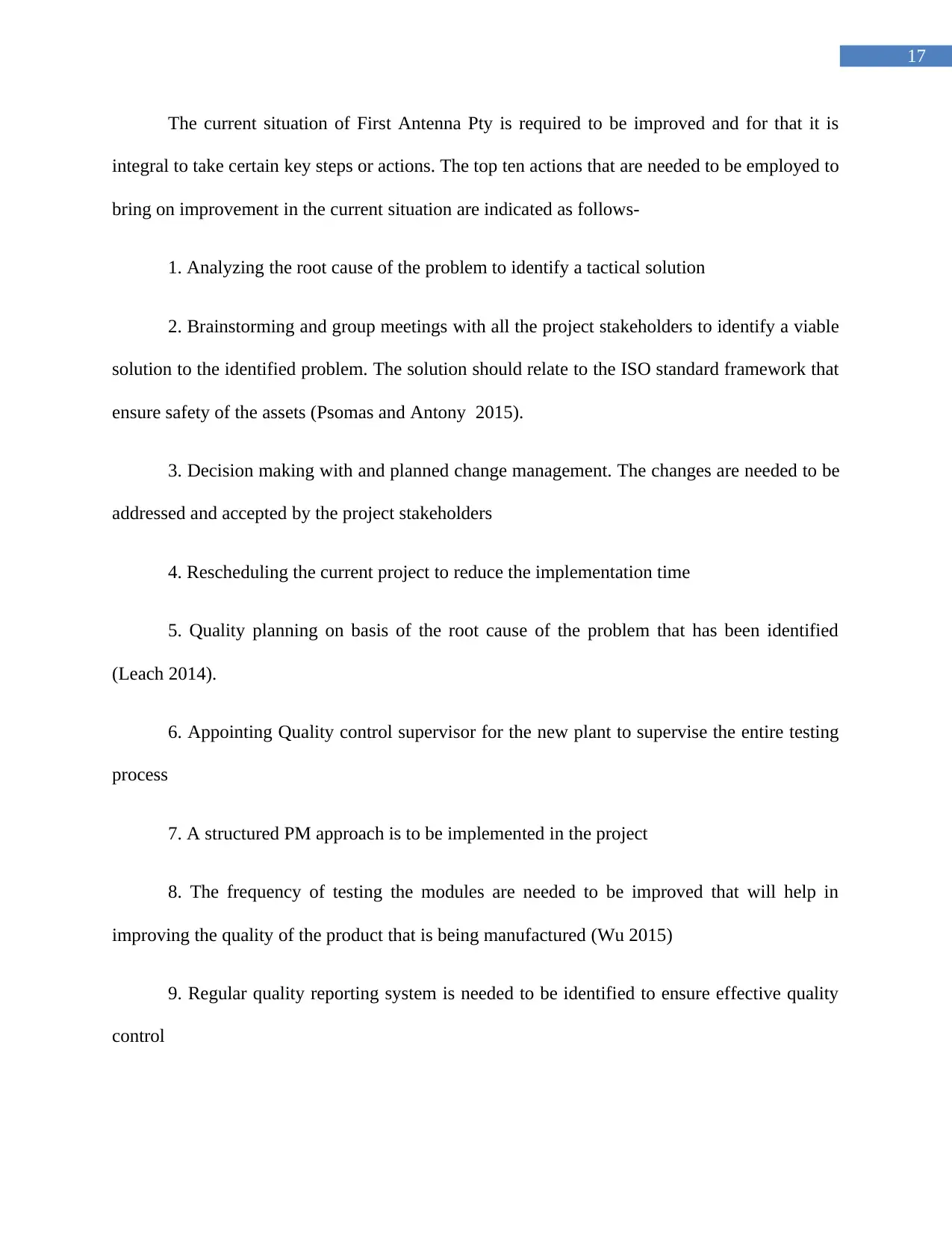
17
The current situation of First Antenna Pty is required to be improved and for that it is
integral to take certain key steps or actions. The top ten actions that are needed to be employed to
bring on improvement in the current situation are indicated as follows-
1. Analyzing the root cause of the problem to identify a tactical solution
2. Brainstorming and group meetings with all the project stakeholders to identify a viable
solution to the identified problem. The solution should relate to the ISO standard framework that
ensure safety of the assets (Psomas and Antony 2015).
3. Decision making with and planned change management. The changes are needed to be
addressed and accepted by the project stakeholders
4. Rescheduling the current project to reduce the implementation time
5. Quality planning on basis of the root cause of the problem that has been identified
(Leach 2014).
6. Appointing Quality control supervisor for the new plant to supervise the entire testing
process
7. A structured PM approach is to be implemented in the project
8. The frequency of testing the modules are needed to be improved that will help in
improving the quality of the product that is being manufactured (Wu 2015)
9. Regular quality reporting system is needed to be identified to ensure effective quality
control
The current situation of First Antenna Pty is required to be improved and for that it is
integral to take certain key steps or actions. The top ten actions that are needed to be employed to
bring on improvement in the current situation are indicated as follows-
1. Analyzing the root cause of the problem to identify a tactical solution
2. Brainstorming and group meetings with all the project stakeholders to identify a viable
solution to the identified problem. The solution should relate to the ISO standard framework that
ensure safety of the assets (Psomas and Antony 2015).
3. Decision making with and planned change management. The changes are needed to be
addressed and accepted by the project stakeholders
4. Rescheduling the current project to reduce the implementation time
5. Quality planning on basis of the root cause of the problem that has been identified
(Leach 2014).
6. Appointing Quality control supervisor for the new plant to supervise the entire testing
process
7. A structured PM approach is to be implemented in the project
8. The frequency of testing the modules are needed to be improved that will help in
improving the quality of the product that is being manufactured (Wu 2015)
9. Regular quality reporting system is needed to be identified to ensure effective quality
control
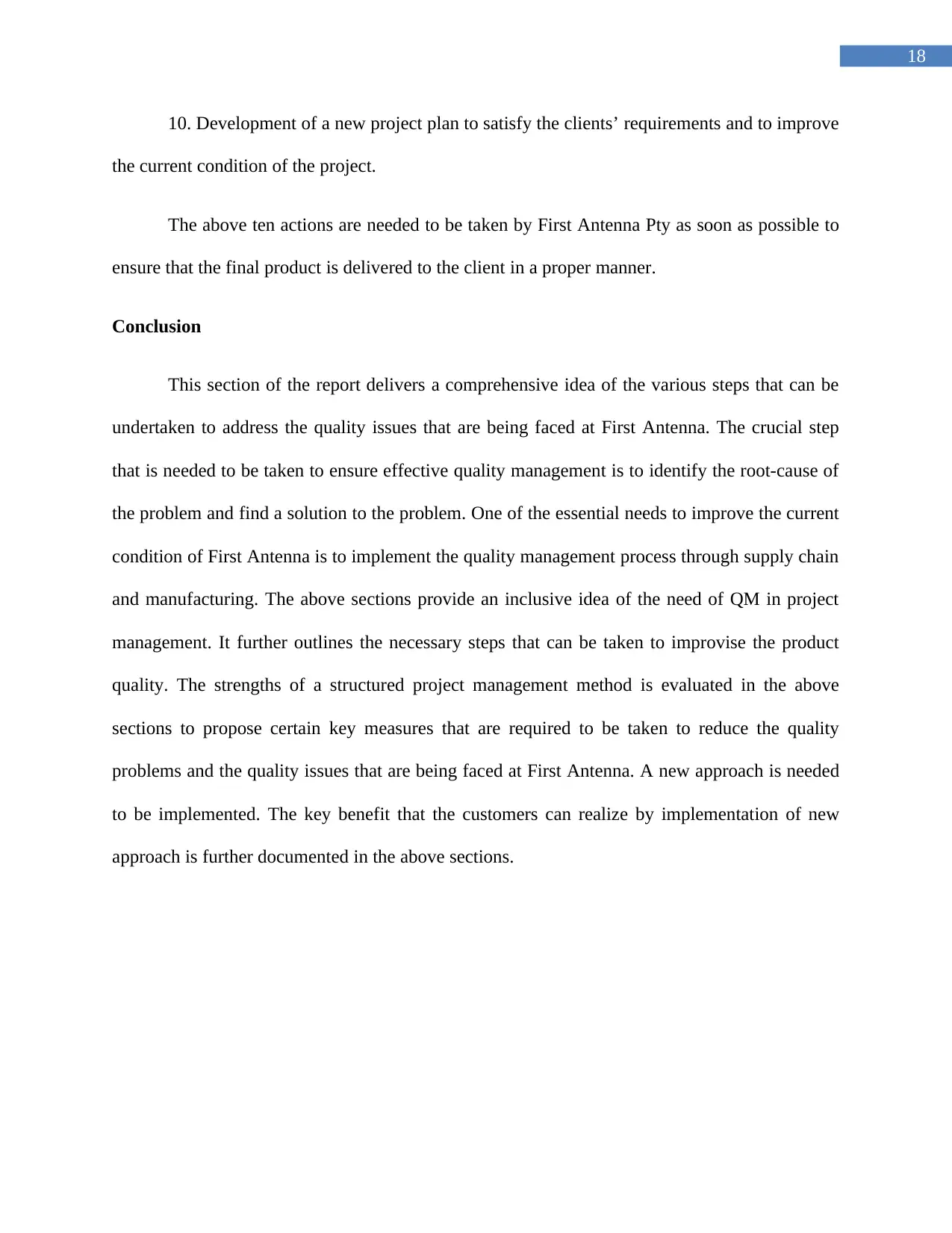
18
10. Development of a new project plan to satisfy the clients’ requirements and to improve
the current condition of the project.
The above ten actions are needed to be taken by First Antenna Pty as soon as possible to
ensure that the final product is delivered to the client in a proper manner.
Conclusion
This section of the report delivers a comprehensive idea of the various steps that can be
undertaken to address the quality issues that are being faced at First Antenna. The crucial step
that is needed to be taken to ensure effective quality management is to identify the root-cause of
the problem and find a solution to the problem. One of the essential needs to improve the current
condition of First Antenna is to implement the quality management process through supply chain
and manufacturing. The above sections provide an inclusive idea of the need of QM in project
management. It further outlines the necessary steps that can be taken to improvise the product
quality. The strengths of a structured project management method is evaluated in the above
sections to propose certain key measures that are required to be taken to reduce the quality
problems and the quality issues that are being faced at First Antenna. A new approach is needed
to be implemented. The key benefit that the customers can realize by implementation of new
approach is further documented in the above sections.
10. Development of a new project plan to satisfy the clients’ requirements and to improve
the current condition of the project.
The above ten actions are needed to be taken by First Antenna Pty as soon as possible to
ensure that the final product is delivered to the client in a proper manner.
Conclusion
This section of the report delivers a comprehensive idea of the various steps that can be
undertaken to address the quality issues that are being faced at First Antenna. The crucial step
that is needed to be taken to ensure effective quality management is to identify the root-cause of
the problem and find a solution to the problem. One of the essential needs to improve the current
condition of First Antenna is to implement the quality management process through supply chain
and manufacturing. The above sections provide an inclusive idea of the need of QM in project
management. It further outlines the necessary steps that can be taken to improvise the product
quality. The strengths of a structured project management method is evaluated in the above
sections to propose certain key measures that are required to be taken to reduce the quality
problems and the quality issues that are being faced at First Antenna. A new approach is needed
to be implemented. The key benefit that the customers can realize by implementation of new
approach is further documented in the above sections.
Paraphrase This Document
Need a fresh take? Get an instant paraphrase of this document with our AI Paraphraser
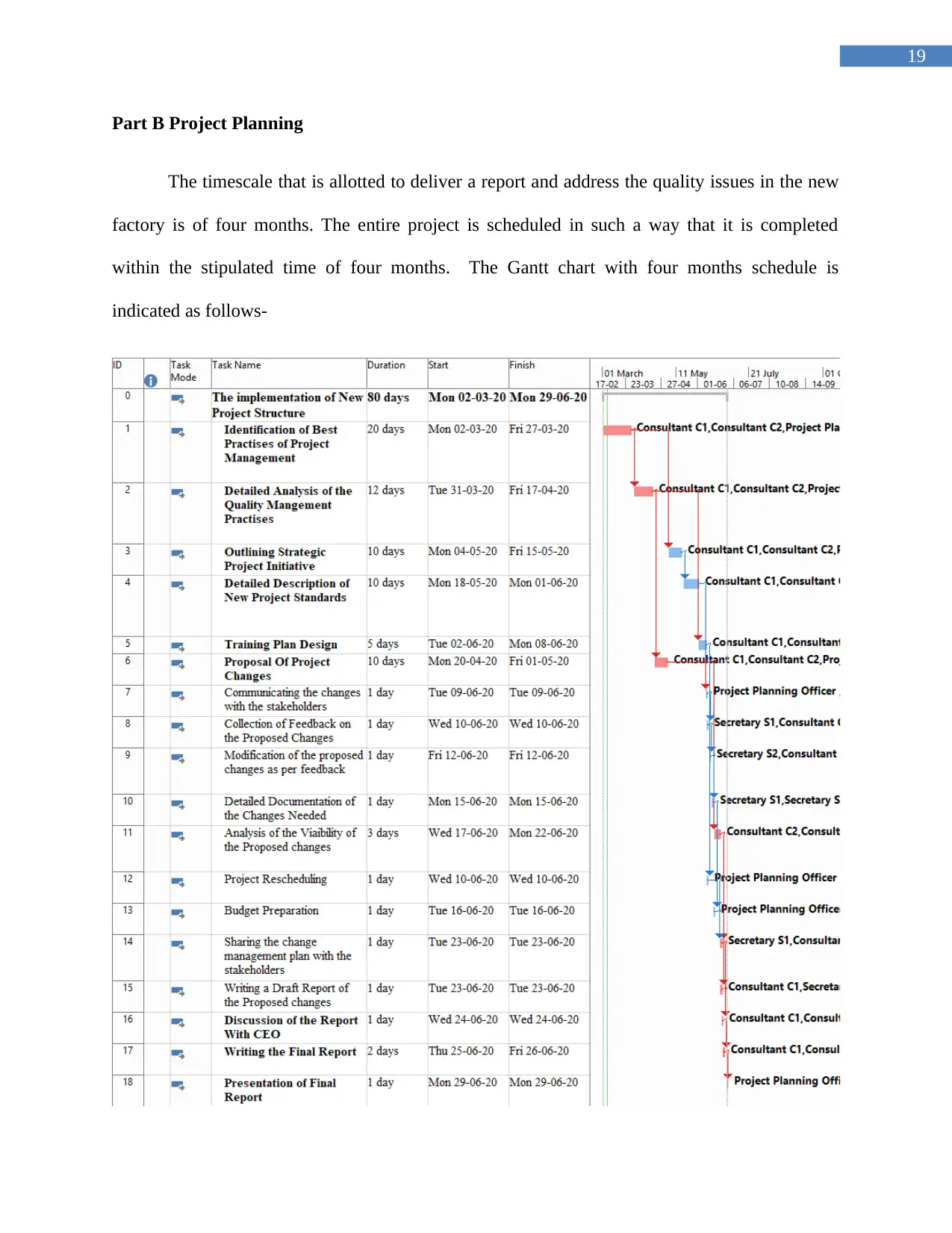
19
Part B Project Planning
The timescale that is allotted to deliver a report and address the quality issues in the new
factory is of four months. The entire project is scheduled in such a way that it is completed
within the stipulated time of four months. The Gantt chart with four months schedule is
indicated as follows-
Part B Project Planning
The timescale that is allotted to deliver a report and address the quality issues in the new
factory is of four months. The entire project is scheduled in such a way that it is completed
within the stipulated time of four months. The Gantt chart with four months schedule is
indicated as follows-
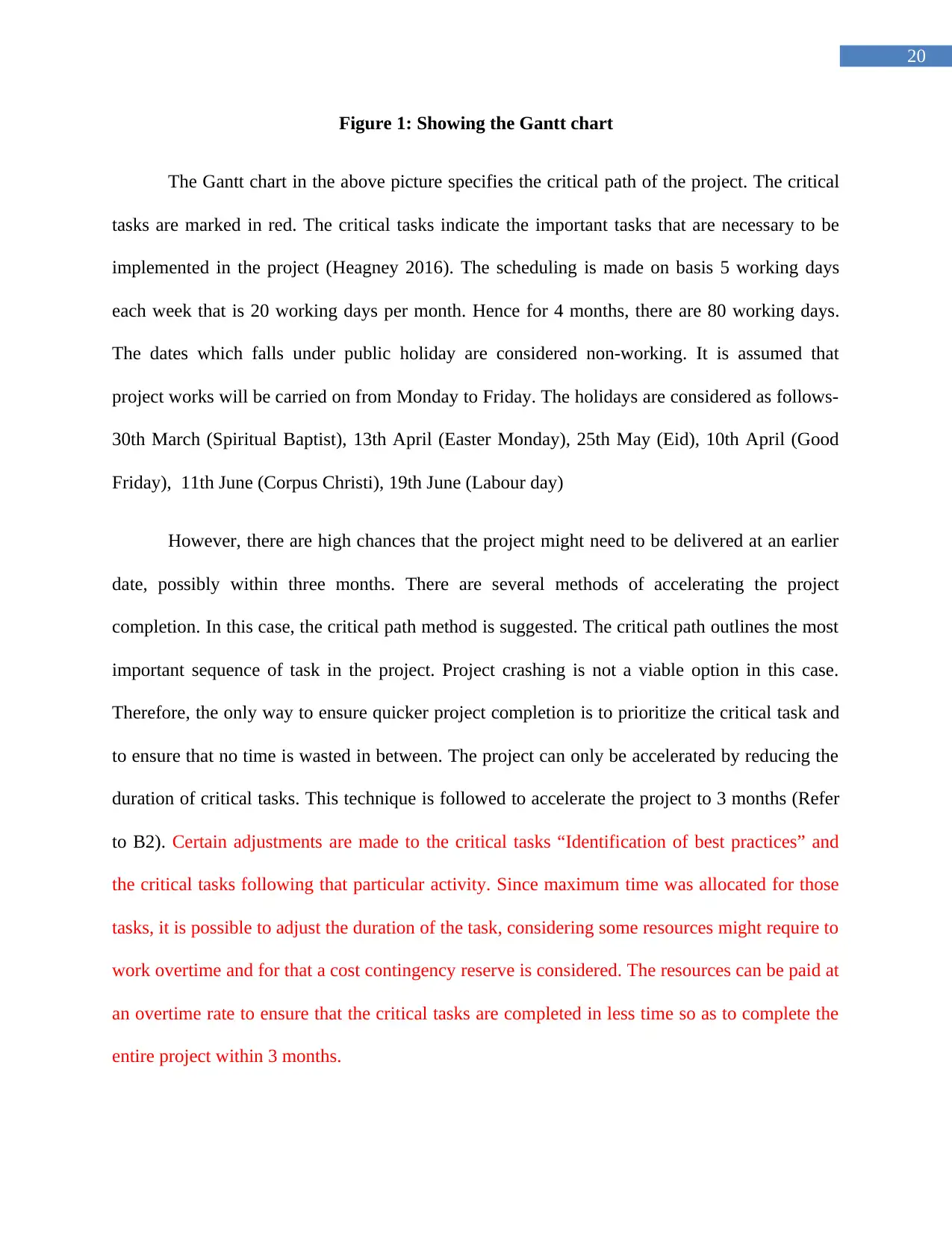
20
Figure 1: Showing the Gantt chart
The Gantt chart in the above picture specifies the critical path of the project. The critical
tasks are marked in red. The critical tasks indicate the important tasks that are necessary to be
implemented in the project (Heagney 2016). The scheduling is made on basis 5 working days
each week that is 20 working days per month. Hence for 4 months, there are 80 working days.
The dates which falls under public holiday are considered non-working. It is assumed that
project works will be carried on from Monday to Friday. The holidays are considered as follows-
30th March (Spiritual Baptist), 13th April (Easter Monday), 25th May (Eid), 10th April (Good
Friday), 11th June (Corpus Christi), 19th June (Labour day)
However, there are high chances that the project might need to be delivered at an earlier
date, possibly within three months. There are several methods of accelerating the project
completion. In this case, the critical path method is suggested. The critical path outlines the most
important sequence of task in the project. Project crashing is not a viable option in this case.
Therefore, the only way to ensure quicker project completion is to prioritize the critical task and
to ensure that no time is wasted in between. The project can only be accelerated by reducing the
duration of critical tasks. This technique is followed to accelerate the project to 3 months (Refer
to B2). Certain adjustments are made to the critical tasks “Identification of best practices” and
the critical tasks following that particular activity. Since maximum time was allocated for those
tasks, it is possible to adjust the duration of the task, considering some resources might require to
work overtime and for that a cost contingency reserve is considered. The resources can be paid at
an overtime rate to ensure that the critical tasks are completed in less time so as to complete the
entire project within 3 months.
Figure 1: Showing the Gantt chart
The Gantt chart in the above picture specifies the critical path of the project. The critical
tasks are marked in red. The critical tasks indicate the important tasks that are necessary to be
implemented in the project (Heagney 2016). The scheduling is made on basis 5 working days
each week that is 20 working days per month. Hence for 4 months, there are 80 working days.
The dates which falls under public holiday are considered non-working. It is assumed that
project works will be carried on from Monday to Friday. The holidays are considered as follows-
30th March (Spiritual Baptist), 13th April (Easter Monday), 25th May (Eid), 10th April (Good
Friday), 11th June (Corpus Christi), 19th June (Labour day)
However, there are high chances that the project might need to be delivered at an earlier
date, possibly within three months. There are several methods of accelerating the project
completion. In this case, the critical path method is suggested. The critical path outlines the most
important sequence of task in the project. Project crashing is not a viable option in this case.
Therefore, the only way to ensure quicker project completion is to prioritize the critical task and
to ensure that no time is wasted in between. The project can only be accelerated by reducing the
duration of critical tasks. This technique is followed to accelerate the project to 3 months (Refer
to B2). Certain adjustments are made to the critical tasks “Identification of best practices” and
the critical tasks following that particular activity. Since maximum time was allocated for those
tasks, it is possible to adjust the duration of the task, considering some resources might require to
work overtime and for that a cost contingency reserve is considered. The resources can be paid at
an overtime rate to ensure that the critical tasks are completed in less time so as to complete the
entire project within 3 months.
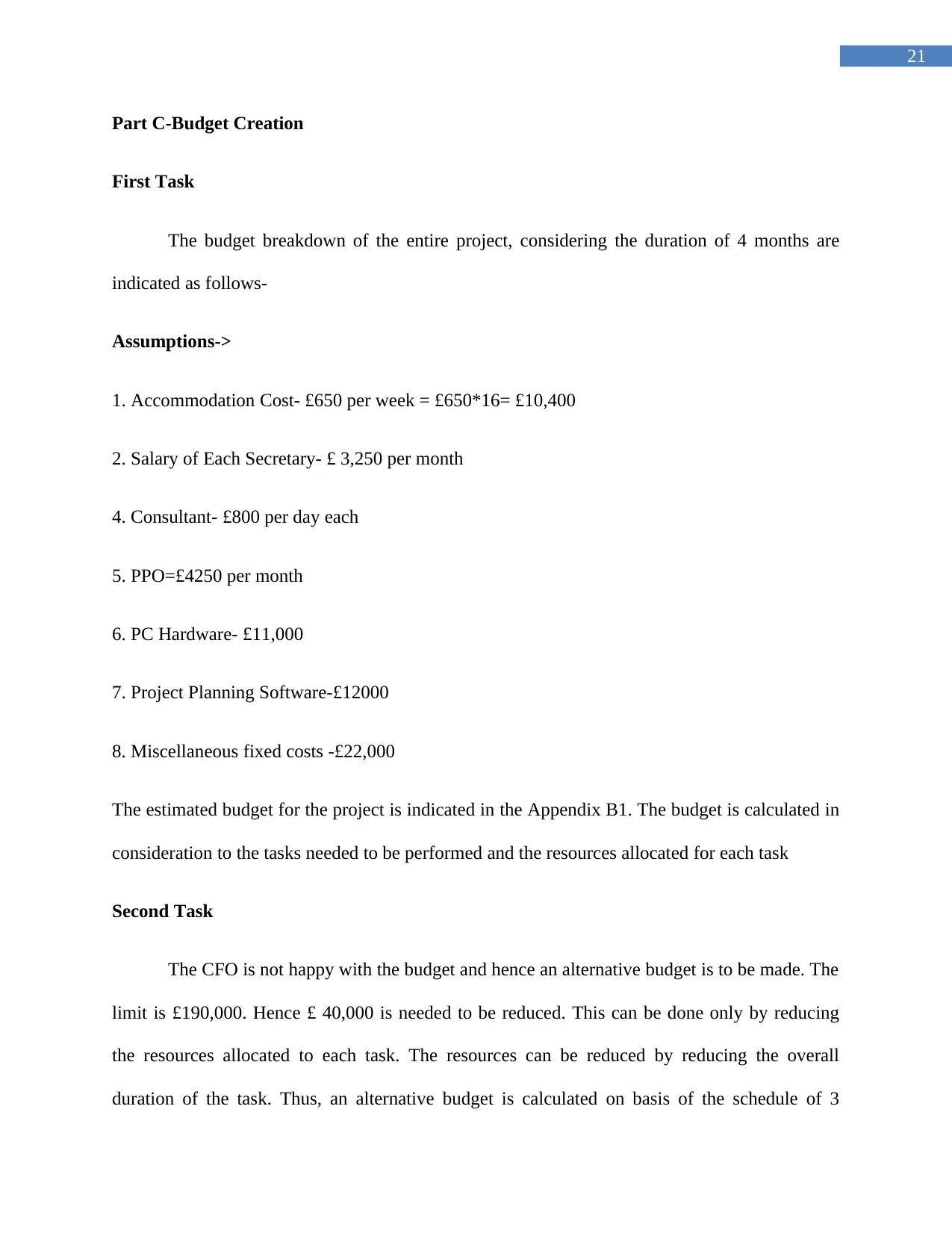
21
Part C-Budget Creation
First Task
The budget breakdown of the entire project, considering the duration of 4 months are
indicated as follows-
Assumptions->
1. Accommodation Cost- £650 per week = £650*16= £10,400
2. Salary of Each Secretary- £ 3,250 per month
4. Consultant- £800 per day each
5. PPO=£4250 per month
6. PC Hardware- £11,000
7. Project Planning Software-£12000
8. Miscellaneous fixed costs -£22,000
The estimated budget for the project is indicated in the Appendix B1. The budget is calculated in
consideration to the tasks needed to be performed and the resources allocated for each task
Second Task
The CFO is not happy with the budget and hence an alternative budget is to be made. The
limit is £190,000. Hence £ 40,000 is needed to be reduced. This can be done only by reducing
the resources allocated to each task. The resources can be reduced by reducing the overall
duration of the task. Thus, an alternative budget is calculated on basis of the schedule of 3
Part C-Budget Creation
First Task
The budget breakdown of the entire project, considering the duration of 4 months are
indicated as follows-
Assumptions->
1. Accommodation Cost- £650 per week = £650*16= £10,400
2. Salary of Each Secretary- £ 3,250 per month
4. Consultant- £800 per day each
5. PPO=£4250 per month
6. PC Hardware- £11,000
7. Project Planning Software-£12000
8. Miscellaneous fixed costs -£22,000
The estimated budget for the project is indicated in the Appendix B1. The budget is calculated in
consideration to the tasks needed to be performed and the resources allocated for each task
Second Task
The CFO is not happy with the budget and hence an alternative budget is to be made. The
limit is £190,000. Hence £ 40,000 is needed to be reduced. This can be done only by reducing
the resources allocated to each task. The resources can be reduced by reducing the overall
duration of the task. Thus, an alternative budget is calculated on basis of the schedule of 3
Secure Best Marks with AI Grader
Need help grading? Try our AI Grader for instant feedback on your assignments.
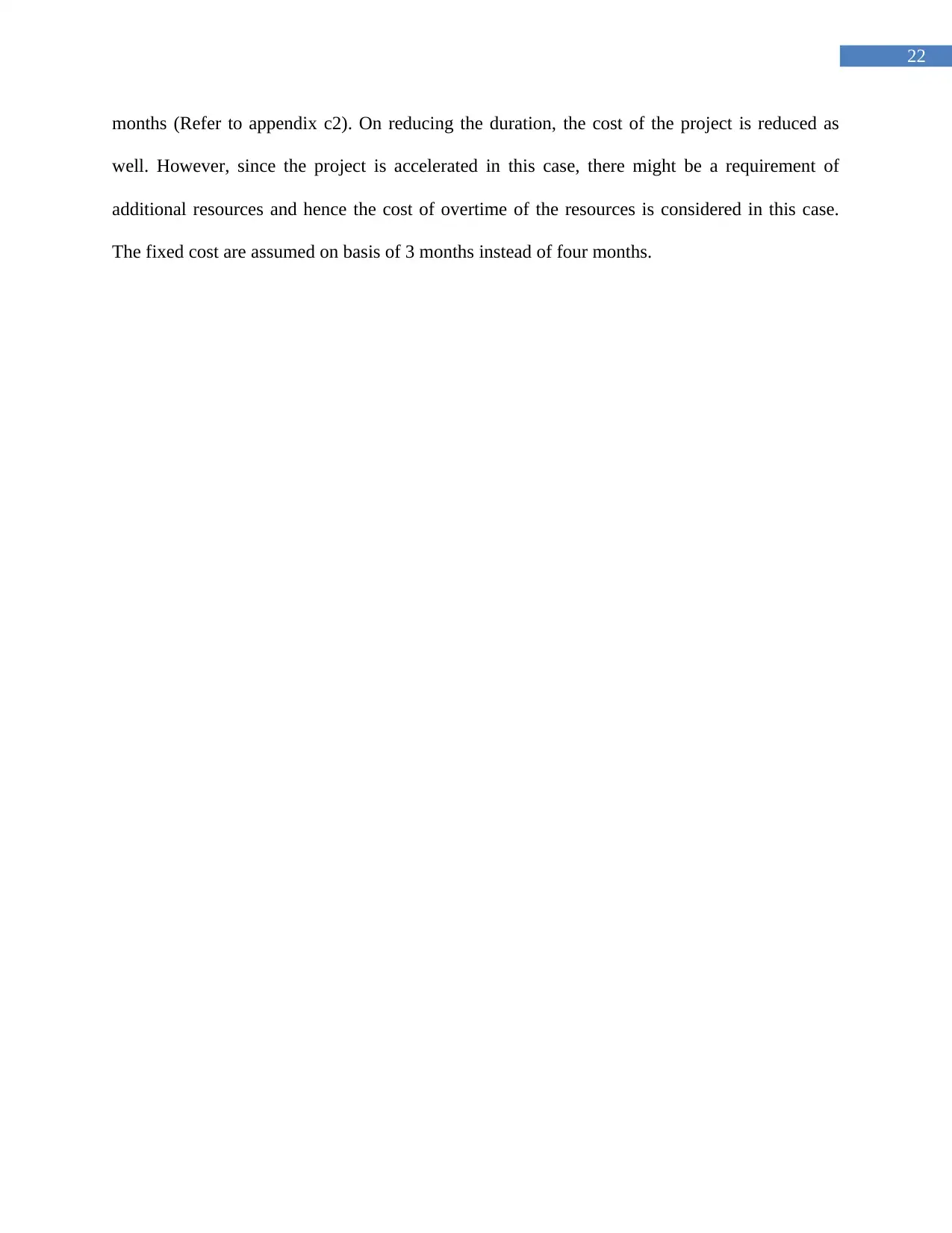
22
months (Refer to appendix c2). On reducing the duration, the cost of the project is reduced as
well. However, since the project is accelerated in this case, there might be a requirement of
additional resources and hence the cost of overtime of the resources is considered in this case.
The fixed cost are assumed on basis of 3 months instead of four months.
months (Refer to appendix c2). On reducing the duration, the cost of the project is reduced as
well. However, since the project is accelerated in this case, there might be a requirement of
additional resources and hence the cost of overtime of the resources is considered in this case.
The fixed cost are assumed on basis of 3 months instead of four months.
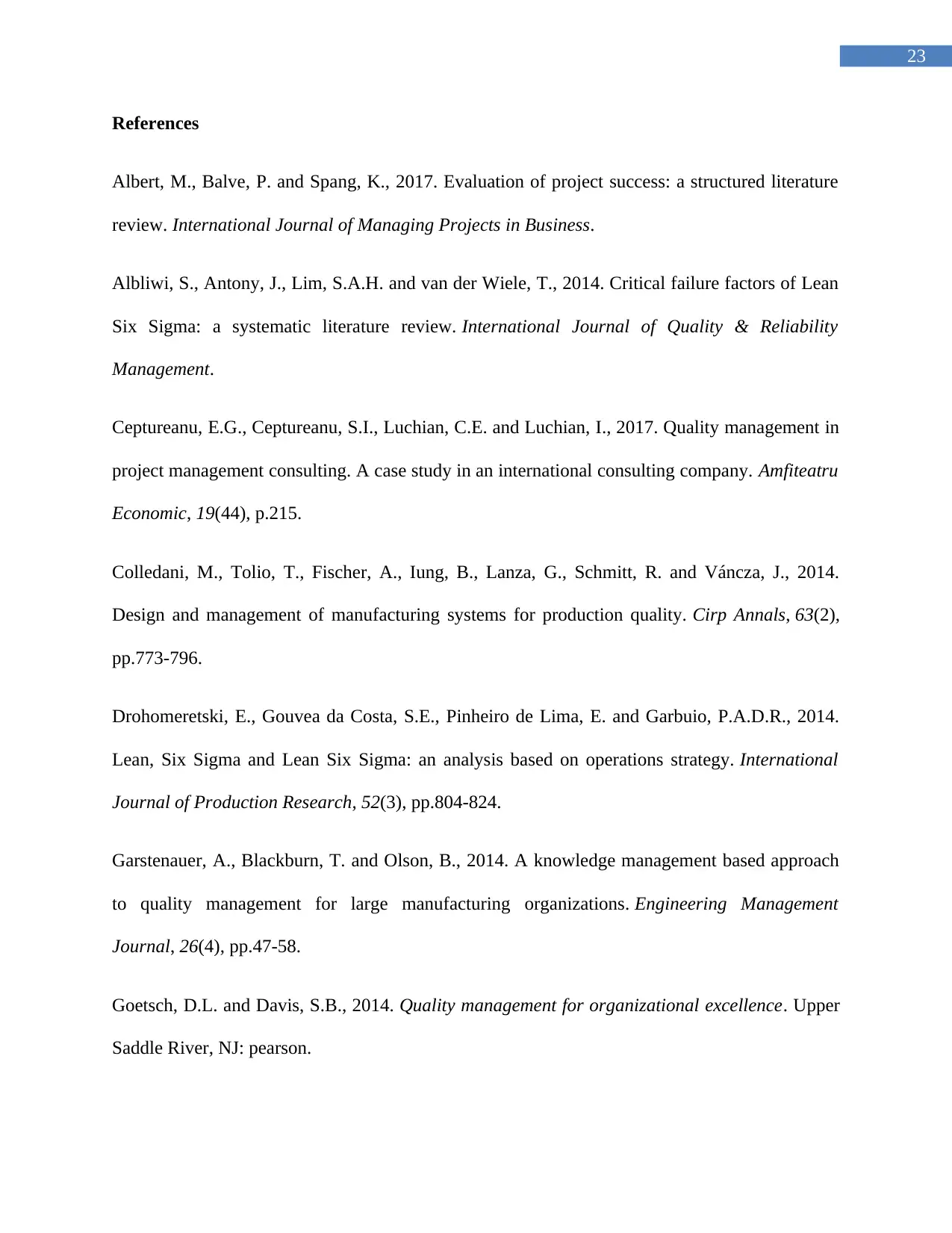
23
References
Albert, M., Balve, P. and Spang, K., 2017. Evaluation of project success: a structured literature
review. International Journal of Managing Projects in Business.
Albliwi, S., Antony, J., Lim, S.A.H. and van der Wiele, T., 2014. Critical failure factors of Lean
Six Sigma: a systematic literature review. International Journal of Quality & Reliability
Management.
Ceptureanu, E.G., Ceptureanu, S.I., Luchian, C.E. and Luchian, I., 2017. Quality management in
project management consulting. A case study in an international consulting company. Amfiteatru
Economic, 19(44), p.215.
Colledani, M., Tolio, T., Fischer, A., Iung, B., Lanza, G., Schmitt, R. and Váncza, J., 2014.
Design and management of manufacturing systems for production quality. Cirp Annals, 63(2),
pp.773-796.
Drohomeretski, E., Gouvea da Costa, S.E., Pinheiro de Lima, E. and Garbuio, P.A.D.R., 2014.
Lean, Six Sigma and Lean Six Sigma: an analysis based on operations strategy. International
Journal of Production Research, 52(3), pp.804-824.
Garstenauer, A., Blackburn, T. and Olson, B., 2014. A knowledge management based approach
to quality management for large manufacturing organizations. Engineering Management
Journal, 26(4), pp.47-58.
Goetsch, D.L. and Davis, S.B., 2014. Quality management for organizational excellence. Upper
Saddle River, NJ: pearson.
References
Albert, M., Balve, P. and Spang, K., 2017. Evaluation of project success: a structured literature
review. International Journal of Managing Projects in Business.
Albliwi, S., Antony, J., Lim, S.A.H. and van der Wiele, T., 2014. Critical failure factors of Lean
Six Sigma: a systematic literature review. International Journal of Quality & Reliability
Management.
Ceptureanu, E.G., Ceptureanu, S.I., Luchian, C.E. and Luchian, I., 2017. Quality management in
project management consulting. A case study in an international consulting company. Amfiteatru
Economic, 19(44), p.215.
Colledani, M., Tolio, T., Fischer, A., Iung, B., Lanza, G., Schmitt, R. and Váncza, J., 2014.
Design and management of manufacturing systems for production quality. Cirp Annals, 63(2),
pp.773-796.
Drohomeretski, E., Gouvea da Costa, S.E., Pinheiro de Lima, E. and Garbuio, P.A.D.R., 2014.
Lean, Six Sigma and Lean Six Sigma: an analysis based on operations strategy. International
Journal of Production Research, 52(3), pp.804-824.
Garstenauer, A., Blackburn, T. and Olson, B., 2014. A knowledge management based approach
to quality management for large manufacturing organizations. Engineering Management
Journal, 26(4), pp.47-58.
Goetsch, D.L. and Davis, S.B., 2014. Quality management for organizational excellence. Upper
Saddle River, NJ: pearson.
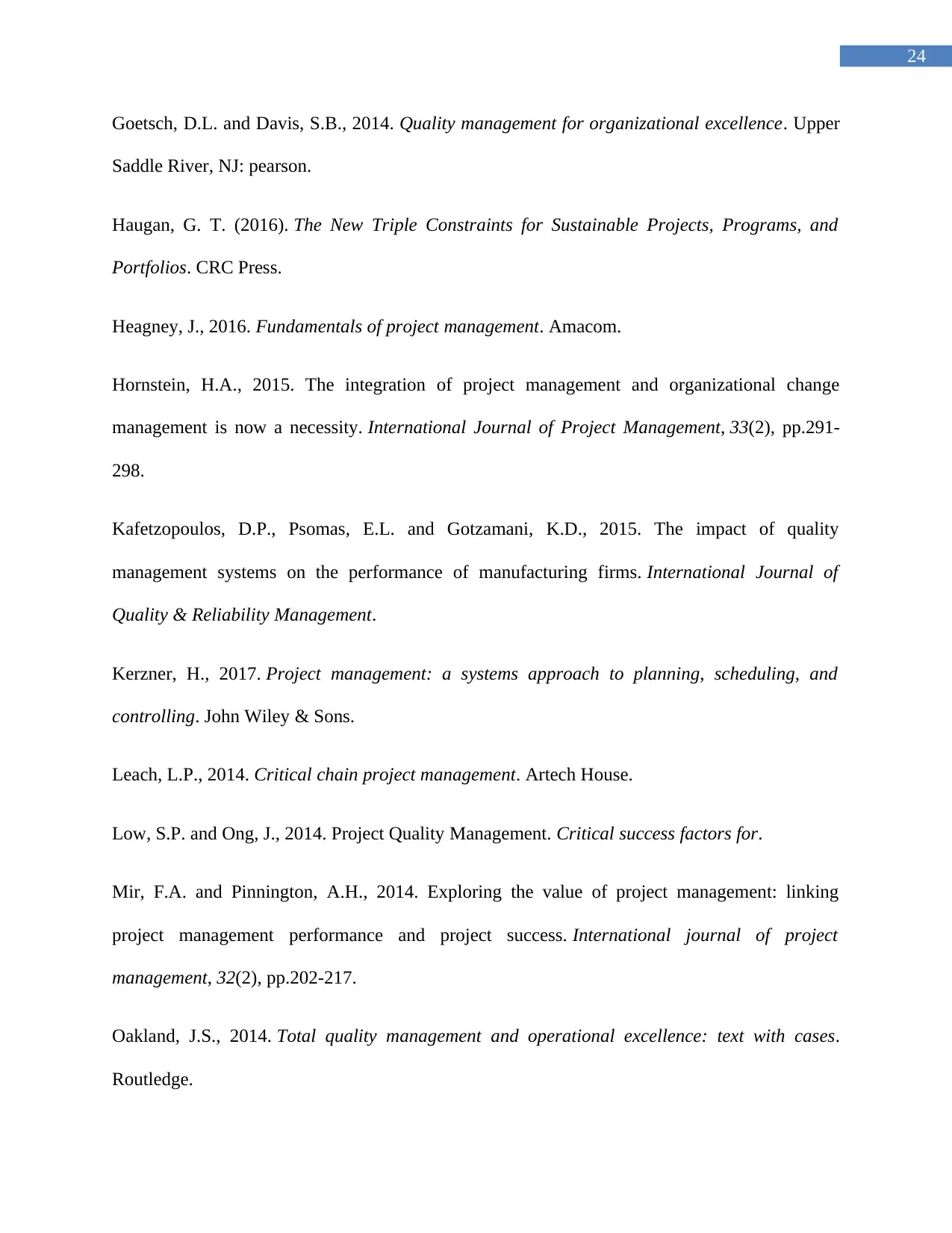
24
Goetsch, D.L. and Davis, S.B., 2014. Quality management for organizational excellence. Upper
Saddle River, NJ: pearson.
Haugan, G. T. (2016). The New Triple Constraints for Sustainable Projects, Programs, and
Portfolios. CRC Press.
Heagney, J., 2016. Fundamentals of project management. Amacom.
Hornstein, H.A., 2015. The integration of project management and organizational change
management is now a necessity. International Journal of Project Management, 33(2), pp.291-
298.
Kafetzopoulos, D.P., Psomas, E.L. and Gotzamani, K.D., 2015. The impact of quality
management systems on the performance of manufacturing firms. International Journal of
Quality & Reliability Management.
Kerzner, H., 2017. Project management: a systems approach to planning, scheduling, and
controlling. John Wiley & Sons.
Leach, L.P., 2014. Critical chain project management. Artech House.
Low, S.P. and Ong, J., 2014. Project Quality Management. Critical success factors for.
Mir, F.A. and Pinnington, A.H., 2014. Exploring the value of project management: linking
project management performance and project success. International journal of project
management, 32(2), pp.202-217.
Oakland, J.S., 2014. Total quality management and operational excellence: text with cases.
Routledge.
Goetsch, D.L. and Davis, S.B., 2014. Quality management for organizational excellence. Upper
Saddle River, NJ: pearson.
Haugan, G. T. (2016). The New Triple Constraints for Sustainable Projects, Programs, and
Portfolios. CRC Press.
Heagney, J., 2016. Fundamentals of project management. Amacom.
Hornstein, H.A., 2015. The integration of project management and organizational change
management is now a necessity. International Journal of Project Management, 33(2), pp.291-
298.
Kafetzopoulos, D.P., Psomas, E.L. and Gotzamani, K.D., 2015. The impact of quality
management systems on the performance of manufacturing firms. International Journal of
Quality & Reliability Management.
Kerzner, H., 2017. Project management: a systems approach to planning, scheduling, and
controlling. John Wiley & Sons.
Leach, L.P., 2014. Critical chain project management. Artech House.
Low, S.P. and Ong, J., 2014. Project Quality Management. Critical success factors for.
Mir, F.A. and Pinnington, A.H., 2014. Exploring the value of project management: linking
project management performance and project success. International journal of project
management, 32(2), pp.202-217.
Oakland, J.S., 2014. Total quality management and operational excellence: text with cases.
Routledge.
Paraphrase This Document
Need a fresh take? Get an instant paraphrase of this document with our AI Paraphraser
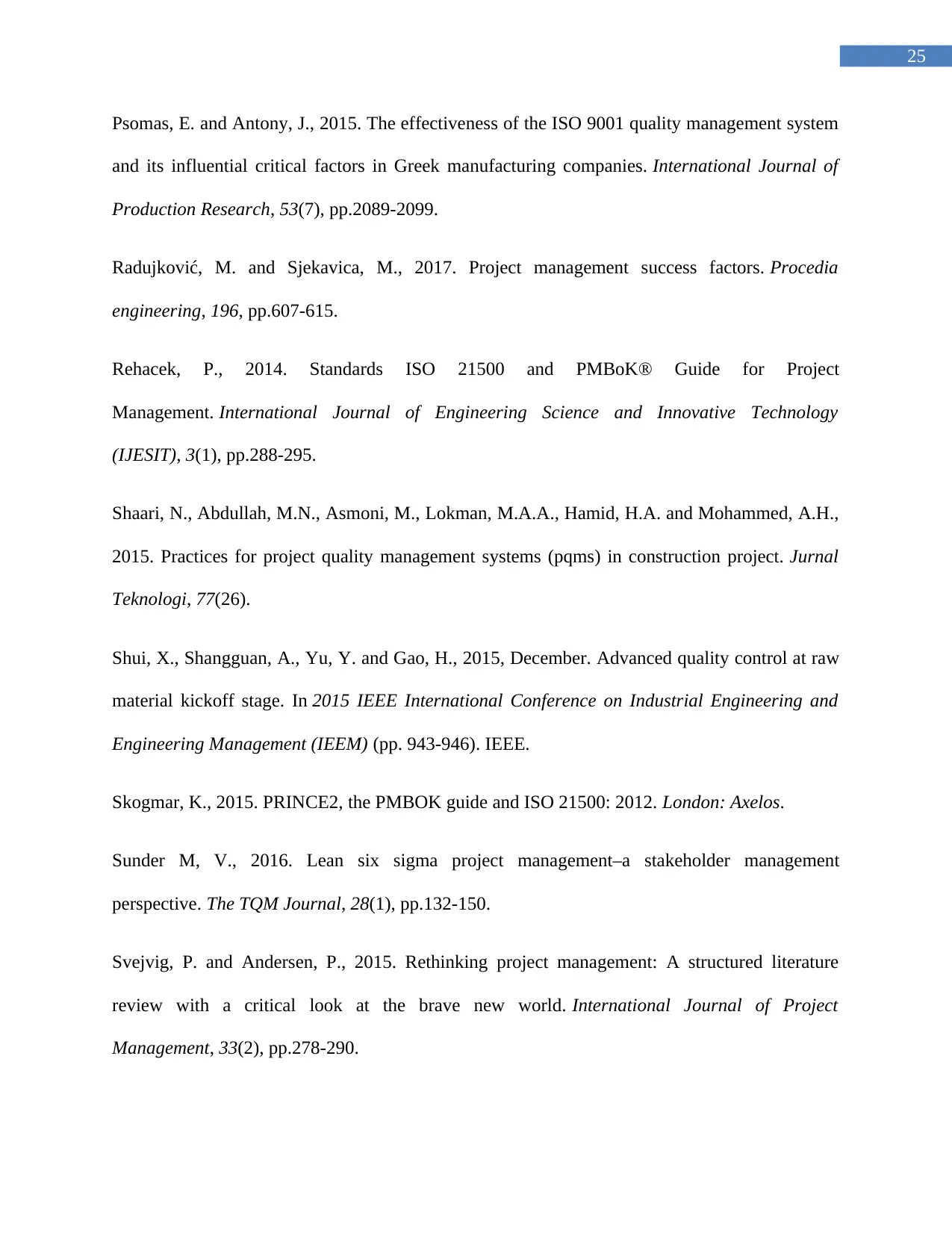
25
Psomas, E. and Antony, J., 2015. The effectiveness of the ISO 9001 quality management system
and its influential critical factors in Greek manufacturing companies. International Journal of
Production Research, 53(7), pp.2089-2099.
Radujković, M. and Sjekavica, M., 2017. Project management success factors. Procedia
engineering, 196, pp.607-615.
Rehacek, P., 2014. Standards ISO 21500 and PMBoK® Guide for Project
Management. International Journal of Engineering Science and Innovative Technology
(IJESIT), 3(1), pp.288-295.
Shaari, N., Abdullah, M.N., Asmoni, M., Lokman, M.A.A., Hamid, H.A. and Mohammed, A.H.,
2015. Practices for project quality management systems (pqms) in construction project. Jurnal
Teknologi, 77(26).
Shui, X., Shangguan, A., Yu, Y. and Gao, H., 2015, December. Advanced quality control at raw
material kickoff stage. In 2015 IEEE International Conference on Industrial Engineering and
Engineering Management (IEEM) (pp. 943-946). IEEE.
Skogmar, K., 2015. PRINCE2, the PMBOK guide and ISO 21500: 2012. London: Axelos.
Sunder M, V., 2016. Lean six sigma project management–a stakeholder management
perspective. The TQM Journal, 28(1), pp.132-150.
Svejvig, P. and Andersen, P., 2015. Rethinking project management: A structured literature
review with a critical look at the brave new world. International Journal of Project
Management, 33(2), pp.278-290.
Psomas, E. and Antony, J., 2015. The effectiveness of the ISO 9001 quality management system
and its influential critical factors in Greek manufacturing companies. International Journal of
Production Research, 53(7), pp.2089-2099.
Radujković, M. and Sjekavica, M., 2017. Project management success factors. Procedia
engineering, 196, pp.607-615.
Rehacek, P., 2014. Standards ISO 21500 and PMBoK® Guide for Project
Management. International Journal of Engineering Science and Innovative Technology
(IJESIT), 3(1), pp.288-295.
Shaari, N., Abdullah, M.N., Asmoni, M., Lokman, M.A.A., Hamid, H.A. and Mohammed, A.H.,
2015. Practices for project quality management systems (pqms) in construction project. Jurnal
Teknologi, 77(26).
Shui, X., Shangguan, A., Yu, Y. and Gao, H., 2015, December. Advanced quality control at raw
material kickoff stage. In 2015 IEEE International Conference on Industrial Engineering and
Engineering Management (IEEM) (pp. 943-946). IEEE.
Skogmar, K., 2015. PRINCE2, the PMBOK guide and ISO 21500: 2012. London: Axelos.
Sunder M, V., 2016. Lean six sigma project management–a stakeholder management
perspective. The TQM Journal, 28(1), pp.132-150.
Svejvig, P. and Andersen, P., 2015. Rethinking project management: A structured literature
review with a critical look at the brave new world. International Journal of Project
Management, 33(2), pp.278-290.
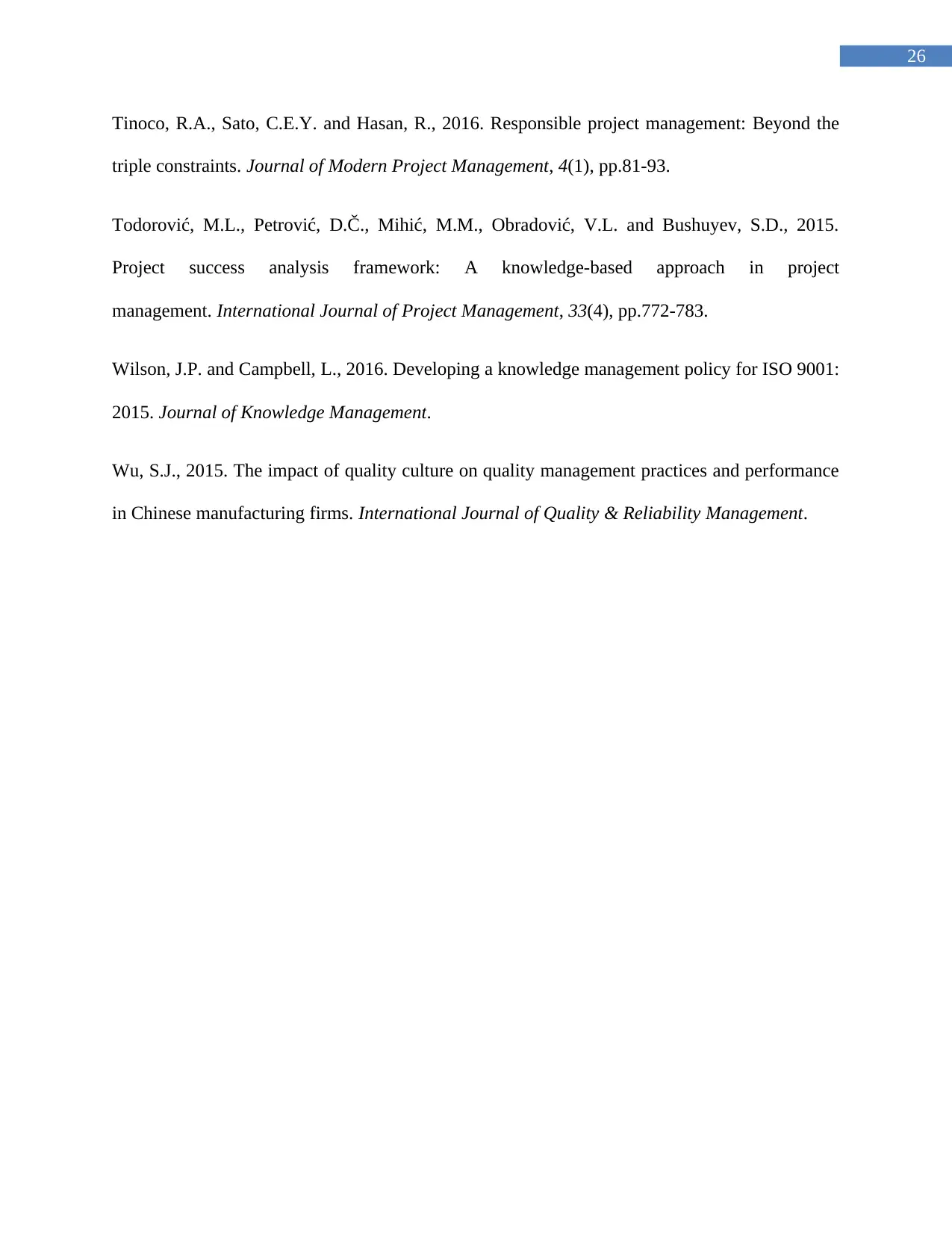
26
Tinoco, R.A., Sato, C.E.Y. and Hasan, R., 2016. Responsible project management: Beyond the
triple constraints. Journal of Modern Project Management, 4(1), pp.81-93.
Todorović, M.L., Petrović, D.Č., Mihić, M.M., Obradović, V.L. and Bushuyev, S.D., 2015.
Project success analysis framework: A knowledge-based approach in project
management. International Journal of Project Management, 33(4), pp.772-783.
Wilson, J.P. and Campbell, L., 2016. Developing a knowledge management policy for ISO 9001:
2015. Journal of Knowledge Management.
Wu, S.J., 2015. The impact of quality culture on quality management practices and performance
in Chinese manufacturing firms. International Journal of Quality & Reliability Management.
Tinoco, R.A., Sato, C.E.Y. and Hasan, R., 2016. Responsible project management: Beyond the
triple constraints. Journal of Modern Project Management, 4(1), pp.81-93.
Todorović, M.L., Petrović, D.Č., Mihić, M.M., Obradović, V.L. and Bushuyev, S.D., 2015.
Project success analysis framework: A knowledge-based approach in project
management. International Journal of Project Management, 33(4), pp.772-783.
Wilson, J.P. and Campbell, L., 2016. Developing a knowledge management policy for ISO 9001:
2015. Journal of Knowledge Management.
Wu, S.J., 2015. The impact of quality culture on quality management practices and performance
in Chinese manufacturing firms. International Journal of Quality & Reliability Management.
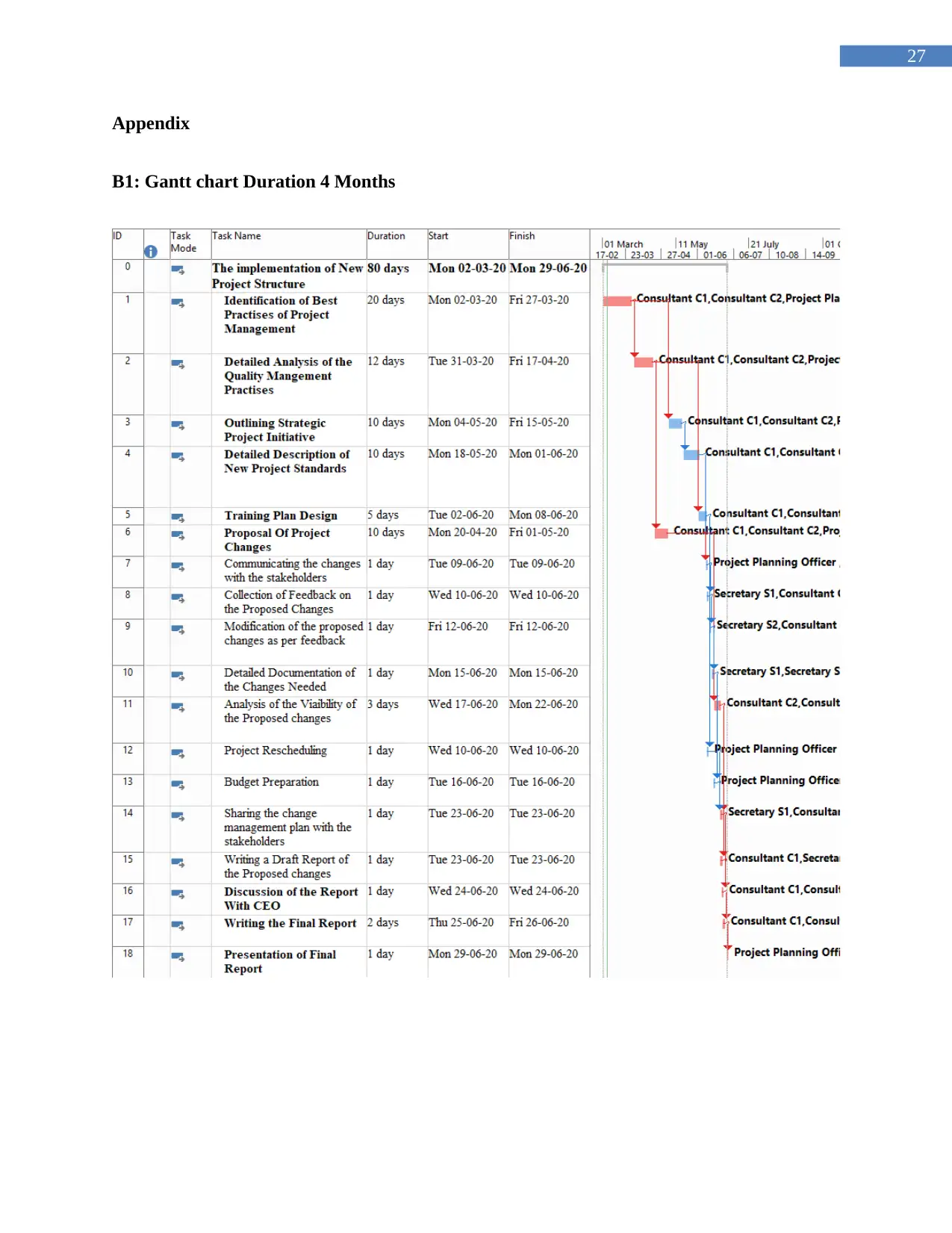
27
Appendix
B1: Gantt chart Duration 4 Months
Appendix
B1: Gantt chart Duration 4 Months
Secure Best Marks with AI Grader
Need help grading? Try our AI Grader for instant feedback on your assignments.
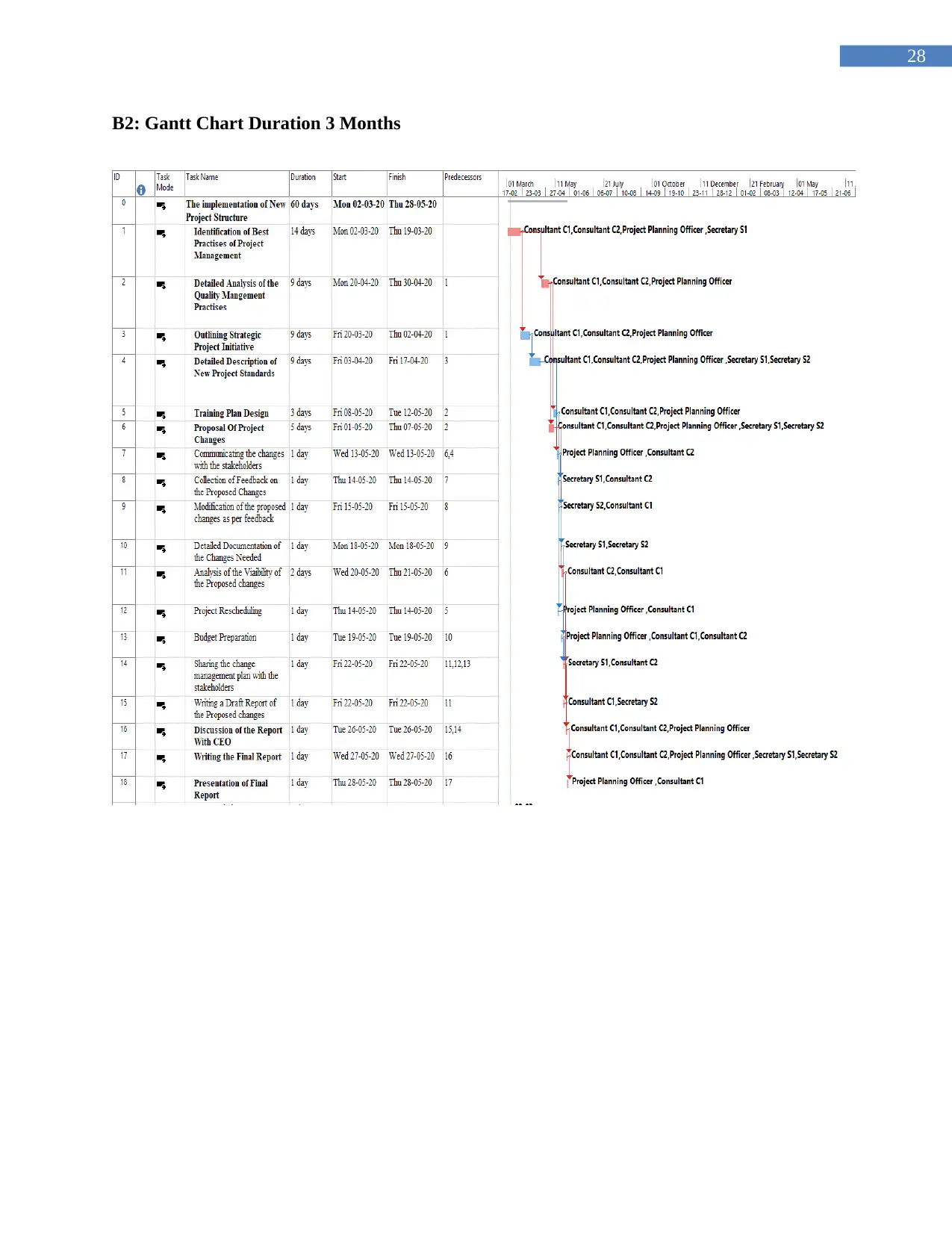
28
B2: Gantt Chart Duration 3 Months
B2: Gantt Chart Duration 3 Months
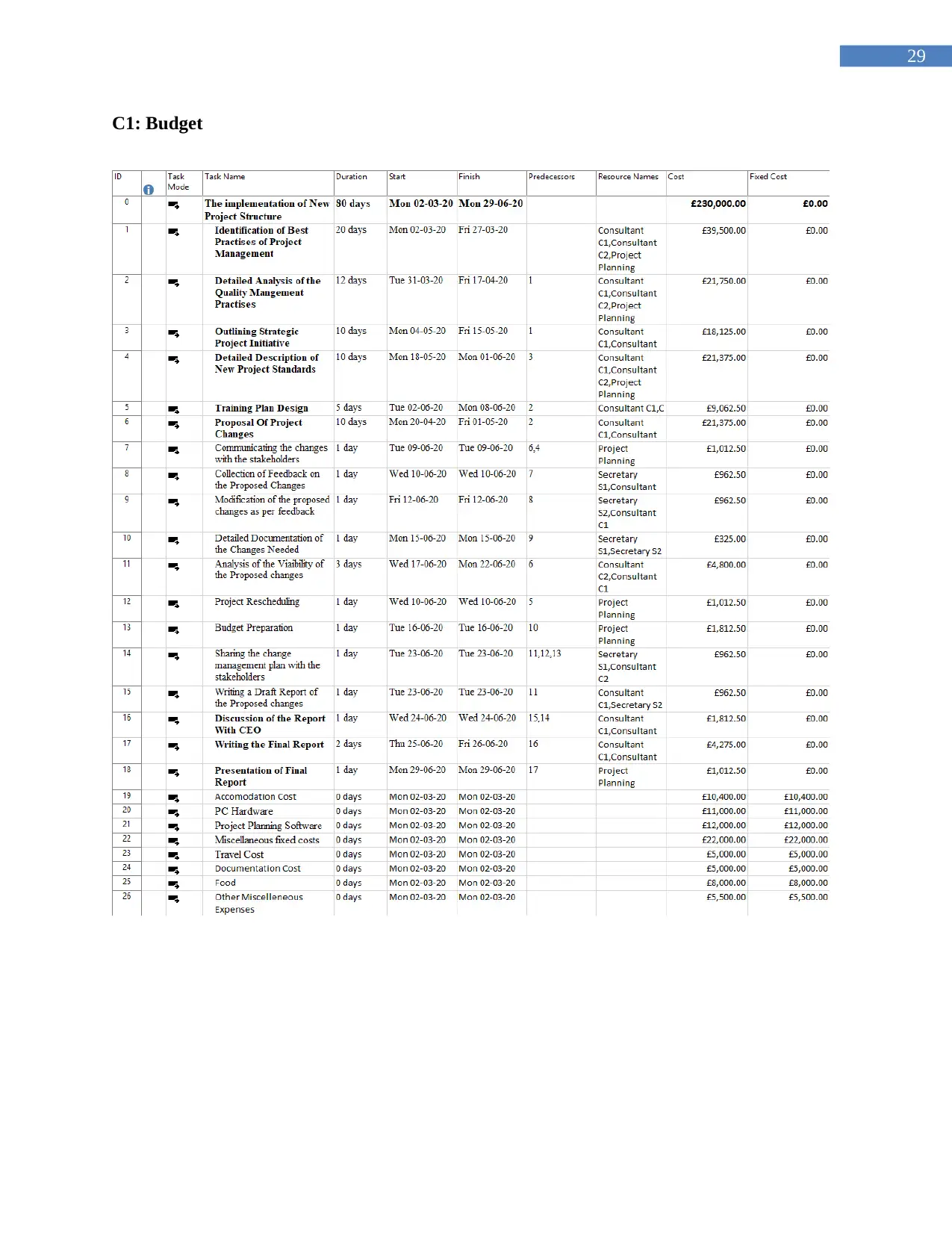
29
C1: Budget
C1: Budget
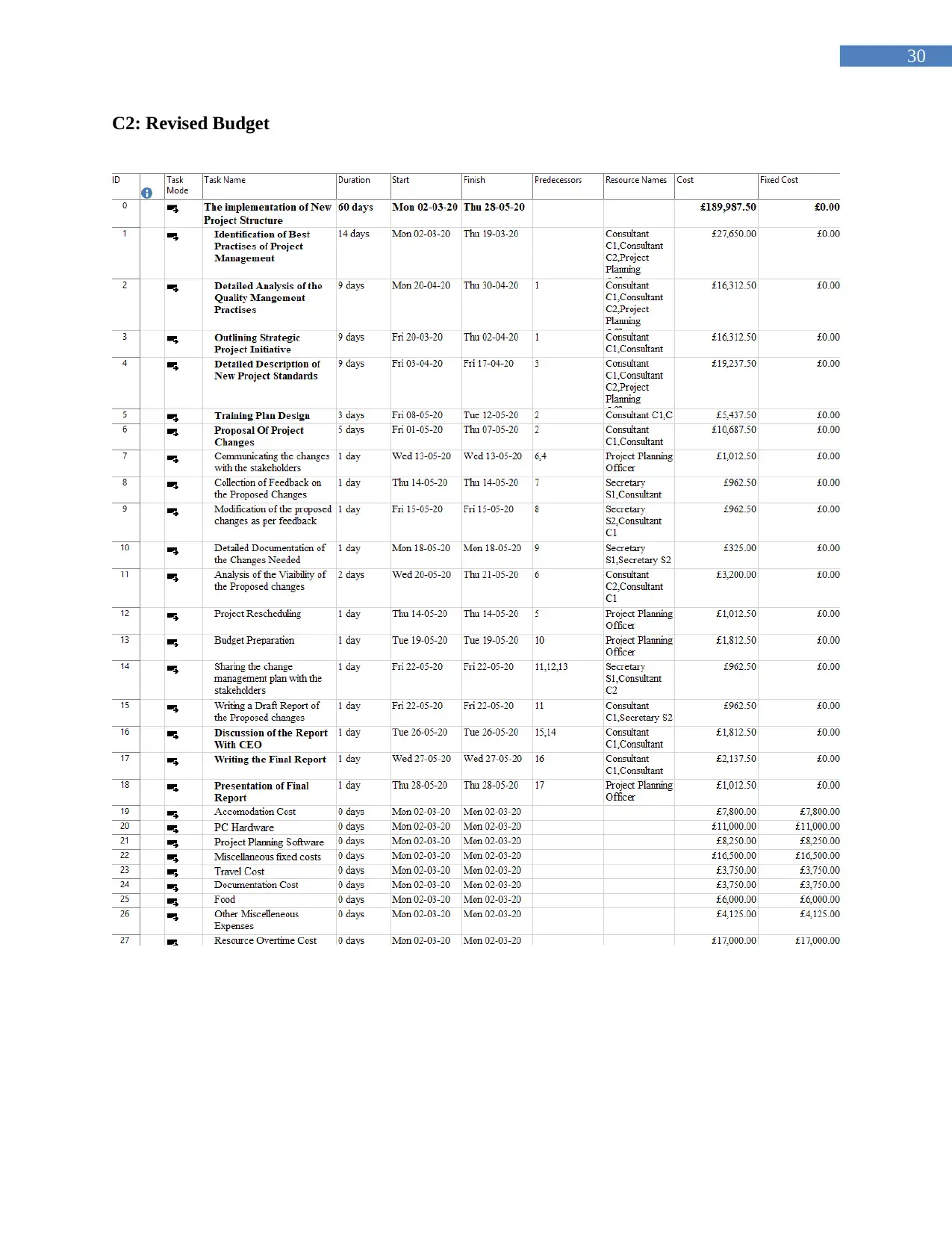
30
C2: Revised Budget
C2: Revised Budget
1 out of 31
Related Documents

Your All-in-One AI-Powered Toolkit for Academic Success.
+13062052269
info@desklib.com
Available 24*7 on WhatsApp / Email
Unlock your academic potential
© 2024 | Zucol Services PVT LTD | All rights reserved.