Project Plan for Swedish Recycling Vehicles in Fingal Residential Area
VerifiedAdded on 2021/09/13
|17
|4214
|24
Report
AI Summary
This project plan outlines the implementation of Swedish recycling vehicles in the Fingal residential area, focusing on enhancing productivity and efficiency through automated trucks. The project aims to address the challenges of operating traditional recycling vehicles on narrow roads by introducin...
Read More
Contribute Materials
Your contribution can guide someone’s learning journey. Share your
documents today.
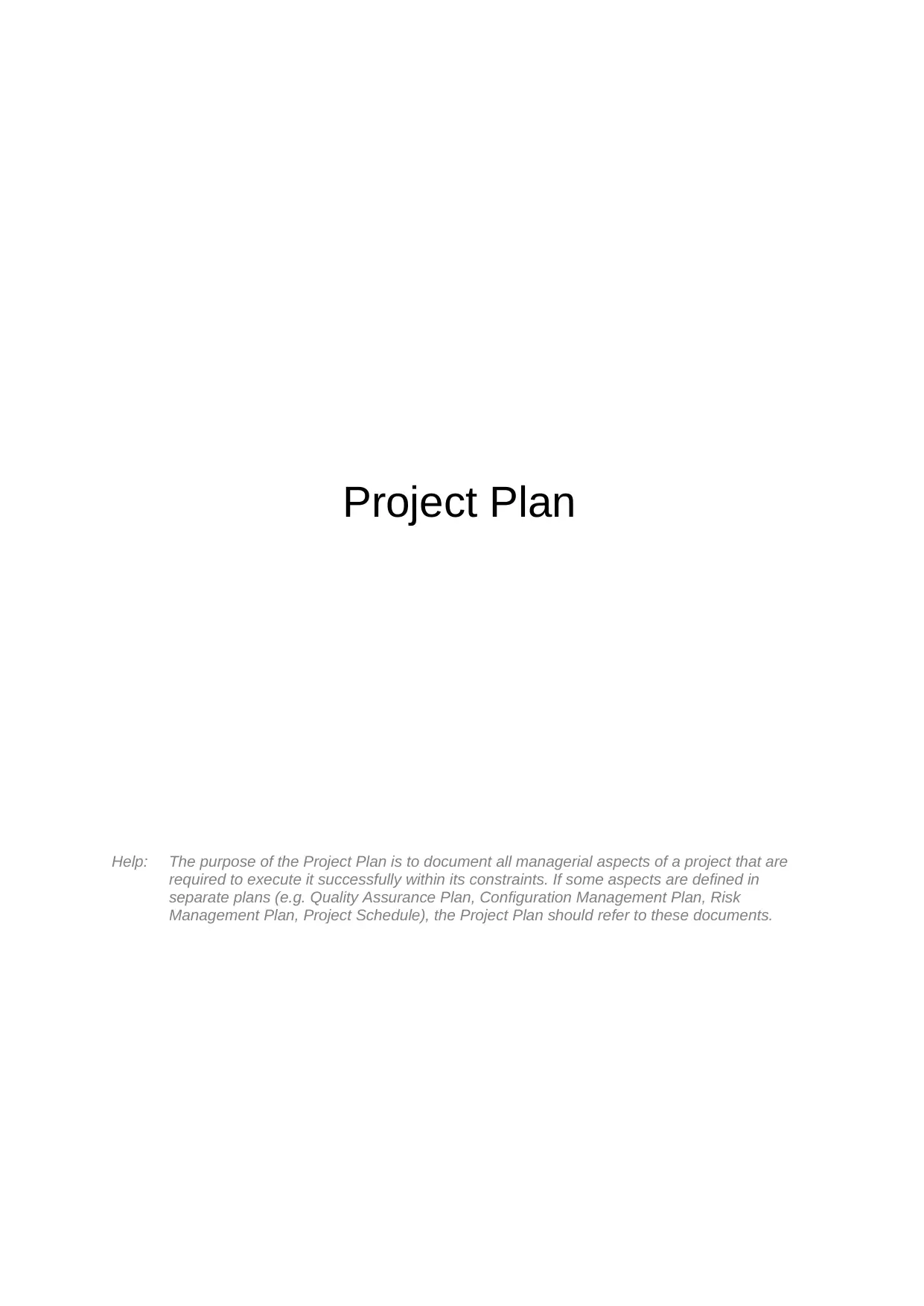
Project Plan
Help: The purpose of the Project Plan is to document all managerial aspects of a project that are
required to execute it successfully within its constraints. If some aspects are defined in
separate plans (e.g. Quality Assurance Plan, Configuration Management Plan, Risk
Management Plan, Project Schedule), the Project Plan should refer to these documents.
Help: The purpose of the Project Plan is to document all managerial aspects of a project that are
required to execute it successfully within its constraints. If some aspects are defined in
separate plans (e.g. Quality Assurance Plan, Configuration Management Plan, Risk
Management Plan, Project Schedule), the Project Plan should refer to these documents.
Secure Best Marks with AI Grader
Need help grading? Try our AI Grader for instant feedback on your assignments.
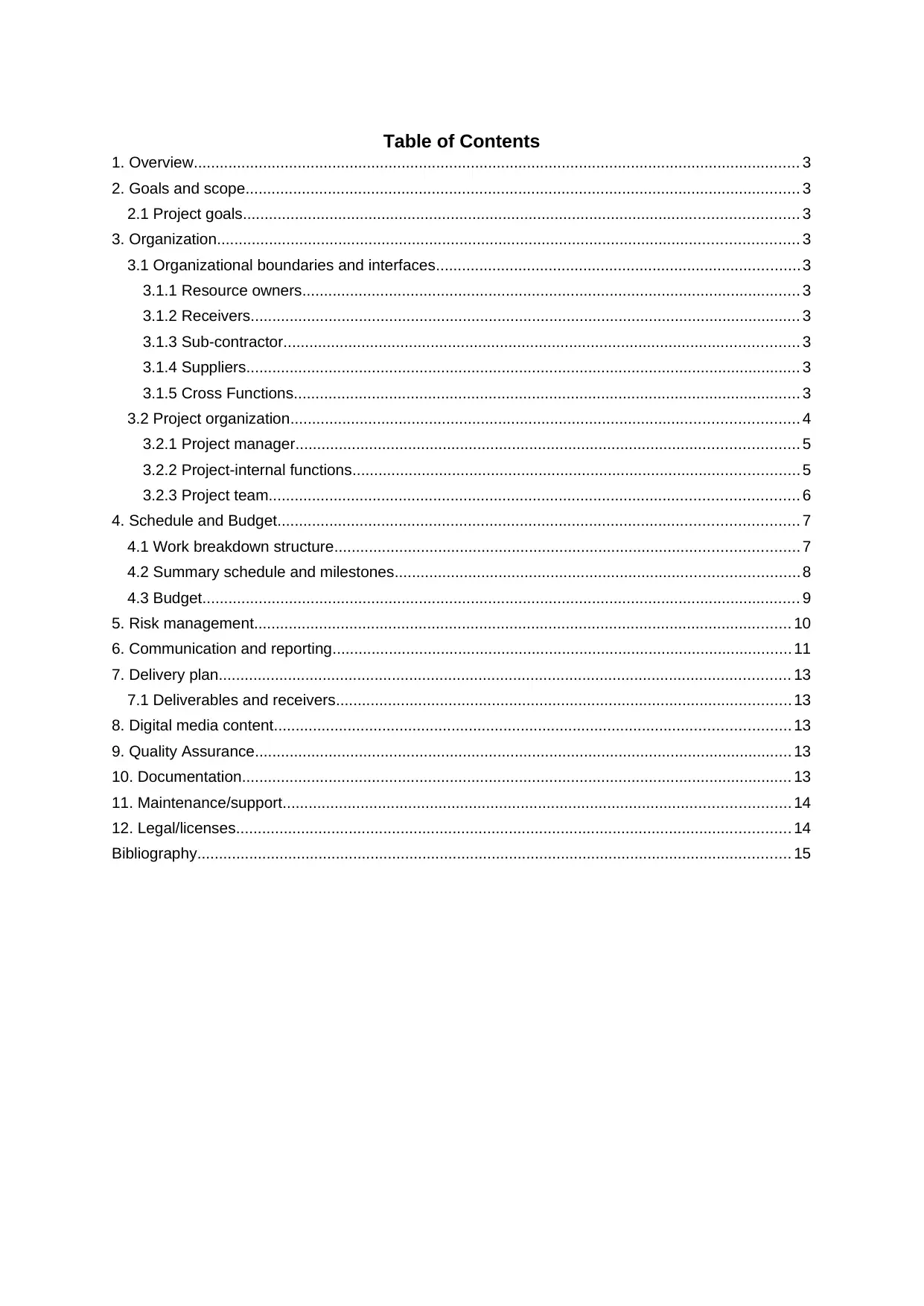
Table of Contents
1. Overview............................................................................................................................................ 3
2. Goals and scope................................................................................................................................ 3
2.1 Project goals................................................................................................................................ 3
3. Organization...................................................................................................................................... 3
3.1 Organizational boundaries and interfaces....................................................................................3
3.1.1 Resource owners................................................................................................................... 3
3.1.2 Receivers............................................................................................................................... 3
3.1.3 Sub-contractor....................................................................................................................... 3
3.1.4 Suppliers................................................................................................................................ 3
3.1.5 Cross Functions..................................................................................................................... 3
3.2 Project organization..................................................................................................................... 4
3.2.1 Project manager.................................................................................................................... 5
3.2.2 Project-internal functions....................................................................................................... 5
3.2.3 Project team.......................................................................................................................... 6
4. Schedule and Budget........................................................................................................................ 7
4.1 Work breakdown structure........................................................................................................... 7
4.2 Summary schedule and milestones............................................................................................. 8
4.3 Budget.......................................................................................................................................... 9
5. Risk management............................................................................................................................ 10
6. Communication and reporting.......................................................................................................... 11
7. Delivery plan.................................................................................................................................... 13
7.1 Deliverables and receivers......................................................................................................... 13
8. Digital media content....................................................................................................................... 13
9. Quality Assurance............................................................................................................................ 13
10. Documentation............................................................................................................................... 13
11. Maintenance/support..................................................................................................................... 14
12. Legal/licenses................................................................................................................................ 14
Bibliography......................................................................................................................................... 15
1. Overview............................................................................................................................................ 3
2. Goals and scope................................................................................................................................ 3
2.1 Project goals................................................................................................................................ 3
3. Organization...................................................................................................................................... 3
3.1 Organizational boundaries and interfaces....................................................................................3
3.1.1 Resource owners................................................................................................................... 3
3.1.2 Receivers............................................................................................................................... 3
3.1.3 Sub-contractor....................................................................................................................... 3
3.1.4 Suppliers................................................................................................................................ 3
3.1.5 Cross Functions..................................................................................................................... 3
3.2 Project organization..................................................................................................................... 4
3.2.1 Project manager.................................................................................................................... 5
3.2.2 Project-internal functions....................................................................................................... 5
3.2.3 Project team.......................................................................................................................... 6
4. Schedule and Budget........................................................................................................................ 7
4.1 Work breakdown structure........................................................................................................... 7
4.2 Summary schedule and milestones............................................................................................. 8
4.3 Budget.......................................................................................................................................... 9
5. Risk management............................................................................................................................ 10
6. Communication and reporting.......................................................................................................... 11
7. Delivery plan.................................................................................................................................... 13
7.1 Deliverables and receivers......................................................................................................... 13
8. Digital media content....................................................................................................................... 13
9. Quality Assurance............................................................................................................................ 13
10. Documentation............................................................................................................................... 13
11. Maintenance/support..................................................................................................................... 14
12. Legal/licenses................................................................................................................................ 14
Bibliography......................................................................................................................................... 15
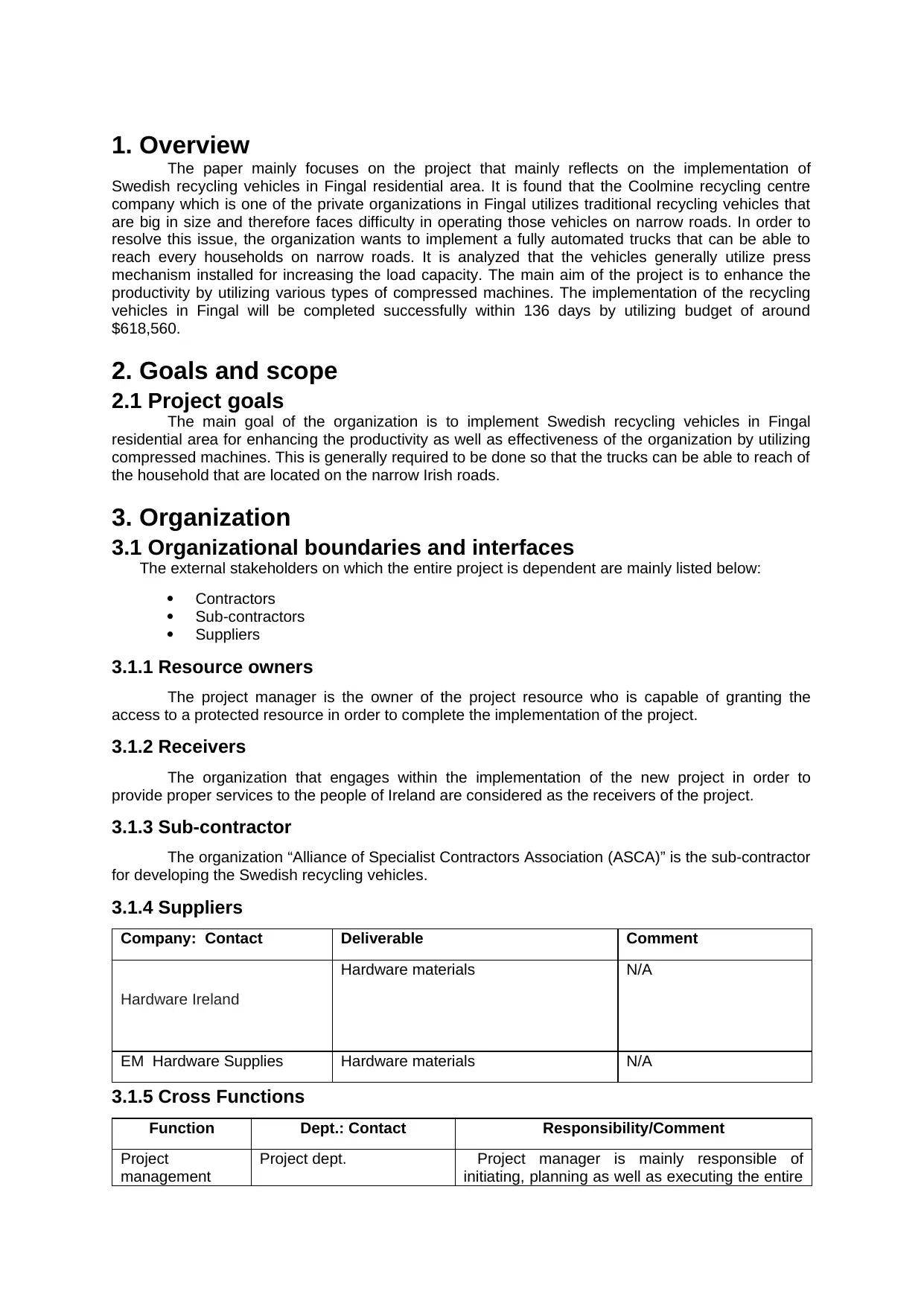
1. Overview
The paper mainly focuses on the project that mainly reflects on the implementation of
Swedish recycling vehicles in Fingal residential area. It is found that the Coolmine recycling centre
company which is one of the private organizations in Fingal utilizes traditional recycling vehicles that
are big in size and therefore faces difficulty in operating those vehicles on narrow roads. In order to
resolve this issue, the organization wants to implement a fully automated trucks that can be able to
reach every households on narrow roads. It is analyzed that the vehicles generally utilize press
mechanism installed for increasing the load capacity. The main aim of the project is to enhance the
productivity by utilizing various types of compressed machines. The implementation of the recycling
vehicles in Fingal will be completed successfully within 136 days by utilizing budget of around
$618,560.
2. Goals and scope
2.1 Project goals
The main goal of the organization is to implement Swedish recycling vehicles in Fingal
residential area for enhancing the productivity as well as effectiveness of the organization by utilizing
compressed machines. This is generally required to be done so that the trucks can be able to reach of
the household that are located on the narrow Irish roads.
3. Organization
3.1 Organizational boundaries and interfaces
The external stakeholders on which the entire project is dependent are mainly listed below:
Contractors
Sub-contractors
Suppliers
3.1.1 Resource owners
The project manager is the owner of the project resource who is capable of granting the
access to a protected resource in order to complete the implementation of the project.
3.1.2 Receivers
The organization that engages within the implementation of the new project in order to
provide proper services to the people of Ireland are considered as the receivers of the project.
3.1.3 Sub-contractor
The organization “Alliance of Specialist Contractors Association (ASCA)” is the sub-contractor
for developing the Swedish recycling vehicles.
3.1.4 Suppliers
Company: Contact Deliverable Comment
Hardware Ireland
Hardware materials N/A
EM Hardware Supplies Hardware materials N/A
3.1.5 Cross Functions
Function Dept.: Contact Responsibility/Comment
Project
management
Project dept. Project manager is mainly responsible of
initiating, planning as well as executing the entire
The paper mainly focuses on the project that mainly reflects on the implementation of
Swedish recycling vehicles in Fingal residential area. It is found that the Coolmine recycling centre
company which is one of the private organizations in Fingal utilizes traditional recycling vehicles that
are big in size and therefore faces difficulty in operating those vehicles on narrow roads. In order to
resolve this issue, the organization wants to implement a fully automated trucks that can be able to
reach every households on narrow roads. It is analyzed that the vehicles generally utilize press
mechanism installed for increasing the load capacity. The main aim of the project is to enhance the
productivity by utilizing various types of compressed machines. The implementation of the recycling
vehicles in Fingal will be completed successfully within 136 days by utilizing budget of around
$618,560.
2. Goals and scope
2.1 Project goals
The main goal of the organization is to implement Swedish recycling vehicles in Fingal
residential area for enhancing the productivity as well as effectiveness of the organization by utilizing
compressed machines. This is generally required to be done so that the trucks can be able to reach of
the household that are located on the narrow Irish roads.
3. Organization
3.1 Organizational boundaries and interfaces
The external stakeholders on which the entire project is dependent are mainly listed below:
Contractors
Sub-contractors
Suppliers
3.1.1 Resource owners
The project manager is the owner of the project resource who is capable of granting the
access to a protected resource in order to complete the implementation of the project.
3.1.2 Receivers
The organization that engages within the implementation of the new project in order to
provide proper services to the people of Ireland are considered as the receivers of the project.
3.1.3 Sub-contractor
The organization “Alliance of Specialist Contractors Association (ASCA)” is the sub-contractor
for developing the Swedish recycling vehicles.
3.1.4 Suppliers
Company: Contact Deliverable Comment
Hardware Ireland
Hardware materials N/A
EM Hardware Supplies Hardware materials N/A
3.1.5 Cross Functions
Function Dept.: Contact Responsibility/Comment
Project
management
Project dept. Project manager is mainly responsible of
initiating, planning as well as executing the entire
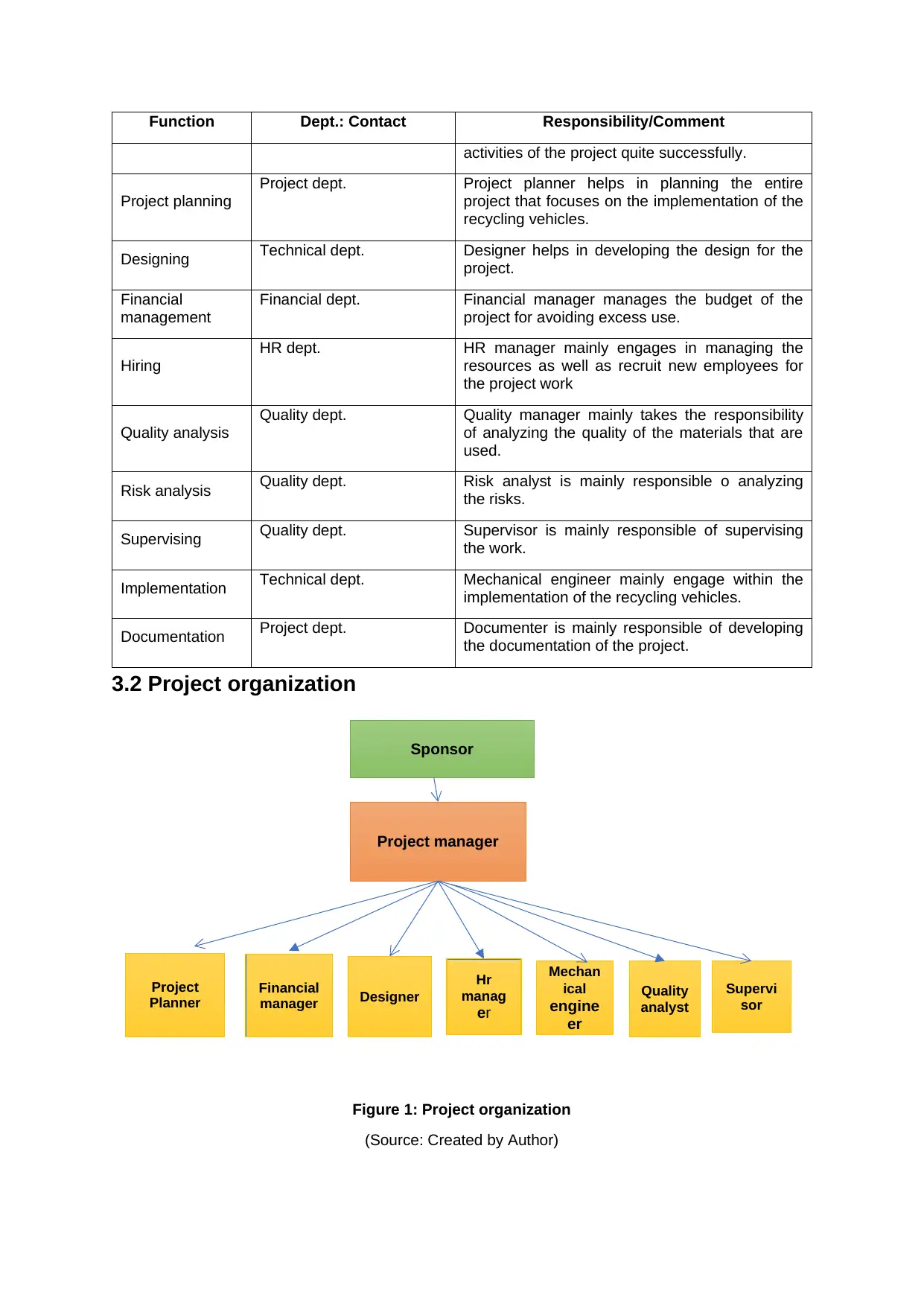
Sponsor
Project
Planner Designer
Mechan
ical
engine
er
Supervi
sor
Project manager
Financial
manager
Hr
manag
er
Quality
analyst
Function Dept.: Contact Responsibility/Comment
activities of the project quite successfully.
Project planning
Project dept. Project planner helps in planning the entire
project that focuses on the implementation of the
recycling vehicles.
Designing Technical dept. Designer helps in developing the design for the
project.
Financial
management
Financial dept. Financial manager manages the budget of the
project for avoiding excess use.
Hiring
HR dept. HR manager mainly engages in managing the
resources as well as recruit new employees for
the project work
Quality analysis
Quality dept. Quality manager mainly takes the responsibility
of analyzing the quality of the materials that are
used.
Risk analysis Quality dept. Risk analyst is mainly responsible o analyzing
the risks.
Supervising Quality dept. Supervisor is mainly responsible of supervising
the work.
Implementation Technical dept. Mechanical engineer mainly engage within the
implementation of the recycling vehicles.
Documentation Project dept. Documenter is mainly responsible of developing
the documentation of the project.
3.2 Project organization
Figure 1: Project organization
(Source: Created by Author)
Project
Planner Designer
Mechan
ical
engine
er
Supervi
sor
Project manager
Financial
manager
Hr
manag
er
Quality
analyst
Function Dept.: Contact Responsibility/Comment
activities of the project quite successfully.
Project planning
Project dept. Project planner helps in planning the entire
project that focuses on the implementation of the
recycling vehicles.
Designing Technical dept. Designer helps in developing the design for the
project.
Financial
management
Financial dept. Financial manager manages the budget of the
project for avoiding excess use.
Hiring
HR dept. HR manager mainly engages in managing the
resources as well as recruit new employees for
the project work
Quality analysis
Quality dept. Quality manager mainly takes the responsibility
of analyzing the quality of the materials that are
used.
Risk analysis Quality dept. Risk analyst is mainly responsible o analyzing
the risks.
Supervising Quality dept. Supervisor is mainly responsible of supervising
the work.
Implementation Technical dept. Mechanical engineer mainly engage within the
implementation of the recycling vehicles.
Documentation Project dept. Documenter is mainly responsible of developing
the documentation of the project.
3.2 Project organization
Figure 1: Project organization
(Source: Created by Author)
Secure Best Marks with AI Grader
Need help grading? Try our AI Grader for instant feedback on your assignments.
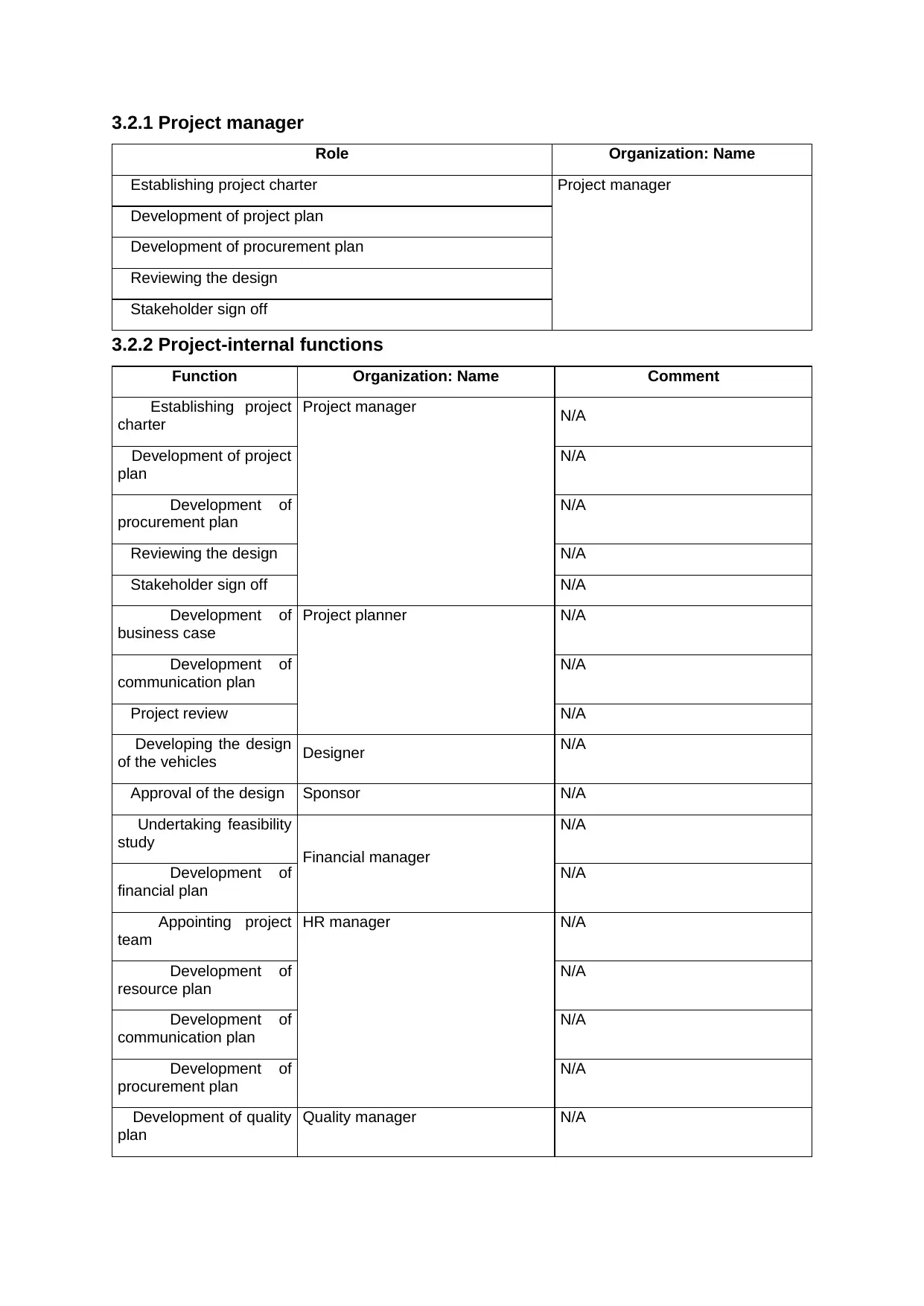
3.2.1 Project manager
Role Organization: Name
Establishing project charter Project manager
Development of project plan
Development of procurement plan
Reviewing the design
Stakeholder sign off
3.2.2 Project-internal functions
Function Organization: Name Comment
Establishing project
charter
Project manager N/A
Development of project
plan
N/A
Development of
procurement plan
N/A
Reviewing the design N/A
Stakeholder sign off N/A
Development of
business case
Project planner N/A
Development of
communication plan
N/A
Project review N/A
Developing the design
of the vehicles Designer N/A
Approval of the design Sponsor N/A
Undertaking feasibility
study Financial manager
N/A
Development of
financial plan
N/A
Appointing project
team
HR manager N/A
Development of
resource plan
N/A
Development of
communication plan
N/A
Development of
procurement plan
N/A
Development of quality
plan
Quality manager N/A
Role Organization: Name
Establishing project charter Project manager
Development of project plan
Development of procurement plan
Reviewing the design
Stakeholder sign off
3.2.2 Project-internal functions
Function Organization: Name Comment
Establishing project
charter
Project manager N/A
Development of project
plan
N/A
Development of
procurement plan
N/A
Reviewing the design N/A
Stakeholder sign off N/A
Development of
business case
Project planner N/A
Development of
communication plan
N/A
Project review N/A
Developing the design
of the vehicles Designer N/A
Approval of the design Sponsor N/A
Undertaking feasibility
study Financial manager
N/A
Development of
financial plan
N/A
Appointing project
team
HR manager N/A
Development of
resource plan
N/A
Development of
communication plan
N/A
Development of
procurement plan
N/A
Development of quality
plan
Quality manager N/A
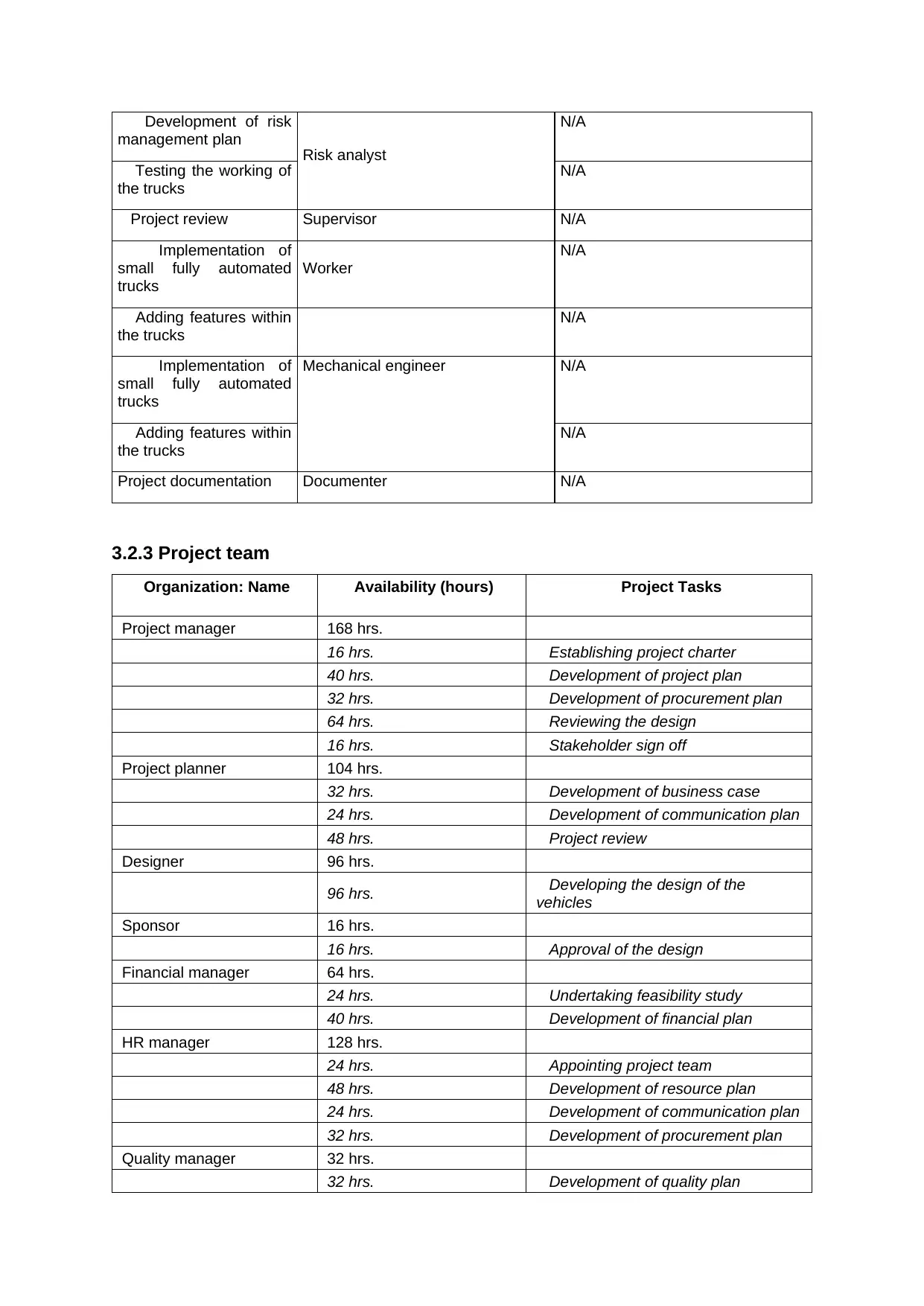
Development of risk
management plan Risk analyst
N/A
Testing the working of
the trucks
N/A
Project review Supervisor N/A
Implementation of
small fully automated
trucks
Worker
N/A
Adding features within
the trucks
N/A
Implementation of
small fully automated
trucks
Mechanical engineer N/A
Adding features within
the trucks
N/A
Project documentation Documenter N/A
3.2.3 Project team
Organization: Name Availability (hours) Project Tasks
Project manager 168 hrs.
16 hrs. Establishing project charter
40 hrs. Development of project plan
32 hrs. Development of procurement plan
64 hrs. Reviewing the design
16 hrs. Stakeholder sign off
Project planner 104 hrs.
32 hrs. Development of business case
24 hrs. Development of communication plan
48 hrs. Project review
Designer 96 hrs.
96 hrs. Developing the design of the
vehicles
Sponsor 16 hrs.
16 hrs. Approval of the design
Financial manager 64 hrs.
24 hrs. Undertaking feasibility study
40 hrs. Development of financial plan
HR manager 128 hrs.
24 hrs. Appointing project team
48 hrs. Development of resource plan
24 hrs. Development of communication plan
32 hrs. Development of procurement plan
Quality manager 32 hrs.
32 hrs. Development of quality plan
management plan Risk analyst
N/A
Testing the working of
the trucks
N/A
Project review Supervisor N/A
Implementation of
small fully automated
trucks
Worker
N/A
Adding features within
the trucks
N/A
Implementation of
small fully automated
trucks
Mechanical engineer N/A
Adding features within
the trucks
N/A
Project documentation Documenter N/A
3.2.3 Project team
Organization: Name Availability (hours) Project Tasks
Project manager 168 hrs.
16 hrs. Establishing project charter
40 hrs. Development of project plan
32 hrs. Development of procurement plan
64 hrs. Reviewing the design
16 hrs. Stakeholder sign off
Project planner 104 hrs.
32 hrs. Development of business case
24 hrs. Development of communication plan
48 hrs. Project review
Designer 96 hrs.
96 hrs. Developing the design of the
vehicles
Sponsor 16 hrs.
16 hrs. Approval of the design
Financial manager 64 hrs.
24 hrs. Undertaking feasibility study
40 hrs. Development of financial plan
HR manager 128 hrs.
24 hrs. Appointing project team
48 hrs. Development of resource plan
24 hrs. Development of communication plan
32 hrs. Development of procurement plan
Quality manager 32 hrs.
32 hrs. Development of quality plan
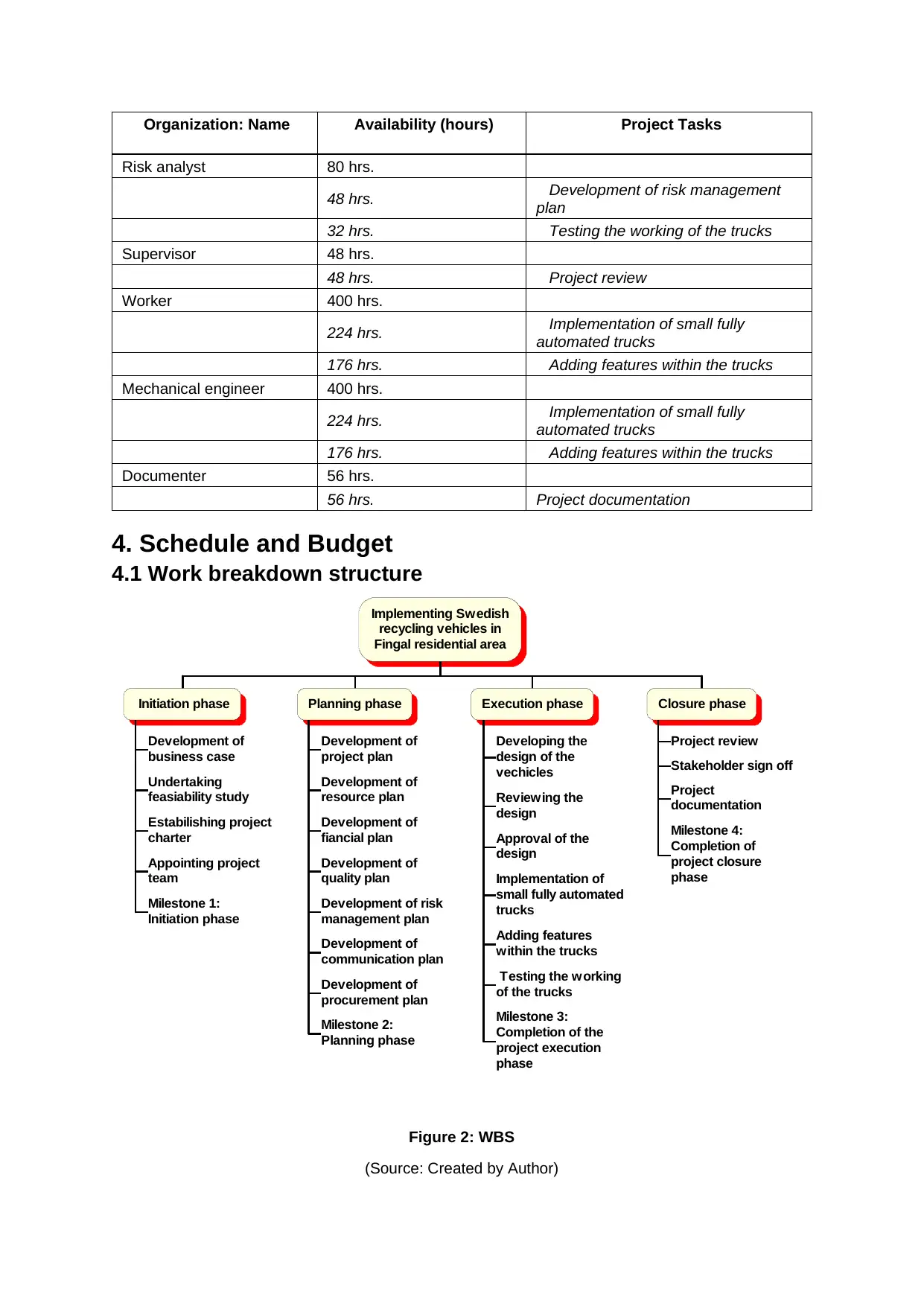
Organization: Name Availability (hours) Project Tasks
Risk analyst 80 hrs.
48 hrs. Development of risk management
plan
32 hrs. Testing the working of the trucks
Supervisor 48 hrs.
48 hrs. Project review
Worker 400 hrs.
224 hrs. Implementation of small fully
automated trucks
176 hrs. Adding features within the trucks
Mechanical engineer 400 hrs.
224 hrs. Implementation of small fully
automated trucks
176 hrs. Adding features within the trucks
Documenter 56 hrs.
56 hrs. Project documentation
4. Schedule and Budget
4.1 Work breakdown structure
Implementing Swedish
recycling vehicles in
Fingal residential area
Initiation phase
Development of
business case
Undertaking
feasiability study
Estabilishing project
charter
Appointing project
team
Milestone 1:
Initiation phase
Planning phase
Development of
project plan
Development of
resource plan
Development of
fiancial plan
Development of
quality plan
Development of risk
management plan
Development of
communication plan
Development of
procurement plan
Milestone 2:
Planning phase
Execution phase
Developing the
design of the
vechicles
Reviewing the
design
Approval of the
design
Implementation of
small fully automated
trucks
Adding features
within the trucks
Testing the working
of the trucks
Milestone 3:
Completion of the
project execution
phase
Closure phase
Project review
Stakeholder sign off
Project
documentation
Milestone 4:
Completion of
project closure
phase
Figure 2: WBS
(Source: Created by Author)
Risk analyst 80 hrs.
48 hrs. Development of risk management
plan
32 hrs. Testing the working of the trucks
Supervisor 48 hrs.
48 hrs. Project review
Worker 400 hrs.
224 hrs. Implementation of small fully
automated trucks
176 hrs. Adding features within the trucks
Mechanical engineer 400 hrs.
224 hrs. Implementation of small fully
automated trucks
176 hrs. Adding features within the trucks
Documenter 56 hrs.
56 hrs. Project documentation
4. Schedule and Budget
4.1 Work breakdown structure
Implementing Swedish
recycling vehicles in
Fingal residential area
Initiation phase
Development of
business case
Undertaking
feasiability study
Estabilishing project
charter
Appointing project
team
Milestone 1:
Initiation phase
Planning phase
Development of
project plan
Development of
resource plan
Development of
fiancial plan
Development of
quality plan
Development of risk
management plan
Development of
communication plan
Development of
procurement plan
Milestone 2:
Planning phase
Execution phase
Developing the
design of the
vechicles
Reviewing the
design
Approval of the
design
Implementation of
small fully automated
trucks
Adding features
within the trucks
Testing the working
of the trucks
Milestone 3:
Completion of the
project execution
phase
Closure phase
Project review
Stakeholder sign off
Project
documentation
Milestone 4:
Completion of
project closure
phase
Figure 2: WBS
(Source: Created by Author)
Paraphrase This Document
Need a fresh take? Get an instant paraphrase of this document with our AI Paraphraser
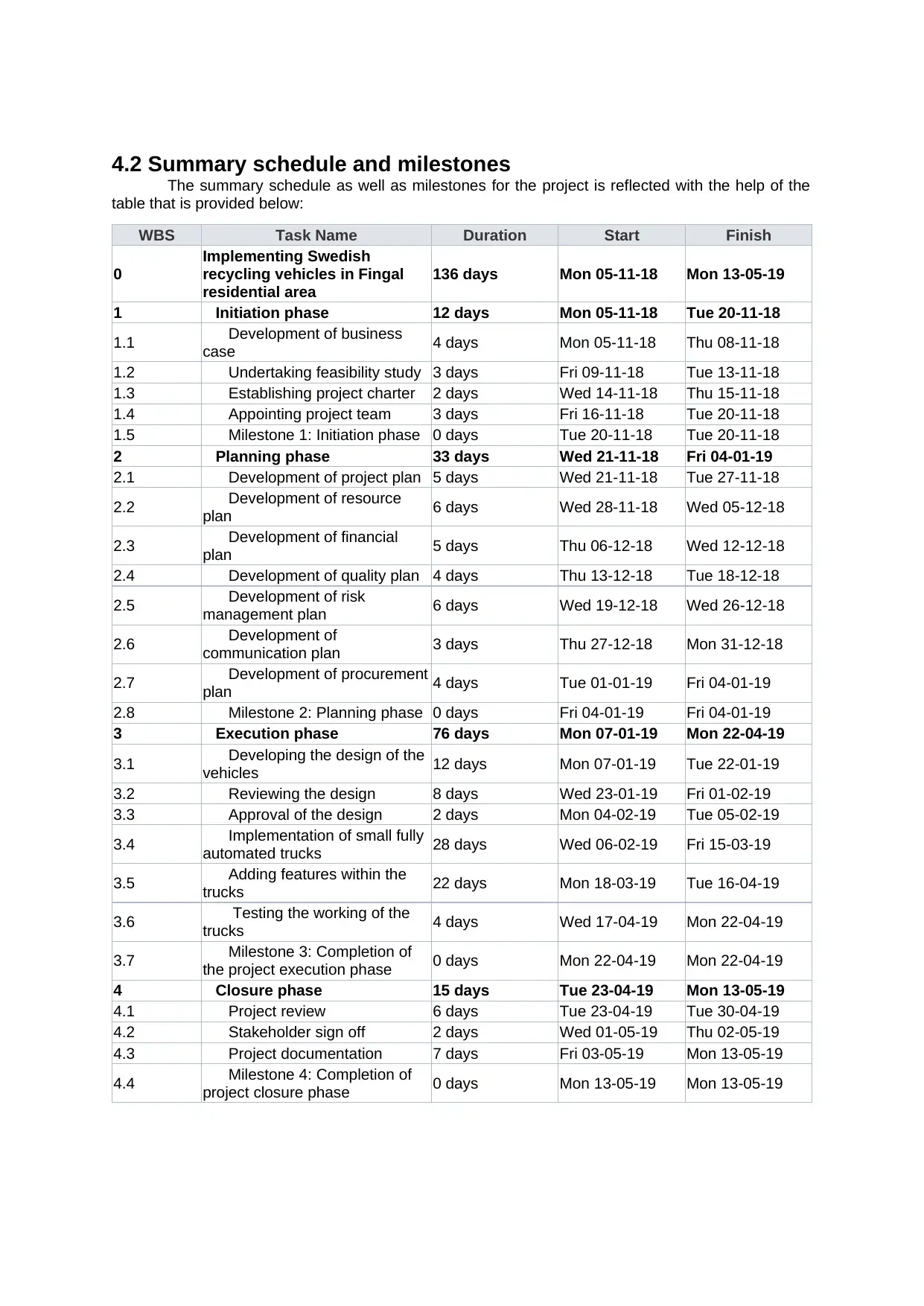
4.2 Summary schedule and milestones
The summary schedule as well as milestones for the project is reflected with the help of the
table that is provided below:
WBS Task Name Duration Start Finish
0
Implementing Swedish
recycling vehicles in Fingal
residential area
136 days Mon 05-11-18 Mon 13-05-19
1 Initiation phase 12 days Mon 05-11-18 Tue 20-11-18
1.1 Development of business
case 4 days Mon 05-11-18 Thu 08-11-18
1.2 Undertaking feasibility study 3 days Fri 09-11-18 Tue 13-11-18
1.3 Establishing project charter 2 days Wed 14-11-18 Thu 15-11-18
1.4 Appointing project team 3 days Fri 16-11-18 Tue 20-11-18
1.5 Milestone 1: Initiation phase 0 days Tue 20-11-18 Tue 20-11-18
2 Planning phase 33 days Wed 21-11-18 Fri 04-01-19
2.1 Development of project plan 5 days Wed 21-11-18 Tue 27-11-18
2.2 Development of resource
plan 6 days Wed 28-11-18 Wed 05-12-18
2.3 Development of financial
plan 5 days Thu 06-12-18 Wed 12-12-18
2.4 Development of quality plan 4 days Thu 13-12-18 Tue 18-12-18
2.5 Development of risk
management plan 6 days Wed 19-12-18 Wed 26-12-18
2.6 Development of
communication plan 3 days Thu 27-12-18 Mon 31-12-18
2.7 Development of procurement
plan 4 days Tue 01-01-19 Fri 04-01-19
2.8 Milestone 2: Planning phase 0 days Fri 04-01-19 Fri 04-01-19
3 Execution phase 76 days Mon 07-01-19 Mon 22-04-19
3.1 Developing the design of the
vehicles 12 days Mon 07-01-19 Tue 22-01-19
3.2 Reviewing the design 8 days Wed 23-01-19 Fri 01-02-19
3.3 Approval of the design 2 days Mon 04-02-19 Tue 05-02-19
3.4 Implementation of small fully
automated trucks 28 days Wed 06-02-19 Fri 15-03-19
3.5 Adding features within the
trucks 22 days Mon 18-03-19 Tue 16-04-19
3.6 Testing the working of the
trucks 4 days Wed 17-04-19 Mon 22-04-19
3.7 Milestone 3: Completion of
the project execution phase 0 days Mon 22-04-19 Mon 22-04-19
4 Closure phase 15 days Tue 23-04-19 Mon 13-05-19
4.1 Project review 6 days Tue 23-04-19 Tue 30-04-19
4.2 Stakeholder sign off 2 days Wed 01-05-19 Thu 02-05-19
4.3 Project documentation 7 days Fri 03-05-19 Mon 13-05-19
4.4 Milestone 4: Completion of
project closure phase 0 days Mon 13-05-19 Mon 13-05-19
The summary schedule as well as milestones for the project is reflected with the help of the
table that is provided below:
WBS Task Name Duration Start Finish
0
Implementing Swedish
recycling vehicles in Fingal
residential area
136 days Mon 05-11-18 Mon 13-05-19
1 Initiation phase 12 days Mon 05-11-18 Tue 20-11-18
1.1 Development of business
case 4 days Mon 05-11-18 Thu 08-11-18
1.2 Undertaking feasibility study 3 days Fri 09-11-18 Tue 13-11-18
1.3 Establishing project charter 2 days Wed 14-11-18 Thu 15-11-18
1.4 Appointing project team 3 days Fri 16-11-18 Tue 20-11-18
1.5 Milestone 1: Initiation phase 0 days Tue 20-11-18 Tue 20-11-18
2 Planning phase 33 days Wed 21-11-18 Fri 04-01-19
2.1 Development of project plan 5 days Wed 21-11-18 Tue 27-11-18
2.2 Development of resource
plan 6 days Wed 28-11-18 Wed 05-12-18
2.3 Development of financial
plan 5 days Thu 06-12-18 Wed 12-12-18
2.4 Development of quality plan 4 days Thu 13-12-18 Tue 18-12-18
2.5 Development of risk
management plan 6 days Wed 19-12-18 Wed 26-12-18
2.6 Development of
communication plan 3 days Thu 27-12-18 Mon 31-12-18
2.7 Development of procurement
plan 4 days Tue 01-01-19 Fri 04-01-19
2.8 Milestone 2: Planning phase 0 days Fri 04-01-19 Fri 04-01-19
3 Execution phase 76 days Mon 07-01-19 Mon 22-04-19
3.1 Developing the design of the
vehicles 12 days Mon 07-01-19 Tue 22-01-19
3.2 Reviewing the design 8 days Wed 23-01-19 Fri 01-02-19
3.3 Approval of the design 2 days Mon 04-02-19 Tue 05-02-19
3.4 Implementation of small fully
automated trucks 28 days Wed 06-02-19 Fri 15-03-19
3.5 Adding features within the
trucks 22 days Mon 18-03-19 Tue 16-04-19
3.6 Testing the working of the
trucks 4 days Wed 17-04-19 Mon 22-04-19
3.7 Milestone 3: Completion of
the project execution phase 0 days Mon 22-04-19 Mon 22-04-19
4 Closure phase 15 days Tue 23-04-19 Mon 13-05-19
4.1 Project review 6 days Tue 23-04-19 Tue 30-04-19
4.2 Stakeholder sign off 2 days Wed 01-05-19 Thu 02-05-19
4.3 Project documentation 7 days Fri 03-05-19 Mon 13-05-19
4.4 Milestone 4: Completion of
project closure phase 0 days Mon 13-05-19 Mon 13-05-19
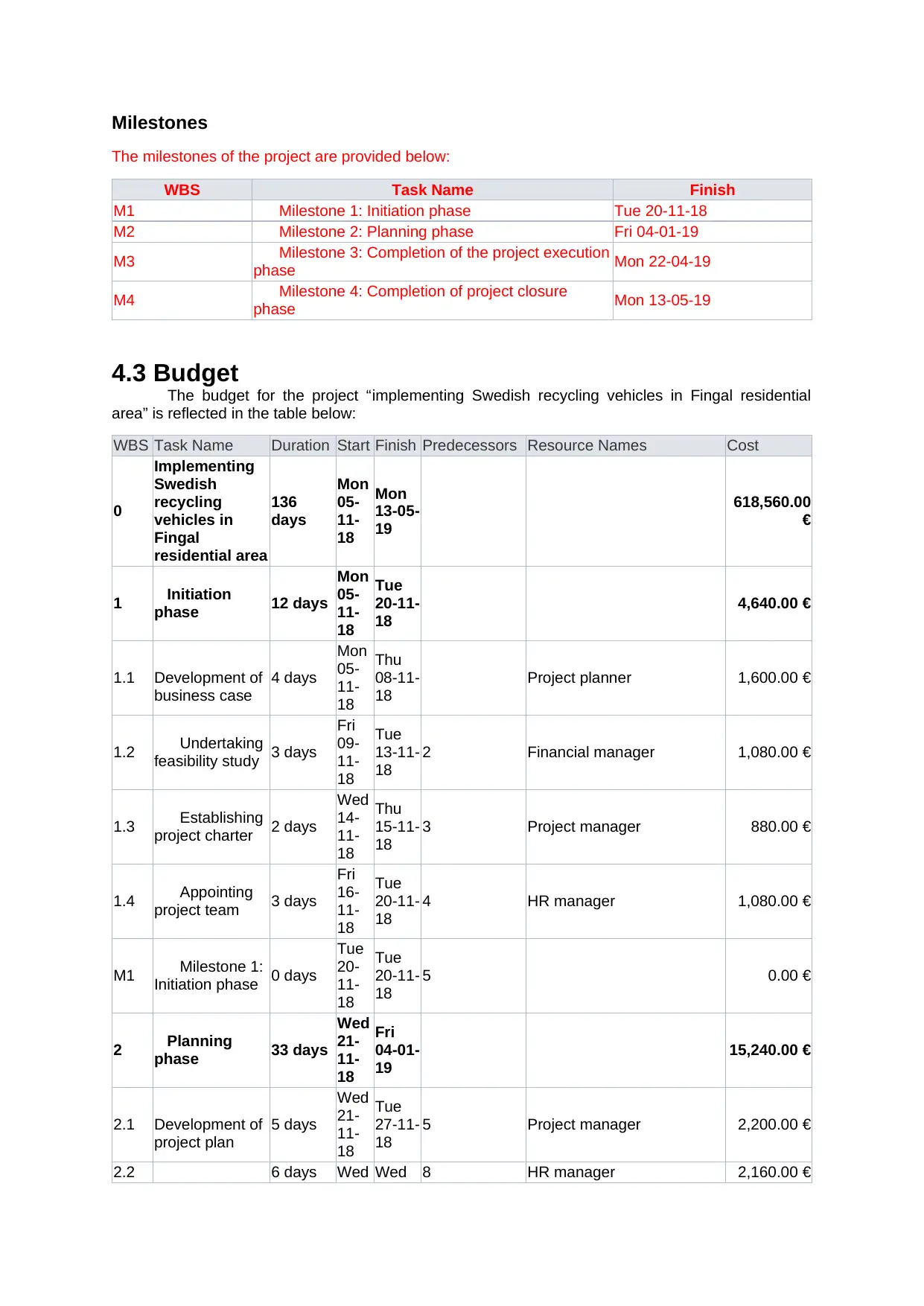
Milestones
The milestones of the project are provided below:
WBS Task Name Finish
M1 Milestone 1: Initiation phase Tue 20-11-18
M2 Milestone 2: Planning phase Fri 04-01-19
M3 Milestone 3: Completion of the project execution
phase Mon 22-04-19
M4 Milestone 4: Completion of project closure
phase Mon 13-05-19
4.3 Budget
The budget for the project “implementing Swedish recycling vehicles in Fingal residential
area” is reflected in the table below:
WBS Task Name Duration Start Finish Predecessors Resource Names Cost
0
Implementing
Swedish
recycling
vehicles in
Fingal
residential area
136
days
Mon
05-
11-
18
Mon
13-05-
19
618,560.00
€
1 Initiation
phase 12 days
Mon
05-
11-
18
Tue
20-11-
18
4,640.00 €
1.1 Development of
business case
4 days
Mon
05-
11-
18
Thu
08-11-
18
Project planner 1,600.00 €
1.2 Undertaking
feasibility study 3 days
Fri
09-
11-
18
Tue
13-11-
18
2 Financial manager 1,080.00 €
1.3 Establishing
project charter 2 days
Wed
14-
11-
18
Thu
15-11-
18
3 Project manager 880.00 €
1.4 Appointing
project team 3 days
Fri
16-
11-
18
Tue
20-11-
18
4 HR manager 1,080.00 €
M1 Milestone 1:
Initiation phase 0 days
Tue
20-
11-
18
Tue
20-11-
18
5 0.00 €
2 Planning
phase 33 days
Wed
21-
11-
18
Fri
04-01-
19
15,240.00 €
2.1 Development of
project plan
5 days
Wed
21-
11-
18
Tue
27-11-
18
5 Project manager 2,200.00 €
2.2 6 days Wed Wed 8 HR manager 2,160.00 €
The milestones of the project are provided below:
WBS Task Name Finish
M1 Milestone 1: Initiation phase Tue 20-11-18
M2 Milestone 2: Planning phase Fri 04-01-19
M3 Milestone 3: Completion of the project execution
phase Mon 22-04-19
M4 Milestone 4: Completion of project closure
phase Mon 13-05-19
4.3 Budget
The budget for the project “implementing Swedish recycling vehicles in Fingal residential
area” is reflected in the table below:
WBS Task Name Duration Start Finish Predecessors Resource Names Cost
0
Implementing
Swedish
recycling
vehicles in
Fingal
residential area
136
days
Mon
05-
11-
18
Mon
13-05-
19
618,560.00
€
1 Initiation
phase 12 days
Mon
05-
11-
18
Tue
20-11-
18
4,640.00 €
1.1 Development of
business case
4 days
Mon
05-
11-
18
Thu
08-11-
18
Project planner 1,600.00 €
1.2 Undertaking
feasibility study 3 days
Fri
09-
11-
18
Tue
13-11-
18
2 Financial manager 1,080.00 €
1.3 Establishing
project charter 2 days
Wed
14-
11-
18
Thu
15-11-
18
3 Project manager 880.00 €
1.4 Appointing
project team 3 days
Fri
16-
11-
18
Tue
20-11-
18
4 HR manager 1,080.00 €
M1 Milestone 1:
Initiation phase 0 days
Tue
20-
11-
18
Tue
20-11-
18
5 0.00 €
2 Planning
phase 33 days
Wed
21-
11-
18
Fri
04-01-
19
15,240.00 €
2.1 Development of
project plan
5 days
Wed
21-
11-
18
Tue
27-11-
18
5 Project manager 2,200.00 €
2.2 6 days Wed Wed 8 HR manager 2,160.00 €
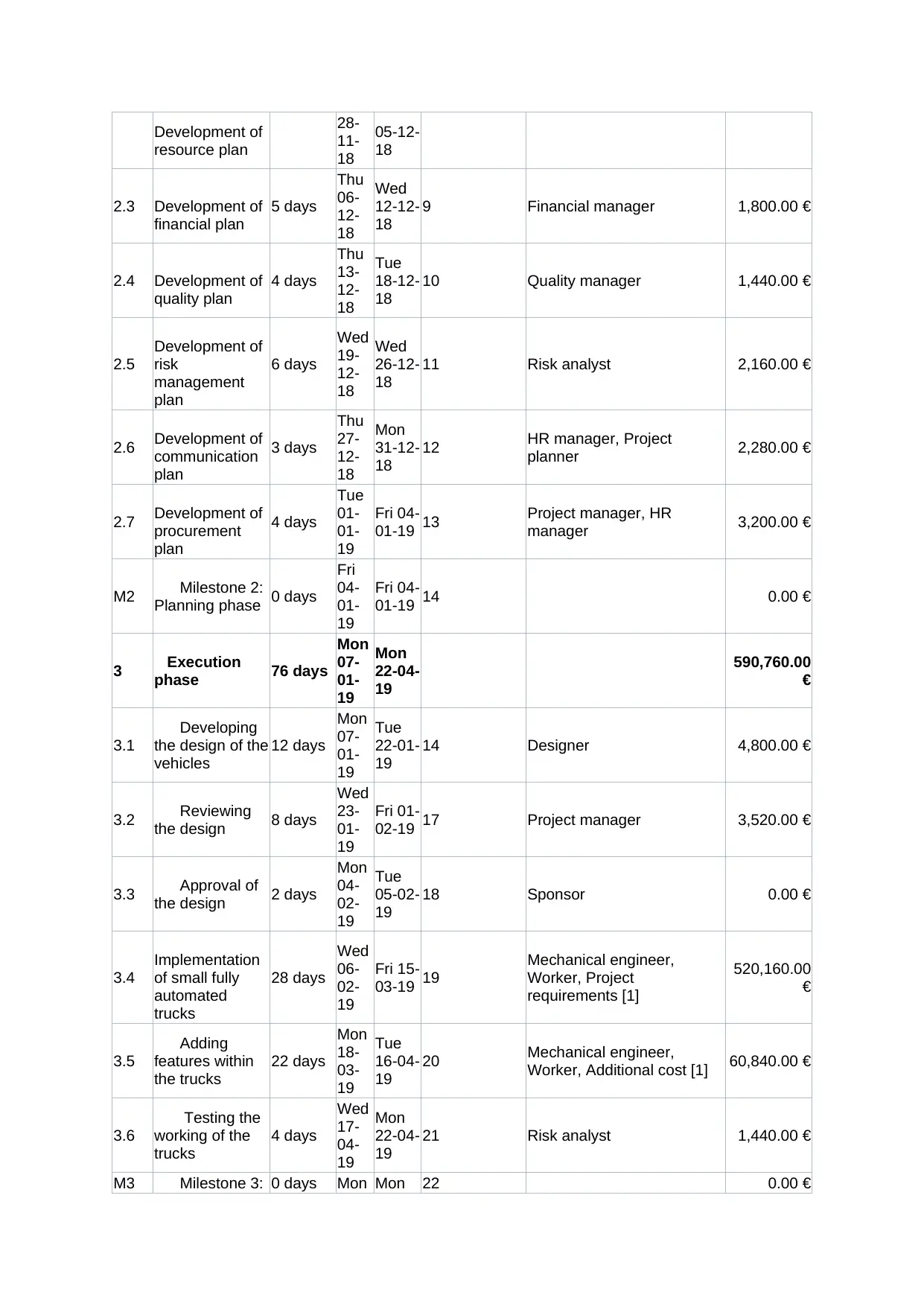
Development of
resource plan
28-
11-
18
05-12-
18
2.3 Development of
financial plan
5 days
Thu
06-
12-
18
Wed
12-12-
18
9 Financial manager 1,800.00 €
2.4 Development of
quality plan
4 days
Thu
13-
12-
18
Tue
18-12-
18
10 Quality manager 1,440.00 €
2.5
Development of
risk
management
plan
6 days
Wed
19-
12-
18
Wed
26-12-
18
11 Risk analyst 2,160.00 €
2.6 Development of
communication
plan
3 days
Thu
27-
12-
18
Mon
31-12-
18
12 HR manager, Project
planner 2,280.00 €
2.7 Development of
procurement
plan
4 days
Tue
01-
01-
19
Fri 04-
01-19 13 Project manager, HR
manager 3,200.00 €
M2 Milestone 2:
Planning phase 0 days
Fri
04-
01-
19
Fri 04-
01-19 14 0.00 €
3 Execution
phase 76 days
Mon
07-
01-
19
Mon
22-04-
19
590,760.00
€
3.1
Developing
the design of the
vehicles
12 days
Mon
07-
01-
19
Tue
22-01-
19
14 Designer 4,800.00 €
3.2 Reviewing
the design 8 days
Wed
23-
01-
19
Fri 01-
02-19 17 Project manager 3,520.00 €
3.3 Approval of
the design 2 days
Mon
04-
02-
19
Tue
05-02-
19
18 Sponsor 0.00 €
3.4
Implementation
of small fully
automated
trucks
28 days
Wed
06-
02-
19
Fri 15-
03-19 19
Mechanical engineer,
Worker, Project
requirements [1]
520,160.00
€
3.5
Adding
features within
the trucks
22 days
Mon
18-
03-
19
Tue
16-04-
19
20 Mechanical engineer,
Worker, Additional cost [1] 60,840.00 €
3.6
Testing the
working of the
trucks
4 days
Wed
17-
04-
19
Mon
22-04-
19
21 Risk analyst 1,440.00 €
M3 Milestone 3: 0 days Mon Mon 22 0.00 €
resource plan
28-
11-
18
05-12-
18
2.3 Development of
financial plan
5 days
Thu
06-
12-
18
Wed
12-12-
18
9 Financial manager 1,800.00 €
2.4 Development of
quality plan
4 days
Thu
13-
12-
18
Tue
18-12-
18
10 Quality manager 1,440.00 €
2.5
Development of
risk
management
plan
6 days
Wed
19-
12-
18
Wed
26-12-
18
11 Risk analyst 2,160.00 €
2.6 Development of
communication
plan
3 days
Thu
27-
12-
18
Mon
31-12-
18
12 HR manager, Project
planner 2,280.00 €
2.7 Development of
procurement
plan
4 days
Tue
01-
01-
19
Fri 04-
01-19 13 Project manager, HR
manager 3,200.00 €
M2 Milestone 2:
Planning phase 0 days
Fri
04-
01-
19
Fri 04-
01-19 14 0.00 €
3 Execution
phase 76 days
Mon
07-
01-
19
Mon
22-04-
19
590,760.00
€
3.1
Developing
the design of the
vehicles
12 days
Mon
07-
01-
19
Tue
22-01-
19
14 Designer 4,800.00 €
3.2 Reviewing
the design 8 days
Wed
23-
01-
19
Fri 01-
02-19 17 Project manager 3,520.00 €
3.3 Approval of
the design 2 days
Mon
04-
02-
19
Tue
05-02-
19
18 Sponsor 0.00 €
3.4
Implementation
of small fully
automated
trucks
28 days
Wed
06-
02-
19
Fri 15-
03-19 19
Mechanical engineer,
Worker, Project
requirements [1]
520,160.00
€
3.5
Adding
features within
the trucks
22 days
Mon
18-
03-
19
Tue
16-04-
19
20 Mechanical engineer,
Worker, Additional cost [1] 60,840.00 €
3.6
Testing the
working of the
trucks
4 days
Wed
17-
04-
19
Mon
22-04-
19
21 Risk analyst 1,440.00 €
M3 Milestone 3: 0 days Mon Mon 22 0.00 €
Secure Best Marks with AI Grader
Need help grading? Try our AI Grader for instant feedback on your assignments.
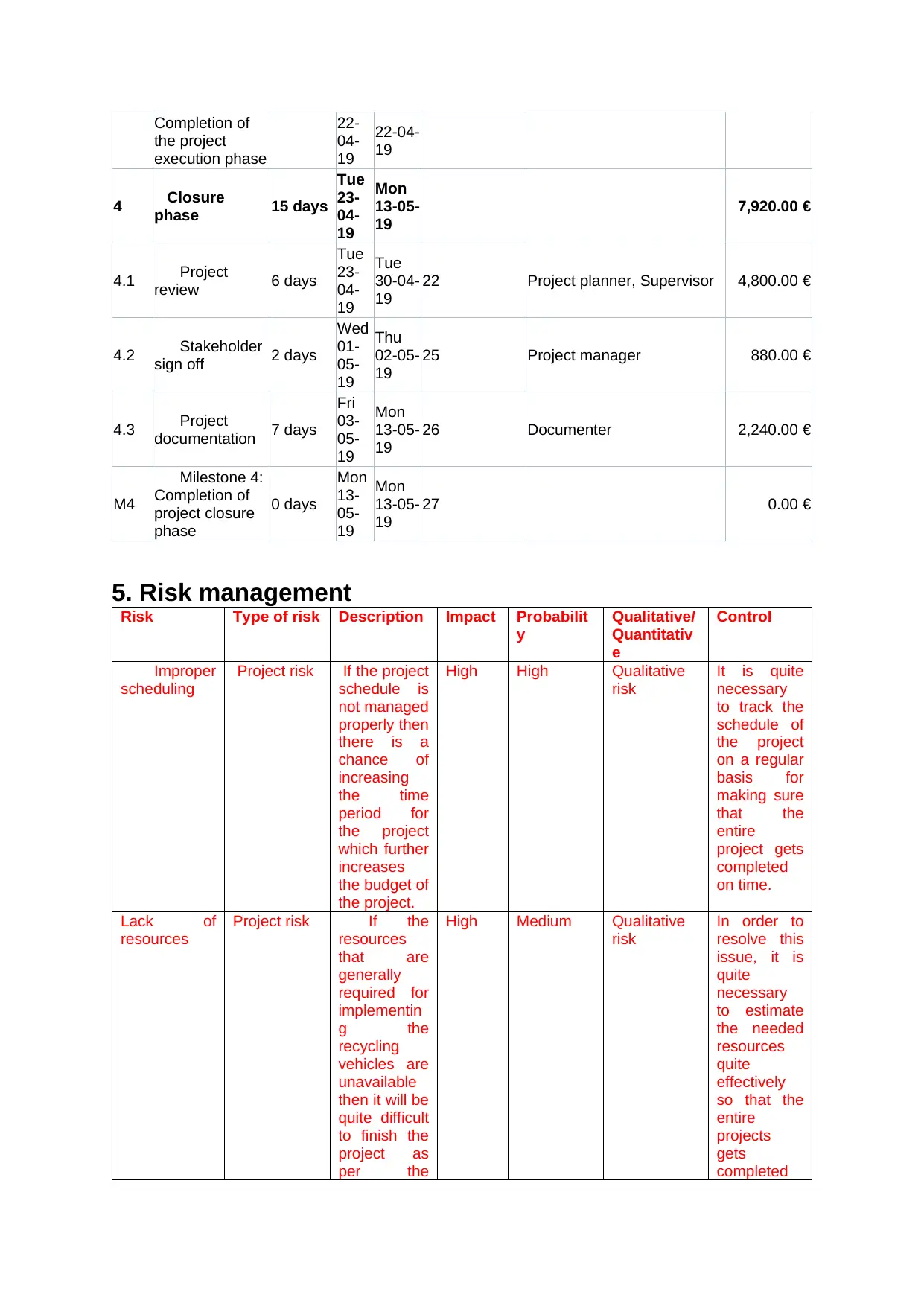
Completion of
the project
execution phase
22-
04-
19
22-04-
19
4 Closure
phase 15 days
Tue
23-
04-
19
Mon
13-05-
19
7,920.00 €
4.1 Project
review 6 days
Tue
23-
04-
19
Tue
30-04-
19
22 Project planner, Supervisor 4,800.00 €
4.2 Stakeholder
sign off 2 days
Wed
01-
05-
19
Thu
02-05-
19
25 Project manager 880.00 €
4.3 Project
documentation 7 days
Fri
03-
05-
19
Mon
13-05-
19
26 Documenter 2,240.00 €
M4
Milestone 4:
Completion of
project closure
phase
0 days
Mon
13-
05-
19
Mon
13-05-
19
27 0.00 €
5. Risk management
Risk Type of risk Description Impact Probabilit
y
Qualitative/
Quantitativ
e
Control
Improper
scheduling
Project risk If the project
schedule is
not managed
properly then
there is a
chance of
increasing
the time
period for
the project
which further
increases
the budget of
the project.
High High Qualitative
risk
It is quite
necessary
to track the
schedule of
the project
on a regular
basis for
making sure
that the
entire
project gets
completed
on time.
Lack of
resources
Project risk If the
resources
that are
generally
required for
implementin
g the
recycling
vehicles are
unavailable
then it will be
quite difficult
to finish the
project as
per the
High Medium Qualitative
risk
In order to
resolve this
issue, it is
quite
necessary
to estimate
the needed
resources
quite
effectively
so that the
entire
projects
gets
completed
the project
execution phase
22-
04-
19
22-04-
19
4 Closure
phase 15 days
Tue
23-
04-
19
Mon
13-05-
19
7,920.00 €
4.1 Project
review 6 days
Tue
23-
04-
19
Tue
30-04-
19
22 Project planner, Supervisor 4,800.00 €
4.2 Stakeholder
sign off 2 days
Wed
01-
05-
19
Thu
02-05-
19
25 Project manager 880.00 €
4.3 Project
documentation 7 days
Fri
03-
05-
19
Mon
13-05-
19
26 Documenter 2,240.00 €
M4
Milestone 4:
Completion of
project closure
phase
0 days
Mon
13-
05-
19
Mon
13-05-
19
27 0.00 €
5. Risk management
Risk Type of risk Description Impact Probabilit
y
Qualitative/
Quantitativ
e
Control
Improper
scheduling
Project risk If the project
schedule is
not managed
properly then
there is a
chance of
increasing
the time
period for
the project
which further
increases
the budget of
the project.
High High Qualitative
risk
It is quite
necessary
to track the
schedule of
the project
on a regular
basis for
making sure
that the
entire
project gets
completed
on time.
Lack of
resources
Project risk If the
resources
that are
generally
required for
implementin
g the
recycling
vehicles are
unavailable
then it will be
quite difficult
to finish the
project as
per the
High Medium Qualitative
risk
In order to
resolve this
issue, it is
quite
necessary
to estimate
the needed
resources
quite
effectively
so that the
entire
projects
gets
completed
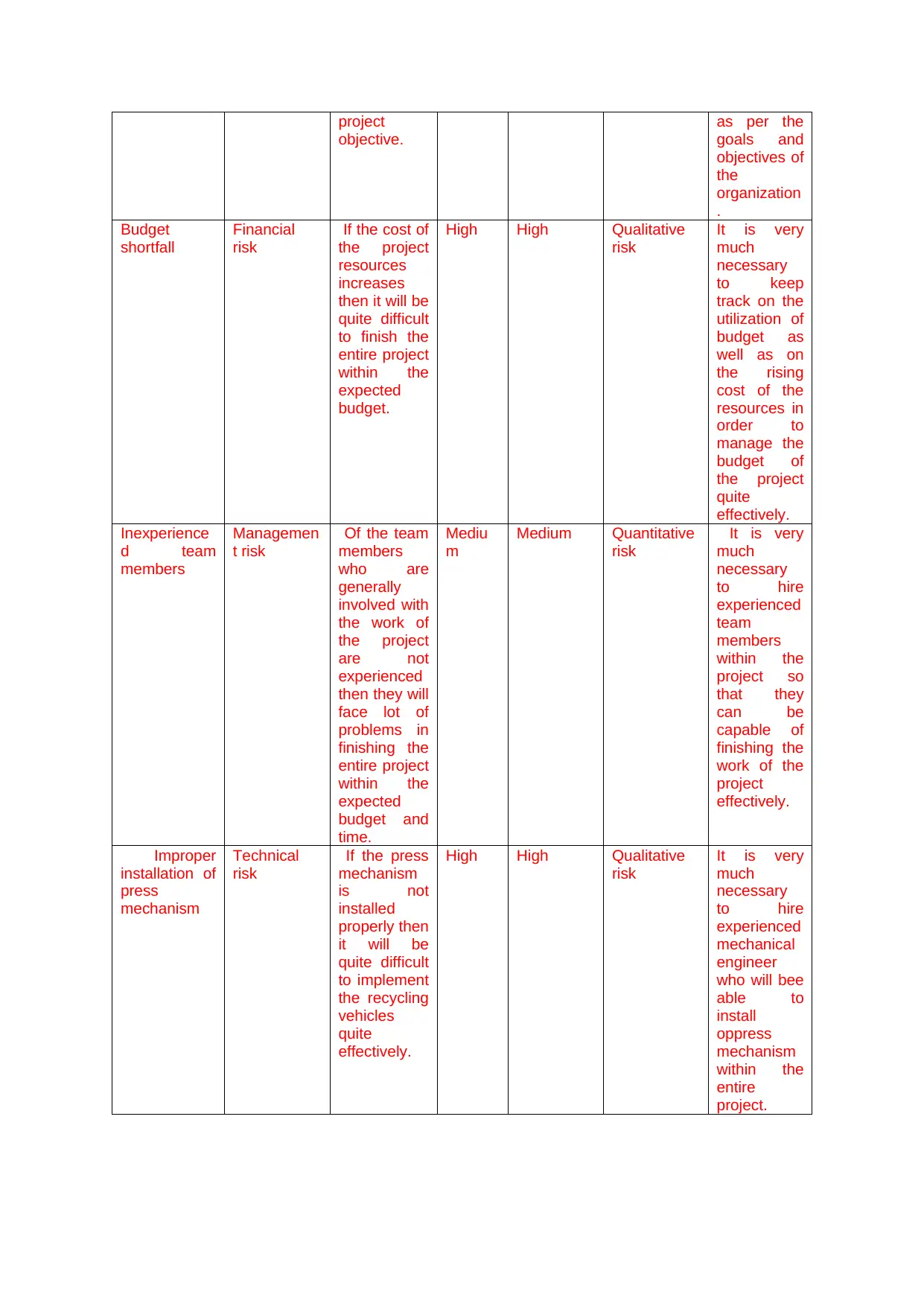
project
objective.
as per the
goals and
objectives of
the
organization
.
Budget
shortfall
Financial
risk
If the cost of
the project
resources
increases
then it will be
quite difficult
to finish the
entire project
within the
expected
budget.
High High Qualitative
risk
It is very
much
necessary
to keep
track on the
utilization of
budget as
well as on
the rising
cost of the
resources in
order to
manage the
budget of
the project
quite
effectively.
Inexperience
d team
members
Managemen
t risk
Of the team
members
who are
generally
involved with
the work of
the project
are not
experienced
then they will
face lot of
problems in
finishing the
entire project
within the
expected
budget and
time.
Mediu
m
Medium Quantitative
risk
It is very
much
necessary
to hire
experienced
team
members
within the
project so
that they
can be
capable of
finishing the
work of the
project
effectively.
Improper
installation of
press
mechanism
Technical
risk
If the press
mechanism
is not
installed
properly then
it will be
quite difficult
to implement
the recycling
vehicles
quite
effectively.
High High Qualitative
risk
It is very
much
necessary
to hire
experienced
mechanical
engineer
who will bee
able to
install
oppress
mechanism
within the
entire
project.
objective.
as per the
goals and
objectives of
the
organization
.
Budget
shortfall
Financial
risk
If the cost of
the project
resources
increases
then it will be
quite difficult
to finish the
entire project
within the
expected
budget.
High High Qualitative
risk
It is very
much
necessary
to keep
track on the
utilization of
budget as
well as on
the rising
cost of the
resources in
order to
manage the
budget of
the project
quite
effectively.
Inexperience
d team
members
Managemen
t risk
Of the team
members
who are
generally
involved with
the work of
the project
are not
experienced
then they will
face lot of
problems in
finishing the
entire project
within the
expected
budget and
time.
Mediu
m
Medium Quantitative
risk
It is very
much
necessary
to hire
experienced
team
members
within the
project so
that they
can be
capable of
finishing the
work of the
project
effectively.
Improper
installation of
press
mechanism
Technical
risk
If the press
mechanism
is not
installed
properly then
it will be
quite difficult
to implement
the recycling
vehicles
quite
effectively.
High High Qualitative
risk
It is very
much
necessary
to hire
experienced
mechanical
engineer
who will bee
able to
install
oppress
mechanism
within the
entire
project.
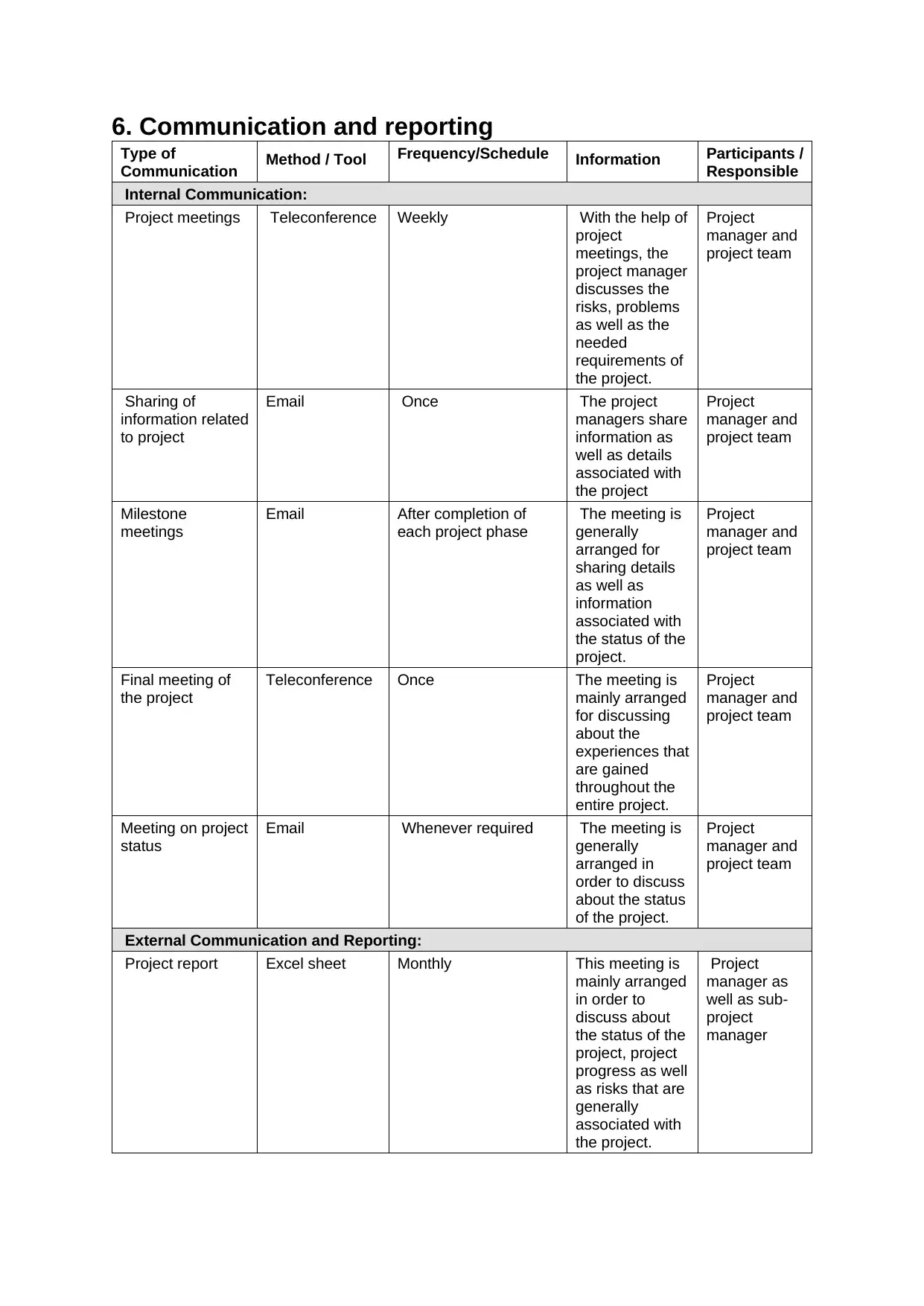
6. Communication and reporting
Type of
Communication Method / Tool Frequency/Schedule Information Participants /
Responsible
Internal Communication:
Project meetings Teleconference Weekly With the help of
project
meetings, the
project manager
discusses the
risks, problems
as well as the
needed
requirements of
the project.
Project
manager and
project team
Sharing of
information related
to project
Email Once The project
managers share
information as
well as details
associated with
the project
Project
manager and
project team
Milestone
meetings
Email After completion of
each project phase
The meeting is
generally
arranged for
sharing details
as well as
information
associated with
the status of the
project.
Project
manager and
project team
Final meeting of
the project
Teleconference Once The meeting is
mainly arranged
for discussing
about the
experiences that
are gained
throughout the
entire project.
Project
manager and
project team
Meeting on project
status
Email Whenever required The meeting is
generally
arranged in
order to discuss
about the status
of the project.
Project
manager and
project team
External Communication and Reporting:
Project report Excel sheet Monthly This meeting is
mainly arranged
in order to
discuss about
the status of the
project, project
progress as well
as risks that are
generally
associated with
the project.
Project
manager as
well as sub-
project
manager
Type of
Communication Method / Tool Frequency/Schedule Information Participants /
Responsible
Internal Communication:
Project meetings Teleconference Weekly With the help of
project
meetings, the
project manager
discusses the
risks, problems
as well as the
needed
requirements of
the project.
Project
manager and
project team
Sharing of
information related
to project
Email Once The project
managers share
information as
well as details
associated with
the project
Project
manager and
project team
Milestone
meetings
Email After completion of
each project phase
The meeting is
generally
arranged for
sharing details
as well as
information
associated with
the status of the
project.
Project
manager and
project team
Final meeting of
the project
Teleconference Once The meeting is
mainly arranged
for discussing
about the
experiences that
are gained
throughout the
entire project.
Project
manager and
project team
Meeting on project
status
Email Whenever required The meeting is
generally
arranged in
order to discuss
about the status
of the project.
Project
manager and
project team
External Communication and Reporting:
Project report Excel sheet Monthly This meeting is
mainly arranged
in order to
discuss about
the status of the
project, project
progress as well
as risks that are
generally
associated with
the project.
Project
manager as
well as sub-
project
manager
Paraphrase This Document
Need a fresh take? Get an instant paraphrase of this document with our AI Paraphraser

Type of
Communication Method / Tool Frequency/Schedule Information Participants /
Responsible
Steering meeting Teleconference Monthly This meeting is
generally
arranged for
discussing
about the
project.
Project
manager,
Steering
Committee.
7. Delivery plan
7.1 Deliverables and receivers
Ident. Deliverable Planned Date Receiver
D1 Installation of the press mechanism 05-11-2018 Mechanical engineers
D2 Implementation of the automated
trucks for finishing the project
successfully.
05-11-2018 Mechanical engineers
D3 Marketing and sales materials are
needed for marketing the project.
05-11-2018 Marketing managers
D4 Training facility is provided by the
workers who are involved within the
project
05-11-2018 workers
D5 Management presentation is done in
order to reflect the entire project to
the managers
05-11-2018 Managers
D6 Project budget is developed for
completing the project as per it.
06-12-18 Project sponsor
D7 Swedish recycling vehicles are
provided to the customers
5-11-18 Customer
8. Digital media content
The digital media content of the project with their specifications are generally elaborated
below:
Audio: Proper audio about the working as well as requirements of the project are generally
kept so that the usefulness of the Swedish recycling vehicles can be known with the help of the audio.
Images: Images about the entire procedure of recycling must be kept as the content of digital
media so that the people can be able to know about the process that are utilized for recycling the
vehicles.
Videos: Videos about the entire process of recycling must be made so that the entire
procedure of recycling with the help of the Swedish recycling vehicles can be properly understood.
9. Quality Assurance
It is found that in order to assure that the quality of the project is maintained during the
implementation of Swedish recycling vehicles, it is very much necessary to follow steps that are
generally elaborated below:
Communication Method / Tool Frequency/Schedule Information Participants /
Responsible
Steering meeting Teleconference Monthly This meeting is
generally
arranged for
discussing
about the
project.
Project
manager,
Steering
Committee.
7. Delivery plan
7.1 Deliverables and receivers
Ident. Deliverable Planned Date Receiver
D1 Installation of the press mechanism 05-11-2018 Mechanical engineers
D2 Implementation of the automated
trucks for finishing the project
successfully.
05-11-2018 Mechanical engineers
D3 Marketing and sales materials are
needed for marketing the project.
05-11-2018 Marketing managers
D4 Training facility is provided by the
workers who are involved within the
project
05-11-2018 workers
D5 Management presentation is done in
order to reflect the entire project to
the managers
05-11-2018 Managers
D6 Project budget is developed for
completing the project as per it.
06-12-18 Project sponsor
D7 Swedish recycling vehicles are
provided to the customers
5-11-18 Customer
8. Digital media content
The digital media content of the project with their specifications are generally elaborated
below:
Audio: Proper audio about the working as well as requirements of the project are generally
kept so that the usefulness of the Swedish recycling vehicles can be known with the help of the audio.
Images: Images about the entire procedure of recycling must be kept as the content of digital
media so that the people can be able to know about the process that are utilized for recycling the
vehicles.
Videos: Videos about the entire process of recycling must be made so that the entire
procedure of recycling with the help of the Swedish recycling vehicles can be properly understood.
9. Quality Assurance
It is found that in order to assure that the quality of the project is maintained during the
implementation of Swedish recycling vehicles, it is very much necessary to follow steps that are
generally elaborated below:
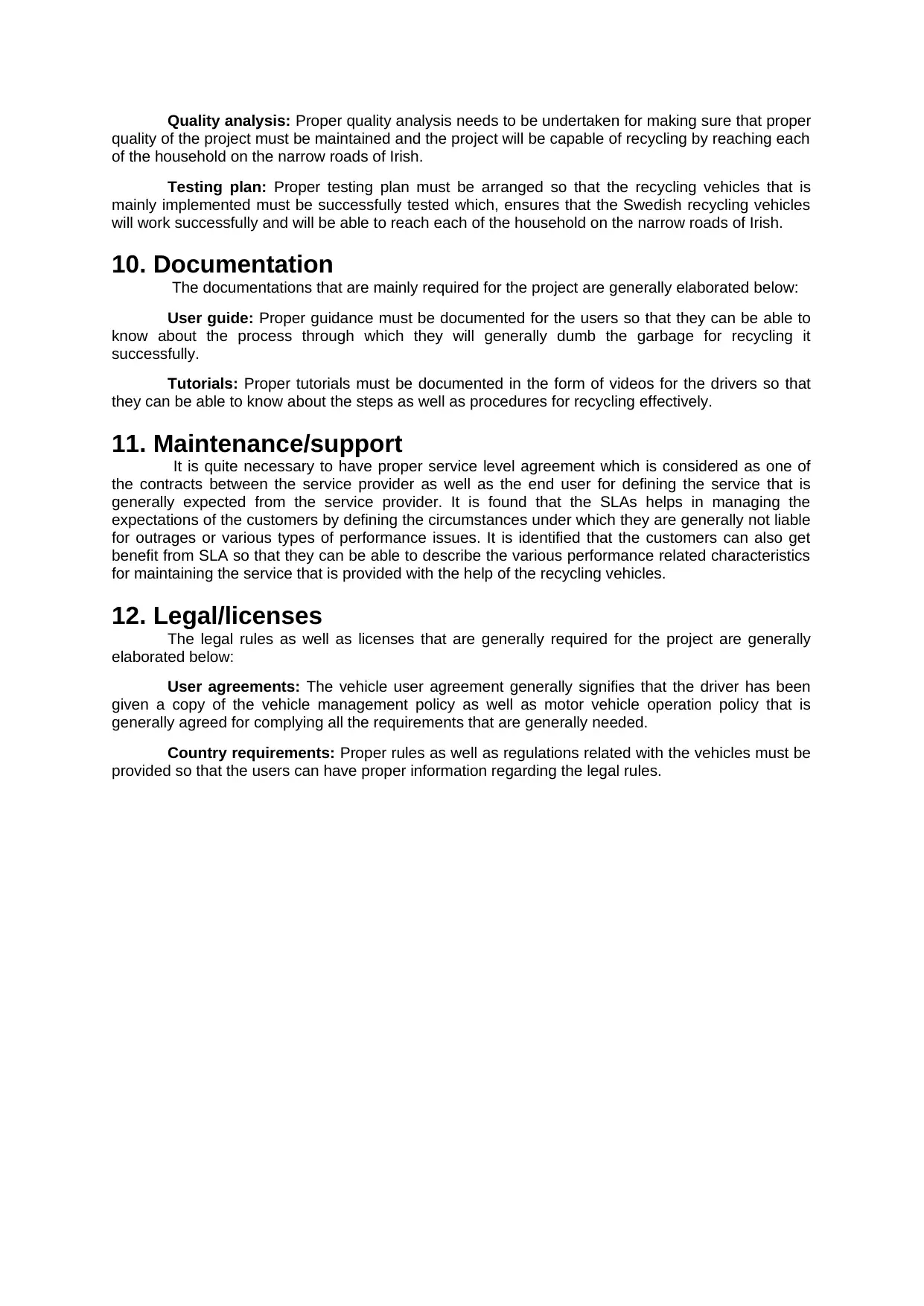
Quality analysis: Proper quality analysis needs to be undertaken for making sure that proper
quality of the project must be maintained and the project will be capable of recycling by reaching each
of the household on the narrow roads of Irish.
Testing plan: Proper testing plan must be arranged so that the recycling vehicles that is
mainly implemented must be successfully tested which, ensures that the Swedish recycling vehicles
will work successfully and will be able to reach each of the household on the narrow roads of Irish.
10. Documentation
The documentations that are mainly required for the project are generally elaborated below:
User guide: Proper guidance must be documented for the users so that they can be able to
know about the process through which they will generally dumb the garbage for recycling it
successfully.
Tutorials: Proper tutorials must be documented in the form of videos for the drivers so that
they can be able to know about the steps as well as procedures for recycling effectively.
11. Maintenance/support
It is quite necessary to have proper service level agreement which is considered as one of
the contracts between the service provider as well as the end user for defining the service that is
generally expected from the service provider. It is found that the SLAs helps in managing the
expectations of the customers by defining the circumstances under which they are generally not liable
for outrages or various types of performance issues. It is identified that the customers can also get
benefit from SLA so that they can be able to describe the various performance related characteristics
for maintaining the service that is provided with the help of the recycling vehicles.
12. Legal/licenses
The legal rules as well as licenses that are generally required for the project are generally
elaborated below:
User agreements: The vehicle user agreement generally signifies that the driver has been
given a copy of the vehicle management policy as well as motor vehicle operation policy that is
generally agreed for complying all the requirements that are generally needed.
Country requirements: Proper rules as well as regulations related with the vehicles must be
provided so that the users can have proper information regarding the legal rules.
quality of the project must be maintained and the project will be capable of recycling by reaching each
of the household on the narrow roads of Irish.
Testing plan: Proper testing plan must be arranged so that the recycling vehicles that is
mainly implemented must be successfully tested which, ensures that the Swedish recycling vehicles
will work successfully and will be able to reach each of the household on the narrow roads of Irish.
10. Documentation
The documentations that are mainly required for the project are generally elaborated below:
User guide: Proper guidance must be documented for the users so that they can be able to
know about the process through which they will generally dumb the garbage for recycling it
successfully.
Tutorials: Proper tutorials must be documented in the form of videos for the drivers so that
they can be able to know about the steps as well as procedures for recycling effectively.
11. Maintenance/support
It is quite necessary to have proper service level agreement which is considered as one of
the contracts between the service provider as well as the end user for defining the service that is
generally expected from the service provider. It is found that the SLAs helps in managing the
expectations of the customers by defining the circumstances under which they are generally not liable
for outrages or various types of performance issues. It is identified that the customers can also get
benefit from SLA so that they can be able to describe the various performance related characteristics
for maintaining the service that is provided with the help of the recycling vehicles.
12. Legal/licenses
The legal rules as well as licenses that are generally required for the project are generally
elaborated below:
User agreements: The vehicle user agreement generally signifies that the driver has been
given a copy of the vehicle management policy as well as motor vehicle operation policy that is
generally agreed for complying all the requirements that are generally needed.
Country requirements: Proper rules as well as regulations related with the vehicles must be
provided so that the users can have proper information regarding the legal rules.
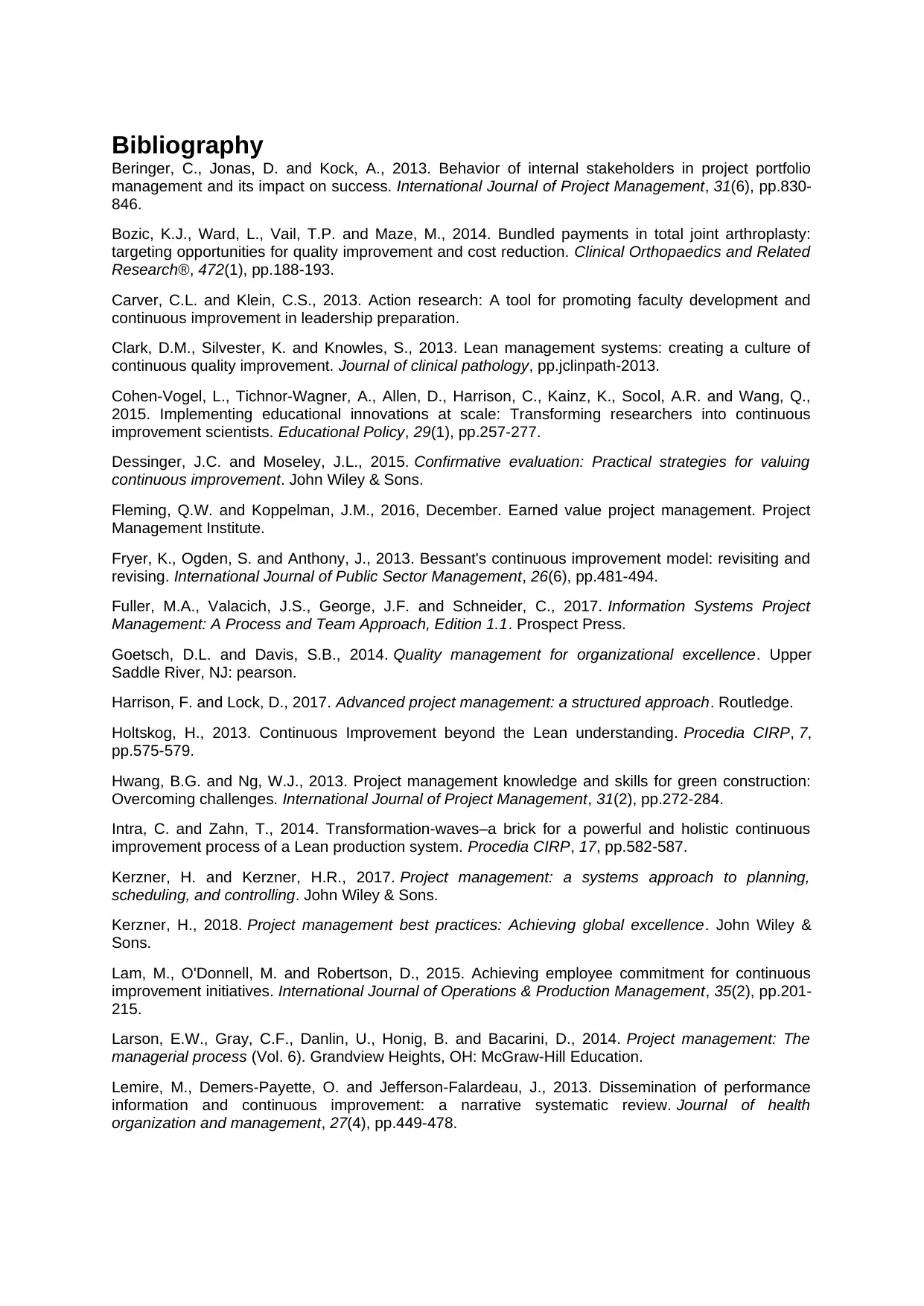
Bibliography
Beringer, C., Jonas, D. and Kock, A., 2013. Behavior of internal stakeholders in project portfolio
management and its impact on success. International Journal of Project Management, 31(6), pp.830-
846.
Bozic, K.J., Ward, L., Vail, T.P. and Maze, M., 2014. Bundled payments in total joint arthroplasty:
targeting opportunities for quality improvement and cost reduction. Clinical Orthopaedics and Related
Research®, 472(1), pp.188-193.
Carver, C.L. and Klein, C.S., 2013. Action research: A tool for promoting faculty development and
continuous improvement in leadership preparation.
Clark, D.M., Silvester, K. and Knowles, S., 2013. Lean management systems: creating a culture of
continuous quality improvement. Journal of clinical pathology, pp.jclinpath-2013.
Cohen-Vogel, L., Tichnor-Wagner, A., Allen, D., Harrison, C., Kainz, K., Socol, A.R. and Wang, Q.,
2015. Implementing educational innovations at scale: Transforming researchers into continuous
improvement scientists. Educational Policy, 29(1), pp.257-277.
Dessinger, J.C. and Moseley, J.L., 2015. Confirmative evaluation: Practical strategies for valuing
continuous improvement. John Wiley & Sons.
Fleming, Q.W. and Koppelman, J.M., 2016, December. Earned value project management. Project
Management Institute.
Fryer, K., Ogden, S. and Anthony, J., 2013. Bessant's continuous improvement model: revisiting and
revising. International Journal of Public Sector Management, 26(6), pp.481-494.
Fuller, M.A., Valacich, J.S., George, J.F. and Schneider, C., 2017. Information Systems Project
Management: A Process and Team Approach, Edition 1.1. Prospect Press.
Goetsch, D.L. and Davis, S.B., 2014. Quality management for organizational excellence. Upper
Saddle River, NJ: pearson.
Harrison, F. and Lock, D., 2017. Advanced project management: a structured approach. Routledge.
Holtskog, H., 2013. Continuous Improvement beyond the Lean understanding. Procedia CIRP, 7,
pp.575-579.
Hwang, B.G. and Ng, W.J., 2013. Project management knowledge and skills for green construction:
Overcoming challenges. International Journal of Project Management, 31(2), pp.272-284.
Intra, C. and Zahn, T., 2014. Transformation-waves–a brick for a powerful and holistic continuous
improvement process of a Lean production system. Procedia CIRP, 17, pp.582-587.
Kerzner, H. and Kerzner, H.R., 2017. Project management: a systems approach to planning,
scheduling, and controlling. John Wiley & Sons.
Kerzner, H., 2018. Project management best practices: Achieving global excellence. John Wiley &
Sons.
Lam, M., O'Donnell, M. and Robertson, D., 2015. Achieving employee commitment for continuous
improvement initiatives. International Journal of Operations & Production Management, 35(2), pp.201-
215.
Larson, E.W., Gray, C.F., Danlin, U., Honig, B. and Bacarini, D., 2014. Project management: The
managerial process (Vol. 6). Grandview Heights, OH: McGraw-Hill Education.
Lemire, M., Demers-Payette, O. and Jefferson-Falardeau, J., 2013. Dissemination of performance
information and continuous improvement: a narrative systematic review. Journal of health
organization and management, 27(4), pp.449-478.
Beringer, C., Jonas, D. and Kock, A., 2013. Behavior of internal stakeholders in project portfolio
management and its impact on success. International Journal of Project Management, 31(6), pp.830-
846.
Bozic, K.J., Ward, L., Vail, T.P. and Maze, M., 2014. Bundled payments in total joint arthroplasty:
targeting opportunities for quality improvement and cost reduction. Clinical Orthopaedics and Related
Research®, 472(1), pp.188-193.
Carver, C.L. and Klein, C.S., 2013. Action research: A tool for promoting faculty development and
continuous improvement in leadership preparation.
Clark, D.M., Silvester, K. and Knowles, S., 2013. Lean management systems: creating a culture of
continuous quality improvement. Journal of clinical pathology, pp.jclinpath-2013.
Cohen-Vogel, L., Tichnor-Wagner, A., Allen, D., Harrison, C., Kainz, K., Socol, A.R. and Wang, Q.,
2015. Implementing educational innovations at scale: Transforming researchers into continuous
improvement scientists. Educational Policy, 29(1), pp.257-277.
Dessinger, J.C. and Moseley, J.L., 2015. Confirmative evaluation: Practical strategies for valuing
continuous improvement. John Wiley & Sons.
Fleming, Q.W. and Koppelman, J.M., 2016, December. Earned value project management. Project
Management Institute.
Fryer, K., Ogden, S. and Anthony, J., 2013. Bessant's continuous improvement model: revisiting and
revising. International Journal of Public Sector Management, 26(6), pp.481-494.
Fuller, M.A., Valacich, J.S., George, J.F. and Schneider, C., 2017. Information Systems Project
Management: A Process and Team Approach, Edition 1.1. Prospect Press.
Goetsch, D.L. and Davis, S.B., 2014. Quality management for organizational excellence. Upper
Saddle River, NJ: pearson.
Harrison, F. and Lock, D., 2017. Advanced project management: a structured approach. Routledge.
Holtskog, H., 2013. Continuous Improvement beyond the Lean understanding. Procedia CIRP, 7,
pp.575-579.
Hwang, B.G. and Ng, W.J., 2013. Project management knowledge and skills for green construction:
Overcoming challenges. International Journal of Project Management, 31(2), pp.272-284.
Intra, C. and Zahn, T., 2014. Transformation-waves–a brick for a powerful and holistic continuous
improvement process of a Lean production system. Procedia CIRP, 17, pp.582-587.
Kerzner, H. and Kerzner, H.R., 2017. Project management: a systems approach to planning,
scheduling, and controlling. John Wiley & Sons.
Kerzner, H., 2018. Project management best practices: Achieving global excellence. John Wiley &
Sons.
Lam, M., O'Donnell, M. and Robertson, D., 2015. Achieving employee commitment for continuous
improvement initiatives. International Journal of Operations & Production Management, 35(2), pp.201-
215.
Larson, E.W., Gray, C.F., Danlin, U., Honig, B. and Bacarini, D., 2014. Project management: The
managerial process (Vol. 6). Grandview Heights, OH: McGraw-Hill Education.
Lemire, M., Demers-Payette, O. and Jefferson-Falardeau, J., 2013. Dissemination of performance
information and continuous improvement: a narrative systematic review. Journal of health
organization and management, 27(4), pp.449-478.
Secure Best Marks with AI Grader
Need help grading? Try our AI Grader for instant feedback on your assignments.
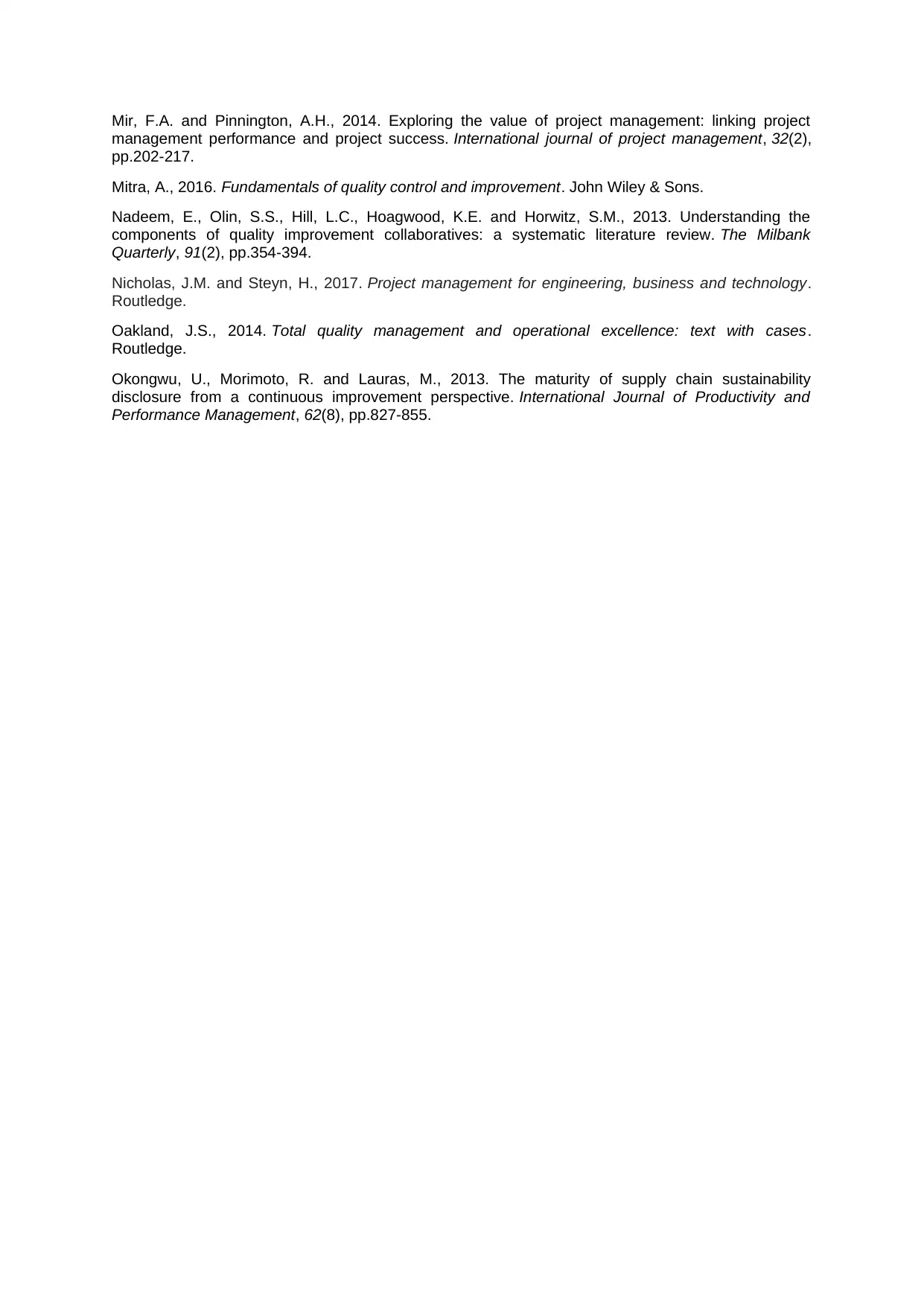
Mir, F.A. and Pinnington, A.H., 2014. Exploring the value of project management: linking project
management performance and project success. International journal of project management, 32(2),
pp.202-217.
Mitra, A., 2016. Fundamentals of quality control and improvement. John Wiley & Sons.
Nadeem, E., Olin, S.S., Hill, L.C., Hoagwood, K.E. and Horwitz, S.M., 2013. Understanding the
components of quality improvement collaboratives: a systematic literature review. The Milbank
Quarterly, 91(2), pp.354-394.
Nicholas, J.M. and Steyn, H., 2017. Project management for engineering, business and technology.
Routledge.
Oakland, J.S., 2014. Total quality management and operational excellence: text with cases.
Routledge.
Okongwu, U., Morimoto, R. and Lauras, M., 2013. The maturity of supply chain sustainability
disclosure from a continuous improvement perspective. International Journal of Productivity and
Performance Management, 62(8), pp.827-855.
management performance and project success. International journal of project management, 32(2),
pp.202-217.
Mitra, A., 2016. Fundamentals of quality control and improvement. John Wiley & Sons.
Nadeem, E., Olin, S.S., Hill, L.C., Hoagwood, K.E. and Horwitz, S.M., 2013. Understanding the
components of quality improvement collaboratives: a systematic literature review. The Milbank
Quarterly, 91(2), pp.354-394.
Nicholas, J.M. and Steyn, H., 2017. Project management for engineering, business and technology.
Routledge.
Oakland, J.S., 2014. Total quality management and operational excellence: text with cases.
Routledge.
Okongwu, U., Morimoto, R. and Lauras, M., 2013. The maturity of supply chain sustainability
disclosure from a continuous improvement perspective. International Journal of Productivity and
Performance Management, 62(8), pp.827-855.
1 out of 17
Related Documents

Your All-in-One AI-Powered Toolkit for Academic Success.
+13062052269
info@desklib.com
Available 24*7 on WhatsApp / Email
Unlock your academic potential
© 2024 | Zucol Services PVT LTD | All rights reserved.