Managerial Accounting Report: TDABC for Australian Paper Pty Ltd
VerifiedAdded on 2020/05/16
|13
|2980
|116
Report
AI Summary
This report provides a detailed analysis of Time-Driven Activity-Based Costing (TDABC) in the context of managerial accounting. It begins with an introduction to cost accounting and highlights the evolution from traditional costing and Activity-Based Costing (ABC) to TDABC. The report then describes the client firm, Australian Paper Pty Ltd, a vertically integrated manufacturing organization. It defines TDABC, outlining its operational process, which involves assigning resource costs to cost objects using time-based estimates. The report explains the features of TDABC, such as ease of cost assignment and integration with ERP systems. It differentiates TDABC from ABC and traditional costing, detailing their respective strengths and weaknesses. Finally, the report analyzes the suitability of TDABC for Australian Paper Pty Ltd, emphasizing its potential to improve cost management, strategic decision-making, and overall production efficiency. The report concludes that TDABC is a superior approach for the company.
Contribute Materials
Your contribution can guide someone’s learning journey. Share your
documents today.
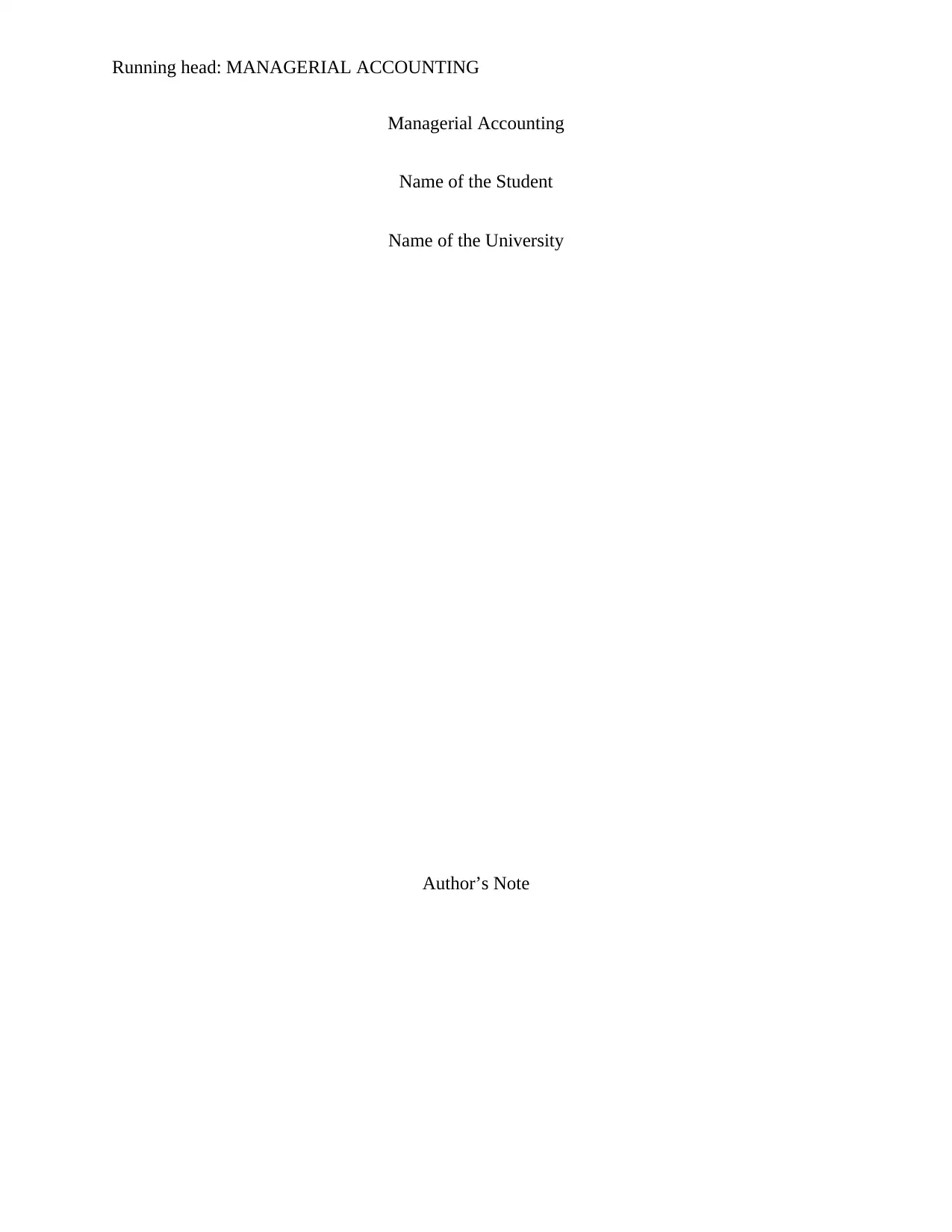
Running head: MANAGERIAL ACCOUNTING
Managerial Accounting
Name of the Student
Name of the University
Author’s Note
Managerial Accounting
Name of the Student
Name of the University
Author’s Note
Secure Best Marks with AI Grader
Need help grading? Try our AI Grader for instant feedback on your assignments.

1MANAGERIAL ACCOUNTING
Table of Contents
Introduction......................................................................................................................................2
Client Firm’s Description................................................................................................................2
Time Driven Activity Based Costing (TDABC).............................................................................3
Description...................................................................................................................................3
Features........................................................................................................................................3
Differences.......................................................................................................................................4
Differences between TDABC and ABC......................................................................................5
Differences between TDABC and Traditional Costing Approach..............................................6
Analysis of the Suitability of TDABC in Client Firm.....................................................................7
Conclusion.......................................................................................................................................8
References......................................................................................................................................10
Table of Contents
Introduction......................................................................................................................................2
Client Firm’s Description................................................................................................................2
Time Driven Activity Based Costing (TDABC).............................................................................3
Description...................................................................................................................................3
Features........................................................................................................................................3
Differences.......................................................................................................................................4
Differences between TDABC and ABC......................................................................................5
Differences between TDABC and Traditional Costing Approach..............................................6
Analysis of the Suitability of TDABC in Client Firm.....................................................................7
Conclusion.......................................................................................................................................8
References......................................................................................................................................10
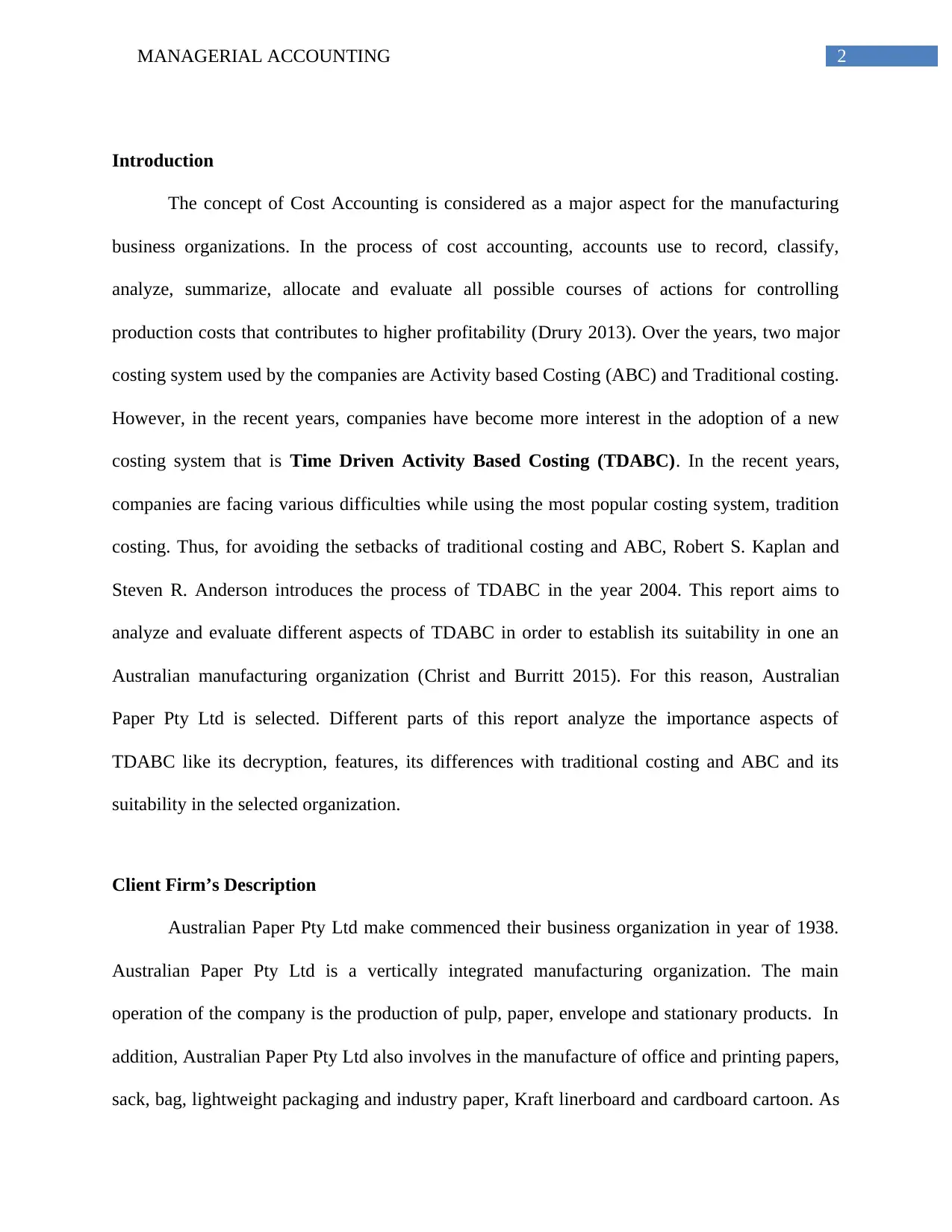
2MANAGERIAL ACCOUNTING
Introduction
The concept of Cost Accounting is considered as a major aspect for the manufacturing
business organizations. In the process of cost accounting, accounts use to record, classify,
analyze, summarize, allocate and evaluate all possible courses of actions for controlling
production costs that contributes to higher profitability (Drury 2013). Over the years, two major
costing system used by the companies are Activity based Costing (ABC) and Traditional costing.
However, in the recent years, companies have become more interest in the adoption of a new
costing system that is Time Driven Activity Based Costing (TDABC). In the recent years,
companies are facing various difficulties while using the most popular costing system, tradition
costing. Thus, for avoiding the setbacks of traditional costing and ABC, Robert S. Kaplan and
Steven R. Anderson introduces the process of TDABC in the year 2004. This report aims to
analyze and evaluate different aspects of TDABC in order to establish its suitability in one an
Australian manufacturing organization (Christ and Burritt 2015). For this reason, Australian
Paper Pty Ltd is selected. Different parts of this report analyze the importance aspects of
TDABC like its decryption, features, its differences with traditional costing and ABC and its
suitability in the selected organization.
Client Firm’s Description
Australian Paper Pty Ltd make commenced their business organization in year of 1938.
Australian Paper Pty Ltd is a vertically integrated manufacturing organization. The main
operation of the company is the production of pulp, paper, envelope and stationary products. In
addition, Australian Paper Pty Ltd also involves in the manufacture of office and printing papers,
sack, bag, lightweight packaging and industry paper, Kraft linerboard and cardboard cartoon. As
Introduction
The concept of Cost Accounting is considered as a major aspect for the manufacturing
business organizations. In the process of cost accounting, accounts use to record, classify,
analyze, summarize, allocate and evaluate all possible courses of actions for controlling
production costs that contributes to higher profitability (Drury 2013). Over the years, two major
costing system used by the companies are Activity based Costing (ABC) and Traditional costing.
However, in the recent years, companies have become more interest in the adoption of a new
costing system that is Time Driven Activity Based Costing (TDABC). In the recent years,
companies are facing various difficulties while using the most popular costing system, tradition
costing. Thus, for avoiding the setbacks of traditional costing and ABC, Robert S. Kaplan and
Steven R. Anderson introduces the process of TDABC in the year 2004. This report aims to
analyze and evaluate different aspects of TDABC in order to establish its suitability in one an
Australian manufacturing organization (Christ and Burritt 2015). For this reason, Australian
Paper Pty Ltd is selected. Different parts of this report analyze the importance aspects of
TDABC like its decryption, features, its differences with traditional costing and ABC and its
suitability in the selected organization.
Client Firm’s Description
Australian Paper Pty Ltd make commenced their business organization in year of 1938.
Australian Paper Pty Ltd is a vertically integrated manufacturing organization. The main
operation of the company is the production of pulp, paper, envelope and stationary products. In
addition, Australian Paper Pty Ltd also involves in the manufacture of office and printing papers,
sack, bag, lightweight packaging and industry paper, Kraft linerboard and cardboard cartoon. As
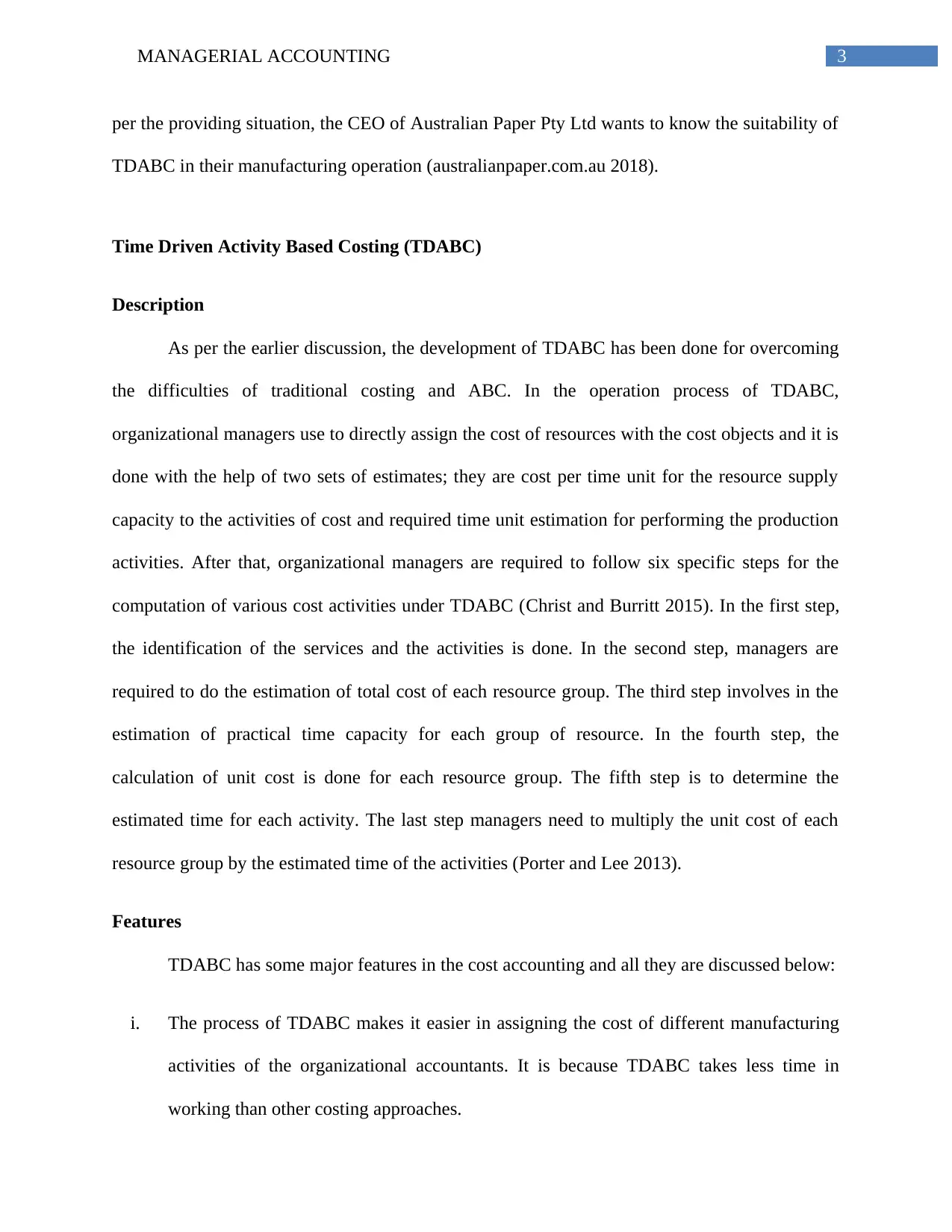
3MANAGERIAL ACCOUNTING
per the providing situation, the CEO of Australian Paper Pty Ltd wants to know the suitability of
TDABC in their manufacturing operation (australianpaper.com.au 2018).
Time Driven Activity Based Costing (TDABC)
Description
As per the earlier discussion, the development of TDABC has been done for overcoming
the difficulties of traditional costing and ABC. In the operation process of TDABC,
organizational managers use to directly assign the cost of resources with the cost objects and it is
done with the help of two sets of estimates; they are cost per time unit for the resource supply
capacity to the activities of cost and required time unit estimation for performing the production
activities. After that, organizational managers are required to follow six specific steps for the
computation of various cost activities under TDABC (Christ and Burritt 2015). In the first step,
the identification of the services and the activities is done. In the second step, managers are
required to do the estimation of total cost of each resource group. The third step involves in the
estimation of practical time capacity for each group of resource. In the fourth step, the
calculation of unit cost is done for each resource group. The fifth step is to determine the
estimated time for each activity. The last step managers need to multiply the unit cost of each
resource group by the estimated time of the activities (Porter and Lee 2013).
Features
TDABC has some major features in the cost accounting and all they are discussed below:
i. The process of TDABC makes it easier in assigning the cost of different manufacturing
activities of the organizational accountants. It is because TDABC takes less time in
working than other costing approaches.
per the providing situation, the CEO of Australian Paper Pty Ltd wants to know the suitability of
TDABC in their manufacturing operation (australianpaper.com.au 2018).
Time Driven Activity Based Costing (TDABC)
Description
As per the earlier discussion, the development of TDABC has been done for overcoming
the difficulties of traditional costing and ABC. In the operation process of TDABC,
organizational managers use to directly assign the cost of resources with the cost objects and it is
done with the help of two sets of estimates; they are cost per time unit for the resource supply
capacity to the activities of cost and required time unit estimation for performing the production
activities. After that, organizational managers are required to follow six specific steps for the
computation of various cost activities under TDABC (Christ and Burritt 2015). In the first step,
the identification of the services and the activities is done. In the second step, managers are
required to do the estimation of total cost of each resource group. The third step involves in the
estimation of practical time capacity for each group of resource. In the fourth step, the
calculation of unit cost is done for each resource group. The fifth step is to determine the
estimated time for each activity. The last step managers need to multiply the unit cost of each
resource group by the estimated time of the activities (Porter and Lee 2013).
Features
TDABC has some major features in the cost accounting and all they are discussed below:
i. The process of TDABC makes it easier in assigning the cost of different manufacturing
activities of the organizational accountants. It is because TDABC takes less time in
working than other costing approaches.
Secure Best Marks with AI Grader
Need help grading? Try our AI Grader for instant feedback on your assignments.
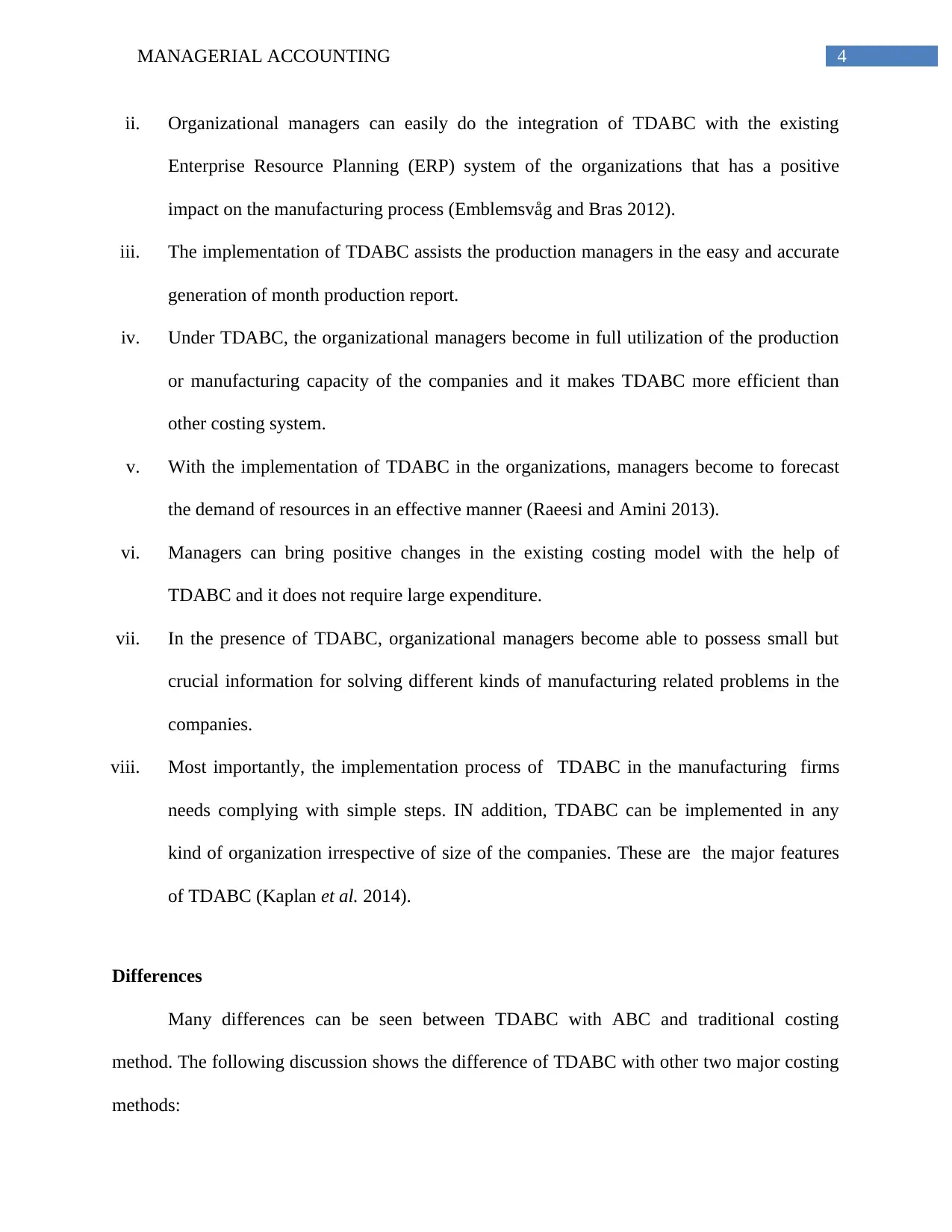
4MANAGERIAL ACCOUNTING
ii. Organizational managers can easily do the integration of TDABC with the existing
Enterprise Resource Planning (ERP) system of the organizations that has a positive
impact on the manufacturing process (Emblemsvåg and Bras 2012).
iii. The implementation of TDABC assists the production managers in the easy and accurate
generation of month production report.
iv. Under TDABC, the organizational managers become in full utilization of the production
or manufacturing capacity of the companies and it makes TDABC more efficient than
other costing system.
v. With the implementation of TDABC in the organizations, managers become to forecast
the demand of resources in an effective manner (Raeesi and Amini 2013).
vi. Managers can bring positive changes in the existing costing model with the help of
TDABC and it does not require large expenditure.
vii. In the presence of TDABC, organizational managers become able to possess small but
crucial information for solving different kinds of manufacturing related problems in the
companies.
viii. Most importantly, the implementation process of TDABC in the manufacturing firms
needs complying with simple steps. IN addition, TDABC can be implemented in any
kind of organization irrespective of size of the companies. These are the major features
of TDABC (Kaplan et al. 2014).
Differences
Many differences can be seen between TDABC with ABC and traditional costing
method. The following discussion shows the difference of TDABC with other two major costing
methods:
ii. Organizational managers can easily do the integration of TDABC with the existing
Enterprise Resource Planning (ERP) system of the organizations that has a positive
impact on the manufacturing process (Emblemsvåg and Bras 2012).
iii. The implementation of TDABC assists the production managers in the easy and accurate
generation of month production report.
iv. Under TDABC, the organizational managers become in full utilization of the production
or manufacturing capacity of the companies and it makes TDABC more efficient than
other costing system.
v. With the implementation of TDABC in the organizations, managers become to forecast
the demand of resources in an effective manner (Raeesi and Amini 2013).
vi. Managers can bring positive changes in the existing costing model with the help of
TDABC and it does not require large expenditure.
vii. In the presence of TDABC, organizational managers become able to possess small but
crucial information for solving different kinds of manufacturing related problems in the
companies.
viii. Most importantly, the implementation process of TDABC in the manufacturing firms
needs complying with simple steps. IN addition, TDABC can be implemented in any
kind of organization irrespective of size of the companies. These are the major features
of TDABC (Kaplan et al. 2014).
Differences
Many differences can be seen between TDABC with ABC and traditional costing
method. The following discussion shows the difference of TDABC with other two major costing
methods:
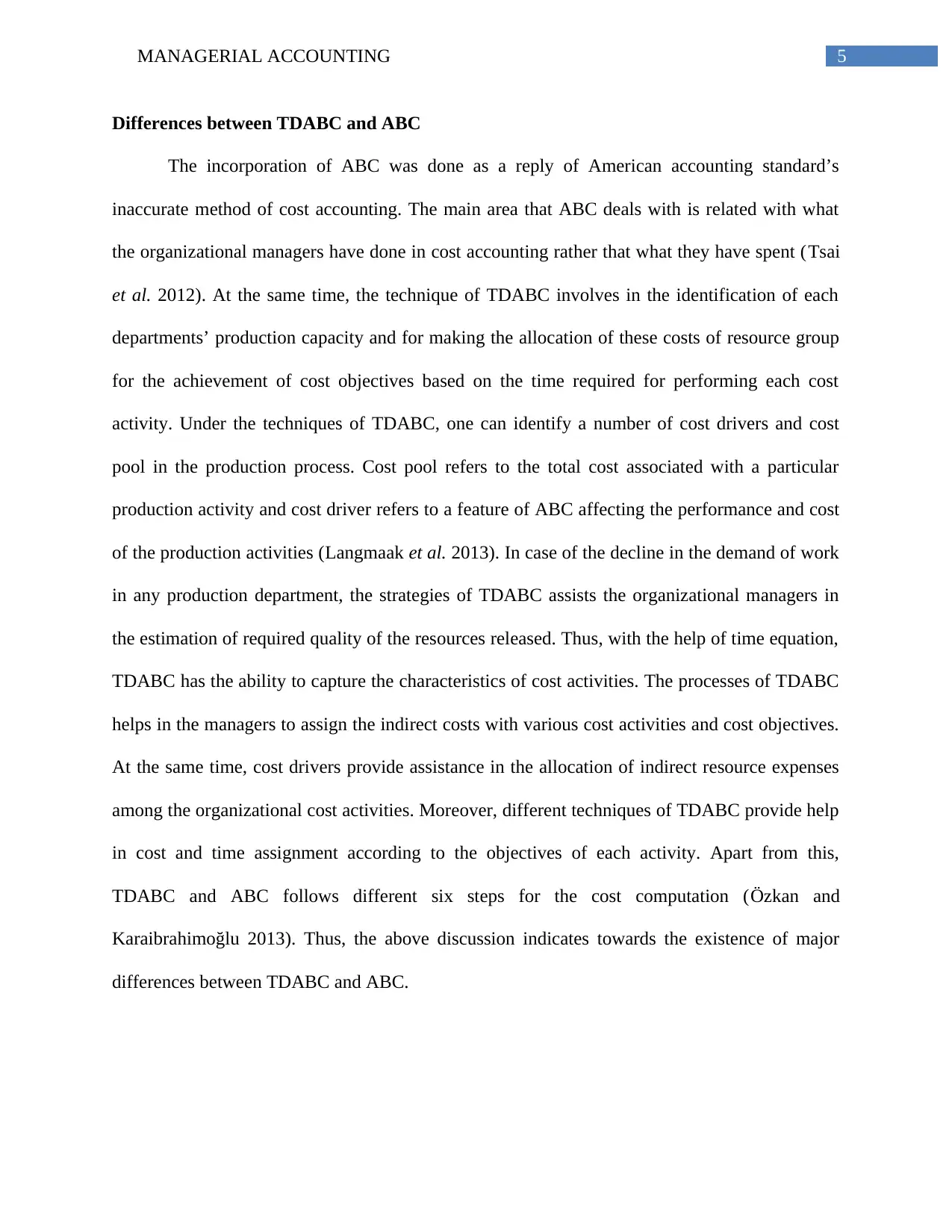
5MANAGERIAL ACCOUNTING
Differences between TDABC and ABC
The incorporation of ABC was done as a reply of American accounting standard’s
inaccurate method of cost accounting. The main area that ABC deals with is related with what
the organizational managers have done in cost accounting rather that what they have spent (Tsai
et al. 2012). At the same time, the technique of TDABC involves in the identification of each
departments’ production capacity and for making the allocation of these costs of resource group
for the achievement of cost objectives based on the time required for performing each cost
activity. Under the techniques of TDABC, one can identify a number of cost drivers and cost
pool in the production process. Cost pool refers to the total cost associated with a particular
production activity and cost driver refers to a feature of ABC affecting the performance and cost
of the production activities (Langmaak et al. 2013). In case of the decline in the demand of work
in any production department, the strategies of TDABC assists the organizational managers in
the estimation of required quality of the resources released. Thus, with the help of time equation,
TDABC has the ability to capture the characteristics of cost activities. The processes of TDABC
helps in the managers to assign the indirect costs with various cost activities and cost objectives.
At the same time, cost drivers provide assistance in the allocation of indirect resource expenses
among the organizational cost activities. Moreover, different techniques of TDABC provide help
in cost and time assignment according to the objectives of each activity. Apart from this,
TDABC and ABC follows different six steps for the cost computation (Özkan and
Karaibrahimoğlu 2013). Thus, the above discussion indicates towards the existence of major
differences between TDABC and ABC.
Differences between TDABC and ABC
The incorporation of ABC was done as a reply of American accounting standard’s
inaccurate method of cost accounting. The main area that ABC deals with is related with what
the organizational managers have done in cost accounting rather that what they have spent (Tsai
et al. 2012). At the same time, the technique of TDABC involves in the identification of each
departments’ production capacity and for making the allocation of these costs of resource group
for the achievement of cost objectives based on the time required for performing each cost
activity. Under the techniques of TDABC, one can identify a number of cost drivers and cost
pool in the production process. Cost pool refers to the total cost associated with a particular
production activity and cost driver refers to a feature of ABC affecting the performance and cost
of the production activities (Langmaak et al. 2013). In case of the decline in the demand of work
in any production department, the strategies of TDABC assists the organizational managers in
the estimation of required quality of the resources released. Thus, with the help of time equation,
TDABC has the ability to capture the characteristics of cost activities. The processes of TDABC
helps in the managers to assign the indirect costs with various cost activities and cost objectives.
At the same time, cost drivers provide assistance in the allocation of indirect resource expenses
among the organizational cost activities. Moreover, different techniques of TDABC provide help
in cost and time assignment according to the objectives of each activity. Apart from this,
TDABC and ABC follows different six steps for the cost computation (Özkan and
Karaibrahimoğlu 2013). Thus, the above discussion indicates towards the existence of major
differences between TDABC and ABC.

6MANAGERIAL ACCOUNTING
Differences between TDABC and Traditional Costing Approach
One of the major differences between TDABC and traditional costing is the lack of
simplicity. The costing approach of traditional costing is easy and simple where TDABC
operates in a complex way. Under the approach of traditional costing, a requirement of cost
objective and used up resources can be seen for the purpose to evaluate different cost activities
(Weygandt, Kimmel and Kieso 2015). However, the situation is different in case of TDABC as
different cost activities have dependency on used activities for achieving the cost objective. It
has been seen that the companies with large amount of overheads and large number of
miscellaneous products have the tendency of the adoption of TDABC and it is adopted out of the
requirement of effective and accurate method for managing the production costs. Under the
techniques of traditional costing method, organizational managers use to use single overhead
pools and they are unable for the accurate and true calculation of manufacturing costs (Laudon
and Laudon 2016). Moreover, under the techniques of traditional costing, managers use to
allocate cost objectives on random basis based machine hours or labor hours and this aspect
differs in TDABC. TDABC wants the inclusion of identifiable products; but traditional costing
requires the inclusion of different expenses like salaries, depreciation and many others. Under
traditional costing approach, managers calculate the total cost of production after the ending of
the whole production process. However, in case of TDABC, feedbacks of the customers are used
for the determination of total cost of production. Most importantly, it has been seen that the
implementation of TDABC helps the organizational managers in the reduction of cost of
production so that profitability can be maximized (Cooper 2017). Hence, the above discussion is
the evidence that there are clear differences between TDABC and traditional costing approach.
Differences between TDABC and Traditional Costing Approach
One of the major differences between TDABC and traditional costing is the lack of
simplicity. The costing approach of traditional costing is easy and simple where TDABC
operates in a complex way. Under the approach of traditional costing, a requirement of cost
objective and used up resources can be seen for the purpose to evaluate different cost activities
(Weygandt, Kimmel and Kieso 2015). However, the situation is different in case of TDABC as
different cost activities have dependency on used activities for achieving the cost objective. It
has been seen that the companies with large amount of overheads and large number of
miscellaneous products have the tendency of the adoption of TDABC and it is adopted out of the
requirement of effective and accurate method for managing the production costs. Under the
techniques of traditional costing method, organizational managers use to use single overhead
pools and they are unable for the accurate and true calculation of manufacturing costs (Laudon
and Laudon 2016). Moreover, under the techniques of traditional costing, managers use to
allocate cost objectives on random basis based machine hours or labor hours and this aspect
differs in TDABC. TDABC wants the inclusion of identifiable products; but traditional costing
requires the inclusion of different expenses like salaries, depreciation and many others. Under
traditional costing approach, managers calculate the total cost of production after the ending of
the whole production process. However, in case of TDABC, feedbacks of the customers are used
for the determination of total cost of production. Most importantly, it has been seen that the
implementation of TDABC helps the organizational managers in the reduction of cost of
production so that profitability can be maximized (Cooper 2017). Hence, the above discussion is
the evidence that there are clear differences between TDABC and traditional costing approach.
Paraphrase This Document
Need a fresh take? Get an instant paraphrase of this document with our AI Paraphraser
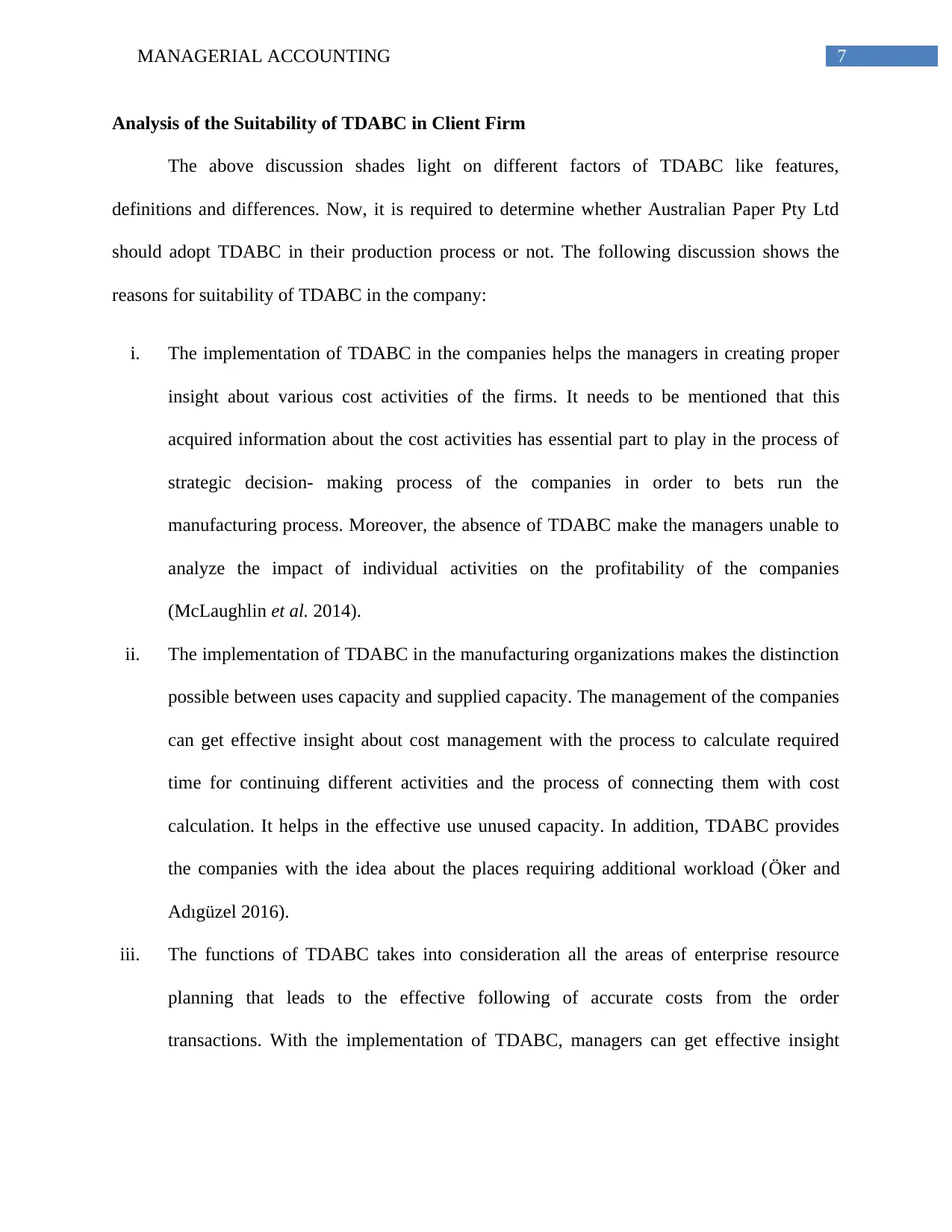
7MANAGERIAL ACCOUNTING
Analysis of the Suitability of TDABC in Client Firm
The above discussion shades light on different factors of TDABC like features,
definitions and differences. Now, it is required to determine whether Australian Paper Pty Ltd
should adopt TDABC in their production process or not. The following discussion shows the
reasons for suitability of TDABC in the company:
i. The implementation of TDABC in the companies helps the managers in creating proper
insight about various cost activities of the firms. It needs to be mentioned that this
acquired information about the cost activities has essential part to play in the process of
strategic decision- making process of the companies in order to bets run the
manufacturing process. Moreover, the absence of TDABC make the managers unable to
analyze the impact of individual activities on the profitability of the companies
(McLaughlin et al. 2014).
ii. The implementation of TDABC in the manufacturing organizations makes the distinction
possible between uses capacity and supplied capacity. The management of the companies
can get effective insight about cost management with the process to calculate required
time for continuing different activities and the process of connecting them with cost
calculation. It helps in the effective use unused capacity. In addition, TDABC provides
the companies with the idea about the places requiring additional workload (Öker and
Adıgüzel 2016).
iii. The functions of TDABC takes into consideration all the areas of enterprise resource
planning that leads to the effective following of accurate costs from the order
transactions. With the implementation of TDABC, managers can get effective insight
Analysis of the Suitability of TDABC in Client Firm
The above discussion shades light on different factors of TDABC like features,
definitions and differences. Now, it is required to determine whether Australian Paper Pty Ltd
should adopt TDABC in their production process or not. The following discussion shows the
reasons for suitability of TDABC in the company:
i. The implementation of TDABC in the companies helps the managers in creating proper
insight about various cost activities of the firms. It needs to be mentioned that this
acquired information about the cost activities has essential part to play in the process of
strategic decision- making process of the companies in order to bets run the
manufacturing process. Moreover, the absence of TDABC make the managers unable to
analyze the impact of individual activities on the profitability of the companies
(McLaughlin et al. 2014).
ii. The implementation of TDABC in the manufacturing organizations makes the distinction
possible between uses capacity and supplied capacity. The management of the companies
can get effective insight about cost management with the process to calculate required
time for continuing different activities and the process of connecting them with cost
calculation. It helps in the effective use unused capacity. In addition, TDABC provides
the companies with the idea about the places requiring additional workload (Öker and
Adıgüzel 2016).
iii. The functions of TDABC takes into consideration all the areas of enterprise resource
planning that leads to the effective following of accurate costs from the order
transactions. With the implementation of TDABC, managers can get effective insight
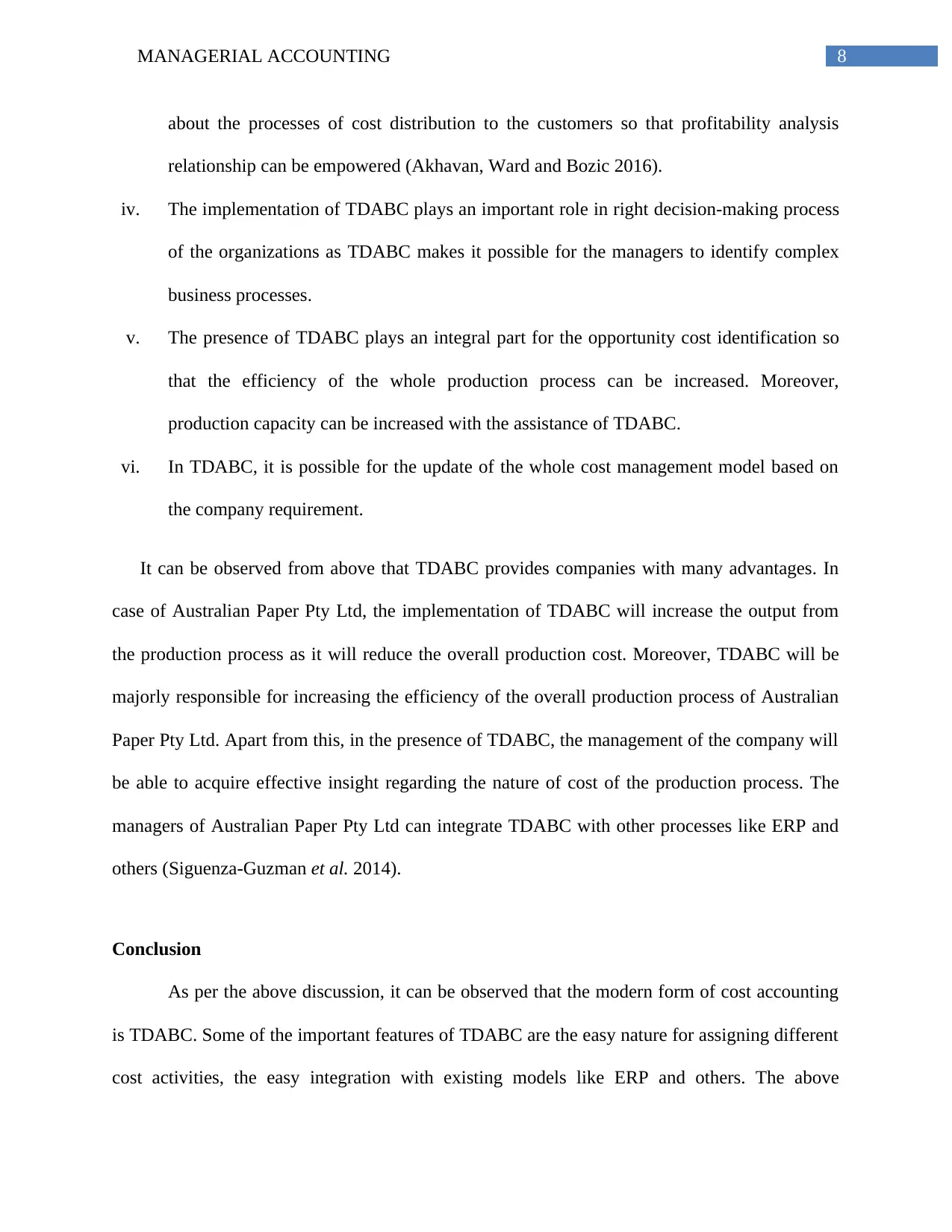
8MANAGERIAL ACCOUNTING
about the processes of cost distribution to the customers so that profitability analysis
relationship can be empowered (Akhavan, Ward and Bozic 2016).
iv. The implementation of TDABC plays an important role in right decision-making process
of the organizations as TDABC makes it possible for the managers to identify complex
business processes.
v. The presence of TDABC plays an integral part for the opportunity cost identification so
that the efficiency of the whole production process can be increased. Moreover,
production capacity can be increased with the assistance of TDABC.
vi. In TDABC, it is possible for the update of the whole cost management model based on
the company requirement.
It can be observed from above that TDABC provides companies with many advantages. In
case of Australian Paper Pty Ltd, the implementation of TDABC will increase the output from
the production process as it will reduce the overall production cost. Moreover, TDABC will be
majorly responsible for increasing the efficiency of the overall production process of Australian
Paper Pty Ltd. Apart from this, in the presence of TDABC, the management of the company will
be able to acquire effective insight regarding the nature of cost of the production process. The
managers of Australian Paper Pty Ltd can integrate TDABC with other processes like ERP and
others (Siguenza-Guzman et al. 2014).
Conclusion
As per the above discussion, it can be observed that the modern form of cost accounting
is TDABC. Some of the important features of TDABC are the easy nature for assigning different
cost activities, the easy integration with existing models like ERP and others. The above
about the processes of cost distribution to the customers so that profitability analysis
relationship can be empowered (Akhavan, Ward and Bozic 2016).
iv. The implementation of TDABC plays an important role in right decision-making process
of the organizations as TDABC makes it possible for the managers to identify complex
business processes.
v. The presence of TDABC plays an integral part for the opportunity cost identification so
that the efficiency of the whole production process can be increased. Moreover,
production capacity can be increased with the assistance of TDABC.
vi. In TDABC, it is possible for the update of the whole cost management model based on
the company requirement.
It can be observed from above that TDABC provides companies with many advantages. In
case of Australian Paper Pty Ltd, the implementation of TDABC will increase the output from
the production process as it will reduce the overall production cost. Moreover, TDABC will be
majorly responsible for increasing the efficiency of the overall production process of Australian
Paper Pty Ltd. Apart from this, in the presence of TDABC, the management of the company will
be able to acquire effective insight regarding the nature of cost of the production process. The
managers of Australian Paper Pty Ltd can integrate TDABC with other processes like ERP and
others (Siguenza-Guzman et al. 2014).
Conclusion
As per the above discussion, it can be observed that the modern form of cost accounting
is TDABC. Some of the important features of TDABC are the easy nature for assigning different
cost activities, the easy integration with existing models like ERP and others. The above
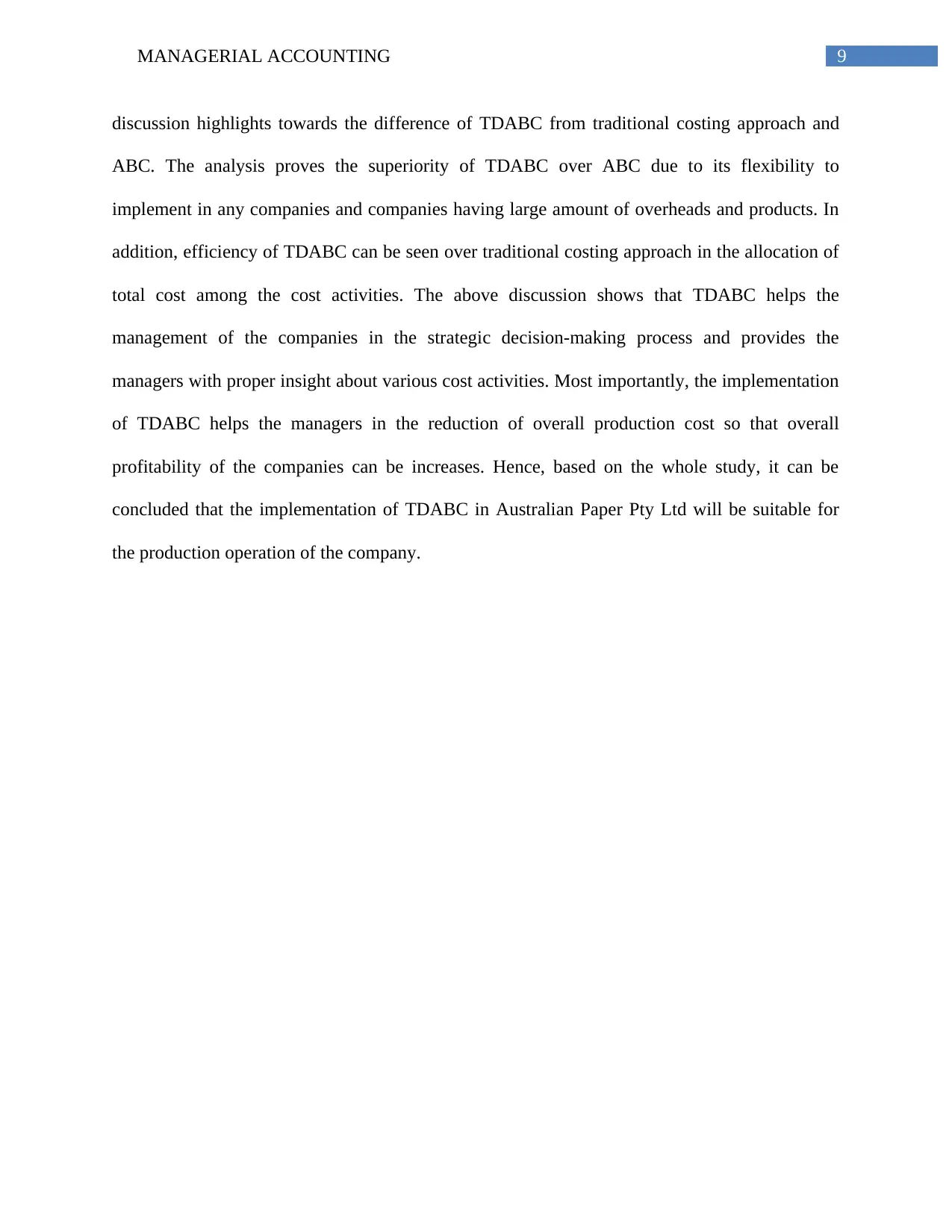
9MANAGERIAL ACCOUNTING
discussion highlights towards the difference of TDABC from traditional costing approach and
ABC. The analysis proves the superiority of TDABC over ABC due to its flexibility to
implement in any companies and companies having large amount of overheads and products. In
addition, efficiency of TDABC can be seen over traditional costing approach in the allocation of
total cost among the cost activities. The above discussion shows that TDABC helps the
management of the companies in the strategic decision-making process and provides the
managers with proper insight about various cost activities. Most importantly, the implementation
of TDABC helps the managers in the reduction of overall production cost so that overall
profitability of the companies can be increases. Hence, based on the whole study, it can be
concluded that the implementation of TDABC in Australian Paper Pty Ltd will be suitable for
the production operation of the company.
discussion highlights towards the difference of TDABC from traditional costing approach and
ABC. The analysis proves the superiority of TDABC over ABC due to its flexibility to
implement in any companies and companies having large amount of overheads and products. In
addition, efficiency of TDABC can be seen over traditional costing approach in the allocation of
total cost among the cost activities. The above discussion shows that TDABC helps the
management of the companies in the strategic decision-making process and provides the
managers with proper insight about various cost activities. Most importantly, the implementation
of TDABC helps the managers in the reduction of overall production cost so that overall
profitability of the companies can be increases. Hence, based on the whole study, it can be
concluded that the implementation of TDABC in Australian Paper Pty Ltd will be suitable for
the production operation of the company.
Secure Best Marks with AI Grader
Need help grading? Try our AI Grader for instant feedback on your assignments.
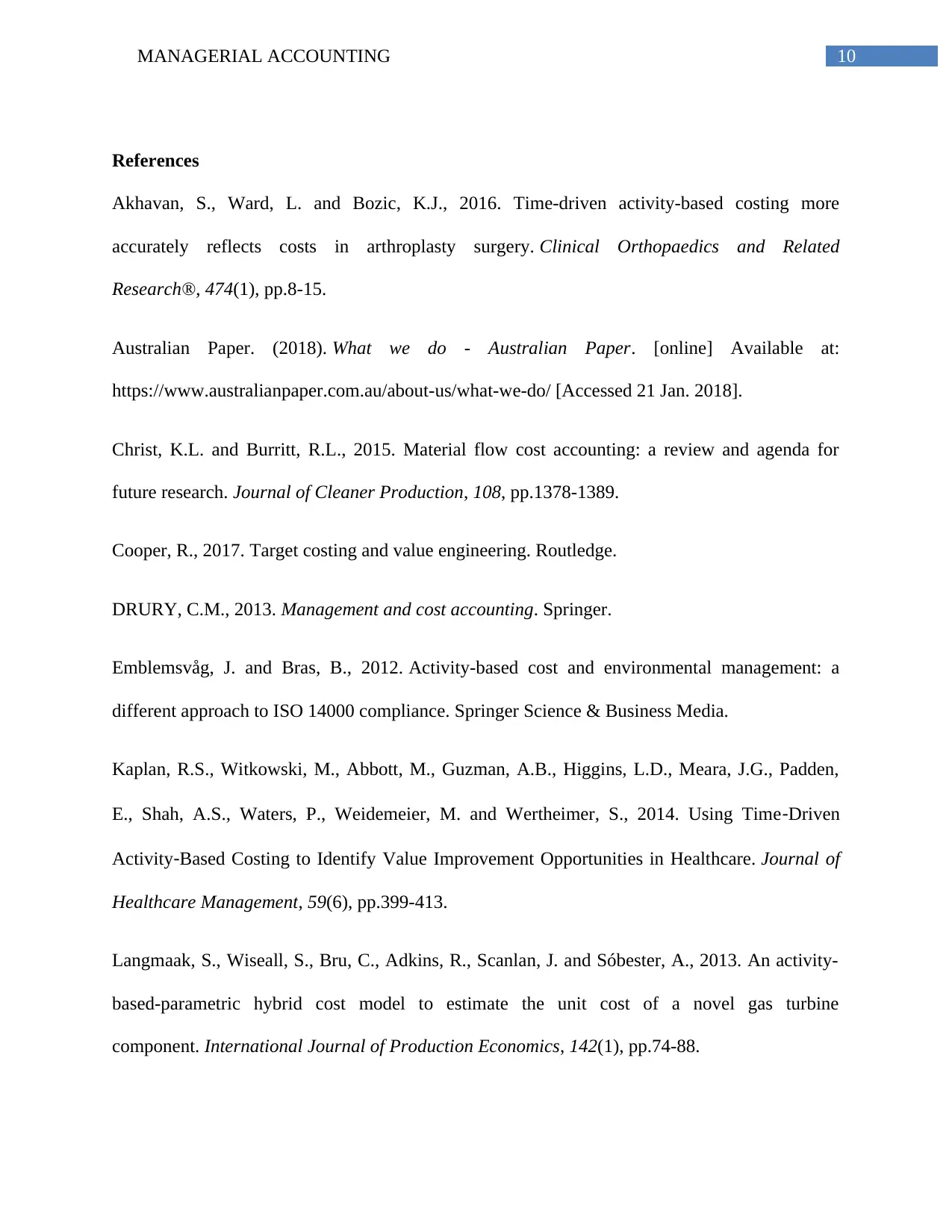
10MANAGERIAL ACCOUNTING
References
Akhavan, S., Ward, L. and Bozic, K.J., 2016. Time-driven activity-based costing more
accurately reflects costs in arthroplasty surgery. Clinical Orthopaedics and Related
Research®, 474(1), pp.8-15.
Australian Paper. (2018). What we do - Australian Paper. [online] Available at:
https://www.australianpaper.com.au/about-us/what-we-do/ [Accessed 21 Jan. 2018].
Christ, K.L. and Burritt, R.L., 2015. Material flow cost accounting: a review and agenda for
future research. Journal of Cleaner Production, 108, pp.1378-1389.
Cooper, R., 2017. Target costing and value engineering. Routledge.
DRURY, C.M., 2013. Management and cost accounting. Springer.
Emblemsvåg, J. and Bras, B., 2012. Activity-based cost and environmental management: a
different approach to ISO 14000 compliance. Springer Science & Business Media.
Kaplan, R.S., Witkowski, M., Abbott, M., Guzman, A.B., Higgins, L.D., Meara, J.G., Padden,
E., Shah, A.S., Waters, P., Weidemeier, M. and Wertheimer, S., 2014. Using Time‐Driven
Activity‐Based Costing to Identify Value Improvement Opportunities in Healthcare. Journal of
Healthcare Management, 59(6), pp.399-413.
Langmaak, S., Wiseall, S., Bru, C., Adkins, R., Scanlan, J. and Sóbester, A., 2013. An activity-
based-parametric hybrid cost model to estimate the unit cost of a novel gas turbine
component. International Journal of Production Economics, 142(1), pp.74-88.
References
Akhavan, S., Ward, L. and Bozic, K.J., 2016. Time-driven activity-based costing more
accurately reflects costs in arthroplasty surgery. Clinical Orthopaedics and Related
Research®, 474(1), pp.8-15.
Australian Paper. (2018). What we do - Australian Paper. [online] Available at:
https://www.australianpaper.com.au/about-us/what-we-do/ [Accessed 21 Jan. 2018].
Christ, K.L. and Burritt, R.L., 2015. Material flow cost accounting: a review and agenda for
future research. Journal of Cleaner Production, 108, pp.1378-1389.
Cooper, R., 2017. Target costing and value engineering. Routledge.
DRURY, C.M., 2013. Management and cost accounting. Springer.
Emblemsvåg, J. and Bras, B., 2012. Activity-based cost and environmental management: a
different approach to ISO 14000 compliance. Springer Science & Business Media.
Kaplan, R.S., Witkowski, M., Abbott, M., Guzman, A.B., Higgins, L.D., Meara, J.G., Padden,
E., Shah, A.S., Waters, P., Weidemeier, M. and Wertheimer, S., 2014. Using Time‐Driven
Activity‐Based Costing to Identify Value Improvement Opportunities in Healthcare. Journal of
Healthcare Management, 59(6), pp.399-413.
Langmaak, S., Wiseall, S., Bru, C., Adkins, R., Scanlan, J. and Sóbester, A., 2013. An activity-
based-parametric hybrid cost model to estimate the unit cost of a novel gas turbine
component. International Journal of Production Economics, 142(1), pp.74-88.
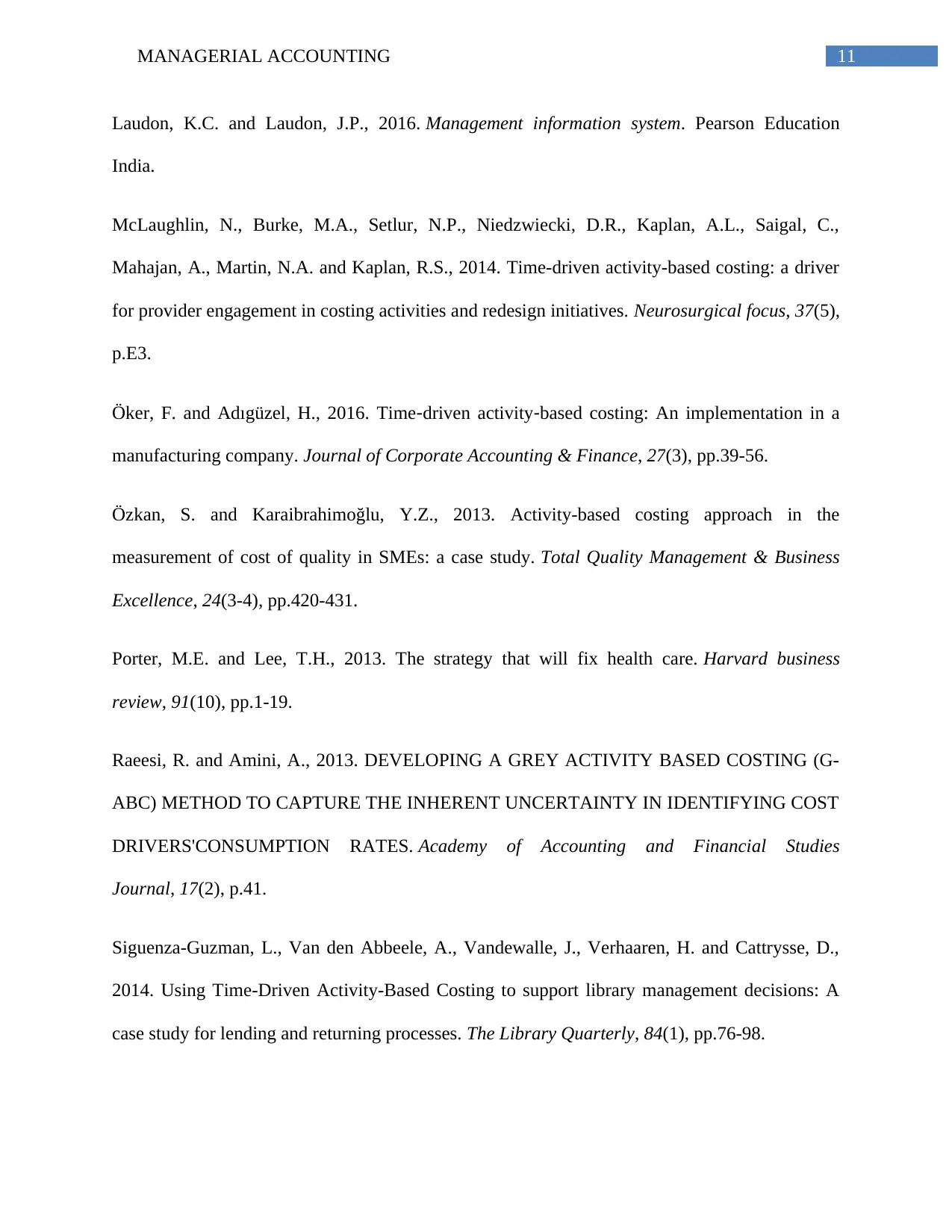
11MANAGERIAL ACCOUNTING
Laudon, K.C. and Laudon, J.P., 2016. Management information system. Pearson Education
India.
McLaughlin, N., Burke, M.A., Setlur, N.P., Niedzwiecki, D.R., Kaplan, A.L., Saigal, C.,
Mahajan, A., Martin, N.A. and Kaplan, R.S., 2014. Time-driven activity-based costing: a driver
for provider engagement in costing activities and redesign initiatives. Neurosurgical focus, 37(5),
p.E3.
Öker, F. and Adıgüzel, H., 2016. Time‐driven activity‐based costing: An implementation in a
manufacturing company. Journal of Corporate Accounting & Finance, 27(3), pp.39-56.
Özkan, S. and Karaibrahimoğlu, Y.Z., 2013. Activity-based costing approach in the
measurement of cost of quality in SMEs: a case study. Total Quality Management & Business
Excellence, 24(3-4), pp.420-431.
Porter, M.E. and Lee, T.H., 2013. The strategy that will fix health care. Harvard business
review, 91(10), pp.1-19.
Raeesi, R. and Amini, A., 2013. DEVELOPING A GREY ACTIVITY BASED COSTING (G-
ABC) METHOD TO CAPTURE THE INHERENT UNCERTAINTY IN IDENTIFYING COST
DRIVERS'CONSUMPTION RATES. Academy of Accounting and Financial Studies
Journal, 17(2), p.41.
Siguenza-Guzman, L., Van den Abbeele, A., Vandewalle, J., Verhaaren, H. and Cattrysse, D.,
2014. Using Time-Driven Activity-Based Costing to support library management decisions: A
case study for lending and returning processes. The Library Quarterly, 84(1), pp.76-98.
Laudon, K.C. and Laudon, J.P., 2016. Management information system. Pearson Education
India.
McLaughlin, N., Burke, M.A., Setlur, N.P., Niedzwiecki, D.R., Kaplan, A.L., Saigal, C.,
Mahajan, A., Martin, N.A. and Kaplan, R.S., 2014. Time-driven activity-based costing: a driver
for provider engagement in costing activities and redesign initiatives. Neurosurgical focus, 37(5),
p.E3.
Öker, F. and Adıgüzel, H., 2016. Time‐driven activity‐based costing: An implementation in a
manufacturing company. Journal of Corporate Accounting & Finance, 27(3), pp.39-56.
Özkan, S. and Karaibrahimoğlu, Y.Z., 2013. Activity-based costing approach in the
measurement of cost of quality in SMEs: a case study. Total Quality Management & Business
Excellence, 24(3-4), pp.420-431.
Porter, M.E. and Lee, T.H., 2013. The strategy that will fix health care. Harvard business
review, 91(10), pp.1-19.
Raeesi, R. and Amini, A., 2013. DEVELOPING A GREY ACTIVITY BASED COSTING (G-
ABC) METHOD TO CAPTURE THE INHERENT UNCERTAINTY IN IDENTIFYING COST
DRIVERS'CONSUMPTION RATES. Academy of Accounting and Financial Studies
Journal, 17(2), p.41.
Siguenza-Guzman, L., Van den Abbeele, A., Vandewalle, J., Verhaaren, H. and Cattrysse, D.,
2014. Using Time-Driven Activity-Based Costing to support library management decisions: A
case study for lending and returning processes. The Library Quarterly, 84(1), pp.76-98.
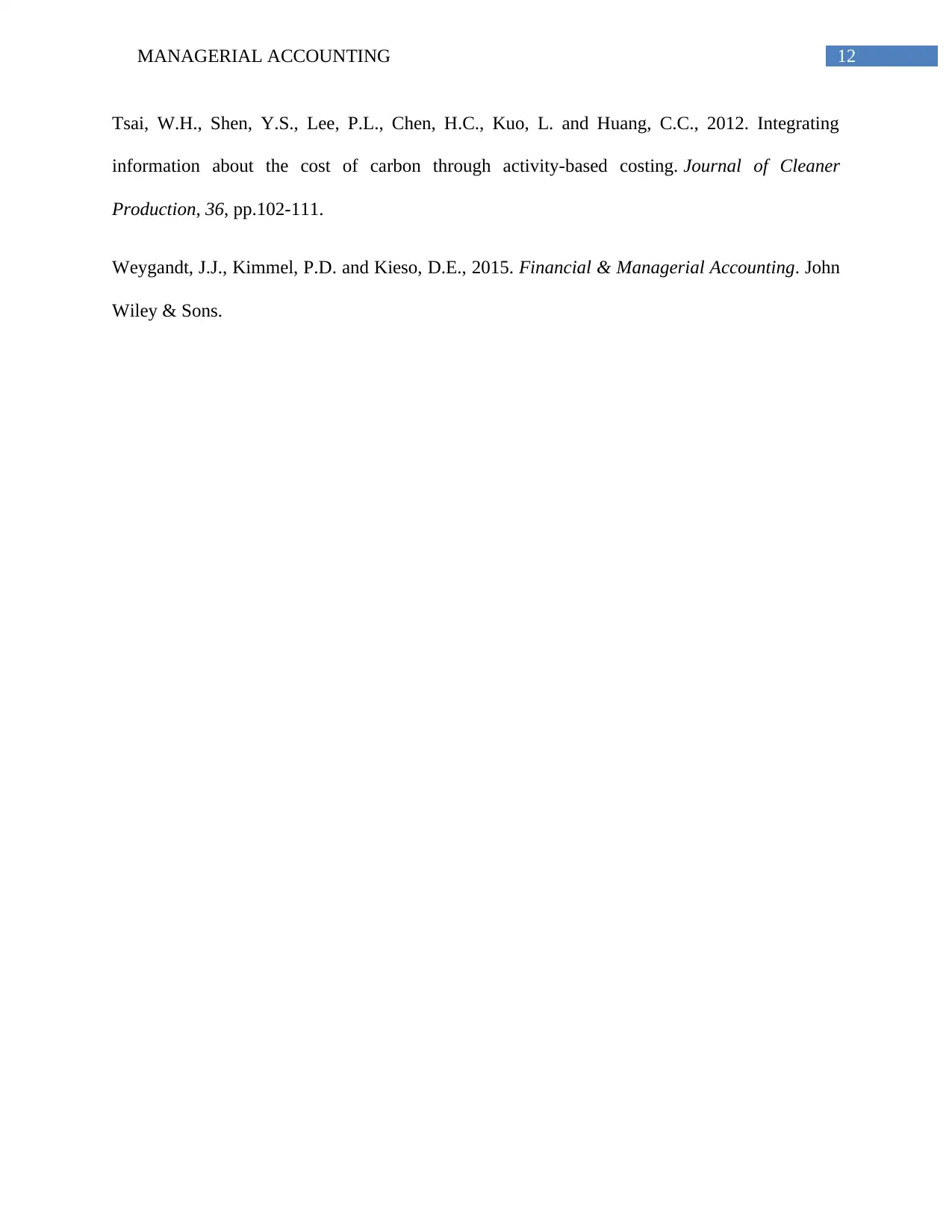
12MANAGERIAL ACCOUNTING
Tsai, W.H., Shen, Y.S., Lee, P.L., Chen, H.C., Kuo, L. and Huang, C.C., 2012. Integrating
information about the cost of carbon through activity-based costing. Journal of Cleaner
Production, 36, pp.102-111.
Weygandt, J.J., Kimmel, P.D. and Kieso, D.E., 2015. Financial & Managerial Accounting. John
Wiley & Sons.
Tsai, W.H., Shen, Y.S., Lee, P.L., Chen, H.C., Kuo, L. and Huang, C.C., 2012. Integrating
information about the cost of carbon through activity-based costing. Journal of Cleaner
Production, 36, pp.102-111.
Weygandt, J.J., Kimmel, P.D. and Kieso, D.E., 2015. Financial & Managerial Accounting. John
Wiley & Sons.
1 out of 13
Related Documents

Your All-in-One AI-Powered Toolkit for Academic Success.
+13062052269
info@desklib.com
Available 24*7 on WhatsApp / Email
Unlock your academic potential
© 2024 | Zucol Services PVT LTD | All rights reserved.