TLIJ - Applying Quality System in Motorola: A Comprehensive Report
VerifiedAdded on  2023/06/18
|10
|2932
|327
Report
AI Summary
This report examines the application of quality control (QC) within Motorola, an Australian-based telecommunications and electronics company. It defines QC, explains its necessity for maintaining and improving product quality, and details the QC methods employed by Motorola, particularly the Six Sigma approach. The report highlights the importance of QC in enhancing production processes, reducing risks, and fostering customer loyalty. It discusses the various types of quality control, such as process control, control charts, and product quality, along with the tools used for quality assessment. The analysis focuses on Motorola's implementation of Six Sigma, outlining steps such as defining the problem, measuring the current process, analyzing issues, improving processes, and implementing controls. The report concludes by emphasizing the contributions of Six Sigma in reducing operational costs, improving efficiency, and ultimately enhancing customer satisfaction. Desklib provides access to this and other solved assignments for students.
Contribute Materials
Your contribution can guide someone’s learning journey. Share your
documents today.
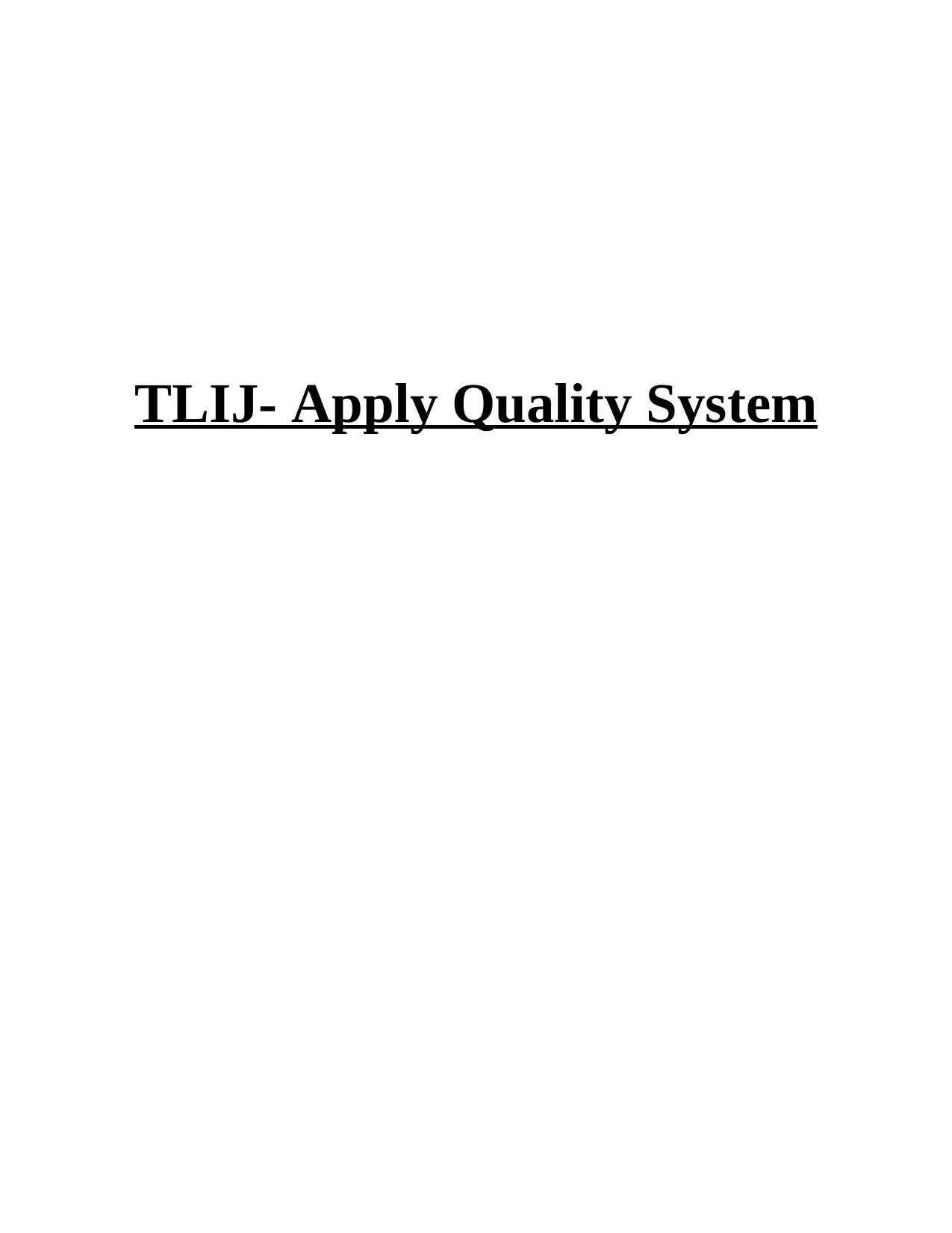
TLIJ- Apply Quality System
Secure Best Marks with AI Grader
Need help grading? Try our AI Grader for instant feedback on your assignments.
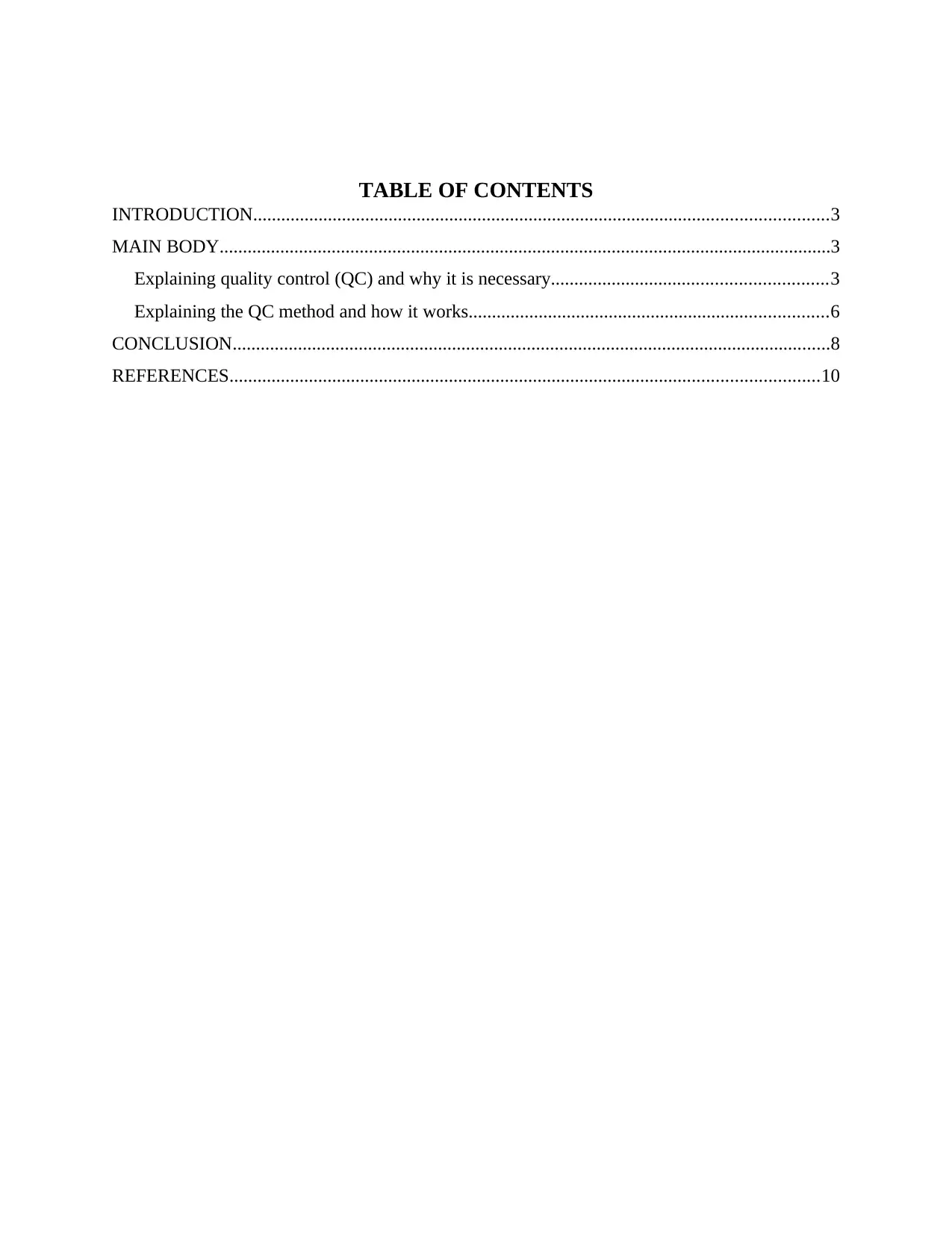
TABLE OF CONTENTS
INTRODUCTION...........................................................................................................................3
MAIN BODY...................................................................................................................................3
Explaining quality control (QC) and why it is necessary...........................................................3
Explaining the QC method and how it works.............................................................................6
CONCLUSION................................................................................................................................8
REFERENCES..............................................................................................................................10
INTRODUCTION...........................................................................................................................3
MAIN BODY...................................................................................................................................3
Explaining quality control (QC) and why it is necessary...........................................................3
Explaining the QC method and how it works.............................................................................6
CONCLUSION................................................................................................................................8
REFERENCES..............................................................................................................................10
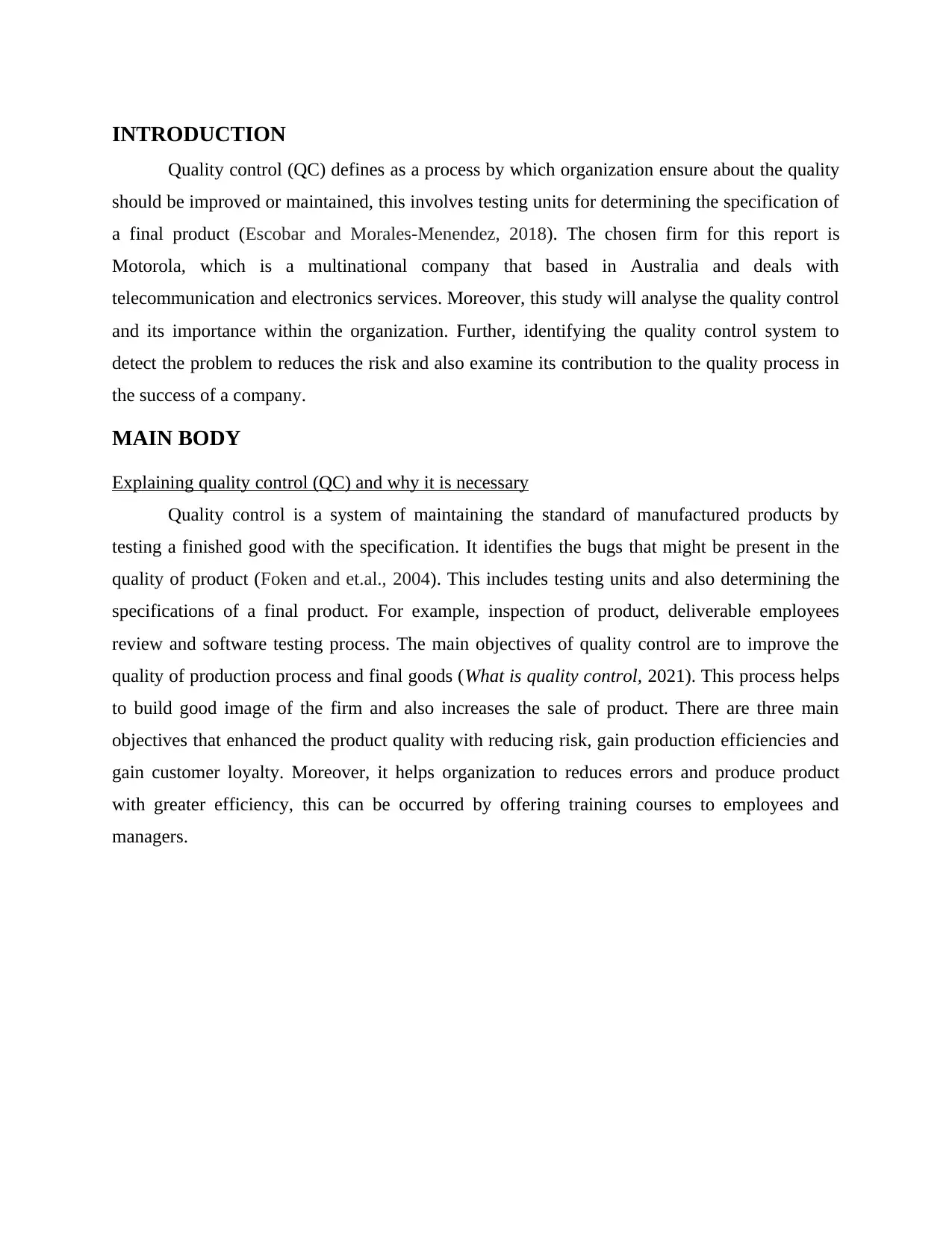
INTRODUCTION
Quality control (QC) defines as a process by which organization ensure about the quality
should be improved or maintained, this involves testing units for determining the specification of
a final product (Escobar and Morales-Menendez, 2018). The chosen firm for this report is
Motorola, which is a multinational company that based in Australia and deals with
telecommunication and electronics services. Moreover, this study will analyse the quality control
and its importance within the organization. Further, identifying the quality control system to
detect the problem to reduces the risk and also examine its contribution to the quality process in
the success of a company.
MAIN BODY
Explaining quality control (QC) and why it is necessary
Quality control is a system of maintaining the standard of manufactured products by
testing a finished good with the specification. It identifies the bugs that might be present in the
quality of product (Foken and et.al., 2004). This includes testing units and also determining the
specifications of a final product. For example, inspection of product, deliverable employees
review and software testing process. The main objectives of quality control are to improve the
quality of production process and final goods (What is quality control, 2021). This process helps
to build good image of the firm and also increases the sale of product. There are three main
objectives that enhanced the product quality with reducing risk, gain production efficiencies and
gain customer loyalty. Moreover, it helps organization to reduces errors and produce product
with greater efficiency, this can be occurred by offering training courses to employees and
managers.
Quality control (QC) defines as a process by which organization ensure about the quality
should be improved or maintained, this involves testing units for determining the specification of
a final product (Escobar and Morales-Menendez, 2018). The chosen firm for this report is
Motorola, which is a multinational company that based in Australia and deals with
telecommunication and electronics services. Moreover, this study will analyse the quality control
and its importance within the organization. Further, identifying the quality control system to
detect the problem to reduces the risk and also examine its contribution to the quality process in
the success of a company.
MAIN BODY
Explaining quality control (QC) and why it is necessary
Quality control is a system of maintaining the standard of manufactured products by
testing a finished good with the specification. It identifies the bugs that might be present in the
quality of product (Foken and et.al., 2004). This includes testing units and also determining the
specifications of a final product. For example, inspection of product, deliverable employees
review and software testing process. The main objectives of quality control are to improve the
quality of production process and final goods (What is quality control, 2021). This process helps
to build good image of the firm and also increases the sale of product. There are three main
objectives that enhanced the product quality with reducing risk, gain production efficiencies and
gain customer loyalty. Moreover, it helps organization to reduces errors and produce product
with greater efficiency, this can be occurred by offering training courses to employees and
managers.
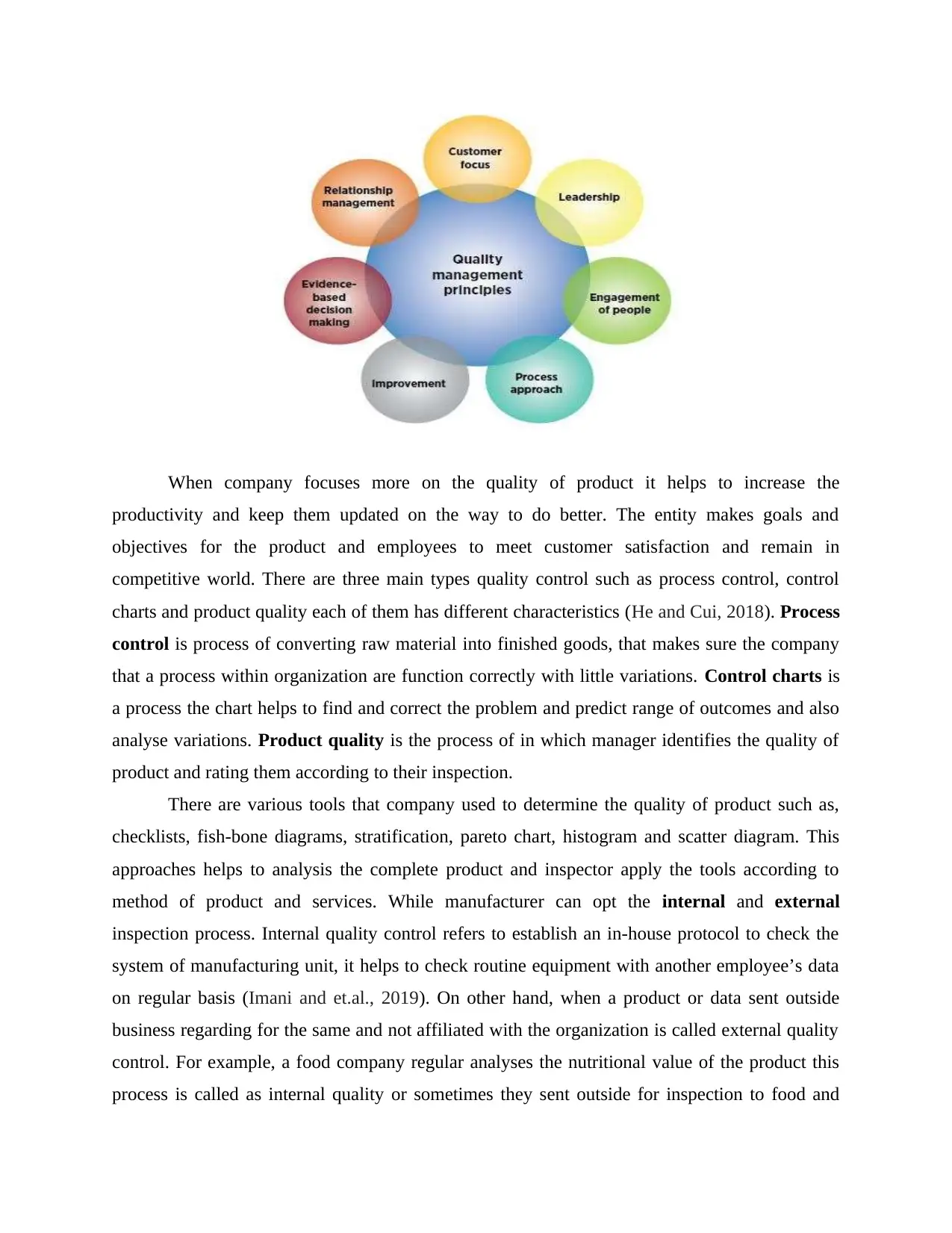
When company focuses more on the quality of product it helps to increase the
productivity and keep them updated on the way to do better. The entity makes goals and
objectives for the product and employees to meet customer satisfaction and remain in
competitive world. There are three main types quality control such as process control, control
charts and product quality each of them has different characteristics (He and Cui, 2018). Process
control is process of converting raw material into finished goods, that makes sure the company
that a process within organization are function correctly with little variations. Control charts is
a process the chart helps to find and correct the problem and predict range of outcomes and also
analyse variations. Product quality is the process of in which manager identifies the quality of
product and rating them according to their inspection.
There are various tools that company used to determine the quality of product such as,
checklists, fish-bone diagrams, stratification, pareto chart, histogram and scatter diagram. This
approaches helps to analysis the complete product and inspector apply the tools according to
method of product and services. While manufacturer can opt the internal and external
inspection process. Internal quality control refers to establish an in-house protocol to check the
system of manufacturing unit, it helps to check routine equipment with another employee’s data
on regular basis (Imani and et.al., 2019). On other hand, when a product or data sent outside
business regarding for the same and not affiliated with the organization is called external quality
control. For example, a food company regular analyses the nutritional value of the product this
process is called as internal quality or sometimes they sent outside for inspection to food and
productivity and keep them updated on the way to do better. The entity makes goals and
objectives for the product and employees to meet customer satisfaction and remain in
competitive world. There are three main types quality control such as process control, control
charts and product quality each of them has different characteristics (He and Cui, 2018). Process
control is process of converting raw material into finished goods, that makes sure the company
that a process within organization are function correctly with little variations. Control charts is
a process the chart helps to find and correct the problem and predict range of outcomes and also
analyse variations. Product quality is the process of in which manager identifies the quality of
product and rating them according to their inspection.
There are various tools that company used to determine the quality of product such as,
checklists, fish-bone diagrams, stratification, pareto chart, histogram and scatter diagram. This
approaches helps to analysis the complete product and inspector apply the tools according to
method of product and services. While manufacturer can opt the internal and external
inspection process. Internal quality control refers to establish an in-house protocol to check the
system of manufacturing unit, it helps to check routine equipment with another employee’s data
on regular basis (Imani and et.al., 2019). On other hand, when a product or data sent outside
business regarding for the same and not affiliated with the organization is called external quality
control. For example, a food company regular analyses the nutritional value of the product this
process is called as internal quality or sometimes they sent outside for inspection to food and
Secure Best Marks with AI Grader
Need help grading? Try our AI Grader for instant feedback on your assignments.
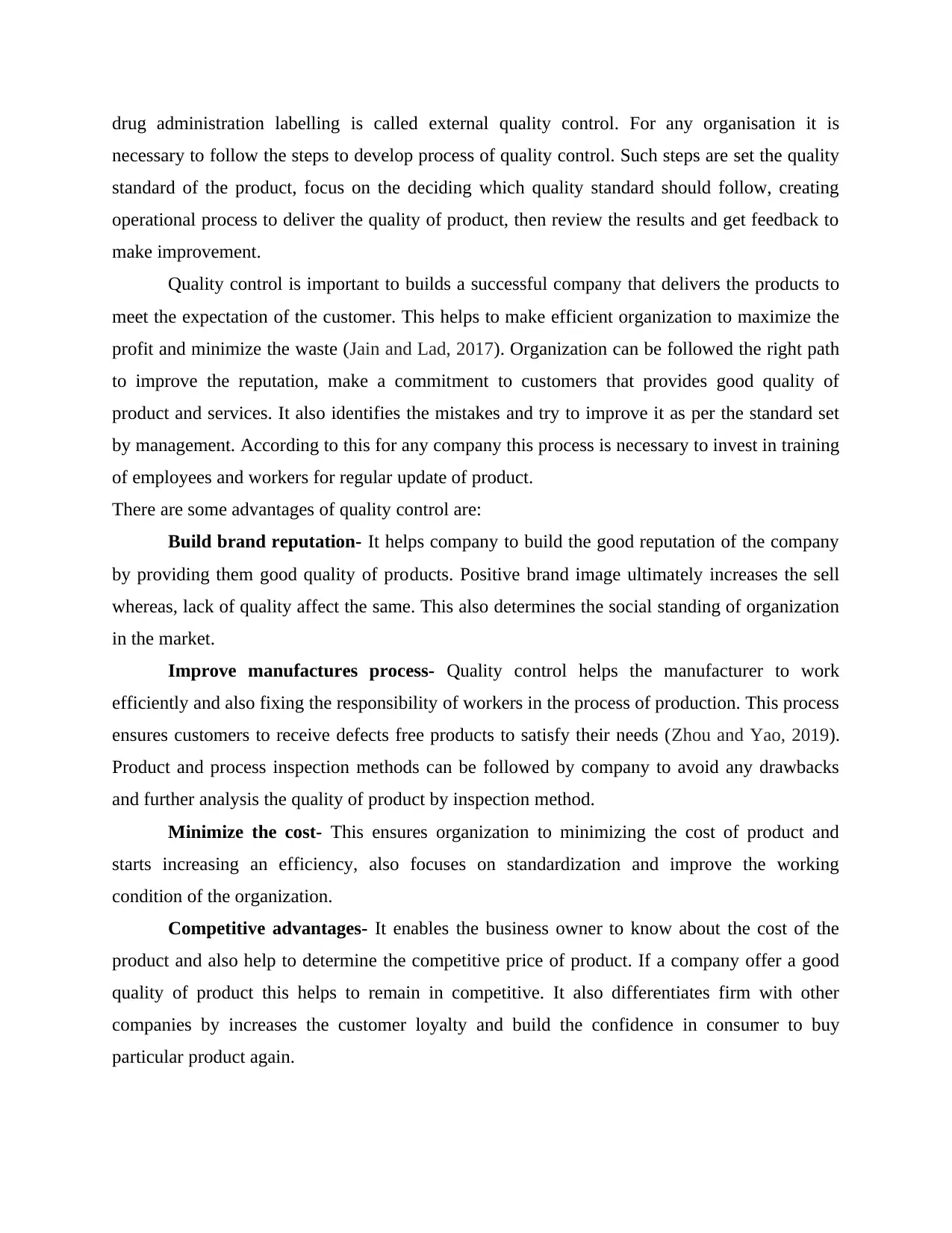
drug administration labelling is called external quality control. For any organisation it is
necessary to follow the steps to develop process of quality control. Such steps are set the quality
standard of the product, focus on the deciding which quality standard should follow, creating
operational process to deliver the quality of product, then review the results and get feedback to
make improvement.
Quality control is important to builds a successful company that delivers the products to
meet the expectation of the customer. This helps to make efficient organization to maximize the
profit and minimize the waste (Jain and Lad, 2017). Organization can be followed the right path
to improve the reputation, make a commitment to customers that provides good quality of
product and services. It also identifies the mistakes and try to improve it as per the standard set
by management. According to this for any company this process is necessary to invest in training
of employees and workers for regular update of product.
There are some advantages of quality control are:
Build brand reputation- It helps company to build the good reputation of the company
by providing them good quality of products. Positive brand image ultimately increases the sell
whereas, lack of quality affect the same. This also determines the social standing of organization
in the market.
Improve manufactures process- Quality control helps the manufacturer to work
efficiently and also fixing the responsibility of workers in the process of production. This process
ensures customers to receive defects free products to satisfy their needs (Zhou and Yao, 2019).
Product and process inspection methods can be followed by company to avoid any drawbacks
and further analysis the quality of product by inspection method.
Minimize the cost- This ensures organization to minimizing the cost of product and
starts increasing an efficiency, also focuses on standardization and improve the working
condition of the organization.
Competitive advantages- It enables the business owner to know about the cost of the
product and also help to determine the competitive price of product. If a company offer a good
quality of product this helps to remain in competitive. It also differentiates firm with other
companies by increases the customer loyalty and build the confidence in consumer to buy
particular product again.
necessary to follow the steps to develop process of quality control. Such steps are set the quality
standard of the product, focus on the deciding which quality standard should follow, creating
operational process to deliver the quality of product, then review the results and get feedback to
make improvement.
Quality control is important to builds a successful company that delivers the products to
meet the expectation of the customer. This helps to make efficient organization to maximize the
profit and minimize the waste (Jain and Lad, 2017). Organization can be followed the right path
to improve the reputation, make a commitment to customers that provides good quality of
product and services. It also identifies the mistakes and try to improve it as per the standard set
by management. According to this for any company this process is necessary to invest in training
of employees and workers for regular update of product.
There are some advantages of quality control are:
Build brand reputation- It helps company to build the good reputation of the company
by providing them good quality of products. Positive brand image ultimately increases the sell
whereas, lack of quality affect the same. This also determines the social standing of organization
in the market.
Improve manufactures process- Quality control helps the manufacturer to work
efficiently and also fixing the responsibility of workers in the process of production. This process
ensures customers to receive defects free products to satisfy their needs (Zhou and Yao, 2019).
Product and process inspection methods can be followed by company to avoid any drawbacks
and further analysis the quality of product by inspection method.
Minimize the cost- This ensures organization to minimizing the cost of product and
starts increasing an efficiency, also focuses on standardization and improve the working
condition of the organization.
Competitive advantages- It enables the business owner to know about the cost of the
product and also help to determine the competitive price of product. If a company offer a good
quality of product this helps to remain in competitive. It also differentiates firm with other
companies by increases the customer loyalty and build the confidence in consumer to buy
particular product again.
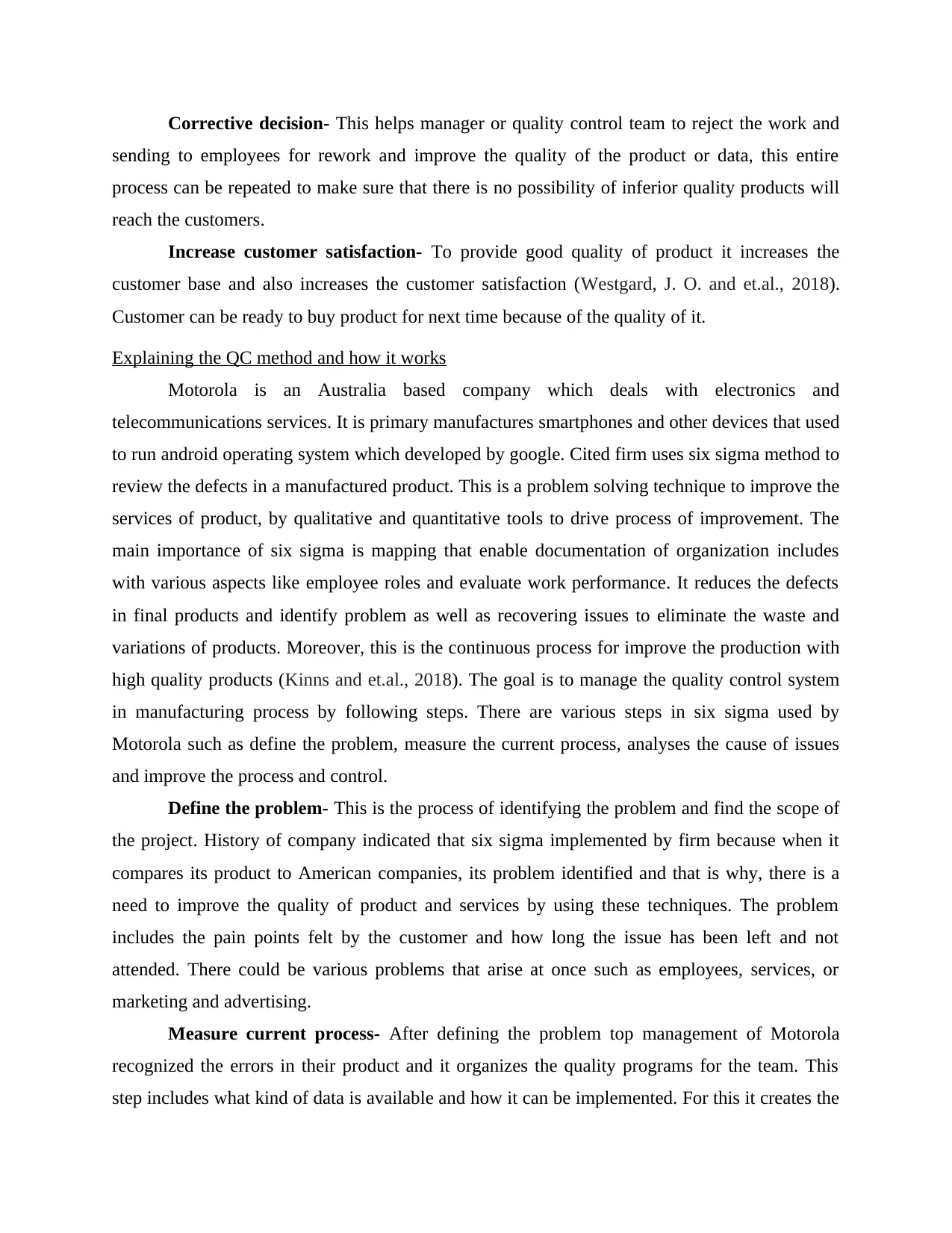
Corrective decision- This helps manager or quality control team to reject the work and
sending to employees for rework and improve the quality of the product or data, this entire
process can be repeated to make sure that there is no possibility of inferior quality products will
reach the customers.
Increase customer satisfaction- To provide good quality of product it increases the
customer base and also increases the customer satisfaction (Westgard, J. O. and et.al., 2018).
Customer can be ready to buy product for next time because of the quality of it.
Explaining the QC method and how it works
Motorola is an Australia based company which deals with electronics and
telecommunications services. It is primary manufactures smartphones and other devices that used
to run android operating system which developed by google. Cited firm uses six sigma method to
review the defects in a manufactured product. This is a problem solving technique to improve the
services of product, by qualitative and quantitative tools to drive process of improvement. The
main importance of six sigma is mapping that enable documentation of organization includes
with various aspects like employee roles and evaluate work performance. It reduces the defects
in final products and identify problem as well as recovering issues to eliminate the waste and
variations of products. Moreover, this is the continuous process for improve the production with
high quality products (Kinns and et.al., 2018). The goal is to manage the quality control system
in manufacturing process by following steps. There are various steps in six sigma used by
Motorola such as define the problem, measure the current process, analyses the cause of issues
and improve the process and control.
Define the problem- This is the process of identifying the problem and find the scope of
the project. History of company indicated that six sigma implemented by firm because when it
compares its product to American companies, its problem identified and that is why, there is a
need to improve the quality of product and services by using these techniques. The problem
includes the pain points felt by the customer and how long the issue has been left and not
attended. There could be various problems that arise at once such as employees, services, or
marketing and advertising.
Measure current process- After defining the problem top management of Motorola
recognized the errors in their product and it organizes the quality programs for the team. This
step includes what kind of data is available and how it can be implemented. For this it creates the
sending to employees for rework and improve the quality of the product or data, this entire
process can be repeated to make sure that there is no possibility of inferior quality products will
reach the customers.
Increase customer satisfaction- To provide good quality of product it increases the
customer base and also increases the customer satisfaction (Westgard, J. O. and et.al., 2018).
Customer can be ready to buy product for next time because of the quality of it.
Explaining the QC method and how it works
Motorola is an Australia based company which deals with electronics and
telecommunications services. It is primary manufactures smartphones and other devices that used
to run android operating system which developed by google. Cited firm uses six sigma method to
review the defects in a manufactured product. This is a problem solving technique to improve the
services of product, by qualitative and quantitative tools to drive process of improvement. The
main importance of six sigma is mapping that enable documentation of organization includes
with various aspects like employee roles and evaluate work performance. It reduces the defects
in final products and identify problem as well as recovering issues to eliminate the waste and
variations of products. Moreover, this is the continuous process for improve the production with
high quality products (Kinns and et.al., 2018). The goal is to manage the quality control system
in manufacturing process by following steps. There are various steps in six sigma used by
Motorola such as define the problem, measure the current process, analyses the cause of issues
and improve the process and control.
Define the problem- This is the process of identifying the problem and find the scope of
the project. History of company indicated that six sigma implemented by firm because when it
compares its product to American companies, its problem identified and that is why, there is a
need to improve the quality of product and services by using these techniques. The problem
includes the pain points felt by the customer and how long the issue has been left and not
attended. There could be various problems that arise at once such as employees, services, or
marketing and advertising.
Measure current process- After defining the problem top management of Motorola
recognized the errors in their product and it organizes the quality programs for the team. This
step includes what kind of data is available and how it can be implemented. For this it creates the
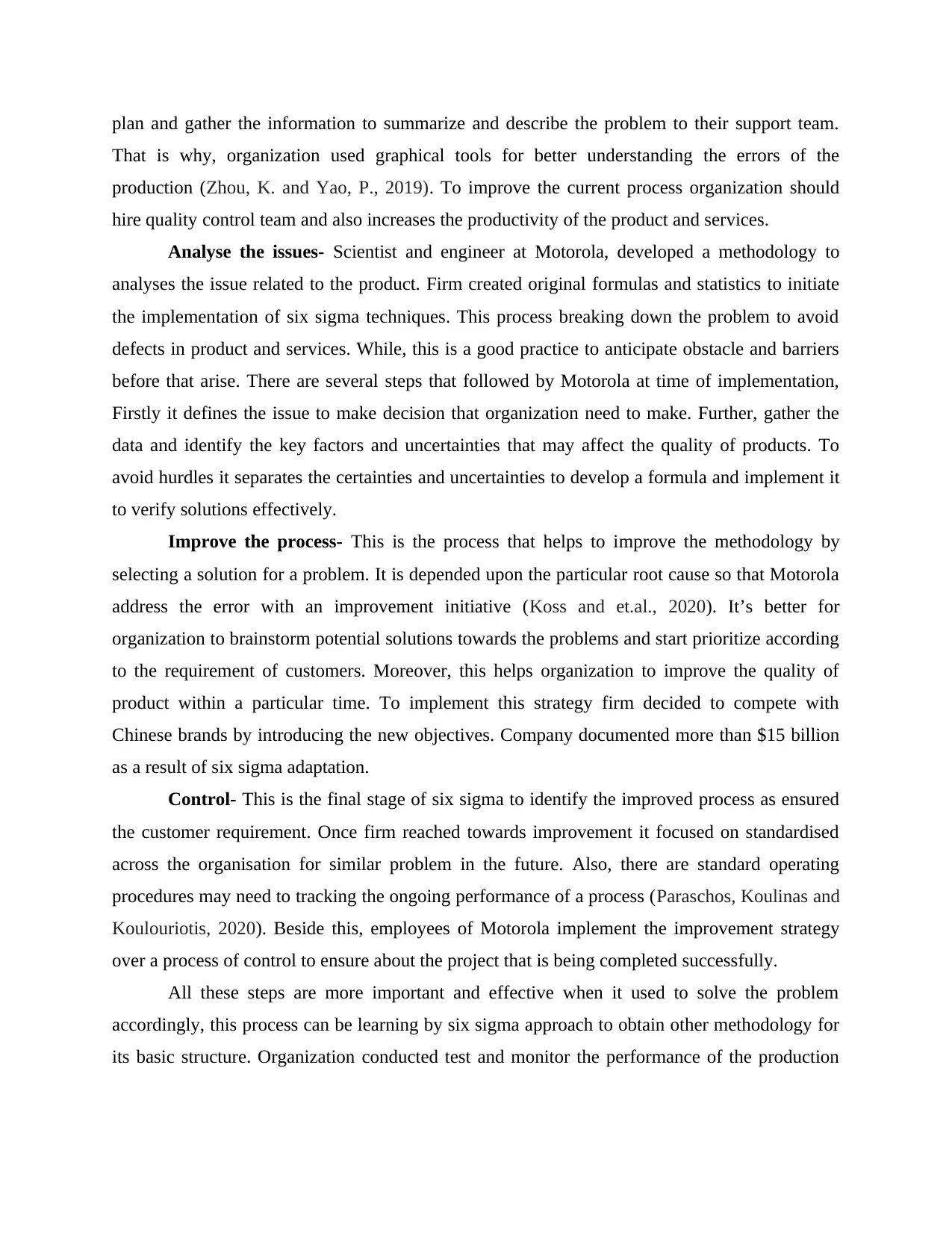
plan and gather the information to summarize and describe the problem to their support team.
That is why, organization used graphical tools for better understanding the errors of the
production (Zhou, K. and Yao, P., 2019). To improve the current process organization should
hire quality control team and also increases the productivity of the product and services.
Analyse the issues- Scientist and engineer at Motorola, developed a methodology to
analyses the issue related to the product. Firm created original formulas and statistics to initiate
the implementation of six sigma techniques. This process breaking down the problem to avoid
defects in product and services. While, this is a good practice to anticipate obstacle and barriers
before that arise. There are several steps that followed by Motorola at time of implementation,
Firstly it defines the issue to make decision that organization need to make. Further, gather the
data and identify the key factors and uncertainties that may affect the quality of products. To
avoid hurdles it separates the certainties and uncertainties to develop a formula and implement it
to verify solutions effectively.
Improve the process- This is the process that helps to improve the methodology by
selecting a solution for a problem. It is depended upon the particular root cause so that Motorola
address the error with an improvement initiative (Koss and et.al., 2020). It’s better for
organization to brainstorm potential solutions towards the problems and start prioritize according
to the requirement of customers. Moreover, this helps organization to improve the quality of
product within a particular time. To implement this strategy firm decided to compete with
Chinese brands by introducing the new objectives. Company documented more than $15 billion
as a result of six sigma adaptation.
Control- This is the final stage of six sigma to identify the improved process as ensured
the customer requirement. Once firm reached towards improvement it focused on standardised
across the organisation for similar problem in the future. Also, there are standard operating
procedures may need to tracking the ongoing performance of a process (Paraschos, Koulinas and
Koulouriotis, 2020). Beside this, employees of Motorola implement the improvement strategy
over a process of control to ensure about the project that is being completed successfully.
All these steps are more important and effective when it used to solve the problem
accordingly, this process can be learning by six sigma approach to obtain other methodology for
its basic structure. Organization conducted test and monitor the performance of the production
That is why, organization used graphical tools for better understanding the errors of the
production (Zhou, K. and Yao, P., 2019). To improve the current process organization should
hire quality control team and also increases the productivity of the product and services.
Analyse the issues- Scientist and engineer at Motorola, developed a methodology to
analyses the issue related to the product. Firm created original formulas and statistics to initiate
the implementation of six sigma techniques. This process breaking down the problem to avoid
defects in product and services. While, this is a good practice to anticipate obstacle and barriers
before that arise. There are several steps that followed by Motorola at time of implementation,
Firstly it defines the issue to make decision that organization need to make. Further, gather the
data and identify the key factors and uncertainties that may affect the quality of products. To
avoid hurdles it separates the certainties and uncertainties to develop a formula and implement it
to verify solutions effectively.
Improve the process- This is the process that helps to improve the methodology by
selecting a solution for a problem. It is depended upon the particular root cause so that Motorola
address the error with an improvement initiative (Koss and et.al., 2020). It’s better for
organization to brainstorm potential solutions towards the problems and start prioritize according
to the requirement of customers. Moreover, this helps organization to improve the quality of
product within a particular time. To implement this strategy firm decided to compete with
Chinese brands by introducing the new objectives. Company documented more than $15 billion
as a result of six sigma adaptation.
Control- This is the final stage of six sigma to identify the improved process as ensured
the customer requirement. Once firm reached towards improvement it focused on standardised
across the organisation for similar problem in the future. Also, there are standard operating
procedures may need to tracking the ongoing performance of a process (Paraschos, Koulinas and
Koulouriotis, 2020). Beside this, employees of Motorola implement the improvement strategy
over a process of control to ensure about the project that is being completed successfully.
All these steps are more important and effective when it used to solve the problem
accordingly, this process can be learning by six sigma approach to obtain other methodology for
its basic structure. Organization conducted test and monitor the performance of the production
Paraphrase This Document
Need a fresh take? Get an instant paraphrase of this document with our AI Paraphraser
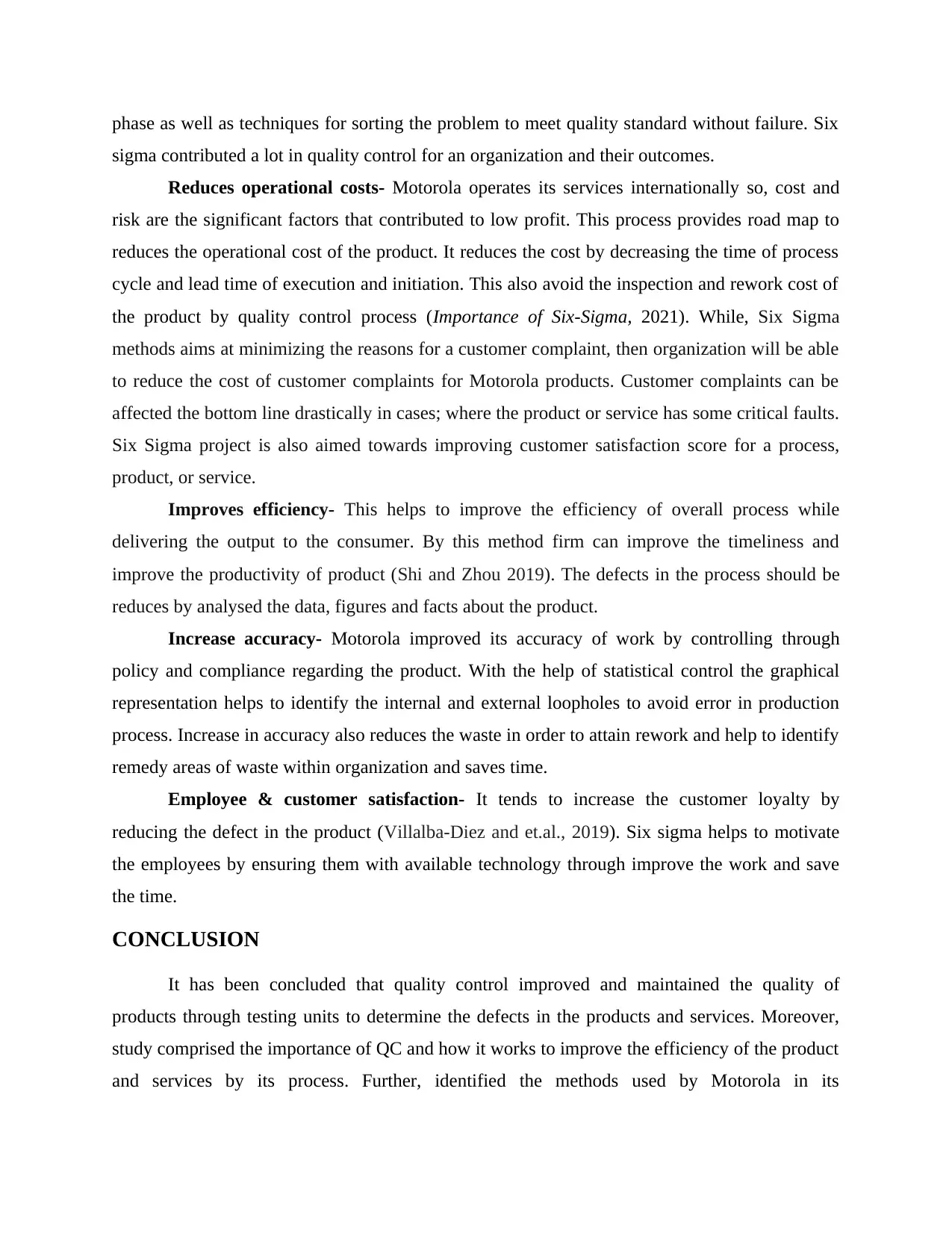
phase as well as techniques for sorting the problem to meet quality standard without failure. Six
sigma contributed a lot in quality control for an organization and their outcomes.
Reduces operational costs- Motorola operates its services internationally so, cost and
risk are the significant factors that contributed to low profit. This process provides road map to
reduces the operational cost of the product. It reduces the cost by decreasing the time of process
cycle and lead time of execution and initiation. This also avoid the inspection and rework cost of
the product by quality control process (Importance of Six-Sigma, 2021). While, Six Sigma
methods aims at minimizing the reasons for a customer complaint, then organization will be able
to reduce the cost of customer complaints for Motorola products. Customer complaints can be
affected the bottom line drastically in cases; where the product or service has some critical faults.
Six Sigma project is also aimed towards improving customer satisfaction score for a process,
product, or service.
Improves efficiency- This helps to improve the efficiency of overall process while
delivering the output to the consumer. By this method firm can improve the timeliness and
improve the productivity of product (Shi and Zhou 2019). The defects in the process should be
reduces by analysed the data, figures and facts about the product.
Increase accuracy- Motorola improved its accuracy of work by controlling through
policy and compliance regarding the product. With the help of statistical control the graphical
representation helps to identify the internal and external loopholes to avoid error in production
process. Increase in accuracy also reduces the waste in order to attain rework and help to identify
remedy areas of waste within organization and saves time.
Employee & customer satisfaction- It tends to increase the customer loyalty by
reducing the defect in the product (Villalba-Diez and et.al., 2019). Six sigma helps to motivate
the employees by ensuring them with available technology through improve the work and save
the time.
CONCLUSION
It has been concluded that quality control improved and maintained the quality of
products through testing units to determine the defects in the products and services. Moreover,
study comprised the importance of QC and how it works to improve the efficiency of the product
and services by its process. Further, identified the methods used by Motorola in its
sigma contributed a lot in quality control for an organization and their outcomes.
Reduces operational costs- Motorola operates its services internationally so, cost and
risk are the significant factors that contributed to low profit. This process provides road map to
reduces the operational cost of the product. It reduces the cost by decreasing the time of process
cycle and lead time of execution and initiation. This also avoid the inspection and rework cost of
the product by quality control process (Importance of Six-Sigma, 2021). While, Six Sigma
methods aims at minimizing the reasons for a customer complaint, then organization will be able
to reduce the cost of customer complaints for Motorola products. Customer complaints can be
affected the bottom line drastically in cases; where the product or service has some critical faults.
Six Sigma project is also aimed towards improving customer satisfaction score for a process,
product, or service.
Improves efficiency- This helps to improve the efficiency of overall process while
delivering the output to the consumer. By this method firm can improve the timeliness and
improve the productivity of product (Shi and Zhou 2019). The defects in the process should be
reduces by analysed the data, figures and facts about the product.
Increase accuracy- Motorola improved its accuracy of work by controlling through
policy and compliance regarding the product. With the help of statistical control the graphical
representation helps to identify the internal and external loopholes to avoid error in production
process. Increase in accuracy also reduces the waste in order to attain rework and help to identify
remedy areas of waste within organization and saves time.
Employee & customer satisfaction- It tends to increase the customer loyalty by
reducing the defect in the product (Villalba-Diez and et.al., 2019). Six sigma helps to motivate
the employees by ensuring them with available technology through improve the work and save
the time.
CONCLUSION
It has been concluded that quality control improved and maintained the quality of
products through testing units to determine the defects in the products and services. Moreover,
study comprised the importance of QC and how it works to improve the efficiency of the product
and services by its process. Further, identified the methods used by Motorola in its
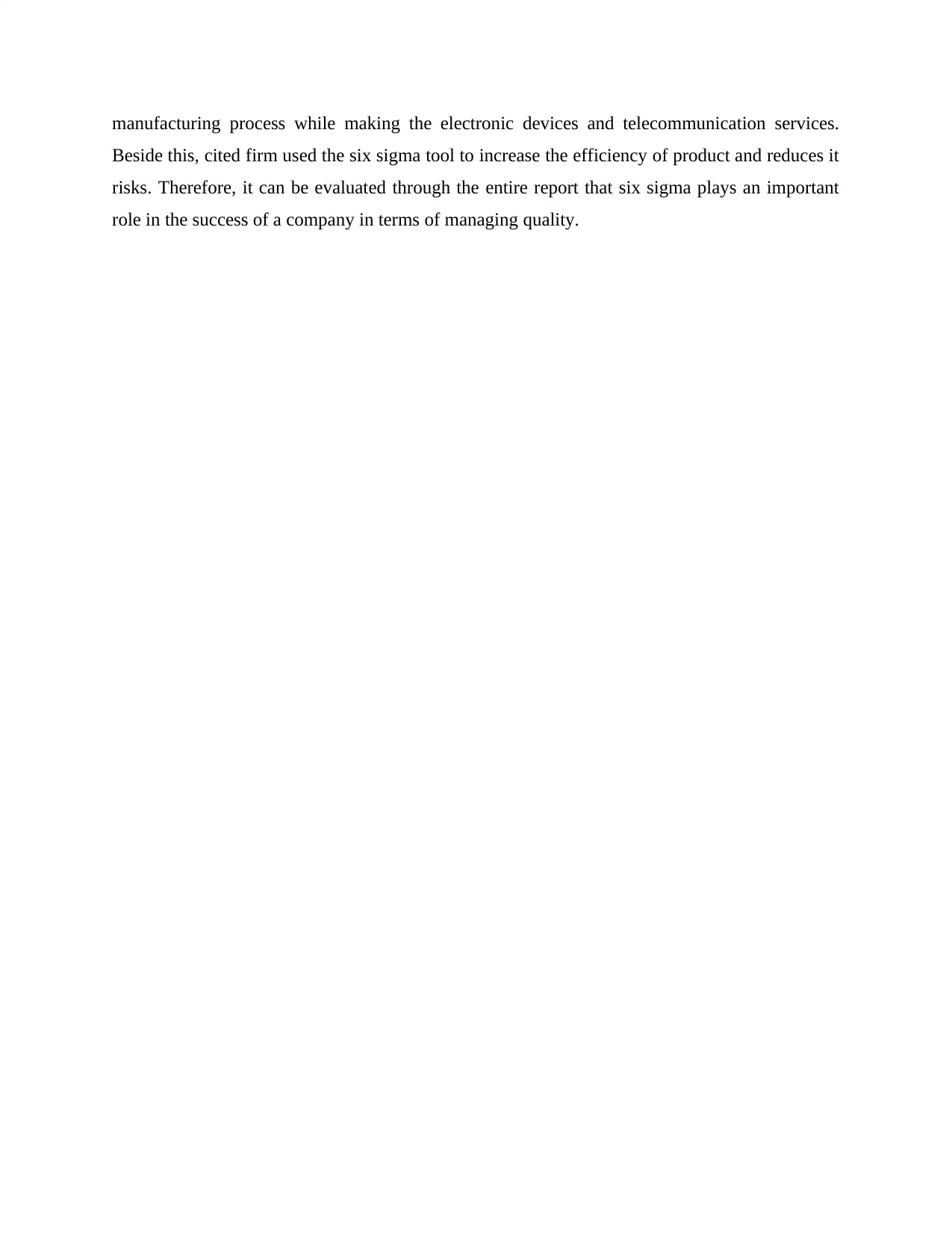
manufacturing process while making the electronic devices and telecommunication services.
Beside this, cited firm used the six sigma tool to increase the efficiency of product and reduces it
risks. Therefore, it can be evaluated through the entire report that six sigma plays an important
role in the success of a company in terms of managing quality.
Beside this, cited firm used the six sigma tool to increase the efficiency of product and reduces it
risks. Therefore, it can be evaluated through the entire report that six sigma plays an important
role in the success of a company in terms of managing quality.
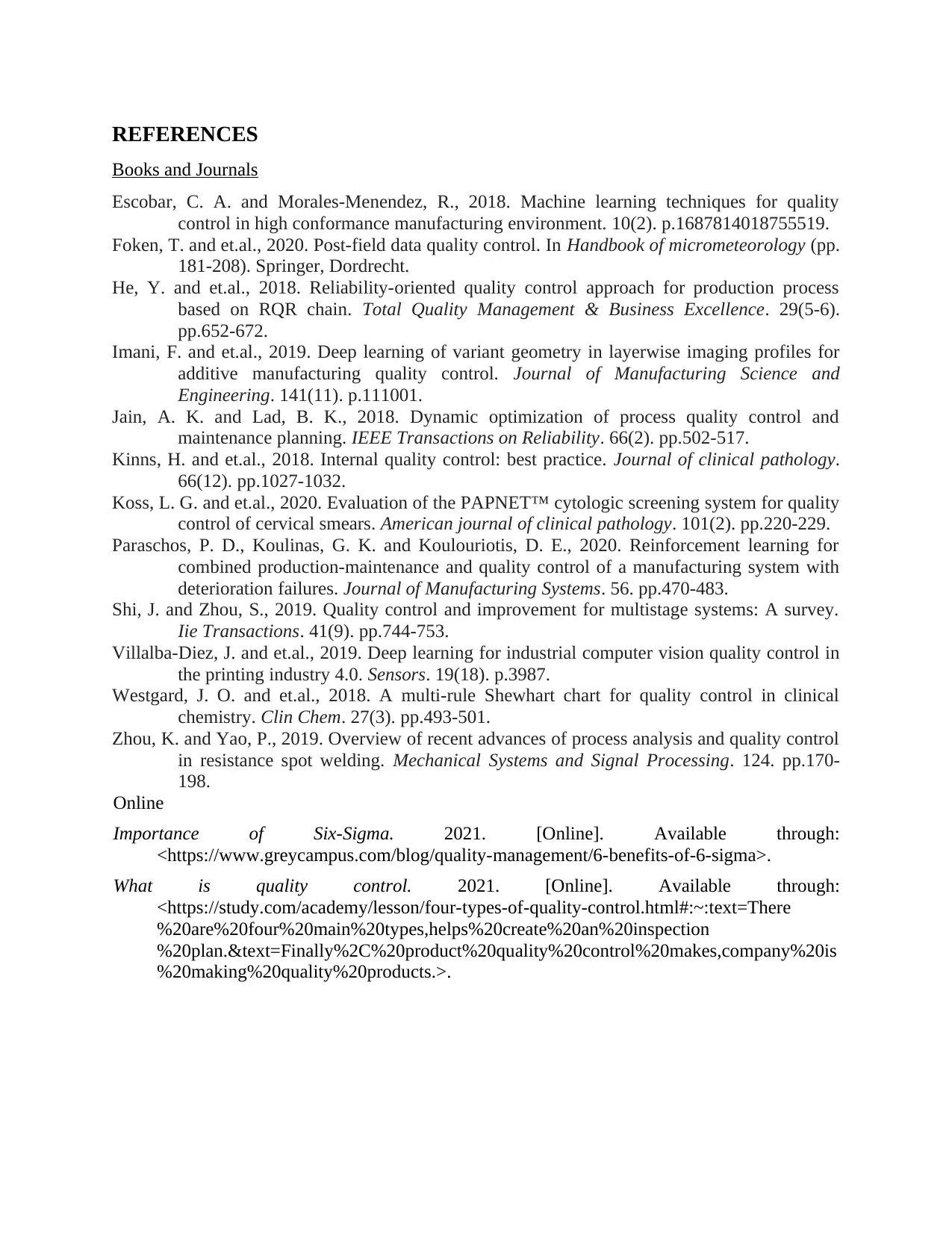
REFERENCES
Books and Journals
Escobar, C. A. and Morales-Menendez, R., 2018. Machine learning techniques for quality
control in high conformance manufacturing environment. 10(2). p.1687814018755519.
Foken, T. and et.al., 2020. Post-field data quality control. In Handbook of micrometeorology (pp.
181-208). Springer, Dordrecht.
He, Y. and et.al., 2018. Reliability-oriented quality control approach for production process
based on RQR chain. Total Quality Management & Business Excellence. 29(5-6).
pp.652-672.
Imani, F. and et.al., 2019. Deep learning of variant geometry in layerwise imaging profiles for
additive manufacturing quality control. Journal of Manufacturing Science and
Engineering. 141(11). p.111001.
Jain, A. K. and Lad, B. K., 2018. Dynamic optimization of process quality control and
maintenance planning. IEEE Transactions on Reliability. 66(2). pp.502-517.
Kinns, H. and et.al., 2018. Internal quality control: best practice. Journal of clinical pathology.
66(12). pp.1027-1032.
Koss, L. G. and et.al., 2020. Evaluation of the PAPNET™ cytologic screening system for quality
control of cervical smears. American journal of clinical pathology. 101(2). pp.220-229.
Paraschos, P. D., Koulinas, G. K. and Koulouriotis, D. E., 2020. Reinforcement learning for
combined production-maintenance and quality control of a manufacturing system with
deterioration failures. Journal of Manufacturing Systems. 56. pp.470-483.
Shi, J. and Zhou, S., 2019. Quality control and improvement for multistage systems: A survey.
Iie Transactions. 41(9). pp.744-753.
Villalba-Diez, J. and et.al., 2019. Deep learning for industrial computer vision quality control in
the printing industry 4.0. Sensors. 19(18). p.3987.
Westgard, J. O. and et.al., 2018. A multi-rule Shewhart chart for quality control in clinical
chemistry. Clin Chem. 27(3). pp.493-501.
Zhou, K. and Yao, P., 2019. Overview of recent advances of process analysis and quality control
in resistance spot welding. Mechanical Systems and Signal Processing. 124. pp.170-
198.
Online
Importance of Six-Sigma. 2021. [Online]. Available through:
<https://www.greycampus.com/blog/quality-management/6-benefits-of-6-sigma>.
What is quality control. 2021. [Online]. Available through:
<https://study.com/academy/lesson/four-types-of-quality-control.html#:~:text=There
%20are%20four%20main%20types,helps%20create%20an%20inspection
%20plan.&text=Finally%2C%20product%20quality%20control%20makes,company%20is
%20making%20quality%20products.>.
Books and Journals
Escobar, C. A. and Morales-Menendez, R., 2018. Machine learning techniques for quality
control in high conformance manufacturing environment. 10(2). p.1687814018755519.
Foken, T. and et.al., 2020. Post-field data quality control. In Handbook of micrometeorology (pp.
181-208). Springer, Dordrecht.
He, Y. and et.al., 2018. Reliability-oriented quality control approach for production process
based on RQR chain. Total Quality Management & Business Excellence. 29(5-6).
pp.652-672.
Imani, F. and et.al., 2019. Deep learning of variant geometry in layerwise imaging profiles for
additive manufacturing quality control. Journal of Manufacturing Science and
Engineering. 141(11). p.111001.
Jain, A. K. and Lad, B. K., 2018. Dynamic optimization of process quality control and
maintenance planning. IEEE Transactions on Reliability. 66(2). pp.502-517.
Kinns, H. and et.al., 2018. Internal quality control: best practice. Journal of clinical pathology.
66(12). pp.1027-1032.
Koss, L. G. and et.al., 2020. Evaluation of the PAPNET™ cytologic screening system for quality
control of cervical smears. American journal of clinical pathology. 101(2). pp.220-229.
Paraschos, P. D., Koulinas, G. K. and Koulouriotis, D. E., 2020. Reinforcement learning for
combined production-maintenance and quality control of a manufacturing system with
deterioration failures. Journal of Manufacturing Systems. 56. pp.470-483.
Shi, J. and Zhou, S., 2019. Quality control and improvement for multistage systems: A survey.
Iie Transactions. 41(9). pp.744-753.
Villalba-Diez, J. and et.al., 2019. Deep learning for industrial computer vision quality control in
the printing industry 4.0. Sensors. 19(18). p.3987.
Westgard, J. O. and et.al., 2018. A multi-rule Shewhart chart for quality control in clinical
chemistry. Clin Chem. 27(3). pp.493-501.
Zhou, K. and Yao, P., 2019. Overview of recent advances of process analysis and quality control
in resistance spot welding. Mechanical Systems and Signal Processing. 124. pp.170-
198.
Online
Importance of Six-Sigma. 2021. [Online]. Available through:
<https://www.greycampus.com/blog/quality-management/6-benefits-of-6-sigma>.
What is quality control. 2021. [Online]. Available through:
<https://study.com/academy/lesson/four-types-of-quality-control.html#:~:text=There
%20are%20four%20main%20types,helps%20create%20an%20inspection
%20plan.&text=Finally%2C%20product%20quality%20control%20makes,company%20is
%20making%20quality%20products.>.
1 out of 10
Related Documents

Your All-in-One AI-Powered Toolkit for Academic Success.
 +13062052269
info@desklib.com
Available 24*7 on WhatsApp / Email
Unlock your academic potential
© 2024  |  Zucol Services PVT LTD  |  All rights reserved.