Evaluating Total Quality Management (TQM) at Ford Motor Company
VerifiedAdded on 2020/01/06
|13
|2835
|124
Report
AI Summary
This report provides a comprehensive analysis of Total Quality Management (TQM), using Ford Motor Company as a case study. It begins with an introduction to operations management and the importance of quality, defining TQM and its core components. The report explores the utility and relevance of TQM in the contemporary business environment, examining Ford's application of TQM, including Deming's chain reaction and the TQM model. It details significant aspects of TQM, such as quality at the source, team approaches, and benchmarking, along with TQM tools and methods like process flowcharting and cause-and-effect diagrams. The report evaluates the success and potential failures of TQM implementation, considering factors like commitment and employee contributions. It also critiques TQM, addressing customer feedback, management influence, and product improvement, concluding with an overview of TQM's impact on business development and quality control within Ford's operations.
Contribute Materials
Your contribution can guide someone’s learning journey. Share your
documents today.
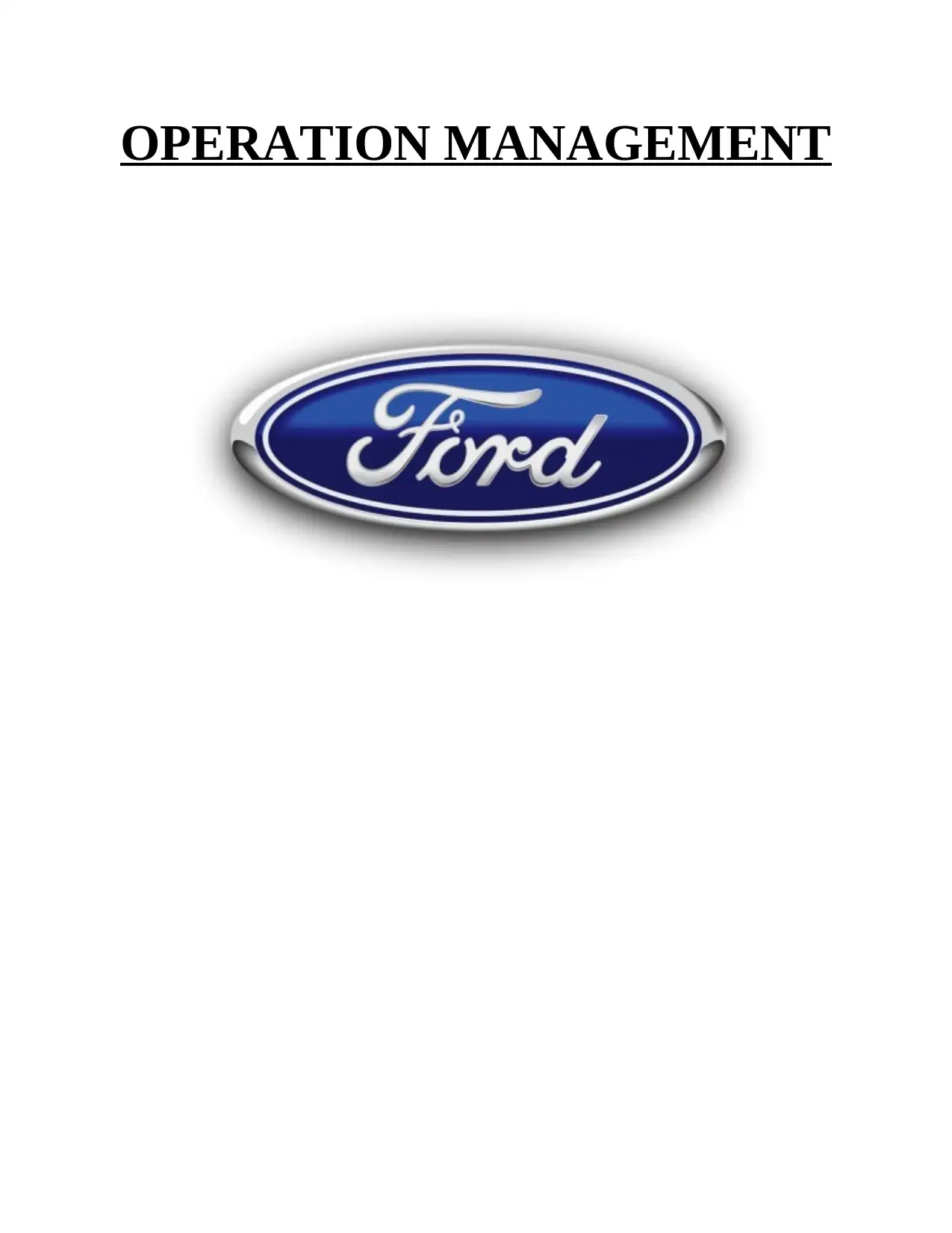
OPERATION MANAGEMENT
Secure Best Marks with AI Grader
Need help grading? Try our AI Grader for instant feedback on your assignments.
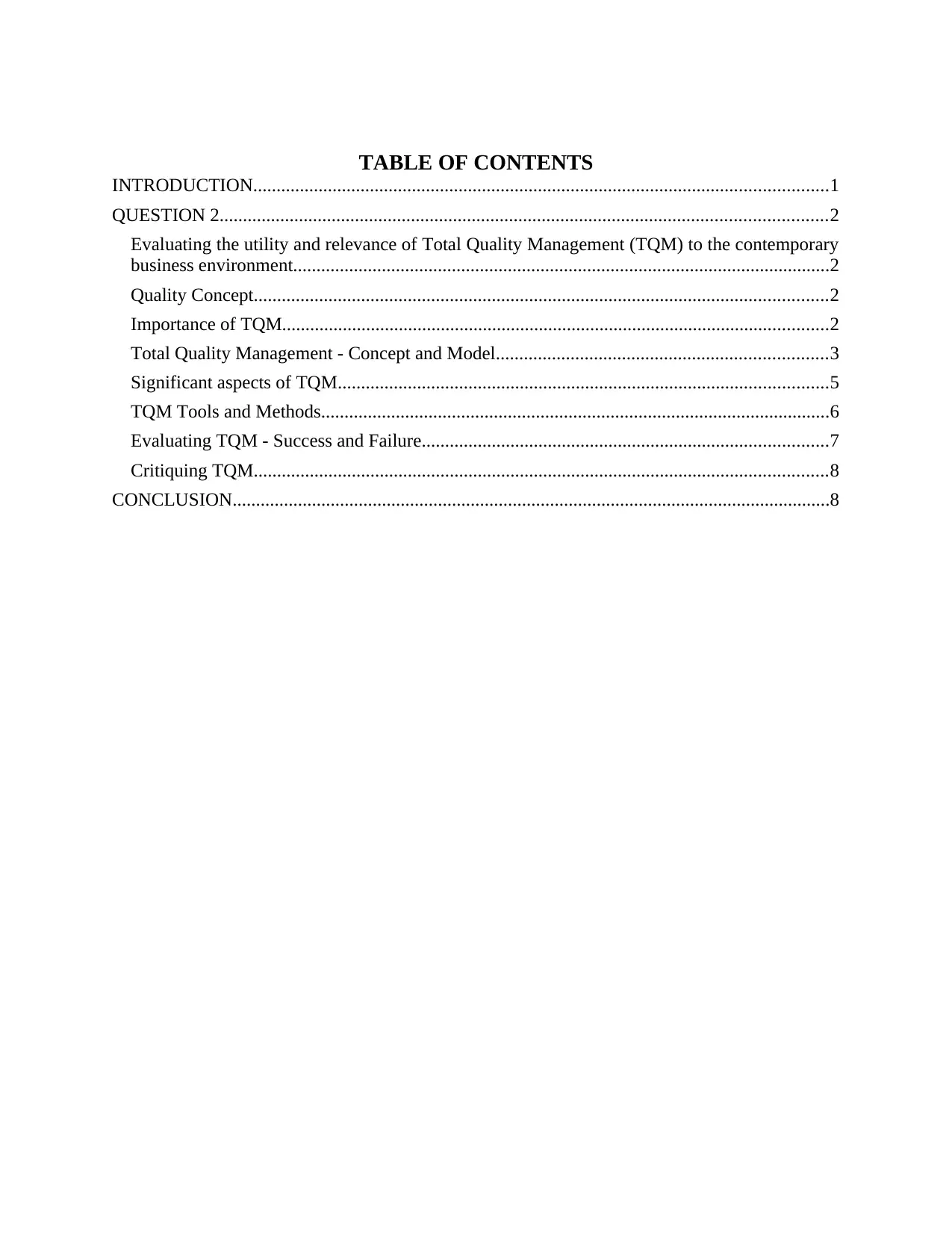
TABLE OF CONTENTS
INTRODUCTION...........................................................................................................................1
QUESTION 2..................................................................................................................................2
Evaluating the utility and relevance of Total Quality Management (TQM) to the contemporary
business environment...................................................................................................................2
Quality Concept...........................................................................................................................2
Importance of TQM.....................................................................................................................2
Total Quality Management - Concept and Model.......................................................................3
Significant aspects of TQM.........................................................................................................5
TQM Tools and Methods.............................................................................................................6
Evaluating TQM - Success and Failure.......................................................................................7
Critiquing TQM...........................................................................................................................8
CONCLUSION................................................................................................................................8
INTRODUCTION...........................................................................................................................1
QUESTION 2..................................................................................................................................2
Evaluating the utility and relevance of Total Quality Management (TQM) to the contemporary
business environment...................................................................................................................2
Quality Concept...........................................................................................................................2
Importance of TQM.....................................................................................................................2
Total Quality Management - Concept and Model.......................................................................3
Significant aspects of TQM.........................................................................................................5
TQM Tools and Methods.............................................................................................................6
Evaluating TQM - Success and Failure.......................................................................................7
Critiquing TQM...........................................................................................................................8
CONCLUSION................................................................................................................................8
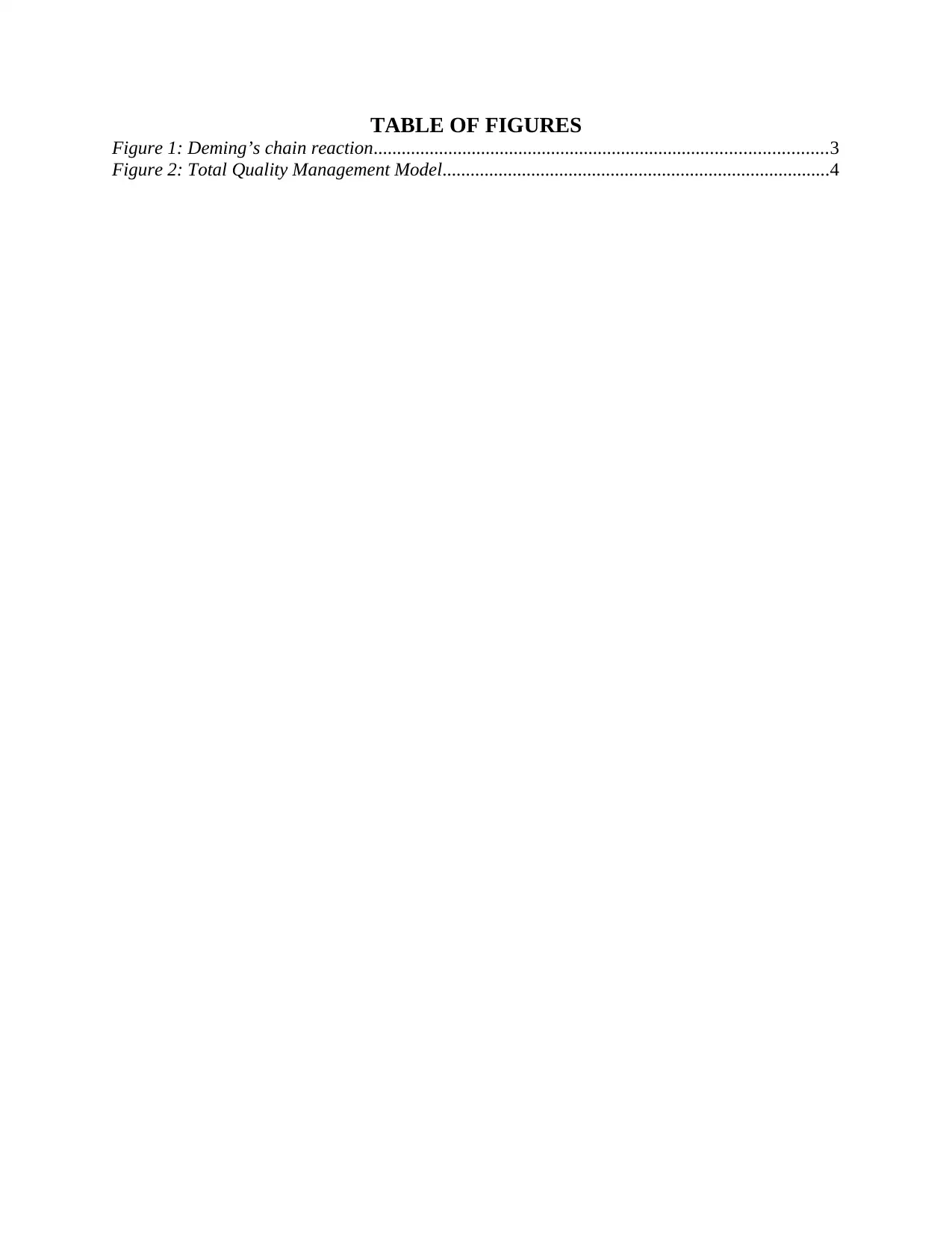
TABLE OF FIGURES
Figure 1: Deming’s chain reaction.................................................................................................3
Figure 2: Total Quality Management Model...................................................................................4
Figure 1: Deming’s chain reaction.................................................................................................3
Figure 2: Total Quality Management Model...................................................................................4
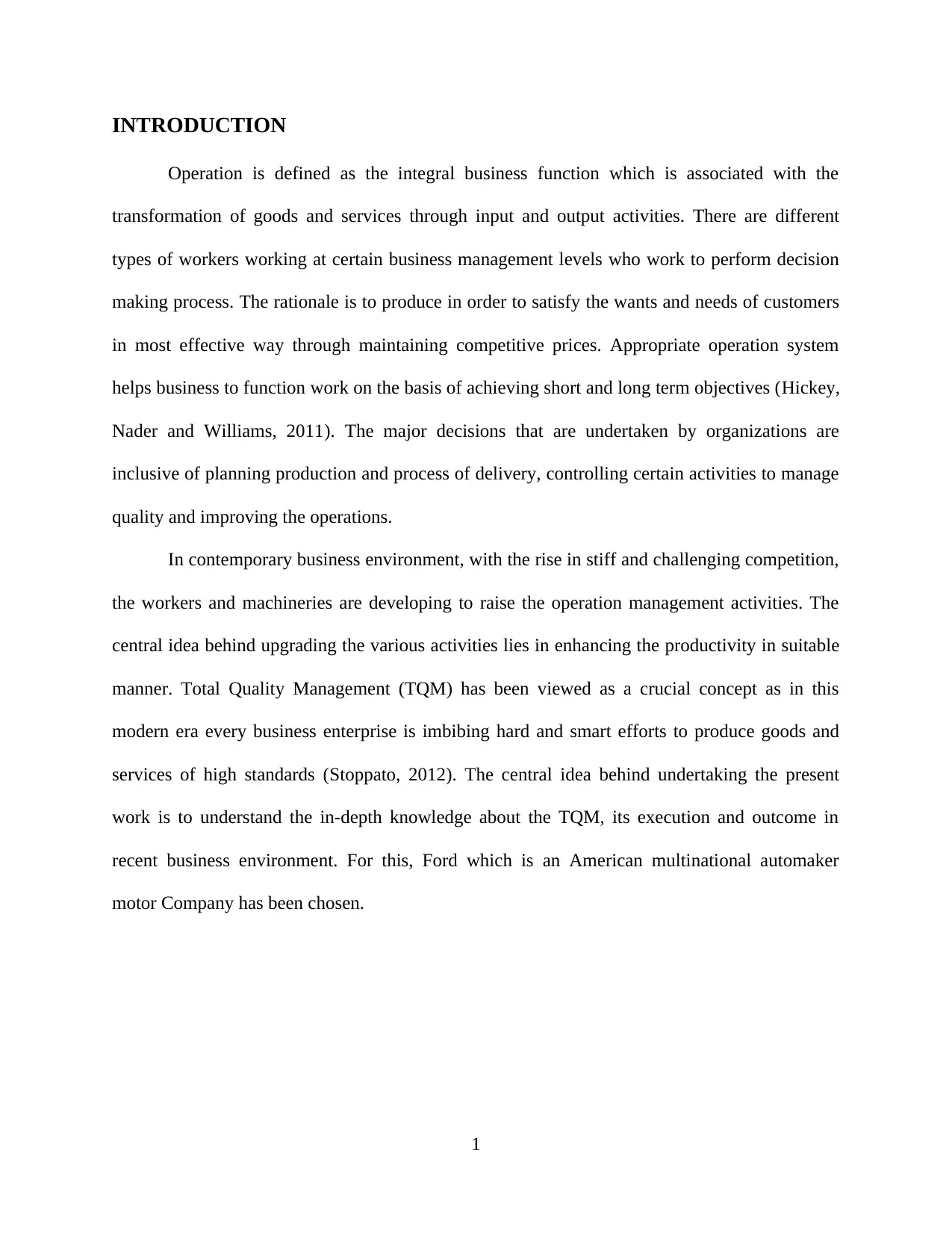
INTRODUCTION
Operation is defined as the integral business function which is associated with the
transformation of goods and services through input and output activities. There are different
types of workers working at certain business management levels who work to perform decision
making process. The rationale is to produce in order to satisfy the wants and needs of customers
in most effective way through maintaining competitive prices. Appropriate operation system
helps business to function work on the basis of achieving short and long term objectives (Hickey,
Nader and Williams, 2011). The major decisions that are undertaken by organizations are
inclusive of planning production and process of delivery, controlling certain activities to manage
quality and improving the operations.
In contemporary business environment, with the rise in stiff and challenging competition,
the workers and machineries are developing to raise the operation management activities. The
central idea behind upgrading the various activities lies in enhancing the productivity in suitable
manner. Total Quality Management (TQM) has been viewed as a crucial concept as in this
modern era every business enterprise is imbibing hard and smart efforts to produce goods and
services of high standards (Stoppato, 2012). The central idea behind undertaking the present
work is to understand the in-depth knowledge about the TQM, its execution and outcome in
recent business environment. For this, Ford which is an American multinational automaker
motor Company has been chosen.
1
Operation is defined as the integral business function which is associated with the
transformation of goods and services through input and output activities. There are different
types of workers working at certain business management levels who work to perform decision
making process. The rationale is to produce in order to satisfy the wants and needs of customers
in most effective way through maintaining competitive prices. Appropriate operation system
helps business to function work on the basis of achieving short and long term objectives (Hickey,
Nader and Williams, 2011). The major decisions that are undertaken by organizations are
inclusive of planning production and process of delivery, controlling certain activities to manage
quality and improving the operations.
In contemporary business environment, with the rise in stiff and challenging competition,
the workers and machineries are developing to raise the operation management activities. The
central idea behind upgrading the various activities lies in enhancing the productivity in suitable
manner. Total Quality Management (TQM) has been viewed as a crucial concept as in this
modern era every business enterprise is imbibing hard and smart efforts to produce goods and
services of high standards (Stoppato, 2012). The central idea behind undertaking the present
work is to understand the in-depth knowledge about the TQM, its execution and outcome in
recent business environment. For this, Ford which is an American multinational automaker
motor Company has been chosen.
1
Secure Best Marks with AI Grader
Need help grading? Try our AI Grader for instant feedback on your assignments.
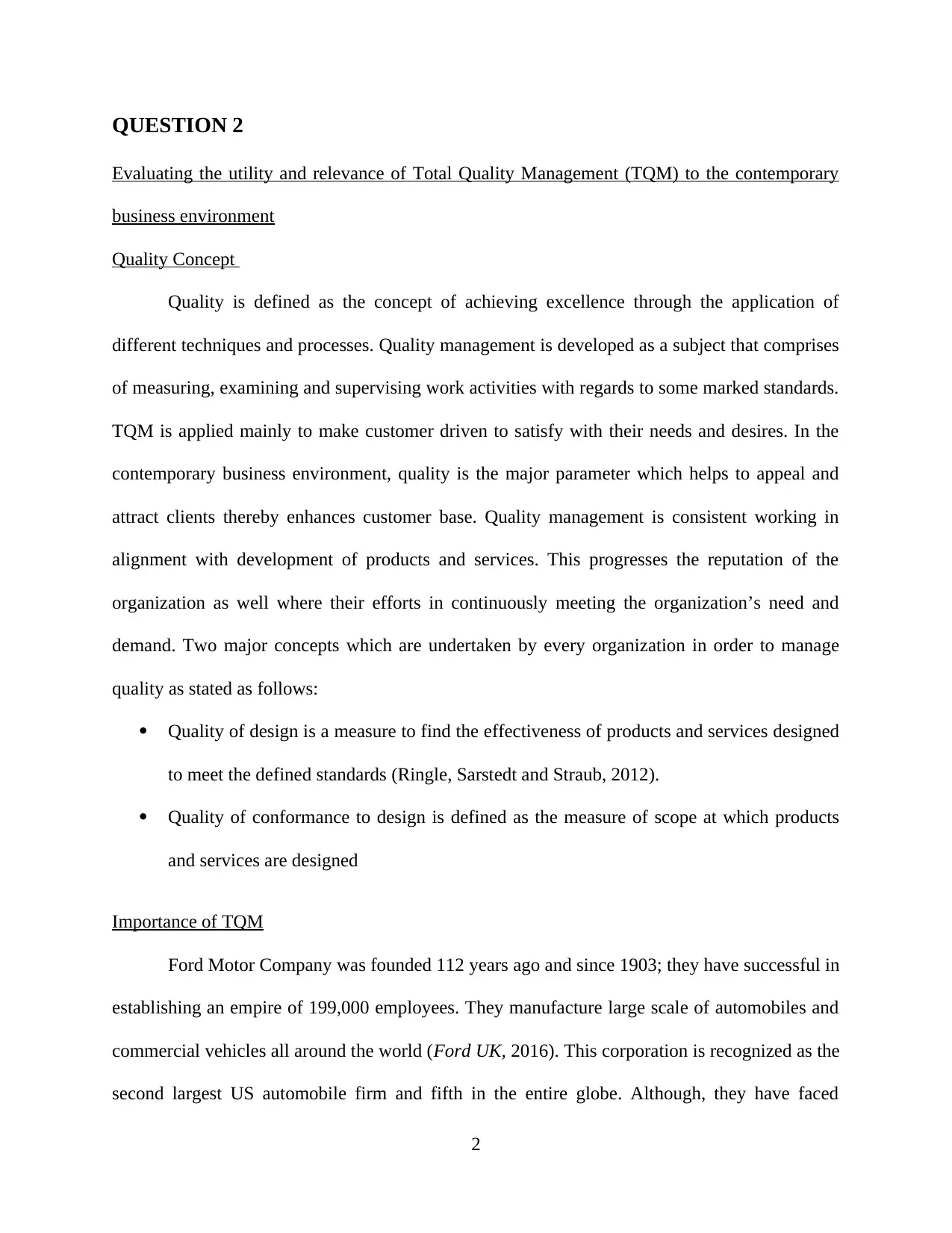
QUESTION 2
Evaluating the utility and relevance of Total Quality Management (TQM) to the contemporary
business environment
Quality Concept
Quality is defined as the concept of achieving excellence through the application of
different techniques and processes. Quality management is developed as a subject that comprises
of measuring, examining and supervising work activities with regards to some marked standards.
TQM is applied mainly to make customer driven to satisfy with their needs and desires. In the
contemporary business environment, quality is the major parameter which helps to appeal and
attract clients thereby enhances customer base. Quality management is consistent working in
alignment with development of products and services. This progresses the reputation of the
organization as well where their efforts in continuously meeting the organization’s need and
demand. Two major concepts which are undertaken by every organization in order to manage
quality as stated as follows:
Quality of design is a measure to find the effectiveness of products and services designed
to meet the defined standards (Ringle, Sarstedt and Straub, 2012).
Quality of conformance to design is defined as the measure of scope at which products
and services are designed
Importance of TQM
Ford Motor Company was founded 112 years ago and since 1903; they have successful in
establishing an empire of 199,000 employees. They manufacture large scale of automobiles and
commercial vehicles all around the world (Ford UK, 2016). This corporation is recognized as the
second largest US automobile firm and fifth in the entire globe. Although, they have faced
2
Evaluating the utility and relevance of Total Quality Management (TQM) to the contemporary
business environment
Quality Concept
Quality is defined as the concept of achieving excellence through the application of
different techniques and processes. Quality management is developed as a subject that comprises
of measuring, examining and supervising work activities with regards to some marked standards.
TQM is applied mainly to make customer driven to satisfy with their needs and desires. In the
contemporary business environment, quality is the major parameter which helps to appeal and
attract clients thereby enhances customer base. Quality management is consistent working in
alignment with development of products and services. This progresses the reputation of the
organization as well where their efforts in continuously meeting the organization’s need and
demand. Two major concepts which are undertaken by every organization in order to manage
quality as stated as follows:
Quality of design is a measure to find the effectiveness of products and services designed
to meet the defined standards (Ringle, Sarstedt and Straub, 2012).
Quality of conformance to design is defined as the measure of scope at which products
and services are designed
Importance of TQM
Ford Motor Company was founded 112 years ago and since 1903; they have successful in
establishing an empire of 199,000 employees. They manufacture large scale of automobiles and
commercial vehicles all around the world (Ford UK, 2016). This corporation is recognized as the
second largest US automobile firm and fifth in the entire globe. Although, they have faced
2
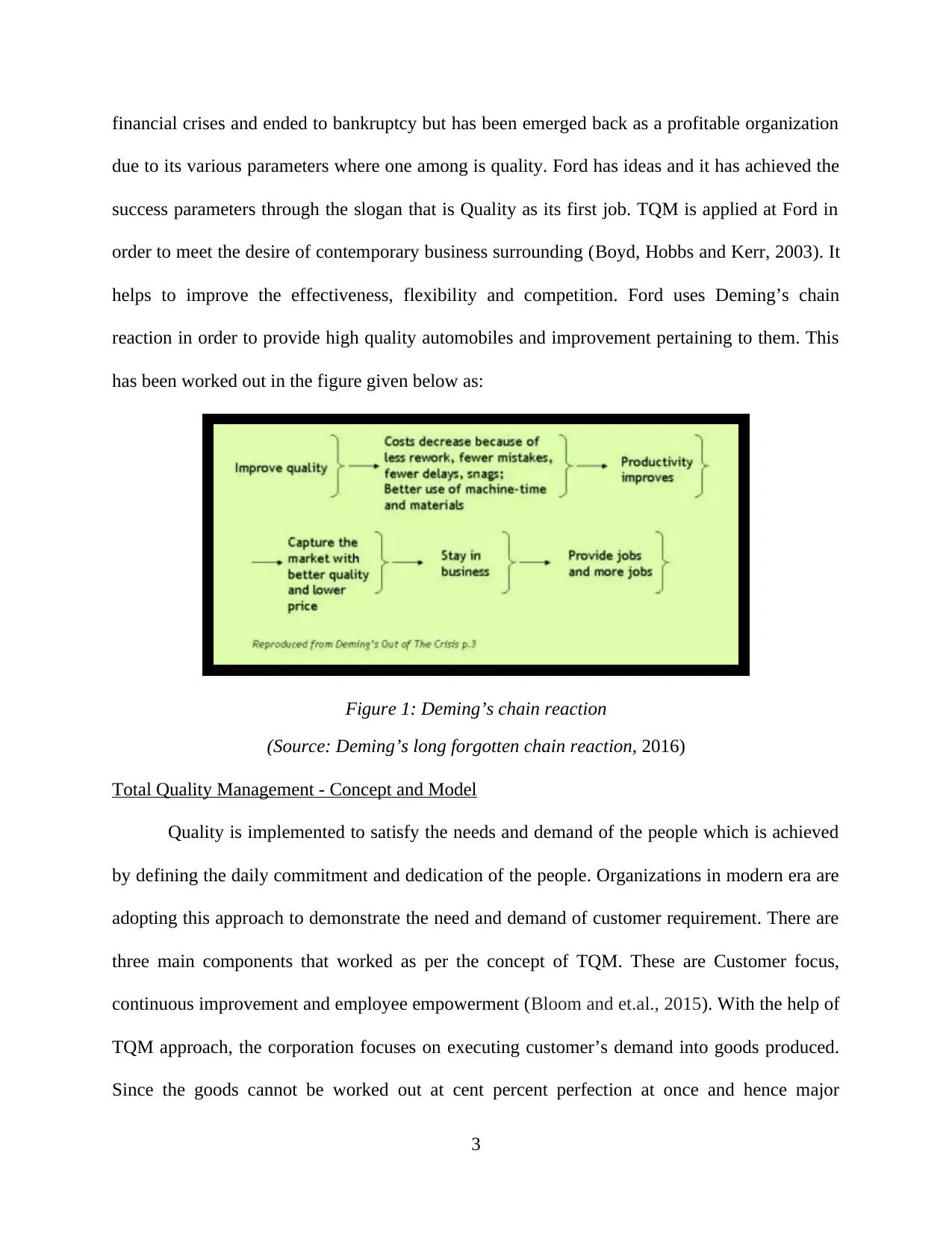
financial crises and ended to bankruptcy but has been emerged back as a profitable organization
due to its various parameters where one among is quality. Ford has ideas and it has achieved the
success parameters through the slogan that is Quality as its first job. TQM is applied at Ford in
order to meet the desire of contemporary business surrounding (Boyd, Hobbs and Kerr, 2003). It
helps to improve the effectiveness, flexibility and competition. Ford uses Deming’s chain
reaction in order to provide high quality automobiles and improvement pertaining to them. This
has been worked out in the figure given below as:
Figure 1: Deming’s chain reaction
(Source: Deming’s long forgotten chain reaction, 2016)
Total Quality Management - Concept and Model
Quality is implemented to satisfy the needs and demand of the people which is achieved
by defining the daily commitment and dedication of the people. Organizations in modern era are
adopting this approach to demonstrate the need and demand of customer requirement. There are
three main components that worked as per the concept of TQM. These are Customer focus,
continuous improvement and employee empowerment (Bloom and et.al., 2015). With the help of
TQM approach, the corporation focuses on executing customer’s demand into goods produced.
Since the goods cannot be worked out at cent percent perfection at once and hence major
3
due to its various parameters where one among is quality. Ford has ideas and it has achieved the
success parameters through the slogan that is Quality as its first job. TQM is applied at Ford in
order to meet the desire of contemporary business surrounding (Boyd, Hobbs and Kerr, 2003). It
helps to improve the effectiveness, flexibility and competition. Ford uses Deming’s chain
reaction in order to provide high quality automobiles and improvement pertaining to them. This
has been worked out in the figure given below as:
Figure 1: Deming’s chain reaction
(Source: Deming’s long forgotten chain reaction, 2016)
Total Quality Management - Concept and Model
Quality is implemented to satisfy the needs and demand of the people which is achieved
by defining the daily commitment and dedication of the people. Organizations in modern era are
adopting this approach to demonstrate the need and demand of customer requirement. There are
three main components that worked as per the concept of TQM. These are Customer focus,
continuous improvement and employee empowerment (Bloom and et.al., 2015). With the help of
TQM approach, the corporation focuses on executing customer’s demand into goods produced.
Since the goods cannot be worked out at cent percent perfection at once and hence major
3
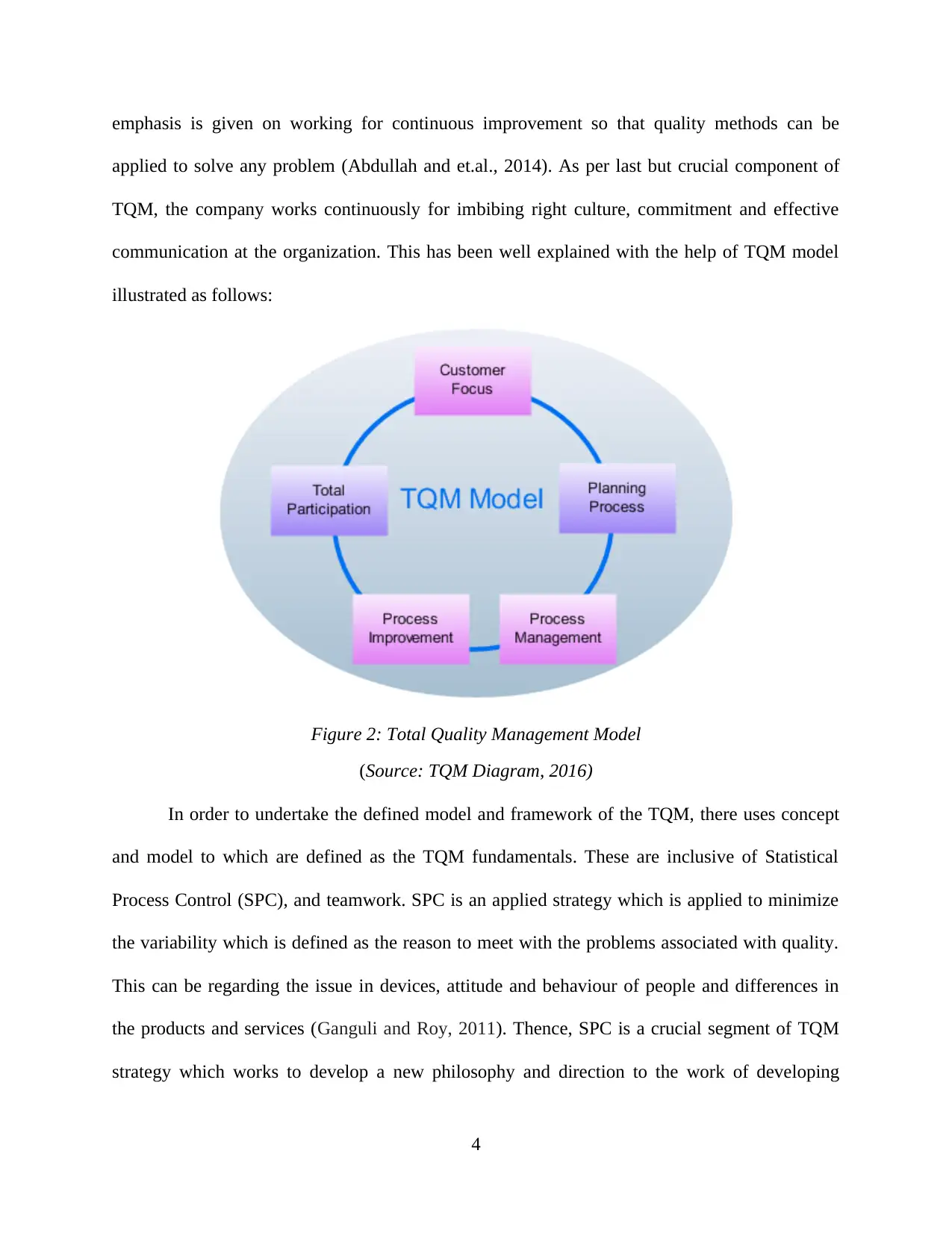
emphasis is given on working for continuous improvement so that quality methods can be
applied to solve any problem (Abdullah and et.al., 2014). As per last but crucial component of
TQM, the company works continuously for imbibing right culture, commitment and effective
communication at the organization. This has been well explained with the help of TQM model
illustrated as follows:
Figure 2: Total Quality Management Model
(Source: TQM Diagram, 2016)
In order to undertake the defined model and framework of the TQM, there uses concept
and model to which are defined as the TQM fundamentals. These are inclusive of Statistical
Process Control (SPC), and teamwork. SPC is an applied strategy which is applied to minimize
the variability which is defined as the reason to meet with the problems associated with quality.
This can be regarding the issue in devices, attitude and behaviour of people and differences in
the products and services (Ganguli and Roy, 2011). Thence, SPC is a crucial segment of TQM
strategy which works to develop a new philosophy and direction to the work of developing
4
applied to solve any problem (Abdullah and et.al., 2014). As per last but crucial component of
TQM, the company works continuously for imbibing right culture, commitment and effective
communication at the organization. This has been well explained with the help of TQM model
illustrated as follows:
Figure 2: Total Quality Management Model
(Source: TQM Diagram, 2016)
In order to undertake the defined model and framework of the TQM, there uses concept
and model to which are defined as the TQM fundamentals. These are inclusive of Statistical
Process Control (SPC), and teamwork. SPC is an applied strategy which is applied to minimize
the variability which is defined as the reason to meet with the problems associated with quality.
This can be regarding the issue in devices, attitude and behaviour of people and differences in
the products and services (Ganguli and Roy, 2011). Thence, SPC is a crucial segment of TQM
strategy which works to develop a new philosophy and direction to the work of developing
4
Paraphrase This Document
Need a fresh take? Get an instant paraphrase of this document with our AI Paraphraser
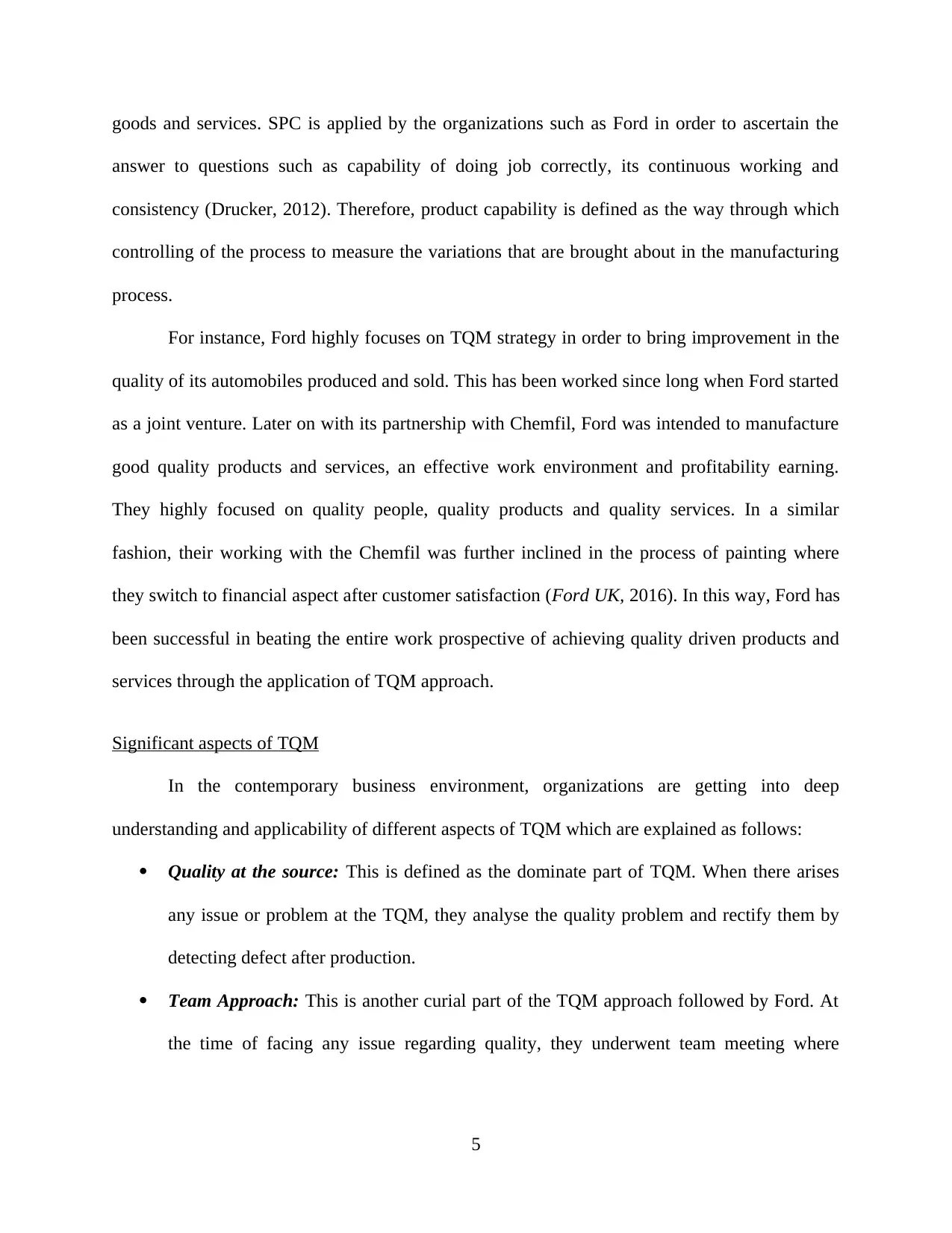
goods and services. SPC is applied by the organizations such as Ford in order to ascertain the
answer to questions such as capability of doing job correctly, its continuous working and
consistency (Drucker, 2012). Therefore, product capability is defined as the way through which
controlling of the process to measure the variations that are brought about in the manufacturing
process.
For instance, Ford highly focuses on TQM strategy in order to bring improvement in the
quality of its automobiles produced and sold. This has been worked since long when Ford started
as a joint venture. Later on with its partnership with Chemfil, Ford was intended to manufacture
good quality products and services, an effective work environment and profitability earning.
They highly focused on quality people, quality products and quality services. In a similar
fashion, their working with the Chemfil was further inclined in the process of painting where
they switch to financial aspect after customer satisfaction (Ford UK, 2016). In this way, Ford has
been successful in beating the entire work prospective of achieving quality driven products and
services through the application of TQM approach.
Significant aspects of TQM
In the contemporary business environment, organizations are getting into deep
understanding and applicability of different aspects of TQM which are explained as follows:
Quality at the source: This is defined as the dominate part of TQM. When there arises
any issue or problem at the TQM, they analyse the quality problem and rectify them by
detecting defect after production.
Team Approach: This is another curial part of the TQM approach followed by Ford. At
the time of facing any issue regarding quality, they underwent team meeting where
5
answer to questions such as capability of doing job correctly, its continuous working and
consistency (Drucker, 2012). Therefore, product capability is defined as the way through which
controlling of the process to measure the variations that are brought about in the manufacturing
process.
For instance, Ford highly focuses on TQM strategy in order to bring improvement in the
quality of its automobiles produced and sold. This has been worked since long when Ford started
as a joint venture. Later on with its partnership with Chemfil, Ford was intended to manufacture
good quality products and services, an effective work environment and profitability earning.
They highly focused on quality people, quality products and quality services. In a similar
fashion, their working with the Chemfil was further inclined in the process of painting where
they switch to financial aspect after customer satisfaction (Ford UK, 2016). In this way, Ford has
been successful in beating the entire work prospective of achieving quality driven products and
services through the application of TQM approach.
Significant aspects of TQM
In the contemporary business environment, organizations are getting into deep
understanding and applicability of different aspects of TQM which are explained as follows:
Quality at the source: This is defined as the dominate part of TQM. When there arises
any issue or problem at the TQM, they analyse the quality problem and rectify them by
detecting defect after production.
Team Approach: This is another curial part of the TQM approach followed by Ford. At
the time of facing any issue regarding quality, they underwent team meeting where
5
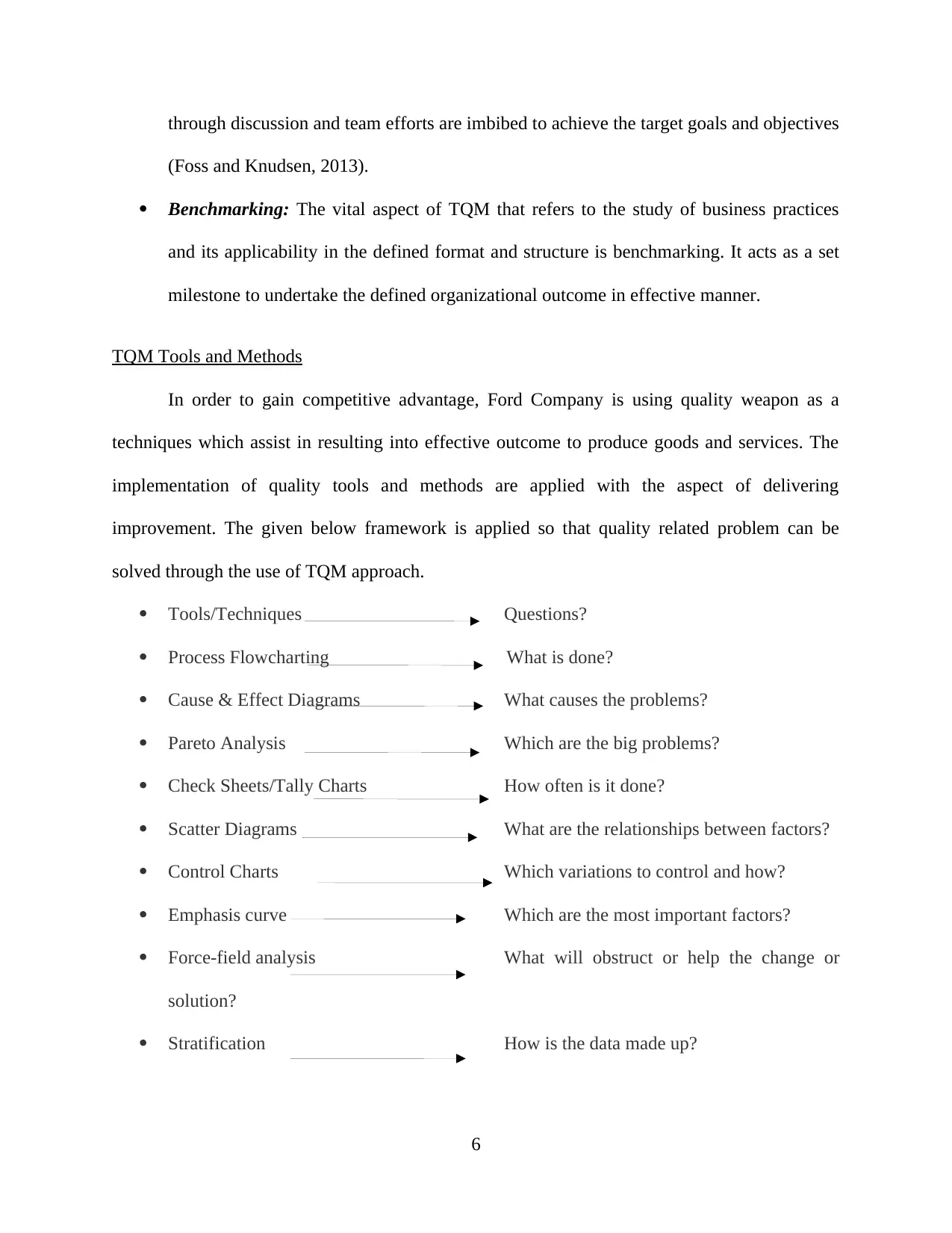
through discussion and team efforts are imbibed to achieve the target goals and objectives
(Foss and Knudsen, 2013).
Benchmarking: The vital aspect of TQM that refers to the study of business practices
and its applicability in the defined format and structure is benchmarking. It acts as a set
milestone to undertake the defined organizational outcome in effective manner.
TQM Tools and Methods
In order to gain competitive advantage, Ford Company is using quality weapon as a
techniques which assist in resulting into effective outcome to produce goods and services. The
implementation of quality tools and methods are applied with the aspect of delivering
improvement. The given below framework is applied so that quality related problem can be
solved through the use of TQM approach.
Tools/Techniques Questions?
Process Flowcharting What is done?
Cause & Effect Diagrams What causes the problems?
Pareto Analysis Which are the big problems?
Check Sheets/Tally Charts How often is it done?
Scatter Diagrams What are the relationships between factors?
Control Charts Which variations to control and how?
Emphasis curve Which are the most important factors?
Force-field analysis What will obstruct or help the change or
solution?
Stratification How is the data made up?
6
(Foss and Knudsen, 2013).
Benchmarking: The vital aspect of TQM that refers to the study of business practices
and its applicability in the defined format and structure is benchmarking. It acts as a set
milestone to undertake the defined organizational outcome in effective manner.
TQM Tools and Methods
In order to gain competitive advantage, Ford Company is using quality weapon as a
techniques which assist in resulting into effective outcome to produce goods and services. The
implementation of quality tools and methods are applied with the aspect of delivering
improvement. The given below framework is applied so that quality related problem can be
solved through the use of TQM approach.
Tools/Techniques Questions?
Process Flowcharting What is done?
Cause & Effect Diagrams What causes the problems?
Pareto Analysis Which are the big problems?
Check Sheets/Tally Charts How often is it done?
Scatter Diagrams What are the relationships between factors?
Control Charts Which variations to control and how?
Emphasis curve Which are the most important factors?
Force-field analysis What will obstruct or help the change or
solution?
Stratification How is the data made up?
6
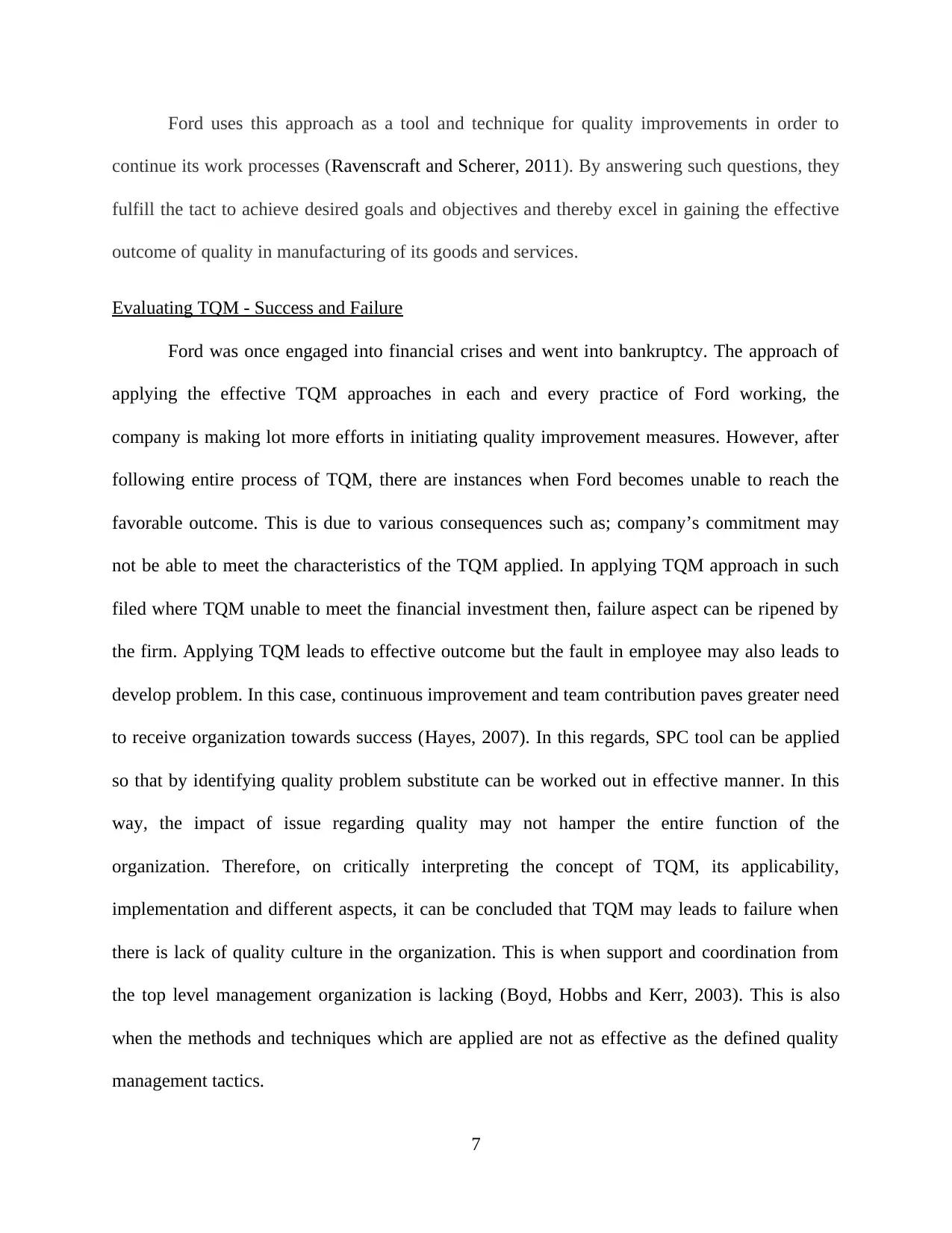
Ford uses this approach as a tool and technique for quality improvements in order to
continue its work processes (Ravenscraft and Scherer, 2011). By answering such questions, they
fulfill the tact to achieve desired goals and objectives and thereby excel in gaining the effective
outcome of quality in manufacturing of its goods and services.
Evaluating TQM - Success and Failure
Ford was once engaged into financial crises and went into bankruptcy. The approach of
applying the effective TQM approaches in each and every practice of Ford working, the
company is making lot more efforts in initiating quality improvement measures. However, after
following entire process of TQM, there are instances when Ford becomes unable to reach the
favorable outcome. This is due to various consequences such as; company’s commitment may
not be able to meet the characteristics of the TQM applied. In applying TQM approach in such
filed where TQM unable to meet the financial investment then, failure aspect can be ripened by
the firm. Applying TQM leads to effective outcome but the fault in employee may also leads to
develop problem. In this case, continuous improvement and team contribution paves greater need
to receive organization towards success (Hayes, 2007). In this regards, SPC tool can be applied
so that by identifying quality problem substitute can be worked out in effective manner. In this
way, the impact of issue regarding quality may not hamper the entire function of the
organization. Therefore, on critically interpreting the concept of TQM, its applicability,
implementation and different aspects, it can be concluded that TQM may leads to failure when
there is lack of quality culture in the organization. This is when support and coordination from
the top level management organization is lacking (Boyd, Hobbs and Kerr, 2003). This is also
when the methods and techniques which are applied are not as effective as the defined quality
management tactics.
7
continue its work processes (Ravenscraft and Scherer, 2011). By answering such questions, they
fulfill the tact to achieve desired goals and objectives and thereby excel in gaining the effective
outcome of quality in manufacturing of its goods and services.
Evaluating TQM - Success and Failure
Ford was once engaged into financial crises and went into bankruptcy. The approach of
applying the effective TQM approaches in each and every practice of Ford working, the
company is making lot more efforts in initiating quality improvement measures. However, after
following entire process of TQM, there are instances when Ford becomes unable to reach the
favorable outcome. This is due to various consequences such as; company’s commitment may
not be able to meet the characteristics of the TQM applied. In applying TQM approach in such
filed where TQM unable to meet the financial investment then, failure aspect can be ripened by
the firm. Applying TQM leads to effective outcome but the fault in employee may also leads to
develop problem. In this case, continuous improvement and team contribution paves greater need
to receive organization towards success (Hayes, 2007). In this regards, SPC tool can be applied
so that by identifying quality problem substitute can be worked out in effective manner. In this
way, the impact of issue regarding quality may not hamper the entire function of the
organization. Therefore, on critically interpreting the concept of TQM, its applicability,
implementation and different aspects, it can be concluded that TQM may leads to failure when
there is lack of quality culture in the organization. This is when support and coordination from
the top level management organization is lacking (Boyd, Hobbs and Kerr, 2003). This is also
when the methods and techniques which are applied are not as effective as the defined quality
management tactics.
7
Secure Best Marks with AI Grader
Need help grading? Try our AI Grader for instant feedback on your assignments.
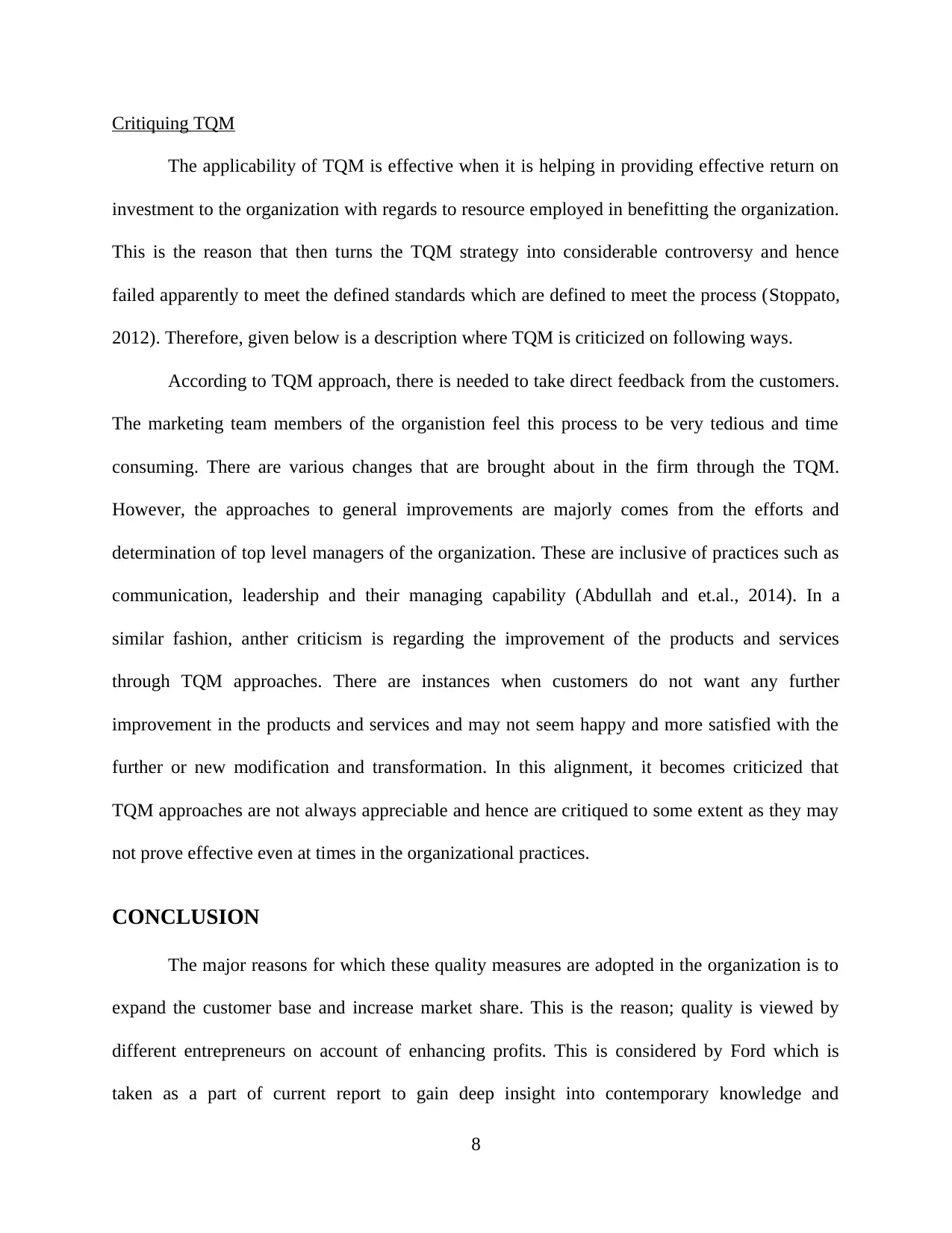
Critiquing TQM
The applicability of TQM is effective when it is helping in providing effective return on
investment to the organization with regards to resource employed in benefitting the organization.
This is the reason that then turns the TQM strategy into considerable controversy and hence
failed apparently to meet the defined standards which are defined to meet the process (Stoppato,
2012). Therefore, given below is a description where TQM is criticized on following ways.
According to TQM approach, there is needed to take direct feedback from the customers.
The marketing team members of the organistion feel this process to be very tedious and time
consuming. There are various changes that are brought about in the firm through the TQM.
However, the approaches to general improvements are majorly comes from the efforts and
determination of top level managers of the organization. These are inclusive of practices such as
communication, leadership and their managing capability (Abdullah and et.al., 2014). In a
similar fashion, anther criticism is regarding the improvement of the products and services
through TQM approaches. There are instances when customers do not want any further
improvement in the products and services and may not seem happy and more satisfied with the
further or new modification and transformation. In this alignment, it becomes criticized that
TQM approaches are not always appreciable and hence are critiqued to some extent as they may
not prove effective even at times in the organizational practices.
CONCLUSION
The major reasons for which these quality measures are adopted in the organization is to
expand the customer base and increase market share. This is the reason; quality is viewed by
different entrepreneurs on account of enhancing profits. This is considered by Ford which is
taken as a part of current report to gain deep insight into contemporary knowledge and
8
The applicability of TQM is effective when it is helping in providing effective return on
investment to the organization with regards to resource employed in benefitting the organization.
This is the reason that then turns the TQM strategy into considerable controversy and hence
failed apparently to meet the defined standards which are defined to meet the process (Stoppato,
2012). Therefore, given below is a description where TQM is criticized on following ways.
According to TQM approach, there is needed to take direct feedback from the customers.
The marketing team members of the organistion feel this process to be very tedious and time
consuming. There are various changes that are brought about in the firm through the TQM.
However, the approaches to general improvements are majorly comes from the efforts and
determination of top level managers of the organization. These are inclusive of practices such as
communication, leadership and their managing capability (Abdullah and et.al., 2014). In a
similar fashion, anther criticism is regarding the improvement of the products and services
through TQM approaches. There are instances when customers do not want any further
improvement in the products and services and may not seem happy and more satisfied with the
further or new modification and transformation. In this alignment, it becomes criticized that
TQM approaches are not always appreciable and hence are critiqued to some extent as they may
not prove effective even at times in the organizational practices.
CONCLUSION
The major reasons for which these quality measures are adopted in the organization is to
expand the customer base and increase market share. This is the reason; quality is viewed by
different entrepreneurs on account of enhancing profits. This is considered by Ford which is
taken as a part of current report to gain deep insight into contemporary knowledge and
8
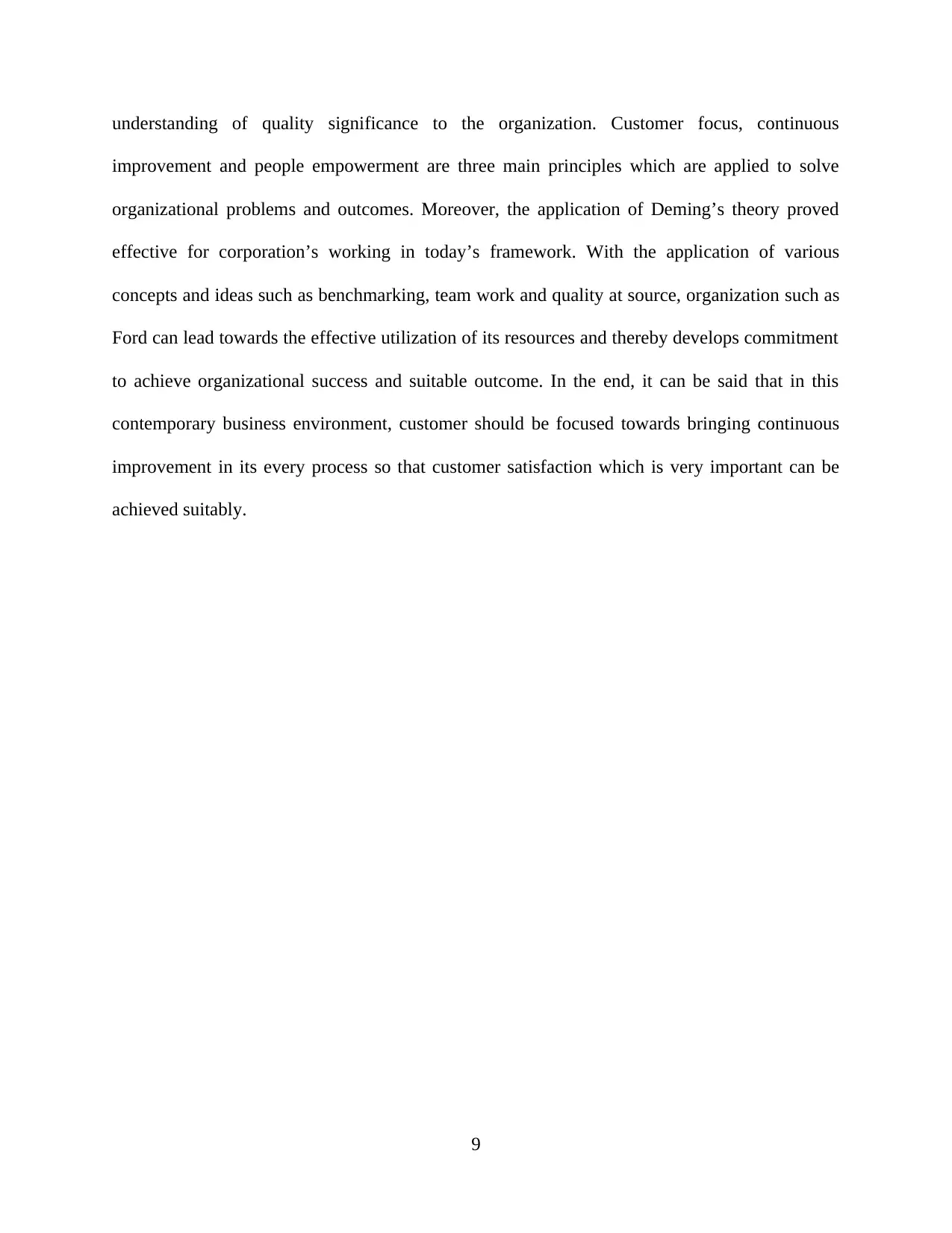
understanding of quality significance to the organization. Customer focus, continuous
improvement and people empowerment are three main principles which are applied to solve
organizational problems and outcomes. Moreover, the application of Deming’s theory proved
effective for corporation’s working in today’s framework. With the application of various
concepts and ideas such as benchmarking, team work and quality at source, organization such as
Ford can lead towards the effective utilization of its resources and thereby develops commitment
to achieve organizational success and suitable outcome. In the end, it can be said that in this
contemporary business environment, customer should be focused towards bringing continuous
improvement in its every process so that customer satisfaction which is very important can be
achieved suitably.
9
improvement and people empowerment are three main principles which are applied to solve
organizational problems and outcomes. Moreover, the application of Deming’s theory proved
effective for corporation’s working in today’s framework. With the application of various
concepts and ideas such as benchmarking, team work and quality at source, organization such as
Ford can lead towards the effective utilization of its resources and thereby develops commitment
to achieve organizational success and suitable outcome. In the end, it can be said that in this
contemporary business environment, customer should be focused towards bringing continuous
improvement in its every process so that customer satisfaction which is very important can be
achieved suitably.
9
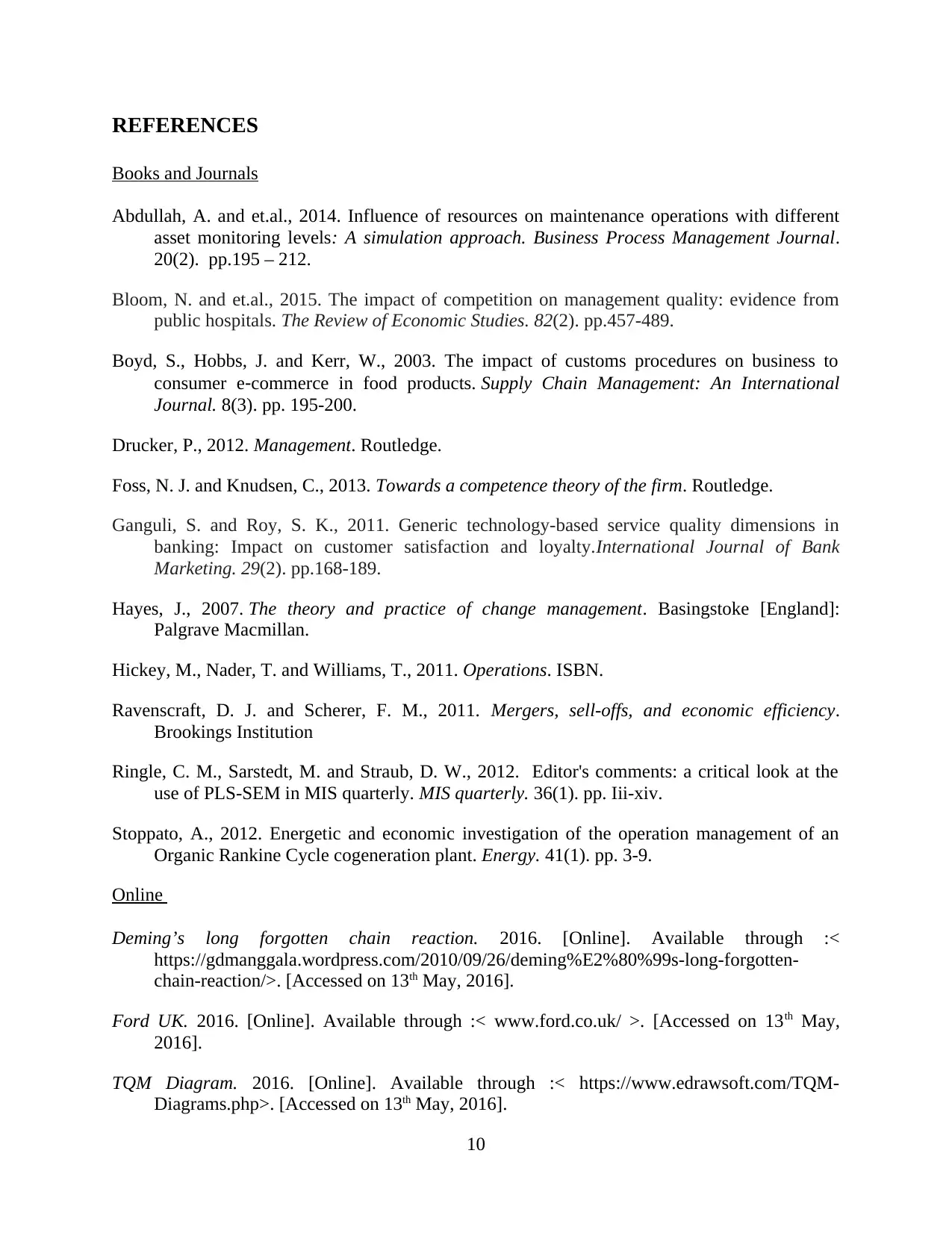
REFERENCES
Books and Journals
Abdullah, A. and et.al., 2014. Influence of resources on maintenance operations with different
asset monitoring levels: A simulation approach. Business Process Management Journal.
20(2). pp.195 – 212.
Bloom, N. and et.al., 2015. The impact of competition on management quality: evidence from
public hospitals. The Review of Economic Studies. 82(2). pp.457-489.
Boyd, S., Hobbs, J. and Kerr, W., 2003. The impact of customs procedures on business to
consumer e‐commerce in food products. Supply Chain Management: An International
Journal. 8(3). pp. 195-200.
Drucker, P., 2012. Management. Routledge.
Foss, N. J. and Knudsen, C., 2013. Towards a competence theory of the firm. Routledge.
Ganguli, S. and Roy, S. K., 2011. Generic technology-based service quality dimensions in
banking: Impact on customer satisfaction and loyalty.International Journal of Bank
Marketing. 29(2). pp.168-189.
Hayes, J., 2007. The theory and practice of change management. Basingstoke [England]:
Palgrave Macmillan.
Hickey, M., Nader, T. and Williams, T., 2011. Operations. ISBN.
Ravenscraft, D. J. and Scherer, F. M., 2011. Mergers, sell-offs, and economic efficiency.
Brookings Institution
Ringle, C. M., Sarstedt, M. and Straub, D. W., 2012. Editor's comments: a critical look at the
use of PLS-SEM in MIS quarterly. MIS quarterly. 36(1). pp. Iii-xiv.
Stoppato, A., 2012. Energetic and economic investigation of the operation management of an
Organic Rankine Cycle cogeneration plant. Energy. 41(1). pp. 3-9.
Online
Deming’s long forgotten chain reaction. 2016. [Online]. Available through :<
https://gdmanggala.wordpress.com/2010/09/26/deming%E2%80%99s-long-forgotten-
chain-reaction/>. [Accessed on 13th May, 2016].
Ford UK. 2016. [Online]. Available through :< www.ford.co.uk/ >. [Accessed on 13th May,
2016].
TQM Diagram. 2016. [Online]. Available through :< https://www.edrawsoft.com/TQM-
Diagrams.php>. [Accessed on 13th May, 2016].
10
Books and Journals
Abdullah, A. and et.al., 2014. Influence of resources on maintenance operations with different
asset monitoring levels: A simulation approach. Business Process Management Journal.
20(2). pp.195 – 212.
Bloom, N. and et.al., 2015. The impact of competition on management quality: evidence from
public hospitals. The Review of Economic Studies. 82(2). pp.457-489.
Boyd, S., Hobbs, J. and Kerr, W., 2003. The impact of customs procedures on business to
consumer e‐commerce in food products. Supply Chain Management: An International
Journal. 8(3). pp. 195-200.
Drucker, P., 2012. Management. Routledge.
Foss, N. J. and Knudsen, C., 2013. Towards a competence theory of the firm. Routledge.
Ganguli, S. and Roy, S. K., 2011. Generic technology-based service quality dimensions in
banking: Impact on customer satisfaction and loyalty.International Journal of Bank
Marketing. 29(2). pp.168-189.
Hayes, J., 2007. The theory and practice of change management. Basingstoke [England]:
Palgrave Macmillan.
Hickey, M., Nader, T. and Williams, T., 2011. Operations. ISBN.
Ravenscraft, D. J. and Scherer, F. M., 2011. Mergers, sell-offs, and economic efficiency.
Brookings Institution
Ringle, C. M., Sarstedt, M. and Straub, D. W., 2012. Editor's comments: a critical look at the
use of PLS-SEM in MIS quarterly. MIS quarterly. 36(1). pp. Iii-xiv.
Stoppato, A., 2012. Energetic and economic investigation of the operation management of an
Organic Rankine Cycle cogeneration plant. Energy. 41(1). pp. 3-9.
Online
Deming’s long forgotten chain reaction. 2016. [Online]. Available through :<
https://gdmanggala.wordpress.com/2010/09/26/deming%E2%80%99s-long-forgotten-
chain-reaction/>. [Accessed on 13th May, 2016].
Ford UK. 2016. [Online]. Available through :< www.ford.co.uk/ >. [Accessed on 13th May,
2016].
TQM Diagram. 2016. [Online]. Available through :< https://www.edrawsoft.com/TQM-
Diagrams.php>. [Accessed on 13th May, 2016].
10
1 out of 13
Related Documents

Your All-in-One AI-Powered Toolkit for Academic Success.
+13062052269
info@desklib.com
Available 24*7 on WhatsApp / Email
Unlock your academic potential
© 2024 | Zucol Services PVT LTD | All rights reserved.