Analysis of Total Quality Management and its Implementation at Nestle
VerifiedAdded on 2020/04/21
|9
|3121
|75
Report
AI Summary
This report provides a comprehensive analysis of Nestle's Total Quality Management (TQM) system. It begins with an introduction to TQM and its importance for business success, followed by a brief overview of Nestle. The report then delves into the TQM tools used by Nestle, with a specific focus on Kaizen and statistical process control. It details the implementation methods employed by Nestle, outlining the steps involved in the Kaizen process. The report further examines the success of TQM implementation at Nestle, highlighting improvements in quality, waste reduction, and employee value. It also addresses how the organization deals with change management. Recommendations are provided for continuous improvement, emphasizing the importance of quality management in a competitive food industry. The report concludes with a summary of the key findings and a list of references.
Contribute Materials
Your contribution can guide someone’s learning journey. Share your
documents today.
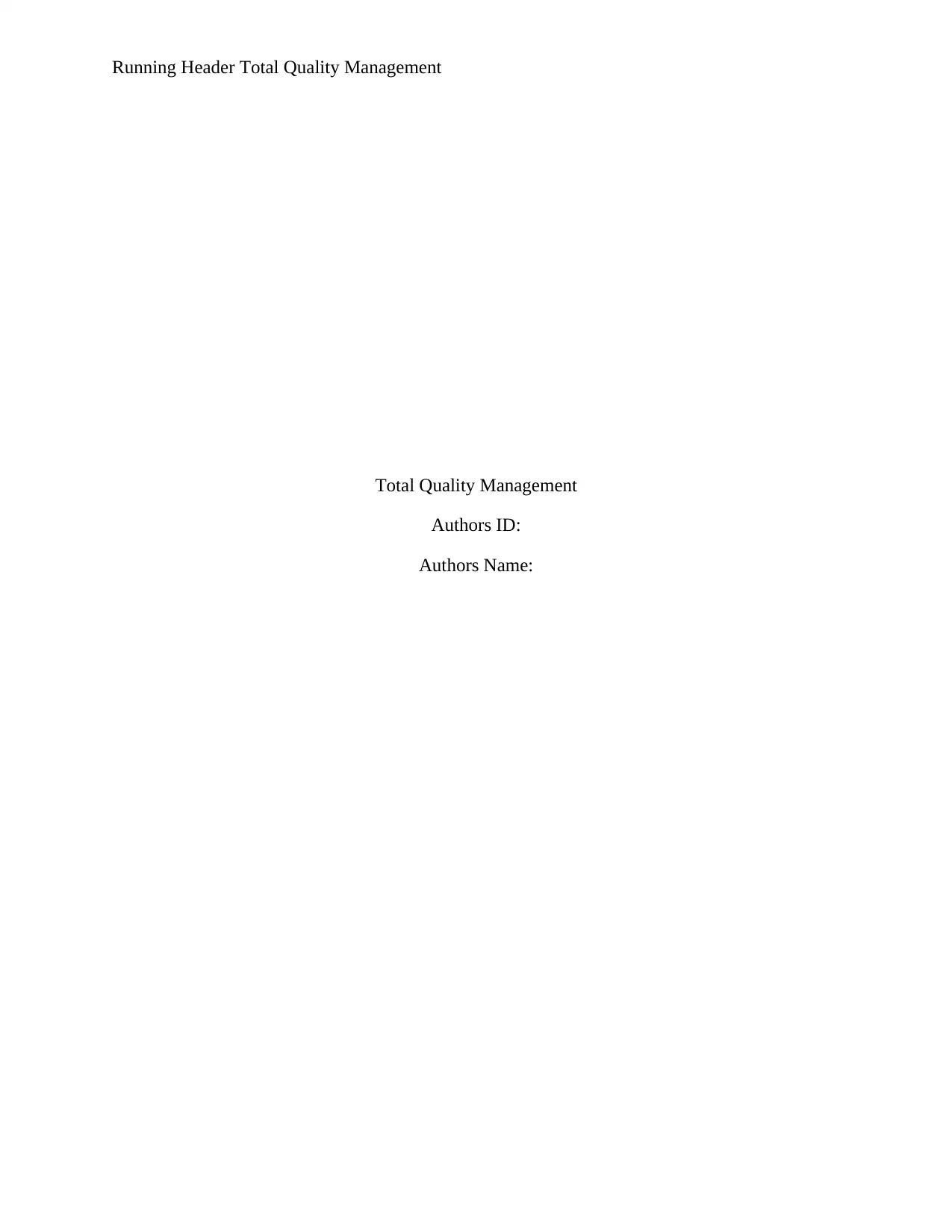
Running Header Total Quality Management
Total Quality Management
Authors ID:
Authors Name:
Total Quality Management
Authors ID:
Authors Name:
Secure Best Marks with AI Grader
Need help grading? Try our AI Grader for instant feedback on your assignments.
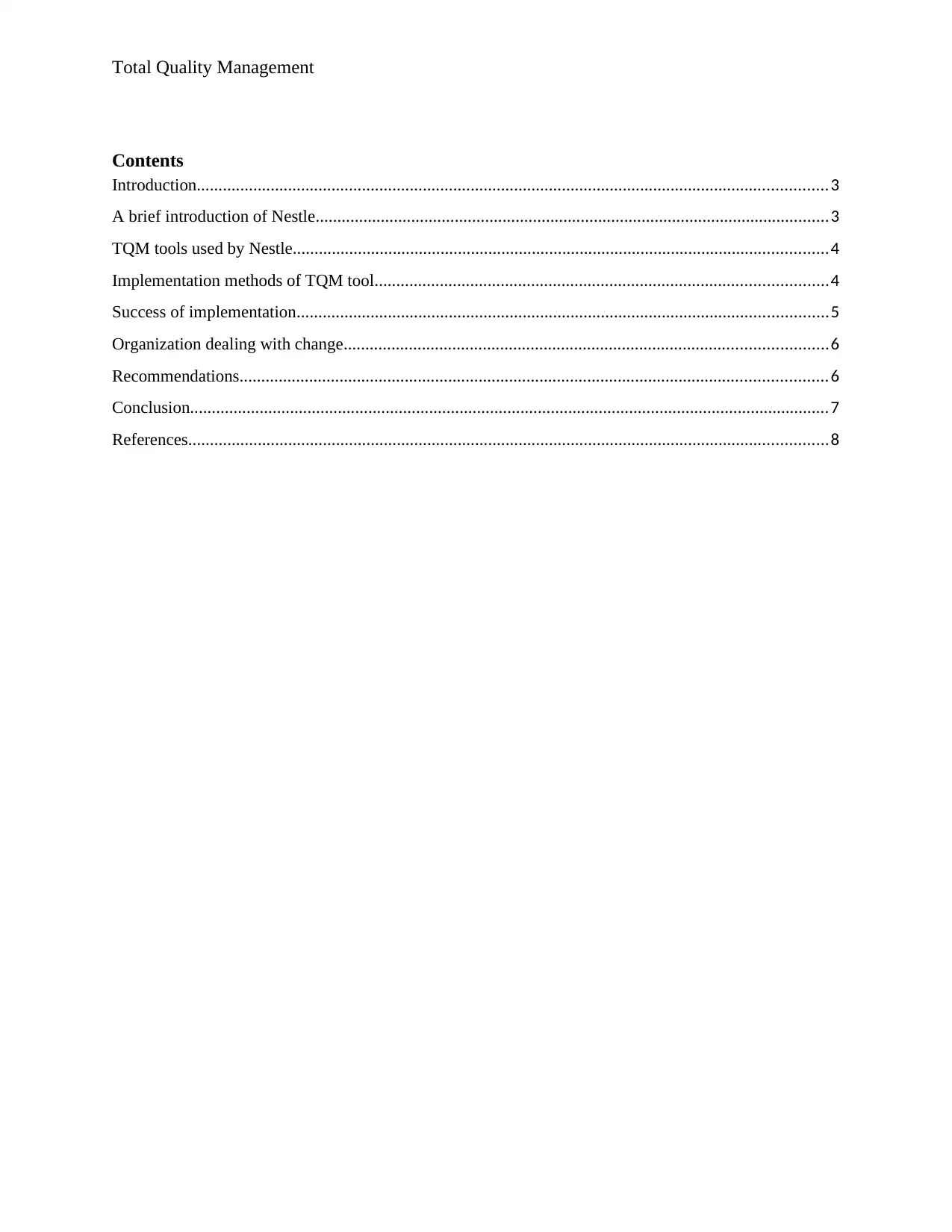
Total Quality Management
Contents
Introduction.................................................................................................................................................3
A brief introduction of Nestle......................................................................................................................3
TQM tools used by Nestle...........................................................................................................................4
Implementation methods of TQM tool........................................................................................................4
Success of implementation..........................................................................................................................5
Organization dealing with change...............................................................................................................6
Recommendations.......................................................................................................................................6
Conclusion...................................................................................................................................................7
References...................................................................................................................................................8
Contents
Introduction.................................................................................................................................................3
A brief introduction of Nestle......................................................................................................................3
TQM tools used by Nestle...........................................................................................................................4
Implementation methods of TQM tool........................................................................................................4
Success of implementation..........................................................................................................................5
Organization dealing with change...............................................................................................................6
Recommendations.......................................................................................................................................6
Conclusion...................................................................................................................................................7
References...................................................................................................................................................8
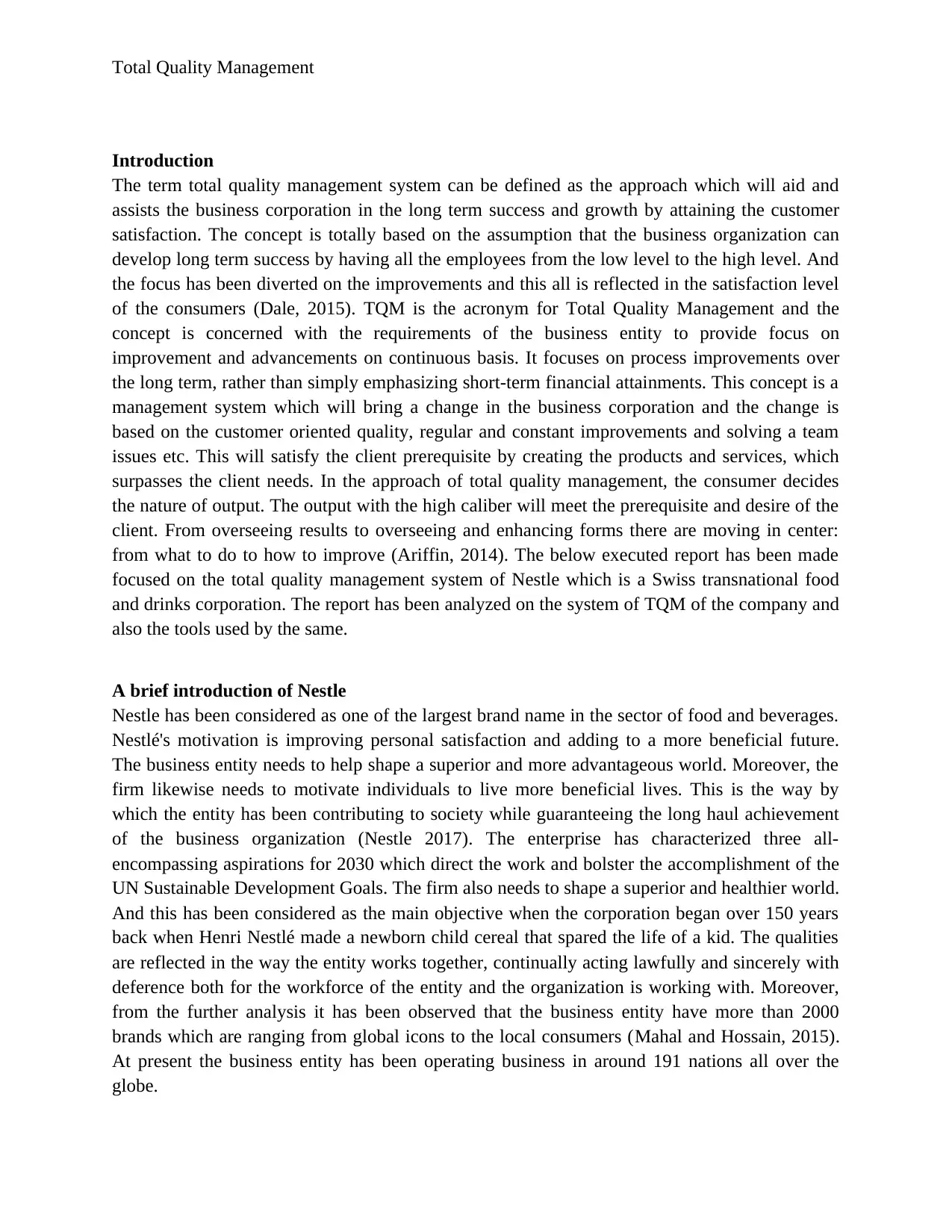
Total Quality Management
Introduction
The term total quality management system can be defined as the approach which will aid and
assists the business corporation in the long term success and growth by attaining the customer
satisfaction. The concept is totally based on the assumption that the business organization can
develop long term success by having all the employees from the low level to the high level. And
the focus has been diverted on the improvements and this all is reflected in the satisfaction level
of the consumers (Dale, 2015). TQM is the acronym for Total Quality Management and the
concept is concerned with the requirements of the business entity to provide focus on
improvement and advancements on continuous basis. It focuses on process improvements over
the long term, rather than simply emphasizing short-term financial attainments. This concept is a
management system which will bring a change in the business corporation and the change is
based on the customer oriented quality, regular and constant improvements and solving a team
issues etc. This will satisfy the client prerequisite by creating the products and services, which
surpasses the client needs. In the approach of total quality management, the consumer decides
the nature of output. The output with the high caliber will meet the prerequisite and desire of the
client. From overseeing results to overseeing and enhancing forms there are moving in center:
from what to do to how to improve (Ariffin, 2014). The below executed report has been made
focused on the total quality management system of Nestle which is a Swiss transnational food
and drinks corporation. The report has been analyzed on the system of TQM of the company and
also the tools used by the same.
A brief introduction of Nestle
Nestle has been considered as one of the largest brand name in the sector of food and beverages.
Nestlé's motivation is improving personal satisfaction and adding to a more beneficial future.
The business entity needs to help shape a superior and more advantageous world. Moreover, the
firm likewise needs to motivate individuals to live more beneficial lives. This is the way by
which the entity has been contributing to society while guaranteeing the long haul achievement
of the business organization (Nestle 2017). The enterprise has characterized three all-
encompassing aspirations for 2030 which direct the work and bolster the accomplishment of the
UN Sustainable Development Goals. The firm also needs to shape a superior and healthier world.
And this has been considered as the main objective when the corporation began over 150 years
back when Henri Nestlé made a newborn child cereal that spared the life of a kid. The qualities
are reflected in the way the entity works together, continually acting lawfully and sincerely with
deference both for the workforce of the entity and the organization is working with. Moreover,
from the further analysis it has been observed that the business entity have more than 2000
brands which are ranging from global icons to the local consumers (Mahal and Hossain, 2015).
At present the business entity has been operating business in around 191 nations all over the
globe.
Introduction
The term total quality management system can be defined as the approach which will aid and
assists the business corporation in the long term success and growth by attaining the customer
satisfaction. The concept is totally based on the assumption that the business organization can
develop long term success by having all the employees from the low level to the high level. And
the focus has been diverted on the improvements and this all is reflected in the satisfaction level
of the consumers (Dale, 2015). TQM is the acronym for Total Quality Management and the
concept is concerned with the requirements of the business entity to provide focus on
improvement and advancements on continuous basis. It focuses on process improvements over
the long term, rather than simply emphasizing short-term financial attainments. This concept is a
management system which will bring a change in the business corporation and the change is
based on the customer oriented quality, regular and constant improvements and solving a team
issues etc. This will satisfy the client prerequisite by creating the products and services, which
surpasses the client needs. In the approach of total quality management, the consumer decides
the nature of output. The output with the high caliber will meet the prerequisite and desire of the
client. From overseeing results to overseeing and enhancing forms there are moving in center:
from what to do to how to improve (Ariffin, 2014). The below executed report has been made
focused on the total quality management system of Nestle which is a Swiss transnational food
and drinks corporation. The report has been analyzed on the system of TQM of the company and
also the tools used by the same.
A brief introduction of Nestle
Nestle has been considered as one of the largest brand name in the sector of food and beverages.
Nestlé's motivation is improving personal satisfaction and adding to a more beneficial future.
The business entity needs to help shape a superior and more advantageous world. Moreover, the
firm likewise needs to motivate individuals to live more beneficial lives. This is the way by
which the entity has been contributing to society while guaranteeing the long haul achievement
of the business organization (Nestle 2017). The enterprise has characterized three all-
encompassing aspirations for 2030 which direct the work and bolster the accomplishment of the
UN Sustainable Development Goals. The firm also needs to shape a superior and healthier world.
And this has been considered as the main objective when the corporation began over 150 years
back when Henri Nestlé made a newborn child cereal that spared the life of a kid. The qualities
are reflected in the way the entity works together, continually acting lawfully and sincerely with
deference both for the workforce of the entity and the organization is working with. Moreover,
from the further analysis it has been observed that the business entity have more than 2000
brands which are ranging from global icons to the local consumers (Mahal and Hossain, 2015).
At present the business entity has been operating business in around 191 nations all over the
globe.
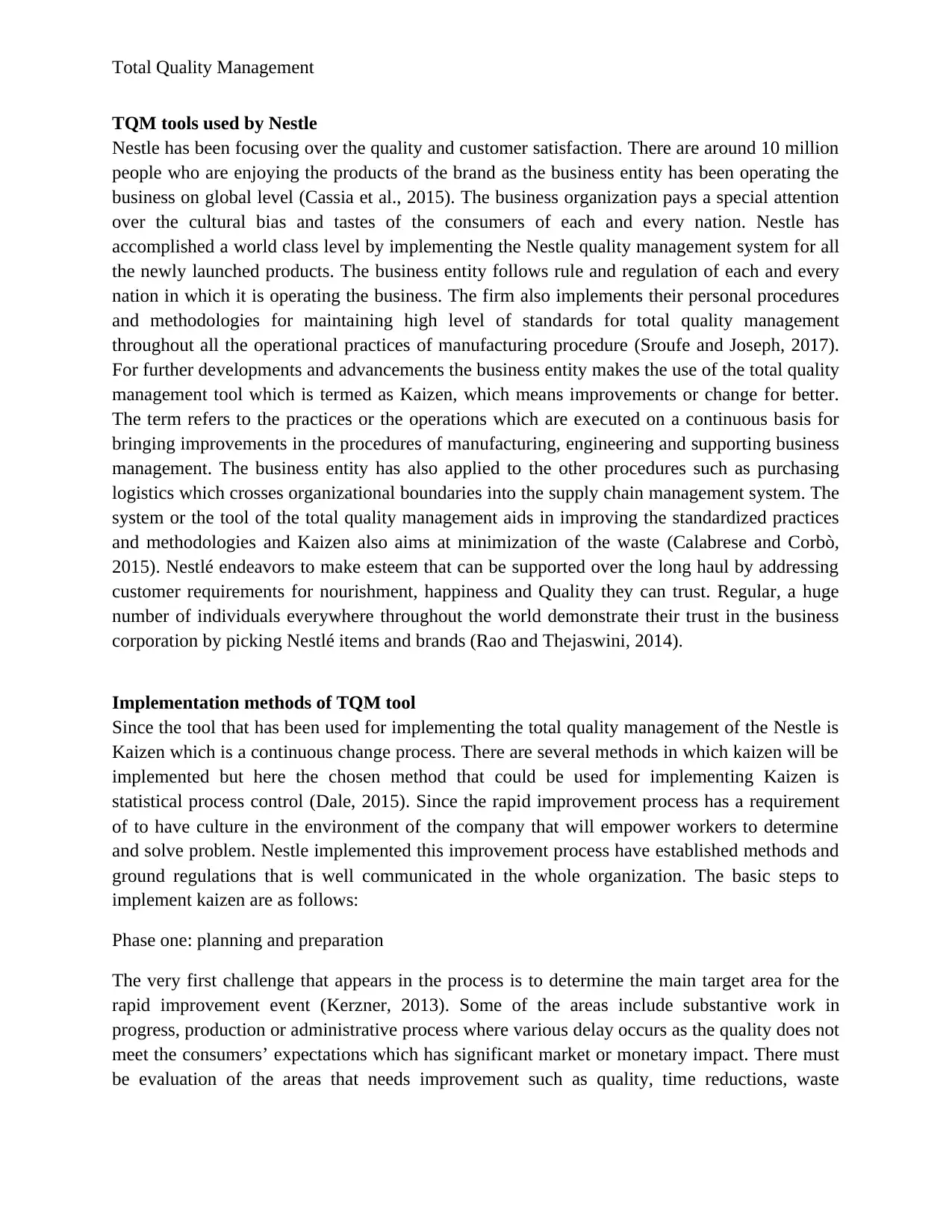
Total Quality Management
TQM tools used by Nestle
Nestle has been focusing over the quality and customer satisfaction. There are around 10 million
people who are enjoying the products of the brand as the business entity has been operating the
business on global level (Cassia et al., 2015). The business organization pays a special attention
over the cultural bias and tastes of the consumers of each and every nation. Nestle has
accomplished a world class level by implementing the Nestle quality management system for all
the newly launched products. The business entity follows rule and regulation of each and every
nation in which it is operating the business. The firm also implements their personal procedures
and methodologies for maintaining high level of standards for total quality management
throughout all the operational practices of manufacturing procedure (Sroufe and Joseph, 2017).
For further developments and advancements the business entity makes the use of the total quality
management tool which is termed as Kaizen, which means improvements or change for better.
The term refers to the practices or the operations which are executed on a continuous basis for
bringing improvements in the procedures of manufacturing, engineering and supporting business
management. The business entity has also applied to the other procedures such as purchasing
logistics which crosses organizational boundaries into the supply chain management system. The
system or the tool of the total quality management aids in improving the standardized practices
and methodologies and Kaizen also aims at minimization of the waste (Calabrese and Corbò,
2015). Nestlé endeavors to make esteem that can be supported over the long haul by addressing
customer requirements for nourishment, happiness and Quality they can trust. Regular, a huge
number of individuals everywhere throughout the world demonstrate their trust in the business
corporation by picking Nestlé items and brands (Rao and Thejaswini, 2014).
Implementation methods of TQM tool
Since the tool that has been used for implementing the total quality management of the Nestle is
Kaizen which is a continuous change process. There are several methods in which kaizen will be
implemented but here the chosen method that could be used for implementing Kaizen is
statistical process control (Dale, 2015). Since the rapid improvement process has a requirement
of to have culture in the environment of the company that will empower workers to determine
and solve problem. Nestle implemented this improvement process have established methods and
ground regulations that is well communicated in the whole organization. The basic steps to
implement kaizen are as follows:
Phase one: planning and preparation
The very first challenge that appears in the process is to determine the main target area for the
rapid improvement event (Kerzner, 2013). Some of the areas include substantive work in
progress, production or administrative process where various delay occurs as the quality does not
meet the consumers’ expectations which has significant market or monetary impact. There must
be evaluation of the areas that needs improvement such as quality, time reductions, waste
TQM tools used by Nestle
Nestle has been focusing over the quality and customer satisfaction. There are around 10 million
people who are enjoying the products of the brand as the business entity has been operating the
business on global level (Cassia et al., 2015). The business organization pays a special attention
over the cultural bias and tastes of the consumers of each and every nation. Nestle has
accomplished a world class level by implementing the Nestle quality management system for all
the newly launched products. The business entity follows rule and regulation of each and every
nation in which it is operating the business. The firm also implements their personal procedures
and methodologies for maintaining high level of standards for total quality management
throughout all the operational practices of manufacturing procedure (Sroufe and Joseph, 2017).
For further developments and advancements the business entity makes the use of the total quality
management tool which is termed as Kaizen, which means improvements or change for better.
The term refers to the practices or the operations which are executed on a continuous basis for
bringing improvements in the procedures of manufacturing, engineering and supporting business
management. The business entity has also applied to the other procedures such as purchasing
logistics which crosses organizational boundaries into the supply chain management system. The
system or the tool of the total quality management aids in improving the standardized practices
and methodologies and Kaizen also aims at minimization of the waste (Calabrese and Corbò,
2015). Nestlé endeavors to make esteem that can be supported over the long haul by addressing
customer requirements for nourishment, happiness and Quality they can trust. Regular, a huge
number of individuals everywhere throughout the world demonstrate their trust in the business
corporation by picking Nestlé items and brands (Rao and Thejaswini, 2014).
Implementation methods of TQM tool
Since the tool that has been used for implementing the total quality management of the Nestle is
Kaizen which is a continuous change process. There are several methods in which kaizen will be
implemented but here the chosen method that could be used for implementing Kaizen is
statistical process control (Dale, 2015). Since the rapid improvement process has a requirement
of to have culture in the environment of the company that will empower workers to determine
and solve problem. Nestle implemented this improvement process have established methods and
ground regulations that is well communicated in the whole organization. The basic steps to
implement kaizen are as follows:
Phase one: planning and preparation
The very first challenge that appears in the process is to determine the main target area for the
rapid improvement event (Kerzner, 2013). Some of the areas include substantive work in
progress, production or administrative process where various delay occurs as the quality does not
meet the consumers’ expectations which has significant market or monetary impact. There must
be evaluation of the areas that needs improvement such as quality, time reductions, waste
Secure Best Marks with AI Grader
Need help grading? Try our AI Grader for instant feedback on your assignments.
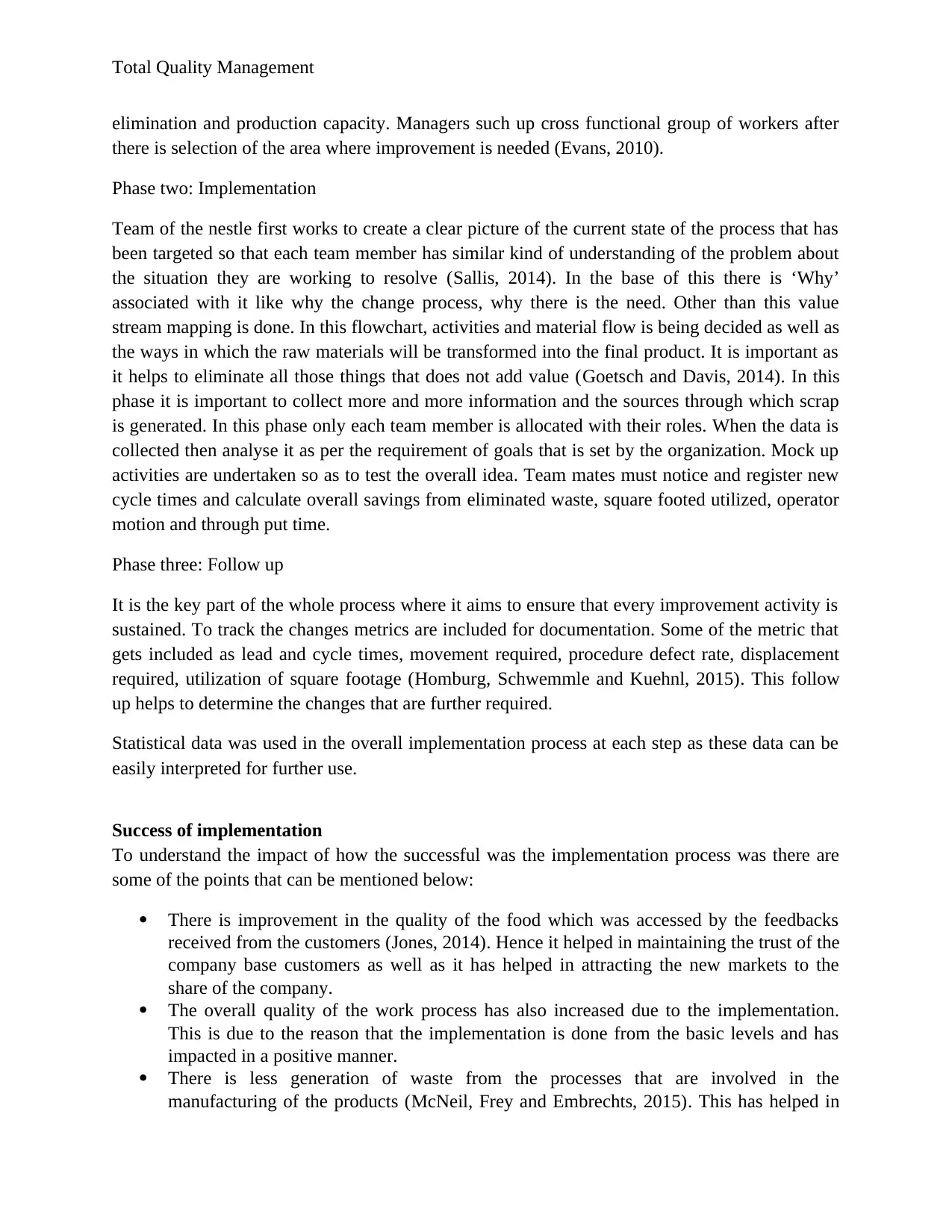
Total Quality Management
elimination and production capacity. Managers such up cross functional group of workers after
there is selection of the area where improvement is needed (Evans, 2010).
Phase two: Implementation
Team of the nestle first works to create a clear picture of the current state of the process that has
been targeted so that each team member has similar kind of understanding of the problem about
the situation they are working to resolve (Sallis, 2014). In the base of this there is ‘Why’
associated with it like why the change process, why there is the need. Other than this value
stream mapping is done. In this flowchart, activities and material flow is being decided as well as
the ways in which the raw materials will be transformed into the final product. It is important as
it helps to eliminate all those things that does not add value (Goetsch and Davis, 2014). In this
phase it is important to collect more and more information and the sources through which scrap
is generated. In this phase only each team member is allocated with their roles. When the data is
collected then analyse it as per the requirement of goals that is set by the organization. Mock up
activities are undertaken so as to test the overall idea. Team mates must notice and register new
cycle times and calculate overall savings from eliminated waste, square footed utilized, operator
motion and through put time.
Phase three: Follow up
It is the key part of the whole process where it aims to ensure that every improvement activity is
sustained. To track the changes metrics are included for documentation. Some of the metric that
gets included as lead and cycle times, movement required, procedure defect rate, displacement
required, utilization of square footage (Homburg, Schwemmle and Kuehnl, 2015). This follow
up helps to determine the changes that are further required.
Statistical data was used in the overall implementation process at each step as these data can be
easily interpreted for further use.
Success of implementation
To understand the impact of how the successful was the implementation process was there are
some of the points that can be mentioned below:
There is improvement in the quality of the food which was accessed by the feedbacks
received from the customers (Jones, 2014). Hence it helped in maintaining the trust of the
company base customers as well as it has helped in attracting the new markets to the
share of the company.
The overall quality of the work process has also increased due to the implementation.
This is due to the reason that the implementation is done from the basic levels and has
impacted in a positive manner.
There is less generation of waste from the processes that are involved in the
manufacturing of the products (McNeil, Frey and Embrechts, 2015). This has helped in
elimination and production capacity. Managers such up cross functional group of workers after
there is selection of the area where improvement is needed (Evans, 2010).
Phase two: Implementation
Team of the nestle first works to create a clear picture of the current state of the process that has
been targeted so that each team member has similar kind of understanding of the problem about
the situation they are working to resolve (Sallis, 2014). In the base of this there is ‘Why’
associated with it like why the change process, why there is the need. Other than this value
stream mapping is done. In this flowchart, activities and material flow is being decided as well as
the ways in which the raw materials will be transformed into the final product. It is important as
it helps to eliminate all those things that does not add value (Goetsch and Davis, 2014). In this
phase it is important to collect more and more information and the sources through which scrap
is generated. In this phase only each team member is allocated with their roles. When the data is
collected then analyse it as per the requirement of goals that is set by the organization. Mock up
activities are undertaken so as to test the overall idea. Team mates must notice and register new
cycle times and calculate overall savings from eliminated waste, square footed utilized, operator
motion and through put time.
Phase three: Follow up
It is the key part of the whole process where it aims to ensure that every improvement activity is
sustained. To track the changes metrics are included for documentation. Some of the metric that
gets included as lead and cycle times, movement required, procedure defect rate, displacement
required, utilization of square footage (Homburg, Schwemmle and Kuehnl, 2015). This follow
up helps to determine the changes that are further required.
Statistical data was used in the overall implementation process at each step as these data can be
easily interpreted for further use.
Success of implementation
To understand the impact of how the successful was the implementation process was there are
some of the points that can be mentioned below:
There is improvement in the quality of the food which was accessed by the feedbacks
received from the customers (Jones, 2014). Hence it helped in maintaining the trust of the
company base customers as well as it has helped in attracting the new markets to the
share of the company.
The overall quality of the work process has also increased due to the implementation.
This is due to the reason that the implementation is done from the basic levels and has
impacted in a positive manner.
There is less generation of waste from the processes that are involved in the
manufacturing of the products (McNeil, Frey and Embrechts, 2015). This has helped in
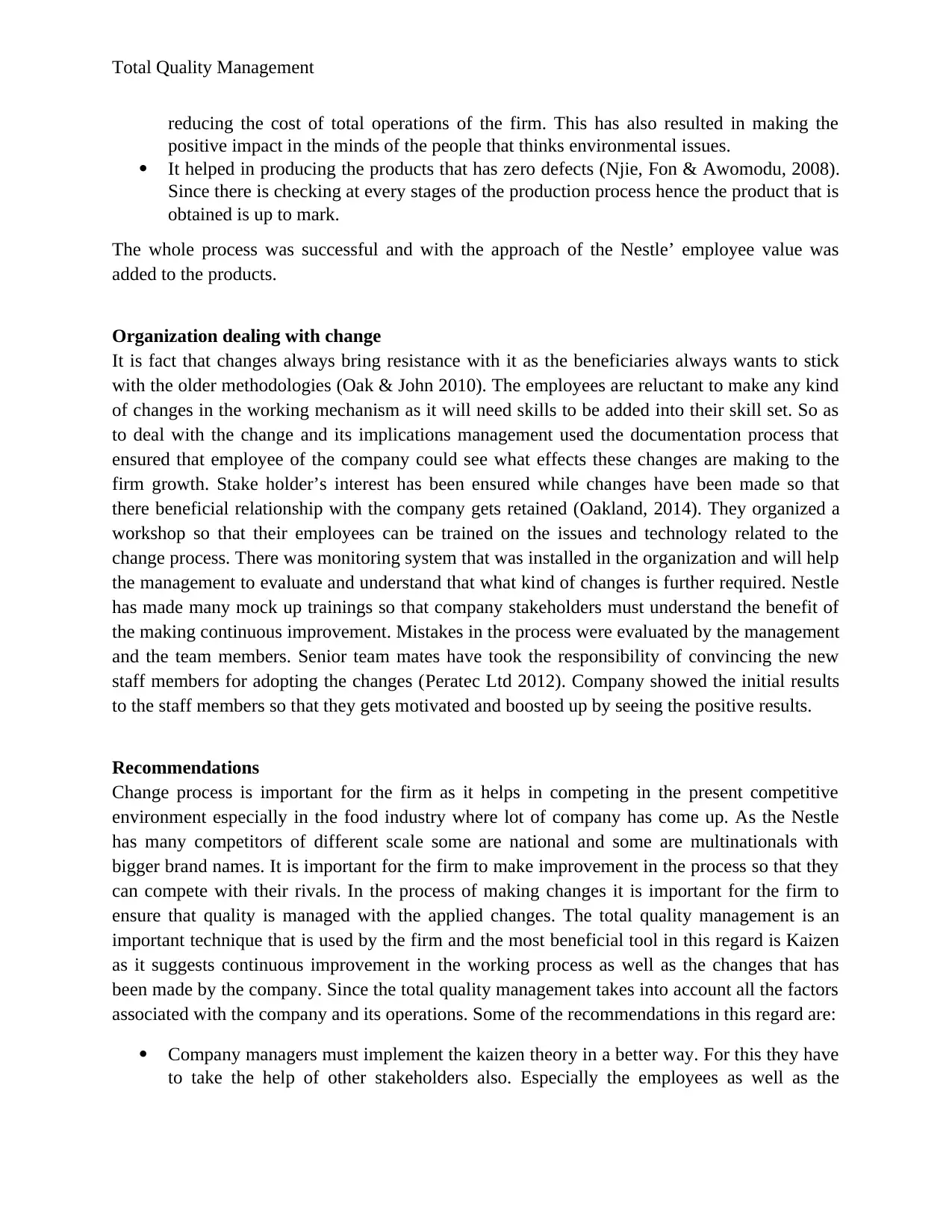
Total Quality Management
reducing the cost of total operations of the firm. This has also resulted in making the
positive impact in the minds of the people that thinks environmental issues.
It helped in producing the products that has zero defects (Njie, Fon & Awomodu, 2008).
Since there is checking at every stages of the production process hence the product that is
obtained is up to mark.
The whole process was successful and with the approach of the Nestle’ employee value was
added to the products.
Organization dealing with change
It is fact that changes always bring resistance with it as the beneficiaries always wants to stick
with the older methodologies (Oak & John 2010). The employees are reluctant to make any kind
of changes in the working mechanism as it will need skills to be added into their skill set. So as
to deal with the change and its implications management used the documentation process that
ensured that employee of the company could see what effects these changes are making to the
firm growth. Stake holder’s interest has been ensured while changes have been made so that
there beneficial relationship with the company gets retained (Oakland, 2014). They organized a
workshop so that their employees can be trained on the issues and technology related to the
change process. There was monitoring system that was installed in the organization and will help
the management to evaluate and understand that what kind of changes is further required. Nestle
has made many mock up trainings so that company stakeholders must understand the benefit of
the making continuous improvement. Mistakes in the process were evaluated by the management
and the team members. Senior team mates have took the responsibility of convincing the new
staff members for adopting the changes (Peratec Ltd 2012). Company showed the initial results
to the staff members so that they gets motivated and boosted up by seeing the positive results.
Recommendations
Change process is important for the firm as it helps in competing in the present competitive
environment especially in the food industry where lot of company has come up. As the Nestle
has many competitors of different scale some are national and some are multinationals with
bigger brand names. It is important for the firm to make improvement in the process so that they
can compete with their rivals. In the process of making changes it is important for the firm to
ensure that quality is managed with the applied changes. The total quality management is an
important technique that is used by the firm and the most beneficial tool in this regard is Kaizen
as it suggests continuous improvement in the working process as well as the changes that has
been made by the company. Since the total quality management takes into account all the factors
associated with the company and its operations. Some of the recommendations in this regard are:
Company managers must implement the kaizen theory in a better way. For this they have
to take the help of other stakeholders also. Especially the employees as well as the
reducing the cost of total operations of the firm. This has also resulted in making the
positive impact in the minds of the people that thinks environmental issues.
It helped in producing the products that has zero defects (Njie, Fon & Awomodu, 2008).
Since there is checking at every stages of the production process hence the product that is
obtained is up to mark.
The whole process was successful and with the approach of the Nestle’ employee value was
added to the products.
Organization dealing with change
It is fact that changes always bring resistance with it as the beneficiaries always wants to stick
with the older methodologies (Oak & John 2010). The employees are reluctant to make any kind
of changes in the working mechanism as it will need skills to be added into their skill set. So as
to deal with the change and its implications management used the documentation process that
ensured that employee of the company could see what effects these changes are making to the
firm growth. Stake holder’s interest has been ensured while changes have been made so that
there beneficial relationship with the company gets retained (Oakland, 2014). They organized a
workshop so that their employees can be trained on the issues and technology related to the
change process. There was monitoring system that was installed in the organization and will help
the management to evaluate and understand that what kind of changes is further required. Nestle
has made many mock up trainings so that company stakeholders must understand the benefit of
the making continuous improvement. Mistakes in the process were evaluated by the management
and the team members. Senior team mates have took the responsibility of convincing the new
staff members for adopting the changes (Peratec Ltd 2012). Company showed the initial results
to the staff members so that they gets motivated and boosted up by seeing the positive results.
Recommendations
Change process is important for the firm as it helps in competing in the present competitive
environment especially in the food industry where lot of company has come up. As the Nestle
has many competitors of different scale some are national and some are multinationals with
bigger brand names. It is important for the firm to make improvement in the process so that they
can compete with their rivals. In the process of making changes it is important for the firm to
ensure that quality is managed with the applied changes. The total quality management is an
important technique that is used by the firm and the most beneficial tool in this regard is Kaizen
as it suggests continuous improvement in the working process as well as the changes that has
been made by the company. Since the total quality management takes into account all the factors
associated with the company and its operations. Some of the recommendations in this regard are:
Company managers must implement the kaizen theory in a better way. For this they have
to take the help of other stakeholders also. Especially the employees as well as the
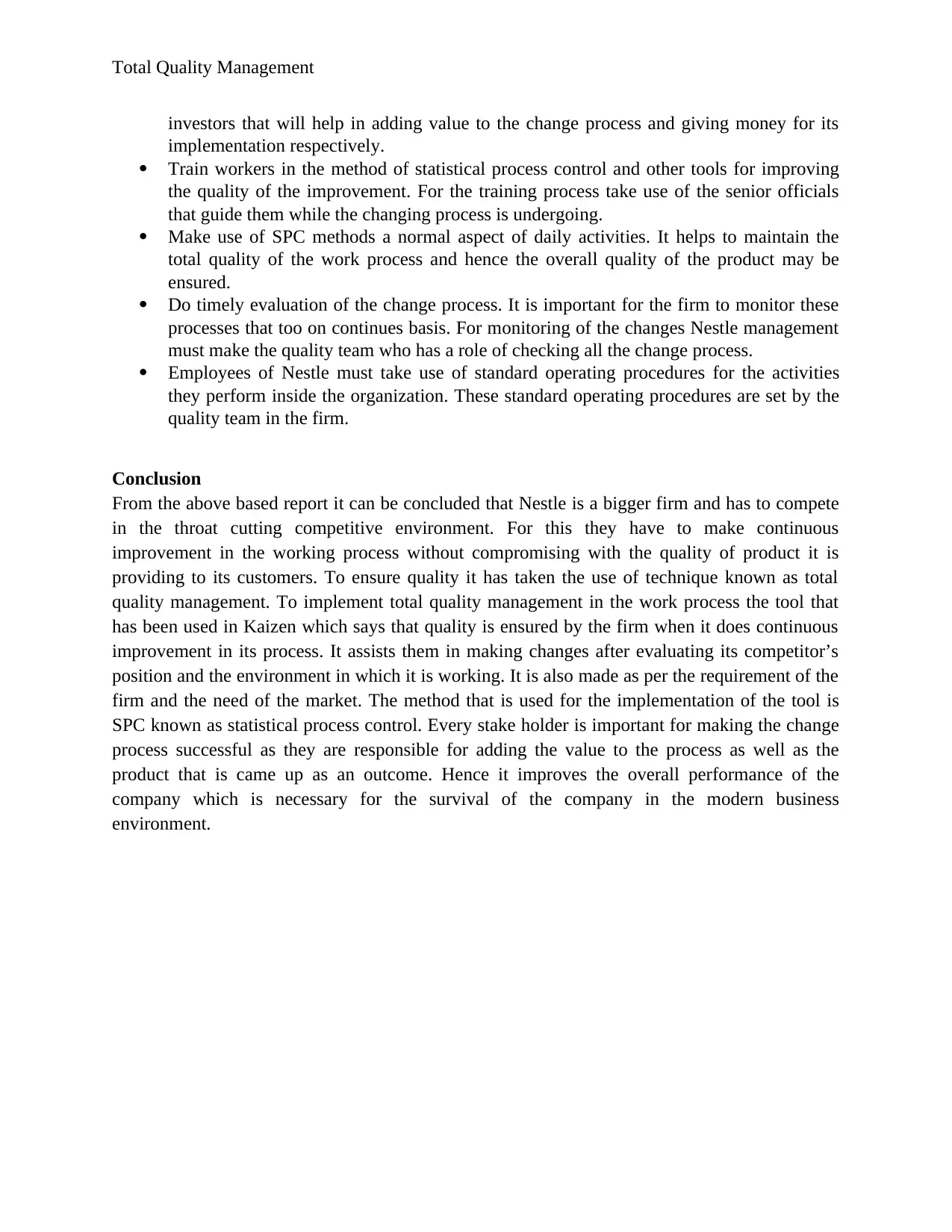
Total Quality Management
investors that will help in adding value to the change process and giving money for its
implementation respectively.
Train workers in the method of statistical process control and other tools for improving
the quality of the improvement. For the training process take use of the senior officials
that guide them while the changing process is undergoing.
Make use of SPC methods a normal aspect of daily activities. It helps to maintain the
total quality of the work process and hence the overall quality of the product may be
ensured.
Do timely evaluation of the change process. It is important for the firm to monitor these
processes that too on continues basis. For monitoring of the changes Nestle management
must make the quality team who has a role of checking all the change process.
Employees of Nestle must take use of standard operating procedures for the activities
they perform inside the organization. These standard operating procedures are set by the
quality team in the firm.
Conclusion
From the above based report it can be concluded that Nestle is a bigger firm and has to compete
in the throat cutting competitive environment. For this they have to make continuous
improvement in the working process without compromising with the quality of product it is
providing to its customers. To ensure quality it has taken the use of technique known as total
quality management. To implement total quality management in the work process the tool that
has been used in Kaizen which says that quality is ensured by the firm when it does continuous
improvement in its process. It assists them in making changes after evaluating its competitor’s
position and the environment in which it is working. It is also made as per the requirement of the
firm and the need of the market. The method that is used for the implementation of the tool is
SPC known as statistical process control. Every stake holder is important for making the change
process successful as they are responsible for adding the value to the process as well as the
product that is came up as an outcome. Hence it improves the overall performance of the
company which is necessary for the survival of the company in the modern business
environment.
investors that will help in adding value to the change process and giving money for its
implementation respectively.
Train workers in the method of statistical process control and other tools for improving
the quality of the improvement. For the training process take use of the senior officials
that guide them while the changing process is undergoing.
Make use of SPC methods a normal aspect of daily activities. It helps to maintain the
total quality of the work process and hence the overall quality of the product may be
ensured.
Do timely evaluation of the change process. It is important for the firm to monitor these
processes that too on continues basis. For monitoring of the changes Nestle management
must make the quality team who has a role of checking all the change process.
Employees of Nestle must take use of standard operating procedures for the activities
they perform inside the organization. These standard operating procedures are set by the
quality team in the firm.
Conclusion
From the above based report it can be concluded that Nestle is a bigger firm and has to compete
in the throat cutting competitive environment. For this they have to make continuous
improvement in the working process without compromising with the quality of product it is
providing to its customers. To ensure quality it has taken the use of technique known as total
quality management. To implement total quality management in the work process the tool that
has been used in Kaizen which says that quality is ensured by the firm when it does continuous
improvement in its process. It assists them in making changes after evaluating its competitor’s
position and the environment in which it is working. It is also made as per the requirement of the
firm and the need of the market. The method that is used for the implementation of the tool is
SPC known as statistical process control. Every stake holder is important for making the change
process successful as they are responsible for adding the value to the process as well as the
product that is came up as an outcome. Hence it improves the overall performance of the
company which is necessary for the survival of the company in the modern business
environment.
Paraphrase This Document
Need a fresh take? Get an instant paraphrase of this document with our AI Paraphraser
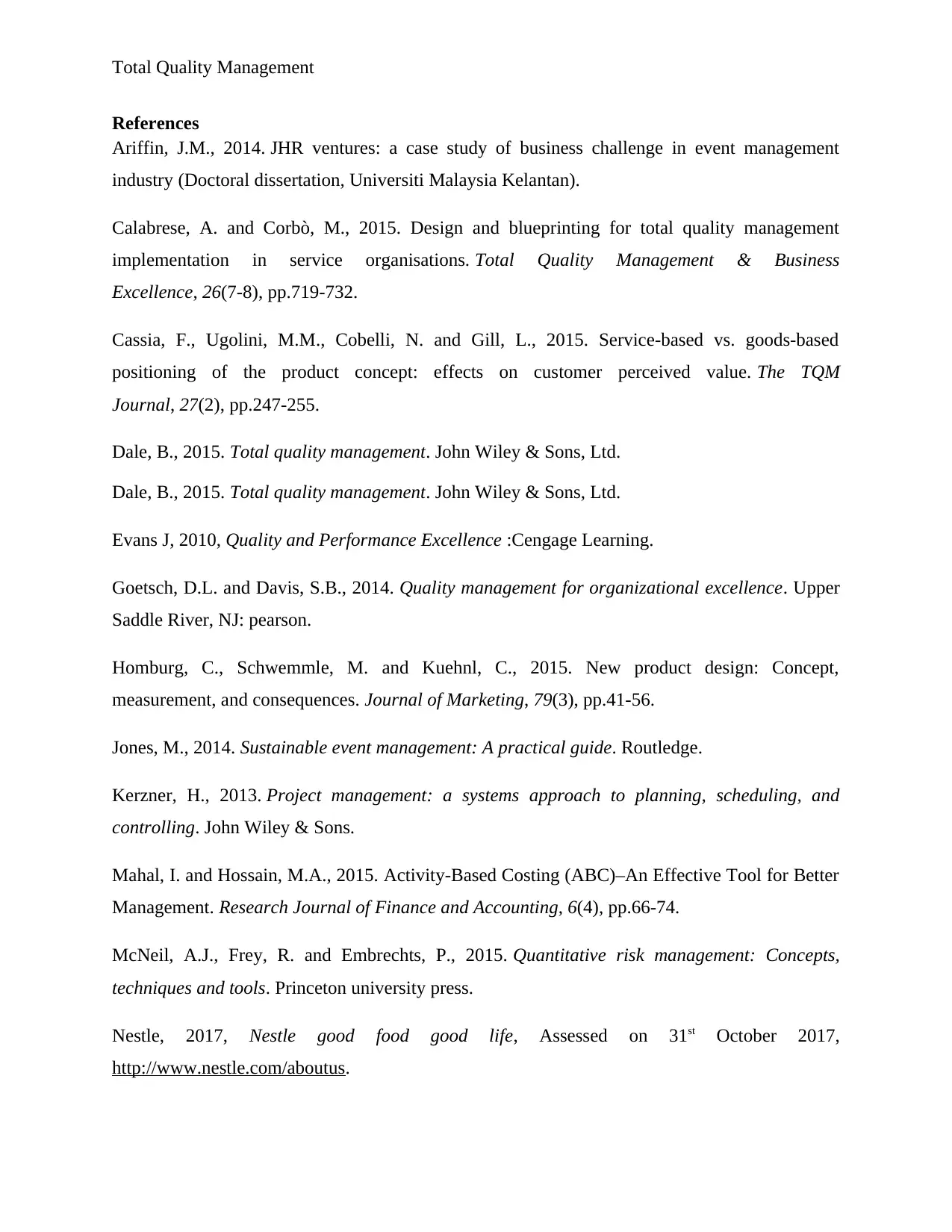
Total Quality Management
References
Ariffin, J.M., 2014. JHR ventures: a case study of business challenge in event management
industry (Doctoral dissertation, Universiti Malaysia Kelantan).
Calabrese, A. and Corbò, M., 2015. Design and blueprinting for total quality management
implementation in service organisations. Total Quality Management & Business
Excellence, 26(7-8), pp.719-732.
Cassia, F., Ugolini, M.M., Cobelli, N. and Gill, L., 2015. Service-based vs. goods-based
positioning of the product concept: effects on customer perceived value. The TQM
Journal, 27(2), pp.247-255.
Dale, B., 2015. Total quality management. John Wiley & Sons, Ltd.
Dale, B., 2015. Total quality management. John Wiley & Sons, Ltd.
Evans J, 2010, Quality and Performance Excellence :Cengage Learning.
Goetsch, D.L. and Davis, S.B., 2014. Quality management for organizational excellence. Upper
Saddle River, NJ: pearson.
Homburg, C., Schwemmle, M. and Kuehnl, C., 2015. New product design: Concept,
measurement, and consequences. Journal of Marketing, 79(3), pp.41-56.
Jones, M., 2014. Sustainable event management: A practical guide. Routledge.
Kerzner, H., 2013. Project management: a systems approach to planning, scheduling, and
controlling. John Wiley & Sons.
Mahal, I. and Hossain, M.A., 2015. Activity-Based Costing (ABC)–An Effective Tool for Better
Management. Research Journal of Finance and Accounting, 6(4), pp.66-74.
McNeil, A.J., Frey, R. and Embrechts, P., 2015. Quantitative risk management: Concepts,
techniques and tools. Princeton university press.
Nestle, 2017, Nestle good food good life, Assessed on 31st October 2017,
http://www.nestle.com/aboutus.
References
Ariffin, J.M., 2014. JHR ventures: a case study of business challenge in event management
industry (Doctoral dissertation, Universiti Malaysia Kelantan).
Calabrese, A. and Corbò, M., 2015. Design and blueprinting for total quality management
implementation in service organisations. Total Quality Management & Business
Excellence, 26(7-8), pp.719-732.
Cassia, F., Ugolini, M.M., Cobelli, N. and Gill, L., 2015. Service-based vs. goods-based
positioning of the product concept: effects on customer perceived value. The TQM
Journal, 27(2), pp.247-255.
Dale, B., 2015. Total quality management. John Wiley & Sons, Ltd.
Dale, B., 2015. Total quality management. John Wiley & Sons, Ltd.
Evans J, 2010, Quality and Performance Excellence :Cengage Learning.
Goetsch, D.L. and Davis, S.B., 2014. Quality management for organizational excellence. Upper
Saddle River, NJ: pearson.
Homburg, C., Schwemmle, M. and Kuehnl, C., 2015. New product design: Concept,
measurement, and consequences. Journal of Marketing, 79(3), pp.41-56.
Jones, M., 2014. Sustainable event management: A practical guide. Routledge.
Kerzner, H., 2013. Project management: a systems approach to planning, scheduling, and
controlling. John Wiley & Sons.
Mahal, I. and Hossain, M.A., 2015. Activity-Based Costing (ABC)–An Effective Tool for Better
Management. Research Journal of Finance and Accounting, 6(4), pp.66-74.
McNeil, A.J., Frey, R. and Embrechts, P., 2015. Quantitative risk management: Concepts,
techniques and tools. Princeton university press.
Nestle, 2017, Nestle good food good life, Assessed on 31st October 2017,
http://www.nestle.com/aboutus.
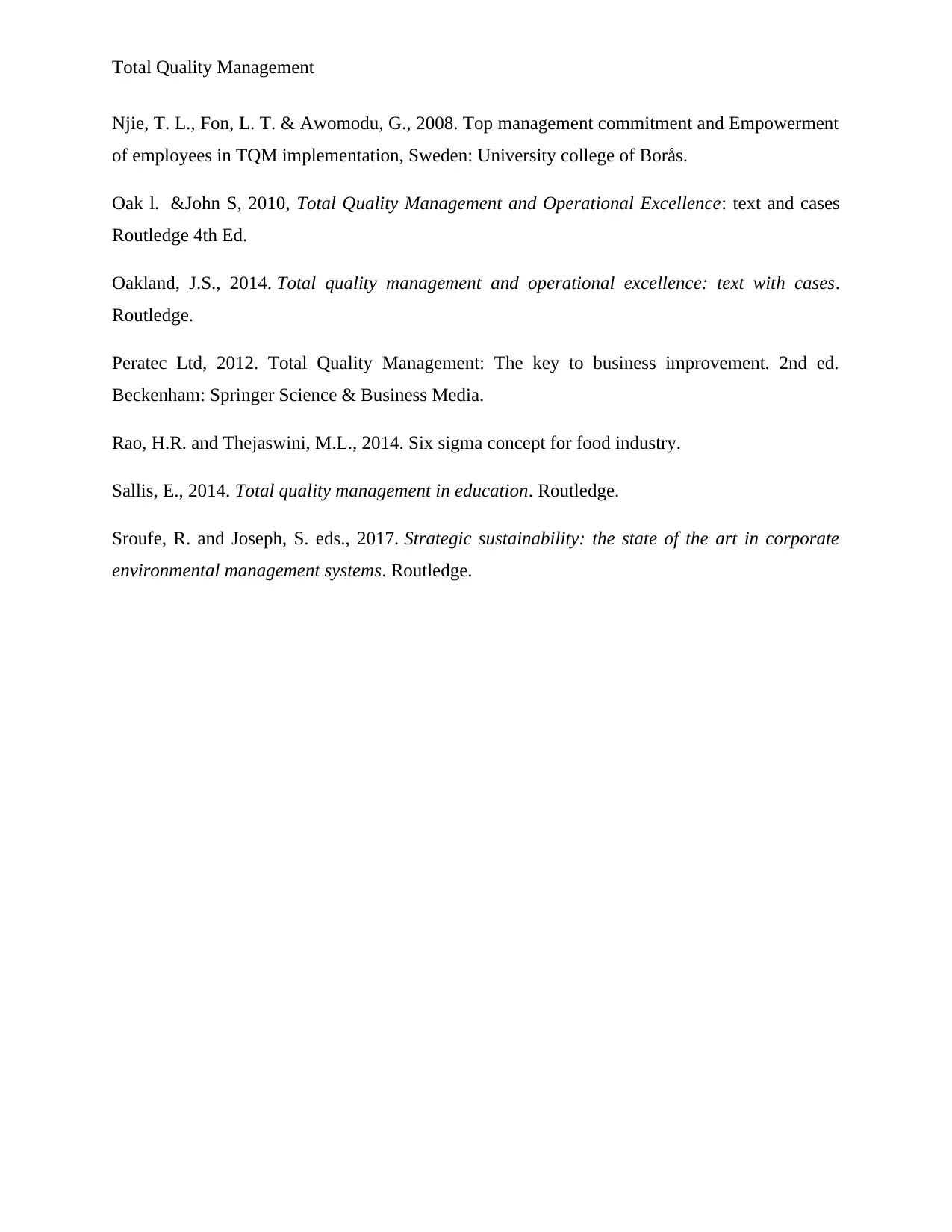
Total Quality Management
Njie, T. L., Fon, L. T. & Awomodu, G., 2008. Top management commitment and Empowerment
of employees in TQM implementation, Sweden: University college of Borås.
Oak l. &John S, 2010, Total Quality Management and Operational Excellence: text and cases
Routledge 4th Ed.
Oakland, J.S., 2014. Total quality management and operational excellence: text with cases.
Routledge.
Peratec Ltd, 2012. Total Quality Management: The key to business improvement. 2nd ed.
Beckenham: Springer Science & Business Media.
Rao, H.R. and Thejaswini, M.L., 2014. Six sigma concept for food industry.
Sallis, E., 2014. Total quality management in education. Routledge.
Sroufe, R. and Joseph, S. eds., 2017. Strategic sustainability: the state of the art in corporate
environmental management systems. Routledge.
Njie, T. L., Fon, L. T. & Awomodu, G., 2008. Top management commitment and Empowerment
of employees in TQM implementation, Sweden: University college of Borås.
Oak l. &John S, 2010, Total Quality Management and Operational Excellence: text and cases
Routledge 4th Ed.
Oakland, J.S., 2014. Total quality management and operational excellence: text with cases.
Routledge.
Peratec Ltd, 2012. Total Quality Management: The key to business improvement. 2nd ed.
Beckenham: Springer Science & Business Media.
Rao, H.R. and Thejaswini, M.L., 2014. Six sigma concept for food industry.
Sallis, E., 2014. Total quality management in education. Routledge.
Sroufe, R. and Joseph, S. eds., 2017. Strategic sustainability: the state of the art in corporate
environmental management systems. Routledge.
1 out of 9
Related Documents

Your All-in-One AI-Powered Toolkit for Academic Success.
+13062052269
info@desklib.com
Available 24*7 on WhatsApp / Email
Unlock your academic potential
© 2024 | Zucol Services PVT LTD | All rights reserved.