Leadership & Operations Analysis: A Toyota Case Study - BTEC
VerifiedAdded on 2023/04/22
|15
|5047
|317
Report
AI Summary
This report delves into the management and operations of Toyota Motor Company, examining the roles of leaders and managers, supported by leadership theories. It differentiates between management and leadership, analyzing their diverse roles within Toyota, and supported by relevant concepts and theories. The report evaluates the strengths and weaknesses of different leadership and management approaches applied at Toyota, including situational leadership, management by objectives, and chaos theory. It also defines key operational functions such as Total Quality Management (TQM) and Continuous Improvement (Kaizen), highlighting the roles of managers in these areas. The report concludes that operational management and leadership theories, when effectively adopted, contribute to Toyota's better performance and profitability and identifies external factors impacting operational management and decisions.
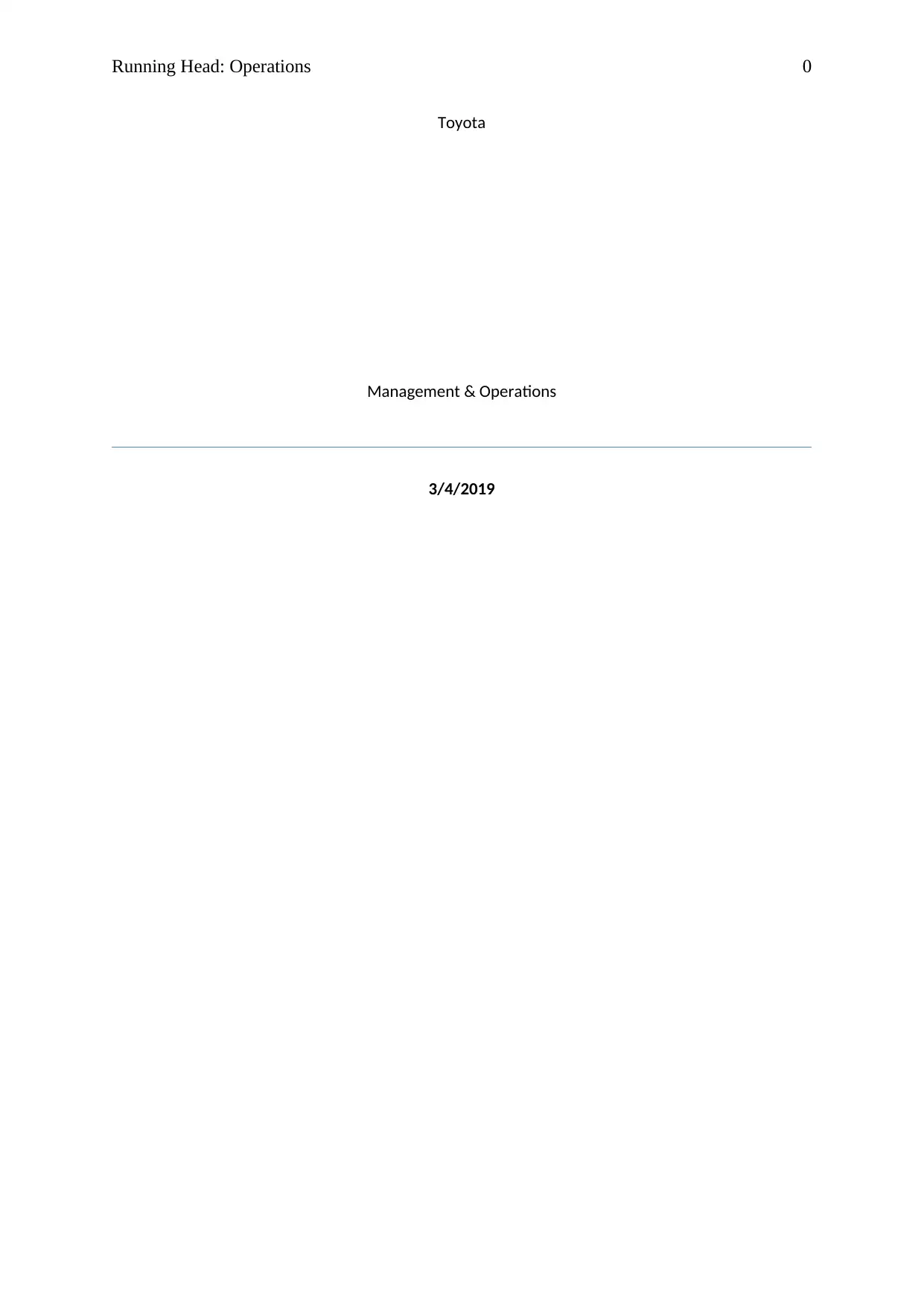
Running Head: Operations 0
Toyota
Management & Operations
3/4/2019
Toyota
Management & Operations
3/4/2019
Secure Best Marks with AI Grader
Need help grading? Try our AI Grader for instant feedback on your assignments.
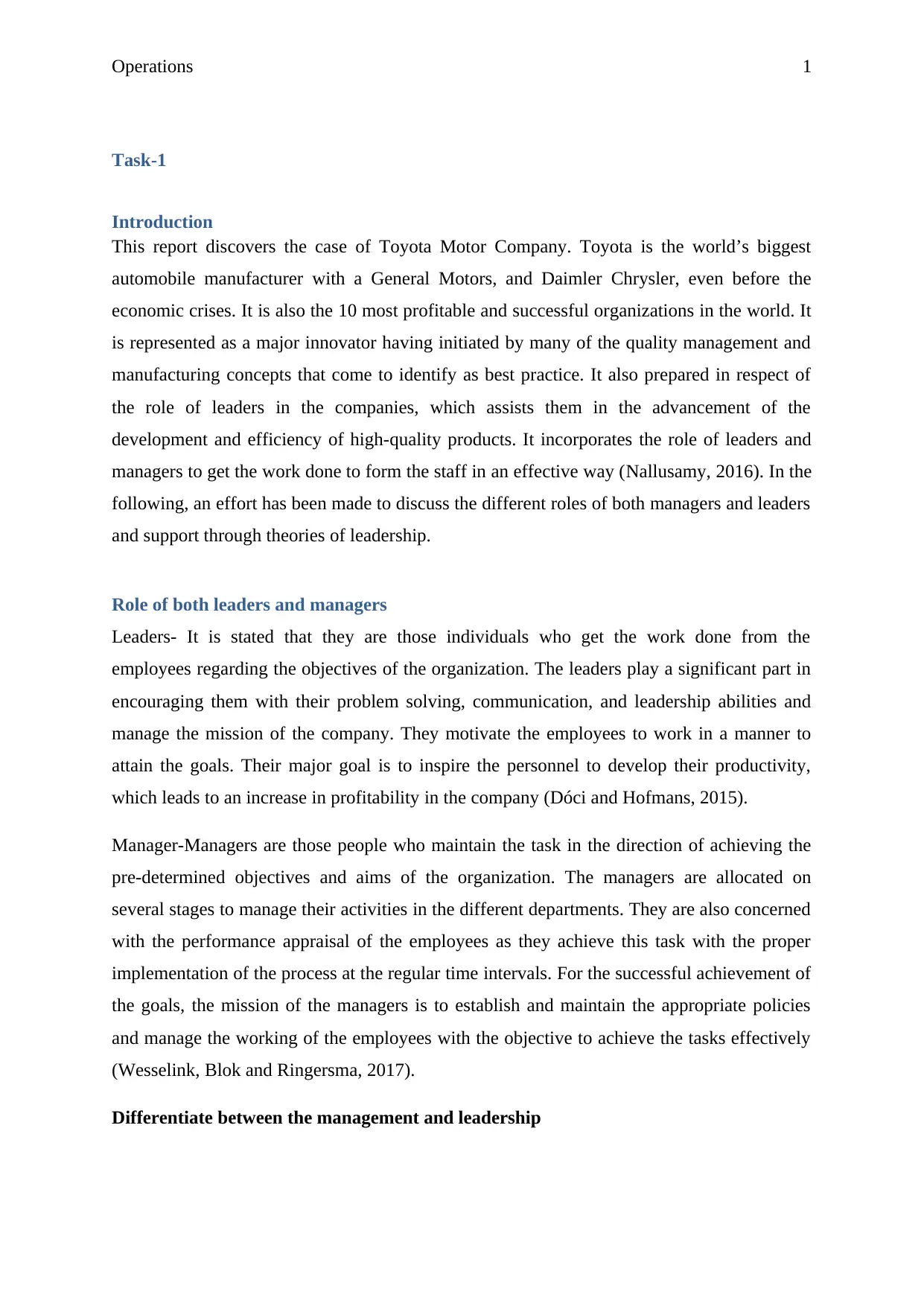
Operations 1
Task-1
Introduction
This report discovers the case of Toyota Motor Company. Toyota is the world’s biggest
automobile manufacturer with a General Motors, and Daimler Chrysler, even before the
economic crises. It is also the 10 most profitable and successful organizations in the world. It
is represented as a major innovator having initiated by many of the quality management and
manufacturing concepts that come to identify as best practice. It also prepared in respect of
the role of leaders in the companies, which assists them in the advancement of the
development and efficiency of high-quality products. It incorporates the role of leaders and
managers to get the work done to form the staff in an effective way (Nallusamy, 2016). In the
following, an effort has been made to discuss the different roles of both managers and leaders
and support through theories of leadership.
Role of both leaders and managers
Leaders- It is stated that they are those individuals who get the work done from the
employees regarding the objectives of the organization. The leaders play a significant part in
encouraging them with their problem solving, communication, and leadership abilities and
manage the mission of the company. They motivate the employees to work in a manner to
attain the goals. Their major goal is to inspire the personnel to develop their productivity,
which leads to an increase in profitability in the company (Dóci and Hofmans, 2015).
Manager-Managers are those people who maintain the task in the direction of achieving the
pre-determined objectives and aims of the organization. The managers are allocated on
several stages to manage their activities in the different departments. They are also concerned
with the performance appraisal of the employees as they achieve this task with the proper
implementation of the process at the regular time intervals. For the successful achievement of
the goals, the mission of the managers is to establish and maintain the appropriate policies
and manage the working of the employees with the objective to achieve the tasks effectively
(Wesselink, Blok and Ringersma, 2017).
Differentiate between the management and leadership
Task-1
Introduction
This report discovers the case of Toyota Motor Company. Toyota is the world’s biggest
automobile manufacturer with a General Motors, and Daimler Chrysler, even before the
economic crises. It is also the 10 most profitable and successful organizations in the world. It
is represented as a major innovator having initiated by many of the quality management and
manufacturing concepts that come to identify as best practice. It also prepared in respect of
the role of leaders in the companies, which assists them in the advancement of the
development and efficiency of high-quality products. It incorporates the role of leaders and
managers to get the work done to form the staff in an effective way (Nallusamy, 2016). In the
following, an effort has been made to discuss the different roles of both managers and leaders
and support through theories of leadership.
Role of both leaders and managers
Leaders- It is stated that they are those individuals who get the work done from the
employees regarding the objectives of the organization. The leaders play a significant part in
encouraging them with their problem solving, communication, and leadership abilities and
manage the mission of the company. They motivate the employees to work in a manner to
attain the goals. Their major goal is to inspire the personnel to develop their productivity,
which leads to an increase in profitability in the company (Dóci and Hofmans, 2015).
Manager-Managers are those people who maintain the task in the direction of achieving the
pre-determined objectives and aims of the organization. The managers are allocated on
several stages to manage their activities in the different departments. They are also concerned
with the performance appraisal of the employees as they achieve this task with the proper
implementation of the process at the regular time intervals. For the successful achievement of
the goals, the mission of the managers is to establish and maintain the appropriate policies
and manage the working of the employees with the objective to achieve the tasks effectively
(Wesselink, Blok and Ringersma, 2017).
Differentiate between the management and leadership
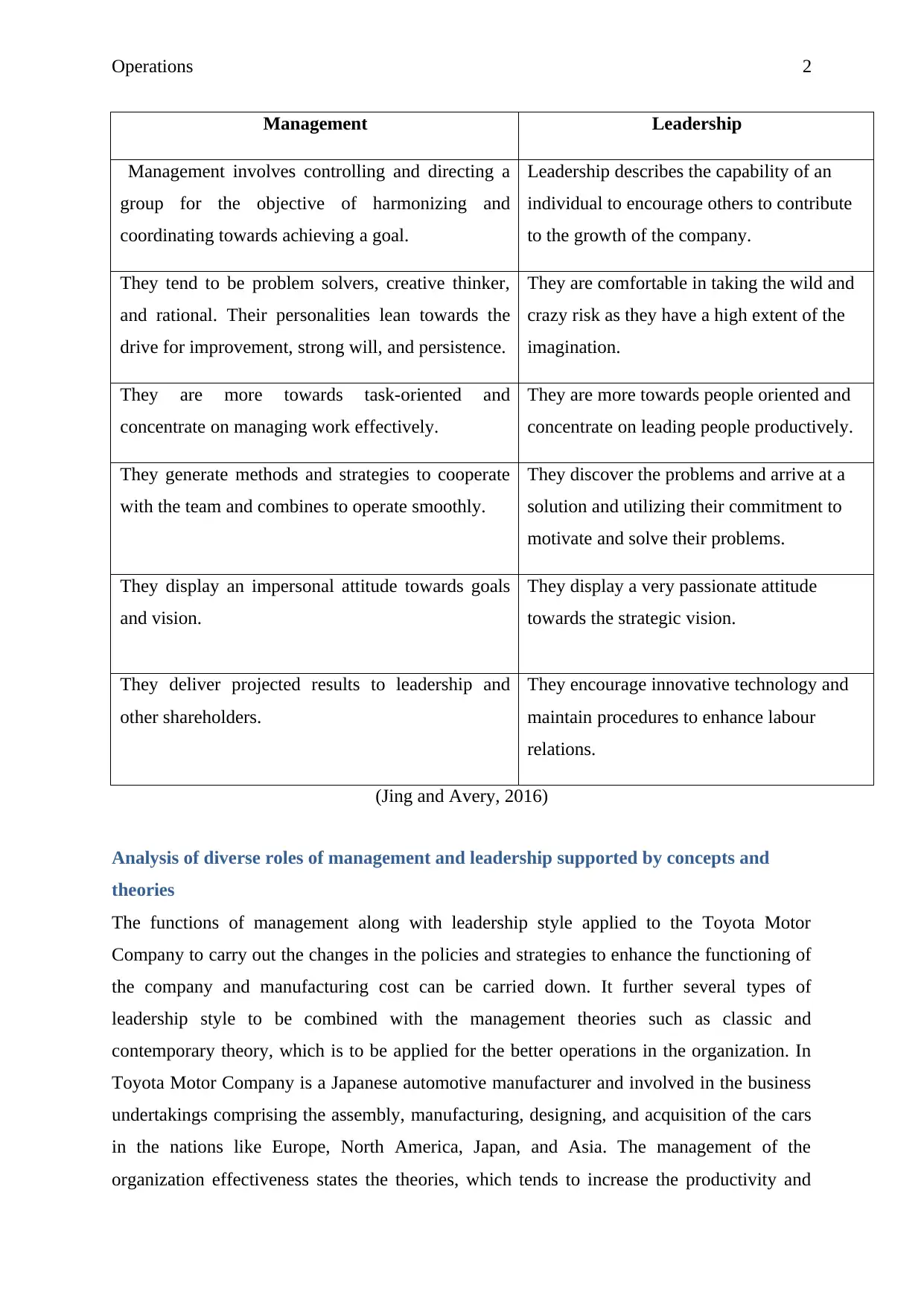
Operations 2
Management Leadership
Management involves controlling and directing a
group for the objective of harmonizing and
coordinating towards achieving a goal.
Leadership describes the capability of an
individual to encourage others to contribute
to the growth of the company.
They tend to be problem solvers, creative thinker,
and rational. Their personalities lean towards the
drive for improvement, strong will, and persistence.
They are comfortable in taking the wild and
crazy risk as they have a high extent of the
imagination.
They are more towards task-oriented and
concentrate on managing work effectively.
They are more towards people oriented and
concentrate on leading people productively.
They generate methods and strategies to cooperate
with the team and combines to operate smoothly.
They discover the problems and arrive at a
solution and utilizing their commitment to
motivate and solve their problems.
They display an impersonal attitude towards goals
and vision.
They display a very passionate attitude
towards the strategic vision.
They deliver projected results to leadership and
other shareholders.
They encourage innovative technology and
maintain procedures to enhance labour
relations.
(Jing and Avery, 2016)
Analysis of diverse roles of management and leadership supported by concepts and
theories
The functions of management along with leadership style applied to the Toyota Motor
Company to carry out the changes in the policies and strategies to enhance the functioning of
the company and manufacturing cost can be carried down. It further several types of
leadership style to be combined with the management theories such as classic and
contemporary theory, which is to be applied for the better operations in the organization. In
Toyota Motor Company is a Japanese automotive manufacturer and involved in the business
undertakings comprising the assembly, manufacturing, designing, and acquisition of the cars
in the nations like Europe, North America, Japan, and Asia. The management of the
organization effectiveness states the theories, which tends to increase the productivity and
Management Leadership
Management involves controlling and directing a
group for the objective of harmonizing and
coordinating towards achieving a goal.
Leadership describes the capability of an
individual to encourage others to contribute
to the growth of the company.
They tend to be problem solvers, creative thinker,
and rational. Their personalities lean towards the
drive for improvement, strong will, and persistence.
They are comfortable in taking the wild and
crazy risk as they have a high extent of the
imagination.
They are more towards task-oriented and
concentrate on managing work effectively.
They are more towards people oriented and
concentrate on leading people productively.
They generate methods and strategies to cooperate
with the team and combines to operate smoothly.
They discover the problems and arrive at a
solution and utilizing their commitment to
motivate and solve their problems.
They display an impersonal attitude towards goals
and vision.
They display a very passionate attitude
towards the strategic vision.
They deliver projected results to leadership and
other shareholders.
They encourage innovative technology and
maintain procedures to enhance labour
relations.
(Jing and Avery, 2016)
Analysis of diverse roles of management and leadership supported by concepts and
theories
The functions of management along with leadership style applied to the Toyota Motor
Company to carry out the changes in the policies and strategies to enhance the functioning of
the company and manufacturing cost can be carried down. It further several types of
leadership style to be combined with the management theories such as classic and
contemporary theory, which is to be applied for the better operations in the organization. In
Toyota Motor Company is a Japanese automotive manufacturer and involved in the business
undertakings comprising the assembly, manufacturing, designing, and acquisition of the cars
in the nations like Europe, North America, Japan, and Asia. The management of the
organization effectiveness states the theories, which tends to increase the productivity and
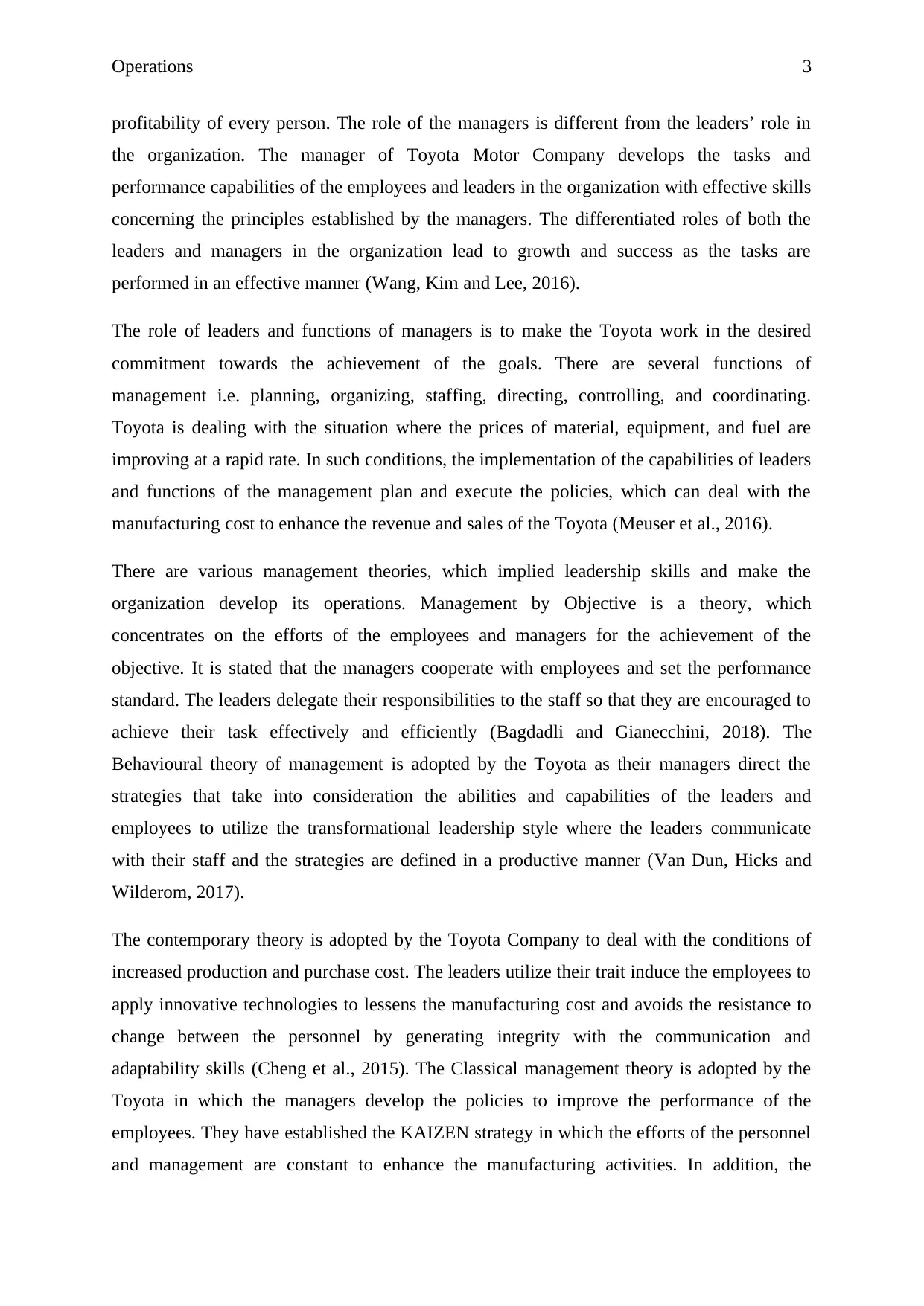
Operations 3
profitability of every person. The role of the managers is different from the leaders’ role in
the organization. The manager of Toyota Motor Company develops the tasks and
performance capabilities of the employees and leaders in the organization with effective skills
concerning the principles established by the managers. The differentiated roles of both the
leaders and managers in the organization lead to growth and success as the tasks are
performed in an effective manner (Wang, Kim and Lee, 2016).
The role of leaders and functions of managers is to make the Toyota work in the desired
commitment towards the achievement of the goals. There are several functions of
management i.e. planning, organizing, staffing, directing, controlling, and coordinating.
Toyota is dealing with the situation where the prices of material, equipment, and fuel are
improving at a rapid rate. In such conditions, the implementation of the capabilities of leaders
and functions of the management plan and execute the policies, which can deal with the
manufacturing cost to enhance the revenue and sales of the Toyota (Meuser et al., 2016).
There are various management theories, which implied leadership skills and make the
organization develop its operations. Management by Objective is a theory, which
concentrates on the efforts of the employees and managers for the achievement of the
objective. It is stated that the managers cooperate with employees and set the performance
standard. The leaders delegate their responsibilities to the staff so that they are encouraged to
achieve their task effectively and efficiently (Bagdadli and Gianecchini, 2018). The
Behavioural theory of management is adopted by the Toyota as their managers direct the
strategies that take into consideration the abilities and capabilities of the leaders and
employees to utilize the transformational leadership style where the leaders communicate
with their staff and the strategies are defined in a productive manner (Van Dun, Hicks and
Wilderom, 2017).
The contemporary theory is adopted by the Toyota Company to deal with the conditions of
increased production and purchase cost. The leaders utilize their trait induce the employees to
apply innovative technologies to lessens the manufacturing cost and avoids the resistance to
change between the personnel by generating integrity with the communication and
adaptability skills (Cheng et al., 2015). The Classical management theory is adopted by the
Toyota in which the managers develop the policies to improve the performance of the
employees. They have established the KAIZEN strategy in which the efforts of the personnel
and management are constant to enhance the manufacturing activities. In addition, the
profitability of every person. The role of the managers is different from the leaders’ role in
the organization. The manager of Toyota Motor Company develops the tasks and
performance capabilities of the employees and leaders in the organization with effective skills
concerning the principles established by the managers. The differentiated roles of both the
leaders and managers in the organization lead to growth and success as the tasks are
performed in an effective manner (Wang, Kim and Lee, 2016).
The role of leaders and functions of managers is to make the Toyota work in the desired
commitment towards the achievement of the goals. There are several functions of
management i.e. planning, organizing, staffing, directing, controlling, and coordinating.
Toyota is dealing with the situation where the prices of material, equipment, and fuel are
improving at a rapid rate. In such conditions, the implementation of the capabilities of leaders
and functions of the management plan and execute the policies, which can deal with the
manufacturing cost to enhance the revenue and sales of the Toyota (Meuser et al., 2016).
There are various management theories, which implied leadership skills and make the
organization develop its operations. Management by Objective is a theory, which
concentrates on the efforts of the employees and managers for the achievement of the
objective. It is stated that the managers cooperate with employees and set the performance
standard. The leaders delegate their responsibilities to the staff so that they are encouraged to
achieve their task effectively and efficiently (Bagdadli and Gianecchini, 2018). The
Behavioural theory of management is adopted by the Toyota as their managers direct the
strategies that take into consideration the abilities and capabilities of the leaders and
employees to utilize the transformational leadership style where the leaders communicate
with their staff and the strategies are defined in a productive manner (Van Dun, Hicks and
Wilderom, 2017).
The contemporary theory is adopted by the Toyota Company to deal with the conditions of
increased production and purchase cost. The leaders utilize their trait induce the employees to
apply innovative technologies to lessens the manufacturing cost and avoids the resistance to
change between the personnel by generating integrity with the communication and
adaptability skills (Cheng et al., 2015). The Classical management theory is adopted by the
Toyota in which the managers develop the policies to improve the performance of the
employees. They have established the KAIZEN strategy in which the efforts of the personnel
and management are constant to enhance the manufacturing activities. In addition, the
Secure Best Marks with AI Grader
Need help grading? Try our AI Grader for instant feedback on your assignments.
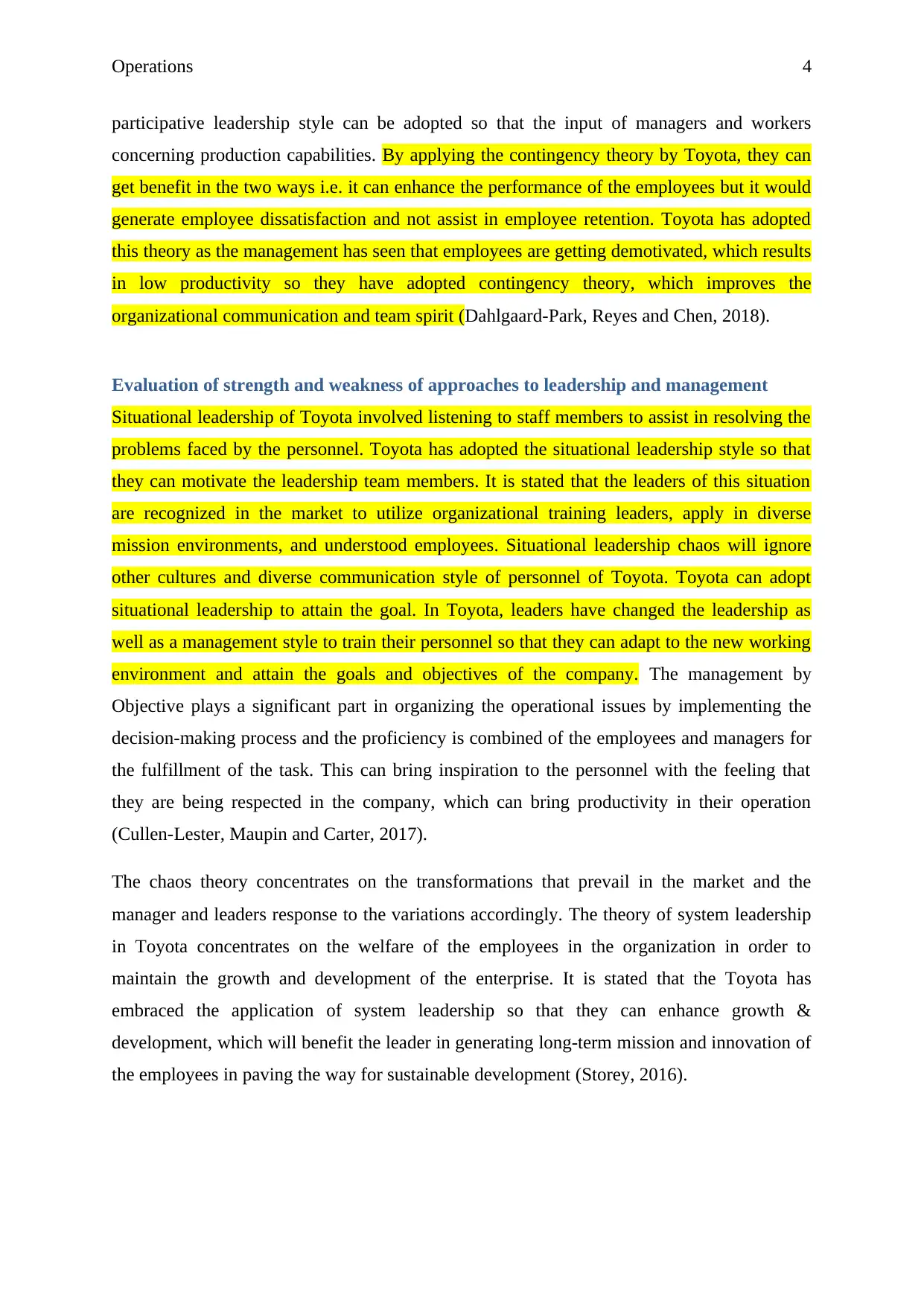
Operations 4
participative leadership style can be adopted so that the input of managers and workers
concerning production capabilities. By applying the contingency theory by Toyota, they can
get benefit in the two ways i.e. it can enhance the performance of the employees but it would
generate employee dissatisfaction and not assist in employee retention. Toyota has adopted
this theory as the management has seen that employees are getting demotivated, which results
in low productivity so they have adopted contingency theory, which improves the
organizational communication and team spirit (Dahlgaard-Park, Reyes and Chen, 2018).
Evaluation of strength and weakness of approaches to leadership and management
Situational leadership of Toyota involved listening to staff members to assist in resolving the
problems faced by the personnel. Toyota has adopted the situational leadership style so that
they can motivate the leadership team members. It is stated that the leaders of this situation
are recognized in the market to utilize organizational training leaders, apply in diverse
mission environments, and understood employees. Situational leadership chaos will ignore
other cultures and diverse communication style of personnel of Toyota. Toyota can adopt
situational leadership to attain the goal. In Toyota, leaders have changed the leadership as
well as a management style to train their personnel so that they can adapt to the new working
environment and attain the goals and objectives of the company. The management by
Objective plays a significant part in organizing the operational issues by implementing the
decision-making process and the proficiency is combined of the employees and managers for
the fulfillment of the task. This can bring inspiration to the personnel with the feeling that
they are being respected in the company, which can bring productivity in their operation
(Cullen-Lester, Maupin and Carter, 2017).
The chaos theory concentrates on the transformations that prevail in the market and the
manager and leaders response to the variations accordingly. The theory of system leadership
in Toyota concentrates on the welfare of the employees in the organization in order to
maintain the growth and development of the enterprise. It is stated that the Toyota has
embraced the application of system leadership so that they can enhance growth &
development, which will benefit the leader in generating long-term mission and innovation of
the employees in paving the way for sustainable development (Storey, 2016).
participative leadership style can be adopted so that the input of managers and workers
concerning production capabilities. By applying the contingency theory by Toyota, they can
get benefit in the two ways i.e. it can enhance the performance of the employees but it would
generate employee dissatisfaction and not assist in employee retention. Toyota has adopted
this theory as the management has seen that employees are getting demotivated, which results
in low productivity so they have adopted contingency theory, which improves the
organizational communication and team spirit (Dahlgaard-Park, Reyes and Chen, 2018).
Evaluation of strength and weakness of approaches to leadership and management
Situational leadership of Toyota involved listening to staff members to assist in resolving the
problems faced by the personnel. Toyota has adopted the situational leadership style so that
they can motivate the leadership team members. It is stated that the leaders of this situation
are recognized in the market to utilize organizational training leaders, apply in diverse
mission environments, and understood employees. Situational leadership chaos will ignore
other cultures and diverse communication style of personnel of Toyota. Toyota can adopt
situational leadership to attain the goal. In Toyota, leaders have changed the leadership as
well as a management style to train their personnel so that they can adapt to the new working
environment and attain the goals and objectives of the company. The management by
Objective plays a significant part in organizing the operational issues by implementing the
decision-making process and the proficiency is combined of the employees and managers for
the fulfillment of the task. This can bring inspiration to the personnel with the feeling that
they are being respected in the company, which can bring productivity in their operation
(Cullen-Lester, Maupin and Carter, 2017).
The chaos theory concentrates on the transformations that prevail in the market and the
manager and leaders response to the variations accordingly. The theory of system leadership
in Toyota concentrates on the welfare of the employees in the organization in order to
maintain the growth and development of the enterprise. It is stated that the Toyota has
embraced the application of system leadership so that they can enhance growth &
development, which will benefit the leader in generating long-term mission and innovation of
the employees in paving the way for sustainable development (Storey, 2016).
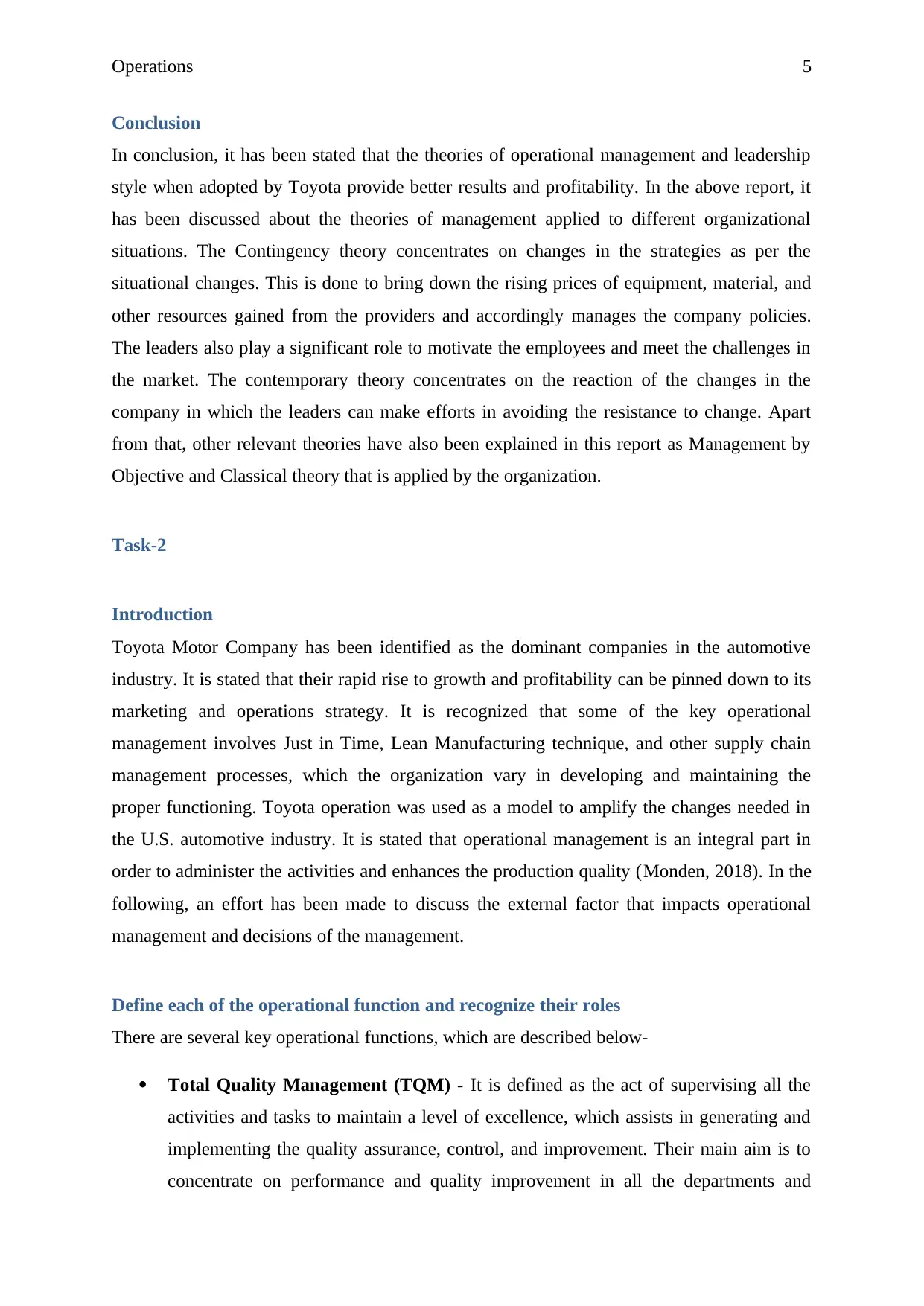
Operations 5
Conclusion
In conclusion, it has been stated that the theories of operational management and leadership
style when adopted by Toyota provide better results and profitability. In the above report, it
has been discussed about the theories of management applied to different organizational
situations. The Contingency theory concentrates on changes in the strategies as per the
situational changes. This is done to bring down the rising prices of equipment, material, and
other resources gained from the providers and accordingly manages the company policies.
The leaders also play a significant role to motivate the employees and meet the challenges in
the market. The contemporary theory concentrates on the reaction of the changes in the
company in which the leaders can make efforts in avoiding the resistance to change. Apart
from that, other relevant theories have also been explained in this report as Management by
Objective and Classical theory that is applied by the organization.
Task-2
Introduction
Toyota Motor Company has been identified as the dominant companies in the automotive
industry. It is stated that their rapid rise to growth and profitability can be pinned down to its
marketing and operations strategy. It is recognized that some of the key operational
management involves Just in Time, Lean Manufacturing technique, and other supply chain
management processes, which the organization vary in developing and maintaining the
proper functioning. Toyota operation was used as a model to amplify the changes needed in
the U.S. automotive industry. It is stated that operational management is an integral part in
order to administer the activities and enhances the production quality (Monden, 2018). In the
following, an effort has been made to discuss the external factor that impacts operational
management and decisions of the management.
Define each of the operational function and recognize their roles
There are several key operational functions, which are described below-
Total Quality Management (TQM) - It is defined as the act of supervising all the
activities and tasks to maintain a level of excellence, which assists in generating and
implementing the quality assurance, control, and improvement. Their main aim is to
concentrate on performance and quality improvement in all the departments and
Conclusion
In conclusion, it has been stated that the theories of operational management and leadership
style when adopted by Toyota provide better results and profitability. In the above report, it
has been discussed about the theories of management applied to different organizational
situations. The Contingency theory concentrates on changes in the strategies as per the
situational changes. This is done to bring down the rising prices of equipment, material, and
other resources gained from the providers and accordingly manages the company policies.
The leaders also play a significant role to motivate the employees and meet the challenges in
the market. The contemporary theory concentrates on the reaction of the changes in the
company in which the leaders can make efforts in avoiding the resistance to change. Apart
from that, other relevant theories have also been explained in this report as Management by
Objective and Classical theory that is applied by the organization.
Task-2
Introduction
Toyota Motor Company has been identified as the dominant companies in the automotive
industry. It is stated that their rapid rise to growth and profitability can be pinned down to its
marketing and operations strategy. It is recognized that some of the key operational
management involves Just in Time, Lean Manufacturing technique, and other supply chain
management processes, which the organization vary in developing and maintaining the
proper functioning. Toyota operation was used as a model to amplify the changes needed in
the U.S. automotive industry. It is stated that operational management is an integral part in
order to administer the activities and enhances the production quality (Monden, 2018). In the
following, an effort has been made to discuss the external factor that impacts operational
management and decisions of the management.
Define each of the operational function and recognize their roles
There are several key operational functions, which are described below-
Total Quality Management (TQM) - It is defined as the act of supervising all the
activities and tasks to maintain a level of excellence, which assists in generating and
implementing the quality assurance, control, and improvement. Their main aim is to
concentrate on performance and quality improvement in all the departments and
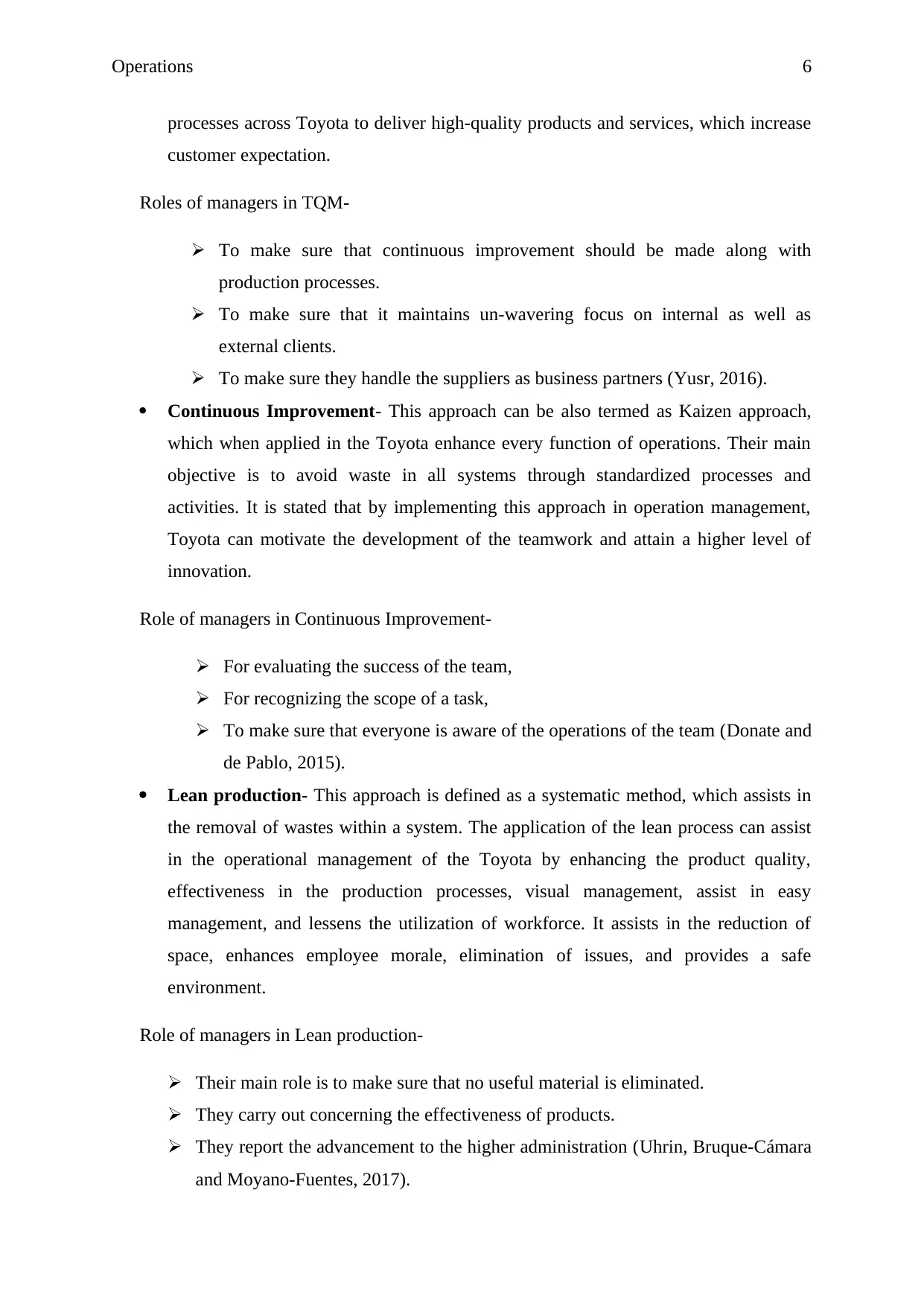
Operations 6
processes across Toyota to deliver high-quality products and services, which increase
customer expectation.
Roles of managers in TQM-
To make sure that continuous improvement should be made along with
production processes.
To make sure that it maintains un-wavering focus on internal as well as
external clients.
To make sure they handle the suppliers as business partners (Yusr, 2016).
Continuous Improvement- This approach can be also termed as Kaizen approach,
which when applied in the Toyota enhance every function of operations. Their main
objective is to avoid waste in all systems through standardized processes and
activities. It is stated that by implementing this approach in operation management,
Toyota can motivate the development of the teamwork and attain a higher level of
innovation.
Role of managers in Continuous Improvement-
For evaluating the success of the team,
For recognizing the scope of a task,
To make sure that everyone is aware of the operations of the team (Donate and
de Pablo, 2015).
Lean production- This approach is defined as a systematic method, which assists in
the removal of wastes within a system. The application of the lean process can assist
in the operational management of the Toyota by enhancing the product quality,
effectiveness in the production processes, visual management, assist in easy
management, and lessens the utilization of workforce. It assists in the reduction of
space, enhances employee morale, elimination of issues, and provides a safe
environment.
Role of managers in Lean production-
Their main role is to make sure that no useful material is eliminated.
They carry out concerning the effectiveness of products.
They report the advancement to the higher administration (Uhrin, Bruque-Cámara
and Moyano-Fuentes, 2017).
processes across Toyota to deliver high-quality products and services, which increase
customer expectation.
Roles of managers in TQM-
To make sure that continuous improvement should be made along with
production processes.
To make sure that it maintains un-wavering focus on internal as well as
external clients.
To make sure they handle the suppliers as business partners (Yusr, 2016).
Continuous Improvement- This approach can be also termed as Kaizen approach,
which when applied in the Toyota enhance every function of operations. Their main
objective is to avoid waste in all systems through standardized processes and
activities. It is stated that by implementing this approach in operation management,
Toyota can motivate the development of the teamwork and attain a higher level of
innovation.
Role of managers in Continuous Improvement-
For evaluating the success of the team,
For recognizing the scope of a task,
To make sure that everyone is aware of the operations of the team (Donate and
de Pablo, 2015).
Lean production- This approach is defined as a systematic method, which assists in
the removal of wastes within a system. The application of the lean process can assist
in the operational management of the Toyota by enhancing the product quality,
effectiveness in the production processes, visual management, assist in easy
management, and lessens the utilization of workforce. It assists in the reduction of
space, enhances employee morale, elimination of issues, and provides a safe
environment.
Role of managers in Lean production-
Their main role is to make sure that no useful material is eliminated.
They carry out concerning the effectiveness of products.
They report the advancement to the higher administration (Uhrin, Bruque-Cámara
and Moyano-Fuentes, 2017).
Paraphrase This Document
Need a fresh take? Get an instant paraphrase of this document with our AI Paraphraser

Operations 7
Just-in-time Inventory (JIT)- This approach is defined as a policy, which reduces
waste and increased efficiency only by receiving goods when they are required in the
production process. The implementation of this approach assists in decreasing the
storage space as the goods are only maintained at the time of their utilization and it
saves the lot of cost of the Toyota.
Role of managers in Just-in-time Approach-
Their main role is to maintain a good connection with the providers to make sure
that they supply the desired supply of the goods.
To order an adequate amount of goods after identifying the demands (Gao, 2017).
Six Sigma- This approach is being defined as an approach, which eliminates defects
in any process ranging from transactional to manufacturing across diverse
organizations other than Toyota. The application of the six sigma approach in the
operational management assists in attaining maximum customer satisfaction by
improving employment growth, prevent defects, minimizing wastes, attain stock value
growth, return on sales, and production processes.
Role of managers in six-sigma approach-
Their role is to evaluate and implement the quality in Toyota.
They should save the cost in management reviews.
Their main role is to support the personnel and top administration to maintain
success in the organization (Tsironis and Psychogios, 2016).
Approaches to operational management
This depicts the approaches to enhance production capabilities and increase the efficiency of
Toyota. Six-Sigma concentrates on team efforts in order to attain tasks and as a result,
performance enhances. The main role of a leader while applying the Six Sigma is to
encourage team effort for the betterment of Toyota. The role of managers in the growth and
success of the global strategy of Toyota is to plan and execute the strategies, which carry out
the fulfillment of assets in a productive way. In Toyota, managers can adopt this approach,
avoids waste, and enhance production capabilities (O’Neill, Sohal and Teng, 2016).
Total Quality management carries out efficiency in the production of Toyota. This approach
concentrates on the constant quality improvement of the products and services offered
Just-in-time Inventory (JIT)- This approach is defined as a policy, which reduces
waste and increased efficiency only by receiving goods when they are required in the
production process. The implementation of this approach assists in decreasing the
storage space as the goods are only maintained at the time of their utilization and it
saves the lot of cost of the Toyota.
Role of managers in Just-in-time Approach-
Their main role is to maintain a good connection with the providers to make sure
that they supply the desired supply of the goods.
To order an adequate amount of goods after identifying the demands (Gao, 2017).
Six Sigma- This approach is being defined as an approach, which eliminates defects
in any process ranging from transactional to manufacturing across diverse
organizations other than Toyota. The application of the six sigma approach in the
operational management assists in attaining maximum customer satisfaction by
improving employment growth, prevent defects, minimizing wastes, attain stock value
growth, return on sales, and production processes.
Role of managers in six-sigma approach-
Their role is to evaluate and implement the quality in Toyota.
They should save the cost in management reviews.
Their main role is to support the personnel and top administration to maintain
success in the organization (Tsironis and Psychogios, 2016).
Approaches to operational management
This depicts the approaches to enhance production capabilities and increase the efficiency of
Toyota. Six-Sigma concentrates on team efforts in order to attain tasks and as a result,
performance enhances. The main role of a leader while applying the Six Sigma is to
encourage team effort for the betterment of Toyota. The role of managers in the growth and
success of the global strategy of Toyota is to plan and execute the strategies, which carry out
the fulfillment of assets in a productive way. In Toyota, managers can adopt this approach,
avoids waste, and enhance production capabilities (O’Neill, Sohal and Teng, 2016).
Total Quality management carries out efficiency in the production of Toyota. This approach
concentrates on the constant quality improvement of the products and services offered
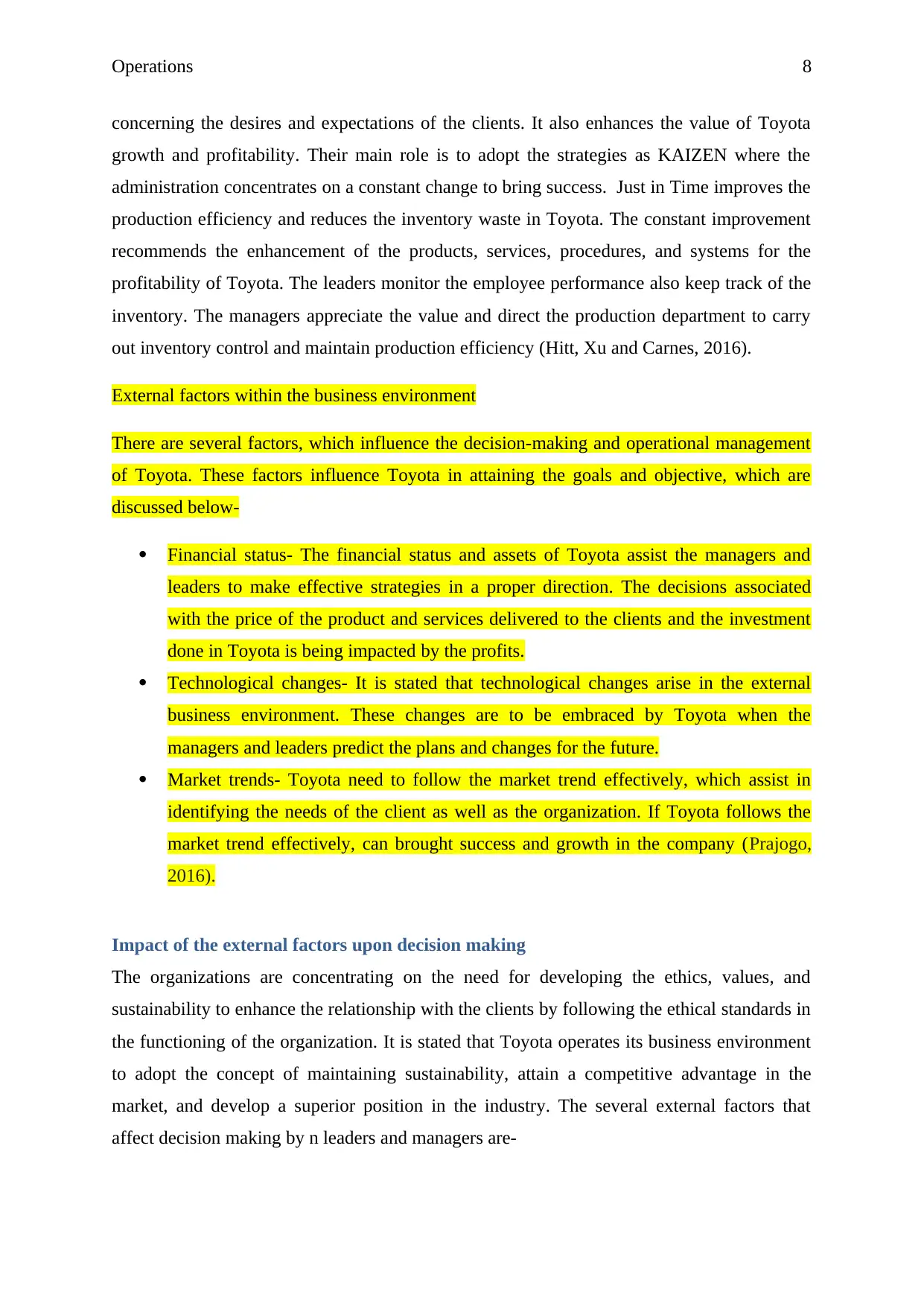
Operations 8
concerning the desires and expectations of the clients. It also enhances the value of Toyota
growth and profitability. Their main role is to adopt the strategies as KAIZEN where the
administration concentrates on a constant change to bring success. Just in Time improves the
production efficiency and reduces the inventory waste in Toyota. The constant improvement
recommends the enhancement of the products, services, procedures, and systems for the
profitability of Toyota. The leaders monitor the employee performance also keep track of the
inventory. The managers appreciate the value and direct the production department to carry
out inventory control and maintain production efficiency (Hitt, Xu and Carnes, 2016).
External factors within the business environment
There are several factors, which influence the decision-making and operational management
of Toyota. These factors influence Toyota in attaining the goals and objective, which are
discussed below-
Financial status- The financial status and assets of Toyota assist the managers and
leaders to make effective strategies in a proper direction. The decisions associated
with the price of the product and services delivered to the clients and the investment
done in Toyota is being impacted by the profits.
Technological changes- It is stated that technological changes arise in the external
business environment. These changes are to be embraced by Toyota when the
managers and leaders predict the plans and changes for the future.
Market trends- Toyota need to follow the market trend effectively, which assist in
identifying the needs of the client as well as the organization. If Toyota follows the
market trend effectively, can brought success and growth in the company (Prajogo,
2016).
Impact of the external factors upon decision making
The organizations are concentrating on the need for developing the ethics, values, and
sustainability to enhance the relationship with the clients by following the ethical standards in
the functioning of the organization. It is stated that Toyota operates its business environment
to adopt the concept of maintaining sustainability, attain a competitive advantage in the
market, and develop a superior position in the industry. The several external factors that
affect decision making by n leaders and managers are-
concerning the desires and expectations of the clients. It also enhances the value of Toyota
growth and profitability. Their main role is to adopt the strategies as KAIZEN where the
administration concentrates on a constant change to bring success. Just in Time improves the
production efficiency and reduces the inventory waste in Toyota. The constant improvement
recommends the enhancement of the products, services, procedures, and systems for the
profitability of Toyota. The leaders monitor the employee performance also keep track of the
inventory. The managers appreciate the value and direct the production department to carry
out inventory control and maintain production efficiency (Hitt, Xu and Carnes, 2016).
External factors within the business environment
There are several factors, which influence the decision-making and operational management
of Toyota. These factors influence Toyota in attaining the goals and objective, which are
discussed below-
Financial status- The financial status and assets of Toyota assist the managers and
leaders to make effective strategies in a proper direction. The decisions associated
with the price of the product and services delivered to the clients and the investment
done in Toyota is being impacted by the profits.
Technological changes- It is stated that technological changes arise in the external
business environment. These changes are to be embraced by Toyota when the
managers and leaders predict the plans and changes for the future.
Market trends- Toyota need to follow the market trend effectively, which assist in
identifying the needs of the client as well as the organization. If Toyota follows the
market trend effectively, can brought success and growth in the company (Prajogo,
2016).
Impact of the external factors upon decision making
The organizations are concentrating on the need for developing the ethics, values, and
sustainability to enhance the relationship with the clients by following the ethical standards in
the functioning of the organization. It is stated that Toyota operates its business environment
to adopt the concept of maintaining sustainability, attain a competitive advantage in the
market, and develop a superior position in the industry. The several external factors that
affect decision making by n leaders and managers are-
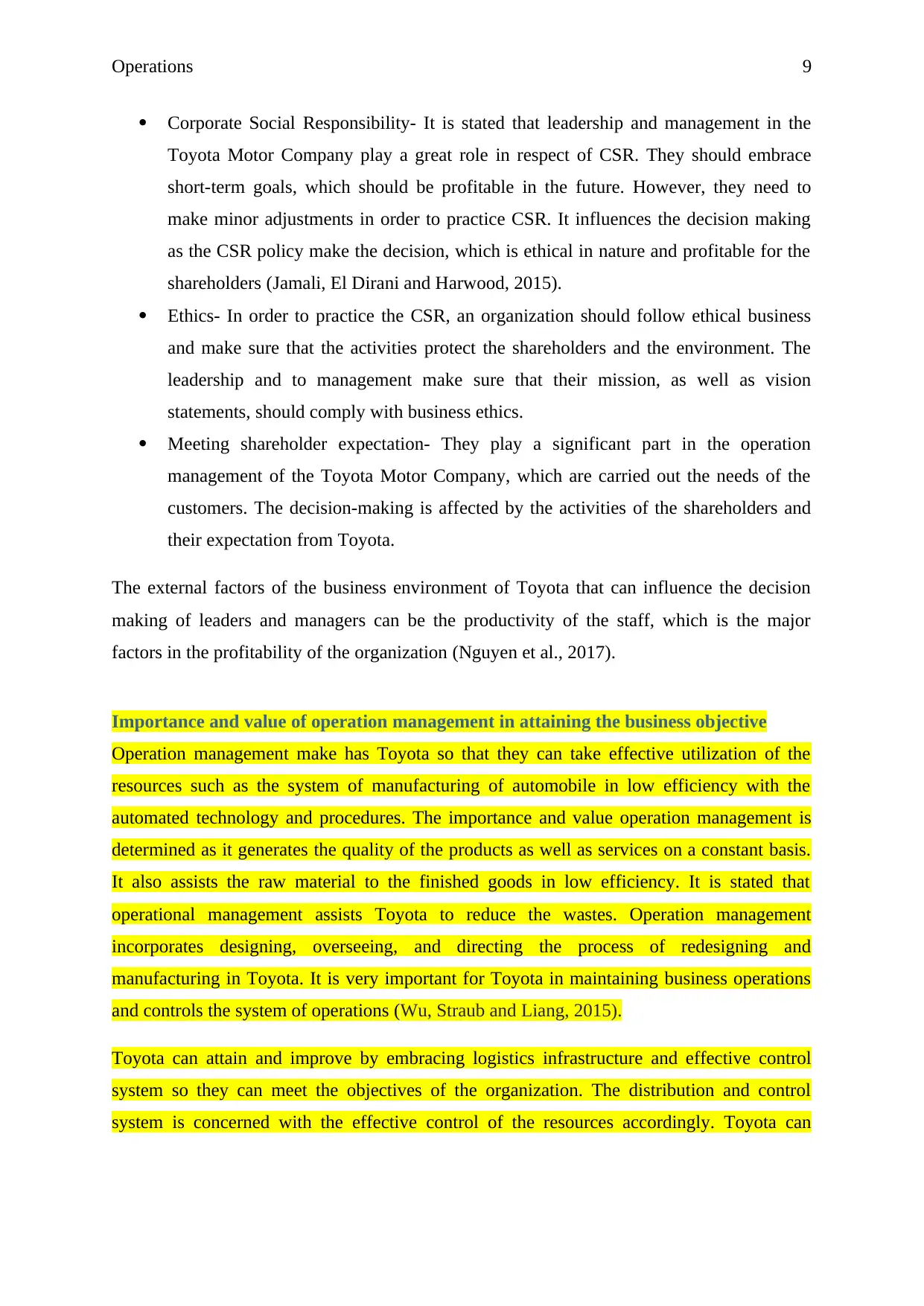
Operations 9
Corporate Social Responsibility- It is stated that leadership and management in the
Toyota Motor Company play a great role in respect of CSR. They should embrace
short-term goals, which should be profitable in the future. However, they need to
make minor adjustments in order to practice CSR. It influences the decision making
as the CSR policy make the decision, which is ethical in nature and profitable for the
shareholders (Jamali, El Dirani and Harwood, 2015).
Ethics- In order to practice the CSR, an organization should follow ethical business
and make sure that the activities protect the shareholders and the environment. The
leadership and to management make sure that their mission, as well as vision
statements, should comply with business ethics.
Meeting shareholder expectation- They play a significant part in the operation
management of the Toyota Motor Company, which are carried out the needs of the
customers. The decision-making is affected by the activities of the shareholders and
their expectation from Toyota.
The external factors of the business environment of Toyota that can influence the decision
making of leaders and managers can be the productivity of the staff, which is the major
factors in the profitability of the organization (Nguyen et al., 2017).
Importance and value of operation management in attaining the business objective
Operation management make has Toyota so that they can take effective utilization of the
resources such as the system of manufacturing of automobile in low efficiency with the
automated technology and procedures. The importance and value operation management is
determined as it generates the quality of the products as well as services on a constant basis.
It also assists the raw material to the finished goods in low efficiency. It is stated that
operational management assists Toyota to reduce the wastes. Operation management
incorporates designing, overseeing, and directing the process of redesigning and
manufacturing in Toyota. It is very important for Toyota in maintaining business operations
and controls the system of operations (Wu, Straub and Liang, 2015).
Toyota can attain and improve by embracing logistics infrastructure and effective control
system so they can meet the objectives of the organization. The distribution and control
system is concerned with the effective control of the resources accordingly. Toyota can
Corporate Social Responsibility- It is stated that leadership and management in the
Toyota Motor Company play a great role in respect of CSR. They should embrace
short-term goals, which should be profitable in the future. However, they need to
make minor adjustments in order to practice CSR. It influences the decision making
as the CSR policy make the decision, which is ethical in nature and profitable for the
shareholders (Jamali, El Dirani and Harwood, 2015).
Ethics- In order to practice the CSR, an organization should follow ethical business
and make sure that the activities protect the shareholders and the environment. The
leadership and to management make sure that their mission, as well as vision
statements, should comply with business ethics.
Meeting shareholder expectation- They play a significant part in the operation
management of the Toyota Motor Company, which are carried out the needs of the
customers. The decision-making is affected by the activities of the shareholders and
their expectation from Toyota.
The external factors of the business environment of Toyota that can influence the decision
making of leaders and managers can be the productivity of the staff, which is the major
factors in the profitability of the organization (Nguyen et al., 2017).
Importance and value of operation management in attaining the business objective
Operation management make has Toyota so that they can take effective utilization of the
resources such as the system of manufacturing of automobile in low efficiency with the
automated technology and procedures. The importance and value operation management is
determined as it generates the quality of the products as well as services on a constant basis.
It also assists the raw material to the finished goods in low efficiency. It is stated that
operational management assists Toyota to reduce the wastes. Operation management
incorporates designing, overseeing, and directing the process of redesigning and
manufacturing in Toyota. It is very important for Toyota in maintaining business operations
and controls the system of operations (Wu, Straub and Liang, 2015).
Toyota can attain and improve by embracing logistics infrastructure and effective control
system so they can meet the objectives of the organization. The distribution and control
system is concerned with the effective control of the resources accordingly. Toyota can
Secure Best Marks with AI Grader
Need help grading? Try our AI Grader for instant feedback on your assignments.
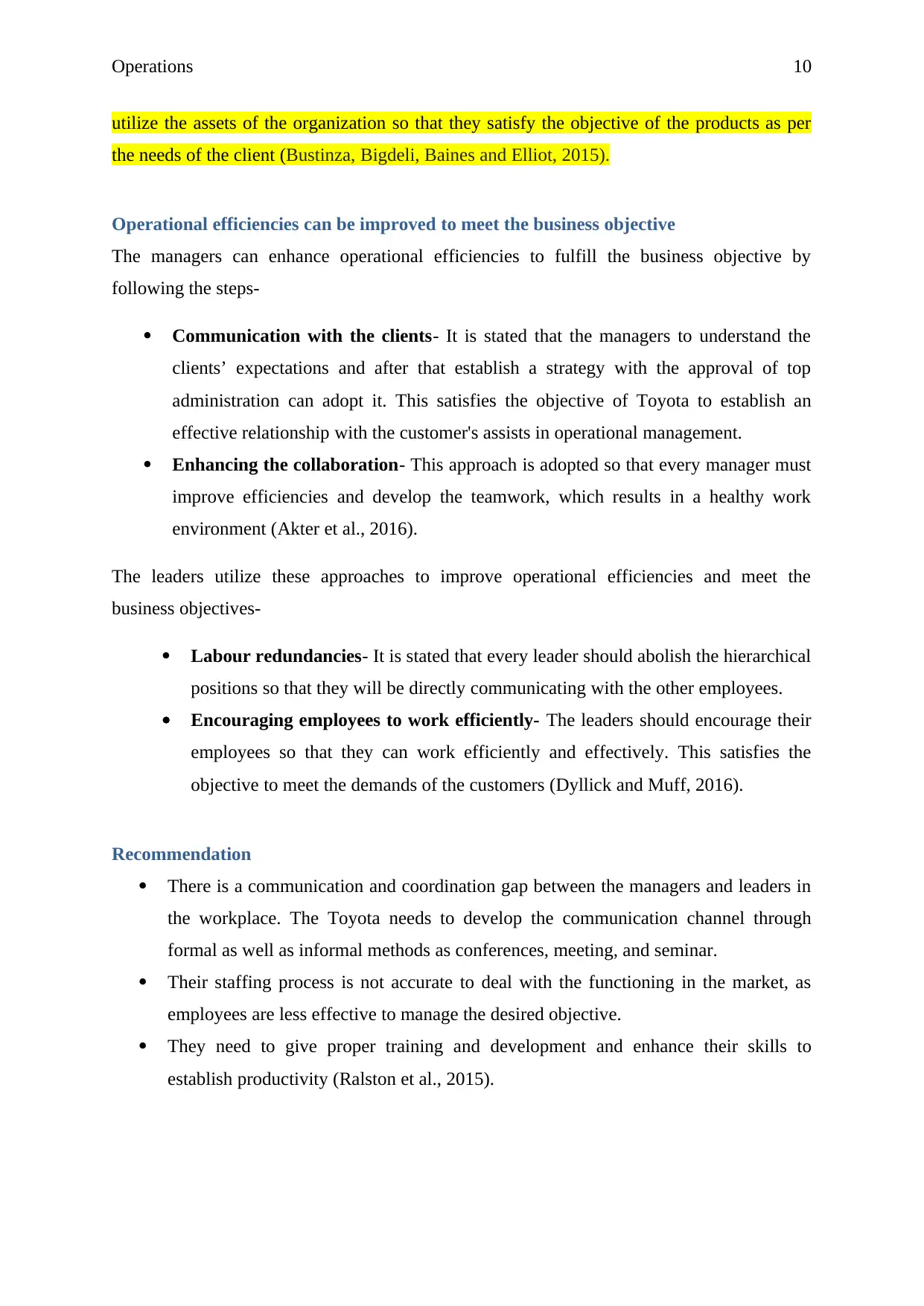
Operations 10
utilize the assets of the organization so that they satisfy the objective of the products as per
the needs of the client (Bustinza, Bigdeli, Baines and Elliot, 2015).
Operational efficiencies can be improved to meet the business objective
The managers can enhance operational efficiencies to fulfill the business objective by
following the steps-
Communication with the clients- It is stated that the managers to understand the
clients’ expectations and after that establish a strategy with the approval of top
administration can adopt it. This satisfies the objective of Toyota to establish an
effective relationship with the customer's assists in operational management.
Enhancing the collaboration- This approach is adopted so that every manager must
improve efficiencies and develop the teamwork, which results in a healthy work
environment (Akter et al., 2016).
The leaders utilize these approaches to improve operational efficiencies and meet the
business objectives-
Labour redundancies- It is stated that every leader should abolish the hierarchical
positions so that they will be directly communicating with the other employees.
Encouraging employees to work efficiently- The leaders should encourage their
employees so that they can work efficiently and effectively. This satisfies the
objective to meet the demands of the customers (Dyllick and Muff, 2016).
Recommendation
There is a communication and coordination gap between the managers and leaders in
the workplace. The Toyota needs to develop the communication channel through
formal as well as informal methods as conferences, meeting, and seminar.
Their staffing process is not accurate to deal with the functioning in the market, as
employees are less effective to manage the desired objective.
They need to give proper training and development and enhance their skills to
establish productivity (Ralston et al., 2015).
utilize the assets of the organization so that they satisfy the objective of the products as per
the needs of the client (Bustinza, Bigdeli, Baines and Elliot, 2015).
Operational efficiencies can be improved to meet the business objective
The managers can enhance operational efficiencies to fulfill the business objective by
following the steps-
Communication with the clients- It is stated that the managers to understand the
clients’ expectations and after that establish a strategy with the approval of top
administration can adopt it. This satisfies the objective of Toyota to establish an
effective relationship with the customer's assists in operational management.
Enhancing the collaboration- This approach is adopted so that every manager must
improve efficiencies and develop the teamwork, which results in a healthy work
environment (Akter et al., 2016).
The leaders utilize these approaches to improve operational efficiencies and meet the
business objectives-
Labour redundancies- It is stated that every leader should abolish the hierarchical
positions so that they will be directly communicating with the other employees.
Encouraging employees to work efficiently- The leaders should encourage their
employees so that they can work efficiently and effectively. This satisfies the
objective to meet the demands of the customers (Dyllick and Muff, 2016).
Recommendation
There is a communication and coordination gap between the managers and leaders in
the workplace. The Toyota needs to develop the communication channel through
formal as well as informal methods as conferences, meeting, and seminar.
Their staffing process is not accurate to deal with the functioning in the market, as
employees are less effective to manage the desired objective.
They need to give proper training and development and enhance their skills to
establish productivity (Ralston et al., 2015).
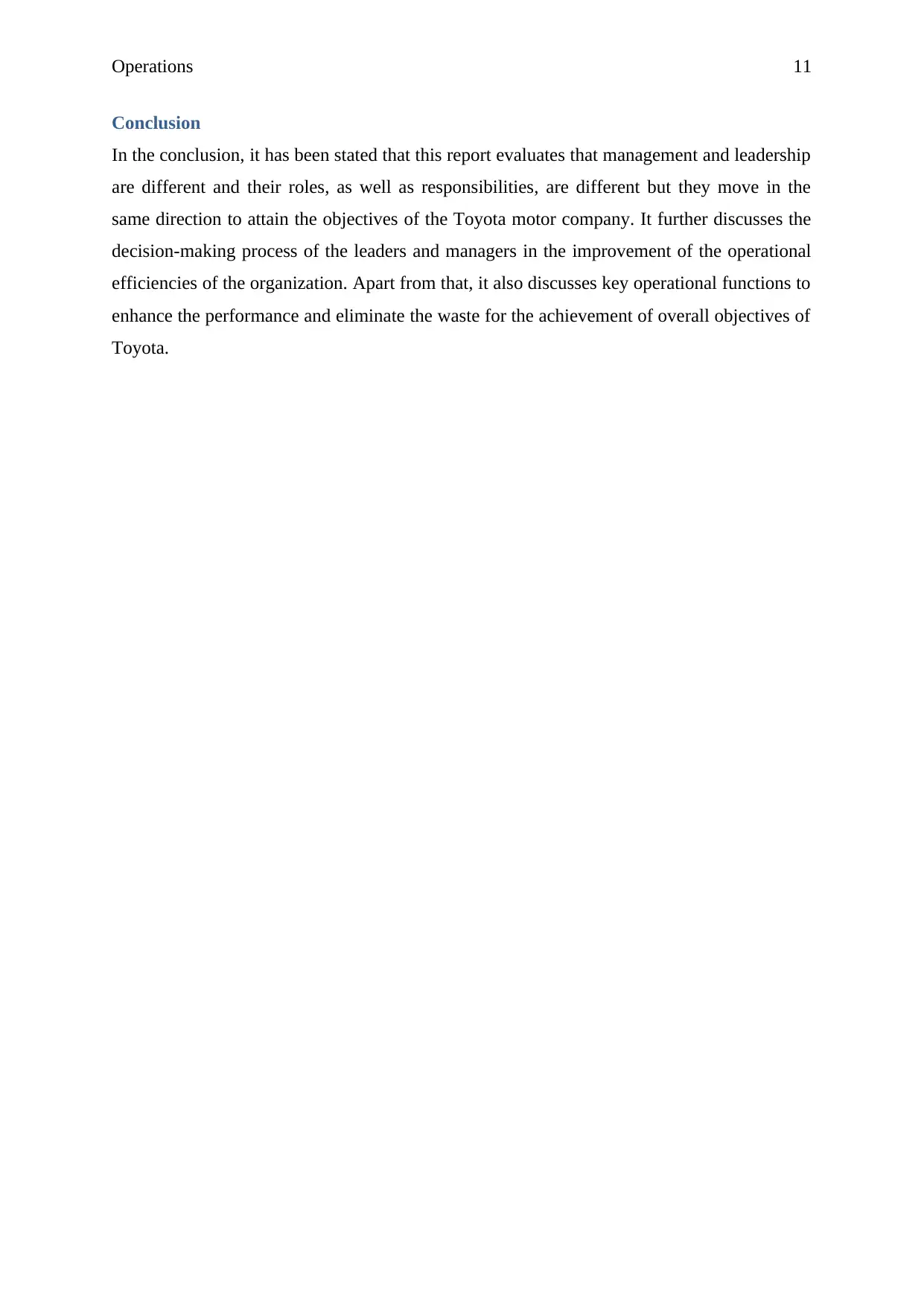
Operations 11
Conclusion
In the conclusion, it has been stated that this report evaluates that management and leadership
are different and their roles, as well as responsibilities, are different but they move in the
same direction to attain the objectives of the Toyota motor company. It further discusses the
decision-making process of the leaders and managers in the improvement of the operational
efficiencies of the organization. Apart from that, it also discusses key operational functions to
enhance the performance and eliminate the waste for the achievement of overall objectives of
Toyota.
Conclusion
In the conclusion, it has been stated that this report evaluates that management and leadership
are different and their roles, as well as responsibilities, are different but they move in the
same direction to attain the objectives of the Toyota motor company. It further discusses the
decision-making process of the leaders and managers in the improvement of the operational
efficiencies of the organization. Apart from that, it also discusses key operational functions to
enhance the performance and eliminate the waste for the achievement of overall objectives of
Toyota.
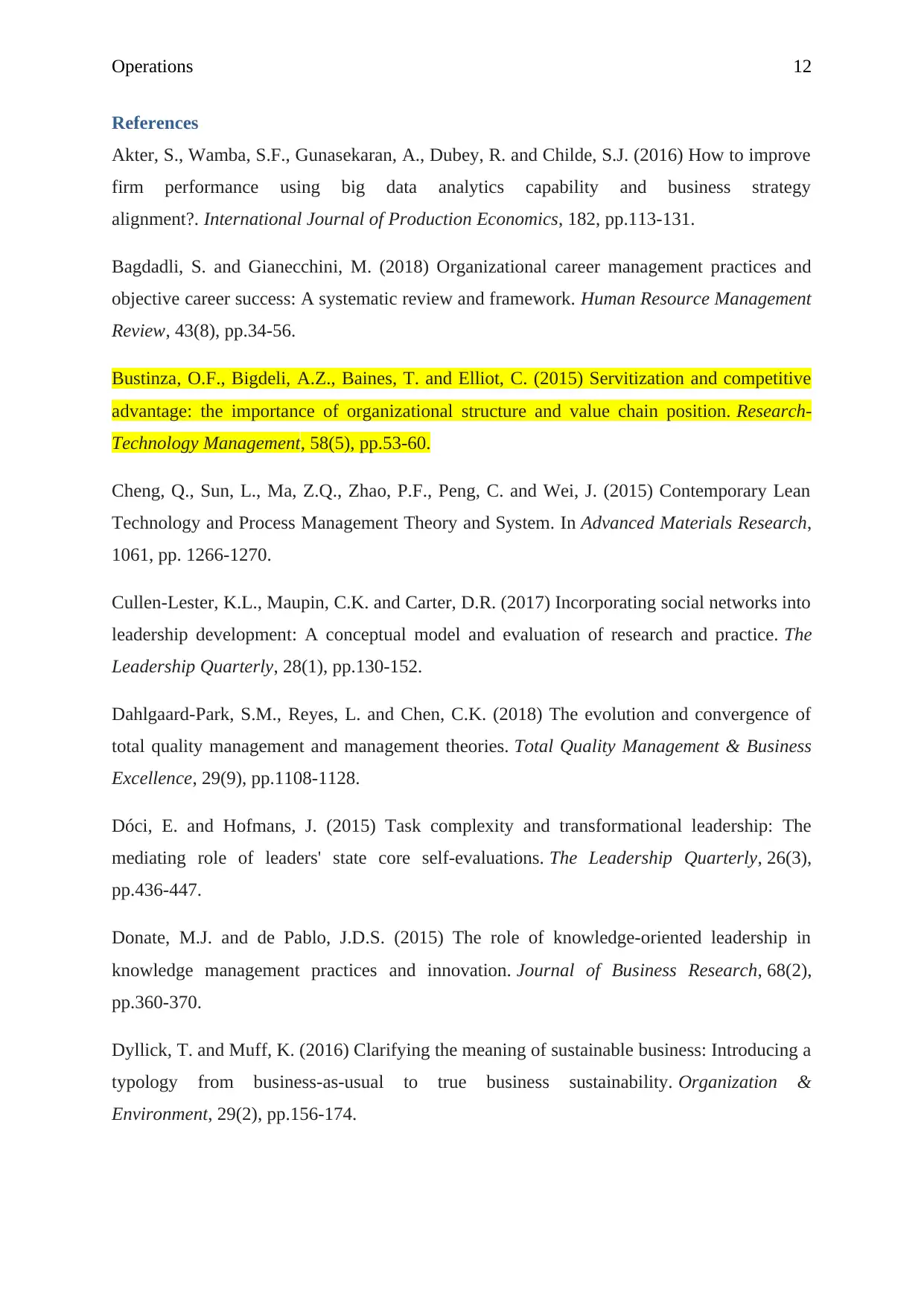
Operations 12
References
Akter, S., Wamba, S.F., Gunasekaran, A., Dubey, R. and Childe, S.J. (2016) How to improve
firm performance using big data analytics capability and business strategy
alignment?. International Journal of Production Economics, 182, pp.113-131.
Bagdadli, S. and Gianecchini, M. (2018) Organizational career management practices and
objective career success: A systematic review and framework. Human Resource Management
Review, 43(8), pp.34-56.
Bustinza, O.F., Bigdeli, A.Z., Baines, T. and Elliot, C. (2015) Servitization and competitive
advantage: the importance of organizational structure and value chain position. Research-
Technology Management, 58(5), pp.53-60.
Cheng, Q., Sun, L., Ma, Z.Q., Zhao, P.F., Peng, C. and Wei, J. (2015) Contemporary Lean
Technology and Process Management Theory and System. In Advanced Materials Research,
1061, pp. 1266-1270.
Cullen-Lester, K.L., Maupin, C.K. and Carter, D.R. (2017) Incorporating social networks into
leadership development: A conceptual model and evaluation of research and practice. The
Leadership Quarterly, 28(1), pp.130-152.
Dahlgaard-Park, S.M., Reyes, L. and Chen, C.K. (2018) The evolution and convergence of
total quality management and management theories. Total Quality Management & Business
Excellence, 29(9), pp.1108-1128.
Dóci, E. and Hofmans, J. (2015) Task complexity and transformational leadership: The
mediating role of leaders' state core self-evaluations. The Leadership Quarterly, 26(3),
pp.436-447.
Donate, M.J. and de Pablo, J.D.S. (2015) The role of knowledge-oriented leadership in
knowledge management practices and innovation. Journal of Business Research, 68(2),
pp.360-370.
Dyllick, T. and Muff, K. (2016) Clarifying the meaning of sustainable business: Introducing a
typology from business-as-usual to true business sustainability. Organization &
Environment, 29(2), pp.156-174.
References
Akter, S., Wamba, S.F., Gunasekaran, A., Dubey, R. and Childe, S.J. (2016) How to improve
firm performance using big data analytics capability and business strategy
alignment?. International Journal of Production Economics, 182, pp.113-131.
Bagdadli, S. and Gianecchini, M. (2018) Organizational career management practices and
objective career success: A systematic review and framework. Human Resource Management
Review, 43(8), pp.34-56.
Bustinza, O.F., Bigdeli, A.Z., Baines, T. and Elliot, C. (2015) Servitization and competitive
advantage: the importance of organizational structure and value chain position. Research-
Technology Management, 58(5), pp.53-60.
Cheng, Q., Sun, L., Ma, Z.Q., Zhao, P.F., Peng, C. and Wei, J. (2015) Contemporary Lean
Technology and Process Management Theory and System. In Advanced Materials Research,
1061, pp. 1266-1270.
Cullen-Lester, K.L., Maupin, C.K. and Carter, D.R. (2017) Incorporating social networks into
leadership development: A conceptual model and evaluation of research and practice. The
Leadership Quarterly, 28(1), pp.130-152.
Dahlgaard-Park, S.M., Reyes, L. and Chen, C.K. (2018) The evolution and convergence of
total quality management and management theories. Total Quality Management & Business
Excellence, 29(9), pp.1108-1128.
Dóci, E. and Hofmans, J. (2015) Task complexity and transformational leadership: The
mediating role of leaders' state core self-evaluations. The Leadership Quarterly, 26(3),
pp.436-447.
Donate, M.J. and de Pablo, J.D.S. (2015) The role of knowledge-oriented leadership in
knowledge management practices and innovation. Journal of Business Research, 68(2),
pp.360-370.
Dyllick, T. and Muff, K. (2016) Clarifying the meaning of sustainable business: Introducing a
typology from business-as-usual to true business sustainability. Organization &
Environment, 29(2), pp.156-174.
Paraphrase This Document
Need a fresh take? Get an instant paraphrase of this document with our AI Paraphraser
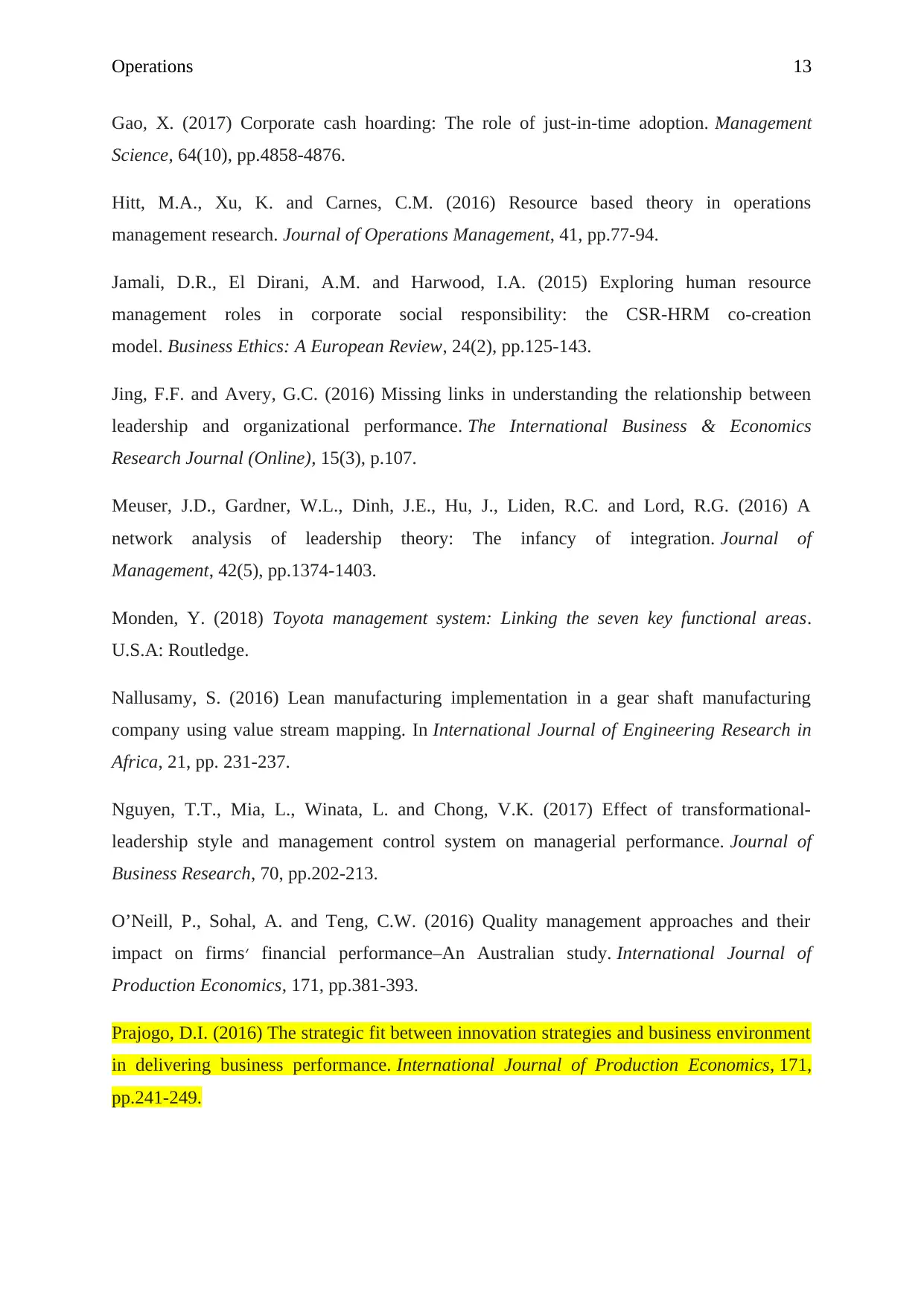
Operations 13
Gao, X. (2017) Corporate cash hoarding: The role of just-in-time adoption. Management
Science, 64(10), pp.4858-4876.
Hitt, M.A., Xu, K. and Carnes, C.M. (2016) Resource based theory in operations
management research. Journal of Operations Management, 41, pp.77-94.
Jamali, D.R., El Dirani, A.M. and Harwood, I.A. (2015) Exploring human resource
management roles in corporate social responsibility: the CSR‐HRM co‐creation
model. Business Ethics: A European Review, 24(2), pp.125-143.
Jing, F.F. and Avery, G.C. (2016) Missing links in understanding the relationship between
leadership and organizational performance. The International Business & Economics
Research Journal (Online), 15(3), p.107.
Meuser, J.D., Gardner, W.L., Dinh, J.E., Hu, J., Liden, R.C. and Lord, R.G. (2016) A
network analysis of leadership theory: The infancy of integration. Journal of
Management, 42(5), pp.1374-1403.
Monden, Y. (2018) Toyota management system: Linking the seven key functional areas.
U.S.A: Routledge.
Nallusamy, S. (2016) Lean manufacturing implementation in a gear shaft manufacturing
company using value stream mapping. In International Journal of Engineering Research in
Africa, 21, pp. 231-237.
Nguyen, T.T., Mia, L., Winata, L. and Chong, V.K. (2017) Effect of transformational-
leadership style and management control system on managerial performance. Journal of
Business Research, 70, pp.202-213.
O’Neill, P., Sohal, A. and Teng, C.W. (2016) Quality management approaches and their
impact on firms׳ financial performance–An Australian study. International Journal of
Production Economics, 171, pp.381-393.
Prajogo, D.I. (2016) The strategic fit between innovation strategies and business environment
in delivering business performance. International Journal of Production Economics, 171,
pp.241-249.
Gao, X. (2017) Corporate cash hoarding: The role of just-in-time adoption. Management
Science, 64(10), pp.4858-4876.
Hitt, M.A., Xu, K. and Carnes, C.M. (2016) Resource based theory in operations
management research. Journal of Operations Management, 41, pp.77-94.
Jamali, D.R., El Dirani, A.M. and Harwood, I.A. (2015) Exploring human resource
management roles in corporate social responsibility: the CSR‐HRM co‐creation
model. Business Ethics: A European Review, 24(2), pp.125-143.
Jing, F.F. and Avery, G.C. (2016) Missing links in understanding the relationship between
leadership and organizational performance. The International Business & Economics
Research Journal (Online), 15(3), p.107.
Meuser, J.D., Gardner, W.L., Dinh, J.E., Hu, J., Liden, R.C. and Lord, R.G. (2016) A
network analysis of leadership theory: The infancy of integration. Journal of
Management, 42(5), pp.1374-1403.
Monden, Y. (2018) Toyota management system: Linking the seven key functional areas.
U.S.A: Routledge.
Nallusamy, S. (2016) Lean manufacturing implementation in a gear shaft manufacturing
company using value stream mapping. In International Journal of Engineering Research in
Africa, 21, pp. 231-237.
Nguyen, T.T., Mia, L., Winata, L. and Chong, V.K. (2017) Effect of transformational-
leadership style and management control system on managerial performance. Journal of
Business Research, 70, pp.202-213.
O’Neill, P., Sohal, A. and Teng, C.W. (2016) Quality management approaches and their
impact on firms׳ financial performance–An Australian study. International Journal of
Production Economics, 171, pp.381-393.
Prajogo, D.I. (2016) The strategic fit between innovation strategies and business environment
in delivering business performance. International Journal of Production Economics, 171,
pp.241-249.
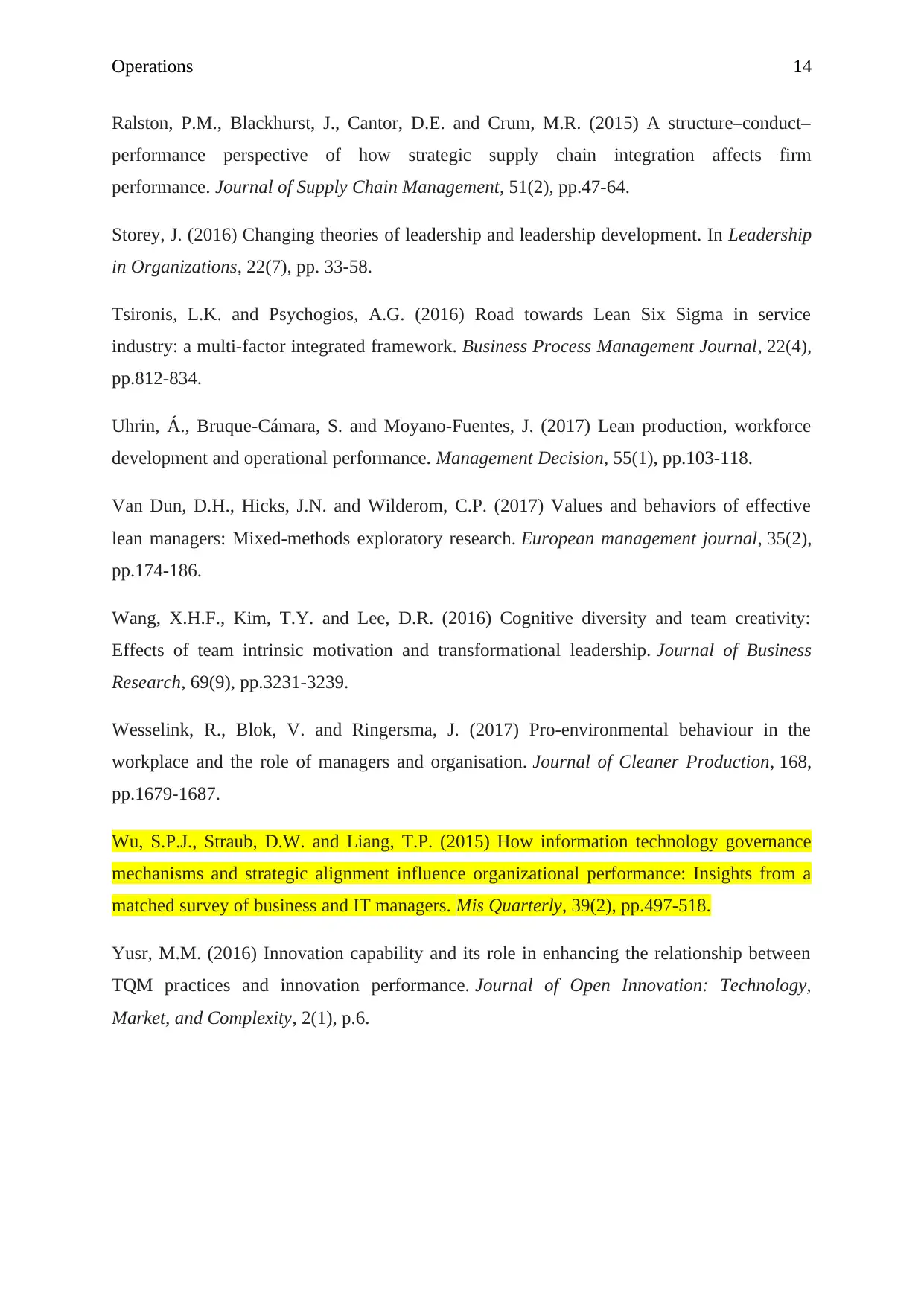
Operations 14
Ralston, P.M., Blackhurst, J., Cantor, D.E. and Crum, M.R. (2015) A structure–conduct–
performance perspective of how strategic supply chain integration affects firm
performance. Journal of Supply Chain Management, 51(2), pp.47-64.
Storey, J. (2016) Changing theories of leadership and leadership development. In Leadership
in Organizations, 22(7), pp. 33-58.
Tsironis, L.K. and Psychogios, A.G. (2016) Road towards Lean Six Sigma in service
industry: a multi-factor integrated framework. Business Process Management Journal, 22(4),
pp.812-834.
Uhrin, Á., Bruque-Cámara, S. and Moyano-Fuentes, J. (2017) Lean production, workforce
development and operational performance. Management Decision, 55(1), pp.103-118.
Van Dun, D.H., Hicks, J.N. and Wilderom, C.P. (2017) Values and behaviors of effective
lean managers: Mixed-methods exploratory research. European management journal, 35(2),
pp.174-186.
Wang, X.H.F., Kim, T.Y. and Lee, D.R. (2016) Cognitive diversity and team creativity:
Effects of team intrinsic motivation and transformational leadership. Journal of Business
Research, 69(9), pp.3231-3239.
Wesselink, R., Blok, V. and Ringersma, J. (2017) Pro-environmental behaviour in the
workplace and the role of managers and organisation. Journal of Cleaner Production, 168,
pp.1679-1687.
Wu, S.P.J., Straub, D.W. and Liang, T.P. (2015) How information technology governance
mechanisms and strategic alignment influence organizational performance: Insights from a
matched survey of business and IT managers. Mis Quarterly, 39(2), pp.497-518.
Yusr, M.M. (2016) Innovation capability and its role in enhancing the relationship between
TQM practices and innovation performance. Journal of Open Innovation: Technology,
Market, and Complexity, 2(1), p.6.
Ralston, P.M., Blackhurst, J., Cantor, D.E. and Crum, M.R. (2015) A structure–conduct–
performance perspective of how strategic supply chain integration affects firm
performance. Journal of Supply Chain Management, 51(2), pp.47-64.
Storey, J. (2016) Changing theories of leadership and leadership development. In Leadership
in Organizations, 22(7), pp. 33-58.
Tsironis, L.K. and Psychogios, A.G. (2016) Road towards Lean Six Sigma in service
industry: a multi-factor integrated framework. Business Process Management Journal, 22(4),
pp.812-834.
Uhrin, Á., Bruque-Cámara, S. and Moyano-Fuentes, J. (2017) Lean production, workforce
development and operational performance. Management Decision, 55(1), pp.103-118.
Van Dun, D.H., Hicks, J.N. and Wilderom, C.P. (2017) Values and behaviors of effective
lean managers: Mixed-methods exploratory research. European management journal, 35(2),
pp.174-186.
Wang, X.H.F., Kim, T.Y. and Lee, D.R. (2016) Cognitive diversity and team creativity:
Effects of team intrinsic motivation and transformational leadership. Journal of Business
Research, 69(9), pp.3231-3239.
Wesselink, R., Blok, V. and Ringersma, J. (2017) Pro-environmental behaviour in the
workplace and the role of managers and organisation. Journal of Cleaner Production, 168,
pp.1679-1687.
Wu, S.P.J., Straub, D.W. and Liang, T.P. (2015) How information technology governance
mechanisms and strategic alignment influence organizational performance: Insights from a
matched survey of business and IT managers. Mis Quarterly, 39(2), pp.497-518.
Yusr, M.M. (2016) Innovation capability and its role in enhancing the relationship between
TQM practices and innovation performance. Journal of Open Innovation: Technology,
Market, and Complexity, 2(1), p.6.
1 out of 15
Related Documents

Your All-in-One AI-Powered Toolkit for Academic Success.
+13062052269
info@desklib.com
Available 24*7 on WhatsApp / Email
Unlock your academic potential
© 2024 | Zucol Services PVT LTD | All rights reserved.