Toyota HRM Case Study: Corporate Culture Impact on Human Resource Mgmt
VerifiedAdded on 2023/06/07
|4
|694
|201
Case Study
AI Summary
This case study examines the human resource management (HRM) practices at Toyota Motor Company, focusing on the impact of its corporate culture. Rooted in Japanese norms, Toyota's organizational structure has traditionally been rigid, with decision-making concentrated at the managerial l...
Read More
Contribute Materials
Your contribution can guide someone’s learning journey. Share your
documents today.
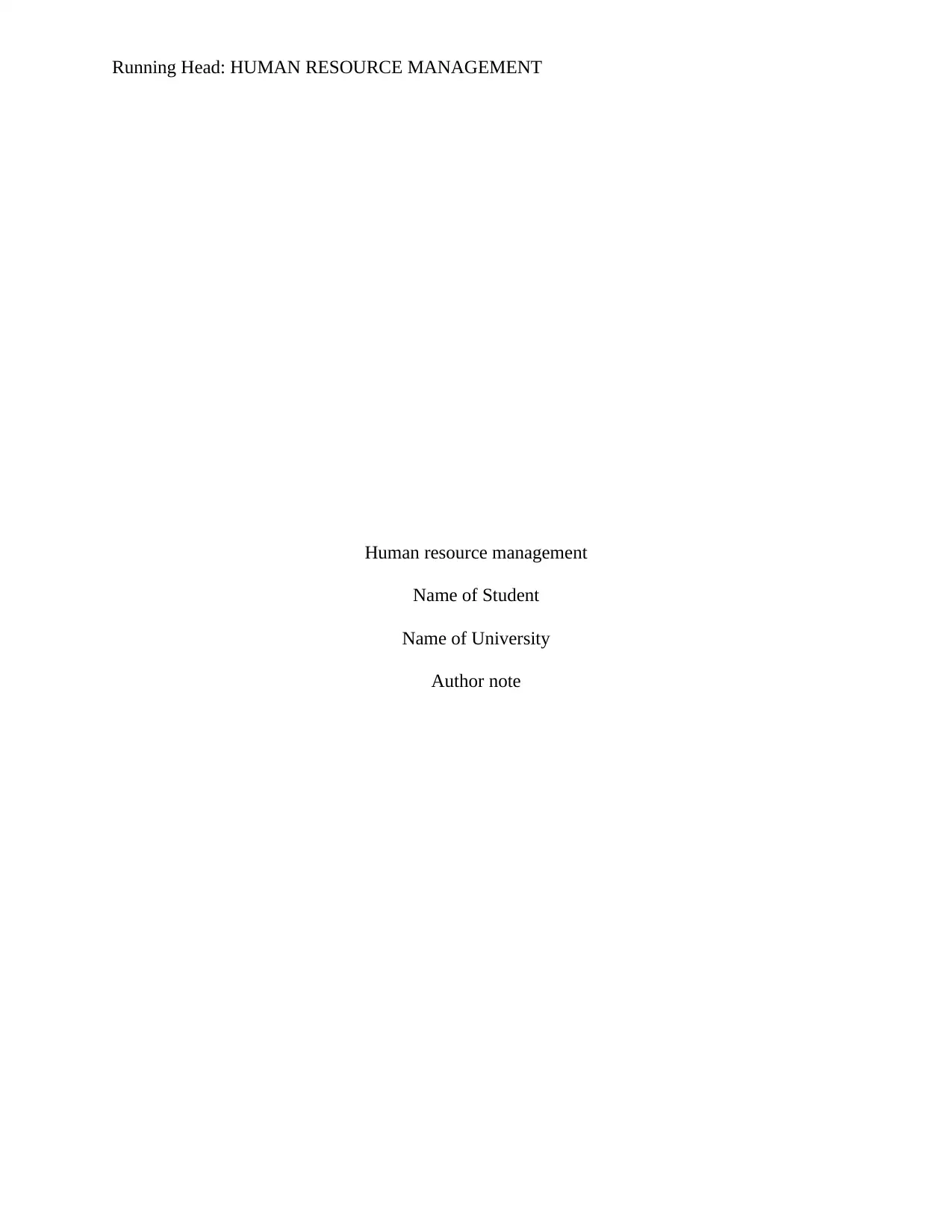
Running Head: HUMAN RESOURCE MANAGEMENT
Human resource management
Name of Student
Name of University
Author note
Human resource management
Name of Student
Name of University
Author note
Secure Best Marks with AI Grader
Need help grading? Try our AI Grader for instant feedback on your assignments.
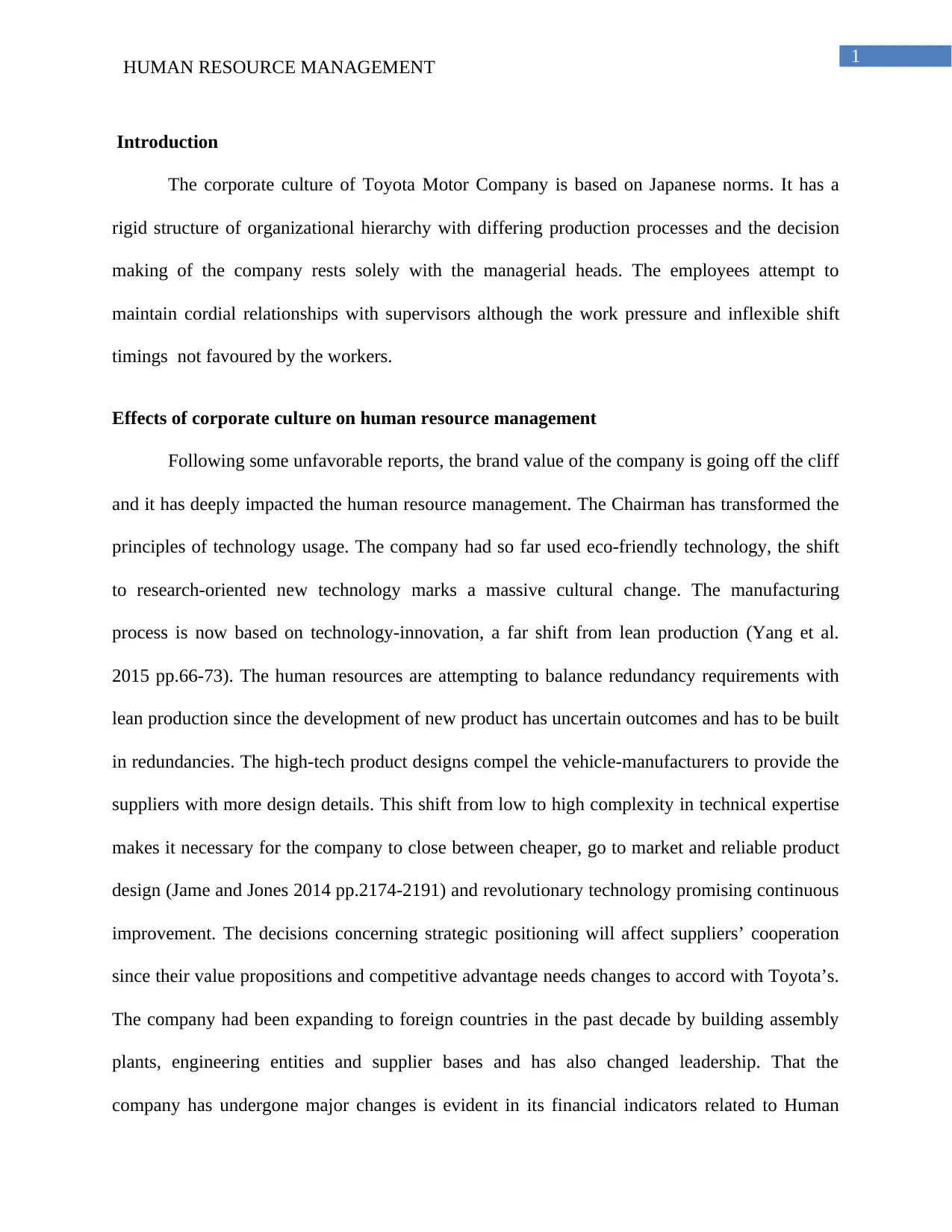
1
HUMAN RESOURCE MANAGEMENT
Introduction
The corporate culture of Toyota Motor Company is based on Japanese norms. It has a
rigid structure of organizational hierarchy with differing production processes and the decision
making of the company rests solely with the managerial heads. The employees attempt to
maintain cordial relationships with supervisors although the work pressure and inflexible shift
timings not favoured by the workers.
Effects of corporate culture on human resource management
Following some unfavorable reports, the brand value of the company is going off the cliff
and it has deeply impacted the human resource management. The Chairman has transformed the
principles of technology usage. The company had so far used eco-friendly technology, the shift
to research-oriented new technology marks a massive cultural change. The manufacturing
process is now based on technology-innovation, a far shift from lean production (Yang et al.
2015 pp.66-73). The human resources are attempting to balance redundancy requirements with
lean production since the development of new product has uncertain outcomes and has to be built
in redundancies. The high-tech product designs compel the vehicle-manufacturers to provide the
suppliers with more design details. This shift from low to high complexity in technical expertise
makes it necessary for the company to close between cheaper, go to market and reliable product
design (Jame and Jones 2014 pp.2174-2191) and revolutionary technology promising continuous
improvement. The decisions concerning strategic positioning will affect suppliers’ cooperation
since their value propositions and competitive advantage needs changes to accord with Toyota’s.
The company had been expanding to foreign countries in the past decade by building assembly
plants, engineering entities and supplier bases and has also changed leadership. That the
company has undergone major changes is evident in its financial indicators related to Human
HUMAN RESOURCE MANAGEMENT
Introduction
The corporate culture of Toyota Motor Company is based on Japanese norms. It has a
rigid structure of organizational hierarchy with differing production processes and the decision
making of the company rests solely with the managerial heads. The employees attempt to
maintain cordial relationships with supervisors although the work pressure and inflexible shift
timings not favoured by the workers.
Effects of corporate culture on human resource management
Following some unfavorable reports, the brand value of the company is going off the cliff
and it has deeply impacted the human resource management. The Chairman has transformed the
principles of technology usage. The company had so far used eco-friendly technology, the shift
to research-oriented new technology marks a massive cultural change. The manufacturing
process is now based on technology-innovation, a far shift from lean production (Yang et al.
2015 pp.66-73). The human resources are attempting to balance redundancy requirements with
lean production since the development of new product has uncertain outcomes and has to be built
in redundancies. The high-tech product designs compel the vehicle-manufacturers to provide the
suppliers with more design details. This shift from low to high complexity in technical expertise
makes it necessary for the company to close between cheaper, go to market and reliable product
design (Jame and Jones 2014 pp.2174-2191) and revolutionary technology promising continuous
improvement. The decisions concerning strategic positioning will affect suppliers’ cooperation
since their value propositions and competitive advantage needs changes to accord with Toyota’s.
The company had been expanding to foreign countries in the past decade by building assembly
plants, engineering entities and supplier bases and has also changed leadership. That the
company has undergone major changes is evident in its financial indicators related to Human
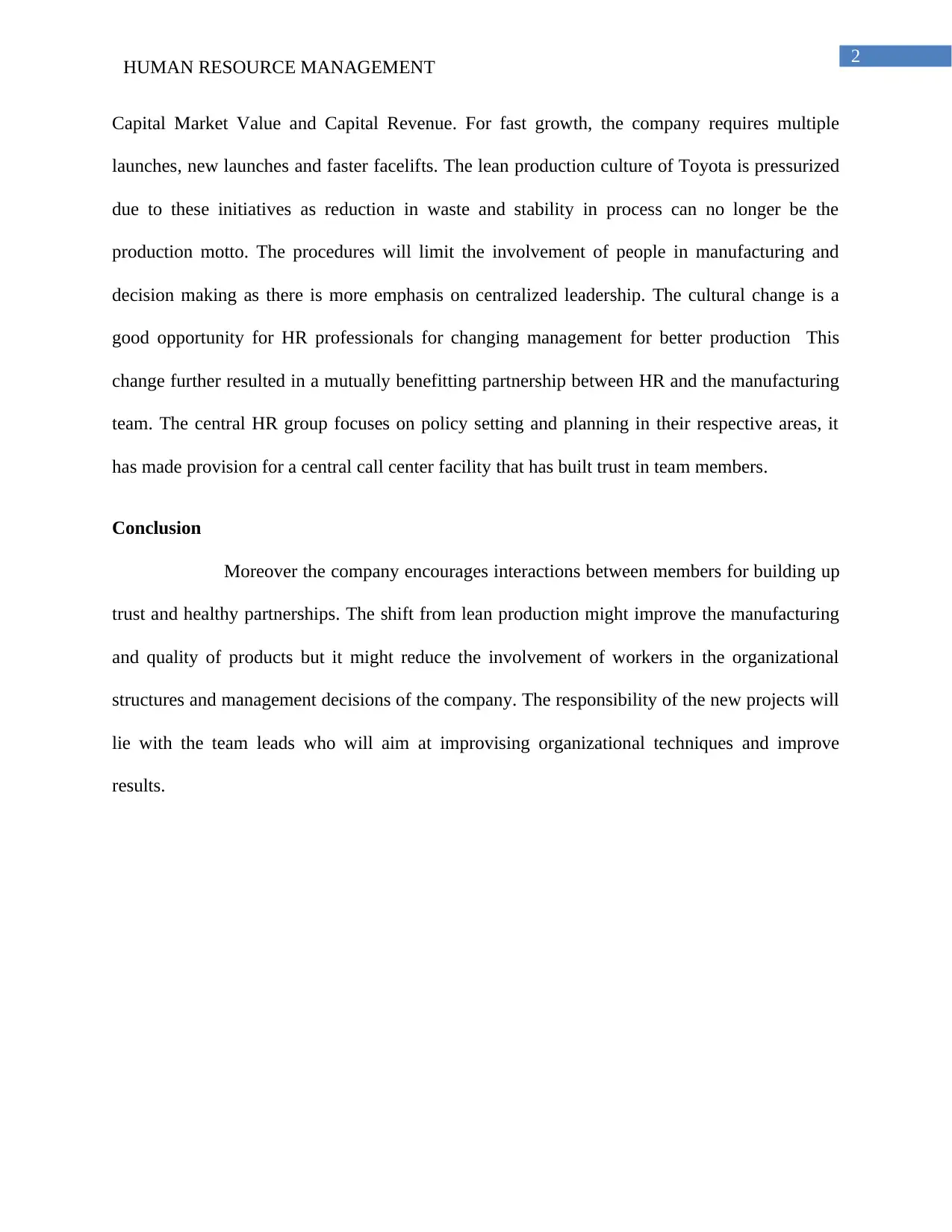
2
HUMAN RESOURCE MANAGEMENT
Capital Market Value and Capital Revenue. For fast growth, the company requires multiple
launches, new launches and faster facelifts. The lean production culture of Toyota is pressurized
due to these initiatives as reduction in waste and stability in process can no longer be the
production motto. The procedures will limit the involvement of people in manufacturing and
decision making as there is more emphasis on centralized leadership. The cultural change is a
good opportunity for HR professionals for changing management for better production This
change further resulted in a mutually benefitting partnership between HR and the manufacturing
team. The central HR group focuses on policy setting and planning in their respective areas, it
has made provision for a central call center facility that has built trust in team members.
Conclusion
Moreover the company encourages interactions between members for building up
trust and healthy partnerships. The shift from lean production might improve the manufacturing
and quality of products but it might reduce the involvement of workers in the organizational
structures and management decisions of the company. The responsibility of the new projects will
lie with the team leads who will aim at improvising organizational techniques and improve
results.
HUMAN RESOURCE MANAGEMENT
Capital Market Value and Capital Revenue. For fast growth, the company requires multiple
launches, new launches and faster facelifts. The lean production culture of Toyota is pressurized
due to these initiatives as reduction in waste and stability in process can no longer be the
production motto. The procedures will limit the involvement of people in manufacturing and
decision making as there is more emphasis on centralized leadership. The cultural change is a
good opportunity for HR professionals for changing management for better production This
change further resulted in a mutually benefitting partnership between HR and the manufacturing
team. The central HR group focuses on policy setting and planning in their respective areas, it
has made provision for a central call center facility that has built trust in team members.
Conclusion
Moreover the company encourages interactions between members for building up
trust and healthy partnerships. The shift from lean production might improve the manufacturing
and quality of products but it might reduce the involvement of workers in the organizational
structures and management decisions of the company. The responsibility of the new projects will
lie with the team leads who will aim at improvising organizational techniques and improve
results.
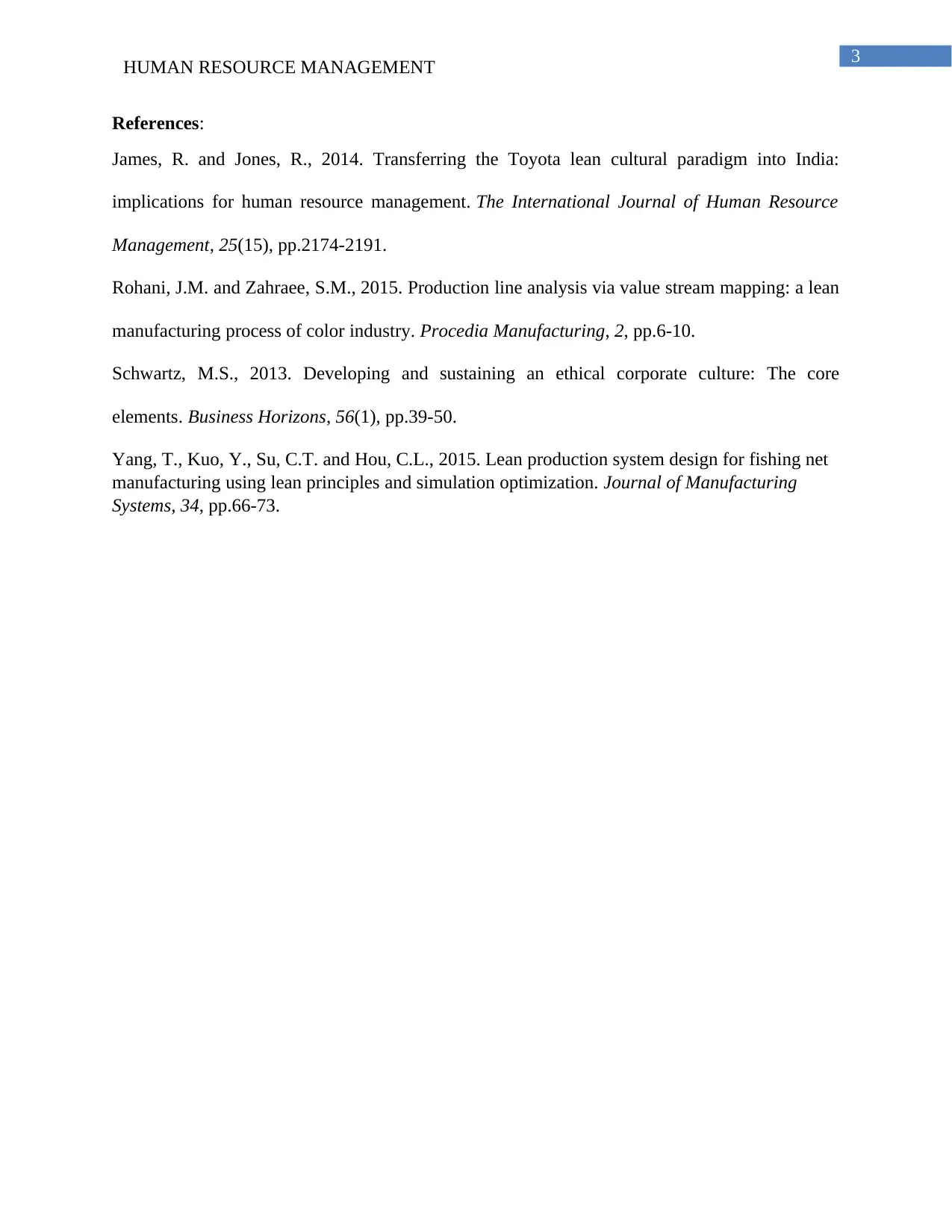
3
HUMAN RESOURCE MANAGEMENT
References:
James, R. and Jones, R., 2014. Transferring the Toyota lean cultural paradigm into India:
implications for human resource management. The International Journal of Human Resource
Management, 25(15), pp.2174-2191.
Rohani, J.M. and Zahraee, S.M., 2015. Production line analysis via value stream mapping: a lean
manufacturing process of color industry. Procedia Manufacturing, 2, pp.6-10.
Schwartz, M.S., 2013. Developing and sustaining an ethical corporate culture: The core
elements. Business Horizons, 56(1), pp.39-50.
Yang, T., Kuo, Y., Su, C.T. and Hou, C.L., 2015. Lean production system design for fishing net
manufacturing using lean principles and simulation optimization. Journal of Manufacturing
Systems, 34, pp.66-73.
HUMAN RESOURCE MANAGEMENT
References:
James, R. and Jones, R., 2014. Transferring the Toyota lean cultural paradigm into India:
implications for human resource management. The International Journal of Human Resource
Management, 25(15), pp.2174-2191.
Rohani, J.M. and Zahraee, S.M., 2015. Production line analysis via value stream mapping: a lean
manufacturing process of color industry. Procedia Manufacturing, 2, pp.6-10.
Schwartz, M.S., 2013. Developing and sustaining an ethical corporate culture: The core
elements. Business Horizons, 56(1), pp.39-50.
Yang, T., Kuo, Y., Su, C.T. and Hou, C.L., 2015. Lean production system design for fishing net
manufacturing using lean principles and simulation optimization. Journal of Manufacturing
Systems, 34, pp.66-73.
1 out of 4
Related Documents

Your All-in-One AI-Powered Toolkit for Academic Success.
+13062052269
info@desklib.com
Available 24*7 on WhatsApp / Email
Unlock your academic potential
© 2024 | Zucol Services PVT LTD | All rights reserved.