Toyota's Operations: Role of Leaders and Managers in Automotive
VerifiedAdded on 2021/01/01
|24
|4812
|474
Report
AI Summary
This report provides a comprehensive analysis of Toyota's operational management, leadership approaches, and key strategies within the automotive industry. It begins with an introduction to Toyota, highlighting its global presence and market position. The report then explores the roles of managers and leaders, contrasting their responsibilities and influences in various situations, including operational inefficiencies and conflicts. Different leadership models, such as the system approach and situational leadership, are evaluated for their effectiveness. The report also examines Toyota's key operational functions, including product design, and the application of lean manufacturing principles. Furthermore, it analyzes the impact of leaders and managers on the organization, discussing practices that enhance production efficiency. The report concludes with suggestions and recommendations for maintaining and improving Toyota's operational effectiveness, drawing on concepts like Jidoka and Just-In-Time production systems, and emphasizes the importance of continuous improvement and employee engagement in achieving organizational goals.
Contribute Materials
Your contribution can guide someone’s learning journey. Share your
documents today.
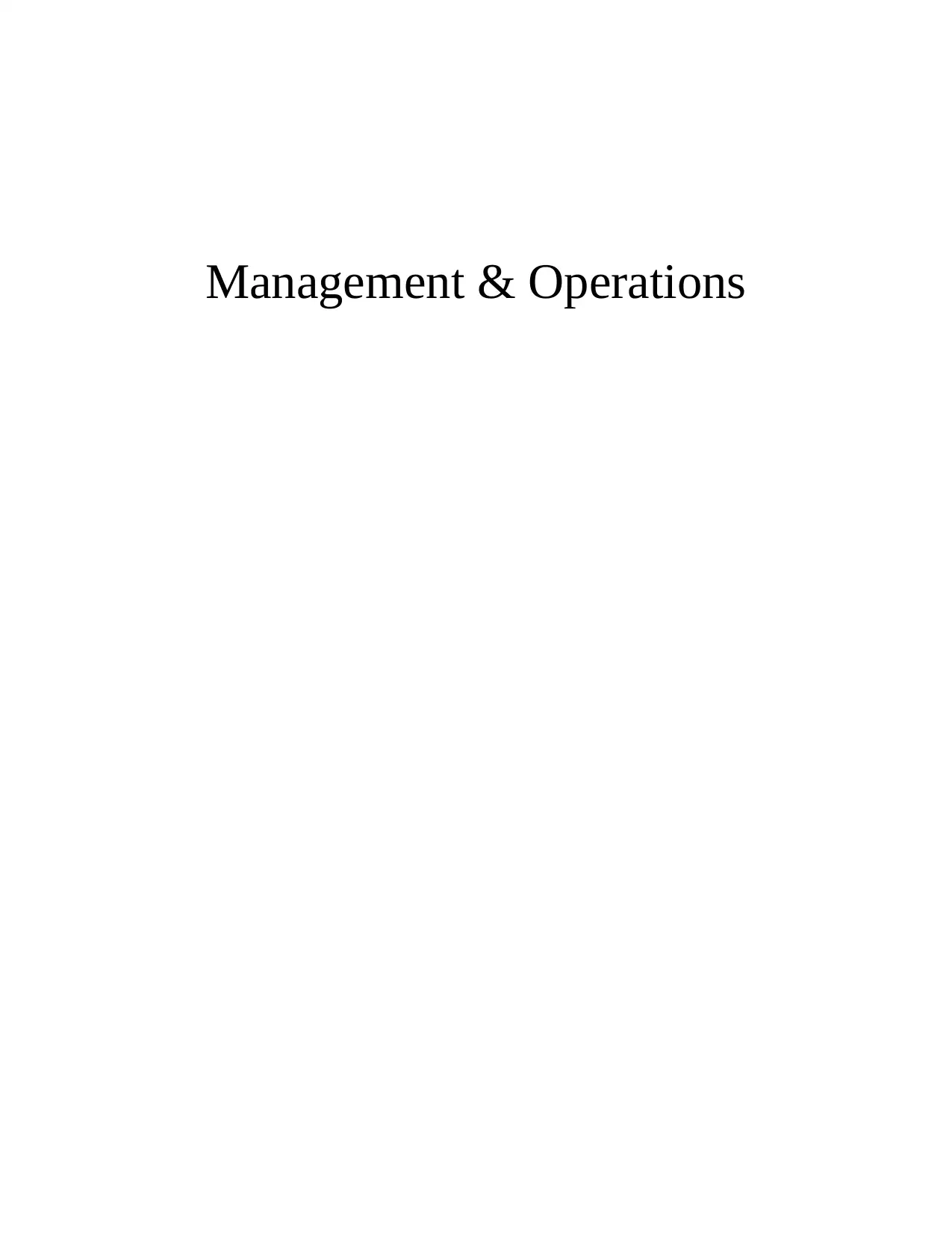
Management & Operations
Secure Best Marks with AI Grader
Need help grading? Try our AI Grader for instant feedback on your assignments.
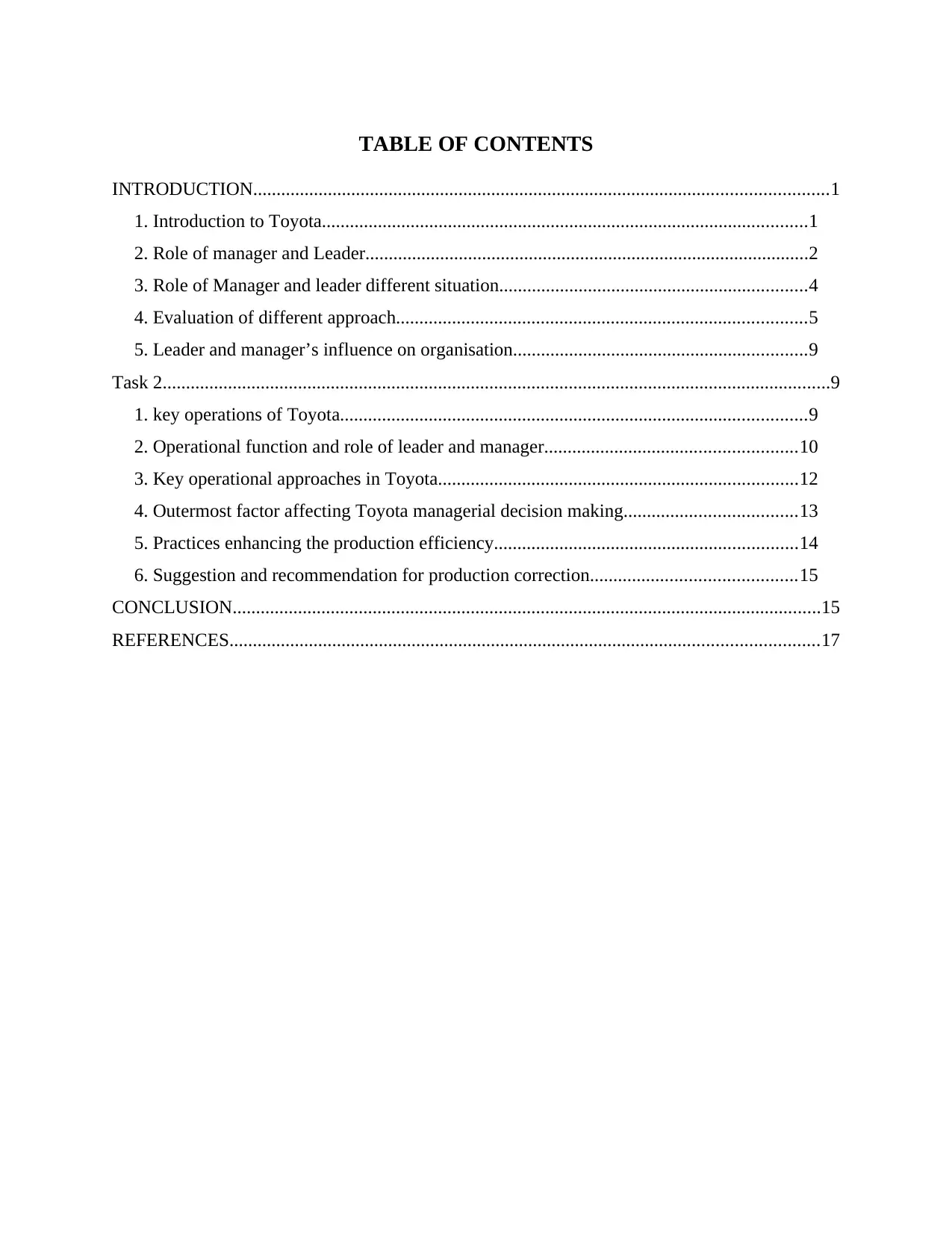
TABLE OF CONTENTS
INTRODUCTION...........................................................................................................................1
1. Introduction to Toyota........................................................................................................1
2. Role of manager and Leader...............................................................................................2
3. Role of Manager and leader different situation..................................................................4
4. Evaluation of different approach........................................................................................5
5. Leader and manager’s influence on organisation...............................................................9
Task 2...............................................................................................................................................9
1. key operations of Toyota....................................................................................................9
2. Operational function and role of leader and manager......................................................10
3. Key operational approaches in Toyota.............................................................................12
4. Outermost factor affecting Toyota managerial decision making.....................................13
5. Practices enhancing the production efficiency.................................................................14
6. Suggestion and recommendation for production correction............................................15
CONCLUSION..............................................................................................................................15
REFERENCES..............................................................................................................................17
INTRODUCTION...........................................................................................................................1
1. Introduction to Toyota........................................................................................................1
2. Role of manager and Leader...............................................................................................2
3. Role of Manager and leader different situation..................................................................4
4. Evaluation of different approach........................................................................................5
5. Leader and manager’s influence on organisation...............................................................9
Task 2...............................................................................................................................................9
1. key operations of Toyota....................................................................................................9
2. Operational function and role of leader and manager......................................................10
3. Key operational approaches in Toyota.............................................................................12
4. Outermost factor affecting Toyota managerial decision making.....................................13
5. Practices enhancing the production efficiency.................................................................14
6. Suggestion and recommendation for production correction............................................15
CONCLUSION..............................................................................................................................15
REFERENCES..............................................................................................................................17
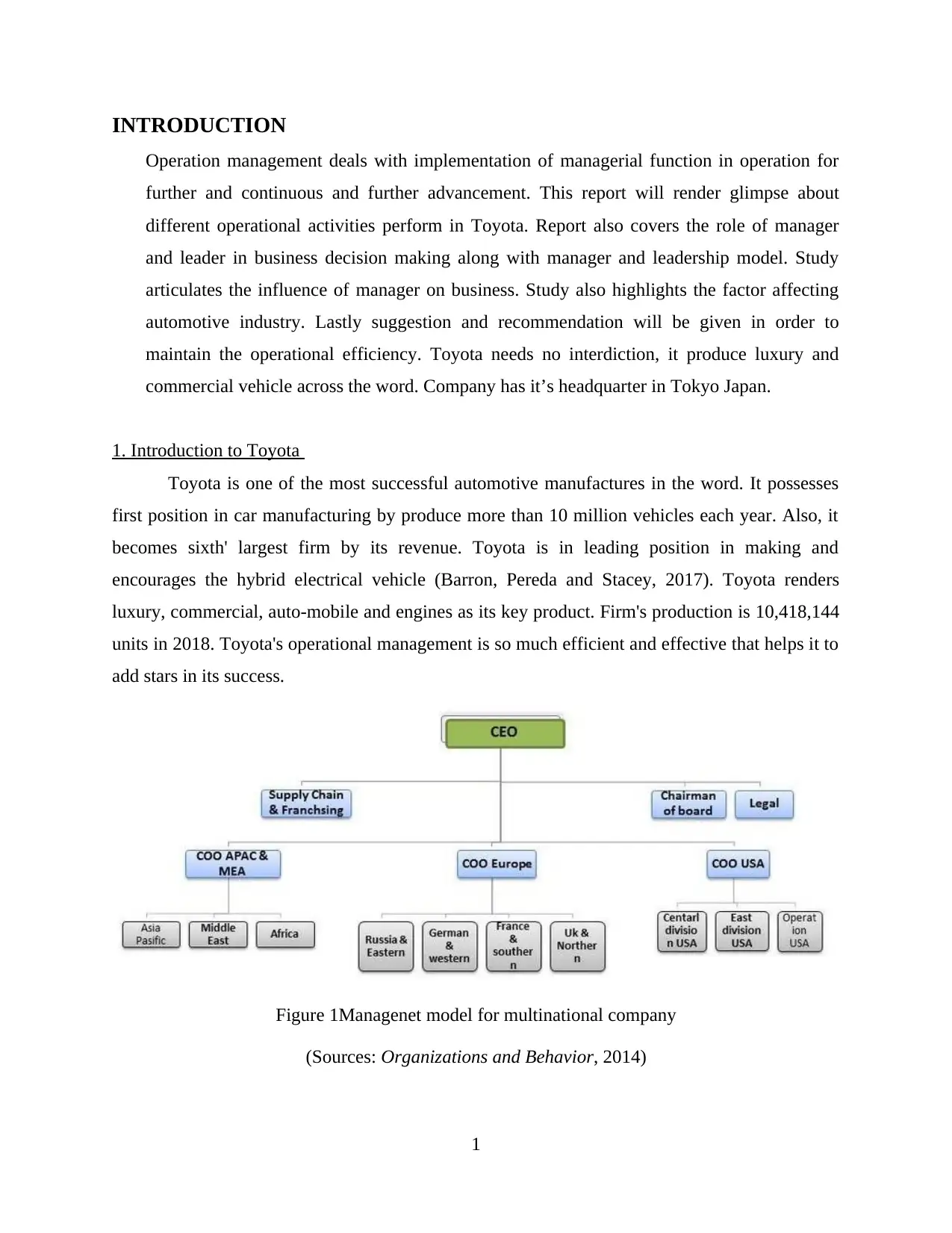
INTRODUCTION
Operation management deals with implementation of managerial function in operation for
further and continuous and further advancement. This report will render glimpse about
different operational activities perform in Toyota. Report also covers the role of manager
and leader in business decision making along with manager and leadership model. Study
articulates the influence of manager on business. Study also highlights the factor affecting
automotive industry. Lastly suggestion and recommendation will be given in order to
maintain the operational efficiency. Toyota needs no interdiction, it produce luxury and
commercial vehicle across the word. Company has it’s headquarter in Tokyo Japan.
1. Introduction to Toyota
Toyota is one of the most successful automotive manufactures in the word. It possesses
first position in car manufacturing by produce more than 10 million vehicles each year. Also, it
becomes sixth' largest firm by its revenue. Toyota is in leading position in making and
encourages the hybrid electrical vehicle (Barron, Pereda and Stacey, 2017). Toyota renders
luxury, commercial, auto-mobile and engines as its key product. Firm's production is 10,418,144
units in 2018. Toyota's operational management is so much efficient and effective that helps it to
add stars in its success.
Figure 1Managenet model for multinational company
(Sources: Organizations and Behavior, 2014)
1
Operation management deals with implementation of managerial function in operation for
further and continuous and further advancement. This report will render glimpse about
different operational activities perform in Toyota. Report also covers the role of manager
and leader in business decision making along with manager and leadership model. Study
articulates the influence of manager on business. Study also highlights the factor affecting
automotive industry. Lastly suggestion and recommendation will be given in order to
maintain the operational efficiency. Toyota needs no interdiction, it produce luxury and
commercial vehicle across the word. Company has it’s headquarter in Tokyo Japan.
1. Introduction to Toyota
Toyota is one of the most successful automotive manufactures in the word. It possesses
first position in car manufacturing by produce more than 10 million vehicles each year. Also, it
becomes sixth' largest firm by its revenue. Toyota is in leading position in making and
encourages the hybrid electrical vehicle (Barron, Pereda and Stacey, 2017). Toyota renders
luxury, commercial, auto-mobile and engines as its key product. Firm's production is 10,418,144
units in 2018. Toyota's operational management is so much efficient and effective that helps it to
add stars in its success.
Figure 1Managenet model for multinational company
(Sources: Organizations and Behavior, 2014)
1
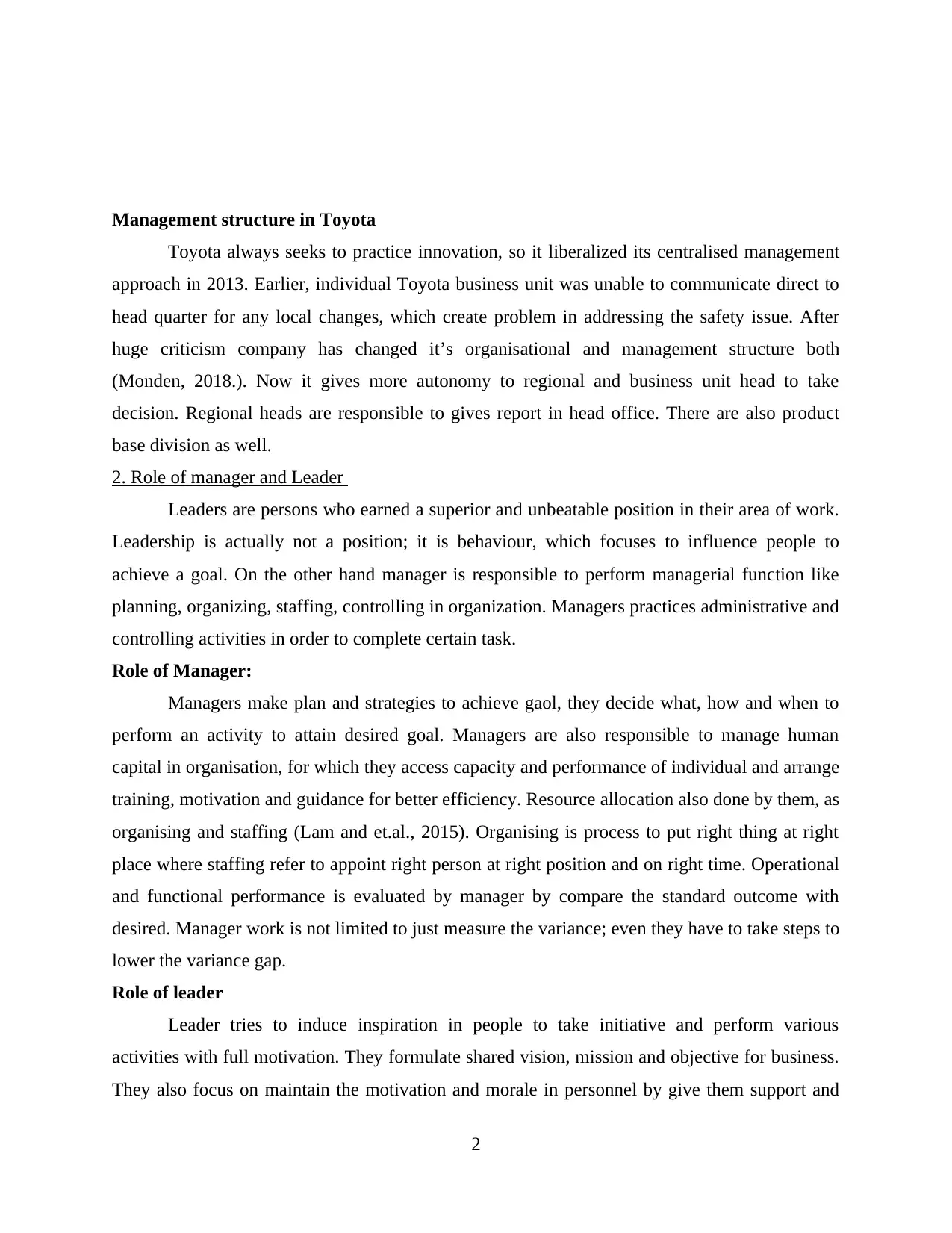
Management structure in Toyota
Toyota always seeks to practice innovation, so it liberalized its centralised management
approach in 2013. Earlier, individual Toyota business unit was unable to communicate direct to
head quarter for any local changes, which create problem in addressing the safety issue. After
huge criticism company has changed it’s organisational and management structure both
(Monden, 2018.). Now it gives more autonomy to regional and business unit head to take
decision. Regional heads are responsible to gives report in head office. There are also product
base division as well.
2. Role of manager and Leader
Leaders are persons who earned a superior and unbeatable position in their area of work.
Leadership is actually not a position; it is behaviour, which focuses to influence people to
achieve a goal. On the other hand manager is responsible to perform managerial function like
planning, organizing, staffing, controlling in organization. Managers practices administrative and
controlling activities in order to complete certain task.
Role of Manager:
Managers make plan and strategies to achieve gaol, they decide what, how and when to
perform an activity to attain desired goal. Managers are also responsible to manage human
capital in organisation, for which they access capacity and performance of individual and arrange
training, motivation and guidance for better efficiency. Resource allocation also done by them, as
organising and staffing (Lam and et.al., 2015). Organising is process to put right thing at right
place where staffing refer to appoint right person at right position and on right time. Operational
and functional performance is evaluated by manager by compare the standard outcome with
desired. Manager work is not limited to just measure the variance; even they have to take steps to
lower the variance gap.
Role of leader
Leader tries to induce inspiration in people to take initiative and perform various
activities with full motivation. They formulate shared vision, mission and objective for business.
They also focus on maintain the motivation and morale in personnel by give them support and
2
Toyota always seeks to practice innovation, so it liberalized its centralised management
approach in 2013. Earlier, individual Toyota business unit was unable to communicate direct to
head quarter for any local changes, which create problem in addressing the safety issue. After
huge criticism company has changed it’s organisational and management structure both
(Monden, 2018.). Now it gives more autonomy to regional and business unit head to take
decision. Regional heads are responsible to gives report in head office. There are also product
base division as well.
2. Role of manager and Leader
Leaders are persons who earned a superior and unbeatable position in their area of work.
Leadership is actually not a position; it is behaviour, which focuses to influence people to
achieve a goal. On the other hand manager is responsible to perform managerial function like
planning, organizing, staffing, controlling in organization. Managers practices administrative and
controlling activities in order to complete certain task.
Role of Manager:
Managers make plan and strategies to achieve gaol, they decide what, how and when to
perform an activity to attain desired goal. Managers are also responsible to manage human
capital in organisation, for which they access capacity and performance of individual and arrange
training, motivation and guidance for better efficiency. Resource allocation also done by them, as
organising and staffing (Lam and et.al., 2015). Organising is process to put right thing at right
place where staffing refer to appoint right person at right position and on right time. Operational
and functional performance is evaluated by manager by compare the standard outcome with
desired. Manager work is not limited to just measure the variance; even they have to take steps to
lower the variance gap.
Role of leader
Leader tries to induce inspiration in people to take initiative and perform various
activities with full motivation. They formulate shared vision, mission and objective for business.
They also focus on maintain the motivation and morale in personnel by give them support and
2
Secure Best Marks with AI Grader
Need help grading? Try our AI Grader for instant feedback on your assignments.
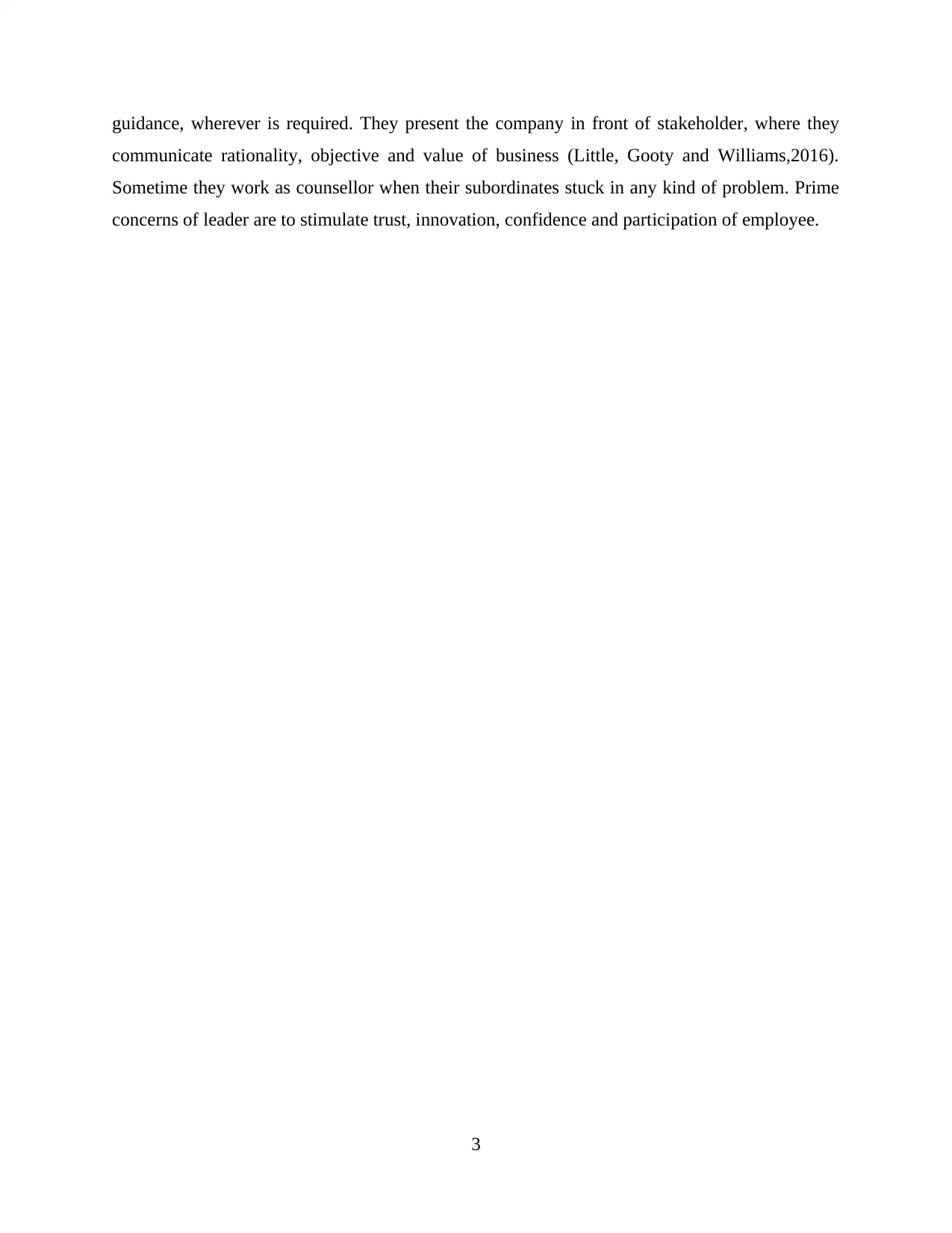
guidance, wherever is required. They present the company in front of stakeholder, where they
communicate rationality, objective and value of business (Little, Gooty and Williams,2016).
Sometime they work as counsellor when their subordinates stuck in any kind of problem. Prime
concerns of leader are to stimulate trust, innovation, confidence and participation of employee.
3
communicate rationality, objective and value of business (Little, Gooty and Williams,2016).
Sometime they work as counsellor when their subordinates stuck in any kind of problem. Prime
concerns of leader are to stimulate trust, innovation, confidence and participation of employee.
3
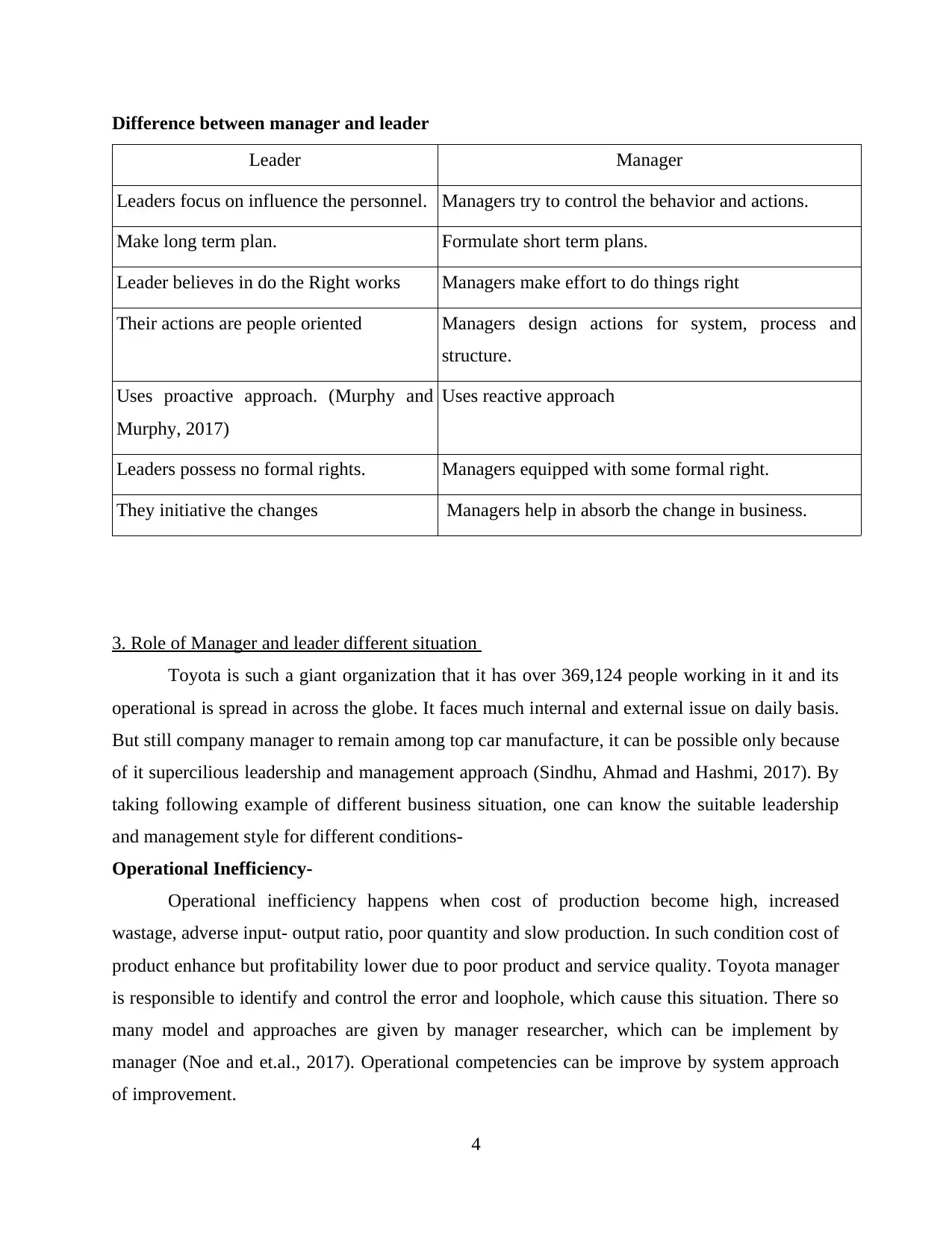
Difference between manager and leader
Leader Manager
Leaders focus on influence the personnel. Managers try to control the behavior and actions.
Make long term plan. Formulate short term plans.
Leader believes in do the Right works Managers make effort to do things right
Their actions are people oriented Managers design actions for system, process and
structure.
Uses proactive approach. (Murphy and
Murphy, 2017)
Uses reactive approach
Leaders possess no formal rights. Managers equipped with some formal right.
They initiative the changes Managers help in absorb the change in business.
3. Role of Manager and leader different situation
Toyota is such a giant organization that it has over 369,124 people working in it and its
operational is spread in across the globe. It faces much internal and external issue on daily basis.
But still company manager to remain among top car manufacture, it can be possible only because
of it supercilious leadership and management approach (Sindhu, Ahmad and Hashmi, 2017). By
taking following example of different business situation, one can know the suitable leadership
and management style for different conditions-
Operational Inefficiency-
Operational inefficiency happens when cost of production become high, increased
wastage, adverse input- output ratio, poor quantity and slow production. In such condition cost of
product enhance but profitability lower due to poor product and service quality. Toyota manager
is responsible to identify and control the error and loophole, which cause this situation. There so
many model and approaches are given by manager researcher, which can be implement by
manager (Noe and et.al., 2017). Operational competencies can be improve by system approach
of improvement.
4
Leader Manager
Leaders focus on influence the personnel. Managers try to control the behavior and actions.
Make long term plan. Formulate short term plans.
Leader believes in do the Right works Managers make effort to do things right
Their actions are people oriented Managers design actions for system, process and
structure.
Uses proactive approach. (Murphy and
Murphy, 2017)
Uses reactive approach
Leaders possess no formal rights. Managers equipped with some formal right.
They initiative the changes Managers help in absorb the change in business.
3. Role of Manager and leader different situation
Toyota is such a giant organization that it has over 369,124 people working in it and its
operational is spread in across the globe. It faces much internal and external issue on daily basis.
But still company manager to remain among top car manufacture, it can be possible only because
of it supercilious leadership and management approach (Sindhu, Ahmad and Hashmi, 2017). By
taking following example of different business situation, one can know the suitable leadership
and management style for different conditions-
Operational Inefficiency-
Operational inefficiency happens when cost of production become high, increased
wastage, adverse input- output ratio, poor quantity and slow production. In such condition cost of
product enhance but profitability lower due to poor product and service quality. Toyota manager
is responsible to identify and control the error and loophole, which cause this situation. There so
many model and approaches are given by manager researcher, which can be implement by
manager (Noe and et.al., 2017). Operational competencies can be improve by system approach
of improvement.
4
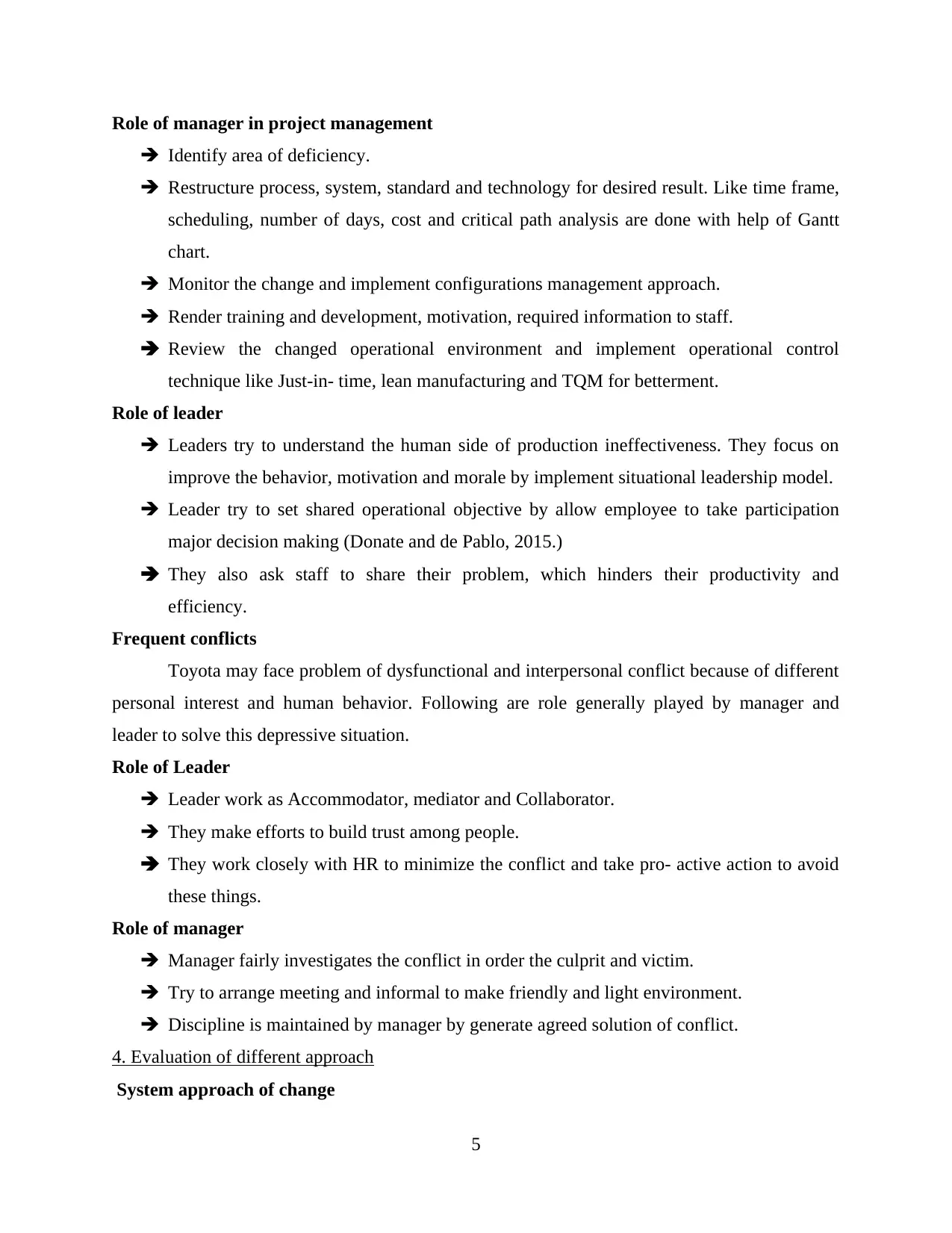
Role of manager in project management
Identify area of deficiency.
Restructure process, system, standard and technology for desired result. Like time frame,
scheduling, number of days, cost and critical path analysis are done with help of Gantt
chart.
Monitor the change and implement configurations management approach.
Render training and development, motivation, required information to staff.
Review the changed operational environment and implement operational control
technique like Just-in- time, lean manufacturing and TQM for betterment.
Role of leader
Leaders try to understand the human side of production ineffectiveness. They focus on
improve the behavior, motivation and morale by implement situational leadership model.
Leader try to set shared operational objective by allow employee to take participation
major decision making (Donate and de Pablo, 2015.)
They also ask staff to share their problem, which hinders their productivity and
efficiency.
Frequent conflicts
Toyota may face problem of dysfunctional and interpersonal conflict because of different
personal interest and human behavior. Following are role generally played by manager and
leader to solve this depressive situation.
Role of Leader
Leader work as Accommodator, mediator and Collaborator.
They make efforts to build trust among people.
They work closely with HR to minimize the conflict and take pro- active action to avoid
these things.
Role of manager
Manager fairly investigates the conflict in order the culprit and victim.
Try to arrange meeting and informal to make friendly and light environment.
Discipline is maintained by manager by generate agreed solution of conflict.
4. Evaluation of different approach
System approach of change
5
Identify area of deficiency.
Restructure process, system, standard and technology for desired result. Like time frame,
scheduling, number of days, cost and critical path analysis are done with help of Gantt
chart.
Monitor the change and implement configurations management approach.
Render training and development, motivation, required information to staff.
Review the changed operational environment and implement operational control
technique like Just-in- time, lean manufacturing and TQM for betterment.
Role of leader
Leaders try to understand the human side of production ineffectiveness. They focus on
improve the behavior, motivation and morale by implement situational leadership model.
Leader try to set shared operational objective by allow employee to take participation
major decision making (Donate and de Pablo, 2015.)
They also ask staff to share their problem, which hinders their productivity and
efficiency.
Frequent conflicts
Toyota may face problem of dysfunctional and interpersonal conflict because of different
personal interest and human behavior. Following are role generally played by manager and
leader to solve this depressive situation.
Role of Leader
Leader work as Accommodator, mediator and Collaborator.
They make efforts to build trust among people.
They work closely with HR to minimize the conflict and take pro- active action to avoid
these things.
Role of manager
Manager fairly investigates the conflict in order the culprit and victim.
Try to arrange meeting and informal to make friendly and light environment.
Discipline is maintained by manager by generate agreed solution of conflict.
4. Evaluation of different approach
System approach of change
5
Paraphrase This Document
Need a fresh take? Get an instant paraphrase of this document with our AI Paraphraser
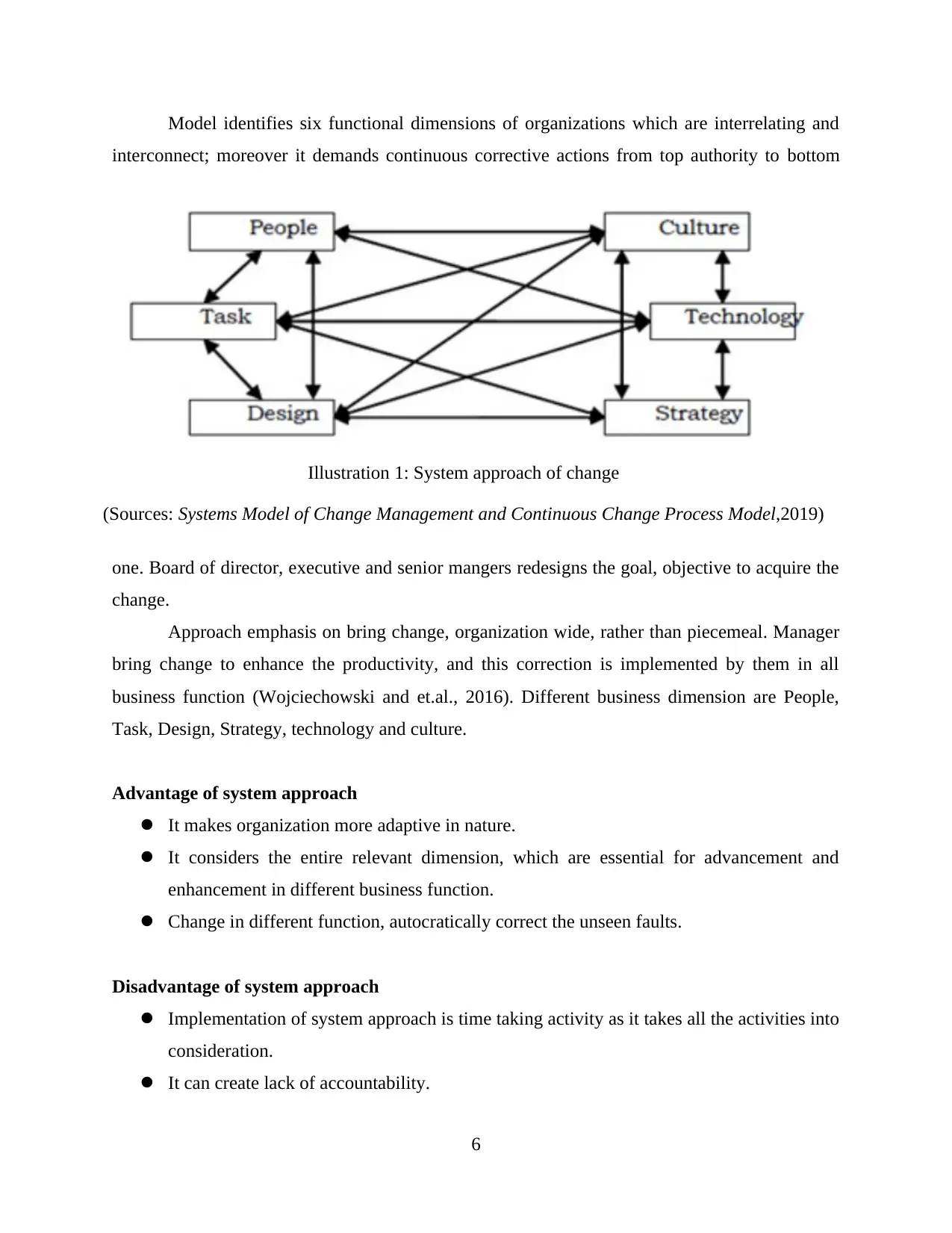
Model identifies six functional dimensions of organizations which are interrelating and
interconnect; moreover it demands continuous corrective actions from top authority to bottom
one. Board of director, executive and senior mangers redesigns the goal, objective to acquire the
change.
Approach emphasis on bring change, organization wide, rather than piecemeal. Manager
bring change to enhance the productivity, and this correction is implemented by them in all
business function (Wojciechowski and et.al., 2016). Different business dimension are People,
Task, Design, Strategy, technology and culture.
Advantage of system approach
It makes organization more adaptive in nature.
It considers the entire relevant dimension, which are essential for advancement and
enhancement in different business function.
Change in different function, autocratically correct the unseen faults.
Disadvantage of system approach
Implementation of system approach is time taking activity as it takes all the activities into
consideration.
It can create lack of accountability.
6
Illustration 1: System approach of change
(Sources: Systems Model of Change Management and Continuous Change Process Model,2019)
interconnect; moreover it demands continuous corrective actions from top authority to bottom
one. Board of director, executive and senior mangers redesigns the goal, objective to acquire the
change.
Approach emphasis on bring change, organization wide, rather than piecemeal. Manager
bring change to enhance the productivity, and this correction is implemented by them in all
business function (Wojciechowski and et.al., 2016). Different business dimension are People,
Task, Design, Strategy, technology and culture.
Advantage of system approach
It makes organization more adaptive in nature.
It considers the entire relevant dimension, which are essential for advancement and
enhancement in different business function.
Change in different function, autocratically correct the unseen faults.
Disadvantage of system approach
Implementation of system approach is time taking activity as it takes all the activities into
consideration.
It can create lack of accountability.
6
Illustration 1: System approach of change
(Sources: Systems Model of Change Management and Continuous Change Process Model,2019)
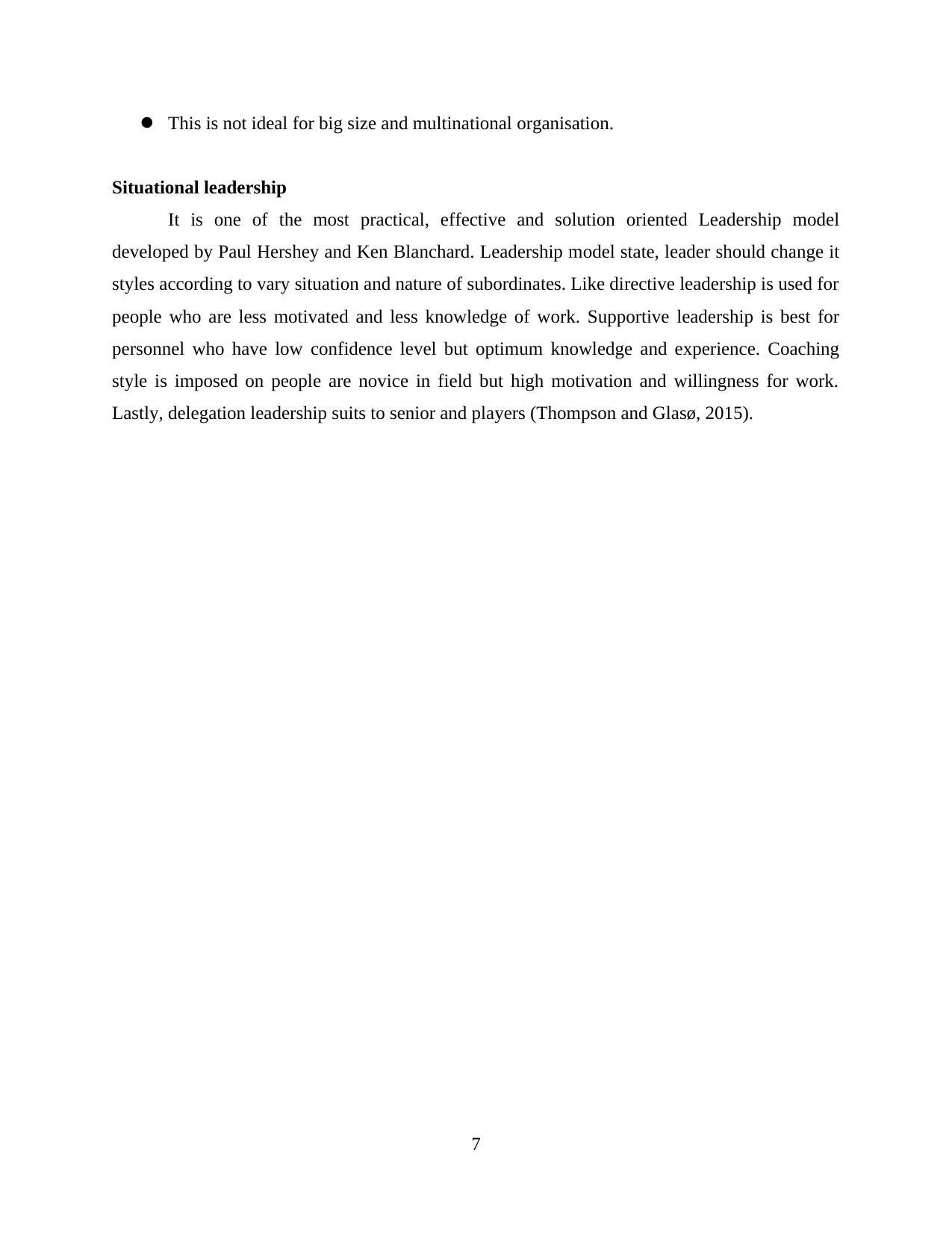
This is not ideal for big size and multinational organisation.
Situational leadership
It is one of the most practical, effective and solution oriented Leadership model
developed by Paul Hershey and Ken Blanchard. Leadership model state, leader should change it
styles according to vary situation and nature of subordinates. Like directive leadership is used for
people who are less motivated and less knowledge of work. Supportive leadership is best for
personnel who have low confidence level but optimum knowledge and experience. Coaching
style is imposed on people are novice in field but high motivation and willingness for work.
Lastly, delegation leadership suits to senior and players (Thompson and Glasø, 2015).
7
Situational leadership
It is one of the most practical, effective and solution oriented Leadership model
developed by Paul Hershey and Ken Blanchard. Leadership model state, leader should change it
styles according to vary situation and nature of subordinates. Like directive leadership is used for
people who are less motivated and less knowledge of work. Supportive leadership is best for
personnel who have low confidence level but optimum knowledge and experience. Coaching
style is imposed on people are novice in field but high motivation and willingness for work.
Lastly, delegation leadership suits to senior and players (Thompson and Glasø, 2015).
7
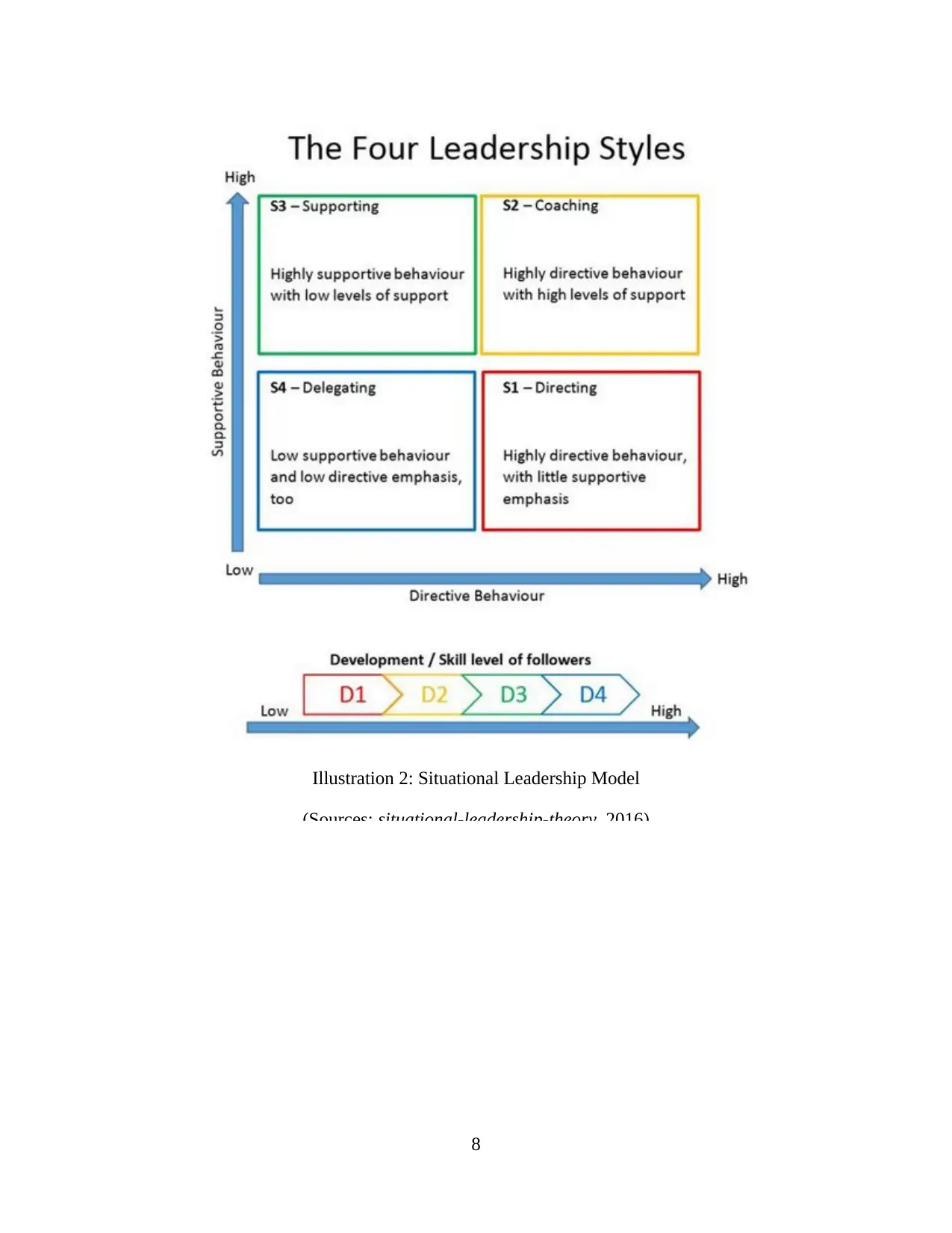
8
Illustration 2: Situational Leadership Model
(Sources: situational-leadership-theory, 2016)
Illustration 2: Situational Leadership Model
(Sources: situational-leadership-theory, 2016)
Secure Best Marks with AI Grader
Need help grading? Try our AI Grader for instant feedback on your assignments.
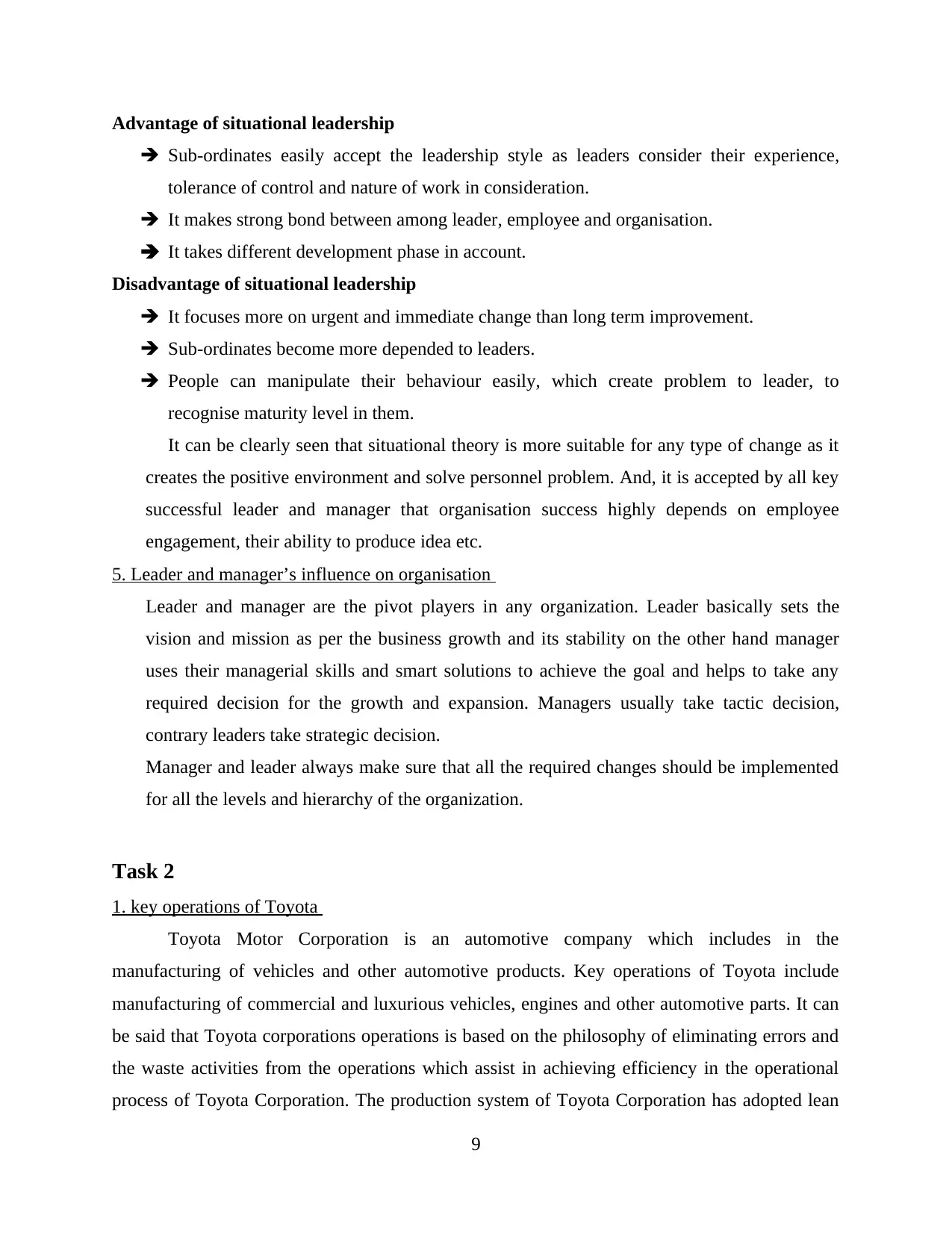
Advantage of situational leadership
Sub-ordinates easily accept the leadership style as leaders consider their experience,
tolerance of control and nature of work in consideration.
It makes strong bond between among leader, employee and organisation.
It takes different development phase in account.
Disadvantage of situational leadership
It focuses more on urgent and immediate change than long term improvement.
Sub-ordinates become more depended to leaders.
People can manipulate their behaviour easily, which create problem to leader, to
recognise maturity level in them.
It can be clearly seen that situational theory is more suitable for any type of change as it
creates the positive environment and solve personnel problem. And, it is accepted by all key
successful leader and manager that organisation success highly depends on employee
engagement, their ability to produce idea etc.
5. Leader and manager’s influence on organisation
Leader and manager are the pivot players in any organization. Leader basically sets the
vision and mission as per the business growth and its stability on the other hand manager
uses their managerial skills and smart solutions to achieve the goal and helps to take any
required decision for the growth and expansion. Managers usually take tactic decision,
contrary leaders take strategic decision.
Manager and leader always make sure that all the required changes should be implemented
for all the levels and hierarchy of the organization.
Task 2
1. key operations of Toyota
Toyota Motor Corporation is an automotive company which includes in the
manufacturing of vehicles and other automotive products. Key operations of Toyota include
manufacturing of commercial and luxurious vehicles, engines and other automotive parts. It can
be said that Toyota corporations operations is based on the philosophy of eliminating errors and
the waste activities from the operations which assist in achieving efficiency in the operational
process of Toyota Corporation. The production system of Toyota Corporation has adopted lean
9
Sub-ordinates easily accept the leadership style as leaders consider their experience,
tolerance of control and nature of work in consideration.
It makes strong bond between among leader, employee and organisation.
It takes different development phase in account.
Disadvantage of situational leadership
It focuses more on urgent and immediate change than long term improvement.
Sub-ordinates become more depended to leaders.
People can manipulate their behaviour easily, which create problem to leader, to
recognise maturity level in them.
It can be clearly seen that situational theory is more suitable for any type of change as it
creates the positive environment and solve personnel problem. And, it is accepted by all key
successful leader and manager that organisation success highly depends on employee
engagement, their ability to produce idea etc.
5. Leader and manager’s influence on organisation
Leader and manager are the pivot players in any organization. Leader basically sets the
vision and mission as per the business growth and its stability on the other hand manager
uses their managerial skills and smart solutions to achieve the goal and helps to take any
required decision for the growth and expansion. Managers usually take tactic decision,
contrary leaders take strategic decision.
Manager and leader always make sure that all the required changes should be implemented
for all the levels and hierarchy of the organization.
Task 2
1. key operations of Toyota
Toyota Motor Corporation is an automotive company which includes in the
manufacturing of vehicles and other automotive products. Key operations of Toyota include
manufacturing of commercial and luxurious vehicles, engines and other automotive parts. It can
be said that Toyota corporations operations is based on the philosophy of eliminating errors and
the waste activities from the operations which assist in achieving efficiency in the operational
process of Toyota Corporation. The production system of Toyota Corporation has adopted lean
9
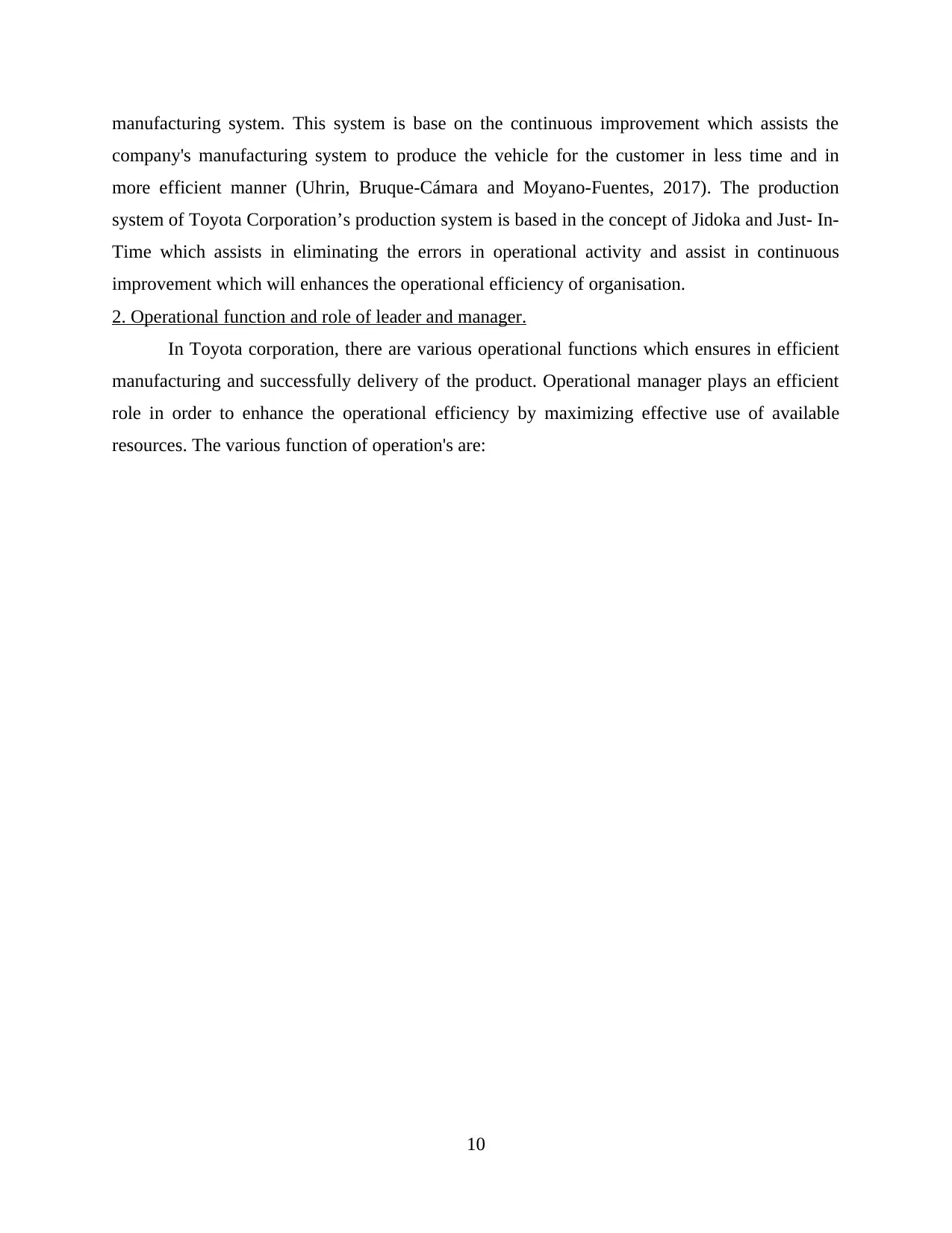
manufacturing system. This system is base on the continuous improvement which assists the
company's manufacturing system to produce the vehicle for the customer in less time and in
more efficient manner (Uhrin, Bruque-Cámara and Moyano-Fuentes, 2017). The production
system of Toyota Corporation’s production system is based in the concept of Jidoka and Just- In-
Time which assists in eliminating the errors in operational activity and assist in continuous
improvement which will enhances the operational efficiency of organisation.
2. Operational function and role of leader and manager.
In Toyota corporation, there are various operational functions which ensures in efficient
manufacturing and successfully delivery of the product. Operational manager plays an efficient
role in order to enhance the operational efficiency by maximizing effective use of available
resources. The various function of operation's are:
10
company's manufacturing system to produce the vehicle for the customer in less time and in
more efficient manner (Uhrin, Bruque-Cámara and Moyano-Fuentes, 2017). The production
system of Toyota Corporation’s production system is based in the concept of Jidoka and Just- In-
Time which assists in eliminating the errors in operational activity and assist in continuous
improvement which will enhances the operational efficiency of organisation.
2. Operational function and role of leader and manager.
In Toyota corporation, there are various operational functions which ensures in efficient
manufacturing and successfully delivery of the product. Operational manager plays an efficient
role in order to enhance the operational efficiency by maximizing effective use of available
resources. The various function of operation's are:
10
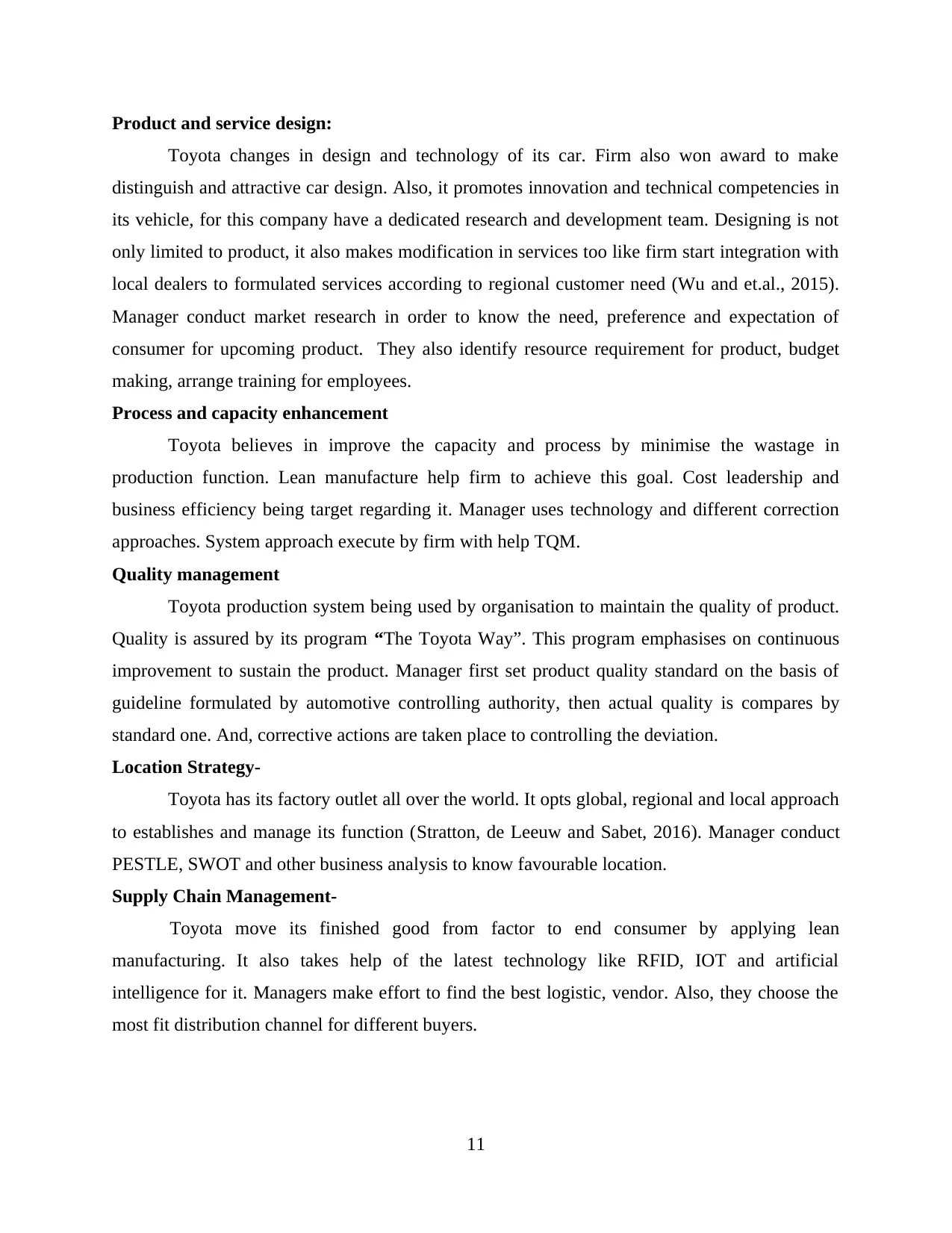
Product and service design:
Toyota changes in design and technology of its car. Firm also won award to make
distinguish and attractive car design. Also, it promotes innovation and technical competencies in
its vehicle, for this company have a dedicated research and development team. Designing is not
only limited to product, it also makes modification in services too like firm start integration with
local dealers to formulated services according to regional customer need (Wu and et.al., 2015).
Manager conduct market research in order to know the need, preference and expectation of
consumer for upcoming product. They also identify resource requirement for product, budget
making, arrange training for employees.
Process and capacity enhancement
Toyota believes in improve the capacity and process by minimise the wastage in
production function. Lean manufacture help firm to achieve this goal. Cost leadership and
business efficiency being target regarding it. Manager uses technology and different correction
approaches. System approach execute by firm with help TQM.
Quality management
Toyota production system being used by organisation to maintain the quality of product.
Quality is assured by its program “The Toyota Way”. This program emphasises on continuous
improvement to sustain the product. Manager first set product quality standard on the basis of
guideline formulated by automotive controlling authority, then actual quality is compares by
standard one. And, corrective actions are taken place to controlling the deviation.
Location Strategy-
Toyota has its factory outlet all over the world. It opts global, regional and local approach
to establishes and manage its function (Stratton, de Leeuw and Sabet, 2016). Manager conduct
PESTLE, SWOT and other business analysis to know favourable location.
Supply Chain Management-
Toyota move its finished good from factor to end consumer by applying lean
manufacturing. It also takes help of the latest technology like RFID, IOT and artificial
intelligence for it. Managers make effort to find the best logistic, vendor. Also, they choose the
most fit distribution channel for different buyers.
11
Toyota changes in design and technology of its car. Firm also won award to make
distinguish and attractive car design. Also, it promotes innovation and technical competencies in
its vehicle, for this company have a dedicated research and development team. Designing is not
only limited to product, it also makes modification in services too like firm start integration with
local dealers to formulated services according to regional customer need (Wu and et.al., 2015).
Manager conduct market research in order to know the need, preference and expectation of
consumer for upcoming product. They also identify resource requirement for product, budget
making, arrange training for employees.
Process and capacity enhancement
Toyota believes in improve the capacity and process by minimise the wastage in
production function. Lean manufacture help firm to achieve this goal. Cost leadership and
business efficiency being target regarding it. Manager uses technology and different correction
approaches. System approach execute by firm with help TQM.
Quality management
Toyota production system being used by organisation to maintain the quality of product.
Quality is assured by its program “The Toyota Way”. This program emphasises on continuous
improvement to sustain the product. Manager first set product quality standard on the basis of
guideline formulated by automotive controlling authority, then actual quality is compares by
standard one. And, corrective actions are taken place to controlling the deviation.
Location Strategy-
Toyota has its factory outlet all over the world. It opts global, regional and local approach
to establishes and manage its function (Stratton, de Leeuw and Sabet, 2016). Manager conduct
PESTLE, SWOT and other business analysis to know favourable location.
Supply Chain Management-
Toyota move its finished good from factor to end consumer by applying lean
manufacturing. It also takes help of the latest technology like RFID, IOT and artificial
intelligence for it. Managers make effort to find the best logistic, vendor. Also, they choose the
most fit distribution channel for different buyers.
11
Paraphrase This Document
Need a fresh take? Get an instant paraphrase of this document with our AI Paraphraser
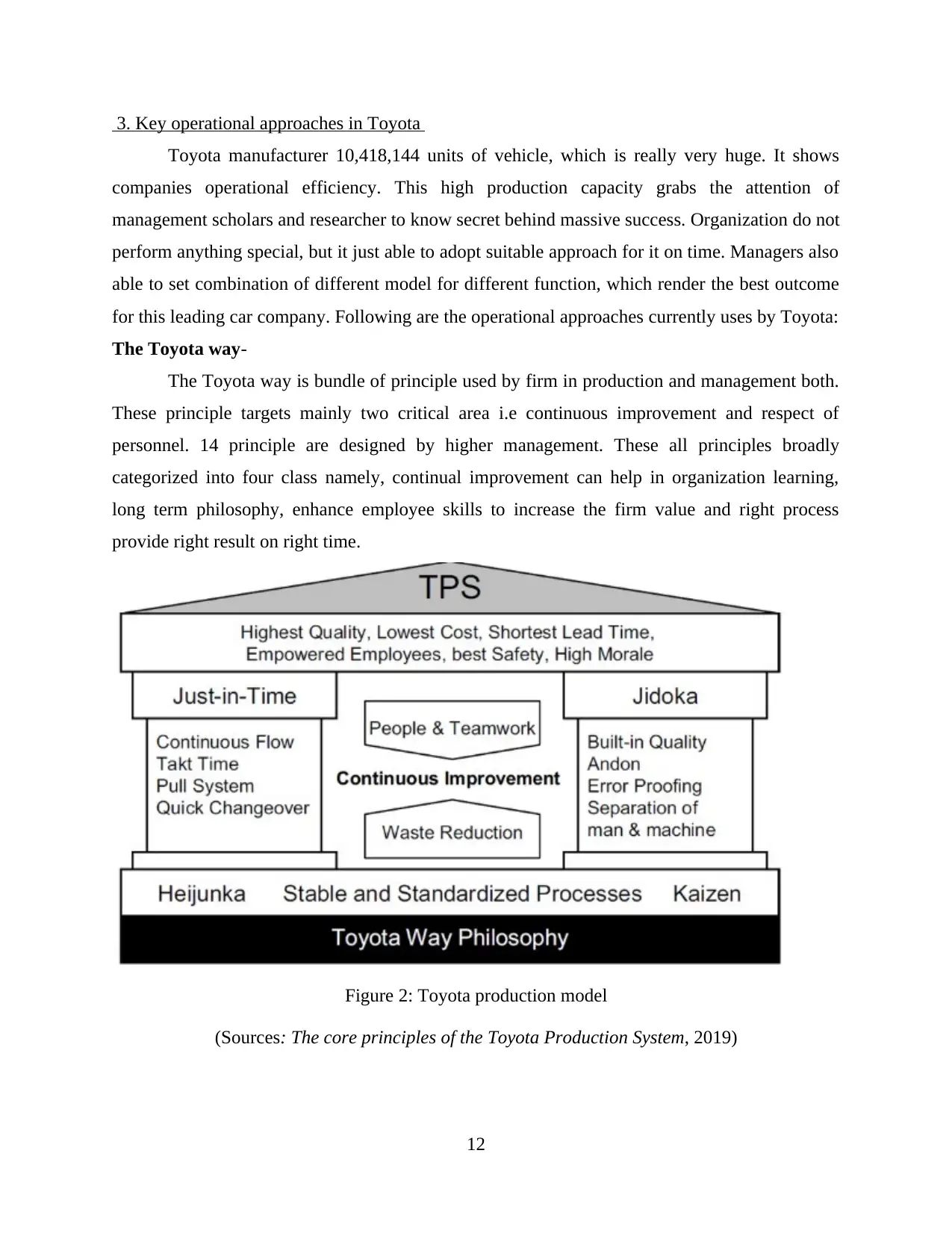
3. Key operational approaches in Toyota
Toyota manufacturer 10,418,144 units of vehicle, which is really very huge. It shows
companies operational efficiency. This high production capacity grabs the attention of
management scholars and researcher to know secret behind massive success. Organization do not
perform anything special, but it just able to adopt suitable approach for it on time. Managers also
able to set combination of different model for different function, which render the best outcome
for this leading car company. Following are the operational approaches currently uses by Toyota:
The Toyota way-
The Toyota way is bundle of principle used by firm in production and management both.
These principle targets mainly two critical area i.e continuous improvement and respect of
personnel. 14 principle are designed by higher management. These all principles broadly
categorized into four class namely, continual improvement can help in organization learning,
long term philosophy, enhance employee skills to increase the firm value and right process
provide right result on right time.
Figure 2: Toyota production model
(Sources: The core principles of the Toyota Production System, 2019)
12
Toyota manufacturer 10,418,144 units of vehicle, which is really very huge. It shows
companies operational efficiency. This high production capacity grabs the attention of
management scholars and researcher to know secret behind massive success. Organization do not
perform anything special, but it just able to adopt suitable approach for it on time. Managers also
able to set combination of different model for different function, which render the best outcome
for this leading car company. Following are the operational approaches currently uses by Toyota:
The Toyota way-
The Toyota way is bundle of principle used by firm in production and management both.
These principle targets mainly two critical area i.e continuous improvement and respect of
personnel. 14 principle are designed by higher management. These all principles broadly
categorized into four class namely, continual improvement can help in organization learning,
long term philosophy, enhance employee skills to increase the firm value and right process
provide right result on right time.
Figure 2: Toyota production model
(Sources: The core principles of the Toyota Production System, 2019)
12
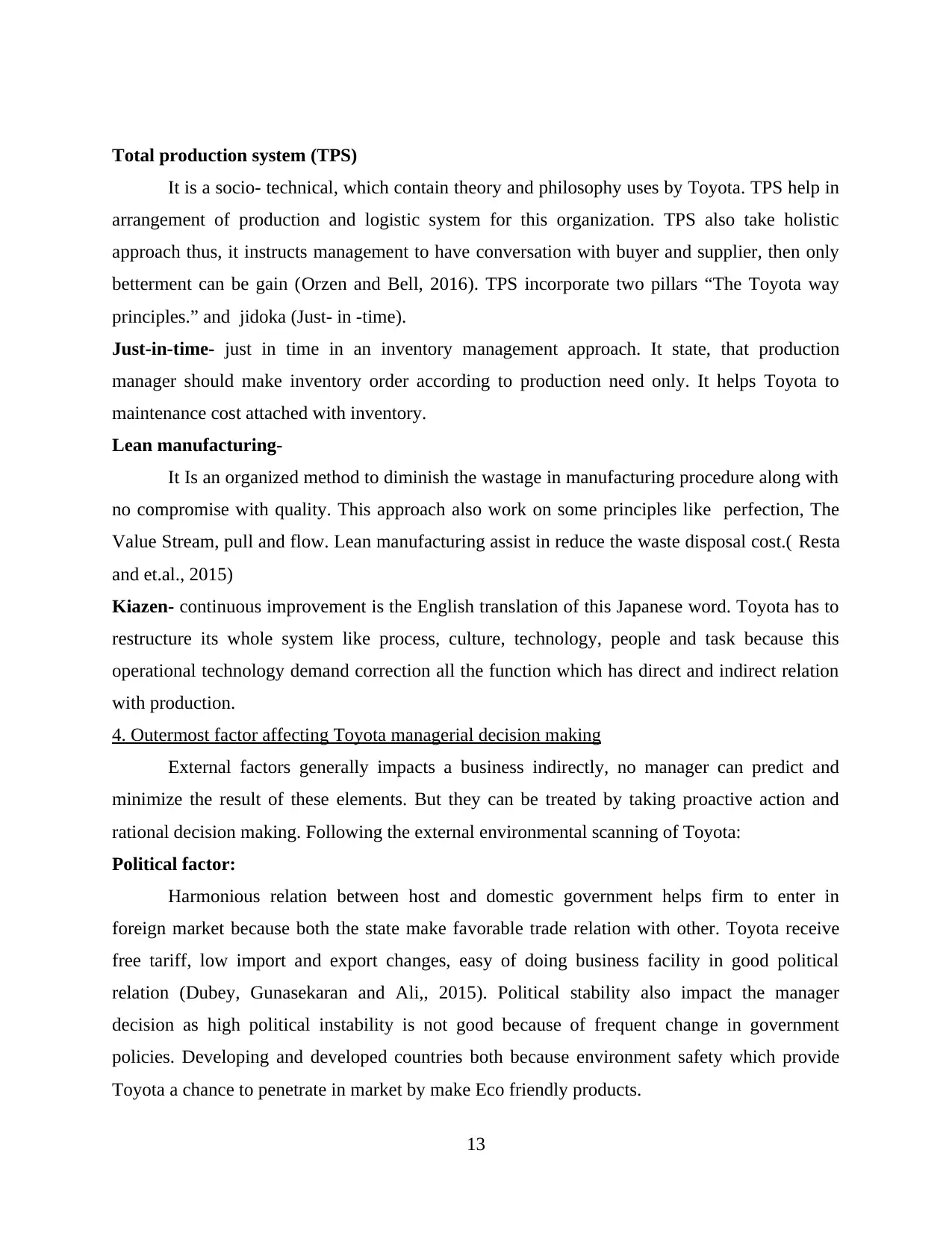
Total production system (TPS)
It is a socio- technical, which contain theory and philosophy uses by Toyota. TPS help in
arrangement of production and logistic system for this organization. TPS also take holistic
approach thus, it instructs management to have conversation with buyer and supplier, then only
betterment can be gain (Orzen and Bell, 2016). TPS incorporate two pillars “The Toyota way
principles.” and jidoka (Just- in -time).
Just-in-time- just in time in an inventory management approach. It state, that production
manager should make inventory order according to production need only. It helps Toyota to
maintenance cost attached with inventory.
Lean manufacturing-
It Is an organized method to diminish the wastage in manufacturing procedure along with
no compromise with quality. This approach also work on some principles like perfection, The
Value Stream, pull and flow. Lean manufacturing assist in reduce the waste disposal cost.( Resta
and et.al., 2015)
Kiazen- continuous improvement is the English translation of this Japanese word. Toyota has to
restructure its whole system like process, culture, technology, people and task because this
operational technology demand correction all the function which has direct and indirect relation
with production.
4. Outermost factor affecting Toyota managerial decision making
External factors generally impacts a business indirectly, no manager can predict and
minimize the result of these elements. But they can be treated by taking proactive action and
rational decision making. Following the external environmental scanning of Toyota:
Political factor:
Harmonious relation between host and domestic government helps firm to enter in
foreign market because both the state make favorable trade relation with other. Toyota receive
free tariff, low import and export changes, easy of doing business facility in good political
relation (Dubey, Gunasekaran and Ali,, 2015). Political stability also impact the manager
decision as high political instability is not good because of frequent change in government
policies. Developing and developed countries both because environment safety which provide
Toyota a chance to penetrate in market by make Eco friendly products.
13
It is a socio- technical, which contain theory and philosophy uses by Toyota. TPS help in
arrangement of production and logistic system for this organization. TPS also take holistic
approach thus, it instructs management to have conversation with buyer and supplier, then only
betterment can be gain (Orzen and Bell, 2016). TPS incorporate two pillars “The Toyota way
principles.” and jidoka (Just- in -time).
Just-in-time- just in time in an inventory management approach. It state, that production
manager should make inventory order according to production need only. It helps Toyota to
maintenance cost attached with inventory.
Lean manufacturing-
It Is an organized method to diminish the wastage in manufacturing procedure along with
no compromise with quality. This approach also work on some principles like perfection, The
Value Stream, pull and flow. Lean manufacturing assist in reduce the waste disposal cost.( Resta
and et.al., 2015)
Kiazen- continuous improvement is the English translation of this Japanese word. Toyota has to
restructure its whole system like process, culture, technology, people and task because this
operational technology demand correction all the function which has direct and indirect relation
with production.
4. Outermost factor affecting Toyota managerial decision making
External factors generally impacts a business indirectly, no manager can predict and
minimize the result of these elements. But they can be treated by taking proactive action and
rational decision making. Following the external environmental scanning of Toyota:
Political factor:
Harmonious relation between host and domestic government helps firm to enter in
foreign market because both the state make favorable trade relation with other. Toyota receive
free tariff, low import and export changes, easy of doing business facility in good political
relation (Dubey, Gunasekaran and Ali,, 2015). Political stability also impact the manager
decision as high political instability is not good because of frequent change in government
policies. Developing and developed countries both because environment safety which provide
Toyota a chance to penetrate in market by make Eco friendly products.
13
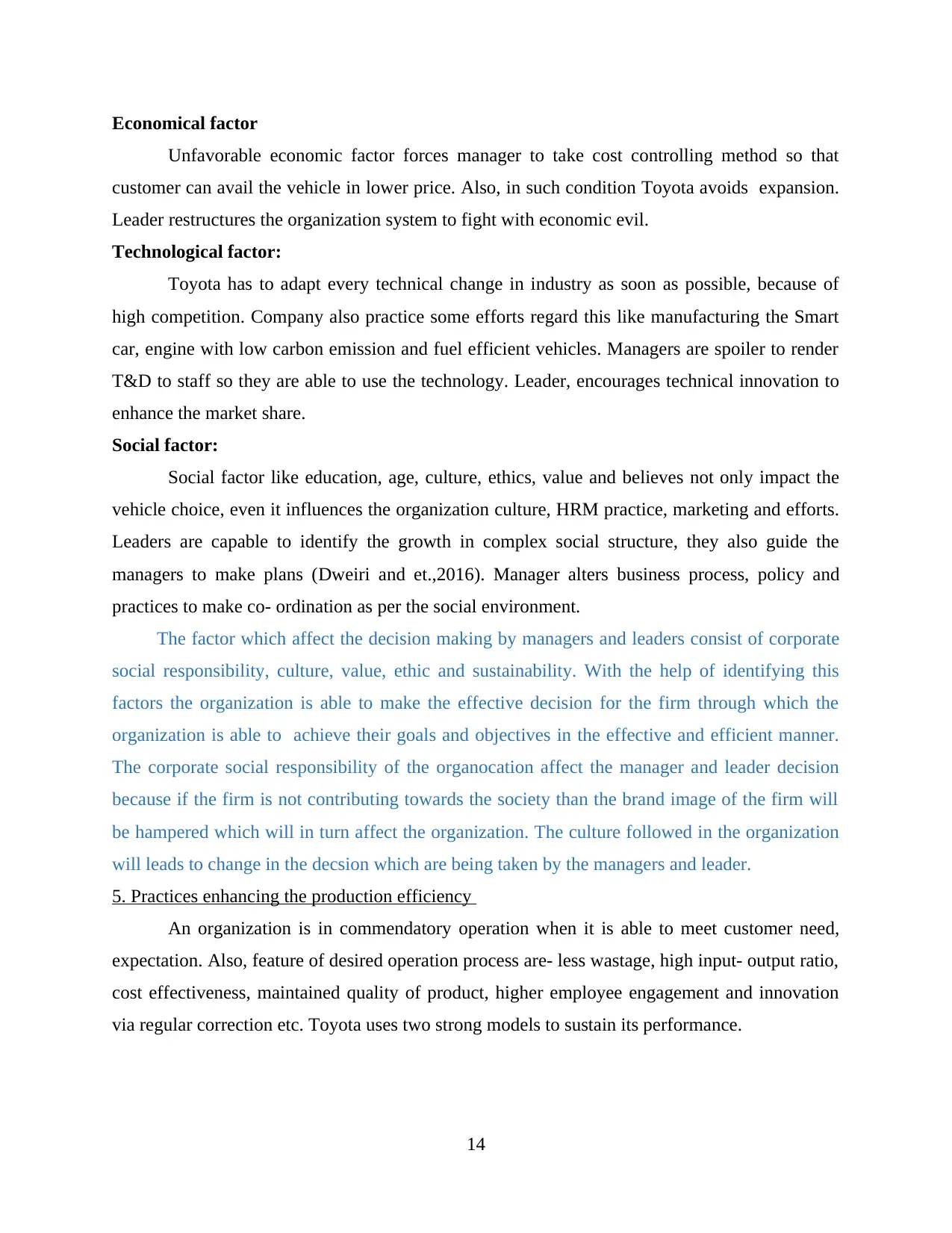
Economical factor
Unfavorable economic factor forces manager to take cost controlling method so that
customer can avail the vehicle in lower price. Also, in such condition Toyota avoids expansion.
Leader restructures the organization system to fight with economic evil.
Technological factor:
Toyota has to adapt every technical change in industry as soon as possible, because of
high competition. Company also practice some efforts regard this like manufacturing the Smart
car, engine with low carbon emission and fuel efficient vehicles. Managers are spoiler to render
T&D to staff so they are able to use the technology. Leader, encourages technical innovation to
enhance the market share.
Social factor:
Social factor like education, age, culture, ethics, value and believes not only impact the
vehicle choice, even it influences the organization culture, HRM practice, marketing and efforts.
Leaders are capable to identify the growth in complex social structure, they also guide the
managers to make plans (Dweiri and et.,2016). Manager alters business process, policy and
practices to make co- ordination as per the social environment.
The factor which affect the decision making by managers and leaders consist of corporate
social responsibility, culture, value, ethic and sustainability. With the help of identifying this
factors the organization is able to make the effective decision for the firm through which the
organization is able to achieve their goals and objectives in the effective and efficient manner.
The corporate social responsibility of the organocation affect the manager and leader decision
because if the firm is not contributing towards the society than the brand image of the firm will
be hampered which will in turn affect the organization. The culture followed in the organization
will leads to change in the decsion which are being taken by the managers and leader.
5. Practices enhancing the production efficiency
An organization is in commendatory operation when it is able to meet customer need,
expectation. Also, feature of desired operation process are- less wastage, high input- output ratio,
cost effectiveness, maintained quality of product, higher employee engagement and innovation
via regular correction etc. Toyota uses two strong models to sustain its performance.
14
Unfavorable economic factor forces manager to take cost controlling method so that
customer can avail the vehicle in lower price. Also, in such condition Toyota avoids expansion.
Leader restructures the organization system to fight with economic evil.
Technological factor:
Toyota has to adapt every technical change in industry as soon as possible, because of
high competition. Company also practice some efforts regard this like manufacturing the Smart
car, engine with low carbon emission and fuel efficient vehicles. Managers are spoiler to render
T&D to staff so they are able to use the technology. Leader, encourages technical innovation to
enhance the market share.
Social factor:
Social factor like education, age, culture, ethics, value and believes not only impact the
vehicle choice, even it influences the organization culture, HRM practice, marketing and efforts.
Leaders are capable to identify the growth in complex social structure, they also guide the
managers to make plans (Dweiri and et.,2016). Manager alters business process, policy and
practices to make co- ordination as per the social environment.
The factor which affect the decision making by managers and leaders consist of corporate
social responsibility, culture, value, ethic and sustainability. With the help of identifying this
factors the organization is able to make the effective decision for the firm through which the
organization is able to achieve their goals and objectives in the effective and efficient manner.
The corporate social responsibility of the organocation affect the manager and leader decision
because if the firm is not contributing towards the society than the brand image of the firm will
be hampered which will in turn affect the organization. The culture followed in the organization
will leads to change in the decsion which are being taken by the managers and leader.
5. Practices enhancing the production efficiency
An organization is in commendatory operation when it is able to meet customer need,
expectation. Also, feature of desired operation process are- less wastage, high input- output ratio,
cost effectiveness, maintained quality of product, higher employee engagement and innovation
via regular correction etc. Toyota uses two strong models to sustain its performance.
14
Secure Best Marks with AI Grader
Need help grading? Try our AI Grader for instant feedback on your assignments.
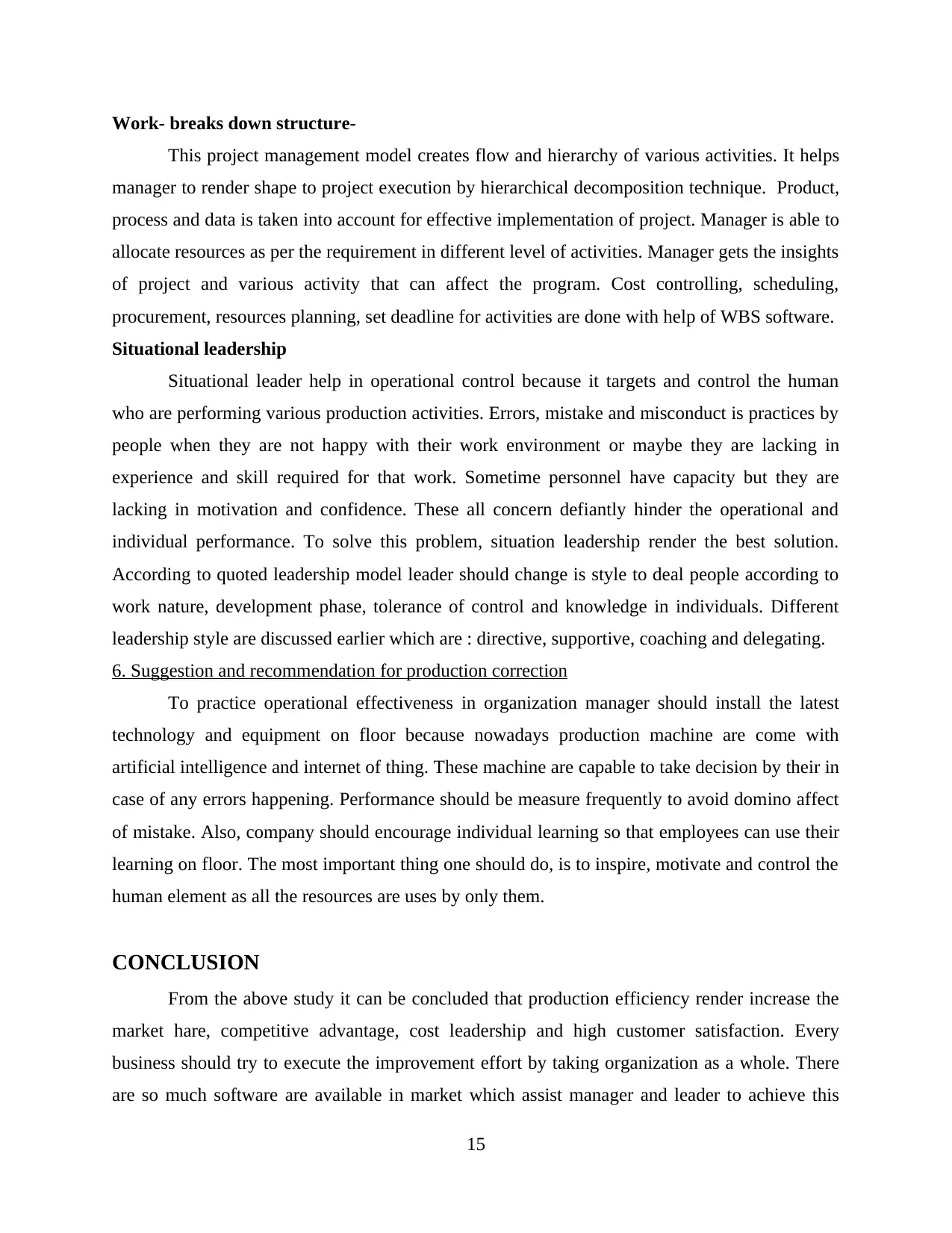
Work- breaks down structure-
This project management model creates flow and hierarchy of various activities. It helps
manager to render shape to project execution by hierarchical decomposition technique. Product,
process and data is taken into account for effective implementation of project. Manager is able to
allocate resources as per the requirement in different level of activities. Manager gets the insights
of project and various activity that can affect the program. Cost controlling, scheduling,
procurement, resources planning, set deadline for activities are done with help of WBS software.
Situational leadership
Situational leader help in operational control because it targets and control the human
who are performing various production activities. Errors, mistake and misconduct is practices by
people when they are not happy with their work environment or maybe they are lacking in
experience and skill required for that work. Sometime personnel have capacity but they are
lacking in motivation and confidence. These all concern defiantly hinder the operational and
individual performance. To solve this problem, situation leadership render the best solution.
According to quoted leadership model leader should change is style to deal people according to
work nature, development phase, tolerance of control and knowledge in individuals. Different
leadership style are discussed earlier which are : directive, supportive, coaching and delegating.
6. Suggestion and recommendation for production correction
To practice operational effectiveness in organization manager should install the latest
technology and equipment on floor because nowadays production machine are come with
artificial intelligence and internet of thing. These machine are capable to take decision by their in
case of any errors happening. Performance should be measure frequently to avoid domino affect
of mistake. Also, company should encourage individual learning so that employees can use their
learning on floor. The most important thing one should do, is to inspire, motivate and control the
human element as all the resources are uses by only them.
CONCLUSION
From the above study it can be concluded that production efficiency render increase the
market hare, competitive advantage, cost leadership and high customer satisfaction. Every
business should try to execute the improvement effort by taking organization as a whole. There
are so much software are available in market which assist manager and leader to achieve this
15
This project management model creates flow and hierarchy of various activities. It helps
manager to render shape to project execution by hierarchical decomposition technique. Product,
process and data is taken into account for effective implementation of project. Manager is able to
allocate resources as per the requirement in different level of activities. Manager gets the insights
of project and various activity that can affect the program. Cost controlling, scheduling,
procurement, resources planning, set deadline for activities are done with help of WBS software.
Situational leadership
Situational leader help in operational control because it targets and control the human
who are performing various production activities. Errors, mistake and misconduct is practices by
people when they are not happy with their work environment or maybe they are lacking in
experience and skill required for that work. Sometime personnel have capacity but they are
lacking in motivation and confidence. These all concern defiantly hinder the operational and
individual performance. To solve this problem, situation leadership render the best solution.
According to quoted leadership model leader should change is style to deal people according to
work nature, development phase, tolerance of control and knowledge in individuals. Different
leadership style are discussed earlier which are : directive, supportive, coaching and delegating.
6. Suggestion and recommendation for production correction
To practice operational effectiveness in organization manager should install the latest
technology and equipment on floor because nowadays production machine are come with
artificial intelligence and internet of thing. These machine are capable to take decision by their in
case of any errors happening. Performance should be measure frequently to avoid domino affect
of mistake. Also, company should encourage individual learning so that employees can use their
learning on floor. The most important thing one should do, is to inspire, motivate and control the
human element as all the resources are uses by only them.
CONCLUSION
From the above study it can be concluded that production efficiency render increase the
market hare, competitive advantage, cost leadership and high customer satisfaction. Every
business should try to execute the improvement effort by taking organization as a whole. There
are so much software are available in market which assist manager and leader to achieve this
15
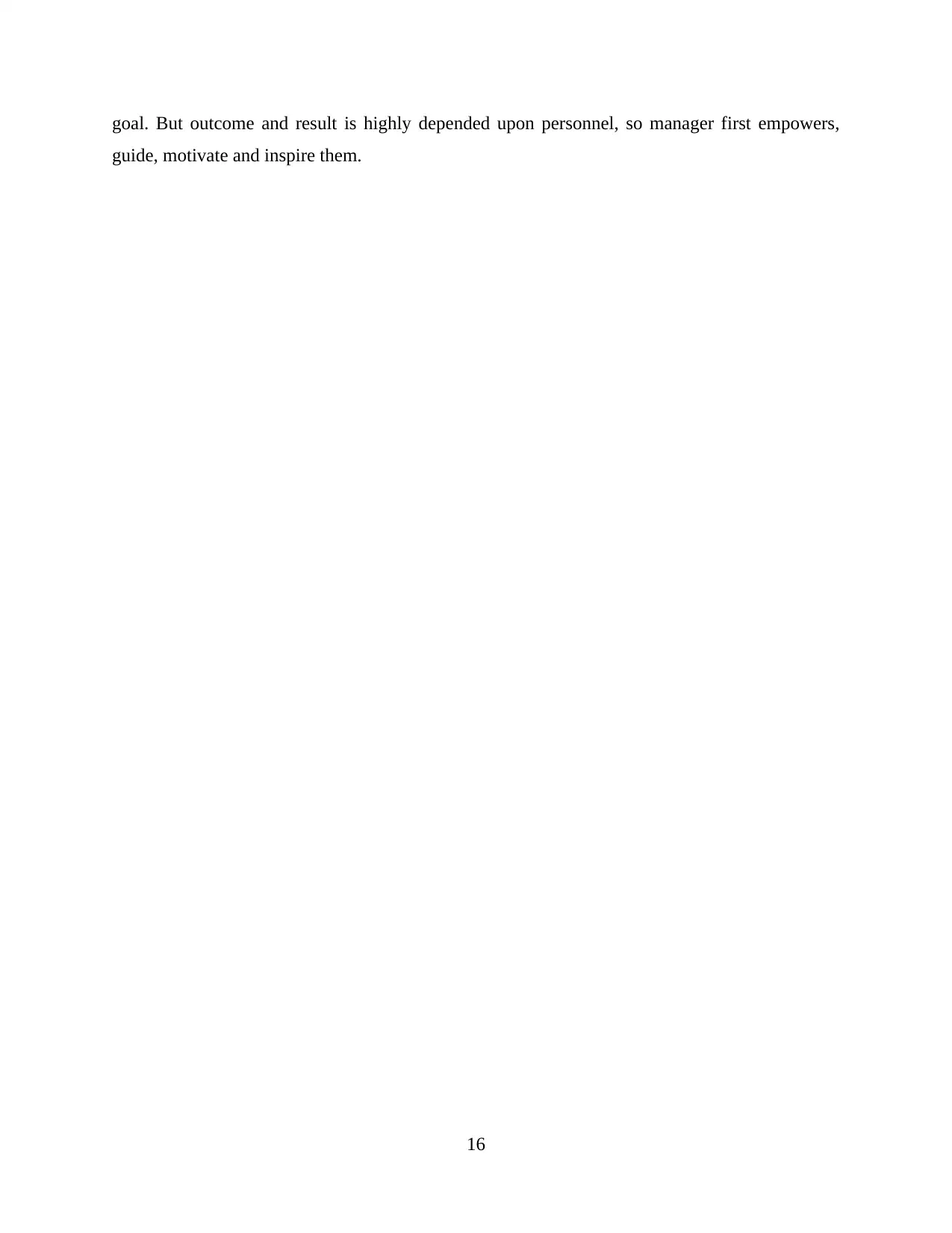
goal. But outcome and result is highly depended upon personnel, so manager first empowers,
guide, motivate and inspire them.
16
guide, motivate and inspire them.
16
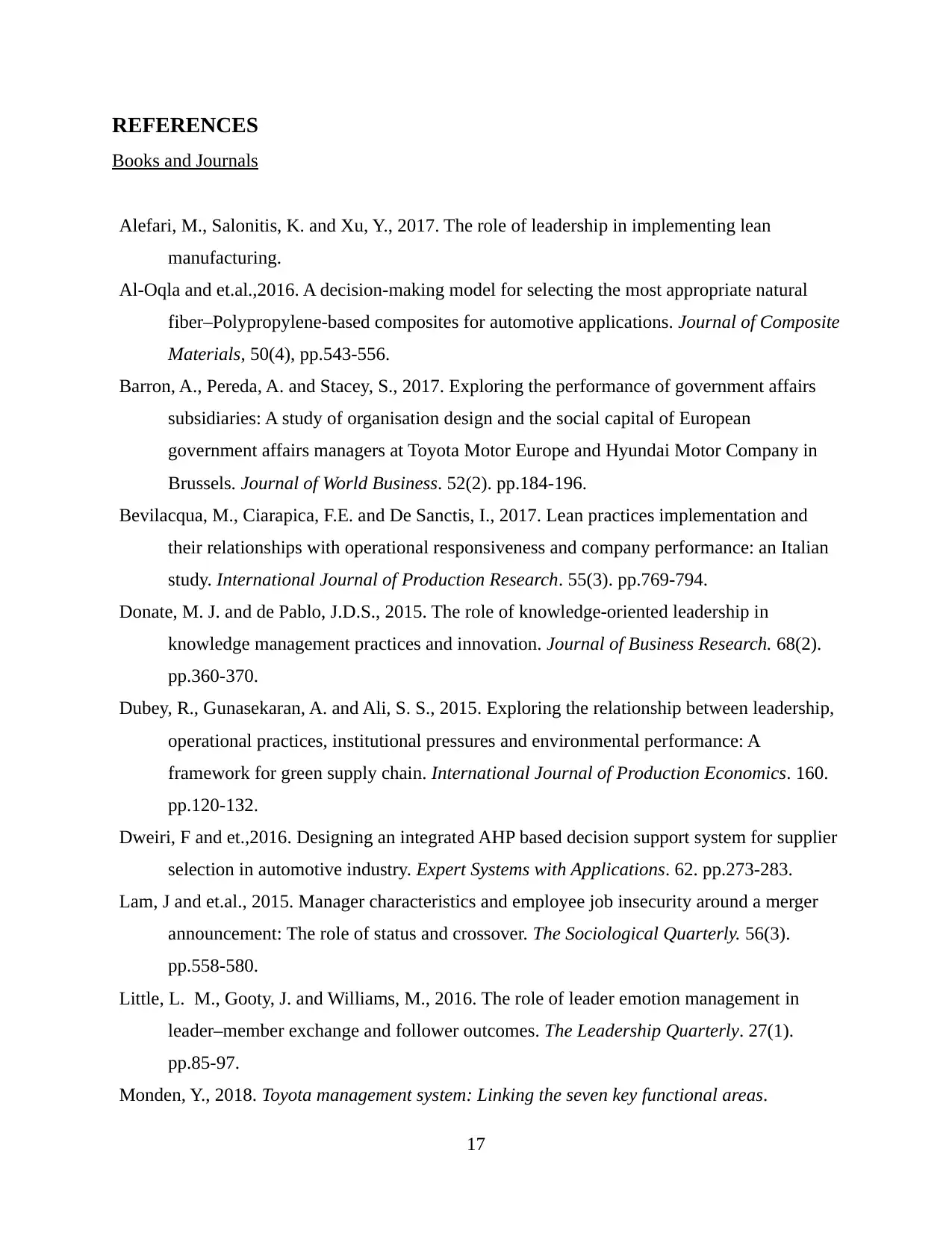
REFERENCES
Books and Journals
Alefari, M., Salonitis, K. and Xu, Y., 2017. The role of leadership in implementing lean
manufacturing.
Al-Oqla and et.al.,2016. A decision-making model for selecting the most appropriate natural
fiber–Polypropylene-based composites for automotive applications. Journal of Composite
Materials, 50(4), pp.543-556.
Barron, A., Pereda, A. and Stacey, S., 2017. Exploring the performance of government affairs
subsidiaries: A study of organisation design and the social capital of European
government affairs managers at Toyota Motor Europe and Hyundai Motor Company in
Brussels. Journal of World Business. 52(2). pp.184-196.
Bevilacqua, M., Ciarapica, F.E. and De Sanctis, I., 2017. Lean practices implementation and
their relationships with operational responsiveness and company performance: an Italian
study. International Journal of Production Research. 55(3). pp.769-794.
Donate, M. J. and de Pablo, J.D.S., 2015. The role of knowledge-oriented leadership in
knowledge management practices and innovation. Journal of Business Research. 68(2).
pp.360-370.
Dubey, R., Gunasekaran, A. and Ali, S. S., 2015. Exploring the relationship between leadership,
operational practices, institutional pressures and environmental performance: A
framework for green supply chain. International Journal of Production Economics. 160.
pp.120-132.
Dweiri, F and et.,2016. Designing an integrated AHP based decision support system for supplier
selection in automotive industry. Expert Systems with Applications. 62. pp.273-283.
Lam, J and et.al., 2015. Manager characteristics and employee job insecurity around a merger
announcement: The role of status and crossover. The Sociological Quarterly. 56(3).
pp.558-580.
Little, L. M., Gooty, J. and Williams, M., 2016. The role of leader emotion management in
leader–member exchange and follower outcomes. The Leadership Quarterly. 27(1).
pp.85-97.
Monden, Y., 2018. Toyota management system: Linking the seven key functional areas.
17
Books and Journals
Alefari, M., Salonitis, K. and Xu, Y., 2017. The role of leadership in implementing lean
manufacturing.
Al-Oqla and et.al.,2016. A decision-making model for selecting the most appropriate natural
fiber–Polypropylene-based composites for automotive applications. Journal of Composite
Materials, 50(4), pp.543-556.
Barron, A., Pereda, A. and Stacey, S., 2017. Exploring the performance of government affairs
subsidiaries: A study of organisation design and the social capital of European
government affairs managers at Toyota Motor Europe and Hyundai Motor Company in
Brussels. Journal of World Business. 52(2). pp.184-196.
Bevilacqua, M., Ciarapica, F.E. and De Sanctis, I., 2017. Lean practices implementation and
their relationships with operational responsiveness and company performance: an Italian
study. International Journal of Production Research. 55(3). pp.769-794.
Donate, M. J. and de Pablo, J.D.S., 2015. The role of knowledge-oriented leadership in
knowledge management practices and innovation. Journal of Business Research. 68(2).
pp.360-370.
Dubey, R., Gunasekaran, A. and Ali, S. S., 2015. Exploring the relationship between leadership,
operational practices, institutional pressures and environmental performance: A
framework for green supply chain. International Journal of Production Economics. 160.
pp.120-132.
Dweiri, F and et.,2016. Designing an integrated AHP based decision support system for supplier
selection in automotive industry. Expert Systems with Applications. 62. pp.273-283.
Lam, J and et.al., 2015. Manager characteristics and employee job insecurity around a merger
announcement: The role of status and crossover. The Sociological Quarterly. 56(3).
pp.558-580.
Little, L. M., Gooty, J. and Williams, M., 2016. The role of leader emotion management in
leader–member exchange and follower outcomes. The Leadership Quarterly. 27(1).
pp.85-97.
Monden, Y., 2018. Toyota management system: Linking the seven key functional areas.
17
Paraphrase This Document
Need a fresh take? Get an instant paraphrase of this document with our AI Paraphraser
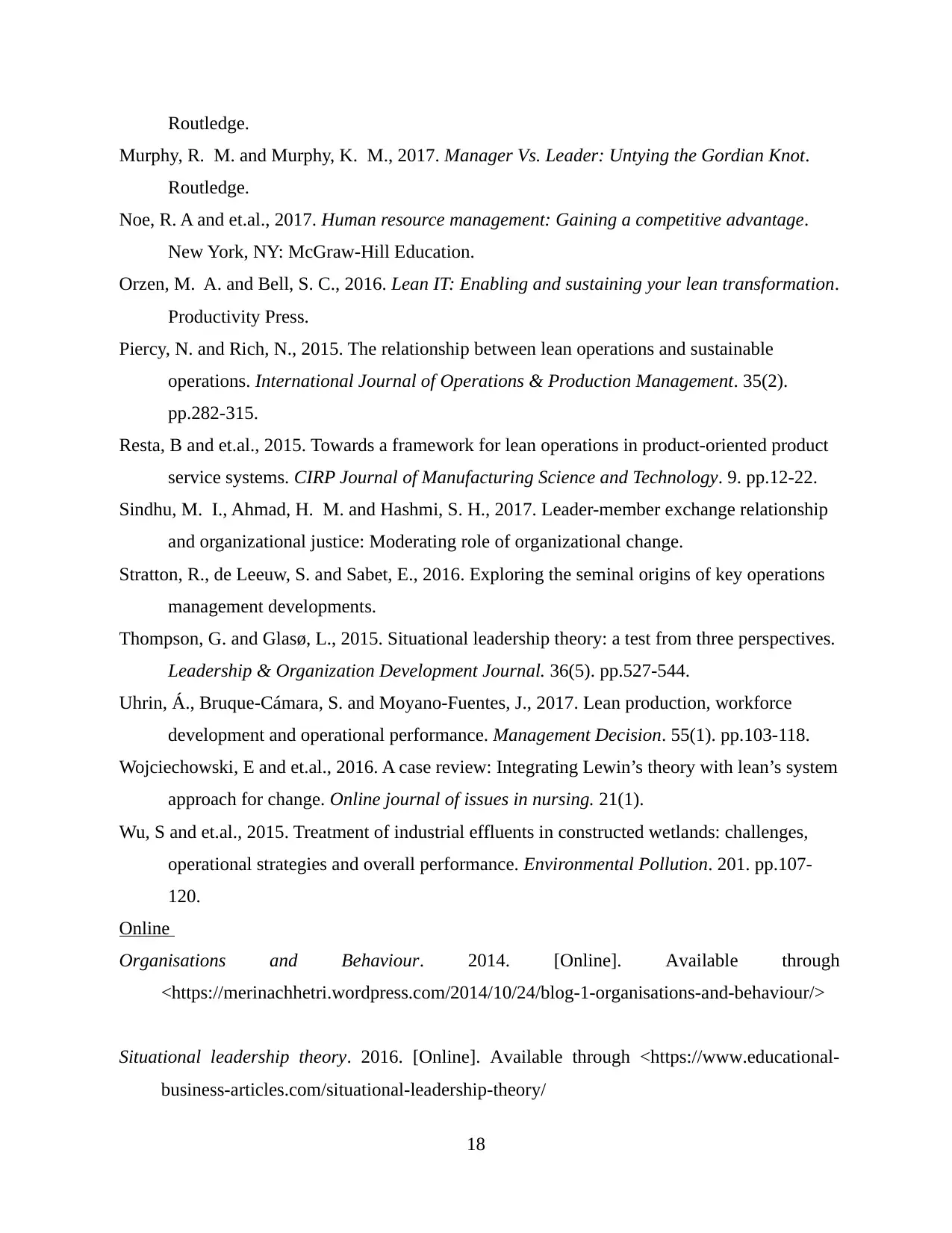
Routledge.
Murphy, R. M. and Murphy, K. M., 2017. Manager Vs. Leader: Untying the Gordian Knot.
Routledge.
Noe, R. A and et.al., 2017. Human resource management: Gaining a competitive advantage.
New York, NY: McGraw-Hill Education.
Orzen, M. A. and Bell, S. C., 2016. Lean IT: Enabling and sustaining your lean transformation.
Productivity Press.
Piercy, N. and Rich, N., 2015. The relationship between lean operations and sustainable
operations. International Journal of Operations & Production Management. 35(2).
pp.282-315.
Resta, B and et.al., 2015. Towards a framework for lean operations in product-oriented product
service systems. CIRP Journal of Manufacturing Science and Technology. 9. pp.12-22.
Sindhu, M. I., Ahmad, H. M. and Hashmi, S. H., 2017. Leader-member exchange relationship
and organizational justice: Moderating role of organizational change.
Stratton, R., de Leeuw, S. and Sabet, E., 2016. Exploring the seminal origins of key operations
management developments.
Thompson, G. and Glasø, L., 2015. Situational leadership theory: a test from three perspectives.
Leadership & Organization Development Journal. 36(5). pp.527-544.
Uhrin, Á., Bruque-Cámara, S. and Moyano-Fuentes, J., 2017. Lean production, workforce
development and operational performance. Management Decision. 55(1). pp.103-118.
Wojciechowski, E and et.al., 2016. A case review: Integrating Lewin’s theory with lean’s system
approach for change. Online journal of issues in nursing. 21(1).
Wu, S and et.al., 2015. Treatment of industrial effluents in constructed wetlands: challenges,
operational strategies and overall performance. Environmental Pollution. 201. pp.107-
120.
Online
Organisations and Behaviour. 2014. [Online]. Available through
<https://merinachhetri.wordpress.com/2014/10/24/blog-1-organisations-and-behaviour/>
Situational leadership theory. 2016. [Online]. Available through <https://www.educational-
business-articles.com/situational-leadership-theory/
18
Murphy, R. M. and Murphy, K. M., 2017. Manager Vs. Leader: Untying the Gordian Knot.
Routledge.
Noe, R. A and et.al., 2017. Human resource management: Gaining a competitive advantage.
New York, NY: McGraw-Hill Education.
Orzen, M. A. and Bell, S. C., 2016. Lean IT: Enabling and sustaining your lean transformation.
Productivity Press.
Piercy, N. and Rich, N., 2015. The relationship between lean operations and sustainable
operations. International Journal of Operations & Production Management. 35(2).
pp.282-315.
Resta, B and et.al., 2015. Towards a framework for lean operations in product-oriented product
service systems. CIRP Journal of Manufacturing Science and Technology. 9. pp.12-22.
Sindhu, M. I., Ahmad, H. M. and Hashmi, S. H., 2017. Leader-member exchange relationship
and organizational justice: Moderating role of organizational change.
Stratton, R., de Leeuw, S. and Sabet, E., 2016. Exploring the seminal origins of key operations
management developments.
Thompson, G. and Glasø, L., 2015. Situational leadership theory: a test from three perspectives.
Leadership & Organization Development Journal. 36(5). pp.527-544.
Uhrin, Á., Bruque-Cámara, S. and Moyano-Fuentes, J., 2017. Lean production, workforce
development and operational performance. Management Decision. 55(1). pp.103-118.
Wojciechowski, E and et.al., 2016. A case review: Integrating Lewin’s theory with lean’s system
approach for change. Online journal of issues in nursing. 21(1).
Wu, S and et.al., 2015. Treatment of industrial effluents in constructed wetlands: challenges,
operational strategies and overall performance. Environmental Pollution. 201. pp.107-
120.
Online
Organisations and Behaviour. 2014. [Online]. Available through
<https://merinachhetri.wordpress.com/2014/10/24/blog-1-organisations-and-behaviour/>
Situational leadership theory. 2016. [Online]. Available through <https://www.educational-
business-articles.com/situational-leadership-theory/
18
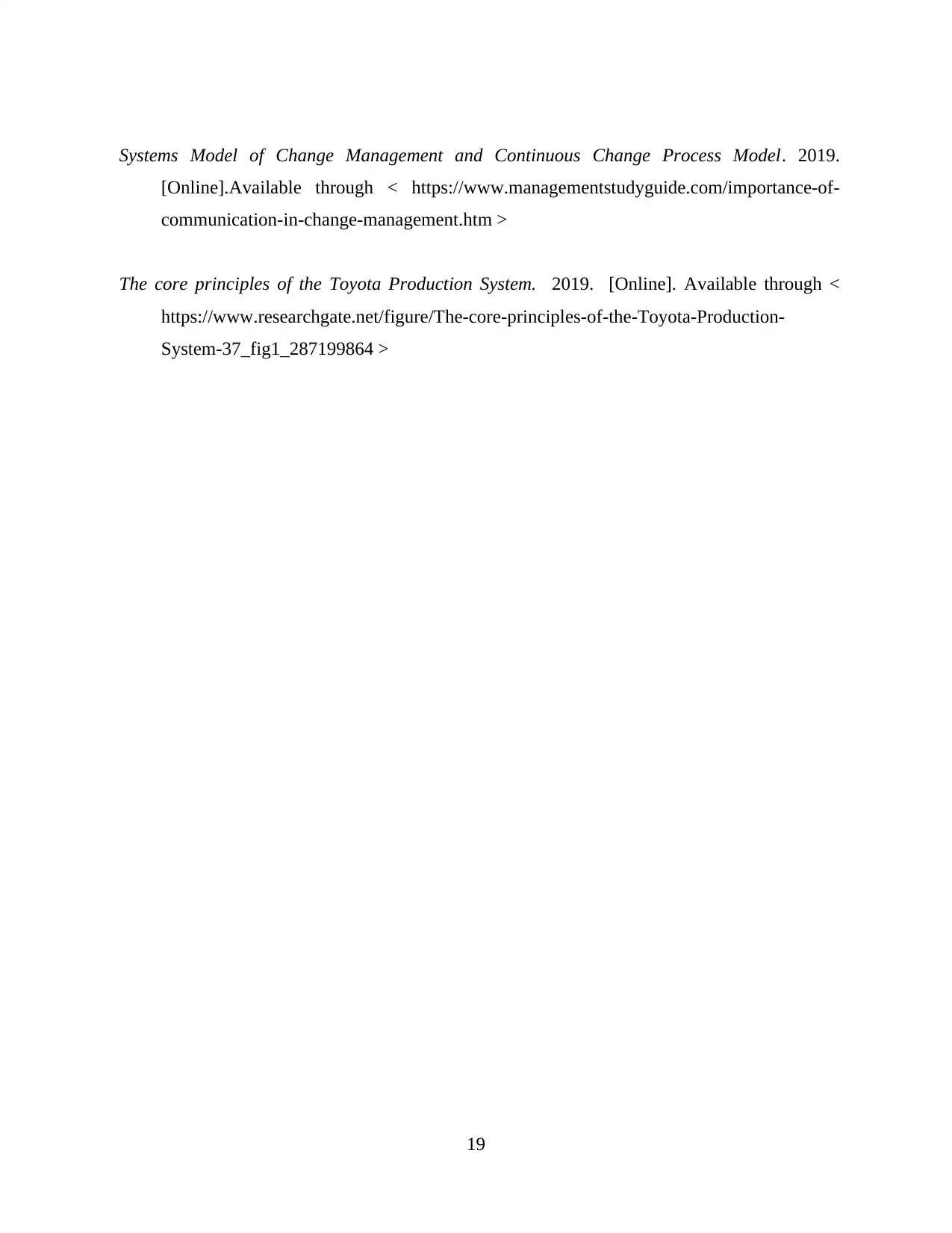
Systems Model of Change Management and Continuous Change Process Model. 2019.
[Online].Available through < https://www.managementstudyguide.com/importance-of-
communication-in-change-management.htm >
The core principles of the Toyota Production System. 2019. [Online]. Available through <
https://www.researchgate.net/figure/The-core-principles-of-the-Toyota-Production-
System-37_fig1_287199864 >
19
[Online].Available through < https://www.managementstudyguide.com/importance-of-
communication-in-change-management.htm >
The core principles of the Toyota Production System. 2019. [Online]. Available through <
https://www.researchgate.net/figure/The-core-principles-of-the-Toyota-Production-
System-37_fig1_287199864 >
19
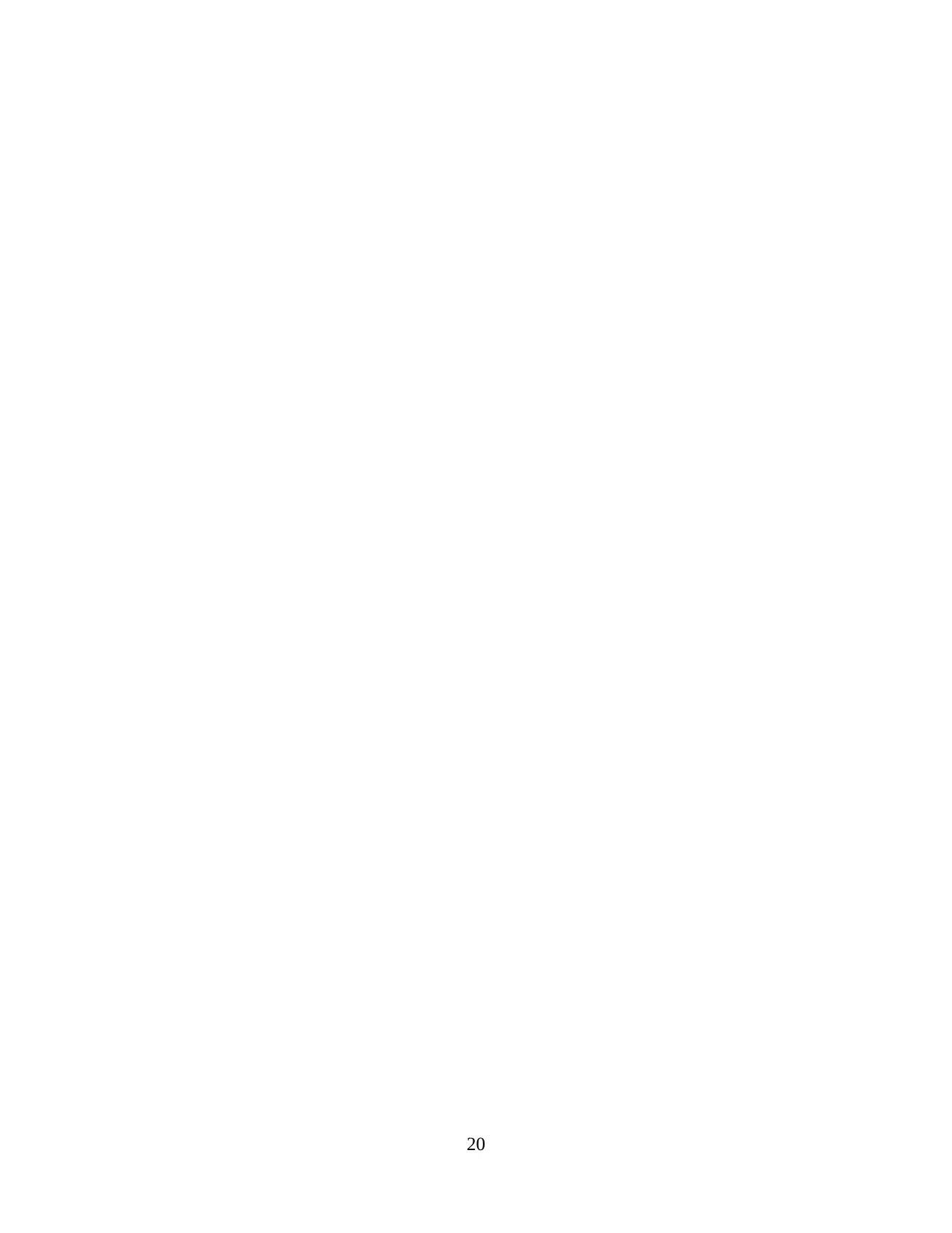
20
Secure Best Marks with AI Grader
Need help grading? Try our AI Grader for instant feedback on your assignments.
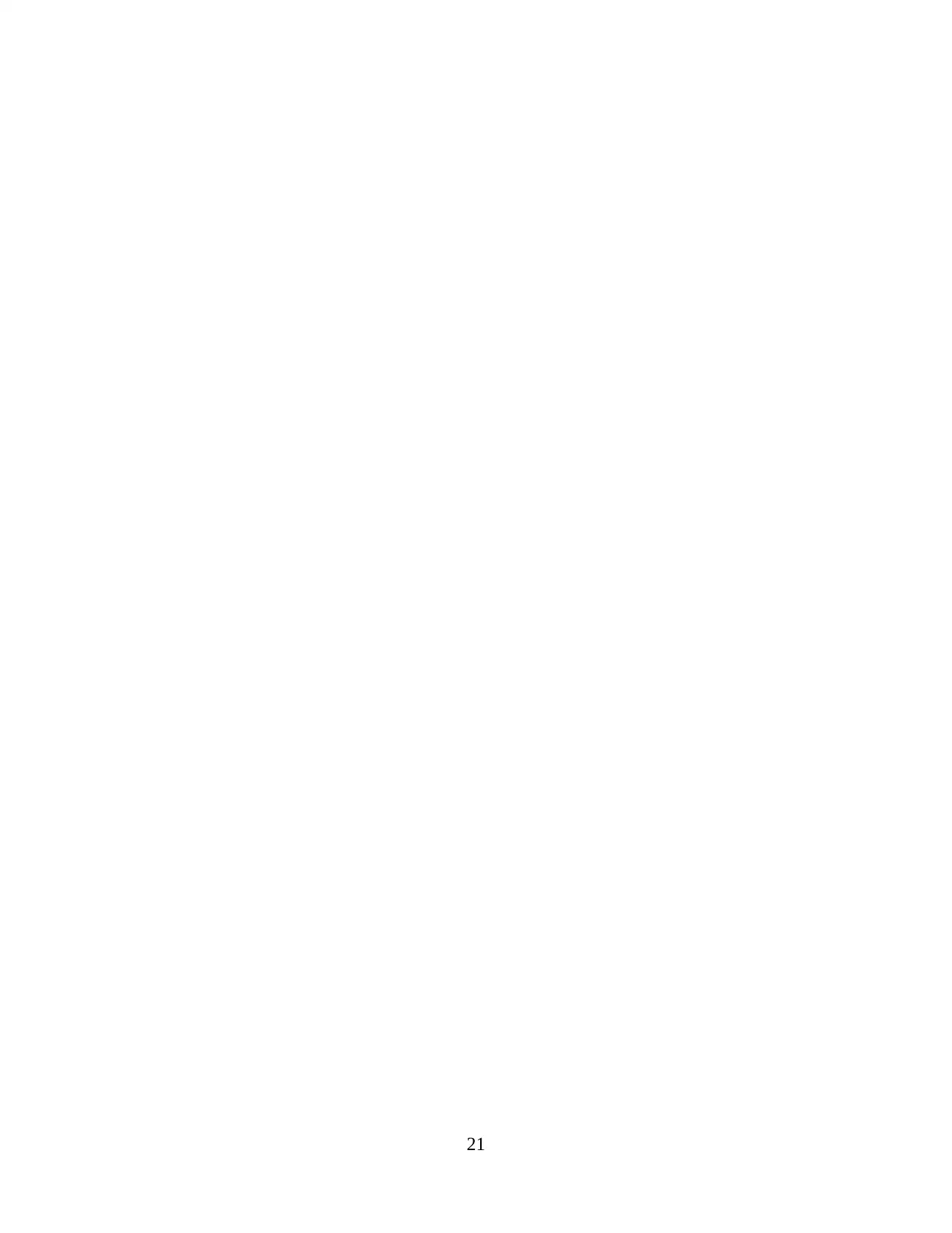
21
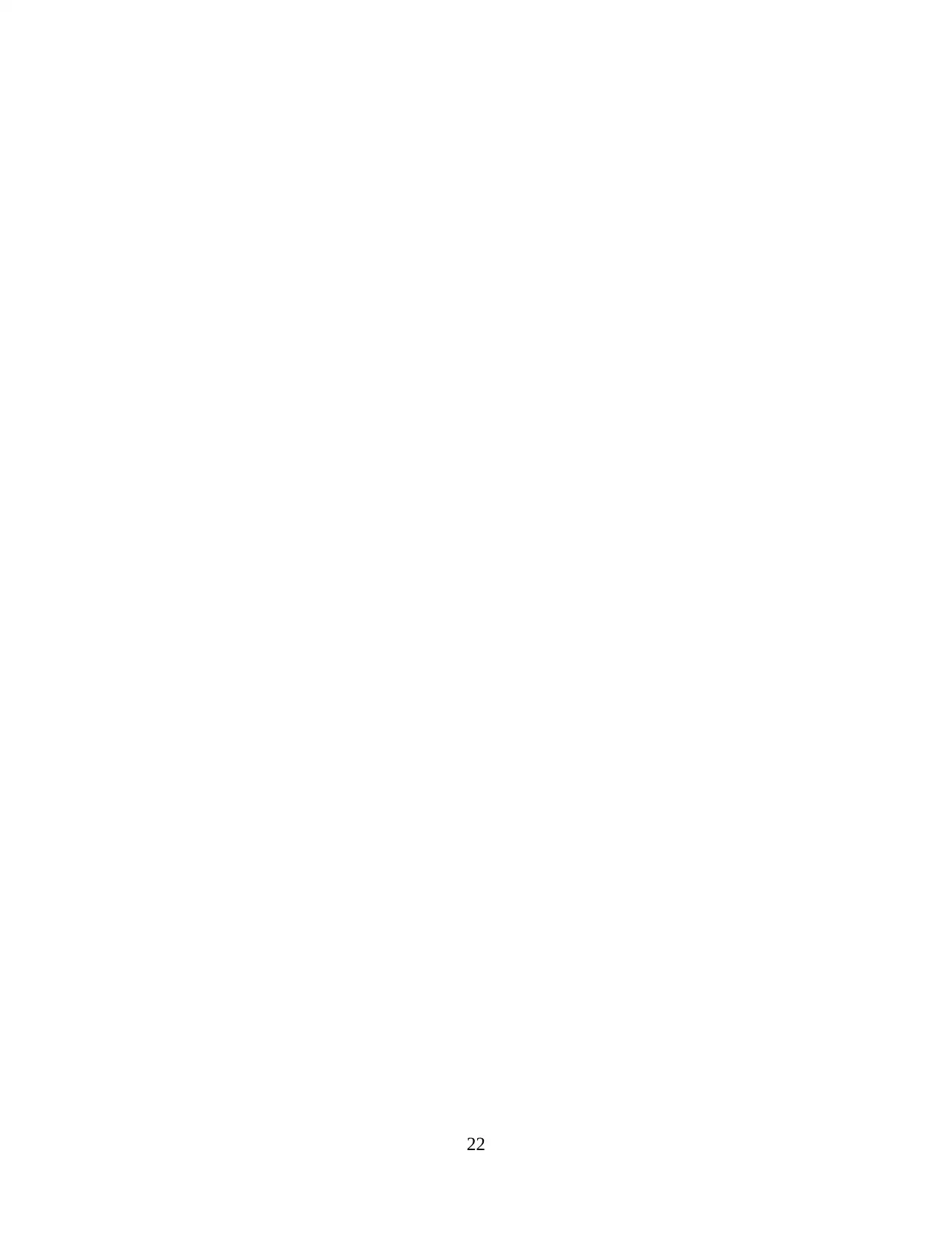
22
1 out of 24
Related Documents

Your All-in-One AI-Powered Toolkit for Academic Success.
+13062052269
info@desklib.com
Available 24*7 on WhatsApp / Email
Unlock your academic potential
© 2024 | Zucol Services PVT LTD | All rights reserved.