Toyota: A Comprehensive Operations Improvement Strategy Analysis
VerifiedAdded on 2021/02/19
|13
|4445
|182
Report
AI Summary
This report delves into Toyota's operations improvement strategy, focusing on enhancing efficiency and market competitiveness. It begins by introducing the importance of continuous improvement in the automotive industry, highlighting Toyota's global presence and commitment to innovation. The ...
Read More
Contribute Materials
Your contribution can guide someone’s learning journey. Share your
documents today.
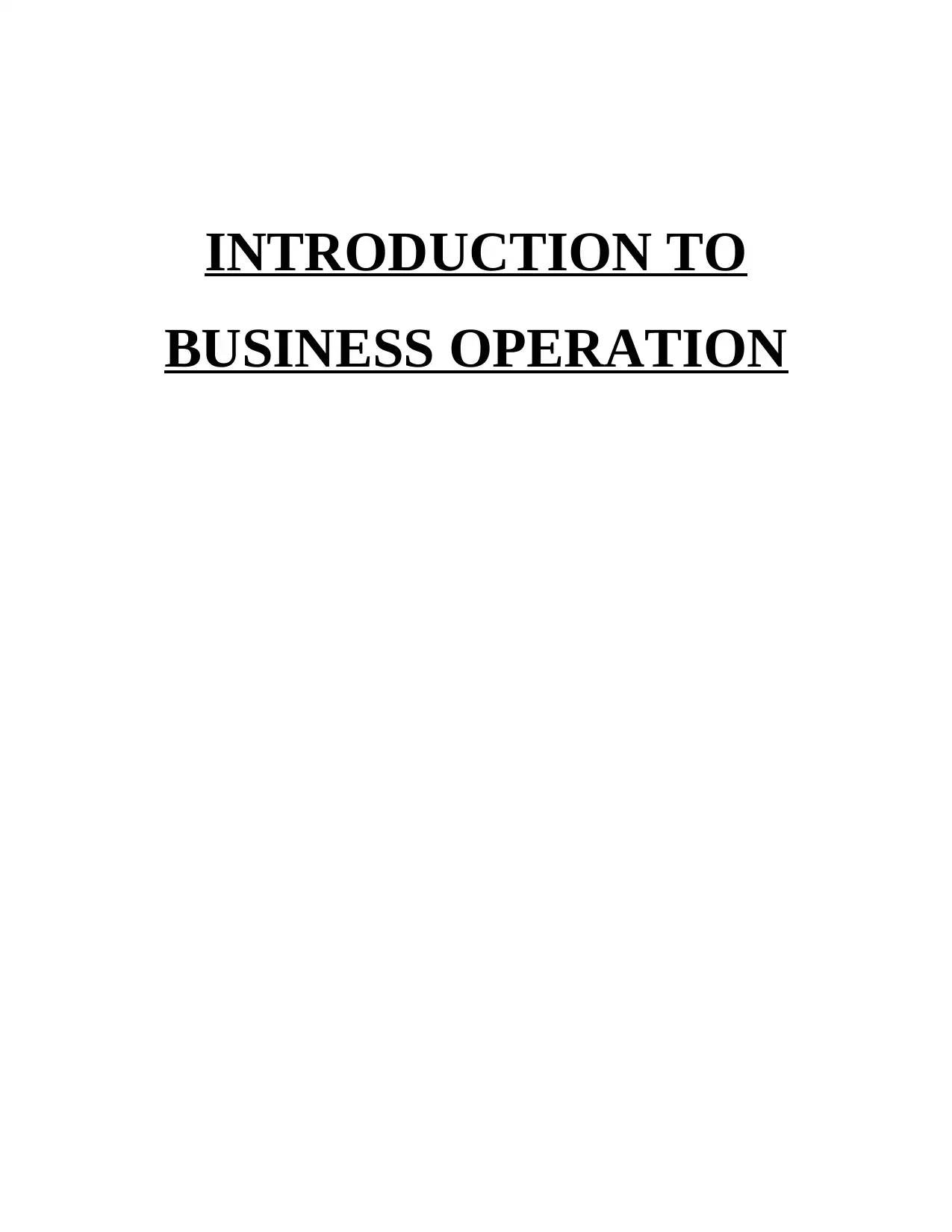
INTRODUCTION TO
BUSINESS OPERATION
BUSINESS OPERATION
Secure Best Marks with AI Grader
Need help grading? Try our AI Grader for instant feedback on your assignments.
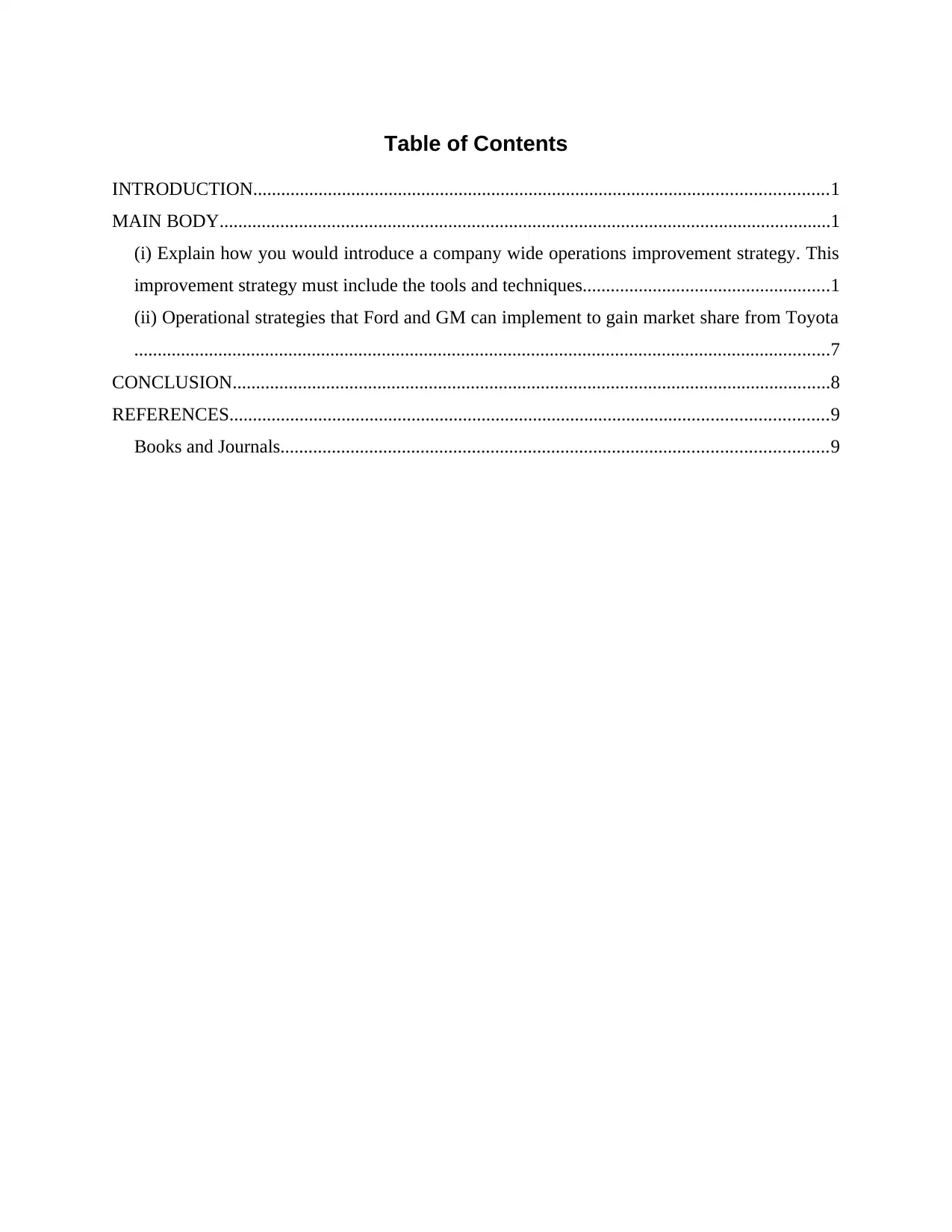
Table of Contents
INTRODUCTION...........................................................................................................................1
MAIN BODY...................................................................................................................................1
(i) Explain how you would introduce a company wide operations improvement strategy. This
improvement strategy must include the tools and techniques.....................................................1
(ii) Operational strategies that Ford and GM can implement to gain market share from Toyota
.....................................................................................................................................................7
CONCLUSION................................................................................................................................8
REFERENCES................................................................................................................................9
Books and Journals.....................................................................................................................9
INTRODUCTION...........................................................................................................................1
MAIN BODY...................................................................................................................................1
(i) Explain how you would introduce a company wide operations improvement strategy. This
improvement strategy must include the tools and techniques.....................................................1
(ii) Operational strategies that Ford and GM can implement to gain market share from Toyota
.....................................................................................................................................................7
CONCLUSION................................................................................................................................8
REFERENCES................................................................................................................................9
Books and Journals.....................................................................................................................9
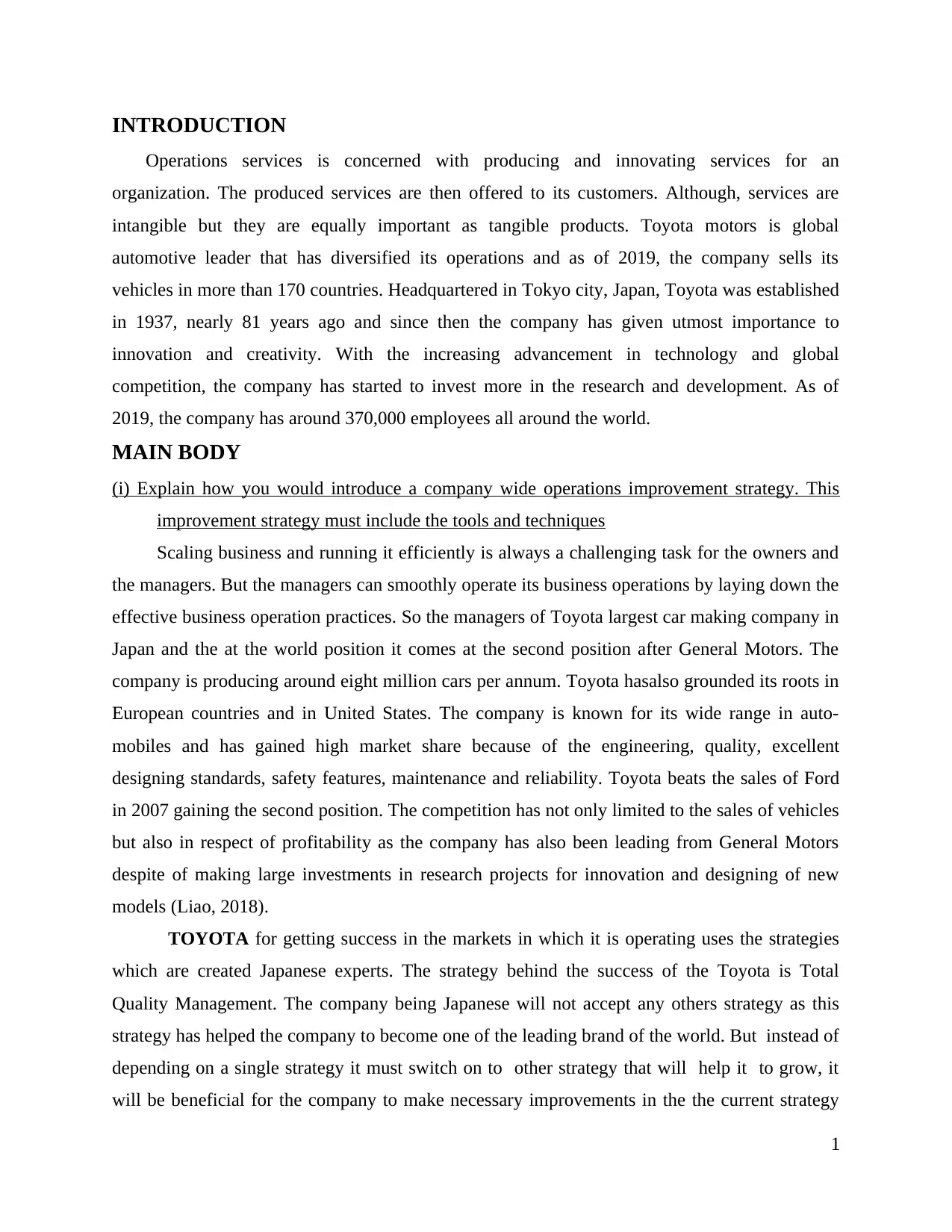
INTRODUCTION
Operations services is concerned with producing and innovating services for an
organization. The produced services are then offered to its customers. Although, services are
intangible but they are equally important as tangible products. Toyota motors is global
automotive leader that has diversified its operations and as of 2019, the company sells its
vehicles in more than 170 countries. Headquartered in Tokyo city, Japan, Toyota was established
in 1937, nearly 81 years ago and since then the company has given utmost importance to
innovation and creativity. With the increasing advancement in technology and global
competition, the company has started to invest more in the research and development. As of
2019, the company has around 370,000 employees all around the world.
MAIN BODY
(i) Explain how you would introduce a company wide operations improvement strategy. This
improvement strategy must include the tools and techniques
Scaling business and running it efficiently is always a challenging task for the owners and
the managers. But the managers can smoothly operate its business operations by laying down the
effective business operation practices. So the managers of Toyota largest car making company in
Japan and the at the world position it comes at the second position after General Motors. The
company is producing around eight million cars per annum. Toyota hasalso grounded its roots in
European countries and in United States. The company is known for its wide range in auto-
mobiles and has gained high market share because of the engineering, quality, excellent
designing standards, safety features, maintenance and reliability. Toyota beats the sales of Ford
in 2007 gaining the second position. The competition has not only limited to the sales of vehicles
but also in respect of profitability as the company has also been leading from General Motors
despite of making large investments in research projects for innovation and designing of new
models (Liao, 2018).
TOYOTA for getting success in the markets in which it is operating uses the strategies
which are created Japanese experts. The strategy behind the success of the Toyota is Total
Quality Management. The company being Japanese will not accept any others strategy as this
strategy has helped the company to become one of the leading brand of the world. But instead of
depending on a single strategy it must switch on to other strategy that will help it to grow, it
will be beneficial for the company to make necessary improvements in the the current strategy
1
Operations services is concerned with producing and innovating services for an
organization. The produced services are then offered to its customers. Although, services are
intangible but they are equally important as tangible products. Toyota motors is global
automotive leader that has diversified its operations and as of 2019, the company sells its
vehicles in more than 170 countries. Headquartered in Tokyo city, Japan, Toyota was established
in 1937, nearly 81 years ago and since then the company has given utmost importance to
innovation and creativity. With the increasing advancement in technology and global
competition, the company has started to invest more in the research and development. As of
2019, the company has around 370,000 employees all around the world.
MAIN BODY
(i) Explain how you would introduce a company wide operations improvement strategy. This
improvement strategy must include the tools and techniques
Scaling business and running it efficiently is always a challenging task for the owners and
the managers. But the managers can smoothly operate its business operations by laying down the
effective business operation practices. So the managers of Toyota largest car making company in
Japan and the at the world position it comes at the second position after General Motors. The
company is producing around eight million cars per annum. Toyota hasalso grounded its roots in
European countries and in United States. The company is known for its wide range in auto-
mobiles and has gained high market share because of the engineering, quality, excellent
designing standards, safety features, maintenance and reliability. Toyota beats the sales of Ford
in 2007 gaining the second position. The competition has not only limited to the sales of vehicles
but also in respect of profitability as the company has also been leading from General Motors
despite of making large investments in research projects for innovation and designing of new
models (Liao, 2018).
TOYOTA for getting success in the markets in which it is operating uses the strategies
which are created Japanese experts. The strategy behind the success of the Toyota is Total
Quality Management. The company being Japanese will not accept any others strategy as this
strategy has helped the company to become one of the leading brand of the world. But instead of
depending on a single strategy it must switch on to other strategy that will help it to grow, it
will be beneficial for the company to make necessary improvements in the the current strategy
1
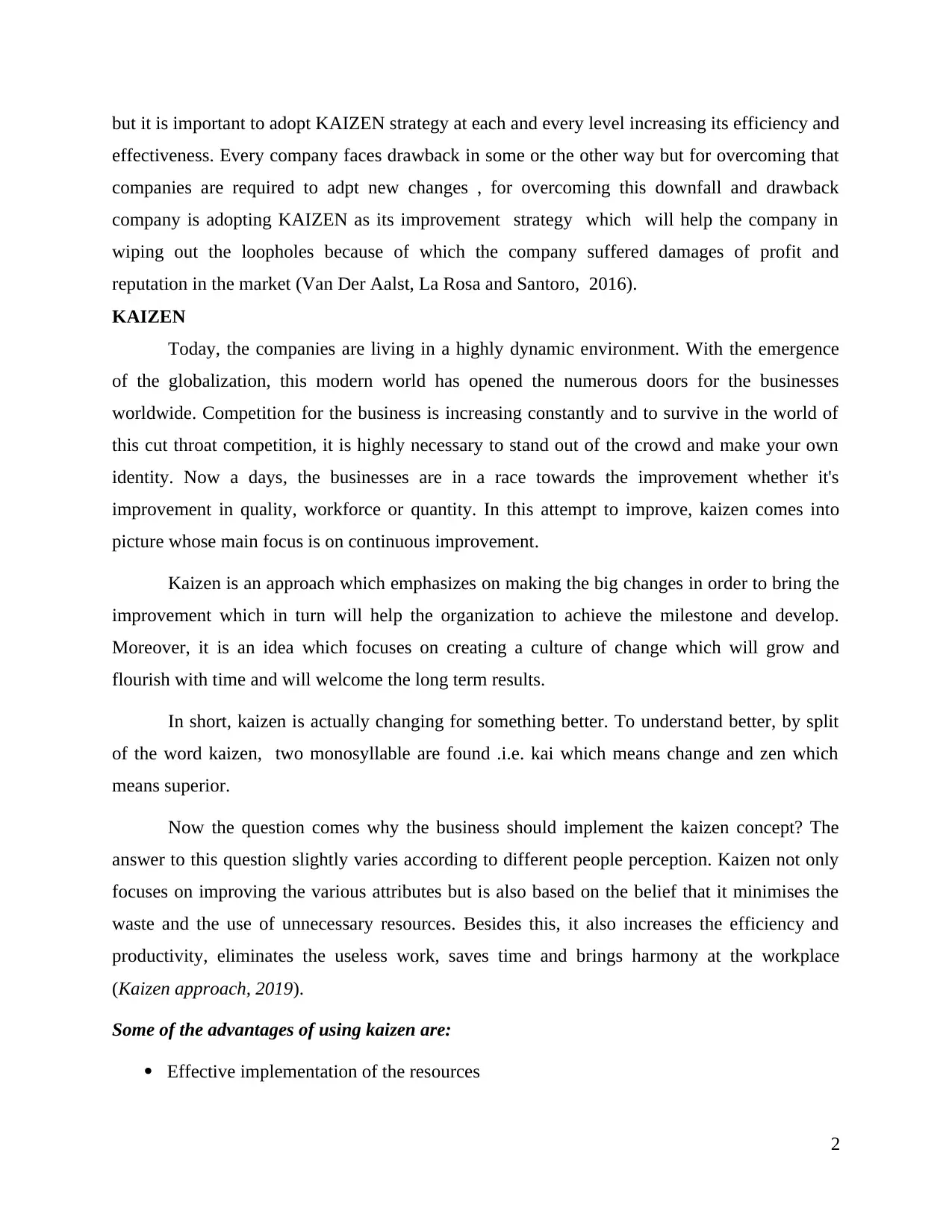
but it is important to adopt KAIZEN strategy at each and every level increasing its efficiency and
effectiveness. Every company faces drawback in some or the other way but for overcoming that
companies are required to adpt new changes , for overcoming this downfall and drawback
company is adopting KAIZEN as its improvement strategy which will help the company in
wiping out the loopholes because of which the company suffered damages of profit and
reputation in the market (Van Der Aalst, La Rosa and Santoro, 2016).
KAIZEN
Today, the companies are living in a highly dynamic environment. With the emergence
of the globalization, this modern world has opened the numerous doors for the businesses
worldwide. Competition for the business is increasing constantly and to survive in the world of
this cut throat competition, it is highly necessary to stand out of the crowd and make your own
identity. Now a days, the businesses are in a race towards the improvement whether it's
improvement in quality, workforce or quantity. In this attempt to improve, kaizen comes into
picture whose main focus is on continuous improvement.
Kaizen is an approach which emphasizes on making the big changes in order to bring the
improvement which in turn will help the organization to achieve the milestone and develop.
Moreover, it is an idea which focuses on creating a culture of change which will grow and
flourish with time and will welcome the long term results.
In short, kaizen is actually changing for something better. To understand better, by split
of the word kaizen, two monosyllable are found .i.e. kai which means change and zen which
means superior.
Now the question comes why the business should implement the kaizen concept? The
answer to this question slightly varies according to different people perception. Kaizen not only
focuses on improving the various attributes but is also based on the belief that it minimises the
waste and the use of unnecessary resources. Besides this, it also increases the efficiency and
productivity, eliminates the useless work, saves time and brings harmony at the workplace
(Kaizen approach, 2019).
Some of the advantages of using kaizen are:
Effective implementation of the resources
2
effectiveness. Every company faces drawback in some or the other way but for overcoming that
companies are required to adpt new changes , for overcoming this downfall and drawback
company is adopting KAIZEN as its improvement strategy which will help the company in
wiping out the loopholes because of which the company suffered damages of profit and
reputation in the market (Van Der Aalst, La Rosa and Santoro, 2016).
KAIZEN
Today, the companies are living in a highly dynamic environment. With the emergence
of the globalization, this modern world has opened the numerous doors for the businesses
worldwide. Competition for the business is increasing constantly and to survive in the world of
this cut throat competition, it is highly necessary to stand out of the crowd and make your own
identity. Now a days, the businesses are in a race towards the improvement whether it's
improvement in quality, workforce or quantity. In this attempt to improve, kaizen comes into
picture whose main focus is on continuous improvement.
Kaizen is an approach which emphasizes on making the big changes in order to bring the
improvement which in turn will help the organization to achieve the milestone and develop.
Moreover, it is an idea which focuses on creating a culture of change which will grow and
flourish with time and will welcome the long term results.
In short, kaizen is actually changing for something better. To understand better, by split
of the word kaizen, two monosyllable are found .i.e. kai which means change and zen which
means superior.
Now the question comes why the business should implement the kaizen concept? The
answer to this question slightly varies according to different people perception. Kaizen not only
focuses on improving the various attributes but is also based on the belief that it minimises the
waste and the use of unnecessary resources. Besides this, it also increases the efficiency and
productivity, eliminates the useless work, saves time and brings harmony at the workplace
(Kaizen approach, 2019).
Some of the advantages of using kaizen are:
Effective implementation of the resources
2
Secure Best Marks with AI Grader
Need help grading? Try our AI Grader for instant feedback on your assignments.
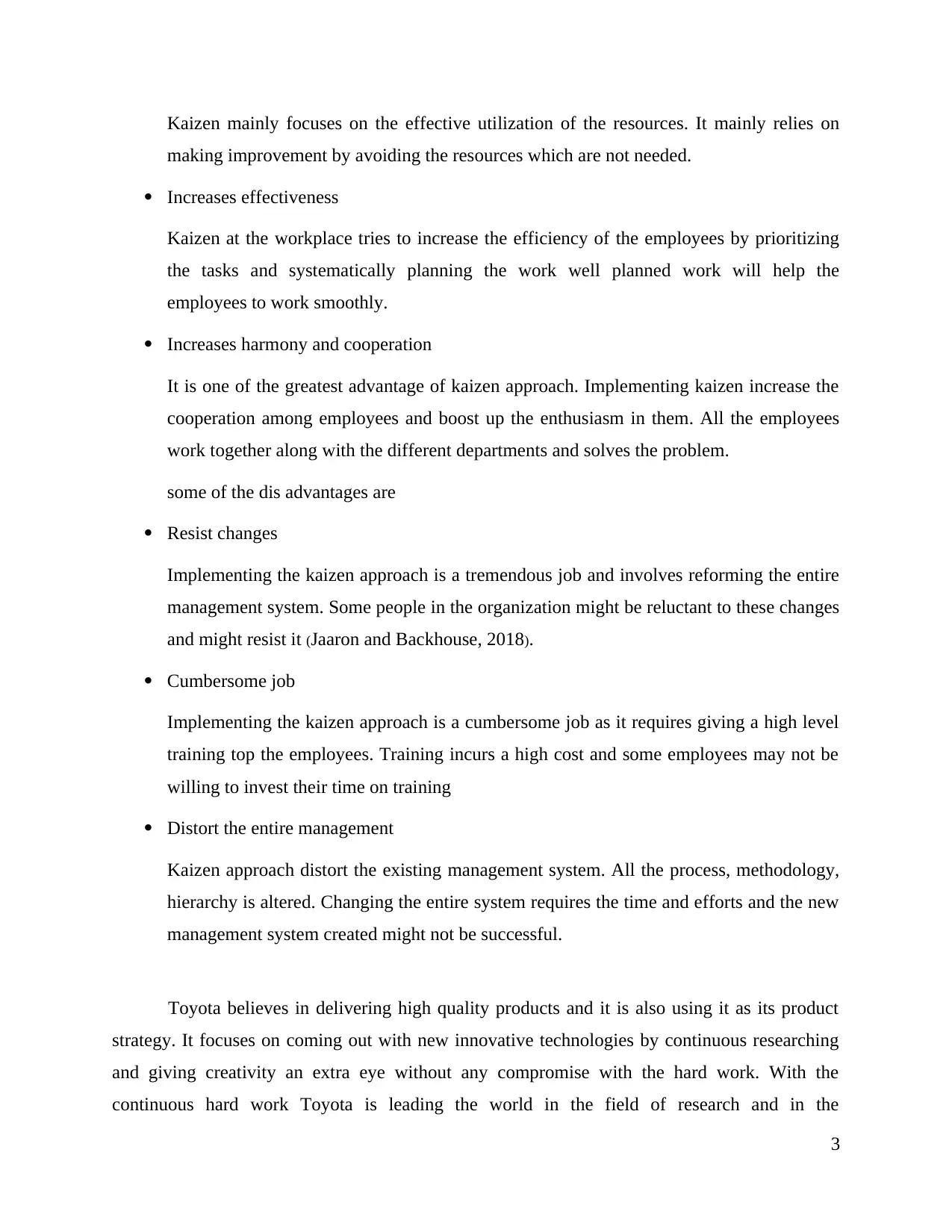
Kaizen mainly focuses on the effective utilization of the resources. It mainly relies on
making improvement by avoiding the resources which are not needed.
Increases effectiveness
Kaizen at the workplace tries to increase the efficiency of the employees by prioritizing
the tasks and systematically planning the work well planned work will help the
employees to work smoothly.
Increases harmony and cooperation
It is one of the greatest advantage of kaizen approach. Implementing kaizen increase the
cooperation among employees and boost up the enthusiasm in them. All the employees
work together along with the different departments and solves the problem.
some of the dis advantages are
Resist changes
Implementing the kaizen approach is a tremendous job and involves reforming the entire
management system. Some people in the organization might be reluctant to these changes
and might resist it (Jaaron and Backhouse, 2018).
Cumbersome job
Implementing the kaizen approach is a cumbersome job as it requires giving a high level
training top the employees. Training incurs a high cost and some employees may not be
willing to invest their time on training
Distort the entire management
Kaizen approach distort the existing management system. All the process, methodology,
hierarchy is altered. Changing the entire system requires the time and efforts and the new
management system created might not be successful.
Toyota believes in delivering high quality products and it is also using it as its product
strategy. It focuses on coming out with new innovative technologies by continuous researching
and giving creativity an extra eye without any compromise with the hard work. With the
continuous hard work Toyota is leading the world in the field of research and in the
3
making improvement by avoiding the resources which are not needed.
Increases effectiveness
Kaizen at the workplace tries to increase the efficiency of the employees by prioritizing
the tasks and systematically planning the work well planned work will help the
employees to work smoothly.
Increases harmony and cooperation
It is one of the greatest advantage of kaizen approach. Implementing kaizen increase the
cooperation among employees and boost up the enthusiasm in them. All the employees
work together along with the different departments and solves the problem.
some of the dis advantages are
Resist changes
Implementing the kaizen approach is a tremendous job and involves reforming the entire
management system. Some people in the organization might be reluctant to these changes
and might resist it (Jaaron and Backhouse, 2018).
Cumbersome job
Implementing the kaizen approach is a cumbersome job as it requires giving a high level
training top the employees. Training incurs a high cost and some employees may not be
willing to invest their time on training
Distort the entire management
Kaizen approach distort the existing management system. All the process, methodology,
hierarchy is altered. Changing the entire system requires the time and efforts and the new
management system created might not be successful.
Toyota believes in delivering high quality products and it is also using it as its product
strategy. It focuses on coming out with new innovative technologies by continuous researching
and giving creativity an extra eye without any compromise with the hard work. With the
continuous hard work Toyota is leading the world in the field of research and in the
3
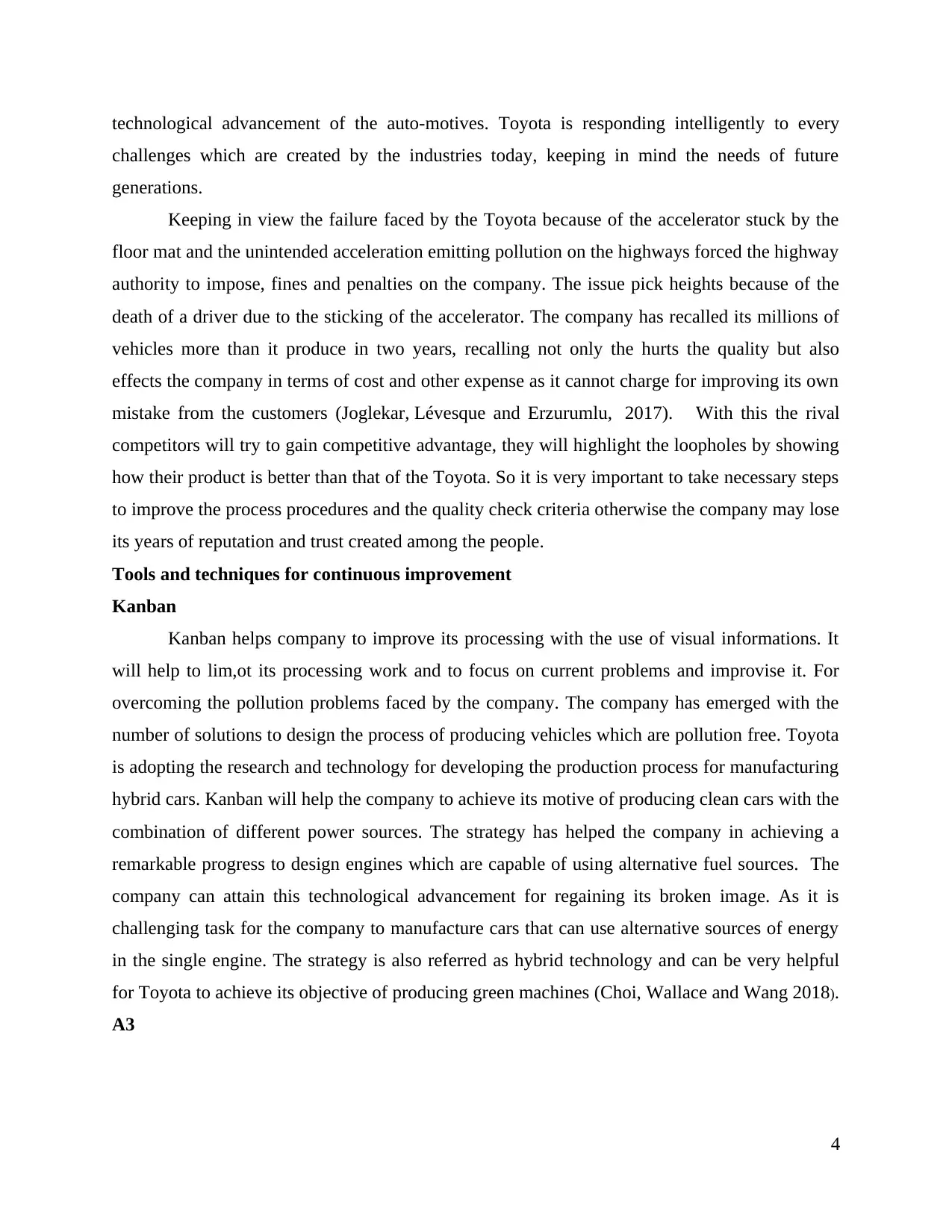
technological advancement of the auto-motives. Toyota is responding intelligently to every
challenges which are created by the industries today, keeping in mind the needs of future
generations.
Keeping in view the failure faced by the Toyota because of the accelerator stuck by the
floor mat and the unintended acceleration emitting pollution on the highways forced the highway
authority to impose, fines and penalties on the company. The issue pick heights because of the
death of a driver due to the sticking of the accelerator. The company has recalled its millions of
vehicles more than it produce in two years, recalling not only the hurts the quality but also
effects the company in terms of cost and other expense as it cannot charge for improving its own
mistake from the customers (Joglekar, Lévesque and Erzurumlu, 2017). With this the rival
competitors will try to gain competitive advantage, they will highlight the loopholes by showing
how their product is better than that of the Toyota. So it is very important to take necessary steps
to improve the process procedures and the quality check criteria otherwise the company may lose
its years of reputation and trust created among the people.
Tools and techniques for continuous improvement
Kanban
Kanban helps company to improve its processing with the use of visual informations. It
will help to lim,ot its processing work and to focus on current problems and improvise it. For
overcoming the pollution problems faced by the company. The company has emerged with the
number of solutions to design the process of producing vehicles which are pollution free. Toyota
is adopting the research and technology for developing the production process for manufacturing
hybrid cars. Kanban will help the company to achieve its motive of producing clean cars with the
combination of different power sources. The strategy has helped the company in achieving a
remarkable progress to design engines which are capable of using alternative fuel sources. The
company can attain this technological advancement for regaining its broken image. As it is
challenging task for the company to manufacture cars that can use alternative sources of energy
in the single engine. The strategy is also referred as hybrid technology and can be very helpful
for Toyota to achieve its objective of producing green machines (Choi, Wallace and Wang 2018).
A3
4
challenges which are created by the industries today, keeping in mind the needs of future
generations.
Keeping in view the failure faced by the Toyota because of the accelerator stuck by the
floor mat and the unintended acceleration emitting pollution on the highways forced the highway
authority to impose, fines and penalties on the company. The issue pick heights because of the
death of a driver due to the sticking of the accelerator. The company has recalled its millions of
vehicles more than it produce in two years, recalling not only the hurts the quality but also
effects the company in terms of cost and other expense as it cannot charge for improving its own
mistake from the customers (Joglekar, Lévesque and Erzurumlu, 2017). With this the rival
competitors will try to gain competitive advantage, they will highlight the loopholes by showing
how their product is better than that of the Toyota. So it is very important to take necessary steps
to improve the process procedures and the quality check criteria otherwise the company may lose
its years of reputation and trust created among the people.
Tools and techniques for continuous improvement
Kanban
Kanban helps company to improve its processing with the use of visual informations. It
will help to lim,ot its processing work and to focus on current problems and improvise it. For
overcoming the pollution problems faced by the company. The company has emerged with the
number of solutions to design the process of producing vehicles which are pollution free. Toyota
is adopting the research and technology for developing the production process for manufacturing
hybrid cars. Kanban will help the company to achieve its motive of producing clean cars with the
combination of different power sources. The strategy has helped the company in achieving a
remarkable progress to design engines which are capable of using alternative fuel sources. The
company can attain this technological advancement for regaining its broken image. As it is
challenging task for the company to manufacture cars that can use alternative sources of energy
in the single engine. The strategy is also referred as hybrid technology and can be very helpful
for Toyota to achieve its objective of producing green machines (Choi, Wallace and Wang 2018).
A3
4
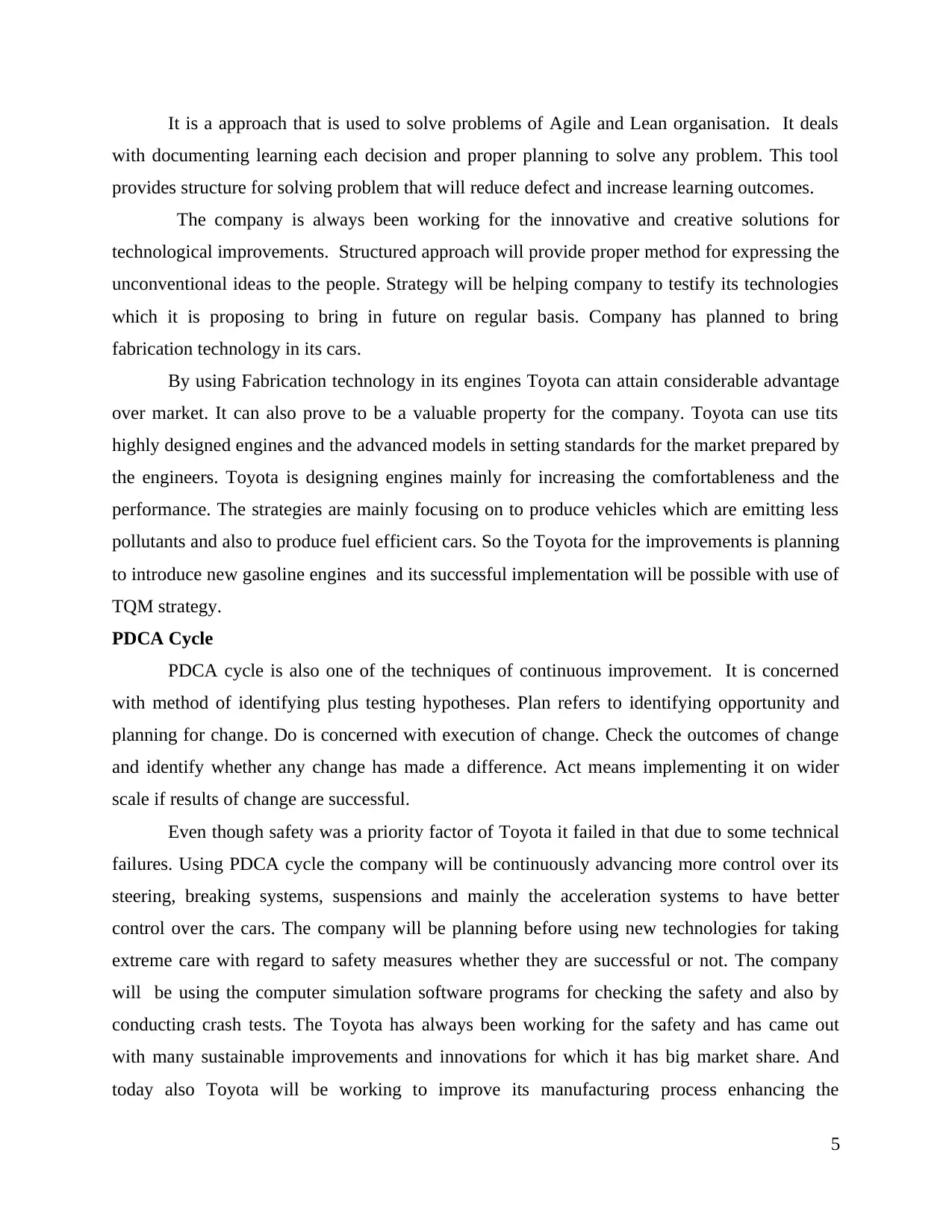
It is a approach that is used to solve problems of Agile and Lean organisation. It deals
with documenting learning each decision and proper planning to solve any problem. This tool
provides structure for solving problem that will reduce defect and increase learning outcomes.
The company is always been working for the innovative and creative solutions for
technological improvements. Structured approach will provide proper method for expressing the
unconventional ideas to the people. Strategy will be helping company to testify its technologies
which it is proposing to bring in future on regular basis. Company has planned to bring
fabrication technology in its cars.
By using Fabrication technology in its engines Toyota can attain considerable advantage
over market. It can also prove to be a valuable property for the company. Toyota can use tits
highly designed engines and the advanced models in setting standards for the market prepared by
the engineers. Toyota is designing engines mainly for increasing the comfortableness and the
performance. The strategies are mainly focusing on to produce vehicles which are emitting less
pollutants and also to produce fuel efficient cars. So the Toyota for the improvements is planning
to introduce new gasoline engines and its successful implementation will be possible with use of
TQM strategy.
PDCA Cycle
PDCA cycle is also one of the techniques of continuous improvement. It is concerned
with method of identifying plus testing hypotheses. Plan refers to identifying opportunity and
planning for change. Do is concerned with execution of change. Check the outcomes of change
and identify whether any change has made a difference. Act means implementing it on wider
scale if results of change are successful.
Even though safety was a priority factor of Toyota it failed in that due to some technical
failures. Using PDCA cycle the company will be continuously advancing more control over its
steering, breaking systems, suspensions and mainly the acceleration systems to have better
control over the cars. The company will be planning before using new technologies for taking
extreme care with regard to safety measures whether they are successful or not. The company
will be using the computer simulation software programs for checking the safety and also by
conducting crash tests. The Toyota has always been working for the safety and has came out
with many sustainable improvements and innovations for which it has big market share. And
today also Toyota will be working to improve its manufacturing process enhancing the
5
with documenting learning each decision and proper planning to solve any problem. This tool
provides structure for solving problem that will reduce defect and increase learning outcomes.
The company is always been working for the innovative and creative solutions for
technological improvements. Structured approach will provide proper method for expressing the
unconventional ideas to the people. Strategy will be helping company to testify its technologies
which it is proposing to bring in future on regular basis. Company has planned to bring
fabrication technology in its cars.
By using Fabrication technology in its engines Toyota can attain considerable advantage
over market. It can also prove to be a valuable property for the company. Toyota can use tits
highly designed engines and the advanced models in setting standards for the market prepared by
the engineers. Toyota is designing engines mainly for increasing the comfortableness and the
performance. The strategies are mainly focusing on to produce vehicles which are emitting less
pollutants and also to produce fuel efficient cars. So the Toyota for the improvements is planning
to introduce new gasoline engines and its successful implementation will be possible with use of
TQM strategy.
PDCA Cycle
PDCA cycle is also one of the techniques of continuous improvement. It is concerned
with method of identifying plus testing hypotheses. Plan refers to identifying opportunity and
planning for change. Do is concerned with execution of change. Check the outcomes of change
and identify whether any change has made a difference. Act means implementing it on wider
scale if results of change are successful.
Even though safety was a priority factor of Toyota it failed in that due to some technical
failures. Using PDCA cycle the company will be continuously advancing more control over its
steering, breaking systems, suspensions and mainly the acceleration systems to have better
control over the cars. The company will be planning before using new technologies for taking
extreme care with regard to safety measures whether they are successful or not. The company
will be using the computer simulation software programs for checking the safety and also by
conducting crash tests. The Toyota has always been working for the safety and has came out
with many sustainable improvements and innovations for which it has big market share. And
today also Toyota will be working to improve its manufacturing process enhancing the
5
Paraphrase This Document
Need a fresh take? Get an instant paraphrase of this document with our AI Paraphraser
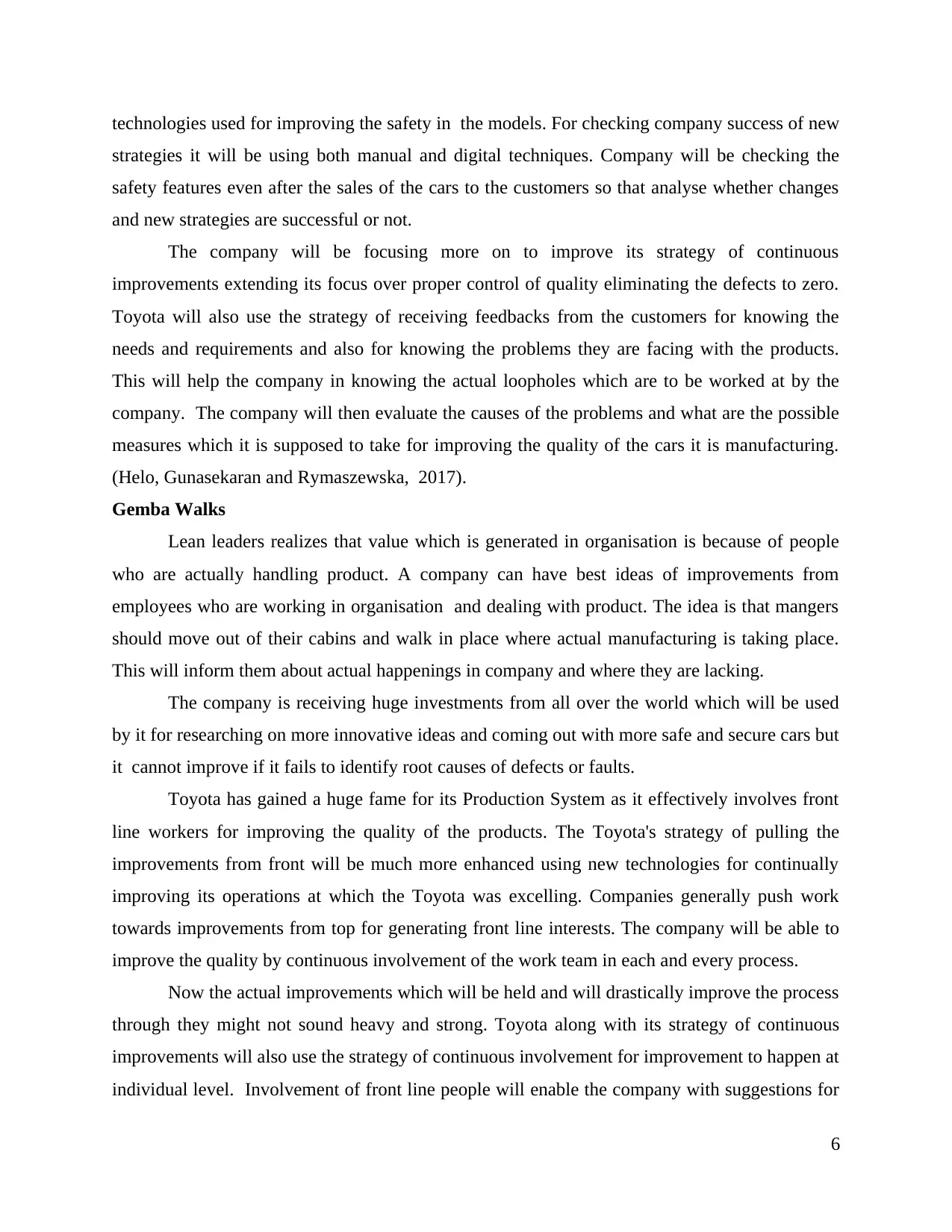
technologies used for improving the safety in the models. For checking company success of new
strategies it will be using both manual and digital techniques. Company will be checking the
safety features even after the sales of the cars to the customers so that analyse whether changes
and new strategies are successful or not.
The company will be focusing more on to improve its strategy of continuous
improvements extending its focus over proper control of quality eliminating the defects to zero.
Toyota will also use the strategy of receiving feedbacks from the customers for knowing the
needs and requirements and also for knowing the problems they are facing with the products.
This will help the company in knowing the actual loopholes which are to be worked at by the
company. The company will then evaluate the causes of the problems and what are the possible
measures which it is supposed to take for improving the quality of the cars it is manufacturing.
(Helo, Gunasekaran and Rymaszewska, 2017).
Gemba Walks
Lean leaders realizes that value which is generated in organisation is because of people
who are actually handling product. A company can have best ideas of improvements from
employees who are working in organisation and dealing with product. The idea is that mangers
should move out of their cabins and walk in place where actual manufacturing is taking place.
This will inform them about actual happenings in company and where they are lacking.
The company is receiving huge investments from all over the world which will be used
by it for researching on more innovative ideas and coming out with more safe and secure cars but
it cannot improve if it fails to identify root causes of defects or faults.
Toyota has gained a huge fame for its Production System as it effectively involves front
line workers for improving the quality of the products. The Toyota's strategy of pulling the
improvements from front will be much more enhanced using new technologies for continually
improving its operations at which the Toyota was excelling. Companies generally push work
towards improvements from top for generating front line interests. The company will be able to
improve the quality by continuous involvement of the work team in each and every process.
Now the actual improvements which will be held and will drastically improve the process
through they might not sound heavy and strong. Toyota along with its strategy of continuous
improvements will also use the strategy of continuous involvement for improvement to happen at
individual level. Involvement of front line people will enable the company with suggestions for
6
strategies it will be using both manual and digital techniques. Company will be checking the
safety features even after the sales of the cars to the customers so that analyse whether changes
and new strategies are successful or not.
The company will be focusing more on to improve its strategy of continuous
improvements extending its focus over proper control of quality eliminating the defects to zero.
Toyota will also use the strategy of receiving feedbacks from the customers for knowing the
needs and requirements and also for knowing the problems they are facing with the products.
This will help the company in knowing the actual loopholes which are to be worked at by the
company. The company will then evaluate the causes of the problems and what are the possible
measures which it is supposed to take for improving the quality of the cars it is manufacturing.
(Helo, Gunasekaran and Rymaszewska, 2017).
Gemba Walks
Lean leaders realizes that value which is generated in organisation is because of people
who are actually handling product. A company can have best ideas of improvements from
employees who are working in organisation and dealing with product. The idea is that mangers
should move out of their cabins and walk in place where actual manufacturing is taking place.
This will inform them about actual happenings in company and where they are lacking.
The company is receiving huge investments from all over the world which will be used
by it for researching on more innovative ideas and coming out with more safe and secure cars but
it cannot improve if it fails to identify root causes of defects or faults.
Toyota has gained a huge fame for its Production System as it effectively involves front
line workers for improving the quality of the products. The Toyota's strategy of pulling the
improvements from front will be much more enhanced using new technologies for continually
improving its operations at which the Toyota was excelling. Companies generally push work
towards improvements from top for generating front line interests. The company will be able to
improve the quality by continuous involvement of the work team in each and every process.
Now the actual improvements which will be held and will drastically improve the process
through they might not sound heavy and strong. Toyota along with its strategy of continuous
improvements will also use the strategy of continuous involvement for improvement to happen at
individual level. Involvement of front line people will enable the company with suggestions for
6
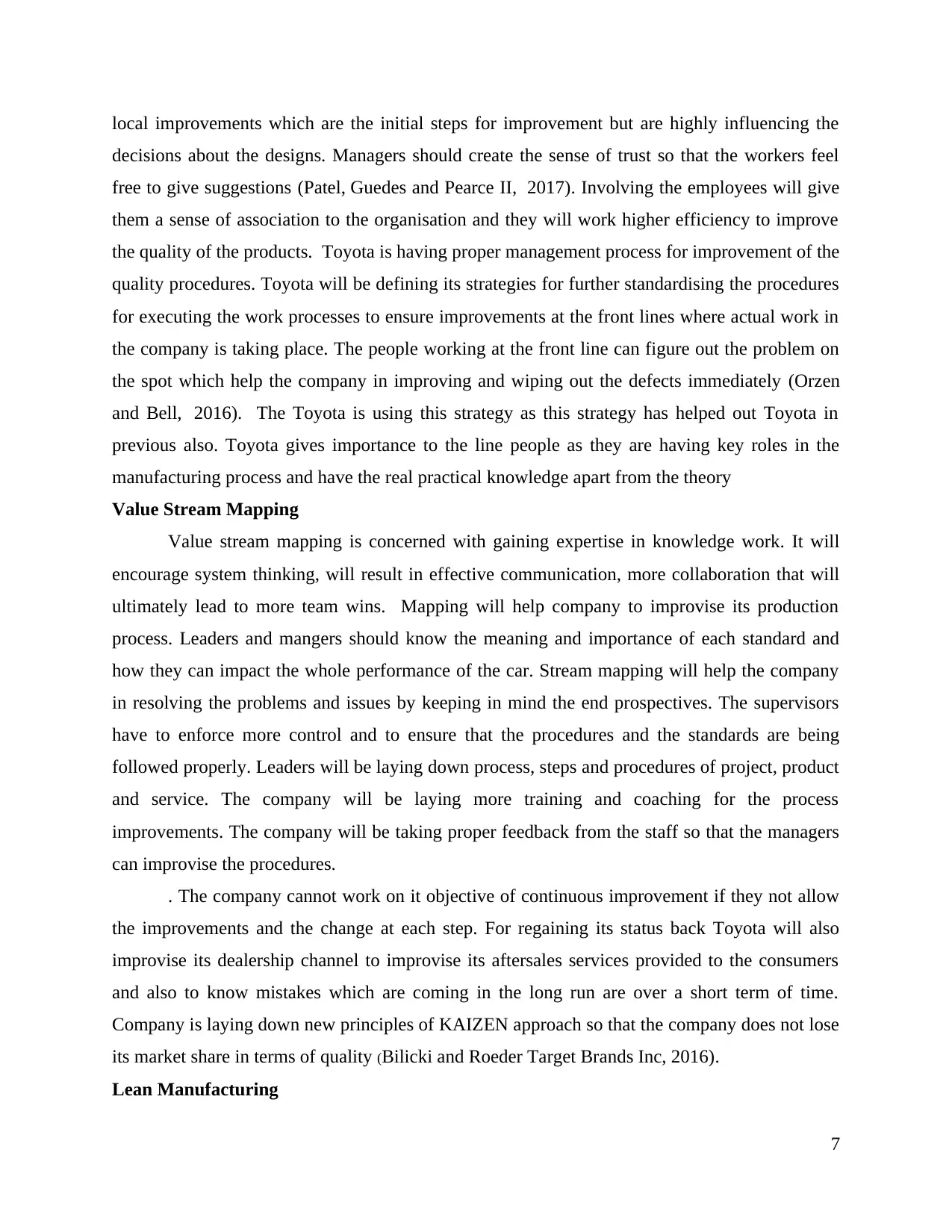
local improvements which are the initial steps for improvement but are highly influencing the
decisions about the designs. Managers should create the sense of trust so that the workers feel
free to give suggestions (Patel, Guedes and Pearce II, 2017). Involving the employees will give
them a sense of association to the organisation and they will work higher efficiency to improve
the quality of the products. Toyota is having proper management process for improvement of the
quality procedures. Toyota will be defining its strategies for further standardising the procedures
for executing the work processes to ensure improvements at the front lines where actual work in
the company is taking place. The people working at the front line can figure out the problem on
the spot which help the company in improving and wiping out the defects immediately (Orzen
and Bell, 2016). The Toyota is using this strategy as this strategy has helped out Toyota in
previous also. Toyota gives importance to the line people as they are having key roles in the
manufacturing process and have the real practical knowledge apart from the theory
Value Stream Mapping
Value stream mapping is concerned with gaining expertise in knowledge work. It will
encourage system thinking, will result in effective communication, more collaboration that will
ultimately lead to more team wins. Mapping will help company to improvise its production
process. Leaders and mangers should know the meaning and importance of each standard and
how they can impact the whole performance of the car. Stream mapping will help the company
in resolving the problems and issues by keeping in mind the end prospectives. The supervisors
have to enforce more control and to ensure that the procedures and the standards are being
followed properly. Leaders will be laying down process, steps and procedures of project, product
and service. The company will be laying more training and coaching for the process
improvements. The company will be taking proper feedback from the staff so that the managers
can improvise the procedures.
. The company cannot work on it objective of continuous improvement if they not allow
the improvements and the change at each step. For regaining its status back Toyota will also
improvise its dealership channel to improvise its aftersales services provided to the consumers
and also to know mistakes which are coming in the long run are over a short term of time.
Company is laying down new principles of KAIZEN approach so that the company does not lose
its market share in terms of quality (Bilicki and Roeder Target Brands Inc, 2016).
Lean Manufacturing
7
decisions about the designs. Managers should create the sense of trust so that the workers feel
free to give suggestions (Patel, Guedes and Pearce II, 2017). Involving the employees will give
them a sense of association to the organisation and they will work higher efficiency to improve
the quality of the products. Toyota is having proper management process for improvement of the
quality procedures. Toyota will be defining its strategies for further standardising the procedures
for executing the work processes to ensure improvements at the front lines where actual work in
the company is taking place. The people working at the front line can figure out the problem on
the spot which help the company in improving and wiping out the defects immediately (Orzen
and Bell, 2016). The Toyota is using this strategy as this strategy has helped out Toyota in
previous also. Toyota gives importance to the line people as they are having key roles in the
manufacturing process and have the real practical knowledge apart from the theory
Value Stream Mapping
Value stream mapping is concerned with gaining expertise in knowledge work. It will
encourage system thinking, will result in effective communication, more collaboration that will
ultimately lead to more team wins. Mapping will help company to improvise its production
process. Leaders and mangers should know the meaning and importance of each standard and
how they can impact the whole performance of the car. Stream mapping will help the company
in resolving the problems and issues by keeping in mind the end prospectives. The supervisors
have to enforce more control and to ensure that the procedures and the standards are being
followed properly. Leaders will be laying down process, steps and procedures of project, product
and service. The company will be laying more training and coaching for the process
improvements. The company will be taking proper feedback from the staff so that the managers
can improvise the procedures.
. The company cannot work on it objective of continuous improvement if they not allow
the improvements and the change at each step. For regaining its status back Toyota will also
improvise its dealership channel to improvise its aftersales services provided to the consumers
and also to know mistakes which are coming in the long run are over a short term of time.
Company is laying down new principles of KAIZEN approach so that the company does not lose
its market share in terms of quality (Bilicki and Roeder Target Brands Inc, 2016).
Lean Manufacturing
7
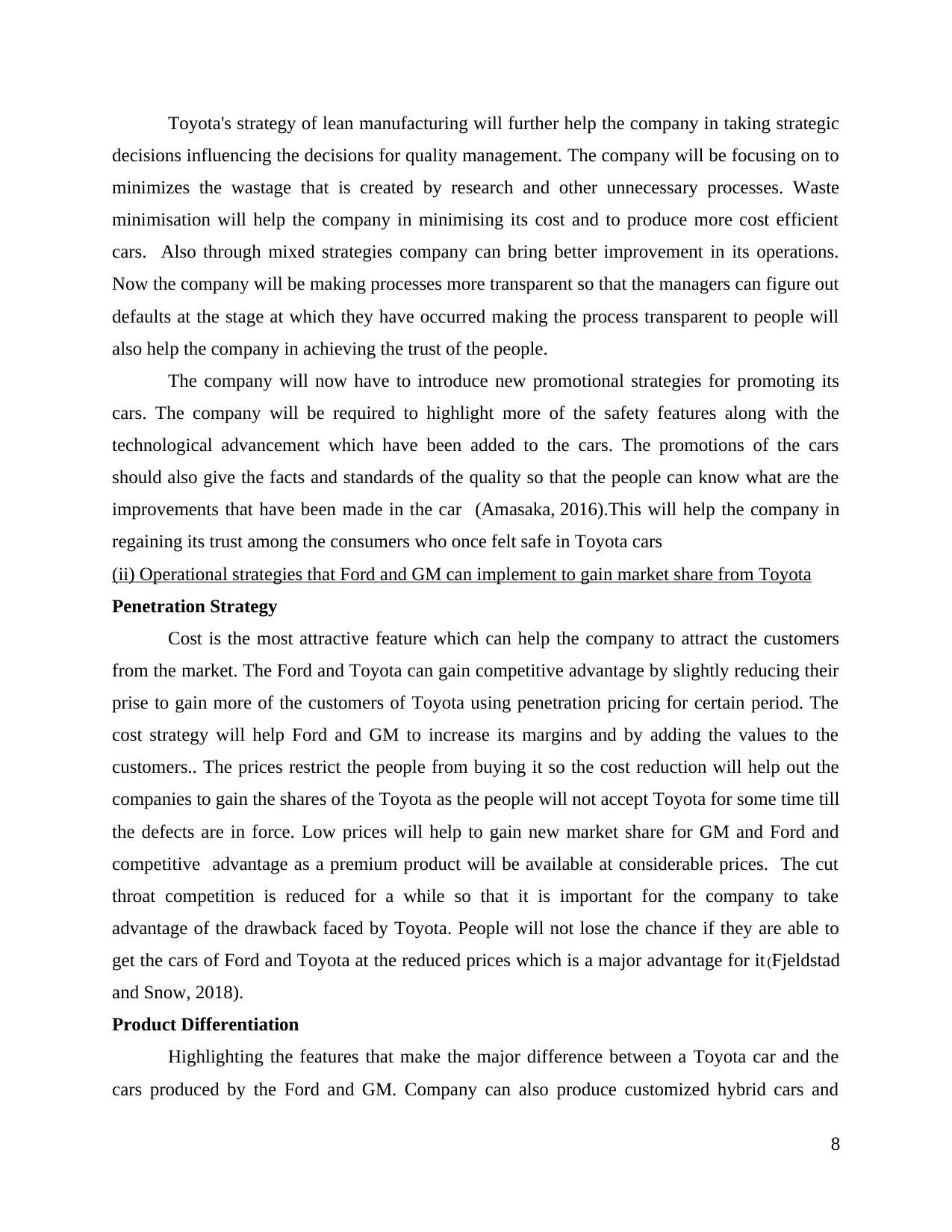
Toyota's strategy of lean manufacturing will further help the company in taking strategic
decisions influencing the decisions for quality management. The company will be focusing on to
minimizes the wastage that is created by research and other unnecessary processes. Waste
minimisation will help the company in minimising its cost and to produce more cost efficient
cars. Also through mixed strategies company can bring better improvement in its operations.
Now the company will be making processes more transparent so that the managers can figure out
defaults at the stage at which they have occurred making the process transparent to people will
also help the company in achieving the trust of the people.
The company will now have to introduce new promotional strategies for promoting its
cars. The company will be required to highlight more of the safety features along with the
technological advancement which have been added to the cars. The promotions of the cars
should also give the facts and standards of the quality so that the people can know what are the
improvements that have been made in the car (Amasaka, 2016).This will help the company in
regaining its trust among the consumers who once felt safe in Toyota cars
(ii) Operational strategies that Ford and GM can implement to gain market share from Toyota
Penetration Strategy
Cost is the most attractive feature which can help the company to attract the customers
from the market. The Ford and Toyota can gain competitive advantage by slightly reducing their
prise to gain more of the customers of Toyota using penetration pricing for certain period. The
cost strategy will help Ford and GM to increase its margins and by adding the values to the
customers.. The prices restrict the people from buying it so the cost reduction will help out the
companies to gain the shares of the Toyota as the people will not accept Toyota for some time till
the defects are in force. Low prices will help to gain new market share for GM and Ford and
competitive advantage as a premium product will be available at considerable prices. The cut
throat competition is reduced for a while so that it is important for the company to take
advantage of the drawback faced by Toyota. People will not lose the chance if they are able to
get the cars of Ford and Toyota at the reduced prices which is a major advantage for it(Fjeldstad
and Snow, 2018).
Product Differentiation
Highlighting the features that make the major difference between a Toyota car and the
cars produced by the Ford and GM. Company can also produce customized hybrid cars and
8
decisions influencing the decisions for quality management. The company will be focusing on to
minimizes the wastage that is created by research and other unnecessary processes. Waste
minimisation will help the company in minimising its cost and to produce more cost efficient
cars. Also through mixed strategies company can bring better improvement in its operations.
Now the company will be making processes more transparent so that the managers can figure out
defaults at the stage at which they have occurred making the process transparent to people will
also help the company in achieving the trust of the people.
The company will now have to introduce new promotional strategies for promoting its
cars. The company will be required to highlight more of the safety features along with the
technological advancement which have been added to the cars. The promotions of the cars
should also give the facts and standards of the quality so that the people can know what are the
improvements that have been made in the car (Amasaka, 2016).This will help the company in
regaining its trust among the consumers who once felt safe in Toyota cars
(ii) Operational strategies that Ford and GM can implement to gain market share from Toyota
Penetration Strategy
Cost is the most attractive feature which can help the company to attract the customers
from the market. The Ford and Toyota can gain competitive advantage by slightly reducing their
prise to gain more of the customers of Toyota using penetration pricing for certain period. The
cost strategy will help Ford and GM to increase its margins and by adding the values to the
customers.. The prices restrict the people from buying it so the cost reduction will help out the
companies to gain the shares of the Toyota as the people will not accept Toyota for some time till
the defects are in force. Low prices will help to gain new market share for GM and Ford and
competitive advantage as a premium product will be available at considerable prices. The cut
throat competition is reduced for a while so that it is important for the company to take
advantage of the drawback faced by Toyota. People will not lose the chance if they are able to
get the cars of Ford and Toyota at the reduced prices which is a major advantage for it(Fjeldstad
and Snow, 2018).
Product Differentiation
Highlighting the features that make the major difference between a Toyota car and the
cars produced by the Ford and GM. Company can also produce customized hybrid cars and
8
Secure Best Marks with AI Grader
Need help grading? Try our AI Grader for instant feedback on your assignments.
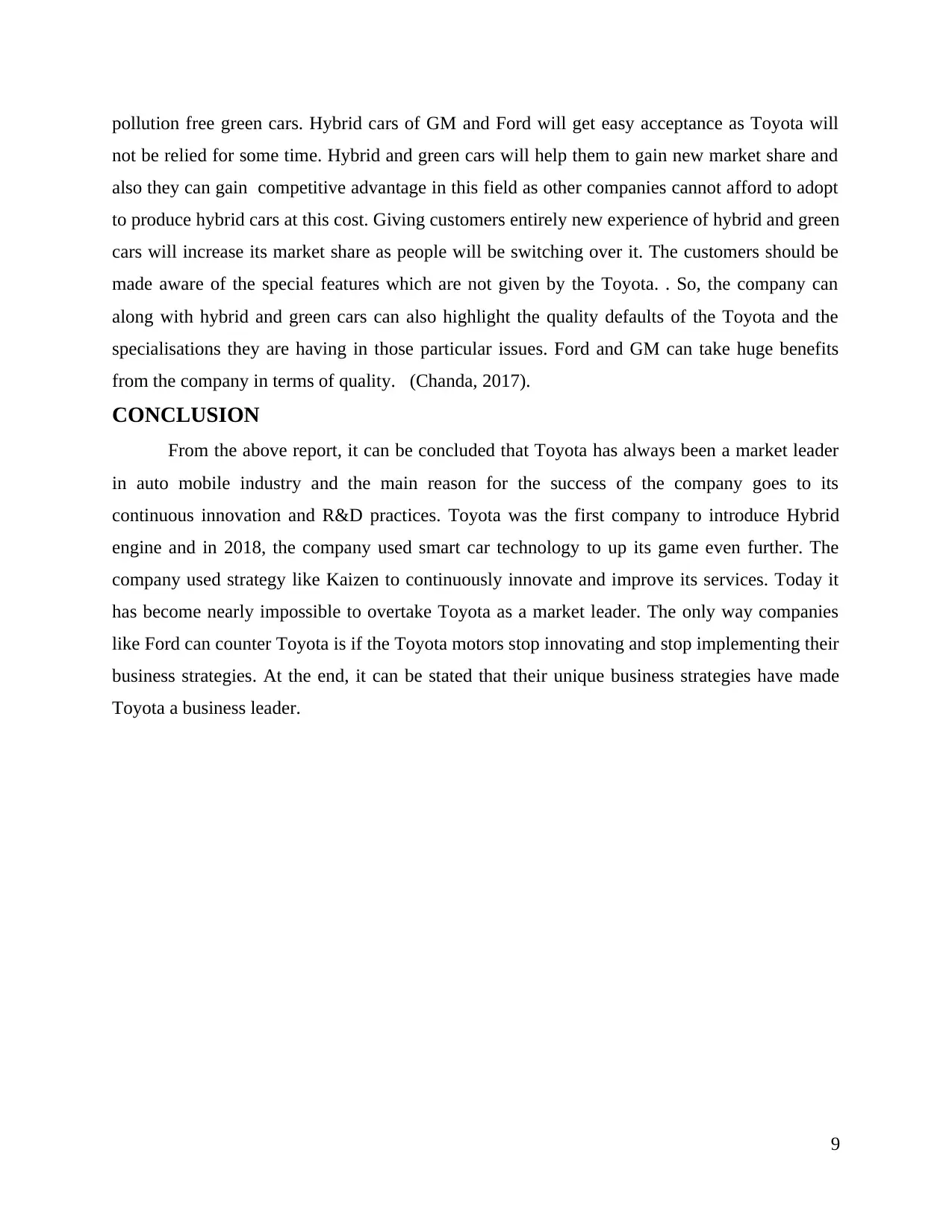
pollution free green cars. Hybrid cars of GM and Ford will get easy acceptance as Toyota will
not be relied for some time. Hybrid and green cars will help them to gain new market share and
also they can gain competitive advantage in this field as other companies cannot afford to adopt
to produce hybrid cars at this cost. Giving customers entirely new experience of hybrid and green
cars will increase its market share as people will be switching over it. The customers should be
made aware of the special features which are not given by the Toyota. . So, the company can
along with hybrid and green cars can also highlight the quality defaults of the Toyota and the
specialisations they are having in those particular issues. Ford and GM can take huge benefits
from the company in terms of quality. (Chanda, 2017).
CONCLUSION
From the above report, it can be concluded that Toyota has always been a market leader
in auto mobile industry and the main reason for the success of the company goes to its
continuous innovation and R&D practices. Toyota was the first company to introduce Hybrid
engine and in 2018, the company used smart car technology to up its game even further. The
company used strategy like Kaizen to continuously innovate and improve its services. Today it
has become nearly impossible to overtake Toyota as a market leader. The only way companies
like Ford can counter Toyota is if the Toyota motors stop innovating and stop implementing their
business strategies. At the end, it can be stated that their unique business strategies have made
Toyota a business leader.
9
not be relied for some time. Hybrid and green cars will help them to gain new market share and
also they can gain competitive advantage in this field as other companies cannot afford to adopt
to produce hybrid cars at this cost. Giving customers entirely new experience of hybrid and green
cars will increase its market share as people will be switching over it. The customers should be
made aware of the special features which are not given by the Toyota. . So, the company can
along with hybrid and green cars can also highlight the quality defaults of the Toyota and the
specialisations they are having in those particular issues. Ford and GM can take huge benefits
from the company in terms of quality. (Chanda, 2017).
CONCLUSION
From the above report, it can be concluded that Toyota has always been a market leader
in auto mobile industry and the main reason for the success of the company goes to its
continuous innovation and R&D practices. Toyota was the first company to introduce Hybrid
engine and in 2018, the company used smart car technology to up its game even further. The
company used strategy like Kaizen to continuously innovate and improve its services. Today it
has become nearly impossible to overtake Toyota as a market leader. The only way companies
like Ford can counter Toyota is if the Toyota motors stop innovating and stop implementing their
business strategies. At the end, it can be stated that their unique business strategies have made
Toyota a business leader.
9
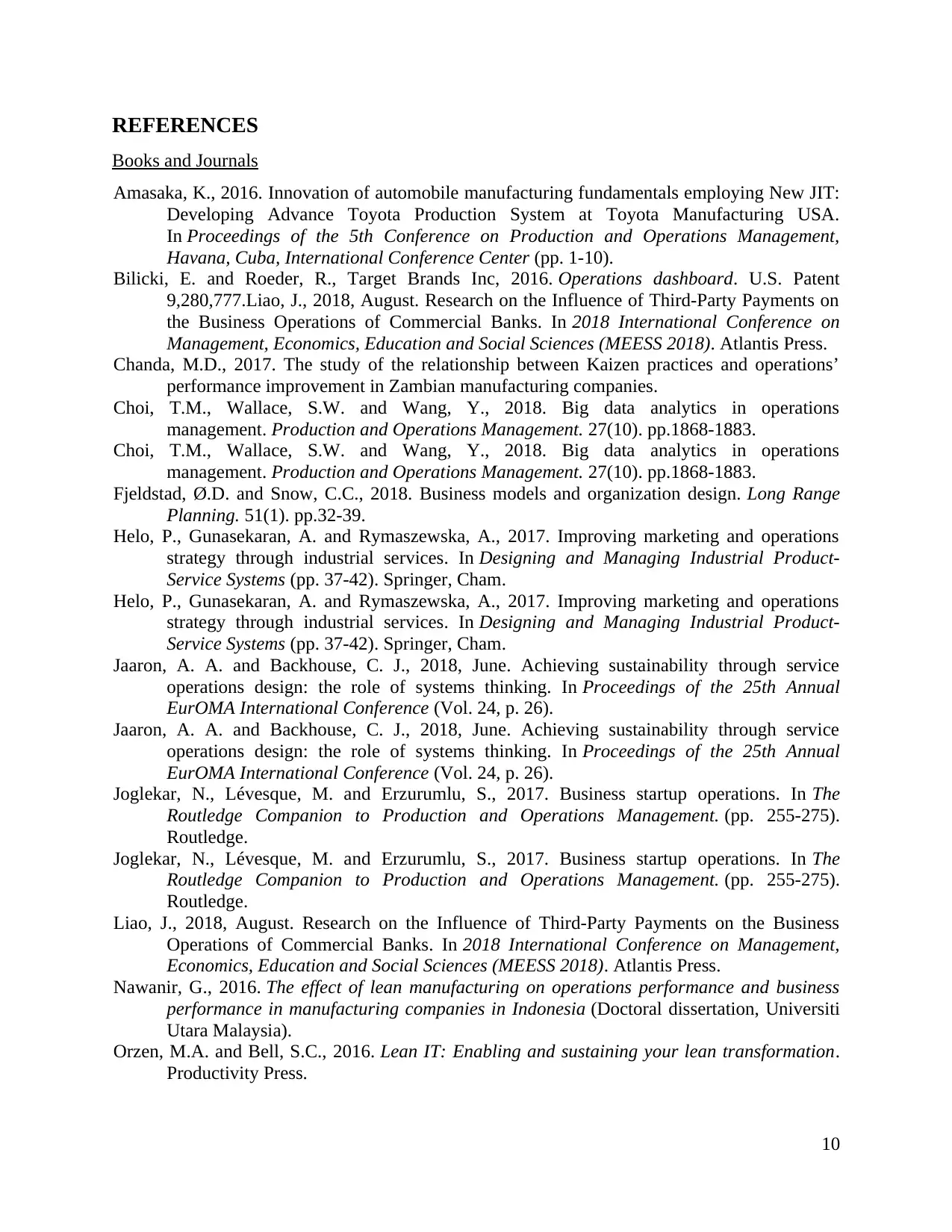
REFERENCES
Books and Journals
Amasaka, K., 2016. Innovation of automobile manufacturing fundamentals employing New JIT:
Developing Advance Toyota Production System at Toyota Manufacturing USA.
In Proceedings of the 5th Conference on Production and Operations Management,
Havana, Cuba, International Conference Center (pp. 1-10).
Bilicki, E. and Roeder, R., Target Brands Inc, 2016. Operations dashboard. U.S. Patent
9,280,777.Liao, J., 2018, August. Research on the Influence of Third-Party Payments on
the Business Operations of Commercial Banks. In 2018 International Conference on
Management, Economics, Education and Social Sciences (MEESS 2018). Atlantis Press.
Chanda, M.D., 2017. The study of the relationship between Kaizen practices and operations’
performance improvement in Zambian manufacturing companies.
Choi, T.M., Wallace, S.W. and Wang, Y., 2018. Big data analytics in operations
management. Production and Operations Management. 27(10). pp.1868-1883.
Choi, T.M., Wallace, S.W. and Wang, Y., 2018. Big data analytics in operations
management. Production and Operations Management. 27(10). pp.1868-1883.
Fjeldstad, Ø.D. and Snow, C.C., 2018. Business models and organization design. Long Range
Planning. 51(1). pp.32-39.
Helo, P., Gunasekaran, A. and Rymaszewska, A., 2017. Improving marketing and operations
strategy through industrial services. In Designing and Managing Industrial Product-
Service Systems (pp. 37-42). Springer, Cham.
Helo, P., Gunasekaran, A. and Rymaszewska, A., 2017. Improving marketing and operations
strategy through industrial services. In Designing and Managing Industrial Product-
Service Systems (pp. 37-42). Springer, Cham.
Jaaron, A. A. and Backhouse, C. J., 2018, June. Achieving sustainability through service
operations design: the role of systems thinking. In Proceedings of the 25th Annual
EurOMA International Conference (Vol. 24, p. 26).
Jaaron, A. A. and Backhouse, C. J., 2018, June. Achieving sustainability through service
operations design: the role of systems thinking. In Proceedings of the 25th Annual
EurOMA International Conference (Vol. 24, p. 26).
Joglekar, N., Lévesque, M. and Erzurumlu, S., 2017. Business startup operations. In The
Routledge Companion to Production and Operations Management. (pp. 255-275).
Routledge.
Joglekar, N., Lévesque, M. and Erzurumlu, S., 2017. Business startup operations. In The
Routledge Companion to Production and Operations Management. (pp. 255-275).
Routledge.
Liao, J., 2018, August. Research on the Influence of Third-Party Payments on the Business
Operations of Commercial Banks. In 2018 International Conference on Management,
Economics, Education and Social Sciences (MEESS 2018). Atlantis Press.
Nawanir, G., 2016. The effect of lean manufacturing on operations performance and business
performance in manufacturing companies in Indonesia (Doctoral dissertation, Universiti
Utara Malaysia).
Orzen, M.A. and Bell, S.C., 2016. Lean IT: Enabling and sustaining your lean transformation.
Productivity Press.
10
Books and Journals
Amasaka, K., 2016. Innovation of automobile manufacturing fundamentals employing New JIT:
Developing Advance Toyota Production System at Toyota Manufacturing USA.
In Proceedings of the 5th Conference on Production and Operations Management,
Havana, Cuba, International Conference Center (pp. 1-10).
Bilicki, E. and Roeder, R., Target Brands Inc, 2016. Operations dashboard. U.S. Patent
9,280,777.Liao, J., 2018, August. Research on the Influence of Third-Party Payments on
the Business Operations of Commercial Banks. In 2018 International Conference on
Management, Economics, Education and Social Sciences (MEESS 2018). Atlantis Press.
Chanda, M.D., 2017. The study of the relationship between Kaizen practices and operations’
performance improvement in Zambian manufacturing companies.
Choi, T.M., Wallace, S.W. and Wang, Y., 2018. Big data analytics in operations
management. Production and Operations Management. 27(10). pp.1868-1883.
Choi, T.M., Wallace, S.W. and Wang, Y., 2018. Big data analytics in operations
management. Production and Operations Management. 27(10). pp.1868-1883.
Fjeldstad, Ø.D. and Snow, C.C., 2018. Business models and organization design. Long Range
Planning. 51(1). pp.32-39.
Helo, P., Gunasekaran, A. and Rymaszewska, A., 2017. Improving marketing and operations
strategy through industrial services. In Designing and Managing Industrial Product-
Service Systems (pp. 37-42). Springer, Cham.
Helo, P., Gunasekaran, A. and Rymaszewska, A., 2017. Improving marketing and operations
strategy through industrial services. In Designing and Managing Industrial Product-
Service Systems (pp. 37-42). Springer, Cham.
Jaaron, A. A. and Backhouse, C. J., 2018, June. Achieving sustainability through service
operations design: the role of systems thinking. In Proceedings of the 25th Annual
EurOMA International Conference (Vol. 24, p. 26).
Jaaron, A. A. and Backhouse, C. J., 2018, June. Achieving sustainability through service
operations design: the role of systems thinking. In Proceedings of the 25th Annual
EurOMA International Conference (Vol. 24, p. 26).
Joglekar, N., Lévesque, M. and Erzurumlu, S., 2017. Business startup operations. In The
Routledge Companion to Production and Operations Management. (pp. 255-275).
Routledge.
Joglekar, N., Lévesque, M. and Erzurumlu, S., 2017. Business startup operations. In The
Routledge Companion to Production and Operations Management. (pp. 255-275).
Routledge.
Liao, J., 2018, August. Research on the Influence of Third-Party Payments on the Business
Operations of Commercial Banks. In 2018 International Conference on Management,
Economics, Education and Social Sciences (MEESS 2018). Atlantis Press.
Nawanir, G., 2016. The effect of lean manufacturing on operations performance and business
performance in manufacturing companies in Indonesia (Doctoral dissertation, Universiti
Utara Malaysia).
Orzen, M.A. and Bell, S.C., 2016. Lean IT: Enabling and sustaining your lean transformation.
Productivity Press.
10
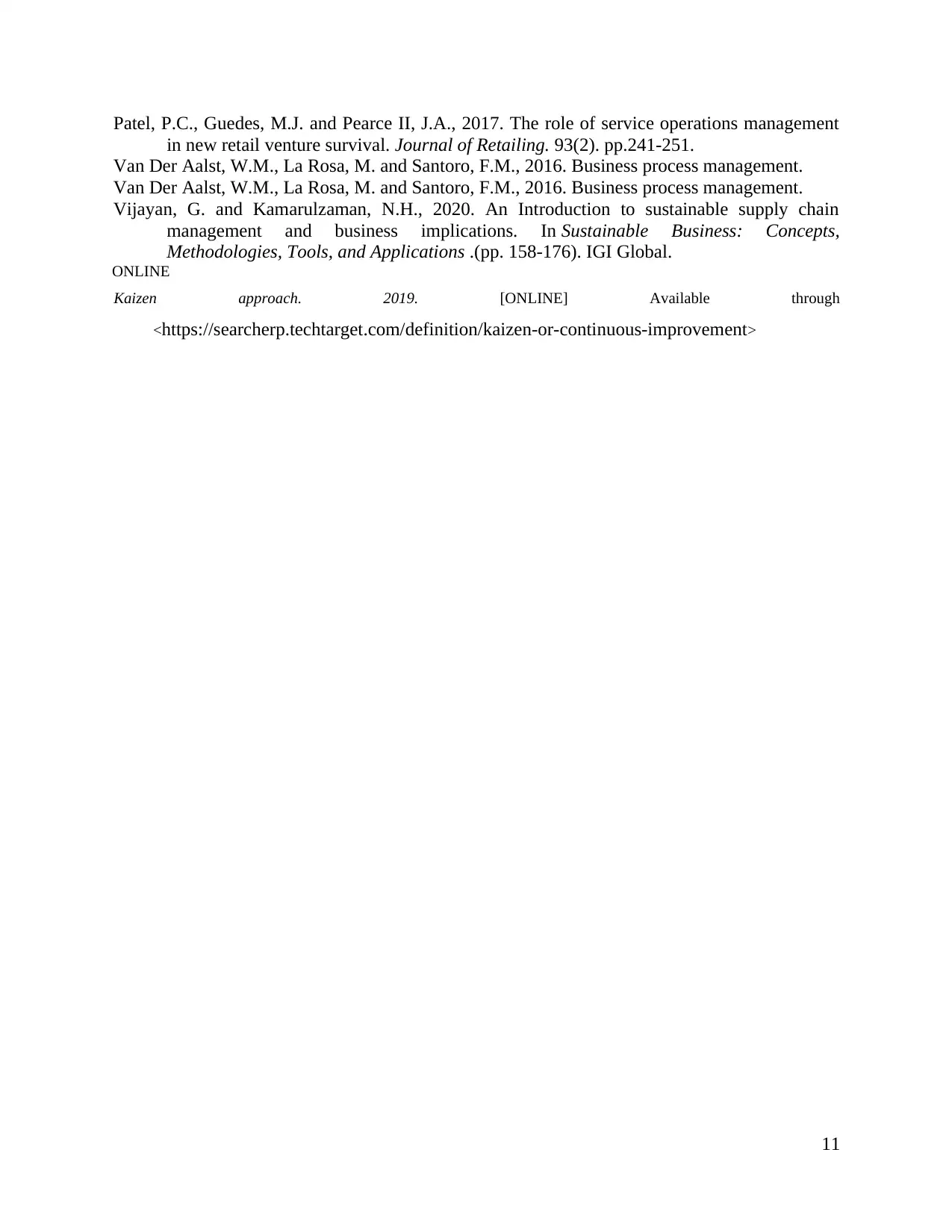
Patel, P.C., Guedes, M.J. and Pearce II, J.A., 2017. The role of service operations management
in new retail venture survival. Journal of Retailing. 93(2). pp.241-251.
Van Der Aalst, W.M., La Rosa, M. and Santoro, F.M., 2016. Business process management.
Van Der Aalst, W.M., La Rosa, M. and Santoro, F.M., 2016. Business process management.
Vijayan, G. and Kamarulzaman, N.H., 2020. An Introduction to sustainable supply chain
management and business implications. In Sustainable Business: Concepts,
Methodologies, Tools, and Applications .(pp. 158-176). IGI Global.
ONLINE
Kaizen approach. 2019. [ONLINE] Available through
<https://searcherp.techtarget.com/definition/kaizen-or-continuous-improvement>
11
in new retail venture survival. Journal of Retailing. 93(2). pp.241-251.
Van Der Aalst, W.M., La Rosa, M. and Santoro, F.M., 2016. Business process management.
Van Der Aalst, W.M., La Rosa, M. and Santoro, F.M., 2016. Business process management.
Vijayan, G. and Kamarulzaman, N.H., 2020. An Introduction to sustainable supply chain
management and business implications. In Sustainable Business: Concepts,
Methodologies, Tools, and Applications .(pp. 158-176). IGI Global.
ONLINE
Kaizen approach. 2019. [ONLINE] Available through
<https://searcherp.techtarget.com/definition/kaizen-or-continuous-improvement>
11
1 out of 13
Related Documents

Your All-in-One AI-Powered Toolkit for Academic Success.
+13062052269
info@desklib.com
Available 24*7 on WhatsApp / Email
Unlock your academic potential
© 2024 | Zucol Services PVT LTD | All rights reserved.