Strategies and Tools to Improve Toyota's Operations and Services
VerifiedAdded on 2020/10/05
|11
|3672
|495
Report
AI Summary
This report delves into the operational strategies and improvement tools that Toyota can employ to enhance its business performance, particularly in light of recent challenges. The introduction sets the stage by defining operations management and its significance in the automotive industry, specifically focusing on Toyota. The discussion section explores various strategies, including asset optimization, quality improvement (with models like PDSA, Six Sigma, and Lean management), safety performance, effective project planning and execution, supply chain management, process improvement, shutdown management, reliability, inventory management, and value engineering. Furthermore, the report examines operational improvement tools such as Lean technology and Six Sigma, illustrating how these tools can be implemented to boost efficiency and address potential issues. The conclusion summarizes the key findings and recommendations, offering insights for Toyota to maintain its market advantage and improve its operations. The report also references the strategies adopted by competitors like Ford and General Motors, providing a comparative perspective.
Contribute Materials
Your contribution can guide someone’s learning journey. Share your
documents today.
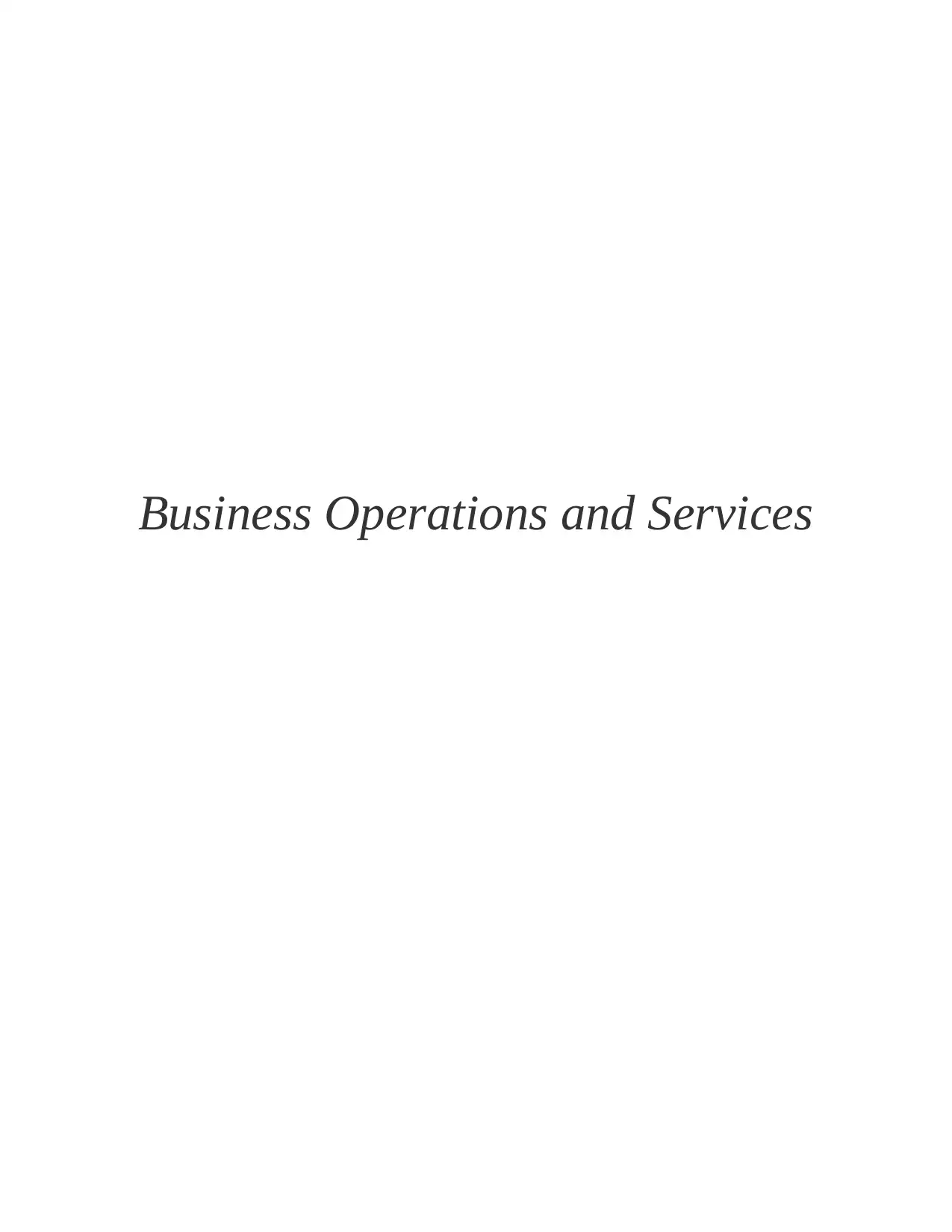
Business Operations and Services
Secure Best Marks with AI Grader
Need help grading? Try our AI Grader for instant feedback on your assignments.

Table of Contents
INTRODUCTION...........................................................................................................................1
DISCUSSION..................................................................................................................................1
Operational Improvement Strategies...........................................................................................1
Operation Improvement Tools.....................................................................................................5
Recommendations for Strategies Used by Market Competitors..................................................7
CONCLUSION................................................................................................................................8
REFERENCES................................................................................................................................9
INTRODUCTION...........................................................................................................................1
DISCUSSION..................................................................................................................................1
Operational Improvement Strategies...........................................................................................1
Operation Improvement Tools.....................................................................................................5
Recommendations for Strategies Used by Market Competitors..................................................7
CONCLUSION................................................................................................................................8
REFERENCES................................................................................................................................9
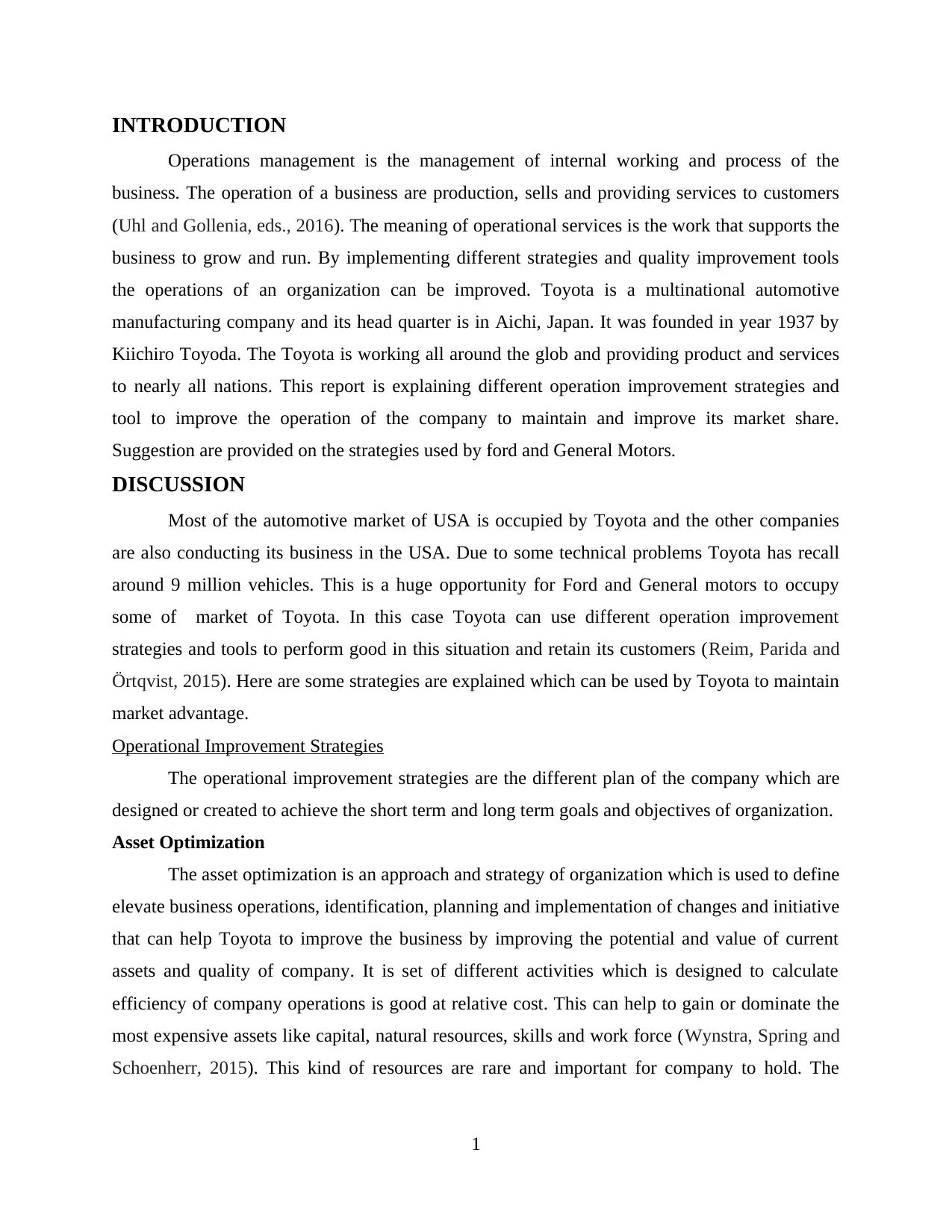
INTRODUCTION
Operations management is the management of internal working and process of the
business. The operation of a business are production, sells and providing services to customers
(Uhl and Gollenia, eds., 2016). The meaning of operational services is the work that supports the
business to grow and run. By implementing different strategies and quality improvement tools
the operations of an organization can be improved. Toyota is a multinational automotive
manufacturing company and its head quarter is in Aichi, Japan. It was founded in year 1937 by
Kiichiro Toyoda. The Toyota is working all around the glob and providing product and services
to nearly all nations. This report is explaining different operation improvement strategies and
tool to improve the operation of the company to maintain and improve its market share.
Suggestion are provided on the strategies used by ford and General Motors.
DISCUSSION
Most of the automotive market of USA is occupied by Toyota and the other companies
are also conducting its business in the USA. Due to some technical problems Toyota has recall
around 9 million vehicles. This is a huge opportunity for Ford and General motors to occupy
some of market of Toyota. In this case Toyota can use different operation improvement
strategies and tools to perform good in this situation and retain its customers (Reim, Parida and
Örtqvist, 2015). Here are some strategies are explained which can be used by Toyota to maintain
market advantage.
Operational Improvement Strategies
The operational improvement strategies are the different plan of the company which are
designed or created to achieve the short term and long term goals and objectives of organization.
Asset Optimization
The asset optimization is an approach and strategy of organization which is used to define
elevate business operations, identification, planning and implementation of changes and initiative
that can help Toyota to improve the business by improving the potential and value of current
assets and quality of company. It is set of different activities which is designed to calculate
efficiency of company operations is good at relative cost. This can help to gain or dominate the
most expensive assets like capital, natural resources, skills and work force (Wynstra, Spring and
Schoenherr, 2015). This kind of resources are rare and important for company to hold. The
1
Operations management is the management of internal working and process of the
business. The operation of a business are production, sells and providing services to customers
(Uhl and Gollenia, eds., 2016). The meaning of operational services is the work that supports the
business to grow and run. By implementing different strategies and quality improvement tools
the operations of an organization can be improved. Toyota is a multinational automotive
manufacturing company and its head quarter is in Aichi, Japan. It was founded in year 1937 by
Kiichiro Toyoda. The Toyota is working all around the glob and providing product and services
to nearly all nations. This report is explaining different operation improvement strategies and
tool to improve the operation of the company to maintain and improve its market share.
Suggestion are provided on the strategies used by ford and General Motors.
DISCUSSION
Most of the automotive market of USA is occupied by Toyota and the other companies
are also conducting its business in the USA. Due to some technical problems Toyota has recall
around 9 million vehicles. This is a huge opportunity for Ford and General motors to occupy
some of market of Toyota. In this case Toyota can use different operation improvement
strategies and tools to perform good in this situation and retain its customers (Reim, Parida and
Örtqvist, 2015). Here are some strategies are explained which can be used by Toyota to maintain
market advantage.
Operational Improvement Strategies
The operational improvement strategies are the different plan of the company which are
designed or created to achieve the short term and long term goals and objectives of organization.
Asset Optimization
The asset optimization is an approach and strategy of organization which is used to define
elevate business operations, identification, planning and implementation of changes and initiative
that can help Toyota to improve the business by improving the potential and value of current
assets and quality of company. It is set of different activities which is designed to calculate
efficiency of company operations is good at relative cost. This can help to gain or dominate the
most expensive assets like capital, natural resources, skills and work force (Wynstra, Spring and
Schoenherr, 2015). This kind of resources are rare and important for company to hold. The
1
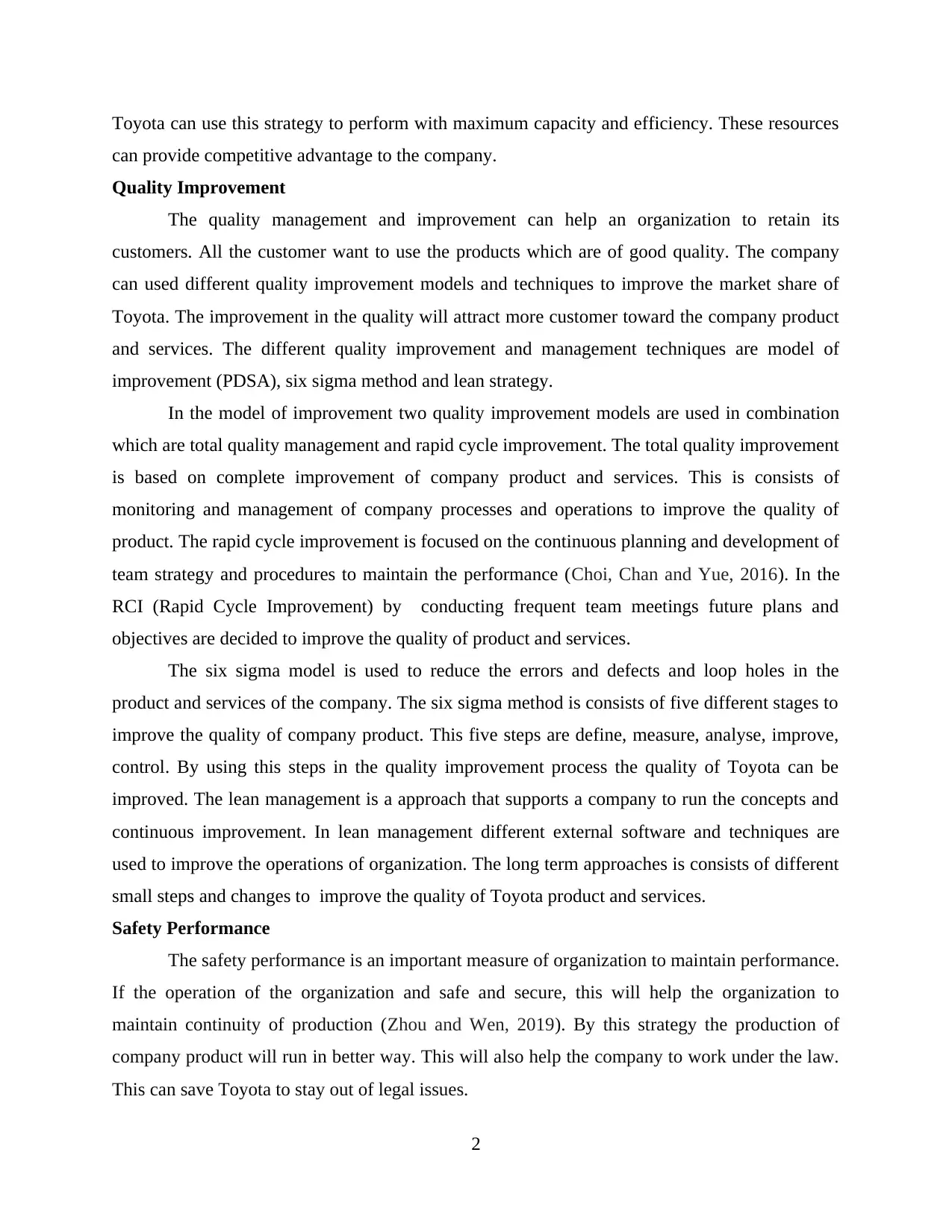
Toyota can use this strategy to perform with maximum capacity and efficiency. These resources
can provide competitive advantage to the company.
Quality Improvement
The quality management and improvement can help an organization to retain its
customers. All the customer want to use the products which are of good quality. The company
can used different quality improvement models and techniques to improve the market share of
Toyota. The improvement in the quality will attract more customer toward the company product
and services. The different quality improvement and management techniques are model of
improvement (PDSA), six sigma method and lean strategy.
In the model of improvement two quality improvement models are used in combination
which are total quality management and rapid cycle improvement. The total quality improvement
is based on complete improvement of company product and services. This is consists of
monitoring and management of company processes and operations to improve the quality of
product. The rapid cycle improvement is focused on the continuous planning and development of
team strategy and procedures to maintain the performance (Choi, Chan and Yue, 2016). In the
RCI (Rapid Cycle Improvement) by conducting frequent team meetings future plans and
objectives are decided to improve the quality of product and services.
The six sigma model is used to reduce the errors and defects and loop holes in the
product and services of the company. The six sigma method is consists of five different stages to
improve the quality of company product. This five steps are define, measure, analyse, improve,
control. By using this steps in the quality improvement process the quality of Toyota can be
improved. The lean management is a approach that supports a company to run the concepts and
continuous improvement. In lean management different external software and techniques are
used to improve the operations of organization. The long term approaches is consists of different
small steps and changes to improve the quality of Toyota product and services.
Safety Performance
The safety performance is an important measure of organization to maintain performance.
If the operation of the organization and safe and secure, this will help the organization to
maintain continuity of production (Zhou and Wen, 2019). By this strategy the production of
company product will run in better way. This will also help the company to work under the law.
This can save Toyota to stay out of legal issues.
2
can provide competitive advantage to the company.
Quality Improvement
The quality management and improvement can help an organization to retain its
customers. All the customer want to use the products which are of good quality. The company
can used different quality improvement models and techniques to improve the market share of
Toyota. The improvement in the quality will attract more customer toward the company product
and services. The different quality improvement and management techniques are model of
improvement (PDSA), six sigma method and lean strategy.
In the model of improvement two quality improvement models are used in combination
which are total quality management and rapid cycle improvement. The total quality improvement
is based on complete improvement of company product and services. This is consists of
monitoring and management of company processes and operations to improve the quality of
product. The rapid cycle improvement is focused on the continuous planning and development of
team strategy and procedures to maintain the performance (Choi, Chan and Yue, 2016). In the
RCI (Rapid Cycle Improvement) by conducting frequent team meetings future plans and
objectives are decided to improve the quality of product and services.
The six sigma model is used to reduce the errors and defects and loop holes in the
product and services of the company. The six sigma method is consists of five different stages to
improve the quality of company product. This five steps are define, measure, analyse, improve,
control. By using this steps in the quality improvement process the quality of Toyota can be
improved. The lean management is a approach that supports a company to run the concepts and
continuous improvement. In lean management different external software and techniques are
used to improve the operations of organization. The long term approaches is consists of different
small steps and changes to improve the quality of Toyota product and services.
Safety Performance
The safety performance is an important measure of organization to maintain performance.
If the operation of the organization and safe and secure, this will help the organization to
maintain continuity of production (Zhou and Wen, 2019). By this strategy the production of
company product will run in better way. This will also help the company to work under the law.
This can save Toyota to stay out of legal issues.
2
Secure Best Marks with AI Grader
Need help grading? Try our AI Grader for instant feedback on your assignments.
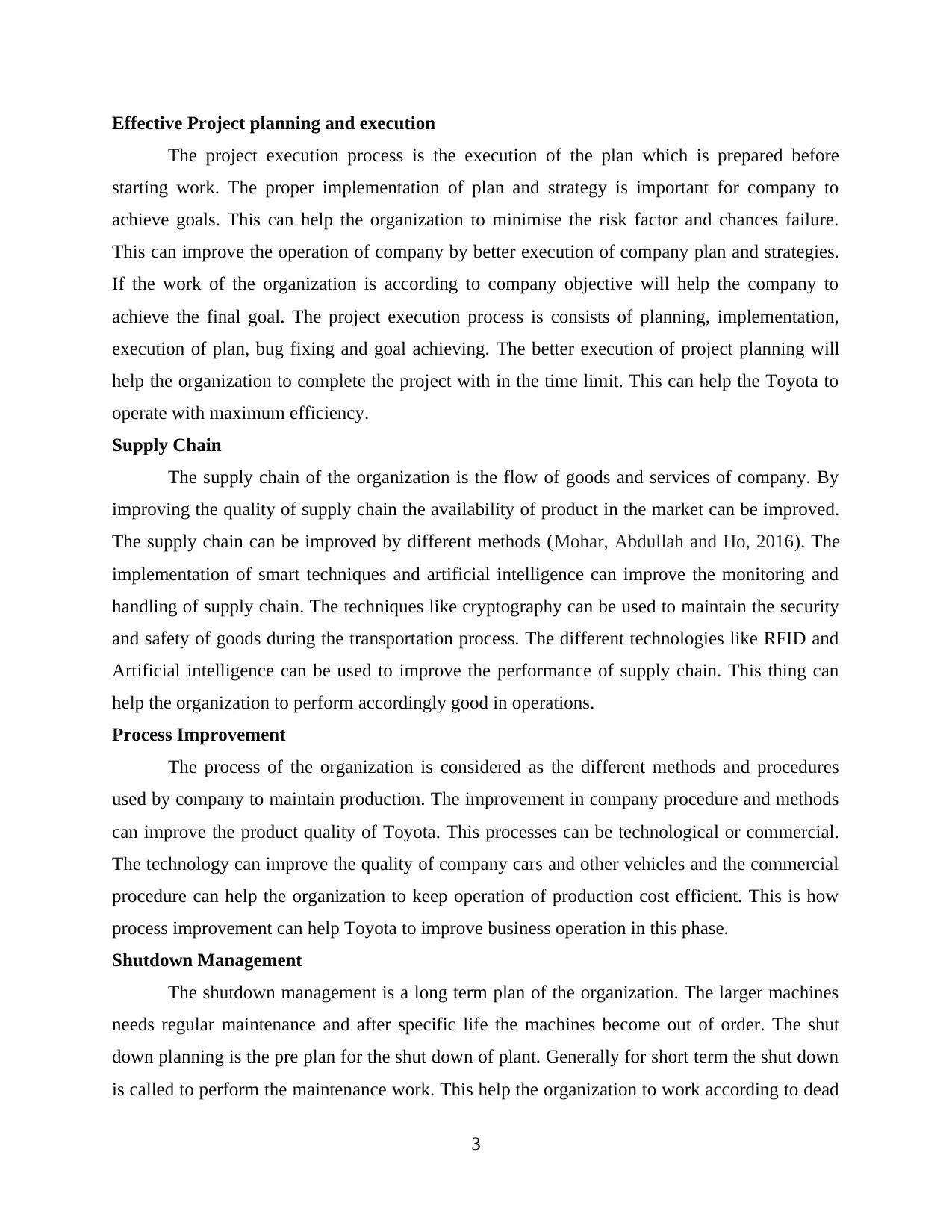
Effective Project planning and execution
The project execution process is the execution of the plan which is prepared before
starting work. The proper implementation of plan and strategy is important for company to
achieve goals. This can help the organization to minimise the risk factor and chances failure.
This can improve the operation of company by better execution of company plan and strategies.
If the work of the organization is according to company objective will help the company to
achieve the final goal. The project execution process is consists of planning, implementation,
execution of plan, bug fixing and goal achieving. The better execution of project planning will
help the organization to complete the project with in the time limit. This can help the Toyota to
operate with maximum efficiency.
Supply Chain
The supply chain of the organization is the flow of goods and services of company. By
improving the quality of supply chain the availability of product in the market can be improved.
The supply chain can be improved by different methods (Mohar, Abdullah and Ho, 2016). The
implementation of smart techniques and artificial intelligence can improve the monitoring and
handling of supply chain. The techniques like cryptography can be used to maintain the security
and safety of goods during the transportation process. The different technologies like RFID and
Artificial intelligence can be used to improve the performance of supply chain. This thing can
help the organization to perform accordingly good in operations.
Process Improvement
The process of the organization is considered as the different methods and procedures
used by company to maintain production. The improvement in company procedure and methods
can improve the product quality of Toyota. This processes can be technological or commercial.
The technology can improve the quality of company cars and other vehicles and the commercial
procedure can help the organization to keep operation of production cost efficient. This is how
process improvement can help Toyota to improve business operation in this phase.
Shutdown Management
The shutdown management is a long term plan of the organization. The larger machines
needs regular maintenance and after specific life the machines become out of order. The shut
down planning is the pre plan for the shut down of plant. Generally for short term the shut down
is called to perform the maintenance work. This help the organization to work according to dead
3
The project execution process is the execution of the plan which is prepared before
starting work. The proper implementation of plan and strategy is important for company to
achieve goals. This can help the organization to minimise the risk factor and chances failure.
This can improve the operation of company by better execution of company plan and strategies.
If the work of the organization is according to company objective will help the company to
achieve the final goal. The project execution process is consists of planning, implementation,
execution of plan, bug fixing and goal achieving. The better execution of project planning will
help the organization to complete the project with in the time limit. This can help the Toyota to
operate with maximum efficiency.
Supply Chain
The supply chain of the organization is the flow of goods and services of company. By
improving the quality of supply chain the availability of product in the market can be improved.
The supply chain can be improved by different methods (Mohar, Abdullah and Ho, 2016). The
implementation of smart techniques and artificial intelligence can improve the monitoring and
handling of supply chain. The techniques like cryptography can be used to maintain the security
and safety of goods during the transportation process. The different technologies like RFID and
Artificial intelligence can be used to improve the performance of supply chain. This thing can
help the organization to perform accordingly good in operations.
Process Improvement
The process of the organization is considered as the different methods and procedures
used by company to maintain production. The improvement in company procedure and methods
can improve the product quality of Toyota. This processes can be technological or commercial.
The technology can improve the quality of company cars and other vehicles and the commercial
procedure can help the organization to keep operation of production cost efficient. This is how
process improvement can help Toyota to improve business operation in this phase.
Shutdown Management
The shutdown management is a long term plan of the organization. The larger machines
needs regular maintenance and after specific life the machines become out of order. The shut
down planning is the pre plan for the shut down of plant. Generally for short term the shut down
is called to perform the maintenance work. This help the organization to work according to dead
3
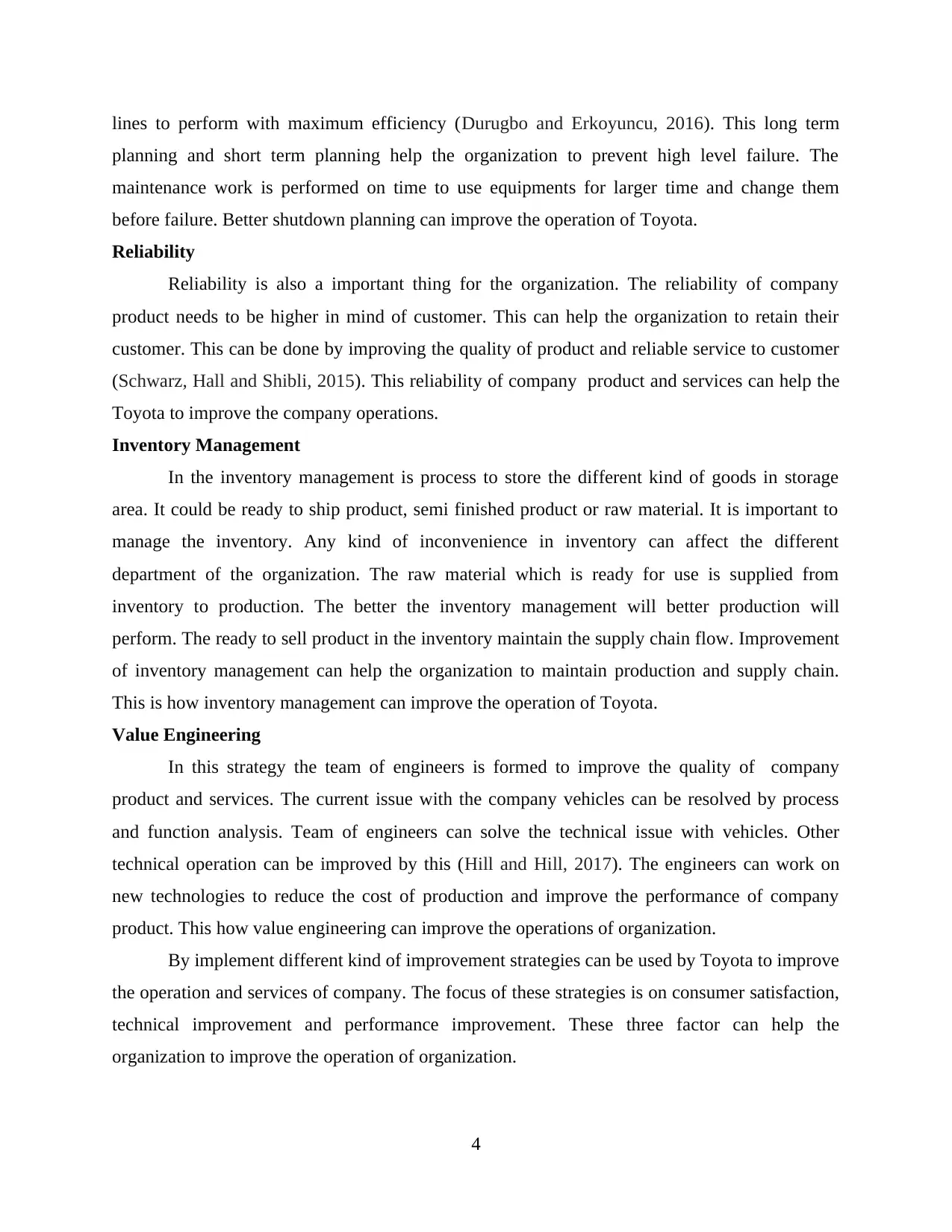
lines to perform with maximum efficiency (Durugbo and Erkoyuncu, 2016). This long term
planning and short term planning help the organization to prevent high level failure. The
maintenance work is performed on time to use equipments for larger time and change them
before failure. Better shutdown planning can improve the operation of Toyota.
Reliability
Reliability is also a important thing for the organization. The reliability of company
product needs to be higher in mind of customer. This can help the organization to retain their
customer. This can be done by improving the quality of product and reliable service to customer
(Schwarz, Hall and Shibli, 2015). This reliability of company product and services can help the
Toyota to improve the company operations.
Inventory Management
In the inventory management is process to store the different kind of goods in storage
area. It could be ready to ship product, semi finished product or raw material. It is important to
manage the inventory. Any kind of inconvenience in inventory can affect the different
department of the organization. The raw material which is ready for use is supplied from
inventory to production. The better the inventory management will better production will
perform. The ready to sell product in the inventory maintain the supply chain flow. Improvement
of inventory management can help the organization to maintain production and supply chain.
This is how inventory management can improve the operation of Toyota.
Value Engineering
In this strategy the team of engineers is formed to improve the quality of company
product and services. The current issue with the company vehicles can be resolved by process
and function analysis. Team of engineers can solve the technical issue with vehicles. Other
technical operation can be improved by this (Hill and Hill, 2017). The engineers can work on
new technologies to reduce the cost of production and improve the performance of company
product. This how value engineering can improve the operations of organization.
By implement different kind of improvement strategies can be used by Toyota to improve
the operation and services of company. The focus of these strategies is on consumer satisfaction,
technical improvement and performance improvement. These three factor can help the
organization to improve the operation of organization.
4
planning and short term planning help the organization to prevent high level failure. The
maintenance work is performed on time to use equipments for larger time and change them
before failure. Better shutdown planning can improve the operation of Toyota.
Reliability
Reliability is also a important thing for the organization. The reliability of company
product needs to be higher in mind of customer. This can help the organization to retain their
customer. This can be done by improving the quality of product and reliable service to customer
(Schwarz, Hall and Shibli, 2015). This reliability of company product and services can help the
Toyota to improve the company operations.
Inventory Management
In the inventory management is process to store the different kind of goods in storage
area. It could be ready to ship product, semi finished product or raw material. It is important to
manage the inventory. Any kind of inconvenience in inventory can affect the different
department of the organization. The raw material which is ready for use is supplied from
inventory to production. The better the inventory management will better production will
perform. The ready to sell product in the inventory maintain the supply chain flow. Improvement
of inventory management can help the organization to maintain production and supply chain.
This is how inventory management can improve the operation of Toyota.
Value Engineering
In this strategy the team of engineers is formed to improve the quality of company
product and services. The current issue with the company vehicles can be resolved by process
and function analysis. Team of engineers can solve the technical issue with vehicles. Other
technical operation can be improved by this (Hill and Hill, 2017). The engineers can work on
new technologies to reduce the cost of production and improve the performance of company
product. This how value engineering can improve the operations of organization.
By implement different kind of improvement strategies can be used by Toyota to improve
the operation and services of company. The focus of these strategies is on consumer satisfaction,
technical improvement and performance improvement. These three factor can help the
organization to improve the operation of organization.
4
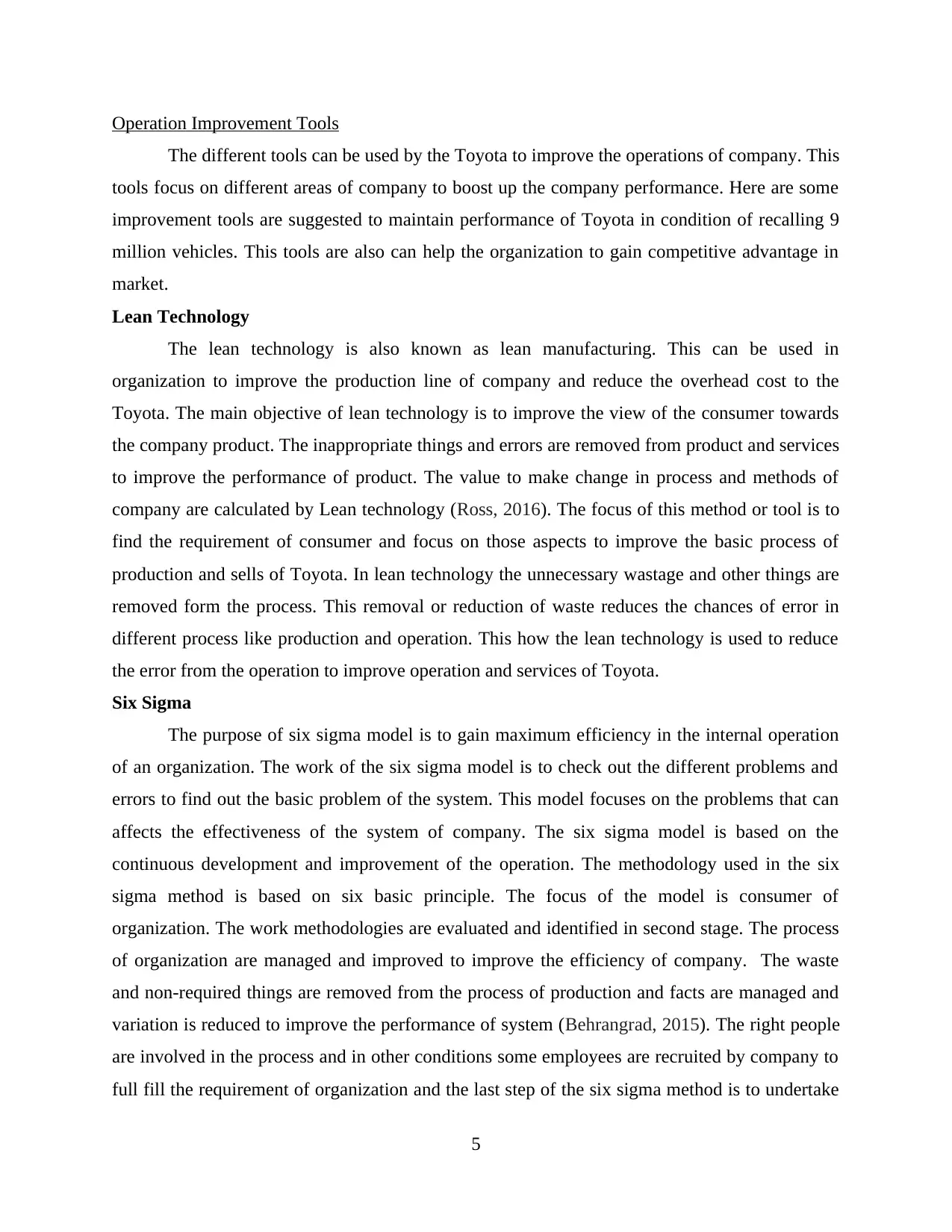
Operation Improvement Tools
The different tools can be used by the Toyota to improve the operations of company. This
tools focus on different areas of company to boost up the company performance. Here are some
improvement tools are suggested to maintain performance of Toyota in condition of recalling 9
million vehicles. This tools are also can help the organization to gain competitive advantage in
market.
Lean Technology
The lean technology is also known as lean manufacturing. This can be used in
organization to improve the production line of company and reduce the overhead cost to the
Toyota. The main objective of lean technology is to improve the view of the consumer towards
the company product. The inappropriate things and errors are removed from product and services
to improve the performance of product. The value to make change in process and methods of
company are calculated by Lean technology (Ross, 2016). The focus of this method or tool is to
find the requirement of consumer and focus on those aspects to improve the basic process of
production and sells of Toyota. In lean technology the unnecessary wastage and other things are
removed form the process. This removal or reduction of waste reduces the chances of error in
different process like production and operation. This how the lean technology is used to reduce
the error from the operation to improve operation and services of Toyota.
Six Sigma
The purpose of six sigma model is to gain maximum efficiency in the internal operation
of an organization. The work of the six sigma model is to check out the different problems and
errors to find out the basic problem of the system. This model focuses on the problems that can
affects the effectiveness of the system of company. The six sigma model is based on the
continuous development and improvement of the operation. The methodology used in the six
sigma method is based on six basic principle. The focus of the model is consumer of
organization. The work methodologies are evaluated and identified in second stage. The process
of organization are managed and improved to improve the efficiency of company. The waste
and non-required things are removed from the process of production and facts are managed and
variation is reduced to improve the performance of system (Behrangrad, 2015). The right people
are involved in the process and in other conditions some employees are recruited by company to
full fill the requirement of organization and the last step of the six sigma method is to undertake
5
The different tools can be used by the Toyota to improve the operations of company. This
tools focus on different areas of company to boost up the company performance. Here are some
improvement tools are suggested to maintain performance of Toyota in condition of recalling 9
million vehicles. This tools are also can help the organization to gain competitive advantage in
market.
Lean Technology
The lean technology is also known as lean manufacturing. This can be used in
organization to improve the production line of company and reduce the overhead cost to the
Toyota. The main objective of lean technology is to improve the view of the consumer towards
the company product. The inappropriate things and errors are removed from product and services
to improve the performance of product. The value to make change in process and methods of
company are calculated by Lean technology (Ross, 2016). The focus of this method or tool is to
find the requirement of consumer and focus on those aspects to improve the basic process of
production and sells of Toyota. In lean technology the unnecessary wastage and other things are
removed form the process. This removal or reduction of waste reduces the chances of error in
different process like production and operation. This how the lean technology is used to reduce
the error from the operation to improve operation and services of Toyota.
Six Sigma
The purpose of six sigma model is to gain maximum efficiency in the internal operation
of an organization. The work of the six sigma model is to check out the different problems and
errors to find out the basic problem of the system. This model focuses on the problems that can
affects the effectiveness of the system of company. The six sigma model is based on the
continuous development and improvement of the operation. The methodology used in the six
sigma method is based on six basic principle. The focus of the model is consumer of
organization. The work methodologies are evaluated and identified in second stage. The process
of organization are managed and improved to improve the efficiency of company. The waste
and non-required things are removed from the process of production and facts are managed and
variation is reduced to improve the performance of system (Behrangrad, 2015). The right people
are involved in the process and in other conditions some employees are recruited by company to
full fill the requirement of organization and the last step of the six sigma method is to undertake
5
Paraphrase This Document
Need a fresh take? Get an instant paraphrase of this document with our AI Paraphraser
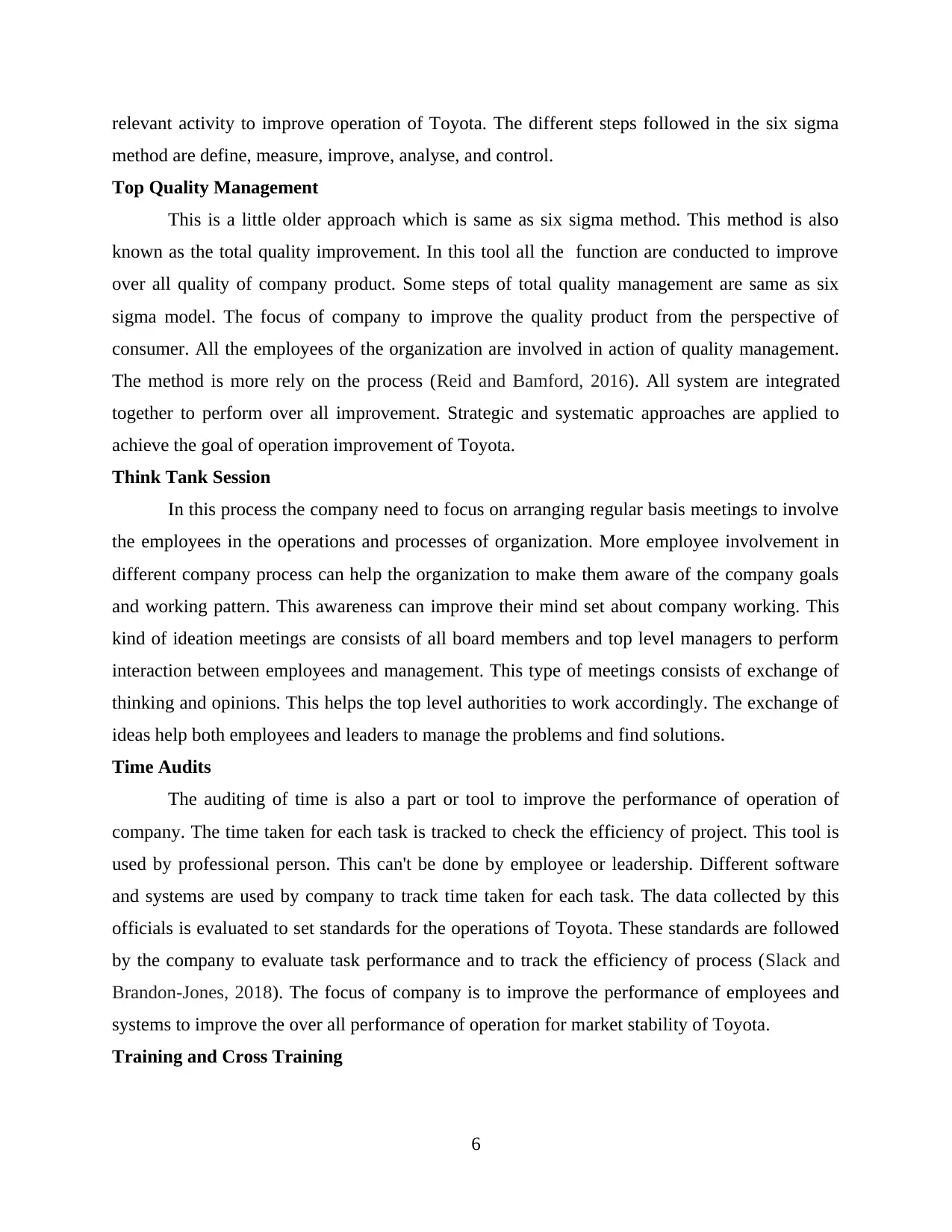
relevant activity to improve operation of Toyota. The different steps followed in the six sigma
method are define, measure, improve, analyse, and control.
Top Quality Management
This is a little older approach which is same as six sigma method. This method is also
known as the total quality improvement. In this tool all the function are conducted to improve
over all quality of company product. Some steps of total quality management are same as six
sigma model. The focus of company to improve the quality product from the perspective of
consumer. All the employees of the organization are involved in action of quality management.
The method is more rely on the process (Reid and Bamford, 2016). All system are integrated
together to perform over all improvement. Strategic and systematic approaches are applied to
achieve the goal of operation improvement of Toyota.
Think Tank Session
In this process the company need to focus on arranging regular basis meetings to involve
the employees in the operations and processes of organization. More employee involvement in
different company process can help the organization to make them aware of the company goals
and working pattern. This awareness can improve their mind set about company working. This
kind of ideation meetings are consists of all board members and top level managers to perform
interaction between employees and management. This type of meetings consists of exchange of
thinking and opinions. This helps the top level authorities to work accordingly. The exchange of
ideas help both employees and leaders to manage the problems and find solutions.
Time Audits
The auditing of time is also a part or tool to improve the performance of operation of
company. The time taken for each task is tracked to check the efficiency of project. This tool is
used by professional person. This can't be done by employee or leadership. Different software
and systems are used by company to track time taken for each task. The data collected by this
officials is evaluated to set standards for the operations of Toyota. These standards are followed
by the company to evaluate task performance and to track the efficiency of process (Slack and
Brandon-Jones, 2018). The focus of company is to improve the performance of employees and
systems to improve the over all performance of operation for market stability of Toyota.
Training and Cross Training
6
method are define, measure, improve, analyse, and control.
Top Quality Management
This is a little older approach which is same as six sigma method. This method is also
known as the total quality improvement. In this tool all the function are conducted to improve
over all quality of company product. Some steps of total quality management are same as six
sigma model. The focus of company to improve the quality product from the perspective of
consumer. All the employees of the organization are involved in action of quality management.
The method is more rely on the process (Reid and Bamford, 2016). All system are integrated
together to perform over all improvement. Strategic and systematic approaches are applied to
achieve the goal of operation improvement of Toyota.
Think Tank Session
In this process the company need to focus on arranging regular basis meetings to involve
the employees in the operations and processes of organization. More employee involvement in
different company process can help the organization to make them aware of the company goals
and working pattern. This awareness can improve their mind set about company working. This
kind of ideation meetings are consists of all board members and top level managers to perform
interaction between employees and management. This type of meetings consists of exchange of
thinking and opinions. This helps the top level authorities to work accordingly. The exchange of
ideas help both employees and leaders to manage the problems and find solutions.
Time Audits
The auditing of time is also a part or tool to improve the performance of operation of
company. The time taken for each task is tracked to check the efficiency of project. This tool is
used by professional person. This can't be done by employee or leadership. Different software
and systems are used by company to track time taken for each task. The data collected by this
officials is evaluated to set standards for the operations of Toyota. These standards are followed
by the company to evaluate task performance and to track the efficiency of process (Slack and
Brandon-Jones, 2018). The focus of company is to improve the performance of employees and
systems to improve the over all performance of operation for market stability of Toyota.
Training and Cross Training
6
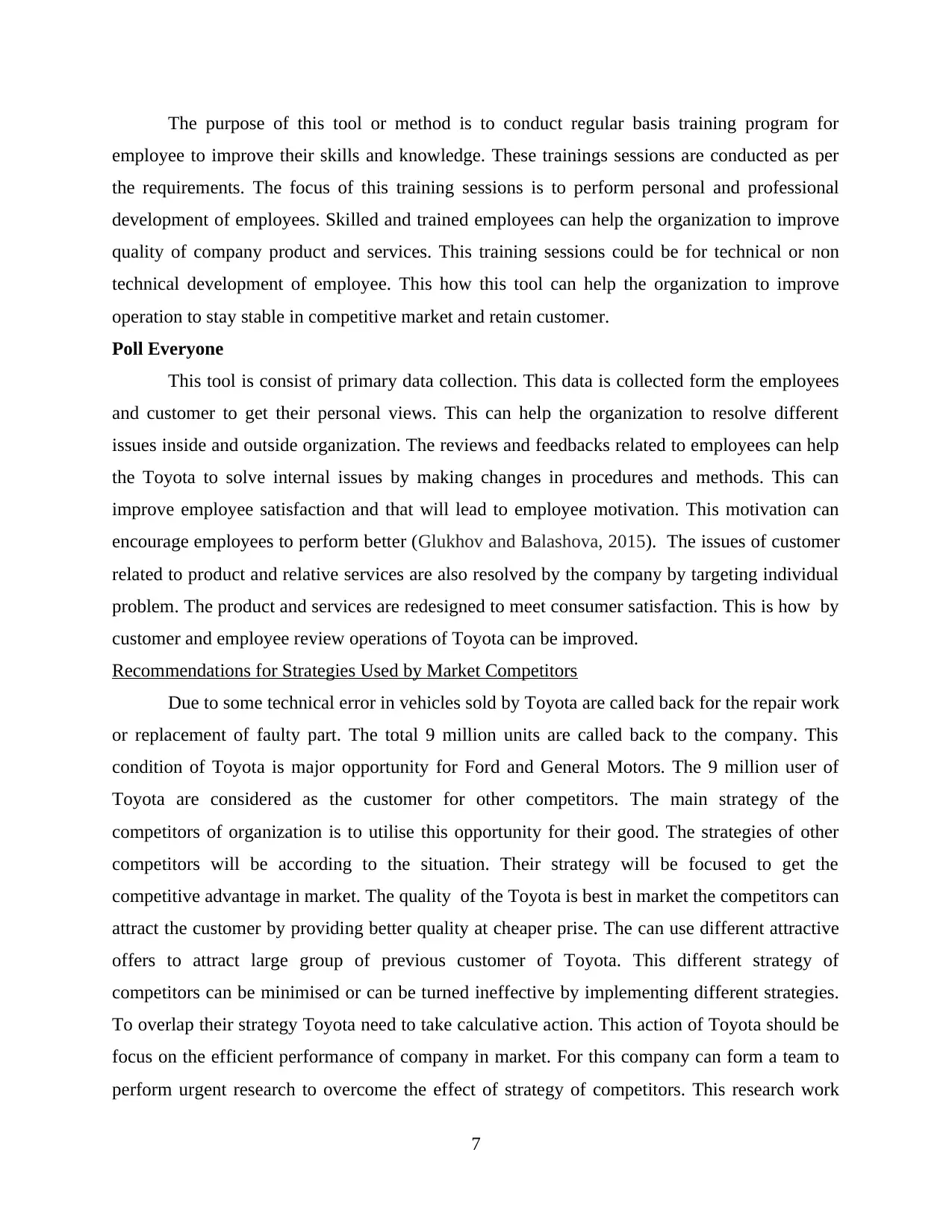
The purpose of this tool or method is to conduct regular basis training program for
employee to improve their skills and knowledge. These trainings sessions are conducted as per
the requirements. The focus of this training sessions is to perform personal and professional
development of employees. Skilled and trained employees can help the organization to improve
quality of company product and services. This training sessions could be for technical or non
technical development of employee. This how this tool can help the organization to improve
operation to stay stable in competitive market and retain customer.
Poll Everyone
This tool is consist of primary data collection. This data is collected form the employees
and customer to get their personal views. This can help the organization to resolve different
issues inside and outside organization. The reviews and feedbacks related to employees can help
the Toyota to solve internal issues by making changes in procedures and methods. This can
improve employee satisfaction and that will lead to employee motivation. This motivation can
encourage employees to perform better (Glukhov and Balashova, 2015). The issues of customer
related to product and relative services are also resolved by the company by targeting individual
problem. The product and services are redesigned to meet consumer satisfaction. This is how by
customer and employee review operations of Toyota can be improved.
Recommendations for Strategies Used by Market Competitors
Due to some technical error in vehicles sold by Toyota are called back for the repair work
or replacement of faulty part. The total 9 million units are called back to the company. This
condition of Toyota is major opportunity for Ford and General Motors. The 9 million user of
Toyota are considered as the customer for other competitors. The main strategy of the
competitors of organization is to utilise this opportunity for their good. The strategies of other
competitors will be according to the situation. Their strategy will be focused to get the
competitive advantage in market. The quality of the Toyota is best in market the competitors can
attract the customer by providing better quality at cheaper prise. The can use different attractive
offers to attract large group of previous customer of Toyota. This different strategy of
competitors can be minimised or can be turned ineffective by implementing different strategies.
To overlap their strategy Toyota need to take calculative action. This action of Toyota should be
focus on the efficient performance of company in market. For this company can form a team to
perform urgent research to overcome the effect of strategy of competitors. This research work
7
employee to improve their skills and knowledge. These trainings sessions are conducted as per
the requirements. The focus of this training sessions is to perform personal and professional
development of employees. Skilled and trained employees can help the organization to improve
quality of company product and services. This training sessions could be for technical or non
technical development of employee. This how this tool can help the organization to improve
operation to stay stable in competitive market and retain customer.
Poll Everyone
This tool is consist of primary data collection. This data is collected form the employees
and customer to get their personal views. This can help the organization to resolve different
issues inside and outside organization. The reviews and feedbacks related to employees can help
the Toyota to solve internal issues by making changes in procedures and methods. This can
improve employee satisfaction and that will lead to employee motivation. This motivation can
encourage employees to perform better (Glukhov and Balashova, 2015). The issues of customer
related to product and relative services are also resolved by the company by targeting individual
problem. The product and services are redesigned to meet consumer satisfaction. This is how by
customer and employee review operations of Toyota can be improved.
Recommendations for Strategies Used by Market Competitors
Due to some technical error in vehicles sold by Toyota are called back for the repair work
or replacement of faulty part. The total 9 million units are called back to the company. This
condition of Toyota is major opportunity for Ford and General Motors. The 9 million user of
Toyota are considered as the customer for other competitors. The main strategy of the
competitors of organization is to utilise this opportunity for their good. The strategies of other
competitors will be according to the situation. Their strategy will be focused to get the
competitive advantage in market. The quality of the Toyota is best in market the competitors can
attract the customer by providing better quality at cheaper prise. The can use different attractive
offers to attract large group of previous customer of Toyota. This different strategy of
competitors can be minimised or can be turned ineffective by implementing different strategies.
To overlap their strategy Toyota need to take calculative action. This action of Toyota should be
focus on the efficient performance of company in market. For this company can form a team to
perform urgent research to overcome the effect of strategy of competitors. This research work
7
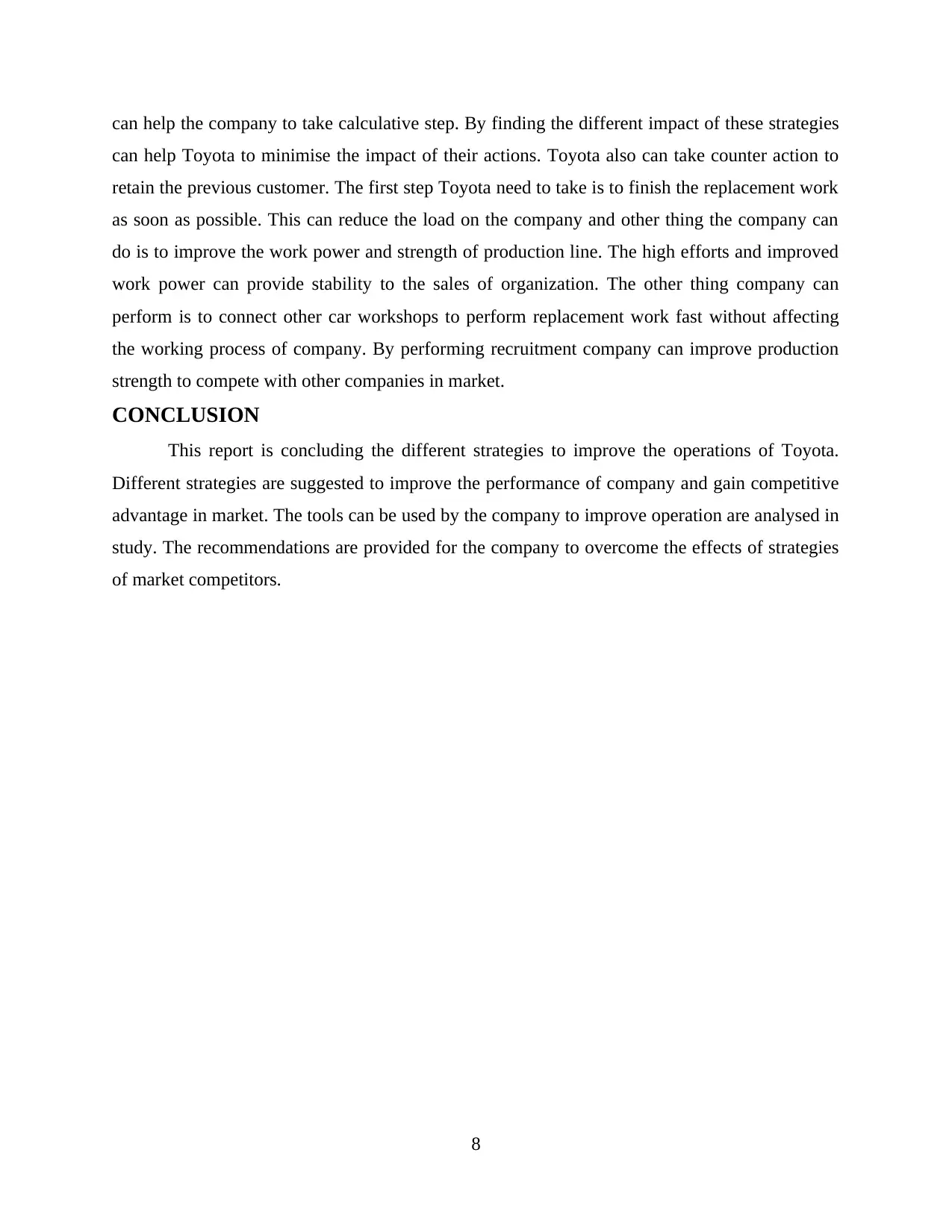
can help the company to take calculative step. By finding the different impact of these strategies
can help Toyota to minimise the impact of their actions. Toyota also can take counter action to
retain the previous customer. The first step Toyota need to take is to finish the replacement work
as soon as possible. This can reduce the load on the company and other thing the company can
do is to improve the work power and strength of production line. The high efforts and improved
work power can provide stability to the sales of organization. The other thing company can
perform is to connect other car workshops to perform replacement work fast without affecting
the working process of company. By performing recruitment company can improve production
strength to compete with other companies in market.
CONCLUSION
This report is concluding the different strategies to improve the operations of Toyota.
Different strategies are suggested to improve the performance of company and gain competitive
advantage in market. The tools can be used by the company to improve operation are analysed in
study. The recommendations are provided for the company to overcome the effects of strategies
of market competitors.
8
can help Toyota to minimise the impact of their actions. Toyota also can take counter action to
retain the previous customer. The first step Toyota need to take is to finish the replacement work
as soon as possible. This can reduce the load on the company and other thing the company can
do is to improve the work power and strength of production line. The high efforts and improved
work power can provide stability to the sales of organization. The other thing company can
perform is to connect other car workshops to perform replacement work fast without affecting
the working process of company. By performing recruitment company can improve production
strength to compete with other companies in market.
CONCLUSION
This report is concluding the different strategies to improve the operations of Toyota.
Different strategies are suggested to improve the performance of company and gain competitive
advantage in market. The tools can be used by the company to improve operation are analysed in
study. The recommendations are provided for the company to overcome the effects of strategies
of market competitors.
8
Secure Best Marks with AI Grader
Need help grading? Try our AI Grader for instant feedback on your assignments.
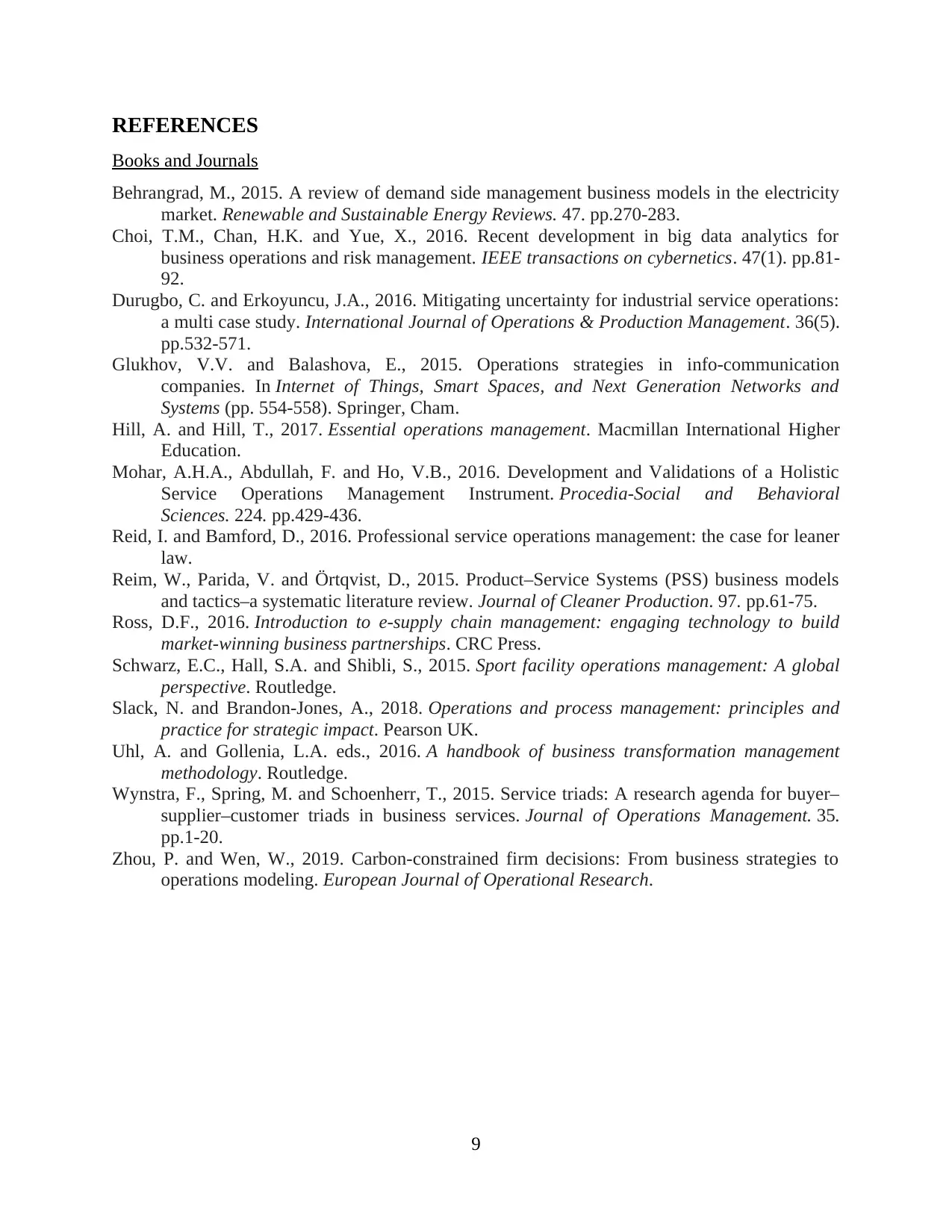
REFERENCES
Books and Journals
Behrangrad, M., 2015. A review of demand side management business models in the electricity
market. Renewable and Sustainable Energy Reviews. 47. pp.270-283.
Choi, T.M., Chan, H.K. and Yue, X., 2016. Recent development in big data analytics for
business operations and risk management. IEEE transactions on cybernetics. 47(1). pp.81-
92.
Durugbo, C. and Erkoyuncu, J.A., 2016. Mitigating uncertainty for industrial service operations:
a multi case study. International Journal of Operations & Production Management. 36(5).
pp.532-571.
Glukhov, V.V. and Balashova, E., 2015. Operations strategies in info-communication
companies. In Internet of Things, Smart Spaces, and Next Generation Networks and
Systems (pp. 554-558). Springer, Cham.
Hill, A. and Hill, T., 2017. Essential operations management. Macmillan International Higher
Education.
Mohar, A.H.A., Abdullah, F. and Ho, V.B., 2016. Development and Validations of a Holistic
Service Operations Management Instrument. Procedia-Social and Behavioral
Sciences. 224. pp.429-436.
Reid, I. and Bamford, D., 2016. Professional service operations management: the case for leaner
law.
Reim, W., Parida, V. and Örtqvist, D., 2015. Product–Service Systems (PSS) business models
and tactics–a systematic literature review. Journal of Cleaner Production. 97. pp.61-75.
Ross, D.F., 2016. Introduction to e-supply chain management: engaging technology to build
market-winning business partnerships. CRC Press.
Schwarz, E.C., Hall, S.A. and Shibli, S., 2015. Sport facility operations management: A global
perspective. Routledge.
Slack, N. and Brandon-Jones, A., 2018. Operations and process management: principles and
practice for strategic impact. Pearson UK.
Uhl, A. and Gollenia, L.A. eds., 2016. A handbook of business transformation management
methodology. Routledge.
Wynstra, F., Spring, M. and Schoenherr, T., 2015. Service triads: A research agenda for buyer–
supplier–customer triads in business services. Journal of Operations Management. 35.
pp.1-20.
Zhou, P. and Wen, W., 2019. Carbon-constrained firm decisions: From business strategies to
operations modeling. European Journal of Operational Research.
9
Books and Journals
Behrangrad, M., 2015. A review of demand side management business models in the electricity
market. Renewable and Sustainable Energy Reviews. 47. pp.270-283.
Choi, T.M., Chan, H.K. and Yue, X., 2016. Recent development in big data analytics for
business operations and risk management. IEEE transactions on cybernetics. 47(1). pp.81-
92.
Durugbo, C. and Erkoyuncu, J.A., 2016. Mitigating uncertainty for industrial service operations:
a multi case study. International Journal of Operations & Production Management. 36(5).
pp.532-571.
Glukhov, V.V. and Balashova, E., 2015. Operations strategies in info-communication
companies. In Internet of Things, Smart Spaces, and Next Generation Networks and
Systems (pp. 554-558). Springer, Cham.
Hill, A. and Hill, T., 2017. Essential operations management. Macmillan International Higher
Education.
Mohar, A.H.A., Abdullah, F. and Ho, V.B., 2016. Development and Validations of a Holistic
Service Operations Management Instrument. Procedia-Social and Behavioral
Sciences. 224. pp.429-436.
Reid, I. and Bamford, D., 2016. Professional service operations management: the case for leaner
law.
Reim, W., Parida, V. and Örtqvist, D., 2015. Product–Service Systems (PSS) business models
and tactics–a systematic literature review. Journal of Cleaner Production. 97. pp.61-75.
Ross, D.F., 2016. Introduction to e-supply chain management: engaging technology to build
market-winning business partnerships. CRC Press.
Schwarz, E.C., Hall, S.A. and Shibli, S., 2015. Sport facility operations management: A global
perspective. Routledge.
Slack, N. and Brandon-Jones, A., 2018. Operations and process management: principles and
practice for strategic impact. Pearson UK.
Uhl, A. and Gollenia, L.A. eds., 2016. A handbook of business transformation management
methodology. Routledge.
Wynstra, F., Spring, M. and Schoenherr, T., 2015. Service triads: A research agenda for buyer–
supplier–customer triads in business services. Journal of Operations Management. 35.
pp.1-20.
Zhou, P. and Wen, W., 2019. Carbon-constrained firm decisions: From business strategies to
operations modeling. European Journal of Operational Research.
9
1 out of 11
Related Documents

Your All-in-One AI-Powered Toolkit for Academic Success.
+13062052269
info@desklib.com
Available 24*7 on WhatsApp / Email
Unlock your academic potential
© 2024 | Zucol Services PVT LTD | All rights reserved.