A Report on Toyota's Organizational Structure, Management, and TPS
VerifiedAdded on 2021/01/07
|8
|2559
|125
Report
AI Summary
This report delves into the organizational structure of Toyota, examining its evolution, the Toyota Production System (TPS), and its implications. It explores the company's global hierarchy, geographical divisions, and product-based divisions, highlighting the advantages and disadvantages of its structure. The report analyzes Toyota's managerial practices, particularly the 'just-in-time' development concepts inherent in TPS, and how they empower frontline workers. It also discusses the challenges Toyota faced, such as product recalls and slow responses to issues, and the cultural aspects of the company, emphasizing long-term sustainability and employee commitment. The report concludes by summarizing Toyota's innovative work environment and its emphasis on employee input and continuous improvement through small innovation teams and mathematical monitoring techniques.
Contribute Materials
Your contribution can guide someone’s learning journey. Share your
documents today.
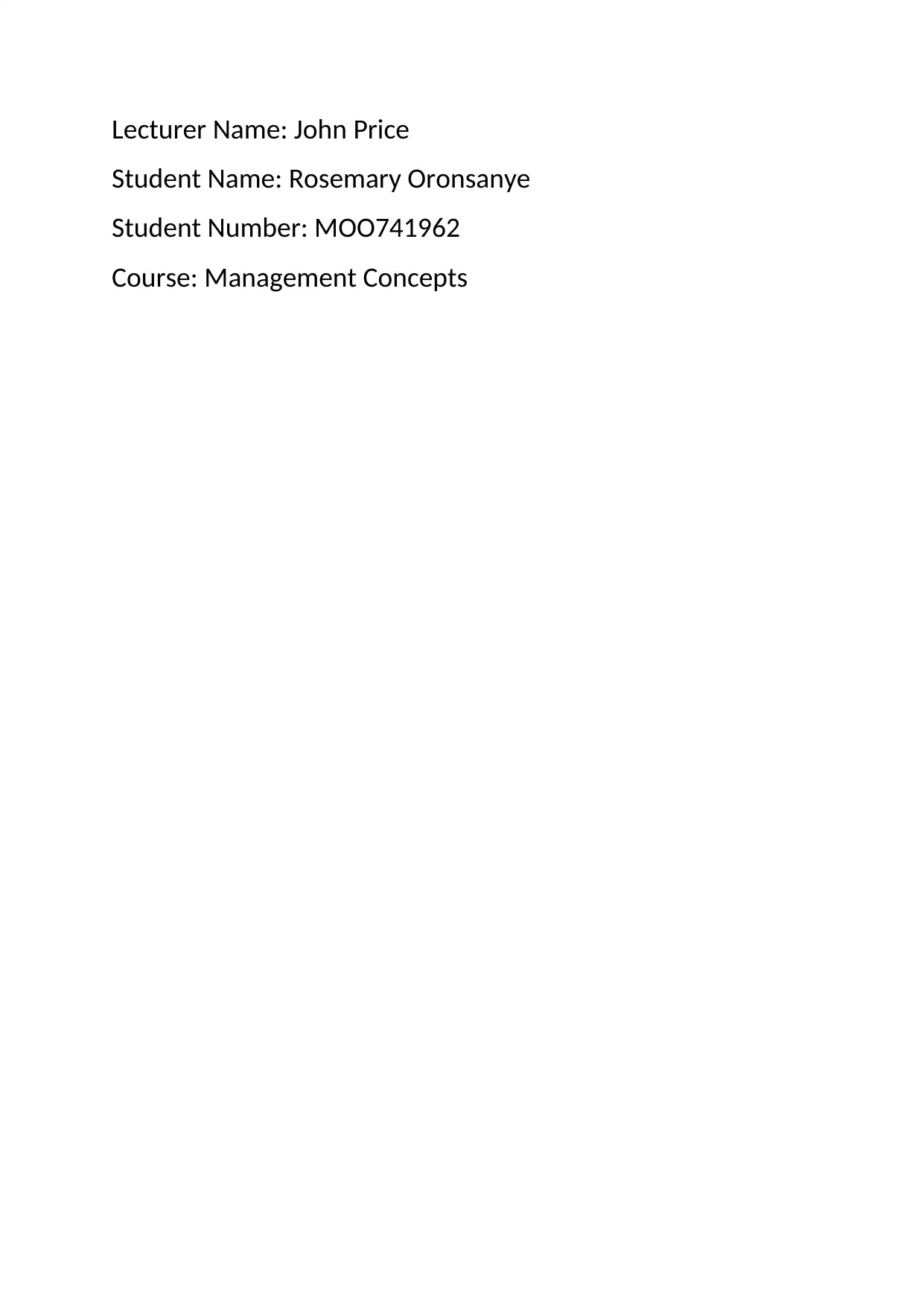
Lecturer Name: John Price
Student Name: Rosemary Oronsanye
Student Number: MOO741962
Course: Management Concepts
Student Name: Rosemary Oronsanye
Student Number: MOO741962
Course: Management Concepts
Secure Best Marks with AI Grader
Need help grading? Try our AI Grader for instant feedback on your assignments.
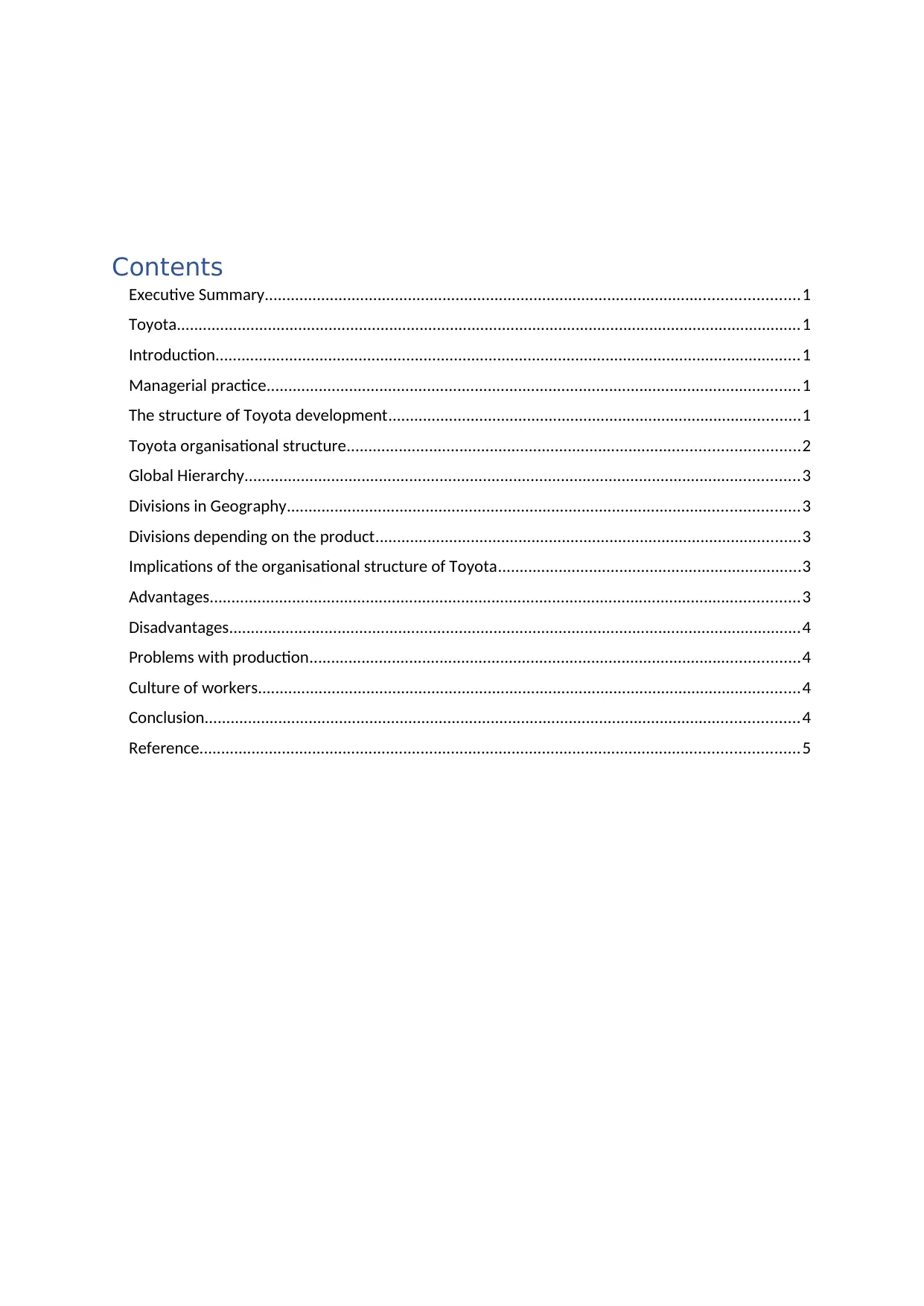
Contents
Executive Summary...........................................................................................................................1
Toyota................................................................................................................................................1
Introduction.......................................................................................................................................1
Managerial practice...........................................................................................................................1
The structure of Toyota development...............................................................................................1
Toyota organisational structure........................................................................................................2
Global Hierarchy................................................................................................................................3
Divisions in Geography......................................................................................................................3
Divisions depending on the product..................................................................................................3
Implications of the organisational structure of Toyota......................................................................3
Advantages........................................................................................................................................3
Disadvantages....................................................................................................................................4
Problems with production.................................................................................................................4
Culture of workers.............................................................................................................................4
Conclusion.........................................................................................................................................4
Reference..........................................................................................................................................5
Executive Summary...........................................................................................................................1
Toyota................................................................................................................................................1
Introduction.......................................................................................................................................1
Managerial practice...........................................................................................................................1
The structure of Toyota development...............................................................................................1
Toyota organisational structure........................................................................................................2
Global Hierarchy................................................................................................................................3
Divisions in Geography......................................................................................................................3
Divisions depending on the product..................................................................................................3
Implications of the organisational structure of Toyota......................................................................3
Advantages........................................................................................................................................3
Disadvantages....................................................................................................................................4
Problems with production.................................................................................................................4
Culture of workers.............................................................................................................................4
Conclusion.........................................................................................................................................4
Reference..........................................................................................................................................5
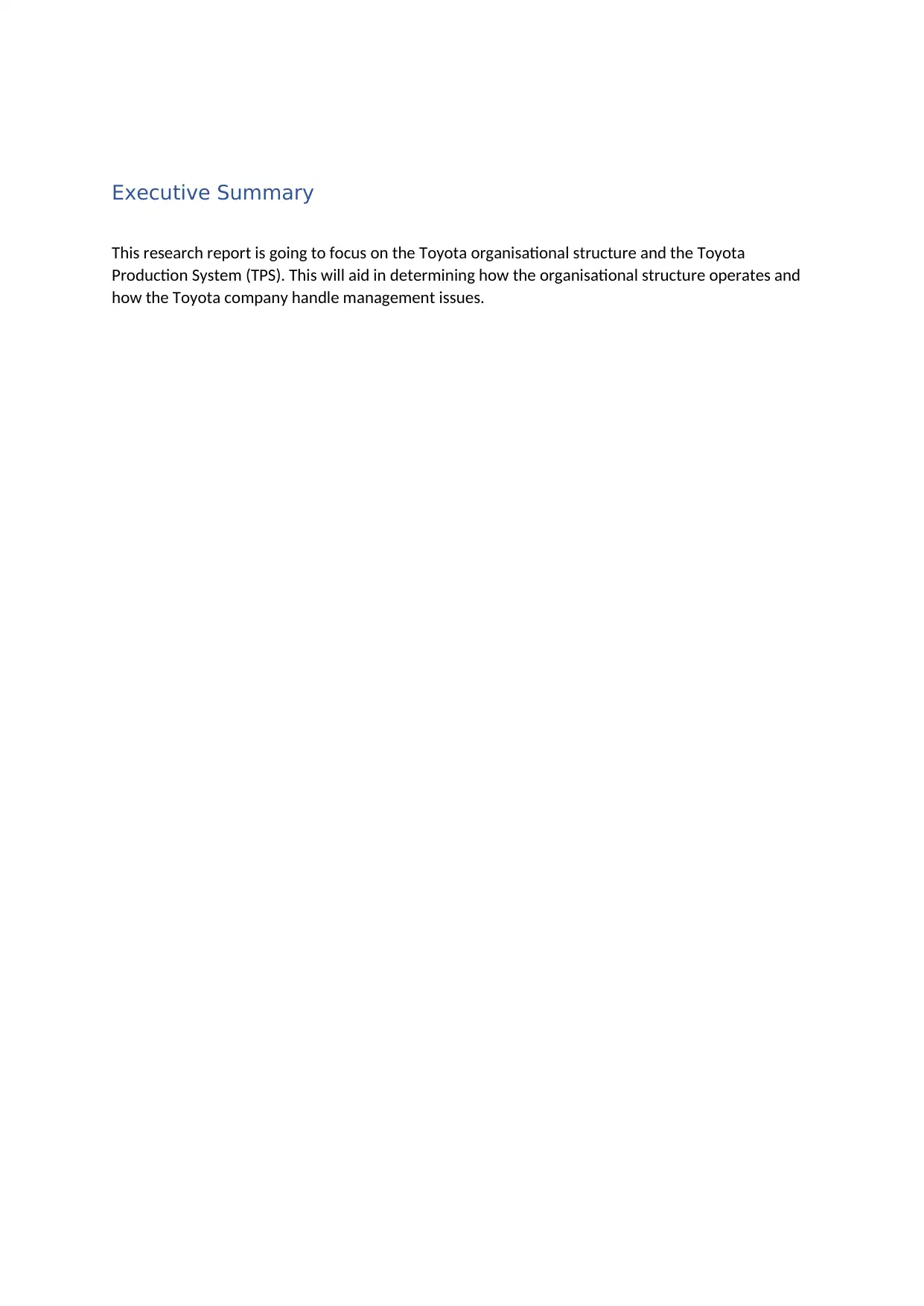
Executive Summary
This research report is going to focus on the Toyota organisational structure and the Toyota
Production System (TPS). This will aid in determining how the organisational structure operates and
how the Toyota company handle management issues.
This research report is going to focus on the Toyota organisational structure and the Toyota
Production System (TPS). This will aid in determining how the organisational structure operates and
how the Toyota company handle management issues.
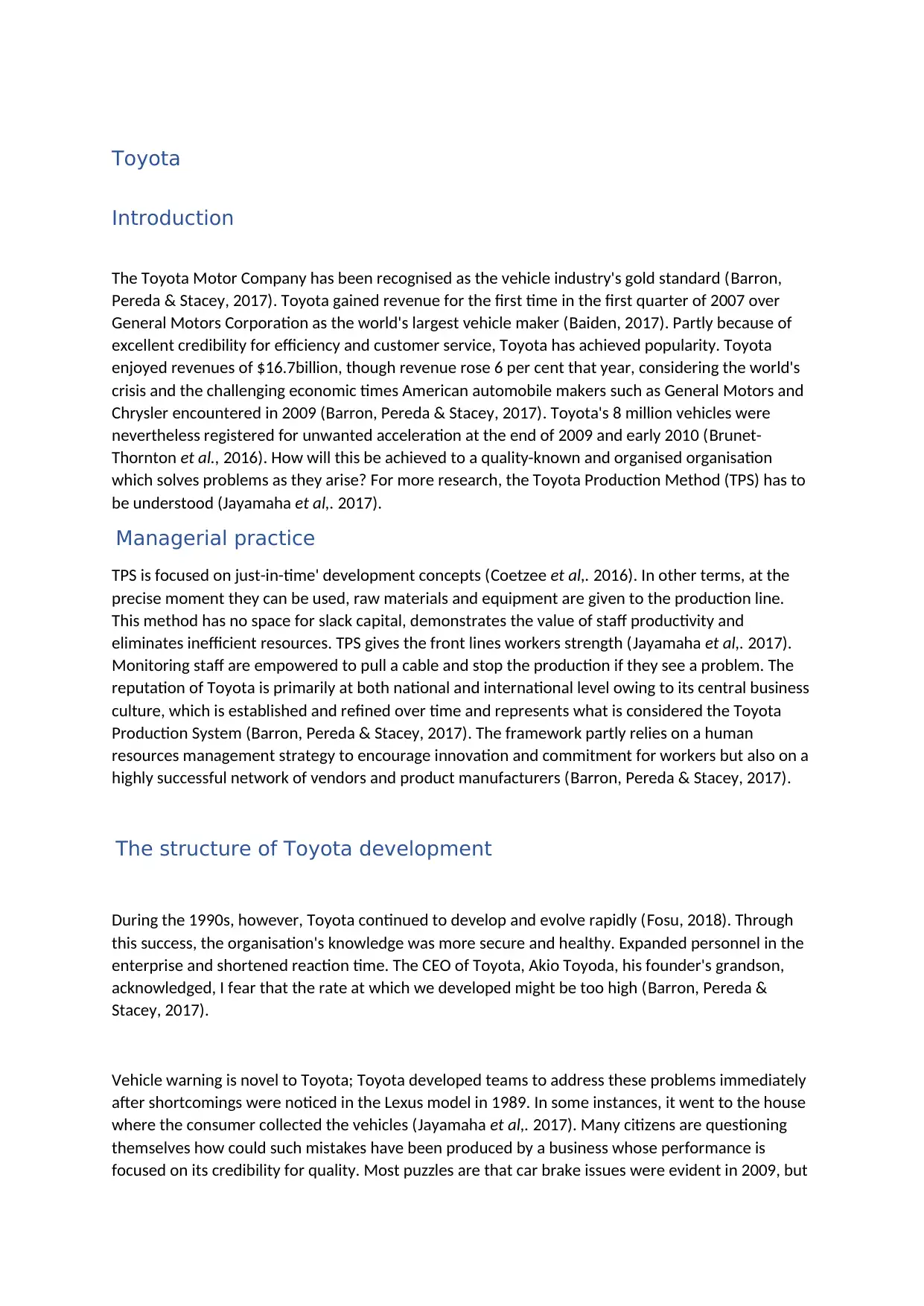
Toyota
Introduction
The Toyota Motor Company has been recognised as the vehicle industry's gold standard (Barron,
Pereda & Stacey, 2017). Toyota gained revenue for the first time in the first quarter of 2007 over
General Motors Corporation as the world's largest vehicle maker (Baiden, 2017). Partly because of
excellent credibility for efficiency and customer service, Toyota has achieved popularity. Toyota
enjoyed revenues of $16.7billion, though revenue rose 6 per cent that year, considering the world's
crisis and the challenging economic times American automobile makers such as General Motors and
Chrysler encountered in 2009 (Barron, Pereda & Stacey, 2017). Toyota's 8 million vehicles were
nevertheless registered for unwanted acceleration at the end of 2009 and early 2010 (Brunet-
Thornton et al., 2016). How will this be achieved to a quality-known and organised organisation
which solves problems as they arise? For more research, the Toyota Production Method (TPS) has to
be understood (Jayamaha et al,. 2017).
Managerial practice
TPS is focused on just-in-time' development concepts (Coetzee et al,. 2016). In other terms, at the
precise moment they can be used, raw materials and equipment are given to the production line.
This method has no space for slack capital, demonstrates the value of staff productivity and
eliminates inefficient resources. TPS gives the front lines workers strength (Jayamaha et al,. 2017).
Monitoring staff are empowered to pull a cable and stop the production if they see a problem. The
reputation of Toyota is primarily at both national and international level owing to its central business
culture, which is established and refined over time and represents what is considered the Toyota
Production System (Barron, Pereda & Stacey, 2017). The framework partly relies on a human
resources management strategy to encourage innovation and commitment for workers but also on a
highly successful network of vendors and product manufacturers (Barron, Pereda & Stacey, 2017).
The structure of Toyota development
During the 1990s, however, Toyota continued to develop and evolve rapidly (Fosu, 2018). Through
this success, the organisation's knowledge was more secure and healthy. Expanded personnel in the
enterprise and shortened reaction time. The CEO of Toyota, Akio Toyoda, his founder's grandson,
acknowledged, I fear that the rate at which we developed might be too high (Barron, Pereda &
Stacey, 2017).
Vehicle warning is novel to Toyota; Toyota developed teams to address these problems immediately
after shortcomings were noticed in the Lexus model in 1989. In some instances, it went to the house
where the consumer collected the vehicles (Jayamaha et al,. 2017). Many citizens are questioning
themselves how could such mistakes have been produced by a business whose performance is
focused on its credibility for quality. Most puzzles are that car brake issues were evident in 2009, but
Introduction
The Toyota Motor Company has been recognised as the vehicle industry's gold standard (Barron,
Pereda & Stacey, 2017). Toyota gained revenue for the first time in the first quarter of 2007 over
General Motors Corporation as the world's largest vehicle maker (Baiden, 2017). Partly because of
excellent credibility for efficiency and customer service, Toyota has achieved popularity. Toyota
enjoyed revenues of $16.7billion, though revenue rose 6 per cent that year, considering the world's
crisis and the challenging economic times American automobile makers such as General Motors and
Chrysler encountered in 2009 (Barron, Pereda & Stacey, 2017). Toyota's 8 million vehicles were
nevertheless registered for unwanted acceleration at the end of 2009 and early 2010 (Brunet-
Thornton et al., 2016). How will this be achieved to a quality-known and organised organisation
which solves problems as they arise? For more research, the Toyota Production Method (TPS) has to
be understood (Jayamaha et al,. 2017).
Managerial practice
TPS is focused on just-in-time' development concepts (Coetzee et al,. 2016). In other terms, at the
precise moment they can be used, raw materials and equipment are given to the production line.
This method has no space for slack capital, demonstrates the value of staff productivity and
eliminates inefficient resources. TPS gives the front lines workers strength (Jayamaha et al,. 2017).
Monitoring staff are empowered to pull a cable and stop the production if they see a problem. The
reputation of Toyota is primarily at both national and international level owing to its central business
culture, which is established and refined over time and represents what is considered the Toyota
Production System (Barron, Pereda & Stacey, 2017). The framework partly relies on a human
resources management strategy to encourage innovation and commitment for workers but also on a
highly successful network of vendors and product manufacturers (Barron, Pereda & Stacey, 2017).
The structure of Toyota development
During the 1990s, however, Toyota continued to develop and evolve rapidly (Fosu, 2018). Through
this success, the organisation's knowledge was more secure and healthy. Expanded personnel in the
enterprise and shortened reaction time. The CEO of Toyota, Akio Toyoda, his founder's grandson,
acknowledged, I fear that the rate at which we developed might be too high (Barron, Pereda &
Stacey, 2017).
Vehicle warning is novel to Toyota; Toyota developed teams to address these problems immediately
after shortcomings were noticed in the Lexus model in 1989. In some instances, it went to the house
where the consumer collected the vehicles (Jayamaha et al,. 2017). Many citizens are questioning
themselves how could such mistakes have been produced by a business whose performance is
focused on its credibility for quality. Most puzzles are that car brake issues were evident in 2009, but
Secure Best Marks with AI Grader
Need help grading? Try our AI Grader for instant feedback on your assignments.
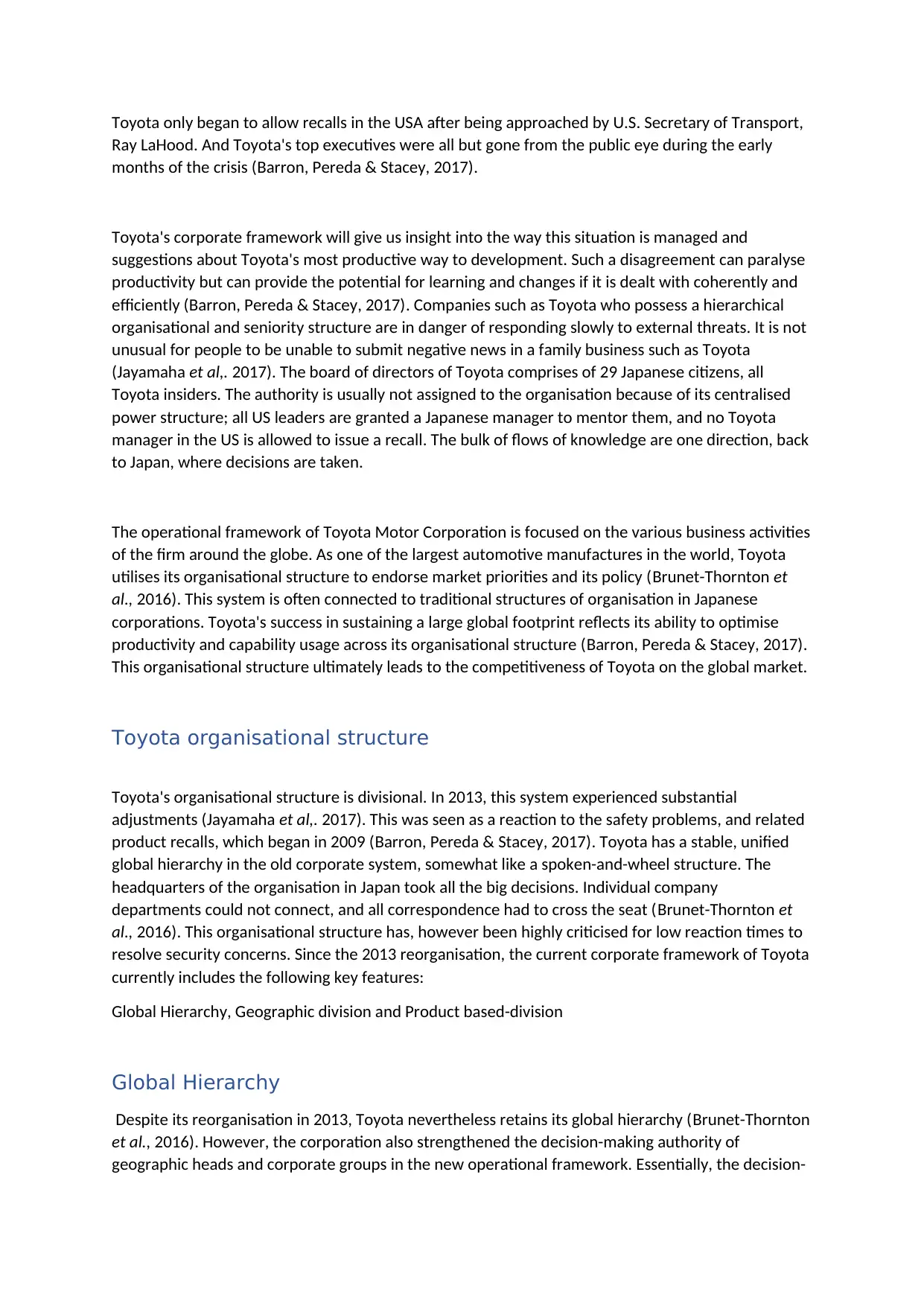
Toyota only began to allow recalls in the USA after being approached by U.S. Secretary of Transport,
Ray LaHood. And Toyota's top executives were all but gone from the public eye during the early
months of the crisis (Barron, Pereda & Stacey, 2017).
Toyota's corporate framework will give us insight into the way this situation is managed and
suggestions about Toyota's most productive way to development. Such a disagreement can paralyse
productivity but can provide the potential for learning and changes if it is dealt with coherently and
efficiently (Barron, Pereda & Stacey, 2017). Companies such as Toyota who possess a hierarchical
organisational and seniority structure are in danger of responding slowly to external threats. It is not
unusual for people to be unable to submit negative news in a family business such as Toyota
(Jayamaha et al,. 2017). The board of directors of Toyota comprises of 29 Japanese citizens, all
Toyota insiders. The authority is usually not assigned to the organisation because of its centralised
power structure; all US leaders are granted a Japanese manager to mentor them, and no Toyota
manager in the US is allowed to issue a recall. The bulk of flows of knowledge are one direction, back
to Japan, where decisions are taken.
The operational framework of Toyota Motor Corporation is focused on the various business activities
of the firm around the globe. As one of the largest automotive manufactures in the world, Toyota
utilises its organisational structure to endorse market priorities and its policy (Brunet-Thornton et
al., 2016). This system is often connected to traditional structures of organisation in Japanese
corporations. Toyota's success in sustaining a large global footprint reflects its ability to optimise
productivity and capability usage across its organisational structure (Barron, Pereda & Stacey, 2017).
This organisational structure ultimately leads to the competitiveness of Toyota on the global market.
Toyota organisational structure
Toyota's organisational structure is divisional. In 2013, this system experienced substantial
adjustments (Jayamaha et al,. 2017). This was seen as a reaction to the safety problems, and related
product recalls, which began in 2009 (Barron, Pereda & Stacey, 2017). Toyota has a stable, unified
global hierarchy in the old corporate system, somewhat like a spoken-and-wheel structure. The
headquarters of the organisation in Japan took all the big decisions. Individual company
departments could not connect, and all correspondence had to cross the seat (Brunet-Thornton et
al., 2016). This organisational structure has, however been highly criticised for low reaction times to
resolve security concerns. Since the 2013 reorganisation, the current corporate framework of Toyota
currently includes the following key features:
Global Hierarchy, Geographic division and Product based-division
Global Hierarchy
Despite its reorganisation in 2013, Toyota nevertheless retains its global hierarchy (Brunet-Thornton
et al., 2016). However, the corporation also strengthened the decision-making authority of
geographic heads and corporate groups in the new operational framework. Essentially, the decision-
Ray LaHood. And Toyota's top executives were all but gone from the public eye during the early
months of the crisis (Barron, Pereda & Stacey, 2017).
Toyota's corporate framework will give us insight into the way this situation is managed and
suggestions about Toyota's most productive way to development. Such a disagreement can paralyse
productivity but can provide the potential for learning and changes if it is dealt with coherently and
efficiently (Barron, Pereda & Stacey, 2017). Companies such as Toyota who possess a hierarchical
organisational and seniority structure are in danger of responding slowly to external threats. It is not
unusual for people to be unable to submit negative news in a family business such as Toyota
(Jayamaha et al,. 2017). The board of directors of Toyota comprises of 29 Japanese citizens, all
Toyota insiders. The authority is usually not assigned to the organisation because of its centralised
power structure; all US leaders are granted a Japanese manager to mentor them, and no Toyota
manager in the US is allowed to issue a recall. The bulk of flows of knowledge are one direction, back
to Japan, where decisions are taken.
The operational framework of Toyota Motor Corporation is focused on the various business activities
of the firm around the globe. As one of the largest automotive manufactures in the world, Toyota
utilises its organisational structure to endorse market priorities and its policy (Brunet-Thornton et
al., 2016). This system is often connected to traditional structures of organisation in Japanese
corporations. Toyota's success in sustaining a large global footprint reflects its ability to optimise
productivity and capability usage across its organisational structure (Barron, Pereda & Stacey, 2017).
This organisational structure ultimately leads to the competitiveness of Toyota on the global market.
Toyota organisational structure
Toyota's organisational structure is divisional. In 2013, this system experienced substantial
adjustments (Jayamaha et al,. 2017). This was seen as a reaction to the safety problems, and related
product recalls, which began in 2009 (Barron, Pereda & Stacey, 2017). Toyota has a stable, unified
global hierarchy in the old corporate system, somewhat like a spoken-and-wheel structure. The
headquarters of the organisation in Japan took all the big decisions. Individual company
departments could not connect, and all correspondence had to cross the seat (Brunet-Thornton et
al., 2016). This organisational structure has, however been highly criticised for low reaction times to
resolve security concerns. Since the 2013 reorganisation, the current corporate framework of Toyota
currently includes the following key features:
Global Hierarchy, Geographic division and Product based-division
Global Hierarchy
Despite its reorganisation in 2013, Toyota nevertheless retains its global hierarchy (Brunet-Thornton
et al., 2016). However, the corporation also strengthened the decision-making authority of
geographic heads and corporate groups in the new operational framework. Essentially, the decision-
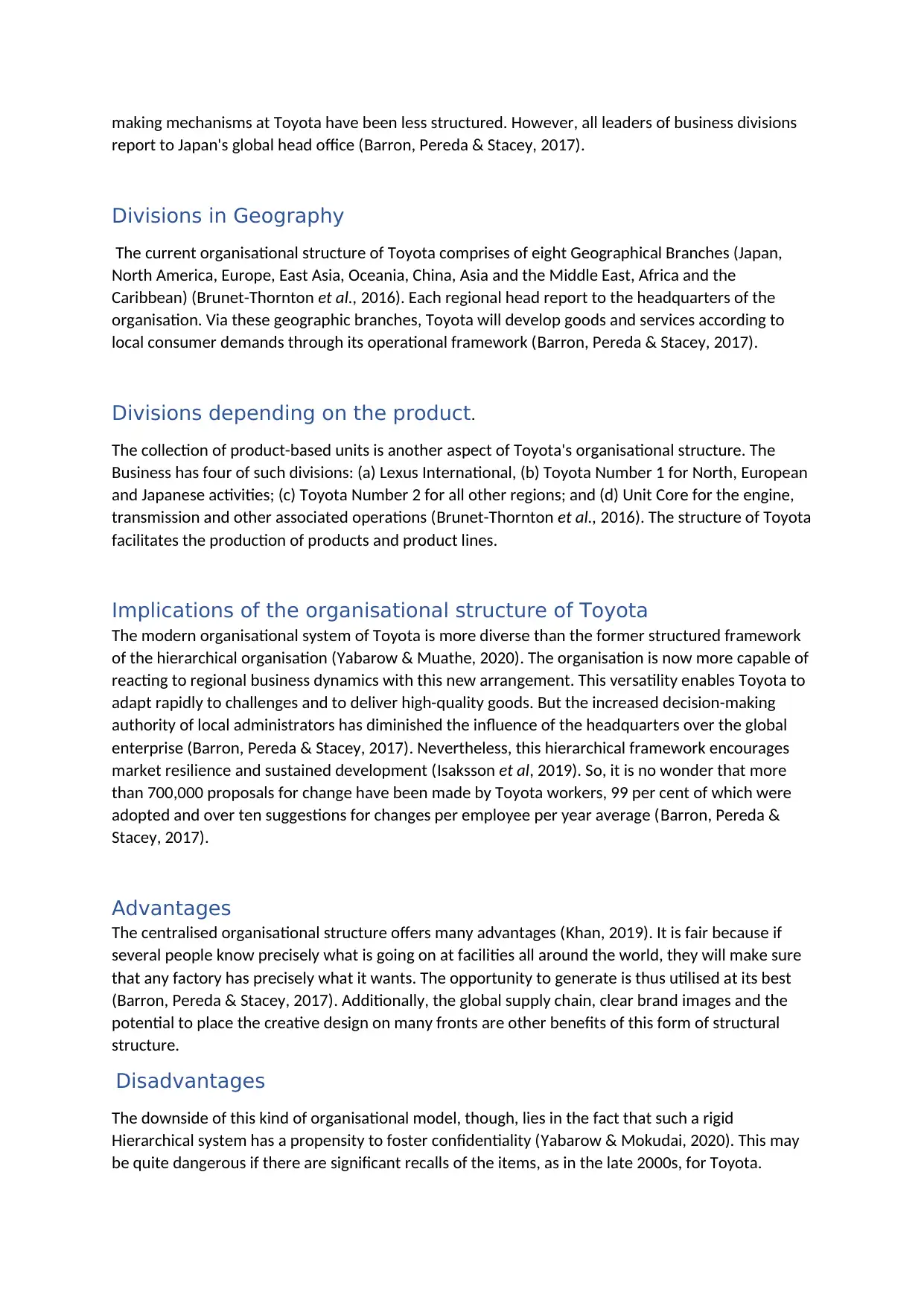
making mechanisms at Toyota have been less structured. However, all leaders of business divisions
report to Japan's global head office (Barron, Pereda & Stacey, 2017).
Divisions in Geography
The current organisational structure of Toyota comprises of eight Geographical Branches (Japan,
North America, Europe, East Asia, Oceania, China, Asia and the Middle East, Africa and the
Caribbean) (Brunet-Thornton et al., 2016). Each regional head report to the headquarters of the
organisation. Via these geographic branches, Toyota will develop goods and services according to
local consumer demands through its operational framework (Barron, Pereda & Stacey, 2017).
Divisions depending on the product.
The collection of product-based units is another aspect of Toyota's organisational structure. The
Business has four of such divisions: (a) Lexus International, (b) Toyota Number 1 for North, European
and Japanese activities; (c) Toyota Number 2 for all other regions; and (d) Unit Core for the engine,
transmission and other associated operations (Brunet-Thornton et al., 2016). The structure of Toyota
facilitates the production of products and product lines.
Implications of the organisational structure of Toyota
The modern organisational system of Toyota is more diverse than the former structured framework
of the hierarchical organisation (Yabarow & Muathe, 2020). The organisation is now more capable of
reacting to regional business dynamics with this new arrangement. This versatility enables Toyota to
adapt rapidly to challenges and to deliver high-quality goods. But the increased decision-making
authority of local administrators has diminished the influence of the headquarters over the global
enterprise (Barron, Pereda & Stacey, 2017). Nevertheless, this hierarchical framework encourages
market resilience and sustained development (Isaksson et al, 2019). So, it is no wonder that more
than 700,000 proposals for change have been made by Toyota workers, 99 per cent of which were
adopted and over ten suggestions for changes per employee per year average (Barron, Pereda &
Stacey, 2017).
Advantages
The centralised organisational structure offers many advantages (Khan, 2019). It is fair because if
several people know precisely what is going on at facilities all around the world, they will make sure
that any factory has precisely what it wants. The opportunity to generate is thus utilised at its best
(Barron, Pereda & Stacey, 2017). Additionally, the global supply chain, clear brand images and the
potential to place the creative design on many fronts are other benefits of this form of structural
structure.
Disadvantages
The downside of this kind of organisational model, though, lies in the fact that such a rigid
Hierarchical system has a propensity to foster confidentiality (Yabarow & Mokudai, 2020). This may
be quite dangerous if there are significant recalls of the items, as in the late 2000s, for Toyota.
report to Japan's global head office (Barron, Pereda & Stacey, 2017).
Divisions in Geography
The current organisational structure of Toyota comprises of eight Geographical Branches (Japan,
North America, Europe, East Asia, Oceania, China, Asia and the Middle East, Africa and the
Caribbean) (Brunet-Thornton et al., 2016). Each regional head report to the headquarters of the
organisation. Via these geographic branches, Toyota will develop goods and services according to
local consumer demands through its operational framework (Barron, Pereda & Stacey, 2017).
Divisions depending on the product.
The collection of product-based units is another aspect of Toyota's organisational structure. The
Business has four of such divisions: (a) Lexus International, (b) Toyota Number 1 for North, European
and Japanese activities; (c) Toyota Number 2 for all other regions; and (d) Unit Core for the engine,
transmission and other associated operations (Brunet-Thornton et al., 2016). The structure of Toyota
facilitates the production of products and product lines.
Implications of the organisational structure of Toyota
The modern organisational system of Toyota is more diverse than the former structured framework
of the hierarchical organisation (Yabarow & Muathe, 2020). The organisation is now more capable of
reacting to regional business dynamics with this new arrangement. This versatility enables Toyota to
adapt rapidly to challenges and to deliver high-quality goods. But the increased decision-making
authority of local administrators has diminished the influence of the headquarters over the global
enterprise (Barron, Pereda & Stacey, 2017). Nevertheless, this hierarchical framework encourages
market resilience and sustained development (Isaksson et al, 2019). So, it is no wonder that more
than 700,000 proposals for change have been made by Toyota workers, 99 per cent of which were
adopted and over ten suggestions for changes per employee per year average (Barron, Pereda &
Stacey, 2017).
Advantages
The centralised organisational structure offers many advantages (Khan, 2019). It is fair because if
several people know precisely what is going on at facilities all around the world, they will make sure
that any factory has precisely what it wants. The opportunity to generate is thus utilised at its best
(Barron, Pereda & Stacey, 2017). Additionally, the global supply chain, clear brand images and the
potential to place the creative design on many fronts are other benefits of this form of structural
structure.
Disadvantages
The downside of this kind of organisational model, though, lies in the fact that such a rigid
Hierarchical system has a propensity to foster confidentiality (Yabarow & Mokudai, 2020). This may
be quite dangerous if there are significant recalls of the items, as in the late 2000s, for Toyota.
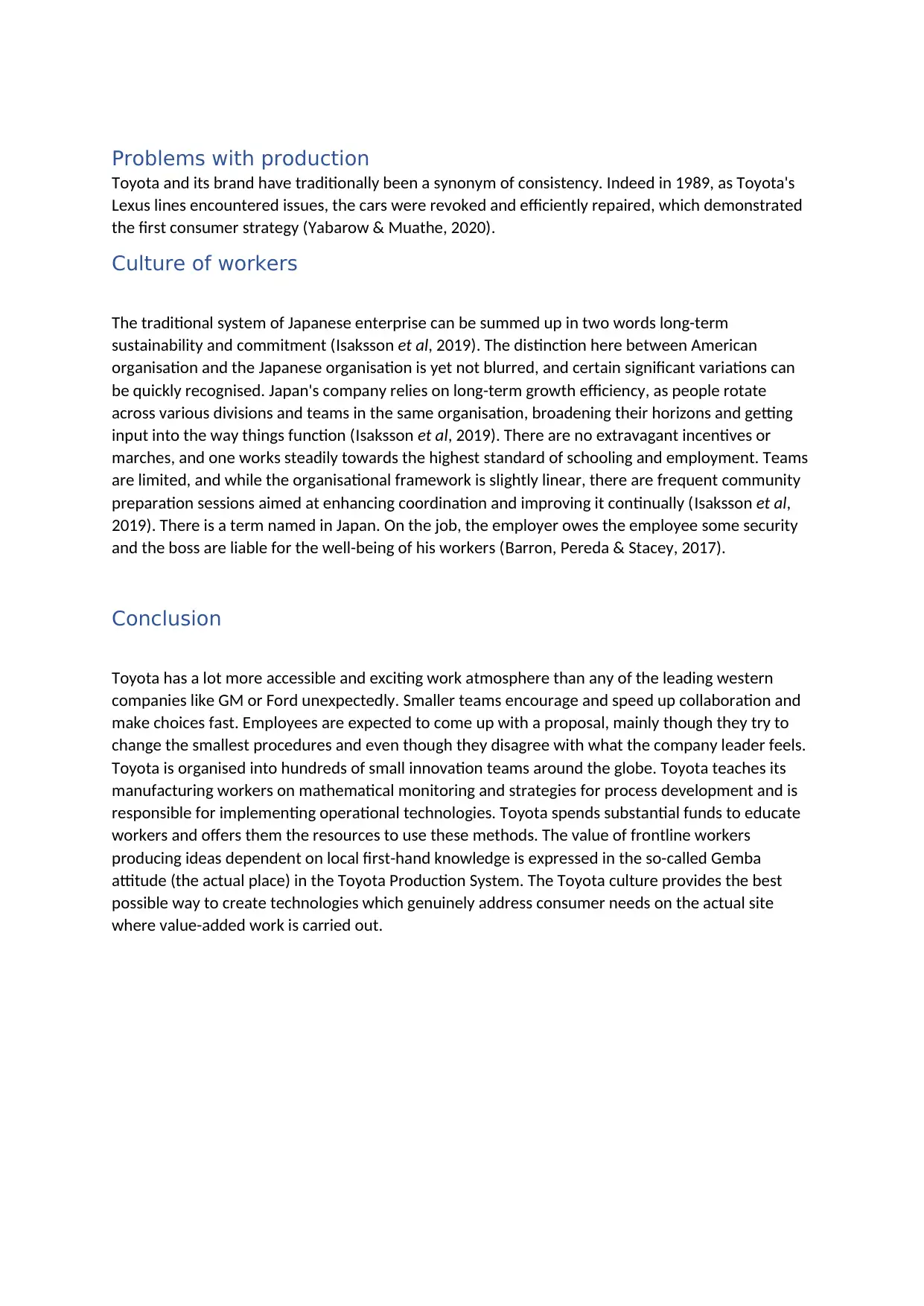
Problems with production
Toyota and its brand have traditionally been a synonym of consistency. Indeed in 1989, as Toyota's
Lexus lines encountered issues, the cars were revoked and efficiently repaired, which demonstrated
the first consumer strategy (Yabarow & Muathe, 2020).
Culture of workers
The traditional system of Japanese enterprise can be summed up in two words long-term
sustainability and commitment (Isaksson et al, 2019). The distinction here between American
organisation and the Japanese organisation is yet not blurred, and certain significant variations can
be quickly recognised. Japan's company relies on long-term growth efficiency, as people rotate
across various divisions and teams in the same organisation, broadening their horizons and getting
input into the way things function (Isaksson et al, 2019). There are no extravagant incentives or
marches, and one works steadily towards the highest standard of schooling and employment. Teams
are limited, and while the organisational framework is slightly linear, there are frequent community
preparation sessions aimed at enhancing coordination and improving it continually (Isaksson et al,
2019). There is a term named in Japan. On the job, the employer owes the employee some security
and the boss are liable for the well-being of his workers (Barron, Pereda & Stacey, 2017).
Conclusion
Toyota has a lot more accessible and exciting work atmosphere than any of the leading western
companies like GM or Ford unexpectedly. Smaller teams encourage and speed up collaboration and
make choices fast. Employees are expected to come up with a proposal, mainly though they try to
change the smallest procedures and even though they disagree with what the company leader feels.
Toyota is organised into hundreds of small innovation teams around the globe. Toyota teaches its
manufacturing workers on mathematical monitoring and strategies for process development and is
responsible for implementing operational technologies. Toyota spends substantial funds to educate
workers and offers them the resources to use these methods. The value of frontline workers
producing ideas dependent on local first-hand knowledge is expressed in the so-called Gemba
attitude (the actual place) in the Toyota Production System. The Toyota culture provides the best
possible way to create technologies which genuinely address consumer needs on the actual site
where value-added work is carried out.
Toyota and its brand have traditionally been a synonym of consistency. Indeed in 1989, as Toyota's
Lexus lines encountered issues, the cars were revoked and efficiently repaired, which demonstrated
the first consumer strategy (Yabarow & Muathe, 2020).
Culture of workers
The traditional system of Japanese enterprise can be summed up in two words long-term
sustainability and commitment (Isaksson et al, 2019). The distinction here between American
organisation and the Japanese organisation is yet not blurred, and certain significant variations can
be quickly recognised. Japan's company relies on long-term growth efficiency, as people rotate
across various divisions and teams in the same organisation, broadening their horizons and getting
input into the way things function (Isaksson et al, 2019). There are no extravagant incentives or
marches, and one works steadily towards the highest standard of schooling and employment. Teams
are limited, and while the organisational framework is slightly linear, there are frequent community
preparation sessions aimed at enhancing coordination and improving it continually (Isaksson et al,
2019). There is a term named in Japan. On the job, the employer owes the employee some security
and the boss are liable for the well-being of his workers (Barron, Pereda & Stacey, 2017).
Conclusion
Toyota has a lot more accessible and exciting work atmosphere than any of the leading western
companies like GM or Ford unexpectedly. Smaller teams encourage and speed up collaboration and
make choices fast. Employees are expected to come up with a proposal, mainly though they try to
change the smallest procedures and even though they disagree with what the company leader feels.
Toyota is organised into hundreds of small innovation teams around the globe. Toyota teaches its
manufacturing workers on mathematical monitoring and strategies for process development and is
responsible for implementing operational technologies. Toyota spends substantial funds to educate
workers and offers them the resources to use these methods. The value of frontline workers
producing ideas dependent on local first-hand knowledge is expressed in the so-called Gemba
attitude (the actual place) in the Toyota Production System. The Toyota culture provides the best
possible way to create technologies which genuinely address consumer needs on the actual site
where value-added work is carried out.
Paraphrase This Document
Need a fresh take? Get an instant paraphrase of this document with our AI Paraphraser
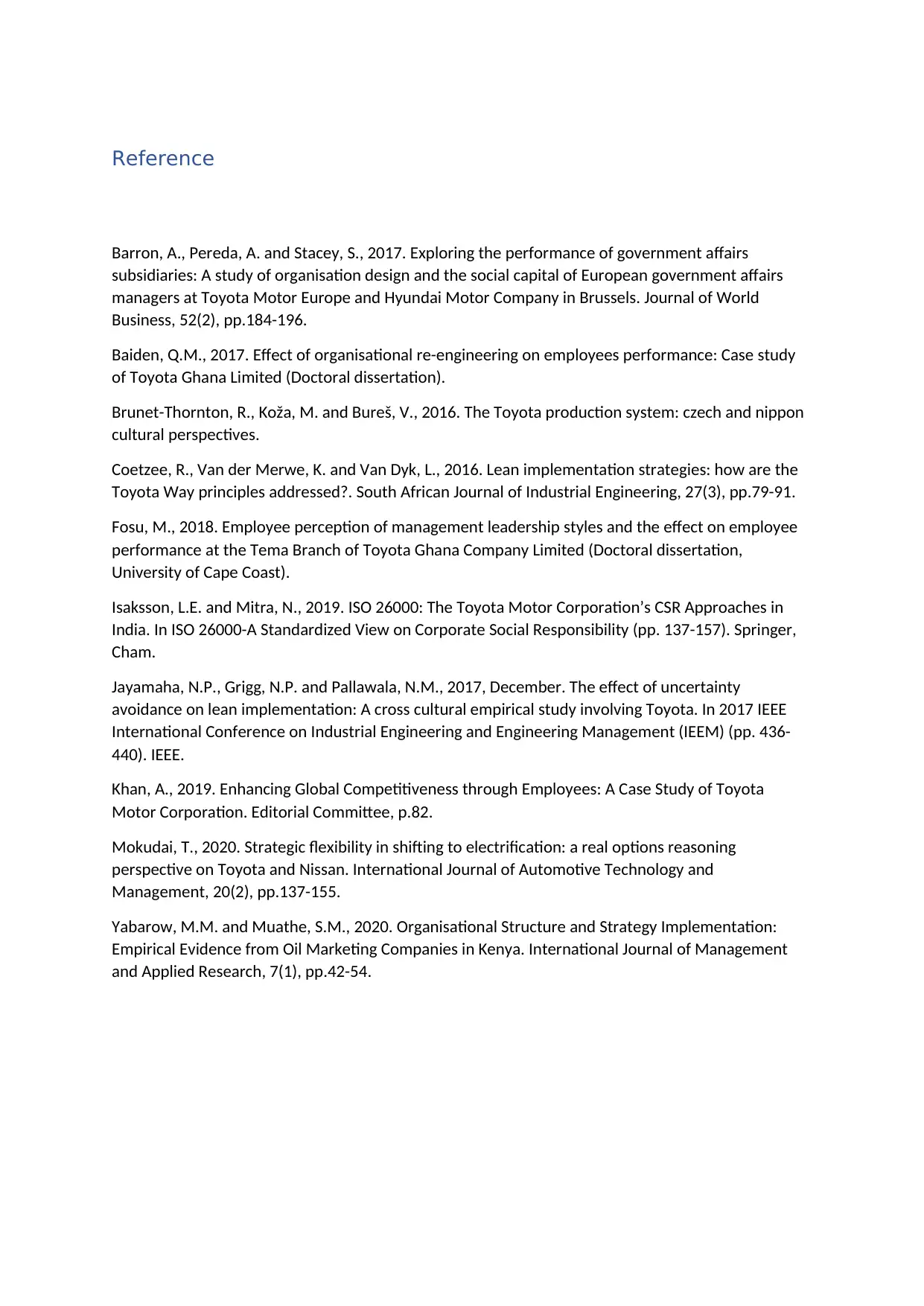
Reference
Barron, A., Pereda, A. and Stacey, S., 2017. Exploring the performance of government affairs
subsidiaries: A study of organisation design and the social capital of European government affairs
managers at Toyota Motor Europe and Hyundai Motor Company in Brussels. Journal of World
Business, 52(2), pp.184-196.
Baiden, Q.M., 2017. Effect of organisational re-engineering on employees performance: Case study
of Toyota Ghana Limited (Doctoral dissertation).
Brunet-Thornton, R., Koža, M. and Bureš, V., 2016. The Toyota production system: czech and nippon
cultural perspectives.
Coetzee, R., Van der Merwe, K. and Van Dyk, L., 2016. Lean implementation strategies: how are the
Toyota Way principles addressed?. South African Journal of Industrial Engineering, 27(3), pp.79-91.
Fosu, M., 2018. Employee perception of management leadership styles and the effect on employee
performance at the Tema Branch of Toyota Ghana Company Limited (Doctoral dissertation,
University of Cape Coast).
Isaksson, L.E. and Mitra, N., 2019. ISO 26000: The Toyota Motor Corporation’s CSR Approaches in
India. In ISO 26000-A Standardized View on Corporate Social Responsibility (pp. 137-157). Springer,
Cham.
Jayamaha, N.P., Grigg, N.P. and Pallawala, N.M., 2017, December. The effect of uncertainty
avoidance on lean implementation: A cross cultural empirical study involving Toyota. In 2017 IEEE
International Conference on Industrial Engineering and Engineering Management (IEEM) (pp. 436-
440). IEEE.
Khan, A., 2019. Enhancing Global Competitiveness through Employees: A Case Study of Toyota
Motor Corporation. Editorial Committee, p.82.
Mokudai, T., 2020. Strategic flexibility in shifting to electrification: a real options reasoning
perspective on Toyota and Nissan. International Journal of Automotive Technology and
Management, 20(2), pp.137-155.
Yabarow, M.M. and Muathe, S.M., 2020. Organisational Structure and Strategy Implementation:
Empirical Evidence from Oil Marketing Companies in Kenya. International Journal of Management
and Applied Research, 7(1), pp.42-54.
Barron, A., Pereda, A. and Stacey, S., 2017. Exploring the performance of government affairs
subsidiaries: A study of organisation design and the social capital of European government affairs
managers at Toyota Motor Europe and Hyundai Motor Company in Brussels. Journal of World
Business, 52(2), pp.184-196.
Baiden, Q.M., 2017. Effect of organisational re-engineering on employees performance: Case study
of Toyota Ghana Limited (Doctoral dissertation).
Brunet-Thornton, R., Koža, M. and Bureš, V., 2016. The Toyota production system: czech and nippon
cultural perspectives.
Coetzee, R., Van der Merwe, K. and Van Dyk, L., 2016. Lean implementation strategies: how are the
Toyota Way principles addressed?. South African Journal of Industrial Engineering, 27(3), pp.79-91.
Fosu, M., 2018. Employee perception of management leadership styles and the effect on employee
performance at the Tema Branch of Toyota Ghana Company Limited (Doctoral dissertation,
University of Cape Coast).
Isaksson, L.E. and Mitra, N., 2019. ISO 26000: The Toyota Motor Corporation’s CSR Approaches in
India. In ISO 26000-A Standardized View on Corporate Social Responsibility (pp. 137-157). Springer,
Cham.
Jayamaha, N.P., Grigg, N.P. and Pallawala, N.M., 2017, December. The effect of uncertainty
avoidance on lean implementation: A cross cultural empirical study involving Toyota. In 2017 IEEE
International Conference on Industrial Engineering and Engineering Management (IEEM) (pp. 436-
440). IEEE.
Khan, A., 2019. Enhancing Global Competitiveness through Employees: A Case Study of Toyota
Motor Corporation. Editorial Committee, p.82.
Mokudai, T., 2020. Strategic flexibility in shifting to electrification: a real options reasoning
perspective on Toyota and Nissan. International Journal of Automotive Technology and
Management, 20(2), pp.137-155.
Yabarow, M.M. and Muathe, S.M., 2020. Organisational Structure and Strategy Implementation:
Empirical Evidence from Oil Marketing Companies in Kenya. International Journal of Management
and Applied Research, 7(1), pp.42-54.
1 out of 8
Related Documents

Your All-in-One AI-Powered Toolkit for Academic Success.
+13062052269
info@desklib.com
Available 24*7 on WhatsApp / Email
Unlock your academic potential
© 2024 | Zucol Services PVT LTD | All rights reserved.