Analyzing Toyota's Supply Chain: Quality Management and Productivity
VerifiedAdded on 2023/06/11
|11
|2872
|466
Case Study
AI Summary
This case study explores Toyota's supply chain management with a focus on quality and productivity. It examines Toyota's journey, including a major crisis in 2009 due to massive recalls and subsequent efforts to reorganize its quality management. The analysis covers Toyota's cost-cutting measures, neglect of quality control, and the resulting product defects. It also highlights Toyota's innovative techniques such as JIT, Kanban, and Kaizen, which contribute to waste elimination, shortened production time, and inventory minimization. Furthermore, the case study discusses Toyota's sales methods, like 'I will be friend for life,' and its benchmarking efforts to increase sales and avoid stagnated growth. The study concludes with Toyota's reorganization of its quality management, its commitment to the Way principle, and its efforts to strengthen the production structure, demonstrating the company's transformation into one that prioritizes quality in all production processes. The document is available on Desklib, a platform offering study tools for students.
Contribute Materials
Your contribution can guide someone’s learning journey. Share your
documents today.
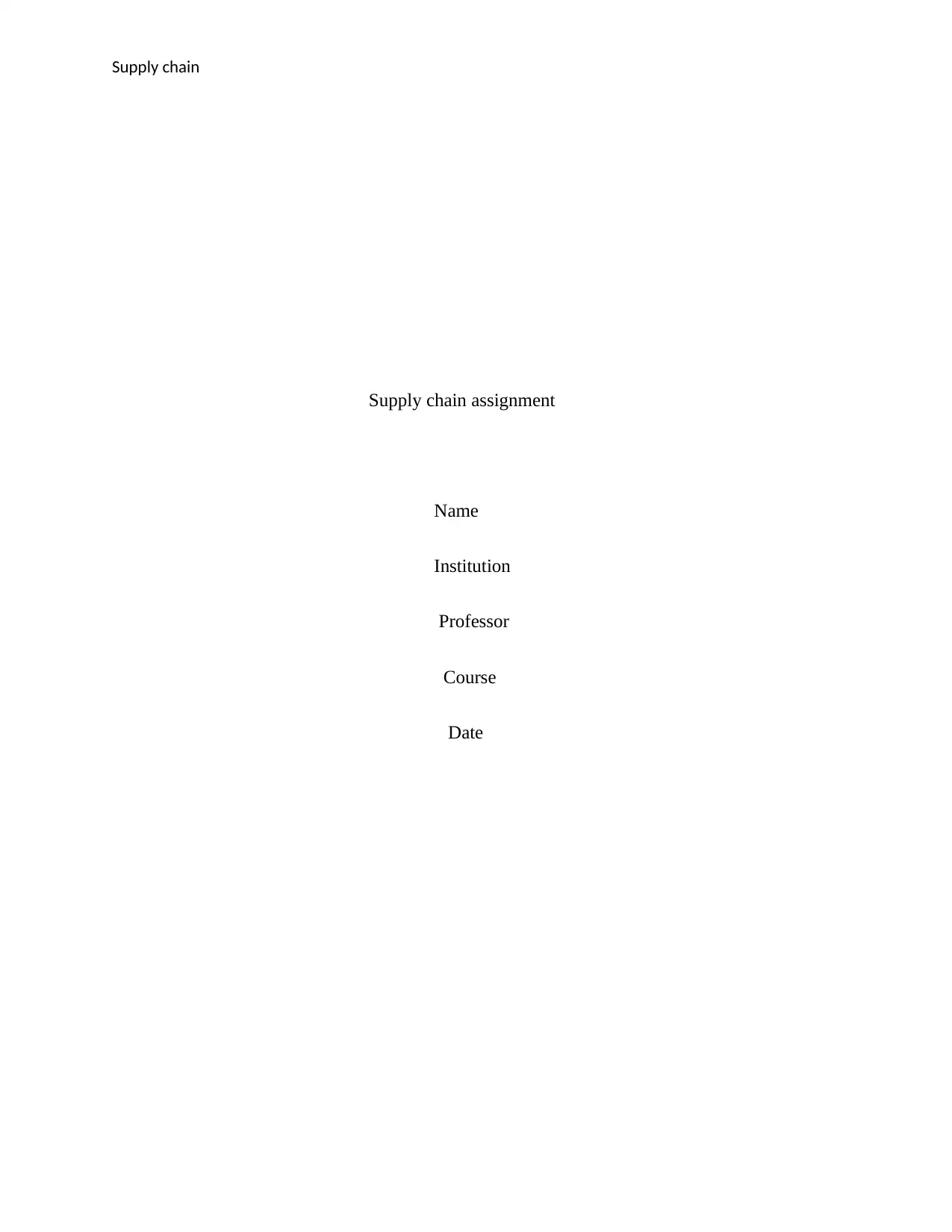
Supply chain
Supply chain assignment
Name
Institution
Professor
Course
Date
Supply chain assignment
Name
Institution
Professor
Course
Date
Secure Best Marks with AI Grader
Need help grading? Try our AI Grader for instant feedback on your assignments.
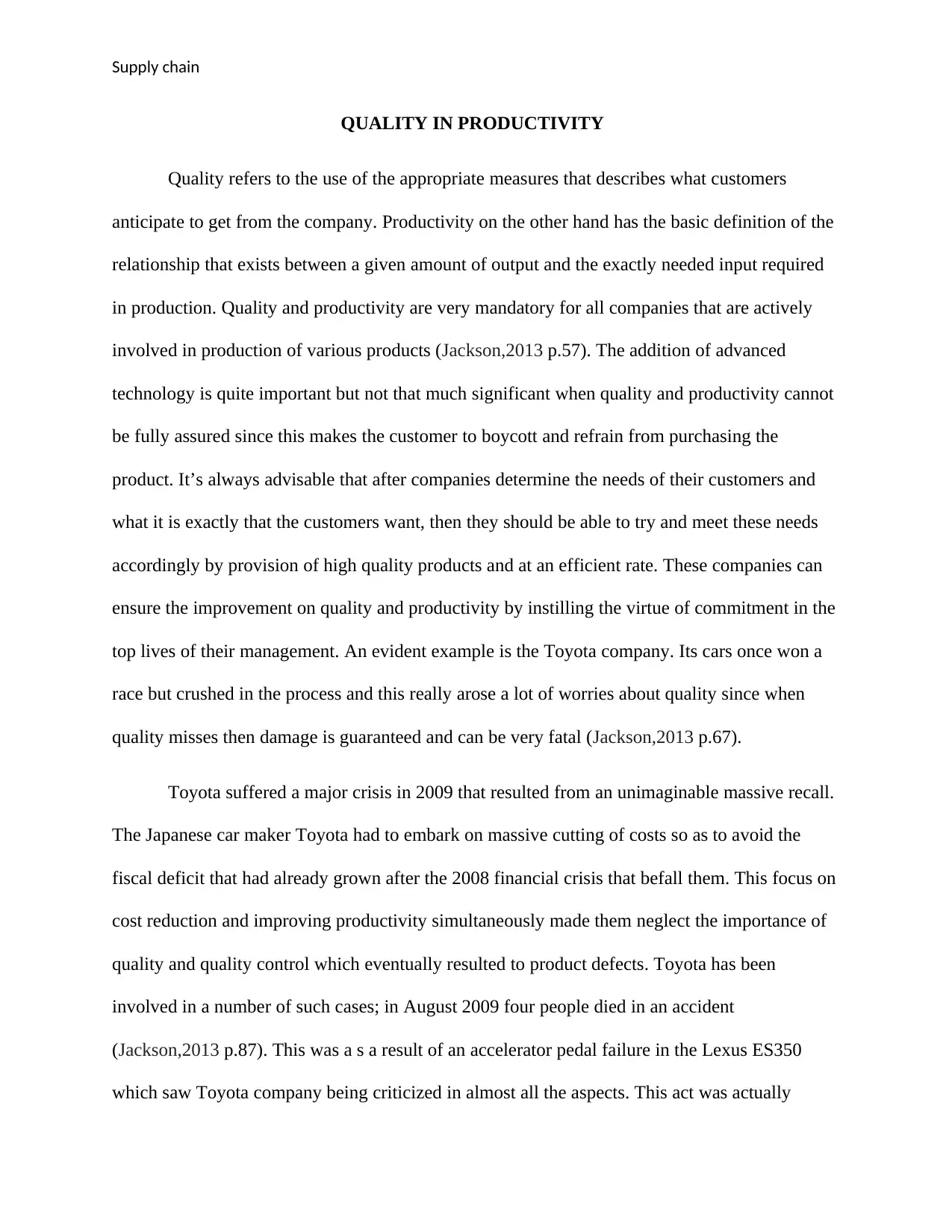
Supply chain
QUALITY IN PRODUCTIVITY
Quality refers to the use of the appropriate measures that describes what customers
anticipate to get from the company. Productivity on the other hand has the basic definition of the
relationship that exists between a given amount of output and the exactly needed input required
in production. Quality and productivity are very mandatory for all companies that are actively
involved in production of various products (Jackson,2013 p.57). The addition of advanced
technology is quite important but not that much significant when quality and productivity cannot
be fully assured since this makes the customer to boycott and refrain from purchasing the
product. It’s always advisable that after companies determine the needs of their customers and
what it is exactly that the customers want, then they should be able to try and meet these needs
accordingly by provision of high quality products and at an efficient rate. These companies can
ensure the improvement on quality and productivity by instilling the virtue of commitment in the
top lives of their management. An evident example is the Toyota company. Its cars once won a
race but crushed in the process and this really arose a lot of worries about quality since when
quality misses then damage is guaranteed and can be very fatal (Jackson,2013 p.67).
Toyota suffered a major crisis in 2009 that resulted from an unimaginable massive recall.
The Japanese car maker Toyota had to embark on massive cutting of costs so as to avoid the
fiscal deficit that had already grown after the 2008 financial crisis that befall them. This focus on
cost reduction and improving productivity simultaneously made them neglect the importance of
quality and quality control which eventually resulted to product defects. Toyota has been
involved in a number of such cases; in August 2009 four people died in an accident
(Jackson,2013 p.87). This was a s a result of an accelerator pedal failure in the Lexus ES350
which saw Toyota company being criticized in almost all the aspects. This act was actually
QUALITY IN PRODUCTIVITY
Quality refers to the use of the appropriate measures that describes what customers
anticipate to get from the company. Productivity on the other hand has the basic definition of the
relationship that exists between a given amount of output and the exactly needed input required
in production. Quality and productivity are very mandatory for all companies that are actively
involved in production of various products (Jackson,2013 p.57). The addition of advanced
technology is quite important but not that much significant when quality and productivity cannot
be fully assured since this makes the customer to boycott and refrain from purchasing the
product. It’s always advisable that after companies determine the needs of their customers and
what it is exactly that the customers want, then they should be able to try and meet these needs
accordingly by provision of high quality products and at an efficient rate. These companies can
ensure the improvement on quality and productivity by instilling the virtue of commitment in the
top lives of their management. An evident example is the Toyota company. Its cars once won a
race but crushed in the process and this really arose a lot of worries about quality since when
quality misses then damage is guaranteed and can be very fatal (Jackson,2013 p.67).
Toyota suffered a major crisis in 2009 that resulted from an unimaginable massive recall.
The Japanese car maker Toyota had to embark on massive cutting of costs so as to avoid the
fiscal deficit that had already grown after the 2008 financial crisis that befall them. This focus on
cost reduction and improving productivity simultaneously made them neglect the importance of
quality and quality control which eventually resulted to product defects. Toyota has been
involved in a number of such cases; in August 2009 four people died in an accident
(Jackson,2013 p.87). This was a s a result of an accelerator pedal failure in the Lexus ES350
which saw Toyota company being criticized in almost all the aspects. This act was actually

Supply chain
among one of many that caused a great crisis to Toyota and saw the sales of Toyota drop very
significantly. On addition to this crisis Toyota has at some point also faced a crisis with a recall
of more than 9 million units due to component defects (Thierfelder & Wall,2012 p.90). Toyota
also recalled in the US, Europe and China due to defects in some of its automobile parts this
went ahead into forcing them to suspend sales in the US.
Shown below is a diagram of the recalls and a representation of the crisis that befall Toyota.
(Goetsch & Davis,2014 p.46).
The following were identified from the diagram above.
In August 28 ,2009 there were four people who died during the Lexus vehicle accident.
After recalling 4.26 million units from the accelerator pedal problem on November 2009, other
recalls were also made to 5.3 million units including the additional 109 ,000 units which were
recalled on 27th (Goetsch & Davis,2014 p.48).
among one of many that caused a great crisis to Toyota and saw the sales of Toyota drop very
significantly. On addition to this crisis Toyota has at some point also faced a crisis with a recall
of more than 9 million units due to component defects (Thierfelder & Wall,2012 p.90). Toyota
also recalled in the US, Europe and China due to defects in some of its automobile parts this
went ahead into forcing them to suspend sales in the US.
Shown below is a diagram of the recalls and a representation of the crisis that befall Toyota.
(Goetsch & Davis,2014 p.46).
The following were identified from the diagram above.
In August 28 ,2009 there were four people who died during the Lexus vehicle accident.
After recalling 4.26 million units from the accelerator pedal problem on November 2009, other
recalls were also made to 5.3 million units including the additional 109 ,000 units which were
recalled on 27th (Goetsch & Davis,2014 p.48).

Supply chain
Five plants in Toyota North America entered production halt for a week on February 4 ,2010.
Toyota recalled additional 109,000 units and other 75,000 units were also recalled from the
Chinese market on February 4,2010.
US department of transportation (USDOT) launched a full-fledged on February 4,2010.
Toyotas share price in the New York stock market reduced from $91.78 on Jan 19 to $71.78 on
4th February giving a fall down of 21% from the previous year.
Toyota is also involved in innovation through the use of the various techniques. The company is
the best in cost saving in the world and some of its production methods are the JIT, Kanban, and
the Kaizen (Goetsch & Davis,2014 p.56). The JIT for instance eliminates waste by producing
only what is needed, it also aims at a shortened production time and minimization of inventory. It
achieves this by use of a pull-base material flow where parts are produced in accordance to the
production schedule. It basically attempts to eliminate defects and rework to keep the material
flow uniform. To however operate the JIT system efficiently, it’s important to keep product
standard and implement all statistical techniques such as Total Quality Management. Workers in
this process control quality from source by acting as quality inspectors (Vasilescu et al,2015
p.78).
The Kanban system on the other hand ensures thorough elimination of waste. It
automatically comes in with JIT. One distinct feature of the Kanban system is that the entire
process is directly visible. Usually the system can be linked to all work places and vendors thus
allowing almost all the production materials have a high visibility through visible on-site control
systems (Filatova et al,2011 p.56). The other way of overcoming a low growth and depression
Five plants in Toyota North America entered production halt for a week on February 4 ,2010.
Toyota recalled additional 109,000 units and other 75,000 units were also recalled from the
Chinese market on February 4,2010.
US department of transportation (USDOT) launched a full-fledged on February 4,2010.
Toyotas share price in the New York stock market reduced from $91.78 on Jan 19 to $71.78 on
4th February giving a fall down of 21% from the previous year.
Toyota is also involved in innovation through the use of the various techniques. The company is
the best in cost saving in the world and some of its production methods are the JIT, Kanban, and
the Kaizen (Goetsch & Davis,2014 p.56). The JIT for instance eliminates waste by producing
only what is needed, it also aims at a shortened production time and minimization of inventory. It
achieves this by use of a pull-base material flow where parts are produced in accordance to the
production schedule. It basically attempts to eliminate defects and rework to keep the material
flow uniform. To however operate the JIT system efficiently, it’s important to keep product
standard and implement all statistical techniques such as Total Quality Management. Workers in
this process control quality from source by acting as quality inspectors (Vasilescu et al,2015
p.78).
The Kanban system on the other hand ensures thorough elimination of waste. It
automatically comes in with JIT. One distinct feature of the Kanban system is that the entire
process is directly visible. Usually the system can be linked to all work places and vendors thus
allowing almost all the production materials have a high visibility through visible on-site control
systems (Filatova et al,2011 p.56). The other way of overcoming a low growth and depression
Secure Best Marks with AI Grader
Need help grading? Try our AI Grader for instant feedback on your assignments.
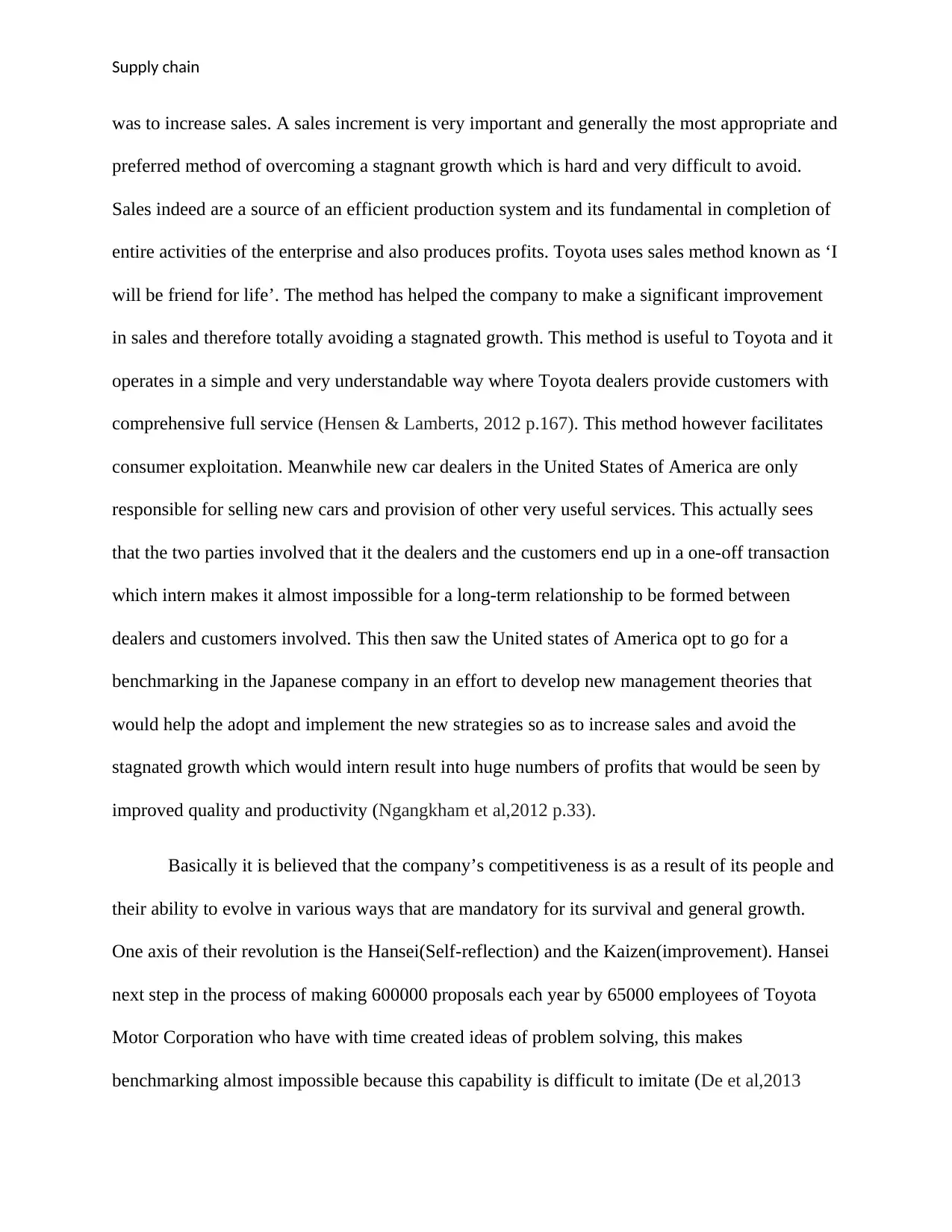
Supply chain
was to increase sales. A sales increment is very important and generally the most appropriate and
preferred method of overcoming a stagnant growth which is hard and very difficult to avoid.
Sales indeed are a source of an efficient production system and its fundamental in completion of
entire activities of the enterprise and also produces profits. Toyota uses sales method known as ‘I
will be friend for life’. The method has helped the company to make a significant improvement
in sales and therefore totally avoiding a stagnated growth. This method is useful to Toyota and it
operates in a simple and very understandable way where Toyota dealers provide customers with
comprehensive full service (Hensen & Lamberts, 2012 p.167). This method however facilitates
consumer exploitation. Meanwhile new car dealers in the United States of America are only
responsible for selling new cars and provision of other very useful services. This actually sees
that the two parties involved that it the dealers and the customers end up in a one-off transaction
which intern makes it almost impossible for a long-term relationship to be formed between
dealers and customers involved. This then saw the United states of America opt to go for a
benchmarking in the Japanese company in an effort to develop new management theories that
would help the adopt and implement the new strategies so as to increase sales and avoid the
stagnated growth which would intern result into huge numbers of profits that would be seen by
improved quality and productivity (Ngangkham et al,2012 p.33).
Basically it is believed that the company’s competitiveness is as a result of its people and
their ability to evolve in various ways that are mandatory for its survival and general growth.
One axis of their revolution is the Hansei(Self-reflection) and the Kaizen(improvement). Hansei
next step in the process of making 600000 proposals each year by 65000 employees of Toyota
Motor Corporation who have with time created ideas of problem solving, this makes
benchmarking almost impossible because this capability is difficult to imitate (De et al,2013
was to increase sales. A sales increment is very important and generally the most appropriate and
preferred method of overcoming a stagnant growth which is hard and very difficult to avoid.
Sales indeed are a source of an efficient production system and its fundamental in completion of
entire activities of the enterprise and also produces profits. Toyota uses sales method known as ‘I
will be friend for life’. The method has helped the company to make a significant improvement
in sales and therefore totally avoiding a stagnated growth. This method is useful to Toyota and it
operates in a simple and very understandable way where Toyota dealers provide customers with
comprehensive full service (Hensen & Lamberts, 2012 p.167). This method however facilitates
consumer exploitation. Meanwhile new car dealers in the United States of America are only
responsible for selling new cars and provision of other very useful services. This actually sees
that the two parties involved that it the dealers and the customers end up in a one-off transaction
which intern makes it almost impossible for a long-term relationship to be formed between
dealers and customers involved. This then saw the United states of America opt to go for a
benchmarking in the Japanese company in an effort to develop new management theories that
would help the adopt and implement the new strategies so as to increase sales and avoid the
stagnated growth which would intern result into huge numbers of profits that would be seen by
improved quality and productivity (Ngangkham et al,2012 p.33).
Basically it is believed that the company’s competitiveness is as a result of its people and
their ability to evolve in various ways that are mandatory for its survival and general growth.
One axis of their revolution is the Hansei(Self-reflection) and the Kaizen(improvement). Hansei
next step in the process of making 600000 proposals each year by 65000 employees of Toyota
Motor Corporation who have with time created ideas of problem solving, this makes
benchmarking almost impossible because this capability is difficult to imitate (De et al,2013
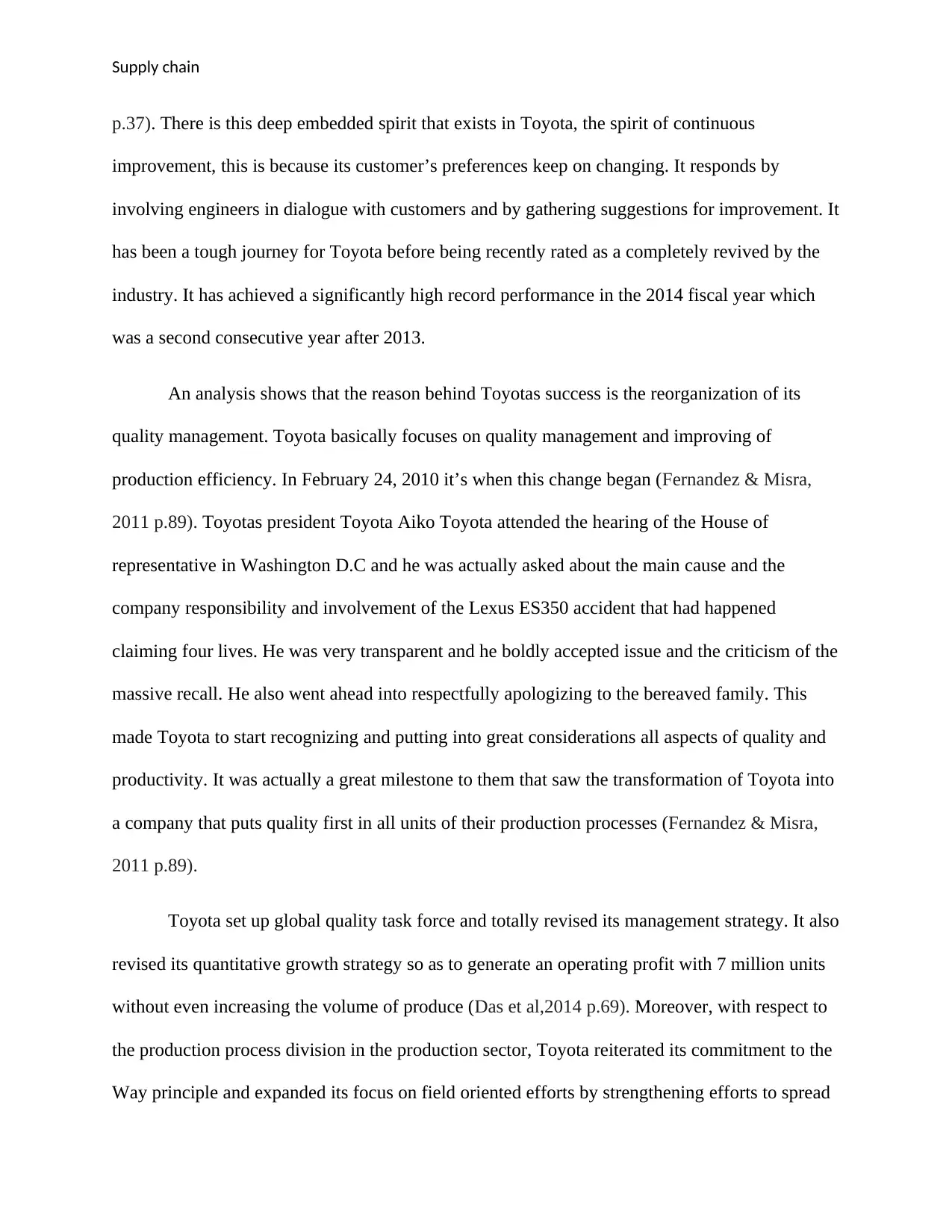
Supply chain
p.37). There is this deep embedded spirit that exists in Toyota, the spirit of continuous
improvement, this is because its customer’s preferences keep on changing. It responds by
involving engineers in dialogue with customers and by gathering suggestions for improvement. It
has been a tough journey for Toyota before being recently rated as a completely revived by the
industry. It has achieved a significantly high record performance in the 2014 fiscal year which
was a second consecutive year after 2013.
An analysis shows that the reason behind Toyotas success is the reorganization of its
quality management. Toyota basically focuses on quality management and improving of
production efficiency. In February 24, 2010 it’s when this change began (Fernandez & Misra,
2011 p.89). Toyotas president Toyota Aiko Toyota attended the hearing of the House of
representative in Washington D.C and he was actually asked about the main cause and the
company responsibility and involvement of the Lexus ES350 accident that had happened
claiming four lives. He was very transparent and he boldly accepted issue and the criticism of the
massive recall. He also went ahead into respectfully apologizing to the bereaved family. This
made Toyota to start recognizing and putting into great considerations all aspects of quality and
productivity. It was actually a great milestone to them that saw the transformation of Toyota into
a company that puts quality first in all units of their production processes (Fernandez & Misra,
2011 p.89).
Toyota set up global quality task force and totally revised its management strategy. It also
revised its quantitative growth strategy so as to generate an operating profit with 7 million units
without even increasing the volume of produce (Das et al,2014 p.69). Moreover, with respect to
the production process division in the production sector, Toyota reiterated its commitment to the
Way principle and expanded its focus on field oriented efforts by strengthening efforts to spread
p.37). There is this deep embedded spirit that exists in Toyota, the spirit of continuous
improvement, this is because its customer’s preferences keep on changing. It responds by
involving engineers in dialogue with customers and by gathering suggestions for improvement. It
has been a tough journey for Toyota before being recently rated as a completely revived by the
industry. It has achieved a significantly high record performance in the 2014 fiscal year which
was a second consecutive year after 2013.
An analysis shows that the reason behind Toyotas success is the reorganization of its
quality management. Toyota basically focuses on quality management and improving of
production efficiency. In February 24, 2010 it’s when this change began (Fernandez & Misra,
2011 p.89). Toyotas president Toyota Aiko Toyota attended the hearing of the House of
representative in Washington D.C and he was actually asked about the main cause and the
company responsibility and involvement of the Lexus ES350 accident that had happened
claiming four lives. He was very transparent and he boldly accepted issue and the criticism of the
massive recall. He also went ahead into respectfully apologizing to the bereaved family. This
made Toyota to start recognizing and putting into great considerations all aspects of quality and
productivity. It was actually a great milestone to them that saw the transformation of Toyota into
a company that puts quality first in all units of their production processes (Fernandez & Misra,
2011 p.89).
Toyota set up global quality task force and totally revised its management strategy. It also
revised its quantitative growth strategy so as to generate an operating profit with 7 million units
without even increasing the volume of produce (Das et al,2014 p.69). Moreover, with respect to
the production process division in the production sector, Toyota reiterated its commitment to the
Way principle and expanded its focus on field oriented efforts by strengthening efforts to spread
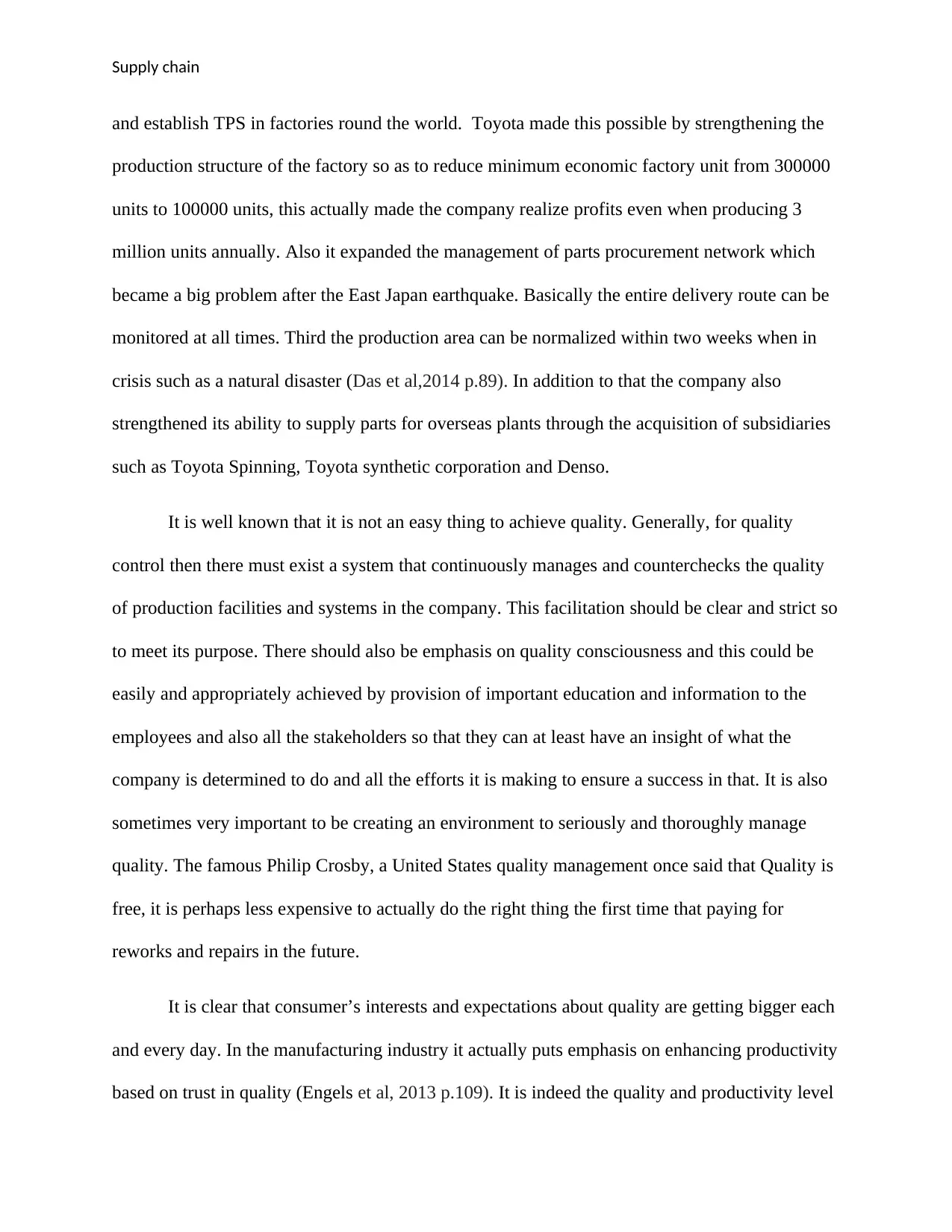
Supply chain
and establish TPS in factories round the world. Toyota made this possible by strengthening the
production structure of the factory so as to reduce minimum economic factory unit from 300000
units to 100000 units, this actually made the company realize profits even when producing 3
million units annually. Also it expanded the management of parts procurement network which
became a big problem after the East Japan earthquake. Basically the entire delivery route can be
monitored at all times. Third the production area can be normalized within two weeks when in
crisis such as a natural disaster (Das et al,2014 p.89). In addition to that the company also
strengthened its ability to supply parts for overseas plants through the acquisition of subsidiaries
such as Toyota Spinning, Toyota synthetic corporation and Denso.
It is well known that it is not an easy thing to achieve quality. Generally, for quality
control then there must exist a system that continuously manages and counterchecks the quality
of production facilities and systems in the company. This facilitation should be clear and strict so
to meet its purpose. There should also be emphasis on quality consciousness and this could be
easily and appropriately achieved by provision of important education and information to the
employees and also all the stakeholders so that they can at least have an insight of what the
company is determined to do and all the efforts it is making to ensure a success in that. It is also
sometimes very important to be creating an environment to seriously and thoroughly manage
quality. The famous Philip Crosby, a United States quality management once said that Quality is
free, it is perhaps less expensive to actually do the right thing the first time that paying for
reworks and repairs in the future.
It is clear that consumer’s interests and expectations about quality are getting bigger each
and every day. In the manufacturing industry it actually puts emphasis on enhancing productivity
based on trust in quality (Engels et al, 2013 p.109). It is indeed the quality and productivity level
and establish TPS in factories round the world. Toyota made this possible by strengthening the
production structure of the factory so as to reduce minimum economic factory unit from 300000
units to 100000 units, this actually made the company realize profits even when producing 3
million units annually. Also it expanded the management of parts procurement network which
became a big problem after the East Japan earthquake. Basically the entire delivery route can be
monitored at all times. Third the production area can be normalized within two weeks when in
crisis such as a natural disaster (Das et al,2014 p.89). In addition to that the company also
strengthened its ability to supply parts for overseas plants through the acquisition of subsidiaries
such as Toyota Spinning, Toyota synthetic corporation and Denso.
It is well known that it is not an easy thing to achieve quality. Generally, for quality
control then there must exist a system that continuously manages and counterchecks the quality
of production facilities and systems in the company. This facilitation should be clear and strict so
to meet its purpose. There should also be emphasis on quality consciousness and this could be
easily and appropriately achieved by provision of important education and information to the
employees and also all the stakeholders so that they can at least have an insight of what the
company is determined to do and all the efforts it is making to ensure a success in that. It is also
sometimes very important to be creating an environment to seriously and thoroughly manage
quality. The famous Philip Crosby, a United States quality management once said that Quality is
free, it is perhaps less expensive to actually do the right thing the first time that paying for
reworks and repairs in the future.
It is clear that consumer’s interests and expectations about quality are getting bigger each
and every day. In the manufacturing industry it actually puts emphasis on enhancing productivity
based on trust in quality (Engels et al, 2013 p.109). It is indeed the quality and productivity level
Paraphrase This Document
Need a fresh take? Get an instant paraphrase of this document with our AI Paraphraser
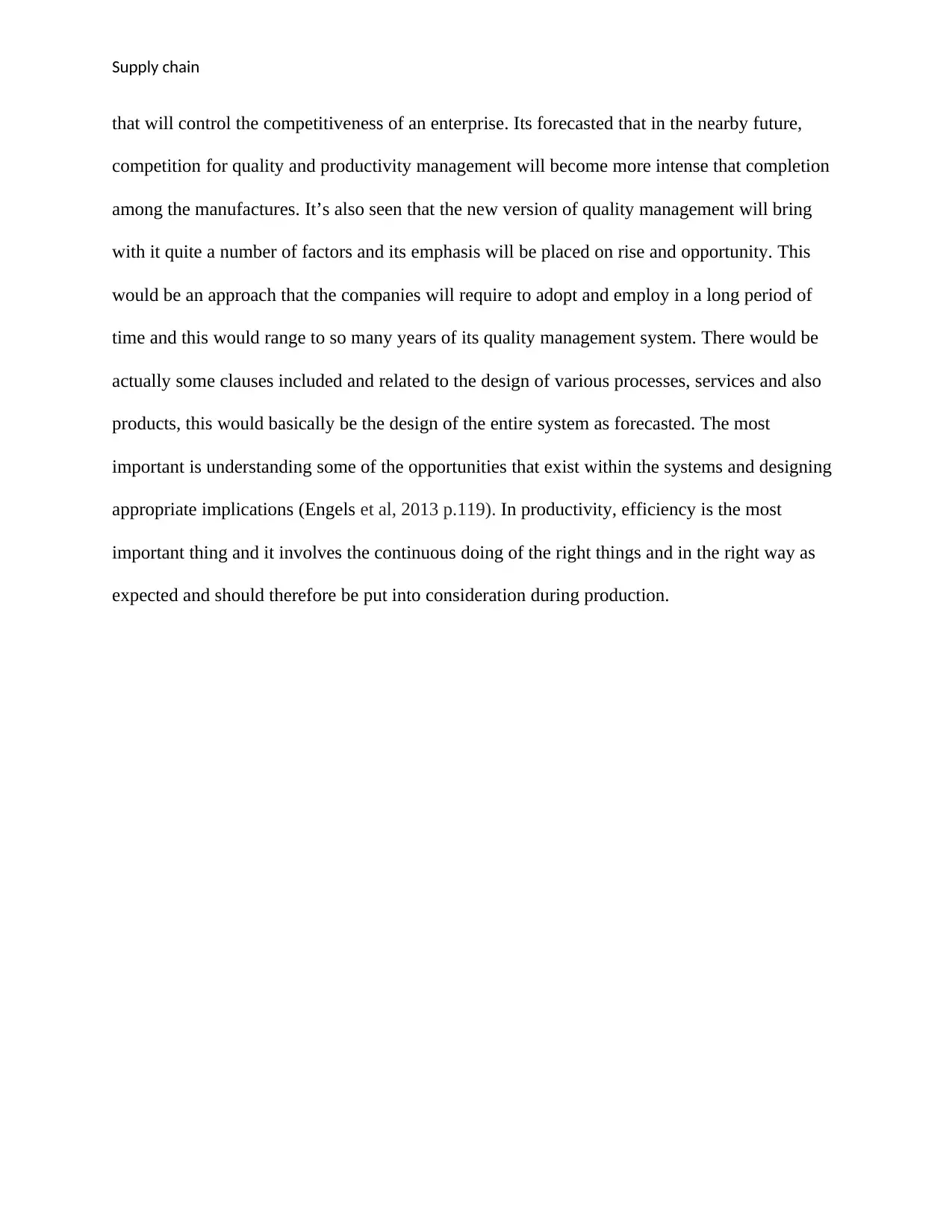
Supply chain
that will control the competitiveness of an enterprise. Its forecasted that in the nearby future,
competition for quality and productivity management will become more intense that completion
among the manufactures. It’s also seen that the new version of quality management will bring
with it quite a number of factors and its emphasis will be placed on rise and opportunity. This
would be an approach that the companies will require to adopt and employ in a long period of
time and this would range to so many years of its quality management system. There would be
actually some clauses included and related to the design of various processes, services and also
products, this would basically be the design of the entire system as forecasted. The most
important is understanding some of the opportunities that exist within the systems and designing
appropriate implications (Engels et al, 2013 p.119). In productivity, efficiency is the most
important thing and it involves the continuous doing of the right things and in the right way as
expected and should therefore be put into consideration during production.
that will control the competitiveness of an enterprise. Its forecasted that in the nearby future,
competition for quality and productivity management will become more intense that completion
among the manufactures. It’s also seen that the new version of quality management will bring
with it quite a number of factors and its emphasis will be placed on rise and opportunity. This
would be an approach that the companies will require to adopt and employ in a long period of
time and this would range to so many years of its quality management system. There would be
actually some clauses included and related to the design of various processes, services and also
products, this would basically be the design of the entire system as forecasted. The most
important is understanding some of the opportunities that exist within the systems and designing
appropriate implications (Engels et al, 2013 p.119). In productivity, efficiency is the most
important thing and it involves the continuous doing of the right things and in the right way as
expected and should therefore be put into consideration during production.
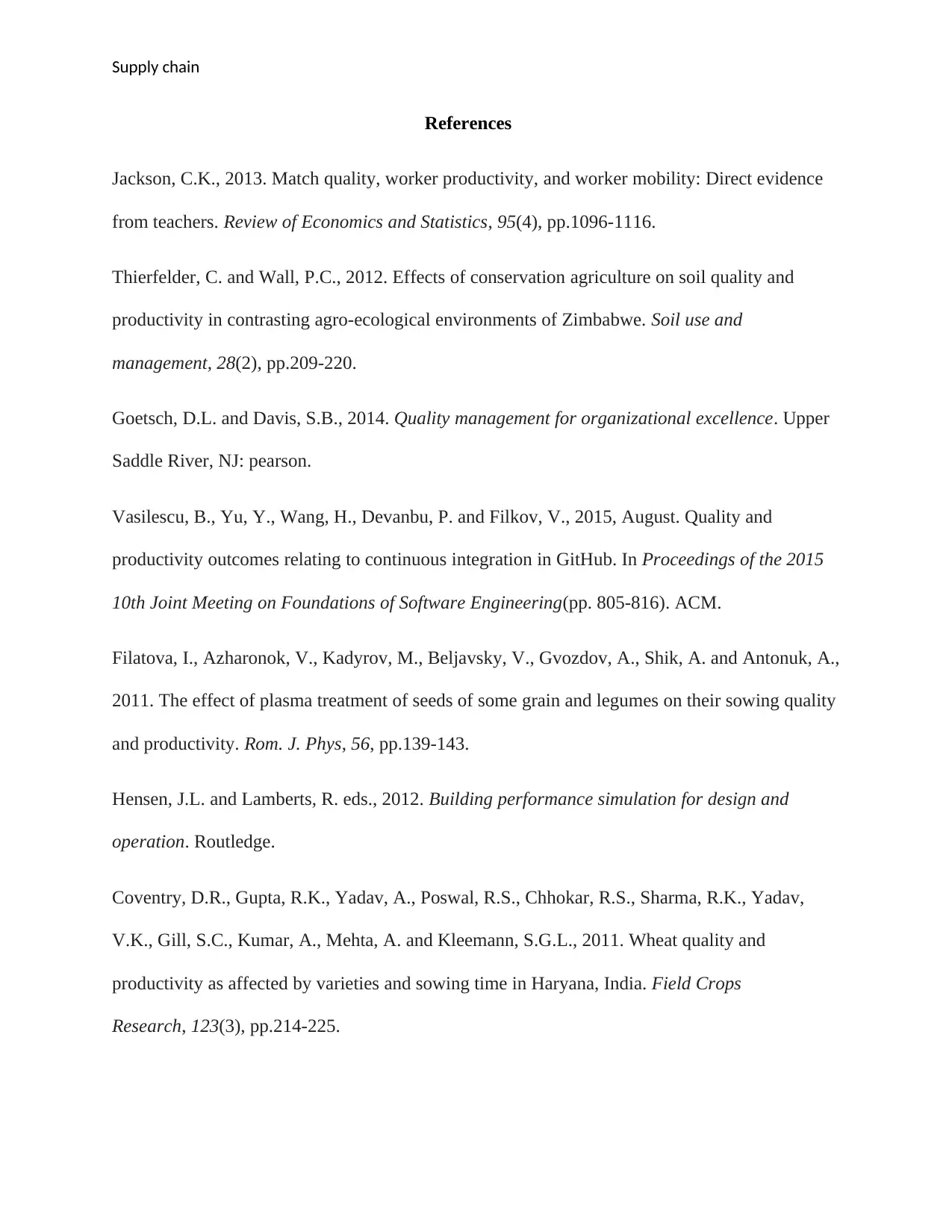
Supply chain
References
Jackson, C.K., 2013. Match quality, worker productivity, and worker mobility: Direct evidence
from teachers. Review of Economics and Statistics, 95(4), pp.1096-1116.
Thierfelder, C. and Wall, P.C., 2012. Effects of conservation agriculture on soil quality and
productivity in contrasting agro‐ecological environments of Zimbabwe. Soil use and
management, 28(2), pp.209-220.
Goetsch, D.L. and Davis, S.B., 2014. Quality management for organizational excellence. Upper
Saddle River, NJ: pearson.
Vasilescu, B., Yu, Y., Wang, H., Devanbu, P. and Filkov, V., 2015, August. Quality and
productivity outcomes relating to continuous integration in GitHub. In Proceedings of the 2015
10th Joint Meeting on Foundations of Software Engineering(pp. 805-816). ACM.
Filatova, I., Azharonok, V., Kadyrov, M., Beljavsky, V., Gvozdov, A., Shik, A. and Antonuk, A.,
2011. The effect of plasma treatment of seeds of some grain and legumes on their sowing quality
and productivity. Rom. J. Phys, 56, pp.139-143.
Hensen, J.L. and Lamberts, R. eds., 2012. Building performance simulation for design and
operation. Routledge.
Coventry, D.R., Gupta, R.K., Yadav, A., Poswal, R.S., Chhokar, R.S., Sharma, R.K., Yadav,
V.K., Gill, S.C., Kumar, A., Mehta, A. and Kleemann, S.G.L., 2011. Wheat quality and
productivity as affected by varieties and sowing time in Haryana, India. Field Crops
Research, 123(3), pp.214-225.
References
Jackson, C.K., 2013. Match quality, worker productivity, and worker mobility: Direct evidence
from teachers. Review of Economics and Statistics, 95(4), pp.1096-1116.
Thierfelder, C. and Wall, P.C., 2012. Effects of conservation agriculture on soil quality and
productivity in contrasting agro‐ecological environments of Zimbabwe. Soil use and
management, 28(2), pp.209-220.
Goetsch, D.L. and Davis, S.B., 2014. Quality management for organizational excellence. Upper
Saddle River, NJ: pearson.
Vasilescu, B., Yu, Y., Wang, H., Devanbu, P. and Filkov, V., 2015, August. Quality and
productivity outcomes relating to continuous integration in GitHub. In Proceedings of the 2015
10th Joint Meeting on Foundations of Software Engineering(pp. 805-816). ACM.
Filatova, I., Azharonok, V., Kadyrov, M., Beljavsky, V., Gvozdov, A., Shik, A. and Antonuk, A.,
2011. The effect of plasma treatment of seeds of some grain and legumes on their sowing quality
and productivity. Rom. J. Phys, 56, pp.139-143.
Hensen, J.L. and Lamberts, R. eds., 2012. Building performance simulation for design and
operation. Routledge.
Coventry, D.R., Gupta, R.K., Yadav, A., Poswal, R.S., Chhokar, R.S., Sharma, R.K., Yadav,
V.K., Gill, S.C., Kumar, A., Mehta, A. and Kleemann, S.G.L., 2011. Wheat quality and
productivity as affected by varieties and sowing time in Haryana, India. Field Crops
Research, 123(3), pp.214-225.
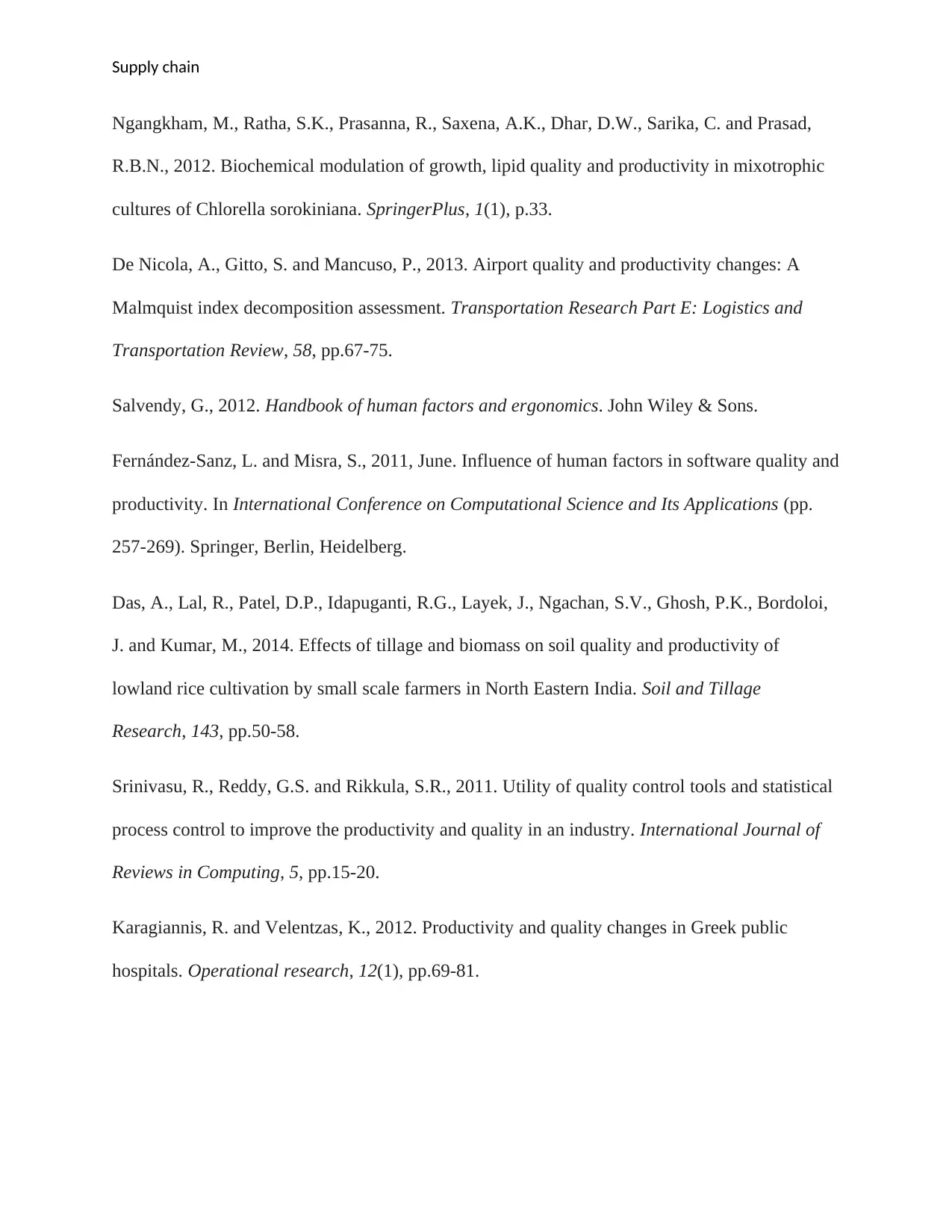
Supply chain
Ngangkham, M., Ratha, S.K., Prasanna, R., Saxena, A.K., Dhar, D.W., Sarika, C. and Prasad,
R.B.N., 2012. Biochemical modulation of growth, lipid quality and productivity in mixotrophic
cultures of Chlorella sorokiniana. SpringerPlus, 1(1), p.33.
De Nicola, A., Gitto, S. and Mancuso, P., 2013. Airport quality and productivity changes: A
Malmquist index decomposition assessment. Transportation Research Part E: Logistics and
Transportation Review, 58, pp.67-75.
Salvendy, G., 2012. Handbook of human factors and ergonomics. John Wiley & Sons.
Fernández-Sanz, L. and Misra, S., 2011, June. Influence of human factors in software quality and
productivity. In International Conference on Computational Science and Its Applications (pp.
257-269). Springer, Berlin, Heidelberg.
Das, A., Lal, R., Patel, D.P., Idapuganti, R.G., Layek, J., Ngachan, S.V., Ghosh, P.K., Bordoloi,
J. and Kumar, M., 2014. Effects of tillage and biomass on soil quality and productivity of
lowland rice cultivation by small scale farmers in North Eastern India. Soil and Tillage
Research, 143, pp.50-58.
Srinivasu, R., Reddy, G.S. and Rikkula, S.R., 2011. Utility of quality control tools and statistical
process control to improve the productivity and quality in an industry. International Journal of
Reviews in Computing, 5, pp.15-20.
Karagiannis, R. and Velentzas, K., 2012. Productivity and quality changes in Greek public
hospitals. Operational research, 12(1), pp.69-81.
Ngangkham, M., Ratha, S.K., Prasanna, R., Saxena, A.K., Dhar, D.W., Sarika, C. and Prasad,
R.B.N., 2012. Biochemical modulation of growth, lipid quality and productivity in mixotrophic
cultures of Chlorella sorokiniana. SpringerPlus, 1(1), p.33.
De Nicola, A., Gitto, S. and Mancuso, P., 2013. Airport quality and productivity changes: A
Malmquist index decomposition assessment. Transportation Research Part E: Logistics and
Transportation Review, 58, pp.67-75.
Salvendy, G., 2012. Handbook of human factors and ergonomics. John Wiley & Sons.
Fernández-Sanz, L. and Misra, S., 2011, June. Influence of human factors in software quality and
productivity. In International Conference on Computational Science and Its Applications (pp.
257-269). Springer, Berlin, Heidelberg.
Das, A., Lal, R., Patel, D.P., Idapuganti, R.G., Layek, J., Ngachan, S.V., Ghosh, P.K., Bordoloi,
J. and Kumar, M., 2014. Effects of tillage and biomass on soil quality and productivity of
lowland rice cultivation by small scale farmers in North Eastern India. Soil and Tillage
Research, 143, pp.50-58.
Srinivasu, R., Reddy, G.S. and Rikkula, S.R., 2011. Utility of quality control tools and statistical
process control to improve the productivity and quality in an industry. International Journal of
Reviews in Computing, 5, pp.15-20.
Karagiannis, R. and Velentzas, K., 2012. Productivity and quality changes in Greek public
hospitals. Operational research, 12(1), pp.69-81.
Secure Best Marks with AI Grader
Need help grading? Try our AI Grader for instant feedback on your assignments.

Supply chain
Islam, M.M., Khan, A.M. and Khan, M.M.R., 2013. Minimization of reworks in quality and
productivity improvement in the apparel industry. International Journal of Engineering, 1(4),
pp.2305-8269.
Engels, T.C., Goos, P., Dexters, N. and Spruyt, E.H., 2013. Group size, h-index, and efficiency
in publishing in top journals explain expert panel assessments of research group quality and
productivity. Research Evaluation, 22(4), pp.224-236.
Islam, M.M., Khan, A.M. and Khan, M.M.R., 2013. Minimization of reworks in quality and
productivity improvement in the apparel industry. International Journal of Engineering, 1(4),
pp.2305-8269.
Engels, T.C., Goos, P., Dexters, N. and Spruyt, E.H., 2013. Group size, h-index, and efficiency
in publishing in top journals explain expert panel assessments of research group quality and
productivity. Research Evaluation, 22(4), pp.224-236.
1 out of 11
Related Documents

Your All-in-One AI-Powered Toolkit for Academic Success.
+13062052269
info@desklib.com
Available 24*7 on WhatsApp / Email
Unlock your academic potential
© 2024 | Zucol Services PVT LTD | All rights reserved.