Implementation, Development, and Impact of TQM System at Toyota Motors
VerifiedAdded on 2020/01/15
|11
|3415
|181
Report
AI Summary
This report provides a detailed analysis of Toyota's Total Quality Management (TQM) system, examining its implementation, development, and impact on the company's operations and performance. It begins with an introduction to TQM and then outlines the specific TQM system employed by Toyota, highlighting key elements such as the Deming cycle and lean manufacturing. The report critically analyzes the implementation and development of the TQM system, discussing the evolution of quality control practices within Toyota, including the adoption of statistical methods, creative idea suggestion systems, and Just-in-Time principles. It then assesses the success of the TQM implementation, demonstrating its impact on customer satisfaction, cost reduction, and employee productivity. The report describes the impact of the TQM system on Toyota before its introduction, during its development, and after implementation, including the shift from a focus on inspection to a focus on process improvement. The report concludes with recommendations for continuous improvement based on the principles of TQM.
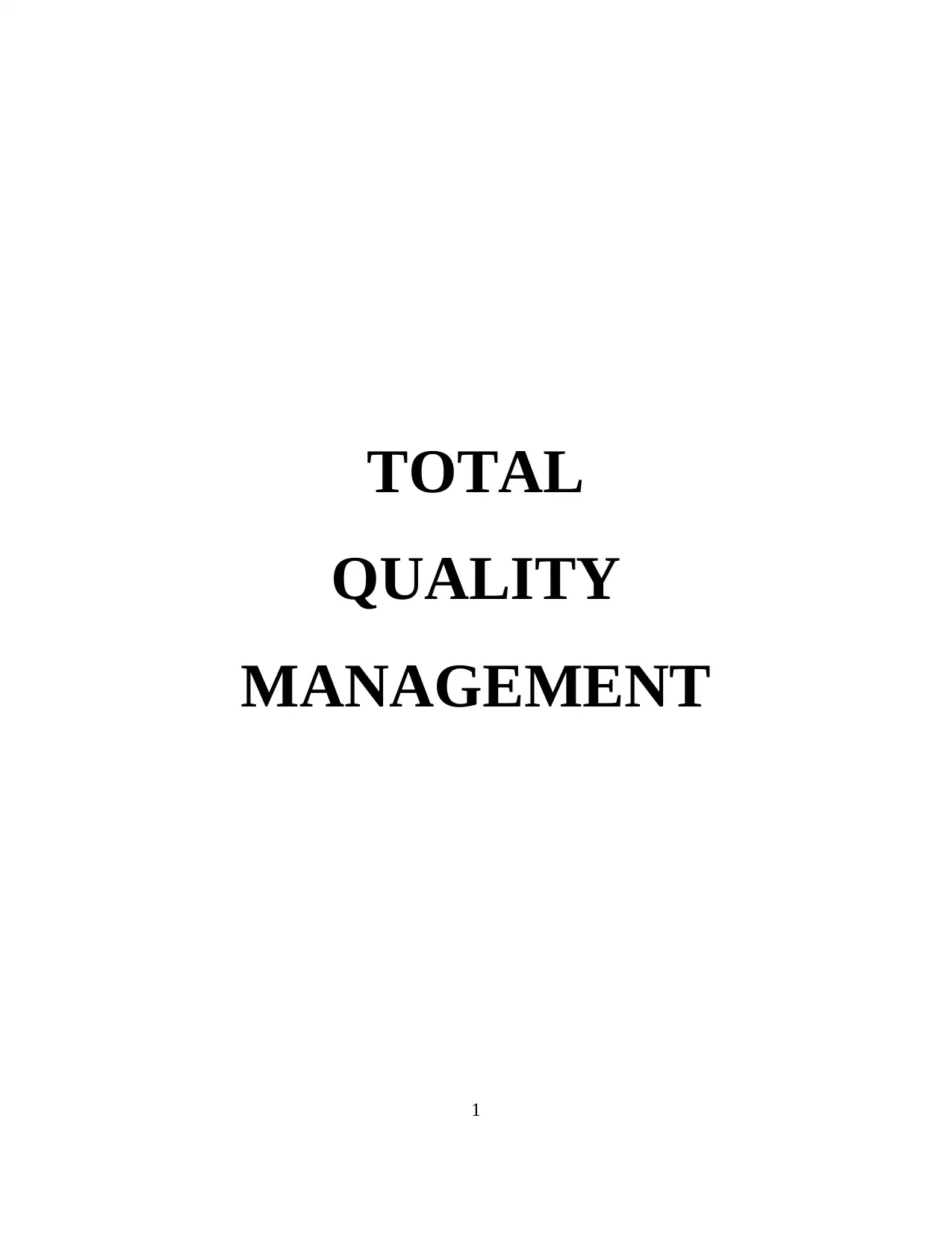
TOTAL
QUALITY
MANAGEMENT
1
QUALITY
MANAGEMENT
1
Paraphrase This Document
Need a fresh take? Get an instant paraphrase of this document with our AI Paraphraser
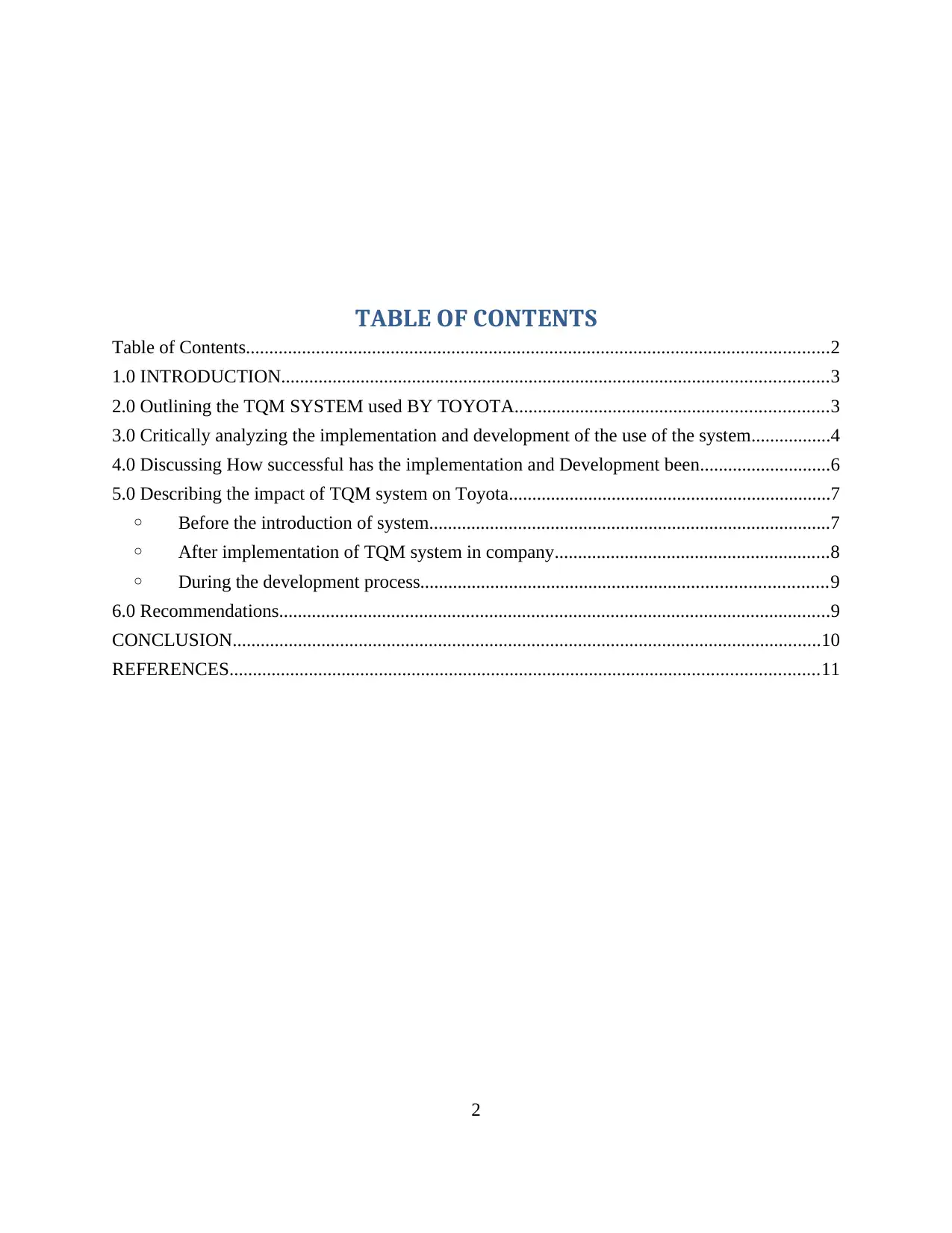
TABLE OF CONTENTS
Table of Contents.............................................................................................................................2
1.0 INTRODUCTION.....................................................................................................................3
2.0 Outlining the TQM SYSTEM used BY TOYOTA...................................................................3
3.0 Critically analyzing the implementation and development of the use of the system.................4
4.0 Discussing How successful has the implementation and Development been............................6
5.0 Describing the impact of TQM system on Toyota.....................................................................7
◦ Before the introduction of system......................................................................................7
◦ After implementation of TQM system in company...........................................................8
◦ During the development process.......................................................................................9
6.0 Recommendations......................................................................................................................9
CONCLUSION..............................................................................................................................10
REFERENCES..............................................................................................................................11
2
Table of Contents.............................................................................................................................2
1.0 INTRODUCTION.....................................................................................................................3
2.0 Outlining the TQM SYSTEM used BY TOYOTA...................................................................3
3.0 Critically analyzing the implementation and development of the use of the system.................4
4.0 Discussing How successful has the implementation and Development been............................6
5.0 Describing the impact of TQM system on Toyota.....................................................................7
◦ Before the introduction of system......................................................................................7
◦ After implementation of TQM system in company...........................................................8
◦ During the development process.......................................................................................9
6.0 Recommendations......................................................................................................................9
CONCLUSION..............................................................................................................................10
REFERENCES..............................................................................................................................11
2
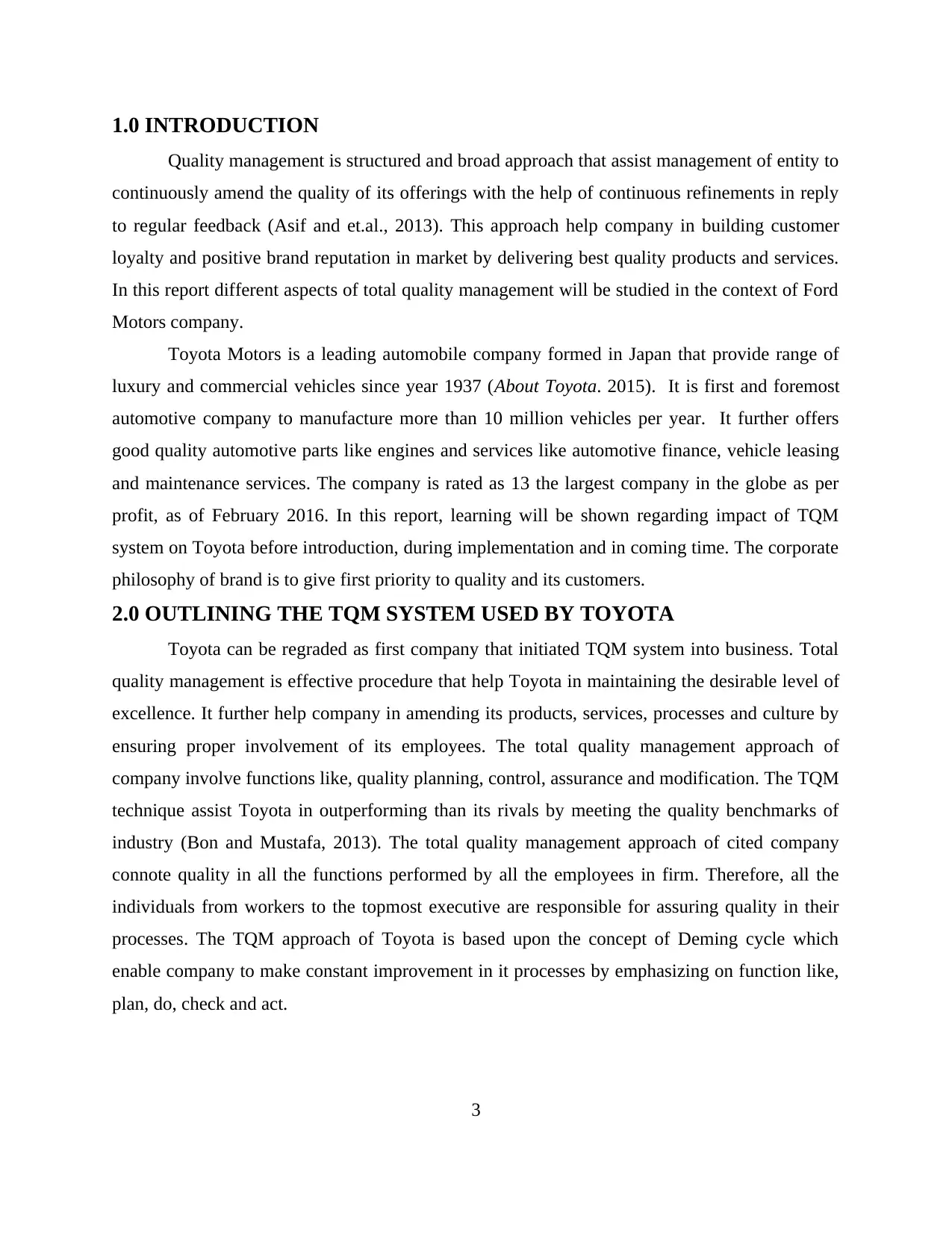
1.0 INTRODUCTION
Quality management is structured and broad approach that assist management of entity to
continuously amend the quality of its offerings with the help of continuous refinements in reply
to regular feedback (Asif and et.al., 2013). This approach help company in building customer
loyalty and positive brand reputation in market by delivering best quality products and services.
In this report different aspects of total quality management will be studied in the context of Ford
Motors company.
Toyota Motors is a leading automobile company formed in Japan that provide range of
luxury and commercial vehicles since year 1937 (About Toyota. 2015). It is first and foremost
automotive company to manufacture more than 10 million vehicles per year. It further offers
good quality automotive parts like engines and services like automotive finance, vehicle leasing
and maintenance services. The company is rated as 13 the largest company in the globe as per
profit, as of February 2016. In this report, learning will be shown regarding impact of TQM
system on Toyota before introduction, during implementation and in coming time. The corporate
philosophy of brand is to give first priority to quality and its customers.
2.0 OUTLINING THE TQM SYSTEM USED BY TOYOTA
Toyota can be regraded as first company that initiated TQM system into business. Total
quality management is effective procedure that help Toyota in maintaining the desirable level of
excellence. It further help company in amending its products, services, processes and culture by
ensuring proper involvement of its employees. The total quality management approach of
company involve functions like, quality planning, control, assurance and modification. The TQM
technique assist Toyota in outperforming than its rivals by meeting the quality benchmarks of
industry (Bon and Mustafa, 2013). The total quality management approach of cited company
connote quality in all the functions performed by all the employees in firm. Therefore, all the
individuals from workers to the topmost executive are responsible for assuring quality in their
processes. The TQM approach of Toyota is based upon the concept of Deming cycle which
enable company to make constant improvement in it processes by emphasizing on function like,
plan, do, check and act.
3
Quality management is structured and broad approach that assist management of entity to
continuously amend the quality of its offerings with the help of continuous refinements in reply
to regular feedback (Asif and et.al., 2013). This approach help company in building customer
loyalty and positive brand reputation in market by delivering best quality products and services.
In this report different aspects of total quality management will be studied in the context of Ford
Motors company.
Toyota Motors is a leading automobile company formed in Japan that provide range of
luxury and commercial vehicles since year 1937 (About Toyota. 2015). It is first and foremost
automotive company to manufacture more than 10 million vehicles per year. It further offers
good quality automotive parts like engines and services like automotive finance, vehicle leasing
and maintenance services. The company is rated as 13 the largest company in the globe as per
profit, as of February 2016. In this report, learning will be shown regarding impact of TQM
system on Toyota before introduction, during implementation and in coming time. The corporate
philosophy of brand is to give first priority to quality and its customers.
2.0 OUTLINING THE TQM SYSTEM USED BY TOYOTA
Toyota can be regraded as first company that initiated TQM system into business. Total
quality management is effective procedure that help Toyota in maintaining the desirable level of
excellence. It further help company in amending its products, services, processes and culture by
ensuring proper involvement of its employees. The total quality management approach of
company involve functions like, quality planning, control, assurance and modification. The TQM
technique assist Toyota in outperforming than its rivals by meeting the quality benchmarks of
industry (Bon and Mustafa, 2013). The total quality management approach of cited company
connote quality in all the functions performed by all the employees in firm. Therefore, all the
individuals from workers to the topmost executive are responsible for assuring quality in their
processes. The TQM approach of Toyota is based upon the concept of Deming cycle which
enable company to make constant improvement in it processes by emphasizing on function like,
plan, do, check and act.
3
⊘ This is a preview!⊘
Do you want full access?
Subscribe today to unlock all pages.

Trusted by 1+ million students worldwide
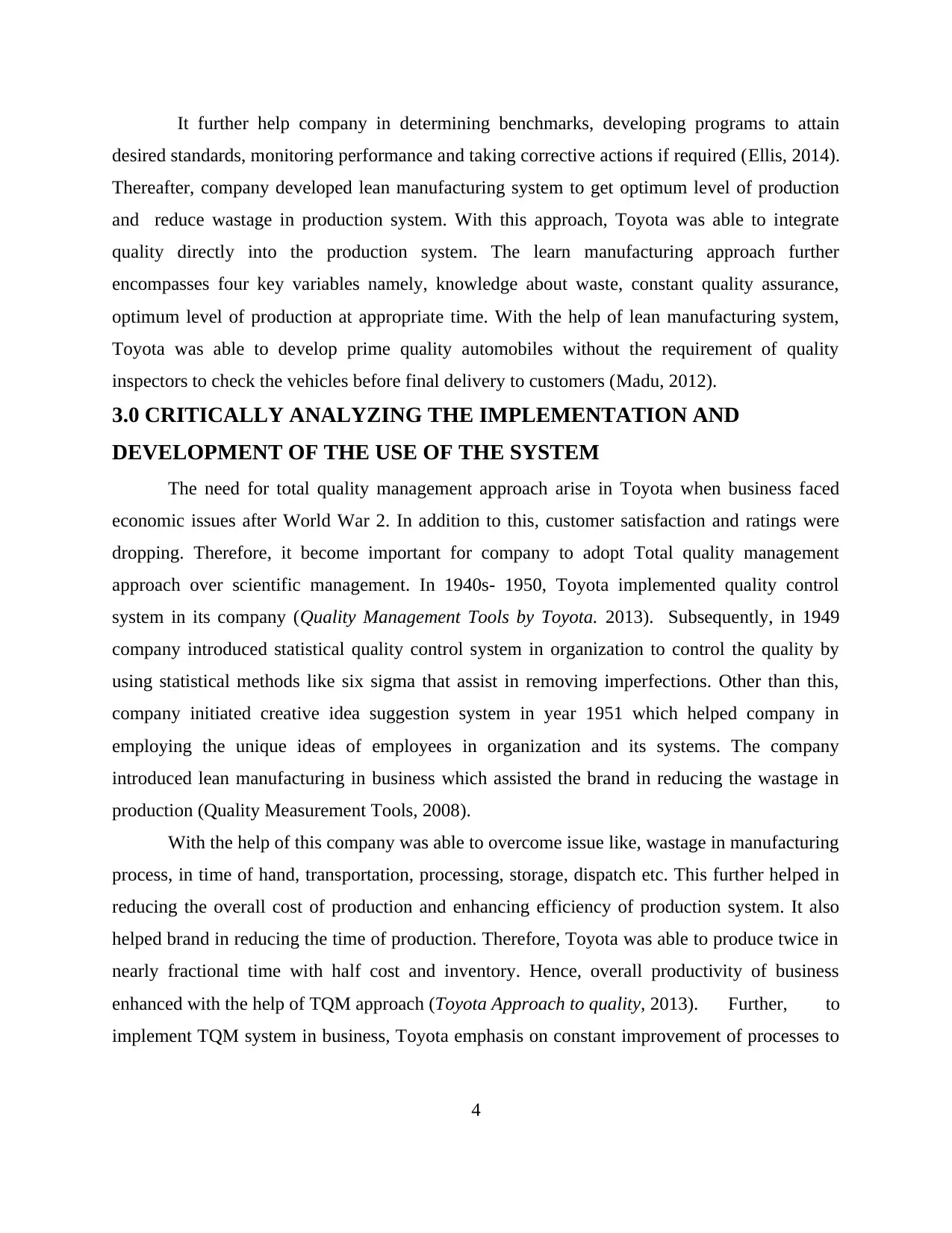
It further help company in determining benchmarks, developing programs to attain
desired standards, monitoring performance and taking corrective actions if required (Ellis, 2014).
Thereafter, company developed lean manufacturing system to get optimum level of production
and reduce wastage in production system. With this approach, Toyota was able to integrate
quality directly into the production system. The learn manufacturing approach further
encompasses four key variables namely, knowledge about waste, constant quality assurance,
optimum level of production at appropriate time. With the help of lean manufacturing system,
Toyota was able to develop prime quality automobiles without the requirement of quality
inspectors to check the vehicles before final delivery to customers (Madu, 2012).
3.0 CRITICALLY ANALYZING THE IMPLEMENTATION AND
DEVELOPMENT OF THE USE OF THE SYSTEM
The need for total quality management approach arise in Toyota when business faced
economic issues after World War 2. In addition to this, customer satisfaction and ratings were
dropping. Therefore, it become important for company to adopt Total quality management
approach over scientific management. In 1940s- 1950, Toyota implemented quality control
system in its company (Quality Management Tools by Toyota. 2013). Subsequently, in 1949
company introduced statistical quality control system in organization to control the quality by
using statistical methods like six sigma that assist in removing imperfections. Other than this,
company initiated creative idea suggestion system in year 1951 which helped company in
employing the unique ideas of employees in organization and its systems. The company
introduced lean manufacturing in business which assisted the brand in reducing the wastage in
production (Quality Measurement Tools, 2008).
With the help of this company was able to overcome issue like, wastage in manufacturing
process, in time of hand, transportation, processing, storage, dispatch etc. This further helped in
reducing the overall cost of production and enhancing efficiency of production system. It also
helped brand in reducing the time of production. Therefore, Toyota was able to produce twice in
nearly fractional time with half cost and inventory. Hence, overall productivity of business
enhanced with the help of TQM approach (Toyota Approach to quality, 2013). Further, to
implement TQM system in business, Toyota emphasis on constant improvement of processes to
4
desired standards, monitoring performance and taking corrective actions if required (Ellis, 2014).
Thereafter, company developed lean manufacturing system to get optimum level of production
and reduce wastage in production system. With this approach, Toyota was able to integrate
quality directly into the production system. The learn manufacturing approach further
encompasses four key variables namely, knowledge about waste, constant quality assurance,
optimum level of production at appropriate time. With the help of lean manufacturing system,
Toyota was able to develop prime quality automobiles without the requirement of quality
inspectors to check the vehicles before final delivery to customers (Madu, 2012).
3.0 CRITICALLY ANALYZING THE IMPLEMENTATION AND
DEVELOPMENT OF THE USE OF THE SYSTEM
The need for total quality management approach arise in Toyota when business faced
economic issues after World War 2. In addition to this, customer satisfaction and ratings were
dropping. Therefore, it become important for company to adopt Total quality management
approach over scientific management. In 1940s- 1950, Toyota implemented quality control
system in its company (Quality Management Tools by Toyota. 2013). Subsequently, in 1949
company introduced statistical quality control system in organization to control the quality by
using statistical methods like six sigma that assist in removing imperfections. Other than this,
company initiated creative idea suggestion system in year 1951 which helped company in
employing the unique ideas of employees in organization and its systems. The company
introduced lean manufacturing in business which assisted the brand in reducing the wastage in
production (Quality Measurement Tools, 2008).
With the help of this company was able to overcome issue like, wastage in manufacturing
process, in time of hand, transportation, processing, storage, dispatch etc. This further helped in
reducing the overall cost of production and enhancing efficiency of production system. It also
helped brand in reducing the time of production. Therefore, Toyota was able to produce twice in
nearly fractional time with half cost and inventory. Hence, overall productivity of business
enhanced with the help of TQM approach (Toyota Approach to quality, 2013). Further, to
implement TQM system in business, Toyota emphasis on constant improvement of processes to
4
Paraphrase This Document
Need a fresh take? Get an instant paraphrase of this document with our AI Paraphraser
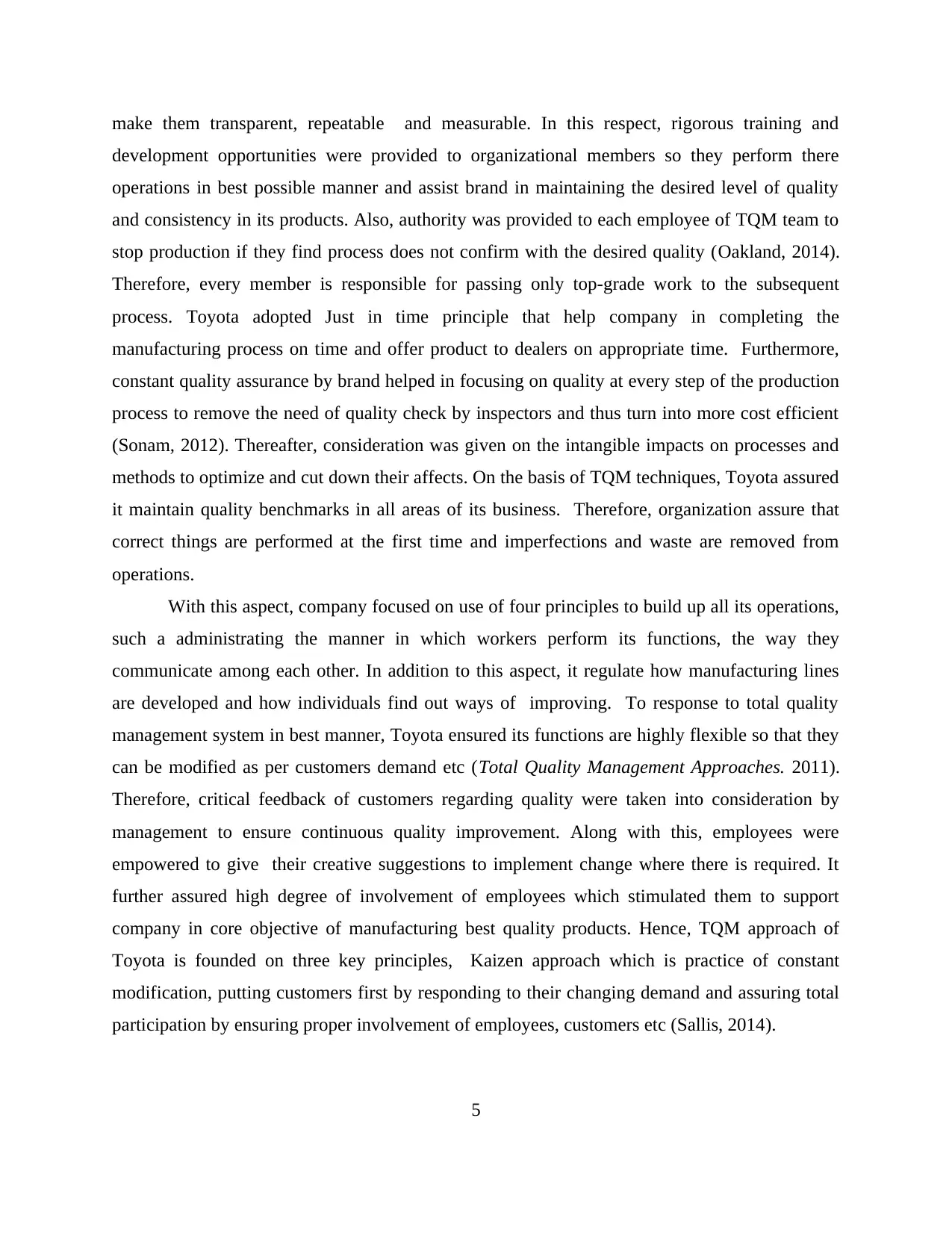
make them transparent, repeatable and measurable. In this respect, rigorous training and
development opportunities were provided to organizational members so they perform there
operations in best possible manner and assist brand in maintaining the desired level of quality
and consistency in its products. Also, authority was provided to each employee of TQM team to
stop production if they find process does not confirm with the desired quality (Oakland, 2014).
Therefore, every member is responsible for passing only top-grade work to the subsequent
process. Toyota adopted Just in time principle that help company in completing the
manufacturing process on time and offer product to dealers on appropriate time. Furthermore,
constant quality assurance by brand helped in focusing on quality at every step of the production
process to remove the need of quality check by inspectors and thus turn into more cost efficient
(Sonam, 2012). Thereafter, consideration was given on the intangible impacts on processes and
methods to optimize and cut down their affects. On the basis of TQM techniques, Toyota assured
it maintain quality benchmarks in all areas of its business. Therefore, organization assure that
correct things are performed at the first time and imperfections and waste are removed from
operations.
With this aspect, company focused on use of four principles to build up all its operations,
such a administrating the manner in which workers perform its functions, the way they
communicate among each other. In addition to this aspect, it regulate how manufacturing lines
are developed and how individuals find out ways of improving. To response to total quality
management system in best manner, Toyota ensured its functions are highly flexible so that they
can be modified as per customers demand etc (Total Quality Management Approaches. 2011).
Therefore, critical feedback of customers regarding quality were taken into consideration by
management to ensure continuous quality improvement. Along with this, employees were
empowered to give their creative suggestions to implement change where there is required. It
further assured high degree of involvement of employees which stimulated them to support
company in core objective of manufacturing best quality products. Hence, TQM approach of
Toyota is founded on three key principles, Kaizen approach which is practice of constant
modification, putting customers first by responding to their changing demand and assuring total
participation by ensuring proper involvement of employees, customers etc (Sallis, 2014).
5
development opportunities were provided to organizational members so they perform there
operations in best possible manner and assist brand in maintaining the desired level of quality
and consistency in its products. Also, authority was provided to each employee of TQM team to
stop production if they find process does not confirm with the desired quality (Oakland, 2014).
Therefore, every member is responsible for passing only top-grade work to the subsequent
process. Toyota adopted Just in time principle that help company in completing the
manufacturing process on time and offer product to dealers on appropriate time. Furthermore,
constant quality assurance by brand helped in focusing on quality at every step of the production
process to remove the need of quality check by inspectors and thus turn into more cost efficient
(Sonam, 2012). Thereafter, consideration was given on the intangible impacts on processes and
methods to optimize and cut down their affects. On the basis of TQM techniques, Toyota assured
it maintain quality benchmarks in all areas of its business. Therefore, organization assure that
correct things are performed at the first time and imperfections and waste are removed from
operations.
With this aspect, company focused on use of four principles to build up all its operations,
such a administrating the manner in which workers perform its functions, the way they
communicate among each other. In addition to this aspect, it regulate how manufacturing lines
are developed and how individuals find out ways of improving. To response to total quality
management system in best manner, Toyota ensured its functions are highly flexible so that they
can be modified as per customers demand etc (Total Quality Management Approaches. 2011).
Therefore, critical feedback of customers regarding quality were taken into consideration by
management to ensure continuous quality improvement. Along with this, employees were
empowered to give their creative suggestions to implement change where there is required. It
further assured high degree of involvement of employees which stimulated them to support
company in core objective of manufacturing best quality products. Hence, TQM approach of
Toyota is founded on three key principles, Kaizen approach which is practice of constant
modification, putting customers first by responding to their changing demand and assuring total
participation by ensuring proper involvement of employees, customers etc (Sallis, 2014).
5
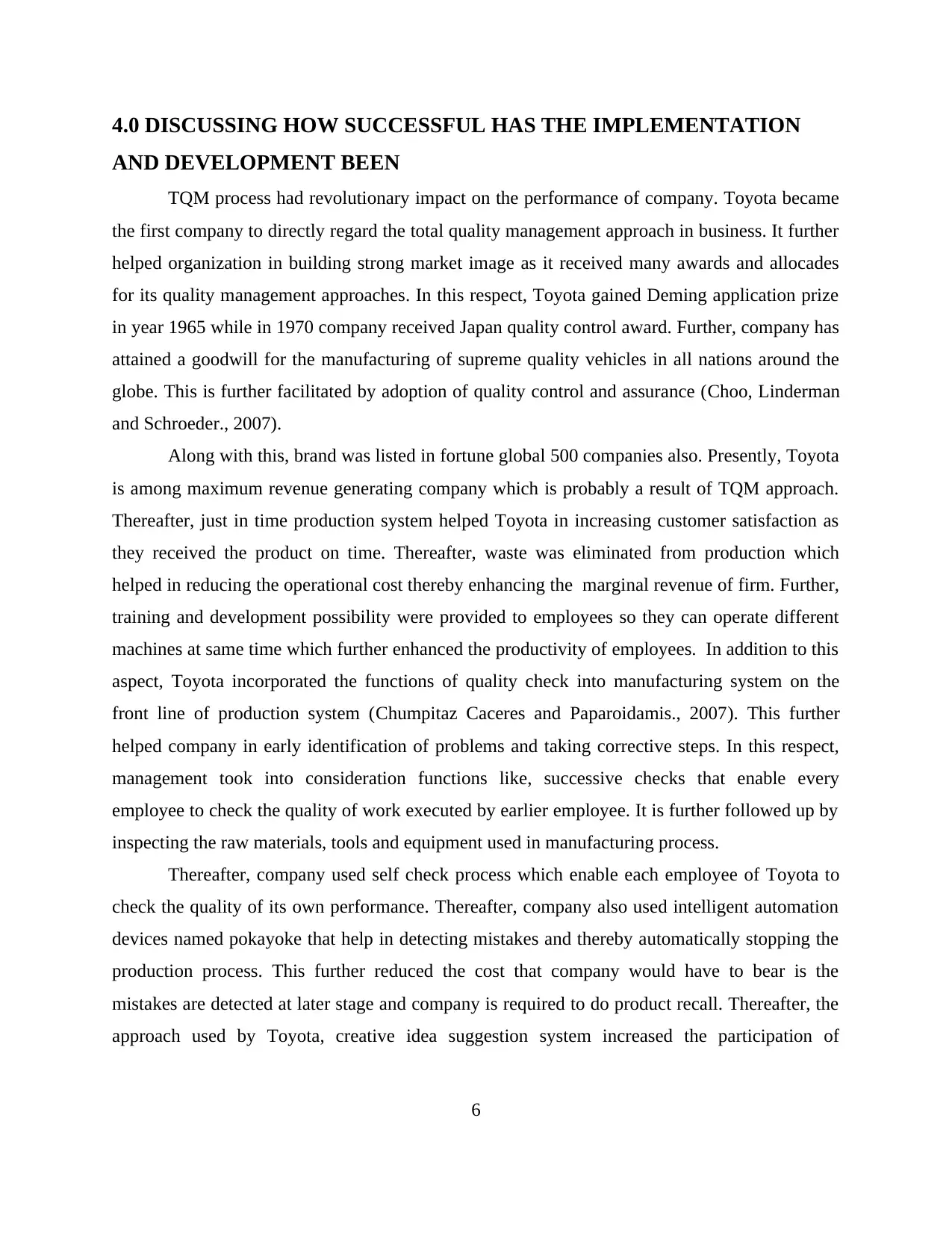
4.0 DISCUSSING HOW SUCCESSFUL HAS THE IMPLEMENTATION
AND DEVELOPMENT BEEN
TQM process had revolutionary impact on the performance of company. Toyota became
the first company to directly regard the total quality management approach in business. It further
helped organization in building strong market image as it received many awards and allocades
for its quality management approaches. In this respect, Toyota gained Deming application prize
in year 1965 while in 1970 company received Japan quality control award. Further, company has
attained a goodwill for the manufacturing of supreme quality vehicles in all nations around the
globe. This is further facilitated by adoption of quality control and assurance (Choo, Linderman
and Schroeder., 2007).
Along with this, brand was listed in fortune global 500 companies also. Presently, Toyota
is among maximum revenue generating company which is probably a result of TQM approach.
Thereafter, just in time production system helped Toyota in increasing customer satisfaction as
they received the product on time. Thereafter, waste was eliminated from production which
helped in reducing the operational cost thereby enhancing the marginal revenue of firm. Further,
training and development possibility were provided to employees so they can operate different
machines at same time which further enhanced the productivity of employees. In addition to this
aspect, Toyota incorporated the functions of quality check into manufacturing system on the
front line of production system (Chumpitaz Caceres and Paparoidamis., 2007). This further
helped company in early identification of problems and taking corrective steps. In this respect,
management took into consideration functions like, successive checks that enable every
employee to check the quality of work executed by earlier employee. It is further followed up by
inspecting the raw materials, tools and equipment used in manufacturing process.
Thereafter, company used self check process which enable each employee of Toyota to
check the quality of its own performance. Thereafter, company also used intelligent automation
devices named pokayoke that help in detecting mistakes and thereby automatically stopping the
production process. This further reduced the cost that company would have to bear is the
mistakes are detected at later stage and company is required to do product recall. Thereafter, the
approach used by Toyota, creative idea suggestion system increased the participation of
6
AND DEVELOPMENT BEEN
TQM process had revolutionary impact on the performance of company. Toyota became
the first company to directly regard the total quality management approach in business. It further
helped organization in building strong market image as it received many awards and allocades
for its quality management approaches. In this respect, Toyota gained Deming application prize
in year 1965 while in 1970 company received Japan quality control award. Further, company has
attained a goodwill for the manufacturing of supreme quality vehicles in all nations around the
globe. This is further facilitated by adoption of quality control and assurance (Choo, Linderman
and Schroeder., 2007).
Along with this, brand was listed in fortune global 500 companies also. Presently, Toyota
is among maximum revenue generating company which is probably a result of TQM approach.
Thereafter, just in time production system helped Toyota in increasing customer satisfaction as
they received the product on time. Thereafter, waste was eliminated from production which
helped in reducing the operational cost thereby enhancing the marginal revenue of firm. Further,
training and development possibility were provided to employees so they can operate different
machines at same time which further enhanced the productivity of employees. In addition to this
aspect, Toyota incorporated the functions of quality check into manufacturing system on the
front line of production system (Chumpitaz Caceres and Paparoidamis., 2007). This further
helped company in early identification of problems and taking corrective steps. In this respect,
management took into consideration functions like, successive checks that enable every
employee to check the quality of work executed by earlier employee. It is further followed up by
inspecting the raw materials, tools and equipment used in manufacturing process.
Thereafter, company used self check process which enable each employee of Toyota to
check the quality of its own performance. Thereafter, company also used intelligent automation
devices named pokayoke that help in detecting mistakes and thereby automatically stopping the
production process. This further reduced the cost that company would have to bear is the
mistakes are detected at later stage and company is required to do product recall. Thereafter, the
approach used by Toyota, creative idea suggestion system increased the participation of
6
⊘ This is a preview!⊘
Do you want full access?
Subscribe today to unlock all pages.

Trusted by 1+ million students worldwide
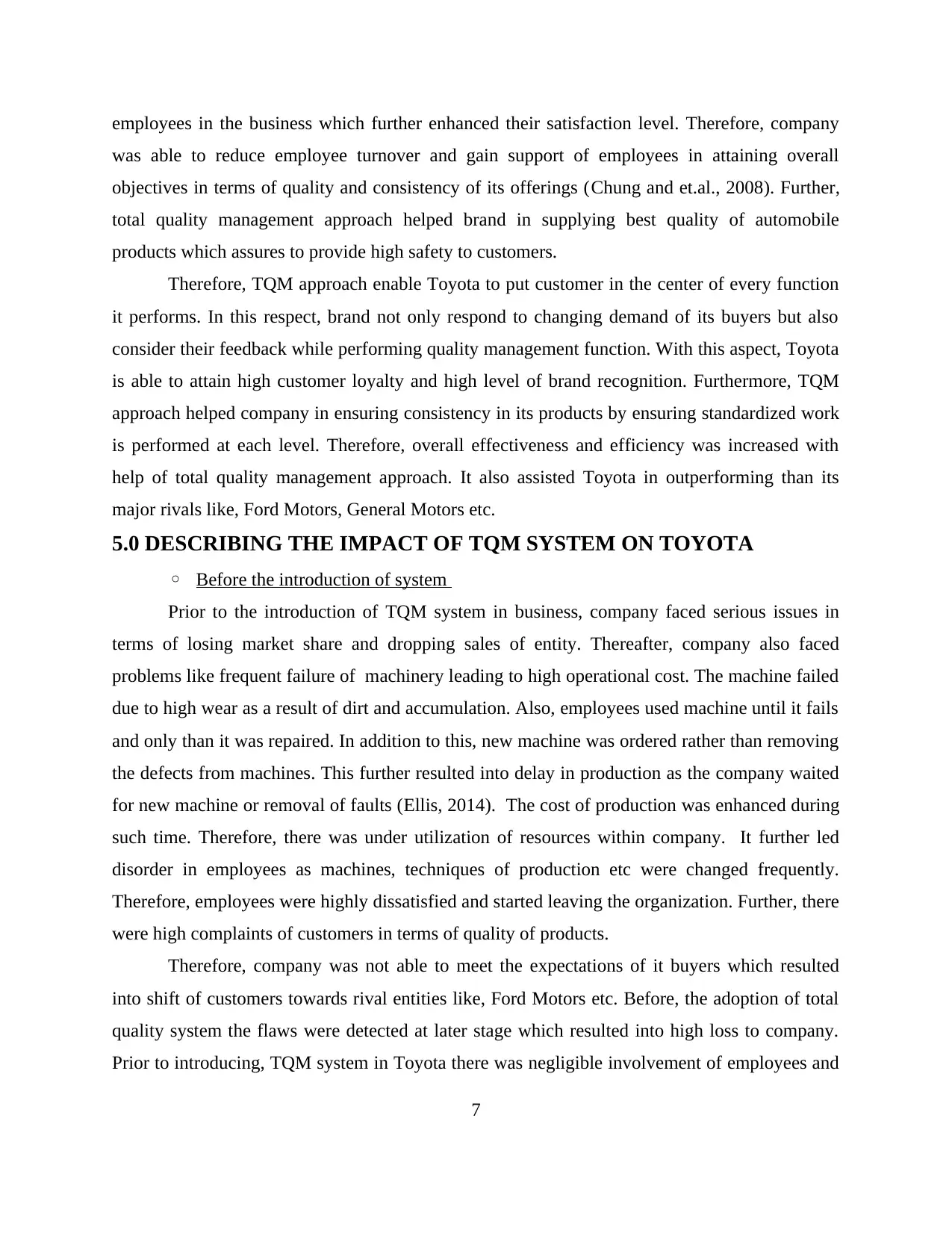
employees in the business which further enhanced their satisfaction level. Therefore, company
was able to reduce employee turnover and gain support of employees in attaining overall
objectives in terms of quality and consistency of its offerings (Chung and et.al., 2008). Further,
total quality management approach helped brand in supplying best quality of automobile
products which assures to provide high safety to customers.
Therefore, TQM approach enable Toyota to put customer in the center of every function
it performs. In this respect, brand not only respond to changing demand of its buyers but also
consider their feedback while performing quality management function. With this aspect, Toyota
is able to attain high customer loyalty and high level of brand recognition. Furthermore, TQM
approach helped company in ensuring consistency in its products by ensuring standardized work
is performed at each level. Therefore, overall effectiveness and efficiency was increased with
help of total quality management approach. It also assisted Toyota in outperforming than its
major rivals like, Ford Motors, General Motors etc.
5.0 DESCRIBING THE IMPACT OF TQM SYSTEM ON TOYOTA
◦ Before the introduction of system
Prior to the introduction of TQM system in business, company faced serious issues in
terms of losing market share and dropping sales of entity. Thereafter, company also faced
problems like frequent failure of machinery leading to high operational cost. The machine failed
due to high wear as a result of dirt and accumulation. Also, employees used machine until it fails
and only than it was repaired. In addition to this, new machine was ordered rather than removing
the defects from machines. This further resulted into delay in production as the company waited
for new machine or removal of faults (Ellis, 2014). The cost of production was enhanced during
such time. Therefore, there was under utilization of resources within company. It further led
disorder in employees as machines, techniques of production etc were changed frequently.
Therefore, employees were highly dissatisfied and started leaving the organization. Further, there
were high complaints of customers in terms of quality of products.
Therefore, company was not able to meet the expectations of it buyers which resulted
into shift of customers towards rival entities like, Ford Motors etc. Before, the adoption of total
quality system the flaws were detected at later stage which resulted into high loss to company.
Prior to introducing, TQM system in Toyota there was negligible involvement of employees and
7
was able to reduce employee turnover and gain support of employees in attaining overall
objectives in terms of quality and consistency of its offerings (Chung and et.al., 2008). Further,
total quality management approach helped brand in supplying best quality of automobile
products which assures to provide high safety to customers.
Therefore, TQM approach enable Toyota to put customer in the center of every function
it performs. In this respect, brand not only respond to changing demand of its buyers but also
consider their feedback while performing quality management function. With this aspect, Toyota
is able to attain high customer loyalty and high level of brand recognition. Furthermore, TQM
approach helped company in ensuring consistency in its products by ensuring standardized work
is performed at each level. Therefore, overall effectiveness and efficiency was increased with
help of total quality management approach. It also assisted Toyota in outperforming than its
major rivals like, Ford Motors, General Motors etc.
5.0 DESCRIBING THE IMPACT OF TQM SYSTEM ON TOYOTA
◦ Before the introduction of system
Prior to the introduction of TQM system in business, company faced serious issues in
terms of losing market share and dropping sales of entity. Thereafter, company also faced
problems like frequent failure of machinery leading to high operational cost. The machine failed
due to high wear as a result of dirt and accumulation. Also, employees used machine until it fails
and only than it was repaired. In addition to this, new machine was ordered rather than removing
the defects from machines. This further resulted into delay in production as the company waited
for new machine or removal of faults (Ellis, 2014). The cost of production was enhanced during
such time. Therefore, there was under utilization of resources within company. It further led
disorder in employees as machines, techniques of production etc were changed frequently.
Therefore, employees were highly dissatisfied and started leaving the organization. Further, there
were high complaints of customers in terms of quality of products.
Therefore, company was not able to meet the expectations of it buyers which resulted
into shift of customers towards rival entities like, Ford Motors etc. Before, the adoption of total
quality system the flaws were detected at later stage which resulted into high loss to company.
Prior to introducing, TQM system in Toyota there was negligible involvement of employees and
7
Paraphrase This Document
Need a fresh take? Get an instant paraphrase of this document with our AI Paraphraser
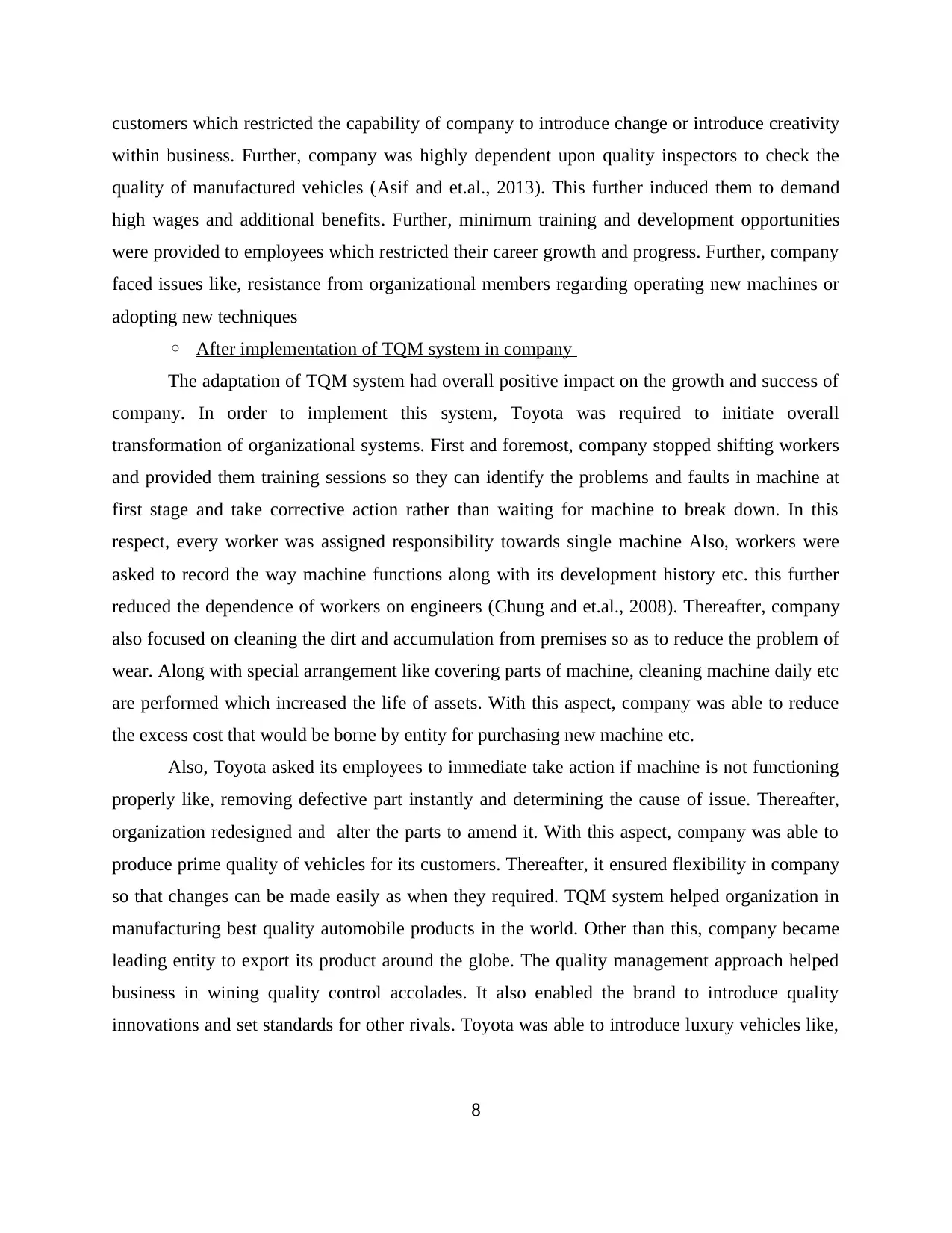
customers which restricted the capability of company to introduce change or introduce creativity
within business. Further, company was highly dependent upon quality inspectors to check the
quality of manufactured vehicles (Asif and et.al., 2013). This further induced them to demand
high wages and additional benefits. Further, minimum training and development opportunities
were provided to employees which restricted their career growth and progress. Further, company
faced issues like, resistance from organizational members regarding operating new machines or
adopting new techniques
◦ After implementation of TQM system in company
The adaptation of TQM system had overall positive impact on the growth and success of
company. In order to implement this system, Toyota was required to initiate overall
transformation of organizational systems. First and foremost, company stopped shifting workers
and provided them training sessions so they can identify the problems and faults in machine at
first stage and take corrective action rather than waiting for machine to break down. In this
respect, every worker was assigned responsibility towards single machine Also, workers were
asked to record the way machine functions along with its development history etc. this further
reduced the dependence of workers on engineers (Chung and et.al., 2008). Thereafter, company
also focused on cleaning the dirt and accumulation from premises so as to reduce the problem of
wear. Along with special arrangement like covering parts of machine, cleaning machine daily etc
are performed which increased the life of assets. With this aspect, company was able to reduce
the excess cost that would be borne by entity for purchasing new machine etc.
Also, Toyota asked its employees to immediate take action if machine is not functioning
properly like, removing defective part instantly and determining the cause of issue. Thereafter,
organization redesigned and alter the parts to amend it. With this aspect, company was able to
produce prime quality of vehicles for its customers. Thereafter, it ensured flexibility in company
so that changes can be made easily as when they required. TQM system helped organization in
manufacturing best quality automobile products in the world. Other than this, company became
leading entity to export its product around the globe. The quality management approach helped
business in wining quality control accolades. It also enabled the brand to introduce quality
innovations and set standards for other rivals. Toyota was able to introduce luxury vehicles like,
8
within business. Further, company was highly dependent upon quality inspectors to check the
quality of manufactured vehicles (Asif and et.al., 2013). This further induced them to demand
high wages and additional benefits. Further, minimum training and development opportunities
were provided to employees which restricted their career growth and progress. Further, company
faced issues like, resistance from organizational members regarding operating new machines or
adopting new techniques
◦ After implementation of TQM system in company
The adaptation of TQM system had overall positive impact on the growth and success of
company. In order to implement this system, Toyota was required to initiate overall
transformation of organizational systems. First and foremost, company stopped shifting workers
and provided them training sessions so they can identify the problems and faults in machine at
first stage and take corrective action rather than waiting for machine to break down. In this
respect, every worker was assigned responsibility towards single machine Also, workers were
asked to record the way machine functions along with its development history etc. this further
reduced the dependence of workers on engineers (Chung and et.al., 2008). Thereafter, company
also focused on cleaning the dirt and accumulation from premises so as to reduce the problem of
wear. Along with special arrangement like covering parts of machine, cleaning machine daily etc
are performed which increased the life of assets. With this aspect, company was able to reduce
the excess cost that would be borne by entity for purchasing new machine etc.
Also, Toyota asked its employees to immediate take action if machine is not functioning
properly like, removing defective part instantly and determining the cause of issue. Thereafter,
organization redesigned and alter the parts to amend it. With this aspect, company was able to
produce prime quality of vehicles for its customers. Thereafter, it ensured flexibility in company
so that changes can be made easily as when they required. TQM system helped organization in
manufacturing best quality automobile products in the world. Other than this, company became
leading entity to export its product around the globe. The quality management approach helped
business in wining quality control accolades. It also enabled the brand to introduce quality
innovations and set standards for other rivals. Toyota was able to introduce luxury vehicles like,
8
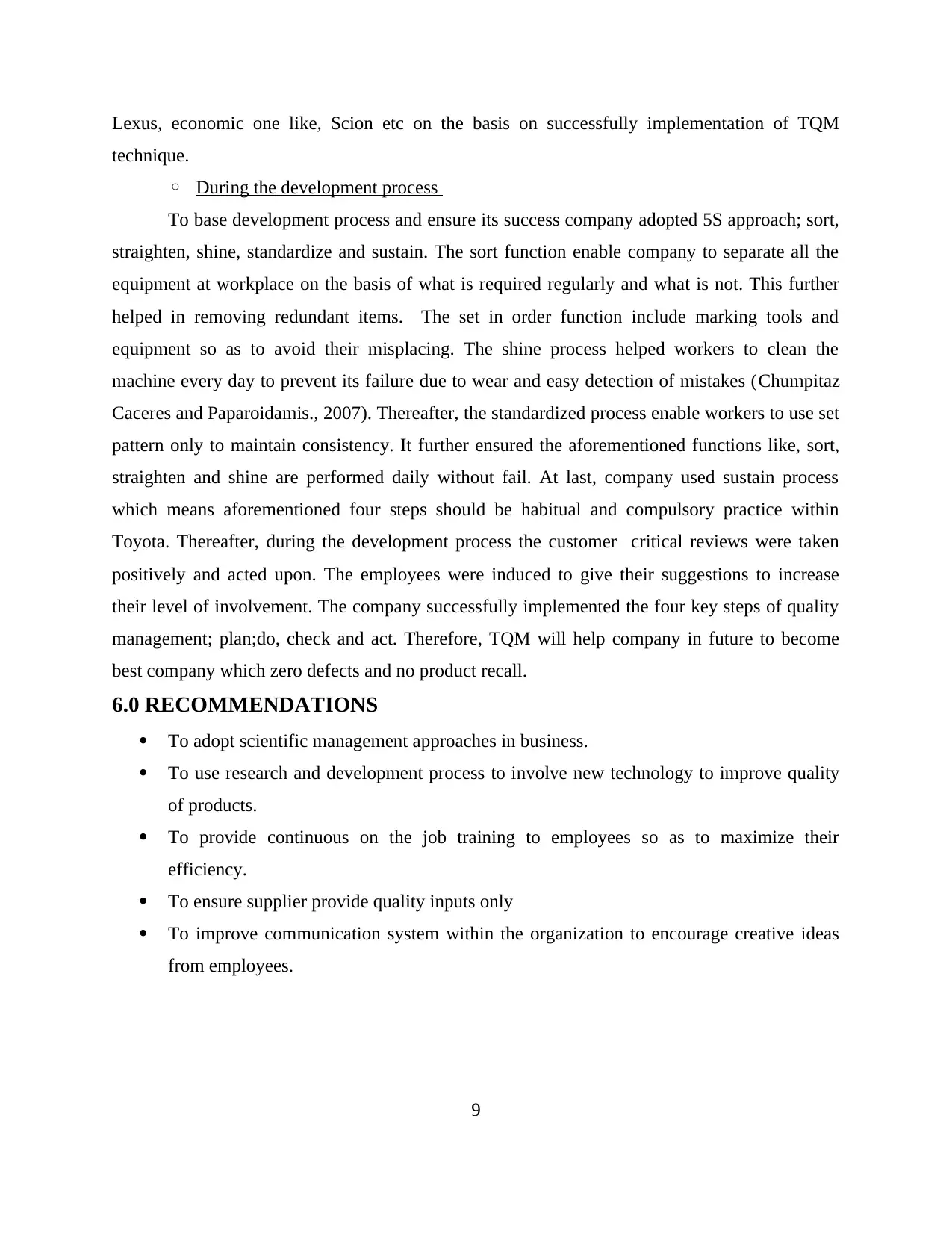
Lexus, economic one like, Scion etc on the basis on successfully implementation of TQM
technique.
◦ During the development process
To base development process and ensure its success company adopted 5S approach; sort,
straighten, shine, standardize and sustain. The sort function enable company to separate all the
equipment at workplace on the basis of what is required regularly and what is not. This further
helped in removing redundant items. The set in order function include marking tools and
equipment so as to avoid their misplacing. The shine process helped workers to clean the
machine every day to prevent its failure due to wear and easy detection of mistakes (Chumpitaz
Caceres and Paparoidamis., 2007). Thereafter, the standardized process enable workers to use set
pattern only to maintain consistency. It further ensured the aforementioned functions like, sort,
straighten and shine are performed daily without fail. At last, company used sustain process
which means aforementioned four steps should be habitual and compulsory practice within
Toyota. Thereafter, during the development process the customer critical reviews were taken
positively and acted upon. The employees were induced to give their suggestions to increase
their level of involvement. The company successfully implemented the four key steps of quality
management; plan;do, check and act. Therefore, TQM will help company in future to become
best company which zero defects and no product recall.
6.0 RECOMMENDATIONS
To adopt scientific management approaches in business.
To use research and development process to involve new technology to improve quality
of products.
To provide continuous on the job training to employees so as to maximize their
efficiency.
To ensure supplier provide quality inputs only
To improve communication system within the organization to encourage creative ideas
from employees.
9
technique.
◦ During the development process
To base development process and ensure its success company adopted 5S approach; sort,
straighten, shine, standardize and sustain. The sort function enable company to separate all the
equipment at workplace on the basis of what is required regularly and what is not. This further
helped in removing redundant items. The set in order function include marking tools and
equipment so as to avoid their misplacing. The shine process helped workers to clean the
machine every day to prevent its failure due to wear and easy detection of mistakes (Chumpitaz
Caceres and Paparoidamis., 2007). Thereafter, the standardized process enable workers to use set
pattern only to maintain consistency. It further ensured the aforementioned functions like, sort,
straighten and shine are performed daily without fail. At last, company used sustain process
which means aforementioned four steps should be habitual and compulsory practice within
Toyota. Thereafter, during the development process the customer critical reviews were taken
positively and acted upon. The employees were induced to give their suggestions to increase
their level of involvement. The company successfully implemented the four key steps of quality
management; plan;do, check and act. Therefore, TQM will help company in future to become
best company which zero defects and no product recall.
6.0 RECOMMENDATIONS
To adopt scientific management approaches in business.
To use research and development process to involve new technology to improve quality
of products.
To provide continuous on the job training to employees so as to maximize their
efficiency.
To ensure supplier provide quality inputs only
To improve communication system within the organization to encourage creative ideas
from employees.
9
⊘ This is a preview!⊘
Do you want full access?
Subscribe today to unlock all pages.

Trusted by 1+ million students worldwide
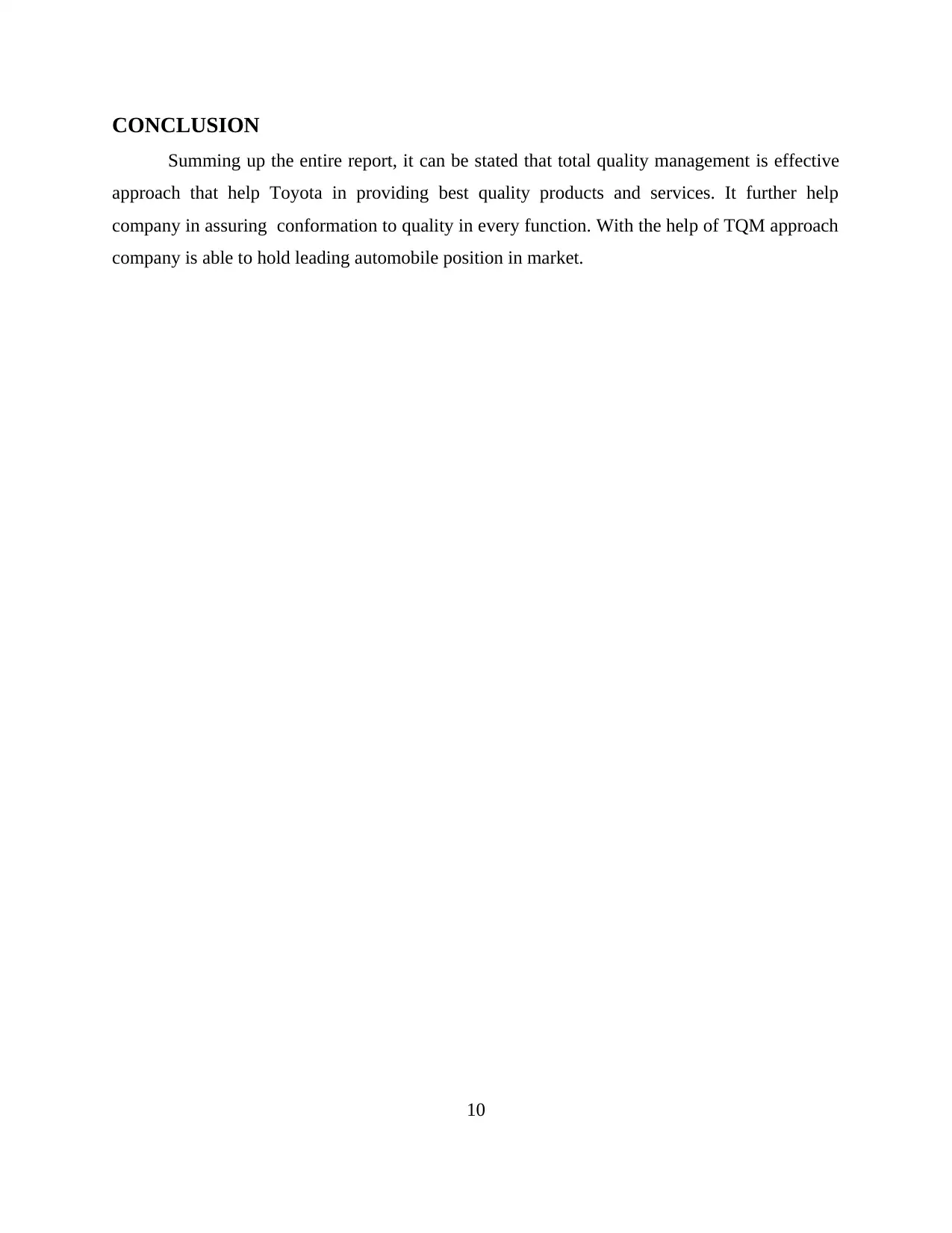
CONCLUSION
Summing up the entire report, it can be stated that total quality management is effective
approach that help Toyota in providing best quality products and services. It further help
company in assuring conformation to quality in every function. With the help of TQM approach
company is able to hold leading automobile position in market.
10
Summing up the entire report, it can be stated that total quality management is effective
approach that help Toyota in providing best quality products and services. It further help
company in assuring conformation to quality in every function. With the help of TQM approach
company is able to hold leading automobile position in market.
10
Paraphrase This Document
Need a fresh take? Get an instant paraphrase of this document with our AI Paraphraser
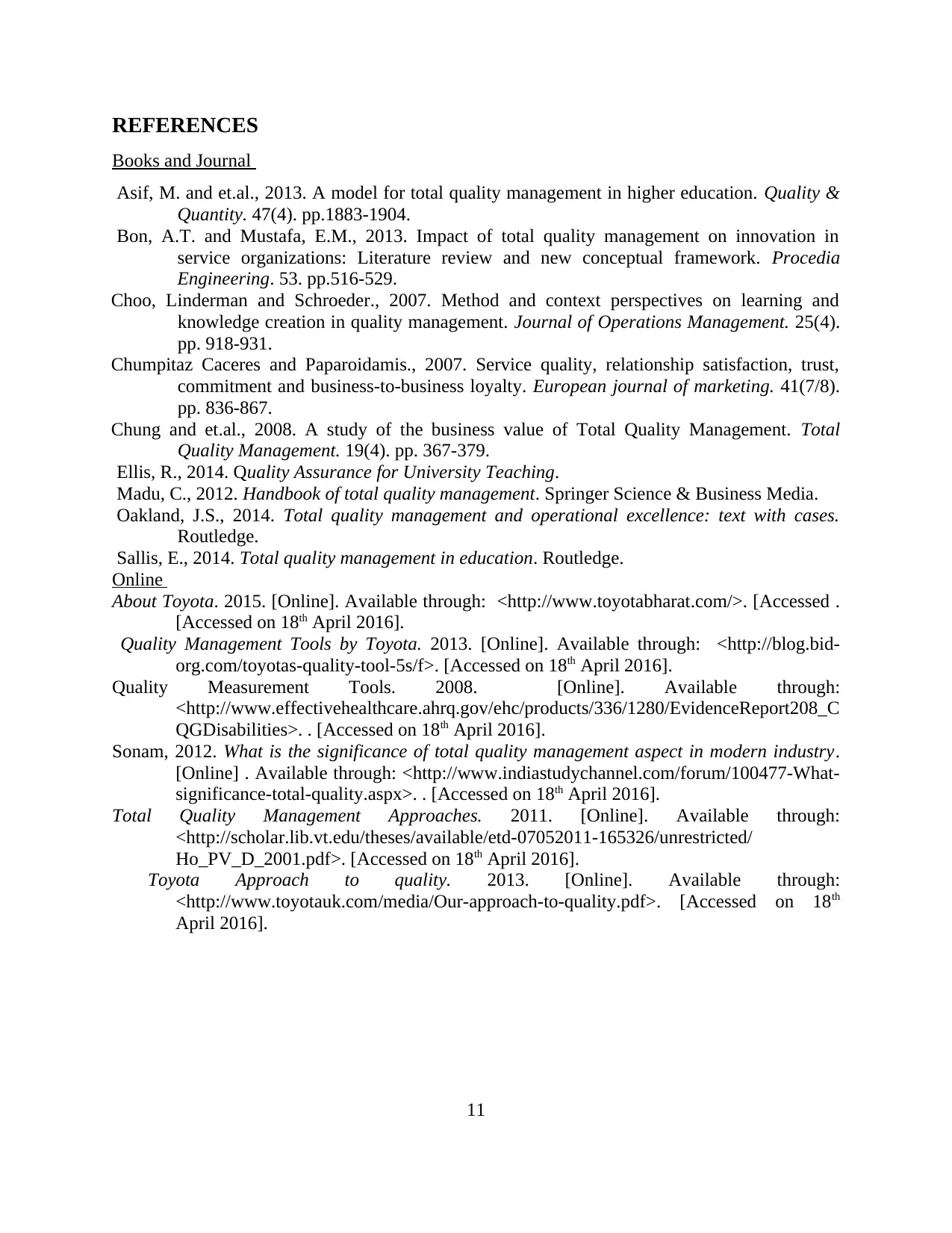
REFERENCES
Books and Journal
Asif, M. and et.al., 2013. A model for total quality management in higher education. Quality &
Quantity. 47(4). pp.1883-1904.
Bon, A.T. and Mustafa, E.M., 2013. Impact of total quality management on innovation in
service organizations: Literature review and new conceptual framework. Procedia
Engineering. 53. pp.516-529.
Choo, Linderman and Schroeder., 2007. Method and context perspectives on learning and
knowledge creation in quality management. Journal of Operations Management. 25(4).
pp. 918-931.
Chumpitaz Caceres and Paparoidamis., 2007. Service quality, relationship satisfaction, trust,
commitment and business-to-business loyalty. European journal of marketing. 41(7/8).
pp. 836-867.
Chung and et.al., 2008. A study of the business value of Total Quality Management. Total
Quality Management. 19(4). pp. 367-379.
Ellis, R., 2014. Quality Assurance for University Teaching.
Madu, C., 2012. Handbook of total quality management. Springer Science & Business Media.
Oakland, J.S., 2014. Total quality management and operational excellence: text with cases.
Routledge.
Sallis, E., 2014. Total quality management in education. Routledge.
Online
About Toyota. 2015. [Online]. Available through: <http://www.toyotabharat.com/>. [Accessed .
[Accessed on 18th April 2016].
Quality Management Tools by Toyota. 2013. [Online]. Available through: <http://blog.bid-
org.com/toyotas-quality-tool-5s/f>. [Accessed on 18th April 2016].
Quality Measurement Tools. 2008. [Online]. Available through:
<http://www.effectivehealthcare.ahrq.gov/ehc/products/336/1280/EvidenceReport208_C
QGDisabilities>. . [Accessed on 18th April 2016].
Sonam, 2012. What is the significance of total quality management aspect in modern industry.
[Online] . Available through: <http://www.indiastudychannel.com/forum/100477-What-
significance-total-quality.aspx>. . [Accessed on 18th April 2016].
Total Quality Management Approaches. 2011. [Online]. Available through:
<http://scholar.lib.vt.edu/theses/available/etd-07052011-165326/unrestricted/
Ho_PV_D_2001.pdf>. [Accessed on 18th April 2016].
Toyota Approach to quality. 2013. [Online]. Available through:
<http://www.toyotauk.com/media/Our-approach-to-quality.pdf>. [Accessed on 18th
April 2016].
11
Books and Journal
Asif, M. and et.al., 2013. A model for total quality management in higher education. Quality &
Quantity. 47(4). pp.1883-1904.
Bon, A.T. and Mustafa, E.M., 2013. Impact of total quality management on innovation in
service organizations: Literature review and new conceptual framework. Procedia
Engineering. 53. pp.516-529.
Choo, Linderman and Schroeder., 2007. Method and context perspectives on learning and
knowledge creation in quality management. Journal of Operations Management. 25(4).
pp. 918-931.
Chumpitaz Caceres and Paparoidamis., 2007. Service quality, relationship satisfaction, trust,
commitment and business-to-business loyalty. European journal of marketing. 41(7/8).
pp. 836-867.
Chung and et.al., 2008. A study of the business value of Total Quality Management. Total
Quality Management. 19(4). pp. 367-379.
Ellis, R., 2014. Quality Assurance for University Teaching.
Madu, C., 2012. Handbook of total quality management. Springer Science & Business Media.
Oakland, J.S., 2014. Total quality management and operational excellence: text with cases.
Routledge.
Sallis, E., 2014. Total quality management in education. Routledge.
Online
About Toyota. 2015. [Online]. Available through: <http://www.toyotabharat.com/>. [Accessed .
[Accessed on 18th April 2016].
Quality Management Tools by Toyota. 2013. [Online]. Available through: <http://blog.bid-
org.com/toyotas-quality-tool-5s/f>. [Accessed on 18th April 2016].
Quality Measurement Tools. 2008. [Online]. Available through:
<http://www.effectivehealthcare.ahrq.gov/ehc/products/336/1280/EvidenceReport208_C
QGDisabilities>. . [Accessed on 18th April 2016].
Sonam, 2012. What is the significance of total quality management aspect in modern industry.
[Online] . Available through: <http://www.indiastudychannel.com/forum/100477-What-
significance-total-quality.aspx>. . [Accessed on 18th April 2016].
Total Quality Management Approaches. 2011. [Online]. Available through:
<http://scholar.lib.vt.edu/theses/available/etd-07052011-165326/unrestricted/
Ho_PV_D_2001.pdf>. [Accessed on 18th April 2016].
Toyota Approach to quality. 2013. [Online]. Available through:
<http://www.toyotauk.com/media/Our-approach-to-quality.pdf>. [Accessed on 18th
April 2016].
11
1 out of 11
Related Documents

Your All-in-One AI-Powered Toolkit for Academic Success.
+13062052269
info@desklib.com
Available 24*7 on WhatsApp / Email
Unlock your academic potential
Copyright © 2020–2025 A2Z Services. All Rights Reserved. Developed and managed by ZUCOL.