BUS298 - Organizational Change Essay: TQM and Lean Production Analysis
VerifiedAdded on 2022/08/11
|12
|3062
|25
Essay
AI Summary
This essay critically evaluates the effectiveness of Total Quality Management (TQM) and Lean Production as change tools in both manufacturing and service industries. The introduction defines organizational change and introduces the essay's focus on TQM and Lean Production, arguing for their usefulness in driving success in both sectors. The essay defines and explains the mechanisms of TQM and Lean Production, highlighting their roles in improving processes, customer satisfaction, and efficiency. The essay then introduces two companies, Grab (service) and Flex Ltd (manufacturing), analyzing their characteristics and identifying key similarities and differences. The application of TQM and Lean Production is discussed for both sectors, including their advantages and shortcomings, supported by academic literature. The essay explores the benefits of TQM in enhancing product quality and revenue in manufacturing, and the role of lean production in improving efficiency. In the service industry, TQM's focus on customer satisfaction and lean production's role in streamlining tasks are examined. The conclusion summarizes the findings, highlighting the appropriateness of each tool for driving organizational change in the respective sectors.
Contribute Materials
Your contribution can guide someone’s learning journey. Share your
documents today.
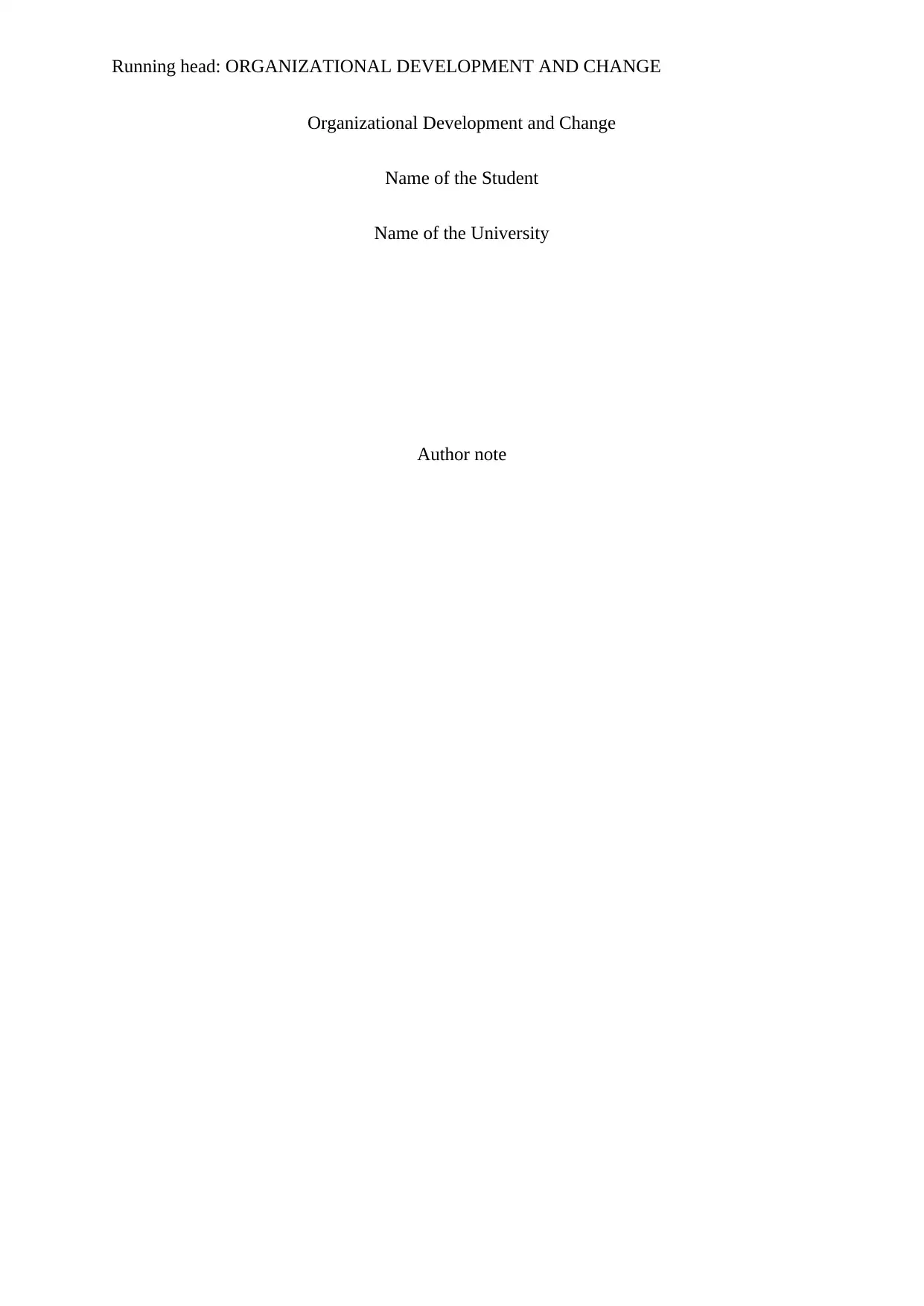
Running head: ORGANIZATIONAL DEVELOPMENT AND CHANGE
Organizational Development and Change
Name of the Student
Name of the University
Author note
Organizational Development and Change
Name of the Student
Name of the University
Author note
Secure Best Marks with AI Grader
Need help grading? Try our AI Grader for instant feedback on your assignments.
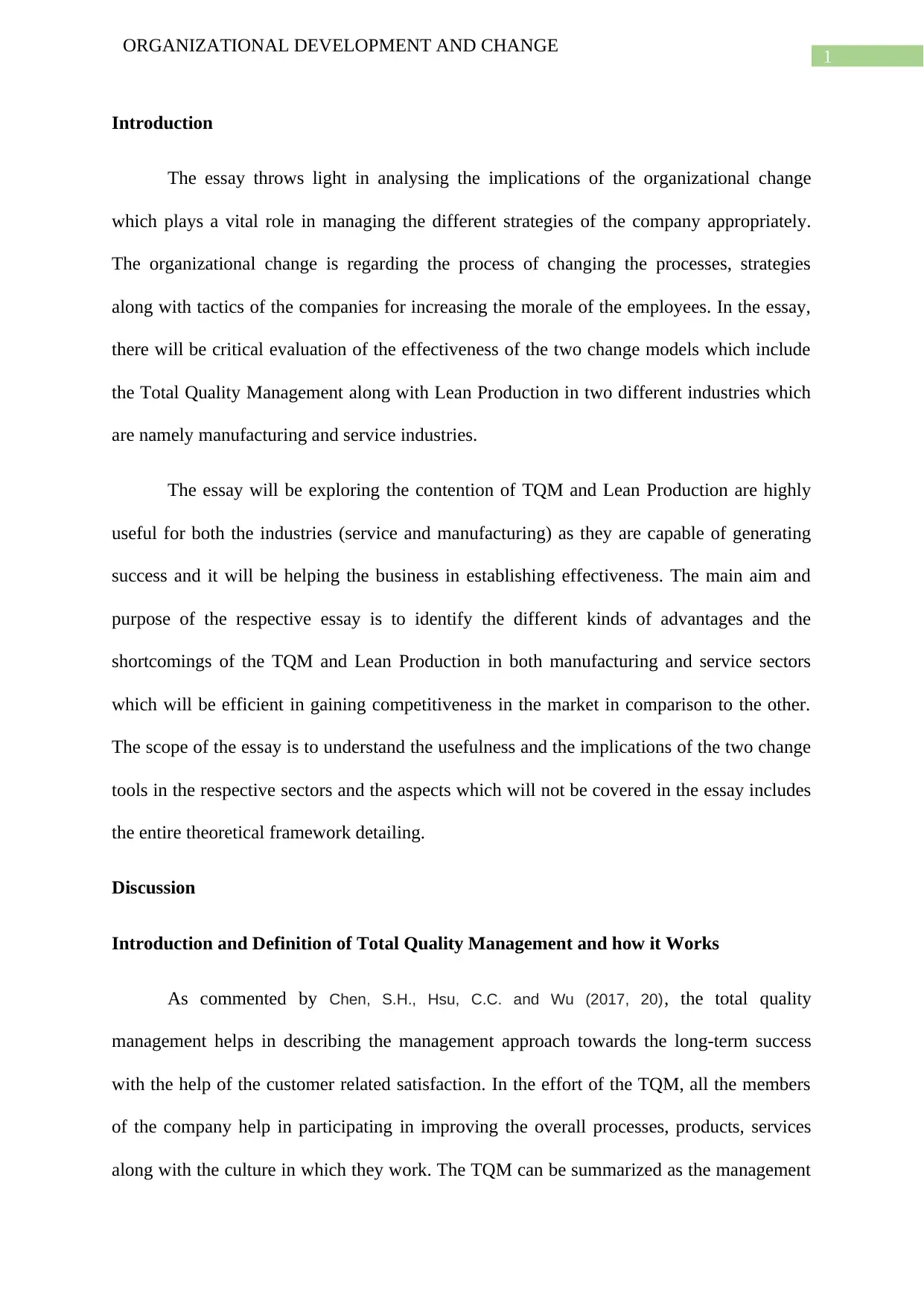
1
ORGANIZATIONAL DEVELOPMENT AND CHANGE
Introduction
The essay throws light in analysing the implications of the organizational change
which plays a vital role in managing the different strategies of the company appropriately.
The organizational change is regarding the process of changing the processes, strategies
along with tactics of the companies for increasing the morale of the employees. In the essay,
there will be critical evaluation of the effectiveness of the two change models which include
the Total Quality Management along with Lean Production in two different industries which
are namely manufacturing and service industries.
The essay will be exploring the contention of TQM and Lean Production are highly
useful for both the industries (service and manufacturing) as they are capable of generating
success and it will be helping the business in establishing effectiveness. The main aim and
purpose of the respective essay is to identify the different kinds of advantages and the
shortcomings of the TQM and Lean Production in both manufacturing and service sectors
which will be efficient in gaining competitiveness in the market in comparison to the other.
The scope of the essay is to understand the usefulness and the implications of the two change
tools in the respective sectors and the aspects which will not be covered in the essay includes
the entire theoretical framework detailing.
Discussion
Introduction and Definition of Total Quality Management and how it Works
As commented by Chen, S.H., Hsu, C.C. and Wu (2017, 20), the total quality
management helps in describing the management approach towards the long-term success
with the help of the customer related satisfaction. In the effort of the TQM, all the members
of the company help in participating in improving the overall processes, products, services
along with the culture in which they work. The TQM can be summarized as the management
ORGANIZATIONAL DEVELOPMENT AND CHANGE
Introduction
The essay throws light in analysing the implications of the organizational change
which plays a vital role in managing the different strategies of the company appropriately.
The organizational change is regarding the process of changing the processes, strategies
along with tactics of the companies for increasing the morale of the employees. In the essay,
there will be critical evaluation of the effectiveness of the two change models which include
the Total Quality Management along with Lean Production in two different industries which
are namely manufacturing and service industries.
The essay will be exploring the contention of TQM and Lean Production are highly
useful for both the industries (service and manufacturing) as they are capable of generating
success and it will be helping the business in establishing effectiveness. The main aim and
purpose of the respective essay is to identify the different kinds of advantages and the
shortcomings of the TQM and Lean Production in both manufacturing and service sectors
which will be efficient in gaining competitiveness in the market in comparison to the other.
The scope of the essay is to understand the usefulness and the implications of the two change
tools in the respective sectors and the aspects which will not be covered in the essay includes
the entire theoretical framework detailing.
Discussion
Introduction and Definition of Total Quality Management and how it Works
As commented by Chen, S.H., Hsu, C.C. and Wu (2017, 20), the total quality
management helps in describing the management approach towards the long-term success
with the help of the customer related satisfaction. In the effort of the TQM, all the members
of the company help in participating in improving the overall processes, products, services
along with the culture in which they work. The TQM can be summarized as the management
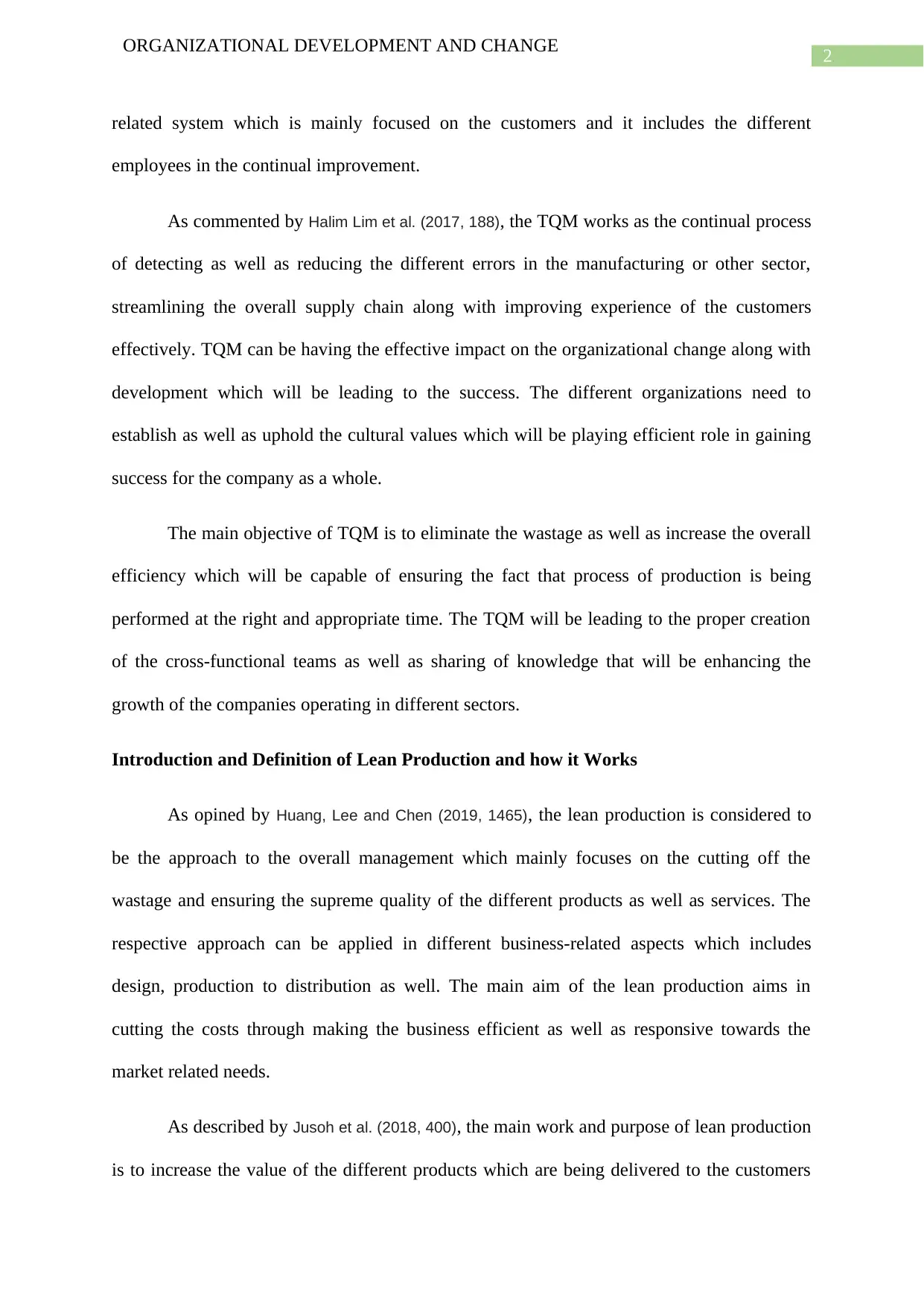
2
ORGANIZATIONAL DEVELOPMENT AND CHANGE
related system which is mainly focused on the customers and it includes the different
employees in the continual improvement.
As commented by Halim Lim et al. (2017, 188), the TQM works as the continual process
of detecting as well as reducing the different errors in the manufacturing or other sector,
streamlining the overall supply chain along with improving experience of the customers
effectively. TQM can be having the effective impact on the organizational change along with
development which will be leading to the success. The different organizations need to
establish as well as uphold the cultural values which will be playing efficient role in gaining
success for the company as a whole.
The main objective of TQM is to eliminate the wastage as well as increase the overall
efficiency which will be capable of ensuring the fact that process of production is being
performed at the right and appropriate time. The TQM will be leading to the proper creation
of the cross-functional teams as well as sharing of knowledge that will be enhancing the
growth of the companies operating in different sectors.
Introduction and Definition of Lean Production and how it Works
As opined by Huang, Lee and Chen (2019, 1465), the lean production is considered to
be the approach to the overall management which mainly focuses on the cutting off the
wastage and ensuring the supreme quality of the different products as well as services. The
respective approach can be applied in different business-related aspects which includes
design, production to distribution as well. The main aim of the lean production aims in
cutting the costs through making the business efficient as well as responsive towards the
market related needs.
As described by Jusoh et al. (2018, 400), the main work and purpose of lean production
is to increase the value of the different products which are being delivered to the customers
ORGANIZATIONAL DEVELOPMENT AND CHANGE
related system which is mainly focused on the customers and it includes the different
employees in the continual improvement.
As commented by Halim Lim et al. (2017, 188), the TQM works as the continual process
of detecting as well as reducing the different errors in the manufacturing or other sector,
streamlining the overall supply chain along with improving experience of the customers
effectively. TQM can be having the effective impact on the organizational change along with
development which will be leading to the success. The different organizations need to
establish as well as uphold the cultural values which will be playing efficient role in gaining
success for the company as a whole.
The main objective of TQM is to eliminate the wastage as well as increase the overall
efficiency which will be capable of ensuring the fact that process of production is being
performed at the right and appropriate time. The TQM will be leading to the proper creation
of the cross-functional teams as well as sharing of knowledge that will be enhancing the
growth of the companies operating in different sectors.
Introduction and Definition of Lean Production and how it Works
As opined by Huang, Lee and Chen (2019, 1465), the lean production is considered to
be the approach to the overall management which mainly focuses on the cutting off the
wastage and ensuring the supreme quality of the different products as well as services. The
respective approach can be applied in different business-related aspects which includes
design, production to distribution as well. The main aim of the lean production aims in
cutting the costs through making the business efficient as well as responsive towards the
market related needs.
As described by Jusoh et al. (2018, 400), the main work and purpose of lean production
is to increase the value of the different products which are being delivered to the customers

3
ORGANIZATIONAL DEVELOPMENT AND CHANGE
for solving the problems of the different customers. The achievement of the respective aim
will be assisting in improving the effectiveness and competitiveness of the companies
through reduction of the costs successfully. Lean mainly puts emphasis on meeting the
different demands of customers with the help of fewer resources and it will be enhancing the
growth patterns of the company successfully. The ultimate goal of the lean production is
providing the perfect value to the different customers through perfect value process of
creation which has zero level of wastage.
Introduce as well as define characteristics of different companies who manufacture
goods and companies who provide services. Analysis of Similarities and differences
The two companies which have been selected in the respective section includes Grab
(Service Provider) and Flex Ltd (Manufacturing). In case of Grab, it falls under the service
industry as it is the Singapore based ridesharing company and moreover, it offers the food
delivery along with digital payment services through the mobile application. There are
different services provided by the company to the customers such as peer to peer ridesharing
as well as food delivery applications (Grab.com.sg 2020).
On the other hand, Flex Ltd is Singaporean domiciled multinational technological
manufacturer which is headquartered at Singapore (Flex.com 2020). The respective
organization manufactures different kinds of electrical devices and equipment such as
Television along with other products and sell the same directly to customers or the other
retail companies. From the analysis of the service and manufacturing companies, it can be
seen that both the companies are delivering the output to the customers or the business in a
direct or indirect manner.
On the other hand, the differences are many wherein the first is the tangibility related
to the output. As commented by Keinan and Karugu (2018, 99), the output of the service firm
ORGANIZATIONAL DEVELOPMENT AND CHANGE
for solving the problems of the different customers. The achievement of the respective aim
will be assisting in improving the effectiveness and competitiveness of the companies
through reduction of the costs successfully. Lean mainly puts emphasis on meeting the
different demands of customers with the help of fewer resources and it will be enhancing the
growth patterns of the company successfully. The ultimate goal of the lean production is
providing the perfect value to the different customers through perfect value process of
creation which has zero level of wastage.
Introduce as well as define characteristics of different companies who manufacture
goods and companies who provide services. Analysis of Similarities and differences
The two companies which have been selected in the respective section includes Grab
(Service Provider) and Flex Ltd (Manufacturing). In case of Grab, it falls under the service
industry as it is the Singapore based ridesharing company and moreover, it offers the food
delivery along with digital payment services through the mobile application. There are
different services provided by the company to the customers such as peer to peer ridesharing
as well as food delivery applications (Grab.com.sg 2020).
On the other hand, Flex Ltd is Singaporean domiciled multinational technological
manufacturer which is headquartered at Singapore (Flex.com 2020). The respective
organization manufactures different kinds of electrical devices and equipment such as
Television along with other products and sell the same directly to customers or the other
retail companies. From the analysis of the service and manufacturing companies, it can be
seen that both the companies are delivering the output to the customers or the business in a
direct or indirect manner.
On the other hand, the differences are many wherein the first is the tangibility related
to the output. As commented by Keinan and Karugu (2018, 99), the output of the service firm
Secure Best Marks with AI Grader
Need help grading? Try our AI Grader for instant feedback on your assignments.
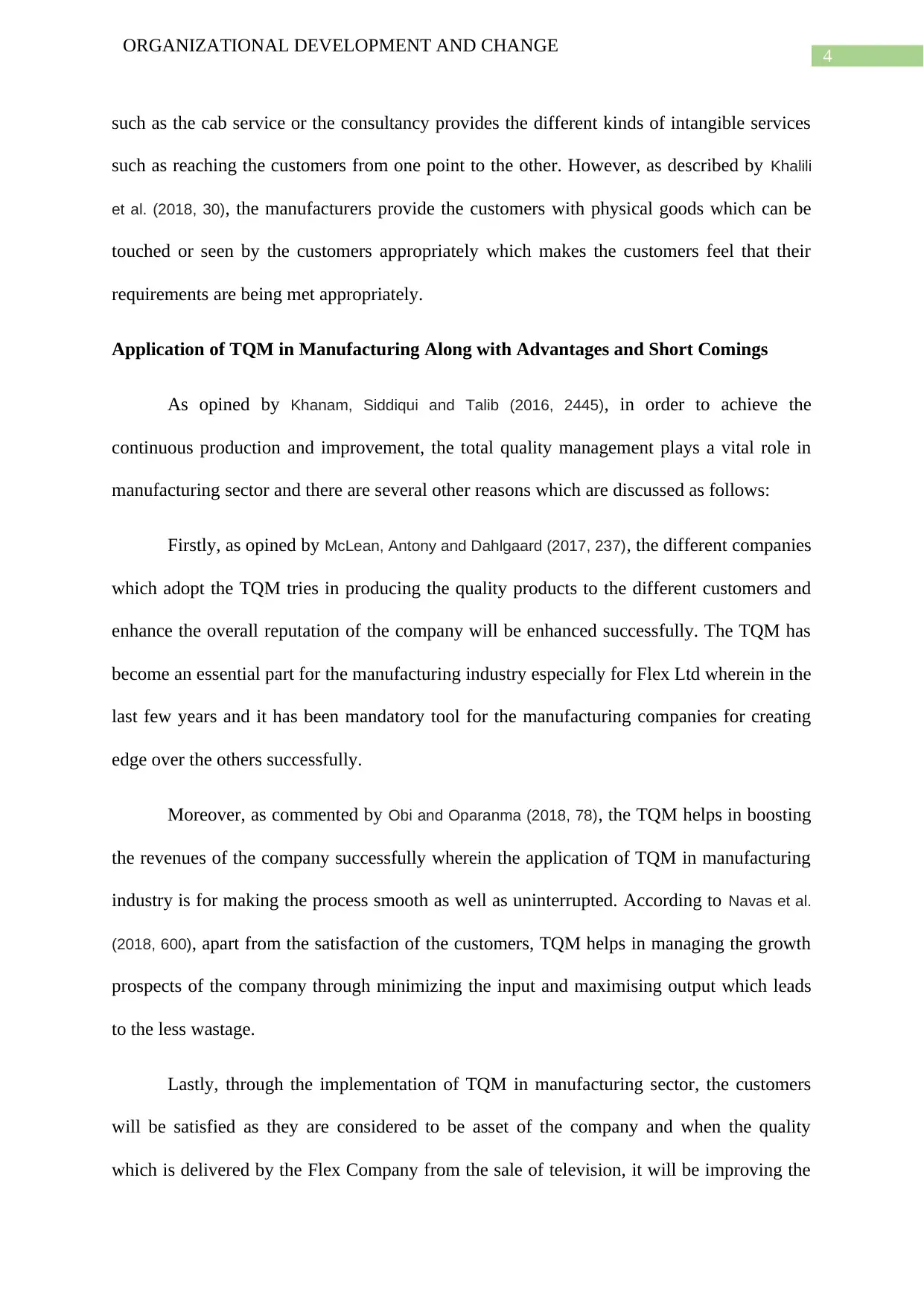
4
ORGANIZATIONAL DEVELOPMENT AND CHANGE
such as the cab service or the consultancy provides the different kinds of intangible services
such as reaching the customers from one point to the other. However, as described by Khalili
et al. (2018, 30), the manufacturers provide the customers with physical goods which can be
touched or seen by the customers appropriately which makes the customers feel that their
requirements are being met appropriately.
Application of TQM in Manufacturing Along with Advantages and Short Comings
As opined by Khanam, Siddiqui and Talib (2016, 2445), in order to achieve the
continuous production and improvement, the total quality management plays a vital role in
manufacturing sector and there are several other reasons which are discussed as follows:
Firstly, as opined by McLean, Antony and Dahlgaard (2017, 237), the different companies
which adopt the TQM tries in producing the quality products to the different customers and
enhance the overall reputation of the company will be enhanced successfully. The TQM has
become an essential part for the manufacturing industry especially for Flex Ltd wherein in the
last few years and it has been mandatory tool for the manufacturing companies for creating
edge over the others successfully.
Moreover, as commented by Obi and Oparanma (2018, 78), the TQM helps in boosting
the revenues of the company successfully wherein the application of TQM in manufacturing
industry is for making the process smooth as well as uninterrupted. According to Navas et al.
(2018, 600), apart from the satisfaction of the customers, TQM helps in managing the growth
prospects of the company through minimizing the input and maximising output which leads
to the less wastage.
Lastly, through the implementation of TQM in manufacturing sector, the customers
will be satisfied as they are considered to be asset of the company and when the quality
which is delivered by the Flex Company from the sale of television, it will be improving the
ORGANIZATIONAL DEVELOPMENT AND CHANGE
such as the cab service or the consultancy provides the different kinds of intangible services
such as reaching the customers from one point to the other. However, as described by Khalili
et al. (2018, 30), the manufacturers provide the customers with physical goods which can be
touched or seen by the customers appropriately which makes the customers feel that their
requirements are being met appropriately.
Application of TQM in Manufacturing Along with Advantages and Short Comings
As opined by Khanam, Siddiqui and Talib (2016, 2445), in order to achieve the
continuous production and improvement, the total quality management plays a vital role in
manufacturing sector and there are several other reasons which are discussed as follows:
Firstly, as opined by McLean, Antony and Dahlgaard (2017, 237), the different companies
which adopt the TQM tries in producing the quality products to the different customers and
enhance the overall reputation of the company will be enhanced successfully. The TQM has
become an essential part for the manufacturing industry especially for Flex Ltd wherein in the
last few years and it has been mandatory tool for the manufacturing companies for creating
edge over the others successfully.
Moreover, as commented by Obi and Oparanma (2018, 78), the TQM helps in boosting
the revenues of the company successfully wherein the application of TQM in manufacturing
industry is for making the process smooth as well as uninterrupted. According to Navas et al.
(2018, 600), apart from the satisfaction of the customers, TQM helps in managing the growth
prospects of the company through minimizing the input and maximising output which leads
to the less wastage.
Lastly, through the implementation of TQM in manufacturing sector, the customers
will be satisfied as they are considered to be asset of the company and when the quality
which is delivered by the Flex Company from the sale of television, it will be improving the
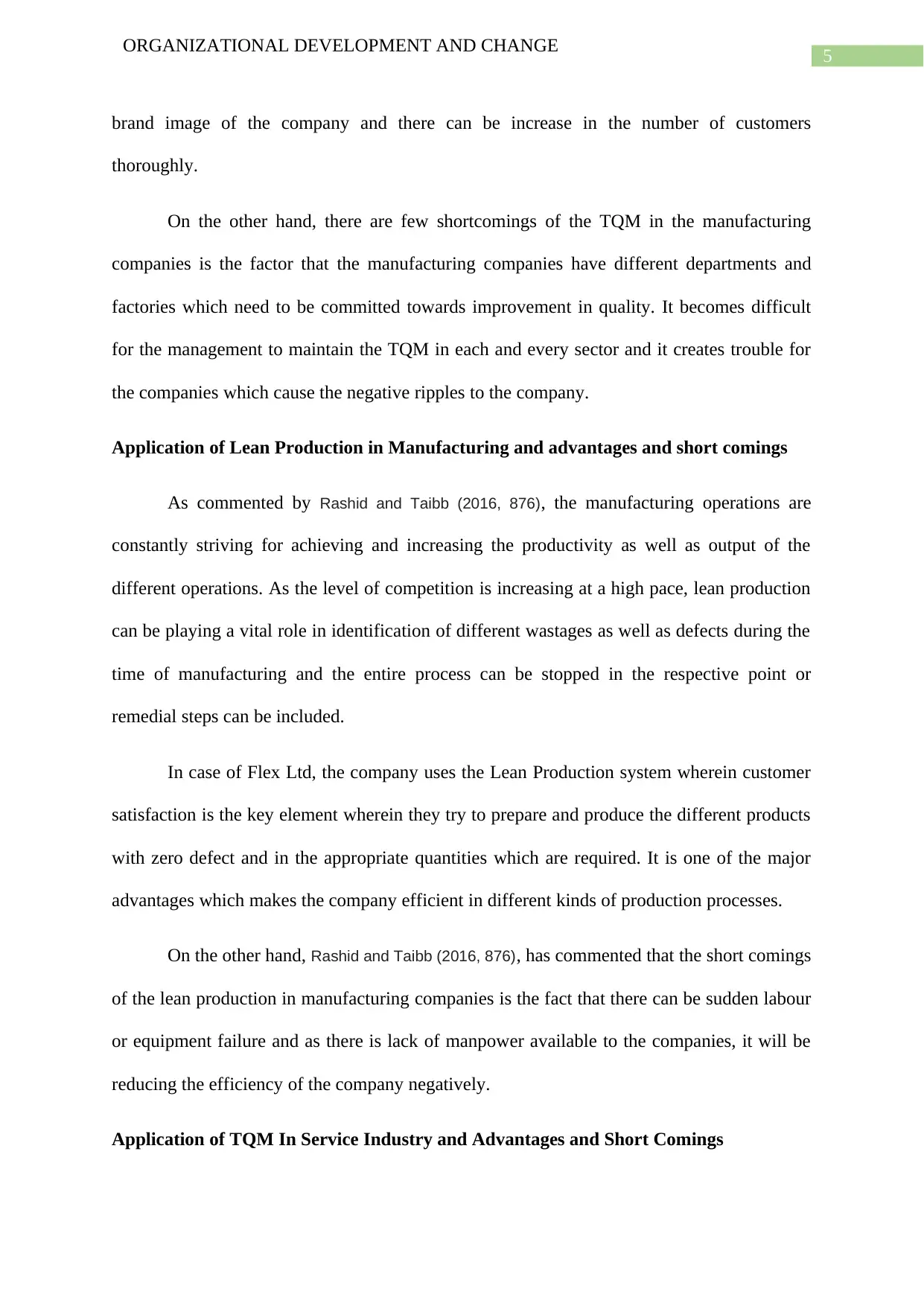
5
ORGANIZATIONAL DEVELOPMENT AND CHANGE
brand image of the company and there can be increase in the number of customers
thoroughly.
On the other hand, there are few shortcomings of the TQM in the manufacturing
companies is the factor that the manufacturing companies have different departments and
factories which need to be committed towards improvement in quality. It becomes difficult
for the management to maintain the TQM in each and every sector and it creates trouble for
the companies which cause the negative ripples to the company.
Application of Lean Production in Manufacturing and advantages and short comings
As commented by Rashid and Taibb (2016, 876), the manufacturing operations are
constantly striving for achieving and increasing the productivity as well as output of the
different operations. As the level of competition is increasing at a high pace, lean production
can be playing a vital role in identification of different wastages as well as defects during the
time of manufacturing and the entire process can be stopped in the respective point or
remedial steps can be included.
In case of Flex Ltd, the company uses the Lean Production system wherein customer
satisfaction is the key element wherein they try to prepare and produce the different products
with zero defect and in the appropriate quantities which are required. It is one of the major
advantages which makes the company efficient in different kinds of production processes.
On the other hand, Rashid and Taibb (2016, 876), has commented that the short comings
of the lean production in manufacturing companies is the fact that there can be sudden labour
or equipment failure and as there is lack of manpower available to the companies, it will be
reducing the efficiency of the company negatively.
Application of TQM In Service Industry and Advantages and Short Comings
ORGANIZATIONAL DEVELOPMENT AND CHANGE
brand image of the company and there can be increase in the number of customers
thoroughly.
On the other hand, there are few shortcomings of the TQM in the manufacturing
companies is the factor that the manufacturing companies have different departments and
factories which need to be committed towards improvement in quality. It becomes difficult
for the management to maintain the TQM in each and every sector and it creates trouble for
the companies which cause the negative ripples to the company.
Application of Lean Production in Manufacturing and advantages and short comings
As commented by Rashid and Taibb (2016, 876), the manufacturing operations are
constantly striving for achieving and increasing the productivity as well as output of the
different operations. As the level of competition is increasing at a high pace, lean production
can be playing a vital role in identification of different wastages as well as defects during the
time of manufacturing and the entire process can be stopped in the respective point or
remedial steps can be included.
In case of Flex Ltd, the company uses the Lean Production system wherein customer
satisfaction is the key element wherein they try to prepare and produce the different products
with zero defect and in the appropriate quantities which are required. It is one of the major
advantages which makes the company efficient in different kinds of production processes.
On the other hand, Rashid and Taibb (2016, 876), has commented that the short comings
of the lean production in manufacturing companies is the fact that there can be sudden labour
or equipment failure and as there is lack of manpower available to the companies, it will be
reducing the efficiency of the company negatively.
Application of TQM In Service Industry and Advantages and Short Comings
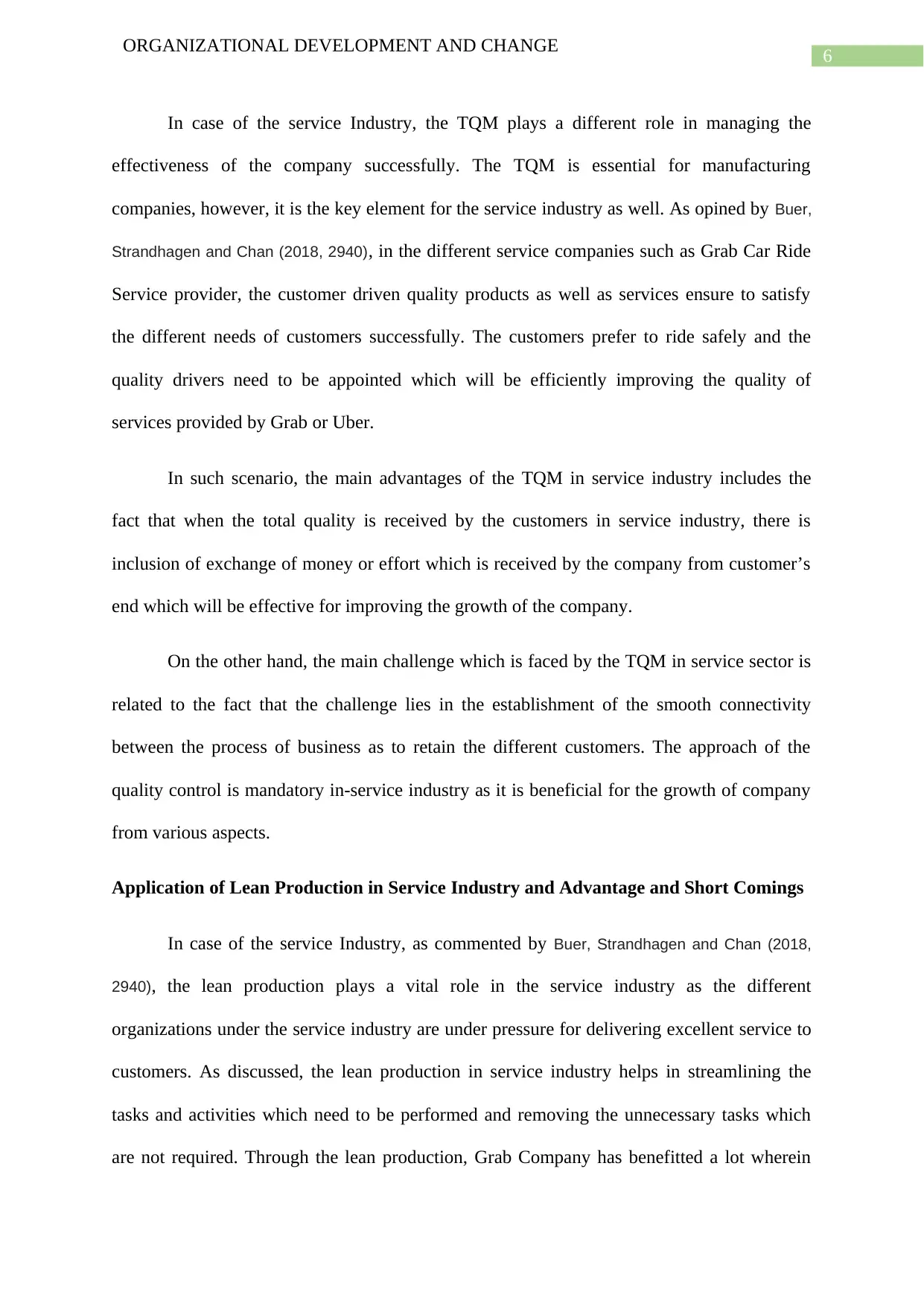
6
ORGANIZATIONAL DEVELOPMENT AND CHANGE
In case of the service Industry, the TQM plays a different role in managing the
effectiveness of the company successfully. The TQM is essential for manufacturing
companies, however, it is the key element for the service industry as well. As opined by Buer,
Strandhagen and Chan (2018, 2940), in the different service companies such as Grab Car Ride
Service provider, the customer driven quality products as well as services ensure to satisfy
the different needs of customers successfully. The customers prefer to ride safely and the
quality drivers need to be appointed which will be efficiently improving the quality of
services provided by Grab or Uber.
In such scenario, the main advantages of the TQM in service industry includes the
fact that when the total quality is received by the customers in service industry, there is
inclusion of exchange of money or effort which is received by the company from customer’s
end which will be effective for improving the growth of the company.
On the other hand, the main challenge which is faced by the TQM in service sector is
related to the fact that the challenge lies in the establishment of the smooth connectivity
between the process of business as to retain the different customers. The approach of the
quality control is mandatory in-service industry as it is beneficial for the growth of company
from various aspects.
Application of Lean Production in Service Industry and Advantage and Short Comings
In case of the service Industry, as commented by Buer, Strandhagen and Chan (2018,
2940), the lean production plays a vital role in the service industry as the different
organizations under the service industry are under pressure for delivering excellent service to
customers. As discussed, the lean production in service industry helps in streamlining the
tasks and activities which need to be performed and removing the unnecessary tasks which
are not required. Through the lean production, Grab Company has benefitted a lot wherein
ORGANIZATIONAL DEVELOPMENT AND CHANGE
In case of the service Industry, the TQM plays a different role in managing the
effectiveness of the company successfully. The TQM is essential for manufacturing
companies, however, it is the key element for the service industry as well. As opined by Buer,
Strandhagen and Chan (2018, 2940), in the different service companies such as Grab Car Ride
Service provider, the customer driven quality products as well as services ensure to satisfy
the different needs of customers successfully. The customers prefer to ride safely and the
quality drivers need to be appointed which will be efficiently improving the quality of
services provided by Grab or Uber.
In such scenario, the main advantages of the TQM in service industry includes the
fact that when the total quality is received by the customers in service industry, there is
inclusion of exchange of money or effort which is received by the company from customer’s
end which will be effective for improving the growth of the company.
On the other hand, the main challenge which is faced by the TQM in service sector is
related to the fact that the challenge lies in the establishment of the smooth connectivity
between the process of business as to retain the different customers. The approach of the
quality control is mandatory in-service industry as it is beneficial for the growth of company
from various aspects.
Application of Lean Production in Service Industry and Advantage and Short Comings
In case of the service Industry, as commented by Buer, Strandhagen and Chan (2018,
2940), the lean production plays a vital role in the service industry as the different
organizations under the service industry are under pressure for delivering excellent service to
customers. As discussed, the lean production in service industry helps in streamlining the
tasks and activities which need to be performed and removing the unnecessary tasks which
are not required. Through the lean production, Grab Company has benefitted a lot wherein
Paraphrase This Document
Need a fresh take? Get an instant paraphrase of this document with our AI Paraphraser
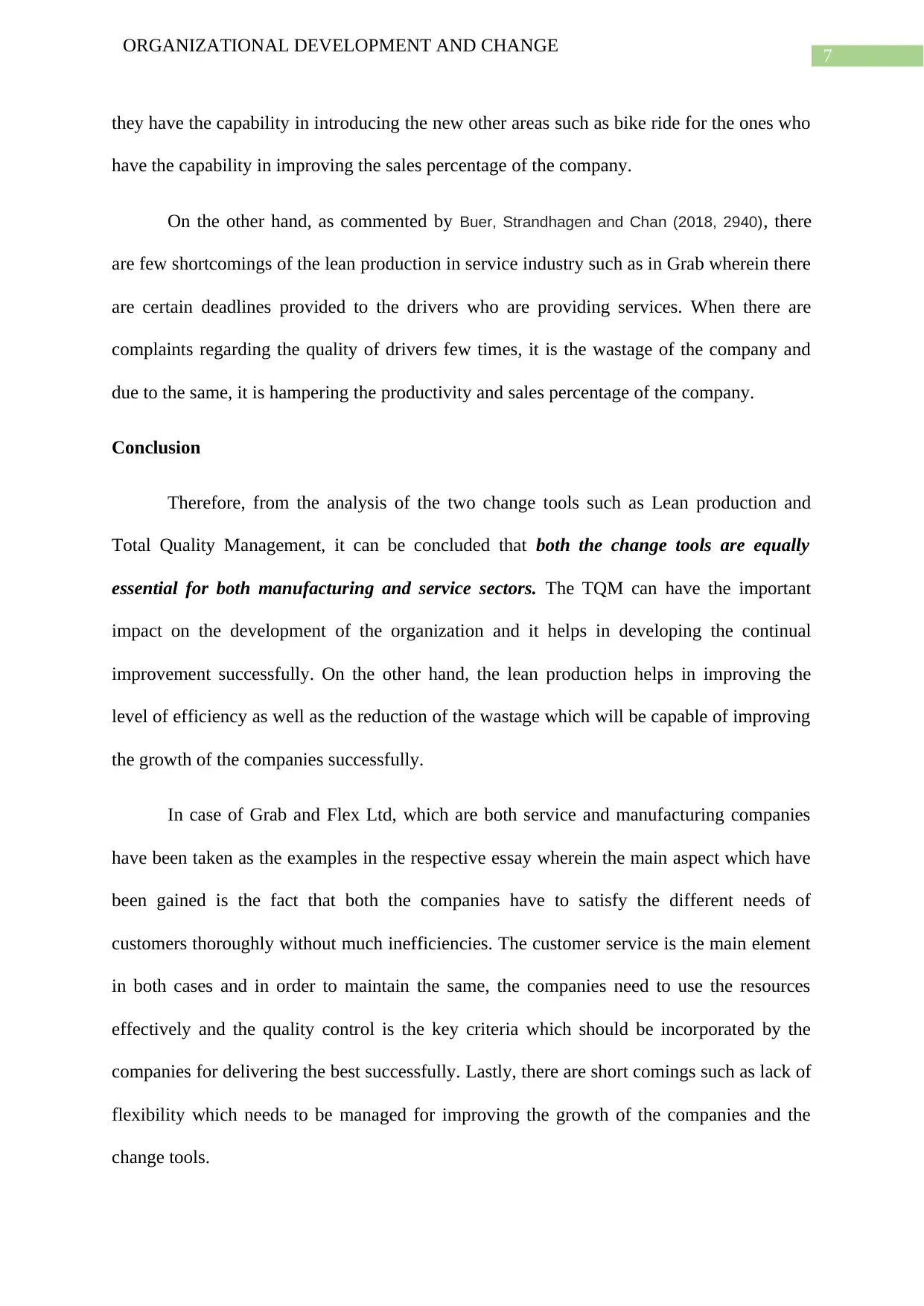
7
ORGANIZATIONAL DEVELOPMENT AND CHANGE
they have the capability in introducing the new other areas such as bike ride for the ones who
have the capability in improving the sales percentage of the company.
On the other hand, as commented by Buer, Strandhagen and Chan (2018, 2940), there
are few shortcomings of the lean production in service industry such as in Grab wherein there
are certain deadlines provided to the drivers who are providing services. When there are
complaints regarding the quality of drivers few times, it is the wastage of the company and
due to the same, it is hampering the productivity and sales percentage of the company.
Conclusion
Therefore, from the analysis of the two change tools such as Lean production and
Total Quality Management, it can be concluded that both the change tools are equally
essential for both manufacturing and service sectors. The TQM can have the important
impact on the development of the organization and it helps in developing the continual
improvement successfully. On the other hand, the lean production helps in improving the
level of efficiency as well as the reduction of the wastage which will be capable of improving
the growth of the companies successfully.
In case of Grab and Flex Ltd, which are both service and manufacturing companies
have been taken as the examples in the respective essay wherein the main aspect which have
been gained is the fact that both the companies have to satisfy the different needs of
customers thoroughly without much inefficiencies. The customer service is the main element
in both cases and in order to maintain the same, the companies need to use the resources
effectively and the quality control is the key criteria which should be incorporated by the
companies for delivering the best successfully. Lastly, there are short comings such as lack of
flexibility which needs to be managed for improving the growth of the companies and the
change tools.
ORGANIZATIONAL DEVELOPMENT AND CHANGE
they have the capability in introducing the new other areas such as bike ride for the ones who
have the capability in improving the sales percentage of the company.
On the other hand, as commented by Buer, Strandhagen and Chan (2018, 2940), there
are few shortcomings of the lean production in service industry such as in Grab wherein there
are certain deadlines provided to the drivers who are providing services. When there are
complaints regarding the quality of drivers few times, it is the wastage of the company and
due to the same, it is hampering the productivity and sales percentage of the company.
Conclusion
Therefore, from the analysis of the two change tools such as Lean production and
Total Quality Management, it can be concluded that both the change tools are equally
essential for both manufacturing and service sectors. The TQM can have the important
impact on the development of the organization and it helps in developing the continual
improvement successfully. On the other hand, the lean production helps in improving the
level of efficiency as well as the reduction of the wastage which will be capable of improving
the growth of the companies successfully.
In case of Grab and Flex Ltd, which are both service and manufacturing companies
have been taken as the examples in the respective essay wherein the main aspect which have
been gained is the fact that both the companies have to satisfy the different needs of
customers thoroughly without much inefficiencies. The customer service is the main element
in both cases and in order to maintain the same, the companies need to use the resources
effectively and the quality control is the key criteria which should be incorporated by the
companies for delivering the best successfully. Lastly, there are short comings such as lack of
flexibility which needs to be managed for improving the growth of the companies and the
change tools.
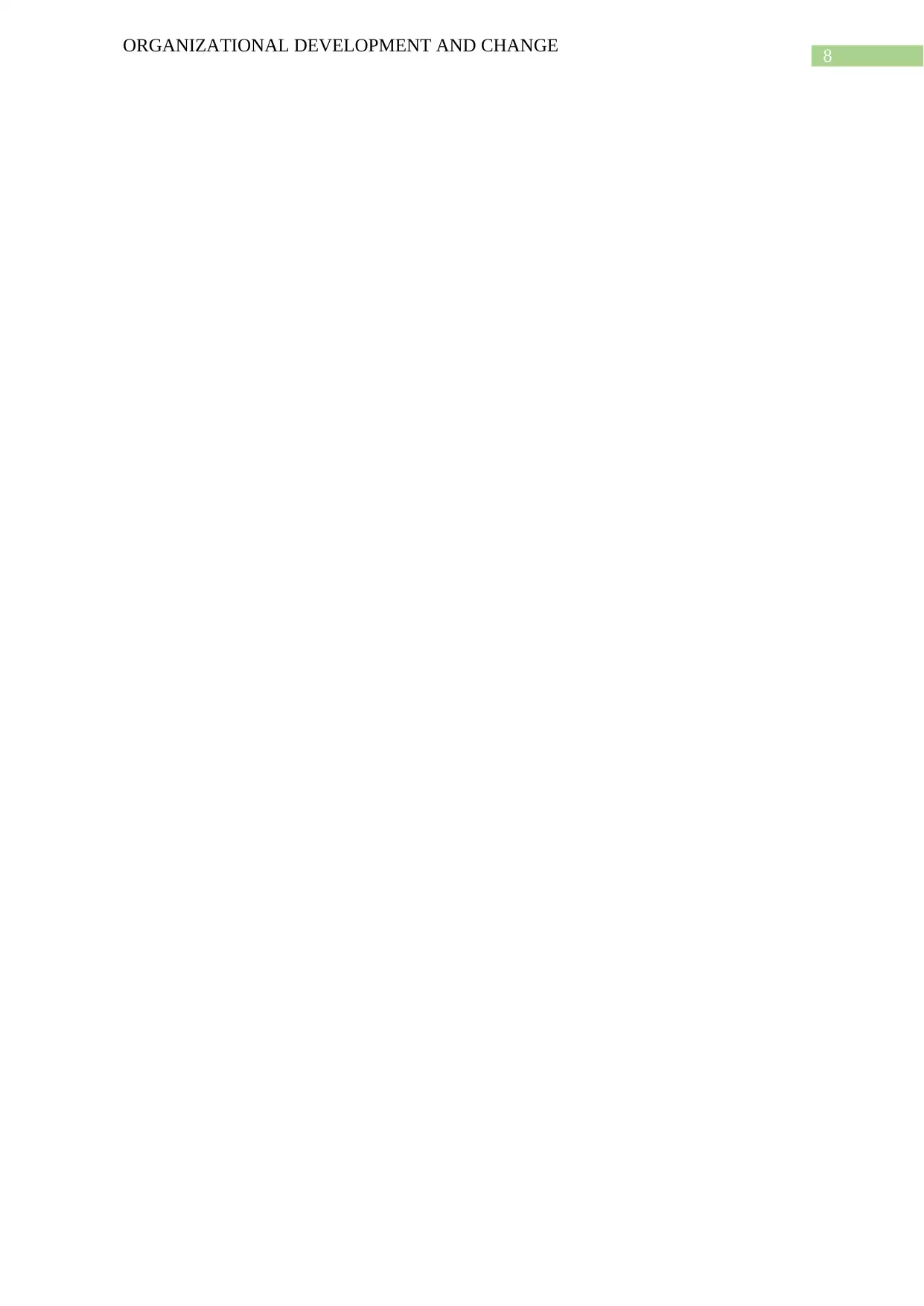
8
ORGANIZATIONAL DEVELOPMENT AND CHANGE
ORGANIZATIONAL DEVELOPMENT AND CHANGE
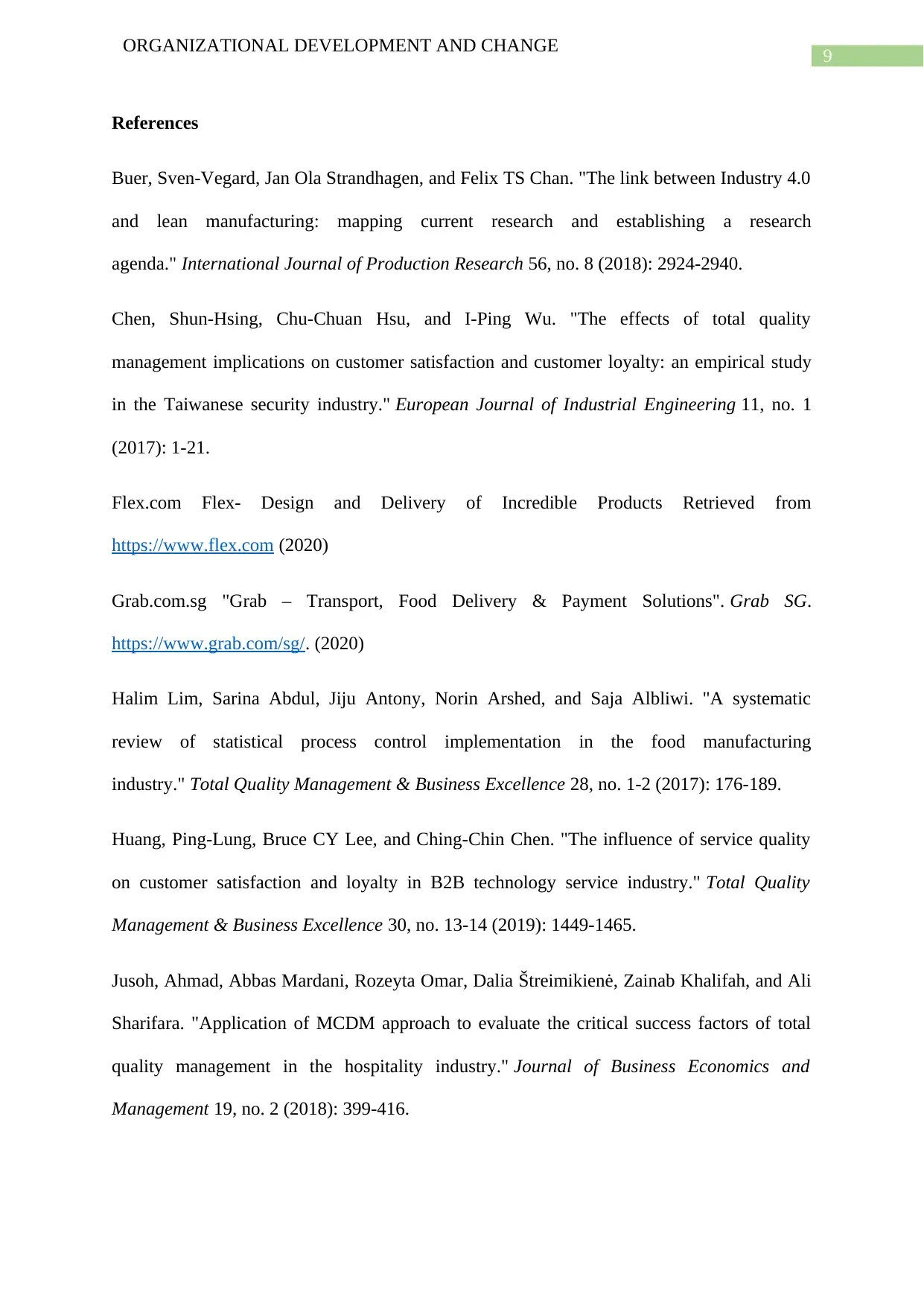
9
ORGANIZATIONAL DEVELOPMENT AND CHANGE
References
Buer, Sven-Vegard, Jan Ola Strandhagen, and Felix TS Chan. "The link between Industry 4.0
and lean manufacturing: mapping current research and establishing a research
agenda." International Journal of Production Research 56, no. 8 (2018): 2924-2940.
Chen, Shun-Hsing, Chu-Chuan Hsu, and I-Ping Wu. "The effects of total quality
management implications on customer satisfaction and customer loyalty: an empirical study
in the Taiwanese security industry." European Journal of Industrial Engineering 11, no. 1
(2017): 1-21.
Flex.com Flex- Design and Delivery of Incredible Products Retrieved from
https://www.flex.com (2020)
Grab.com.sg "Grab – Transport, Food Delivery & Payment Solutions". Grab SG.
https://www.grab.com/sg/. (2020)
Halim Lim, Sarina Abdul, Jiju Antony, Norin Arshed, and Saja Albliwi. "A systematic
review of statistical process control implementation in the food manufacturing
industry." Total Quality Management & Business Excellence 28, no. 1-2 (2017): 176-189.
Huang, Ping-Lung, Bruce CY Lee, and Ching-Chin Chen. "The influence of service quality
on customer satisfaction and loyalty in B2B technology service industry." Total Quality
Management & Business Excellence 30, no. 13-14 (2019): 1449-1465.
Jusoh, Ahmad, Abbas Mardani, Rozeyta Omar, Dalia Štreimikienė, Zainab Khalifah, and Ali
Sharifara. "Application of MCDM approach to evaluate the critical success factors of total
quality management in the hospitality industry." Journal of Business Economics and
Management 19, no. 2 (2018): 399-416.
ORGANIZATIONAL DEVELOPMENT AND CHANGE
References
Buer, Sven-Vegard, Jan Ola Strandhagen, and Felix TS Chan. "The link between Industry 4.0
and lean manufacturing: mapping current research and establishing a research
agenda." International Journal of Production Research 56, no. 8 (2018): 2924-2940.
Chen, Shun-Hsing, Chu-Chuan Hsu, and I-Ping Wu. "The effects of total quality
management implications on customer satisfaction and customer loyalty: an empirical study
in the Taiwanese security industry." European Journal of Industrial Engineering 11, no. 1
(2017): 1-21.
Flex.com Flex- Design and Delivery of Incredible Products Retrieved from
https://www.flex.com (2020)
Grab.com.sg "Grab – Transport, Food Delivery & Payment Solutions". Grab SG.
https://www.grab.com/sg/. (2020)
Halim Lim, Sarina Abdul, Jiju Antony, Norin Arshed, and Saja Albliwi. "A systematic
review of statistical process control implementation in the food manufacturing
industry." Total Quality Management & Business Excellence 28, no. 1-2 (2017): 176-189.
Huang, Ping-Lung, Bruce CY Lee, and Ching-Chin Chen. "The influence of service quality
on customer satisfaction and loyalty in B2B technology service industry." Total Quality
Management & Business Excellence 30, no. 13-14 (2019): 1449-1465.
Jusoh, Ahmad, Abbas Mardani, Rozeyta Omar, Dalia Štreimikienė, Zainab Khalifah, and Ali
Sharifara. "Application of MCDM approach to evaluate the critical success factors of total
quality management in the hospitality industry." Journal of Business Economics and
Management 19, no. 2 (2018): 399-416.
Secure Best Marks with AI Grader
Need help grading? Try our AI Grader for instant feedback on your assignments.
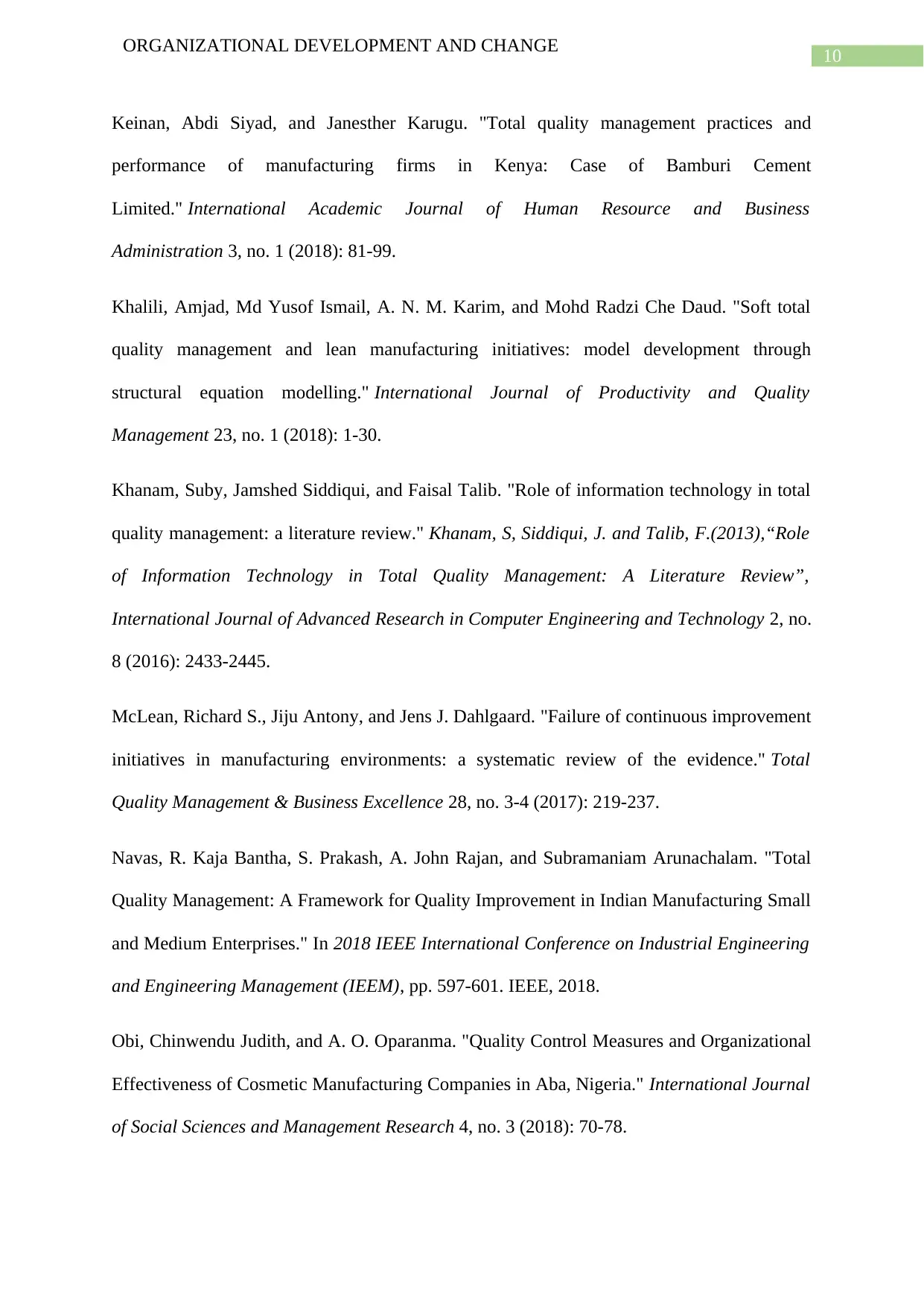
10
ORGANIZATIONAL DEVELOPMENT AND CHANGE
Keinan, Abdi Siyad, and Janesther Karugu. "Total quality management practices and
performance of manufacturing firms in Kenya: Case of Bamburi Cement
Limited." International Academic Journal of Human Resource and Business
Administration 3, no. 1 (2018): 81-99.
Khalili, Amjad, Md Yusof Ismail, A. N. M. Karim, and Mohd Radzi Che Daud. "Soft total
quality management and lean manufacturing initiatives: model development through
structural equation modelling." International Journal of Productivity and Quality
Management 23, no. 1 (2018): 1-30.
Khanam, Suby, Jamshed Siddiqui, and Faisal Talib. "Role of information technology in total
quality management: a literature review." Khanam, S, Siddiqui, J. and Talib, F.(2013),“Role
of Information Technology in Total Quality Management: A Literature Review”,
International Journal of Advanced Research in Computer Engineering and Technology 2, no.
8 (2016): 2433-2445.
McLean, Richard S., Jiju Antony, and Jens J. Dahlgaard. "Failure of continuous improvement
initiatives in manufacturing environments: a systematic review of the evidence." Total
Quality Management & Business Excellence 28, no. 3-4 (2017): 219-237.
Navas, R. Kaja Bantha, S. Prakash, A. John Rajan, and Subramaniam Arunachalam. "Total
Quality Management: A Framework for Quality Improvement in Indian Manufacturing Small
and Medium Enterprises." In 2018 IEEE International Conference on Industrial Engineering
and Engineering Management (IEEM), pp. 597-601. IEEE, 2018.
Obi, Chinwendu Judith, and A. O. Oparanma. "Quality Control Measures and Organizational
Effectiveness of Cosmetic Manufacturing Companies in Aba, Nigeria." International Journal
of Social Sciences and Management Research 4, no. 3 (2018): 70-78.
ORGANIZATIONAL DEVELOPMENT AND CHANGE
Keinan, Abdi Siyad, and Janesther Karugu. "Total quality management practices and
performance of manufacturing firms in Kenya: Case of Bamburi Cement
Limited." International Academic Journal of Human Resource and Business
Administration 3, no. 1 (2018): 81-99.
Khalili, Amjad, Md Yusof Ismail, A. N. M. Karim, and Mohd Radzi Che Daud. "Soft total
quality management and lean manufacturing initiatives: model development through
structural equation modelling." International Journal of Productivity and Quality
Management 23, no. 1 (2018): 1-30.
Khanam, Suby, Jamshed Siddiqui, and Faisal Talib. "Role of information technology in total
quality management: a literature review." Khanam, S, Siddiqui, J. and Talib, F.(2013),“Role
of Information Technology in Total Quality Management: A Literature Review”,
International Journal of Advanced Research in Computer Engineering and Technology 2, no.
8 (2016): 2433-2445.
McLean, Richard S., Jiju Antony, and Jens J. Dahlgaard. "Failure of continuous improvement
initiatives in manufacturing environments: a systematic review of the evidence." Total
Quality Management & Business Excellence 28, no. 3-4 (2017): 219-237.
Navas, R. Kaja Bantha, S. Prakash, A. John Rajan, and Subramaniam Arunachalam. "Total
Quality Management: A Framework for Quality Improvement in Indian Manufacturing Small
and Medium Enterprises." In 2018 IEEE International Conference on Industrial Engineering
and Engineering Management (IEEM), pp. 597-601. IEEE, 2018.
Obi, Chinwendu Judith, and A. O. Oparanma. "Quality Control Measures and Organizational
Effectiveness of Cosmetic Manufacturing Companies in Aba, Nigeria." International Journal
of Social Sciences and Management Research 4, no. 3 (2018): 70-78.
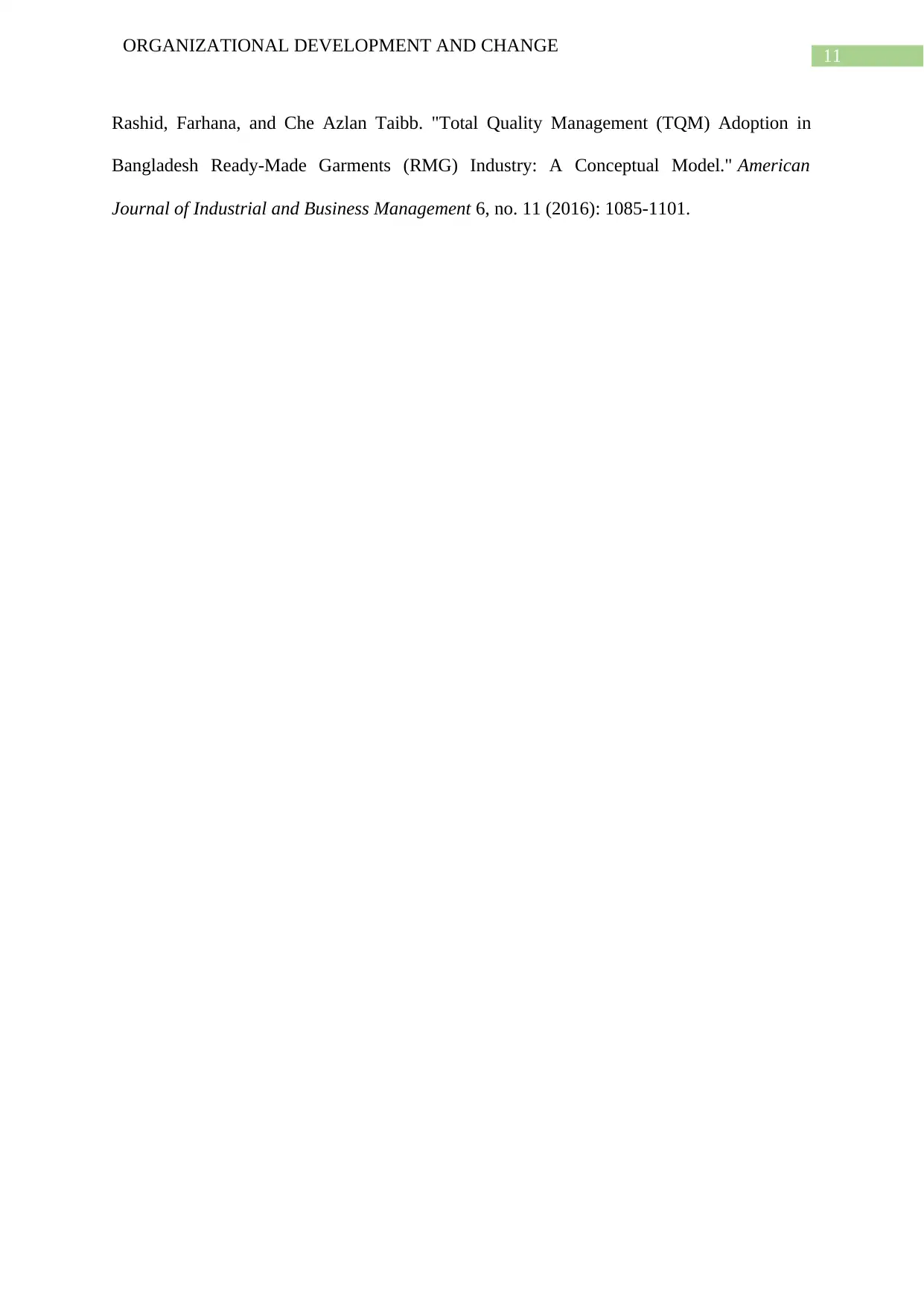
11
ORGANIZATIONAL DEVELOPMENT AND CHANGE
Rashid, Farhana, and Che Azlan Taibb. "Total Quality Management (TQM) Adoption in
Bangladesh Ready-Made Garments (RMG) Industry: A Conceptual Model." American
Journal of Industrial and Business Management 6, no. 11 (2016): 1085-1101.
ORGANIZATIONAL DEVELOPMENT AND CHANGE
Rashid, Farhana, and Che Azlan Taibb. "Total Quality Management (TQM) Adoption in
Bangladesh Ready-Made Garments (RMG) Industry: A Conceptual Model." American
Journal of Industrial and Business Management 6, no. 11 (2016): 1085-1101.
1 out of 12
Related Documents

Your All-in-One AI-Powered Toolkit for Academic Success.
+13062052269
info@desklib.com
Available 24*7 on WhatsApp / Email
Unlock your academic potential
© 2024 | Zucol Services PVT LTD | All rights reserved.