Analysis of Costing Methods: Traditional vs. Activity-Based Costing
VerifiedAdded on  2021/05/31
|15
|2611
|225
Homework Assignment
AI Summary
This assignment analyzes cost accounting methods, focusing on traditional and activity-based costing (ABC) approaches. It begins with a comparative analysis of two models, Basic and Advance, using the traditional costing method, calculating total costs and cost per unit. The solution then presents the same models using ABC, demonstrating how overhead costs are allocated differently, impacting the final cost per unit. A profit and loss statement is then created using both costing methods, showing how sales prices and profit margins are affected. The assignment then examines overhead expenses and how they are allocated, discussing the impact of under and over absorption of overheads. Finally, it explores the advantages and disadvantages of ABC, highlighting its accuracy in calculating product costs, its role in cost control, and its limitations, such as complexity and suitability for certain industries. This assignment is a comprehensive overview of cost accounting principles and their practical application.
Contribute Materials
Your contribution can guide someone’s learning journey. Share your
documents today.
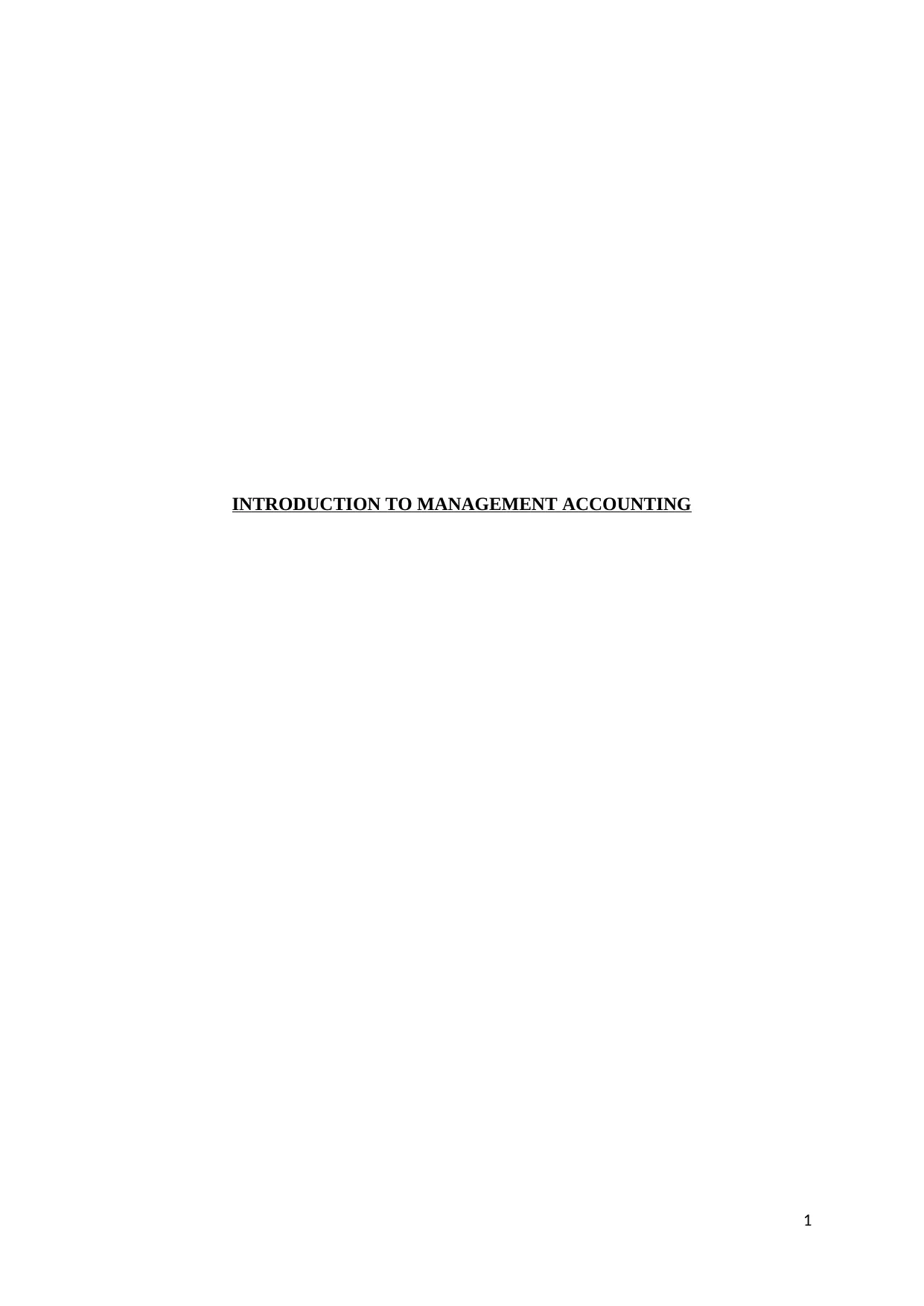
INTRODUCTION TO MANAGEMENT ACCOUNTING
1
1
Secure Best Marks with AI Grader
Need help grading? Try our AI Grader for instant feedback on your assignments.
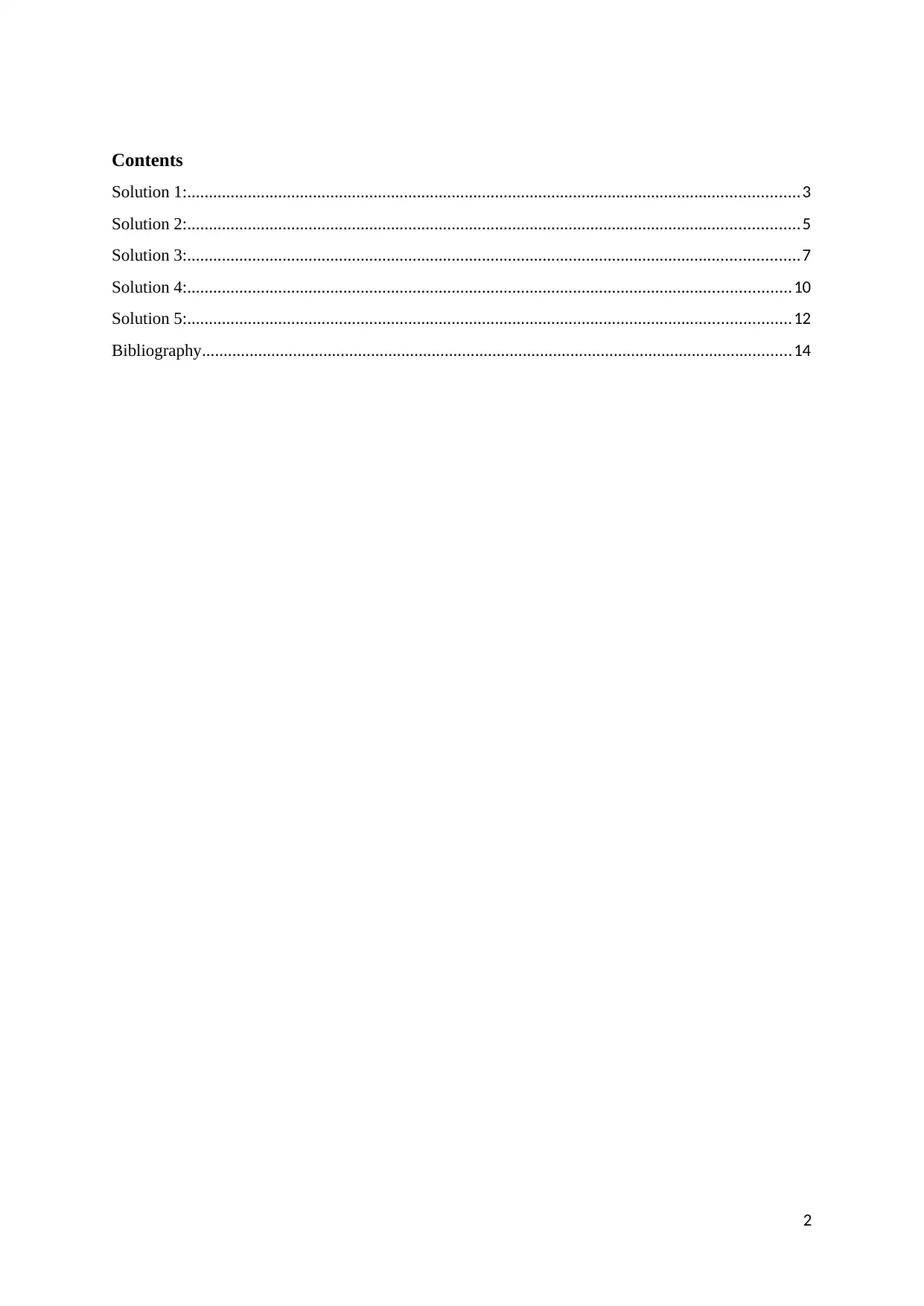
Contents
Solution 1:.............................................................................................................................................3
Solution 2:.............................................................................................................................................5
Solution 3:.............................................................................................................................................7
Solution 4:...........................................................................................................................................10
Solution 5:...........................................................................................................................................12
Bibliography........................................................................................................................................14
2
Solution 1:.............................................................................................................................................3
Solution 2:.............................................................................................................................................5
Solution 3:.............................................................................................................................................7
Solution 4:...........................................................................................................................................10
Solution 5:...........................................................................................................................................12
Bibliography........................................................................................................................................14
2
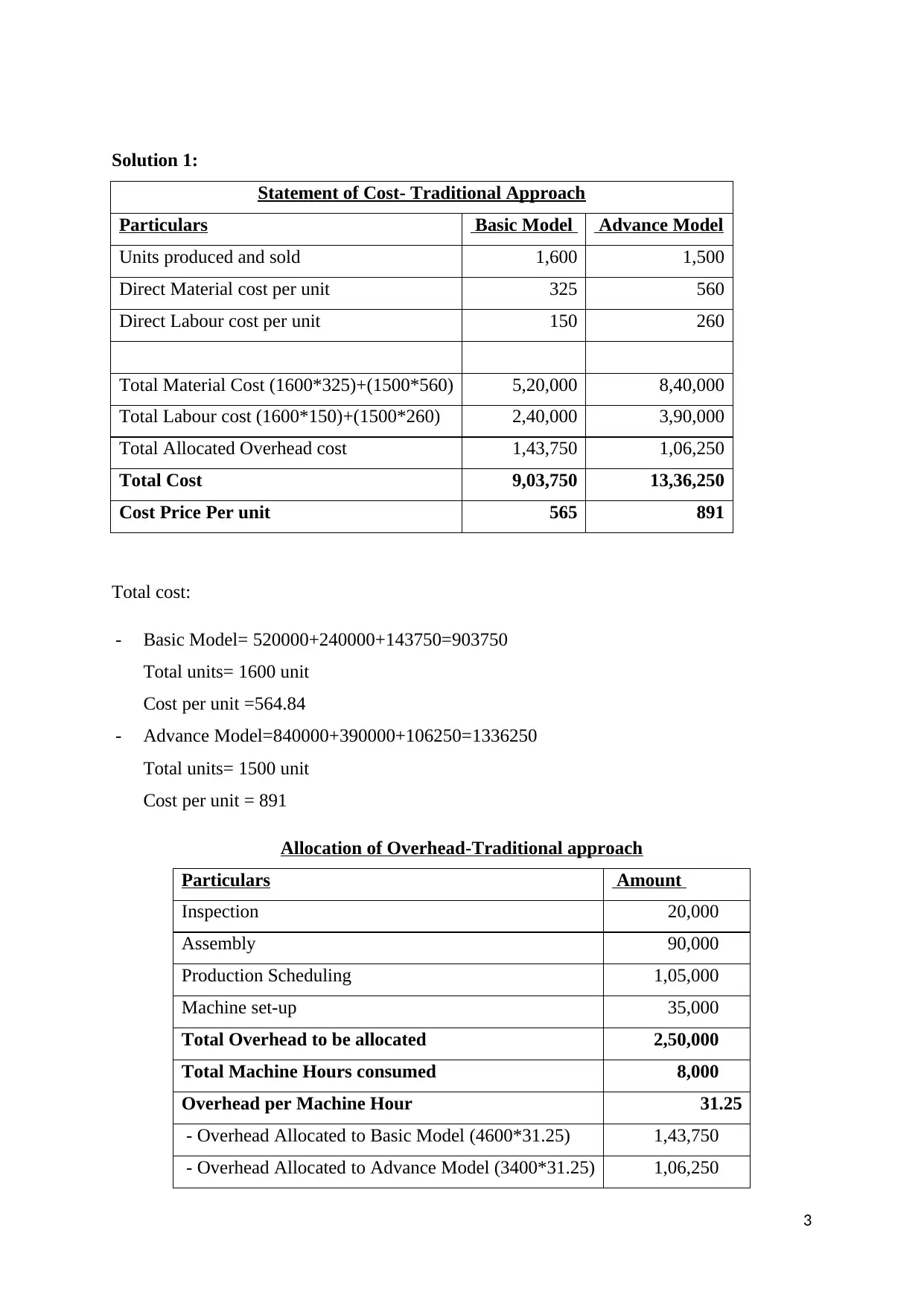
Solution 1:
Statement of Cost- Traditional Approach
Particulars Basic Model Advance Model
Units produced and sold 1,600 1,500
Direct Material cost per unit 325 560
Direct Labour cost per unit 150 260
Total Material Cost (1600*325)+(1500*560) 5,20,000 8,40,000
Total Labour cost (1600*150)+(1500*260) 2,40,000 3,90,000
Total Allocated Overhead cost 1,43,750 1,06,250
Total Cost 9,03,750 13,36,250
Cost Price Per unit 565 891
Total cost:
- Basic Model= 520000+240000+143750=903750
Total units= 1600 unit
Cost per unit =564.84
- Advance Model=840000+390000+106250=1336250
Total units= 1500 unit
Cost per unit = 891
Allocation of Overhead-Traditional approach
Particulars Amount
Inspection 20,000
Assembly 90,000
Production Scheduling 1,05,000
Machine set-up 35,000
Total Overhead to be allocated 2,50,000
Total Machine Hours consumed 8,000
Overhead per Machine Hour 31.25
- Overhead Allocated to Basic Model (4600*31.25) 1,43,750
- Overhead Allocated to Advance Model (3400*31.25) 1,06,250
3
Statement of Cost- Traditional Approach
Particulars Basic Model Advance Model
Units produced and sold 1,600 1,500
Direct Material cost per unit 325 560
Direct Labour cost per unit 150 260
Total Material Cost (1600*325)+(1500*560) 5,20,000 8,40,000
Total Labour cost (1600*150)+(1500*260) 2,40,000 3,90,000
Total Allocated Overhead cost 1,43,750 1,06,250
Total Cost 9,03,750 13,36,250
Cost Price Per unit 565 891
Total cost:
- Basic Model= 520000+240000+143750=903750
Total units= 1600 unit
Cost per unit =564.84
- Advance Model=840000+390000+106250=1336250
Total units= 1500 unit
Cost per unit = 891
Allocation of Overhead-Traditional approach
Particulars Amount
Inspection 20,000
Assembly 90,000
Production Scheduling 1,05,000
Machine set-up 35,000
Total Overhead to be allocated 2,50,000
Total Machine Hours consumed 8,000
Overhead per Machine Hour 31.25
- Overhead Allocated to Basic Model (4600*31.25) 1,43,750
- Overhead Allocated to Advance Model (3400*31.25) 1,06,250
3
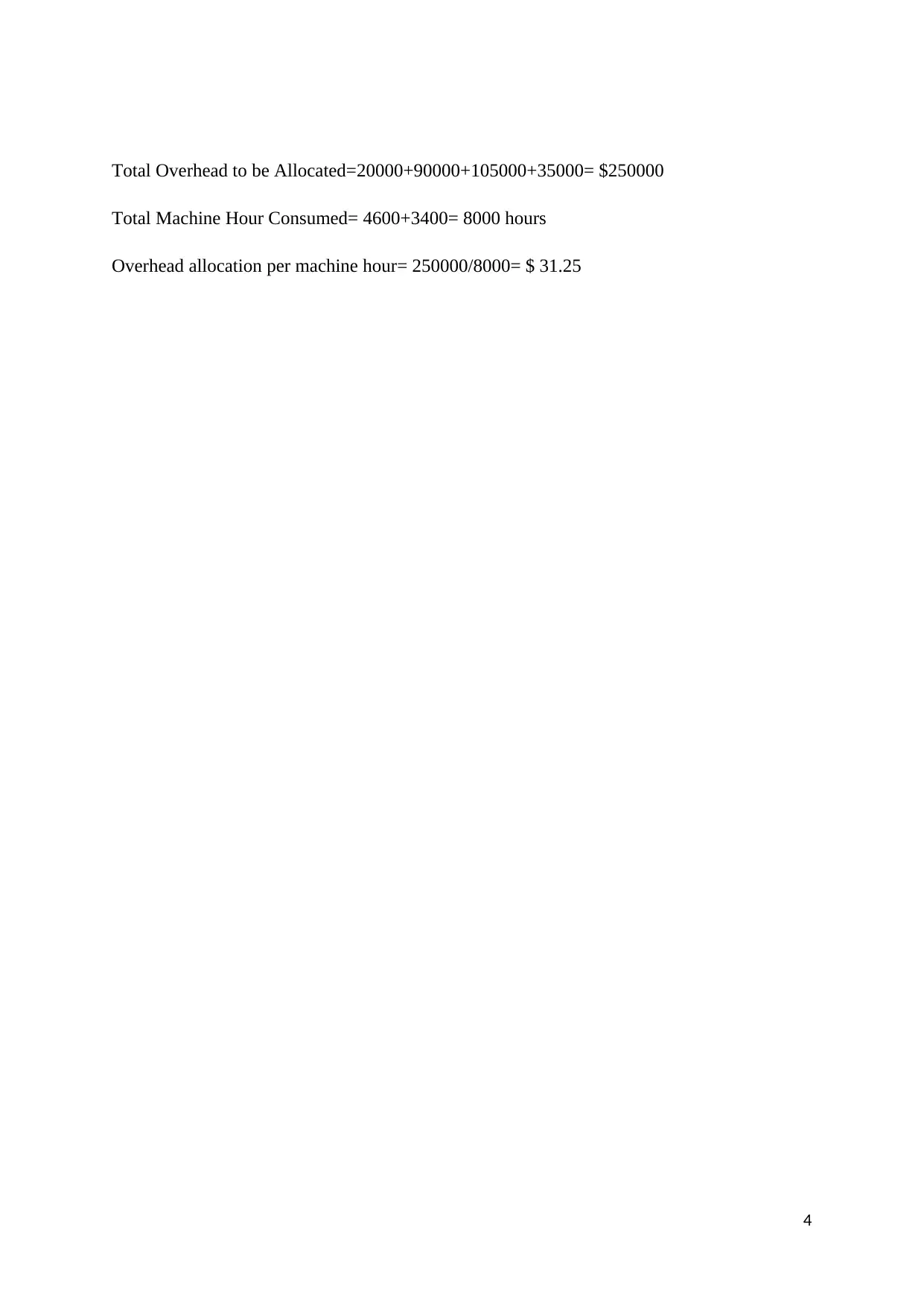
Total Overhead to be Allocated=20000+90000+105000+35000= $250000
Total Machine Hour Consumed= 4600+3400= 8000 hours
Overhead allocation per machine hour= 250000/8000= $ 31.25
4
Total Machine Hour Consumed= 4600+3400= 8000 hours
Overhead allocation per machine hour= 250000/8000= $ 31.25
4
Secure Best Marks with AI Grader
Need help grading? Try our AI Grader for instant feedback on your assignments.

Solution 2:
Statement of Cost- ABC approach
Particulars Basic Model Advance Model
Units produced and sold 1,600 1,500
Direct Material cost per unit 325 560
Direct Labour cost per unit 150 260
Total Material Cost (1600*325)+(1500*560) 5,20,000 8,40,000
Total Labour cost (1600*150)+(1500*260) 2,40,000 3,90,000
Total Allocated Overhead cost 75,506 1,74,494
Total Cost 8,35,506 14,04,494
Cost Price Per unit 522 936
Total cost:
- Basic Model= 520000+240000+75506=835506
Total units= 1600 unit
Cost per unit = $522
- Advance Model=840000+390000+174494=1404494
Total units= 1500 unit
Cost per unit = $936
Allocation of Overhead-ABC Approach
Particulars Inspection
Assem
bly
Production
Scheduling
Machine
set-up
Total
Cost
Cost 20,000 90,000 1,05,000 35,000 2,50,000
Units 950 8,000 550 350
Cost per unit 21 11 191 100
Units for Basic
Model 200 4,600 50 100
Units for Advance 750 3,400 500 250
5
Statement of Cost- ABC approach
Particulars Basic Model Advance Model
Units produced and sold 1,600 1,500
Direct Material cost per unit 325 560
Direct Labour cost per unit 150 260
Total Material Cost (1600*325)+(1500*560) 5,20,000 8,40,000
Total Labour cost (1600*150)+(1500*260) 2,40,000 3,90,000
Total Allocated Overhead cost 75,506 1,74,494
Total Cost 8,35,506 14,04,494
Cost Price Per unit 522 936
Total cost:
- Basic Model= 520000+240000+75506=835506
Total units= 1600 unit
Cost per unit = $522
- Advance Model=840000+390000+174494=1404494
Total units= 1500 unit
Cost per unit = $936
Allocation of Overhead-ABC Approach
Particulars Inspection
Assem
bly
Production
Scheduling
Machine
set-up
Total
Cost
Cost 20,000 90,000 1,05,000 35,000 2,50,000
Units 950 8,000 550 350
Cost per unit 21 11 191 100
Units for Basic
Model 200 4,600 50 100
Units for Advance 750 3,400 500 250
5
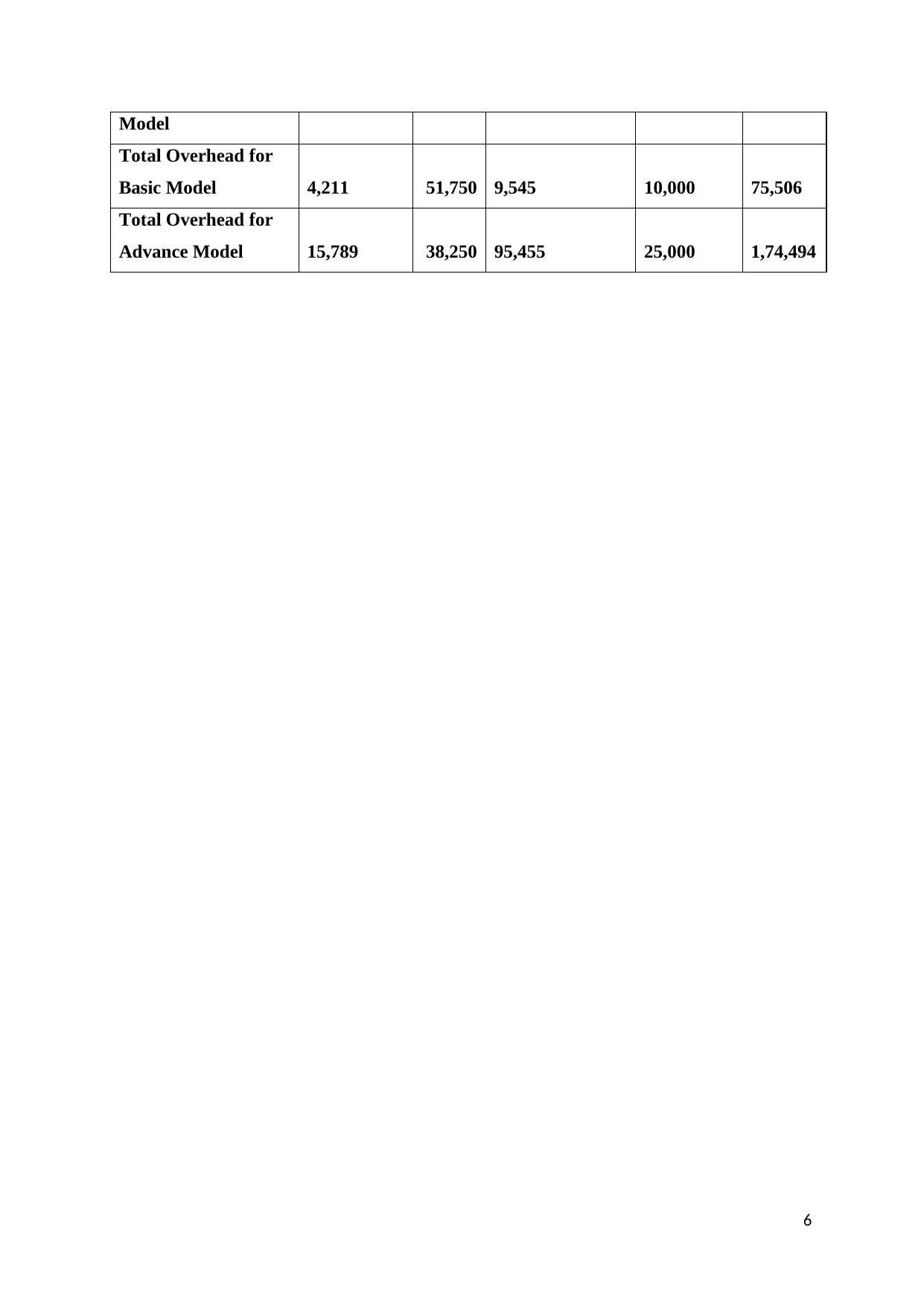
Model
Total Overhead for
Basic Model 4,211 51,750 9,545 10,000 75,506
Total Overhead for
Advance Model 15,789 38,250 95,455 25,000 1,74,494
6
Total Overhead for
Basic Model 4,211 51,750 9,545 10,000 75,506
Total Overhead for
Advance Model 15,789 38,250 95,455 25,000 1,74,494
6
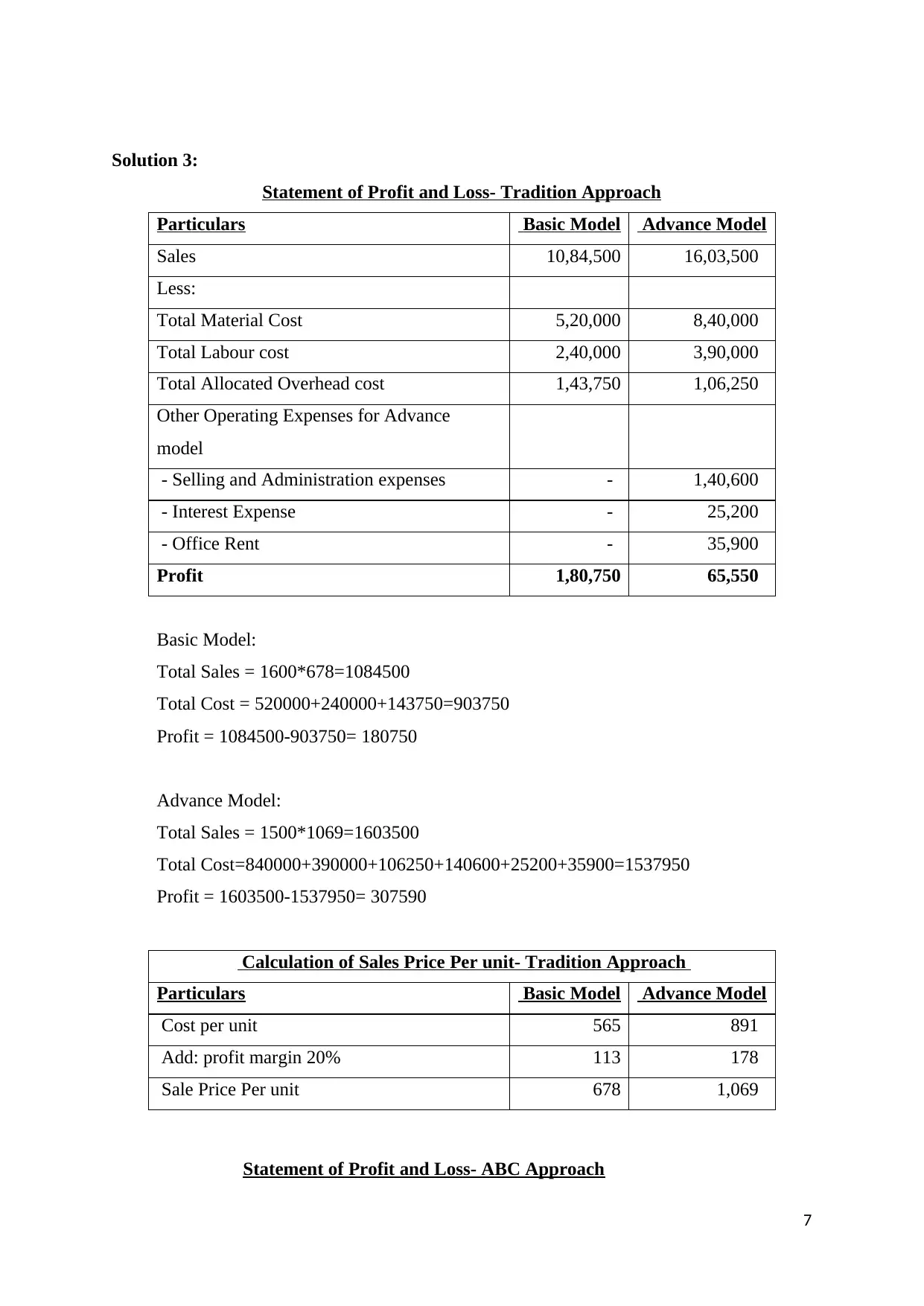
Solution 3:
Statement of Profit and Loss- Tradition Approach
Particulars Basic Model Advance Model
Sales 10,84,500 16,03,500
Less:
Total Material Cost 5,20,000 8,40,000
Total Labour cost 2,40,000 3,90,000
Total Allocated Overhead cost 1,43,750 1,06,250
Other Operating Expenses for Advance
model
- Selling and Administration expenses - 1,40,600
- Interest Expense - 25,200
- Office Rent - 35,900
Profit 1,80,750 65,550
Basic Model:
Total Sales = 1600*678=1084500
Total Cost = 520000+240000+143750=903750
Profit = 1084500-903750= 180750
Advance Model:
Total Sales = 1500*1069=1603500
Total Cost=840000+390000+106250+140600+25200+35900=1537950
Profit = 1603500-1537950= 307590
Calculation of Sales Price Per unit- Tradition Approach
Particulars Basic Model Advance Model
Cost per unit 565 891
Add: profit margin 20% 113 178
Sale Price Per unit 678 1,069
Statement of Profit and Loss- ABC Approach
7
Statement of Profit and Loss- Tradition Approach
Particulars Basic Model Advance Model
Sales 10,84,500 16,03,500
Less:
Total Material Cost 5,20,000 8,40,000
Total Labour cost 2,40,000 3,90,000
Total Allocated Overhead cost 1,43,750 1,06,250
Other Operating Expenses for Advance
model
- Selling and Administration expenses - 1,40,600
- Interest Expense - 25,200
- Office Rent - 35,900
Profit 1,80,750 65,550
Basic Model:
Total Sales = 1600*678=1084500
Total Cost = 520000+240000+143750=903750
Profit = 1084500-903750= 180750
Advance Model:
Total Sales = 1500*1069=1603500
Total Cost=840000+390000+106250+140600+25200+35900=1537950
Profit = 1603500-1537950= 307590
Calculation of Sales Price Per unit- Tradition Approach
Particulars Basic Model Advance Model
Cost per unit 565 891
Add: profit margin 20% 113 178
Sale Price Per unit 678 1,069
Statement of Profit and Loss- ABC Approach
7
Paraphrase This Document
Need a fresh take? Get an instant paraphrase of this document with our AI Paraphraser

Particulars Basic Model Advance Model
Sales 10,02,607 16,85,393
Less:
Total Material Cost 5,20,000 8,40,000
Total Labour cost 2,40,000 3,90,000
Total Allocated Overhead cost 75,506 1,74,494
Other Operating Expenses for Advance
model
- Selling and Administration expenses - 1,40,600
- Interest Expense - 25,200
- Office Rent - 35,900
Profit 1,67,101 79,199
Basic Model:
Total Sales = 1600*624=998178
Total Cost = 520000+240000+75506=835506
Profit = 998178-835506= 167101
Advance Model:
Total Sales = 1500*1124=1685393
Total Cost=840000+390000+174494+140600+25200+35900=1606194
Profit = 1685393-1606194=79199
Calculation of Sales Price Per unit- ABC Approach
Particulars Basic Model Advance Model
Cost per unit 522 936
Add: profit margin 20% 104 187
Sale Price Per unit 627 1,124
In the given case we see that the overseas buyer is interested in buying only the advance
model and not the basic model of the sewing machines. Also, that the company has been
currently using traditional costing practices. From the table above we can see that the price
which the company would have offered to the overseas buyer would have been $1069 per
8
Sales 10,02,607 16,85,393
Less:
Total Material Cost 5,20,000 8,40,000
Total Labour cost 2,40,000 3,90,000
Total Allocated Overhead cost 75,506 1,74,494
Other Operating Expenses for Advance
model
- Selling and Administration expenses - 1,40,600
- Interest Expense - 25,200
- Office Rent - 35,900
Profit 1,67,101 79,199
Basic Model:
Total Sales = 1600*624=998178
Total Cost = 520000+240000+75506=835506
Profit = 998178-835506= 167101
Advance Model:
Total Sales = 1500*1124=1685393
Total Cost=840000+390000+174494+140600+25200+35900=1606194
Profit = 1685393-1606194=79199
Calculation of Sales Price Per unit- ABC Approach
Particulars Basic Model Advance Model
Cost per unit 522 936
Add: profit margin 20% 104 187
Sale Price Per unit 627 1,124
In the given case we see that the overseas buyer is interested in buying only the advance
model and not the basic model of the sewing machines. Also, that the company has been
currently using traditional costing practices. From the table above we can see that the price
which the company would have offered to the overseas buyer would have been $1069 per
8
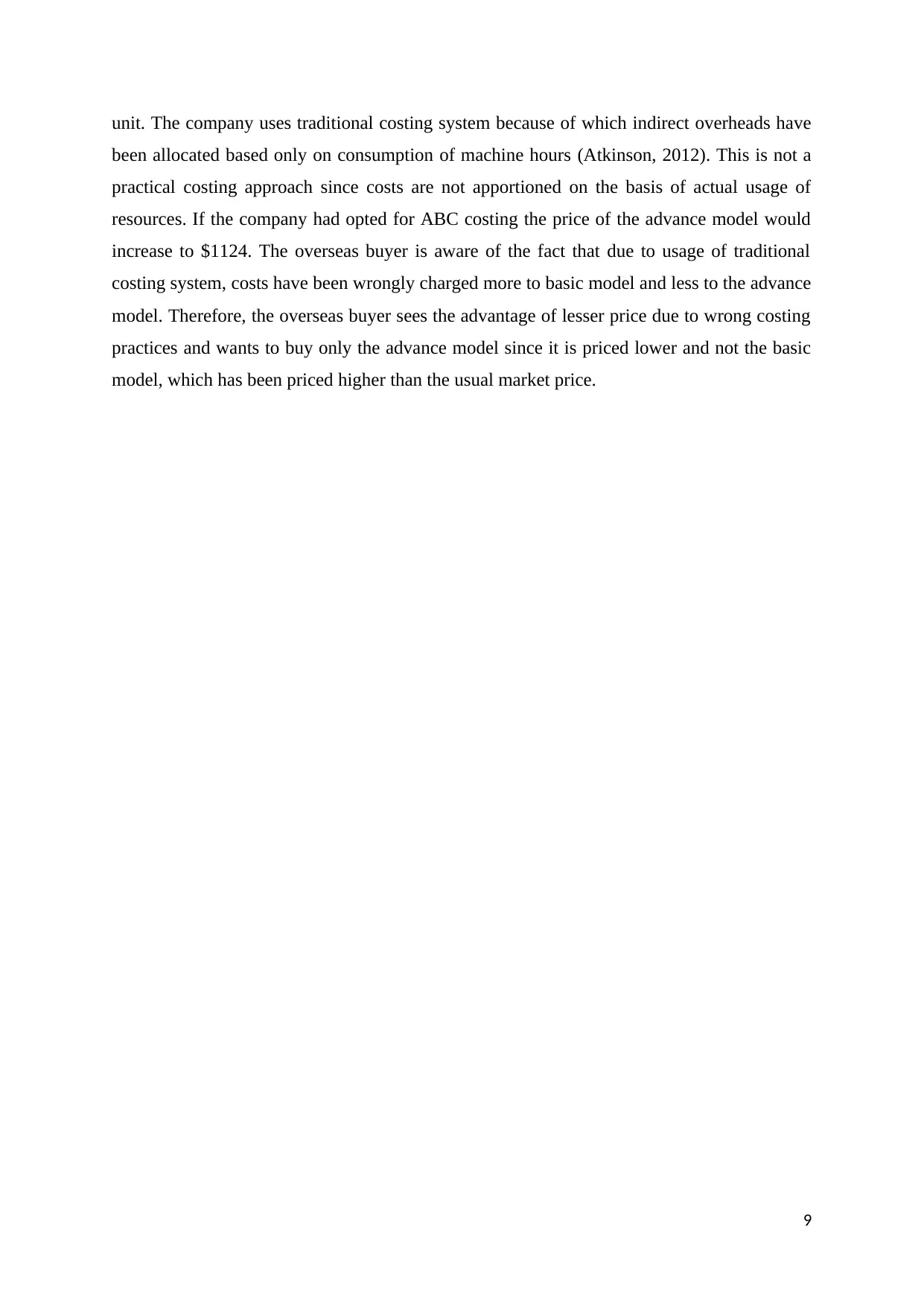
unit. The company uses traditional costing system because of which indirect overheads have
been allocated based only on consumption of machine hours (Atkinson, 2012). This is not a
practical costing approach since costs are not apportioned on the basis of actual usage of
resources. If the company had opted for ABC costing the price of the advance model would
increase to $1124. The overseas buyer is aware of the fact that due to usage of traditional
costing system, costs have been wrongly charged more to basic model and less to the advance
model. Therefore, the overseas buyer sees the advantage of lesser price due to wrong costing
practices and wants to buy only the advance model since it is priced lower and not the basic
model, which has been priced higher than the usual market price.
9
been allocated based only on consumption of machine hours (Atkinson, 2012). This is not a
practical costing approach since costs are not apportioned on the basis of actual usage of
resources. If the company had opted for ABC costing the price of the advance model would
increase to $1124. The overseas buyer is aware of the fact that due to usage of traditional
costing system, costs have been wrongly charged more to basic model and less to the advance
model. Therefore, the overseas buyer sees the advantage of lesser price due to wrong costing
practices and wants to buy only the advance model since it is priced lower and not the basic
model, which has been priced higher than the usual market price.
9
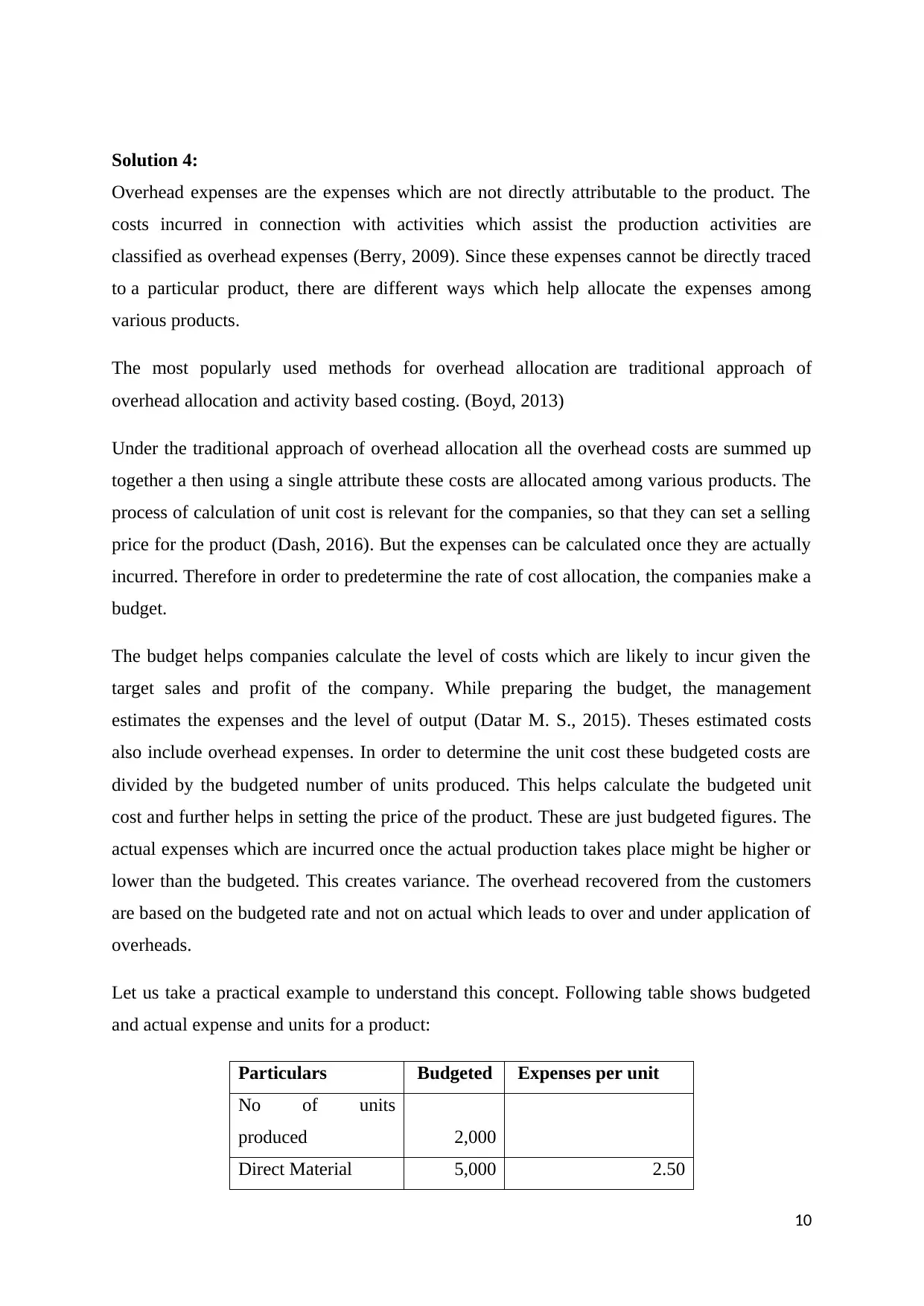
Solution 4:
Overhead expenses are the expenses which are not directly attributable to the product. The
costs incurred in connection with activities which assist the production activities are
classified as overhead expenses (Berry, 2009). Since these expenses cannot be directly traced
to a particular product, there are different ways which help allocate the expenses among
various products.
The most popularly used methods for overhead allocation are traditional approach of
overhead allocation and activity based costing. (Boyd, 2013)
Under the traditional approach of overhead allocation all the overhead costs are summed up
together a then using a single attribute these costs are allocated among various products. The
process of calculation of unit cost is relevant for the companies, so that they can set a selling
price for the product (Dash, 2016). But the expenses can be calculated once they are actually
incurred. Therefore in order to predetermine the rate of cost allocation, the companies make a
budget.
The budget helps companies calculate the level of costs which are likely to incur given the
target sales and profit of the company. While preparing the budget, the management
estimates the expenses and the level of output (Datar M. S., 2015). Theses estimated costs
also include overhead expenses. In order to determine the unit cost these budgeted costs are
divided by the budgeted number of units produced. This helps calculate the budgeted unit
cost and further helps in setting the price of the product. These are just budgeted figures. The
actual expenses which are incurred once the actual production takes place might be higher or
lower than the budgeted. This creates variance. The overhead recovered from the customers
are based on the budgeted rate and not on actual which leads to over and under application of
overheads.
Let us take a practical example to understand this concept. Following table shows budgeted
and actual expense and units for a product:
Particulars Budgeted Expenses per unit
No of units
produced 2,000
Direct Material 5,000 2.50
10
Overhead expenses are the expenses which are not directly attributable to the product. The
costs incurred in connection with activities which assist the production activities are
classified as overhead expenses (Berry, 2009). Since these expenses cannot be directly traced
to a particular product, there are different ways which help allocate the expenses among
various products.
The most popularly used methods for overhead allocation are traditional approach of
overhead allocation and activity based costing. (Boyd, 2013)
Under the traditional approach of overhead allocation all the overhead costs are summed up
together a then using a single attribute these costs are allocated among various products. The
process of calculation of unit cost is relevant for the companies, so that they can set a selling
price for the product (Dash, 2016). But the expenses can be calculated once they are actually
incurred. Therefore in order to predetermine the rate of cost allocation, the companies make a
budget.
The budget helps companies calculate the level of costs which are likely to incur given the
target sales and profit of the company. While preparing the budget, the management
estimates the expenses and the level of output (Datar M. S., 2015). Theses estimated costs
also include overhead expenses. In order to determine the unit cost these budgeted costs are
divided by the budgeted number of units produced. This helps calculate the budgeted unit
cost and further helps in setting the price of the product. These are just budgeted figures. The
actual expenses which are incurred once the actual production takes place might be higher or
lower than the budgeted. This creates variance. The overhead recovered from the customers
are based on the budgeted rate and not on actual which leads to over and under application of
overheads.
Let us take a practical example to understand this concept. Following table shows budgeted
and actual expense and units for a product:
Particulars Budgeted Expenses per unit
No of units
produced 2,000
Direct Material 5,000 2.50
10
Secure Best Marks with AI Grader
Need help grading? Try our AI Grader for instant feedback on your assignments.
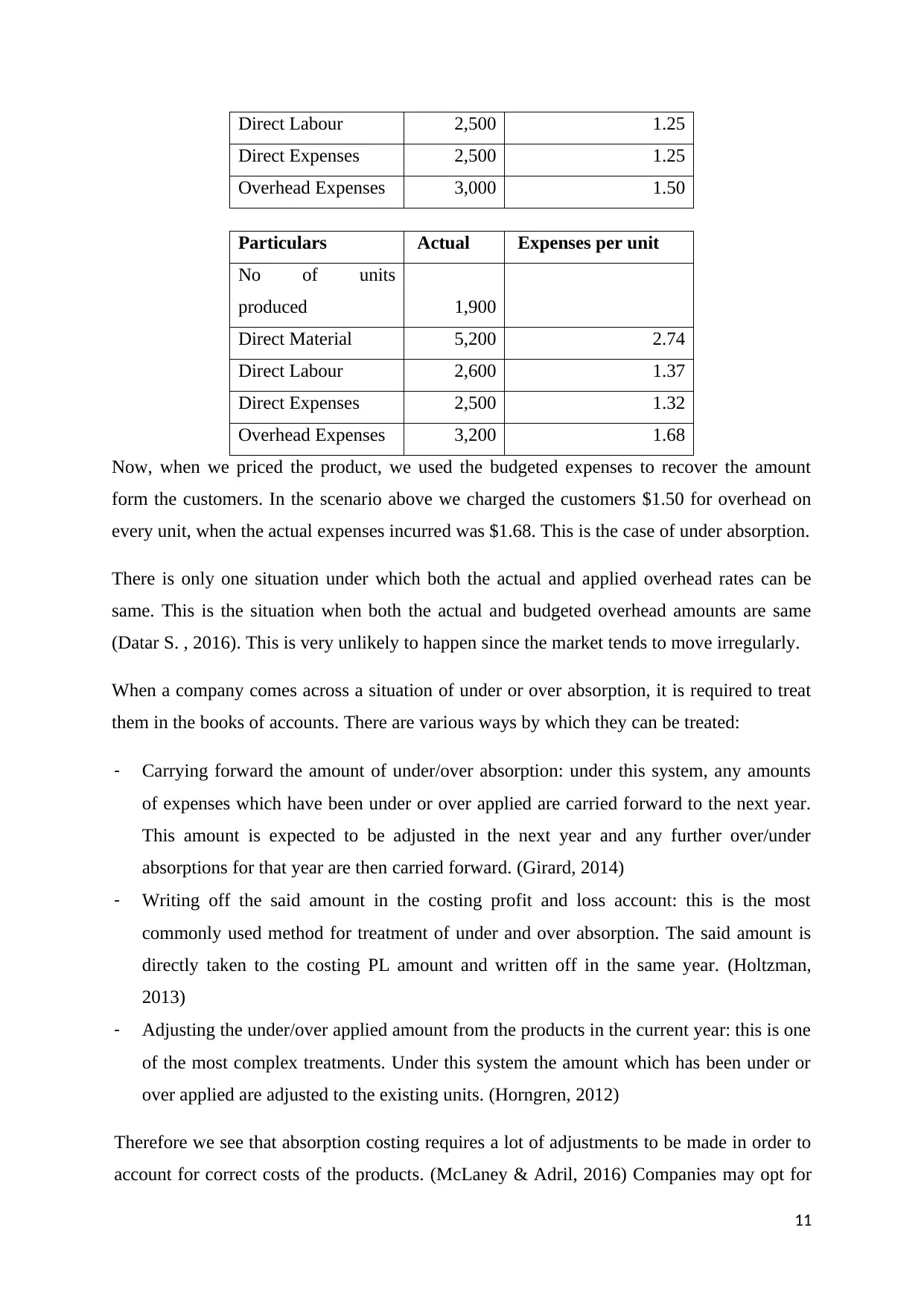
Direct Labour 2,500 1.25
Direct Expenses 2,500 1.25
Overhead Expenses 3,000 1.50
Particulars Actual Expenses per unit
No of units
produced 1,900
Direct Material 5,200 2.74
Direct Labour 2,600 1.37
Direct Expenses 2,500 1.32
Overhead Expenses 3,200 1.68
Now, when we priced the product, we used the budgeted expenses to recover the amount
form the customers. In the scenario above we charged the customers $1.50 for overhead on
every unit, when the actual expenses incurred was $1.68. This is the case of under absorption.
There is only one situation under which both the actual and applied overhead rates can be
same. This is the situation when both the actual and budgeted overhead amounts are same
(Datar S. , 2016). This is very unlikely to happen since the market tends to move irregularly.
When a company comes across a situation of under or over absorption, it is required to treat
them in the books of accounts. There are various ways by which they can be treated:
- Carrying forward the amount of under/over absorption: under this system, any amounts
of expenses which have been under or over applied are carried forward to the next year.
This amount is expected to be adjusted in the next year and any further over/under
absorptions for that year are then carried forward. (Girard, 2014)
- Writing off the said amount in the costing profit and loss account: this is the most
commonly used method for treatment of under and over absorption. The said amount is
directly taken to the costing PL amount and written off in the same year. (Holtzman,
2013)
- Adjusting the under/over applied amount from the products in the current year: this is one
of the most complex treatments. Under this system the amount which has been under or
over applied are adjusted to the existing units. (Horngren, 2012)
Therefore we see that absorption costing requires a lot of adjustments to be made in order to
account for correct costs of the products. (McLaney & Adril, 2016) Companies may opt for
11
Direct Expenses 2,500 1.25
Overhead Expenses 3,000 1.50
Particulars Actual Expenses per unit
No of units
produced 1,900
Direct Material 5,200 2.74
Direct Labour 2,600 1.37
Direct Expenses 2,500 1.32
Overhead Expenses 3,200 1.68
Now, when we priced the product, we used the budgeted expenses to recover the amount
form the customers. In the scenario above we charged the customers $1.50 for overhead on
every unit, when the actual expenses incurred was $1.68. This is the case of under absorption.
There is only one situation under which both the actual and applied overhead rates can be
same. This is the situation when both the actual and budgeted overhead amounts are same
(Datar S. , 2016). This is very unlikely to happen since the market tends to move irregularly.
When a company comes across a situation of under or over absorption, it is required to treat
them in the books of accounts. There are various ways by which they can be treated:
- Carrying forward the amount of under/over absorption: under this system, any amounts
of expenses which have been under or over applied are carried forward to the next year.
This amount is expected to be adjusted in the next year and any further over/under
absorptions for that year are then carried forward. (Girard, 2014)
- Writing off the said amount in the costing profit and loss account: this is the most
commonly used method for treatment of under and over absorption. The said amount is
directly taken to the costing PL amount and written off in the same year. (Holtzman,
2013)
- Adjusting the under/over applied amount from the products in the current year: this is one
of the most complex treatments. Under this system the amount which has been under or
over applied are adjusted to the existing units. (Horngren, 2012)
Therefore we see that absorption costing requires a lot of adjustments to be made in order to
account for correct costs of the products. (McLaney & Adril, 2016) Companies may opt for
11
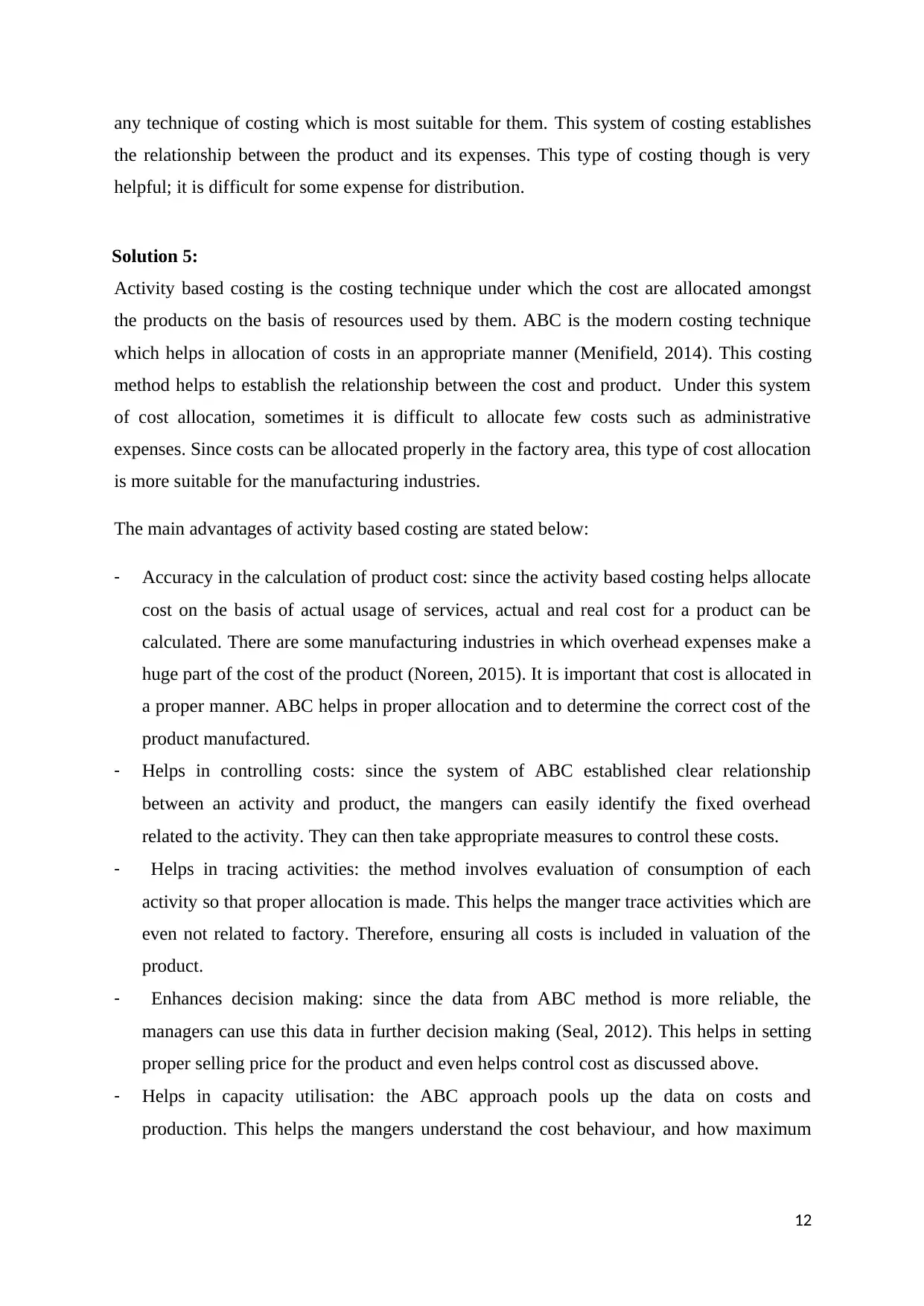
any technique of costing which is most suitable for them. This system of costing establishes
the relationship between the product and its expenses. This type of costing though is very
helpful; it is difficult for some expense for distribution.
Solution 5:
Activity based costing is the costing technique under which the cost are allocated amongst
the products on the basis of resources used by them. ABC is the modern costing technique
which helps in allocation of costs in an appropriate manner (Menifield, 2014). This costing
method helps to establish the relationship between the cost and product. Under this system
of cost allocation, sometimes it is difficult to allocate few costs such as administrative
expenses. Since costs can be allocated properly in the factory area, this type of cost allocation
is more suitable for the manufacturing industries.
The main advantages of activity based costing are stated below:
- Accuracy in the calculation of product cost: since the activity based costing helps allocate
cost on the basis of actual usage of services, actual and real cost for a product can be
calculated. There are some manufacturing industries in which overhead expenses make a
huge part of the cost of the product (Noreen, 2015). It is important that cost is allocated in
a proper manner. ABC helps in proper allocation and to determine the correct cost of the
product manufactured.
- Helps in controlling costs: since the system of ABC established clear relationship
between an activity and product, the mangers can easily identify the fixed overhead
related to the activity. They can then take appropriate measures to control these costs.
- Helps in tracing activities: the method involves evaluation of consumption of each
activity so that proper allocation is made. This helps the manger trace activities which are
even not related to factory. Therefore, ensuring all costs is included in valuation of the
product.
- Enhances decision making: since the data from ABC method is more reliable, the
managers can use this data in further decision making (Seal, 2012). This helps in setting
proper selling price for the product and even helps control cost as discussed above.
- Helps in capacity utilisation: the ABC approach pools up the data on costs and
production. This helps the mangers understand the cost behaviour, and how maximum
12
the relationship between the product and its expenses. This type of costing though is very
helpful; it is difficult for some expense for distribution.
Solution 5:
Activity based costing is the costing technique under which the cost are allocated amongst
the products on the basis of resources used by them. ABC is the modern costing technique
which helps in allocation of costs in an appropriate manner (Menifield, 2014). This costing
method helps to establish the relationship between the cost and product. Under this system
of cost allocation, sometimes it is difficult to allocate few costs such as administrative
expenses. Since costs can be allocated properly in the factory area, this type of cost allocation
is more suitable for the manufacturing industries.
The main advantages of activity based costing are stated below:
- Accuracy in the calculation of product cost: since the activity based costing helps allocate
cost on the basis of actual usage of services, actual and real cost for a product can be
calculated. There are some manufacturing industries in which overhead expenses make a
huge part of the cost of the product (Noreen, 2015). It is important that cost is allocated in
a proper manner. ABC helps in proper allocation and to determine the correct cost of the
product manufactured.
- Helps in controlling costs: since the system of ABC established clear relationship
between an activity and product, the mangers can easily identify the fixed overhead
related to the activity. They can then take appropriate measures to control these costs.
- Helps in tracing activities: the method involves evaluation of consumption of each
activity so that proper allocation is made. This helps the manger trace activities which are
even not related to factory. Therefore, ensuring all costs is included in valuation of the
product.
- Enhances decision making: since the data from ABC method is more reliable, the
managers can use this data in further decision making (Seal, 2012). This helps in setting
proper selling price for the product and even helps control cost as discussed above.
- Helps in capacity utilisation: the ABC approach pools up the data on costs and
production. This helps the mangers understand the cost behaviour, and how maximum
12
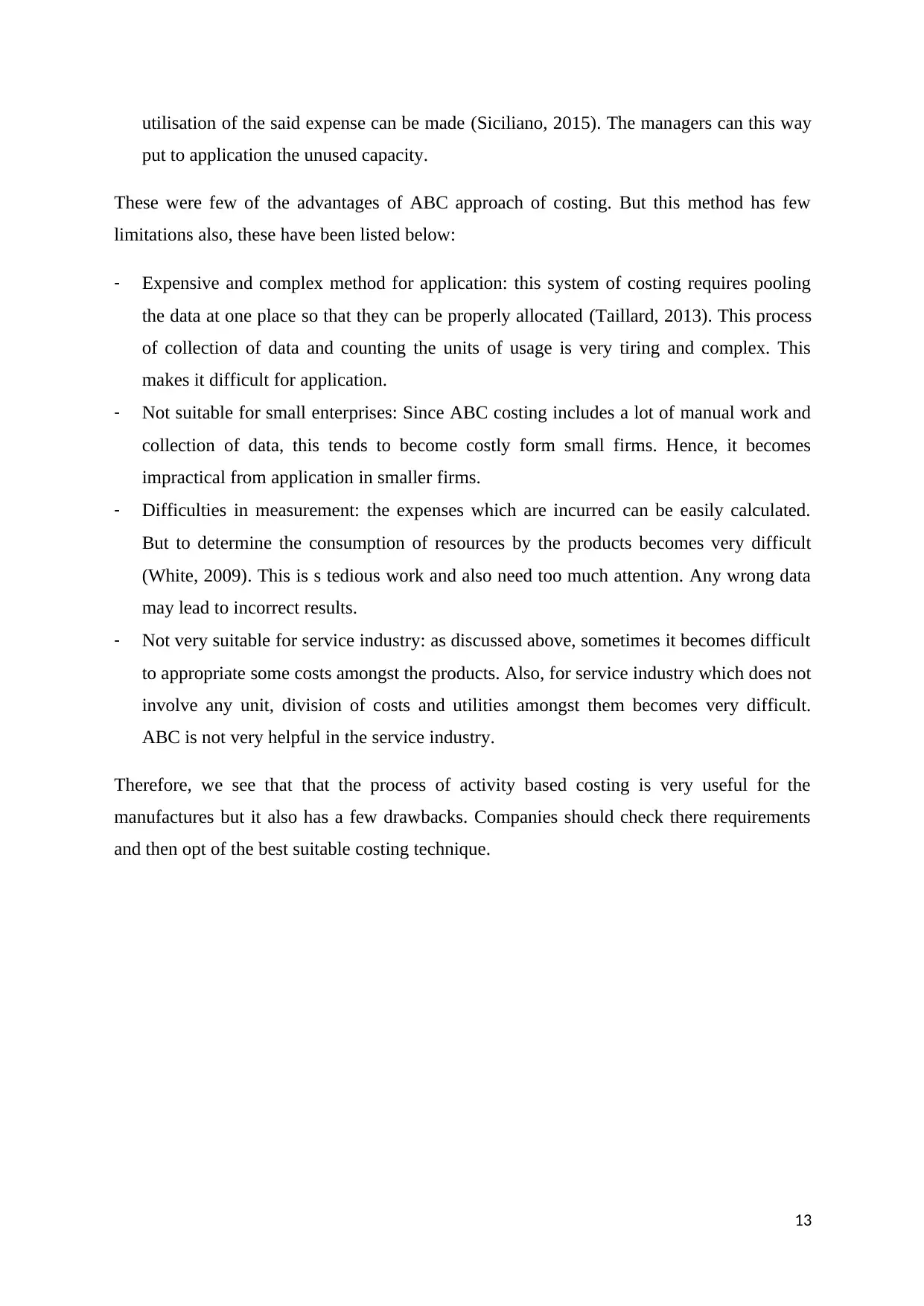
utilisation of the said expense can be made (Siciliano, 2015). The managers can this way
put to application the unused capacity.
These were few of the advantages of ABC approach of costing. But this method has few
limitations also, these have been listed below:
- Expensive and complex method for application: this system of costing requires pooling
the data at one place so that they can be properly allocated (Taillard, 2013). This process
of collection of data and counting the units of usage is very tiring and complex. This
makes it difficult for application.
- Not suitable for small enterprises: Since ABC costing includes a lot of manual work and
collection of data, this tends to become costly form small firms. Hence, it becomes
impractical from application in smaller firms.
- Difficulties in measurement: the expenses which are incurred can be easily calculated.
But to determine the consumption of resources by the products becomes very difficult
(White, 2009). This is s tedious work and also need too much attention. Any wrong data
may lead to incorrect results.
- Not very suitable for service industry: as discussed above, sometimes it becomes difficult
to appropriate some costs amongst the products. Also, for service industry which does not
involve any unit, division of costs and utilities amongst them becomes very difficult.
ABC is not very helpful in the service industry.
Therefore, we see that that the process of activity based costing is very useful for the
manufactures but it also has a few drawbacks. Companies should check there requirements
and then opt of the best suitable costing technique.
13
put to application the unused capacity.
These were few of the advantages of ABC approach of costing. But this method has few
limitations also, these have been listed below:
- Expensive and complex method for application: this system of costing requires pooling
the data at one place so that they can be properly allocated (Taillard, 2013). This process
of collection of data and counting the units of usage is very tiring and complex. This
makes it difficult for application.
- Not suitable for small enterprises: Since ABC costing includes a lot of manual work and
collection of data, this tends to become costly form small firms. Hence, it becomes
impractical from application in smaller firms.
- Difficulties in measurement: the expenses which are incurred can be easily calculated.
But to determine the consumption of resources by the products becomes very difficult
(White, 2009). This is s tedious work and also need too much attention. Any wrong data
may lead to incorrect results.
- Not very suitable for service industry: as discussed above, sometimes it becomes difficult
to appropriate some costs amongst the products. Also, for service industry which does not
involve any unit, division of costs and utilities amongst them becomes very difficult.
ABC is not very helpful in the service industry.
Therefore, we see that that the process of activity based costing is very useful for the
manufactures but it also has a few drawbacks. Companies should check there requirements
and then opt of the best suitable costing technique.
13
Paraphrase This Document
Need a fresh take? Get an instant paraphrase of this document with our AI Paraphraser
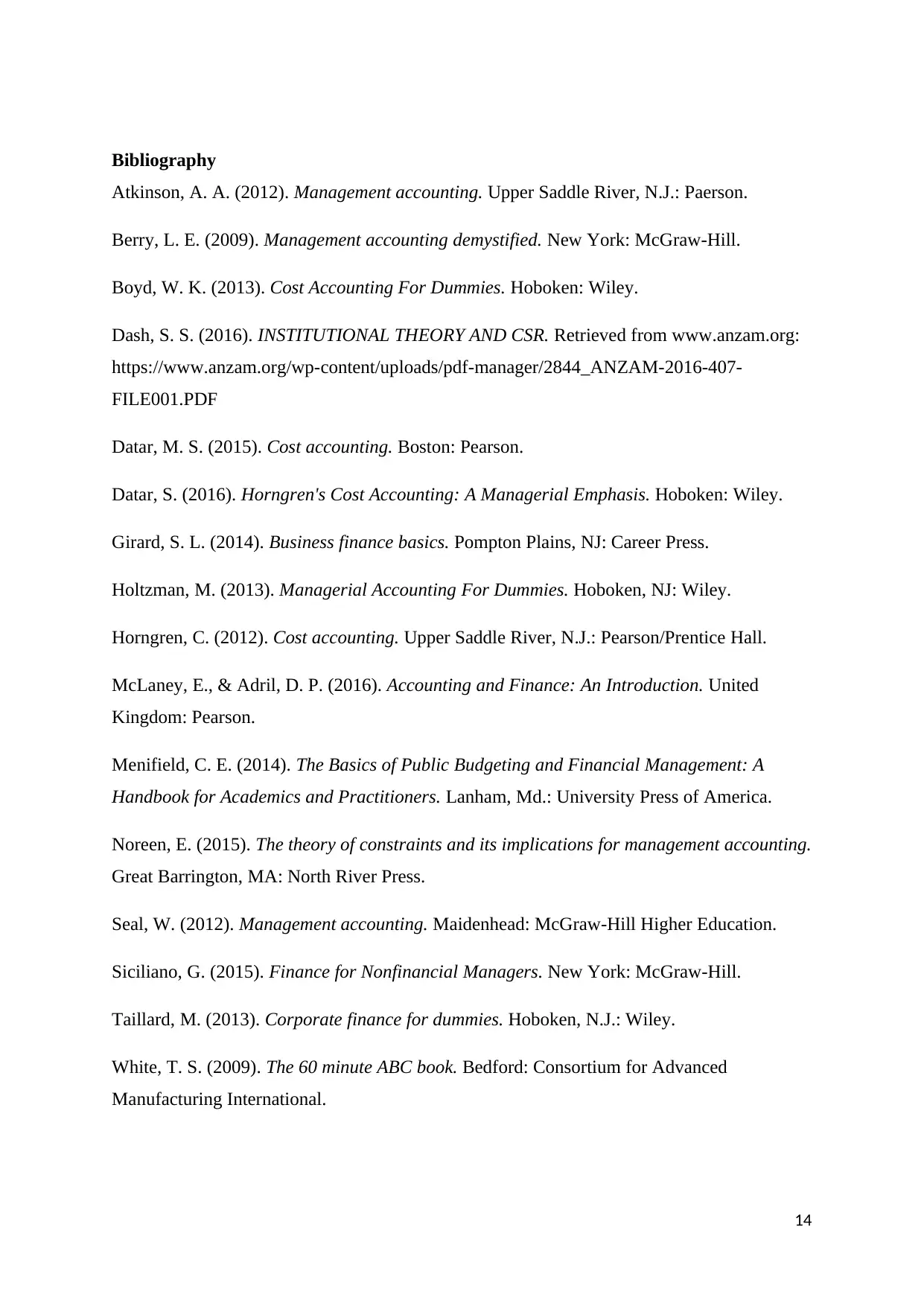
Bibliography
Atkinson, A. A. (2012). Management accounting. Upper Saddle River, N.J.: Paerson.
Berry, L. E. (2009). Management accounting demystified. New York: McGraw-Hill.
Boyd, W. K. (2013). Cost Accounting For Dummies. Hoboken: Wiley.
Dash, S. S. (2016). INSTITUTIONAL THEORY AND CSR. Retrieved from www.anzam.org:
https://www.anzam.org/wp-content/uploads/pdf-manager/2844_ANZAM-2016-407-
FILE001.PDF
Datar, M. S. (2015). Cost accounting. Boston: Pearson.
Datar, S. (2016). Horngren's Cost Accounting: A Managerial Emphasis. Hoboken: Wiley.
Girard, S. L. (2014). Business finance basics. Pompton Plains, NJ: Career Press.
Holtzman, M. (2013). Managerial Accounting For Dummies. Hoboken, NJ: Wiley.
Horngren, C. (2012). Cost accounting. Upper Saddle River, N.J.: Pearson/Prentice Hall.
McLaney, E., & Adril, D. P. (2016). Accounting and Finance: An Introduction. United
Kingdom: Pearson.
Menifield, C. E. (2014). The Basics of Public Budgeting and Financial Management: A
Handbook for Academics and Practitioners. Lanham, Md.: University Press of America.
Noreen, E. (2015). The theory of constraints and its implications for management accounting.
Great Barrington, MA: North River Press.
Seal, W. (2012). Management accounting. Maidenhead: McGraw-Hill Higher Education.
Siciliano, G. (2015). Finance for Nonfinancial Managers. New York: McGraw-Hill.
Taillard, M. (2013). Corporate finance for dummies. Hoboken, N.J.: Wiley.
White, T. S. (2009). The 60 minute ABC book. Bedford: Consortium for Advanced
Manufacturing International.
14
Atkinson, A. A. (2012). Management accounting. Upper Saddle River, N.J.: Paerson.
Berry, L. E. (2009). Management accounting demystified. New York: McGraw-Hill.
Boyd, W. K. (2013). Cost Accounting For Dummies. Hoboken: Wiley.
Dash, S. S. (2016). INSTITUTIONAL THEORY AND CSR. Retrieved from www.anzam.org:
https://www.anzam.org/wp-content/uploads/pdf-manager/2844_ANZAM-2016-407-
FILE001.PDF
Datar, M. S. (2015). Cost accounting. Boston: Pearson.
Datar, S. (2016). Horngren's Cost Accounting: A Managerial Emphasis. Hoboken: Wiley.
Girard, S. L. (2014). Business finance basics. Pompton Plains, NJ: Career Press.
Holtzman, M. (2013). Managerial Accounting For Dummies. Hoboken, NJ: Wiley.
Horngren, C. (2012). Cost accounting. Upper Saddle River, N.J.: Pearson/Prentice Hall.
McLaney, E., & Adril, D. P. (2016). Accounting and Finance: An Introduction. United
Kingdom: Pearson.
Menifield, C. E. (2014). The Basics of Public Budgeting and Financial Management: A
Handbook for Academics and Practitioners. Lanham, Md.: University Press of America.
Noreen, E. (2015). The theory of constraints and its implications for management accounting.
Great Barrington, MA: North River Press.
Seal, W. (2012). Management accounting. Maidenhead: McGraw-Hill Higher Education.
Siciliano, G. (2015). Finance for Nonfinancial Managers. New York: McGraw-Hill.
Taillard, M. (2013). Corporate finance for dummies. Hoboken, N.J.: Wiley.
White, T. S. (2009). The 60 minute ABC book. Bedford: Consortium for Advanced
Manufacturing International.
14
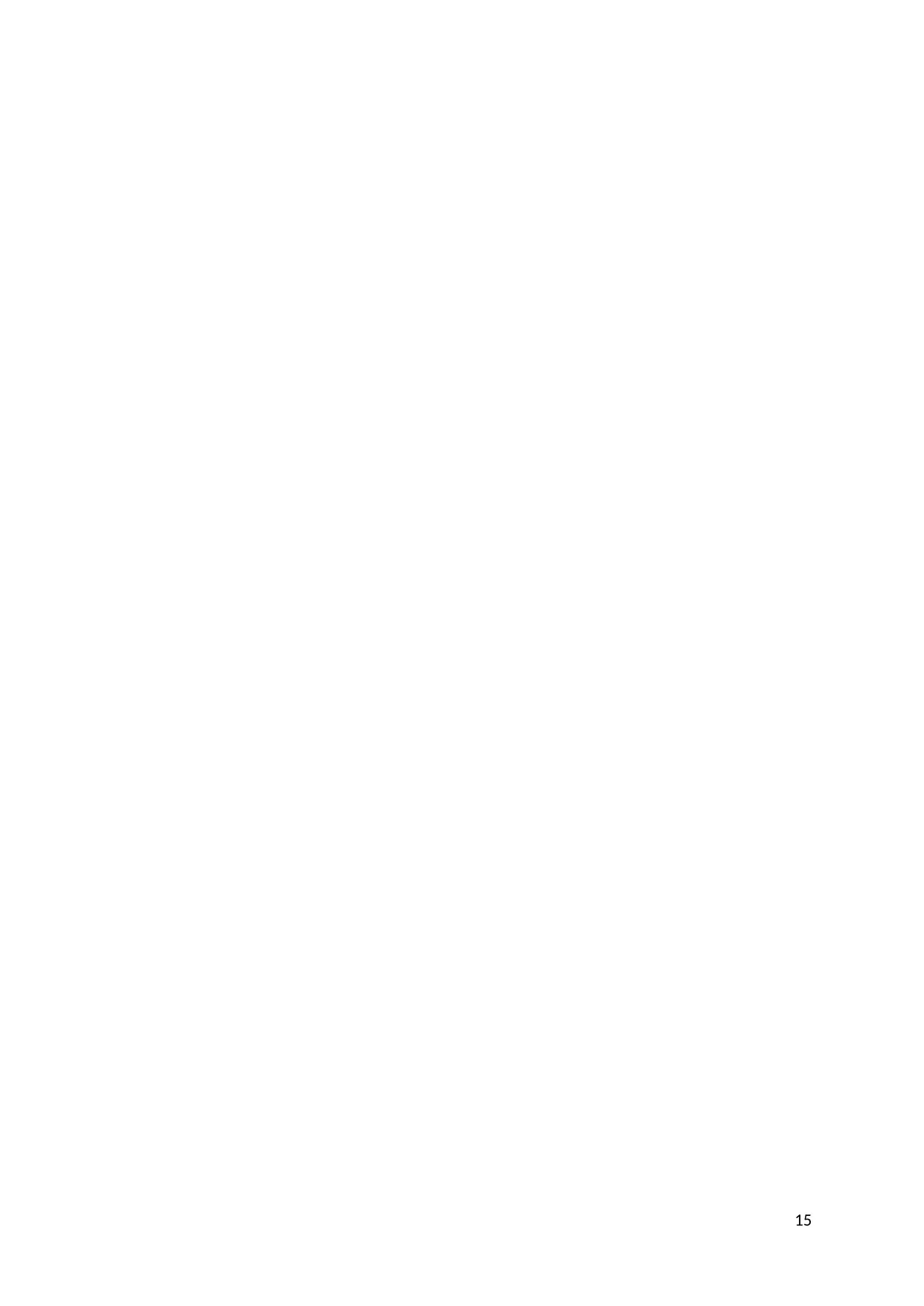
15
1 out of 15
Related Documents

Your All-in-One AI-Powered Toolkit for Academic Success.
 +13062052269
info@desklib.com
Available 24*7 on WhatsApp / Email
Unlock your academic potential
© 2024  |  Zucol Services PVT LTD  |  All rights reserved.