CVA005: Analysis and Design of Trusses vs. Beams in Structures
VerifiedAdded on 2023/04/19
|30
|6718
|130
Report
AI Summary
This report analyzes the structural behavior of trusses and beams through calculations and comparisons. Task 1 involves selecting the best beam cross-section based on bending stress analysis. Task 2 focuses on a simply supported overhang beam, calculating external forces, drawing shear force and bending moment diagrams, and determining maximum normal stress. Task 3 calculates external reactions and internal forces within a steel truss. Finally, Task 4 determines a suitable diameter for truss elements and compares the beam and truss designs to identify the most convenient solution.
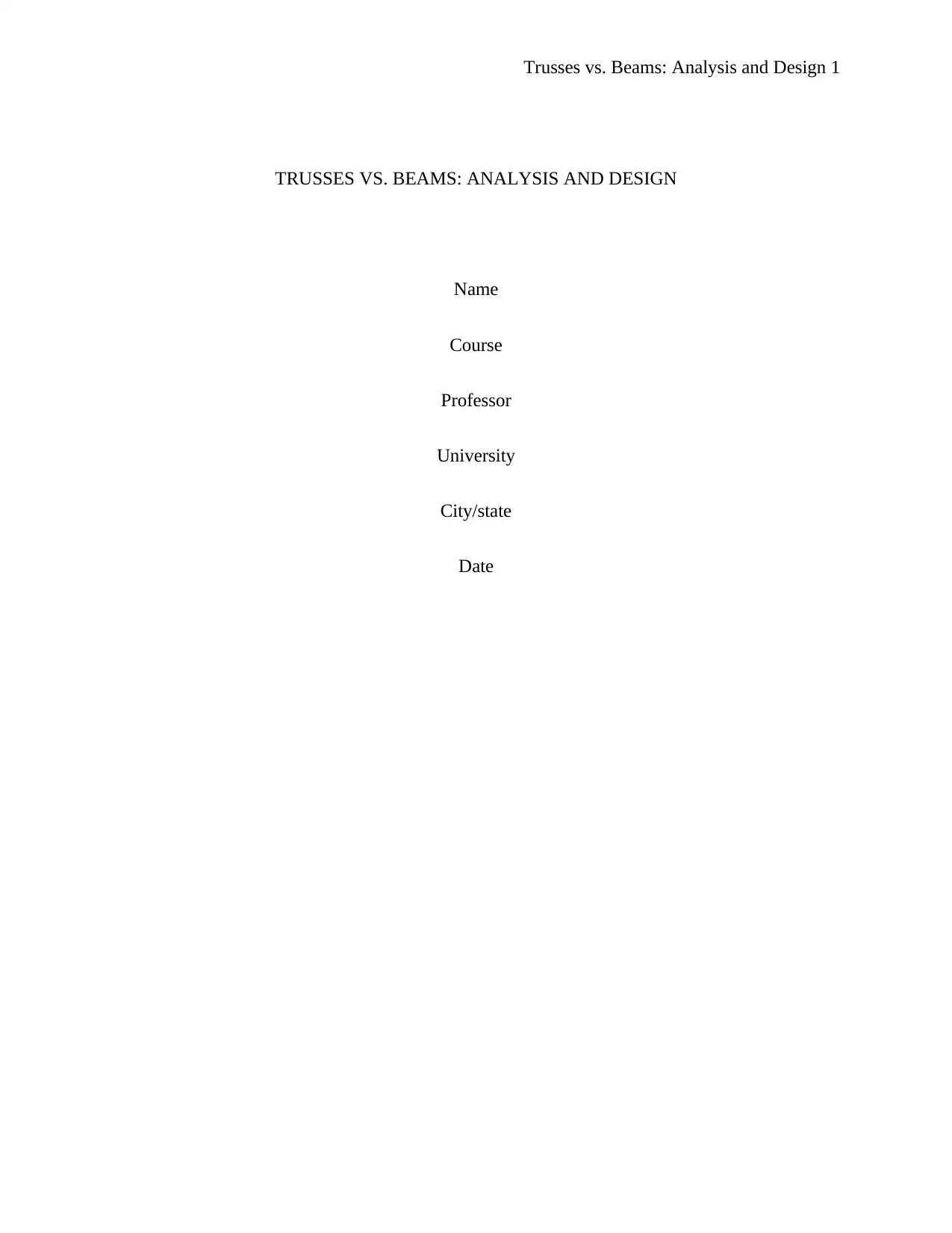
Trusses vs. Beams: Analysis and Design 1
TRUSSES VS. BEAMS: ANALYSIS AND DESIGN
Name
Course
Professor
University
City/state
Date
TRUSSES VS. BEAMS: ANALYSIS AND DESIGN
Name
Course
Professor
University
City/state
Date
Secure Best Marks with AI Grader
Need help grading? Try our AI Grader for instant feedback on your assignments.
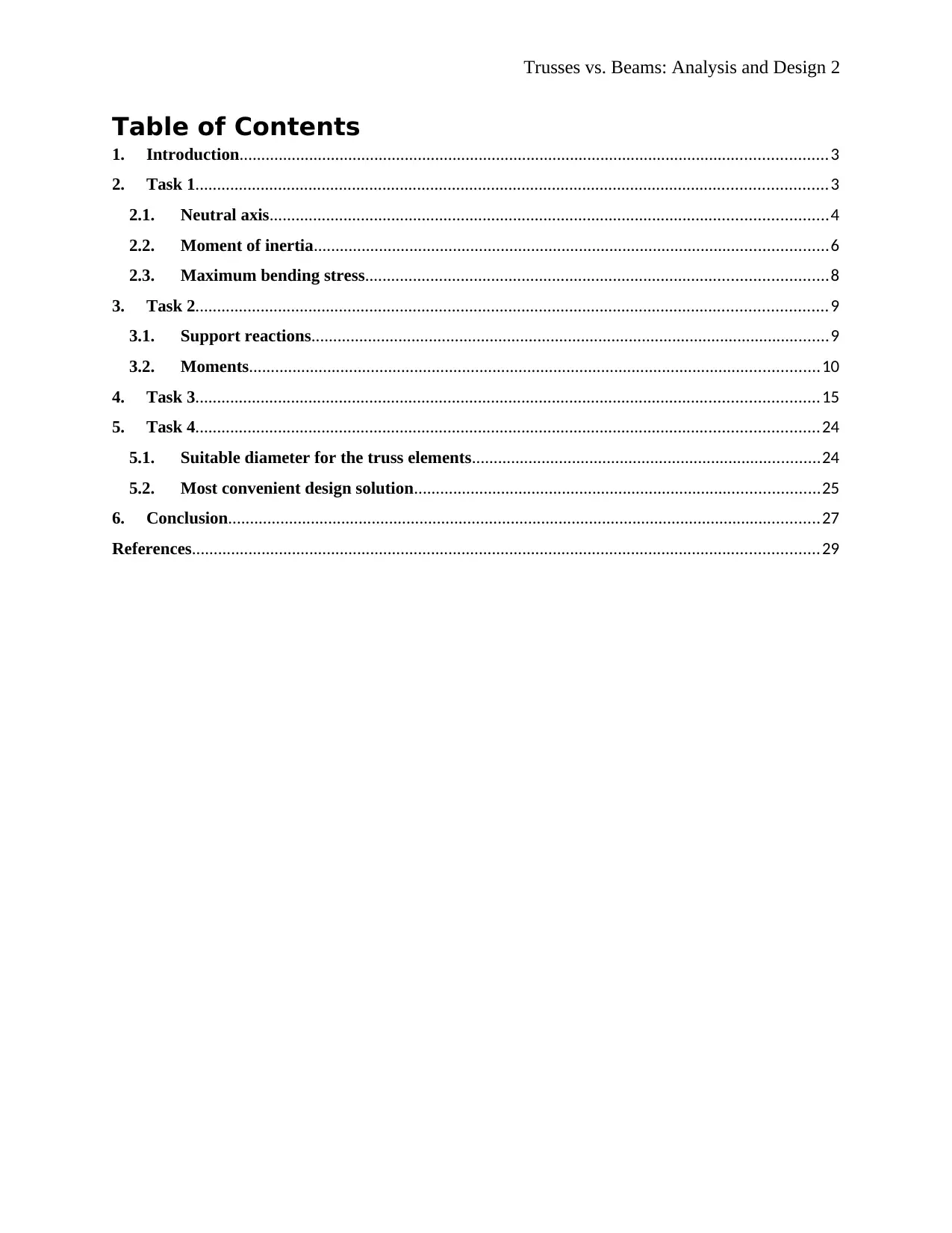
Trusses vs. Beams: Analysis and Design 2
Table of Contents
1. Introduction.......................................................................................................................................3
2. Task 1.................................................................................................................................................3
2.1. Neutral axis................................................................................................................................4
2.2. Moment of inertia......................................................................................................................6
2.3. Maximum bending stress..........................................................................................................8
3. Task 2.................................................................................................................................................9
3.1. Support reactions.......................................................................................................................9
3.2. Moments...................................................................................................................................10
4. Task 3...............................................................................................................................................15
5. Task 4...............................................................................................................................................24
5.1. Suitable diameter for the truss elements................................................................................24
5.2. Most convenient design solution.............................................................................................25
6. Conclusion........................................................................................................................................27
References................................................................................................................................................29
Table of Contents
1. Introduction.......................................................................................................................................3
2. Task 1.................................................................................................................................................3
2.1. Neutral axis................................................................................................................................4
2.2. Moment of inertia......................................................................................................................6
2.3. Maximum bending stress..........................................................................................................8
3. Task 2.................................................................................................................................................9
3.1. Support reactions.......................................................................................................................9
3.2. Moments...................................................................................................................................10
4. Task 3...............................................................................................................................................15
5. Task 4...............................................................................................................................................24
5.1. Suitable diameter for the truss elements................................................................................24
5.2. Most convenient design solution.............................................................................................25
6. Conclusion........................................................................................................................................27
References................................................................................................................................................29
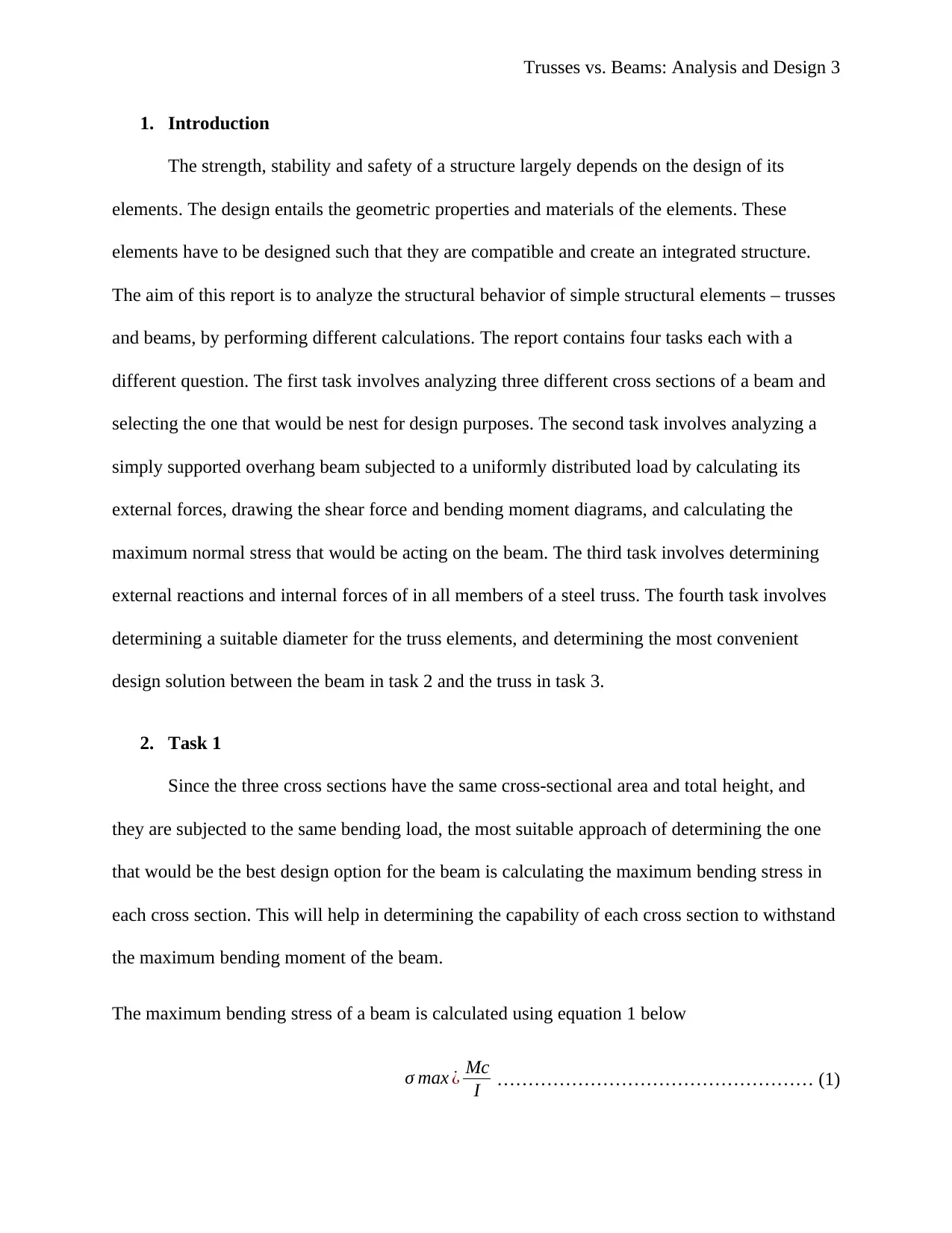
Trusses vs. Beams: Analysis and Design 3
1. Introduction
The strength, stability and safety of a structure largely depends on the design of its
elements. The design entails the geometric properties and materials of the elements. These
elements have to be designed such that they are compatible and create an integrated structure.
The aim of this report is to analyze the structural behavior of simple structural elements – trusses
and beams, by performing different calculations. The report contains four tasks each with a
different question. The first task involves analyzing three different cross sections of a beam and
selecting the one that would be nest for design purposes. The second task involves analyzing a
simply supported overhang beam subjected to a uniformly distributed load by calculating its
external forces, drawing the shear force and bending moment diagrams, and calculating the
maximum normal stress that would be acting on the beam. The third task involves determining
external reactions and internal forces of in all members of a steel truss. The fourth task involves
determining a suitable diameter for the truss elements, and determining the most convenient
design solution between the beam in task 2 and the truss in task 3.
2. Task 1
Since the three cross sections have the same cross-sectional area and total height, and
they are subjected to the same bending load, the most suitable approach of determining the one
that would be the best design option for the beam is calculating the maximum bending stress in
each cross section. This will help in determining the capability of each cross section to withstand
the maximum bending moment of the beam.
The maximum bending stress of a beam is calculated using equation 1 below
σ max ¿ Mc
I …………………………………………… (1)
1. Introduction
The strength, stability and safety of a structure largely depends on the design of its
elements. The design entails the geometric properties and materials of the elements. These
elements have to be designed such that they are compatible and create an integrated structure.
The aim of this report is to analyze the structural behavior of simple structural elements – trusses
and beams, by performing different calculations. The report contains four tasks each with a
different question. The first task involves analyzing three different cross sections of a beam and
selecting the one that would be nest for design purposes. The second task involves analyzing a
simply supported overhang beam subjected to a uniformly distributed load by calculating its
external forces, drawing the shear force and bending moment diagrams, and calculating the
maximum normal stress that would be acting on the beam. The third task involves determining
external reactions and internal forces of in all members of a steel truss. The fourth task involves
determining a suitable diameter for the truss elements, and determining the most convenient
design solution between the beam in task 2 and the truss in task 3.
2. Task 1
Since the three cross sections have the same cross-sectional area and total height, and
they are subjected to the same bending load, the most suitable approach of determining the one
that would be the best design option for the beam is calculating the maximum bending stress in
each cross section. This will help in determining the capability of each cross section to withstand
the maximum bending moment of the beam.
The maximum bending stress of a beam is calculated using equation 1 below
σ max ¿ Mc
I …………………………………………… (1)
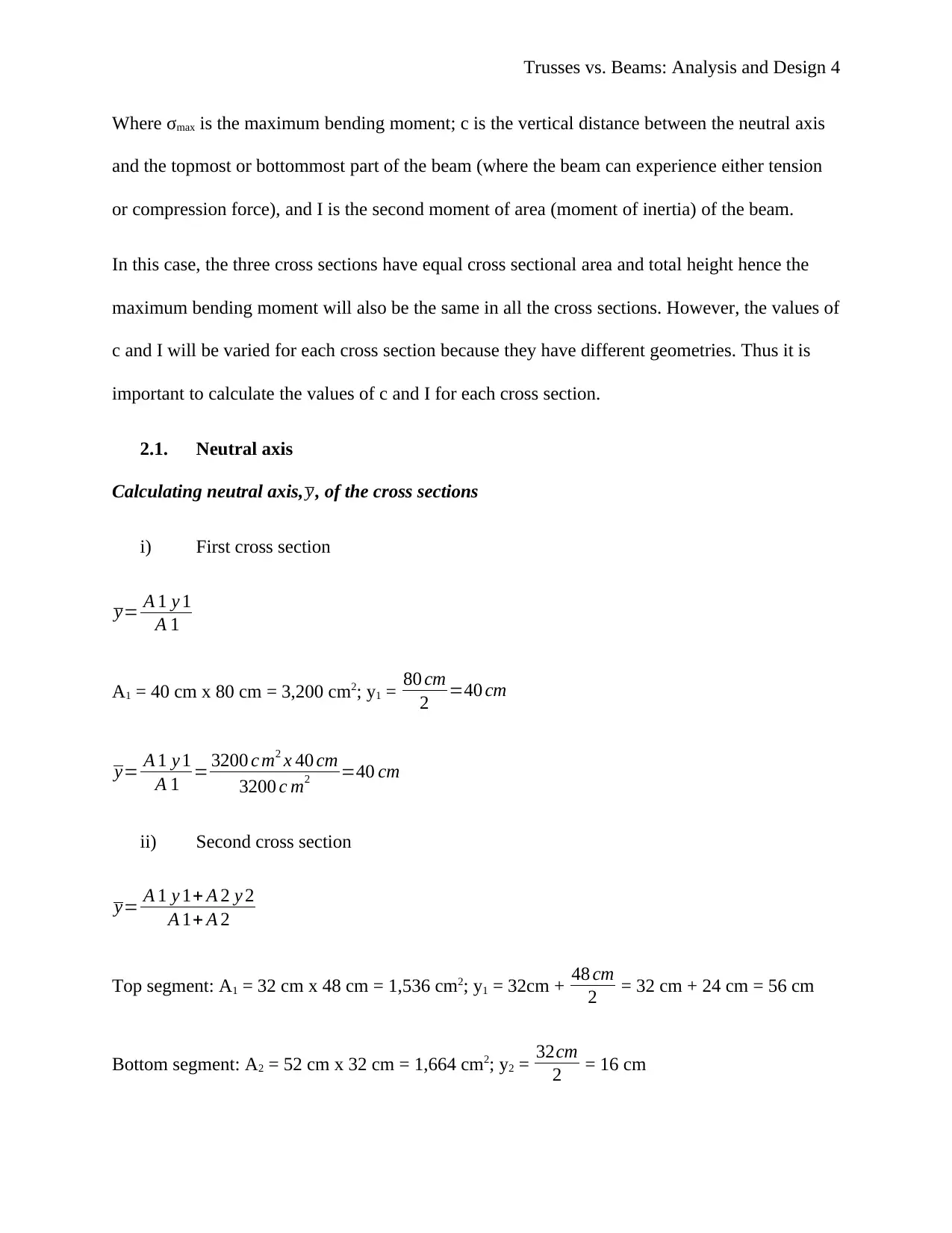
Trusses vs. Beams: Analysis and Design 4
Where σmax is the maximum bending moment; c is the vertical distance between the neutral axis
and the topmost or bottommost part of the beam (where the beam can experience either tension
or compression force), and I is the second moment of area (moment of inertia) of the beam.
In this case, the three cross sections have equal cross sectional area and total height hence the
maximum bending moment will also be the same in all the cross sections. However, the values of
c and I will be varied for each cross section because they have different geometries. Thus it is
important to calculate the values of c and I for each cross section.
2.1. Neutral axis
Calculating neutral axis, y, of the cross sections
i) First cross section
y= A 1 y 1
A 1
A1 = 40 cm x 80 cm = 3,200 cm2; y1 = 80 cm
2 =40 cm
y= A 1 y 1
A 1 = 3200 c m2 x 40 cm
3200 c m2 =40 cm
ii) Second cross section
y= A 1 y 1+ A 2 y 2
A 1+ A 2
Top segment: A1 = 32 cm x 48 cm = 1,536 cm2; y1 = 32cm + 48 cm
2 = 32 cm + 24 cm = 56 cm
Bottom segment: A2 = 52 cm x 32 cm = 1,664 cm2; y2 = 32cm
2 = 16 cm
Where σmax is the maximum bending moment; c is the vertical distance between the neutral axis
and the topmost or bottommost part of the beam (where the beam can experience either tension
or compression force), and I is the second moment of area (moment of inertia) of the beam.
In this case, the three cross sections have equal cross sectional area and total height hence the
maximum bending moment will also be the same in all the cross sections. However, the values of
c and I will be varied for each cross section because they have different geometries. Thus it is
important to calculate the values of c and I for each cross section.
2.1. Neutral axis
Calculating neutral axis, y, of the cross sections
i) First cross section
y= A 1 y 1
A 1
A1 = 40 cm x 80 cm = 3,200 cm2; y1 = 80 cm
2 =40 cm
y= A 1 y 1
A 1 = 3200 c m2 x 40 cm
3200 c m2 =40 cm
ii) Second cross section
y= A 1 y 1+ A 2 y 2
A 1+ A 2
Top segment: A1 = 32 cm x 48 cm = 1,536 cm2; y1 = 32cm + 48 cm
2 = 32 cm + 24 cm = 56 cm
Bottom segment: A2 = 52 cm x 32 cm = 1,664 cm2; y2 = 32cm
2 = 16 cm
Secure Best Marks with AI Grader
Need help grading? Try our AI Grader for instant feedback on your assignments.
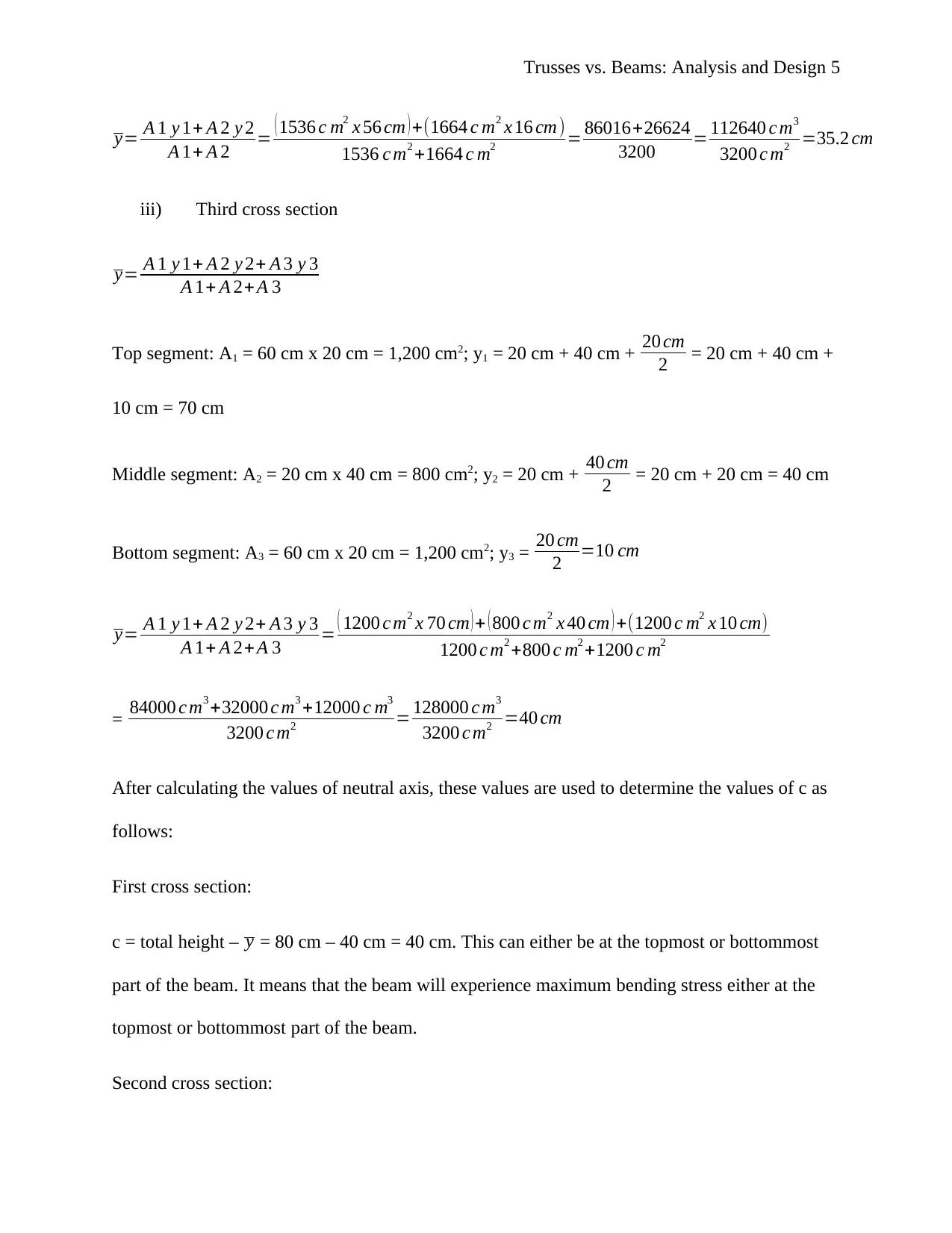
Trusses vs. Beams: Analysis and Design 5
y= A 1 y 1+ A 2 y 2
A 1+ A 2 = ( 1536 c m2 x 56 cm ) +(1664 c m2 x 16 cm )
1536 c m2 +1664 c m2 = 86016+26624
3200 = 112640 c m3
3200 c m2 =35.2 cm
iii) Third cross section
y= A 1 y 1+ A 2 y 2+ A 3 y 3
A 1+ A 2+A 3
Top segment: A1 = 60 cm x 20 cm = 1,200 cm2; y1 = 20 cm + 40 cm + 20 cm
2 = 20 cm + 40 cm +
10 cm = 70 cm
Middle segment: A2 = 20 cm x 40 cm = 800 cm2; y2 = 20 cm + 40 cm
2 = 20 cm + 20 cm = 40 cm
Bottom segment: A3 = 60 cm x 20 cm = 1,200 cm2; y3 = 20 cm
2 =10 cm
y= A 1 y 1+ A 2 y 2+ A 3 y 3
A 1+ A 2+A 3 = ( 1200 c m2 x 70 cm ) + ( 800 c m2 x 40 cm ) +(1200 c m2 x 10 cm)
1200 c m2 +800 c m2 +1200 c m2
= 84000 c m3 +32000 c m3 +12000 c m3
3200 c m2 = 128000 c m3
3200 c m2 =40 cm
After calculating the values of neutral axis, these values are used to determine the values of c as
follows:
First cross section:
c = total height – y = 80 cm – 40 cm = 40 cm. This can either be at the topmost or bottommost
part of the beam. It means that the beam will experience maximum bending stress either at the
topmost or bottommost part of the beam.
Second cross section:
y= A 1 y 1+ A 2 y 2
A 1+ A 2 = ( 1536 c m2 x 56 cm ) +(1664 c m2 x 16 cm )
1536 c m2 +1664 c m2 = 86016+26624
3200 = 112640 c m3
3200 c m2 =35.2 cm
iii) Third cross section
y= A 1 y 1+ A 2 y 2+ A 3 y 3
A 1+ A 2+A 3
Top segment: A1 = 60 cm x 20 cm = 1,200 cm2; y1 = 20 cm + 40 cm + 20 cm
2 = 20 cm + 40 cm +
10 cm = 70 cm
Middle segment: A2 = 20 cm x 40 cm = 800 cm2; y2 = 20 cm + 40 cm
2 = 20 cm + 20 cm = 40 cm
Bottom segment: A3 = 60 cm x 20 cm = 1,200 cm2; y3 = 20 cm
2 =10 cm
y= A 1 y 1+ A 2 y 2+ A 3 y 3
A 1+ A 2+A 3 = ( 1200 c m2 x 70 cm ) + ( 800 c m2 x 40 cm ) +(1200 c m2 x 10 cm)
1200 c m2 +800 c m2 +1200 c m2
= 84000 c m3 +32000 c m3 +12000 c m3
3200 c m2 = 128000 c m3
3200 c m2 =40 cm
After calculating the values of neutral axis, these values are used to determine the values of c as
follows:
First cross section:
c = total height – y = 80 cm – 40 cm = 40 cm. This can either be at the topmost or bottommost
part of the beam. It means that the beam will experience maximum bending stress either at the
topmost or bottommost part of the beam.
Second cross section:
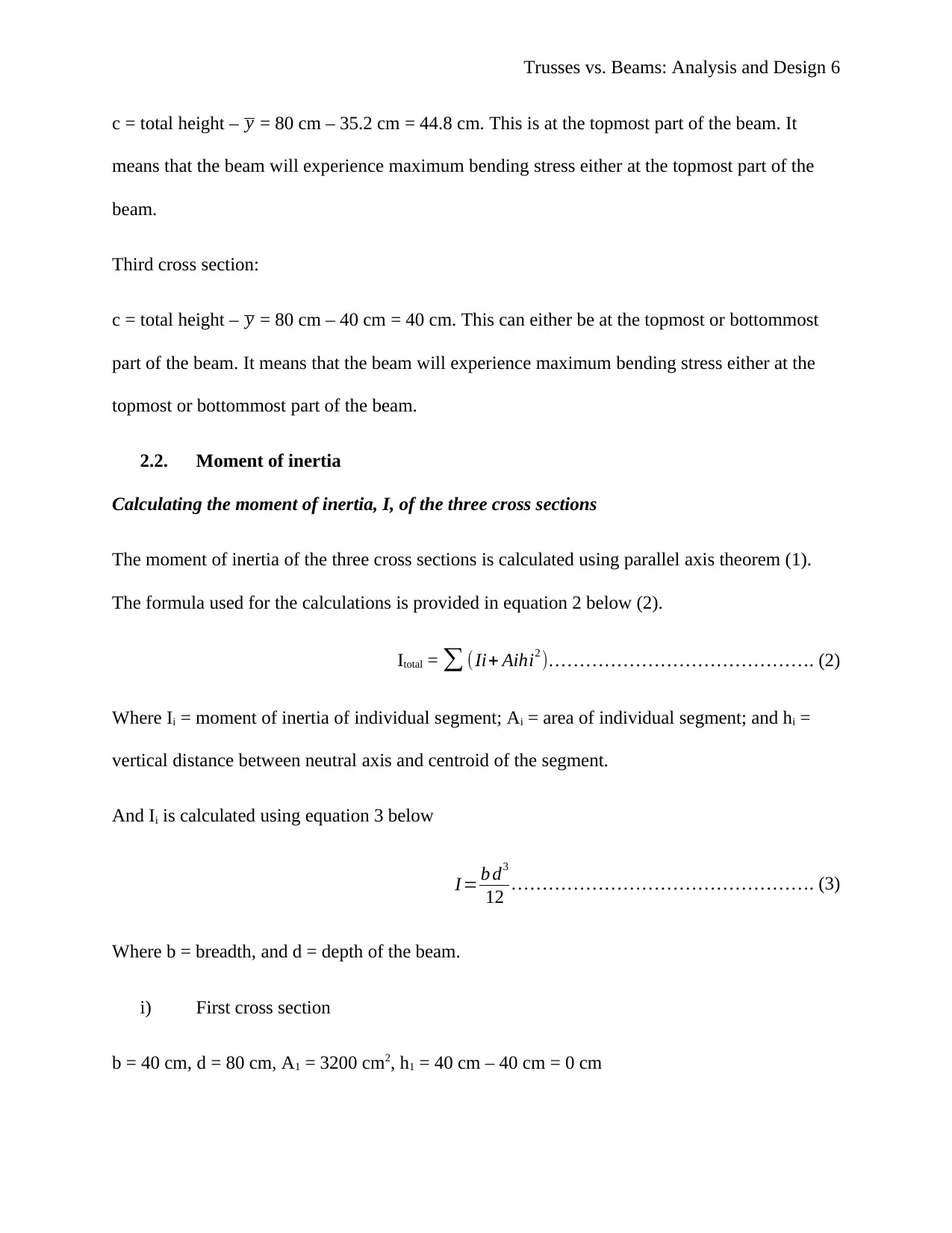
Trusses vs. Beams: Analysis and Design 6
c = total height – y = 80 cm – 35.2 cm = 44.8 cm. This is at the topmost part of the beam. It
means that the beam will experience maximum bending stress either at the topmost part of the
beam.
Third cross section:
c = total height – y = 80 cm – 40 cm = 40 cm. This can either be at the topmost or bottommost
part of the beam. It means that the beam will experience maximum bending stress either at the
topmost or bottommost part of the beam.
2.2. Moment of inertia
Calculating the moment of inertia, I, of the three cross sections
The moment of inertia of the three cross sections is calculated using parallel axis theorem (1).
The formula used for the calculations is provided in equation 2 below (2).
Itotal = ∑ (Ii+ Aihi2 )……………………………………. (2)
Where Ii = moment of inertia of individual segment; Ai = area of individual segment; and hi =
vertical distance between neutral axis and centroid of the segment.
And Ii is calculated using equation 3 below
I = b d3
12 …………………………………………. (3)
Where b = breadth, and d = depth of the beam.
i) First cross section
b = 40 cm, d = 80 cm, A1 = 3200 cm2, h1 = 40 cm – 40 cm = 0 cm
c = total height – y = 80 cm – 35.2 cm = 44.8 cm. This is at the topmost part of the beam. It
means that the beam will experience maximum bending stress either at the topmost part of the
beam.
Third cross section:
c = total height – y = 80 cm – 40 cm = 40 cm. This can either be at the topmost or bottommost
part of the beam. It means that the beam will experience maximum bending stress either at the
topmost or bottommost part of the beam.
2.2. Moment of inertia
Calculating the moment of inertia, I, of the three cross sections
The moment of inertia of the three cross sections is calculated using parallel axis theorem (1).
The formula used for the calculations is provided in equation 2 below (2).
Itotal = ∑ (Ii+ Aihi2 )……………………………………. (2)
Where Ii = moment of inertia of individual segment; Ai = area of individual segment; and hi =
vertical distance between neutral axis and centroid of the segment.
And Ii is calculated using equation 3 below
I = b d3
12 …………………………………………. (3)
Where b = breadth, and d = depth of the beam.
i) First cross section
b = 40 cm, d = 80 cm, A1 = 3200 cm2, h1 = 40 cm – 40 cm = 0 cm

Trusses vs. Beams: Analysis and Design 7
I 1=( 40 x 803
12 )+ ( 3200 x 02 ) =1.707 x 106 c m4
ii) Second cross section
Top segment:
b = 32 cm, d = 48 cm, A1 = 1536 cm2, h1 = 56 cm – 35.2 cm = 20.8 cm
I 1=( 32 x 483
12 ) + ( 1536 x 20.82 ) =294,912c m4 +664,535.04 c m4=959,447.04 c m4
Bottom segment:
b = 52 cm, d = 32 cm, A2 = 1664 cm2, h2 = 35.2 cm – 16 cm = 19.2 cm
I 2=( 52 x 323
12 ) + ( 1664 x 19.22 ) =141,994.67 c m4 + 613,416.96 c m4 =755,411.63 c m4
Itotal = I1 + I2 = 959,447.04 cm4 + 755,411.63 cm4 = 1714858.67 cm4 = 1.715 x 106 cm4
iii) Third cross section
Top segment:
b = 60 cm, d = 20 cm, A1 = 1200 cm2, h1 = 70 cm – 40 cm = 30 cm
I 1=( 60 x 203
12 ) + ( 1200 x 302 ) =40,000 c m4 +1080000 c m4=1,120,000 c m4
Middle segment:
b = 20 cm, d = 40 cm, A2 = 800 cm2, h2 = 40 cm – 40 cm = 0 cm
I 2=( 20 x 403
12 ) + ( 800 x 02 )=106,666.67 c m4 +0 c m4=106,666.67 c m4
I 1=( 40 x 803
12 )+ ( 3200 x 02 ) =1.707 x 106 c m4
ii) Second cross section
Top segment:
b = 32 cm, d = 48 cm, A1 = 1536 cm2, h1 = 56 cm – 35.2 cm = 20.8 cm
I 1=( 32 x 483
12 ) + ( 1536 x 20.82 ) =294,912c m4 +664,535.04 c m4=959,447.04 c m4
Bottom segment:
b = 52 cm, d = 32 cm, A2 = 1664 cm2, h2 = 35.2 cm – 16 cm = 19.2 cm
I 2=( 52 x 323
12 ) + ( 1664 x 19.22 ) =141,994.67 c m4 + 613,416.96 c m4 =755,411.63 c m4
Itotal = I1 + I2 = 959,447.04 cm4 + 755,411.63 cm4 = 1714858.67 cm4 = 1.715 x 106 cm4
iii) Third cross section
Top segment:
b = 60 cm, d = 20 cm, A1 = 1200 cm2, h1 = 70 cm – 40 cm = 30 cm
I 1=( 60 x 203
12 ) + ( 1200 x 302 ) =40,000 c m4 +1080000 c m4=1,120,000 c m4
Middle segment:
b = 20 cm, d = 40 cm, A2 = 800 cm2, h2 = 40 cm – 40 cm = 0 cm
I 2=( 20 x 403
12 ) + ( 800 x 02 )=106,666.67 c m4 +0 c m4=106,666.67 c m4
Paraphrase This Document
Need a fresh take? Get an instant paraphrase of this document with our AI Paraphraser
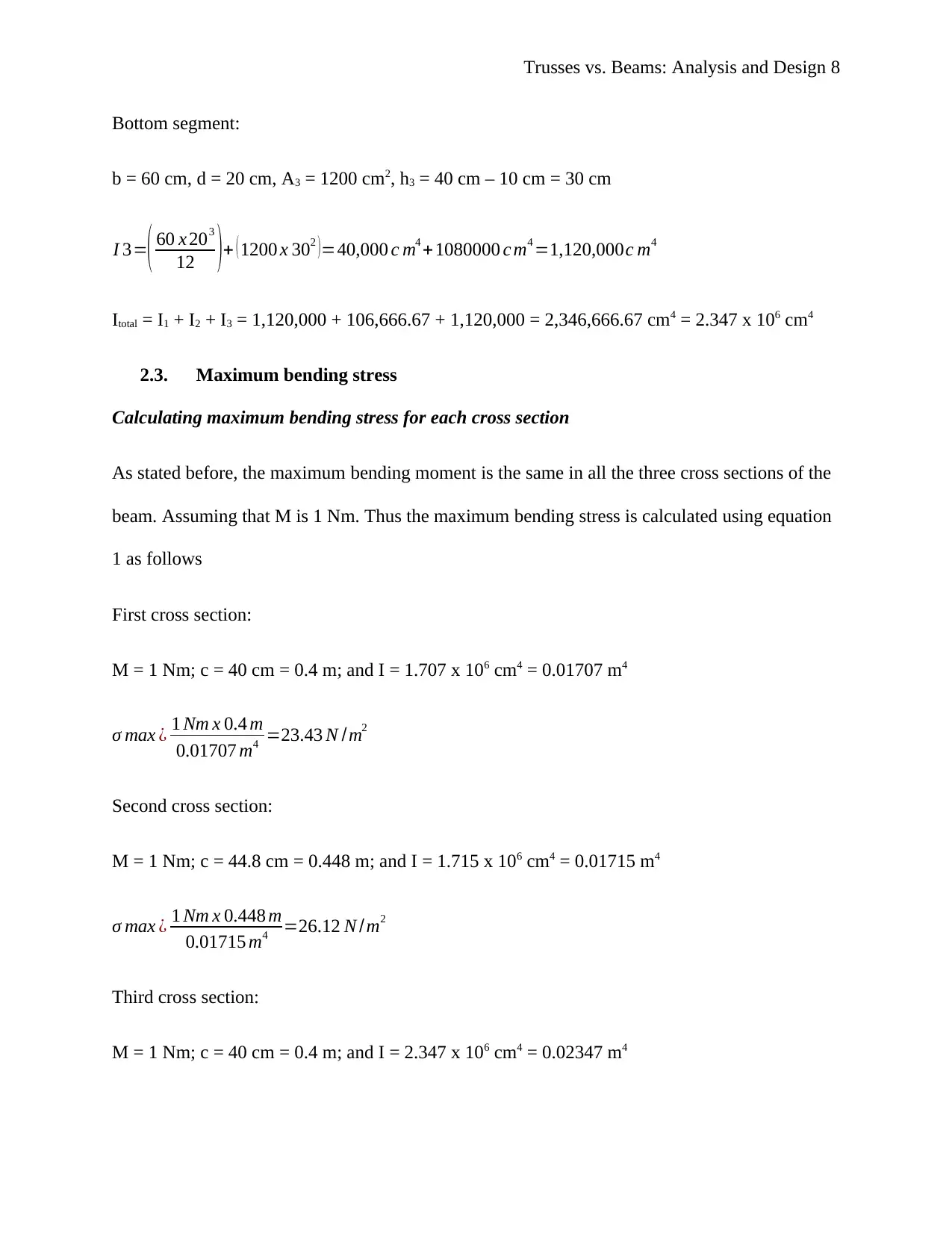
Trusses vs. Beams: Analysis and Design 8
Bottom segment:
b = 60 cm, d = 20 cm, A3 = 1200 cm2, h3 = 40 cm – 10 cm = 30 cm
I 3=( 60 x 203
12 )+ ( 1200 x 302 ) =40,000 c m4 +1080000 c m4 =1,120,000c m4
Itotal = I1 + I2 + I3 = 1,120,000 + 106,666.67 + 1,120,000 = 2,346,666.67 cm4 = 2.347 x 106 cm4
2.3. Maximum bending stress
Calculating maximum bending stress for each cross section
As stated before, the maximum bending moment is the same in all the three cross sections of the
beam. Assuming that M is 1 Nm. Thus the maximum bending stress is calculated using equation
1 as follows
First cross section:
M = 1 Nm; c = 40 cm = 0.4 m; and I = 1.707 x 106 cm4 = 0.01707 m4
σ max ¿ 1 Nm x 0.4 m
0.01707 m4 =23.43 N /m2
Second cross section:
M = 1 Nm; c = 44.8 cm = 0.448 m; and I = 1.715 x 106 cm4 = 0.01715 m4
σ max ¿ 1 Nm x 0.448 m
0.01715 m4 =26.12 N /m2
Third cross section:
M = 1 Nm; c = 40 cm = 0.4 m; and I = 2.347 x 106 cm4 = 0.02347 m4
Bottom segment:
b = 60 cm, d = 20 cm, A3 = 1200 cm2, h3 = 40 cm – 10 cm = 30 cm
I 3=( 60 x 203
12 )+ ( 1200 x 302 ) =40,000 c m4 +1080000 c m4 =1,120,000c m4
Itotal = I1 + I2 + I3 = 1,120,000 + 106,666.67 + 1,120,000 = 2,346,666.67 cm4 = 2.347 x 106 cm4
2.3. Maximum bending stress
Calculating maximum bending stress for each cross section
As stated before, the maximum bending moment is the same in all the three cross sections of the
beam. Assuming that M is 1 Nm. Thus the maximum bending stress is calculated using equation
1 as follows
First cross section:
M = 1 Nm; c = 40 cm = 0.4 m; and I = 1.707 x 106 cm4 = 0.01707 m4
σ max ¿ 1 Nm x 0.4 m
0.01707 m4 =23.43 N /m2
Second cross section:
M = 1 Nm; c = 44.8 cm = 0.448 m; and I = 1.715 x 106 cm4 = 0.01715 m4
σ max ¿ 1 Nm x 0.448 m
0.01715 m4 =26.12 N /m2
Third cross section:
M = 1 Nm; c = 40 cm = 0.4 m; and I = 2.347 x 106 cm4 = 0.02347 m4
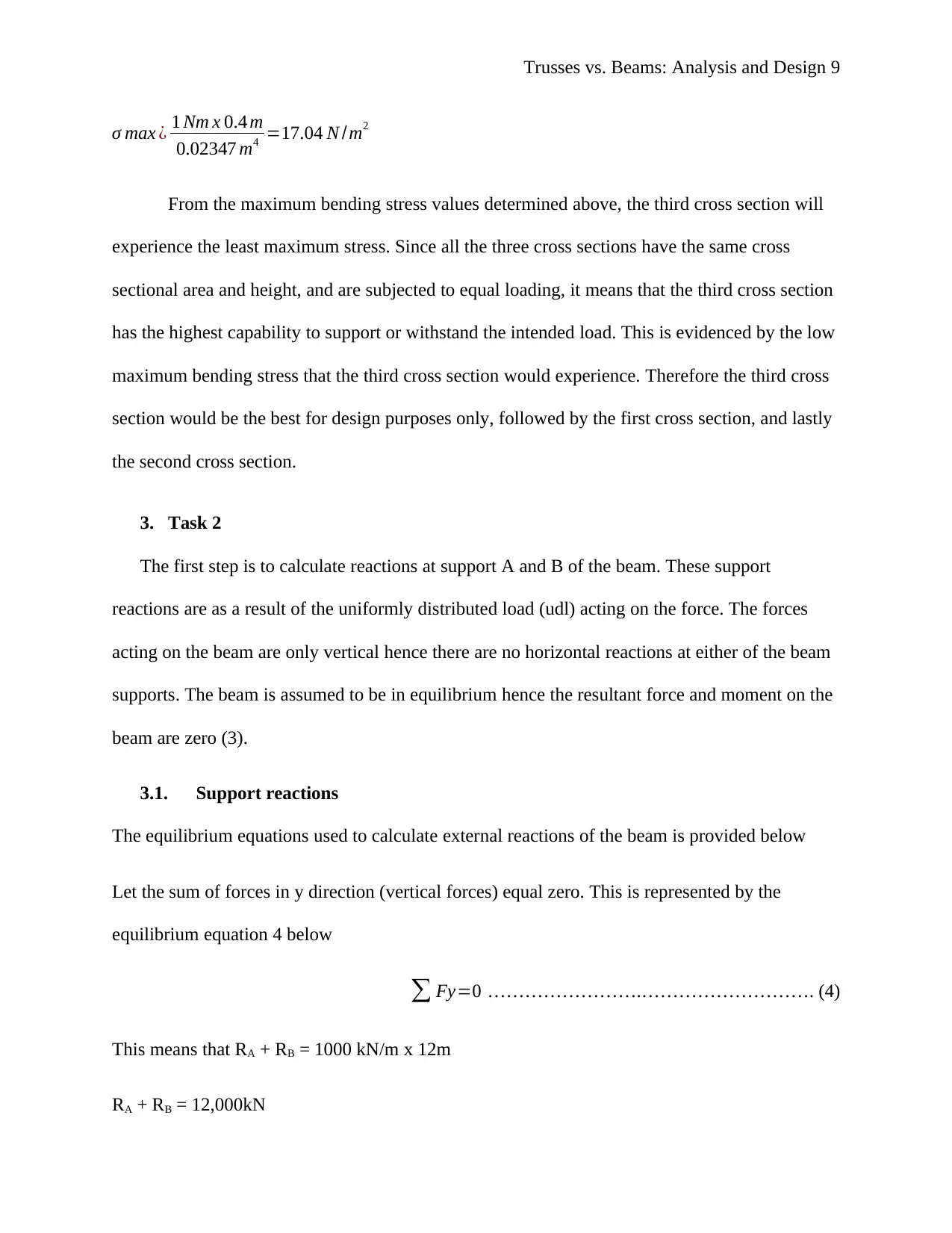
Trusses vs. Beams: Analysis and Design 9
σ max ¿ 1 Nm x 0.4 m
0.02347 m4 =17.04 N /m2
From the maximum bending stress values determined above, the third cross section will
experience the least maximum stress. Since all the three cross sections have the same cross
sectional area and height, and are subjected to equal loading, it means that the third cross section
has the highest capability to support or withstand the intended load. This is evidenced by the low
maximum bending stress that the third cross section would experience. Therefore the third cross
section would be the best for design purposes only, followed by the first cross section, and lastly
the second cross section.
3. Task 2
The first step is to calculate reactions at support A and B of the beam. These support
reactions are as a result of the uniformly distributed load (udl) acting on the force. The forces
acting on the beam are only vertical hence there are no horizontal reactions at either of the beam
supports. The beam is assumed to be in equilibrium hence the resultant force and moment on the
beam are zero (3).
3.1. Support reactions
The equilibrium equations used to calculate external reactions of the beam is provided below
Let the sum of forces in y direction (vertical forces) equal zero. This is represented by the
equilibrium equation 4 below
∑ Fy=0 …………………….………………………. (4)
This means that RA + RB = 1000 kN/m x 12m
RA + RB = 12,000kN
σ max ¿ 1 Nm x 0.4 m
0.02347 m4 =17.04 N /m2
From the maximum bending stress values determined above, the third cross section will
experience the least maximum stress. Since all the three cross sections have the same cross
sectional area and height, and are subjected to equal loading, it means that the third cross section
has the highest capability to support or withstand the intended load. This is evidenced by the low
maximum bending stress that the third cross section would experience. Therefore the third cross
section would be the best for design purposes only, followed by the first cross section, and lastly
the second cross section.
3. Task 2
The first step is to calculate reactions at support A and B of the beam. These support
reactions are as a result of the uniformly distributed load (udl) acting on the force. The forces
acting on the beam are only vertical hence there are no horizontal reactions at either of the beam
supports. The beam is assumed to be in equilibrium hence the resultant force and moment on the
beam are zero (3).
3.1. Support reactions
The equilibrium equations used to calculate external reactions of the beam is provided below
Let the sum of forces in y direction (vertical forces) equal zero. This is represented by the
equilibrium equation 4 below
∑ Fy=0 …………………….………………………. (4)
This means that RA + RB = 1000 kN/m x 12m
RA + RB = 12,000kN
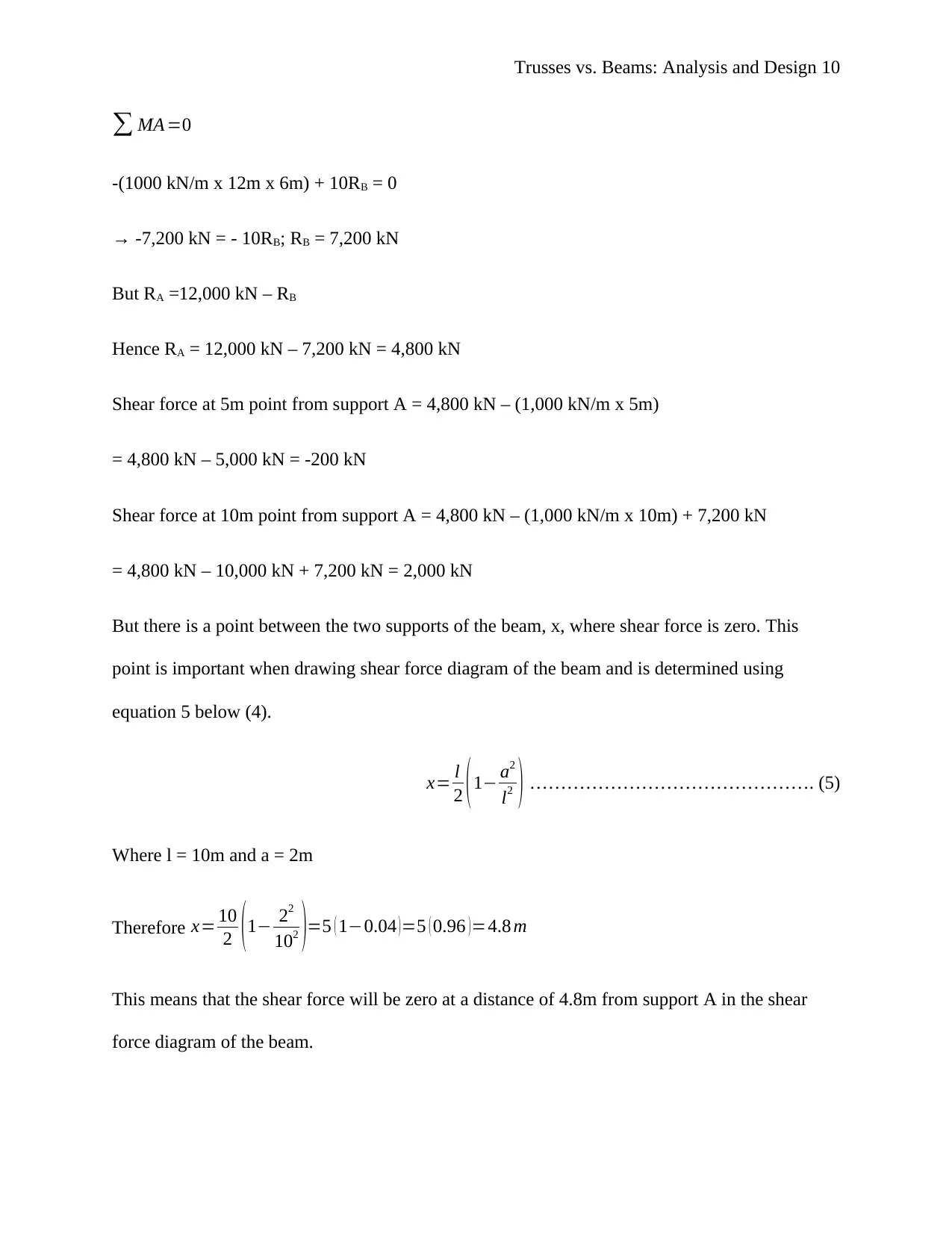
Trusses vs. Beams: Analysis and Design 10
∑ MA =0
-(1000 kN/m x 12m x 6m) + 10RB = 0
→ -7,200 kN = - 10RB; RB = 7,200 kN
But RA =12,000 kN – RB
Hence RA = 12,000 kN – 7,200 kN = 4,800 kN
Shear force at 5m point from support A = 4,800 kN – (1,000 kN/m x 5m)
= 4,800 kN – 5,000 kN = -200 kN
Shear force at 10m point from support A = 4,800 kN – (1,000 kN/m x 10m) + 7,200 kN
= 4,800 kN – 10,000 kN + 7,200 kN = 2,000 kN
But there is a point between the two supports of the beam, x, where shear force is zero. This
point is important when drawing shear force diagram of the beam and is determined using
equation 5 below (4).
x= l
2 ( 1− a2
l2 ) ………………………………………. (5)
Where l = 10m and a = 2m
Therefore x= 10
2 ( 1− 22
102 )=5 ( 1−0.04 ) =5 ( 0.96 ) =4.8 m
This means that the shear force will be zero at a distance of 4.8m from support A in the shear
force diagram of the beam.
∑ MA =0
-(1000 kN/m x 12m x 6m) + 10RB = 0
→ -7,200 kN = - 10RB; RB = 7,200 kN
But RA =12,000 kN – RB
Hence RA = 12,000 kN – 7,200 kN = 4,800 kN
Shear force at 5m point from support A = 4,800 kN – (1,000 kN/m x 5m)
= 4,800 kN – 5,000 kN = -200 kN
Shear force at 10m point from support A = 4,800 kN – (1,000 kN/m x 10m) + 7,200 kN
= 4,800 kN – 10,000 kN + 7,200 kN = 2,000 kN
But there is a point between the two supports of the beam, x, where shear force is zero. This
point is important when drawing shear force diagram of the beam and is determined using
equation 5 below (4).
x= l
2 ( 1− a2
l2 ) ………………………………………. (5)
Where l = 10m and a = 2m
Therefore x= 10
2 ( 1− 22
102 )=5 ( 1−0.04 ) =5 ( 0.96 ) =4.8 m
This means that the shear force will be zero at a distance of 4.8m from support A in the shear
force diagram of the beam.
Secure Best Marks with AI Grader
Need help grading? Try our AI Grader for instant feedback on your assignments.
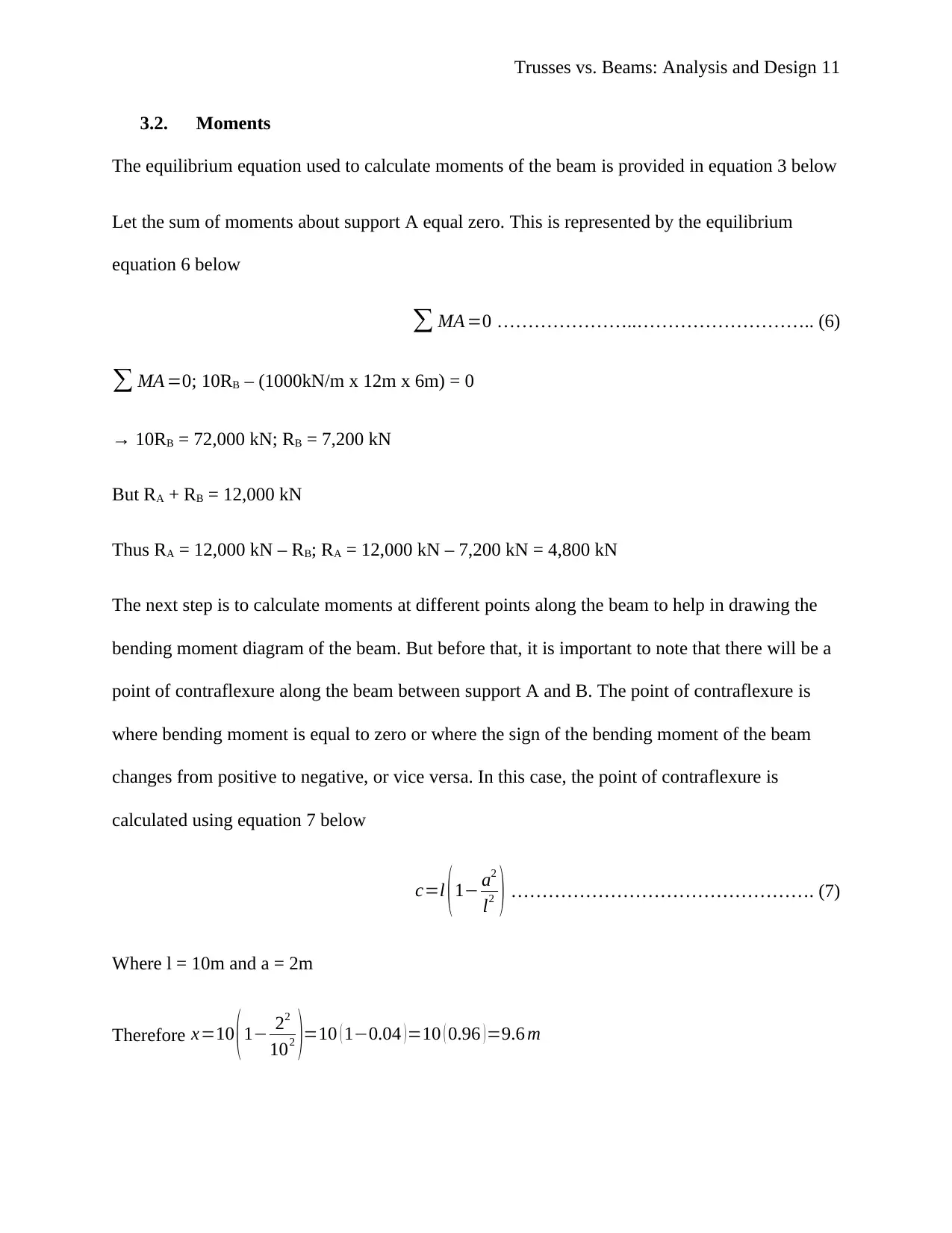
Trusses vs. Beams: Analysis and Design 11
3.2. Moments
The equilibrium equation used to calculate moments of the beam is provided in equation 3 below
Let the sum of moments about support A equal zero. This is represented by the equilibrium
equation 6 below
∑ MA =0 …………………..……………………….. (6)
∑ MA =0; 10RB – (1000kN/m x 12m x 6m) = 0
→ 10RB = 72,000 kN; RB = 7,200 kN
But RA + RB = 12,000 kN
Thus RA = 12,000 kN – RB; RA = 12,000 kN – 7,200 kN = 4,800 kN
The next step is to calculate moments at different points along the beam to help in drawing the
bending moment diagram of the beam. But before that, it is important to note that there will be a
point of contraflexure along the beam between support A and B. The point of contraflexure is
where bending moment is equal to zero or where the sign of the bending moment of the beam
changes from positive to negative, or vice versa. In this case, the point of contraflexure is
calculated using equation 7 below
c=l (1− a2
l2 ) …………………………………………. (7)
Where l = 10m and a = 2m
Therefore x=10 ( 1− 22
102 )=10 ( 1−0.04 ) =10 ( 0.96 ) =9.6 m
3.2. Moments
The equilibrium equation used to calculate moments of the beam is provided in equation 3 below
Let the sum of moments about support A equal zero. This is represented by the equilibrium
equation 6 below
∑ MA =0 …………………..……………………….. (6)
∑ MA =0; 10RB – (1000kN/m x 12m x 6m) = 0
→ 10RB = 72,000 kN; RB = 7,200 kN
But RA + RB = 12,000 kN
Thus RA = 12,000 kN – RB; RA = 12,000 kN – 7,200 kN = 4,800 kN
The next step is to calculate moments at different points along the beam to help in drawing the
bending moment diagram of the beam. But before that, it is important to note that there will be a
point of contraflexure along the beam between support A and B. The point of contraflexure is
where bending moment is equal to zero or where the sign of the bending moment of the beam
changes from positive to negative, or vice versa. In this case, the point of contraflexure is
calculated using equation 7 below
c=l (1− a2
l2 ) …………………………………………. (7)
Where l = 10m and a = 2m
Therefore x=10 ( 1− 22
102 )=10 ( 1−0.04 ) =10 ( 0.96 ) =9.6 m
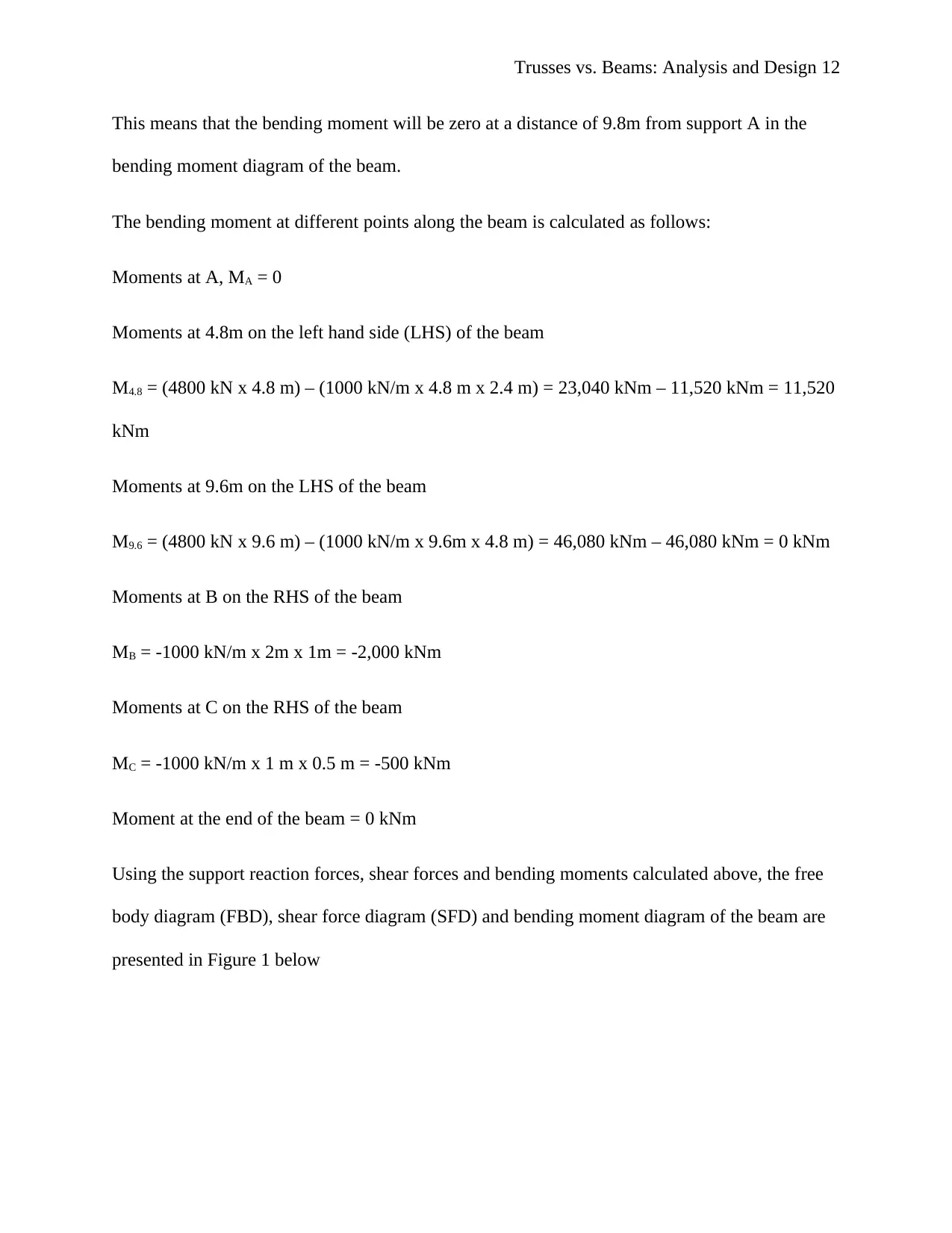
Trusses vs. Beams: Analysis and Design 12
This means that the bending moment will be zero at a distance of 9.8m from support A in the
bending moment diagram of the beam.
The bending moment at different points along the beam is calculated as follows:
Moments at A, MA = 0
Moments at 4.8m on the left hand side (LHS) of the beam
M4.8 = (4800 kN x 4.8 m) – (1000 kN/m x 4.8 m x 2.4 m) = 23,040 kNm – 11,520 kNm = 11,520
kNm
Moments at 9.6m on the LHS of the beam
M9.6 = (4800 kN x 9.6 m) – (1000 kN/m x 9.6m x 4.8 m) = 46,080 kNm – 46,080 kNm = 0 kNm
Moments at B on the RHS of the beam
MB = -1000 kN/m x 2m x 1m = -2,000 kNm
Moments at C on the RHS of the beam
MC = -1000 kN/m x 1 m x 0.5 m = -500 kNm
Moment at the end of the beam = 0 kNm
Using the support reaction forces, shear forces and bending moments calculated above, the free
body diagram (FBD), shear force diagram (SFD) and bending moment diagram of the beam are
presented in Figure 1 below
This means that the bending moment will be zero at a distance of 9.8m from support A in the
bending moment diagram of the beam.
The bending moment at different points along the beam is calculated as follows:
Moments at A, MA = 0
Moments at 4.8m on the left hand side (LHS) of the beam
M4.8 = (4800 kN x 4.8 m) – (1000 kN/m x 4.8 m x 2.4 m) = 23,040 kNm – 11,520 kNm = 11,520
kNm
Moments at 9.6m on the LHS of the beam
M9.6 = (4800 kN x 9.6 m) – (1000 kN/m x 9.6m x 4.8 m) = 46,080 kNm – 46,080 kNm = 0 kNm
Moments at B on the RHS of the beam
MB = -1000 kN/m x 2m x 1m = -2,000 kNm
Moments at C on the RHS of the beam
MC = -1000 kN/m x 1 m x 0.5 m = -500 kNm
Moment at the end of the beam = 0 kNm
Using the support reaction forces, shear forces and bending moments calculated above, the free
body diagram (FBD), shear force diagram (SFD) and bending moment diagram of the beam are
presented in Figure 1 below
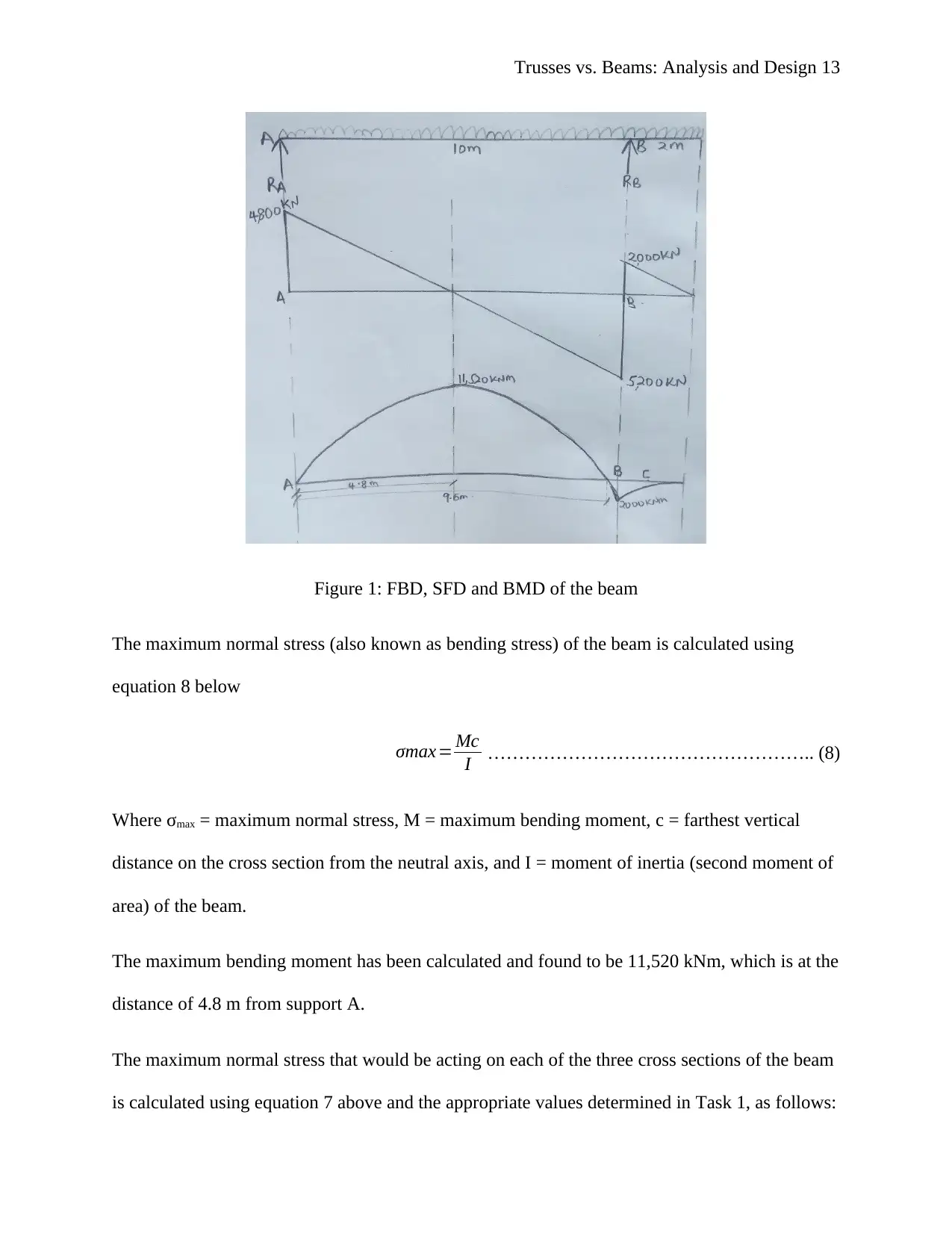
Trusses vs. Beams: Analysis and Design 13
Figure 1: FBD, SFD and BMD of the beam
The maximum normal stress (also known as bending stress) of the beam is calculated using
equation 8 below
σmax= Mc
I …………………………………………….. (8)
Where σmax = maximum normal stress, M = maximum bending moment, c = farthest vertical
distance on the cross section from the neutral axis, and I = moment of inertia (second moment of
area) of the beam.
The maximum bending moment has been calculated and found to be 11,520 kNm, which is at the
distance of 4.8 m from support A.
The maximum normal stress that would be acting on each of the three cross sections of the beam
is calculated using equation 7 above and the appropriate values determined in Task 1, as follows:
Figure 1: FBD, SFD and BMD of the beam
The maximum normal stress (also known as bending stress) of the beam is calculated using
equation 8 below
σmax= Mc
I …………………………………………….. (8)
Where σmax = maximum normal stress, M = maximum bending moment, c = farthest vertical
distance on the cross section from the neutral axis, and I = moment of inertia (second moment of
area) of the beam.
The maximum bending moment has been calculated and found to be 11,520 kNm, which is at the
distance of 4.8 m from support A.
The maximum normal stress that would be acting on each of the three cross sections of the beam
is calculated using equation 7 above and the appropriate values determined in Task 1, as follows:
Paraphrase This Document
Need a fresh take? Get an instant paraphrase of this document with our AI Paraphraser
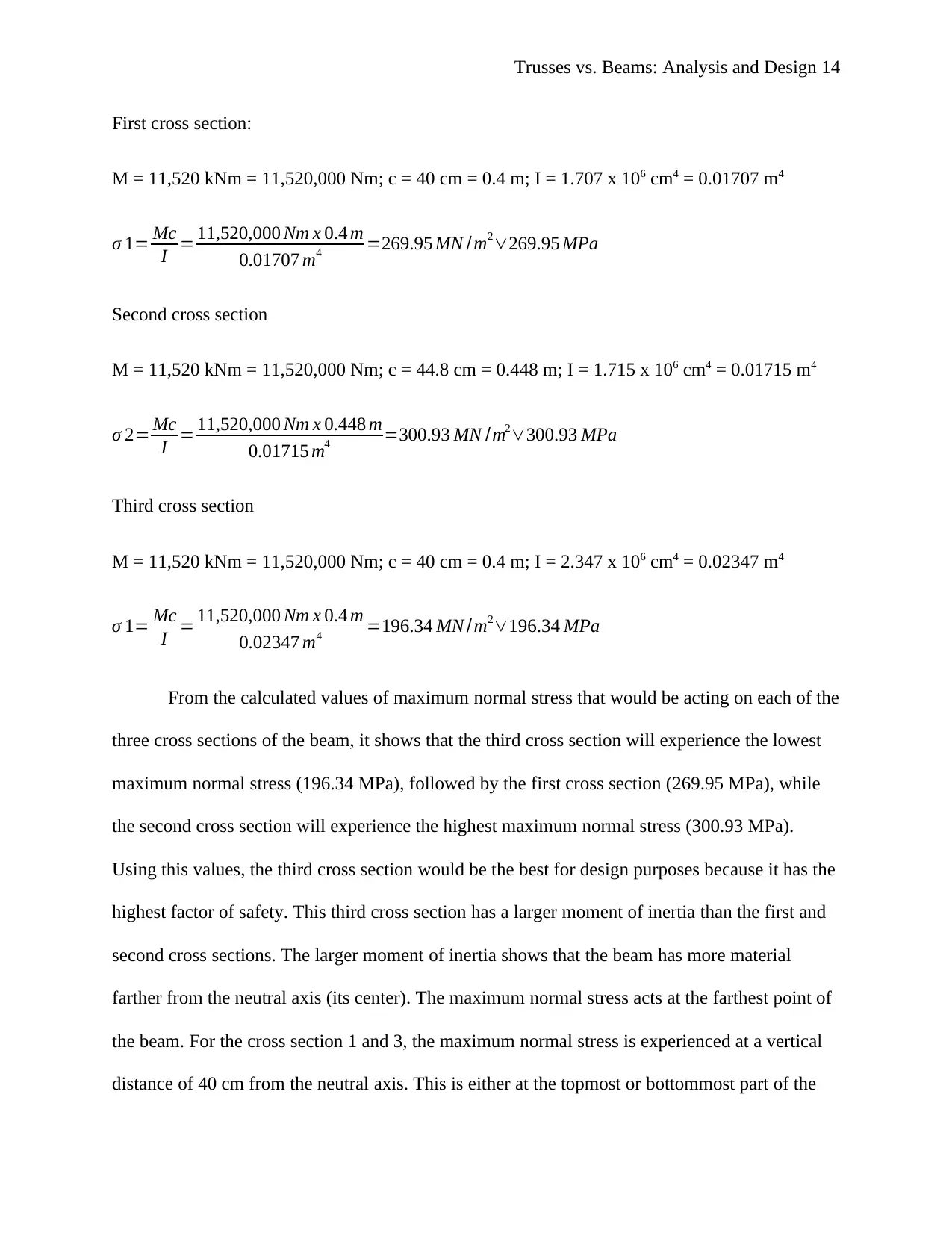
Trusses vs. Beams: Analysis and Design 14
First cross section:
M = 11,520 kNm = 11,520,000 Nm; c = 40 cm = 0.4 m; I = 1.707 x 106 cm4 = 0.01707 m4
σ 1= Mc
I = 11,520,000 Nm x 0.4 m
0.01707 m4 =269.95 MN /m2∨269.95 MPa
Second cross section
M = 11,520 kNm = 11,520,000 Nm; c = 44.8 cm = 0.448 m; I = 1.715 x 106 cm4 = 0.01715 m4
σ 2= Mc
I = 11,520,000 Nm x 0.448 m
0.01715 m4 =300.93 MN /m2∨300.93 MPa
Third cross section
M = 11,520 kNm = 11,520,000 Nm; c = 40 cm = 0.4 m; I = 2.347 x 106 cm4 = 0.02347 m4
σ 1= Mc
I = 11,520,000 Nm x 0.4 m
0.02347 m4 =196.34 MN /m2∨196.34 MPa
From the calculated values of maximum normal stress that would be acting on each of the
three cross sections of the beam, it shows that the third cross section will experience the lowest
maximum normal stress (196.34 MPa), followed by the first cross section (269.95 MPa), while
the second cross section will experience the highest maximum normal stress (300.93 MPa).
Using this values, the third cross section would be the best for design purposes because it has the
highest factor of safety. This third cross section has a larger moment of inertia than the first and
second cross sections. The larger moment of inertia shows that the beam has more material
farther from the neutral axis (its center). The maximum normal stress acts at the farthest point of
the beam. For the cross section 1 and 3, the maximum normal stress is experienced at a vertical
distance of 40 cm from the neutral axis. This is either at the topmost or bottommost part of the
First cross section:
M = 11,520 kNm = 11,520,000 Nm; c = 40 cm = 0.4 m; I = 1.707 x 106 cm4 = 0.01707 m4
σ 1= Mc
I = 11,520,000 Nm x 0.4 m
0.01707 m4 =269.95 MN /m2∨269.95 MPa
Second cross section
M = 11,520 kNm = 11,520,000 Nm; c = 44.8 cm = 0.448 m; I = 1.715 x 106 cm4 = 0.01715 m4
σ 2= Mc
I = 11,520,000 Nm x 0.448 m
0.01715 m4 =300.93 MN /m2∨300.93 MPa
Third cross section
M = 11,520 kNm = 11,520,000 Nm; c = 40 cm = 0.4 m; I = 2.347 x 106 cm4 = 0.02347 m4
σ 1= Mc
I = 11,520,000 Nm x 0.4 m
0.02347 m4 =196.34 MN /m2∨196.34 MPa
From the calculated values of maximum normal stress that would be acting on each of the
three cross sections of the beam, it shows that the third cross section will experience the lowest
maximum normal stress (196.34 MPa), followed by the first cross section (269.95 MPa), while
the second cross section will experience the highest maximum normal stress (300.93 MPa).
Using this values, the third cross section would be the best for design purposes because it has the
highest factor of safety. This third cross section has a larger moment of inertia than the first and
second cross sections. The larger moment of inertia shows that the beam has more material
farther from the neutral axis (its center). The maximum normal stress acts at the farthest point of
the beam. For the cross section 1 and 3, the maximum normal stress is experienced at a vertical
distance of 40 cm from the neutral axis. This is either at the topmost or bottommost part of the
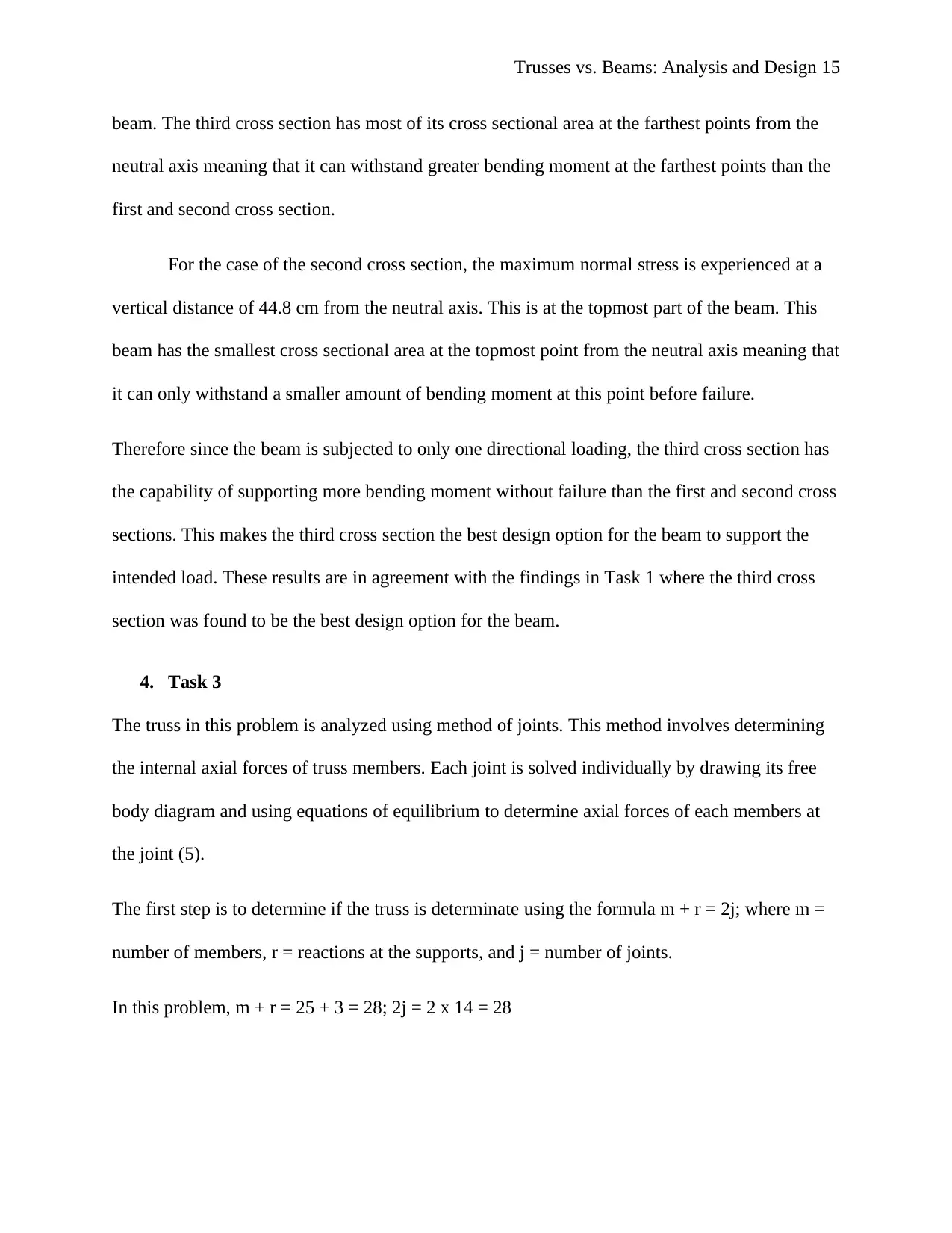
Trusses vs. Beams: Analysis and Design 15
beam. The third cross section has most of its cross sectional area at the farthest points from the
neutral axis meaning that it can withstand greater bending moment at the farthest points than the
first and second cross section.
For the case of the second cross section, the maximum normal stress is experienced at a
vertical distance of 44.8 cm from the neutral axis. This is at the topmost part of the beam. This
beam has the smallest cross sectional area at the topmost point from the neutral axis meaning that
it can only withstand a smaller amount of bending moment at this point before failure.
Therefore since the beam is subjected to only one directional loading, the third cross section has
the capability of supporting more bending moment without failure than the first and second cross
sections. This makes the third cross section the best design option for the beam to support the
intended load. These results are in agreement with the findings in Task 1 where the third cross
section was found to be the best design option for the beam.
4. Task 3
The truss in this problem is analyzed using method of joints. This method involves determining
the internal axial forces of truss members. Each joint is solved individually by drawing its free
body diagram and using equations of equilibrium to determine axial forces of each members at
the joint (5).
The first step is to determine if the truss is determinate using the formula m + r = 2j; where m =
number of members, r = reactions at the supports, and j = number of joints.
In this problem, m + r = 25 + 3 = 28; 2j = 2 x 14 = 28
beam. The third cross section has most of its cross sectional area at the farthest points from the
neutral axis meaning that it can withstand greater bending moment at the farthest points than the
first and second cross section.
For the case of the second cross section, the maximum normal stress is experienced at a
vertical distance of 44.8 cm from the neutral axis. This is at the topmost part of the beam. This
beam has the smallest cross sectional area at the topmost point from the neutral axis meaning that
it can only withstand a smaller amount of bending moment at this point before failure.
Therefore since the beam is subjected to only one directional loading, the third cross section has
the capability of supporting more bending moment without failure than the first and second cross
sections. This makes the third cross section the best design option for the beam to support the
intended load. These results are in agreement with the findings in Task 1 where the third cross
section was found to be the best design option for the beam.
4. Task 3
The truss in this problem is analyzed using method of joints. This method involves determining
the internal axial forces of truss members. Each joint is solved individually by drawing its free
body diagram and using equations of equilibrium to determine axial forces of each members at
the joint (5).
The first step is to determine if the truss is determinate using the formula m + r = 2j; where m =
number of members, r = reactions at the supports, and j = number of joints.
In this problem, m + r = 25 + 3 = 28; 2j = 2 x 14 = 28
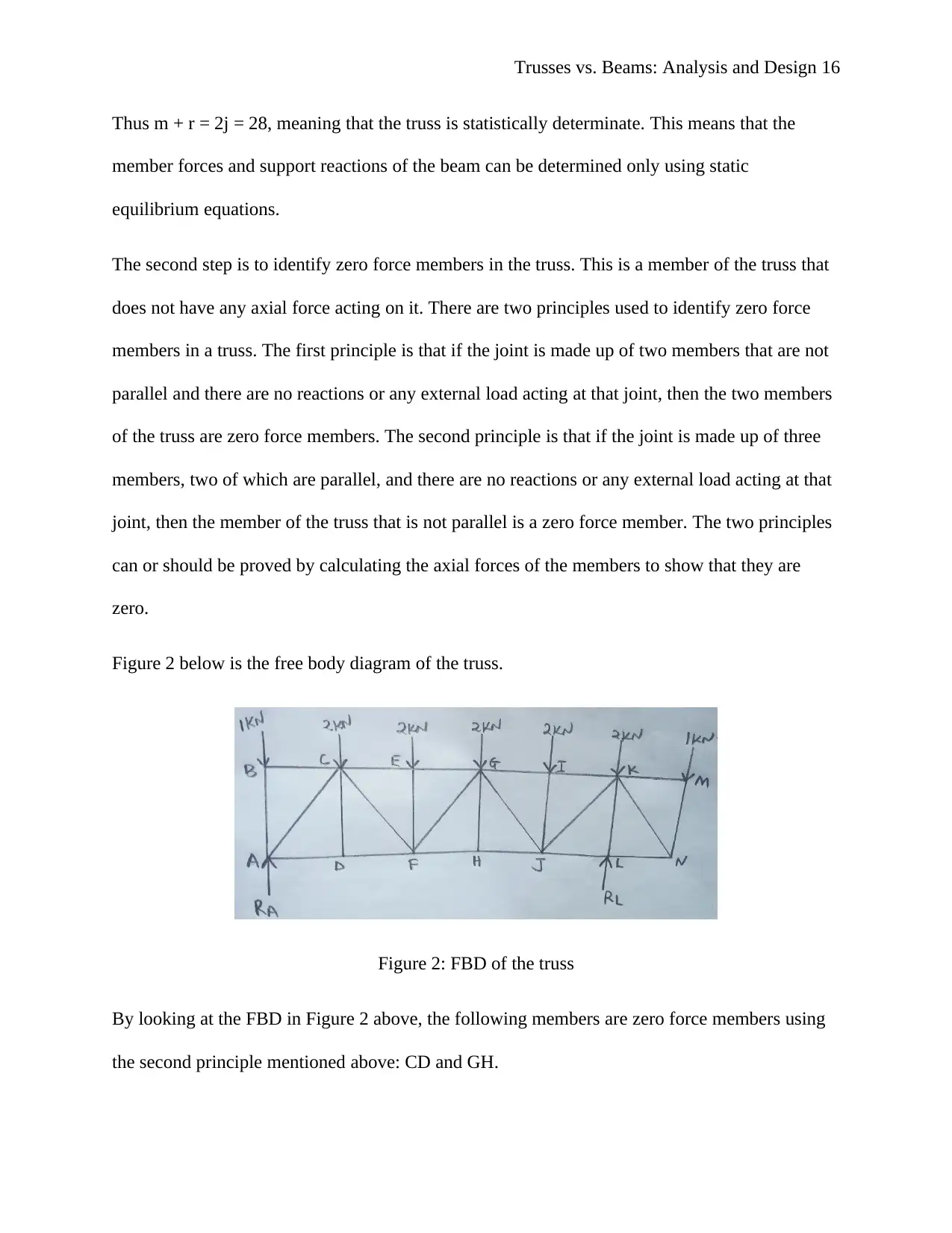
Trusses vs. Beams: Analysis and Design 16
Thus m + r = 2j = 28, meaning that the truss is statistically determinate. This means that the
member forces and support reactions of the beam can be determined only using static
equilibrium equations.
The second step is to identify zero force members in the truss. This is a member of the truss that
does not have any axial force acting on it. There are two principles used to identify zero force
members in a truss. The first principle is that if the joint is made up of two members that are not
parallel and there are no reactions or any external load acting at that joint, then the two members
of the truss are zero force members. The second principle is that if the joint is made up of three
members, two of which are parallel, and there are no reactions or any external load acting at that
joint, then the member of the truss that is not parallel is a zero force member. The two principles
can or should be proved by calculating the axial forces of the members to show that they are
zero.
Figure 2 below is the free body diagram of the truss.
Figure 2: FBD of the truss
By looking at the FBD in Figure 2 above, the following members are zero force members using
the second principle mentioned above: CD and GH.
Thus m + r = 2j = 28, meaning that the truss is statistically determinate. This means that the
member forces and support reactions of the beam can be determined only using static
equilibrium equations.
The second step is to identify zero force members in the truss. This is a member of the truss that
does not have any axial force acting on it. There are two principles used to identify zero force
members in a truss. The first principle is that if the joint is made up of two members that are not
parallel and there are no reactions or any external load acting at that joint, then the two members
of the truss are zero force members. The second principle is that if the joint is made up of three
members, two of which are parallel, and there are no reactions or any external load acting at that
joint, then the member of the truss that is not parallel is a zero force member. The two principles
can or should be proved by calculating the axial forces of the members to show that they are
zero.
Figure 2 below is the free body diagram of the truss.
Figure 2: FBD of the truss
By looking at the FBD in Figure 2 above, the following members are zero force members using
the second principle mentioned above: CD and GH.
Secure Best Marks with AI Grader
Need help grading? Try our AI Grader for instant feedback on your assignments.
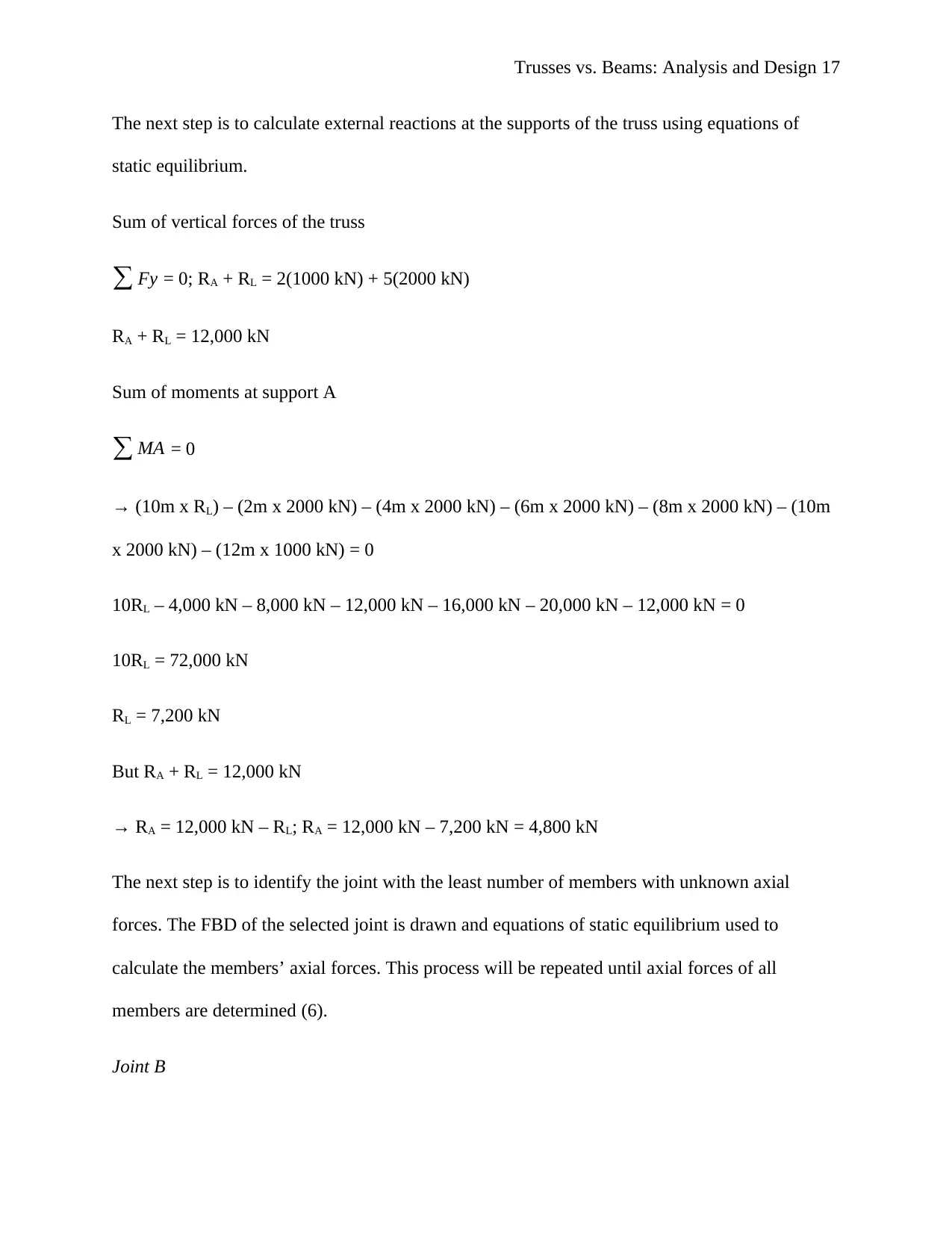
Trusses vs. Beams: Analysis and Design 17
The next step is to calculate external reactions at the supports of the truss using equations of
static equilibrium.
Sum of vertical forces of the truss
∑ Fy = 0; RA + RL = 2(1000 kN) + 5(2000 kN)
RA + RL = 12,000 kN
Sum of moments at support A
∑ MA = 0
→ (10m x RL) – (2m x 2000 kN) – (4m x 2000 kN) – (6m x 2000 kN) – (8m x 2000 kN) – (10m
x 2000 kN) – (12m x 1000 kN) = 0
10RL – 4,000 kN – 8,000 kN – 12,000 kN – 16,000 kN – 20,000 kN – 12,000 kN = 0
10RL = 72,000 kN
RL = 7,200 kN
But RA + RL = 12,000 kN
→ RA = 12,000 kN – RL; RA = 12,000 kN – 7,200 kN = 4,800 kN
The next step is to identify the joint with the least number of members with unknown axial
forces. The FBD of the selected joint is drawn and equations of static equilibrium used to
calculate the members’ axial forces. This process will be repeated until axial forces of all
members are determined (6).
Joint B
The next step is to calculate external reactions at the supports of the truss using equations of
static equilibrium.
Sum of vertical forces of the truss
∑ Fy = 0; RA + RL = 2(1000 kN) + 5(2000 kN)
RA + RL = 12,000 kN
Sum of moments at support A
∑ MA = 0
→ (10m x RL) – (2m x 2000 kN) – (4m x 2000 kN) – (6m x 2000 kN) – (8m x 2000 kN) – (10m
x 2000 kN) – (12m x 1000 kN) = 0
10RL – 4,000 kN – 8,000 kN – 12,000 kN – 16,000 kN – 20,000 kN – 12,000 kN = 0
10RL = 72,000 kN
RL = 7,200 kN
But RA + RL = 12,000 kN
→ RA = 12,000 kN – RL; RA = 12,000 kN – 7,200 kN = 4,800 kN
The next step is to identify the joint with the least number of members with unknown axial
forces. The FBD of the selected joint is drawn and equations of static equilibrium used to
calculate the members’ axial forces. This process will be repeated until axial forces of all
members are determined (6).
Joint B
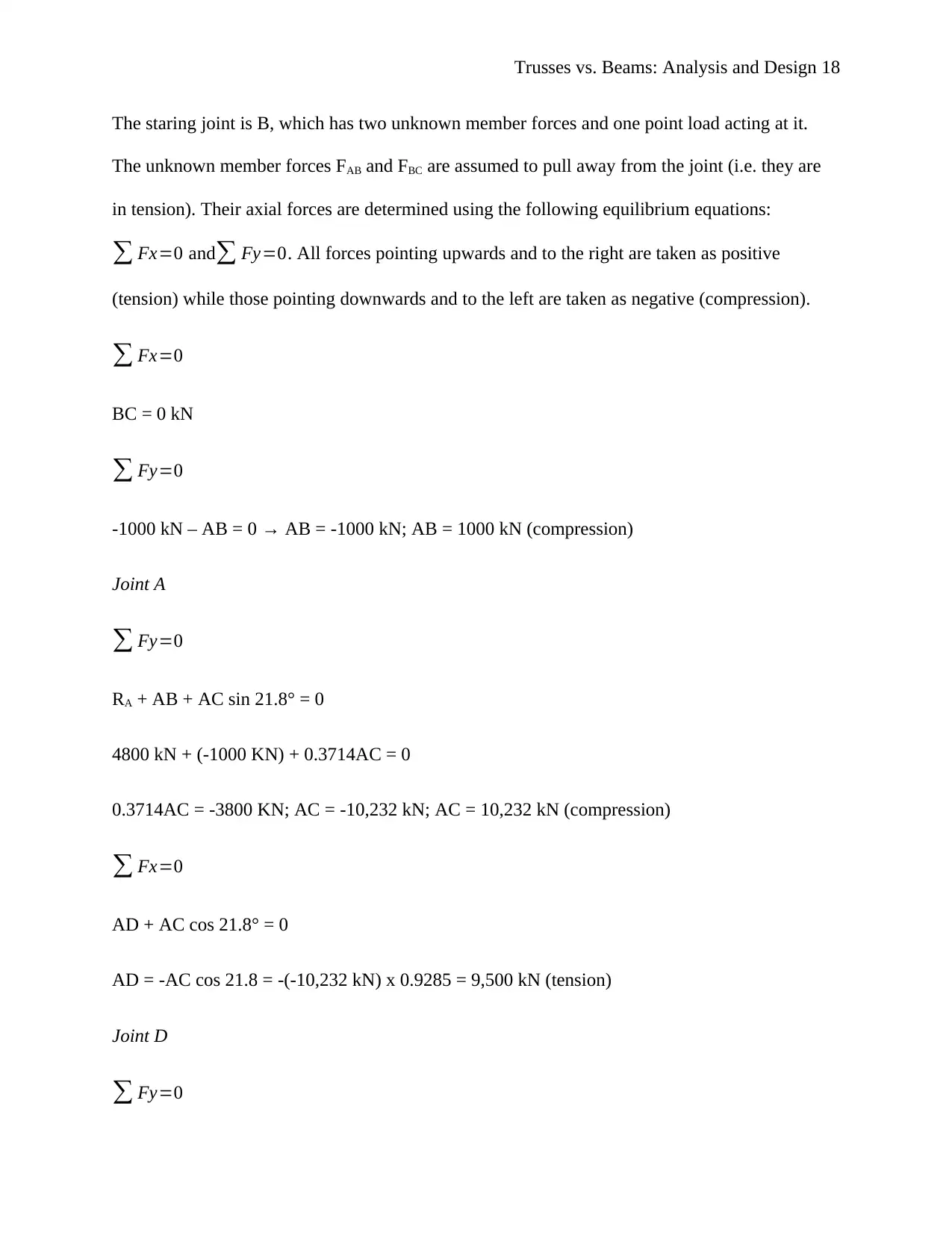
Trusses vs. Beams: Analysis and Design 18
The staring joint is B, which has two unknown member forces and one point load acting at it.
The unknown member forces FAB and FBC are assumed to pull away from the joint (i.e. they are
in tension). Their axial forces are determined using the following equilibrium equations:
∑ Fx=0 and∑ Fy=0. All forces pointing upwards and to the right are taken as positive
(tension) while those pointing downwards and to the left are taken as negative (compression).
∑ Fx=0
BC = 0 kN
∑ Fy=0
-1000 kN – AB = 0 → AB = -1000 kN; AB = 1000 kN (compression)
Joint A
∑ Fy=0
RA + AB + AC sin 21.8° = 0
4800 kN + (-1000 KN) + 0.3714AC = 0
0.3714AC = -3800 KN; AC = -10,232 kN; AC = 10,232 kN (compression)
∑ Fx=0
AD + AC cos 21.8° = 0
AD = -AC cos 21.8 = -(-10,232 kN) x 0.9285 = 9,500 kN (tension)
Joint D
∑ Fy=0
The staring joint is B, which has two unknown member forces and one point load acting at it.
The unknown member forces FAB and FBC are assumed to pull away from the joint (i.e. they are
in tension). Their axial forces are determined using the following equilibrium equations:
∑ Fx=0 and∑ Fy=0. All forces pointing upwards and to the right are taken as positive
(tension) while those pointing downwards and to the left are taken as negative (compression).
∑ Fx=0
BC = 0 kN
∑ Fy=0
-1000 kN – AB = 0 → AB = -1000 kN; AB = 1000 kN (compression)
Joint A
∑ Fy=0
RA + AB + AC sin 21.8° = 0
4800 kN + (-1000 KN) + 0.3714AC = 0
0.3714AC = -3800 KN; AC = -10,232 kN; AC = 10,232 kN (compression)
∑ Fx=0
AD + AC cos 21.8° = 0
AD = -AC cos 21.8 = -(-10,232 kN) x 0.9285 = 9,500 kN (tension)
Joint D
∑ Fy=0
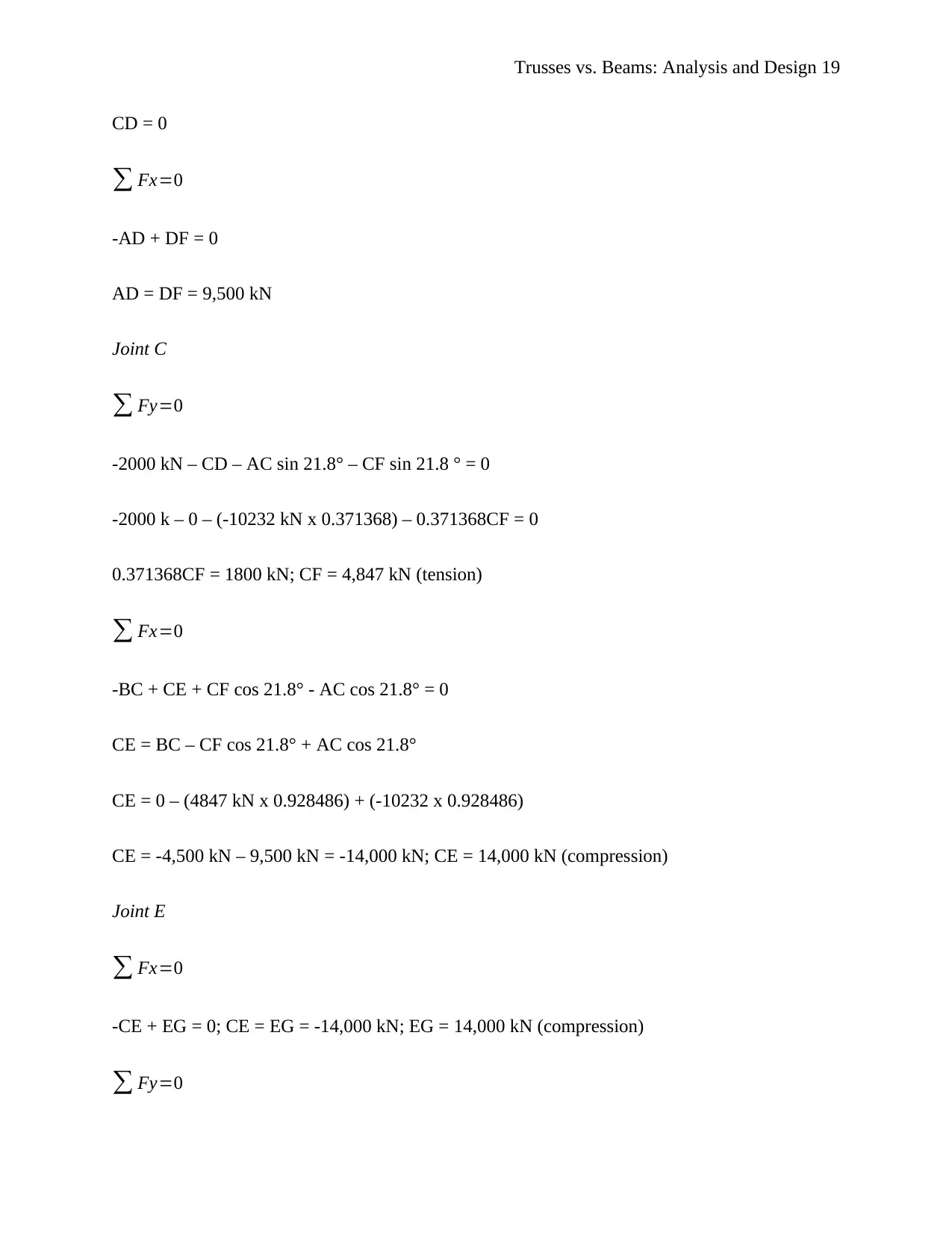
Trusses vs. Beams: Analysis and Design 19
CD = 0
∑ Fx=0
-AD + DF = 0
AD = DF = 9,500 kN
Joint C
∑ Fy=0
-2000 kN – CD – AC sin 21.8° – CF sin 21.8 ° = 0
-2000 k – 0 – (-10232 kN x 0.371368) – 0.371368CF = 0
0.371368CF = 1800 kN; CF = 4,847 kN (tension)
∑ Fx=0
-BC + CE + CF cos 21.8° - AC cos 21.8° = 0
CE = BC – CF cos 21.8° + AC cos 21.8°
CE = 0 – (4847 kN x 0.928486) + (-10232 x 0.928486)
CE = -4,500 kN – 9,500 kN = -14,000 kN; CE = 14,000 kN (compression)
Joint E
∑ Fx=0
-CE + EG = 0; CE = EG = -14,000 kN; EG = 14,000 kN (compression)
∑ Fy=0
CD = 0
∑ Fx=0
-AD + DF = 0
AD = DF = 9,500 kN
Joint C
∑ Fy=0
-2000 kN – CD – AC sin 21.8° – CF sin 21.8 ° = 0
-2000 k – 0 – (-10232 kN x 0.371368) – 0.371368CF = 0
0.371368CF = 1800 kN; CF = 4,847 kN (tension)
∑ Fx=0
-BC + CE + CF cos 21.8° - AC cos 21.8° = 0
CE = BC – CF cos 21.8° + AC cos 21.8°
CE = 0 – (4847 kN x 0.928486) + (-10232 x 0.928486)
CE = -4,500 kN – 9,500 kN = -14,000 kN; CE = 14,000 kN (compression)
Joint E
∑ Fx=0
-CE + EG = 0; CE = EG = -14,000 kN; EG = 14,000 kN (compression)
∑ Fy=0
Paraphrase This Document
Need a fresh take? Get an instant paraphrase of this document with our AI Paraphraser
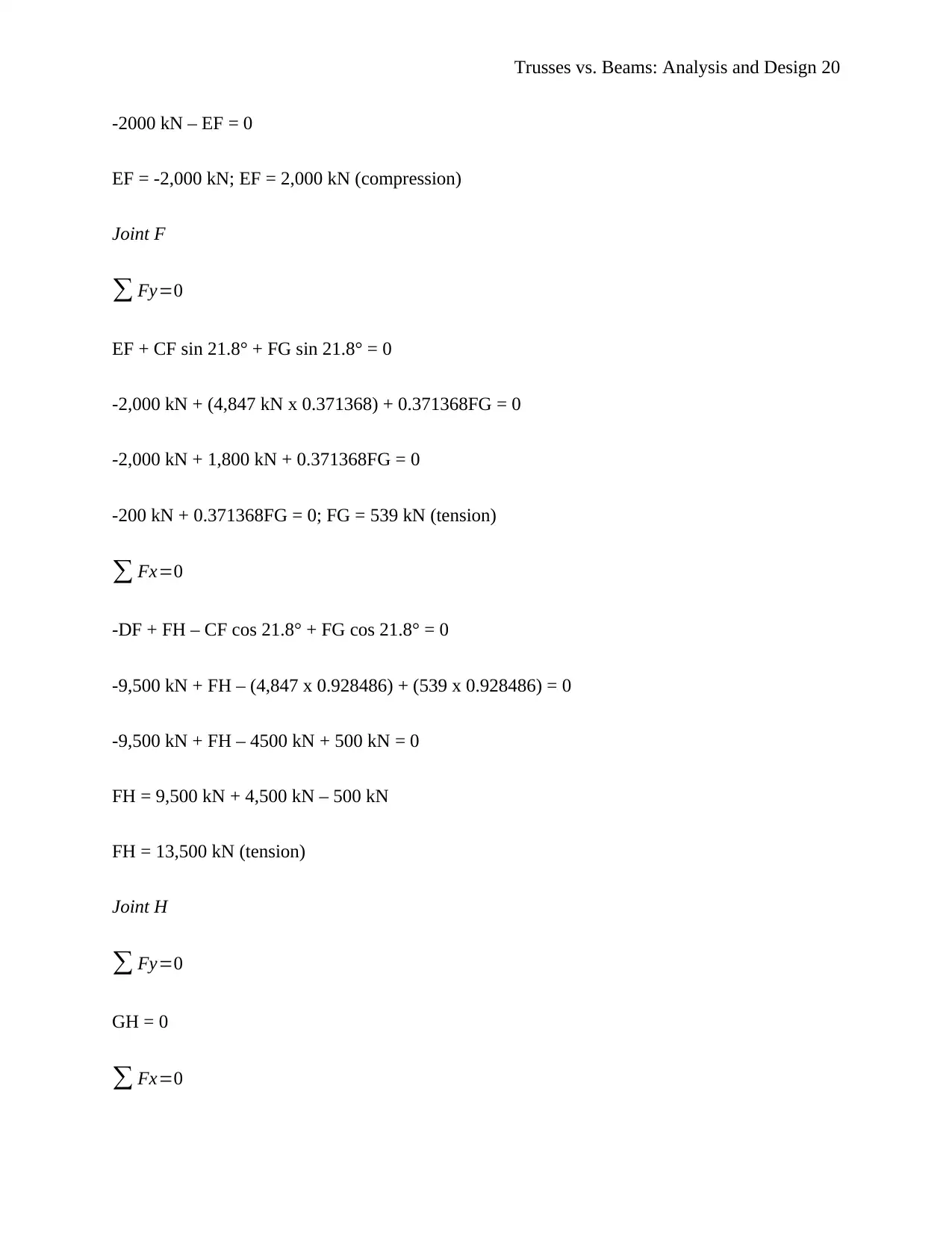
Trusses vs. Beams: Analysis and Design 20
-2000 kN – EF = 0
EF = -2,000 kN; EF = 2,000 kN (compression)
Joint F
∑ Fy=0
EF + CF sin 21.8° + FG sin 21.8° = 0
-2,000 kN + (4,847 kN x 0.371368) + 0.371368FG = 0
-2,000 kN + 1,800 kN + 0.371368FG = 0
-200 kN + 0.371368FG = 0; FG = 539 kN (tension)
∑ Fx=0
-DF + FH – CF cos 21.8° + FG cos 21.8° = 0
-9,500 kN + FH – (4,847 x 0.928486) + (539 x 0.928486) = 0
-9,500 kN + FH – 4500 kN + 500 kN = 0
FH = 9,500 kN + 4,500 kN – 500 kN
FH = 13,500 kN (tension)
Joint H
∑ Fy=0
GH = 0
∑ Fx=0
-2000 kN – EF = 0
EF = -2,000 kN; EF = 2,000 kN (compression)
Joint F
∑ Fy=0
EF + CF sin 21.8° + FG sin 21.8° = 0
-2,000 kN + (4,847 kN x 0.371368) + 0.371368FG = 0
-2,000 kN + 1,800 kN + 0.371368FG = 0
-200 kN + 0.371368FG = 0; FG = 539 kN (tension)
∑ Fx=0
-DF + FH – CF cos 21.8° + FG cos 21.8° = 0
-9,500 kN + FH – (4,847 x 0.928486) + (539 x 0.928486) = 0
-9,500 kN + FH – 4500 kN + 500 kN = 0
FH = 9,500 kN + 4,500 kN – 500 kN
FH = 13,500 kN (tension)
Joint H
∑ Fy=0
GH = 0
∑ Fx=0
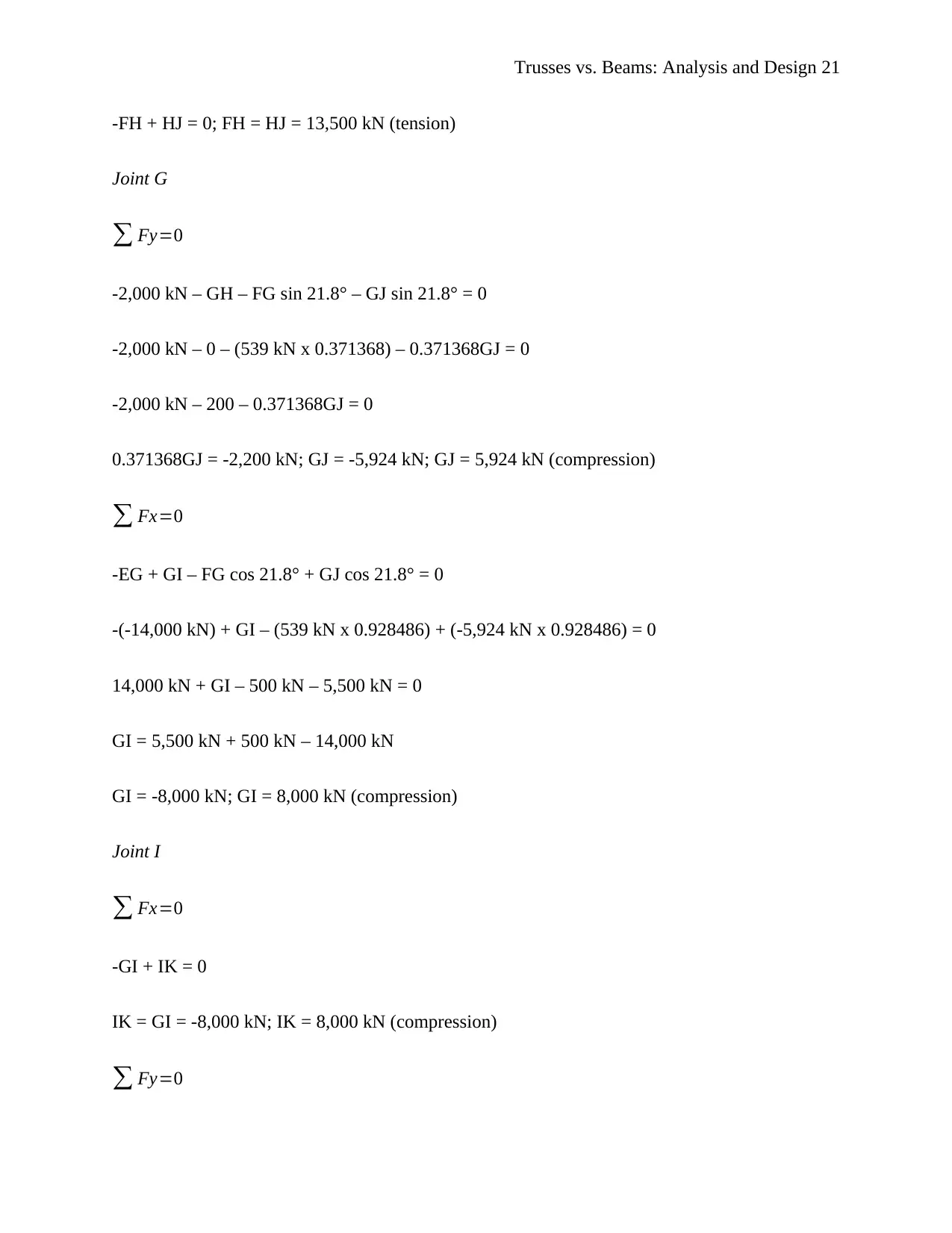
Trusses vs. Beams: Analysis and Design 21
-FH + HJ = 0; FH = HJ = 13,500 kN (tension)
Joint G
∑ Fy=0
-2,000 kN – GH – FG sin 21.8° – GJ sin 21.8° = 0
-2,000 kN – 0 – (539 kN x 0.371368) – 0.371368GJ = 0
-2,000 kN – 200 – 0.371368GJ = 0
0.371368GJ = -2,200 kN; GJ = -5,924 kN; GJ = 5,924 kN (compression)
∑ Fx=0
-EG + GI – FG cos 21.8° + GJ cos 21.8° = 0
-(-14,000 kN) + GI – (539 kN x 0.928486) + (-5,924 kN x 0.928486) = 0
14,000 kN + GI – 500 kN – 5,500 kN = 0
GI = 5,500 kN + 500 kN – 14,000 kN
GI = -8,000 kN; GI = 8,000 kN (compression)
Joint I
∑ Fx=0
-GI + IK = 0
IK = GI = -8,000 kN; IK = 8,000 kN (compression)
∑ Fy=0
-FH + HJ = 0; FH = HJ = 13,500 kN (tension)
Joint G
∑ Fy=0
-2,000 kN – GH – FG sin 21.8° – GJ sin 21.8° = 0
-2,000 kN – 0 – (539 kN x 0.371368) – 0.371368GJ = 0
-2,000 kN – 200 – 0.371368GJ = 0
0.371368GJ = -2,200 kN; GJ = -5,924 kN; GJ = 5,924 kN (compression)
∑ Fx=0
-EG + GI – FG cos 21.8° + GJ cos 21.8° = 0
-(-14,000 kN) + GI – (539 kN x 0.928486) + (-5,924 kN x 0.928486) = 0
14,000 kN + GI – 500 kN – 5,500 kN = 0
GI = 5,500 kN + 500 kN – 14,000 kN
GI = -8,000 kN; GI = 8,000 kN (compression)
Joint I
∑ Fx=0
-GI + IK = 0
IK = GI = -8,000 kN; IK = 8,000 kN (compression)
∑ Fy=0
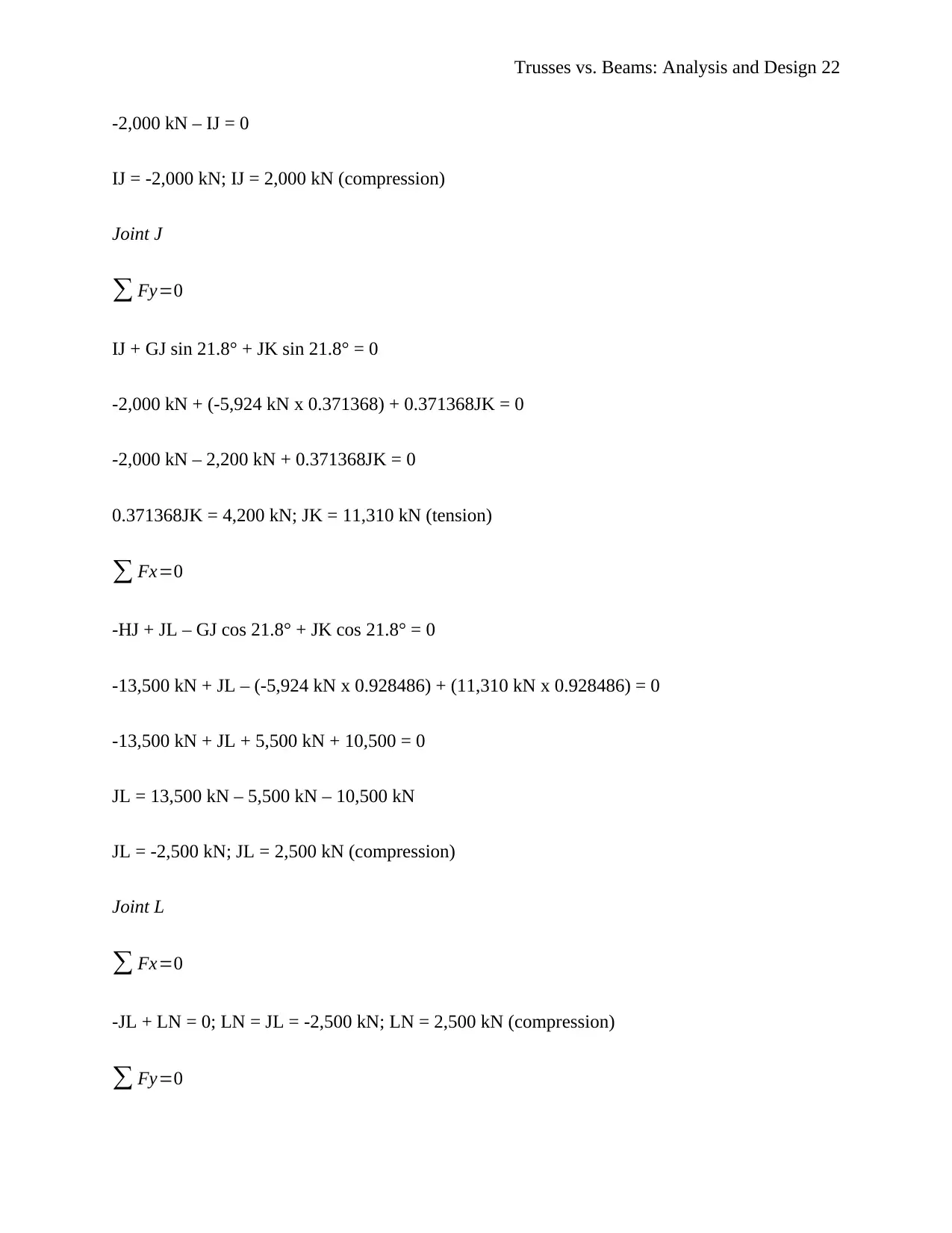
Trusses vs. Beams: Analysis and Design 22
-2,000 kN – IJ = 0
IJ = -2,000 kN; IJ = 2,000 kN (compression)
Joint J
∑ Fy=0
IJ + GJ sin 21.8° + JK sin 21.8° = 0
-2,000 kN + (-5,924 kN x 0.371368) + 0.371368JK = 0
-2,000 kN – 2,200 kN + 0.371368JK = 0
0.371368JK = 4,200 kN; JK = 11,310 kN (tension)
∑ Fx=0
-HJ + JL – GJ cos 21.8° + JK cos 21.8° = 0
-13,500 kN + JL – (-5,924 kN x 0.928486) + (11,310 kN x 0.928486) = 0
-13,500 kN + JL + 5,500 kN + 10,500 = 0
JL = 13,500 kN – 5,500 kN – 10,500 kN
JL = -2,500 kN; JL = 2,500 kN (compression)
Joint L
∑ Fx=0
-JL + LN = 0; LN = JL = -2,500 kN; LN = 2,500 kN (compression)
∑ Fy=0
-2,000 kN – IJ = 0
IJ = -2,000 kN; IJ = 2,000 kN (compression)
Joint J
∑ Fy=0
IJ + GJ sin 21.8° + JK sin 21.8° = 0
-2,000 kN + (-5,924 kN x 0.371368) + 0.371368JK = 0
-2,000 kN – 2,200 kN + 0.371368JK = 0
0.371368JK = 4,200 kN; JK = 11,310 kN (tension)
∑ Fx=0
-HJ + JL – GJ cos 21.8° + JK cos 21.8° = 0
-13,500 kN + JL – (-5,924 kN x 0.928486) + (11,310 kN x 0.928486) = 0
-13,500 kN + JL + 5,500 kN + 10,500 = 0
JL = 13,500 kN – 5,500 kN – 10,500 kN
JL = -2,500 kN; JL = 2,500 kN (compression)
Joint L
∑ Fx=0
-JL + LN = 0; LN = JL = -2,500 kN; LN = 2,500 kN (compression)
∑ Fy=0
Secure Best Marks with AI Grader
Need help grading? Try our AI Grader for instant feedback on your assignments.
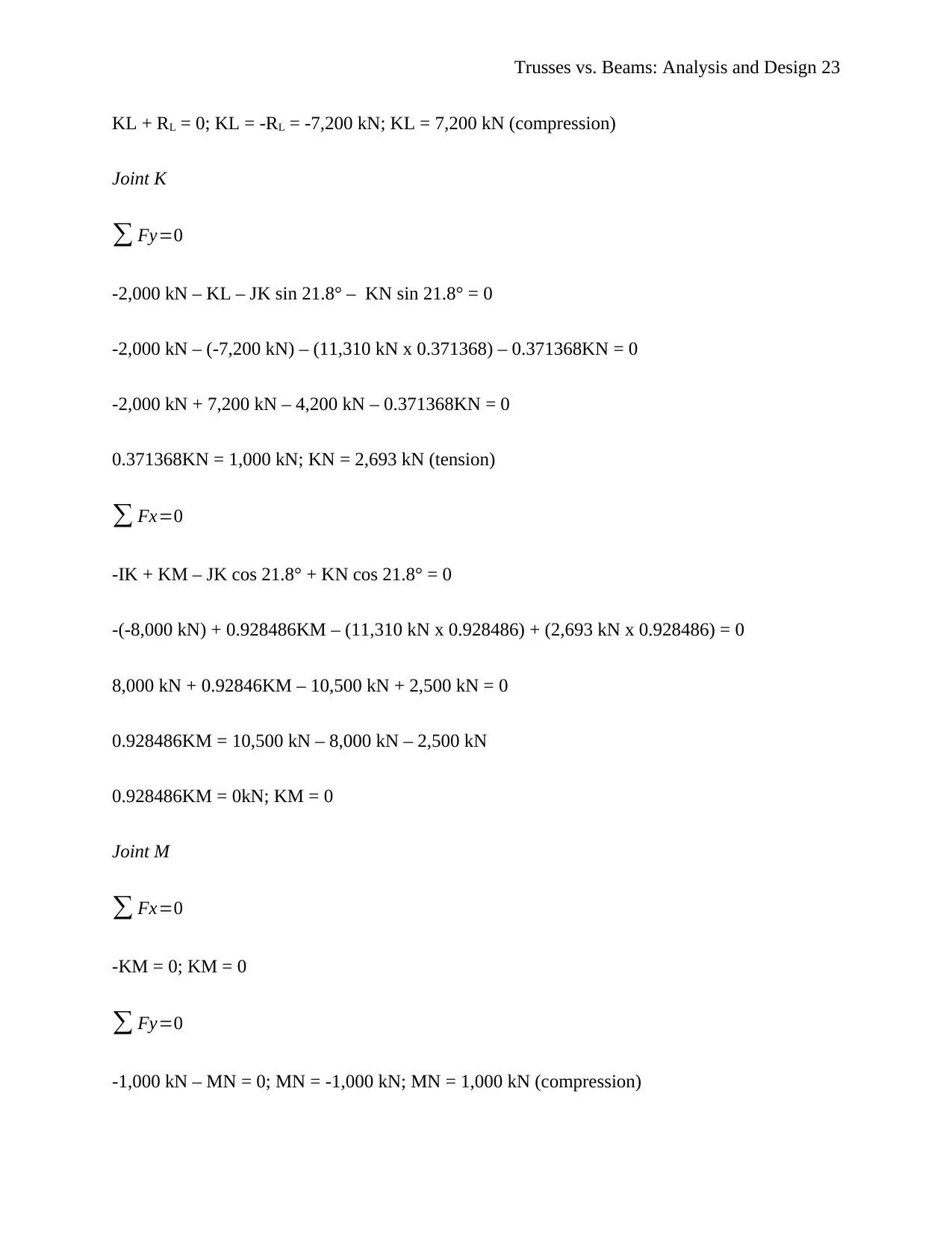
Trusses vs. Beams: Analysis and Design 23
KL + RL = 0; KL = -RL = -7,200 kN; KL = 7,200 kN (compression)
Joint K
∑ Fy=0
-2,000 kN – KL – JK sin 21.8° – KN sin 21.8° = 0
-2,000 kN – (-7,200 kN) – (11,310 kN x 0.371368) – 0.371368KN = 0
-2,000 kN + 7,200 kN – 4,200 kN – 0.371368KN = 0
0.371368KN = 1,000 kN; KN = 2,693 kN (tension)
∑ Fx=0
-IK + KM – JK cos 21.8° + KN cos 21.8° = 0
-(-8,000 kN) + 0.928486KM – (11,310 kN x 0.928486) + (2,693 kN x 0.928486) = 0
8,000 kN + 0.92846KM – 10,500 kN + 2,500 kN = 0
0.928486KM = 10,500 kN – 8,000 kN – 2,500 kN
0.928486KM = 0kN; KM = 0
Joint M
∑ Fx=0
-KM = 0; KM = 0
∑ Fy=0
-1,000 kN – MN = 0; MN = -1,000 kN; MN = 1,000 kN (compression)
KL + RL = 0; KL = -RL = -7,200 kN; KL = 7,200 kN (compression)
Joint K
∑ Fy=0
-2,000 kN – KL – JK sin 21.8° – KN sin 21.8° = 0
-2,000 kN – (-7,200 kN) – (11,310 kN x 0.371368) – 0.371368KN = 0
-2,000 kN + 7,200 kN – 4,200 kN – 0.371368KN = 0
0.371368KN = 1,000 kN; KN = 2,693 kN (tension)
∑ Fx=0
-IK + KM – JK cos 21.8° + KN cos 21.8° = 0
-(-8,000 kN) + 0.928486KM – (11,310 kN x 0.928486) + (2,693 kN x 0.928486) = 0
8,000 kN + 0.92846KM – 10,500 kN + 2,500 kN = 0
0.928486KM = 10,500 kN – 8,000 kN – 2,500 kN
0.928486KM = 0kN; KM = 0
Joint M
∑ Fx=0
-KM = 0; KM = 0
∑ Fy=0
-1,000 kN – MN = 0; MN = -1,000 kN; MN = 1,000 kN (compression)
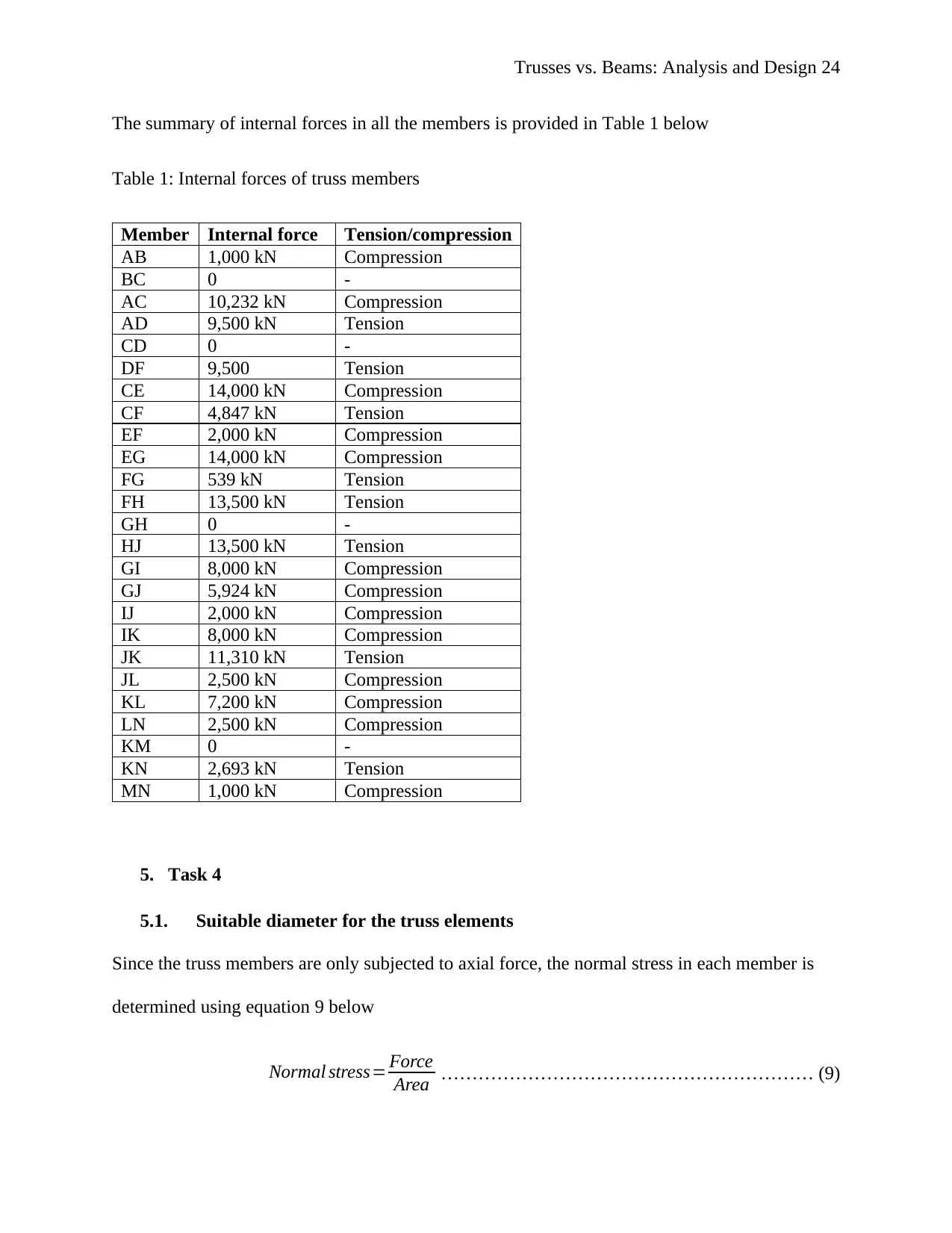
Trusses vs. Beams: Analysis and Design 24
The summary of internal forces in all the members is provided in Table 1 below
Table 1: Internal forces of truss members
Member Internal force Tension/compression
AB 1,000 kN Compression
BC 0 -
AC 10,232 kN Compression
AD 9,500 kN Tension
CD 0 -
DF 9,500 Tension
CE 14,000 kN Compression
CF 4,847 kN Tension
EF 2,000 kN Compression
EG 14,000 kN Compression
FG 539 kN Tension
FH 13,500 kN Tension
GH 0 -
HJ 13,500 kN Tension
GI 8,000 kN Compression
GJ 5,924 kN Compression
IJ 2,000 kN Compression
IK 8,000 kN Compression
JK 11,310 kN Tension
JL 2,500 kN Compression
KL 7,200 kN Compression
LN 2,500 kN Compression
KM 0 -
KN 2,693 kN Tension
MN 1,000 kN Compression
5. Task 4
5.1. Suitable diameter for the truss elements
Since the truss members are only subjected to axial force, the normal stress in each member is
determined using equation 9 below
Normal stress= Force
Area …………………………………………………… (9)
The summary of internal forces in all the members is provided in Table 1 below
Table 1: Internal forces of truss members
Member Internal force Tension/compression
AB 1,000 kN Compression
BC 0 -
AC 10,232 kN Compression
AD 9,500 kN Tension
CD 0 -
DF 9,500 Tension
CE 14,000 kN Compression
CF 4,847 kN Tension
EF 2,000 kN Compression
EG 14,000 kN Compression
FG 539 kN Tension
FH 13,500 kN Tension
GH 0 -
HJ 13,500 kN Tension
GI 8,000 kN Compression
GJ 5,924 kN Compression
IJ 2,000 kN Compression
IK 8,000 kN Compression
JK 11,310 kN Tension
JL 2,500 kN Compression
KL 7,200 kN Compression
LN 2,500 kN Compression
KM 0 -
KN 2,693 kN Tension
MN 1,000 kN Compression
5. Task 4
5.1. Suitable diameter for the truss elements
Since the truss members are only subjected to axial force, the normal stress in each member is
determined using equation 9 below
Normal stress= Force
Area …………………………………………………… (9)
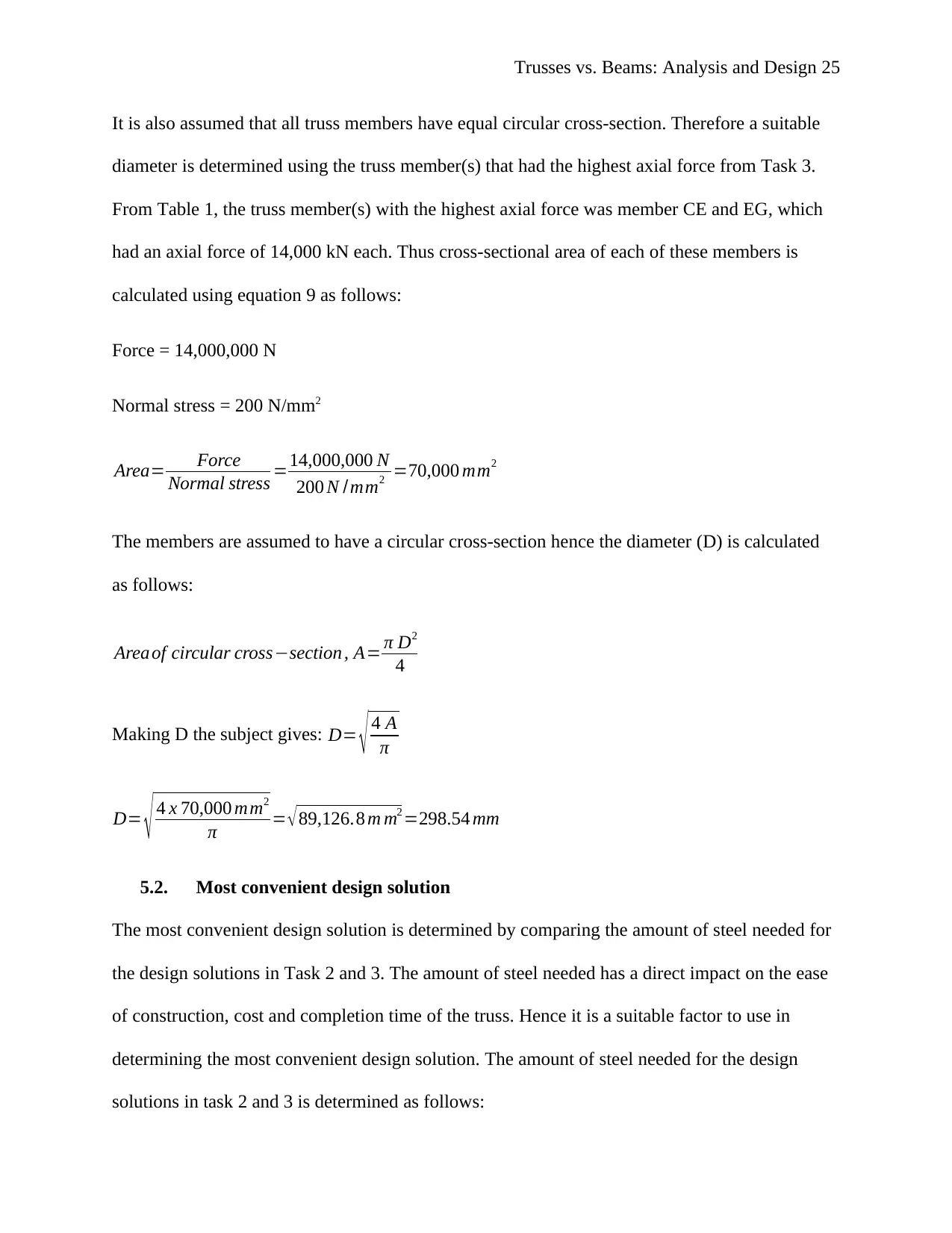
Trusses vs. Beams: Analysis and Design 25
It is also assumed that all truss members have equal circular cross-section. Therefore a suitable
diameter is determined using the truss member(s) that had the highest axial force from Task 3.
From Table 1, the truss member(s) with the highest axial force was member CE and EG, which
had an axial force of 14,000 kN each. Thus cross-sectional area of each of these members is
calculated using equation 9 as follows:
Force = 14,000,000 N
Normal stress = 200 N/mm2
Area= Force
Normal stress =14,000,000 N
200 N /mm2 =70,000 mm2
The members are assumed to have a circular cross-section hence the diameter (D) is calculated
as follows:
Area of circular cross−section , A= π D2
4
Making D the subject gives: D= √ 4 A
π
D= √ 4 x 70,000 mm2
π = √89,126.8 m m2 =298.54 mm
5.2. Most convenient design solution
The most convenient design solution is determined by comparing the amount of steel needed for
the design solutions in Task 2 and 3. The amount of steel needed has a direct impact on the ease
of construction, cost and completion time of the truss. Hence it is a suitable factor to use in
determining the most convenient design solution. The amount of steel needed for the design
solutions in task 2 and 3 is determined as follows:
It is also assumed that all truss members have equal circular cross-section. Therefore a suitable
diameter is determined using the truss member(s) that had the highest axial force from Task 3.
From Table 1, the truss member(s) with the highest axial force was member CE and EG, which
had an axial force of 14,000 kN each. Thus cross-sectional area of each of these members is
calculated using equation 9 as follows:
Force = 14,000,000 N
Normal stress = 200 N/mm2
Area= Force
Normal stress =14,000,000 N
200 N /mm2 =70,000 mm2
The members are assumed to have a circular cross-section hence the diameter (D) is calculated
as follows:
Area of circular cross−section , A= π D2
4
Making D the subject gives: D= √ 4 A
π
D= √ 4 x 70,000 mm2
π = √89,126.8 m m2 =298.54 mm
5.2. Most convenient design solution
The most convenient design solution is determined by comparing the amount of steel needed for
the design solutions in Task 2 and 3. The amount of steel needed has a direct impact on the ease
of construction, cost and completion time of the truss. Hence it is a suitable factor to use in
determining the most convenient design solution. The amount of steel needed for the design
solutions in task 2 and 3 is determined as follows:
Paraphrase This Document
Need a fresh take? Get an instant paraphrase of this document with our AI Paraphraser
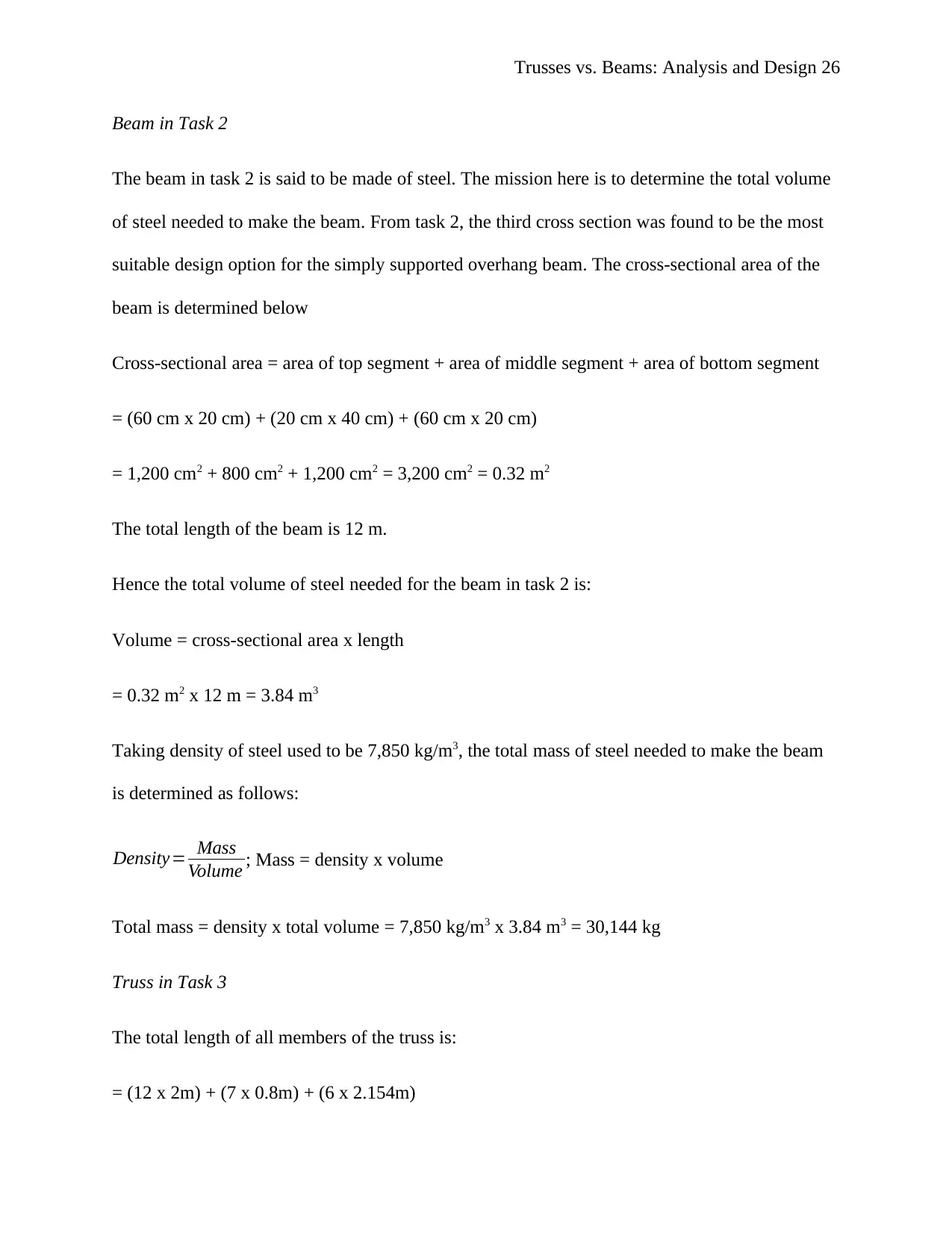
Trusses vs. Beams: Analysis and Design 26
Beam in Task 2
The beam in task 2 is said to be made of steel. The mission here is to determine the total volume
of steel needed to make the beam. From task 2, the third cross section was found to be the most
suitable design option for the simply supported overhang beam. The cross-sectional area of the
beam is determined below
Cross-sectional area = area of top segment + area of middle segment + area of bottom segment
= (60 cm x 20 cm) + (20 cm x 40 cm) + (60 cm x 20 cm)
= 1,200 cm2 + 800 cm2 + 1,200 cm2 = 3,200 cm2 = 0.32 m2
The total length of the beam is 12 m.
Hence the total volume of steel needed for the beam in task 2 is:
Volume = cross-sectional area x length
= 0.32 m2 x 12 m = 3.84 m3
Taking density of steel used to be 7,850 kg/m3, the total mass of steel needed to make the beam
is determined as follows:
Density= Mass
Volume ; Mass = density x volume
Total mass = density x total volume = 7,850 kg/m3 x 3.84 m3 = 30,144 kg
Truss in Task 3
The total length of all members of the truss is:
= (12 x 2m) + (7 x 0.8m) + (6 x 2.154m)
Beam in Task 2
The beam in task 2 is said to be made of steel. The mission here is to determine the total volume
of steel needed to make the beam. From task 2, the third cross section was found to be the most
suitable design option for the simply supported overhang beam. The cross-sectional area of the
beam is determined below
Cross-sectional area = area of top segment + area of middle segment + area of bottom segment
= (60 cm x 20 cm) + (20 cm x 40 cm) + (60 cm x 20 cm)
= 1,200 cm2 + 800 cm2 + 1,200 cm2 = 3,200 cm2 = 0.32 m2
The total length of the beam is 12 m.
Hence the total volume of steel needed for the beam in task 2 is:
Volume = cross-sectional area x length
= 0.32 m2 x 12 m = 3.84 m3
Taking density of steel used to be 7,850 kg/m3, the total mass of steel needed to make the beam
is determined as follows:
Density= Mass
Volume ; Mass = density x volume
Total mass = density x total volume = 7,850 kg/m3 x 3.84 m3 = 30,144 kg
Truss in Task 3
The total length of all members of the truss is:
= (12 x 2m) + (7 x 0.8m) + (6 x 2.154m)
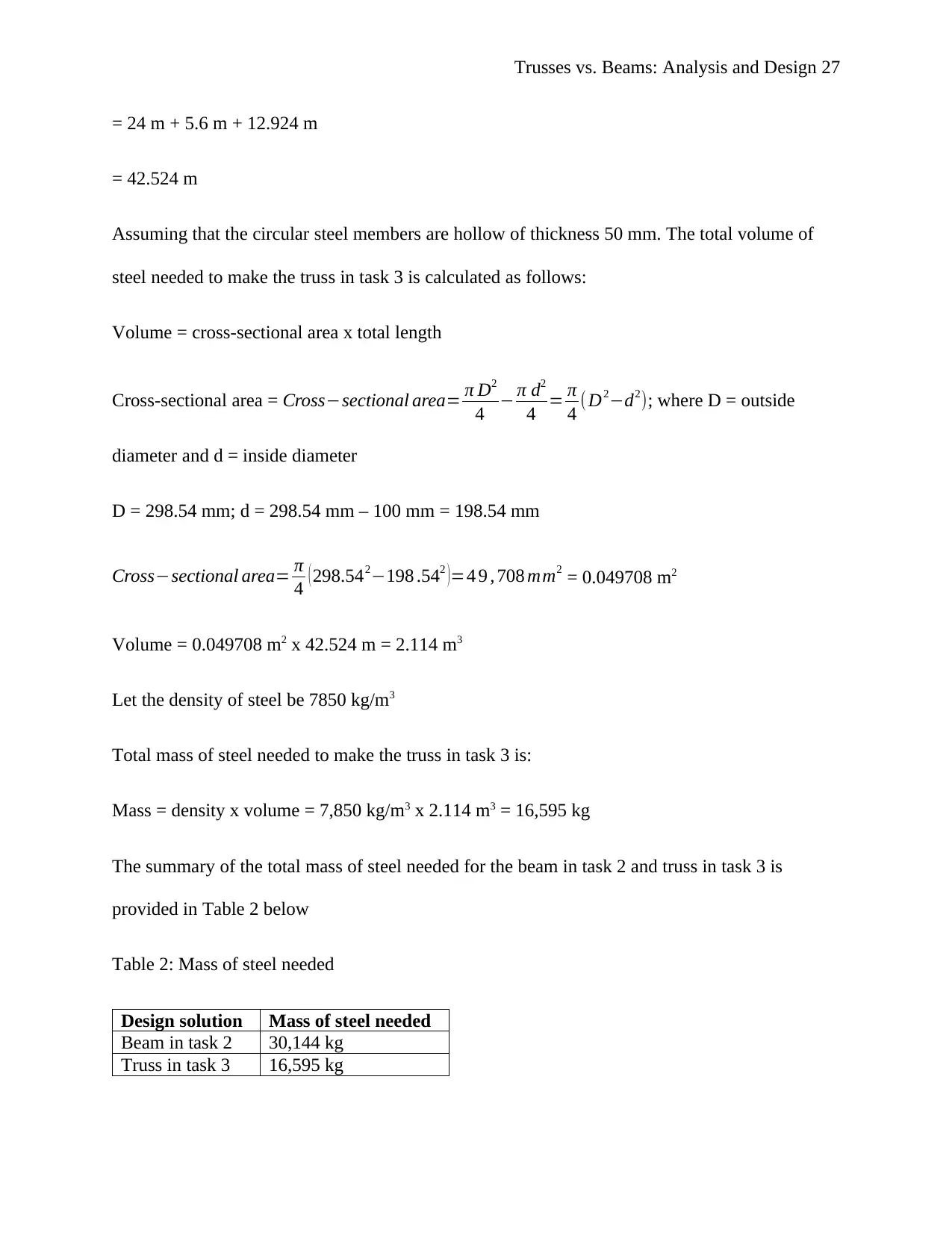
Trusses vs. Beams: Analysis and Design 27
= 24 m + 5.6 m + 12.924 m
= 42.524 m
Assuming that the circular steel members are hollow of thickness 50 mm. The total volume of
steel needed to make the truss in task 3 is calculated as follows:
Volume = cross-sectional area x total length
Cross-sectional area = Cross−sectional area= π D2
4 − π d2
4 = π
4 (D2−d2); where D = outside
diameter and d = inside diameter
D = 298.54 mm; d = 298.54 mm – 100 mm = 198.54 mm
Cross−sectional area= π
4 ( 298.542−198 .542 )=4 9 , 708 mm2 = 0.049708 m2
Volume = 0.049708 m2 x 42.524 m = 2.114 m3
Let the density of steel be 7850 kg/m3
Total mass of steel needed to make the truss in task 3 is:
Mass = density x volume = 7,850 kg/m3 x 2.114 m3 = 16,595 kg
The summary of the total mass of steel needed for the beam in task 2 and truss in task 3 is
provided in Table 2 below
Table 2: Mass of steel needed
Design solution Mass of steel needed
Beam in task 2 30,144 kg
Truss in task 3 16,595 kg
= 24 m + 5.6 m + 12.924 m
= 42.524 m
Assuming that the circular steel members are hollow of thickness 50 mm. The total volume of
steel needed to make the truss in task 3 is calculated as follows:
Volume = cross-sectional area x total length
Cross-sectional area = Cross−sectional area= π D2
4 − π d2
4 = π
4 (D2−d2); where D = outside
diameter and d = inside diameter
D = 298.54 mm; d = 298.54 mm – 100 mm = 198.54 mm
Cross−sectional area= π
4 ( 298.542−198 .542 )=4 9 , 708 mm2 = 0.049708 m2
Volume = 0.049708 m2 x 42.524 m = 2.114 m3
Let the density of steel be 7850 kg/m3
Total mass of steel needed to make the truss in task 3 is:
Mass = density x volume = 7,850 kg/m3 x 2.114 m3 = 16,595 kg
The summary of the total mass of steel needed for the beam in task 2 and truss in task 3 is
provided in Table 2 below
Table 2: Mass of steel needed
Design solution Mass of steel needed
Beam in task 2 30,144 kg
Truss in task 3 16,595 kg
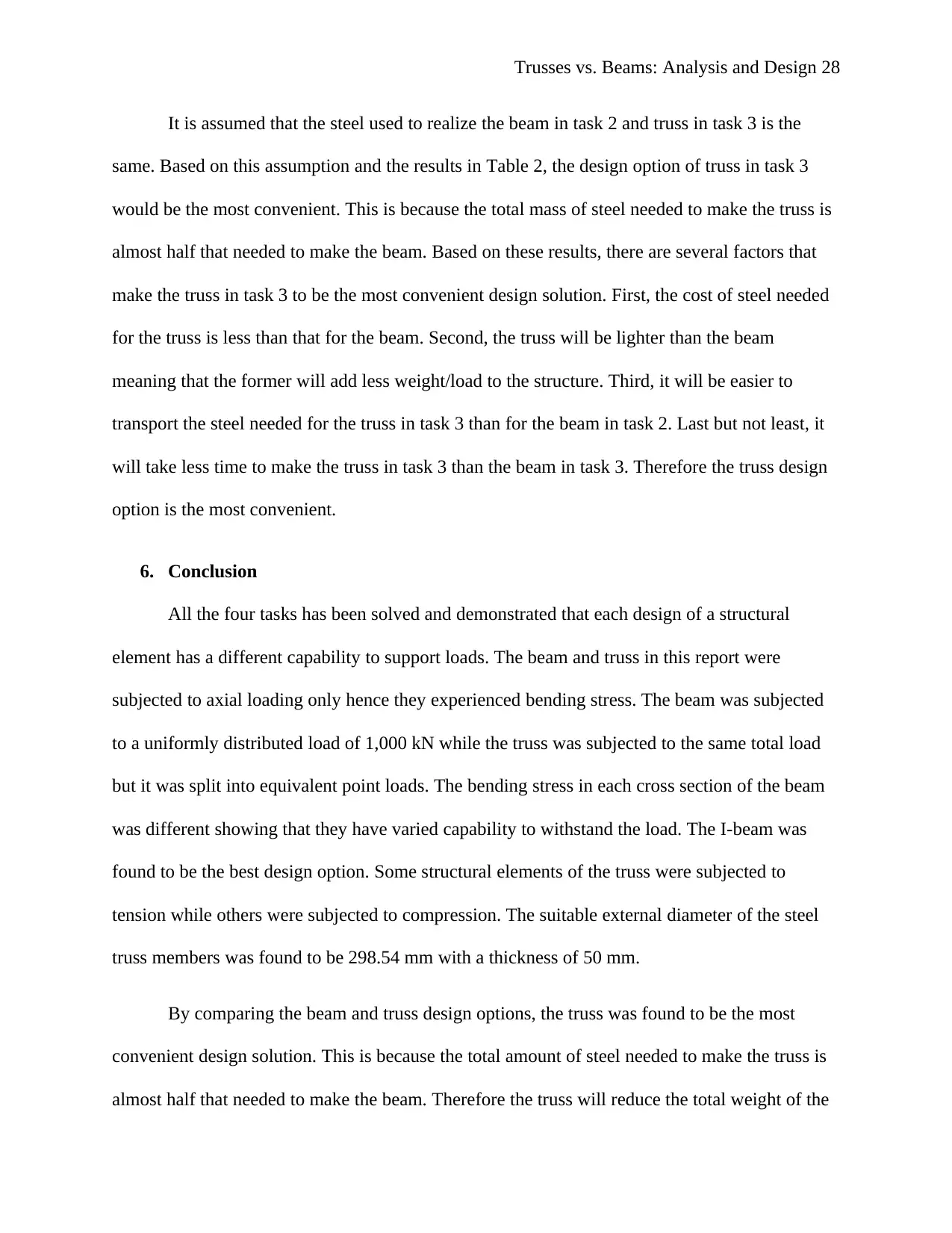
Trusses vs. Beams: Analysis and Design 28
It is assumed that the steel used to realize the beam in task 2 and truss in task 3 is the
same. Based on this assumption and the results in Table 2, the design option of truss in task 3
would be the most convenient. This is because the total mass of steel needed to make the truss is
almost half that needed to make the beam. Based on these results, there are several factors that
make the truss in task 3 to be the most convenient design solution. First, the cost of steel needed
for the truss is less than that for the beam. Second, the truss will be lighter than the beam
meaning that the former will add less weight/load to the structure. Third, it will be easier to
transport the steel needed for the truss in task 3 than for the beam in task 2. Last but not least, it
will take less time to make the truss in task 3 than the beam in task 3. Therefore the truss design
option is the most convenient.
6. Conclusion
All the four tasks has been solved and demonstrated that each design of a structural
element has a different capability to support loads. The beam and truss in this report were
subjected to axial loading only hence they experienced bending stress. The beam was subjected
to a uniformly distributed load of 1,000 kN while the truss was subjected to the same total load
but it was split into equivalent point loads. The bending stress in each cross section of the beam
was different showing that they have varied capability to withstand the load. The I-beam was
found to be the best design option. Some structural elements of the truss were subjected to
tension while others were subjected to compression. The suitable external diameter of the steel
truss members was found to be 298.54 mm with a thickness of 50 mm.
By comparing the beam and truss design options, the truss was found to be the most
convenient design solution. This is because the total amount of steel needed to make the truss is
almost half that needed to make the beam. Therefore the truss will reduce the total weight of the
It is assumed that the steel used to realize the beam in task 2 and truss in task 3 is the
same. Based on this assumption and the results in Table 2, the design option of truss in task 3
would be the most convenient. This is because the total mass of steel needed to make the truss is
almost half that needed to make the beam. Based on these results, there are several factors that
make the truss in task 3 to be the most convenient design solution. First, the cost of steel needed
for the truss is less than that for the beam. Second, the truss will be lighter than the beam
meaning that the former will add less weight/load to the structure. Third, it will be easier to
transport the steel needed for the truss in task 3 than for the beam in task 2. Last but not least, it
will take less time to make the truss in task 3 than the beam in task 3. Therefore the truss design
option is the most convenient.
6. Conclusion
All the four tasks has been solved and demonstrated that each design of a structural
element has a different capability to support loads. The beam and truss in this report were
subjected to axial loading only hence they experienced bending stress. The beam was subjected
to a uniformly distributed load of 1,000 kN while the truss was subjected to the same total load
but it was split into equivalent point loads. The bending stress in each cross section of the beam
was different showing that they have varied capability to withstand the load. The I-beam was
found to be the best design option. Some structural elements of the truss were subjected to
tension while others were subjected to compression. The suitable external diameter of the steel
truss members was found to be 298.54 mm with a thickness of 50 mm.
By comparing the beam and truss design options, the truss was found to be the most
convenient design solution. This is because the total amount of steel needed to make the truss is
almost half that needed to make the beam. Therefore the truss will reduce the total weight of the
Secure Best Marks with AI Grader
Need help grading? Try our AI Grader for instant feedback on your assignments.
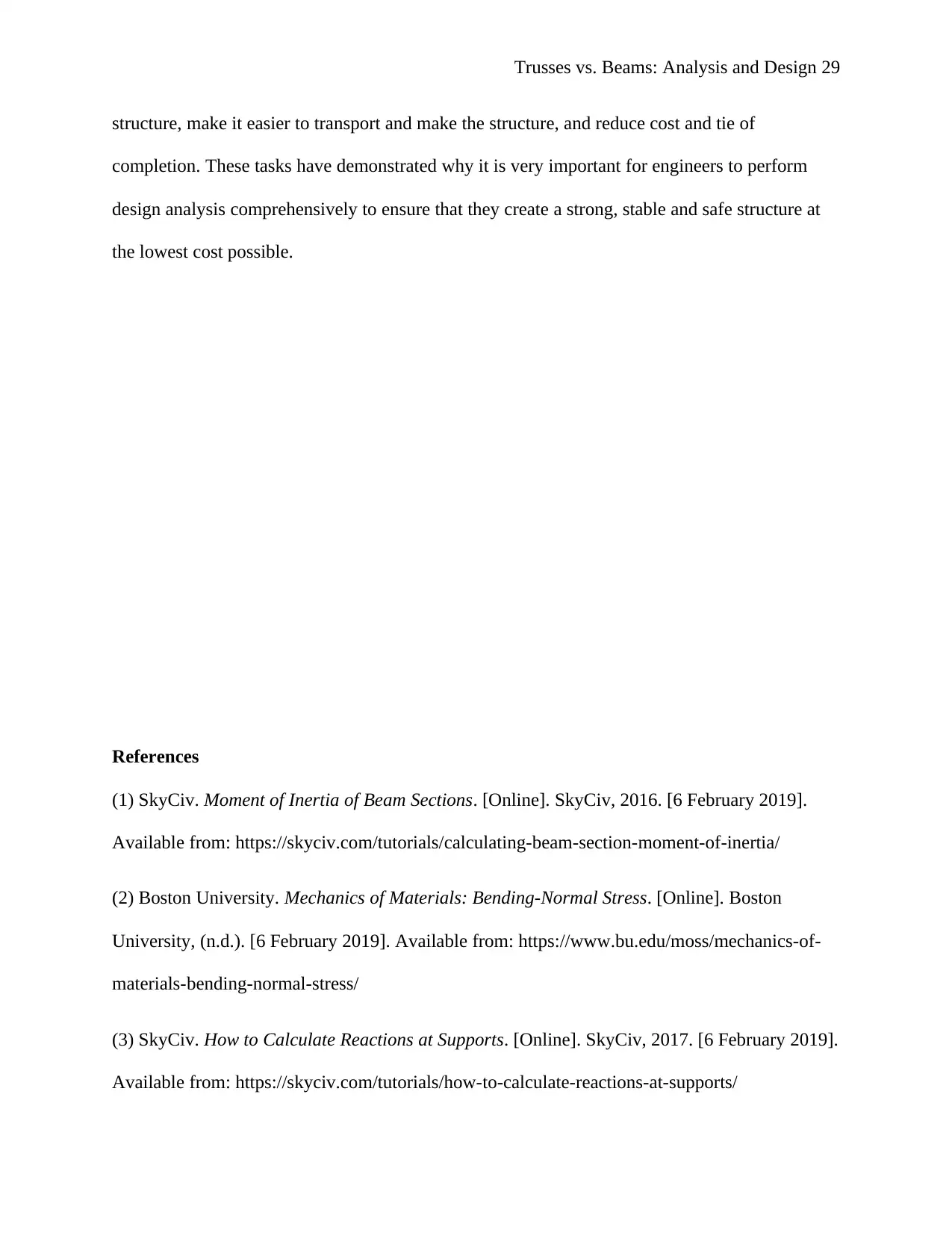
Trusses vs. Beams: Analysis and Design 29
structure, make it easier to transport and make the structure, and reduce cost and tie of
completion. These tasks have demonstrated why it is very important for engineers to perform
design analysis comprehensively to ensure that they create a strong, stable and safe structure at
the lowest cost possible.
References
(1) SkyCiv. Moment of Inertia of Beam Sections. [Online]. SkyCiv, 2016. [6 February 2019].
Available from: https://skyciv.com/tutorials/calculating-beam-section-moment-of-inertia/
(2) Boston University. Mechanics of Materials: Bending-Normal Stress. [Online]. Boston
University, (n.d.). [6 February 2019]. Available from: https://www.bu.edu/moss/mechanics-of-
materials-bending-normal-stress/
(3) SkyCiv. How to Calculate Reactions at Supports. [Online]. SkyCiv, 2017. [6 February 2019].
Available from: https://skyciv.com/tutorials/how-to-calculate-reactions-at-supports/
structure, make it easier to transport and make the structure, and reduce cost and tie of
completion. These tasks have demonstrated why it is very important for engineers to perform
design analysis comprehensively to ensure that they create a strong, stable and safe structure at
the lowest cost possible.
References
(1) SkyCiv. Moment of Inertia of Beam Sections. [Online]. SkyCiv, 2016. [6 February 2019].
Available from: https://skyciv.com/tutorials/calculating-beam-section-moment-of-inertia/
(2) Boston University. Mechanics of Materials: Bending-Normal Stress. [Online]. Boston
University, (n.d.). [6 February 2019]. Available from: https://www.bu.edu/moss/mechanics-of-
materials-bending-normal-stress/
(3) SkyCiv. How to Calculate Reactions at Supports. [Online]. SkyCiv, 2017. [6 February 2019].
Available from: https://skyciv.com/tutorials/how-to-calculate-reactions-at-supports/
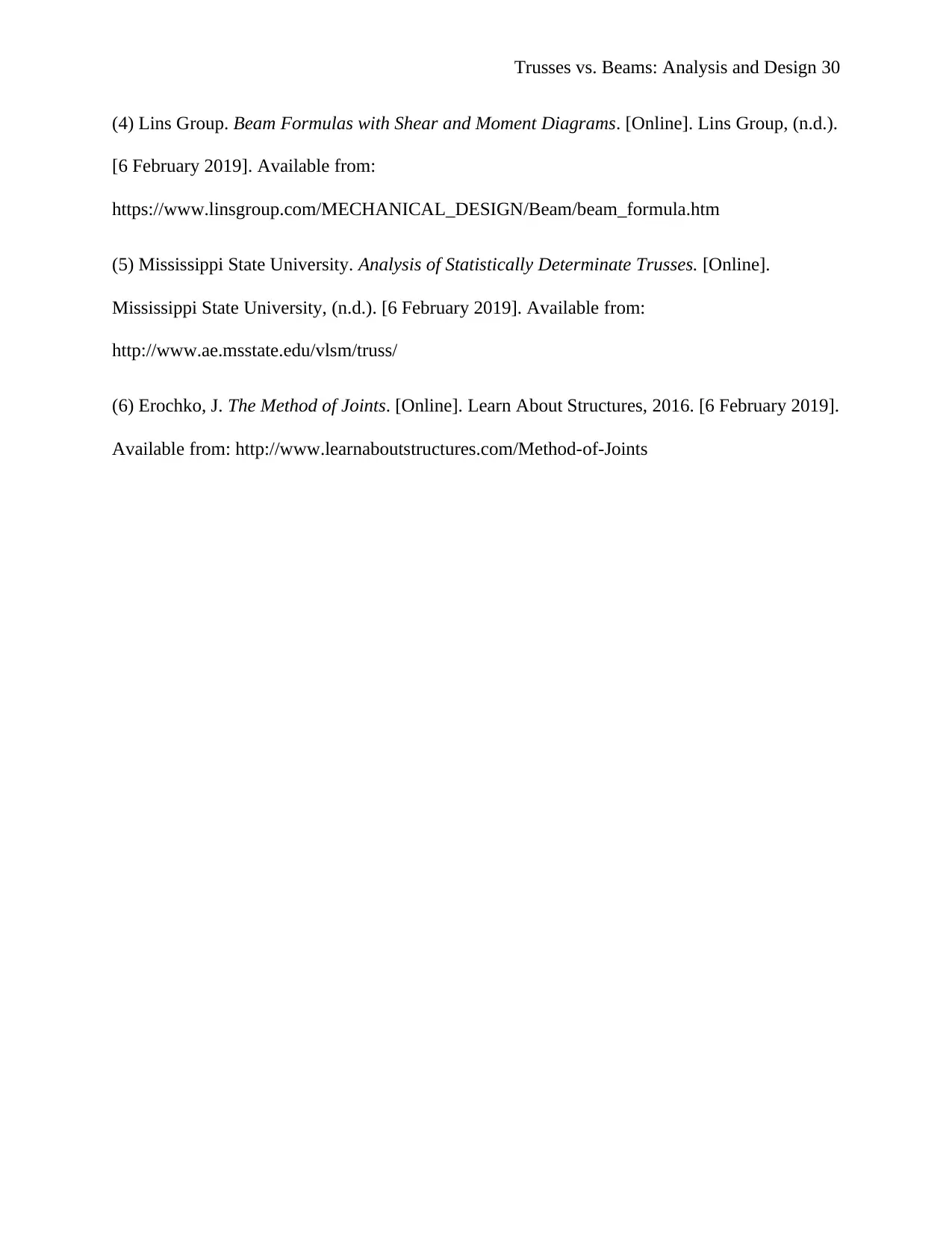
Trusses vs. Beams: Analysis and Design 30
(4) Lins Group. Beam Formulas with Shear and Moment Diagrams. [Online]. Lins Group, (n.d.).
[6 February 2019]. Available from:
https://www.linsgroup.com/MECHANICAL_DESIGN/Beam/beam_formula.htm
(5) Mississippi State University. Analysis of Statistically Determinate Trusses. [Online].
Mississippi State University, (n.d.). [6 February 2019]. Available from:
http://www.ae.msstate.edu/vlsm/truss/
(6) Erochko, J. The Method of Joints. [Online]. Learn About Structures, 2016. [6 February 2019].
Available from: http://www.learnaboutstructures.com/Method-of-Joints
(4) Lins Group. Beam Formulas with Shear and Moment Diagrams. [Online]. Lins Group, (n.d.).
[6 February 2019]. Available from:
https://www.linsgroup.com/MECHANICAL_DESIGN/Beam/beam_formula.htm
(5) Mississippi State University. Analysis of Statistically Determinate Trusses. [Online].
Mississippi State University, (n.d.). [6 February 2019]. Available from:
http://www.ae.msstate.edu/vlsm/truss/
(6) Erochko, J. The Method of Joints. [Online]. Learn About Structures, 2016. [6 February 2019].
Available from: http://www.learnaboutstructures.com/Method-of-Joints
1 out of 30
Related Documents

Your All-in-One AI-Powered Toolkit for Academic Success.
+13062052269
info@desklib.com
Available 24*7 on WhatsApp / Email
Unlock your academic potential
© 2024 | Zucol Services PVT LTD | All rights reserved.