Ultrasonic Vibration-Assisted Laser Net Shaping Energy Analysis
VerifiedAdded on 2022/12/27
|16
|3791
|24
Report
AI Summary
This report presents a statistical analysis of energy consumption in Ultrasonic Vibration-Assisted Laser Assisted Net Shaping (LANS) of Inconel 718 parts. It investigates the impact of parameters like laser power, scanning speed, and powder feed rate on energy consumption. The study includes data c...
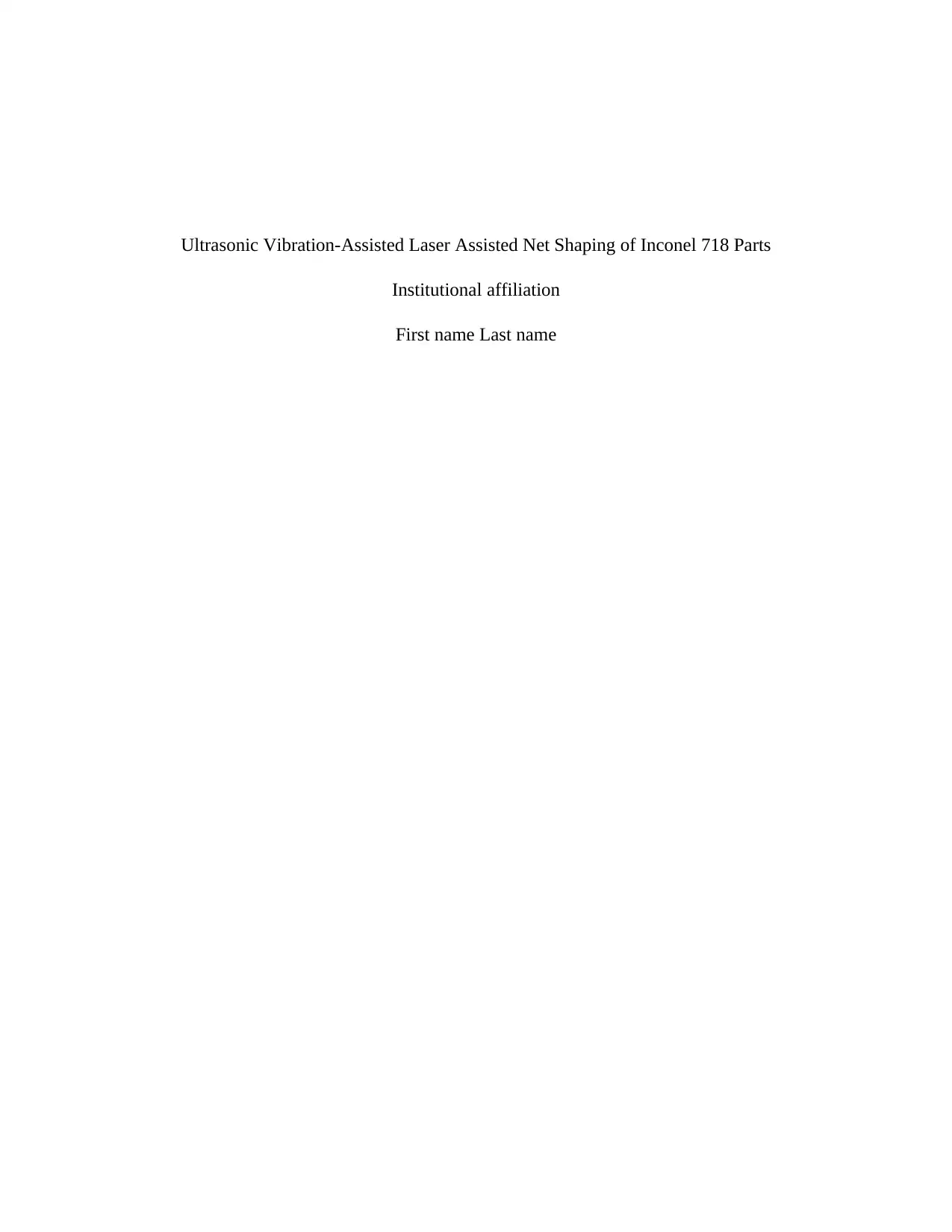
Ultrasonic Vibration-Assisted Laser Assisted Net Shaping of Inconel 718 Parts
Institutional affiliation
First name Last name
Institutional affiliation
First name Last name
Secure Best Marks with AI Grader
Need help grading? Try our AI Grader for instant feedback on your assignments.
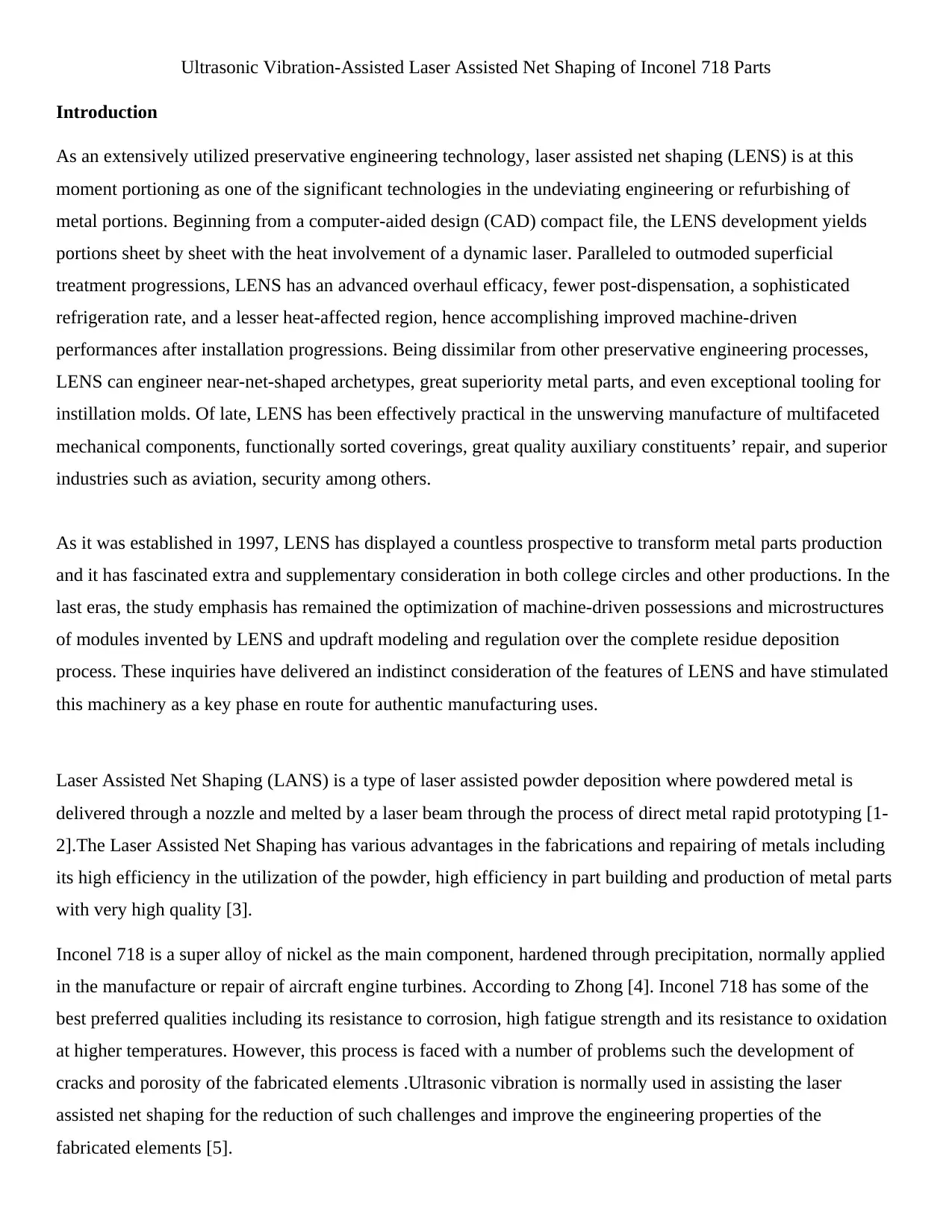
Ultrasonic Vibration-Assisted Laser Assisted Net Shaping of Inconel 718 Parts
Introduction
As an extensively utilized preservative engineering technology, laser assisted net shaping (LENS) is at this
moment portioning as one of the significant technologies in the undeviating engineering or refurbishing of
metal portions. Beginning from a computer-aided design (CAD) compact file, the LENS development yields
portions sheet by sheet with the heat involvement of a dynamic laser. Paralleled to outmoded superficial
treatment progressions, LENS has an advanced overhaul efficacy, fewer post-dispensation, a sophisticated
refrigeration rate, and a lesser heat-affected region, hence accomplishing improved machine-driven
performances after installation progressions. Being dissimilar from other preservative engineering processes,
LENS can engineer near-net-shaped archetypes, great superiority metal parts, and even exceptional tooling for
instillation molds. Of late, LENS has been effectively practical in the unswerving manufacture of multifaceted
mechanical components, functionally sorted coverings, great quality auxiliary constituents’ repair, and superior
industries such as aviation, security among others.
As it was established in 1997, LENS has displayed a countless prospective to transform metal parts production
and it has fascinated extra and supplementary consideration in both college circles and other productions. In the
last eras, the study emphasis has remained the optimization of machine-driven possessions and microstructures
of modules invented by LENS and updraft modeling and regulation over the complete residue deposition
process. These inquiries have delivered an indistinct consideration of the features of LENS and have stimulated
this machinery as a key phase en route for authentic manufacturing uses.
Laser Assisted Net Shaping (LANS) is a type of laser assisted powder deposition where powdered metal is
delivered through a nozzle and melted by a laser beam through the process of direct metal rapid prototyping [1-
2].The Laser Assisted Net Shaping has various advantages in the fabrications and repairing of metals including
its high efficiency in the utilization of the powder, high efficiency in part building and production of metal parts
with very high quality [3].
Inconel 718 is a super alloy of nickel as the main component, hardened through precipitation, normally applied
in the manufacture or repair of aircraft engine turbines. According to Zhong [4]. Inconel 718 has some of the
best preferred qualities including its resistance to corrosion, high fatigue strength and its resistance to oxidation
at higher temperatures. However, this process is faced with a number of problems such the development of
cracks and porosity of the fabricated elements .Ultrasonic vibration is normally used in assisting the laser
assisted net shaping for the reduction of such challenges and improve the engineering properties of the
fabricated elements [5].
Introduction
As an extensively utilized preservative engineering technology, laser assisted net shaping (LENS) is at this
moment portioning as one of the significant technologies in the undeviating engineering or refurbishing of
metal portions. Beginning from a computer-aided design (CAD) compact file, the LENS development yields
portions sheet by sheet with the heat involvement of a dynamic laser. Paralleled to outmoded superficial
treatment progressions, LENS has an advanced overhaul efficacy, fewer post-dispensation, a sophisticated
refrigeration rate, and a lesser heat-affected region, hence accomplishing improved machine-driven
performances after installation progressions. Being dissimilar from other preservative engineering processes,
LENS can engineer near-net-shaped archetypes, great superiority metal parts, and even exceptional tooling for
instillation molds. Of late, LENS has been effectively practical in the unswerving manufacture of multifaceted
mechanical components, functionally sorted coverings, great quality auxiliary constituents’ repair, and superior
industries such as aviation, security among others.
As it was established in 1997, LENS has displayed a countless prospective to transform metal parts production
and it has fascinated extra and supplementary consideration in both college circles and other productions. In the
last eras, the study emphasis has remained the optimization of machine-driven possessions and microstructures
of modules invented by LENS and updraft modeling and regulation over the complete residue deposition
process. These inquiries have delivered an indistinct consideration of the features of LENS and have stimulated
this machinery as a key phase en route for authentic manufacturing uses.
Laser Assisted Net Shaping (LANS) is a type of laser assisted powder deposition where powdered metal is
delivered through a nozzle and melted by a laser beam through the process of direct metal rapid prototyping [1-
2].The Laser Assisted Net Shaping has various advantages in the fabrications and repairing of metals including
its high efficiency in the utilization of the powder, high efficiency in part building and production of metal parts
with very high quality [3].
Inconel 718 is a super alloy of nickel as the main component, hardened through precipitation, normally applied
in the manufacture or repair of aircraft engine turbines. According to Zhong [4]. Inconel 718 has some of the
best preferred qualities including its resistance to corrosion, high fatigue strength and its resistance to oxidation
at higher temperatures. However, this process is faced with a number of problems such the development of
cracks and porosity of the fabricated elements .Ultrasonic vibration is normally used in assisting the laser
assisted net shaping for the reduction of such challenges and improve the engineering properties of the
fabricated elements [5].
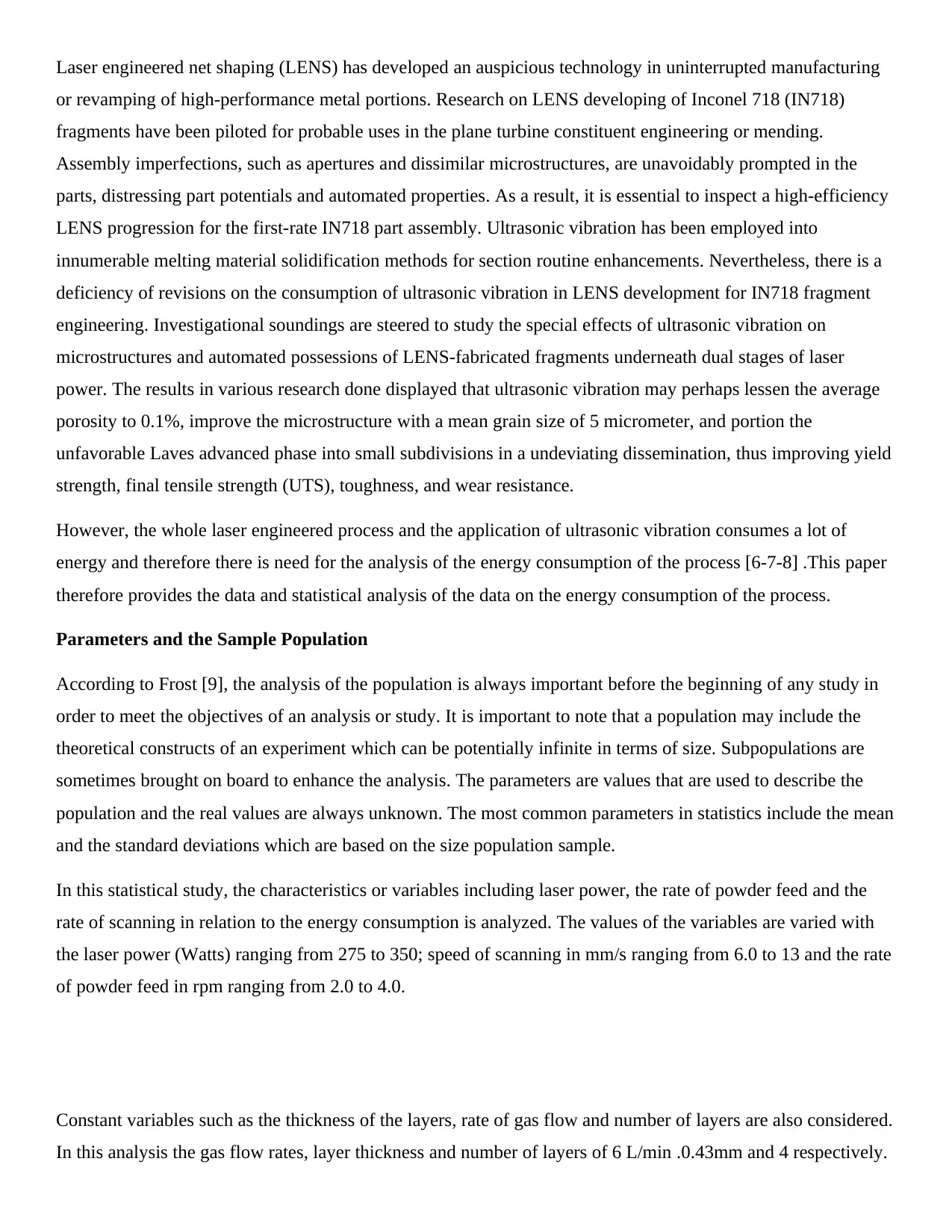
Laser engineered net shaping (LENS) has developed an auspicious technology in uninterrupted manufacturing
or revamping of high-performance metal portions. Research on LENS developing of Inconel 718 (IN718)
fragments have been piloted for probable uses in the plane turbine constituent engineering or mending.
Assembly imperfections, such as apertures and dissimilar microstructures, are unavoidably prompted in the
parts, distressing part potentials and automated properties. As a result, it is essential to inspect a high-efficiency
LENS progression for the first-rate IN718 part assembly. Ultrasonic vibration has been employed into
innumerable melting material solidification methods for section routine enhancements. Nevertheless, there is a
deficiency of revisions on the consumption of ultrasonic vibration in LENS development for IN718 fragment
engineering. Investigational soundings are steered to study the special effects of ultrasonic vibration on
microstructures and automated possessions of LENS-fabricated fragments underneath dual stages of laser
power. The results in various research done displayed that ultrasonic vibration may perhaps lessen the average
porosity to 0.1%, improve the microstructure with a mean grain size of 5 micrometer, and portion the
unfavorable Laves advanced phase into small subdivisions in a undeviating dissemination, thus improving yield
strength, final tensile strength (UTS), toughness, and wear resistance.
However, the whole laser engineered process and the application of ultrasonic vibration consumes a lot of
energy and therefore there is need for the analysis of the energy consumption of the process [6-7-8] .This paper
therefore provides the data and statistical analysis of the data on the energy consumption of the process.
Parameters and the Sample Population
According to Frost [9], the analysis of the population is always important before the beginning of any study in
order to meet the objectives of an analysis or study. It is important to note that a population may include the
theoretical constructs of an experiment which can be potentially infinite in terms of size. Subpopulations are
sometimes brought on board to enhance the analysis. The parameters are values that are used to describe the
population and the real values are always unknown. The most common parameters in statistics include the mean
and the standard deviations which are based on the size population sample.
In this statistical study, the characteristics or variables including laser power, the rate of powder feed and the
rate of scanning in relation to the energy consumption is analyzed. The values of the variables are varied with
the laser power (Watts) ranging from 275 to 350; speed of scanning in mm/s ranging from 6.0 to 13 and the rate
of powder feed in rpm ranging from 2.0 to 4.0.
Constant variables such as the thickness of the layers, rate of gas flow and number of layers are also considered.
In this analysis the gas flow rates, layer thickness and number of layers of 6 L/min .0.43mm and 4 respectively.
or revamping of high-performance metal portions. Research on LENS developing of Inconel 718 (IN718)
fragments have been piloted for probable uses in the plane turbine constituent engineering or mending.
Assembly imperfections, such as apertures and dissimilar microstructures, are unavoidably prompted in the
parts, distressing part potentials and automated properties. As a result, it is essential to inspect a high-efficiency
LENS progression for the first-rate IN718 part assembly. Ultrasonic vibration has been employed into
innumerable melting material solidification methods for section routine enhancements. Nevertheless, there is a
deficiency of revisions on the consumption of ultrasonic vibration in LENS development for IN718 fragment
engineering. Investigational soundings are steered to study the special effects of ultrasonic vibration on
microstructures and automated possessions of LENS-fabricated fragments underneath dual stages of laser
power. The results in various research done displayed that ultrasonic vibration may perhaps lessen the average
porosity to 0.1%, improve the microstructure with a mean grain size of 5 micrometer, and portion the
unfavorable Laves advanced phase into small subdivisions in a undeviating dissemination, thus improving yield
strength, final tensile strength (UTS), toughness, and wear resistance.
However, the whole laser engineered process and the application of ultrasonic vibration consumes a lot of
energy and therefore there is need for the analysis of the energy consumption of the process [6-7-8] .This paper
therefore provides the data and statistical analysis of the data on the energy consumption of the process.
Parameters and the Sample Population
According to Frost [9], the analysis of the population is always important before the beginning of any study in
order to meet the objectives of an analysis or study. It is important to note that a population may include the
theoretical constructs of an experiment which can be potentially infinite in terms of size. Subpopulations are
sometimes brought on board to enhance the analysis. The parameters are values that are used to describe the
population and the real values are always unknown. The most common parameters in statistics include the mean
and the standard deviations which are based on the size population sample.
In this statistical study, the characteristics or variables including laser power, the rate of powder feed and the
rate of scanning in relation to the energy consumption is analyzed. The values of the variables are varied with
the laser power (Watts) ranging from 275 to 350; speed of scanning in mm/s ranging from 6.0 to 13 and the rate
of powder feed in rpm ranging from 2.0 to 4.0.
Constant variables such as the thickness of the layers, rate of gas flow and number of layers are also considered.
In this analysis the gas flow rates, layer thickness and number of layers of 6 L/min .0.43mm and 4 respectively.
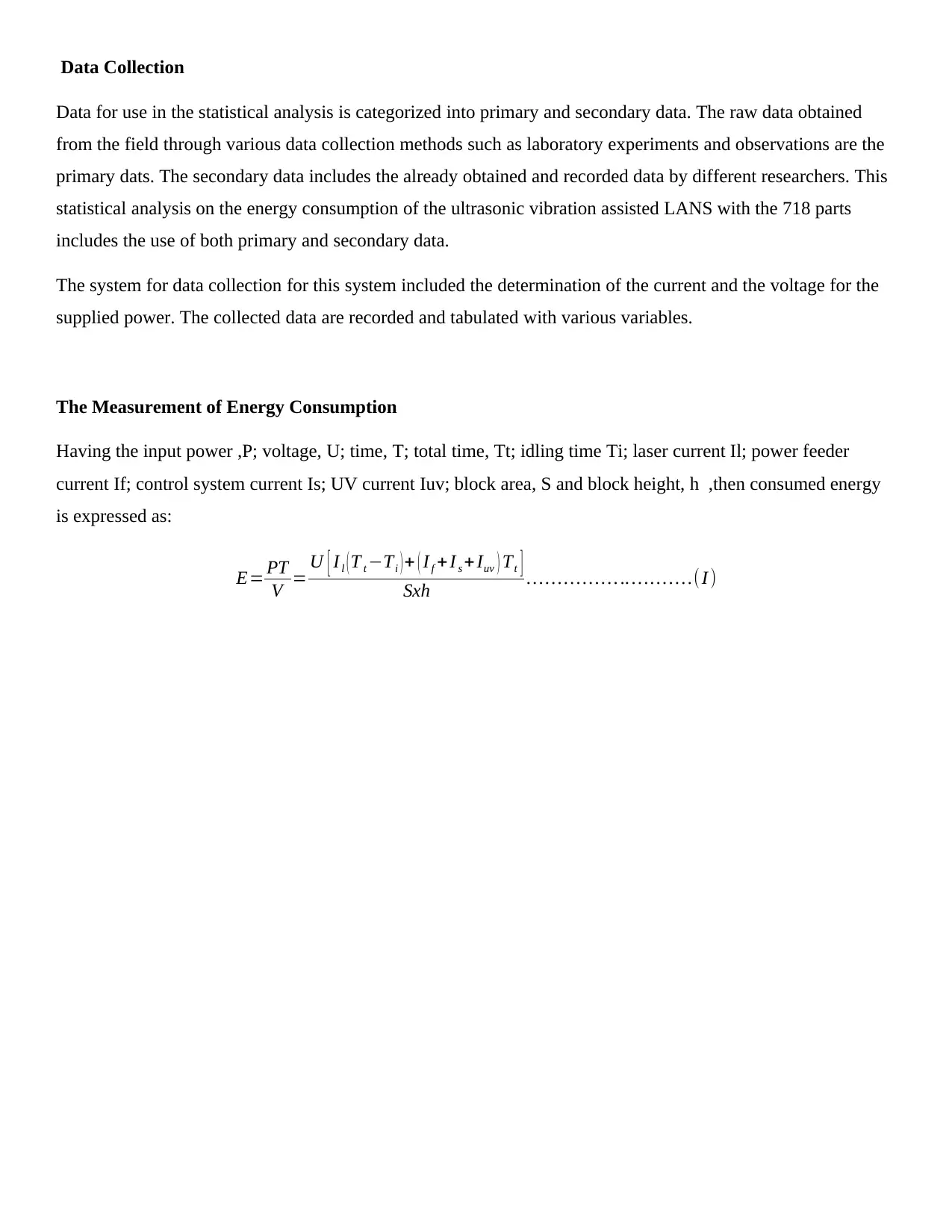
Data Collection
Data for use in the statistical analysis is categorized into primary and secondary data. The raw data obtained
from the field through various data collection methods such as laboratory experiments and observations are the
primary dats. The secondary data includes the already obtained and recorded data by different researchers. This
statistical analysis on the energy consumption of the ultrasonic vibration assisted LANS with the 718 parts
includes the use of both primary and secondary data.
The system for data collection for this system included the determination of the current and the voltage for the
supplied power. The collected data are recorded and tabulated with various variables.
The Measurement of Energy Consumption
Having the input power ,P; voltage, U; time, T; total time, Tt; idling time Ti; laser current Il; power feeder
current If; control system current Is; UV current Iuv; block area, S and block height, h ,then consumed energy
is expressed as:
E= PT
V = U [ I l (T t −Ti )+ ( If + I s + Iuv ) Tt ]
Sxh … … … … … .. … … … .( I )
Data for use in the statistical analysis is categorized into primary and secondary data. The raw data obtained
from the field through various data collection methods such as laboratory experiments and observations are the
primary dats. The secondary data includes the already obtained and recorded data by different researchers. This
statistical analysis on the energy consumption of the ultrasonic vibration assisted LANS with the 718 parts
includes the use of both primary and secondary data.
The system for data collection for this system included the determination of the current and the voltage for the
supplied power. The collected data are recorded and tabulated with various variables.
The Measurement of Energy Consumption
Having the input power ,P; voltage, U; time, T; total time, Tt; idling time Ti; laser current Il; power feeder
current If; control system current Is; UV current Iuv; block area, S and block height, h ,then consumed energy
is expressed as:
E= PT
V = U [ I l (T t −Ti )+ ( If + I s + Iuv ) Tt ]
Sxh … … … … … .. … … … .( I )
Secure Best Marks with AI Grader
Need help grading? Try our AI Grader for instant feedback on your assignments.
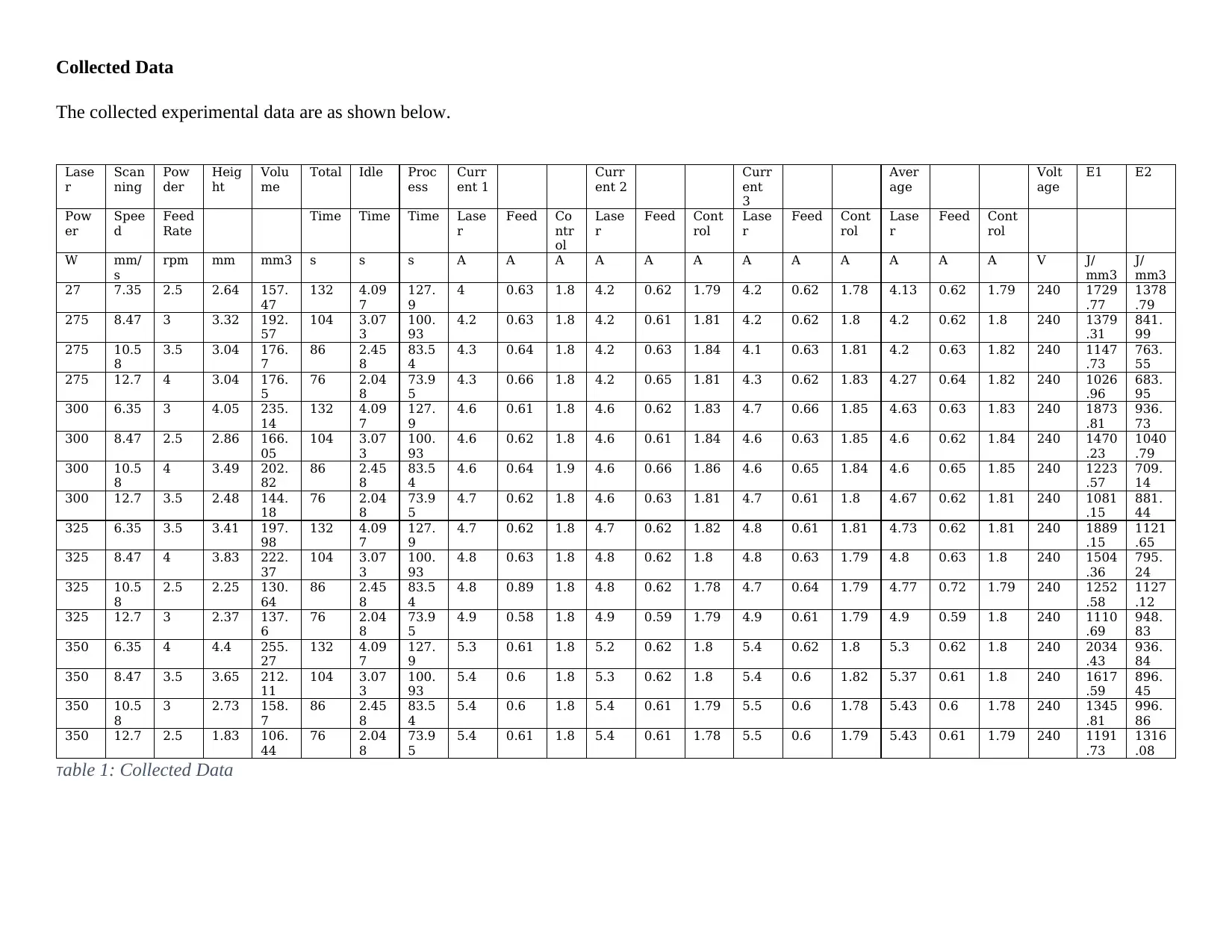
Collected Data
The collected experimental data are as shown below.
Lase
r
Scan
ning
Pow
der
Heig
ht
Volu
me
Total Idle Proc
ess
Curr
ent 1
Curr
ent 2
Curr
ent
3
Aver
age
Volt
age
E1 E2
Pow
er
Spee
d
Feed
Rate
Time Time Time Lase
r
Feed Co
ntr
ol
Lase
r
Feed Cont
rol
Lase
r
Feed Cont
rol
Lase
r
Feed Cont
rol
W mm/
s
rpm mm mm3 s s s A A A A A A A A A A A A V J/
mm3
J/
mm3
27 7.35 2.5 2.64 157.
47
132 4.09
7
127.
9
4 0.63 1.8 4.2 0.62 1.79 4.2 0.62 1.78 4.13 0.62 1.79 240 1729
.77
1378
.79
275 8.47 3 3.32 192.
57
104 3.07
3
100.
93
4.2 0.63 1.8 4.2 0.61 1.81 4.2 0.62 1.8 4.2 0.62 1.8 240 1379
.31
841.
99
275 10.5
8
3.5 3.04 176.
7
86 2.45
8
83.5
4
4.3 0.64 1.8 4.2 0.63 1.84 4.1 0.63 1.81 4.2 0.63 1.82 240 1147
.73
763.
55
275 12.7 4 3.04 176.
5
76 2.04
8
73.9
5
4.3 0.66 1.8 4.2 0.65 1.81 4.3 0.62 1.83 4.27 0.64 1.82 240 1026
.96
683.
95
300 6.35 3 4.05 235.
14
132 4.09
7
127.
9
4.6 0.61 1.8 4.6 0.62 1.83 4.7 0.66 1.85 4.63 0.63 1.83 240 1873
.81
936.
73
300 8.47 2.5 2.86 166.
05
104 3.07
3
100.
93
4.6 0.62 1.8 4.6 0.61 1.84 4.6 0.63 1.85 4.6 0.62 1.84 240 1470
.23
1040
.79
300 10.5
8
4 3.49 202.
82
86 2.45
8
83.5
4
4.6 0.64 1.9 4.6 0.66 1.86 4.6 0.65 1.84 4.6 0.65 1.85 240 1223
.57
709.
14
300 12.7 3.5 2.48 144.
18
76 2.04
8
73.9
5
4.7 0.62 1.8 4.6 0.63 1.81 4.7 0.61 1.8 4.67 0.62 1.81 240 1081
.15
881.
44
325 6.35 3.5 3.41 197.
98
132 4.09
7
127.
9
4.7 0.62 1.8 4.7 0.62 1.82 4.8 0.61 1.81 4.73 0.62 1.81 240 1889
.15
1121
.65
325 8.47 4 3.83 222.
37
104 3.07
3
100.
93
4.8 0.63 1.8 4.8 0.62 1.8 4.8 0.63 1.79 4.8 0.63 1.8 240 1504
.36
795.
24
325 10.5
8
2.5 2.25 130.
64
86 2.45
8
83.5
4
4.8 0.89 1.8 4.8 0.62 1.78 4.7 0.64 1.79 4.77 0.72 1.79 240 1252
.58
1127
.12
325 12.7 3 2.37 137.
6
76 2.04
8
73.9
5
4.9 0.58 1.8 4.9 0.59 1.79 4.9 0.61 1.79 4.9 0.59 1.8 240 1110
.69
948.
83
350 6.35 4 4.4 255.
27
132 4.09
7
127.
9
5.3 0.61 1.8 5.2 0.62 1.8 5.4 0.62 1.8 5.3 0.62 1.8 240 2034
.43
936.
84
350 8.47 3.5 3.65 212.
11
104 3.07
3
100.
93
5.4 0.6 1.8 5.3 0.62 1.8 5.4 0.6 1.82 5.37 0.61 1.8 240 1617
.59
896.
45
350 10.5
8
3 2.73 158.
7
86 2.45
8
83.5
4
5.4 0.6 1.8 5.4 0.61 1.79 5.5 0.6 1.78 5.43 0.6 1.78 240 1345
.81
996.
86
350 12.7 2.5 1.83 106.
44
76 2.04
8
73.9
5
5.4 0.61 1.8 5.4 0.61 1.78 5.5 0.6 1.79 5.43 0.61 1.79 240 1191
.73
1316
.08
Table 1: Collected Data
The collected experimental data are as shown below.
Lase
r
Scan
ning
Pow
der
Heig
ht
Volu
me
Total Idle Proc
ess
Curr
ent 1
Curr
ent 2
Curr
ent
3
Aver
age
Volt
age
E1 E2
Pow
er
Spee
d
Feed
Rate
Time Time Time Lase
r
Feed Co
ntr
ol
Lase
r
Feed Cont
rol
Lase
r
Feed Cont
rol
Lase
r
Feed Cont
rol
W mm/
s
rpm mm mm3 s s s A A A A A A A A A A A A V J/
mm3
J/
mm3
27 7.35 2.5 2.64 157.
47
132 4.09
7
127.
9
4 0.63 1.8 4.2 0.62 1.79 4.2 0.62 1.78 4.13 0.62 1.79 240 1729
.77
1378
.79
275 8.47 3 3.32 192.
57
104 3.07
3
100.
93
4.2 0.63 1.8 4.2 0.61 1.81 4.2 0.62 1.8 4.2 0.62 1.8 240 1379
.31
841.
99
275 10.5
8
3.5 3.04 176.
7
86 2.45
8
83.5
4
4.3 0.64 1.8 4.2 0.63 1.84 4.1 0.63 1.81 4.2 0.63 1.82 240 1147
.73
763.
55
275 12.7 4 3.04 176.
5
76 2.04
8
73.9
5
4.3 0.66 1.8 4.2 0.65 1.81 4.3 0.62 1.83 4.27 0.64 1.82 240 1026
.96
683.
95
300 6.35 3 4.05 235.
14
132 4.09
7
127.
9
4.6 0.61 1.8 4.6 0.62 1.83 4.7 0.66 1.85 4.63 0.63 1.83 240 1873
.81
936.
73
300 8.47 2.5 2.86 166.
05
104 3.07
3
100.
93
4.6 0.62 1.8 4.6 0.61 1.84 4.6 0.63 1.85 4.6 0.62 1.84 240 1470
.23
1040
.79
300 10.5
8
4 3.49 202.
82
86 2.45
8
83.5
4
4.6 0.64 1.9 4.6 0.66 1.86 4.6 0.65 1.84 4.6 0.65 1.85 240 1223
.57
709.
14
300 12.7 3.5 2.48 144.
18
76 2.04
8
73.9
5
4.7 0.62 1.8 4.6 0.63 1.81 4.7 0.61 1.8 4.67 0.62 1.81 240 1081
.15
881.
44
325 6.35 3.5 3.41 197.
98
132 4.09
7
127.
9
4.7 0.62 1.8 4.7 0.62 1.82 4.8 0.61 1.81 4.73 0.62 1.81 240 1889
.15
1121
.65
325 8.47 4 3.83 222.
37
104 3.07
3
100.
93
4.8 0.63 1.8 4.8 0.62 1.8 4.8 0.63 1.79 4.8 0.63 1.8 240 1504
.36
795.
24
325 10.5
8
2.5 2.25 130.
64
86 2.45
8
83.5
4
4.8 0.89 1.8 4.8 0.62 1.78 4.7 0.64 1.79 4.77 0.72 1.79 240 1252
.58
1127
.12
325 12.7 3 2.37 137.
6
76 2.04
8
73.9
5
4.9 0.58 1.8 4.9 0.59 1.79 4.9 0.61 1.79 4.9 0.59 1.8 240 1110
.69
948.
83
350 6.35 4 4.4 255.
27
132 4.09
7
127.
9
5.3 0.61 1.8 5.2 0.62 1.8 5.4 0.62 1.8 5.3 0.62 1.8 240 2034
.43
936.
84
350 8.47 3.5 3.65 212.
11
104 3.07
3
100.
93
5.4 0.6 1.8 5.3 0.62 1.8 5.4 0.6 1.82 5.37 0.61 1.8 240 1617
.59
896.
45
350 10.5
8
3 2.73 158.
7
86 2.45
8
83.5
4
5.4 0.6 1.8 5.4 0.61 1.79 5.5 0.6 1.78 5.43 0.6 1.78 240 1345
.81
996.
86
350 12.7 2.5 1.83 106.
44
76 2.04
8
73.9
5
5.4 0.61 1.8 5.4 0.61 1.78 5.5 0.6 1.79 5.43 0.61 1.79 240 1191
.73
1316
.08
Table 1: Collected Data
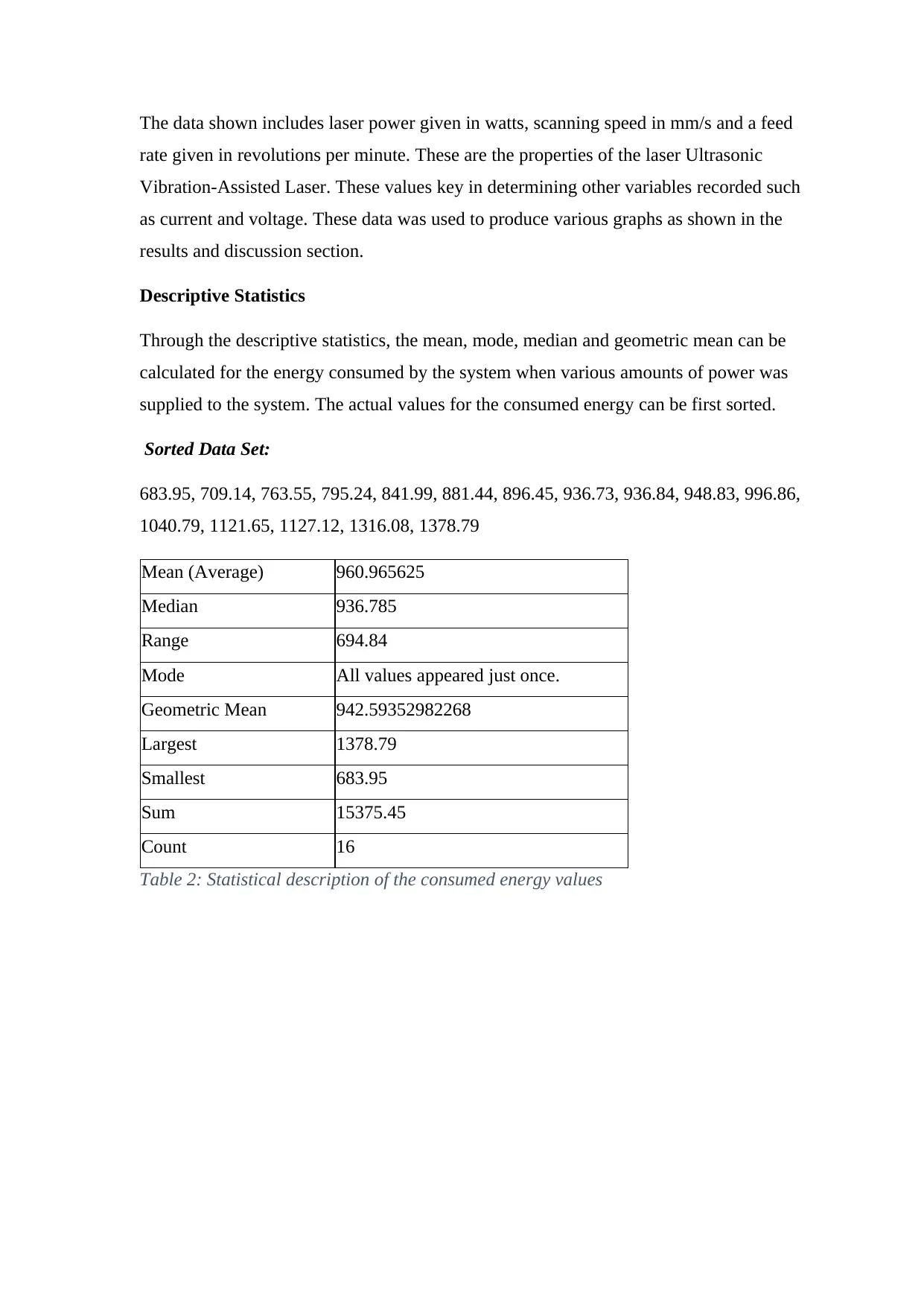
The data shown includes laser power given in watts, scanning speed in mm/s and a feed
rate given in revolutions per minute. These are the properties of the laser Ultrasonic
Vibration-Assisted Laser. These values key in determining other variables recorded such
as current and voltage. These data was used to produce various graphs as shown in the
results and discussion section.
Descriptive Statistics
Through the descriptive statistics, the mean, mode, median and geometric mean can be
calculated for the energy consumed by the system when various amounts of power was
supplied to the system. The actual values for the consumed energy can be first sorted.
Sorted Data Set:
683.95, 709.14, 763.55, 795.24, 841.99, 881.44, 896.45, 936.73, 936.84, 948.83, 996.86,
1040.79, 1121.65, 1127.12, 1316.08, 1378.79
Mean (Average) 960.965625
Median 936.785
Range 694.84
Mode All values appeared just once.
Geometric Mean 942.59352982268
Largest 1378.79
Smallest 683.95
Sum 15375.45
Count 16
Table 2: Statistical description of the consumed energy values
rate given in revolutions per minute. These are the properties of the laser Ultrasonic
Vibration-Assisted Laser. These values key in determining other variables recorded such
as current and voltage. These data was used to produce various graphs as shown in the
results and discussion section.
Descriptive Statistics
Through the descriptive statistics, the mean, mode, median and geometric mean can be
calculated for the energy consumed by the system when various amounts of power was
supplied to the system. The actual values for the consumed energy can be first sorted.
Sorted Data Set:
683.95, 709.14, 763.55, 795.24, 841.99, 881.44, 896.45, 936.73, 936.84, 948.83, 996.86,
1040.79, 1121.65, 1127.12, 1316.08, 1378.79
Mean (Average) 960.965625
Median 936.785
Range 694.84
Mode All values appeared just once.
Geometric Mean 942.59352982268
Largest 1378.79
Smallest 683.95
Sum 15375.45
Count 16
Table 2: Statistical description of the consumed energy values
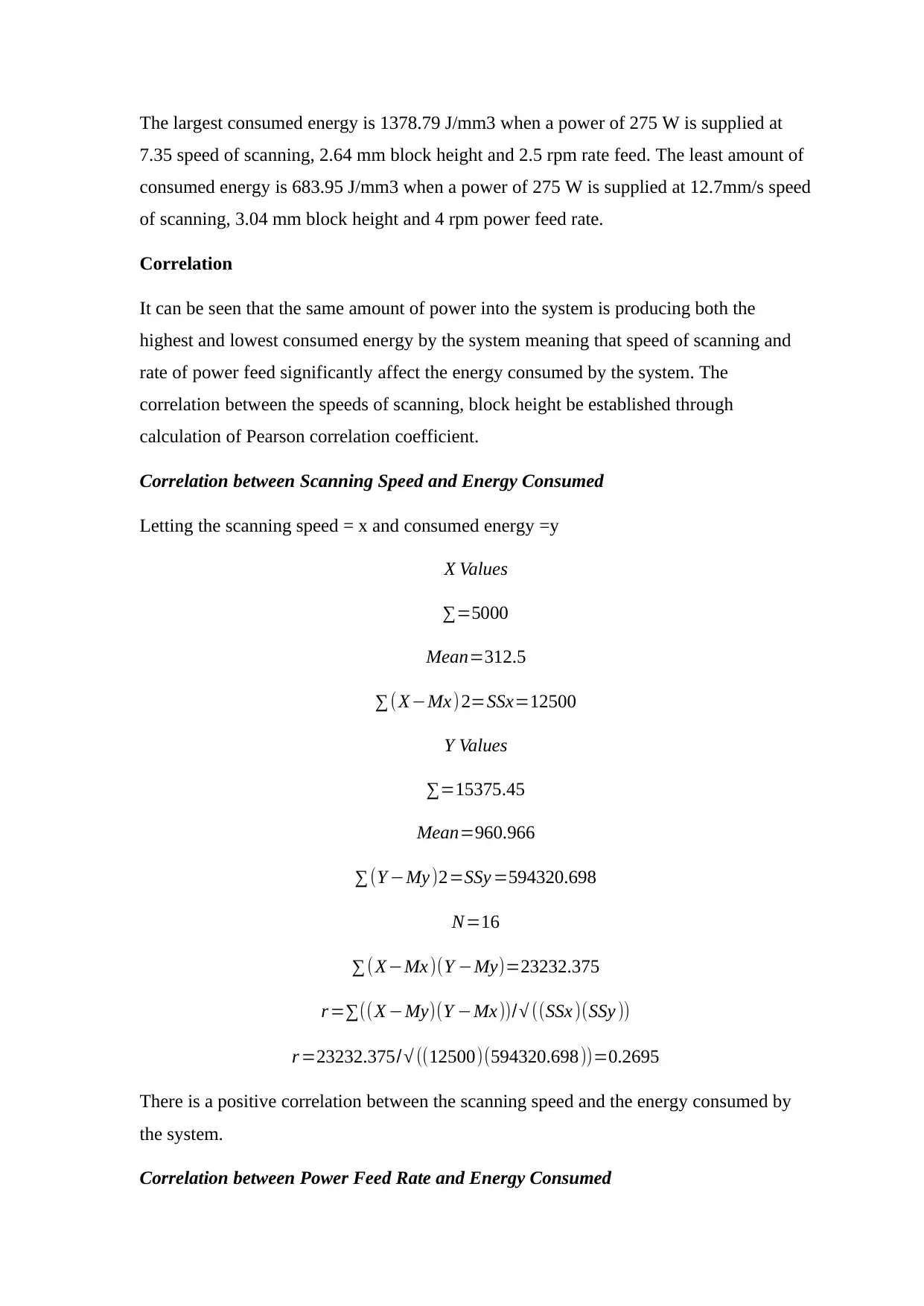
The largest consumed energy is 1378.79 J/mm3 when a power of 275 W is supplied at
7.35 speed of scanning, 2.64 mm block height and 2.5 rpm rate feed. The least amount of
consumed energy is 683.95 J/mm3 when a power of 275 W is supplied at 12.7mm/s speed
of scanning, 3.04 mm block height and 4 rpm power feed rate.
Correlation
It can be seen that the same amount of power into the system is producing both the
highest and lowest consumed energy by the system meaning that speed of scanning and
rate of power feed significantly affect the energy consumed by the system. The
correlation between the speeds of scanning, block height be established through
calculation of Pearson correlation coefficient.
Correlation between Scanning Speed and Energy Consumed
Letting the scanning speed = x and consumed energy =y
X Values
∑=5000
Mean=312.5
∑ (X−Mx)2=SSx=12500
Y Values
∑=15375.45
Mean=960.966
∑ (Y −My)2=SSy =594320.698
N=16
∑ (X−Mx)(Y −My)=23232.375
r =∑((X −My)(Y −Mx))/√ ((SSx )(SSy ))
r =23232.375/√ ((12500)(594320.698))=0.2695
There is a positive correlation between the scanning speed and the energy consumed by
the system.
Correlation between Power Feed Rate and Energy Consumed
7.35 speed of scanning, 2.64 mm block height and 2.5 rpm rate feed. The least amount of
consumed energy is 683.95 J/mm3 when a power of 275 W is supplied at 12.7mm/s speed
of scanning, 3.04 mm block height and 4 rpm power feed rate.
Correlation
It can be seen that the same amount of power into the system is producing both the
highest and lowest consumed energy by the system meaning that speed of scanning and
rate of power feed significantly affect the energy consumed by the system. The
correlation between the speeds of scanning, block height be established through
calculation of Pearson correlation coefficient.
Correlation between Scanning Speed and Energy Consumed
Letting the scanning speed = x and consumed energy =y
X Values
∑=5000
Mean=312.5
∑ (X−Mx)2=SSx=12500
Y Values
∑=15375.45
Mean=960.966
∑ (Y −My)2=SSy =594320.698
N=16
∑ (X−Mx)(Y −My)=23232.375
r =∑((X −My)(Y −Mx))/√ ((SSx )(SSy ))
r =23232.375/√ ((12500)(594320.698))=0.2695
There is a positive correlation between the scanning speed and the energy consumed by
the system.
Correlation between Power Feed Rate and Energy Consumed
Paraphrase This Document
Need a fresh take? Get an instant paraphrase of this document with our AI Paraphraser
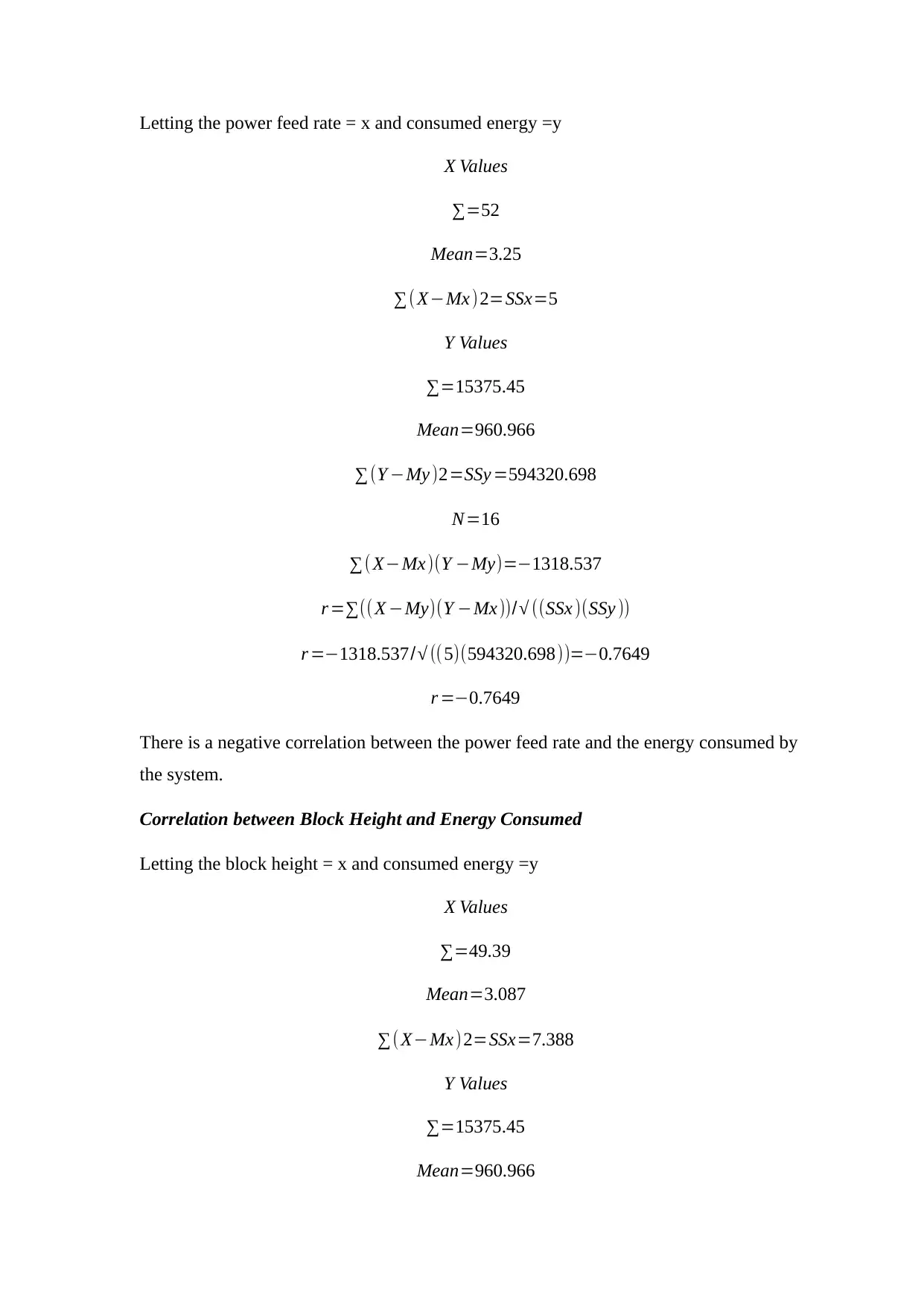
Letting the power feed rate = x and consumed energy =y
X Values
∑=52
Mean=3.25
∑ (X−Mx)2=SSx=5
Y Values
∑=15375.45
Mean=960.966
∑ (Y −My)2=SSy =594320.698
N=16
∑( X−Mx )(Y −My)=−1318.537
r =∑((X −My)(Y −Mx))/√ ((SSx )(SSy ))
r =−1318.537/√ ((5)(594320.698))=−0.7649
r =−0.7649
There is a negative correlation between the power feed rate and the energy consumed by
the system.
Correlation between Block Height and Energy Consumed
Letting the block height = x and consumed energy =y
X Values
∑=49.39
Mean=3.087
∑( X−Mx )2=SSx=7.388
Y Values
∑=15375.45
Mean=960.966
X Values
∑=52
Mean=3.25
∑ (X−Mx)2=SSx=5
Y Values
∑=15375.45
Mean=960.966
∑ (Y −My)2=SSy =594320.698
N=16
∑( X−Mx )(Y −My)=−1318.537
r =∑((X −My)(Y −Mx))/√ ((SSx )(SSy ))
r =−1318.537/√ ((5)(594320.698))=−0.7649
r =−0.7649
There is a negative correlation between the power feed rate and the energy consumed by
the system.
Correlation between Block Height and Energy Consumed
Letting the block height = x and consumed energy =y
X Values
∑=49.39
Mean=3.087
∑( X−Mx )2=SSx=7.388
Y Values
∑=15375.45
Mean=960.966
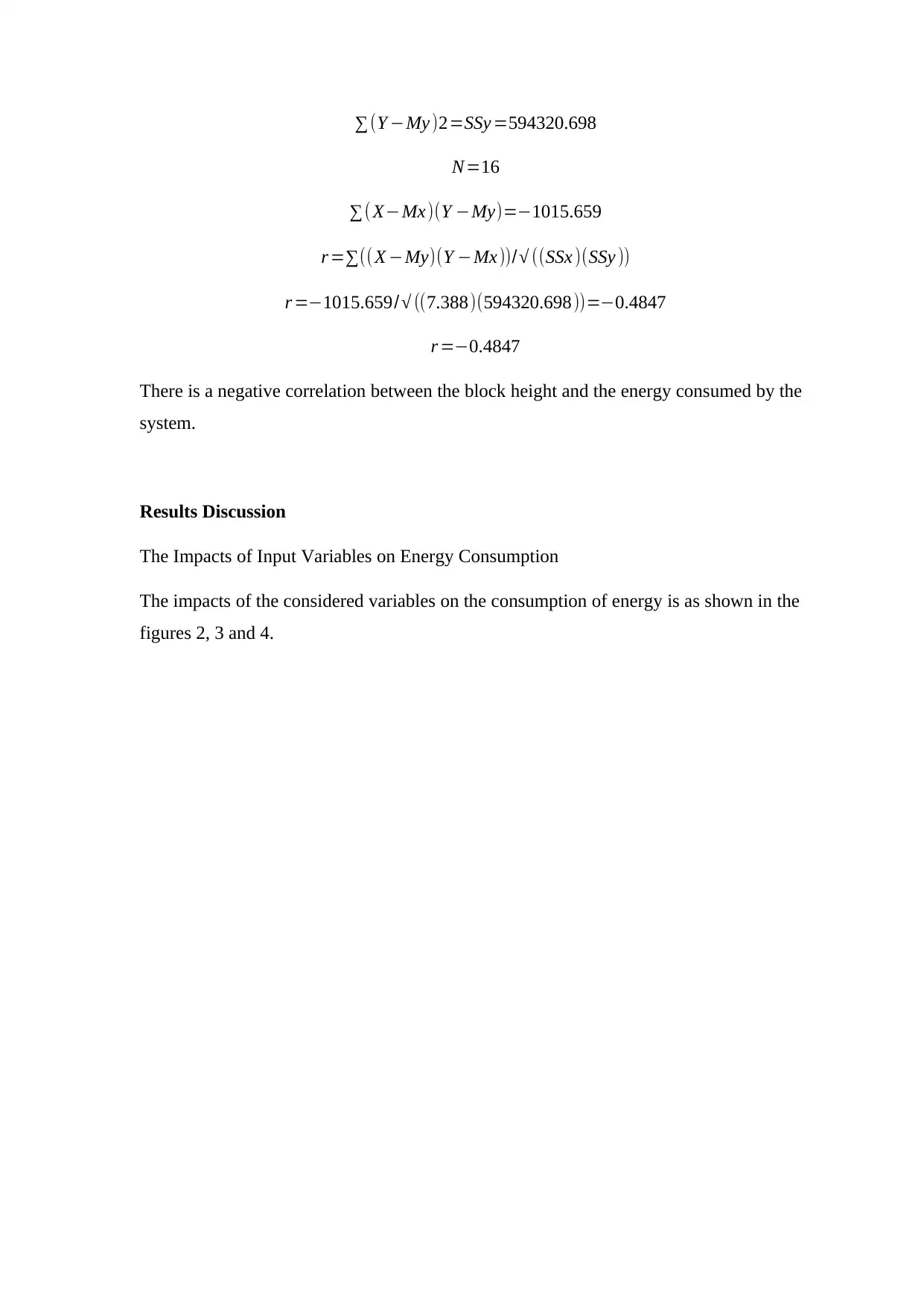
∑ (Y −My)2=SSy =594320.698
N=16
∑( X−Mx )(Y −My)=−1015.659
r =∑((X −My)(Y −Mx))/√ ((SSx )(SSy ))
r =−1015.659/√ ((7.388)(594320.698))=−0.4847
r =−0.4847
There is a negative correlation between the block height and the energy consumed by the
system.
Results Discussion
The Impacts of Input Variables on Energy Consumption
The impacts of the considered variables on the consumption of energy is as shown in the
figures 2, 3 and 4.
N=16
∑( X−Mx )(Y −My)=−1015.659
r =∑((X −My)(Y −Mx))/√ ((SSx )(SSy ))
r =−1015.659/√ ((7.388)(594320.698))=−0.4847
r =−0.4847
There is a negative correlation between the block height and the energy consumed by the
system.
Results Discussion
The Impacts of Input Variables on Energy Consumption
The impacts of the considered variables on the consumption of energy is as shown in the
figures 2, 3 and 4.
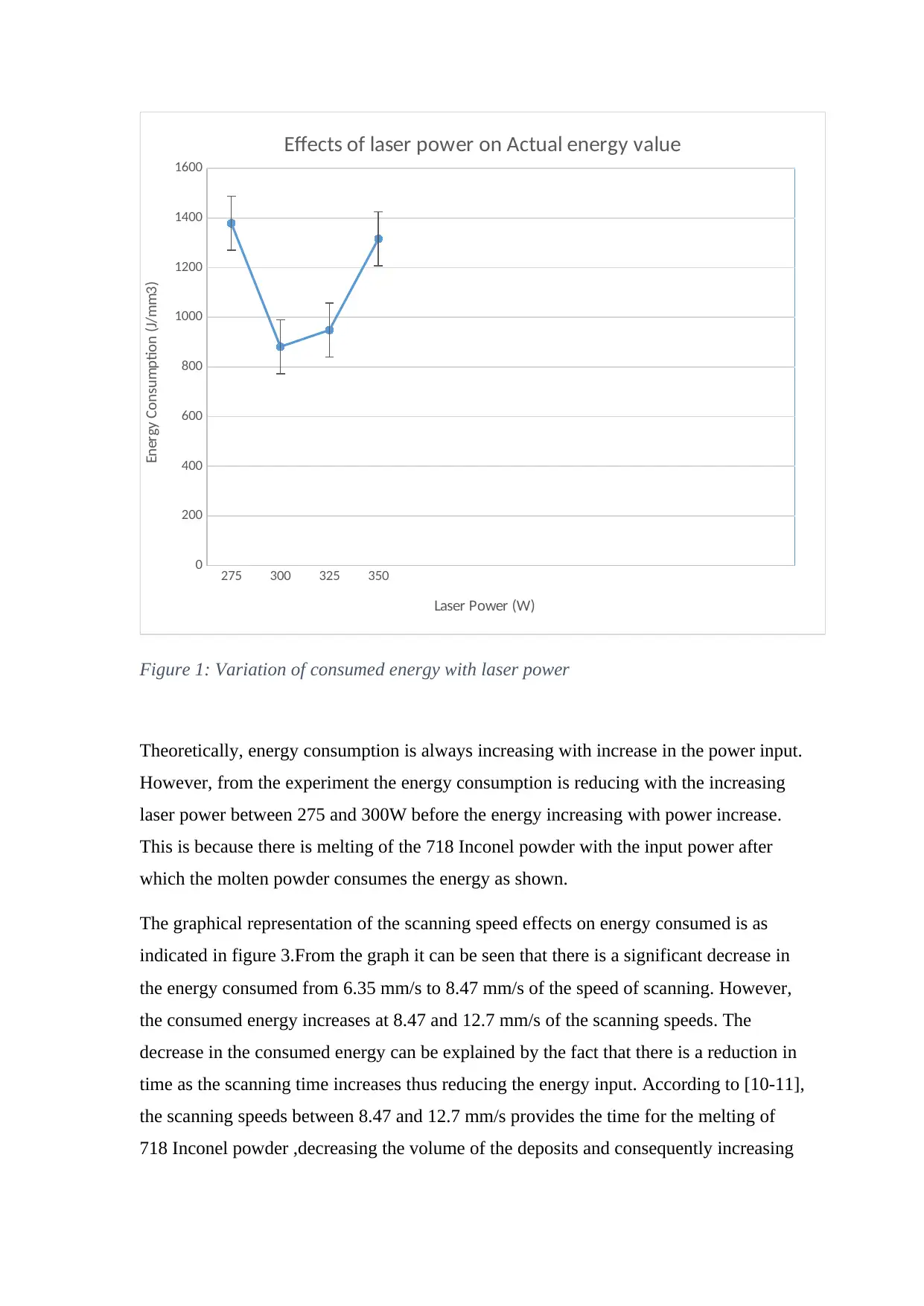
275 300 325 350
0
200
400
600
800
1000
1200
1400
1600
Effects of laser power on Actual energy value
Laser Power (W)
Energy Consumption (J/mm3)
Figure 1: Variation of consumed energy with laser power
Theoretically, energy consumption is always increasing with increase in the power input.
However, from the experiment the energy consumption is reducing with the increasing
laser power between 275 and 300W before the energy increasing with power increase.
This is because there is melting of the 718 Inconel powder with the input power after
which the molten powder consumes the energy as shown.
The graphical representation of the scanning speed effects on energy consumed is as
indicated in figure 3.From the graph it can be seen that there is a significant decrease in
the energy consumed from 6.35 mm/s to 8.47 mm/s of the speed of scanning. However,
the consumed energy increases at 8.47 and 12.7 mm/s of the scanning speeds. The
decrease in the consumed energy can be explained by the fact that there is a reduction in
time as the scanning time increases thus reducing the energy input. According to [10-11],
the scanning speeds between 8.47 and 12.7 mm/s provides the time for the melting of
718 Inconel powder ,decreasing the volume of the deposits and consequently increasing
0
200
400
600
800
1000
1200
1400
1600
Effects of laser power on Actual energy value
Laser Power (W)
Energy Consumption (J/mm3)
Figure 1: Variation of consumed energy with laser power
Theoretically, energy consumption is always increasing with increase in the power input.
However, from the experiment the energy consumption is reducing with the increasing
laser power between 275 and 300W before the energy increasing with power increase.
This is because there is melting of the 718 Inconel powder with the input power after
which the molten powder consumes the energy as shown.
The graphical representation of the scanning speed effects on energy consumed is as
indicated in figure 3.From the graph it can be seen that there is a significant decrease in
the energy consumed from 6.35 mm/s to 8.47 mm/s of the speed of scanning. However,
the consumed energy increases at 8.47 and 12.7 mm/s of the scanning speeds. The
decrease in the consumed energy can be explained by the fact that there is a reduction in
time as the scanning time increases thus reducing the energy input. According to [10-11],
the scanning speeds between 8.47 and 12.7 mm/s provides the time for the melting of
718 Inconel powder ,decreasing the volume of the deposits and consequently increasing
Secure Best Marks with AI Grader
Need help grading? Try our AI Grader for instant feedback on your assignments.
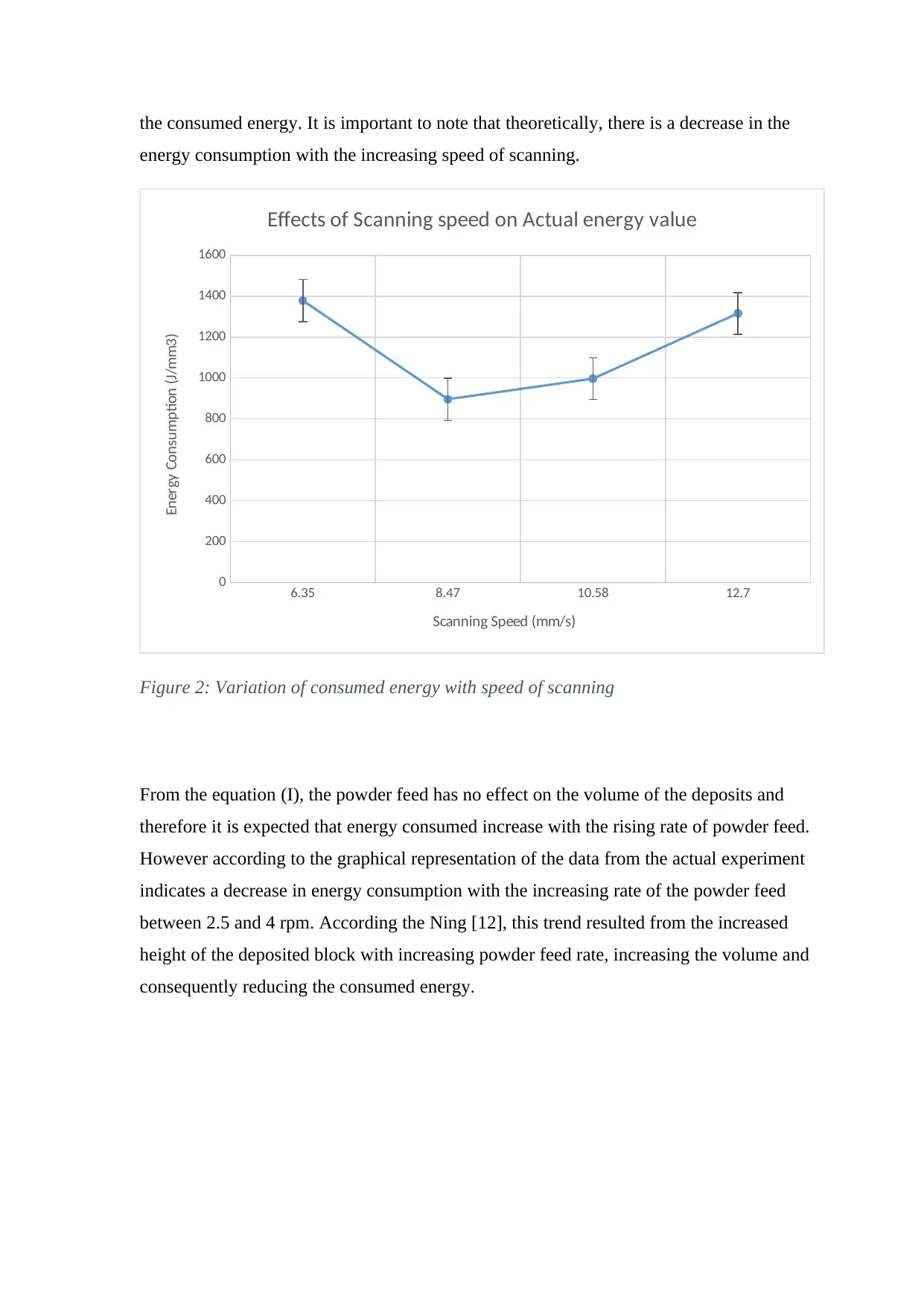
the consumed energy. It is important to note that theoretically, there is a decrease in the
energy consumption with the increasing speed of scanning.
6.35 8.47 10.58 12.7
0
200
400
600
800
1000
1200
1400
1600
Effects of Scanning speed on Actual energy value
Scanning Speed (mm/s)
Energy Consumption (J/mm3)
Figure 2: Variation of consumed energy with speed of scanning
From the equation (I), the powder feed has no effect on the volume of the deposits and
therefore it is expected that energy consumed increase with the rising rate of powder feed.
However according to the graphical representation of the data from the actual experiment
indicates a decrease in energy consumption with the increasing rate of the powder feed
between 2.5 and 4 rpm. According the Ning [12], this trend resulted from the increased
height of the deposited block with increasing powder feed rate, increasing the volume and
consequently reducing the consumed energy.
energy consumption with the increasing speed of scanning.
6.35 8.47 10.58 12.7
0
200
400
600
800
1000
1200
1400
1600
Effects of Scanning speed on Actual energy value
Scanning Speed (mm/s)
Energy Consumption (J/mm3)
Figure 2: Variation of consumed energy with speed of scanning
From the equation (I), the powder feed has no effect on the volume of the deposits and
therefore it is expected that energy consumed increase with the rising rate of powder feed.
However according to the graphical representation of the data from the actual experiment
indicates a decrease in energy consumption with the increasing rate of the powder feed
between 2.5 and 4 rpm. According the Ning [12], this trend resulted from the increased
height of the deposited block with increasing powder feed rate, increasing the volume and
consequently reducing the consumed energy.
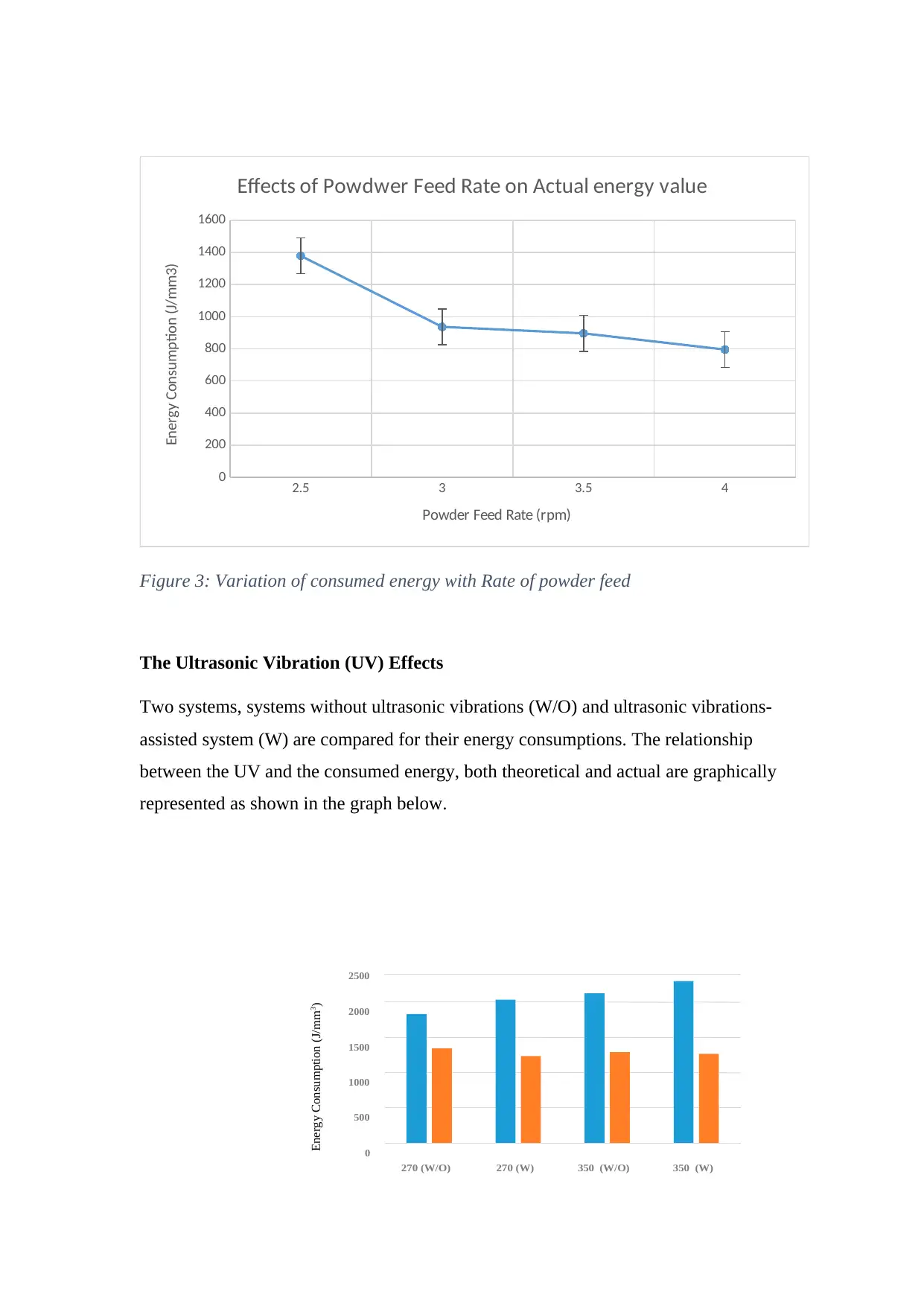
2.5 3 3.5 4
0
200
400
600
800
1000
1200
1400
1600
Effects of Powdwer Feed Rate on Actual energy value
Powder Feed Rate (rpm)
Energy Consumption (J/mm3)
Figure 3: Variation of consumed energy with Rate of powder feed
The Ultrasonic Vibration (UV) Effects
Two systems, systems without ultrasonic vibrations (W/O) and ultrasonic vibrations-
assisted system (W) are compared for their energy consumptions. The relationship
between the UV and the consumed energy, both theoretical and actual are graphically
represented as shown in the graph below.
2500
2000
1500
1000
500
0
270 (W/O) 270 (W) 350 (W/O) 350 (W)
Energy Consumption (J/mm3)
0
200
400
600
800
1000
1200
1400
1600
Effects of Powdwer Feed Rate on Actual energy value
Powder Feed Rate (rpm)
Energy Consumption (J/mm3)
Figure 3: Variation of consumed energy with Rate of powder feed
The Ultrasonic Vibration (UV) Effects
Two systems, systems without ultrasonic vibrations (W/O) and ultrasonic vibrations-
assisted system (W) are compared for their energy consumptions. The relationship
between the UV and the consumed energy, both theoretical and actual are graphically
represented as shown in the graph below.
2500
2000
1500
1000
500
0
270 (W/O) 270 (W) 350 (W/O) 350 (W)
Energy Consumption (J/mm3)
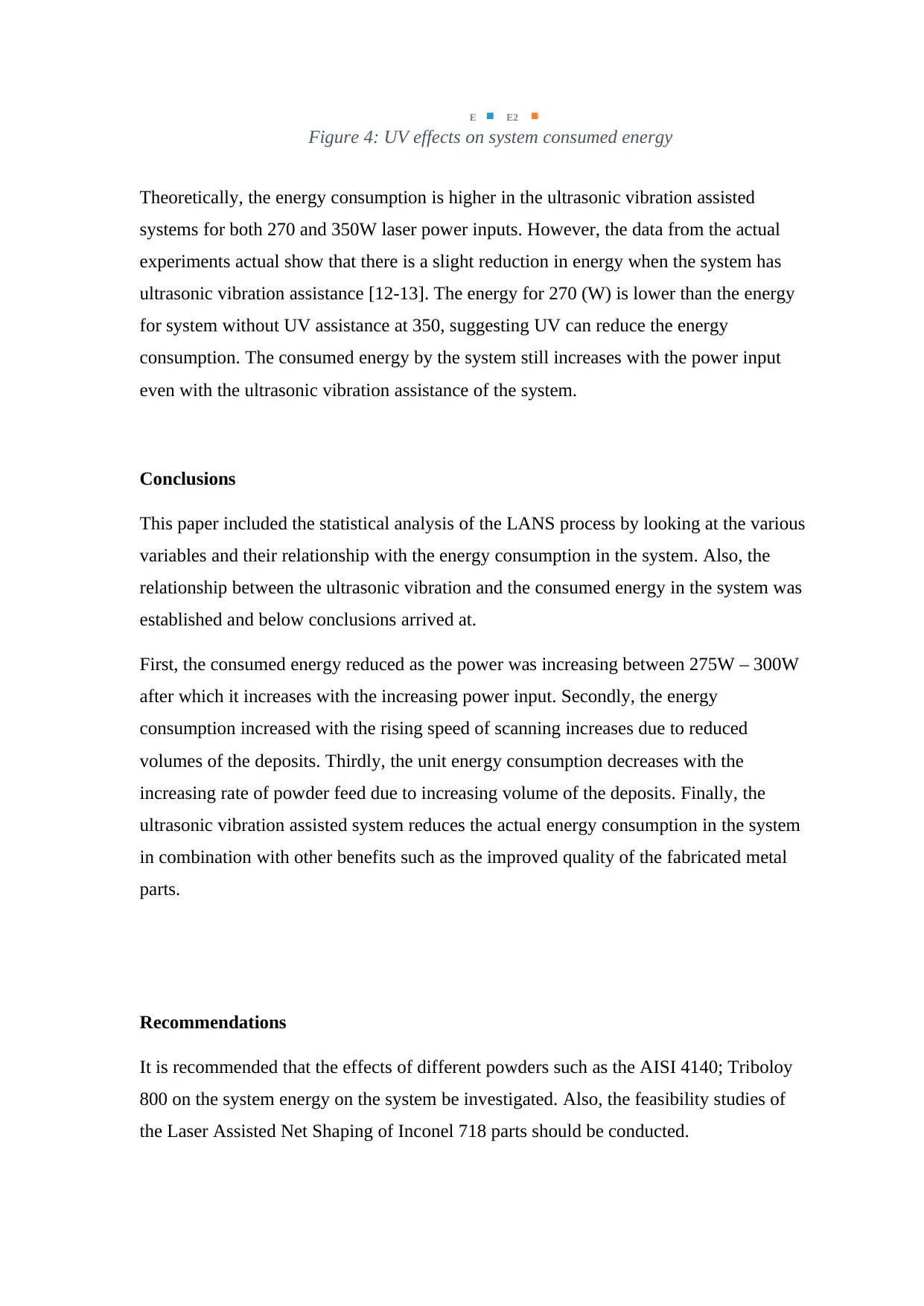
Figure 4: UV effects on system consumed energy
E E2
Theoretically, the energy consumption is higher in the ultrasonic vibration assisted
systems for both 270 and 350W laser power inputs. However, the data from the actual
experiments actual show that there is a slight reduction in energy when the system has
ultrasonic vibration assistance [12-13]. The energy for 270 (W) is lower than the energy
for system without UV assistance at 350, suggesting UV can reduce the energy
consumption. The consumed energy by the system still increases with the power input
even with the ultrasonic vibration assistance of the system.
Conclusions
This paper included the statistical analysis of the LANS process by looking at the various
variables and their relationship with the energy consumption in the system. Also, the
relationship between the ultrasonic vibration and the consumed energy in the system was
established and below conclusions arrived at.
First, the consumed energy reduced as the power was increasing between 275W – 300W
after which it increases with the increasing power input. Secondly, the energy
consumption increased with the rising speed of scanning increases due to reduced
volumes of the deposits. Thirdly, the unit energy consumption decreases with the
increasing rate of powder feed due to increasing volume of the deposits. Finally, the
ultrasonic vibration assisted system reduces the actual energy consumption in the system
in combination with other benefits such as the improved quality of the fabricated metal
parts.
Recommendations
It is recommended that the effects of different powders such as the AISI 4140; Triboloy
800 on the system energy on the system be investigated. Also, the feasibility studies of
the Laser Assisted Net Shaping of Inconel 718 parts should be conducted.
E E2
Theoretically, the energy consumption is higher in the ultrasonic vibration assisted
systems for both 270 and 350W laser power inputs. However, the data from the actual
experiments actual show that there is a slight reduction in energy when the system has
ultrasonic vibration assistance [12-13]. The energy for 270 (W) is lower than the energy
for system without UV assistance at 350, suggesting UV can reduce the energy
consumption. The consumed energy by the system still increases with the power input
even with the ultrasonic vibration assistance of the system.
Conclusions
This paper included the statistical analysis of the LANS process by looking at the various
variables and their relationship with the energy consumption in the system. Also, the
relationship between the ultrasonic vibration and the consumed energy in the system was
established and below conclusions arrived at.
First, the consumed energy reduced as the power was increasing between 275W – 300W
after which it increases with the increasing power input. Secondly, the energy
consumption increased with the rising speed of scanning increases due to reduced
volumes of the deposits. Thirdly, the unit energy consumption decreases with the
increasing rate of powder feed due to increasing volume of the deposits. Finally, the
ultrasonic vibration assisted system reduces the actual energy consumption in the system
in combination with other benefits such as the improved quality of the fabricated metal
parts.
Recommendations
It is recommended that the effects of different powders such as the AISI 4140; Triboloy
800 on the system energy on the system be investigated. Also, the feasibility studies of
the Laser Assisted Net Shaping of Inconel 718 parts should be conducted.
Paraphrase This Document
Need a fresh take? Get an instant paraphrase of this document with our AI Paraphraser
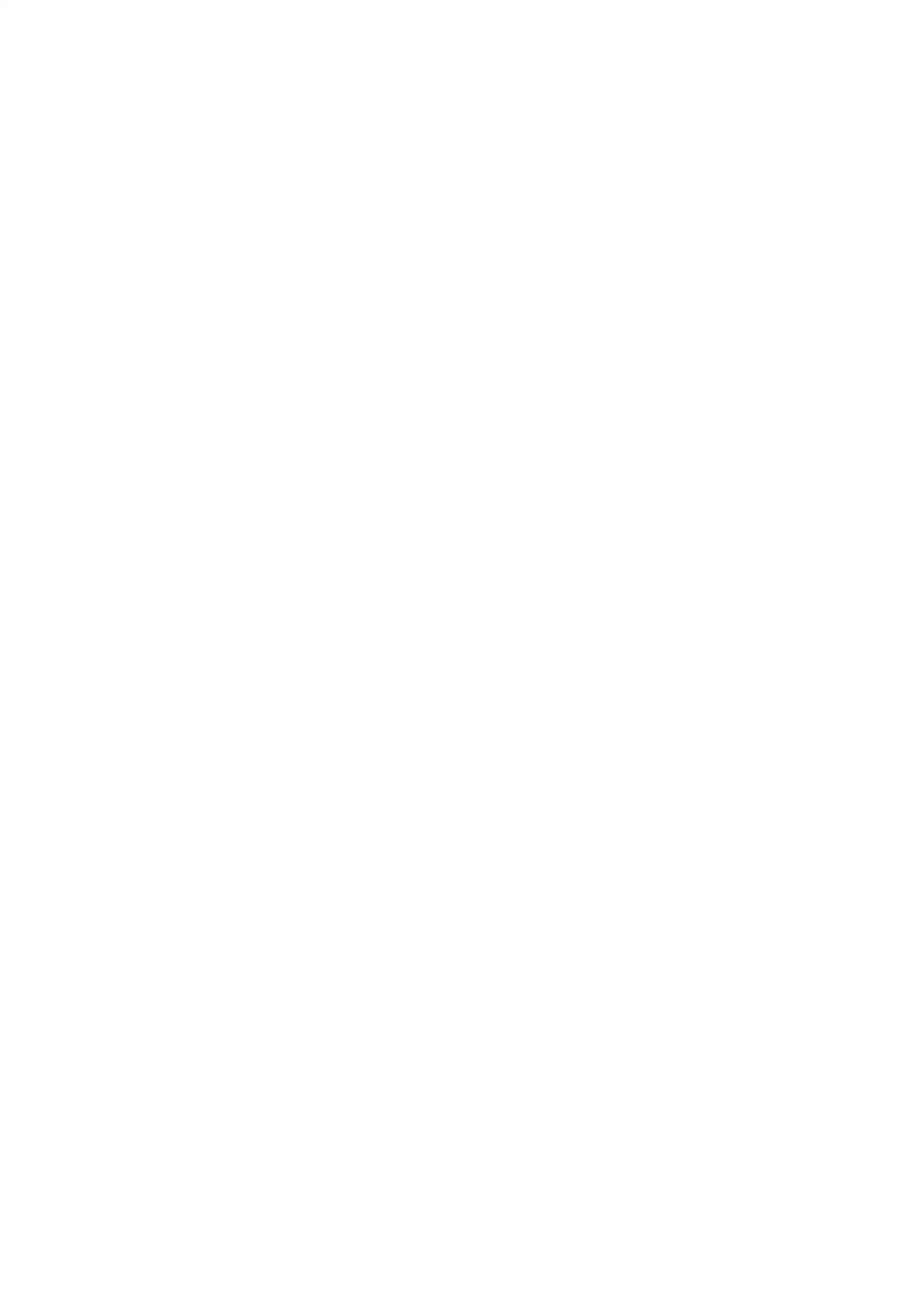
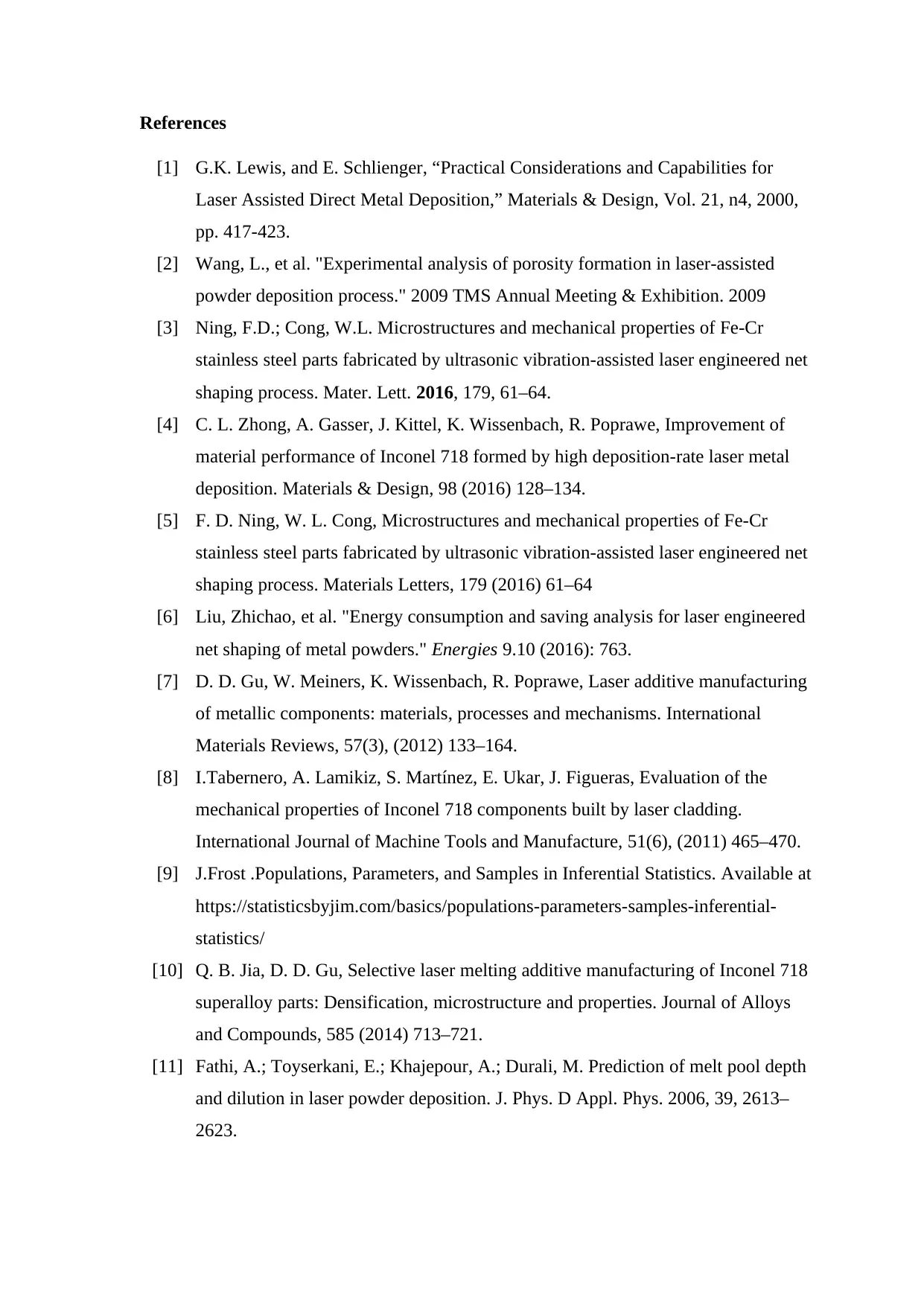
References
[1] G.K. Lewis, and E. Schlienger, “Practical Considerations and Capabilities for
Laser Assisted Direct Metal Deposition,” Materials & Design, Vol. 21, n4, 2000,
pp. 417-423.
[2] Wang, L., et al. "Experimental analysis of porosity formation in laser-assisted
powder deposition process." 2009 TMS Annual Meeting & Exhibition. 2009
[3] Ning, F.D.; Cong, W.L. Microstructures and mechanical properties of Fe-Cr
stainless steel parts fabricated by ultrasonic vibration-assisted laser engineered net
shaping process. Mater. Lett. 2016, 179, 61–64.
[4] C. L. Zhong, A. Gasser, J. Kittel, K. Wissenbach, R. Poprawe, Improvement of
material performance of Inconel 718 formed by high deposition-rate laser metal
deposition. Materials & Design, 98 (2016) 128–134.
[5] F. D. Ning, W. L. Cong, Microstructures and mechanical properties of Fe-Cr
stainless steel parts fabricated by ultrasonic vibration-assisted laser engineered net
shaping process. Materials Letters, 179 (2016) 61–64
[6] Liu, Zhichao, et al. "Energy consumption and saving analysis for laser engineered
net shaping of metal powders." Energies 9.10 (2016): 763.
[7] D. D. Gu, W. Meiners, K. Wissenbach, R. Poprawe, Laser additive manufacturing
of metallic components: materials, processes and mechanisms. International
Materials Reviews, 57(3), (2012) 133–164.
[8] I.Tabernero, A. Lamikiz, S. Martínez, E. Ukar, J. Figueras, Evaluation of the
mechanical properties of Inconel 718 components built by laser cladding.
International Journal of Machine Tools and Manufacture, 51(6), (2011) 465–470.
[9] J.Frost .Populations, Parameters, and Samples in Inferential Statistics. Available at
https://statisticsbyjim.com/basics/populations-parameters-samples-inferential-
statistics/
[10] Q. B. Jia, D. D. Gu, Selective laser melting additive manufacturing of Inconel 718
superalloy parts: Densification, microstructure and properties. Journal of Alloys
and Compounds, 585 (2014) 713–721.
[11] Fathi, A.; Toyserkani, E.; Khajepour, A.; Durali, M. Prediction of melt pool depth
and dilution in laser powder deposition. J. Phys. D Appl. Phys. 2006, 39, 2613–
2623.
[1] G.K. Lewis, and E. Schlienger, “Practical Considerations and Capabilities for
Laser Assisted Direct Metal Deposition,” Materials & Design, Vol. 21, n4, 2000,
pp. 417-423.
[2] Wang, L., et al. "Experimental analysis of porosity formation in laser-assisted
powder deposition process." 2009 TMS Annual Meeting & Exhibition. 2009
[3] Ning, F.D.; Cong, W.L. Microstructures and mechanical properties of Fe-Cr
stainless steel parts fabricated by ultrasonic vibration-assisted laser engineered net
shaping process. Mater. Lett. 2016, 179, 61–64.
[4] C. L. Zhong, A. Gasser, J. Kittel, K. Wissenbach, R. Poprawe, Improvement of
material performance of Inconel 718 formed by high deposition-rate laser metal
deposition. Materials & Design, 98 (2016) 128–134.
[5] F. D. Ning, W. L. Cong, Microstructures and mechanical properties of Fe-Cr
stainless steel parts fabricated by ultrasonic vibration-assisted laser engineered net
shaping process. Materials Letters, 179 (2016) 61–64
[6] Liu, Zhichao, et al. "Energy consumption and saving analysis for laser engineered
net shaping of metal powders." Energies 9.10 (2016): 763.
[7] D. D. Gu, W. Meiners, K. Wissenbach, R. Poprawe, Laser additive manufacturing
of metallic components: materials, processes and mechanisms. International
Materials Reviews, 57(3), (2012) 133–164.
[8] I.Tabernero, A. Lamikiz, S. Martínez, E. Ukar, J. Figueras, Evaluation of the
mechanical properties of Inconel 718 components built by laser cladding.
International Journal of Machine Tools and Manufacture, 51(6), (2011) 465–470.
[9] J.Frost .Populations, Parameters, and Samples in Inferential Statistics. Available at
https://statisticsbyjim.com/basics/populations-parameters-samples-inferential-
statistics/
[10] Q. B. Jia, D. D. Gu, Selective laser melting additive manufacturing of Inconel 718
superalloy parts: Densification, microstructure and properties. Journal of Alloys
and Compounds, 585 (2014) 713–721.
[11] Fathi, A.; Toyserkani, E.; Khajepour, A.; Durali, M. Prediction of melt pool depth
and dilution in laser powder deposition. J. Phys. D Appl. Phys. 2006, 39, 2613–
2623.
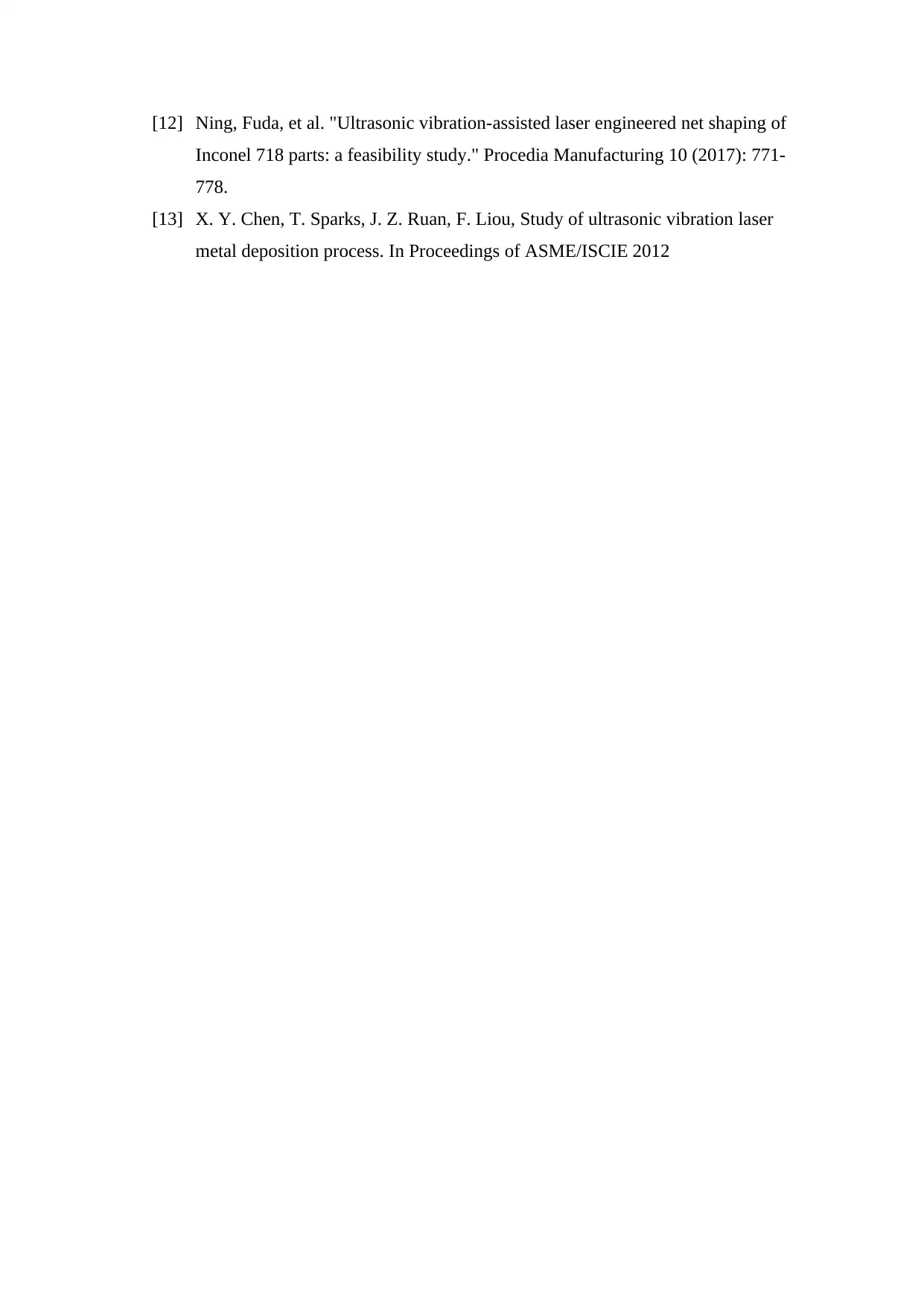
[12] Ning, Fuda, et al. "Ultrasonic vibration-assisted laser engineered net shaping of
Inconel 718 parts: a feasibility study." Procedia Manufacturing 10 (2017): 771-
778.
[13] X. Y. Chen, T. Sparks, J. Z. Ruan, F. Liou, Study of ultrasonic vibration laser
metal deposition process. In Proceedings of ASME/ISCIE 2012
Inconel 718 parts: a feasibility study." Procedia Manufacturing 10 (2017): 771-
778.
[13] X. Y. Chen, T. Sparks, J. Z. Ruan, F. Liou, Study of ultrasonic vibration laser
metal deposition process. In Proceedings of ASME/ISCIE 2012
1 out of 16
Related Documents

Your All-in-One AI-Powered Toolkit for Academic Success.
+13062052269
info@desklib.com
Available 24*7 on WhatsApp / Email
Unlock your academic potential
© 2024 | Zucol Services PVT LTD | All rights reserved.