Report on Business Operations: Unilever's Strategies and Analysis
VerifiedAdded on 2022/12/30
|11
|3086
|77
Report
AI Summary
This report provides a comprehensive analysis of Unilever's business operations. It begins with an introduction to the company and its core business activities, followed by an exploration of the best practices employed by Unilever, including lean manufacturing, automation, employee training, environmental sustainability, and quality management systems. The report then delves into the analytical frameworks utilized, such as Total Quality Management (TQM) and Just-in-Time (JIT) inventory management, outlining their application and benefits. Furthermore, the report examines various approaches to quality management, including Total Quality Control (TQC), technology deployment, process improvement, and customer-aided design. Finally, it discusses specific quality management techniques, such as continuous improvement and Business Process Re-engineering (BPR), highlighting their role in enhancing product quality and operational efficiency. The report concludes by synthesizing these elements to offer a holistic view of Unilever's operational strategies and their impact on business performance. This report is a valuable resource for students seeking to understand real-world business operations and management practices.
Contribute Materials
Your contribution can guide someone’s learning journey. Share your
documents today.
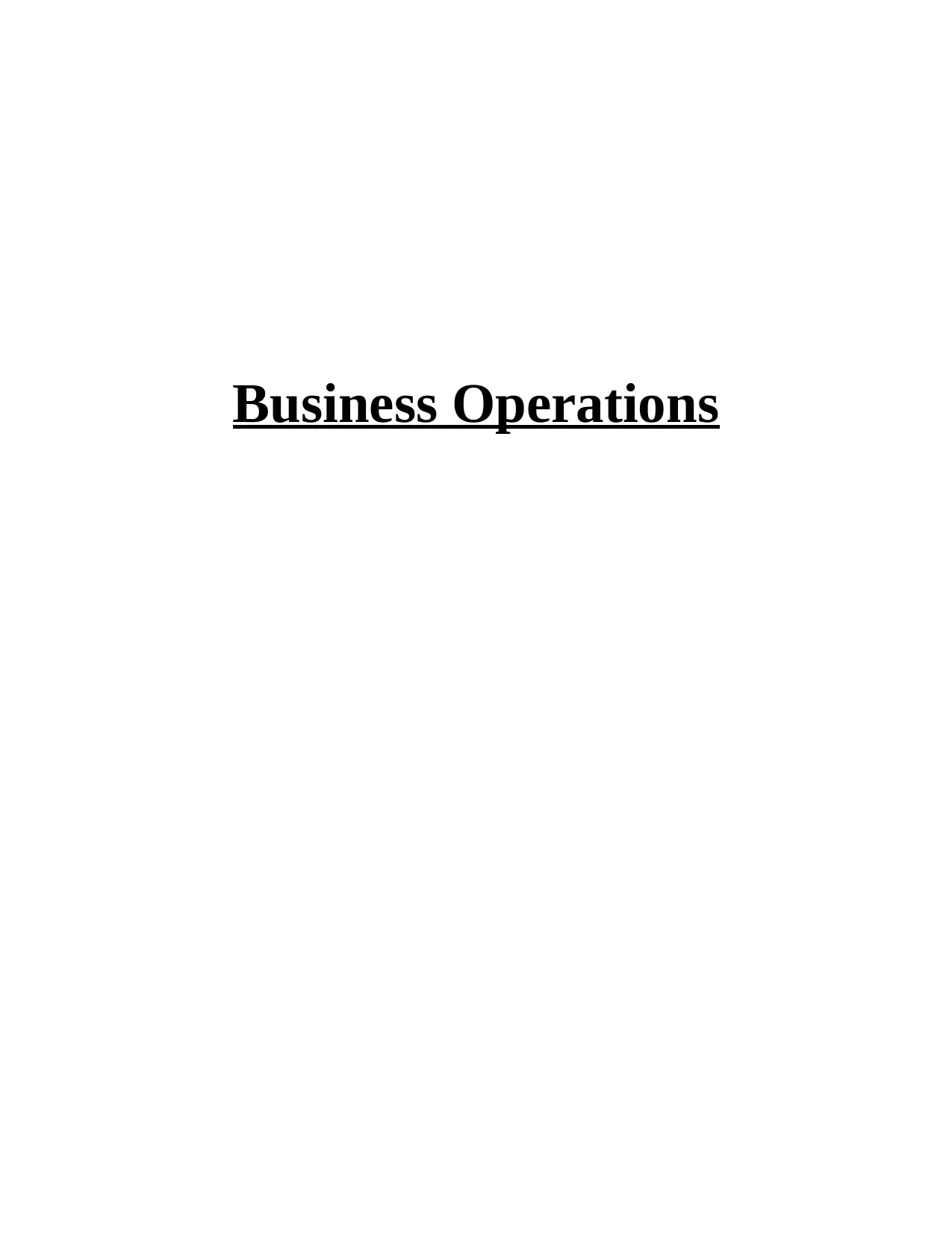
Business Operations
Secure Best Marks with AI Grader
Need help grading? Try our AI Grader for instant feedback on your assignments.
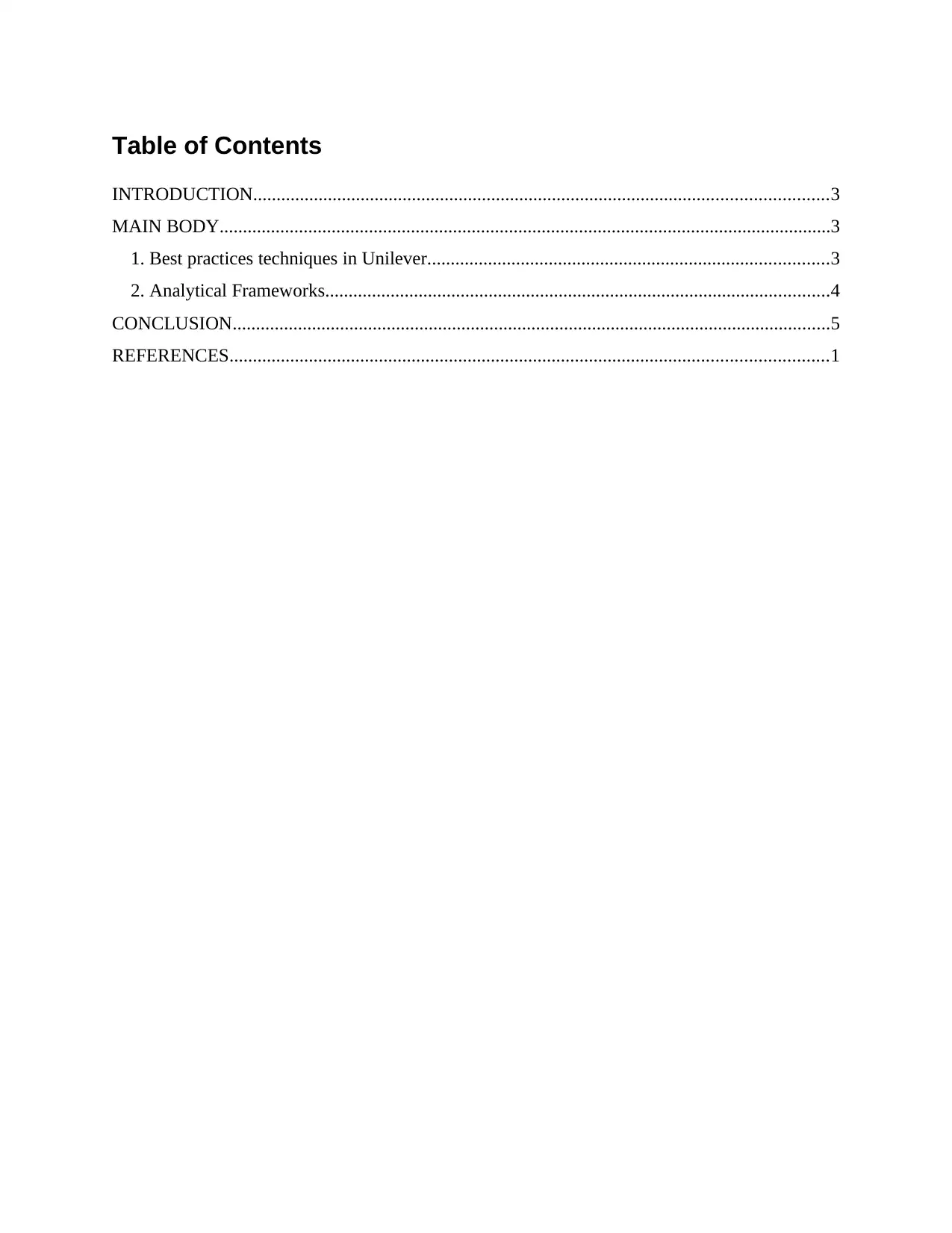
Table of Contents
INTRODUCTION...........................................................................................................................3
MAIN BODY...................................................................................................................................3
1. Best practices techniques in Unilever......................................................................................3
2. Analytical Frameworks............................................................................................................4
CONCLUSION................................................................................................................................5
REFERENCES................................................................................................................................1
INTRODUCTION...........................................................................................................................3
MAIN BODY...................................................................................................................................3
1. Best practices techniques in Unilever......................................................................................3
2. Analytical Frameworks............................................................................................................4
CONCLUSION................................................................................................................................5
REFERENCES................................................................................................................................1
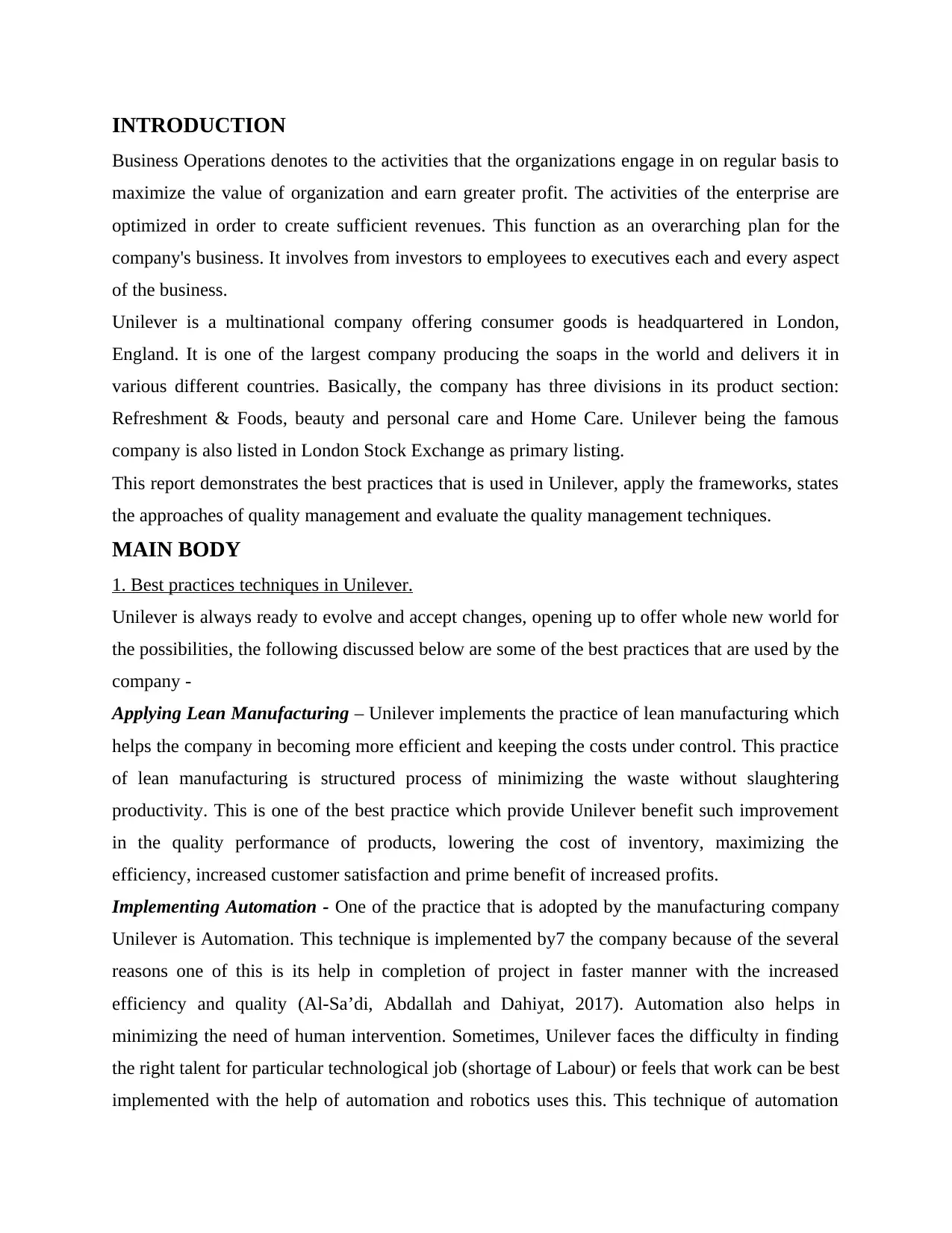
INTRODUCTION
Business Operations denotes to the activities that the organizations engage in on regular basis to
maximize the value of organization and earn greater profit. The activities of the enterprise are
optimized in order to create sufficient revenues. This function as an overarching plan for the
company's business. It involves from investors to employees to executives each and every aspect
of the business.
Unilever is a multinational company offering consumer goods is headquartered in London,
England. It is one of the largest company producing the soaps in the world and delivers it in
various different countries. Basically, the company has three divisions in its product section:
Refreshment & Foods, beauty and personal care and Home Care. Unilever being the famous
company is also listed in London Stock Exchange as primary listing.
This report demonstrates the best practices that is used in Unilever, apply the frameworks, states
the approaches of quality management and evaluate the quality management techniques.
MAIN BODY
1. Best practices techniques in Unilever.
Unilever is always ready to evolve and accept changes, opening up to offer whole new world for
the possibilities, the following discussed below are some of the best practices that are used by the
company -
Applying Lean Manufacturing – Unilever implements the practice of lean manufacturing which
helps the company in becoming more efficient and keeping the costs under control. This practice
of lean manufacturing is structured process of minimizing the waste without slaughtering
productivity. This is one of the best practice which provide Unilever benefit such improvement
in the quality performance of products, lowering the cost of inventory, maximizing the
efficiency, increased customer satisfaction and prime benefit of increased profits.
Implementing Automation - One of the practice that is adopted by the manufacturing company
Unilever is Automation. This technique is implemented by7 the company because of the several
reasons one of this is its help in completion of project in faster manner with the increased
efficiency and quality (Al-Sa’di, Abdallah and Dahiyat, 2017). Automation also helps in
minimizing the need of human intervention. Sometimes, Unilever faces the difficulty in finding
the right talent for particular technological job (shortage of Labour) or feels that work can be best
implemented with the help of automation and robotics uses this. This technique of automation
Business Operations denotes to the activities that the organizations engage in on regular basis to
maximize the value of organization and earn greater profit. The activities of the enterprise are
optimized in order to create sufficient revenues. This function as an overarching plan for the
company's business. It involves from investors to employees to executives each and every aspect
of the business.
Unilever is a multinational company offering consumer goods is headquartered in London,
England. It is one of the largest company producing the soaps in the world and delivers it in
various different countries. Basically, the company has three divisions in its product section:
Refreshment & Foods, beauty and personal care and Home Care. Unilever being the famous
company is also listed in London Stock Exchange as primary listing.
This report demonstrates the best practices that is used in Unilever, apply the frameworks, states
the approaches of quality management and evaluate the quality management techniques.
MAIN BODY
1. Best practices techniques in Unilever.
Unilever is always ready to evolve and accept changes, opening up to offer whole new world for
the possibilities, the following discussed below are some of the best practices that are used by the
company -
Applying Lean Manufacturing – Unilever implements the practice of lean manufacturing which
helps the company in becoming more efficient and keeping the costs under control. This practice
of lean manufacturing is structured process of minimizing the waste without slaughtering
productivity. This is one of the best practice which provide Unilever benefit such improvement
in the quality performance of products, lowering the cost of inventory, maximizing the
efficiency, increased customer satisfaction and prime benefit of increased profits.
Implementing Automation - One of the practice that is adopted by the manufacturing company
Unilever is Automation. This technique is implemented by7 the company because of the several
reasons one of this is its help in completion of project in faster manner with the increased
efficiency and quality (Al-Sa’di, Abdallah and Dahiyat, 2017). Automation also helps in
minimizing the need of human intervention. Sometimes, Unilever faces the difficulty in finding
the right talent for particular technological job (shortage of Labour) or feels that work can be best
implemented with the help of automation and robotics uses this. This technique of automation
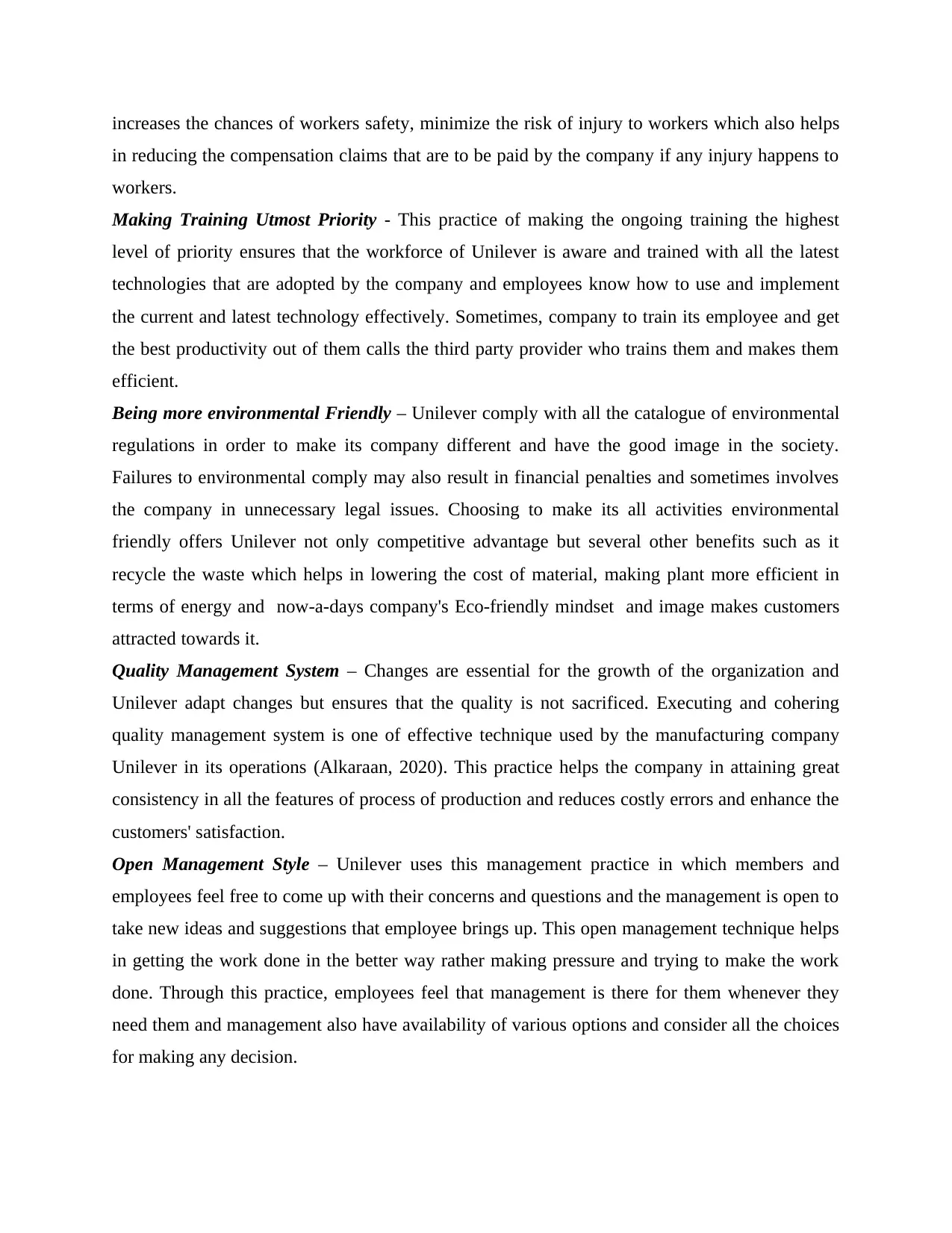
increases the chances of workers safety, minimize the risk of injury to workers which also helps
in reducing the compensation claims that are to be paid by the company if any injury happens to
workers.
Making Training Utmost Priority - This practice of making the ongoing training the highest
level of priority ensures that the workforce of Unilever is aware and trained with all the latest
technologies that are adopted by the company and employees know how to use and implement
the current and latest technology effectively. Sometimes, company to train its employee and get
the best productivity out of them calls the third party provider who trains them and makes them
efficient.
Being more environmental Friendly – Unilever comply with all the catalogue of environmental
regulations in order to make its company different and have the good image in the society.
Failures to environmental comply may also result in financial penalties and sometimes involves
the company in unnecessary legal issues. Choosing to make its all activities environmental
friendly offers Unilever not only competitive advantage but several other benefits such as it
recycle the waste which helps in lowering the cost of material, making plant more efficient in
terms of energy and now-a-days company's Eco-friendly mindset and image makes customers
attracted towards it.
Quality Management System – Changes are essential for the growth of the organization and
Unilever adapt changes but ensures that the quality is not sacrificed. Executing and cohering
quality management system is one of effective technique used by the manufacturing company
Unilever in its operations (Alkaraan, 2020). This practice helps the company in attaining great
consistency in all the features of process of production and reduces costly errors and enhance the
customers' satisfaction.
Open Management Style – Unilever uses this management practice in which members and
employees feel free to come up with their concerns and questions and the management is open to
take new ideas and suggestions that employee brings up. This open management technique helps
in getting the work done in the better way rather making pressure and trying to make the work
done. Through this practice, employees feel that management is there for them whenever they
need them and management also have availability of various options and consider all the choices
for making any decision.
in reducing the compensation claims that are to be paid by the company if any injury happens to
workers.
Making Training Utmost Priority - This practice of making the ongoing training the highest
level of priority ensures that the workforce of Unilever is aware and trained with all the latest
technologies that are adopted by the company and employees know how to use and implement
the current and latest technology effectively. Sometimes, company to train its employee and get
the best productivity out of them calls the third party provider who trains them and makes them
efficient.
Being more environmental Friendly – Unilever comply with all the catalogue of environmental
regulations in order to make its company different and have the good image in the society.
Failures to environmental comply may also result in financial penalties and sometimes involves
the company in unnecessary legal issues. Choosing to make its all activities environmental
friendly offers Unilever not only competitive advantage but several other benefits such as it
recycle the waste which helps in lowering the cost of material, making plant more efficient in
terms of energy and now-a-days company's Eco-friendly mindset and image makes customers
attracted towards it.
Quality Management System – Changes are essential for the growth of the organization and
Unilever adapt changes but ensures that the quality is not sacrificed. Executing and cohering
quality management system is one of effective technique used by the manufacturing company
Unilever in its operations (Alkaraan, 2020). This practice helps the company in attaining great
consistency in all the features of process of production and reduces costly errors and enhance the
customers' satisfaction.
Open Management Style – Unilever uses this management practice in which members and
employees feel free to come up with their concerns and questions and the management is open to
take new ideas and suggestions that employee brings up. This open management technique helps
in getting the work done in the better way rather making pressure and trying to make the work
done. Through this practice, employees feel that management is there for them whenever they
need them and management also have availability of various options and consider all the choices
for making any decision.
Secure Best Marks with AI Grader
Need help grading? Try our AI Grader for instant feedback on your assignments.
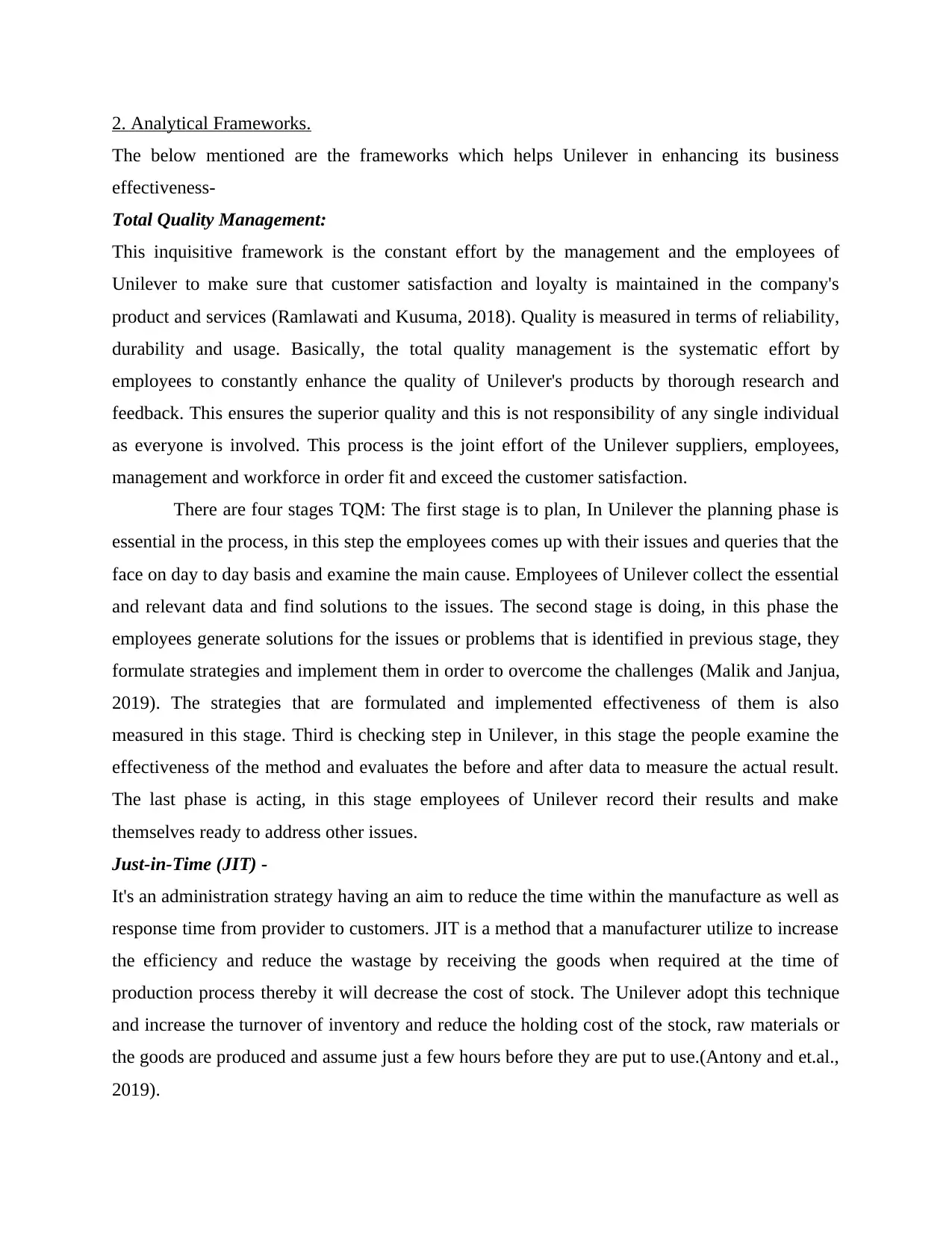
2. Analytical Frameworks.
The below mentioned are the frameworks which helps Unilever in enhancing its business
effectiveness-
Total Quality Management:
This inquisitive framework is the constant effort by the management and the employees of
Unilever to make sure that customer satisfaction and loyalty is maintained in the company's
product and services (Ramlawati and Kusuma, 2018). Quality is measured in terms of reliability,
durability and usage. Basically, the total quality management is the systematic effort by
employees to constantly enhance the quality of Unilever's products by thorough research and
feedback. This ensures the superior quality and this is not responsibility of any single individual
as everyone is involved. This process is the joint effort of the Unilever suppliers, employees,
management and workforce in order fit and exceed the customer satisfaction.
There are four stages TQM: The first stage is to plan, In Unilever the planning phase is
essential in the process, in this step the employees comes up with their issues and queries that the
face on day to day basis and examine the main cause. Employees of Unilever collect the essential
and relevant data and find solutions to the issues. The second stage is doing, in this phase the
employees generate solutions for the issues or problems that is identified in previous stage, they
formulate strategies and implement them in order to overcome the challenges (Malik and Janjua,
2019). The strategies that are formulated and implemented effectiveness of them is also
measured in this stage. Third is checking step in Unilever, in this stage the people examine the
effectiveness of the method and evaluates the before and after data to measure the actual result.
The last phase is acting, in this stage employees of Unilever record their results and make
themselves ready to address other issues.
Just-in-Time (JIT) -
It's an administration strategy having an aim to reduce the time within the manufacture as well as
response time from provider to customers. JIT is a method that a manufacturer utilize to increase
the efficiency and reduce the wastage by receiving the goods when required at the time of
production process thereby it will decrease the cost of stock. The Unilever adopt this technique
and increase the turnover of inventory and reduce the holding cost of the stock, raw materials or
the goods are produced and assume just a few hours before they are put to use.(Antony and et.al.,
2019).
The below mentioned are the frameworks which helps Unilever in enhancing its business
effectiveness-
Total Quality Management:
This inquisitive framework is the constant effort by the management and the employees of
Unilever to make sure that customer satisfaction and loyalty is maintained in the company's
product and services (Ramlawati and Kusuma, 2018). Quality is measured in terms of reliability,
durability and usage. Basically, the total quality management is the systematic effort by
employees to constantly enhance the quality of Unilever's products by thorough research and
feedback. This ensures the superior quality and this is not responsibility of any single individual
as everyone is involved. This process is the joint effort of the Unilever suppliers, employees,
management and workforce in order fit and exceed the customer satisfaction.
There are four stages TQM: The first stage is to plan, In Unilever the planning phase is
essential in the process, in this step the employees comes up with their issues and queries that the
face on day to day basis and examine the main cause. Employees of Unilever collect the essential
and relevant data and find solutions to the issues. The second stage is doing, in this phase the
employees generate solutions for the issues or problems that is identified in previous stage, they
formulate strategies and implement them in order to overcome the challenges (Malik and Janjua,
2019). The strategies that are formulated and implemented effectiveness of them is also
measured in this stage. Third is checking step in Unilever, in this stage the people examine the
effectiveness of the method and evaluates the before and after data to measure the actual result.
The last phase is acting, in this stage employees of Unilever record their results and make
themselves ready to address other issues.
Just-in-Time (JIT) -
It's an administration strategy having an aim to reduce the time within the manufacture as well as
response time from provider to customers. JIT is a method that a manufacturer utilize to increase
the efficiency and reduce the wastage by receiving the goods when required at the time of
production process thereby it will decrease the cost of stock. The Unilever adopt this technique
and increase the turnover of inventory and reduce the holding cost of the stock, raw materials or
the goods are produced and assume just a few hours before they are put to use.(Antony and et.al.,
2019).
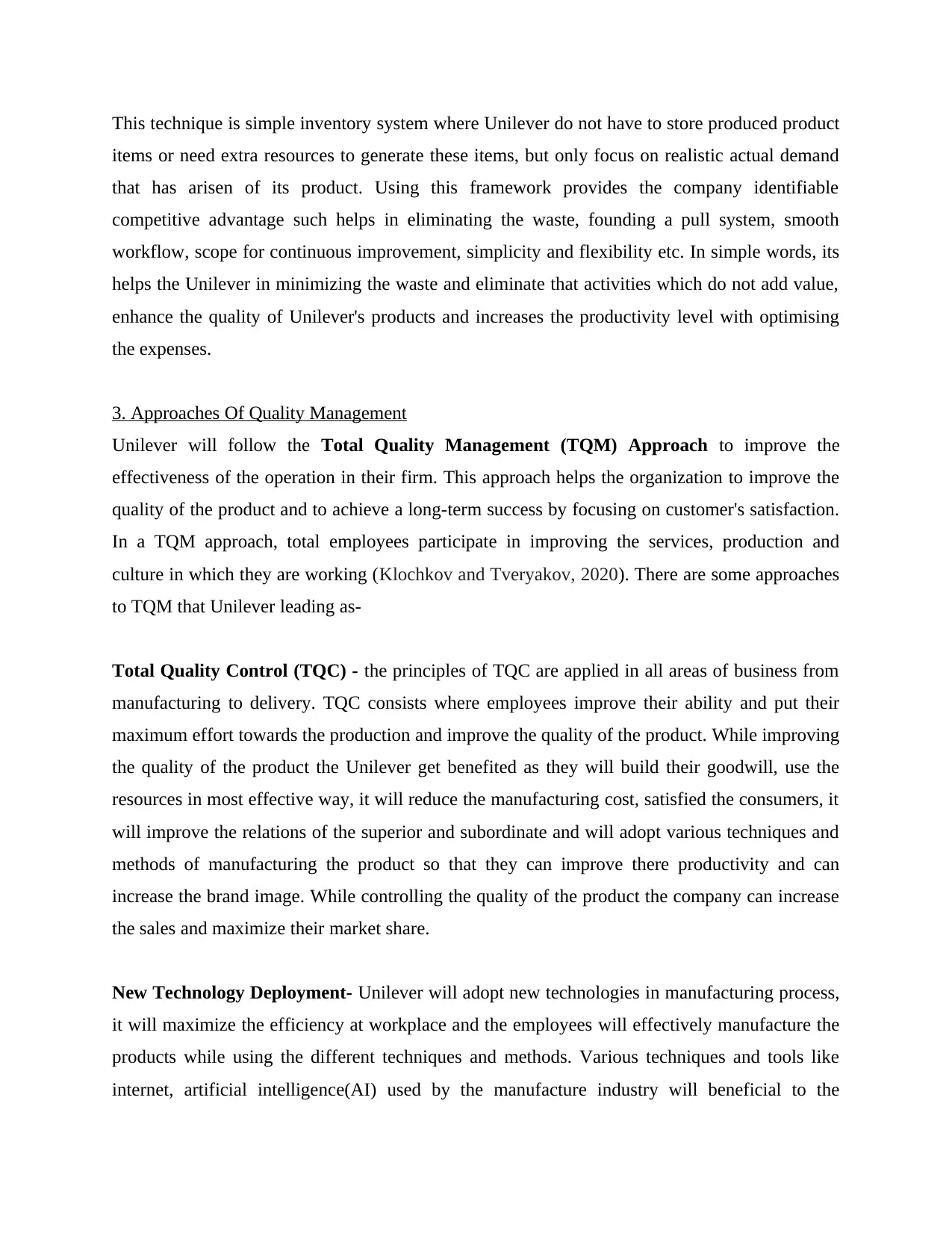
This technique is simple inventory system where Unilever do not have to store produced product
items or need extra resources to generate these items, but only focus on realistic actual demand
that has arisen of its product. Using this framework provides the company identifiable
competitive advantage such helps in eliminating the waste, founding a pull system, smooth
workflow, scope for continuous improvement, simplicity and flexibility etc. In simple words, its
helps the Unilever in minimizing the waste and eliminate that activities which do not add value,
enhance the quality of Unilever's products and increases the productivity level with optimising
the expenses.
3. Approaches Of Quality Management
Unilever will follow the Total Quality Management (TQM) Approach to improve the
effectiveness of the operation in their firm. This approach helps the organization to improve the
quality of the product and to achieve a long-term success by focusing on customer's satisfaction.
In a TQM approach, total employees participate in improving the services, production and
culture in which they are working (Klochkov and Tveryakov, 2020). There are some approaches
to TQM that Unilever leading as-
Total Quality Control (TQC) - the principles of TQC are applied in all areas of business from
manufacturing to delivery. TQC consists where employees improve their ability and put their
maximum effort towards the production and improve the quality of the product. While improving
the quality of the product the Unilever get benefited as they will build their goodwill, use the
resources in most effective way, it will reduce the manufacturing cost, satisfied the consumers, it
will improve the relations of the superior and subordinate and will adopt various techniques and
methods of manufacturing the product so that they can improve there productivity and can
increase the brand image. While controlling the quality of the product the company can increase
the sales and maximize their market share.
New Technology Deployment- Unilever will adopt new technologies in manufacturing process,
it will maximize the efficiency at workplace and the employees will effectively manufacture the
products while using the different techniques and methods. Various techniques and tools like
internet, artificial intelligence(AI) used by the manufacture industry will beneficial to the
items or need extra resources to generate these items, but only focus on realistic actual demand
that has arisen of its product. Using this framework provides the company identifiable
competitive advantage such helps in eliminating the waste, founding a pull system, smooth
workflow, scope for continuous improvement, simplicity and flexibility etc. In simple words, its
helps the Unilever in minimizing the waste and eliminate that activities which do not add value,
enhance the quality of Unilever's products and increases the productivity level with optimising
the expenses.
3. Approaches Of Quality Management
Unilever will follow the Total Quality Management (TQM) Approach to improve the
effectiveness of the operation in their firm. This approach helps the organization to improve the
quality of the product and to achieve a long-term success by focusing on customer's satisfaction.
In a TQM approach, total employees participate in improving the services, production and
culture in which they are working (Klochkov and Tveryakov, 2020). There are some approaches
to TQM that Unilever leading as-
Total Quality Control (TQC) - the principles of TQC are applied in all areas of business from
manufacturing to delivery. TQC consists where employees improve their ability and put their
maximum effort towards the production and improve the quality of the product. While improving
the quality of the product the Unilever get benefited as they will build their goodwill, use the
resources in most effective way, it will reduce the manufacturing cost, satisfied the consumers, it
will improve the relations of the superior and subordinate and will adopt various techniques and
methods of manufacturing the product so that they can improve there productivity and can
increase the brand image. While controlling the quality of the product the company can increase
the sales and maximize their market share.
New Technology Deployment- Unilever will adopt new technologies in manufacturing process,
it will maximize the efficiency at workplace and the employees will effectively manufacture the
products while using the different techniques and methods. Various techniques and tools like
internet, artificial intelligence(AI) used by the manufacture industry will beneficial to the
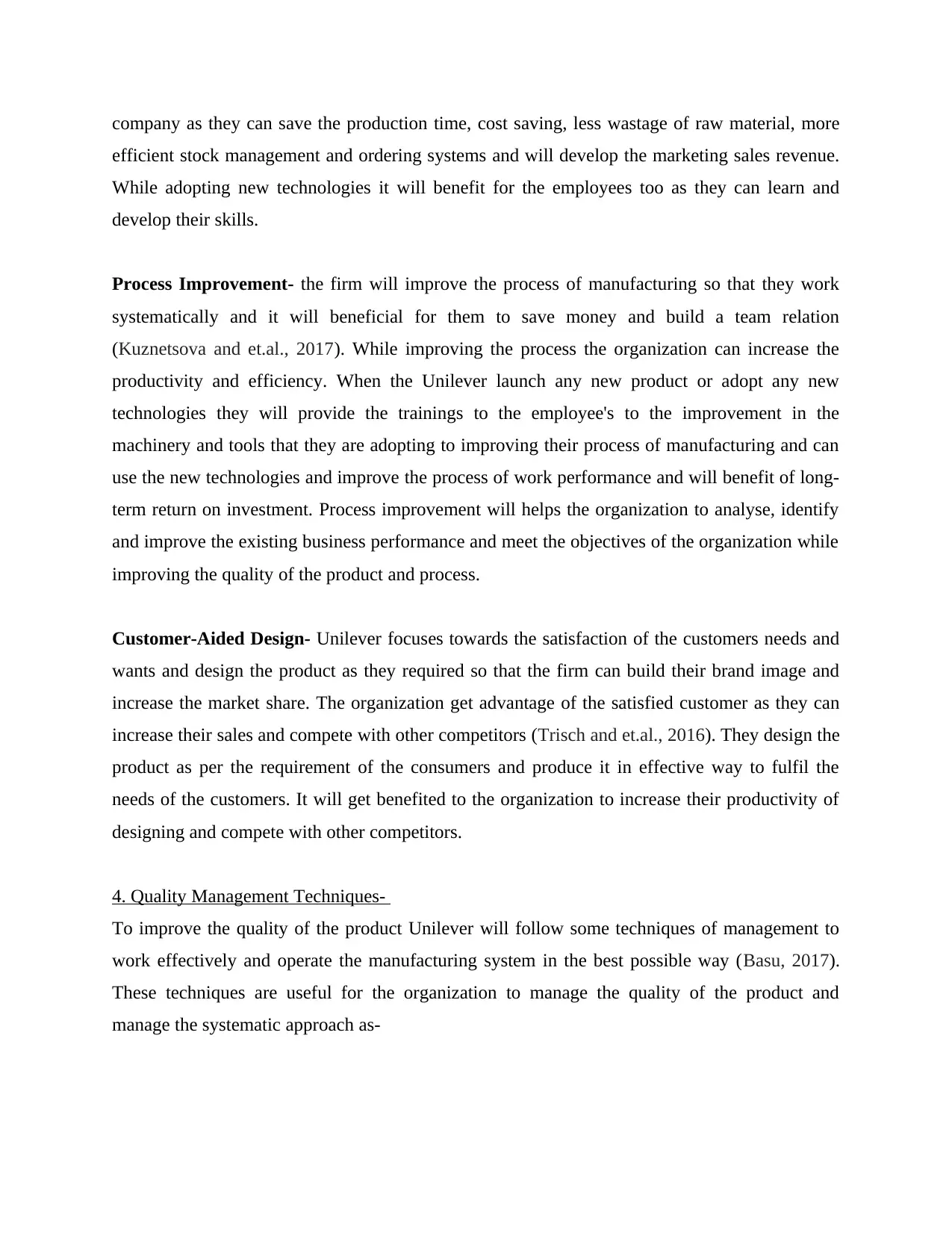
company as they can save the production time, cost saving, less wastage of raw material, more
efficient stock management and ordering systems and will develop the marketing sales revenue.
While adopting new technologies it will benefit for the employees too as they can learn and
develop their skills.
Process Improvement- the firm will improve the process of manufacturing so that they work
systematically and it will beneficial for them to save money and build a team relation
(Kuznetsova and et.al., 2017). While improving the process the organization can increase the
productivity and efficiency. When the Unilever launch any new product or adopt any new
technologies they will provide the trainings to the employee's to the improvement in the
machinery and tools that they are adopting to improving their process of manufacturing and can
use the new technologies and improve the process of work performance and will benefit of long-
term return on investment. Process improvement will helps the organization to analyse, identify
and improve the existing business performance and meet the objectives of the organization while
improving the quality of the product and process.
Customer-Aided Design- Unilever focuses towards the satisfaction of the customers needs and
wants and design the product as they required so that the firm can build their brand image and
increase the market share. The organization get advantage of the satisfied customer as they can
increase their sales and compete with other competitors (Trisch and et.al., 2016). They design the
product as per the requirement of the consumers and produce it in effective way to fulfil the
needs of the customers. It will get benefited to the organization to increase their productivity of
designing and compete with other competitors.
4. Quality Management Techniques-
To improve the quality of the product Unilever will follow some techniques of management to
work effectively and operate the manufacturing system in the best possible way (Basu, 2017).
These techniques are useful for the organization to manage the quality of the product and
manage the systematic approach as-
efficient stock management and ordering systems and will develop the marketing sales revenue.
While adopting new technologies it will benefit for the employees too as they can learn and
develop their skills.
Process Improvement- the firm will improve the process of manufacturing so that they work
systematically and it will beneficial for them to save money and build a team relation
(Kuznetsova and et.al., 2017). While improving the process the organization can increase the
productivity and efficiency. When the Unilever launch any new product or adopt any new
technologies they will provide the trainings to the employee's to the improvement in the
machinery and tools that they are adopting to improving their process of manufacturing and can
use the new technologies and improve the process of work performance and will benefit of long-
term return on investment. Process improvement will helps the organization to analyse, identify
and improve the existing business performance and meet the objectives of the organization while
improving the quality of the product and process.
Customer-Aided Design- Unilever focuses towards the satisfaction of the customers needs and
wants and design the product as they required so that the firm can build their brand image and
increase the market share. The organization get advantage of the satisfied customer as they can
increase their sales and compete with other competitors (Trisch and et.al., 2016). They design the
product as per the requirement of the consumers and produce it in effective way to fulfil the
needs of the customers. It will get benefited to the organization to increase their productivity of
designing and compete with other competitors.
4. Quality Management Techniques-
To improve the quality of the product Unilever will follow some techniques of management to
work effectively and operate the manufacturing system in the best possible way (Basu, 2017).
These techniques are useful for the organization to manage the quality of the product and
manage the systematic approach as-
Paraphrase This Document
Need a fresh take? Get an instant paraphrase of this document with our AI Paraphraser
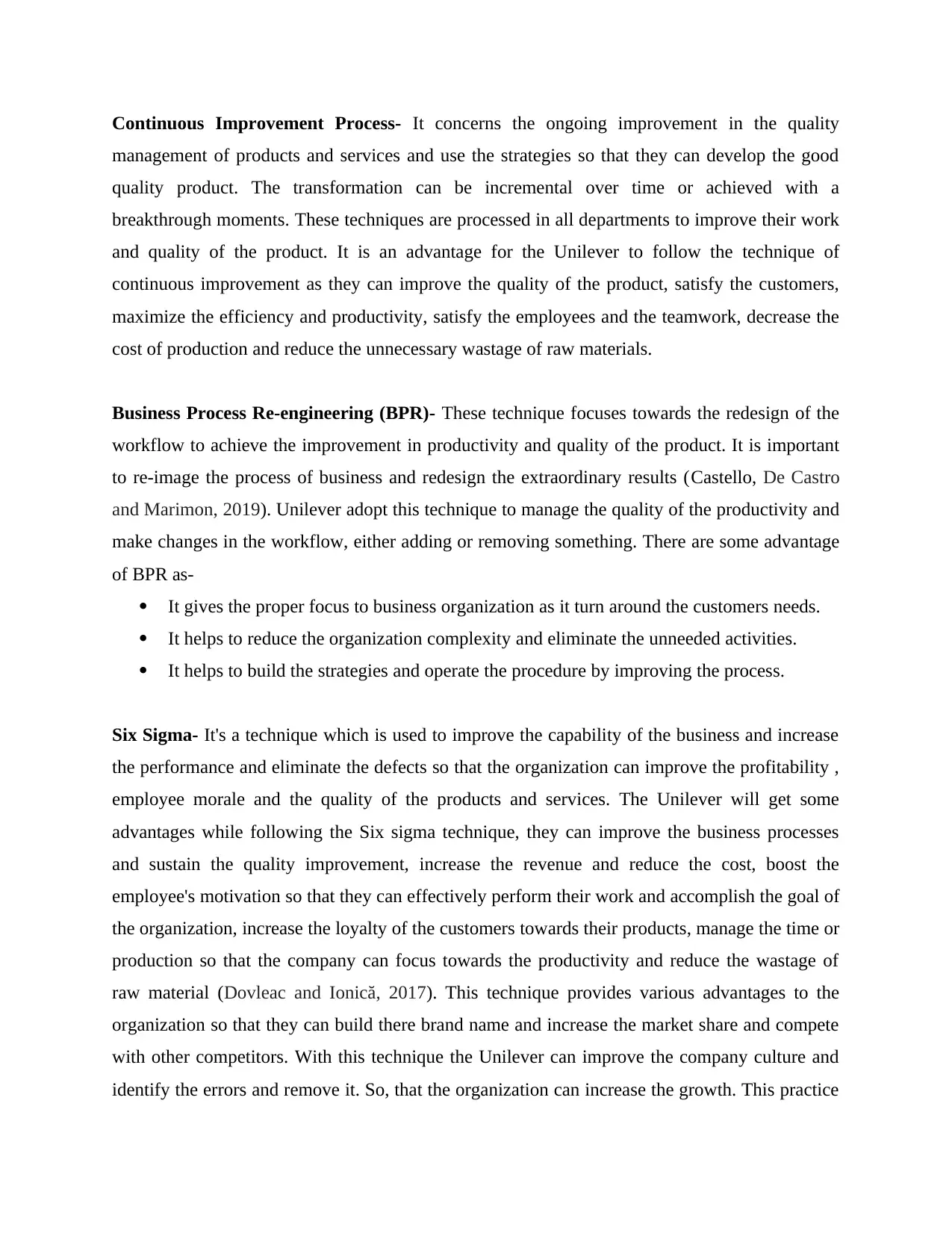
Continuous Improvement Process- It concerns the ongoing improvement in the quality
management of products and services and use the strategies so that they can develop the good
quality product. The transformation can be incremental over time or achieved with a
breakthrough moments. These techniques are processed in all departments to improve their work
and quality of the product. It is an advantage for the Unilever to follow the technique of
continuous improvement as they can improve the quality of the product, satisfy the customers,
maximize the efficiency and productivity, satisfy the employees and the teamwork, decrease the
cost of production and reduce the unnecessary wastage of raw materials.
Business Process Re-engineering (BPR)- These technique focuses towards the redesign of the
workflow to achieve the improvement in productivity and quality of the product. It is important
to re-image the process of business and redesign the extraordinary results (Castello, De Castro
and Marimon, 2019). Unilever adopt this technique to manage the quality of the productivity and
make changes in the workflow, either adding or removing something. There are some advantage
of BPR as-
It gives the proper focus to business organization as it turn around the customers needs.
It helps to reduce the organization complexity and eliminate the unneeded activities.
It helps to build the strategies and operate the procedure by improving the process.
Six Sigma- It's a technique which is used to improve the capability of the business and increase
the performance and eliminate the defects so that the organization can improve the profitability ,
employee morale and the quality of the products and services. The Unilever will get some
advantages while following the Six sigma technique, they can improve the business processes
and sustain the quality improvement, increase the revenue and reduce the cost, boost the
employee's motivation so that they can effectively perform their work and accomplish the goal of
the organization, increase the loyalty of the customers towards their products, manage the time or
production so that the company can focus towards the productivity and reduce the wastage of
raw material (Dovleac and Ionică, 2017). This technique provides various advantages to the
organization so that they can build there brand name and increase the market share and compete
with other competitors. With this technique the Unilever can improve the company culture and
identify the errors and remove it. So, that the organization can increase the growth. This practice
management of products and services and use the strategies so that they can develop the good
quality product. The transformation can be incremental over time or achieved with a
breakthrough moments. These techniques are processed in all departments to improve their work
and quality of the product. It is an advantage for the Unilever to follow the technique of
continuous improvement as they can improve the quality of the product, satisfy the customers,
maximize the efficiency and productivity, satisfy the employees and the teamwork, decrease the
cost of production and reduce the unnecessary wastage of raw materials.
Business Process Re-engineering (BPR)- These technique focuses towards the redesign of the
workflow to achieve the improvement in productivity and quality of the product. It is important
to re-image the process of business and redesign the extraordinary results (Castello, De Castro
and Marimon, 2019). Unilever adopt this technique to manage the quality of the productivity and
make changes in the workflow, either adding or removing something. There are some advantage
of BPR as-
It gives the proper focus to business organization as it turn around the customers needs.
It helps to reduce the organization complexity and eliminate the unneeded activities.
It helps to build the strategies and operate the procedure by improving the process.
Six Sigma- It's a technique which is used to improve the capability of the business and increase
the performance and eliminate the defects so that the organization can improve the profitability ,
employee morale and the quality of the products and services. The Unilever will get some
advantages while following the Six sigma technique, they can improve the business processes
and sustain the quality improvement, increase the revenue and reduce the cost, boost the
employee's motivation so that they can effectively perform their work and accomplish the goal of
the organization, increase the loyalty of the customers towards their products, manage the time or
production so that the company can focus towards the productivity and reduce the wastage of
raw material (Dovleac and Ionică, 2017). This technique provides various advantages to the
organization so that they can build there brand name and increase the market share and compete
with other competitors. With this technique the Unilever can improve the company culture and
identify the errors and remove it. So, that the organization can increase the growth. This practice
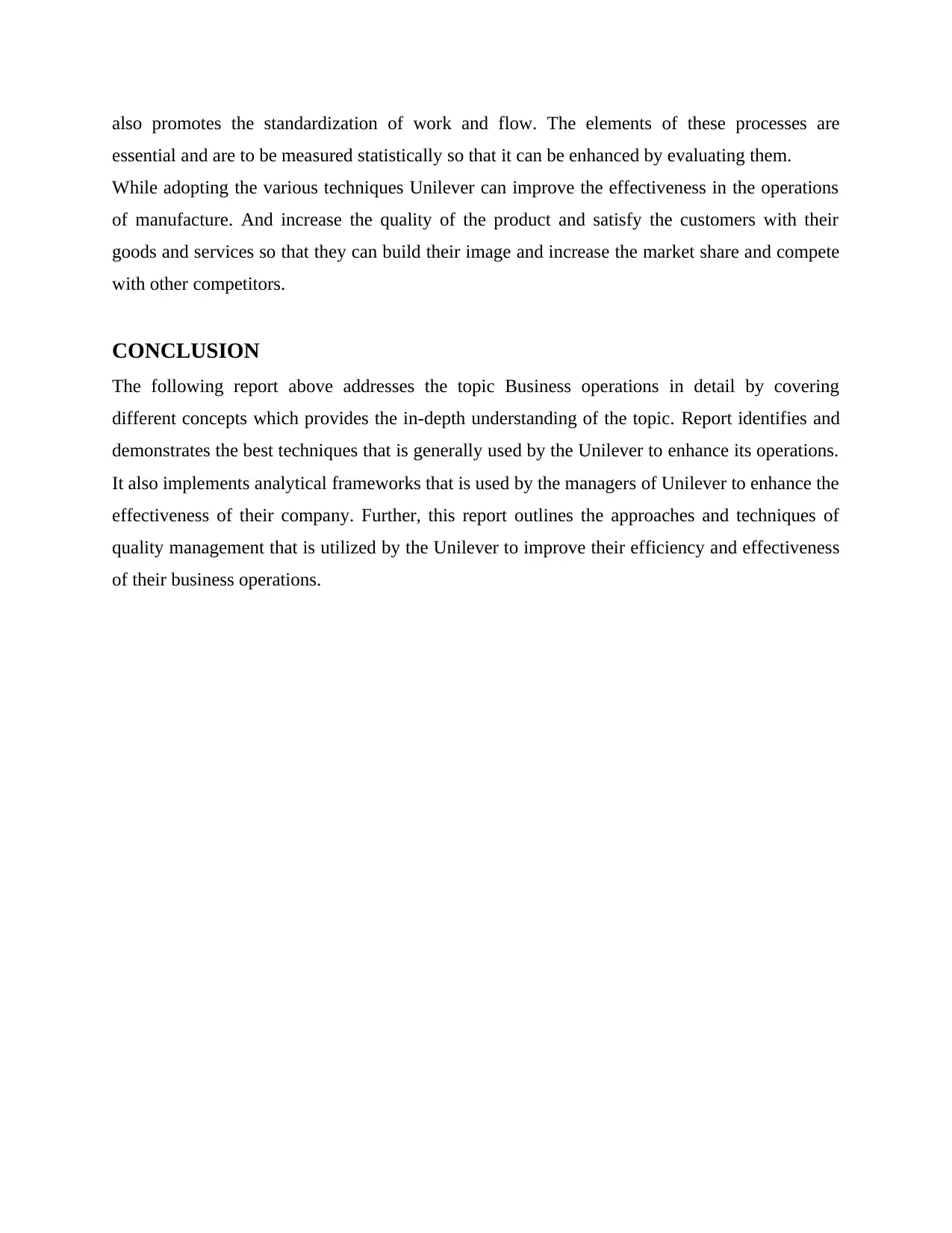
also promotes the standardization of work and flow. The elements of these processes are
essential and are to be measured statistically so that it can be enhanced by evaluating them.
While adopting the various techniques Unilever can improve the effectiveness in the operations
of manufacture. And increase the quality of the product and satisfy the customers with their
goods and services so that they can build their image and increase the market share and compete
with other competitors.
CONCLUSION
The following report above addresses the topic Business operations in detail by covering
different concepts which provides the in-depth understanding of the topic. Report identifies and
demonstrates the best techniques that is generally used by the Unilever to enhance its operations.
It also implements analytical frameworks that is used by the managers of Unilever to enhance the
effectiveness of their company. Further, this report outlines the approaches and techniques of
quality management that is utilized by the Unilever to improve their efficiency and effectiveness
of their business operations.
essential and are to be measured statistically so that it can be enhanced by evaluating them.
While adopting the various techniques Unilever can improve the effectiveness in the operations
of manufacture. And increase the quality of the product and satisfy the customers with their
goods and services so that they can build their image and increase the market share and compete
with other competitors.
CONCLUSION
The following report above addresses the topic Business operations in detail by covering
different concepts which provides the in-depth understanding of the topic. Report identifies and
demonstrates the best techniques that is generally used by the Unilever to enhance its operations.
It also implements analytical frameworks that is used by the managers of Unilever to enhance the
effectiveness of their company. Further, this report outlines the approaches and techniques of
quality management that is utilized by the Unilever to improve their efficiency and effectiveness
of their business operations.
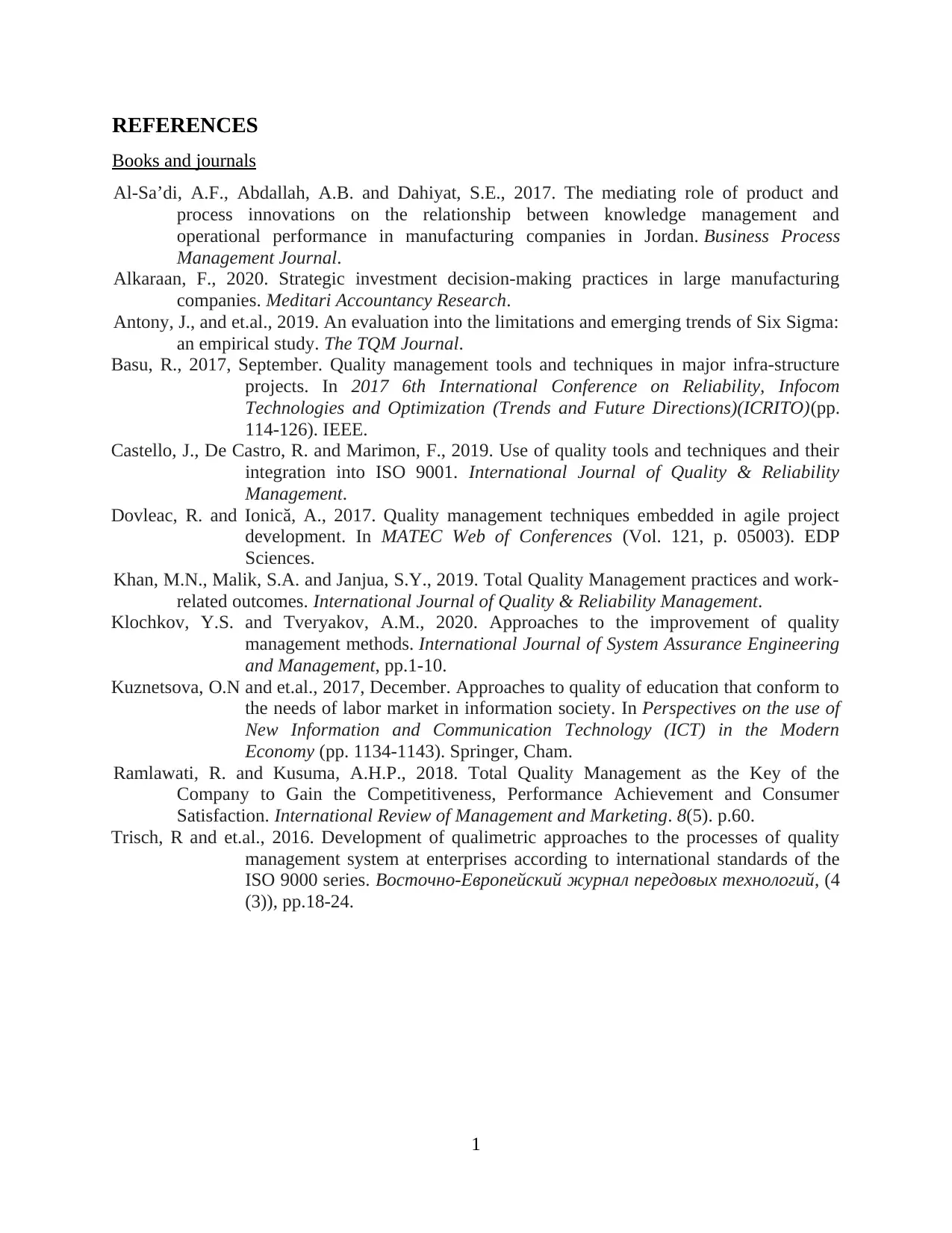
REFERENCES
Books and journals
Al-Sa’di, A.F., Abdallah, A.B. and Dahiyat, S.E., 2017. The mediating role of product and
process innovations on the relationship between knowledge management and
operational performance in manufacturing companies in Jordan. Business Process
Management Journal.
Alkaraan, F., 2020. Strategic investment decision-making practices in large manufacturing
companies. Meditari Accountancy Research.
Antony, J., and et.al., 2019. An evaluation into the limitations and emerging trends of Six Sigma:
an empirical study. The TQM Journal.
Basu, R., 2017, September. Quality management tools and techniques in major infra-structure
projects. In 2017 6th International Conference on Reliability, Infocom
Technologies and Optimization (Trends and Future Directions)(ICRITO)(pp.
114-126). IEEE.
Castello, J., De Castro, R. and Marimon, F., 2019. Use of quality tools and techniques and their
integration into ISO 9001. International Journal of Quality & Reliability
Management.
Dovleac, R. and Ionică, A., 2017. Quality management techniques embedded in agile project
development. In MATEC Web of Conferences (Vol. 121, p. 05003). EDP
Sciences.
Khan, M.N., Malik, S.A. and Janjua, S.Y., 2019. Total Quality Management practices and work-
related outcomes. International Journal of Quality & Reliability Management.
Klochkov, Y.S. and Tveryakov, A.M., 2020. Approaches to the improvement of quality
management methods. International Journal of System Assurance Engineering
and Management, pp.1-10.
Kuznetsova, O.N and et.al., 2017, December. Approaches to quality of education that conform to
the needs of labor market in information society. In Perspectives on the use of
New Information and Communication Technology (ICT) in the Modern
Economy (pp. 1134-1143). Springer, Cham.
Ramlawati, R. and Kusuma, A.H.P., 2018. Total Quality Management as the Key of the
Company to Gain the Competitiveness, Performance Achievement and Consumer
Satisfaction. International Review of Management and Marketing. 8(5). p.60.
Trisch, R and et.al., 2016. Development of qualimetric approaches to the processes of quality
management system at enterprises according to international standards of the
ISO 9000 series. Восточно-Европейский журнал передовых технологий, (4
(3)), pp.18-24.
1
Books and journals
Al-Sa’di, A.F., Abdallah, A.B. and Dahiyat, S.E., 2017. The mediating role of product and
process innovations on the relationship between knowledge management and
operational performance in manufacturing companies in Jordan. Business Process
Management Journal.
Alkaraan, F., 2020. Strategic investment decision-making practices in large manufacturing
companies. Meditari Accountancy Research.
Antony, J., and et.al., 2019. An evaluation into the limitations and emerging trends of Six Sigma:
an empirical study. The TQM Journal.
Basu, R., 2017, September. Quality management tools and techniques in major infra-structure
projects. In 2017 6th International Conference on Reliability, Infocom
Technologies and Optimization (Trends and Future Directions)(ICRITO)(pp.
114-126). IEEE.
Castello, J., De Castro, R. and Marimon, F., 2019. Use of quality tools and techniques and their
integration into ISO 9001. International Journal of Quality & Reliability
Management.
Dovleac, R. and Ionică, A., 2017. Quality management techniques embedded in agile project
development. In MATEC Web of Conferences (Vol. 121, p. 05003). EDP
Sciences.
Khan, M.N., Malik, S.A. and Janjua, S.Y., 2019. Total Quality Management practices and work-
related outcomes. International Journal of Quality & Reliability Management.
Klochkov, Y.S. and Tveryakov, A.M., 2020. Approaches to the improvement of quality
management methods. International Journal of System Assurance Engineering
and Management, pp.1-10.
Kuznetsova, O.N and et.al., 2017, December. Approaches to quality of education that conform to
the needs of labor market in information society. In Perspectives on the use of
New Information and Communication Technology (ICT) in the Modern
Economy (pp. 1134-1143). Springer, Cham.
Ramlawati, R. and Kusuma, A.H.P., 2018. Total Quality Management as the Key of the
Company to Gain the Competitiveness, Performance Achievement and Consumer
Satisfaction. International Review of Management and Marketing. 8(5). p.60.
Trisch, R and et.al., 2016. Development of qualimetric approaches to the processes of quality
management system at enterprises according to international standards of the
ISO 9000 series. Восточно-Европейский журнал передовых технологий, (4
(3)), pp.18-24.
1
Secure Best Marks with AI Grader
Need help grading? Try our AI Grader for instant feedback on your assignments.
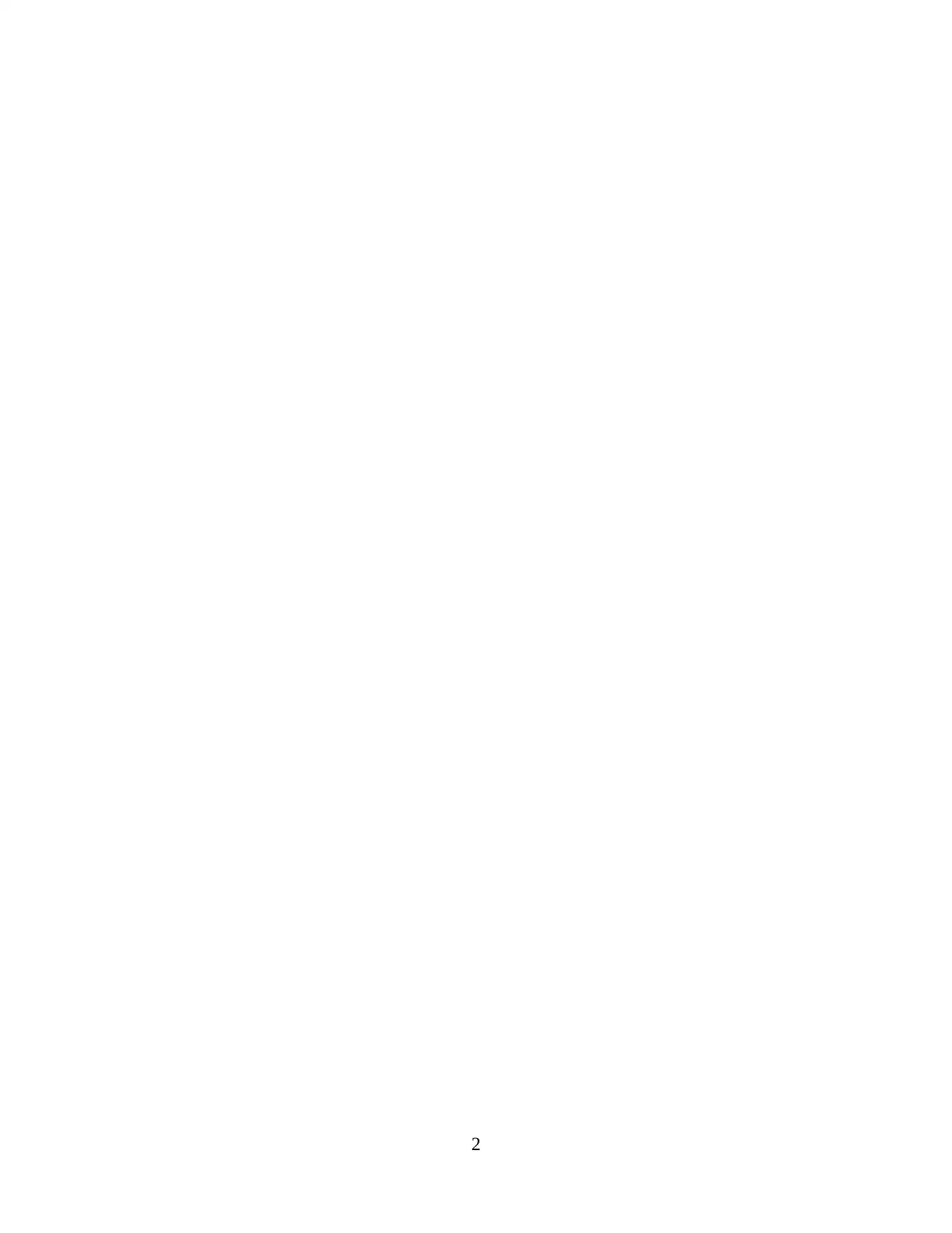
2
1 out of 11
Related Documents

Your All-in-One AI-Powered Toolkit for Academic Success.
+13062052269
info@desklib.com
Available 24*7 on WhatsApp / Email
Unlock your academic potential
© 2024 | Zucol Services PVT LTD | All rights reserved.