Value Management and Whole Life Cycle Costing: Project Analysis Report
VerifiedAdded on 2022/08/16
|14
|3603
|11
Report
AI Summary
This report delves into the theory and application of value management and whole life cycle costing within the context of construction projects. It begins by defining value management and its historical development, emphasizing its role in balancing cost and quality. The report then outlines the key functions of value management procedures, particularly in design and construction projects, and discusses the significance of life cycle cost analysis (LCCA) in assessing total project costs. It addresses the purpose, background, and problems associated with construction projects, including the absence of skilled workers, poor communication, and funding shortages. The report explores potential solutions to increase project value through enhanced planning, construction management software, building information modeling, and staff involvement. Furthermore, it acknowledges the limitations and assumptions inherent in the research, such as the complexity of global projects and the impact of regional market dynamics. The report includes an analysis of design buildability considerations and alternative design options, evaluating them in terms of whole life cycle costing and buildability. The conclusion summarizes key findings and their implications for project success.
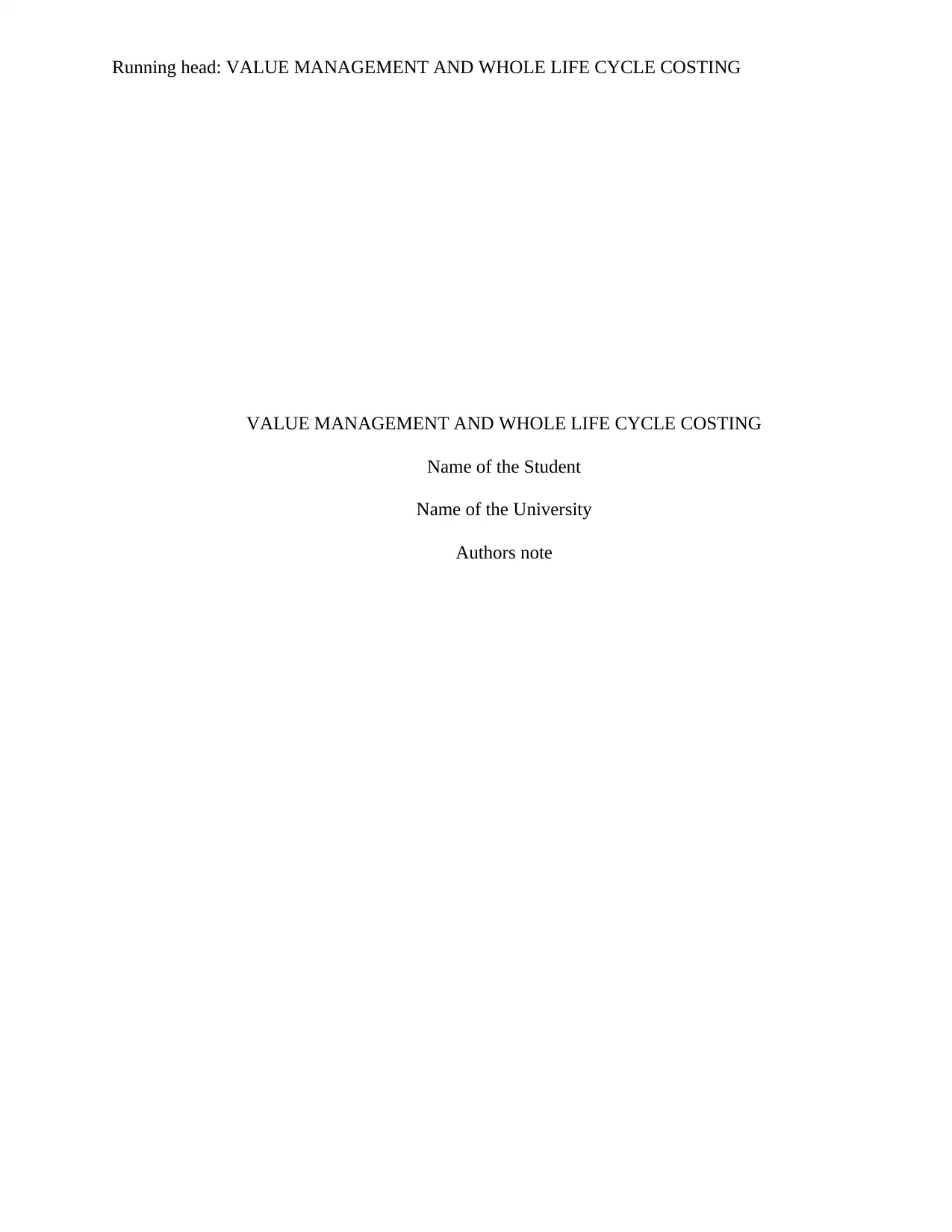
Running head: VALUE MANAGEMENT AND WHOLE LIFE CYCLE COSTING
VALUE MANAGEMENT AND WHOLE LIFE CYCLE COSTING
Name of the Student
Name of the University
Authors note
VALUE MANAGEMENT AND WHOLE LIFE CYCLE COSTING
Name of the Student
Name of the University
Authors note
Secure Best Marks with AI Grader
Need help grading? Try our AI Grader for instant feedback on your assignments.
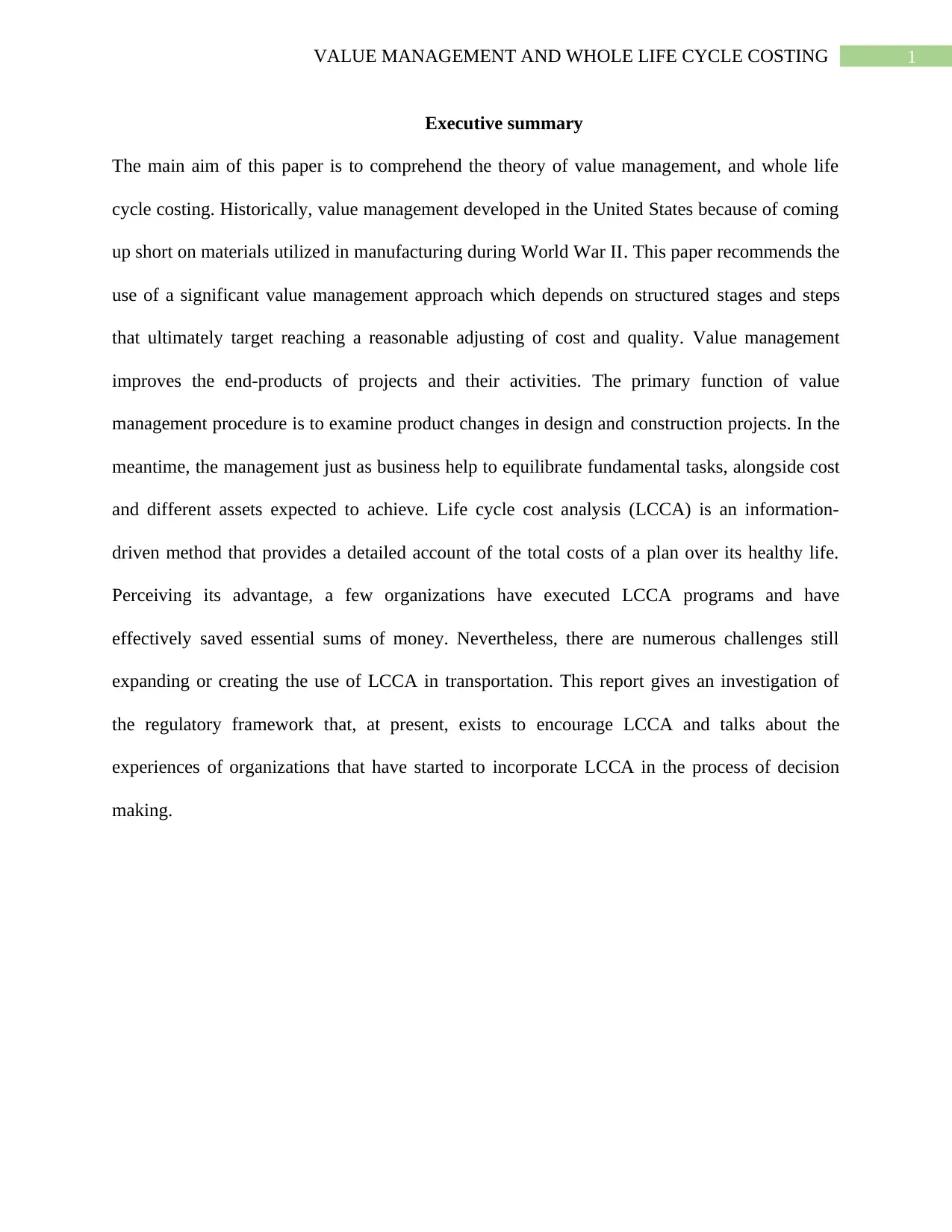
1VALUE MANAGEMENT AND WHOLE LIFE CYCLE COSTING
Executive summary
The main aim of this paper is to comprehend the theory of value management, and whole life
cycle costing. Historically, value management developed in the United States because of coming
up short on materials utilized in manufacturing during World War II. This paper recommends the
use of a significant value management approach which depends on structured stages and steps
that ultimately target reaching a reasonable adjusting of cost and quality. Value management
improves the end-products of projects and their activities. The primary function of value
management procedure is to examine product changes in design and construction projects. In the
meantime, the management just as business help to equilibrate fundamental tasks, alongside cost
and different assets expected to achieve. Life cycle cost analysis (LCCA) is an information-
driven method that provides a detailed account of the total costs of a plan over its healthy life.
Perceiving its advantage, a few organizations have executed LCCA programs and have
effectively saved essential sums of money. Nevertheless, there are numerous challenges still
expanding or creating the use of LCCA in transportation. This report gives an investigation of
the regulatory framework that, at present, exists to encourage LCCA and talks about the
experiences of organizations that have started to incorporate LCCA in the process of decision
making.
Executive summary
The main aim of this paper is to comprehend the theory of value management, and whole life
cycle costing. Historically, value management developed in the United States because of coming
up short on materials utilized in manufacturing during World War II. This paper recommends the
use of a significant value management approach which depends on structured stages and steps
that ultimately target reaching a reasonable adjusting of cost and quality. Value management
improves the end-products of projects and their activities. The primary function of value
management procedure is to examine product changes in design and construction projects. In the
meantime, the management just as business help to equilibrate fundamental tasks, alongside cost
and different assets expected to achieve. Life cycle cost analysis (LCCA) is an information-
driven method that provides a detailed account of the total costs of a plan over its healthy life.
Perceiving its advantage, a few organizations have executed LCCA programs and have
effectively saved essential sums of money. Nevertheless, there are numerous challenges still
expanding or creating the use of LCCA in transportation. This report gives an investigation of
the regulatory framework that, at present, exists to encourage LCCA and talks about the
experiences of organizations that have started to incorporate LCCA in the process of decision
making.
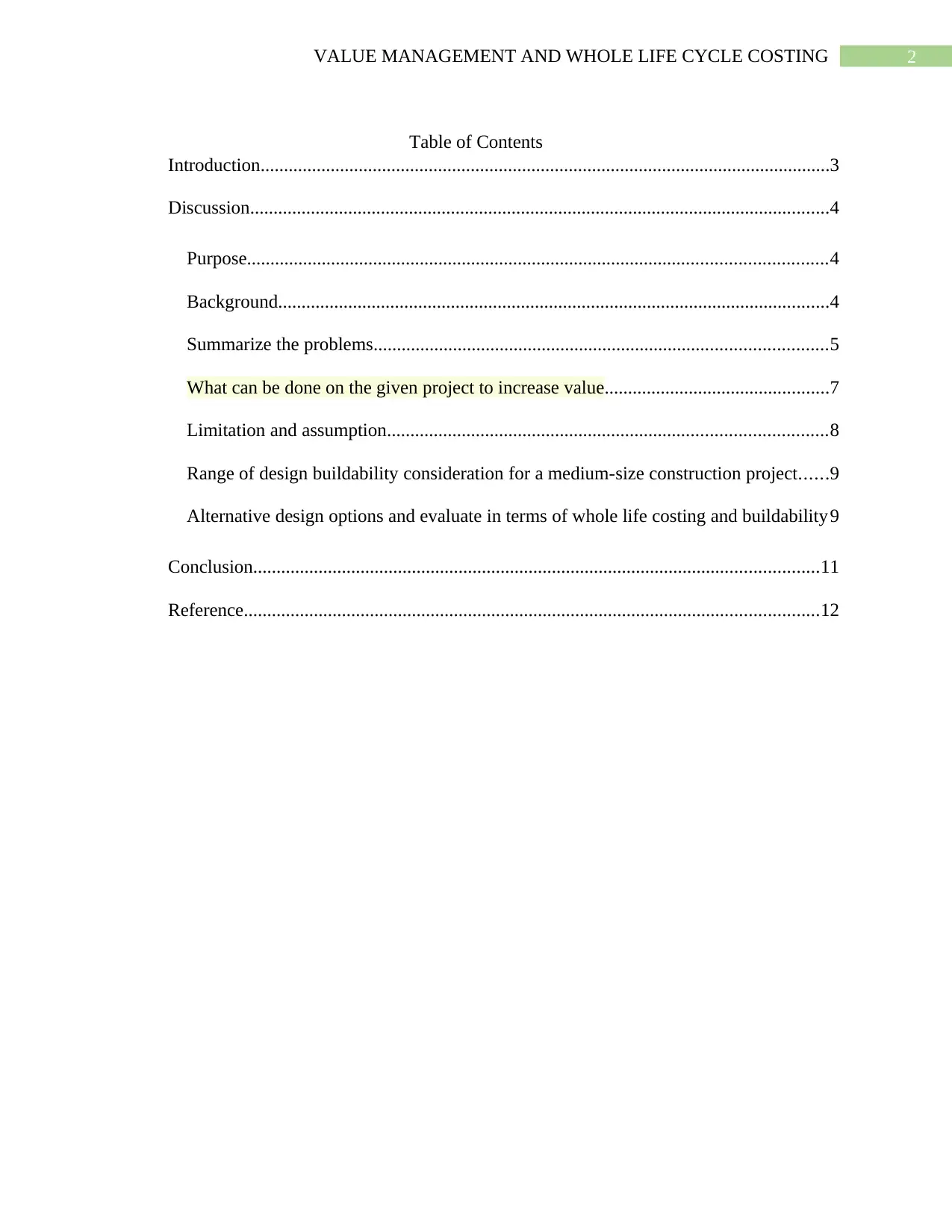
2VALUE MANAGEMENT AND WHOLE LIFE CYCLE COSTING
Table of Contents
Introduction..........................................................................................................................3
Discussion............................................................................................................................4
Purpose............................................................................................................................4
Background......................................................................................................................4
Summarize the problems.................................................................................................5
What can be done on the given project to increase value................................................7
Limitation and assumption..............................................................................................8
Range of design buildability consideration for a medium-size construction project......9
Alternative design options and evaluate in terms of whole life costing and buildability 9
Conclusion.........................................................................................................................11
Reference...........................................................................................................................12
Table of Contents
Introduction..........................................................................................................................3
Discussion............................................................................................................................4
Purpose............................................................................................................................4
Background......................................................................................................................4
Summarize the problems.................................................................................................5
What can be done on the given project to increase value................................................7
Limitation and assumption..............................................................................................8
Range of design buildability consideration for a medium-size construction project......9
Alternative design options and evaluate in terms of whole life costing and buildability 9
Conclusion.........................................................................................................................11
Reference...........................................................................................................................12
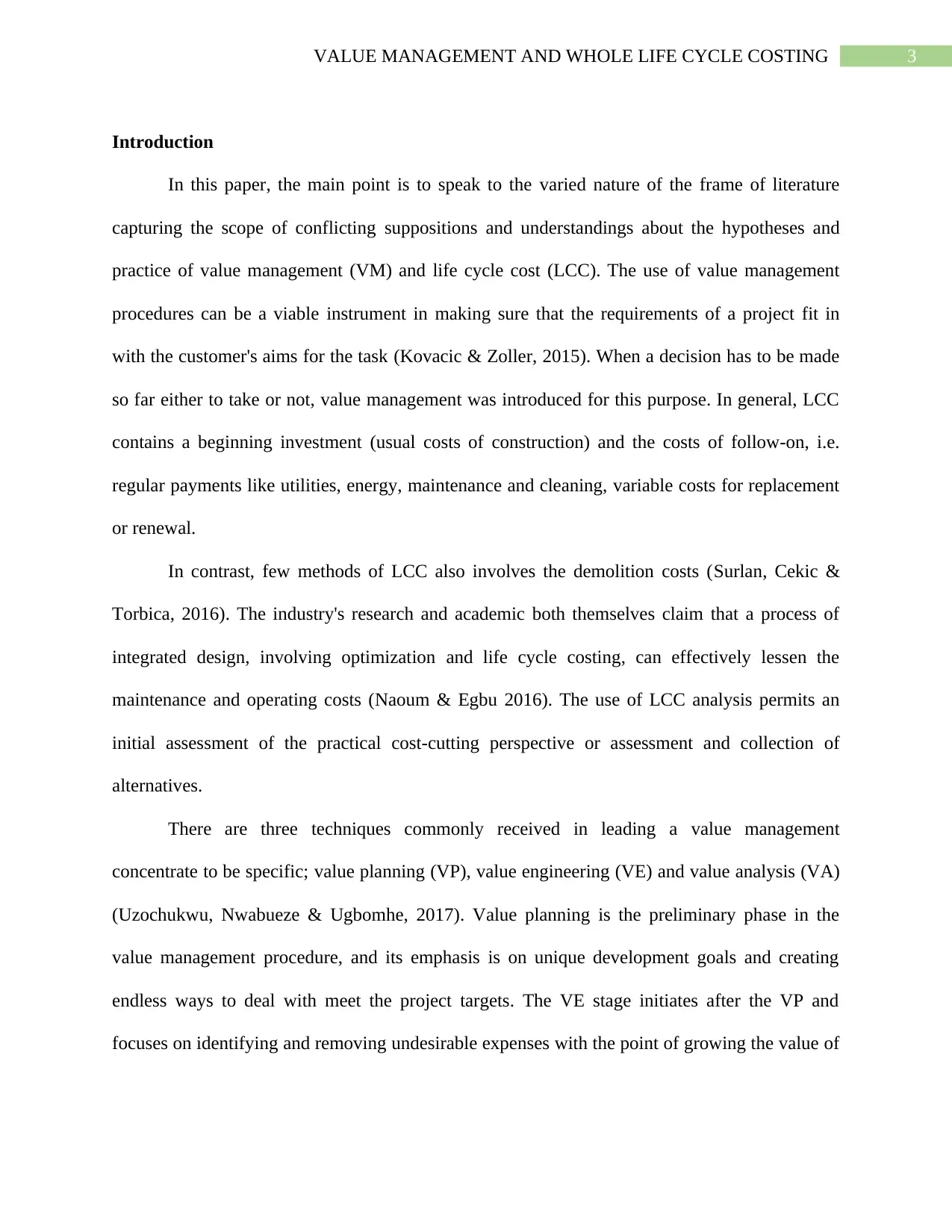
3VALUE MANAGEMENT AND WHOLE LIFE CYCLE COSTING
Introduction
In this paper, the main point is to speak to the varied nature of the frame of literature
capturing the scope of conflicting suppositions and understandings about the hypotheses and
practice of value management (VM) and life cycle cost (LCC). The use of value management
procedures can be a viable instrument in making sure that the requirements of a project fit in
with the customer's aims for the task (Kovacic & Zoller, 2015). When a decision has to be made
so far either to take or not, value management was introduced for this purpose. In general, LCC
contains a beginning investment (usual costs of construction) and the costs of follow-on, i.e.
regular payments like utilities, energy, maintenance and cleaning, variable costs for replacement
or renewal.
In contrast, few methods of LCC also involves the demolition costs (Surlan, Cekic &
Torbica, 2016). The industry's research and academic both themselves claim that a process of
integrated design, involving optimization and life cycle costing, can effectively lessen the
maintenance and operating costs (Naoum & Egbu 2016). The use of LCC analysis permits an
initial assessment of the practical cost-cutting perspective or assessment and collection of
alternatives.
There are three techniques commonly received in leading a value management
concentrate to be specific; value planning (VP), value engineering (VE) and value analysis (VA)
(Uzochukwu, Nwabueze & Ugbomhe, 2017). Value planning is the preliminary phase in the
value management procedure, and its emphasis is on unique development goals and creating
endless ways to deal with meet the project targets. The VE stage initiates after the VP and
focuses on identifying and removing undesirable expenses with the point of growing the value of
Introduction
In this paper, the main point is to speak to the varied nature of the frame of literature
capturing the scope of conflicting suppositions and understandings about the hypotheses and
practice of value management (VM) and life cycle cost (LCC). The use of value management
procedures can be a viable instrument in making sure that the requirements of a project fit in
with the customer's aims for the task (Kovacic & Zoller, 2015). When a decision has to be made
so far either to take or not, value management was introduced for this purpose. In general, LCC
contains a beginning investment (usual costs of construction) and the costs of follow-on, i.e.
regular payments like utilities, energy, maintenance and cleaning, variable costs for replacement
or renewal.
In contrast, few methods of LCC also involves the demolition costs (Surlan, Cekic &
Torbica, 2016). The industry's research and academic both themselves claim that a process of
integrated design, involving optimization and life cycle costing, can effectively lessen the
maintenance and operating costs (Naoum & Egbu 2016). The use of LCC analysis permits an
initial assessment of the practical cost-cutting perspective or assessment and collection of
alternatives.
There are three techniques commonly received in leading a value management
concentrate to be specific; value planning (VP), value engineering (VE) and value analysis (VA)
(Uzochukwu, Nwabueze & Ugbomhe, 2017). Value planning is the preliminary phase in the
value management procedure, and its emphasis is on unique development goals and creating
endless ways to deal with meet the project targets. The VE stage initiates after the VP and
focuses on identifying and removing undesirable expenses with the point of growing the value of
Secure Best Marks with AI Grader
Need help grading? Try our AI Grader for instant feedback on your assignments.
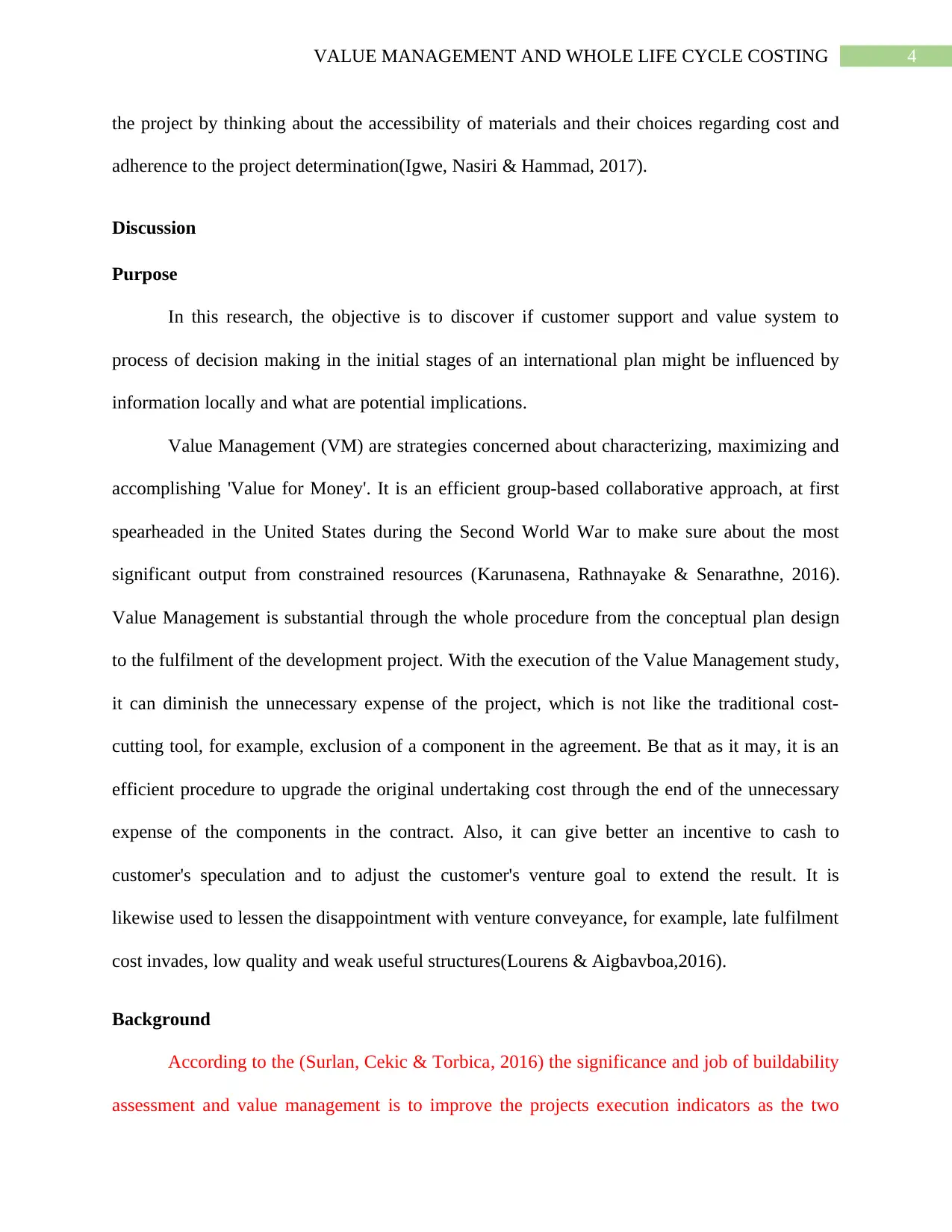
4VALUE MANAGEMENT AND WHOLE LIFE CYCLE COSTING
the project by thinking about the accessibility of materials and their choices regarding cost and
adherence to the project determination(Igwe, Nasiri & Hammad, 2017).
Discussion
Purpose
In this research, the objective is to discover if customer support and value system to
process of decision making in the initial stages of an international plan might be influenced by
information locally and what are potential implications.
Value Management (VM) are strategies concerned about characterizing, maximizing and
accomplishing 'Value for Money'. It is an efficient group-based collaborative approach, at first
spearheaded in the United States during the Second World War to make sure about the most
significant output from constrained resources (Karunasena, Rathnayake & Senarathne, 2016).
Value Management is substantial through the whole procedure from the conceptual plan design
to the fulfilment of the development project. With the execution of the Value Management study,
it can diminish the unnecessary expense of the project, which is not like the traditional cost-
cutting tool, for example, exclusion of a component in the agreement. Be that as it may, it is an
efficient procedure to upgrade the original undertaking cost through the end of the unnecessary
expense of the components in the contract. Also, it can give better an incentive to cash to
customer's speculation and to adjust the customer's venture goal to extend the result. It is
likewise used to lessen the disappointment with venture conveyance, for example, late fulfilment
cost invades, low quality and weak useful structures(Lourens & Aigbavboa,2016).
Background
According to the (Surlan, Cekic & Torbica, 2016) the significance and job of buildability
assessment and value management is to improve the projects execution indicators as the two
the project by thinking about the accessibility of materials and their choices regarding cost and
adherence to the project determination(Igwe, Nasiri & Hammad, 2017).
Discussion
Purpose
In this research, the objective is to discover if customer support and value system to
process of decision making in the initial stages of an international plan might be influenced by
information locally and what are potential implications.
Value Management (VM) are strategies concerned about characterizing, maximizing and
accomplishing 'Value for Money'. It is an efficient group-based collaborative approach, at first
spearheaded in the United States during the Second World War to make sure about the most
significant output from constrained resources (Karunasena, Rathnayake & Senarathne, 2016).
Value Management is substantial through the whole procedure from the conceptual plan design
to the fulfilment of the development project. With the execution of the Value Management study,
it can diminish the unnecessary expense of the project, which is not like the traditional cost-
cutting tool, for example, exclusion of a component in the agreement. Be that as it may, it is an
efficient procedure to upgrade the original undertaking cost through the end of the unnecessary
expense of the components in the contract. Also, it can give better an incentive to cash to
customer's speculation and to adjust the customer's venture goal to extend the result. It is
likewise used to lessen the disappointment with venture conveyance, for example, late fulfilment
cost invades, low quality and weak useful structures(Lourens & Aigbavboa,2016).
Background
According to the (Surlan, Cekic & Torbica, 2016) the significance and job of buildability
assessment and value management is to improve the projects execution indicators as the two
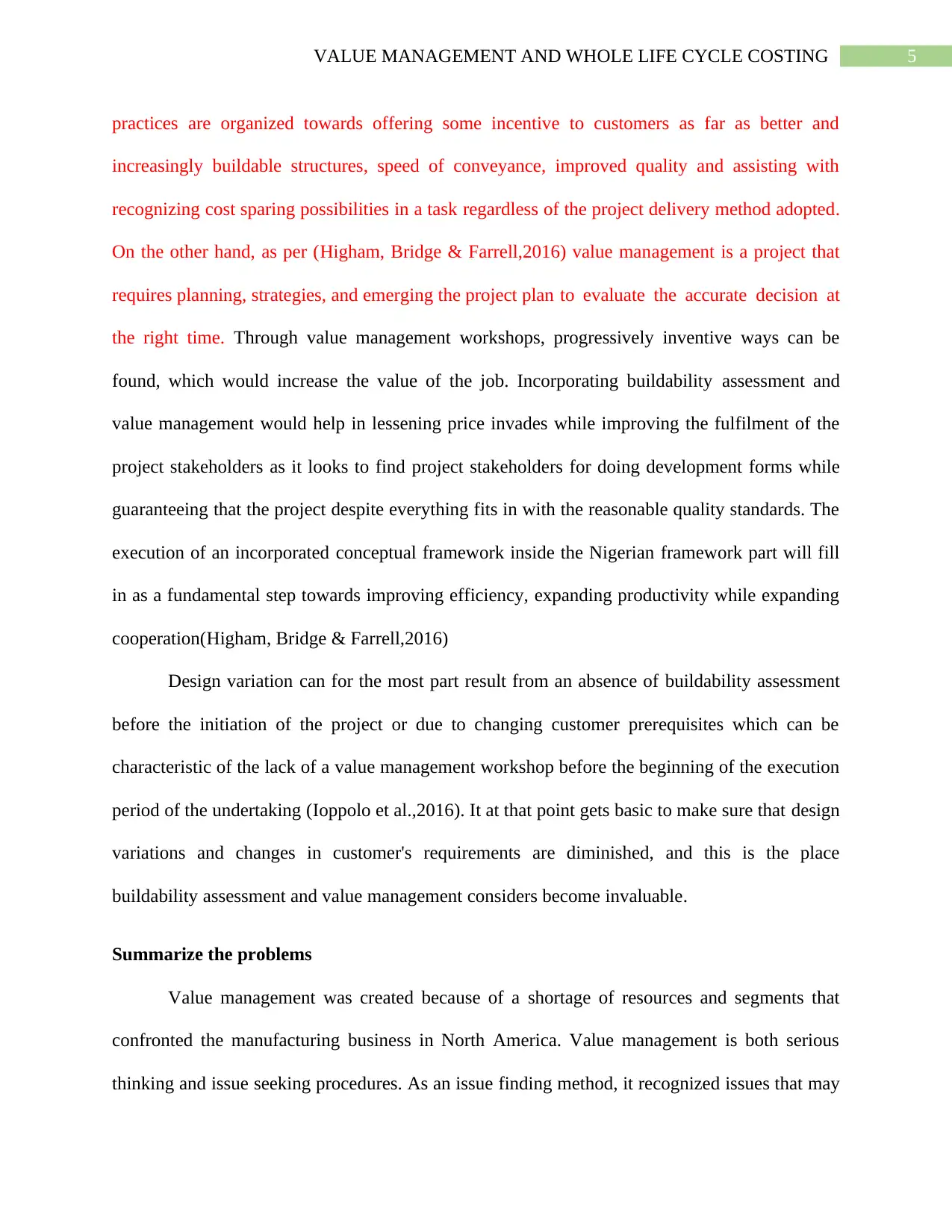
5VALUE MANAGEMENT AND WHOLE LIFE CYCLE COSTING
practices are organized towards offering some incentive to customers as far as better and
increasingly buildable structures, speed of conveyance, improved quality and assisting with
recognizing cost sparing possibilities in a task regardless of the project delivery method adopted.
On the other hand, as per (Higham, Bridge & Farrell,2016) value management is a project that
requires planning, strategies, and emerging the project plan to evaluate the accurate decision at
the right time. Through value management workshops, progressively inventive ways can be
found, which would increase the value of the job. Incorporating buildability assessment and
value management would help in lessening price invades while improving the fulfilment of the
project stakeholders as it looks to find project stakeholders for doing development forms while
guaranteeing that the project despite everything fits in with the reasonable quality standards. The
execution of an incorporated conceptual framework inside the Nigerian framework part will fill
in as a fundamental step towards improving efficiency, expanding productivity while expanding
cooperation(Higham, Bridge & Farrell,2016)
Design variation can for the most part result from an absence of buildability assessment
before the initiation of the project or due to changing customer prerequisites which can be
characteristic of the lack of a value management workshop before the beginning of the execution
period of the undertaking (Ioppolo et al.,2016). It at that point gets basic to make sure that design
variations and changes in customer's requirements are diminished, and this is the place
buildability assessment and value management considers become invaluable.
Summarize the problems
Value management was created because of a shortage of resources and segments that
confronted the manufacturing business in North America. Value management is both serious
thinking and issue seeking procedures. As an issue finding method, it recognized issues that may
practices are organized towards offering some incentive to customers as far as better and
increasingly buildable structures, speed of conveyance, improved quality and assisting with
recognizing cost sparing possibilities in a task regardless of the project delivery method adopted.
On the other hand, as per (Higham, Bridge & Farrell,2016) value management is a project that
requires planning, strategies, and emerging the project plan to evaluate the accurate decision at
the right time. Through value management workshops, progressively inventive ways can be
found, which would increase the value of the job. Incorporating buildability assessment and
value management would help in lessening price invades while improving the fulfilment of the
project stakeholders as it looks to find project stakeholders for doing development forms while
guaranteeing that the project despite everything fits in with the reasonable quality standards. The
execution of an incorporated conceptual framework inside the Nigerian framework part will fill
in as a fundamental step towards improving efficiency, expanding productivity while expanding
cooperation(Higham, Bridge & Farrell,2016)
Design variation can for the most part result from an absence of buildability assessment
before the initiation of the project or due to changing customer prerequisites which can be
characteristic of the lack of a value management workshop before the beginning of the execution
period of the undertaking (Ioppolo et al.,2016). It at that point gets basic to make sure that design
variations and changes in customer's requirements are diminished, and this is the place
buildability assessment and value management considers become invaluable.
Summarize the problems
Value management was created because of a shortage of resources and segments that
confronted the manufacturing business in North America. Value management is both serious
thinking and issue seeking procedures. As an issue finding method, it recognized issues that may
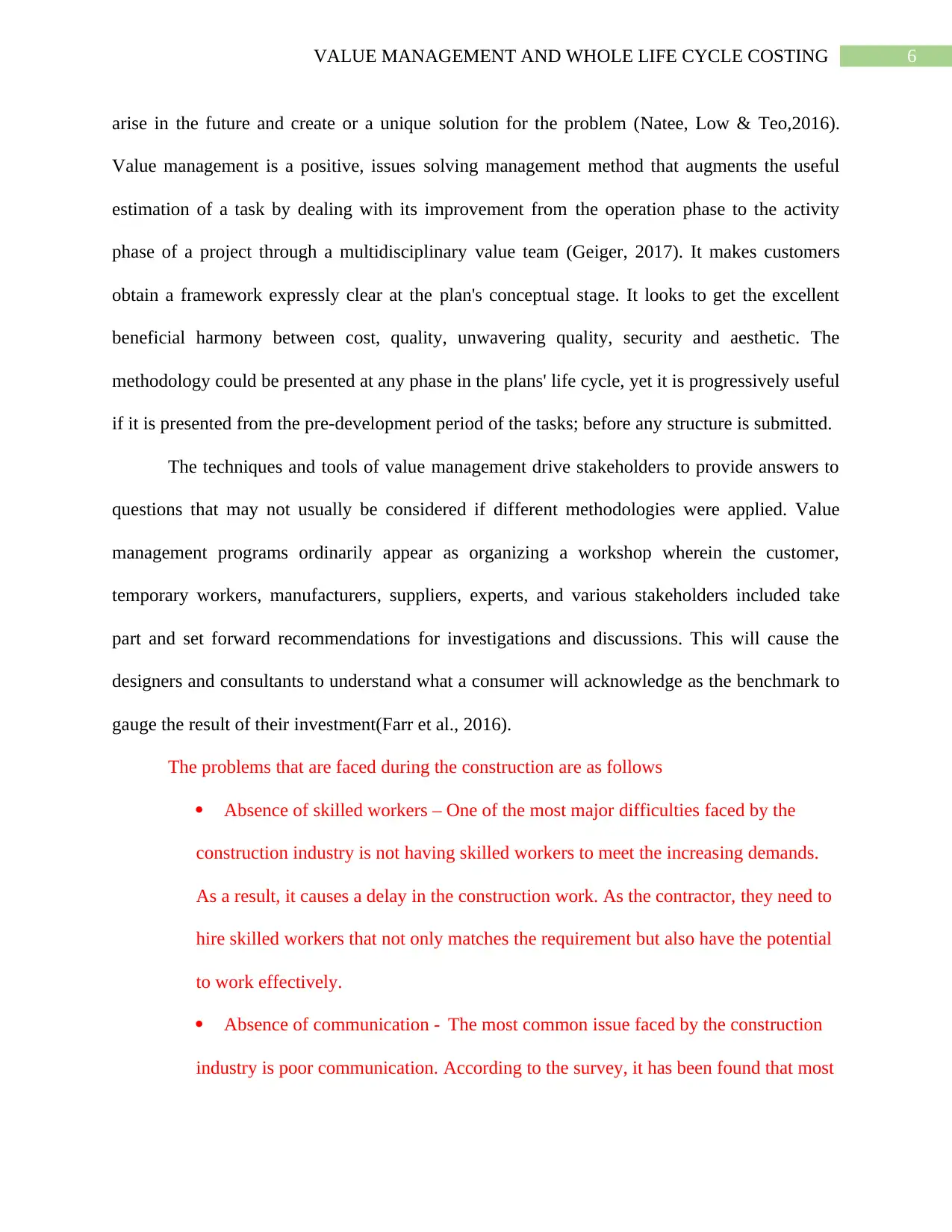
6VALUE MANAGEMENT AND WHOLE LIFE CYCLE COSTING
arise in the future and create or a unique solution for the problem (Natee, Low & Teo,2016).
Value management is a positive, issues solving management method that augments the useful
estimation of a task by dealing with its improvement from the operation phase to the activity
phase of a project through a multidisciplinary value team (Geiger, 2017). It makes customers
obtain a framework expressly clear at the plan's conceptual stage. It looks to get the excellent
beneficial harmony between cost, quality, unwavering quality, security and aesthetic. The
methodology could be presented at any phase in the plans' life cycle, yet it is progressively useful
if it is presented from the pre-development period of the tasks; before any structure is submitted.
The techniques and tools of value management drive stakeholders to provide answers to
questions that may not usually be considered if different methodologies were applied. Value
management programs ordinarily appear as organizing a workshop wherein the customer,
temporary workers, manufacturers, suppliers, experts, and various stakeholders included take
part and set forward recommendations for investigations and discussions. This will cause the
designers and consultants to understand what a consumer will acknowledge as the benchmark to
gauge the result of their investment(Farr et al., 2016).
The problems that are faced during the construction are as follows
Absence of skilled workers – One of the most major difficulties faced by the
construction industry is not having skilled workers to meet the increasing demands.
As a result, it causes a delay in the construction work. As the contractor, they need to
hire skilled workers that not only matches the requirement but also have the potential
to work effectively.
Absence of communication - The most common issue faced by the construction
industry is poor communication. According to the survey, it has been found that most
arise in the future and create or a unique solution for the problem (Natee, Low & Teo,2016).
Value management is a positive, issues solving management method that augments the useful
estimation of a task by dealing with its improvement from the operation phase to the activity
phase of a project through a multidisciplinary value team (Geiger, 2017). It makes customers
obtain a framework expressly clear at the plan's conceptual stage. It looks to get the excellent
beneficial harmony between cost, quality, unwavering quality, security and aesthetic. The
methodology could be presented at any phase in the plans' life cycle, yet it is progressively useful
if it is presented from the pre-development period of the tasks; before any structure is submitted.
The techniques and tools of value management drive stakeholders to provide answers to
questions that may not usually be considered if different methodologies were applied. Value
management programs ordinarily appear as organizing a workshop wherein the customer,
temporary workers, manufacturers, suppliers, experts, and various stakeholders included take
part and set forward recommendations for investigations and discussions. This will cause the
designers and consultants to understand what a consumer will acknowledge as the benchmark to
gauge the result of their investment(Farr et al., 2016).
The problems that are faced during the construction are as follows
Absence of skilled workers – One of the most major difficulties faced by the
construction industry is not having skilled workers to meet the increasing demands.
As a result, it causes a delay in the construction work. As the contractor, they need to
hire skilled workers that not only matches the requirement but also have the potential
to work effectively.
Absence of communication - The most common issue faced by the construction
industry is poor communication. According to the survey, it has been found that most
Paraphrase This Document
Need a fresh take? Get an instant paraphrase of this document with our AI Paraphraser
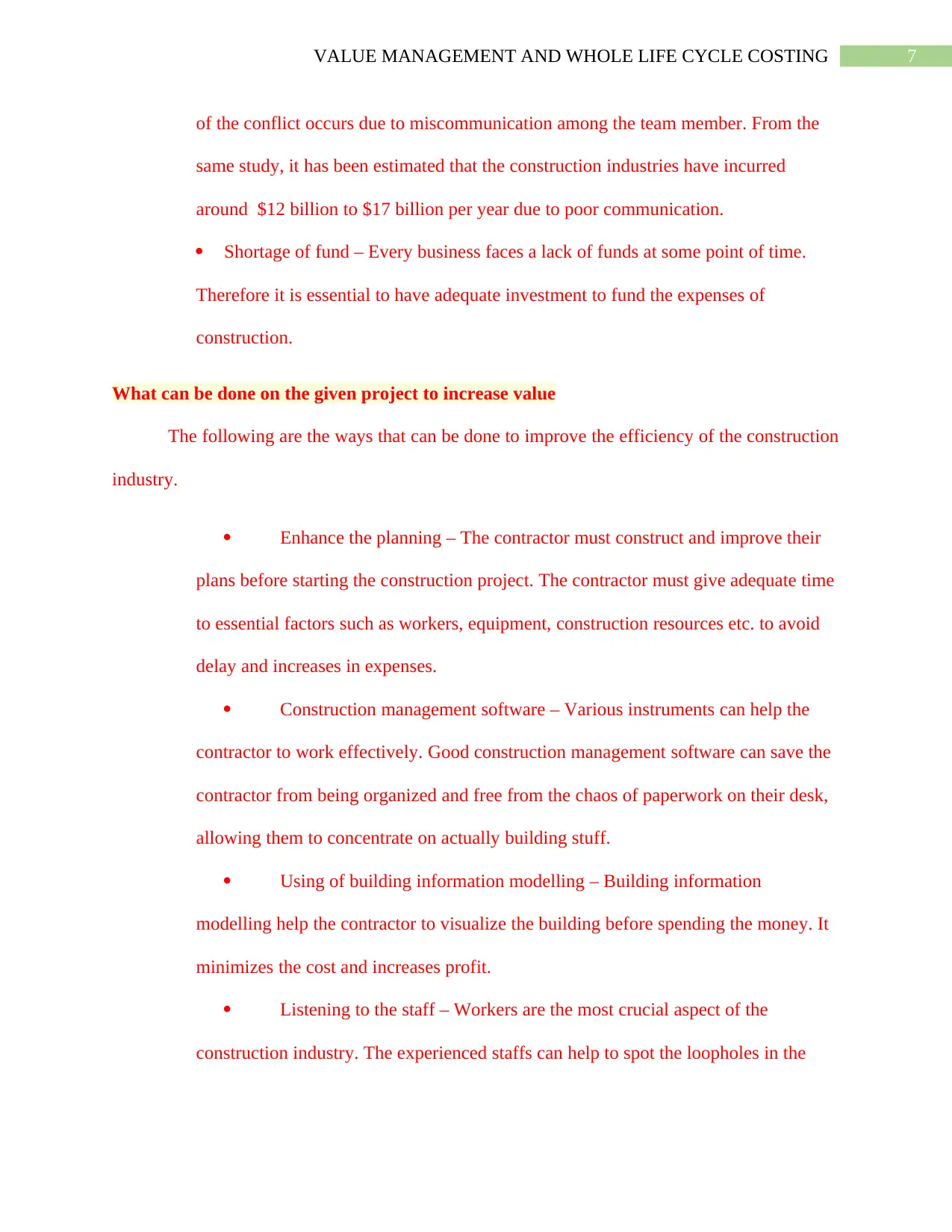
7VALUE MANAGEMENT AND WHOLE LIFE CYCLE COSTING
of the conflict occurs due to miscommunication among the team member. From the
same study, it has been estimated that the construction industries have incurred
around $12 billion to $17 billion per year due to poor communication.
Shortage of fund – Every business faces a lack of funds at some point of time.
Therefore it is essential to have adequate investment to fund the expenses of
construction.
What can be done on the given project to increase value
The following are the ways that can be done to improve the efficiency of the construction
industry.
Enhance the planning – The contractor must construct and improve their
plans before starting the construction project. The contractor must give adequate time
to essential factors such as workers, equipment, construction resources etc. to avoid
delay and increases in expenses.
Construction management software – Various instruments can help the
contractor to work effectively. Good construction management software can save the
contractor from being organized and free from the chaos of paperwork on their desk,
allowing them to concentrate on actually building stuff.
Using of building information modelling – Building information
modelling help the contractor to visualize the building before spending the money. It
minimizes the cost and increases profit.
Listening to the staff – Workers are the most crucial aspect of the
construction industry. The experienced staffs can help to spot the loopholes in the
of the conflict occurs due to miscommunication among the team member. From the
same study, it has been estimated that the construction industries have incurred
around $12 billion to $17 billion per year due to poor communication.
Shortage of fund – Every business faces a lack of funds at some point of time.
Therefore it is essential to have adequate investment to fund the expenses of
construction.
What can be done on the given project to increase value
The following are the ways that can be done to improve the efficiency of the construction
industry.
Enhance the planning – The contractor must construct and improve their
plans before starting the construction project. The contractor must give adequate time
to essential factors such as workers, equipment, construction resources etc. to avoid
delay and increases in expenses.
Construction management software – Various instruments can help the
contractor to work effectively. Good construction management software can save the
contractor from being organized and free from the chaos of paperwork on their desk,
allowing them to concentrate on actually building stuff.
Using of building information modelling – Building information
modelling help the contractor to visualize the building before spending the money. It
minimizes the cost and increases profit.
Listening to the staff – Workers are the most crucial aspect of the
construction industry. The experienced staffs can help to spot the loopholes in the
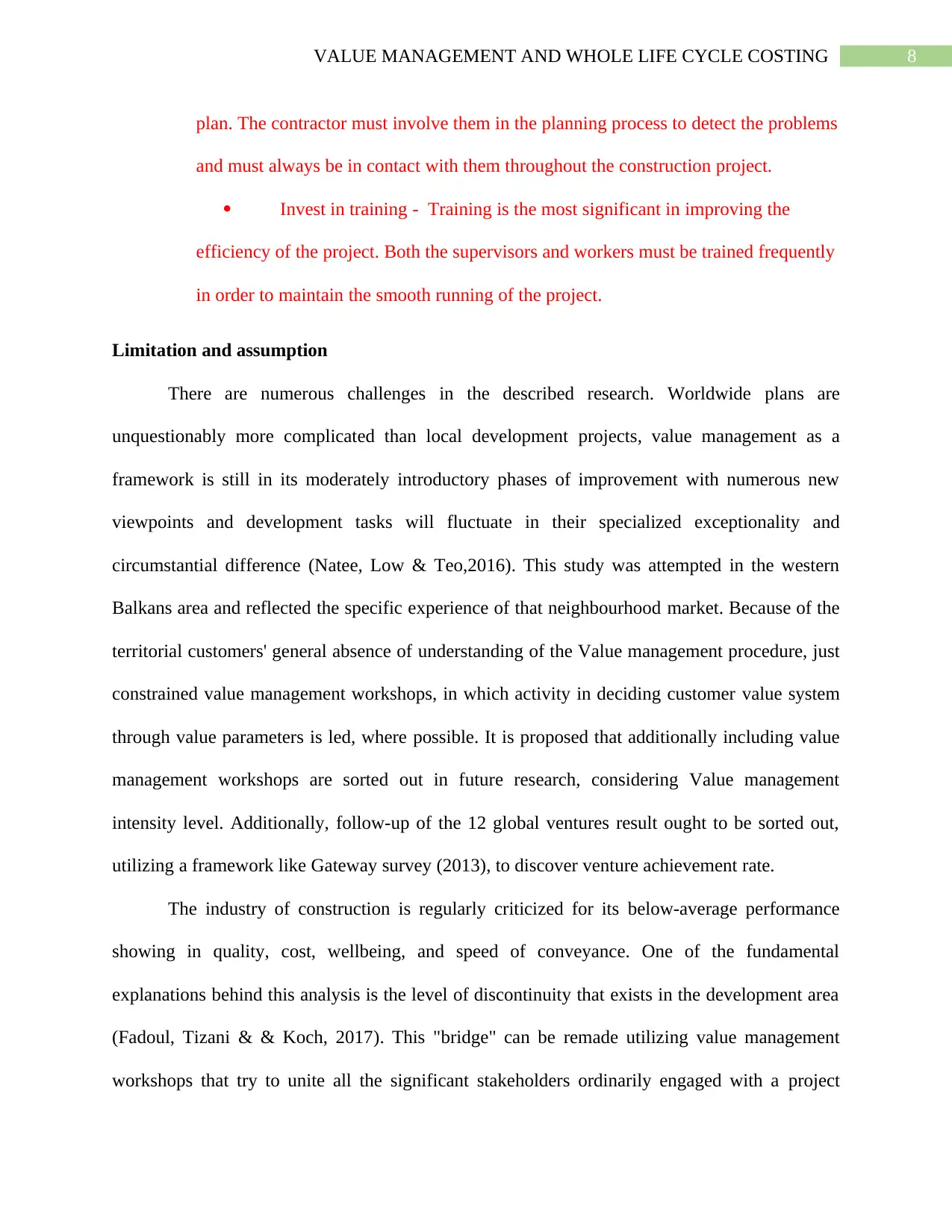
8VALUE MANAGEMENT AND WHOLE LIFE CYCLE COSTING
plan. The contractor must involve them in the planning process to detect the problems
and must always be in contact with them throughout the construction project.
Invest in training - Training is the most significant in improving the
efficiency of the project. Both the supervisors and workers must be trained frequently
in order to maintain the smooth running of the project.
Limitation and assumption
There are numerous challenges in the described research. Worldwide plans are
unquestionably more complicated than local development projects, value management as a
framework is still in its moderately introductory phases of improvement with numerous new
viewpoints and development tasks will fluctuate in their specialized exceptionality and
circumstantial difference (Natee, Low & Teo,2016). This study was attempted in the western
Balkans area and reflected the specific experience of that neighbourhood market. Because of the
territorial customers' general absence of understanding of the Value management procedure, just
constrained value management workshops, in which activity in deciding customer value system
through value parameters is led, where possible. It is proposed that additionally including value
management workshops are sorted out in future research, considering Value management
intensity level. Additionally, follow-up of the 12 global ventures result ought to be sorted out,
utilizing a framework like Gateway survey (2013), to discover venture achievement rate.
The industry of construction is regularly criticized for its below-average performance
showing in quality, cost, wellbeing, and speed of conveyance. One of the fundamental
explanations behind this analysis is the level of discontinuity that exists in the development area
(Fadoul, Tizani & & Koch, 2017). This "bridge" can be remade utilizing value management
workshops that try to unite all the significant stakeholders ordinarily engaged with a project
plan. The contractor must involve them in the planning process to detect the problems
and must always be in contact with them throughout the construction project.
Invest in training - Training is the most significant in improving the
efficiency of the project. Both the supervisors and workers must be trained frequently
in order to maintain the smooth running of the project.
Limitation and assumption
There are numerous challenges in the described research. Worldwide plans are
unquestionably more complicated than local development projects, value management as a
framework is still in its moderately introductory phases of improvement with numerous new
viewpoints and development tasks will fluctuate in their specialized exceptionality and
circumstantial difference (Natee, Low & Teo,2016). This study was attempted in the western
Balkans area and reflected the specific experience of that neighbourhood market. Because of the
territorial customers' general absence of understanding of the Value management procedure, just
constrained value management workshops, in which activity in deciding customer value system
through value parameters is led, where possible. It is proposed that additionally including value
management workshops are sorted out in future research, considering Value management
intensity level. Additionally, follow-up of the 12 global ventures result ought to be sorted out,
utilizing a framework like Gateway survey (2013), to discover venture achievement rate.
The industry of construction is regularly criticized for its below-average performance
showing in quality, cost, wellbeing, and speed of conveyance. One of the fundamental
explanations behind this analysis is the level of discontinuity that exists in the development area
(Fadoul, Tizani & & Koch, 2017). This "bridge" can be remade utilizing value management
workshops that try to unite all the significant stakeholders ordinarily engaged with a project
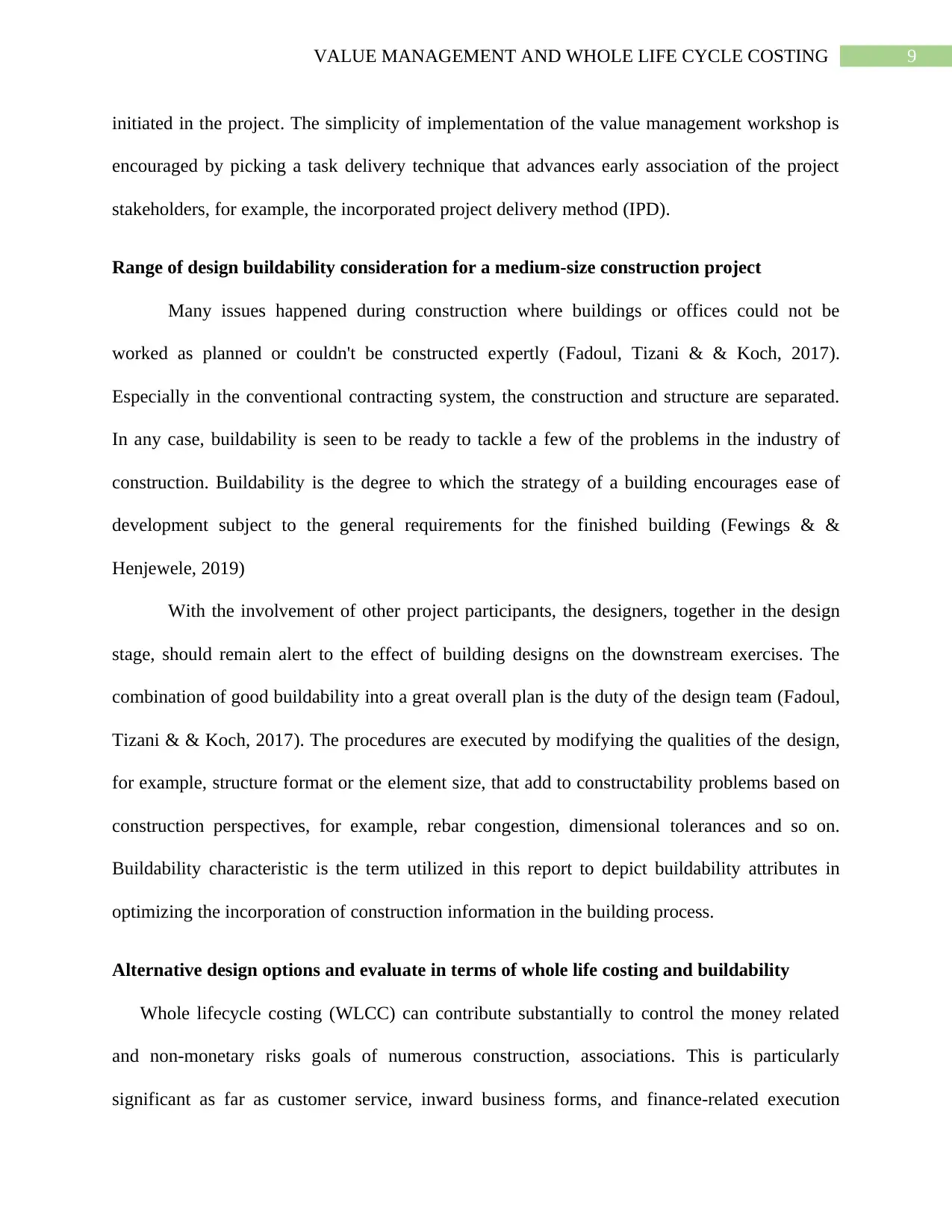
9VALUE MANAGEMENT AND WHOLE LIFE CYCLE COSTING
initiated in the project. The simplicity of implementation of the value management workshop is
encouraged by picking a task delivery technique that advances early association of the project
stakeholders, for example, the incorporated project delivery method (IPD).
Range of design buildability consideration for a medium-size construction project
Many issues happened during construction where buildings or offices could not be
worked as planned or couldn't be constructed expertly (Fadoul, Tizani & & Koch, 2017).
Especially in the conventional contracting system, the construction and structure are separated.
In any case, buildability is seen to be ready to tackle a few of the problems in the industry of
construction. Buildability is the degree to which the strategy of a building encourages ease of
development subject to the general requirements for the finished building (Fewings & &
Henjewele, 2019)
With the involvement of other project participants, the designers, together in the design
stage, should remain alert to the effect of building designs on the downstream exercises. The
combination of good buildability into a great overall plan is the duty of the design team (Fadoul,
Tizani & & Koch, 2017). The procedures are executed by modifying the qualities of the design,
for example, structure format or the element size, that add to constructability problems based on
construction perspectives, for example, rebar congestion, dimensional tolerances and so on.
Buildability characteristic is the term utilized in this report to depict buildability attributes in
optimizing the incorporation of construction information in the building process.
Alternative design options and evaluate in terms of whole life costing and buildability
Whole lifecycle costing (WLCC) can contribute substantially to control the money related
and non-monetary risks goals of numerous construction, associations. This is particularly
significant as far as customer service, inward business forms, and finance-related execution
initiated in the project. The simplicity of implementation of the value management workshop is
encouraged by picking a task delivery technique that advances early association of the project
stakeholders, for example, the incorporated project delivery method (IPD).
Range of design buildability consideration for a medium-size construction project
Many issues happened during construction where buildings or offices could not be
worked as planned or couldn't be constructed expertly (Fadoul, Tizani & & Koch, 2017).
Especially in the conventional contracting system, the construction and structure are separated.
In any case, buildability is seen to be ready to tackle a few of the problems in the industry of
construction. Buildability is the degree to which the strategy of a building encourages ease of
development subject to the general requirements for the finished building (Fewings & &
Henjewele, 2019)
With the involvement of other project participants, the designers, together in the design
stage, should remain alert to the effect of building designs on the downstream exercises. The
combination of good buildability into a great overall plan is the duty of the design team (Fadoul,
Tizani & & Koch, 2017). The procedures are executed by modifying the qualities of the design,
for example, structure format or the element size, that add to constructability problems based on
construction perspectives, for example, rebar congestion, dimensional tolerances and so on.
Buildability characteristic is the term utilized in this report to depict buildability attributes in
optimizing the incorporation of construction information in the building process.
Alternative design options and evaluate in terms of whole life costing and buildability
Whole lifecycle costing (WLCC) can contribute substantially to control the money related
and non-monetary risks goals of numerous construction, associations. This is particularly
significant as far as customer service, inward business forms, and finance-related execution
Secure Best Marks with AI Grader
Need help grading? Try our AI Grader for instant feedback on your assignments.
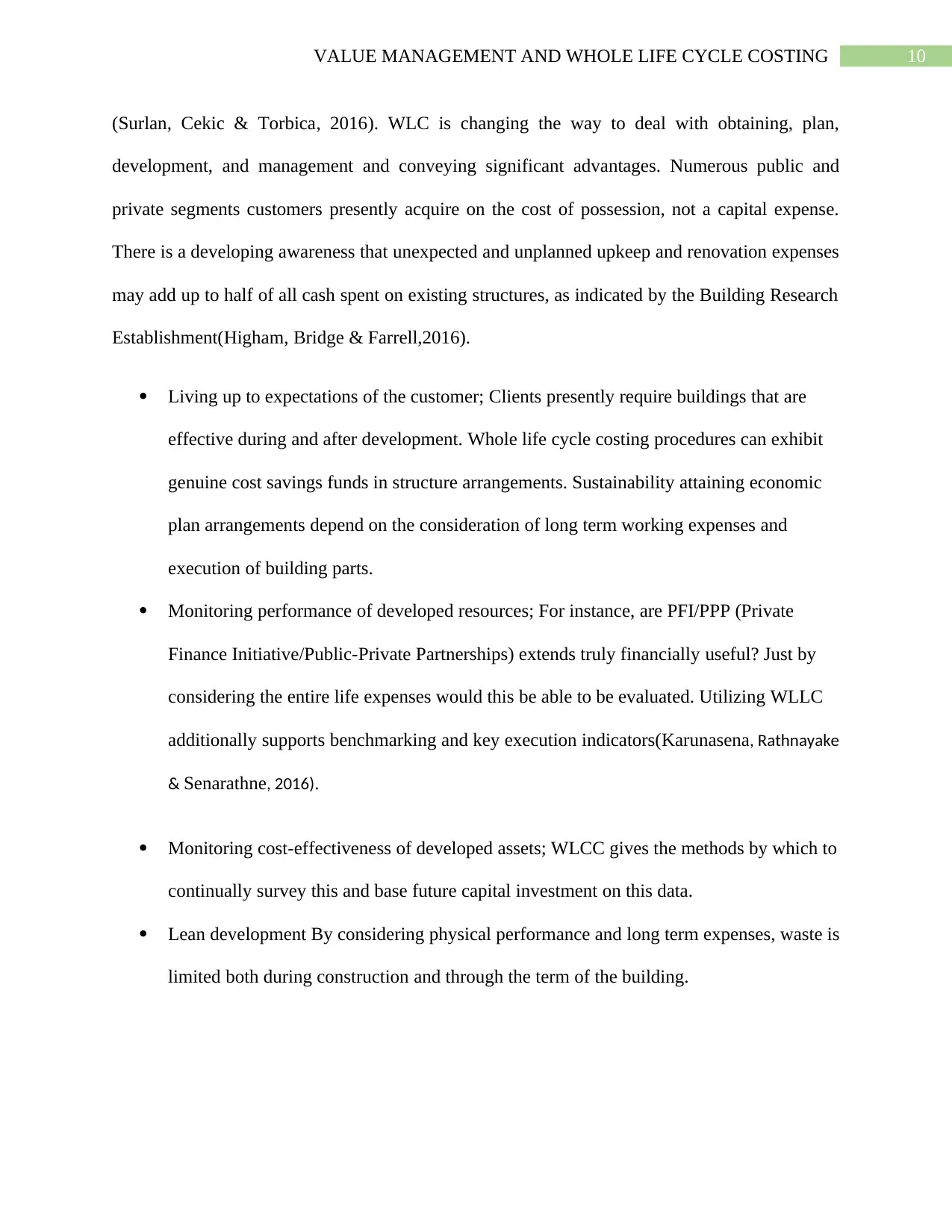
10VALUE MANAGEMENT AND WHOLE LIFE CYCLE COSTING
(Surlan, Cekic & Torbica, 2016). WLC is changing the way to deal with obtaining, plan,
development, and management and conveying significant advantages. Numerous public and
private segments customers presently acquire on the cost of possession, not a capital expense.
There is a developing awareness that unexpected and unplanned upkeep and renovation expenses
may add up to half of all cash spent on existing structures, as indicated by the Building Research
Establishment(Higham, Bridge & Farrell,2016).
Living up to expectations of the customer; Clients presently require buildings that are
effective during and after development. Whole life cycle costing procedures can exhibit
genuine cost savings funds in structure arrangements. Sustainability attaining economic
plan arrangements depend on the consideration of long term working expenses and
execution of building parts.
Monitoring performance of developed resources; For instance, are PFI/PPP (Private
Finance Initiative/Public-Private Partnerships) extends truly financially useful? Just by
considering the entire life expenses would this be able to be evaluated. Utilizing WLLC
additionally supports benchmarking and key execution indicators(Karunasena, Rathnayake
& Senarathne, 2016).
Monitoring cost-effectiveness of developed assets; WLCC gives the methods by which to
continually survey this and base future capital investment on this data.
Lean development By considering physical performance and long term expenses, waste is
limited both during construction and through the term of the building.
(Surlan, Cekic & Torbica, 2016). WLC is changing the way to deal with obtaining, plan,
development, and management and conveying significant advantages. Numerous public and
private segments customers presently acquire on the cost of possession, not a capital expense.
There is a developing awareness that unexpected and unplanned upkeep and renovation expenses
may add up to half of all cash spent on existing structures, as indicated by the Building Research
Establishment(Higham, Bridge & Farrell,2016).
Living up to expectations of the customer; Clients presently require buildings that are
effective during and after development. Whole life cycle costing procedures can exhibit
genuine cost savings funds in structure arrangements. Sustainability attaining economic
plan arrangements depend on the consideration of long term working expenses and
execution of building parts.
Monitoring performance of developed resources; For instance, are PFI/PPP (Private
Finance Initiative/Public-Private Partnerships) extends truly financially useful? Just by
considering the entire life expenses would this be able to be evaluated. Utilizing WLLC
additionally supports benchmarking and key execution indicators(Karunasena, Rathnayake
& Senarathne, 2016).
Monitoring cost-effectiveness of developed assets; WLCC gives the methods by which to
continually survey this and base future capital investment on this data.
Lean development By considering physical performance and long term expenses, waste is
limited both during construction and through the term of the building.
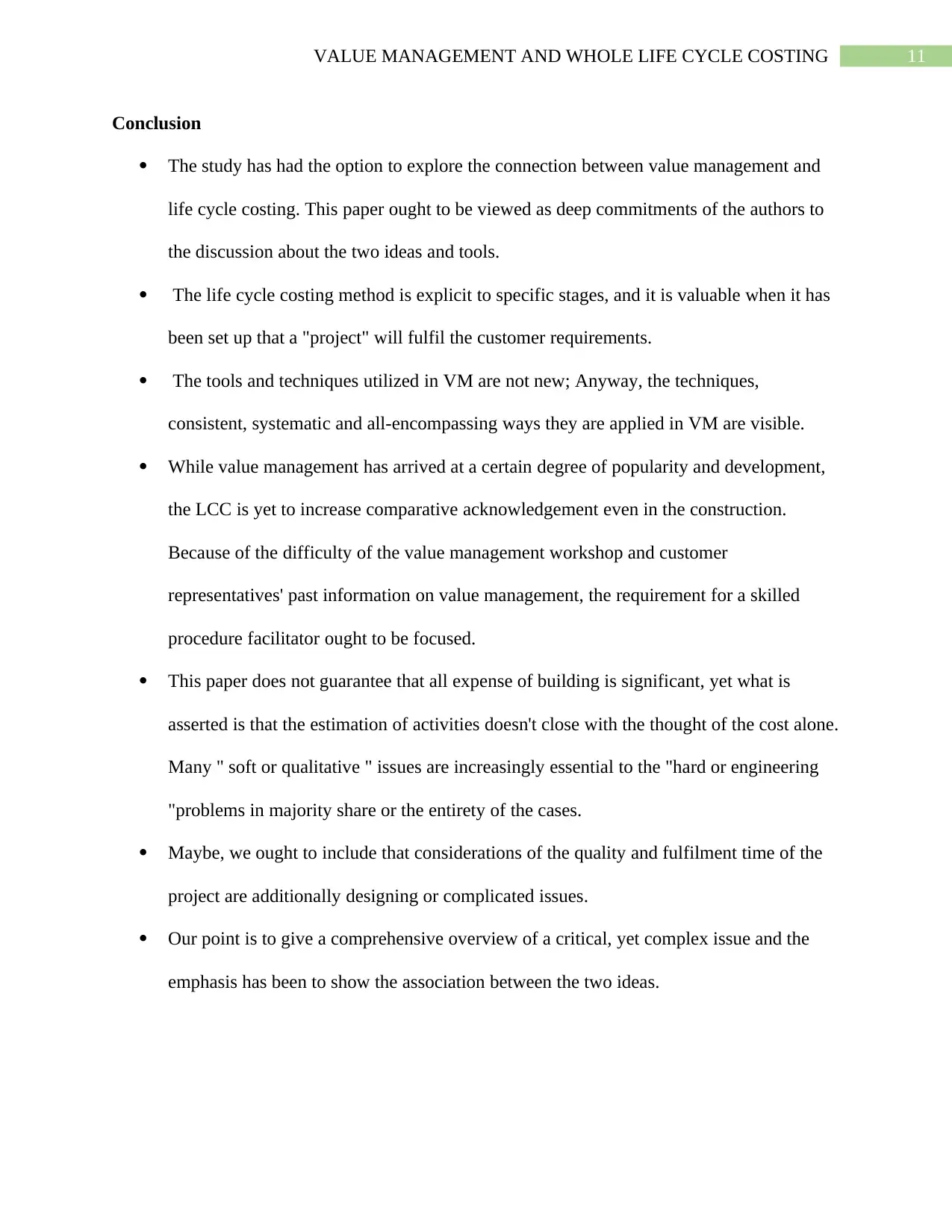
11VALUE MANAGEMENT AND WHOLE LIFE CYCLE COSTING
Conclusion
The study has had the option to explore the connection between value management and
life cycle costing. This paper ought to be viewed as deep commitments of the authors to
the discussion about the two ideas and tools.
The life cycle costing method is explicit to specific stages, and it is valuable when it has
been set up that a "project" will fulfil the customer requirements.
The tools and techniques utilized in VM are not new; Anyway, the techniques,
consistent, systematic and all-encompassing ways they are applied in VM are visible.
While value management has arrived at a certain degree of popularity and development,
the LCC is yet to increase comparative acknowledgement even in the construction.
Because of the difficulty of the value management workshop and customer
representatives' past information on value management, the requirement for a skilled
procedure facilitator ought to be focused.
This paper does not guarantee that all expense of building is significant, yet what is
asserted is that the estimation of activities doesn't close with the thought of the cost alone.
Many " soft or qualitative " issues are increasingly essential to the "hard or engineering
"problems in majority share or the entirety of the cases.
Maybe, we ought to include that considerations of the quality and fulfilment time of the
project are additionally designing or complicated issues.
Our point is to give a comprehensive overview of a critical, yet complex issue and the
emphasis has been to show the association between the two ideas.
Conclusion
The study has had the option to explore the connection between value management and
life cycle costing. This paper ought to be viewed as deep commitments of the authors to
the discussion about the two ideas and tools.
The life cycle costing method is explicit to specific stages, and it is valuable when it has
been set up that a "project" will fulfil the customer requirements.
The tools and techniques utilized in VM are not new; Anyway, the techniques,
consistent, systematic and all-encompassing ways they are applied in VM are visible.
While value management has arrived at a certain degree of popularity and development,
the LCC is yet to increase comparative acknowledgement even in the construction.
Because of the difficulty of the value management workshop and customer
representatives' past information on value management, the requirement for a skilled
procedure facilitator ought to be focused.
This paper does not guarantee that all expense of building is significant, yet what is
asserted is that the estimation of activities doesn't close with the thought of the cost alone.
Many " soft or qualitative " issues are increasingly essential to the "hard or engineering
"problems in majority share or the entirety of the cases.
Maybe, we ought to include that considerations of the quality and fulfilment time of the
project are additionally designing or complicated issues.
Our point is to give a comprehensive overview of a critical, yet complex issue and the
emphasis has been to show the association between the two ideas.
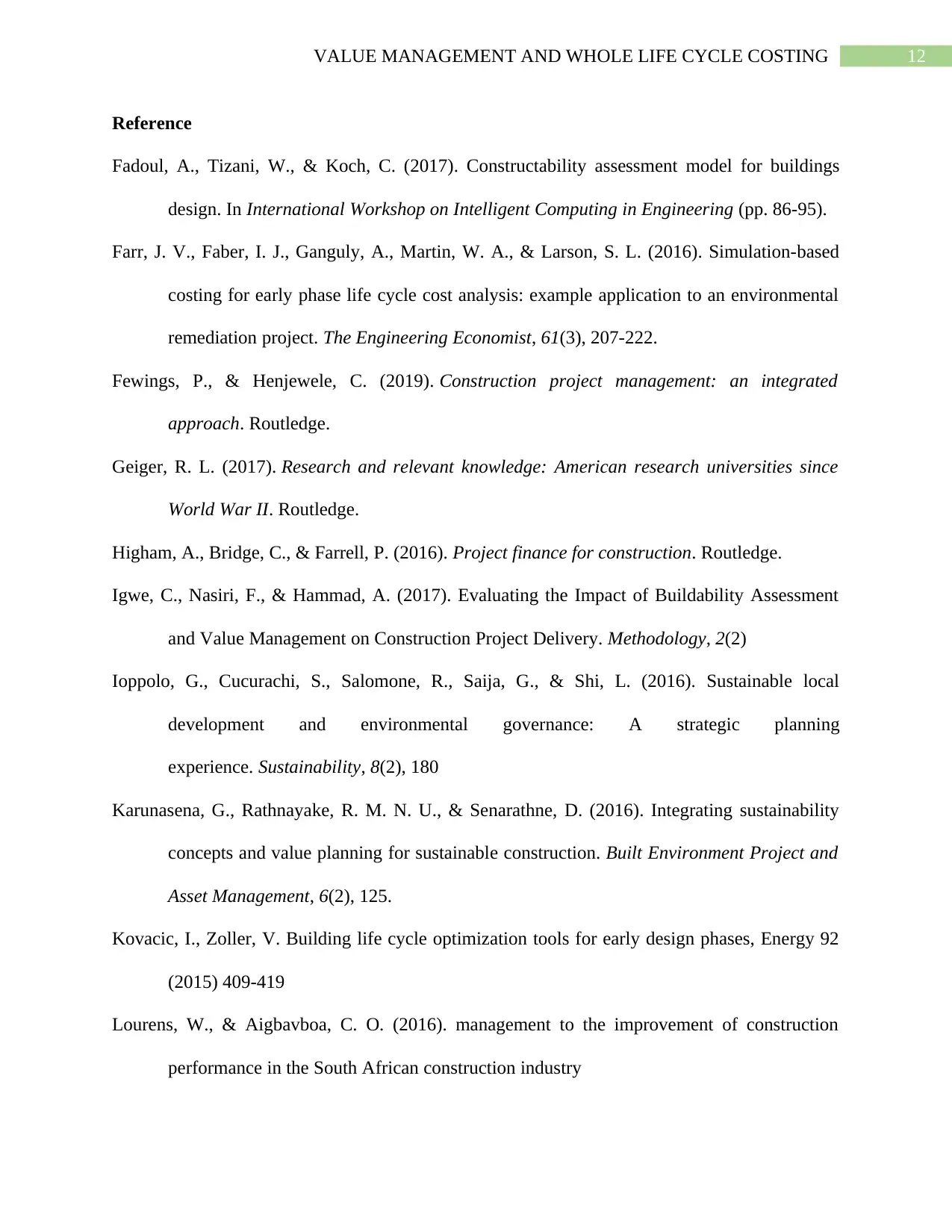
12VALUE MANAGEMENT AND WHOLE LIFE CYCLE COSTING
Reference
Fadoul, A., Tizani, W., & Koch, C. (2017). Constructability assessment model for buildings
design. In International Workshop on Intelligent Computing in Engineering (pp. 86-95).
Farr, J. V., Faber, I. J., Ganguly, A., Martin, W. A., & Larson, S. L. (2016). Simulation-based
costing for early phase life cycle cost analysis: example application to an environmental
remediation project. The Engineering Economist, 61(3), 207-222.
Fewings, P., & Henjewele, C. (2019). Construction project management: an integrated
approach. Routledge.
Geiger, R. L. (2017). Research and relevant knowledge: American research universities since
World War II. Routledge.
Higham, A., Bridge, C., & Farrell, P. (2016). Project finance for construction. Routledge.
Igwe, C., Nasiri, F., & Hammad, A. (2017). Evaluating the Impact of Buildability Assessment
and Value Management on Construction Project Delivery. Methodology, 2(2)
Ioppolo, G., Cucurachi, S., Salomone, R., Saija, G., & Shi, L. (2016). Sustainable local
development and environmental governance: A strategic planning
experience. Sustainability, 8(2), 180
Karunasena, G., Rathnayake, R. M. N. U., & Senarathne, D. (2016). Integrating sustainability
concepts and value planning for sustainable construction. Built Environment Project and
Asset Management, 6(2), 125.
Kovacic, I., Zoller, V. Building life cycle optimization tools for early design phases, Energy 92
(2015) 409-419
Lourens, W., & Aigbavboa, C. O. (2016). management to the improvement of construction
performance in the South African construction industry
Reference
Fadoul, A., Tizani, W., & Koch, C. (2017). Constructability assessment model for buildings
design. In International Workshop on Intelligent Computing in Engineering (pp. 86-95).
Farr, J. V., Faber, I. J., Ganguly, A., Martin, W. A., & Larson, S. L. (2016). Simulation-based
costing for early phase life cycle cost analysis: example application to an environmental
remediation project. The Engineering Economist, 61(3), 207-222.
Fewings, P., & Henjewele, C. (2019). Construction project management: an integrated
approach. Routledge.
Geiger, R. L. (2017). Research and relevant knowledge: American research universities since
World War II. Routledge.
Higham, A., Bridge, C., & Farrell, P. (2016). Project finance for construction. Routledge.
Igwe, C., Nasiri, F., & Hammad, A. (2017). Evaluating the Impact of Buildability Assessment
and Value Management on Construction Project Delivery. Methodology, 2(2)
Ioppolo, G., Cucurachi, S., Salomone, R., Saija, G., & Shi, L. (2016). Sustainable local
development and environmental governance: A strategic planning
experience. Sustainability, 8(2), 180
Karunasena, G., Rathnayake, R. M. N. U., & Senarathne, D. (2016). Integrating sustainability
concepts and value planning for sustainable construction. Built Environment Project and
Asset Management, 6(2), 125.
Kovacic, I., Zoller, V. Building life cycle optimization tools for early design phases, Energy 92
(2015) 409-419
Lourens, W., & Aigbavboa, C. O. (2016). management to the improvement of construction
performance in the South African construction industry
Paraphrase This Document
Need a fresh take? Get an instant paraphrase of this document with our AI Paraphraser
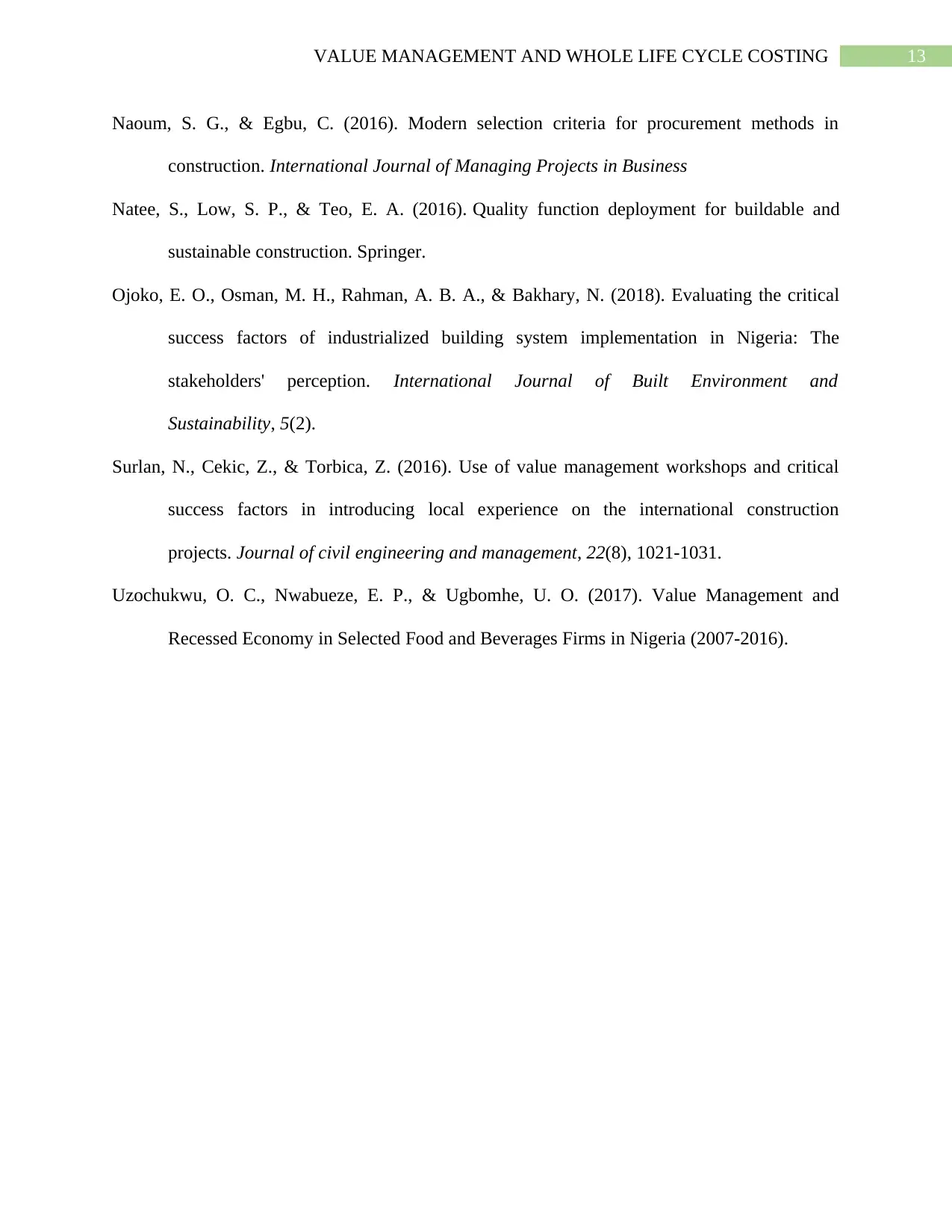
13VALUE MANAGEMENT AND WHOLE LIFE CYCLE COSTING
Naoum, S. G., & Egbu, C. (2016). Modern selection criteria for procurement methods in
construction. International Journal of Managing Projects in Business
Natee, S., Low, S. P., & Teo, E. A. (2016). Quality function deployment for buildable and
sustainable construction. Springer.
Ojoko, E. O., Osman, M. H., Rahman, A. B. A., & Bakhary, N. (2018). Evaluating the critical
success factors of industrialized building system implementation in Nigeria: The
stakeholders' perception. International Journal of Built Environment and
Sustainability, 5(2).
Surlan, N., Cekic, Z., & Torbica, Z. (2016). Use of value management workshops and critical
success factors in introducing local experience on the international construction
projects. Journal of civil engineering and management, 22(8), 1021-1031.
Uzochukwu, O. C., Nwabueze, E. P., & Ugbomhe, U. O. (2017). Value Management and
Recessed Economy in Selected Food and Beverages Firms in Nigeria (2007-2016).
Naoum, S. G., & Egbu, C. (2016). Modern selection criteria for procurement methods in
construction. International Journal of Managing Projects in Business
Natee, S., Low, S. P., & Teo, E. A. (2016). Quality function deployment for buildable and
sustainable construction. Springer.
Ojoko, E. O., Osman, M. H., Rahman, A. B. A., & Bakhary, N. (2018). Evaluating the critical
success factors of industrialized building system implementation in Nigeria: The
stakeholders' perception. International Journal of Built Environment and
Sustainability, 5(2).
Surlan, N., Cekic, Z., & Torbica, Z. (2016). Use of value management workshops and critical
success factors in introducing local experience on the international construction
projects. Journal of civil engineering and management, 22(8), 1021-1031.
Uzochukwu, O. C., Nwabueze, E. P., & Ugbomhe, U. O. (2017). Value Management and
Recessed Economy in Selected Food and Beverages Firms in Nigeria (2007-2016).
1 out of 14
Related Documents

Your All-in-One AI-Powered Toolkit for Academic Success.
+13062052269
info@desklib.com
Available 24*7 on WhatsApp / Email
Unlock your academic potential
© 2024 | Zucol Services PVT LTD | All rights reserved.