A Study on Virtual and Physical Testing Methods Across Industries
VerifiedAdded on 2023/04/24
|70
|14533
|488
Project
AI Summary
This project undertakes a comprehensive comparison of virtual and physical testing methodologies, investigating their application and efficacy across diverse industries. The research employs a mixed-methods approach, including industry surveys and case studies, to evaluate the advantages ...
Read More
Contribute Materials
Your contribution can guide someone’s learning journey. Share your
documents today.
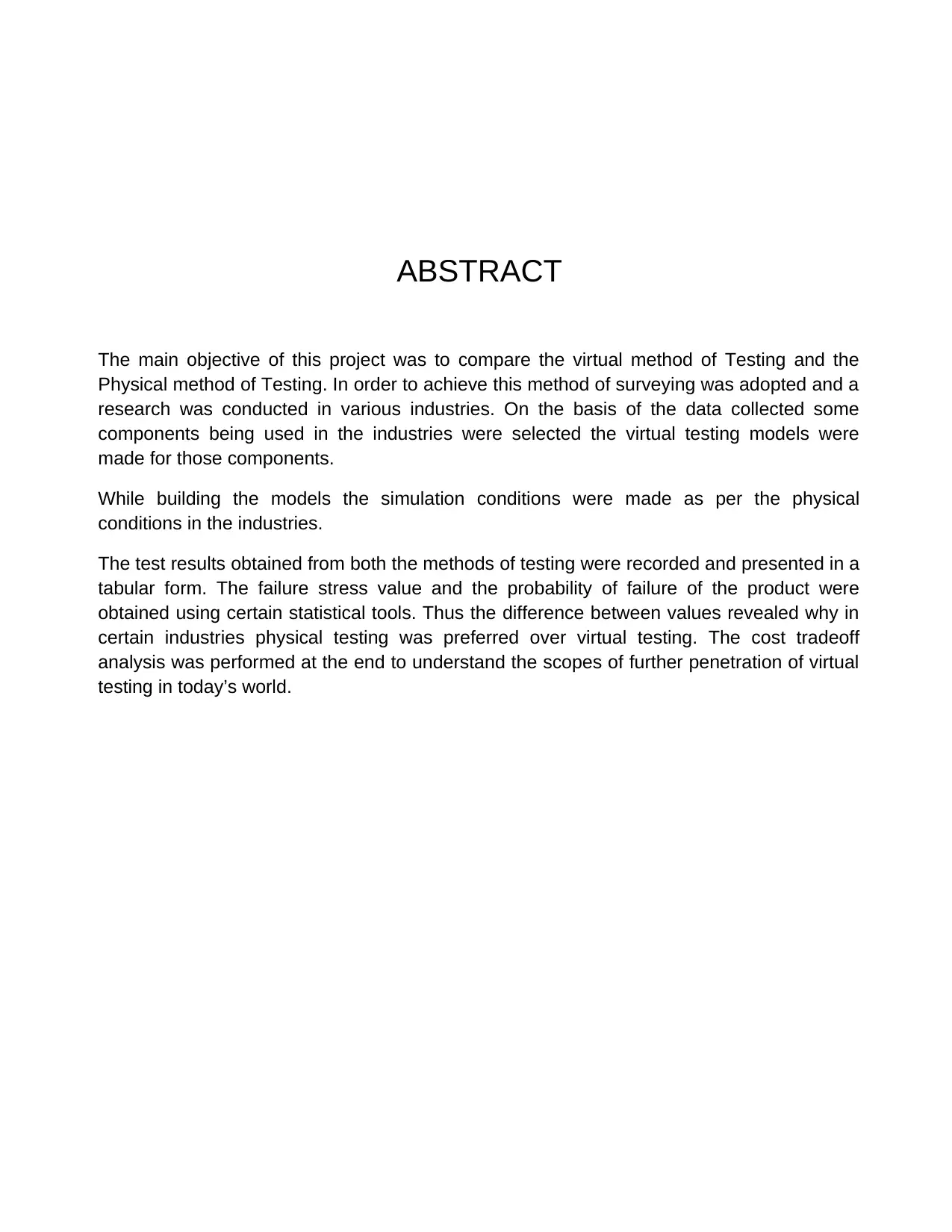
ABSTRACT
The main objective of this project was to compare the virtual method of Testing and the
Physical method of Testing. In order to achieve this method of surveying was adopted and a
research was conducted in various industries. On the basis of the data collected some
components being used in the industries were selected the virtual testing models were
made for those components.
While building the models the simulation conditions were made as per the physical
conditions in the industries.
The test results obtained from both the methods of testing were recorded and presented in a
tabular form. The failure stress value and the probability of failure of the product were
obtained using certain statistical tools. Thus the difference between values revealed why in
certain industries physical testing was preferred over virtual testing. The cost tradeoff
analysis was performed at the end to understand the scopes of further penetration of virtual
testing in today’s world.
The main objective of this project was to compare the virtual method of Testing and the
Physical method of Testing. In order to achieve this method of surveying was adopted and a
research was conducted in various industries. On the basis of the data collected some
components being used in the industries were selected the virtual testing models were
made for those components.
While building the models the simulation conditions were made as per the physical
conditions in the industries.
The test results obtained from both the methods of testing were recorded and presented in a
tabular form. The failure stress value and the probability of failure of the product were
obtained using certain statistical tools. Thus the difference between values revealed why in
certain industries physical testing was preferred over virtual testing. The cost tradeoff
analysis was performed at the end to understand the scopes of further penetration of virtual
testing in today’s world.
Secure Best Marks with AI Grader
Need help grading? Try our AI Grader for instant feedback on your assignments.
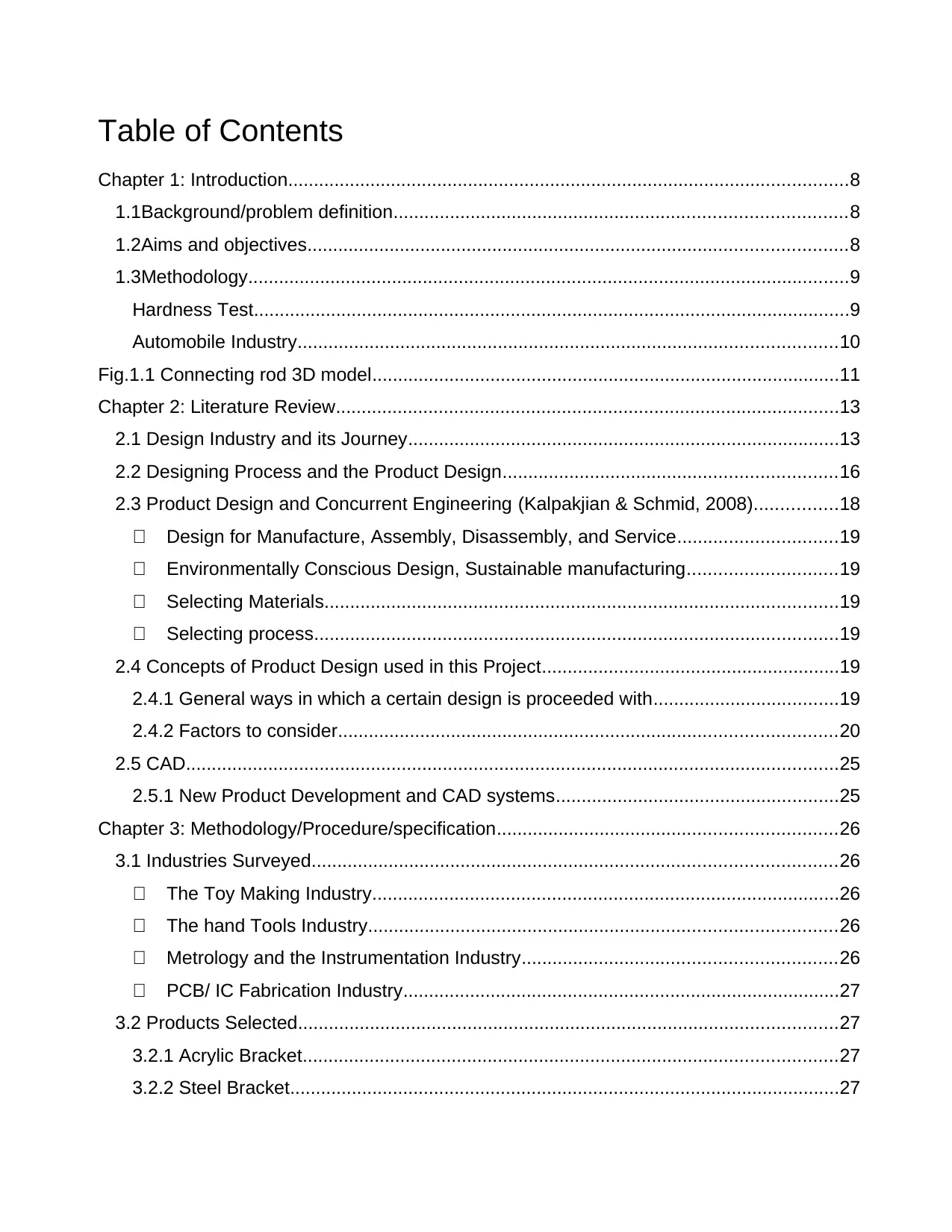
Table of Contents
Chapter 1: Introduction.............................................................................................................8
1.1Background/problem definition........................................................................................8
1.2Aims and objectives.........................................................................................................8
1.3Methodology.....................................................................................................................9
Hardness Test....................................................................................................................9
Automobile Industry.........................................................................................................10
Fig.1.1 Connecting rod 3D model...........................................................................................11
Chapter 2: Literature Review..................................................................................................13
2.1 Design Industry and its Journey....................................................................................13
2.2 Designing Process and the Product Design.................................................................16
2.3 Product Design and Concurrent Engineering (Kalpakjian & Schmid, 2008)................18
Design for Manufacture, Assembly, Disassembly, and Service...............................19
Environmentally Conscious Design, Sustainable manufacturing.............................19
Selecting Materials....................................................................................................19
Selecting process......................................................................................................19
2.4 Concepts of Product Design used in this Project..........................................................19
2.4.1 General ways in which a certain design is proceeded with....................................19
2.4.2 Factors to consider.................................................................................................20
2.5 CAD...............................................................................................................................25
2.5.1 New Product Development and CAD systems.......................................................25
Chapter 3: Methodology/Procedure/specification..................................................................26
3.1 Industries Surveyed......................................................................................................26
The Toy Making Industry...........................................................................................26
The hand Tools Industry...........................................................................................26
Metrology and the Instrumentation Industry.............................................................26
PCB/ IC Fabrication Industry.....................................................................................27
3.2 Products Selected.........................................................................................................27
3.2.1 Acrylic Bracket........................................................................................................27
3.2.2 Steel Bracket...........................................................................................................27
Chapter 1: Introduction.............................................................................................................8
1.1Background/problem definition........................................................................................8
1.2Aims and objectives.........................................................................................................8
1.3Methodology.....................................................................................................................9
Hardness Test....................................................................................................................9
Automobile Industry.........................................................................................................10
Fig.1.1 Connecting rod 3D model...........................................................................................11
Chapter 2: Literature Review..................................................................................................13
2.1 Design Industry and its Journey....................................................................................13
2.2 Designing Process and the Product Design.................................................................16
2.3 Product Design and Concurrent Engineering (Kalpakjian & Schmid, 2008)................18
Design for Manufacture, Assembly, Disassembly, and Service...............................19
Environmentally Conscious Design, Sustainable manufacturing.............................19
Selecting Materials....................................................................................................19
Selecting process......................................................................................................19
2.4 Concepts of Product Design used in this Project..........................................................19
2.4.1 General ways in which a certain design is proceeded with....................................19
2.4.2 Factors to consider.................................................................................................20
2.5 CAD...............................................................................................................................25
2.5.1 New Product Development and CAD systems.......................................................25
Chapter 3: Methodology/Procedure/specification..................................................................26
3.1 Industries Surveyed......................................................................................................26
The Toy Making Industry...........................................................................................26
The hand Tools Industry...........................................................................................26
Metrology and the Instrumentation Industry.............................................................26
PCB/ IC Fabrication Industry.....................................................................................27
3.2 Products Selected.........................................................................................................27
3.2.1 Acrylic Bracket........................................................................................................27
3.2.2 Steel Bracket...........................................................................................................27
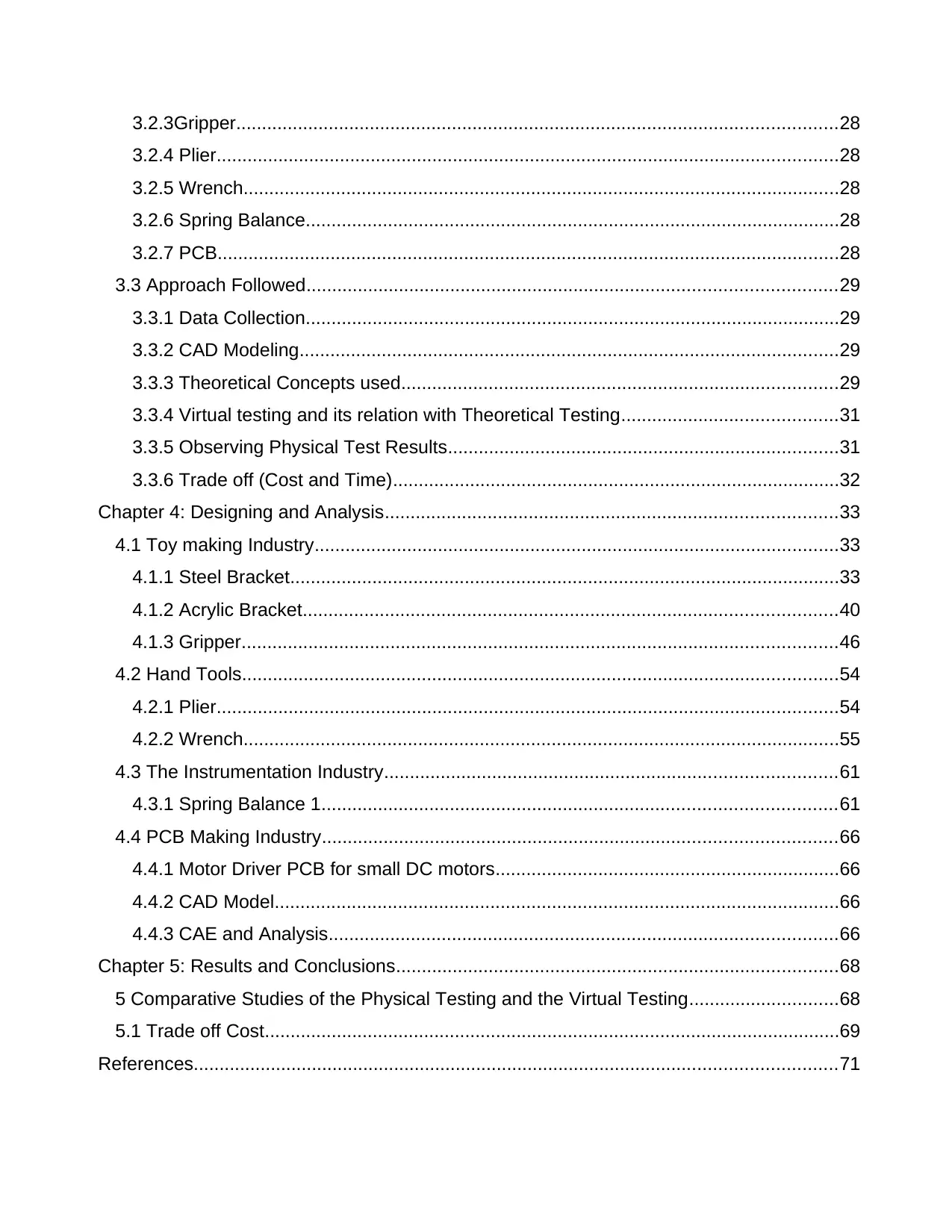
3.2.3Gripper.....................................................................................................................28
3.2.4 Plier.........................................................................................................................28
3.2.5 Wrench....................................................................................................................28
3.2.6 Spring Balance........................................................................................................28
3.2.7 PCB.........................................................................................................................28
3.3 Approach Followed.......................................................................................................29
3.3.1 Data Collection........................................................................................................29
3.3.2 CAD Modeling.........................................................................................................29
3.3.3 Theoretical Concepts used.....................................................................................29
3.3.4 Virtual testing and its relation with Theoretical Testing..........................................31
3.3.5 Observing Physical Test Results............................................................................31
3.3.6 Trade off (Cost and Time).......................................................................................32
Chapter 4: Designing and Analysis........................................................................................33
4.1 Toy making Industry......................................................................................................33
4.1.1 Steel Bracket...........................................................................................................33
4.1.2 Acrylic Bracket........................................................................................................40
4.1.3 Gripper....................................................................................................................46
4.2 Hand Tools....................................................................................................................54
4.2.1 Plier.........................................................................................................................54
4.2.2 Wrench....................................................................................................................55
4.3 The Instrumentation Industry........................................................................................61
4.3.1 Spring Balance 1....................................................................................................61
4.4 PCB Making Industry....................................................................................................66
4.4.1 Motor Driver PCB for small DC motors...................................................................66
4.4.2 CAD Model..............................................................................................................66
4.4.3 CAE and Analysis...................................................................................................66
Chapter 5: Results and Conclusions......................................................................................68
5 Comparative Studies of the Physical Testing and the Virtual Testing.............................68
5.1 Trade off Cost................................................................................................................69
References.............................................................................................................................71
3.2.4 Plier.........................................................................................................................28
3.2.5 Wrench....................................................................................................................28
3.2.6 Spring Balance........................................................................................................28
3.2.7 PCB.........................................................................................................................28
3.3 Approach Followed.......................................................................................................29
3.3.1 Data Collection........................................................................................................29
3.3.2 CAD Modeling.........................................................................................................29
3.3.3 Theoretical Concepts used.....................................................................................29
3.3.4 Virtual testing and its relation with Theoretical Testing..........................................31
3.3.5 Observing Physical Test Results............................................................................31
3.3.6 Trade off (Cost and Time).......................................................................................32
Chapter 4: Designing and Analysis........................................................................................33
4.1 Toy making Industry......................................................................................................33
4.1.1 Steel Bracket...........................................................................................................33
4.1.2 Acrylic Bracket........................................................................................................40
4.1.3 Gripper....................................................................................................................46
4.2 Hand Tools....................................................................................................................54
4.2.1 Plier.........................................................................................................................54
4.2.2 Wrench....................................................................................................................55
4.3 The Instrumentation Industry........................................................................................61
4.3.1 Spring Balance 1....................................................................................................61
4.4 PCB Making Industry....................................................................................................66
4.4.1 Motor Driver PCB for small DC motors...................................................................66
4.4.2 CAD Model..............................................................................................................66
4.4.3 CAE and Analysis...................................................................................................66
Chapter 5: Results and Conclusions......................................................................................68
5 Comparative Studies of the Physical Testing and the Virtual Testing.............................68
5.1 Trade off Cost................................................................................................................69
References.............................................................................................................................71
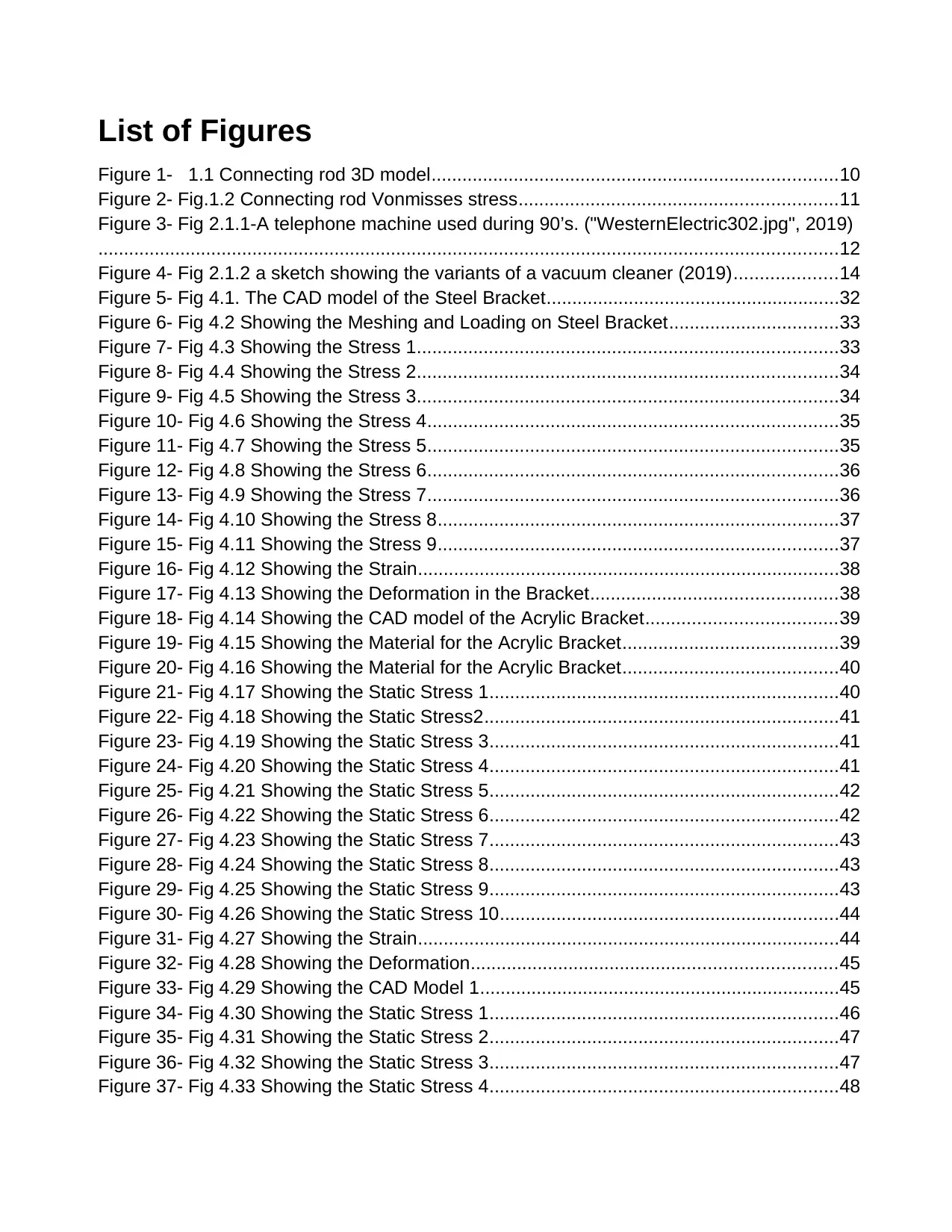
List of Figures
Figure 1- 1.1 Connecting rod 3D model...............................................................................10
Figure 2- Fig.1.2 Connecting rod Vonmisses stress..............................................................11
Figure 3- Fig 2.1.1-A telephone machine used during 90’s. ("WesternElectric302.jpg", 2019)
................................................................................................................................................12
Figure 4- Fig 2.1.2 a sketch showing the variants of a vacuum cleaner (2019)....................14
Figure 5- Fig 4.1. The CAD model of the Steel Bracket.........................................................32
Figure 6- Fig 4.2 Showing the Meshing and Loading on Steel Bracket.................................33
Figure 7- Fig 4.3 Showing the Stress 1..................................................................................33
Figure 8- Fig 4.4 Showing the Stress 2..................................................................................34
Figure 9- Fig 4.5 Showing the Stress 3..................................................................................34
Figure 10- Fig 4.6 Showing the Stress 4................................................................................35
Figure 11- Fig 4.7 Showing the Stress 5................................................................................35
Figure 12- Fig 4.8 Showing the Stress 6................................................................................36
Figure 13- Fig 4.9 Showing the Stress 7................................................................................36
Figure 14- Fig 4.10 Showing the Stress 8..............................................................................37
Figure 15- Fig 4.11 Showing the Stress 9..............................................................................37
Figure 16- Fig 4.12 Showing the Strain..................................................................................38
Figure 17- Fig 4.13 Showing the Deformation in the Bracket................................................38
Figure 18- Fig 4.14 Showing the CAD model of the Acrylic Bracket.....................................39
Figure 19- Fig 4.15 Showing the Material for the Acrylic Bracket..........................................39
Figure 20- Fig 4.16 Showing the Material for the Acrylic Bracket..........................................40
Figure 21- Fig 4.17 Showing the Static Stress 1....................................................................40
Figure 22- Fig 4.18 Showing the Static Stress2.....................................................................41
Figure 23- Fig 4.19 Showing the Static Stress 3....................................................................41
Figure 24- Fig 4.20 Showing the Static Stress 4....................................................................41
Figure 25- Fig 4.21 Showing the Static Stress 5....................................................................42
Figure 26- Fig 4.22 Showing the Static Stress 6....................................................................42
Figure 27- Fig 4.23 Showing the Static Stress 7....................................................................43
Figure 28- Fig 4.24 Showing the Static Stress 8....................................................................43
Figure 29- Fig 4.25 Showing the Static Stress 9....................................................................43
Figure 30- Fig 4.26 Showing the Static Stress 10..................................................................44
Figure 31- Fig 4.27 Showing the Strain..................................................................................44
Figure 32- Fig 4.28 Showing the Deformation.......................................................................45
Figure 33- Fig 4.29 Showing the CAD Model 1......................................................................45
Figure 34- Fig 4.30 Showing the Static Stress 1....................................................................46
Figure 35- Fig 4.31 Showing the Static Stress 2....................................................................47
Figure 36- Fig 4.32 Showing the Static Stress 3....................................................................47
Figure 37- Fig 4.33 Showing the Static Stress 4....................................................................48
Figure 1- 1.1 Connecting rod 3D model...............................................................................10
Figure 2- Fig.1.2 Connecting rod Vonmisses stress..............................................................11
Figure 3- Fig 2.1.1-A telephone machine used during 90’s. ("WesternElectric302.jpg", 2019)
................................................................................................................................................12
Figure 4- Fig 2.1.2 a sketch showing the variants of a vacuum cleaner (2019)....................14
Figure 5- Fig 4.1. The CAD model of the Steel Bracket.........................................................32
Figure 6- Fig 4.2 Showing the Meshing and Loading on Steel Bracket.................................33
Figure 7- Fig 4.3 Showing the Stress 1..................................................................................33
Figure 8- Fig 4.4 Showing the Stress 2..................................................................................34
Figure 9- Fig 4.5 Showing the Stress 3..................................................................................34
Figure 10- Fig 4.6 Showing the Stress 4................................................................................35
Figure 11- Fig 4.7 Showing the Stress 5................................................................................35
Figure 12- Fig 4.8 Showing the Stress 6................................................................................36
Figure 13- Fig 4.9 Showing the Stress 7................................................................................36
Figure 14- Fig 4.10 Showing the Stress 8..............................................................................37
Figure 15- Fig 4.11 Showing the Stress 9..............................................................................37
Figure 16- Fig 4.12 Showing the Strain..................................................................................38
Figure 17- Fig 4.13 Showing the Deformation in the Bracket................................................38
Figure 18- Fig 4.14 Showing the CAD model of the Acrylic Bracket.....................................39
Figure 19- Fig 4.15 Showing the Material for the Acrylic Bracket..........................................39
Figure 20- Fig 4.16 Showing the Material for the Acrylic Bracket..........................................40
Figure 21- Fig 4.17 Showing the Static Stress 1....................................................................40
Figure 22- Fig 4.18 Showing the Static Stress2.....................................................................41
Figure 23- Fig 4.19 Showing the Static Stress 3....................................................................41
Figure 24- Fig 4.20 Showing the Static Stress 4....................................................................41
Figure 25- Fig 4.21 Showing the Static Stress 5....................................................................42
Figure 26- Fig 4.22 Showing the Static Stress 6....................................................................42
Figure 27- Fig 4.23 Showing the Static Stress 7....................................................................43
Figure 28- Fig 4.24 Showing the Static Stress 8....................................................................43
Figure 29- Fig 4.25 Showing the Static Stress 9....................................................................43
Figure 30- Fig 4.26 Showing the Static Stress 10..................................................................44
Figure 31- Fig 4.27 Showing the Strain..................................................................................44
Figure 32- Fig 4.28 Showing the Deformation.......................................................................45
Figure 33- Fig 4.29 Showing the CAD Model 1......................................................................45
Figure 34- Fig 4.30 Showing the Static Stress 1....................................................................46
Figure 35- Fig 4.31 Showing the Static Stress 2....................................................................47
Figure 36- Fig 4.32 Showing the Static Stress 3....................................................................47
Figure 37- Fig 4.33 Showing the Static Stress 4....................................................................48
Secure Best Marks with AI Grader
Need help grading? Try our AI Grader for instant feedback on your assignments.
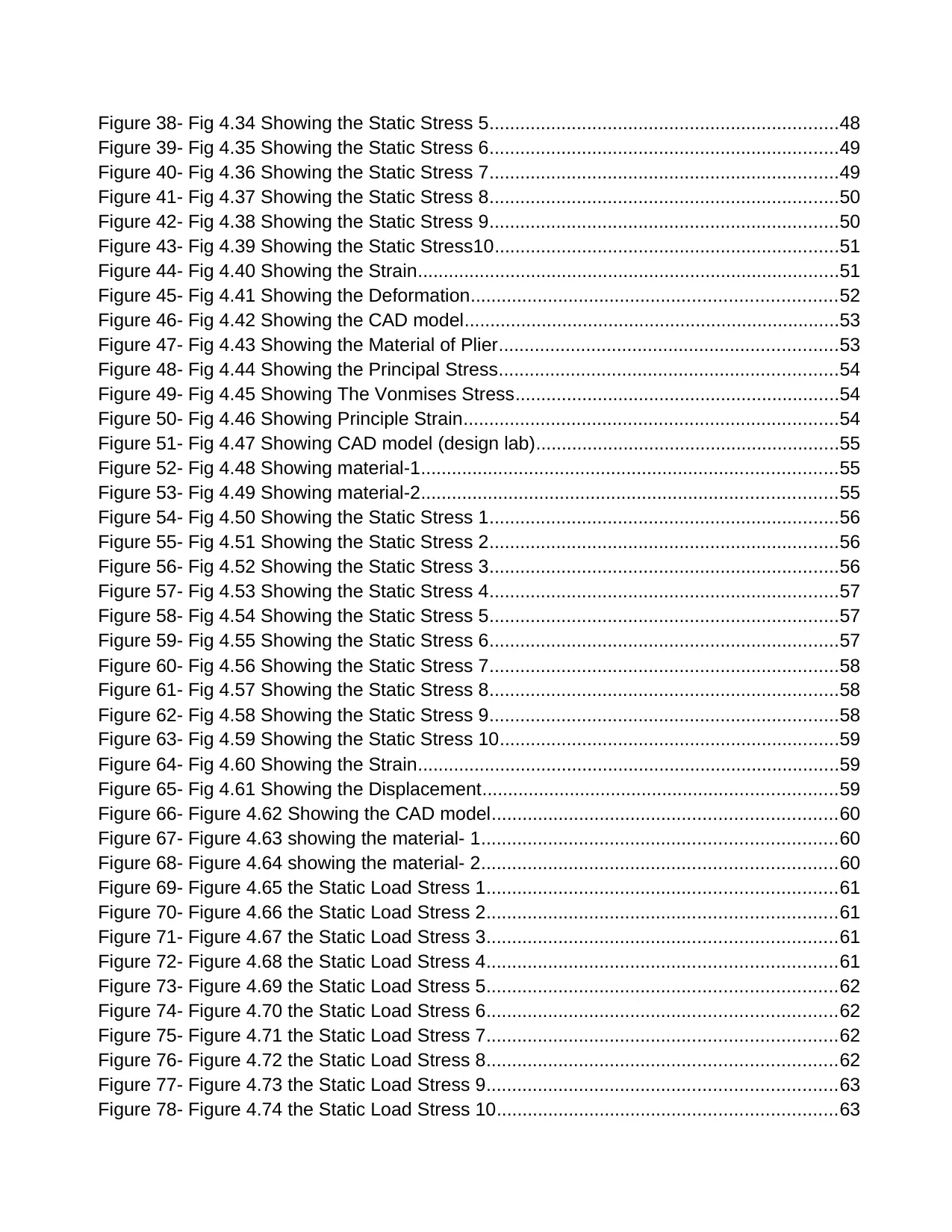
Figure 38- Fig 4.34 Showing the Static Stress 5....................................................................48
Figure 39- Fig 4.35 Showing the Static Stress 6....................................................................49
Figure 40- Fig 4.36 Showing the Static Stress 7....................................................................49
Figure 41- Fig 4.37 Showing the Static Stress 8....................................................................50
Figure 42- Fig 4.38 Showing the Static Stress 9....................................................................50
Figure 43- Fig 4.39 Showing the Static Stress10...................................................................51
Figure 44- Fig 4.40 Showing the Strain..................................................................................51
Figure 45- Fig 4.41 Showing the Deformation.......................................................................52
Figure 46- Fig 4.42 Showing the CAD model.........................................................................53
Figure 47- Fig 4.43 Showing the Material of Plier..................................................................53
Figure 48- Fig 4.44 Showing the Principal Stress..................................................................54
Figure 49- Fig 4.45 Showing The Vonmises Stress...............................................................54
Figure 50- Fig 4.46 Showing Principle Strain.........................................................................54
Figure 51- Fig 4.47 Showing CAD model (design lab)...........................................................55
Figure 52- Fig 4.48 Showing material-1.................................................................................55
Figure 53- Fig 4.49 Showing material-2.................................................................................55
Figure 54- Fig 4.50 Showing the Static Stress 1....................................................................56
Figure 55- Fig 4.51 Showing the Static Stress 2....................................................................56
Figure 56- Fig 4.52 Showing the Static Stress 3....................................................................56
Figure 57- Fig 4.53 Showing the Static Stress 4....................................................................57
Figure 58- Fig 4.54 Showing the Static Stress 5....................................................................57
Figure 59- Fig 4.55 Showing the Static Stress 6....................................................................57
Figure 60- Fig 4.56 Showing the Static Stress 7....................................................................58
Figure 61- Fig 4.57 Showing the Static Stress 8....................................................................58
Figure 62- Fig 4.58 Showing the Static Stress 9....................................................................58
Figure 63- Fig 4.59 Showing the Static Stress 10..................................................................59
Figure 64- Fig 4.60 Showing the Strain..................................................................................59
Figure 65- Fig 4.61 Showing the Displacement.....................................................................59
Figure 66- Figure 4.62 Showing the CAD model...................................................................60
Figure 67- Figure 4.63 showing the material- 1.....................................................................60
Figure 68- Figure 4.64 showing the material- 2.....................................................................60
Figure 69- Figure 4.65 the Static Load Stress 1....................................................................61
Figure 70- Figure 4.66 the Static Load Stress 2....................................................................61
Figure 71- Figure 4.67 the Static Load Stress 3....................................................................61
Figure 72- Figure 4.68 the Static Load Stress 4....................................................................61
Figure 73- Figure 4.69 the Static Load Stress 5....................................................................62
Figure 74- Figure 4.70 the Static Load Stress 6....................................................................62
Figure 75- Figure 4.71 the Static Load Stress 7....................................................................62
Figure 76- Figure 4.72 the Static Load Stress 8....................................................................62
Figure 77- Figure 4.73 the Static Load Stress 9....................................................................63
Figure 78- Figure 4.74 the Static Load Stress 10..................................................................63
Figure 39- Fig 4.35 Showing the Static Stress 6....................................................................49
Figure 40- Fig 4.36 Showing the Static Stress 7....................................................................49
Figure 41- Fig 4.37 Showing the Static Stress 8....................................................................50
Figure 42- Fig 4.38 Showing the Static Stress 9....................................................................50
Figure 43- Fig 4.39 Showing the Static Stress10...................................................................51
Figure 44- Fig 4.40 Showing the Strain..................................................................................51
Figure 45- Fig 4.41 Showing the Deformation.......................................................................52
Figure 46- Fig 4.42 Showing the CAD model.........................................................................53
Figure 47- Fig 4.43 Showing the Material of Plier..................................................................53
Figure 48- Fig 4.44 Showing the Principal Stress..................................................................54
Figure 49- Fig 4.45 Showing The Vonmises Stress...............................................................54
Figure 50- Fig 4.46 Showing Principle Strain.........................................................................54
Figure 51- Fig 4.47 Showing CAD model (design lab)...........................................................55
Figure 52- Fig 4.48 Showing material-1.................................................................................55
Figure 53- Fig 4.49 Showing material-2.................................................................................55
Figure 54- Fig 4.50 Showing the Static Stress 1....................................................................56
Figure 55- Fig 4.51 Showing the Static Stress 2....................................................................56
Figure 56- Fig 4.52 Showing the Static Stress 3....................................................................56
Figure 57- Fig 4.53 Showing the Static Stress 4....................................................................57
Figure 58- Fig 4.54 Showing the Static Stress 5....................................................................57
Figure 59- Fig 4.55 Showing the Static Stress 6....................................................................57
Figure 60- Fig 4.56 Showing the Static Stress 7....................................................................58
Figure 61- Fig 4.57 Showing the Static Stress 8....................................................................58
Figure 62- Fig 4.58 Showing the Static Stress 9....................................................................58
Figure 63- Fig 4.59 Showing the Static Stress 10..................................................................59
Figure 64- Fig 4.60 Showing the Strain..................................................................................59
Figure 65- Fig 4.61 Showing the Displacement.....................................................................59
Figure 66- Figure 4.62 Showing the CAD model...................................................................60
Figure 67- Figure 4.63 showing the material- 1.....................................................................60
Figure 68- Figure 4.64 showing the material- 2.....................................................................60
Figure 69- Figure 4.65 the Static Load Stress 1....................................................................61
Figure 70- Figure 4.66 the Static Load Stress 2....................................................................61
Figure 71- Figure 4.67 the Static Load Stress 3....................................................................61
Figure 72- Figure 4.68 the Static Load Stress 4....................................................................61
Figure 73- Figure 4.69 the Static Load Stress 5....................................................................62
Figure 74- Figure 4.70 the Static Load Stress 6....................................................................62
Figure 75- Figure 4.71 the Static Load Stress 7....................................................................62
Figure 76- Figure 4.72 the Static Load Stress 8....................................................................62
Figure 77- Figure 4.73 the Static Load Stress 9....................................................................63
Figure 78- Figure 4.74 the Static Load Stress 10..................................................................63
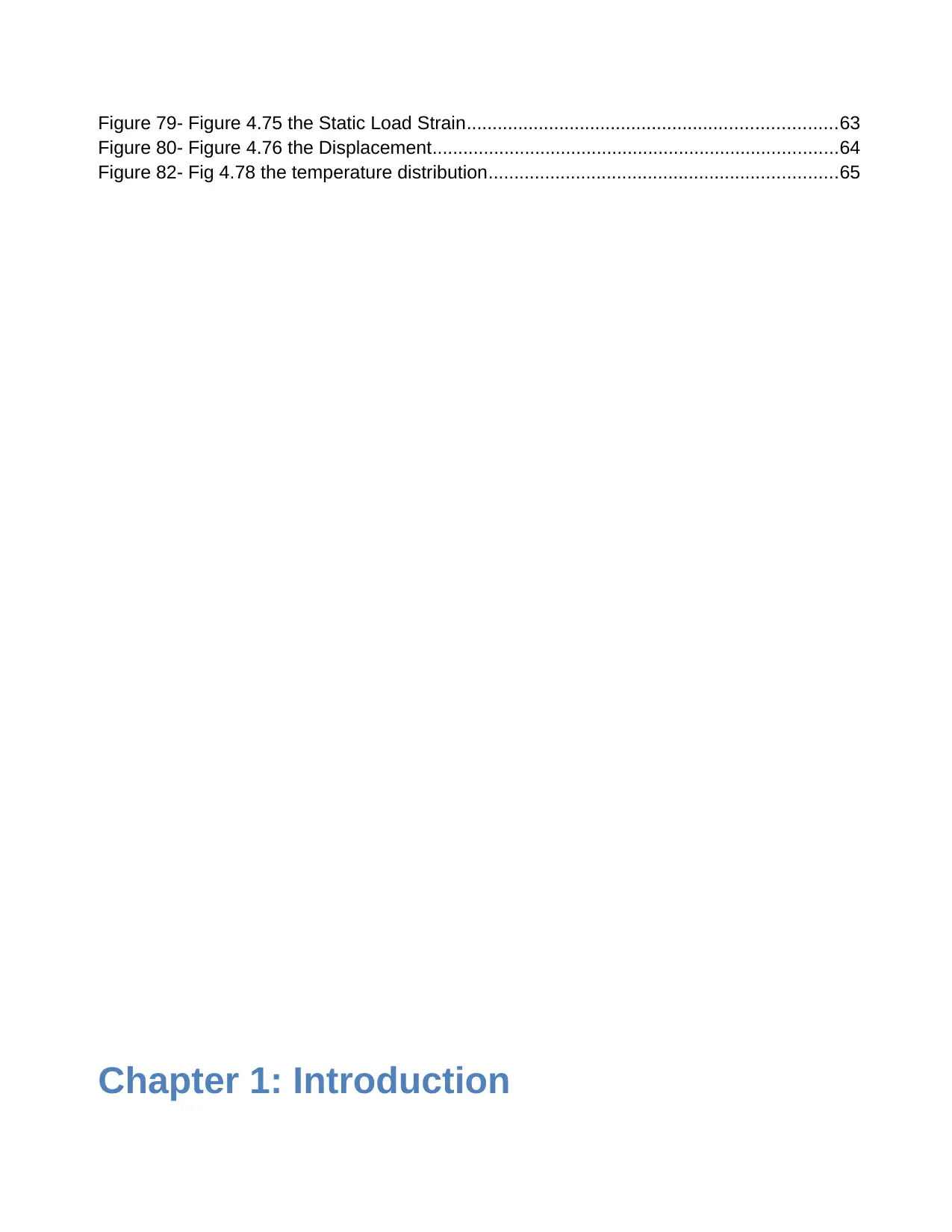
Figure 79- Figure 4.75 the Static Load Strain........................................................................63
Figure 80- Figure 4.76 the Displacement...............................................................................64
Figure 82- Fig 4.78 the temperature distribution....................................................................65
Chapter 1: Introduction
Figure 80- Figure 4.76 the Displacement...............................................................................64
Figure 82- Fig 4.78 the temperature distribution....................................................................65
Chapter 1: Introduction
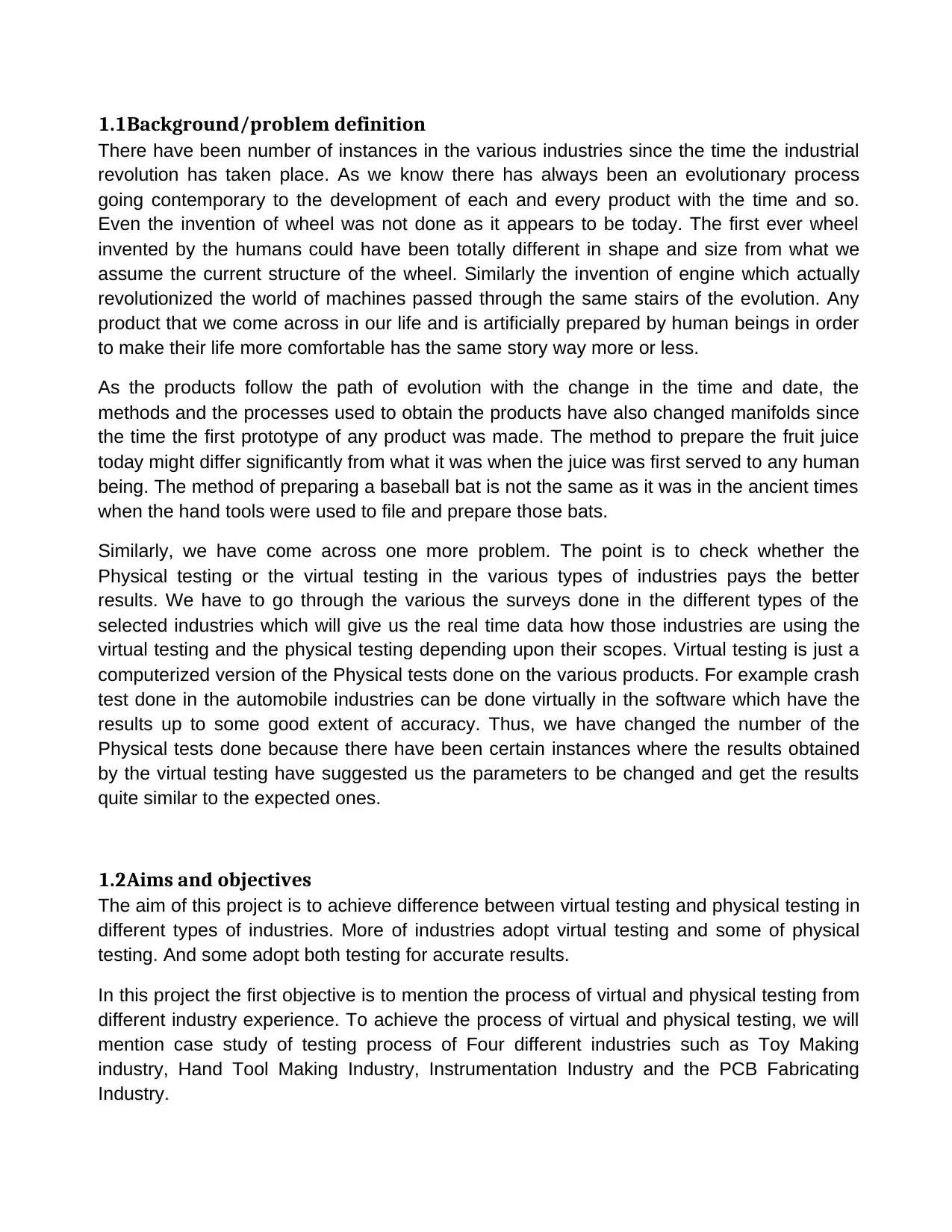
1.1Background/problem definition
There have been number of instances in the various industries since the time the industrial
revolution has taken place. As we know there has always been an evolutionary process
going contemporary to the development of each and every product with the time and so.
Even the invention of wheel was not done as it appears to be today. The first ever wheel
invented by the humans could have been totally different in shape and size from what we
assume the current structure of the wheel. Similarly the invention of engine which actually
revolutionized the world of machines passed through the same stairs of the evolution. Any
product that we come across in our life and is artificially prepared by human beings in order
to make their life more comfortable has the same story way more or less.
As the products follow the path of evolution with the change in the time and date, the
methods and the processes used to obtain the products have also changed manifolds since
the time the first prototype of any product was made. The method to prepare the fruit juice
today might differ significantly from what it was when the juice was first served to any human
being. The method of preparing a baseball bat is not the same as it was in the ancient times
when the hand tools were used to file and prepare those bats.
Similarly, we have come across one more problem. The point is to check whether the
Physical testing or the virtual testing in the various types of industries pays the better
results. We have to go through the various the surveys done in the different types of the
selected industries which will give us the real time data how those industries are using the
virtual testing and the physical testing depending upon their scopes. Virtual testing is just a
computerized version of the Physical tests done on the various products. For example crash
test done in the automobile industries can be done virtually in the software which have the
results up to some good extent of accuracy. Thus, we have changed the number of the
Physical tests done because there have been certain instances where the results obtained
by the virtual testing have suggested us the parameters to be changed and get the results
quite similar to the expected ones.
1.2Aims and objectives
The aim of this project is to achieve difference between virtual testing and physical testing in
different types of industries. More of industries adopt virtual testing and some of physical
testing. And some adopt both testing for accurate results.
In this project the first objective is to mention the process of virtual and physical testing from
different industry experience. To achieve the process of virtual and physical testing, we will
mention case study of testing process of Four different industries such as Toy Making
industry, Hand Tool Making Industry, Instrumentation Industry and the PCB Fabricating
Industry.
There have been number of instances in the various industries since the time the industrial
revolution has taken place. As we know there has always been an evolutionary process
going contemporary to the development of each and every product with the time and so.
Even the invention of wheel was not done as it appears to be today. The first ever wheel
invented by the humans could have been totally different in shape and size from what we
assume the current structure of the wheel. Similarly the invention of engine which actually
revolutionized the world of machines passed through the same stairs of the evolution. Any
product that we come across in our life and is artificially prepared by human beings in order
to make their life more comfortable has the same story way more or less.
As the products follow the path of evolution with the change in the time and date, the
methods and the processes used to obtain the products have also changed manifolds since
the time the first prototype of any product was made. The method to prepare the fruit juice
today might differ significantly from what it was when the juice was first served to any human
being. The method of preparing a baseball bat is not the same as it was in the ancient times
when the hand tools were used to file and prepare those bats.
Similarly, we have come across one more problem. The point is to check whether the
Physical testing or the virtual testing in the various types of industries pays the better
results. We have to go through the various the surveys done in the different types of the
selected industries which will give us the real time data how those industries are using the
virtual testing and the physical testing depending upon their scopes. Virtual testing is just a
computerized version of the Physical tests done on the various products. For example crash
test done in the automobile industries can be done virtually in the software which have the
results up to some good extent of accuracy. Thus, we have changed the number of the
Physical tests done because there have been certain instances where the results obtained
by the virtual testing have suggested us the parameters to be changed and get the results
quite similar to the expected ones.
1.2Aims and objectives
The aim of this project is to achieve difference between virtual testing and physical testing in
different types of industries. More of industries adopt virtual testing and some of physical
testing. And some adopt both testing for accurate results.
In this project the first objective is to mention the process of virtual and physical testing from
different industry experience. To achieve the process of virtual and physical testing, we will
mention case study of testing process of Four different industries such as Toy Making
industry, Hand Tool Making Industry, Instrumentation Industry and the PCB Fabricating
Industry.
Paraphrase This Document
Need a fresh take? Get an instant paraphrase of this document with our AI Paraphraser
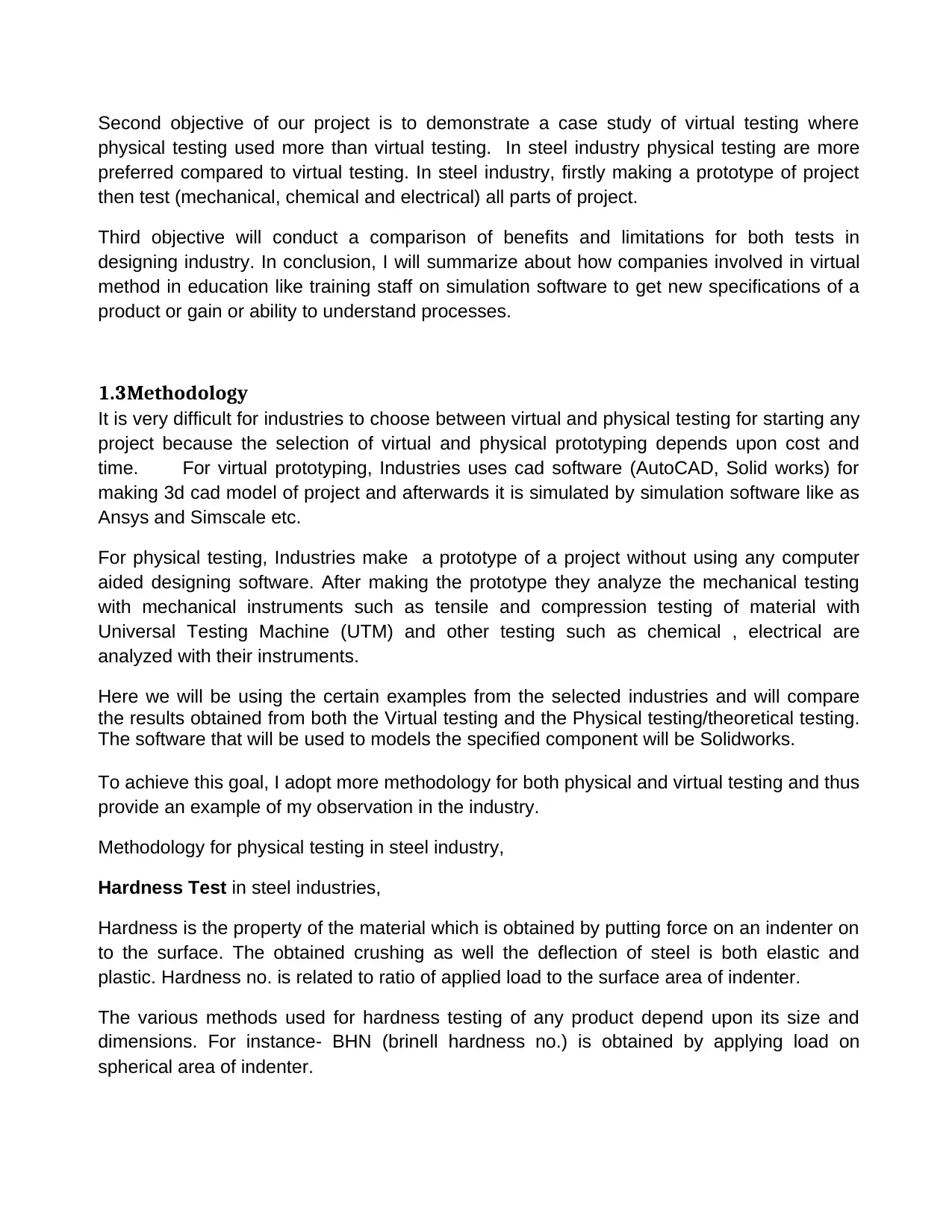
Second objective of our project is to demonstrate a case study of virtual testing where
physical testing used more than virtual testing. In steel industry physical testing are more
preferred compared to virtual testing. In steel industry, firstly making a prototype of project
then test (mechanical, chemical and electrical) all parts of project.
Third objective will conduct a comparison of benefits and limitations for both tests in
designing industry. In conclusion, I will summarize about how companies involved in virtual
method in education like training staff on simulation software to get new specifications of a
product or gain or ability to understand processes.
1.3Methodology
It is very difficult for industries to choose between virtual and physical testing for starting any
project because the selection of virtual and physical prototyping depends upon cost and
time. For virtual prototyping, Industries uses cad software (AutoCAD, Solid works) for
making 3d cad model of project and afterwards it is simulated by simulation software like as
Ansys and Simscale etc.
For physical testing, Industries make a prototype of a project without using any computer
aided designing software. After making the prototype they analyze the mechanical testing
with mechanical instruments such as tensile and compression testing of material with
Universal Testing Machine (UTM) and other testing such as chemical , electrical are
analyzed with their instruments.
Here we will be using the certain examples from the selected industries and will compare
the results obtained from both the Virtual testing and the Physical testing/theoretical testing.
The software that will be used to models the specified component will be Solidworks.
To achieve this goal, I adopt more methodology for both physical and virtual testing and thus
provide an example of my observation in the industry.
Methodology for physical testing in steel industry,
Hardness Test in steel industries,
Hardness is the property of the material which is obtained by putting force on an indenter on
to the surface. The obtained crushing as well the deflection of steel is both elastic and
plastic. Hardness no. is related to ratio of applied load to the surface area of indenter.
The various methods used for hardness testing of any product depend upon its size and
dimensions. For instance- BHN (brinell hardness no.) is obtained by applying load on
spherical area of indenter.
physical testing used more than virtual testing. In steel industry physical testing are more
preferred compared to virtual testing. In steel industry, firstly making a prototype of project
then test (mechanical, chemical and electrical) all parts of project.
Third objective will conduct a comparison of benefits and limitations for both tests in
designing industry. In conclusion, I will summarize about how companies involved in virtual
method in education like training staff on simulation software to get new specifications of a
product or gain or ability to understand processes.
1.3Methodology
It is very difficult for industries to choose between virtual and physical testing for starting any
project because the selection of virtual and physical prototyping depends upon cost and
time. For virtual prototyping, Industries uses cad software (AutoCAD, Solid works) for
making 3d cad model of project and afterwards it is simulated by simulation software like as
Ansys and Simscale etc.
For physical testing, Industries make a prototype of a project without using any computer
aided designing software. After making the prototype they analyze the mechanical testing
with mechanical instruments such as tensile and compression testing of material with
Universal Testing Machine (UTM) and other testing such as chemical , electrical are
analyzed with their instruments.
Here we will be using the certain examples from the selected industries and will compare
the results obtained from both the Virtual testing and the Physical testing/theoretical testing.
The software that will be used to models the specified component will be Solidworks.
To achieve this goal, I adopt more methodology for both physical and virtual testing and thus
provide an example of my observation in the industry.
Methodology for physical testing in steel industry,
Hardness Test in steel industries,
Hardness is the property of the material which is obtained by putting force on an indenter on
to the surface. The obtained crushing as well the deflection of steel is both elastic and
plastic. Hardness no. is related to ratio of applied load to the surface area of indenter.
The various methods used for hardness testing of any product depend upon its size and
dimensions. For instance- BHN (brinell hardness no.) is obtained by applying load on
spherical area of indenter.
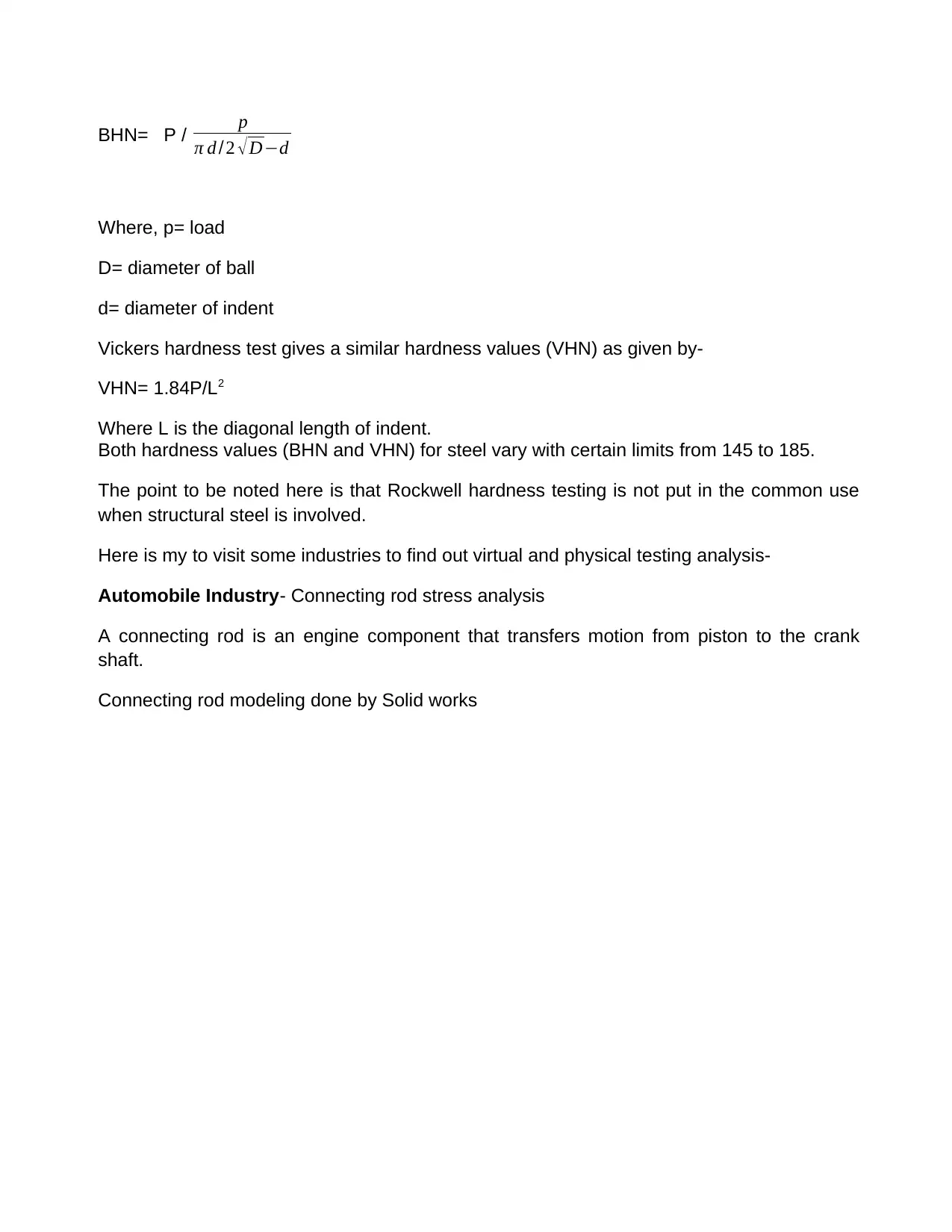
BHN= P / p
π d /2 √ D−d
Where, p= load
D= diameter of ball
d= diameter of indent
Vickers hardness test gives a similar hardness values (VHN) as given by-
VHN= 1.84P/L2
Where L is the diagonal length of indent.
Both hardness values (BHN and VHN) for steel vary with certain limits from 145 to 185.
The point to be noted here is that Rockwell hardness testing is not put in the common use
when structural steel is involved.
Here is my to visit some industries to find out virtual and physical testing analysis-
Automobile Industry- Connecting rod stress analysis
A connecting rod is an engine component that transfers motion from piston to the crank
shaft.
Connecting rod modeling done by Solid works
π d /2 √ D−d
Where, p= load
D= diameter of ball
d= diameter of indent
Vickers hardness test gives a similar hardness values (VHN) as given by-
VHN= 1.84P/L2
Where L is the diagonal length of indent.
Both hardness values (BHN and VHN) for steel vary with certain limits from 145 to 185.
The point to be noted here is that Rockwell hardness testing is not put in the common use
when structural steel is involved.
Here is my to visit some industries to find out virtual and physical testing analysis-
Automobile Industry- Connecting rod stress analysis
A connecting rod is an engine component that transfers motion from piston to the crank
shaft.
Connecting rod modeling done by Solid works
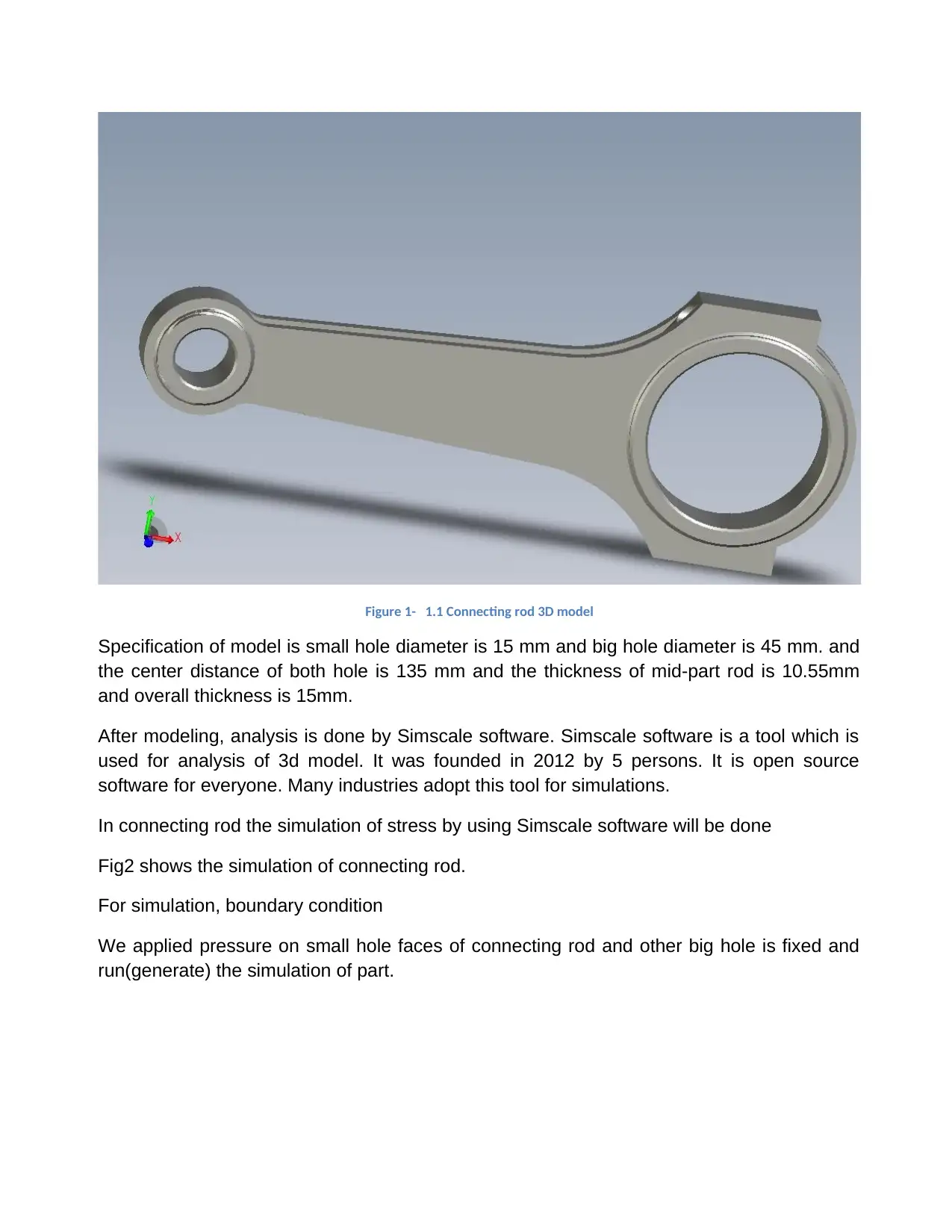
Figure 1- 1.1 Connecting rod 3D model
Specification of model is small hole diameter is 15 mm and big hole diameter is 45 mm. and
the center distance of both hole is 135 mm and the thickness of mid-part rod is 10.55mm
and overall thickness is 15mm.
After modeling, analysis is done by Simscale software. Simscale software is a tool which is
used for analysis of 3d model. It was founded in 2012 by 5 persons. It is open source
software for everyone. Many industries adopt this tool for simulations.
In connecting rod the simulation of stress by using Simscale software will be done
Fig2 shows the simulation of connecting rod.
For simulation, boundary condition
We applied pressure on small hole faces of connecting rod and other big hole is fixed and
run(generate) the simulation of part.
Specification of model is small hole diameter is 15 mm and big hole diameter is 45 mm. and
the center distance of both hole is 135 mm and the thickness of mid-part rod is 10.55mm
and overall thickness is 15mm.
After modeling, analysis is done by Simscale software. Simscale software is a tool which is
used for analysis of 3d model. It was founded in 2012 by 5 persons. It is open source
software for everyone. Many industries adopt this tool for simulations.
In connecting rod the simulation of stress by using Simscale software will be done
Fig2 shows the simulation of connecting rod.
For simulation, boundary condition
We applied pressure on small hole faces of connecting rod and other big hole is fixed and
run(generate) the simulation of part.
Secure Best Marks with AI Grader
Need help grading? Try our AI Grader for instant feedback on your assignments.
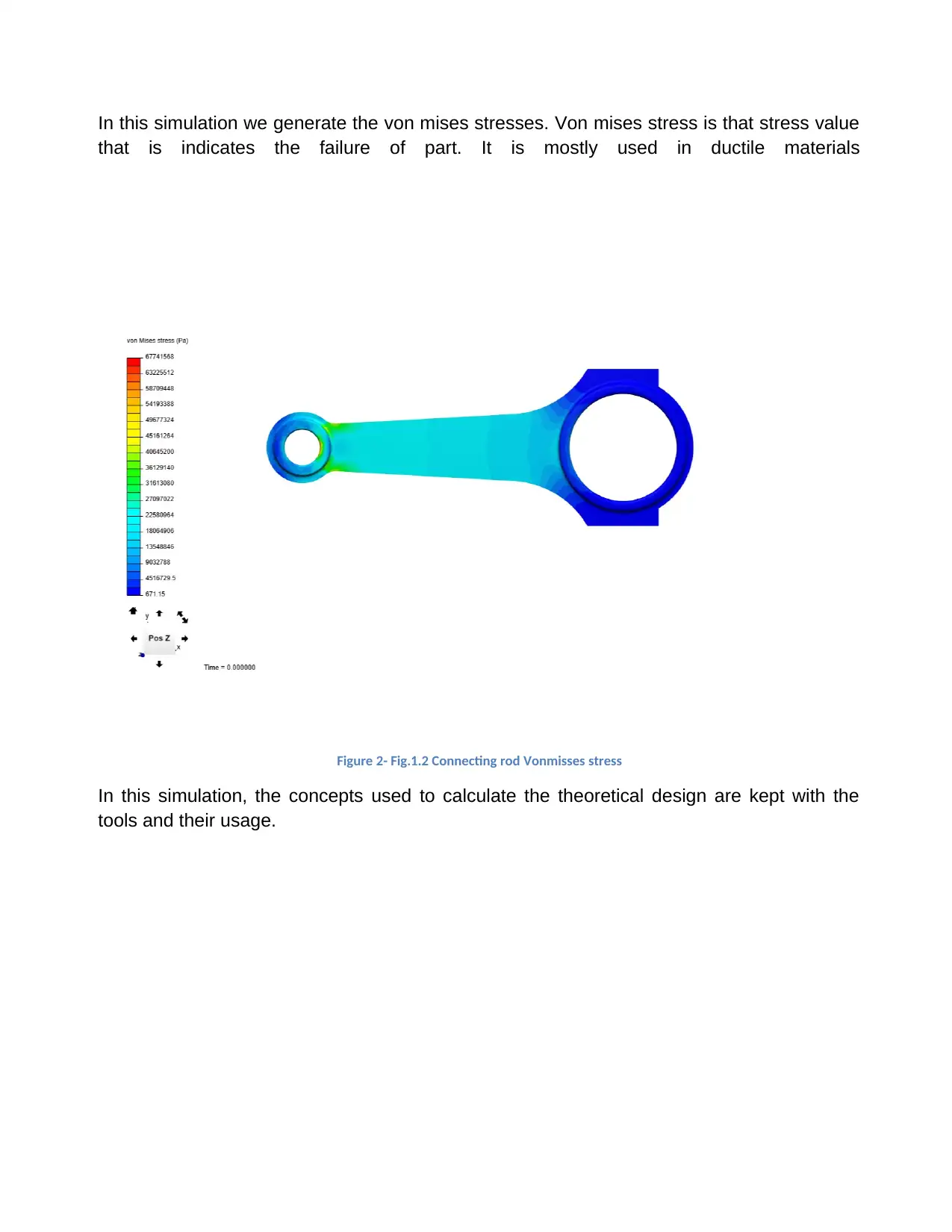
In this simulation we generate the von mises stresses. Von mises stress is that stress value
that is indicates the failure of part. It is mostly used in ductile materials
Figure 2- Fig.1.2 Connecting rod Vonmisses stress
In this simulation, the concepts used to calculate the theoretical design are kept with the
tools and their usage.
that is indicates the failure of part. It is mostly used in ductile materials
Figure 2- Fig.1.2 Connecting rod Vonmisses stress
In this simulation, the concepts used to calculate the theoretical design are kept with the
tools and their usage.
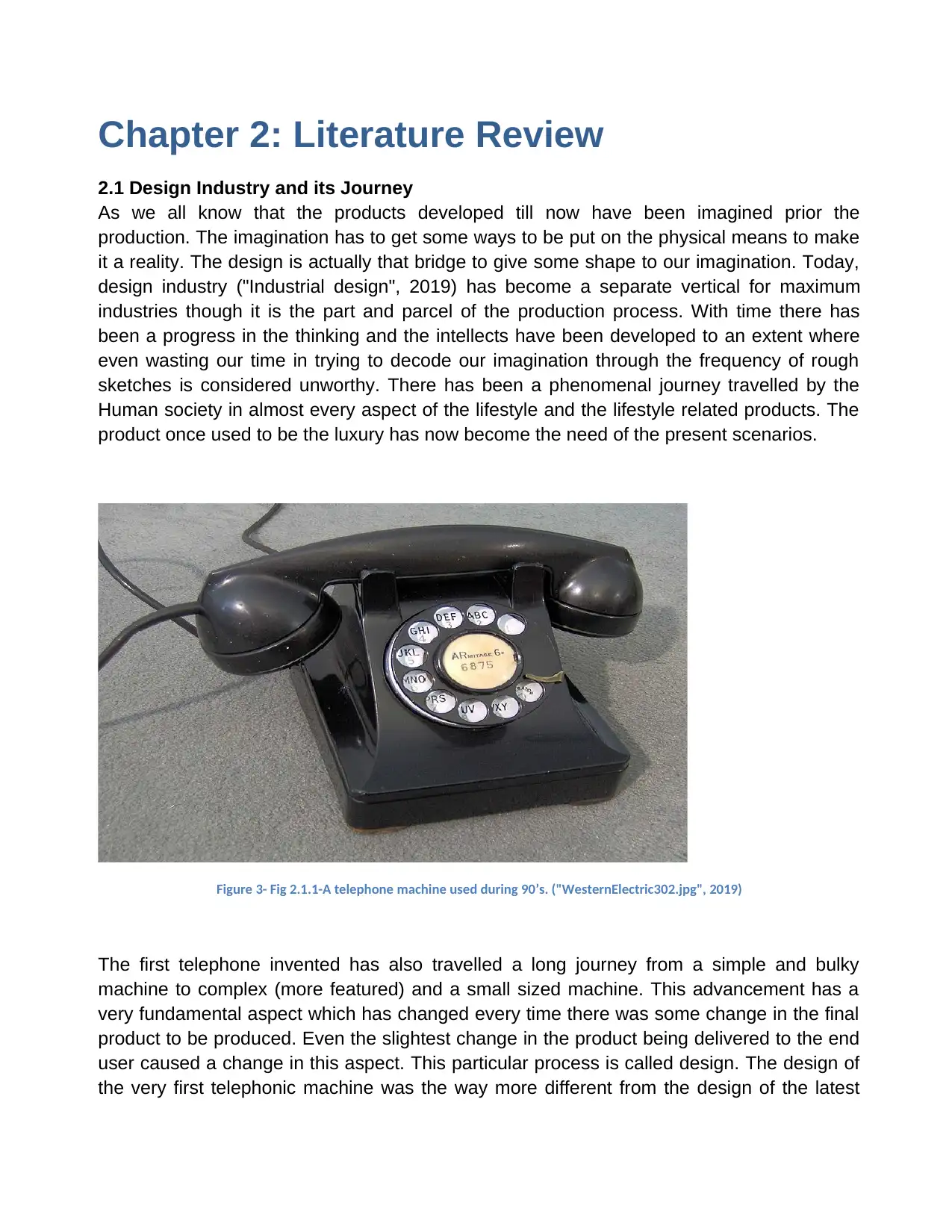
Chapter 2: Literature Review
2.1 Design Industry and its Journey
As we all know that the products developed till now have been imagined prior the
production. The imagination has to get some ways to be put on the physical means to make
it a reality. The design is actually that bridge to give some shape to our imagination. Today,
design industry ("Industrial design", 2019) has become a separate vertical for maximum
industries though it is the part and parcel of the production process. With time there has
been a progress in the thinking and the intellects have been developed to an extent where
even wasting our time in trying to decode our imagination through the frequency of rough
sketches is considered unworthy. There has been a phenomenal journey travelled by the
Human society in almost every aspect of the lifestyle and the lifestyle related products. The
product once used to be the luxury has now become the need of the present scenarios.
Figure 3- Fig 2.1.1-A telephone machine used during 90’s. ("WesternElectric302.jpg", 2019)
The first telephone invented has also travelled a long journey from a simple and bulky
machine to complex (more featured) and a small sized machine. This advancement has a
very fundamental aspect which has changed every time there was some change in the final
product to be produced. Even the slightest change in the product being delivered to the end
user caused a change in this aspect. This particular process is called design. The design of
the very first telephonic machine was the way more different from the design of the latest
2.1 Design Industry and its Journey
As we all know that the products developed till now have been imagined prior the
production. The imagination has to get some ways to be put on the physical means to make
it a reality. The design is actually that bridge to give some shape to our imagination. Today,
design industry ("Industrial design", 2019) has become a separate vertical for maximum
industries though it is the part and parcel of the production process. With time there has
been a progress in the thinking and the intellects have been developed to an extent where
even wasting our time in trying to decode our imagination through the frequency of rough
sketches is considered unworthy. There has been a phenomenal journey travelled by the
Human society in almost every aspect of the lifestyle and the lifestyle related products. The
product once used to be the luxury has now become the need of the present scenarios.
Figure 3- Fig 2.1.1-A telephone machine used during 90’s. ("WesternElectric302.jpg", 2019)
The first telephone invented has also travelled a long journey from a simple and bulky
machine to complex (more featured) and a small sized machine. This advancement has a
very fundamental aspect which has changed every time there was some change in the final
product to be produced. Even the slightest change in the product being delivered to the end
user caused a change in this aspect. This particular process is called design. The design of
the very first telephonic machine was the way more different from the design of the latest
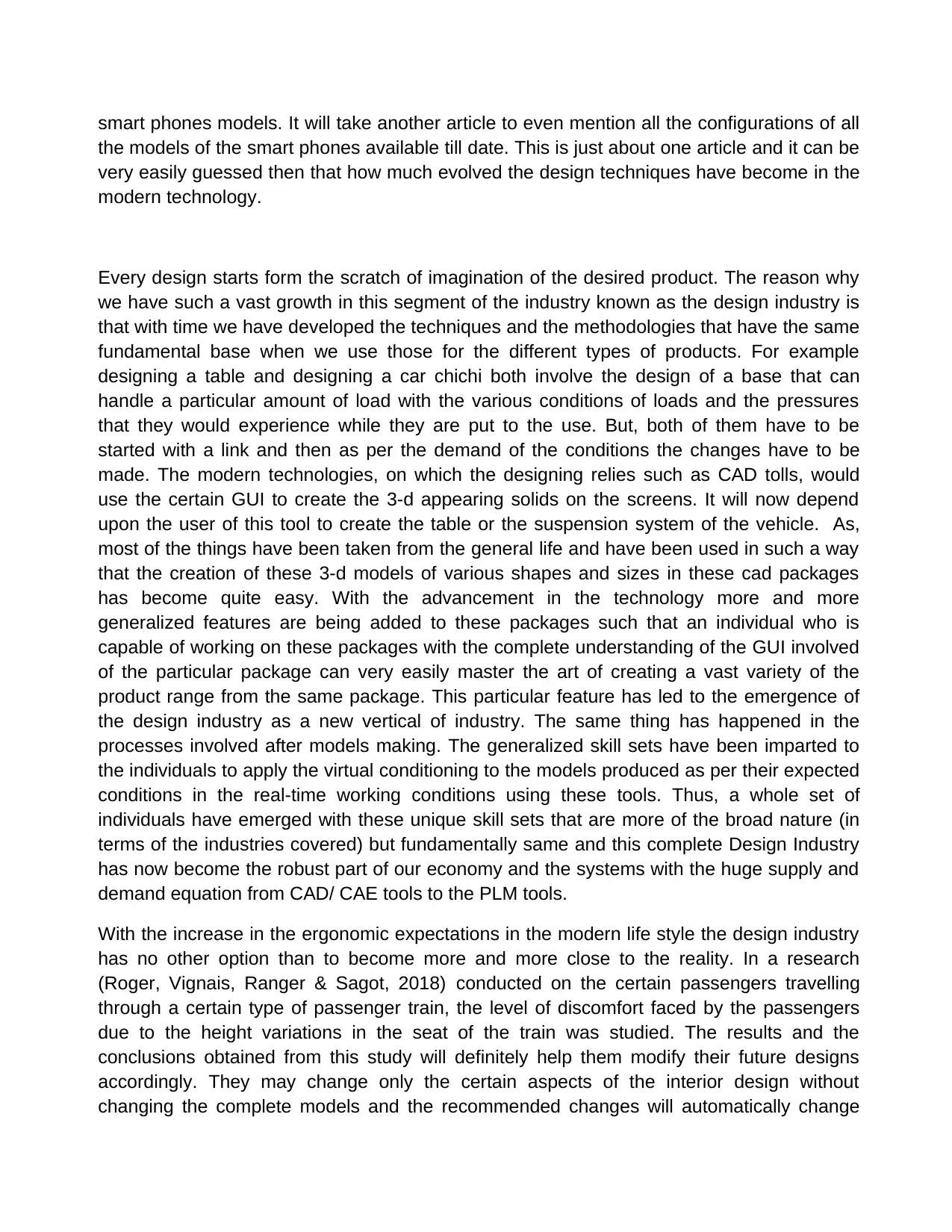
smart phones models. It will take another article to even mention all the configurations of all
the models of the smart phones available till date. This is just about one article and it can be
very easily guessed then that how much evolved the design techniques have become in the
modern technology.
Every design starts form the scratch of imagination of the desired product. The reason why
we have such a vast growth in this segment of the industry known as the design industry is
that with time we have developed the techniques and the methodologies that have the same
fundamental base when we use those for the different types of products. For example
designing a table and designing a car chichi both involve the design of a base that can
handle a particular amount of load with the various conditions of loads and the pressures
that they would experience while they are put to the use. But, both of them have to be
started with a link and then as per the demand of the conditions the changes have to be
made. The modern technologies, on which the designing relies such as CAD tolls, would
use the certain GUI to create the 3-d appearing solids on the screens. It will now depend
upon the user of this tool to create the table or the suspension system of the vehicle. As,
most of the things have been taken from the general life and have been used in such a way
that the creation of these 3-d models of various shapes and sizes in these cad packages
has become quite easy. With the advancement in the technology more and more
generalized features are being added to these packages such that an individual who is
capable of working on these packages with the complete understanding of the GUI involved
of the particular package can very easily master the art of creating a vast variety of the
product range from the same package. This particular feature has led to the emergence of
the design industry as a new vertical of industry. The same thing has happened in the
processes involved after models making. The generalized skill sets have been imparted to
the individuals to apply the virtual conditioning to the models produced as per their expected
conditions in the real-time working conditions using these tools. Thus, a whole set of
individuals have emerged with these unique skill sets that are more of the broad nature (in
terms of the industries covered) but fundamentally same and this complete Design Industry
has now become the robust part of our economy and the systems with the huge supply and
demand equation from CAD/ CAE tools to the PLM tools.
With the increase in the ergonomic expectations in the modern life style the design industry
has no other option than to become more and more close to the reality. In a research
(Roger, Vignais, Ranger & Sagot, 2018) conducted on the certain passengers travelling
through a certain type of passenger train, the level of discomfort faced by the passengers
due to the height variations in the seat of the train was studied. The results and the
conclusions obtained from this study will definitely help them modify their future designs
accordingly. They may change only the certain aspects of the interior design without
changing the complete models and the recommended changes will automatically change
the models of the smart phones available till date. This is just about one article and it can be
very easily guessed then that how much evolved the design techniques have become in the
modern technology.
Every design starts form the scratch of imagination of the desired product. The reason why
we have such a vast growth in this segment of the industry known as the design industry is
that with time we have developed the techniques and the methodologies that have the same
fundamental base when we use those for the different types of products. For example
designing a table and designing a car chichi both involve the design of a base that can
handle a particular amount of load with the various conditions of loads and the pressures
that they would experience while they are put to the use. But, both of them have to be
started with a link and then as per the demand of the conditions the changes have to be
made. The modern technologies, on which the designing relies such as CAD tolls, would
use the certain GUI to create the 3-d appearing solids on the screens. It will now depend
upon the user of this tool to create the table or the suspension system of the vehicle. As,
most of the things have been taken from the general life and have been used in such a way
that the creation of these 3-d models of various shapes and sizes in these cad packages
has become quite easy. With the advancement in the technology more and more
generalized features are being added to these packages such that an individual who is
capable of working on these packages with the complete understanding of the GUI involved
of the particular package can very easily master the art of creating a vast variety of the
product range from the same package. This particular feature has led to the emergence of
the design industry as a new vertical of industry. The same thing has happened in the
processes involved after models making. The generalized skill sets have been imparted to
the individuals to apply the virtual conditioning to the models produced as per their expected
conditions in the real-time working conditions using these tools. Thus, a whole set of
individuals have emerged with these unique skill sets that are more of the broad nature (in
terms of the industries covered) but fundamentally same and this complete Design Industry
has now become the robust part of our economy and the systems with the huge supply and
demand equation from CAD/ CAE tools to the PLM tools.
With the increase in the ergonomic expectations in the modern life style the design industry
has no other option than to become more and more close to the reality. In a research
(Roger, Vignais, Ranger & Sagot, 2018) conducted on the certain passengers travelling
through a certain type of passenger train, the level of discomfort faced by the passengers
due to the height variations in the seat of the train was studied. The results and the
conclusions obtained from this study will definitely help them modify their future designs
accordingly. They may change only the certain aspects of the interior design without
changing the complete models and the recommended changes will automatically change
Paraphrase This Document
Need a fresh take? Get an instant paraphrase of this document with our AI Paraphraser
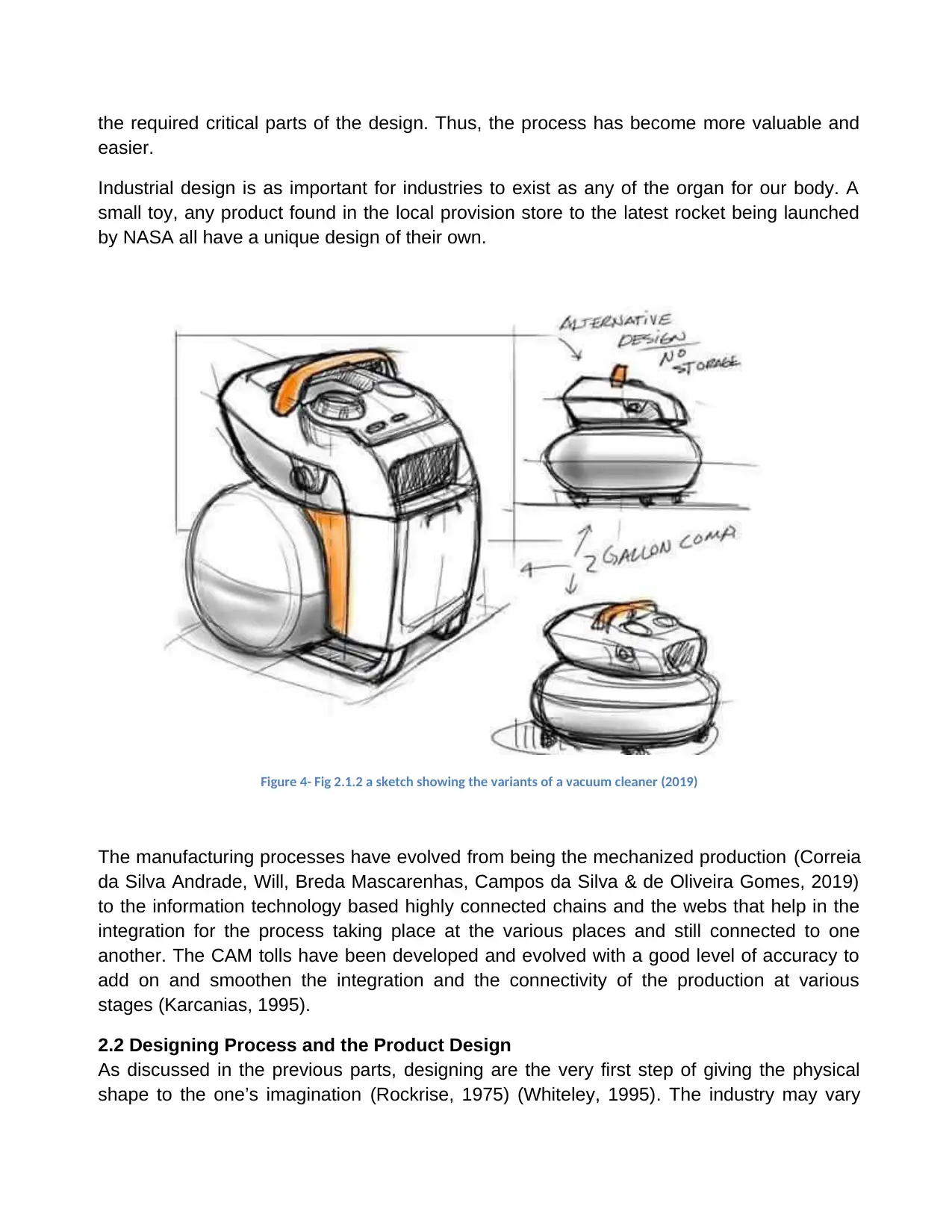
the required critical parts of the design. Thus, the process has become more valuable and
easier.
Industrial design is as important for industries to exist as any of the organ for our body. A
small toy, any product found in the local provision store to the latest rocket being launched
by NASA all have a unique design of their own.
Figure 4- Fig 2.1.2 a sketch showing the variants of a vacuum cleaner (2019)
The manufacturing processes have evolved from being the mechanized production (Correia
da Silva Andrade, Will, Breda Mascarenhas, Campos da Silva & de Oliveira Gomes, 2019)
to the information technology based highly connected chains and the webs that help in the
integration for the process taking place at the various places and still connected to one
another. The CAM tolls have been developed and evolved with a good level of accuracy to
add on and smoothen the integration and the connectivity of the production at various
stages (Karcanias, 1995).
2.2 Designing Process and the Product Design
As discussed in the previous parts, designing are the very first step of giving the physical
shape to the one’s imagination (Rockrise, 1975) (Whiteley, 1995). The industry may vary
easier.
Industrial design is as important for industries to exist as any of the organ for our body. A
small toy, any product found in the local provision store to the latest rocket being launched
by NASA all have a unique design of their own.
Figure 4- Fig 2.1.2 a sketch showing the variants of a vacuum cleaner (2019)
The manufacturing processes have evolved from being the mechanized production (Correia
da Silva Andrade, Will, Breda Mascarenhas, Campos da Silva & de Oliveira Gomes, 2019)
to the information technology based highly connected chains and the webs that help in the
integration for the process taking place at the various places and still connected to one
another. The CAM tolls have been developed and evolved with a good level of accuracy to
add on and smoothen the integration and the connectivity of the production at various
stages (Karcanias, 1995).
2.2 Designing Process and the Product Design
As discussed in the previous parts, designing are the very first step of giving the physical
shape to the one’s imagination (Rockrise, 1975) (Whiteley, 1995). The industry may vary
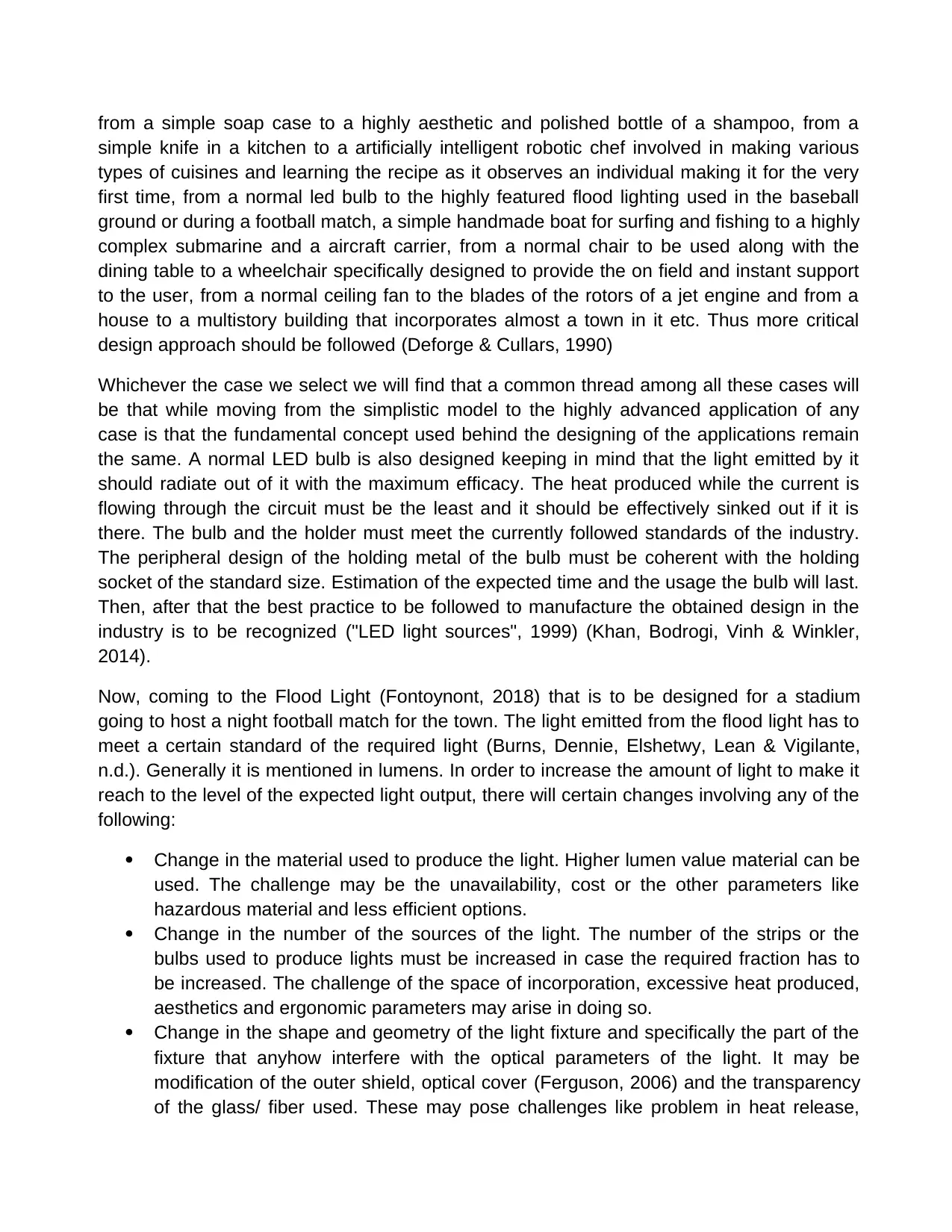
from a simple soap case to a highly aesthetic and polished bottle of a shampoo, from a
simple knife in a kitchen to a artificially intelligent robotic chef involved in making various
types of cuisines and learning the recipe as it observes an individual making it for the very
first time, from a normal led bulb to the highly featured flood lighting used in the baseball
ground or during a football match, a simple handmade boat for surfing and fishing to a highly
complex submarine and a aircraft carrier, from a normal chair to be used along with the
dining table to a wheelchair specifically designed to provide the on field and instant support
to the user, from a normal ceiling fan to the blades of the rotors of a jet engine and from a
house to a multistory building that incorporates almost a town in it etc. Thus more critical
design approach should be followed (Deforge & Cullars, 1990)
Whichever the case we select we will find that a common thread among all these cases will
be that while moving from the simplistic model to the highly advanced application of any
case is that the fundamental concept used behind the designing of the applications remain
the same. A normal LED bulb is also designed keeping in mind that the light emitted by it
should radiate out of it with the maximum efficacy. The heat produced while the current is
flowing through the circuit must be the least and it should be effectively sinked out if it is
there. The bulb and the holder must meet the currently followed standards of the industry.
The peripheral design of the holding metal of the bulb must be coherent with the holding
socket of the standard size. Estimation of the expected time and the usage the bulb will last.
Then, after that the best practice to be followed to manufacture the obtained design in the
industry is to be recognized ("LED light sources", 1999) (Khan, Bodrogi, Vinh & Winkler,
2014).
Now, coming to the Flood Light (Fontoynont, 2018) that is to be designed for a stadium
going to host a night football match for the town. The light emitted from the flood light has to
meet a certain standard of the required light (Burns, Dennie, Elshetwy, Lean & Vigilante,
n.d.). Generally it is mentioned in lumens. In order to increase the amount of light to make it
reach to the level of the expected light output, there will certain changes involving any of the
following:
Change in the material used to produce the light. Higher lumen value material can be
used. The challenge may be the unavailability, cost or the other parameters like
hazardous material and less efficient options.
Change in the number of the sources of the light. The number of the strips or the
bulbs used to produce lights must be increased in case the required fraction has to
be increased. The challenge of the space of incorporation, excessive heat produced,
aesthetics and ergonomic parameters may arise in doing so.
Change in the shape and geometry of the light fixture and specifically the part of the
fixture that anyhow interfere with the optical parameters of the light. It may be
modification of the outer shield, optical cover (Ferguson, 2006) and the transparency
of the glass/ fiber used. These may pose challenges like problem in heat release,
simple knife in a kitchen to a artificially intelligent robotic chef involved in making various
types of cuisines and learning the recipe as it observes an individual making it for the very
first time, from a normal led bulb to the highly featured flood lighting used in the baseball
ground or during a football match, a simple handmade boat for surfing and fishing to a highly
complex submarine and a aircraft carrier, from a normal chair to be used along with the
dining table to a wheelchair specifically designed to provide the on field and instant support
to the user, from a normal ceiling fan to the blades of the rotors of a jet engine and from a
house to a multistory building that incorporates almost a town in it etc. Thus more critical
design approach should be followed (Deforge & Cullars, 1990)
Whichever the case we select we will find that a common thread among all these cases will
be that while moving from the simplistic model to the highly advanced application of any
case is that the fundamental concept used behind the designing of the applications remain
the same. A normal LED bulb is also designed keeping in mind that the light emitted by it
should radiate out of it with the maximum efficacy. The heat produced while the current is
flowing through the circuit must be the least and it should be effectively sinked out if it is
there. The bulb and the holder must meet the currently followed standards of the industry.
The peripheral design of the holding metal of the bulb must be coherent with the holding
socket of the standard size. Estimation of the expected time and the usage the bulb will last.
Then, after that the best practice to be followed to manufacture the obtained design in the
industry is to be recognized ("LED light sources", 1999) (Khan, Bodrogi, Vinh & Winkler,
2014).
Now, coming to the Flood Light (Fontoynont, 2018) that is to be designed for a stadium
going to host a night football match for the town. The light emitted from the flood light has to
meet a certain standard of the required light (Burns, Dennie, Elshetwy, Lean & Vigilante,
n.d.). Generally it is mentioned in lumens. In order to increase the amount of light to make it
reach to the level of the expected light output, there will certain changes involving any of the
following:
Change in the material used to produce the light. Higher lumen value material can be
used. The challenge may be the unavailability, cost or the other parameters like
hazardous material and less efficient options.
Change in the number of the sources of the light. The number of the strips or the
bulbs used to produce lights must be increased in case the required fraction has to
be increased. The challenge of the space of incorporation, excessive heat produced,
aesthetics and ergonomic parameters may arise in doing so.
Change in the shape and geometry of the light fixture and specifically the part of the
fixture that anyhow interfere with the optical parameters of the light. It may be
modification of the outer shield, optical cover (Ferguson, 2006) and the transparency
of the glass/ fiber used. These may pose challenges like problem in heat release,
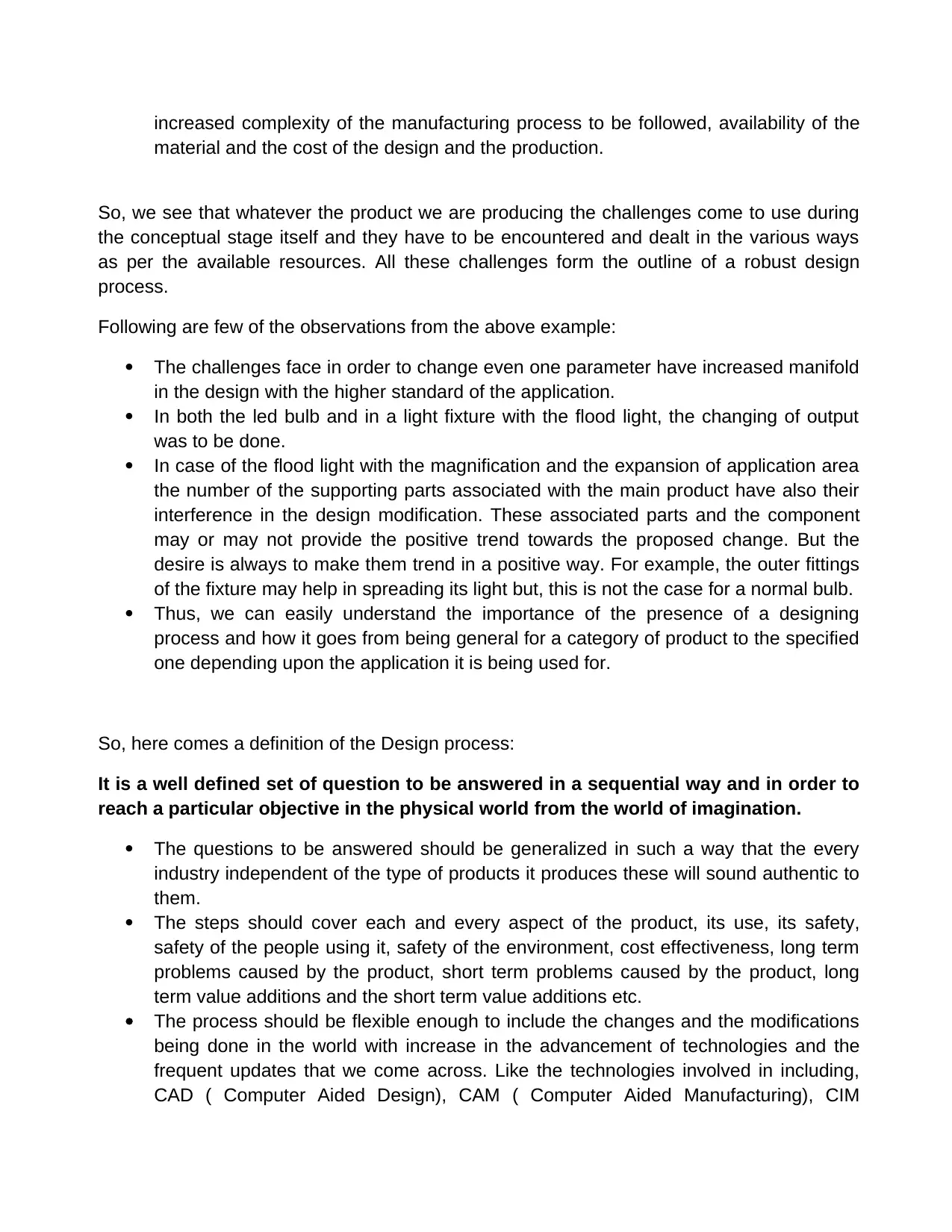
increased complexity of the manufacturing process to be followed, availability of the
material and the cost of the design and the production.
So, we see that whatever the product we are producing the challenges come to use during
the conceptual stage itself and they have to be encountered and dealt in the various ways
as per the available resources. All these challenges form the outline of a robust design
process.
Following are few of the observations from the above example:
The challenges face in order to change even one parameter have increased manifold
in the design with the higher standard of the application.
In both the led bulb and in a light fixture with the flood light, the changing of output
was to be done.
In case of the flood light with the magnification and the expansion of application area
the number of the supporting parts associated with the main product have also their
interference in the design modification. These associated parts and the component
may or may not provide the positive trend towards the proposed change. But the
desire is always to make them trend in a positive way. For example, the outer fittings
of the fixture may help in spreading its light but, this is not the case for a normal bulb.
Thus, we can easily understand the importance of the presence of a designing
process and how it goes from being general for a category of product to the specified
one depending upon the application it is being used for.
So, here comes a definition of the Design process:
It is a well defined set of question to be answered in a sequential way and in order to
reach a particular objective in the physical world from the world of imagination.
The questions to be answered should be generalized in such a way that the every
industry independent of the type of products it produces these will sound authentic to
them.
The steps should cover each and every aspect of the product, its use, its safety,
safety of the people using it, safety of the environment, cost effectiveness, long term
problems caused by the product, short term problems caused by the product, long
term value additions and the short term value additions etc.
The process should be flexible enough to include the changes and the modifications
being done in the world with increase in the advancement of technologies and the
frequent updates that we come across. Like the technologies involved in including,
CAD ( Computer Aided Design), CAM ( Computer Aided Manufacturing), CIM
material and the cost of the design and the production.
So, we see that whatever the product we are producing the challenges come to use during
the conceptual stage itself and they have to be encountered and dealt in the various ways
as per the available resources. All these challenges form the outline of a robust design
process.
Following are few of the observations from the above example:
The challenges face in order to change even one parameter have increased manifold
in the design with the higher standard of the application.
In both the led bulb and in a light fixture with the flood light, the changing of output
was to be done.
In case of the flood light with the magnification and the expansion of application area
the number of the supporting parts associated with the main product have also their
interference in the design modification. These associated parts and the component
may or may not provide the positive trend towards the proposed change. But the
desire is always to make them trend in a positive way. For example, the outer fittings
of the fixture may help in spreading its light but, this is not the case for a normal bulb.
Thus, we can easily understand the importance of the presence of a designing
process and how it goes from being general for a category of product to the specified
one depending upon the application it is being used for.
So, here comes a definition of the Design process:
It is a well defined set of question to be answered in a sequential way and in order to
reach a particular objective in the physical world from the world of imagination.
The questions to be answered should be generalized in such a way that the every
industry independent of the type of products it produces these will sound authentic to
them.
The steps should cover each and every aspect of the product, its use, its safety,
safety of the people using it, safety of the environment, cost effectiveness, long term
problems caused by the product, short term problems caused by the product, long
term value additions and the short term value additions etc.
The process should be flexible enough to include the changes and the modifications
being done in the world with increase in the advancement of technologies and the
frequent updates that we come across. Like the technologies involved in including,
CAD ( Computer Aided Design), CAM ( Computer Aided Manufacturing), CIM
Secure Best Marks with AI Grader
Need help grading? Try our AI Grader for instant feedback on your assignments.
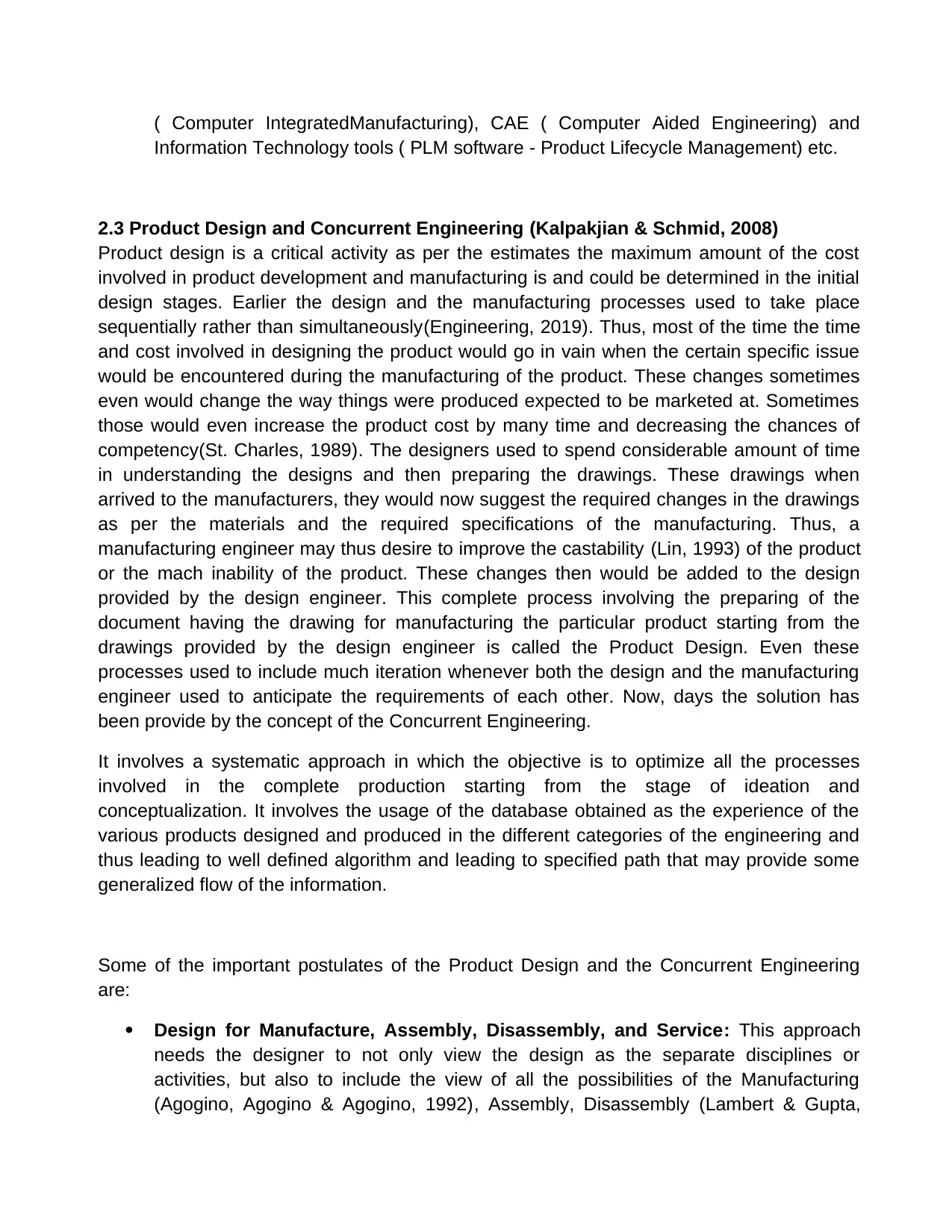
( Computer IntegratedManufacturing), CAE ( Computer Aided Engineering) and
Information Technology tools ( PLM software - Product Lifecycle Management) etc.
2.3 Product Design and Concurrent Engineering (Kalpakjian & Schmid, 2008)
Product design is a critical activity as per the estimates the maximum amount of the cost
involved in product development and manufacturing is and could be determined in the initial
design stages. Earlier the design and the manufacturing processes used to take place
sequentially rather than simultaneously(Engineering, 2019). Thus, most of the time the time
and cost involved in designing the product would go in vain when the certain specific issue
would be encountered during the manufacturing of the product. These changes sometimes
even would change the way things were produced expected to be marketed at. Sometimes
those would even increase the product cost by many time and decreasing the chances of
competency(St. Charles, 1989). The designers used to spend considerable amount of time
in understanding the designs and then preparing the drawings. These drawings when
arrived to the manufacturers, they would now suggest the required changes in the drawings
as per the materials and the required specifications of the manufacturing. Thus, a
manufacturing engineer may thus desire to improve the castability (Lin, 1993) of the product
or the mach inability of the product. These changes then would be added to the design
provided by the design engineer. This complete process involving the preparing of the
document having the drawing for manufacturing the particular product starting from the
drawings provided by the design engineer is called the Product Design. Even these
processes used to include much iteration whenever both the design and the manufacturing
engineer used to anticipate the requirements of each other. Now, days the solution has
been provide by the concept of the Concurrent Engineering.
It involves a systematic approach in which the objective is to optimize all the processes
involved in the complete production starting from the stage of ideation and
conceptualization. It involves the usage of the database obtained as the experience of the
various products designed and produced in the different categories of the engineering and
thus leading to well defined algorithm and leading to specified path that may provide some
generalized flow of the information.
Some of the important postulates of the Product Design and the Concurrent Engineering
are:
Design for Manufacture, Assembly, Disassembly, and Service: This approach
needs the designer to not only view the design as the separate disciplines or
activities, but also to include the view of all the possibilities of the Manufacturing
(Agogino, Agogino & Agogino, 1992), Assembly, Disassembly (Lambert & Gupta,
Information Technology tools ( PLM software - Product Lifecycle Management) etc.
2.3 Product Design and Concurrent Engineering (Kalpakjian & Schmid, 2008)
Product design is a critical activity as per the estimates the maximum amount of the cost
involved in product development and manufacturing is and could be determined in the initial
design stages. Earlier the design and the manufacturing processes used to take place
sequentially rather than simultaneously(Engineering, 2019). Thus, most of the time the time
and cost involved in designing the product would go in vain when the certain specific issue
would be encountered during the manufacturing of the product. These changes sometimes
even would change the way things were produced expected to be marketed at. Sometimes
those would even increase the product cost by many time and decreasing the chances of
competency(St. Charles, 1989). The designers used to spend considerable amount of time
in understanding the designs and then preparing the drawings. These drawings when
arrived to the manufacturers, they would now suggest the required changes in the drawings
as per the materials and the required specifications of the manufacturing. Thus, a
manufacturing engineer may thus desire to improve the castability (Lin, 1993) of the product
or the mach inability of the product. These changes then would be added to the design
provided by the design engineer. This complete process involving the preparing of the
document having the drawing for manufacturing the particular product starting from the
drawings provided by the design engineer is called the Product Design. Even these
processes used to include much iteration whenever both the design and the manufacturing
engineer used to anticipate the requirements of each other. Now, days the solution has
been provide by the concept of the Concurrent Engineering.
It involves a systematic approach in which the objective is to optimize all the processes
involved in the complete production starting from the stage of ideation and
conceptualization. It involves the usage of the database obtained as the experience of the
various products designed and produced in the different categories of the engineering and
thus leading to well defined algorithm and leading to specified path that may provide some
generalized flow of the information.
Some of the important postulates of the Product Design and the Concurrent Engineering
are:
Design for Manufacture, Assembly, Disassembly, and Service: This approach
needs the designer to not only view the design as the separate disciplines or
activities, but also to include the view of all the possibilities of the Manufacturing
(Agogino, Agogino & Agogino, 1992), Assembly, Disassembly (Lambert & Gupta,
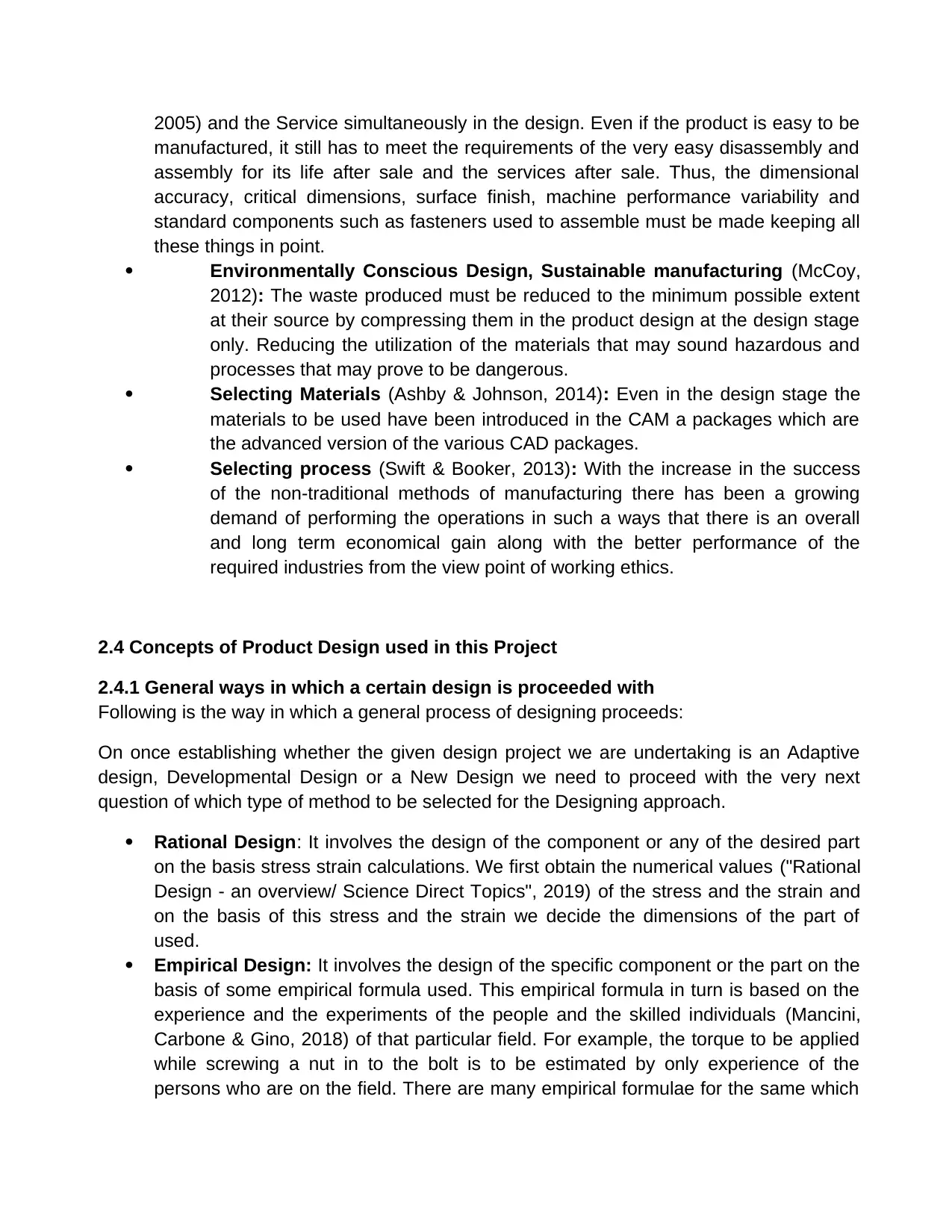
2005) and the Service simultaneously in the design. Even if the product is easy to be
manufactured, it still has to meet the requirements of the very easy disassembly and
assembly for its life after sale and the services after sale. Thus, the dimensional
accuracy, critical dimensions, surface finish, machine performance variability and
standard components such as fasteners used to assemble must be made keeping all
these things in point.
Environmentally Conscious Design, Sustainable manufacturing (McCoy,
2012): The waste produced must be reduced to the minimum possible extent
at their source by compressing them in the product design at the design stage
only. Reducing the utilization of the materials that may sound hazardous and
processes that may prove to be dangerous.
Selecting Materials (Ashby & Johnson, 2014): Even in the design stage the
materials to be used have been introduced in the CAM a packages which are
the advanced version of the various CAD packages.
Selecting process (Swift & Booker, 2013): With the increase in the success
of the non-traditional methods of manufacturing there has been a growing
demand of performing the operations in such a ways that there is an overall
and long term economical gain along with the better performance of the
required industries from the view point of working ethics.
2.4 Concepts of Product Design used in this Project
2.4.1 General ways in which a certain design is proceeded with
Following is the way in which a general process of designing proceeds:
On once establishing whether the given design project we are undertaking is an Adaptive
design, Developmental Design or a New Design we need to proceed with the very next
question of which type of method to be selected for the Designing approach.
Rational Design: It involves the design of the component or any of the desired part
on the basis stress strain calculations. We first obtain the numerical values ("Rational
Design - an overview/ Science Direct Topics", 2019) of the stress and the strain and
on the basis of this stress and the strain we decide the dimensions of the part of
used.
Empirical Design: It involves the design of the specific component or the part on the
basis of some empirical formula used. This empirical formula in turn is based on the
experience and the experiments of the people and the skilled individuals (Mancini,
Carbone & Gino, 2018) of that particular field. For example, the torque to be applied
while screwing a nut in to the bolt is to be estimated by only experience of the
persons who are on the field. There are many empirical formulae for the same which
manufactured, it still has to meet the requirements of the very easy disassembly and
assembly for its life after sale and the services after sale. Thus, the dimensional
accuracy, critical dimensions, surface finish, machine performance variability and
standard components such as fasteners used to assemble must be made keeping all
these things in point.
Environmentally Conscious Design, Sustainable manufacturing (McCoy,
2012): The waste produced must be reduced to the minimum possible extent
at their source by compressing them in the product design at the design stage
only. Reducing the utilization of the materials that may sound hazardous and
processes that may prove to be dangerous.
Selecting Materials (Ashby & Johnson, 2014): Even in the design stage the
materials to be used have been introduced in the CAM a packages which are
the advanced version of the various CAD packages.
Selecting process (Swift & Booker, 2013): With the increase in the success
of the non-traditional methods of manufacturing there has been a growing
demand of performing the operations in such a ways that there is an overall
and long term economical gain along with the better performance of the
required industries from the view point of working ethics.
2.4 Concepts of Product Design used in this Project
2.4.1 General ways in which a certain design is proceeded with
Following is the way in which a general process of designing proceeds:
On once establishing whether the given design project we are undertaking is an Adaptive
design, Developmental Design or a New Design we need to proceed with the very next
question of which type of method to be selected for the Designing approach.
Rational Design: It involves the design of the component or any of the desired part
on the basis stress strain calculations. We first obtain the numerical values ("Rational
Design - an overview/ Science Direct Topics", 2019) of the stress and the strain and
on the basis of this stress and the strain we decide the dimensions of the part of
used.
Empirical Design: It involves the design of the specific component or the part on the
basis of some empirical formula used. This empirical formula in turn is based on the
experience and the experiments of the people and the skilled individuals (Mancini,
Carbone & Gino, 2018) of that particular field. For example, the torque to be applied
while screwing a nut in to the bolt is to be estimated by only experience of the
persons who are on the field. There are many empirical formulae for the same which
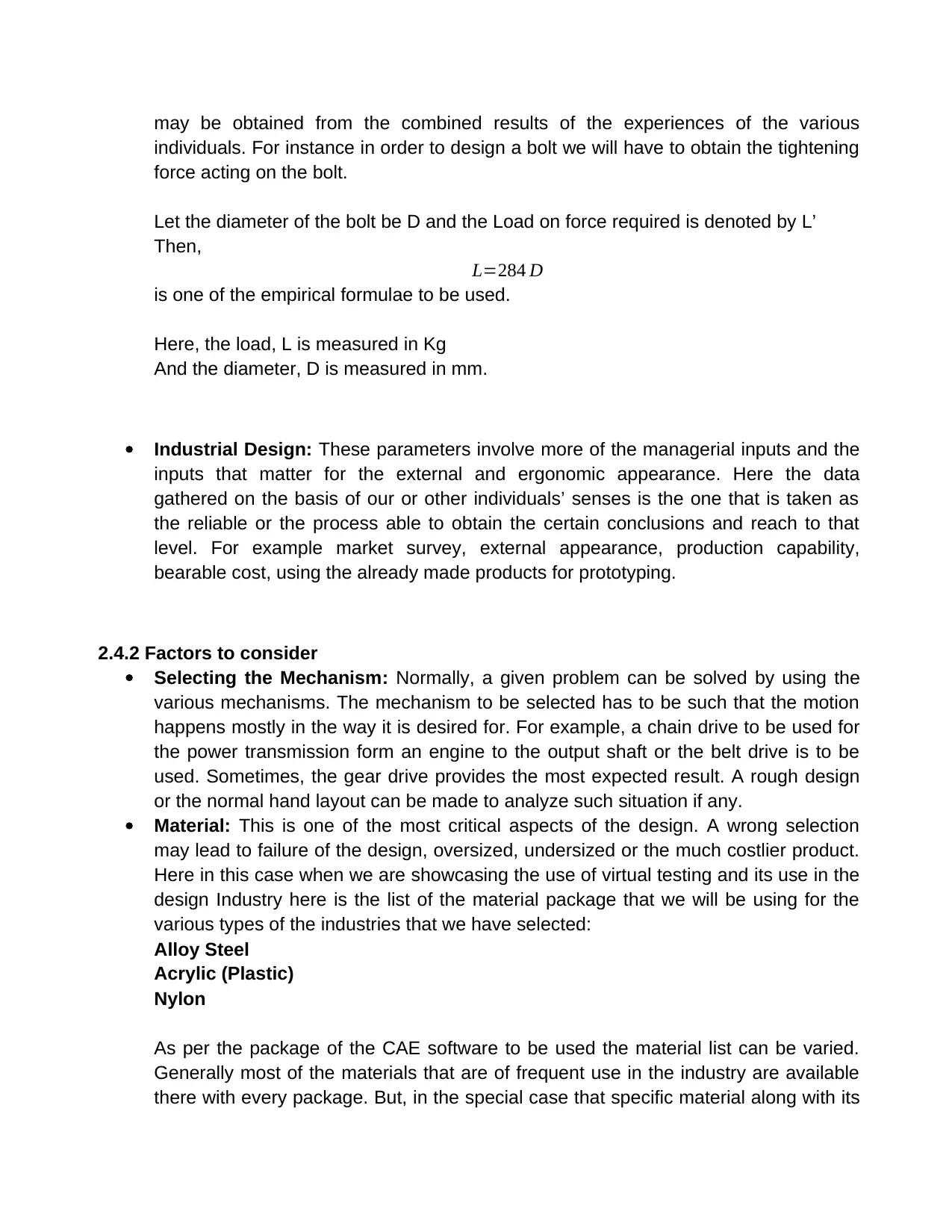
may be obtained from the combined results of the experiences of the various
individuals. For instance in order to design a bolt we will have to obtain the tightening
force acting on the bolt.
Let the diameter of the bolt be D and the Load on force required is denoted by L’
Then,
L=284 D
is one of the empirical formulae to be used.
Here, the load, L is measured in Kg
And the diameter, D is measured in mm.
Industrial Design: These parameters involve more of the managerial inputs and the
inputs that matter for the external and ergonomic appearance. Here the data
gathered on the basis of our or other individuals’ senses is the one that is taken as
the reliable or the process able to obtain the certain conclusions and reach to that
level. For example market survey, external appearance, production capability,
bearable cost, using the already made products for prototyping.
2.4.2 Factors to consider
Selecting the Mechanism: Normally, a given problem can be solved by using the
various mechanisms. The mechanism to be selected has to be such that the motion
happens mostly in the way it is desired for. For example, a chain drive to be used for
the power transmission form an engine to the output shaft or the belt drive is to be
used. Sometimes, the gear drive provides the most expected result. A rough design
or the normal hand layout can be made to analyze such situation if any.
Material: This is one of the most critical aspects of the design. A wrong selection
may lead to failure of the design, oversized, undersized or the much costlier product.
Here in this case when we are showcasing the use of virtual testing and its use in the
design Industry here is the list of the material package that we will be using for the
various types of the industries that we have selected:
Alloy Steel
Acrylic (Plastic)
Nylon
As per the package of the CAE software to be used the material list can be varied.
Generally most of the materials that are of frequent use in the industry are available
there with every package. But, in the special case that specific material along with its
individuals. For instance in order to design a bolt we will have to obtain the tightening
force acting on the bolt.
Let the diameter of the bolt be D and the Load on force required is denoted by L’
Then,
L=284 D
is one of the empirical formulae to be used.
Here, the load, L is measured in Kg
And the diameter, D is measured in mm.
Industrial Design: These parameters involve more of the managerial inputs and the
inputs that matter for the external and ergonomic appearance. Here the data
gathered on the basis of our or other individuals’ senses is the one that is taken as
the reliable or the process able to obtain the certain conclusions and reach to that
level. For example market survey, external appearance, production capability,
bearable cost, using the already made products for prototyping.
2.4.2 Factors to consider
Selecting the Mechanism: Normally, a given problem can be solved by using the
various mechanisms. The mechanism to be selected has to be such that the motion
happens mostly in the way it is desired for. For example, a chain drive to be used for
the power transmission form an engine to the output shaft or the belt drive is to be
used. Sometimes, the gear drive provides the most expected result. A rough design
or the normal hand layout can be made to analyze such situation if any.
Material: This is one of the most critical aspects of the design. A wrong selection
may lead to failure of the design, oversized, undersized or the much costlier product.
Here in this case when we are showcasing the use of virtual testing and its use in the
design Industry here is the list of the material package that we will be using for the
various types of the industries that we have selected:
Alloy Steel
Acrylic (Plastic)
Nylon
As per the package of the CAE software to be used the material list can be varied.
Generally most of the materials that are of frequent use in the industry are available
there with every package. But, in the special case that specific material along with its
Paraphrase This Document
Need a fresh take? Get an instant paraphrase of this document with our AI Paraphraser
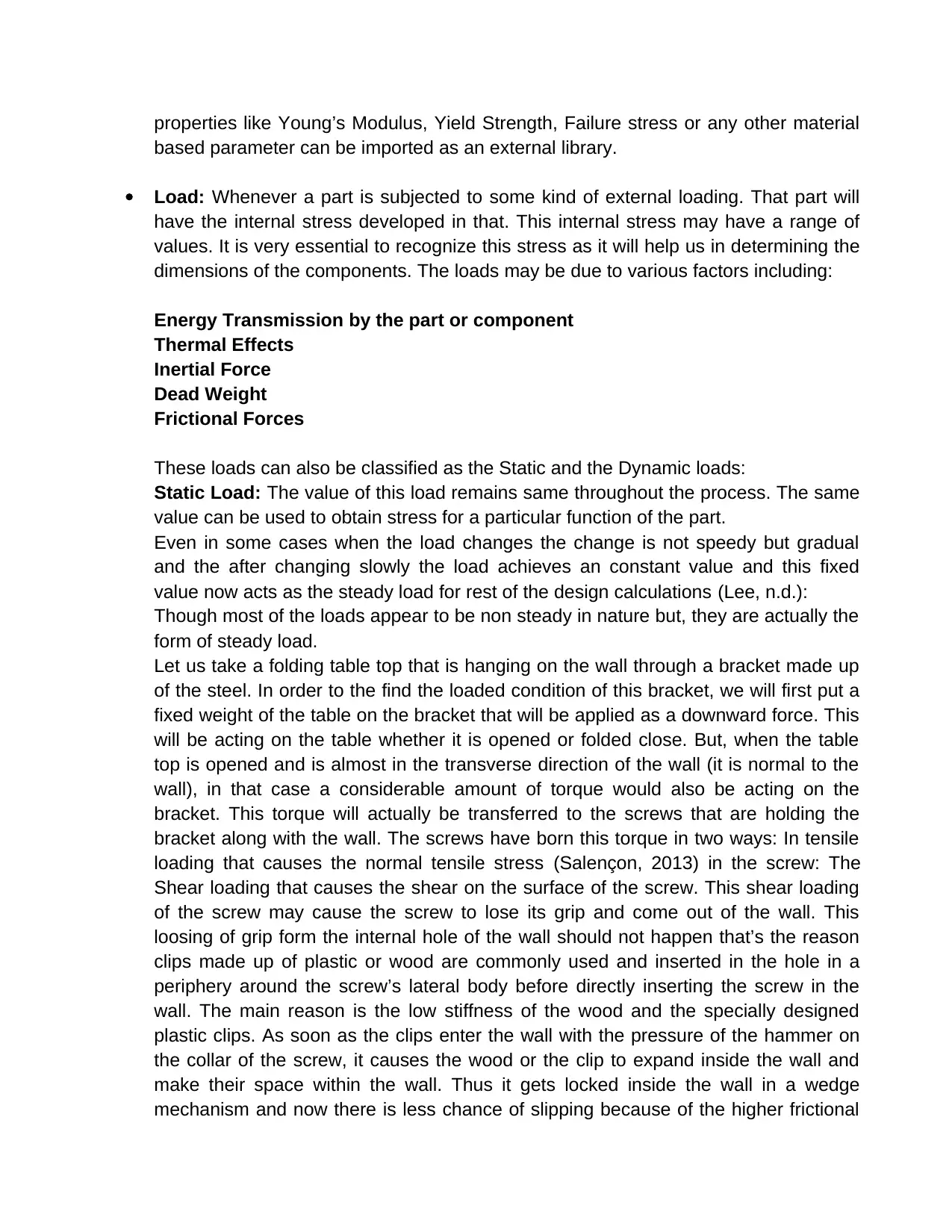
properties like Young’s Modulus, Yield Strength, Failure stress or any other material
based parameter can be imported as an external library.
Load: Whenever a part is subjected to some kind of external loading. That part will
have the internal stress developed in that. This internal stress may have a range of
values. It is very essential to recognize this stress as it will help us in determining the
dimensions of the components. The loads may be due to various factors including:
Energy Transmission by the part or component
Thermal Effects
Inertial Force
Dead Weight
Frictional Forces
These loads can also be classified as the Static and the Dynamic loads:
Static Load: The value of this load remains same throughout the process. The same
value can be used to obtain stress for a particular function of the part.
Even in some cases when the load changes the change is not speedy but gradual
and the after changing slowly the load achieves an constant value and this fixed
value now acts as the steady load for rest of the design calculations (Lee, n.d.):
Though most of the loads appear to be non steady in nature but, they are actually the
form of steady load.
Let us take a folding table top that is hanging on the wall through a bracket made up
of the steel. In order to the find the loaded condition of this bracket, we will first put a
fixed weight of the table on the bracket that will be applied as a downward force. This
will be acting on the table whether it is opened or folded close. But, when the table
top is opened and is almost in the transverse direction of the wall (it is normal to the
wall), in that case a considerable amount of torque would also be acting on the
bracket. This torque will actually be transferred to the screws that are holding the
bracket along with the wall. The screws have born this torque in two ways: In tensile
loading that causes the normal tensile stress (Salençon, 2013) in the screw: The
Shear loading that causes the shear on the surface of the screw. This shear loading
of the screw may cause the screw to lose its grip and come out of the wall. This
loosing of grip form the internal hole of the wall should not happen that’s the reason
clips made up of plastic or wood are commonly used and inserted in the hole in a
periphery around the screw’s lateral body before directly inserting the screw in the
wall. The main reason is the low stiffness of the wood and the specially designed
plastic clips. As soon as the clips enter the wall with the pressure of the hammer on
the collar of the screw, it causes the wood or the clip to expand inside the wall and
make their space within the wall. Thus it gets locked inside the wall in a wedge
mechanism and now there is less chance of slipping because of the higher frictional
based parameter can be imported as an external library.
Load: Whenever a part is subjected to some kind of external loading. That part will
have the internal stress developed in that. This internal stress may have a range of
values. It is very essential to recognize this stress as it will help us in determining the
dimensions of the components. The loads may be due to various factors including:
Energy Transmission by the part or component
Thermal Effects
Inertial Force
Dead Weight
Frictional Forces
These loads can also be classified as the Static and the Dynamic loads:
Static Load: The value of this load remains same throughout the process. The same
value can be used to obtain stress for a particular function of the part.
Even in some cases when the load changes the change is not speedy but gradual
and the after changing slowly the load achieves an constant value and this fixed
value now acts as the steady load for rest of the design calculations (Lee, n.d.):
Though most of the loads appear to be non steady in nature but, they are actually the
form of steady load.
Let us take a folding table top that is hanging on the wall through a bracket made up
of the steel. In order to the find the loaded condition of this bracket, we will first put a
fixed weight of the table on the bracket that will be applied as a downward force. This
will be acting on the table whether it is opened or folded close. But, when the table
top is opened and is almost in the transverse direction of the wall (it is normal to the
wall), in that case a considerable amount of torque would also be acting on the
bracket. This torque will actually be transferred to the screws that are holding the
bracket along with the wall. The screws have born this torque in two ways: In tensile
loading that causes the normal tensile stress (Salençon, 2013) in the screw: The
Shear loading that causes the shear on the surface of the screw. This shear loading
of the screw may cause the screw to lose its grip and come out of the wall. This
loosing of grip form the internal hole of the wall should not happen that’s the reason
clips made up of plastic or wood are commonly used and inserted in the hole in a
periphery around the screw’s lateral body before directly inserting the screw in the
wall. The main reason is the low stiffness of the wood and the specially designed
plastic clips. As soon as the clips enter the wall with the pressure of the hammer on
the collar of the screw, it causes the wood or the clip to expand inside the wall and
make their space within the wall. Thus it gets locked inside the wall in a wedge
mechanism and now there is less chance of slipping because of the higher frictional
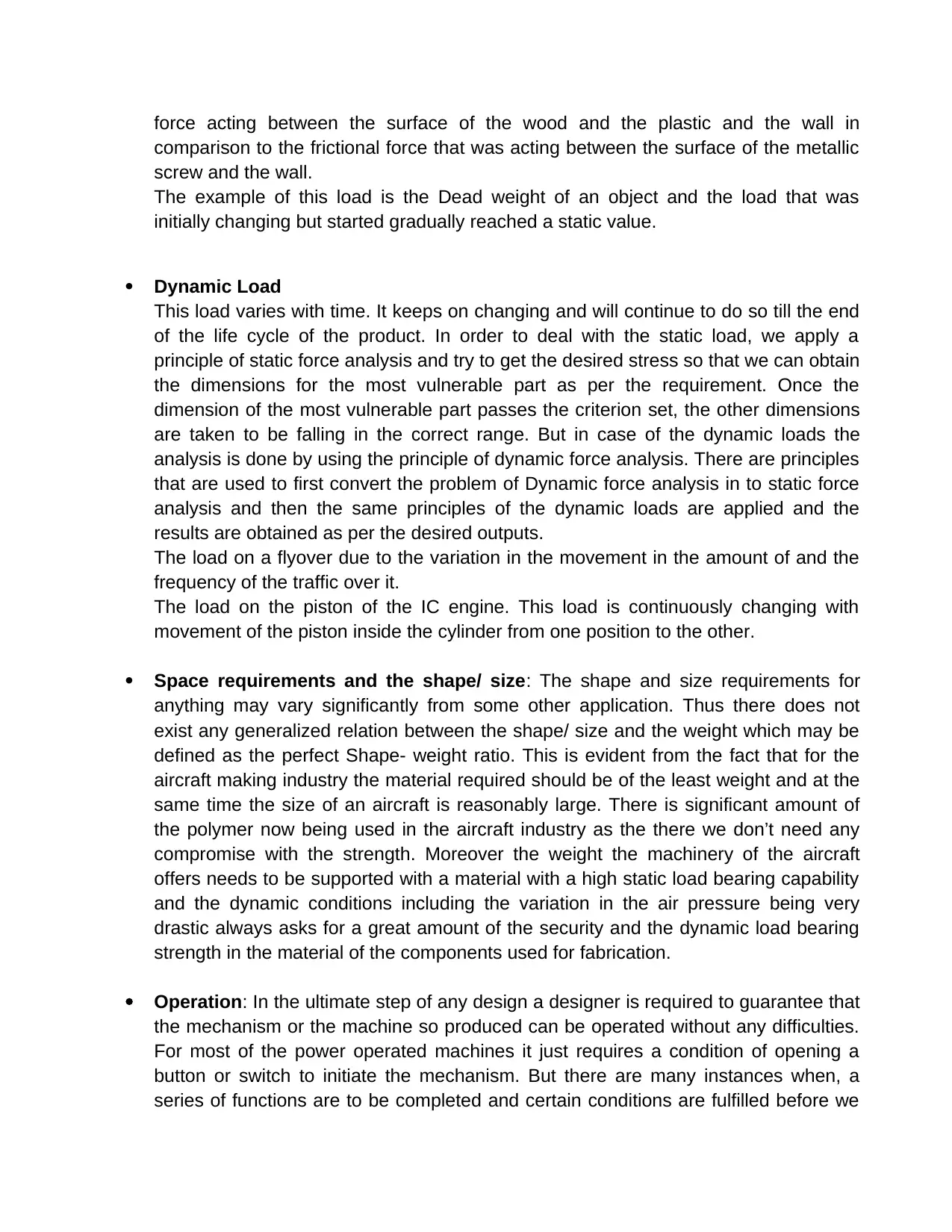
force acting between the surface of the wood and the plastic and the wall in
comparison to the frictional force that was acting between the surface of the metallic
screw and the wall.
The example of this load is the Dead weight of an object and the load that was
initially changing but started gradually reached a static value.
Dynamic Load
This load varies with time. It keeps on changing and will continue to do so till the end
of the life cycle of the product. In order to deal with the static load, we apply a
principle of static force analysis and try to get the desired stress so that we can obtain
the dimensions for the most vulnerable part as per the requirement. Once the
dimension of the most vulnerable part passes the criterion set, the other dimensions
are taken to be falling in the correct range. But in case of the dynamic loads the
analysis is done by using the principle of dynamic force analysis. There are principles
that are used to first convert the problem of Dynamic force analysis in to static force
analysis and then the same principles of the dynamic loads are applied and the
results are obtained as per the desired outputs.
The load on a flyover due to the variation in the movement in the amount of and the
frequency of the traffic over it.
The load on the piston of the IC engine. This load is continuously changing with
movement of the piston inside the cylinder from one position to the other.
Space requirements and the shape/ size: The shape and size requirements for
anything may vary significantly from some other application. Thus there does not
exist any generalized relation between the shape/ size and the weight which may be
defined as the perfect Shape- weight ratio. This is evident from the fact that for the
aircraft making industry the material required should be of the least weight and at the
same time the size of an aircraft is reasonably large. There is significant amount of
the polymer now being used in the aircraft industry as the there we don’t need any
compromise with the strength. Moreover the weight the machinery of the aircraft
offers needs to be supported with a material with a high static load bearing capability
and the dynamic conditions including the variation in the air pressure being very
drastic always asks for a great amount of the security and the dynamic load bearing
strength in the material of the components used for fabrication.
Operation: In the ultimate step of any design a designer is required to guarantee that
the mechanism or the machine so produced can be operated without any difficulties.
For most of the power operated machines it just requires a condition of opening a
button or switch to initiate the mechanism. But there are many instances when, a
series of functions are to be completed and certain conditions are fulfilled before we
comparison to the frictional force that was acting between the surface of the metallic
screw and the wall.
The example of this load is the Dead weight of an object and the load that was
initially changing but started gradually reached a static value.
Dynamic Load
This load varies with time. It keeps on changing and will continue to do so till the end
of the life cycle of the product. In order to deal with the static load, we apply a
principle of static force analysis and try to get the desired stress so that we can obtain
the dimensions for the most vulnerable part as per the requirement. Once the
dimension of the most vulnerable part passes the criterion set, the other dimensions
are taken to be falling in the correct range. But in case of the dynamic loads the
analysis is done by using the principle of dynamic force analysis. There are principles
that are used to first convert the problem of Dynamic force analysis in to static force
analysis and then the same principles of the dynamic loads are applied and the
results are obtained as per the desired outputs.
The load on a flyover due to the variation in the movement in the amount of and the
frequency of the traffic over it.
The load on the piston of the IC engine. This load is continuously changing with
movement of the piston inside the cylinder from one position to the other.
Space requirements and the shape/ size: The shape and size requirements for
anything may vary significantly from some other application. Thus there does not
exist any generalized relation between the shape/ size and the weight which may be
defined as the perfect Shape- weight ratio. This is evident from the fact that for the
aircraft making industry the material required should be of the least weight and at the
same time the size of an aircraft is reasonably large. There is significant amount of
the polymer now being used in the aircraft industry as the there we don’t need any
compromise with the strength. Moreover the weight the machinery of the aircraft
offers needs to be supported with a material with a high static load bearing capability
and the dynamic conditions including the variation in the air pressure being very
drastic always asks for a great amount of the security and the dynamic load bearing
strength in the material of the components used for fabrication.
Operation: In the ultimate step of any design a designer is required to guarantee that
the mechanism or the machine so produced can be operated without any difficulties.
For most of the power operated machines it just requires a condition of opening a
button or switch to initiate the mechanism. But there are many instances when, a
series of functions are to be completed and certain conditions are fulfilled before we
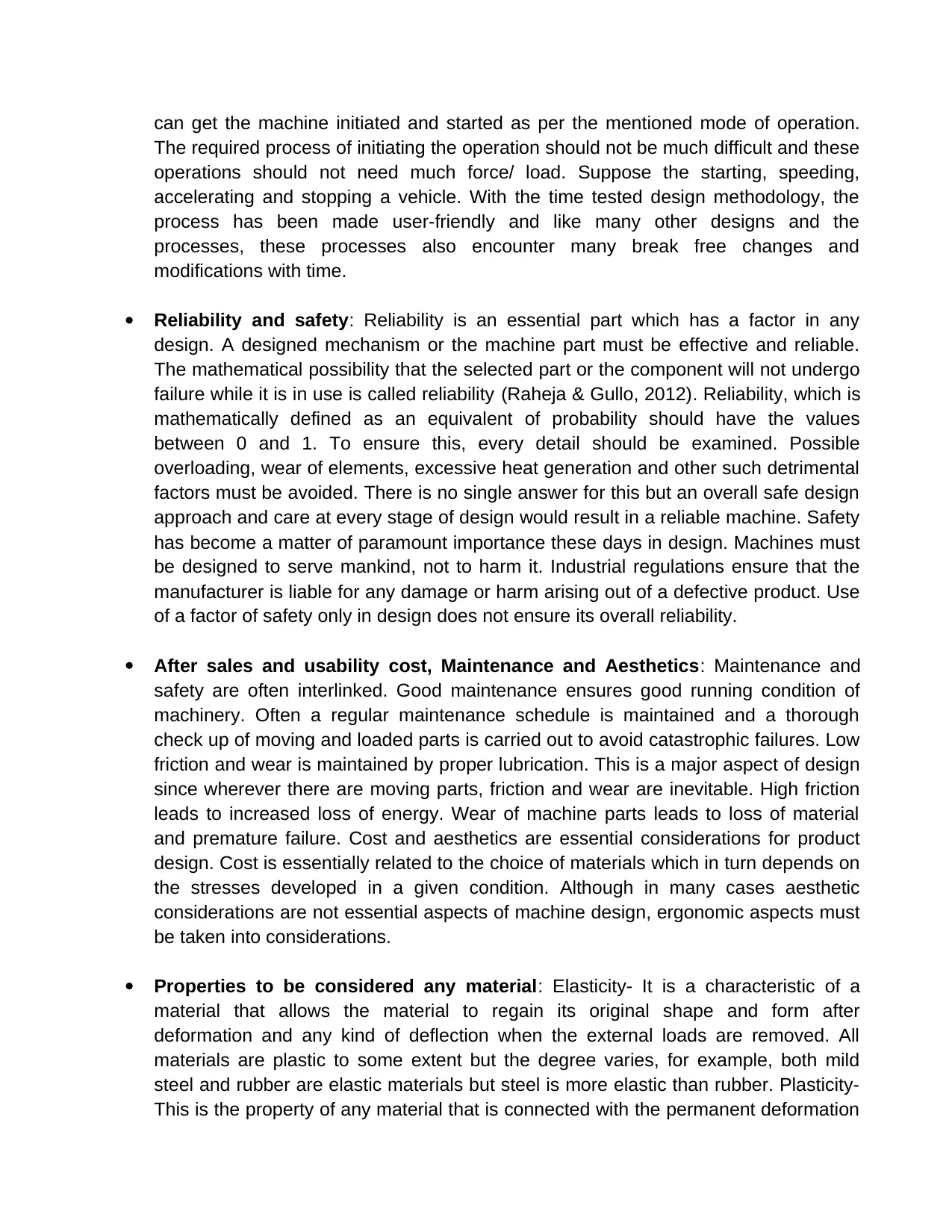
can get the machine initiated and started as per the mentioned mode of operation.
The required process of initiating the operation should not be much difficult and these
operations should not need much force/ load. Suppose the starting, speeding,
accelerating and stopping a vehicle. With the time tested design methodology, the
process has been made user-friendly and like many other designs and the
processes, these processes also encounter many break free changes and
modifications with time.
Reliability and safety: Reliability is an essential part which has a factor in any
design. A designed mechanism or the machine part must be effective and reliable.
The mathematical possibility that the selected part or the component will not undergo
failure while it is in use is called reliability (Raheja & Gullo, 2012). Reliability, which is
mathematically defined as an equivalent of probability should have the values
between 0 and 1. To ensure this, every detail should be examined. Possible
overloading, wear of elements, excessive heat generation and other such detrimental
factors must be avoided. There is no single answer for this but an overall safe design
approach and care at every stage of design would result in a reliable machine. Safety
has become a matter of paramount importance these days in design. Machines must
be designed to serve mankind, not to harm it. Industrial regulations ensure that the
manufacturer is liable for any damage or harm arising out of a defective product. Use
of a factor of safety only in design does not ensure its overall reliability.
After sales and usability cost, Maintenance and Aesthetics: Maintenance and
safety are often interlinked. Good maintenance ensures good running condition of
machinery. Often a regular maintenance schedule is maintained and a thorough
check up of moving and loaded parts is carried out to avoid catastrophic failures. Low
friction and wear is maintained by proper lubrication. This is a major aspect of design
since wherever there are moving parts, friction and wear are inevitable. High friction
leads to increased loss of energy. Wear of machine parts leads to loss of material
and premature failure. Cost and aesthetics are essential considerations for product
design. Cost is essentially related to the choice of materials which in turn depends on
the stresses developed in a given condition. Although in many cases aesthetic
considerations are not essential aspects of machine design, ergonomic aspects must
be taken into considerations.
Properties to be considered any material: Elasticity- It is a characteristic of a
material that allows the material to regain its original shape and form after
deformation and any kind of deflection when the external loads are removed. All
materials are plastic to some extent but the degree varies, for example, both mild
steel and rubber are elastic materials but steel is more elastic than rubber. Plasticity-
This is the property of any material that is connected with the permanent deformation
The required process of initiating the operation should not be much difficult and these
operations should not need much force/ load. Suppose the starting, speeding,
accelerating and stopping a vehicle. With the time tested design methodology, the
process has been made user-friendly and like many other designs and the
processes, these processes also encounter many break free changes and
modifications with time.
Reliability and safety: Reliability is an essential part which has a factor in any
design. A designed mechanism or the machine part must be effective and reliable.
The mathematical possibility that the selected part or the component will not undergo
failure while it is in use is called reliability (Raheja & Gullo, 2012). Reliability, which is
mathematically defined as an equivalent of probability should have the values
between 0 and 1. To ensure this, every detail should be examined. Possible
overloading, wear of elements, excessive heat generation and other such detrimental
factors must be avoided. There is no single answer for this but an overall safe design
approach and care at every stage of design would result in a reliable machine. Safety
has become a matter of paramount importance these days in design. Machines must
be designed to serve mankind, not to harm it. Industrial regulations ensure that the
manufacturer is liable for any damage or harm arising out of a defective product. Use
of a factor of safety only in design does not ensure its overall reliability.
After sales and usability cost, Maintenance and Aesthetics: Maintenance and
safety are often interlinked. Good maintenance ensures good running condition of
machinery. Often a regular maintenance schedule is maintained and a thorough
check up of moving and loaded parts is carried out to avoid catastrophic failures. Low
friction and wear is maintained by proper lubrication. This is a major aspect of design
since wherever there are moving parts, friction and wear are inevitable. High friction
leads to increased loss of energy. Wear of machine parts leads to loss of material
and premature failure. Cost and aesthetics are essential considerations for product
design. Cost is essentially related to the choice of materials which in turn depends on
the stresses developed in a given condition. Although in many cases aesthetic
considerations are not essential aspects of machine design, ergonomic aspects must
be taken into considerations.
Properties to be considered any material: Elasticity- It is a characteristic of a
material that allows the material to regain its original shape and form after
deformation and any kind of deflection when the external loads are removed. All
materials are plastic to some extent but the degree varies, for example, both mild
steel and rubber are elastic materials but steel is more elastic than rubber. Plasticity-
This is the property of any material that is connected with the permanent deformation
Secure Best Marks with AI Grader
Need help grading? Try our AI Grader for instant feedback on your assignments.
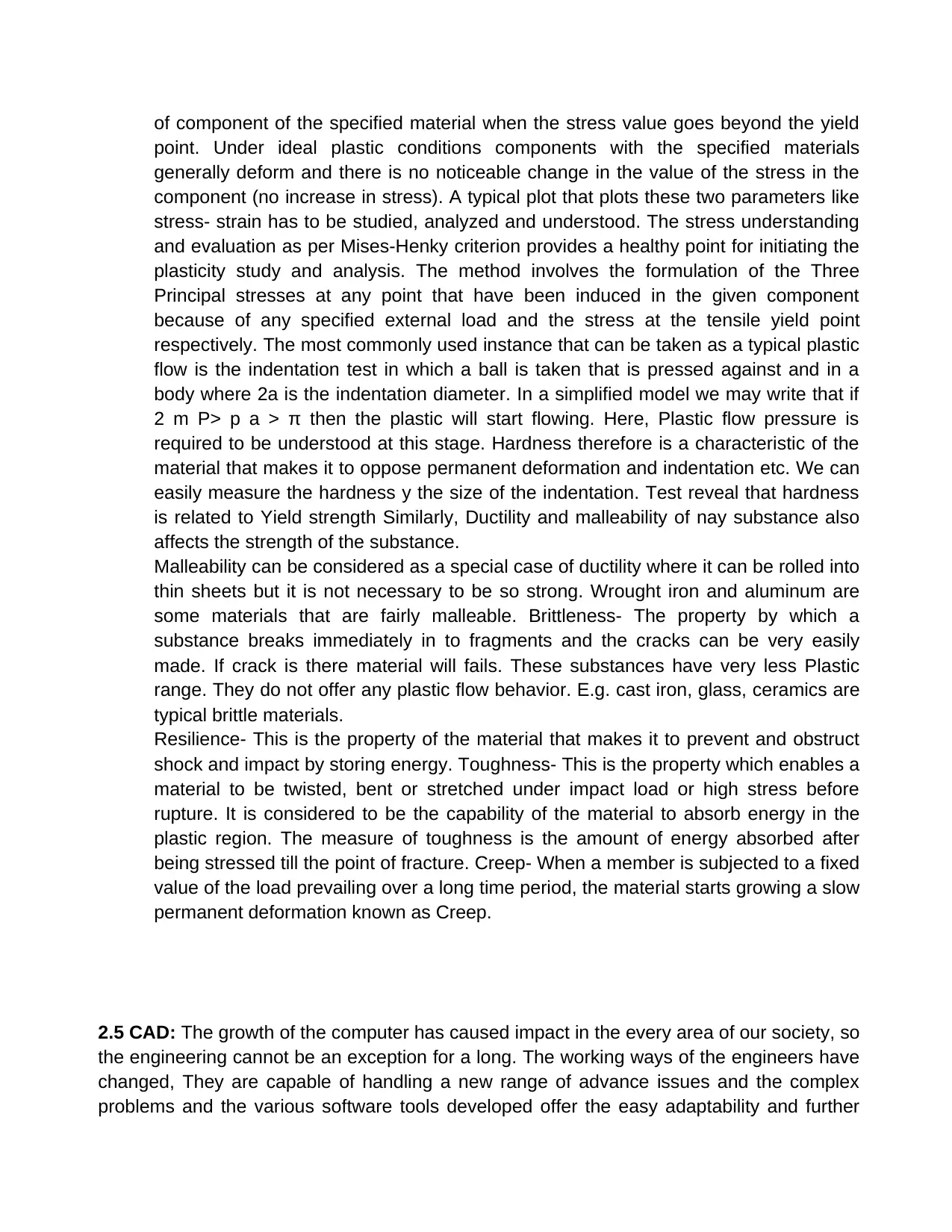
of component of the specified material when the stress value goes beyond the yield
point. Under ideal plastic conditions components with the specified materials
generally deform and there is no noticeable change in the value of the stress in the
component (no increase in stress). A typical plot that plots these two parameters like
stress- strain has to be studied, analyzed and understood. The stress understanding
and evaluation as per Mises-Henky criterion provides a healthy point for initiating the
plasticity study and analysis. The method involves the formulation of the Three
Principal stresses at any point that have been induced in the given component
because of any specified external load and the stress at the tensile yield point
respectively. The most commonly used instance that can be taken as a typical plastic
flow is the indentation test in which a ball is taken that is pressed against and in a
body where 2a is the indentation diameter. In a simplified model we may write that if
2 m P> p a > π then the plastic will start flowing. Here, Plastic flow pressure is
required to be understood at this stage. Hardness therefore is a characteristic of the
material that makes it to oppose permanent deformation and indentation etc. We can
easily measure the hardness y the size of the indentation. Test reveal that hardness
is related to Yield strength Similarly, Ductility and malleability of nay substance also
affects the strength of the substance.
Malleability can be considered as a special case of ductility where it can be rolled into
thin sheets but it is not necessary to be so strong. Wrought iron and aluminum are
some materials that are fairly malleable. Brittleness- The property by which a
substance breaks immediately in to fragments and the cracks can be very easily
made. If crack is there material will fails. These substances have very less Plastic
range. They do not offer any plastic flow behavior. E.g. cast iron, glass, ceramics are
typical brittle materials.
Resilience- This is the property of the material that makes it to prevent and obstruct
shock and impact by storing energy. Toughness- This is the property which enables a
material to be twisted, bent or stretched under impact load or high stress before
rupture. It is considered to be the capability of the material to absorb energy in the
plastic region. The measure of toughness is the amount of energy absorbed after
being stressed till the point of fracture. Creep- When a member is subjected to a fixed
value of the load prevailing over a long time period, the material starts growing a slow
permanent deformation known as Creep.
2.5 CAD: The growth of the computer has caused impact in the every area of our society, so
the engineering cannot be an exception for a long. The working ways of the engineers have
changed, They are capable of handling a new range of advance issues and the complex
problems and the various software tools developed offer the easy adaptability and further
point. Under ideal plastic conditions components with the specified materials
generally deform and there is no noticeable change in the value of the stress in the
component (no increase in stress). A typical plot that plots these two parameters like
stress- strain has to be studied, analyzed and understood. The stress understanding
and evaluation as per Mises-Henky criterion provides a healthy point for initiating the
plasticity study and analysis. The method involves the formulation of the Three
Principal stresses at any point that have been induced in the given component
because of any specified external load and the stress at the tensile yield point
respectively. The most commonly used instance that can be taken as a typical plastic
flow is the indentation test in which a ball is taken that is pressed against and in a
body where 2a is the indentation diameter. In a simplified model we may write that if
2 m P> p a > π then the plastic will start flowing. Here, Plastic flow pressure is
required to be understood at this stage. Hardness therefore is a characteristic of the
material that makes it to oppose permanent deformation and indentation etc. We can
easily measure the hardness y the size of the indentation. Test reveal that hardness
is related to Yield strength Similarly, Ductility and malleability of nay substance also
affects the strength of the substance.
Malleability can be considered as a special case of ductility where it can be rolled into
thin sheets but it is not necessary to be so strong. Wrought iron and aluminum are
some materials that are fairly malleable. Brittleness- The property by which a
substance breaks immediately in to fragments and the cracks can be very easily
made. If crack is there material will fails. These substances have very less Plastic
range. They do not offer any plastic flow behavior. E.g. cast iron, glass, ceramics are
typical brittle materials.
Resilience- This is the property of the material that makes it to prevent and obstruct
shock and impact by storing energy. Toughness- This is the property which enables a
material to be twisted, bent or stretched under impact load or high stress before
rupture. It is considered to be the capability of the material to absorb energy in the
plastic region. The measure of toughness is the amount of energy absorbed after
being stressed till the point of fracture. Creep- When a member is subjected to a fixed
value of the load prevailing over a long time period, the material starts growing a slow
permanent deformation known as Creep.
2.5 CAD: The growth of the computer has caused impact in the every area of our society, so
the engineering cannot be an exception for a long. The working ways of the engineers have
changed, They are capable of handling a new range of advance issues and the complex
problems and the various software tools developed offer the easy adaptability and further
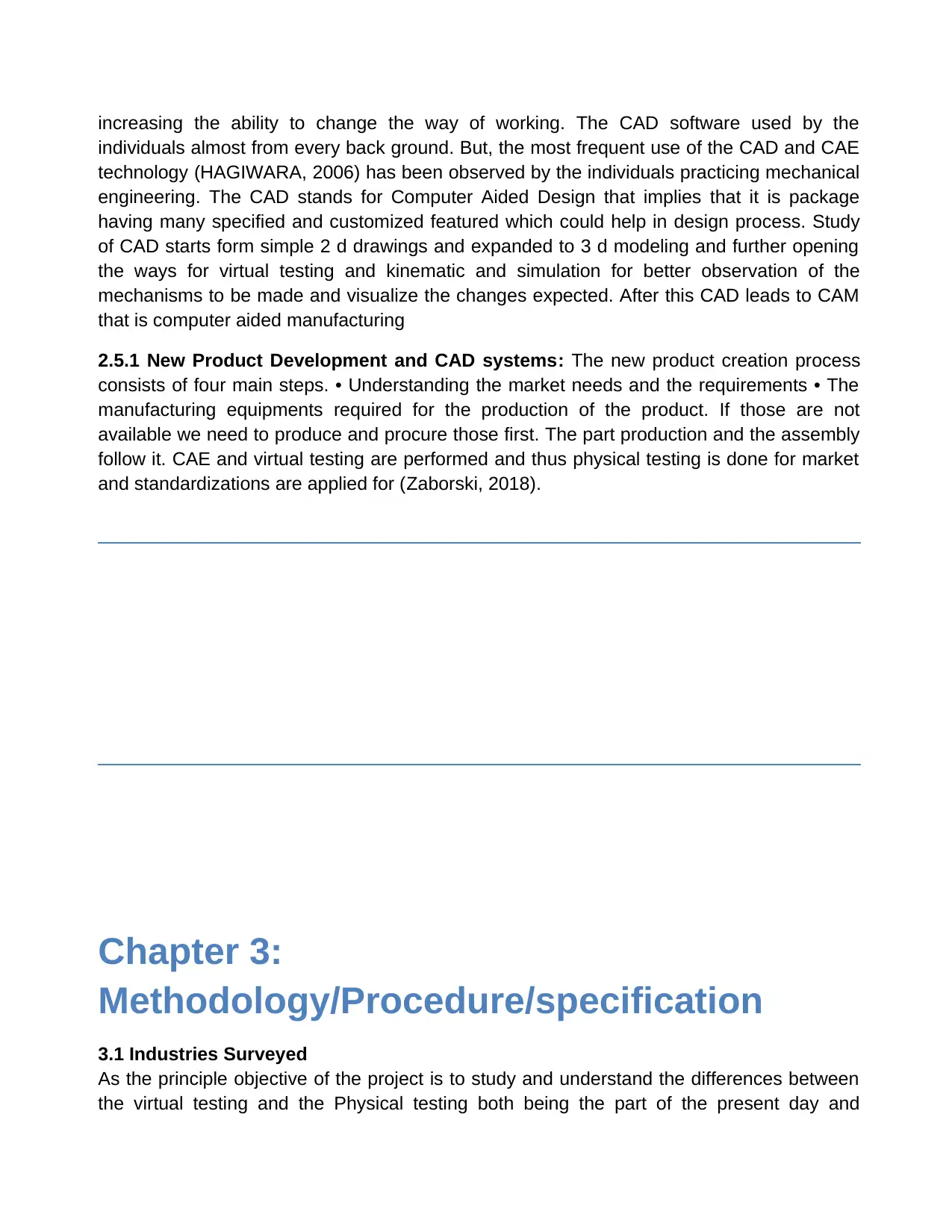
increasing the ability to change the way of working. The CAD software used by the
individuals almost from every back ground. But, the most frequent use of the CAD and CAE
technology (HAGIWARA, 2006) has been observed by the individuals practicing mechanical
engineering. The CAD stands for Computer Aided Design that implies that it is package
having many specified and customized featured which could help in design process. Study
of CAD starts form simple 2 d drawings and expanded to 3 d modeling and further opening
the ways for virtual testing and kinematic and simulation for better observation of the
mechanisms to be made and visualize the changes expected. After this CAD leads to CAM
that is computer aided manufacturing
2.5.1 New Product Development and CAD systems: The new product creation process
consists of four main steps. • Understanding the market needs and the requirements • The
manufacturing equipments required for the production of the product. If those are not
available we need to produce and procure those first. The part production and the assembly
follow it. CAE and virtual testing are performed and thus physical testing is done for market
and standardizations are applied for (Zaborski, 2018).
Chapter 3:
Methodology/Procedure/specification
3.1 Industries Surveyed
As the principle objective of the project is to study and understand the differences between
the virtual testing and the Physical testing both being the part of the present day and
individuals almost from every back ground. But, the most frequent use of the CAD and CAE
technology (HAGIWARA, 2006) has been observed by the individuals practicing mechanical
engineering. The CAD stands for Computer Aided Design that implies that it is package
having many specified and customized featured which could help in design process. Study
of CAD starts form simple 2 d drawings and expanded to 3 d modeling and further opening
the ways for virtual testing and kinematic and simulation for better observation of the
mechanisms to be made and visualize the changes expected. After this CAD leads to CAM
that is computer aided manufacturing
2.5.1 New Product Development and CAD systems: The new product creation process
consists of four main steps. • Understanding the market needs and the requirements • The
manufacturing equipments required for the production of the product. If those are not
available we need to produce and procure those first. The part production and the assembly
follow it. CAE and virtual testing are performed and thus physical testing is done for market
and standardizations are applied for (Zaborski, 2018).
Chapter 3:
Methodology/Procedure/specification
3.1 Industries Surveyed
As the principle objective of the project is to study and understand the differences between
the virtual testing and the Physical testing both being the part of the present day and
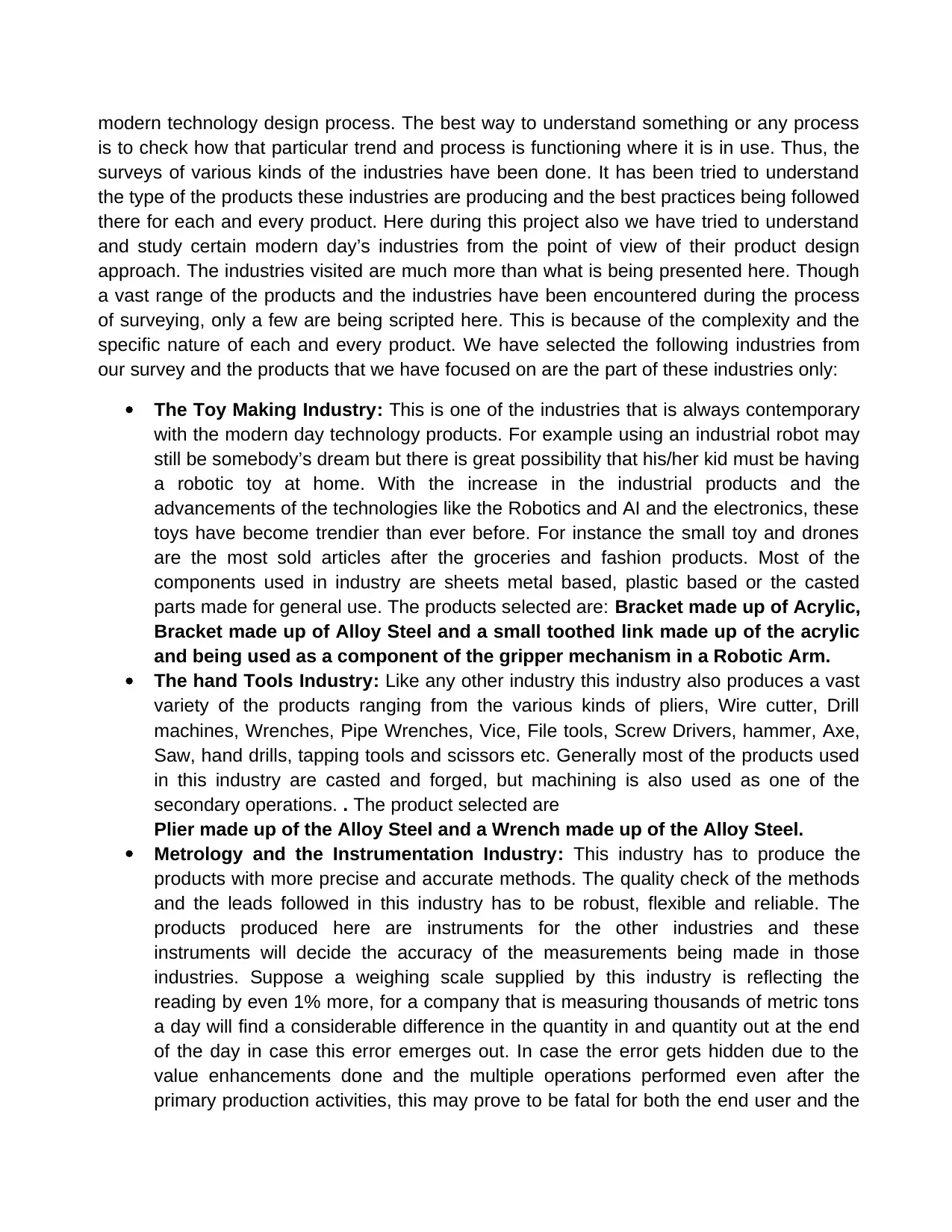
modern technology design process. The best way to understand something or any process
is to check how that particular trend and process is functioning where it is in use. Thus, the
surveys of various kinds of the industries have been done. It has been tried to understand
the type of the products these industries are producing and the best practices being followed
there for each and every product. Here during this project also we have tried to understand
and study certain modern day’s industries from the point of view of their product design
approach. The industries visited are much more than what is being presented here. Though
a vast range of the products and the industries have been encountered during the process
of surveying, only a few are being scripted here. This is because of the complexity and the
specific nature of each and every product. We have selected the following industries from
our survey and the products that we have focused on are the part of these industries only:
The Toy Making Industry: This is one of the industries that is always contemporary
with the modern day technology products. For example using an industrial robot may
still be somebody’s dream but there is great possibility that his/her kid must be having
a robotic toy at home. With the increase in the industrial products and the
advancements of the technologies like the Robotics and AI and the electronics, these
toys have become trendier than ever before. For instance the small toy and drones
are the most sold articles after the groceries and fashion products. Most of the
components used in industry are sheets metal based, plastic based or the casted
parts made for general use. The products selected are: Bracket made up of Acrylic,
Bracket made up of Alloy Steel and a small toothed link made up of the acrylic
and being used as a component of the gripper mechanism in a Robotic Arm.
The hand Tools Industry: Like any other industry this industry also produces a vast
variety of the products ranging from the various kinds of pliers, Wire cutter, Drill
machines, Wrenches, Pipe Wrenches, Vice, File tools, Screw Drivers, hammer, Axe,
Saw, hand drills, tapping tools and scissors etc. Generally most of the products used
in this industry are casted and forged, but machining is also used as one of the
secondary operations. . The product selected are
Plier made up of the Alloy Steel and a Wrench made up of the Alloy Steel.
Metrology and the Instrumentation Industry: This industry has to produce the
products with more precise and accurate methods. The quality check of the methods
and the leads followed in this industry has to be robust, flexible and reliable. The
products produced here are instruments for the other industries and these
instruments will decide the accuracy of the measurements being made in those
industries. Suppose a weighing scale supplied by this industry is reflecting the
reading by even 1% more, for a company that is measuring thousands of metric tons
a day will find a considerable difference in the quantity in and quantity out at the end
of the day in case this error emerges out. In case the error gets hidden due to the
value enhancements done and the multiple operations performed even after the
primary production activities, this may prove to be fatal for both the end user and the
is to check how that particular trend and process is functioning where it is in use. Thus, the
surveys of various kinds of the industries have been done. It has been tried to understand
the type of the products these industries are producing and the best practices being followed
there for each and every product. Here during this project also we have tried to understand
and study certain modern day’s industries from the point of view of their product design
approach. The industries visited are much more than what is being presented here. Though
a vast range of the products and the industries have been encountered during the process
of surveying, only a few are being scripted here. This is because of the complexity and the
specific nature of each and every product. We have selected the following industries from
our survey and the products that we have focused on are the part of these industries only:
The Toy Making Industry: This is one of the industries that is always contemporary
with the modern day technology products. For example using an industrial robot may
still be somebody’s dream but there is great possibility that his/her kid must be having
a robotic toy at home. With the increase in the industrial products and the
advancements of the technologies like the Robotics and AI and the electronics, these
toys have become trendier than ever before. For instance the small toy and drones
are the most sold articles after the groceries and fashion products. Most of the
components used in industry are sheets metal based, plastic based or the casted
parts made for general use. The products selected are: Bracket made up of Acrylic,
Bracket made up of Alloy Steel and a small toothed link made up of the acrylic
and being used as a component of the gripper mechanism in a Robotic Arm.
The hand Tools Industry: Like any other industry this industry also produces a vast
variety of the products ranging from the various kinds of pliers, Wire cutter, Drill
machines, Wrenches, Pipe Wrenches, Vice, File tools, Screw Drivers, hammer, Axe,
Saw, hand drills, tapping tools and scissors etc. Generally most of the products used
in this industry are casted and forged, but machining is also used as one of the
secondary operations. . The product selected are
Plier made up of the Alloy Steel and a Wrench made up of the Alloy Steel.
Metrology and the Instrumentation Industry: This industry has to produce the
products with more precise and accurate methods. The quality check of the methods
and the leads followed in this industry has to be robust, flexible and reliable. The
products produced here are instruments for the other industries and these
instruments will decide the accuracy of the measurements being made in those
industries. Suppose a weighing scale supplied by this industry is reflecting the
reading by even 1% more, for a company that is measuring thousands of metric tons
a day will find a considerable difference in the quantity in and quantity out at the end
of the day in case this error emerges out. In case the error gets hidden due to the
value enhancements done and the multiple operations performed even after the
primary production activities, this may prove to be fatal for both the end user and the
Paraphrase This Document
Need a fresh take? Get an instant paraphrase of this document with our AI Paraphraser
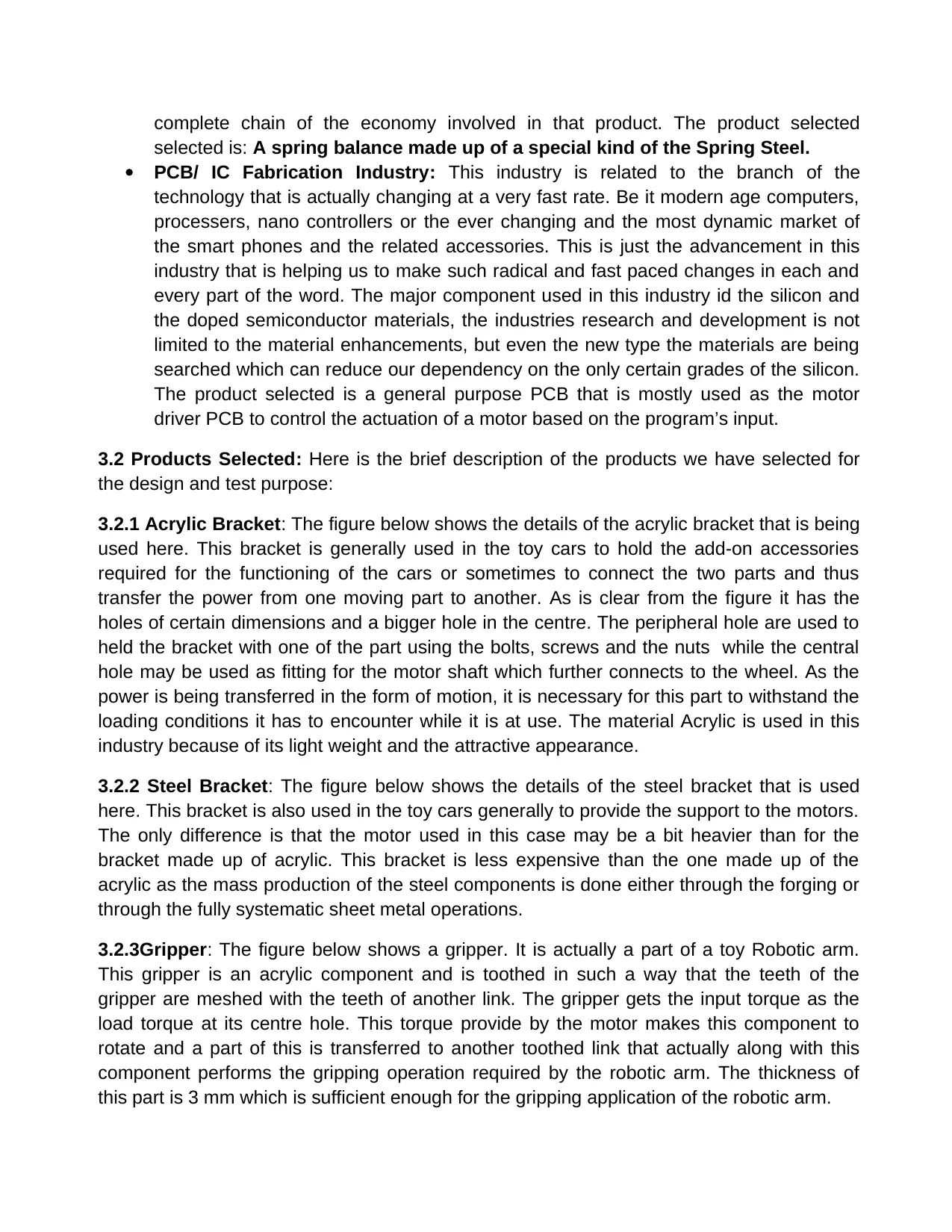
complete chain of the economy involved in that product. The product selected
selected is: A spring balance made up of a special kind of the Spring Steel.
PCB/ IC Fabrication Industry: This industry is related to the branch of the
technology that is actually changing at a very fast rate. Be it modern age computers,
processers, nano controllers or the ever changing and the most dynamic market of
the smart phones and the related accessories. This is just the advancement in this
industry that is helping us to make such radical and fast paced changes in each and
every part of the word. The major component used in this industry id the silicon and
the doped semiconductor materials, the industries research and development is not
limited to the material enhancements, but even the new type the materials are being
searched which can reduce our dependency on the only certain grades of the silicon.
The product selected is a general purpose PCB that is mostly used as the motor
driver PCB to control the actuation of a motor based on the program’s input.
3.2 Products Selected: Here is the brief description of the products we have selected for
the design and test purpose:
3.2.1 Acrylic Bracket: The figure below shows the details of the acrylic bracket that is being
used here. This bracket is generally used in the toy cars to hold the add-on accessories
required for the functioning of the cars or sometimes to connect the two parts and thus
transfer the power from one moving part to another. As is clear from the figure it has the
holes of certain dimensions and a bigger hole in the centre. The peripheral hole are used to
held the bracket with one of the part using the bolts, screws and the nuts while the central
hole may be used as fitting for the motor shaft which further connects to the wheel. As the
power is being transferred in the form of motion, it is necessary for this part to withstand the
loading conditions it has to encounter while it is at use. The material Acrylic is used in this
industry because of its light weight and the attractive appearance.
3.2.2 Steel Bracket: The figure below shows the details of the steel bracket that is used
here. This bracket is also used in the toy cars generally to provide the support to the motors.
The only difference is that the motor used in this case may be a bit heavier than for the
bracket made up of acrylic. This bracket is less expensive than the one made up of the
acrylic as the mass production of the steel components is done either through the forging or
through the fully systematic sheet metal operations.
3.2.3Gripper: The figure below shows a gripper. It is actually a part of a toy Robotic arm.
This gripper is an acrylic component and is toothed in such a way that the teeth of the
gripper are meshed with the teeth of another link. The gripper gets the input torque as the
load torque at its centre hole. This torque provide by the motor makes this component to
rotate and a part of this is transferred to another toothed link that actually along with this
component performs the gripping operation required by the robotic arm. The thickness of
this part is 3 mm which is sufficient enough for the gripping application of the robotic arm.
selected is: A spring balance made up of a special kind of the Spring Steel.
PCB/ IC Fabrication Industry: This industry is related to the branch of the
technology that is actually changing at a very fast rate. Be it modern age computers,
processers, nano controllers or the ever changing and the most dynamic market of
the smart phones and the related accessories. This is just the advancement in this
industry that is helping us to make such radical and fast paced changes in each and
every part of the word. The major component used in this industry id the silicon and
the doped semiconductor materials, the industries research and development is not
limited to the material enhancements, but even the new type the materials are being
searched which can reduce our dependency on the only certain grades of the silicon.
The product selected is a general purpose PCB that is mostly used as the motor
driver PCB to control the actuation of a motor based on the program’s input.
3.2 Products Selected: Here is the brief description of the products we have selected for
the design and test purpose:
3.2.1 Acrylic Bracket: The figure below shows the details of the acrylic bracket that is being
used here. This bracket is generally used in the toy cars to hold the add-on accessories
required for the functioning of the cars or sometimes to connect the two parts and thus
transfer the power from one moving part to another. As is clear from the figure it has the
holes of certain dimensions and a bigger hole in the centre. The peripheral hole are used to
held the bracket with one of the part using the bolts, screws and the nuts while the central
hole may be used as fitting for the motor shaft which further connects to the wheel. As the
power is being transferred in the form of motion, it is necessary for this part to withstand the
loading conditions it has to encounter while it is at use. The material Acrylic is used in this
industry because of its light weight and the attractive appearance.
3.2.2 Steel Bracket: The figure below shows the details of the steel bracket that is used
here. This bracket is also used in the toy cars generally to provide the support to the motors.
The only difference is that the motor used in this case may be a bit heavier than for the
bracket made up of acrylic. This bracket is less expensive than the one made up of the
acrylic as the mass production of the steel components is done either through the forging or
through the fully systematic sheet metal operations.
3.2.3Gripper: The figure below shows a gripper. It is actually a part of a toy Robotic arm.
This gripper is an acrylic component and is toothed in such a way that the teeth of the
gripper are meshed with the teeth of another link. The gripper gets the input torque as the
load torque at its centre hole. This torque provide by the motor makes this component to
rotate and a part of this is transferred to another toothed link that actually along with this
component performs the gripping operation required by the robotic arm. The thickness of
this part is 3 mm which is sufficient enough for the gripping application of the robotic arm.
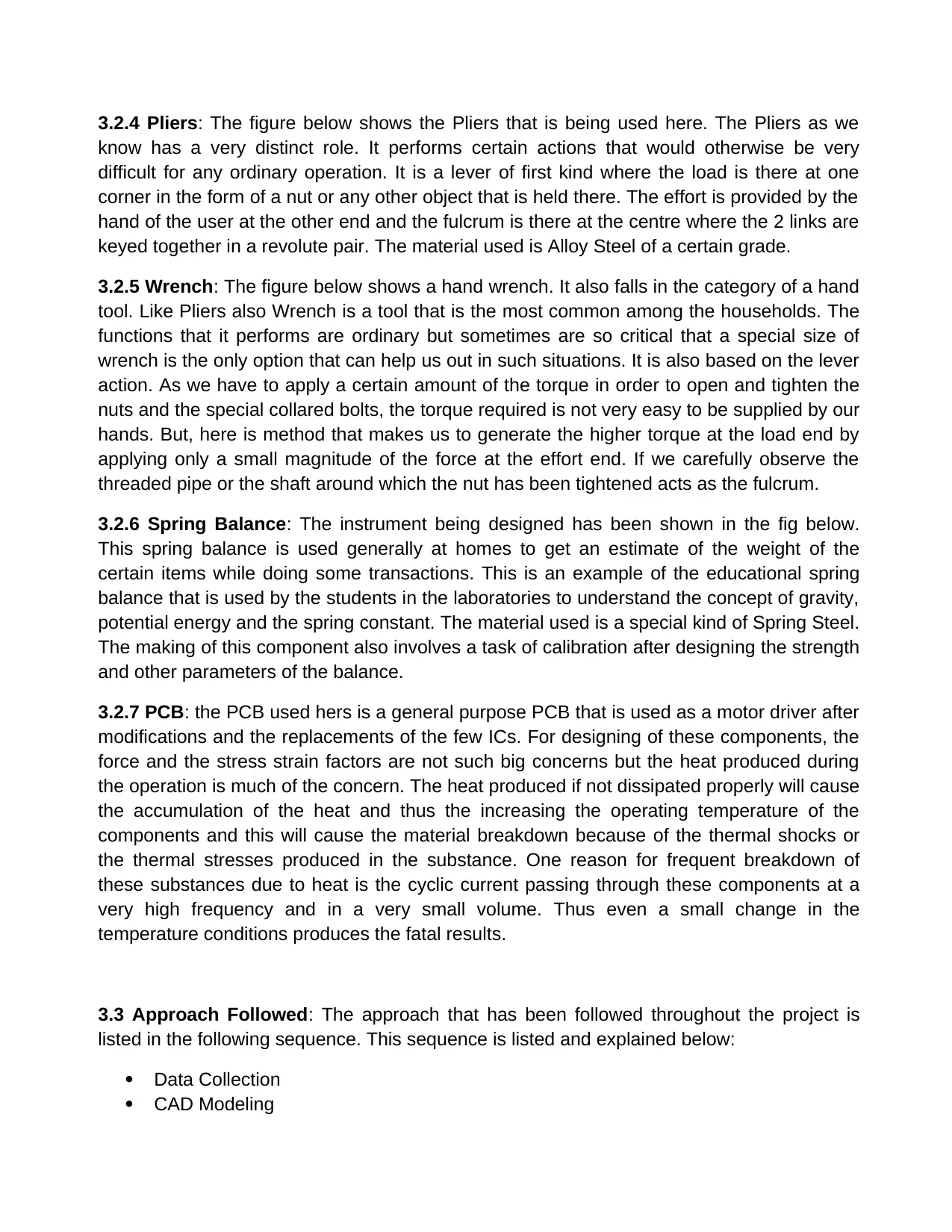
3.2.4 Pliers: The figure below shows the Pliers that is being used here. The Pliers as we
know has a very distinct role. It performs certain actions that would otherwise be very
difficult for any ordinary operation. It is a lever of first kind where the load is there at one
corner in the form of a nut or any other object that is held there. The effort is provided by the
hand of the user at the other end and the fulcrum is there at the centre where the 2 links are
keyed together in a revolute pair. The material used is Alloy Steel of a certain grade.
3.2.5 Wrench: The figure below shows a hand wrench. It also falls in the category of a hand
tool. Like Pliers also Wrench is a tool that is the most common among the households. The
functions that it performs are ordinary but sometimes are so critical that a special size of
wrench is the only option that can help us out in such situations. It is also based on the lever
action. As we have to apply a certain amount of the torque in order to open and tighten the
nuts and the special collared bolts, the torque required is not very easy to be supplied by our
hands. But, here is method that makes us to generate the higher torque at the load end by
applying only a small magnitude of the force at the effort end. If we carefully observe the
threaded pipe or the shaft around which the nut has been tightened acts as the fulcrum.
3.2.6 Spring Balance: The instrument being designed has been shown in the fig below.
This spring balance is used generally at homes to get an estimate of the weight of the
certain items while doing some transactions. This is an example of the educational spring
balance that is used by the students in the laboratories to understand the concept of gravity,
potential energy and the spring constant. The material used is a special kind of Spring Steel.
The making of this component also involves a task of calibration after designing the strength
and other parameters of the balance.
3.2.7 PCB: the PCB used hers is a general purpose PCB that is used as a motor driver after
modifications and the replacements of the few ICs. For designing of these components, the
force and the stress strain factors are not such big concerns but the heat produced during
the operation is much of the concern. The heat produced if not dissipated properly will cause
the accumulation of the heat and thus the increasing the operating temperature of the
components and this will cause the material breakdown because of the thermal shocks or
the thermal stresses produced in the substance. One reason for frequent breakdown of
these substances due to heat is the cyclic current passing through these components at a
very high frequency and in a very small volume. Thus even a small change in the
temperature conditions produces the fatal results.
3.3 Approach Followed: The approach that has been followed throughout the project is
listed in the following sequence. This sequence is listed and explained below:
Data Collection
CAD Modeling
know has a very distinct role. It performs certain actions that would otherwise be very
difficult for any ordinary operation. It is a lever of first kind where the load is there at one
corner in the form of a nut or any other object that is held there. The effort is provided by the
hand of the user at the other end and the fulcrum is there at the centre where the 2 links are
keyed together in a revolute pair. The material used is Alloy Steel of a certain grade.
3.2.5 Wrench: The figure below shows a hand wrench. It also falls in the category of a hand
tool. Like Pliers also Wrench is a tool that is the most common among the households. The
functions that it performs are ordinary but sometimes are so critical that a special size of
wrench is the only option that can help us out in such situations. It is also based on the lever
action. As we have to apply a certain amount of the torque in order to open and tighten the
nuts and the special collared bolts, the torque required is not very easy to be supplied by our
hands. But, here is method that makes us to generate the higher torque at the load end by
applying only a small magnitude of the force at the effort end. If we carefully observe the
threaded pipe or the shaft around which the nut has been tightened acts as the fulcrum.
3.2.6 Spring Balance: The instrument being designed has been shown in the fig below.
This spring balance is used generally at homes to get an estimate of the weight of the
certain items while doing some transactions. This is an example of the educational spring
balance that is used by the students in the laboratories to understand the concept of gravity,
potential energy and the spring constant. The material used is a special kind of Spring Steel.
The making of this component also involves a task of calibration after designing the strength
and other parameters of the balance.
3.2.7 PCB: the PCB used hers is a general purpose PCB that is used as a motor driver after
modifications and the replacements of the few ICs. For designing of these components, the
force and the stress strain factors are not such big concerns but the heat produced during
the operation is much of the concern. The heat produced if not dissipated properly will cause
the accumulation of the heat and thus the increasing the operating temperature of the
components and this will cause the material breakdown because of the thermal shocks or
the thermal stresses produced in the substance. One reason for frequent breakdown of
these substances due to heat is the cyclic current passing through these components at a
very high frequency and in a very small volume. Thus even a small change in the
temperature conditions produces the fatal results.
3.3 Approach Followed: The approach that has been followed throughout the project is
listed in the following sequence. This sequence is listed and explained below:
Data Collection
CAD Modeling
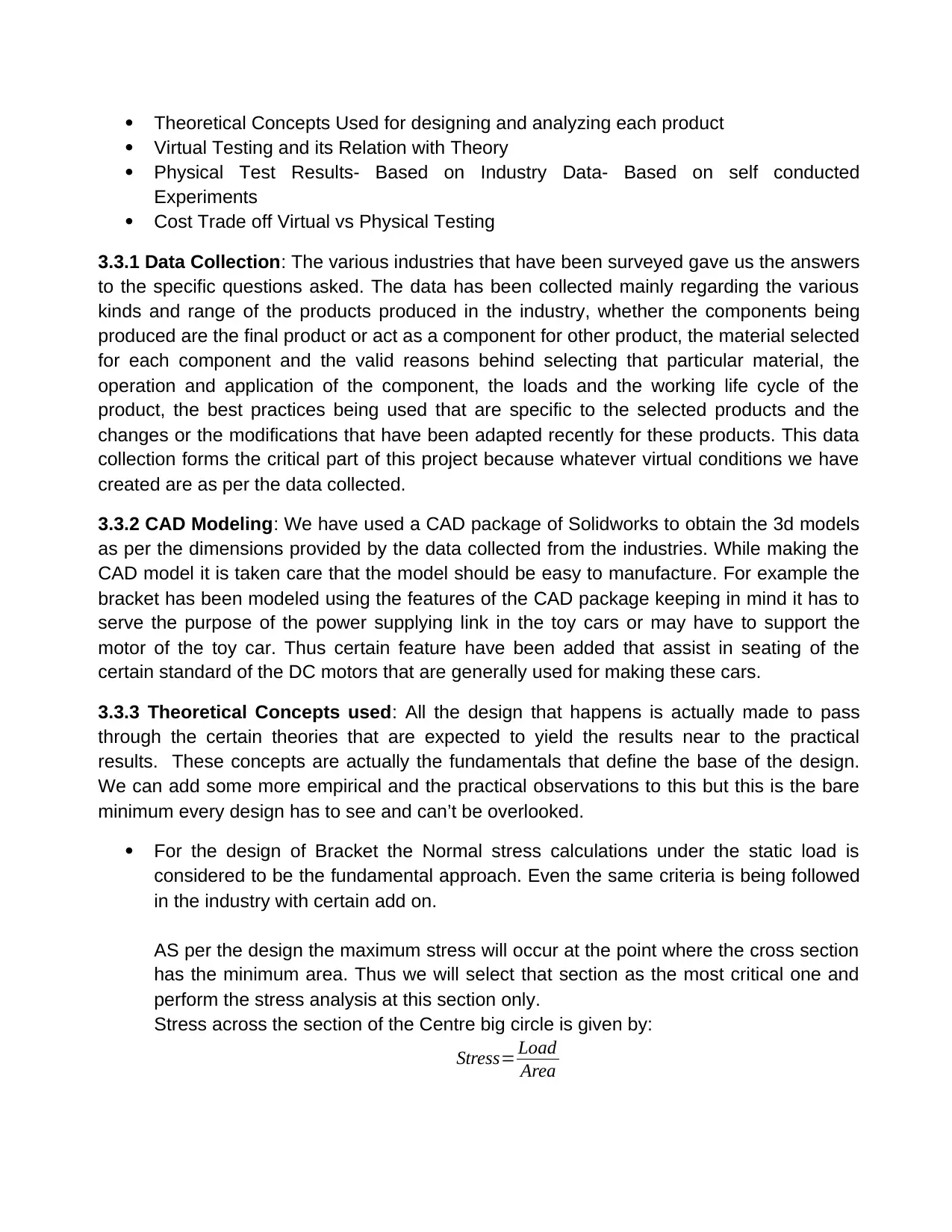
Theoretical Concepts Used for designing and analyzing each product
Virtual Testing and its Relation with Theory
Physical Test Results- Based on Industry Data- Based on self conducted
Experiments
Cost Trade off Virtual vs Physical Testing
3.3.1 Data Collection: The various industries that have been surveyed gave us the answers
to the specific questions asked. The data has been collected mainly regarding the various
kinds and range of the products produced in the industry, whether the components being
produced are the final product or act as a component for other product, the material selected
for each component and the valid reasons behind selecting that particular material, the
operation and application of the component, the loads and the working life cycle of the
product, the best practices being used that are specific to the selected products and the
changes or the modifications that have been adapted recently for these products. This data
collection forms the critical part of this project because whatever virtual conditions we have
created are as per the data collected.
3.3.2 CAD Modeling: We have used a CAD package of Solidworks to obtain the 3d models
as per the dimensions provided by the data collected from the industries. While making the
CAD model it is taken care that the model should be easy to manufacture. For example the
bracket has been modeled using the features of the CAD package keeping in mind it has to
serve the purpose of the power supplying link in the toy cars or may have to support the
motor of the toy car. Thus certain feature have been added that assist in seating of the
certain standard of the DC motors that are generally used for making these cars.
3.3.3 Theoretical Concepts used: All the design that happens is actually made to pass
through the certain theories that are expected to yield the results near to the practical
results. These concepts are actually the fundamentals that define the base of the design.
We can add some more empirical and the practical observations to this but this is the bare
minimum every design has to see and can’t be overlooked.
For the design of Bracket the Normal stress calculations under the static load is
considered to be the fundamental approach. Even the same criteria is being followed
in the industry with certain add on.
AS per the design the maximum stress will occur at the point where the cross section
has the minimum area. Thus we will select that section as the most critical one and
perform the stress analysis at this section only.
Stress across the section of the Centre big circle is given by:
Stress= Load
Area
Virtual Testing and its Relation with Theory
Physical Test Results- Based on Industry Data- Based on self conducted
Experiments
Cost Trade off Virtual vs Physical Testing
3.3.1 Data Collection: The various industries that have been surveyed gave us the answers
to the specific questions asked. The data has been collected mainly regarding the various
kinds and range of the products produced in the industry, whether the components being
produced are the final product or act as a component for other product, the material selected
for each component and the valid reasons behind selecting that particular material, the
operation and application of the component, the loads and the working life cycle of the
product, the best practices being used that are specific to the selected products and the
changes or the modifications that have been adapted recently for these products. This data
collection forms the critical part of this project because whatever virtual conditions we have
created are as per the data collected.
3.3.2 CAD Modeling: We have used a CAD package of Solidworks to obtain the 3d models
as per the dimensions provided by the data collected from the industries. While making the
CAD model it is taken care that the model should be easy to manufacture. For example the
bracket has been modeled using the features of the CAD package keeping in mind it has to
serve the purpose of the power supplying link in the toy cars or may have to support the
motor of the toy car. Thus certain feature have been added that assist in seating of the
certain standard of the DC motors that are generally used for making these cars.
3.3.3 Theoretical Concepts used: All the design that happens is actually made to pass
through the certain theories that are expected to yield the results near to the practical
results. These concepts are actually the fundamentals that define the base of the design.
We can add some more empirical and the practical observations to this but this is the bare
minimum every design has to see and can’t be overlooked.
For the design of Bracket the Normal stress calculations under the static load is
considered to be the fundamental approach. Even the same criteria is being followed
in the industry with certain add on.
AS per the design the maximum stress will occur at the point where the cross section
has the minimum area. Thus we will select that section as the most critical one and
perform the stress analysis at this section only.
Stress across the section of the Centre big circle is given by:
Stress= Load
Area
Secure Best Marks with AI Grader
Need help grading? Try our AI Grader for instant feedback on your assignments.
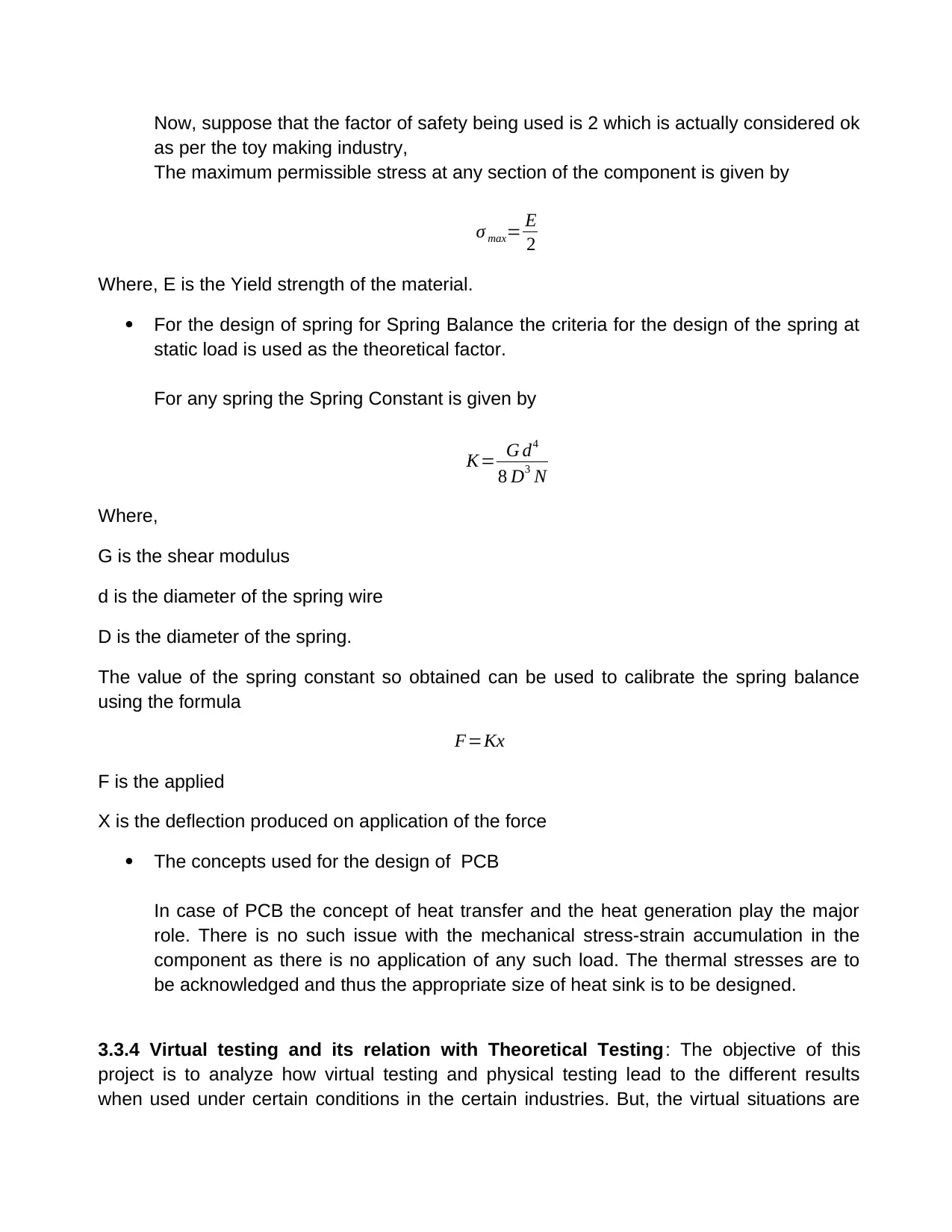
Now, suppose that the factor of safety being used is 2 which is actually considered ok
as per the toy making industry,
The maximum permissible stress at any section of the component is given by
σ max= E
2
Where, E is the Yield strength of the material.
For the design of spring for Spring Balance the criteria for the design of the spring at
static load is used as the theoretical factor.
For any spring the Spring Constant is given by
K= G d4
8 D3 N
Where,
G is the shear modulus
d is the diameter of the spring wire
D is the diameter of the spring.
The value of the spring constant so obtained can be used to calibrate the spring balance
using the formula
F=Kx
F is the applied
X is the deflection produced on application of the force
The concepts used for the design of PCB
In case of PCB the concept of heat transfer and the heat generation play the major
role. There is no such issue with the mechanical stress-strain accumulation in the
component as there is no application of any such load. The thermal stresses are to
be acknowledged and thus the appropriate size of heat sink is to be designed.
3.3.4 Virtual testing and its relation with Theoretical Testing: The objective of this
project is to analyze how virtual testing and physical testing lead to the different results
when used under certain conditions in the certain industries. But, the virtual situations are
as per the toy making industry,
The maximum permissible stress at any section of the component is given by
σ max= E
2
Where, E is the Yield strength of the material.
For the design of spring for Spring Balance the criteria for the design of the spring at
static load is used as the theoretical factor.
For any spring the Spring Constant is given by
K= G d4
8 D3 N
Where,
G is the shear modulus
d is the diameter of the spring wire
D is the diameter of the spring.
The value of the spring constant so obtained can be used to calibrate the spring balance
using the formula
F=Kx
F is the applied
X is the deflection produced on application of the force
The concepts used for the design of PCB
In case of PCB the concept of heat transfer and the heat generation play the major
role. There is no such issue with the mechanical stress-strain accumulation in the
component as there is no application of any such load. The thermal stresses are to
be acknowledged and thus the appropriate size of heat sink is to be designed.
3.3.4 Virtual testing and its relation with Theoretical Testing: The objective of this
project is to analyze how virtual testing and physical testing lead to the different results
when used under certain conditions in the certain industries. But, the virtual situations are
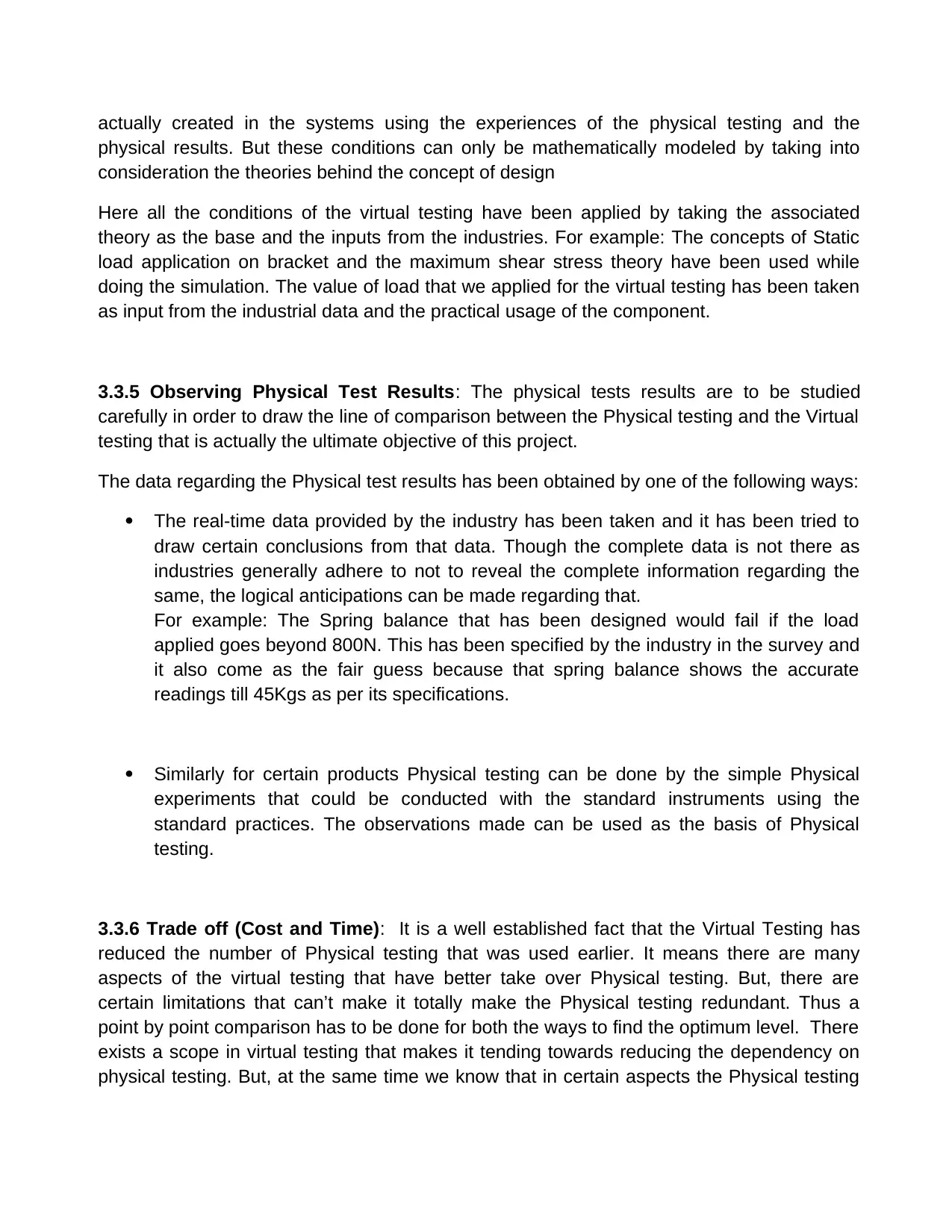
actually created in the systems using the experiences of the physical testing and the
physical results. But these conditions can only be mathematically modeled by taking into
consideration the theories behind the concept of design
Here all the conditions of the virtual testing have been applied by taking the associated
theory as the base and the inputs from the industries. For example: The concepts of Static
load application on bracket and the maximum shear stress theory have been used while
doing the simulation. The value of load that we applied for the virtual testing has been taken
as input from the industrial data and the practical usage of the component.
3.3.5 Observing Physical Test Results: The physical tests results are to be studied
carefully in order to draw the line of comparison between the Physical testing and the Virtual
testing that is actually the ultimate objective of this project.
The data regarding the Physical test results has been obtained by one of the following ways:
The real-time data provided by the industry has been taken and it has been tried to
draw certain conclusions from that data. Though the complete data is not there as
industries generally adhere to not to reveal the complete information regarding the
same, the logical anticipations can be made regarding that.
For example: The Spring balance that has been designed would fail if the load
applied goes beyond 800N. This has been specified by the industry in the survey and
it also come as the fair guess because that spring balance shows the accurate
readings till 45Kgs as per its specifications.
Similarly for certain products Physical testing can be done by the simple Physical
experiments that could be conducted with the standard instruments using the
standard practices. The observations made can be used as the basis of Physical
testing.
3.3.6 Trade off (Cost and Time): It is a well established fact that the Virtual Testing has
reduced the number of Physical testing that was used earlier. It means there are many
aspects of the virtual testing that have better take over Physical testing. But, there are
certain limitations that can’t make it totally make the Physical testing redundant. Thus a
point by point comparison has to be done for both the ways to find the optimum level. There
exists a scope in virtual testing that makes it tending towards reducing the dependency on
physical testing. But, at the same time we know that in certain aspects the Physical testing
physical results. But these conditions can only be mathematically modeled by taking into
consideration the theories behind the concept of design
Here all the conditions of the virtual testing have been applied by taking the associated
theory as the base and the inputs from the industries. For example: The concepts of Static
load application on bracket and the maximum shear stress theory have been used while
doing the simulation. The value of load that we applied for the virtual testing has been taken
as input from the industrial data and the practical usage of the component.
3.3.5 Observing Physical Test Results: The physical tests results are to be studied
carefully in order to draw the line of comparison between the Physical testing and the Virtual
testing that is actually the ultimate objective of this project.
The data regarding the Physical test results has been obtained by one of the following ways:
The real-time data provided by the industry has been taken and it has been tried to
draw certain conclusions from that data. Though the complete data is not there as
industries generally adhere to not to reveal the complete information regarding the
same, the logical anticipations can be made regarding that.
For example: The Spring balance that has been designed would fail if the load
applied goes beyond 800N. This has been specified by the industry in the survey and
it also come as the fair guess because that spring balance shows the accurate
readings till 45Kgs as per its specifications.
Similarly for certain products Physical testing can be done by the simple Physical
experiments that could be conducted with the standard instruments using the
standard practices. The observations made can be used as the basis of Physical
testing.
3.3.6 Trade off (Cost and Time): It is a well established fact that the Virtual Testing has
reduced the number of Physical testing that was used earlier. It means there are many
aspects of the virtual testing that have better take over Physical testing. But, there are
certain limitations that can’t make it totally make the Physical testing redundant. Thus a
point by point comparison has to be done for both the ways to find the optimum level. There
exists a scope in virtual testing that makes it tending towards reducing the dependency on
physical testing. But, at the same time we know that in certain aspects the Physical testing
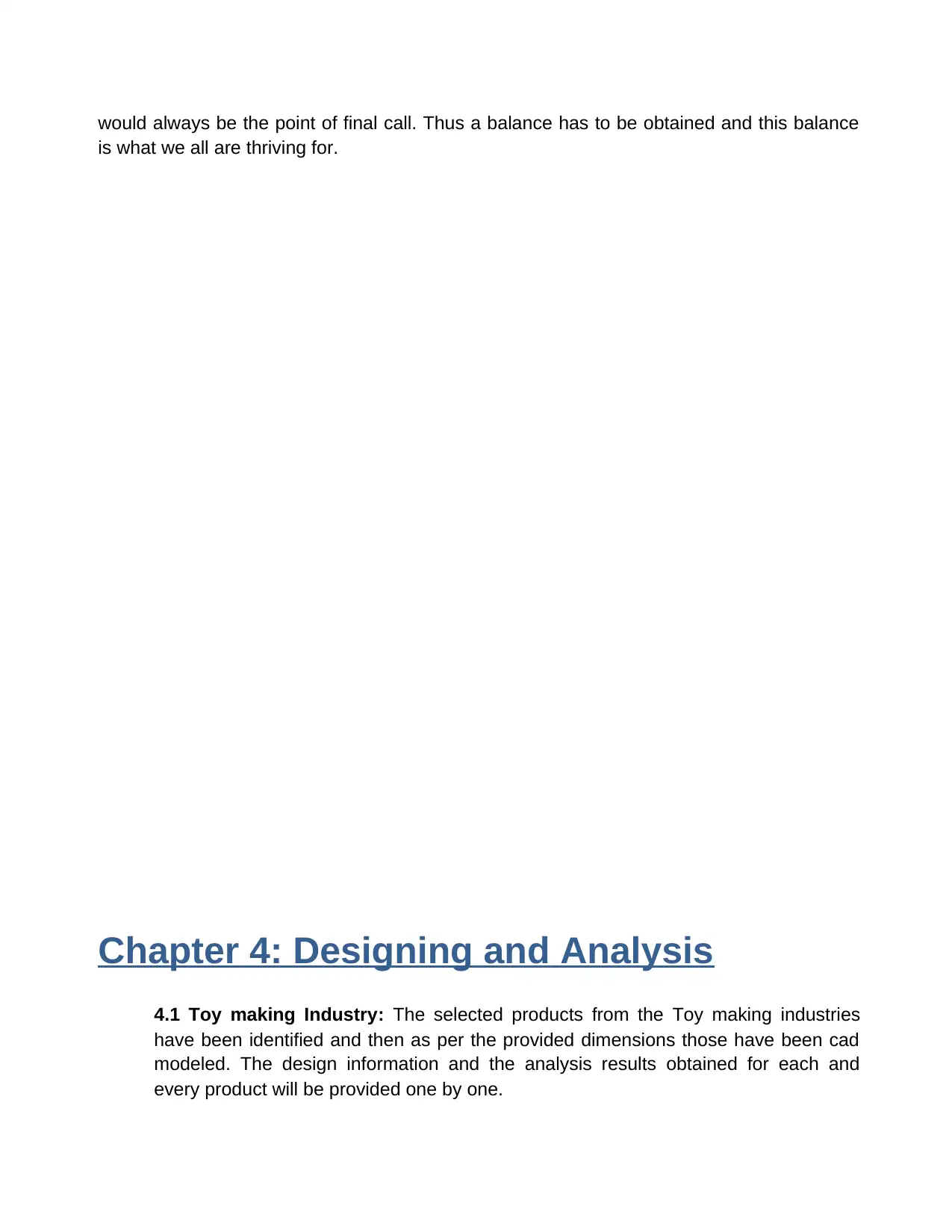
would always be the point of final call. Thus a balance has to be obtained and this balance
is what we all are thriving for.
Chapter 4: Designing and Analysis
4.1 Toy making Industry: The selected products from the Toy making industries
have been identified and then as per the provided dimensions those have been cad
modeled. The design information and the analysis results obtained for each and
every product will be provided one by one.
is what we all are thriving for.
Chapter 4: Designing and Analysis
4.1 Toy making Industry: The selected products from the Toy making industries
have been identified and then as per the provided dimensions those have been cad
modeled. The design information and the analysis results obtained for each and
every product will be provided one by one.
Paraphrase This Document
Need a fresh take? Get an instant paraphrase of this document with our AI Paraphraser
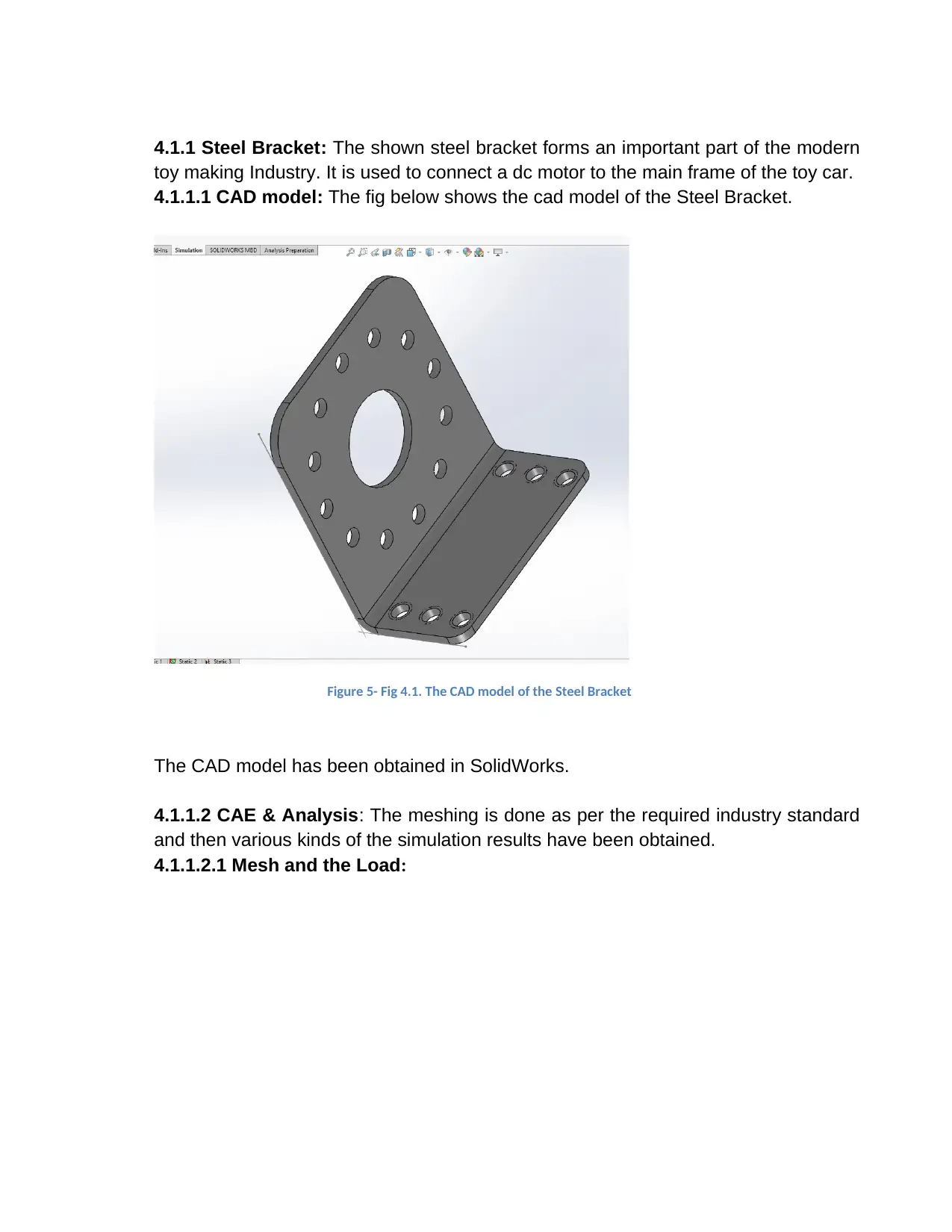
4.1.1 Steel Bracket: The shown steel bracket forms an important part of the modern
toy making Industry. It is used to connect a dc motor to the main frame of the toy car.
4.1.1.1 CAD model: The fig below shows the cad model of the Steel Bracket.
Figure 5- Fig 4.1. The CAD model of the Steel Bracket
The CAD model has been obtained in SolidWorks.
4.1.1.2 CAE & Analysis: The meshing is done as per the required industry standard
and then various kinds of the simulation results have been obtained.
4.1.1.2.1 Mesh and the Load:
toy making Industry. It is used to connect a dc motor to the main frame of the toy car.
4.1.1.1 CAD model: The fig below shows the cad model of the Steel Bracket.
Figure 5- Fig 4.1. The CAD model of the Steel Bracket
The CAD model has been obtained in SolidWorks.
4.1.1.2 CAE & Analysis: The meshing is done as per the required industry standard
and then various kinds of the simulation results have been obtained.
4.1.1.2.1 Mesh and the Load:
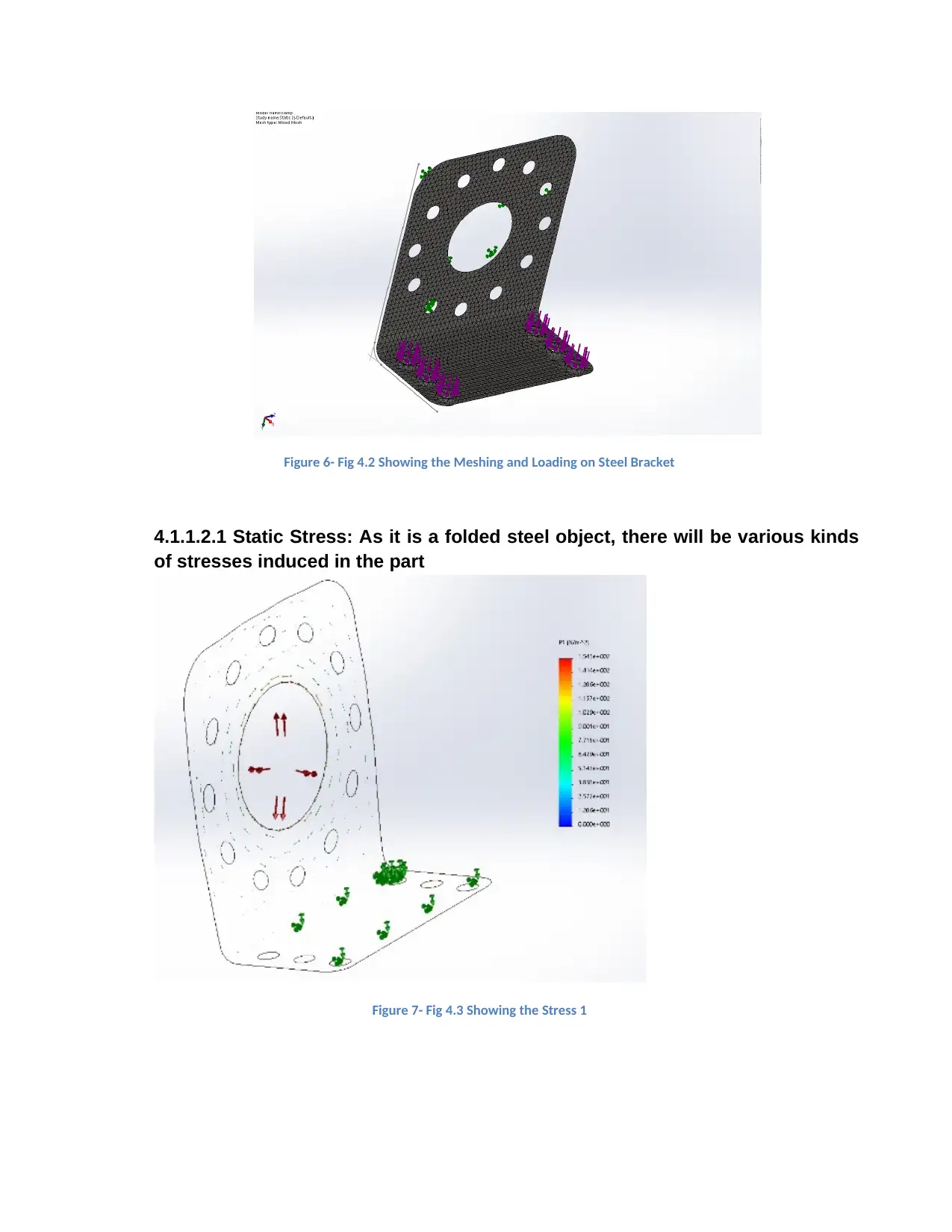
Figure 6- Fig 4.2 Showing the Meshing and Loading on Steel Bracket
4.1.1.2.1 Static Stress: As it is a folded steel object, there will be various kinds
of stresses induced in the part
Figure 7- Fig 4.3 Showing the Stress 1
4.1.1.2.1 Static Stress: As it is a folded steel object, there will be various kinds
of stresses induced in the part
Figure 7- Fig 4.3 Showing the Stress 1
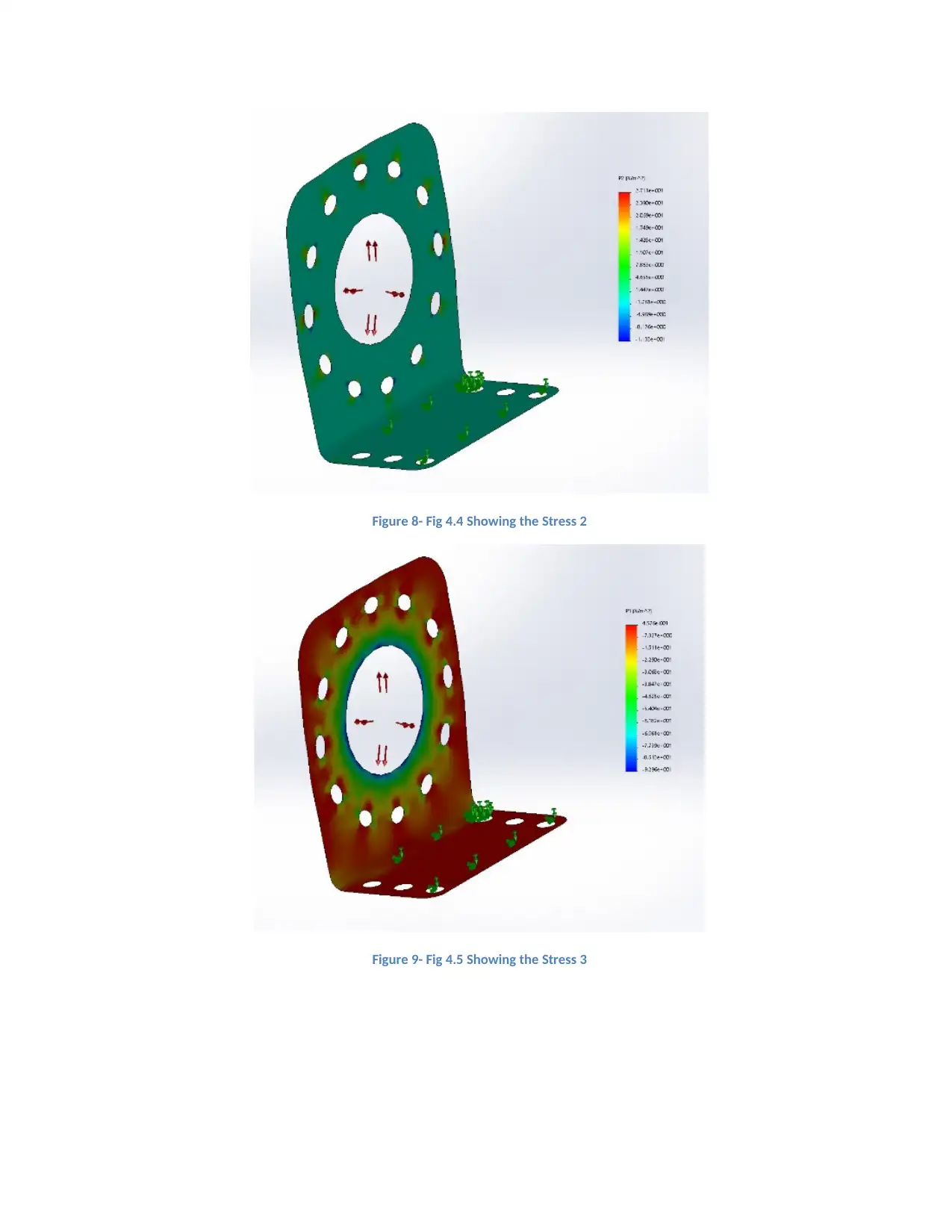
Figure 8- Fig 4.4 Showing the Stress 2
Figure 9- Fig 4.5 Showing the Stress 3
Figure 9- Fig 4.5 Showing the Stress 3
Secure Best Marks with AI Grader
Need help grading? Try our AI Grader for instant feedback on your assignments.
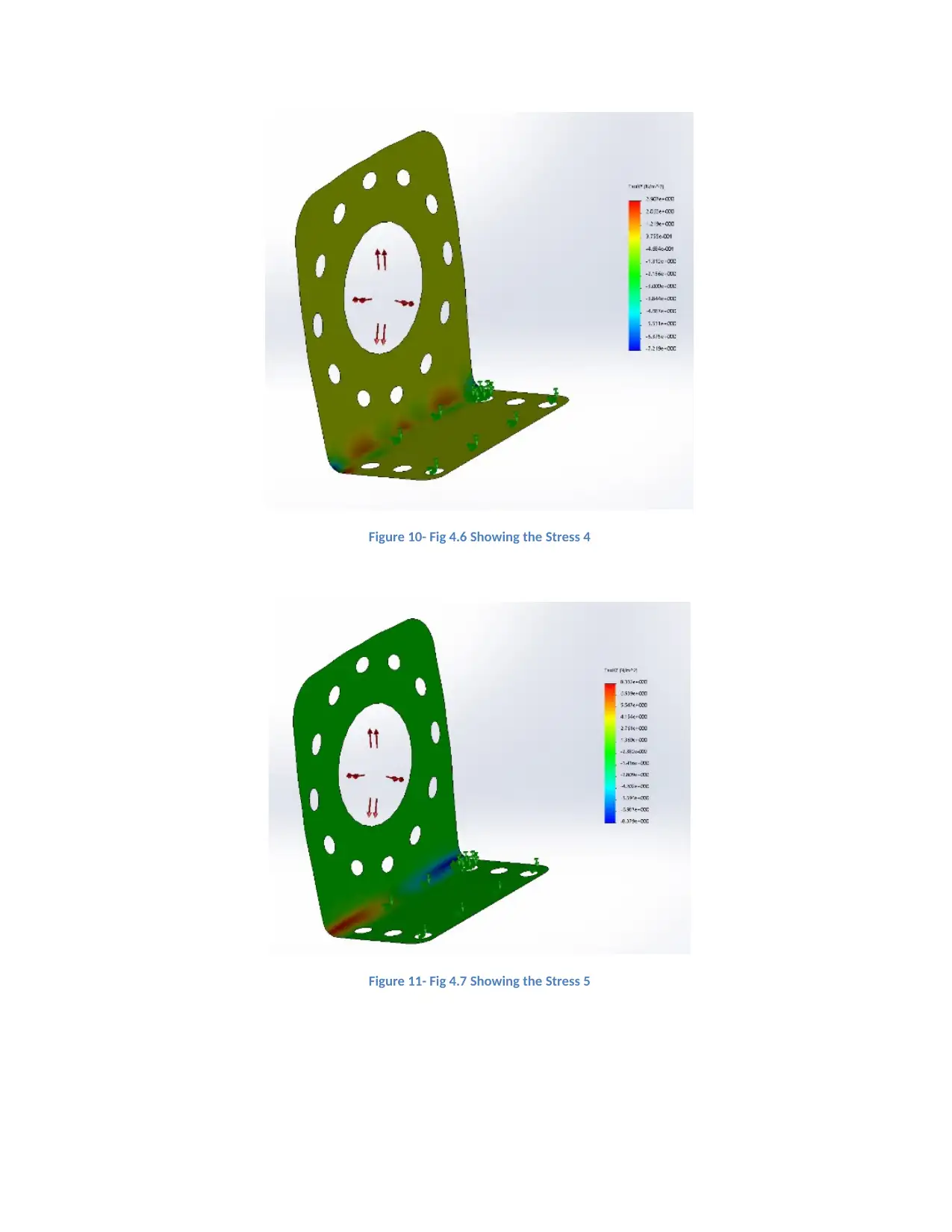
Figure 10- Fig 4.6 Showing the Stress 4
Figure 11- Fig 4.7 Showing the Stress 5
Figure 11- Fig 4.7 Showing the Stress 5
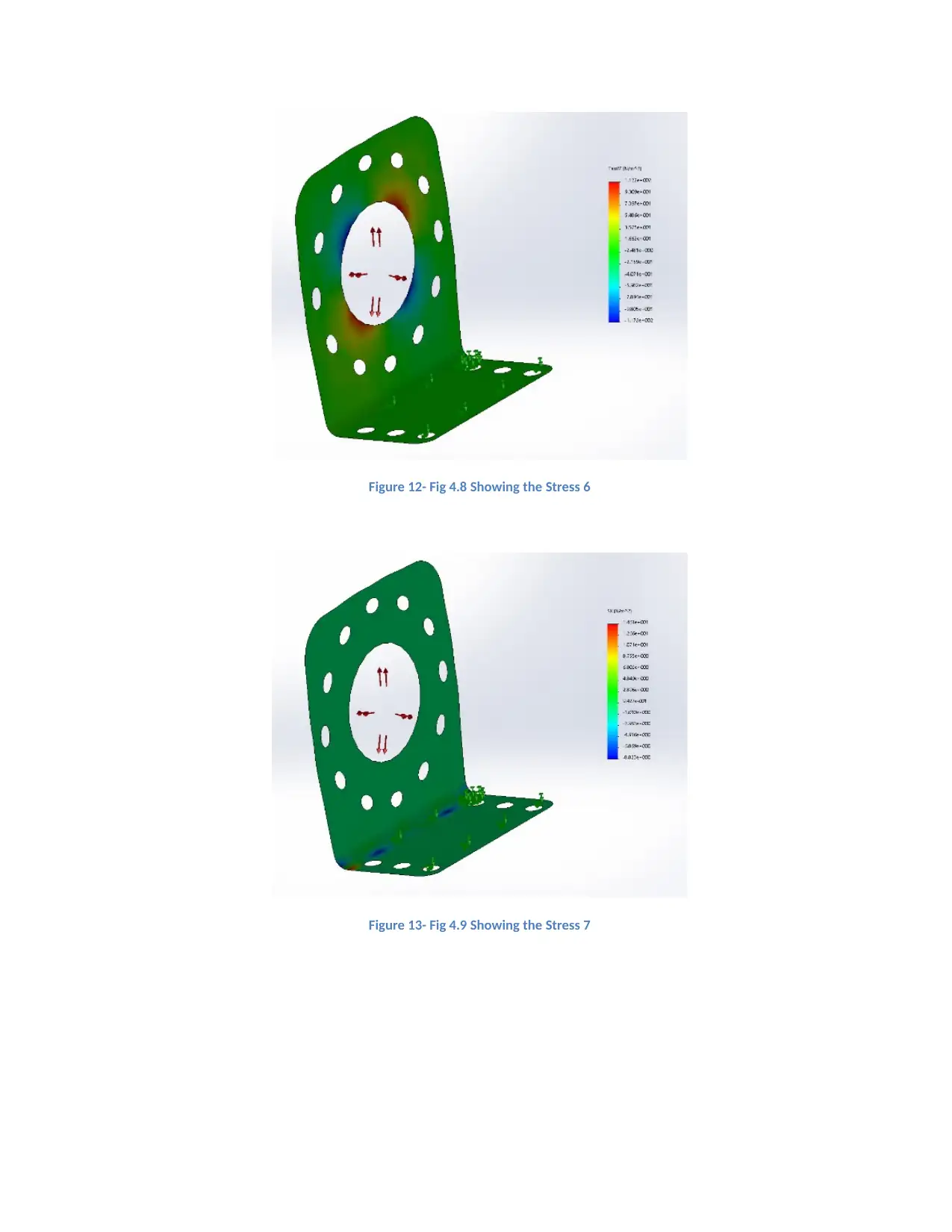
Figure 12- Fig 4.8 Showing the Stress 6
Figure 13- Fig 4.9 Showing the Stress 7
Figure 13- Fig 4.9 Showing the Stress 7
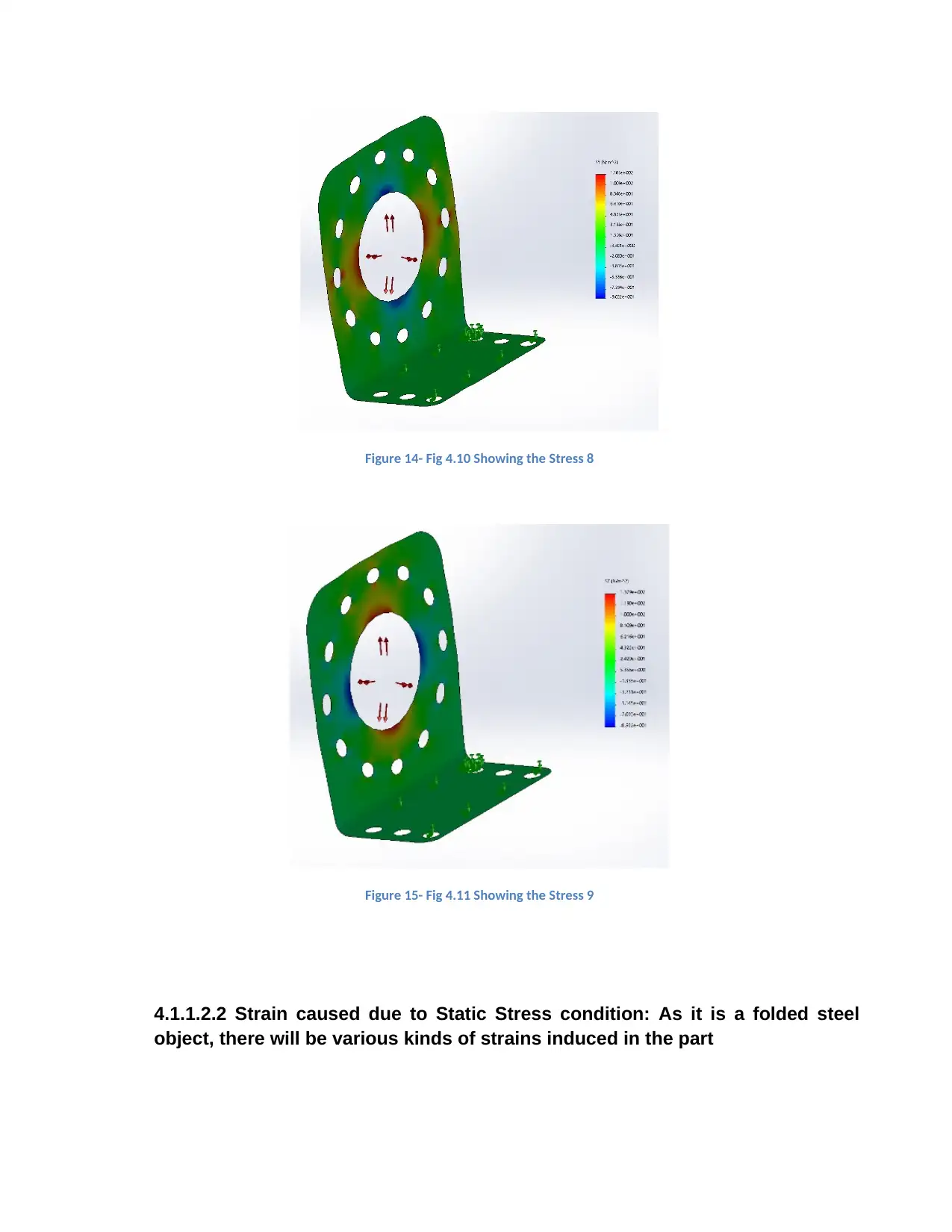
Figure 14- Fig 4.10 Showing the Stress 8
Figure 15- Fig 4.11 Showing the Stress 9
4.1.1.2.2 Strain caused due to Static Stress condition: As it is a folded steel
object, there will be various kinds of strains induced in the part
Figure 15- Fig 4.11 Showing the Stress 9
4.1.1.2.2 Strain caused due to Static Stress condition: As it is a folded steel
object, there will be various kinds of strains induced in the part
Paraphrase This Document
Need a fresh take? Get an instant paraphrase of this document with our AI Paraphraser
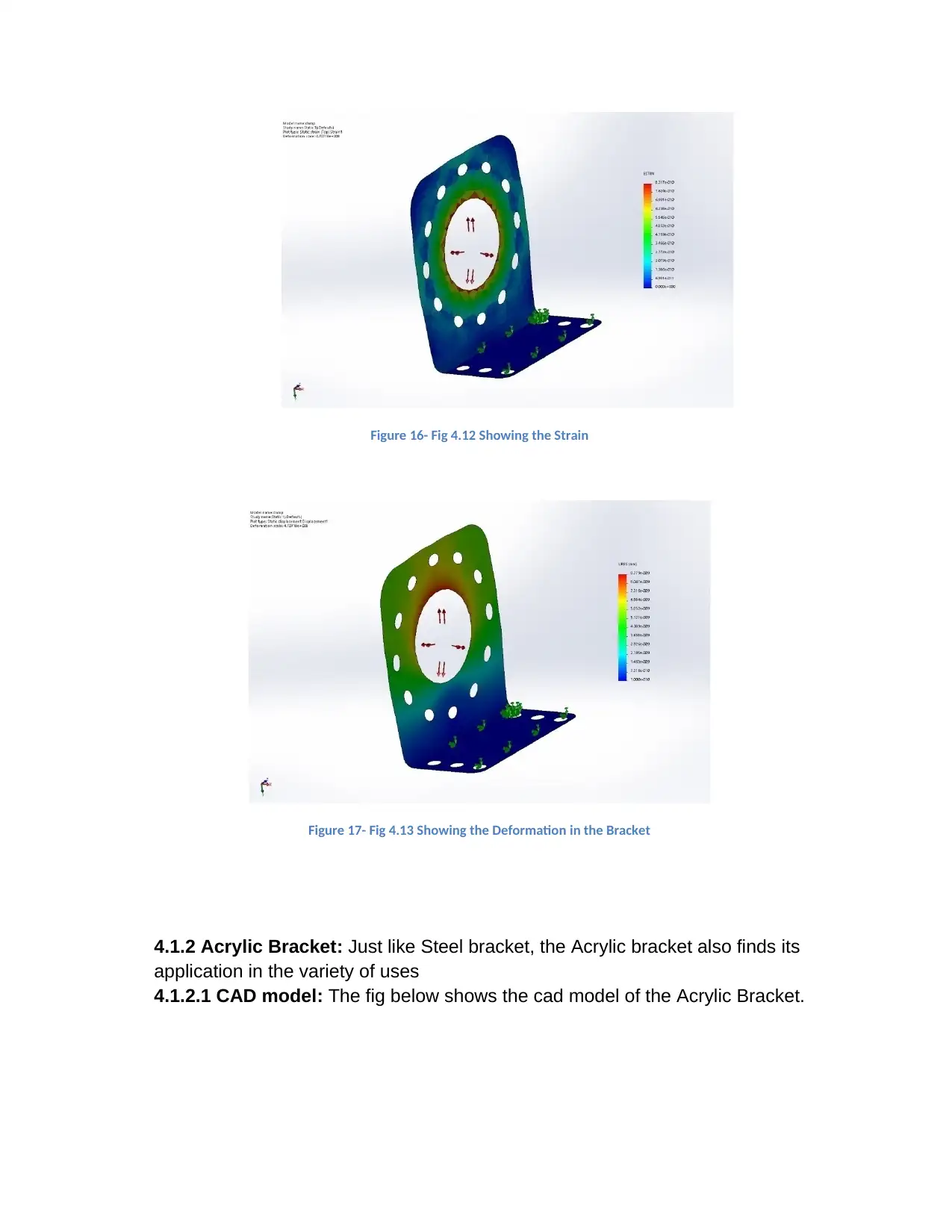
Figure 16- Fig 4.12 Showing the Strain
Figure 17- Fig 4.13 Showing the Deformation in the Bracket
4.1.2 Acrylic Bracket: Just like Steel bracket, the Acrylic bracket also finds its
application in the variety of uses
4.1.2.1 CAD model: The fig below shows the cad model of the Acrylic Bracket.
Figure 17- Fig 4.13 Showing the Deformation in the Bracket
4.1.2 Acrylic Bracket: Just like Steel bracket, the Acrylic bracket also finds its
application in the variety of uses
4.1.2.1 CAD model: The fig below shows the cad model of the Acrylic Bracket.
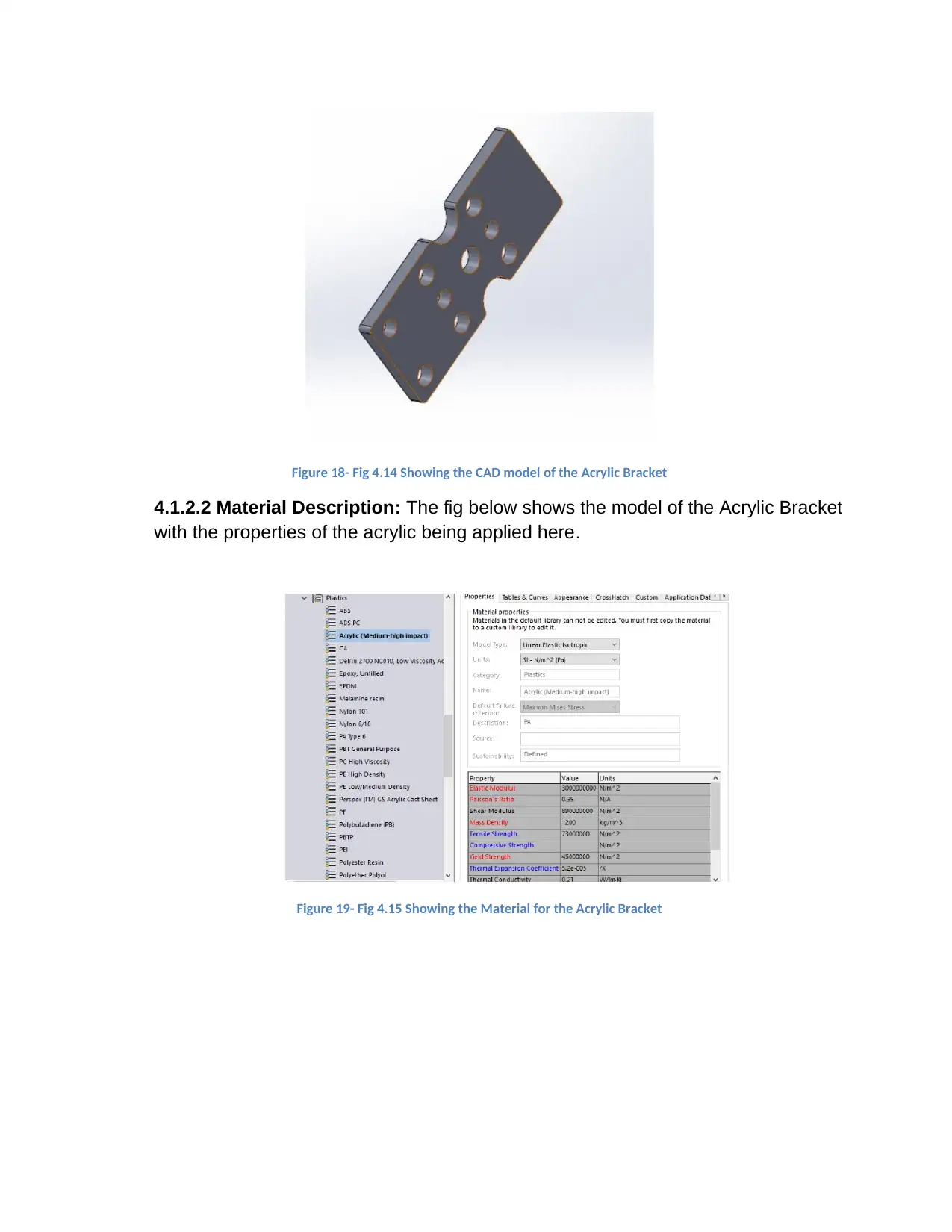
Figure 18- Fig 4.14 Showing the CAD model of the Acrylic Bracket
4.1.2.2 Material Description: The fig below shows the model of the Acrylic Bracket
with the properties of the acrylic being applied here.
Figure 19- Fig 4.15 Showing the Material for the Acrylic Bracket
4.1.2.2 Material Description: The fig below shows the model of the Acrylic Bracket
with the properties of the acrylic being applied here.
Figure 19- Fig 4.15 Showing the Material for the Acrylic Bracket
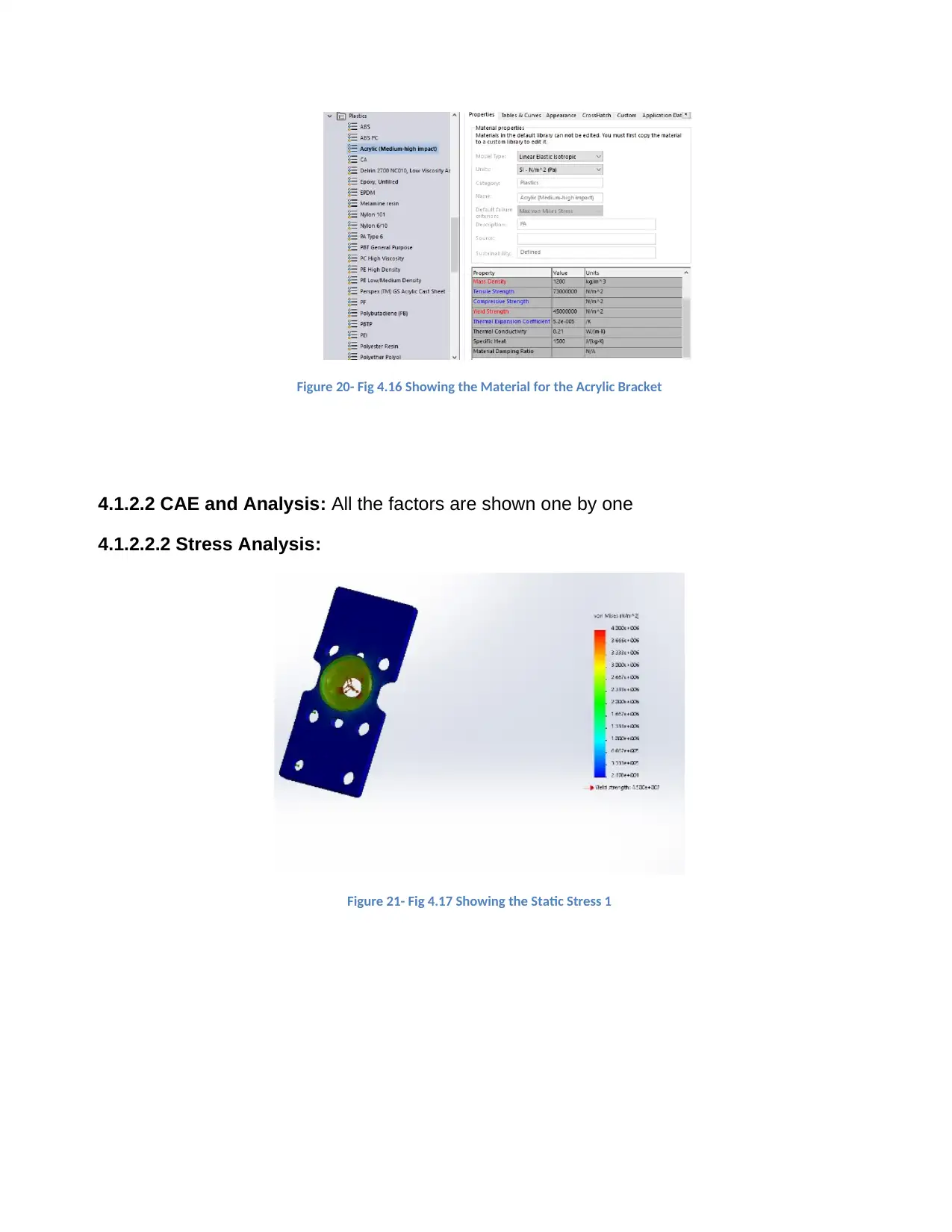
Figure 20- Fig 4.16 Showing the Material for the Acrylic Bracket
4.1.2.2 CAE and Analysis: All the factors are shown one by one
4.1.2.2.2 Stress Analysis:
Figure 21- Fig 4.17 Showing the Static Stress 1
4.1.2.2 CAE and Analysis: All the factors are shown one by one
4.1.2.2.2 Stress Analysis:
Figure 21- Fig 4.17 Showing the Static Stress 1
Secure Best Marks with AI Grader
Need help grading? Try our AI Grader for instant feedback on your assignments.
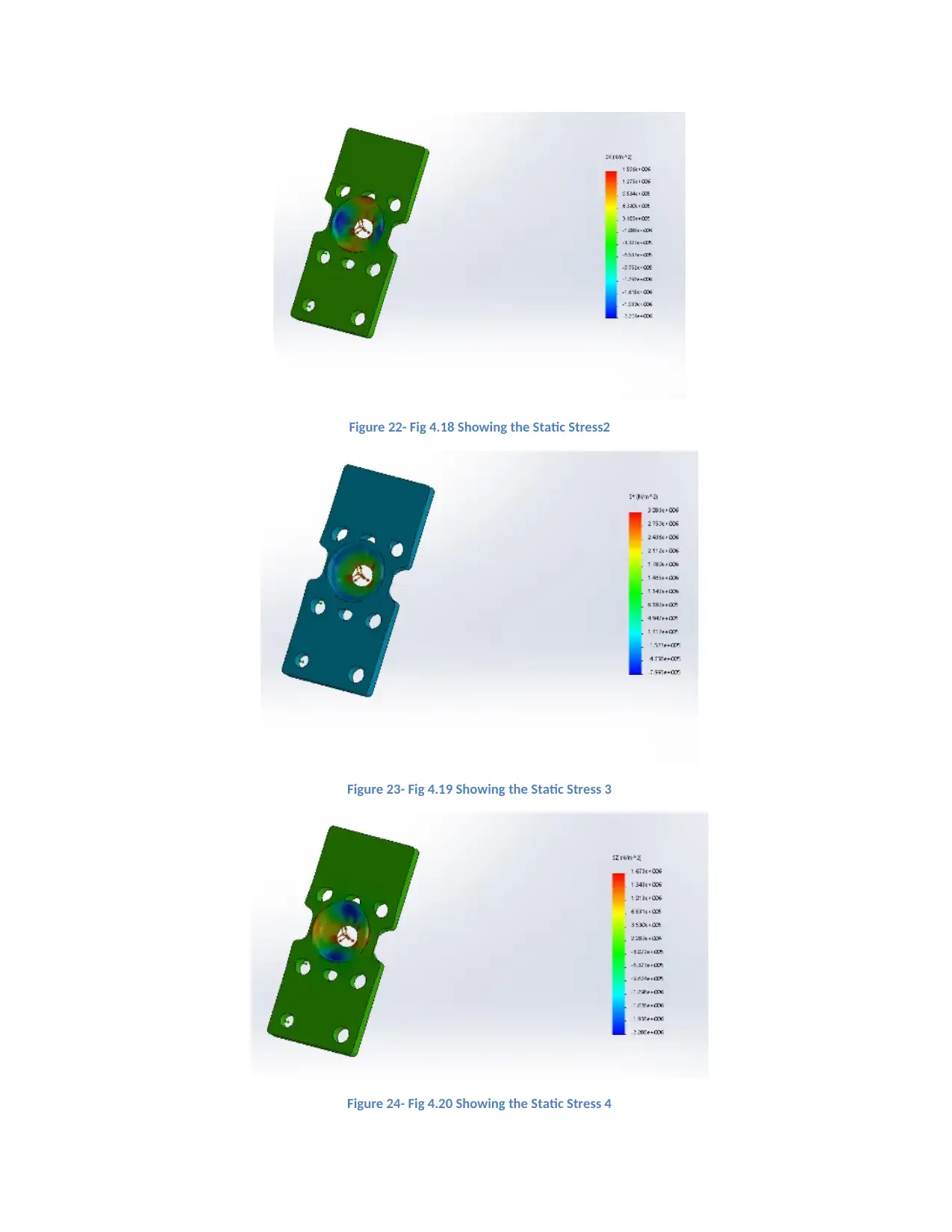
Figure 22- Fig 4.18 Showing the Static Stress2
Figure 23- Fig 4.19 Showing the Static Stress 3
Figure 24- Fig 4.20 Showing the Static Stress 4
Figure 23- Fig 4.19 Showing the Static Stress 3
Figure 24- Fig 4.20 Showing the Static Stress 4
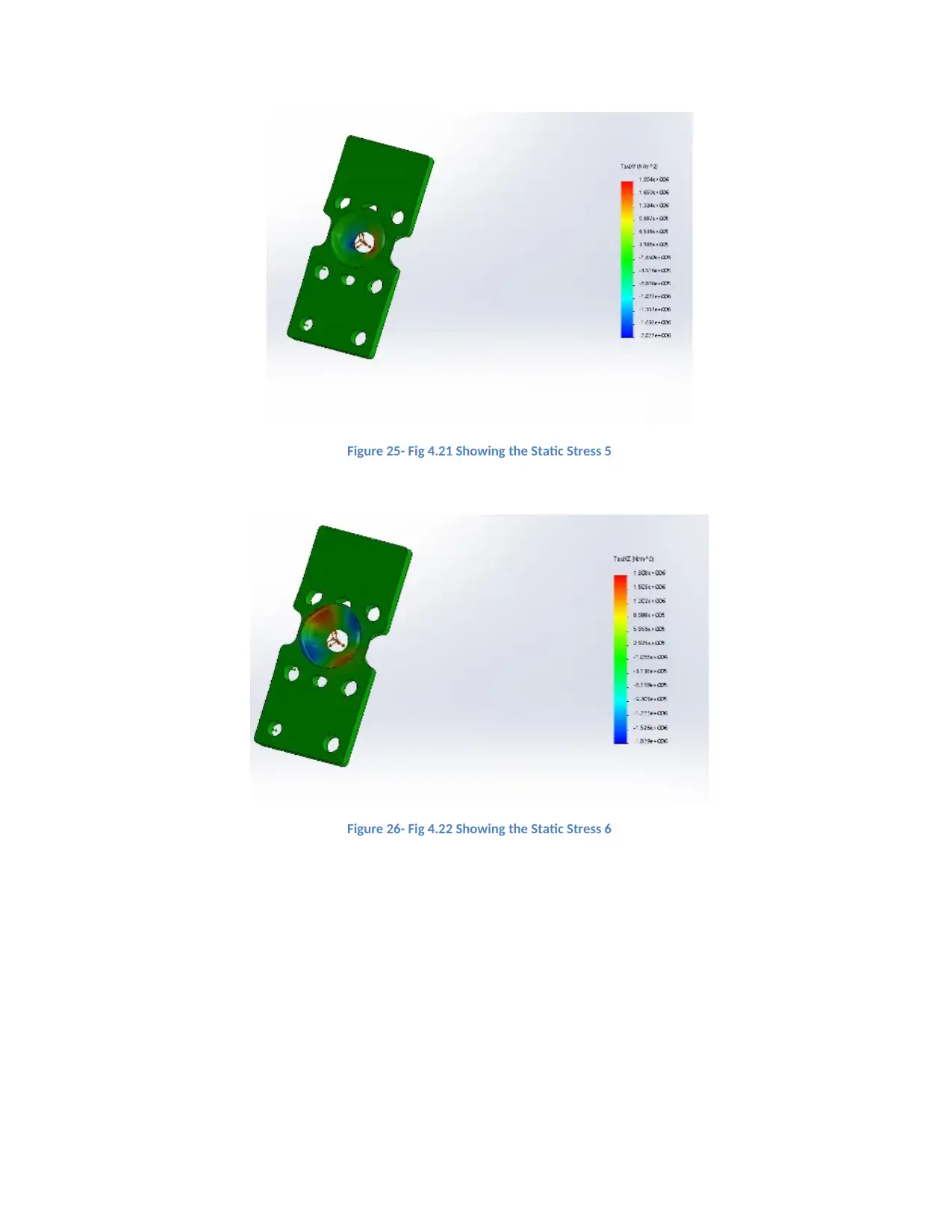
Figure 25- Fig 4.21 Showing the Static Stress 5
Figure 26- Fig 4.22 Showing the Static Stress 6
Figure 26- Fig 4.22 Showing the Static Stress 6
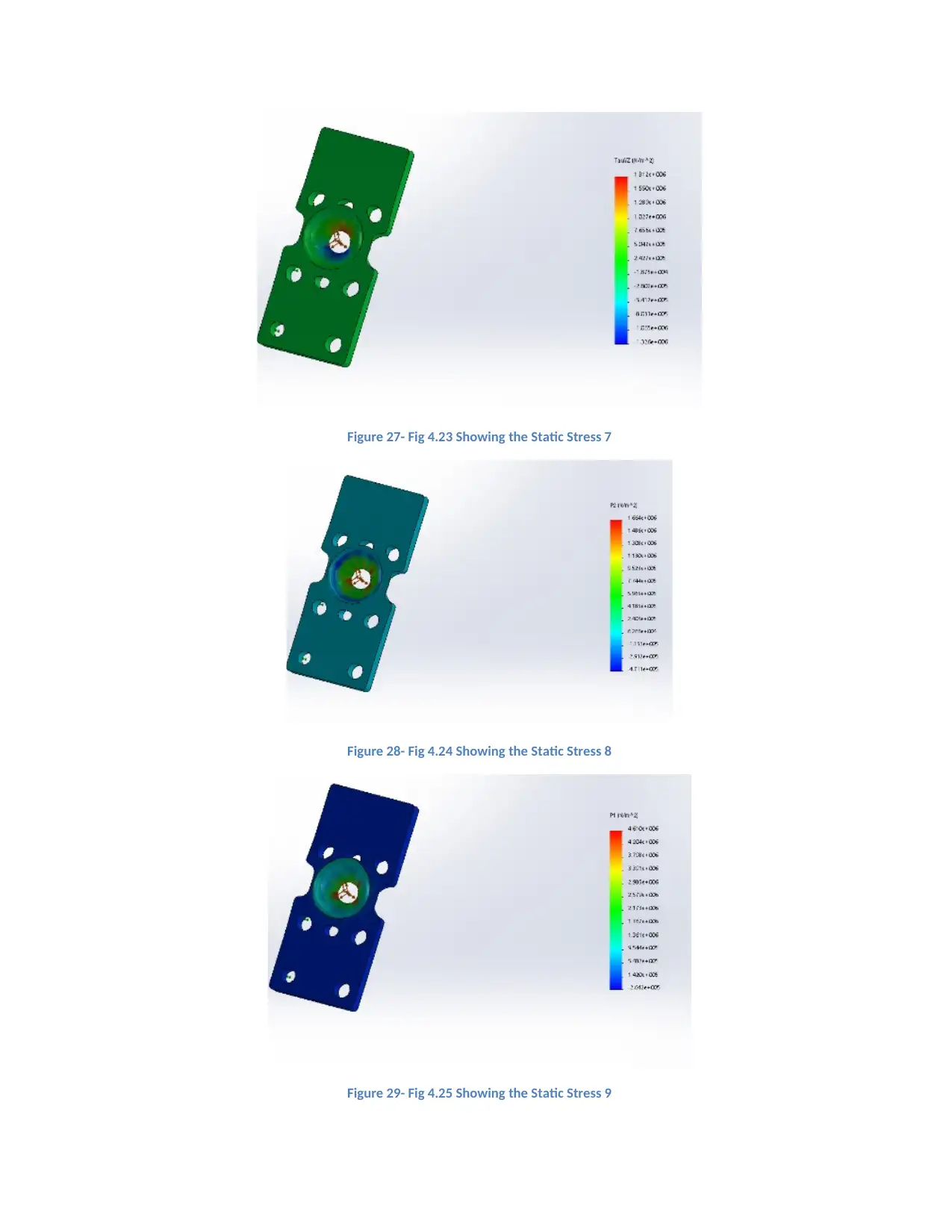
Figure 27- Fig 4.23 Showing the Static Stress 7
Figure 28- Fig 4.24 Showing the Static Stress 8
Figure 29- Fig 4.25 Showing the Static Stress 9
Figure 28- Fig 4.24 Showing the Static Stress 8
Figure 29- Fig 4.25 Showing the Static Stress 9
Paraphrase This Document
Need a fresh take? Get an instant paraphrase of this document with our AI Paraphraser
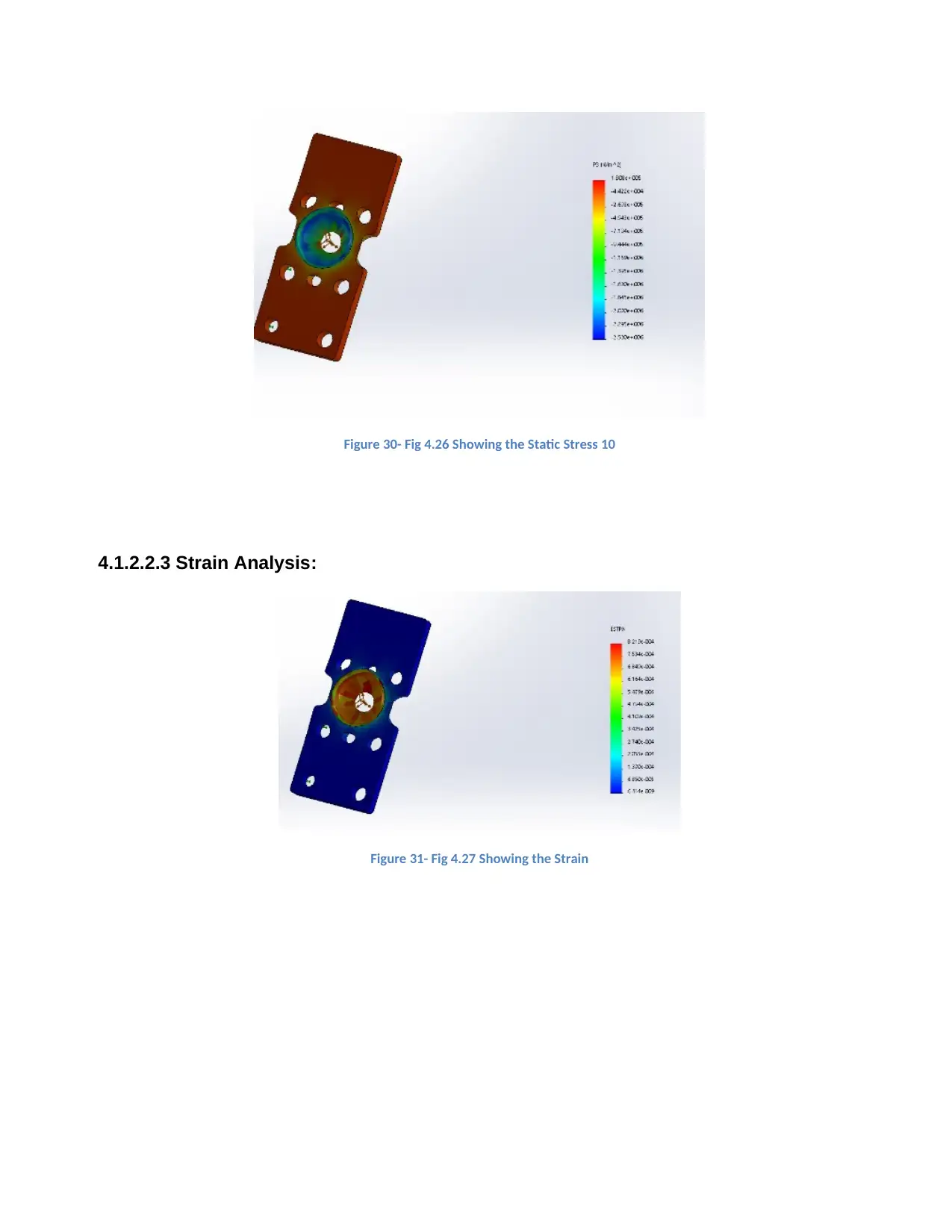
Figure 30- Fig 4.26 Showing the Static Stress 10
4.1.2.2.3 Strain Analysis:
Figure 31- Fig 4.27 Showing the Strain
4.1.2.2.3 Strain Analysis:
Figure 31- Fig 4.27 Showing the Strain
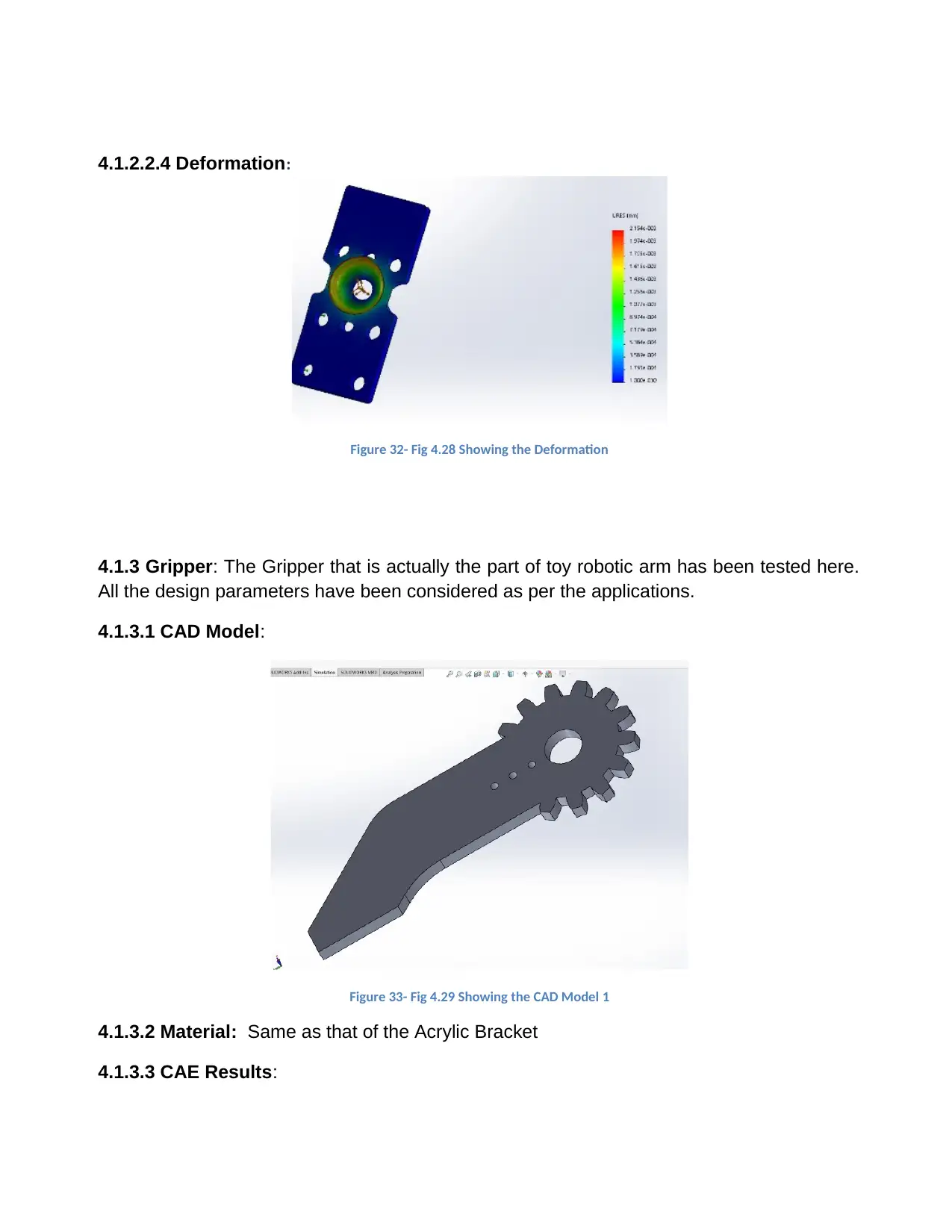
4.1.2.2.4 Deformation:
Figure 32- Fig 4.28 Showing the Deformation
4.1.3 Gripper: The Gripper that is actually the part of toy robotic arm has been tested here.
All the design parameters have been considered as per the applications.
4.1.3.1 CAD Model:
Figure 33- Fig 4.29 Showing the CAD Model 1
4.1.3.2 Material: Same as that of the Acrylic Bracket
4.1.3.3 CAE Results:
Figure 32- Fig 4.28 Showing the Deformation
4.1.3 Gripper: The Gripper that is actually the part of toy robotic arm has been tested here.
All the design parameters have been considered as per the applications.
4.1.3.1 CAD Model:
Figure 33- Fig 4.29 Showing the CAD Model 1
4.1.3.2 Material: Same as that of the Acrylic Bracket
4.1.3.3 CAE Results:
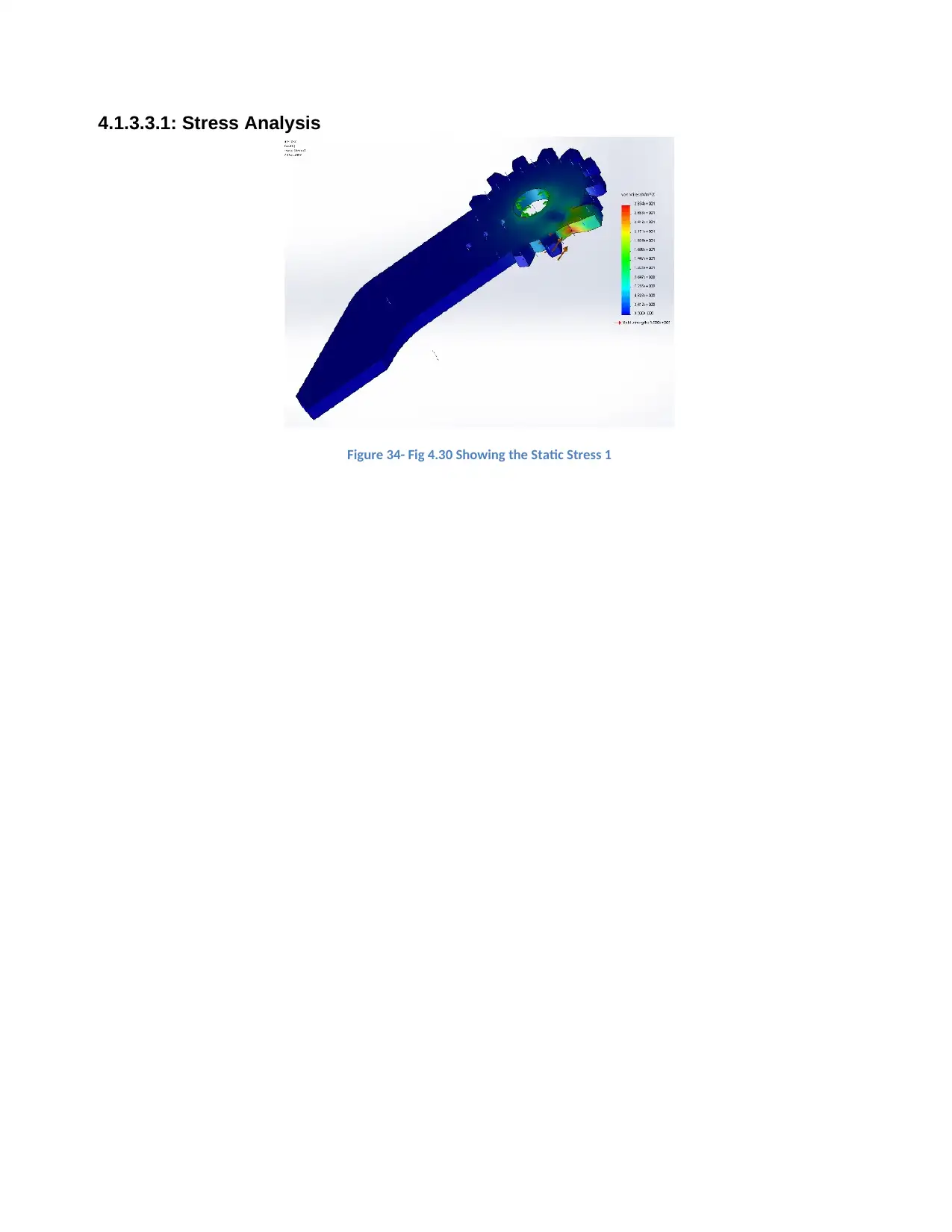
4.1.3.3.1: Stress Analysis
Figure 34- Fig 4.30 Showing the Static Stress 1
Figure 34- Fig 4.30 Showing the Static Stress 1
Secure Best Marks with AI Grader
Need help grading? Try our AI Grader for instant feedback on your assignments.
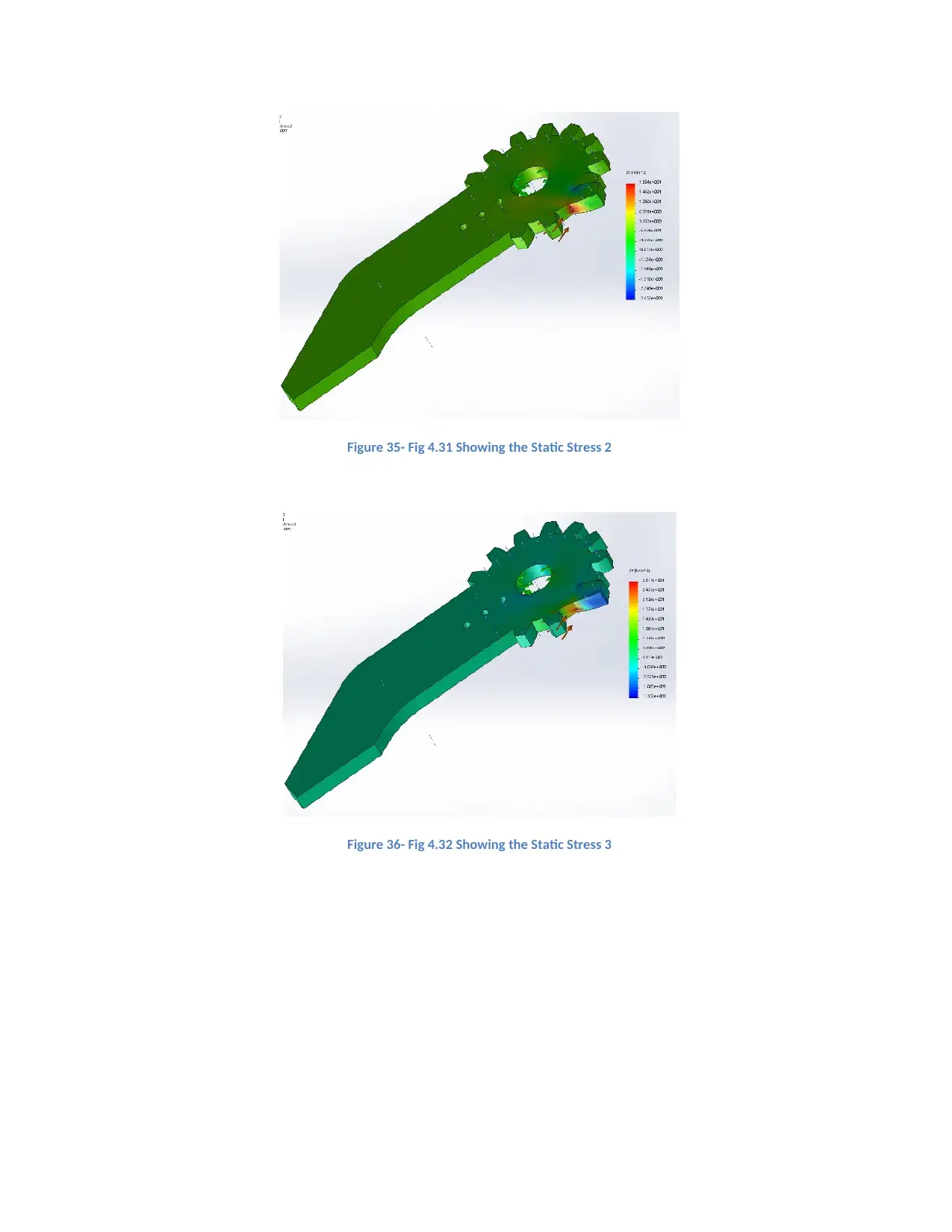
Figure 35- Fig 4.31 Showing the Static Stress 2
Figure 36- Fig 4.32 Showing the Static Stress 3
Figure 36- Fig 4.32 Showing the Static Stress 3
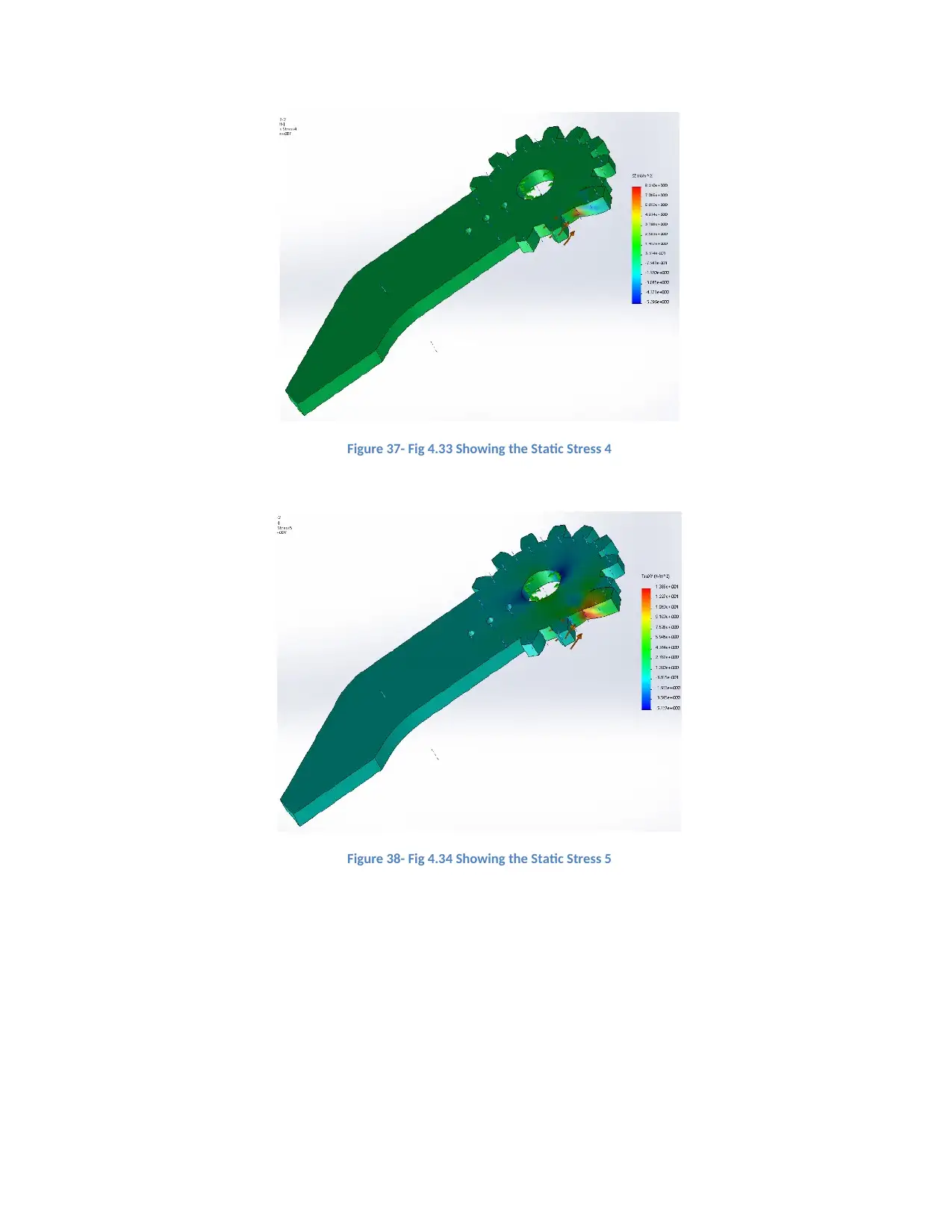
Figure 37- Fig 4.33 Showing the Static Stress 4
Figure 38- Fig 4.34 Showing the Static Stress 5
Figure 38- Fig 4.34 Showing the Static Stress 5
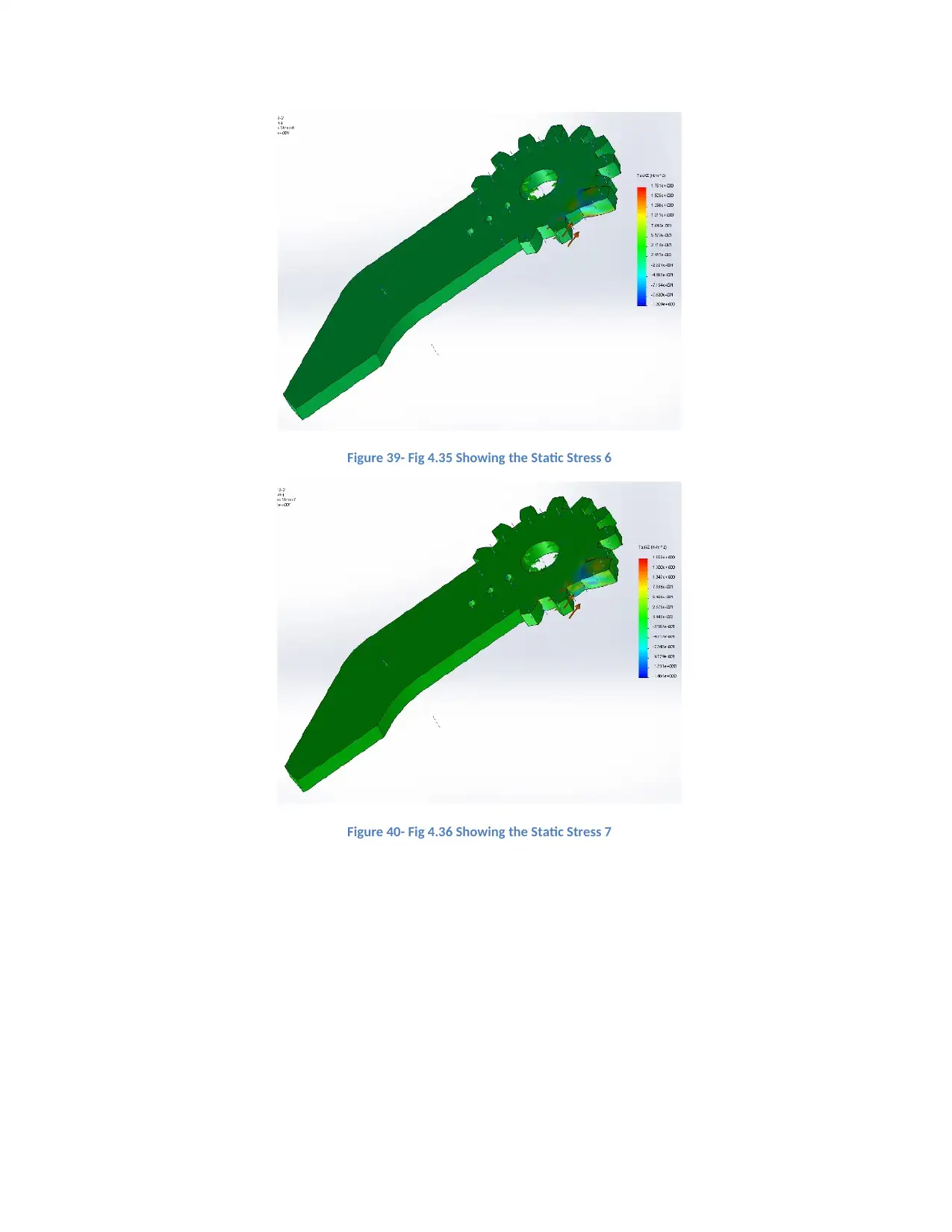
Figure 39- Fig 4.35 Showing the Static Stress 6
Figure 40- Fig 4.36 Showing the Static Stress 7
Figure 40- Fig 4.36 Showing the Static Stress 7
Paraphrase This Document
Need a fresh take? Get an instant paraphrase of this document with our AI Paraphraser
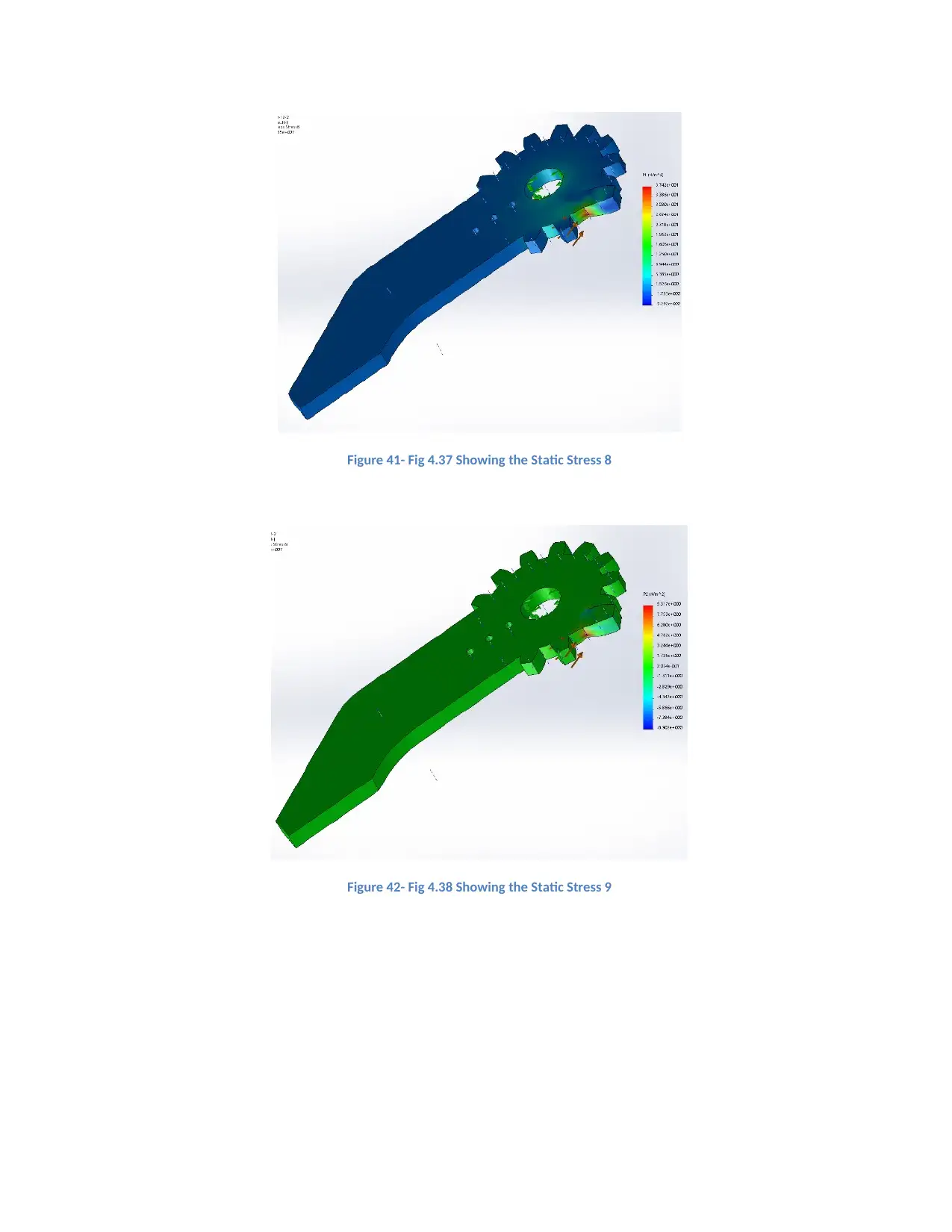
Figure 41- Fig 4.37 Showing the Static Stress 8
Figure 42- Fig 4.38 Showing the Static Stress 9
Figure 42- Fig 4.38 Showing the Static Stress 9
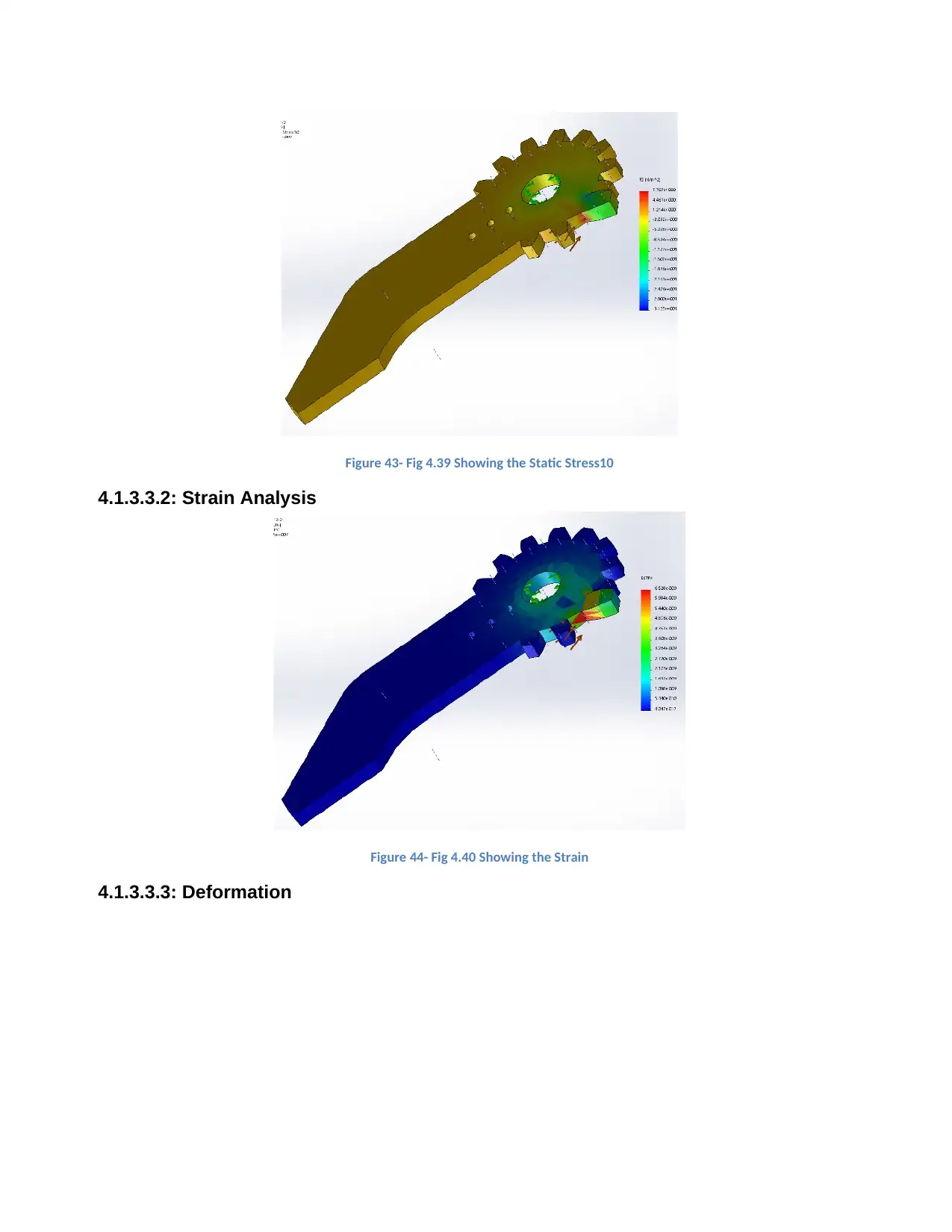
Figure 43- Fig 4.39 Showing the Static Stress10
4.1.3.3.2: Strain Analysis
Figure 44- Fig 4.40 Showing the Strain
4.1.3.3.3: Deformation
4.1.3.3.2: Strain Analysis
Figure 44- Fig 4.40 Showing the Strain
4.1.3.3.3: Deformation
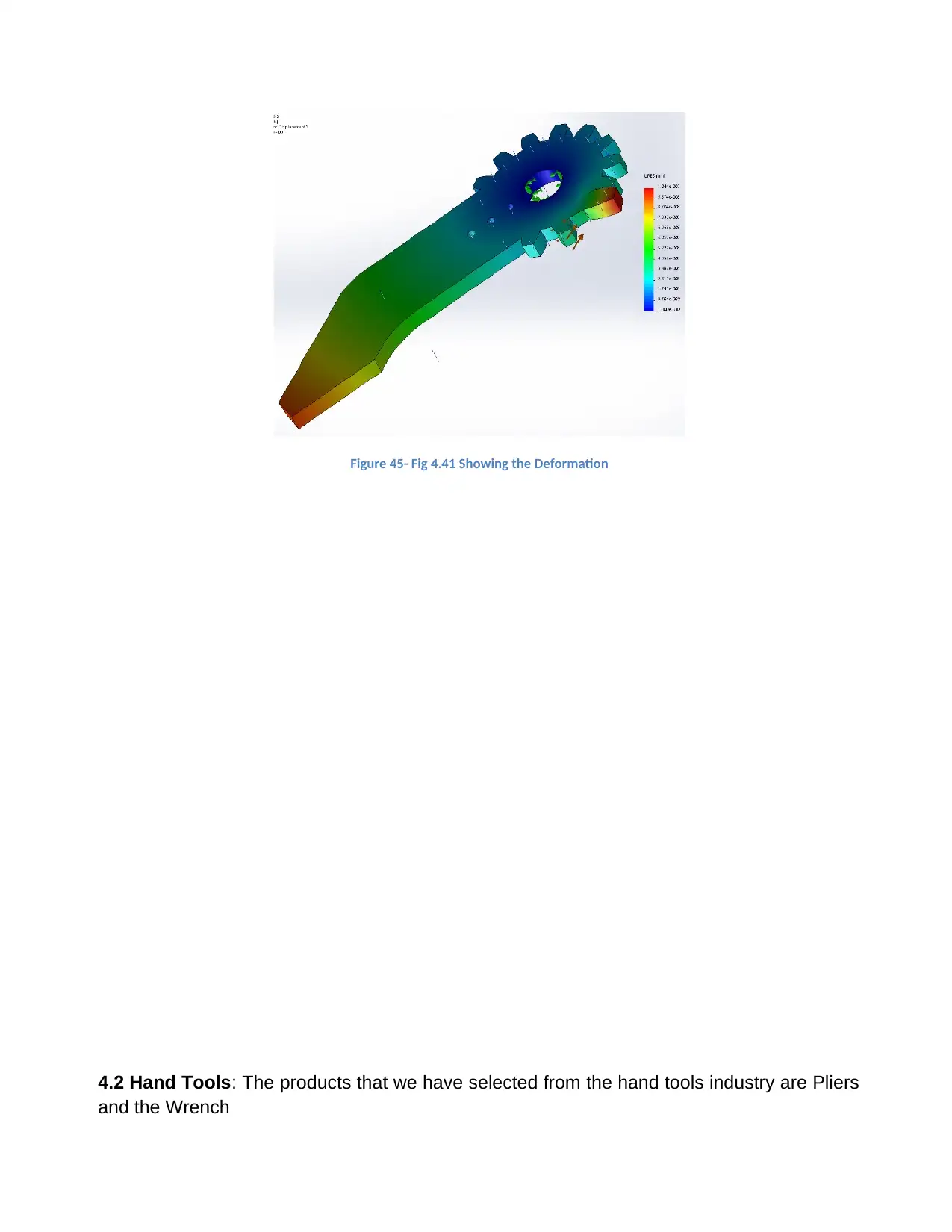
Figure 45- Fig 4.41 Showing the Deformation
4.2 Hand Tools: The products that we have selected from the hand tools industry are Pliers
and the Wrench
4.2 Hand Tools: The products that we have selected from the hand tools industry are Pliers
and the Wrench
Secure Best Marks with AI Grader
Need help grading? Try our AI Grader for instant feedback on your assignments.
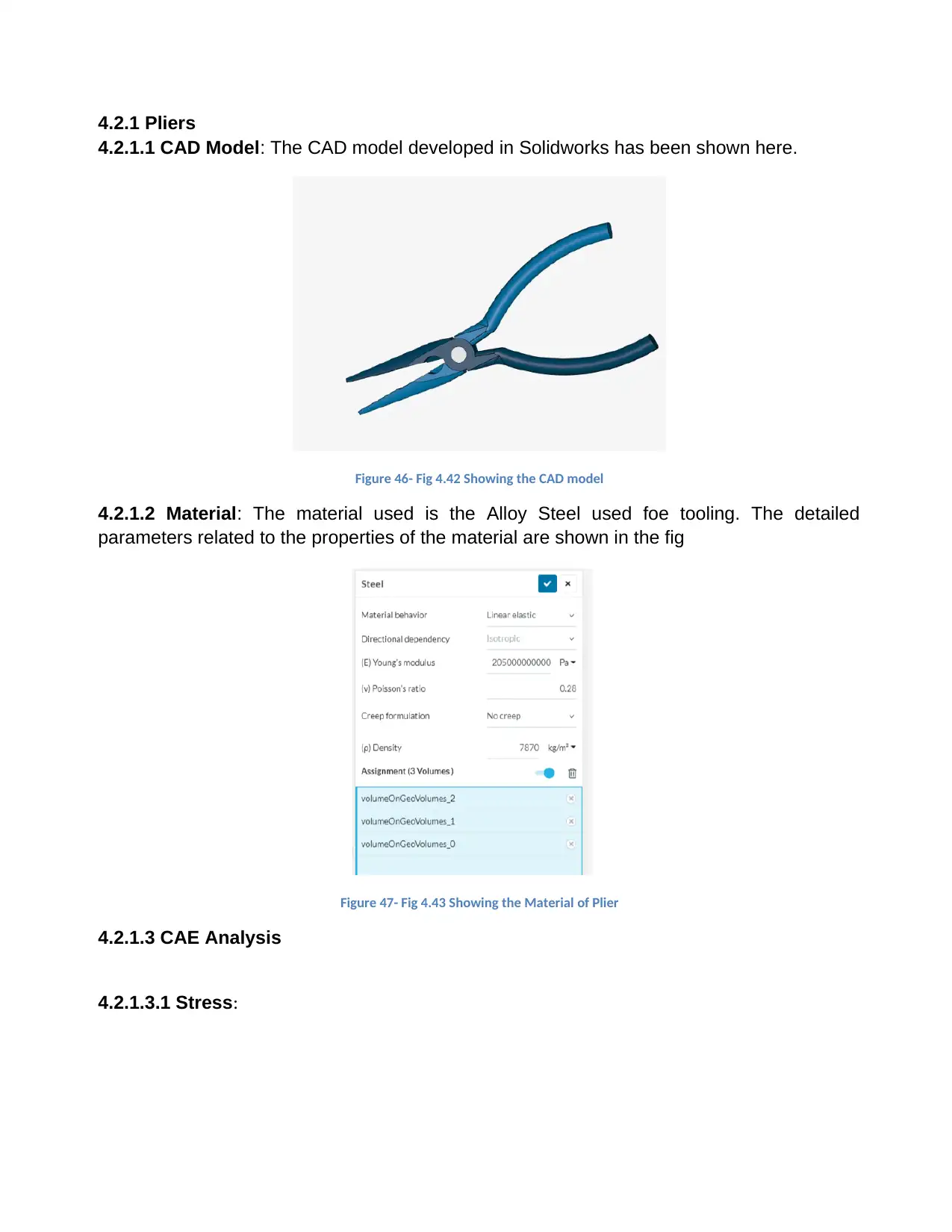
4.2.1 Pliers
4.2.1.1 CAD Model: The CAD model developed in Solidworks has been shown here.
Figure 46- Fig 4.42 Showing the CAD model
4.2.1.2 Material: The material used is the Alloy Steel used foe tooling. The detailed
parameters related to the properties of the material are shown in the fig
Figure 47- Fig 4.43 Showing the Material of Plier
4.2.1.3 CAE Analysis
4.2.1.3.1 Stress:
4.2.1.1 CAD Model: The CAD model developed in Solidworks has been shown here.
Figure 46- Fig 4.42 Showing the CAD model
4.2.1.2 Material: The material used is the Alloy Steel used foe tooling. The detailed
parameters related to the properties of the material are shown in the fig
Figure 47- Fig 4.43 Showing the Material of Plier
4.2.1.3 CAE Analysis
4.2.1.3.1 Stress:
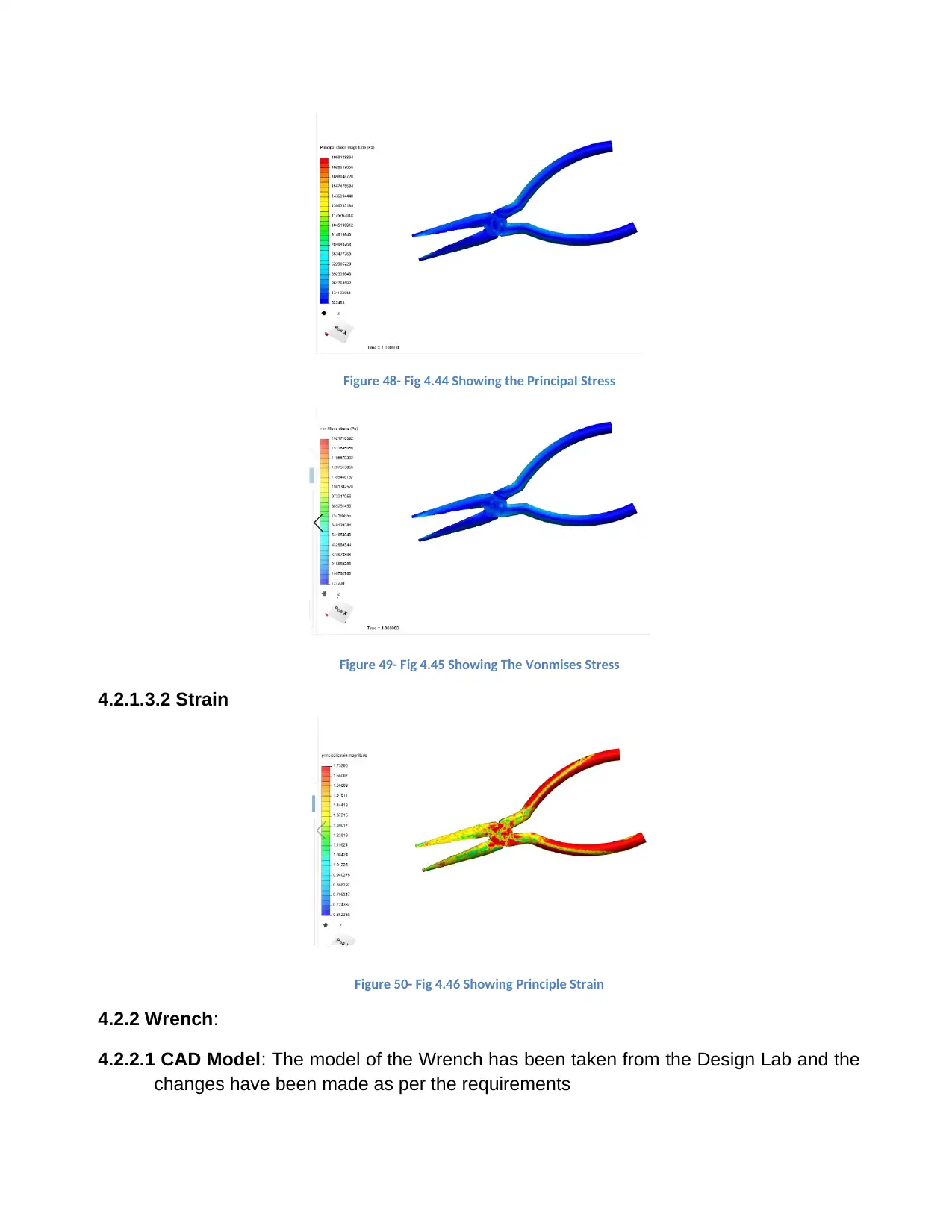
Figure 48- Fig 4.44 Showing the Principal Stress
Figure 49- Fig 4.45 Showing The Vonmises Stress
4.2.1.3.2 Strain
Figure 50- Fig 4.46 Showing Principle Strain
4.2.2 Wrench:
4.2.2.1 CAD Model: The model of the Wrench has been taken from the Design Lab and the
changes have been made as per the requirements
Figure 49- Fig 4.45 Showing The Vonmises Stress
4.2.1.3.2 Strain
Figure 50- Fig 4.46 Showing Principle Strain
4.2.2 Wrench:
4.2.2.1 CAD Model: The model of the Wrench has been taken from the Design Lab and the
changes have been made as per the requirements
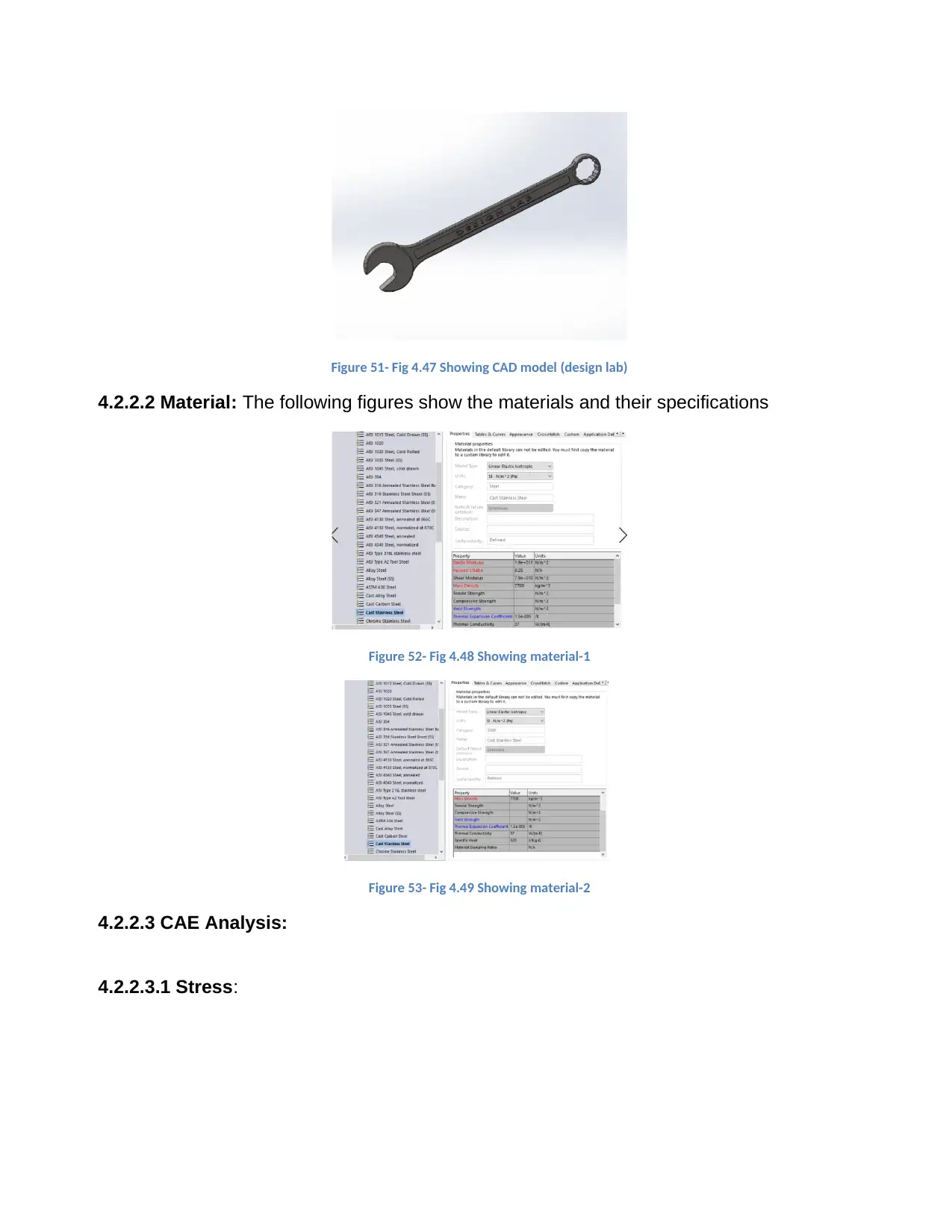
Figure 51- Fig 4.47 Showing CAD model (design lab)
4.2.2.2 Material: The following figures show the materials and their specifications
Figure 52- Fig 4.48 Showing material-1
Figure 53- Fig 4.49 Showing material-2
4.2.2.3 CAE Analysis:
4.2.2.3.1 Stress:
4.2.2.2 Material: The following figures show the materials and their specifications
Figure 52- Fig 4.48 Showing material-1
Figure 53- Fig 4.49 Showing material-2
4.2.2.3 CAE Analysis:
4.2.2.3.1 Stress:
Paraphrase This Document
Need a fresh take? Get an instant paraphrase of this document with our AI Paraphraser
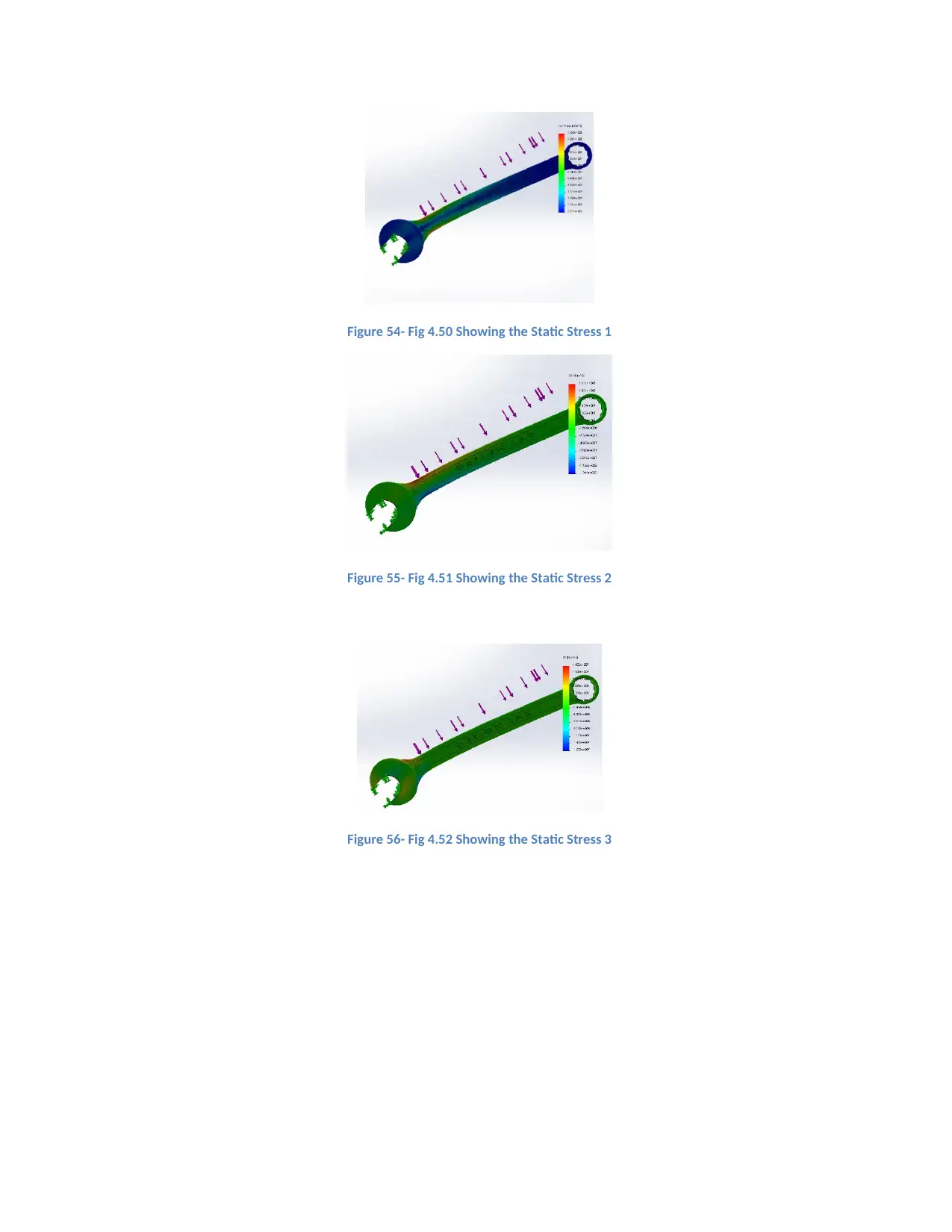
Figure 54- Fig 4.50 Showing the Static Stress 1
Figure 55- Fig 4.51 Showing the Static Stress 2
Figure 56- Fig 4.52 Showing the Static Stress 3
Figure 55- Fig 4.51 Showing the Static Stress 2
Figure 56- Fig 4.52 Showing the Static Stress 3
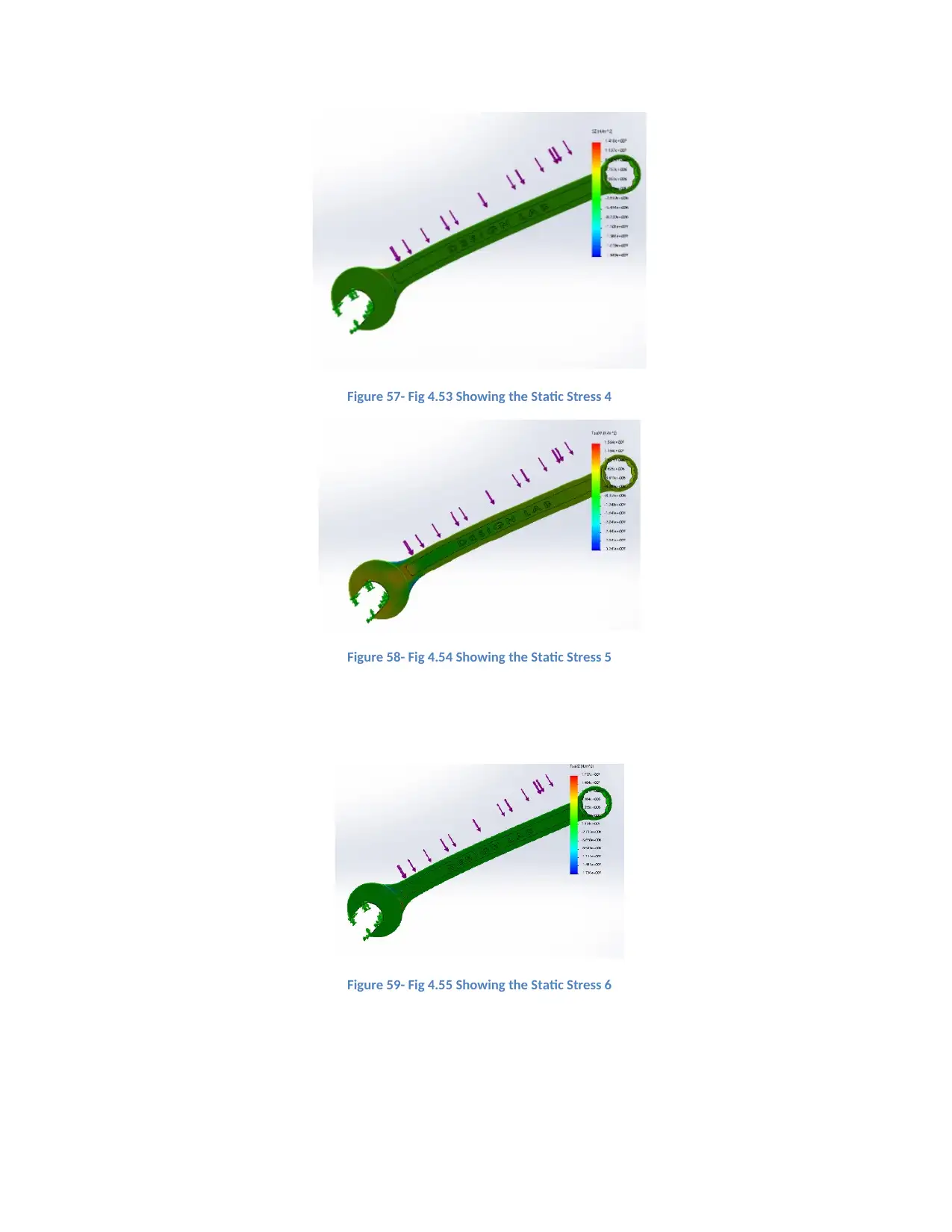
Figure 57- Fig 4.53 Showing the Static Stress 4
Figure 58- Fig 4.54 Showing the Static Stress 5
Figure 59- Fig 4.55 Showing the Static Stress 6
Figure 58- Fig 4.54 Showing the Static Stress 5
Figure 59- Fig 4.55 Showing the Static Stress 6

Figure 60- Fig 4.56 Showing the Static Stress 7
Figure 61- Fig 4.57 Showing the Static Stress 8
Figure 62- Fig 4.58 Showing the Static Stress 9
Figure 61- Fig 4.57 Showing the Static Stress 8
Figure 62- Fig 4.58 Showing the Static Stress 9
Secure Best Marks with AI Grader
Need help grading? Try our AI Grader for instant feedback on your assignments.
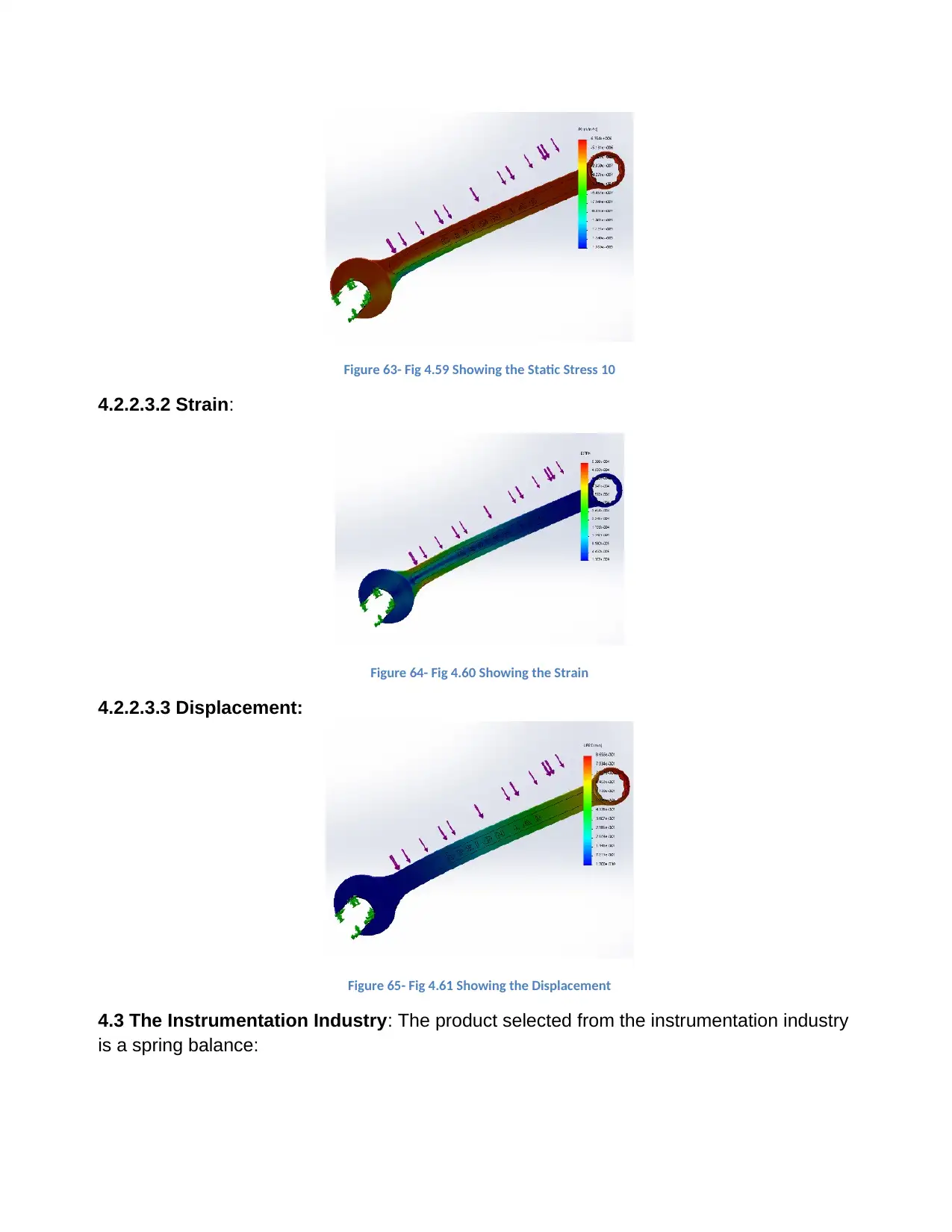
Figure 63- Fig 4.59 Showing the Static Stress 10
4.2.2.3.2 Strain:
Figure 64- Fig 4.60 Showing the Strain
4.2.2.3.3 Displacement:
Figure 65- Fig 4.61 Showing the Displacement
4.3 The Instrumentation Industry: The product selected from the instrumentation industry
is a spring balance:
4.2.2.3.2 Strain:
Figure 64- Fig 4.60 Showing the Strain
4.2.2.3.3 Displacement:
Figure 65- Fig 4.61 Showing the Displacement
4.3 The Instrumentation Industry: The product selected from the instrumentation industry
is a spring balance:
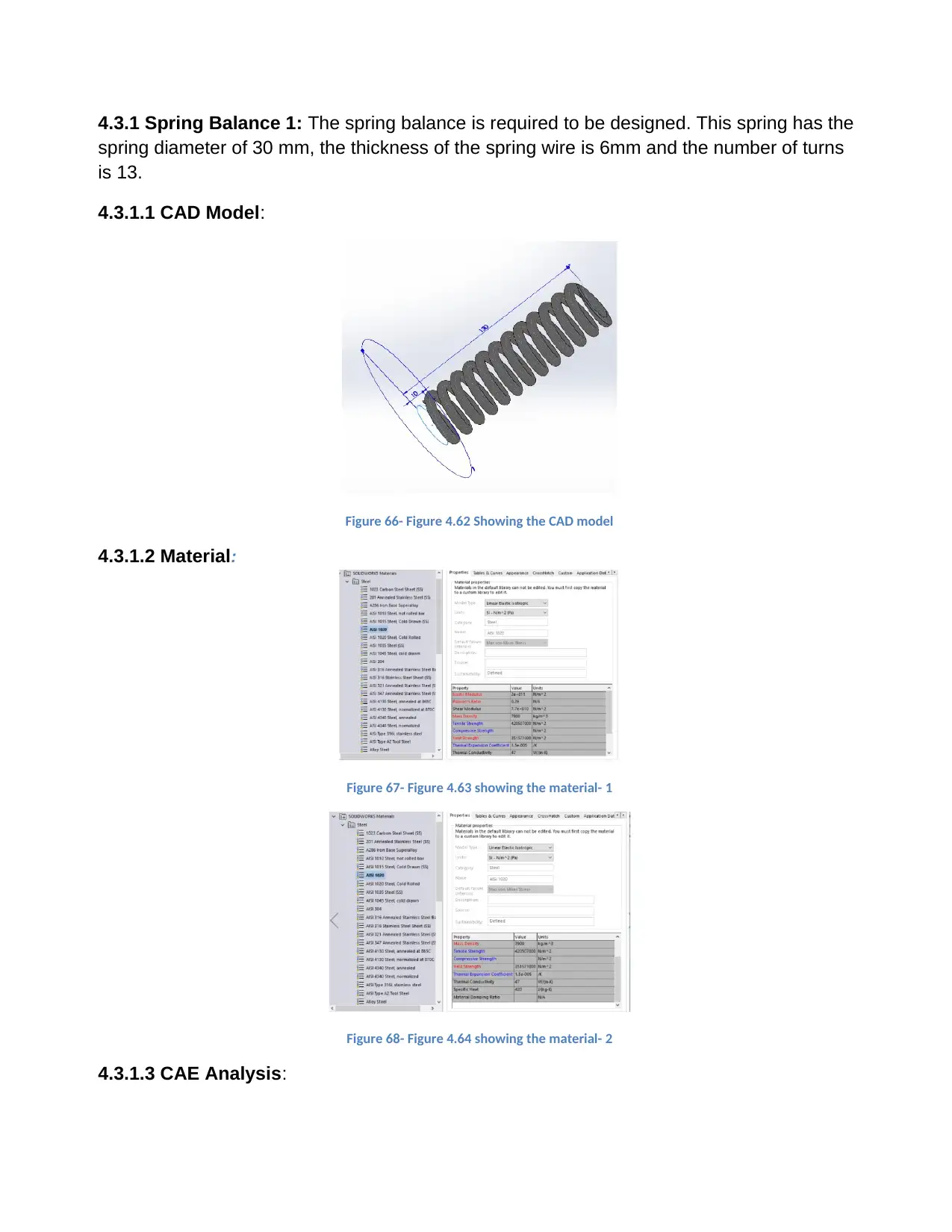
4.3.1 Spring Balance 1: The spring balance is required to be designed. This spring has the
spring diameter of 30 mm, the thickness of the spring wire is 6mm and the number of turns
is 13.
4.3.1.1 CAD Model:
Figure 66- Figure 4.62 Showing the CAD model
4.3.1.2 Material:
Figure 67- Figure 4.63 showing the material- 1
Figure 68- Figure 4.64 showing the material- 2
4.3.1.3 CAE Analysis:
spring diameter of 30 mm, the thickness of the spring wire is 6mm and the number of turns
is 13.
4.3.1.1 CAD Model:
Figure 66- Figure 4.62 Showing the CAD model
4.3.1.2 Material:
Figure 67- Figure 4.63 showing the material- 1
Figure 68- Figure 4.64 showing the material- 2
4.3.1.3 CAE Analysis:
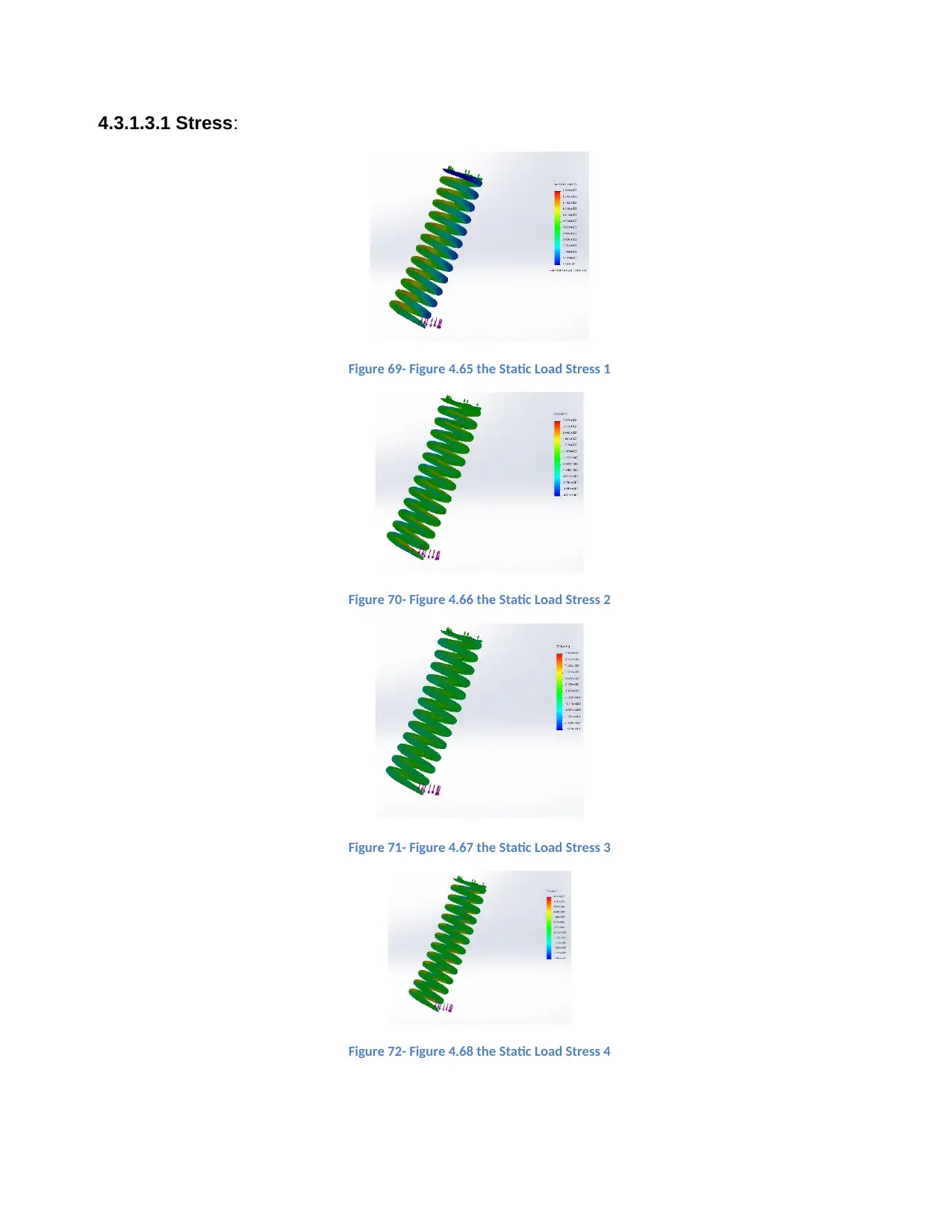
4.3.1.3.1 Stress:
Figure 69- Figure 4.65 the Static Load Stress 1
Figure 70- Figure 4.66 the Static Load Stress 2
Figure 71- Figure 4.67 the Static Load Stress 3
Figure 72- Figure 4.68 the Static Load Stress 4
Figure 69- Figure 4.65 the Static Load Stress 1
Figure 70- Figure 4.66 the Static Load Stress 2
Figure 71- Figure 4.67 the Static Load Stress 3
Figure 72- Figure 4.68 the Static Load Stress 4
Paraphrase This Document
Need a fresh take? Get an instant paraphrase of this document with our AI Paraphraser
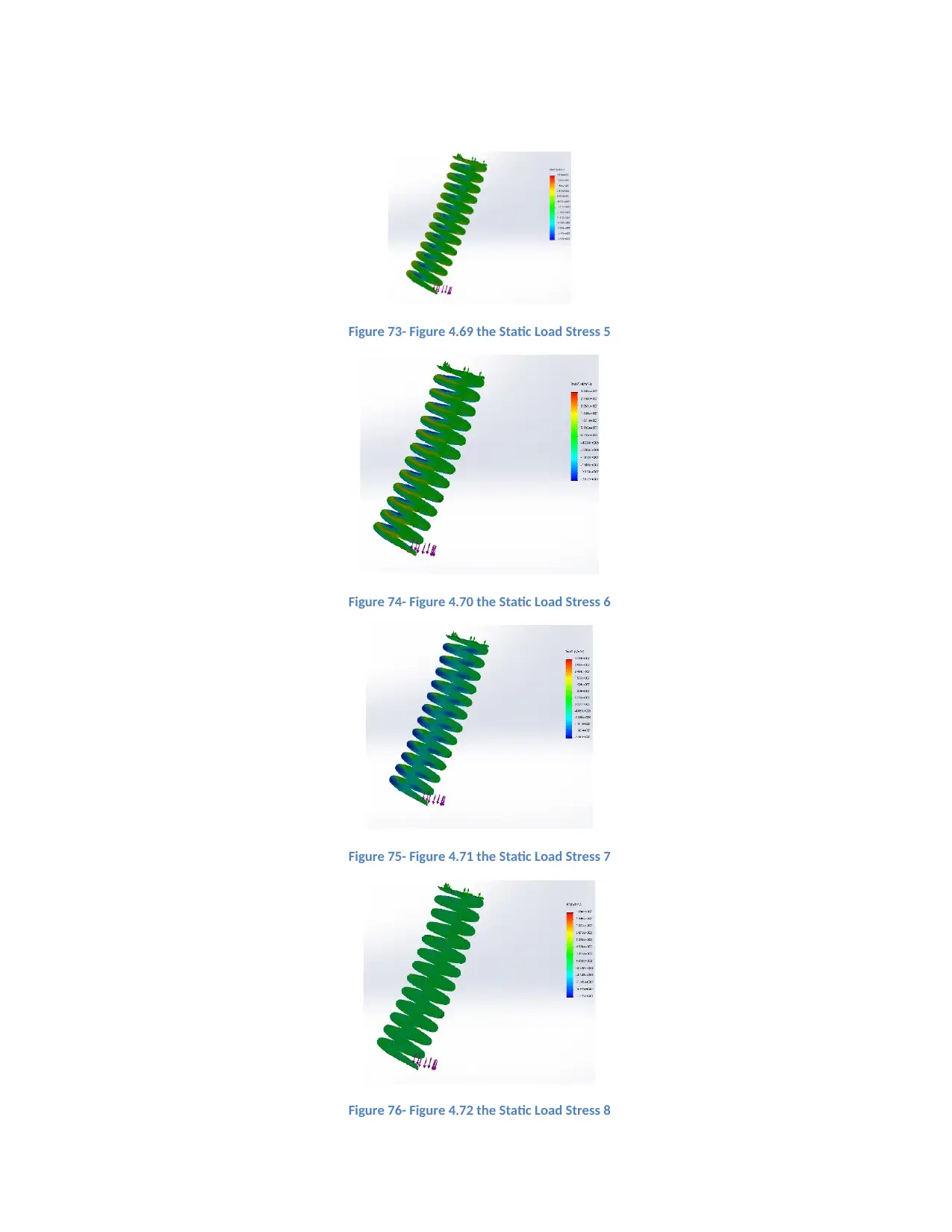
Figure 73- Figure 4.69 the Static Load Stress 5
Figure 74- Figure 4.70 the Static Load Stress 6
Figure 75- Figure 4.71 the Static Load Stress 7
Figure 76- Figure 4.72 the Static Load Stress 8
Figure 74- Figure 4.70 the Static Load Stress 6
Figure 75- Figure 4.71 the Static Load Stress 7
Figure 76- Figure 4.72 the Static Load Stress 8
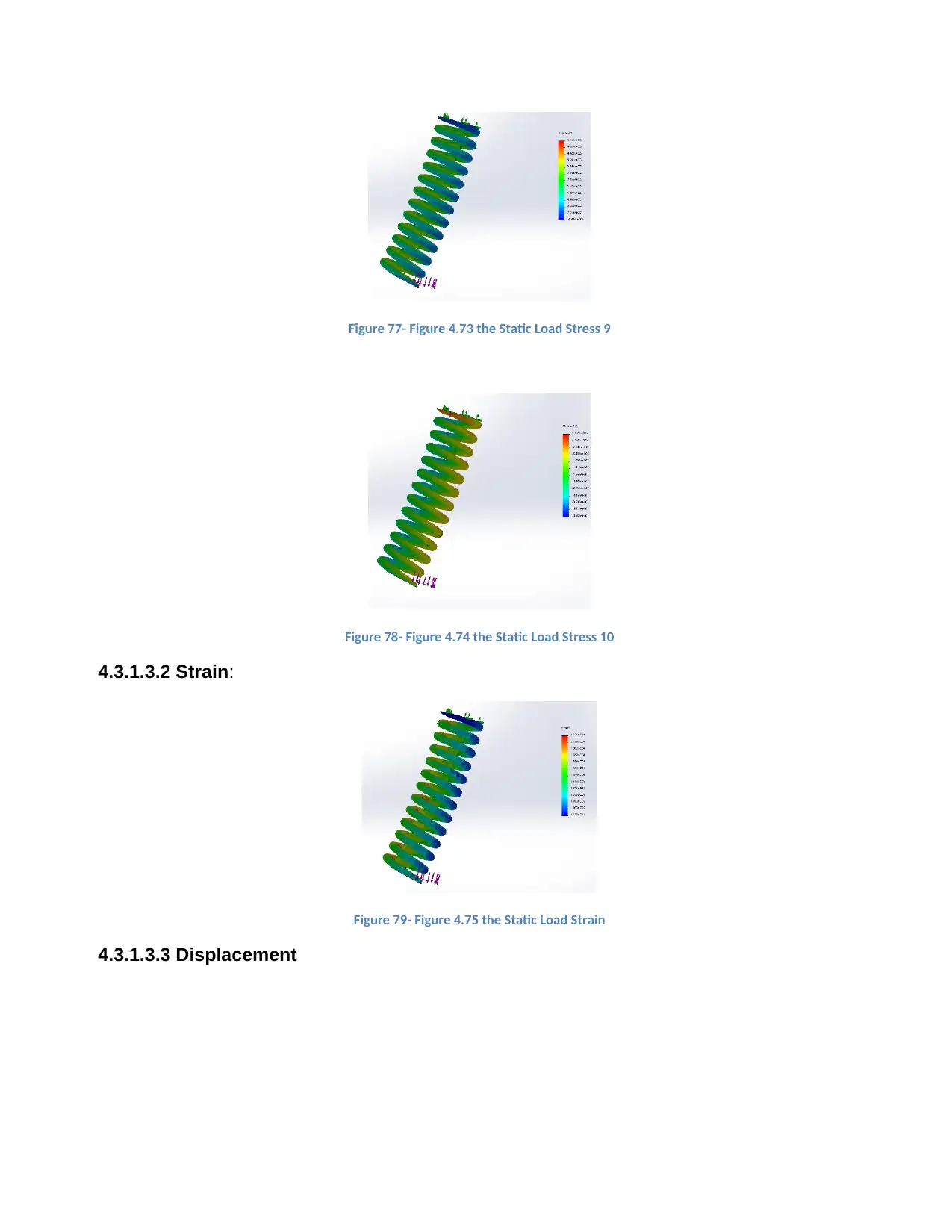
Figure 77- Figure 4.73 the Static Load Stress 9
Figure 78- Figure 4.74 the Static Load Stress 10
4.3.1.3.2 Strain:
Figure 79- Figure 4.75 the Static Load Strain
4.3.1.3.3 Displacement
Figure 78- Figure 4.74 the Static Load Stress 10
4.3.1.3.2 Strain:
Figure 79- Figure 4.75 the Static Load Strain
4.3.1.3.3 Displacement
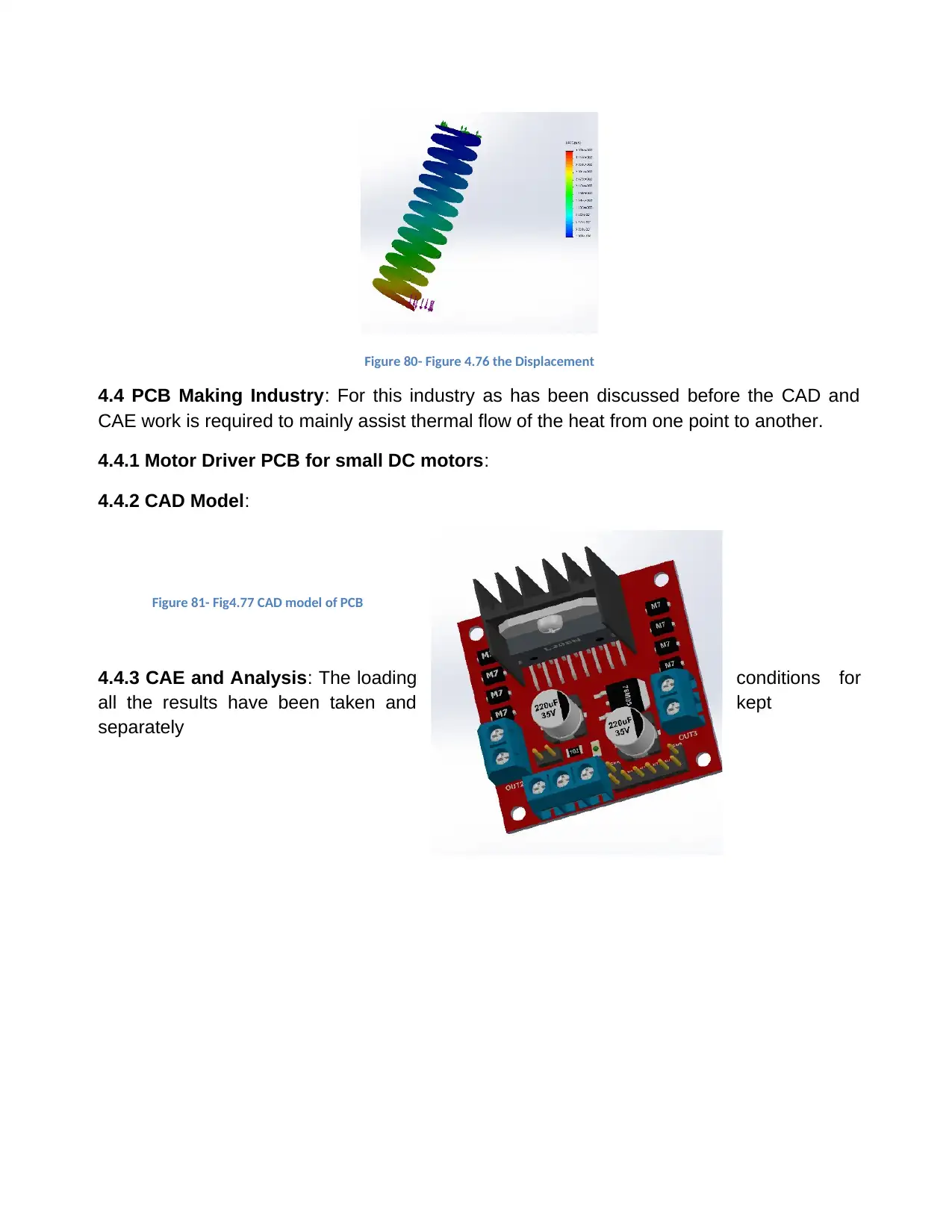
Figure 80- Figure 4.76 the Displacement
4.4 PCB Making Industry: For this industry as has been discussed before the CAD and
CAE work is required to mainly assist thermal flow of the heat from one point to another.
4.4.1 Motor Driver PCB for small DC motors:
4.4.2 CAD Model:
Figure 81- Fig4.77 CAD model of PCB
4.4.3 CAE and Analysis: The loading conditions for
all the results have been taken and kept
separately
4.4 PCB Making Industry: For this industry as has been discussed before the CAD and
CAE work is required to mainly assist thermal flow of the heat from one point to another.
4.4.1 Motor Driver PCB for small DC motors:
4.4.2 CAD Model:
Figure 81- Fig4.77 CAD model of PCB
4.4.3 CAE and Analysis: The loading conditions for
all the results have been taken and kept
separately
Secure Best Marks with AI Grader
Need help grading? Try our AI Grader for instant feedback on your assignments.
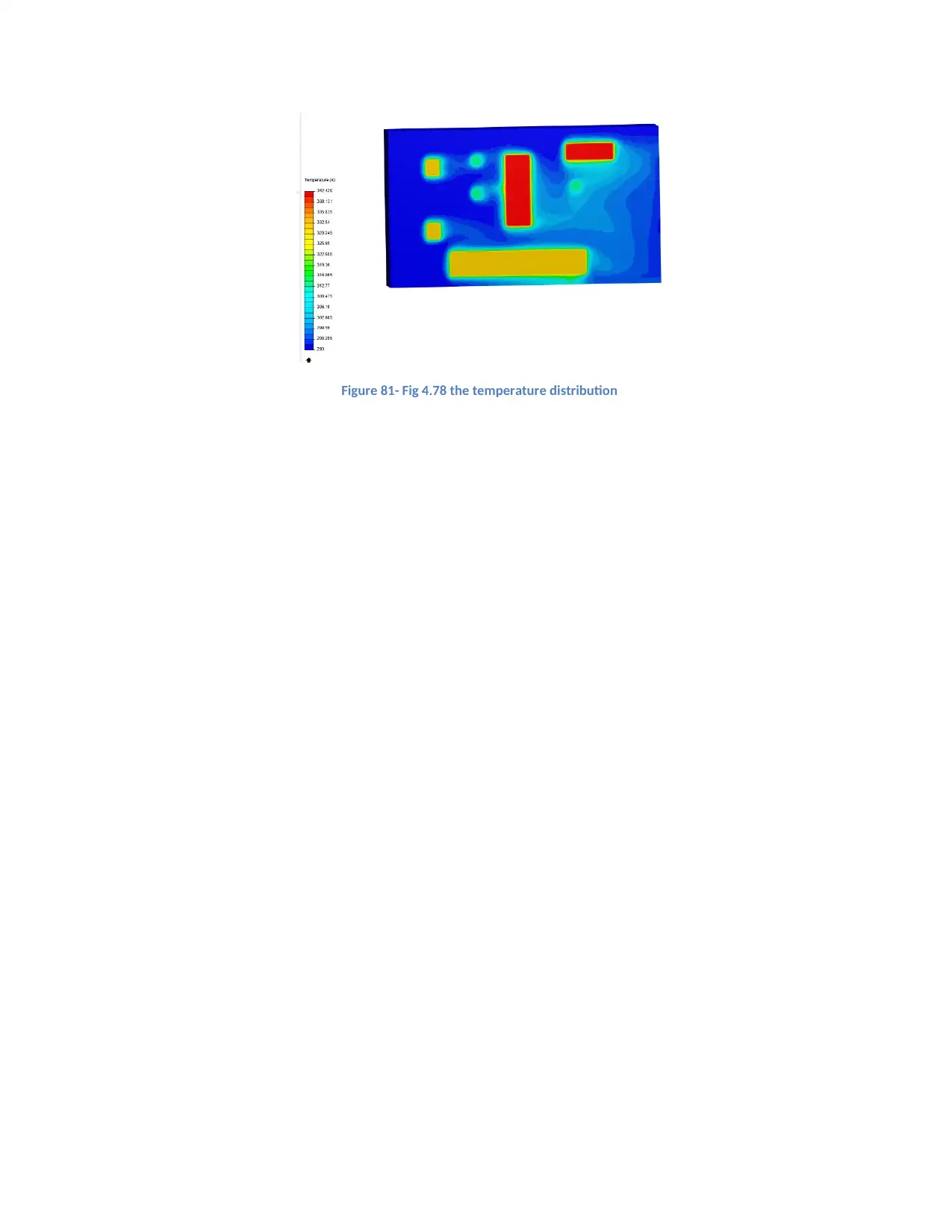
Figure 81- Fig 4.78 the temperature distribution
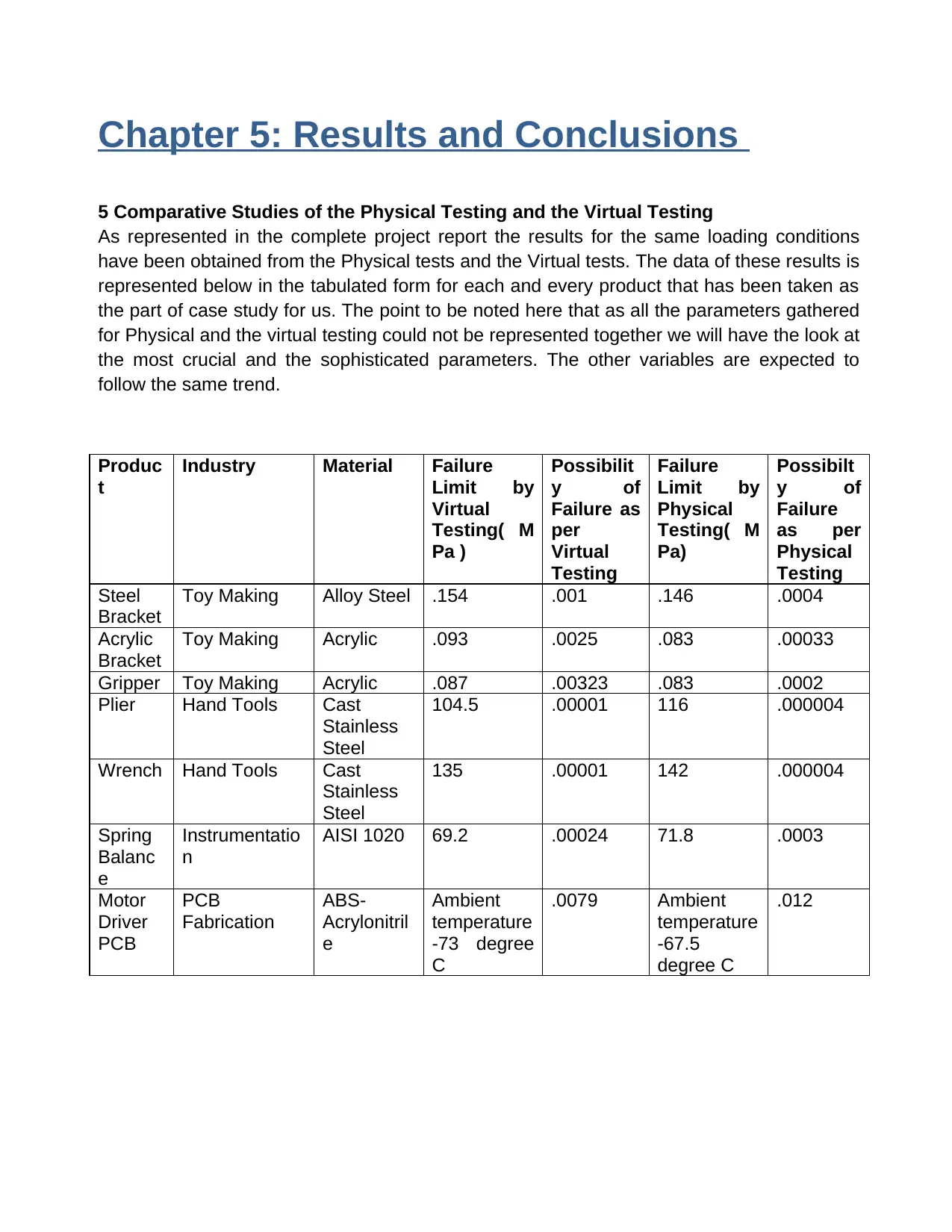
Chapter 5: Results and Conclusions
5 Comparative Studies of the Physical Testing and the Virtual Testing
As represented in the complete project report the results for the same loading conditions
have been obtained from the Physical tests and the Virtual tests. The data of these results is
represented below in the tabulated form for each and every product that has been taken as
the part of case study for us. The point to be noted here that as all the parameters gathered
for Physical and the virtual testing could not be represented together we will have the look at
the most crucial and the sophisticated parameters. The other variables are expected to
follow the same trend.
Produc
t
Industry Material Failure
Limit by
Virtual
Testing( M
Pa )
Possibilit
y of
Failure as
per
Virtual
Testing
Failure
Limit by
Physical
Testing( M
Pa)
Possibilt
y of
Failure
as per
Physical
Testing
Steel
Bracket
Toy Making Alloy Steel .154 .001 .146 .0004
Acrylic
Bracket
Toy Making Acrylic .093 .0025 .083 .00033
Gripper Toy Making Acrylic .087 .00323 .083 .0002
Plier Hand Tools Cast
Stainless
Steel
104.5 .00001 116 .000004
Wrench Hand Tools Cast
Stainless
Steel
135 .00001 142 .000004
Spring
Balanc
e
Instrumentatio
n
AISI 1020 69.2 .00024 71.8 .0003
Motor
Driver
PCB
PCB
Fabrication
ABS-
Acrylonitril
e
Ambient
temperature
-73 degree
C
.0079 Ambient
temperature
-67.5
degree C
.012
5 Comparative Studies of the Physical Testing and the Virtual Testing
As represented in the complete project report the results for the same loading conditions
have been obtained from the Physical tests and the Virtual tests. The data of these results is
represented below in the tabulated form for each and every product that has been taken as
the part of case study for us. The point to be noted here that as all the parameters gathered
for Physical and the virtual testing could not be represented together we will have the look at
the most crucial and the sophisticated parameters. The other variables are expected to
follow the same trend.
Produc
t
Industry Material Failure
Limit by
Virtual
Testing( M
Pa )
Possibilit
y of
Failure as
per
Virtual
Testing
Failure
Limit by
Physical
Testing( M
Pa)
Possibilt
y of
Failure
as per
Physical
Testing
Steel
Bracket
Toy Making Alloy Steel .154 .001 .146 .0004
Acrylic
Bracket
Toy Making Acrylic .093 .0025 .083 .00033
Gripper Toy Making Acrylic .087 .00323 .083 .0002
Plier Hand Tools Cast
Stainless
Steel
104.5 .00001 116 .000004
Wrench Hand Tools Cast
Stainless
Steel
135 .00001 142 .000004
Spring
Balanc
e
Instrumentatio
n
AISI 1020 69.2 .00024 71.8 .0003
Motor
Driver
PCB
PCB
Fabrication
ABS-
Acrylonitril
e
Ambient
temperature
-73 degree
C
.0079 Ambient
temperature
-67.5
degree C
.012
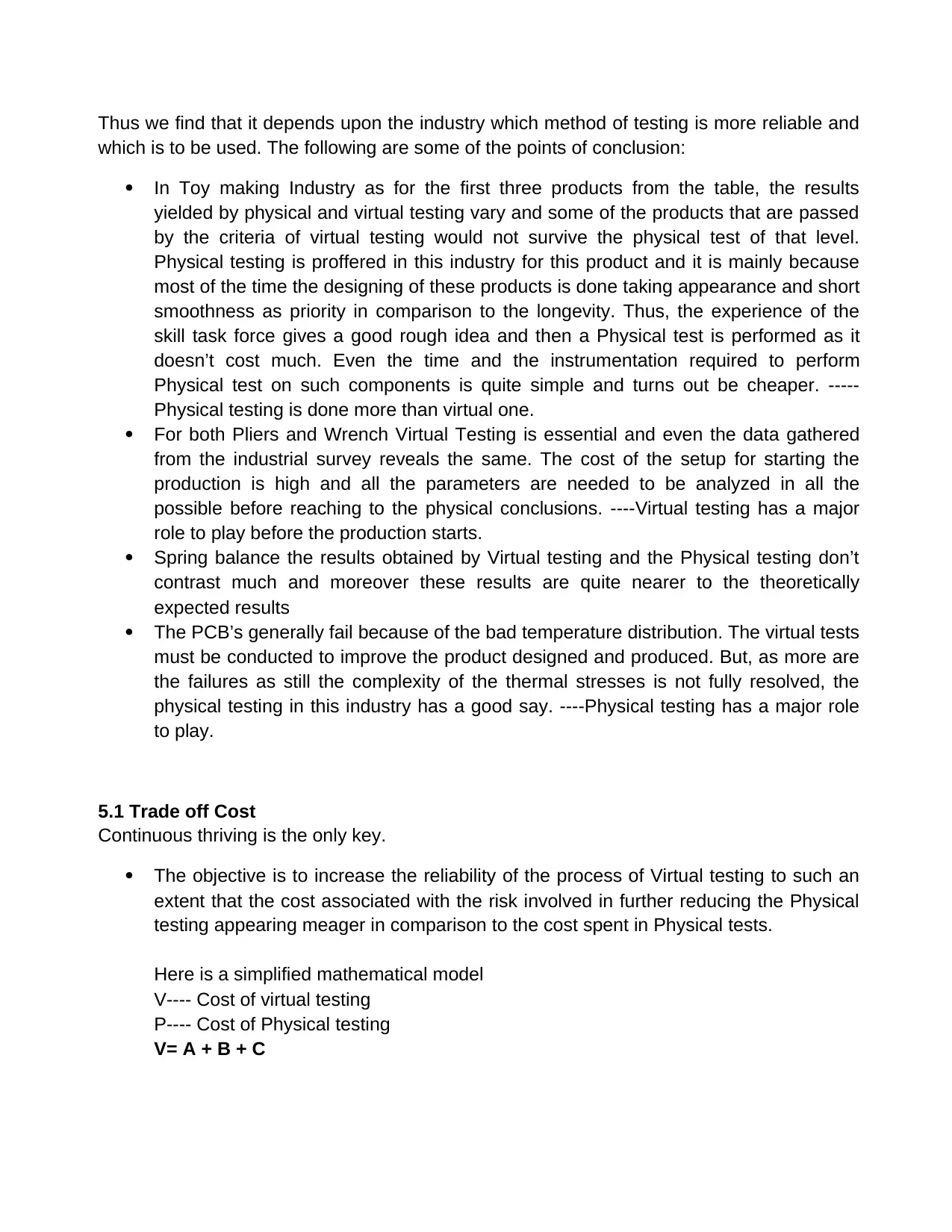
Thus we find that it depends upon the industry which method of testing is more reliable and
which is to be used. The following are some of the points of conclusion:
In Toy making Industry as for the first three products from the table, the results
yielded by physical and virtual testing vary and some of the products that are passed
by the criteria of virtual testing would not survive the physical test of that level.
Physical testing is proffered in this industry for this product and it is mainly because
most of the time the designing of these products is done taking appearance and short
smoothness as priority in comparison to the longevity. Thus, the experience of the
skill task force gives a good rough idea and then a Physical test is performed as it
doesn’t cost much. Even the time and the instrumentation required to perform
Physical test on such components is quite simple and turns out be cheaper. -----
Physical testing is done more than virtual one.
For both Pliers and Wrench Virtual Testing is essential and even the data gathered
from the industrial survey reveals the same. The cost of the setup for starting the
production is high and all the parameters are needed to be analyzed in all the
possible before reaching to the physical conclusions. ----Virtual testing has a major
role to play before the production starts.
Spring balance the results obtained by Virtual testing and the Physical testing don’t
contrast much and moreover these results are quite nearer to the theoretically
expected results
The PCB’s generally fail because of the bad temperature distribution. The virtual tests
must be conducted to improve the product designed and produced. But, as more are
the failures as still the complexity of the thermal stresses is not fully resolved, the
physical testing in this industry has a good say. ----Physical testing has a major role
to play.
5.1 Trade off Cost
Continuous thriving is the only key.
The objective is to increase the reliability of the process of Virtual testing to such an
extent that the cost associated with the risk involved in further reducing the Physical
testing appearing meager in comparison to the cost spent in Physical tests.
Here is a simplified mathematical model
V---- Cost of virtual testing
P---- Cost of Physical testing
V= A + B + C
which is to be used. The following are some of the points of conclusion:
In Toy making Industry as for the first three products from the table, the results
yielded by physical and virtual testing vary and some of the products that are passed
by the criteria of virtual testing would not survive the physical test of that level.
Physical testing is proffered in this industry for this product and it is mainly because
most of the time the designing of these products is done taking appearance and short
smoothness as priority in comparison to the longevity. Thus, the experience of the
skill task force gives a good rough idea and then a Physical test is performed as it
doesn’t cost much. Even the time and the instrumentation required to perform
Physical test on such components is quite simple and turns out be cheaper. -----
Physical testing is done more than virtual one.
For both Pliers and Wrench Virtual Testing is essential and even the data gathered
from the industrial survey reveals the same. The cost of the setup for starting the
production is high and all the parameters are needed to be analyzed in all the
possible before reaching to the physical conclusions. ----Virtual testing has a major
role to play before the production starts.
Spring balance the results obtained by Virtual testing and the Physical testing don’t
contrast much and moreover these results are quite nearer to the theoretically
expected results
The PCB’s generally fail because of the bad temperature distribution. The virtual tests
must be conducted to improve the product designed and produced. But, as more are
the failures as still the complexity of the thermal stresses is not fully resolved, the
physical testing in this industry has a good say. ----Physical testing has a major role
to play.
5.1 Trade off Cost
Continuous thriving is the only key.
The objective is to increase the reliability of the process of Virtual testing to such an
extent that the cost associated with the risk involved in further reducing the Physical
testing appearing meager in comparison to the cost spent in Physical tests.
Here is a simplified mathematical model
V---- Cost of virtual testing
P---- Cost of Physical testing
V= A + B + C
Paraphrase This Document
Need a fresh take? Get an instant paraphrase of this document with our AI Paraphraser
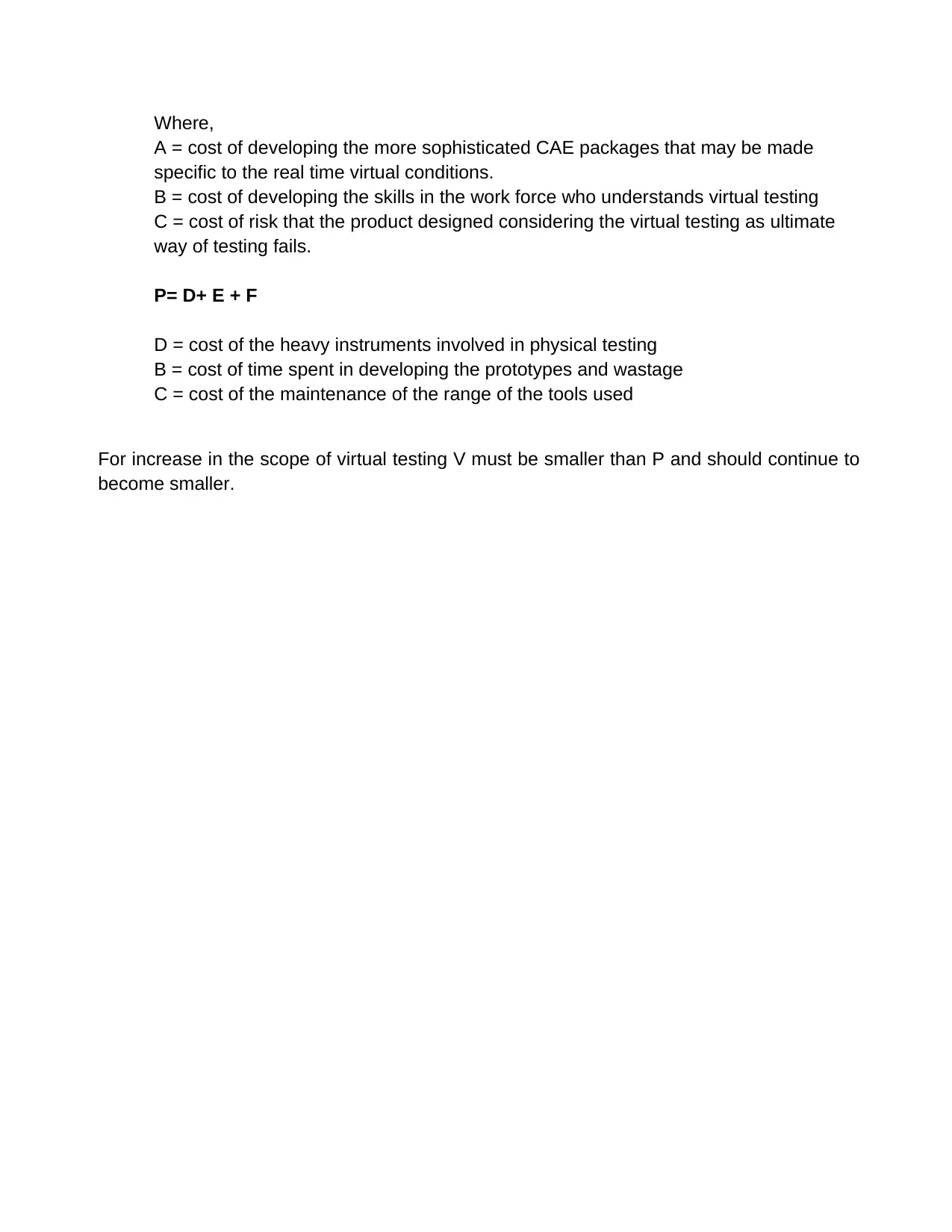
Where,
A = cost of developing the more sophisticated CAE packages that may be made
specific to the real time virtual conditions.
B = cost of developing the skills in the work force who understands virtual testing
C = cost of risk that the product designed considering the virtual testing as ultimate
way of testing fails.
P= D+ E + F
D = cost of the heavy instruments involved in physical testing
B = cost of time spent in developing the prototypes and wastage
C = cost of the maintenance of the range of the tools used
For increase in the scope of virtual testing V must be smaller than P and should continue to
become smaller.
A = cost of developing the more sophisticated CAE packages that may be made
specific to the real time virtual conditions.
B = cost of developing the skills in the work force who understands virtual testing
C = cost of risk that the product designed considering the virtual testing as ultimate
way of testing fails.
P= D+ E + F
D = cost of the heavy instruments involved in physical testing
B = cost of time spent in developing the prototypes and wastage
C = cost of the maintenance of the range of the tools used
For increase in the scope of virtual testing V must be smaller than P and should continue to
become smaller.
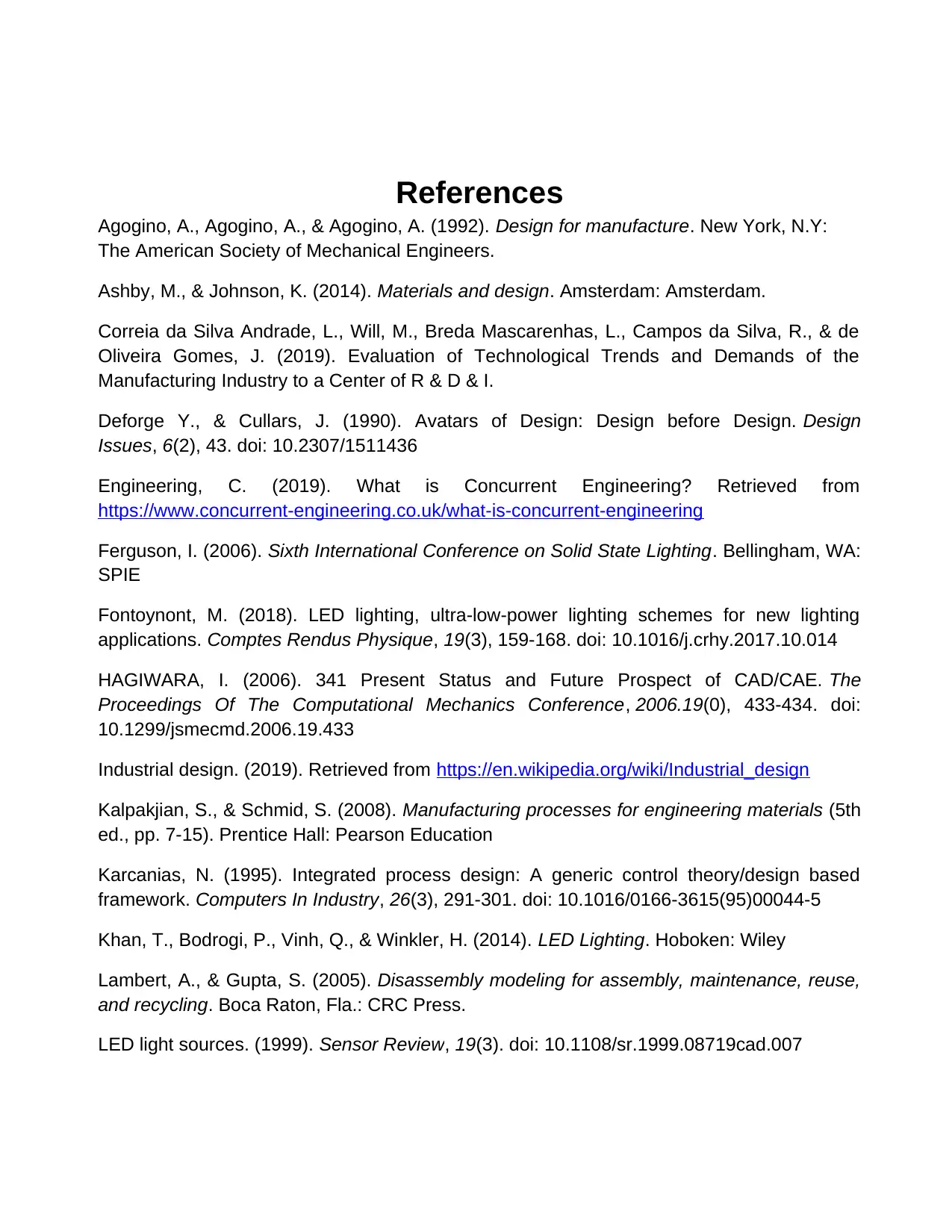
References
Agogino, A., Agogino, A., & Agogino, A. (1992). Design for manufacture. New York, N.Y:
The American Society of Mechanical Engineers.
Ashby, M., & Johnson, K. (2014). Materials and design. Amsterdam: Amsterdam.
Correia da Silva Andrade, L., Will, M., Breda Mascarenhas, L., Campos da Silva, R., & de
Oliveira Gomes, J. (2019). Evaluation of Technological Trends and Demands of the
Manufacturing Industry to a Center of R & D & I.
Deforge Y., & Cullars, J. (1990). Avatars of Design: Design before Design. Design
Issues, 6(2), 43. doi: 10.2307/1511436
Engineering, C. (2019). What is Concurrent Engineering? Retrieved from
https://www.concurrent-engineering.co.uk/what-is-concurrent-engineering
Ferguson, I. (2006). Sixth International Conference on Solid State Lighting. Bellingham, WA:
SPIE
Fontoynont, M. (2018). LED lighting, ultra-low-power lighting schemes for new lighting
applications. Comptes Rendus Physique, 19(3), 159-168. doi: 10.1016/j.crhy.2017.10.014
HAGIWARA, I. (2006). 341 Present Status and Future Prospect of CAD/CAE. The
Proceedings Of The Computational Mechanics Conference, 2006.19(0), 433-434. doi:
10.1299/jsmecmd.2006.19.433
Industrial design. (2019). Retrieved from https://en.wikipedia.org/wiki/Industrial_design
Kalpakjian, S., & Schmid, S. (2008). Manufacturing processes for engineering materials (5th
ed., pp. 7-15). Prentice Hall: Pearson Education
Karcanias, N. (1995). Integrated process design: A generic control theory/design based
framework. Computers In Industry, 26(3), 291-301. doi: 10.1016/0166-3615(95)00044-5
Khan, T., Bodrogi, P., Vinh, Q., & Winkler, H. (2014). LED Lighting. Hoboken: Wiley
Lambert, A., & Gupta, S. (2005). Disassembly modeling for assembly, maintenance, reuse,
and recycling. Boca Raton, Fla.: CRC Press.
LED light sources. (1999). Sensor Review, 19(3). doi: 10.1108/sr.1999.08719cad.007
Agogino, A., Agogino, A., & Agogino, A. (1992). Design for manufacture. New York, N.Y:
The American Society of Mechanical Engineers.
Ashby, M., & Johnson, K. (2014). Materials and design. Amsterdam: Amsterdam.
Correia da Silva Andrade, L., Will, M., Breda Mascarenhas, L., Campos da Silva, R., & de
Oliveira Gomes, J. (2019). Evaluation of Technological Trends and Demands of the
Manufacturing Industry to a Center of R & D & I.
Deforge Y., & Cullars, J. (1990). Avatars of Design: Design before Design. Design
Issues, 6(2), 43. doi: 10.2307/1511436
Engineering, C. (2019). What is Concurrent Engineering? Retrieved from
https://www.concurrent-engineering.co.uk/what-is-concurrent-engineering
Ferguson, I. (2006). Sixth International Conference on Solid State Lighting. Bellingham, WA:
SPIE
Fontoynont, M. (2018). LED lighting, ultra-low-power lighting schemes for new lighting
applications. Comptes Rendus Physique, 19(3), 159-168. doi: 10.1016/j.crhy.2017.10.014
HAGIWARA, I. (2006). 341 Present Status and Future Prospect of CAD/CAE. The
Proceedings Of The Computational Mechanics Conference, 2006.19(0), 433-434. doi:
10.1299/jsmecmd.2006.19.433
Industrial design. (2019). Retrieved from https://en.wikipedia.org/wiki/Industrial_design
Kalpakjian, S., & Schmid, S. (2008). Manufacturing processes for engineering materials (5th
ed., pp. 7-15). Prentice Hall: Pearson Education
Karcanias, N. (1995). Integrated process design: A generic control theory/design based
framework. Computers In Industry, 26(3), 291-301. doi: 10.1016/0166-3615(95)00044-5
Khan, T., Bodrogi, P., Vinh, Q., & Winkler, H. (2014). LED Lighting. Hoboken: Wiley
Lambert, A., & Gupta, S. (2005). Disassembly modeling for assembly, maintenance, reuse,
and recycling. Boca Raton, Fla.: CRC Press.
LED light sources. (1999). Sensor Review, 19(3). doi: 10.1108/sr.1999.08719cad.007
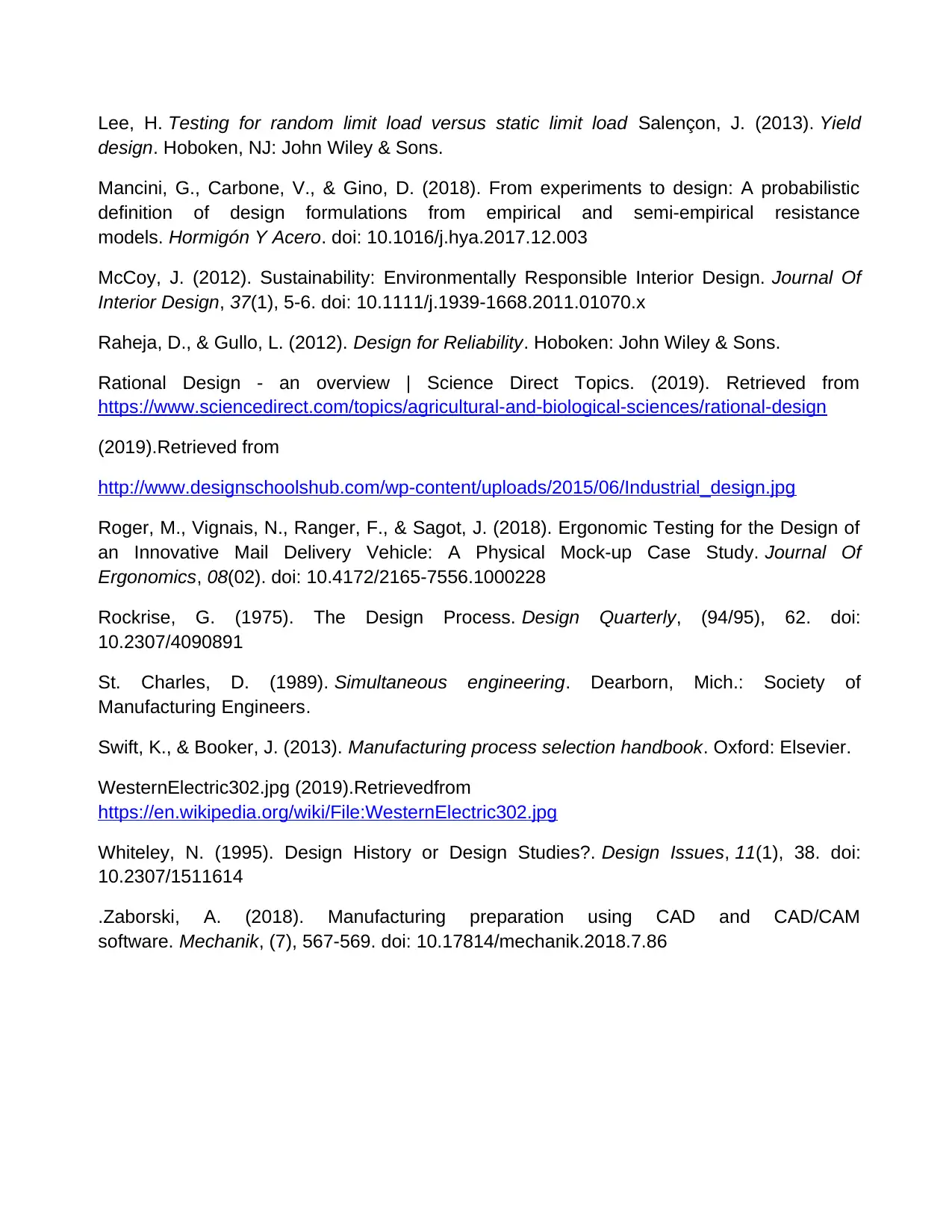
Lee, H. Testing for random limit load versus static limit load Salençon, J. (2013). Yield
design. Hoboken, NJ: John Wiley & Sons.
Mancini, G., Carbone, V., & Gino, D. (2018). From experiments to design: A probabilistic
definition of design formulations from empirical and semi-empirical resistance
models. Hormigón Y Acero. doi: 10.1016/j.hya.2017.12.003
McCoy, J. (2012). Sustainability: Environmentally Responsible Interior Design. Journal Of
Interior Design, 37(1), 5-6. doi: 10.1111/j.1939-1668.2011.01070.x
Raheja, D., & Gullo, L. (2012). Design for Reliability. Hoboken: John Wiley & Sons.
Rational Design - an overview | Science Direct Topics. (2019). Retrieved from
https://www.sciencedirect.com/topics/agricultural-and-biological-sciences/rational-design
(2019).Retrieved from
http://www.designschoolshub.com/wp-content/uploads/2015/06/Industrial_design.jpg
Roger, M., Vignais, N., Ranger, F., & Sagot, J. (2018). Ergonomic Testing for the Design of
an Innovative Mail Delivery Vehicle: A Physical Mock-up Case Study. Journal Of
Ergonomics, 08(02). doi: 10.4172/2165-7556.1000228
Rockrise, G. (1975). The Design Process. Design Quarterly, (94/95), 62. doi:
10.2307/4090891
St. Charles, D. (1989). Simultaneous engineering. Dearborn, Mich.: Society of
Manufacturing Engineers.
Swift, K., & Booker, J. (2013). Manufacturing process selection handbook. Oxford: Elsevier.
WesternElectric302.jpg (2019).Retrievedfrom
https://en.wikipedia.org/wiki/File:WesternElectric302.jpg
Whiteley, N. (1995). Design History or Design Studies?. Design Issues, 11(1), 38. doi:
10.2307/1511614
.Zaborski, A. (2018). Manufacturing preparation using CAD and CAD/CAM
software. Mechanik, (7), 567-569. doi: 10.17814/mechanik.2018.7.86
design. Hoboken, NJ: John Wiley & Sons.
Mancini, G., Carbone, V., & Gino, D. (2018). From experiments to design: A probabilistic
definition of design formulations from empirical and semi-empirical resistance
models. Hormigón Y Acero. doi: 10.1016/j.hya.2017.12.003
McCoy, J. (2012). Sustainability: Environmentally Responsible Interior Design. Journal Of
Interior Design, 37(1), 5-6. doi: 10.1111/j.1939-1668.2011.01070.x
Raheja, D., & Gullo, L. (2012). Design for Reliability. Hoboken: John Wiley & Sons.
Rational Design - an overview | Science Direct Topics. (2019). Retrieved from
https://www.sciencedirect.com/topics/agricultural-and-biological-sciences/rational-design
(2019).Retrieved from
http://www.designschoolshub.com/wp-content/uploads/2015/06/Industrial_design.jpg
Roger, M., Vignais, N., Ranger, F., & Sagot, J. (2018). Ergonomic Testing for the Design of
an Innovative Mail Delivery Vehicle: A Physical Mock-up Case Study. Journal Of
Ergonomics, 08(02). doi: 10.4172/2165-7556.1000228
Rockrise, G. (1975). The Design Process. Design Quarterly, (94/95), 62. doi:
10.2307/4090891
St. Charles, D. (1989). Simultaneous engineering. Dearborn, Mich.: Society of
Manufacturing Engineers.
Swift, K., & Booker, J. (2013). Manufacturing process selection handbook. Oxford: Elsevier.
WesternElectric302.jpg (2019).Retrievedfrom
https://en.wikipedia.org/wiki/File:WesternElectric302.jpg
Whiteley, N. (1995). Design History or Design Studies?. Design Issues, 11(1), 38. doi:
10.2307/1511614
.Zaborski, A. (2018). Manufacturing preparation using CAD and CAD/CAM
software. Mechanik, (7), 567-569. doi: 10.17814/mechanik.2018.7.86
1 out of 70

Your All-in-One AI-Powered Toolkit for Academic Success.
+13062052269
info@desklib.com
Available 24*7 on WhatsApp / Email
Unlock your academic potential
© 2024 | Zucol Services PVT LTD | All rights reserved.