Business Process Improvement for Watson Engineering Tooling Company
VerifiedAdded on 2020/10/05
|11
|3487
|364
Report
AI Summary
This report provides a comprehensive analysis of the Watson Engineering Tooling Company, focusing on strategies to improve its operations and services. The study explores the company's evolution, from its initial product offerings to its global expansion efforts. The report highlights the significance of business process modeling, business process engineering, and the PCDA cycle (Plan-Do-Check-Act) as key strategies for operational enhancement. Furthermore, the report delves into the application of Lean principles, including techniques like continuous flow, Jidoka, and Kanban, to eliminate waste and improve efficiency. It also discusses the importance of knowledge management and throughout experience life-cycle in the context of business process improvement. The report offers recommendations for the company to optimize its processes, reduce costs, and enhance its competitive position in the market. The study also emphasizes the importance of ethical and cultural influences in the workplace. This report is a valuable resource for students and professionals studying business development and operations management, and is available on Desklib.
Contribute Materials
Your contribution can guide someone’s learning journey. Share your
documents today.
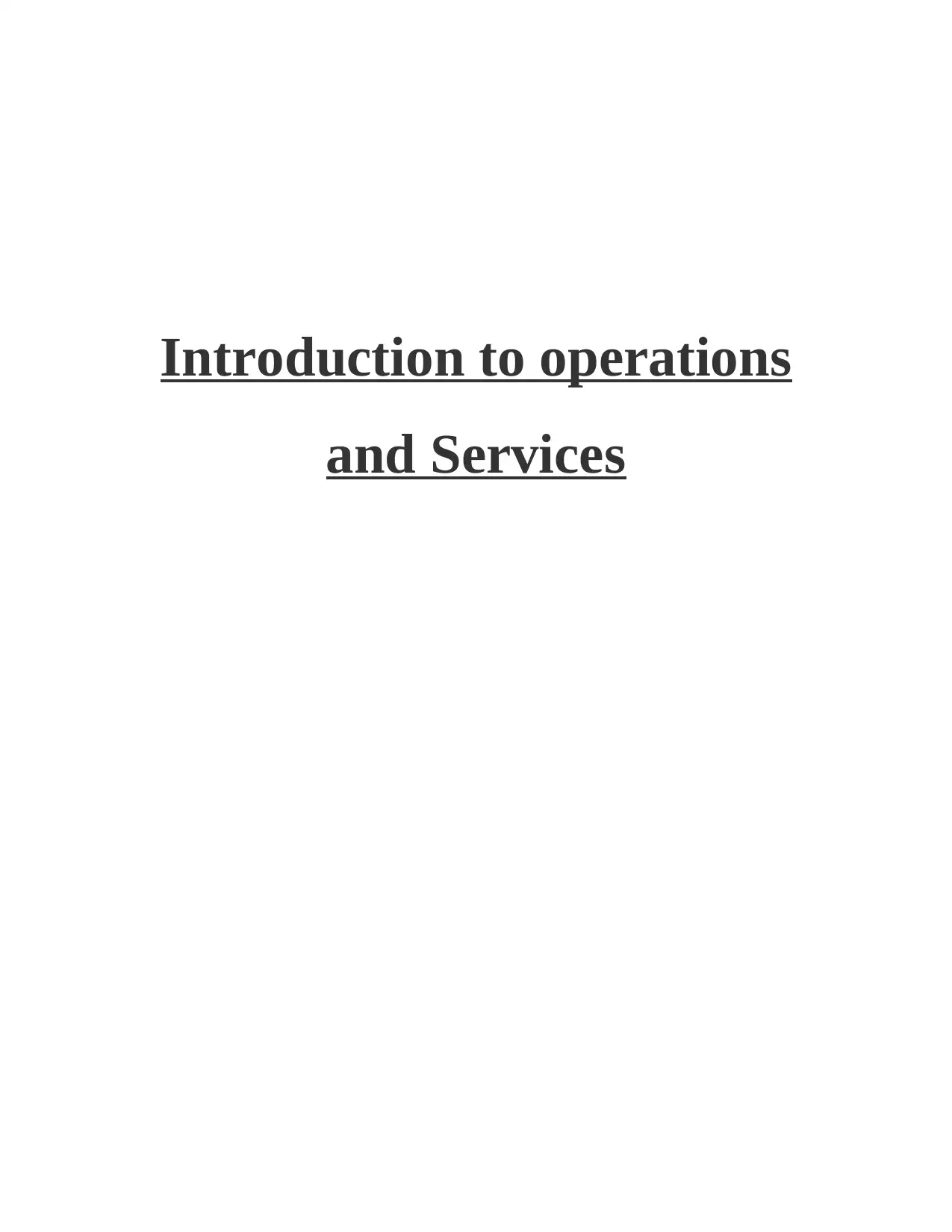
Introduction to operations
and Services
and Services
Secure Best Marks with AI Grader
Need help grading? Try our AI Grader for instant feedback on your assignments.
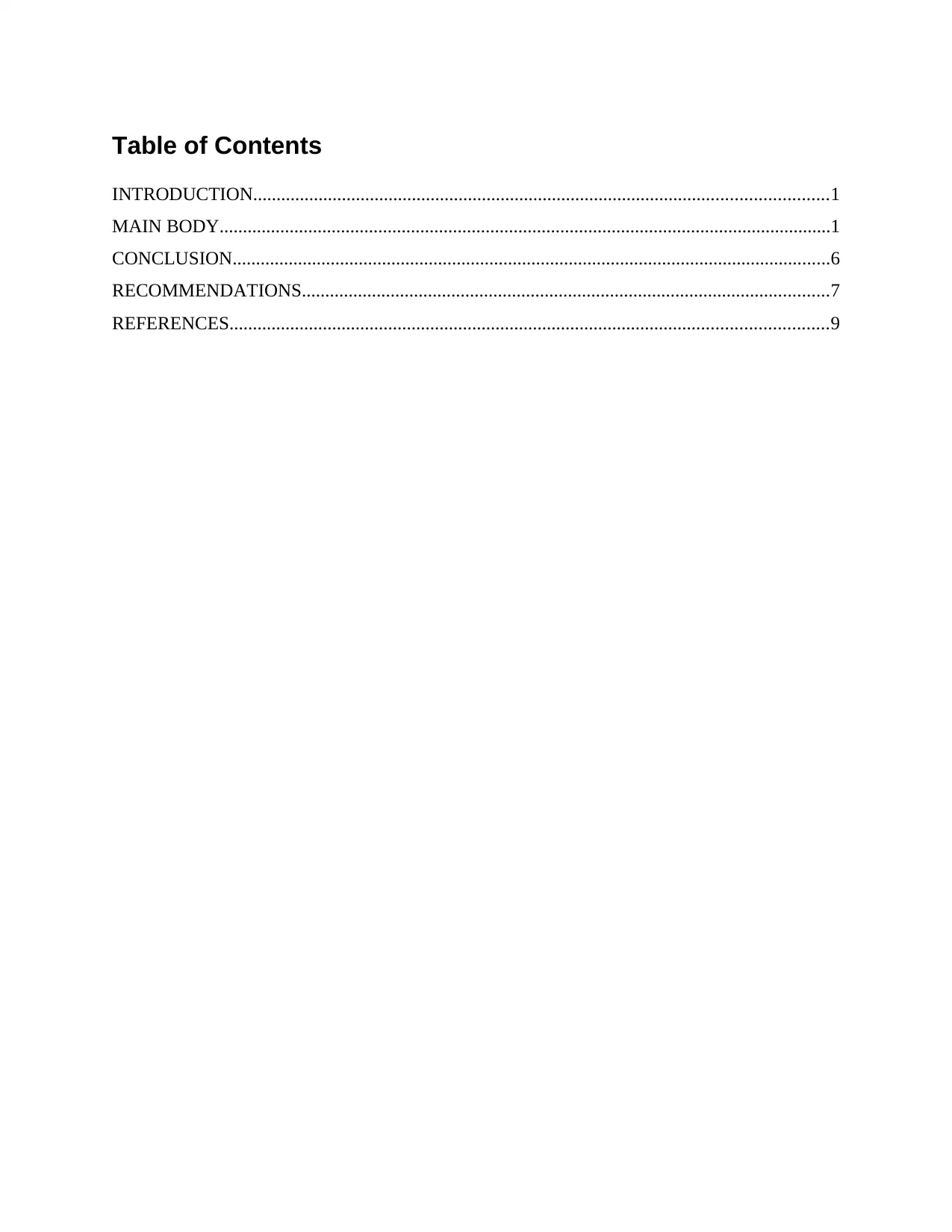
Table of Contents
INTRODUCTION...........................................................................................................................1
MAIN BODY...................................................................................................................................1
CONCLUSION................................................................................................................................6
RECOMMENDATIONS.................................................................................................................7
REFERENCES................................................................................................................................9
INTRODUCTION...........................................................................................................................1
MAIN BODY...................................................................................................................................1
CONCLUSION................................................................................................................................6
RECOMMENDATIONS.................................................................................................................7
REFERENCES................................................................................................................................9
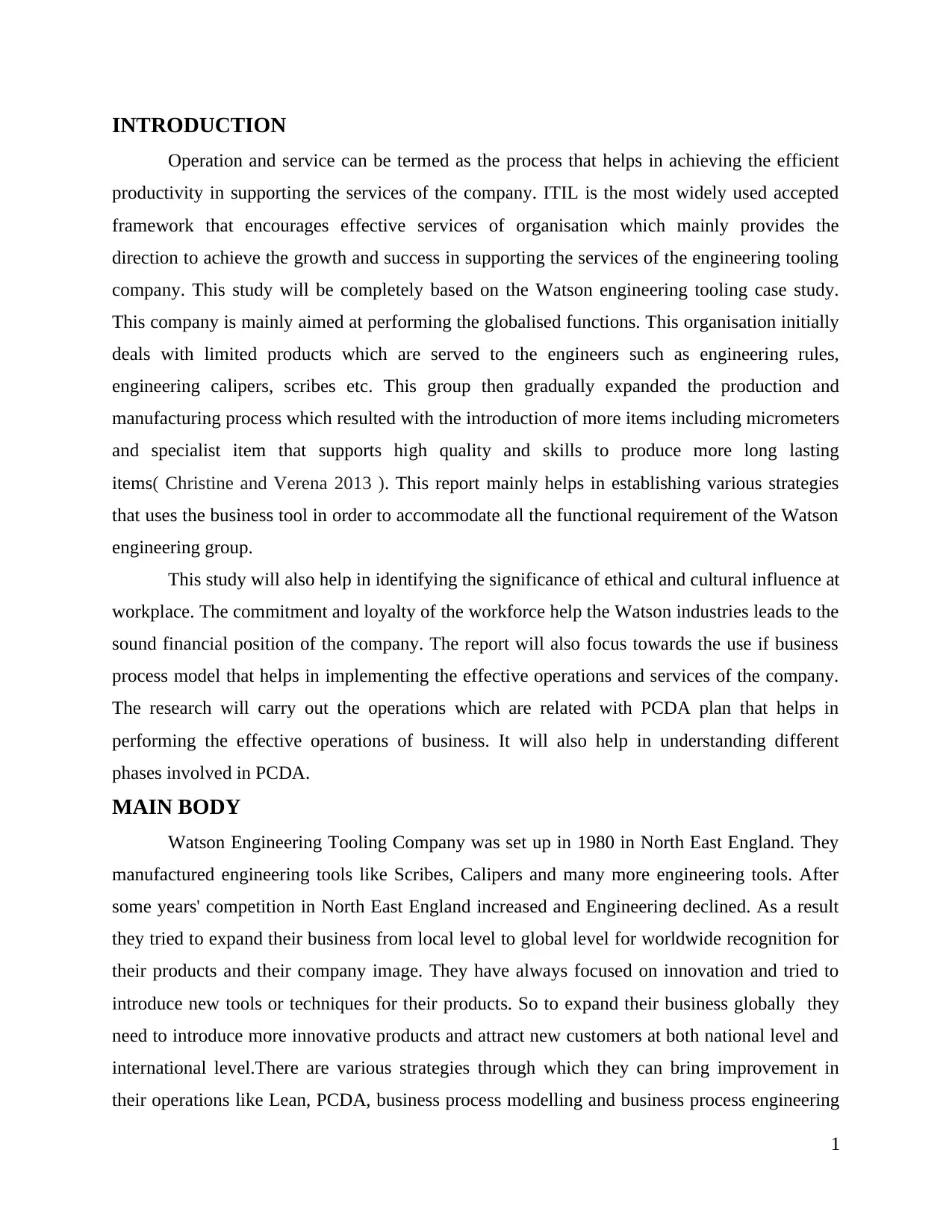
INTRODUCTION
Operation and service can be termed as the process that helps in achieving the efficient
productivity in supporting the services of the company. ITIL is the most widely used accepted
framework that encourages effective services of organisation which mainly provides the
direction to achieve the growth and success in supporting the services of the engineering tooling
company. This study will be completely based on the Watson engineering tooling case study.
This company is mainly aimed at performing the globalised functions. This organisation initially
deals with limited products which are served to the engineers such as engineering rules,
engineering calipers, scribes etc. This group then gradually expanded the production and
manufacturing process which resulted with the introduction of more items including micrometers
and specialist item that supports high quality and skills to produce more long lasting
items( Christine and Verena 2013 ). This report mainly helps in establishing various strategies
that uses the business tool in order to accommodate all the functional requirement of the Watson
engineering group.
This study will also help in identifying the significance of ethical and cultural influence at
workplace. The commitment and loyalty of the workforce help the Watson industries leads to the
sound financial position of the company. The report will also focus towards the use if business
process model that helps in implementing the effective operations and services of the company.
The research will carry out the operations which are related with PCDA plan that helps in
performing the effective operations of business. It will also help in understanding different
phases involved in PCDA.
MAIN BODY
Watson Engineering Tooling Company was set up in 1980 in North East England. They
manufactured engineering tools like Scribes, Calipers and many more engineering tools. After
some years' competition in North East England increased and Engineering declined. As a result
they tried to expand their business from local level to global level for worldwide recognition for
their products and their company image. They have always focused on innovation and tried to
introduce new tools or techniques for their products. So to expand their business globally they
need to introduce more innovative products and attract new customers at both national level and
international level.There are various strategies through which they can bring improvement in
their operations like Lean, PCDA, business process modelling and business process engineering
1
Operation and service can be termed as the process that helps in achieving the efficient
productivity in supporting the services of the company. ITIL is the most widely used accepted
framework that encourages effective services of organisation which mainly provides the
direction to achieve the growth and success in supporting the services of the engineering tooling
company. This study will be completely based on the Watson engineering tooling case study.
This company is mainly aimed at performing the globalised functions. This organisation initially
deals with limited products which are served to the engineers such as engineering rules,
engineering calipers, scribes etc. This group then gradually expanded the production and
manufacturing process which resulted with the introduction of more items including micrometers
and specialist item that supports high quality and skills to produce more long lasting
items( Christine and Verena 2013 ). This report mainly helps in establishing various strategies
that uses the business tool in order to accommodate all the functional requirement of the Watson
engineering group.
This study will also help in identifying the significance of ethical and cultural influence at
workplace. The commitment and loyalty of the workforce help the Watson industries leads to the
sound financial position of the company. The report will also focus towards the use if business
process model that helps in implementing the effective operations and services of the company.
The research will carry out the operations which are related with PCDA plan that helps in
performing the effective operations of business. It will also help in understanding different
phases involved in PCDA.
MAIN BODY
Watson Engineering Tooling Company was set up in 1980 in North East England. They
manufactured engineering tools like Scribes, Calipers and many more engineering tools. After
some years' competition in North East England increased and Engineering declined. As a result
they tried to expand their business from local level to global level for worldwide recognition for
their products and their company image. They have always focused on innovation and tried to
introduce new tools or techniques for their products. So to expand their business globally they
need to introduce more innovative products and attract new customers at both national level and
international level.There are various strategies through which they can bring improvement in
their operations like Lean, PCDA, business process modelling and business process engineering
1
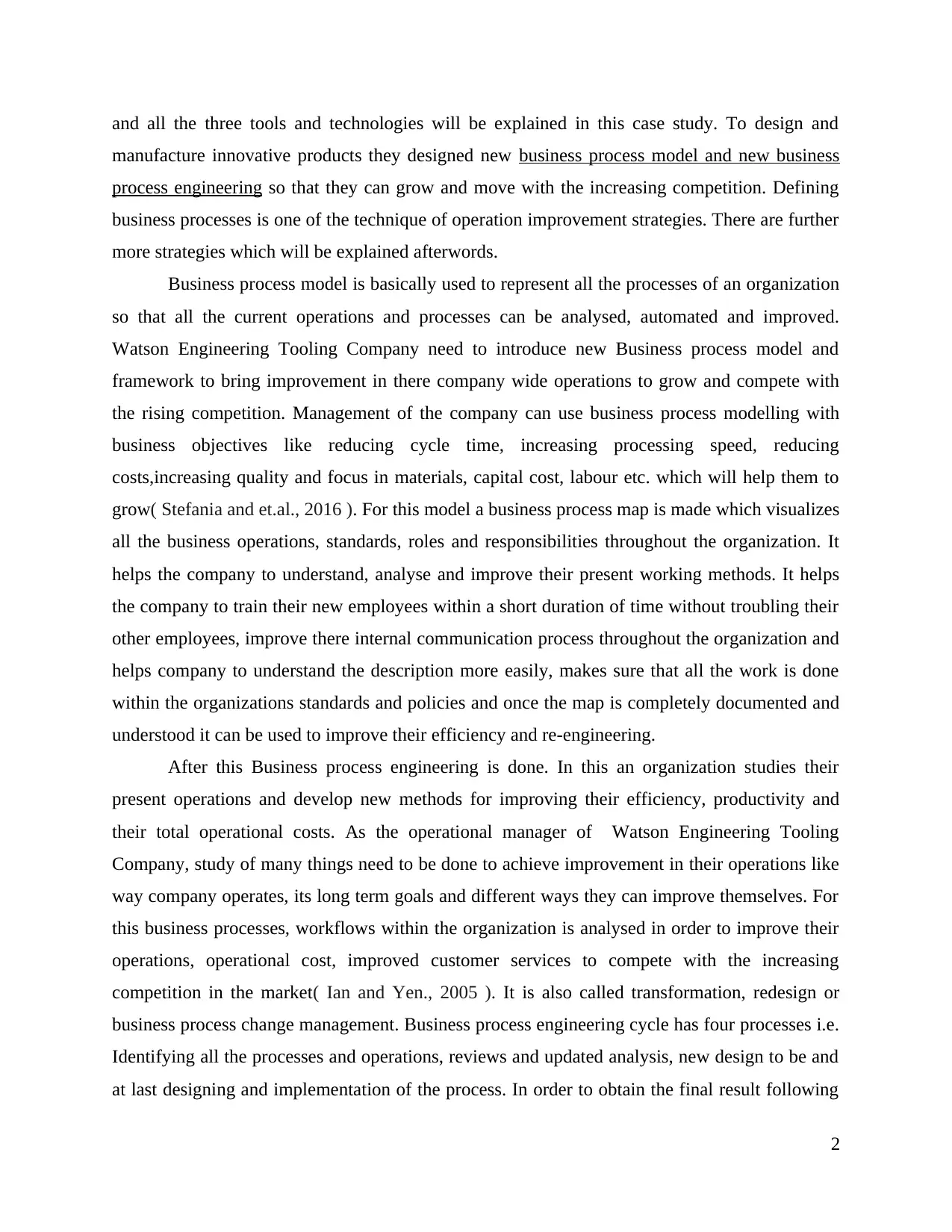
and all the three tools and technologies will be explained in this case study. To design and
manufacture innovative products they designed new business process model and new business
process engineering so that they can grow and move with the increasing competition. Defining
business processes is one of the technique of operation improvement strategies. There are further
more strategies which will be explained afterwords.
Business process model is basically used to represent all the processes of an organization
so that all the current operations and processes can be analysed, automated and improved.
Watson Engineering Tooling Company need to introduce new Business process model and
framework to bring improvement in there company wide operations to grow and compete with
the rising competition. Management of the company can use business process modelling with
business objectives like reducing cycle time, increasing processing speed, reducing
costs,increasing quality and focus in materials, capital cost, labour etc. which will help them to
grow( Stefania and et.al., 2016 ). For this model a business process map is made which visualizes
all the business operations, standards, roles and responsibilities throughout the organization. It
helps the company to understand, analyse and improve their present working methods. It helps
the company to train their new employees within a short duration of time without troubling their
other employees, improve there internal communication process throughout the organization and
helps company to understand the description more easily, makes sure that all the work is done
within the organizations standards and policies and once the map is completely documented and
understood it can be used to improve their efficiency and re-engineering.
After this Business process engineering is done. In this an organization studies their
present operations and develop new methods for improving their efficiency, productivity and
their total operational costs. As the operational manager of Watson Engineering Tooling
Company, study of many things need to be done to achieve improvement in their operations like
way company operates, its long term goals and different ways they can improve themselves. For
this business processes, workflows within the organization is analysed in order to improve their
operations, operational cost, improved customer services to compete with the increasing
competition in the market( Ian and Yen., 2005 ). It is also called transformation, redesign or
business process change management. Business process engineering cycle has four processes i.e.
Identifying all the processes and operations, reviews and updated analysis, new design to be and
at last designing and implementation of the process. In order to obtain the final result following
2
manufacture innovative products they designed new business process model and new business
process engineering so that they can grow and move with the increasing competition. Defining
business processes is one of the technique of operation improvement strategies. There are further
more strategies which will be explained afterwords.
Business process model is basically used to represent all the processes of an organization
so that all the current operations and processes can be analysed, automated and improved.
Watson Engineering Tooling Company need to introduce new Business process model and
framework to bring improvement in there company wide operations to grow and compete with
the rising competition. Management of the company can use business process modelling with
business objectives like reducing cycle time, increasing processing speed, reducing
costs,increasing quality and focus in materials, capital cost, labour etc. which will help them to
grow( Stefania and et.al., 2016 ). For this model a business process map is made which visualizes
all the business operations, standards, roles and responsibilities throughout the organization. It
helps the company to understand, analyse and improve their present working methods. It helps
the company to train their new employees within a short duration of time without troubling their
other employees, improve there internal communication process throughout the organization and
helps company to understand the description more easily, makes sure that all the work is done
within the organizations standards and policies and once the map is completely documented and
understood it can be used to improve their efficiency and re-engineering.
After this Business process engineering is done. In this an organization studies their
present operations and develop new methods for improving their efficiency, productivity and
their total operational costs. As the operational manager of Watson Engineering Tooling
Company, study of many things need to be done to achieve improvement in their operations like
way company operates, its long term goals and different ways they can improve themselves. For
this business processes, workflows within the organization is analysed in order to improve their
operations, operational cost, improved customer services to compete with the increasing
competition in the market( Ian and Yen., 2005 ). It is also called transformation, redesign or
business process change management. Business process engineering cycle has four processes i.e.
Identifying all the processes and operations, reviews and updated analysis, new design to be and
at last designing and implementation of the process. In order to obtain the final result following
2
Secure Best Marks with AI Grader
Need help grading? Try our AI Grader for instant feedback on your assignments.
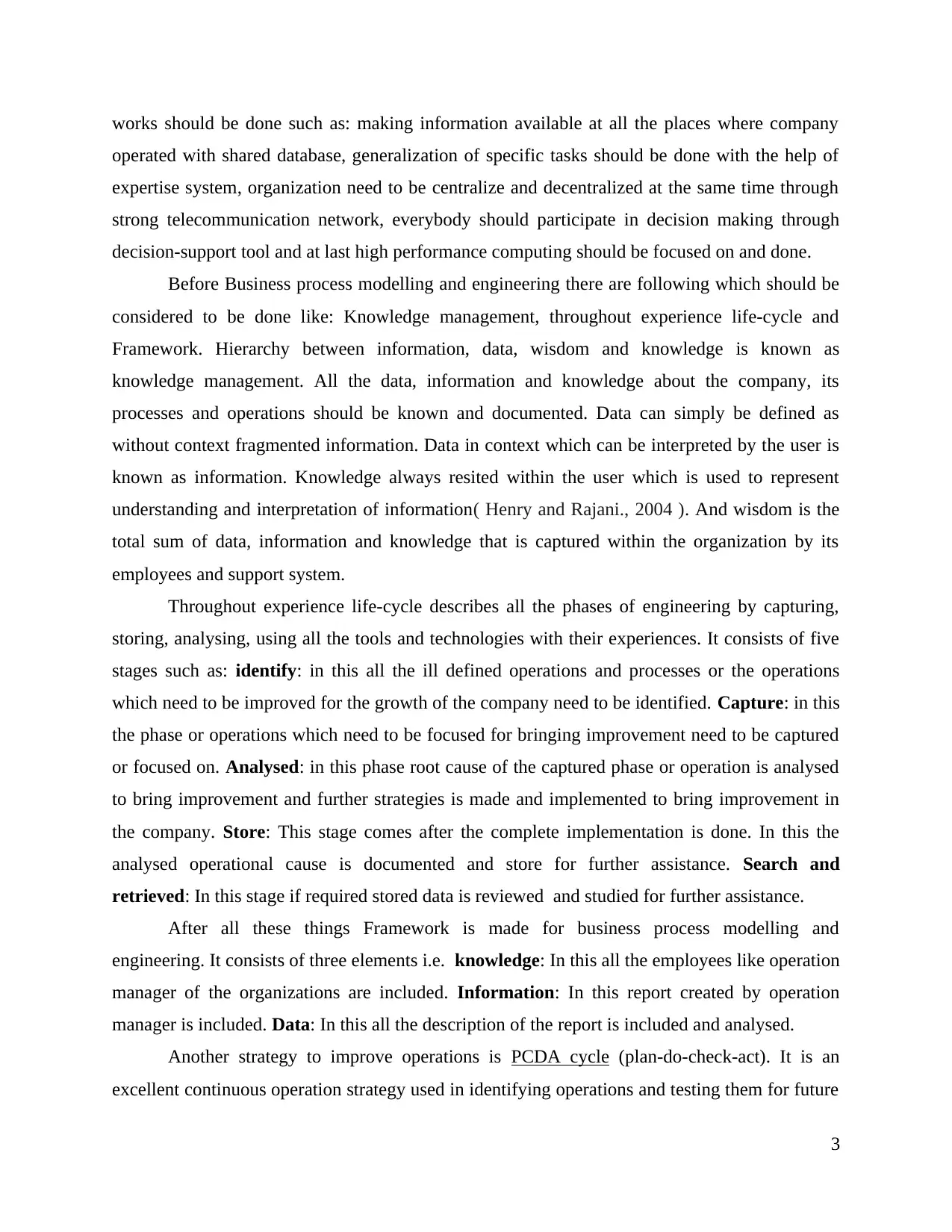
works should be done such as: making information available at all the places where company
operated with shared database, generalization of specific tasks should be done with the help of
expertise system, organization need to be centralize and decentralized at the same time through
strong telecommunication network, everybody should participate in decision making through
decision-support tool and at last high performance computing should be focused on and done.
Before Business process modelling and engineering there are following which should be
considered to be done like: Knowledge management, throughout experience life-cycle and
Framework. Hierarchy between information, data, wisdom and knowledge is known as
knowledge management. All the data, information and knowledge about the company, its
processes and operations should be known and documented. Data can simply be defined as
without context fragmented information. Data in context which can be interpreted by the user is
known as information. Knowledge always resited within the user which is used to represent
understanding and interpretation of information( Henry and Rajani., 2004 ). And wisdom is the
total sum of data, information and knowledge that is captured within the organization by its
employees and support system.
Throughout experience life-cycle describes all the phases of engineering by capturing,
storing, analysing, using all the tools and technologies with their experiences. It consists of five
stages such as: identify: in this all the ill defined operations and processes or the operations
which need to be improved for the growth of the company need to be identified. Capture: in this
the phase or operations which need to be focused for bringing improvement need to be captured
or focused on. Analysed: in this phase root cause of the captured phase or operation is analysed
to bring improvement and further strategies is made and implemented to bring improvement in
the company. Store: This stage comes after the complete implementation is done. In this the
analysed operational cause is documented and store for further assistance. Search and
retrieved: In this stage if required stored data is reviewed and studied for further assistance.
After all these things Framework is made for business process modelling and
engineering. It consists of three elements i.e. knowledge: In this all the employees like operation
manager of the organizations are included. Information: In this report created by operation
manager is included. Data: In this all the description of the report is included and analysed.
Another strategy to improve operations is PCDA cycle (plan-do-check-act). It is an
excellent continuous operation strategy used in identifying operations and testing them for future
3
operated with shared database, generalization of specific tasks should be done with the help of
expertise system, organization need to be centralize and decentralized at the same time through
strong telecommunication network, everybody should participate in decision making through
decision-support tool and at last high performance computing should be focused on and done.
Before Business process modelling and engineering there are following which should be
considered to be done like: Knowledge management, throughout experience life-cycle and
Framework. Hierarchy between information, data, wisdom and knowledge is known as
knowledge management. All the data, information and knowledge about the company, its
processes and operations should be known and documented. Data can simply be defined as
without context fragmented information. Data in context which can be interpreted by the user is
known as information. Knowledge always resited within the user which is used to represent
understanding and interpretation of information( Henry and Rajani., 2004 ). And wisdom is the
total sum of data, information and knowledge that is captured within the organization by its
employees and support system.
Throughout experience life-cycle describes all the phases of engineering by capturing,
storing, analysing, using all the tools and technologies with their experiences. It consists of five
stages such as: identify: in this all the ill defined operations and processes or the operations
which need to be improved for the growth of the company need to be identified. Capture: in this
the phase or operations which need to be focused for bringing improvement need to be captured
or focused on. Analysed: in this phase root cause of the captured phase or operation is analysed
to bring improvement and further strategies is made and implemented to bring improvement in
the company. Store: This stage comes after the complete implementation is done. In this the
analysed operational cause is documented and store for further assistance. Search and
retrieved: In this stage if required stored data is reviewed and studied for further assistance.
After all these things Framework is made for business process modelling and
engineering. It consists of three elements i.e. knowledge: In this all the employees like operation
manager of the organizations are included. Information: In this report created by operation
manager is included. Data: In this all the description of the report is included and analysed.
Another strategy to improve operations is PCDA cycle (plan-do-check-act). It is an
excellent continuous operation strategy used in identifying operations and testing them for future
3
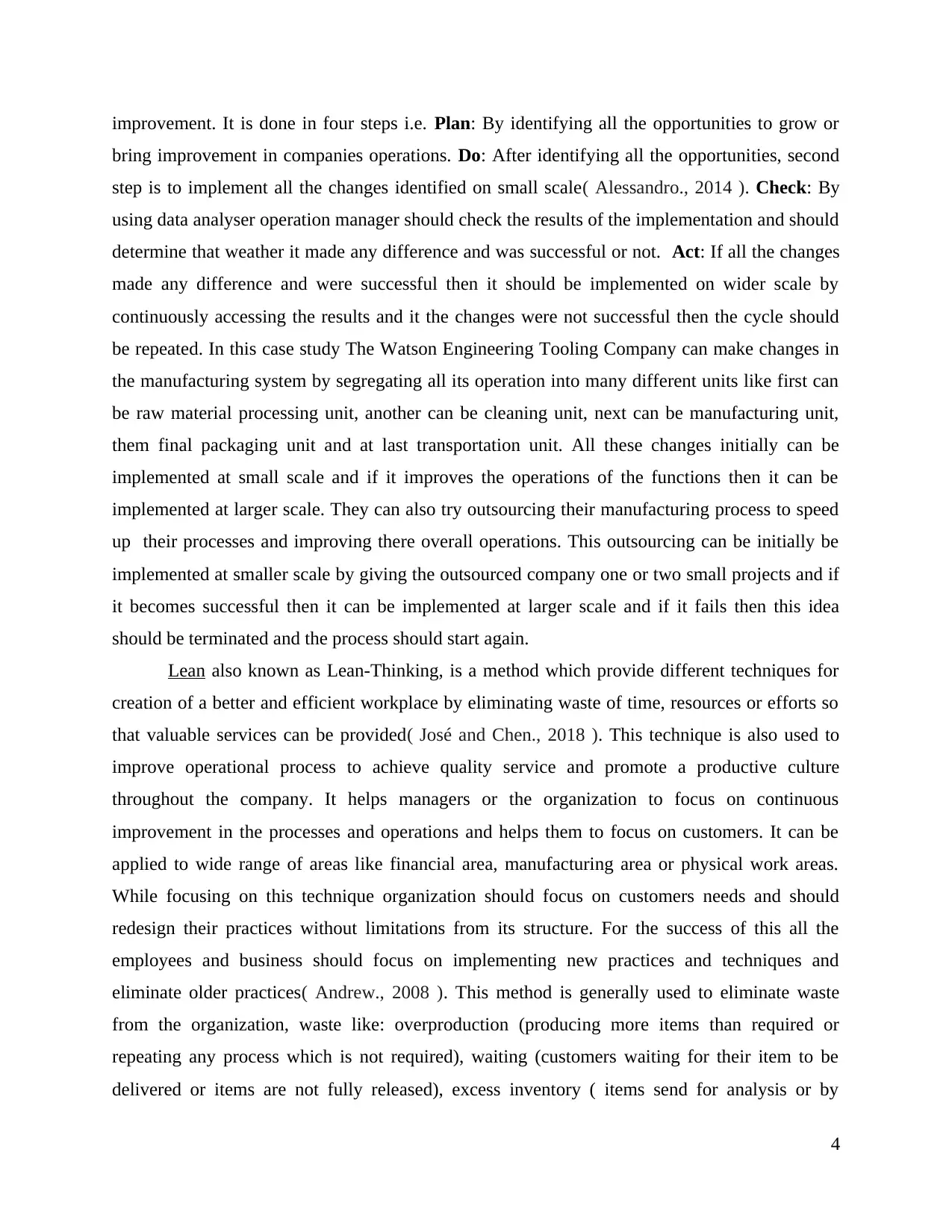
improvement. It is done in four steps i.e. Plan: By identifying all the opportunities to grow or
bring improvement in companies operations. Do: After identifying all the opportunities, second
step is to implement all the changes identified on small scale( Alessandro., 2014 ). Check: By
using data analyser operation manager should check the results of the implementation and should
determine that weather it made any difference and was successful or not. Act: If all the changes
made any difference and were successful then it should be implemented on wider scale by
continuously accessing the results and it the changes were not successful then the cycle should
be repeated. In this case study The Watson Engineering Tooling Company can make changes in
the manufacturing system by segregating all its operation into many different units like first can
be raw material processing unit, another can be cleaning unit, next can be manufacturing unit,
them final packaging unit and at last transportation unit. All these changes initially can be
implemented at small scale and if it improves the operations of the functions then it can be
implemented at larger scale. They can also try outsourcing their manufacturing process to speed
up their processes and improving there overall operations. This outsourcing can be initially be
implemented at smaller scale by giving the outsourced company one or two small projects and if
it becomes successful then it can be implemented at larger scale and if it fails then this idea
should be terminated and the process should start again.
Lean also known as Lean-Thinking, is a method which provide different techniques for
creation of a better and efficient workplace by eliminating waste of time, resources or efforts so
that valuable services can be provided( José and Chen., 2018 ). This technique is also used to
improve operational process to achieve quality service and promote a productive culture
throughout the company. It helps managers or the organization to focus on continuous
improvement in the processes and operations and helps them to focus on customers. It can be
applied to wide range of areas like financial area, manufacturing area or physical work areas.
While focusing on this technique organization should focus on customers needs and should
redesign their practices without limitations from its structure. For the success of this all the
employees and business should focus on implementing new practices and techniques and
eliminate older practices( Andrew., 2008 ). This method is generally used to eliminate waste
from the organization, waste like: overproduction (producing more items than required or
repeating any process which is not required), waiting (customers waiting for their item to be
delivered or items are not fully released), excess inventory ( items send for analysis or by
4
bring improvement in companies operations. Do: After identifying all the opportunities, second
step is to implement all the changes identified on small scale( Alessandro., 2014 ). Check: By
using data analyser operation manager should check the results of the implementation and should
determine that weather it made any difference and was successful or not. Act: If all the changes
made any difference and were successful then it should be implemented on wider scale by
continuously accessing the results and it the changes were not successful then the cycle should
be repeated. In this case study The Watson Engineering Tooling Company can make changes in
the manufacturing system by segregating all its operation into many different units like first can
be raw material processing unit, another can be cleaning unit, next can be manufacturing unit,
them final packaging unit and at last transportation unit. All these changes initially can be
implemented at small scale and if it improves the operations of the functions then it can be
implemented at larger scale. They can also try outsourcing their manufacturing process to speed
up their processes and improving there overall operations. This outsourcing can be initially be
implemented at smaller scale by giving the outsourced company one or two small projects and if
it becomes successful then it can be implemented at larger scale and if it fails then this idea
should be terminated and the process should start again.
Lean also known as Lean-Thinking, is a method which provide different techniques for
creation of a better and efficient workplace by eliminating waste of time, resources or efforts so
that valuable services can be provided( José and Chen., 2018 ). This technique is also used to
improve operational process to achieve quality service and promote a productive culture
throughout the company. It helps managers or the organization to focus on continuous
improvement in the processes and operations and helps them to focus on customers. It can be
applied to wide range of areas like financial area, manufacturing area or physical work areas.
While focusing on this technique organization should focus on customers needs and should
redesign their practices without limitations from its structure. For the success of this all the
employees and business should focus on implementing new practices and techniques and
eliminate older practices( Andrew., 2008 ). This method is generally used to eliminate waste
from the organization, waste like: overproduction (producing more items than required or
repeating any process which is not required), waiting (customers waiting for their item to be
delivered or items are not fully released), excess inventory ( items send for analysis or by
4
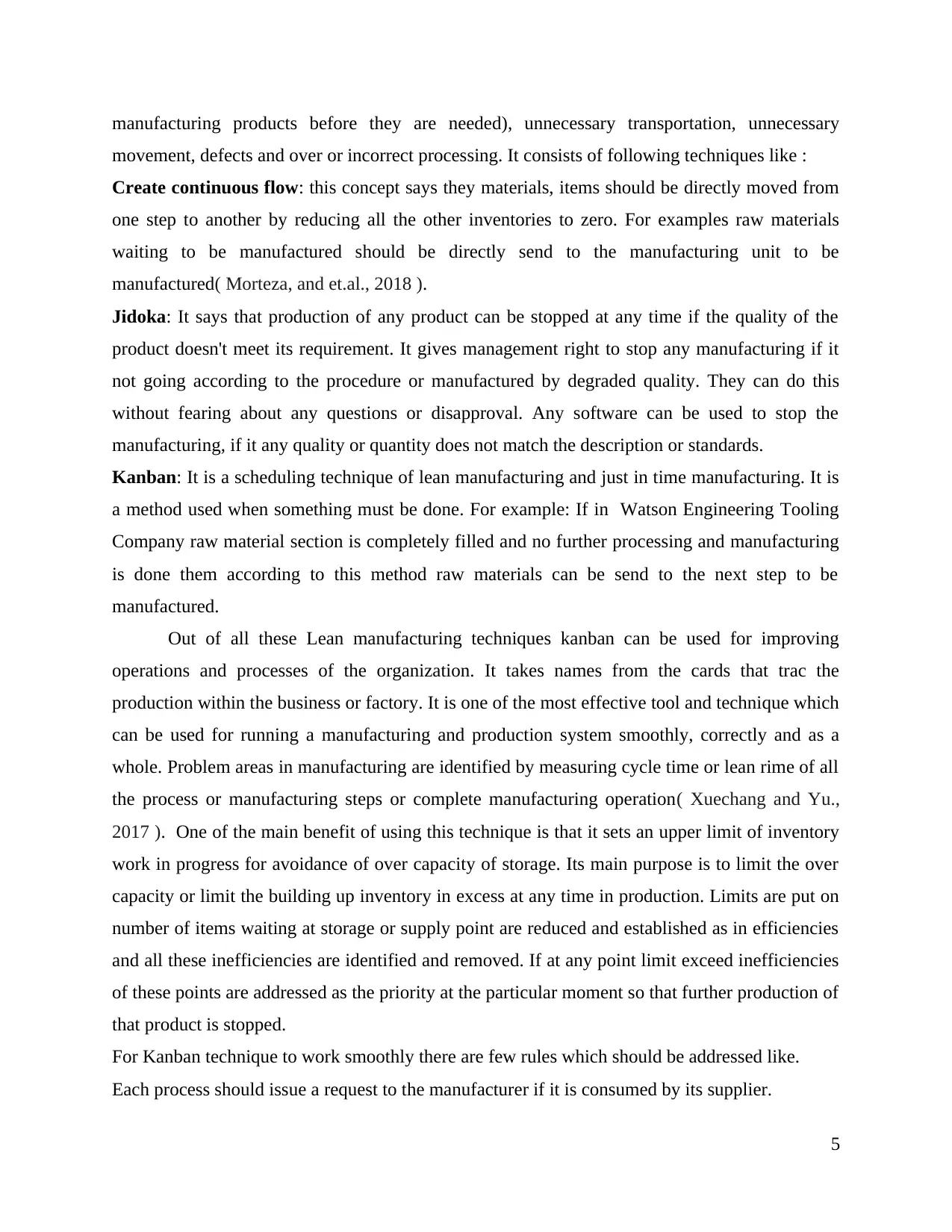
manufacturing products before they are needed), unnecessary transportation, unnecessary
movement, defects and over or incorrect processing. It consists of following techniques like :
Create continuous flow: this concept says they materials, items should be directly moved from
one step to another by reducing all the other inventories to zero. For examples raw materials
waiting to be manufactured should be directly send to the manufacturing unit to be
manufactured( Morteza, and et.al., 2018 ).
Jidoka: It says that production of any product can be stopped at any time if the quality of the
product doesn't meet its requirement. It gives management right to stop any manufacturing if it
not going according to the procedure or manufactured by degraded quality. They can do this
without fearing about any questions or disapproval. Any software can be used to stop the
manufacturing, if it any quality or quantity does not match the description or standards.
Kanban: It is a scheduling technique of lean manufacturing and just in time manufacturing. It is
a method used when something must be done. For example: If in Watson Engineering Tooling
Company raw material section is completely filled and no further processing and manufacturing
is done them according to this method raw materials can be send to the next step to be
manufactured.
Out of all these Lean manufacturing techniques kanban can be used for improving
operations and processes of the organization. It takes names from the cards that trac the
production within the business or factory. It is one of the most effective tool and technique which
can be used for running a manufacturing and production system smoothly, correctly and as a
whole. Problem areas in manufacturing are identified by measuring cycle time or lean rime of all
the process or manufacturing steps or complete manufacturing operation( Xuechang and Yu.,
2017 ). One of the main benefit of using this technique is that it sets an upper limit of inventory
work in progress for avoidance of over capacity of storage. Its main purpose is to limit the over
capacity or limit the building up inventory in excess at any time in production. Limits are put on
number of items waiting at storage or supply point are reduced and established as in efficiencies
and all these inefficiencies are identified and removed. If at any point limit exceed inefficiencies
of these points are addressed as the priority at the particular moment so that further production of
that product is stopped.
For Kanban technique to work smoothly there are few rules which should be addressed like.
Each process should issue a request to the manufacturer if it is consumed by its supplier.
5
movement, defects and over or incorrect processing. It consists of following techniques like :
Create continuous flow: this concept says they materials, items should be directly moved from
one step to another by reducing all the other inventories to zero. For examples raw materials
waiting to be manufactured should be directly send to the manufacturing unit to be
manufactured( Morteza, and et.al., 2018 ).
Jidoka: It says that production of any product can be stopped at any time if the quality of the
product doesn't meet its requirement. It gives management right to stop any manufacturing if it
not going according to the procedure or manufactured by degraded quality. They can do this
without fearing about any questions or disapproval. Any software can be used to stop the
manufacturing, if it any quality or quantity does not match the description or standards.
Kanban: It is a scheduling technique of lean manufacturing and just in time manufacturing. It is
a method used when something must be done. For example: If in Watson Engineering Tooling
Company raw material section is completely filled and no further processing and manufacturing
is done them according to this method raw materials can be send to the next step to be
manufactured.
Out of all these Lean manufacturing techniques kanban can be used for improving
operations and processes of the organization. It takes names from the cards that trac the
production within the business or factory. It is one of the most effective tool and technique which
can be used for running a manufacturing and production system smoothly, correctly and as a
whole. Problem areas in manufacturing are identified by measuring cycle time or lean rime of all
the process or manufacturing steps or complete manufacturing operation( Xuechang and Yu.,
2017 ). One of the main benefit of using this technique is that it sets an upper limit of inventory
work in progress for avoidance of over capacity of storage. Its main purpose is to limit the over
capacity or limit the building up inventory in excess at any time in production. Limits are put on
number of items waiting at storage or supply point are reduced and established as in efficiencies
and all these inefficiencies are identified and removed. If at any point limit exceed inefficiencies
of these points are addressed as the priority at the particular moment so that further production of
that product is stopped.
For Kanban technique to work smoothly there are few rules which should be addressed like.
Each process should issue a request to the manufacturer if it is consumed by its supplier.
5
Paraphrase This Document
Need a fresh take? Get an instant paraphrase of this document with our AI Paraphraser
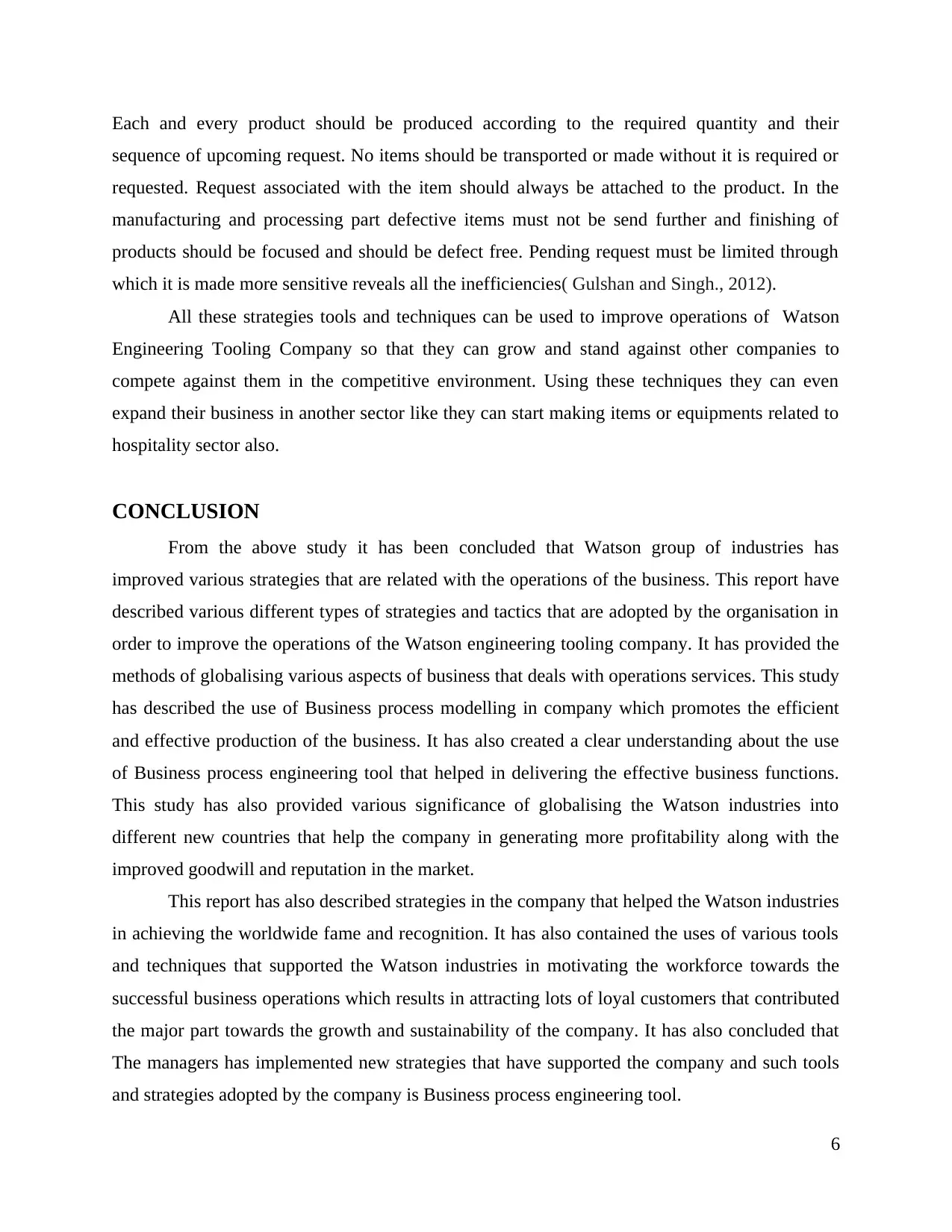
Each and every product should be produced according to the required quantity and their
sequence of upcoming request. No items should be transported or made without it is required or
requested. Request associated with the item should always be attached to the product. In the
manufacturing and processing part defective items must not be send further and finishing of
products should be focused and should be defect free. Pending request must be limited through
which it is made more sensitive reveals all the inefficiencies( Gulshan and Singh., 2012).
All these strategies tools and techniques can be used to improve operations of Watson
Engineering Tooling Company so that they can grow and stand against other companies to
compete against them in the competitive environment. Using these techniques they can even
expand their business in another sector like they can start making items or equipments related to
hospitality sector also.
CONCLUSION
From the above study it has been concluded that Watson group of industries has
improved various strategies that are related with the operations of the business. This report have
described various different types of strategies and tactics that are adopted by the organisation in
order to improve the operations of the Watson engineering tooling company. It has provided the
methods of globalising various aspects of business that deals with operations services. This study
has described the use of Business process modelling in company which promotes the efficient
and effective production of the business. It has also created a clear understanding about the use
of Business process engineering tool that helped in delivering the effective business functions.
This study has also provided various significance of globalising the Watson industries into
different new countries that help the company in generating more profitability along with the
improved goodwill and reputation in the market.
This report has also described strategies in the company that helped the Watson industries
in achieving the worldwide fame and recognition. It has also contained the uses of various tools
and techniques that supported the Watson industries in motivating the workforce towards the
successful business operations which results in attracting lots of loyal customers that contributed
the major part towards the growth and sustainability of the company. It has also concluded that
The managers has implemented new strategies that have supported the company and such tools
and strategies adopted by the company is Business process engineering tool.
6
sequence of upcoming request. No items should be transported or made without it is required or
requested. Request associated with the item should always be attached to the product. In the
manufacturing and processing part defective items must not be send further and finishing of
products should be focused and should be defect free. Pending request must be limited through
which it is made more sensitive reveals all the inefficiencies( Gulshan and Singh., 2012).
All these strategies tools and techniques can be used to improve operations of Watson
Engineering Tooling Company so that they can grow and stand against other companies to
compete against them in the competitive environment. Using these techniques they can even
expand their business in another sector like they can start making items or equipments related to
hospitality sector also.
CONCLUSION
From the above study it has been concluded that Watson group of industries has
improved various strategies that are related with the operations of the business. This report have
described various different types of strategies and tactics that are adopted by the organisation in
order to improve the operations of the Watson engineering tooling company. It has provided the
methods of globalising various aspects of business that deals with operations services. This study
has described the use of Business process modelling in company which promotes the efficient
and effective production of the business. It has also created a clear understanding about the use
of Business process engineering tool that helped in delivering the effective business functions.
This study has also provided various significance of globalising the Watson industries into
different new countries that help the company in generating more profitability along with the
improved goodwill and reputation in the market.
This report has also described strategies in the company that helped the Watson industries
in achieving the worldwide fame and recognition. It has also contained the uses of various tools
and techniques that supported the Watson industries in motivating the workforce towards the
successful business operations which results in attracting lots of loyal customers that contributed
the major part towards the growth and sustainability of the company. It has also concluded that
The managers has implemented new strategies that have supported the company and such tools
and strategies adopted by the company is Business process engineering tool.
6
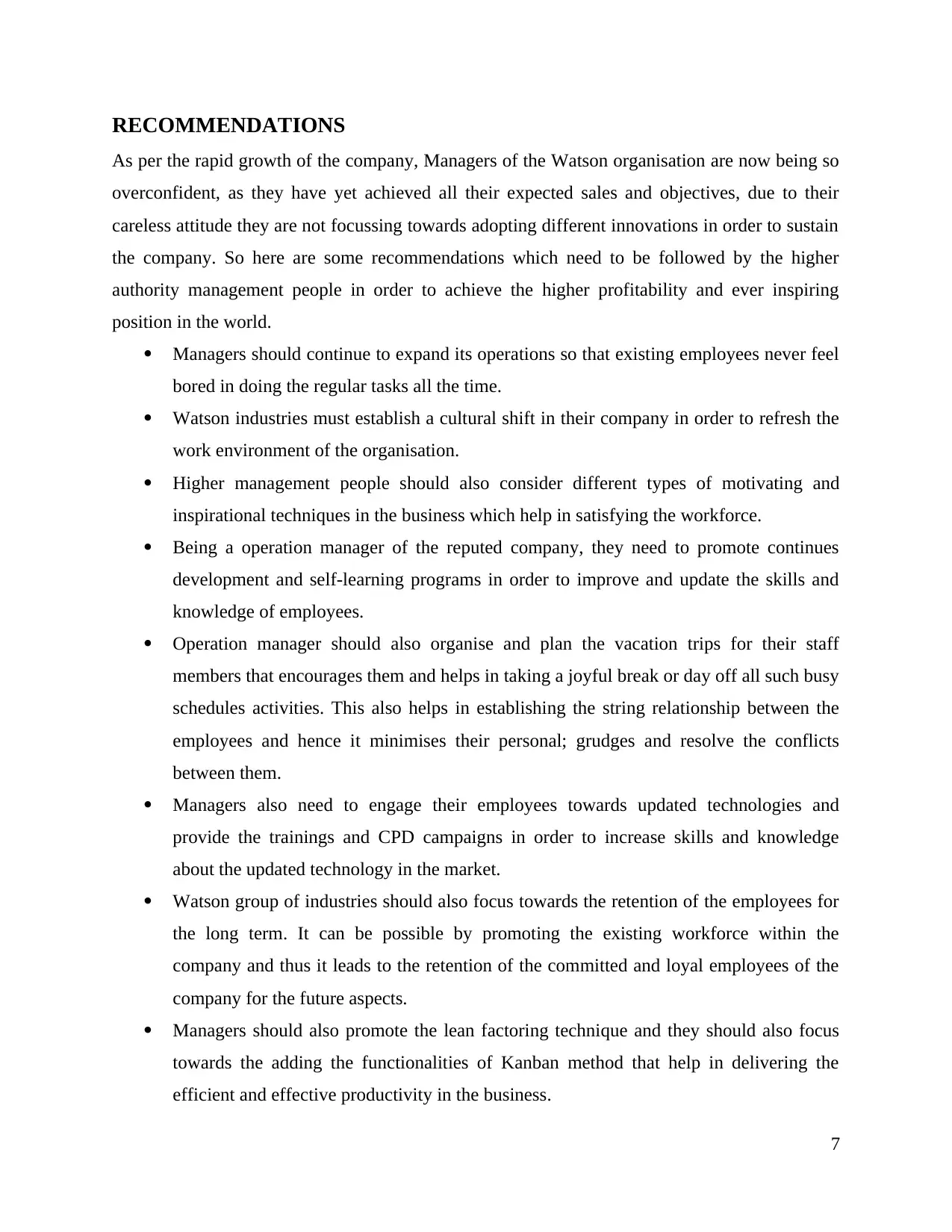
RECOMMENDATIONS
As per the rapid growth of the company, Managers of the Watson organisation are now being so
overconfident, as they have yet achieved all their expected sales and objectives, due to their
careless attitude they are not focussing towards adopting different innovations in order to sustain
the company. So here are some recommendations which need to be followed by the higher
authority management people in order to achieve the higher profitability and ever inspiring
position in the world.
Managers should continue to expand its operations so that existing employees never feel
bored in doing the regular tasks all the time.
Watson industries must establish a cultural shift in their company in order to refresh the
work environment of the organisation.
Higher management people should also consider different types of motivating and
inspirational techniques in the business which help in satisfying the workforce.
Being a operation manager of the reputed company, they need to promote continues
development and self-learning programs in order to improve and update the skills and
knowledge of employees.
Operation manager should also organise and plan the vacation trips for their staff
members that encourages them and helps in taking a joyful break or day off all such busy
schedules activities. This also helps in establishing the string relationship between the
employees and hence it minimises their personal; grudges and resolve the conflicts
between them.
Managers also need to engage their employees towards updated technologies and
provide the trainings and CPD campaigns in order to increase skills and knowledge
about the updated technology in the market.
Watson group of industries should also focus towards the retention of the employees for
the long term. It can be possible by promoting the existing workforce within the
company and thus it leads to the retention of the committed and loyal employees of the
company for the future aspects.
Managers should also promote the lean factoring technique and they should also focus
towards the adding the functionalities of Kanban method that help in delivering the
efficient and effective productivity in the business.
7
As per the rapid growth of the company, Managers of the Watson organisation are now being so
overconfident, as they have yet achieved all their expected sales and objectives, due to their
careless attitude they are not focussing towards adopting different innovations in order to sustain
the company. So here are some recommendations which need to be followed by the higher
authority management people in order to achieve the higher profitability and ever inspiring
position in the world.
Managers should continue to expand its operations so that existing employees never feel
bored in doing the regular tasks all the time.
Watson industries must establish a cultural shift in their company in order to refresh the
work environment of the organisation.
Higher management people should also consider different types of motivating and
inspirational techniques in the business which help in satisfying the workforce.
Being a operation manager of the reputed company, they need to promote continues
development and self-learning programs in order to improve and update the skills and
knowledge of employees.
Operation manager should also organise and plan the vacation trips for their staff
members that encourages them and helps in taking a joyful break or day off all such busy
schedules activities. This also helps in establishing the string relationship between the
employees and hence it minimises their personal; grudges and resolve the conflicts
between them.
Managers also need to engage their employees towards updated technologies and
provide the trainings and CPD campaigns in order to increase skills and knowledge
about the updated technology in the market.
Watson group of industries should also focus towards the retention of the employees for
the long term. It can be possible by promoting the existing workforce within the
company and thus it leads to the retention of the committed and loyal employees of the
company for the future aspects.
Managers should also promote the lean factoring technique and they should also focus
towards the adding the functionalities of Kanban method that help in delivering the
efficient and effective productivity in the business.
7
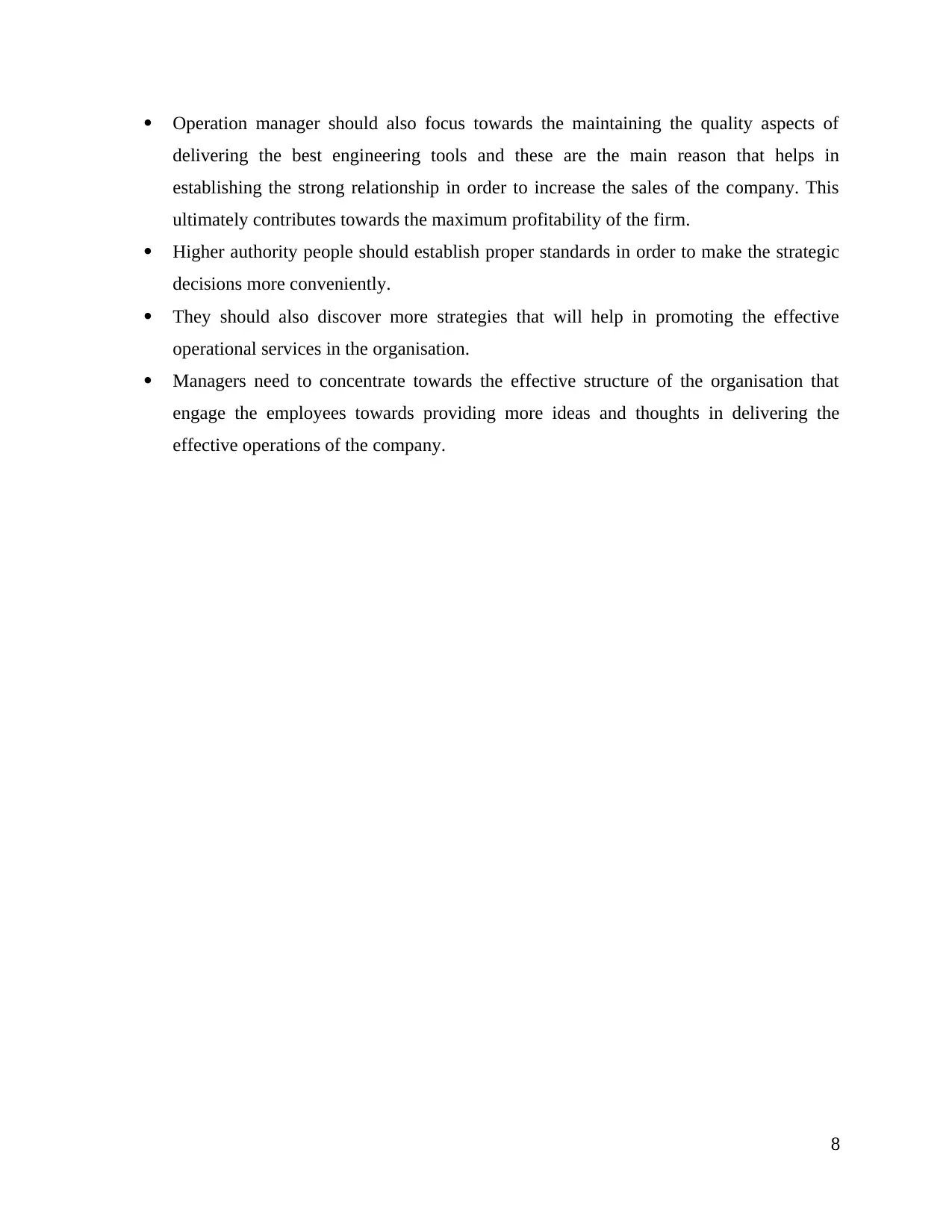
Operation manager should also focus towards the maintaining the quality aspects of
delivering the best engineering tools and these are the main reason that helps in
establishing the strong relationship in order to increase the sales of the company. This
ultimately contributes towards the maximum profitability of the firm.
Higher authority people should establish proper standards in order to make the strategic
decisions more conveniently.
They should also discover more strategies that will help in promoting the effective
operational services in the organisation.
Managers need to concentrate towards the effective structure of the organisation that
engage the employees towards providing more ideas and thoughts in delivering the
effective operations of the company.
8
delivering the best engineering tools and these are the main reason that helps in
establishing the strong relationship in order to increase the sales of the company. This
ultimately contributes towards the maximum profitability of the firm.
Higher authority people should establish proper standards in order to make the strategic
decisions more conveniently.
They should also discover more strategies that will help in promoting the effective
operational services in the organisation.
Managers need to concentrate towards the effective structure of the organisation that
engage the employees towards providing more ideas and thoughts in delivering the
effective operations of the company.
8
Secure Best Marks with AI Grader
Need help grading? Try our AI Grader for instant feedback on your assignments.
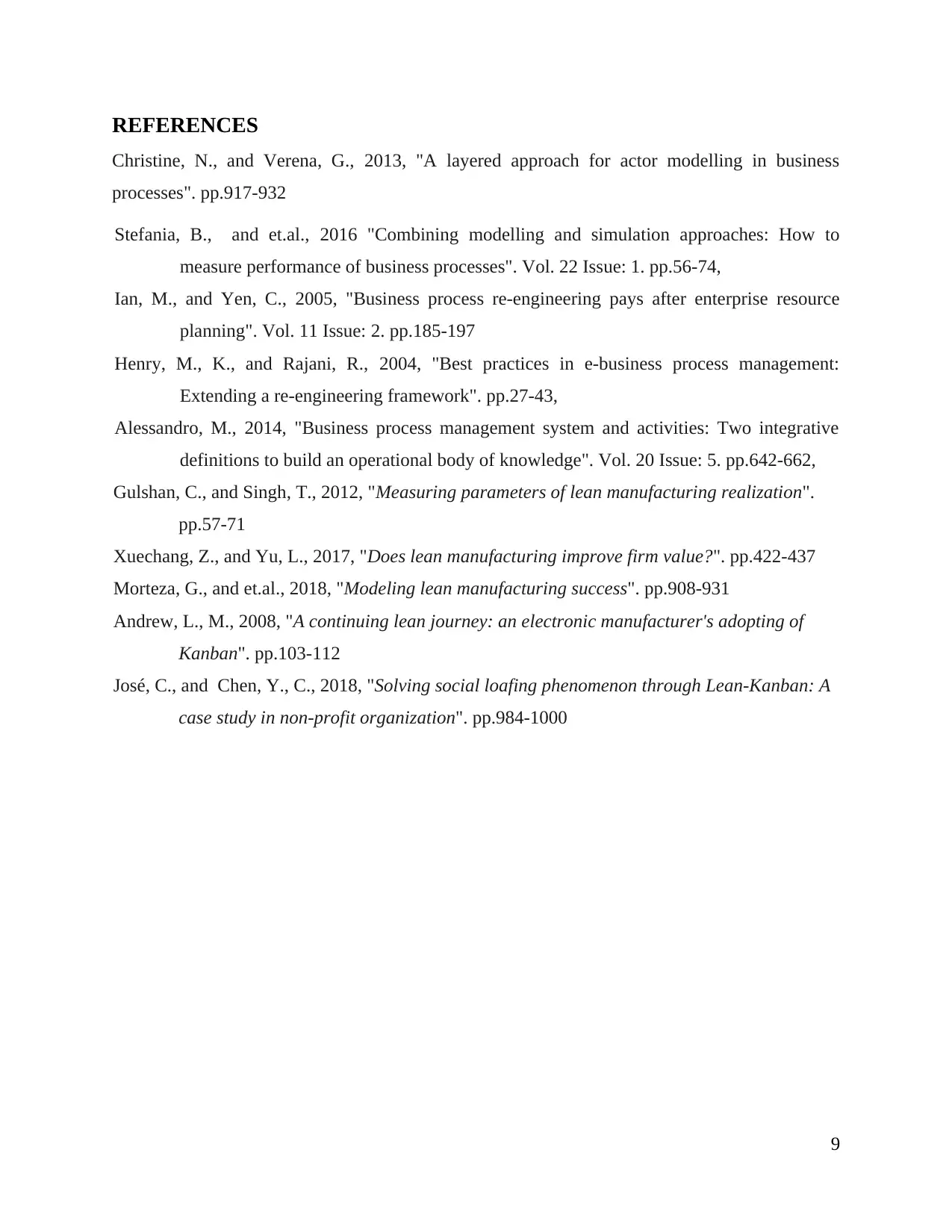
REFERENCES
Christine, N., and Verena, G., 2013, "A layered approach for actor modelling in business
processes". pp.917-932
Stefania, B., and et.al., 2016 "Combining modelling and simulation approaches: How to
measure performance of business processes". Vol. 22 Issue: 1. pp.56-74,
Ian, M., and Yen, C., 2005, "Business process re‐engineering pays after enterprise resource
planning". Vol. 11 Issue: 2. pp.185-197
Henry, M., K., and Rajani, R., 2004, "Best practices in e‐business process management:
Extending a re‐engineering framework". pp.27-43,
Alessandro, M., 2014, "Business process management system and activities: Two integrative
definitions to build an operational body of knowledge". Vol. 20 Issue: 5. pp.642-662,
Gulshan, C., and Singh, T., 2012, "Measuring parameters of lean manufacturing realization".
pp.57-71
Xuechang, Z., and Yu, L., 2017, "Does lean manufacturing improve firm value?". pp.422-437
Morteza, G., and et.al., 2018, "Modeling lean manufacturing success". pp.908-931
Andrew, L., M., 2008, "A continuing lean journey: an electronic manufacturer's adopting of
Kanban". pp.103-112
José, C., and Chen, Y., C., 2018, "Solving social loafing phenomenon through Lean-Kanban: A
case study in non-profit organization". pp.984-1000
9
Christine, N., and Verena, G., 2013, "A layered approach for actor modelling in business
processes". pp.917-932
Stefania, B., and et.al., 2016 "Combining modelling and simulation approaches: How to
measure performance of business processes". Vol. 22 Issue: 1. pp.56-74,
Ian, M., and Yen, C., 2005, "Business process re‐engineering pays after enterprise resource
planning". Vol. 11 Issue: 2. pp.185-197
Henry, M., K., and Rajani, R., 2004, "Best practices in e‐business process management:
Extending a re‐engineering framework". pp.27-43,
Alessandro, M., 2014, "Business process management system and activities: Two integrative
definitions to build an operational body of knowledge". Vol. 20 Issue: 5. pp.642-662,
Gulshan, C., and Singh, T., 2012, "Measuring parameters of lean manufacturing realization".
pp.57-71
Xuechang, Z., and Yu, L., 2017, "Does lean manufacturing improve firm value?". pp.422-437
Morteza, G., and et.al., 2018, "Modeling lean manufacturing success". pp.908-931
Andrew, L., M., 2008, "A continuing lean journey: an electronic manufacturer's adopting of
Kanban". pp.103-112
José, C., and Chen, Y., C., 2018, "Solving social loafing phenomenon through Lean-Kanban: A
case study in non-profit organization". pp.984-1000
9
1 out of 11
Related Documents

Your All-in-One AI-Powered Toolkit for Academic Success.
+13062052269
info@desklib.com
Available 24*7 on WhatsApp / Email
Unlock your academic potential
© 2024 | Zucol Services PVT LTD | All rights reserved.