BSBWHS501: Report on WHS Management System at Australian Hardware
VerifiedAdded on 2022/11/13
|12
|2789
|291
Report
AI Summary
This report, developed for the BSBWHS501 unit, details the implementation and evaluation of a WHS management system at Australian Hardware. The report encompasses three assessment tasks. The first task involves establishing and maintaining the WHS management system, including the development of a safety plan, WHS policies, and resource allocation for training and management. Task 2 focuses on undertaking consultation and managing WHS risks through role-playing scenarios with a Health and Safety Representative and a store manager, addressing identified hazards and proposing solutions. Task 3 centers on evaluating the effectiveness of the WHS management system, identifying areas for improvement based on the provided scenario data, and formulating recommendations for enhanced workplace safety, including implementation plans for the suggested improvements. The report also addresses record-keeping, risk management, and consultation procedures to ensure a safe working environment.
Contribute Materials
Your contribution can guide someone’s learning journey. Share your
documents today.
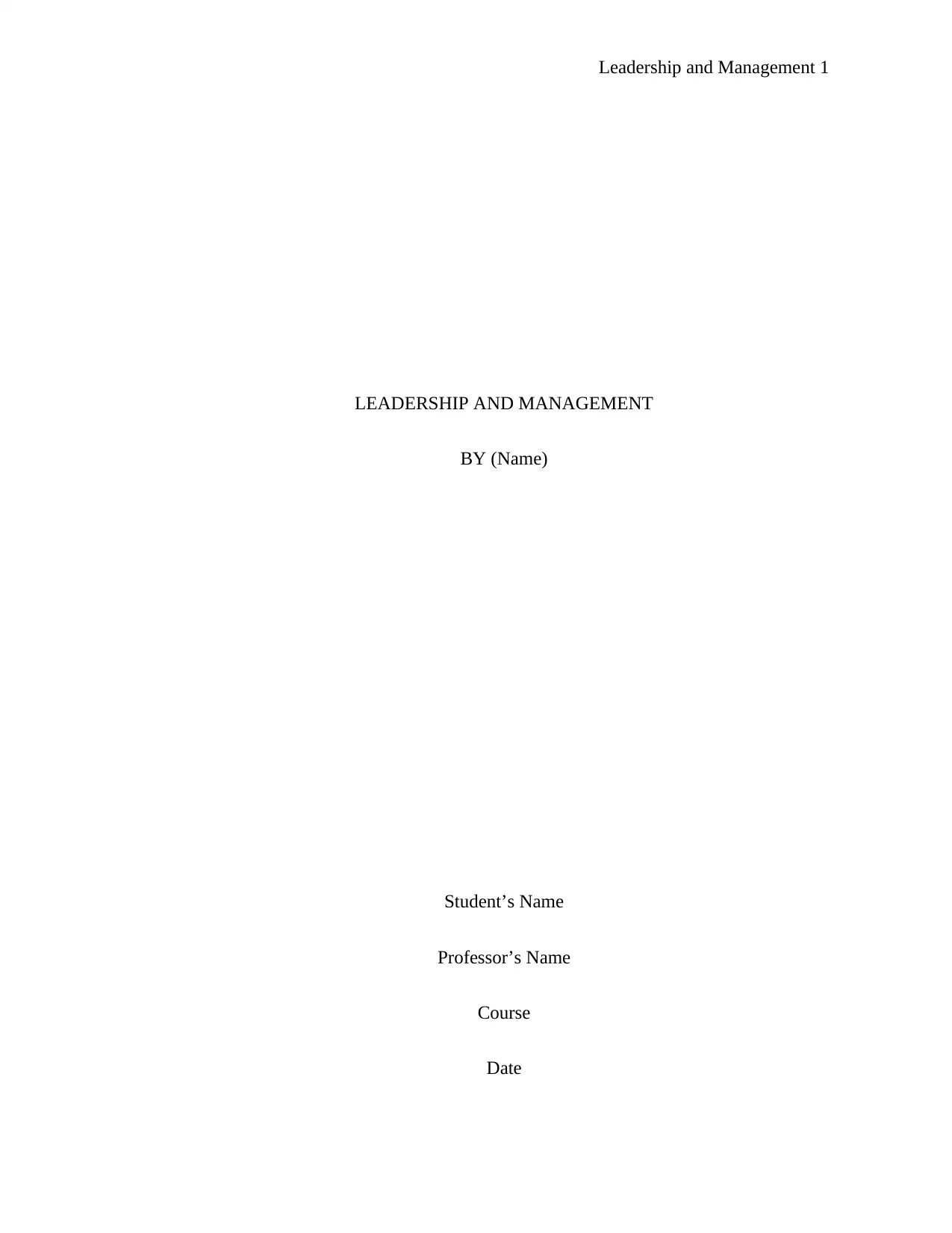
Leadership and Management 1
LEADERSHIP AND MANAGEMENT
BY (Name)
Student’s Name
Professor’s Name
Course
Date
LEADERSHIP AND MANAGEMENT
BY (Name)
Student’s Name
Professor’s Name
Course
Date
Secure Best Marks with AI Grader
Need help grading? Try our AI Grader for instant feedback on your assignments.
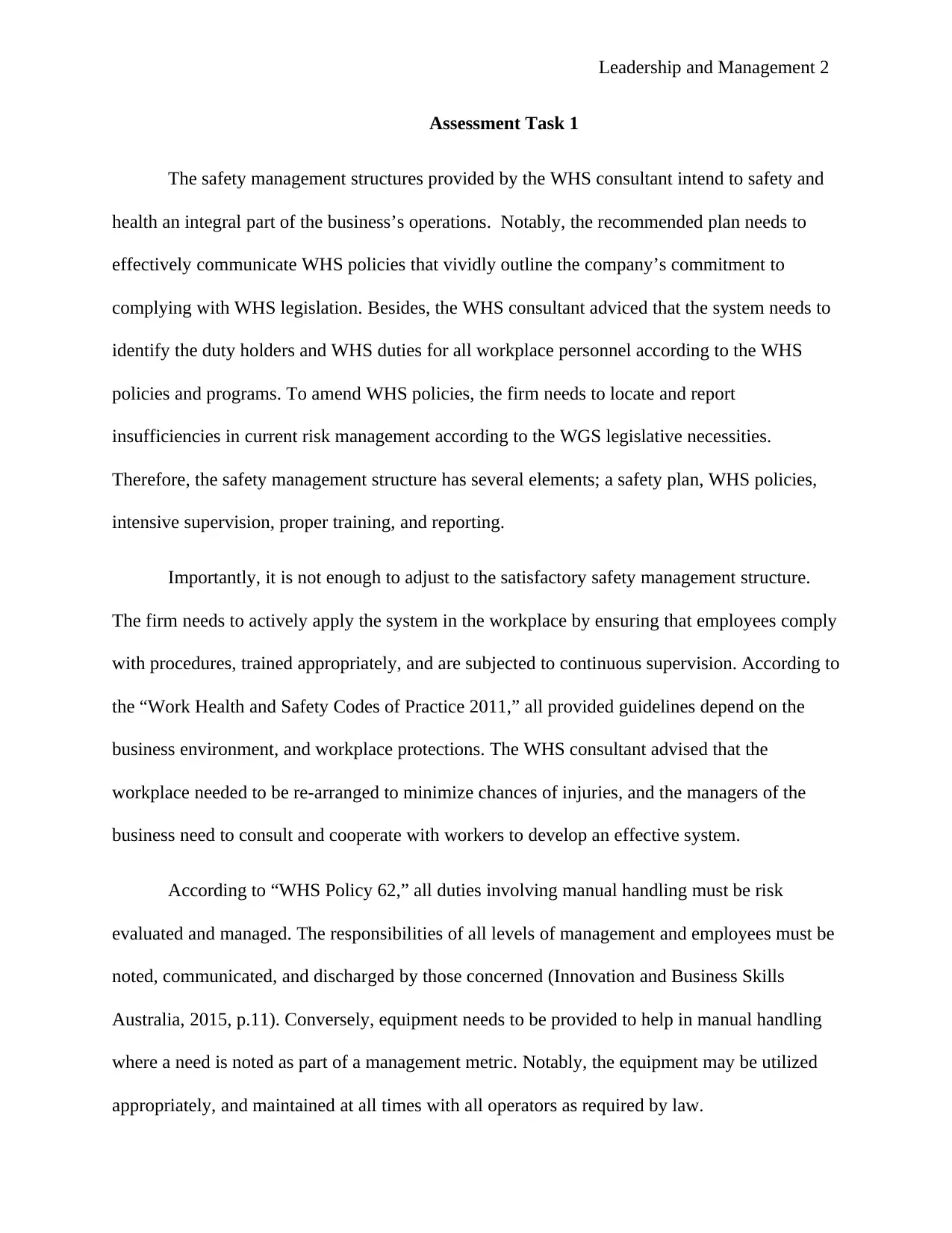
Leadership and Management 2
Assessment Task 1
The safety management structures provided by the WHS consultant intend to safety and
health an integral part of the business’s operations. Notably, the recommended plan needs to
effectively communicate WHS policies that vividly outline the company’s commitment to
complying with WHS legislation. Besides, the WHS consultant adviced that the system needs to
identify the duty holders and WHS duties for all workplace personnel according to the WHS
policies and programs. To amend WHS policies, the firm needs to locate and report
insufficiencies in current risk management according to the WGS legislative necessities.
Therefore, the safety management structure has several elements; a safety plan, WHS policies,
intensive supervision, proper training, and reporting.
Importantly, it is not enough to adjust to the satisfactory safety management structure.
The firm needs to actively apply the system in the workplace by ensuring that employees comply
with procedures, trained appropriately, and are subjected to continuous supervision. According to
the “Work Health and Safety Codes of Practice 2011,” all provided guidelines depend on the
business environment, and workplace protections. The WHS consultant advised that the
workplace needed to be re-arranged to minimize chances of injuries, and the managers of the
business need to consult and cooperate with workers to develop an effective system.
According to “WHS Policy 62,” all duties involving manual handling must be risk
evaluated and managed. The responsibilities of all levels of management and employees must be
noted, communicated, and discharged by those concerned (Innovation and Business Skills
Australia, 2015, p.11). Conversely, equipment needs to be provided to help in manual handling
where a need is noted as part of a management metric. Notably, the equipment may be utilized
appropriately, and maintained at all times with all operators as required by law.
Assessment Task 1
The safety management structures provided by the WHS consultant intend to safety and
health an integral part of the business’s operations. Notably, the recommended plan needs to
effectively communicate WHS policies that vividly outline the company’s commitment to
complying with WHS legislation. Besides, the WHS consultant adviced that the system needs to
identify the duty holders and WHS duties for all workplace personnel according to the WHS
policies and programs. To amend WHS policies, the firm needs to locate and report
insufficiencies in current risk management according to the WGS legislative necessities.
Therefore, the safety management structure has several elements; a safety plan, WHS policies,
intensive supervision, proper training, and reporting.
Importantly, it is not enough to adjust to the satisfactory safety management structure.
The firm needs to actively apply the system in the workplace by ensuring that employees comply
with procedures, trained appropriately, and are subjected to continuous supervision. According to
the “Work Health and Safety Codes of Practice 2011,” all provided guidelines depend on the
business environment, and workplace protections. The WHS consultant advised that the
workplace needed to be re-arranged to minimize chances of injuries, and the managers of the
business need to consult and cooperate with workers to develop an effective system.
According to “WHS Policy 62,” all duties involving manual handling must be risk
evaluated and managed. The responsibilities of all levels of management and employees must be
noted, communicated, and discharged by those concerned (Innovation and Business Skills
Australia, 2015, p.11). Conversely, equipment needs to be provided to help in manual handling
where a need is noted as part of a management metric. Notably, the equipment may be utilized
appropriately, and maintained at all times with all operators as required by law.
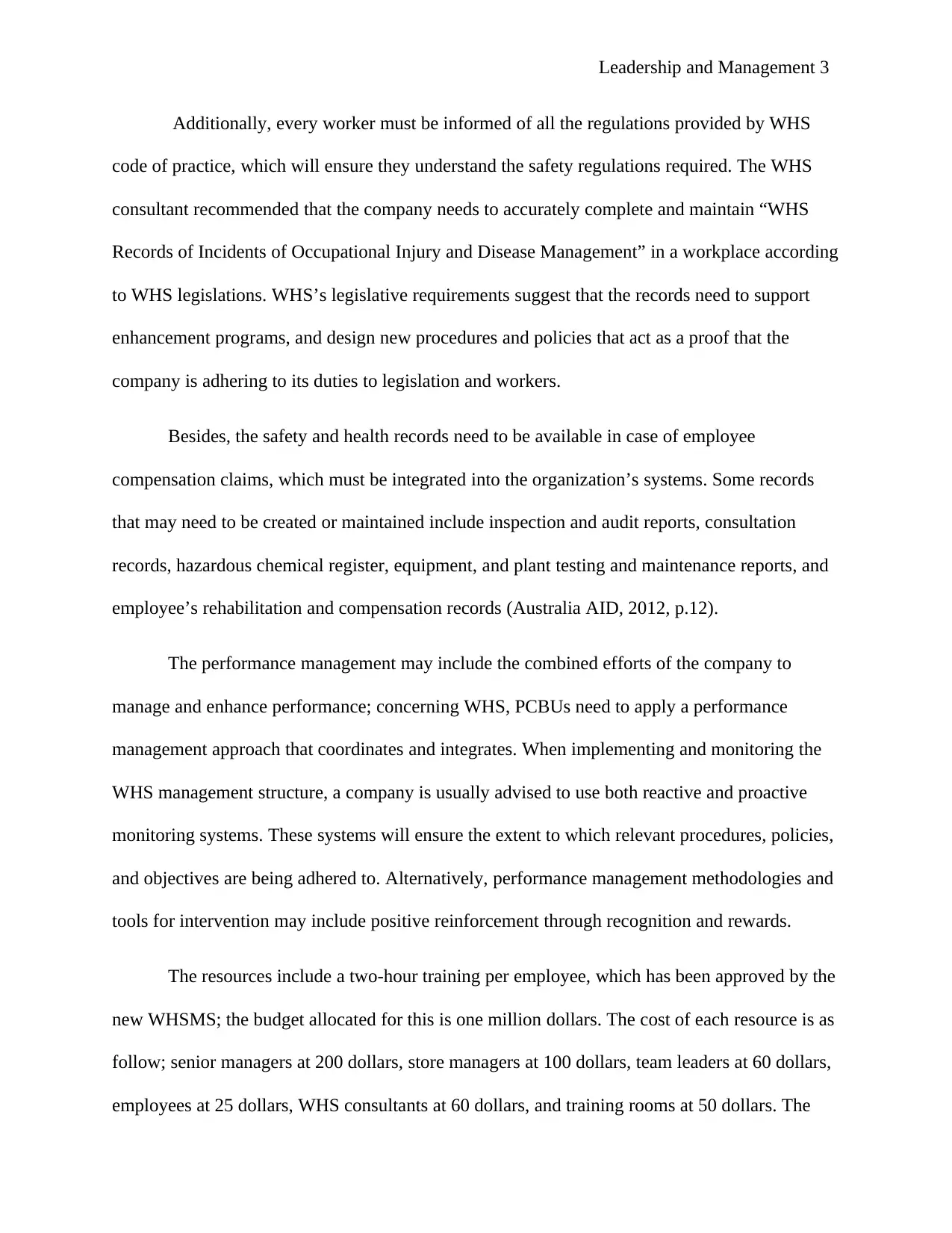
Leadership and Management 3
Additionally, every worker must be informed of all the regulations provided by WHS
code of practice, which will ensure they understand the safety regulations required. The WHS
consultant recommended that the company needs to accurately complete and maintain “WHS
Records of Incidents of Occupational Injury and Disease Management” in a workplace according
to WHS legislations. WHS’s legislative requirements suggest that the records need to support
enhancement programs, and design new procedures and policies that act as a proof that the
company is adhering to its duties to legislation and workers.
Besides, the safety and health records need to be available in case of employee
compensation claims, which must be integrated into the organization’s systems. Some records
that may need to be created or maintained include inspection and audit reports, consultation
records, hazardous chemical register, equipment, and plant testing and maintenance reports, and
employee’s rehabilitation and compensation records (Australia AID, 2012, p.12).
The performance management may include the combined efforts of the company to
manage and enhance performance; concerning WHS, PCBUs need to apply a performance
management approach that coordinates and integrates. When implementing and monitoring the
WHS management structure, a company is usually advised to use both reactive and proactive
monitoring systems. These systems will ensure the extent to which relevant procedures, policies,
and objectives are being adhered to. Alternatively, performance management methodologies and
tools for intervention may include positive reinforcement through recognition and rewards.
The resources include a two-hour training per employee, which has been approved by the
new WHSMS; the budget allocated for this is one million dollars. The cost of each resource is as
follow; senior managers at 200 dollars, store managers at 100 dollars, team leaders at 60 dollars,
employees at 25 dollars, WHS consultants at 60 dollars, and training rooms at 50 dollars. The
Additionally, every worker must be informed of all the regulations provided by WHS
code of practice, which will ensure they understand the safety regulations required. The WHS
consultant recommended that the company needs to accurately complete and maintain “WHS
Records of Incidents of Occupational Injury and Disease Management” in a workplace according
to WHS legislations. WHS’s legislative requirements suggest that the records need to support
enhancement programs, and design new procedures and policies that act as a proof that the
company is adhering to its duties to legislation and workers.
Besides, the safety and health records need to be available in case of employee
compensation claims, which must be integrated into the organization’s systems. Some records
that may need to be created or maintained include inspection and audit reports, consultation
records, hazardous chemical register, equipment, and plant testing and maintenance reports, and
employee’s rehabilitation and compensation records (Australia AID, 2012, p.12).
The performance management may include the combined efforts of the company to
manage and enhance performance; concerning WHS, PCBUs need to apply a performance
management approach that coordinates and integrates. When implementing and monitoring the
WHS management structure, a company is usually advised to use both reactive and proactive
monitoring systems. These systems will ensure the extent to which relevant procedures, policies,
and objectives are being adhered to. Alternatively, performance management methodologies and
tools for intervention may include positive reinforcement through recognition and rewards.
The resources include a two-hour training per employee, which has been approved by the
new WHSMS; the budget allocated for this is one million dollars. The cost of each resource is as
follow; senior managers at 200 dollars, store managers at 100 dollars, team leaders at 60 dollars,
employees at 25 dollars, WHS consultants at 60 dollars, and training rooms at 50 dollars. The
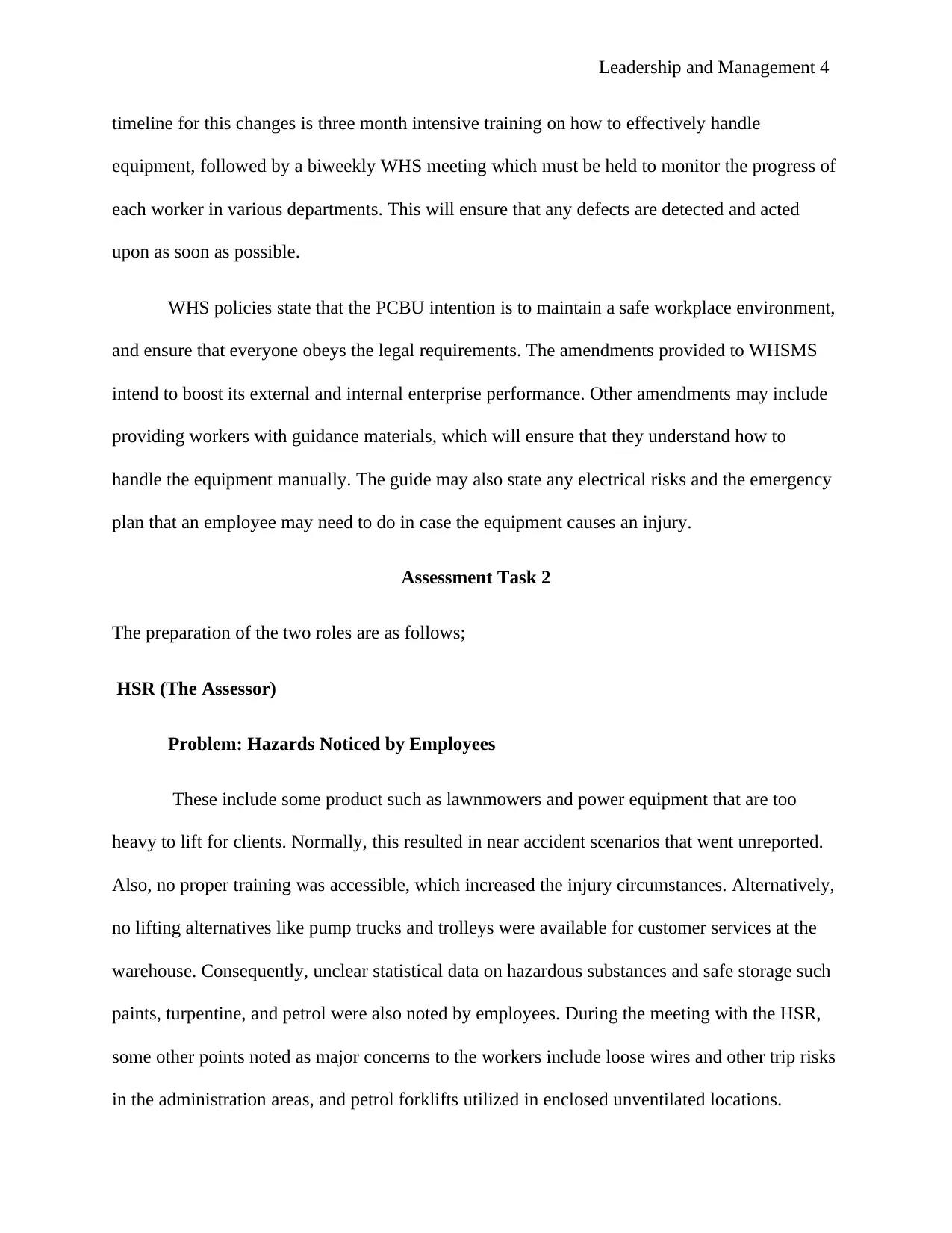
Leadership and Management 4
timeline for this changes is three month intensive training on how to effectively handle
equipment, followed by a biweekly WHS meeting which must be held to monitor the progress of
each worker in various departments. This will ensure that any defects are detected and acted
upon as soon as possible.
WHS policies state that the PCBU intention is to maintain a safe workplace environment,
and ensure that everyone obeys the legal requirements. The amendments provided to WHSMS
intend to boost its external and internal enterprise performance. Other amendments may include
providing workers with guidance materials, which will ensure that they understand how to
handle the equipment manually. The guide may also state any electrical risks and the emergency
plan that an employee may need to do in case the equipment causes an injury.
Assessment Task 2
The preparation of the two roles are as follows;
HSR (The Assessor)
Problem: Hazards Noticed by Employees
These include some product such as lawnmowers and power equipment that are too
heavy to lift for clients. Normally, this resulted in near accident scenarios that went unreported.
Also, no proper training was accessible, which increased the injury circumstances. Alternatively,
no lifting alternatives like pump trucks and trolleys were available for customer services at the
warehouse. Consequently, unclear statistical data on hazardous substances and safe storage such
paints, turpentine, and petrol were also noted by employees. During the meeting with the HSR,
some other points noted as major concerns to the workers include loose wires and other trip risks
in the administration areas, and petrol forklifts utilized in enclosed unventilated locations.
timeline for this changes is three month intensive training on how to effectively handle
equipment, followed by a biweekly WHS meeting which must be held to monitor the progress of
each worker in various departments. This will ensure that any defects are detected and acted
upon as soon as possible.
WHS policies state that the PCBU intention is to maintain a safe workplace environment,
and ensure that everyone obeys the legal requirements. The amendments provided to WHSMS
intend to boost its external and internal enterprise performance. Other amendments may include
providing workers with guidance materials, which will ensure that they understand how to
handle the equipment manually. The guide may also state any electrical risks and the emergency
plan that an employee may need to do in case the equipment causes an injury.
Assessment Task 2
The preparation of the two roles are as follows;
HSR (The Assessor)
Problem: Hazards Noticed by Employees
These include some product such as lawnmowers and power equipment that are too
heavy to lift for clients. Normally, this resulted in near accident scenarios that went unreported.
Also, no proper training was accessible, which increased the injury circumstances. Alternatively,
no lifting alternatives like pump trucks and trolleys were available for customer services at the
warehouse. Consequently, unclear statistical data on hazardous substances and safe storage such
paints, turpentine, and petrol were also noted by employees. During the meeting with the HSR,
some other points noted as major concerns to the workers include loose wires and other trip risks
in the administration areas, and petrol forklifts utilized in enclosed unventilated locations.
Secure Best Marks with AI Grader
Need help grading? Try our AI Grader for instant feedback on your assignments.
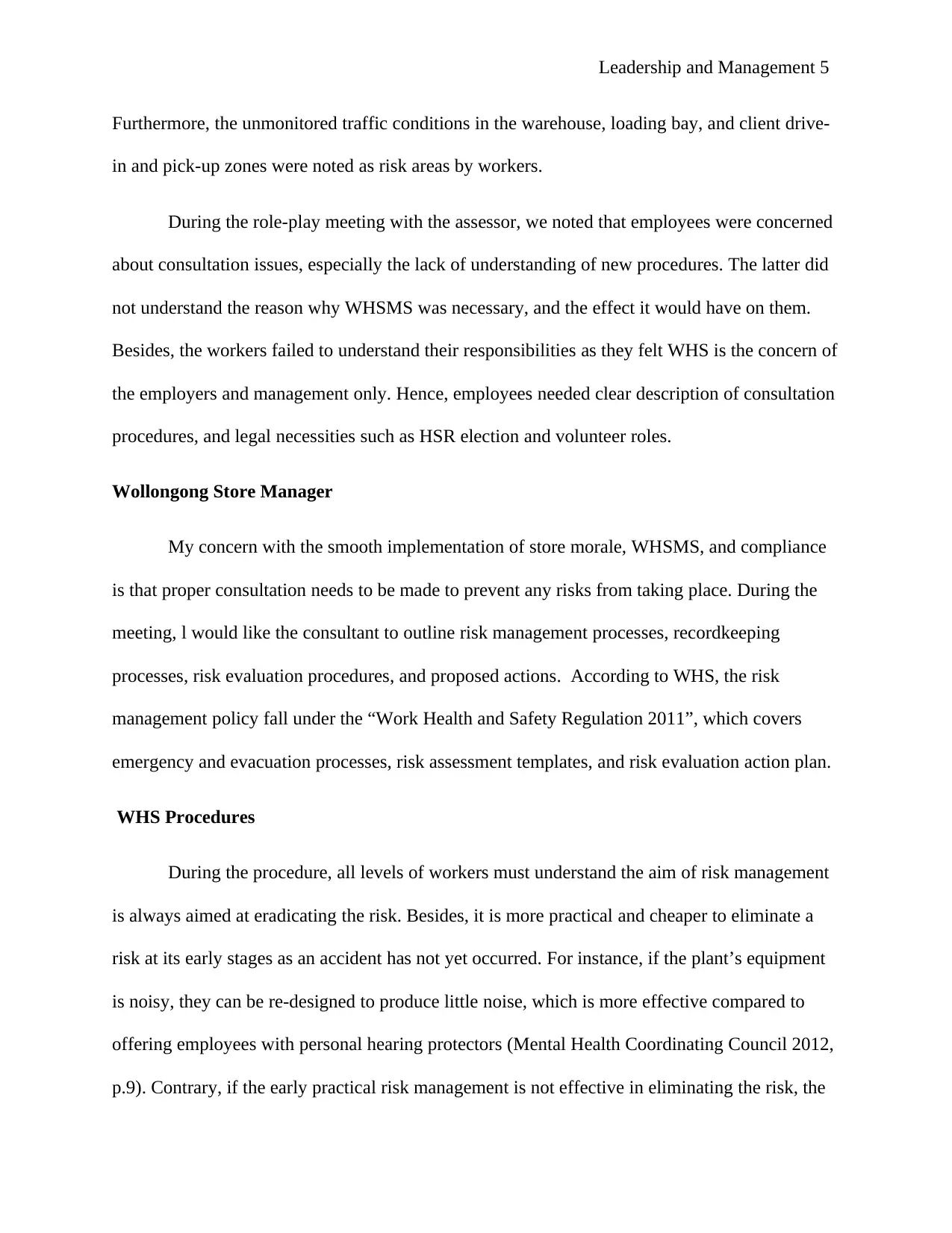
Leadership and Management 5
Furthermore, the unmonitored traffic conditions in the warehouse, loading bay, and client drive-
in and pick-up zones were noted as risk areas by workers.
During the role-play meeting with the assessor, we noted that employees were concerned
about consultation issues, especially the lack of understanding of new procedures. The latter did
not understand the reason why WHSMS was necessary, and the effect it would have on them.
Besides, the workers failed to understand their responsibilities as they felt WHS is the concern of
the employers and management only. Hence, employees needed clear description of consultation
procedures, and legal necessities such as HSR election and volunteer roles.
Wollongong Store Manager
My concern with the smooth implementation of store morale, WHSMS, and compliance
is that proper consultation needs to be made to prevent any risks from taking place. During the
meeting, l would like the consultant to outline risk management processes, recordkeeping
processes, risk evaluation procedures, and proposed actions. According to WHS, the risk
management policy fall under the “Work Health and Safety Regulation 2011”, which covers
emergency and evacuation processes, risk assessment templates, and risk evaluation action plan.
WHS Procedures
During the procedure, all levels of workers must understand the aim of risk management
is always aimed at eradicating the risk. Besides, it is more practical and cheaper to eliminate a
risk at its early stages as an accident has not yet occurred. For instance, if the plant’s equipment
is noisy, they can be re-designed to produce little noise, which is more effective compared to
offering employees with personal hearing protectors (Mental Health Coordinating Council 2012,
p.9). Contrary, if the early practical risk management is not effective in eliminating the risk, the
Furthermore, the unmonitored traffic conditions in the warehouse, loading bay, and client drive-
in and pick-up zones were noted as risk areas by workers.
During the role-play meeting with the assessor, we noted that employees were concerned
about consultation issues, especially the lack of understanding of new procedures. The latter did
not understand the reason why WHSMS was necessary, and the effect it would have on them.
Besides, the workers failed to understand their responsibilities as they felt WHS is the concern of
the employers and management only. Hence, employees needed clear description of consultation
procedures, and legal necessities such as HSR election and volunteer roles.
Wollongong Store Manager
My concern with the smooth implementation of store morale, WHSMS, and compliance
is that proper consultation needs to be made to prevent any risks from taking place. During the
meeting, l would like the consultant to outline risk management processes, recordkeeping
processes, risk evaluation procedures, and proposed actions. According to WHS, the risk
management policy fall under the “Work Health and Safety Regulation 2011”, which covers
emergency and evacuation processes, risk assessment templates, and risk evaluation action plan.
WHS Procedures
During the procedure, all levels of workers must understand the aim of risk management
is always aimed at eradicating the risk. Besides, it is more practical and cheaper to eliminate a
risk at its early stages as an accident has not yet occurred. For instance, if the plant’s equipment
is noisy, they can be re-designed to produce little noise, which is more effective compared to
offering employees with personal hearing protectors (Mental Health Coordinating Council 2012,
p.9). Contrary, if the early practical risk management is not effective in eliminating the risk, the
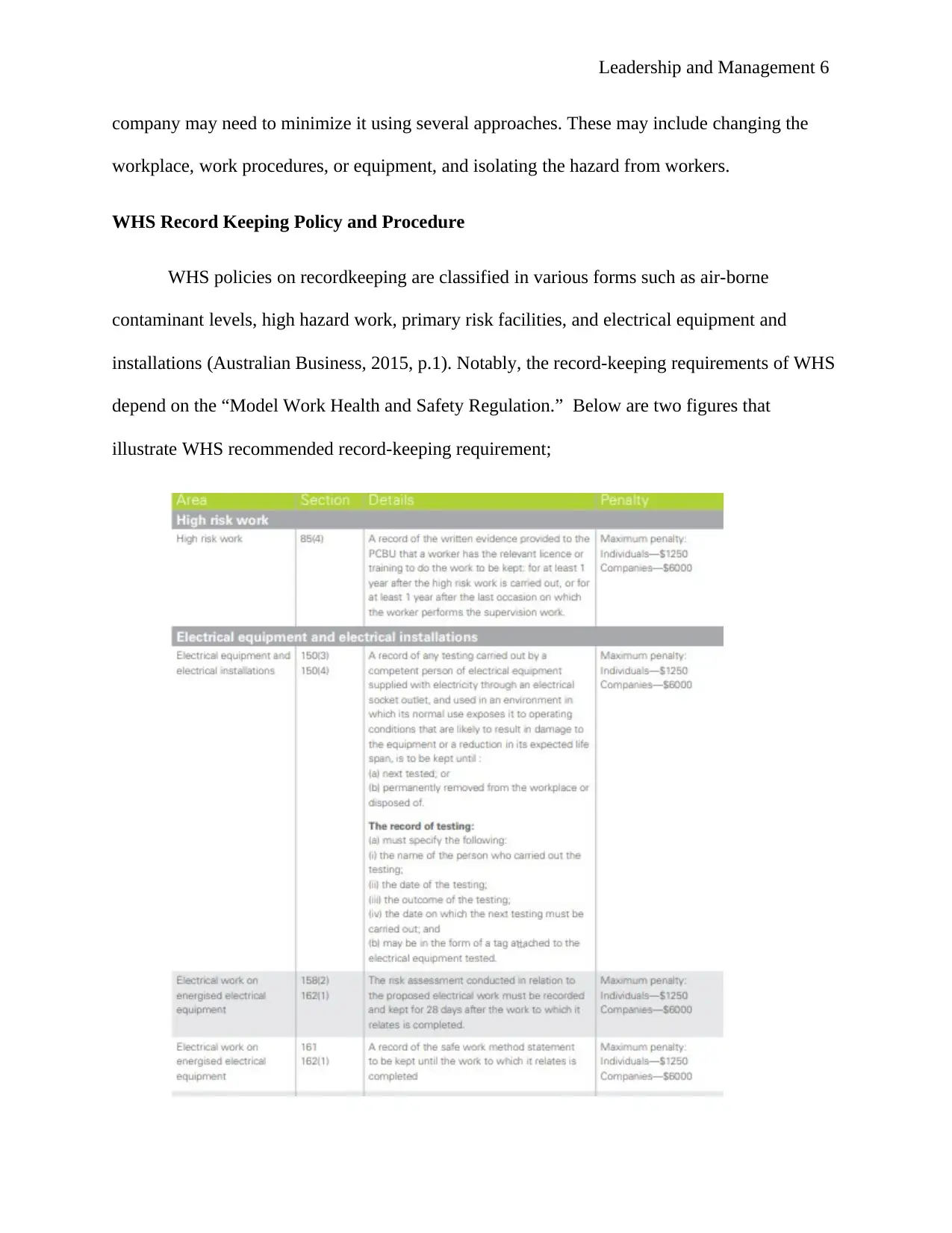
Leadership and Management 6
company may need to minimize it using several approaches. These may include changing the
workplace, work procedures, or equipment, and isolating the hazard from workers.
WHS Record Keeping Policy and Procedure
WHS policies on recordkeeping are classified in various forms such as air-borne
contaminant levels, high hazard work, primary risk facilities, and electrical equipment and
installations (Australian Business, 2015, p.1). Notably, the record-keeping requirements of WHS
depend on the “Model Work Health and Safety Regulation.” Below are two figures that
illustrate WHS recommended record-keeping requirement;
company may need to minimize it using several approaches. These may include changing the
workplace, work procedures, or equipment, and isolating the hazard from workers.
WHS Record Keeping Policy and Procedure
WHS policies on recordkeeping are classified in various forms such as air-borne
contaminant levels, high hazard work, primary risk facilities, and electrical equipment and
installations (Australian Business, 2015, p.1). Notably, the record-keeping requirements of WHS
depend on the “Model Work Health and Safety Regulation.” Below are two figures that
illustrate WHS recommended record-keeping requirement;
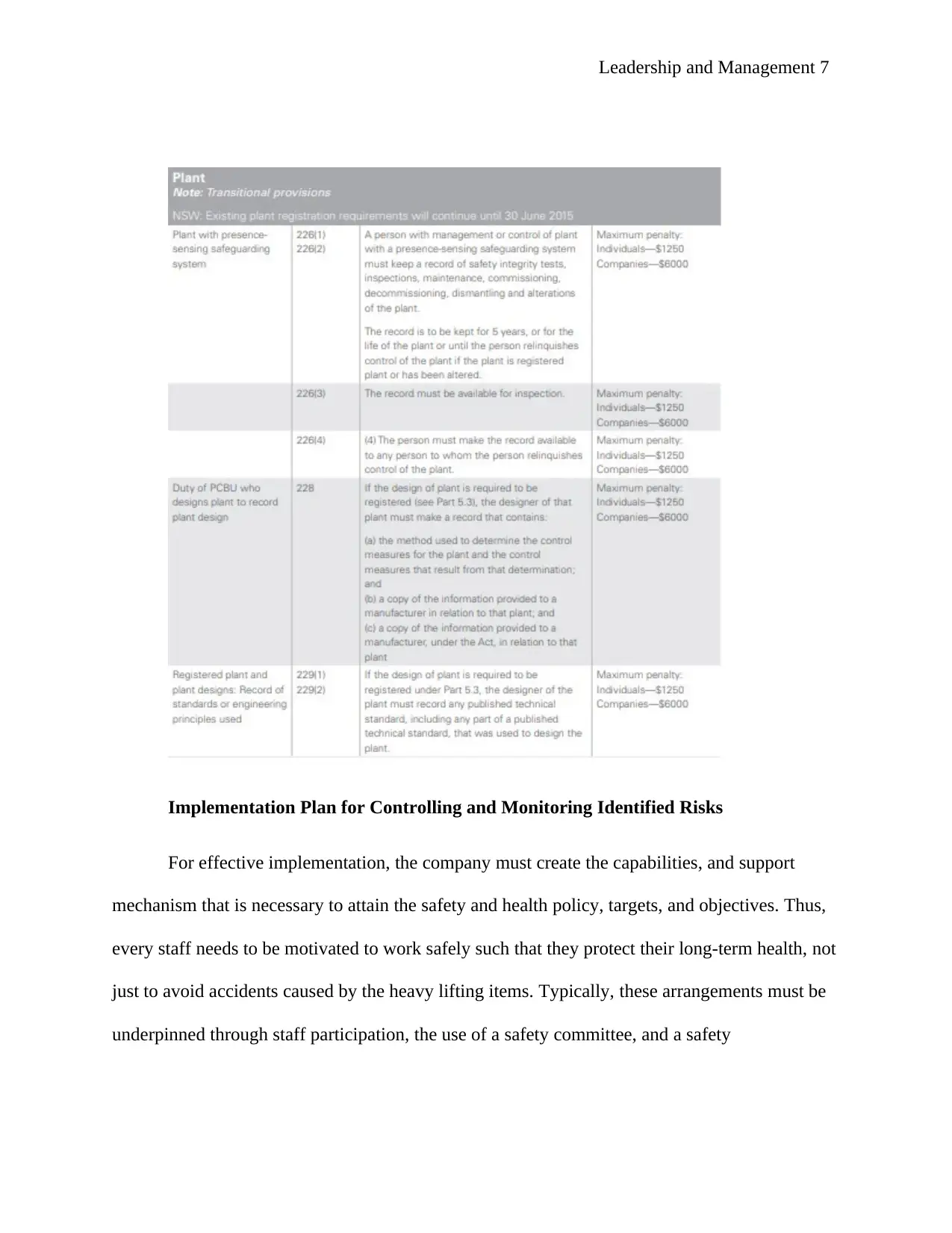
Leadership and Management 7
Implementation Plan for Controlling and Monitoring Identified Risks
For effective implementation, the company must create the capabilities, and support
mechanism that is necessary to attain the safety and health policy, targets, and objectives. Thus,
every staff needs to be motivated to work safely such that they protect their long-term health, not
just to avoid accidents caused by the heavy lifting items. Typically, these arrangements must be
underpinned through staff participation, the use of a safety committee, and a safety
Implementation Plan for Controlling and Monitoring Identified Risks
For effective implementation, the company must create the capabilities, and support
mechanism that is necessary to attain the safety and health policy, targets, and objectives. Thus,
every staff needs to be motivated to work safely such that they protect their long-term health, not
just to avoid accidents caused by the heavy lifting items. Typically, these arrangements must be
underpinned through staff participation, the use of a safety committee, and a safety
Paraphrase This Document
Need a fresh take? Get an instant paraphrase of this document with our AI Paraphraser
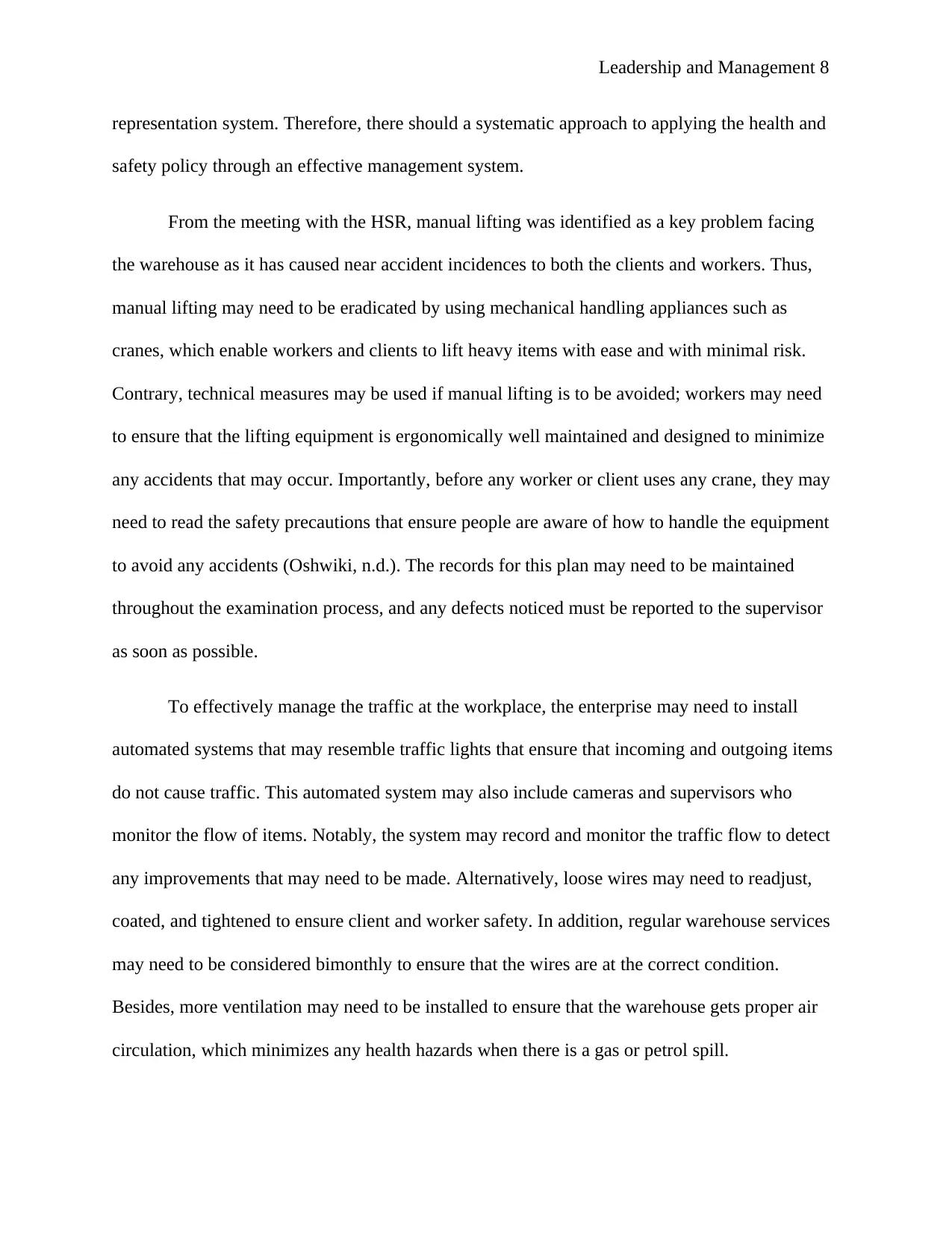
Leadership and Management 8
representation system. Therefore, there should a systematic approach to applying the health and
safety policy through an effective management system.
From the meeting with the HSR, manual lifting was identified as a key problem facing
the warehouse as it has caused near accident incidences to both the clients and workers. Thus,
manual lifting may need to be eradicated by using mechanical handling appliances such as
cranes, which enable workers and clients to lift heavy items with ease and with minimal risk.
Contrary, technical measures may be used if manual lifting is to be avoided; workers may need
to ensure that the lifting equipment is ergonomically well maintained and designed to minimize
any accidents that may occur. Importantly, before any worker or client uses any crane, they may
need to read the safety precautions that ensure people are aware of how to handle the equipment
to avoid any accidents (Oshwiki, n.d.). The records for this plan may need to be maintained
throughout the examination process, and any defects noticed must be reported to the supervisor
as soon as possible.
To effectively manage the traffic at the workplace, the enterprise may need to install
automated systems that may resemble traffic lights that ensure that incoming and outgoing items
do not cause traffic. This automated system may also include cameras and supervisors who
monitor the flow of items. Notably, the system may record and monitor the traffic flow to detect
any improvements that may need to be made. Alternatively, loose wires may need to readjust,
coated, and tightened to ensure client and worker safety. In addition, regular warehouse services
may need to be considered bimonthly to ensure that the wires are at the correct condition.
Besides, more ventilation may need to be installed to ensure that the warehouse gets proper air
circulation, which minimizes any health hazards when there is a gas or petrol spill.
representation system. Therefore, there should a systematic approach to applying the health and
safety policy through an effective management system.
From the meeting with the HSR, manual lifting was identified as a key problem facing
the warehouse as it has caused near accident incidences to both the clients and workers. Thus,
manual lifting may need to be eradicated by using mechanical handling appliances such as
cranes, which enable workers and clients to lift heavy items with ease and with minimal risk.
Contrary, technical measures may be used if manual lifting is to be avoided; workers may need
to ensure that the lifting equipment is ergonomically well maintained and designed to minimize
any accidents that may occur. Importantly, before any worker or client uses any crane, they may
need to read the safety precautions that ensure people are aware of how to handle the equipment
to avoid any accidents (Oshwiki, n.d.). The records for this plan may need to be maintained
throughout the examination process, and any defects noticed must be reported to the supervisor
as soon as possible.
To effectively manage the traffic at the workplace, the enterprise may need to install
automated systems that may resemble traffic lights that ensure that incoming and outgoing items
do not cause traffic. This automated system may also include cameras and supervisors who
monitor the flow of items. Notably, the system may record and monitor the traffic flow to detect
any improvements that may need to be made. Alternatively, loose wires may need to readjust,
coated, and tightened to ensure client and worker safety. In addition, regular warehouse services
may need to be considered bimonthly to ensure that the wires are at the correct condition.
Besides, more ventilation may need to be installed to ensure that the warehouse gets proper air
circulation, which minimizes any health hazards when there is a gas or petrol spill.
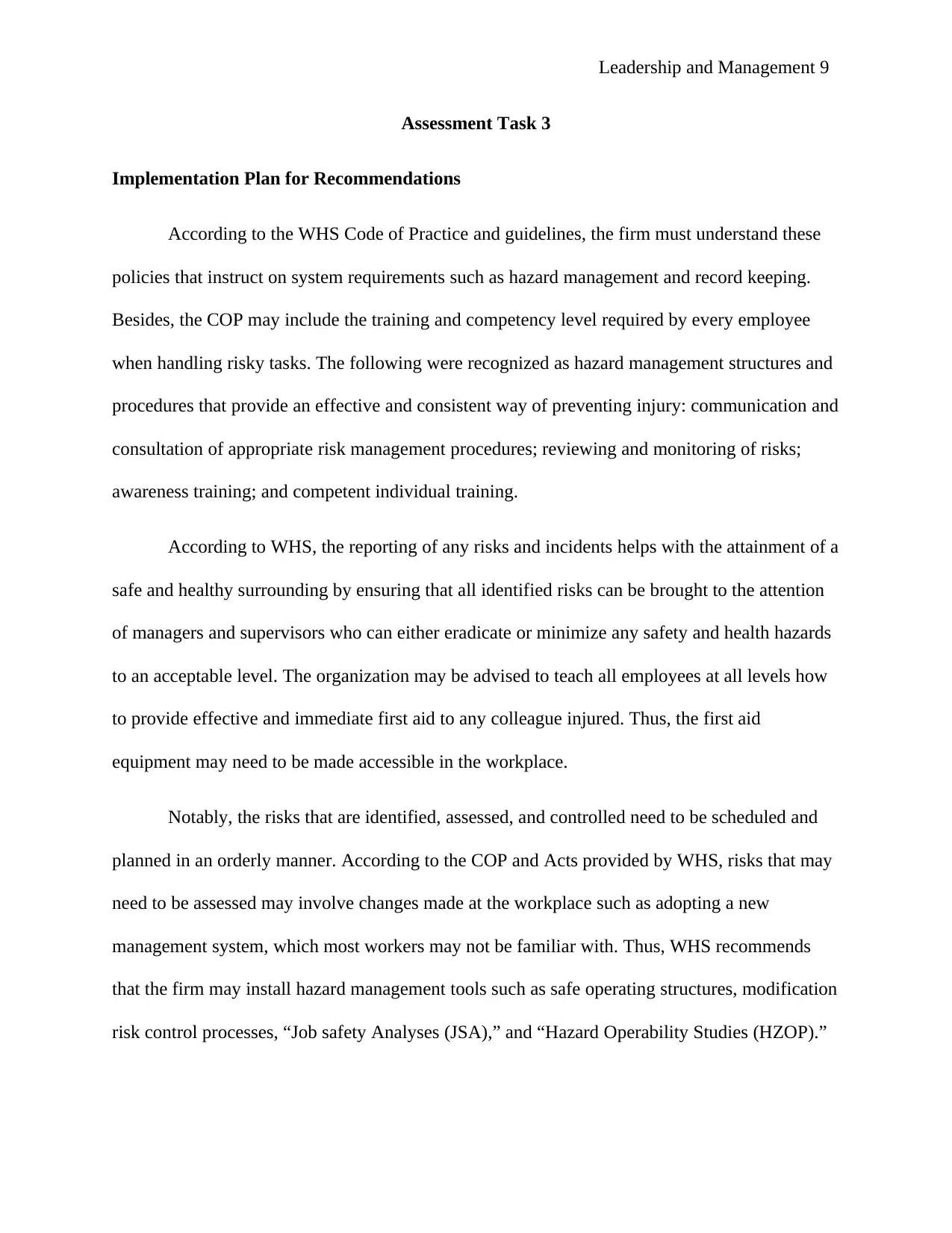
Leadership and Management 9
Assessment Task 3
Implementation Plan for Recommendations
According to the WHS Code of Practice and guidelines, the firm must understand these
policies that instruct on system requirements such as hazard management and record keeping.
Besides, the COP may include the training and competency level required by every employee
when handling risky tasks. The following were recognized as hazard management structures and
procedures that provide an effective and consistent way of preventing injury: communication and
consultation of appropriate risk management procedures; reviewing and monitoring of risks;
awareness training; and competent individual training.
According to WHS, the reporting of any risks and incidents helps with the attainment of a
safe and healthy surrounding by ensuring that all identified risks can be brought to the attention
of managers and supervisors who can either eradicate or minimize any safety and health hazards
to an acceptable level. The organization may be advised to teach all employees at all levels how
to provide effective and immediate first aid to any colleague injured. Thus, the first aid
equipment may need to be made accessible in the workplace.
Notably, the risks that are identified, assessed, and controlled need to be scheduled and
planned in an orderly manner. According to the COP and Acts provided by WHS, risks that may
need to be assessed may involve changes made at the workplace such as adopting a new
management system, which most workers may not be familiar with. Thus, WHS recommends
that the firm may install hazard management tools such as safe operating structures, modification
risk control processes, “Job safety Analyses (JSA),” and “Hazard Operability Studies (HZOP).”
Assessment Task 3
Implementation Plan for Recommendations
According to the WHS Code of Practice and guidelines, the firm must understand these
policies that instruct on system requirements such as hazard management and record keeping.
Besides, the COP may include the training and competency level required by every employee
when handling risky tasks. The following were recognized as hazard management structures and
procedures that provide an effective and consistent way of preventing injury: communication and
consultation of appropriate risk management procedures; reviewing and monitoring of risks;
awareness training; and competent individual training.
According to WHS, the reporting of any risks and incidents helps with the attainment of a
safe and healthy surrounding by ensuring that all identified risks can be brought to the attention
of managers and supervisors who can either eradicate or minimize any safety and health hazards
to an acceptable level. The organization may be advised to teach all employees at all levels how
to provide effective and immediate first aid to any colleague injured. Thus, the first aid
equipment may need to be made accessible in the workplace.
Notably, the risks that are identified, assessed, and controlled need to be scheduled and
planned in an orderly manner. According to the COP and Acts provided by WHS, risks that may
need to be assessed may involve changes made at the workplace such as adopting a new
management system, which most workers may not be familiar with. Thus, WHS recommends
that the firm may install hazard management tools such as safe operating structures, modification
risk control processes, “Job safety Analyses (JSA),” and “Hazard Operability Studies (HZOP).”
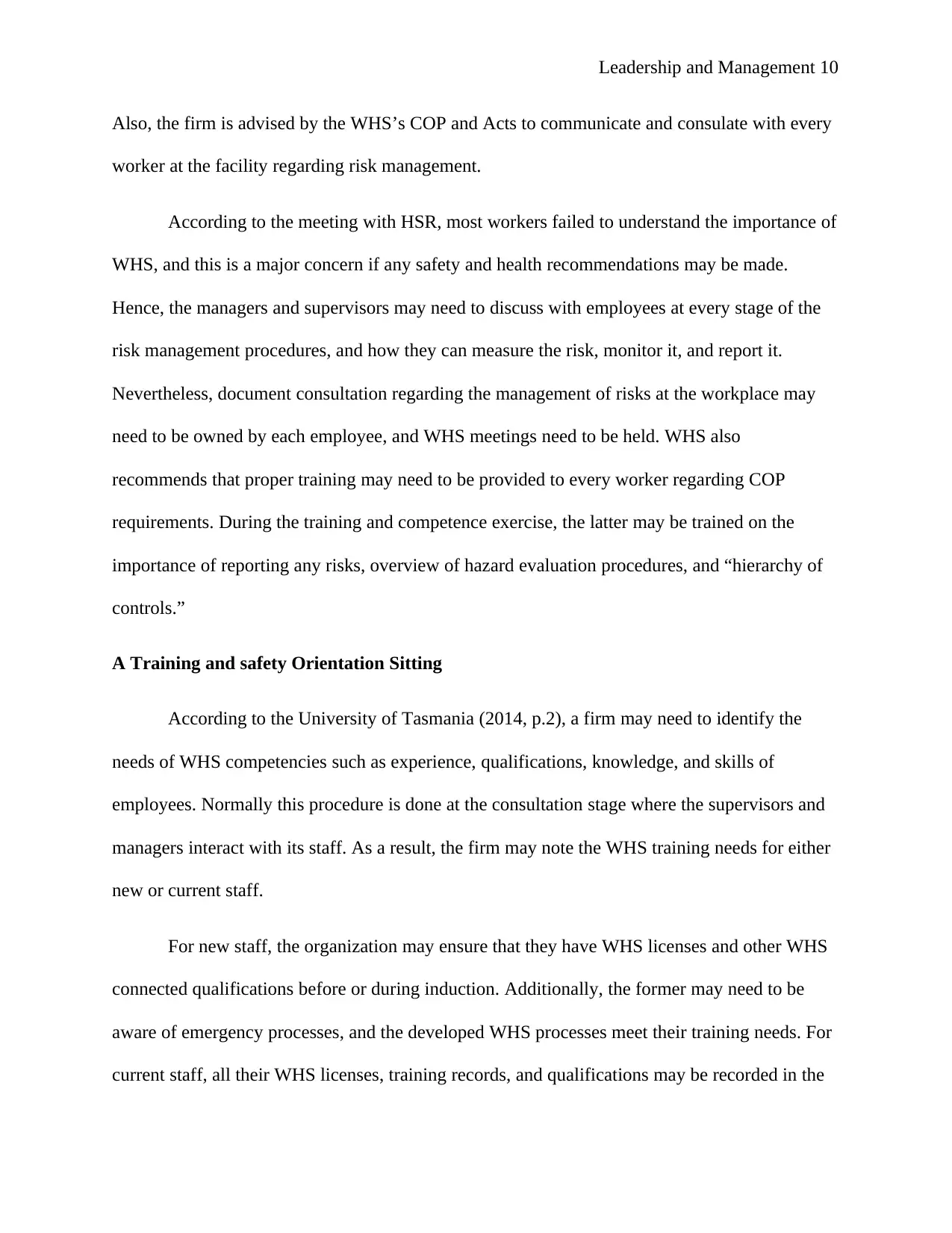
Leadership and Management 10
Also, the firm is advised by the WHS’s COP and Acts to communicate and consulate with every
worker at the facility regarding risk management.
According to the meeting with HSR, most workers failed to understand the importance of
WHS, and this is a major concern if any safety and health recommendations may be made.
Hence, the managers and supervisors may need to discuss with employees at every stage of the
risk management procedures, and how they can measure the risk, monitor it, and report it.
Nevertheless, document consultation regarding the management of risks at the workplace may
need to be owned by each employee, and WHS meetings need to be held. WHS also
recommends that proper training may need to be provided to every worker regarding COP
requirements. During the training and competence exercise, the latter may be trained on the
importance of reporting any risks, overview of hazard evaluation procedures, and “hierarchy of
controls.”
A Training and safety Orientation Sitting
According to the University of Tasmania (2014, p.2), a firm may need to identify the
needs of WHS competencies such as experience, qualifications, knowledge, and skills of
employees. Normally this procedure is done at the consultation stage where the supervisors and
managers interact with its staff. As a result, the firm may note the WHS training needs for either
new or current staff.
For new staff, the organization may ensure that they have WHS licenses and other WHS
connected qualifications before or during induction. Additionally, the former may need to be
aware of emergency processes, and the developed WHS processes meet their training needs. For
current staff, all their WHS licenses, training records, and qualifications may be recorded in the
Also, the firm is advised by the WHS’s COP and Acts to communicate and consulate with every
worker at the facility regarding risk management.
According to the meeting with HSR, most workers failed to understand the importance of
WHS, and this is a major concern if any safety and health recommendations may be made.
Hence, the managers and supervisors may need to discuss with employees at every stage of the
risk management procedures, and how they can measure the risk, monitor it, and report it.
Nevertheless, document consultation regarding the management of risks at the workplace may
need to be owned by each employee, and WHS meetings need to be held. WHS also
recommends that proper training may need to be provided to every worker regarding COP
requirements. During the training and competence exercise, the latter may be trained on the
importance of reporting any risks, overview of hazard evaluation procedures, and “hierarchy of
controls.”
A Training and safety Orientation Sitting
According to the University of Tasmania (2014, p.2), a firm may need to identify the
needs of WHS competencies such as experience, qualifications, knowledge, and skills of
employees. Normally this procedure is done at the consultation stage where the supervisors and
managers interact with its staff. As a result, the firm may note the WHS training needs for either
new or current staff.
For new staff, the organization may ensure that they have WHS licenses and other WHS
connected qualifications before or during induction. Additionally, the former may need to be
aware of emergency processes, and the developed WHS processes meet their training needs. For
current staff, all their WHS licenses, training records, and qualifications may be recorded in the
Secure Best Marks with AI Grader
Need help grading? Try our AI Grader for instant feedback on your assignments.
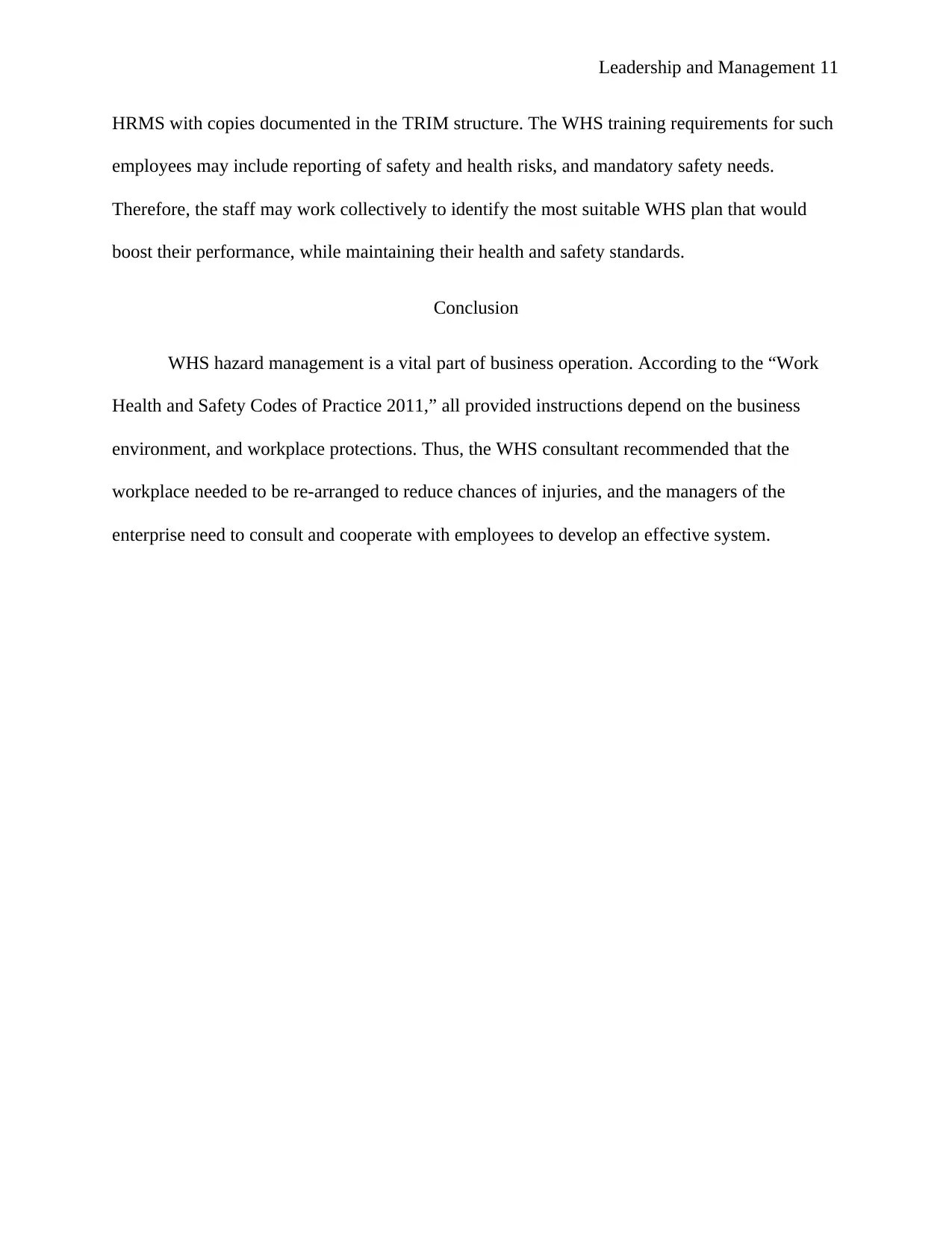
Leadership and Management 11
HRMS with copies documented in the TRIM structure. The WHS training requirements for such
employees may include reporting of safety and health risks, and mandatory safety needs.
Therefore, the staff may work collectively to identify the most suitable WHS plan that would
boost their performance, while maintaining their health and safety standards.
Conclusion
WHS hazard management is a vital part of business operation. According to the “Work
Health and Safety Codes of Practice 2011,” all provided instructions depend on the business
environment, and workplace protections. Thus, the WHS consultant recommended that the
workplace needed to be re-arranged to reduce chances of injuries, and the managers of the
enterprise need to consult and cooperate with employees to develop an effective system.
HRMS with copies documented in the TRIM structure. The WHS training requirements for such
employees may include reporting of safety and health risks, and mandatory safety needs.
Therefore, the staff may work collectively to identify the most suitable WHS plan that would
boost their performance, while maintaining their health and safety standards.
Conclusion
WHS hazard management is a vital part of business operation. According to the “Work
Health and Safety Codes of Practice 2011,” all provided instructions depend on the business
environment, and workplace protections. Thus, the WHS consultant recommended that the
workplace needed to be re-arranged to reduce chances of injuries, and the managers of the
enterprise need to consult and cooperate with employees to develop an effective system.
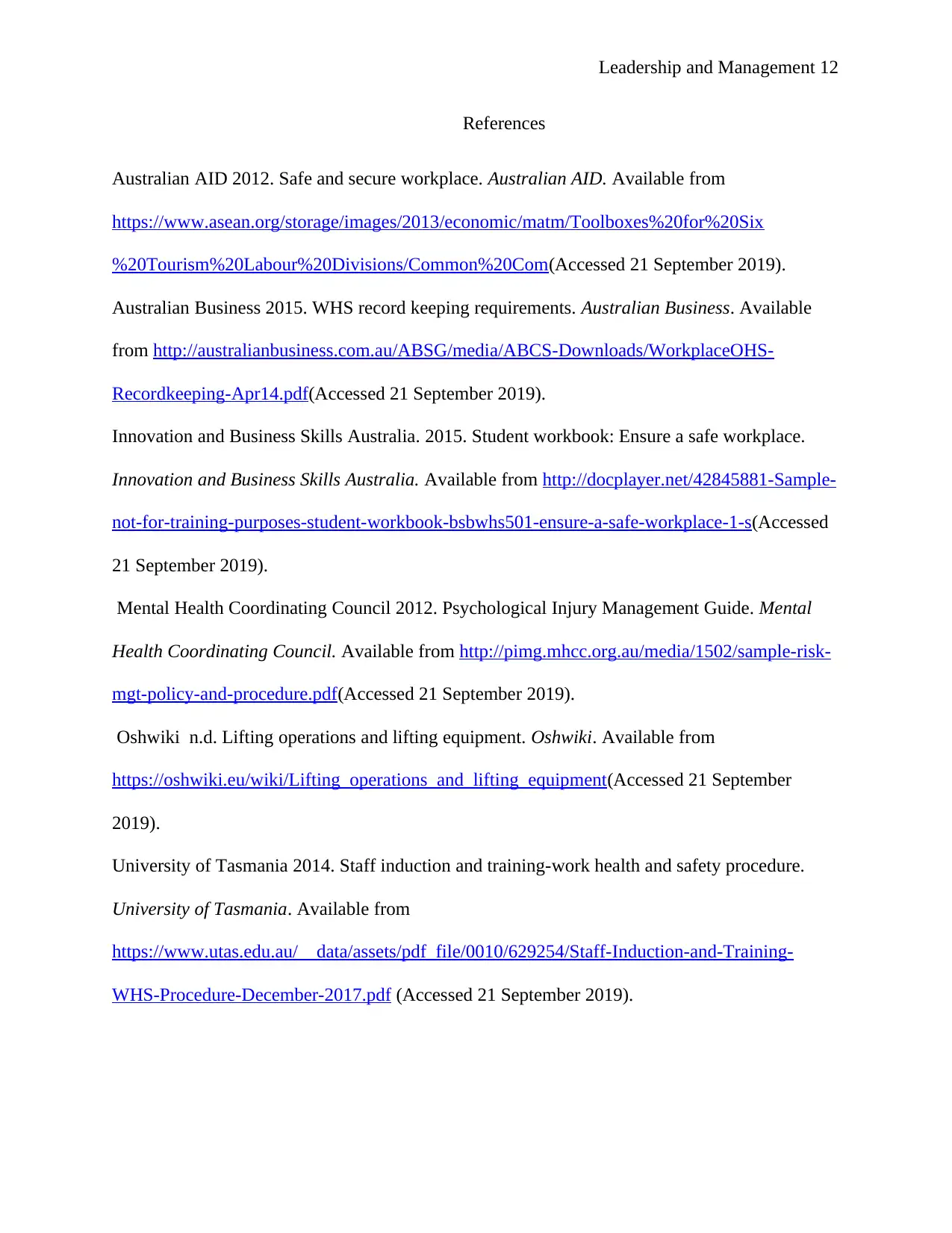
Leadership and Management 12
References
Australian AID 2012. Safe and secure workplace. Australian AID. Available from
https://www.asean.org/storage/images/2013/economic/matm/Toolboxes%20for%20Six
%20Tourism%20Labour%20Divisions/Common%20Com(Accessed 21 September 2019).
Australian Business 2015. WHS record keeping requirements. Australian Business. Available
from http://australianbusiness.com.au/ABSG/media/ABCS-Downloads/WorkplaceOHS-
Recordkeeping-Apr14.pdf(Accessed 21 September 2019).
Innovation and Business Skills Australia. 2015. Student workbook: Ensure a safe workplace.
Innovation and Business Skills Australia. Available from http://docplayer.net/42845881-Sample-
not-for-training-purposes-student-workbook-bsbwhs501-ensure-a-safe-workplace-1-s(Accessed
21 September 2019).
Mental Health Coordinating Council 2012. Psychological Injury Management Guide. Mental
Health Coordinating Council. Available from http://pimg.mhcc.org.au/media/1502/sample-risk-
mgt-policy-and-procedure.pdf(Accessed 21 September 2019).
Oshwiki n.d. Lifting operations and lifting equipment. Oshwiki. Available from
https://oshwiki.eu/wiki/Lifting_operations_and_lifting_equipment(Accessed 21 September
2019).
University of Tasmania 2014. Staff induction and training-work health and safety procedure.
University of Tasmania. Available from
https://www.utas.edu.au/__data/assets/pdf_file/0010/629254/Staff-Induction-and-Training-
WHS-Procedure-December-2017.pdf (Accessed 21 September 2019).
References
Australian AID 2012. Safe and secure workplace. Australian AID. Available from
https://www.asean.org/storage/images/2013/economic/matm/Toolboxes%20for%20Six
%20Tourism%20Labour%20Divisions/Common%20Com(Accessed 21 September 2019).
Australian Business 2015. WHS record keeping requirements. Australian Business. Available
from http://australianbusiness.com.au/ABSG/media/ABCS-Downloads/WorkplaceOHS-
Recordkeeping-Apr14.pdf(Accessed 21 September 2019).
Innovation and Business Skills Australia. 2015. Student workbook: Ensure a safe workplace.
Innovation and Business Skills Australia. Available from http://docplayer.net/42845881-Sample-
not-for-training-purposes-student-workbook-bsbwhs501-ensure-a-safe-workplace-1-s(Accessed
21 September 2019).
Mental Health Coordinating Council 2012. Psychological Injury Management Guide. Mental
Health Coordinating Council. Available from http://pimg.mhcc.org.au/media/1502/sample-risk-
mgt-policy-and-procedure.pdf(Accessed 21 September 2019).
Oshwiki n.d. Lifting operations and lifting equipment. Oshwiki. Available from
https://oshwiki.eu/wiki/Lifting_operations_and_lifting_equipment(Accessed 21 September
2019).
University of Tasmania 2014. Staff induction and training-work health and safety procedure.
University of Tasmania. Available from
https://www.utas.edu.au/__data/assets/pdf_file/0010/629254/Staff-Induction-and-Training-
WHS-Procedure-December-2017.pdf (Accessed 21 September 2019).
1 out of 12
Related Documents

Your All-in-One AI-Powered Toolkit for Academic Success.
+13062052269
info@desklib.com
Available 24*7 on WhatsApp / Email
Unlock your academic potential
© 2024 | Zucol Services PVT LTD | All rights reserved.