Develop, Implement & Maintain WHS Management System Report - Pitstop
VerifiedAdded on 2022/08/18
|12
|3617
|16
Report
AI Summary
This report analyzes the current WHS management practices of Pitstop Pty Ltd, a company facing workplace safety challenges. The report begins by outlining the company's background and the issues it faces, including fuel spills, fires, and employee fatigue, which highlight the need for an improved WHS management system. It then addresses the responsibilities of various stakeholders, including employees, managers, and the management team, and proposes solutions such as continuous training, adherence to regulations, and the implementation of safety measures like fire extinguishers and first aid kits. The report includes a proposed WHS policy, addressing work-life balance, break times, and harassment, and also suggests changes to address issues like lack of resources, employee trust, and training gaps. The report then delves into the objectives of the WHS plan, emphasizing hazard identification, risk assessment, and control, along with implementation strategies for a specific store location. The report concludes by emphasizing the importance of safety audits, analyzing key performance indicators, and comparing post-implementation results to pre-implementation data to assess the effectiveness of the implemented strategies.
Contribute Materials
Your contribution can guide someone’s learning journey. Share your
documents today.
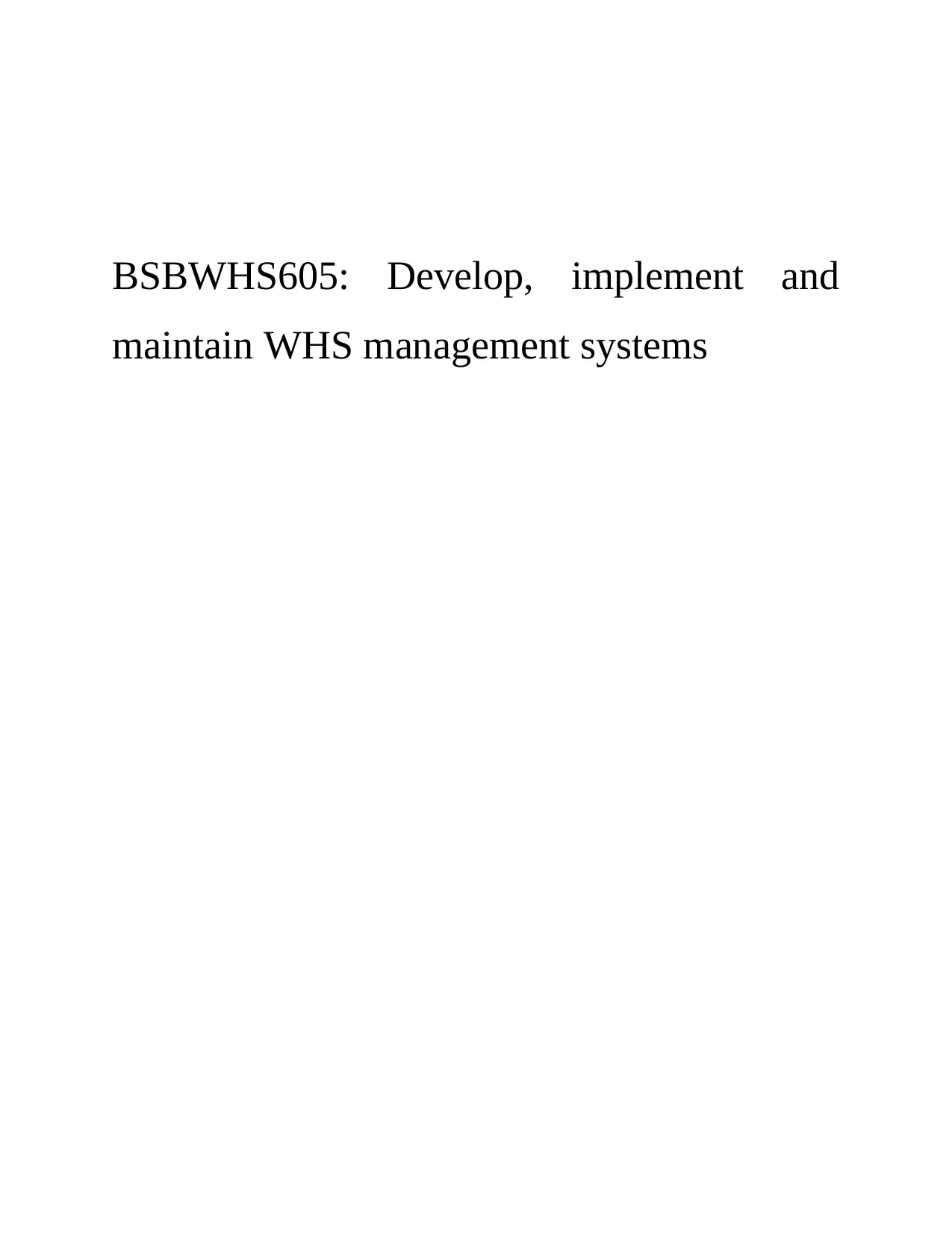
BSBWHS605: Develop, implement and
maintain WHS management systems
maintain WHS management systems
Secure Best Marks with AI Grader
Need help grading? Try our AI Grader for instant feedback on your assignments.
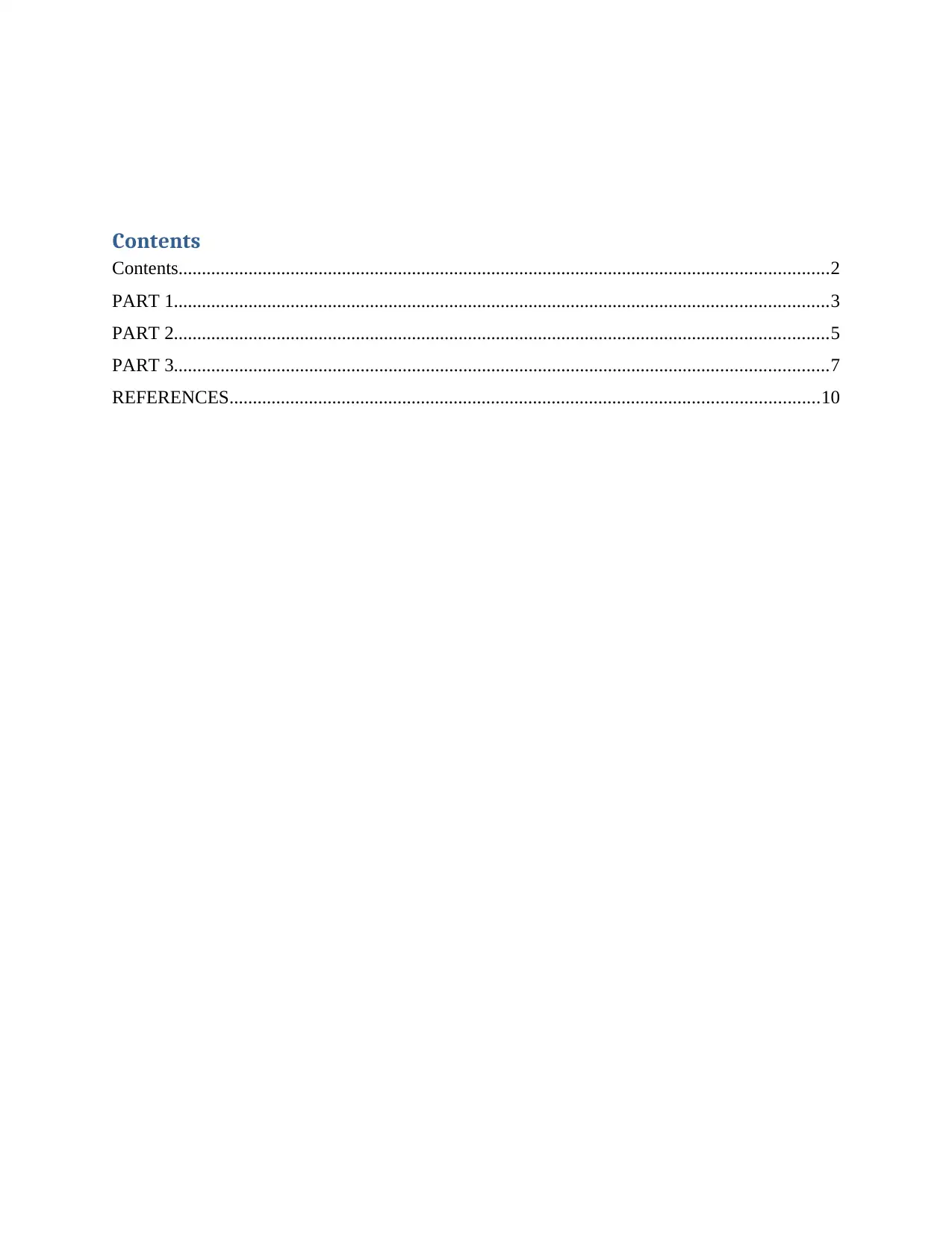
Contents
Contents...........................................................................................................................................2
PART 1............................................................................................................................................3
PART 2............................................................................................................................................5
PART 3............................................................................................................................................7
REFERENCES..............................................................................................................................10
Contents...........................................................................................................................................2
PART 1............................................................................................................................................3
PART 2............................................................................................................................................5
PART 3............................................................................................................................................7
REFERENCES..............................................................................................................................10
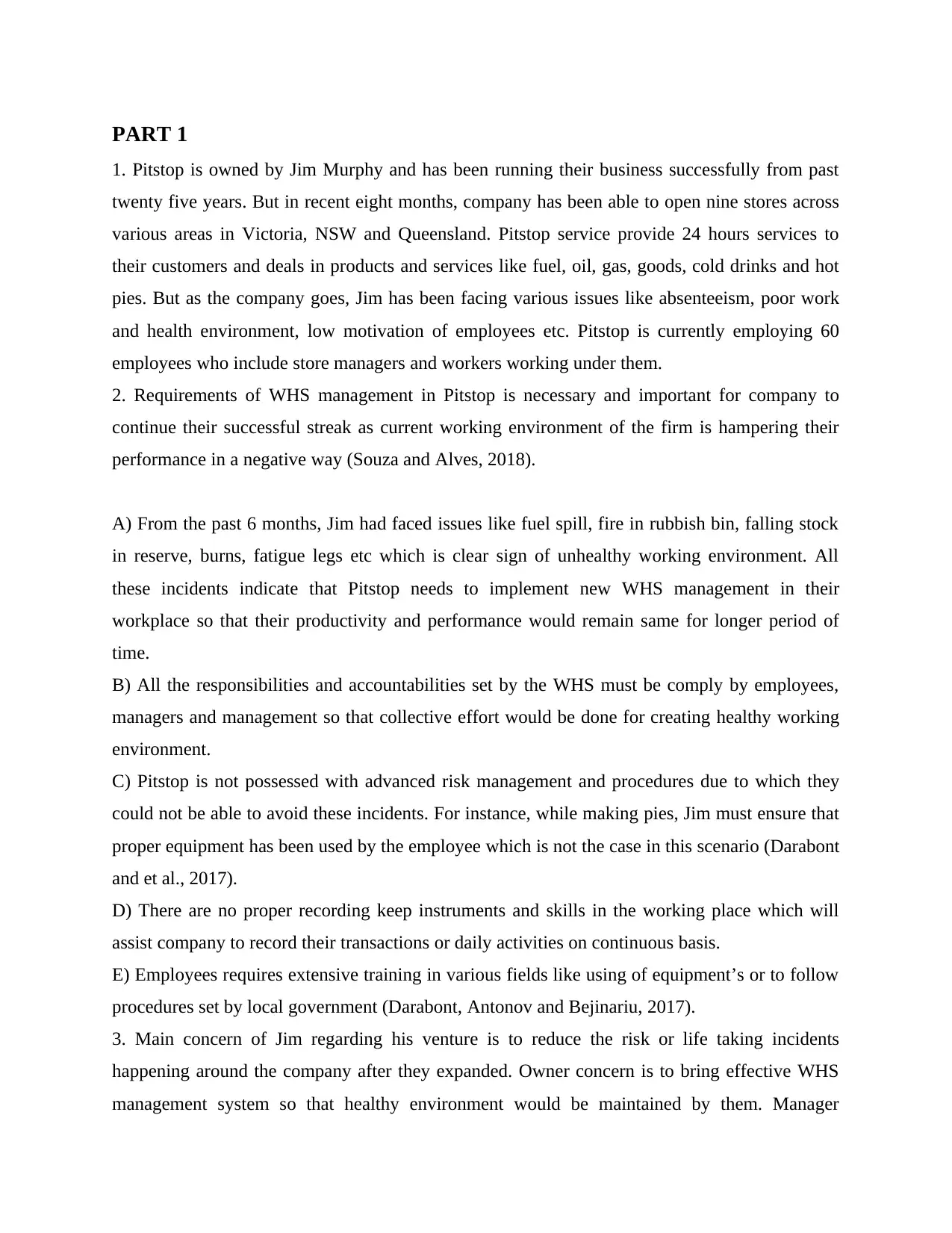
PART 1
1. Pitstop is owned by Jim Murphy and has been running their business successfully from past
twenty five years. But in recent eight months, company has been able to open nine stores across
various areas in Victoria, NSW and Queensland. Pitstop service provide 24 hours services to
their customers and deals in products and services like fuel, oil, gas, goods, cold drinks and hot
pies. But as the company goes, Jim has been facing various issues like absenteeism, poor work
and health environment, low motivation of employees etc. Pitstop is currently employing 60
employees who include store managers and workers working under them.
2. Requirements of WHS management in Pitstop is necessary and important for company to
continue their successful streak as current working environment of the firm is hampering their
performance in a negative way (Souza and Alves, 2018).
A) From the past 6 months, Jim had faced issues like fuel spill, fire in rubbish bin, falling stock
in reserve, burns, fatigue legs etc which is clear sign of unhealthy working environment. All
these incidents indicate that Pitstop needs to implement new WHS management in their
workplace so that their productivity and performance would remain same for longer period of
time.
B) All the responsibilities and accountabilities set by the WHS must be comply by employees,
managers and management so that collective effort would be done for creating healthy working
environment.
C) Pitstop is not possessed with advanced risk management and procedures due to which they
could not be able to avoid these incidents. For instance, while making pies, Jim must ensure that
proper equipment has been used by the employee which is not the case in this scenario (Darabont
and et al., 2017).
D) There are no proper recording keep instruments and skills in the working place which will
assist company to record their transactions or daily activities on continuous basis.
E) Employees requires extensive training in various fields like using of equipment’s or to follow
procedures set by local government (Darabont, Antonov and Bejinariu, 2017).
3. Main concern of Jim regarding his venture is to reduce the risk or life taking incidents
happening around the company after they expanded. Owner concern is to bring effective WHS
management system so that healthy environment would be maintained by them. Manager
1. Pitstop is owned by Jim Murphy and has been running their business successfully from past
twenty five years. But in recent eight months, company has been able to open nine stores across
various areas in Victoria, NSW and Queensland. Pitstop service provide 24 hours services to
their customers and deals in products and services like fuel, oil, gas, goods, cold drinks and hot
pies. But as the company goes, Jim has been facing various issues like absenteeism, poor work
and health environment, low motivation of employees etc. Pitstop is currently employing 60
employees who include store managers and workers working under them.
2. Requirements of WHS management in Pitstop is necessary and important for company to
continue their successful streak as current working environment of the firm is hampering their
performance in a negative way (Souza and Alves, 2018).
A) From the past 6 months, Jim had faced issues like fuel spill, fire in rubbish bin, falling stock
in reserve, burns, fatigue legs etc which is clear sign of unhealthy working environment. All
these incidents indicate that Pitstop needs to implement new WHS management in their
workplace so that their productivity and performance would remain same for longer period of
time.
B) All the responsibilities and accountabilities set by the WHS must be comply by employees,
managers and management so that collective effort would be done for creating healthy working
environment.
C) Pitstop is not possessed with advanced risk management and procedures due to which they
could not be able to avoid these incidents. For instance, while making pies, Jim must ensure that
proper equipment has been used by the employee which is not the case in this scenario (Darabont
and et al., 2017).
D) There are no proper recording keep instruments and skills in the working place which will
assist company to record their transactions or daily activities on continuous basis.
E) Employees requires extensive training in various fields like using of equipment’s or to follow
procedures set by local government (Darabont, Antonov and Bejinariu, 2017).
3. Main concern of Jim regarding his venture is to reduce the risk or life taking incidents
happening around the company after they expanded. Owner concern is to bring effective WHS
management system so that healthy environment would be maintained by them. Manager
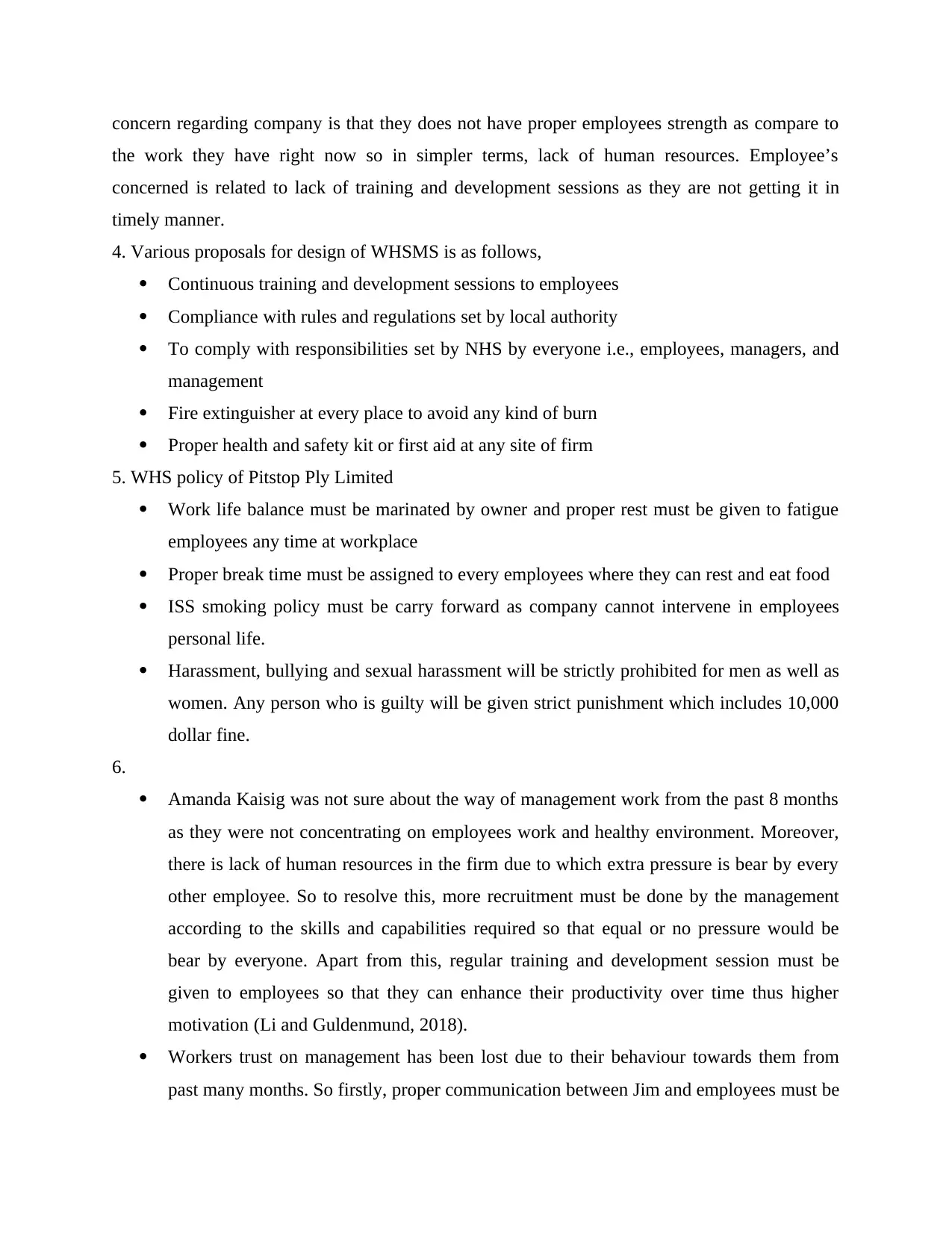
concern regarding company is that they does not have proper employees strength as compare to
the work they have right now so in simpler terms, lack of human resources. Employee’s
concerned is related to lack of training and development sessions as they are not getting it in
timely manner.
4. Various proposals for design of WHSMS is as follows,
Continuous training and development sessions to employees
Compliance with rules and regulations set by local authority
To comply with responsibilities set by NHS by everyone i.e., employees, managers, and
management
Fire extinguisher at every place to avoid any kind of burn
Proper health and safety kit or first aid at any site of firm
5. WHS policy of Pitstop Ply Limited
Work life balance must be marinated by owner and proper rest must be given to fatigue
employees any time at workplace
Proper break time must be assigned to every employees where they can rest and eat food
ISS smoking policy must be carry forward as company cannot intervene in employees
personal life.
Harassment, bullying and sexual harassment will be strictly prohibited for men as well as
women. Any person who is guilty will be given strict punishment which includes 10,000
dollar fine.
6.
Amanda Kaisig was not sure about the way of management work from the past 8 months
as they were not concentrating on employees work and healthy environment. Moreover,
there is lack of human resources in the firm due to which extra pressure is bear by every
other employee. So to resolve this, more recruitment must be done by the management
according to the skills and capabilities required so that equal or no pressure would be
bear by everyone. Apart from this, regular training and development session must be
given to employees so that they can enhance their productivity over time thus higher
motivation (Li and Guldenmund, 2018).
Workers trust on management has been lost due to their behaviour towards them from
past many months. So firstly, proper communication between Jim and employees must be
the work they have right now so in simpler terms, lack of human resources. Employee’s
concerned is related to lack of training and development sessions as they are not getting it in
timely manner.
4. Various proposals for design of WHSMS is as follows,
Continuous training and development sessions to employees
Compliance with rules and regulations set by local authority
To comply with responsibilities set by NHS by everyone i.e., employees, managers, and
management
Fire extinguisher at every place to avoid any kind of burn
Proper health and safety kit or first aid at any site of firm
5. WHS policy of Pitstop Ply Limited
Work life balance must be marinated by owner and proper rest must be given to fatigue
employees any time at workplace
Proper break time must be assigned to every employees where they can rest and eat food
ISS smoking policy must be carry forward as company cannot intervene in employees
personal life.
Harassment, bullying and sexual harassment will be strictly prohibited for men as well as
women. Any person who is guilty will be given strict punishment which includes 10,000
dollar fine.
6.
Amanda Kaisig was not sure about the way of management work from the past 8 months
as they were not concentrating on employees work and healthy environment. Moreover,
there is lack of human resources in the firm due to which extra pressure is bear by every
other employee. So to resolve this, more recruitment must be done by the management
according to the skills and capabilities required so that equal or no pressure would be
bear by everyone. Apart from this, regular training and development session must be
given to employees so that they can enhance their productivity over time thus higher
motivation (Li and Guldenmund, 2018).
Workers trust on management has been lost due to their behaviour towards them from
past many months. So firstly, proper communication between Jim and employees must be
Secure Best Marks with AI Grader
Need help grading? Try our AI Grader for instant feedback on your assignments.
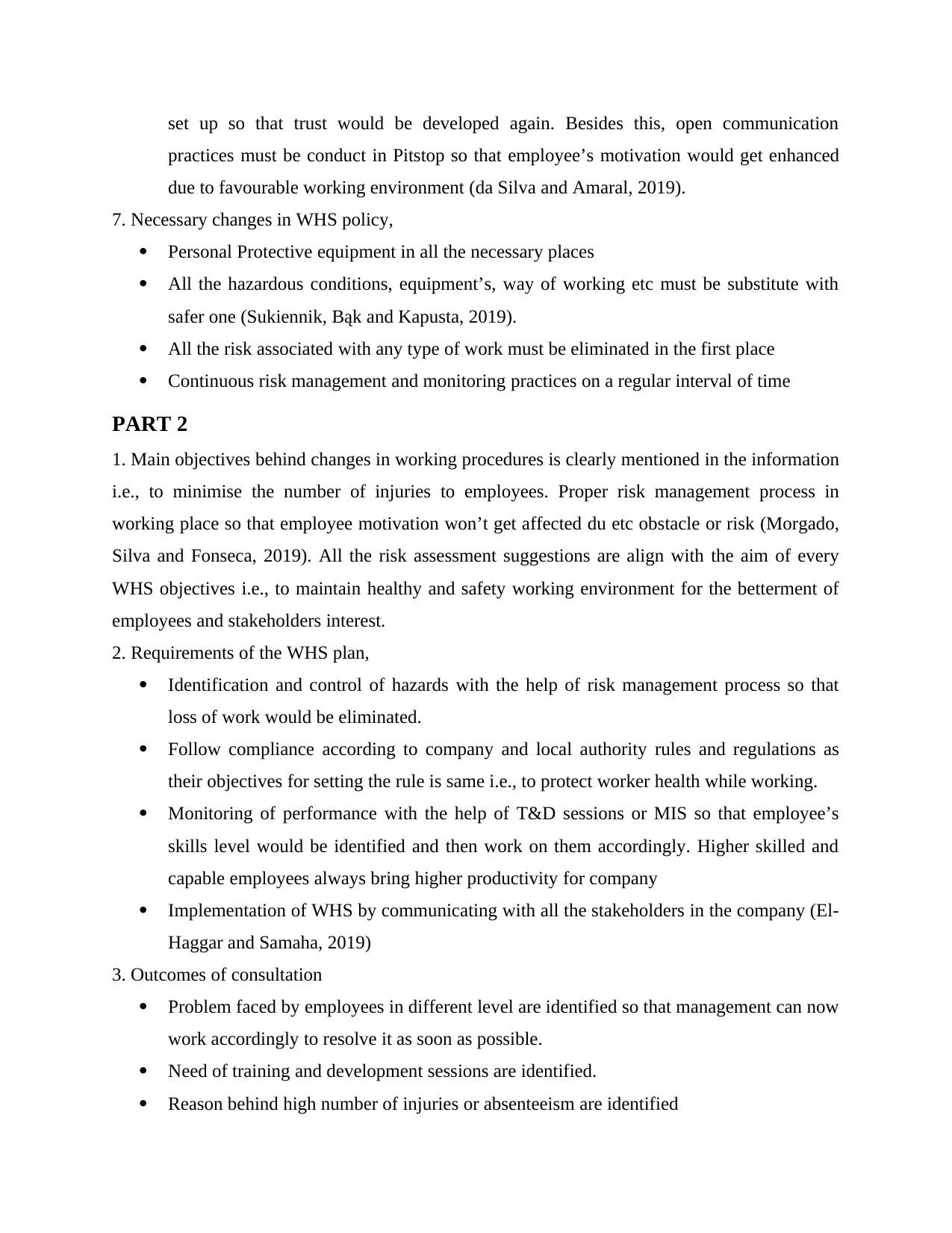
set up so that trust would be developed again. Besides this, open communication
practices must be conduct in Pitstop so that employee’s motivation would get enhanced
due to favourable working environment (da Silva and Amaral, 2019).
7. Necessary changes in WHS policy,
Personal Protective equipment in all the necessary places
All the hazardous conditions, equipment’s, way of working etc must be substitute with
safer one (Sukiennik, Bąk and Kapusta, 2019).
All the risk associated with any type of work must be eliminated in the first place
Continuous risk management and monitoring practices on a regular interval of time
PART 2
1. Main objectives behind changes in working procedures is clearly mentioned in the information
i.e., to minimise the number of injuries to employees. Proper risk management process in
working place so that employee motivation won’t get affected du etc obstacle or risk (Morgado,
Silva and Fonseca, 2019). All the risk assessment suggestions are align with the aim of every
WHS objectives i.e., to maintain healthy and safety working environment for the betterment of
employees and stakeholders interest.
2. Requirements of the WHS plan,
Identification and control of hazards with the help of risk management process so that
loss of work would be eliminated.
Follow compliance according to company and local authority rules and regulations as
their objectives for setting the rule is same i.e., to protect worker health while working.
Monitoring of performance with the help of T&D sessions or MIS so that employee’s
skills level would be identified and then work on them accordingly. Higher skilled and
capable employees always bring higher productivity for company
Implementation of WHS by communicating with all the stakeholders in the company (El-
Haggar and Samaha, 2019)
3. Outcomes of consultation
Problem faced by employees in different level are identified so that management can now
work accordingly to resolve it as soon as possible.
Need of training and development sessions are identified.
Reason behind high number of injuries or absenteeism are identified
practices must be conduct in Pitstop so that employee’s motivation would get enhanced
due to favourable working environment (da Silva and Amaral, 2019).
7. Necessary changes in WHS policy,
Personal Protective equipment in all the necessary places
All the hazardous conditions, equipment’s, way of working etc must be substitute with
safer one (Sukiennik, Bąk and Kapusta, 2019).
All the risk associated with any type of work must be eliminated in the first place
Continuous risk management and monitoring practices on a regular interval of time
PART 2
1. Main objectives behind changes in working procedures is clearly mentioned in the information
i.e., to minimise the number of injuries to employees. Proper risk management process in
working place so that employee motivation won’t get affected du etc obstacle or risk (Morgado,
Silva and Fonseca, 2019). All the risk assessment suggestions are align with the aim of every
WHS objectives i.e., to maintain healthy and safety working environment for the betterment of
employees and stakeholders interest.
2. Requirements of the WHS plan,
Identification and control of hazards with the help of risk management process so that
loss of work would be eliminated.
Follow compliance according to company and local authority rules and regulations as
their objectives for setting the rule is same i.e., to protect worker health while working.
Monitoring of performance with the help of T&D sessions or MIS so that employee’s
skills level would be identified and then work on them accordingly. Higher skilled and
capable employees always bring higher productivity for company
Implementation of WHS by communicating with all the stakeholders in the company (El-
Haggar and Samaha, 2019)
3. Outcomes of consultation
Problem faced by employees in different level are identified so that management can now
work accordingly to resolve it as soon as possible.
Need of training and development sessions are identified.
Reason behind high number of injuries or absenteeism are identified
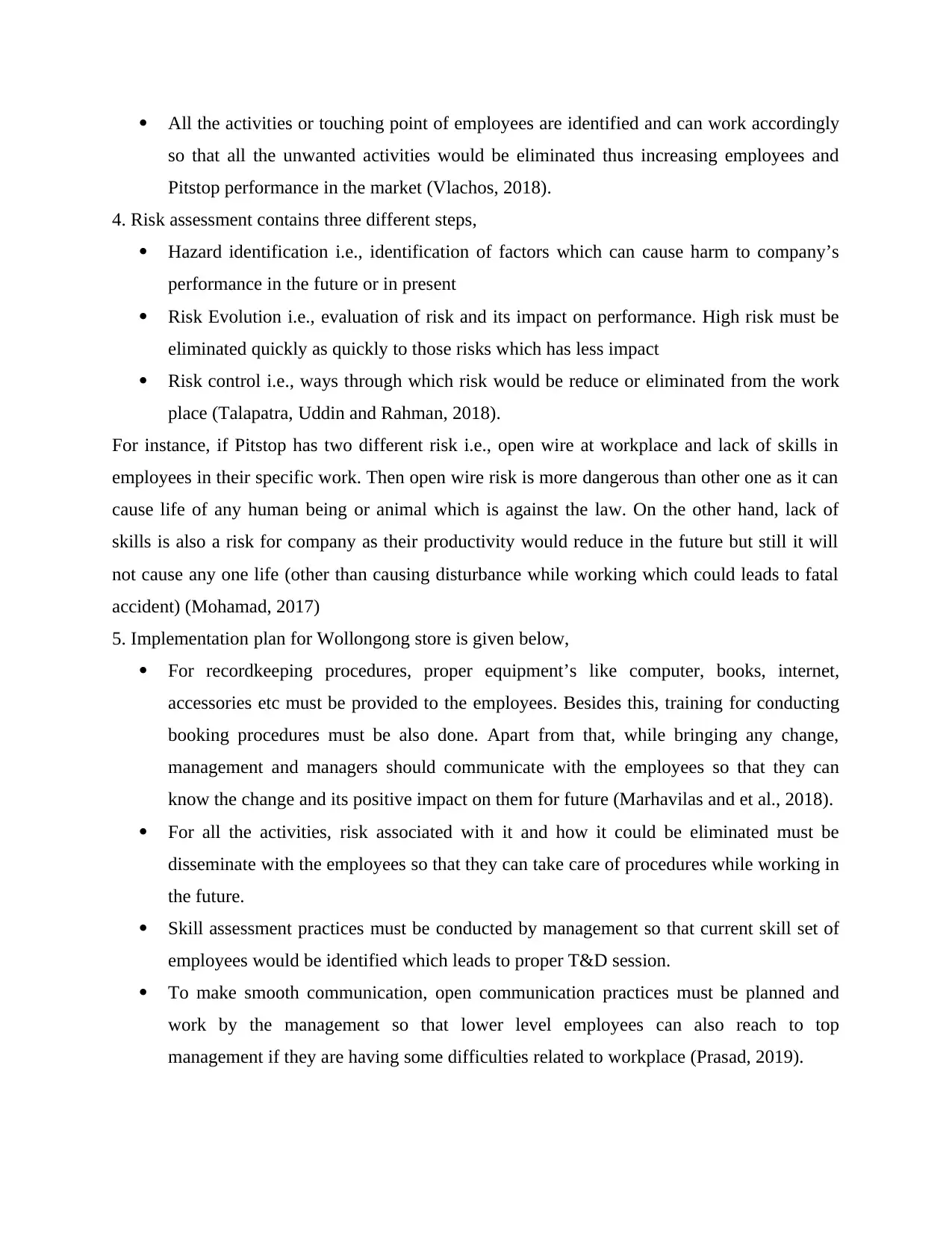
All the activities or touching point of employees are identified and can work accordingly
so that all the unwanted activities would be eliminated thus increasing employees and
Pitstop performance in the market (Vlachos, 2018).
4. Risk assessment contains three different steps,
Hazard identification i.e., identification of factors which can cause harm to company’s
performance in the future or in present
Risk Evolution i.e., evaluation of risk and its impact on performance. High risk must be
eliminated quickly as quickly to those risks which has less impact
Risk control i.e., ways through which risk would be reduce or eliminated from the work
place (Talapatra, Uddin and Rahman, 2018).
For instance, if Pitstop has two different risk i.e., open wire at workplace and lack of skills in
employees in their specific work. Then open wire risk is more dangerous than other one as it can
cause life of any human being or animal which is against the law. On the other hand, lack of
skills is also a risk for company as their productivity would reduce in the future but still it will
not cause any one life (other than causing disturbance while working which could leads to fatal
accident) (Mohamad, 2017)
5. Implementation plan for Wollongong store is given below,
For recordkeeping procedures, proper equipment’s like computer, books, internet,
accessories etc must be provided to the employees. Besides this, training for conducting
booking procedures must be also done. Apart from that, while bringing any change,
management and managers should communicate with the employees so that they can
know the change and its positive impact on them for future (Marhavilas and et al., 2018).
For all the activities, risk associated with it and how it could be eliminated must be
disseminate with the employees so that they can take care of procedures while working in
the future.
Skill assessment practices must be conducted by management so that current skill set of
employees would be identified which leads to proper T&D session.
To make smooth communication, open communication practices must be planned and
work by the management so that lower level employees can also reach to top
management if they are having some difficulties related to workplace (Prasad, 2019).
so that all the unwanted activities would be eliminated thus increasing employees and
Pitstop performance in the market (Vlachos, 2018).
4. Risk assessment contains three different steps,
Hazard identification i.e., identification of factors which can cause harm to company’s
performance in the future or in present
Risk Evolution i.e., evaluation of risk and its impact on performance. High risk must be
eliminated quickly as quickly to those risks which has less impact
Risk control i.e., ways through which risk would be reduce or eliminated from the work
place (Talapatra, Uddin and Rahman, 2018).
For instance, if Pitstop has two different risk i.e., open wire at workplace and lack of skills in
employees in their specific work. Then open wire risk is more dangerous than other one as it can
cause life of any human being or animal which is against the law. On the other hand, lack of
skills is also a risk for company as their productivity would reduce in the future but still it will
not cause any one life (other than causing disturbance while working which could leads to fatal
accident) (Mohamad, 2017)
5. Implementation plan for Wollongong store is given below,
For recordkeeping procedures, proper equipment’s like computer, books, internet,
accessories etc must be provided to the employees. Besides this, training for conducting
booking procedures must be also done. Apart from that, while bringing any change,
management and managers should communicate with the employees so that they can
know the change and its positive impact on them for future (Marhavilas and et al., 2018).
For all the activities, risk associated with it and how it could be eliminated must be
disseminate with the employees so that they can take care of procedures while working in
the future.
Skill assessment practices must be conducted by management so that current skill set of
employees would be identified which leads to proper T&D session.
To make smooth communication, open communication practices must be planned and
work by the management so that lower level employees can also reach to top
management if they are having some difficulties related to workplace (Prasad, 2019).
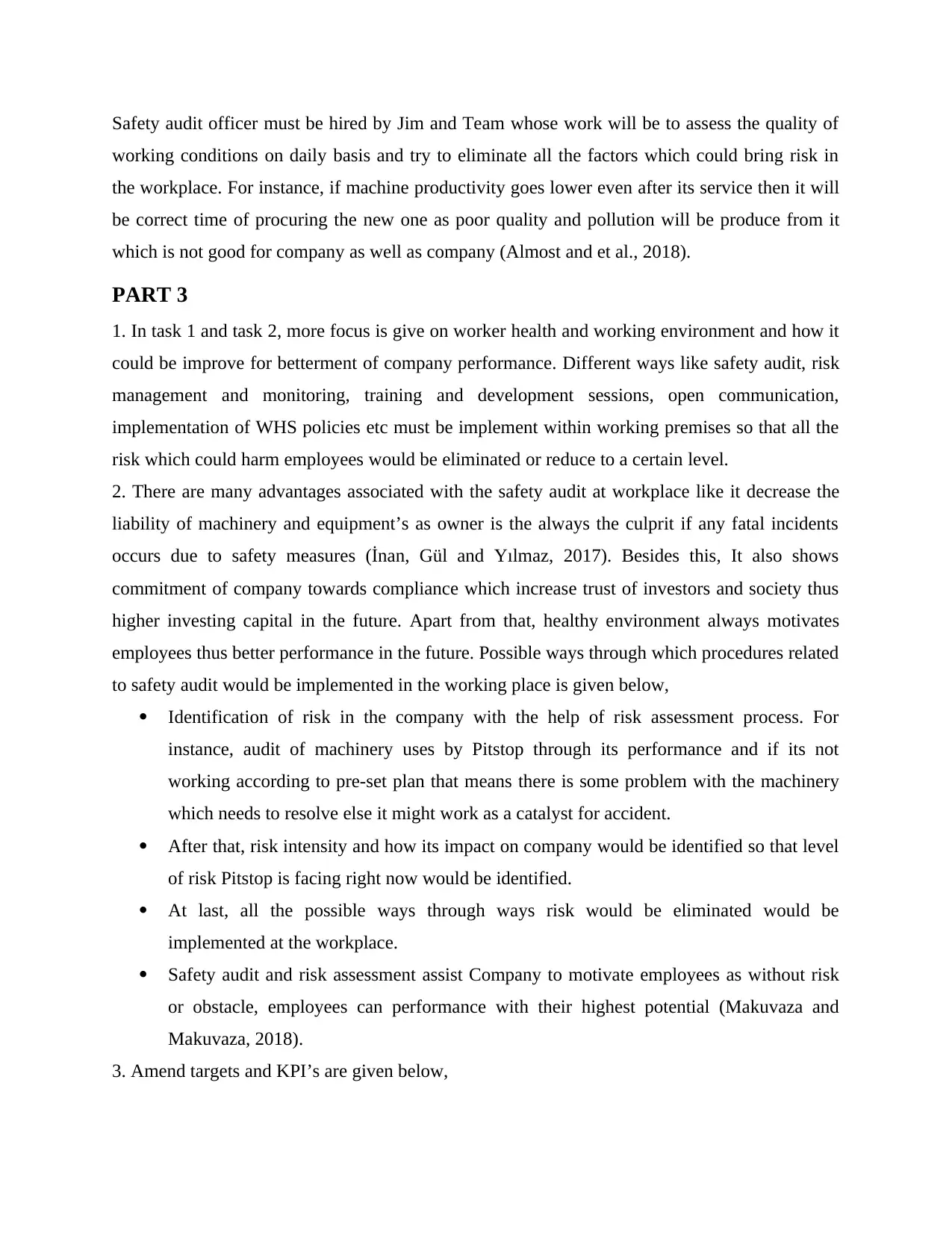
Safety audit officer must be hired by Jim and Team whose work will be to assess the quality of
working conditions on daily basis and try to eliminate all the factors which could bring risk in
the workplace. For instance, if machine productivity goes lower even after its service then it will
be correct time of procuring the new one as poor quality and pollution will be produce from it
which is not good for company as well as company (Almost and et al., 2018).
PART 3
1. In task 1 and task 2, more focus is give on worker health and working environment and how it
could be improve for betterment of company performance. Different ways like safety audit, risk
management and monitoring, training and development sessions, open communication,
implementation of WHS policies etc must be implement within working premises so that all the
risk which could harm employees would be eliminated or reduce to a certain level.
2. There are many advantages associated with the safety audit at workplace like it decrease the
liability of machinery and equipment’s as owner is the always the culprit if any fatal incidents
occurs due to safety measures (İnan, Gül and Yılmaz, 2017). Besides this, It also shows
commitment of company towards compliance which increase trust of investors and society thus
higher investing capital in the future. Apart from that, healthy environment always motivates
employees thus better performance in the future. Possible ways through which procedures related
to safety audit would be implemented in the working place is given below,
Identification of risk in the company with the help of risk assessment process. For
instance, audit of machinery uses by Pitstop through its performance and if its not
working according to pre-set plan that means there is some problem with the machinery
which needs to resolve else it might work as a catalyst for accident.
After that, risk intensity and how its impact on company would be identified so that level
of risk Pitstop is facing right now would be identified.
At last, all the possible ways through ways risk would be eliminated would be
implemented at the workplace.
Safety audit and risk assessment assist Company to motivate employees as without risk
or obstacle, employees can performance with their highest potential (Makuvaza and
Makuvaza, 2018).
3. Amend targets and KPI’s are given below,
working conditions on daily basis and try to eliminate all the factors which could bring risk in
the workplace. For instance, if machine productivity goes lower even after its service then it will
be correct time of procuring the new one as poor quality and pollution will be produce from it
which is not good for company as well as company (Almost and et al., 2018).
PART 3
1. In task 1 and task 2, more focus is give on worker health and working environment and how it
could be improve for betterment of company performance. Different ways like safety audit, risk
management and monitoring, training and development sessions, open communication,
implementation of WHS policies etc must be implement within working premises so that all the
risk which could harm employees would be eliminated or reduce to a certain level.
2. There are many advantages associated with the safety audit at workplace like it decrease the
liability of machinery and equipment’s as owner is the always the culprit if any fatal incidents
occurs due to safety measures (İnan, Gül and Yılmaz, 2017). Besides this, It also shows
commitment of company towards compliance which increase trust of investors and society thus
higher investing capital in the future. Apart from that, healthy environment always motivates
employees thus better performance in the future. Possible ways through which procedures related
to safety audit would be implemented in the working place is given below,
Identification of risk in the company with the help of risk assessment process. For
instance, audit of machinery uses by Pitstop through its performance and if its not
working according to pre-set plan that means there is some problem with the machinery
which needs to resolve else it might work as a catalyst for accident.
After that, risk intensity and how its impact on company would be identified so that level
of risk Pitstop is facing right now would be identified.
At last, all the possible ways through ways risk would be eliminated would be
implemented at the workplace.
Safety audit and risk assessment assist Company to motivate employees as without risk
or obstacle, employees can performance with their highest potential (Makuvaza and
Makuvaza, 2018).
3. Amend targets and KPI’s are given below,
Paraphrase This Document
Need a fresh take? Get an instant paraphrase of this document with our AI Paraphraser
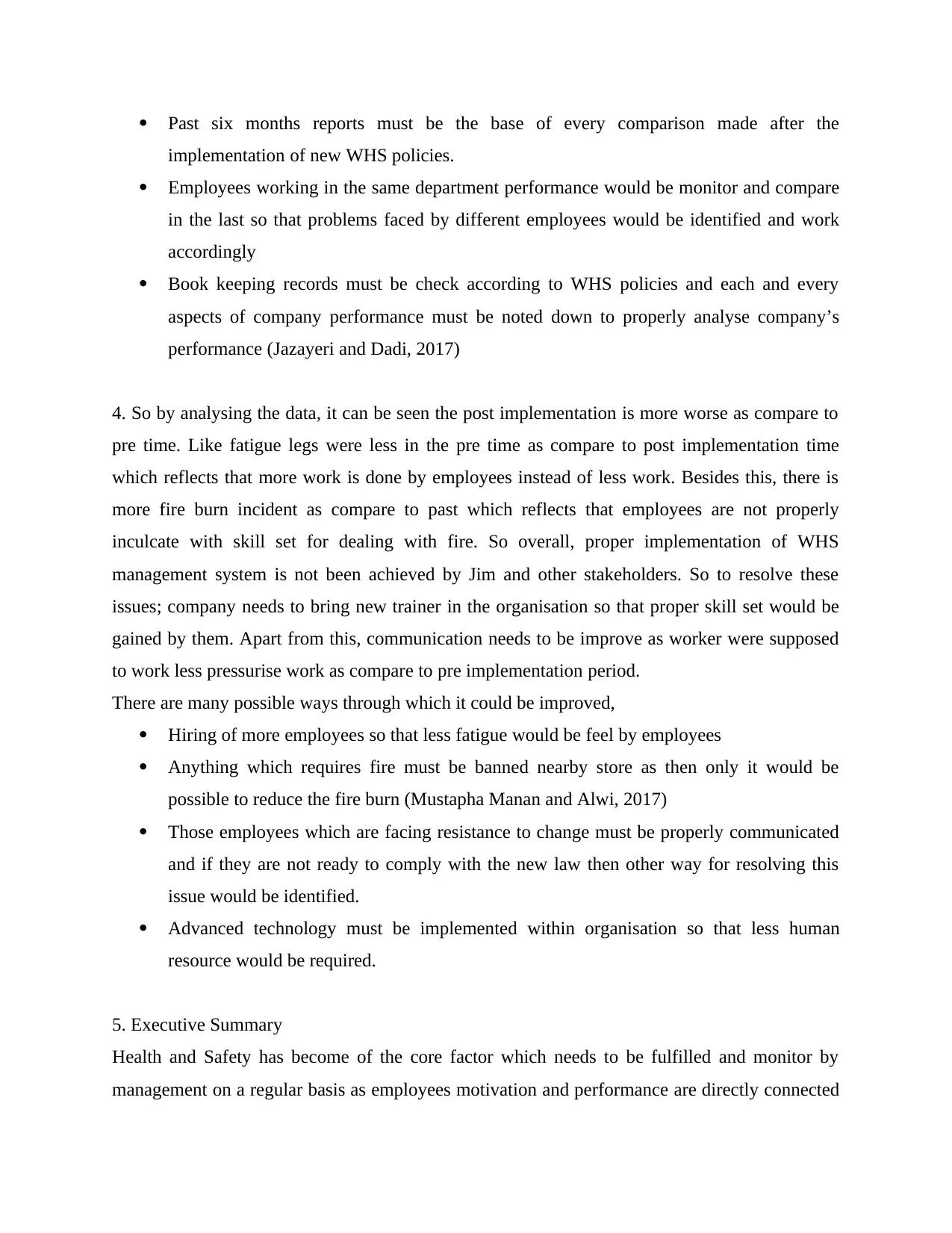
Past six months reports must be the base of every comparison made after the
implementation of new WHS policies.
Employees working in the same department performance would be monitor and compare
in the last so that problems faced by different employees would be identified and work
accordingly
Book keeping records must be check according to WHS policies and each and every
aspects of company performance must be noted down to properly analyse company’s
performance (Jazayeri and Dadi, 2017)
4. So by analysing the data, it can be seen the post implementation is more worse as compare to
pre time. Like fatigue legs were less in the pre time as compare to post implementation time
which reflects that more work is done by employees instead of less work. Besides this, there is
more fire burn incident as compare to past which reflects that employees are not properly
inculcate with skill set for dealing with fire. So overall, proper implementation of WHS
management system is not been achieved by Jim and other stakeholders. So to resolve these
issues; company needs to bring new trainer in the organisation so that proper skill set would be
gained by them. Apart from this, communication needs to be improve as worker were supposed
to work less pressurise work as compare to pre implementation period.
There are many possible ways through which it could be improved,
Hiring of more employees so that less fatigue would be feel by employees
Anything which requires fire must be banned nearby store as then only it would be
possible to reduce the fire burn (Mustapha Manan and Alwi, 2017)
Those employees which are facing resistance to change must be properly communicated
and if they are not ready to comply with the new law then other way for resolving this
issue would be identified.
Advanced technology must be implemented within organisation so that less human
resource would be required.
5. Executive Summary
Health and Safety has become of the core factor which needs to be fulfilled and monitor by
management on a regular basis as employees motivation and performance are directly connected
implementation of new WHS policies.
Employees working in the same department performance would be monitor and compare
in the last so that problems faced by different employees would be identified and work
accordingly
Book keeping records must be check according to WHS policies and each and every
aspects of company performance must be noted down to properly analyse company’s
performance (Jazayeri and Dadi, 2017)
4. So by analysing the data, it can be seen the post implementation is more worse as compare to
pre time. Like fatigue legs were less in the pre time as compare to post implementation time
which reflects that more work is done by employees instead of less work. Besides this, there is
more fire burn incident as compare to past which reflects that employees are not properly
inculcate with skill set for dealing with fire. So overall, proper implementation of WHS
management system is not been achieved by Jim and other stakeholders. So to resolve these
issues; company needs to bring new trainer in the organisation so that proper skill set would be
gained by them. Apart from this, communication needs to be improve as worker were supposed
to work less pressurise work as compare to pre implementation period.
There are many possible ways through which it could be improved,
Hiring of more employees so that less fatigue would be feel by employees
Anything which requires fire must be banned nearby store as then only it would be
possible to reduce the fire burn (Mustapha Manan and Alwi, 2017)
Those employees which are facing resistance to change must be properly communicated
and if they are not ready to comply with the new law then other way for resolving this
issue would be identified.
Advanced technology must be implemented within organisation so that less human
resource would be required.
5. Executive Summary
Health and Safety has become of the core factor which needs to be fulfilled and monitor by
management on a regular basis as employees motivation and performance are directly connected
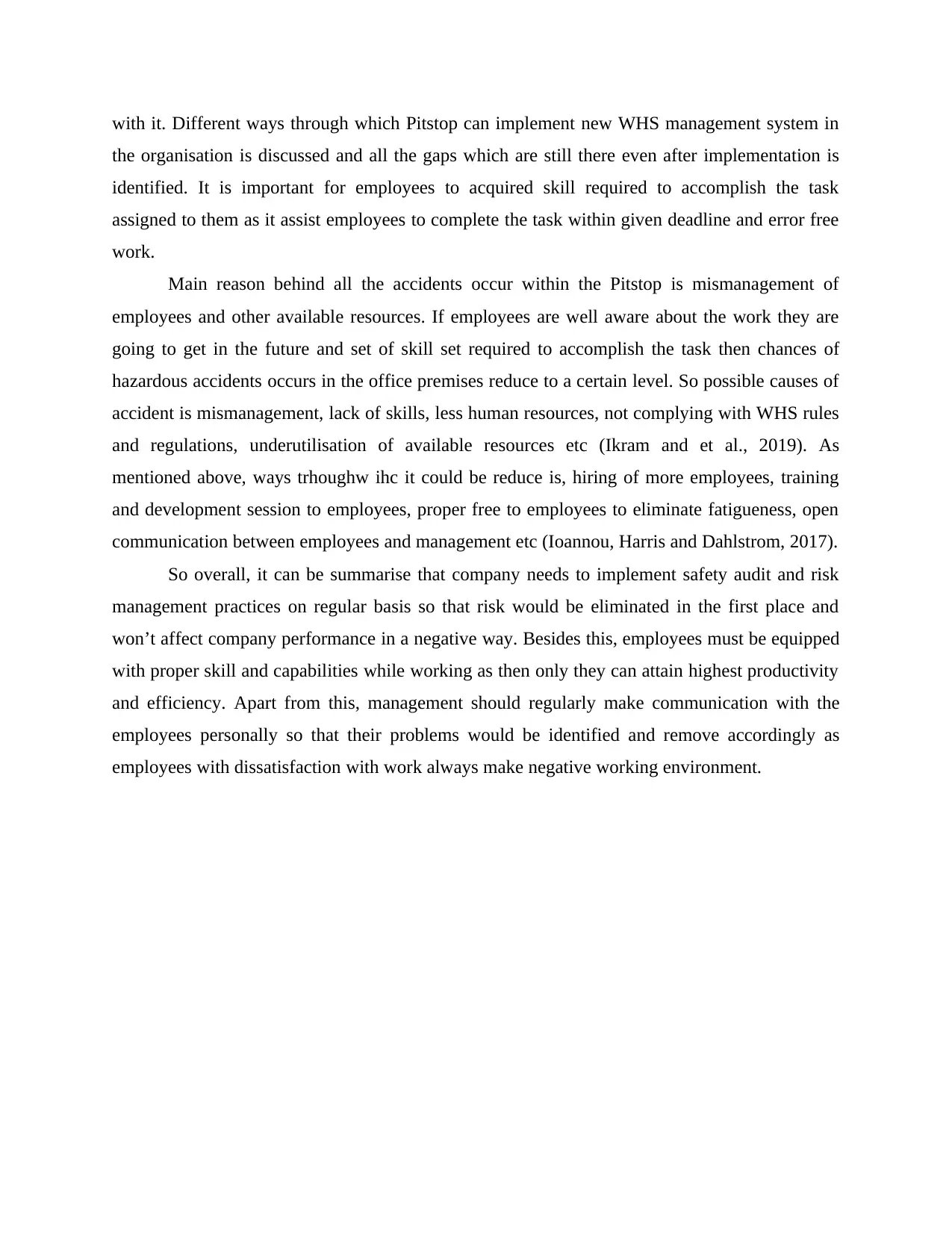
with it. Different ways through which Pitstop can implement new WHS management system in
the organisation is discussed and all the gaps which are still there even after implementation is
identified. It is important for employees to acquired skill required to accomplish the task
assigned to them as it assist employees to complete the task within given deadline and error free
work.
Main reason behind all the accidents occur within the Pitstop is mismanagement of
employees and other available resources. If employees are well aware about the work they are
going to get in the future and set of skill set required to accomplish the task then chances of
hazardous accidents occurs in the office premises reduce to a certain level. So possible causes of
accident is mismanagement, lack of skills, less human resources, not complying with WHS rules
and regulations, underutilisation of available resources etc (Ikram and et al., 2019). As
mentioned above, ways trhoughw ihc it could be reduce is, hiring of more employees, training
and development session to employees, proper free to employees to eliminate fatigueness, open
communication between employees and management etc (Ioannou, Harris and Dahlstrom, 2017).
So overall, it can be summarise that company needs to implement safety audit and risk
management practices on regular basis so that risk would be eliminated in the first place and
won’t affect company performance in a negative way. Besides this, employees must be equipped
with proper skill and capabilities while working as then only they can attain highest productivity
and efficiency. Apart from this, management should regularly make communication with the
employees personally so that their problems would be identified and remove accordingly as
employees with dissatisfaction with work always make negative working environment.
the organisation is discussed and all the gaps which are still there even after implementation is
identified. It is important for employees to acquired skill required to accomplish the task
assigned to them as it assist employees to complete the task within given deadline and error free
work.
Main reason behind all the accidents occur within the Pitstop is mismanagement of
employees and other available resources. If employees are well aware about the work they are
going to get in the future and set of skill set required to accomplish the task then chances of
hazardous accidents occurs in the office premises reduce to a certain level. So possible causes of
accident is mismanagement, lack of skills, less human resources, not complying with WHS rules
and regulations, underutilisation of available resources etc (Ikram and et al., 2019). As
mentioned above, ways trhoughw ihc it could be reduce is, hiring of more employees, training
and development session to employees, proper free to employees to eliminate fatigueness, open
communication between employees and management etc (Ioannou, Harris and Dahlstrom, 2017).
So overall, it can be summarise that company needs to implement safety audit and risk
management practices on regular basis so that risk would be eliminated in the first place and
won’t affect company performance in a negative way. Besides this, employees must be equipped
with proper skill and capabilities while working as then only they can attain highest productivity
and efficiency. Apart from this, management should regularly make communication with the
employees personally so that their problems would be identified and remove accordingly as
employees with dissatisfaction with work always make negative working environment.
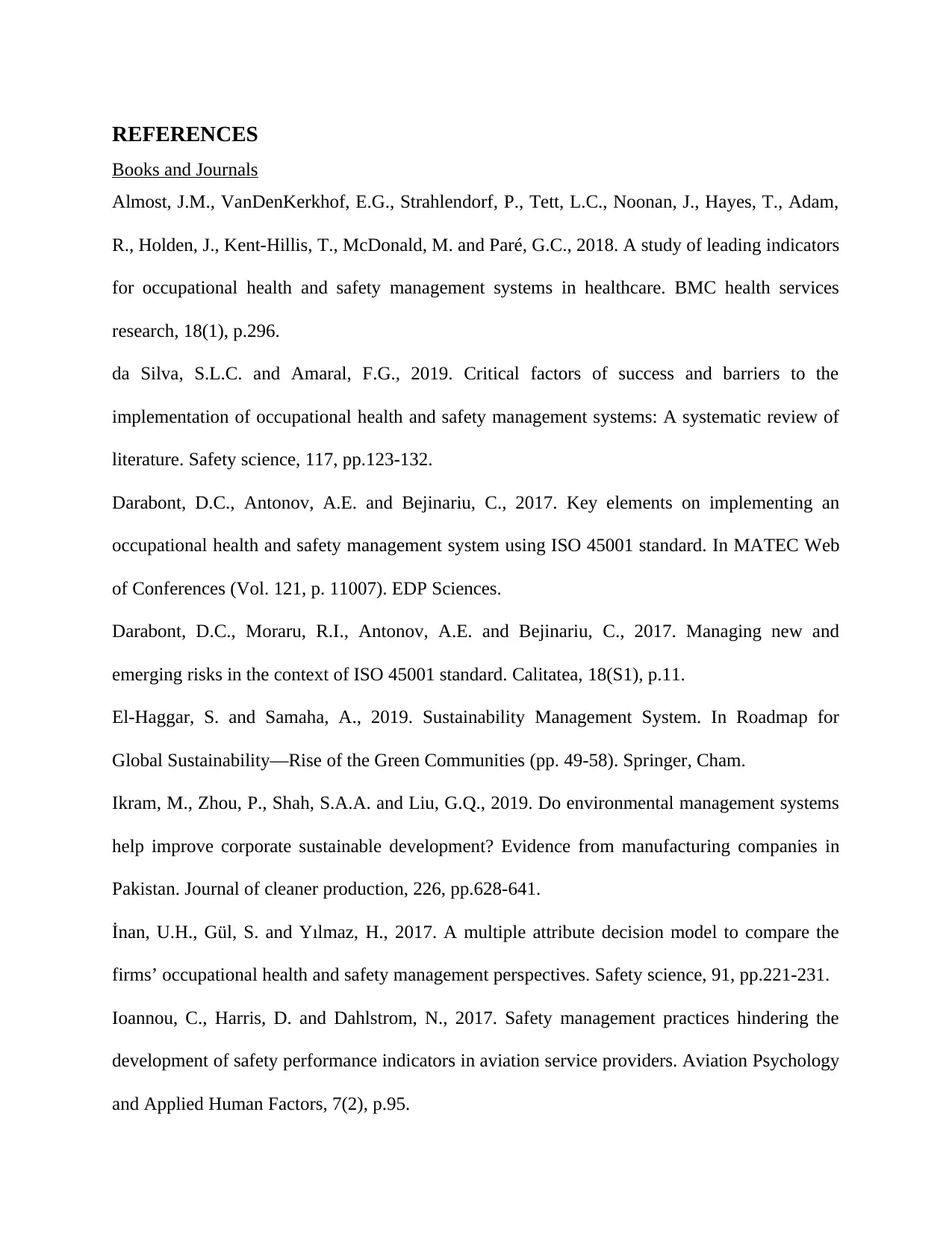
REFERENCES
Books and Journals
Almost, J.M., VanDenKerkhof, E.G., Strahlendorf, P., Tett, L.C., Noonan, J., Hayes, T., Adam,
R., Holden, J., Kent-Hillis, T., McDonald, M. and Paré, G.C., 2018. A study of leading indicators
for occupational health and safety management systems in healthcare. BMC health services
research, 18(1), p.296.
da Silva, S.L.C. and Amaral, F.G., 2019. Critical factors of success and barriers to the
implementation of occupational health and safety management systems: A systematic review of
literature. Safety science, 117, pp.123-132.
Darabont, D.C., Antonov, A.E. and Bejinariu, C., 2017. Key elements on implementing an
occupational health and safety management system using ISO 45001 standard. In MATEC Web
of Conferences (Vol. 121, p. 11007). EDP Sciences.
Darabont, D.C., Moraru, R.I., Antonov, A.E. and Bejinariu, C., 2017. Managing new and
emerging risks in the context of ISO 45001 standard. Calitatea, 18(S1), p.11.
El-Haggar, S. and Samaha, A., 2019. Sustainability Management System. In Roadmap for
Global Sustainability—Rise of the Green Communities (pp. 49-58). Springer, Cham.
Ikram, M., Zhou, P., Shah, S.A.A. and Liu, G.Q., 2019. Do environmental management systems
help improve corporate sustainable development? Evidence from manufacturing companies in
Pakistan. Journal of cleaner production, 226, pp.628-641.
İnan, U.H., Gül, S. and Yılmaz, H., 2017. A multiple attribute decision model to compare the
firms’ occupational health and safety management perspectives. Safety science, 91, pp.221-231.
Ioannou, C., Harris, D. and Dahlstrom, N., 2017. Safety management practices hindering the
development of safety performance indicators in aviation service providers. Aviation Psychology
and Applied Human Factors, 7(2), p.95.
Books and Journals
Almost, J.M., VanDenKerkhof, E.G., Strahlendorf, P., Tett, L.C., Noonan, J., Hayes, T., Adam,
R., Holden, J., Kent-Hillis, T., McDonald, M. and Paré, G.C., 2018. A study of leading indicators
for occupational health and safety management systems in healthcare. BMC health services
research, 18(1), p.296.
da Silva, S.L.C. and Amaral, F.G., 2019. Critical factors of success and barriers to the
implementation of occupational health and safety management systems: A systematic review of
literature. Safety science, 117, pp.123-132.
Darabont, D.C., Antonov, A.E. and Bejinariu, C., 2017. Key elements on implementing an
occupational health and safety management system using ISO 45001 standard. In MATEC Web
of Conferences (Vol. 121, p. 11007). EDP Sciences.
Darabont, D.C., Moraru, R.I., Antonov, A.E. and Bejinariu, C., 2017. Managing new and
emerging risks in the context of ISO 45001 standard. Calitatea, 18(S1), p.11.
El-Haggar, S. and Samaha, A., 2019. Sustainability Management System. In Roadmap for
Global Sustainability—Rise of the Green Communities (pp. 49-58). Springer, Cham.
Ikram, M., Zhou, P., Shah, S.A.A. and Liu, G.Q., 2019. Do environmental management systems
help improve corporate sustainable development? Evidence from manufacturing companies in
Pakistan. Journal of cleaner production, 226, pp.628-641.
İnan, U.H., Gül, S. and Yılmaz, H., 2017. A multiple attribute decision model to compare the
firms’ occupational health and safety management perspectives. Safety science, 91, pp.221-231.
Ioannou, C., Harris, D. and Dahlstrom, N., 2017. Safety management practices hindering the
development of safety performance indicators in aviation service providers. Aviation Psychology
and Applied Human Factors, 7(2), p.95.
Secure Best Marks with AI Grader
Need help grading? Try our AI Grader for instant feedback on your assignments.
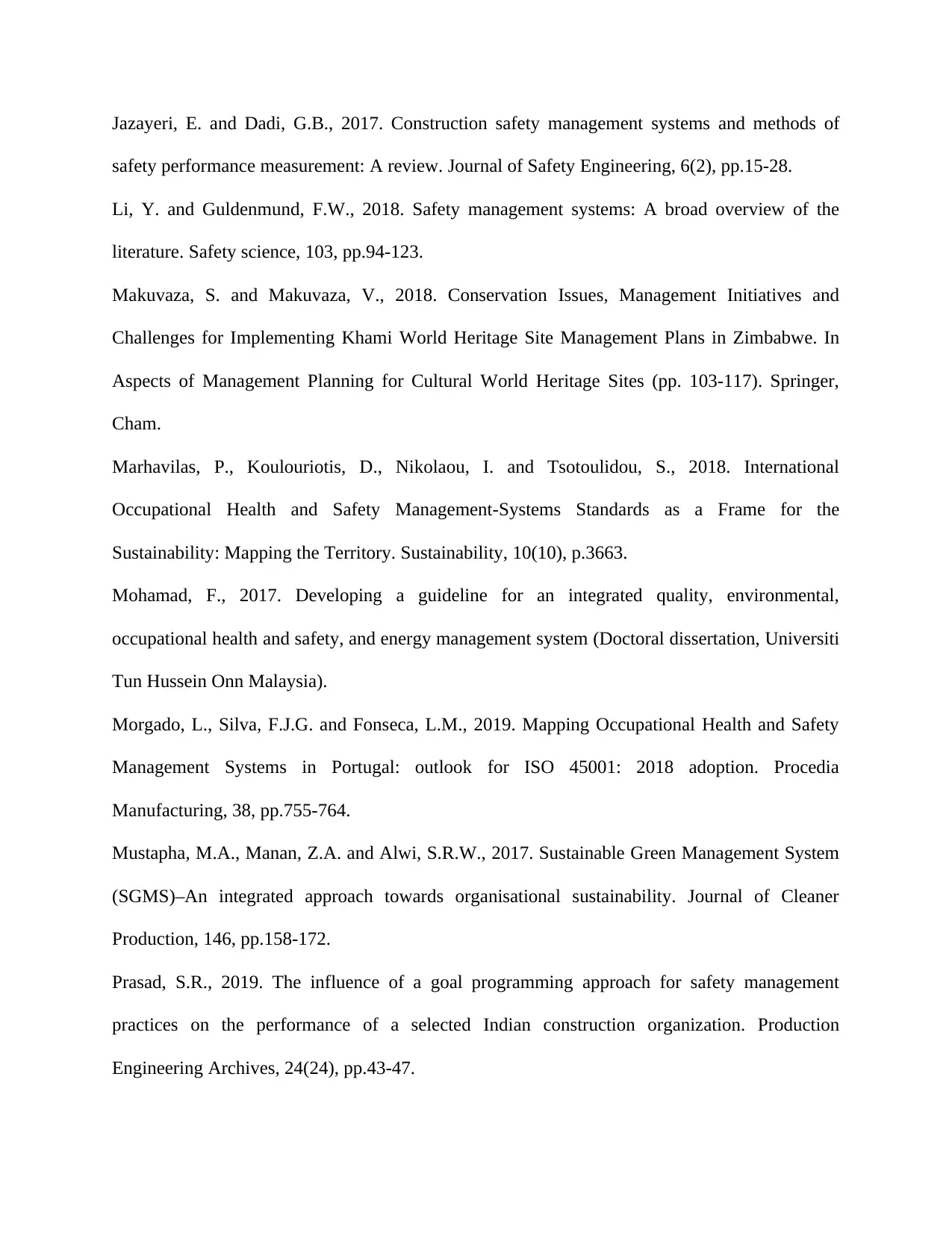
Jazayeri, E. and Dadi, G.B., 2017. Construction safety management systems and methods of
safety performance measurement: A review. Journal of Safety Engineering, 6(2), pp.15-28.
Li, Y. and Guldenmund, F.W., 2018. Safety management systems: A broad overview of the
literature. Safety science, 103, pp.94-123.
Makuvaza, S. and Makuvaza, V., 2018. Conservation Issues, Management Initiatives and
Challenges for Implementing Khami World Heritage Site Management Plans in Zimbabwe. In
Aspects of Management Planning for Cultural World Heritage Sites (pp. 103-117). Springer,
Cham.
Marhavilas, P., Koulouriotis, D., Nikolaou, I. and Tsotoulidou, S., 2018. International
Occupational Health and Safety Management-Systems Standards as a Frame for the
Sustainability: Mapping the Territory. Sustainability, 10(10), p.3663.
Mohamad, F., 2017. Developing a guideline for an integrated quality, environmental,
occupational health and safety, and energy management system (Doctoral dissertation, Universiti
Tun Hussein Onn Malaysia).
Morgado, L., Silva, F.J.G. and Fonseca, L.M., 2019. Mapping Occupational Health and Safety
Management Systems in Portugal: outlook for ISO 45001: 2018 adoption. Procedia
Manufacturing, 38, pp.755-764.
Mustapha, M.A., Manan, Z.A. and Alwi, S.R.W., 2017. Sustainable Green Management System
(SGMS)–An integrated approach towards organisational sustainability. Journal of Cleaner
Production, 146, pp.158-172.
Prasad, S.R., 2019. The influence of a goal programming approach for safety management
practices on the performance of a selected Indian construction organization. Production
Engineering Archives, 24(24), pp.43-47.
safety performance measurement: A review. Journal of Safety Engineering, 6(2), pp.15-28.
Li, Y. and Guldenmund, F.W., 2018. Safety management systems: A broad overview of the
literature. Safety science, 103, pp.94-123.
Makuvaza, S. and Makuvaza, V., 2018. Conservation Issues, Management Initiatives and
Challenges for Implementing Khami World Heritage Site Management Plans in Zimbabwe. In
Aspects of Management Planning for Cultural World Heritage Sites (pp. 103-117). Springer,
Cham.
Marhavilas, P., Koulouriotis, D., Nikolaou, I. and Tsotoulidou, S., 2018. International
Occupational Health and Safety Management-Systems Standards as a Frame for the
Sustainability: Mapping the Territory. Sustainability, 10(10), p.3663.
Mohamad, F., 2017. Developing a guideline for an integrated quality, environmental,
occupational health and safety, and energy management system (Doctoral dissertation, Universiti
Tun Hussein Onn Malaysia).
Morgado, L., Silva, F.J.G. and Fonseca, L.M., 2019. Mapping Occupational Health and Safety
Management Systems in Portugal: outlook for ISO 45001: 2018 adoption. Procedia
Manufacturing, 38, pp.755-764.
Mustapha, M.A., Manan, Z.A. and Alwi, S.R.W., 2017. Sustainable Green Management System
(SGMS)–An integrated approach towards organisational sustainability. Journal of Cleaner
Production, 146, pp.158-172.
Prasad, S.R., 2019. The influence of a goal programming approach for safety management
practices on the performance of a selected Indian construction organization. Production
Engineering Archives, 24(24), pp.43-47.
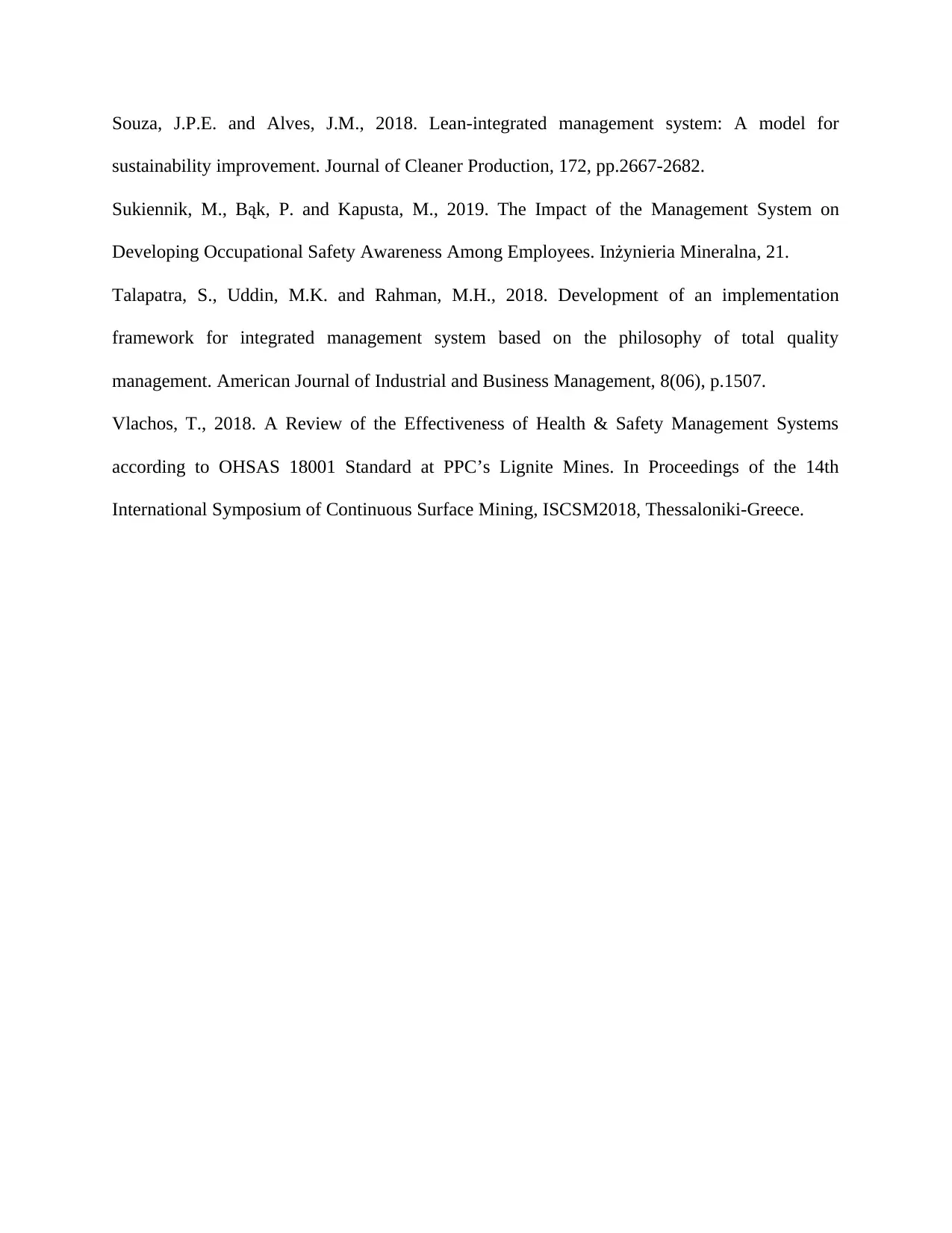
Souza, J.P.E. and Alves, J.M., 2018. Lean-integrated management system: A model for
sustainability improvement. Journal of Cleaner Production, 172, pp.2667-2682.
Sukiennik, M., Bąk, P. and Kapusta, M., 2019. The Impact of the Management System on
Developing Occupational Safety Awareness Among Employees. Inżynieria Mineralna, 21.
Talapatra, S., Uddin, M.K. and Rahman, M.H., 2018. Development of an implementation
framework for integrated management system based on the philosophy of total quality
management. American Journal of Industrial and Business Management, 8(06), p.1507.
Vlachos, T., 2018. A Review of the Effectiveness of Health & Safety Management Systems
according to OHSAS 18001 Standard at PPC’s Lignite Mines. In Proceedings of the 14th
International Symposium of Continuous Surface Mining, ISCSM2018, Thessaloniki-Greece.
sustainability improvement. Journal of Cleaner Production, 172, pp.2667-2682.
Sukiennik, M., Bąk, P. and Kapusta, M., 2019. The Impact of the Management System on
Developing Occupational Safety Awareness Among Employees. Inżynieria Mineralna, 21.
Talapatra, S., Uddin, M.K. and Rahman, M.H., 2018. Development of an implementation
framework for integrated management system based on the philosophy of total quality
management. American Journal of Industrial and Business Management, 8(06), p.1507.
Vlachos, T., 2018. A Review of the Effectiveness of Health & Safety Management Systems
according to OHSAS 18001 Standard at PPC’s Lignite Mines. In Proceedings of the 14th
International Symposium of Continuous Surface Mining, ISCSM2018, Thessaloniki-Greece.
1 out of 12
Related Documents

Your All-in-One AI-Powered Toolkit for Academic Success.
+13062052269
info@desklib.com
Available 24*7 on WhatsApp / Email
Unlock your academic potential
© 2024 | Zucol Services PVT LTD | All rights reserved.