Implement and Monitor WHS Policies, Procedures and Programs Report
VerifiedAdded on 2022/09/12
|24
|7442
|32
Report
AI Summary
This report delves into the critical aspects of implementing and monitoring Workplace Health and Safety (WHS) policies, procedures, and programs. It examines the obligations of managers and business owners, emphasizing their responsibilities in ensuring employee safety and well-being. The report covers key elements such as hazard identification, risk assessment, and control measures, providing a comprehensive understanding of these processes. It explores the purpose and application of codes of practice, including first aid in the workplace, and discusses the importance of employee training and communication. Through case studies and practical examples, the report illustrates how to identify and address workplace hazards, implement risk control procedures, and maintain a safe and healthy work environment. Furthermore, it highlights the significance of promptly implementing hazard reports, providing ongoing training, and maintaining injury registers to ensure continuous improvement in WHS practices. The report also addresses the purpose of the hierarchy of control and the importance of consulting with staff when implementing or reviewing WHS procedures.
Contribute Materials
Your contribution can guide someone’s learning journey. Share your
documents today.
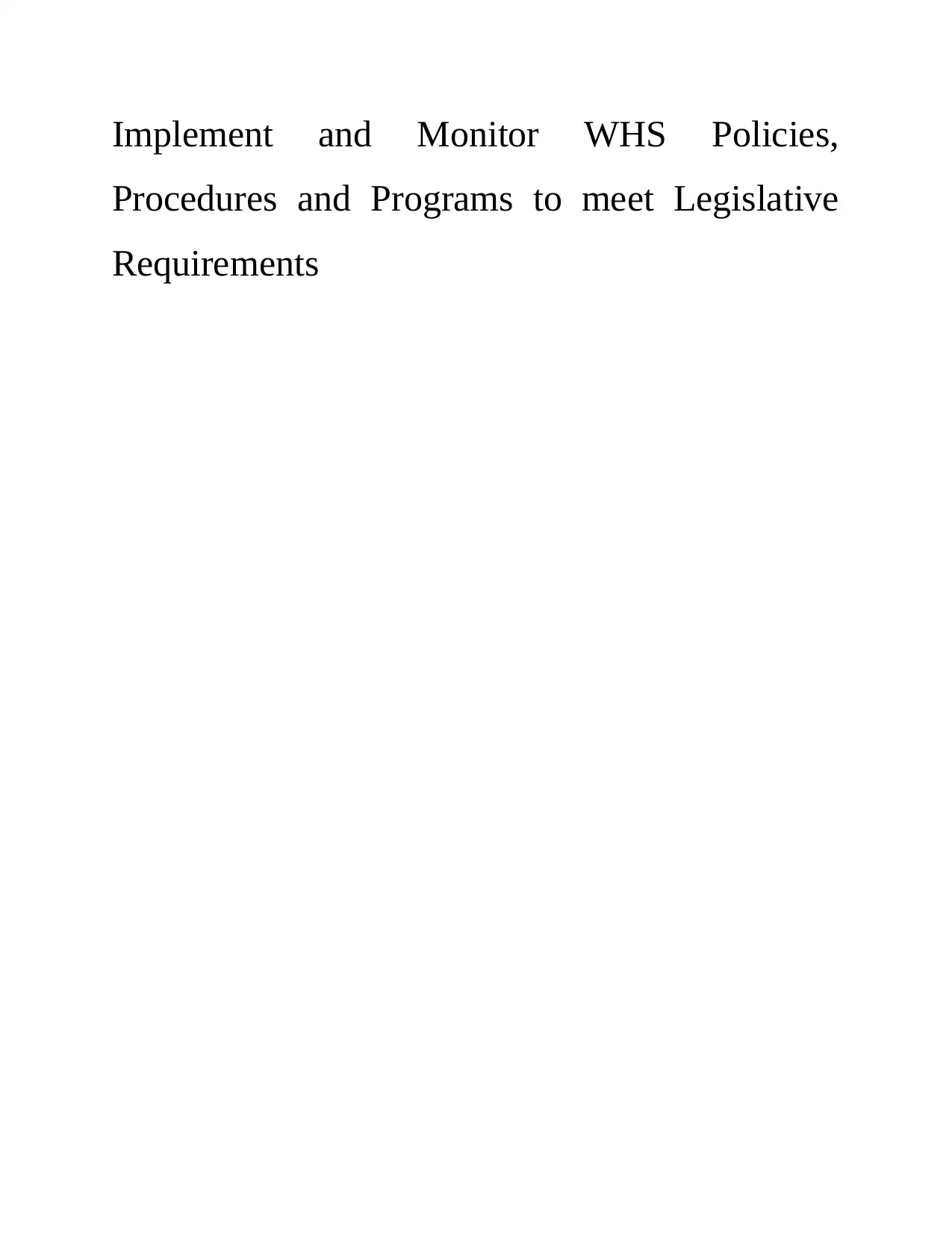
Implement and Monitor WHS Policies,
Procedures and Programs to meet Legislative
Requirements
Procedures and Programs to meet Legislative
Requirements
Secure Best Marks with AI Grader
Need help grading? Try our AI Grader for instant feedback on your assignments.
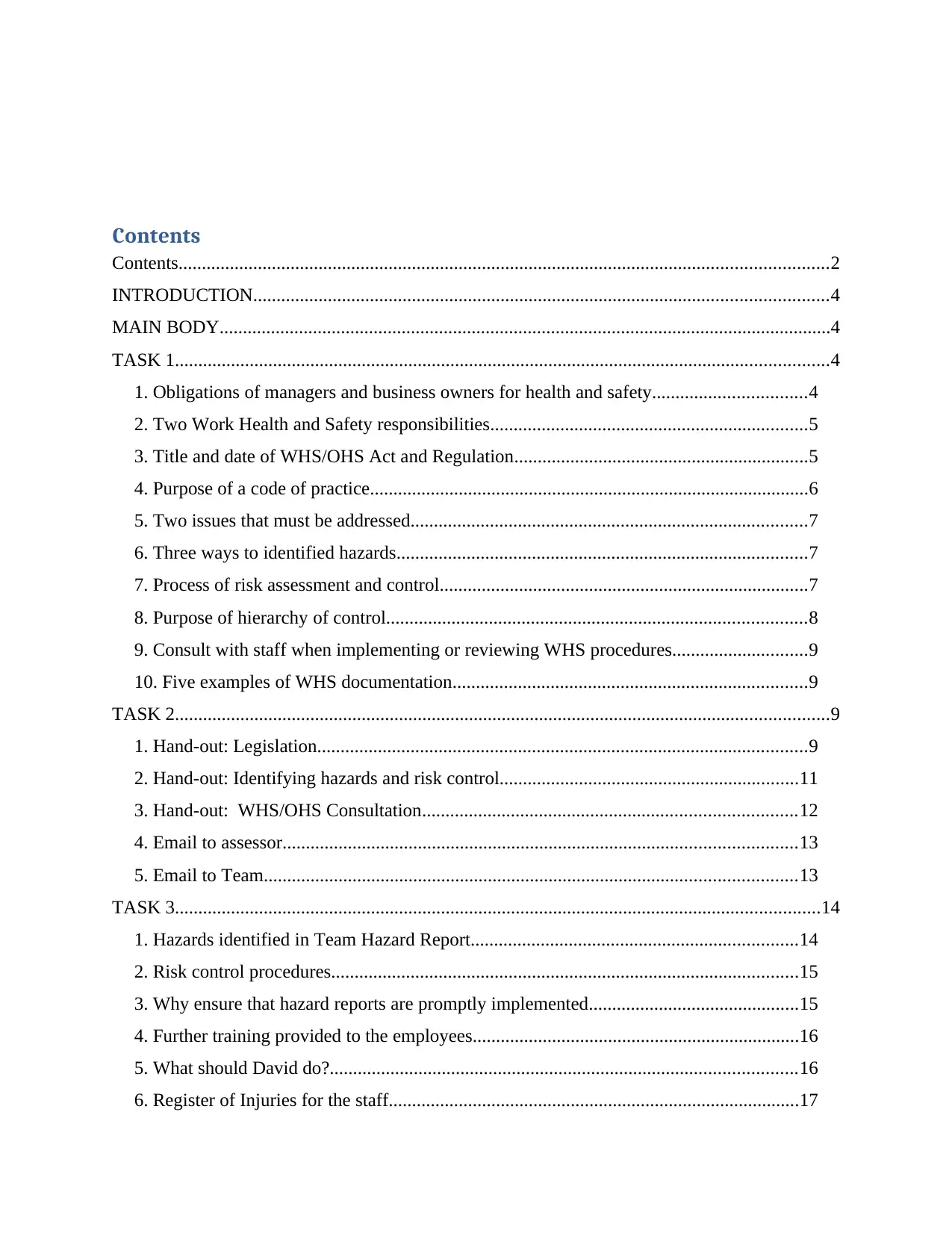
Contents
Contents...........................................................................................................................................2
INTRODUCTION...........................................................................................................................4
MAIN BODY...................................................................................................................................4
TASK 1............................................................................................................................................4
1. Obligations of managers and business owners for health and safety.................................4
2. Two Work Health and Safety responsibilities....................................................................5
3. Title and date of WHS/OHS Act and Regulation...............................................................5
4. Purpose of a code of practice..............................................................................................6
5. Two issues that must be addressed.....................................................................................7
6. Three ways to identified hazards........................................................................................7
7. Process of risk assessment and control...............................................................................7
8. Purpose of hierarchy of control..........................................................................................8
9. Consult with staff when implementing or reviewing WHS procedures.............................9
10. Five examples of WHS documentation............................................................................9
TASK 2............................................................................................................................................9
1. Hand-out: Legislation.........................................................................................................9
2. Hand-out: Identifying hazards and risk control................................................................11
3. Hand-out: WHS/OHS Consultation................................................................................12
4. Email to assessor..............................................................................................................13
5. Email to Team..................................................................................................................13
TASK 3..........................................................................................................................................14
1. Hazards identified in Team Hazard Report......................................................................14
2. Risk control procedures....................................................................................................15
3. Why ensure that hazard reports are promptly implemented.............................................15
4. Further training provided to the employees......................................................................16
5. What should David do?....................................................................................................16
6. Register of Injuries for the staff........................................................................................17
Contents...........................................................................................................................................2
INTRODUCTION...........................................................................................................................4
MAIN BODY...................................................................................................................................4
TASK 1............................................................................................................................................4
1. Obligations of managers and business owners for health and safety.................................4
2. Two Work Health and Safety responsibilities....................................................................5
3. Title and date of WHS/OHS Act and Regulation...............................................................5
4. Purpose of a code of practice..............................................................................................6
5. Two issues that must be addressed.....................................................................................7
6. Three ways to identified hazards........................................................................................7
7. Process of risk assessment and control...............................................................................7
8. Purpose of hierarchy of control..........................................................................................8
9. Consult with staff when implementing or reviewing WHS procedures.............................9
10. Five examples of WHS documentation............................................................................9
TASK 2............................................................................................................................................9
1. Hand-out: Legislation.........................................................................................................9
2. Hand-out: Identifying hazards and risk control................................................................11
3. Hand-out: WHS/OHS Consultation................................................................................12
4. Email to assessor..............................................................................................................13
5. Email to Team..................................................................................................................13
TASK 3..........................................................................................................................................14
1. Hazards identified in Team Hazard Report......................................................................14
2. Risk control procedures....................................................................................................15
3. Why ensure that hazard reports are promptly implemented.............................................15
4. Further training provided to the employees......................................................................16
5. What should David do?....................................................................................................16
6. Register of Injuries for the staff........................................................................................17
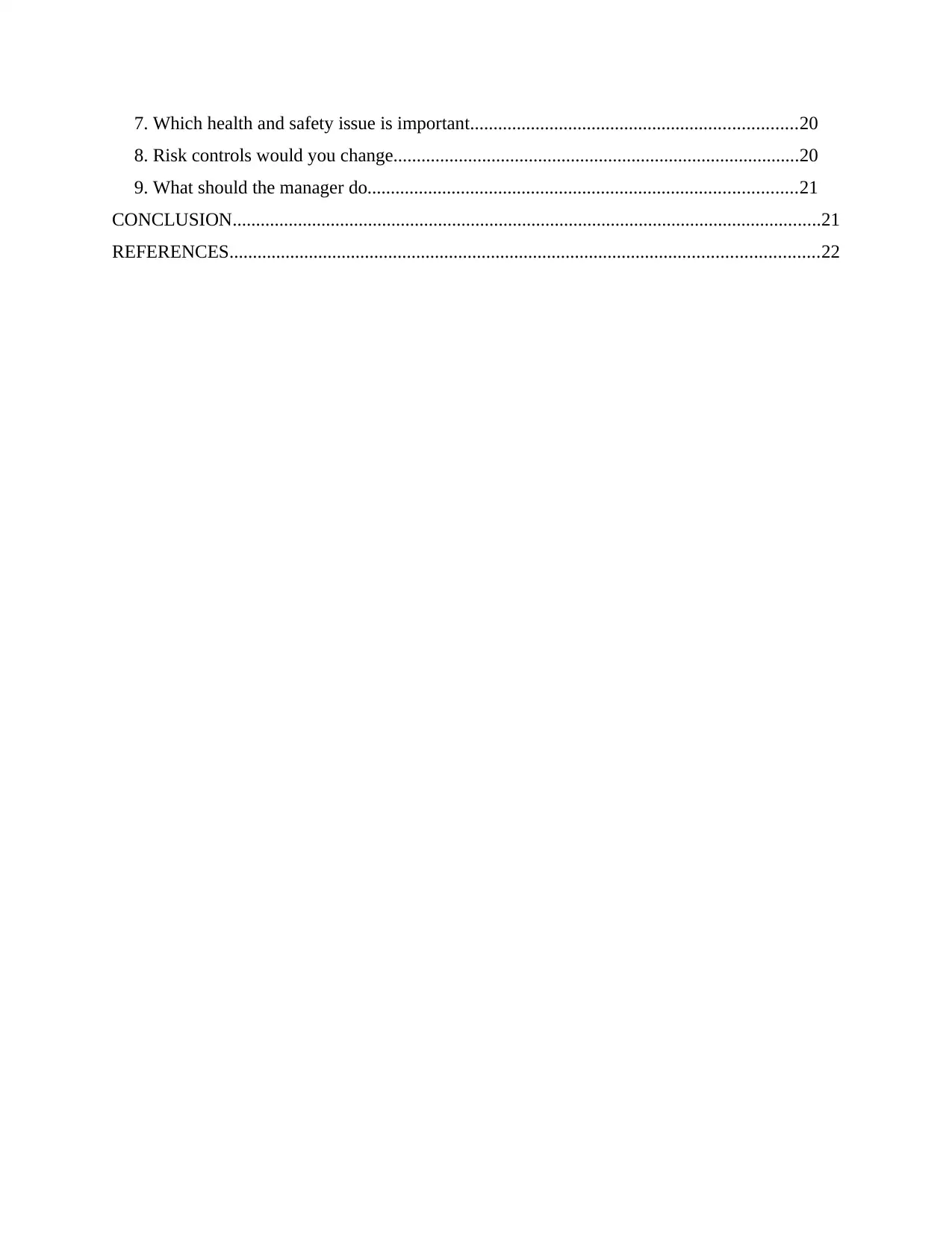
7. Which health and safety issue is important......................................................................20
8. Risk controls would you change.......................................................................................20
9. What should the manager do............................................................................................21
CONCLUSION..............................................................................................................................21
REFERENCES..............................................................................................................................22
8. Risk controls would you change.......................................................................................20
9. What should the manager do............................................................................................21
CONCLUSION..............................................................................................................................21
REFERENCES..............................................................................................................................22
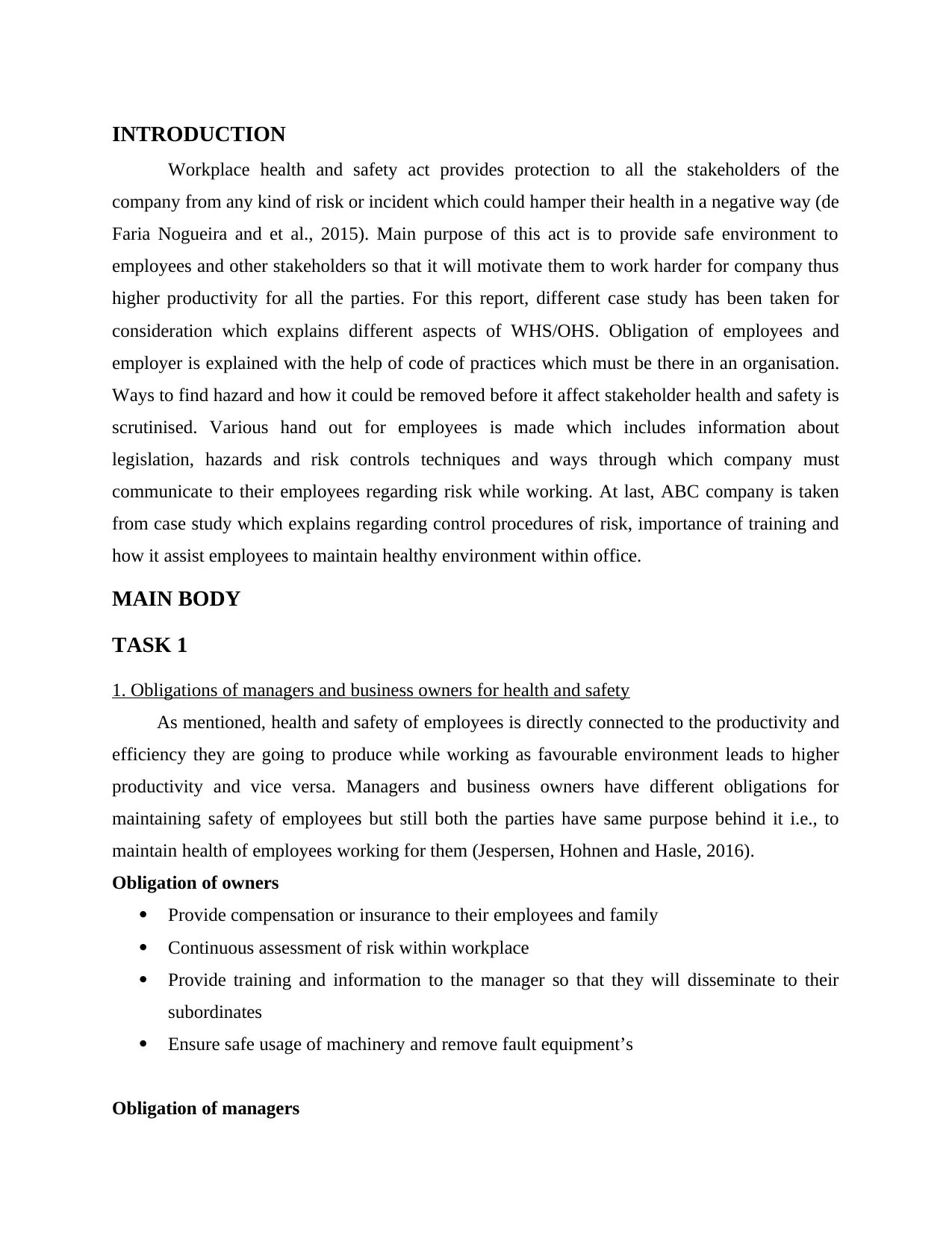
INTRODUCTION
Workplace health and safety act provides protection to all the stakeholders of the
company from any kind of risk or incident which could hamper their health in a negative way (de
Faria Nogueira and et al., 2015). Main purpose of this act is to provide safe environment to
employees and other stakeholders so that it will motivate them to work harder for company thus
higher productivity for all the parties. For this report, different case study has been taken for
consideration which explains different aspects of WHS/OHS. Obligation of employees and
employer is explained with the help of code of practices which must be there in an organisation.
Ways to find hazard and how it could be removed before it affect stakeholder health and safety is
scrutinised. Various hand out for employees is made which includes information about
legislation, hazards and risk controls techniques and ways through which company must
communicate to their employees regarding risk while working. At last, ABC company is taken
from case study which explains regarding control procedures of risk, importance of training and
how it assist employees to maintain healthy environment within office.
MAIN BODY
TASK 1
1. Obligations of managers and business owners for health and safety
As mentioned, health and safety of employees is directly connected to the productivity and
efficiency they are going to produce while working as favourable environment leads to higher
productivity and vice versa. Managers and business owners have different obligations for
maintaining safety of employees but still both the parties have same purpose behind it i.e., to
maintain health of employees working for them (Jespersen, Hohnen and Hasle, 2016).
Obligation of owners
Provide compensation or insurance to their employees and family
Continuous assessment of risk within workplace
Provide training and information to the manager so that they will disseminate to their
subordinates
Ensure safe usage of machinery and remove fault equipment’s
Obligation of managers
Workplace health and safety act provides protection to all the stakeholders of the
company from any kind of risk or incident which could hamper their health in a negative way (de
Faria Nogueira and et al., 2015). Main purpose of this act is to provide safe environment to
employees and other stakeholders so that it will motivate them to work harder for company thus
higher productivity for all the parties. For this report, different case study has been taken for
consideration which explains different aspects of WHS/OHS. Obligation of employees and
employer is explained with the help of code of practices which must be there in an organisation.
Ways to find hazard and how it could be removed before it affect stakeholder health and safety is
scrutinised. Various hand out for employees is made which includes information about
legislation, hazards and risk controls techniques and ways through which company must
communicate to their employees regarding risk while working. At last, ABC company is taken
from case study which explains regarding control procedures of risk, importance of training and
how it assist employees to maintain healthy environment within office.
MAIN BODY
TASK 1
1. Obligations of managers and business owners for health and safety
As mentioned, health and safety of employees is directly connected to the productivity and
efficiency they are going to produce while working as favourable environment leads to higher
productivity and vice versa. Managers and business owners have different obligations for
maintaining safety of employees but still both the parties have same purpose behind it i.e., to
maintain health of employees working for them (Jespersen, Hohnen and Hasle, 2016).
Obligation of owners
Provide compensation or insurance to their employees and family
Continuous assessment of risk within workplace
Provide training and information to the manager so that they will disseminate to their
subordinates
Ensure safe usage of machinery and remove fault equipment’s
Obligation of managers
Secure Best Marks with AI Grader
Need help grading? Try our AI Grader for instant feedback on your assignments.
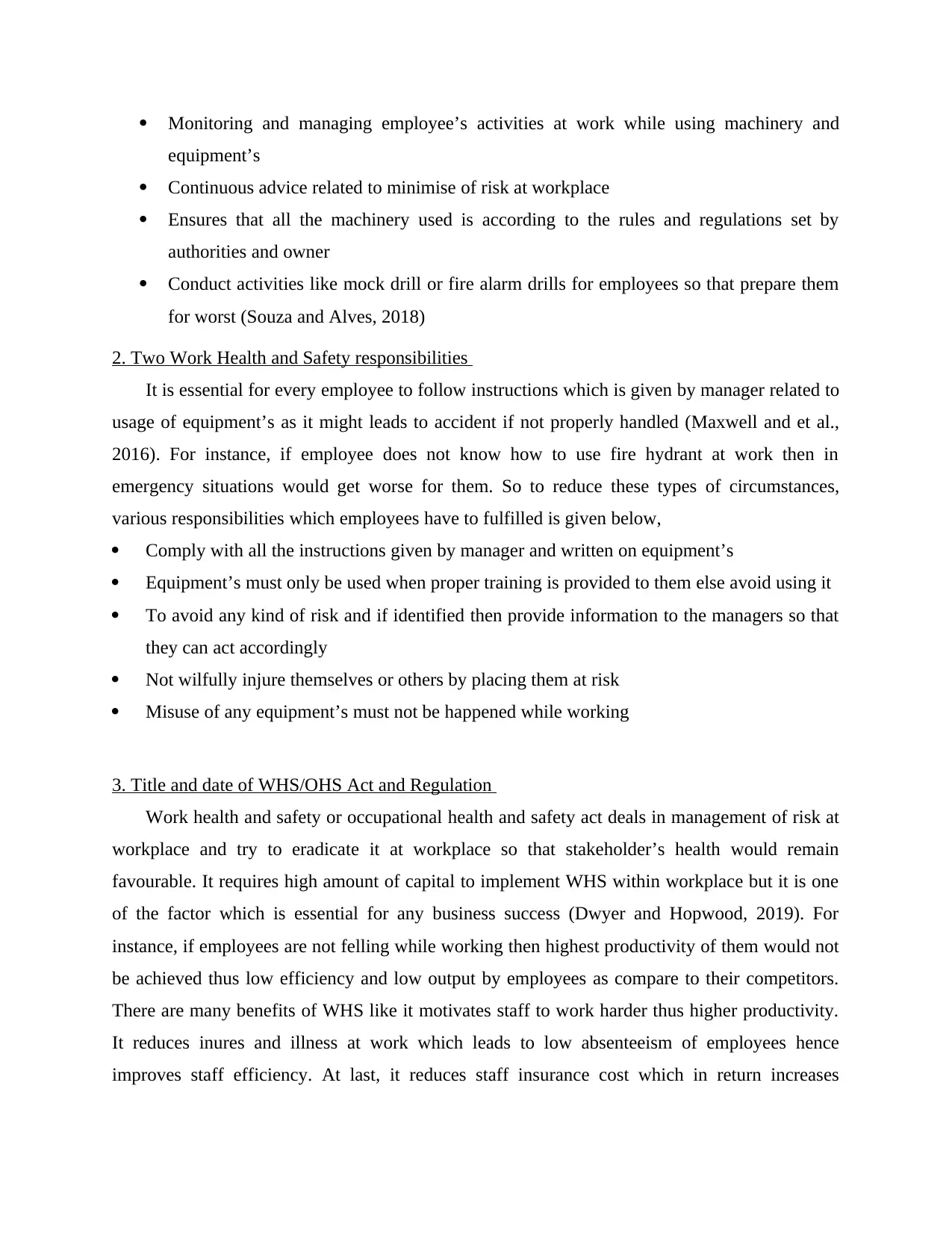
Monitoring and managing employee’s activities at work while using machinery and
equipment’s
Continuous advice related to minimise of risk at workplace
Ensures that all the machinery used is according to the rules and regulations set by
authorities and owner
Conduct activities like mock drill or fire alarm drills for employees so that prepare them
for worst (Souza and Alves, 2018)
2. Two Work Health and Safety responsibilities
It is essential for every employee to follow instructions which is given by manager related to
usage of equipment’s as it might leads to accident if not properly handled (Maxwell and et al.,
2016). For instance, if employee does not know how to use fire hydrant at work then in
emergency situations would get worse for them. So to reduce these types of circumstances,
various responsibilities which employees have to fulfilled is given below,
Comply with all the instructions given by manager and written on equipment’s
Equipment’s must only be used when proper training is provided to them else avoid using it
To avoid any kind of risk and if identified then provide information to the managers so that
they can act accordingly
Not wilfully injure themselves or others by placing them at risk
Misuse of any equipment’s must not be happened while working
3. Title and date of WHS/OHS Act and Regulation
Work health and safety or occupational health and safety act deals in management of risk at
workplace and try to eradicate it at workplace so that stakeholder’s health would remain
favourable. It requires high amount of capital to implement WHS within workplace but it is one
of the factor which is essential for any business success (Dwyer and Hopwood, 2019). For
instance, if employees are not felling while working then highest productivity of them would not
be achieved thus low efficiency and low output by employees as compare to their competitors.
There are many benefits of WHS like it motivates staff to work harder thus higher productivity.
It reduces inures and illness at work which leads to low absenteeism of employees hence
improves staff efficiency. At last, it reduces staff insurance cost which in return increases
equipment’s
Continuous advice related to minimise of risk at workplace
Ensures that all the machinery used is according to the rules and regulations set by
authorities and owner
Conduct activities like mock drill or fire alarm drills for employees so that prepare them
for worst (Souza and Alves, 2018)
2. Two Work Health and Safety responsibilities
It is essential for every employee to follow instructions which is given by manager related to
usage of equipment’s as it might leads to accident if not properly handled (Maxwell and et al.,
2016). For instance, if employee does not know how to use fire hydrant at work then in
emergency situations would get worse for them. So to reduce these types of circumstances,
various responsibilities which employees have to fulfilled is given below,
Comply with all the instructions given by manager and written on equipment’s
Equipment’s must only be used when proper training is provided to them else avoid using it
To avoid any kind of risk and if identified then provide information to the managers so that
they can act accordingly
Not wilfully injure themselves or others by placing them at risk
Misuse of any equipment’s must not be happened while working
3. Title and date of WHS/OHS Act and Regulation
Work health and safety or occupational health and safety act deals in management of risk at
workplace and try to eradicate it at workplace so that stakeholder’s health would remain
favourable. It requires high amount of capital to implement WHS within workplace but it is one
of the factor which is essential for any business success (Dwyer and Hopwood, 2019). For
instance, if employees are not felling while working then highest productivity of them would not
be achieved thus low efficiency and low output by employees as compare to their competitors.
There are many benefits of WHS like it motivates staff to work harder thus higher productivity.
It reduces inures and illness at work which leads to low absenteeism of employees hence
improves staff efficiency. At last, it reduces staff insurance cost which in return increases
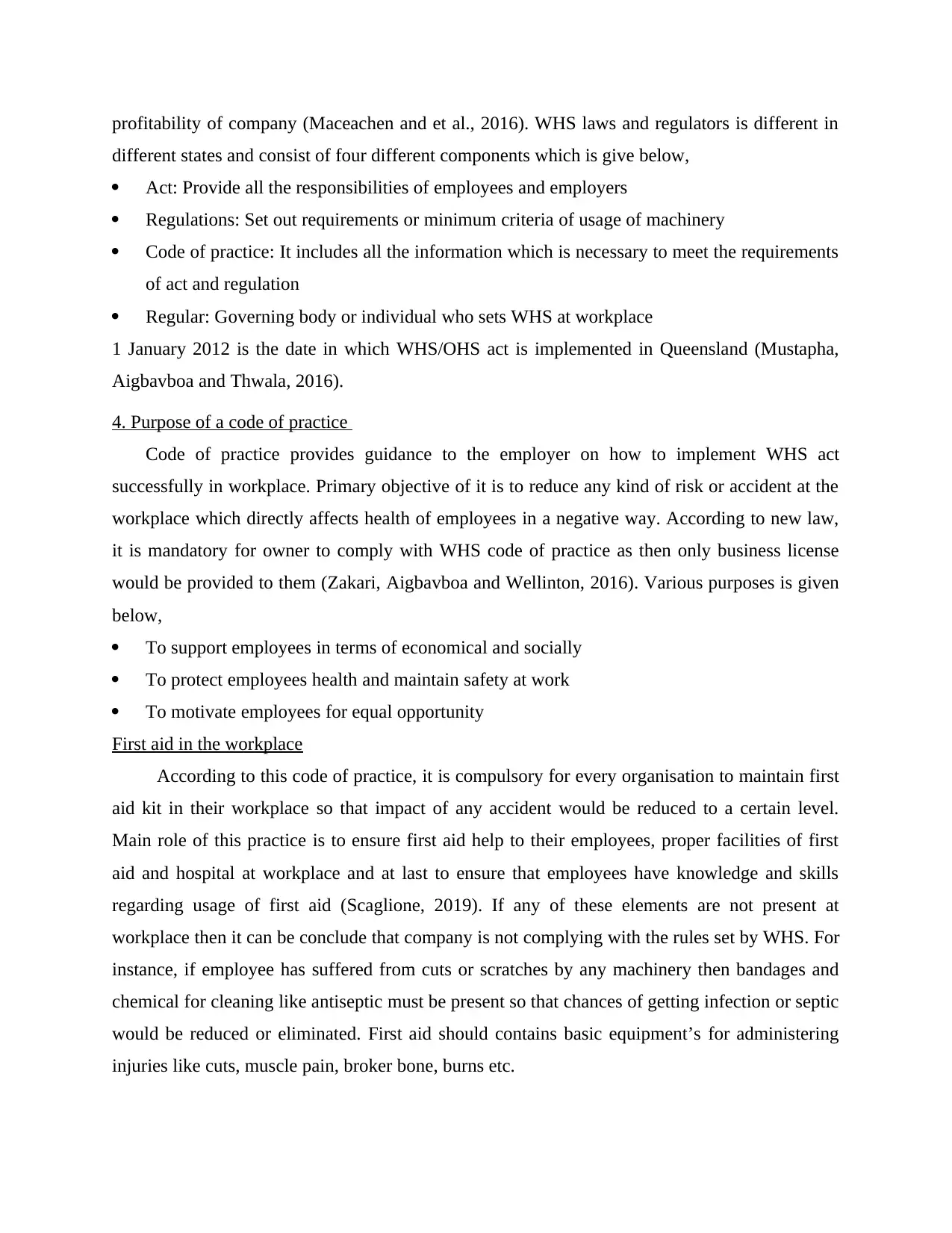
profitability of company (Maceachen and et al., 2016). WHS laws and regulators is different in
different states and consist of four different components which is give below,
Act: Provide all the responsibilities of employees and employers
Regulations: Set out requirements or minimum criteria of usage of machinery
Code of practice: It includes all the information which is necessary to meet the requirements
of act and regulation
Regular: Governing body or individual who sets WHS at workplace
1 January 2012 is the date in which WHS/OHS act is implemented in Queensland (Mustapha,
Aigbavboa and Thwala, 2016).
4. Purpose of a code of practice
Code of practice provides guidance to the employer on how to implement WHS act
successfully in workplace. Primary objective of it is to reduce any kind of risk or accident at the
workplace which directly affects health of employees in a negative way. According to new law,
it is mandatory for owner to comply with WHS code of practice as then only business license
would be provided to them (Zakari, Aigbavboa and Wellinton, 2016). Various purposes is given
below,
To support employees in terms of economical and socially
To protect employees health and maintain safety at work
To motivate employees for equal opportunity
First aid in the workplace
According to this code of practice, it is compulsory for every organisation to maintain first
aid kit in their workplace so that impact of any accident would be reduced to a certain level.
Main role of this practice is to ensure first aid help to their employees, proper facilities of first
aid and hospital at workplace and at last to ensure that employees have knowledge and skills
regarding usage of first aid (Scaglione, 2019). If any of these elements are not present at
workplace then it can be conclude that company is not complying with the rules set by WHS. For
instance, if employee has suffered from cuts or scratches by any machinery then bandages and
chemical for cleaning like antiseptic must be present so that chances of getting infection or septic
would be reduced or eliminated. First aid should contains basic equipment’s for administering
injuries like cuts, muscle pain, broker bone, burns etc.
different states and consist of four different components which is give below,
Act: Provide all the responsibilities of employees and employers
Regulations: Set out requirements or minimum criteria of usage of machinery
Code of practice: It includes all the information which is necessary to meet the requirements
of act and regulation
Regular: Governing body or individual who sets WHS at workplace
1 January 2012 is the date in which WHS/OHS act is implemented in Queensland (Mustapha,
Aigbavboa and Thwala, 2016).
4. Purpose of a code of practice
Code of practice provides guidance to the employer on how to implement WHS act
successfully in workplace. Primary objective of it is to reduce any kind of risk or accident at the
workplace which directly affects health of employees in a negative way. According to new law,
it is mandatory for owner to comply with WHS code of practice as then only business license
would be provided to them (Zakari, Aigbavboa and Wellinton, 2016). Various purposes is given
below,
To support employees in terms of economical and socially
To protect employees health and maintain safety at work
To motivate employees for equal opportunity
First aid in the workplace
According to this code of practice, it is compulsory for every organisation to maintain first
aid kit in their workplace so that impact of any accident would be reduced to a certain level.
Main role of this practice is to ensure first aid help to their employees, proper facilities of first
aid and hospital at workplace and at last to ensure that employees have knowledge and skills
regarding usage of first aid (Scaglione, 2019). If any of these elements are not present at
workplace then it can be conclude that company is not complying with the rules set by WHS. For
instance, if employee has suffered from cuts or scratches by any machinery then bandages and
chemical for cleaning like antiseptic must be present so that chances of getting infection or septic
would be reduced or eliminated. First aid should contains basic equipment’s for administering
injuries like cuts, muscle pain, broker bone, burns etc.
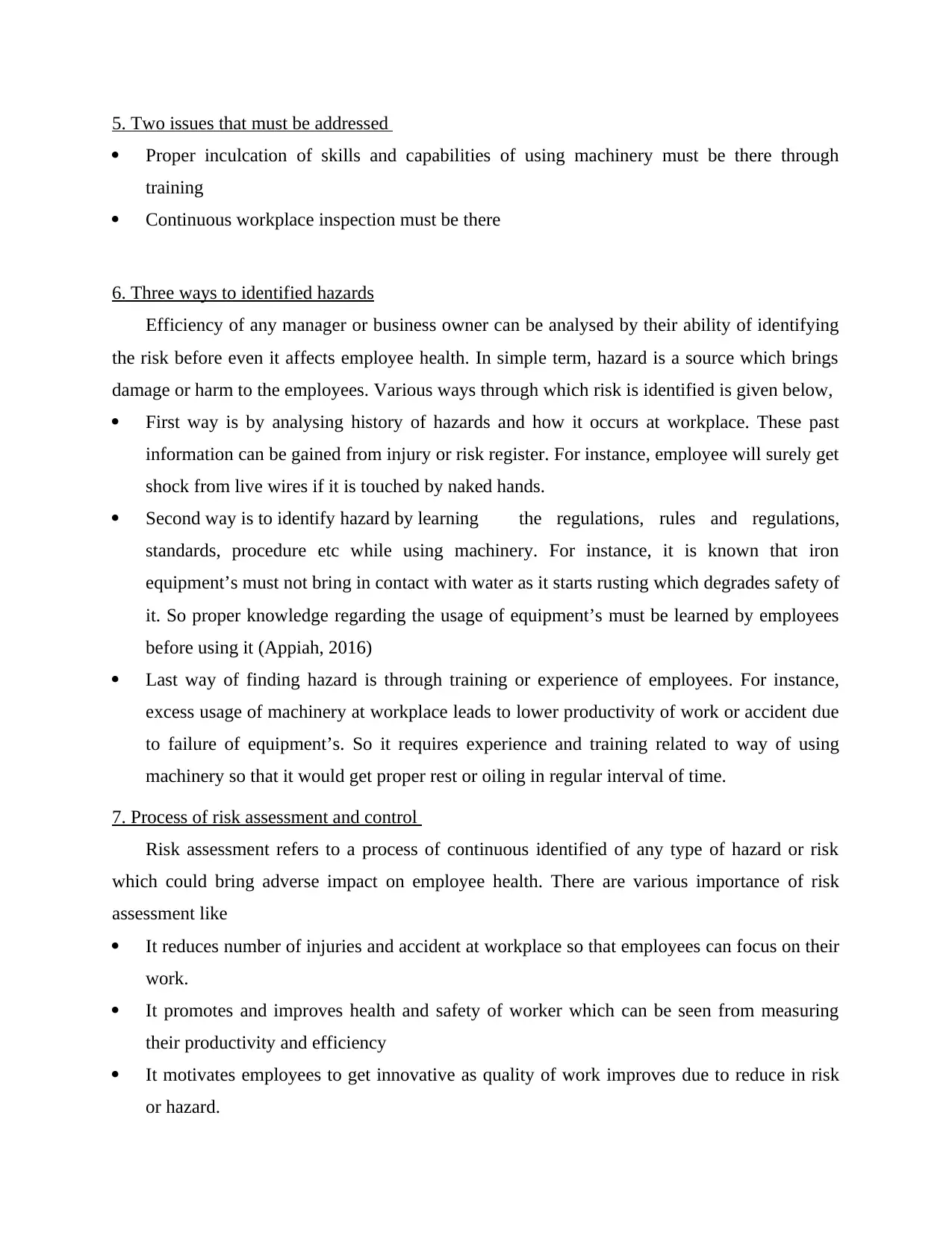
5. Two issues that must be addressed
Proper inculcation of skills and capabilities of using machinery must be there through
training
Continuous workplace inspection must be there
6. Three ways to identified hazards
Efficiency of any manager or business owner can be analysed by their ability of identifying
the risk before even it affects employee health. In simple term, hazard is a source which brings
damage or harm to the employees. Various ways through which risk is identified is given below,
First way is by analysing history of hazards and how it occurs at workplace. These past
information can be gained from injury or risk register. For instance, employee will surely get
shock from live wires if it is touched by naked hands.
Second way is to identify hazard by learning the regulations, rules and regulations,
standards, procedure etc while using machinery. For instance, it is known that iron
equipment’s must not bring in contact with water as it starts rusting which degrades safety of
it. So proper knowledge regarding the usage of equipment’s must be learned by employees
before using it (Appiah, 2016)
Last way of finding hazard is through training or experience of employees. For instance,
excess usage of machinery at workplace leads to lower productivity of work or accident due
to failure of equipment’s. So it requires experience and training related to way of using
machinery so that it would get proper rest or oiling in regular interval of time.
7. Process of risk assessment and control
Risk assessment refers to a process of continuous identified of any type of hazard or risk
which could bring adverse impact on employee health. There are various importance of risk
assessment like
It reduces number of injuries and accident at workplace so that employees can focus on their
work.
It promotes and improves health and safety of worker which can be seen from measuring
their productivity and efficiency
It motivates employees to get innovative as quality of work improves due to reduce in risk
or hazard.
Proper inculcation of skills and capabilities of using machinery must be there through
training
Continuous workplace inspection must be there
6. Three ways to identified hazards
Efficiency of any manager or business owner can be analysed by their ability of identifying
the risk before even it affects employee health. In simple term, hazard is a source which brings
damage or harm to the employees. Various ways through which risk is identified is given below,
First way is by analysing history of hazards and how it occurs at workplace. These past
information can be gained from injury or risk register. For instance, employee will surely get
shock from live wires if it is touched by naked hands.
Second way is to identify hazard by learning the regulations, rules and regulations,
standards, procedure etc while using machinery. For instance, it is known that iron
equipment’s must not bring in contact with water as it starts rusting which degrades safety of
it. So proper knowledge regarding the usage of equipment’s must be learned by employees
before using it (Appiah, 2016)
Last way of finding hazard is through training or experience of employees. For instance,
excess usage of machinery at workplace leads to lower productivity of work or accident due
to failure of equipment’s. So it requires experience and training related to way of using
machinery so that it would get proper rest or oiling in regular interval of time.
7. Process of risk assessment and control
Risk assessment refers to a process of continuous identified of any type of hazard or risk
which could bring adverse impact on employee health. There are various importance of risk
assessment like
It reduces number of injuries and accident at workplace so that employees can focus on their
work.
It promotes and improves health and safety of worker which can be seen from measuring
their productivity and efficiency
It motivates employees to get innovative as quality of work improves due to reduce in risk
or hazard.
Paraphrase This Document
Need a fresh take? Get an instant paraphrase of this document with our AI Paraphraser
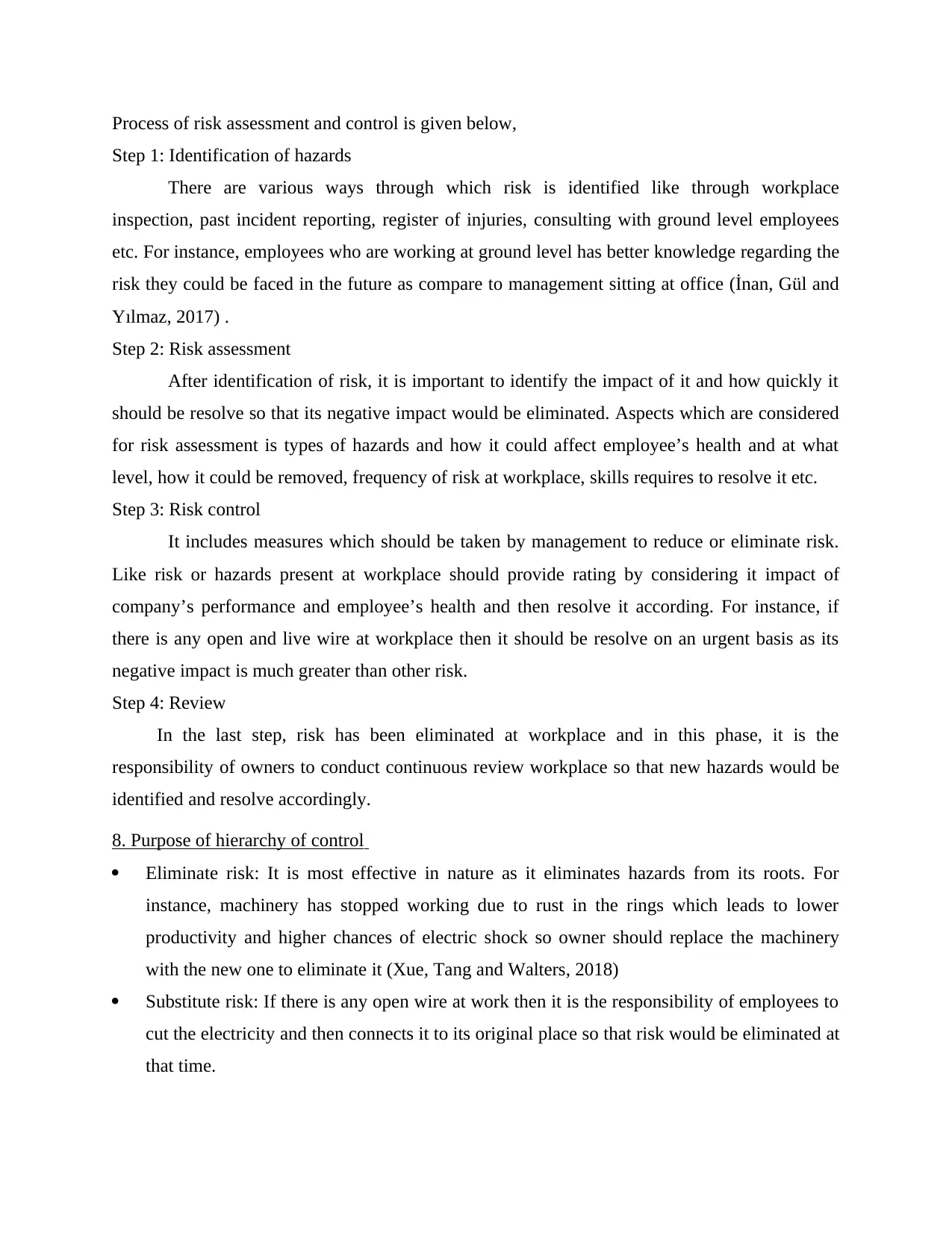
Process of risk assessment and control is given below,
Step 1: Identification of hazards
There are various ways through which risk is identified like through workplace
inspection, past incident reporting, register of injuries, consulting with ground level employees
etc. For instance, employees who are working at ground level has better knowledge regarding the
risk they could be faced in the future as compare to management sitting at office (İnan, Gül and
Yılmaz, 2017) .
Step 2: Risk assessment
After identification of risk, it is important to identify the impact of it and how quickly it
should be resolve so that its negative impact would be eliminated. Aspects which are considered
for risk assessment is types of hazards and how it could affect employee’s health and at what
level, how it could be removed, frequency of risk at workplace, skills requires to resolve it etc.
Step 3: Risk control
It includes measures which should be taken by management to reduce or eliminate risk.
Like risk or hazards present at workplace should provide rating by considering it impact of
company’s performance and employee’s health and then resolve it according. For instance, if
there is any open and live wire at workplace then it should be resolve on an urgent basis as its
negative impact is much greater than other risk.
Step 4: Review
In the last step, risk has been eliminated at workplace and in this phase, it is the
responsibility of owners to conduct continuous review workplace so that new hazards would be
identified and resolve accordingly.
8. Purpose of hierarchy of control
Eliminate risk: It is most effective in nature as it eliminates hazards from its roots. For
instance, machinery has stopped working due to rust in the rings which leads to lower
productivity and higher chances of electric shock so owner should replace the machinery
with the new one to eliminate it (Xue, Tang and Walters, 2018)
Substitute risk: If there is any open wire at work then it is the responsibility of employees to
cut the electricity and then connects it to its original place so that risk would be eliminated at
that time.
Step 1: Identification of hazards
There are various ways through which risk is identified like through workplace
inspection, past incident reporting, register of injuries, consulting with ground level employees
etc. For instance, employees who are working at ground level has better knowledge regarding the
risk they could be faced in the future as compare to management sitting at office (İnan, Gül and
Yılmaz, 2017) .
Step 2: Risk assessment
After identification of risk, it is important to identify the impact of it and how quickly it
should be resolve so that its negative impact would be eliminated. Aspects which are considered
for risk assessment is types of hazards and how it could affect employee’s health and at what
level, how it could be removed, frequency of risk at workplace, skills requires to resolve it etc.
Step 3: Risk control
It includes measures which should be taken by management to reduce or eliminate risk.
Like risk or hazards present at workplace should provide rating by considering it impact of
company’s performance and employee’s health and then resolve it according. For instance, if
there is any open and live wire at workplace then it should be resolve on an urgent basis as its
negative impact is much greater than other risk.
Step 4: Review
In the last step, risk has been eliminated at workplace and in this phase, it is the
responsibility of owners to conduct continuous review workplace so that new hazards would be
identified and resolve accordingly.
8. Purpose of hierarchy of control
Eliminate risk: It is most effective in nature as it eliminates hazards from its roots. For
instance, machinery has stopped working due to rust in the rings which leads to lower
productivity and higher chances of electric shock so owner should replace the machinery
with the new one to eliminate it (Xue, Tang and Walters, 2018)
Substitute risk: If there is any open wire at work then it is the responsibility of employees to
cut the electricity and then connects it to its original place so that risk would be eliminated at
that time.
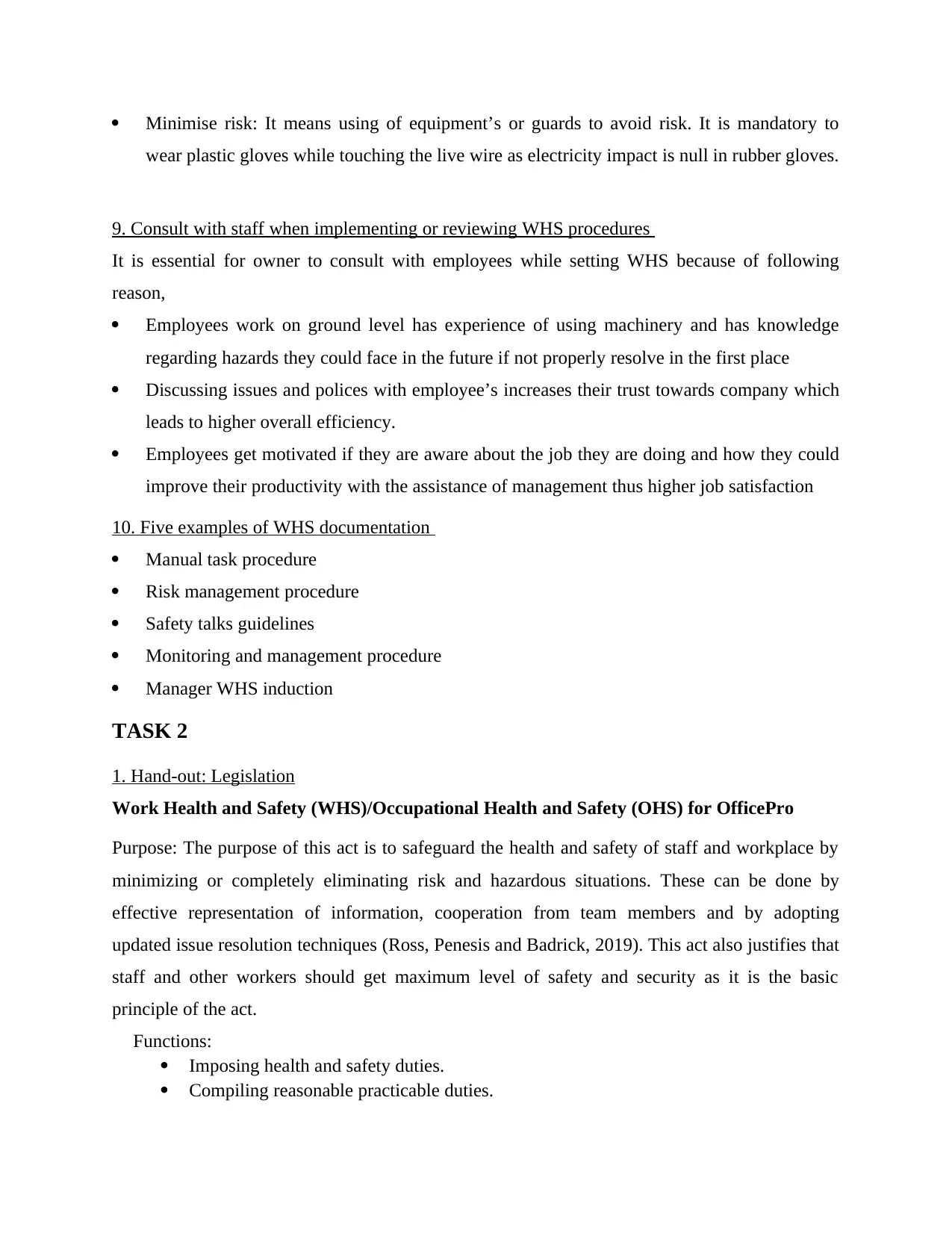
Minimise risk: It means using of equipment’s or guards to avoid risk. It is mandatory to
wear plastic gloves while touching the live wire as electricity impact is null in rubber gloves.
9. Consult with staff when implementing or reviewing WHS procedures
It is essential for owner to consult with employees while setting WHS because of following
reason,
Employees work on ground level has experience of using machinery and has knowledge
regarding hazards they could face in the future if not properly resolve in the first place
Discussing issues and polices with employee’s increases their trust towards company which
leads to higher overall efficiency.
Employees get motivated if they are aware about the job they are doing and how they could
improve their productivity with the assistance of management thus higher job satisfaction
10. Five examples of WHS documentation
Manual task procedure
Risk management procedure
Safety talks guidelines
Monitoring and management procedure
Manager WHS induction
TASK 2
1. Hand-out: Legislation
Work Health and Safety (WHS)/Occupational Health and Safety (OHS) for OfficePro
Purpose: The purpose of this act is to safeguard the health and safety of staff and workplace by
minimizing or completely eliminating risk and hazardous situations. These can be done by
effective representation of information, cooperation from team members and by adopting
updated issue resolution techniques (Ross, Penesis and Badrick, 2019). This act also justifies that
staff and other workers should get maximum level of safety and security as it is the basic
principle of the act.
Functions:
Imposing health and safety duties.
Compiling reasonable practicable duties.
wear plastic gloves while touching the live wire as electricity impact is null in rubber gloves.
9. Consult with staff when implementing or reviewing WHS procedures
It is essential for owner to consult with employees while setting WHS because of following
reason,
Employees work on ground level has experience of using machinery and has knowledge
regarding hazards they could face in the future if not properly resolve in the first place
Discussing issues and polices with employee’s increases their trust towards company which
leads to higher overall efficiency.
Employees get motivated if they are aware about the job they are doing and how they could
improve their productivity with the assistance of management thus higher job satisfaction
10. Five examples of WHS documentation
Manual task procedure
Risk management procedure
Safety talks guidelines
Monitoring and management procedure
Manager WHS induction
TASK 2
1. Hand-out: Legislation
Work Health and Safety (WHS)/Occupational Health and Safety (OHS) for OfficePro
Purpose: The purpose of this act is to safeguard the health and safety of staff and workplace by
minimizing or completely eliminating risk and hazardous situations. These can be done by
effective representation of information, cooperation from team members and by adopting
updated issue resolution techniques (Ross, Penesis and Badrick, 2019). This act also justifies that
staff and other workers should get maximum level of safety and security as it is the basic
principle of the act.
Functions:
Imposing health and safety duties.
Compiling reasonable practicable duties.
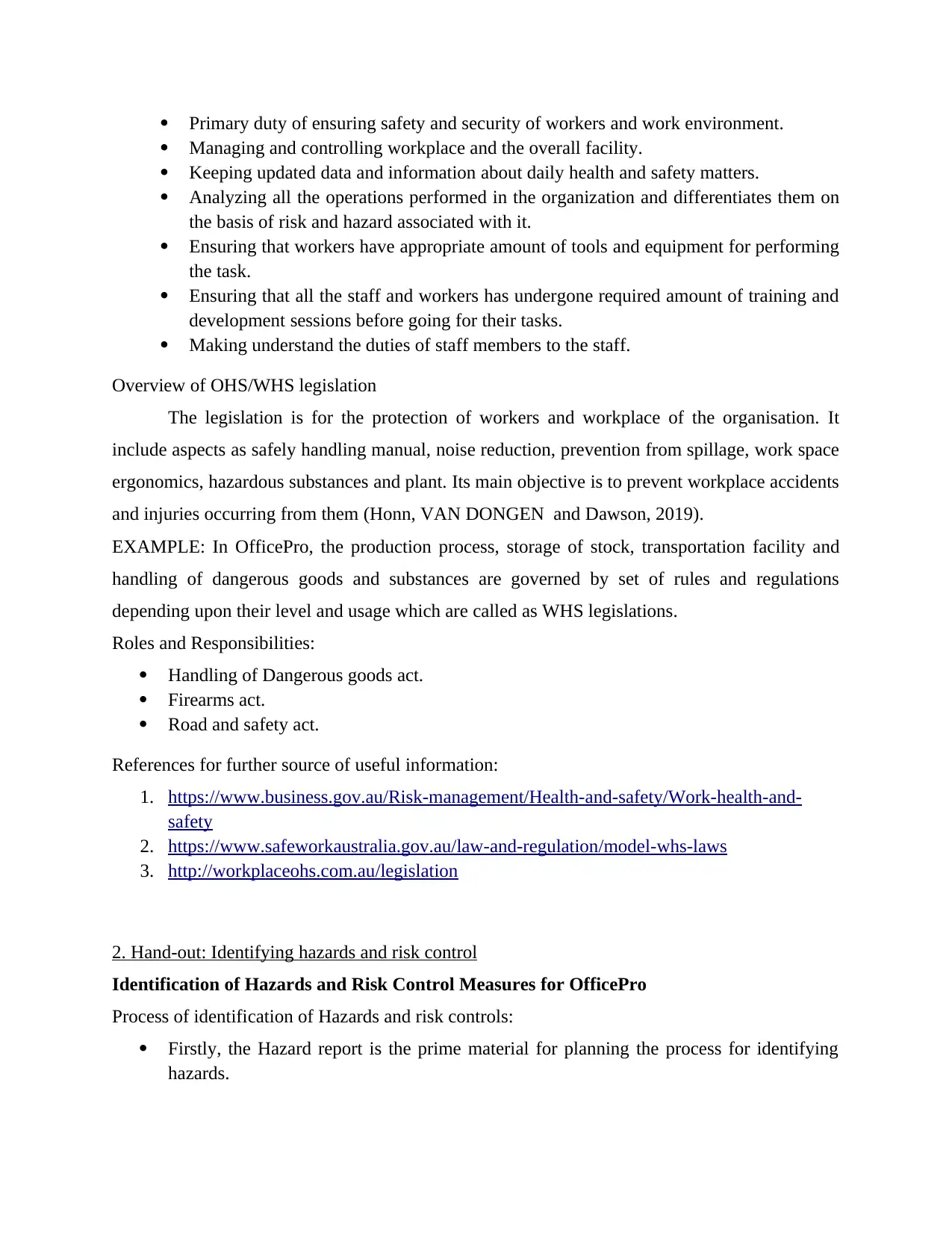
Primary duty of ensuring safety and security of workers and work environment.
Managing and controlling workplace and the overall facility.
Keeping updated data and information about daily health and safety matters.
Analyzing all the operations performed in the organization and differentiates them on
the basis of risk and hazard associated with it.
Ensuring that workers have appropriate amount of tools and equipment for performing
the task.
Ensuring that all the staff and workers has undergone required amount of training and
development sessions before going for their tasks.
Making understand the duties of staff members to the staff.
Overview of OHS/WHS legislation
The legislation is for the protection of workers and workplace of the organisation. It
include aspects as safely handling manual, noise reduction, prevention from spillage, work space
ergonomics, hazardous substances and plant. Its main objective is to prevent workplace accidents
and injuries occurring from them (Honn, VAN DONGEN and Dawson, 2019).
EXAMPLE: In OfficePro, the production process, storage of stock, transportation facility and
handling of dangerous goods and substances are governed by set of rules and regulations
depending upon their level and usage which are called as WHS legislations.
Roles and Responsibilities:
Handling of Dangerous goods act.
Firearms act.
Road and safety act.
References for further source of useful information:
1. https://www.business.gov.au/Risk-management/Health-and-safety/Work-health-and-
safety
2. https://www.safeworkaustralia.gov.au/law-and-regulation/model-whs-laws
3. http://workplaceohs.com.au/legislation
2. Hand-out: Identifying hazards and risk control
Identification of Hazards and Risk Control Measures for OfficePro
Process of identification of Hazards and risk controls:
Firstly, the Hazard report is the prime material for planning the process for identifying
hazards.
Managing and controlling workplace and the overall facility.
Keeping updated data and information about daily health and safety matters.
Analyzing all the operations performed in the organization and differentiates them on
the basis of risk and hazard associated with it.
Ensuring that workers have appropriate amount of tools and equipment for performing
the task.
Ensuring that all the staff and workers has undergone required amount of training and
development sessions before going for their tasks.
Making understand the duties of staff members to the staff.
Overview of OHS/WHS legislation
The legislation is for the protection of workers and workplace of the organisation. It
include aspects as safely handling manual, noise reduction, prevention from spillage, work space
ergonomics, hazardous substances and plant. Its main objective is to prevent workplace accidents
and injuries occurring from them (Honn, VAN DONGEN and Dawson, 2019).
EXAMPLE: In OfficePro, the production process, storage of stock, transportation facility and
handling of dangerous goods and substances are governed by set of rules and regulations
depending upon their level and usage which are called as WHS legislations.
Roles and Responsibilities:
Handling of Dangerous goods act.
Firearms act.
Road and safety act.
References for further source of useful information:
1. https://www.business.gov.au/Risk-management/Health-and-safety/Work-health-and-
safety
2. https://www.safeworkaustralia.gov.au/law-and-regulation/model-whs-laws
3. http://workplaceohs.com.au/legislation
2. Hand-out: Identifying hazards and risk control
Identification of Hazards and Risk Control Measures for OfficePro
Process of identification of Hazards and risk controls:
Firstly, the Hazard report is the prime material for planning the process for identifying
hazards.
Secure Best Marks with AI Grader
Need help grading? Try our AI Grader for instant feedback on your assignments.
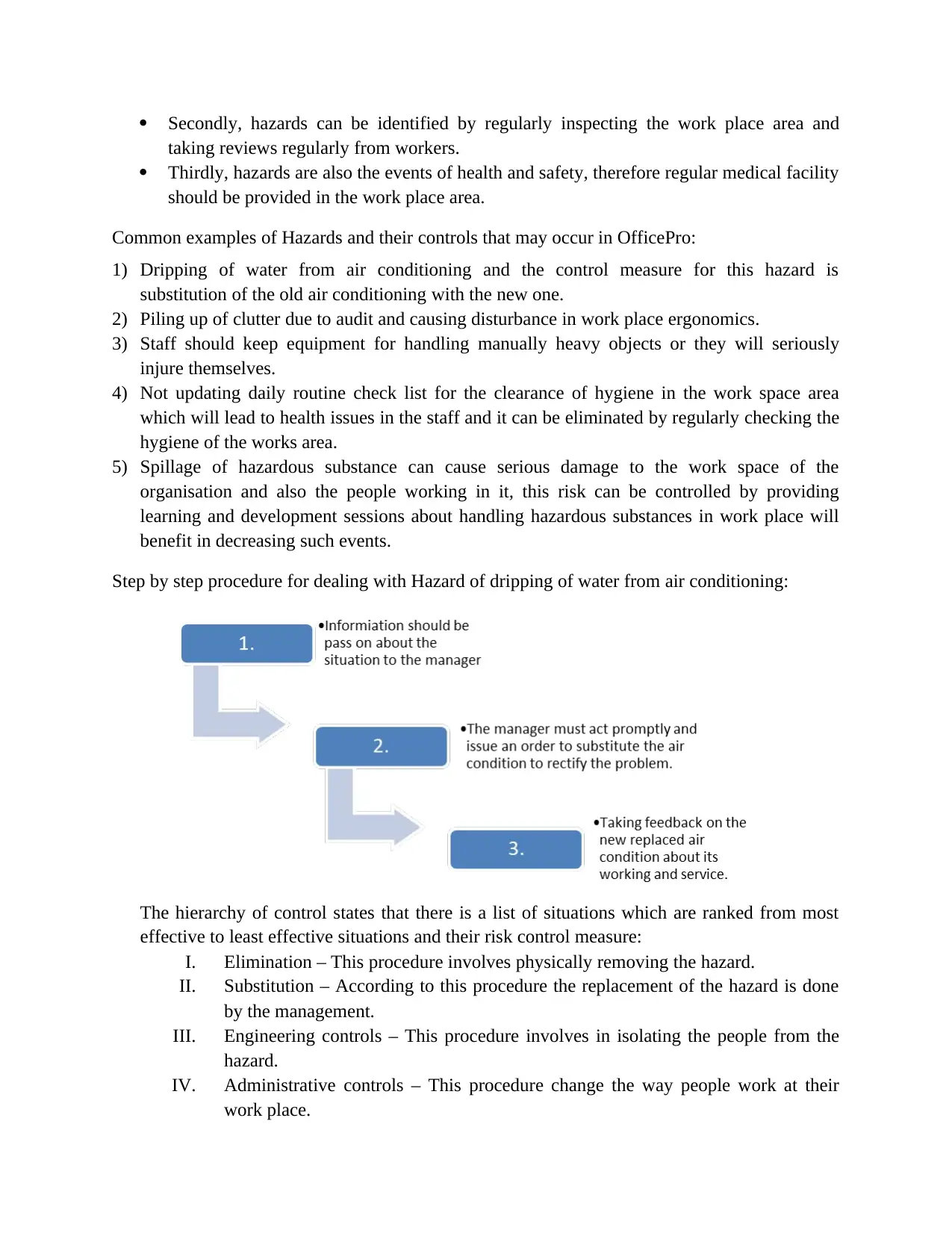
Secondly, hazards can be identified by regularly inspecting the work place area and
taking reviews regularly from workers.
Thirdly, hazards are also the events of health and safety, therefore regular medical facility
should be provided in the work place area.
Common examples of Hazards and their controls that may occur in OfficePro:
1) Dripping of water from air conditioning and the control measure for this hazard is
substitution of the old air conditioning with the new one.
2) Piling up of clutter due to audit and causing disturbance in work place ergonomics.
3) Staff should keep equipment for handling manually heavy objects or they will seriously
injure themselves.
4) Not updating daily routine check list for the clearance of hygiene in the work space area
which will lead to health issues in the staff and it can be eliminated by regularly checking the
hygiene of the works area.
5) Spillage of hazardous substance can cause serious damage to the work space of the
organisation and also the people working in it, this risk can be controlled by providing
learning and development sessions about handling hazardous substances in work place will
benefit in decreasing such events.
Step by step procedure for dealing with Hazard of dripping of water from air conditioning:
The hierarchy of control states that there is a list of situations which are ranked from most
effective to least effective situations and their risk control measure:
I. Elimination – This procedure involves physically removing the hazard.
II. Substitution – According to this procedure the replacement of the hazard is done
by the management.
III. Engineering controls – This procedure involves in isolating the people from the
hazard.
IV. Administrative controls – This procedure change the way people work at their
work place.
taking reviews regularly from workers.
Thirdly, hazards are also the events of health and safety, therefore regular medical facility
should be provided in the work place area.
Common examples of Hazards and their controls that may occur in OfficePro:
1) Dripping of water from air conditioning and the control measure for this hazard is
substitution of the old air conditioning with the new one.
2) Piling up of clutter due to audit and causing disturbance in work place ergonomics.
3) Staff should keep equipment for handling manually heavy objects or they will seriously
injure themselves.
4) Not updating daily routine check list for the clearance of hygiene in the work space area
which will lead to health issues in the staff and it can be eliminated by regularly checking the
hygiene of the works area.
5) Spillage of hazardous substance can cause serious damage to the work space of the
organisation and also the people working in it, this risk can be controlled by providing
learning and development sessions about handling hazardous substances in work place will
benefit in decreasing such events.
Step by step procedure for dealing with Hazard of dripping of water from air conditioning:
The hierarchy of control states that there is a list of situations which are ranked from most
effective to least effective situations and their risk control measure:
I. Elimination – This procedure involves physically removing the hazard.
II. Substitution – According to this procedure the replacement of the hazard is done
by the management.
III. Engineering controls – This procedure involves in isolating the people from the
hazard.
IV. Administrative controls – This procedure change the way people work at their
work place.
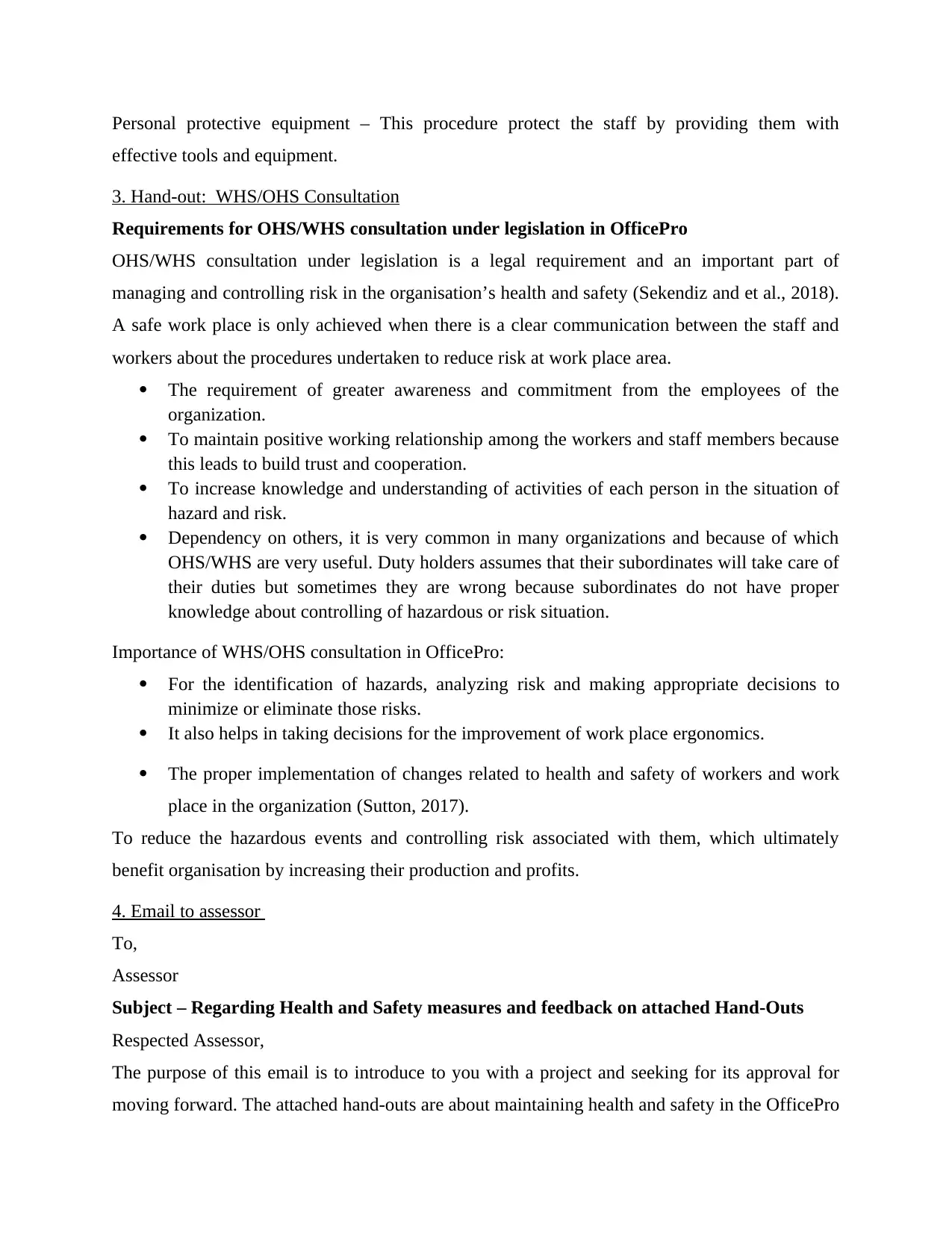
Personal protective equipment – This procedure protect the staff by providing them with
effective tools and equipment.
3. Hand-out: WHS/OHS Consultation
Requirements for OHS/WHS consultation under legislation in OfficePro
OHS/WHS consultation under legislation is a legal requirement and an important part of
managing and controlling risk in the organisation’s health and safety (Sekendiz and et al., 2018).
A safe work place is only achieved when there is a clear communication between the staff and
workers about the procedures undertaken to reduce risk at work place area.
The requirement of greater awareness and commitment from the employees of the
organization.
To maintain positive working relationship among the workers and staff members because
this leads to build trust and cooperation.
To increase knowledge and understanding of activities of each person in the situation of
hazard and risk.
Dependency on others, it is very common in many organizations and because of which
OHS/WHS are very useful. Duty holders assumes that their subordinates will take care of
their duties but sometimes they are wrong because subordinates do not have proper
knowledge about controlling of hazardous or risk situation.
Importance of WHS/OHS consultation in OfficePro:
For the identification of hazards, analyzing risk and making appropriate decisions to
minimize or eliminate those risks.
It also helps in taking decisions for the improvement of work place ergonomics.
The proper implementation of changes related to health and safety of workers and work
place in the organization (Sutton, 2017).
To reduce the hazardous events and controlling risk associated with them, which ultimately
benefit organisation by increasing their production and profits.
4. Email to assessor
To,
Assessor
Subject – Regarding Health and Safety measures and feedback on attached Hand-Outs
Respected Assessor,
The purpose of this email is to introduce to you with a project and seeking for its approval for
moving forward. The attached hand-outs are about maintaining health and safety in the OfficePro
effective tools and equipment.
3. Hand-out: WHS/OHS Consultation
Requirements for OHS/WHS consultation under legislation in OfficePro
OHS/WHS consultation under legislation is a legal requirement and an important part of
managing and controlling risk in the organisation’s health and safety (Sekendiz and et al., 2018).
A safe work place is only achieved when there is a clear communication between the staff and
workers about the procedures undertaken to reduce risk at work place area.
The requirement of greater awareness and commitment from the employees of the
organization.
To maintain positive working relationship among the workers and staff members because
this leads to build trust and cooperation.
To increase knowledge and understanding of activities of each person in the situation of
hazard and risk.
Dependency on others, it is very common in many organizations and because of which
OHS/WHS are very useful. Duty holders assumes that their subordinates will take care of
their duties but sometimes they are wrong because subordinates do not have proper
knowledge about controlling of hazardous or risk situation.
Importance of WHS/OHS consultation in OfficePro:
For the identification of hazards, analyzing risk and making appropriate decisions to
minimize or eliminate those risks.
It also helps in taking decisions for the improvement of work place ergonomics.
The proper implementation of changes related to health and safety of workers and work
place in the organization (Sutton, 2017).
To reduce the hazardous events and controlling risk associated with them, which ultimately
benefit organisation by increasing their production and profits.
4. Email to assessor
To,
Assessor
Subject – Regarding Health and Safety measures and feedback on attached Hand-Outs
Respected Assessor,
The purpose of this email is to introduce to you with a project and seeking for its approval for
moving forward. The attached hand-outs are about maintaining health and safety in the OfficePro
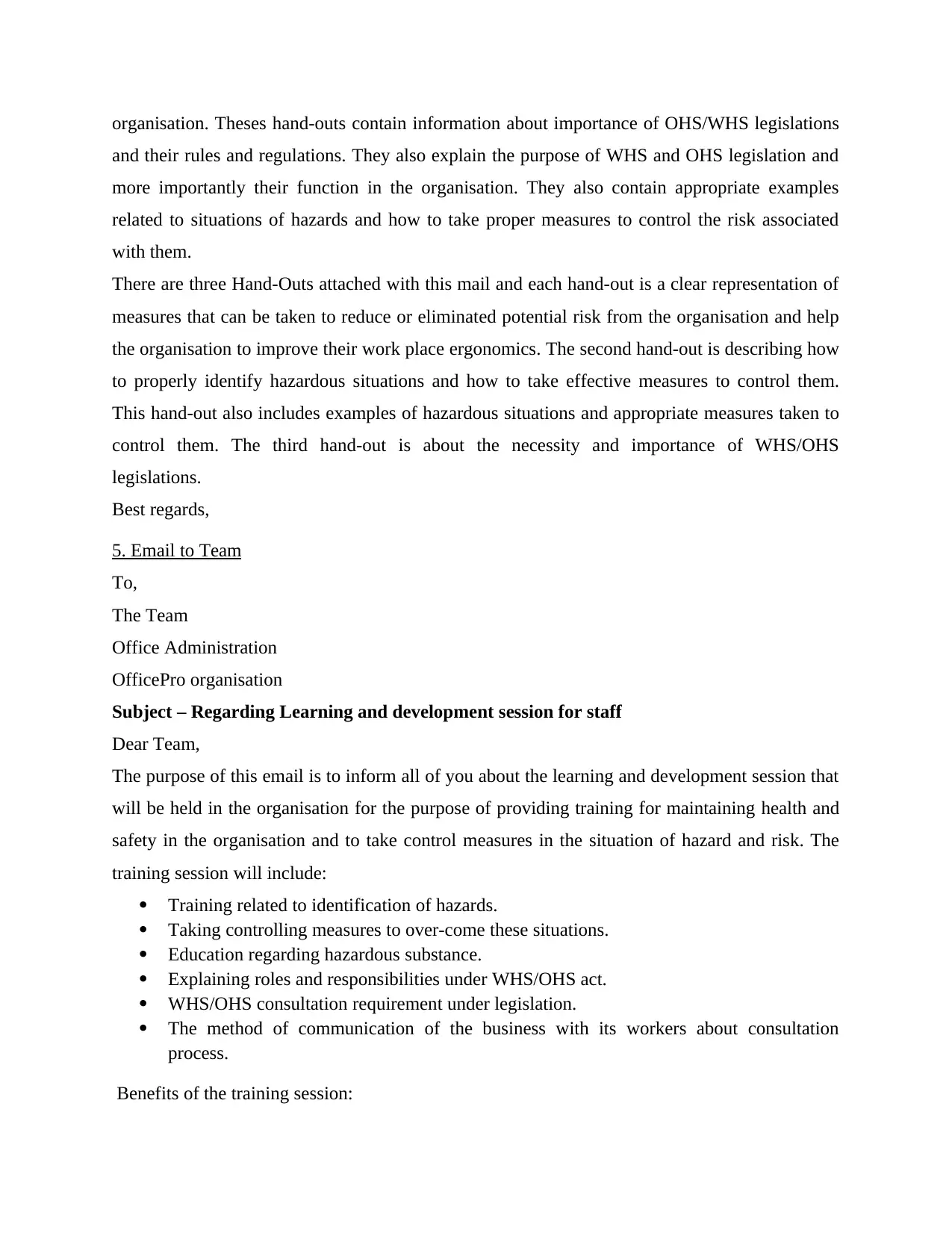
organisation. Theses hand-outs contain information about importance of OHS/WHS legislations
and their rules and regulations. They also explain the purpose of WHS and OHS legislation and
more importantly their function in the organisation. They also contain appropriate examples
related to situations of hazards and how to take proper measures to control the risk associated
with them.
There are three Hand-Outs attached with this mail and each hand-out is a clear representation of
measures that can be taken to reduce or eliminated potential risk from the organisation and help
the organisation to improve their work place ergonomics. The second hand-out is describing how
to properly identify hazardous situations and how to take effective measures to control them.
This hand-out also includes examples of hazardous situations and appropriate measures taken to
control them. The third hand-out is about the necessity and importance of WHS/OHS
legislations.
Best regards,
5. Email to Team
To,
The Team
Office Administration
OfficePro organisation
Subject – Regarding Learning and development session for staff
Dear Team,
The purpose of this email is to inform all of you about the learning and development session that
will be held in the organisation for the purpose of providing training for maintaining health and
safety in the organisation and to take control measures in the situation of hazard and risk. The
training session will include:
Training related to identification of hazards.
Taking controlling measures to over-come these situations.
Education regarding hazardous substance.
Explaining roles and responsibilities under WHS/OHS act.
WHS/OHS consultation requirement under legislation.
The method of communication of the business with its workers about consultation
process.
Benefits of the training session:
and their rules and regulations. They also explain the purpose of WHS and OHS legislation and
more importantly their function in the organisation. They also contain appropriate examples
related to situations of hazards and how to take proper measures to control the risk associated
with them.
There are three Hand-Outs attached with this mail and each hand-out is a clear representation of
measures that can be taken to reduce or eliminated potential risk from the organisation and help
the organisation to improve their work place ergonomics. The second hand-out is describing how
to properly identify hazardous situations and how to take effective measures to control them.
This hand-out also includes examples of hazardous situations and appropriate measures taken to
control them. The third hand-out is about the necessity and importance of WHS/OHS
legislations.
Best regards,
5. Email to Team
To,
The Team
Office Administration
OfficePro organisation
Subject – Regarding Learning and development session for staff
Dear Team,
The purpose of this email is to inform all of you about the learning and development session that
will be held in the organisation for the purpose of providing training for maintaining health and
safety in the organisation and to take control measures in the situation of hazard and risk. The
training session will include:
Training related to identification of hazards.
Taking controlling measures to over-come these situations.
Education regarding hazardous substance.
Explaining roles and responsibilities under WHS/OHS act.
WHS/OHS consultation requirement under legislation.
The method of communication of the business with its workers about consultation
process.
Benefits of the training session:
Paraphrase This Document
Need a fresh take? Get an instant paraphrase of this document with our AI Paraphraser
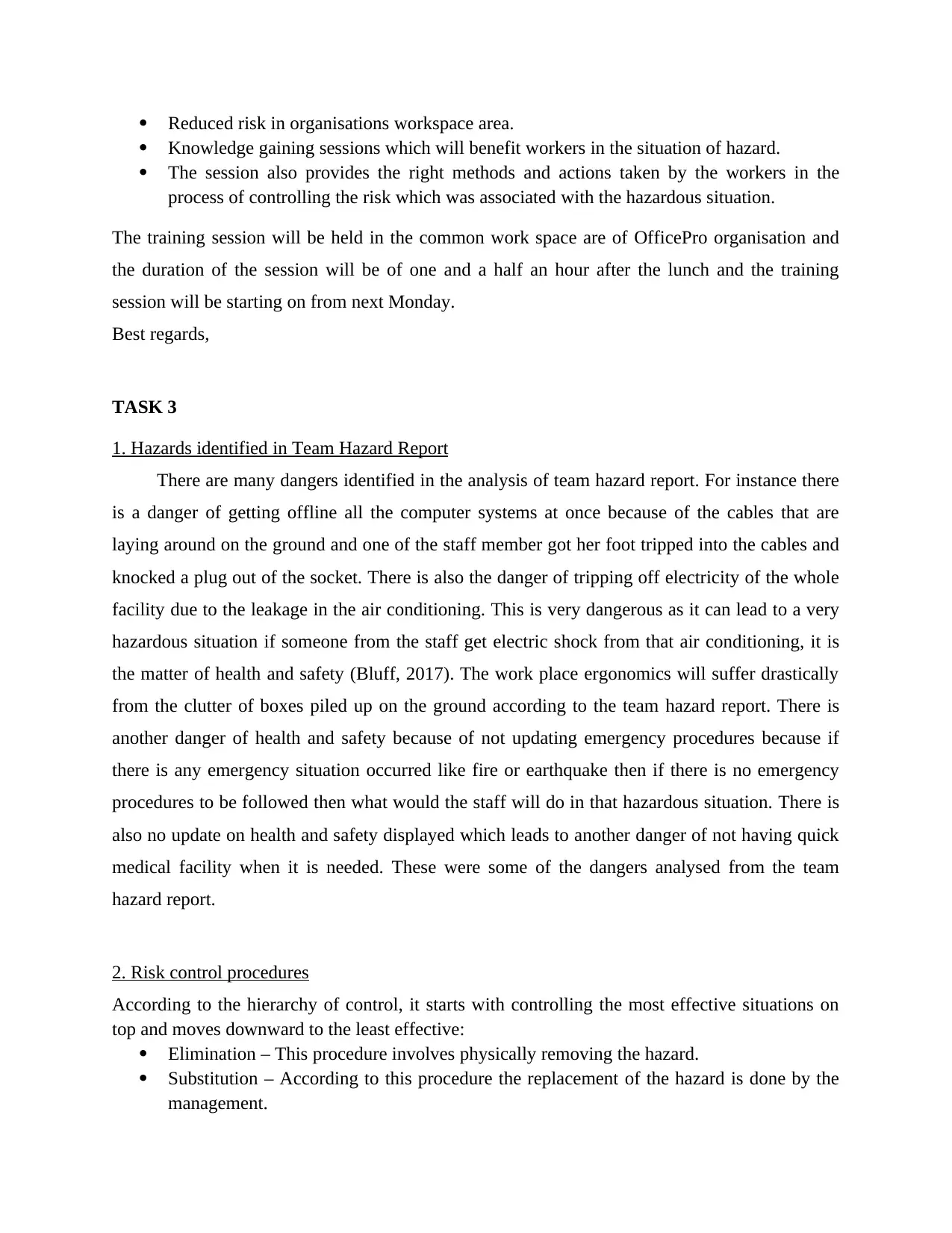
Reduced risk in organisations workspace area.
Knowledge gaining sessions which will benefit workers in the situation of hazard.
The session also provides the right methods and actions taken by the workers in the
process of controlling the risk which was associated with the hazardous situation.
The training session will be held in the common work space are of OfficePro organisation and
the duration of the session will be of one and a half an hour after the lunch and the training
session will be starting on from next Monday.
Best regards,
TASK 3
1. Hazards identified in Team Hazard Report
There are many dangers identified in the analysis of team hazard report. For instance there
is a danger of getting offline all the computer systems at once because of the cables that are
laying around on the ground and one of the staff member got her foot tripped into the cables and
knocked a plug out of the socket. There is also the danger of tripping off electricity of the whole
facility due to the leakage in the air conditioning. This is very dangerous as it can lead to a very
hazardous situation if someone from the staff get electric shock from that air conditioning, it is
the matter of health and safety (Bluff, 2017). The work place ergonomics will suffer drastically
from the clutter of boxes piled up on the ground according to the team hazard report. There is
another danger of health and safety because of not updating emergency procedures because if
there is any emergency situation occurred like fire or earthquake then if there is no emergency
procedures to be followed then what would the staff will do in that hazardous situation. There is
also no update on health and safety displayed which leads to another danger of not having quick
medical facility when it is needed. These were some of the dangers analysed from the team
hazard report.
2. Risk control procedures
According to the hierarchy of control, it starts with controlling the most effective situations on
top and moves downward to the least effective:
Elimination – This procedure involves physically removing the hazard.
Substitution – According to this procedure the replacement of the hazard is done by the
management.
Knowledge gaining sessions which will benefit workers in the situation of hazard.
The session also provides the right methods and actions taken by the workers in the
process of controlling the risk which was associated with the hazardous situation.
The training session will be held in the common work space are of OfficePro organisation and
the duration of the session will be of one and a half an hour after the lunch and the training
session will be starting on from next Monday.
Best regards,
TASK 3
1. Hazards identified in Team Hazard Report
There are many dangers identified in the analysis of team hazard report. For instance there
is a danger of getting offline all the computer systems at once because of the cables that are
laying around on the ground and one of the staff member got her foot tripped into the cables and
knocked a plug out of the socket. There is also the danger of tripping off electricity of the whole
facility due to the leakage in the air conditioning. This is very dangerous as it can lead to a very
hazardous situation if someone from the staff get electric shock from that air conditioning, it is
the matter of health and safety (Bluff, 2017). The work place ergonomics will suffer drastically
from the clutter of boxes piled up on the ground according to the team hazard report. There is
another danger of health and safety because of not updating emergency procedures because if
there is any emergency situation occurred like fire or earthquake then if there is no emergency
procedures to be followed then what would the staff will do in that hazardous situation. There is
also no update on health and safety displayed which leads to another danger of not having quick
medical facility when it is needed. These were some of the dangers analysed from the team
hazard report.
2. Risk control procedures
According to the hierarchy of control, it starts with controlling the most effective situations on
top and moves downward to the least effective:
Elimination – This procedure involves physically removing the hazard.
Substitution – According to this procedure the replacement of the hazard is done by the
management.
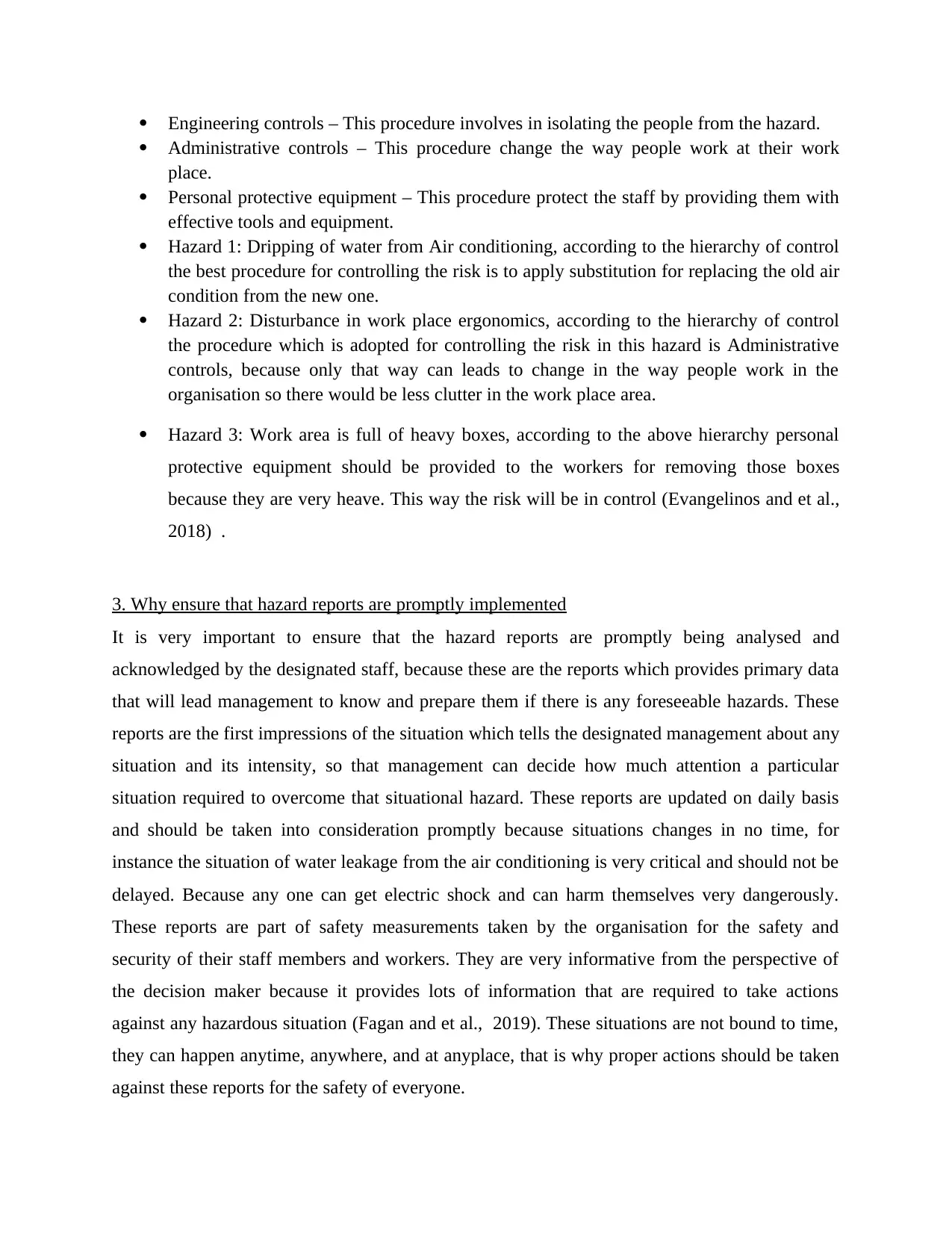
Engineering controls – This procedure involves in isolating the people from the hazard.
Administrative controls – This procedure change the way people work at their work
place.
Personal protective equipment – This procedure protect the staff by providing them with
effective tools and equipment.
Hazard 1: Dripping of water from Air conditioning, according to the hierarchy of control
the best procedure for controlling the risk is to apply substitution for replacing the old air
condition from the new one.
Hazard 2: Disturbance in work place ergonomics, according to the hierarchy of control
the procedure which is adopted for controlling the risk in this hazard is Administrative
controls, because only that way can leads to change in the way people work in the
organisation so there would be less clutter in the work place area.
Hazard 3: Work area is full of heavy boxes, according to the above hierarchy personal
protective equipment should be provided to the workers for removing those boxes
because they are very heave. This way the risk will be in control (Evangelinos and et al.,
2018) .
3. Why ensure that hazard reports are promptly implemented
It is very important to ensure that the hazard reports are promptly being analysed and
acknowledged by the designated staff, because these are the reports which provides primary data
that will lead management to know and prepare them if there is any foreseeable hazards. These
reports are the first impressions of the situation which tells the designated management about any
situation and its intensity, so that management can decide how much attention a particular
situation required to overcome that situational hazard. These reports are updated on daily basis
and should be taken into consideration promptly because situations changes in no time, for
instance the situation of water leakage from the air conditioning is very critical and should not be
delayed. Because any one can get electric shock and can harm themselves very dangerously.
These reports are part of safety measurements taken by the organisation for the safety and
security of their staff members and workers. They are very informative from the perspective of
the decision maker because it provides lots of information that are required to take actions
against any hazardous situation (Fagan and et al., 2019). These situations are not bound to time,
they can happen anytime, anywhere, and at anyplace, that is why proper actions should be taken
against these reports for the safety of everyone.
Administrative controls – This procedure change the way people work at their work
place.
Personal protective equipment – This procedure protect the staff by providing them with
effective tools and equipment.
Hazard 1: Dripping of water from Air conditioning, according to the hierarchy of control
the best procedure for controlling the risk is to apply substitution for replacing the old air
condition from the new one.
Hazard 2: Disturbance in work place ergonomics, according to the hierarchy of control
the procedure which is adopted for controlling the risk in this hazard is Administrative
controls, because only that way can leads to change in the way people work in the
organisation so there would be less clutter in the work place area.
Hazard 3: Work area is full of heavy boxes, according to the above hierarchy personal
protective equipment should be provided to the workers for removing those boxes
because they are very heave. This way the risk will be in control (Evangelinos and et al.,
2018) .
3. Why ensure that hazard reports are promptly implemented
It is very important to ensure that the hazard reports are promptly being analysed and
acknowledged by the designated staff, because these are the reports which provides primary data
that will lead management to know and prepare them if there is any foreseeable hazards. These
reports are the first impressions of the situation which tells the designated management about any
situation and its intensity, so that management can decide how much attention a particular
situation required to overcome that situational hazard. These reports are updated on daily basis
and should be taken into consideration promptly because situations changes in no time, for
instance the situation of water leakage from the air conditioning is very critical and should not be
delayed. Because any one can get electric shock and can harm themselves very dangerously.
These reports are part of safety measurements taken by the organisation for the safety and
security of their staff members and workers. They are very informative from the perspective of
the decision maker because it provides lots of information that are required to take actions
against any hazardous situation (Fagan and et al., 2019). These situations are not bound to time,
they can happen anytime, anywhere, and at anyplace, that is why proper actions should be taken
against these reports for the safety of everyone.

4. Further training provided to the employees
According to the Team Hazard Report from Andrew, there are some WHS training courses
which are still required by the staff for the complete safety of the work place environment. The
frequency of training and its amount shows the level of risk involved in the hazardous situation.
The training must by very thorough and covers all the elements of risks involved. It does not
matter that the staff is from which department health and safety training should be attended by
everyone in the organisation (Bluff, 2019). These training courses are based on the analysis of
the hazard report and are as follows:
Safe manual handling – According to the hazard report some workers hurt their back in
moving those heavy boxes which are lying on the floor of the work area.
First aid – As according to the report there is no updated medical and health services. The
staff members should understand how important first aid box is in the situation of
emergency.
Hazard identification – The staff should be able to identify situations that may lead to a
hazardous situation if not attended. For identifying these incidents the staff must get
training for hazard identification.
Emergency procedures – As from the report it is very clear that there are no updated
emergency procedures followed in the organisation. This is very dangerous and it could
lead to a situation of life or death.
5. What should David do?
David Santos the Manager of ABC company, should analyse the situation based on facts and
evidences provided in the report and based on that analysis David Santos should start training
courses in Effective manual handling procedures instantly. This could affect the profitability of
the organisation. Because if more people have started taking leaves for two days every week then
the production the company will suffer drastically which leads to decrease in production and
ultimately profits of the organisation (Potter and et al., 2019). David Santos should implement
distribution of safe manual handling instructions booklet so that even if a worker miss signs or
would not be able to attend training at least he/she can have safety manual for handling heavy
things.
The changes that David Santos could implement are as follows:
I. The training programs must be strict and forced on the staff for attending it.
According to the Team Hazard Report from Andrew, there are some WHS training courses
which are still required by the staff for the complete safety of the work place environment. The
frequency of training and its amount shows the level of risk involved in the hazardous situation.
The training must by very thorough and covers all the elements of risks involved. It does not
matter that the staff is from which department health and safety training should be attended by
everyone in the organisation (Bluff, 2019). These training courses are based on the analysis of
the hazard report and are as follows:
Safe manual handling – According to the hazard report some workers hurt their back in
moving those heavy boxes which are lying on the floor of the work area.
First aid – As according to the report there is no updated medical and health services. The
staff members should understand how important first aid box is in the situation of
emergency.
Hazard identification – The staff should be able to identify situations that may lead to a
hazardous situation if not attended. For identifying these incidents the staff must get
training for hazard identification.
Emergency procedures – As from the report it is very clear that there are no updated
emergency procedures followed in the organisation. This is very dangerous and it could
lead to a situation of life or death.
5. What should David do?
David Santos the Manager of ABC company, should analyse the situation based on facts and
evidences provided in the report and based on that analysis David Santos should start training
courses in Effective manual handling procedures instantly. This could affect the profitability of
the organisation. Because if more people have started taking leaves for two days every week then
the production the company will suffer drastically which leads to decrease in production and
ultimately profits of the organisation (Potter and et al., 2019). David Santos should implement
distribution of safe manual handling instructions booklet so that even if a worker miss signs or
would not be able to attend training at least he/she can have safety manual for handling heavy
things.
The changes that David Santos could implement are as follows:
I. The training programs must be strict and forced on the staff for attending it.
Secure Best Marks with AI Grader
Need help grading? Try our AI Grader for instant feedback on your assignments.
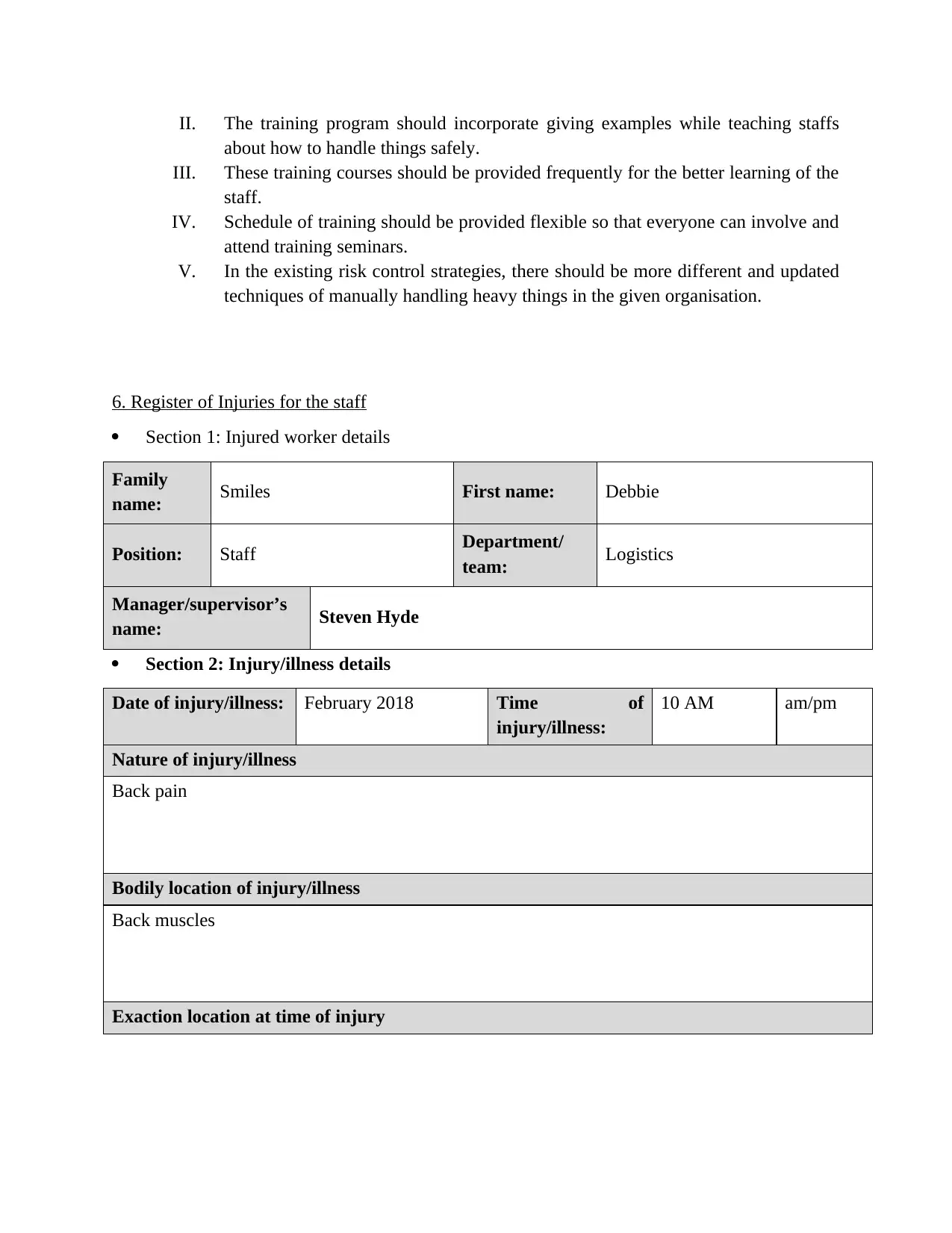
II. The training program should incorporate giving examples while teaching staffs
about how to handle things safely.
III. These training courses should be provided frequently for the better learning of the
staff.
IV. Schedule of training should be provided flexible so that everyone can involve and
attend training seminars.
V. In the existing risk control strategies, there should be more different and updated
techniques of manually handling heavy things in the given organisation.
6. Register of Injuries for the staff
Section 1: Injured worker details
Family
name: Smiles First name: Debbie
Position: Staff Department/
team: Logistics
Manager/supervisor’s
name: Steven Hyde
Section 2: Injury/illness details
Date of injury/illness: February 2018 Time of
injury/illness:
10 AM am/pm
Nature of injury/illness
Back pain
Bodily location of injury/illness
Back muscles
Exaction location at time of injury
about how to handle things safely.
III. These training courses should be provided frequently for the better learning of the
staff.
IV. Schedule of training should be provided flexible so that everyone can involve and
attend training seminars.
V. In the existing risk control strategies, there should be more different and updated
techniques of manually handling heavy things in the given organisation.
6. Register of Injuries for the staff
Section 1: Injured worker details
Family
name: Smiles First name: Debbie
Position: Staff Department/
team: Logistics
Manager/supervisor’s
name: Steven Hyde
Section 2: Injury/illness details
Date of injury/illness: February 2018 Time of
injury/illness:
10 AM am/pm
Nature of injury/illness
Back pain
Bodily location of injury/illness
Back muscles
Exaction location at time of injury
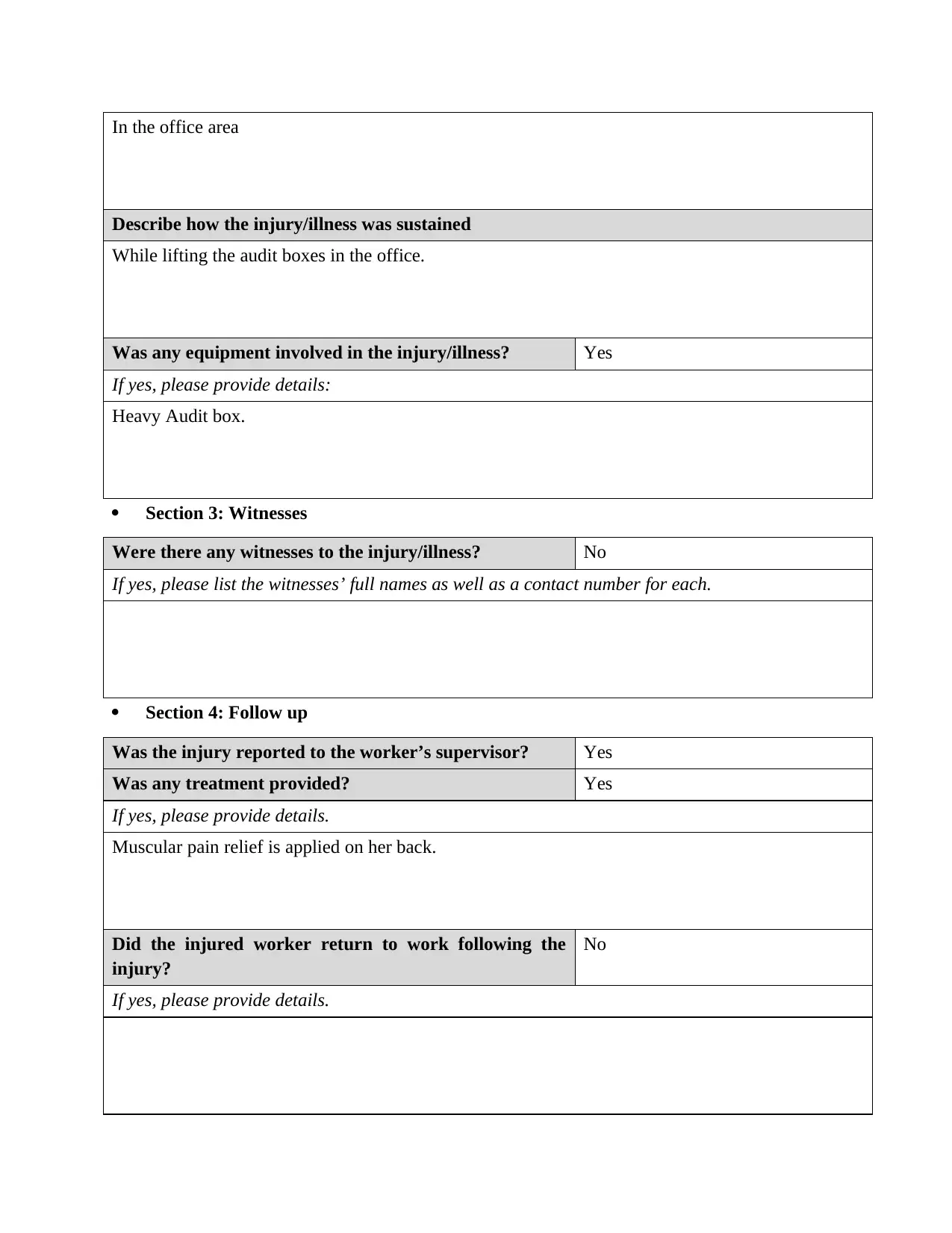
In the office area
Describe how the injury/illness was sustained
While lifting the audit boxes in the office.
Was any equipment involved in the injury/illness? Yes
If yes, please provide details:
Heavy Audit box.
Section 3: Witnesses
Were there any witnesses to the injury/illness? No
If yes, please list the witnesses’ full names as well as a contact number for each.
Section 4: Follow up
Was the injury reported to the worker’s supervisor? Yes
Was any treatment provided? Yes
If yes, please provide details.
Muscular pain relief is applied on her back.
Did the injured worker return to work following the
injury?
No
If yes, please provide details.
Describe how the injury/illness was sustained
While lifting the audit boxes in the office.
Was any equipment involved in the injury/illness? Yes
If yes, please provide details:
Heavy Audit box.
Section 3: Witnesses
Were there any witnesses to the injury/illness? No
If yes, please list the witnesses’ full names as well as a contact number for each.
Section 4: Follow up
Was the injury reported to the worker’s supervisor? Yes
Was any treatment provided? Yes
If yes, please provide details.
Muscular pain relief is applied on her back.
Did the injured worker return to work following the
injury?
No
If yes, please provide details.
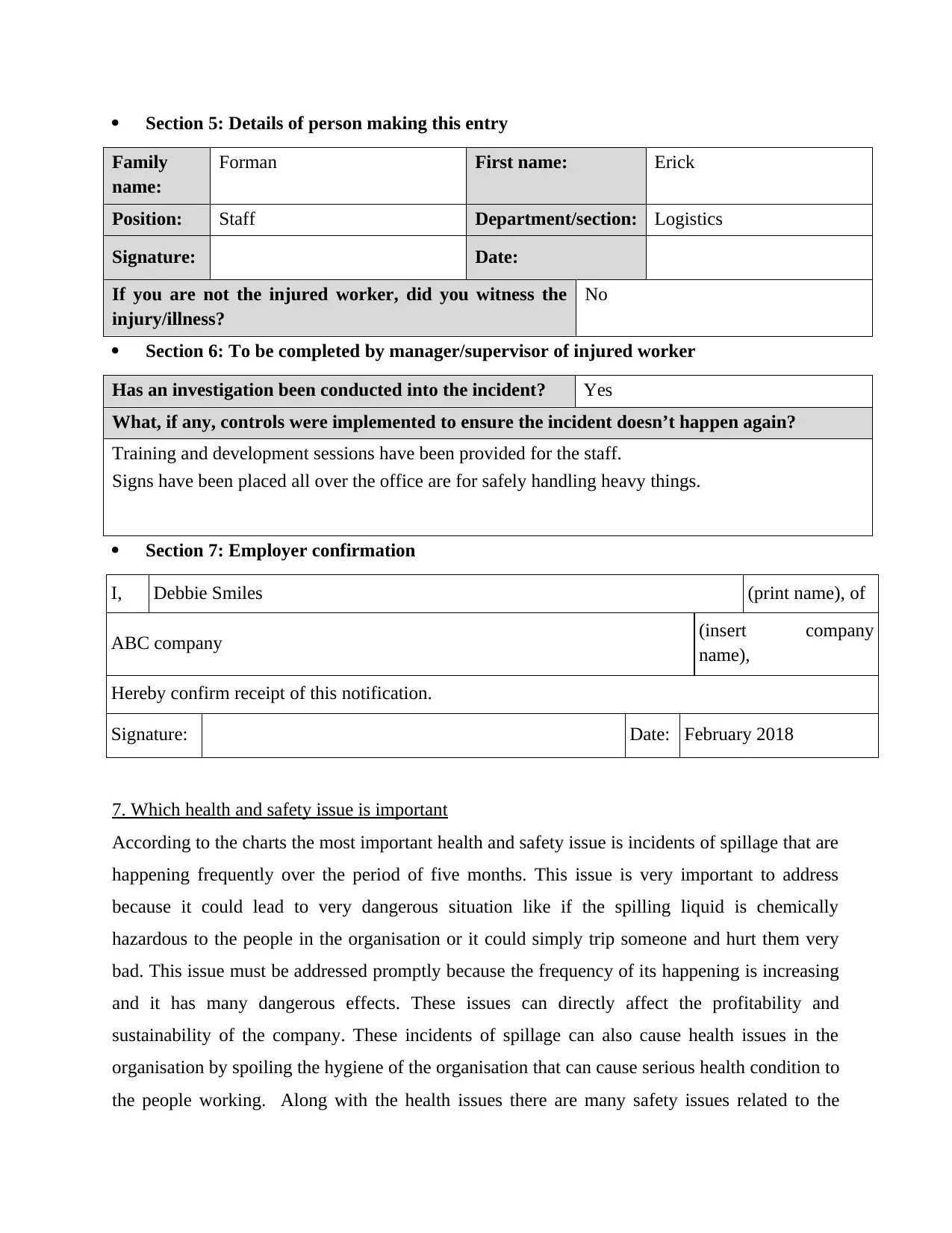
Section 5: Details of person making this entry
Family
name:
Forman First name: Erick
Position: Staff Department/section: Logistics
Signature: Date:
If you are not the injured worker, did you witness the
injury/illness?
No
Section 6: To be completed by manager/supervisor of injured worker
Has an investigation been conducted into the incident? Yes
What, if any, controls were implemented to ensure the incident doesn’t happen again?
Training and development sessions have been provided for the staff.
Signs have been placed all over the office are for safely handling heavy things.
Section 7: Employer confirmation
I, Debbie Smiles (print name), of
ABC company (insert company
name),
Hereby confirm receipt of this notification.
Signature: Date: February 2018
7. Which health and safety issue is important
According to the charts the most important health and safety issue is incidents of spillage that are
happening frequently over the period of five months. This issue is very important to address
because it could lead to very dangerous situation like if the spilling liquid is chemically
hazardous to the people in the organisation or it could simply trip someone and hurt them very
bad. This issue must be addressed promptly because the frequency of its happening is increasing
and it has many dangerous effects. These issues can directly affect the profitability and
sustainability of the company. These incidents of spillage can also cause health issues in the
organisation by spoiling the hygiene of the organisation that can cause serious health condition to
the people working. Along with the health issues there are many safety issues related to the
Family
name:
Forman First name: Erick
Position: Staff Department/section: Logistics
Signature: Date:
If you are not the injured worker, did you witness the
injury/illness?
No
Section 6: To be completed by manager/supervisor of injured worker
Has an investigation been conducted into the incident? Yes
What, if any, controls were implemented to ensure the incident doesn’t happen again?
Training and development sessions have been provided for the staff.
Signs have been placed all over the office are for safely handling heavy things.
Section 7: Employer confirmation
I, Debbie Smiles (print name), of
ABC company (insert company
name),
Hereby confirm receipt of this notification.
Signature: Date: February 2018
7. Which health and safety issue is important
According to the charts the most important health and safety issue is incidents of spillage that are
happening frequently over the period of five months. This issue is very important to address
because it could lead to very dangerous situation like if the spilling liquid is chemically
hazardous to the people in the organisation or it could simply trip someone and hurt them very
bad. This issue must be addressed promptly because the frequency of its happening is increasing
and it has many dangerous effects. These issues can directly affect the profitability and
sustainability of the company. These incidents of spillage can also cause health issues in the
organisation by spoiling the hygiene of the organisation that can cause serious health condition to
the people working. Along with the health issues there are many safety issues related to the
Paraphrase This Document
Need a fresh take? Get an instant paraphrase of this document with our AI Paraphraser
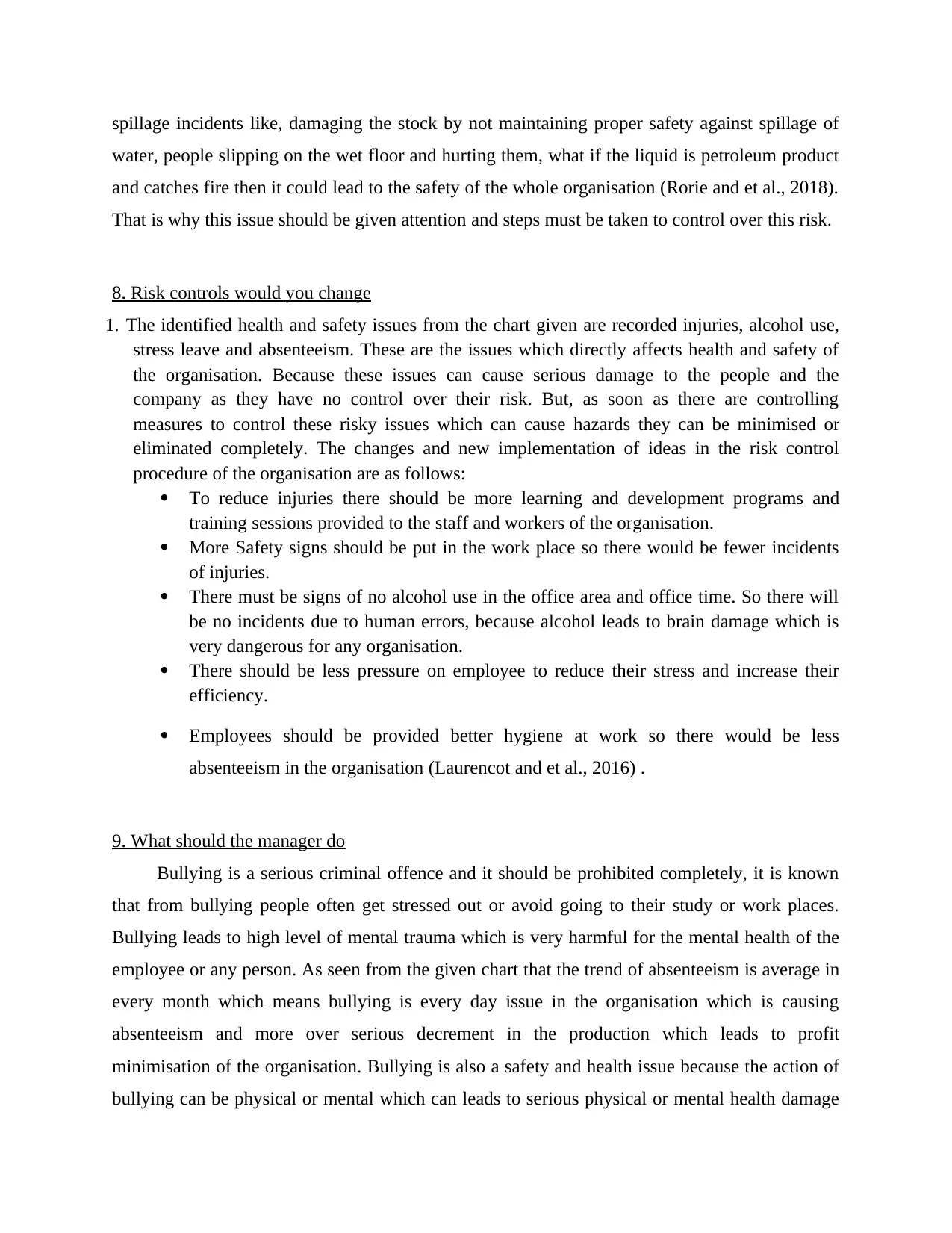
spillage incidents like, damaging the stock by not maintaining proper safety against spillage of
water, people slipping on the wet floor and hurting them, what if the liquid is petroleum product
and catches fire then it could lead to the safety of the whole organisation (Rorie and et al., 2018).
That is why this issue should be given attention and steps must be taken to control over this risk.
8. Risk controls would you change
1. The identified health and safety issues from the chart given are recorded injuries, alcohol use,
stress leave and absenteeism. These are the issues which directly affects health and safety of
the organisation. Because these issues can cause serious damage to the people and the
company as they have no control over their risk. But, as soon as there are controlling
measures to control these risky issues which can cause hazards they can be minimised or
eliminated completely. The changes and new implementation of ideas in the risk control
procedure of the organisation are as follows:
To reduce injuries there should be more learning and development programs and
training sessions provided to the staff and workers of the organisation.
More Safety signs should be put in the work place so there would be fewer incidents
of injuries.
There must be signs of no alcohol use in the office area and office time. So there will
be no incidents due to human errors, because alcohol leads to brain damage which is
very dangerous for any organisation.
There should be less pressure on employee to reduce their stress and increase their
efficiency.
Employees should be provided better hygiene at work so there would be less
absenteeism in the organisation (Laurencot and et al., 2016) .
9. What should the manager do
Bullying is a serious criminal offence and it should be prohibited completely, it is known
that from bullying people often get stressed out or avoid going to their study or work places.
Bullying leads to high level of mental trauma which is very harmful for the mental health of the
employee or any person. As seen from the given chart that the trend of absenteeism is average in
every month which means bullying is every day issue in the organisation which is causing
absenteeism and more over serious decrement in the production which leads to profit
minimisation of the organisation. Bullying is also a safety and health issue because the action of
bullying can be physical or mental which can leads to serious physical or mental health damage
water, people slipping on the wet floor and hurting them, what if the liquid is petroleum product
and catches fire then it could lead to the safety of the whole organisation (Rorie and et al., 2018).
That is why this issue should be given attention and steps must be taken to control over this risk.
8. Risk controls would you change
1. The identified health and safety issues from the chart given are recorded injuries, alcohol use,
stress leave and absenteeism. These are the issues which directly affects health and safety of
the organisation. Because these issues can cause serious damage to the people and the
company as they have no control over their risk. But, as soon as there are controlling
measures to control these risky issues which can cause hazards they can be minimised or
eliminated completely. The changes and new implementation of ideas in the risk control
procedure of the organisation are as follows:
To reduce injuries there should be more learning and development programs and
training sessions provided to the staff and workers of the organisation.
More Safety signs should be put in the work place so there would be fewer incidents
of injuries.
There must be signs of no alcohol use in the office area and office time. So there will
be no incidents due to human errors, because alcohol leads to brain damage which is
very dangerous for any organisation.
There should be less pressure on employee to reduce their stress and increase their
efficiency.
Employees should be provided better hygiene at work so there would be less
absenteeism in the organisation (Laurencot and et al., 2016) .
9. What should the manager do
Bullying is a serious criminal offence and it should be prohibited completely, it is known
that from bullying people often get stressed out or avoid going to their study or work places.
Bullying leads to high level of mental trauma which is very harmful for the mental health of the
employee or any person. As seen from the given chart that the trend of absenteeism is average in
every month which means bullying is every day issue in the organisation which is causing
absenteeism and more over serious decrement in the production which leads to profit
minimisation of the organisation. Bullying is also a safety and health issue because the action of
bullying can be physical or mental which can leads to serious physical or mental health damage
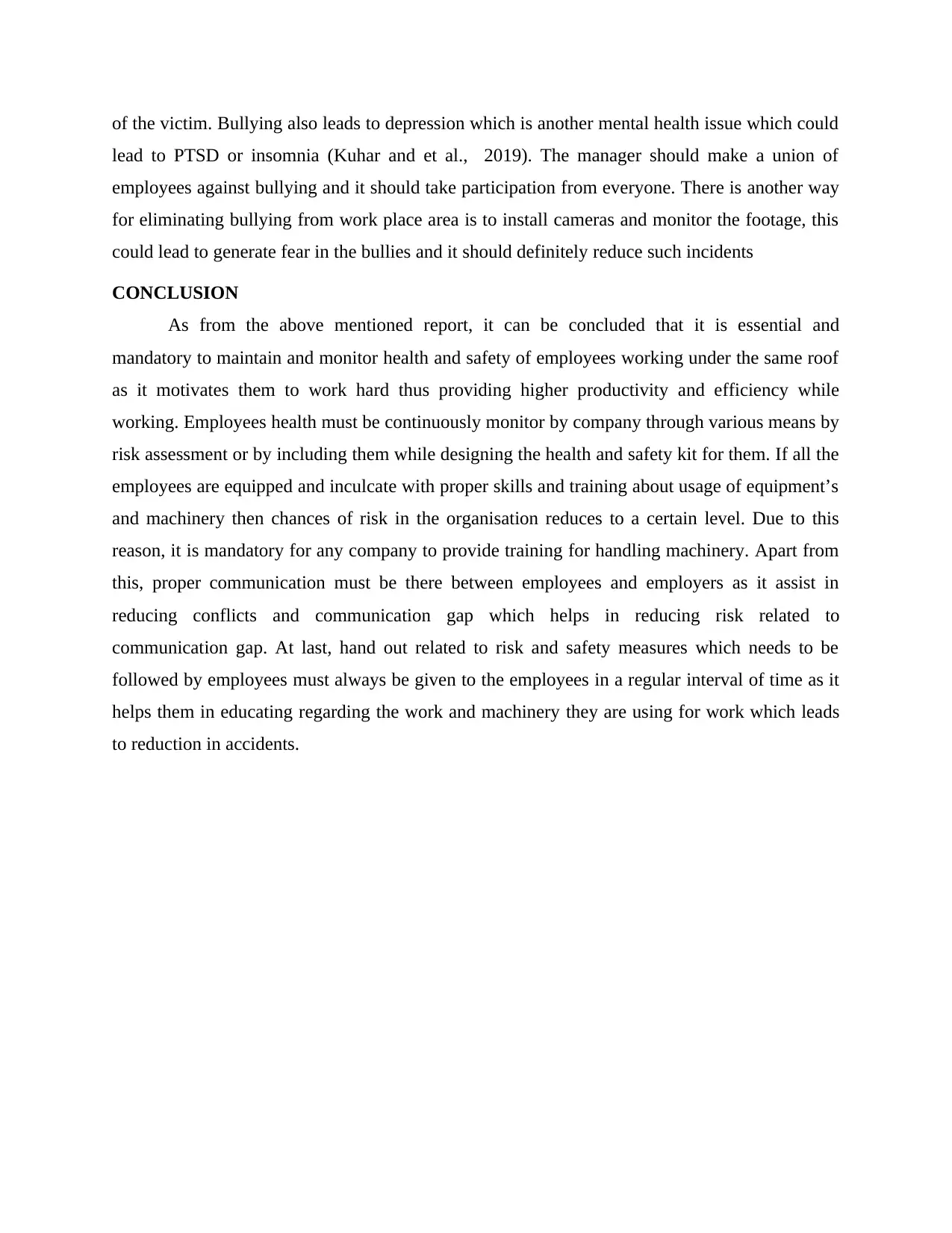
of the victim. Bullying also leads to depression which is another mental health issue which could
lead to PTSD or insomnia (Kuhar and et al., 2019). The manager should make a union of
employees against bullying and it should take participation from everyone. There is another way
for eliminating bullying from work place area is to install cameras and monitor the footage, this
could lead to generate fear in the bullies and it should definitely reduce such incidents
CONCLUSION
As from the above mentioned report, it can be concluded that it is essential and
mandatory to maintain and monitor health and safety of employees working under the same roof
as it motivates them to work hard thus providing higher productivity and efficiency while
working. Employees health must be continuously monitor by company through various means by
risk assessment or by including them while designing the health and safety kit for them. If all the
employees are equipped and inculcate with proper skills and training about usage of equipment’s
and machinery then chances of risk in the organisation reduces to a certain level. Due to this
reason, it is mandatory for any company to provide training for handling machinery. Apart from
this, proper communication must be there between employees and employers as it assist in
reducing conflicts and communication gap which helps in reducing risk related to
communication gap. At last, hand out related to risk and safety measures which needs to be
followed by employees must always be given to the employees in a regular interval of time as it
helps them in educating regarding the work and machinery they are using for work which leads
to reduction in accidents.
lead to PTSD or insomnia (Kuhar and et al., 2019). The manager should make a union of
employees against bullying and it should take participation from everyone. There is another way
for eliminating bullying from work place area is to install cameras and monitor the footage, this
could lead to generate fear in the bullies and it should definitely reduce such incidents
CONCLUSION
As from the above mentioned report, it can be concluded that it is essential and
mandatory to maintain and monitor health and safety of employees working under the same roof
as it motivates them to work hard thus providing higher productivity and efficiency while
working. Employees health must be continuously monitor by company through various means by
risk assessment or by including them while designing the health and safety kit for them. If all the
employees are equipped and inculcate with proper skills and training about usage of equipment’s
and machinery then chances of risk in the organisation reduces to a certain level. Due to this
reason, it is mandatory for any company to provide training for handling machinery. Apart from
this, proper communication must be there between employees and employers as it assist in
reducing conflicts and communication gap which helps in reducing risk related to
communication gap. At last, hand out related to risk and safety measures which needs to be
followed by employees must always be given to the employees in a regular interval of time as it
helps them in educating regarding the work and machinery they are using for work which leads
to reduction in accidents.

REFERENCES
Books and Journals
Appiah, S., 2016. Connecting occupational safety awareness, legislation, implementation and
enforcement within the Ghanaian industrial economy. Journal of environmental and occupational
science, 5(2), pp.e53-e53.
Bluff, E., 2017. The regulation of work health and safety. REGULATORY THEORY, p.611.
Bluff, E., 2019. How SMEs respond to legal requirements to provide information, training,
instruction and supervision to workers about work health and safety matters. Safety science, 116,
pp.45-57.
de Faria Nogueira, E.C., Luiz, O., Quelhas, G., França, S.L., Meiriño, M.J. and Mosca Cunha,
L.A., 2015. IMPLEMENTATION OF A SAFETY PROGRAM FOR THE WORK
ACCIDENTS'CONTROL. A CASE STUDY IN THE CHEMICAL INDUSTRY. International
Journal for Quality Research, 9(1).
Dwyer, J. and Hopwood, N., 2019. The business communication handbook. Cengage AU.
Evangelinos, K., Fotiadis, S., Skouloudis, A., Khan, N., Konstandakopoulou, F., Nikolaou, I. and
Lundy, S., 2018. Occupational health and safety disclosures in sustainability reports: An
overview of trends among corporate leaders. Corporate Social Responsibility and Environmental
Management, 25(5), pp.961-970.
Fagan, A.A., Bumbarger, B.K., Barth, R.P., Bradshaw, C.P., Cooper, B.R., Supplee, L.H. and
Walker, D.K., 2019. Scaling up evidence-based interventions in US public systems to prevent
behavioral health problems: challenges and opportunities. Prevention Science, pp.1-22.
Honn, K.A., VAN DONGEN, H.P. and Dawson, D., 2019. Working Time Society consensus
statements: Prescriptive rule sets and risk management-based approaches for the management of
fatigue-related risk in working time arrangements. Industrial health, pp.SW-8.
Books and Journals
Appiah, S., 2016. Connecting occupational safety awareness, legislation, implementation and
enforcement within the Ghanaian industrial economy. Journal of environmental and occupational
science, 5(2), pp.e53-e53.
Bluff, E., 2017. The regulation of work health and safety. REGULATORY THEORY, p.611.
Bluff, E., 2019. How SMEs respond to legal requirements to provide information, training,
instruction and supervision to workers about work health and safety matters. Safety science, 116,
pp.45-57.
de Faria Nogueira, E.C., Luiz, O., Quelhas, G., França, S.L., Meiriño, M.J. and Mosca Cunha,
L.A., 2015. IMPLEMENTATION OF A SAFETY PROGRAM FOR THE WORK
ACCIDENTS'CONTROL. A CASE STUDY IN THE CHEMICAL INDUSTRY. International
Journal for Quality Research, 9(1).
Dwyer, J. and Hopwood, N., 2019. The business communication handbook. Cengage AU.
Evangelinos, K., Fotiadis, S., Skouloudis, A., Khan, N., Konstandakopoulou, F., Nikolaou, I. and
Lundy, S., 2018. Occupational health and safety disclosures in sustainability reports: An
overview of trends among corporate leaders. Corporate Social Responsibility and Environmental
Management, 25(5), pp.961-970.
Fagan, A.A., Bumbarger, B.K., Barth, R.P., Bradshaw, C.P., Cooper, B.R., Supplee, L.H. and
Walker, D.K., 2019. Scaling up evidence-based interventions in US public systems to prevent
behavioral health problems: challenges and opportunities. Prevention Science, pp.1-22.
Honn, K.A., VAN DONGEN, H.P. and Dawson, D., 2019. Working Time Society consensus
statements: Prescriptive rule sets and risk management-based approaches for the management of
fatigue-related risk in working time arrangements. Industrial health, pp.SW-8.
Secure Best Marks with AI Grader
Need help grading? Try our AI Grader for instant feedback on your assignments.
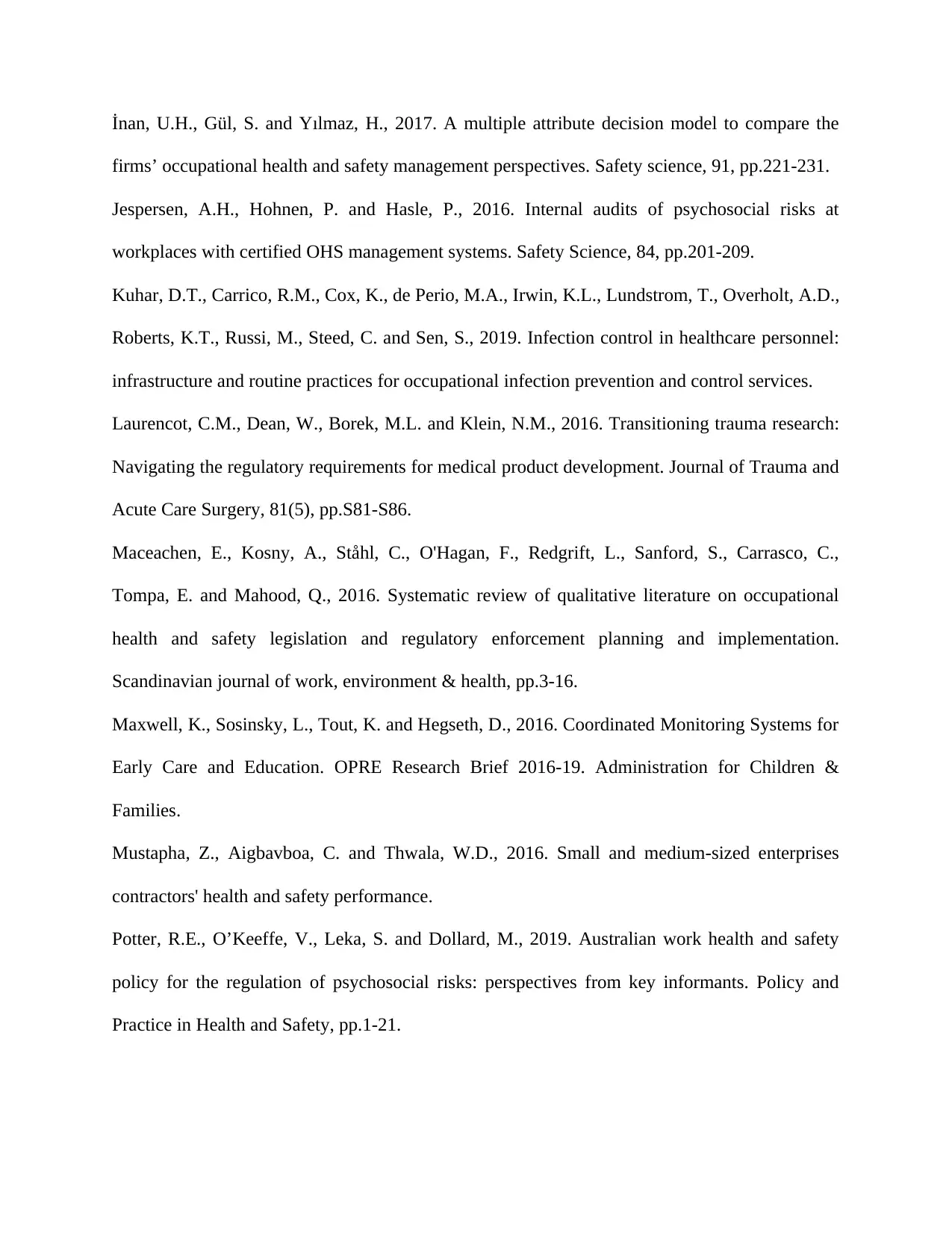
İnan, U.H., Gül, S. and Yılmaz, H., 2017. A multiple attribute decision model to compare the
firms’ occupational health and safety management perspectives. Safety science, 91, pp.221-231.
Jespersen, A.H., Hohnen, P. and Hasle, P., 2016. Internal audits of psychosocial risks at
workplaces with certified OHS management systems. Safety Science, 84, pp.201-209.
Kuhar, D.T., Carrico, R.M., Cox, K., de Perio, M.A., Irwin, K.L., Lundstrom, T., Overholt, A.D.,
Roberts, K.T., Russi, M., Steed, C. and Sen, S., 2019. Infection control in healthcare personnel:
infrastructure and routine practices for occupational infection prevention and control services.
Laurencot, C.M., Dean, W., Borek, M.L. and Klein, N.M., 2016. Transitioning trauma research:
Navigating the regulatory requirements for medical product development. Journal of Trauma and
Acute Care Surgery, 81(5), pp.S81-S86.
Maceachen, E., Kosny, A., Ståhl, C., O'Hagan, F., Redgrift, L., Sanford, S., Carrasco, C.,
Tompa, E. and Mahood, Q., 2016. Systematic review of qualitative literature on occupational
health and safety legislation and regulatory enforcement planning and implementation.
Scandinavian journal of work, environment & health, pp.3-16.
Maxwell, K., Sosinsky, L., Tout, K. and Hegseth, D., 2016. Coordinated Monitoring Systems for
Early Care and Education. OPRE Research Brief 2016-19. Administration for Children &
Families.
Mustapha, Z., Aigbavboa, C. and Thwala, W.D., 2016. Small and medium-sized enterprises
contractors' health and safety performance.
Potter, R.E., O’Keeffe, V., Leka, S. and Dollard, M., 2019. Australian work health and safety
policy for the regulation of psychosocial risks: perspectives from key informants. Policy and
Practice in Health and Safety, pp.1-21.
firms’ occupational health and safety management perspectives. Safety science, 91, pp.221-231.
Jespersen, A.H., Hohnen, P. and Hasle, P., 2016. Internal audits of psychosocial risks at
workplaces with certified OHS management systems. Safety Science, 84, pp.201-209.
Kuhar, D.T., Carrico, R.M., Cox, K., de Perio, M.A., Irwin, K.L., Lundstrom, T., Overholt, A.D.,
Roberts, K.T., Russi, M., Steed, C. and Sen, S., 2019. Infection control in healthcare personnel:
infrastructure and routine practices for occupational infection prevention and control services.
Laurencot, C.M., Dean, W., Borek, M.L. and Klein, N.M., 2016. Transitioning trauma research:
Navigating the regulatory requirements for medical product development. Journal of Trauma and
Acute Care Surgery, 81(5), pp.S81-S86.
Maceachen, E., Kosny, A., Ståhl, C., O'Hagan, F., Redgrift, L., Sanford, S., Carrasco, C.,
Tompa, E. and Mahood, Q., 2016. Systematic review of qualitative literature on occupational
health and safety legislation and regulatory enforcement planning and implementation.
Scandinavian journal of work, environment & health, pp.3-16.
Maxwell, K., Sosinsky, L., Tout, K. and Hegseth, D., 2016. Coordinated Monitoring Systems for
Early Care and Education. OPRE Research Brief 2016-19. Administration for Children &
Families.
Mustapha, Z., Aigbavboa, C. and Thwala, W.D., 2016. Small and medium-sized enterprises
contractors' health and safety performance.
Potter, R.E., O’Keeffe, V., Leka, S. and Dollard, M., 2019. Australian work health and safety
policy for the regulation of psychosocial risks: perspectives from key informants. Policy and
Practice in Health and Safety, pp.1-21.
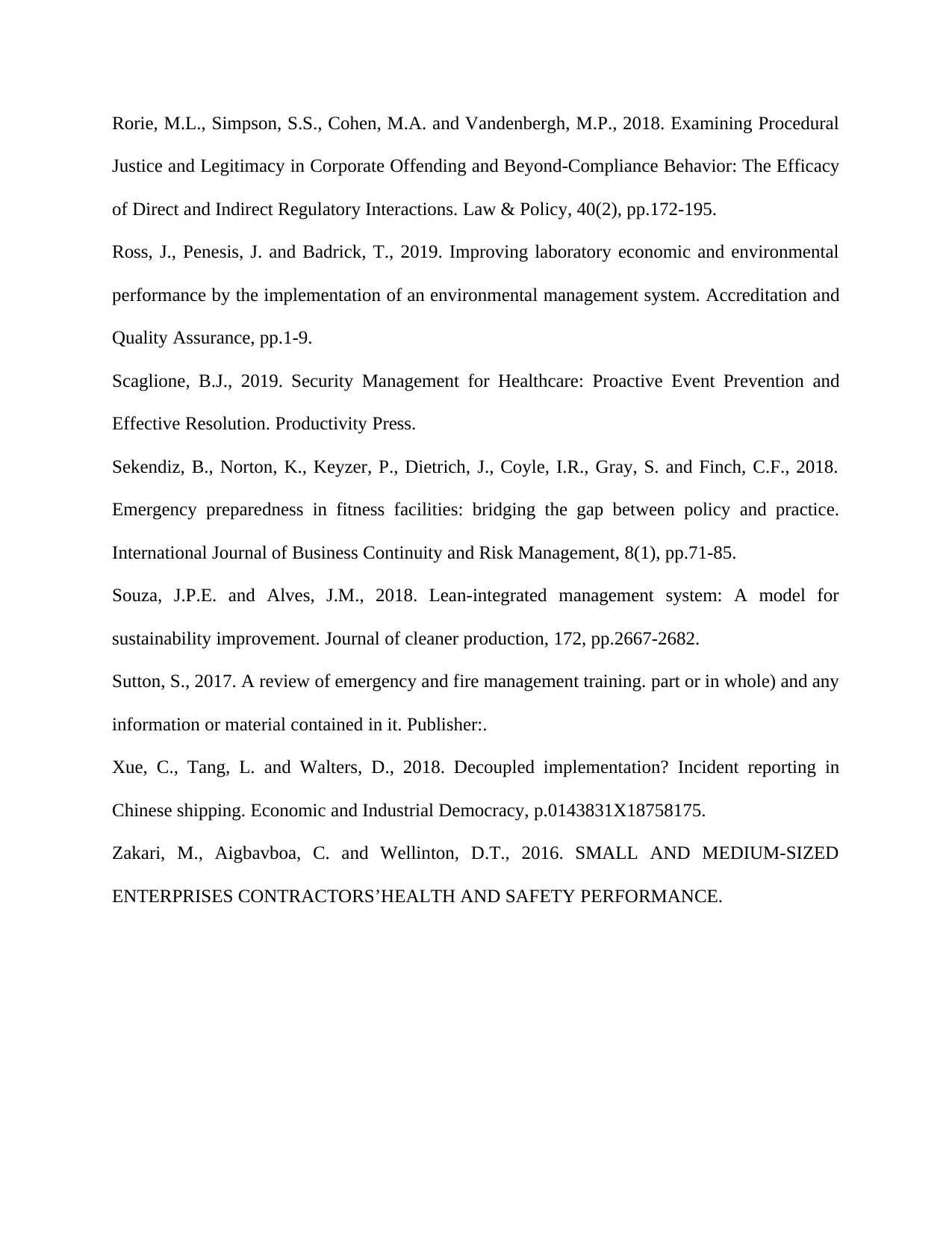
Rorie, M.L., Simpson, S.S., Cohen, M.A. and Vandenbergh, M.P., 2018. Examining Procedural
Justice and Legitimacy in Corporate Offending and Beyond‐Compliance Behavior: The Efficacy
of Direct and Indirect Regulatory Interactions. Law & Policy, 40(2), pp.172-195.
Ross, J., Penesis, J. and Badrick, T., 2019. Improving laboratory economic and environmental
performance by the implementation of an environmental management system. Accreditation and
Quality Assurance, pp.1-9.
Scaglione, B.J., 2019. Security Management for Healthcare: Proactive Event Prevention and
Effective Resolution. Productivity Press.
Sekendiz, B., Norton, K., Keyzer, P., Dietrich, J., Coyle, I.R., Gray, S. and Finch, C.F., 2018.
Emergency preparedness in fitness facilities: bridging the gap between policy and practice.
International Journal of Business Continuity and Risk Management, 8(1), pp.71-85.
Souza, J.P.E. and Alves, J.M., 2018. Lean-integrated management system: A model for
sustainability improvement. Journal of cleaner production, 172, pp.2667-2682.
Sutton, S., 2017. A review of emergency and fire management training. part or in whole) and any
information or material contained in it. Publisher:.
Xue, C., Tang, L. and Walters, D., 2018. Decoupled implementation? Incident reporting in
Chinese shipping. Economic and Industrial Democracy, p.0143831X18758175.
Zakari, M., Aigbavboa, C. and Wellinton, D.T., 2016. SMALL AND MEDIUM-SIZED
ENTERPRISES CONTRACTORS’HEALTH AND SAFETY PERFORMANCE.
Justice and Legitimacy in Corporate Offending and Beyond‐Compliance Behavior: The Efficacy
of Direct and Indirect Regulatory Interactions. Law & Policy, 40(2), pp.172-195.
Ross, J., Penesis, J. and Badrick, T., 2019. Improving laboratory economic and environmental
performance by the implementation of an environmental management system. Accreditation and
Quality Assurance, pp.1-9.
Scaglione, B.J., 2019. Security Management for Healthcare: Proactive Event Prevention and
Effective Resolution. Productivity Press.
Sekendiz, B., Norton, K., Keyzer, P., Dietrich, J., Coyle, I.R., Gray, S. and Finch, C.F., 2018.
Emergency preparedness in fitness facilities: bridging the gap between policy and practice.
International Journal of Business Continuity and Risk Management, 8(1), pp.71-85.
Souza, J.P.E. and Alves, J.M., 2018. Lean-integrated management system: A model for
sustainability improvement. Journal of cleaner production, 172, pp.2667-2682.
Sutton, S., 2017. A review of emergency and fire management training. part or in whole) and any
information or material contained in it. Publisher:.
Xue, C., Tang, L. and Walters, D., 2018. Decoupled implementation? Incident reporting in
Chinese shipping. Economic and Industrial Democracy, p.0143831X18758175.
Zakari, M., Aigbavboa, C. and Wellinton, D.T., 2016. SMALL AND MEDIUM-SIZED
ENTERPRISES CONTRACTORS’HEALTH AND SAFETY PERFORMANCE.
1 out of 24
Related Documents

Your All-in-One AI-Powered Toolkit for Academic Success.
+13062052269
info@desklib.com
Available 24*7 on WhatsApp / Email
Unlock your academic potential
© 2024 | Zucol Services PVT LTD | All rights reserved.