PROC6001 Assessment 1 Part B: Wood Substitutes and Market Analysis
VerifiedAdded on 2022/09/18
|12
|2902
|24
Report
AI Summary
This report examines the evolution of wood-based substitutes and their influence on the wood market over the past two decades. It delves into the properties, advantages, and disadvantages of various engineered wood products, including MDF, particleboard, OSB, triboard, scrimber, and laminated timber. The analysis explores how these substitutes have helped wood regain market share and expand into new areas, considering factors such as environmental concerns, performance characteristics, cost-effectiveness, and ease of use. The report highlights the increasing demand for these materials due to their durability, design flexibility, and ability to meet specific application requirements. It also addresses the environmental and legislative impacts, emphasizing the role of wood-based substitutes in conserving natural resources. The conclusion summarizes the key findings and underscores the importance of these materials in the context of deforestation and sustainable practices.
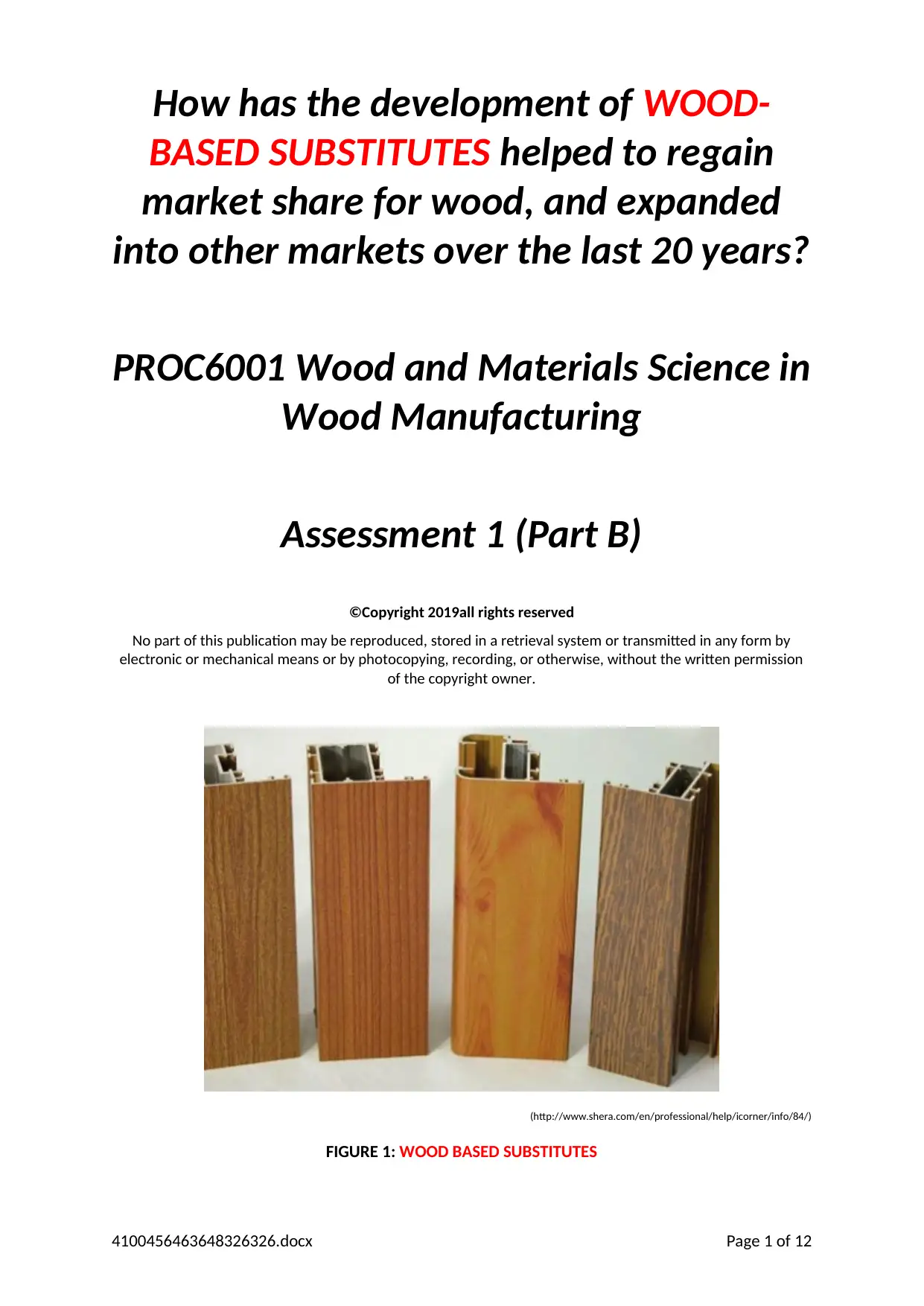
How has the development of WOOD-
BASED SUBSTITUTES helped to regain
market share for wood, and expanded
into other markets over the last 20 years?
PROC6001 Wood and Materials Science in
Wood Manufacturing
Assessment 1 (Part B)
©Copyright 2019all rights reserved
No part of this publication may be reproduced, stored in a retrieval system or transmitted in any form by
electronic or mechanical means or by photocopying, recording, or otherwise, without the written permission
of the copyright owner.
(http://www.shera.com/en/professional/help/icorner/info/84/)
FIGURE 1: WOOD BASED SUBSTITUTES
4100456463648326326.docx Page 1 of 12
BASED SUBSTITUTES helped to regain
market share for wood, and expanded
into other markets over the last 20 years?
PROC6001 Wood and Materials Science in
Wood Manufacturing
Assessment 1 (Part B)
©Copyright 2019all rights reserved
No part of this publication may be reproduced, stored in a retrieval system or transmitted in any form by
electronic or mechanical means or by photocopying, recording, or otherwise, without the written permission
of the copyright owner.
(http://www.shera.com/en/professional/help/icorner/info/84/)
FIGURE 1: WOOD BASED SUBSTITUTES
4100456463648326326.docx Page 1 of 12
Secure Best Marks with AI Grader
Need help grading? Try our AI Grader for instant feedback on your assignments.
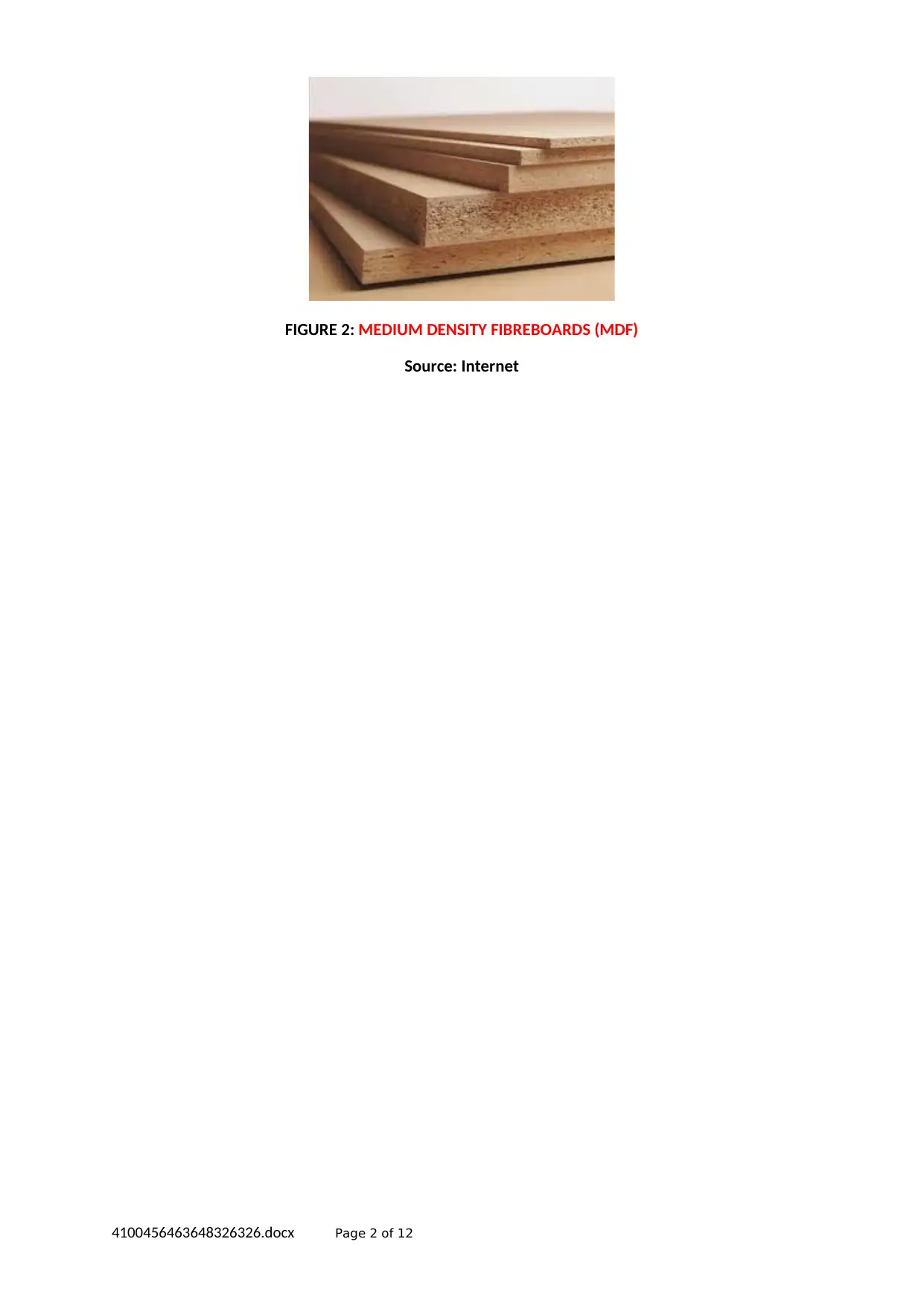
FIGURE 2: MEDIUM DENSITY FIBREBOARDS (MDF)
Source: Internet
4100456463648326326.docx Page 2 of 12
Source: Internet
4100456463648326326.docx Page 2 of 12
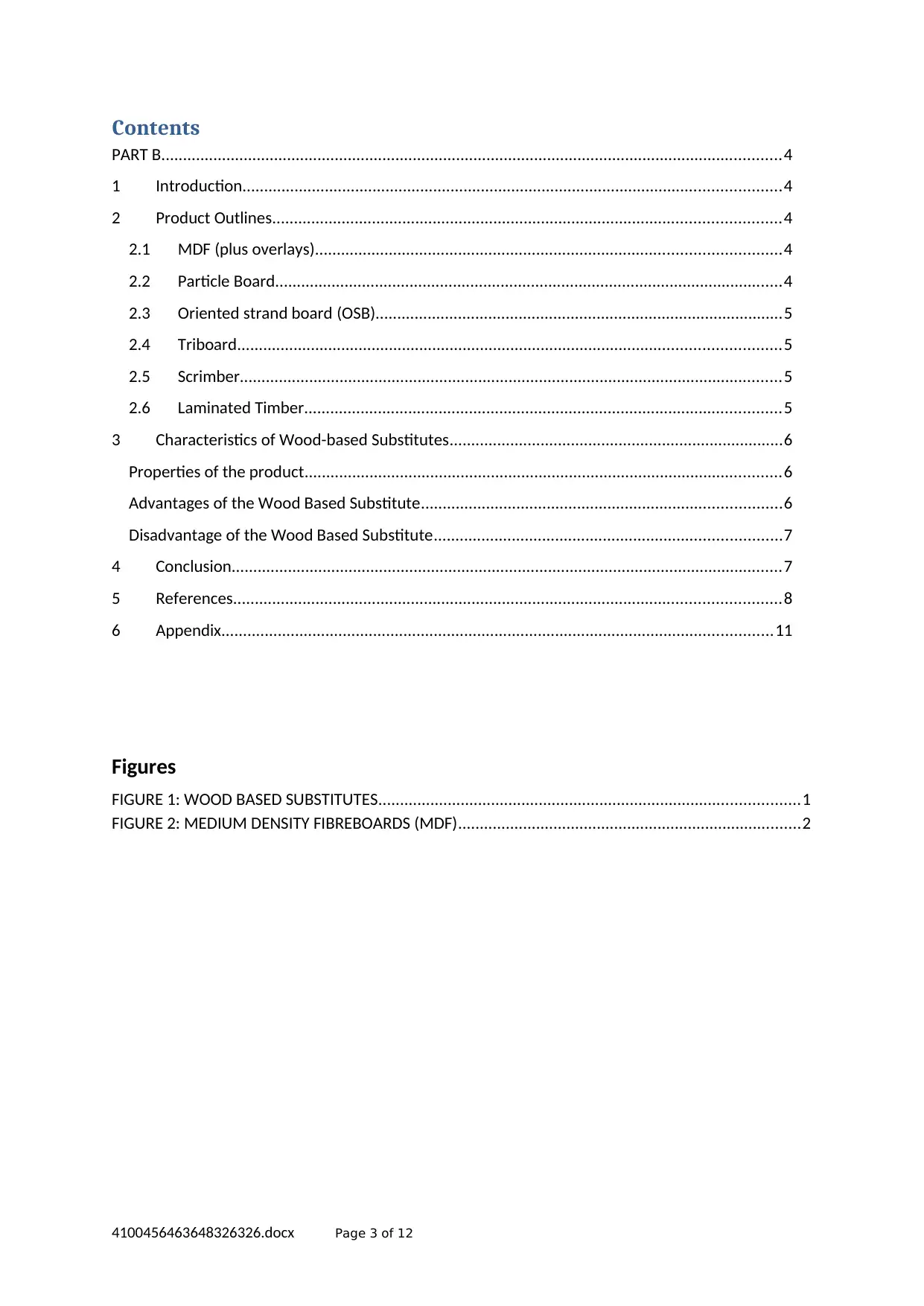
Contents
PART B...............................................................................................................................................4
1 Introduction............................................................................................................................4
2 Product Outlines.....................................................................................................................4
2.1 MDF (plus overlays)...........................................................................................................4
2.2 Particle Board.....................................................................................................................4
2.3 Oriented strand board (OSB)..............................................................................................5
2.4 Triboard.............................................................................................................................5
2.5 Scrimber.............................................................................................................................5
2.6 Laminated Timber..............................................................................................................5
3 Characteristics of Wood-based Substitutes.............................................................................6
Properties of the product..............................................................................................................6
Advantages of the Wood Based Substitute...................................................................................6
Disadvantage of the Wood Based Substitute................................................................................7
4 Conclusion...............................................................................................................................7
5 References..............................................................................................................................8
6 Appendix...............................................................................................................................11
Figures
FIGURE 1: WOOD BASED SUBSTITUTES.................................................................................................1
FIGURE 2: MEDIUM DENSITY FIBREBOARDS (MDF)...............................................................................2
4100456463648326326.docx Page 3 of 12
PART B...............................................................................................................................................4
1 Introduction............................................................................................................................4
2 Product Outlines.....................................................................................................................4
2.1 MDF (plus overlays)...........................................................................................................4
2.2 Particle Board.....................................................................................................................4
2.3 Oriented strand board (OSB)..............................................................................................5
2.4 Triboard.............................................................................................................................5
2.5 Scrimber.............................................................................................................................5
2.6 Laminated Timber..............................................................................................................5
3 Characteristics of Wood-based Substitutes.............................................................................6
Properties of the product..............................................................................................................6
Advantages of the Wood Based Substitute...................................................................................6
Disadvantage of the Wood Based Substitute................................................................................7
4 Conclusion...............................................................................................................................7
5 References..............................................................................................................................8
6 Appendix...............................................................................................................................11
Figures
FIGURE 1: WOOD BASED SUBSTITUTES.................................................................................................1
FIGURE 2: MEDIUM DENSITY FIBREBOARDS (MDF)...............................................................................2
4100456463648326326.docx Page 3 of 12
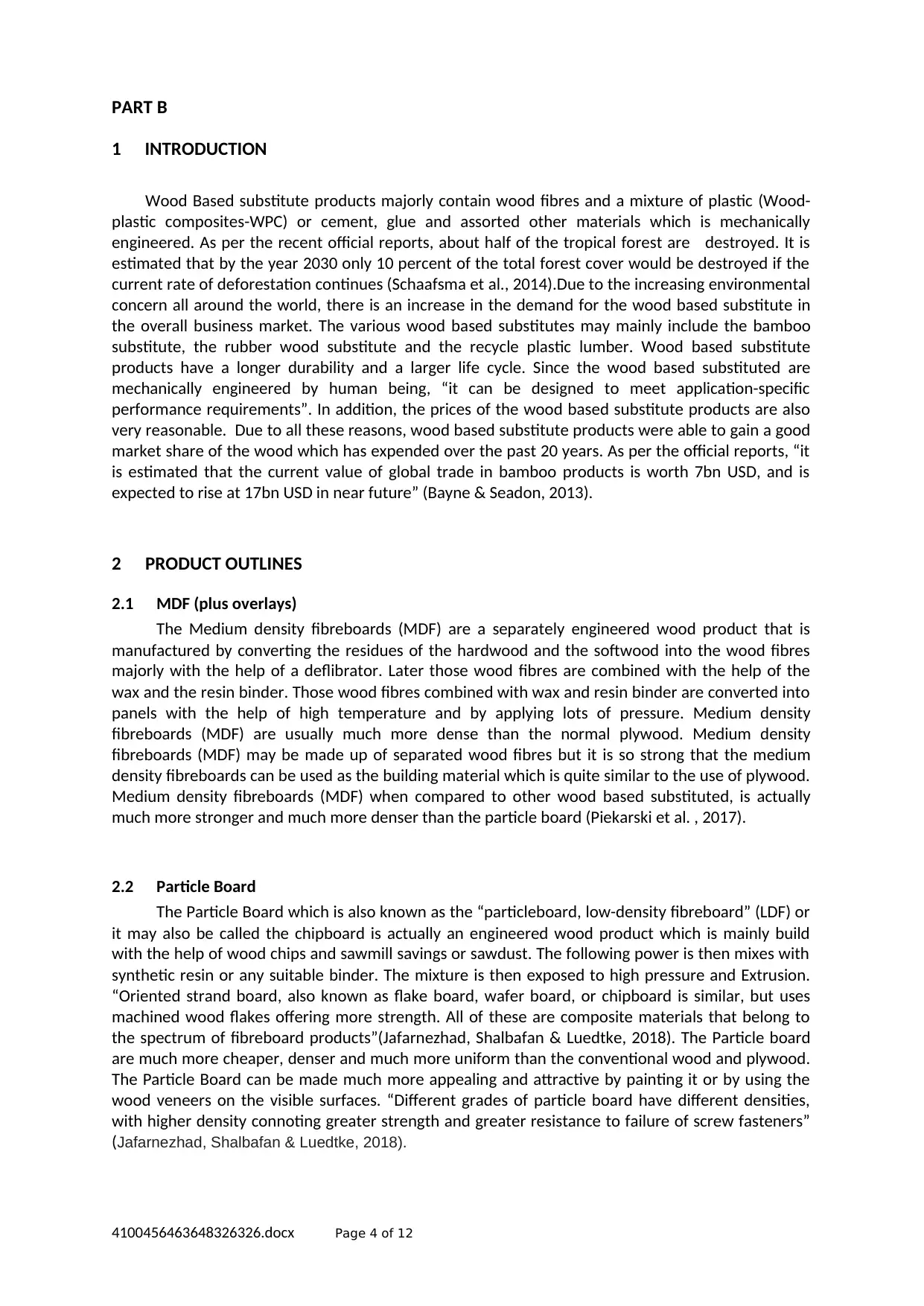
PART B
1 INTRODUCTION
Wood Based substitute products majorly contain wood fibres and a mixture of plastic (Wood-
plastic composites-WPC) or cement, glue and assorted other materials which is mechanically
engineered. As per the recent official reports, about half of the tropical forest are destroyed. It is
estimated that by the year 2030 only 10 percent of the total forest cover would be destroyed if the
current rate of deforestation continues (Schaafsma et al., 2014).Due to the increasing environmental
concern all around the world, there is an increase in the demand for the wood based substitute in
the overall business market. The various wood based substitutes may mainly include the bamboo
substitute, the rubber wood substitute and the recycle plastic lumber. Wood based substitute
products have a longer durability and a larger life cycle. Since the wood based substituted are
mechanically engineered by human being, “it can be designed to meet application-specific
performance requirements”. In addition, the prices of the wood based substitute products are also
very reasonable. Due to all these reasons, wood based substitute products were able to gain a good
market share of the wood which has expended over the past 20 years. As per the official reports, “it
is estimated that the current value of global trade in bamboo products is worth 7bn USD, and is
expected to rise at 17bn USD in near future” (Bayne & Seadon, 2013).
2 PRODUCT OUTLINES
2.1 MDF (plus overlays)
The Medium density fibreboards (MDF) are a separately engineered wood product that is
manufactured by converting the residues of the hardwood and the softwood into the wood fibres
majorly with the help of a deflibrator. Later those wood fibres are combined with the help of the
wax and the resin binder. Those wood fibres combined with wax and resin binder are converted into
panels with the help of high temperature and by applying lots of pressure. Medium density
fibreboards (MDF) are usually much more dense than the normal plywood. Medium density
fibreboards (MDF) may be made up of separated wood fibres but it is so strong that the medium
density fibreboards can be used as the building material which is quite similar to the use of plywood.
Medium density fibreboards (MDF) when compared to other wood based substituted, is actually
much more stronger and much more denser than the particle board (Piekarski et al. , 2017).
2.2 Particle Board
The Particle Board which is also known as the “particleboard, low-density fibreboard” (LDF) or
it may also be called the chipboard is actually an engineered wood product which is mainly build
with the help of wood chips and sawmill savings or sawdust. The following power is then mixes with
synthetic resin or any suitable binder. The mixture is then exposed to high pressure and Extrusion.
“Oriented strand board, also known as flake board, wafer board, or chipboard is similar, but uses
machined wood flakes offering more strength. All of these are composite materials that belong to
the spectrum of fibreboard products”(Jafarnezhad, Shalbafan & Luedtke, 2018). The Particle board
are much more cheaper, denser and much more uniform than the conventional wood and plywood.
The Particle Board can be made much more appealing and attractive by painting it or by using the
wood veneers on the visible surfaces. “Different grades of particle board have different densities,
with higher density connoting greater strength and greater resistance to failure of screw fasteners”
(Jafarnezhad, Shalbafan & Luedtke, 2018).
4100456463648326326.docx Page 4 of 12
1 INTRODUCTION
Wood Based substitute products majorly contain wood fibres and a mixture of plastic (Wood-
plastic composites-WPC) or cement, glue and assorted other materials which is mechanically
engineered. As per the recent official reports, about half of the tropical forest are destroyed. It is
estimated that by the year 2030 only 10 percent of the total forest cover would be destroyed if the
current rate of deforestation continues (Schaafsma et al., 2014).Due to the increasing environmental
concern all around the world, there is an increase in the demand for the wood based substitute in
the overall business market. The various wood based substitutes may mainly include the bamboo
substitute, the rubber wood substitute and the recycle plastic lumber. Wood based substitute
products have a longer durability and a larger life cycle. Since the wood based substituted are
mechanically engineered by human being, “it can be designed to meet application-specific
performance requirements”. In addition, the prices of the wood based substitute products are also
very reasonable. Due to all these reasons, wood based substitute products were able to gain a good
market share of the wood which has expended over the past 20 years. As per the official reports, “it
is estimated that the current value of global trade in bamboo products is worth 7bn USD, and is
expected to rise at 17bn USD in near future” (Bayne & Seadon, 2013).
2 PRODUCT OUTLINES
2.1 MDF (plus overlays)
The Medium density fibreboards (MDF) are a separately engineered wood product that is
manufactured by converting the residues of the hardwood and the softwood into the wood fibres
majorly with the help of a deflibrator. Later those wood fibres are combined with the help of the
wax and the resin binder. Those wood fibres combined with wax and resin binder are converted into
panels with the help of high temperature and by applying lots of pressure. Medium density
fibreboards (MDF) are usually much more dense than the normal plywood. Medium density
fibreboards (MDF) may be made up of separated wood fibres but it is so strong that the medium
density fibreboards can be used as the building material which is quite similar to the use of plywood.
Medium density fibreboards (MDF) when compared to other wood based substituted, is actually
much more stronger and much more denser than the particle board (Piekarski et al. , 2017).
2.2 Particle Board
The Particle Board which is also known as the “particleboard, low-density fibreboard” (LDF) or
it may also be called the chipboard is actually an engineered wood product which is mainly build
with the help of wood chips and sawmill savings or sawdust. The following power is then mixes with
synthetic resin or any suitable binder. The mixture is then exposed to high pressure and Extrusion.
“Oriented strand board, also known as flake board, wafer board, or chipboard is similar, but uses
machined wood flakes offering more strength. All of these are composite materials that belong to
the spectrum of fibreboard products”(Jafarnezhad, Shalbafan & Luedtke, 2018). The Particle board
are much more cheaper, denser and much more uniform than the conventional wood and plywood.
The Particle Board can be made much more appealing and attractive by painting it or by using the
wood veneers on the visible surfaces. “Different grades of particle board have different densities,
with higher density connoting greater strength and greater resistance to failure of screw fasteners”
(Jafarnezhad, Shalbafan & Luedtke, 2018).
4100456463648326326.docx Page 4 of 12
Secure Best Marks with AI Grader
Need help grading? Try our AI Grader for instant feedback on your assignments.
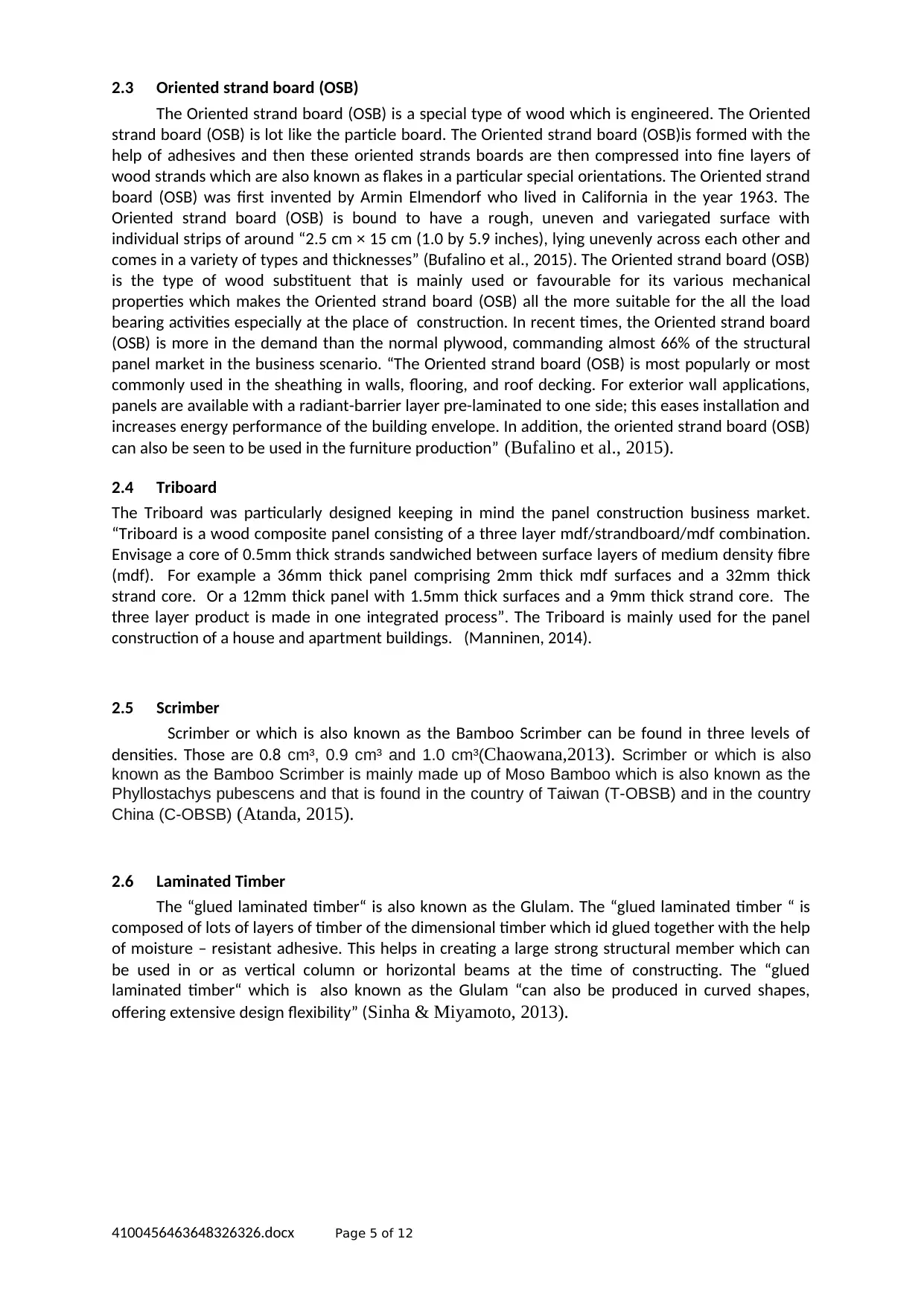
2.3 Oriented strand board (OSB)
The Oriented strand board (OSB) is a special type of wood which is engineered. The Oriented
strand board (OSB) is lot like the particle board. The Oriented strand board (OSB)is formed with the
help of adhesives and then these oriented strands boards are then compressed into fine layers of
wood strands which are also known as flakes in a particular special orientations. The Oriented strand
board (OSB) was first invented by Armin Elmendorf who lived in California in the year 1963. The
Oriented strand board (OSB) is bound to have a rough, uneven and variegated surface with
individual strips of around “2.5 cm × 15 cm (1.0 by 5.9 inches), lying unevenly across each other and
comes in a variety of types and thicknesses” (Bufalino et al., 2015). The Oriented strand board (OSB)
is the type of wood substituent that is mainly used or favourable for its various mechanical
properties which makes the Oriented strand board (OSB) all the more suitable for the all the load
bearing activities especially at the place of construction. In recent times, the Oriented strand board
(OSB) is more in the demand than the normal plywood, commanding almost 66% of the structural
panel market in the business scenario. “The Oriented strand board (OSB) is most popularly or most
commonly used in the sheathing in walls, flooring, and roof decking. For exterior wall applications,
panels are available with a radiant-barrier layer pre-laminated to one side; this eases installation and
increases energy performance of the building envelope. In addition, the oriented strand board (OSB)
can also be seen to be used in the furniture production” (Bufalino et al., 2015).
2.4 Triboard
The Triboard was particularly designed keeping in mind the panel construction business market.
“Triboard is a wood composite panel consisting of a three layer mdf/strandboard/mdf combination.
Envisage a core of 0.5mm thick strands sandwiched between surface layers of medium density fibre
(mdf). For example a 36mm thick panel comprising 2mm thick mdf surfaces and a 32mm thick
strand core. Or a 12mm thick panel with 1.5mm thick surfaces and a 9mm thick strand core. The
three layer product is made in one integrated process”. The Triboard is mainly used for the panel
construction of a house and apartment buildings. (Manninen, 2014).
2.5 Scrimber
Scrimber or which is also known as the Bamboo Scrimber can be found in three levels of
densities. Those are 0.8 cm³, 0.9 cm³ and 1.0 cm³(Chaowana,2013). Scrimber or which is also
known as the Bamboo Scrimber is mainly made up of Moso Bamboo which is also known as the
Phyllostachys pubescens and that is found in the country of Taiwan (T-OBSB) and in the country
China (C-OBSB) (Atanda, 2015).
2.6 Laminated Timber
The “glued laminated timber“ is also known as the Glulam. The “glued laminated timber “ is
composed of lots of layers of timber of the dimensional timber which id glued together with the help
of moisture – resistant adhesive. This helps in creating a large strong structural member which can
be used in or as vertical column or horizontal beams at the time of constructing. The “glued
laminated timber“ which is also known as the Glulam “can also be produced in curved shapes,
offering extensive design flexibility” (Sinha & Miyamoto, 2013).
4100456463648326326.docx Page 5 of 12
The Oriented strand board (OSB) is a special type of wood which is engineered. The Oriented
strand board (OSB) is lot like the particle board. The Oriented strand board (OSB)is formed with the
help of adhesives and then these oriented strands boards are then compressed into fine layers of
wood strands which are also known as flakes in a particular special orientations. The Oriented strand
board (OSB) was first invented by Armin Elmendorf who lived in California in the year 1963. The
Oriented strand board (OSB) is bound to have a rough, uneven and variegated surface with
individual strips of around “2.5 cm × 15 cm (1.0 by 5.9 inches), lying unevenly across each other and
comes in a variety of types and thicknesses” (Bufalino et al., 2015). The Oriented strand board (OSB)
is the type of wood substituent that is mainly used or favourable for its various mechanical
properties which makes the Oriented strand board (OSB) all the more suitable for the all the load
bearing activities especially at the place of construction. In recent times, the Oriented strand board
(OSB) is more in the demand than the normal plywood, commanding almost 66% of the structural
panel market in the business scenario. “The Oriented strand board (OSB) is most popularly or most
commonly used in the sheathing in walls, flooring, and roof decking. For exterior wall applications,
panels are available with a radiant-barrier layer pre-laminated to one side; this eases installation and
increases energy performance of the building envelope. In addition, the oriented strand board (OSB)
can also be seen to be used in the furniture production” (Bufalino et al., 2015).
2.4 Triboard
The Triboard was particularly designed keeping in mind the panel construction business market.
“Triboard is a wood composite panel consisting of a three layer mdf/strandboard/mdf combination.
Envisage a core of 0.5mm thick strands sandwiched between surface layers of medium density fibre
(mdf). For example a 36mm thick panel comprising 2mm thick mdf surfaces and a 32mm thick
strand core. Or a 12mm thick panel with 1.5mm thick surfaces and a 9mm thick strand core. The
three layer product is made in one integrated process”. The Triboard is mainly used for the panel
construction of a house and apartment buildings. (Manninen, 2014).
2.5 Scrimber
Scrimber or which is also known as the Bamboo Scrimber can be found in three levels of
densities. Those are 0.8 cm³, 0.9 cm³ and 1.0 cm³(Chaowana,2013). Scrimber or which is also
known as the Bamboo Scrimber is mainly made up of Moso Bamboo which is also known as the
Phyllostachys pubescens and that is found in the country of Taiwan (T-OBSB) and in the country
China (C-OBSB) (Atanda, 2015).
2.6 Laminated Timber
The “glued laminated timber“ is also known as the Glulam. The “glued laminated timber “ is
composed of lots of layers of timber of the dimensional timber which id glued together with the help
of moisture – resistant adhesive. This helps in creating a large strong structural member which can
be used in or as vertical column or horizontal beams at the time of constructing. The “glued
laminated timber“ which is also known as the Glulam “can also be produced in curved shapes,
offering extensive design flexibility” (Sinha & Miyamoto, 2013).
4100456463648326326.docx Page 5 of 12
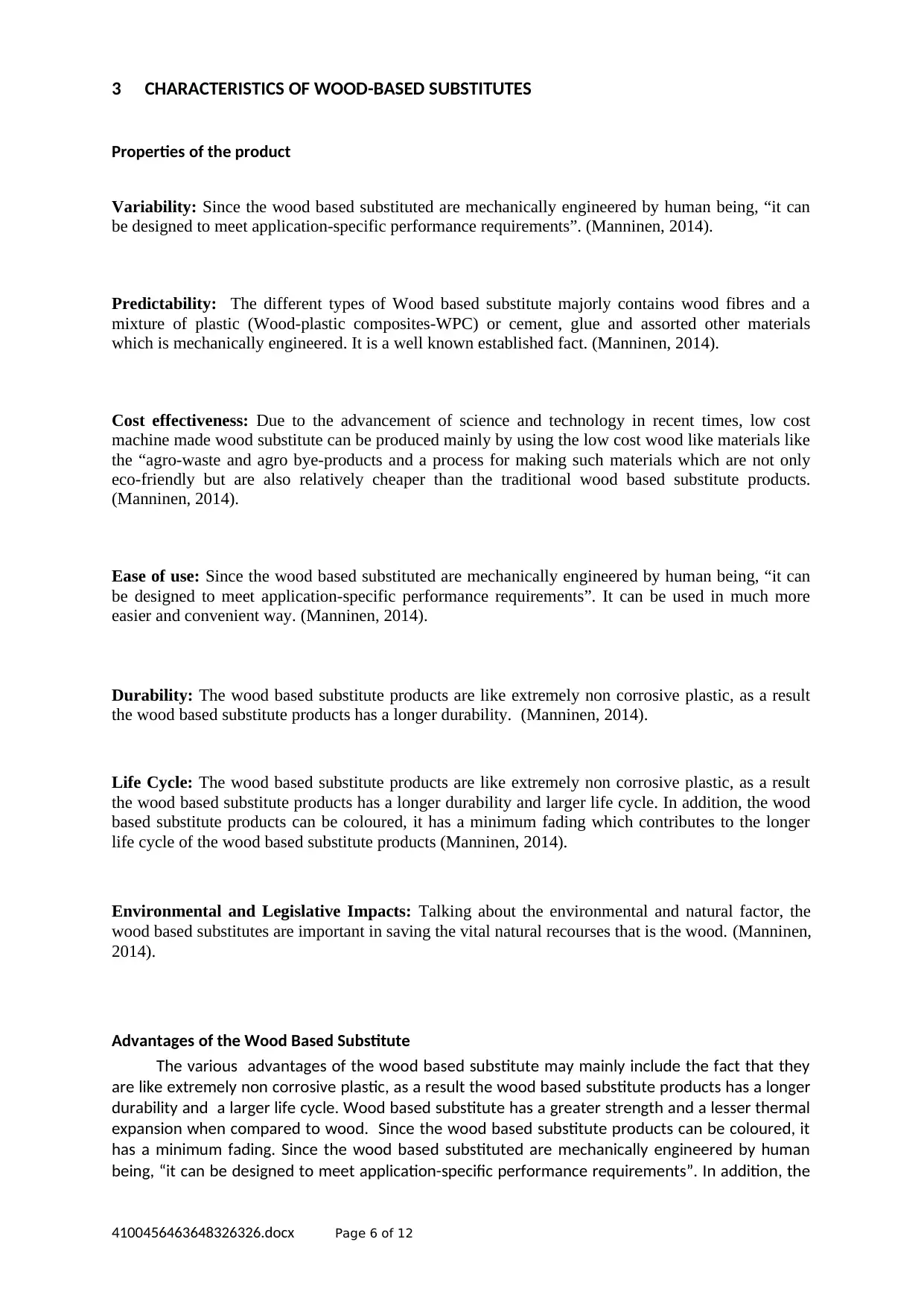
3 CHARACTERISTICS OF WOOD-BASED SUBSTITUTES
Properties of the product
Variability: Since the wood based substituted are mechanically engineered by human being, “it can
be designed to meet application-specific performance requirements”. (Manninen, 2014).
Predictability: The different types of Wood based substitute majorly contains wood fibres and a
mixture of plastic (Wood-plastic composites-WPC) or cement, glue and assorted other materials
which is mechanically engineered. It is a well known established fact. (Manninen, 2014).
Cost effectiveness: Due to the advancement of science and technology in recent times, low cost
machine made wood substitute can be produced mainly by using the low cost wood like materials like
the “agro-waste and agro bye-products and a process for making such materials which are not only
eco-friendly but are also relatively cheaper than the traditional wood based substitute products.
(Manninen, 2014).
Ease of use: Since the wood based substituted are mechanically engineered by human being, “it can
be designed to meet application-specific performance requirements”. It can be used in much more
easier and convenient way. (Manninen, 2014).
Durability: The wood based substitute products are like extremely non corrosive plastic, as a result
the wood based substitute products has a longer durability. (Manninen, 2014).
Life Cycle: The wood based substitute products are like extremely non corrosive plastic, as a result
the wood based substitute products has a longer durability and larger life cycle. In addition, the wood
based substitute products can be coloured, it has a minimum fading which contributes to the longer
life cycle of the wood based substitute products (Manninen, 2014).
Environmental and Legislative Impacts: Talking about the environmental and natural factor, the
wood based substitutes are important in saving the vital natural recourses that is the wood. (Manninen,
2014).
Advantages of the Wood Based Substitute
The various advantages of the wood based substitute may mainly include the fact that they
are like extremely non corrosive plastic, as a result the wood based substitute products has a longer
durability and a larger life cycle. Wood based substitute has a greater strength and a lesser thermal
expansion when compared to wood. Since the wood based substitute products can be coloured, it
has a minimum fading. Since the wood based substituted are mechanically engineered by human
being, “it can be designed to meet application-specific performance requirements”. In addition, the
4100456463648326326.docx Page 6 of 12
Properties of the product
Variability: Since the wood based substituted are mechanically engineered by human being, “it can
be designed to meet application-specific performance requirements”. (Manninen, 2014).
Predictability: The different types of Wood based substitute majorly contains wood fibres and a
mixture of plastic (Wood-plastic composites-WPC) or cement, glue and assorted other materials
which is mechanically engineered. It is a well known established fact. (Manninen, 2014).
Cost effectiveness: Due to the advancement of science and technology in recent times, low cost
machine made wood substitute can be produced mainly by using the low cost wood like materials like
the “agro-waste and agro bye-products and a process for making such materials which are not only
eco-friendly but are also relatively cheaper than the traditional wood based substitute products.
(Manninen, 2014).
Ease of use: Since the wood based substituted are mechanically engineered by human being, “it can
be designed to meet application-specific performance requirements”. It can be used in much more
easier and convenient way. (Manninen, 2014).
Durability: The wood based substitute products are like extremely non corrosive plastic, as a result
the wood based substitute products has a longer durability. (Manninen, 2014).
Life Cycle: The wood based substitute products are like extremely non corrosive plastic, as a result
the wood based substitute products has a longer durability and larger life cycle. In addition, the wood
based substitute products can be coloured, it has a minimum fading which contributes to the longer
life cycle of the wood based substitute products (Manninen, 2014).
Environmental and Legislative Impacts: Talking about the environmental and natural factor, the
wood based substitutes are important in saving the vital natural recourses that is the wood. (Manninen,
2014).
Advantages of the Wood Based Substitute
The various advantages of the wood based substitute may mainly include the fact that they
are like extremely non corrosive plastic, as a result the wood based substitute products has a longer
durability and a larger life cycle. Wood based substitute has a greater strength and a lesser thermal
expansion when compared to wood. Since the wood based substitute products can be coloured, it
has a minimum fading. Since the wood based substituted are mechanically engineered by human
being, “it can be designed to meet application-specific performance requirements”. In addition, the
4100456463648326326.docx Page 6 of 12
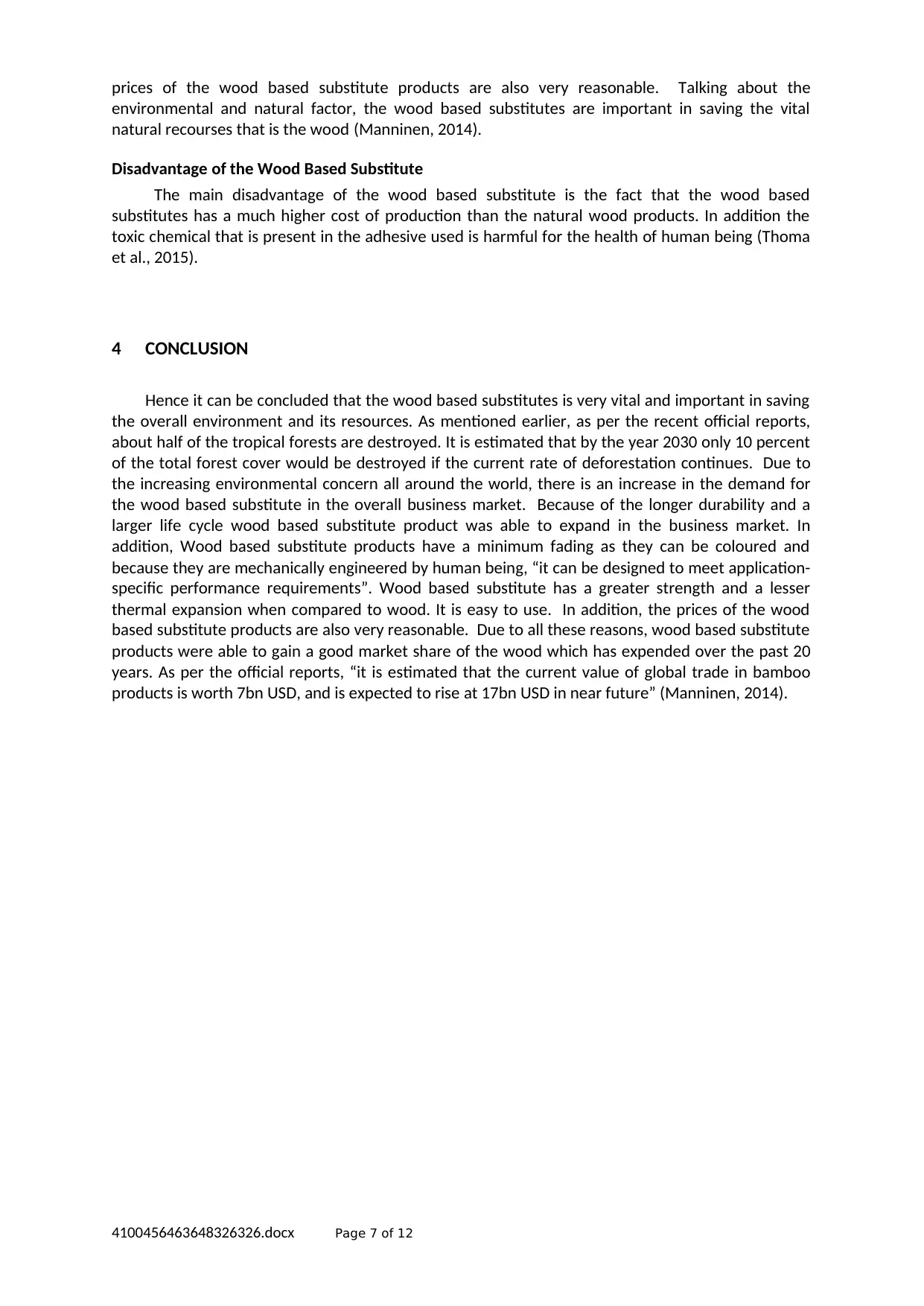
prices of the wood based substitute products are also very reasonable. Talking about the
environmental and natural factor, the wood based substitutes are important in saving the vital
natural recourses that is the wood (Manninen, 2014).
Disadvantage of the Wood Based Substitute
The main disadvantage of the wood based substitute is the fact that the wood based
substitutes has a much higher cost of production than the natural wood products. In addition the
toxic chemical that is present in the adhesive used is harmful for the health of human being (Thoma
et al., 2015).
4 CONCLUSION
Hence it can be concluded that the wood based substitutes is very vital and important in saving
the overall environment and its resources. As mentioned earlier, as per the recent official reports,
about half of the tropical forests are destroyed. It is estimated that by the year 2030 only 10 percent
of the total forest cover would be destroyed if the current rate of deforestation continues. Due to
the increasing environmental concern all around the world, there is an increase in the demand for
the wood based substitute in the overall business market. Because of the longer durability and a
larger life cycle wood based substitute product was able to expand in the business market. In
addition, Wood based substitute products have a minimum fading as they can be coloured and
because they are mechanically engineered by human being, “it can be designed to meet application-
specific performance requirements”. Wood based substitute has a greater strength and a lesser
thermal expansion when compared to wood. It is easy to use. In addition, the prices of the wood
based substitute products are also very reasonable. Due to all these reasons, wood based substitute
products were able to gain a good market share of the wood which has expended over the past 20
years. As per the official reports, “it is estimated that the current value of global trade in bamboo
products is worth 7bn USD, and is expected to rise at 17bn USD in near future” (Manninen, 2014).
4100456463648326326.docx Page 7 of 12
environmental and natural factor, the wood based substitutes are important in saving the vital
natural recourses that is the wood (Manninen, 2014).
Disadvantage of the Wood Based Substitute
The main disadvantage of the wood based substitute is the fact that the wood based
substitutes has a much higher cost of production than the natural wood products. In addition the
toxic chemical that is present in the adhesive used is harmful for the health of human being (Thoma
et al., 2015).
4 CONCLUSION
Hence it can be concluded that the wood based substitutes is very vital and important in saving
the overall environment and its resources. As mentioned earlier, as per the recent official reports,
about half of the tropical forests are destroyed. It is estimated that by the year 2030 only 10 percent
of the total forest cover would be destroyed if the current rate of deforestation continues. Due to
the increasing environmental concern all around the world, there is an increase in the demand for
the wood based substitute in the overall business market. Because of the longer durability and a
larger life cycle wood based substitute product was able to expand in the business market. In
addition, Wood based substitute products have a minimum fading as they can be coloured and
because they are mechanically engineered by human being, “it can be designed to meet application-
specific performance requirements”. Wood based substitute has a greater strength and a lesser
thermal expansion when compared to wood. It is easy to use. In addition, the prices of the wood
based substitute products are also very reasonable. Due to all these reasons, wood based substitute
products were able to gain a good market share of the wood which has expended over the past 20
years. As per the official reports, “it is estimated that the current value of global trade in bamboo
products is worth 7bn USD, and is expected to rise at 17bn USD in near future” (Manninen, 2014).
4100456463648326326.docx Page 7 of 12
Paraphrase This Document
Need a fresh take? Get an instant paraphrase of this document with our AI Paraphraser
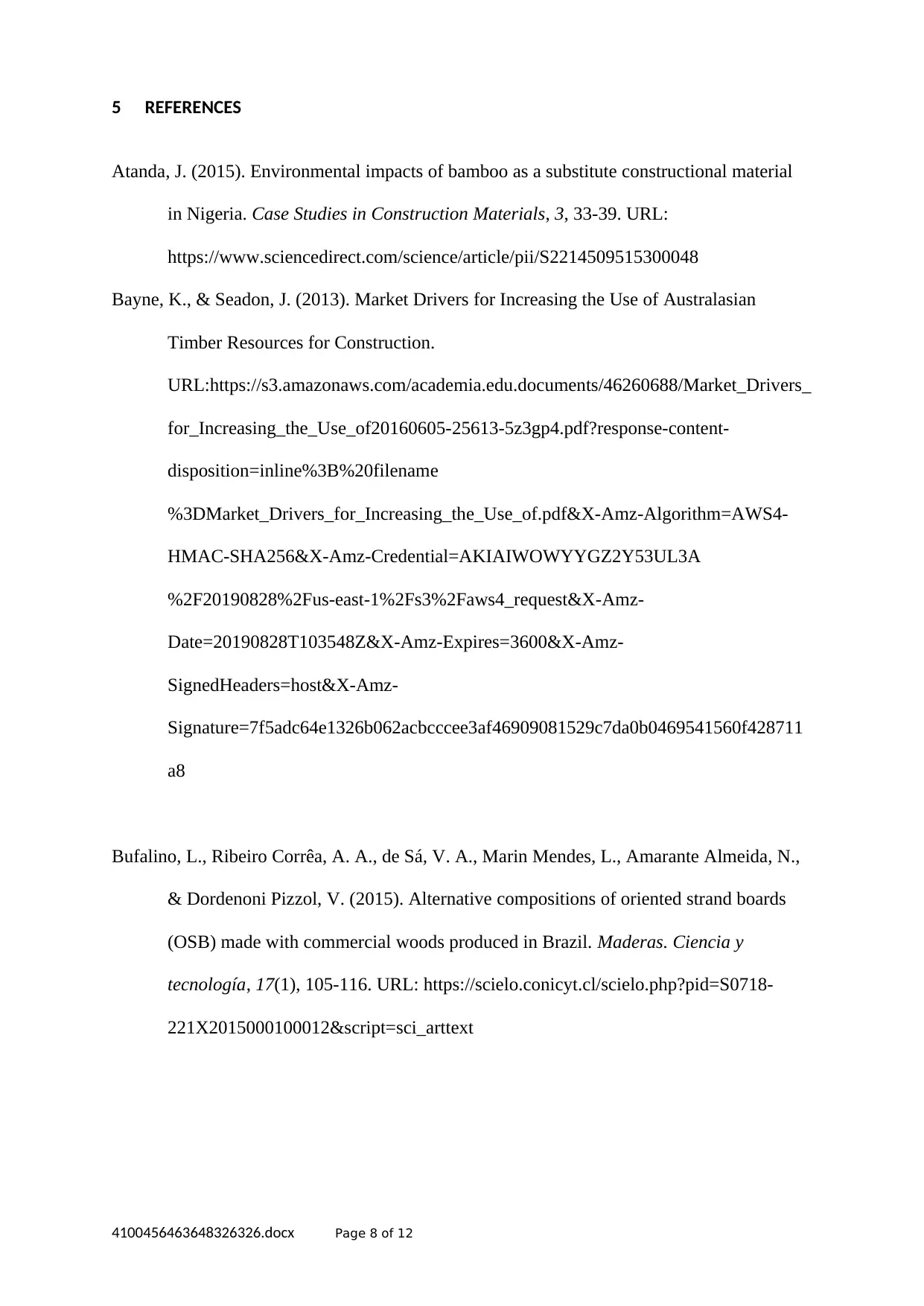
5 REFERENCES
Atanda, J. (2015). Environmental impacts of bamboo as a substitute constructional material
in Nigeria. Case Studies in Construction Materials, 3, 33-39. URL:
https://www.sciencedirect.com/science/article/pii/S2214509515300048
Bayne, K., & Seadon, J. (2013). Market Drivers for Increasing the Use of Australasian
Timber Resources for Construction.
URL:https://s3.amazonaws.com/academia.edu.documents/46260688/Market_Drivers_
for_Increasing_the_Use_of20160605-25613-5z3gp4.pdf?response-content-
disposition=inline%3B%20filename
%3DMarket_Drivers_for_Increasing_the_Use_of.pdf&X-Amz-Algorithm=AWS4-
HMAC-SHA256&X-Amz-Credential=AKIAIWOWYYGZ2Y53UL3A
%2F20190828%2Fus-east-1%2Fs3%2Faws4_request&X-Amz-
Date=20190828T103548Z&X-Amz-Expires=3600&X-Amz-
SignedHeaders=host&X-Amz-
Signature=7f5adc64e1326b062acbcccee3af46909081529c7da0b0469541560f428711
a8
Bufalino, L., Ribeiro Corrêa, A. A., de Sá, V. A., Marin Mendes, L., Amarante Almeida, N.,
& Dordenoni Pizzol, V. (2015). Alternative compositions of oriented strand boards
(OSB) made with commercial woods produced in Brazil. Maderas. Ciencia y
tecnología, 17(1), 105-116. URL: https://scielo.conicyt.cl/scielo.php?pid=S0718-
221X2015000100012&script=sci_arttext
4100456463648326326.docx Page 8 of 12
Atanda, J. (2015). Environmental impacts of bamboo as a substitute constructional material
in Nigeria. Case Studies in Construction Materials, 3, 33-39. URL:
https://www.sciencedirect.com/science/article/pii/S2214509515300048
Bayne, K., & Seadon, J. (2013). Market Drivers for Increasing the Use of Australasian
Timber Resources for Construction.
URL:https://s3.amazonaws.com/academia.edu.documents/46260688/Market_Drivers_
for_Increasing_the_Use_of20160605-25613-5z3gp4.pdf?response-content-
disposition=inline%3B%20filename
%3DMarket_Drivers_for_Increasing_the_Use_of.pdf&X-Amz-Algorithm=AWS4-
HMAC-SHA256&X-Amz-Credential=AKIAIWOWYYGZ2Y53UL3A
%2F20190828%2Fus-east-1%2Fs3%2Faws4_request&X-Amz-
Date=20190828T103548Z&X-Amz-Expires=3600&X-Amz-
SignedHeaders=host&X-Amz-
Signature=7f5adc64e1326b062acbcccee3af46909081529c7da0b0469541560f428711
a8
Bufalino, L., Ribeiro Corrêa, A. A., de Sá, V. A., Marin Mendes, L., Amarante Almeida, N.,
& Dordenoni Pizzol, V. (2015). Alternative compositions of oriented strand boards
(OSB) made with commercial woods produced in Brazil. Maderas. Ciencia y
tecnología, 17(1), 105-116. URL: https://scielo.conicyt.cl/scielo.php?pid=S0718-
221X2015000100012&script=sci_arttext
4100456463648326326.docx Page 8 of 12
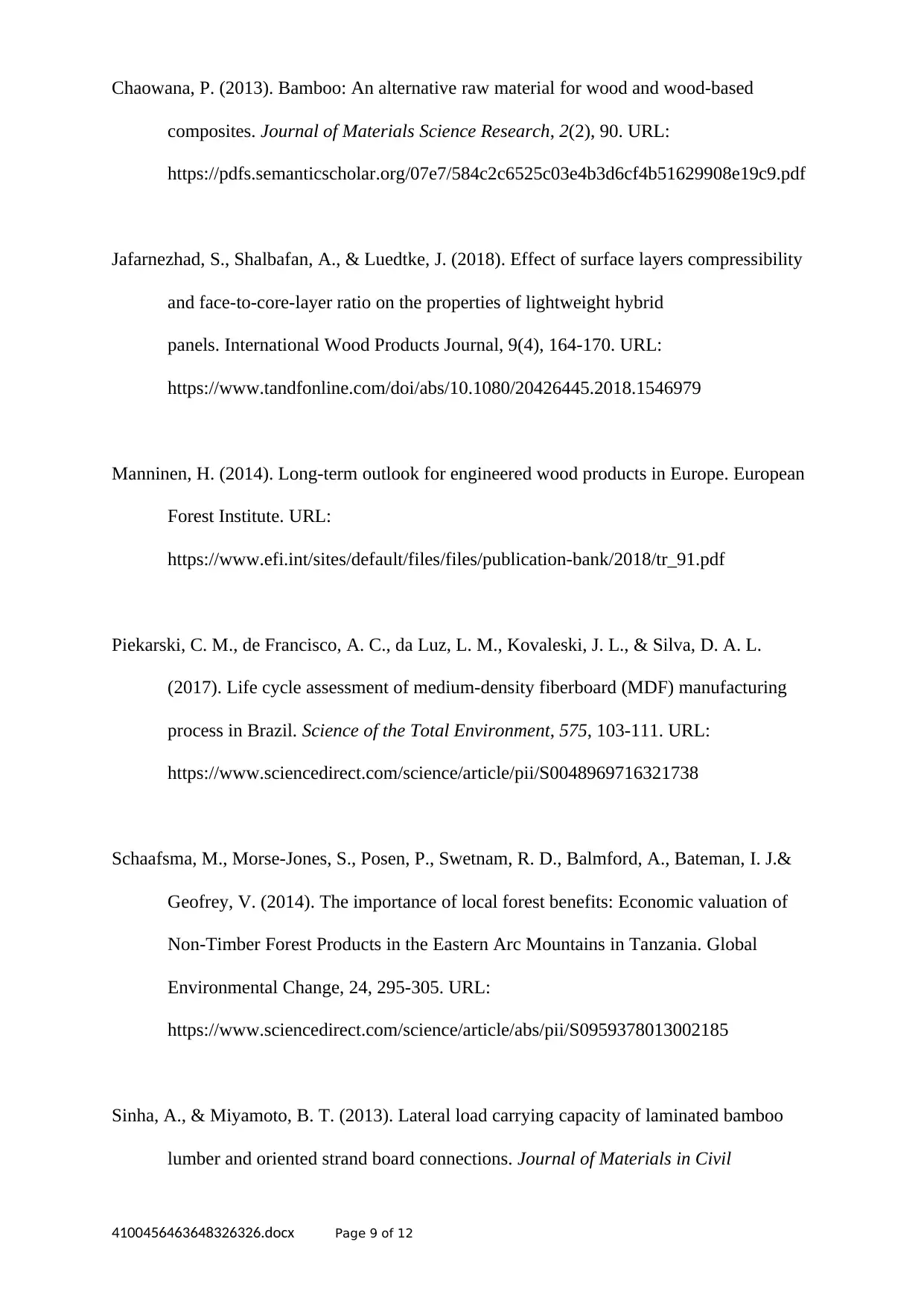
Chaowana, P. (2013). Bamboo: An alternative raw material for wood and wood-based
composites. Journal of Materials Science Research, 2(2), 90. URL:
https://pdfs.semanticscholar.org/07e7/584c2c6525c03e4b3d6cf4b51629908e19c9.pdf
Jafarnezhad, S., Shalbafan, A., & Luedtke, J. (2018). Effect of surface layers compressibility
and face-to-core-layer ratio on the properties of lightweight hybrid
panels. International Wood Products Journal, 9(4), 164-170. URL:
https://www.tandfonline.com/doi/abs/10.1080/20426445.2018.1546979
Manninen, H. (2014). Long-term outlook for engineered wood products in Europe. European
Forest Institute. URL:
https://www.efi.int/sites/default/files/files/publication-bank/2018/tr_91.pdf
Piekarski, C. M., de Francisco, A. C., da Luz, L. M., Kovaleski, J. L., & Silva, D. A. L.
(2017). Life cycle assessment of medium-density fiberboard (MDF) manufacturing
process in Brazil. Science of the Total Environment, 575, 103-111. URL:
https://www.sciencedirect.com/science/article/pii/S0048969716321738
Schaafsma, M., Morse-Jones, S., Posen, P., Swetnam, R. D., Balmford, A., Bateman, I. J.&
Geofrey, V. (2014). The importance of local forest benefits: Economic valuation of
Non-Timber Forest Products in the Eastern Arc Mountains in Tanzania. Global
Environmental Change, 24, 295-305. URL:
https://www.sciencedirect.com/science/article/abs/pii/S0959378013002185
Sinha, A., & Miyamoto, B. T. (2013). Lateral load carrying capacity of laminated bamboo
lumber and oriented strand board connections. Journal of Materials in Civil
4100456463648326326.docx Page 9 of 12
composites. Journal of Materials Science Research, 2(2), 90. URL:
https://pdfs.semanticscholar.org/07e7/584c2c6525c03e4b3d6cf4b51629908e19c9.pdf
Jafarnezhad, S., Shalbafan, A., & Luedtke, J. (2018). Effect of surface layers compressibility
and face-to-core-layer ratio on the properties of lightweight hybrid
panels. International Wood Products Journal, 9(4), 164-170. URL:
https://www.tandfonline.com/doi/abs/10.1080/20426445.2018.1546979
Manninen, H. (2014). Long-term outlook for engineered wood products in Europe. European
Forest Institute. URL:
https://www.efi.int/sites/default/files/files/publication-bank/2018/tr_91.pdf
Piekarski, C. M., de Francisco, A. C., da Luz, L. M., Kovaleski, J. L., & Silva, D. A. L.
(2017). Life cycle assessment of medium-density fiberboard (MDF) manufacturing
process in Brazil. Science of the Total Environment, 575, 103-111. URL:
https://www.sciencedirect.com/science/article/pii/S0048969716321738
Schaafsma, M., Morse-Jones, S., Posen, P., Swetnam, R. D., Balmford, A., Bateman, I. J.&
Geofrey, V. (2014). The importance of local forest benefits: Economic valuation of
Non-Timber Forest Products in the Eastern Arc Mountains in Tanzania. Global
Environmental Change, 24, 295-305. URL:
https://www.sciencedirect.com/science/article/abs/pii/S0959378013002185
Sinha, A., & Miyamoto, B. T. (2013). Lateral load carrying capacity of laminated bamboo
lumber and oriented strand board connections. Journal of Materials in Civil
4100456463648326326.docx Page 9 of 12
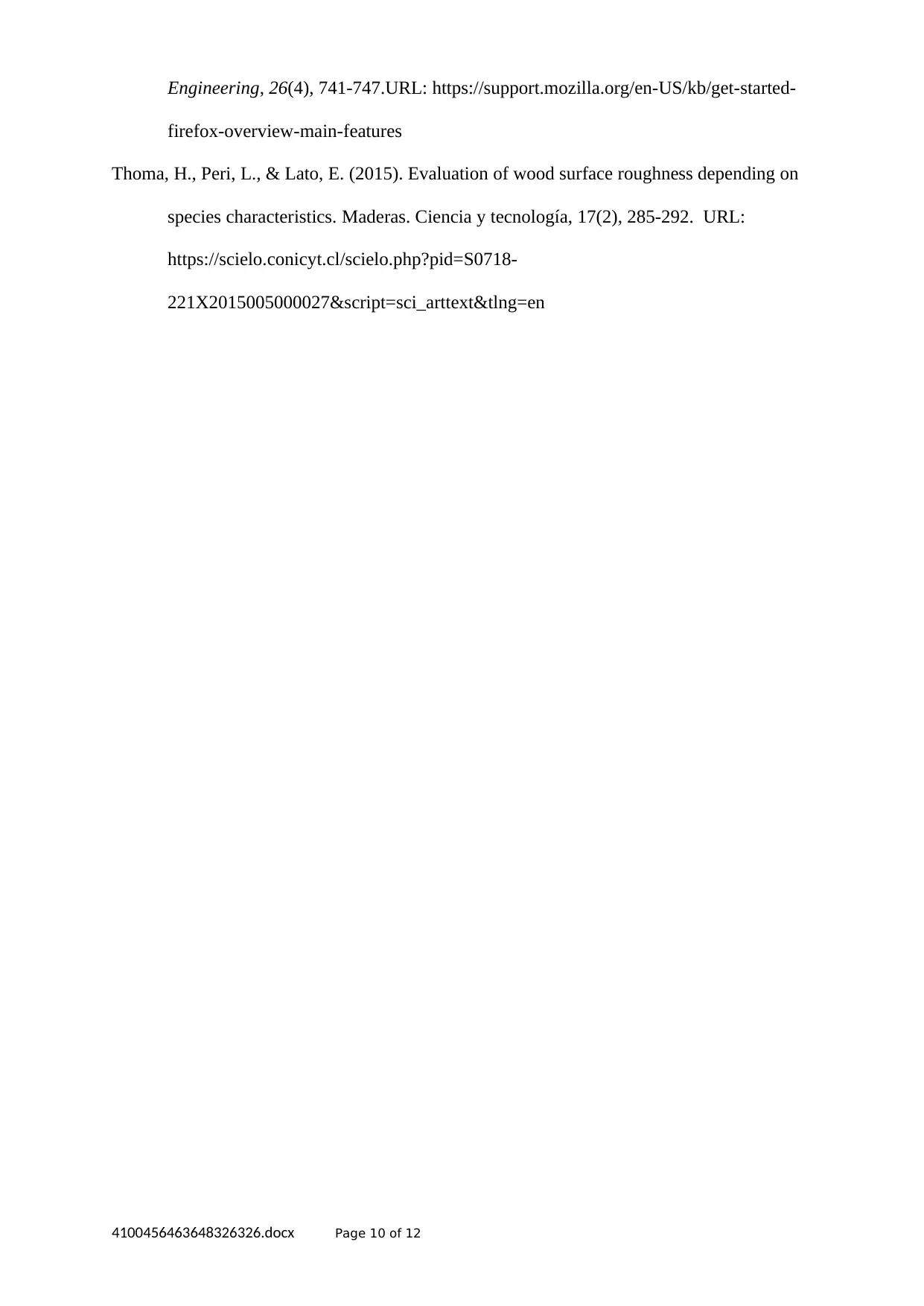
Engineering, 26(4), 741-747.URL: https://support.mozilla.org/en-US/kb/get-started-
firefox-overview-main-features
Thoma, H., Peri, L., & Lato, E. (2015). Evaluation of wood surface roughness depending on
species characteristics. Maderas. Ciencia y tecnología, 17(2), 285-292. URL:
https://scielo.conicyt.cl/scielo.php?pid=S0718-
221X2015005000027&script=sci_arttext&tlng=en
4100456463648326326.docx Page 10 of 12
firefox-overview-main-features
Thoma, H., Peri, L., & Lato, E. (2015). Evaluation of wood surface roughness depending on
species characteristics. Maderas. Ciencia y tecnología, 17(2), 285-292. URL:
https://scielo.conicyt.cl/scielo.php?pid=S0718-
221X2015005000027&script=sci_arttext&tlng=en
4100456463648326326.docx Page 10 of 12
Secure Best Marks with AI Grader
Need help grading? Try our AI Grader for instant feedback on your assignments.
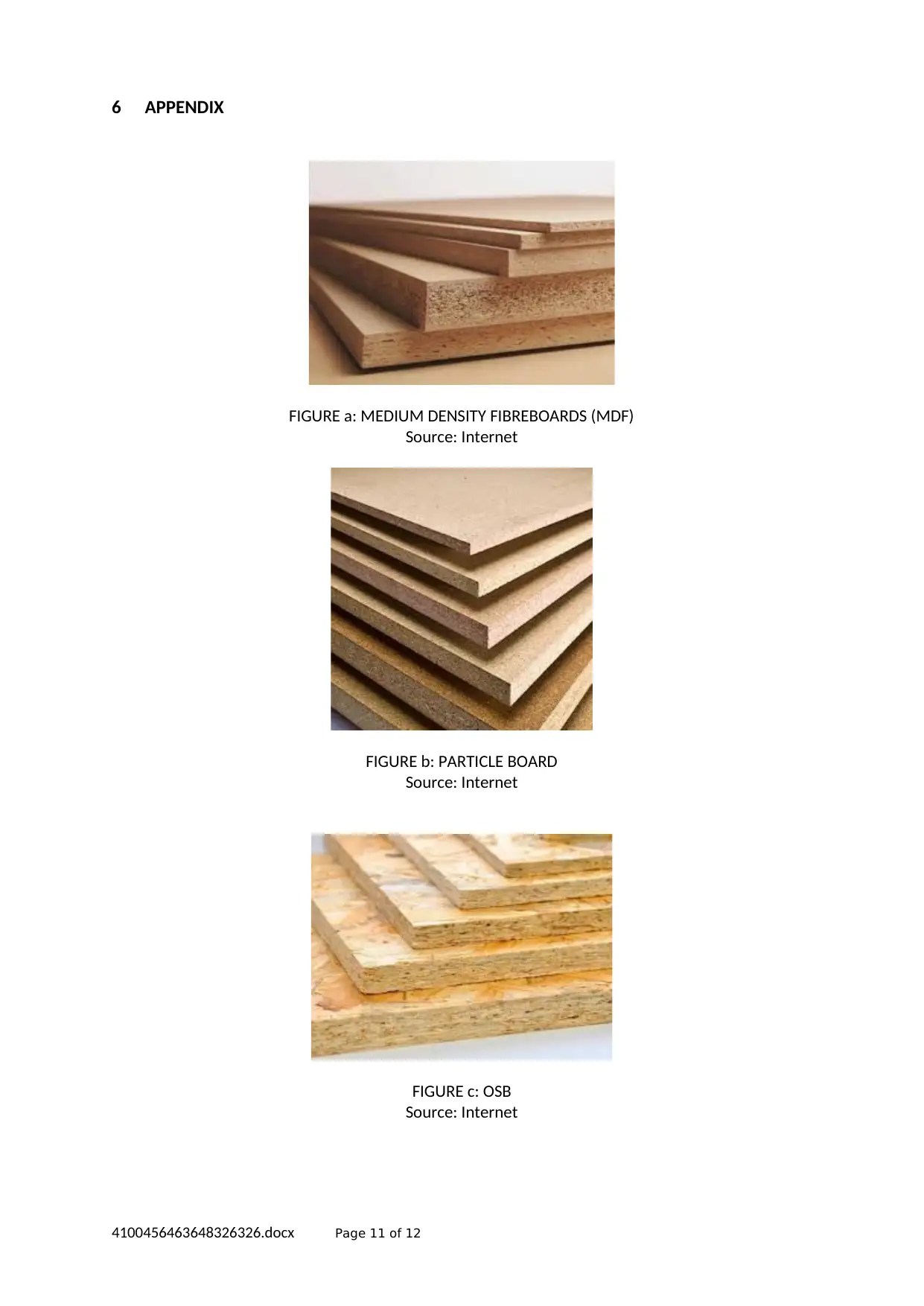
6 APPENDIX
FIGURE a: MEDIUM DENSITY FIBREBOARDS (MDF)
Source: Internet
FIGURE b: PARTICLE BOARD
Source: Internet
FIGURE c: OSB
Source: Internet
4100456463648326326.docx Page 11 of 12
FIGURE a: MEDIUM DENSITY FIBREBOARDS (MDF)
Source: Internet
FIGURE b: PARTICLE BOARD
Source: Internet
FIGURE c: OSB
Source: Internet
4100456463648326326.docx Page 11 of 12
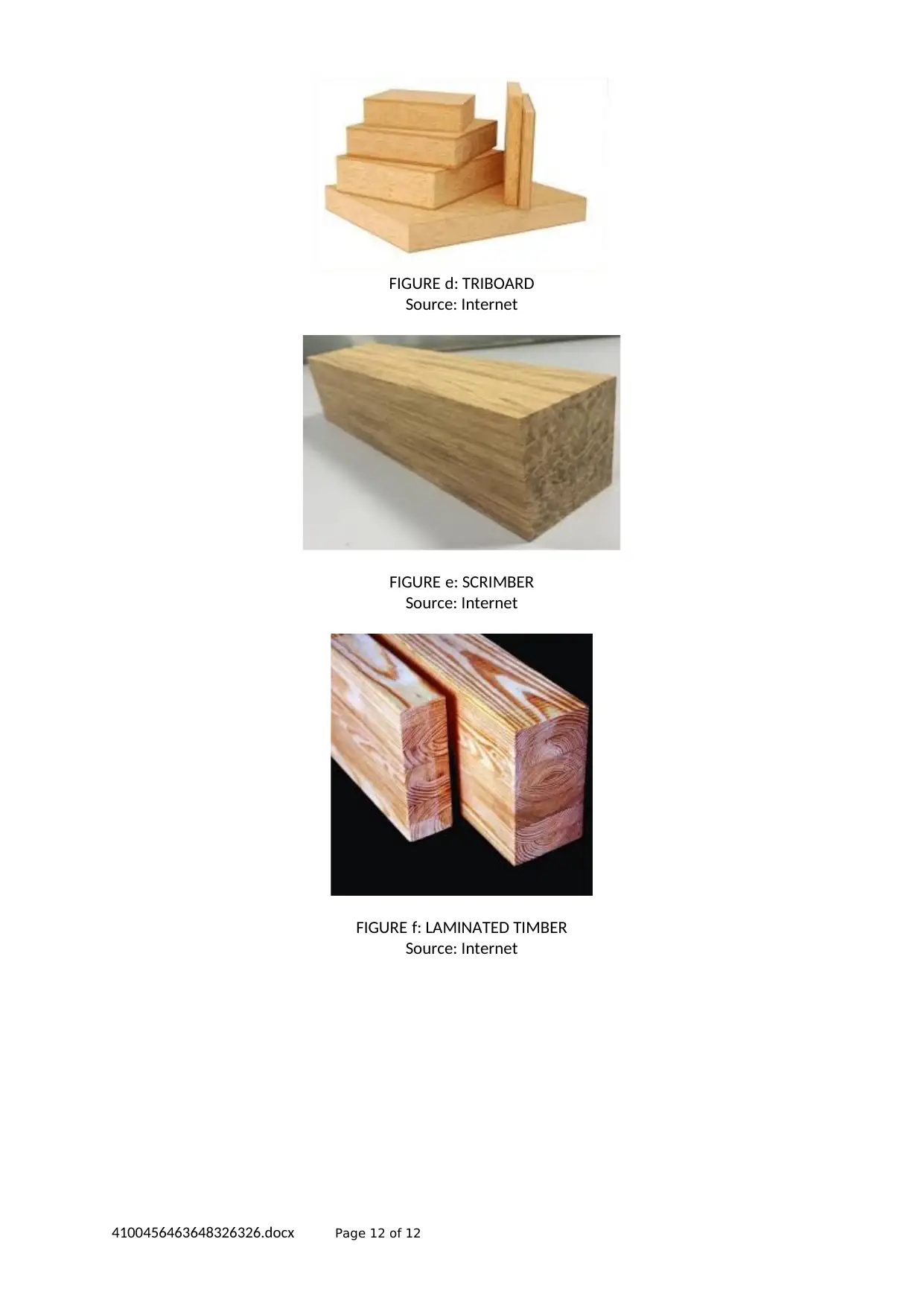
FIGURE d: TRIBOARD
Source: Internet
FIGURE e: SCRIMBER
Source: Internet
FIGURE f: LAMINATED TIMBER
Source: Internet
4100456463648326326.docx Page 12 of 12
Source: Internet
FIGURE e: SCRIMBER
Source: Internet
FIGURE f: LAMINATED TIMBER
Source: Internet
4100456463648326326.docx Page 12 of 12
1 out of 12

Your All-in-One AI-Powered Toolkit for Academic Success.
+13062052269
info@desklib.com
Available 24*7 on WhatsApp / Email
Unlock your academic potential
© 2024 | Zucol Services PVT LTD | All rights reserved.