BHM356: Workplace Design and Health - Accident Prevention Report
VerifiedAdded on 2021/01/08
|11
|2695
|163
Report
AI Summary
This report, prepared for the BHM356 module on Workplace Design and Health, delves into the causes and prevention of workplace accidents. It explores the concepts of active and latent failures, referencing James Reason's Swiss Cheese Model to illustrate how multiple layers of failures can lead to incidents. The report defines active failures as immediate errors by frontline staff and latent failures as underlying issues created by management, such as inadequate training or poor design. It provides examples of each failure type and suggests various preventive measures, including risk assessments, ergonomic design, proper training, and adherence to safety protocols. The report emphasizes the importance of a proactive safety culture, where both employers and employees work collaboratively to minimize risks and ensure a safe working environment. It concludes by highlighting the employer's duty to prevent latent failures to avoid accidents, as emphasized by the court in Polyflor Ltd vs. Health and Safety Executive (2014).
Contribute Materials
Your contribution can guide someone’s learning journey. Share your
documents today.
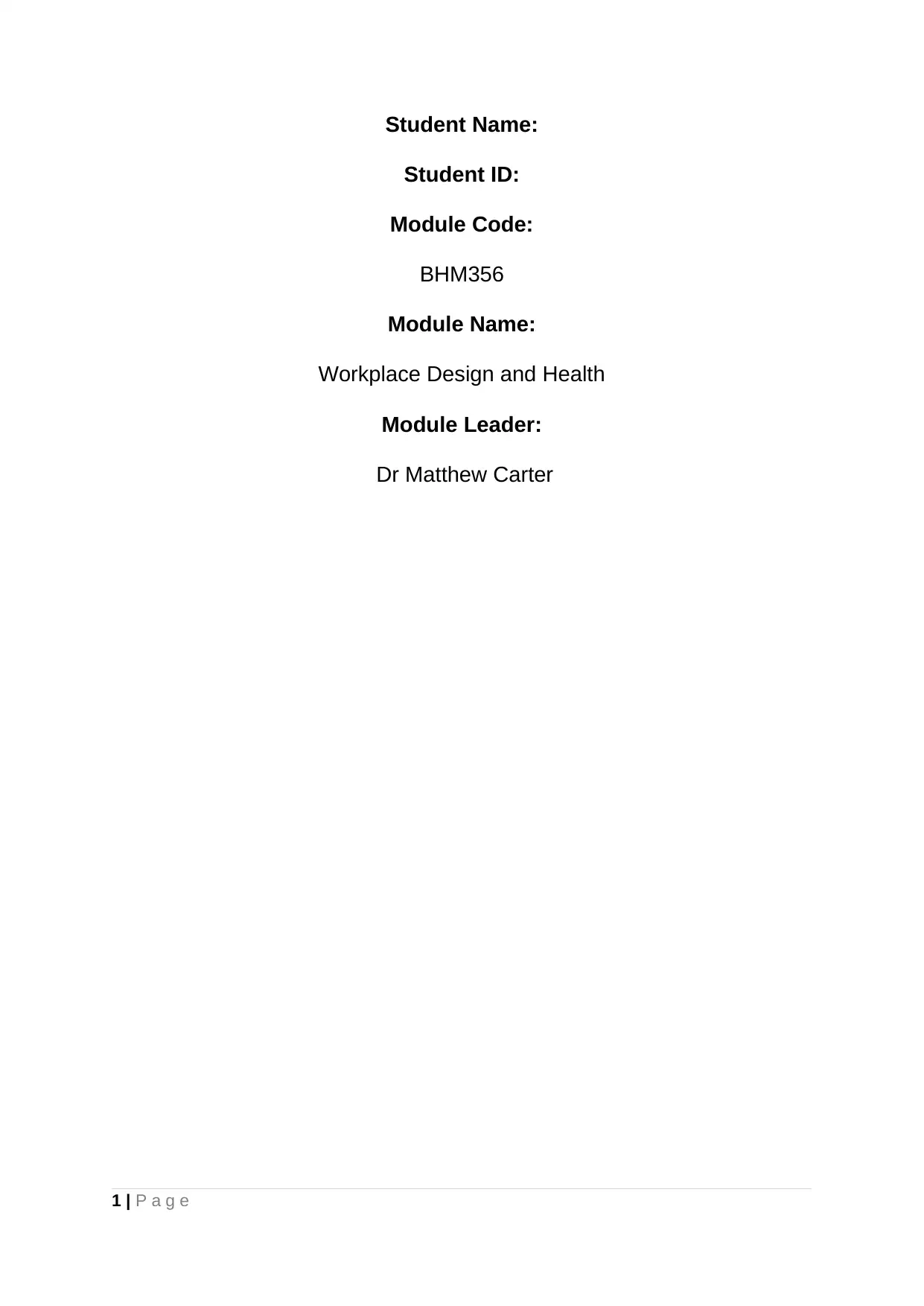
Student Name:
Student ID:
Module Code:
BHM356
Module Name:
Workplace Design and Health
Module Leader:
Dr Matthew Carter
1 | P a g e
Student ID:
Module Code:
BHM356
Module Name:
Workplace Design and Health
Module Leader:
Dr Matthew Carter
1 | P a g e
Secure Best Marks with AI Grader
Need help grading? Try our AI Grader for instant feedback on your assignments.
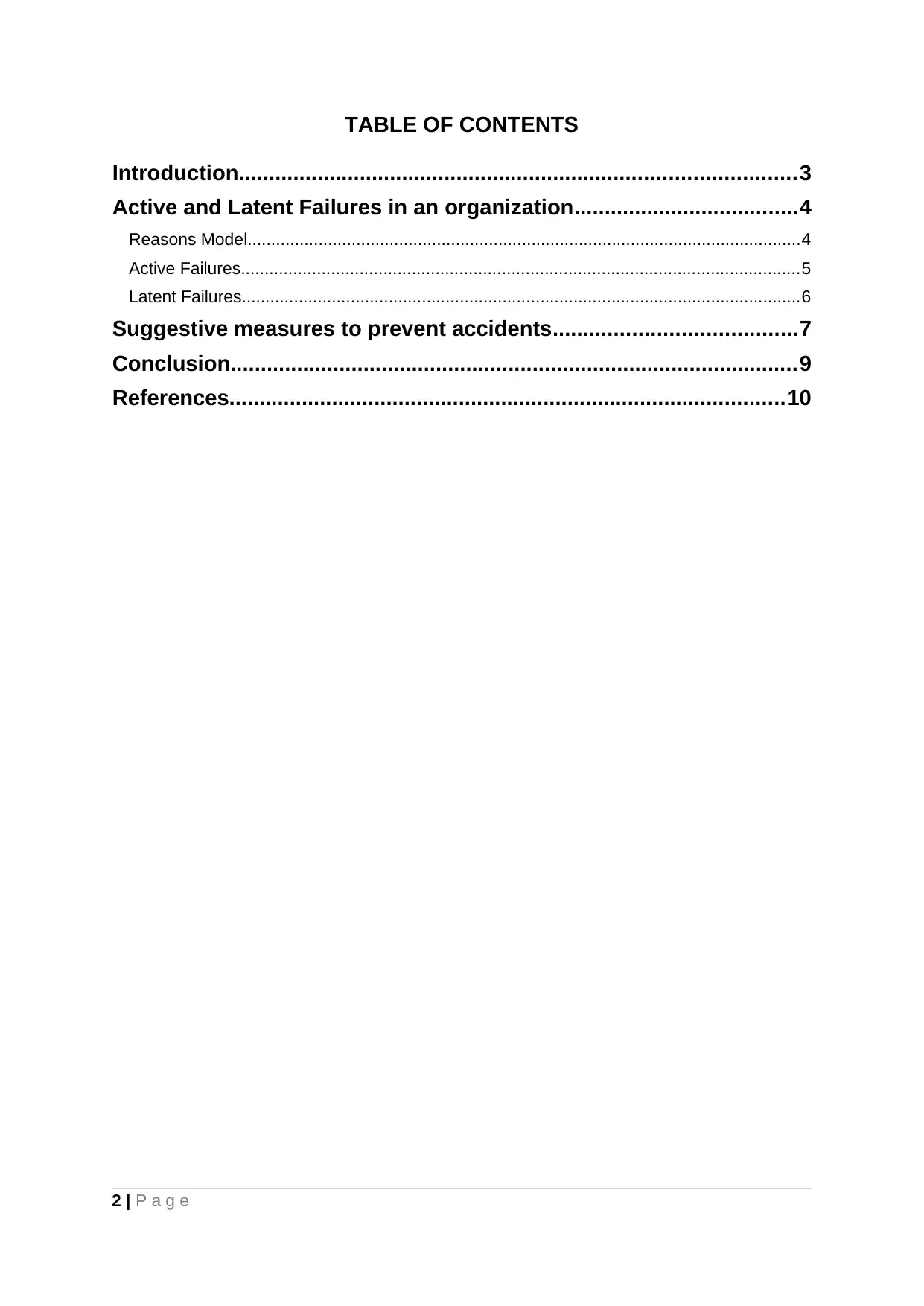
TABLE OF CONTENTS
Introduction............................................................................................3
Active and Latent Failures in an organization.....................................4
Reasons Model.....................................................................................................................4
Active Failures......................................................................................................................5
Latent Failures......................................................................................................................6
Suggestive measures to prevent accidents........................................7
Conclusion..............................................................................................9
References............................................................................................10
2 | P a g e
Introduction............................................................................................3
Active and Latent Failures in an organization.....................................4
Reasons Model.....................................................................................................................4
Active Failures......................................................................................................................5
Latent Failures......................................................................................................................6
Suggestive measures to prevent accidents........................................7
Conclusion..............................................................................................9
References............................................................................................10
2 | P a g e
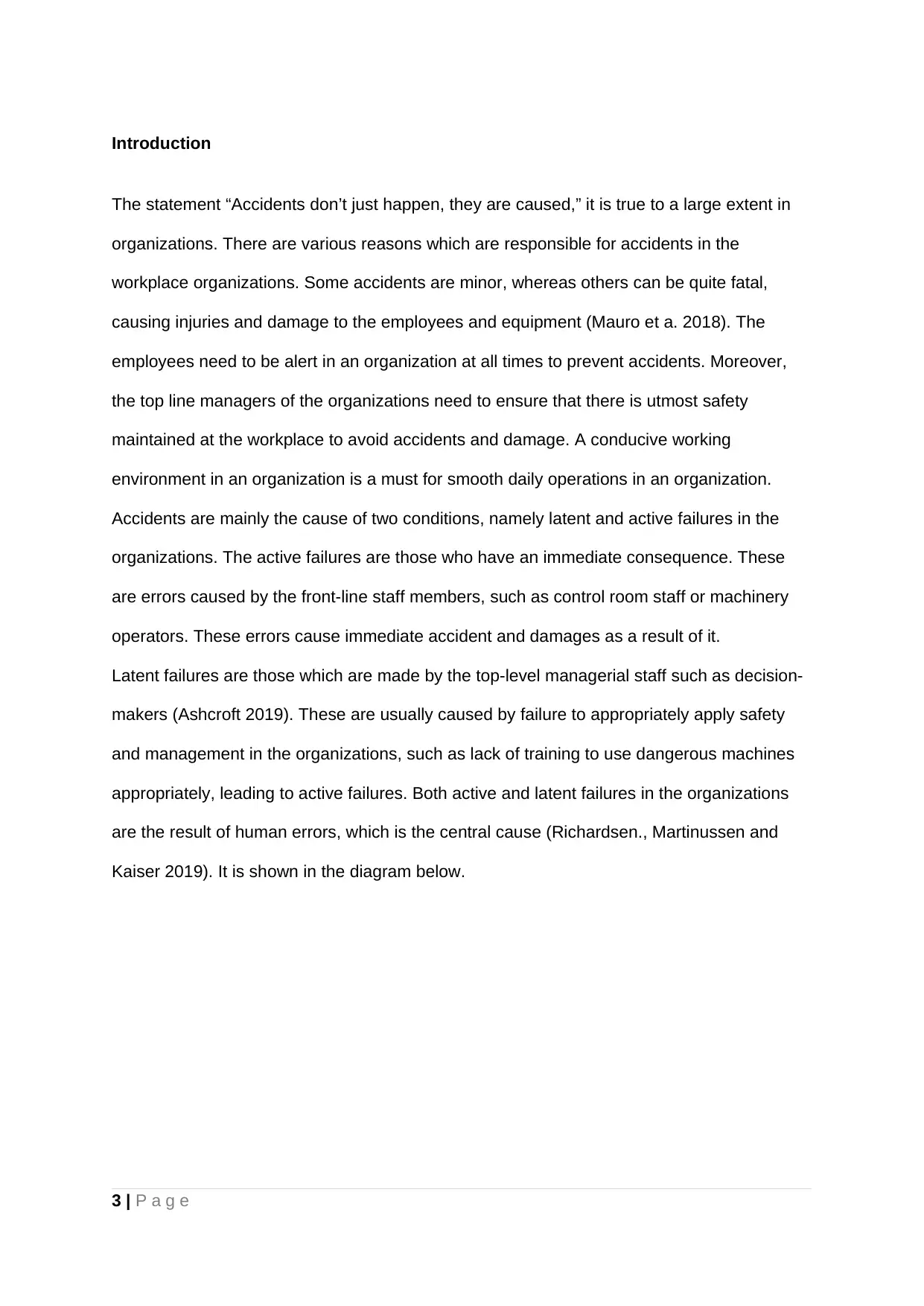
Introduction
The statement “Accidents don’t just happen, they are caused,” it is true to a large extent in
organizations. There are various reasons which are responsible for accidents in the
workplace organizations. Some accidents are minor, whereas others can be quite fatal,
causing injuries and damage to the employees and equipment (Mauro et a. 2018). The
employees need to be alert in an organization at all times to prevent accidents. Moreover,
the top line managers of the organizations need to ensure that there is utmost safety
maintained at the workplace to avoid accidents and damage. A conducive working
environment in an organization is a must for smooth daily operations in an organization.
Accidents are mainly the cause of two conditions, namely latent and active failures in the
organizations. The active failures are those who have an immediate consequence. These
are errors caused by the front-line staff members, such as control room staff or machinery
operators. These errors cause immediate accident and damages as a result of it.
Latent failures are those which are made by the top-level managerial staff such as decision-
makers (Ashcroft 2019). These are usually caused by failure to appropriately apply safety
and management in the organizations, such as lack of training to use dangerous machines
appropriately, leading to active failures. Both active and latent failures in the organizations
are the result of human errors, which is the central cause (Richardsen., Martinussen and
Kaiser 2019). It is shown in the diagram below.
3 | P a g e
The statement “Accidents don’t just happen, they are caused,” it is true to a large extent in
organizations. There are various reasons which are responsible for accidents in the
workplace organizations. Some accidents are minor, whereas others can be quite fatal,
causing injuries and damage to the employees and equipment (Mauro et a. 2018). The
employees need to be alert in an organization at all times to prevent accidents. Moreover,
the top line managers of the organizations need to ensure that there is utmost safety
maintained at the workplace to avoid accidents and damage. A conducive working
environment in an organization is a must for smooth daily operations in an organization.
Accidents are mainly the cause of two conditions, namely latent and active failures in the
organizations. The active failures are those who have an immediate consequence. These
are errors caused by the front-line staff members, such as control room staff or machinery
operators. These errors cause immediate accident and damages as a result of it.
Latent failures are those which are made by the top-level managerial staff such as decision-
makers (Ashcroft 2019). These are usually caused by failure to appropriately apply safety
and management in the organizations, such as lack of training to use dangerous machines
appropriately, leading to active failures. Both active and latent failures in the organizations
are the result of human errors, which is the central cause (Richardsen., Martinussen and
Kaiser 2019). It is shown in the diagram below.
3 | P a g e
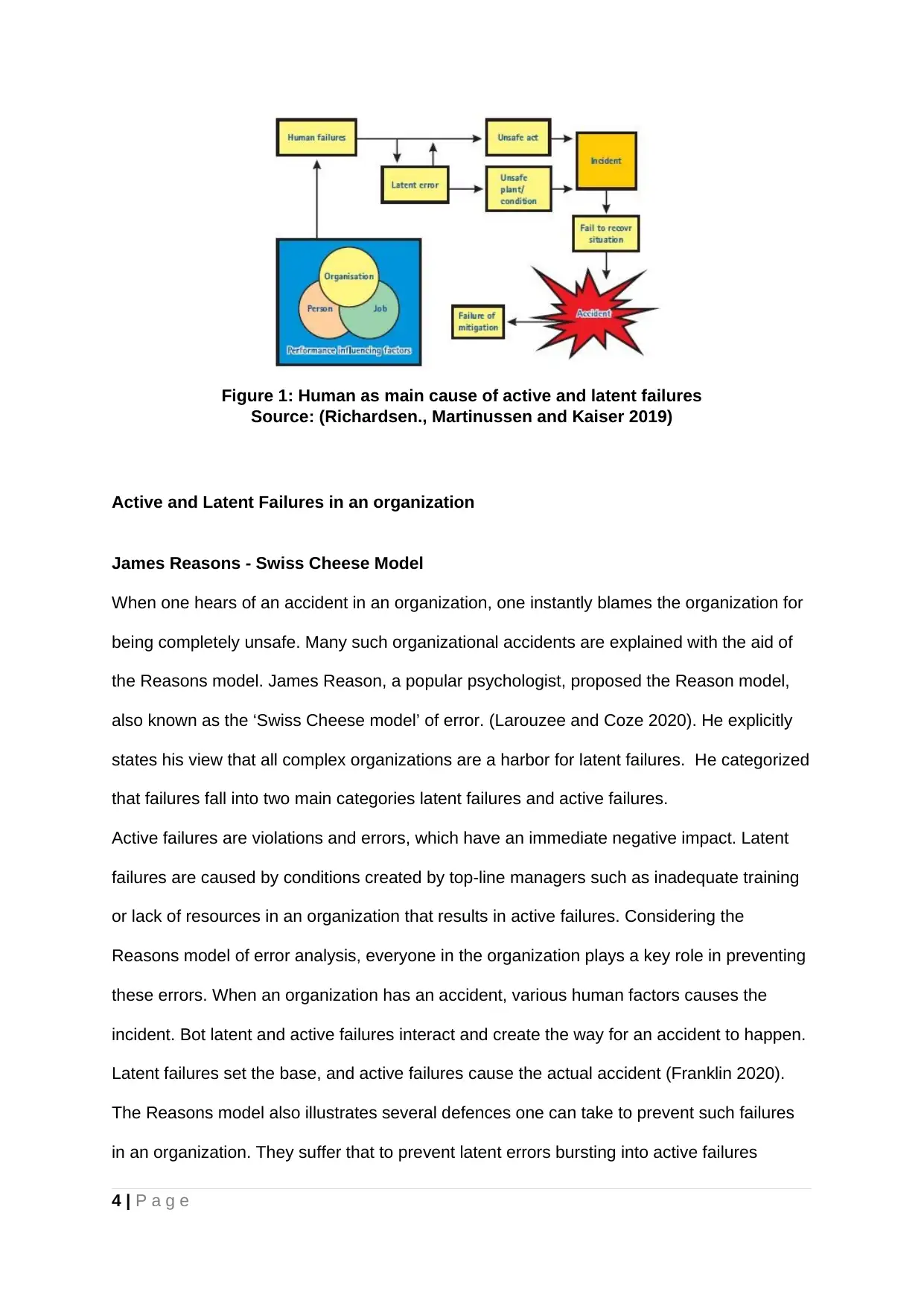
Figure 1: Human as main cause of active and latent failures
Source: (Richardsen., Martinussen and Kaiser 2019)
Active and Latent Failures in an organization
James Reasons - Swiss Cheese Model
When one hears of an accident in an organization, one instantly blames the organization for
being completely unsafe. Many such organizational accidents are explained with the aid of
the Reasons model. James Reason, a popular psychologist, proposed the Reason model,
also known as the ‘Swiss Cheese model’ of error. (Larouzee and Coze 2020). He explicitly
states his view that all complex organizations are a harbor for latent failures. He categorized
that failures fall into two main categories latent failures and active failures.
Active failures are violations and errors, which have an immediate negative impact. Latent
failures are caused by conditions created by top-line managers such as inadequate training
or lack of resources in an organization that results in active failures. Considering the
Reasons model of error analysis, everyone in the organization plays a key role in preventing
these errors. When an organization has an accident, various human factors causes the
incident. Bot latent and active failures interact and create the way for an accident to happen.
Latent failures set the base, and active failures cause the actual accident (Franklin 2020).
The Reasons model also illustrates several defences one can take to prevent such failures
in an organization. They suffer that to prevent latent errors bursting into active failures
4 | P a g e
Source: (Richardsen., Martinussen and Kaiser 2019)
Active and Latent Failures in an organization
James Reasons - Swiss Cheese Model
When one hears of an accident in an organization, one instantly blames the organization for
being completely unsafe. Many such organizational accidents are explained with the aid of
the Reasons model. James Reason, a popular psychologist, proposed the Reason model,
also known as the ‘Swiss Cheese model’ of error. (Larouzee and Coze 2020). He explicitly
states his view that all complex organizations are a harbor for latent failures. He categorized
that failures fall into two main categories latent failures and active failures.
Active failures are violations and errors, which have an immediate negative impact. Latent
failures are caused by conditions created by top-line managers such as inadequate training
or lack of resources in an organization that results in active failures. Considering the
Reasons model of error analysis, everyone in the organization plays a key role in preventing
these errors. When an organization has an accident, various human factors causes the
incident. Bot latent and active failures interact and create the way for an accident to happen.
Latent failures set the base, and active failures cause the actual accident (Franklin 2020).
The Reasons model also illustrates several defences one can take to prevent such failures
in an organization. They suffer that to prevent latent errors bursting into active failures
4 | P a g e
Secure Best Marks with AI Grader
Need help grading? Try our AI Grader for instant feedback on your assignments.
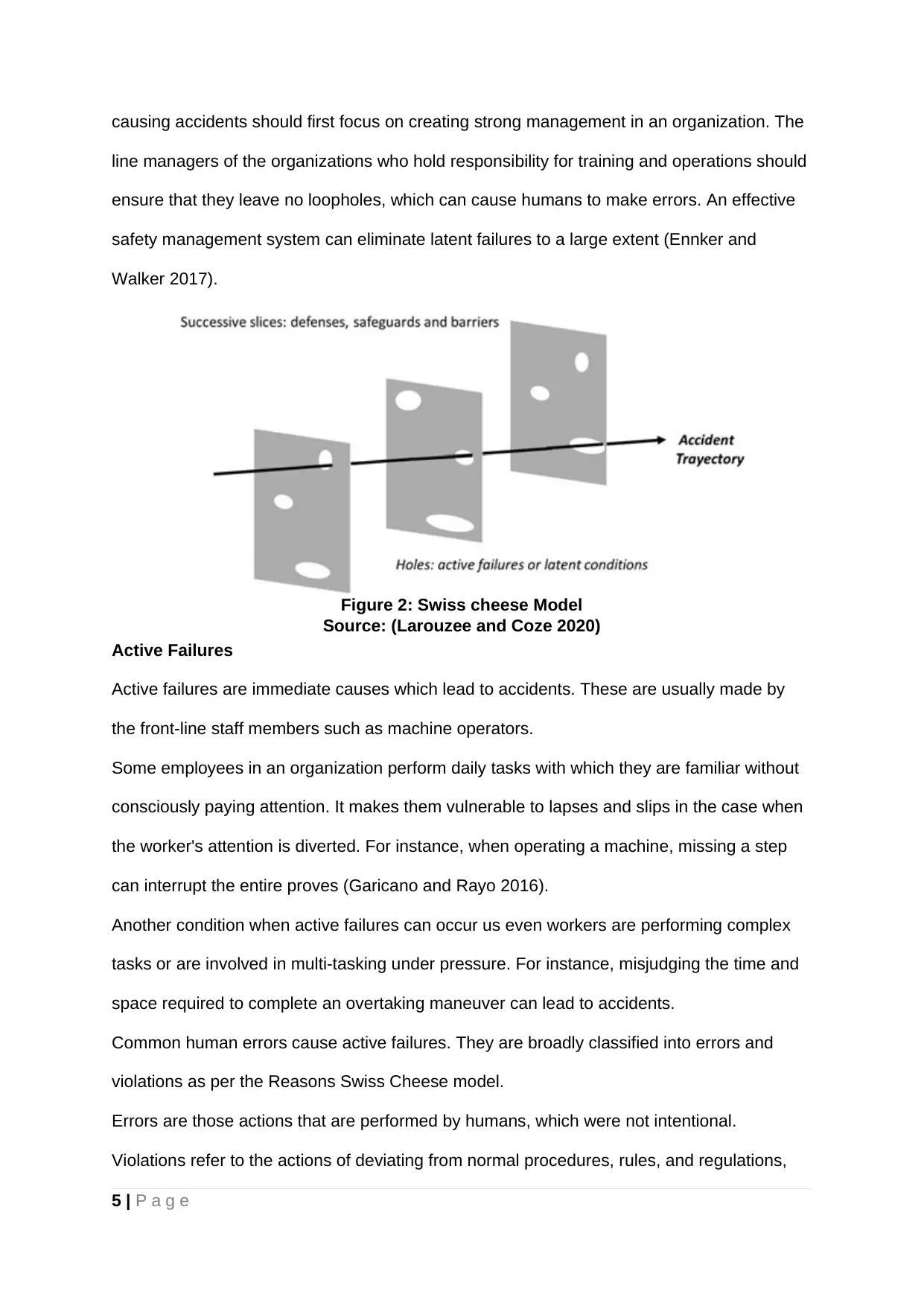
causing accidents should first focus on creating strong management in an organization. The
line managers of the organizations who hold responsibility for training and operations should
ensure that they leave no loopholes, which can cause humans to make errors. An effective
safety management system can eliminate latent failures to a large extent (Ennker and
Walker 2017).
Figure 2: Swiss cheese Model
Source: (Larouzee and Coze 2020)
Active Failures
Active failures are immediate causes which lead to accidents. These are usually made by
the front-line staff members such as machine operators.
Some employees in an organization perform daily tasks with which they are familiar without
consciously paying attention. It makes them vulnerable to lapses and slips in the case when
the worker's attention is diverted. For instance, when operating a machine, missing a step
can interrupt the entire proves (Garicano and Rayo 2016).
Another condition when active failures can occur us even workers are performing complex
tasks or are involved in multi-tasking under pressure. For instance, misjudging the time and
space required to complete an overtaking maneuver can lead to accidents.
Common human errors cause active failures. They are broadly classified into errors and
violations as per the Reasons Swiss Cheese model.
Errors are those actions that are performed by humans, which were not intentional.
Violations refer to the actions of deviating from normal procedures, rules, and regulations,
5 | P a g e
line managers of the organizations who hold responsibility for training and operations should
ensure that they leave no loopholes, which can cause humans to make errors. An effective
safety management system can eliminate latent failures to a large extent (Ennker and
Walker 2017).
Figure 2: Swiss cheese Model
Source: (Larouzee and Coze 2020)
Active Failures
Active failures are immediate causes which lead to accidents. These are usually made by
the front-line staff members such as machine operators.
Some employees in an organization perform daily tasks with which they are familiar without
consciously paying attention. It makes them vulnerable to lapses and slips in the case when
the worker's attention is diverted. For instance, when operating a machine, missing a step
can interrupt the entire proves (Garicano and Rayo 2016).
Another condition when active failures can occur us even workers are performing complex
tasks or are involved in multi-tasking under pressure. For instance, misjudging the time and
space required to complete an overtaking maneuver can lead to accidents.
Common human errors cause active failures. They are broadly classified into errors and
violations as per the Reasons Swiss Cheese model.
Errors are those actions that are performed by humans, which were not intentional.
Violations refer to the actions of deviating from normal procedures, rules, and regulations,
5 | P a g e
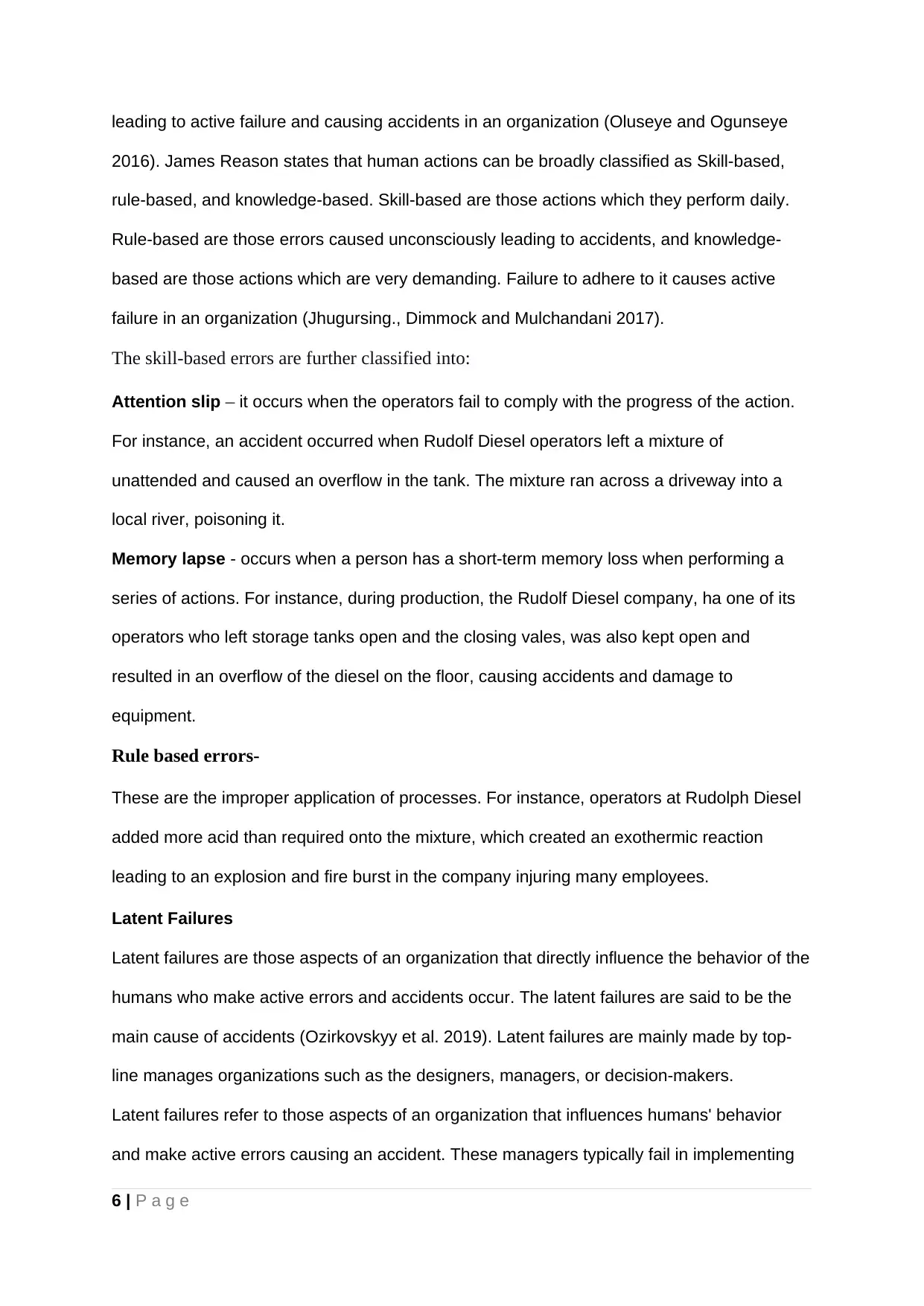
leading to active failure and causing accidents in an organization (Oluseye and Ogunseye
2016). James Reason states that human actions can be broadly classified as Skill-based,
rule-based, and knowledge-based. Skill-based are those actions which they perform daily.
Rule-based are those errors caused unconsciously leading to accidents, and knowledge-
based are those actions which are very demanding. Failure to adhere to it causes active
failure in an organization (Jhugursing., Dimmock and Mulchandani 2017).
The skill-based errors are further classified into:
Attention slip – it occurs when the operators fail to comply with the progress of the action.
For instance, an accident occurred when Rudolf Diesel operators left a mixture of
unattended and caused an overflow in the tank. The mixture ran across a driveway into a
local river, poisoning it.
Memory lapse - occurs when a person has a short-term memory loss when performing a
series of actions. For instance, during production, the Rudolf Diesel company, ha one of its
operators who left storage tanks open and the closing vales, was also kept open and
resulted in an overflow of the diesel on the floor, causing accidents and damage to
equipment.
Rule based errors-
These are the improper application of processes. For instance, operators at Rudolph Diesel
added more acid than required onto the mixture, which created an exothermic reaction
leading to an explosion and fire burst in the company injuring many employees.
Latent Failures
Latent failures are those aspects of an organization that directly influence the behavior of the
humans who make active errors and accidents occur. The latent failures are said to be the
main cause of accidents (Ozirkovskyy et al. 2019). Latent failures are mainly made by top-
line manages organizations such as the designers, managers, or decision-makers.
Latent failures refer to those aspects of an organization that influences humans' behavior
and make active errors causing an accident. These managers typically fail in implementing
6 | P a g e
2016). James Reason states that human actions can be broadly classified as Skill-based,
rule-based, and knowledge-based. Skill-based are those actions which they perform daily.
Rule-based are those errors caused unconsciously leading to accidents, and knowledge-
based are those actions which are very demanding. Failure to adhere to it causes active
failure in an organization (Jhugursing., Dimmock and Mulchandani 2017).
The skill-based errors are further classified into:
Attention slip – it occurs when the operators fail to comply with the progress of the action.
For instance, an accident occurred when Rudolf Diesel operators left a mixture of
unattended and caused an overflow in the tank. The mixture ran across a driveway into a
local river, poisoning it.
Memory lapse - occurs when a person has a short-term memory loss when performing a
series of actions. For instance, during production, the Rudolf Diesel company, ha one of its
operators who left storage tanks open and the closing vales, was also kept open and
resulted in an overflow of the diesel on the floor, causing accidents and damage to
equipment.
Rule based errors-
These are the improper application of processes. For instance, operators at Rudolph Diesel
added more acid than required onto the mixture, which created an exothermic reaction
leading to an explosion and fire burst in the company injuring many employees.
Latent Failures
Latent failures are those aspects of an organization that directly influence the behavior of the
humans who make active errors and accidents occur. The latent failures are said to be the
main cause of accidents (Ozirkovskyy et al. 2019). Latent failures are mainly made by top-
line manages organizations such as the designers, managers, or decision-makers.
Latent failures refer to those aspects of an organization that influences humans' behavior
and make active errors causing an accident. These managers typically fail in implementing
6 | P a g e
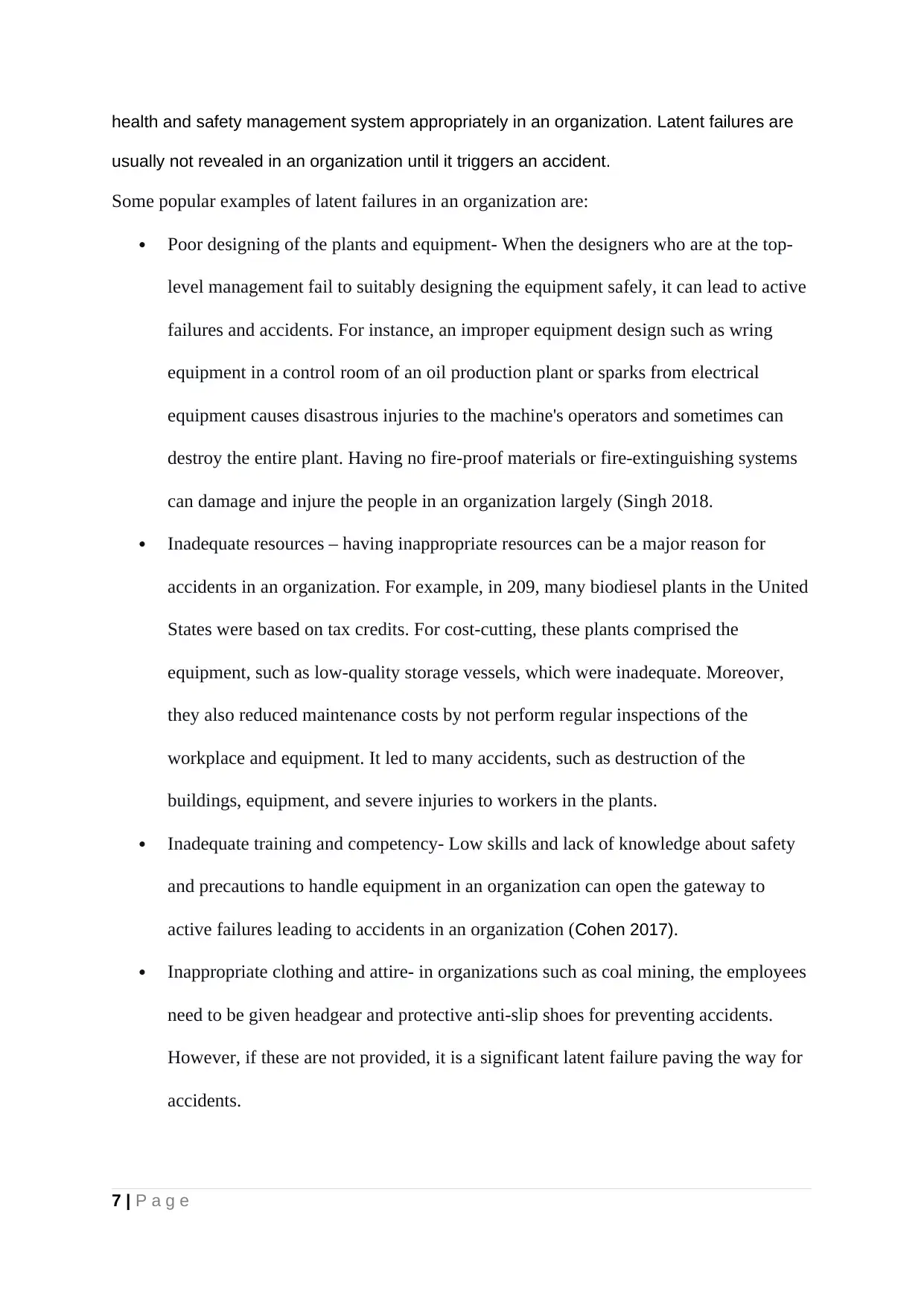
health and safety management system appropriately in an organization. Latent failures are
usually not revealed in an organization until it triggers an accident.
Some popular examples of latent failures in an organization are:
Poor designing of the plants and equipment- When the designers who are at the top-
level management fail to suitably designing the equipment safely, it can lead to active
failures and accidents. For instance, an improper equipment design such as wring
equipment in a control room of an oil production plant or sparks from electrical
equipment causes disastrous injuries to the machine's operators and sometimes can
destroy the entire plant. Having no fire-proof materials or fire-extinguishing systems
can damage and injure the people in an organization largely (Singh 2018.
Inadequate resources – having inappropriate resources can be a major reason for
accidents in an organization. For example, in 209, many biodiesel plants in the United
States were based on tax credits. For cost-cutting, these plants comprised the
equipment, such as low-quality storage vessels, which were inadequate. Moreover,
they also reduced maintenance costs by not perform regular inspections of the
workplace and equipment. It led to many accidents, such as destruction of the
buildings, equipment, and severe injuries to workers in the plants.
Inadequate training and competency- Low skills and lack of knowledge about safety
and precautions to handle equipment in an organization can open the gateway to
active failures leading to accidents in an organization (Cohen 2017).
Inappropriate clothing and attire- in organizations such as coal mining, the employees
need to be given headgear and protective anti-slip shoes for preventing accidents.
However, if these are not provided, it is a significant latent failure paving the way for
accidents.
7 | P a g e
usually not revealed in an organization until it triggers an accident.
Some popular examples of latent failures in an organization are:
Poor designing of the plants and equipment- When the designers who are at the top-
level management fail to suitably designing the equipment safely, it can lead to active
failures and accidents. For instance, an improper equipment design such as wring
equipment in a control room of an oil production plant or sparks from electrical
equipment causes disastrous injuries to the machine's operators and sometimes can
destroy the entire plant. Having no fire-proof materials or fire-extinguishing systems
can damage and injure the people in an organization largely (Singh 2018.
Inadequate resources – having inappropriate resources can be a major reason for
accidents in an organization. For example, in 209, many biodiesel plants in the United
States were based on tax credits. For cost-cutting, these plants comprised the
equipment, such as low-quality storage vessels, which were inadequate. Moreover,
they also reduced maintenance costs by not perform regular inspections of the
workplace and equipment. It led to many accidents, such as destruction of the
buildings, equipment, and severe injuries to workers in the plants.
Inadequate training and competency- Low skills and lack of knowledge about safety
and precautions to handle equipment in an organization can open the gateway to
active failures leading to accidents in an organization (Cohen 2017).
Inappropriate clothing and attire- in organizations such as coal mining, the employees
need to be given headgear and protective anti-slip shoes for preventing accidents.
However, if these are not provided, it is a significant latent failure paving the way for
accidents.
7 | P a g e
Paraphrase This Document
Need a fresh take? Get an instant paraphrase of this document with our AI Paraphraser
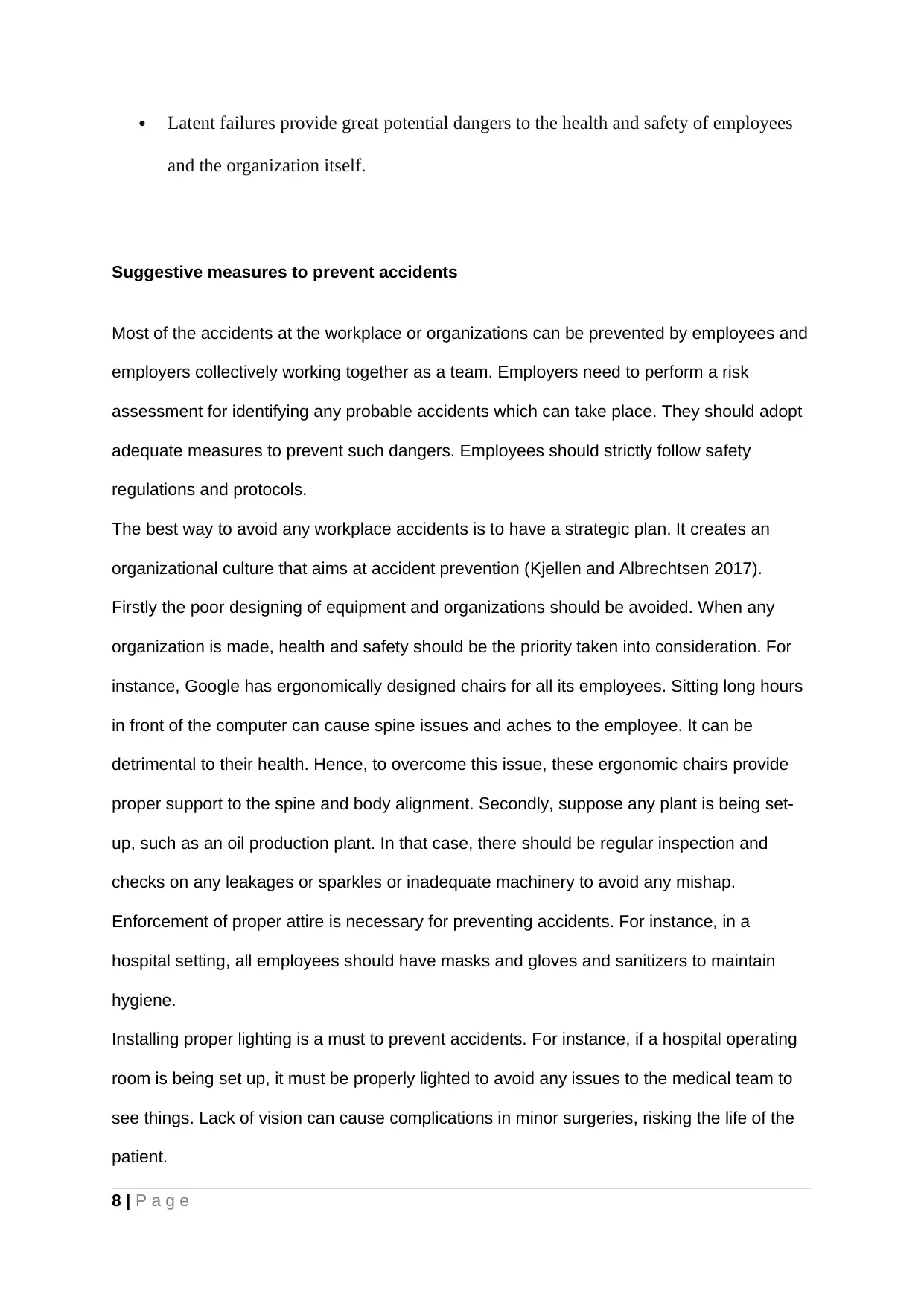
Latent failures provide great potential dangers to the health and safety of employees
and the organization itself.
Suggestive measures to prevent accidents
Most of the accidents at the workplace or organizations can be prevented by employees and
employers collectively working together as a team. Employers need to perform a risk
assessment for identifying any probable accidents which can take place. They should adopt
adequate measures to prevent such dangers. Employees should strictly follow safety
regulations and protocols.
The best way to avoid any workplace accidents is to have a strategic plan. It creates an
organizational culture that aims at accident prevention (Kjellen and Albrechtsen 2017).
Firstly the poor designing of equipment and organizations should be avoided. When any
organization is made, health and safety should be the priority taken into consideration. For
instance, Google has ergonomically designed chairs for all its employees. Sitting long hours
in front of the computer can cause spine issues and aches to the employee. It can be
detrimental to their health. Hence, to overcome this issue, these ergonomic chairs provide
proper support to the spine and body alignment. Secondly, suppose any plant is being set-
up, such as an oil production plant. In that case, there should be regular inspection and
checks on any leakages or sparkles or inadequate machinery to avoid any mishap.
Enforcement of proper attire is necessary for preventing accidents. For instance, in a
hospital setting, all employees should have masks and gloves and sanitizers to maintain
hygiene.
Installing proper lighting is a must to prevent accidents. For instance, if a hospital operating
room is being set up, it must be properly lighted to avoid any issues to the medical team to
see things. Lack of vision can cause complications in minor surgeries, risking the life of the
patient.
8 | P a g e
and the organization itself.
Suggestive measures to prevent accidents
Most of the accidents at the workplace or organizations can be prevented by employees and
employers collectively working together as a team. Employers need to perform a risk
assessment for identifying any probable accidents which can take place. They should adopt
adequate measures to prevent such dangers. Employees should strictly follow safety
regulations and protocols.
The best way to avoid any workplace accidents is to have a strategic plan. It creates an
organizational culture that aims at accident prevention (Kjellen and Albrechtsen 2017).
Firstly the poor designing of equipment and organizations should be avoided. When any
organization is made, health and safety should be the priority taken into consideration. For
instance, Google has ergonomically designed chairs for all its employees. Sitting long hours
in front of the computer can cause spine issues and aches to the employee. It can be
detrimental to their health. Hence, to overcome this issue, these ergonomic chairs provide
proper support to the spine and body alignment. Secondly, suppose any plant is being set-
up, such as an oil production plant. In that case, there should be regular inspection and
checks on any leakages or sparkles or inadequate machinery to avoid any mishap.
Enforcement of proper attire is necessary for preventing accidents. For instance, in a
hospital setting, all employees should have masks and gloves and sanitizers to maintain
hygiene.
Installing proper lighting is a must to prevent accidents. For instance, if a hospital operating
room is being set up, it must be properly lighted to avoid any issues to the medical team to
see things. Lack of vision can cause complications in minor surgeries, risking the life of the
patient.
8 | P a g e
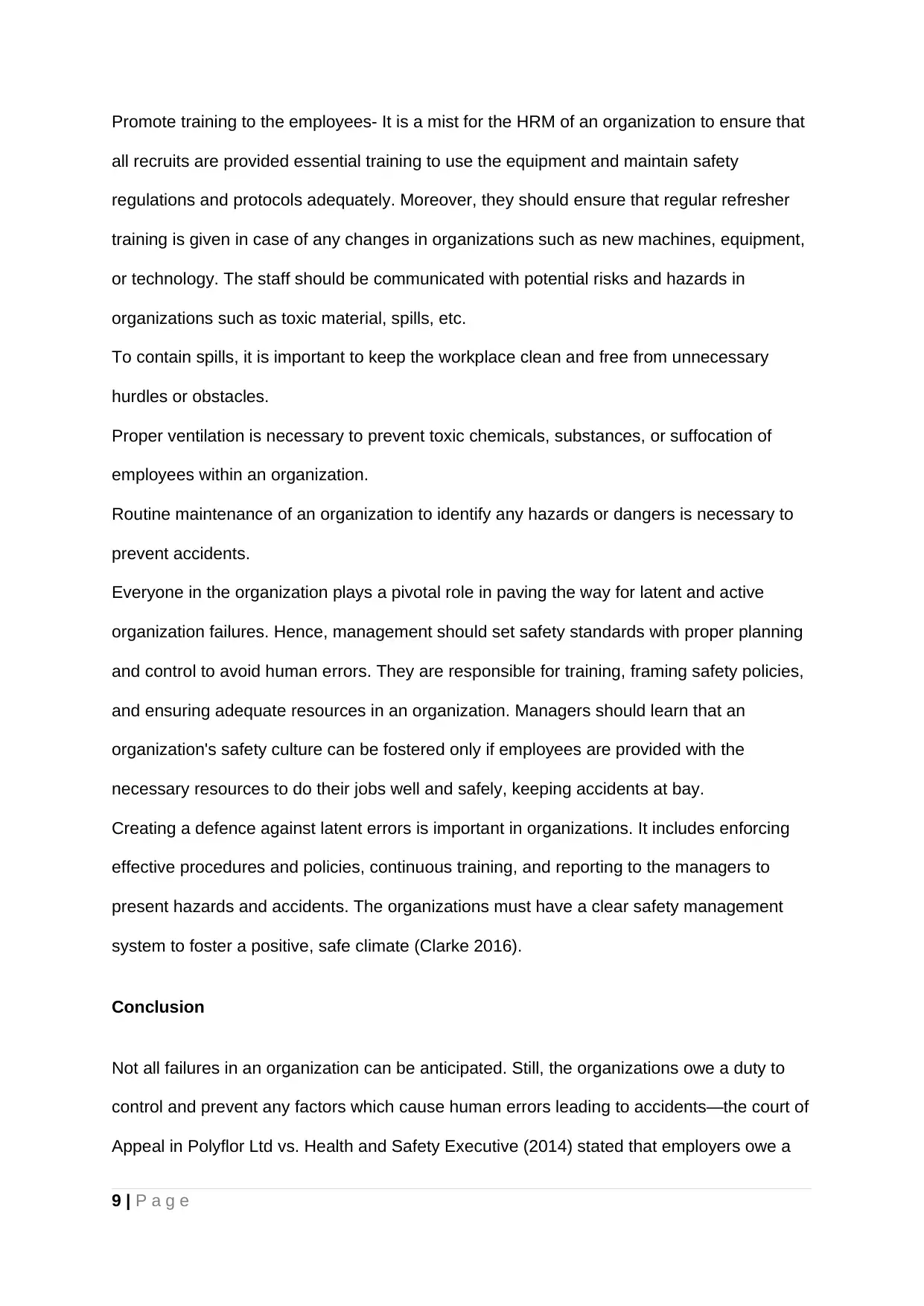
Promote training to the employees- It is a mist for the HRM of an organization to ensure that
all recruits are provided essential training to use the equipment and maintain safety
regulations and protocols adequately. Moreover, they should ensure that regular refresher
training is given in case of any changes in organizations such as new machines, equipment,
or technology. The staff should be communicated with potential risks and hazards in
organizations such as toxic material, spills, etc.
To contain spills, it is important to keep the workplace clean and free from unnecessary
hurdles or obstacles.
Proper ventilation is necessary to prevent toxic chemicals, substances, or suffocation of
employees within an organization.
Routine maintenance of an organization to identify any hazards or dangers is necessary to
prevent accidents.
Everyone in the organization plays a pivotal role in paving the way for latent and active
organization failures. Hence, management should set safety standards with proper planning
and control to avoid human errors. They are responsible for training, framing safety policies,
and ensuring adequate resources in an organization. Managers should learn that an
organization's safety culture can be fostered only if employees are provided with the
necessary resources to do their jobs well and safely, keeping accidents at bay.
Creating a defence against latent errors is important in organizations. It includes enforcing
effective procedures and policies, continuous training, and reporting to the managers to
present hazards and accidents. The organizations must have a clear safety management
system to foster a positive, safe climate (Clarke 2016).
Conclusion
Not all failures in an organization can be anticipated. Still, the organizations owe a duty to
control and prevent any factors which cause human errors leading to accidents—the court of
Appeal in Polyflor Ltd vs. Health and Safety Executive (2014) stated that employers owe a
9 | P a g e
all recruits are provided essential training to use the equipment and maintain safety
regulations and protocols adequately. Moreover, they should ensure that regular refresher
training is given in case of any changes in organizations such as new machines, equipment,
or technology. The staff should be communicated with potential risks and hazards in
organizations such as toxic material, spills, etc.
To contain spills, it is important to keep the workplace clean and free from unnecessary
hurdles or obstacles.
Proper ventilation is necessary to prevent toxic chemicals, substances, or suffocation of
employees within an organization.
Routine maintenance of an organization to identify any hazards or dangers is necessary to
prevent accidents.
Everyone in the organization plays a pivotal role in paving the way for latent and active
organization failures. Hence, management should set safety standards with proper planning
and control to avoid human errors. They are responsible for training, framing safety policies,
and ensuring adequate resources in an organization. Managers should learn that an
organization's safety culture can be fostered only if employees are provided with the
necessary resources to do their jobs well and safely, keeping accidents at bay.
Creating a defence against latent errors is important in organizations. It includes enforcing
effective procedures and policies, continuous training, and reporting to the managers to
present hazards and accidents. The organizations must have a clear safety management
system to foster a positive, safe climate (Clarke 2016).
Conclusion
Not all failures in an organization can be anticipated. Still, the organizations owe a duty to
control and prevent any factors which cause human errors leading to accidents—the court of
Appeal in Polyflor Ltd vs. Health and Safety Executive (2014) stated that employers owe a
9 | P a g e
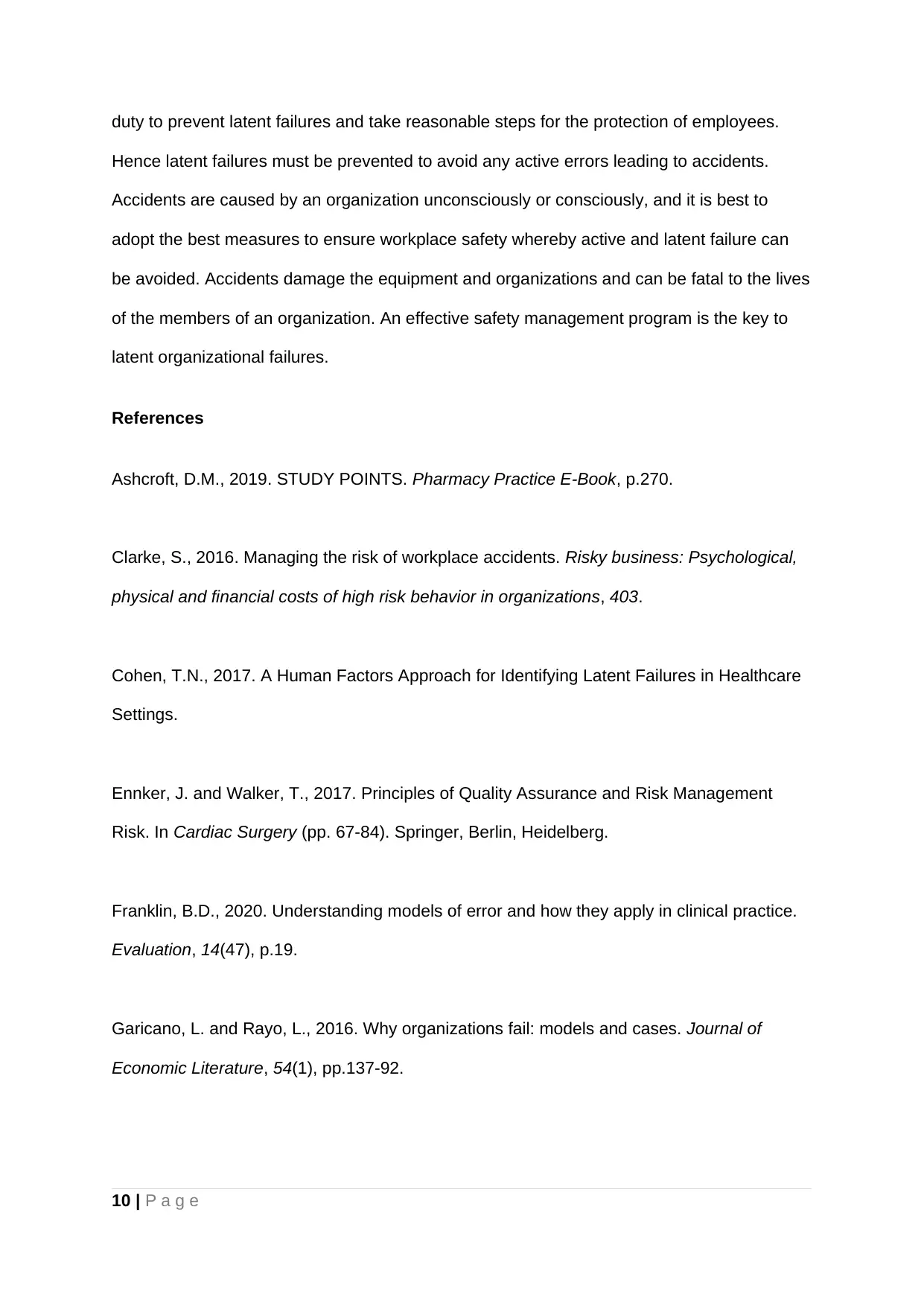
duty to prevent latent failures and take reasonable steps for the protection of employees.
Hence latent failures must be prevented to avoid any active errors leading to accidents.
Accidents are caused by an organization unconsciously or consciously, and it is best to
adopt the best measures to ensure workplace safety whereby active and latent failure can
be avoided. Accidents damage the equipment and organizations and can be fatal to the lives
of the members of an organization. An effective safety management program is the key to
latent organizational failures.
References
Ashcroft, D.M., 2019. STUDY POINTS. Pharmacy Practice E-Book, p.270.
Clarke, S., 2016. Managing the risk of workplace accidents. Risky business: Psychological,
physical and financial costs of high risk behavior in organizations, 403.
Cohen, T.N., 2017. A Human Factors Approach for Identifying Latent Failures in Healthcare
Settings.
Ennker, J. and Walker, T., 2017. Principles of Quality Assurance and Risk Management
Risk. In Cardiac Surgery (pp. 67-84). Springer, Berlin, Heidelberg.
Franklin, B.D., 2020. Understanding models of error and how they apply in clinical practice.
Evaluation, 14(47), p.19.
Garicano, L. and Rayo, L., 2016. Why organizations fail: models and cases. Journal of
Economic Literature, 54(1), pp.137-92.
10 | P a g e
Hence latent failures must be prevented to avoid any active errors leading to accidents.
Accidents are caused by an organization unconsciously or consciously, and it is best to
adopt the best measures to ensure workplace safety whereby active and latent failure can
be avoided. Accidents damage the equipment and organizations and can be fatal to the lives
of the members of an organization. An effective safety management program is the key to
latent organizational failures.
References
Ashcroft, D.M., 2019. STUDY POINTS. Pharmacy Practice E-Book, p.270.
Clarke, S., 2016. Managing the risk of workplace accidents. Risky business: Psychological,
physical and financial costs of high risk behavior in organizations, 403.
Cohen, T.N., 2017. A Human Factors Approach for Identifying Latent Failures in Healthcare
Settings.
Ennker, J. and Walker, T., 2017. Principles of Quality Assurance and Risk Management
Risk. In Cardiac Surgery (pp. 67-84). Springer, Berlin, Heidelberg.
Franklin, B.D., 2020. Understanding models of error and how they apply in clinical practice.
Evaluation, 14(47), p.19.
Garicano, L. and Rayo, L., 2016. Why organizations fail: models and cases. Journal of
Economic Literature, 54(1), pp.137-92.
10 | P a g e
Secure Best Marks with AI Grader
Need help grading? Try our AI Grader for instant feedback on your assignments.
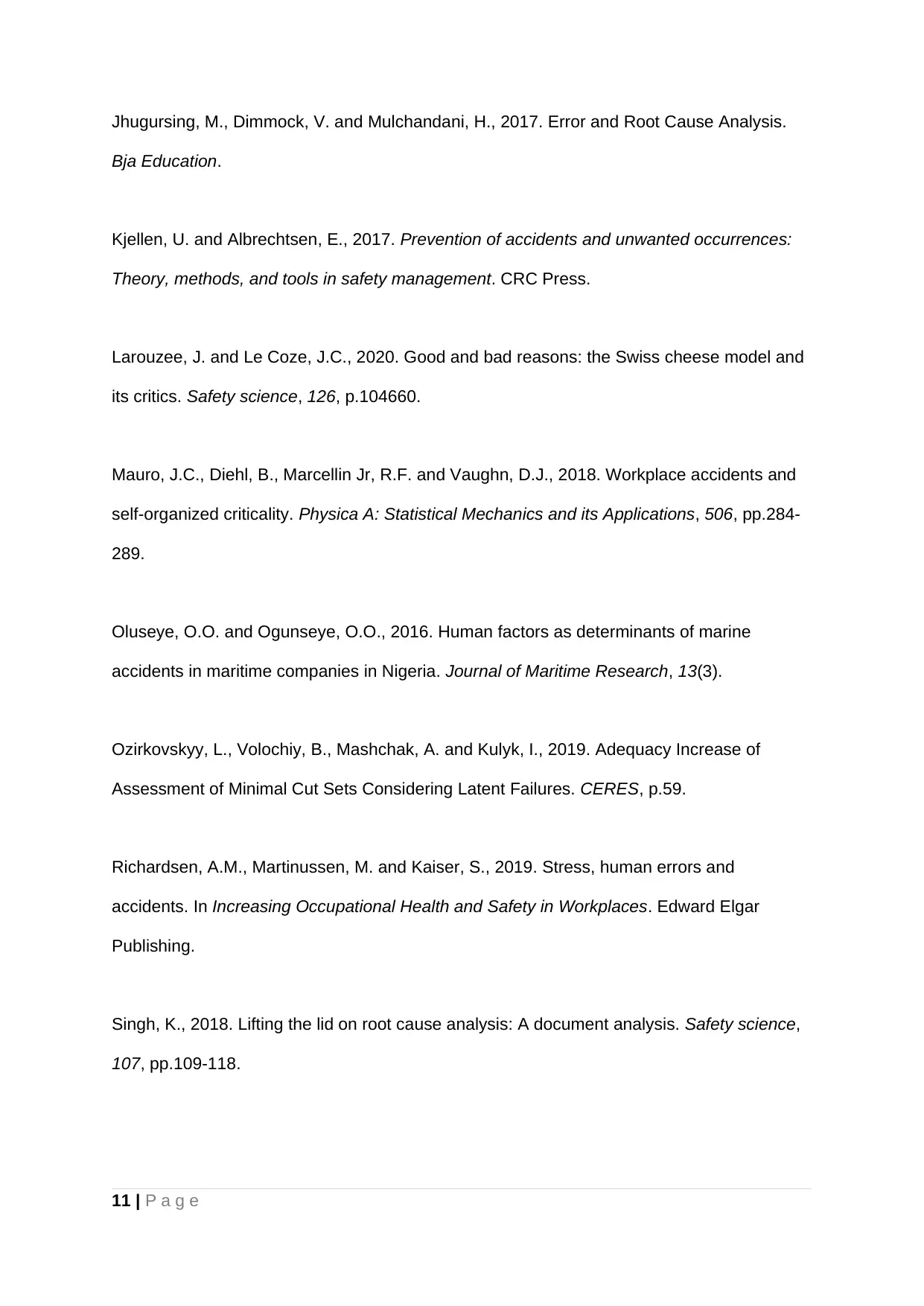
Jhugursing, M., Dimmock, V. and Mulchandani, H., 2017. Error and Root Cause Analysis.
Bja Education.
Kjellen, U. and Albrechtsen, E., 2017. Prevention of accidents and unwanted occurrences:
Theory, methods, and tools in safety management. CRC Press.
Larouzee, J. and Le Coze, J.C., 2020. Good and bad reasons: the Swiss cheese model and
its critics. Safety science, 126, p.104660.
Mauro, J.C., Diehl, B., Marcellin Jr, R.F. and Vaughn, D.J., 2018. Workplace accidents and
self-organized criticality. Physica A: Statistical Mechanics and its Applications, 506, pp.284-
289.
Oluseye, O.O. and Ogunseye, O.O., 2016. Human factors as determinants of marine
accidents in maritime companies in Nigeria. Journal of Maritime Research, 13(3).
Ozirkovskyy, L., Volochiy, B., Mashchak, A. and Kulyk, I., 2019. Adequacy Increase of
Assessment of Minimal Cut Sets Considering Latent Failures. CERES, p.59.
Richardsen, A.M., Martinussen, M. and Kaiser, S., 2019. Stress, human errors and
accidents. In Increasing Occupational Health and Safety in Workplaces. Edward Elgar
Publishing.
Singh, K., 2018. Lifting the lid on root cause analysis: A document analysis. Safety science,
107, pp.109-118.
11 | P a g e
Bja Education.
Kjellen, U. and Albrechtsen, E., 2017. Prevention of accidents and unwanted occurrences:
Theory, methods, and tools in safety management. CRC Press.
Larouzee, J. and Le Coze, J.C., 2020. Good and bad reasons: the Swiss cheese model and
its critics. Safety science, 126, p.104660.
Mauro, J.C., Diehl, B., Marcellin Jr, R.F. and Vaughn, D.J., 2018. Workplace accidents and
self-organized criticality. Physica A: Statistical Mechanics and its Applications, 506, pp.284-
289.
Oluseye, O.O. and Ogunseye, O.O., 2016. Human factors as determinants of marine
accidents in maritime companies in Nigeria. Journal of Maritime Research, 13(3).
Ozirkovskyy, L., Volochiy, B., Mashchak, A. and Kulyk, I., 2019. Adequacy Increase of
Assessment of Minimal Cut Sets Considering Latent Failures. CERES, p.59.
Richardsen, A.M., Martinussen, M. and Kaiser, S., 2019. Stress, human errors and
accidents. In Increasing Occupational Health and Safety in Workplaces. Edward Elgar
Publishing.
Singh, K., 2018. Lifting the lid on root cause analysis: A document analysis. Safety science,
107, pp.109-118.
11 | P a g e
1 out of 11
Related Documents

Your All-in-One AI-Powered Toolkit for Academic Success.
+13062052269
info@desklib.com
Available 24*7 on WhatsApp / Email
Unlock your academic potential
© 2024 | Zucol Services PVT LTD | All rights reserved.