Graduate Diploma in Purchasing and Supply Chain: Quality Circle Report
VerifiedAdded on 2023/01/17
|11
|2262
|34
Report
AI Summary
This report, submitted by a student for the Graduate Diploma in Purchasing and Supply Chain Management, Module 14, delves into the implementation of a quality circle to enhance workplace quality. The report outlines the formation of a quality circle, emphasizing the involvement of top managem...
Read More
Contribute Materials
Your contribution can guide someone’s learning journey. Share your
documents today.
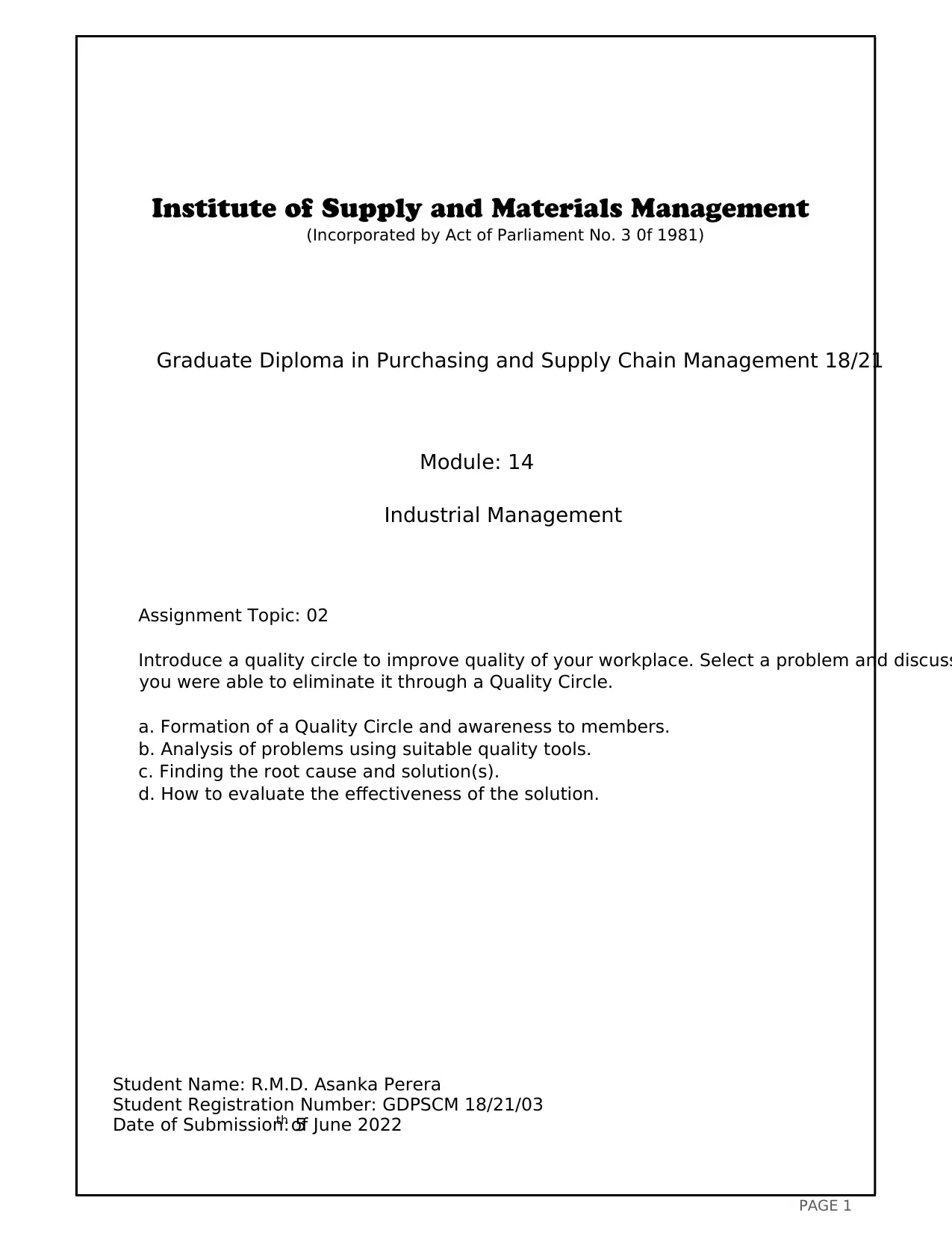
PAGE 1
(Incorporated by Act of Parliament No. 3 0f 1981)
Graduate Diploma in Purchasing and Supply Chain Management 18/21
Module: 14
Industrial Management
Assignment Topic: 02
Introduce a quality circle to improve quality of your workplace. Select a problem and discuss
you were able to eliminate it through a Quality Circle.
a. Formation of a Quality Circle and awareness to members.
b. Analysis of problems using suitable quality tools.
c. Finding the root cause and solution(s).
d. How to evaluate the effectiveness of the solution.
Student Name: R.M.D. Asanka Perera
Student Registration Number: GDPSCM 18/21/03
Date of Submission: 5th of June 2022
(Incorporated by Act of Parliament No. 3 0f 1981)
Graduate Diploma in Purchasing and Supply Chain Management 18/21
Module: 14
Industrial Management
Assignment Topic: 02
Introduce a quality circle to improve quality of your workplace. Select a problem and discuss
you were able to eliminate it through a Quality Circle.
a. Formation of a Quality Circle and awareness to members.
b. Analysis of problems using suitable quality tools.
c. Finding the root cause and solution(s).
d. How to evaluate the effectiveness of the solution.
Student Name: R.M.D. Asanka Perera
Student Registration Number: GDPSCM 18/21/03
Date of Submission: 5th of June 2022
Secure Best Marks with AI Grader
Need help grading? Try our AI Grader for instant feedback on your assignments.
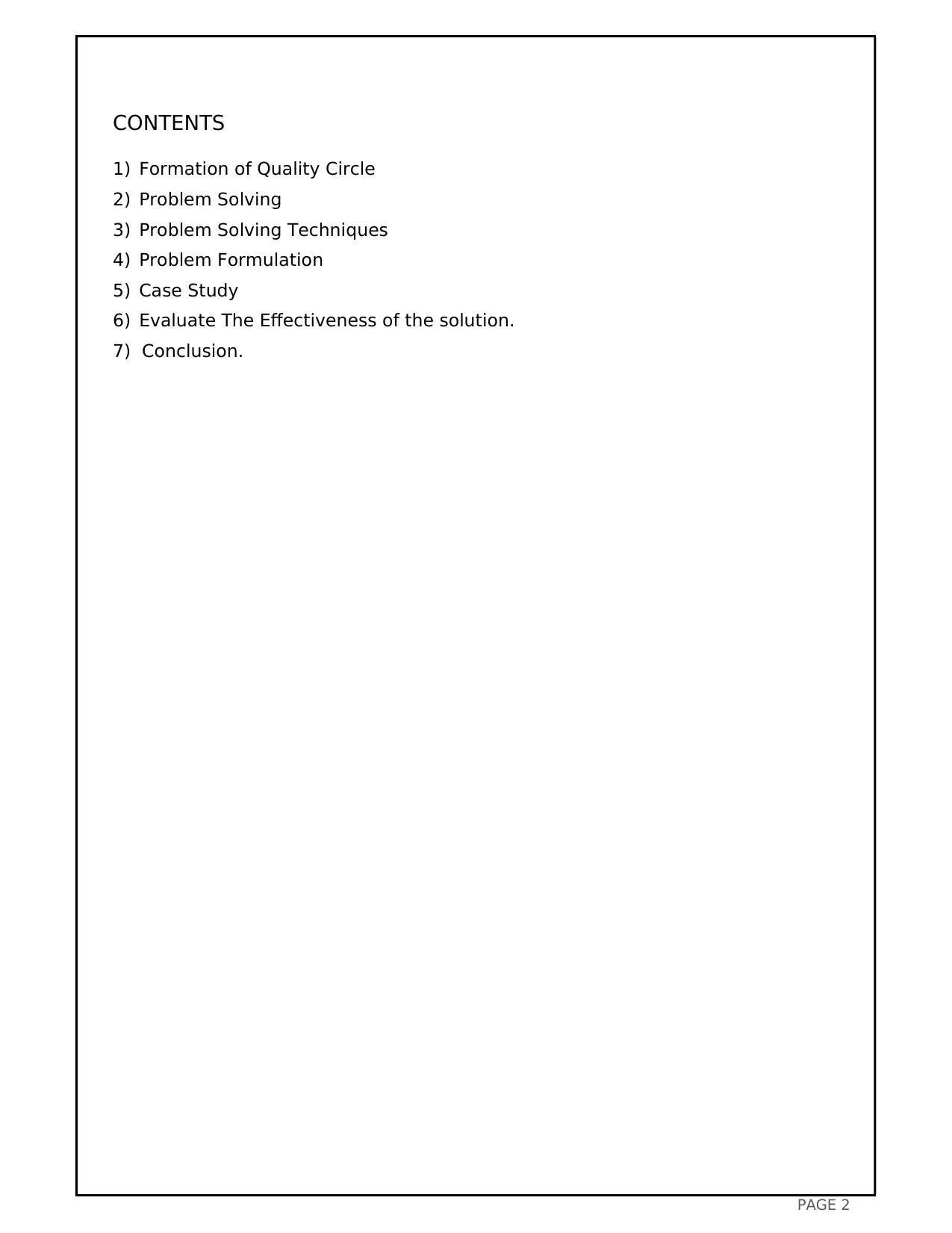
PAGE 2
CONTENTS
1) Formation of Quality Circle
2) Problem Solving
3) Problem Solving Techniques
4) Problem Formulation
5) Case Study
6) Evaluate The Effectiveness of the solution.
7) Conclusion.
CONTENTS
1) Formation of Quality Circle
2) Problem Solving
3) Problem Solving Techniques
4) Problem Formulation
5) Case Study
6) Evaluate The Effectiveness of the solution.
7) Conclusion.
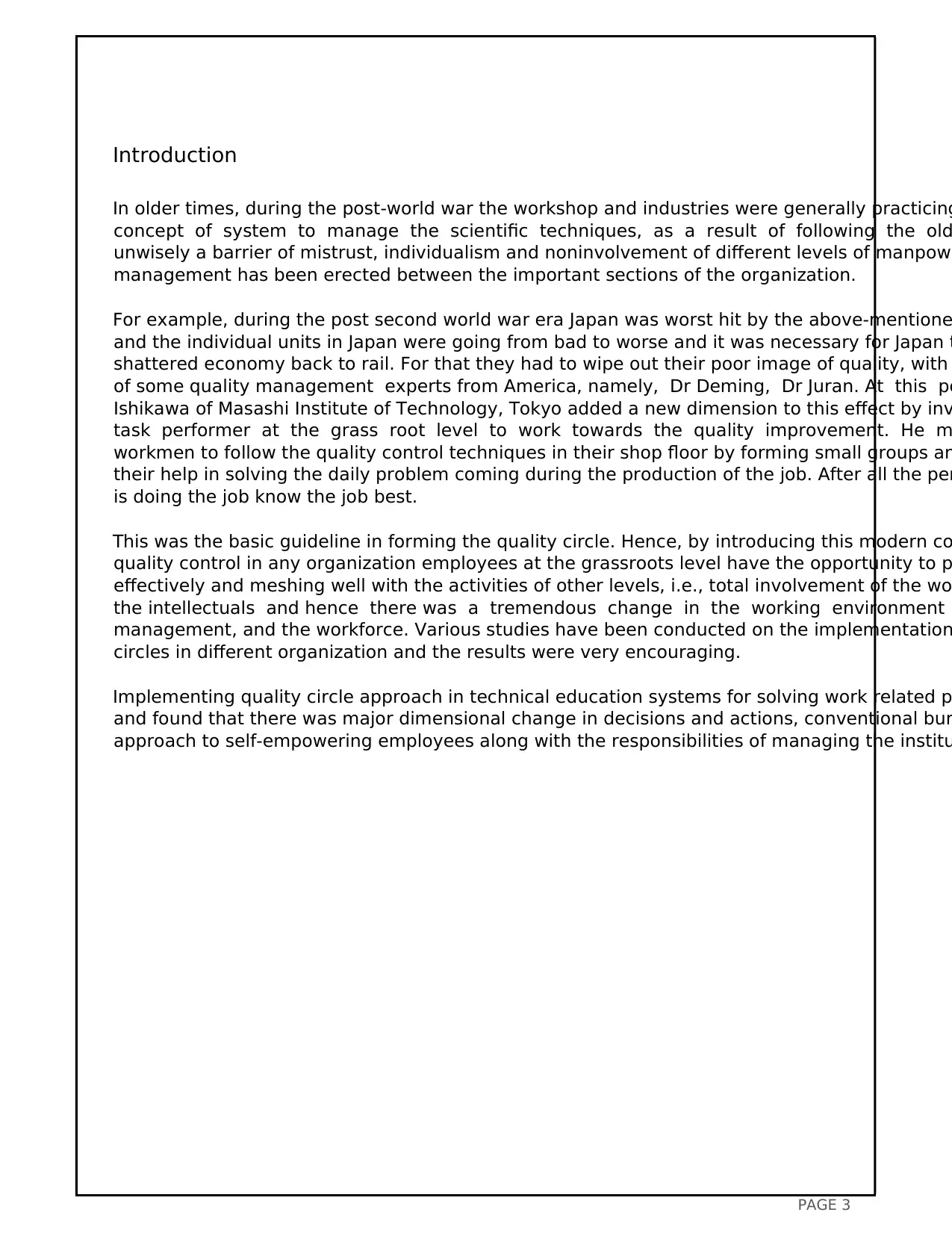
PAGE 3
Introduction
In older times, during the post-world war the workshop and industries were generally practicing
concept of system to manage the scientific techniques, as a result of following the old
unwisely a barrier of mistrust, individualism and noninvolvement of different levels of manpowe
management has been erected between the important sections of the organization.
For example, during the post second world war era Japan was worst hit by the above-mentione
and the individual units in Japan were going from bad to worse and it was necessary for Japan t
shattered economy back to rail. For that they had to wipe out their poor image of quality, with
of some quality management experts from America, namely, Dr Deming, Dr Juran. At this po
Ishikawa of Masashi Institute of Technology, Tokyo added a new dimension to this effect by inv
task performer at the grass root level to work towards the quality improvement. He m
workmen to follow the quality control techniques in their shop floor by forming small groups an
their help in solving the daily problem coming during the production of the job. After all the per
is doing the job know the job best.
This was the basic guideline in forming the quality circle. Hence, by introducing this modern co
quality control in any organization employees at the grassroots level have the opportunity to p
effectively and meshing well with the activities of other levels, i.e., total involvement of the wo
the intellectuals and hence there was a tremendous change in the working environment
management, and the workforce. Various studies have been conducted on the implementation
circles in different organization and the results were very encouraging.
Implementing quality circle approach in technical education systems for solving work related p
and found that there was major dimensional change in decisions and actions, conventional bur
approach to self-empowering employees along with the responsibilities of managing the institu
Introduction
In older times, during the post-world war the workshop and industries were generally practicing
concept of system to manage the scientific techniques, as a result of following the old
unwisely a barrier of mistrust, individualism and noninvolvement of different levels of manpowe
management has been erected between the important sections of the organization.
For example, during the post second world war era Japan was worst hit by the above-mentione
and the individual units in Japan were going from bad to worse and it was necessary for Japan t
shattered economy back to rail. For that they had to wipe out their poor image of quality, with
of some quality management experts from America, namely, Dr Deming, Dr Juran. At this po
Ishikawa of Masashi Institute of Technology, Tokyo added a new dimension to this effect by inv
task performer at the grass root level to work towards the quality improvement. He m
workmen to follow the quality control techniques in their shop floor by forming small groups an
their help in solving the daily problem coming during the production of the job. After all the per
is doing the job know the job best.
This was the basic guideline in forming the quality circle. Hence, by introducing this modern co
quality control in any organization employees at the grassroots level have the opportunity to p
effectively and meshing well with the activities of other levels, i.e., total involvement of the wo
the intellectuals and hence there was a tremendous change in the working environment
management, and the workforce. Various studies have been conducted on the implementation
circles in different organization and the results were very encouraging.
Implementing quality circle approach in technical education systems for solving work related p
and found that there was major dimensional change in decisions and actions, conventional bur
approach to self-empowering employees along with the responsibilities of managing the institu
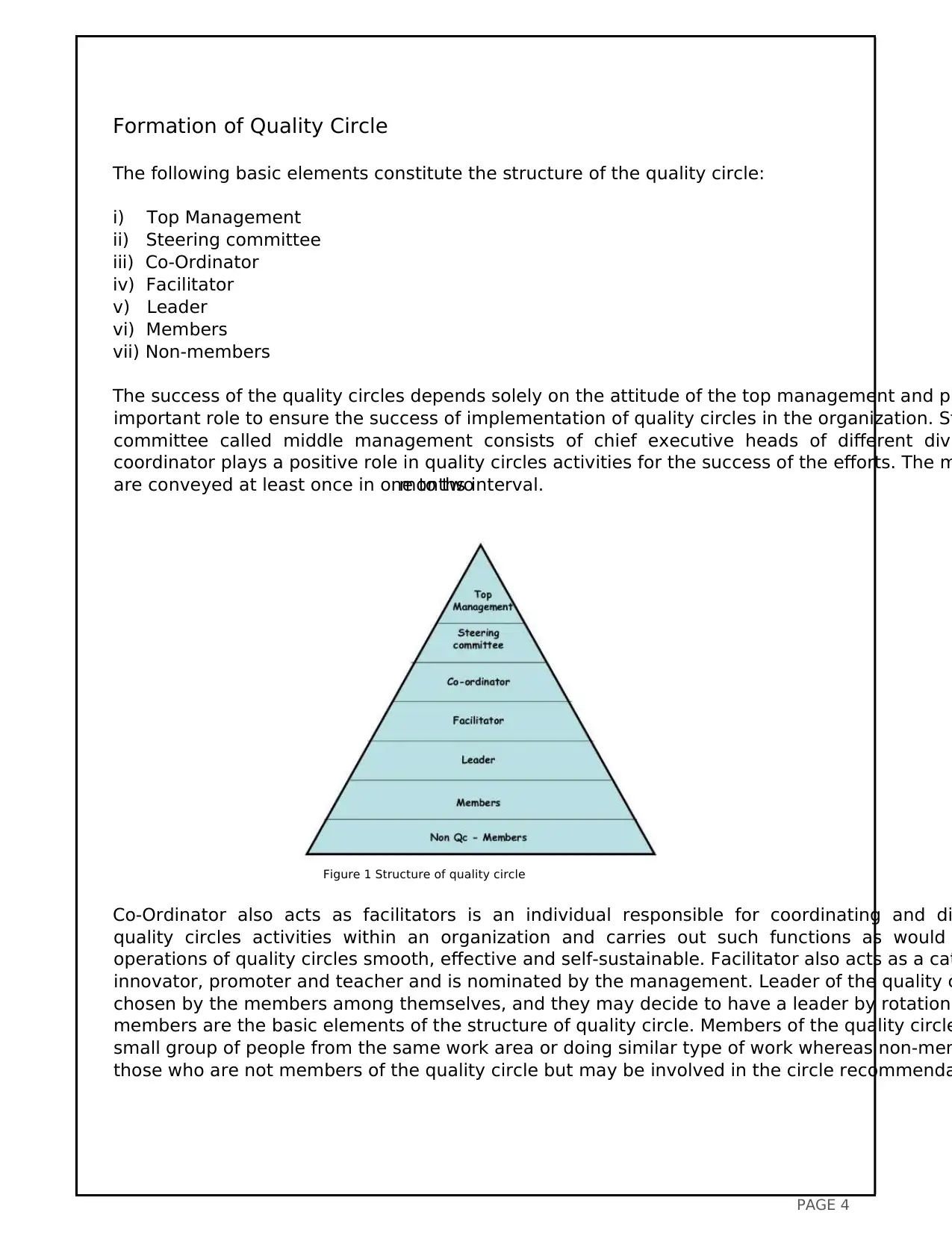
PAGE 4
Formation of Quality Circle
The following basic elements constitute the structure of the quality circle:
i) Top Management
ii) Steering committee
iii) Co-Ordinator
iv) Facilitator
v) Leader
vi) Members
vii) Non-members
The success of the quality circles depends solely on the attitude of the top management and pl
important role to ensure the success of implementation of quality circles in the organization. St
committee called middle management consists of chief executive heads of different divi
coordinator plays a positive role in quality circles activities for the success of the efforts. The m
are conveyed at least once in one to twomonths interval.
Figure 1 Structure of quality circle
Co-Ordinator also acts as facilitators is an individual responsible for coordinating and di
quality circles activities within an organization and carries out such functions as would
operations of quality circles smooth, effective and self-sustainable. Facilitator also acts as a cat
innovator, promoter and teacher and is nominated by the management. Leader of the quality c
chosen by the members among themselves, and they may decide to have a leader by rotation
members are the basic elements of the structure of quality circle. Members of the quality circle
small group of people from the same work area or doing similar type of work whereas non-mem
those who are not members of the quality circle but may be involved in the circle recommenda
Formation of Quality Circle
The following basic elements constitute the structure of the quality circle:
i) Top Management
ii) Steering committee
iii) Co-Ordinator
iv) Facilitator
v) Leader
vi) Members
vii) Non-members
The success of the quality circles depends solely on the attitude of the top management and pl
important role to ensure the success of implementation of quality circles in the organization. St
committee called middle management consists of chief executive heads of different divi
coordinator plays a positive role in quality circles activities for the success of the efforts. The m
are conveyed at least once in one to twomonths interval.
Figure 1 Structure of quality circle
Co-Ordinator also acts as facilitators is an individual responsible for coordinating and di
quality circles activities within an organization and carries out such functions as would
operations of quality circles smooth, effective and self-sustainable. Facilitator also acts as a cat
innovator, promoter and teacher and is nominated by the management. Leader of the quality c
chosen by the members among themselves, and they may decide to have a leader by rotation
members are the basic elements of the structure of quality circle. Members of the quality circle
small group of people from the same work area or doing similar type of work whereas non-mem
those who are not members of the quality circle but may be involved in the circle recommenda
Secure Best Marks with AI Grader
Need help grading? Try our AI Grader for instant feedback on your assignments.
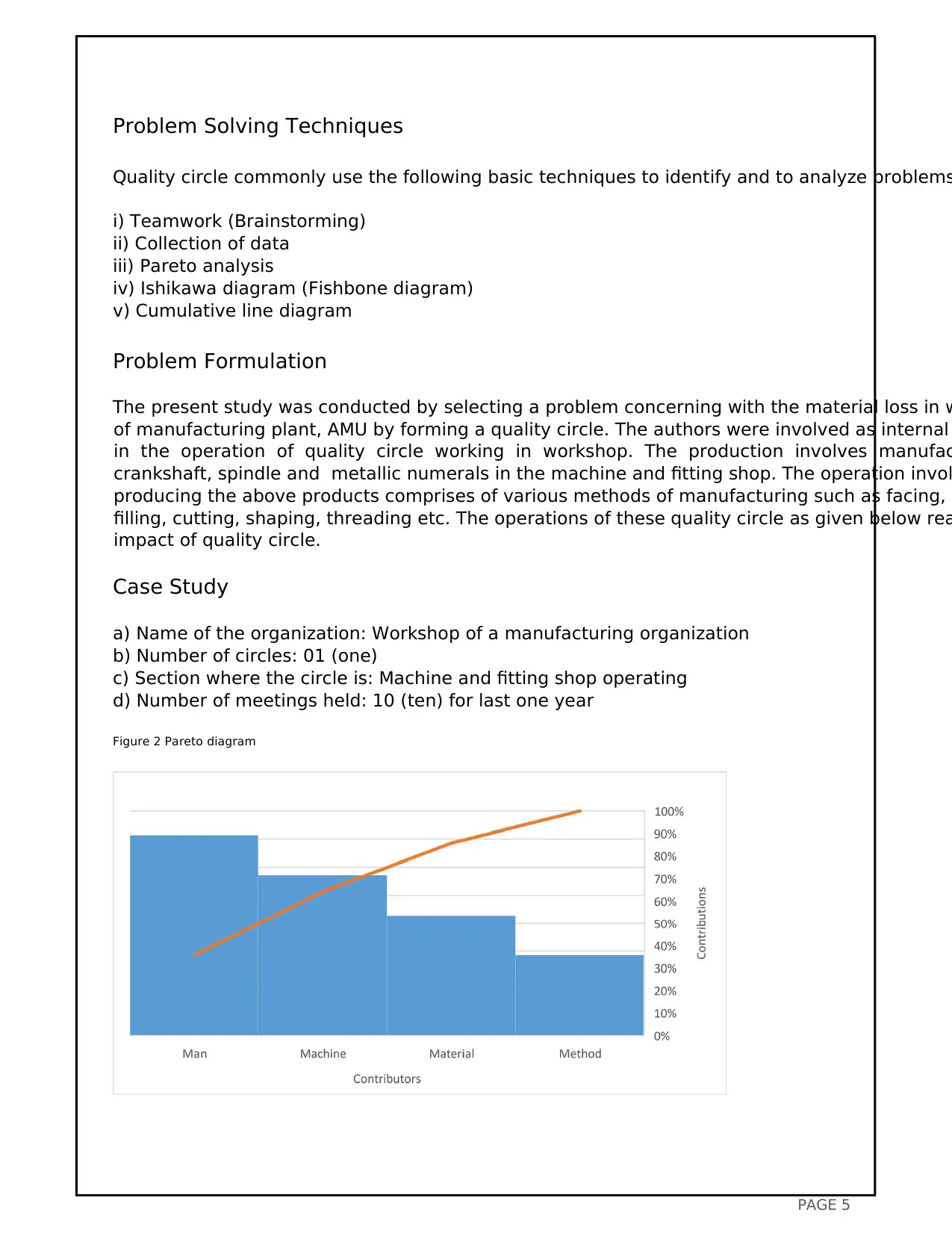
PAGE 5
Problem Solving Techniques
Quality circle commonly use the following basic techniques to identify and to analyze problems
i) Teamwork (Brainstorming)
ii) Collection of data
iii) Pareto analysis
iv) Ishikawa diagram (Fishbone diagram)
v) Cumulative line diagram
Problem Formulation
The present study was conducted by selecting a problem concerning with the material loss in w
of manufacturing plant, AMU by forming a quality circle. The authors were involved as internal
in the operation of quality circle working in workshop. The production involves manufac
crankshaft, spindle and metallic numerals in the machine and fitting shop. The operation invol
producing the above products comprises of various methods of manufacturing such as facing, d
filling, cutting, shaping, threading etc. The operations of these quality circle as given below rea
impact of quality circle.
Case Study
a) Name of the organization: Workshop of a manufacturing organization
b) Number of circles: 01 (one)
c) Section where the circle is: Machine and fitting shop operating
d) Number of meetings held: 10 (ten) for last one year
Figure 2 Pareto diagram
Problem Solving Techniques
Quality circle commonly use the following basic techniques to identify and to analyze problems
i) Teamwork (Brainstorming)
ii) Collection of data
iii) Pareto analysis
iv) Ishikawa diagram (Fishbone diagram)
v) Cumulative line diagram
Problem Formulation
The present study was conducted by selecting a problem concerning with the material loss in w
of manufacturing plant, AMU by forming a quality circle. The authors were involved as internal
in the operation of quality circle working in workshop. The production involves manufac
crankshaft, spindle and metallic numerals in the machine and fitting shop. The operation invol
producing the above products comprises of various methods of manufacturing such as facing, d
filling, cutting, shaping, threading etc. The operations of these quality circle as given below rea
impact of quality circle.
Case Study
a) Name of the organization: Workshop of a manufacturing organization
b) Number of circles: 01 (one)
c) Section where the circle is: Machine and fitting shop operating
d) Number of meetings held: 10 (ten) for last one year
Figure 2 Pareto diagram
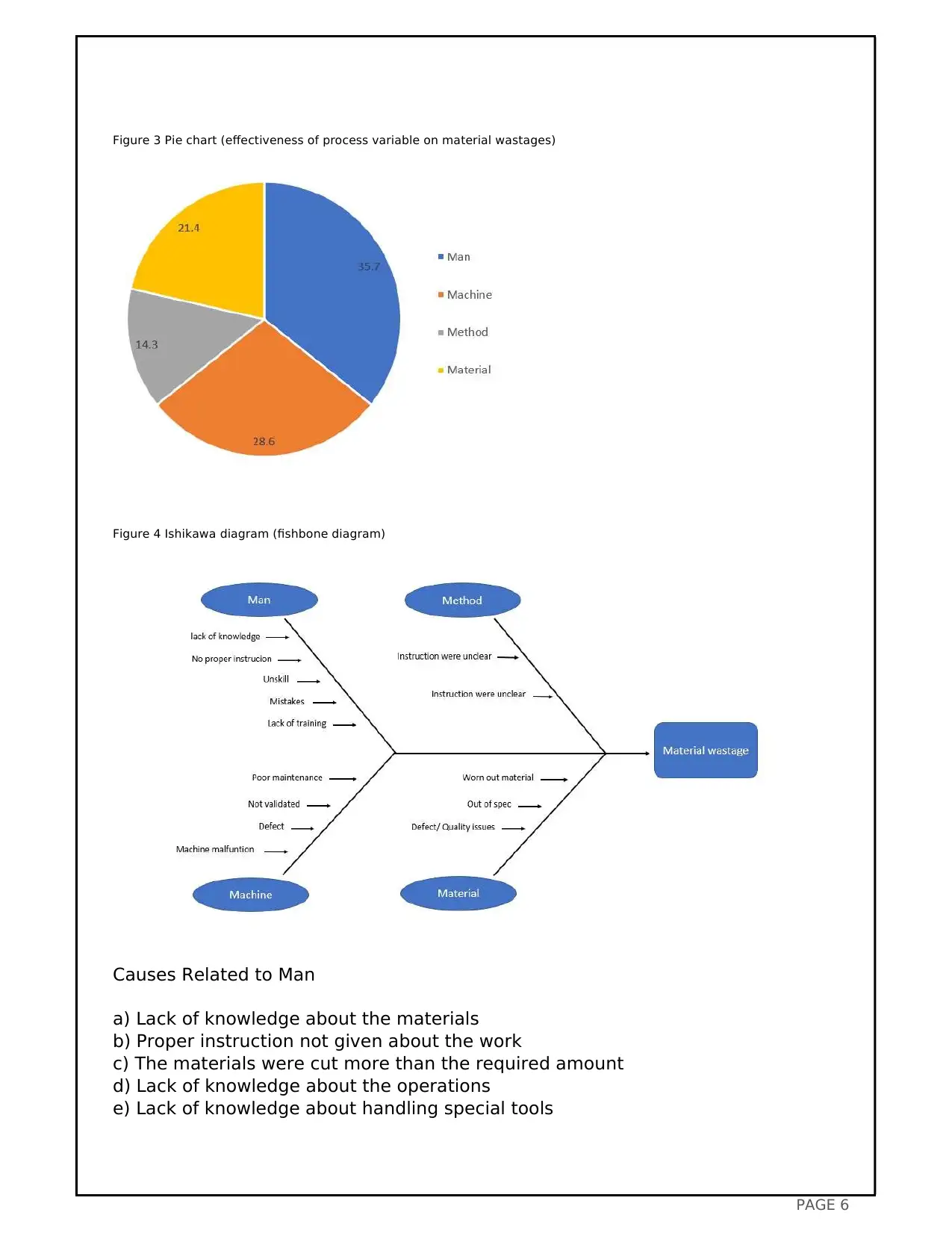
PAGE 6
Figure 3 Pie chart (effectiveness of process variable on material wastages)
Figure 4 Ishikawa diagram (fishbone diagram)
Causes Related to Man
a) Lack of knowledge about the materials
b) Proper instruction not given about the work
c) The materials were cut more than the required amount
d) Lack of knowledge about the operations
e) Lack of knowledge about handling special tools
Figure 3 Pie chart (effectiveness of process variable on material wastages)
Figure 4 Ishikawa diagram (fishbone diagram)
Causes Related to Man
a) Lack of knowledge about the materials
b) Proper instruction not given about the work
c) The materials were cut more than the required amount
d) Lack of knowledge about the operations
e) Lack of knowledge about handling special tools
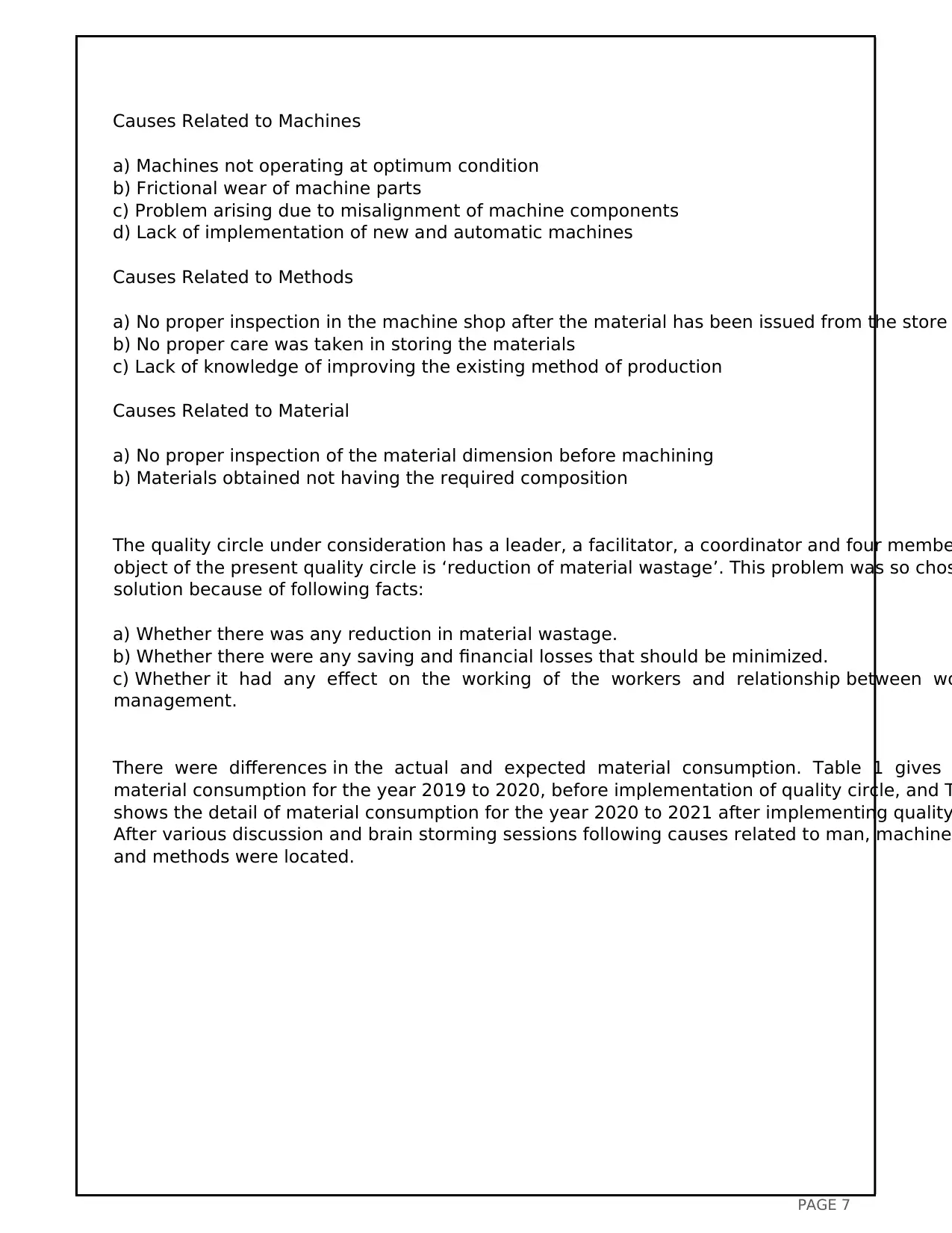
PAGE 7
Causes Related to Machines
a) Machines not operating at optimum condition
b) Frictional wear of machine parts
c) Problem arising due to misalignment of machine components
d) Lack of implementation of new and automatic machines
Causes Related to Methods
a) No proper inspection in the machine shop after the material has been issued from the store
b) No proper care was taken in storing the materials
c) Lack of knowledge of improving the existing method of production
Causes Related to Material
a) No proper inspection of the material dimension before machining
b) Materials obtained not having the required composition
The quality circle under consideration has a leader, a facilitator, a coordinator and four membe
object of the present quality circle is ‘reduction of material wastage’. This problem was so chos
solution because of following facts:
a) Whether there was any reduction in material wastage.
b) Whether there were any saving and financial losses that should be minimized.
c) Whether it had any effect on the working of the workers and relationship between wo
management.
There were differences in the actual and expected material consumption. Table 1 gives
material consumption for the year 2019 to 2020, before implementation of quality circle, and T
shows the detail of material consumption for the year 2020 to 2021 after implementing quality
After various discussion and brain storming sessions following causes related to man, machine,
and methods were located.
Causes Related to Machines
a) Machines not operating at optimum condition
b) Frictional wear of machine parts
c) Problem arising due to misalignment of machine components
d) Lack of implementation of new and automatic machines
Causes Related to Methods
a) No proper inspection in the machine shop after the material has been issued from the store
b) No proper care was taken in storing the materials
c) Lack of knowledge of improving the existing method of production
Causes Related to Material
a) No proper inspection of the material dimension before machining
b) Materials obtained not having the required composition
The quality circle under consideration has a leader, a facilitator, a coordinator and four membe
object of the present quality circle is ‘reduction of material wastage’. This problem was so chos
solution because of following facts:
a) Whether there was any reduction in material wastage.
b) Whether there were any saving and financial losses that should be minimized.
c) Whether it had any effect on the working of the workers and relationship between wo
management.
There were differences in the actual and expected material consumption. Table 1 gives
material consumption for the year 2019 to 2020, before implementation of quality circle, and T
shows the detail of material consumption for the year 2020 to 2021 after implementing quality
After various discussion and brain storming sessions following causes related to man, machine,
and methods were located.
Paraphrase This Document
Need a fresh take? Get an instant paraphrase of this document with our AI Paraphraser
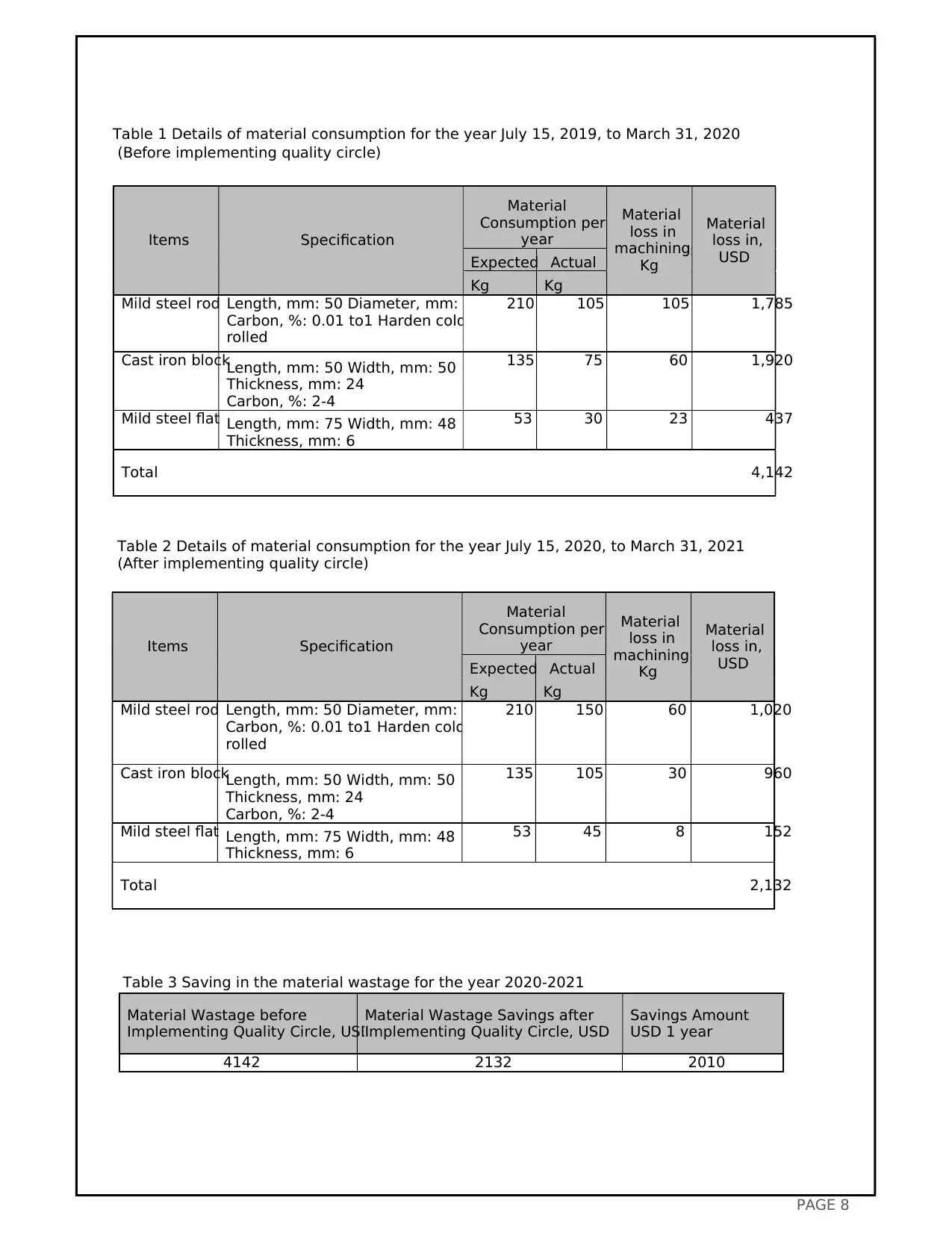
PAGE 8
Table 1 Details of material consumption for the year July 15, 2019, to March 31, 2020
(Before implementing quality circle)
Items Specification
Material
Consumption per
year
Material
loss in
machining,
Kg
Material
loss in,
USDExpected Actual
Kg Kg
Mild steel rod Length, mm: 50 Diameter, mm: 31
Carbon, %: 0.01 to1 Harden cold
rolled
210 105 105 1,785
Cast iron block
Length, mm: 50 Width, mm: 50
Thickness, mm: 24
Carbon, %: 2-4
135 75 60 1,920
Mild steel flat Length, mm: 75 Width, mm: 48
Thickness, mm: 6
53 30 23 437
Total 4,142
Table 2 Details of material consumption for the year July 15, 2020, to March 31, 2021
(After implementing quality circle)
Items Specification
Material
Consumption per
year
Material
loss in
machining,
Kg
Material
loss in,
USDExpected Actual
Kg Kg
Mild steel rod Length, mm: 50 Diameter, mm: 31
Carbon, %: 0.01 to1 Harden cold
rolled
210 150 60 1,020
Cast iron blockLength, mm: 50 Width, mm: 50
Thickness, mm: 24
Carbon, %: 2-4
135 105 30 960
Mild steel flat Length, mm: 75 Width, mm: 48
Thickness, mm: 6
53 45 8 152
Total 2,132
Table 3 Saving in the material wastage for the year 2020-2021
Material Wastage before
Implementing Quality Circle, USD
Material Wastage Savings after
Implementing Quality Circle, USD
Savings Amount
USD 1 year
4142 2132 2010
Table 1 Details of material consumption for the year July 15, 2019, to March 31, 2020
(Before implementing quality circle)
Items Specification
Material
Consumption per
year
Material
loss in
machining,
Kg
Material
loss in,
USDExpected Actual
Kg Kg
Mild steel rod Length, mm: 50 Diameter, mm: 31
Carbon, %: 0.01 to1 Harden cold
rolled
210 105 105 1,785
Cast iron block
Length, mm: 50 Width, mm: 50
Thickness, mm: 24
Carbon, %: 2-4
135 75 60 1,920
Mild steel flat Length, mm: 75 Width, mm: 48
Thickness, mm: 6
53 30 23 437
Total 4,142
Table 2 Details of material consumption for the year July 15, 2020, to March 31, 2021
(After implementing quality circle)
Items Specification
Material
Consumption per
year
Material
loss in
machining,
Kg
Material
loss in,
USDExpected Actual
Kg Kg
Mild steel rod Length, mm: 50 Diameter, mm: 31
Carbon, %: 0.01 to1 Harden cold
rolled
210 150 60 1,020
Cast iron blockLength, mm: 50 Width, mm: 50
Thickness, mm: 24
Carbon, %: 2-4
135 105 30 960
Mild steel flat Length, mm: 75 Width, mm: 48
Thickness, mm: 6
53 45 8 152
Total 2,132
Table 3 Saving in the material wastage for the year 2020-2021
Material Wastage before
Implementing Quality Circle, USD
Material Wastage Savings after
Implementing Quality Circle, USD
Savings Amount
USD 1 year
4142 2132 2010
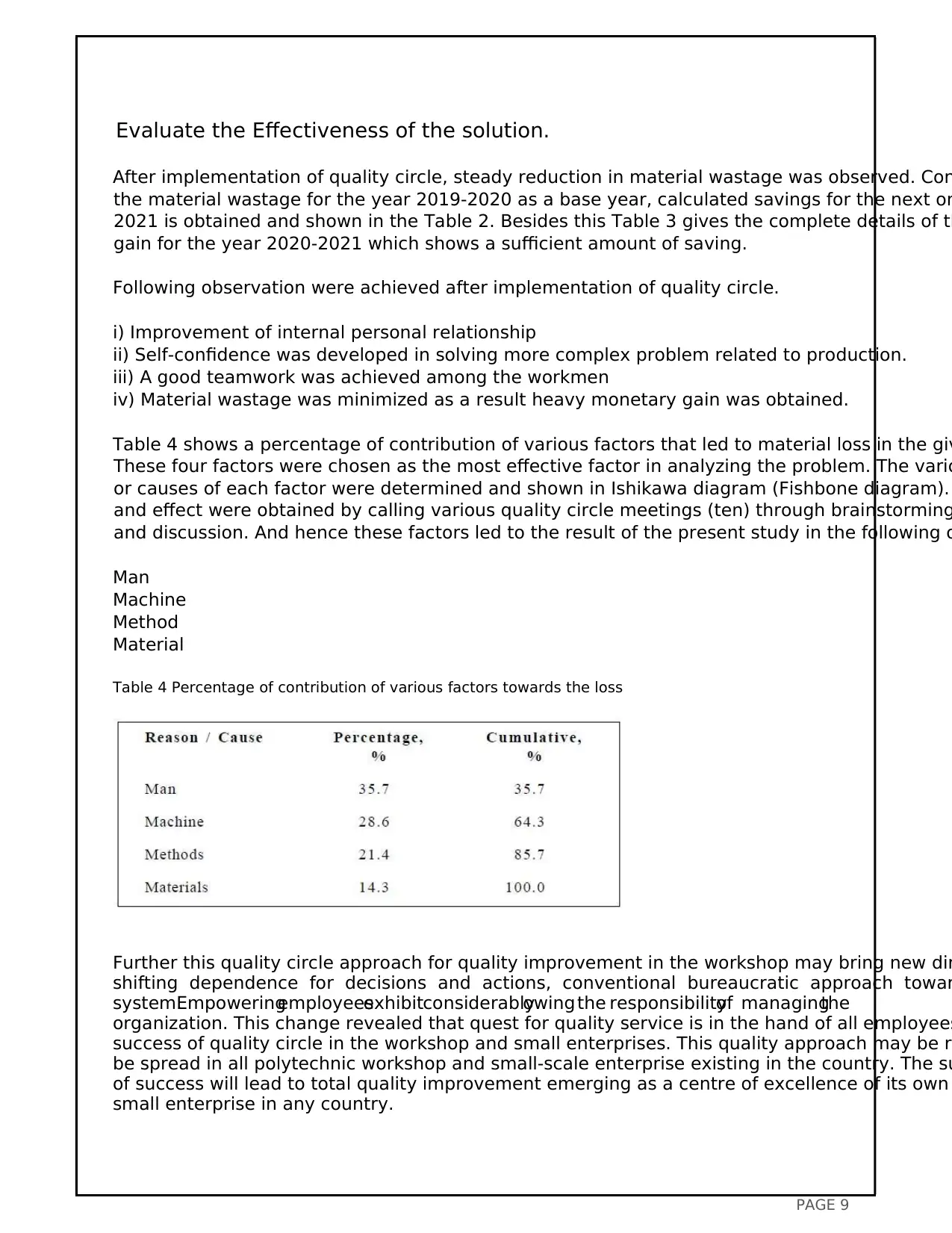
PAGE 9
Evaluate the Effectiveness of the solution.
After implementation of quality circle, steady reduction in material wastage was observed. Con
the material wastage for the year 2019-2020 as a base year, calculated savings for the next on
2021 is obtained and shown in the Table 2. Besides this Table 3 gives the complete details of th
gain for the year 2020-2021 which shows a sufficient amount of saving.
Following observation were achieved after implementation of quality circle.
i) Improvement of internal personal relationship
ii) Self-confidence was developed in solving more complex problem related to production.
iii) A good teamwork was achieved among the workmen
iv) Material wastage was minimized as a result heavy monetary gain was obtained.
Table 4 shows a percentage of contribution of various factors that led to material loss in the giv
These four factors were chosen as the most effective factor in analyzing the problem. The vario
or causes of each factor were determined and shown in Ishikawa diagram (Fishbone diagram).
and effect were obtained by calling various quality circle meetings (ten) through brainstorming
and discussion. And hence these factors led to the result of the present study in the following o
Man
Machine
Method
Material
Table 4 Percentage of contribution of various factors towards the loss
Further this quality circle approach for quality improvement in the workshop may bring new dim
shifting dependence for decisions and actions, conventional bureaucratic approach towar
system.Empoweringemployeesexhibitconsiderablyowing the responsibilityof managingthe
organization. This change revealed that quest for quality service is in the hand of all employees
success of quality circle in the workshop and small enterprises. This quality approach may be re
be spread in all polytechnic workshop and small-scale enterprise existing in the country. The su
of success will lead to total quality improvement emerging as a centre of excellence of its own
small enterprise in any country.
Evaluate the Effectiveness of the solution.
After implementation of quality circle, steady reduction in material wastage was observed. Con
the material wastage for the year 2019-2020 as a base year, calculated savings for the next on
2021 is obtained and shown in the Table 2. Besides this Table 3 gives the complete details of th
gain for the year 2020-2021 which shows a sufficient amount of saving.
Following observation were achieved after implementation of quality circle.
i) Improvement of internal personal relationship
ii) Self-confidence was developed in solving more complex problem related to production.
iii) A good teamwork was achieved among the workmen
iv) Material wastage was minimized as a result heavy monetary gain was obtained.
Table 4 shows a percentage of contribution of various factors that led to material loss in the giv
These four factors were chosen as the most effective factor in analyzing the problem. The vario
or causes of each factor were determined and shown in Ishikawa diagram (Fishbone diagram).
and effect were obtained by calling various quality circle meetings (ten) through brainstorming
and discussion. And hence these factors led to the result of the present study in the following o
Man
Machine
Method
Material
Table 4 Percentage of contribution of various factors towards the loss
Further this quality circle approach for quality improvement in the workshop may bring new dim
shifting dependence for decisions and actions, conventional bureaucratic approach towar
system.Empoweringemployeesexhibitconsiderablyowing the responsibilityof managingthe
organization. This change revealed that quest for quality service is in the hand of all employees
success of quality circle in the workshop and small enterprises. This quality approach may be re
be spread in all polytechnic workshop and small-scale enterprise existing in the country. The su
of success will lead to total quality improvement emerging as a centre of excellence of its own
small enterprise in any country.

PAGE 10
Conclusion
Quality circle is an important and effective tool used to solve problems in the organization at di
levels. The Quality circle helps to find out relationship between different factors in the organiza
their effect on each other so that we can find out major and minor factors based upon which m
can take action to improve organization effectiveness. Quality circle approach for quality impro
in workshop may bring new dimension, shifting dependence for decisions and actions towards
system. This change revealed that quest for quality service is in the hand of all employees. A q
circle program is very simple and does not overlap company structures. The impact of Quality c
towards employees and organization has become very important for improving a firm's
capabilities in order to achieve fit and sustain competitive advantages. Quality circle can be lin
with productivity which cannot be measured only by money. There are various factors
developing the employees’ attitude towards quality circle. The organization plays a facilitator r
developing Quality circle. The transparency and integrity of the organization is very much impo
the smooth functioning of quality circles. The culture has great impact on the quality circles ba
employeeinvolvement,employeeempowerment,perceivedorganizationalsupport& employee
engagement.
Conclusion
Quality circle is an important and effective tool used to solve problems in the organization at di
levels. The Quality circle helps to find out relationship between different factors in the organiza
their effect on each other so that we can find out major and minor factors based upon which m
can take action to improve organization effectiveness. Quality circle approach for quality impro
in workshop may bring new dimension, shifting dependence for decisions and actions towards
system. This change revealed that quest for quality service is in the hand of all employees. A q
circle program is very simple and does not overlap company structures. The impact of Quality c
towards employees and organization has become very important for improving a firm's
capabilities in order to achieve fit and sustain competitive advantages. Quality circle can be lin
with productivity which cannot be measured only by money. There are various factors
developing the employees’ attitude towards quality circle. The organization plays a facilitator r
developing Quality circle. The transparency and integrity of the organization is very much impo
the smooth functioning of quality circles. The culture has great impact on the quality circles ba
employeeinvolvement,employeeempowerment,perceivedorganizationalsupport& employee
engagement.
Secure Best Marks with AI Grader
Need help grading? Try our AI Grader for instant feedback on your assignments.
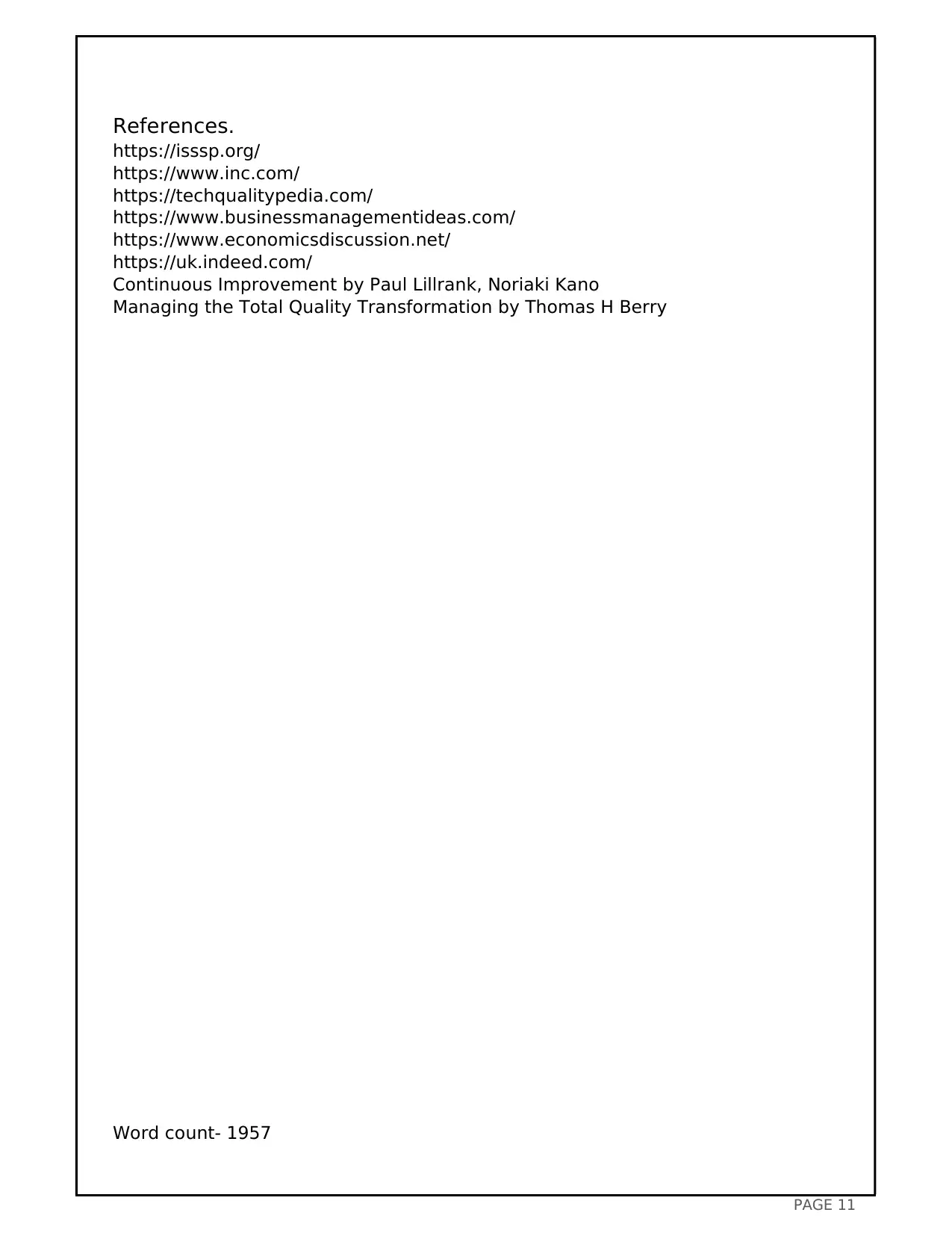
PAGE 11
References.
https://isssp.org/
https://www.inc.com/
https://techqualitypedia.com/
https://www.businessmanagementideas.com/
https://www.economicsdiscussion.net/
https://uk.indeed.com/
Continuous Improvement by Paul Lillrank, Noriaki Kano
Managing the Total Quality Transformation by Thomas H Berry
Word count- 1957
References.
https://isssp.org/
https://www.inc.com/
https://techqualitypedia.com/
https://www.businessmanagementideas.com/
https://www.economicsdiscussion.net/
https://uk.indeed.com/
Continuous Improvement by Paul Lillrank, Noriaki Kano
Managing the Total Quality Transformation by Thomas H Berry
Word count- 1957
1 out of 11

Your All-in-One AI-Powered Toolkit for Academic Success.
+13062052269
info@desklib.com
Available 24*7 on WhatsApp / Email
Unlock your academic potential
© 2024 | Zucol Services PVT LTD | All rights reserved.