OHS Law 13: Case Study Analysis of Workplace Accident at Do More Steel
VerifiedAdded on 2020/03/16
|13
|3439
|59
Case Study
AI Summary
This case study examines a workplace accident at the Do More Steel Manufacturing Company, focusing on violations of the Work Health and Safety (WHS) Act 2011 in Queensland. The accident, resulting in a fatal injury, is analyzed in detail, identifying various duty holders including the PCBU (Do Mor...
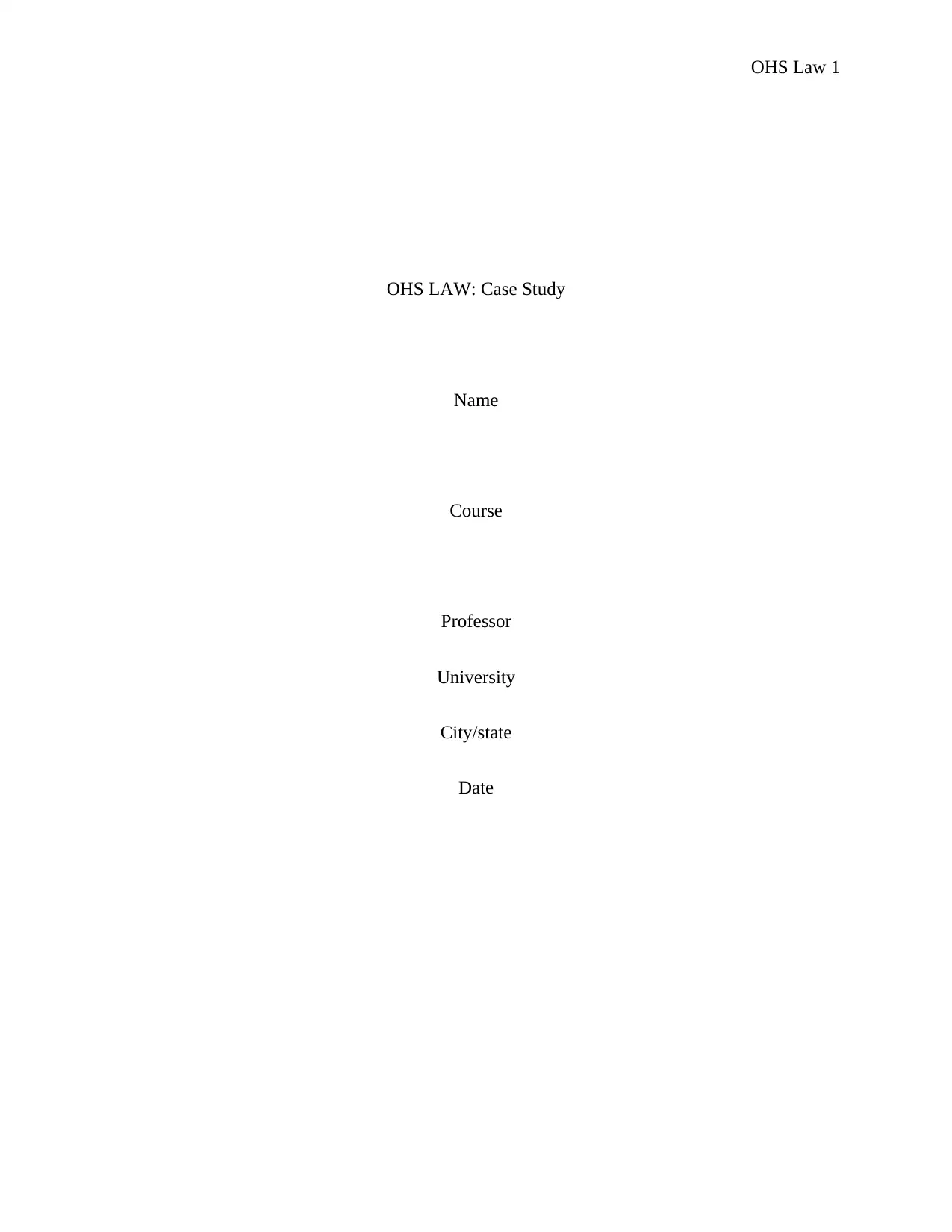
OHS Law 1
OHS LAW: Case Study
Name
Course
Professor
University
City/state
Date
OHS LAW: Case Study
Name
Course
Professor
University
City/state
Date
Paraphrase This Document
Need a fresh take? Get an instant paraphrase of this document with our AI Paraphraser
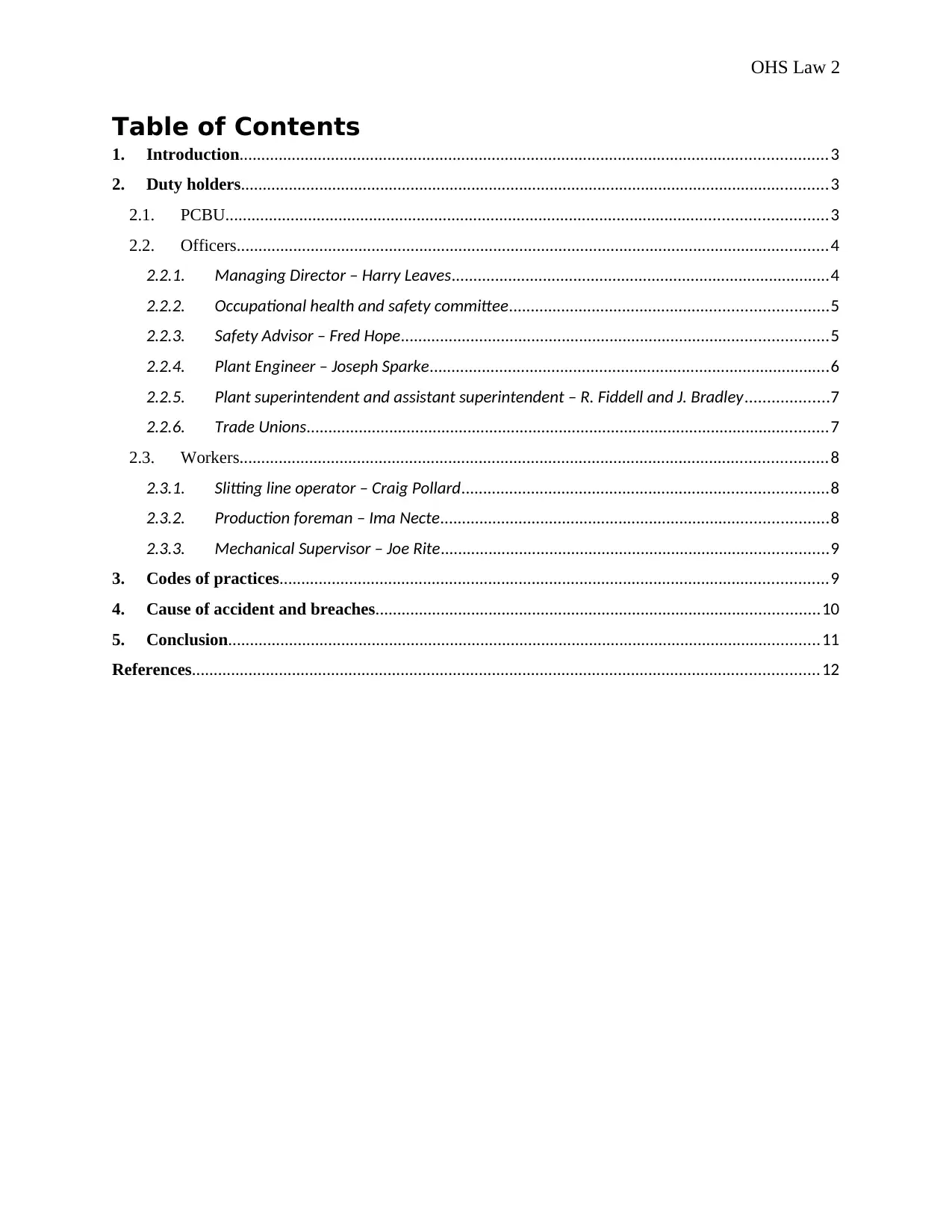
OHS Law 2
Table of Contents
1. Introduction.......................................................................................................................................3
2. Duty holders.......................................................................................................................................3
2.1. PCBU..........................................................................................................................................3
2.2. Officers........................................................................................................................................4
2.2.1. Managing Director – Harry Leaves.......................................................................................4
2.2.2. Occupational health and safety committee.........................................................................5
2.2.3. Safety Advisor – Fred Hope..................................................................................................5
2.2.4. Plant Engineer – Joseph Sparke............................................................................................6
2.2.5. Plant superintendent and assistant superintendent – R. Fiddell and J. Bradley...................7
2.2.6. Trade Unions........................................................................................................................7
2.3. Workers.......................................................................................................................................8
2.3.1. Slitting line operator – Craig Pollard....................................................................................8
2.3.2. Production foreman – Ima Necte.........................................................................................8
2.3.3. Mechanical Supervisor – Joe Rite.........................................................................................9
3. Codes of practices..............................................................................................................................9
4. Cause of accident and breaches......................................................................................................10
5. Conclusion........................................................................................................................................11
References................................................................................................................................................12
Table of Contents
1. Introduction.......................................................................................................................................3
2. Duty holders.......................................................................................................................................3
2.1. PCBU..........................................................................................................................................3
2.2. Officers........................................................................................................................................4
2.2.1. Managing Director – Harry Leaves.......................................................................................4
2.2.2. Occupational health and safety committee.........................................................................5
2.2.3. Safety Advisor – Fred Hope..................................................................................................5
2.2.4. Plant Engineer – Joseph Sparke............................................................................................6
2.2.5. Plant superintendent and assistant superintendent – R. Fiddell and J. Bradley...................7
2.2.6. Trade Unions........................................................................................................................7
2.3. Workers.......................................................................................................................................8
2.3.1. Slitting line operator – Craig Pollard....................................................................................8
2.3.2. Production foreman – Ima Necte.........................................................................................8
2.3.3. Mechanical Supervisor – Joe Rite.........................................................................................9
3. Codes of practices..............................................................................................................................9
4. Cause of accident and breaches......................................................................................................10
5. Conclusion........................................................................................................................................11
References................................................................................................................................................12
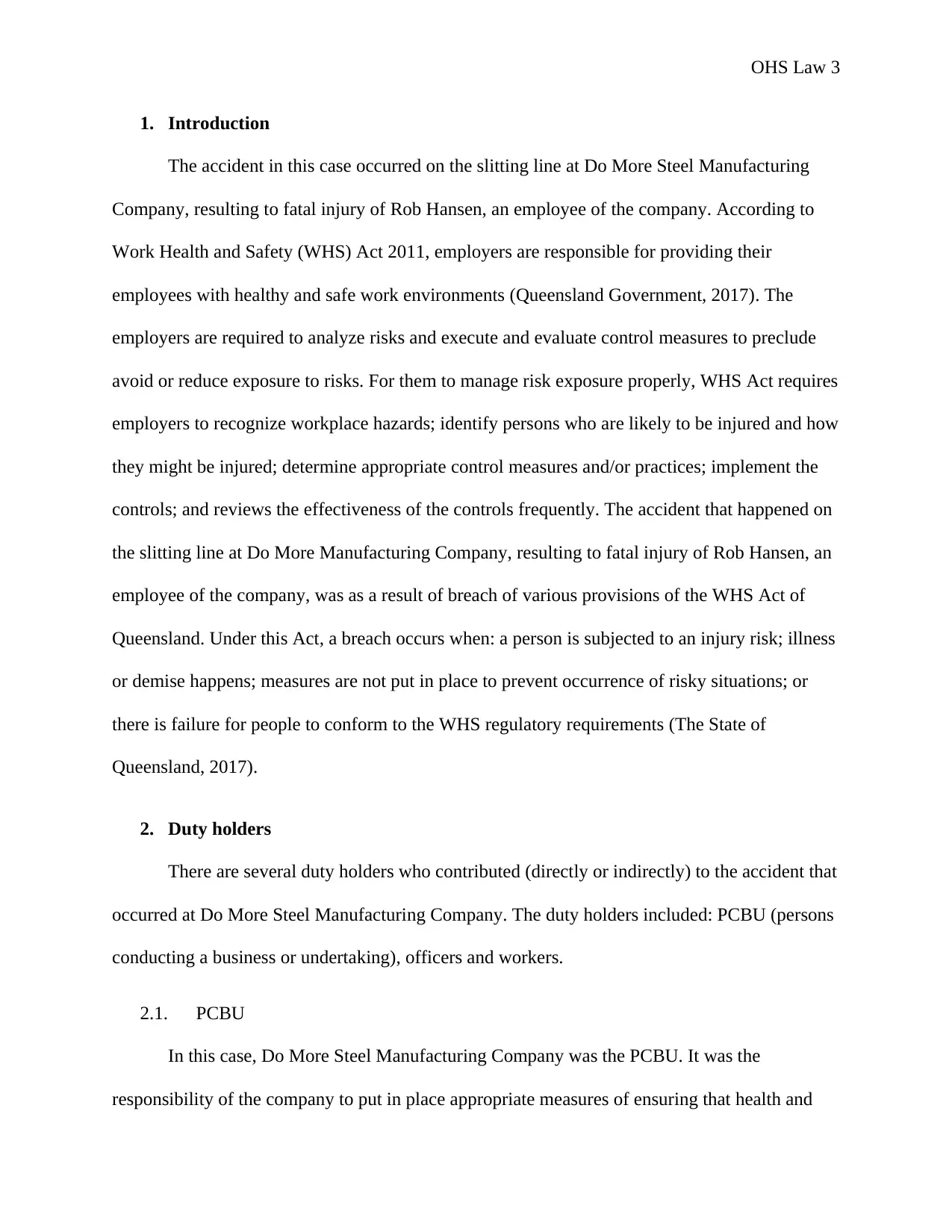
OHS Law 3
1. Introduction
The accident in this case occurred on the slitting line at Do More Steel Manufacturing
Company, resulting to fatal injury of Rob Hansen, an employee of the company. According to
Work Health and Safety (WHS) Act 2011, employers are responsible for providing their
employees with healthy and safe work environments (Queensland Government, 2017). The
employers are required to analyze risks and execute and evaluate control measures to preclude
avoid or reduce exposure to risks. For them to manage risk exposure properly, WHS Act requires
employers to recognize workplace hazards; identify persons who are likely to be injured and how
they might be injured; determine appropriate control measures and/or practices; implement the
controls; and reviews the effectiveness of the controls frequently. The accident that happened on
the slitting line at Do More Manufacturing Company, resulting to fatal injury of Rob Hansen, an
employee of the company, was as a result of breach of various provisions of the WHS Act of
Queensland. Under this Act, a breach occurs when: a person is subjected to an injury risk; illness
or demise happens; measures are not put in place to prevent occurrence of risky situations; or
there is failure for people to conform to the WHS regulatory requirements (The State of
Queensland, 2017).
2. Duty holders
There are several duty holders who contributed (directly or indirectly) to the accident that
occurred at Do More Steel Manufacturing Company. The duty holders included: PCBU (persons
conducting a business or undertaking), officers and workers.
2.1. PCBU
In this case, Do More Steel Manufacturing Company was the PCBU. It was the
responsibility of the company to put in place appropriate measures of ensuring that health and
1. Introduction
The accident in this case occurred on the slitting line at Do More Steel Manufacturing
Company, resulting to fatal injury of Rob Hansen, an employee of the company. According to
Work Health and Safety (WHS) Act 2011, employers are responsible for providing their
employees with healthy and safe work environments (Queensland Government, 2017). The
employers are required to analyze risks and execute and evaluate control measures to preclude
avoid or reduce exposure to risks. For them to manage risk exposure properly, WHS Act requires
employers to recognize workplace hazards; identify persons who are likely to be injured and how
they might be injured; determine appropriate control measures and/or practices; implement the
controls; and reviews the effectiveness of the controls frequently. The accident that happened on
the slitting line at Do More Manufacturing Company, resulting to fatal injury of Rob Hansen, an
employee of the company, was as a result of breach of various provisions of the WHS Act of
Queensland. Under this Act, a breach occurs when: a person is subjected to an injury risk; illness
or demise happens; measures are not put in place to prevent occurrence of risky situations; or
there is failure for people to conform to the WHS regulatory requirements (The State of
Queensland, 2017).
2. Duty holders
There are several duty holders who contributed (directly or indirectly) to the accident that
occurred at Do More Steel Manufacturing Company. The duty holders included: PCBU (persons
conducting a business or undertaking), officers and workers.
2.1. PCBU
In this case, Do More Steel Manufacturing Company was the PCBU. It was the
responsibility of the company to put in place appropriate measures of ensuring that health and
⊘ This is a preview!⊘
Do you want full access?
Subscribe today to unlock all pages.

Trusted by 1+ million students worldwide
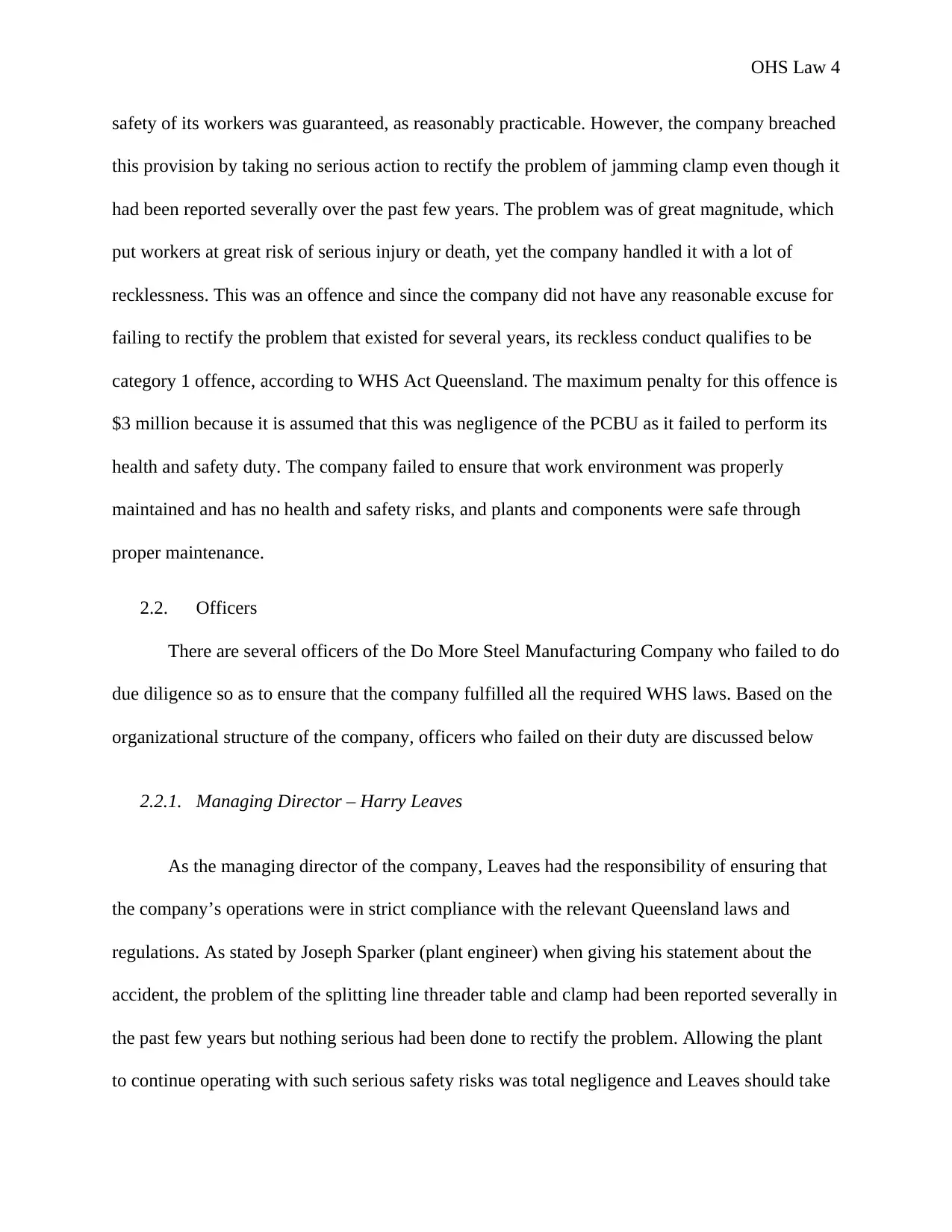
OHS Law 4
safety of its workers was guaranteed, as reasonably practicable. However, the company breached
this provision by taking no serious action to rectify the problem of jamming clamp even though it
had been reported severally over the past few years. The problem was of great magnitude, which
put workers at great risk of serious injury or death, yet the company handled it with a lot of
recklessness. This was an offence and since the company did not have any reasonable excuse for
failing to rectify the problem that existed for several years, its reckless conduct qualifies to be
category 1 offence, according to WHS Act Queensland. The maximum penalty for this offence is
$3 million because it is assumed that this was negligence of the PCBU as it failed to perform its
health and safety duty. The company failed to ensure that work environment was properly
maintained and has no health and safety risks, and plants and components were safe through
proper maintenance.
2.2. Officers
There are several officers of the Do More Steel Manufacturing Company who failed to do
due diligence so as to ensure that the company fulfilled all the required WHS laws. Based on the
organizational structure of the company, officers who failed on their duty are discussed below
2.2.1. Managing Director – Harry Leaves
As the managing director of the company, Leaves had the responsibility of ensuring that
the company’s operations were in strict compliance with the relevant Queensland laws and
regulations. As stated by Joseph Sparker (plant engineer) when giving his statement about the
accident, the problem of the splitting line threader table and clamp had been reported severally in
the past few years but nothing serious had been done to rectify the problem. Allowing the plant
to continue operating with such serious safety risks was total negligence and Leaves should take
safety of its workers was guaranteed, as reasonably practicable. However, the company breached
this provision by taking no serious action to rectify the problem of jamming clamp even though it
had been reported severally over the past few years. The problem was of great magnitude, which
put workers at great risk of serious injury or death, yet the company handled it with a lot of
recklessness. This was an offence and since the company did not have any reasonable excuse for
failing to rectify the problem that existed for several years, its reckless conduct qualifies to be
category 1 offence, according to WHS Act Queensland. The maximum penalty for this offence is
$3 million because it is assumed that this was negligence of the PCBU as it failed to perform its
health and safety duty. The company failed to ensure that work environment was properly
maintained and has no health and safety risks, and plants and components were safe through
proper maintenance.
2.2. Officers
There are several officers of the Do More Steel Manufacturing Company who failed to do
due diligence so as to ensure that the company fulfilled all the required WHS laws. Based on the
organizational structure of the company, officers who failed on their duty are discussed below
2.2.1. Managing Director – Harry Leaves
As the managing director of the company, Leaves had the responsibility of ensuring that
the company’s operations were in strict compliance with the relevant Queensland laws and
regulations. As stated by Joseph Sparker (plant engineer) when giving his statement about the
accident, the problem of the splitting line threader table and clamp had been reported severally in
the past few years but nothing serious had been done to rectify the problem. Allowing the plant
to continue operating with such serious safety risks was total negligence and Leaves should take
Paraphrase This Document
Need a fresh take? Get an instant paraphrase of this document with our AI Paraphraser
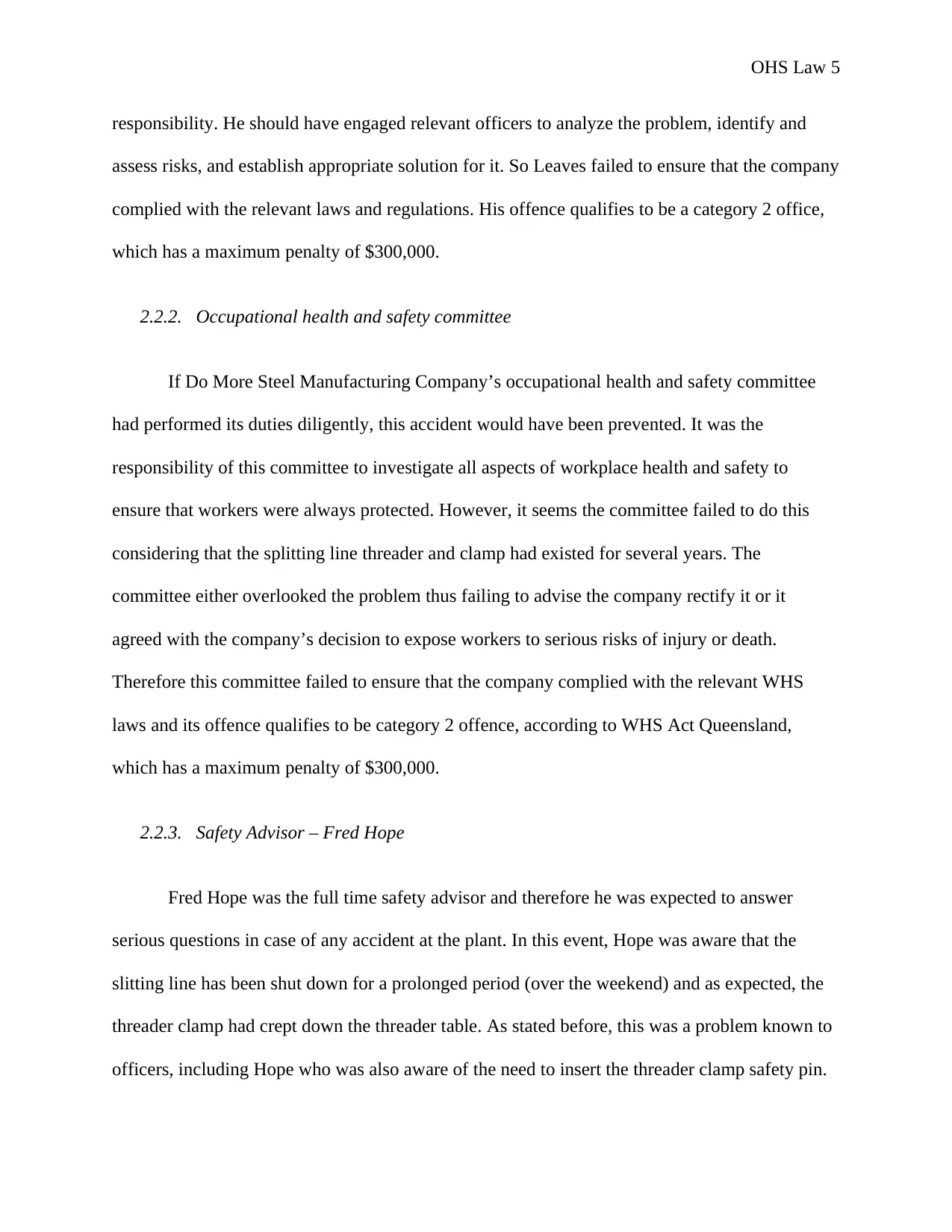
OHS Law 5
responsibility. He should have engaged relevant officers to analyze the problem, identify and
assess risks, and establish appropriate solution for it. So Leaves failed to ensure that the company
complied with the relevant laws and regulations. His offence qualifies to be a category 2 office,
which has a maximum penalty of $300,000.
2.2.2. Occupational health and safety committee
If Do More Steel Manufacturing Company’s occupational health and safety committee
had performed its duties diligently, this accident would have been prevented. It was the
responsibility of this committee to investigate all aspects of workplace health and safety to
ensure that workers were always protected. However, it seems the committee failed to do this
considering that the splitting line threader and clamp had existed for several years. The
committee either overlooked the problem thus failing to advise the company rectify it or it
agreed with the company’s decision to expose workers to serious risks of injury or death.
Therefore this committee failed to ensure that the company complied with the relevant WHS
laws and its offence qualifies to be category 2 offence, according to WHS Act Queensland,
which has a maximum penalty of $300,000.
2.2.3. Safety Advisor – Fred Hope
Fred Hope was the full time safety advisor and therefore he was expected to answer
serious questions in case of any accident at the plant. In this event, Hope was aware that the
slitting line has been shut down for a prolonged period (over the weekend) and as expected, the
threader clamp had crept down the threader table. As stated before, this was a problem known to
officers, including Hope who was also aware of the need to insert the threader clamp safety pin.
responsibility. He should have engaged relevant officers to analyze the problem, identify and
assess risks, and establish appropriate solution for it. So Leaves failed to ensure that the company
complied with the relevant laws and regulations. His offence qualifies to be a category 2 office,
which has a maximum penalty of $300,000.
2.2.2. Occupational health and safety committee
If Do More Steel Manufacturing Company’s occupational health and safety committee
had performed its duties diligently, this accident would have been prevented. It was the
responsibility of this committee to investigate all aspects of workplace health and safety to
ensure that workers were always protected. However, it seems the committee failed to do this
considering that the splitting line threader and clamp had existed for several years. The
committee either overlooked the problem thus failing to advise the company rectify it or it
agreed with the company’s decision to expose workers to serious risks of injury or death.
Therefore this committee failed to ensure that the company complied with the relevant WHS
laws and its offence qualifies to be category 2 offence, according to WHS Act Queensland,
which has a maximum penalty of $300,000.
2.2.3. Safety Advisor – Fred Hope
Fred Hope was the full time safety advisor and therefore he was expected to answer
serious questions in case of any accident at the plant. In this event, Hope was aware that the
slitting line has been shut down for a prolonged period (over the weekend) and as expected, the
threader clamp had crept down the threader table. As stated before, this was a problem known to
officers, including Hope who was also aware of the need to insert the threader clamp safety pin.
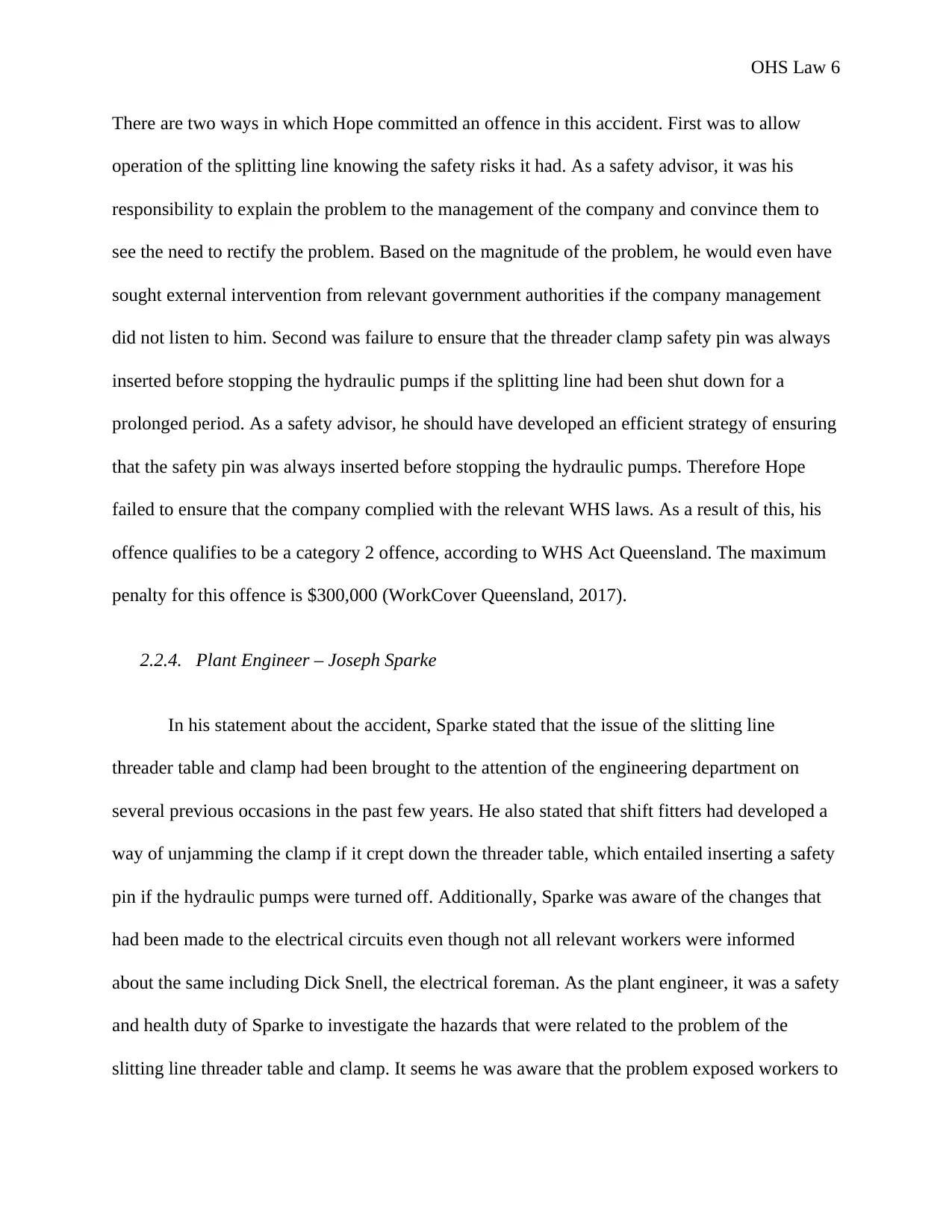
OHS Law 6
There are two ways in which Hope committed an offence in this accident. First was to allow
operation of the splitting line knowing the safety risks it had. As a safety advisor, it was his
responsibility to explain the problem to the management of the company and convince them to
see the need to rectify the problem. Based on the magnitude of the problem, he would even have
sought external intervention from relevant government authorities if the company management
did not listen to him. Second was failure to ensure that the threader clamp safety pin was always
inserted before stopping the hydraulic pumps if the splitting line had been shut down for a
prolonged period. As a safety advisor, he should have developed an efficient strategy of ensuring
that the safety pin was always inserted before stopping the hydraulic pumps. Therefore Hope
failed to ensure that the company complied with the relevant WHS laws. As a result of this, his
offence qualifies to be a category 2 offence, according to WHS Act Queensland. The maximum
penalty for this offence is $300,000 (WorkCover Queensland, 2017).
2.2.4. Plant Engineer – Joseph Sparke
In his statement about the accident, Sparke stated that the issue of the slitting line
threader table and clamp had been brought to the attention of the engineering department on
several previous occasions in the past few years. He also stated that shift fitters had developed a
way of unjamming the clamp if it crept down the threader table, which entailed inserting a safety
pin if the hydraulic pumps were turned off. Additionally, Sparke was aware of the changes that
had been made to the electrical circuits even though not all relevant workers were informed
about the same including Dick Snell, the electrical foreman. As the plant engineer, it was a safety
and health duty of Sparke to investigate the hazards that were related to the problem of the
slitting line threader table and clamp. It seems he was aware that the problem exposed workers to
There are two ways in which Hope committed an offence in this accident. First was to allow
operation of the splitting line knowing the safety risks it had. As a safety advisor, it was his
responsibility to explain the problem to the management of the company and convince them to
see the need to rectify the problem. Based on the magnitude of the problem, he would even have
sought external intervention from relevant government authorities if the company management
did not listen to him. Second was failure to ensure that the threader clamp safety pin was always
inserted before stopping the hydraulic pumps if the splitting line had been shut down for a
prolonged period. As a safety advisor, he should have developed an efficient strategy of ensuring
that the safety pin was always inserted before stopping the hydraulic pumps. Therefore Hope
failed to ensure that the company complied with the relevant WHS laws. As a result of this, his
offence qualifies to be a category 2 offence, according to WHS Act Queensland. The maximum
penalty for this offence is $300,000 (WorkCover Queensland, 2017).
2.2.4. Plant Engineer – Joseph Sparke
In his statement about the accident, Sparke stated that the issue of the slitting line
threader table and clamp had been brought to the attention of the engineering department on
several previous occasions in the past few years. He also stated that shift fitters had developed a
way of unjamming the clamp if it crept down the threader table, which entailed inserting a safety
pin if the hydraulic pumps were turned off. Additionally, Sparke was aware of the changes that
had been made to the electrical circuits even though not all relevant workers were informed
about the same including Dick Snell, the electrical foreman. As the plant engineer, it was a safety
and health duty of Sparke to investigate the hazards that were related to the problem of the
slitting line threader table and clamp. It seems he was aware that the problem exposed workers to
⊘ This is a preview!⊘
Do you want full access?
Subscribe today to unlock all pages.

Trusted by 1+ million students worldwide
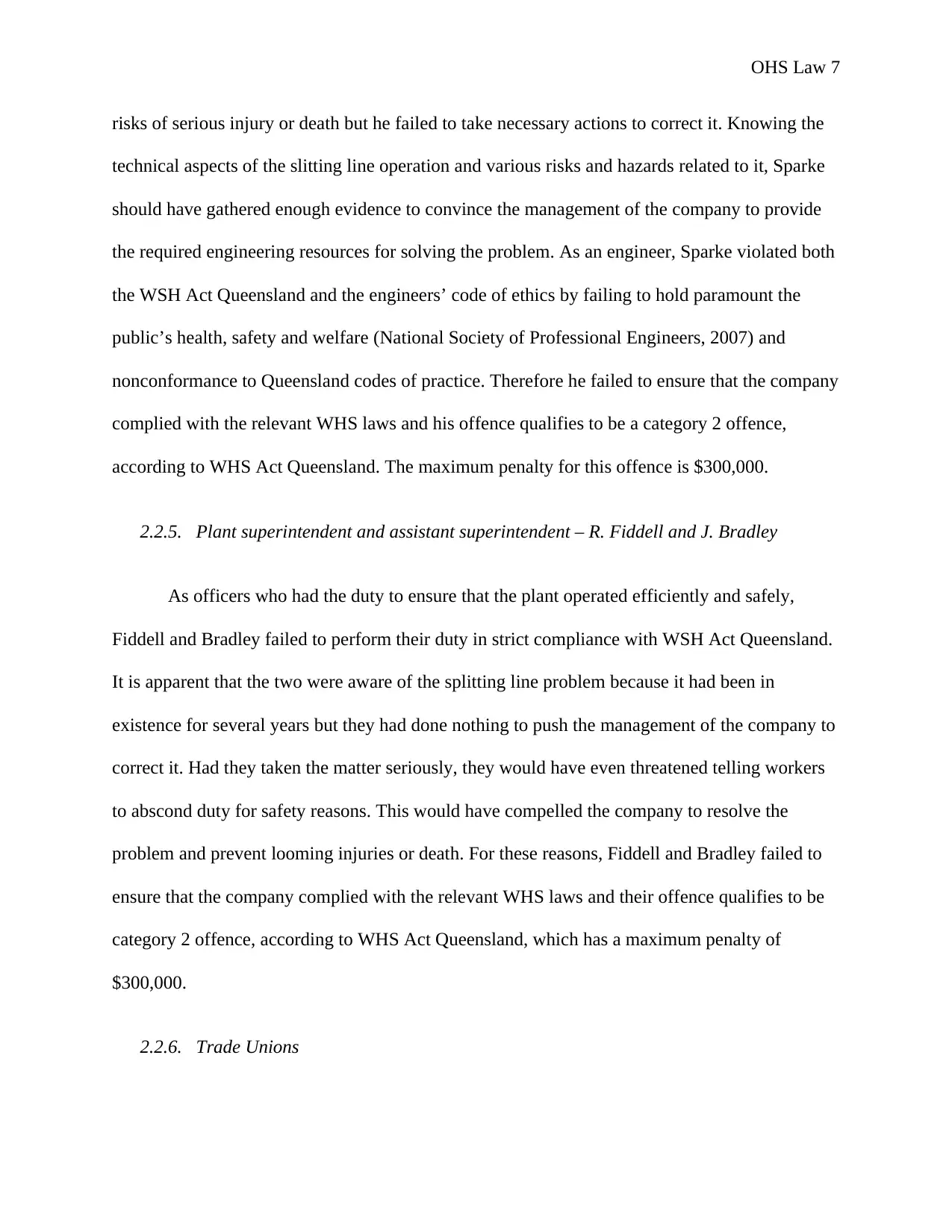
OHS Law 7
risks of serious injury or death but he failed to take necessary actions to correct it. Knowing the
technical aspects of the slitting line operation and various risks and hazards related to it, Sparke
should have gathered enough evidence to convince the management of the company to provide
the required engineering resources for solving the problem. As an engineer, Sparke violated both
the WSH Act Queensland and the engineers’ code of ethics by failing to hold paramount the
public’s health, safety and welfare (National Society of Professional Engineers, 2007) and
nonconformance to Queensland codes of practice. Therefore he failed to ensure that the company
complied with the relevant WHS laws and his offence qualifies to be a category 2 offence,
according to WHS Act Queensland. The maximum penalty for this offence is $300,000.
2.2.5. Plant superintendent and assistant superintendent – R. Fiddell and J. Bradley
As officers who had the duty to ensure that the plant operated efficiently and safely,
Fiddell and Bradley failed to perform their duty in strict compliance with WSH Act Queensland.
It is apparent that the two were aware of the splitting line problem because it had been in
existence for several years but they had done nothing to push the management of the company to
correct it. Had they taken the matter seriously, they would have even threatened telling workers
to abscond duty for safety reasons. This would have compelled the company to resolve the
problem and prevent looming injuries or death. For these reasons, Fiddell and Bradley failed to
ensure that the company complied with the relevant WHS laws and their offence qualifies to be
category 2 offence, according to WHS Act Queensland, which has a maximum penalty of
$300,000.
2.2.6. Trade Unions
risks of serious injury or death but he failed to take necessary actions to correct it. Knowing the
technical aspects of the slitting line operation and various risks and hazards related to it, Sparke
should have gathered enough evidence to convince the management of the company to provide
the required engineering resources for solving the problem. As an engineer, Sparke violated both
the WSH Act Queensland and the engineers’ code of ethics by failing to hold paramount the
public’s health, safety and welfare (National Society of Professional Engineers, 2007) and
nonconformance to Queensland codes of practice. Therefore he failed to ensure that the company
complied with the relevant WHS laws and his offence qualifies to be a category 2 offence,
according to WHS Act Queensland. The maximum penalty for this offence is $300,000.
2.2.5. Plant superintendent and assistant superintendent – R. Fiddell and J. Bradley
As officers who had the duty to ensure that the plant operated efficiently and safely,
Fiddell and Bradley failed to perform their duty in strict compliance with WSH Act Queensland.
It is apparent that the two were aware of the splitting line problem because it had been in
existence for several years but they had done nothing to push the management of the company to
correct it. Had they taken the matter seriously, they would have even threatened telling workers
to abscond duty for safety reasons. This would have compelled the company to resolve the
problem and prevent looming injuries or death. For these reasons, Fiddell and Bradley failed to
ensure that the company complied with the relevant WHS laws and their offence qualifies to be
category 2 offence, according to WHS Act Queensland, which has a maximum penalty of
$300,000.
2.2.6. Trade Unions
Paraphrase This Document
Need a fresh take? Get an instant paraphrase of this document with our AI Paraphraser
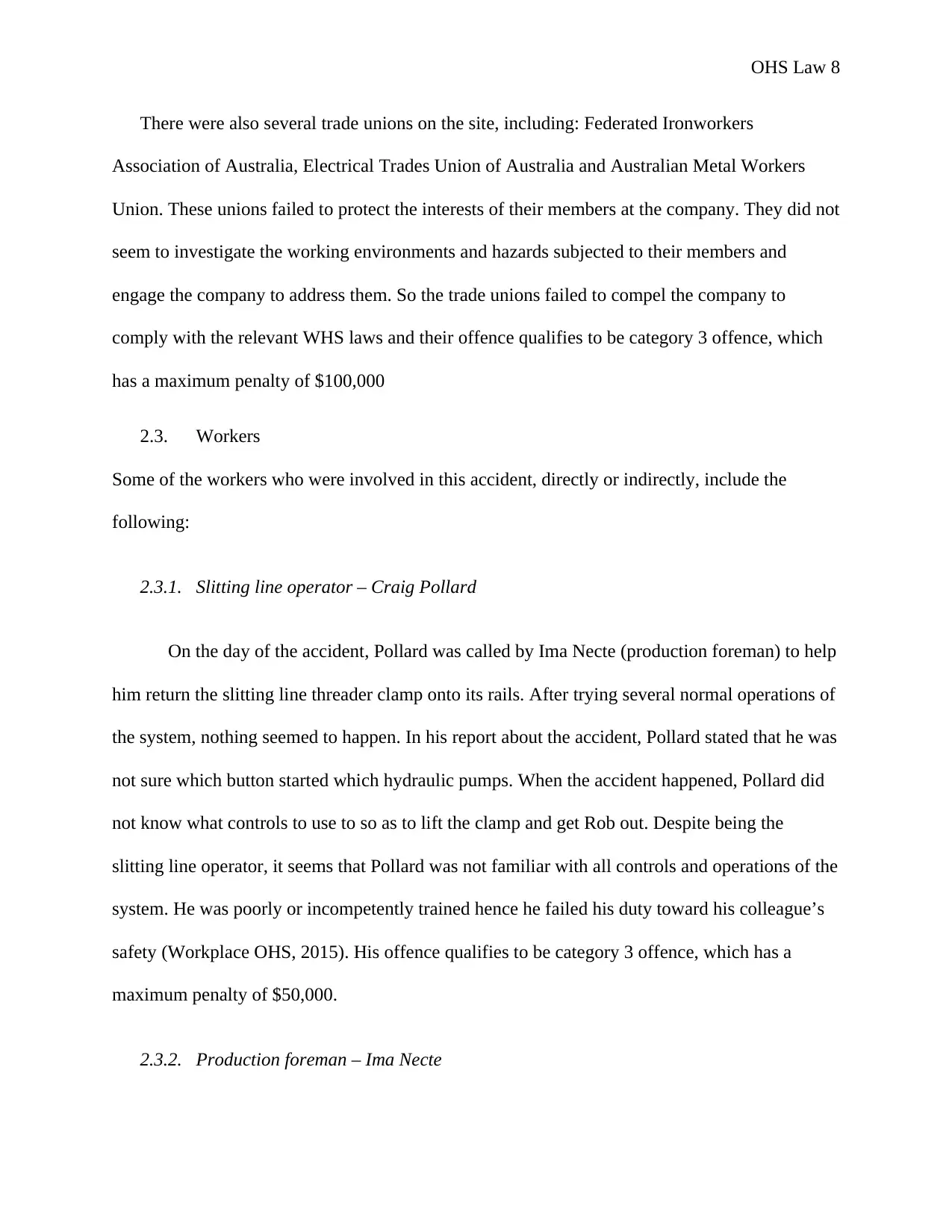
OHS Law 8
There were also several trade unions on the site, including: Federated Ironworkers
Association of Australia, Electrical Trades Union of Australia and Australian Metal Workers
Union. These unions failed to protect the interests of their members at the company. They did not
seem to investigate the working environments and hazards subjected to their members and
engage the company to address them. So the trade unions failed to compel the company to
comply with the relevant WHS laws and their offence qualifies to be category 3 offence, which
has a maximum penalty of $100,000
2.3. Workers
Some of the workers who were involved in this accident, directly or indirectly, include the
following:
2.3.1. Slitting line operator – Craig Pollard
On the day of the accident, Pollard was called by Ima Necte (production foreman) to help
him return the slitting line threader clamp onto its rails. After trying several normal operations of
the system, nothing seemed to happen. In his report about the accident, Pollard stated that he was
not sure which button started which hydraulic pumps. When the accident happened, Pollard did
not know what controls to use to so as to lift the clamp and get Rob out. Despite being the
slitting line operator, it seems that Pollard was not familiar with all controls and operations of the
system. He was poorly or incompetently trained hence he failed his duty toward his colleague’s
safety (Workplace OHS, 2015). His offence qualifies to be category 3 offence, which has a
maximum penalty of $50,000.
2.3.2. Production foreman – Ima Necte
There were also several trade unions on the site, including: Federated Ironworkers
Association of Australia, Electrical Trades Union of Australia and Australian Metal Workers
Union. These unions failed to protect the interests of their members at the company. They did not
seem to investigate the working environments and hazards subjected to their members and
engage the company to address them. So the trade unions failed to compel the company to
comply with the relevant WHS laws and their offence qualifies to be category 3 offence, which
has a maximum penalty of $100,000
2.3. Workers
Some of the workers who were involved in this accident, directly or indirectly, include the
following:
2.3.1. Slitting line operator – Craig Pollard
On the day of the accident, Pollard was called by Ima Necte (production foreman) to help
him return the slitting line threader clamp onto its rails. After trying several normal operations of
the system, nothing seemed to happen. In his report about the accident, Pollard stated that he was
not sure which button started which hydraulic pumps. When the accident happened, Pollard did
not know what controls to use to so as to lift the clamp and get Rob out. Despite being the
slitting line operator, it seems that Pollard was not familiar with all controls and operations of the
system. He was poorly or incompetently trained hence he failed his duty toward his colleague’s
safety (Workplace OHS, 2015). His offence qualifies to be category 3 offence, which has a
maximum penalty of $50,000.
2.3.2. Production foreman – Ima Necte
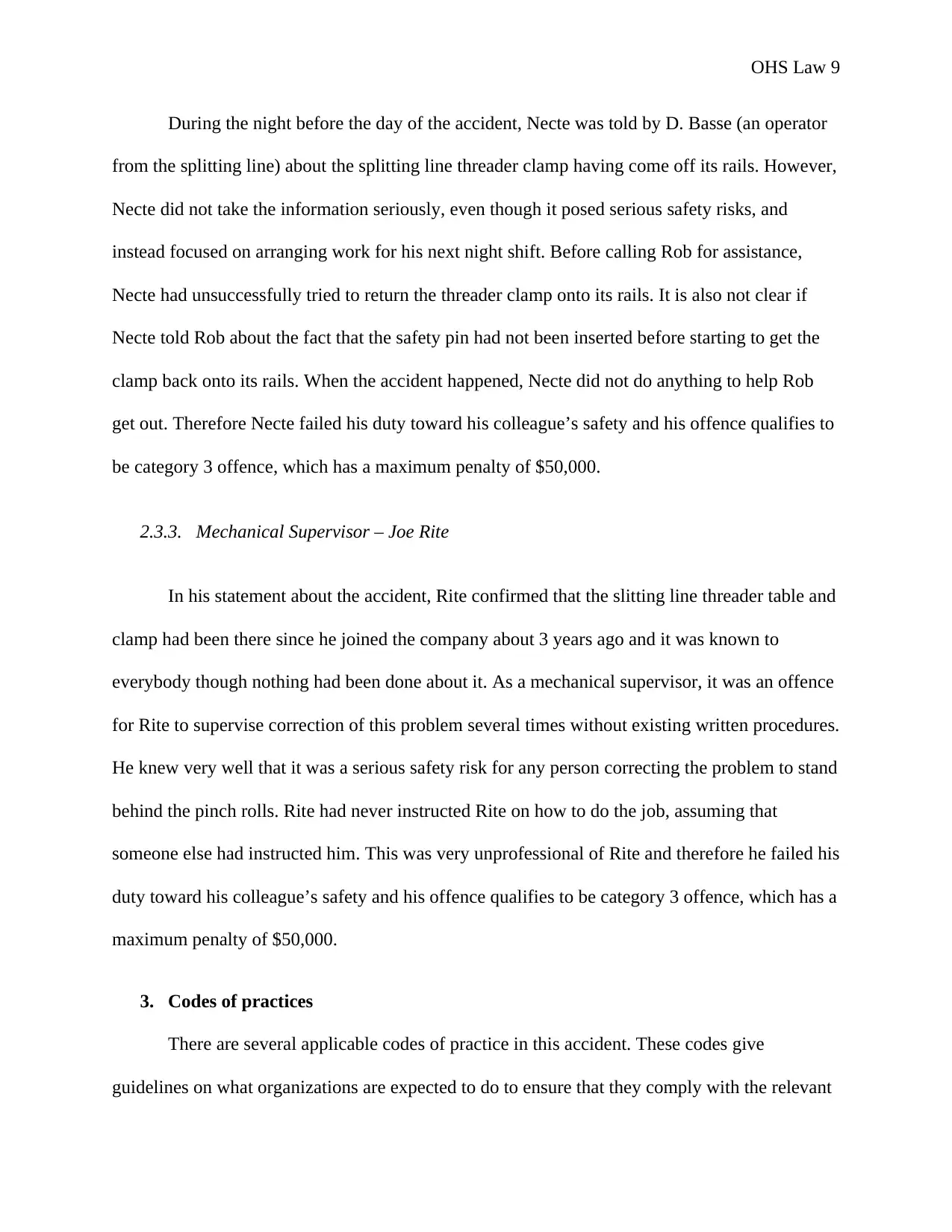
OHS Law 9
During the night before the day of the accident, Necte was told by D. Basse (an operator
from the splitting line) about the splitting line threader clamp having come off its rails. However,
Necte did not take the information seriously, even though it posed serious safety risks, and
instead focused on arranging work for his next night shift. Before calling Rob for assistance,
Necte had unsuccessfully tried to return the threader clamp onto its rails. It is also not clear if
Necte told Rob about the fact that the safety pin had not been inserted before starting to get the
clamp back onto its rails. When the accident happened, Necte did not do anything to help Rob
get out. Therefore Necte failed his duty toward his colleague’s safety and his offence qualifies to
be category 3 offence, which has a maximum penalty of $50,000.
2.3.3. Mechanical Supervisor – Joe Rite
In his statement about the accident, Rite confirmed that the slitting line threader table and
clamp had been there since he joined the company about 3 years ago and it was known to
everybody though nothing had been done about it. As a mechanical supervisor, it was an offence
for Rite to supervise correction of this problem several times without existing written procedures.
He knew very well that it was a serious safety risk for any person correcting the problem to stand
behind the pinch rolls. Rite had never instructed Rite on how to do the job, assuming that
someone else had instructed him. This was very unprofessional of Rite and therefore he failed his
duty toward his colleague’s safety and his offence qualifies to be category 3 offence, which has a
maximum penalty of $50,000.
3. Codes of practices
There are several applicable codes of practice in this accident. These codes give
guidelines on what organizations are expected to do to ensure that they comply with the relevant
During the night before the day of the accident, Necte was told by D. Basse (an operator
from the splitting line) about the splitting line threader clamp having come off its rails. However,
Necte did not take the information seriously, even though it posed serious safety risks, and
instead focused on arranging work for his next night shift. Before calling Rob for assistance,
Necte had unsuccessfully tried to return the threader clamp onto its rails. It is also not clear if
Necte told Rob about the fact that the safety pin had not been inserted before starting to get the
clamp back onto its rails. When the accident happened, Necte did not do anything to help Rob
get out. Therefore Necte failed his duty toward his colleague’s safety and his offence qualifies to
be category 3 offence, which has a maximum penalty of $50,000.
2.3.3. Mechanical Supervisor – Joe Rite
In his statement about the accident, Rite confirmed that the slitting line threader table and
clamp had been there since he joined the company about 3 years ago and it was known to
everybody though nothing had been done about it. As a mechanical supervisor, it was an offence
for Rite to supervise correction of this problem several times without existing written procedures.
He knew very well that it was a serious safety risk for any person correcting the problem to stand
behind the pinch rolls. Rite had never instructed Rite on how to do the job, assuming that
someone else had instructed him. This was very unprofessional of Rite and therefore he failed his
duty toward his colleague’s safety and his offence qualifies to be category 3 offence, which has a
maximum penalty of $50,000.
3. Codes of practices
There are several applicable codes of practice in this accident. These codes give
guidelines on what organizations are expected to do to ensure that they comply with the relevant
⊘ This is a preview!⊘
Do you want full access?
Subscribe today to unlock all pages.

Trusted by 1+ million students worldwide
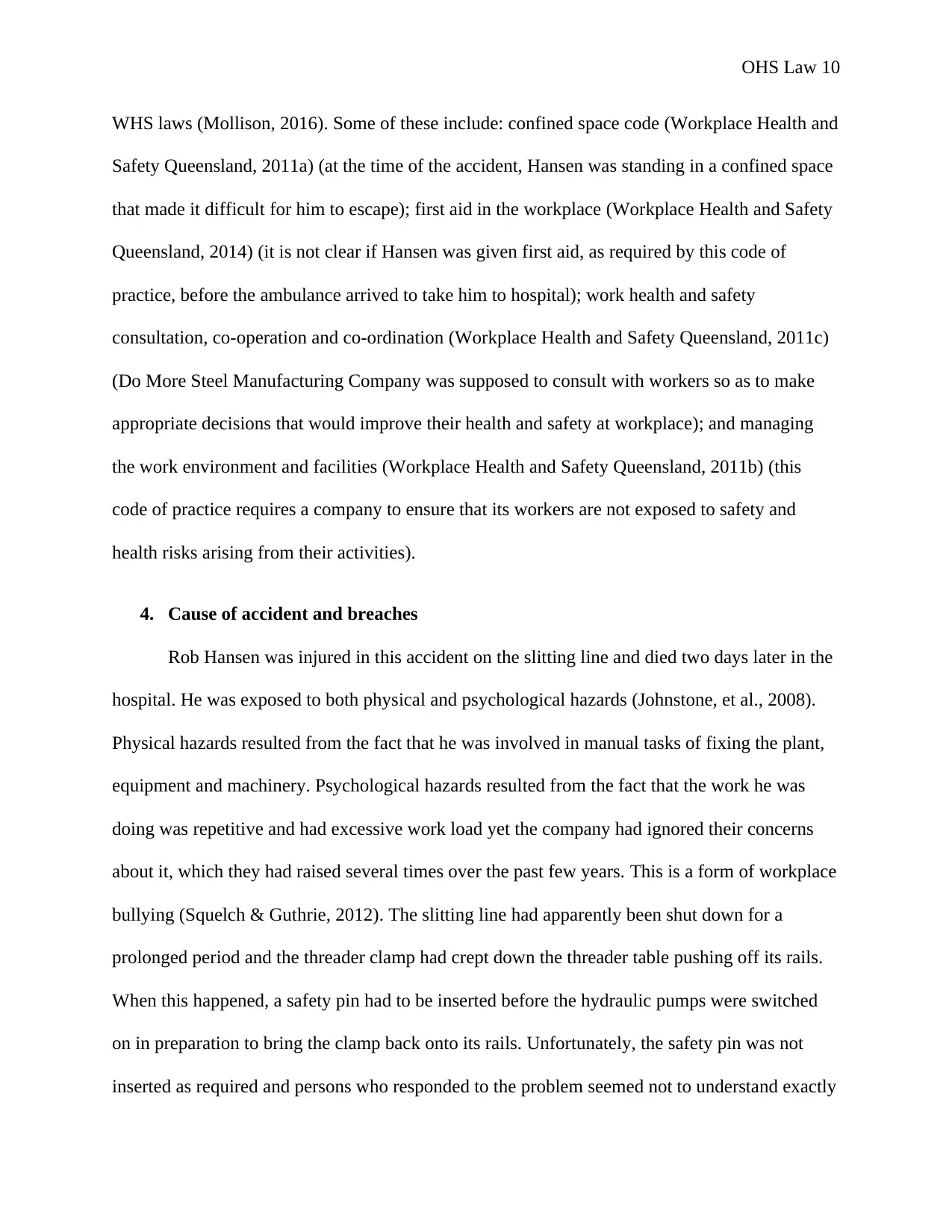
OHS Law 10
WHS laws (Mollison, 2016). Some of these include: confined space code (Workplace Health and
Safety Queensland, 2011a) (at the time of the accident, Hansen was standing in a confined space
that made it difficult for him to escape); first aid in the workplace (Workplace Health and Safety
Queensland, 2014) (it is not clear if Hansen was given first aid, as required by this code of
practice, before the ambulance arrived to take him to hospital); work health and safety
consultation, co-operation and co-ordination (Workplace Health and Safety Queensland, 2011c)
(Do More Steel Manufacturing Company was supposed to consult with workers so as to make
appropriate decisions that would improve their health and safety at workplace); and managing
the work environment and facilities (Workplace Health and Safety Queensland, 2011b) (this
code of practice requires a company to ensure that its workers are not exposed to safety and
health risks arising from their activities).
4. Cause of accident and breaches
Rob Hansen was injured in this accident on the slitting line and died two days later in the
hospital. He was exposed to both physical and psychological hazards (Johnstone, et al., 2008).
Physical hazards resulted from the fact that he was involved in manual tasks of fixing the plant,
equipment and machinery. Psychological hazards resulted from the fact that the work he was
doing was repetitive and had excessive work load yet the company had ignored their concerns
about it, which they had raised several times over the past few years. This is a form of workplace
bullying (Squelch & Guthrie, 2012). The slitting line had apparently been shut down for a
prolonged period and the threader clamp had crept down the threader table pushing off its rails.
When this happened, a safety pin had to be inserted before the hydraulic pumps were switched
on in preparation to bring the clamp back onto its rails. Unfortunately, the safety pin was not
inserted as required and persons who responded to the problem seemed not to understand exactly
WHS laws (Mollison, 2016). Some of these include: confined space code (Workplace Health and
Safety Queensland, 2011a) (at the time of the accident, Hansen was standing in a confined space
that made it difficult for him to escape); first aid in the workplace (Workplace Health and Safety
Queensland, 2014) (it is not clear if Hansen was given first aid, as required by this code of
practice, before the ambulance arrived to take him to hospital); work health and safety
consultation, co-operation and co-ordination (Workplace Health and Safety Queensland, 2011c)
(Do More Steel Manufacturing Company was supposed to consult with workers so as to make
appropriate decisions that would improve their health and safety at workplace); and managing
the work environment and facilities (Workplace Health and Safety Queensland, 2011b) (this
code of practice requires a company to ensure that its workers are not exposed to safety and
health risks arising from their activities).
4. Cause of accident and breaches
Rob Hansen was injured in this accident on the slitting line and died two days later in the
hospital. He was exposed to both physical and psychological hazards (Johnstone, et al., 2008).
Physical hazards resulted from the fact that he was involved in manual tasks of fixing the plant,
equipment and machinery. Psychological hazards resulted from the fact that the work he was
doing was repetitive and had excessive work load yet the company had ignored their concerns
about it, which they had raised several times over the past few years. This is a form of workplace
bullying (Squelch & Guthrie, 2012). The slitting line had apparently been shut down for a
prolonged period and the threader clamp had crept down the threader table pushing off its rails.
When this happened, a safety pin had to be inserted before the hydraulic pumps were switched
on in preparation to bring the clamp back onto its rails. Unfortunately, the safety pin was not
inserted as required and persons who responded to the problem seemed not to understand exactly
Paraphrase This Document
Need a fresh take? Get an instant paraphrase of this document with our AI Paraphraser
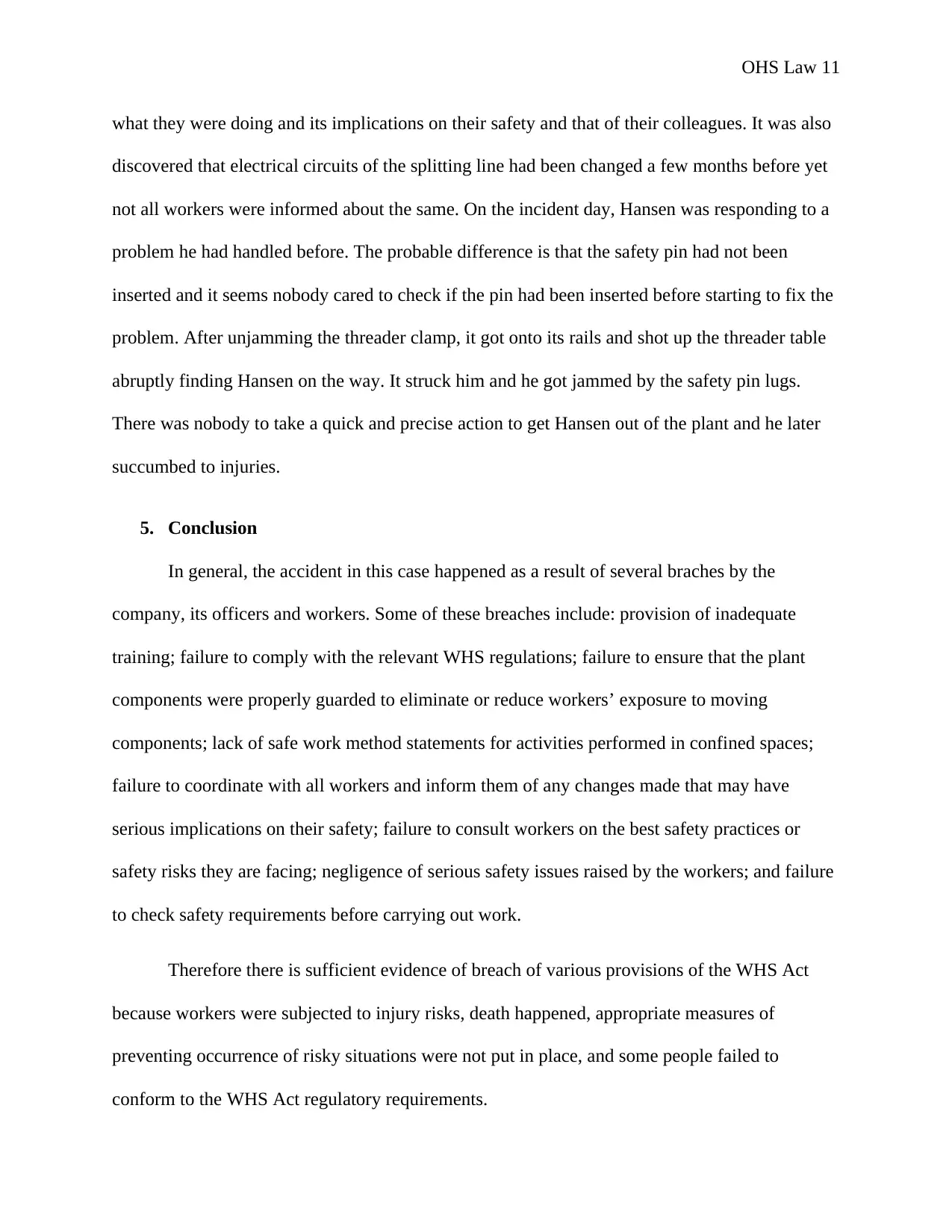
OHS Law 11
what they were doing and its implications on their safety and that of their colleagues. It was also
discovered that electrical circuits of the splitting line had been changed a few months before yet
not all workers were informed about the same. On the incident day, Hansen was responding to a
problem he had handled before. The probable difference is that the safety pin had not been
inserted and it seems nobody cared to check if the pin had been inserted before starting to fix the
problem. After unjamming the threader clamp, it got onto its rails and shot up the threader table
abruptly finding Hansen on the way. It struck him and he got jammed by the safety pin lugs.
There was nobody to take a quick and precise action to get Hansen out of the plant and he later
succumbed to injuries.
5. Conclusion
In general, the accident in this case happened as a result of several braches by the
company, its officers and workers. Some of these breaches include: provision of inadequate
training; failure to comply with the relevant WHS regulations; failure to ensure that the plant
components were properly guarded to eliminate or reduce workers’ exposure to moving
components; lack of safe work method statements for activities performed in confined spaces;
failure to coordinate with all workers and inform them of any changes made that may have
serious implications on their safety; failure to consult workers on the best safety practices or
safety risks they are facing; negligence of serious safety issues raised by the workers; and failure
to check safety requirements before carrying out work.
Therefore there is sufficient evidence of breach of various provisions of the WHS Act
because workers were subjected to injury risks, death happened, appropriate measures of
preventing occurrence of risky situations were not put in place, and some people failed to
conform to the WHS Act regulatory requirements.
what they were doing and its implications on their safety and that of their colleagues. It was also
discovered that electrical circuits of the splitting line had been changed a few months before yet
not all workers were informed about the same. On the incident day, Hansen was responding to a
problem he had handled before. The probable difference is that the safety pin had not been
inserted and it seems nobody cared to check if the pin had been inserted before starting to fix the
problem. After unjamming the threader clamp, it got onto its rails and shot up the threader table
abruptly finding Hansen on the way. It struck him and he got jammed by the safety pin lugs.
There was nobody to take a quick and precise action to get Hansen out of the plant and he later
succumbed to injuries.
5. Conclusion
In general, the accident in this case happened as a result of several braches by the
company, its officers and workers. Some of these breaches include: provision of inadequate
training; failure to comply with the relevant WHS regulations; failure to ensure that the plant
components were properly guarded to eliminate or reduce workers’ exposure to moving
components; lack of safe work method statements for activities performed in confined spaces;
failure to coordinate with all workers and inform them of any changes made that may have
serious implications on their safety; failure to consult workers on the best safety practices or
safety risks they are facing; negligence of serious safety issues raised by the workers; and failure
to check safety requirements before carrying out work.
Therefore there is sufficient evidence of breach of various provisions of the WHS Act
because workers were subjected to injury risks, death happened, appropriate measures of
preventing occurrence of risky situations were not put in place, and some people failed to
conform to the WHS Act regulatory requirements.
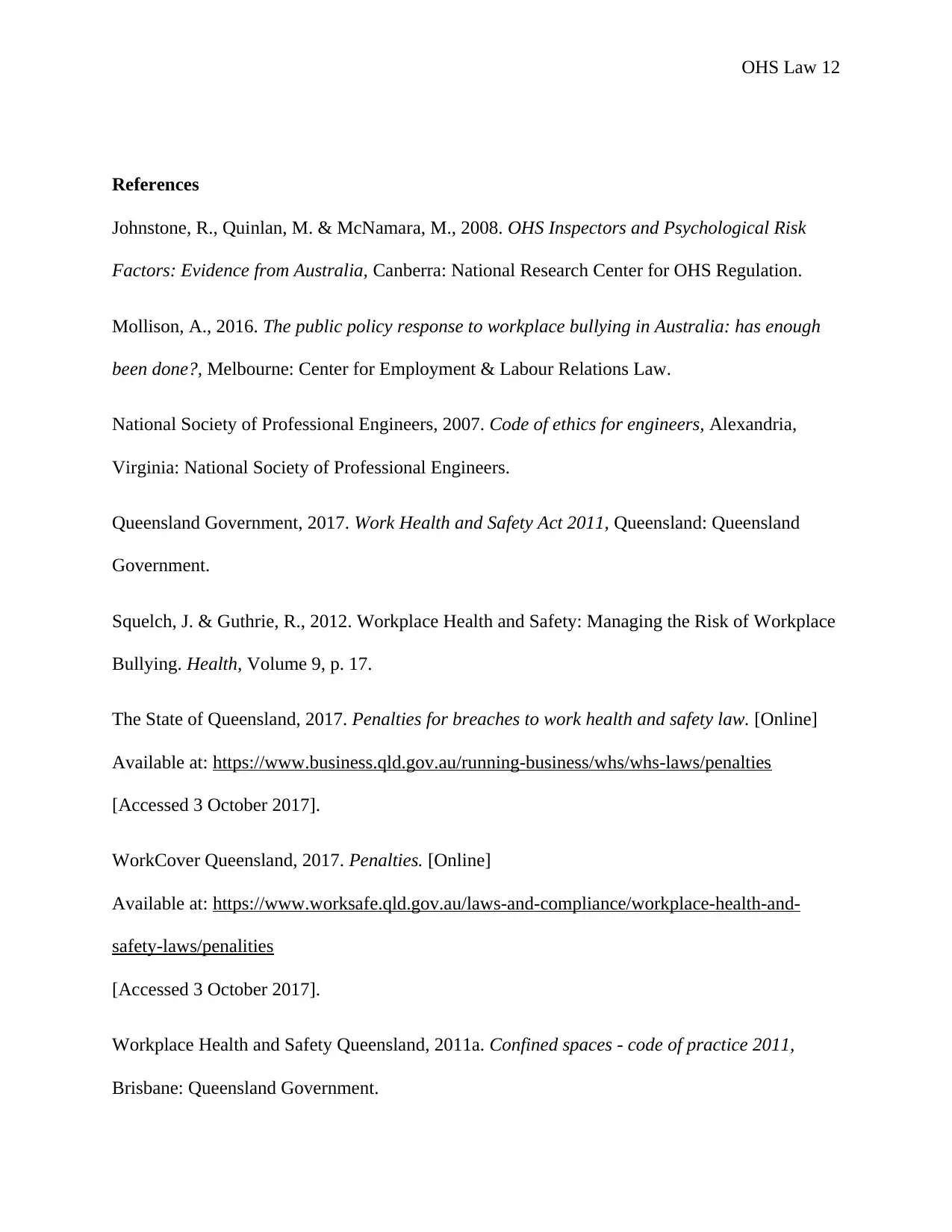
OHS Law 12
References
Johnstone, R., Quinlan, M. & McNamara, M., 2008. OHS Inspectors and Psychological Risk
Factors: Evidence from Australia, Canberra: National Research Center for OHS Regulation.
Mollison, A., 2016. The public policy response to workplace bullying in Australia: has enough
been done?, Melbourne: Center for Employment & Labour Relations Law.
National Society of Professional Engineers, 2007. Code of ethics for engineers, Alexandria,
Virginia: National Society of Professional Engineers.
Queensland Government, 2017. Work Health and Safety Act 2011, Queensland: Queensland
Government.
Squelch, J. & Guthrie, R., 2012. Workplace Health and Safety: Managing the Risk of Workplace
Bullying. Health, Volume 9, p. 17.
The State of Queensland, 2017. Penalties for breaches to work health and safety law. [Online]
Available at: https://www.business.qld.gov.au/running-business/whs/whs-laws/penalties
[Accessed 3 October 2017].
WorkCover Queensland, 2017. Penalties. [Online]
Available at: https://www.worksafe.qld.gov.au/laws-and-compliance/workplace-health-and-
safety-laws/penalities
[Accessed 3 October 2017].
Workplace Health and Safety Queensland, 2011a. Confined spaces - code of practice 2011,
Brisbane: Queensland Government.
References
Johnstone, R., Quinlan, M. & McNamara, M., 2008. OHS Inspectors and Psychological Risk
Factors: Evidence from Australia, Canberra: National Research Center for OHS Regulation.
Mollison, A., 2016. The public policy response to workplace bullying in Australia: has enough
been done?, Melbourne: Center for Employment & Labour Relations Law.
National Society of Professional Engineers, 2007. Code of ethics for engineers, Alexandria,
Virginia: National Society of Professional Engineers.
Queensland Government, 2017. Work Health and Safety Act 2011, Queensland: Queensland
Government.
Squelch, J. & Guthrie, R., 2012. Workplace Health and Safety: Managing the Risk of Workplace
Bullying. Health, Volume 9, p. 17.
The State of Queensland, 2017. Penalties for breaches to work health and safety law. [Online]
Available at: https://www.business.qld.gov.au/running-business/whs/whs-laws/penalties
[Accessed 3 October 2017].
WorkCover Queensland, 2017. Penalties. [Online]
Available at: https://www.worksafe.qld.gov.au/laws-and-compliance/workplace-health-and-
safety-laws/penalities
[Accessed 3 October 2017].
Workplace Health and Safety Queensland, 2011a. Confined spaces - code of practice 2011,
Brisbane: Queensland Government.
⊘ This is a preview!⊘
Do you want full access?
Subscribe today to unlock all pages.

Trusted by 1+ million students worldwide
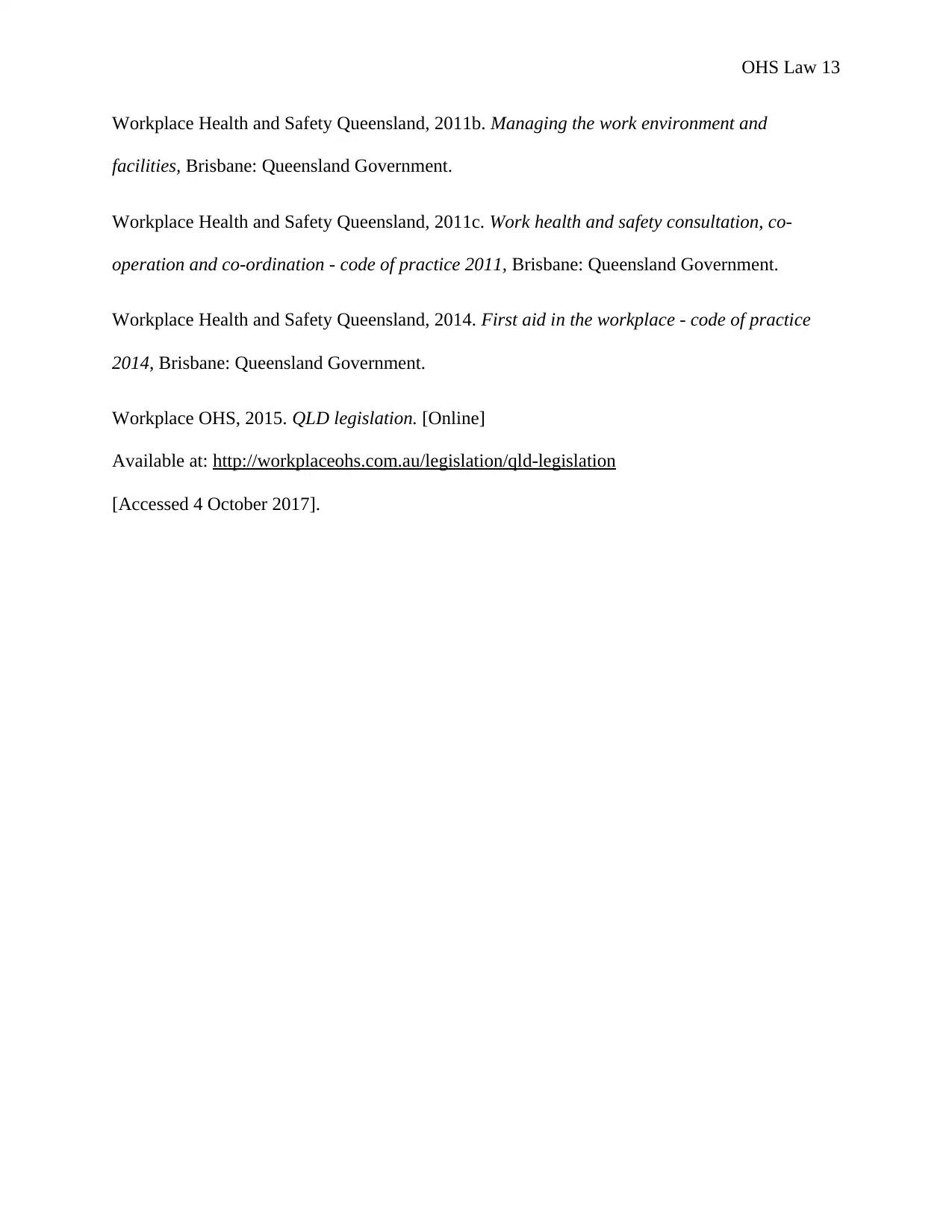
OHS Law 13
Workplace Health and Safety Queensland, 2011b. Managing the work environment and
facilities, Brisbane: Queensland Government.
Workplace Health and Safety Queensland, 2011c. Work health and safety consultation, co-
operation and co-ordination - code of practice 2011, Brisbane: Queensland Government.
Workplace Health and Safety Queensland, 2014. First aid in the workplace - code of practice
2014, Brisbane: Queensland Government.
Workplace OHS, 2015. QLD legislation. [Online]
Available at: http://workplaceohs.com.au/legislation/qld-legislation
[Accessed 4 October 2017].
Workplace Health and Safety Queensland, 2011b. Managing the work environment and
facilities, Brisbane: Queensland Government.
Workplace Health and Safety Queensland, 2011c. Work health and safety consultation, co-
operation and co-ordination - code of practice 2011, Brisbane: Queensland Government.
Workplace Health and Safety Queensland, 2014. First aid in the workplace - code of practice
2014, Brisbane: Queensland Government.
Workplace OHS, 2015. QLD legislation. [Online]
Available at: http://workplaceohs.com.au/legislation/qld-legislation
[Accessed 4 October 2017].
1 out of 13

Your All-in-One AI-Powered Toolkit for Academic Success.
+13062052269
info@desklib.com
Available 24*7 on WhatsApp / Email
Unlock your academic potential
© 2024 | Zucol Services PVT LTD | All rights reserved.