WSI Blue Mountains College: Detailed Quality Management Plan
VerifiedAdded on  2023/06/09
|10
|2081
|227
Report
AI Summary
This document presents a quality management plan for the WSI Blue Mountains College project, focusing on the construction of beauty therapy and complementary health classrooms and offices. The plan adheres to Australian standards and ISO 9001:2008 requirements, detailing the project's objectives, team roles, and quality policies. It includes procedures for cost control, document and drawing management, site instructions, and non-conformance handling. The plan also outlines audit schedules, program registers, and filing systems to ensure effective project management and quality assurance. The aim is to provide a framework for managing the project effectively, confirming responsibilities, and addressing potential issues to achieve successful project outcomes.
Contribute Materials
Your contribution can guide someone’s learning journey. Share your
documents today.
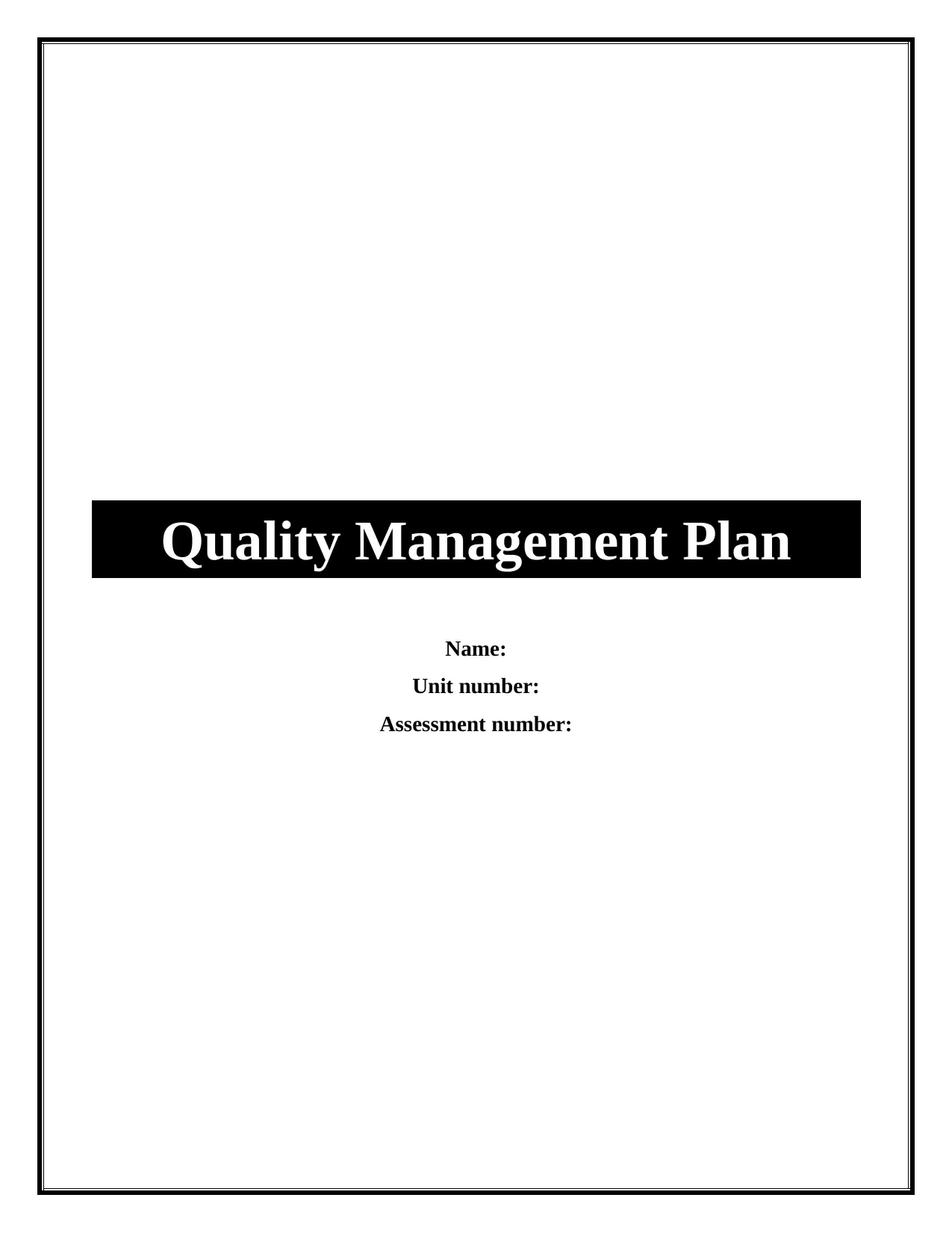
Name:
Unit number:
Assessment number:
Quality Management Plan
Unit number:
Assessment number:
Quality Management Plan
Secure Best Marks with AI Grader
Need help grading? Try our AI Grader for instant feedback on your assignments.
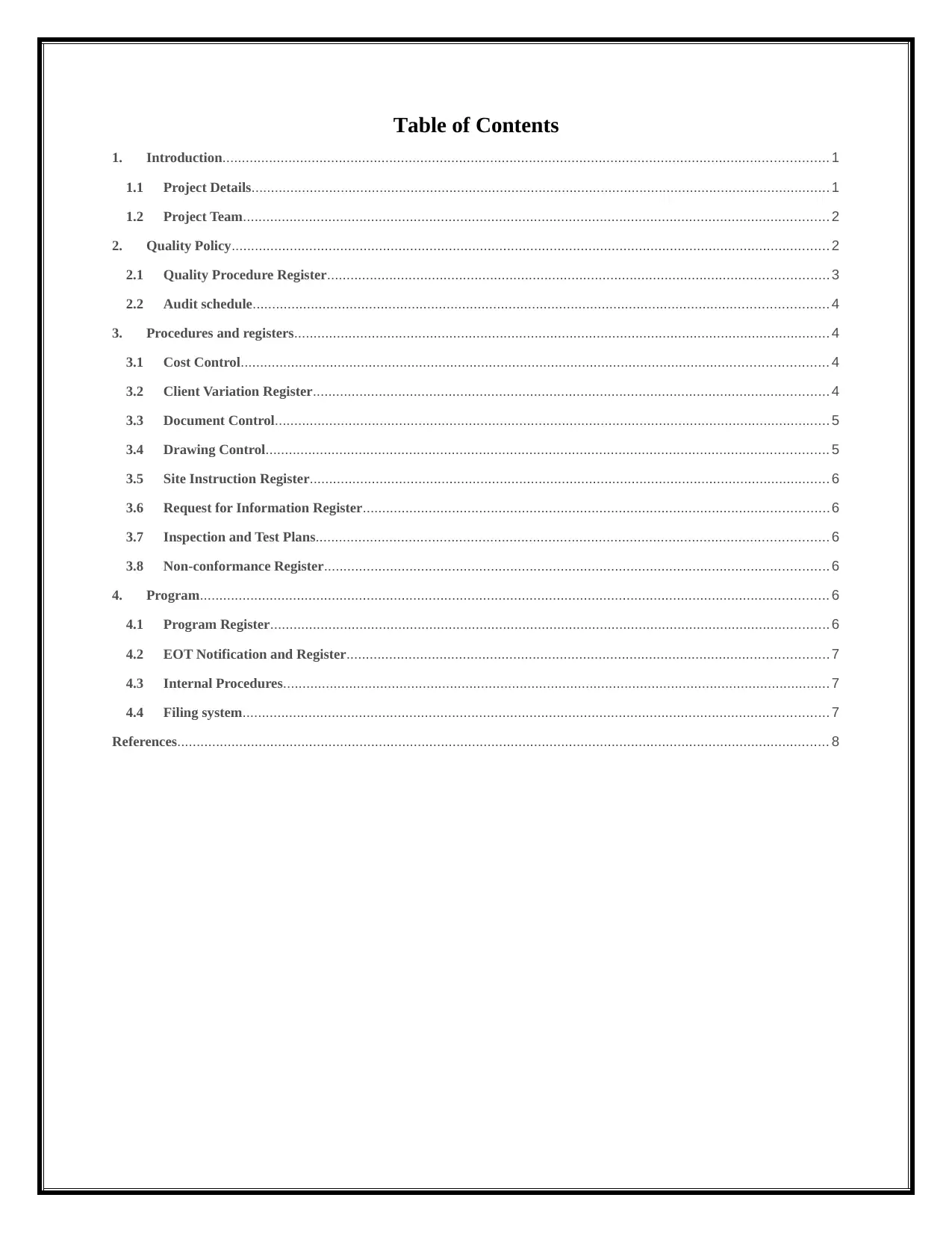
Table of Contents
1. Introduction............................................................................................................................................................ 1
1.1 Project Details..................................................................................................................................................... 1
1.2 Project Team....................................................................................................................................................... 2
2. Quality Policy.......................................................................................................................................................... 2
2.1 Quality Procedure Register................................................................................................................................. 3
2.2 Audit schedule.................................................................................................................................................... 4
3. Procedures and registers.......................................................................................................................................... 4
3.1 Cost Control....................................................................................................................................................... 4
3.2 Client Variation Register..................................................................................................................................... 4
3.3 Document Control............................................................................................................................................... 5
3.4 Drawing Control................................................................................................................................................. 5
3.5 Site Instruction Register...................................................................................................................................... 6
3.6 Request for Information Register........................................................................................................................6
3.7 Inspection and Test Plans.................................................................................................................................... 6
3.8 Non-conformance Register.................................................................................................................................. 6
4. Program.................................................................................................................................................................. 6
4.1 Program Register................................................................................................................................................ 6
4.2 EOT Notification and Register............................................................................................................................ 7
4.3 Internal Procedures............................................................................................................................................. 7
4.4 Filing system....................................................................................................................................................... 7
References........................................................................................................................................................................ 8
1. Introduction............................................................................................................................................................ 1
1.1 Project Details..................................................................................................................................................... 1
1.2 Project Team....................................................................................................................................................... 2
2. Quality Policy.......................................................................................................................................................... 2
2.1 Quality Procedure Register................................................................................................................................. 3
2.2 Audit schedule.................................................................................................................................................... 4
3. Procedures and registers.......................................................................................................................................... 4
3.1 Cost Control....................................................................................................................................................... 4
3.2 Client Variation Register..................................................................................................................................... 4
3.3 Document Control............................................................................................................................................... 5
3.4 Drawing Control................................................................................................................................................. 5
3.5 Site Instruction Register...................................................................................................................................... 6
3.6 Request for Information Register........................................................................................................................6
3.7 Inspection and Test Plans.................................................................................................................................... 6
3.8 Non-conformance Register.................................................................................................................................. 6
4. Program.................................................................................................................................................................. 6
4.1 Program Register................................................................................................................................................ 6
4.2 EOT Notification and Register............................................................................................................................ 7
4.3 Internal Procedures............................................................................................................................................. 7
4.4 Filing system....................................................................................................................................................... 7
References........................................................................................................................................................................ 8
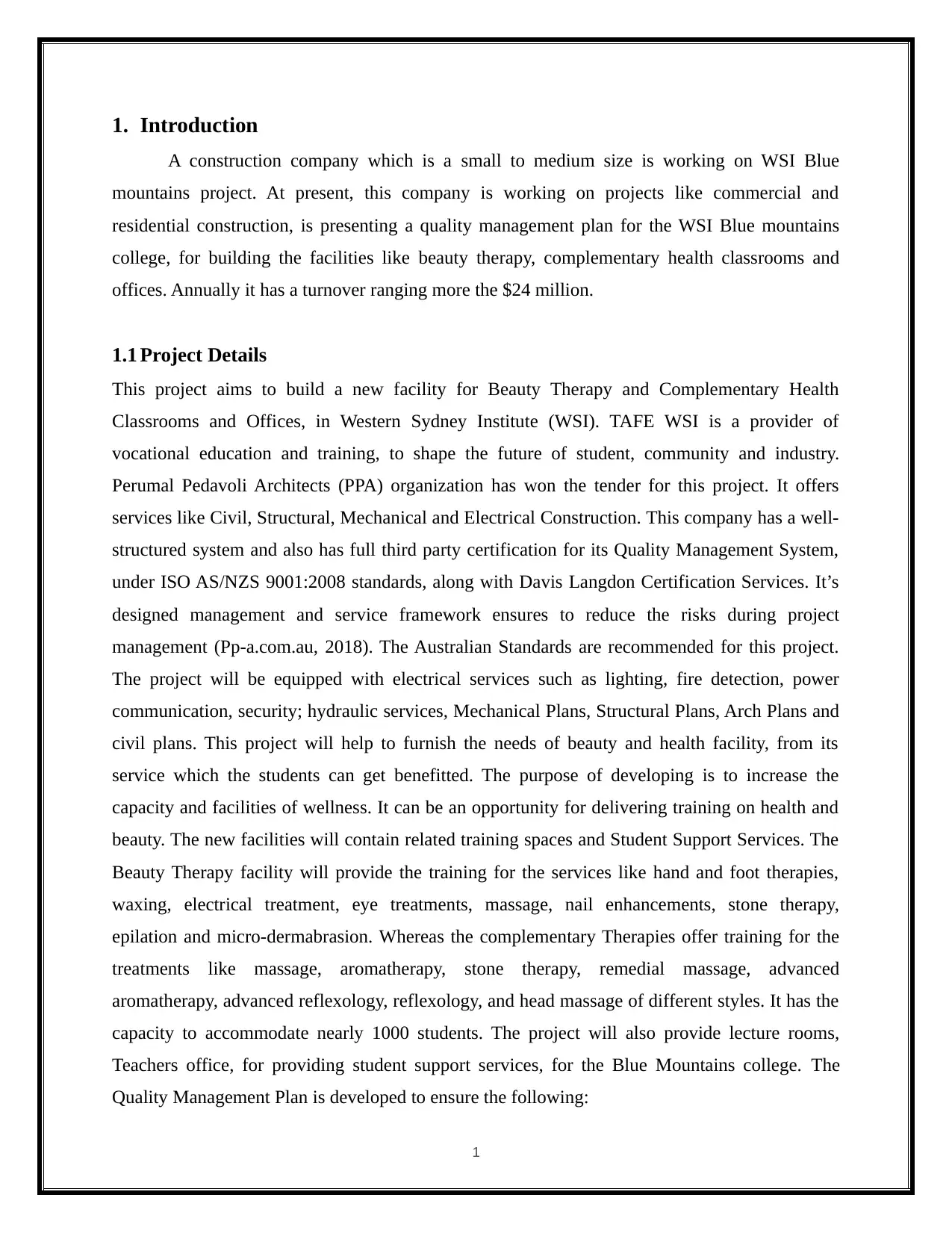
1. Introduction
A construction company which is a small to medium size is working on WSI Blue
mountains project. At present, this company is working on projects like commercial and
residential construction, is presenting a quality management plan for the WSI Blue mountains
college, for building the facilities like beauty therapy, complementary health classrooms and
offices. Annually it has a turnover ranging more the $24 million.
1.1 Project Details
This project aims to build a new facility for Beauty Therapy and Complementary Health
Classrooms and Offices, in Western Sydney Institute (WSI). TAFE WSI is a provider of
vocational education and training, to shape the future of student, community and industry.
Perumal Pedavoli Architects (PPA) organization has won the tender for this project. It offers
services like Civil, Structural, Mechanical and Electrical Construction. This company has a well-
structured system and also has full third party certification for its Quality Management System,
under ISO AS/NZS 9001:2008 standards, along with Davis Langdon Certification Services. It’s
designed management and service framework ensures to reduce the risks during project
management (Pp-a.com.au, 2018). The Australian Standards are recommended for this project.
The project will be equipped with electrical services such as lighting, fire detection, power
communication, security; hydraulic services, Mechanical Plans, Structural Plans, Arch Plans and
civil plans. This project will help to furnish the needs of beauty and health facility, from its
service which the students can get benefitted. The purpose of developing is to increase the
capacity and facilities of wellness. It can be an opportunity for delivering training on health and
beauty. The new facilities will contain related training spaces and Student Support Services. The
Beauty Therapy facility will provide the training for the services like hand and foot therapies,
waxing, electrical treatment, eye treatments, massage, nail enhancements, stone therapy,
epilation and micro-dermabrasion. Whereas the complementary Therapies offer training for the
treatments like massage, aromatherapy, stone therapy, remedial massage, advanced
aromatherapy, advanced reflexology, reflexology, and head massage of different styles. It has the
capacity to accommodate nearly 1000 students. The project will also provide lecture rooms,
Teachers office, for providing student support services, for the Blue Mountains college. The
Quality Management Plan is developed to ensure the following:
1
A construction company which is a small to medium size is working on WSI Blue
mountains project. At present, this company is working on projects like commercial and
residential construction, is presenting a quality management plan for the WSI Blue mountains
college, for building the facilities like beauty therapy, complementary health classrooms and
offices. Annually it has a turnover ranging more the $24 million.
1.1 Project Details
This project aims to build a new facility for Beauty Therapy and Complementary Health
Classrooms and Offices, in Western Sydney Institute (WSI). TAFE WSI is a provider of
vocational education and training, to shape the future of student, community and industry.
Perumal Pedavoli Architects (PPA) organization has won the tender for this project. It offers
services like Civil, Structural, Mechanical and Electrical Construction. This company has a well-
structured system and also has full third party certification for its Quality Management System,
under ISO AS/NZS 9001:2008 standards, along with Davis Langdon Certification Services. It’s
designed management and service framework ensures to reduce the risks during project
management (Pp-a.com.au, 2018). The Australian Standards are recommended for this project.
The project will be equipped with electrical services such as lighting, fire detection, power
communication, security; hydraulic services, Mechanical Plans, Structural Plans, Arch Plans and
civil plans. This project will help to furnish the needs of beauty and health facility, from its
service which the students can get benefitted. The purpose of developing is to increase the
capacity and facilities of wellness. It can be an opportunity for delivering training on health and
beauty. The new facilities will contain related training spaces and Student Support Services. The
Beauty Therapy facility will provide the training for the services like hand and foot therapies,
waxing, electrical treatment, eye treatments, massage, nail enhancements, stone therapy,
epilation and micro-dermabrasion. Whereas the complementary Therapies offer training for the
treatments like massage, aromatherapy, stone therapy, remedial massage, advanced
aromatherapy, advanced reflexology, reflexology, and head massage of different styles. It has the
capacity to accommodate nearly 1000 students. The project will also provide lecture rooms,
Teachers office, for providing student support services, for the Blue Mountains college. The
Quality Management Plan is developed to ensure the following:
1
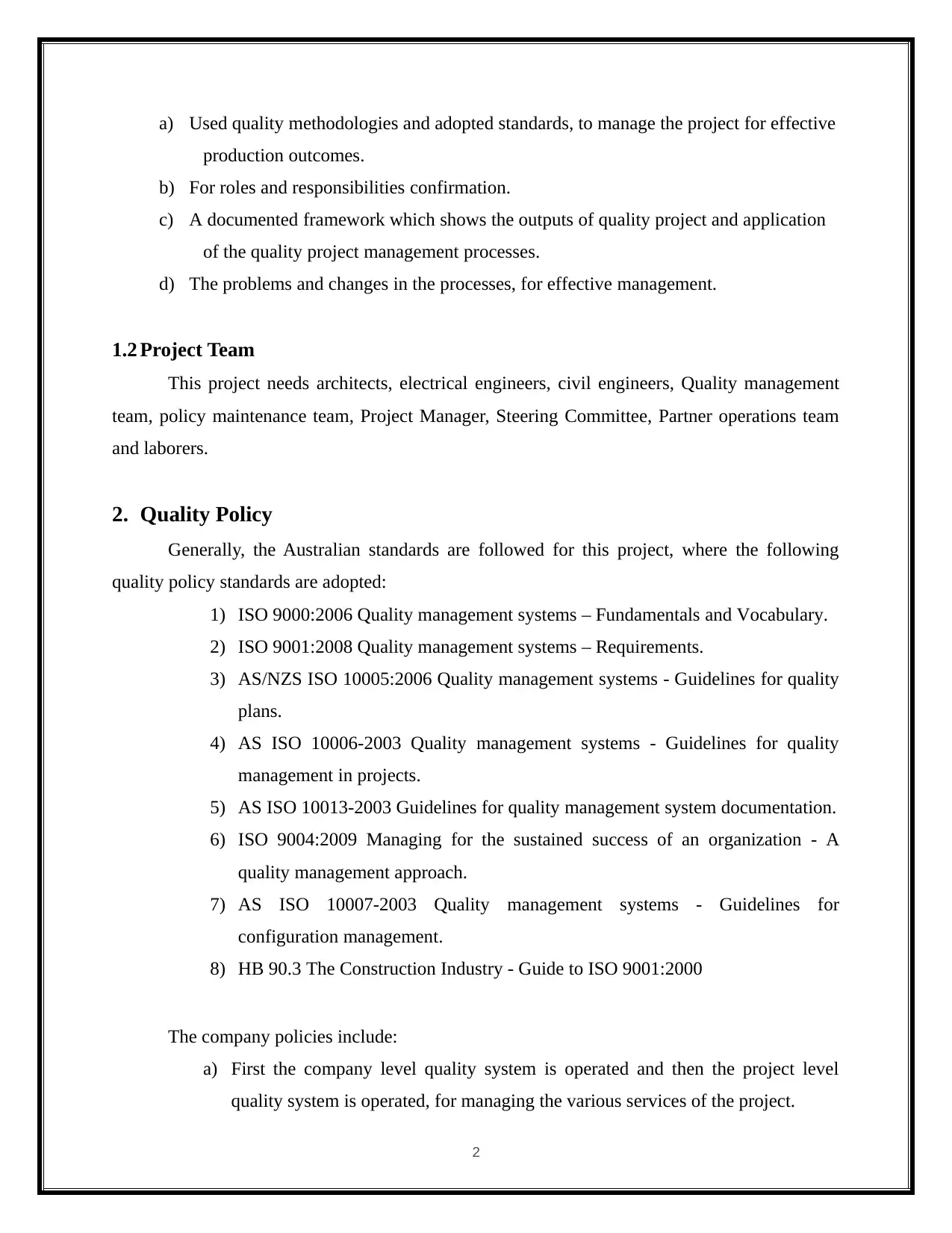
a) Used quality methodologies and adopted standards, to manage the project for effective
production outcomes.
b) For roles and responsibilities confirmation.
c) A documented framework which shows the outputs of quality project and application
of the quality project management processes.
d) The problems and changes in the processes, for effective management.
1.2 Project Team
This project needs architects, electrical engineers, civil engineers, Quality management
team, policy maintenance team, Project Manager, Steering Committee, Partner operations team
and laborers.
2. Quality Policy
Generally, the Australian standards are followed for this project, where the following
quality policy standards are adopted:
1) ISO 9000:2006 Quality management systems – Fundamentals and Vocabulary.
2) ISO 9001:2008 Quality management systems – Requirements.
3) AS/NZS ISO 10005:2006 Quality management systems - Guidelines for quality
plans.
4) AS ISO 10006-2003 Quality management systems - Guidelines for quality
management in projects.
5) AS ISO 10013-2003 Guidelines for quality management system documentation.
6) ISO 9004:2009 Managing for the sustained success of an organization - A
quality management approach.
7) AS ISO 10007-2003 Quality management systems - Guidelines for
configuration management.
8) HB 90.3 The Construction Industry - Guide to ISO 9001:2000
The company policies include:
a) First the company level quality system is operated and then the project level
quality system is operated, for managing the various services of the project.
2
production outcomes.
b) For roles and responsibilities confirmation.
c) A documented framework which shows the outputs of quality project and application
of the quality project management processes.
d) The problems and changes in the processes, for effective management.
1.2 Project Team
This project needs architects, electrical engineers, civil engineers, Quality management
team, policy maintenance team, Project Manager, Steering Committee, Partner operations team
and laborers.
2. Quality Policy
Generally, the Australian standards are followed for this project, where the following
quality policy standards are adopted:
1) ISO 9000:2006 Quality management systems – Fundamentals and Vocabulary.
2) ISO 9001:2008 Quality management systems – Requirements.
3) AS/NZS ISO 10005:2006 Quality management systems - Guidelines for quality
plans.
4) AS ISO 10006-2003 Quality management systems - Guidelines for quality
management in projects.
5) AS ISO 10013-2003 Guidelines for quality management system documentation.
6) ISO 9004:2009 Managing for the sustained success of an organization - A
quality management approach.
7) AS ISO 10007-2003 Quality management systems - Guidelines for
configuration management.
8) HB 90.3 The Construction Industry - Guide to ISO 9001:2000
The company policies include:
a) First the company level quality system is operated and then the project level
quality system is operated, for managing the various services of the project.
2
Secure Best Marks with AI Grader
Need help grading? Try our AI Grader for instant feedback on your assignments.
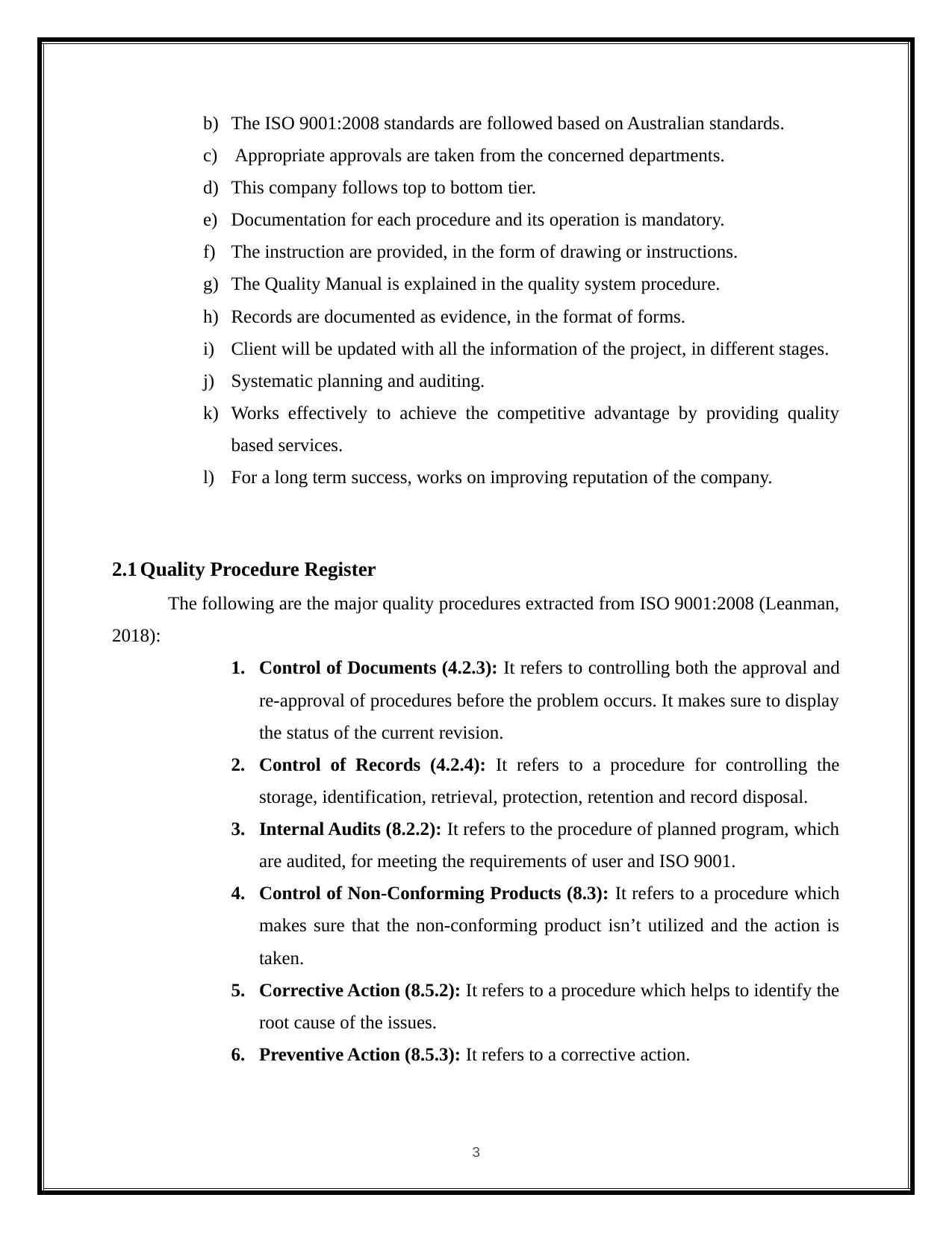
b) The ISO 9001:2008 standards are followed based on Australian standards.
c) Appropriate approvals are taken from the concerned departments.
d) This company follows top to bottom tier.
e) Documentation for each procedure and its operation is mandatory.
f) The instruction are provided, in the form of drawing or instructions.
g) The Quality Manual is explained in the quality system procedure.
h) Records are documented as evidence, in the format of forms.
i) Client will be updated with all the information of the project, in different stages.
j) Systematic planning and auditing.
k) Works effectively to achieve the competitive advantage by providing quality
based services.
l) For a long term success, works on improving reputation of the company.
2.1 Quality Procedure Register
The following are the major quality procedures extracted from ISO 9001:2008 (Leanman,
2018):
1. Control of Documents (4.2.3): It refers to controlling both the approval and
re-approval of procedures before the problem occurs. It makes sure to display
the status of the current revision.
2. Control of Records (4.2.4): It refers to a procedure for controlling the
storage, identification, retrieval, protection, retention and record disposal.
3. Internal Audits (8.2.2): It refers to the procedure of planned program, which
are audited, for meeting the requirements of user and ISO 9001.
4. Control of Non-Conforming Products (8.3): It refers to a procedure which
makes sure that the non-conforming product isn’t utilized and the action is
taken.
5. Corrective Action (8.5.2): It refers to a procedure which helps to identify the
root cause of the issues.
6. Preventive Action (8.5.3): It refers to a corrective action.
3
c) Appropriate approvals are taken from the concerned departments.
d) This company follows top to bottom tier.
e) Documentation for each procedure and its operation is mandatory.
f) The instruction are provided, in the form of drawing or instructions.
g) The Quality Manual is explained in the quality system procedure.
h) Records are documented as evidence, in the format of forms.
i) Client will be updated with all the information of the project, in different stages.
j) Systematic planning and auditing.
k) Works effectively to achieve the competitive advantage by providing quality
based services.
l) For a long term success, works on improving reputation of the company.
2.1 Quality Procedure Register
The following are the major quality procedures extracted from ISO 9001:2008 (Leanman,
2018):
1. Control of Documents (4.2.3): It refers to controlling both the approval and
re-approval of procedures before the problem occurs. It makes sure to display
the status of the current revision.
2. Control of Records (4.2.4): It refers to a procedure for controlling the
storage, identification, retrieval, protection, retention and record disposal.
3. Internal Audits (8.2.2): It refers to the procedure of planned program, which
are audited, for meeting the requirements of user and ISO 9001.
4. Control of Non-Conforming Products (8.3): It refers to a procedure which
makes sure that the non-conforming product isn’t utilized and the action is
taken.
5. Corrective Action (8.5.2): It refers to a procedure which helps to identify the
root cause of the issues.
6. Preventive Action (8.5.3): It refers to a corrective action.
3
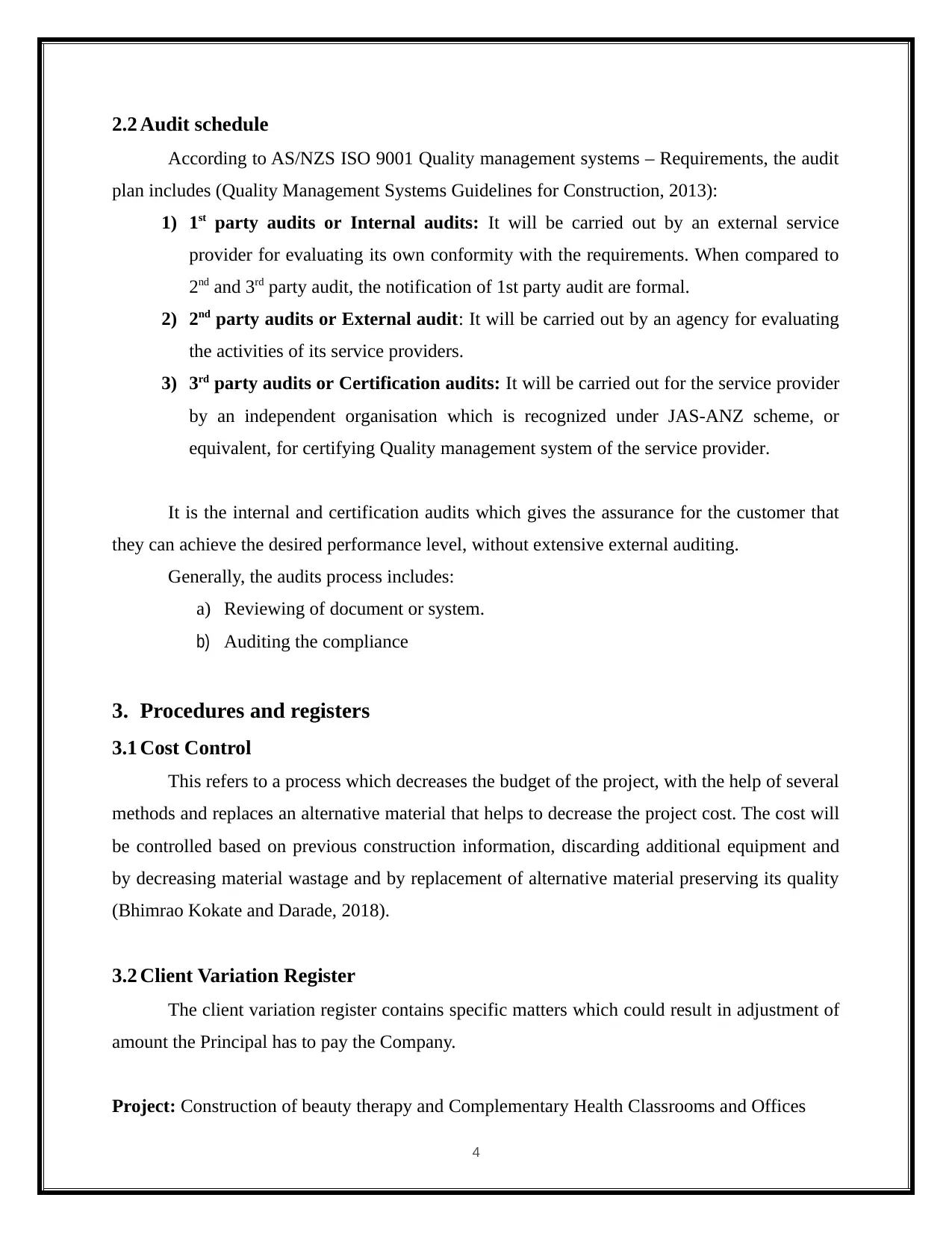
2.2 Audit schedule
According to AS/NZS ISO 9001 Quality management systems – Requirements, the audit
plan includes (Quality Management Systems Guidelines for Construction, 2013):
1) 1st party audits or Internal audits: It will be carried out by an external service
provider for evaluating its own conformity with the requirements. When compared to
2nd and 3rd party audit, the notification of 1st party audit are formal.
2) 2nd party audits or External audit: It will be carried out by an agency for evaluating
the activities of its service providers.
3) 3rd party audits or Certification audits: It will be carried out for the service provider
by an independent organisation which is recognized under JAS-ANZ scheme, or
equivalent, for certifying Quality management system of the service provider.
It is the internal and certification audits which gives the assurance for the customer that
they can achieve the desired performance level, without extensive external auditing.
Generally, the audits process includes:
a) Reviewing of document or system.
b) Auditing the compliance
3. Procedures and registers
3.1 Cost Control
This refers to a process which decreases the budget of the project, with the help of several
methods and replaces an alternative material that helps to decrease the project cost. The cost will
be controlled based on previous construction information, discarding additional equipment and
by decreasing material wastage and by replacement of alternative material preserving its quality
(Bhimrao Kokate and Darade, 2018).
3.2 Client Variation Register
The client variation register contains specific matters which could result in adjustment of
amount the Principal has to pay the Company.
Project: Construction of beauty therapy and Complementary Health Classrooms and Offices
4
According to AS/NZS ISO 9001 Quality management systems – Requirements, the audit
plan includes (Quality Management Systems Guidelines for Construction, 2013):
1) 1st party audits or Internal audits: It will be carried out by an external service
provider for evaluating its own conformity with the requirements. When compared to
2nd and 3rd party audit, the notification of 1st party audit are formal.
2) 2nd party audits or External audit: It will be carried out by an agency for evaluating
the activities of its service providers.
3) 3rd party audits or Certification audits: It will be carried out for the service provider
by an independent organisation which is recognized under JAS-ANZ scheme, or
equivalent, for certifying Quality management system of the service provider.
It is the internal and certification audits which gives the assurance for the customer that
they can achieve the desired performance level, without extensive external auditing.
Generally, the audits process includes:
a) Reviewing of document or system.
b) Auditing the compliance
3. Procedures and registers
3.1 Cost Control
This refers to a process which decreases the budget of the project, with the help of several
methods and replaces an alternative material that helps to decrease the project cost. The cost will
be controlled based on previous construction information, discarding additional equipment and
by decreasing material wastage and by replacement of alternative material preserving its quality
(Bhimrao Kokate and Darade, 2018).
3.2 Client Variation Register
The client variation register contains specific matters which could result in adjustment of
amount the Principal has to pay the Company.
Project: Construction of beauty therapy and Complementary Health Classrooms and Offices
4
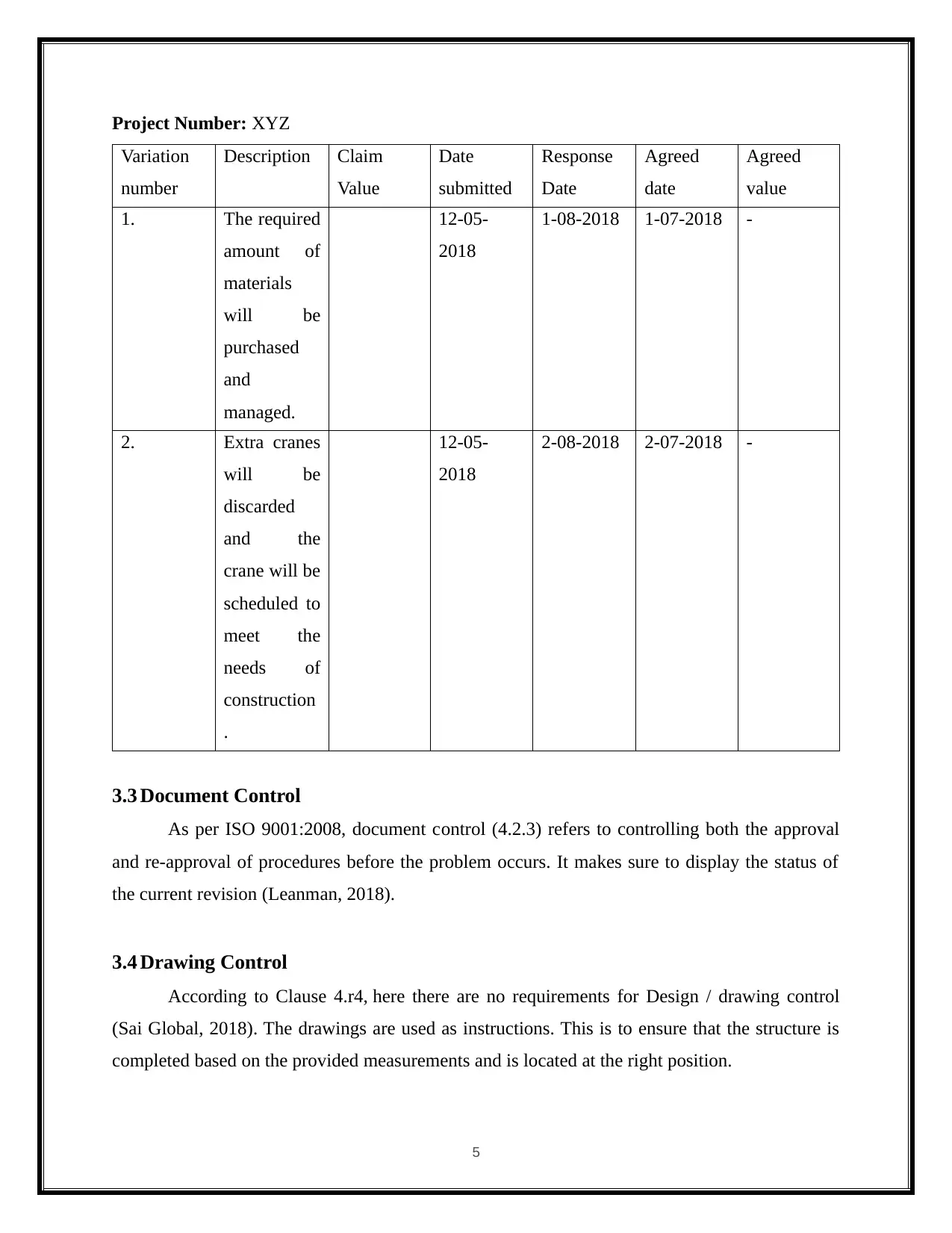
Project Number: XYZ
Variation
number
Description Claim
Value
Date
submitted
Response
Date
Agreed
date
Agreed
value
1. The required
amount of
materials
will be
purchased
and
managed.
12-05-
2018
1-08-2018 1-07-2018 -
2. Extra cranes
will be
discarded
and the
crane will be
scheduled to
meet the
needs of
construction
.
12-05-
2018
2-08-2018 2-07-2018 -
3.3 Document Control
As per ISO 9001:2008, document control (4.2.3) refers to controlling both the approval
and re-approval of procedures before the problem occurs. It makes sure to display the status of
the current revision (Leanman, 2018).
3.4 Drawing Control
According to Clause 4.r4, here there are no requirements for Design / drawing control
(Sai Global, 2018). The drawings are used as instructions. This is to ensure that the structure is
completed based on the provided measurements and is located at the right position.
5
Variation
number
Description Claim
Value
Date
submitted
Response
Date
Agreed
date
Agreed
value
1. The required
amount of
materials
will be
purchased
and
managed.
12-05-
2018
1-08-2018 1-07-2018 -
2. Extra cranes
will be
discarded
and the
crane will be
scheduled to
meet the
needs of
construction
.
12-05-
2018
2-08-2018 2-07-2018 -
3.3 Document Control
As per ISO 9001:2008, document control (4.2.3) refers to controlling both the approval
and re-approval of procedures before the problem occurs. It makes sure to display the status of
the current revision (Leanman, 2018).
3.4 Drawing Control
According to Clause 4.r4, here there are no requirements for Design / drawing control
(Sai Global, 2018). The drawings are used as instructions. This is to ensure that the structure is
completed based on the provided measurements and is located at the right position.
5
Paraphrase This Document
Need a fresh take? Get an instant paraphrase of this document with our AI Paraphraser

3.5 Site Instruction Register
The site instruction register helps to keep track of all the site instructions, which are
raised for the project. The head contractor sets the directives for the contractors who are
currently working on a project.
3.6 Request for Information Register
The required information is collected from the suppliers, for shortlisting potential
suppliers. This helps to compare the businesses which offer the required products ad services that
are needed to complete the project.
3.7 Inspection and Test Plans
Based on ISO standards, an effective plan will be designed to test the designed plan. The
following will be carried out:
1) monitoring
2) Measurement
3) analysis
4) evaluation
5) Internal audit
6) Management review
3.8 Non-conformance Register
It refers to a procedure which makes sure that the non-conforming product isn’t utilized
and the action is taken. The quality audit team maintains non-conformance report. Project Design
Form and Compliance Checklist; and Project Construction Form and Compliance Checklist help
to find non-conformance in the project.
4. Program
4.1 Program Register
The details of the project and the workflow will be registered.
6
The site instruction register helps to keep track of all the site instructions, which are
raised for the project. The head contractor sets the directives for the contractors who are
currently working on a project.
3.6 Request for Information Register
The required information is collected from the suppliers, for shortlisting potential
suppliers. This helps to compare the businesses which offer the required products ad services that
are needed to complete the project.
3.7 Inspection and Test Plans
Based on ISO standards, an effective plan will be designed to test the designed plan. The
following will be carried out:
1) monitoring
2) Measurement
3) analysis
4) evaluation
5) Internal audit
6) Management review
3.8 Non-conformance Register
It refers to a procedure which makes sure that the non-conforming product isn’t utilized
and the action is taken. The quality audit team maintains non-conformance report. Project Design
Form and Compliance Checklist; and Project Construction Form and Compliance Checklist help
to find non-conformance in the project.
4. Program
4.1 Program Register
The details of the project and the workflow will be registered.
6
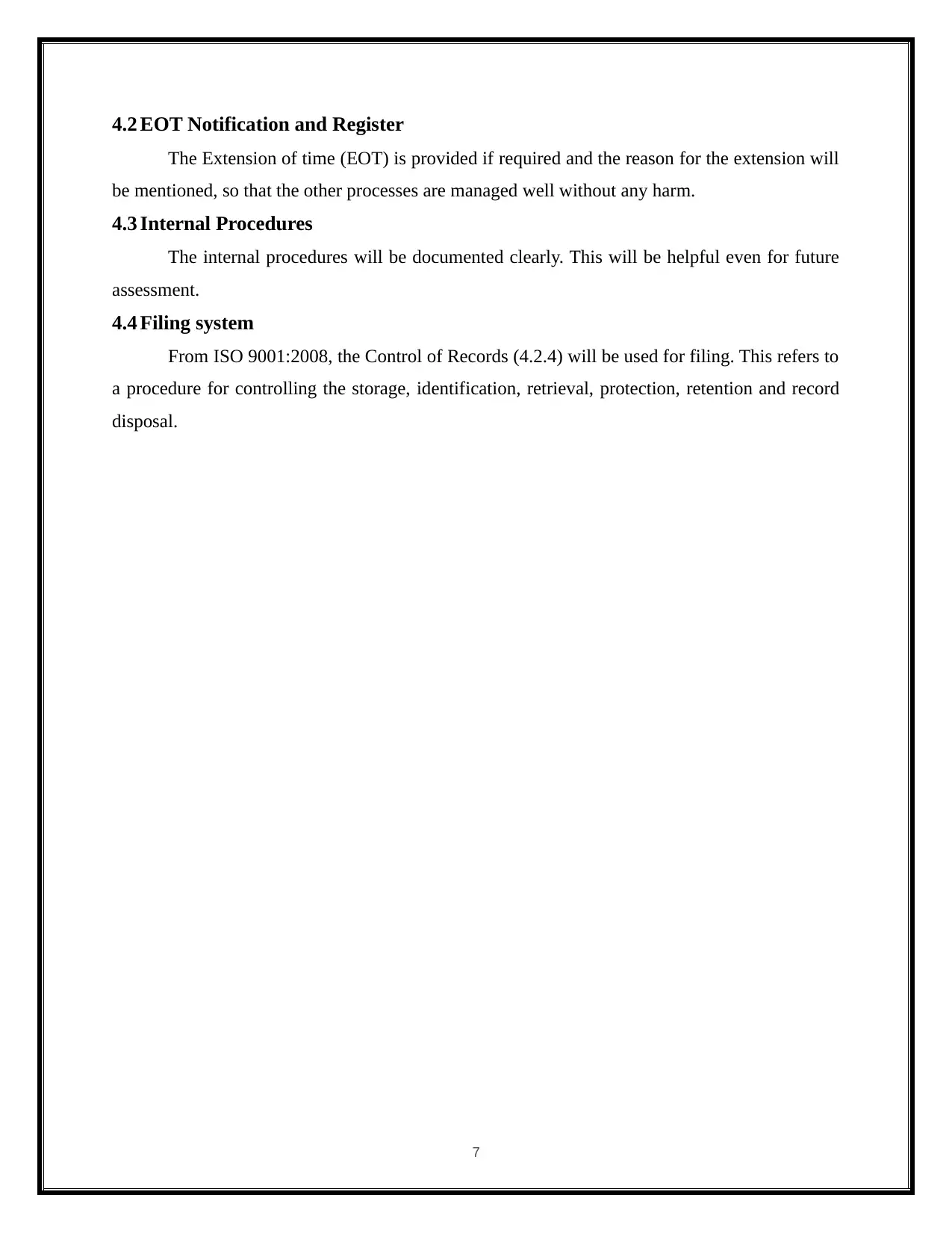
4.2 EOT Notification and Register
The Extension of time (EOT) is provided if required and the reason for the extension will
be mentioned, so that the other processes are managed well without any harm.
4.3 Internal Procedures
The internal procedures will be documented clearly. This will be helpful even for future
assessment.
4.4 Filing system
From ISO 9001:2008, the Control of Records (4.2.4) will be used for filing. This refers to
a procedure for controlling the storage, identification, retrieval, protection, retention and record
disposal.
7
The Extension of time (EOT) is provided if required and the reason for the extension will
be mentioned, so that the other processes are managed well without any harm.
4.3 Internal Procedures
The internal procedures will be documented clearly. This will be helpful even for future
assessment.
4.4 Filing system
From ISO 9001:2008, the Control of Records (4.2.4) will be used for filing. This refers to
a procedure for controlling the storage, identification, retrieval, protection, retention and record
disposal.
7
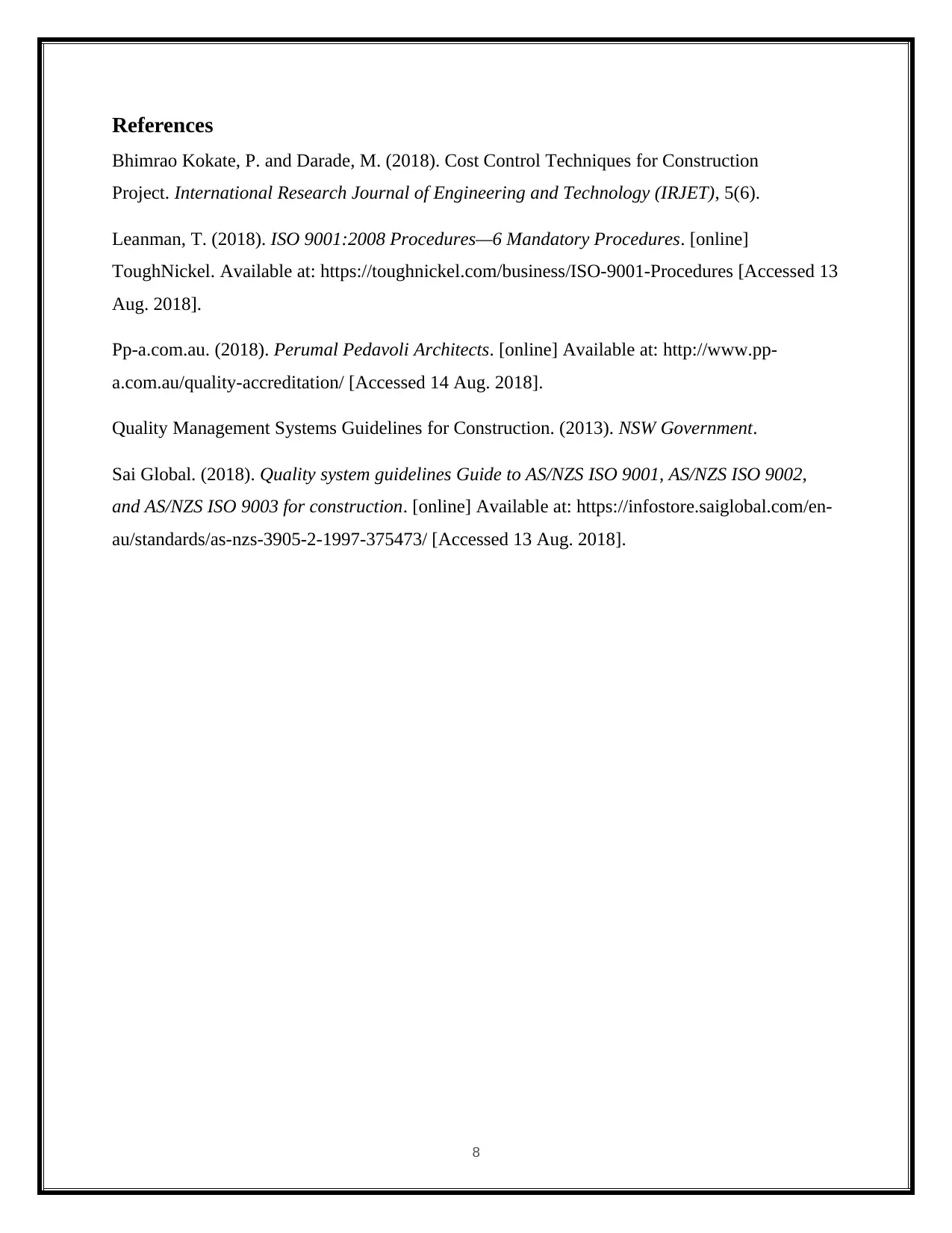
References
Bhimrao Kokate, P. and Darade, M. (2018). Cost Control Techniques for Construction
Project. International Research Journal of Engineering and Technology (IRJET), 5(6).
Leanman, T. (2018). ISO 9001:2008 Procedures—6 Mandatory Procedures. [online]
ToughNickel. Available at: https://toughnickel.com/business/ISO-9001-Procedures [Accessed 13
Aug. 2018].
Pp-a.com.au. (2018). Perumal Pedavoli Architects. [online] Available at: http://www.pp-
a.com.au/quality-accreditation/ [Accessed 14 Aug. 2018].
Quality Management Systems Guidelines for Construction. (2013). NSW Government.
Sai Global. (2018). Quality system guidelines Guide to AS/NZS ISO 9001, AS/NZS ISO 9002,
and AS/NZS ISO 9003 for construction. [online] Available at: https://infostore.saiglobal.com/en-
au/standards/as-nzs-3905-2-1997-375473/ [Accessed 13 Aug. 2018].
8
Bhimrao Kokate, P. and Darade, M. (2018). Cost Control Techniques for Construction
Project. International Research Journal of Engineering and Technology (IRJET), 5(6).
Leanman, T. (2018). ISO 9001:2008 Procedures—6 Mandatory Procedures. [online]
ToughNickel. Available at: https://toughnickel.com/business/ISO-9001-Procedures [Accessed 13
Aug. 2018].
Pp-a.com.au. (2018). Perumal Pedavoli Architects. [online] Available at: http://www.pp-
a.com.au/quality-accreditation/ [Accessed 14 Aug. 2018].
Quality Management Systems Guidelines for Construction. (2013). NSW Government.
Sai Global. (2018). Quality system guidelines Guide to AS/NZS ISO 9001, AS/NZS ISO 9002,
and AS/NZS ISO 9003 for construction. [online] Available at: https://infostore.saiglobal.com/en-
au/standards/as-nzs-3905-2-1997-375473/ [Accessed 13 Aug. 2018].
8
1 out of 10
Related Documents

Your All-in-One AI-Powered Toolkit for Academic Success.
 +13062052269
info@desklib.com
Available 24*7 on WhatsApp / Email
Unlock your academic potential
© 2024  |  Zucol Services PVT LTD  |  All rights reserved.