Safety in Work Place
VerifiedAdded on 2023/04/22
|8
|1867
|62
AI Summary
This document provides a hazard identification checklist for the automotive service and repair industry. It helps identify potential health and safety problems in the workplace and provides guidance on making necessary changes. The checklist covers manual tasks, machinery and equipment, chemicals, slips, trips and falls, noise, electrical, first aid, fire and emergency procedures, lighting, and hand tools.
Contribute Materials
Your contribution can guide someone’s learning journey. Share your
documents today.
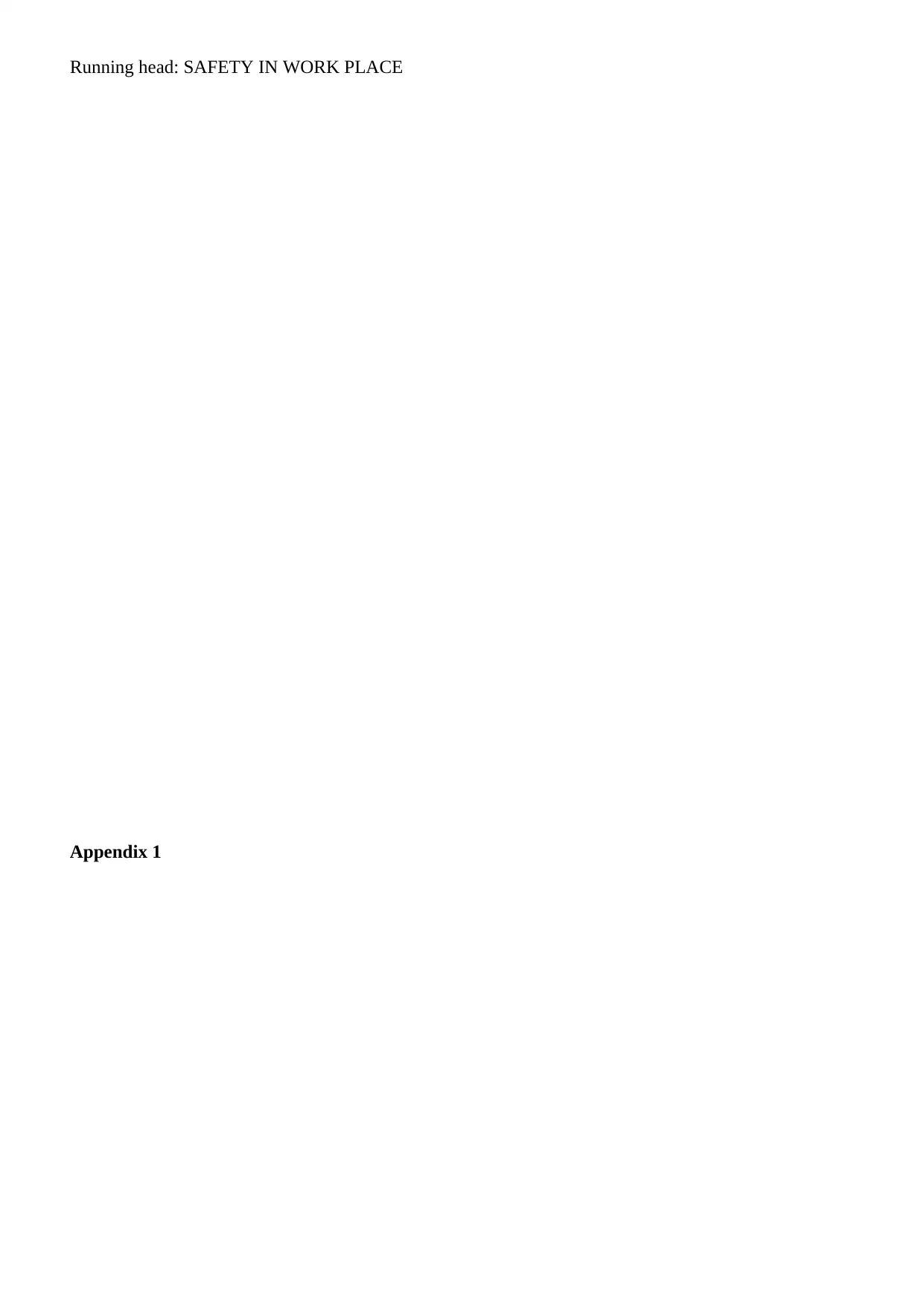
Running head: SAFETY IN WORK PLACE
Appendix 1
Appendix 1
Secure Best Marks with AI Grader
Need help grading? Try our AI Grader for instant feedback on your assignments.
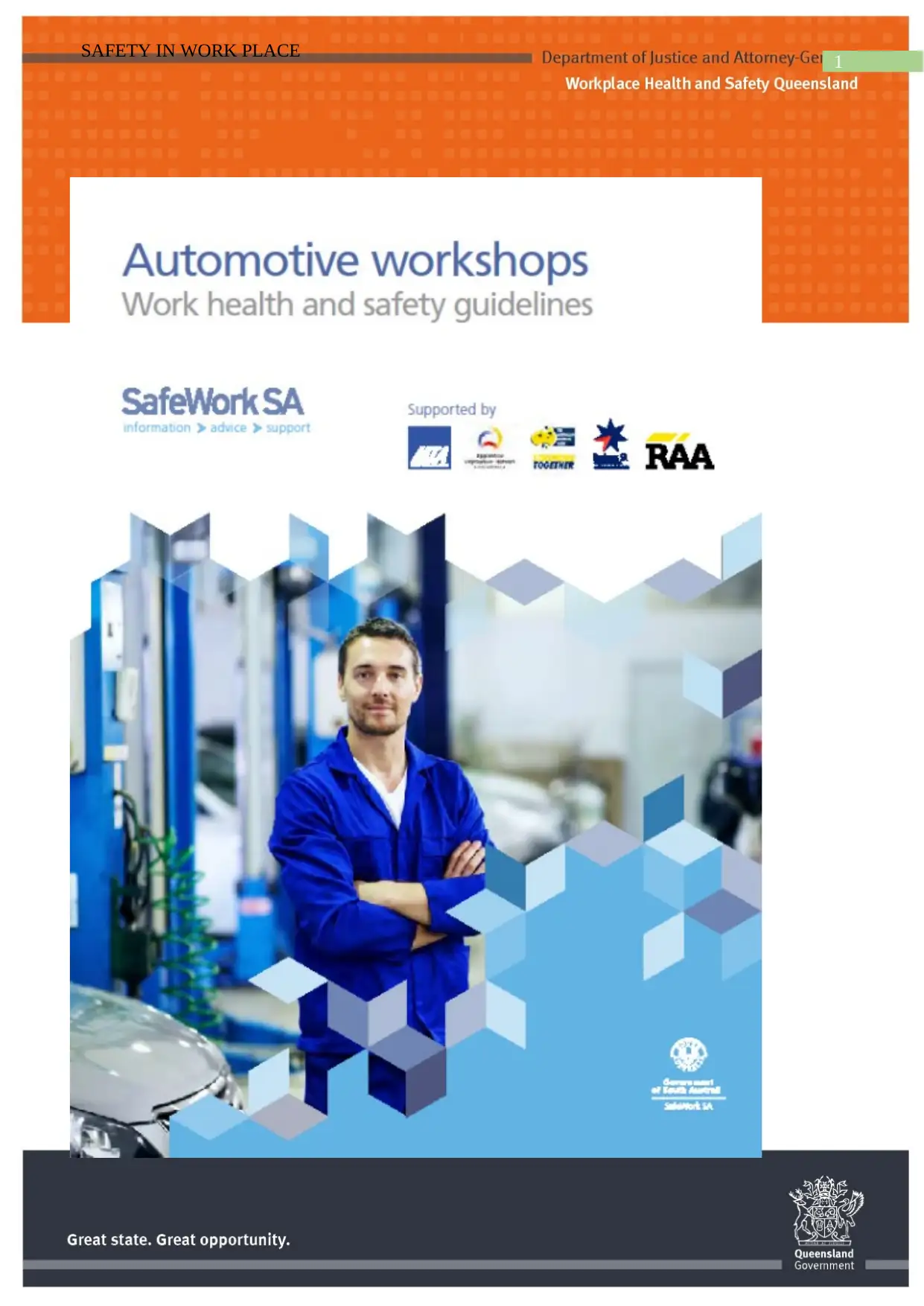
1
SAFETY IN WORK PLACE
SAFETY IN WORK PLACE
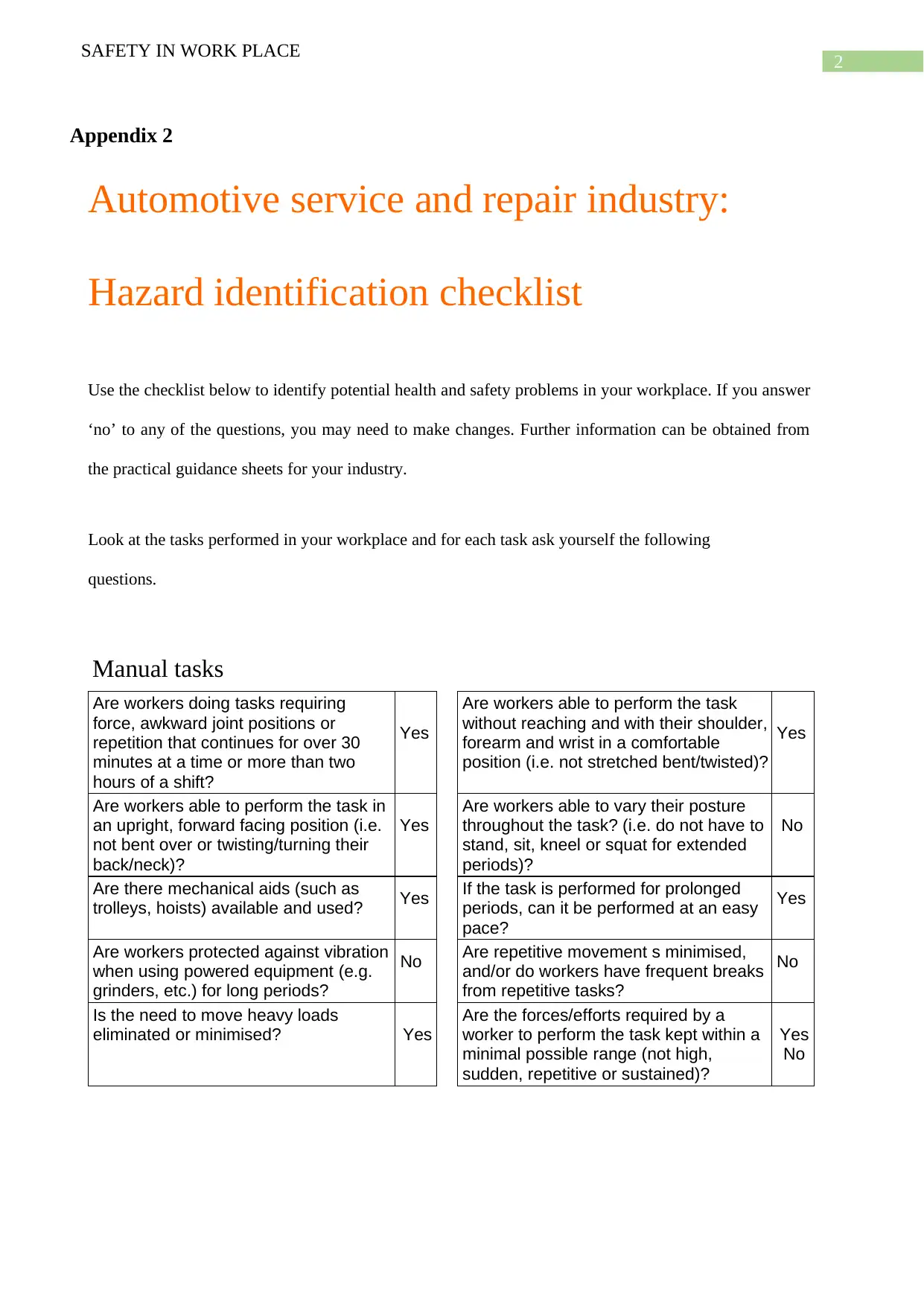
2
SAFETY IN WORK PLACE
Appendix 2
Automotive service and repair industry:
Hazard identification checklist
Use the checklist below to identify potential health and safety problems in your workplace. If you answer
‘no’ to any of the questions, you may need to make changes. Further information can be obtained from
the practical guidance sheets for your industry.
Look at the tasks performed in your workplace and for each task ask yourself the following
questions.
Manual tasks
Are workers doing tasks requiring
force, awkward joint positions or
repetition that continues for over 30
minutes at a time or more than two
hours of a shift?
Yes
Are workers able to perform the task in
an upright, forward facing position (i.e.
not bent over or twisting/turning their
back/neck)?
Yes
Are there mechanical aids (such as
trolleys, hoists) available and used? Yes
Are workers protected against vibration
when using powered equipment (e.g.
grinders, etc.) for long periods?
No
Is the need to move heavy loads
eliminated or minimised? Yes
Are workers able to perform the task
without reaching and with their shoulder,
forearm and wrist in a comfortable
position (i.e. not stretched bent/twisted)?
Yes
Are workers able to vary their posture
throughout the task? (i.e. do not have to
stand, sit, kneel or squat for extended
periods)?
No
If the task is performed for prolonged
periods, can it be performed at an easy
pace?
Yes
Are repetitive movement s minimised,
and/or do workers have frequent breaks
from repetitive tasks?
No
Are the forces/efforts required by a
worker to perform the task kept within a
minimal possible range (not high,
sudden, repetitive or sustained)?
Yes
No
SAFETY IN WORK PLACE
Appendix 2
Automotive service and repair industry:
Hazard identification checklist
Use the checklist below to identify potential health and safety problems in your workplace. If you answer
‘no’ to any of the questions, you may need to make changes. Further information can be obtained from
the practical guidance sheets for your industry.
Look at the tasks performed in your workplace and for each task ask yourself the following
questions.
Manual tasks
Are workers doing tasks requiring
force, awkward joint positions or
repetition that continues for over 30
minutes at a time or more than two
hours of a shift?
Yes
Are workers able to perform the task in
an upright, forward facing position (i.e.
not bent over or twisting/turning their
back/neck)?
Yes
Are there mechanical aids (such as
trolleys, hoists) available and used? Yes
Are workers protected against vibration
when using powered equipment (e.g.
grinders, etc.) for long periods?
No
Is the need to move heavy loads
eliminated or minimised? Yes
Are workers able to perform the task
without reaching and with their shoulder,
forearm and wrist in a comfortable
position (i.e. not stretched bent/twisted)?
Yes
Are workers able to vary their posture
throughout the task? (i.e. do not have to
stand, sit, kneel or squat for extended
periods)?
No
If the task is performed for prolonged
periods, can it be performed at an easy
pace?
Yes
Are repetitive movement s minimised,
and/or do workers have frequent breaks
from repetitive tasks?
No
Are the forces/efforts required by a
worker to perform the task kept within a
minimal possible range (not high,
sudden, repetitive or sustained)?
Yes
No
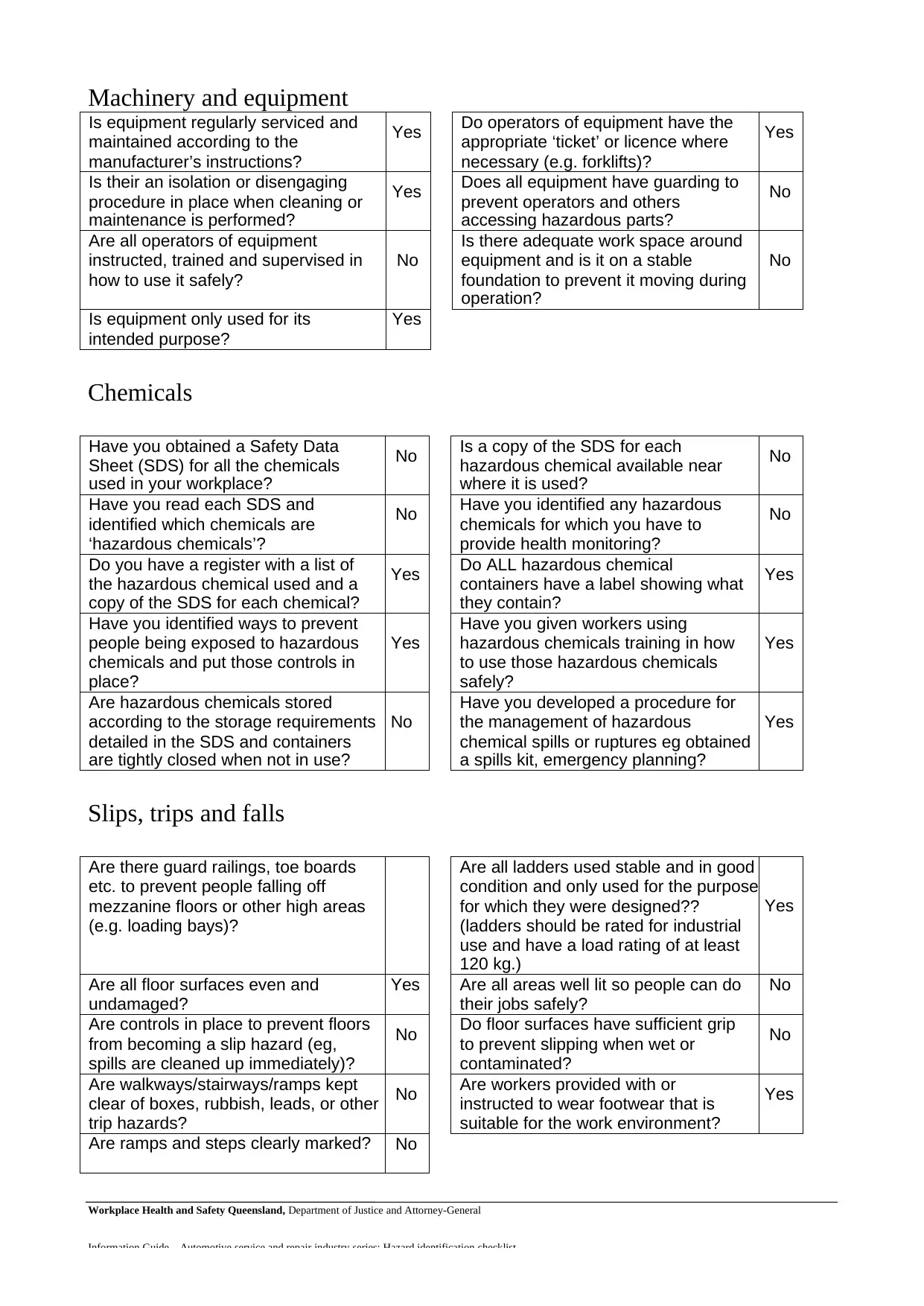
Machinery and equipment
Workplace Health and Safety Queensland, Department of Justice and Attorney-General
Information Guide – Automotive service and repair industry series: Hazard identification checklist
Is equipment regularly serviced and
maintained according to the
manufacturer’s instructions?
Yes Do operators of equipment have the
appropriate ‘ticket’ or licence where
necessary (e.g. forklifts)?
Yes
Is their an isolation or disengaging
procedure in place when cleaning or
maintenance is performed?
Yes Does all equipment have guarding to
prevent operators and others
accessing hazardous parts?
No
Are all operators of equipment
instructed, trained and supervised in
how to use it safely?
No
Is there adequate work space around
equipment and is it on a stable
foundation to prevent it moving during
operation?
No
Is equipment only used for its
intended purpose?
Yes
Chemicals
Have you obtained a Safety Data
Sheet (SDS) for all the chemicals
used in your workplace?
No Is a copy of the SDS for each
hazardous chemical available near
where it is used?
No
Have you read each SDS and
identified which chemicals are
‘hazardous chemicals’?
No Have you identified any hazardous
chemicals for which you have to
provide health monitoring?
No
Do you have a register with a list of
the hazardous chemical used and a
copy of the SDS for each chemical?
Yes Do ALL hazardous chemical
containers have a label showing what
they contain?
Yes
Have you identified ways to prevent
people being exposed to hazardous
chemicals and put those controls in
place?
Yes
Have you given workers using
hazardous chemicals training in how
to use those hazardous chemicals
safely?
Yes
Are hazardous chemicals stored
according to the storage requirements
detailed in the SDS and containers
are tightly closed when not in use?
No
Have you developed a procedure for
the management of hazardous
chemical spills or ruptures eg obtained
a spills kit, emergency planning?
Yes
Slips, trips and falls
Are there guard railings, toe boards
etc. to prevent people falling off
mezzanine floors or other high areas
(e.g. loading bays)?
Are all ladders used stable and in good
condition and only used for the purpose
for which they were designed??
(ladders should be rated for industrial
use and have a load rating of at least
120 kg.)
Yes
Are all floor surfaces even and
undamaged?
Yes Are all areas well lit so people can do
their jobs safely?
No
Are controls in place to prevent floors
from becoming a slip hazard (eg,
spills are cleaned up immediately)?
No Do floor surfaces have sufficient grip
to prevent slipping when wet or
contaminated?
No
Are walkways/stairways/ramps kept
clear of boxes, rubbish, leads, or other
trip hazards?
No Are workers provided with or
instructed to wear footwear that is
suitable for the work environment?
Yes
Are ramps and steps clearly marked? No
Workplace Health and Safety Queensland, Department of Justice and Attorney-General
Information Guide – Automotive service and repair industry series: Hazard identification checklist
Is equipment regularly serviced and
maintained according to the
manufacturer’s instructions?
Yes Do operators of equipment have the
appropriate ‘ticket’ or licence where
necessary (e.g. forklifts)?
Yes
Is their an isolation or disengaging
procedure in place when cleaning or
maintenance is performed?
Yes Does all equipment have guarding to
prevent operators and others
accessing hazardous parts?
No
Are all operators of equipment
instructed, trained and supervised in
how to use it safely?
No
Is there adequate work space around
equipment and is it on a stable
foundation to prevent it moving during
operation?
No
Is equipment only used for its
intended purpose?
Yes
Chemicals
Have you obtained a Safety Data
Sheet (SDS) for all the chemicals
used in your workplace?
No Is a copy of the SDS for each
hazardous chemical available near
where it is used?
No
Have you read each SDS and
identified which chemicals are
‘hazardous chemicals’?
No Have you identified any hazardous
chemicals for which you have to
provide health monitoring?
No
Do you have a register with a list of
the hazardous chemical used and a
copy of the SDS for each chemical?
Yes Do ALL hazardous chemical
containers have a label showing what
they contain?
Yes
Have you identified ways to prevent
people being exposed to hazardous
chemicals and put those controls in
place?
Yes
Have you given workers using
hazardous chemicals training in how
to use those hazardous chemicals
safely?
Yes
Are hazardous chemicals stored
according to the storage requirements
detailed in the SDS and containers
are tightly closed when not in use?
No
Have you developed a procedure for
the management of hazardous
chemical spills or ruptures eg obtained
a spills kit, emergency planning?
Yes
Slips, trips and falls
Are there guard railings, toe boards
etc. to prevent people falling off
mezzanine floors or other high areas
(e.g. loading bays)?
Are all ladders used stable and in good
condition and only used for the purpose
for which they were designed??
(ladders should be rated for industrial
use and have a load rating of at least
120 kg.)
Yes
Are all floor surfaces even and
undamaged?
Yes Are all areas well lit so people can do
their jobs safely?
No
Are controls in place to prevent floors
from becoming a slip hazard (eg,
spills are cleaned up immediately)?
No Do floor surfaces have sufficient grip
to prevent slipping when wet or
contaminated?
No
Are walkways/stairways/ramps kept
clear of boxes, rubbish, leads, or other
trip hazards?
No Are workers provided with or
instructed to wear footwear that is
suitable for the work environment?
Yes
Are ramps and steps clearly marked? No
Secure Best Marks with AI Grader
Need help grading? Try our AI Grader for instant feedback on your assignments.
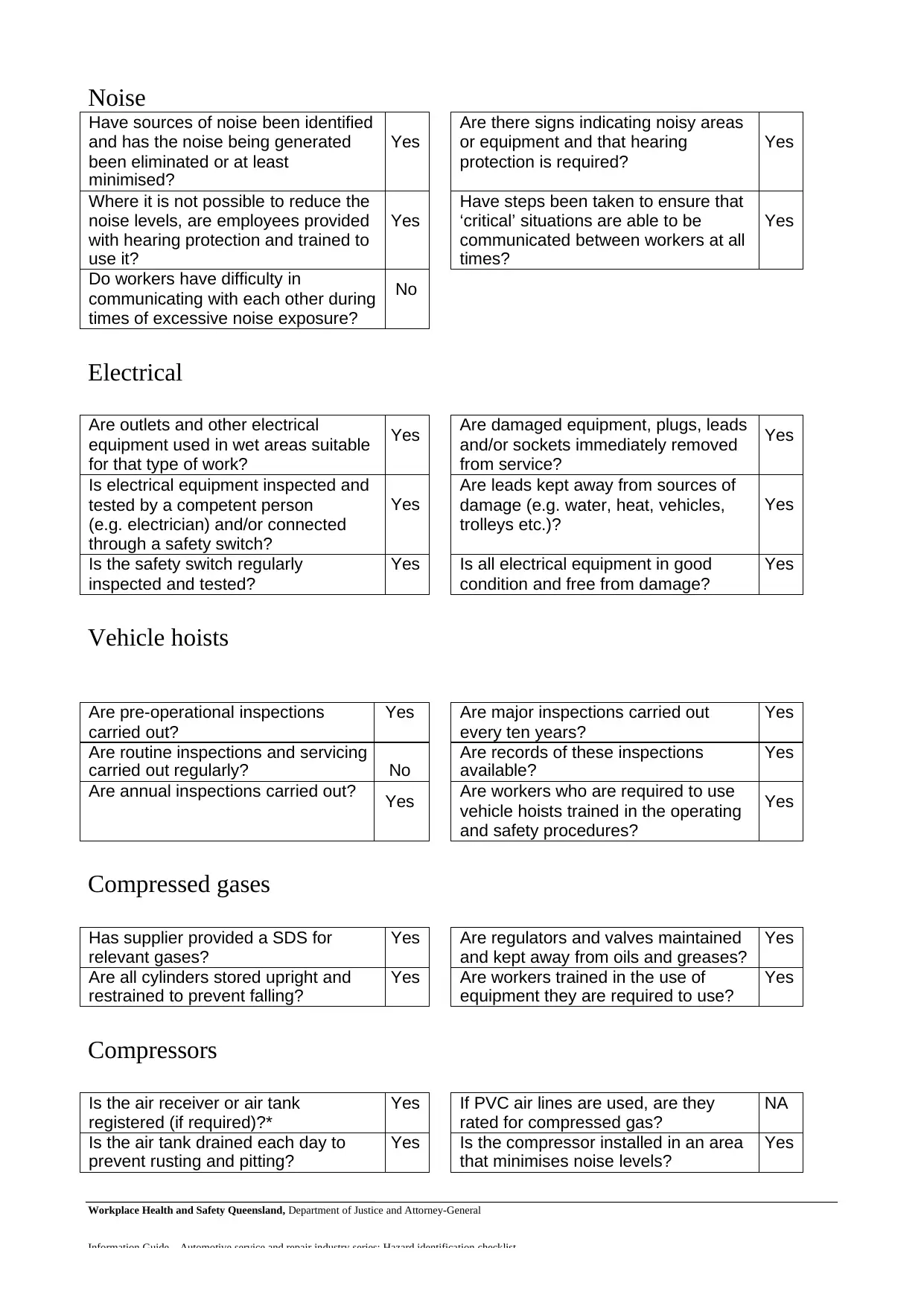
Noise
Workplace Health and Safety Queensland, Department of Justice and Attorney-General
Information Guide – Automotive service and repair industry series: Hazard identification checklist
Have sources of noise been identified
and has the noise being generated
been eliminated or at least
minimised?
Yes
Are there signs indicating noisy areas
or equipment and that hearing
protection is required?
Yes
Where it is not possible to reduce the
noise levels, are employees provided
with hearing protection and trained to
use it?
Yes
Have steps been taken to ensure that
‘critical’ situations are able to be
communicated between workers at all
times?
Yes
Do workers have difficulty in
communicating with each other during
times of excessive noise exposure?
No
Electrical
Are outlets and other electrical
equipment used in wet areas suitable
for that type of work?
Yes Are damaged equipment, plugs, leads
and/or sockets immediately removed
from service?
Yes
Is electrical equipment inspected and
tested by a competent person
(e.g. electrician) and/or connected
through a safety switch?
Yes
Are leads kept away from sources of
damage (e.g. water, heat, vehicles,
trolleys etc.)?
Yes
Is the safety switch regularly
inspected and tested?
Yes Is all electrical equipment in good
condition and free from damage?
Yes
Vehicle hoists
Are pre-operational inspections
carried out?
Yes Are major inspections carried out
every ten years?
Yes
Are routine inspections and servicing
carried out regularly? No
Are records of these inspections
available?
Yes
Are annual inspections carried out? Yes Are workers who are required to use
vehicle hoists trained in the operating
and safety procedures?
Yes
Compressed gases
Has supplier provided a SDS for
relevant gases?
Yes Are regulators and valves maintained
and kept away from oils and greases?
Yes
Are all cylinders stored upright and
restrained to prevent falling?
Yes Are workers trained in the use of
equipment they are required to use?
Yes
Compressors
Is the air receiver or air tank
registered (if required)?*
Yes If PVC air lines are used, are they
rated for compressed gas?
NA
Is the air tank drained each day to
prevent rusting and pitting?
Yes Is the compressor installed in an area
that minimises noise levels?
Yes
Workplace Health and Safety Queensland, Department of Justice and Attorney-General
Information Guide – Automotive service and repair industry series: Hazard identification checklist
Have sources of noise been identified
and has the noise being generated
been eliminated or at least
minimised?
Yes
Are there signs indicating noisy areas
or equipment and that hearing
protection is required?
Yes
Where it is not possible to reduce the
noise levels, are employees provided
with hearing protection and trained to
use it?
Yes
Have steps been taken to ensure that
‘critical’ situations are able to be
communicated between workers at all
times?
Yes
Do workers have difficulty in
communicating with each other during
times of excessive noise exposure?
No
Electrical
Are outlets and other electrical
equipment used in wet areas suitable
for that type of work?
Yes Are damaged equipment, plugs, leads
and/or sockets immediately removed
from service?
Yes
Is electrical equipment inspected and
tested by a competent person
(e.g. electrician) and/or connected
through a safety switch?
Yes
Are leads kept away from sources of
damage (e.g. water, heat, vehicles,
trolleys etc.)?
Yes
Is the safety switch regularly
inspected and tested?
Yes Is all electrical equipment in good
condition and free from damage?
Yes
Vehicle hoists
Are pre-operational inspections
carried out?
Yes Are major inspections carried out
every ten years?
Yes
Are routine inspections and servicing
carried out regularly? No
Are records of these inspections
available?
Yes
Are annual inspections carried out? Yes Are workers who are required to use
vehicle hoists trained in the operating
and safety procedures?
Yes
Compressed gases
Has supplier provided a SDS for
relevant gases?
Yes Are regulators and valves maintained
and kept away from oils and greases?
Yes
Are all cylinders stored upright and
restrained to prevent falling?
Yes Are workers trained in the use of
equipment they are required to use?
Yes
Compressors
Is the air receiver or air tank
registered (if required)?*
Yes If PVC air lines are used, are they
rated for compressed gas?
NA
Is the air tank drained each day to
prevent rusting and pitting?
Yes Is the compressor installed in an area
that minimises noise levels?
Yes
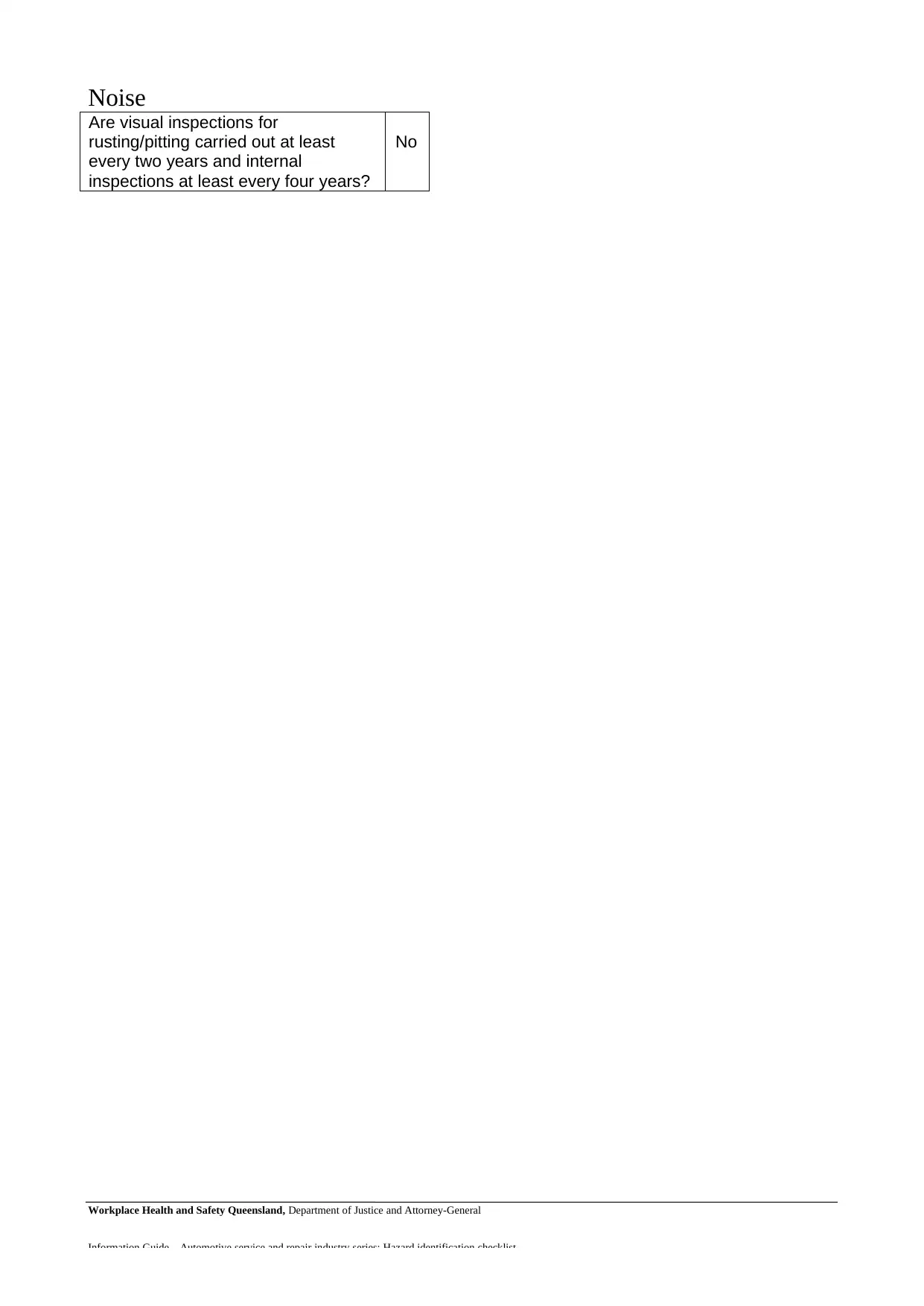
Noise
Workplace Health and Safety Queensland, Department of Justice and Attorney-General
Information Guide – Automotive service and repair industry series: Hazard identification checklist
Are visual inspections for
rusting/pitting carried out at least
every two years and internal
inspections at least every four years?
No
Workplace Health and Safety Queensland, Department of Justice and Attorney-General
Information Guide – Automotive service and repair industry series: Hazard identification checklist
Are visual inspections for
rusting/pitting carried out at least
every two years and internal
inspections at least every four years?
No
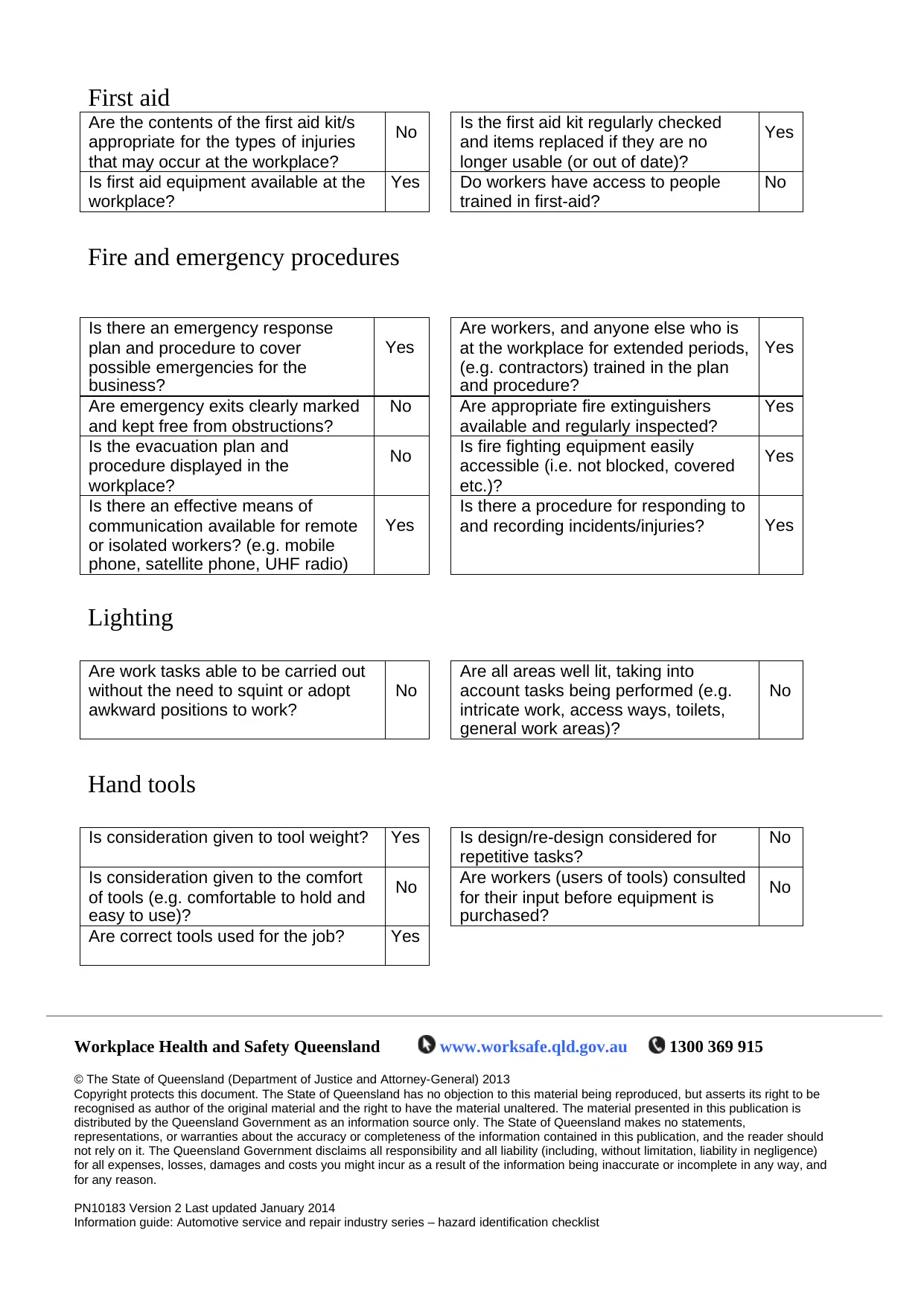
First aid
Workplace Health and Safety Queensland www.worksafe.qld.gov.au 1300 369 915
© The State of Queensland (Department of Justice and Attorney-General) 2013
Copyright protects this document. The State of Queensland has no objection to this material being reproduced, but asserts its right to be
recognised as author of the original material and the right to have the material unaltered. The material presented in this publication is
distributed by the Queensland Government as an information source only. The State of Queensland makes no statements,
representations, or warranties about the accuracy or completeness of the information contained in this publication, and the reader should
not rely on it. The Queensland Government disclaims all responsibility and all liability (including, without limitation, liability in negligence)
for all expenses, losses, damages and costs you might incur as a result of the information being inaccurate or incomplete in any way, and
for any reason.
PN10183 Version 2 Last updated January 2014
Information guide: Automotive service and repair industry series – hazard identification checklist
Are the contents of the first aid kit/s
appropriate for the types of injuries
that may occur at the workplace?
No Is the first aid kit regularly checked
and items replaced if they are no
longer usable (or out of date)?
Yes
Is first aid equipment available at the
workplace?
Yes Do workers have access to people
trained in first-aid?
No
Fire and emergency procedures
Is there an emergency response
plan and procedure to cover
possible emergencies for the
business?
Yes
Are workers, and anyone else who is
at the workplace for extended periods,
(e.g. contractors) trained in the plan
and procedure?
Yes
Are emergency exits clearly marked
and kept free from obstructions?
No Are appropriate fire extinguishers
available and regularly inspected?
Yes
Is the evacuation plan and
procedure displayed in the
workplace?
No Is fire fighting equipment easily
accessible (i.e. not blocked, covered
etc.)?
Yes
Is there an effective means of
communication available for remote
or isolated workers? (e.g. mobile
phone, satellite phone, UHF radio)
Yes
Is there a procedure for responding to
and recording incidents/injuries? Yes
Lighting
Are work tasks able to be carried out
without the need to squint or adopt
awkward positions to work?
No
Are all areas well lit, taking into
account tasks being performed (e.g.
intricate work, access ways, toilets,
general work areas)?
No
Hand tools
Is consideration given to tool weight? Yes Is design/re-design considered for
repetitive tasks?
No
Is consideration given to the comfort
of tools (e.g. comfortable to hold and
easy to use)?
No Are workers (users of tools) consulted
for their input before equipment is
purchased?
No
Are correct tools used for the job? Yes
Workplace Health and Safety Queensland www.worksafe.qld.gov.au 1300 369 915
© The State of Queensland (Department of Justice and Attorney-General) 2013
Copyright protects this document. The State of Queensland has no objection to this material being reproduced, but asserts its right to be
recognised as author of the original material and the right to have the material unaltered. The material presented in this publication is
distributed by the Queensland Government as an information source only. The State of Queensland makes no statements,
representations, or warranties about the accuracy or completeness of the information contained in this publication, and the reader should
not rely on it. The Queensland Government disclaims all responsibility and all liability (including, without limitation, liability in negligence)
for all expenses, losses, damages and costs you might incur as a result of the information being inaccurate or incomplete in any way, and
for any reason.
PN10183 Version 2 Last updated January 2014
Information guide: Automotive service and repair industry series – hazard identification checklist
Are the contents of the first aid kit/s
appropriate for the types of injuries
that may occur at the workplace?
No Is the first aid kit regularly checked
and items replaced if they are no
longer usable (or out of date)?
Yes
Is first aid equipment available at the
workplace?
Yes Do workers have access to people
trained in first-aid?
No
Fire and emergency procedures
Is there an emergency response
plan and procedure to cover
possible emergencies for the
business?
Yes
Are workers, and anyone else who is
at the workplace for extended periods,
(e.g. contractors) trained in the plan
and procedure?
Yes
Are emergency exits clearly marked
and kept free from obstructions?
No Are appropriate fire extinguishers
available and regularly inspected?
Yes
Is the evacuation plan and
procedure displayed in the
workplace?
No Is fire fighting equipment easily
accessible (i.e. not blocked, covered
etc.)?
Yes
Is there an effective means of
communication available for remote
or isolated workers? (e.g. mobile
phone, satellite phone, UHF radio)
Yes
Is there a procedure for responding to
and recording incidents/injuries? Yes
Lighting
Are work tasks able to be carried out
without the need to squint or adopt
awkward positions to work?
No
Are all areas well lit, taking into
account tasks being performed (e.g.
intricate work, access ways, toilets,
general work areas)?
No
Hand tools
Is consideration given to tool weight? Yes Is design/re-design considered for
repetitive tasks?
No
Is consideration given to the comfort
of tools (e.g. comfortable to hold and
easy to use)?
No Are workers (users of tools) consulted
for their input before equipment is
purchased?
No
Are correct tools used for the job? Yes
Paraphrase This Document
Need a fresh take? Get an instant paraphrase of this document with our AI Paraphraser
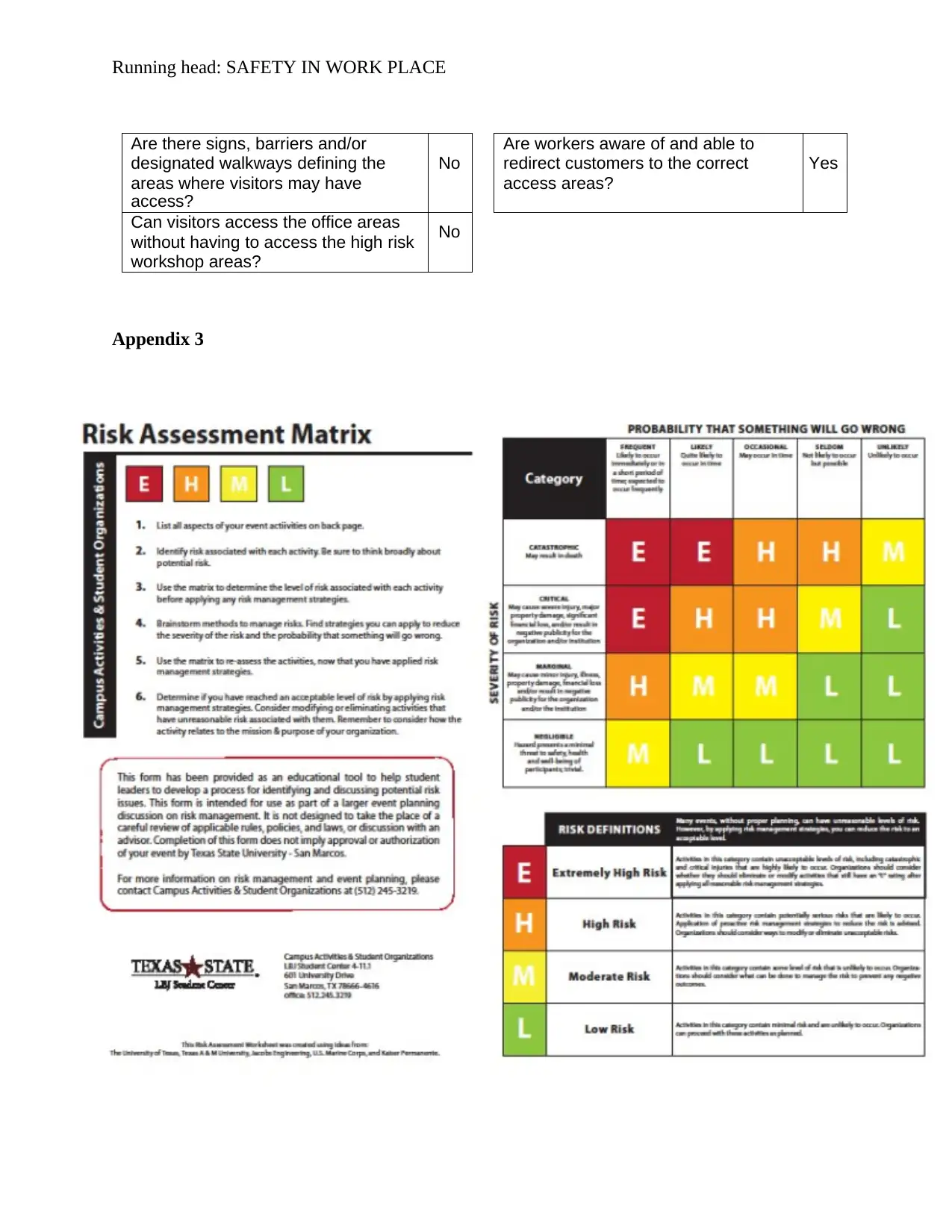
Running head: SAFETY IN WORK PLACE
Are there signs, barriers and/or
designated walkways defining the
areas where visitors may have
access?
No
Are workers aware of and able to
redirect customers to the correct
access areas?
Yes
Can visitors access the office areas
without having to access the high risk
workshop areas?
No
Appendix 3
Are there signs, barriers and/or
designated walkways defining the
areas where visitors may have
access?
No
Are workers aware of and able to
redirect customers to the correct
access areas?
Yes
Can visitors access the office areas
without having to access the high risk
workshop areas?
No
Appendix 3
1 out of 8
Related Documents
![[object Object]](/_next/image/?url=%2F_next%2Fstatic%2Fmedia%2Flogo.6d15ce61.png&w=640&q=75)
Your All-in-One AI-Powered Toolkit for Academic Success.
+13062052269
info@desklib.com
Available 24*7 on WhatsApp / Email
Unlock your academic potential
© 2024 | Zucol Services PVT LTD | All rights reserved.