Comparison of Absorption Costing and Activity Based Costing
VerifiedAdded on 2022/11/14
|15
|2569
|153
AI Summary
This document compares Absorption Costing and Activity Based Costing techniques for allocating overhead costs. It includes schedules and lists of activities and resource drivers used in the production process. The analysis shows a significant difference in the allocation of overhead costs between the two techniques. The document also discusses the reasons for changes in the cost of the product and concludes that both products' costs are overstated. It provides insights on how to allocate overhead costs using Activity Based Costing.
Contribute Materials
Your contribution can guide someone’s learning journey. Share your
documents today.

ABSORPTION COSTING
VS
ACTIVITY BASED COSTING
VS
ACTIVITY BASED COSTING
Secure Best Marks with AI Grader
Need help grading? Try our AI Grader for instant feedback on your assignments.
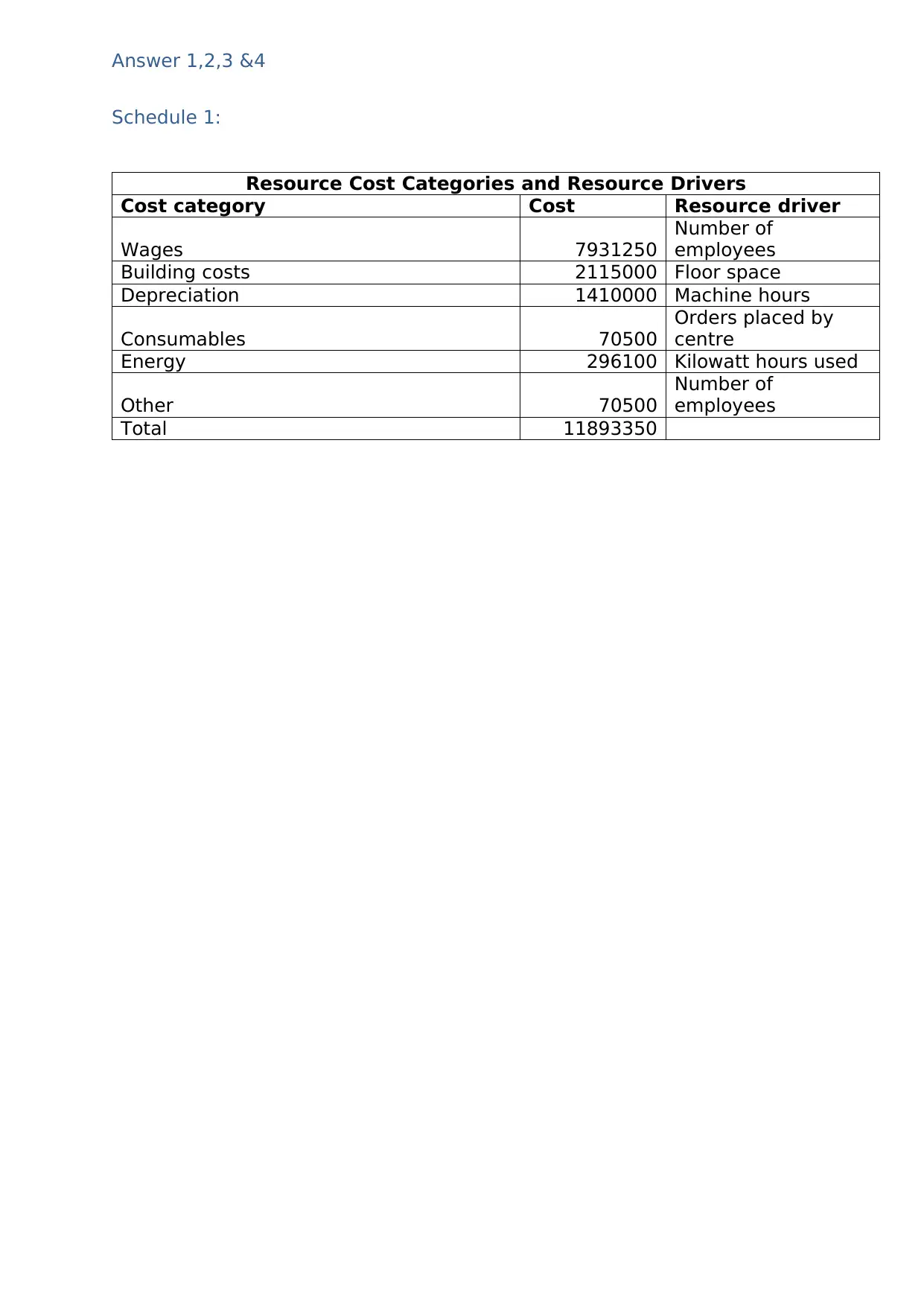
Answer 1,2,3 &4
Schedule 1:
Resource Cost Categories and Resource Drivers
Cost category Cost Resource driver
Wages 7931250
Number of
employees
Building costs 2115000 Floor space
Depreciation 1410000 Machine hours
Consumables 70500
Orders placed by
centre
Energy 296100 Kilowatt hours used
Other 70500
Number of
employees
Total 11893350
Schedule 1:
Resource Cost Categories and Resource Drivers
Cost category Cost Resource driver
Wages 7931250
Number of
employees
Building costs 2115000 Floor space
Depreciation 1410000 Machine hours
Consumables 70500
Orders placed by
centre
Energy 296100 Kilowatt hours used
Other 70500
Number of
employees
Total 11893350
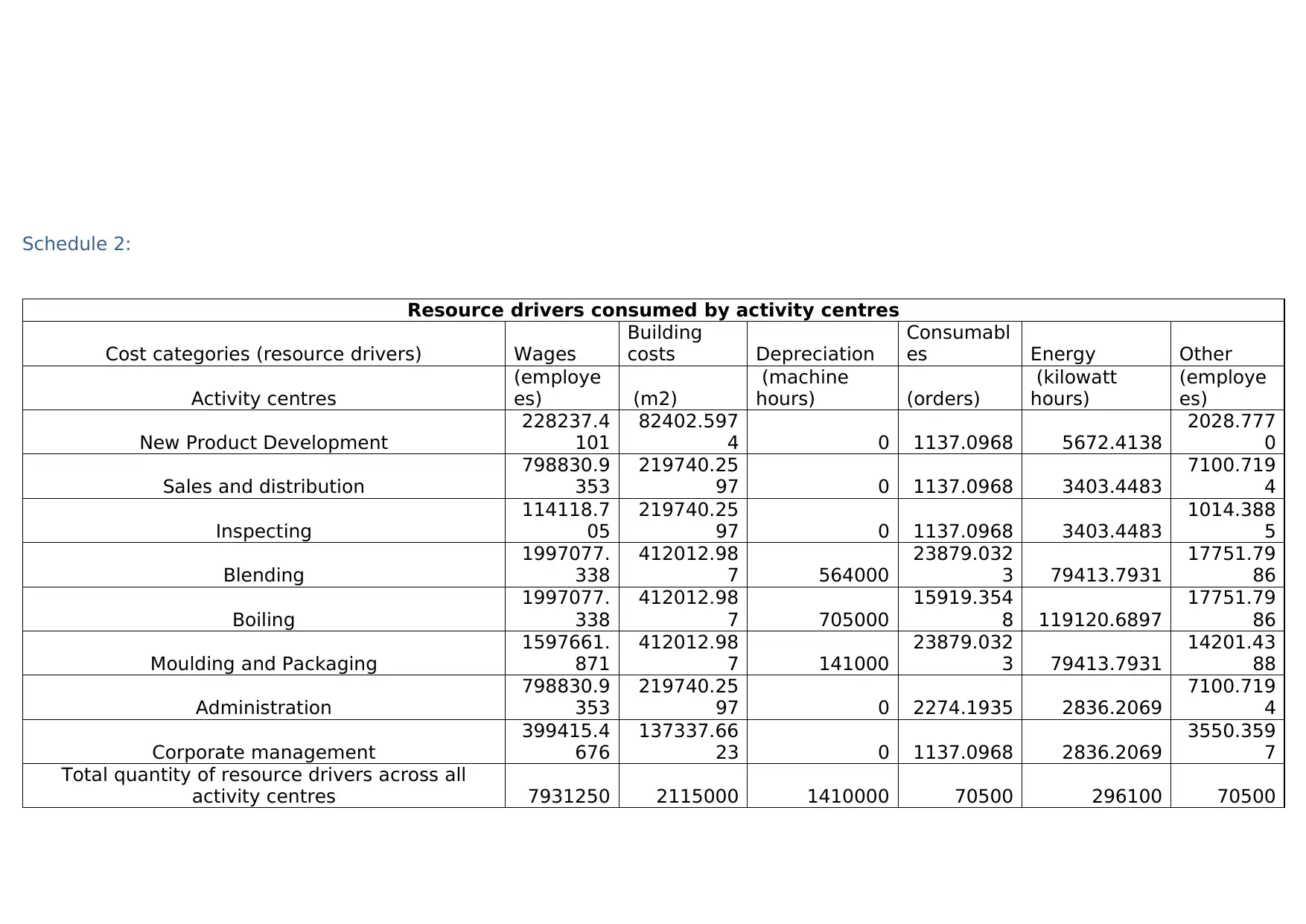
Schedule 2:
Resource drivers consumed by activity centres
Cost categories (resource drivers) Wages
Building
costs Depreciation
Consumabl
es Energy Other
Activity centres
(employe
es) (m2)
(machine
hours) (orders)
(kilowatt
hours)
(employe
es)
New Product Development
228237.4
101
82402.597
4 0 1137.0968 5672.4138
2028.777
0
Sales and distribution
798830.9
353
219740.25
97 0 1137.0968 3403.4483
7100.719
4
Inspecting
114118.7
05
219740.25
97 0 1137.0968 3403.4483
1014.388
5
Blending
1997077.
338
412012.98
7 564000
23879.032
3 79413.7931
17751.79
86
Boiling
1997077.
338
412012.98
7 705000
15919.354
8 119120.6897
17751.79
86
Moulding and Packaging
1597661.
871
412012.98
7 141000
23879.032
3 79413.7931
14201.43
88
Administration
798830.9
353
219740.25
97 0 2274.1935 2836.2069
7100.719
4
Corporate management
399415.4
676
137337.66
23 0 1137.0968 2836.2069
3550.359
7
Total quantity of resource drivers across all
activity centres 7931250 2115000 1410000 70500 296100 70500
Resource drivers consumed by activity centres
Cost categories (resource drivers) Wages
Building
costs Depreciation
Consumabl
es Energy Other
Activity centres
(employe
es) (m2)
(machine
hours) (orders)
(kilowatt
hours)
(employe
es)
New Product Development
228237.4
101
82402.597
4 0 1137.0968 5672.4138
2028.777
0
Sales and distribution
798830.9
353
219740.25
97 0 1137.0968 3403.4483
7100.719
4
Inspecting
114118.7
05
219740.25
97 0 1137.0968 3403.4483
1014.388
5
Blending
1997077.
338
412012.98
7 564000
23879.032
3 79413.7931
17751.79
86
Boiling
1997077.
338
412012.98
7 705000
15919.354
8 119120.6897
17751.79
86
Moulding and Packaging
1597661.
871
412012.98
7 141000
23879.032
3 79413.7931
14201.43
88
Administration
798830.9
353
219740.25
97 0 2274.1935 2836.2069
7100.719
4
Corporate management
399415.4
676
137337.66
23 0 1137.0968 2836.2069
3550.359
7
Total quantity of resource drivers across all
activity centres 7931250 2115000 1410000 70500 296100 70500
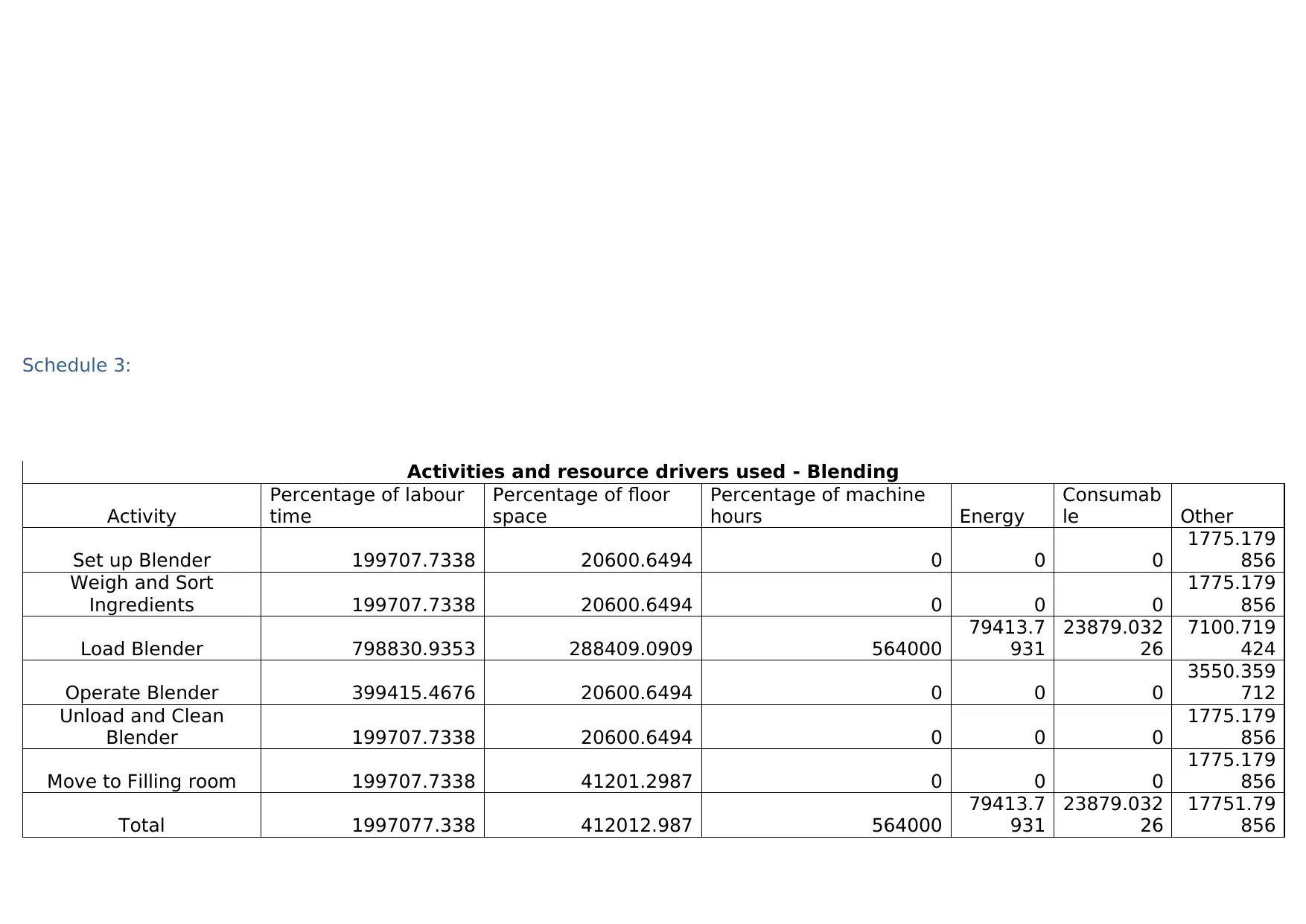
Schedule 3:
Activities and resource drivers used - Blending
Activity
Percentage of labour
time
Percentage of floor
space
Percentage of machine
hours Energy
Consumab
le Other
Set up Blender 199707.7338 20600.6494 0 0 0
1775.179
856
Weigh and Sort
Ingredients 199707.7338 20600.6494 0 0 0
1775.179
856
Load Blender 798830.9353 288409.0909 564000
79413.7
931
23879.032
26
7100.719
424
Operate Blender 399415.4676 20600.6494 0 0 0
3550.359
712
Unload and Clean
Blender 199707.7338 20600.6494 0 0 0
1775.179
856
Move to Filling room 199707.7338 41201.2987 0 0 0
1775.179
856
Total 1997077.338 412012.987 564000
79413.7
931
23879.032
26
17751.79
856
Activities and resource drivers used - Blending
Activity
Percentage of labour
time
Percentage of floor
space
Percentage of machine
hours Energy
Consumab
le Other
Set up Blender 199707.7338 20600.6494 0 0 0
1775.179
856
Weigh and Sort
Ingredients 199707.7338 20600.6494 0 0 0
1775.179
856
Load Blender 798830.9353 288409.0909 564000
79413.7
931
23879.032
26
7100.719
424
Operate Blender 399415.4676 20600.6494 0 0 0
3550.359
712
Unload and Clean
Blender 199707.7338 20600.6494 0 0 0
1775.179
856
Move to Filling room 199707.7338 41201.2987 0 0 0
1775.179
856
Total 1997077.338 412012.987 564000
79413.7
931
23879.032
26
17751.79
856
Secure Best Marks with AI Grader
Need help grading? Try our AI Grader for instant feedback on your assignments.
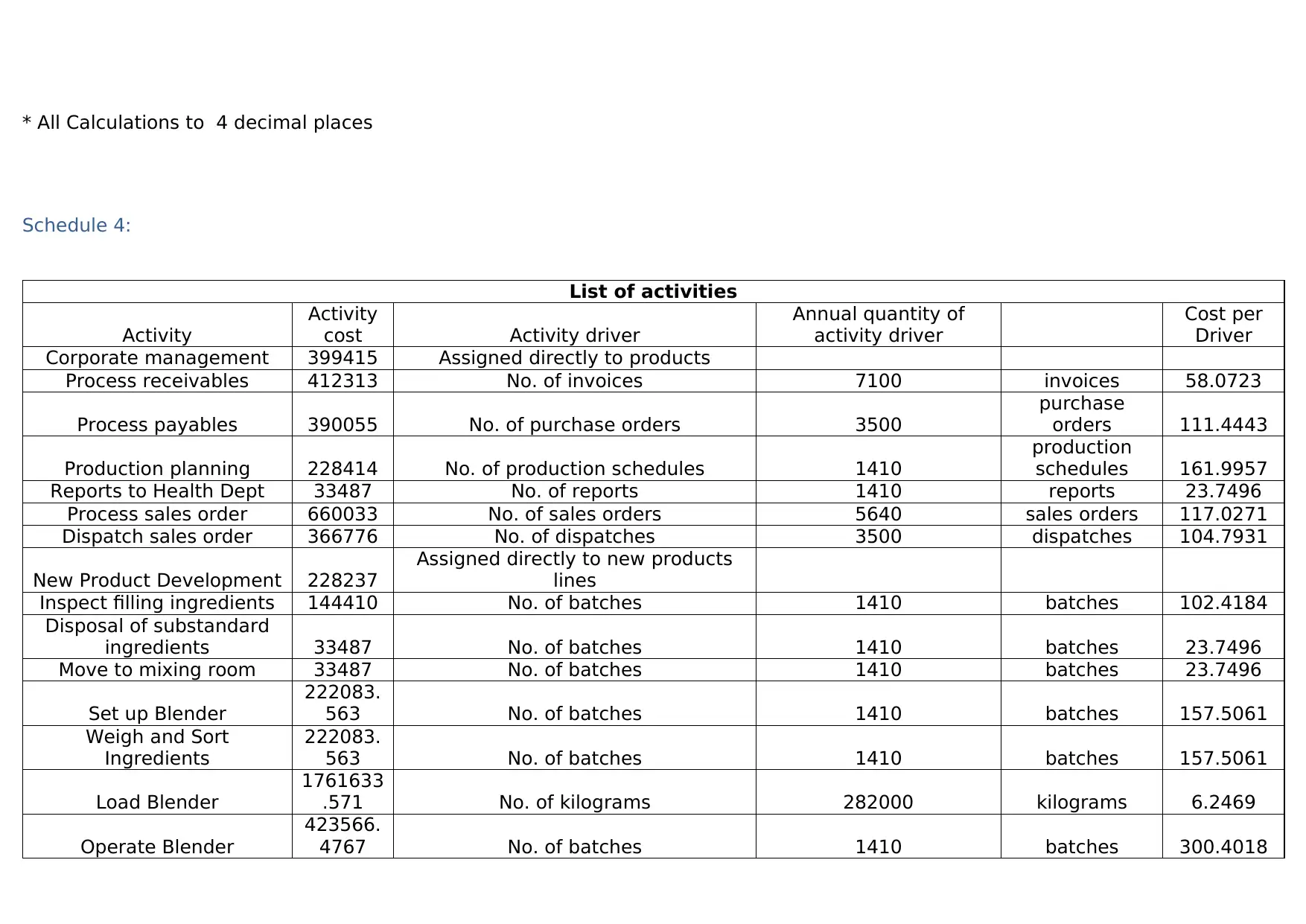
* All Calculations to 4 decimal places
Schedule 4:
List of activities
Activity
Activity
cost Activity driver
Annual quantity of
activity driver
Cost per
Driver
Corporate management 399415 Assigned directly to products
Process receivables 412313 No. of invoices 7100 invoices 58.0723
Process payables 390055 No. of purchase orders 3500
purchase
orders 111.4443
Production planning 228414 No. of production schedules 1410
production
schedules 161.9957
Reports to Health Dept 33487 No. of reports 1410 reports 23.7496
Process sales order 660033 No. of sales orders 5640 sales orders 117.0271
Dispatch sales order 366776 No. of dispatches 3500 dispatches 104.7931
New Product Development 228237
Assigned directly to new products
lines
Inspect filling ingredients 144410 No. of batches 1410 batches 102.4184
Disposal of substandard
ingredients 33487 No. of batches 1410 batches 23.7496
Move to mixing room 33487 No. of batches 1410 batches 23.7496
Set up Blender
222083.
563 No. of batches 1410 batches 157.5061
Weigh and Sort
Ingredients
222083.
563 No. of batches 1410 batches 157.5061
Load Blender
1761633
.571 No. of kilograms 282000 kilograms 6.2469
Operate Blender
423566.
4767 No. of batches 1410 batches 300.4018
Schedule 4:
List of activities
Activity
Activity
cost Activity driver
Annual quantity of
activity driver
Cost per
Driver
Corporate management 399415 Assigned directly to products
Process receivables 412313 No. of invoices 7100 invoices 58.0723
Process payables 390055 No. of purchase orders 3500
purchase
orders 111.4443
Production planning 228414 No. of production schedules 1410
production
schedules 161.9957
Reports to Health Dept 33487 No. of reports 1410 reports 23.7496
Process sales order 660033 No. of sales orders 5640 sales orders 117.0271
Dispatch sales order 366776 No. of dispatches 3500 dispatches 104.7931
New Product Development 228237
Assigned directly to new products
lines
Inspect filling ingredients 144410 No. of batches 1410 batches 102.4184
Disposal of substandard
ingredients 33487 No. of batches 1410 batches 23.7496
Move to mixing room 33487 No. of batches 1410 batches 23.7496
Set up Blender
222083.
563 No. of batches 1410 batches 157.5061
Weigh and Sort
Ingredients
222083.
563 No. of batches 1410 batches 157.5061
Load Blender
1761633
.571 No. of kilograms 282000 kilograms 6.2469
Operate Blender
423566.
4767 No. of batches 1410 batches 300.4018
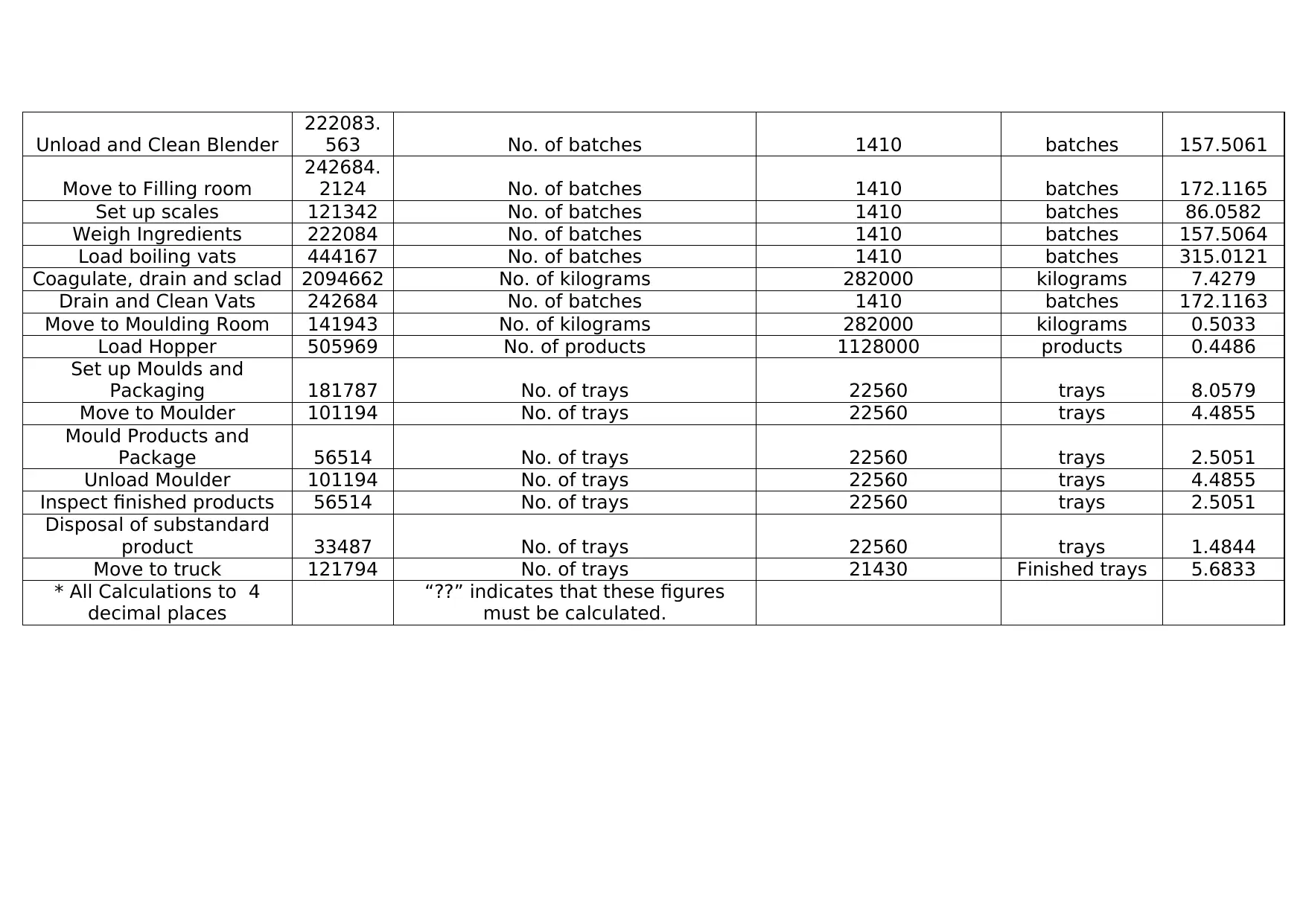
Unload and Clean Blender
222083.
563 No. of batches 1410 batches 157.5061
Move to Filling room
242684.
2124 No. of batches 1410 batches 172.1165
Set up scales 121342 No. of batches 1410 batches 86.0582
Weigh Ingredients 222084 No. of batches 1410 batches 157.5064
Load boiling vats 444167 No. of batches 1410 batches 315.0121
Coagulate, drain and sclad 2094662 No. of kilograms 282000 kilograms 7.4279
Drain and Clean Vats 242684 No. of batches 1410 batches 172.1163
Move to Moulding Room 141943 No. of kilograms 282000 kilograms 0.5033
Load Hopper 505969 No. of products 1128000 products 0.4486
Set up Moulds and
Packaging 181787 No. of trays 22560 trays 8.0579
Move to Moulder 101194 No. of trays 22560 trays 4.4855
Mould Products and
Package 56514 No. of trays 22560 trays 2.5051
Unload Moulder 101194 No. of trays 22560 trays 4.4855
Inspect finished products 56514 No. of trays 22560 trays 2.5051
Disposal of substandard
product 33487 No. of trays 22560 trays 1.4844
Move to truck 121794 No. of trays 21430 Finished trays 5.6833
* All Calculations to 4
decimal places
“??” indicates that these figures
must be calculated.
222083.
563 No. of batches 1410 batches 157.5061
Move to Filling room
242684.
2124 No. of batches 1410 batches 172.1165
Set up scales 121342 No. of batches 1410 batches 86.0582
Weigh Ingredients 222084 No. of batches 1410 batches 157.5064
Load boiling vats 444167 No. of batches 1410 batches 315.0121
Coagulate, drain and sclad 2094662 No. of kilograms 282000 kilograms 7.4279
Drain and Clean Vats 242684 No. of batches 1410 batches 172.1163
Move to Moulding Room 141943 No. of kilograms 282000 kilograms 0.5033
Load Hopper 505969 No. of products 1128000 products 0.4486
Set up Moulds and
Packaging 181787 No. of trays 22560 trays 8.0579
Move to Moulder 101194 No. of trays 22560 trays 4.4855
Mould Products and
Package 56514 No. of trays 22560 trays 2.5051
Unload Moulder 101194 No. of trays 22560 trays 4.4855
Inspect finished products 56514 No. of trays 22560 trays 2.5051
Disposal of substandard
product 33487 No. of trays 22560 trays 1.4844
Move to truck 121794 No. of trays 21430 Finished trays 5.6833
* All Calculations to 4
decimal places
“??” indicates that these figures
must be calculated.
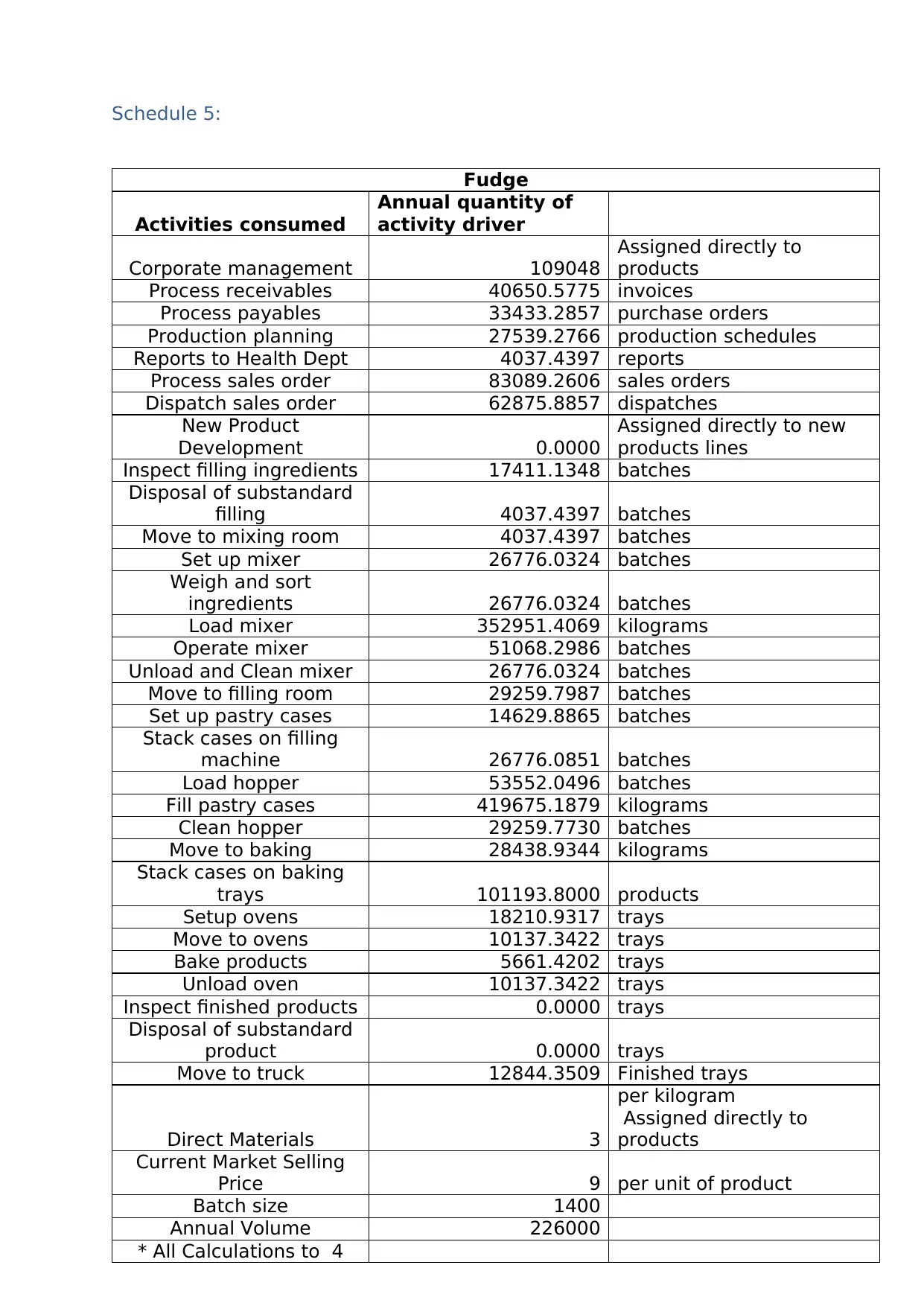
Schedule 5:
Fudge
Activities consumed
Annual quantity of
activity driver
Corporate management 109048
Assigned directly to
products
Process receivables 40650.5775 invoices
Process payables 33433.2857 purchase orders
Production planning 27539.2766 production schedules
Reports to Health Dept 4037.4397 reports
Process sales order 83089.2606 sales orders
Dispatch sales order 62875.8857 dispatches
New Product
Development 0.0000
Assigned directly to new
products lines
Inspect filling ingredients 17411.1348 batches
Disposal of substandard
filling 4037.4397 batches
Move to mixing room 4037.4397 batches
Set up mixer 26776.0324 batches
Weigh and sort
ingredients 26776.0324 batches
Load mixer 352951.4069 kilograms
Operate mixer 51068.2986 batches
Unload and Clean mixer 26776.0324 batches
Move to filling room 29259.7987 batches
Set up pastry cases 14629.8865 batches
Stack cases on filling
machine 26776.0851 batches
Load hopper 53552.0496 batches
Fill pastry cases 419675.1879 kilograms
Clean hopper 29259.7730 batches
Move to baking 28438.9344 kilograms
Stack cases on baking
trays 101193.8000 products
Setup ovens 18210.9317 trays
Move to ovens 10137.3422 trays
Bake products 5661.4202 trays
Unload oven 10137.3422 trays
Inspect finished products 0.0000 trays
Disposal of substandard
product 0.0000 trays
Move to truck 12844.3509 Finished trays
Direct Materials 3
per kilogram
Assigned directly to
products
Current Market Selling
Price 9 per unit of product
Batch size 1400
Annual Volume 226000
* All Calculations to 4
Fudge
Activities consumed
Annual quantity of
activity driver
Corporate management 109048
Assigned directly to
products
Process receivables 40650.5775 invoices
Process payables 33433.2857 purchase orders
Production planning 27539.2766 production schedules
Reports to Health Dept 4037.4397 reports
Process sales order 83089.2606 sales orders
Dispatch sales order 62875.8857 dispatches
New Product
Development 0.0000
Assigned directly to new
products lines
Inspect filling ingredients 17411.1348 batches
Disposal of substandard
filling 4037.4397 batches
Move to mixing room 4037.4397 batches
Set up mixer 26776.0324 batches
Weigh and sort
ingredients 26776.0324 batches
Load mixer 352951.4069 kilograms
Operate mixer 51068.2986 batches
Unload and Clean mixer 26776.0324 batches
Move to filling room 29259.7987 batches
Set up pastry cases 14629.8865 batches
Stack cases on filling
machine 26776.0851 batches
Load hopper 53552.0496 batches
Fill pastry cases 419675.1879 kilograms
Clean hopper 29259.7730 batches
Move to baking 28438.9344 kilograms
Stack cases on baking
trays 101193.8000 products
Setup ovens 18210.9317 trays
Move to ovens 10137.3422 trays
Bake products 5661.4202 trays
Unload oven 10137.3422 trays
Inspect finished products 0.0000 trays
Disposal of substandard
product 0.0000 trays
Move to truck 12844.3509 Finished trays
Direct Materials 3
per kilogram
Assigned directly to
products
Current Market Selling
Price 9 per unit of product
Batch size 1400
Annual Volume 226000
* All Calculations to 4
Paraphrase This Document
Need a fresh take? Get an instant paraphrase of this document with our AI Paraphraser
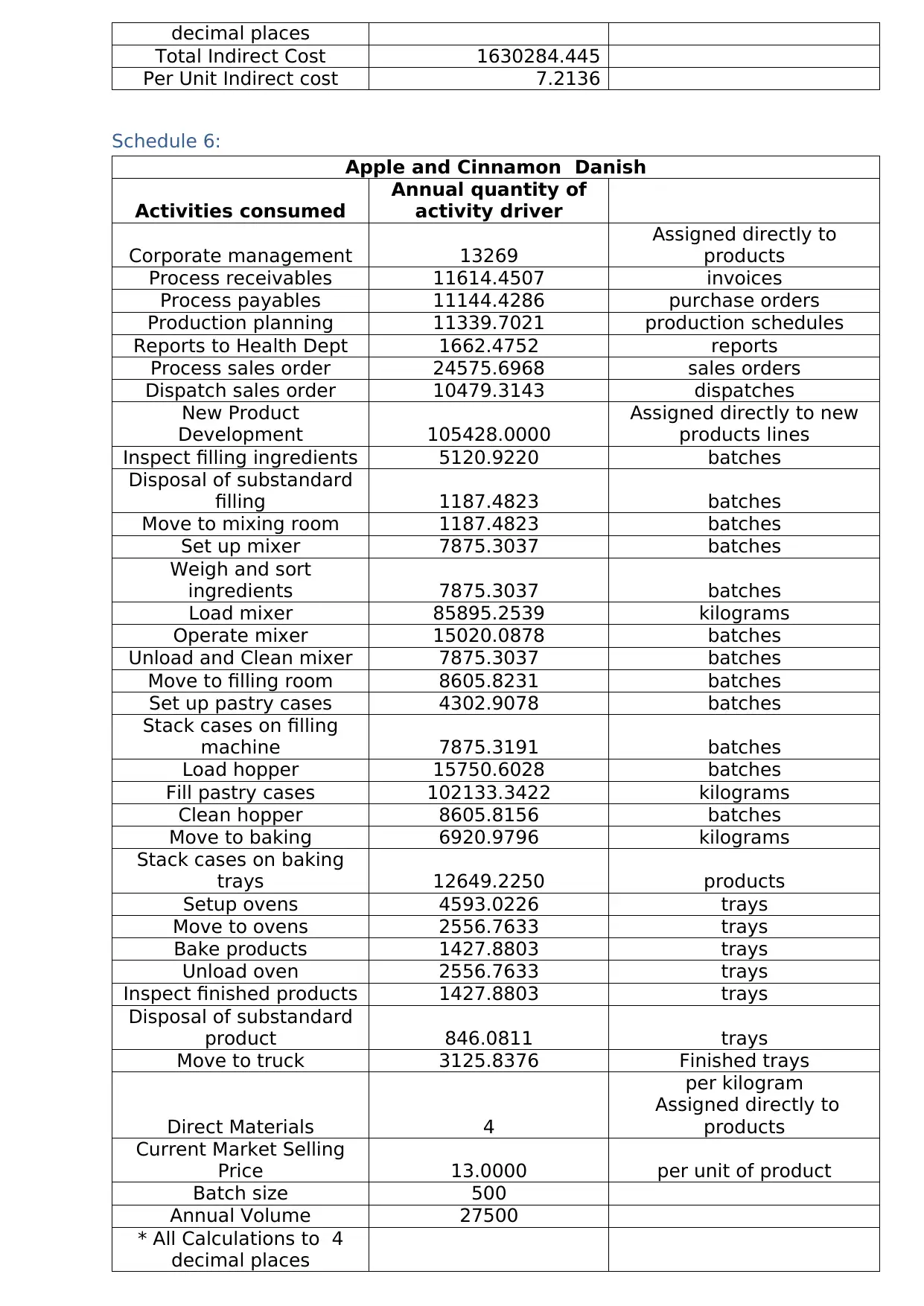
decimal places
Total Indirect Cost 1630284.445
Per Unit Indirect cost 7.2136
Schedule 6:
Apple and Cinnamon Danish
Activities consumed
Annual quantity of
activity driver
Corporate management 13269
Assigned directly to
products
Process receivables 11614.4507 invoices
Process payables 11144.4286 purchase orders
Production planning 11339.7021 production schedules
Reports to Health Dept 1662.4752 reports
Process sales order 24575.6968 sales orders
Dispatch sales order 10479.3143 dispatches
New Product
Development 105428.0000
Assigned directly to new
products lines
Inspect filling ingredients 5120.9220 batches
Disposal of substandard
filling 1187.4823 batches
Move to mixing room 1187.4823 batches
Set up mixer 7875.3037 batches
Weigh and sort
ingredients 7875.3037 batches
Load mixer 85895.2539 kilograms
Operate mixer 15020.0878 batches
Unload and Clean mixer 7875.3037 batches
Move to filling room 8605.8231 batches
Set up pastry cases 4302.9078 batches
Stack cases on filling
machine 7875.3191 batches
Load hopper 15750.6028 batches
Fill pastry cases 102133.3422 kilograms
Clean hopper 8605.8156 batches
Move to baking 6920.9796 kilograms
Stack cases on baking
trays 12649.2250 products
Setup ovens 4593.0226 trays
Move to ovens 2556.7633 trays
Bake products 1427.8803 trays
Unload oven 2556.7633 trays
Inspect finished products 1427.8803 trays
Disposal of substandard
product 846.0811 trays
Move to truck 3125.8376 Finished trays
Direct Materials 4
per kilogram
Assigned directly to
products
Current Market Selling
Price 13.0000 per unit of product
Batch size 500
Annual Volume 27500
* All Calculations to 4
decimal places
Total Indirect Cost 1630284.445
Per Unit Indirect cost 7.2136
Schedule 6:
Apple and Cinnamon Danish
Activities consumed
Annual quantity of
activity driver
Corporate management 13269
Assigned directly to
products
Process receivables 11614.4507 invoices
Process payables 11144.4286 purchase orders
Production planning 11339.7021 production schedules
Reports to Health Dept 1662.4752 reports
Process sales order 24575.6968 sales orders
Dispatch sales order 10479.3143 dispatches
New Product
Development 105428.0000
Assigned directly to new
products lines
Inspect filling ingredients 5120.9220 batches
Disposal of substandard
filling 1187.4823 batches
Move to mixing room 1187.4823 batches
Set up mixer 7875.3037 batches
Weigh and sort
ingredients 7875.3037 batches
Load mixer 85895.2539 kilograms
Operate mixer 15020.0878 batches
Unload and Clean mixer 7875.3037 batches
Move to filling room 8605.8231 batches
Set up pastry cases 4302.9078 batches
Stack cases on filling
machine 7875.3191 batches
Load hopper 15750.6028 batches
Fill pastry cases 102133.3422 kilograms
Clean hopper 8605.8156 batches
Move to baking 6920.9796 kilograms
Stack cases on baking
trays 12649.2250 products
Setup ovens 4593.0226 trays
Move to ovens 2556.7633 trays
Bake products 1427.8803 trays
Unload oven 2556.7633 trays
Inspect finished products 1427.8803 trays
Disposal of substandard
product 846.0811 trays
Move to truck 3125.8376 Finished trays
Direct Materials 4
per kilogram
Assigned directly to
products
Current Market Selling
Price 13.0000 per unit of product
Batch size 500
Annual Volume 27500
* All Calculations to 4
decimal places
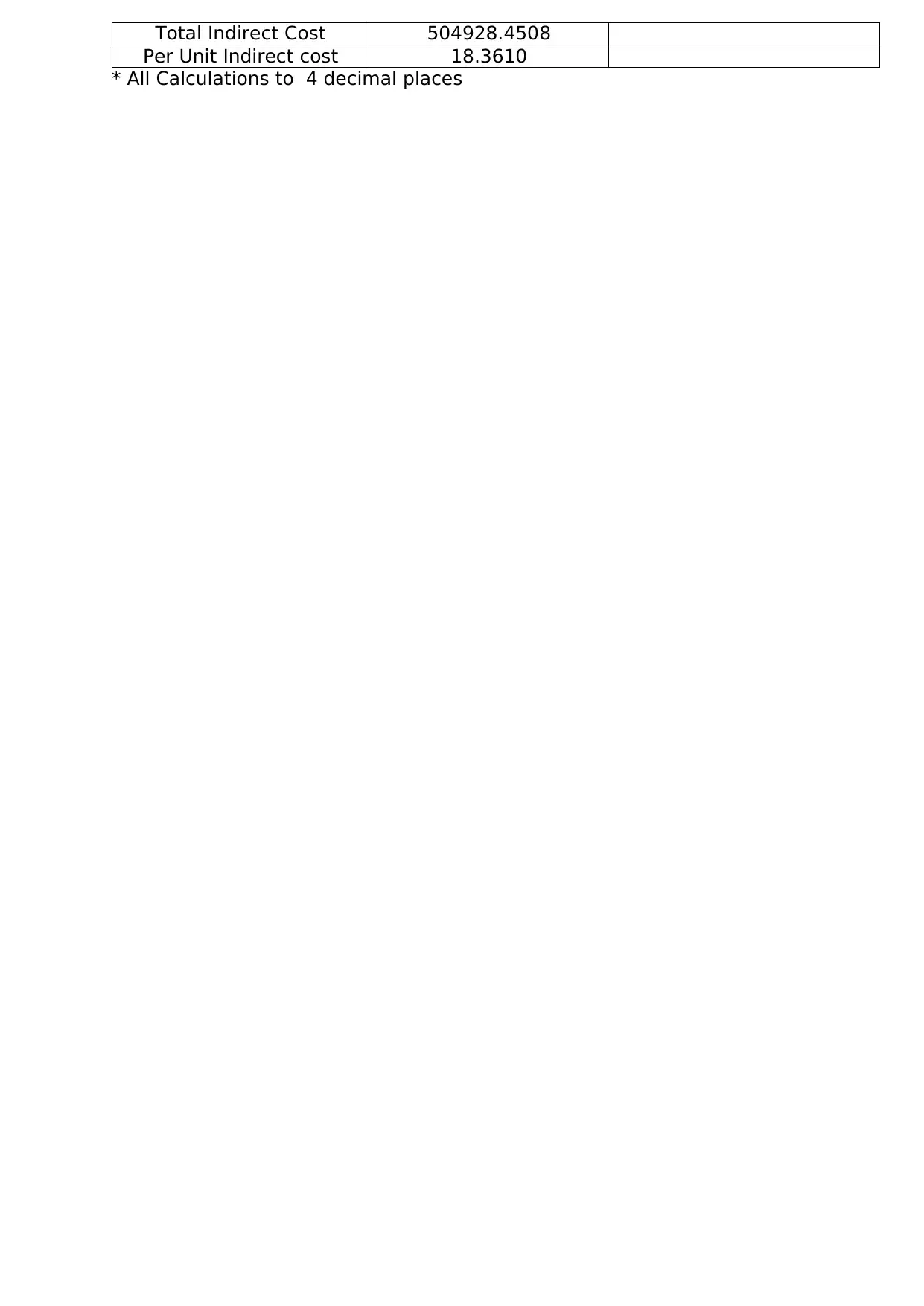
Total Indirect Cost 504928.4508
Per Unit Indirect cost 18.3610
* All Calculations to 4 decimal places
Per Unit Indirect cost 18.3610
* All Calculations to 4 decimal places
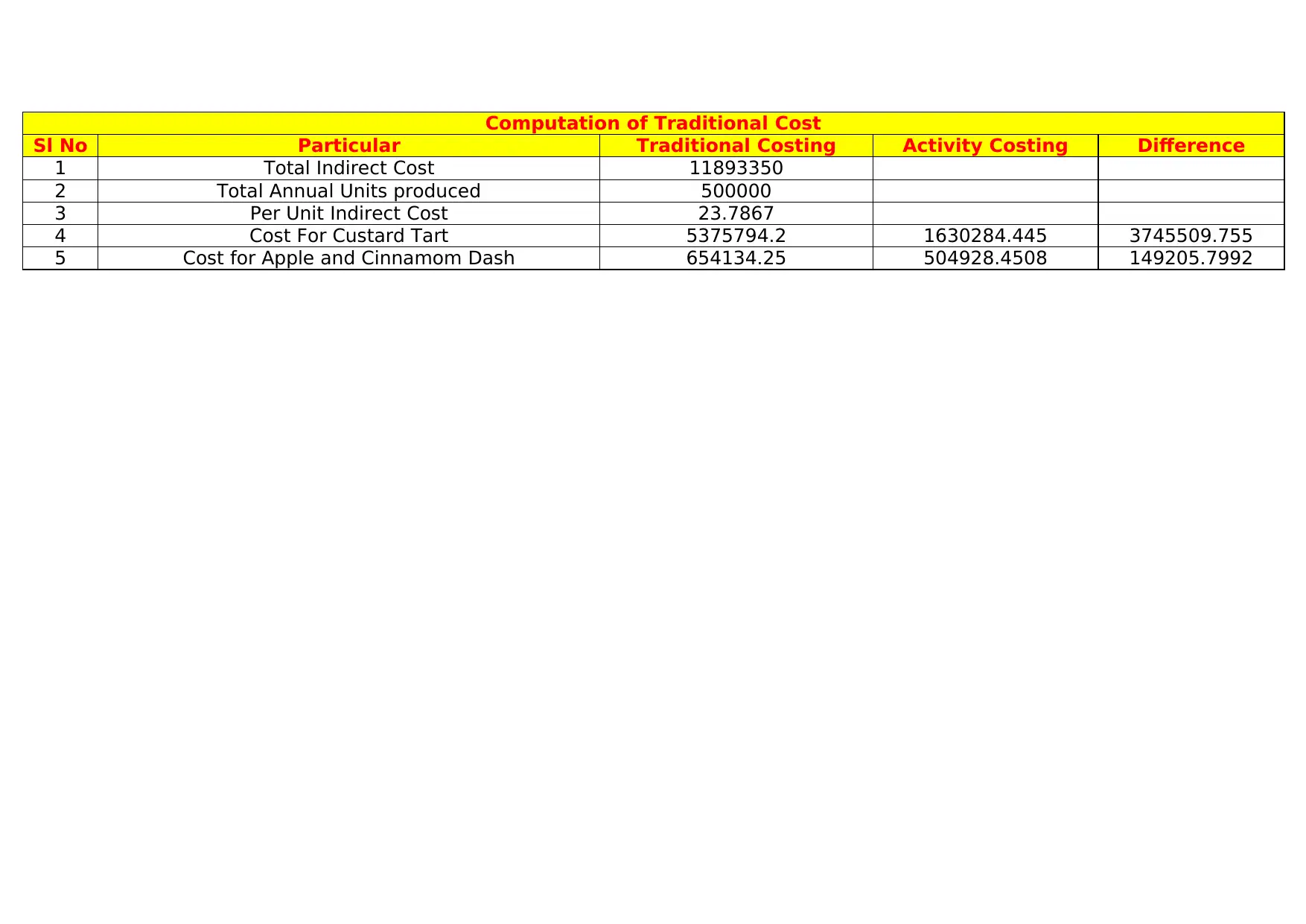
Computation of Traditional Cost
Sl No Particular Traditional Costing Activity Costing Difference
1 Total Indirect Cost 11893350
2 Total Annual Units produced 500000
3 Per Unit Indirect Cost 23.7867
4 Cost For Custard Tart 5375794.2 1630284.445 3745509.755
5 Cost for Apple and Cinnamom Dash 654134.25 504928.4508 149205.7992
Sl No Particular Traditional Costing Activity Costing Difference
1 Total Indirect Cost 11893350
2 Total Annual Units produced 500000
3 Per Unit Indirect Cost 23.7867
4 Cost For Custard Tart 5375794.2 1630284.445 3745509.755
5 Cost for Apple and Cinnamom Dash 654134.25 504928.4508 149205.7992
Secure Best Marks with AI Grader
Need help grading? Try our AI Grader for instant feedback on your assignments.
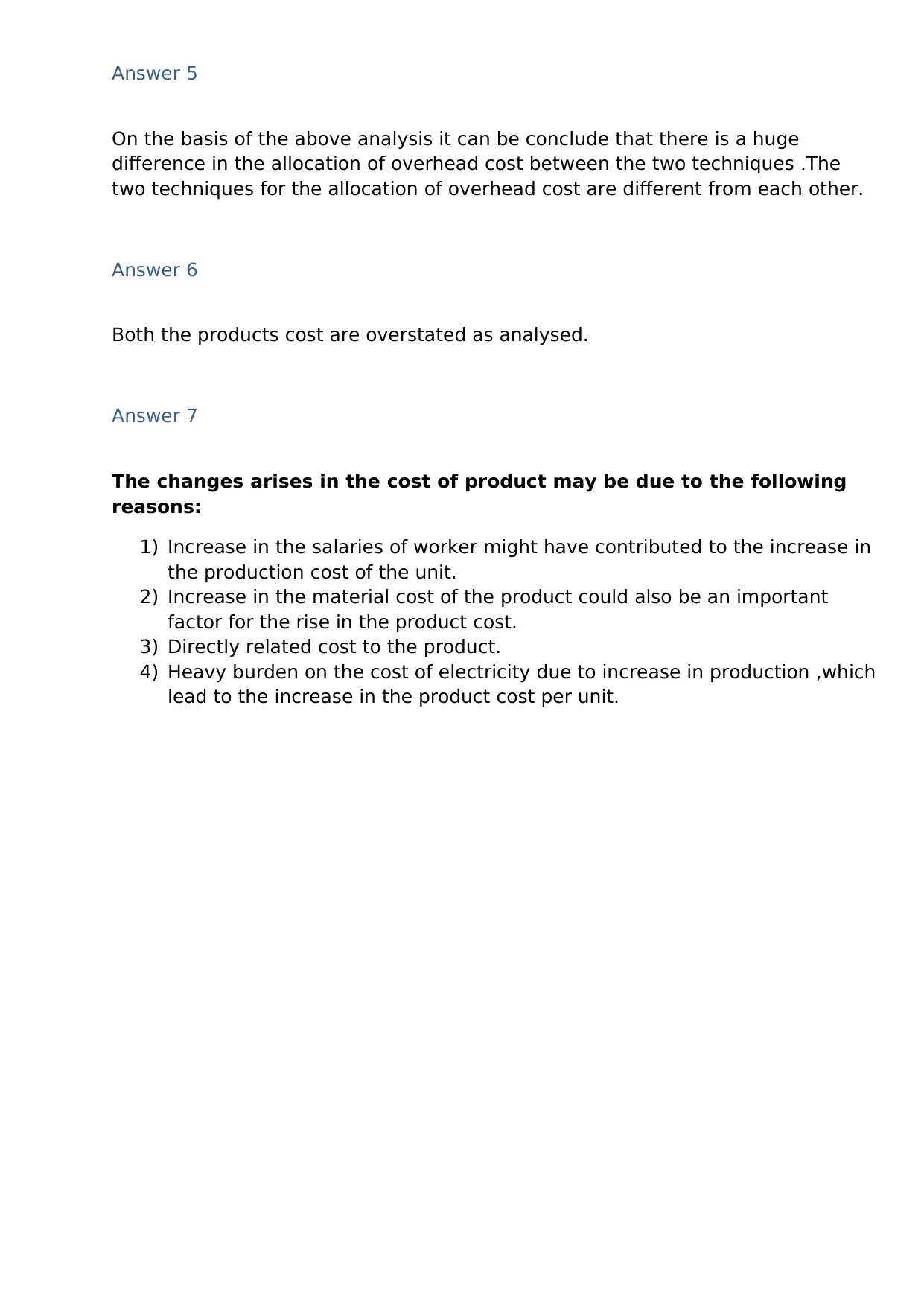
Answer 5
On the basis of the above analysis it can be conclude that there is a huge
difference in the allocation of overhead cost between the two techniques .The
two techniques for the allocation of overhead cost are different from each other.
Answer 6
Both the products cost are overstated as analysed.
Answer 7
The changes arises in the cost of product may be due to the following
reasons:
1) Increase in the salaries of worker might have contributed to the increase in
the production cost of the unit.
2) Increase in the material cost of the product could also be an important
factor for the rise in the product cost.
3) Directly related cost to the product.
4) Heavy burden on the cost of electricity due to increase in production ,which
lead to the increase in the product cost per unit.
On the basis of the above analysis it can be conclude that there is a huge
difference in the allocation of overhead cost between the two techniques .The
two techniques for the allocation of overhead cost are different from each other.
Answer 6
Both the products cost are overstated as analysed.
Answer 7
The changes arises in the cost of product may be due to the following
reasons:
1) Increase in the salaries of worker might have contributed to the increase in
the production cost of the unit.
2) Increase in the material cost of the product could also be an important
factor for the rise in the product cost.
3) Directly related cost to the product.
4) Heavy burden on the cost of electricity due to increase in production ,which
lead to the increase in the product cost per unit.
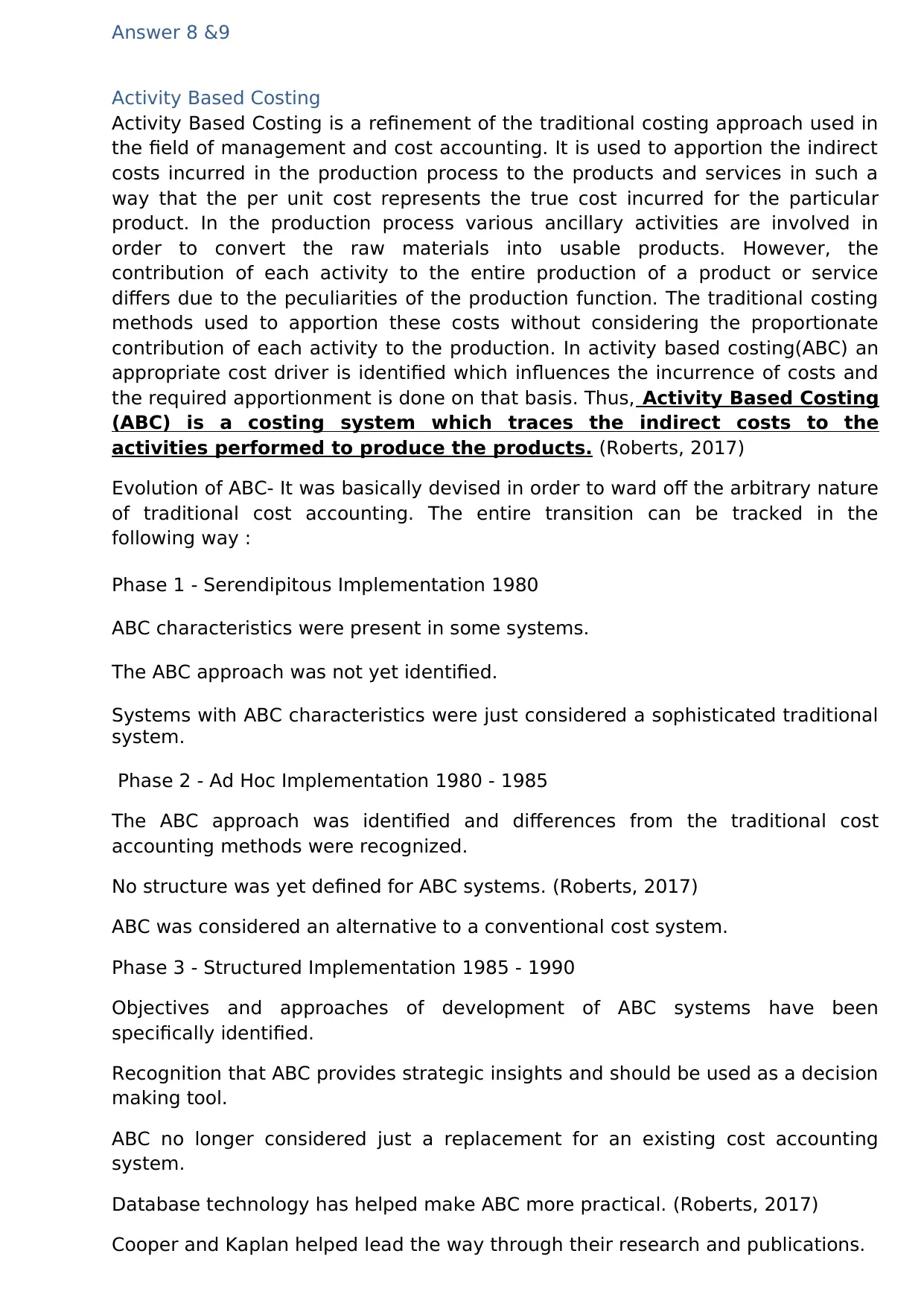
Answer 8 &9
Activity Based Costing
Activity Based Costing is a refinement of the traditional costing approach used in
the field of management and cost accounting. It is used to apportion the indirect
costs incurred in the production process to the products and services in such a
way that the per unit cost represents the true cost incurred for the particular
product. In the production process various ancillary activities are involved in
order to convert the raw materials into usable products. However, the
contribution of each activity to the entire production of a product or service
differs due to the peculiarities of the production function. The traditional costing
methods used to apportion these costs without considering the proportionate
contribution of each activity to the production. In activity based costing(ABC) an
appropriate cost driver is identified which influences the incurrence of costs and
the required apportionment is done on that basis. Thus, Activity Based Costing
(ABC) is a costing system which traces the indirect costs to the
activities performed to produce the products. (Roberts, 2017)
Evolution of ABC- It was basically devised in order to ward off the arbitrary nature
of traditional cost accounting. The entire transition can be tracked in the
following way :
Phase 1 - Serendipitous Implementation 1980
ABC characteristics were present in some systems.
The ABC approach was not yet identified.
Systems with ABC characteristics were just considered a sophisticated traditional
system.
Phase 2 - Ad Hoc Implementation 1980 - 1985
The ABC approach was identified and differences from the traditional cost
accounting methods were recognized.
No structure was yet defined for ABC systems. (Roberts, 2017)
ABC was considered an alternative to a conventional cost system.
Phase 3 - Structured Implementation 1985 - 1990
Objectives and approaches of development of ABC systems have been
specifically identified.
Recognition that ABC provides strategic insights and should be used as a decision
making tool.
ABC no longer considered just a replacement for an existing cost accounting
system.
Database technology has helped make ABC more practical. (Roberts, 2017)
Cooper and Kaplan helped lead the way through their research and publications.
Activity Based Costing
Activity Based Costing is a refinement of the traditional costing approach used in
the field of management and cost accounting. It is used to apportion the indirect
costs incurred in the production process to the products and services in such a
way that the per unit cost represents the true cost incurred for the particular
product. In the production process various ancillary activities are involved in
order to convert the raw materials into usable products. However, the
contribution of each activity to the entire production of a product or service
differs due to the peculiarities of the production function. The traditional costing
methods used to apportion these costs without considering the proportionate
contribution of each activity to the production. In activity based costing(ABC) an
appropriate cost driver is identified which influences the incurrence of costs and
the required apportionment is done on that basis. Thus, Activity Based Costing
(ABC) is a costing system which traces the indirect costs to the
activities performed to produce the products. (Roberts, 2017)
Evolution of ABC- It was basically devised in order to ward off the arbitrary nature
of traditional cost accounting. The entire transition can be tracked in the
following way :
Phase 1 - Serendipitous Implementation 1980
ABC characteristics were present in some systems.
The ABC approach was not yet identified.
Systems with ABC characteristics were just considered a sophisticated traditional
system.
Phase 2 - Ad Hoc Implementation 1980 - 1985
The ABC approach was identified and differences from the traditional cost
accounting methods were recognized.
No structure was yet defined for ABC systems. (Roberts, 2017)
ABC was considered an alternative to a conventional cost system.
Phase 3 - Structured Implementation 1985 - 1990
Objectives and approaches of development of ABC systems have been
specifically identified.
Recognition that ABC provides strategic insights and should be used as a decision
making tool.
ABC no longer considered just a replacement for an existing cost accounting
system.
Database technology has helped make ABC more practical. (Roberts, 2017)
Cooper and Kaplan helped lead the way through their research and publications.

The following are the advantages of ABC system:
It takes into account all the costs associated with the production of a
product or a service.
It facilitates the bifurcation of production costs from administration costs.
It provides a more scientific and prudent base for decision making as the
cost figures are more reliable.
In contrast, the following are the disadvantages of ABC system:
It is not recognised by Generally Accepted Accounting Principles (GAAP), so,
it cannot be used for official record keeping.
This ABC costing technique is much more complex as compared to the
traditional approach.
ABSORPTION COSTING
Absorption costing is a method a costing in which all overhead are apportioned
on the basis of the cost centers.This method of costing particularly consider that
whatever cost is incurred during the production of goods is ultimately recovered
from the final consumer of goods. (CFI Education Inc., 2019)
EVOLUTION OF ABSORPTION COSTING
The history of absorption costing is closely linked with the history of cost
accounting. At beginning, companies usually dealt with single or narrow range of
products. The direct labour was larger parts of production cost and overhead cost
was therefore smaller. Therefore there was no distortion that resulted from
inappropriate overhead allocation were not evident.
Advantages of Absorption Costing
This method of costing is used for internal purpose and is also recognised by
Financial Accounting Standards Board(FASB).
It is the simple , inexpensive and less complex type of costing. (Singh, 2017)
This costing technique report is also required for the preparation of tax by
Internal Revenue Service..
This method of costing is very easy to compute and very reliable as it
consider fixed overhead also in arriving at the cost per unit of production.
(Singh, 2017).
Responsibility of the managers and staff also increases in case of absorption
costing method . (Audit It, 2019)
DISADVANTAGES OF ABSORPTION COSTING
Absorption costing is dependent on level of output; so different unit costs are
obtained for different levels of output. An increase in the volume of output
normally results in reduced unit cost and a reduction in output results in an
increased cost per unit due to the existence of fixed expenses. This makes
comparison and control of cost difficult.
In this technique of costing the fixed cost incurred is transferred to the next
year also as the closing stock is inclusive of the fixed cost incurred.
It takes into account all the costs associated with the production of a
product or a service.
It facilitates the bifurcation of production costs from administration costs.
It provides a more scientific and prudent base for decision making as the
cost figures are more reliable.
In contrast, the following are the disadvantages of ABC system:
It is not recognised by Generally Accepted Accounting Principles (GAAP), so,
it cannot be used for official record keeping.
This ABC costing technique is much more complex as compared to the
traditional approach.
ABSORPTION COSTING
Absorption costing is a method a costing in which all overhead are apportioned
on the basis of the cost centers.This method of costing particularly consider that
whatever cost is incurred during the production of goods is ultimately recovered
from the final consumer of goods. (CFI Education Inc., 2019)
EVOLUTION OF ABSORPTION COSTING
The history of absorption costing is closely linked with the history of cost
accounting. At beginning, companies usually dealt with single or narrow range of
products. The direct labour was larger parts of production cost and overhead cost
was therefore smaller. Therefore there was no distortion that resulted from
inappropriate overhead allocation were not evident.
Advantages of Absorption Costing
This method of costing is used for internal purpose and is also recognised by
Financial Accounting Standards Board(FASB).
It is the simple , inexpensive and less complex type of costing. (Singh, 2017)
This costing technique report is also required for the preparation of tax by
Internal Revenue Service..
This method of costing is very easy to compute and very reliable as it
consider fixed overhead also in arriving at the cost per unit of production.
(Singh, 2017).
Responsibility of the managers and staff also increases in case of absorption
costing method . (Audit It, 2019)
DISADVANTAGES OF ABSORPTION COSTING
Absorption costing is dependent on level of output; so different unit costs are
obtained for different levels of output. An increase in the volume of output
normally results in reduced unit cost and a reduction in output results in an
increased cost per unit due to the existence of fixed expenses. This makes
comparison and control of cost difficult.
In this technique of costing the fixed cost incurred is transferred to the next
year also as the closing stock is inclusive of the fixed cost incurred.
Paraphrase This Document
Need a fresh take? Get an instant paraphrase of this document with our AI Paraphraser
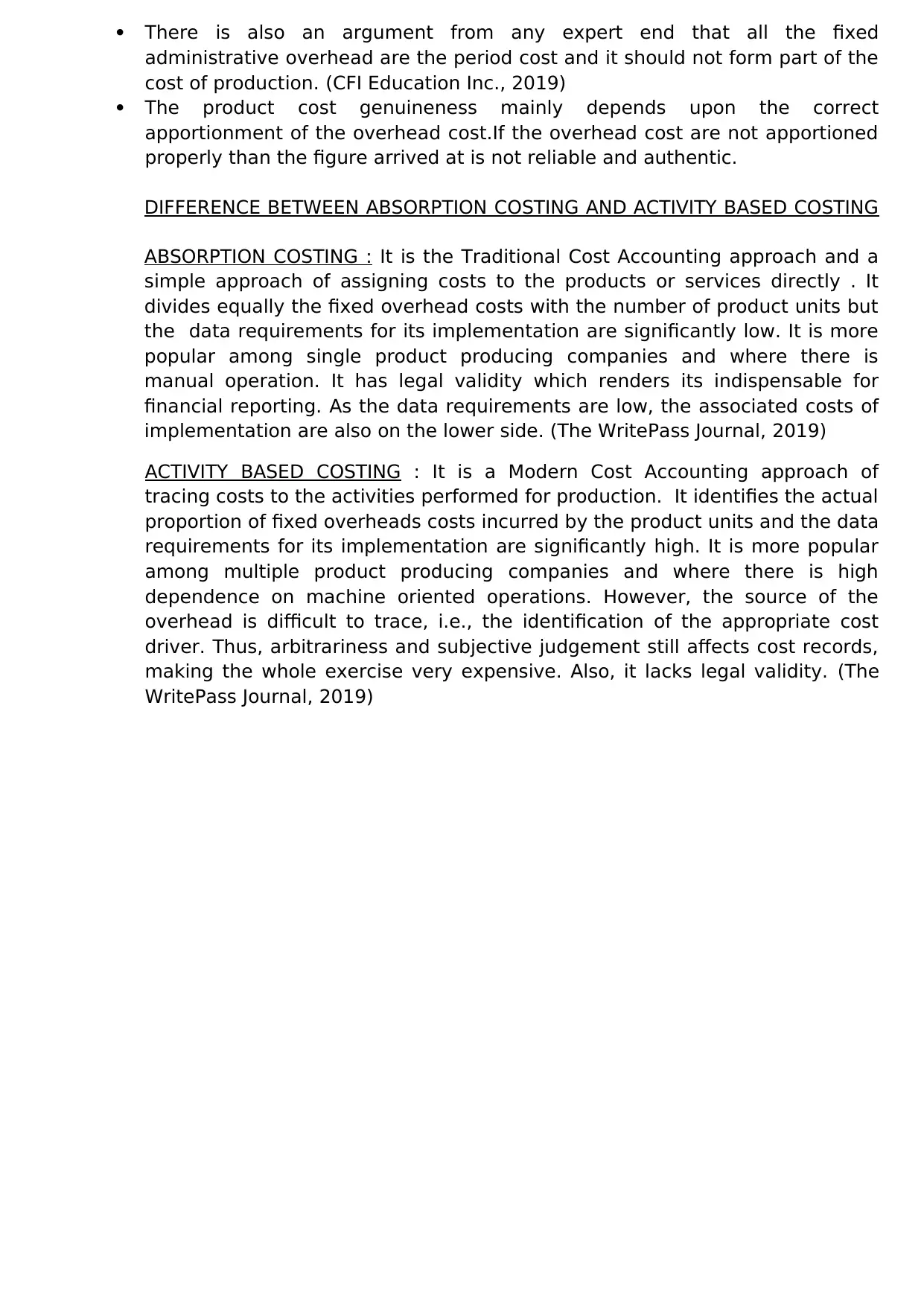
There is also an argument from any expert end that all the fixed
administrative overhead are the period cost and it should not form part of the
cost of production. (CFI Education Inc., 2019)
The product cost genuineness mainly depends upon the correct
apportionment of the overhead cost.If the overhead cost are not apportioned
properly than the figure arrived at is not reliable and authentic.
DIFFERENCE BETWEEN ABSORPTION COSTING AND ACTIVITY BASED COSTING
ABSORPTION COSTING : It is the Traditional Cost Accounting approach and a
simple approach of assigning costs to the products or services directly . It
divides equally the fixed overhead costs with the number of product units but
the data requirements for its implementation are significantly low. It is more
popular among single product producing companies and where there is
manual operation. It has legal validity which renders its indispensable for
financial reporting. As the data requirements are low, the associated costs of
implementation are also on the lower side. (The WritePass Journal, 2019)
ACTIVITY BASED COSTING : It is a Modern Cost Accounting approach of
tracing costs to the activities performed for production. It identifies the actual
proportion of fixed overheads costs incurred by the product units and the data
requirements for its implementation are significantly high. It is more popular
among multiple product producing companies and where there is high
dependence on machine oriented operations. However, the source of the
overhead is difficult to trace, i.e., the identification of the appropriate cost
driver. Thus, arbitrariness and subjective judgement still affects cost records,
making the whole exercise very expensive. Also, it lacks legal validity. (The
WritePass Journal, 2019)
administrative overhead are the period cost and it should not form part of the
cost of production. (CFI Education Inc., 2019)
The product cost genuineness mainly depends upon the correct
apportionment of the overhead cost.If the overhead cost are not apportioned
properly than the figure arrived at is not reliable and authentic.
DIFFERENCE BETWEEN ABSORPTION COSTING AND ACTIVITY BASED COSTING
ABSORPTION COSTING : It is the Traditional Cost Accounting approach and a
simple approach of assigning costs to the products or services directly . It
divides equally the fixed overhead costs with the number of product units but
the data requirements for its implementation are significantly low. It is more
popular among single product producing companies and where there is
manual operation. It has legal validity which renders its indispensable for
financial reporting. As the data requirements are low, the associated costs of
implementation are also on the lower side. (The WritePass Journal, 2019)
ACTIVITY BASED COSTING : It is a Modern Cost Accounting approach of
tracing costs to the activities performed for production. It identifies the actual
proportion of fixed overheads costs incurred by the product units and the data
requirements for its implementation are significantly high. It is more popular
among multiple product producing companies and where there is high
dependence on machine oriented operations. However, the source of the
overhead is difficult to trace, i.e., the identification of the appropriate cost
driver. Thus, arbitrariness and subjective judgement still affects cost records,
making the whole exercise very expensive. Also, it lacks legal validity. (The
WritePass Journal, 2019)
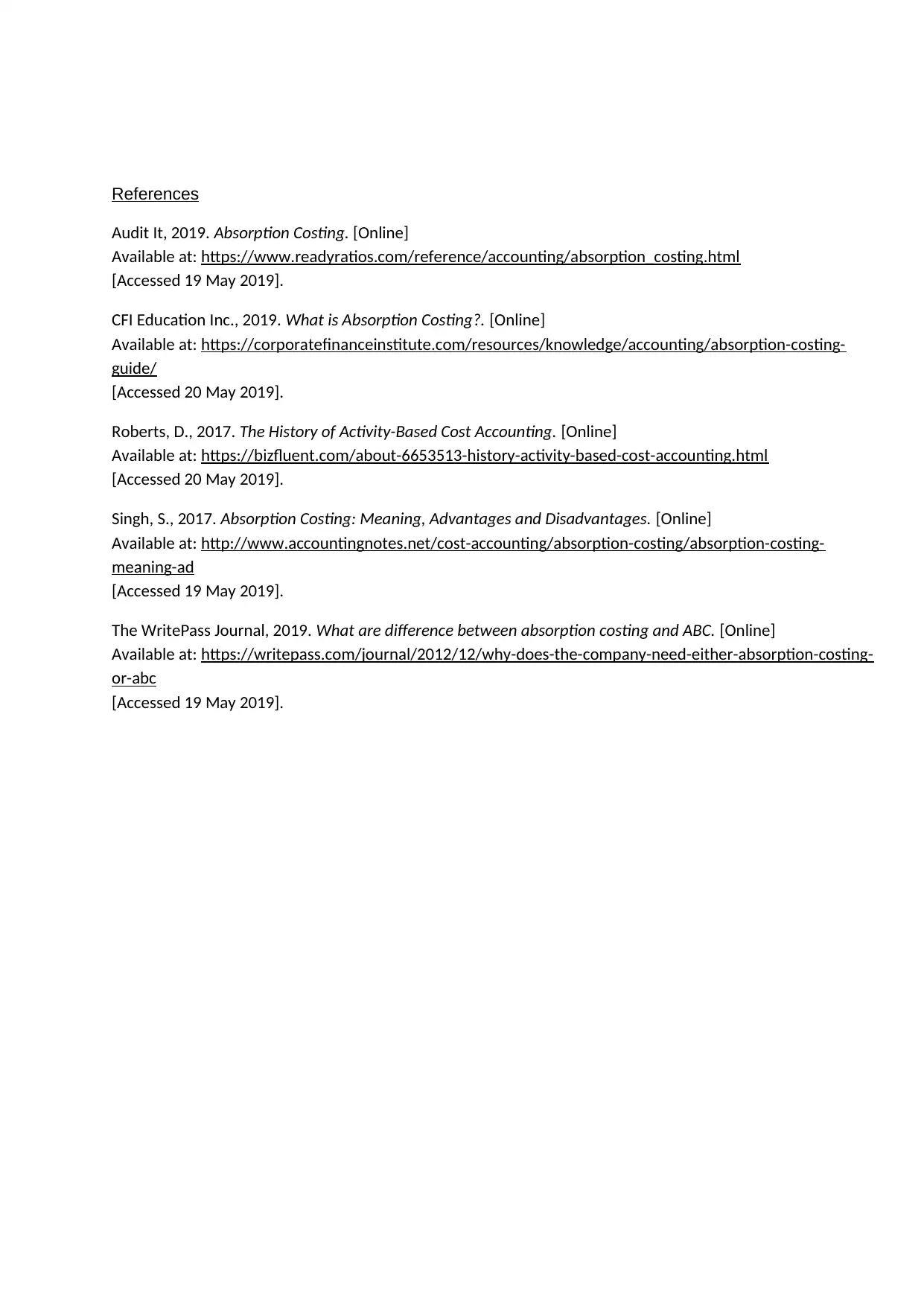
References
Audit It, 2019. Absorption Costing. [Online]
Available at: https://www.readyratios.com/reference/accounting/absorption_costing.html
[Accessed 19 May 2019].
CFI Education Inc., 2019. What is Absorption Costing?. [Online]
Available at: https://corporatefinanceinstitute.com/resources/knowledge/accounting/absorption-costing-
guide/
[Accessed 20 May 2019].
Roberts, D., 2017. The History of Activity-Based Cost Accounting. [Online]
Available at: https://bizfluent.com/about-6653513-history-activity-based-cost-accounting.html
[Accessed 20 May 2019].
Singh, S., 2017. Absorption Costing: Meaning, Advantages and Disadvantages. [Online]
Available at: http://www.accountingnotes.net/cost-accounting/absorption-costing/absorption-costing-
meaning-ad
[Accessed 19 May 2019].
The WritePass Journal, 2019. What are difference between absorption costing and ABC. [Online]
Available at: https://writepass.com/journal/2012/12/why-does-the-company-need-either-absorption-costing-
or-abc
[Accessed 19 May 2019].
Audit It, 2019. Absorption Costing. [Online]
Available at: https://www.readyratios.com/reference/accounting/absorption_costing.html
[Accessed 19 May 2019].
CFI Education Inc., 2019. What is Absorption Costing?. [Online]
Available at: https://corporatefinanceinstitute.com/resources/knowledge/accounting/absorption-costing-
guide/
[Accessed 20 May 2019].
Roberts, D., 2017. The History of Activity-Based Cost Accounting. [Online]
Available at: https://bizfluent.com/about-6653513-history-activity-based-cost-accounting.html
[Accessed 20 May 2019].
Singh, S., 2017. Absorption Costing: Meaning, Advantages and Disadvantages. [Online]
Available at: http://www.accountingnotes.net/cost-accounting/absorption-costing/absorption-costing-
meaning-ad
[Accessed 19 May 2019].
The WritePass Journal, 2019. What are difference between absorption costing and ABC. [Online]
Available at: https://writepass.com/journal/2012/12/why-does-the-company-need-either-absorption-costing-
or-abc
[Accessed 19 May 2019].
1 out of 15
Related Documents
![[object Object]](/_next/image/?url=%2F_next%2Fstatic%2Fmedia%2Flogo.6d15ce61.png&w=640&q=75)
Your All-in-One AI-Powered Toolkit for Academic Success.
+13062052269
info@desklib.com
Available 24*7 on WhatsApp / Email
Unlock your academic potential
© 2024 | Zucol Services PVT LTD | All rights reserved.