Additive manufacturing popularly PDF
6 Pages1992 Words58 Views
Added on 2021-05-31
Additive manufacturing popularly PDF
Added on 2021-05-31
ShareRelated Documents
INTRODUCION:Additive manufacturing popularly said as rapid prototyping or 3D printing has gained itsattention recently that uses the principle of addition of materials in a layer with the particularprocesses. This requires an additional material to be fitted which seems to be designed with thehelp of certain software in a 3-dimensional structure. This can be directly implemented in thereal-time application purpose, thereby decreasing its time and the complication. Instead ofremoving the materials, the addition of materials serves the system as a better head conductorand makes them lighter (Guan, Qin, Liu, Yin, Peng, Lv, Sun and Wu, 2016). This could removecertain constrains that are created by the conventional manufacturing by adding the materialslayer by layer. At first, the materials are added in a thin powdered layer to the building platformand with the help of the laser, the powder diffuses in certain points by a computer-generatedcomponent design data. Then another layer is placed that fuses the material to form a predefinedstructure. The additive manufacturing technology can be used in wide variety of fields startingfrom the medical and marine application to the electronics and consumer accessories. Process involved in Additive Manufacturing:Several processes are involved in a metal additive manufacturing and they are as follows.Figure 1: Block diagram of the stages involved in the metal additive manufacturing.Material deposition process:
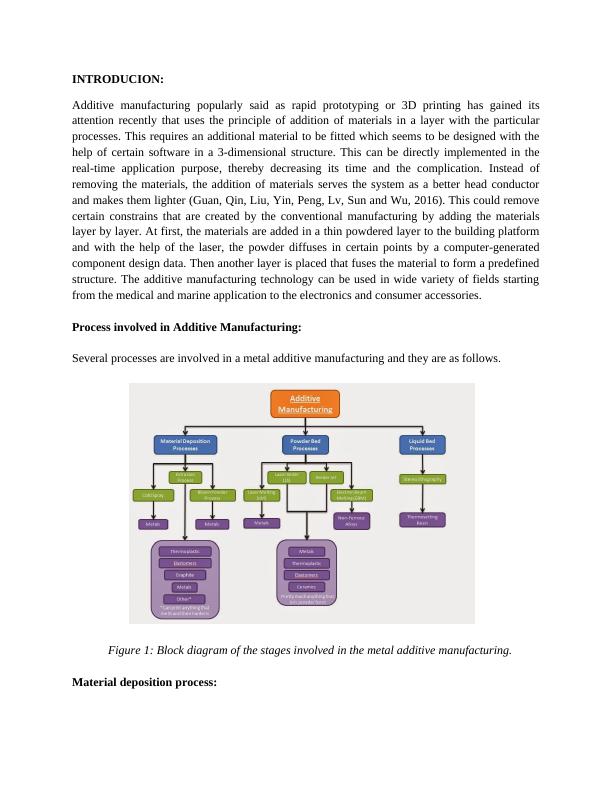
This method transports the material from the powder jet or the filament into the surface. Thedepth of the layer could vary in a certain micrometers range. The important factor monitoredover here is the flow rates of the material either a powder or a polymer. Depending on thepowder size the flow rate should be estimated. The material is supplied in 2 axes although it’s a3D axes. With the help of this process we could eliminate the usage of any support material thatdoes not cause a viable geometry. Material deposition could be done with the help of cold spray,Extrusion process, and blown powder process. Power bed process:a) Laser beam Melting:Additive manufacturing involves several ways in the deposition of the layers. Selective LaserMelting (SLM) and Selective Laser Sintering (SLS) process melts and softens the layer settled inthe material. Certain industries use the metal powder or the polymer in the production of thelayers. In the process of laser beam, the high intensity laser is used to melt the metal. Meltingprocess involves the material of powdered form. The powder is spread equally with the help ofrecoater arm, and the laser power of about 50-2000 W has been used to solidify the process.When this is done, then another layer of powder is coated thereby lowering the depth of thematerial. This particular process is carried out in an inert temperature of argon or heliumatmosphere since the powder can easily oxidize. When the depth of the layer is small then themanufacturing part is well defined, although the time of manufacturing increases. A heat post-treatment is necessarily carried out to remove the deformation of the materials or polishing thesurface. This should be done in a controlled environment in order to increase its precision rate.Similarly, the material used in the Laser polymerization is the photosensitive resin. This processis cured with the help of the UV radiation from the low intense laser source.b)Electron Beam Melting:This process is more productive when compared to the laser in its features. This process uses anelectron beam of maximum power of about 3kW. This is also carried out with the certaintemperature in an inert gas environment. The powder used should be preheated that neglects thethermal gradient. Although the temperature (Yang, Yhang, Song, Chen, Shen and Yang, 2016)used here is very high, the cooling procedure is also carried out to avoid the internal stress of thematerial. The powder could move at a faster rate that works well with the huge depth of thelayers. But due to its broad beam width, this method is not precise and it is not sufficient whencompared to the laser beam method. Liquid Bed process:This involves the process of Stereo lithography and thermosetting resin. The principle of photo-polymerization is involved in the Stereo lithography procedure. The lower power helium-
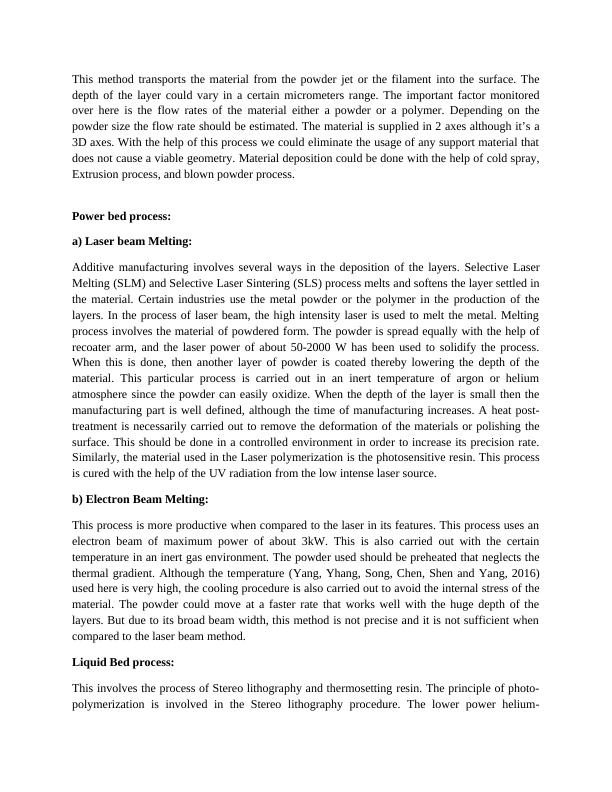
cadmium UV radiation has been used in this process. This UV radiation coagulates to form a thinlayer in the surface of the material. A SLA machine is built in such a way that the whole processis engrossed in a liquid resin with the laser source and the required hardware and softwareplatform is also built. With the CAD model (Wilkinson, Turnbull, Yan, Stitt and Marigo, 2017),the layer is being scanned and once this process is done the inner portion is engraved andundated below a layer. A blade is used to remove the extra fitted layer to ensure the flatness ofthe surface. After this process the next layer is deposited and again the procedure is carried outlike the previous one. With this method we can able to produce a highly accurate polymer parts.The process of Stereo lithography is shown in the FigureFigure 2: Parts involved in Stereo lithographyQuality of the surface and their accuracy:Surface quality is the most important feature to be considered in the Additive manufacturing.Depending on the particle size, the surface should be used in manufacturing. When the particlesize is huge of above 30μm, then the surface produced by the Selective Laser Melting will becoarse (Giuntini, Chen and Olevsky, 2016). However, less particle size of below 20 μm couldproduce a smooth and a polished surface. There is a drawback in using the fine sized particle asit could hinders the flow rate of the particle in the layer thereby increasing the cost. The surfacequality is the most important concern in the quality estimation (Molla, Bjork, Olevsky, Pryds andFrandsen, 2014). Certain process involves the fine powder layer for instance, Binder jettingprocess (BJG). The tolerance level should also been taken into consideration due to its heat
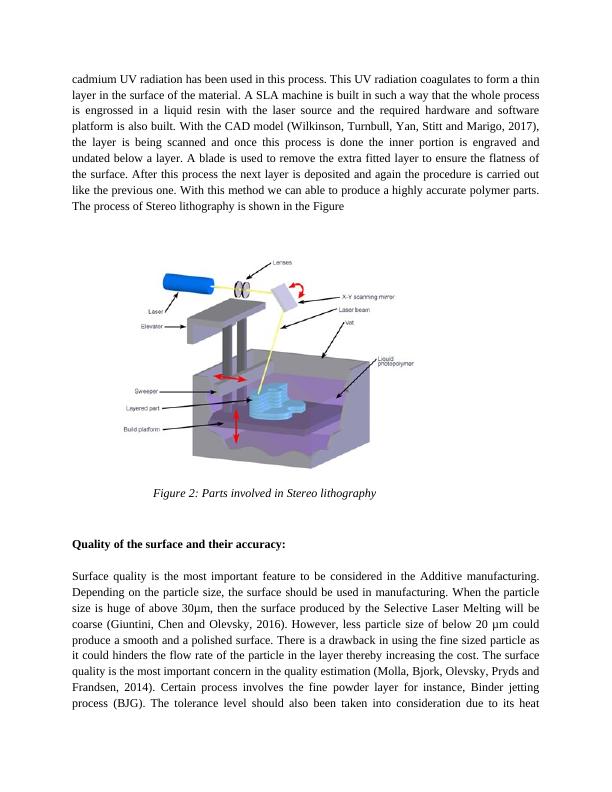
End of preview
Want to access all the pages? Upload your documents or become a member.
Related Documents
Laser Metal Deposition: Additive Manufacturing Technologylg...
|39
|8927
|249
Ultrasonic Vibration Assisted Laser Engineered Net Shapinglg...
|8
|1750
|98
Report on Selective Laser Meltinglg...
|6
|690
|316
Metal Additive Manufacturing (AM)lg...
|15
|3036
|95
(PDF) The Processes and Technologies of 3D Printinglg...
|5
|2828
|46
Laser Cladding Materialslg...
|32
|8841
|144