Asset Management - Question and Answer
Overview of RCM methodology, benefits and limitations; Overview of FMEA process, benefits and limitations; Review of one Journal Article on RCM implementation case study
7 Pages3315 Words10 Views
Added on 2022-09-14
Asset Management - Question and Answer
Overview of RCM methodology, benefits and limitations; Overview of FMEA process, benefits and limitations; Review of one Journal Article on RCM implementation case study
Added on 2022-09-14
ShareRelated Documents
Asset Management 1
Managing assets
By (name)
College:
Date:
Managing assets
By (name)
College:
Date:
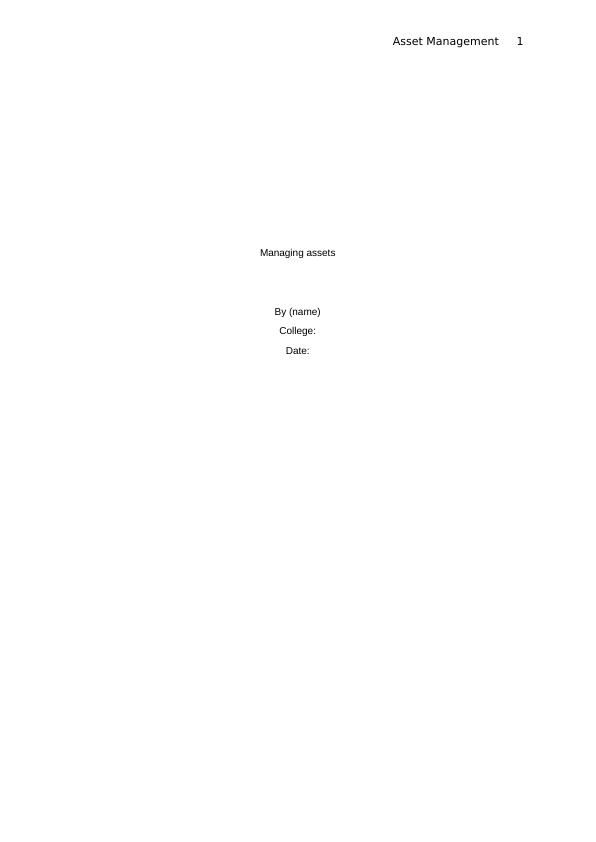
Asset Management 2
Question 1: Reflective Essay
An overview of RCM methodology
Reliability centered maintenance is a decision procedure or process that is designed to establish
management policies for the identification, selection and prioritization of system component failures
(Anderson & Neri, 2012). These policies are usually in the form of system design modifications,
operational changes, maintenance activities or actions aimed to reduce failure consequences. It is a
systematic method that assesses and optimizes the performance of preventive maintenance tasks.
Through reliability centered maintenance, effective preventive maintenance demands for equipment
are identified with respect to safety economic and operational consequences as well as the
degradation ways responsible for the system failures (Besnard, Fischer, & Bertling, 2010). Developed
in the 1960s for the aviation sector, RCM application has spread and is currently used in many
assorted industries such as the marine and power distribution systems (Almeida et al., 2015). RCM
involves the consideration of system characteristics such as system functions, the ways these
functions can fail, safety and economics based on priorities and the identification of effective and
applicable preventive maintenance actions (Raheja & Gullo, 2012). The principles of reliability
centered maintenance can be summarised as follows:
i) To maintain the functionalities of a system or its components
ii) To identify possible failure modes that can cripple system functions
iii) To assign system functions priorities according to corresponding failure modes
iv) To select effective and reasonable preventive maintenance actions for failure modes
assigned high priorities.
The steps involved in the implementation of reliability centered processes or programs include
(Gehris, 2015):
i) The identification of functions
ii) Determination of the causes of function failures
iii) The identification of system or component failure modes
iv) Establishment of the effects resulting from the identified failure modes
v) Determination of the consequences associated with these failure modes
vi) The development of tasks and actions for the maintenance of the system or its
components
Some important terminologies associated with reliability centered maintenance include (Carnero &
González-Prida, 2016):
Functional failure
This refers to the inability of a component or equipment to satisfactorily perform its intended function.
Failure mode
This specifies the manner in which the equipment fails to meet its performance specifications
Failure effect
This can be defined as the impact the failure has on the overall expectations the component is to
fulfill.
Reliability
This is the possibility that given equipment will perform its specified function satisfactorily under
certain operating conditions and a given time frame.
Advantages of RCM
i) With RCM, it is possible to considerably lower the cost required to maintain and repair an
apparatus as a result of the great focus on the improvement of equipment reliability
ii) RCM eliminates or minimizes the consequences of system failure which may be fatal
leading to the compromise of human safety (Selvik & Aven, 2011)
iii) It eliminates the unnecessary replacement of system components unless it is necessary
Question 1: Reflective Essay
An overview of RCM methodology
Reliability centered maintenance is a decision procedure or process that is designed to establish
management policies for the identification, selection and prioritization of system component failures
(Anderson & Neri, 2012). These policies are usually in the form of system design modifications,
operational changes, maintenance activities or actions aimed to reduce failure consequences. It is a
systematic method that assesses and optimizes the performance of preventive maintenance tasks.
Through reliability centered maintenance, effective preventive maintenance demands for equipment
are identified with respect to safety economic and operational consequences as well as the
degradation ways responsible for the system failures (Besnard, Fischer, & Bertling, 2010). Developed
in the 1960s for the aviation sector, RCM application has spread and is currently used in many
assorted industries such as the marine and power distribution systems (Almeida et al., 2015). RCM
involves the consideration of system characteristics such as system functions, the ways these
functions can fail, safety and economics based on priorities and the identification of effective and
applicable preventive maintenance actions (Raheja & Gullo, 2012). The principles of reliability
centered maintenance can be summarised as follows:
i) To maintain the functionalities of a system or its components
ii) To identify possible failure modes that can cripple system functions
iii) To assign system functions priorities according to corresponding failure modes
iv) To select effective and reasonable preventive maintenance actions for failure modes
assigned high priorities.
The steps involved in the implementation of reliability centered processes or programs include
(Gehris, 2015):
i) The identification of functions
ii) Determination of the causes of function failures
iii) The identification of system or component failure modes
iv) Establishment of the effects resulting from the identified failure modes
v) Determination of the consequences associated with these failure modes
vi) The development of tasks and actions for the maintenance of the system or its
components
Some important terminologies associated with reliability centered maintenance include (Carnero &
González-Prida, 2016):
Functional failure
This refers to the inability of a component or equipment to satisfactorily perform its intended function.
Failure mode
This specifies the manner in which the equipment fails to meet its performance specifications
Failure effect
This can be defined as the impact the failure has on the overall expectations the component is to
fulfill.
Reliability
This is the possibility that given equipment will perform its specified function satisfactorily under
certain operating conditions and a given time frame.
Advantages of RCM
i) With RCM, it is possible to considerably lower the cost required to maintain and repair an
apparatus as a result of the great focus on the improvement of equipment reliability
ii) RCM eliminates or minimizes the consequences of system failure which may be fatal
leading to the compromise of human safety (Selvik & Aven, 2011)
iii) It eliminates the unnecessary replacement of system components unless it is necessary
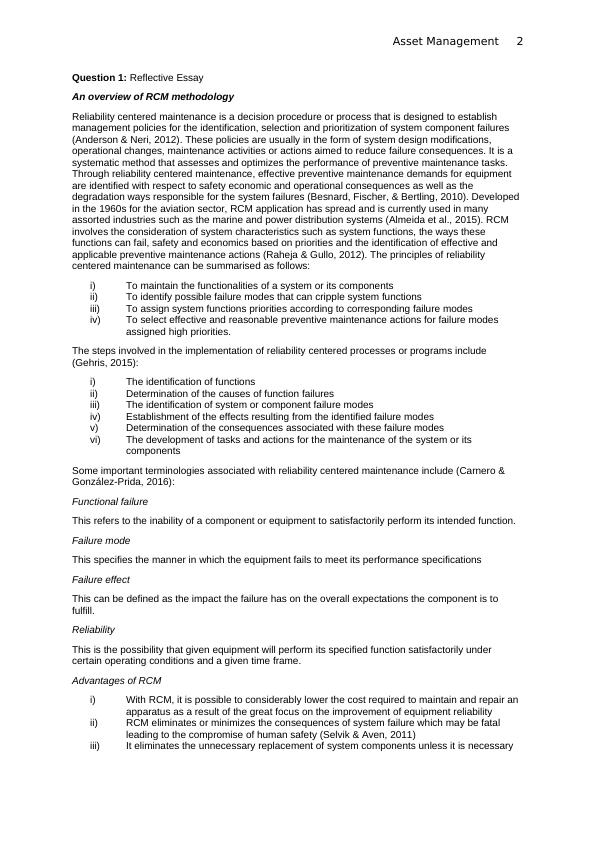
Asset Management 3
Disadvantages of RCM
i) It is usually very expensive to initiate an RCM program because it is necessary to
purchase technological equipment
ii) Industries normally have large a number of equipment hence selection of maintenance
procedures for components is time-consuming
iii) The high initial cost of its initiation makes RCM’s ability to save costs somehow blurred to
the management (Clifton A. Ericson, 2015).
An overview of FMEA process
Failure mode and effects analysis is a process for the systematic analysis of a system with the aim to
identify possible system failure modes, their causes as well as the effects they have on the
performance of the system (Sarno Severi, 2014). This process requires a team effort and can be
applied at various levels of system abstraction. FMEA is an iterative process. This means that new
steps are added with the increase in the knowledge and understanding of the system or equipment
(Carlson, 2012). FMEA aims to achieve the following objectives (Carlson, 2012):
i) To enable system reliability improvement and safety through design modifications, quality
assurance, and maintainability
ii) To set the foundation for the establishment of priority corrective actions
iii) To identify possible system failures, their magnitude and effects
iv) Ensure that all probable system failure modes are identified including their effects on the
functionality of the system
v) Help in the evaluation of redundancies related to system requirements, manual and
automatic override and systems for failure detection
vi) To allow for the documentation of system operations for future reference in the analysis of
failures and design alterations
Major terminologies associated with FMEA analysis
Failure severity
This estimates how adversely the effects of failure will impact the system under consideration
Failure probability
This is a number that gives the probability or possibility or the likelihood of the failure happening
Failure detectability
This gives an estimate of the ability to identify and eliminate system failure before it can adversely
affect the system
Risk priority number
The risk priority number (RPN) = failure severity × failure probability × failure detectability (Raheja &
Gullo, 2012)
A universal method of conducting the FMEA procedure does not exist (Singh, 2017). However, the
following steps are generally followed (Dietz, 2015):
i) Identification of system elements and functions
ii) Identification of possible system failure modes which are dependent on the life cycle
profile of the system components
iii) Determination of the causes leading to system failure
iv) Identification of possible failure mechanisms and the development of failure models
v) Prioritization of the failure mechanisms
vi) Documentation of the entire FMEA process
Benefits of FMEA analysis
i) FMEA makes it possible to detect design deficiencies early enough to prevent
catastrophic system failure (Haimes, 2015)
Disadvantages of RCM
i) It is usually very expensive to initiate an RCM program because it is necessary to
purchase technological equipment
ii) Industries normally have large a number of equipment hence selection of maintenance
procedures for components is time-consuming
iii) The high initial cost of its initiation makes RCM’s ability to save costs somehow blurred to
the management (Clifton A. Ericson, 2015).
An overview of FMEA process
Failure mode and effects analysis is a process for the systematic analysis of a system with the aim to
identify possible system failure modes, their causes as well as the effects they have on the
performance of the system (Sarno Severi, 2014). This process requires a team effort and can be
applied at various levels of system abstraction. FMEA is an iterative process. This means that new
steps are added with the increase in the knowledge and understanding of the system or equipment
(Carlson, 2012). FMEA aims to achieve the following objectives (Carlson, 2012):
i) To enable system reliability improvement and safety through design modifications, quality
assurance, and maintainability
ii) To set the foundation for the establishment of priority corrective actions
iii) To identify possible system failures, their magnitude and effects
iv) Ensure that all probable system failure modes are identified including their effects on the
functionality of the system
v) Help in the evaluation of redundancies related to system requirements, manual and
automatic override and systems for failure detection
vi) To allow for the documentation of system operations for future reference in the analysis of
failures and design alterations
Major terminologies associated with FMEA analysis
Failure severity
This estimates how adversely the effects of failure will impact the system under consideration
Failure probability
This is a number that gives the probability or possibility or the likelihood of the failure happening
Failure detectability
This gives an estimate of the ability to identify and eliminate system failure before it can adversely
affect the system
Risk priority number
The risk priority number (RPN) = failure severity × failure probability × failure detectability (Raheja &
Gullo, 2012)
A universal method of conducting the FMEA procedure does not exist (Singh, 2017). However, the
following steps are generally followed (Dietz, 2015):
i) Identification of system elements and functions
ii) Identification of possible system failure modes which are dependent on the life cycle
profile of the system components
iii) Determination of the causes leading to system failure
iv) Identification of possible failure mechanisms and the development of failure models
v) Prioritization of the failure mechanisms
vi) Documentation of the entire FMEA process
Benefits of FMEA analysis
i) FMEA makes it possible to detect design deficiencies early enough to prevent
catastrophic system failure (Haimes, 2015)
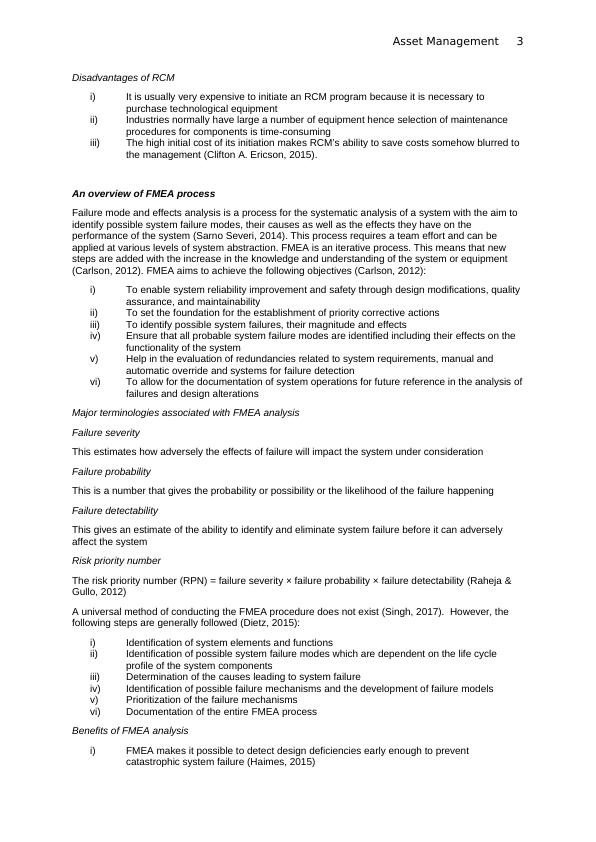
End of preview
Want to access all the pages? Upload your documents or become a member.
Related Documents
RCM Methodology Reliabilitylg...
|14
|3194
|84
The program thus focusses on the systemlg...
|7
|3308
|17
The final step involves the evaluation of the worthlg...
|6
|3250
|23
An overview of RCM and FMEAlg...
|7
|3530
|23
Reliable Centered Maintenancelg...
|6
|1208
|41
Reliability Centred Maintenance: Principles, Analysis, and Advantageslg...
|21
|1406
|27