The final step involves the evaluation of the worth
Provide an overview of RCM methodology, identify the benefits and limitations of this process. Provide an overview of FMEA process, identify its benefits and limitations. Review one Journal Article on RCM implementation case study and provide a summary. Develop an FMEA Worksheet for a given system and identify top three failure modes successfully mitigated by the team's recommended actions.
Added on 2022-09-18
The final step involves the evaluation of the worth
Provide an overview of RCM methodology, identify the benefits and limitations of this process. Provide an overview of FMEA process, identify its benefits and limitations. Review one Journal Article on RCM implementation case study and provide a summary. Develop an FMEA Worksheet for a given system and identify top three failure modes successfully mitigated by the team's recommended actions.
Added on 2022-09-18
Author:
Question 1: Reflective Essay
An overview of RCM methodology
Reliability Centred maintenance is a method that qualitatively analyses and determines the most
effective and applicable preventive maintenance tasks that can be used to maintain the primary
function of a certain system or its components [1]. Initially, it was developed primarily for the aviation
sector in the 1960s [1]. It is widely applied in industrial systems due to its ability to boost the cost-
effectiveness of programs aimed at maintaining these systems and providing a crucial understanding
of the severity of failure modes that may interfere with the normal operation of a system. RCM uses a
philosophy of preventive maintenance, real-time monitoring, predictive maintenance, and proactive
maintenance. It integrates all these techniques in a manner that increases the probability of a
component or a system functioning in a desired manner over the life cycle of its design with minimal
maintenance [2]. The RCM procedure can be generally summarized through the steps listed below:
i) The first step is to have an outline and definition of the functions of the critical
components in the desired system [2].
ii) The next step involves the identification of the dominant failure modes associated with
each component identified in step one. The failure mode severity is then prioritized from
the history of the components’ failure consequences [2].
iii) The preventive maintenance tasks are then determined for the critical failure modes.
iv) An RCM process or program is then formulated for the system’s components.
v) The final step involves the evaluation of the worth of the RCM program. This usually
includes cost analysis [2].
The operation of RCM involves a balance between the cost of predictive or preventive policies and the
high maintenance costs while taking into consideration the possibility of shortening the useful life of
the considered item or component [3].
Advantages of RCM
i) The major advantage of RCM is that it achieves the maximum utilisation of equipment. A
component is replaced based on its actual condition rather than a pre-determined life-
length [4]
ii) Repair and maintenance costs are reduced due to the great emphasis placed on
improving equipment reliability.
iii) It helps avoid environmental and property damage as well as injury or the loss of human
life.
Disadvantages of RCM
i) The selection of an appropriate maintenance strategy for each component and its failure
modes is difficult due to the great quantity of industrial equipment and associated
uncertainty factors.
ii) Its initiation involves substantial capital for training staff and the purchase of the
necessary equipment.
iii) Its potential to save costs is not readily apparent to the management.
As a result of the high initial cost of investment in purchasing technological equipment and training
operating staff, a newly endorsed RCM program normally leads to an increased maintenance cost.
However, this rise is usually short-lived ranging from two to three years. Thereafter, the cost of repair
declines as the probability of failures is reduced and condition monitoring replaces preventive
maintenance tasks [5]. Besides, savings in energy are realized via the application of condition
monitoring methods.
An overview of FMEA process
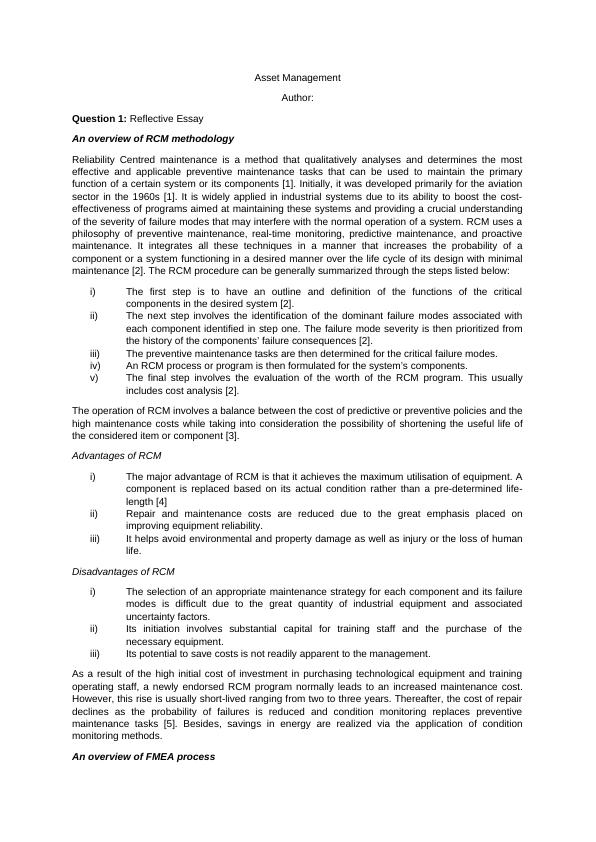
the identification and the addressing of the potential failures or problems that a system or a
component may encounter as well as their effects on the system before an adverse event occurs [6].
This idea was developed in the 1940s but it was not applied until the 1960s in the Apollo missions [6].
Therefore, FMEA aims to prevent the occurrence of an undesirable event by identifying and
eliminating process failures. FMEA looks into each system function, every possible system failure as
well as the major failure modes related to each failure [6].
FMEA can be used to evaluate both existing and new systems/processes. In the case of new
systems, it helps identify possible bottlenecks and unwanted consequences before the
implementation of the new system [7]. In the case of existing systems, it is useful in understanding
how planned changes will affect the operation of the system.
There are three common levels of FMEAs namely:
i) System FMEA: This focuses on system-related deficiencies. It is the highest level and
involves the analysis of the whole system.
ii) Design FMEA: It focuses on the deficiencies related to the design of the product. It is
applied at the sub-system or component level
iii) Process FMEA: it focuses on the deficiencies related to the manufacturing of a product. It
is applied at the assembly or manufacturing level
FMEA procedure
i) The first step is to determine the ways in which the inputs to the desired process can go
wrong which is called the failure mode. This is done for each process input.
ii) Next, the severity level for each failure mode is determined
iii) The potential cause for each failure mode is identified and an occurrence level for each
cause selected
iv) Outline the current controls for each cause and select the level of detection for every
cause
v) Compute the Risk Priority Number (RPN)
vi) Establish recommended actions and assign them to responsible persons. High RPNs are
given priority
vii) Lastly, the predicted detection levels, occurrence, and severity are assigned and RPNs
compared
Benefits of FMEA
i) It helps us to pinpoint the areas a systems design that mostly impacts customers or
patients
ii) It is possible to take actions to eliminate or reduce failures according to quantitative RPN
iii) With FMEA, one can track product failure modes, their causes, and effects. This provides
useful knowledge for process and product designs in the future.
iv) It gives the designer an indication of the major failures that should be given significant
attention while designing a product [7].
Disadvantages
i) Tracing the failure of components through FMEA charts is tedious and time-consuming.
ii) The application of FMEA is usually too late to affect the decision making and design
process.
iii) FMEA disregards the relationships between the assorted failure components
iv) This methodology is subjective and is dependent on engineers’ experience and are fairly
unknown at the enterprise level [8]
Question 2: Article review
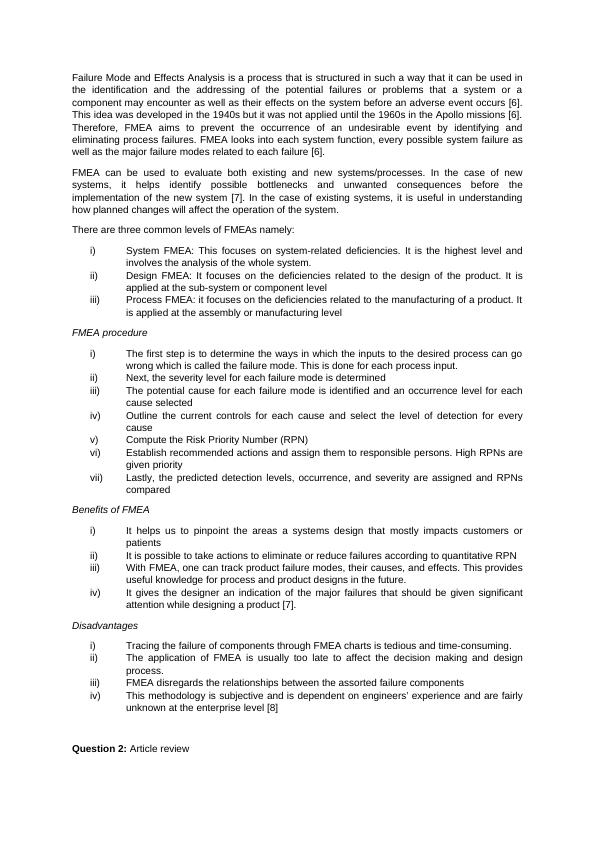
Introduction
This article investigated the trend in the breakdown of automated production systems. Its aim was to
gather enough data and information which could then be used to recommend the use of reliability
centered maintenance to improve system productivity through a previously unimplemented preventive
maintenance program. The case study used a glass bottle making machine (individual section-forming
machine, ISM) as the automated production system. Focusing on the procedures and processes, the
different parts of the machine and the working mechanisms were analyzed. This was done in order for
the maintenance department for the ISM to run more smoothly, ensuring the smooth operation of the
machines and reducing machine breakdown.
Article summary
Okwuobi et al., [11] described the ISM as an automated machine for the production of hollow glass
bottles with narrow or wide necks.
Review of RCM related work
According to Okwuobi et al., [11], safety is the top-most priority of RCM. Assuming that safety is not
compromised, the next top priority is maintenance. A justification for this is the ability to achieve
availability and reliability with the final priority being based on cost-effectiveness. These together
necessitate the use of RCM in the design of the system, the modes of operation of the system, the
methods of maintenance and practices, cost data and logistics so as to boost the capability of
operation of such a system. Okwuobi et al., [11] described RCM as a continuous process requiring
sustainability considering that a system’s best maintenance is only capable of sustaining the system
to its inherent availability and reliability. To investigate the conditions causing the failure mode for the
ISM, it is necessary to use sensors such as pressure sensors, thermal sensors and accelerometers
[11].
Failure risk analysis
Okwuobi et al., [11] conducted a risk analysis for every identified component of the ISM system for
any failure form experienced. The available data was used as a basis for the analysis which was done
using FMEA effect analysis and failure modes. Besides, they also considered the downtime analysis
of the components. They followed the steps below:
i) They reviewed all the processes necessary to get the products
ii) They highlighted the probable failure modes
iii) Each failure mode was then analyzed for its possible effects
iv) The severity of each effect was then assigned a rank
v) The possibility of each failure mode happening was assigned a rank (O)
vi) The detection ease of every failure mode was then assigned a rank (D)
vii) They then computed the risk priority number (RPN) using the following formula:
Risk priority number (RPN) = Severity (S) × Occurrence (O) × Detection (D) [11]
Results and discussion
Okwuobi et al., [11] performed a downtime analysis and the causes of failure for the following
components of the ISM system:
i) Pusher cylinder
Through the conducted RCM analysis, Okwuobi et al., [11] established that inappropriate tightening of
the bolted parts is the cause for a significant number of the failures of the pusher cylinder. They found
out that the highest risk priority number was due to wear as a result of inadequate or lack of
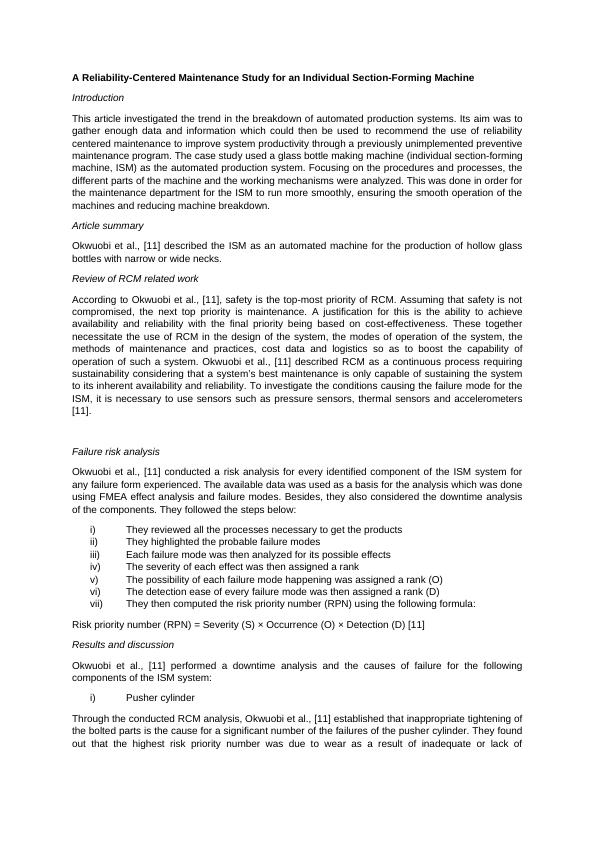
End of preview
Want to access all the pages? Upload your documents or become a member.