Relevance of Lean Manufacturing in Present Business World
VerifiedAdded on 2023/04/23
|16
|5023
|286
AI Summary
This paper critically analyses the concept of lean manufacturing and shows that it is relevant even in the modern business world. It discusses the main approaches to Organisational Management, explicit or implicit assumptions underpin the approaches to Organisational Management, and more.
Contribute Materials
Your contribution can guide someone’s learning journey. Share your
documents today.
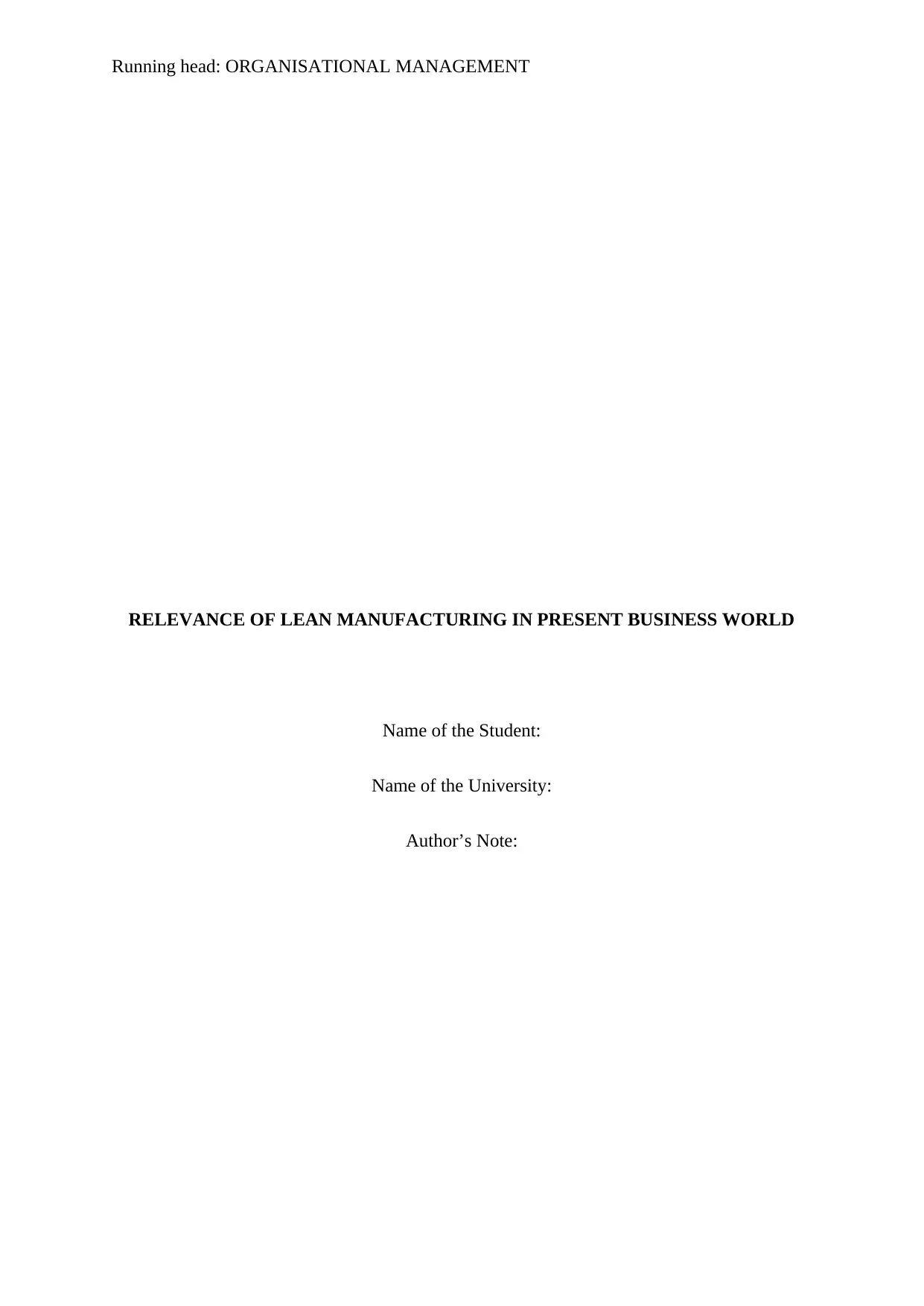
Running head: ORGANISATIONAL MANAGEMENT
RELEVANCE OF LEAN MANUFACTURING IN PRESENT BUSINESS WORLD
Name of the Student:
Name of the University:
Author’s Note:
RELEVANCE OF LEAN MANUFACTURING IN PRESENT BUSINESS WORLD
Name of the Student:
Name of the University:
Author’s Note:
Secure Best Marks with AI Grader
Need help grading? Try our AI Grader for instant feedback on your assignments.
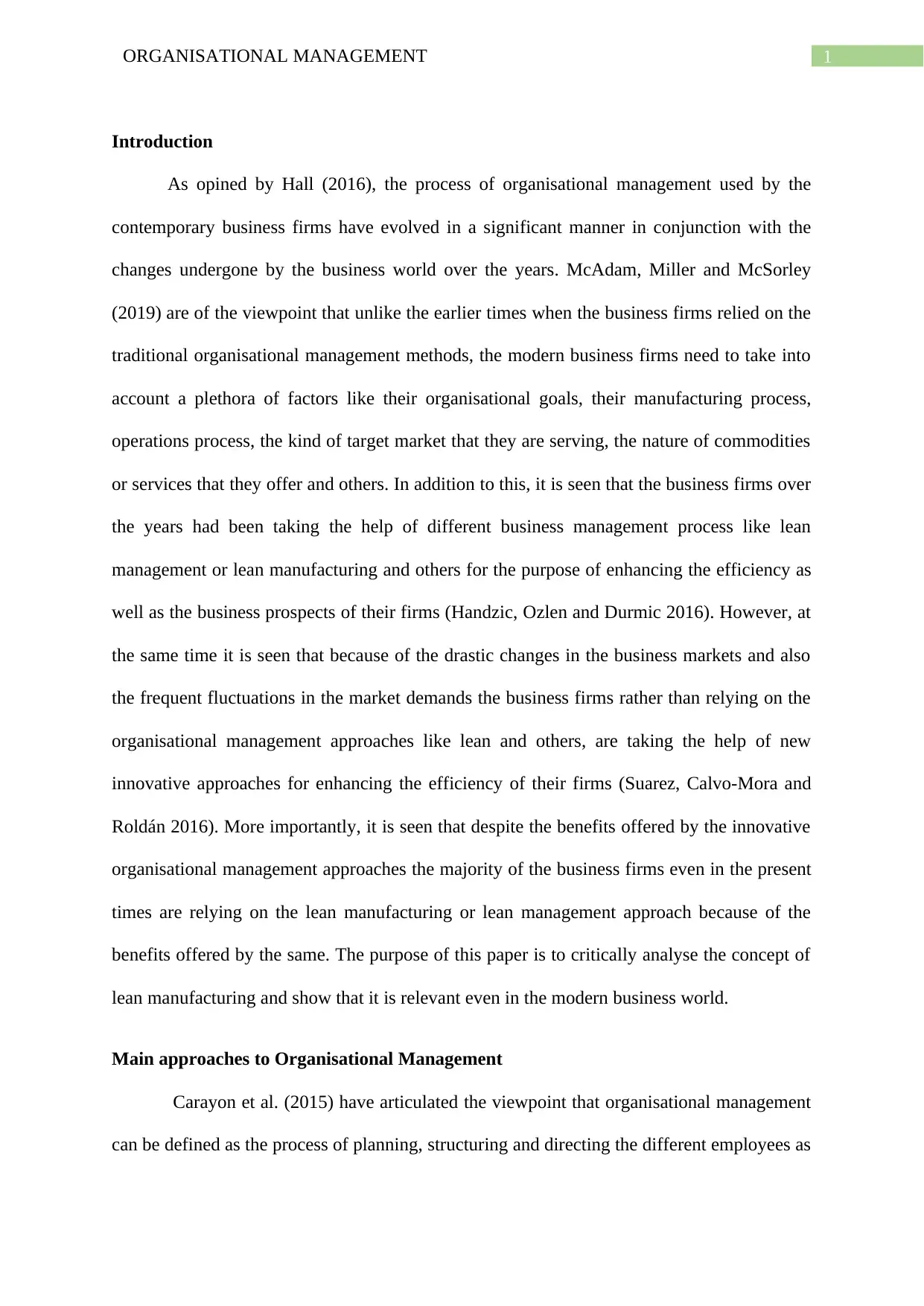
1ORGANISATIONAL MANAGEMENT
Introduction
As opined by Hall (2016), the process of organisational management used by the
contemporary business firms have evolved in a significant manner in conjunction with the
changes undergone by the business world over the years. McAdam, Miller and McSorley
(2019) are of the viewpoint that unlike the earlier times when the business firms relied on the
traditional organisational management methods, the modern business firms need to take into
account a plethora of factors like their organisational goals, their manufacturing process,
operations process, the kind of target market that they are serving, the nature of commodities
or services that they offer and others. In addition to this, it is seen that the business firms over
the years had been taking the help of different business management process like lean
management or lean manufacturing and others for the purpose of enhancing the efficiency as
well as the business prospects of their firms (Handzic, Ozlen and Durmic 2016). However, at
the same time it is seen that because of the drastic changes in the business markets and also
the frequent fluctuations in the market demands the business firms rather than relying on the
organisational management approaches like lean and others, are taking the help of new
innovative approaches for enhancing the efficiency of their firms (Suarez, Calvo-Mora and
Roldán 2016). More importantly, it is seen that despite the benefits offered by the innovative
organisational management approaches the majority of the business firms even in the present
times are relying on the lean manufacturing or lean management approach because of the
benefits offered by the same. The purpose of this paper is to critically analyse the concept of
lean manufacturing and show that it is relevant even in the modern business world.
Main approaches to Organisational Management
Carayon et al. (2015) have articulated the viewpoint that organisational management
can be defined as the process of planning, structuring and directing the different employees as
Introduction
As opined by Hall (2016), the process of organisational management used by the
contemporary business firms have evolved in a significant manner in conjunction with the
changes undergone by the business world over the years. McAdam, Miller and McSorley
(2019) are of the viewpoint that unlike the earlier times when the business firms relied on the
traditional organisational management methods, the modern business firms need to take into
account a plethora of factors like their organisational goals, their manufacturing process,
operations process, the kind of target market that they are serving, the nature of commodities
or services that they offer and others. In addition to this, it is seen that the business firms over
the years had been taking the help of different business management process like lean
management or lean manufacturing and others for the purpose of enhancing the efficiency as
well as the business prospects of their firms (Handzic, Ozlen and Durmic 2016). However, at
the same time it is seen that because of the drastic changes in the business markets and also
the frequent fluctuations in the market demands the business firms rather than relying on the
organisational management approaches like lean and others, are taking the help of new
innovative approaches for enhancing the efficiency of their firms (Suarez, Calvo-Mora and
Roldán 2016). More importantly, it is seen that despite the benefits offered by the innovative
organisational management approaches the majority of the business firms even in the present
times are relying on the lean manufacturing or lean management approach because of the
benefits offered by the same. The purpose of this paper is to critically analyse the concept of
lean manufacturing and show that it is relevant even in the modern business world.
Main approaches to Organisational Management
Carayon et al. (2015) have articulated the viewpoint that organisational management
can be defined as the process of planning, structuring and directing the different employees as

2ORGANISATIONAL MANAGEMENT
well as the resources of a firm for the attainment or the achievement of its business objectives
or goals. On the other hand, Ivens et al. (2016) have noted that the process of organisational
management can be seen as an applied behaviour analysis that “applies psychological
principles of organizational behaviour and the experimental analysis of behaviour to
organizations to improve individual and group performance and worker safety”. As opined by
Chandler (2017), the prominence held by the concept of organisational management over the
years can be explained on the basis of the fact that the financial returns earned by an
organisation or for that matter its business prospects greatly depend on the kind of
organisational management approaches or processes which are being used by the concerned
organisation. The resultant effect of this is that over the years, different kinds of
organisational management approaches have gained popularity which are being extensively
used by the different business firms. Some of the most important ones in this regard are listed
below-
Classical Management Approach
Berry, Broadbent and Otley (2016) have articulated the viewpoint that one of the most
important aspects of the classical management approach is the belief that the employees
within the spectrum of a business firm have only physical or economic needs. More
importantly, this approach of management relegates the social needs, job satisfaction, work-
life balance and others of the employees completely to the background stating that the
primary focus of the employees is on the effective fulfilment of their physical or economic
needs (Clegg 2017). The resultant effect of this is that the business firms often take the help
of the kind of organisational management approach which seeks the specialisation of labour
or for that matter maximisation of profit and loss or decision making (Wehrmeyer 2017).
Thus, it had been seen that the business firms over the years had taken the help of these
aspects for the formulation of the kind of management approach which will enable them to
well as the resources of a firm for the attainment or the achievement of its business objectives
or goals. On the other hand, Ivens et al. (2016) have noted that the process of organisational
management can be seen as an applied behaviour analysis that “applies psychological
principles of organizational behaviour and the experimental analysis of behaviour to
organizations to improve individual and group performance and worker safety”. As opined by
Chandler (2017), the prominence held by the concept of organisational management over the
years can be explained on the basis of the fact that the financial returns earned by an
organisation or for that matter its business prospects greatly depend on the kind of
organisational management approaches or processes which are being used by the concerned
organisation. The resultant effect of this is that over the years, different kinds of
organisational management approaches have gained popularity which are being extensively
used by the different business firms. Some of the most important ones in this regard are listed
below-
Classical Management Approach
Berry, Broadbent and Otley (2016) have articulated the viewpoint that one of the most
important aspects of the classical management approach is the belief that the employees
within the spectrum of a business firm have only physical or economic needs. More
importantly, this approach of management relegates the social needs, job satisfaction, work-
life balance and others of the employees completely to the background stating that the
primary focus of the employees is on the effective fulfilment of their physical or economic
needs (Clegg 2017). The resultant effect of this is that the business firms often take the help
of the kind of organisational management approach which seeks the specialisation of labour
or for that matter maximisation of profit and loss or decision making (Wehrmeyer 2017).
Thus, it had been seen that the business firms over the years had taken the help of these
aspects for the formulation of the kind of management approach which will enable them to

3ORGANISATIONAL MANAGEMENT
maximise the productivity of the employees and thereby the profitability or the financial
returns of the firm. In this regard, it needs to be said that the machinery of lean manufacturing
or lean management over the years had served as an important process which had been used
by the business firms for the attainment of the desired ends. As a matter of fact, Jasti and
Kodali (2016) have noted that one of the most important aspects of the construct of lean
manufacturing is the fact that it focuses on the minimisation of the waste generated by a firm
within its manufacturing department, in terms of wastage or resources, without hampering the
productivity or the performance of the concerned firm. More importantly, it is seen that the
process of lean manufacturing intends to minimise the waste generated by a firm on the score
of the over-burden on the manufacturing unit of the concerned firm or for matter because of
the unevenness of the work that the different employees are required to perform (Nhema
2015). In this regard, in needs to be said that back in the 20th century, automobile firms like
Ford company and others and also the Firearm industry were taking the help of the machinery
of lean manufacturing for reducing the amount of wastage of their resources and thereby to
improve the financial returns earned by them (Ghobakhloo and Azar 2018). Furthermore, it
was seen that the concept of lean manufacturing was used by these firms in conjunction with
the classical management approach used by them which focused on the effective fulfilment of
the economic as well as the physical needs of the employees.
According to Clegg (2017), the business firms using the classical organisational
management approach along with the usage of the process of lean management also take the
help of the 14 principles “Administrative Management Theory” of Henri Foyal. In this
context, it needs to be said that the 14 principles of this theory were meant as guidelines for
the managers of the 20th century who did not believed in the usage of the scientific
management approach. The 14 principles articulated by the theory under discussion are listed
below-
maximise the productivity of the employees and thereby the profitability or the financial
returns of the firm. In this regard, it needs to be said that the machinery of lean manufacturing
or lean management over the years had served as an important process which had been used
by the business firms for the attainment of the desired ends. As a matter of fact, Jasti and
Kodali (2016) have noted that one of the most important aspects of the construct of lean
manufacturing is the fact that it focuses on the minimisation of the waste generated by a firm
within its manufacturing department, in terms of wastage or resources, without hampering the
productivity or the performance of the concerned firm. More importantly, it is seen that the
process of lean manufacturing intends to minimise the waste generated by a firm on the score
of the over-burden on the manufacturing unit of the concerned firm or for matter because of
the unevenness of the work that the different employees are required to perform (Nhema
2015). In this regard, in needs to be said that back in the 20th century, automobile firms like
Ford company and others and also the Firearm industry were taking the help of the machinery
of lean manufacturing for reducing the amount of wastage of their resources and thereby to
improve the financial returns earned by them (Ghobakhloo and Azar 2018). Furthermore, it
was seen that the concept of lean manufacturing was used by these firms in conjunction with
the classical management approach used by them which focused on the effective fulfilment of
the economic as well as the physical needs of the employees.
According to Clegg (2017), the business firms using the classical organisational
management approach along with the usage of the process of lean management also take the
help of the 14 principles “Administrative Management Theory” of Henri Foyal. In this
context, it needs to be said that the 14 principles of this theory were meant as guidelines for
the managers of the 20th century who did not believed in the usage of the scientific
management approach. The 14 principles articulated by the theory under discussion are listed
below-
Secure Best Marks with AI Grader
Need help grading? Try our AI Grader for instant feedback on your assignments.

4ORGANISATIONAL MANAGEMENT
Initiative: This is the desired level of freedom that the firms need to offer to their
employees so that they are being able to execute their plans in an effective manner
without forcing the employees.
Equity: This principle dictates that all the members of a firm are equal and thereby
treated in likewise manner.
Scalar Chain: This principle states that there should be adequate number of
superiors from the top management level of the firms to the lower level so as to
facilitate the effective flow of information which in turn is likely to help in a better
completion of the work of the concerned firms.
Renumeration: The firms need to offer adequate monetary as well as non-
monetary remunerations to the workers on the basis of the labour that they do.
However, it is seen that rather than focusing on the monetary remunerations, Fayol
focuses more on the non-monetary remunerations since they are likely to motivate
the workers in a much better manner.
Unity of Direction: As per this principle there should a unity of direction in the
instructions which are being given to the team members under a manager and this
should be in conjunction with the overall strategic objectives or goals of the firms.
Discipline: The employees are required to be obedient and also comply with the
principles which are being followed within the firm.
Division of Work: There should be an equal division of labour on the basis of the
abilities or the capabilities of the workers.
Authority and Responsibility: There should be an effective balance between the
authority of the firm and the responsibility that the employees are required to
shoulder.
Initiative: This is the desired level of freedom that the firms need to offer to their
employees so that they are being able to execute their plans in an effective manner
without forcing the employees.
Equity: This principle dictates that all the members of a firm are equal and thereby
treated in likewise manner.
Scalar Chain: This principle states that there should be adequate number of
superiors from the top management level of the firms to the lower level so as to
facilitate the effective flow of information which in turn is likely to help in a better
completion of the work of the concerned firms.
Renumeration: The firms need to offer adequate monetary as well as non-
monetary remunerations to the workers on the basis of the labour that they do.
However, it is seen that rather than focusing on the monetary remunerations, Fayol
focuses more on the non-monetary remunerations since they are likely to motivate
the workers in a much better manner.
Unity of Direction: As per this principle there should a unity of direction in the
instructions which are being given to the team members under a manager and this
should be in conjunction with the overall strategic objectives or goals of the firms.
Discipline: The employees are required to be obedient and also comply with the
principles which are being followed within the firm.
Division of Work: There should be an equal division of labour on the basis of the
abilities or the capabilities of the workers.
Authority and Responsibility: There should be an effective balance between the
authority of the firm and the responsibility that the employees are required to
shoulder.

5ORGANISATIONAL MANAGEMENT
Unity of Command: There needs to be a unity within the different commands
which are being given to the employees and they should come from the immediate
supervisors or the managers of the employees.
Superiority of the general interests: The employees rather than focusing on the
attainment of their individual interests should focus on the attainment of the general
interests of the firm which is not only likely to benefit them but also the firm itself.
Centralisation: The top most authority of the firm should be the source of all
power or authority of the firms.
Order: The different employees should be given a proper place within the firm so
as to maintain an effective order.
Stability of Tenure: The employees need to have job security so as to perform in
an effective manner.
Espirit de Corps: The employees as well as the firm need to believe in the idea
that ‘unity is strength’.
Human Relations Approach
Ruiz-Benitez, López and Real (2017) are of the viewpoint that “Elton Mayo’s Human
Relations Approach” to organisational management focuses on the study of the human
relations or for that matter an analysis of the social behaviour of the employees or the
workers within the spectrum of a business firm. More importantly, it had been seen that the
fulcrum point of this approach to management is on the effective understanding of the human
relations and thereby shaping not only the organisational culture but at the same time the job
designs of the employees on the basis of the same (Bhasin 2015). This is important because
of the fact that within the spectrum of business firms it had been that the majority of the
wastage of the resources of the firms occur because of the fact that the employees are often
overburdened with work or for that matter on the score of the unevenness of the distribution
Unity of Command: There needs to be a unity within the different commands
which are being given to the employees and they should come from the immediate
supervisors or the managers of the employees.
Superiority of the general interests: The employees rather than focusing on the
attainment of their individual interests should focus on the attainment of the general
interests of the firm which is not only likely to benefit them but also the firm itself.
Centralisation: The top most authority of the firm should be the source of all
power or authority of the firms.
Order: The different employees should be given a proper place within the firm so
as to maintain an effective order.
Stability of Tenure: The employees need to have job security so as to perform in
an effective manner.
Espirit de Corps: The employees as well as the firm need to believe in the idea
that ‘unity is strength’.
Human Relations Approach
Ruiz-Benitez, López and Real (2017) are of the viewpoint that “Elton Mayo’s Human
Relations Approach” to organisational management focuses on the study of the human
relations or for that matter an analysis of the social behaviour of the employees or the
workers within the spectrum of a business firm. More importantly, it had been seen that the
fulcrum point of this approach to management is on the effective understanding of the human
relations and thereby shaping not only the organisational culture but at the same time the job
designs of the employees on the basis of the same (Bhasin 2015). This is important because
of the fact that within the spectrum of business firms it had been that the majority of the
wastage of the resources of the firms occur because of the fact that the employees are often
overburdened with work or for that matter on the score of the unevenness of the distribution

6ORGANISATIONAL MANAGEMENT
of the work that they are required to perform within the firm. In this regard, it needs to be
said that the firm Toyota was facing precisely this problem back in the 20th century when it
was seen that the concerned firm was facing a high amount of wastage of its organisational
resources because of the fact that the employees were over-burdened with work and also
there was not adequate distribution of work among the different employees or the workers of
the firm (Kumar, Sharma and Agarwal 2015). It is precisely here that the machinery of lean
manufacturing or lean management becomes important within the framework of the human
relations management that the firms had been using over the years. As a matter of fact, it had
been seen that the business firms like Toyota, Wipro and others had been able to integrate the
machinery of lean manufacturing within the human relations management approach that they
had been using so as to enhance the performance of their firm (Tortorella, Miorando and
Tlapa 2017).
Systems Approach
Rinehart, Huxley and Robertson (2018) have noted that the systems management
approach considers the entire business firm to be an organic unit with different sub-systems
which are inter-related to each other and the entire performance of the firm greatly depends
on the interrelation or the coordination between these different units. The resultant effect of
this is that the business firms in order to attain the desired level of performance synchronise
the different departments or the sub-systems of their firm. However, at the same time it needs
to be said that this is the interlinking of the departments of a firm not only places extra work
pressure on the different employees of the firm but at the same time hinders the effective
distribution of the work as well and this in turn enhances the level of wastage of the resources
of the firms (Tortorella, Miorando and Marodin 2017). The resultant effect of this is that the
firms over the years along with the usage of this approach to organisational management have
of the work that they are required to perform within the firm. In this regard, it needs to be
said that the firm Toyota was facing precisely this problem back in the 20th century when it
was seen that the concerned firm was facing a high amount of wastage of its organisational
resources because of the fact that the employees were over-burdened with work and also
there was not adequate distribution of work among the different employees or the workers of
the firm (Kumar, Sharma and Agarwal 2015). It is precisely here that the machinery of lean
manufacturing or lean management becomes important within the framework of the human
relations management that the firms had been using over the years. As a matter of fact, it had
been seen that the business firms like Toyota, Wipro and others had been able to integrate the
machinery of lean manufacturing within the human relations management approach that they
had been using so as to enhance the performance of their firm (Tortorella, Miorando and
Tlapa 2017).
Systems Approach
Rinehart, Huxley and Robertson (2018) have noted that the systems management
approach considers the entire business firm to be an organic unit with different sub-systems
which are inter-related to each other and the entire performance of the firm greatly depends
on the interrelation or the coordination between these different units. The resultant effect of
this is that the business firms in order to attain the desired level of performance synchronise
the different departments or the sub-systems of their firm. However, at the same time it needs
to be said that this is the interlinking of the departments of a firm not only places extra work
pressure on the different employees of the firm but at the same time hinders the effective
distribution of the work as well and this in turn enhances the level of wastage of the resources
of the firms (Tortorella, Miorando and Marodin 2017). The resultant effect of this is that the
firms over the years along with the usage of this approach to organisational management have
Paraphrase This Document
Need a fresh take? Get an instant paraphrase of this document with our AI Paraphraser

7ORGANISATIONAL MANAGEMENT
been taking the help of the machinery of lean management or manufacturing for reducing the
wastage of the resources of the firm and also to earn a higher amount of profitability as well.
Contingency Approach
Souza and Alves (2018) have articulated the viewpoint that the situational
management approach or commonly called by the name of contingency approach to
management is the one which articulates the idea that the usage of one management approach
cannot help a particular business firm in the effective management of its diverse business
activities. The resultant effect of this is that the firms need to take the help of a
conglomerative approach which will take into account the positive aspects of the majority of
the organisational management approaches for the effective management of a firm. As a
matter of fact, it had been seen over the years that the different business firms had been
taking the help of the process of lean management or manufacturing in conjunction with the
other management approaches for the attainment of the goals or the objectives of their firms
(Zokaei et al. 2016). More importantly, the effectiveness of this organisational management
approach becomes apparent from the fact that over the years business firms like Toyota,
Wipro and others in addition to the other management approaches that they have been using
also took the help of the machinery of lean manufacturing or management so as to attain the
desired level of growth or success (Agarwal and Sharma 2016).
Explicit or implicit assumptions underpin the approaches to Organisational
Management
According to Andrés-López, González-Requena and Sanz-Lobera (2015), the
different business firms over the years for the effective management of the diverse aspects of
their firm as well as for the attainment of the desired level of success had taken the help of
different kinds of assumptions regarding the organisational management approaches that they
had followed. As a matter of fact, it is seen that one of the most important assumptions that
been taking the help of the machinery of lean management or manufacturing for reducing the
wastage of the resources of the firm and also to earn a higher amount of profitability as well.
Contingency Approach
Souza and Alves (2018) have articulated the viewpoint that the situational
management approach or commonly called by the name of contingency approach to
management is the one which articulates the idea that the usage of one management approach
cannot help a particular business firm in the effective management of its diverse business
activities. The resultant effect of this is that the firms need to take the help of a
conglomerative approach which will take into account the positive aspects of the majority of
the organisational management approaches for the effective management of a firm. As a
matter of fact, it had been seen over the years that the different business firms had been
taking the help of the process of lean management or manufacturing in conjunction with the
other management approaches for the attainment of the goals or the objectives of their firms
(Zokaei et al. 2016). More importantly, the effectiveness of this organisational management
approach becomes apparent from the fact that over the years business firms like Toyota,
Wipro and others in addition to the other management approaches that they have been using
also took the help of the machinery of lean manufacturing or management so as to attain the
desired level of growth or success (Agarwal and Sharma 2016).
Explicit or implicit assumptions underpin the approaches to Organisational
Management
According to Andrés-López, González-Requena and Sanz-Lobera (2015), the
different business firms over the years for the effective management of the diverse aspects of
their firm as well as for the attainment of the desired level of success had taken the help of
different kinds of assumptions regarding the organisational management approaches that they
had followed. As a matter of fact, it is seen that one of the most important assumptions that

8ORGANISATIONAL MANAGEMENT
the different business firms had taken the help of is the fact that the effective usage of the
process of lean management or manufacturing is likely to help them to attain the business
objectives or the goals that they have outlined for their firms. In this regard, it needs to be
said that the business firms over the years had simply assumed the fact that the mere
reduction of the wastage of organisational resources is likely to help them to attain the
desired level of business success (Clegg 2017). However, the thing that the business firms fail
to take into account is the fact that along with focusing on the aspect of the reduction of the
wastage of organisational resources they also need to take into account the other aspects of
the process of lean manufacturing or for that matter take into account the process through
which they need to reduce the wastage of organisational resources (Chandler 2017). The
resultant effect of this is that the business firms despite using the process of lean
manufacturing or lean management within the spectrum of their firm have failed to attain the
desired level of success that they were hoping to attain through the usage of the same. More
importantly, it had seen that another important assumption that the different firms have made
regarding the lean manufacturing process is the fact that they do not need to provide any
specialised training to the employees for the usage of the same process whereas it had seen
that the firms using the lean management approach need to offer specialised training to their
employees (Nhema 2015).
As opined by Berry, Broadbent and Otley (2016), some aspects of the process of lean
manufacturing that the firms need to take into account are a centralised organisational
structure, effective division of labour, segregation of work and personal life, adequate wages
and others. However, it is seen that the firms merely assume that they are fulfilling these
criteria within their workplace and there fail to get the desired kind of results from the usage
of the lean manufacturing process (Jasti and Kodali 2016). As a matter of fact, it had been
seen that the other management approaches also make some assumptions which in turn
the different business firms had taken the help of is the fact that the effective usage of the
process of lean management or manufacturing is likely to help them to attain the business
objectives or the goals that they have outlined for their firms. In this regard, it needs to be
said that the business firms over the years had simply assumed the fact that the mere
reduction of the wastage of organisational resources is likely to help them to attain the
desired level of business success (Clegg 2017). However, the thing that the business firms fail
to take into account is the fact that along with focusing on the aspect of the reduction of the
wastage of organisational resources they also need to take into account the other aspects of
the process of lean manufacturing or for that matter take into account the process through
which they need to reduce the wastage of organisational resources (Chandler 2017). The
resultant effect of this is that the business firms despite using the process of lean
manufacturing or lean management within the spectrum of their firm have failed to attain the
desired level of success that they were hoping to attain through the usage of the same. More
importantly, it had seen that another important assumption that the different firms have made
regarding the lean manufacturing process is the fact that they do not need to provide any
specialised training to the employees for the usage of the same process whereas it had seen
that the firms using the lean management approach need to offer specialised training to their
employees (Nhema 2015).
As opined by Berry, Broadbent and Otley (2016), some aspects of the process of lean
manufacturing that the firms need to take into account are a centralised organisational
structure, effective division of labour, segregation of work and personal life, adequate wages
and others. However, it is seen that the firms merely assume that they are fulfilling these
criteria within their workplace and there fail to get the desired kind of results from the usage
of the lean manufacturing process (Jasti and Kodali 2016). As a matter of fact, it had been
seen that the other management approaches also make some assumptions which in turn

9ORGANISATIONAL MANAGEMENT
hinder the effective usage of the same by the firms. For example, it is seen that one of the
major assumptions that the contingency approach makes is the fact that one single
management approach cannot help the firms to effectively manage the different aspects of
their firms (Hall 2016). On the other hand, the major assumption that the systems approach
makes is the fact that the entire firm is an organic unit and thereby cannot be considered to be
composed of individual units or systems (McAdam, Miller and McSorley 2019). Lastly, the
assumption that the human relations approach is the fact that the employees are dedicated
towards the achievement of the organisational goals without taking into consideration the fact
that the employees can have individual objectives or goals.
Interrelation between approaches to Organisational Management
An analysis of the different organisational management approaches that had been
used by the business firms over the years in a succinct manner shows that there is an
interrelation or correlation between these approaches. As a matter of fact, it is seen that the
different organisational management approaches are intended to enhance the efficiency or the
effectiveness of the business firms and also the kind of business activities that they perform.
More importantly, they are also intended to help the business firms to enhance the effective
utilisation of the organisational resources and thereby reduce the wastage of the same
(Suarez, Calvo-Mora and Roldán 2016). However, at the same time it needs to be said that
for the attainment of these ends the business firms apart from the usage of the above-
mentioned organisational management approaches also need to take the help of the process of
lean management or lean manufacturing (Carayon et al. 2015). This becomes especially
important from the perspective of the different benefits that the effective usage of the process
of lean management offers to the firms like the reduction in the operations cost of the firms,
employee empowerment and others.
hinder the effective usage of the same by the firms. For example, it is seen that one of the
major assumptions that the contingency approach makes is the fact that one single
management approach cannot help the firms to effectively manage the different aspects of
their firms (Hall 2016). On the other hand, the major assumption that the systems approach
makes is the fact that the entire firm is an organic unit and thereby cannot be considered to be
composed of individual units or systems (McAdam, Miller and McSorley 2019). Lastly, the
assumption that the human relations approach is the fact that the employees are dedicated
towards the achievement of the organisational goals without taking into consideration the fact
that the employees can have individual objectives or goals.
Interrelation between approaches to Organisational Management
An analysis of the different organisational management approaches that had been
used by the business firms over the years in a succinct manner shows that there is an
interrelation or correlation between these approaches. As a matter of fact, it is seen that the
different organisational management approaches are intended to enhance the efficiency or the
effectiveness of the business firms and also the kind of business activities that they perform.
More importantly, they are also intended to help the business firms to enhance the effective
utilisation of the organisational resources and thereby reduce the wastage of the same
(Suarez, Calvo-Mora and Roldán 2016). However, at the same time it needs to be said that
for the attainment of these ends the business firms apart from the usage of the above-
mentioned organisational management approaches also need to take the help of the process of
lean management or lean manufacturing (Carayon et al. 2015). This becomes especially
important from the perspective of the different benefits that the effective usage of the process
of lean management offers to the firms like the reduction in the operations cost of the firms,
employee empowerment and others.
Secure Best Marks with AI Grader
Need help grading? Try our AI Grader for instant feedback on your assignments.
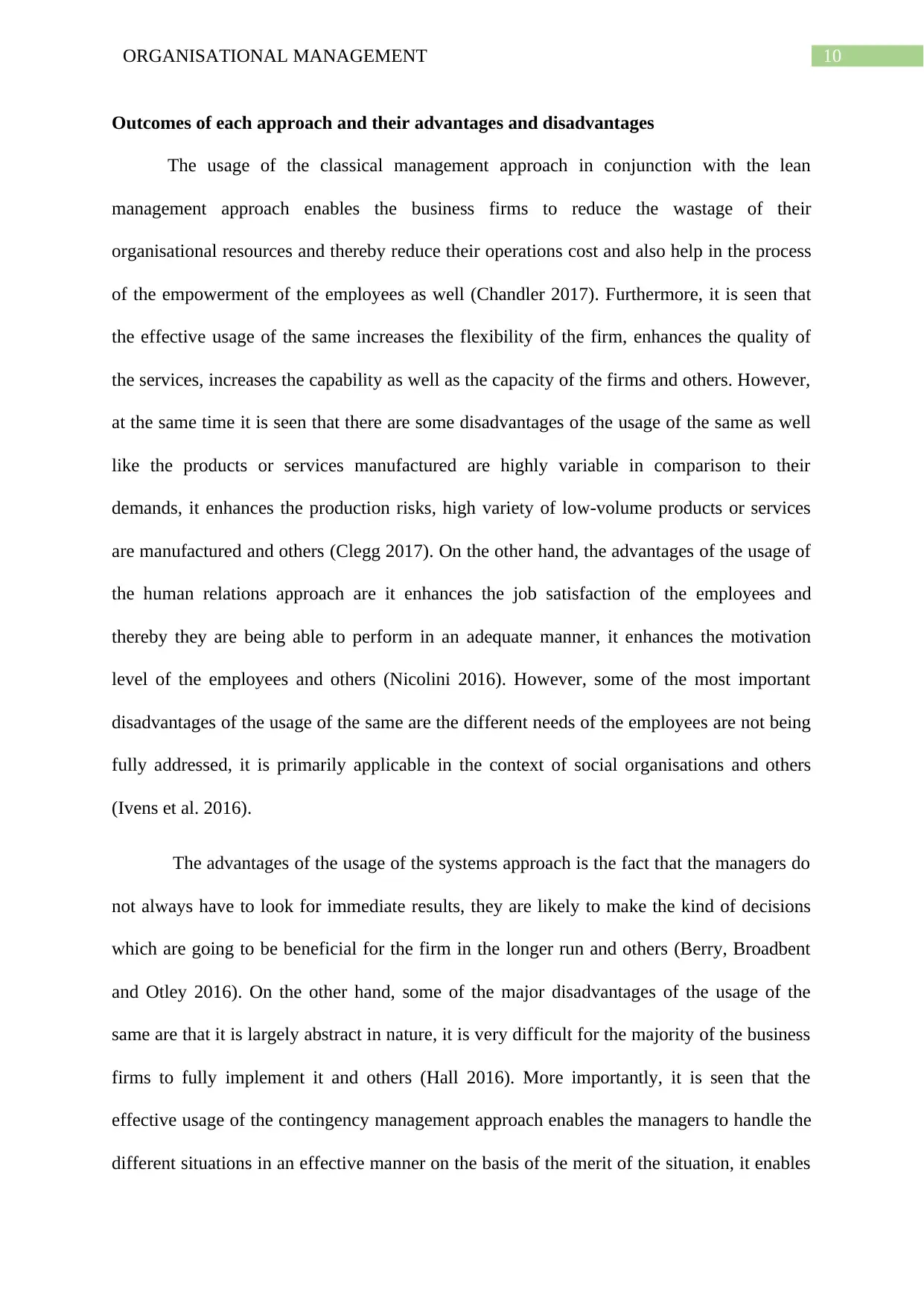
10ORGANISATIONAL MANAGEMENT
Outcomes of each approach and their advantages and disadvantages
The usage of the classical management approach in conjunction with the lean
management approach enables the business firms to reduce the wastage of their
organisational resources and thereby reduce their operations cost and also help in the process
of the empowerment of the employees as well (Chandler 2017). Furthermore, it is seen that
the effective usage of the same increases the flexibility of the firm, enhances the quality of
the services, increases the capability as well as the capacity of the firms and others. However,
at the same time it is seen that there are some disadvantages of the usage of the same as well
like the products or services manufactured are highly variable in comparison to their
demands, it enhances the production risks, high variety of low-volume products or services
are manufactured and others (Clegg 2017). On the other hand, the advantages of the usage of
the human relations approach are it enhances the job satisfaction of the employees and
thereby they are being able to perform in an adequate manner, it enhances the motivation
level of the employees and others (Nicolini 2016). However, some of the most important
disadvantages of the usage of the same are the different needs of the employees are not being
fully addressed, it is primarily applicable in the context of social organisations and others
(Ivens et al. 2016).
The advantages of the usage of the systems approach is the fact that the managers do
not always have to look for immediate results, they are likely to make the kind of decisions
which are going to be beneficial for the firm in the longer run and others (Berry, Broadbent
and Otley 2016). On the other hand, some of the major disadvantages of the usage of the
same are that it is largely abstract in nature, it is very difficult for the majority of the business
firms to fully implement it and others (Hall 2016). More importantly, it is seen that the
effective usage of the contingency management approach enables the managers to handle the
different situations in an effective manner on the basis of the merit of the situation, it enables
Outcomes of each approach and their advantages and disadvantages
The usage of the classical management approach in conjunction with the lean
management approach enables the business firms to reduce the wastage of their
organisational resources and thereby reduce their operations cost and also help in the process
of the empowerment of the employees as well (Chandler 2017). Furthermore, it is seen that
the effective usage of the same increases the flexibility of the firm, enhances the quality of
the services, increases the capability as well as the capacity of the firms and others. However,
at the same time it is seen that there are some disadvantages of the usage of the same as well
like the products or services manufactured are highly variable in comparison to their
demands, it enhances the production risks, high variety of low-volume products or services
are manufactured and others (Clegg 2017). On the other hand, the advantages of the usage of
the human relations approach are it enhances the job satisfaction of the employees and
thereby they are being able to perform in an adequate manner, it enhances the motivation
level of the employees and others (Nicolini 2016). However, some of the most important
disadvantages of the usage of the same are the different needs of the employees are not being
fully addressed, it is primarily applicable in the context of social organisations and others
(Ivens et al. 2016).
The advantages of the usage of the systems approach is the fact that the managers do
not always have to look for immediate results, they are likely to make the kind of decisions
which are going to be beneficial for the firm in the longer run and others (Berry, Broadbent
and Otley 2016). On the other hand, some of the major disadvantages of the usage of the
same are that it is largely abstract in nature, it is very difficult for the majority of the business
firms to fully implement it and others (Hall 2016). More importantly, it is seen that the
effective usage of the contingency management approach enables the managers to handle the
different situations in an effective manner on the basis of the merit of the situation, it enables

11ORGANISATIONAL MANAGEMENT
the managers to make the best possible decisions and others (Wehrmeyer 2017). However,
there are some disadvantages of the usage of this management approach like at times it
becomes very difficult to determine the right kind of approach for the management of the
diverse situations, difficulty in analysing the situations and others.
Effectiveness and relevance of lean manufacturing in present business world
The above discussion makes it clear that there are various difficulties or roadblocks
that the business firms face for the effective usage of the process of lean manufacturing like
lack of experience, ineffective understanding of the concept and others and this in turn deter
the business firms from the usage of the same. However, it is seen that despite the
disadvantages of the process of lean management the firms especially the ones related to the
manufacturing and the automobile industry are using this process even in the 21st century
because of the benefits offered by the same. As a matter of fact, it is seen that the effective
usage of the process of lean management had enabled the firms to not only enhance the
efficiency of their firm but at the same time offer better quality services or products to the
customers which in turn had greatly improved their profitability (Ruiz-Benitez, López and
Real 2017). In addition to this, it is seen that the effective usage of the same had significantly
reduced the space requirements of the firms, the amount of resources that they need,
empowerment of the employees and others. On the score of these benefits that the process of
lean management offers to the firms and also from the fact that the different business firms
are extensively using the process of lean management it can be said that the same is not only
an effective management approach but at the same time a completely relevant one even in the
21st century.
the managers to make the best possible decisions and others (Wehrmeyer 2017). However,
there are some disadvantages of the usage of this management approach like at times it
becomes very difficult to determine the right kind of approach for the management of the
diverse situations, difficulty in analysing the situations and others.
Effectiveness and relevance of lean manufacturing in present business world
The above discussion makes it clear that there are various difficulties or roadblocks
that the business firms face for the effective usage of the process of lean manufacturing like
lack of experience, ineffective understanding of the concept and others and this in turn deter
the business firms from the usage of the same. However, it is seen that despite the
disadvantages of the process of lean management the firms especially the ones related to the
manufacturing and the automobile industry are using this process even in the 21st century
because of the benefits offered by the same. As a matter of fact, it is seen that the effective
usage of the process of lean management had enabled the firms to not only enhance the
efficiency of their firm but at the same time offer better quality services or products to the
customers which in turn had greatly improved their profitability (Ruiz-Benitez, López and
Real 2017). In addition to this, it is seen that the effective usage of the same had significantly
reduced the space requirements of the firms, the amount of resources that they need,
empowerment of the employees and others. On the score of these benefits that the process of
lean management offers to the firms and also from the fact that the different business firms
are extensively using the process of lean management it can be said that the same is not only
an effective management approach but at the same time a completely relevant one even in the
21st century.

12ORGANISATIONAL MANAGEMENT
Conclusion
To conclude, the transition that the business world had undergone in the present times
becomes apparent from the increasingly diverse organisational management approaches that
the business firms are presently using. As a matter of fact, it had been seen that the different
organisational management approaches which are being used by the firms take into account
the different requirements of the business firms and thereby try to increase the efficiency of
the firms and also their profitability as well. In this regard, mention needs to be made of the
organisational management approach of lean management which although a traditional one is
still used extensively even in the present times because of the benefits offered by the same.
For example, it is seen that the process of lean management offers the opportunity to the
business firms to reduce the wastage of organisational resources, reduce their operations cost,
empower the employees and others. Thus, on the score of these aspects it can be said that the
process of lean management is a relevant one even in the present times. These aspects of the
process of lean management become apparent from the above analysis.
Conclusion
To conclude, the transition that the business world had undergone in the present times
becomes apparent from the increasingly diverse organisational management approaches that
the business firms are presently using. As a matter of fact, it had been seen that the different
organisational management approaches which are being used by the firms take into account
the different requirements of the business firms and thereby try to increase the efficiency of
the firms and also their profitability as well. In this regard, mention needs to be made of the
organisational management approach of lean management which although a traditional one is
still used extensively even in the present times because of the benefits offered by the same.
For example, it is seen that the process of lean management offers the opportunity to the
business firms to reduce the wastage of organisational resources, reduce their operations cost,
empower the employees and others. Thus, on the score of these aspects it can be said that the
process of lean management is a relevant one even in the present times. These aspects of the
process of lean management become apparent from the above analysis.
Paraphrase This Document
Need a fresh take? Get an instant paraphrase of this document with our AI Paraphraser
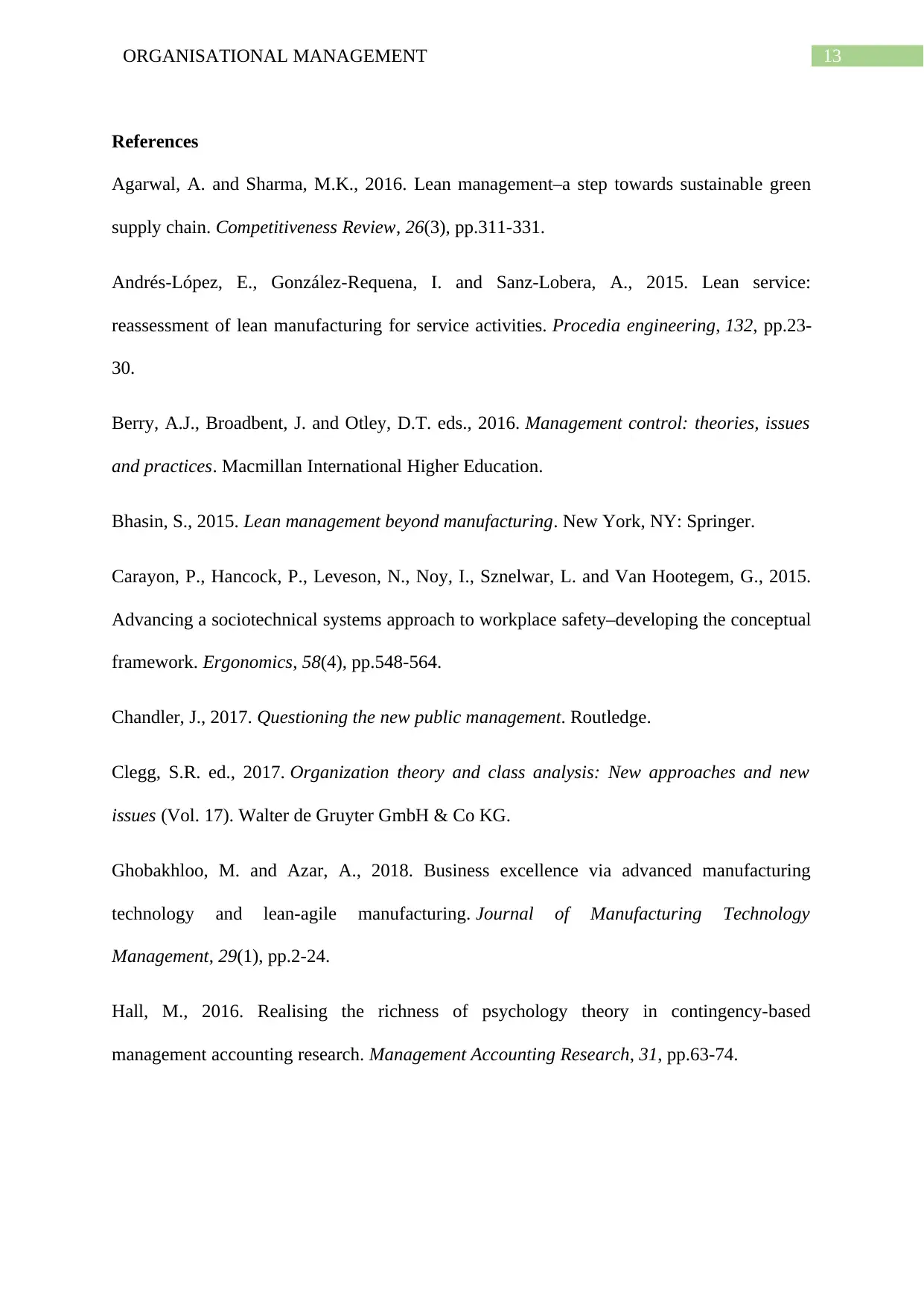
13ORGANISATIONAL MANAGEMENT
References
Agarwal, A. and Sharma, M.K., 2016. Lean management–a step towards sustainable green
supply chain. Competitiveness Review, 26(3), pp.311-331.
Andrés-López, E., González-Requena, I. and Sanz-Lobera, A., 2015. Lean service:
reassessment of lean manufacturing for service activities. Procedia engineering, 132, pp.23-
30.
Berry, A.J., Broadbent, J. and Otley, D.T. eds., 2016. Management control: theories, issues
and practices. Macmillan International Higher Education.
Bhasin, S., 2015. Lean management beyond manufacturing. New York, NY: Springer.
Carayon, P., Hancock, P., Leveson, N., Noy, I., Sznelwar, L. and Van Hootegem, G., 2015.
Advancing a sociotechnical systems approach to workplace safety–developing the conceptual
framework. Ergonomics, 58(4), pp.548-564.
Chandler, J., 2017. Questioning the new public management. Routledge.
Clegg, S.R. ed., 2017. Organization theory and class analysis: New approaches and new
issues (Vol. 17). Walter de Gruyter GmbH & Co KG.
Ghobakhloo, M. and Azar, A., 2018. Business excellence via advanced manufacturing
technology and lean-agile manufacturing. Journal of Manufacturing Technology
Management, 29(1), pp.2-24.
Hall, M., 2016. Realising the richness of psychology theory in contingency-based
management accounting research. Management Accounting Research, 31, pp.63-74.
References
Agarwal, A. and Sharma, M.K., 2016. Lean management–a step towards sustainable green
supply chain. Competitiveness Review, 26(3), pp.311-331.
Andrés-López, E., González-Requena, I. and Sanz-Lobera, A., 2015. Lean service:
reassessment of lean manufacturing for service activities. Procedia engineering, 132, pp.23-
30.
Berry, A.J., Broadbent, J. and Otley, D.T. eds., 2016. Management control: theories, issues
and practices. Macmillan International Higher Education.
Bhasin, S., 2015. Lean management beyond manufacturing. New York, NY: Springer.
Carayon, P., Hancock, P., Leveson, N., Noy, I., Sznelwar, L. and Van Hootegem, G., 2015.
Advancing a sociotechnical systems approach to workplace safety–developing the conceptual
framework. Ergonomics, 58(4), pp.548-564.
Chandler, J., 2017. Questioning the new public management. Routledge.
Clegg, S.R. ed., 2017. Organization theory and class analysis: New approaches and new
issues (Vol. 17). Walter de Gruyter GmbH & Co KG.
Ghobakhloo, M. and Azar, A., 2018. Business excellence via advanced manufacturing
technology and lean-agile manufacturing. Journal of Manufacturing Technology
Management, 29(1), pp.2-24.
Hall, M., 2016. Realising the richness of psychology theory in contingency-based
management accounting research. Management Accounting Research, 31, pp.63-74.

14ORGANISATIONAL MANAGEMENT
Handzic, M., Ozlen, K. and Durmic, N., 2016. A contingency approach to knowledge
management: Finding the best fit. International Journal of Knowledge Management
(IJKM), 12(1), pp.31-44.
Ivens, B.S., Pardo, C., Niersbach, B. and Leischnig, A., 2016. Firm-internal key account
management networks: Framework, case study, avenues for future research. Industrial
Marketing Management, 58, pp.102-113.
Jasti, N.V.K. and Kodali, R., 2016. An empirical study for implementation of lean principles
in Indian manufacturing industry. Benchmarking: An International Journal, 23(1), pp.183-
207.
Kumar BR, R., Sharma, M.K. and Agarwal, A., 2015. An experimental investigation of lean
management in aviation: Avoiding unforced errors for better supply chain. Journal of
Manufacturing Technology Management, 26(2), pp.231-260.
McAdam, R., Miller, K. and McSorley, C., 2019. Towards a contingency theory perspective
of quality management in enabling strategic alignment. International Journal of Production
Economics, 207, pp.195-209.
Nhema, A.G., 2015. Relevance of classical management theories to modern public
administration: A review. Journal of Public Administration and Governance, 5(3), pp.165-
179.
Nicolini, D., 2016. Knowing in Organizations: A Practice-Based Approach: A Practice-
Based Approach. Routledge.
Rinehart, J., Huxley, C. and Robertson, D., 2018. Just another car factory?: Lean production
and its discontents. Cornell University Press.
Handzic, M., Ozlen, K. and Durmic, N., 2016. A contingency approach to knowledge
management: Finding the best fit. International Journal of Knowledge Management
(IJKM), 12(1), pp.31-44.
Ivens, B.S., Pardo, C., Niersbach, B. and Leischnig, A., 2016. Firm-internal key account
management networks: Framework, case study, avenues for future research. Industrial
Marketing Management, 58, pp.102-113.
Jasti, N.V.K. and Kodali, R., 2016. An empirical study for implementation of lean principles
in Indian manufacturing industry. Benchmarking: An International Journal, 23(1), pp.183-
207.
Kumar BR, R., Sharma, M.K. and Agarwal, A., 2015. An experimental investigation of lean
management in aviation: Avoiding unforced errors for better supply chain. Journal of
Manufacturing Technology Management, 26(2), pp.231-260.
McAdam, R., Miller, K. and McSorley, C., 2019. Towards a contingency theory perspective
of quality management in enabling strategic alignment. International Journal of Production
Economics, 207, pp.195-209.
Nhema, A.G., 2015. Relevance of classical management theories to modern public
administration: A review. Journal of Public Administration and Governance, 5(3), pp.165-
179.
Nicolini, D., 2016. Knowing in Organizations: A Practice-Based Approach: A Practice-
Based Approach. Routledge.
Rinehart, J., Huxley, C. and Robertson, D., 2018. Just another car factory?: Lean production
and its discontents. Cornell University Press.
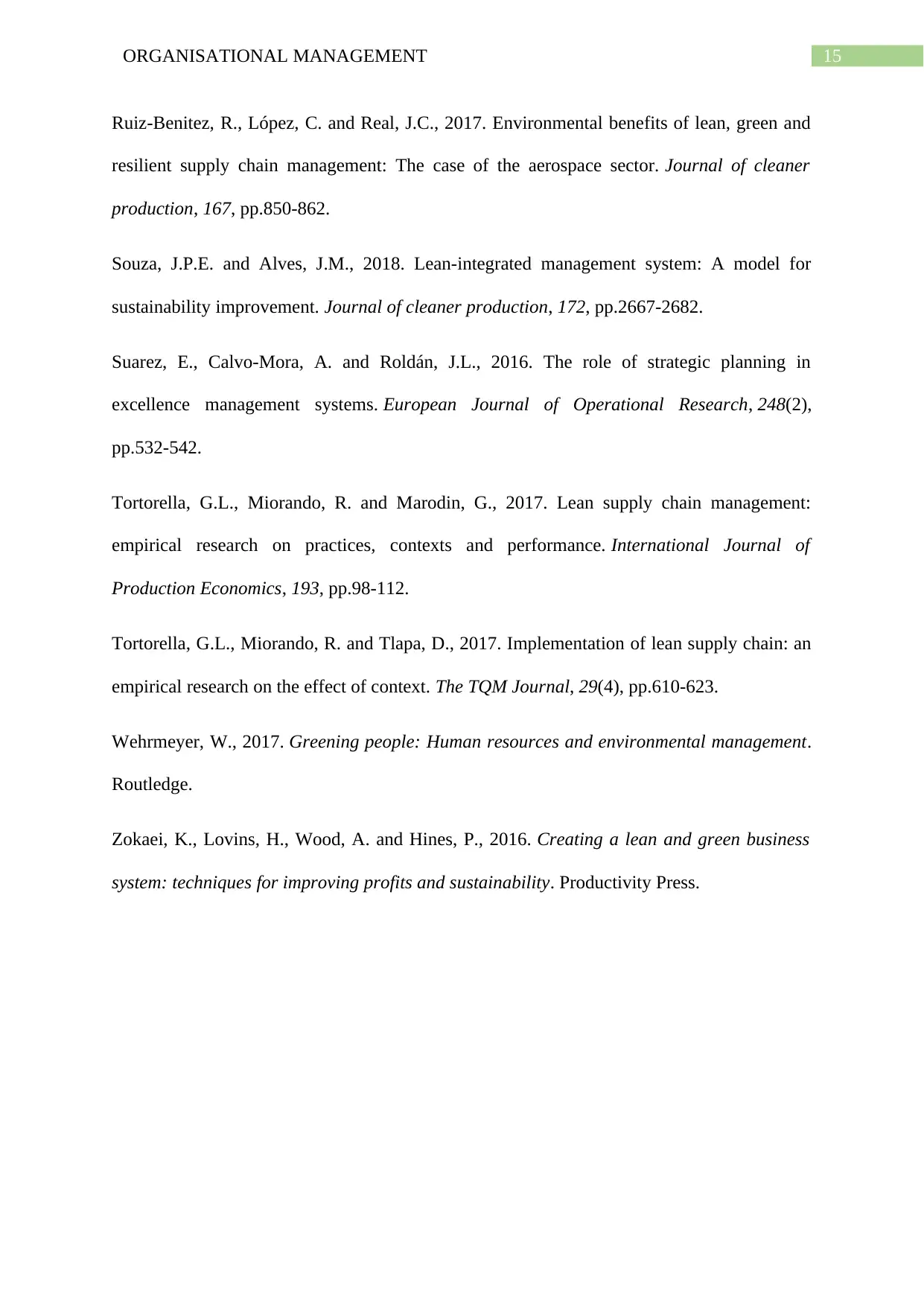
15ORGANISATIONAL MANAGEMENT
Ruiz-Benitez, R., López, C. and Real, J.C., 2017. Environmental benefits of lean, green and
resilient supply chain management: The case of the aerospace sector. Journal of cleaner
production, 167, pp.850-862.
Souza, J.P.E. and Alves, J.M., 2018. Lean-integrated management system: A model for
sustainability improvement. Journal of cleaner production, 172, pp.2667-2682.
Suarez, E., Calvo-Mora, A. and Roldán, J.L., 2016. The role of strategic planning in
excellence management systems. European Journal of Operational Research, 248(2),
pp.532-542.
Tortorella, G.L., Miorando, R. and Marodin, G., 2017. Lean supply chain management:
empirical research on practices, contexts and performance. International Journal of
Production Economics, 193, pp.98-112.
Tortorella, G.L., Miorando, R. and Tlapa, D., 2017. Implementation of lean supply chain: an
empirical research on the effect of context. The TQM Journal, 29(4), pp.610-623.
Wehrmeyer, W., 2017. Greening people: Human resources and environmental management.
Routledge.
Zokaei, K., Lovins, H., Wood, A. and Hines, P., 2016. Creating a lean and green business
system: techniques for improving profits and sustainability. Productivity Press.
Ruiz-Benitez, R., López, C. and Real, J.C., 2017. Environmental benefits of lean, green and
resilient supply chain management: The case of the aerospace sector. Journal of cleaner
production, 167, pp.850-862.
Souza, J.P.E. and Alves, J.M., 2018. Lean-integrated management system: A model for
sustainability improvement. Journal of cleaner production, 172, pp.2667-2682.
Suarez, E., Calvo-Mora, A. and Roldán, J.L., 2016. The role of strategic planning in
excellence management systems. European Journal of Operational Research, 248(2),
pp.532-542.
Tortorella, G.L., Miorando, R. and Marodin, G., 2017. Lean supply chain management:
empirical research on practices, contexts and performance. International Journal of
Production Economics, 193, pp.98-112.
Tortorella, G.L., Miorando, R. and Tlapa, D., 2017. Implementation of lean supply chain: an
empirical research on the effect of context. The TQM Journal, 29(4), pp.610-623.
Wehrmeyer, W., 2017. Greening people: Human resources and environmental management.
Routledge.
Zokaei, K., Lovins, H., Wood, A. and Hines, P., 2016. Creating a lean and green business
system: techniques for improving profits and sustainability. Productivity Press.
1 out of 16
Related Documents
![[object Object]](/_next/image/?url=%2F_next%2Fstatic%2Fmedia%2Flogo.6d15ce61.png&w=640&q=75)
Your All-in-One AI-Powered Toolkit for Academic Success.
+13062052269
info@desklib.com
Available 24*7 on WhatsApp / Email
Unlock your academic potential
© 2024 | Zucol Services PVT LTD | All rights reserved.