Business Process Management
VerifiedAdded on 2022/11/17
|9
|1721
|136
AI Summary
This article discusses the issues faced by Swinburne Logistics and the best practices that can be employed to address them. It also describes the advantages and disadvantages of each practice. The article focuses on Lean Six Sigma as an approach to improving quality, reducing variation, and eliminating waste. It also provides a list of steps to implement Lean Six Sigma. The article is relevant to students and professionals interested in business process management.
Contribute Materials
Your contribution can guide someone’s learning journey. Share your
documents today.
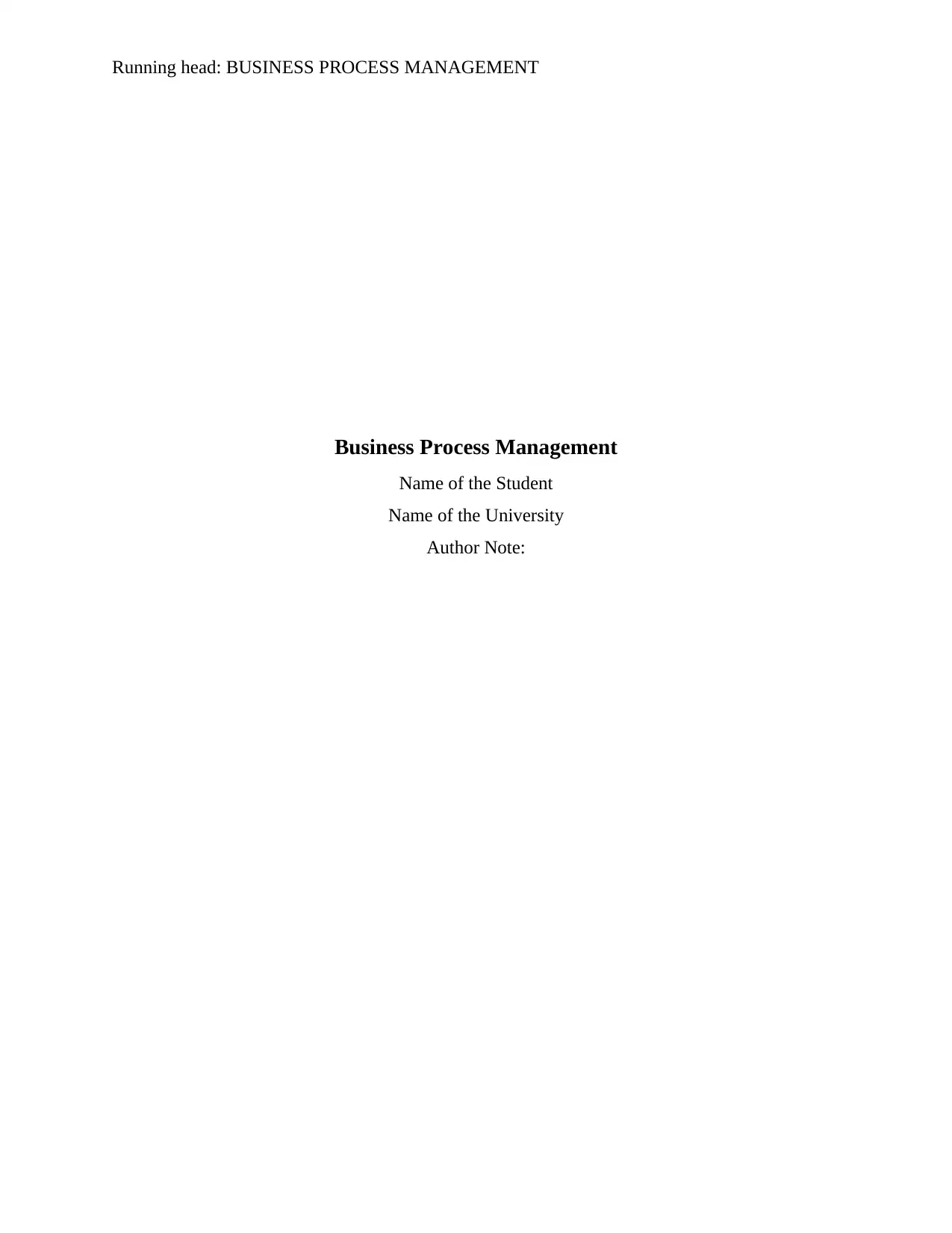
Running head: BUSINESS PROCESS MANAGEMENT
Business Process Management
Name of the Student
Name of the University
Author Note:
Business Process Management
Name of the Student
Name of the University
Author Note:
Secure Best Marks with AI Grader
Need help grading? Try our AI Grader for instant feedback on your assignments.
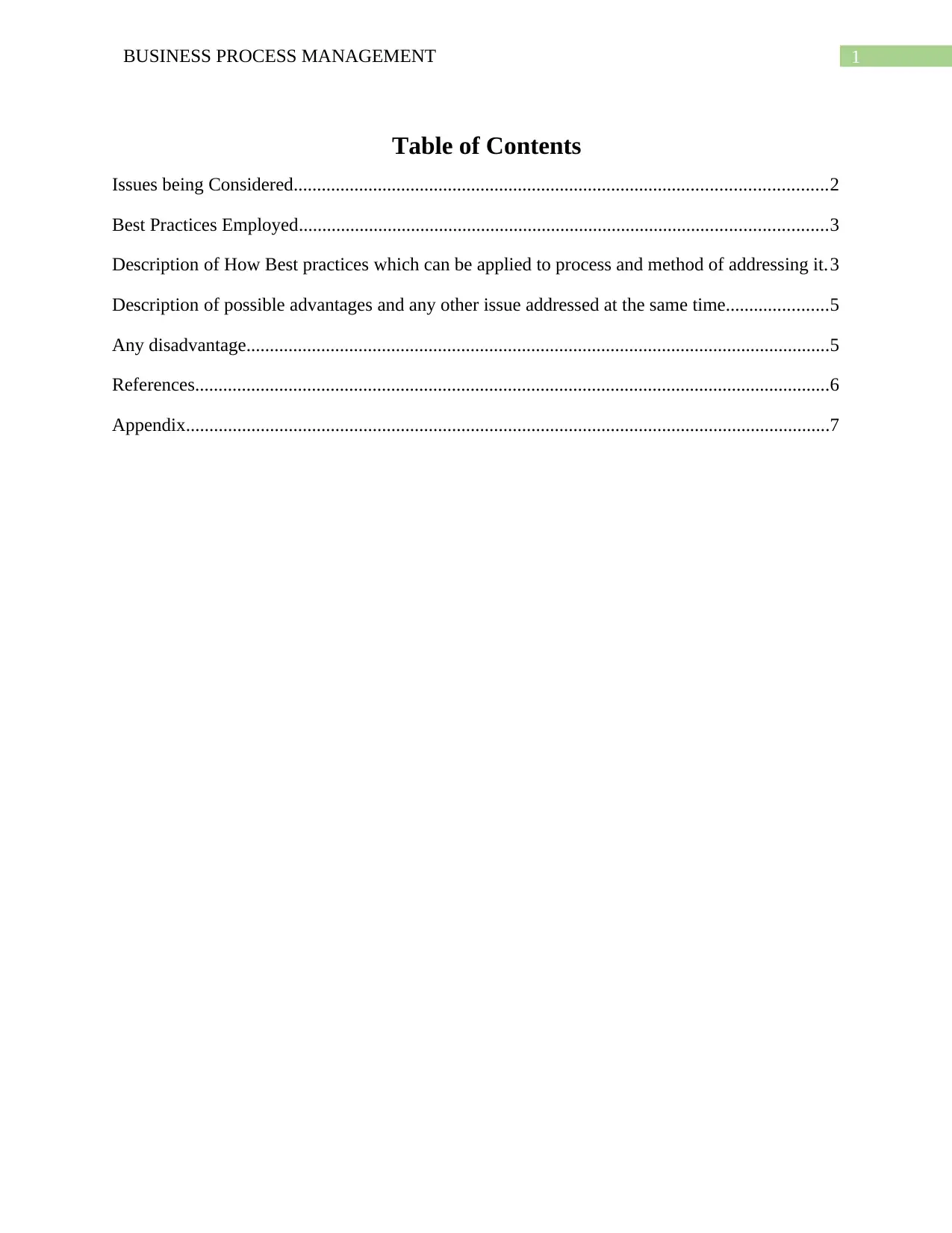
1BUSINESS PROCESS MANAGEMENT
Table of Contents
Issues being Considered..................................................................................................................2
Best Practices Employed.................................................................................................................3
Description of How Best practices which can be applied to process and method of addressing it.3
Description of possible advantages and any other issue addressed at the same time......................5
Any disadvantage.............................................................................................................................5
References........................................................................................................................................6
Appendix..........................................................................................................................................7
Table of Contents
Issues being Considered..................................................................................................................2
Best Practices Employed.................................................................................................................3
Description of How Best practices which can be applied to process and method of addressing it.3
Description of possible advantages and any other issue addressed at the same time......................5
Any disadvantage.............................................................................................................................5
References........................................................................................................................................6
Appendix..........................................................................................................................................7
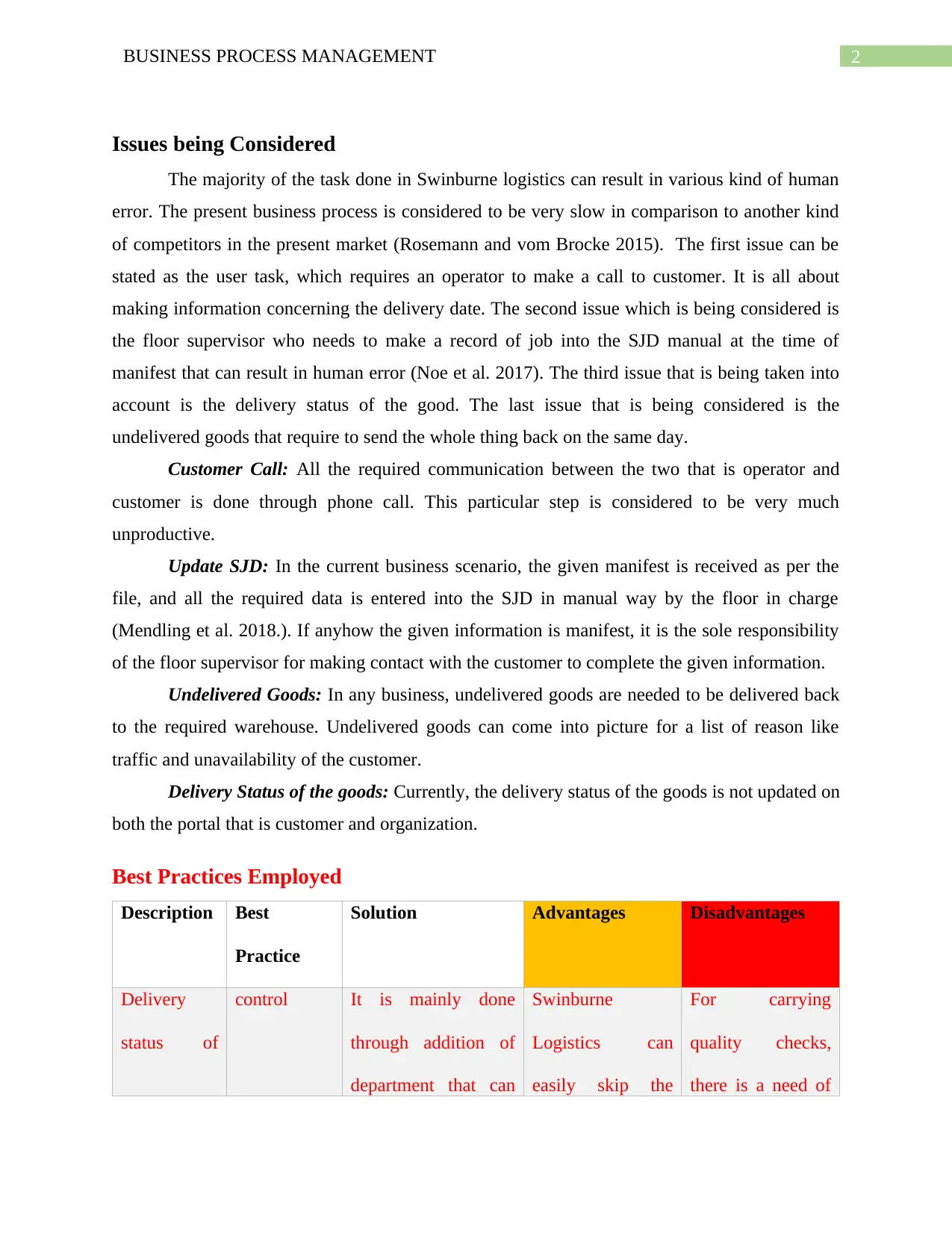
2BUSINESS PROCESS MANAGEMENT
Issues being Considered
The majority of the task done in Swinburne logistics can result in various kind of human
error. The present business process is considered to be very slow in comparison to another kind
of competitors in the present market (Rosemann and vom Brocke 2015). The first issue can be
stated as the user task, which requires an operator to make a call to customer. It is all about
making information concerning the delivery date. The second issue which is being considered is
the floor supervisor who needs to make a record of job into the SJD manual at the time of
manifest that can result in human error (Noe et al. 2017). The third issue that is being taken into
account is the delivery status of the good. The last issue that is being considered is the
undelivered goods that require to send the whole thing back on the same day.
Customer Call: All the required communication between the two that is operator and
customer is done through phone call. This particular step is considered to be very much
unproductive.
Update SJD: In the current business scenario, the given manifest is received as per the
file, and all the required data is entered into the SJD in manual way by the floor in charge
(Mendling et al. 2018.). If anyhow the given information is manifest, it is the sole responsibility
of the floor supervisor for making contact with the customer to complete the given information.
Undelivered Goods: In any business, undelivered goods are needed to be delivered back
to the required warehouse. Undelivered goods can come into picture for a list of reason like
traffic and unavailability of the customer.
Delivery Status of the goods: Currently, the delivery status of the goods is not updated on
both the portal that is customer and organization.
Best Practices Employed
Description Best
Practice
Solution Advantages Disadvantages
Delivery
status of
control It is mainly done
through addition of
department that can
Swinburne
Logistics can
easily skip the
For carrying
quality checks,
there is a need of
Issues being Considered
The majority of the task done in Swinburne logistics can result in various kind of human
error. The present business process is considered to be very slow in comparison to another kind
of competitors in the present market (Rosemann and vom Brocke 2015). The first issue can be
stated as the user task, which requires an operator to make a call to customer. It is all about
making information concerning the delivery date. The second issue which is being considered is
the floor supervisor who needs to make a record of job into the SJD manual at the time of
manifest that can result in human error (Noe et al. 2017). The third issue that is being taken into
account is the delivery status of the good. The last issue that is being considered is the
undelivered goods that require to send the whole thing back on the same day.
Customer Call: All the required communication between the two that is operator and
customer is done through phone call. This particular step is considered to be very much
unproductive.
Update SJD: In the current business scenario, the given manifest is received as per the
file, and all the required data is entered into the SJD in manual way by the floor in charge
(Mendling et al. 2018.). If anyhow the given information is manifest, it is the sole responsibility
of the floor supervisor for making contact with the customer to complete the given information.
Undelivered Goods: In any business, undelivered goods are needed to be delivered back
to the required warehouse. Undelivered goods can come into picture for a list of reason like
traffic and unavailability of the customer.
Delivery Status of the goods: Currently, the delivery status of the goods is not updated on
both the portal that is customer and organization.
Best Practices Employed
Description Best
Practice
Solution Advantages Disadvantages
Delivery
status of
control It is mainly done
through addition of
department that can
Swinburne
Logistics can
easily skip the
For carrying
quality checks,
there is a need of
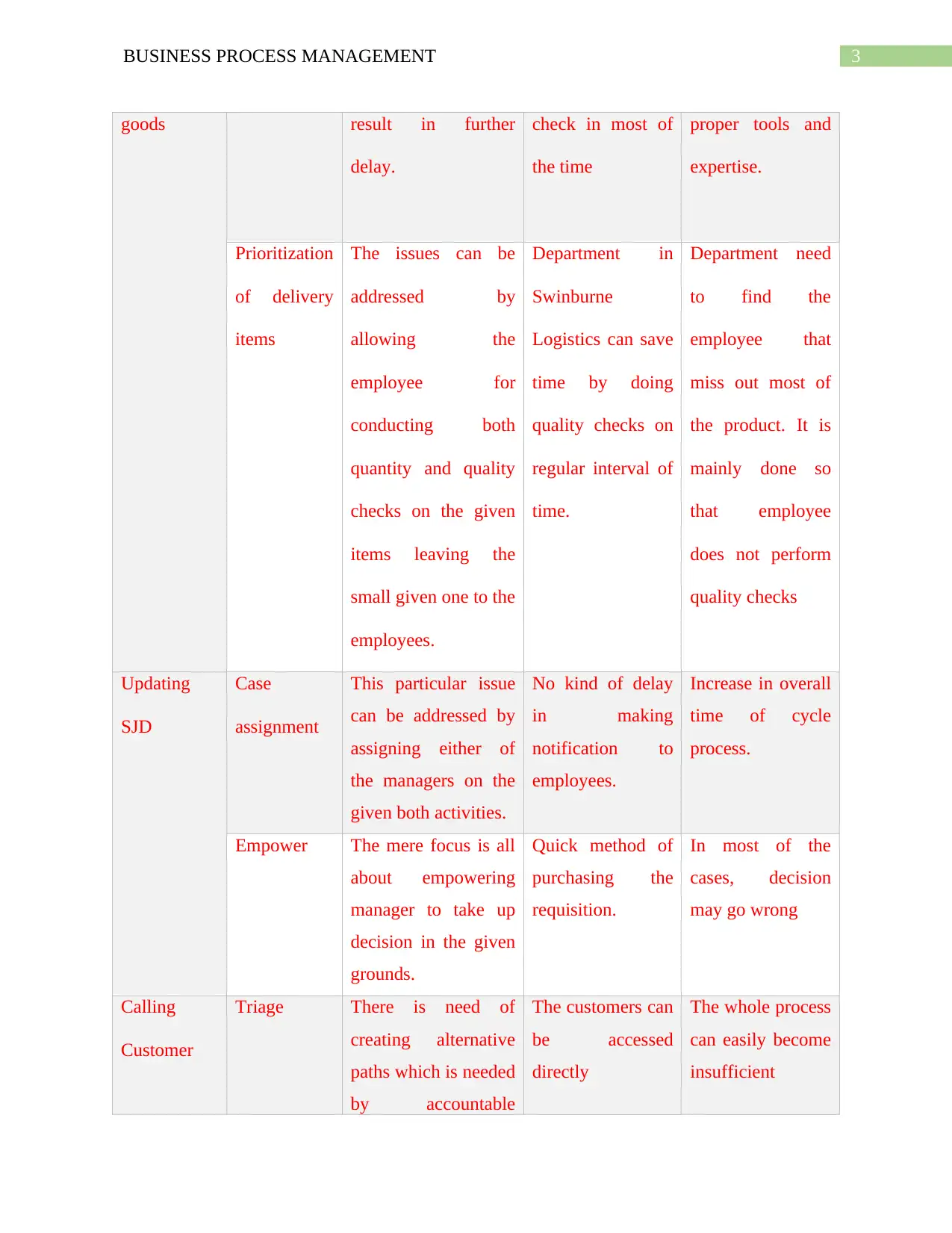
3BUSINESS PROCESS MANAGEMENT
goods result in further
delay.
check in most of
the time
proper tools and
expertise.
Prioritization
of delivery
items
The issues can be
addressed by
allowing the
employee for
conducting both
quantity and quality
checks on the given
items leaving the
small given one to the
employees.
Department in
Swinburne
Logistics can save
time by doing
quality checks on
regular interval of
time.
Department need
to find the
employee that
miss out most of
the product. It is
mainly done so
that employee
does not perform
quality checks
Updating
SJD
Case
assignment
This particular issue
can be addressed by
assigning either of
the managers on the
given both activities.
No kind of delay
in making
notification to
employees.
Increase in overall
time of cycle
process.
Empower The mere focus is all
about empowering
manager to take up
decision in the given
grounds.
Quick method of
purchasing the
requisition.
In most of the
cases, decision
may go wrong
Calling
Customer
Triage There is need of
creating alternative
paths which is needed
by accountable
The customers can
be accessed
directly
The whole process
can easily become
insufficient
goods result in further
delay.
check in most of
the time
proper tools and
expertise.
Prioritization
of delivery
items
The issues can be
addressed by
allowing the
employee for
conducting both
quantity and quality
checks on the given
items leaving the
small given one to the
employees.
Department in
Swinburne
Logistics can save
time by doing
quality checks on
regular interval of
time.
Department need
to find the
employee that
miss out most of
the product. It is
mainly done so
that employee
does not perform
quality checks
Updating
SJD
Case
assignment
This particular issue
can be addressed by
assigning either of
the managers on the
given both activities.
No kind of delay
in making
notification to
employees.
Increase in overall
time of cycle
process.
Empower The mere focus is all
about empowering
manager to take up
decision in the given
grounds.
Quick method of
purchasing the
requisition.
In most of the
cases, decision
may go wrong
Calling
Customer
Triage There is need of
creating alternative
paths which is needed
by accountable
The customers can
be accessed
directly
The whole process
can easily become
insufficient
Secure Best Marks with AI Grader
Need help grading? Try our AI Grader for instant feedback on your assignments.
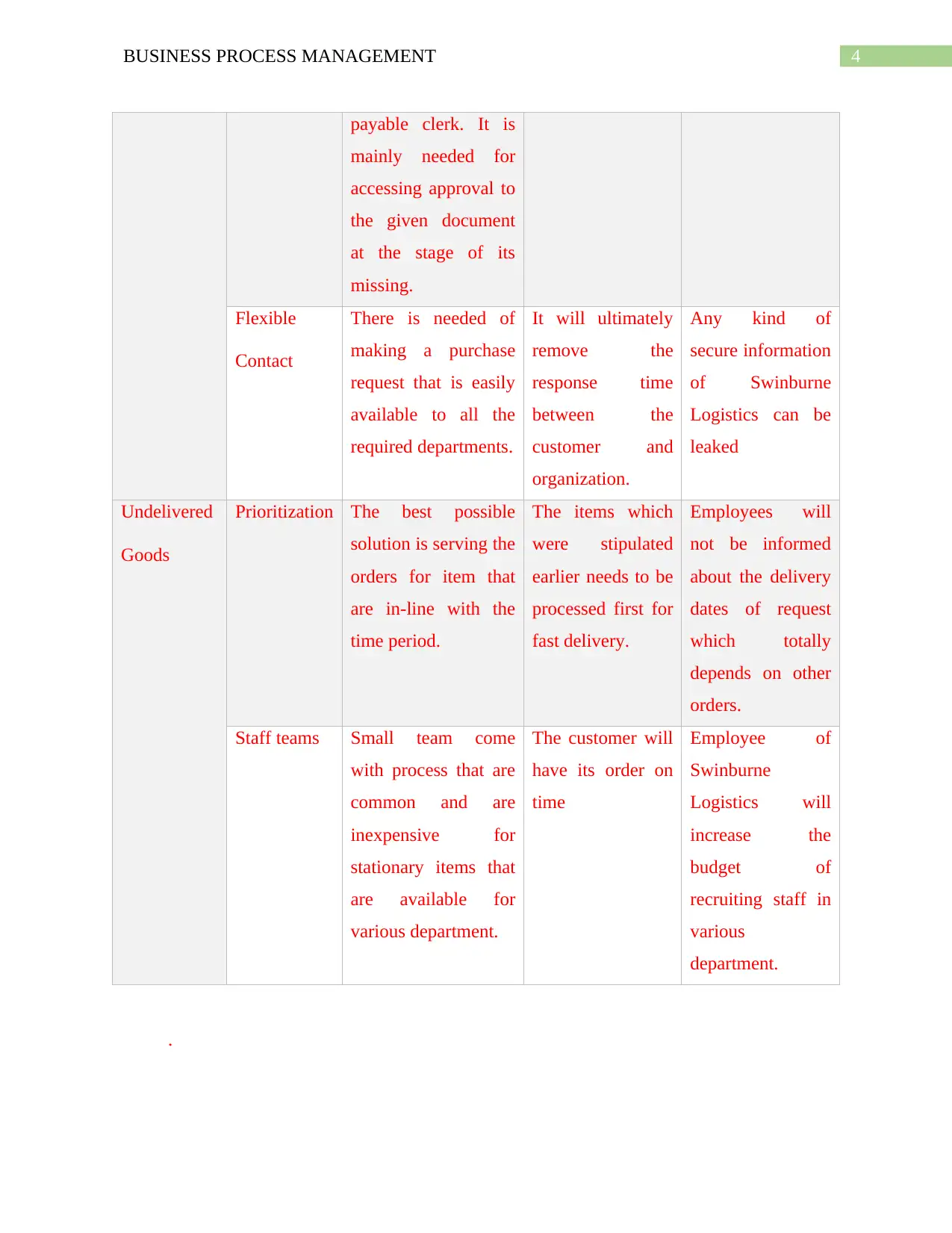
4BUSINESS PROCESS MANAGEMENT
payable clerk. It is
mainly needed for
accessing approval to
the given document
at the stage of its
missing.
Flexible
Contact
There is needed of
making a purchase
request that is easily
available to all the
required departments.
It will ultimately
remove the
response time
between the
customer and
organization.
Any kind of
secure information
of Swinburne
Logistics can be
leaked
Undelivered
Goods
Prioritization The best possible
solution is serving the
orders for item that
are in-line with the
time period.
The items which
were stipulated
earlier needs to be
processed first for
fast delivery.
Employees will
not be informed
about the delivery
dates of request
which totally
depends on other
orders.
Staff teams Small team come
with process that are
common and are
inexpensive for
stationary items that
are available for
various department.
The customer will
have its order on
time
Employee of
Swinburne
Logistics will
increase the
budget of
recruiting staff in
various
department.
.
payable clerk. It is
mainly needed for
accessing approval to
the given document
at the stage of its
missing.
Flexible
Contact
There is needed of
making a purchase
request that is easily
available to all the
required departments.
It will ultimately
remove the
response time
between the
customer and
organization.
Any kind of
secure information
of Swinburne
Logistics can be
leaked
Undelivered
Goods
Prioritization The best possible
solution is serving the
orders for item that
are in-line with the
time period.
The items which
were stipulated
earlier needs to be
processed first for
fast delivery.
Employees will
not be informed
about the delivery
dates of request
which totally
depends on other
orders.
Staff teams Small team come
with process that are
common and are
inexpensive for
stationary items that
are available for
various department.
The customer will
have its order on
time
Employee of
Swinburne
Logistics will
increase the
budget of
recruiting staff in
various
department.
.
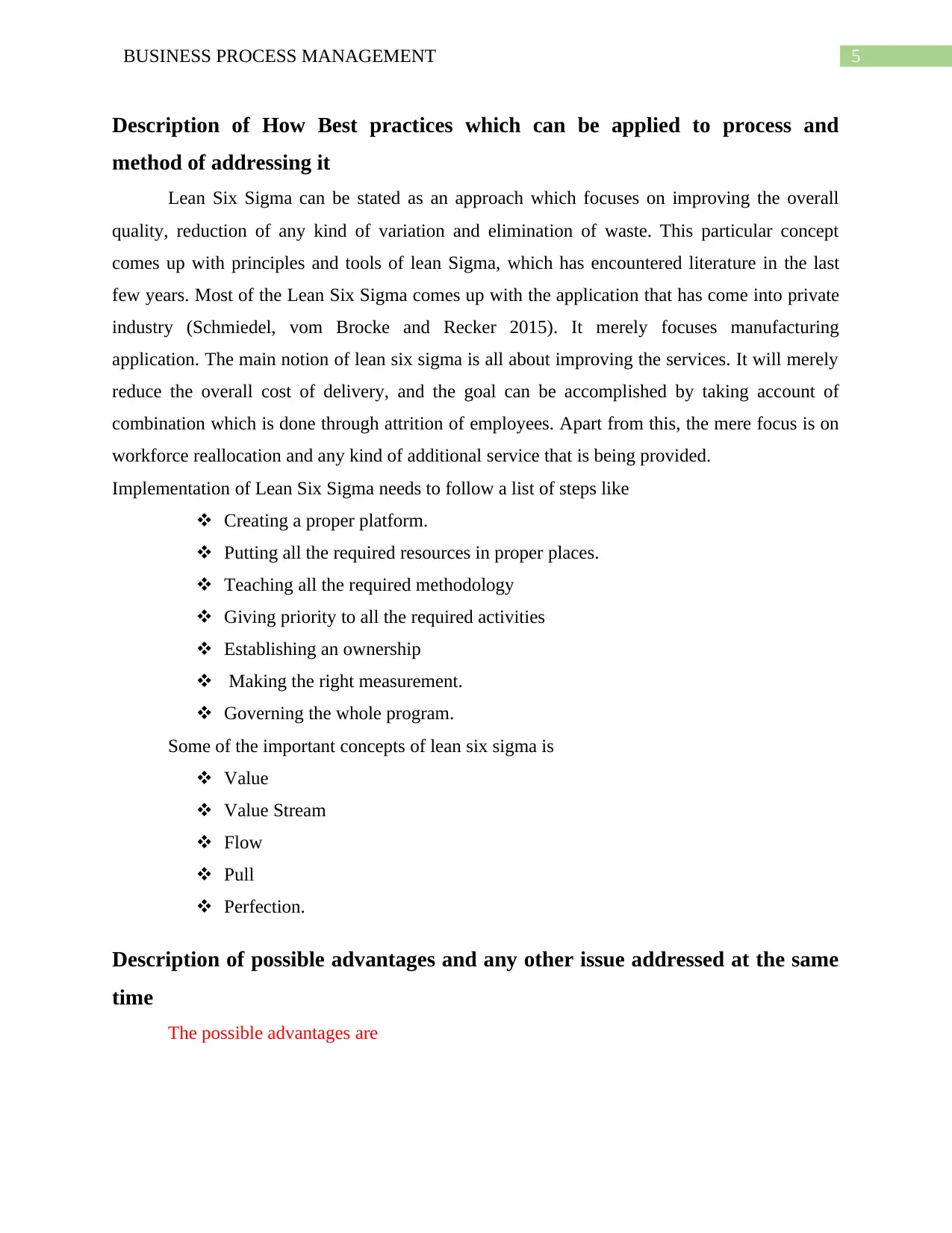
5BUSINESS PROCESS MANAGEMENT
Description of How Best practices which can be applied to process and
method of addressing it
Lean Six Sigma can be stated as an approach which focuses on improving the overall
quality, reduction of any kind of variation and elimination of waste. This particular concept
comes up with principles and tools of lean Sigma, which has encountered literature in the last
few years. Most of the Lean Six Sigma comes up with the application that has come into private
industry (Schmiedel, vom Brocke and Recker 2015). It merely focuses manufacturing
application. The main notion of lean six sigma is all about improving the services. It will merely
reduce the overall cost of delivery, and the goal can be accomplished by taking account of
combination which is done through attrition of employees. Apart from this, the mere focus is on
workforce reallocation and any kind of additional service that is being provided.
Implementation of Lean Six Sigma needs to follow a list of steps like
Creating a proper platform.
Putting all the required resources in proper places.
Teaching all the required methodology
Giving priority to all the required activities
Establishing an ownership
Making the right measurement.
Governing the whole program.
Some of the important concepts of lean six sigma is
Value
Value Stream
Flow
Pull
Perfection.
Description of possible advantages and any other issue addressed at the same
time
The possible advantages are
Description of How Best practices which can be applied to process and
method of addressing it
Lean Six Sigma can be stated as an approach which focuses on improving the overall
quality, reduction of any kind of variation and elimination of waste. This particular concept
comes up with principles and tools of lean Sigma, which has encountered literature in the last
few years. Most of the Lean Six Sigma comes up with the application that has come into private
industry (Schmiedel, vom Brocke and Recker 2015). It merely focuses manufacturing
application. The main notion of lean six sigma is all about improving the services. It will merely
reduce the overall cost of delivery, and the goal can be accomplished by taking account of
combination which is done through attrition of employees. Apart from this, the mere focus is on
workforce reallocation and any kind of additional service that is being provided.
Implementation of Lean Six Sigma needs to follow a list of steps like
Creating a proper platform.
Putting all the required resources in proper places.
Teaching all the required methodology
Giving priority to all the required activities
Establishing an ownership
Making the right measurement.
Governing the whole program.
Some of the important concepts of lean six sigma is
Value
Value Stream
Flow
Pull
Perfection.
Description of possible advantages and any other issue addressed at the same
time
The possible advantages are
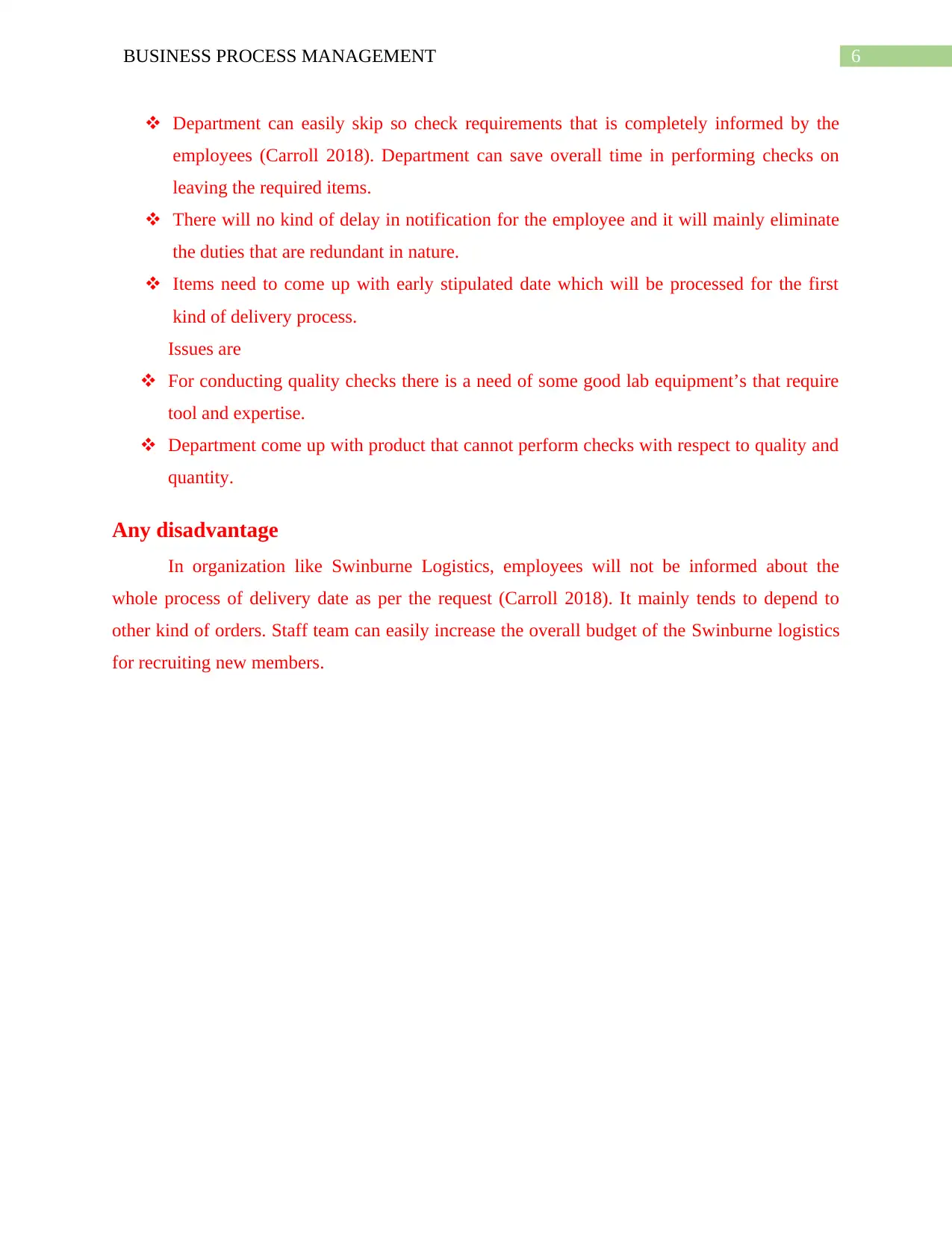
6BUSINESS PROCESS MANAGEMENT
Department can easily skip so check requirements that is completely informed by the
employees (Carroll 2018). Department can save overall time in performing checks on
leaving the required items.
There will no kind of delay in notification for the employee and it will mainly eliminate
the duties that are redundant in nature.
Items need to come up with early stipulated date which will be processed for the first
kind of delivery process.
Issues are
For conducting quality checks there is a need of some good lab equipment’s that require
tool and expertise.
Department come up with product that cannot perform checks with respect to quality and
quantity.
Any disadvantage
In organization like Swinburne Logistics, employees will not be informed about the
whole process of delivery date as per the request (Carroll 2018). It mainly tends to depend to
other kind of orders. Staff team can easily increase the overall budget of the Swinburne logistics
for recruiting new members.
Department can easily skip so check requirements that is completely informed by the
employees (Carroll 2018). Department can save overall time in performing checks on
leaving the required items.
There will no kind of delay in notification for the employee and it will mainly eliminate
the duties that are redundant in nature.
Items need to come up with early stipulated date which will be processed for the first
kind of delivery process.
Issues are
For conducting quality checks there is a need of some good lab equipment’s that require
tool and expertise.
Department come up with product that cannot perform checks with respect to quality and
quantity.
Any disadvantage
In organization like Swinburne Logistics, employees will not be informed about the
whole process of delivery date as per the request (Carroll 2018). It mainly tends to depend to
other kind of orders. Staff team can easily increase the overall budget of the Swinburne logistics
for recruiting new members.
Paraphrase This Document
Need a fresh take? Get an instant paraphrase of this document with our AI Paraphraser
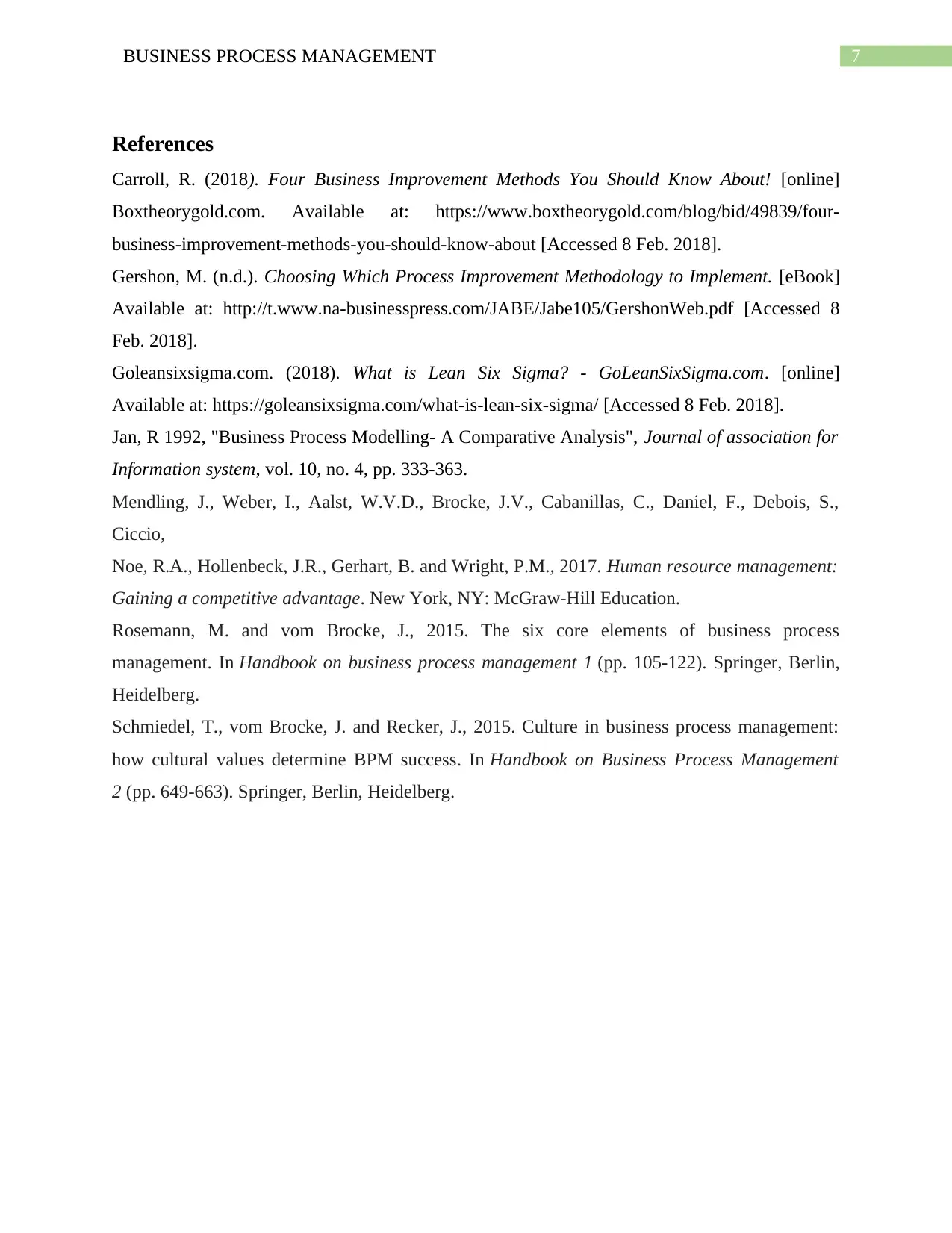
7BUSINESS PROCESS MANAGEMENT
References
Carroll, R. (2018). Four Business Improvement Methods You Should Know About! [online]
Boxtheorygold.com. Available at: https://www.boxtheorygold.com/blog/bid/49839/four-
business-improvement-methods-you-should-know-about [Accessed 8 Feb. 2018].
Gershon, M. (n.d.). Choosing Which Process Improvement Methodology to Implement. [eBook]
Available at: http://t.www.na-businesspress.com/JABE/Jabe105/GershonWeb.pdf [Accessed 8
Feb. 2018].
Goleansixsigma.com. (2018). What is Lean Six Sigma? - GoLeanSixSigma.com. [online]
Available at: https://goleansixsigma.com/what-is-lean-six-sigma/ [Accessed 8 Feb. 2018].
Jan, R 1992, "Business Process Modelling- A Comparative Analysis", Journal of association for
Information system, vol. 10, no. 4, pp. 333-363.
Mendling, J., Weber, I., Aalst, W.V.D., Brocke, J.V., Cabanillas, C., Daniel, F., Debois, S.,
Ciccio,
Noe, R.A., Hollenbeck, J.R., Gerhart, B. and Wright, P.M., 2017. Human resource management:
Gaining a competitive advantage. New York, NY: McGraw-Hill Education.
Rosemann, M. and vom Brocke, J., 2015. The six core elements of business process
management. In Handbook on business process management 1 (pp. 105-122). Springer, Berlin,
Heidelberg.
Schmiedel, T., vom Brocke, J. and Recker, J., 2015. Culture in business process management:
how cultural values determine BPM success. In Handbook on Business Process Management
2 (pp. 649-663). Springer, Berlin, Heidelberg.
References
Carroll, R. (2018). Four Business Improvement Methods You Should Know About! [online]
Boxtheorygold.com. Available at: https://www.boxtheorygold.com/blog/bid/49839/four-
business-improvement-methods-you-should-know-about [Accessed 8 Feb. 2018].
Gershon, M. (n.d.). Choosing Which Process Improvement Methodology to Implement. [eBook]
Available at: http://t.www.na-businesspress.com/JABE/Jabe105/GershonWeb.pdf [Accessed 8
Feb. 2018].
Goleansixsigma.com. (2018). What is Lean Six Sigma? - GoLeanSixSigma.com. [online]
Available at: https://goleansixsigma.com/what-is-lean-six-sigma/ [Accessed 8 Feb. 2018].
Jan, R 1992, "Business Process Modelling- A Comparative Analysis", Journal of association for
Information system, vol. 10, no. 4, pp. 333-363.
Mendling, J., Weber, I., Aalst, W.V.D., Brocke, J.V., Cabanillas, C., Daniel, F., Debois, S.,
Ciccio,
Noe, R.A., Hollenbeck, J.R., Gerhart, B. and Wright, P.M., 2017. Human resource management:
Gaining a competitive advantage. New York, NY: McGraw-Hill Education.
Rosemann, M. and vom Brocke, J., 2015. The six core elements of business process
management. In Handbook on business process management 1 (pp. 105-122). Springer, Berlin,
Heidelberg.
Schmiedel, T., vom Brocke, J. and Recker, J., 2015. Culture in business process management:
how cultural values determine BPM success. In Handbook on Business Process Management
2 (pp. 649-663). Springer, Berlin, Heidelberg.
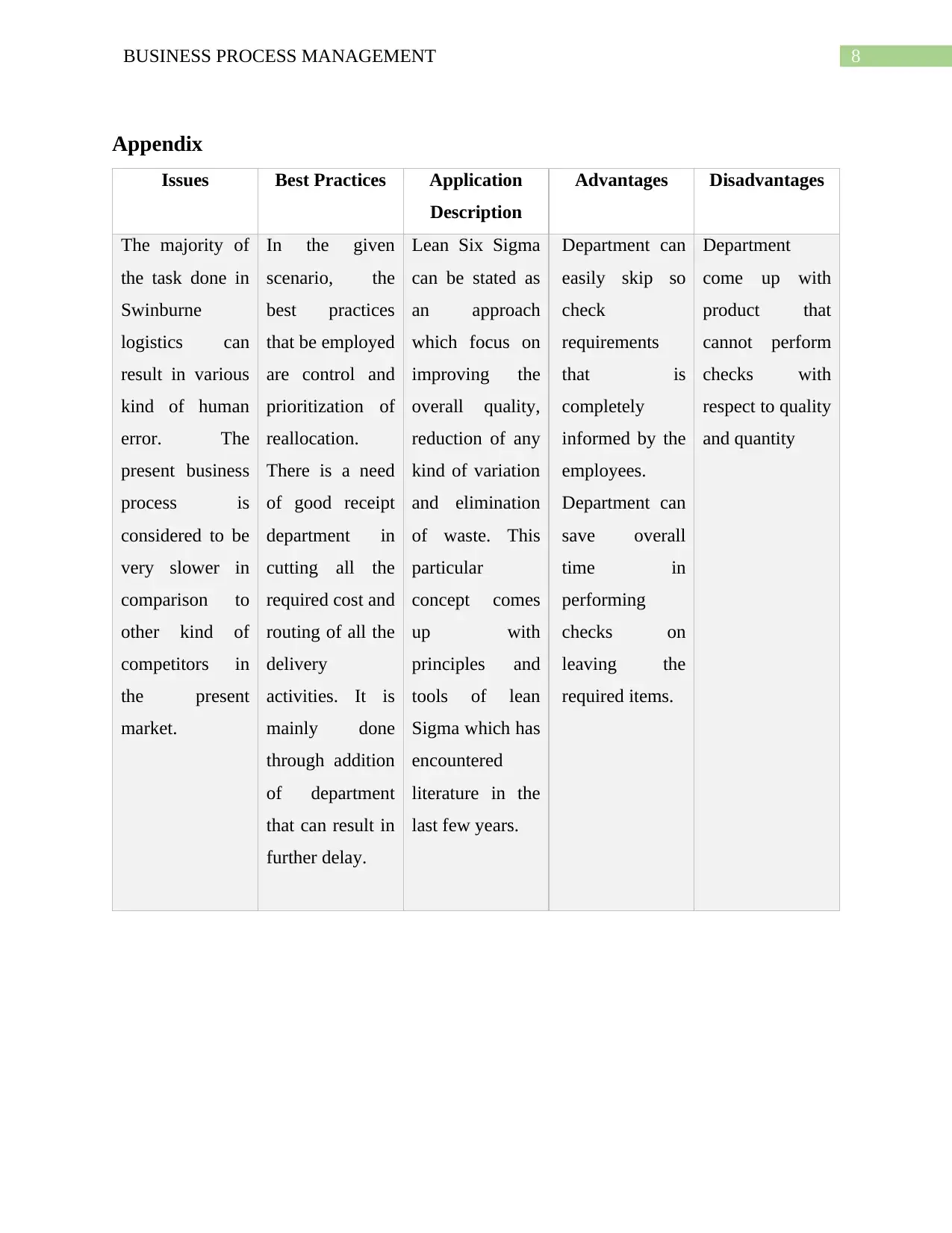
8BUSINESS PROCESS MANAGEMENT
Appendix
Issues Best Practices Application
Description
Advantages Disadvantages
The majority of
the task done in
Swinburne
logistics can
result in various
kind of human
error. The
present business
process is
considered to be
very slower in
comparison to
other kind of
competitors in
the present
market.
In the given
scenario, the
best practices
that be employed
are control and
prioritization of
reallocation.
There is a need
of good receipt
department in
cutting all the
required cost and
routing of all the
delivery
activities. It is
mainly done
through addition
of department
that can result in
further delay.
Lean Six Sigma
can be stated as
an approach
which focus on
improving the
overall quality,
reduction of any
kind of variation
and elimination
of waste. This
particular
concept comes
up with
principles and
tools of lean
Sigma which has
encountered
literature in the
last few years.
Department can
easily skip so
check
requirements
that is
completely
informed by the
employees.
Department can
save overall
time in
performing
checks on
leaving the
required items.
Department
come up with
product that
cannot perform
checks with
respect to quality
and quantity
Appendix
Issues Best Practices Application
Description
Advantages Disadvantages
The majority of
the task done in
Swinburne
logistics can
result in various
kind of human
error. The
present business
process is
considered to be
very slower in
comparison to
other kind of
competitors in
the present
market.
In the given
scenario, the
best practices
that be employed
are control and
prioritization of
reallocation.
There is a need
of good receipt
department in
cutting all the
required cost and
routing of all the
delivery
activities. It is
mainly done
through addition
of department
that can result in
further delay.
Lean Six Sigma
can be stated as
an approach
which focus on
improving the
overall quality,
reduction of any
kind of variation
and elimination
of waste. This
particular
concept comes
up with
principles and
tools of lean
Sigma which has
encountered
literature in the
last few years.
Department can
easily skip so
check
requirements
that is
completely
informed by the
employees.
Department can
save overall
time in
performing
checks on
leaving the
required items.
Department
come up with
product that
cannot perform
checks with
respect to quality
and quantity
1 out of 9
Related Documents
![[object Object]](/_next/image/?url=%2F_next%2Fstatic%2Fmedia%2Flogo.6d15ce61.png&w=640&q=75)
Your All-in-One AI-Powered Toolkit for Academic Success.
+13062052269
info@desklib.com
Available 24*7 on WhatsApp / Email
Unlock your academic potential
© 2024 | Zucol Services PVT LTD | All rights reserved.