Capacity and Inventory Management for Call-Us Plumbing Supply
VerifiedAdded on  2023/06/05
|17
|3469
|498
AI Summary
This article discusses capacity planning, effective capacity management, inventory management, and supply chain management for Call-Us Plumbing Supply. It includes explanations, calculations, and recommendations for improvement.
Contribute Materials
Your contribution can guide someone’s learning journey. Share your
documents today.
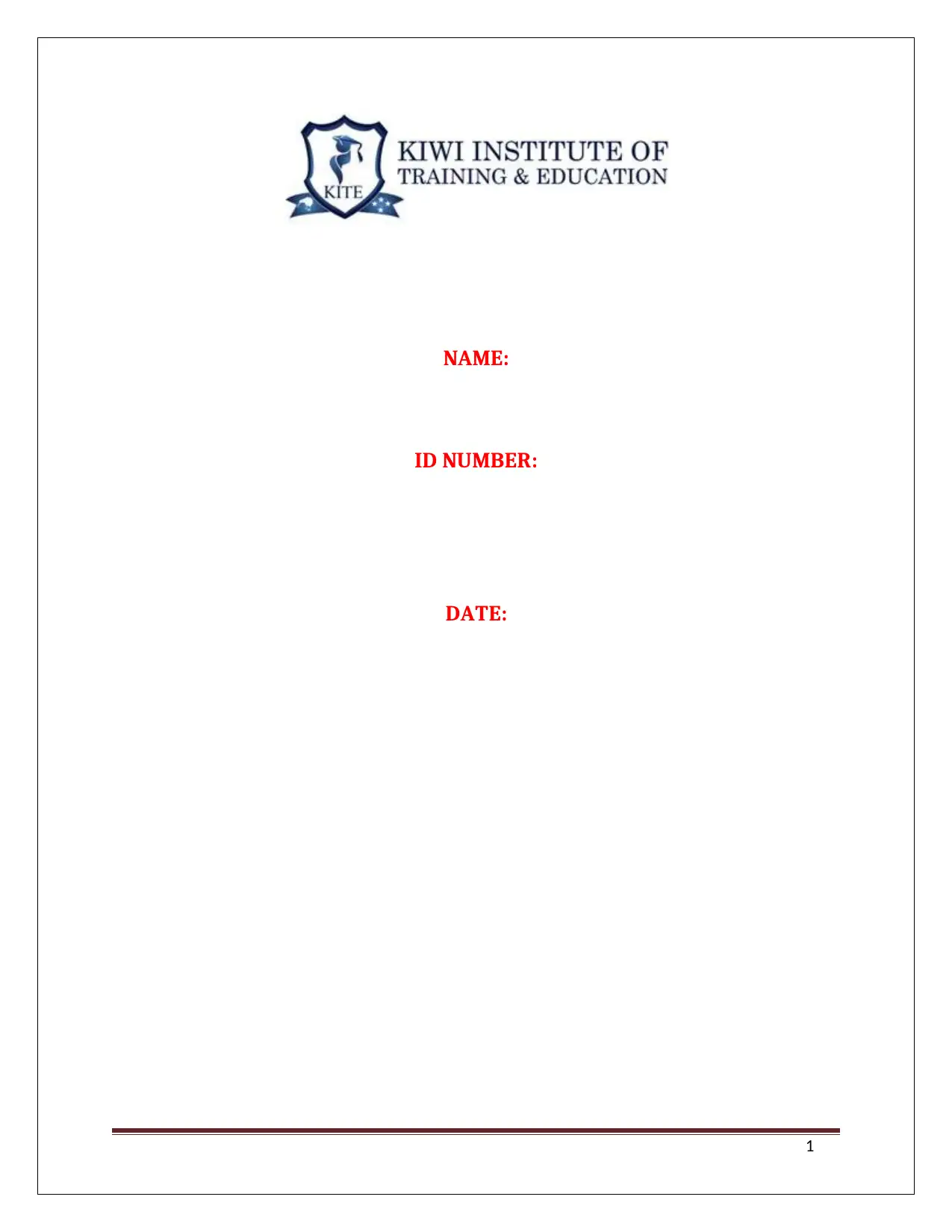
NAME:
ID NUMBER:
DATE:
1
ID NUMBER:
DATE:
1
Secure Best Marks with AI Grader
Need help grading? Try our AI Grader for instant feedback on your assignments.
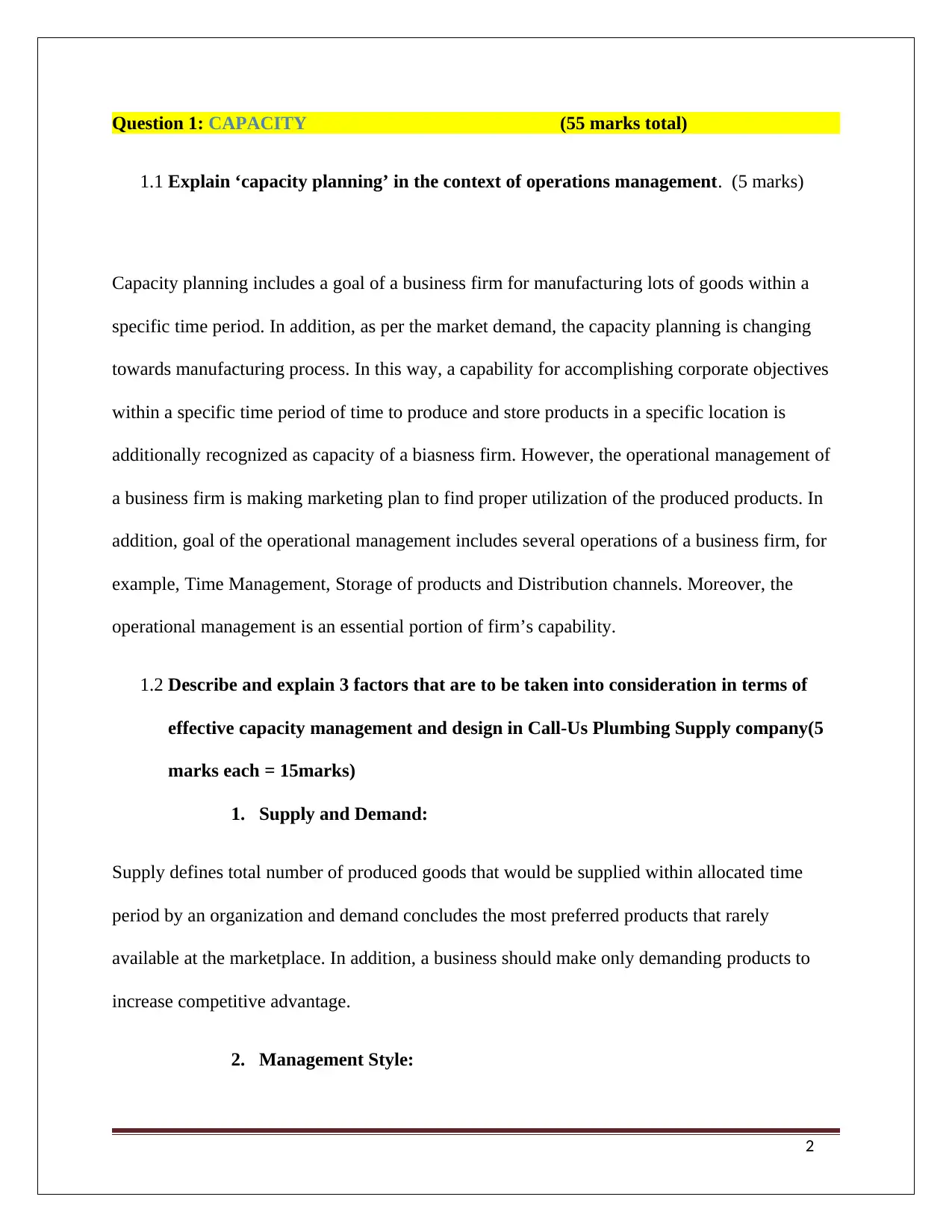
Question 1: CAPACITY (55 marks total)
1.1 Explain ‘capacity planning’ in the context of operations management. (5 marks)
Capacity planning includes a goal of a business firm for manufacturing lots of goods within a
specific time period. In addition, as per the market demand, the capacity planning is changing
towards manufacturing process. In this way, a capability for accomplishing corporate objectives
within a specific time period of time to produce and store products in a specific location is
additionally recognized as capacity of a biasness firm. However, the operational management of
a business firm is making marketing plan to find proper utilization of the produced products. In
addition, goal of the operational management includes several operations of a business firm, for
example, Time Management, Storage of products and Distribution channels. Moreover, the
operational management is an essential portion of firm’s capability.
1.2 Describe and explain 3 factors that are to be taken into consideration in terms of
effective capacity management and design in Call-Us Plumbing Supply company(5
marks each = 15marks)
1. Supply and Demand:
Supply defines total number of produced goods that would be supplied within allocated time
period by an organization and demand concludes the most preferred products that rarely
available at the marketplace. In addition, a business should make only demanding products to
increase competitive advantage.
2. Management Style:
2
1.1 Explain ‘capacity planning’ in the context of operations management. (5 marks)
Capacity planning includes a goal of a business firm for manufacturing lots of goods within a
specific time period. In addition, as per the market demand, the capacity planning is changing
towards manufacturing process. In this way, a capability for accomplishing corporate objectives
within a specific time period of time to produce and store products in a specific location is
additionally recognized as capacity of a biasness firm. However, the operational management of
a business firm is making marketing plan to find proper utilization of the produced products. In
addition, goal of the operational management includes several operations of a business firm, for
example, Time Management, Storage of products and Distribution channels. Moreover, the
operational management is an essential portion of firm’s capability.
1.2 Describe and explain 3 factors that are to be taken into consideration in terms of
effective capacity management and design in Call-Us Plumbing Supply company(5
marks each = 15marks)
1. Supply and Demand:
Supply defines total number of produced goods that would be supplied within allocated time
period by an organization and demand concludes the most preferred products that rarely
available at the marketplace. In addition, a business should make only demanding products to
increase competitive advantage.
2. Management Style:
2

The management style of a business firm is highly influenced by the employee performance
including skills and abilities. The Manager of business firm must have following skills:
ï‚· Excellent communication skills
ï‚· Friendly Behavior
ï‚· Time management
ï‚· Decision Making
ï‚· Co-operative
ï‚· Motivational
The working style of the employees can be measured by active support of the managers in the
workplace. Moreover, with the support of effective management skills, the employees can
produce high quality products under tight deadline to earn more revenue.
3. Machineries:
In order to increase the productivity, the leaders of a business firm should provide advanced
machinery to their workers. In addition, the employees of a business firm can update themselves
time to time by advanced machinery. Due to technical errors, the machineries might generate
difficulties for the workers of a business firm and in that case, the management should hire
qualified technicians to repair the defected machineries.
1.3 Calculate the capacity utilization rate of their production (5 marks)
Capacity utilization rate= actual capacity/potential capacity* 100
=300,000/458,333* 100
=0.065*100
3
including skills and abilities. The Manager of business firm must have following skills:
ï‚· Excellent communication skills
ï‚· Friendly Behavior
ï‚· Time management
ï‚· Decision Making
ï‚· Co-operative
ï‚· Motivational
The working style of the employees can be measured by active support of the managers in the
workplace. Moreover, with the support of effective management skills, the employees can
produce high quality products under tight deadline to earn more revenue.
3. Machineries:
In order to increase the productivity, the leaders of a business firm should provide advanced
machinery to their workers. In addition, the employees of a business firm can update themselves
time to time by advanced machinery. Due to technical errors, the machineries might generate
difficulties for the workers of a business firm and in that case, the management should hire
qualified technicians to repair the defected machineries.
1.3 Calculate the capacity utilization rate of their production (5 marks)
Capacity utilization rate= actual capacity/potential capacity* 100
=300,000/458,333* 100
=0.065*100
3
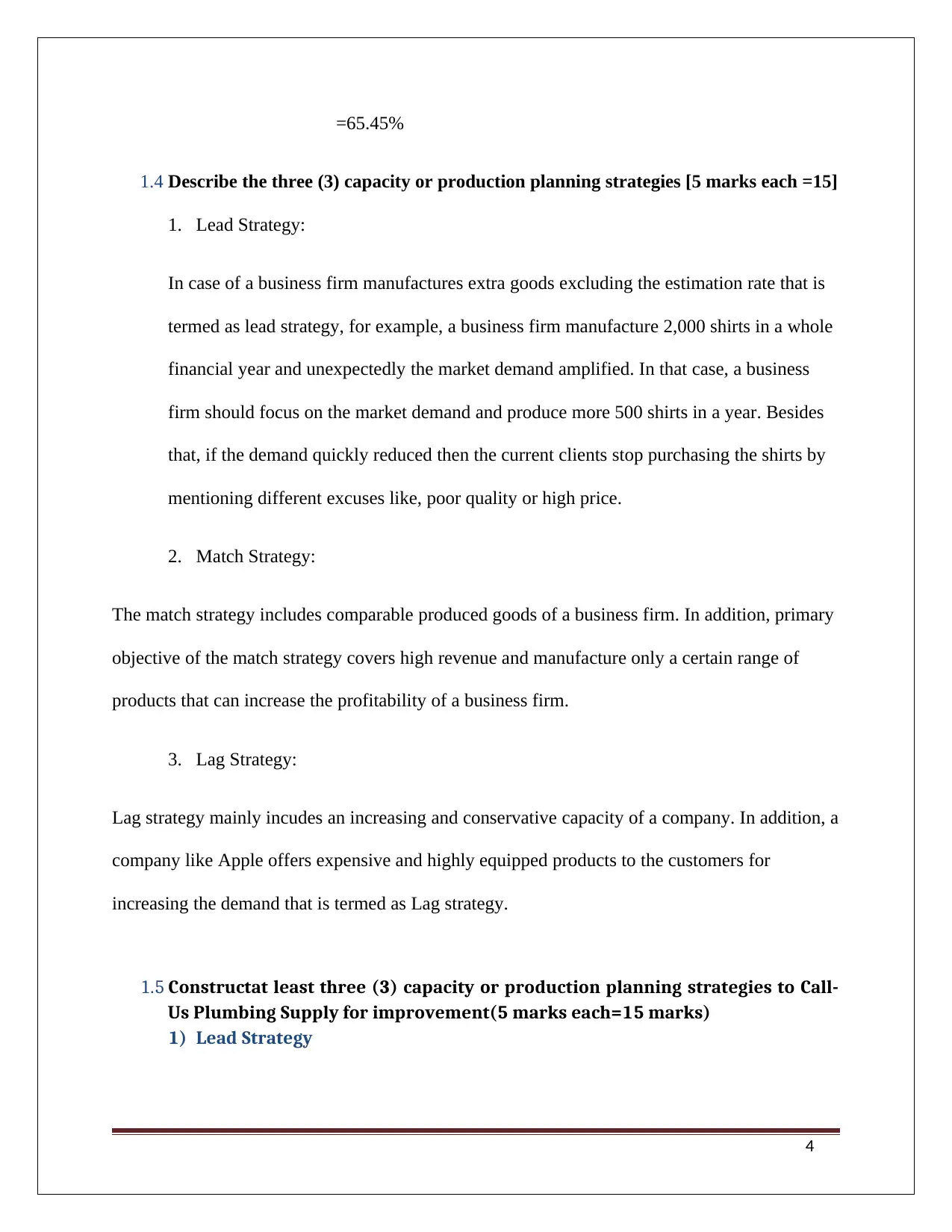
=65.45%
1.4 Describe the three (3) capacity or production planning strategies [5 marks each =15]
1. Lead Strategy:
In case of a business firm manufactures extra goods excluding the estimation rate that is
termed as lead strategy, for example, a business firm manufacture 2,000 shirts in a whole
financial year and unexpectedly the market demand amplified. In that case, a business
firm should focus on the market demand and produce more 500 shirts in a year. Besides
that, if the demand quickly reduced then the current clients stop purchasing the shirts by
mentioning different excuses like, poor quality or high price.
2. Match Strategy:
The match strategy includes comparable produced goods of a business firm. In addition, primary
objective of the match strategy covers high revenue and manufacture only a certain range of
products that can increase the profitability of a business firm.
3. Lag Strategy:
Lag strategy mainly incudes an increasing and conservative capacity of a company. In addition, a
company like Apple offers expensive and highly equipped products to the customers for
increasing the demand that is termed as Lag strategy.
1.5 Constructat least three (3) capacity or production planning strategies to Call-
Us Plumbing Supply for improvement(5 marks each=15 marks)
1) Lead Strategy
4
1.4 Describe the three (3) capacity or production planning strategies [5 marks each =15]
1. Lead Strategy:
In case of a business firm manufactures extra goods excluding the estimation rate that is
termed as lead strategy, for example, a business firm manufacture 2,000 shirts in a whole
financial year and unexpectedly the market demand amplified. In that case, a business
firm should focus on the market demand and produce more 500 shirts in a year. Besides
that, if the demand quickly reduced then the current clients stop purchasing the shirts by
mentioning different excuses like, poor quality or high price.
2. Match Strategy:
The match strategy includes comparable produced goods of a business firm. In addition, primary
objective of the match strategy covers high revenue and manufacture only a certain range of
products that can increase the profitability of a business firm.
3. Lag Strategy:
Lag strategy mainly incudes an increasing and conservative capacity of a company. In addition, a
company like Apple offers expensive and highly equipped products to the customers for
increasing the demand that is termed as Lag strategy.
1.5 Constructat least three (3) capacity or production planning strategies to Call-
Us Plumbing Supply for improvement(5 marks each=15 marks)
1) Lead Strategy
4
Secure Best Marks with AI Grader
Need help grading? Try our AI Grader for instant feedback on your assignments.
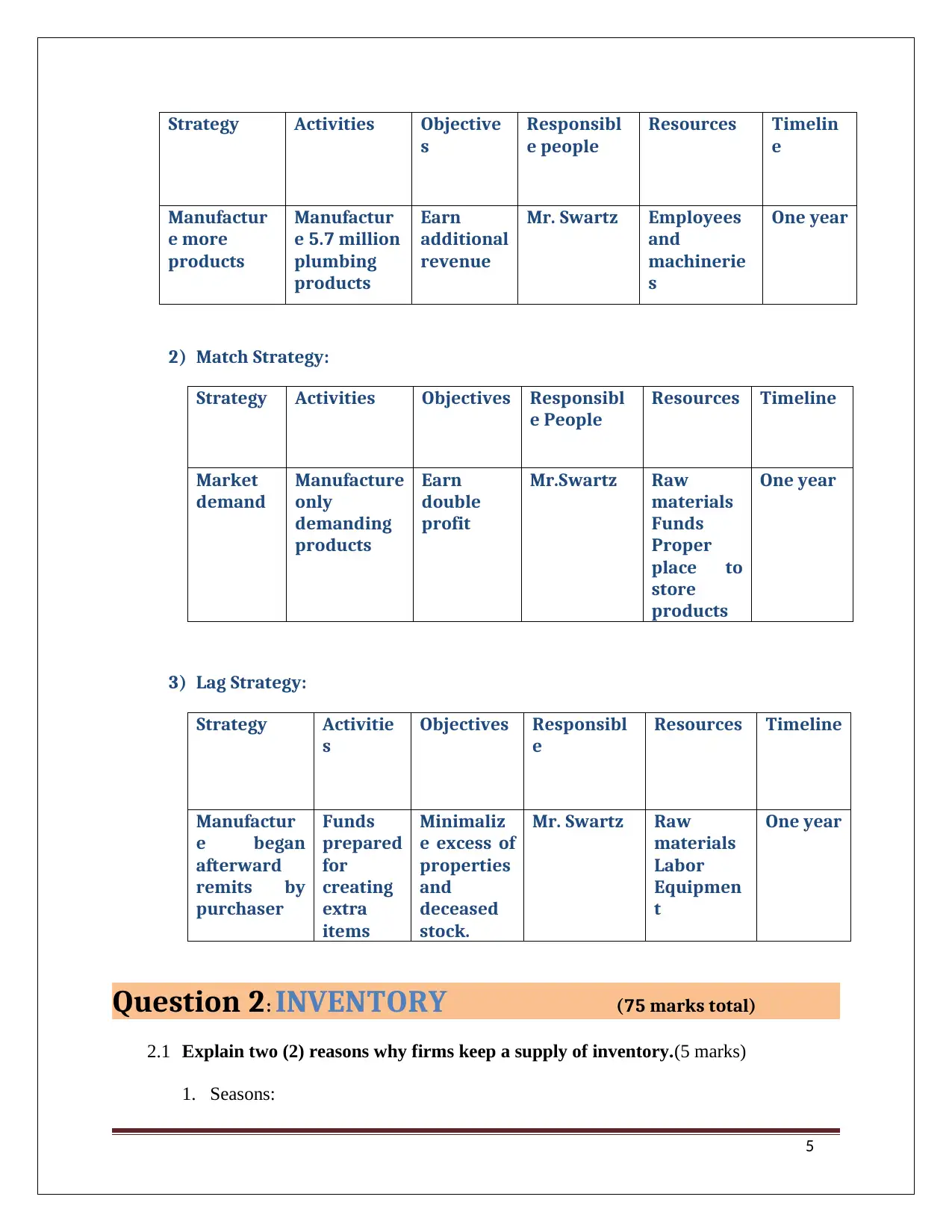
Strategy Activities Objective
s
Responsibl
e people
Resources Timelin
e
Manufactur
e more
products
Manufactur
e 5.7 million
plumbing
products
Earn
additional
revenue
Mr. Swartz Employees
and
machinerie
s
One year
2) Match Strategy:
Strategy Activities Objectives Responsibl
e People
Resources Timeline
Market
demand
Manufacture
only
demanding
products
Earn
double
profit
Mr.Swartz Raw
materials
Funds
Proper
place to
store
products
One year
3) Lag Strategy:
Strategy Activitie
s
Objectives Responsibl
e
Resources Timeline
Manufactur
e began
afterward
remits by
purchaser
Funds
prepared
for
creating
extra
items
Minimaliz
e excess of
properties
and
deceased
stock.
Mr. Swartz Raw
materials
Labor
Equipmen
t
One year
Question 2: INVENTORY (75 marks total)
2.1 Explain two (2) reasons why firms keep a supply of inventory.(5 marks)
1. Seasons:
5
s
Responsibl
e people
Resources Timelin
e
Manufactur
e more
products
Manufactur
e 5.7 million
plumbing
products
Earn
additional
revenue
Mr. Swartz Employees
and
machinerie
s
One year
2) Match Strategy:
Strategy Activities Objectives Responsibl
e People
Resources Timeline
Market
demand
Manufacture
only
demanding
products
Earn
double
profit
Mr.Swartz Raw
materials
Funds
Proper
place to
store
products
One year
3) Lag Strategy:
Strategy Activitie
s
Objectives Responsibl
e
Resources Timeline
Manufactur
e began
afterward
remits by
purchaser
Funds
prepared
for
creating
extra
items
Minimaliz
e excess of
properties
and
deceased
stock.
Mr. Swartz Raw
materials
Labor
Equipmen
t
One year
Question 2: INVENTORY (75 marks total)
2.1 Explain two (2) reasons why firms keep a supply of inventory.(5 marks)
1. Seasons:
5
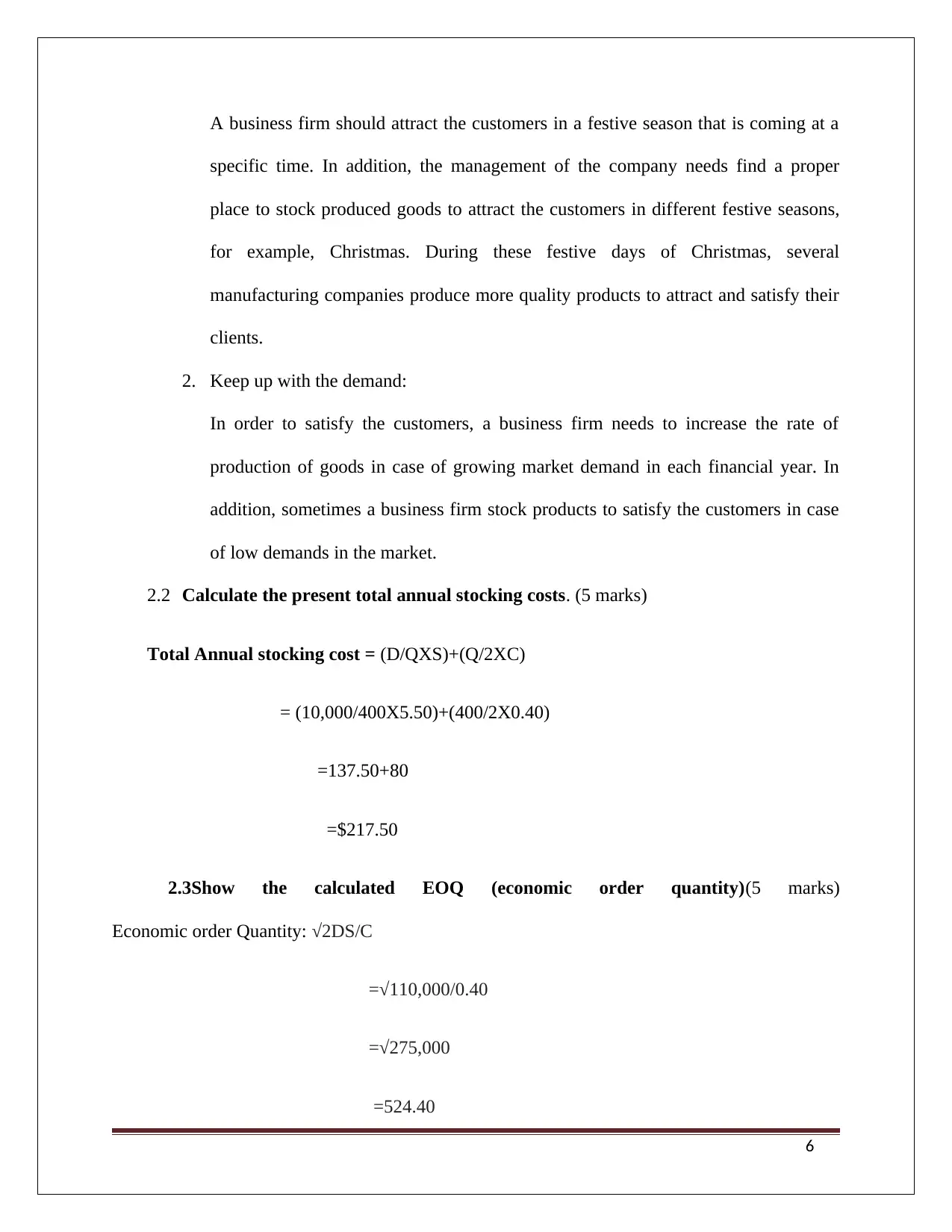
A business firm should attract the customers in a festive season that is coming at a
specific time. In addition, the management of the company needs find a proper
place to stock produced goods to attract the customers in different festive seasons,
for example, Christmas. During these festive days of Christmas, several
manufacturing companies produce more quality products to attract and satisfy their
clients.
2. Keep up with the demand:
In order to satisfy the customers, a business firm needs to increase the rate of
production of goods in case of growing market demand in each financial year. In
addition, sometimes a business firm stock products to satisfy the customers in case
of low demands in the market.
2.2 Calculate the present total annual stocking costs. (5 marks)
Total Annual stocking cost = (D/QXS)+(Q/2XC)
= (10,000/400X5.50)+(400/2X0.40)
=137.50+80
=$217.50
2.3Show the calculated EOQ (economic order quantity)(5 marks)
Economic order Quantity: √2DS/C
=√110,000/0.40
=√275,000
=524.40
6
specific time. In addition, the management of the company needs find a proper
place to stock produced goods to attract the customers in different festive seasons,
for example, Christmas. During these festive days of Christmas, several
manufacturing companies produce more quality products to attract and satisfy their
clients.
2. Keep up with the demand:
In order to satisfy the customers, a business firm needs to increase the rate of
production of goods in case of growing market demand in each financial year. In
addition, sometimes a business firm stock products to satisfy the customers in case
of low demands in the market.
2.2 Calculate the present total annual stocking costs. (5 marks)
Total Annual stocking cost = (D/QXS)+(Q/2XC)
= (10,000/400X5.50)+(400/2X0.40)
=137.50+80
=$217.50
2.3Show the calculated EOQ (economic order quantity)(5 marks)
Economic order Quantity: √2DS/C
=√110,000/0.40
=√275,000
=524.40
6
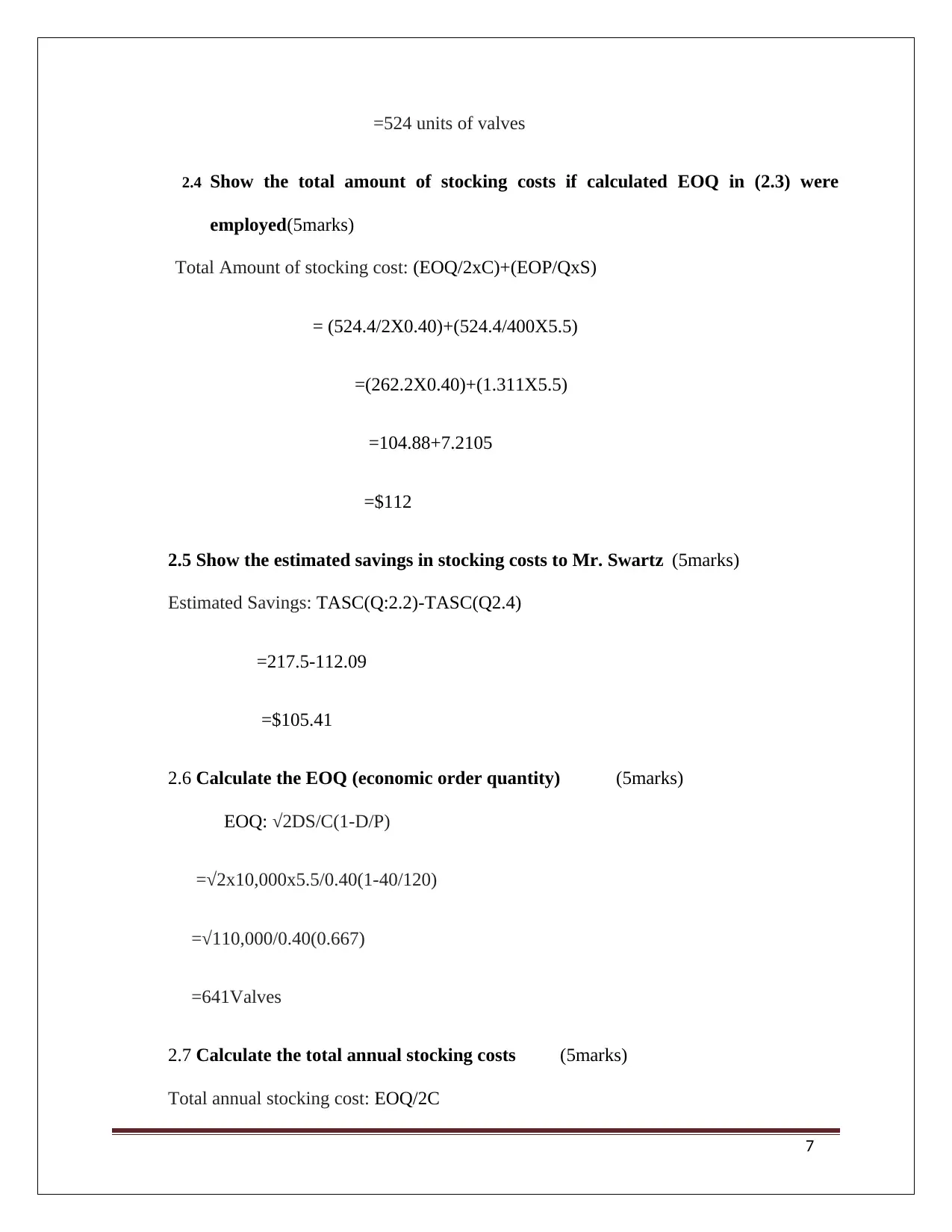
=524 units of valves
2.4 Show the total amount of stocking costs if calculated EOQ in (2.3) were
employed(5marks)
Total Amount of stocking cost: (EOQ/2xC)+(EOP/QxS)
= (524.4/2X0.40)+(524.4/400X5.5)
=(262.2X0.40)+(1.311X5.5)
=104.88+7.2105
=$112
2.5 Show the estimated savings in stocking costs to Mr. Swartz (5marks)
Estimated Savings: TASC(Q:2.2)-TASC(Q2.4)
=217.5-112.09
=$105.41
2.6 Calculate the EOQ (economic order quantity) (5marks)
EOQ: √2DS/C(1-D/P)
=√2x10,000x5.5/0.40(1-40/120)
=√110,000/0.40(0.667)
=641Valves
2.7 Calculate the total annual stocking costs (5marks)
Total annual stocking cost: EOQ/2C
7
2.4 Show the total amount of stocking costs if calculated EOQ in (2.3) were
employed(5marks)
Total Amount of stocking cost: (EOQ/2xC)+(EOP/QxS)
= (524.4/2X0.40)+(524.4/400X5.5)
=(262.2X0.40)+(1.311X5.5)
=104.88+7.2105
=$112
2.5 Show the estimated savings in stocking costs to Mr. Swartz (5marks)
Estimated Savings: TASC(Q:2.2)-TASC(Q2.4)
=217.5-112.09
=$105.41
2.6 Calculate the EOQ (economic order quantity) (5marks)
EOQ: √2DS/C(1-D/P)
=√2x10,000x5.5/0.40(1-40/120)
=√110,000/0.40(0.667)
=641Valves
2.7 Calculate the total annual stocking costs (5marks)
Total annual stocking cost: EOQ/2C
7
Paraphrase This Document
Need a fresh take? Get an instant paraphrase of this document with our AI Paraphraser
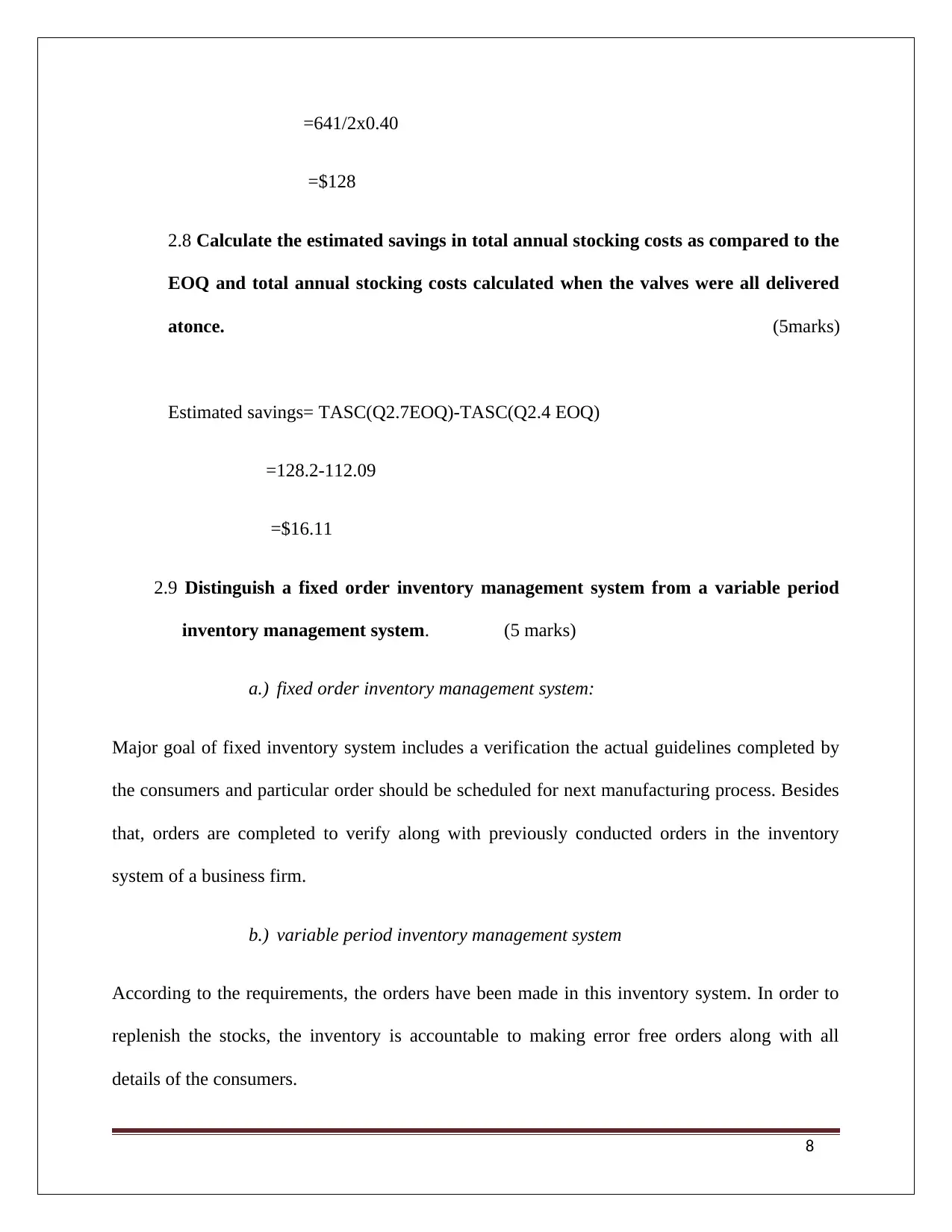
=641/2x0.40
=$128
2.8 Calculate the estimated savings in total annual stocking costs as compared to the
EOQ and total annual stocking costs calculated when the valves were all delivered
atonce. (5marks)
Estimated savings= TASC(Q2.7EOQ)-TASC(Q2.4 EOQ)
=128.2-112.09
=$16.11
2.9 Distinguish a fixed order inventory management system from a variable period
inventory management system. (5 marks)
a.) fixed order inventory management system:
Major goal of fixed inventory system includes a verification the actual guidelines completed by
the consumers and particular order should be scheduled for next manufacturing process. Besides
that, orders are completed to verify along with previously conducted orders in the inventory
system of a business firm.
b.) variable period inventory management system
According to the requirements, the orders have been made in this inventory system. In order to
replenish the stocks, the inventory is accountable to making error free orders along with all
details of the consumers.
8
=$128
2.8 Calculate the estimated savings in total annual stocking costs as compared to the
EOQ and total annual stocking costs calculated when the valves were all delivered
atonce. (5marks)
Estimated savings= TASC(Q2.7EOQ)-TASC(Q2.4 EOQ)
=128.2-112.09
=$16.11
2.9 Distinguish a fixed order inventory management system from a variable period
inventory management system. (5 marks)
a.) fixed order inventory management system:
Major goal of fixed inventory system includes a verification the actual guidelines completed by
the consumers and particular order should be scheduled for next manufacturing process. Besides
that, orders are completed to verify along with previously conducted orders in the inventory
system of a business firm.
b.) variable period inventory management system
According to the requirements, the orders have been made in this inventory system. In order to
replenish the stocks, the inventory is accountable to making error free orders along with all
details of the consumers.
8
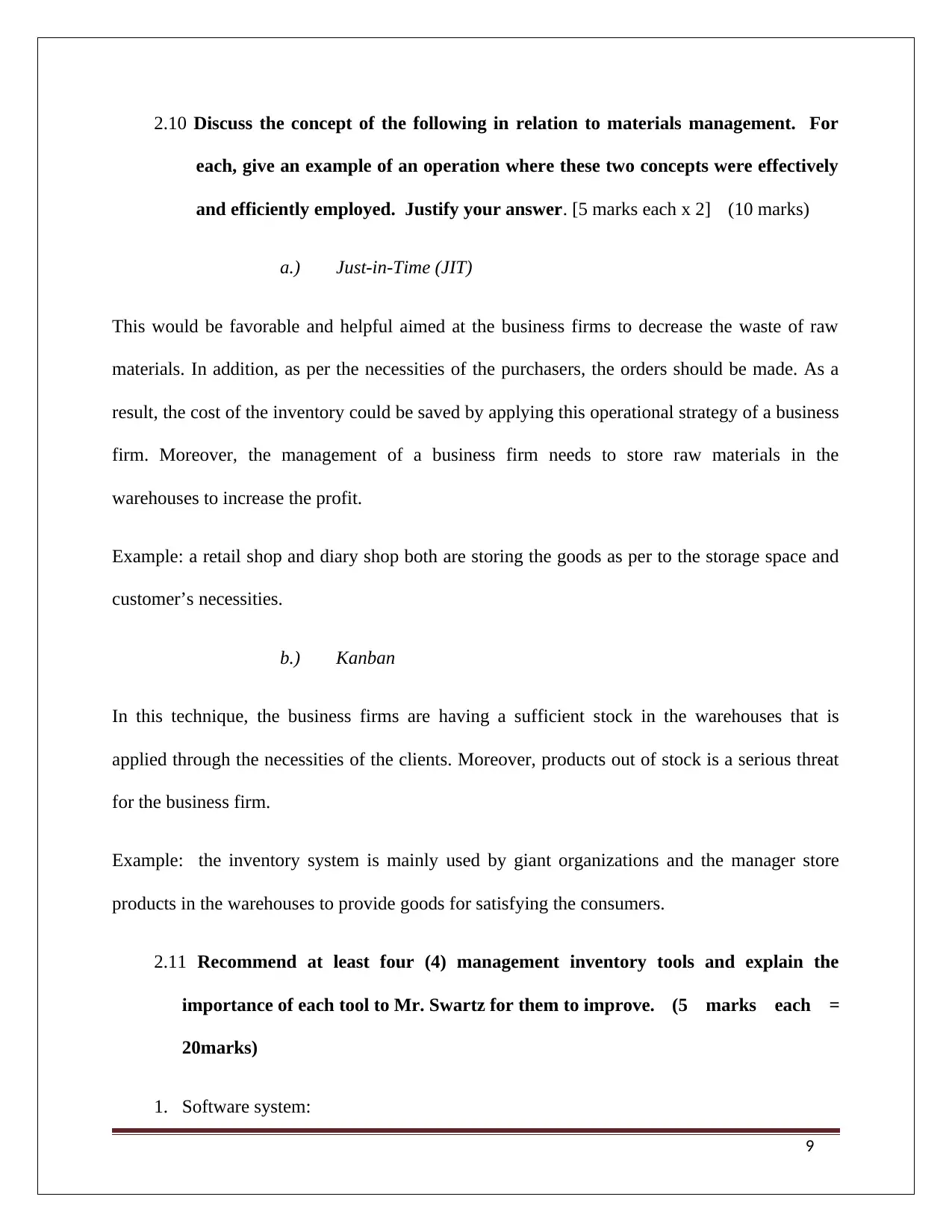
2.10 Discuss the concept of the following in relation to materials management. For
each, give an example of an operation where these two concepts were effectively
and efficiently employed. Justify your answer. [5 marks each x 2] (10 marks)
a.) Just-in-Time (JIT)
This would be favorable and helpful aimed at the business firms to decrease the waste of raw
materials. In addition, as per the necessities of the purchasers, the orders should be made. As a
result, the cost of the inventory could be saved by applying this operational strategy of a business
firm. Moreover, the management of a business firm needs to store raw materials in the
warehouses to increase the profit.
Example: a retail shop and diary shop both are storing the goods as per to the storage space and
customer’s necessities.
b.) Kanban
In this technique, the business firms are having a sufficient stock in the warehouses that is
applied through the necessities of the clients. Moreover, products out of stock is a serious threat
for the business firm.
Example: the inventory system is mainly used by giant organizations and the manager store
products in the warehouses to provide goods for satisfying the consumers.
2.11 Recommend at least four (4) management inventory tools and explain the
importance of each tool to Mr. Swartz for them to improve. (5 marks each =
20marks)
1. Software system:
9
each, give an example of an operation where these two concepts were effectively
and efficiently employed. Justify your answer. [5 marks each x 2] (10 marks)
a.) Just-in-Time (JIT)
This would be favorable and helpful aimed at the business firms to decrease the waste of raw
materials. In addition, as per the necessities of the purchasers, the orders should be made. As a
result, the cost of the inventory could be saved by applying this operational strategy of a business
firm. Moreover, the management of a business firm needs to store raw materials in the
warehouses to increase the profit.
Example: a retail shop and diary shop both are storing the goods as per to the storage space and
customer’s necessities.
b.) Kanban
In this technique, the business firms are having a sufficient stock in the warehouses that is
applied through the necessities of the clients. Moreover, products out of stock is a serious threat
for the business firm.
Example: the inventory system is mainly used by giant organizations and the manager store
products in the warehouses to provide goods for satisfying the consumers.
2.11 Recommend at least four (4) management inventory tools and explain the
importance of each tool to Mr. Swartz for them to improve. (5 marks each =
20marks)
1. Software system:
9
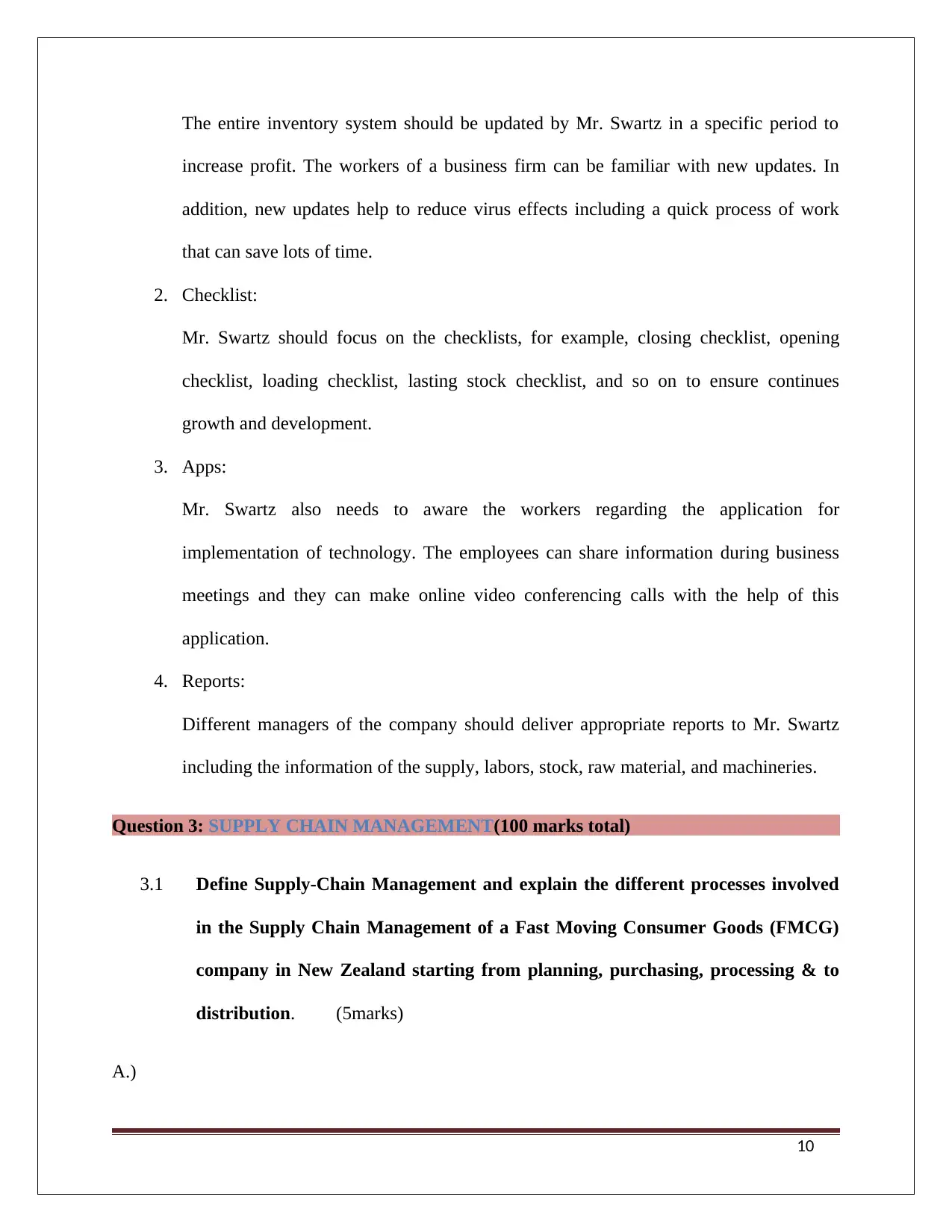
The entire inventory system should be updated by Mr. Swartz in a specific period to
increase profit. The workers of a business firm can be familiar with new updates. In
addition, new updates help to reduce virus effects including a quick process of work
that can save lots of time.
2. Checklist:
Mr. Swartz should focus on the checklists, for example, closing checklist, opening
checklist, loading checklist, lasting stock checklist, and so on to ensure continues
growth and development.
3. Apps:
Mr. Swartz also needs to aware the workers regarding the application for
implementation of technology. The employees can share information during business
meetings and they can make online video conferencing calls with the help of this
application.
4. Reports:
Different managers of the company should deliver appropriate reports to Mr. Swartz
including the information of the supply, labors, stock, raw material, and machineries.
Question 3: SUPPLY CHAIN MANAGEMENT(100 marks total)
3.1 Define Supply-Chain Management and explain the different processes involved
in the Supply Chain Management of a Fast Moving Consumer Goods (FMCG)
company in New Zealand starting from planning, purchasing, processing & to
distribution. (5marks)
A.)
10
increase profit. The workers of a business firm can be familiar with new updates. In
addition, new updates help to reduce virus effects including a quick process of work
that can save lots of time.
2. Checklist:
Mr. Swartz should focus on the checklists, for example, closing checklist, opening
checklist, loading checklist, lasting stock checklist, and so on to ensure continues
growth and development.
3. Apps:
Mr. Swartz also needs to aware the workers regarding the application for
implementation of technology. The employees can share information during business
meetings and they can make online video conferencing calls with the help of this
application.
4. Reports:
Different managers of the company should deliver appropriate reports to Mr. Swartz
including the information of the supply, labors, stock, raw material, and machineries.
Question 3: SUPPLY CHAIN MANAGEMENT(100 marks total)
3.1 Define Supply-Chain Management and explain the different processes involved
in the Supply Chain Management of a Fast Moving Consumer Goods (FMCG)
company in New Zealand starting from planning, purchasing, processing & to
distribution. (5marks)
A.)
10
Secure Best Marks with AI Grader
Need help grading? Try our AI Grader for instant feedback on your assignments.
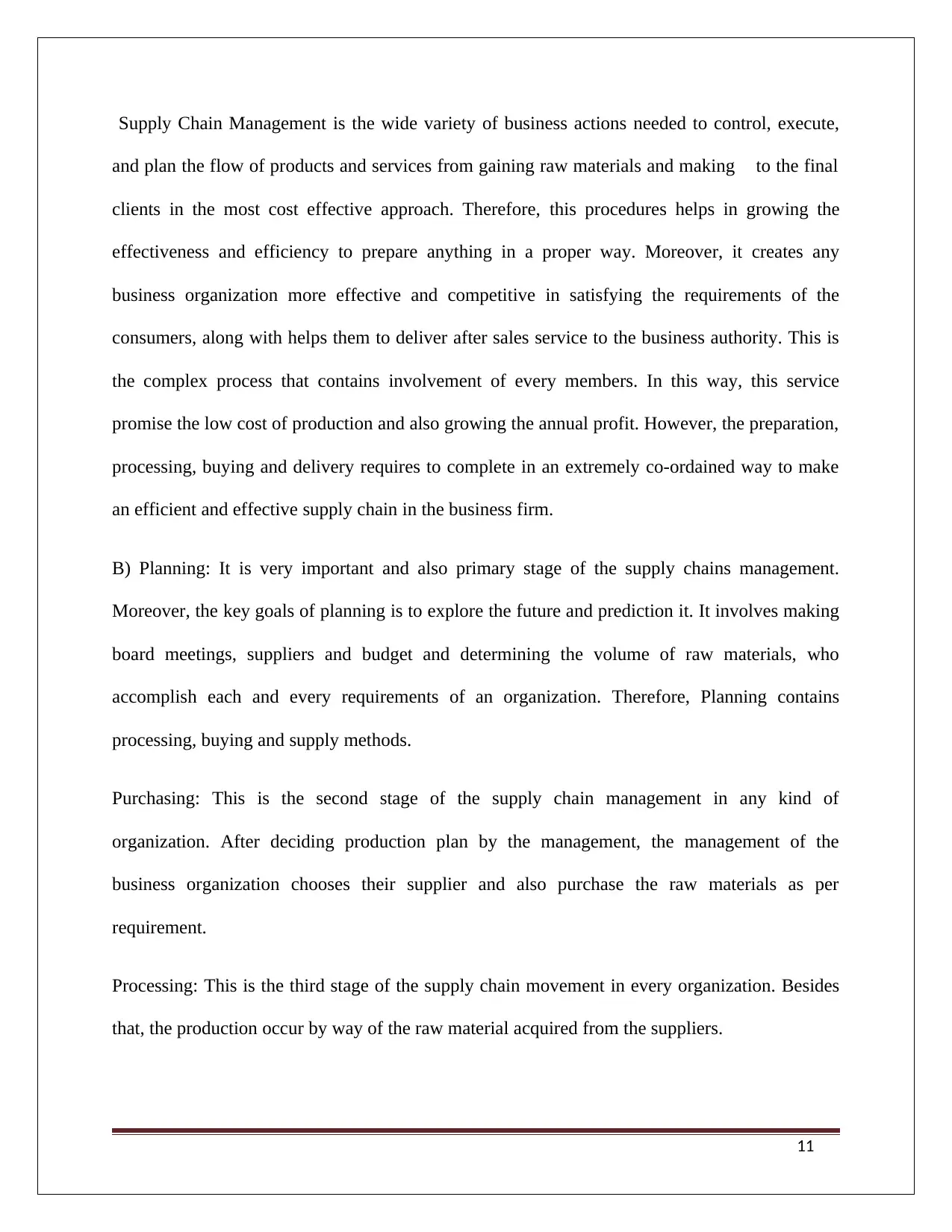
Supply Chain Management is the wide variety of business actions needed to control, execute,
and plan the flow of products and services from gaining raw materials and making to the final
clients in the most cost effective approach. Therefore, this procedures helps in growing the
effectiveness and efficiency to prepare anything in a proper way. Moreover, it creates any
business organization more effective and competitive in satisfying the requirements of the
consumers, along with helps them to deliver after sales service to the business authority. This is
the complex process that contains involvement of every members. In this way, this service
promise the low cost of production and also growing the annual profit. However, the preparation,
processing, buying and delivery requires to complete in an extremely co-ordained way to make
an efficient and effective supply chain in the business firm.
B) Planning: It is very important and also primary stage of the supply chains management.
Moreover, the key goals of planning is to explore the future and prediction it. It involves making
board meetings, suppliers and budget and determining the volume of raw materials, who
accomplish each and every requirements of an organization. Therefore, Planning contains
processing, buying and supply methods.
Purchasing: This is the second stage of the supply chain management in any kind of
organization. After deciding production plan by the management, the management of the
business organization chooses their supplier and also purchase the raw materials as per
requirement.
Processing: This is the third stage of the supply chain movement in every organization. Besides
that, the production occur by way of the raw material acquired from the suppliers.
11
and plan the flow of products and services from gaining raw materials and making to the final
clients in the most cost effective approach. Therefore, this procedures helps in growing the
effectiveness and efficiency to prepare anything in a proper way. Moreover, it creates any
business organization more effective and competitive in satisfying the requirements of the
consumers, along with helps them to deliver after sales service to the business authority. This is
the complex process that contains involvement of every members. In this way, this service
promise the low cost of production and also growing the annual profit. However, the preparation,
processing, buying and delivery requires to complete in an extremely co-ordained way to make
an efficient and effective supply chain in the business firm.
B) Planning: It is very important and also primary stage of the supply chains management.
Moreover, the key goals of planning is to explore the future and prediction it. It involves making
board meetings, suppliers and budget and determining the volume of raw materials, who
accomplish each and every requirements of an organization. Therefore, Planning contains
processing, buying and supply methods.
Purchasing: This is the second stage of the supply chain management in any kind of
organization. After deciding production plan by the management, the management of the
business organization chooses their supplier and also purchase the raw materials as per
requirement.
Processing: This is the third stage of the supply chain movement in every organization. Besides
that, the production occur by way of the raw material acquired from the suppliers.
11
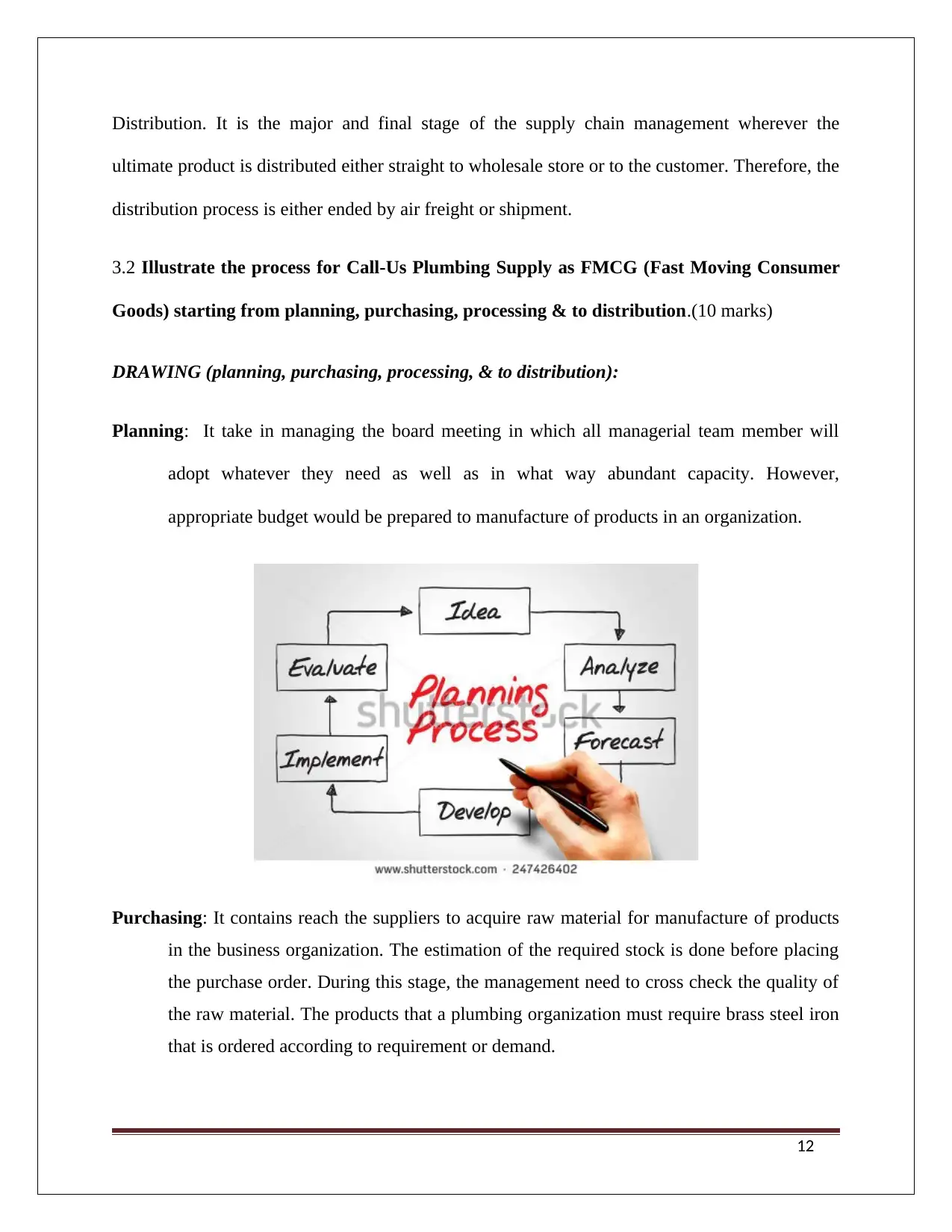
Distribution. It is the major and final stage of the supply chain management wherever the
ultimate product is distributed either straight to wholesale store or to the customer. Therefore, the
distribution process is either ended by air freight or shipment.
3.2 Illustrate the process for Call-Us Plumbing Supply as FMCG (Fast Moving Consumer
Goods) starting from planning, purchasing, processing & to distribution.(10 marks)
DRAWING (planning, purchasing, processing, & to distribution):
Planning: It take in managing the board meeting in which all managerial team member will
adopt whatever they need as well as in what way abundant capacity. However,
appropriate budget would be prepared to manufacture of products in an organization.
Purchasing: It contains reach the suppliers to acquire raw material for manufacture of products
in the business organization. The estimation of the required stock is done before placing
the purchase order. During this stage, the management need to cross check the quality of
the raw material. The products that a plumbing organization must require brass steel iron
that is ordered according to requirement or demand.
12
ultimate product is distributed either straight to wholesale store or to the customer. Therefore, the
distribution process is either ended by air freight or shipment.
3.2 Illustrate the process for Call-Us Plumbing Supply as FMCG (Fast Moving Consumer
Goods) starting from planning, purchasing, processing & to distribution.(10 marks)
DRAWING (planning, purchasing, processing, & to distribution):
Planning: It take in managing the board meeting in which all managerial team member will
adopt whatever they need as well as in what way abundant capacity. However,
appropriate budget would be prepared to manufacture of products in an organization.
Purchasing: It contains reach the suppliers to acquire raw material for manufacture of products
in the business organization. The estimation of the required stock is done before placing
the purchase order. During this stage, the management need to cross check the quality of
the raw material. The products that a plumbing organization must require brass steel iron
that is ordered according to requirement or demand.
12

Processing: There are several kinds of process that the organization similar to Call us plumbing
would succeeding but greatest usually Call us plumbing, are as below
Step 1: Melting cooper or the raw steel
Step 2: Pouring the melted material in a cast to give exact structure
Step 3: Sand blasting it
Step 4: Examine and assembling the parts
Step 5: Testing the completed product and then selling it
13
would succeeding but greatest usually Call us plumbing, are as below
Step 1: Melting cooper or the raw steel
Step 2: Pouring the melted material in a cast to give exact structure
Step 3: Sand blasting it
Step 4: Examine and assembling the parts
Step 5: Testing the completed product and then selling it
13
Paraphrase This Document
Need a fresh take? Get an instant paraphrase of this document with our AI Paraphraser
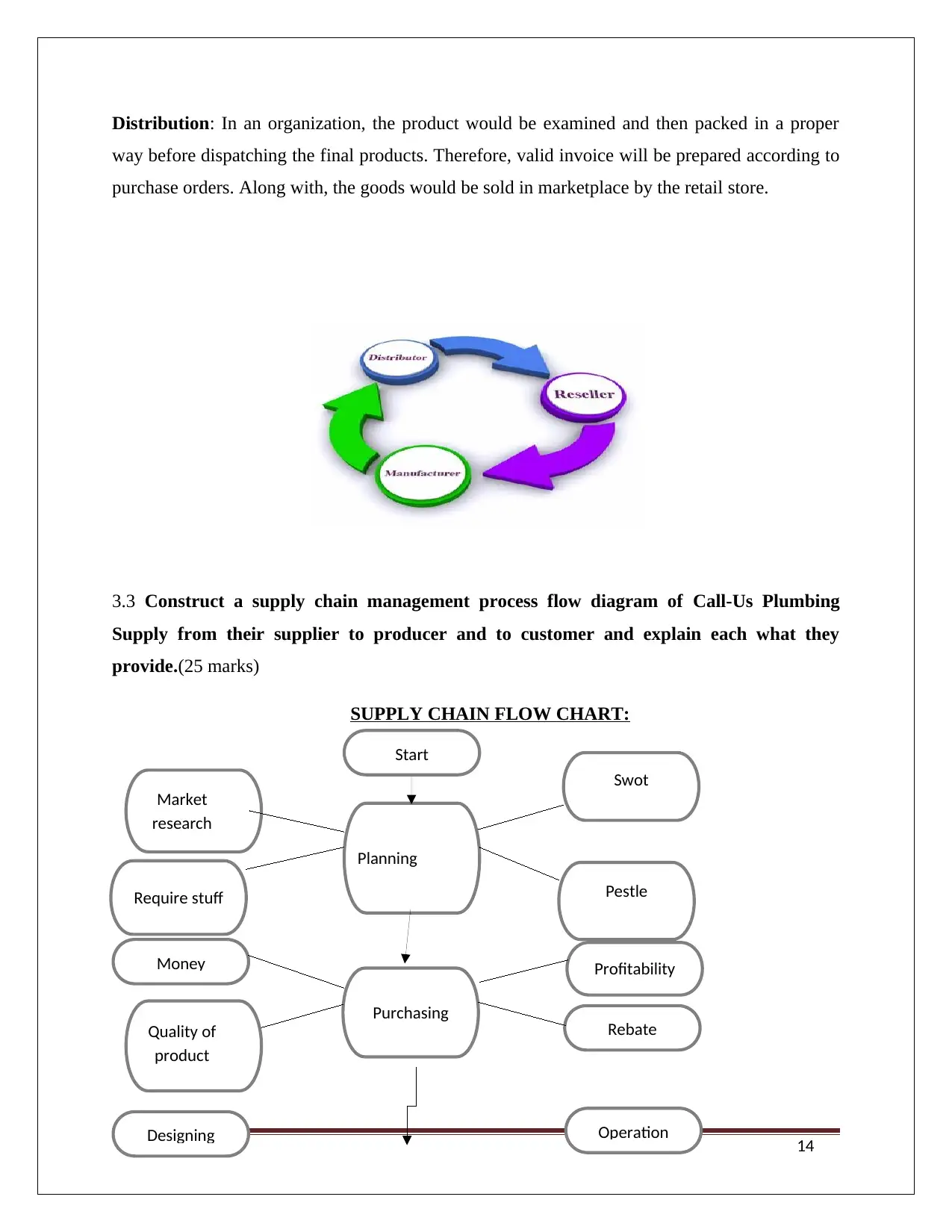
Distribution: In an organization, the product would be examined and then packed in a proper
way before dispatching the final products. Therefore, valid invoice will be prepared according to
purchase orders. Along with, the goods would be sold in marketplace by the retail store.
3.3 Construct a supply chain management process flow diagram of Call-Us Plumbing
Supply from their supplier to producer and to customer and explain each what they
provide.(25 marks)
SUPPLY CHAIN FLOW CHART:
14
Start
Planning
Purchasing
Swot
Market
research
Require stuff Pestle
Money
Rebate
Designing
Quality of
product
Profitability
Operation
way before dispatching the final products. Therefore, valid invoice will be prepared according to
purchase orders. Along with, the goods would be sold in marketplace by the retail store.
3.3 Construct a supply chain management process flow diagram of Call-Us Plumbing
Supply from their supplier to producer and to customer and explain each what they
provide.(25 marks)
SUPPLY CHAIN FLOW CHART:
14
Start
Planning
Purchasing
Swot
Market
research
Require stuff Pestle
Money
Rebate
Designing
Quality of
product
Profitability
Operation
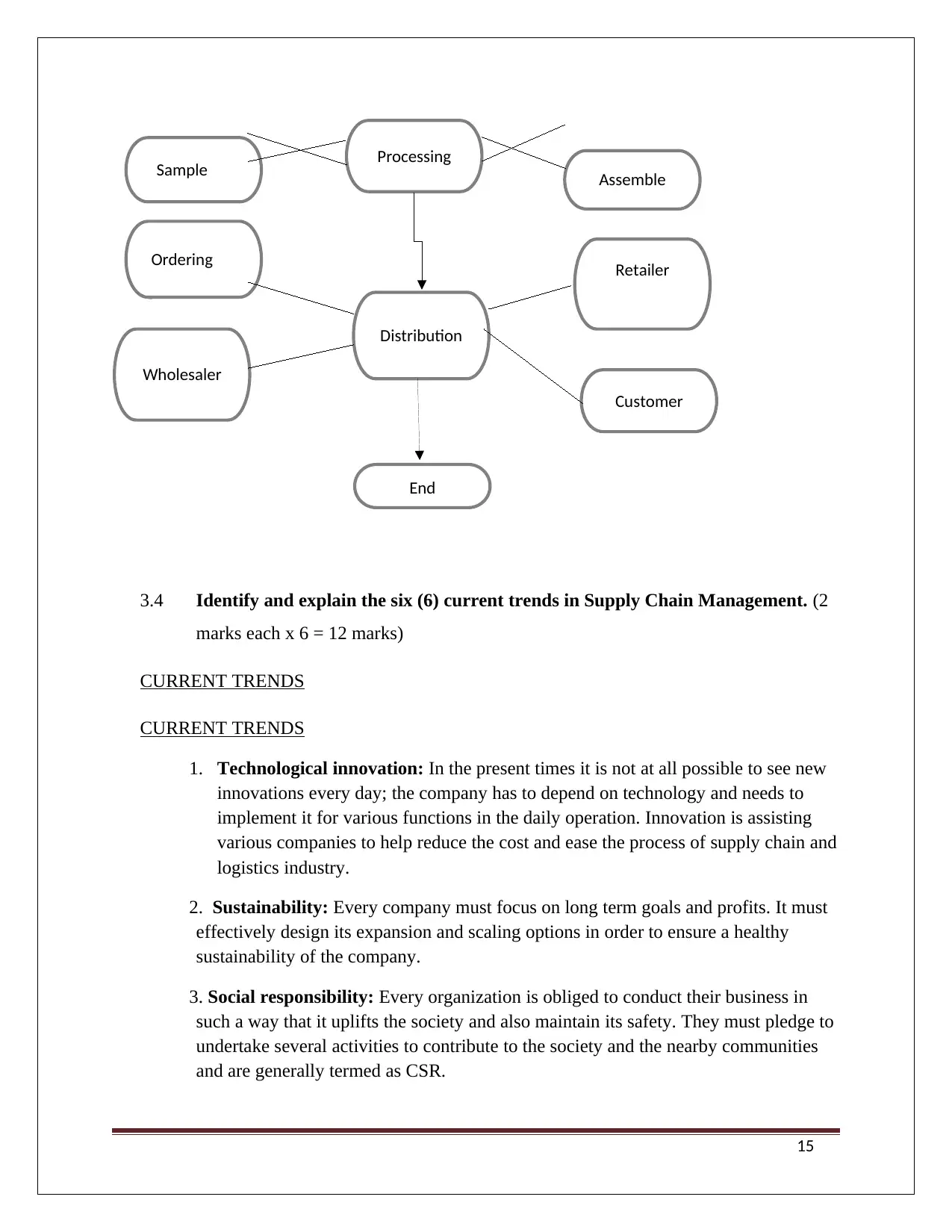
3.4 Identify and explain the six (6) current trends in Supply Chain Management. (2
marks each x 6 = 12 marks)
CURRENT TRENDS
CURRENT TRENDS
1. Technological innovation: In the present times it is not at all possible to see new
innovations every day; the company has to depend on technology and needs to
implement it for various functions in the daily operation. Innovation is assisting
various companies to help reduce the cost and ease the process of supply chain and
logistics industry.
2. Sustainability: Every company must focus on long term goals and profits. It must
effectively design its expansion and scaling options in order to ensure a healthy
sustainability of the company.
3. Social responsibility: Every organization is obliged to conduct their business in
such a way that it uplifts the society and also maintain its safety. They must pledge to
undertake several activities to contribute to the society and the nearby communities
and are generally termed as CSR.
15
Processing
Distribution
End
Sample Assemble
Ordering
Wholesaler
Customer
Retailer
marks each x 6 = 12 marks)
CURRENT TRENDS
CURRENT TRENDS
1. Technological innovation: In the present times it is not at all possible to see new
innovations every day; the company has to depend on technology and needs to
implement it for various functions in the daily operation. Innovation is assisting
various companies to help reduce the cost and ease the process of supply chain and
logistics industry.
2. Sustainability: Every company must focus on long term goals and profits. It must
effectively design its expansion and scaling options in order to ensure a healthy
sustainability of the company.
3. Social responsibility: Every organization is obliged to conduct their business in
such a way that it uplifts the society and also maintain its safety. They must pledge to
undertake several activities to contribute to the society and the nearby communities
and are generally termed as CSR.
15
Processing
Distribution
End
Sample Assemble
Ordering
Wholesaler
Customer
Retailer
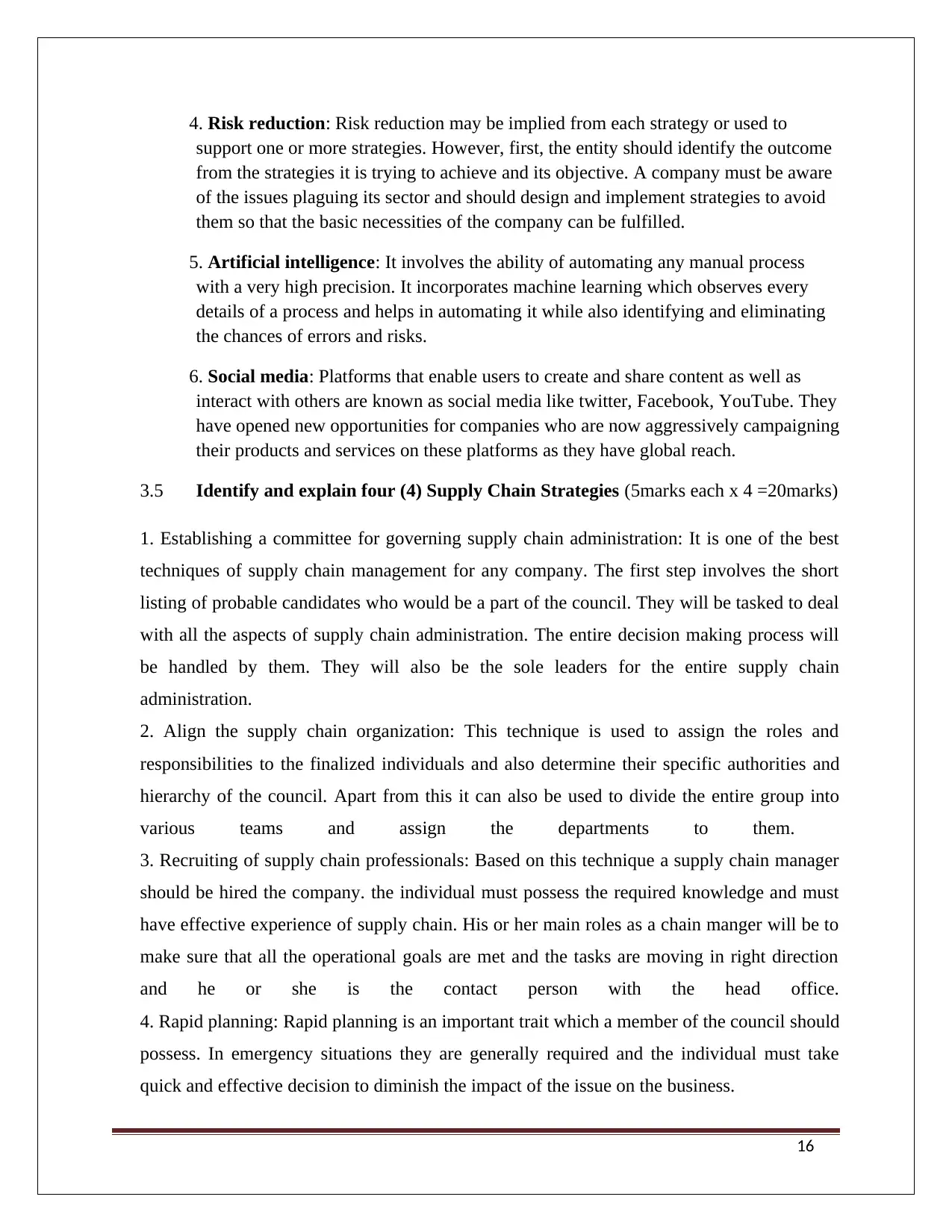
4. Risk reduction: Risk reduction may be implied from each strategy or used to
support one or more strategies. However, first, the entity should identify the outcome
from the strategies it is trying to achieve and its objective. A company must be aware
of the issues plaguing its sector and should design and implement strategies to avoid
them so that the basic necessities of the company can be fulfilled.
5. Artificial intelligence: It involves the ability of automating any manual process
with a very high precision. It incorporates machine learning which observes every
details of a process and helps in automating it while also identifying and eliminating
the chances of errors and risks.
6. Social media: Platforms that enable users to create and share content as well as
interact with others are known as social media like twitter, Facebook, YouTube. They
have opened new opportunities for companies who are now aggressively campaigning
their products and services on these platforms as they have global reach.
3.5 Identify and explain four (4) Supply Chain Strategies (5marks each x 4 =20marks)
1. Establishing a committee for governing supply chain administration: It is one of the best
techniques of supply chain management for any company. The first step involves the short
listing of probable candidates who would be a part of the council. They will be tasked to deal
with all the aspects of supply chain administration. The entire decision making process will
be handled by them. They will also be the sole leaders for the entire supply chain
administration.
2. Align the supply chain organization: This technique is used to assign the roles and
responsibilities to the finalized individuals and also determine their specific authorities and
hierarchy of the council. Apart from this it can also be used to divide the entire group into
various teams and assign the departments to them.
3. Recruiting of supply chain professionals: Based on this technique a supply chain manager
should be hired the company. the individual must possess the required knowledge and must
have effective experience of supply chain. His or her main roles as a chain manger will be to
make sure that all the operational goals are met and the tasks are moving in right direction
and he or she is the contact person with the head office.
4. Rapid planning: Rapid planning is an important trait which a member of the council should
possess. In emergency situations they are generally required and the individual must take
quick and effective decision to diminish the impact of the issue on the business.
16
support one or more strategies. However, first, the entity should identify the outcome
from the strategies it is trying to achieve and its objective. A company must be aware
of the issues plaguing its sector and should design and implement strategies to avoid
them so that the basic necessities of the company can be fulfilled.
5. Artificial intelligence: It involves the ability of automating any manual process
with a very high precision. It incorporates machine learning which observes every
details of a process and helps in automating it while also identifying and eliminating
the chances of errors and risks.
6. Social media: Platforms that enable users to create and share content as well as
interact with others are known as social media like twitter, Facebook, YouTube. They
have opened new opportunities for companies who are now aggressively campaigning
their products and services on these platforms as they have global reach.
3.5 Identify and explain four (4) Supply Chain Strategies (5marks each x 4 =20marks)
1. Establishing a committee for governing supply chain administration: It is one of the best
techniques of supply chain management for any company. The first step involves the short
listing of probable candidates who would be a part of the council. They will be tasked to deal
with all the aspects of supply chain administration. The entire decision making process will
be handled by them. They will also be the sole leaders for the entire supply chain
administration.
2. Align the supply chain organization: This technique is used to assign the roles and
responsibilities to the finalized individuals and also determine their specific authorities and
hierarchy of the council. Apart from this it can also be used to divide the entire group into
various teams and assign the departments to them.
3. Recruiting of supply chain professionals: Based on this technique a supply chain manager
should be hired the company. the individual must possess the required knowledge and must
have effective experience of supply chain. His or her main roles as a chain manger will be to
make sure that all the operational goals are met and the tasks are moving in right direction
and he or she is the contact person with the head office.
4. Rapid planning: Rapid planning is an important trait which a member of the council should
possess. In emergency situations they are generally required and the individual must take
quick and effective decision to diminish the impact of the issue on the business.
16
Secure Best Marks with AI Grader
Need help grading? Try our AI Grader for instant feedback on your assignments.
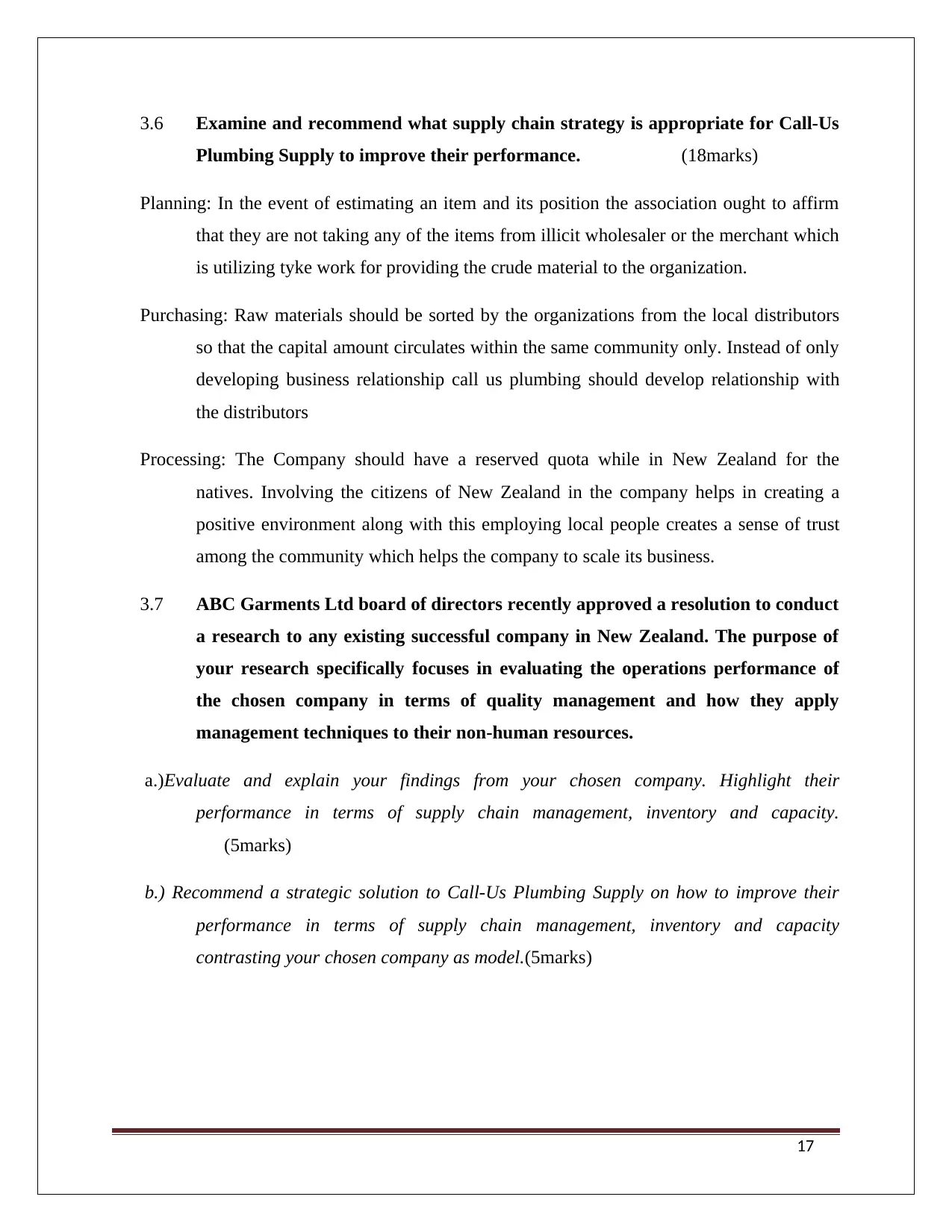
3.6 Examine and recommend what supply chain strategy is appropriate for Call-Us
Plumbing Supply to improve their performance. (18marks)
Planning: In the event of estimating an item and its position the association ought to affirm
that they are not taking any of the items from illicit wholesaler or the merchant which
is utilizing tyke work for providing the crude material to the organization.
Purchasing: Raw materials should be sorted by the organizations from the local distributors
so that the capital amount circulates within the same community only. Instead of only
developing business relationship call us plumbing should develop relationship with
the distributors
Processing: The Company should have a reserved quota while in New Zealand for the
natives. Involving the citizens of New Zealand in the company helps in creating a
positive environment along with this employing local people creates a sense of trust
among the community which helps the company to scale its business.
3.7 ABC Garments Ltd board of directors recently approved a resolution to conduct
a research to any existing successful company in New Zealand. The purpose of
your research specifically focuses in evaluating the operations performance of
the chosen company in terms of quality management and how they apply
management techniques to their non-human resources.
a.)Evaluate and explain your findings from your chosen company. Highlight their
performance in terms of supply chain management, inventory and capacity.
(5marks)
b.) Recommend a strategic solution to Call-Us Plumbing Supply on how to improve their
performance in terms of supply chain management, inventory and capacity
contrasting your chosen company as model.(5marks)
17
Plumbing Supply to improve their performance. (18marks)
Planning: In the event of estimating an item and its position the association ought to affirm
that they are not taking any of the items from illicit wholesaler or the merchant which
is utilizing tyke work for providing the crude material to the organization.
Purchasing: Raw materials should be sorted by the organizations from the local distributors
so that the capital amount circulates within the same community only. Instead of only
developing business relationship call us plumbing should develop relationship with
the distributors
Processing: The Company should have a reserved quota while in New Zealand for the
natives. Involving the citizens of New Zealand in the company helps in creating a
positive environment along with this employing local people creates a sense of trust
among the community which helps the company to scale its business.
3.7 ABC Garments Ltd board of directors recently approved a resolution to conduct
a research to any existing successful company in New Zealand. The purpose of
your research specifically focuses in evaluating the operations performance of
the chosen company in terms of quality management and how they apply
management techniques to their non-human resources.
a.)Evaluate and explain your findings from your chosen company. Highlight their
performance in terms of supply chain management, inventory and capacity.
(5marks)
b.) Recommend a strategic solution to Call-Us Plumbing Supply on how to improve their
performance in terms of supply chain management, inventory and capacity
contrasting your chosen company as model.(5marks)
17
1 out of 17
![[object Object]](/_next/image/?url=%2F_next%2Fstatic%2Fmedia%2Flogo.6d15ce61.png&w=640&q=75)
Your All-in-One AI-Powered Toolkit for Academic Success.
 +13062052269
info@desklib.com
Available 24*7 on WhatsApp / Email
Unlock your academic potential
© 2024  |  Zucol Services PVT LTD  |  All rights reserved.