Effective Management of Mechanical Production System
VerifiedAdded on  2019/10/30
|9
|1733
|376
Report
AI Summary
The assignment content discusses the author's experience in a mechanical production system project, which involved implementing SAP exercises, reviewing and critiquing senior choices, and designing material accessibility deliberately. The author applied engineering knowledge and skills, including CNC machining, laser cutting, and die squeeze, to comprehend fabricating procedures and lead times required for assembling different parts. They also conducted time studies and observed vendor operations to analyze the number of vehicles visiting the Ford automobile pallet line for material movement per hour.
Contribute Materials
Your contribution can guide someone’s learning journey. Share your
documents today.
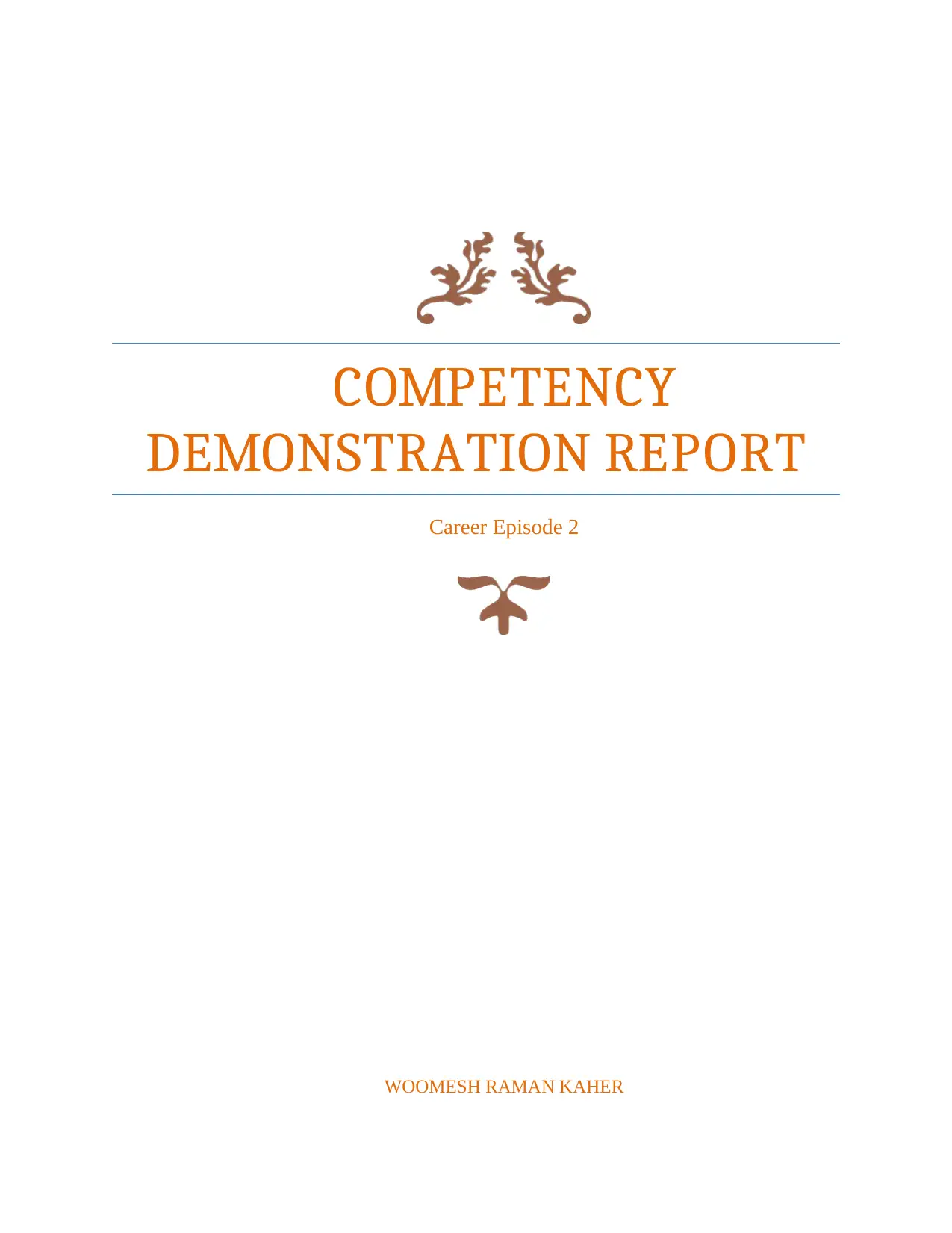
COMPETENCY
DEMONSTRATION REPORT
Career Episode 2
WOOMESH RAMAN KAHER
DEMONSTRATION REPORT
Career Episode 2
WOOMESH RAMAN KAHER
Secure Best Marks with AI Grader
Need help grading? Try our AI Grader for instant feedback on your assignments.
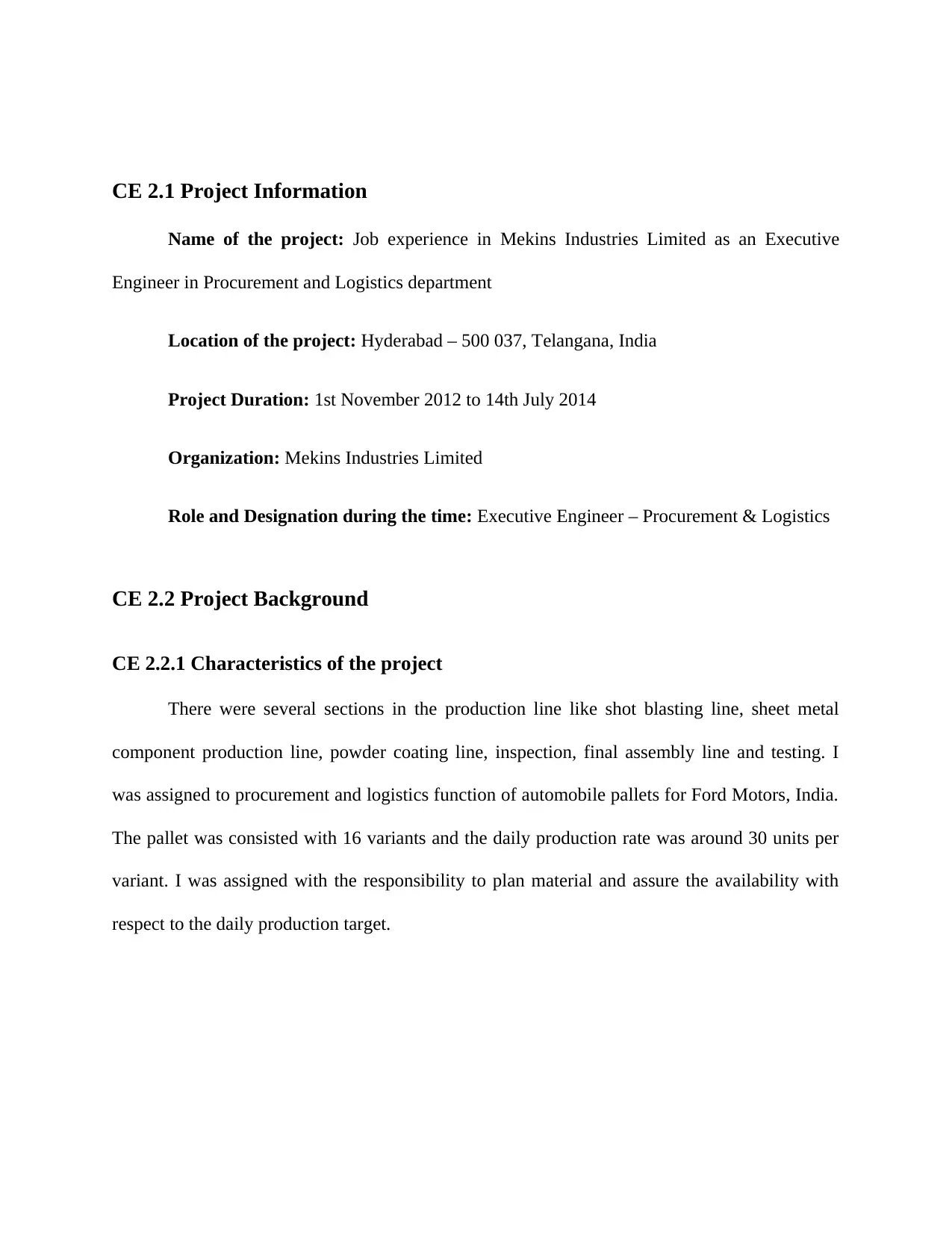
CE 2.1 Project Information
Name of the project: Job experience in Mekins Industries Limited as an Executive
Engineer in Procurement and Logistics department
Location of the project: Hyderabad – 500 037, Telangana, India
Project Duration: 1st November 2012 to 14th July 2014
Organization: Mekins Industries Limited
Role and Designation during the time: Executive Engineer – Procurement & Logistics
CE 2.2 Project Background
CE 2.2.1 Characteristics of the project
There were several sections in the production line like shot blasting line, sheet metal
component production line, powder coating line, inspection, final assembly line and testing. I
was assigned to procurement and logistics function of automobile pallets for Ford Motors, India.
The pallet was consisted with 16 variants and the daily production rate was around 30 units per
variant. I was assigned with the responsibility to plan material and assure the availability with
respect to the daily production target.
Name of the project: Job experience in Mekins Industries Limited as an Executive
Engineer in Procurement and Logistics department
Location of the project: Hyderabad – 500 037, Telangana, India
Project Duration: 1st November 2012 to 14th July 2014
Organization: Mekins Industries Limited
Role and Designation during the time: Executive Engineer – Procurement & Logistics
CE 2.2 Project Background
CE 2.2.1 Characteristics of the project
There were several sections in the production line like shot blasting line, sheet metal
component production line, powder coating line, inspection, final assembly line and testing. I
was assigned to procurement and logistics function of automobile pallets for Ford Motors, India.
The pallet was consisted with 16 variants and the daily production rate was around 30 units per
variant. I was assigned with the responsibility to plan material and assure the availability with
respect to the daily production target.
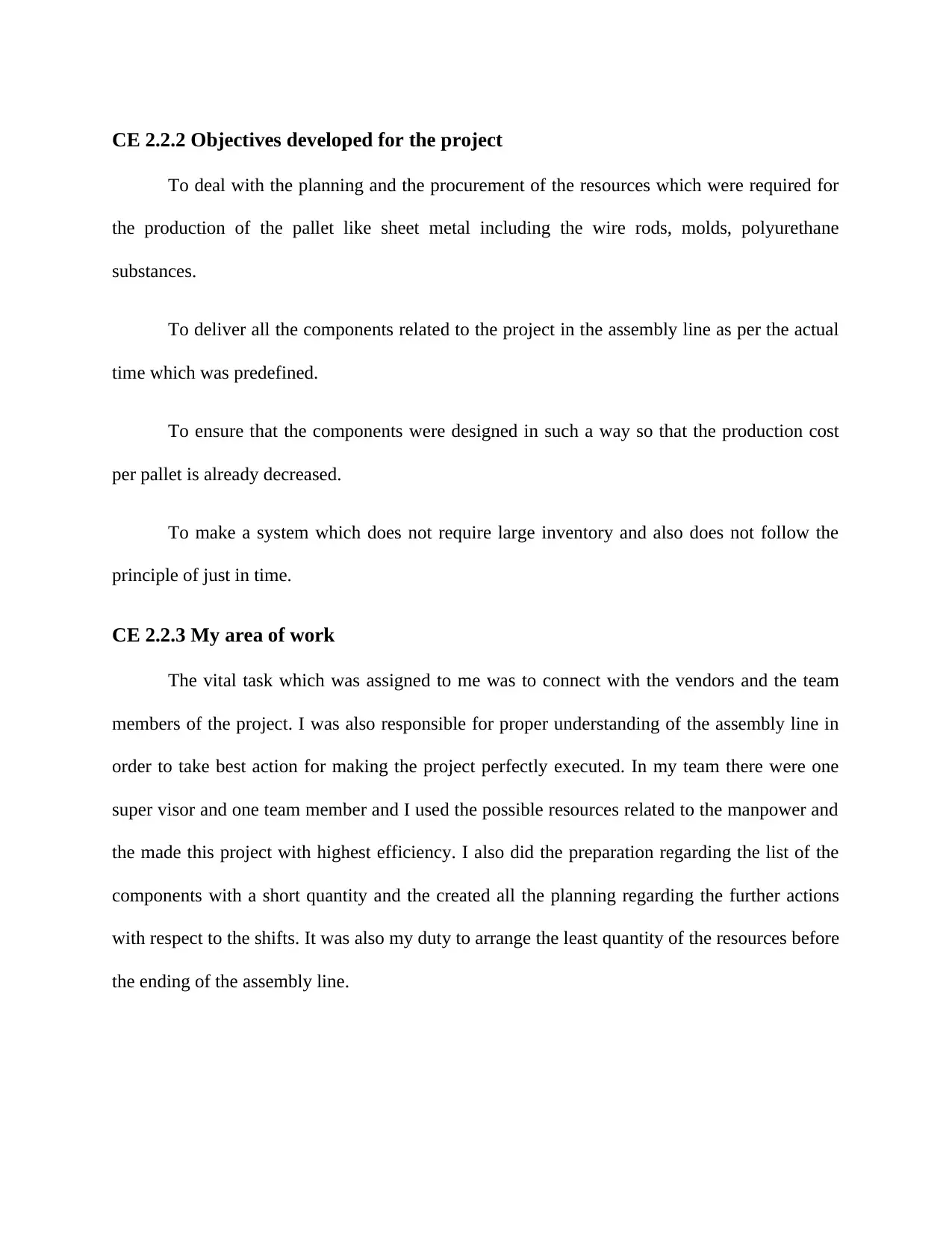
CE 2.2.2 Objectives developed for the project
To deal with the planning and the procurement of the resources which were required for
the production of the pallet like sheet metal including the wire rods, molds, polyurethane
substances.
To deliver all the components related to the project in the assembly line as per the actual
time which was predefined.
To ensure that the components were designed in such a way so that the production cost
per pallet is already decreased.
To make a system which does not require large inventory and also does not follow the
principle of just in time.
CE 2.2.3 My area of work
The vital task which was assigned to me was to connect with the vendors and the team
members of the project. I was also responsible for proper understanding of the assembly line in
order to take best action for making the project perfectly executed. In my team there were one
super visor and one team member and I used the possible resources related to the manpower and
the made this project with highest efficiency. I also did the preparation regarding the list of the
components with a short quantity and the created all the planning regarding the further actions
with respect to the shifts. It was also my duty to arrange the least quantity of the resources before
the ending of the assembly line.
To deal with the planning and the procurement of the resources which were required for
the production of the pallet like sheet metal including the wire rods, molds, polyurethane
substances.
To deliver all the components related to the project in the assembly line as per the actual
time which was predefined.
To ensure that the components were designed in such a way so that the production cost
per pallet is already decreased.
To make a system which does not require large inventory and also does not follow the
principle of just in time.
CE 2.2.3 My area of work
The vital task which was assigned to me was to connect with the vendors and the team
members of the project. I was also responsible for proper understanding of the assembly line in
order to take best action for making the project perfectly executed. In my team there were one
super visor and one team member and I used the possible resources related to the manpower and
the made this project with highest efficiency. I also did the preparation regarding the list of the
components with a short quantity and the created all the planning regarding the further actions
with respect to the shifts. It was also my duty to arrange the least quantity of the resources before
the ending of the assembly line.
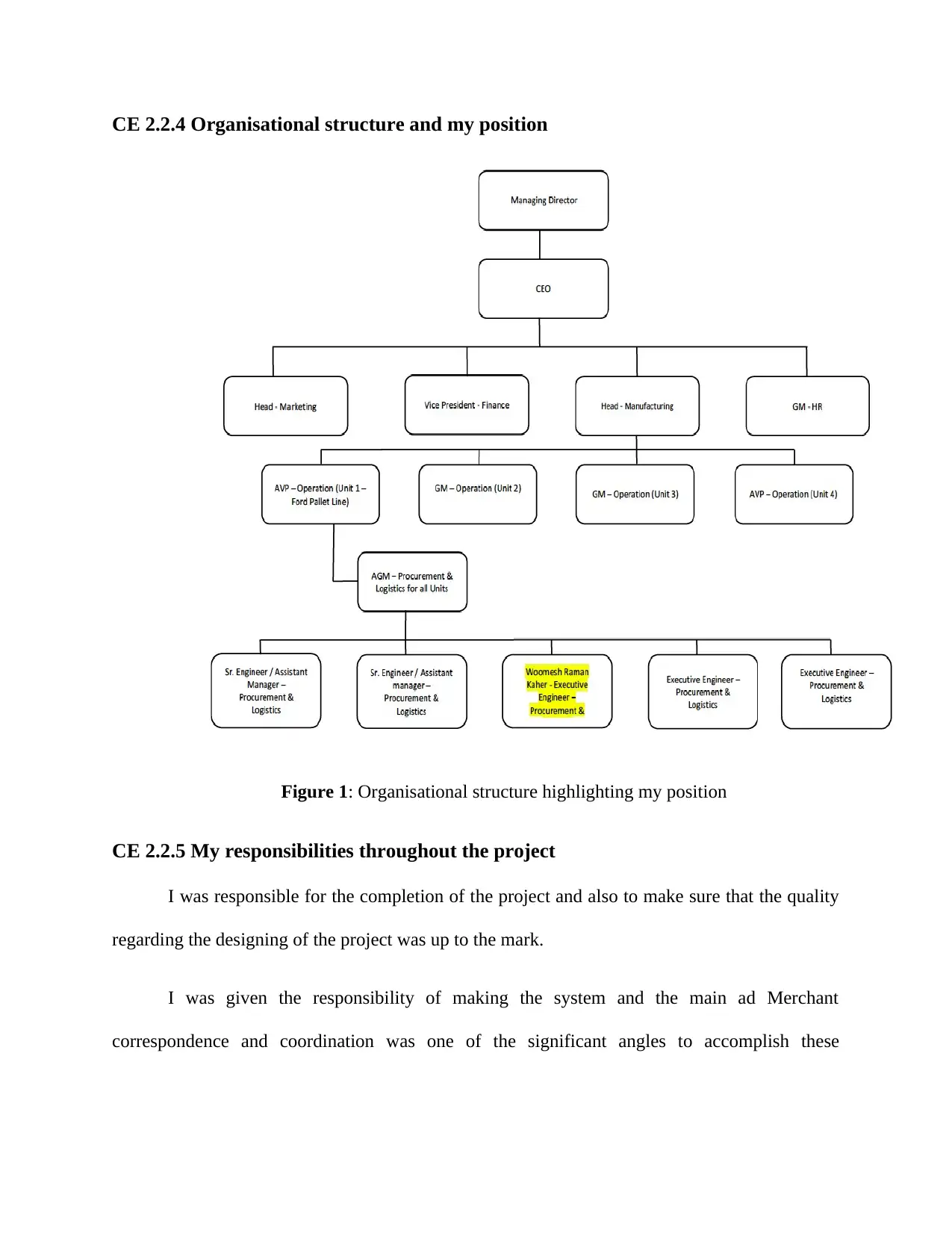
CE 2.2.4 Organisational structure and my position
Figure 1: Organisational structure highlighting my position
CE 2.2.5 My responsibilities throughout the project
I was responsible for the completion of the project and also to make sure that the quality
regarding the designing of the project was up to the mark.
I was given the responsibility of making the system and the main ad Merchant
correspondence and coordination was one of the significant angles to accomplish these
Figure 1: Organisational structure highlighting my position
CE 2.2.5 My responsibilities throughout the project
I was responsible for the completion of the project and also to make sure that the quality
regarding the designing of the project was up to the mark.
I was given the responsibility of making the system and the main ad Merchant
correspondence and coordination was one of the significant angles to accomplish these
Secure Best Marks with AI Grader
Need help grading? Try our AI Grader for instant feedback on your assignments.
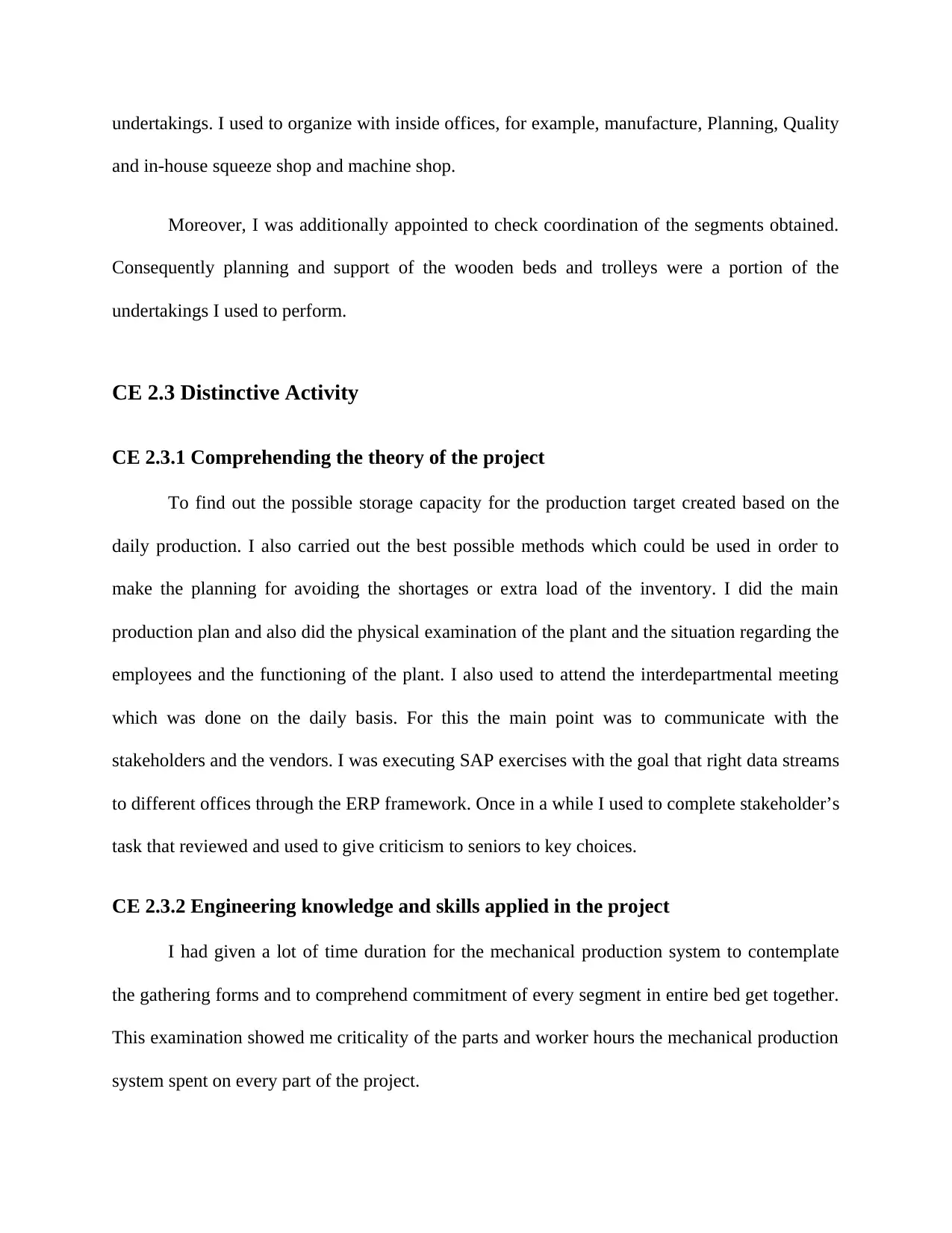
undertakings. I used to organize with inside offices, for example, manufacture, Planning, Quality
and in-house squeeze shop and machine shop.
Moreover, I was additionally appointed to check coordination of the segments obtained.
Consequently planning and support of the wooden beds and trolleys were a portion of the
undertakings I used to perform.
CE 2.3 Distinctive Activity
CE 2.3.1 Comprehending the theory of the project
To find out the possible storage capacity for the production target created based on the
daily production. I also carried out the best possible methods which could be used in order to
make the planning for avoiding the shortages or extra load of the inventory. I did the main
production plan and also did the physical examination of the plant and the situation regarding the
employees and the functioning of the plant. I also used to attend the interdepartmental meeting
which was done on the daily basis. For this the main point was to communicate with the
stakeholders and the vendors. I was executing SAP exercises with the goal that right data streams
to different offices through the ERP framework. Once in a while I used to complete stakeholder’s
task that reviewed and used to give criticism to seniors to key choices.
CE 2.3.2 Engineering knowledge and skills applied in the project
I had given a lot of time duration for the mechanical production system to contemplate
the gathering forms and to comprehend commitment of every segment in entire bed get together.
This examination showed me criticality of the parts and worker hours the mechanical production
system spent on every part of the project.
and in-house squeeze shop and machine shop.
Moreover, I was additionally appointed to check coordination of the segments obtained.
Consequently planning and support of the wooden beds and trolleys were a portion of the
undertakings I used to perform.
CE 2.3 Distinctive Activity
CE 2.3.1 Comprehending the theory of the project
To find out the possible storage capacity for the production target created based on the
daily production. I also carried out the best possible methods which could be used in order to
make the planning for avoiding the shortages or extra load of the inventory. I did the main
production plan and also did the physical examination of the plant and the situation regarding the
employees and the functioning of the plant. I also used to attend the interdepartmental meeting
which was done on the daily basis. For this the main point was to communicate with the
stakeholders and the vendors. I was executing SAP exercises with the goal that right data streams
to different offices through the ERP framework. Once in a while I used to complete stakeholder’s
task that reviewed and used to give criticism to seniors to key choices.
CE 2.3.2 Engineering knowledge and skills applied in the project
I had given a lot of time duration for the mechanical production system to contemplate
the gathering forms and to comprehend commitment of every segment in entire bed get together.
This examination showed me criticality of the parts and worker hours the mechanical production
system spent on every part of the project.
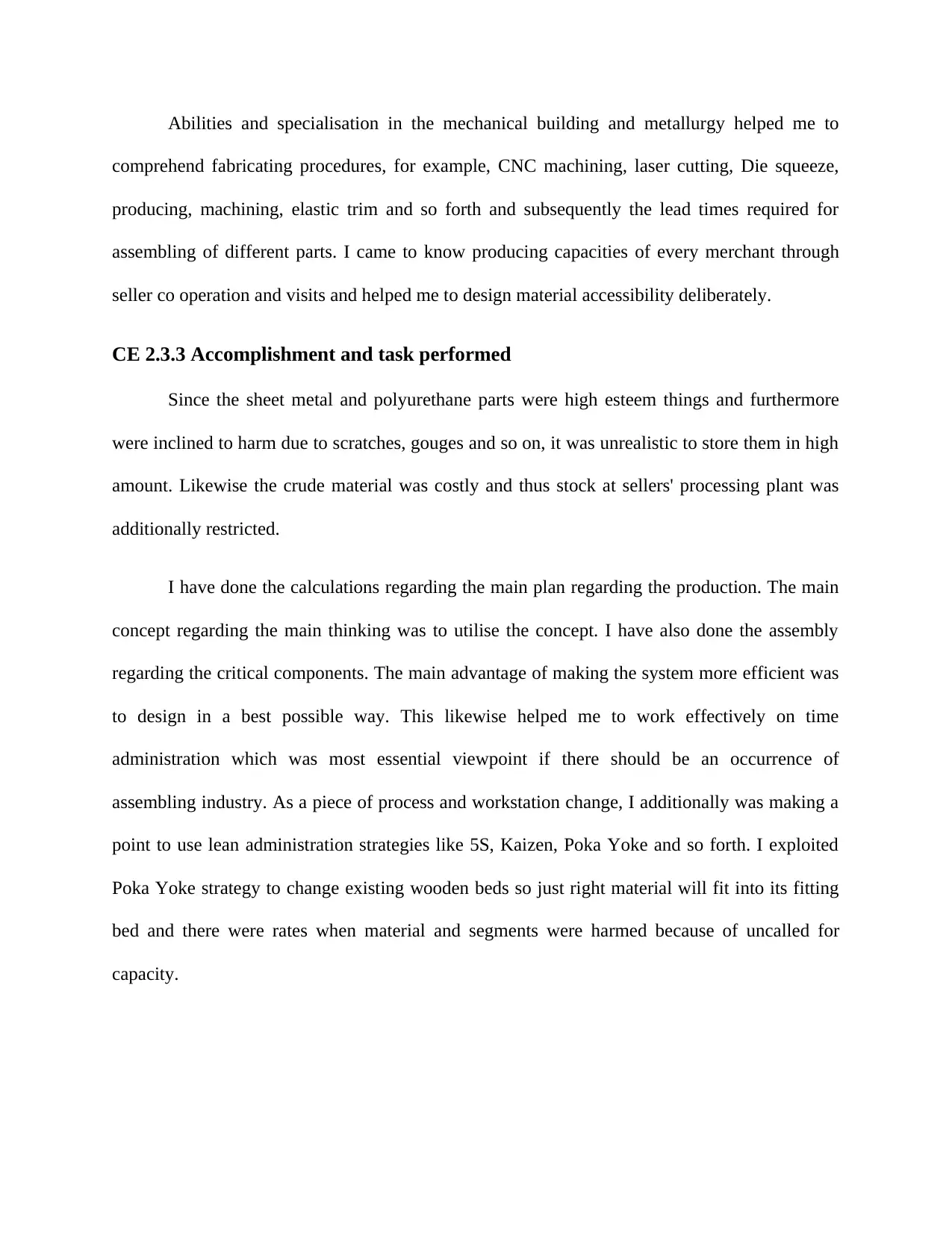
Abilities and specialisation in the mechanical building and metallurgy helped me to
comprehend fabricating procedures, for example, CNC machining, laser cutting, Die squeeze,
producing, machining, elastic trim and so forth and subsequently the lead times required for
assembling of different parts. I came to know producing capacities of every merchant through
seller co operation and visits and helped me to design material accessibility deliberately.
CE 2.3.3 Accomplishment and task performed
Since the sheet metal and polyurethane parts were high esteem things and furthermore
were inclined to harm due to scratches, gouges and so on, it was unrealistic to store them in high
amount. Likewise the crude material was costly and thus stock at sellers' processing plant was
additionally restricted.
I have done the calculations regarding the main plan regarding the production. The main
concept regarding the main thinking was to utilise the concept. I have also done the assembly
regarding the critical components. The main advantage of making the system more efficient was
to design in a best possible way. This likewise helped me to work effectively on time
administration which was most essential viewpoint if there should be an occurrence of
assembling industry. As a piece of process and workstation change, I additionally was making a
point to use lean administration strategies like 5S, Kaizen, Poka Yoke and so forth. I exploited
Poka Yoke strategy to change existing wooden beds so just right material will fit into its fitting
bed and there were rates when material and segments were harmed because of uncalled for
capacity.
comprehend fabricating procedures, for example, CNC machining, laser cutting, Die squeeze,
producing, machining, elastic trim and so forth and subsequently the lead times required for
assembling of different parts. I came to know producing capacities of every merchant through
seller co operation and visits and helped me to design material accessibility deliberately.
CE 2.3.3 Accomplishment and task performed
Since the sheet metal and polyurethane parts were high esteem things and furthermore
were inclined to harm due to scratches, gouges and so on, it was unrealistic to store them in high
amount. Likewise the crude material was costly and thus stock at sellers' processing plant was
additionally restricted.
I have done the calculations regarding the main plan regarding the production. The main
concept regarding the main thinking was to utilise the concept. I have also done the assembly
regarding the critical components. The main advantage of making the system more efficient was
to design in a best possible way. This likewise helped me to work effectively on time
administration which was most essential viewpoint if there should be an occurrence of
assembling industry. As a piece of process and workstation change, I additionally was making a
point to use lean administration strategies like 5S, Kaizen, Poka Yoke and so forth. I exploited
Poka Yoke strategy to change existing wooden beds so just right material will fit into its fitting
bed and there were rates when material and segments were harmed because of uncalled for
capacity.
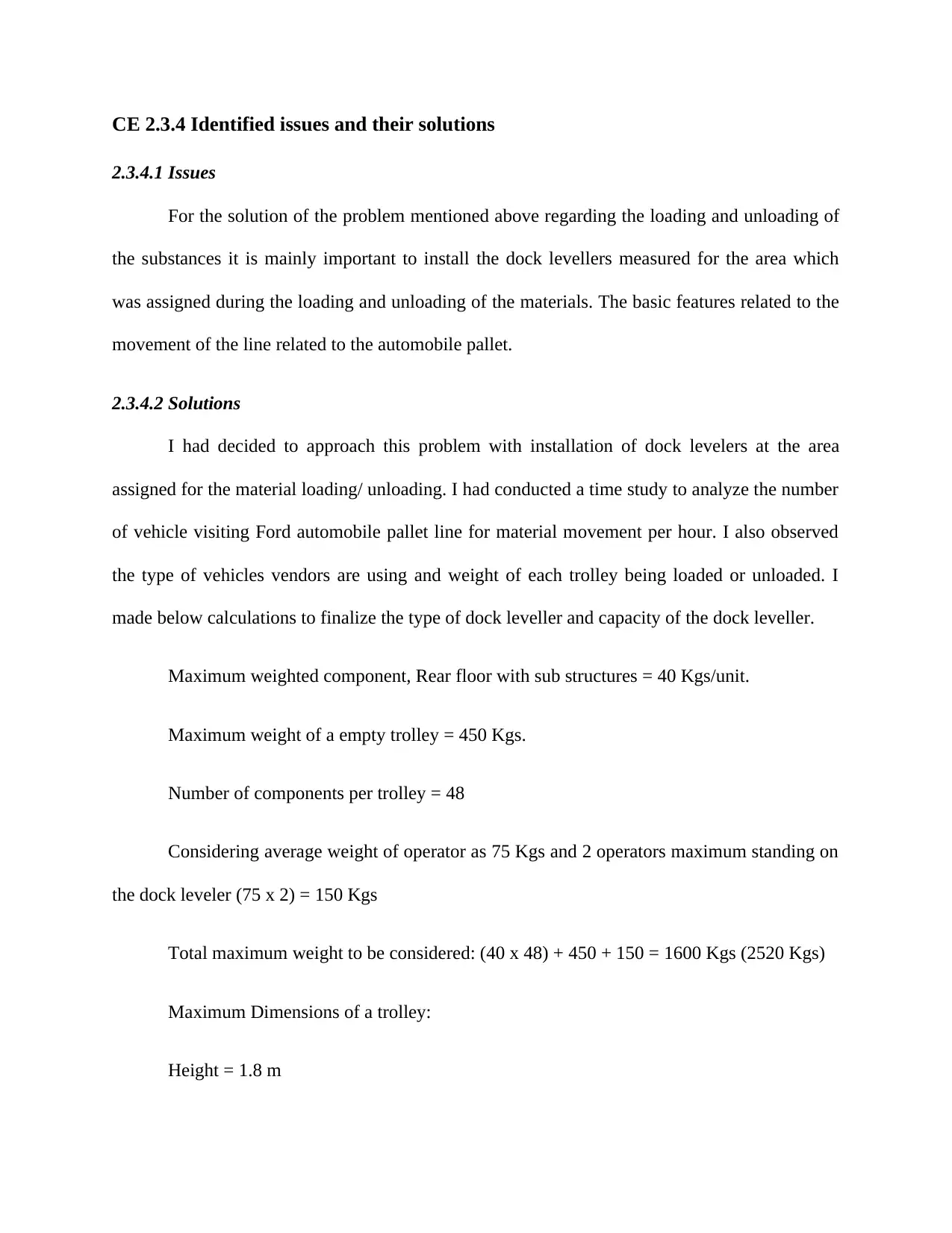
CE 2.3.4 Identified issues and their solutions
2.3.4.1 Issues
For the solution of the problem mentioned above regarding the loading and unloading of
the substances it is mainly important to install the dock levellers measured for the area which
was assigned during the loading and unloading of the materials. The basic features related to the
movement of the line related to the automobile pallet.
2.3.4.2 Solutions
I had decided to approach this problem with installation of dock levelers at the area
assigned for the material loading/ unloading. I had conducted a time study to analyze the number
of vehicle visiting Ford automobile pallet line for material movement per hour. I also observed
the type of vehicles vendors are using and weight of each trolley being loaded or unloaded. I
made below calculations to finalize the type of dock leveller and capacity of the dock leveller.
Maximum weighted component, Rear floor with sub structures = 40 Kgs/unit.
Maximum weight of a empty trolley = 450 Kgs.
Number of components per trolley = 48
Considering average weight of operator as 75 Kgs and 2 operators maximum standing on
the dock leveler (75 x 2) = 150 Kgs
Total maximum weight to be considered: (40 x 48) + 450 + 150 = 1600 Kgs (2520 Kgs)
Maximum Dimensions of a trolley:
Height = 1.8 m
2.3.4.1 Issues
For the solution of the problem mentioned above regarding the loading and unloading of
the substances it is mainly important to install the dock levellers measured for the area which
was assigned during the loading and unloading of the materials. The basic features related to the
movement of the line related to the automobile pallet.
2.3.4.2 Solutions
I had decided to approach this problem with installation of dock levelers at the area
assigned for the material loading/ unloading. I had conducted a time study to analyze the number
of vehicle visiting Ford automobile pallet line for material movement per hour. I also observed
the type of vehicles vendors are using and weight of each trolley being loaded or unloaded. I
made below calculations to finalize the type of dock leveller and capacity of the dock leveller.
Maximum weighted component, Rear floor with sub structures = 40 Kgs/unit.
Maximum weight of a empty trolley = 450 Kgs.
Number of components per trolley = 48
Considering average weight of operator as 75 Kgs and 2 operators maximum standing on
the dock leveler (75 x 2) = 150 Kgs
Total maximum weight to be considered: (40 x 48) + 450 + 150 = 1600 Kgs (2520 Kgs)
Maximum Dimensions of a trolley:
Height = 1.8 m
Paraphrase This Document
Need a fresh take? Get an instant paraphrase of this document with our AI Paraphraser
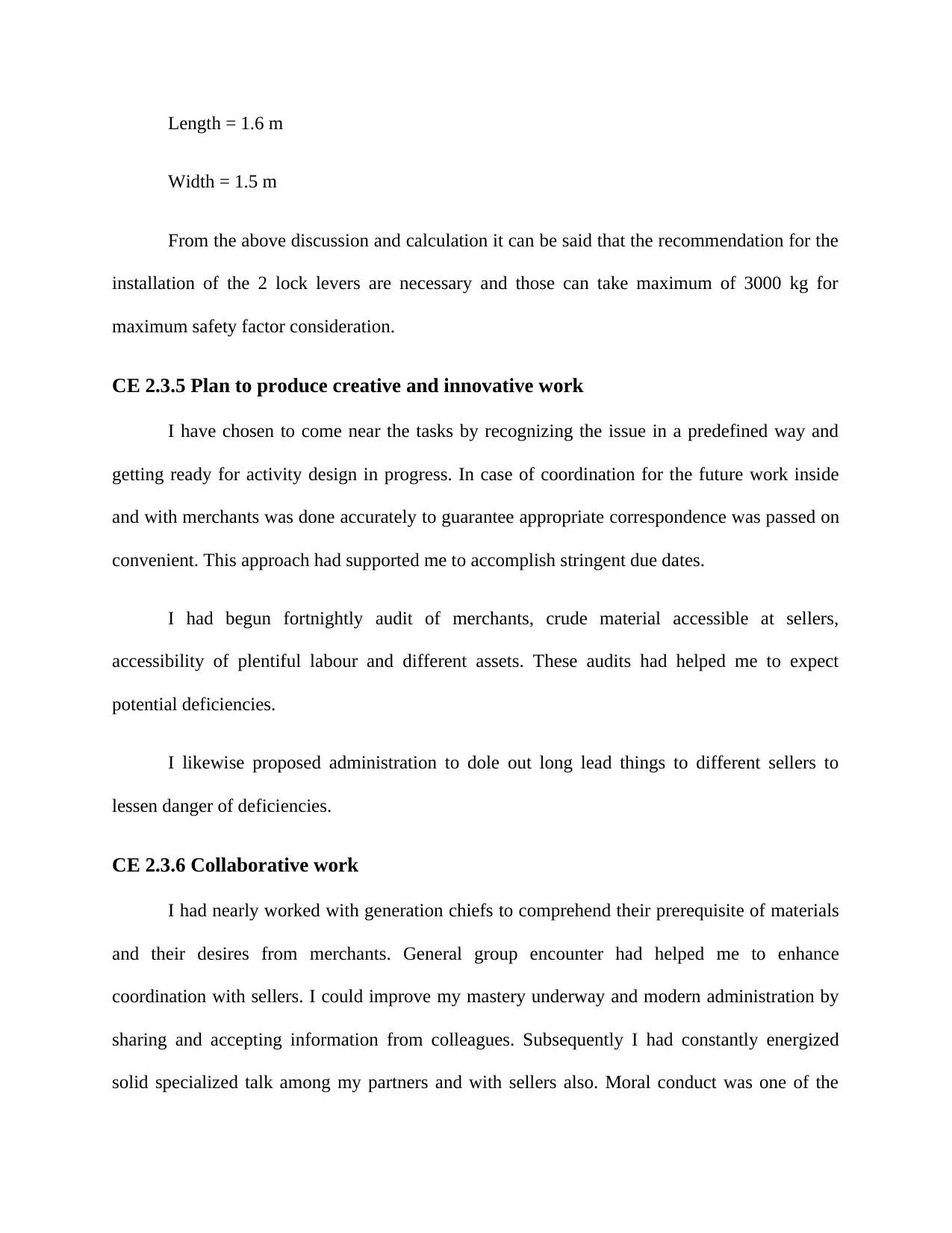
Length = 1.6 m
Width = 1.5 m
From the above discussion and calculation it can be said that the recommendation for the
installation of the 2 lock levers are necessary and those can take maximum of 3000 kg for
maximum safety factor consideration.
CE 2.3.5 Plan to produce creative and innovative work
I have chosen to come near the tasks by recognizing the issue in a predefined way and
getting ready for activity design in progress. In case of coordination for the future work inside
and with merchants was done accurately to guarantee appropriate correspondence was passed on
convenient. This approach had supported me to accomplish stringent due dates.
I had begun fortnightly audit of merchants, crude material accessible at sellers,
accessibility of plentiful labour and different assets. These audits had helped me to expect
potential deficiencies.
I likewise proposed administration to dole out long lead things to different sellers to
lessen danger of deficiencies.
CE 2.3.6 Collaborative work
I had nearly worked with generation chiefs to comprehend their prerequisite of materials
and their desires from merchants. General group encounter had helped me to enhance
coordination with sellers. I could improve my mastery underway and modern administration by
sharing and accepting information from colleagues. Subsequently I had constantly energized
solid specialized talk among my partners and with sellers also. Moral conduct was one of the
Width = 1.5 m
From the above discussion and calculation it can be said that the recommendation for the
installation of the 2 lock levers are necessary and those can take maximum of 3000 kg for
maximum safety factor consideration.
CE 2.3.5 Plan to produce creative and innovative work
I have chosen to come near the tasks by recognizing the issue in a predefined way and
getting ready for activity design in progress. In case of coordination for the future work inside
and with merchants was done accurately to guarantee appropriate correspondence was passed on
convenient. This approach had supported me to accomplish stringent due dates.
I had begun fortnightly audit of merchants, crude material accessible at sellers,
accessibility of plentiful labour and different assets. These audits had helped me to expect
potential deficiencies.
I likewise proposed administration to dole out long lead things to different sellers to
lessen danger of deficiencies.
CE 2.3.6 Collaborative work
I had nearly worked with generation chiefs to comprehend their prerequisite of materials
and their desires from merchants. General group encounter had helped me to enhance
coordination with sellers. I could improve my mastery underway and modern administration by
sharing and accepting information from colleagues. Subsequently I had constantly energized
solid specialized talk among my partners and with sellers also. Moral conduct was one of the
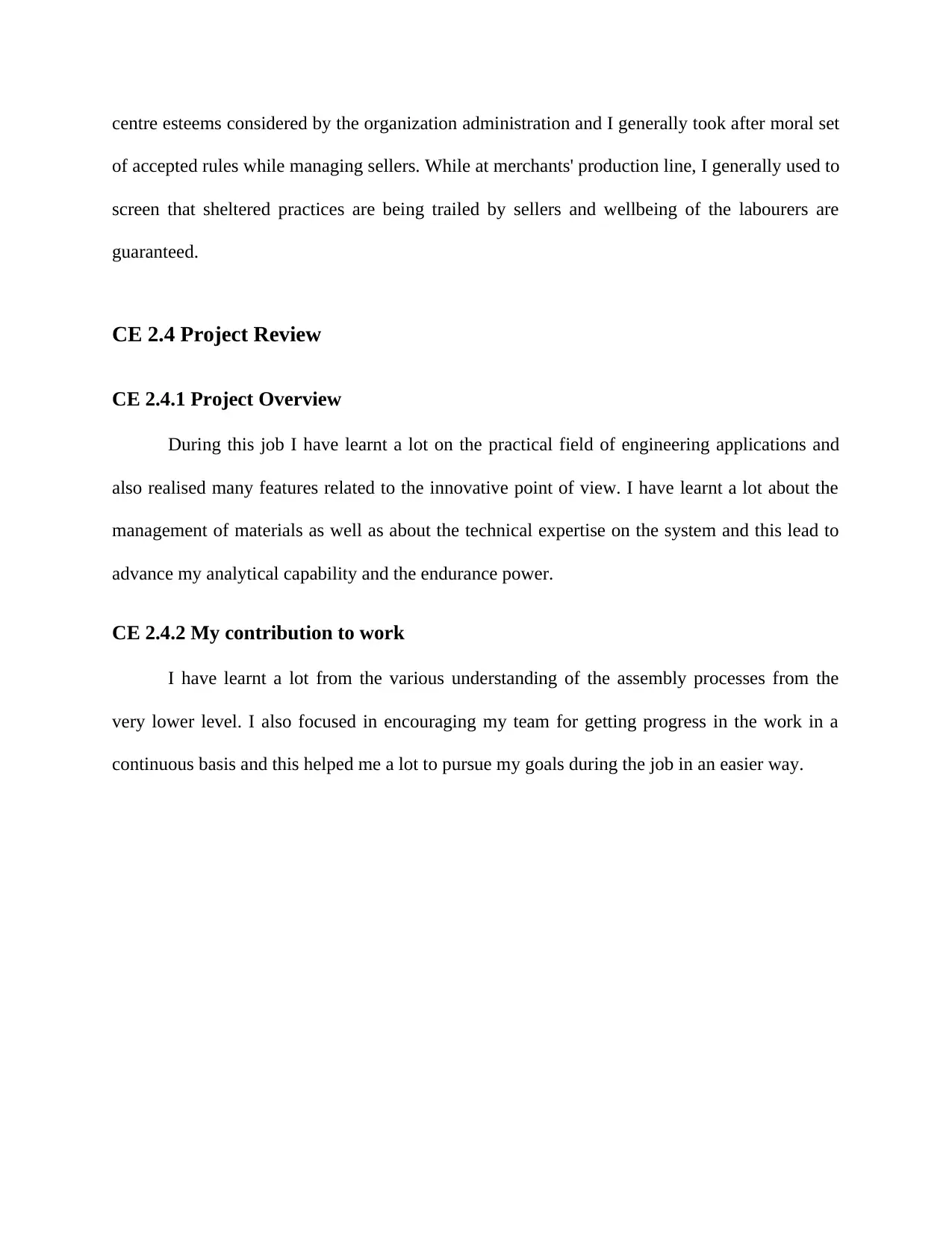
centre esteems considered by the organization administration and I generally took after moral set
of accepted rules while managing sellers. While at merchants' production line, I generally used to
screen that sheltered practices are being trailed by sellers and wellbeing of the labourers are
guaranteed.
CE 2.4 Project Review
CE 2.4.1 Project Overview
During this job I have learnt a lot on the practical field of engineering applications and
also realised many features related to the innovative point of view. I have learnt a lot about the
management of materials as well as about the technical expertise on the system and this lead to
advance my analytical capability and the endurance power.
CE 2.4.2 My contribution to work
I have learnt a lot from the various understanding of the assembly processes from the
very lower level. I also focused in encouraging my team for getting progress in the work in a
continuous basis and this helped me a lot to pursue my goals during the job in an easier way.
of accepted rules while managing sellers. While at merchants' production line, I generally used to
screen that sheltered practices are being trailed by sellers and wellbeing of the labourers are
guaranteed.
CE 2.4 Project Review
CE 2.4.1 Project Overview
During this job I have learnt a lot on the practical field of engineering applications and
also realised many features related to the innovative point of view. I have learnt a lot about the
management of materials as well as about the technical expertise on the system and this lead to
advance my analytical capability and the endurance power.
CE 2.4.2 My contribution to work
I have learnt a lot from the various understanding of the assembly processes from the
very lower level. I also focused in encouraging my team for getting progress in the work in a
continuous basis and this helped me a lot to pursue my goals during the job in an easier way.
1 out of 9
Related Documents
![[object Object]](/_next/image/?url=%2F_next%2Fstatic%2Fmedia%2Flogo.6d15ce61.png&w=640&q=75)
Your All-in-One AI-Powered Toolkit for Academic Success.
 +13062052269
info@desklib.com
Available 24*7 on WhatsApp / Email
Unlock your academic potential
© 2024  |  Zucol Services PVT LTD  |  All rights reserved.