Conventional Cost Allocation with Job Order Costing - Week 4 Notes
VerifiedAdded on 2024/04/29
|26
|5222
|55
AI Summary
This document covers conventional cost allocation with job order costing, discussing product and service costing, flow of costs in manufacturing firms, types of product costing systems, job-order costing, and more.
Contribute Materials
Your contribution can guide someone’s learning journey. Share your
documents today.
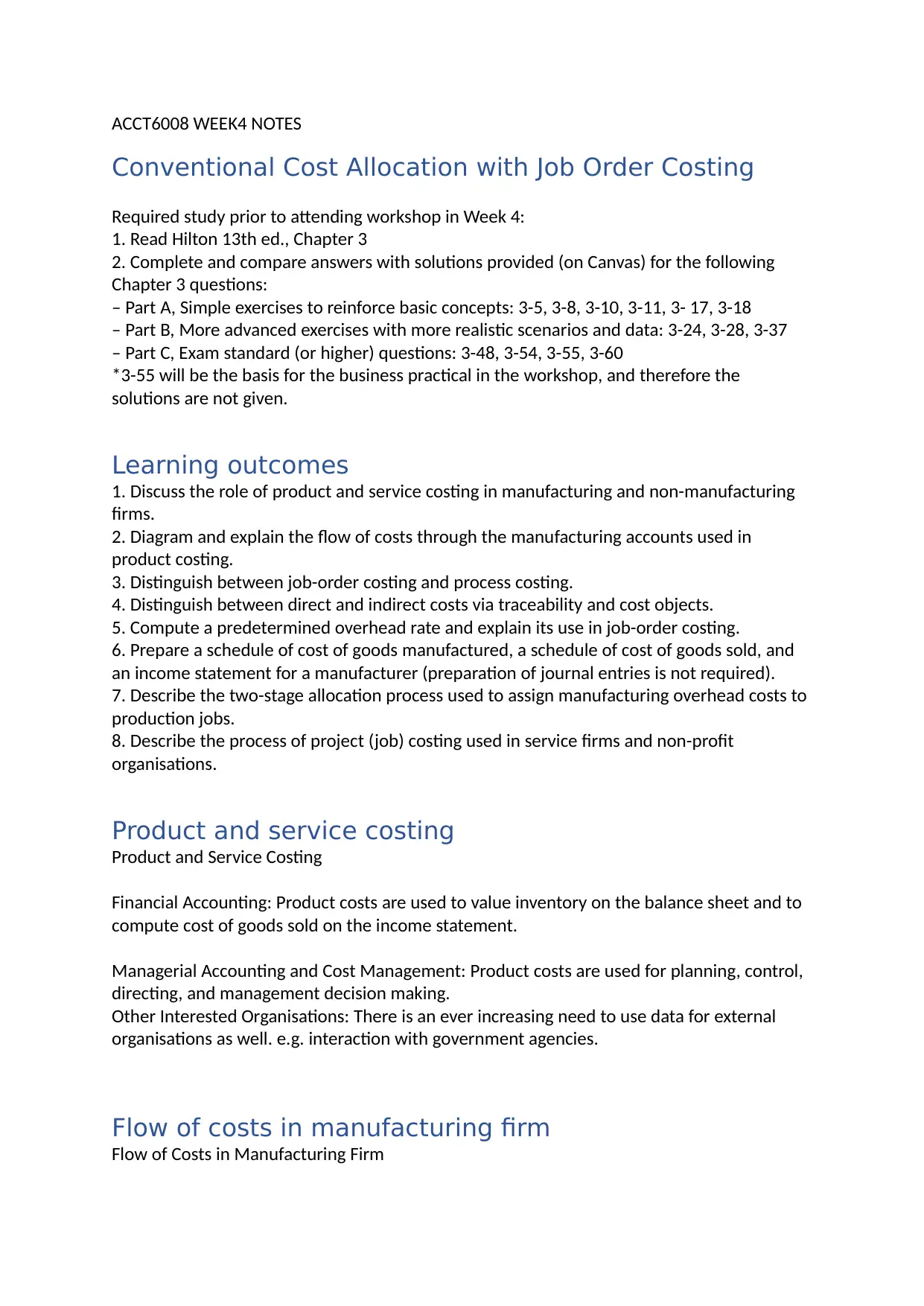
ACCT6008 WEEK4 NOTES
Conventional Cost Allocation with Job Order Costing
Required study prior to attending workshop in Week 4:
1. Read Hilton 13th ed., Chapter 3
2. Complete and compare answers with solutions provided (on Canvas) for the following
Chapter 3 questions:
– Part A, Simple exercises to reinforce basic concepts: 3-5, 3-8, 3-10, 3-11, 3- 17, 3-18
– Part B, More advanced exercises with more realistic scenarios and data: 3-24, 3-28, 3-37
– Part C, Exam standard (or higher) questions: 3-48, 3-54, 3-55, 3-60
*3-55 will be the basis for the business practical in the workshop, and therefore the
solutions are not given.
Learning outcomes
1. Discuss the role of product and service costing in manufacturing and non-manufacturing
firms.
2. Diagram and explain the flow of costs through the manufacturing accounts used in
product costing.
3. Distinguish between job-order costing and process costing.
4. Distinguish between direct and indirect costs via traceability and cost objects.
5. Compute a predetermined overhead rate and explain its use in job-order costing.
6. Prepare a schedule of cost of goods manufactured, a schedule of cost of goods sold, and
an income statement for a manufacturer (preparation of journal entries is not required).
7. Describe the two-stage allocation process used to assign manufacturing overhead costs to
production jobs.
8. Describe the process of project (job) costing used in service firms and non-profit
organisations.
Product and service costing
Product and Service Costing
Financial Accounting: Product costs are used to value inventory on the balance sheet and to
compute cost of goods sold on the income statement.
Managerial Accounting and Cost Management: Product costs are used for planning, control,
directing, and management decision making.
Other Interested Organisations: There is an ever increasing need to use data for external
organisations as well. e.g. interaction with government agencies.
Flow of costs in manufacturing firm
Flow of Costs in Manufacturing Firm
Conventional Cost Allocation with Job Order Costing
Required study prior to attending workshop in Week 4:
1. Read Hilton 13th ed., Chapter 3
2. Complete and compare answers with solutions provided (on Canvas) for the following
Chapter 3 questions:
– Part A, Simple exercises to reinforce basic concepts: 3-5, 3-8, 3-10, 3-11, 3- 17, 3-18
– Part B, More advanced exercises with more realistic scenarios and data: 3-24, 3-28, 3-37
– Part C, Exam standard (or higher) questions: 3-48, 3-54, 3-55, 3-60
*3-55 will be the basis for the business practical in the workshop, and therefore the
solutions are not given.
Learning outcomes
1. Discuss the role of product and service costing in manufacturing and non-manufacturing
firms.
2. Diagram and explain the flow of costs through the manufacturing accounts used in
product costing.
3. Distinguish between job-order costing and process costing.
4. Distinguish between direct and indirect costs via traceability and cost objects.
5. Compute a predetermined overhead rate and explain its use in job-order costing.
6. Prepare a schedule of cost of goods manufactured, a schedule of cost of goods sold, and
an income statement for a manufacturer (preparation of journal entries is not required).
7. Describe the two-stage allocation process used to assign manufacturing overhead costs to
production jobs.
8. Describe the process of project (job) costing used in service firms and non-profit
organisations.
Product and service costing
Product and Service Costing
Financial Accounting: Product costs are used to value inventory on the balance sheet and to
compute cost of goods sold on the income statement.
Managerial Accounting and Cost Management: Product costs are used for planning, control,
directing, and management decision making.
Other Interested Organisations: There is an ever increasing need to use data for external
organisations as well. e.g. interaction with government agencies.
Flow of costs in manufacturing firm
Flow of Costs in Manufacturing Firm
Secure Best Marks with AI Grader
Need help grading? Try our AI Grader for instant feedback on your assignments.
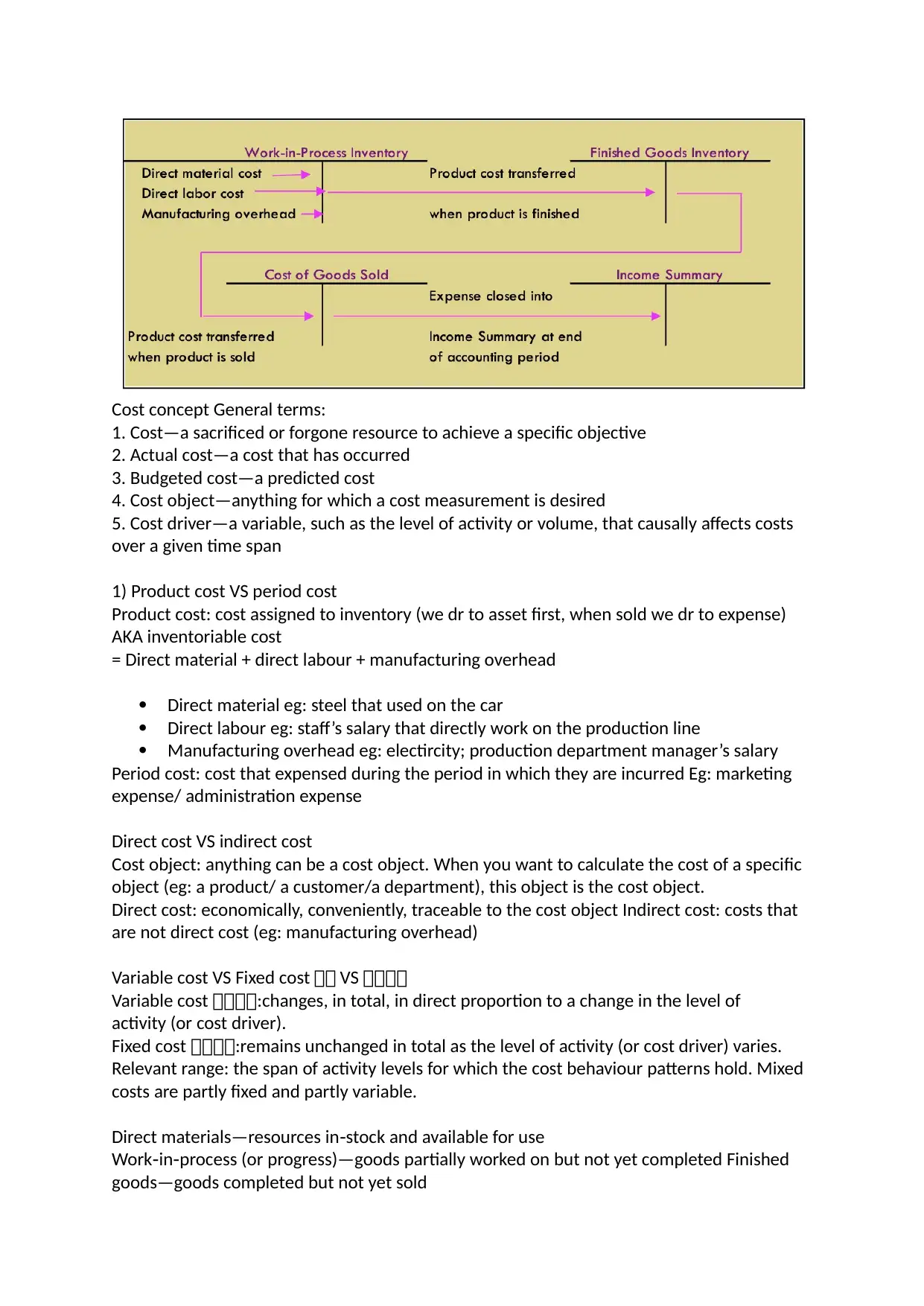
Cost concept General terms:
1. Cost—a sacrificed or forgone resource to achieve a specific objective
2. Actual cost—a cost that has occurred
3. Budgeted cost—a predicted cost
4. Cost object—anything for which a cost measurement is desired
5. Cost driver—a variable, such as the level of activity or volume, that causally affects costs
over a given time span
1) Product cost VS period cost
Product cost: cost assigned to inventory (we dr to asset first, when sold we dr to expense)
AKA inventoriable cost
= Direct material + direct labour + manufacturing overhead
Direct material eg: steel that used on the car
Direct labour eg: staff’s salary that directly work on the production line
Manufacturing overhead eg: electircity; production department manager’s salary
Period cost: cost that expensed during the period in which they are incurred Eg: marketing
expense/ administration expense
Direct cost VS indirect cost
Cost object: anything can be a cost object. When you want to calculate the cost of a specific
object (eg: a product/ a customer/a department), this object is the cost object.
Direct cost: economically, conveniently, traceable to the cost object Indirect cost: costs that
are not direct cost (eg: manufacturing overhead)
Variable cost VS Fixed cost 可可 VS 可可可可
Variable cost 可可可可:changes, in total, in direct proportion to a change in the level of
activity (or cost driver).
Fixed cost 可可可可:remains unchanged in total as the level of activity (or cost driver) varies.
Relevant range: the span of activity levels for which the cost behaviour patterns hold. Mixed
costs are partly fixed and partly variable.
Direct materials—resources in stock and available for use‐
Work in process (or progress)—goods partially worked on but not yet completed Finished‐ ‐
goods—goods completed but not yet sold
1. Cost—a sacrificed or forgone resource to achieve a specific objective
2. Actual cost—a cost that has occurred
3. Budgeted cost—a predicted cost
4. Cost object—anything for which a cost measurement is desired
5. Cost driver—a variable, such as the level of activity or volume, that causally affects costs
over a given time span
1) Product cost VS period cost
Product cost: cost assigned to inventory (we dr to asset first, when sold we dr to expense)
AKA inventoriable cost
= Direct material + direct labour + manufacturing overhead
Direct material eg: steel that used on the car
Direct labour eg: staff’s salary that directly work on the production line
Manufacturing overhead eg: electircity; production department manager’s salary
Period cost: cost that expensed during the period in which they are incurred Eg: marketing
expense/ administration expense
Direct cost VS indirect cost
Cost object: anything can be a cost object. When you want to calculate the cost of a specific
object (eg: a product/ a customer/a department), this object is the cost object.
Direct cost: economically, conveniently, traceable to the cost object Indirect cost: costs that
are not direct cost (eg: manufacturing overhead)
Variable cost VS Fixed cost 可可 VS 可可可可
Variable cost 可可可可:changes, in total, in direct proportion to a change in the level of
activity (or cost driver).
Fixed cost 可可可可:remains unchanged in total as the level of activity (or cost driver) varies.
Relevant range: the span of activity levels for which the cost behaviour patterns hold. Mixed
costs are partly fixed and partly variable.
Direct materials—resources in stock and available for use‐
Work in process (or progress)—goods partially worked on but not yet completed Finished‐ ‐
goods—goods completed but not yet sold
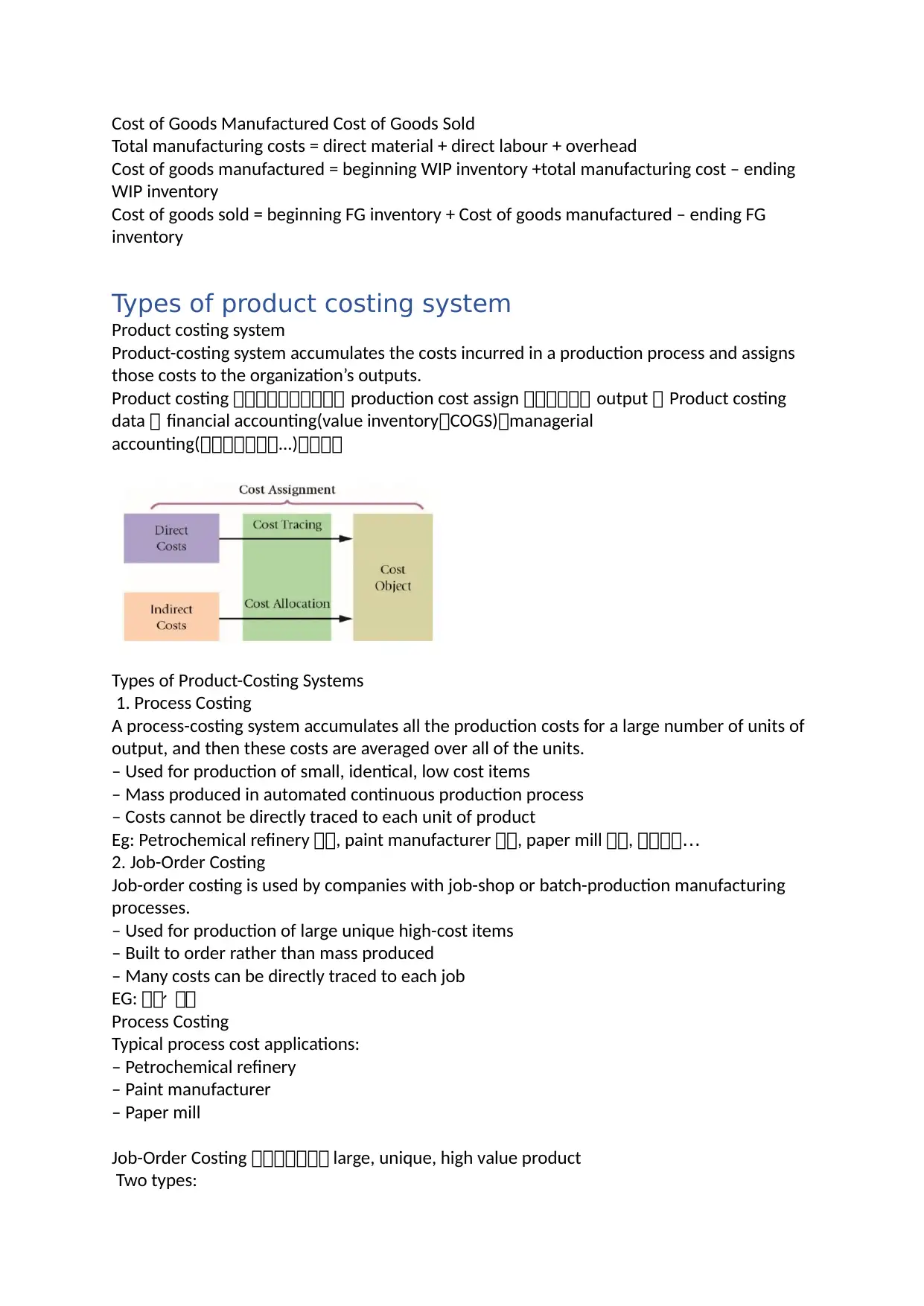
Cost of Goods Manufactured Cost of Goods Sold
Total manufacturing costs = direct material + direct labour + overhead
Cost of goods manufactured = beginning WIP inventory +total manufacturing cost – ending
WIP inventory
Cost of goods sold = beginning FG inventory + Cost of goods manufactured – ending FG
inventory
Types of product costing system
Product costing system
Product-costing system accumulates the costs incurred in a production process and assigns
those costs to the organization’s outputs.
Product costing 可可可可可可可可可可 production cost assign 可可可可可可 output 可 Product costing
data 可 financial accounting(value inventory可COGS)可managerial
accounting(可可可可可可可...)可可可可
Types of Product-Costing Systems
1. Process Costing
A process-costing system accumulates all the production costs for a large number of units of
output, and then these costs are averaged over all of the units.
– Used for production of small, identical, low cost items
– Mass produced in automated continuous production process
– Costs cannot be directly traced to each unit of product
Eg: Petrochemical refinery 可可, paint manufacturer 可可, paper mill 可可, 可可可可…
2. Job-Order Costing
Job-order costing is used by companies with job-shop or batch-production manufacturing
processes.
– Used for production of large unique high-cost items
– Built to order rather than mass produced
– Many costs can be directly traced to each job
EG: 可可 可可、
Process Costing
Typical process cost applications:
– Petrochemical refinery
– Paint manufacturer
– Paper mill
Job-Order Costing 可可可可可可可 large, unique, high value product
Two types:
Total manufacturing costs = direct material + direct labour + overhead
Cost of goods manufactured = beginning WIP inventory +total manufacturing cost – ending
WIP inventory
Cost of goods sold = beginning FG inventory + Cost of goods manufactured – ending FG
inventory
Types of product costing system
Product costing system
Product-costing system accumulates the costs incurred in a production process and assigns
those costs to the organization’s outputs.
Product costing 可可可可可可可可可可 production cost assign 可可可可可可 output 可 Product costing
data 可 financial accounting(value inventory可COGS)可managerial
accounting(可可可可可可可...)可可可可
Types of Product-Costing Systems
1. Process Costing
A process-costing system accumulates all the production costs for a large number of units of
output, and then these costs are averaged over all of the units.
– Used for production of small, identical, low cost items
– Mass produced in automated continuous production process
– Costs cannot be directly traced to each unit of product
Eg: Petrochemical refinery 可可, paint manufacturer 可可, paper mill 可可, 可可可可…
2. Job-Order Costing
Job-order costing is used by companies with job-shop or batch-production manufacturing
processes.
– Used for production of large unique high-cost items
– Built to order rather than mass produced
– Many costs can be directly traced to each job
EG: 可可 可可、
Process Costing
Typical process cost applications:
– Petrochemical refinery
– Paint manufacturer
– Paper mill
Job-Order Costing 可可可可可可可 large, unique, high value product
Two types:
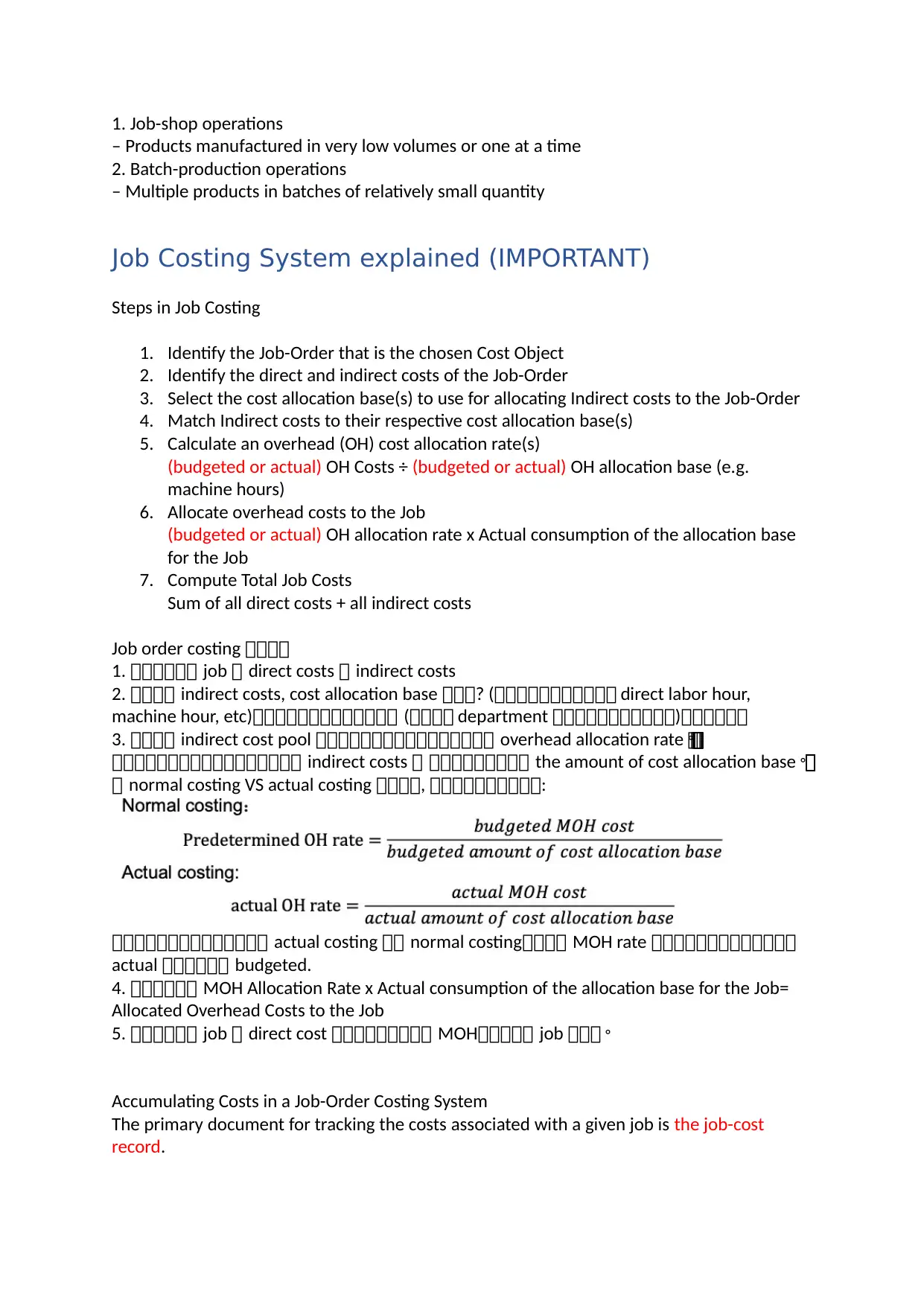
1. Job-shop operations
– Products manufactured in very low volumes or one at a time
2. Batch-production operations
– Multiple products in batches of relatively small quantity
Job Costing System explained (IMPORTANT)
Steps in Job Costing
1. Identify the Job-Order that is the chosen Cost Object
2. Identify the direct and indirect costs of the Job-Order
3. Select the cost allocation base(s) to use for allocating Indirect costs to the Job-Order
4. Match Indirect costs to their respective cost allocation base(s)
5. Calculate an overhead (OH) cost allocation rate(s)
(budgeted or actual) OH Costs ÷ (budgeted or actual) OH allocation base (e.g.
machine hours)
6. Allocate overhead costs to the Job
(budgeted or actual) OH allocation rate x Actual consumption of the allocation base
for the Job
7. Compute Total Job Costs
Sum of all direct costs + all indirect costs
Job order costing 可可可可
1. 可可可可可可 job 可 direct costs 可 indirect costs
2. 可可可可 indirect costs, cost allocation base 可可可? (可可可可可可可可可可可 direct labor hour,
machine hour, etc)可可可可可可可可可可可可可 (可可可可 department 可可可可可可可可可可可)可可可可可可
3. 可可可可 indirect cost pool 可可可可可可可可可可可可可可可可 overhead allocation rate 可可可可可可可可可可。
可可可可可可可可可可可可可可可可可 indirect costs 可 可可可可可可可可可 the amount of cost allocation base 可可可可可可。
可 normal costing VS actual costing 可可可可, 可可可可可可可可可可:
可可可可可可可可可可可可可可 actual costing 可可 normal costing可可可可 MOH rate 可可可可可可可可可可可可可
actual 可可可可可可 budgeted.
4. 可可可可可可 MOH Allocation Rate x Actual consumption of the allocation base for the Job=
Allocated Overhead Costs to the Job
5. 可可可可可可 job 可 direct cost 可可可可可可可可可 MOH可可可可可 job 可可可。
Accumulating Costs in a Job-Order Costing System
The primary document for tracking the costs associated with a given job is the job-cost
record.
– Products manufactured in very low volumes or one at a time
2. Batch-production operations
– Multiple products in batches of relatively small quantity
Job Costing System explained (IMPORTANT)
Steps in Job Costing
1. Identify the Job-Order that is the chosen Cost Object
2. Identify the direct and indirect costs of the Job-Order
3. Select the cost allocation base(s) to use for allocating Indirect costs to the Job-Order
4. Match Indirect costs to their respective cost allocation base(s)
5. Calculate an overhead (OH) cost allocation rate(s)
(budgeted or actual) OH Costs ÷ (budgeted or actual) OH allocation base (e.g.
machine hours)
6. Allocate overhead costs to the Job
(budgeted or actual) OH allocation rate x Actual consumption of the allocation base
for the Job
7. Compute Total Job Costs
Sum of all direct costs + all indirect costs
Job order costing 可可可可
1. 可可可可可可 job 可 direct costs 可 indirect costs
2. 可可可可 indirect costs, cost allocation base 可可可? (可可可可可可可可可可可 direct labor hour,
machine hour, etc)可可可可可可可可可可可可可 (可可可可 department 可可可可可可可可可可可)可可可可可可
3. 可可可可 indirect cost pool 可可可可可可可可可可可可可可可可 overhead allocation rate 可可可可可可可可可可。
可可可可可可可可可可可可可可可可可 indirect costs 可 可可可可可可可可可 the amount of cost allocation base 可可可可可可。
可 normal costing VS actual costing 可可可可, 可可可可可可可可可可:
可可可可可可可可可可可可可可 actual costing 可可 normal costing可可可可 MOH rate 可可可可可可可可可可可可可
actual 可可可可可可 budgeted.
4. 可可可可可可 MOH Allocation Rate x Actual consumption of the allocation base for the Job=
Allocated Overhead Costs to the Job
5. 可可可可可可 job 可 direct cost 可可可可可可可可可 MOH可可可可可 job 可可可。
Accumulating Costs in a Job-Order Costing System
The primary document for tracking the costs associated with a given job is the job-cost
record.
Secure Best Marks with AI Grader
Need help grading? Try our AI Grader for instant feedback on your assignments.
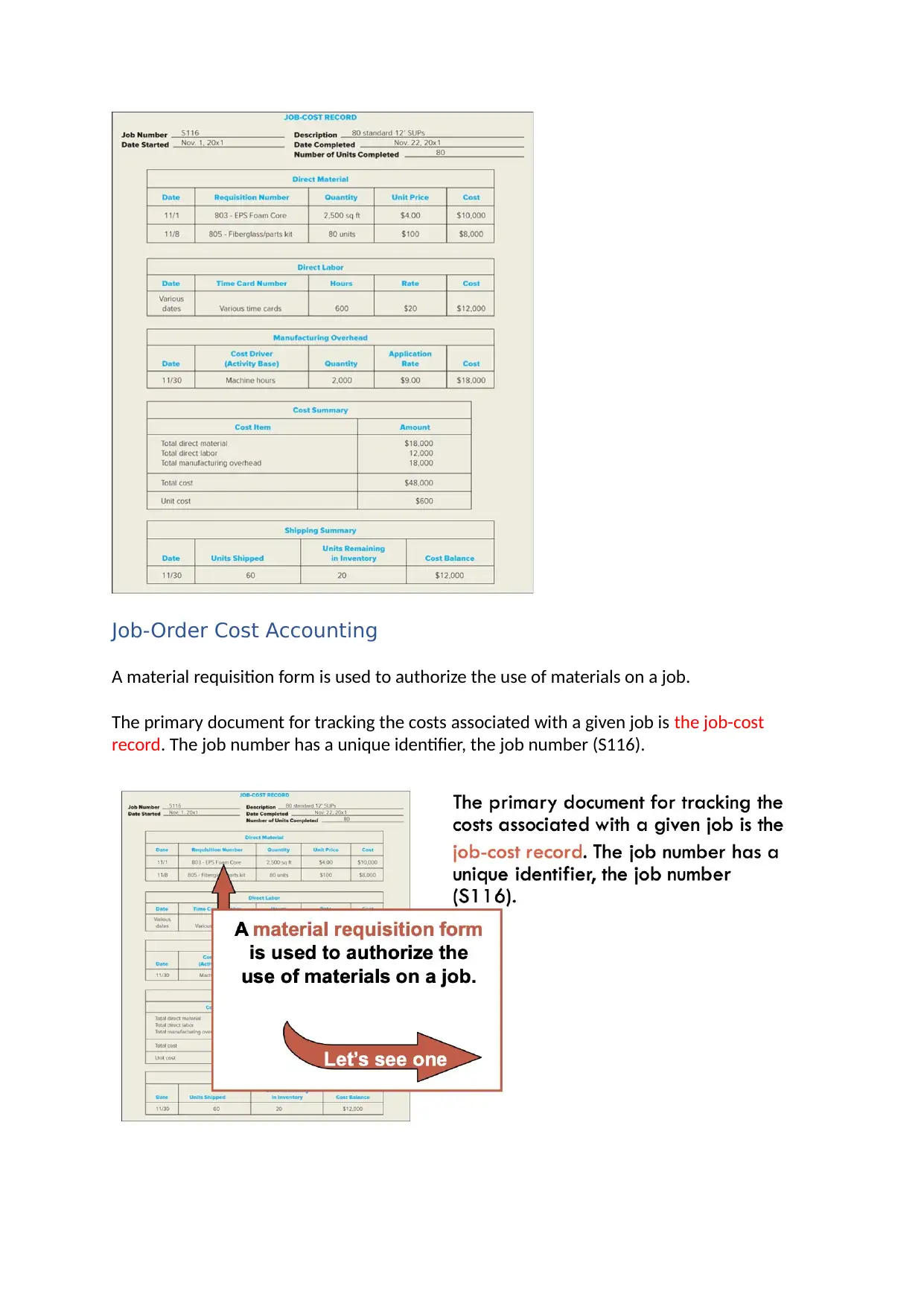
Job-Order Cost Accounting
A material requisition form is used to authorize the use of materials on a job.
The primary document for tracking the costs associated with a given job is the job-cost
record. The job number has a unique identifier, the job number (S116).
A material requisition form is used to authorize the use of materials on a job.
The primary document for tracking the costs associated with a given job is the job-cost
record. The job number has a unique identifier, the job number (S116).
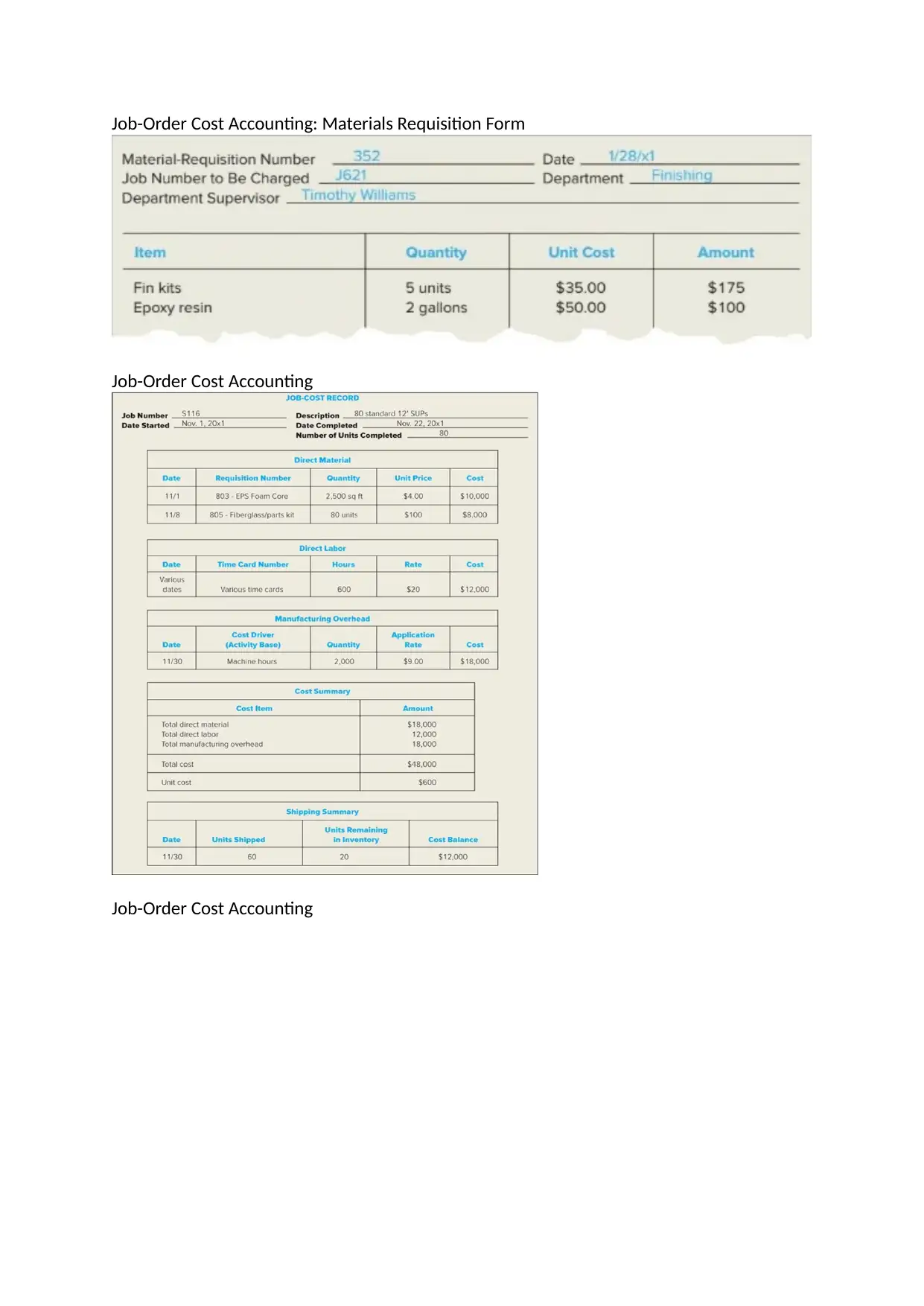
Job-Order Cost Accounting: Materials Requisition Form
Job-Order Cost Accounting
Job-Order Cost Accounting
Job-Order Cost Accounting
Job-Order Cost Accounting
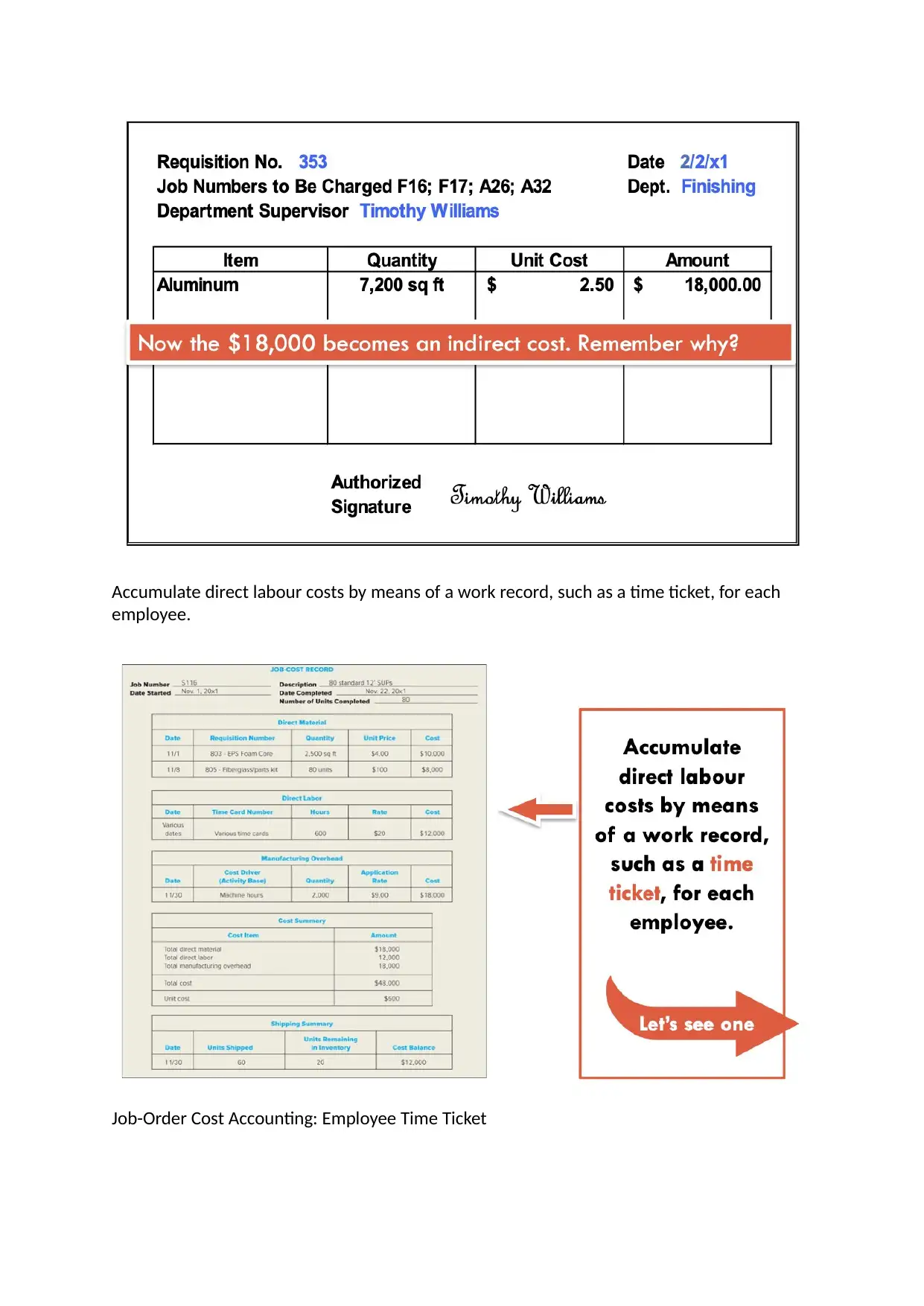
Accumulate direct labour costs by means of a work record, such as a time ticket, for each
employee.
Job-Order Cost Accounting: Employee Time Ticket
employee.
Job-Order Cost Accounting: Employee Time Ticket
Paraphrase This Document
Need a fresh take? Get an instant paraphrase of this document with our AI Paraphraser
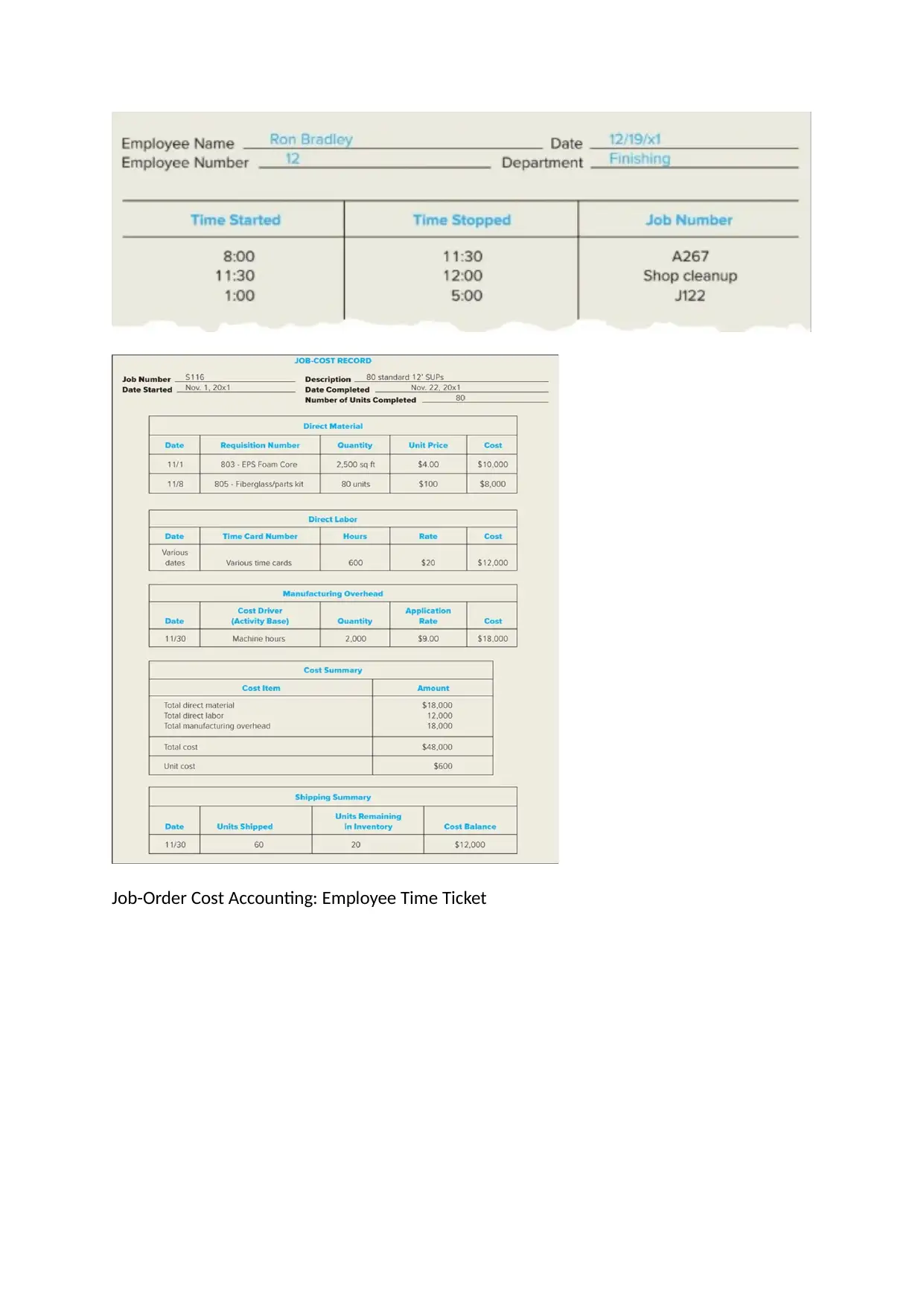
Job-Order Cost Accounting: Employee Time Ticket
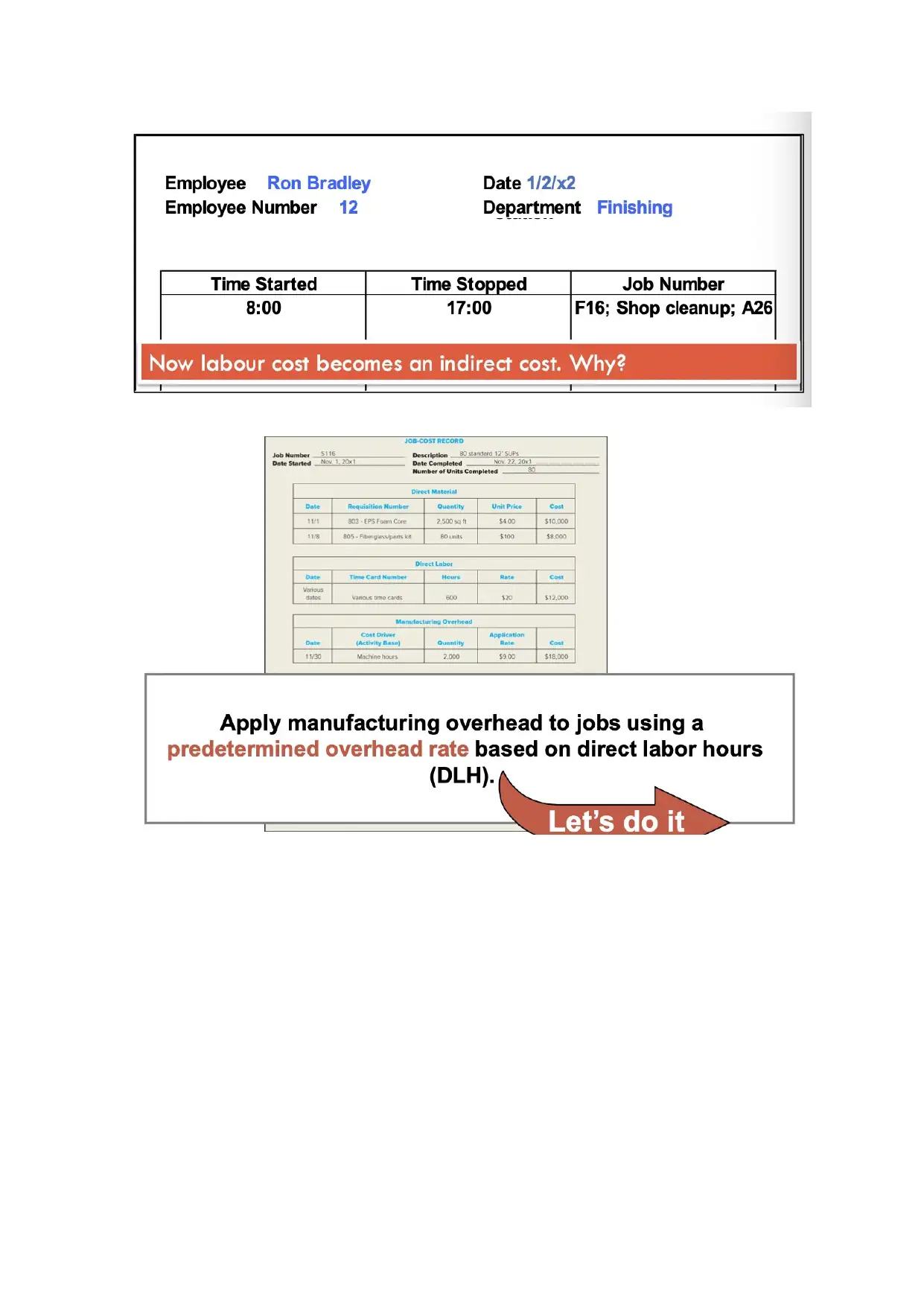
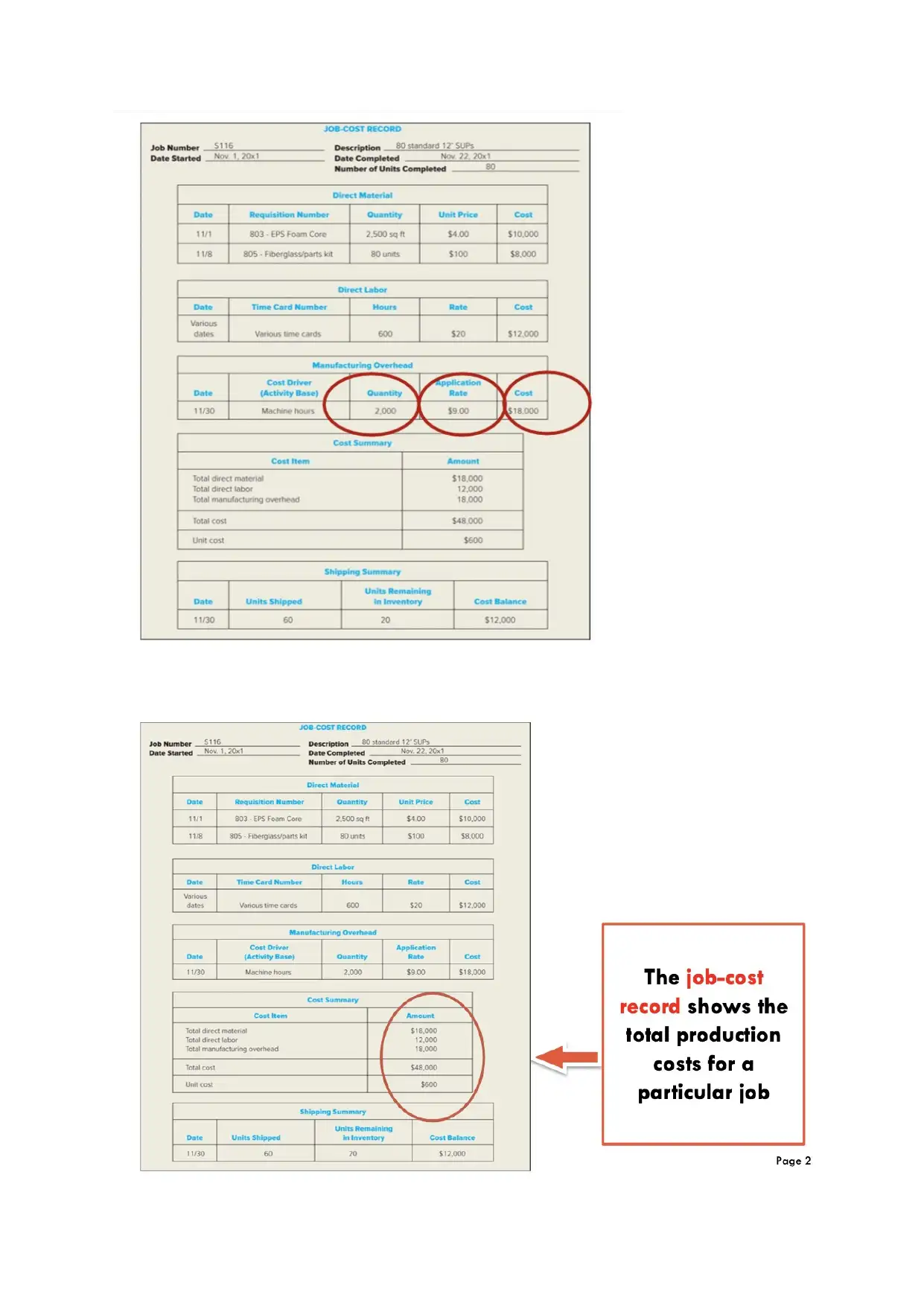
Secure Best Marks with AI Grader
Need help grading? Try our AI Grader for instant feedback on your assignments.

Manufacturing Overhead Costs
This approach works by computing, in advance, a rate for expected manufacturing overhead
that is then used in applying overhead costs throughout the period.
traditional product-costing systems tend to rely on a single, volume-based cost driver.
Manufacturing overhead costs
Overhead is applied to jobs using a predetermined overhead rate based on estimates made
at the beginning of the accounting period (normal costing).
Overhead is applied to jobs using a predetermined overhead rate (POHR) based on
estimates made at the beginning of the accounting period.
This approach works by computing, in advance, a rate for expected manufacturing overhead
that is then used in applying overhead costs throughout the period.
traditional product-costing systems tend to rely on a single, volume-based cost driver.
Manufacturing overhead costs
Overhead is applied to jobs using a predetermined overhead rate based on estimates made
at the beginning of the accounting period (normal costing).
Overhead is applied to jobs using a predetermined overhead rate (POHR) based on
estimates made at the beginning of the accounting period.
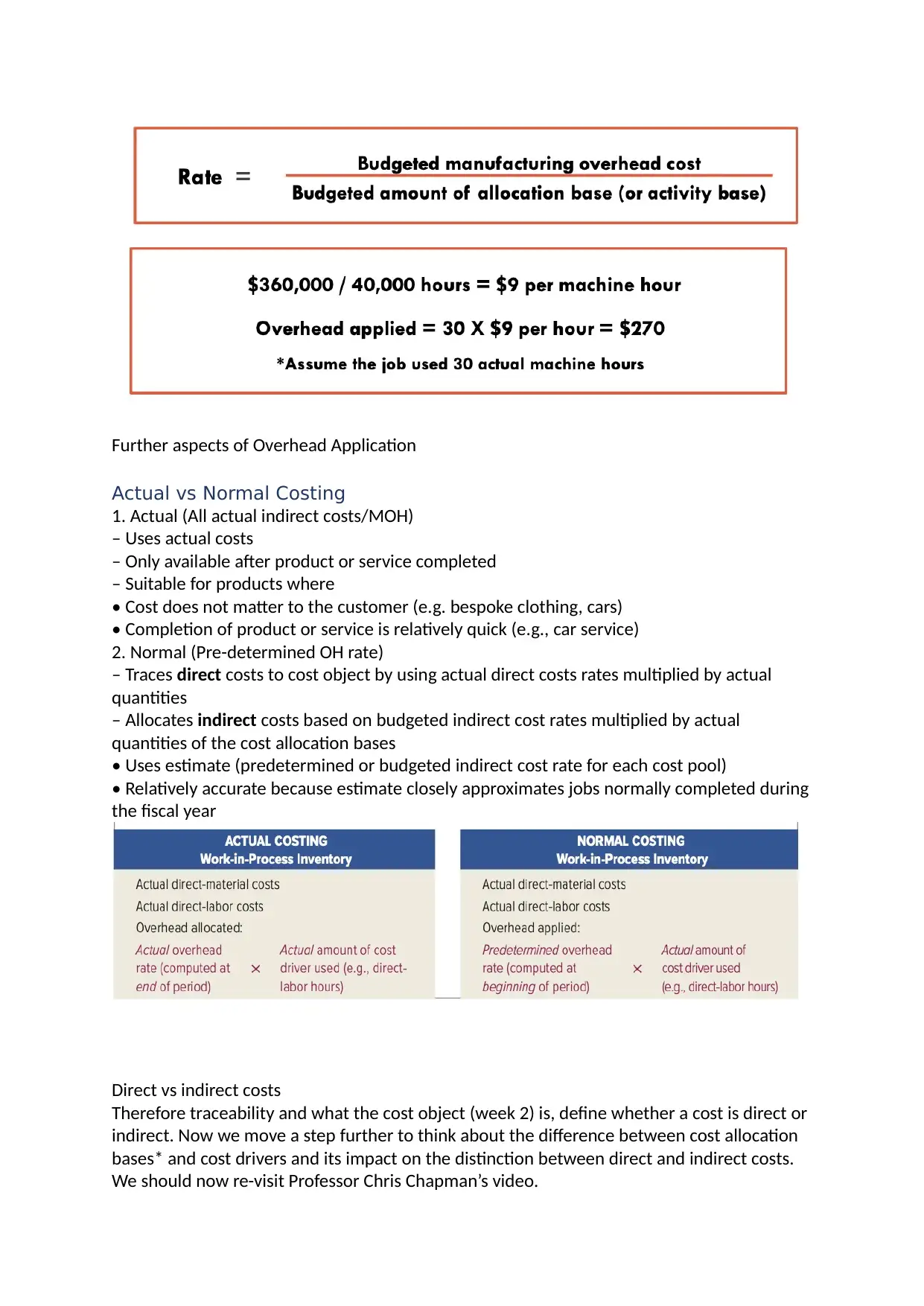
Further aspects of Overhead Application
Actual vs Normal Costing
1. Actual (All actual indirect costs/MOH)
– Uses actual costs
– Only available after product or service completed
– Suitable for products where
• Cost does not matter to the customer (e.g. bespoke clothing, cars)
• Completion of product or service is relatively quick (e.g., car service)
2. Normal (Pre-determined OH rate)
– Traces direct costs to cost object by using actual direct costs rates multiplied by actual
quantities
– Allocates indirect costs based on budgeted indirect cost rates multiplied by actual
quantities of the cost allocation bases
• Uses estimate (predetermined or budgeted indirect cost rate for each cost pool)
• Relatively accurate because estimate closely approximates jobs normally completed during
the fiscal year
Direct vs indirect costs
Therefore traceability and what the cost object (week 2) is, define whether a cost is direct or
indirect. Now we move a step further to think about the difference between cost allocation
bases* and cost drivers and its impact on the distinction between direct and indirect costs.
We should now re-visit Professor Chris Chapman’s video.
Actual vs Normal Costing
1. Actual (All actual indirect costs/MOH)
– Uses actual costs
– Only available after product or service completed
– Suitable for products where
• Cost does not matter to the customer (e.g. bespoke clothing, cars)
• Completion of product or service is relatively quick (e.g., car service)
2. Normal (Pre-determined OH rate)
– Traces direct costs to cost object by using actual direct costs rates multiplied by actual
quantities
– Allocates indirect costs based on budgeted indirect cost rates multiplied by actual
quantities of the cost allocation bases
• Uses estimate (predetermined or budgeted indirect cost rate for each cost pool)
• Relatively accurate because estimate closely approximates jobs normally completed during
the fiscal year
Direct vs indirect costs
Therefore traceability and what the cost object (week 2) is, define whether a cost is direct or
indirect. Now we move a step further to think about the difference between cost allocation
bases* and cost drivers and its impact on the distinction between direct and indirect costs.
We should now re-visit Professor Chris Chapman’s video.
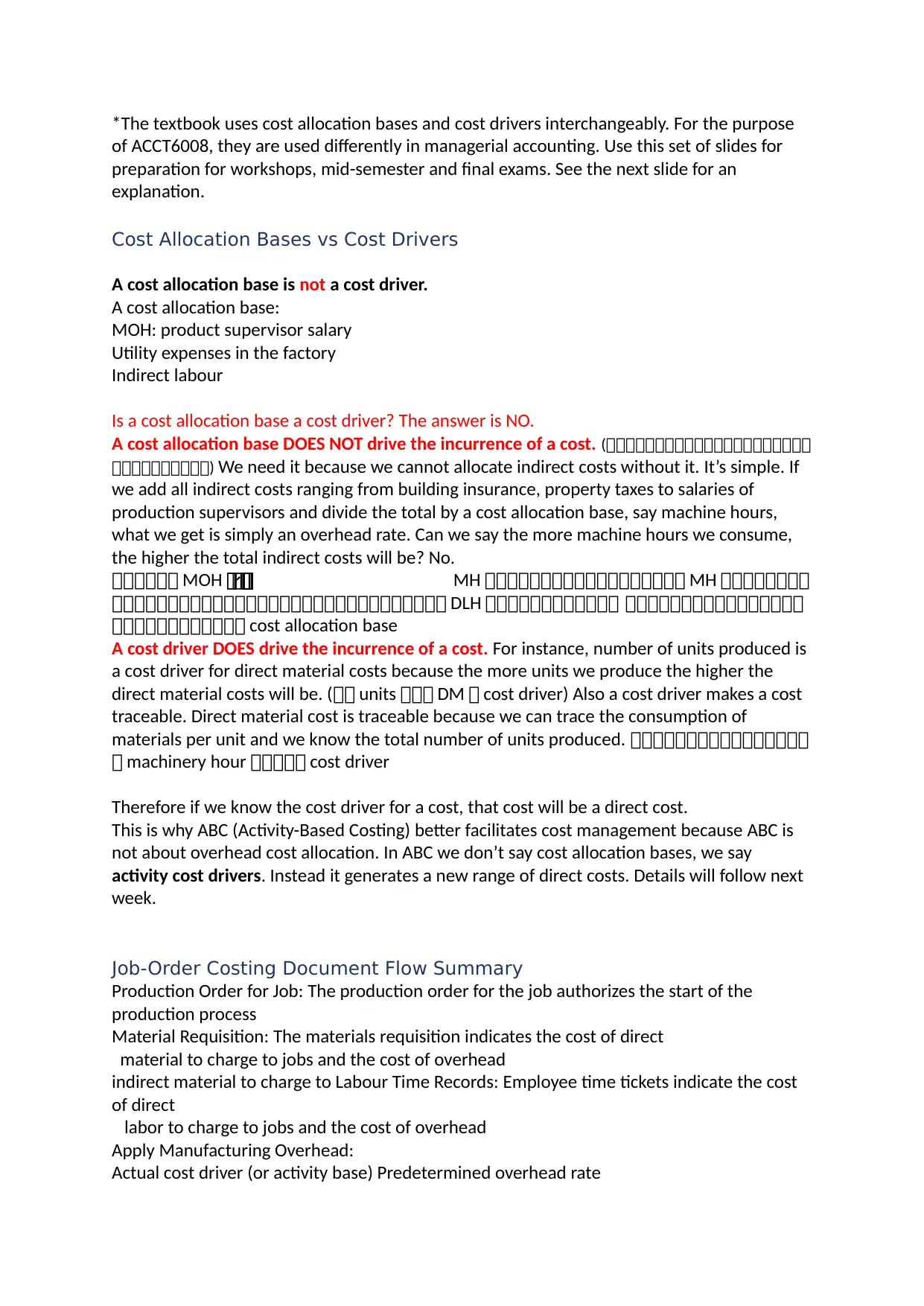
*The textbook uses cost allocation bases and cost drivers interchangeably. For the purpose
of ACCT6008, they are used differently in managerial accounting. Use this set of slides for
preparation for workshops, mid-semester and final exams. See the next slide for an
explanation.
Cost Allocation Bases vs Cost Drivers
A cost allocation base is not a cost driver.
A cost allocation base:
MOH: product supervisor salary
Utility expenses in the factory
Indirect labour
Is a cost allocation base a cost driver? The answer is NO.
A cost allocation base DOES NOT drive the incurrence of a cost. (可可可可可可可可可可可可可可可可可可可可可
可可可可可可可可可可) We need it because we cannot allocate indirect costs without it. It’s simple. If
we add all indirect costs ranging from building insurance, property taxes to salaries of
production supervisors and divide the total by a cost allocation base, say machine hours,
what we get is simply an overhead rate. Can we say the more machine hours we consume,
the higher the total indirect costs will be? No.
可可可可可可 MOH 可可可可可可可可可可可可可可可可可可可、、 MH 可可可可可可可可可可可可可可可可可可 MH 可可可可可可可可
可可可可可可可可可可可可可可可可可可可可可可可可可可可可可可 DLH 可可可可可可可可可可可可 可可可可可可可可可可可可可可可可
可可可可可可可可可可可可 cost allocation base
A cost driver DOES drive the incurrence of a cost. For instance, number of units produced is
a cost driver for direct material costs because the more units we produce the higher the
direct material costs will be. (可可 units 可可可 DM 可 cost driver) Also a cost driver makes a cost
traceable. Direct material cost is traceable because we can trace the consumption of
materials per unit and we know the total number of units produced. 可可可可可可可可可可可可可可可可
可 machinery hour 可可可可可 cost driver
Therefore if we know the cost driver for a cost, that cost will be a direct cost.
This is why ABC (Activity-Based Costing) better facilitates cost management because ABC is
not about overhead cost allocation. In ABC we don’t say cost allocation bases, we say
activity cost drivers. Instead it generates a new range of direct costs. Details will follow next
week.
Job-Order Costing Document Flow Summary
Production Order for Job: The production order for the job authorizes the start of the
production process
Material Requisition: The materials requisition indicates the cost of direct
material to charge to jobs and the cost of overhead
indirect material to charge to Labour Time Records: Employee time tickets indicate the cost
of direct
labor to charge to jobs and the cost of overhead
Apply Manufacturing Overhead:
Actual cost driver (or activity base) Predetermined overhead rate
of ACCT6008, they are used differently in managerial accounting. Use this set of slides for
preparation for workshops, mid-semester and final exams. See the next slide for an
explanation.
Cost Allocation Bases vs Cost Drivers
A cost allocation base is not a cost driver.
A cost allocation base:
MOH: product supervisor salary
Utility expenses in the factory
Indirect labour
Is a cost allocation base a cost driver? The answer is NO.
A cost allocation base DOES NOT drive the incurrence of a cost. (可可可可可可可可可可可可可可可可可可可可可
可可可可可可可可可可) We need it because we cannot allocate indirect costs without it. It’s simple. If
we add all indirect costs ranging from building insurance, property taxes to salaries of
production supervisors and divide the total by a cost allocation base, say machine hours,
what we get is simply an overhead rate. Can we say the more machine hours we consume,
the higher the total indirect costs will be? No.
可可可可可可 MOH 可可可可可可可可可可可可可可可可可可可、、 MH 可可可可可可可可可可可可可可可可可可 MH 可可可可可可可可
可可可可可可可可可可可可可可可可可可可可可可可可可可可可可可 DLH 可可可可可可可可可可可可 可可可可可可可可可可可可可可可可
可可可可可可可可可可可可 cost allocation base
A cost driver DOES drive the incurrence of a cost. For instance, number of units produced is
a cost driver for direct material costs because the more units we produce the higher the
direct material costs will be. (可可 units 可可可 DM 可 cost driver) Also a cost driver makes a cost
traceable. Direct material cost is traceable because we can trace the consumption of
materials per unit and we know the total number of units produced. 可可可可可可可可可可可可可可可可
可 machinery hour 可可可可可 cost driver
Therefore if we know the cost driver for a cost, that cost will be a direct cost.
This is why ABC (Activity-Based Costing) better facilitates cost management because ABC is
not about overhead cost allocation. In ABC we don’t say cost allocation bases, we say
activity cost drivers. Instead it generates a new range of direct costs. Details will follow next
week.
Job-Order Costing Document Flow Summary
Production Order for Job: The production order for the job authorizes the start of the
production process
Material Requisition: The materials requisition indicates the cost of direct
material to charge to jobs and the cost of overhead
indirect material to charge to Labour Time Records: Employee time tickets indicate the cost
of direct
labor to charge to jobs and the cost of overhead
Apply Manufacturing Overhead:
Actual cost driver (or activity base) Predetermined overhead rate
Paraphrase This Document
Need a fresh take? Get an instant paraphrase of this document with our AI Paraphraser
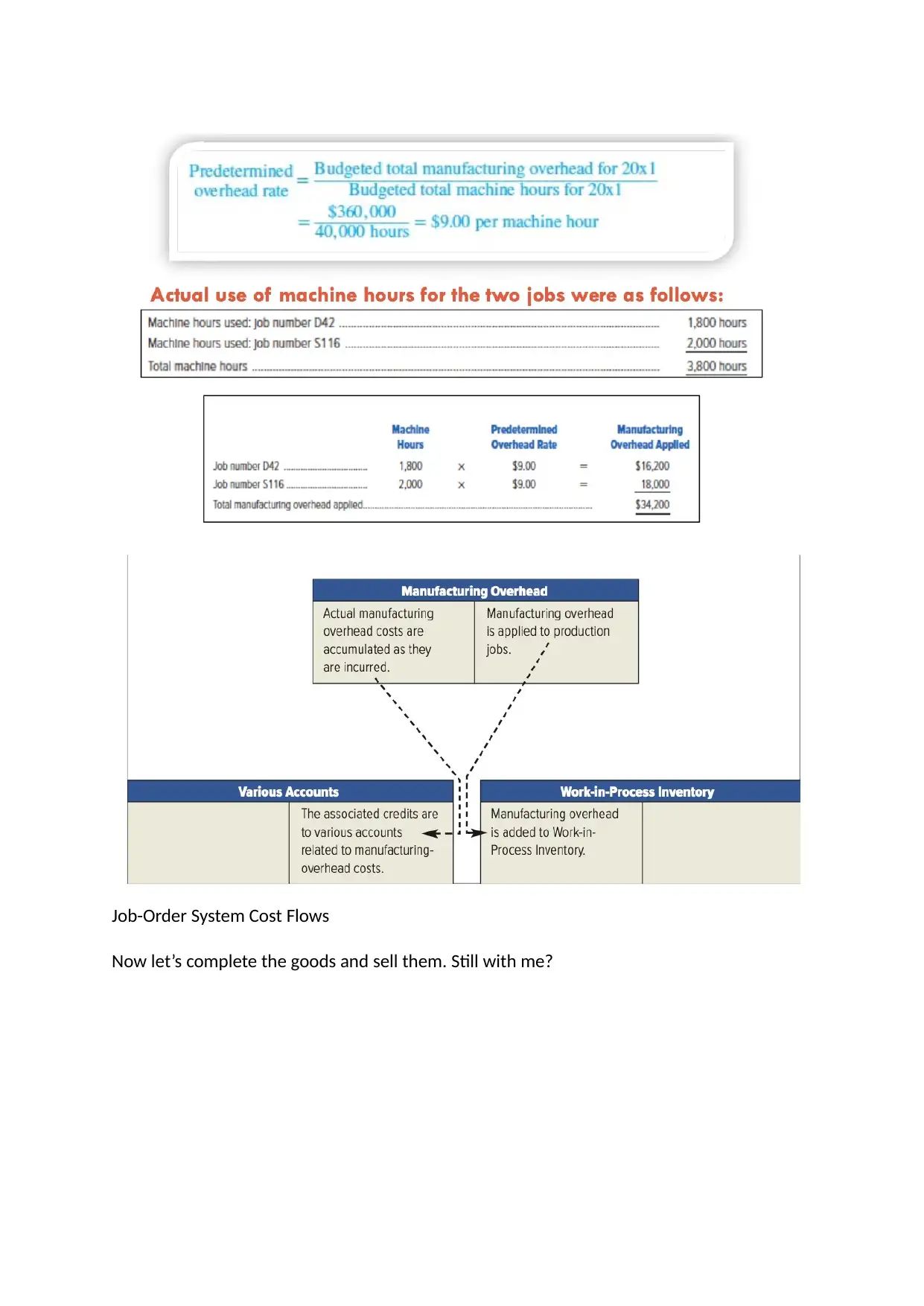
Job-Order System Cost Flows
Now let’s complete the goods and sell them. Still with me?
Now let’s complete the goods and sell them. Still with me?
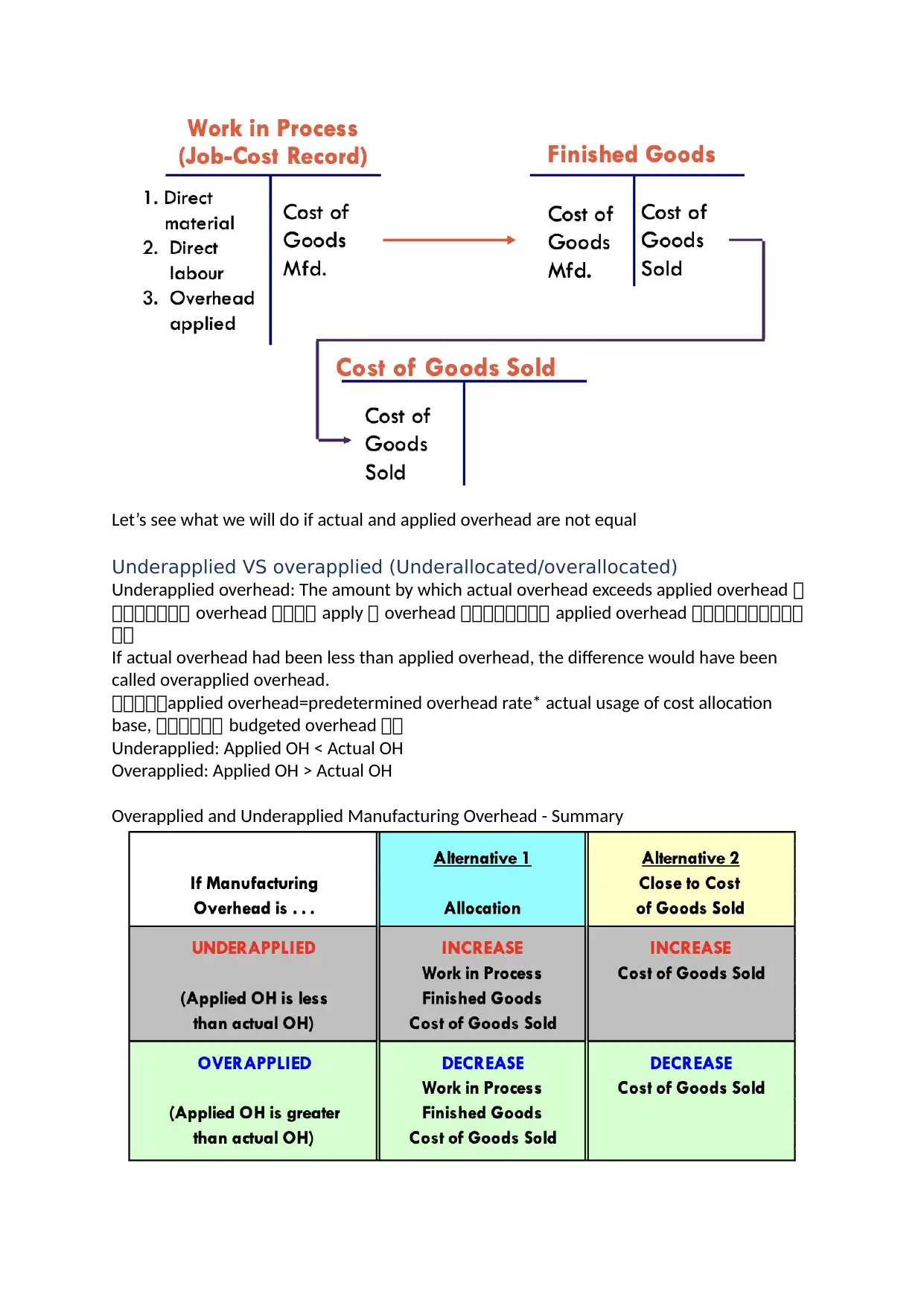
Let’s see what we will do if actual and applied overhead are not equal
Underapplied VS overapplied (Underallocated/overallocated)
Underapplied overhead: The amount by which actual overhead exceeds applied overhead 可
可可可可可可可 overhead 可可可可 apply 可 overhead 可可可可可可可可 applied overhead 可可可可可可可可可可
可可
If actual overhead had been less than applied overhead, the difference would have been
called overapplied overhead.
可可可可可applied overhead=predetermined overhead rate* actual usage of cost allocation
base, 可可可可可可 budgeted overhead 可可
Underapplied: Applied OH < Actual OH
Overapplied: Applied OH > Actual OH
Overapplied and Underapplied Manufacturing Overhead - Summary
Underapplied VS overapplied (Underallocated/overallocated)
Underapplied overhead: The amount by which actual overhead exceeds applied overhead 可
可可可可可可可 overhead 可可可可 apply 可 overhead 可可可可可可可可 applied overhead 可可可可可可可可可可
可可
If actual overhead had been less than applied overhead, the difference would have been
called overapplied overhead.
可可可可可applied overhead=predetermined overhead rate* actual usage of cost allocation
base, 可可可可可可 budgeted overhead 可可
Underapplied: Applied OH < Actual OH
Overapplied: Applied OH > Actual OH
Overapplied and Underapplied Manufacturing Overhead - Summary
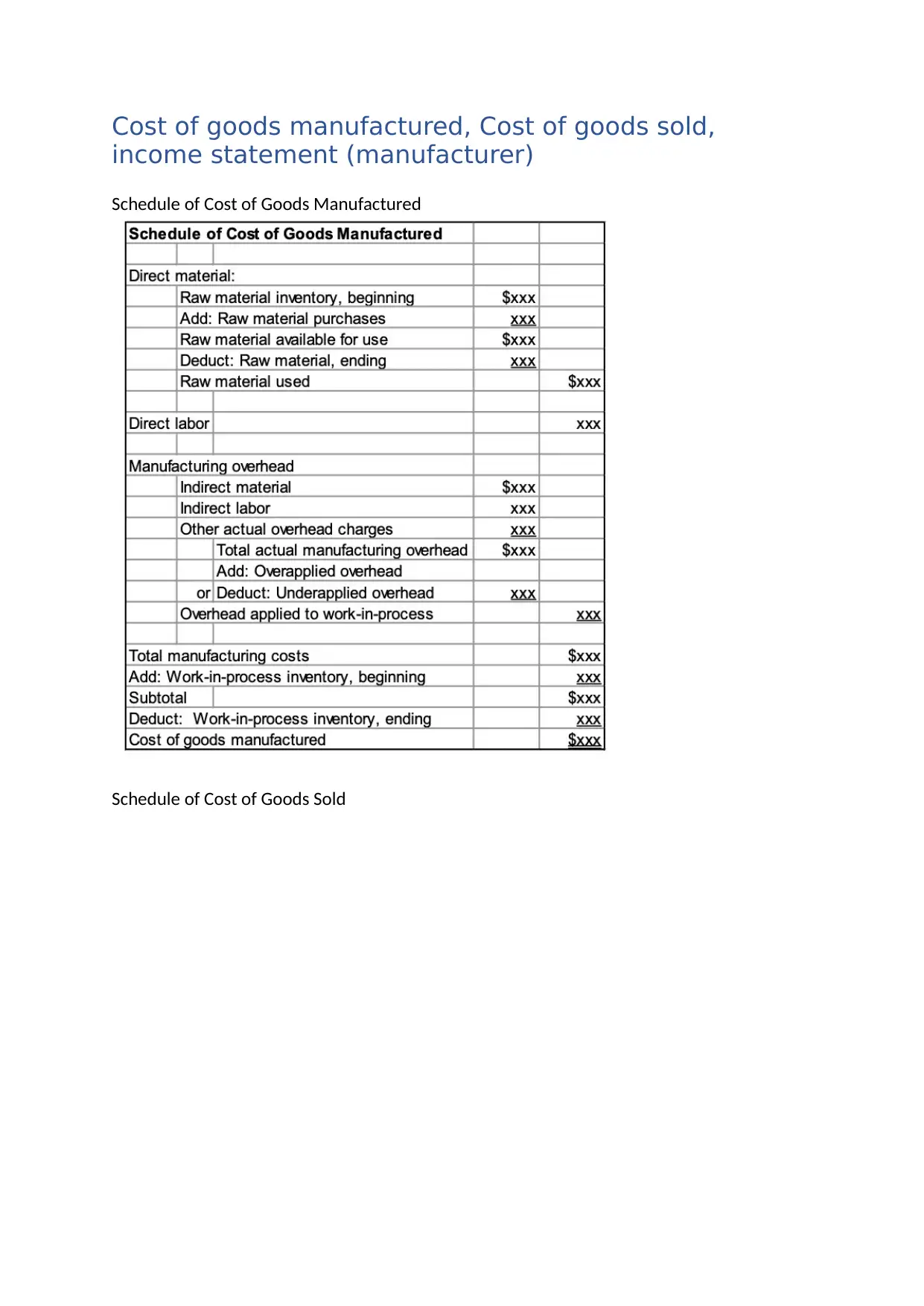
Cost of goods manufactured, Cost of goods sold,
income statement (manufacturer)
Schedule of Cost of Goods Manufactured
Schedule of Cost of Goods Sold
income statement (manufacturer)
Schedule of Cost of Goods Manufactured
Schedule of Cost of Goods Sold
Secure Best Marks with AI Grader
Need help grading? Try our AI Grader for instant feedback on your assignments.
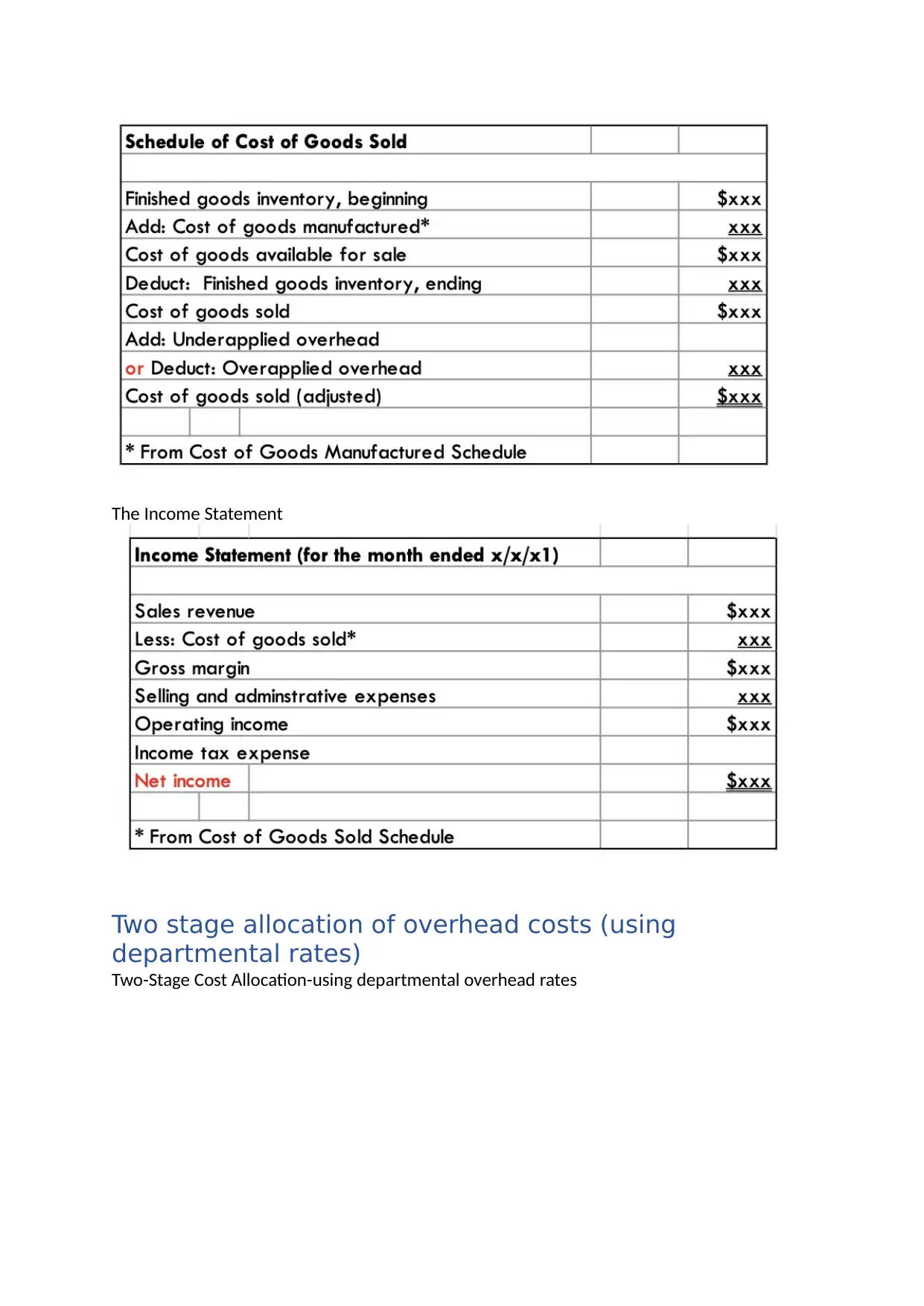
The Income Statement
Two stage allocation of overhead costs (using
departmental rates)
Two-Stage Cost Allocation-using departmental overhead rates
Two stage allocation of overhead costs (using
departmental rates)
Two-Stage Cost Allocation-using departmental overhead rates
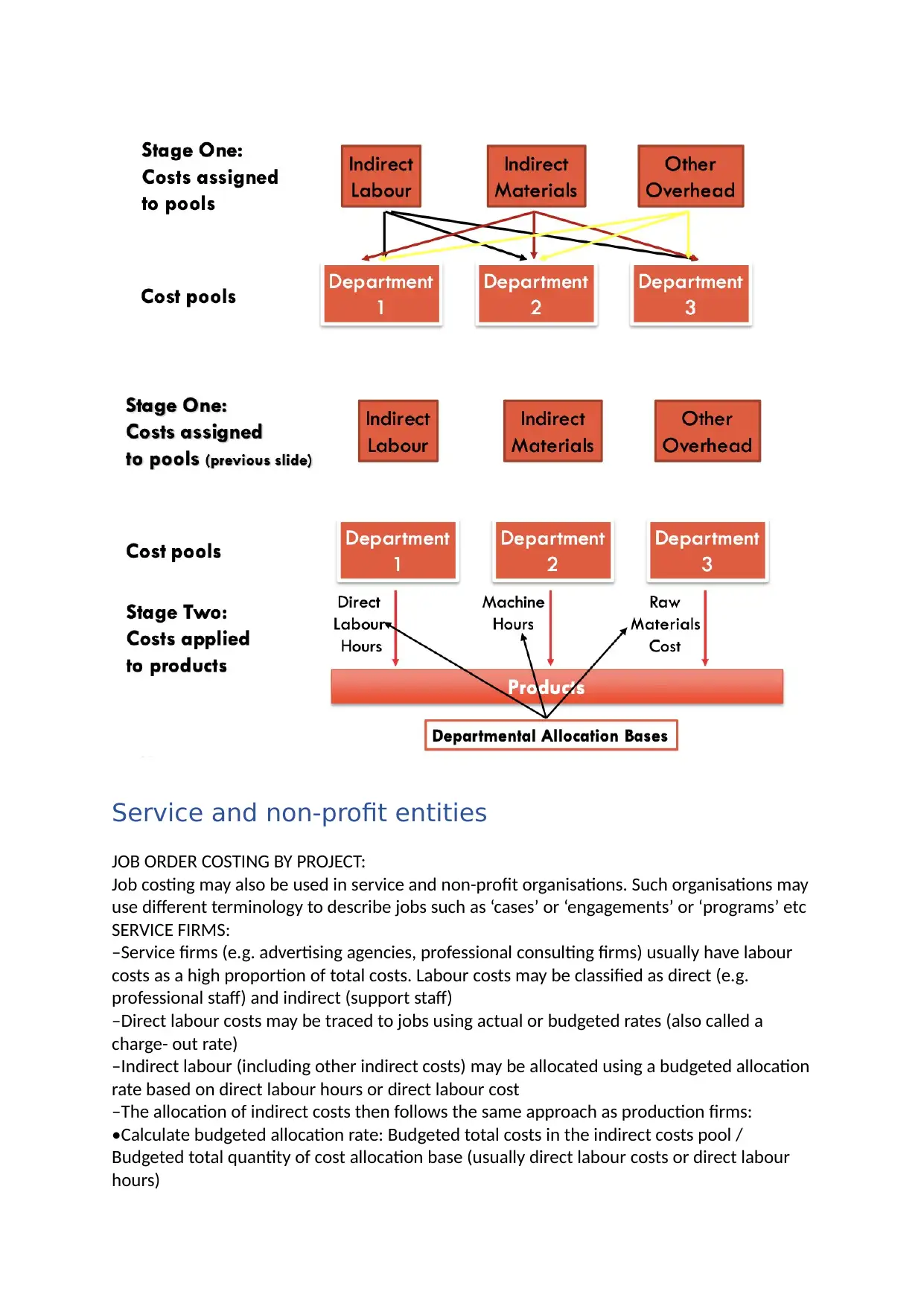
Service and non-profit entities
JOB ORDER COSTING BY PROJECT:
Job costing may also be used in service and non-profit organisations. Such organisations may
use different terminology to describe jobs such as ‘cases’ or ‘engagements’ or ‘programs’ etc
SERVICE FIRMS:
–Service firms (e.g. advertising agencies, professional consulting firms) usually have labour
costs as a high proportion of total costs. Labour costs may be classified as direct (e.g.
professional staff) and indirect (support staff)
–Direct labour costs may be traced to jobs using actual or budgeted rates (also called a
charge- out rate)
–Indirect labour (including other indirect costs) may be allocated using a budgeted allocation
rate based on direct labour hours or direct labour cost
–The allocation of indirect costs then follows the same approach as production firms:
•Calculate budgeted allocation rate: Budgeted total costs in the indirect costs pool /
Budgeted total quantity of cost allocation base (usually direct labour costs or direct labour
hours)
JOB ORDER COSTING BY PROJECT:
Job costing may also be used in service and non-profit organisations. Such organisations may
use different terminology to describe jobs such as ‘cases’ or ‘engagements’ or ‘programs’ etc
SERVICE FIRMS:
–Service firms (e.g. advertising agencies, professional consulting firms) usually have labour
costs as a high proportion of total costs. Labour costs may be classified as direct (e.g.
professional staff) and indirect (support staff)
–Direct labour costs may be traced to jobs using actual or budgeted rates (also called a
charge- out rate)
–Indirect labour (including other indirect costs) may be allocated using a budgeted allocation
rate based on direct labour hours or direct labour cost
–The allocation of indirect costs then follows the same approach as production firms:
•Calculate budgeted allocation rate: Budgeted total costs in the indirect costs pool /
Budgeted total quantity of cost allocation base (usually direct labour costs or direct labour
hours)
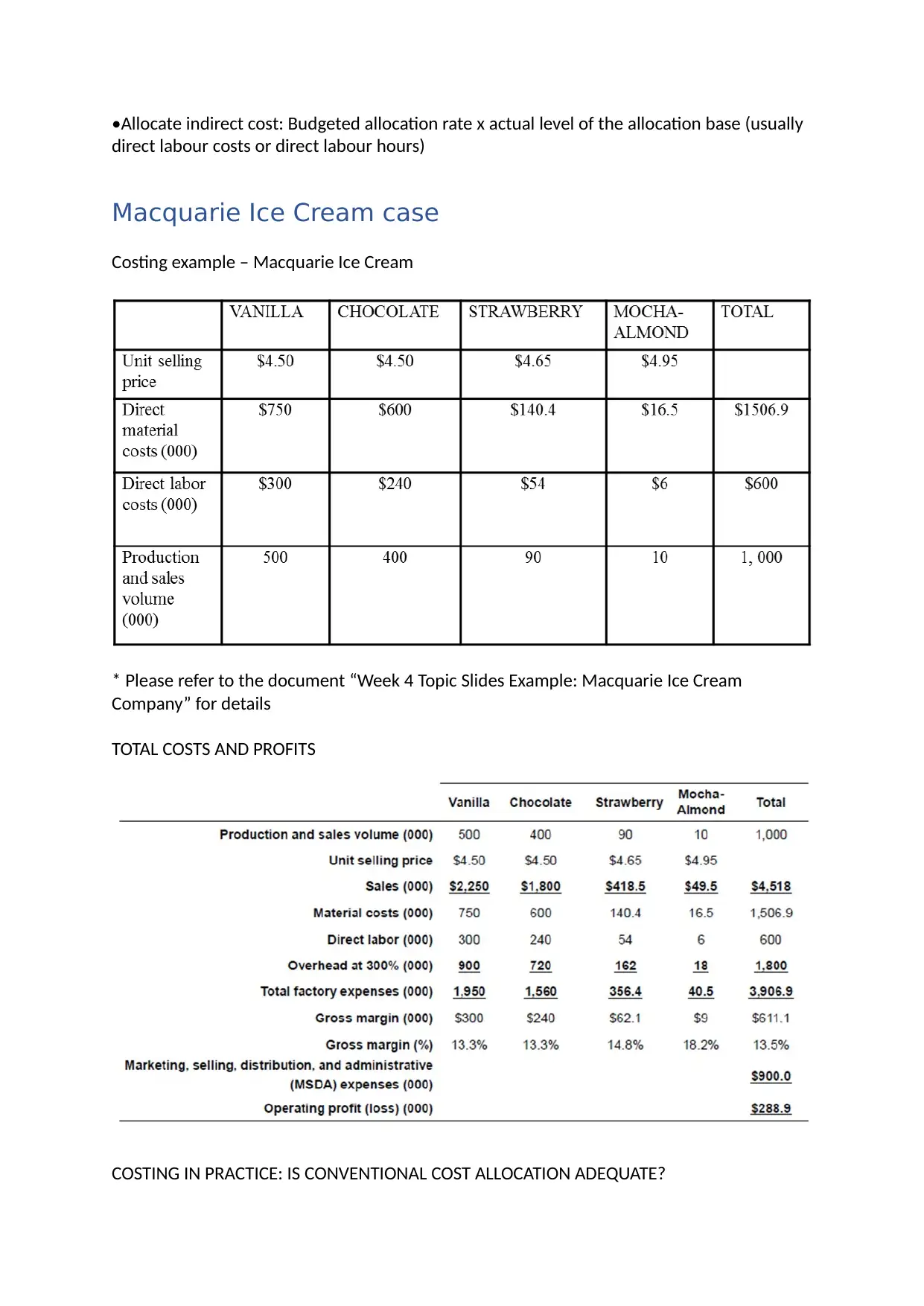
•Allocate indirect cost: Budgeted allocation rate x actual level of the allocation base (usually
direct labour costs or direct labour hours)
Macquarie Ice Cream case
Costing example – Macquarie Ice Cream
* Please refer to the document “Week 4 Topic Slides Example: Macquarie Ice Cream
Company” for details
TOTAL COSTS AND PROFITS
COSTING IN PRACTICE: IS CONVENTIONAL COST ALLOCATION ADEQUATE?
direct labour costs or direct labour hours)
Macquarie Ice Cream case
Costing example – Macquarie Ice Cream
* Please refer to the document “Week 4 Topic Slides Example: Macquarie Ice Cream
Company” for details
TOTAL COSTS AND PROFITS
COSTING IN PRACTICE: IS CONVENTIONAL COST ALLOCATION ADEQUATE?
Paraphrase This Document
Need a fresh take? Get an instant paraphrase of this document with our AI Paraphraser
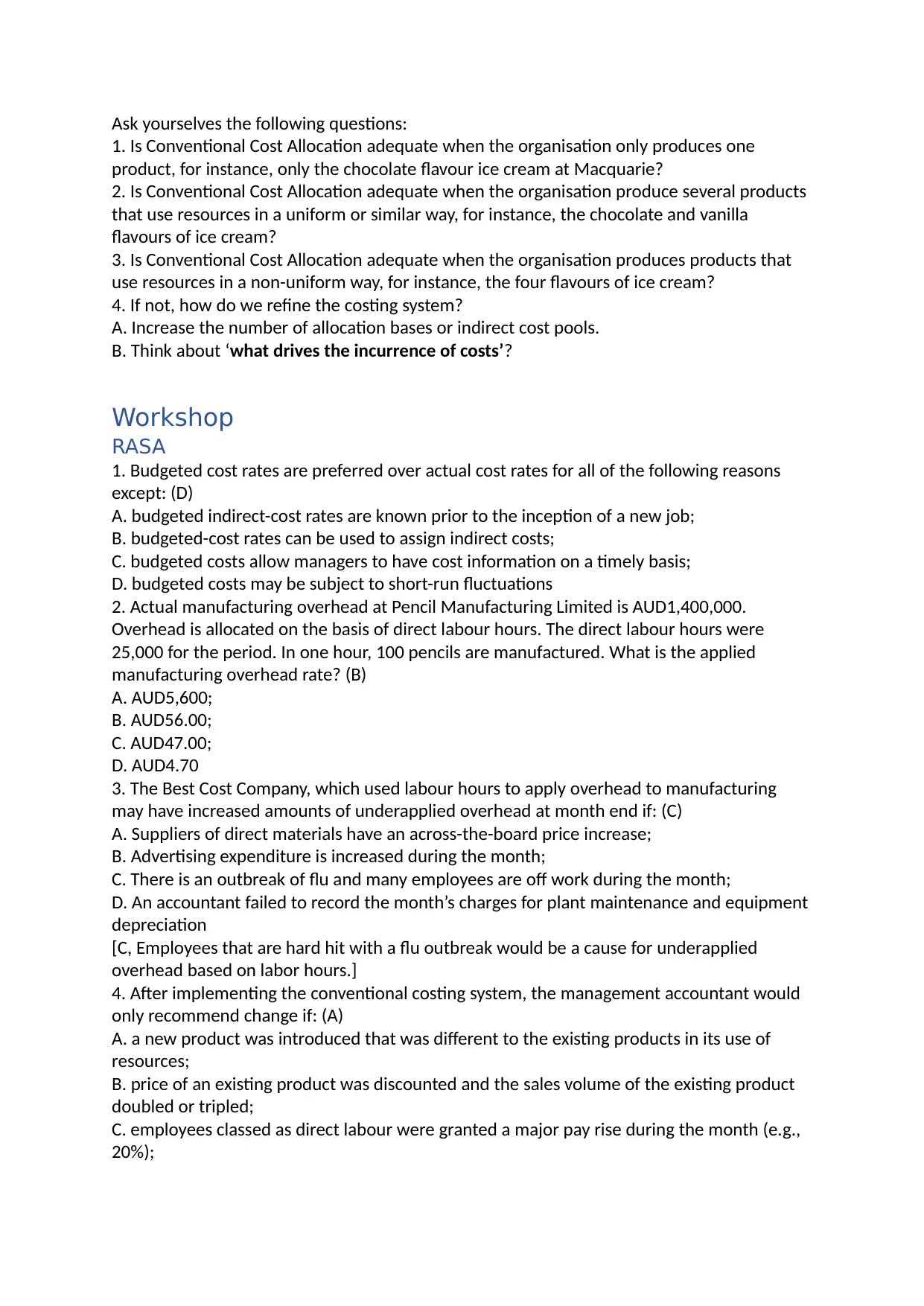
Ask yourselves the following questions:
1. Is Conventional Cost Allocation adequate when the organisation only produces one
product, for instance, only the chocolate flavour ice cream at Macquarie?
2. Is Conventional Cost Allocation adequate when the organisation produce several products
that use resources in a uniform or similar way, for instance, the chocolate and vanilla
flavours of ice cream?
3. Is Conventional Cost Allocation adequate when the organisation produces products that
use resources in a non-uniform way, for instance, the four flavours of ice cream?
4. If not, how do we refine the costing system?
A. Increase the number of allocation bases or indirect cost pools.
B. Think about ‘what drives the incurrence of costs’?
Workshop
RASA
1. Budgeted cost rates are preferred over actual cost rates for all of the following reasons
except: (D)
A. budgeted indirect-cost rates are known prior to the inception of a new job;
B. budgeted-cost rates can be used to assign indirect costs;
C. budgeted costs allow managers to have cost information on a timely basis;
D. budgeted costs may be subject to short-run fluctuations
2. Actual manufacturing overhead at Pencil Manufacturing Limited is AUD1,400,000.
Overhead is allocated on the basis of direct labour hours. The direct labour hours were
25,000 for the period. In one hour, 100 pencils are manufactured. What is the applied
manufacturing overhead rate? (B)
A. AUD5,600;
B. AUD56.00;
C. AUD47.00;
D. AUD4.70
3. The Best Cost Company, which used labour hours to apply overhead to manufacturing
may have increased amounts of underapplied overhead at month end if: (C)
A. Suppliers of direct materials have an across-the-board price increase;
B. Advertising expenditure is increased during the month;
C. There is an outbreak of flu and many employees are off work during the month;
D. An accountant failed to record the month’s charges for plant maintenance and equipment
depreciation
[C, Employees that are hard hit with a flu outbreak would be a cause for underapplied
overhead based on labor hours.]
4. After implementing the conventional costing system, the management accountant would
only recommend change if: (A)
A. a new product was introduced that was different to the existing products in its use of
resources;
B. price of an existing product was discounted and the sales volume of the existing product
doubled or tripled;
C. employees classed as direct labour were granted a major pay rise during the month (e.g.,
20%);
1. Is Conventional Cost Allocation adequate when the organisation only produces one
product, for instance, only the chocolate flavour ice cream at Macquarie?
2. Is Conventional Cost Allocation adequate when the organisation produce several products
that use resources in a uniform or similar way, for instance, the chocolate and vanilla
flavours of ice cream?
3. Is Conventional Cost Allocation adequate when the organisation produces products that
use resources in a non-uniform way, for instance, the four flavours of ice cream?
4. If not, how do we refine the costing system?
A. Increase the number of allocation bases or indirect cost pools.
B. Think about ‘what drives the incurrence of costs’?
Workshop
RASA
1. Budgeted cost rates are preferred over actual cost rates for all of the following reasons
except: (D)
A. budgeted indirect-cost rates are known prior to the inception of a new job;
B. budgeted-cost rates can be used to assign indirect costs;
C. budgeted costs allow managers to have cost information on a timely basis;
D. budgeted costs may be subject to short-run fluctuations
2. Actual manufacturing overhead at Pencil Manufacturing Limited is AUD1,400,000.
Overhead is allocated on the basis of direct labour hours. The direct labour hours were
25,000 for the period. In one hour, 100 pencils are manufactured. What is the applied
manufacturing overhead rate? (B)
A. AUD5,600;
B. AUD56.00;
C. AUD47.00;
D. AUD4.70
3. The Best Cost Company, which used labour hours to apply overhead to manufacturing
may have increased amounts of underapplied overhead at month end if: (C)
A. Suppliers of direct materials have an across-the-board price increase;
B. Advertising expenditure is increased during the month;
C. There is an outbreak of flu and many employees are off work during the month;
D. An accountant failed to record the month’s charges for plant maintenance and equipment
depreciation
[C, Employees that are hard hit with a flu outbreak would be a cause for underapplied
overhead based on labor hours.]
4. After implementing the conventional costing system, the management accountant would
only recommend change if: (A)
A. a new product was introduced that was different to the existing products in its use of
resources;
B. price of an existing product was discounted and the sales volume of the existing product
doubled or tripled;
C. employees classed as direct labour were granted a major pay rise during the month (e.g.,
20%);
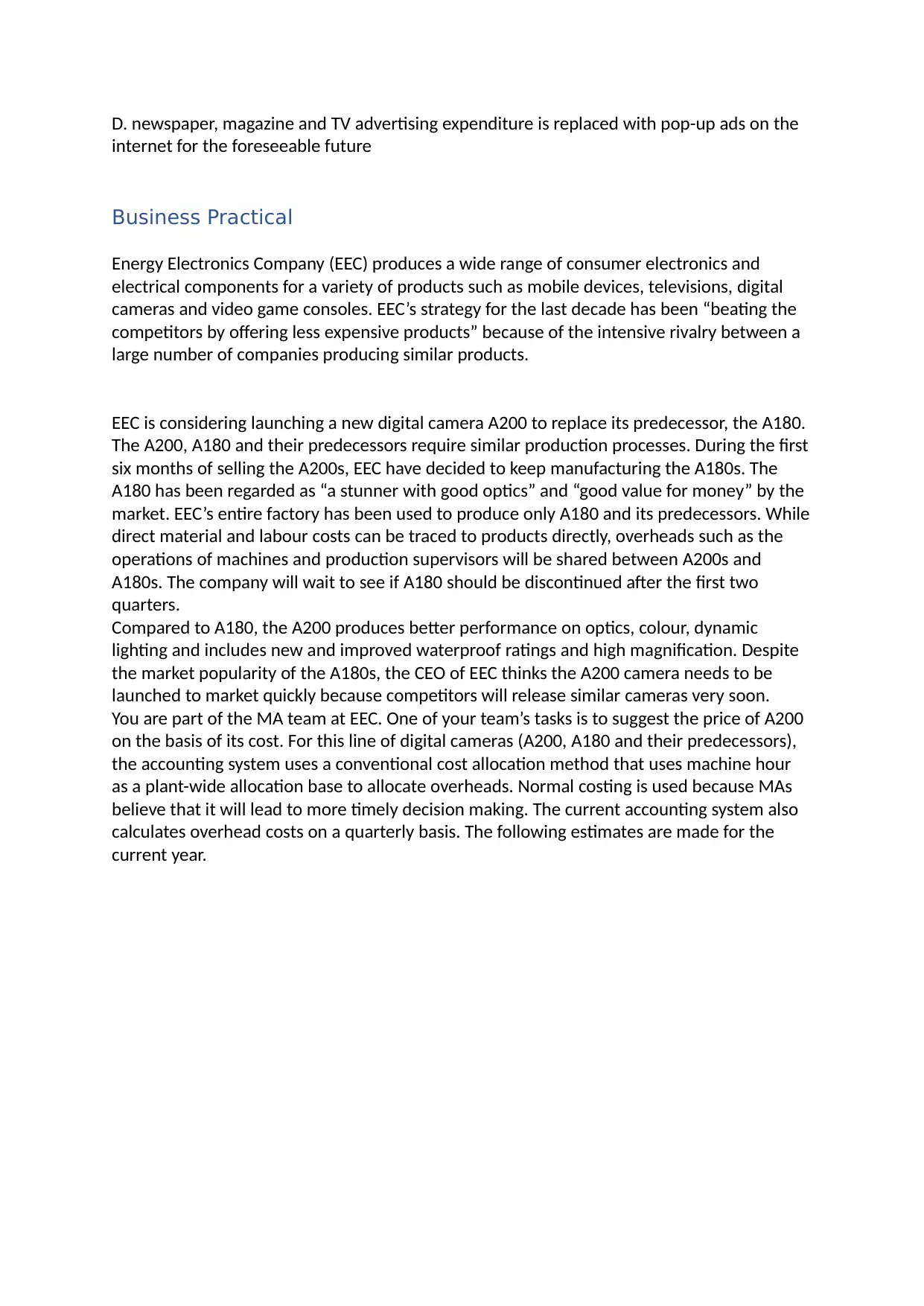
D. newspaper, magazine and TV advertising expenditure is replaced with pop-up ads on the
internet for the foreseeable future
Business Practical
Energy Electronics Company (EEC) produces a wide range of consumer electronics and
electrical components for a variety of products such as mobile devices, televisions, digital
cameras and video game consoles. EEC’s strategy for the last decade has been “beating the
competitors by offering less expensive products” because of the intensive rivalry between a
large number of companies producing similar products.
EEC is considering launching a new digital camera A200 to replace its predecessor, the A180.
The A200, A180 and their predecessors require similar production processes. During the first
six months of selling the A200s, EEC have decided to keep manufacturing the A180s. The
A180 has been regarded as “a stunner with good optics” and “good value for money” by the
market. EEC’s entire factory has been used to produce only A180 and its predecessors. While
direct material and labour costs can be traced to products directly, overheads such as the
operations of machines and production supervisors will be shared between A200s and
A180s. The company will wait to see if A180 should be discontinued after the first two
quarters.
Compared to A180, the A200 produces better performance on optics, colour, dynamic
lighting and includes new and improved waterproof ratings and high magnification. Despite
the market popularity of the A180s, the CEO of EEC thinks the A200 camera needs to be
launched to market quickly because competitors will release similar cameras very soon.
You are part of the MA team at EEC. One of your team’s tasks is to suggest the price of A200
on the basis of its cost. For this line of digital cameras (A200, A180 and their predecessors),
the accounting system uses a conventional cost allocation method that uses machine hour
as a plant-wide allocation base to allocate overheads. Normal costing is used because MAs
believe that it will lead to more timely decision making. The current accounting system also
calculates overhead costs on a quarterly basis. The following estimates are made for the
current year.
internet for the foreseeable future
Business Practical
Energy Electronics Company (EEC) produces a wide range of consumer electronics and
electrical components for a variety of products such as mobile devices, televisions, digital
cameras and video game consoles. EEC’s strategy for the last decade has been “beating the
competitors by offering less expensive products” because of the intensive rivalry between a
large number of companies producing similar products.
EEC is considering launching a new digital camera A200 to replace its predecessor, the A180.
The A200, A180 and their predecessors require similar production processes. During the first
six months of selling the A200s, EEC have decided to keep manufacturing the A180s. The
A180 has been regarded as “a stunner with good optics” and “good value for money” by the
market. EEC’s entire factory has been used to produce only A180 and its predecessors. While
direct material and labour costs can be traced to products directly, overheads such as the
operations of machines and production supervisors will be shared between A200s and
A180s. The company will wait to see if A180 should be discontinued after the first two
quarters.
Compared to A180, the A200 produces better performance on optics, colour, dynamic
lighting and includes new and improved waterproof ratings and high magnification. Despite
the market popularity of the A180s, the CEO of EEC thinks the A200 camera needs to be
launched to market quickly because competitors will release similar cameras very soon.
You are part of the MA team at EEC. One of your team’s tasks is to suggest the price of A200
on the basis of its cost. For this line of digital cameras (A200, A180 and their predecessors),
the accounting system uses a conventional cost allocation method that uses machine hour
as a plant-wide allocation base to allocate overheads. Normal costing is used because MAs
believe that it will lead to more timely decision making. The current accounting system also
calculates overhead costs on a quarterly basis. The following estimates are made for the
current year.
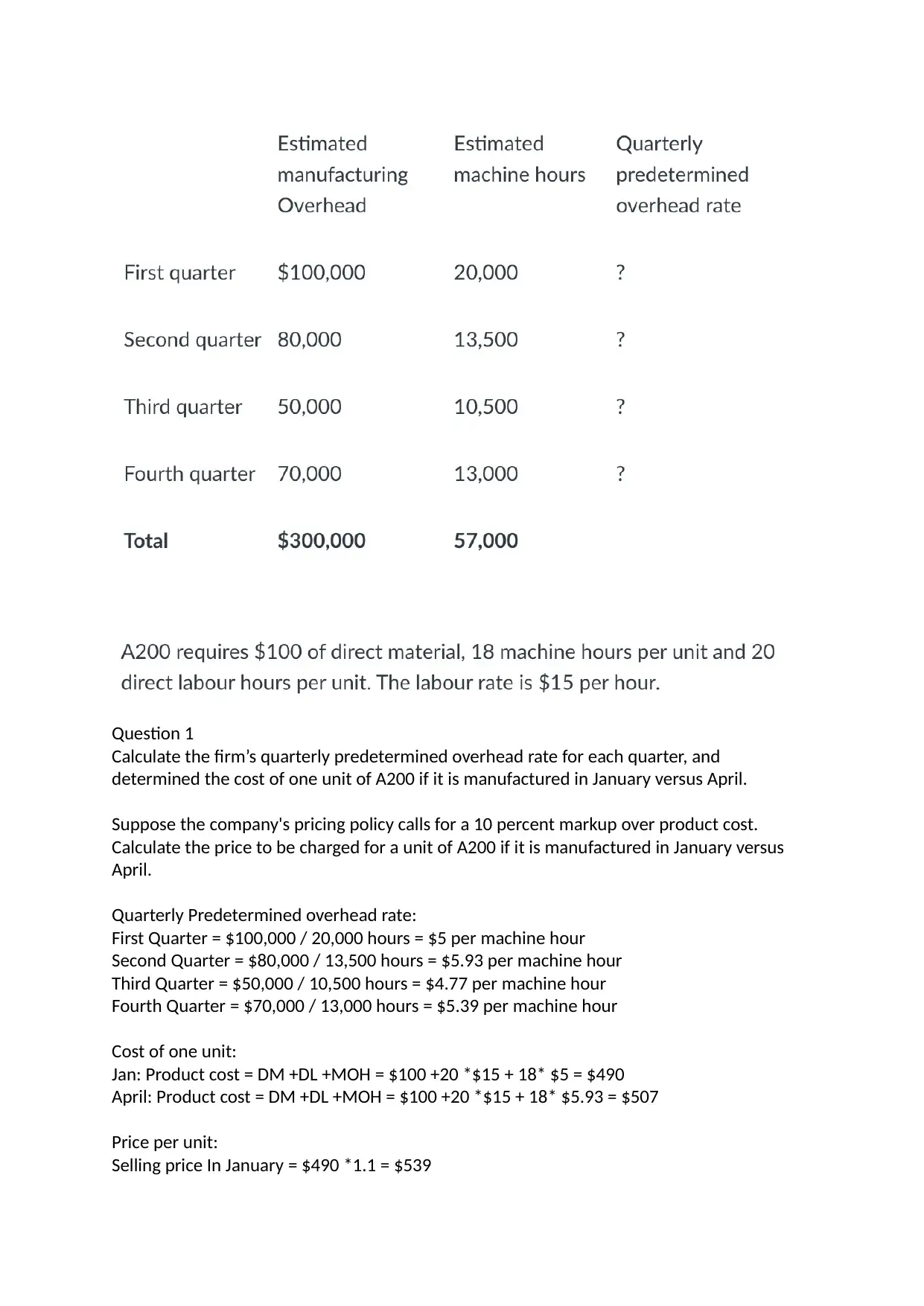
Question 1
Calculate the firm’s quarterly predetermined overhead rate for each quarter, and
determined the cost of one unit of A200 if it is manufactured in January versus April.
Suppose the company's pricing policy calls for a 10 percent markup over product cost.
Calculate the price to be charged for a unit of A200 if it is manufactured in January versus
April.
Quarterly Predetermined overhead rate:
First Quarter = $100,000 / 20,000 hours = $5 per machine hour
Second Quarter = $80,000 / 13,500 hours = $5.93 per machine hour
Third Quarter = $50,000 / 10,500 hours = $4.77 per machine hour
Fourth Quarter = $70,000 / 13,000 hours = $5.39 per machine hour
Cost of one unit:
Jan: Product cost = DM +DL +MOH = $100 +20 *$15 + 18* $5 = $490
April: Product cost = DM +DL +MOH = $100 +20 *$15 + 18* $5.93 = $507
Price per unit:
Selling price In January = $490 *1.1 = $539
Calculate the firm’s quarterly predetermined overhead rate for each quarter, and
determined the cost of one unit of A200 if it is manufactured in January versus April.
Suppose the company's pricing policy calls for a 10 percent markup over product cost.
Calculate the price to be charged for a unit of A200 if it is manufactured in January versus
April.
Quarterly Predetermined overhead rate:
First Quarter = $100,000 / 20,000 hours = $5 per machine hour
Second Quarter = $80,000 / 13,500 hours = $5.93 per machine hour
Third Quarter = $50,000 / 10,500 hours = $4.77 per machine hour
Fourth Quarter = $70,000 / 13,000 hours = $5.39 per machine hour
Cost of one unit:
Jan: Product cost = DM +DL +MOH = $100 +20 *$15 + 18* $5 = $490
April: Product cost = DM +DL +MOH = $100 +20 *$15 + 18* $5.93 = $507
Price per unit:
Selling price In January = $490 *1.1 = $539
Secure Best Marks with AI Grader
Need help grading? Try our AI Grader for instant feedback on your assignments.
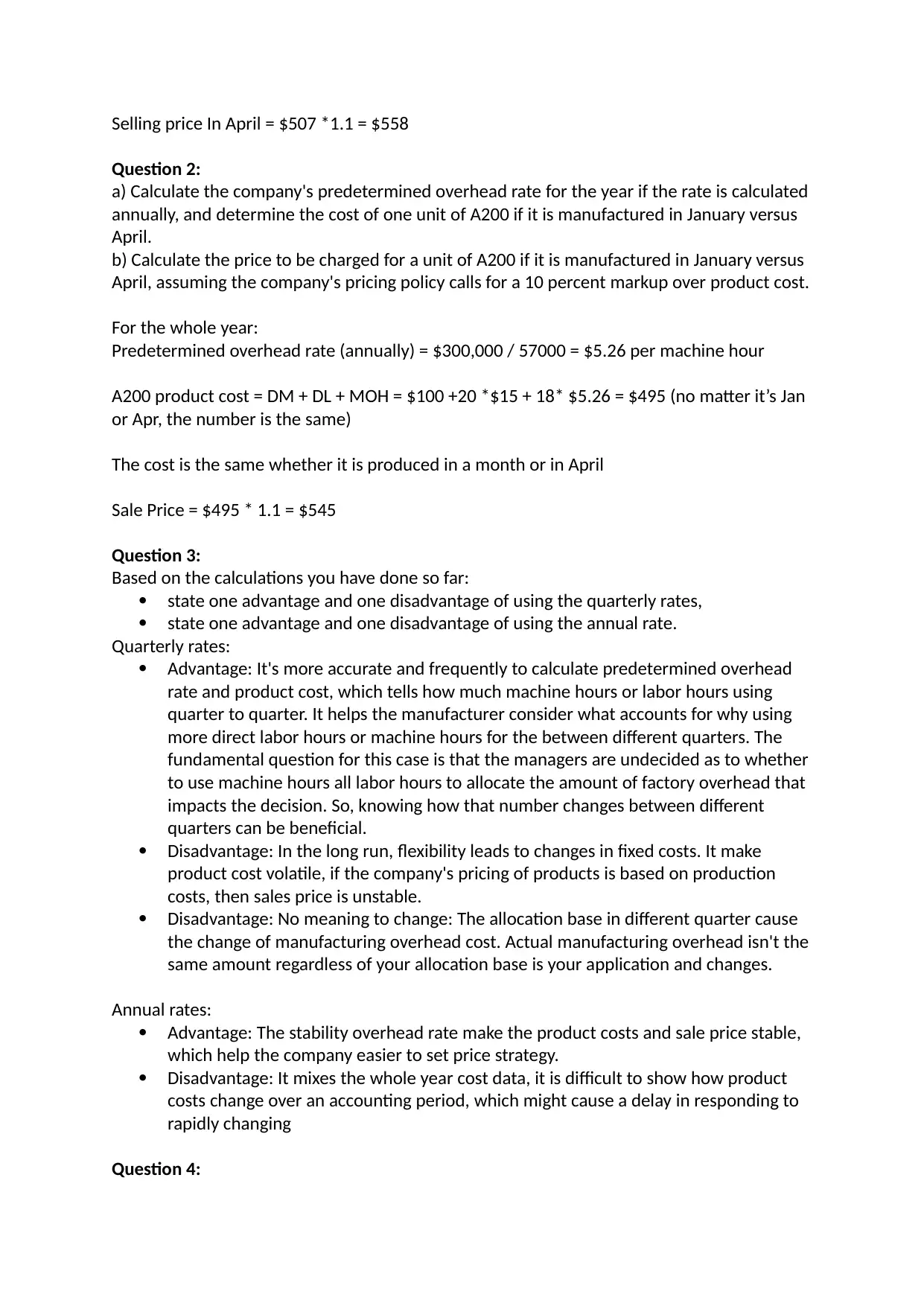
Selling price In April = $507 *1.1 = $558
Question 2:
a) Calculate the company's predetermined overhead rate for the year if the rate is calculated
annually, and determine the cost of one unit of A200 if it is manufactured in January versus
April.
b) Calculate the price to be charged for a unit of A200 if it is manufactured in January versus
April, assuming the company's pricing policy calls for a 10 percent markup over product cost.
For the whole year:
Predetermined overhead rate (annually) = $300,000 / 57000 = $5.26 per machine hour
A200 product cost = DM + DL + MOH = $100 +20 *$15 + 18* $5.26 = $495 (no matter it’s Jan
or Apr, the number is the same)
The cost is the same whether it is produced in a month or in April
Sale Price = $495 * 1.1 = $545
Question 3:
Based on the calculations you have done so far:
state one advantage and one disadvantage of using the quarterly rates,
state one advantage and one disadvantage of using the annual rate.
Quarterly rates:
Advantage: It's more accurate and frequently to calculate predetermined overhead
rate and product cost, which tells how much machine hours or labor hours using
quarter to quarter. It helps the manufacturer consider what accounts for why using
more direct labor hours or machine hours for the between different quarters. The
fundamental question for this case is that the managers are undecided as to whether
to use machine hours all labor hours to allocate the amount of factory overhead that
impacts the decision. So, knowing how that number changes between different
quarters can be beneficial.
Disadvantage: In the long run, flexibility leads to changes in fixed costs. It make
product cost volatile, if the company's pricing of products is based on production
costs, then sales price is unstable.
Disadvantage: No meaning to change: The allocation base in different quarter cause
the change of manufacturing overhead cost. Actual manufacturing overhead isn't the
same amount regardless of your allocation base is your application and changes.
Annual rates:
Advantage: The stability overhead rate make the product costs and sale price stable,
which help the company easier to set price strategy.
Disadvantage: It mixes the whole year cost data, it is difficult to show how product
costs change over an accounting period, which might cause a delay in responding to
rapidly changing
Question 4:
Question 2:
a) Calculate the company's predetermined overhead rate for the year if the rate is calculated
annually, and determine the cost of one unit of A200 if it is manufactured in January versus
April.
b) Calculate the price to be charged for a unit of A200 if it is manufactured in January versus
April, assuming the company's pricing policy calls for a 10 percent markup over product cost.
For the whole year:
Predetermined overhead rate (annually) = $300,000 / 57000 = $5.26 per machine hour
A200 product cost = DM + DL + MOH = $100 +20 *$15 + 18* $5.26 = $495 (no matter it’s Jan
or Apr, the number is the same)
The cost is the same whether it is produced in a month or in April
Sale Price = $495 * 1.1 = $545
Question 3:
Based on the calculations you have done so far:
state one advantage and one disadvantage of using the quarterly rates,
state one advantage and one disadvantage of using the annual rate.
Quarterly rates:
Advantage: It's more accurate and frequently to calculate predetermined overhead
rate and product cost, which tells how much machine hours or labor hours using
quarter to quarter. It helps the manufacturer consider what accounts for why using
more direct labor hours or machine hours for the between different quarters. The
fundamental question for this case is that the managers are undecided as to whether
to use machine hours all labor hours to allocate the amount of factory overhead that
impacts the decision. So, knowing how that number changes between different
quarters can be beneficial.
Disadvantage: In the long run, flexibility leads to changes in fixed costs. It make
product cost volatile, if the company's pricing of products is based on production
costs, then sales price is unstable.
Disadvantage: No meaning to change: The allocation base in different quarter cause
the change of manufacturing overhead cost. Actual manufacturing overhead isn't the
same amount regardless of your allocation base is your application and changes.
Annual rates:
Advantage: The stability overhead rate make the product costs and sale price stable,
which help the company easier to set price strategy.
Disadvantage: It mixes the whole year cost data, it is difficult to show how product
costs change over an accounting period, which might cause a delay in responding to
rapidly changing
Question 4:
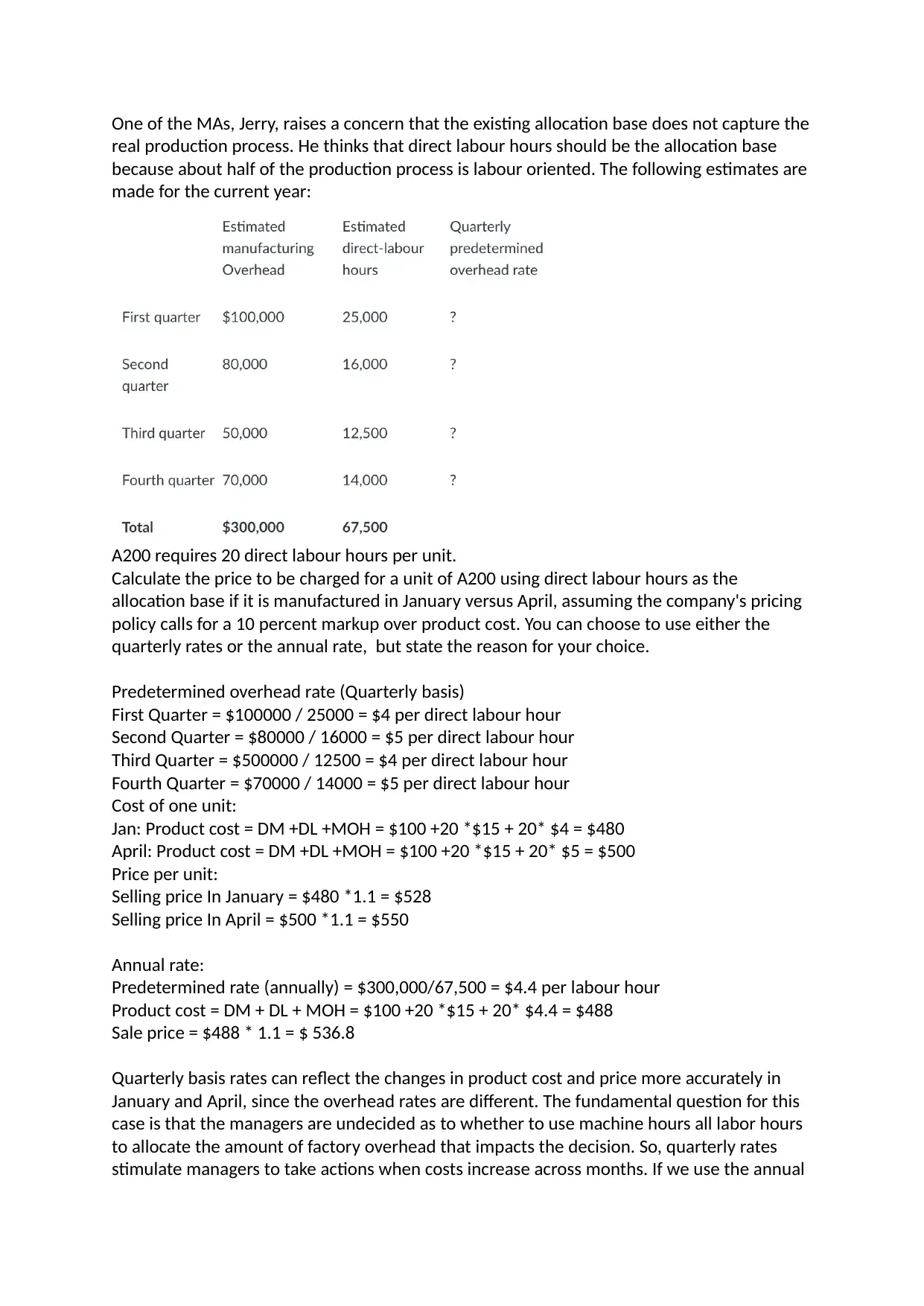
One of the MAs, Jerry, raises a concern that the existing allocation base does not capture the
real production process. He thinks that direct labour hours should be the allocation base
because about half of the production process is labour oriented. The following estimates are
made for the current year:
A200 requires 20 direct labour hours per unit.
Calculate the price to be charged for a unit of A200 using direct labour hours as the
allocation base if it is manufactured in January versus April, assuming the company's pricing
policy calls for a 10 percent markup over product cost. You can choose to use either the
quarterly rates or the annual rate, but state the reason for your choice.
Predetermined overhead rate (Quarterly basis)
First Quarter = $100000 / 25000 = $4 per direct labour hour
Second Quarter = $80000 / 16000 = $5 per direct labour hour
Third Quarter = $500000 / 12500 = $4 per direct labour hour
Fourth Quarter = $70000 / 14000 = $5 per direct labour hour
Cost of one unit:
Jan: Product cost = DM +DL +MOH = $100 +20 *$15 + 20* $4 = $480
April: Product cost = DM +DL +MOH = $100 +20 *$15 + 20* $5 = $500
Price per unit:
Selling price In January = $480 *1.1 = $528
Selling price In April = $500 *1.1 = $550
Annual rate:
Predetermined rate (annually) = $300,000/67,500 = $4.4 per labour hour
Product cost = DM + DL + MOH = $100 +20 *$15 + 20* $4.4 = $488
Sale price = $488 * 1.1 = $ 536.8
Quarterly basis rates can reflect the changes in product cost and price more accurately in
January and April, since the overhead rates are different. The fundamental question for this
case is that the managers are undecided as to whether to use machine hours all labor hours
to allocate the amount of factory overhead that impacts the decision. So, quarterly rates
stimulate managers to take actions when costs increase across months. If we use the annual
real production process. He thinks that direct labour hours should be the allocation base
because about half of the production process is labour oriented. The following estimates are
made for the current year:
A200 requires 20 direct labour hours per unit.
Calculate the price to be charged for a unit of A200 using direct labour hours as the
allocation base if it is manufactured in January versus April, assuming the company's pricing
policy calls for a 10 percent markup over product cost. You can choose to use either the
quarterly rates or the annual rate, but state the reason for your choice.
Predetermined overhead rate (Quarterly basis)
First Quarter = $100000 / 25000 = $4 per direct labour hour
Second Quarter = $80000 / 16000 = $5 per direct labour hour
Third Quarter = $500000 / 12500 = $4 per direct labour hour
Fourth Quarter = $70000 / 14000 = $5 per direct labour hour
Cost of one unit:
Jan: Product cost = DM +DL +MOH = $100 +20 *$15 + 20* $4 = $480
April: Product cost = DM +DL +MOH = $100 +20 *$15 + 20* $5 = $500
Price per unit:
Selling price In January = $480 *1.1 = $528
Selling price In April = $500 *1.1 = $550
Annual rate:
Predetermined rate (annually) = $300,000/67,500 = $4.4 per labour hour
Product cost = DM + DL + MOH = $100 +20 *$15 + 20* $4.4 = $488
Sale price = $488 * 1.1 = $ 536.8
Quarterly basis rates can reflect the changes in product cost and price more accurately in
January and April, since the overhead rates are different. The fundamental question for this
case is that the managers are undecided as to whether to use machine hours all labor hours
to allocate the amount of factory overhead that impacts the decision. So, quarterly rates
stimulate managers to take actions when costs increase across months. If we use the annual
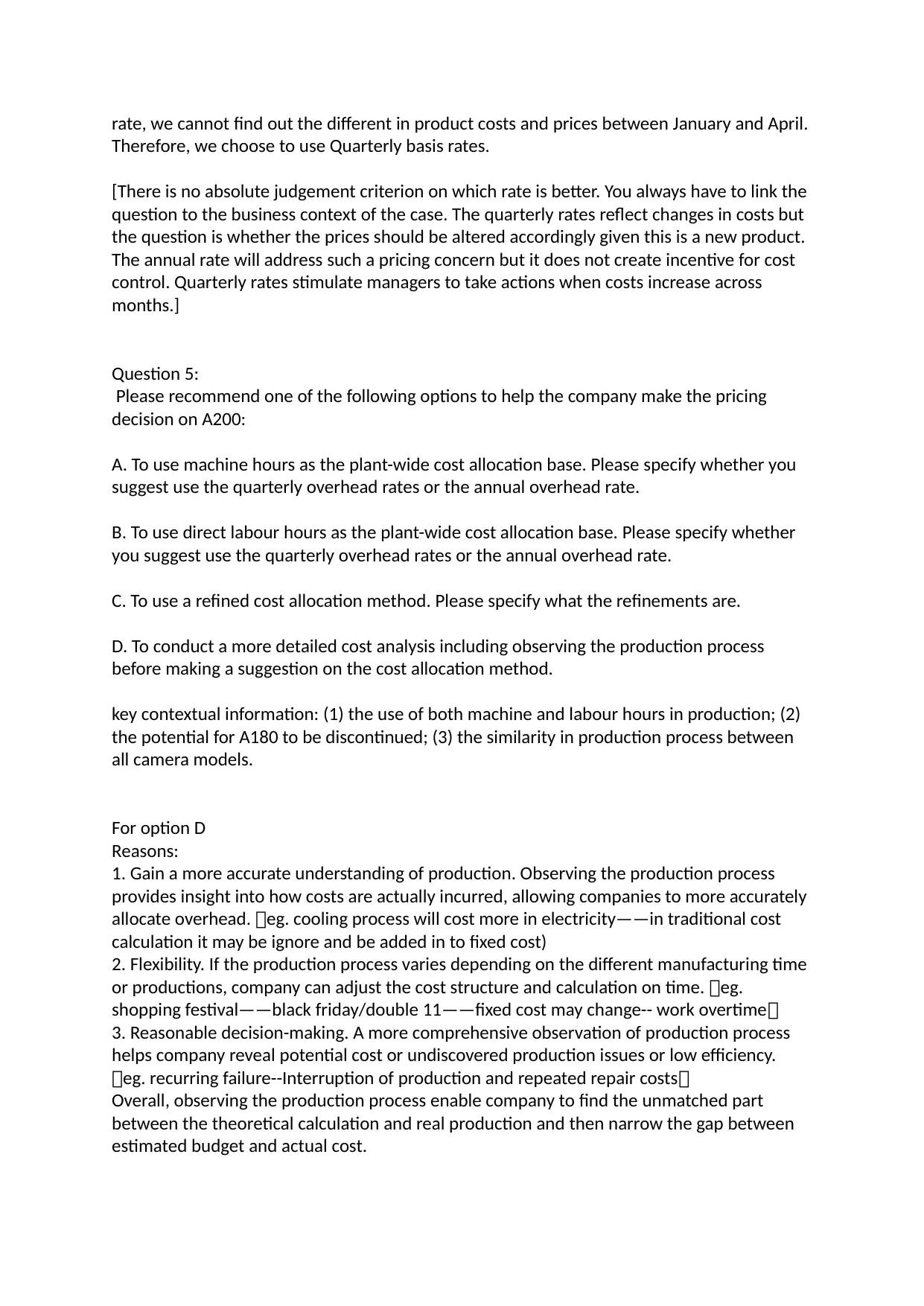
rate, we cannot find out the different in product costs and prices between January and April.
Therefore, we choose to use Quarterly basis rates.
[There is no absolute judgement criterion on which rate is better. You always have to link the
question to the business context of the case. The quarterly rates reflect changes in costs but
the question is whether the prices should be altered accordingly given this is a new product.
The annual rate will address such a pricing concern but it does not create incentive for cost
control. Quarterly rates stimulate managers to take actions when costs increase across
months.]
Question 5:
Please recommend one of the following options to help the company make the pricing
decision on A200:
A. To use machine hours as the plant-wide cost allocation base. Please specify whether you
suggest use the quarterly overhead rates or the annual overhead rate.
B. To use direct labour hours as the plant-wide cost allocation base. Please specify whether
you suggest use the quarterly overhead rates or the annual overhead rate.
C. To use a refined cost allocation method. Please specify what the refinements are.
D. To conduct a more detailed cost analysis including observing the production process
before making a suggestion on the cost allocation method.
key contextual information: (1) the use of both machine and labour hours in production; (2)
the potential for A180 to be discontinued; (3) the similarity in production process between
all camera models.
For option D
Reasons:
1. Gain a more accurate understanding of production. Observing the production process
provides insight into how costs are actually incurred, allowing companies to more accurately
allocate overhead. 可eg. cooling process will cost more in electricity——in traditional cost
calculation it may be ignore and be added in to fixed cost)
2. Flexibility. If the production process varies depending on the different manufacturing time
or productions, company can adjust the cost structure and calculation on time. 可eg.
shopping festival——black friday/double 11——fixed cost may change-- work overtime可
3. Reasonable decision-making. A more comprehensive observation of production process
helps company reveal potential cost or undiscovered production issues or low efficiency.
可eg. recurring failure--Interruption of production and repeated repair costs可
Overall, observing the production process enable company to find the unmatched part
between the theoretical calculation and real production and then narrow the gap between
estimated budget and actual cost.
Therefore, we choose to use Quarterly basis rates.
[There is no absolute judgement criterion on which rate is better. You always have to link the
question to the business context of the case. The quarterly rates reflect changes in costs but
the question is whether the prices should be altered accordingly given this is a new product.
The annual rate will address such a pricing concern but it does not create incentive for cost
control. Quarterly rates stimulate managers to take actions when costs increase across
months.]
Question 5:
Please recommend one of the following options to help the company make the pricing
decision on A200:
A. To use machine hours as the plant-wide cost allocation base. Please specify whether you
suggest use the quarterly overhead rates or the annual overhead rate.
B. To use direct labour hours as the plant-wide cost allocation base. Please specify whether
you suggest use the quarterly overhead rates or the annual overhead rate.
C. To use a refined cost allocation method. Please specify what the refinements are.
D. To conduct a more detailed cost analysis including observing the production process
before making a suggestion on the cost allocation method.
key contextual information: (1) the use of both machine and labour hours in production; (2)
the potential for A180 to be discontinued; (3) the similarity in production process between
all camera models.
For option D
Reasons:
1. Gain a more accurate understanding of production. Observing the production process
provides insight into how costs are actually incurred, allowing companies to more accurately
allocate overhead. 可eg. cooling process will cost more in electricity——in traditional cost
calculation it may be ignore and be added in to fixed cost)
2. Flexibility. If the production process varies depending on the different manufacturing time
or productions, company can adjust the cost structure and calculation on time. 可eg.
shopping festival——black friday/double 11——fixed cost may change-- work overtime可
3. Reasonable decision-making. A more comprehensive observation of production process
helps company reveal potential cost or undiscovered production issues or low efficiency.
可eg. recurring failure--Interruption of production and repeated repair costs可
Overall, observing the production process enable company to find the unmatched part
between the theoretical calculation and real production and then narrow the gap between
estimated budget and actual cost.
Paraphrase This Document
Need a fresh take? Get an instant paraphrase of this document with our AI Paraphraser
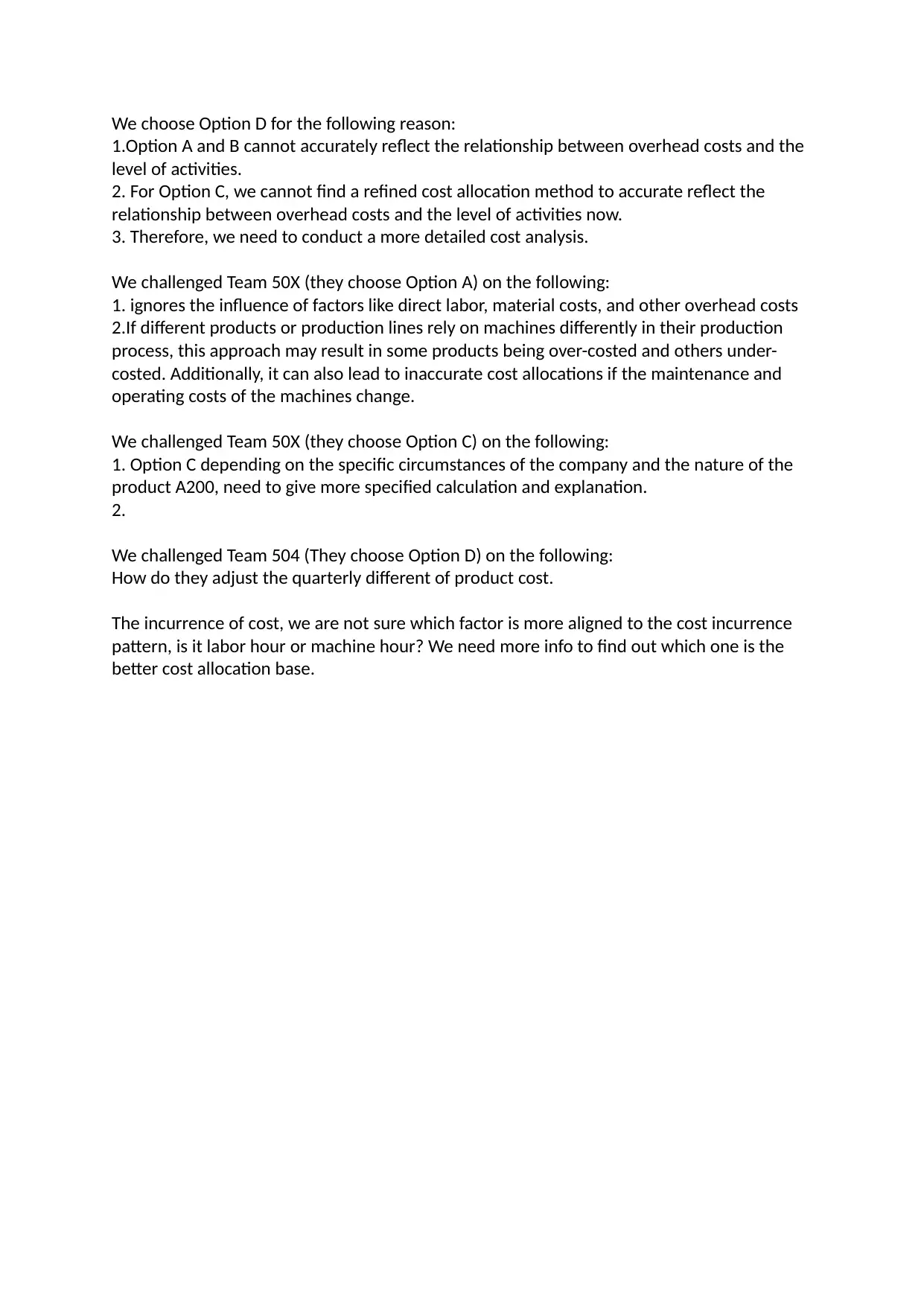
We choose Option D for the following reason:
1.Option A and B cannot accurately reflect the relationship between overhead costs and the
level of activities.
2. For Option C, we cannot find a refined cost allocation method to accurate reflect the
relationship between overhead costs and the level of activities now.
3. Therefore, we need to conduct a more detailed cost analysis.
We challenged Team 50X (they choose Option A) on the following:
1. ignores the influence of factors like direct labor, material costs, and other overhead costs
2.If different products or production lines rely on machines differently in their production
process, this approach may result in some products being over-costed and others under-
costed. Additionally, it can also lead to inaccurate cost allocations if the maintenance and
operating costs of the machines change.
We challenged Team 50X (they choose Option C) on the following:
1. Option C depending on the specific circumstances of the company and the nature of the
product A200, need to give more specified calculation and explanation.
2.
We challenged Team 504 (They choose Option D) on the following:
How do they adjust the quarterly different of product cost.
The incurrence of cost, we are not sure which factor is more aligned to the cost incurrence
pattern, is it labor hour or machine hour? We need more info to find out which one is the
better cost allocation base.
1.Option A and B cannot accurately reflect the relationship between overhead costs and the
level of activities.
2. For Option C, we cannot find a refined cost allocation method to accurate reflect the
relationship between overhead costs and the level of activities now.
3. Therefore, we need to conduct a more detailed cost analysis.
We challenged Team 50X (they choose Option A) on the following:
1. ignores the influence of factors like direct labor, material costs, and other overhead costs
2.If different products or production lines rely on machines differently in their production
process, this approach may result in some products being over-costed and others under-
costed. Additionally, it can also lead to inaccurate cost allocations if the maintenance and
operating costs of the machines change.
We challenged Team 50X (they choose Option C) on the following:
1. Option C depending on the specific circumstances of the company and the nature of the
product A200, need to give more specified calculation and explanation.
2.
We challenged Team 504 (They choose Option D) on the following:
How do they adjust the quarterly different of product cost.
The incurrence of cost, we are not sure which factor is more aligned to the cost incurrence
pattern, is it labor hour or machine hour? We need more info to find out which one is the
better cost allocation base.
1 out of 26
Related Documents
![[object Object]](/_next/image/?url=%2F_next%2Fstatic%2Fmedia%2Flogo.6d15ce61.png&w=640&q=75)
Your All-in-One AI-Powered Toolkit for Academic Success.
+13062052269
info@desklib.com
Available 24*7 on WhatsApp / Email
Unlock your academic potential
© 2024 | Zucol Services PVT LTD | All rights reserved.