Modular Construction Methods Designing Research Project 2022
Added on 2022-09-18
13 Pages2922 Words23 Views
Designing Research Project 1
MODULAR CONSTRUCTION METHODS
By Students Name
Course
Professors Name
University
City/State
Date
MODULAR CONSTRUCTION METHODS
By Students Name
Course
Professors Name
University
City/State
Date
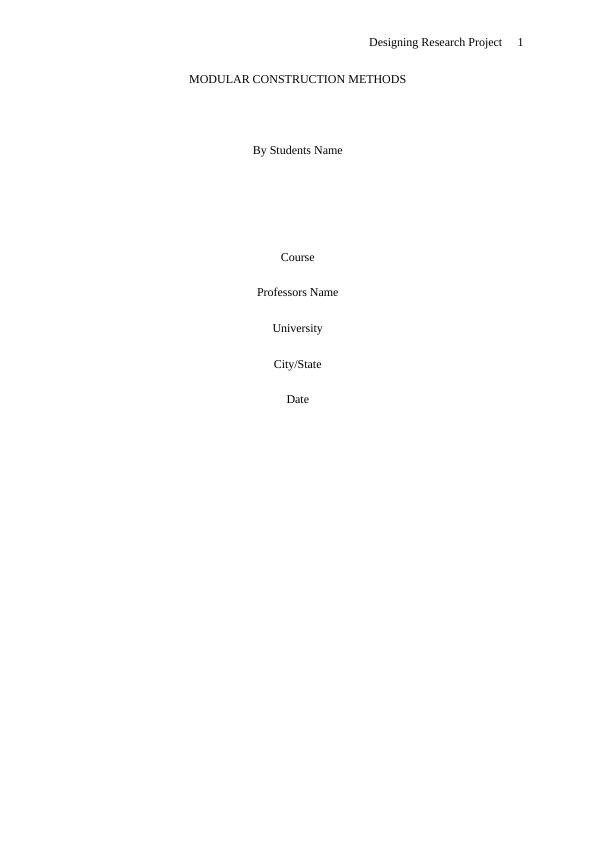
Designing Research Project 2
Table of Contents Page
Introduction 3
Modular Construction Types and Products 4
Advantages and disadvantages 6
Likely Products and Installation costs 8
Conclusion 9
References 10
Table of Contents Page
Introduction 3
Modular Construction Types and Products 4
Advantages and disadvantages 6
Likely Products and Installation costs 8
Conclusion 9
References 10
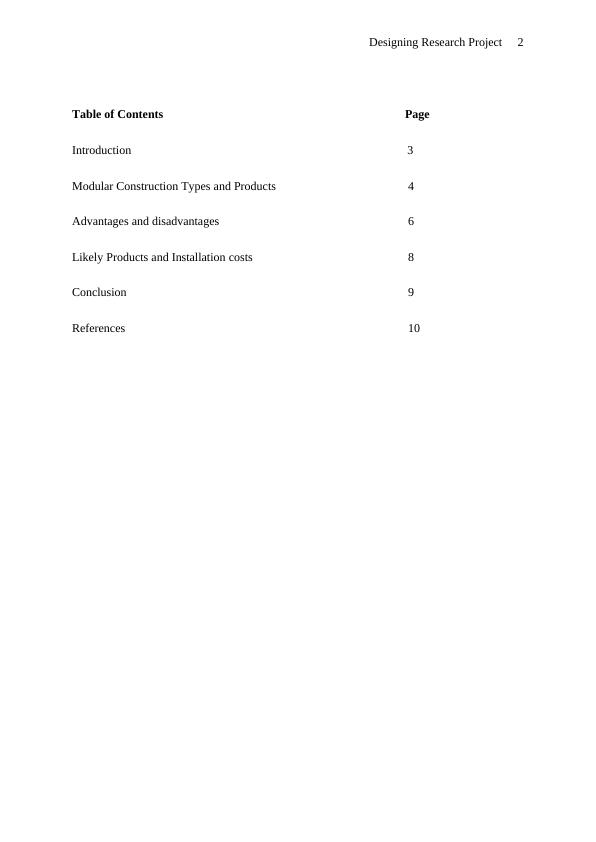
Designing Research Project 3
Modular Construction Methods
Introduction
For decades, the construction industry has lagged when it comes to product
performance in comparison to other sectors. However, there has been a recent change of tides
and a chance to step up, moving away from the traditional building activity of on-site
manufacturing to off-site construction style projects (Baldwin & MacDonald, 2012).
Prefabricated is a not so new idea although a fresh wave of interest and investment has stung
the industry concerning shifts in the environment and technological advancements.
Construction industries make one of the largest sectors in the global market and a profound
change like modular construction has a major impact. The current projects have accelerated
projected timelines by 20 to 50 per cent (Bernstein, et al., 2011).
Modular constructions entail a procedure where a building is constructed off-site,
utilizing materials and designing similar to conventionally build facilities as well as the same
codes and standards. This process is under controlled plant conditions and takes about half
the time used by conventionally build facilities (Blismas & Wakefield, 2009). The
structures are constructed in modules that when assembled on the plot area, showcase the
same specifications and similar design intended of the most advanced site build center.
Countries like Japan and Scandinavia have a sustainable foothold in modular
construction. The United States and United Kingdom markets have been in and out of favor
regarding prefabricated construction since the post-war era (Blismas & Wakefield, 2009).
Thus, multiple key factors determine whether modular construction is likely to be embraced
by the market or not. Among the key determinants, two stand out as the biggest determinants:
the relative costs of skilled construction labor and real estate demand. In areas like Australia's
East Coast, the southern part of the United Kingdom, Germany major cities and the United
Modular Construction Methods
Introduction
For decades, the construction industry has lagged when it comes to product
performance in comparison to other sectors. However, there has been a recent change of tides
and a chance to step up, moving away from the traditional building activity of on-site
manufacturing to off-site construction style projects (Baldwin & MacDonald, 2012).
Prefabricated is a not so new idea although a fresh wave of interest and investment has stung
the industry concerning shifts in the environment and technological advancements.
Construction industries make one of the largest sectors in the global market and a profound
change like modular construction has a major impact. The current projects have accelerated
projected timelines by 20 to 50 per cent (Bernstein, et al., 2011).
Modular constructions entail a procedure where a building is constructed off-site,
utilizing materials and designing similar to conventionally build facilities as well as the same
codes and standards. This process is under controlled plant conditions and takes about half
the time used by conventionally build facilities (Blismas & Wakefield, 2009). The
structures are constructed in modules that when assembled on the plot area, showcase the
same specifications and similar design intended of the most advanced site build center.
Countries like Japan and Scandinavia have a sustainable foothold in modular
construction. The United States and United Kingdom markets have been in and out of favor
regarding prefabricated construction since the post-war era (Blismas & Wakefield, 2009).
Thus, multiple key factors determine whether modular construction is likely to be embraced
by the market or not. Among the key determinants, two stand out as the biggest determinants:
the relative costs of skilled construction labor and real estate demand. In areas like Australia's
East Coast, the southern part of the United Kingdom, Germany major cities and the United
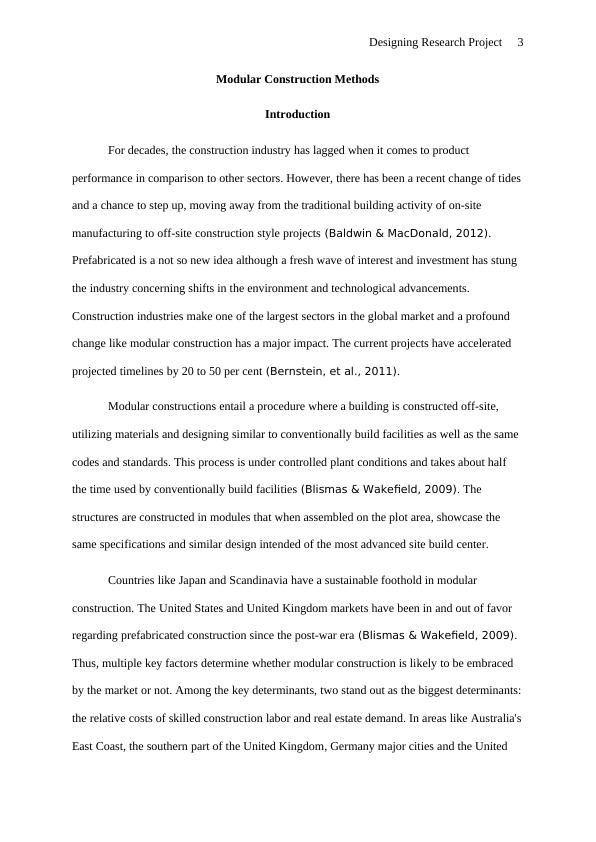
Designing Research Project 4
States west coast have unmet demands in the housing sector and labor shortages making this
model particularly relevant (Burleton, et al., 2015).
Capturing the productivity benefits and total cost of prefabricated housing is not a
straightforward task. Multiple considerations have to be made ranging from optimizing and
choosing the relevant materials; obtaining the preferred solution between 3D modules or 2D
panels, mastering the risks in design, hybrid designs, the technology, logistics and assembly
(Gambatese & Hallowell, 2010). Moreover, it depends whether the market can sustain
builders operation on large scale and repeatability. The regulators and public owners can
affect the industry structure too.
Historical Background of Modular Construction
Modular construction is among the oldest inventions in the construction industry. It
has since evolved from the 20th century to date (Gambatese & Hallowell, 2010). The
company that pioneered this invention is the Sears, Roebuck and Company, it started by
selling its catalogue to different construction companies. Housed constructed by this
catalogue where the very first to have a complete construction system (Gambatese &
Hallowell, 2011). A sears house had a complete house kit having almost 75 pages manual
containing instructions and a 3000 complete pieces. Henry Ford, who is a renowned
automotive pioneer, in the year 1913, introduces an assembly line in the automotive sector,
this helped minimize on production time and maintenance.
Almost a half century later, the invention was implemented in the construction sector
too. Sears, Roebuck and Company combined the technology to come up with a modular
construction. After World War II, after the much destruction of buildings and structures, there
was need to come up with more buildings within a very short time (Ghassemi & Becerik-
Gerber, 2011). Therefore, companies decided to construct buildings from factories. These
housed looked similar to the modern day mobile house, also known as HUD-code house.
States west coast have unmet demands in the housing sector and labor shortages making this
model particularly relevant (Burleton, et al., 2015).
Capturing the productivity benefits and total cost of prefabricated housing is not a
straightforward task. Multiple considerations have to be made ranging from optimizing and
choosing the relevant materials; obtaining the preferred solution between 3D modules or 2D
panels, mastering the risks in design, hybrid designs, the technology, logistics and assembly
(Gambatese & Hallowell, 2010). Moreover, it depends whether the market can sustain
builders operation on large scale and repeatability. The regulators and public owners can
affect the industry structure too.
Historical Background of Modular Construction
Modular construction is among the oldest inventions in the construction industry. It
has since evolved from the 20th century to date (Gambatese & Hallowell, 2010). The
company that pioneered this invention is the Sears, Roebuck and Company, it started by
selling its catalogue to different construction companies. Housed constructed by this
catalogue where the very first to have a complete construction system (Gambatese &
Hallowell, 2011). A sears house had a complete house kit having almost 75 pages manual
containing instructions and a 3000 complete pieces. Henry Ford, who is a renowned
automotive pioneer, in the year 1913, introduces an assembly line in the automotive sector,
this helped minimize on production time and maintenance.
Almost a half century later, the invention was implemented in the construction sector
too. Sears, Roebuck and Company combined the technology to come up with a modular
construction. After World War II, after the much destruction of buildings and structures, there
was need to come up with more buildings within a very short time (Ghassemi & Becerik-
Gerber, 2011). Therefore, companies decided to construct buildings from factories. These
housed looked similar to the modern day mobile house, also known as HUD-code house.
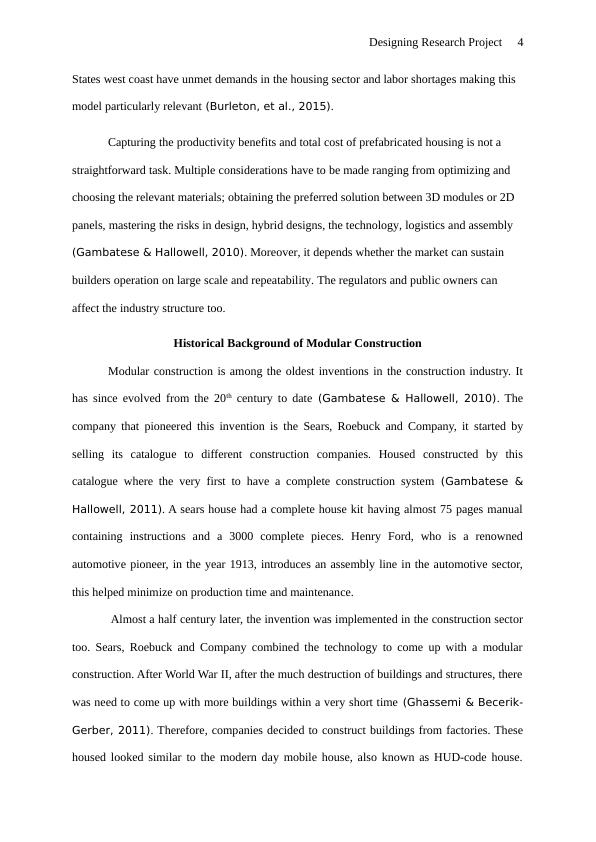
End of preview
Want to access all the pages? Upload your documents or become a member.
Related Documents
Identifying the barriers of modular construction in Australialg...
|12
|2358
|136
Modular Construction Methods Assignmentlg...
|10
|2395
|19
Risk management based on the intelligent Prefabricated Building Literature Review 2022lg...
|12
|4516
|12
Modern Construction Projectlg...
|15
|3138
|56
Modular Construction: Uses, Benefits, Challenges, Theories & Strategieslg...
|2
|500
|233
Prefabrication: A Research Paper on Fabricationlg...
|23
|6064
|461