Basement Design Proposal, Retaining Walls Design, and Piling Design for Desklib
VerifiedAdded on 2023/06/16
|4
|1379
|205
AI Summary
This article provides expert advice on the best construction methods, waterproofing, excavation plant, retaining walls design, and piling design for Desklib. It also discusses the possible causes of sinking retaining walls and how to fix them.
Contribute Materials
Your contribution can guide someone’s learning journey. Share your
documents today.
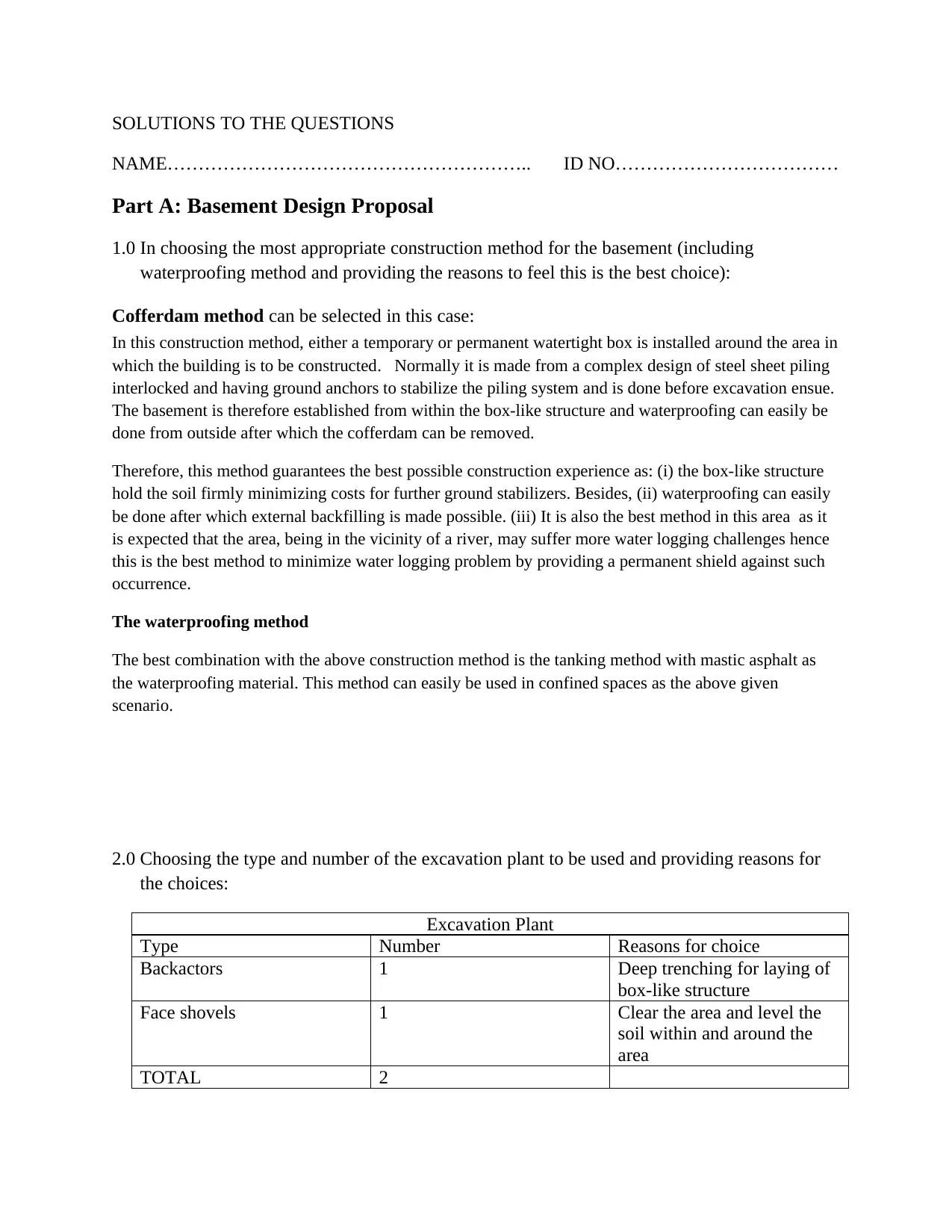
SOLUTIONS TO THE QUESTIONS
NAME………………………………………………….. ID NO………………………………
Part A: Basement Design Proposal
1.0 In choosing the most appropriate construction method for the basement (including
waterproofing method and providing the reasons to feel this is the best choice):
Cofferdam method can be selected in this case:
In this construction method, either a temporary or permanent watertight box is installed around the area in
which the building is to be constructed. Normally it is made from a complex design of steel sheet piling
interlocked and having ground anchors to stabilize the piling system and is done before excavation ensue.
The basement is therefore established from within the box-like structure and waterproofing can easily be
done from outside after which the cofferdam can be removed.
Therefore, this method guarantees the best possible construction experience as: (i) the box-like structure
hold the soil firmly minimizing costs for further ground stabilizers. Besides, (ii) waterproofing can easily
be done after which external backfilling is made possible. (iii) It is also the best method in this area as it
is expected that the area, being in the vicinity of a river, may suffer more water logging challenges hence
this is the best method to minimize water logging problem by providing a permanent shield against such
occurrence.
The waterproofing method
The best combination with the above construction method is the tanking method with mastic asphalt as
the waterproofing material. This method can easily be used in confined spaces as the above given
scenario.
2.0 Choosing the type and number of the excavation plant to be used and providing reasons for
the choices:
Excavation Plant
Type Number Reasons for choice
Backactors 1 Deep trenching for laying of
box-like structure
Face shovels 1 Clear the area and level the
soil within and around the
area
TOTAL 2
NAME………………………………………………….. ID NO………………………………
Part A: Basement Design Proposal
1.0 In choosing the most appropriate construction method for the basement (including
waterproofing method and providing the reasons to feel this is the best choice):
Cofferdam method can be selected in this case:
In this construction method, either a temporary or permanent watertight box is installed around the area in
which the building is to be constructed. Normally it is made from a complex design of steel sheet piling
interlocked and having ground anchors to stabilize the piling system and is done before excavation ensue.
The basement is therefore established from within the box-like structure and waterproofing can easily be
done from outside after which the cofferdam can be removed.
Therefore, this method guarantees the best possible construction experience as: (i) the box-like structure
hold the soil firmly minimizing costs for further ground stabilizers. Besides, (ii) waterproofing can easily
be done after which external backfilling is made possible. (iii) It is also the best method in this area as it
is expected that the area, being in the vicinity of a river, may suffer more water logging challenges hence
this is the best method to minimize water logging problem by providing a permanent shield against such
occurrence.
The waterproofing method
The best combination with the above construction method is the tanking method with mastic asphalt as
the waterproofing material. This method can easily be used in confined spaces as the above given
scenario.
2.0 Choosing the type and number of the excavation plant to be used and providing reasons for
the choices:
Excavation Plant
Type Number Reasons for choice
Backactors 1 Deep trenching for laying of
box-like structure
Face shovels 1 Clear the area and level the
soil within and around the
area
TOTAL 2
Secure Best Marks with AI Grader
Need help grading? Try our AI Grader for instant feedback on your assignments.

Part B: Retaining walls Design
3.0 Stage one
Because you have no previous knowledge of the site you will need to find out all about the
project (specifically the retaining wall details). Prepare a list of questions that you will need
answering before you can prepare your advice:
LIST OF QUESTIONS FOR ANSWERING
(i) Were the retaining walls used adequate in strength to prevent the excessive vertical
displacement that was expected?
(ii) Did the contractor use all the required materials in their correct proportion as was
purportedly directed by the consultant?
(iii) Is the area under active earth pressure and were the engineers in the know? Did they
consider this situation beforehand? If yes, what were the safeguards imposed for this
kind of scenario?
(iv) Did the nature and characteristics of the soil established? If yes, did the safe load
bearing capacity exceeded?
(v) Did the height of water table vehemently featured in the design? How was it
accommodated and was that adequate?
THE ADVICE
Many a time building collapse is mostly caused by inappropriate selection of the right materials
and methods to construct the retaining walls. As provided in the above questions (that need
answering) this unfortunate incident may have been caused by neglecting of the small design
issues that could make a big difference. For instance, inappropriate choice of material can put too
much stress on the weak retaining walls causing subtle failures that would only be manifested
later when the building is trying to ‘settle’ in. Secondly, it is often important that the issue of
establishing the height of water table be vehemently revisited during the pre-design stage. This
would require the engineer to make several site visits in order to establish the true scenario of the
area before undertaking the design. However, sometimes, client’s requirements may be way
above the budget requirements; the engineer-in-charge should always advice the client
accordingly about every aspect of the building construction requirements. Notably, in this case,
and without pre-empting the case direction, it was important for regular review meetings to be
held and the above issues discussed at every stage of construction, at least after every floor was
completed.
3.0 Stage one
Because you have no previous knowledge of the site you will need to find out all about the
project (specifically the retaining wall details). Prepare a list of questions that you will need
answering before you can prepare your advice:
LIST OF QUESTIONS FOR ANSWERING
(i) Were the retaining walls used adequate in strength to prevent the excessive vertical
displacement that was expected?
(ii) Did the contractor use all the required materials in their correct proportion as was
purportedly directed by the consultant?
(iii) Is the area under active earth pressure and were the engineers in the know? Did they
consider this situation beforehand? If yes, what were the safeguards imposed for this
kind of scenario?
(iv) Did the nature and characteristics of the soil established? If yes, did the safe load
bearing capacity exceeded?
(v) Did the height of water table vehemently featured in the design? How was it
accommodated and was that adequate?
THE ADVICE
Many a time building collapse is mostly caused by inappropriate selection of the right materials
and methods to construct the retaining walls. As provided in the above questions (that need
answering) this unfortunate incident may have been caused by neglecting of the small design
issues that could make a big difference. For instance, inappropriate choice of material can put too
much stress on the weak retaining walls causing subtle failures that would only be manifested
later when the building is trying to ‘settle’ in. Secondly, it is often important that the issue of
establishing the height of water table be vehemently revisited during the pre-design stage. This
would require the engineer to make several site visits in order to establish the true scenario of the
area before undertaking the design. However, sometimes, client’s requirements may be way
above the budget requirements; the engineer-in-charge should always advice the client
accordingly about every aspect of the building construction requirements. Notably, in this case,
and without pre-empting the case direction, it was important for regular review meetings to be
held and the above issues discussed at every stage of construction, at least after every floor was
completed.

4.0 Stage Two
Provide an assessment of what the possible causes for the sinking of the retaining wall could be
and write a series of dot points describing them. Make your recommendation to the developer on
how the problem might be rectified in terms of how to fix the retaining wall and how you would
protect the building itself during the repair works.
As mentioned earlier, the sinking of the retaining wall could be attributed to the following
factors:
(i) Inadequate and inappropriate materials use
This is normally results from the poor choices of materials given the structural
realities of the building.
In a case, like this one where it is a tall storey buildings, it will be very critical
to adequately supply the right materials in their right quantity
(ii) The water table height was ignored
Water logging problems are a major concern to the buildings as they cause
further weakening of the supporting strata especially when water table height
is such that it is nearer the surface.
However, moving forward would require the engineer-in-charge and his team to brainstorm
about these issues and reflect on them before coming up with a concrete plan to rectify the
problem. Notably, the geological make-up of the area will have to be relooked and possibly soil
analysis done and approved at every stage. The construction methods must follow all the local
standards in construction and appropriate methods will depend on the real scenario of the area.
The materials to be supplied must be in tandem with the structural design requirements. The
contracting engineer will also have to undertake review meetings with the developer so as to
make him/her be informed of the construction happenings. Above all, construction budget must
reciprocate with the construction work. There is no need to put up an expensive design with very
limited resources as this is often the genesis of problems, apart from the technical hitches from
the side of the engineer. Lastly, the engineer-in-charge must be a qualified and very experienced
professional engineer having undertaken several of such projects in the locality.
Part C: Piling Design
5.0 Select the most appropriate type of piling for this project and justify why this is the best
option.
The replacement piles can be used in this case; as less noise and vibration is produced
hence suitable this area as it is bordering other existing buildings.
Provide an assessment of what the possible causes for the sinking of the retaining wall could be
and write a series of dot points describing them. Make your recommendation to the developer on
how the problem might be rectified in terms of how to fix the retaining wall and how you would
protect the building itself during the repair works.
As mentioned earlier, the sinking of the retaining wall could be attributed to the following
factors:
(i) Inadequate and inappropriate materials use
This is normally results from the poor choices of materials given the structural
realities of the building.
In a case, like this one where it is a tall storey buildings, it will be very critical
to adequately supply the right materials in their right quantity
(ii) The water table height was ignored
Water logging problems are a major concern to the buildings as they cause
further weakening of the supporting strata especially when water table height
is such that it is nearer the surface.
However, moving forward would require the engineer-in-charge and his team to brainstorm
about these issues and reflect on them before coming up with a concrete plan to rectify the
problem. Notably, the geological make-up of the area will have to be relooked and possibly soil
analysis done and approved at every stage. The construction methods must follow all the local
standards in construction and appropriate methods will depend on the real scenario of the area.
The materials to be supplied must be in tandem with the structural design requirements. The
contracting engineer will also have to undertake review meetings with the developer so as to
make him/her be informed of the construction happenings. Above all, construction budget must
reciprocate with the construction work. There is no need to put up an expensive design with very
limited resources as this is often the genesis of problems, apart from the technical hitches from
the side of the engineer. Lastly, the engineer-in-charge must be a qualified and very experienced
professional engineer having undertaken several of such projects in the locality.
Part C: Piling Design
5.0 Select the most appropriate type of piling for this project and justify why this is the best
option.
The replacement piles can be used in this case; as less noise and vibration is produced
hence suitable this area as it is bordering other existing buildings.
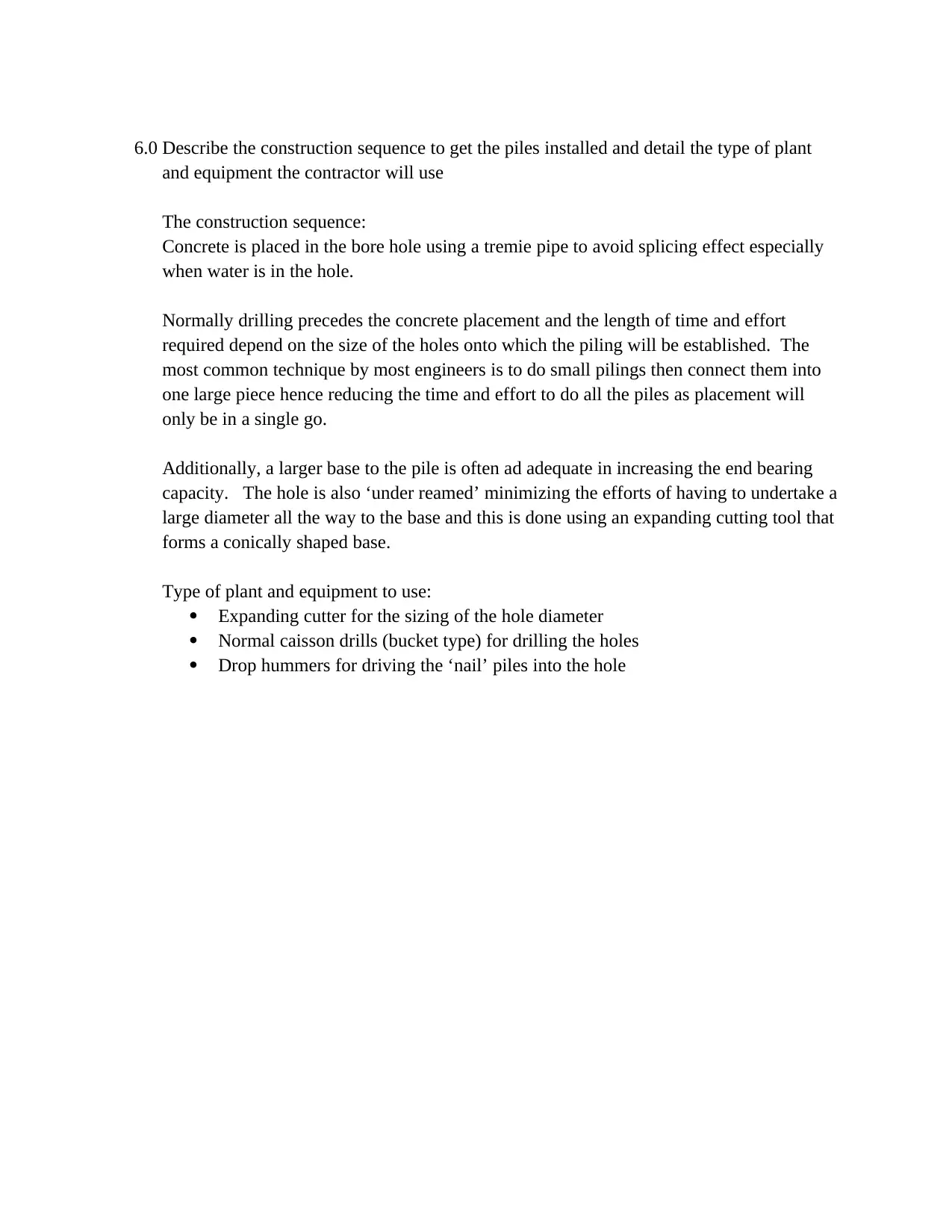
6.0 Describe the construction sequence to get the piles installed and detail the type of plant
and equipment the contractor will use
The construction sequence:
Concrete is placed in the bore hole using a tremie pipe to avoid splicing effect especially
when water is in the hole.
Normally drilling precedes the concrete placement and the length of time and effort
required depend on the size of the holes onto which the piling will be established. The
most common technique by most engineers is to do small pilings then connect them into
one large piece hence reducing the time and effort to do all the piles as placement will
only be in a single go.
Additionally, a larger base to the pile is often ad adequate in increasing the end bearing
capacity. The hole is also ‘under reamed’ minimizing the efforts of having to undertake a
large diameter all the way to the base and this is done using an expanding cutting tool that
forms a conically shaped base.
Type of plant and equipment to use:
Expanding cutter for the sizing of the hole diameter
Normal caisson drills (bucket type) for drilling the holes
Drop hummers for driving the ‘nail’ piles into the hole
and equipment the contractor will use
The construction sequence:
Concrete is placed in the bore hole using a tremie pipe to avoid splicing effect especially
when water is in the hole.
Normally drilling precedes the concrete placement and the length of time and effort
required depend on the size of the holes onto which the piling will be established. The
most common technique by most engineers is to do small pilings then connect them into
one large piece hence reducing the time and effort to do all the piles as placement will
only be in a single go.
Additionally, a larger base to the pile is often ad adequate in increasing the end bearing
capacity. The hole is also ‘under reamed’ minimizing the efforts of having to undertake a
large diameter all the way to the base and this is done using an expanding cutting tool that
forms a conically shaped base.
Type of plant and equipment to use:
Expanding cutter for the sizing of the hole diameter
Normal caisson drills (bucket type) for drilling the holes
Drop hummers for driving the ‘nail’ piles into the hole
1 out of 4
Related Documents
![[object Object]](/_next/image/?url=%2F_next%2Fstatic%2Fmedia%2Flogo.6d15ce61.png&w=640&q=75)
Your All-in-One AI-Powered Toolkit for Academic Success.
+13062052269
info@desklib.com
Available 24*7 on WhatsApp / Email
Unlock your academic potential
© 2024 | Zucol Services PVT LTD | All rights reserved.