Engineering Maths and Modelling
VerifiedAdded on 2023/04/20
|50
|9794
|479
AI Summary
This document discusses the process of solving the governing equations of a spring-mass system using Matlab. It explores the use of analytical, Euler, and ODE45 methods and discusses the findings and key conclusions. The effects of mass, spring constant, and initial conditions on the displacement are also analyzed.
Contribute Materials
Your contribution can guide someone’s learning journey. Share your
documents today.
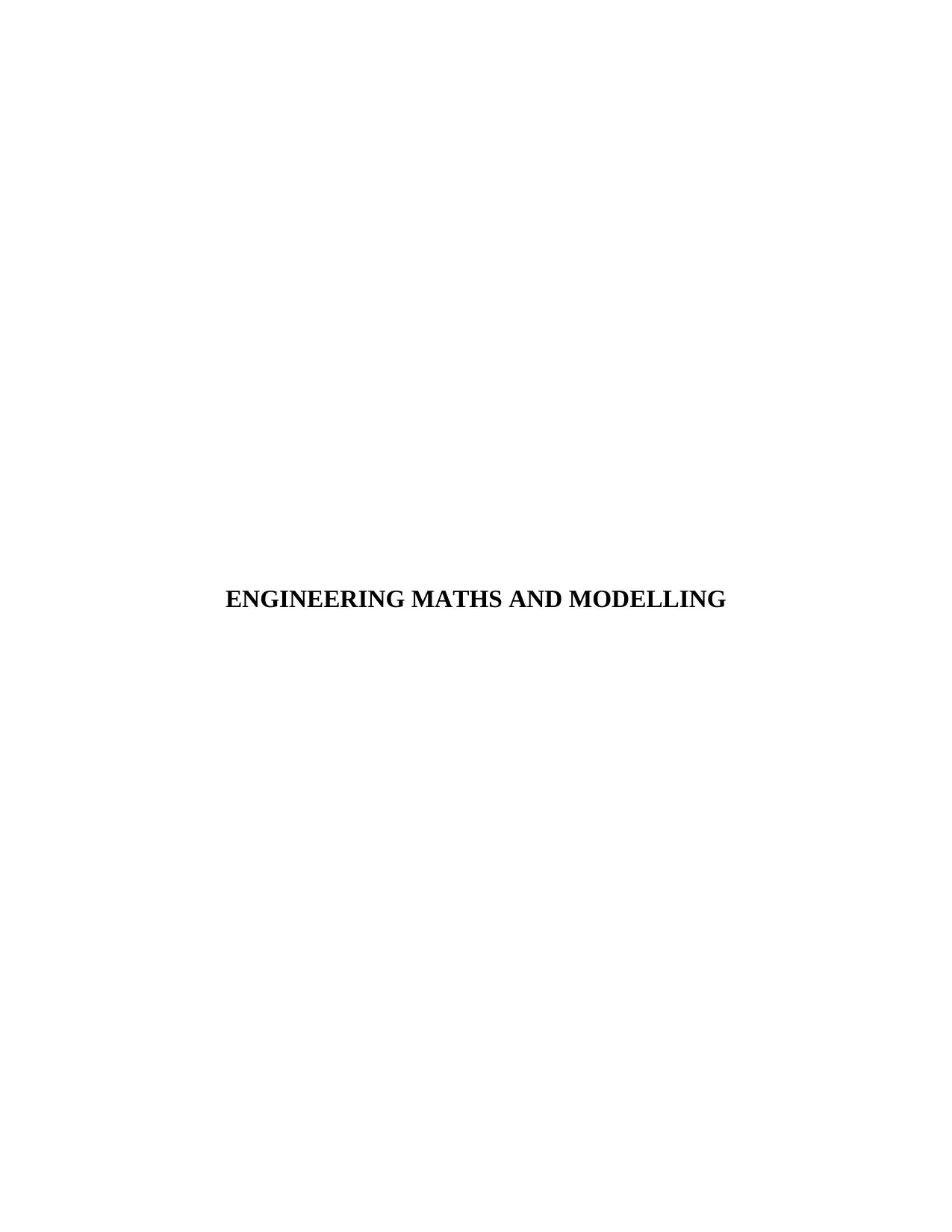
ENGINEERING MATHS AND MODELLING
Secure Best Marks with AI Grader
Need help grading? Try our AI Grader for instant feedback on your assignments.
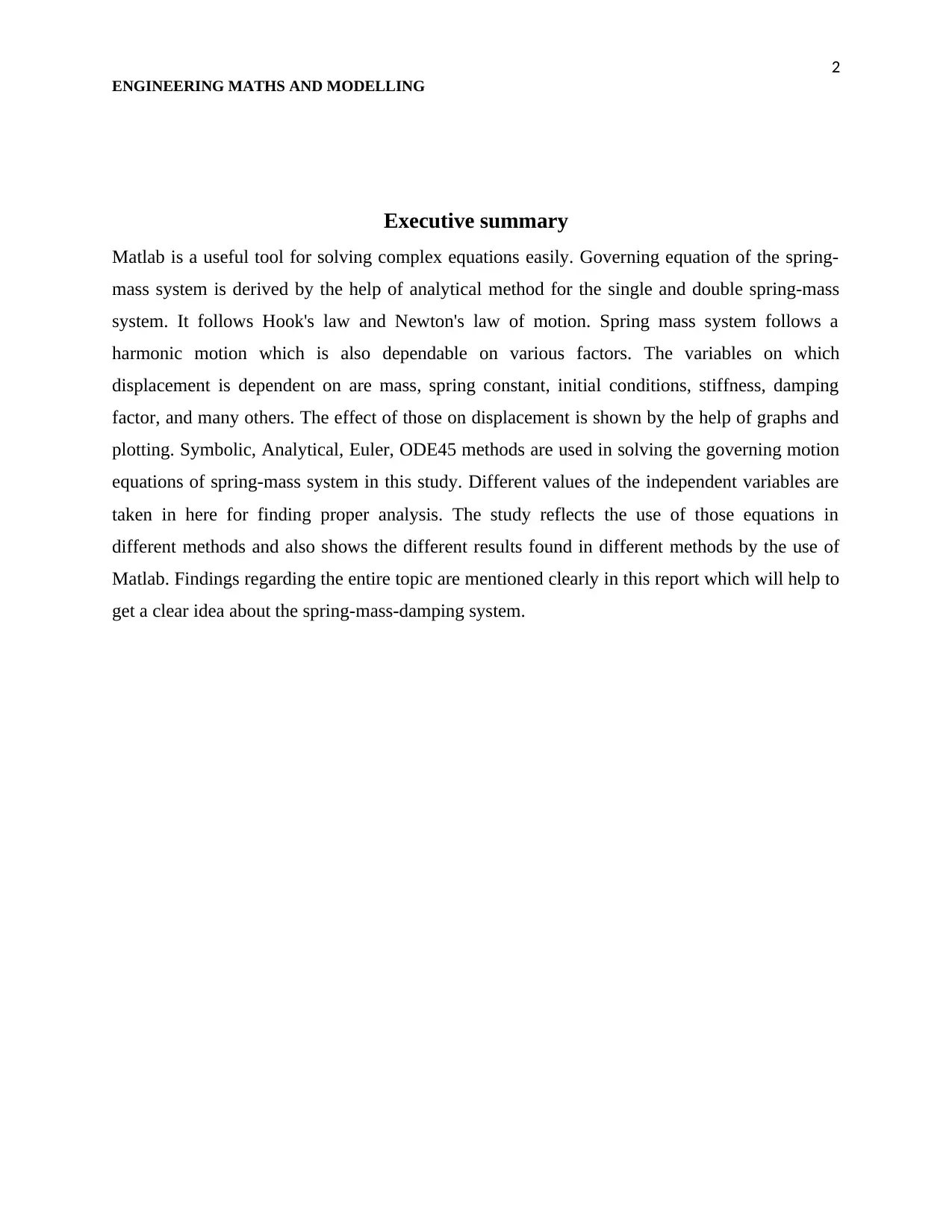
2
ENGINEERING MATHS AND MODELLING
Executive summary
Matlab is a useful tool for solving complex equations easily. Governing equation of the spring-
mass system is derived by the help of analytical method for the single and double spring-mass
system. It follows Hook's law and Newton's law of motion. Spring mass system follows a
harmonic motion which is also dependable on various factors. The variables on which
displacement is dependent on are mass, spring constant, initial conditions, stiffness, damping
factor, and many others. The effect of those on displacement is shown by the help of graphs and
plotting. Symbolic, Analytical, Euler, ODE45 methods are used in solving the governing motion
equations of spring-mass system in this study. Different values of the independent variables are
taken in here for finding proper analysis. The study reflects the use of those equations in
different methods and also shows the different results found in different methods by the use of
Matlab. Findings regarding the entire topic are mentioned clearly in this report which will help to
get a clear idea about the spring-mass-damping system.
ENGINEERING MATHS AND MODELLING
Executive summary
Matlab is a useful tool for solving complex equations easily. Governing equation of the spring-
mass system is derived by the help of analytical method for the single and double spring-mass
system. It follows Hook's law and Newton's law of motion. Spring mass system follows a
harmonic motion which is also dependable on various factors. The variables on which
displacement is dependent on are mass, spring constant, initial conditions, stiffness, damping
factor, and many others. The effect of those on displacement is shown by the help of graphs and
plotting. Symbolic, Analytical, Euler, ODE45 methods are used in solving the governing motion
equations of spring-mass system in this study. Different values of the independent variables are
taken in here for finding proper analysis. The study reflects the use of those equations in
different methods and also shows the different results found in different methods by the use of
Matlab. Findings regarding the entire topic are mentioned clearly in this report which will help to
get a clear idea about the spring-mass-damping system.
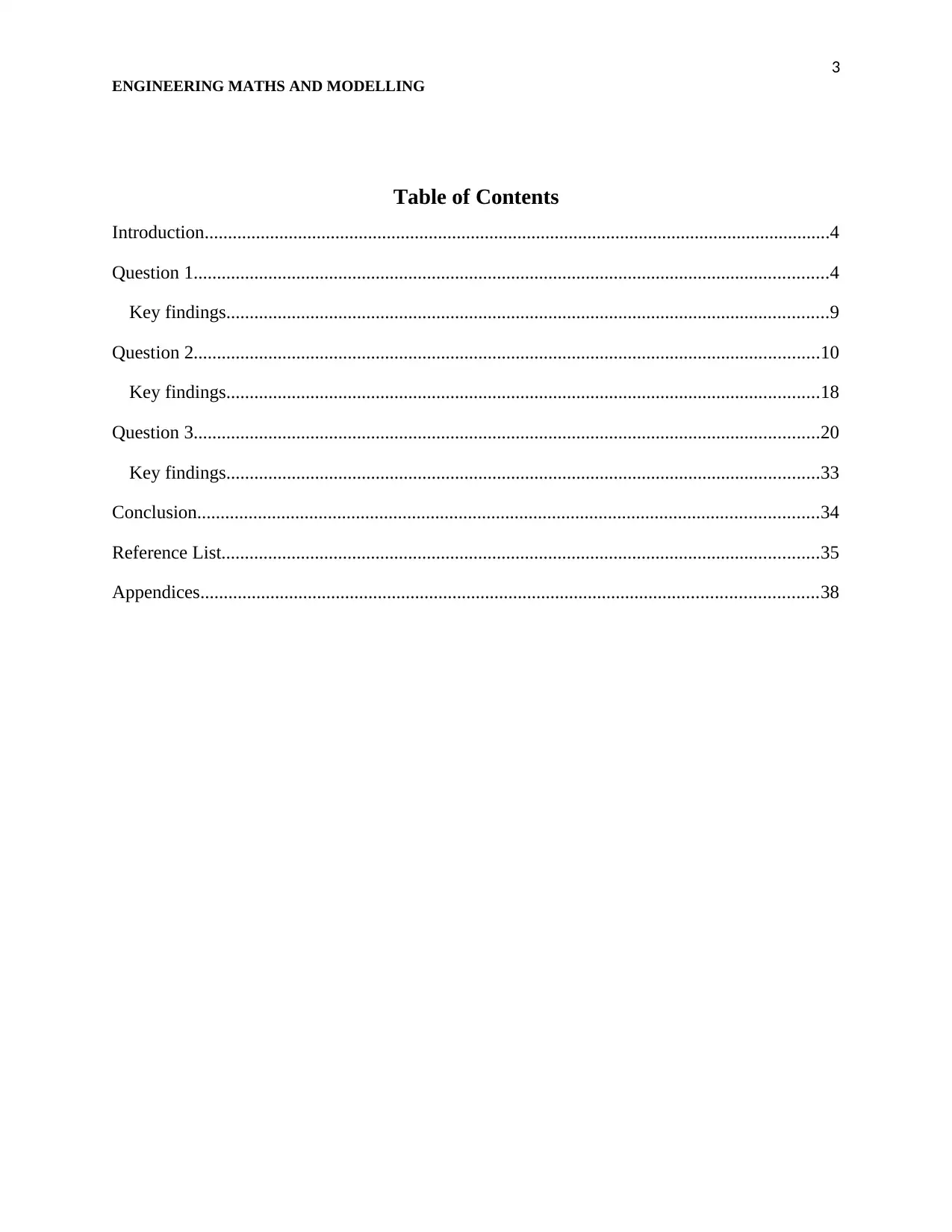
3
ENGINEERING MATHS AND MODELLING
Table of Contents
Introduction......................................................................................................................................4
Question 1........................................................................................................................................4
Key findings.................................................................................................................................9
Question 2......................................................................................................................................10
Key findings...............................................................................................................................18
Question 3......................................................................................................................................20
Key findings...............................................................................................................................33
Conclusion.....................................................................................................................................34
Reference List................................................................................................................................35
Appendices....................................................................................................................................38
ENGINEERING MATHS AND MODELLING
Table of Contents
Introduction......................................................................................................................................4
Question 1........................................................................................................................................4
Key findings.................................................................................................................................9
Question 2......................................................................................................................................10
Key findings...............................................................................................................................18
Question 3......................................................................................................................................20
Key findings...............................................................................................................................33
Conclusion.....................................................................................................................................34
Reference List................................................................................................................................35
Appendices....................................................................................................................................38
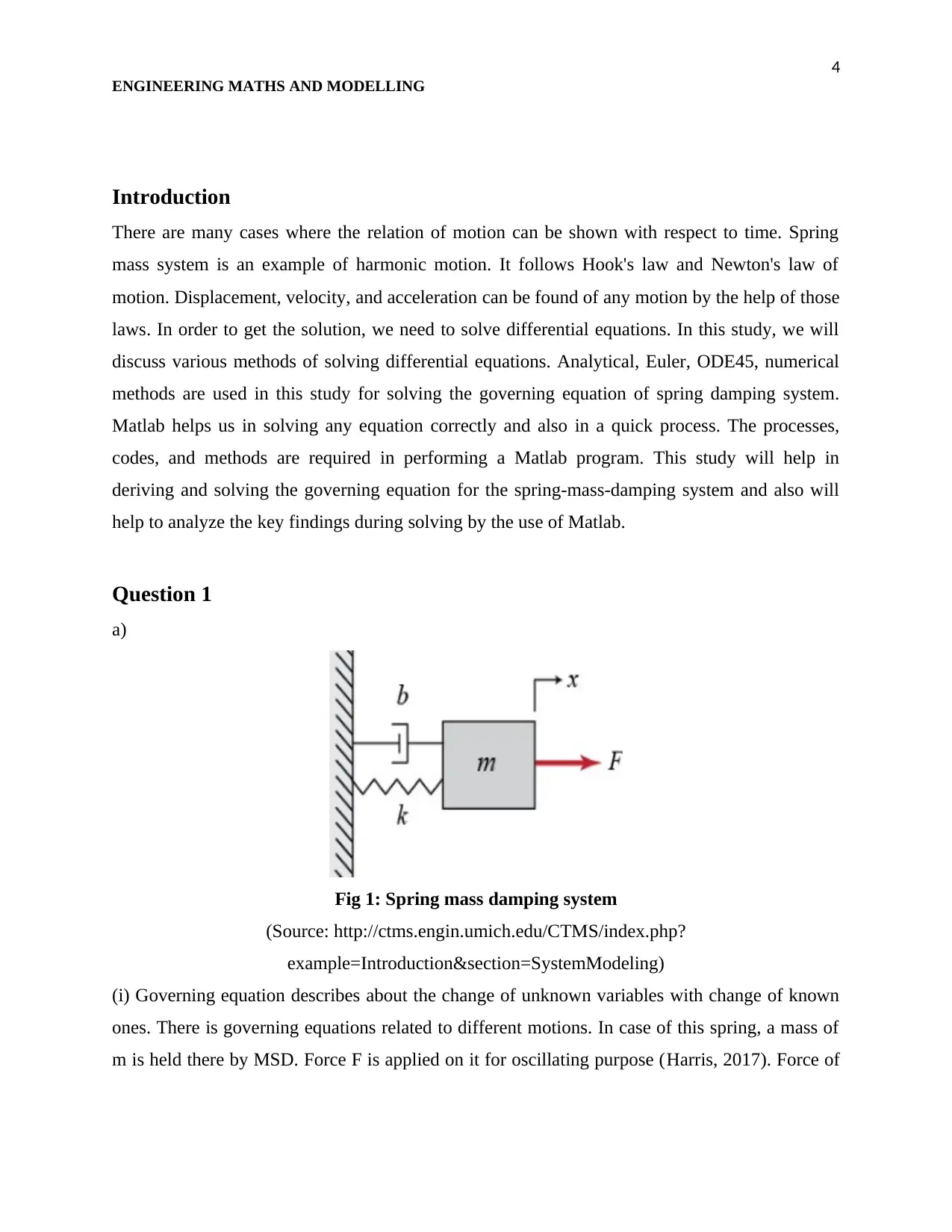
4
ENGINEERING MATHS AND MODELLING
Introduction
There are many cases where the relation of motion can be shown with respect to time. Spring
mass system is an example of harmonic motion. It follows Hook's law and Newton's law of
motion. Displacement, velocity, and acceleration can be found of any motion by the help of those
laws. In order to get the solution, we need to solve differential equations. In this study, we will
discuss various methods of solving differential equations. Analytical, Euler, ODE45, numerical
methods are used in this study for solving the governing equation of spring damping system.
Matlab helps us in solving any equation correctly and also in a quick process. The processes,
codes, and methods are required in performing a Matlab program. This study will help in
deriving and solving the governing equation for the spring-mass-damping system and also will
help to analyze the key findings during solving by the use of Matlab.
Question 1
a)
Fig 1: Spring mass damping system
(Source: http://ctms.engin.umich.edu/CTMS/index.php?
example=Introduction§ion=SystemModeling)
(i) Governing equation describes about the change of unknown variables with change of known
ones. There is governing equations related to different motions. In case of this spring, a mass of
m is held there by MSD. Force F is applied on it for oscillating purpose (Harris, 2017). Force of
ENGINEERING MATHS AND MODELLING
Introduction
There are many cases where the relation of motion can be shown with respect to time. Spring
mass system is an example of harmonic motion. It follows Hook's law and Newton's law of
motion. Displacement, velocity, and acceleration can be found of any motion by the help of those
laws. In order to get the solution, we need to solve differential equations. In this study, we will
discuss various methods of solving differential equations. Analytical, Euler, ODE45, numerical
methods are used in this study for solving the governing equation of spring damping system.
Matlab helps us in solving any equation correctly and also in a quick process. The processes,
codes, and methods are required in performing a Matlab program. This study will help in
deriving and solving the governing equation for the spring-mass-damping system and also will
help to analyze the key findings during solving by the use of Matlab.
Question 1
a)
Fig 1: Spring mass damping system
(Source: http://ctms.engin.umich.edu/CTMS/index.php?
example=Introduction§ion=SystemModeling)
(i) Governing equation describes about the change of unknown variables with change of known
ones. There is governing equations related to different motions. In case of this spring, a mass of
m is held there by MSD. Force F is applied on it for oscillating purpose (Harris, 2017). Force of
Secure Best Marks with AI Grader
Need help grading? Try our AI Grader for instant feedback on your assignments.
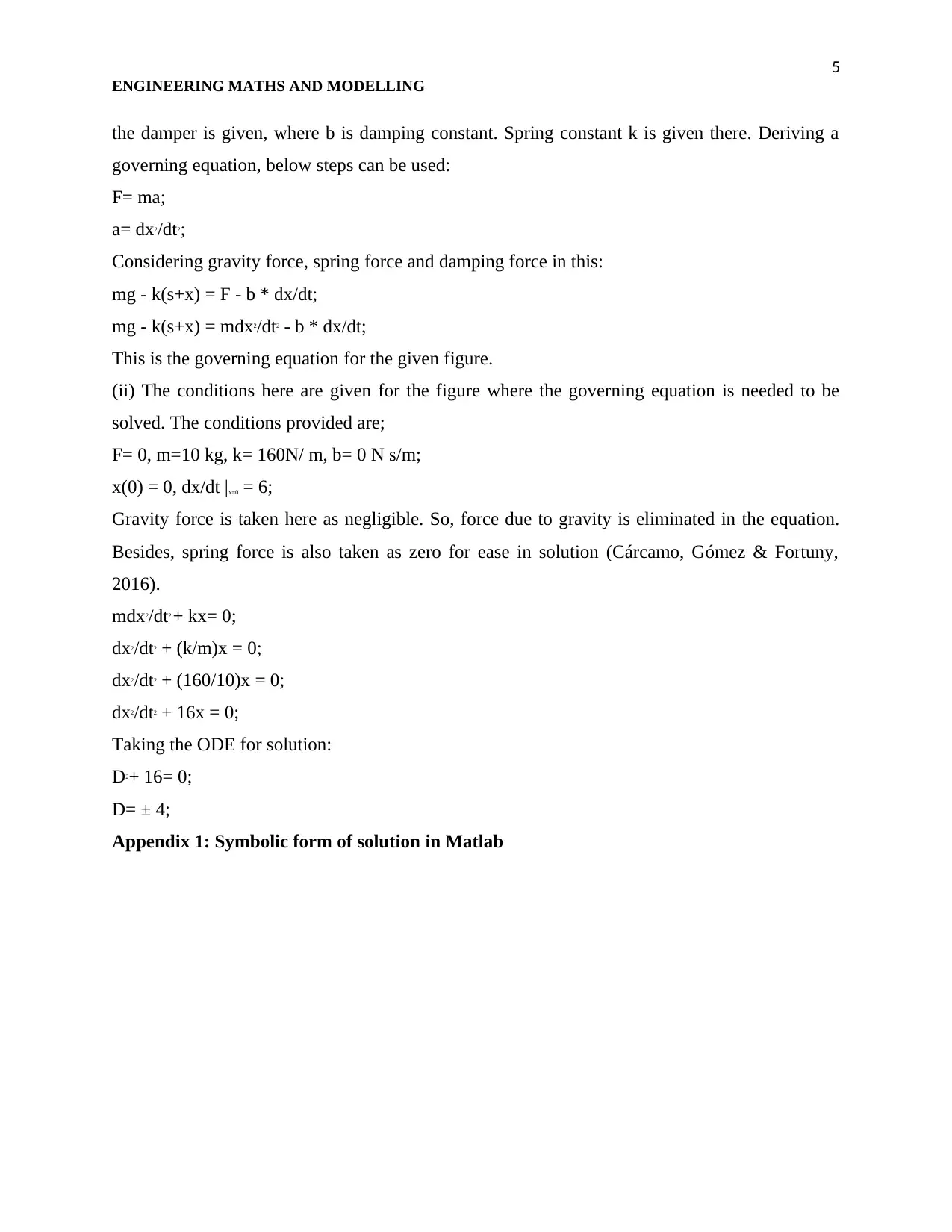
5
ENGINEERING MATHS AND MODELLING
the damper is given, where b is damping constant. Spring constant k is given there. Deriving a
governing equation, below steps can be used:
F= ma;
a= dx2/dt2;
Considering gravity force, spring force and damping force in this:
mg - k(s+x) = F - b * dx/dt;
mg - k(s+x) = mdx2/dt2 - b * dx/dt;
This is the governing equation for the given figure.
(ii) The conditions here are given for the figure where the governing equation is needed to be
solved. The conditions provided are;
F= 0, m=10 kg, k= 160N/ m, b= 0 N s/m;
x(0) = 0, dx/dt |x=0 = 6;
Gravity force is taken here as negligible. So, force due to gravity is eliminated in the equation.
Besides, spring force is also taken as zero for ease in solution (Cárcamo, Gómez & Fortuny,
2016).
mdx2/dt2 + kx= 0;
dx2/dt2 + (k/m)x = 0;
dx2/dt2 + (160/10)x = 0;
dx2/dt2 + 16x = 0;
Taking the ODE for solution:
D2+ 16= 0;
D= ± 4;
Appendix 1: Symbolic form of solution in Matlab
ENGINEERING MATHS AND MODELLING
the damper is given, where b is damping constant. Spring constant k is given there. Deriving a
governing equation, below steps can be used:
F= ma;
a= dx2/dt2;
Considering gravity force, spring force and damping force in this:
mg - k(s+x) = F - b * dx/dt;
mg - k(s+x) = mdx2/dt2 - b * dx/dt;
This is the governing equation for the given figure.
(ii) The conditions here are given for the figure where the governing equation is needed to be
solved. The conditions provided are;
F= 0, m=10 kg, k= 160N/ m, b= 0 N s/m;
x(0) = 0, dx/dt |x=0 = 6;
Gravity force is taken here as negligible. So, force due to gravity is eliminated in the equation.
Besides, spring force is also taken as zero for ease in solution (Cárcamo, Gómez & Fortuny,
2016).
mdx2/dt2 + kx= 0;
dx2/dt2 + (k/m)x = 0;
dx2/dt2 + (160/10)x = 0;
dx2/dt2 + 16x = 0;
Taking the ODE for solution:
D2+ 16= 0;
D= ± 4;
Appendix 1: Symbolic form of solution in Matlab
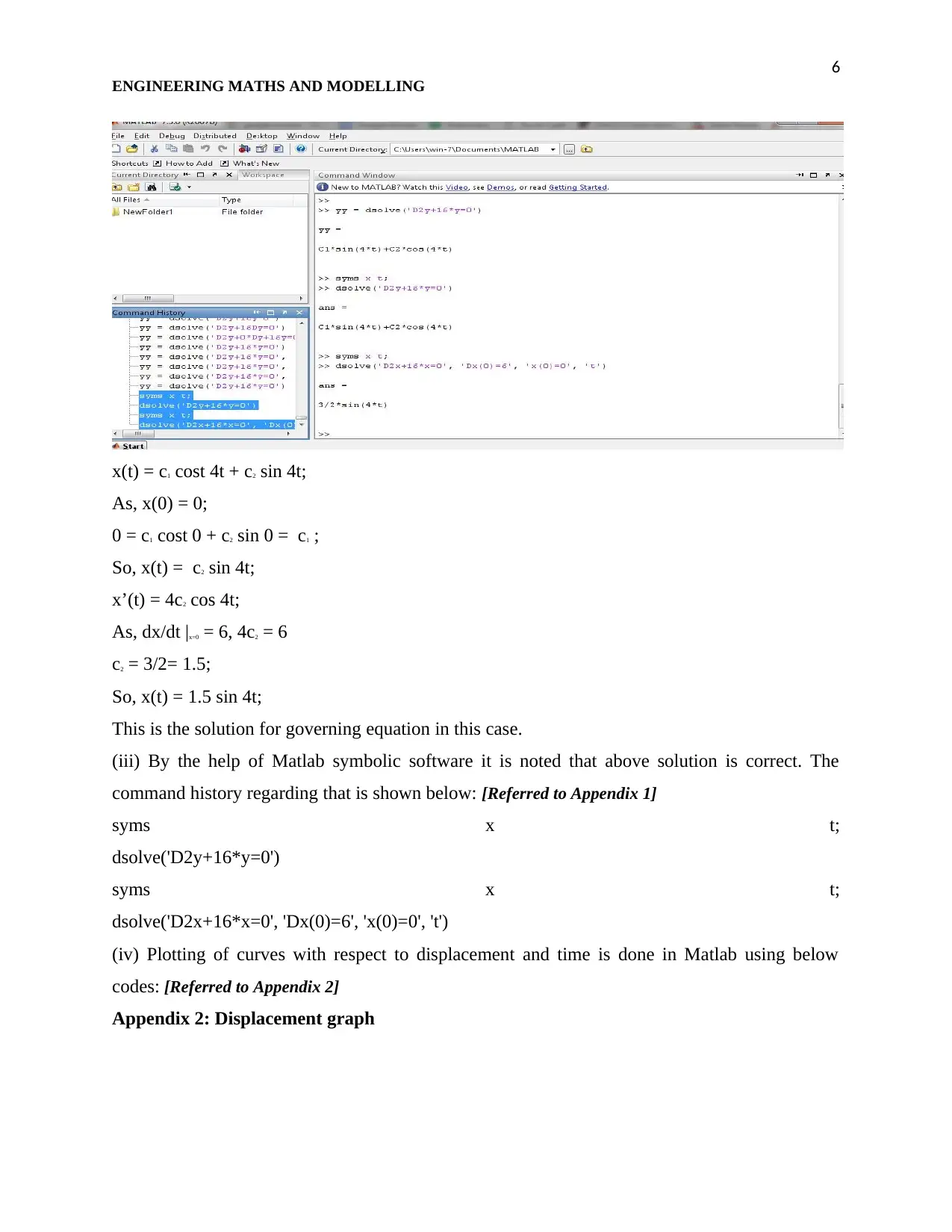
6
ENGINEERING MATHS AND MODELLING
x(t) = c1 cost 4t + c2 sin 4t;
As, x(0) = 0;
0 = c1 cost 0 + c2 sin 0 = c1 ;
So, x(t) = c2 sin 4t;
x’(t) = 4c2 cos 4t;
As, dx/dt |x=0 = 6, 4c2 = 6
c2 = 3/2= 1.5;
So, x(t) = 1.5 sin 4t;
This is the solution for governing equation in this case.
(iii) By the help of Matlab symbolic software it is noted that above solution is correct. The
command history regarding that is shown below: [Referred to Appendix 1]
syms x t;
dsolve('D2y+16*y=0')
syms x t;
dsolve('D2x+16*x=0', 'Dx(0)=6', 'x(0)=0', 't')
(iv) Plotting of curves with respect to displacement and time is done in Matlab using below
codes: [Referred to Appendix 2]
Appendix 2: Displacement graph
ENGINEERING MATHS AND MODELLING
x(t) = c1 cost 4t + c2 sin 4t;
As, x(0) = 0;
0 = c1 cost 0 + c2 sin 0 = c1 ;
So, x(t) = c2 sin 4t;
x’(t) = 4c2 cos 4t;
As, dx/dt |x=0 = 6, 4c2 = 6
c2 = 3/2= 1.5;
So, x(t) = 1.5 sin 4t;
This is the solution for governing equation in this case.
(iii) By the help of Matlab symbolic software it is noted that above solution is correct. The
command history regarding that is shown below: [Referred to Appendix 1]
syms x t;
dsolve('D2y+16*y=0')
syms x t;
dsolve('D2x+16*x=0', 'Dx(0)=6', 'x(0)=0', 't')
(iv) Plotting of curves with respect to displacement and time is done in Matlab using below
codes: [Referred to Appendix 2]
Appendix 2: Displacement graph
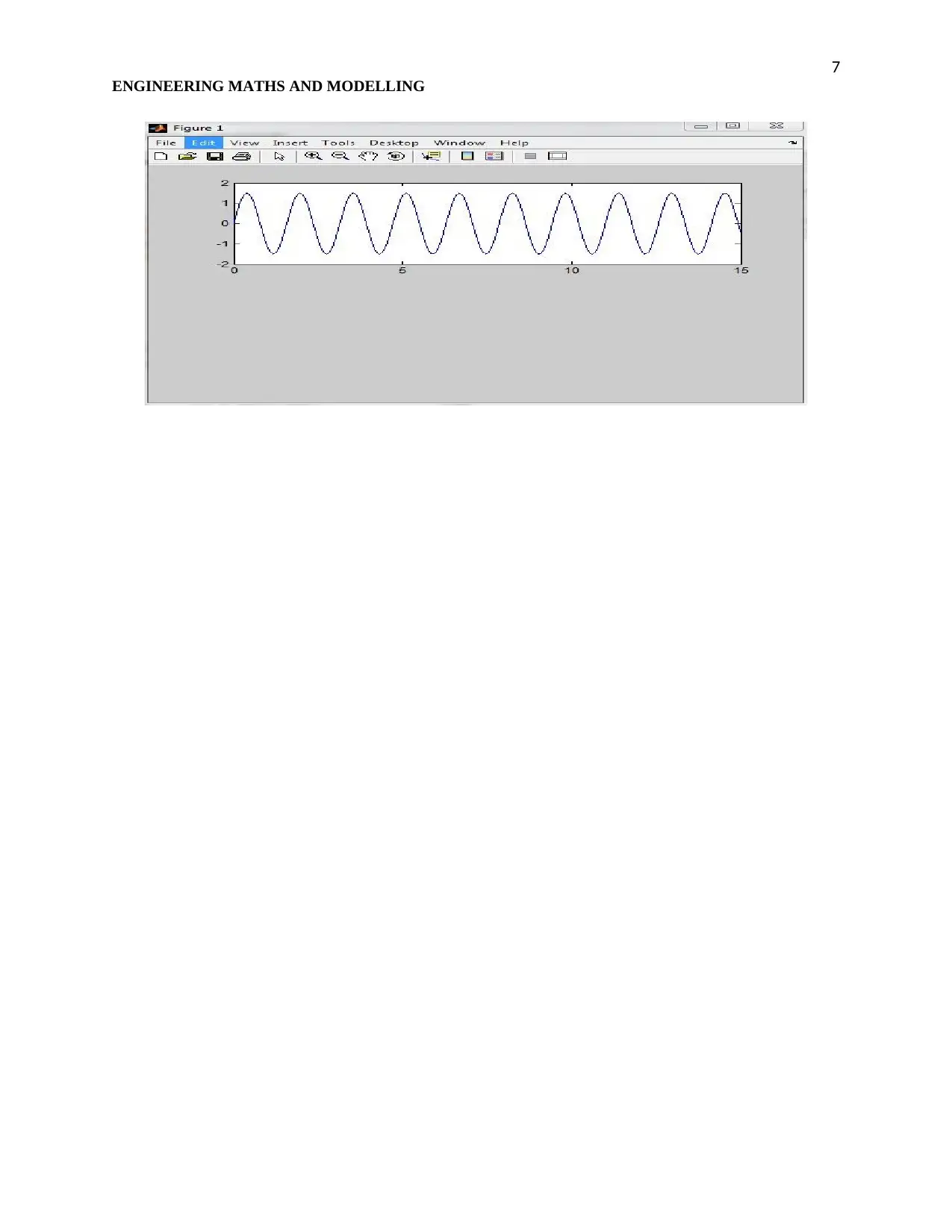
7
ENGINEERING MATHS AND MODELLING
ENGINEERING MATHS AND MODELLING
Paraphrase This Document
Need a fresh take? Get an instant paraphrase of this document with our AI Paraphraser
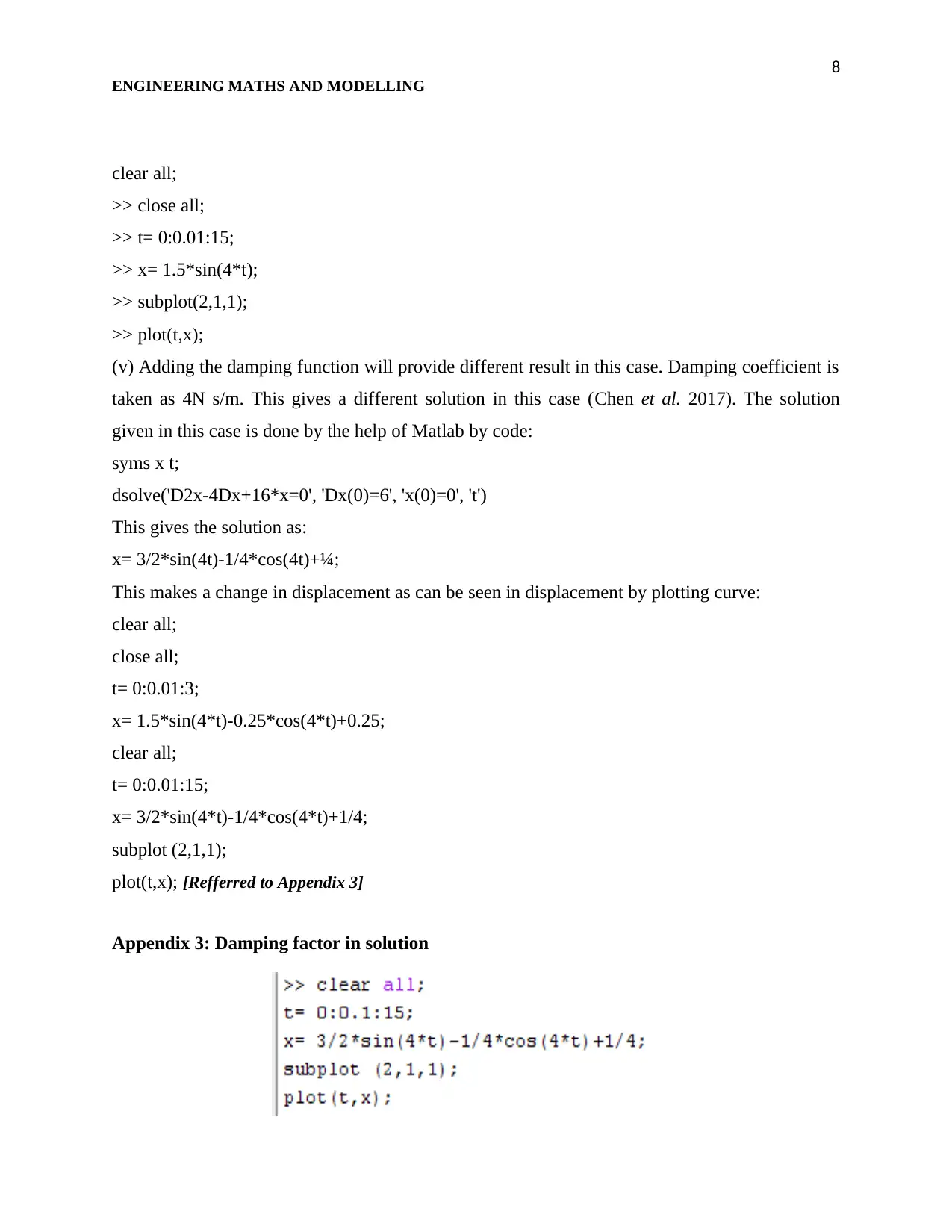
8
ENGINEERING MATHS AND MODELLING
clear all;
>> close all;
>> t= 0:0.01:15;
>> x= 1.5*sin(4*t);
>> subplot(2,1,1);
>> plot(t,x);
(v) Adding the damping function will provide different result in this case. Damping coefficient is
taken as 4N s/m. This gives a different solution in this case (Chen et al. 2017). The solution
given in this case is done by the help of Matlab by code:
syms x t;
dsolve('D2x-4Dx+16*x=0', 'Dx(0)=6', 'x(0)=0', 't')
This gives the solution as:
x= 3/2*sin(4t)-1/4*cos(4t)+¼;
This makes a change in displacement as can be seen in displacement by plotting curve:
clear all;
close all;
t= 0:0.01:3;
x= 1.5*sin(4*t)-0.25*cos(4*t)+0.25;
clear all;
t= 0:0.01:15;
x= 3/2*sin(4*t)-1/4*cos(4*t)+1/4;
subplot (2,1,1);
plot(t,x); [Refferred to Appendix 3]
Appendix 3: Damping factor in solution
ENGINEERING MATHS AND MODELLING
clear all;
>> close all;
>> t= 0:0.01:15;
>> x= 1.5*sin(4*t);
>> subplot(2,1,1);
>> plot(t,x);
(v) Adding the damping function will provide different result in this case. Damping coefficient is
taken as 4N s/m. This gives a different solution in this case (Chen et al. 2017). The solution
given in this case is done by the help of Matlab by code:
syms x t;
dsolve('D2x-4Dx+16*x=0', 'Dx(0)=6', 'x(0)=0', 't')
This gives the solution as:
x= 3/2*sin(4t)-1/4*cos(4t)+¼;
This makes a change in displacement as can be seen in displacement by plotting curve:
clear all;
close all;
t= 0:0.01:3;
x= 1.5*sin(4*t)-0.25*cos(4*t)+0.25;
clear all;
t= 0:0.01:15;
x= 3/2*sin(4*t)-1/4*cos(4*t)+1/4;
subplot (2,1,1);
plot(t,x); [Refferred to Appendix 3]
Appendix 3: Damping factor in solution
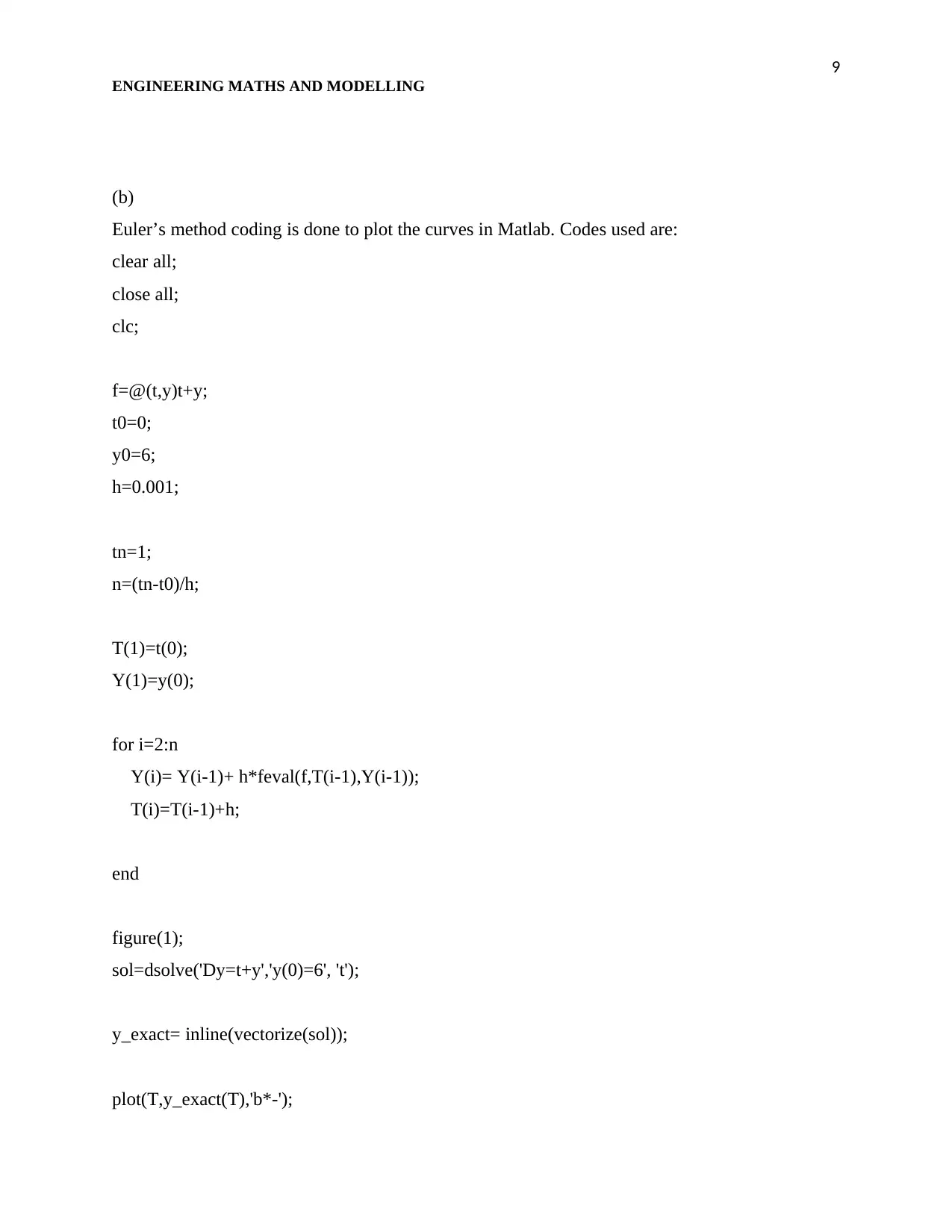
9
ENGINEERING MATHS AND MODELLING
(b)
Euler’s method coding is done to plot the curves in Matlab. Codes used are:
clear all;
close all;
clc;
f=@(t,y)t+y;
t0=0;
y0=6;
h=0.001;
tn=1;
n=(tn-t0)/h;
T(1)=t(0);
Y(1)=y(0);
for i=2:n
Y(i)= Y(i-1)+ h*feval(f,T(i-1),Y(i-1));
T(i)=T(i-1)+h;
end
figure(1);
sol=dsolve('Dy=t+y','y(0)=6', 't');
y_exact= inline(vectorize(sol));
plot(T,y_exact(T),'b*-');
ENGINEERING MATHS AND MODELLING
(b)
Euler’s method coding is done to plot the curves in Matlab. Codes used are:
clear all;
close all;
clc;
f=@(t,y)t+y;
t0=0;
y0=6;
h=0.001;
tn=1;
n=(tn-t0)/h;
T(1)=t(0);
Y(1)=y(0);
for i=2:n
Y(i)= Y(i-1)+ h*feval(f,T(i-1),Y(i-1));
T(i)=T(i-1)+h;
end
figure(1);
sol=dsolve('Dy=t+y','y(0)=6', 't');
y_exact= inline(vectorize(sol));
plot(T,y_exact(T),'b*-');
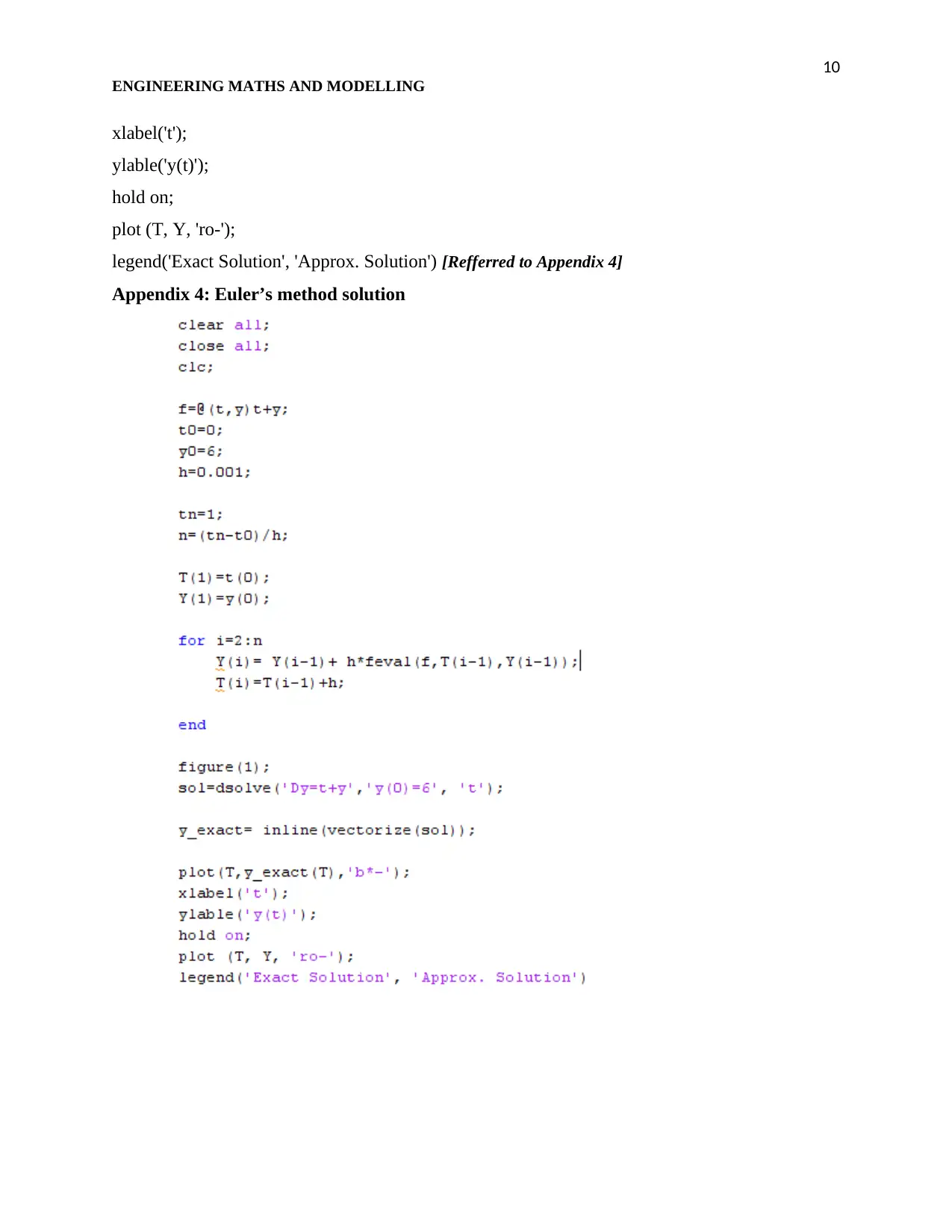
10
ENGINEERING MATHS AND MODELLING
xlabel('t');
ylable('y(t)');
hold on;
plot (T, Y, 'ro-');
legend('Exact Solution', 'Approx. Solution') [Refferred to Appendix 4]
Appendix 4: Euler’s method solution
ENGINEERING MATHS AND MODELLING
xlabel('t');
ylable('y(t)');
hold on;
plot (T, Y, 'ro-');
legend('Exact Solution', 'Approx. Solution') [Refferred to Appendix 4]
Appendix 4: Euler’s method solution
Secure Best Marks with AI Grader
Need help grading? Try our AI Grader for instant feedback on your assignments.
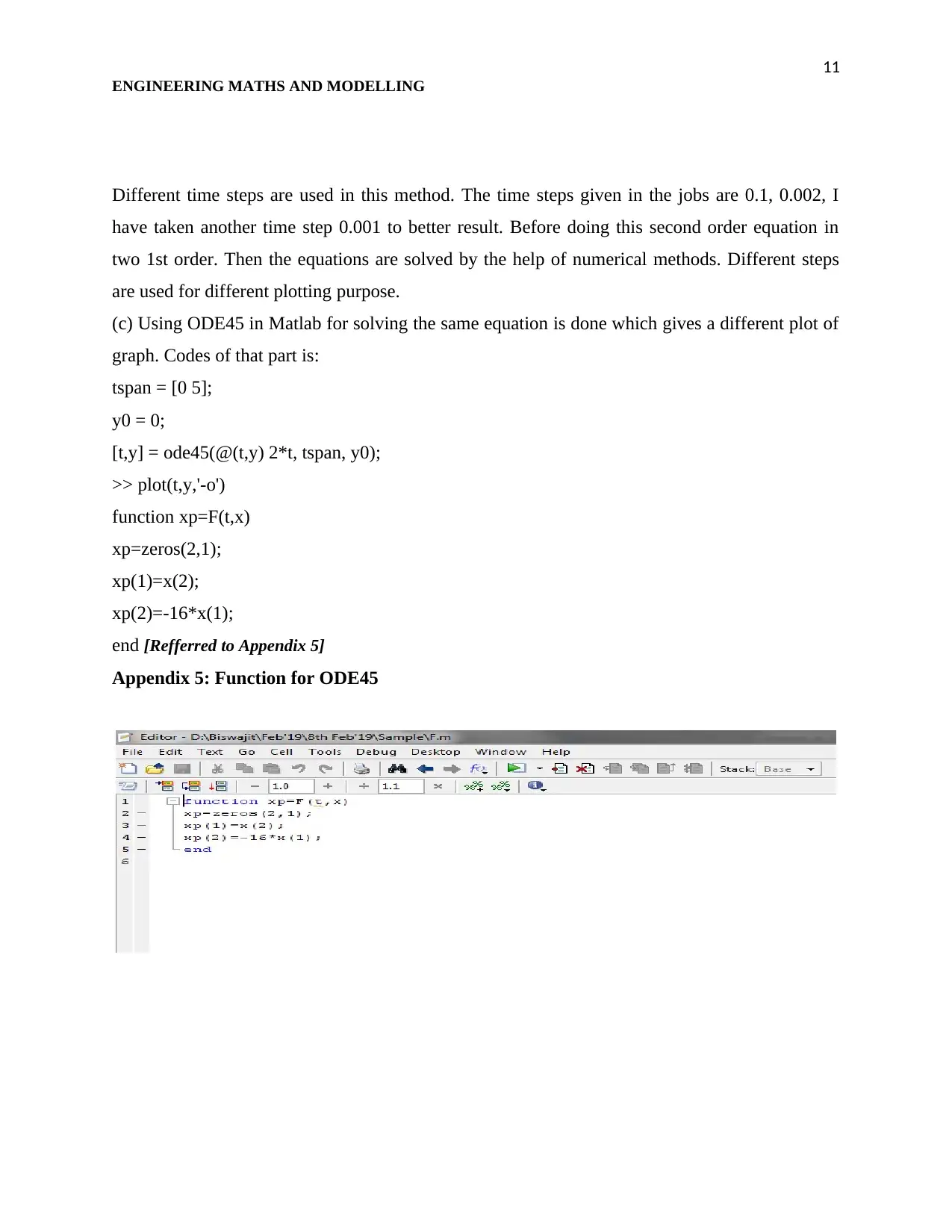
11
ENGINEERING MATHS AND MODELLING
Different time steps are used in this method. The time steps given in the jobs are 0.1, 0.002, I
have taken another time step 0.001 to better result. Before doing this second order equation in
two 1st order. Then the equations are solved by the help of numerical methods. Different steps
are used for different plotting purpose.
(c) Using ODE45 in Matlab for solving the same equation is done which gives a different plot of
graph. Codes of that part is:
tspan = [0 5];
y0 = 0;
[t,y] = ode45(@(t,y) 2*t, tspan, y0);
>> plot(t,y,'-o')
function xp=F(t,x)
xp=zeros(2,1);
xp(1)=x(2);
xp(2)=-16*x(1);
end [Refferred to Appendix 5]
Appendix 5: Function for ODE45
ENGINEERING MATHS AND MODELLING
Different time steps are used in this method. The time steps given in the jobs are 0.1, 0.002, I
have taken another time step 0.001 to better result. Before doing this second order equation in
two 1st order. Then the equations are solved by the help of numerical methods. Different steps
are used for different plotting purpose.
(c) Using ODE45 in Matlab for solving the same equation is done which gives a different plot of
graph. Codes of that part is:
tspan = [0 5];
y0 = 0;
[t,y] = ode45(@(t,y) 2*t, tspan, y0);
>> plot(t,y,'-o')
function xp=F(t,x)
xp=zeros(2,1);
xp(1)=x(2);
xp(2)=-16*x(1);
end [Refferred to Appendix 5]
Appendix 5: Function for ODE45
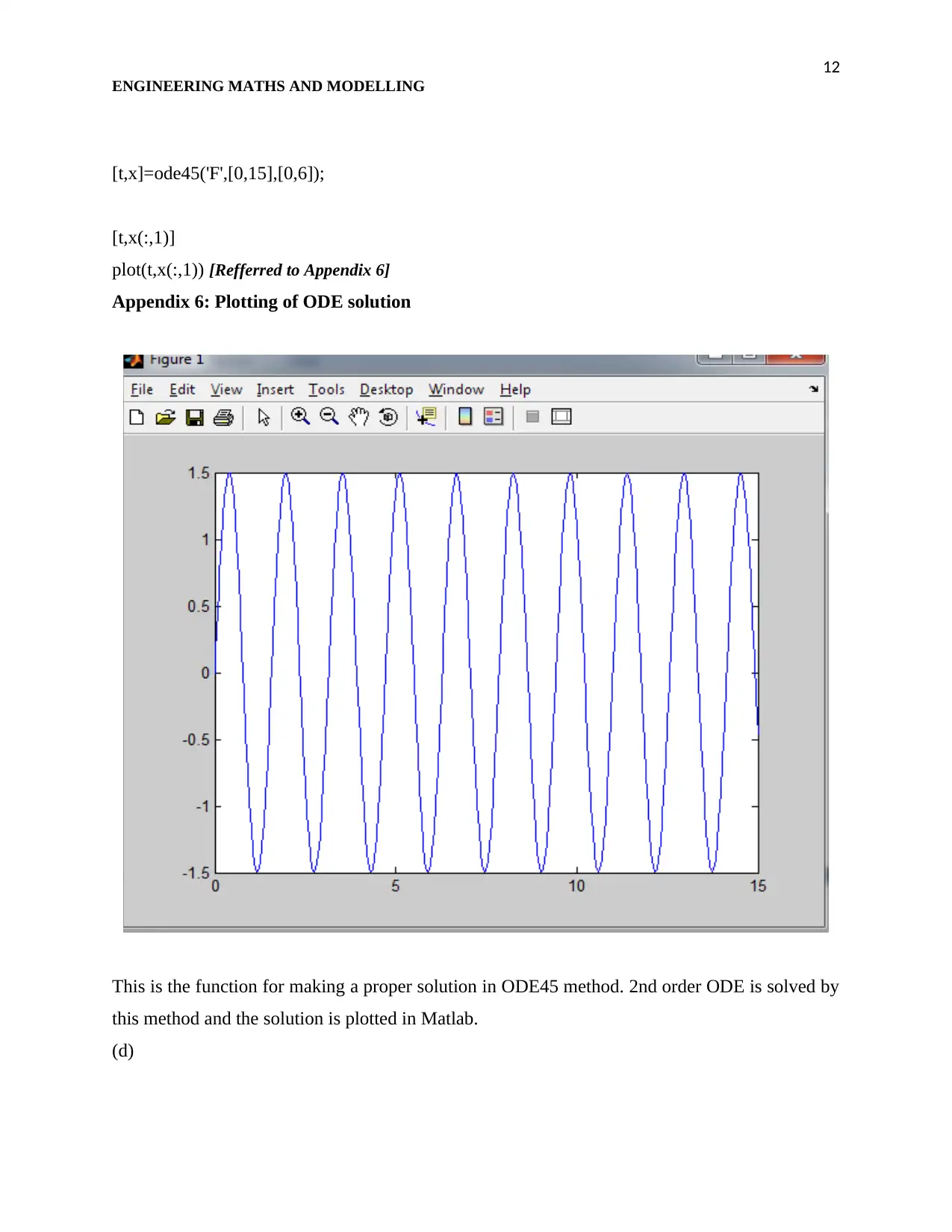
12
ENGINEERING MATHS AND MODELLING
[t,x]=ode45('F',[0,15],[0,6]);
[t,x(:,1)]
plot(t,x(:,1)) [Refferred to Appendix 6]
Appendix 6: Plotting of ODE solution
This is the function for making a proper solution in ODE45 method. 2nd order ODE is solved by
this method and the solution is plotted in Matlab.
(d)
ENGINEERING MATHS AND MODELLING
[t,x]=ode45('F',[0,15],[0,6]);
[t,x(:,1)]
plot(t,x(:,1)) [Refferred to Appendix 6]
Appendix 6: Plotting of ODE solution
This is the function for making a proper solution in ODE45 method. 2nd order ODE is solved by
this method and the solution is plotted in Matlab.
(d)
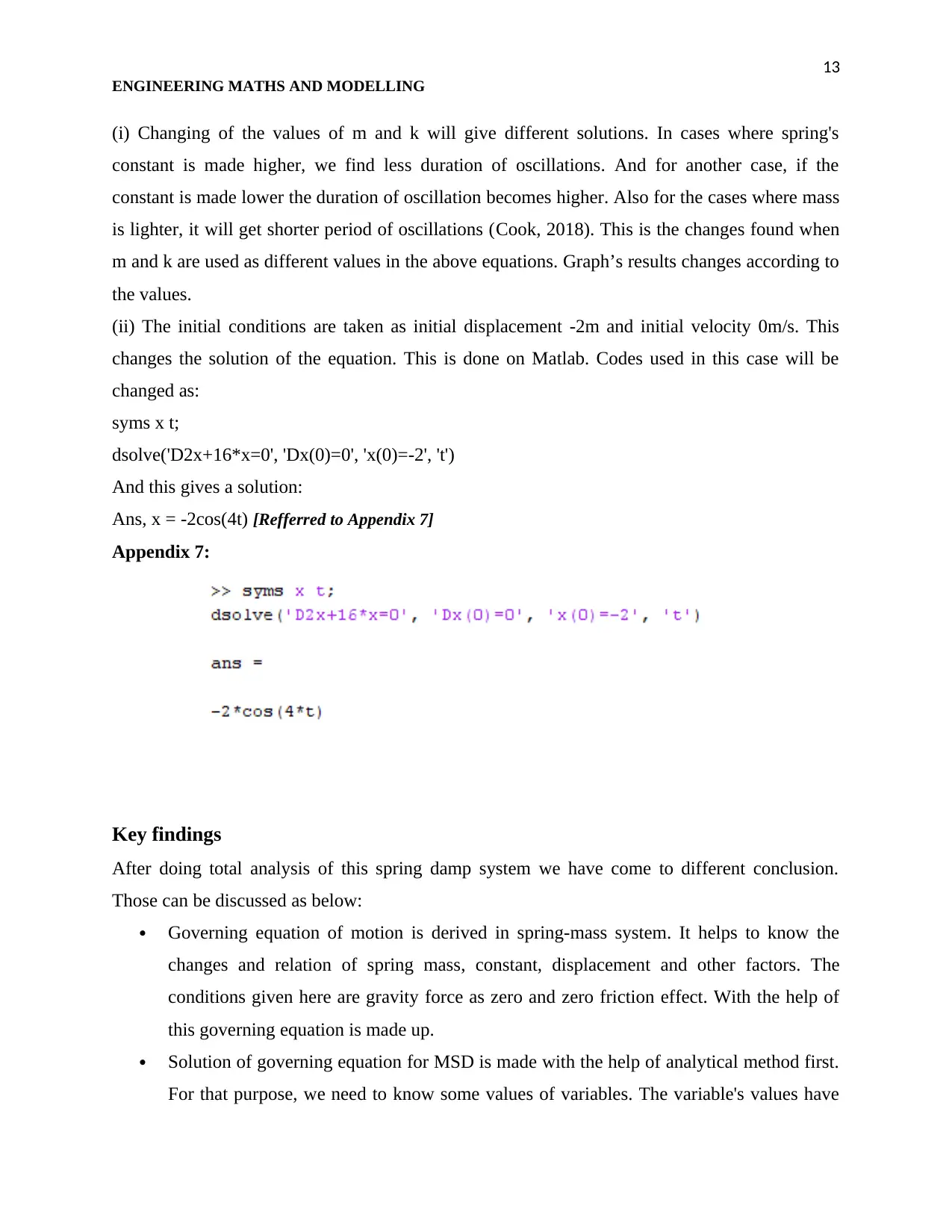
13
ENGINEERING MATHS AND MODELLING
(i) Changing of the values of m and k will give different solutions. In cases where spring's
constant is made higher, we find less duration of oscillations. And for another case, if the
constant is made lower the duration of oscillation becomes higher. Also for the cases where mass
is lighter, it will get shorter period of oscillations (Cook, 2018). This is the changes found when
m and k are used as different values in the above equations. Graph’s results changes according to
the values.
(ii) The initial conditions are taken as initial displacement -2m and initial velocity 0m/s. This
changes the solution of the equation. This is done on Matlab. Codes used in this case will be
changed as:
syms x t;
dsolve('D2x+16*x=0', 'Dx(0)=0', 'x(0)=-2', 't')
And this gives a solution:
Ans, x = -2cos(4t) [Refferred to Appendix 7]
Appendix 7:
Key findings
After doing total analysis of this spring damp system we have come to different conclusion.
Those can be discussed as below:
Governing equation of motion is derived in spring-mass system. It helps to know the
changes and relation of spring mass, constant, displacement and other factors. The
conditions given here are gravity force as zero and zero friction effect. With the help of
this governing equation is made up.
Solution of governing equation for MSD is made with the help of analytical method first.
For that purpose, we need to know some values of variables. The variable's values have
ENGINEERING MATHS AND MODELLING
(i) Changing of the values of m and k will give different solutions. In cases where spring's
constant is made higher, we find less duration of oscillations. And for another case, if the
constant is made lower the duration of oscillation becomes higher. Also for the cases where mass
is lighter, it will get shorter period of oscillations (Cook, 2018). This is the changes found when
m and k are used as different values in the above equations. Graph’s results changes according to
the values.
(ii) The initial conditions are taken as initial displacement -2m and initial velocity 0m/s. This
changes the solution of the equation. This is done on Matlab. Codes used in this case will be
changed as:
syms x t;
dsolve('D2x+16*x=0', 'Dx(0)=0', 'x(0)=-2', 't')
And this gives a solution:
Ans, x = -2cos(4t) [Refferred to Appendix 7]
Appendix 7:
Key findings
After doing total analysis of this spring damp system we have come to different conclusion.
Those can be discussed as below:
Governing equation of motion is derived in spring-mass system. It helps to know the
changes and relation of spring mass, constant, displacement and other factors. The
conditions given here are gravity force as zero and zero friction effect. With the help of
this governing equation is made up.
Solution of governing equation for MSD is made with the help of analytical method first.
For that purpose, we need to know some values of variables. The variable's values have
Paraphrase This Document
Need a fresh take? Get an instant paraphrase of this document with our AI Paraphraser
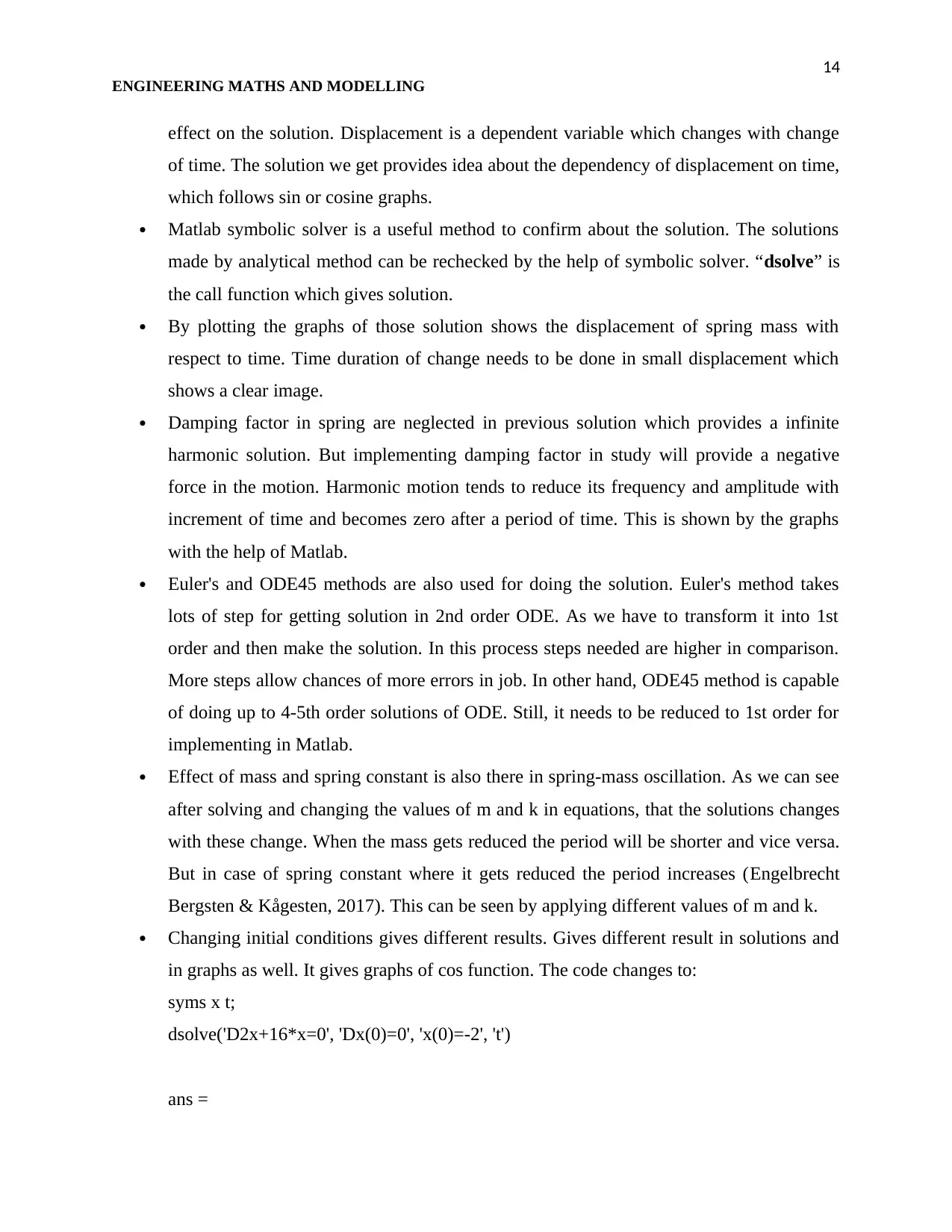
14
ENGINEERING MATHS AND MODELLING
effect on the solution. Displacement is a dependent variable which changes with change
of time. The solution we get provides idea about the dependency of displacement on time,
which follows sin or cosine graphs.
Matlab symbolic solver is a useful method to confirm about the solution. The solutions
made by analytical method can be rechecked by the help of symbolic solver. “dsolve” is
the call function which gives solution.
By plotting the graphs of those solution shows the displacement of spring mass with
respect to time. Time duration of change needs to be done in small displacement which
shows a clear image.
Damping factor in spring are neglected in previous solution which provides a infinite
harmonic solution. But implementing damping factor in study will provide a negative
force in the motion. Harmonic motion tends to reduce its frequency and amplitude with
increment of time and becomes zero after a period of time. This is shown by the graphs
with the help of Matlab.
Euler's and ODE45 methods are also used for doing the solution. Euler's method takes
lots of step for getting solution in 2nd order ODE. As we have to transform it into 1st
order and then make the solution. In this process steps needed are higher in comparison.
More steps allow chances of more errors in job. In other hand, ODE45 method is capable
of doing up to 4-5th order solutions of ODE. Still, it needs to be reduced to 1st order for
implementing in Matlab.
Effect of mass and spring constant is also there in spring-mass oscillation. As we can see
after solving and changing the values of m and k in equations, that the solutions changes
with these change. When the mass gets reduced the period will be shorter and vice versa.
But in case of spring constant where it gets reduced the period increases (Engelbrecht
Bergsten & Kågesten, 2017). This can be seen by applying different values of m and k.
Changing initial conditions gives different results. Gives different result in solutions and
in graphs as well. It gives graphs of cos function. The code changes to:
syms x t;
dsolve('D2x+16*x=0', 'Dx(0)=0', 'x(0)=-2', 't')
ans =
ENGINEERING MATHS AND MODELLING
effect on the solution. Displacement is a dependent variable which changes with change
of time. The solution we get provides idea about the dependency of displacement on time,
which follows sin or cosine graphs.
Matlab symbolic solver is a useful method to confirm about the solution. The solutions
made by analytical method can be rechecked by the help of symbolic solver. “dsolve” is
the call function which gives solution.
By plotting the graphs of those solution shows the displacement of spring mass with
respect to time. Time duration of change needs to be done in small displacement which
shows a clear image.
Damping factor in spring are neglected in previous solution which provides a infinite
harmonic solution. But implementing damping factor in study will provide a negative
force in the motion. Harmonic motion tends to reduce its frequency and amplitude with
increment of time and becomes zero after a period of time. This is shown by the graphs
with the help of Matlab.
Euler's and ODE45 methods are also used for doing the solution. Euler's method takes
lots of step for getting solution in 2nd order ODE. As we have to transform it into 1st
order and then make the solution. In this process steps needed are higher in comparison.
More steps allow chances of more errors in job. In other hand, ODE45 method is capable
of doing up to 4-5th order solutions of ODE. Still, it needs to be reduced to 1st order for
implementing in Matlab.
Effect of mass and spring constant is also there in spring-mass oscillation. As we can see
after solving and changing the values of m and k in equations, that the solutions changes
with these change. When the mass gets reduced the period will be shorter and vice versa.
But in case of spring constant where it gets reduced the period increases (Engelbrecht
Bergsten & Kågesten, 2017). This can be seen by applying different values of m and k.
Changing initial conditions gives different results. Gives different result in solutions and
in graphs as well. It gives graphs of cos function. The code changes to:
syms x t;
dsolve('D2x+16*x=0', 'Dx(0)=0', 'x(0)=-2', 't')
ans =
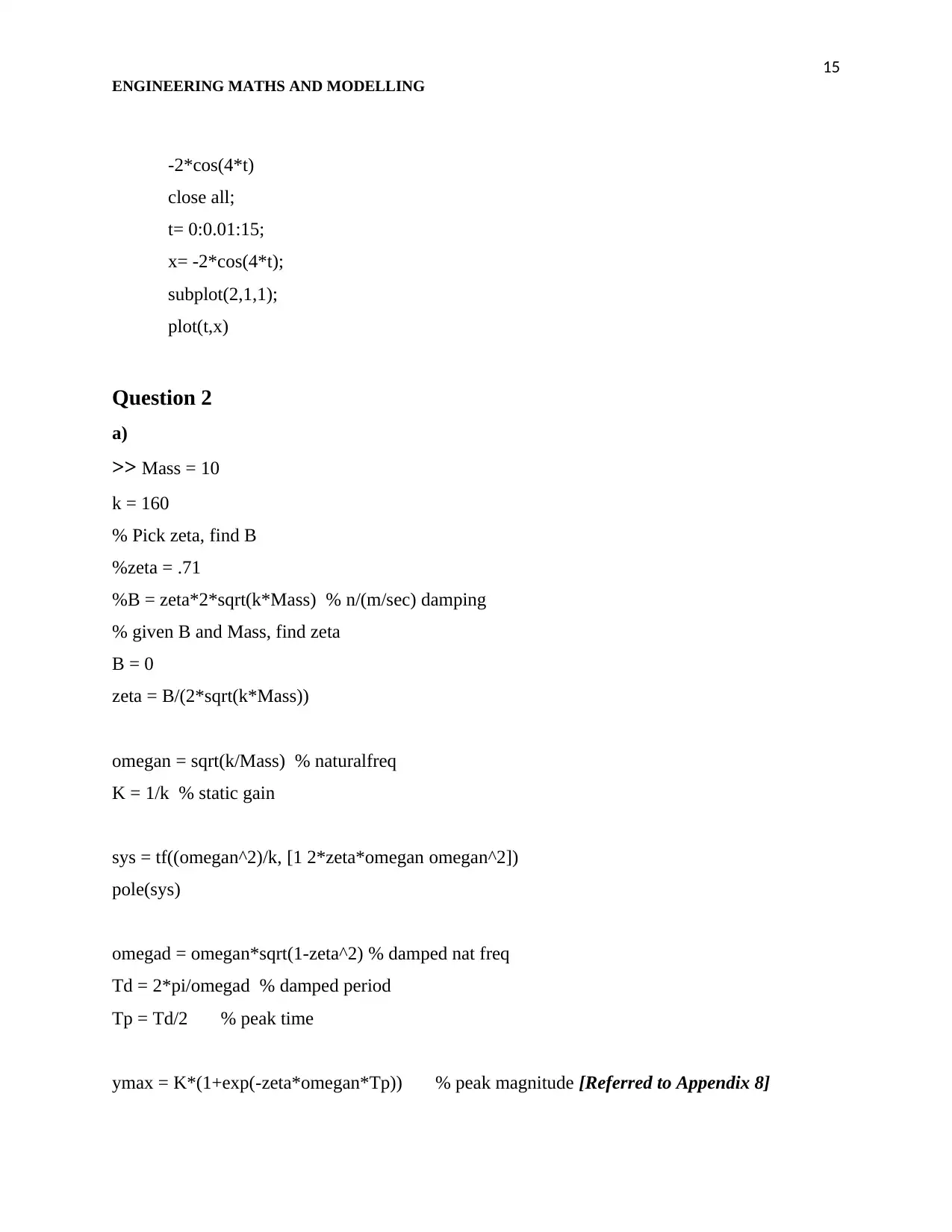
15
ENGINEERING MATHS AND MODELLING
-2*cos(4*t)
close all;
t= 0:0.01:15;
x= -2*cos(4*t);
subplot(2,1,1);
plot(t,x)
Question 2
a)
>> Mass = 10
k = 160
% Pick zeta, find B
%zeta = .71
%B = zeta*2*sqrt(k*Mass) % n/(m/sec) damping
% given B and Mass, find zeta
B = 0
zeta = B/(2*sqrt(k*Mass))
omegan = sqrt(k/Mass) % naturalfreq
K = 1/k % static gain
sys = tf((omegan^2)/k, [1 2*zeta*omegan omegan^2])
pole(sys)
omegad = omegan*sqrt(1-zeta^2) % damped nat freq
Td = 2*pi/omegad % damped period
Tp = Td/2 % peak time
ymax = K*(1+exp(-zeta*omegan*Tp)) % peak magnitude [Referred to Appendix 8]
ENGINEERING MATHS AND MODELLING
-2*cos(4*t)
close all;
t= 0:0.01:15;
x= -2*cos(4*t);
subplot(2,1,1);
plot(t,x)
Question 2
a)
>> Mass = 10
k = 160
% Pick zeta, find B
%zeta = .71
%B = zeta*2*sqrt(k*Mass) % n/(m/sec) damping
% given B and Mass, find zeta
B = 0
zeta = B/(2*sqrt(k*Mass))
omegan = sqrt(k/Mass) % naturalfreq
K = 1/k % static gain
sys = tf((omegan^2)/k, [1 2*zeta*omegan omegan^2])
pole(sys)
omegad = omegan*sqrt(1-zeta^2) % damped nat freq
Td = 2*pi/omegad % damped period
Tp = Td/2 % peak time
ymax = K*(1+exp(-zeta*omegan*Tp)) % peak magnitude [Referred to Appendix 8]
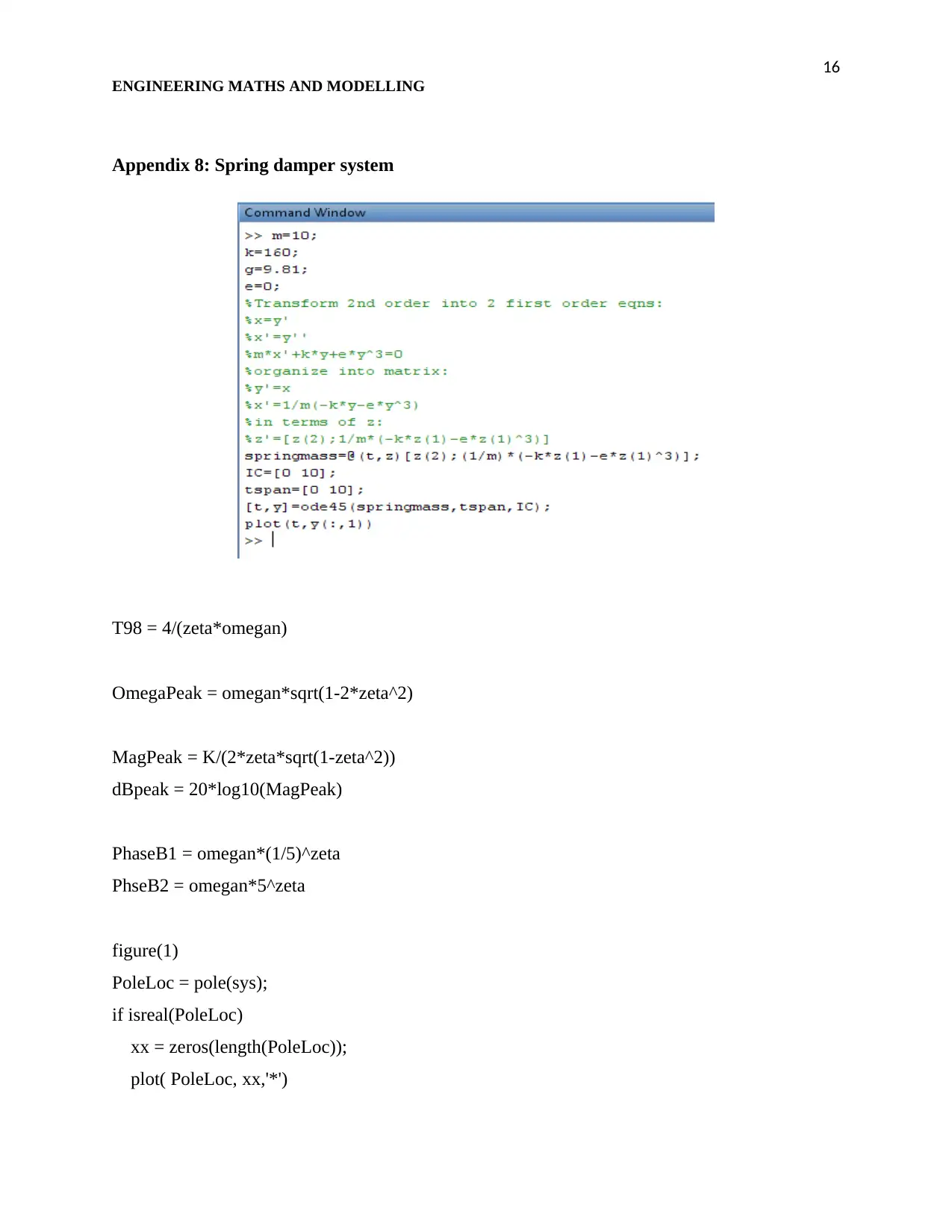
16
ENGINEERING MATHS AND MODELLING
Appendix 8: Spring damper system
T98 = 4/(zeta*omegan)
OmegaPeak = omegan*sqrt(1-2*zeta^2)
MagPeak = K/(2*zeta*sqrt(1-zeta^2))
dBpeak = 20*log10(MagPeak)
PhaseB1 = omegan*(1/5)^zeta
PhseB2 = omegan*5^zeta
figure(1)
PoleLoc = pole(sys);
if isreal(PoleLoc)
xx = zeros(length(PoleLoc));
plot( PoleLoc, xx,'*')
ENGINEERING MATHS AND MODELLING
Appendix 8: Spring damper system
T98 = 4/(zeta*omegan)
OmegaPeak = omegan*sqrt(1-2*zeta^2)
MagPeak = K/(2*zeta*sqrt(1-zeta^2))
dBpeak = 20*log10(MagPeak)
PhaseB1 = omegan*(1/5)^zeta
PhseB2 = omegan*5^zeta
figure(1)
PoleLoc = pole(sys);
if isreal(PoleLoc)
xx = zeros(length(PoleLoc));
plot( PoleLoc, xx,'*')
Secure Best Marks with AI Grader
Need help grading? Try our AI Grader for instant feedback on your assignments.
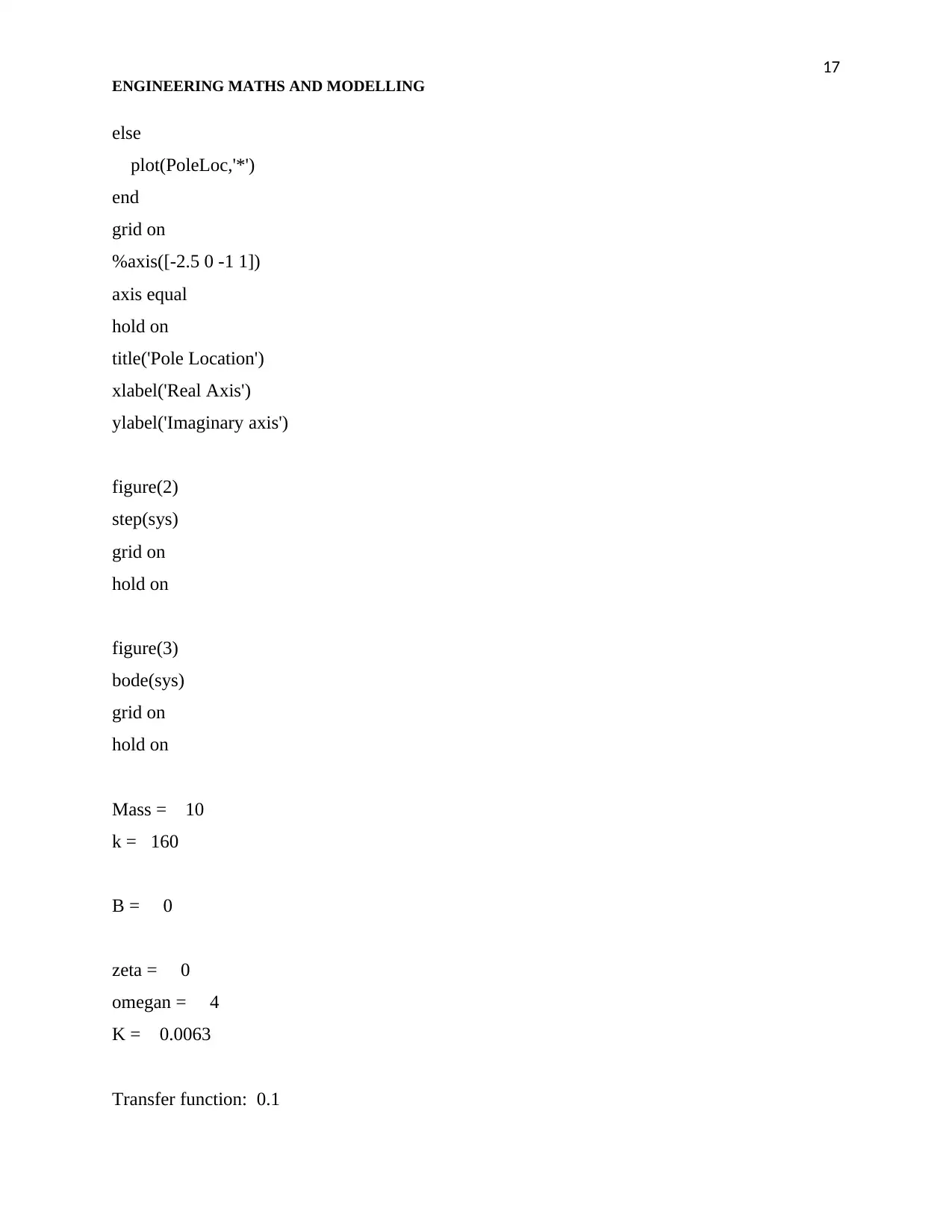
17
ENGINEERING MATHS AND MODELLING
else
plot(PoleLoc,'*')
end
grid on
%axis([-2.5 0 -1 1])
axis equal
hold on
title('Pole Location')
xlabel('Real Axis')
ylabel('Imaginary axis')
figure(2)
step(sys)
grid on
hold on
figure(3)
bode(sys)
grid on
hold on
Mass = 10
k = 160
B = 0
zeta = 0
omegan = 4
K = 0.0063
Transfer function: 0.1
ENGINEERING MATHS AND MODELLING
else
plot(PoleLoc,'*')
end
grid on
%axis([-2.5 0 -1 1])
axis equal
hold on
title('Pole Location')
xlabel('Real Axis')
ylabel('Imaginary axis')
figure(2)
step(sys)
grid on
hold on
figure(3)
bode(sys)
grid on
hold on
Mass = 10
k = 160
B = 0
zeta = 0
omegan = 4
K = 0.0063
Transfer function: 0.1
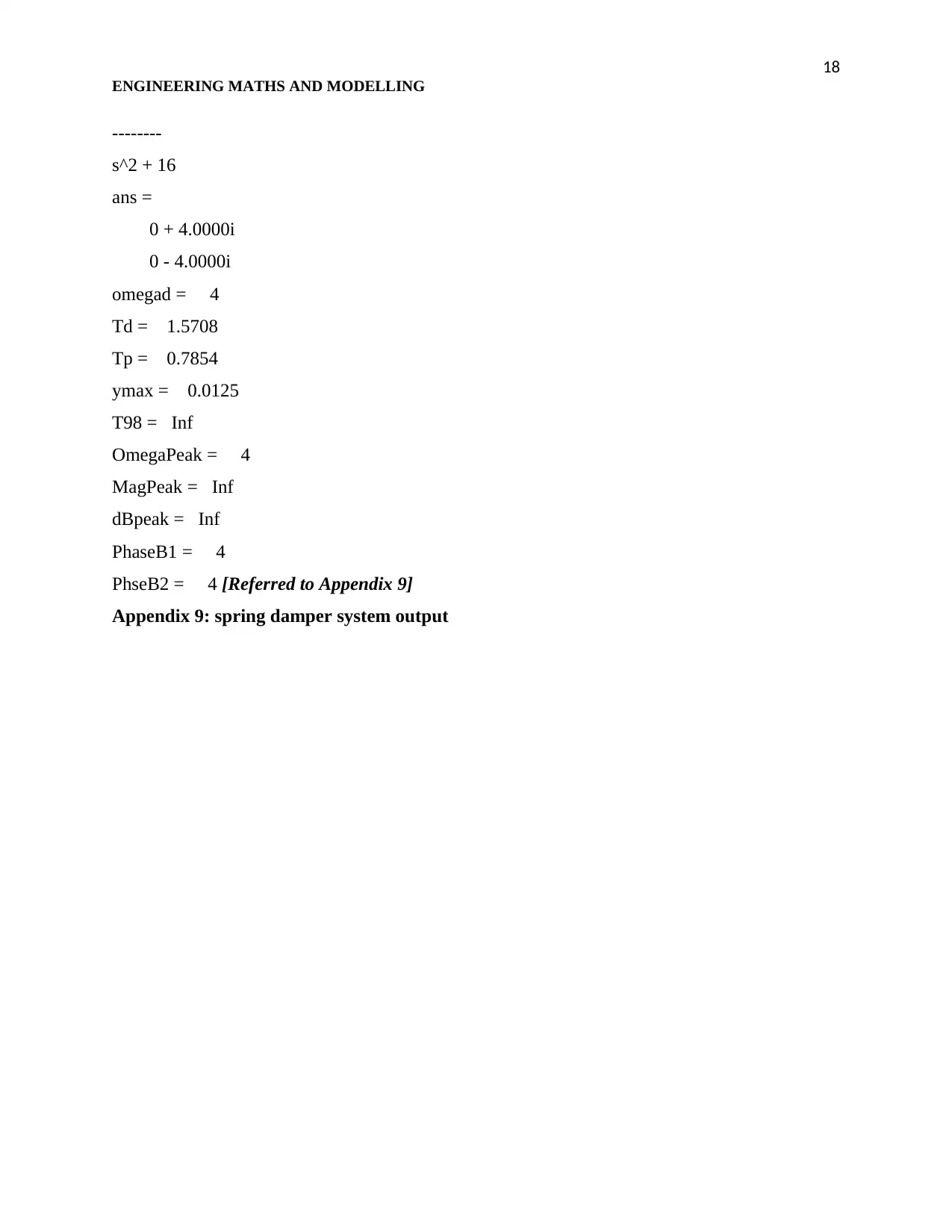
18
ENGINEERING MATHS AND MODELLING
--------
s^2 + 16
ans =
0 + 4.0000i
0 - 4.0000i
omegad = 4
Td = 1.5708
Tp = 0.7854
ymax = 0.0125
T98 = Inf
OmegaPeak = 4
MagPeak = Inf
dBpeak = Inf
PhaseB1 = 4
PhseB2 = 4 [Referred to Appendix 9]
Appendix 9: spring damper system output
ENGINEERING MATHS AND MODELLING
--------
s^2 + 16
ans =
0 + 4.0000i
0 - 4.0000i
omegad = 4
Td = 1.5708
Tp = 0.7854
ymax = 0.0125
T98 = Inf
OmegaPeak = 4
MagPeak = Inf
dBpeak = Inf
PhaseB1 = 4
PhseB2 = 4 [Referred to Appendix 9]
Appendix 9: spring damper system output
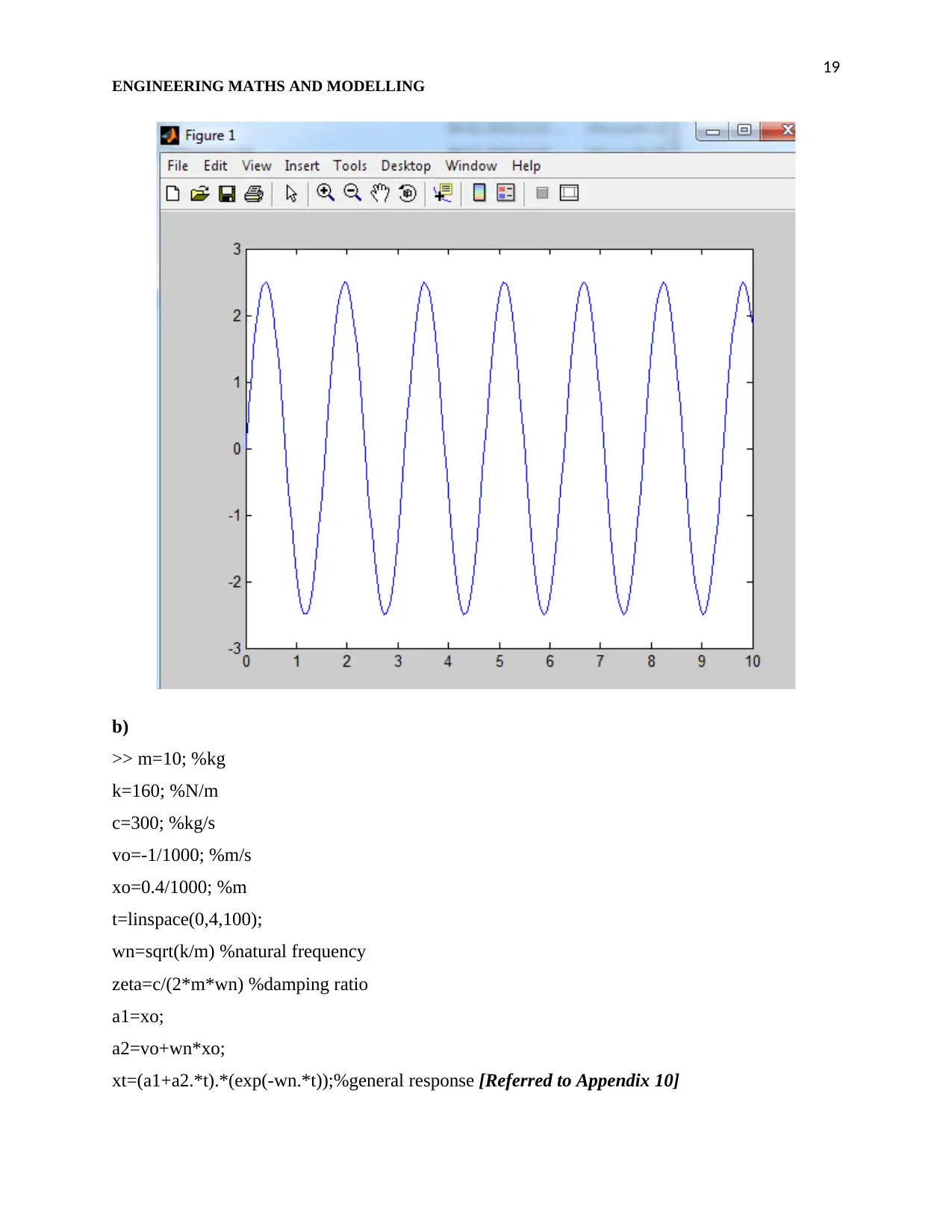
19
ENGINEERING MATHS AND MODELLING
b)
>> m=10; %kg
k=160; %N/m
c=300; %kg/s
vo=-1/1000; %m/s
xo=0.4/1000; %m
t=linspace(0,4,100);
wn=sqrt(k/m) %natural frequency
zeta=c/(2*m*wn) %damping ratio
a1=xo;
a2=vo+wn*xo;
xt=(a1+a2.*t).*(exp(-wn.*t));%general response [Referred to Appendix 10]
ENGINEERING MATHS AND MODELLING
b)
>> m=10; %kg
k=160; %N/m
c=300; %kg/s
vo=-1/1000; %m/s
xo=0.4/1000; %m
t=linspace(0,4,100);
wn=sqrt(k/m) %natural frequency
zeta=c/(2*m*wn) %damping ratio
a1=xo;
a2=vo+wn*xo;
xt=(a1+a2.*t).*(exp(-wn.*t));%general response [Referred to Appendix 10]
Paraphrase This Document
Need a fresh take? Get an instant paraphrase of this document with our AI Paraphraser
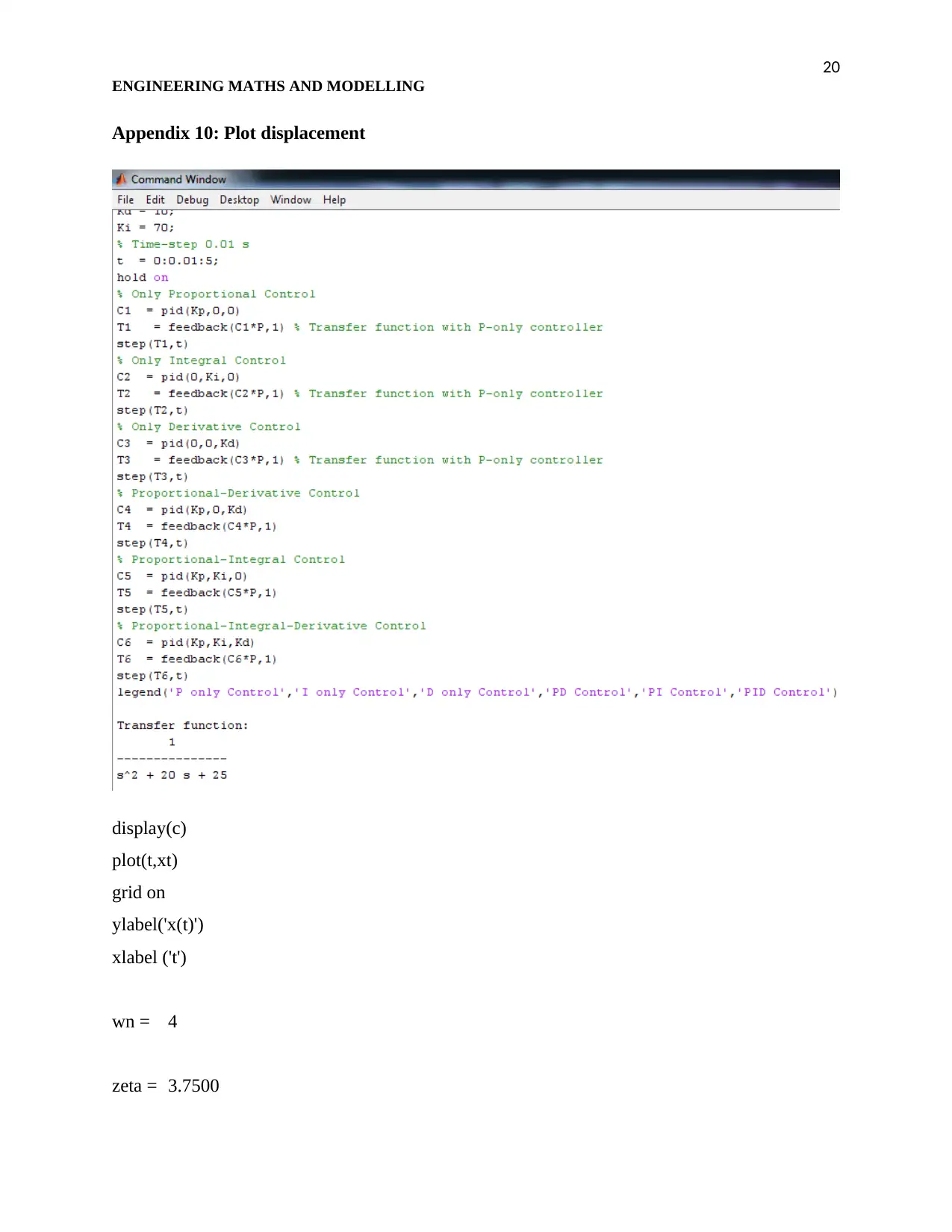
20
ENGINEERING MATHS AND MODELLING
Appendix 10: Plot displacement
display(c)
plot(t,xt)
grid on
ylabel('x(t)')
xlabel ('t')
wn = 4
zeta = 3.7500
ENGINEERING MATHS AND MODELLING
Appendix 10: Plot displacement
display(c)
plot(t,xt)
grid on
ylabel('x(t)')
xlabel ('t')
wn = 4
zeta = 3.7500
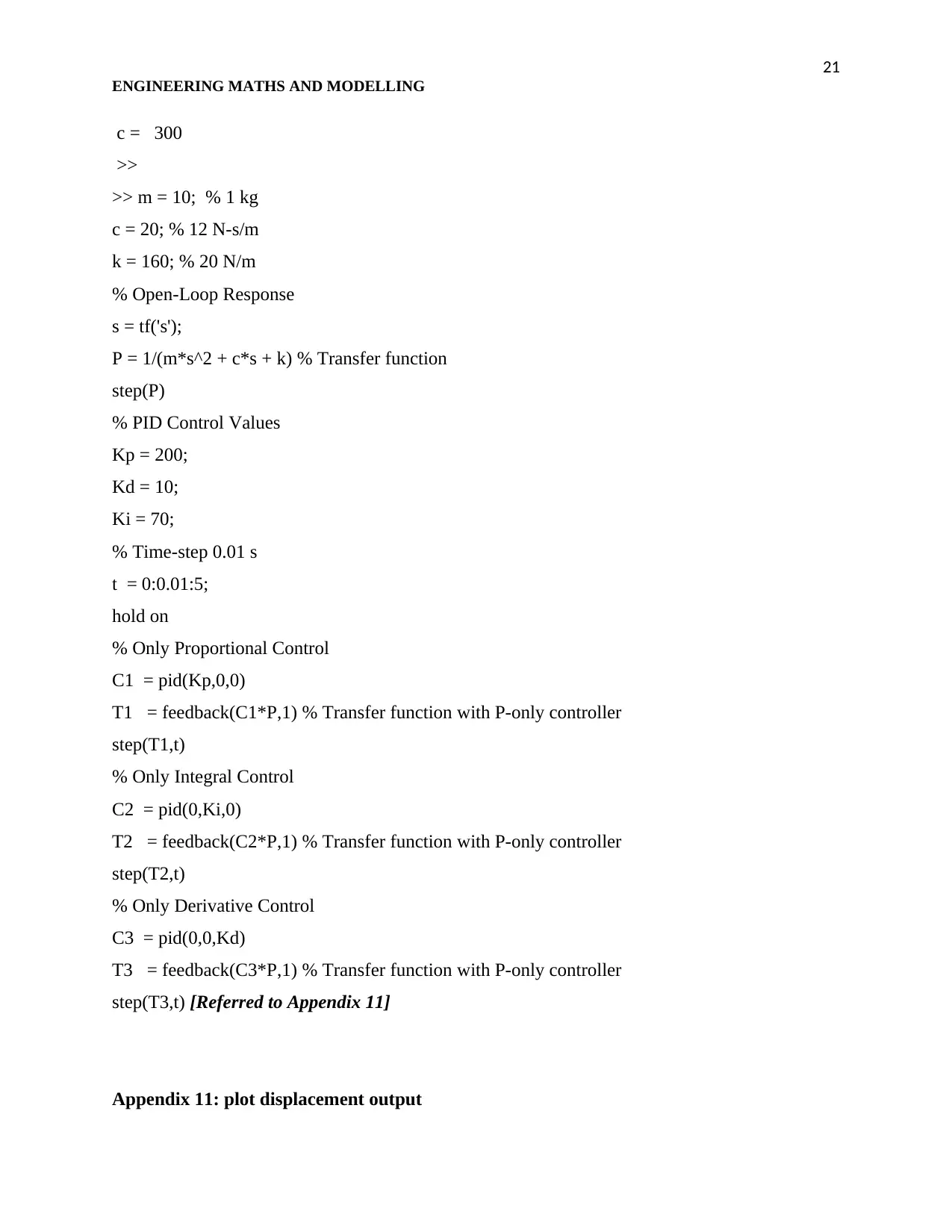
21
ENGINEERING MATHS AND MODELLING
c = 300
>>
>> m = 10; % 1 kg
c = 20; % 12 N-s/m
k = 160; % 20 N/m
% Open-Loop Response
s = tf('s');
P = 1/(m*s^2 + c*s + k) % Transfer function
step(P)
% PID Control Values
Kp = 200;
Kd = 10;
Ki = 70;
% Time-step 0.01 s
t = 0:0.01:5;
hold on
% Only Proportional Control
C1 = pid(Kp,0,0)
T1 = feedback(C1*P,1) % Transfer function with P-only controller
step(T1,t)
% Only Integral Control
C2 = pid(0,Ki,0)
T2 = feedback(C2*P,1) % Transfer function with P-only controller
step(T2,t)
% Only Derivative Control
C3 = pid(0,0,Kd)
T3 = feedback(C3*P,1) % Transfer function with P-only controller
step(T3,t) [Referred to Appendix 11]
Appendix 11: plot displacement output
ENGINEERING MATHS AND MODELLING
c = 300
>>
>> m = 10; % 1 kg
c = 20; % 12 N-s/m
k = 160; % 20 N/m
% Open-Loop Response
s = tf('s');
P = 1/(m*s^2 + c*s + k) % Transfer function
step(P)
% PID Control Values
Kp = 200;
Kd = 10;
Ki = 70;
% Time-step 0.01 s
t = 0:0.01:5;
hold on
% Only Proportional Control
C1 = pid(Kp,0,0)
T1 = feedback(C1*P,1) % Transfer function with P-only controller
step(T1,t)
% Only Integral Control
C2 = pid(0,Ki,0)
T2 = feedback(C2*P,1) % Transfer function with P-only controller
step(T2,t)
% Only Derivative Control
C3 = pid(0,0,Kd)
T3 = feedback(C3*P,1) % Transfer function with P-only controller
step(T3,t) [Referred to Appendix 11]
Appendix 11: plot displacement output
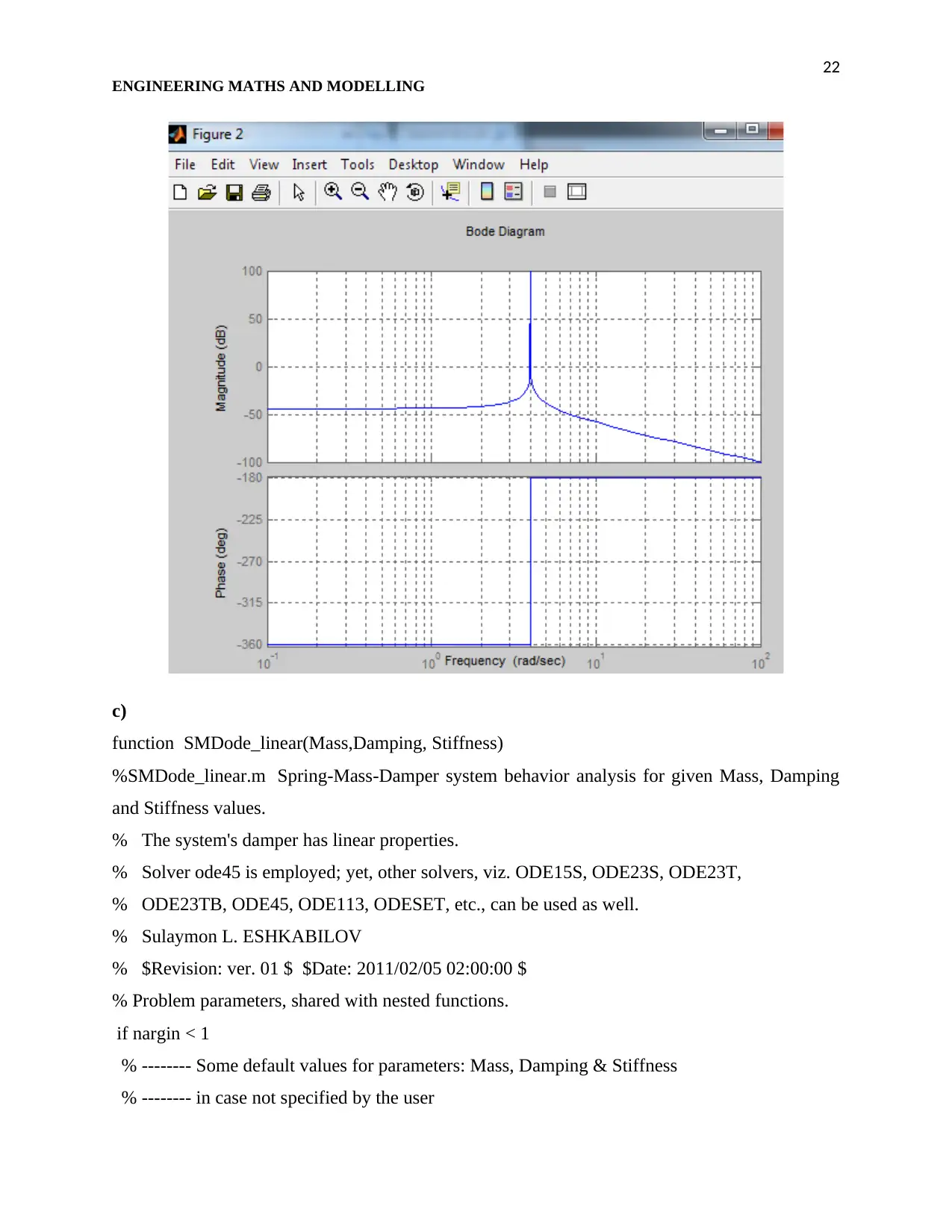
22
ENGINEERING MATHS AND MODELLING
c)
function SMDode_linear(Mass,Damping, Stiffness)
%SMDode_linear.m Spring-Mass-Damper system behavior analysis for given Mass, Damping
and Stiffness values.
% The system's damper has linear properties.
% Solver ode45 is employed; yet, other solvers, viz. ODE15S, ODE23S, ODE23T,
% ODE23TB, ODE45, ODE113, ODESET, etc., can be used as well.
% Sulaymon L. ESHKABILOV
% $Revision: ver. 01 $ $Date: 2011/02/05 02:00:00 $
% Problem parameters, shared with nested functions.
if nargin < 1
% -------- Some default values for parameters: Mass, Damping & Stiffness
% -------- in case not specified by the user
ENGINEERING MATHS AND MODELLING
c)
function SMDode_linear(Mass,Damping, Stiffness)
%SMDode_linear.m Spring-Mass-Damper system behavior analysis for given Mass, Damping
and Stiffness values.
% The system's damper has linear properties.
% Solver ode45 is employed; yet, other solvers, viz. ODE15S, ODE23S, ODE23T,
% ODE23TB, ODE45, ODE113, ODESET, etc., can be used as well.
% Sulaymon L. ESHKABILOV
% $Revision: ver. 01 $ $Date: 2011/02/05 02:00:00 $
% Problem parameters, shared with nested functions.
if nargin < 1
% -------- Some default values for parameters: Mass, Damping & Stiffness
% -------- in case not specified by the user
Secure Best Marks with AI Grader
Need help grading? Try our AI Grader for instant feedback on your assignments.
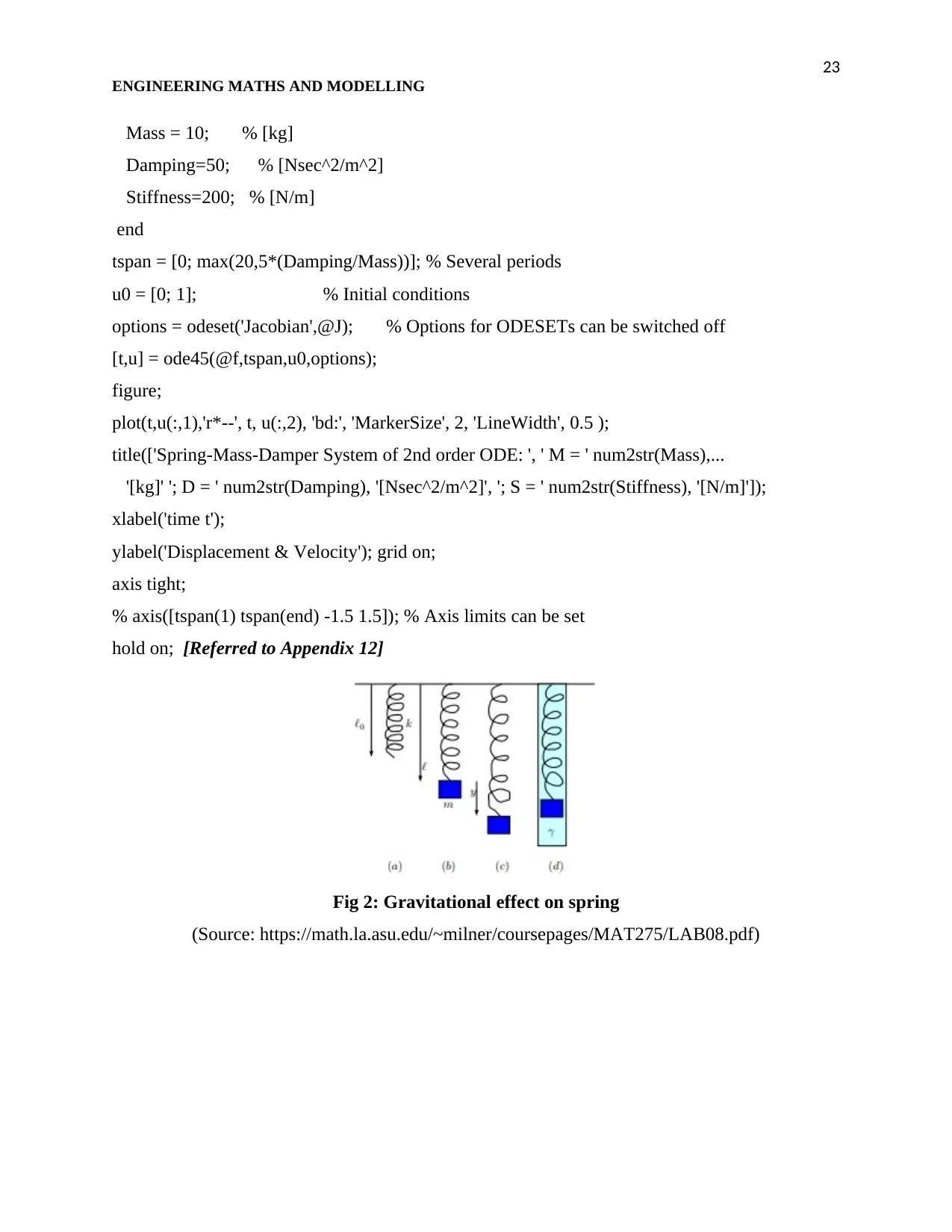
23
ENGINEERING MATHS AND MODELLING
Mass = 10; % [kg]
Damping=50; % [Nsec^2/m^2]
Stiffness=200; % [N/m]
end
tspan = [0; max(20,5*(Damping/Mass))]; % Several periods
u0 = [0; 1]; % Initial conditions
options = odeset('Jacobian',@J); % Options for ODESETs can be switched off
[t,u] = ode45(@f,tspan,u0,options);
figure;
plot(t,u(:,1),'r*--', t, u(:,2), 'bd:', 'MarkerSize', 2, 'LineWidth', 0.5 );
title(['Spring-Mass-Damper System of 2nd order ODE: ', ' M = ' num2str(Mass),...
'[kg]' '; D = ' num2str(Damping), '[Nsec^2/m^2]', '; S = ' num2str(Stiffness), '[N/m]']);
xlabel('time t');
ylabel('Displacement & Velocity'); grid on;
axis tight;
% axis([tspan(1) tspan(end) -1.5 1.5]); % Axis limits can be set
hold on; [Referred to Appendix 12]
Fig 2: Gravitational effect on spring
(Source: https://math.la.asu.edu/~milner/coursepages/MAT275/LAB08.pdf)
ENGINEERING MATHS AND MODELLING
Mass = 10; % [kg]
Damping=50; % [Nsec^2/m^2]
Stiffness=200; % [N/m]
end
tspan = [0; max(20,5*(Damping/Mass))]; % Several periods
u0 = [0; 1]; % Initial conditions
options = odeset('Jacobian',@J); % Options for ODESETs can be switched off
[t,u] = ode45(@f,tspan,u0,options);
figure;
plot(t,u(:,1),'r*--', t, u(:,2), 'bd:', 'MarkerSize', 2, 'LineWidth', 0.5 );
title(['Spring-Mass-Damper System of 2nd order ODE: ', ' M = ' num2str(Mass),...
'[kg]' '; D = ' num2str(Damping), '[Nsec^2/m^2]', '; S = ' num2str(Stiffness), '[N/m]']);
xlabel('time t');
ylabel('Displacement & Velocity'); grid on;
axis tight;
% axis([tspan(1) tspan(end) -1.5 1.5]); % Axis limits can be set
hold on; [Referred to Appendix 12]
Fig 2: Gravitational effect on spring
(Source: https://math.la.asu.edu/~milner/coursepages/MAT275/LAB08.pdf)
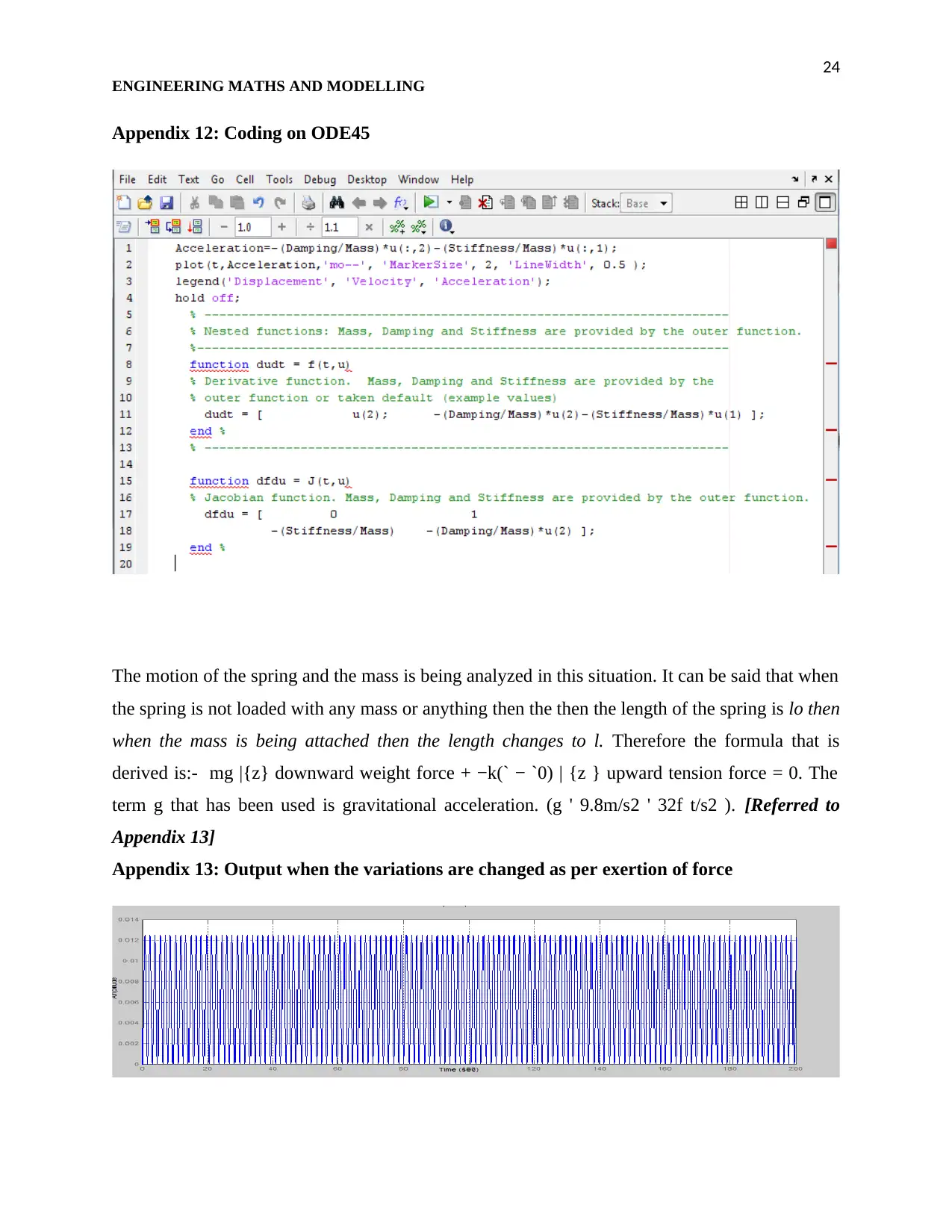
24
ENGINEERING MATHS AND MODELLING
Appendix 12: Coding on ODE45
The motion of the spring and the mass is being analyzed in this situation. It can be said that when
the spring is not loaded with any mass or anything then the then the length of the spring is lo then
when the mass is being attached then the length changes to l. Therefore the formula that is
derived is:- mg |{z} downward weight force + −k(` − `0) | {z } upward tension force = 0. The
term g that has been used is gravitational acceleration. (g ' 9.8m/s2 ' 32f t/s2 ). [Referred to
Appendix 13]
Appendix 13: Output when the variations are changed as per exertion of force
ENGINEERING MATHS AND MODELLING
Appendix 12: Coding on ODE45
The motion of the spring and the mass is being analyzed in this situation. It can be said that when
the spring is not loaded with any mass or anything then the then the length of the spring is lo then
when the mass is being attached then the length changes to l. Therefore the formula that is
derived is:- mg |{z} downward weight force + −k(` − `0) | {z } upward tension force = 0. The
term g that has been used is gravitational acceleration. (g ' 9.8m/s2 ' 32f t/s2 ). [Referred to
Appendix 13]
Appendix 13: Output when the variations are changed as per exertion of force
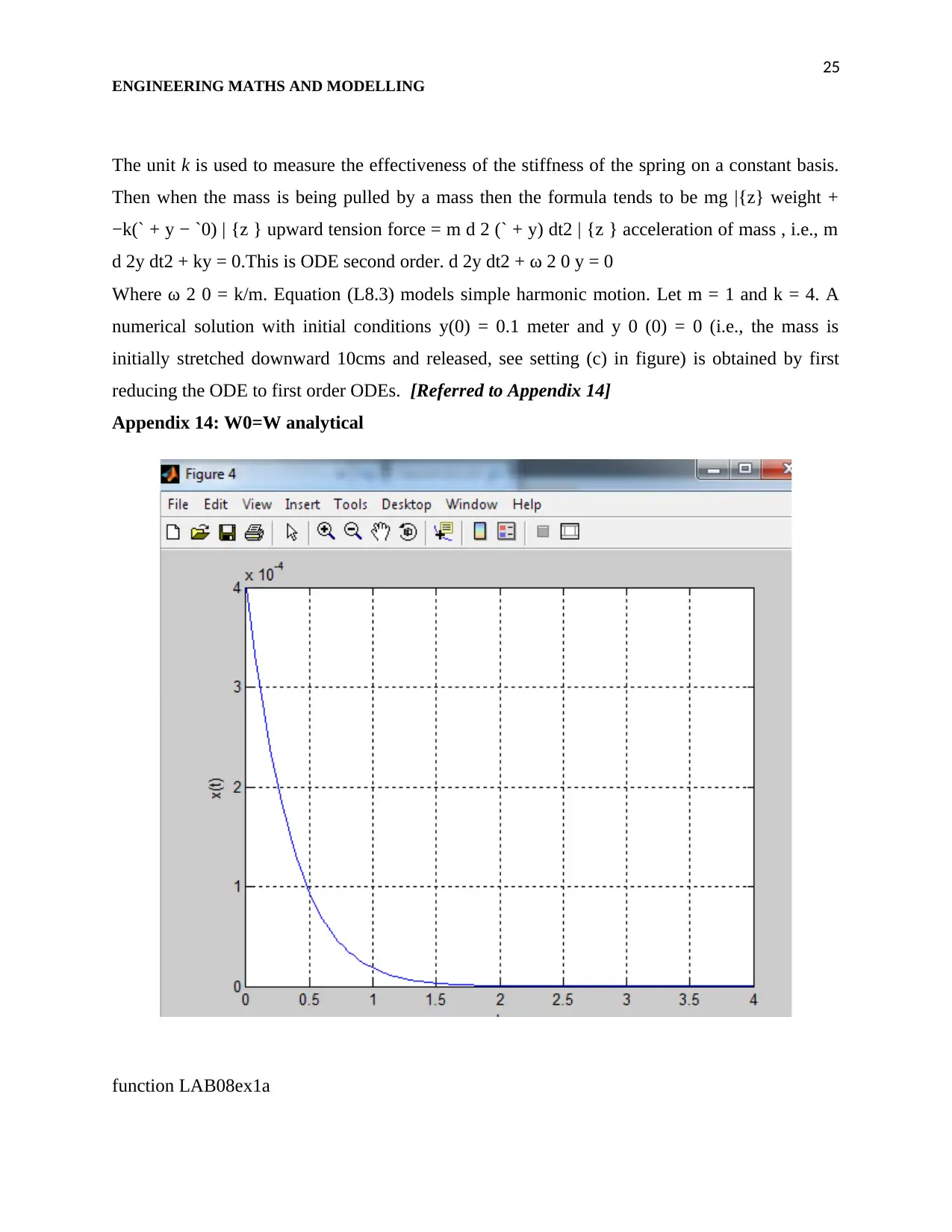
25
ENGINEERING MATHS AND MODELLING
The unit k is used to measure the effectiveness of the stiffness of the spring on a constant basis.
Then when the mass is being pulled by a mass then the formula tends to be mg |{z} weight +
−k(` + y − `0) | {z } upward tension force = m d 2 (` + y) dt2 | {z } acceleration of mass , i.e., m
d 2y dt2 + ky = 0.This is ODE second order. d 2y dt2 + ω 2 0 y = 0
Where ω 2 0 = k/m. Equation (L8.3) models simple harmonic motion. Let m = 1 and k = 4. A
numerical solution with initial conditions y(0) = 0.1 meter and y 0 (0) = 0 (i.e., the mass is
initially stretched downward 10cms and released, see setting (c) in figure) is obtained by first
reducing the ODE to first order ODEs. [Referred to Appendix 14]
Appendix 14: W0=W analytical
function LAB08ex1a
ENGINEERING MATHS AND MODELLING
The unit k is used to measure the effectiveness of the stiffness of the spring on a constant basis.
Then when the mass is being pulled by a mass then the formula tends to be mg |{z} weight +
−k(` + y − `0) | {z } upward tension force = m d 2 (` + y) dt2 | {z } acceleration of mass , i.e., m
d 2y dt2 + ky = 0.This is ODE second order. d 2y dt2 + ω 2 0 y = 0
Where ω 2 0 = k/m. Equation (L8.3) models simple harmonic motion. Let m = 1 and k = 4. A
numerical solution with initial conditions y(0) = 0.1 meter and y 0 (0) = 0 (i.e., the mass is
initially stretched downward 10cms and released, see setting (c) in figure) is obtained by first
reducing the ODE to first order ODEs. [Referred to Appendix 14]
Appendix 14: W0=W analytical
function LAB08ex1a
Paraphrase This Document
Need a fresh take? Get an instant paraphrase of this document with our AI Paraphraser
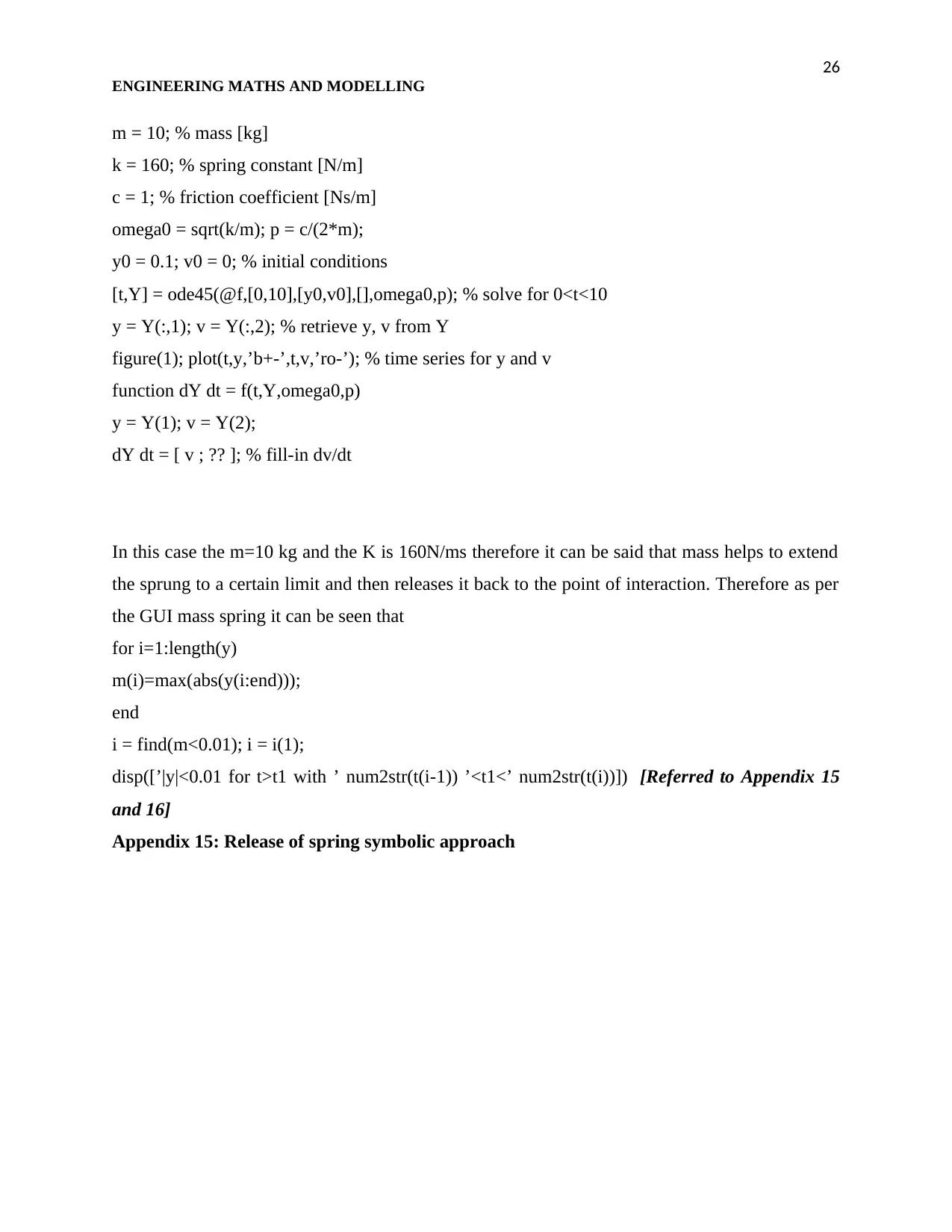
26
ENGINEERING MATHS AND MODELLING
m = 10; % mass [kg]
k = 160; % spring constant [N/m]
c = 1; % friction coefficient [Ns/m]
omega0 = sqrt(k/m); p = c/(2*m);
y0 = 0.1; v0 = 0; % initial conditions
[t,Y] = ode45(@f,[0,10],[y0,v0],[],omega0,p); % solve for 0<t<10
y = Y(:,1); v = Y(:,2); % retrieve y, v from Y
figure(1); plot(t,y,’b+-’,t,v,’ro-’); % time series for y and v
function dY dt = f(t,Y,omega0,p)
y = Y(1); v = Y(2);
dY dt = [ v ; ?? ]; % fill-in dv/dt
In this case the m=10 kg and the K is 160N/ms therefore it can be said that mass helps to extend
the sprung to a certain limit and then releases it back to the point of interaction. Therefore as per
the GUI mass spring it can be seen that
for i=1:length(y)
m(i)=max(abs(y(i:end)));
end
i = find(m<0.01); i = i(1);
disp([’|y|<0.01 for t>t1 with ’ num2str(t(i-1)) ’<t1<’ num2str(t(i))]) [Referred to Appendix 15
and 16]
Appendix 15: Release of spring symbolic approach
ENGINEERING MATHS AND MODELLING
m = 10; % mass [kg]
k = 160; % spring constant [N/m]
c = 1; % friction coefficient [Ns/m]
omega0 = sqrt(k/m); p = c/(2*m);
y0 = 0.1; v0 = 0; % initial conditions
[t,Y] = ode45(@f,[0,10],[y0,v0],[],omega0,p); % solve for 0<t<10
y = Y(:,1); v = Y(:,2); % retrieve y, v from Y
figure(1); plot(t,y,’b+-’,t,v,’ro-’); % time series for y and v
function dY dt = f(t,Y,omega0,p)
y = Y(1); v = Y(2);
dY dt = [ v ; ?? ]; % fill-in dv/dt
In this case the m=10 kg and the K is 160N/ms therefore it can be said that mass helps to extend
the sprung to a certain limit and then releases it back to the point of interaction. Therefore as per
the GUI mass spring it can be seen that
for i=1:length(y)
m(i)=max(abs(y(i:end)));
end
i = find(m<0.01); i = i(1);
disp([’|y|<0.01 for t>t1 with ’ num2str(t(i-1)) ’<t1<’ num2str(t(i))]) [Referred to Appendix 15
and 16]
Appendix 15: Release of spring symbolic approach
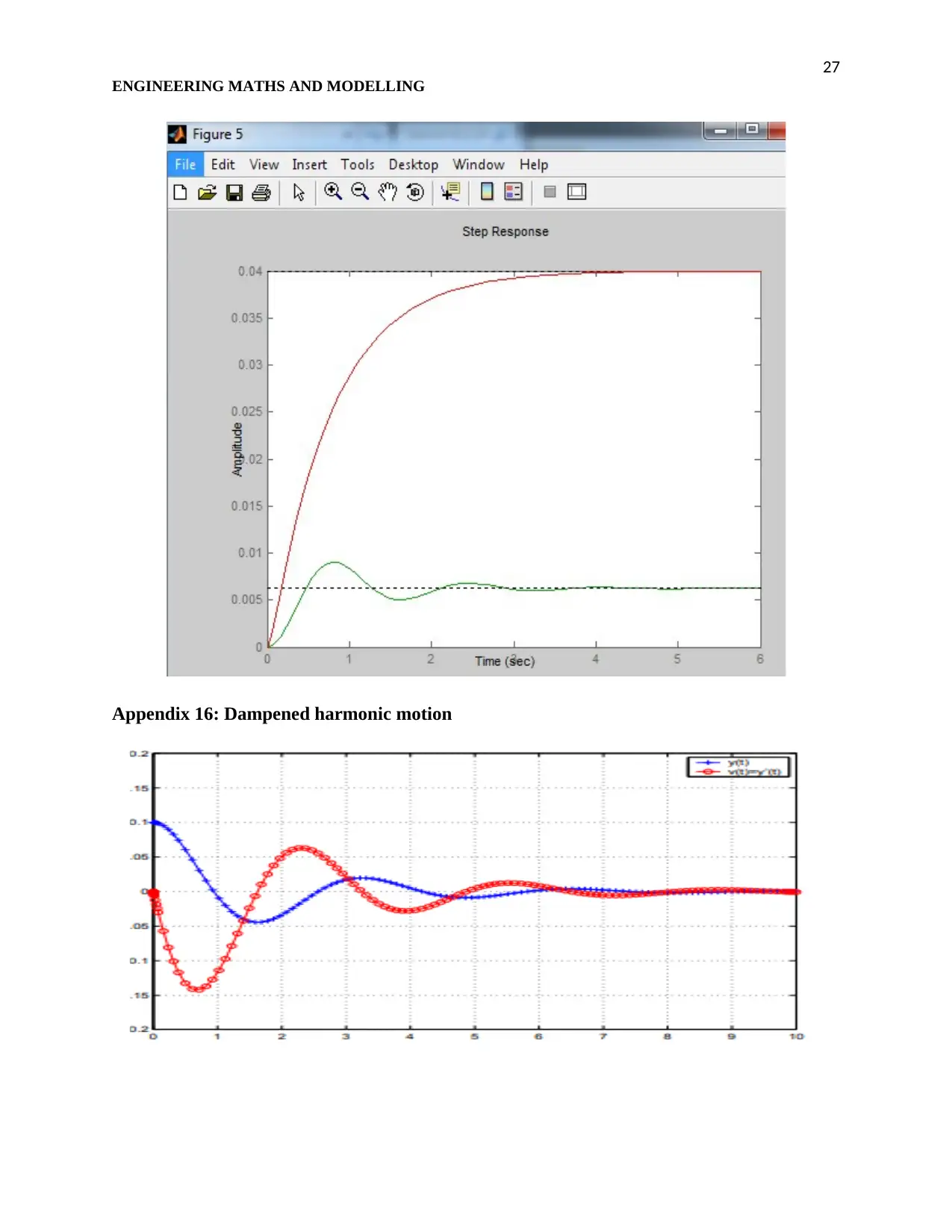
27
ENGINEERING MATHS AND MODELLING
Appendix 16: Dampened harmonic motion
ENGINEERING MATHS AND MODELLING
Appendix 16: Dampened harmonic motion
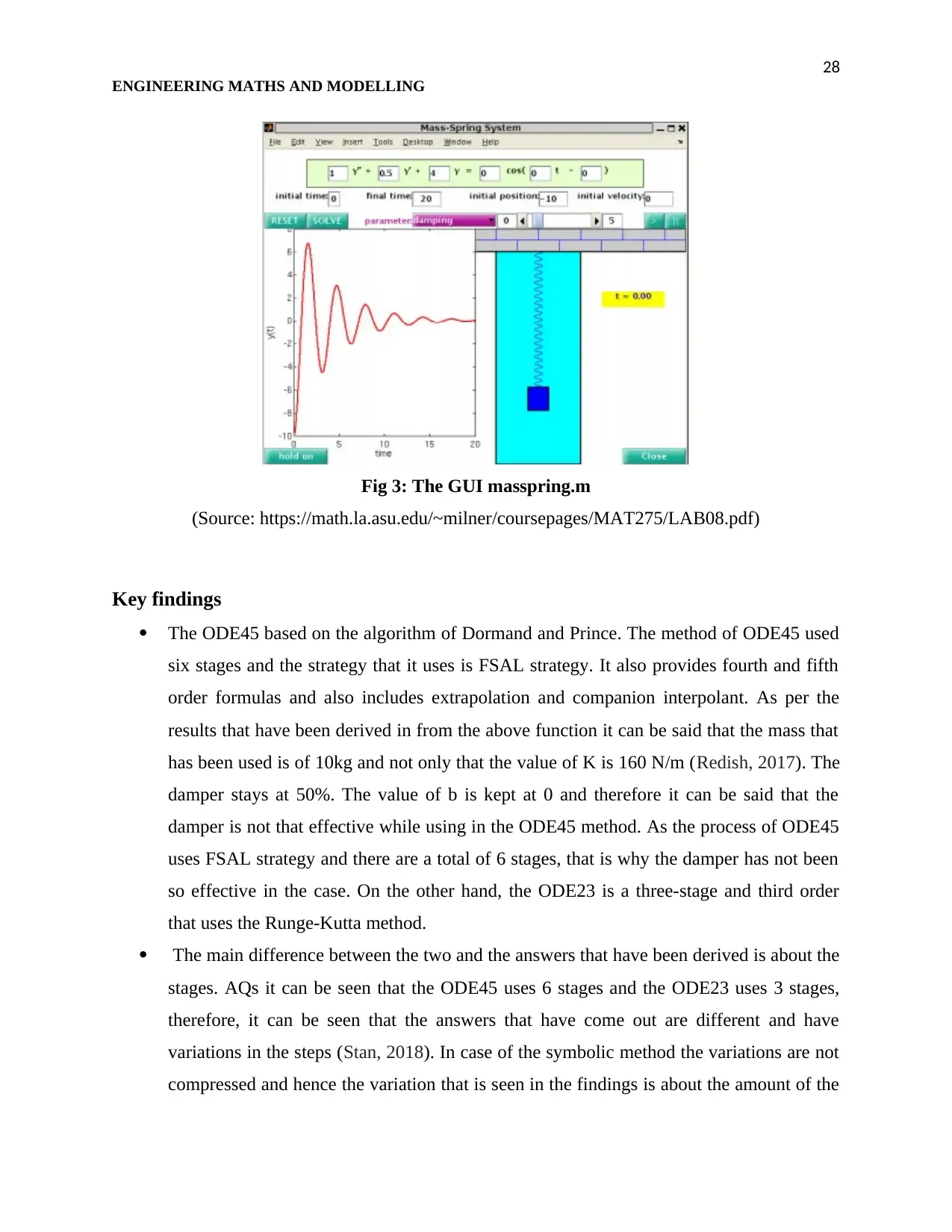
28
ENGINEERING MATHS AND MODELLING
Fig 3: The GUI masspring.m
(Source: https://math.la.asu.edu/~milner/coursepages/MAT275/LAB08.pdf)
Key findings
The ODE45 based on the algorithm of Dormand and Prince. The method of ODE45 used
six stages and the strategy that it uses is FSAL strategy. It also provides fourth and fifth
order formulas and also includes extrapolation and companion interpolant. As per the
results that have been derived in from the above function it can be said that the mass that
has been used is of 10kg and not only that the value of K is 160 N/m (Redish, 2017). The
damper stays at 50%. The value of b is kept at 0 and therefore it can be said that the
damper is not that effective while using in the ODE45 method. As the process of ODE45
uses FSAL strategy and there are a total of 6 stages, that is why the damper has not been
so effective in the case. On the other hand, the ODE23 is a three-stage and third order
that uses the Runge-Kutta method.
The main difference between the two and the answers that have been derived is about the
stages. AQs it can be seen that the ODE45 uses 6 stages and the ODE23 uses 3 stages,
therefore, it can be seen that the answers that have come out are different and have
variations in the steps (Stan, 2018). In case of the symbolic method the variations are not
compressed and hence the variation that is seen in the findings is about the amount of the
ENGINEERING MATHS AND MODELLING
Fig 3: The GUI masspring.m
(Source: https://math.la.asu.edu/~milner/coursepages/MAT275/LAB08.pdf)
Key findings
The ODE45 based on the algorithm of Dormand and Prince. The method of ODE45 used
six stages and the strategy that it uses is FSAL strategy. It also provides fourth and fifth
order formulas and also includes extrapolation and companion interpolant. As per the
results that have been derived in from the above function it can be said that the mass that
has been used is of 10kg and not only that the value of K is 160 N/m (Redish, 2017). The
damper stays at 50%. The value of b is kept at 0 and therefore it can be said that the
damper is not that effective while using in the ODE45 method. As the process of ODE45
uses FSAL strategy and there are a total of 6 stages, that is why the damper has not been
so effective in the case. On the other hand, the ODE23 is a three-stage and third order
that uses the Runge-Kutta method.
The main difference between the two and the answers that have been derived is about the
stages. AQs it can be seen that the ODE45 uses 6 stages and the ODE23 uses 3 stages,
therefore, it can be seen that the answers that have come out are different and have
variations in the steps (Stan, 2018). In case of the symbolic method the variations are not
compressed and hence the variation that is seen in the findings is about the amount of the
Secure Best Marks with AI Grader
Need help grading? Try our AI Grader for instant feedback on your assignments.
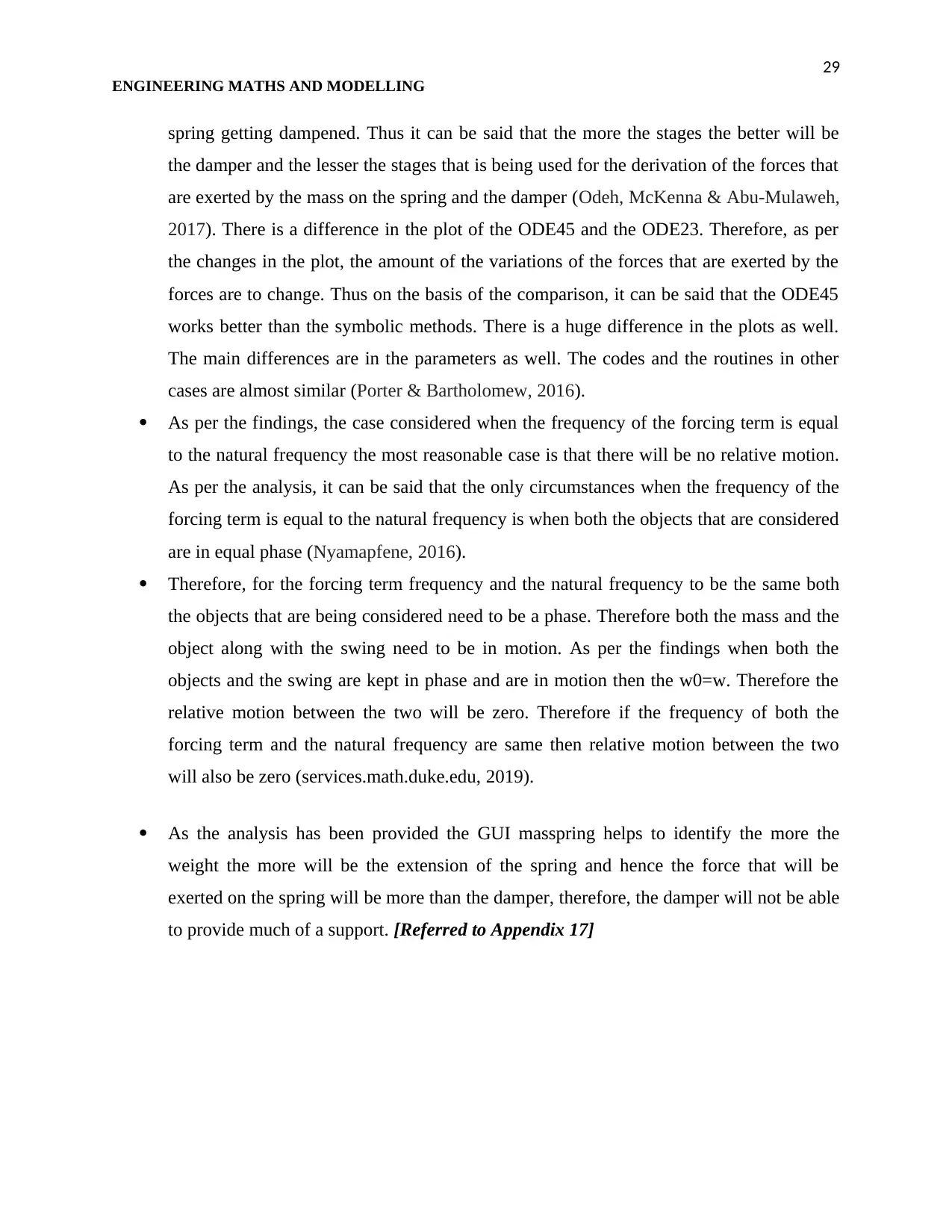
29
ENGINEERING MATHS AND MODELLING
spring getting dampened. Thus it can be said that the more the stages the better will be
the damper and the lesser the stages that is being used for the derivation of the forces that
are exerted by the mass on the spring and the damper (Odeh, McKenna & Abu-Mulaweh,
2017). There is a difference in the plot of the ODE45 and the ODE23. Therefore, as per
the changes in the plot, the amount of the variations of the forces that are exerted by the
forces are to change. Thus on the basis of the comparison, it can be said that the ODE45
works better than the symbolic methods. There is a huge difference in the plots as well.
The main differences are in the parameters as well. The codes and the routines in other
cases are almost similar (Porter & Bartholomew, 2016).
As per the findings, the case considered when the frequency of the forcing term is equal
to the natural frequency the most reasonable case is that there will be no relative motion.
As per the analysis, it can be said that the only circumstances when the frequency of the
forcing term is equal to the natural frequency is when both the objects that are considered
are in equal phase (Nyamapfene, 2016).
Therefore, for the forcing term frequency and the natural frequency to be the same both
the objects that are being considered need to be a phase. Therefore both the mass and the
object along with the swing need to be in motion. As per the findings when both the
objects and the swing are kept in phase and are in motion then the w0=w. Therefore the
relative motion between the two will be zero. Therefore if the frequency of both the
forcing term and the natural frequency are same then relative motion between the two
will also be zero (services.math.duke.edu, 2019).
As the analysis has been provided the GUI masspring helps to identify the more the
weight the more will be the extension of the spring and hence the force that will be
exerted on the spring will be more than the damper, therefore, the damper will not be able
to provide much of a support. [Referred to Appendix 17]
ENGINEERING MATHS AND MODELLING
spring getting dampened. Thus it can be said that the more the stages the better will be
the damper and the lesser the stages that is being used for the derivation of the forces that
are exerted by the mass on the spring and the damper (Odeh, McKenna & Abu-Mulaweh,
2017). There is a difference in the plot of the ODE45 and the ODE23. Therefore, as per
the changes in the plot, the amount of the variations of the forces that are exerted by the
forces are to change. Thus on the basis of the comparison, it can be said that the ODE45
works better than the symbolic methods. There is a huge difference in the plots as well.
The main differences are in the parameters as well. The codes and the routines in other
cases are almost similar (Porter & Bartholomew, 2016).
As per the findings, the case considered when the frequency of the forcing term is equal
to the natural frequency the most reasonable case is that there will be no relative motion.
As per the analysis, it can be said that the only circumstances when the frequency of the
forcing term is equal to the natural frequency is when both the objects that are considered
are in equal phase (Nyamapfene, 2016).
Therefore, for the forcing term frequency and the natural frequency to be the same both
the objects that are being considered need to be a phase. Therefore both the mass and the
object along with the swing need to be in motion. As per the findings when both the
objects and the swing are kept in phase and are in motion then the w0=w. Therefore the
relative motion between the two will be zero. Therefore if the frequency of both the
forcing term and the natural frequency are same then relative motion between the two
will also be zero (services.math.duke.edu, 2019).
As the analysis has been provided the GUI masspring helps to identify the more the
weight the more will be the extension of the spring and hence the force that will be
exerted on the spring will be more than the damper, therefore, the damper will not be able
to provide much of a support. [Referred to Appendix 17]
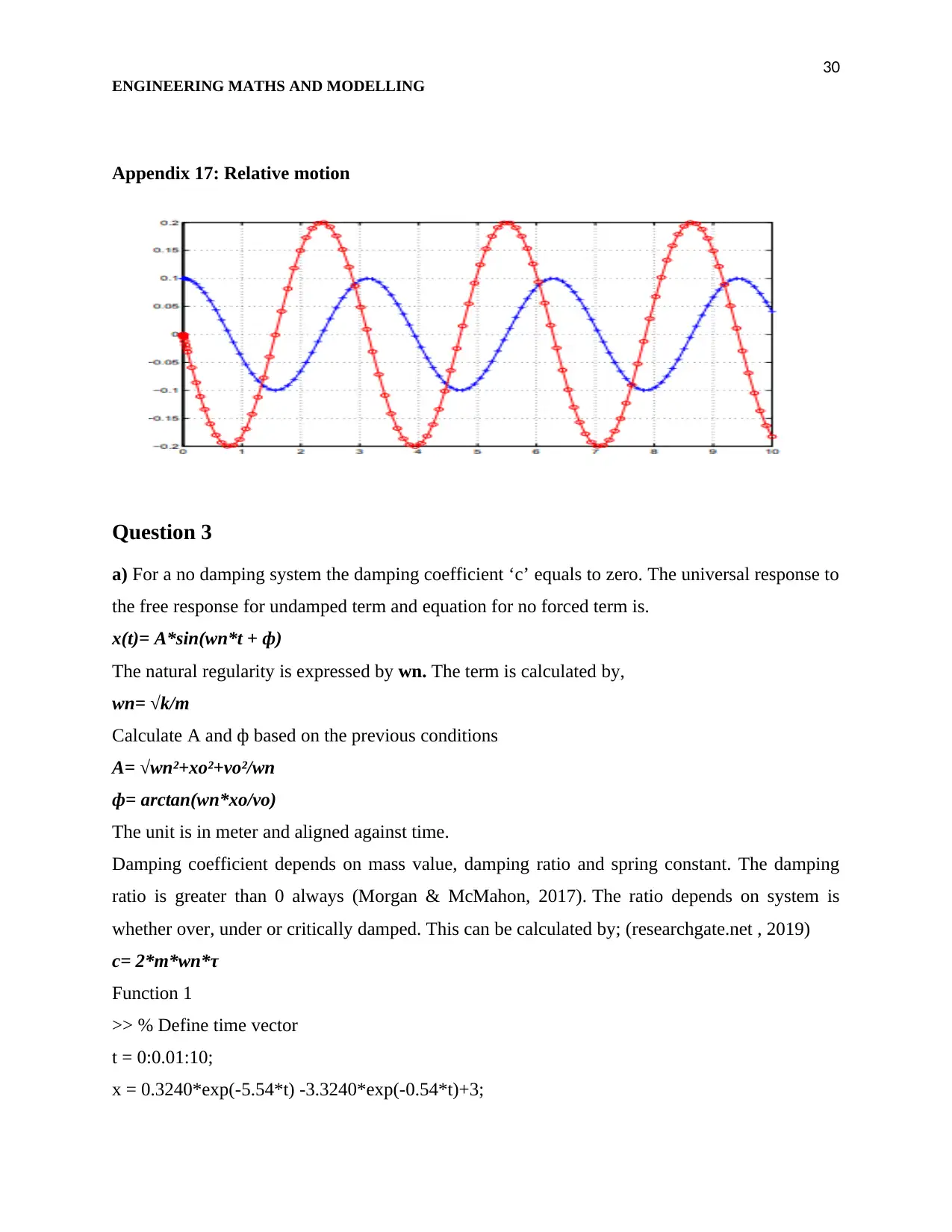
30
ENGINEERING MATHS AND MODELLING
Appendix 17: Relative motion
Question 3
a) For a no damping system the damping coefficient ‘c’ equals to zero. The universal response to
the free response for undamped term and equation for no forced term is.
x(t)= A*sin(wn*t + ф)
The natural regularity is expressed by wn. The term is calculated by,
wn= √k/m
Calculate A and ф based on the previous conditions
A= √wn²+xo²+vo²/wn
ф= arctan(wn*xo/vo)
The unit is in meter and aligned against time.
Damping coefficient depends on mass value, damping ratio and spring constant. The damping
ratio is greater than 0 always (Morgan & McMahon, 2017). The ratio depends on system is
whether over, under or critically damped. This can be calculated by; (researchgate.net , 2019)
c= 2*m*wn*τ
Function 1
>> % Define time vector
t = 0:0.01:10;
x = 0.3240*exp(-5.54*t) -3.3240*exp(-0.54*t)+3;
ENGINEERING MATHS AND MODELLING
Appendix 17: Relative motion
Question 3
a) For a no damping system the damping coefficient ‘c’ equals to zero. The universal response to
the free response for undamped term and equation for no forced term is.
x(t)= A*sin(wn*t + ф)
The natural regularity is expressed by wn. The term is calculated by,
wn= √k/m
Calculate A and ф based on the previous conditions
A= √wn²+xo²+vo²/wn
ф= arctan(wn*xo/vo)
The unit is in meter and aligned against time.
Damping coefficient depends on mass value, damping ratio and spring constant. The damping
ratio is greater than 0 always (Morgan & McMahon, 2017). The ratio depends on system is
whether over, under or critically damped. This can be calculated by; (researchgate.net , 2019)
c= 2*m*wn*τ
Function 1
>> % Define time vector
t = 0:0.01:10;
x = 0.3240*exp(-5.54*t) -3.3240*exp(-0.54*t)+3;
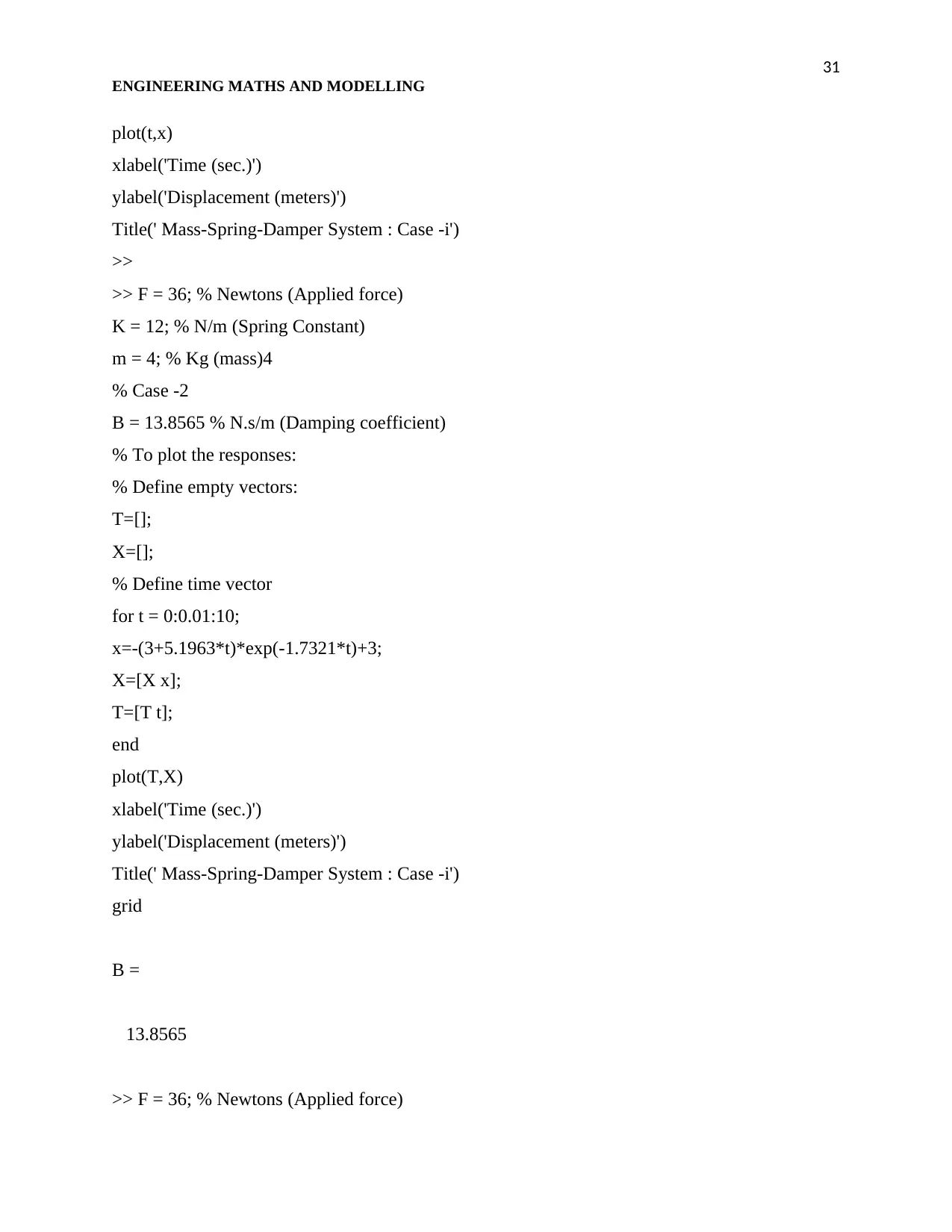
31
ENGINEERING MATHS AND MODELLING
plot(t,x)
xlabel('Time (sec.)')
ylabel('Displacement (meters)')
Title(' Mass-Spring-Damper System : Case -i')
>>
>> F = 36; % Newtons (Applied force)
K = 12; % N/m (Spring Constant)
m = 4; % Kg (mass)4
% Case -2
B = 13.8565 % N.s/m (Damping coefficient)
% To plot the responses:
% Define empty vectors:
T=[];
X=[];
% Define time vector
for t = 0:0.01:10;
x=-(3+5.1963*t)*exp(-1.7321*t)+3;
X=[X x];
T=[T t];
end
plot(T,X)
xlabel('Time (sec.)')
ylabel('Displacement (meters)')
Title(' Mass-Spring-Damper System : Case -i')
grid
B =
13.8565
>> F = 36; % Newtons (Applied force)
ENGINEERING MATHS AND MODELLING
plot(t,x)
xlabel('Time (sec.)')
ylabel('Displacement (meters)')
Title(' Mass-Spring-Damper System : Case -i')
>>
>> F = 36; % Newtons (Applied force)
K = 12; % N/m (Spring Constant)
m = 4; % Kg (mass)4
% Case -2
B = 13.8565 % N.s/m (Damping coefficient)
% To plot the responses:
% Define empty vectors:
T=[];
X=[];
% Define time vector
for t = 0:0.01:10;
x=-(3+5.1963*t)*exp(-1.7321*t)+3;
X=[X x];
T=[T t];
end
plot(T,X)
xlabel('Time (sec.)')
ylabel('Displacement (meters)')
Title(' Mass-Spring-Damper System : Case -i')
grid
B =
13.8565
>> F = 36; % Newtons (Applied force)
Paraphrase This Document
Need a fresh take? Get an instant paraphrase of this document with our AI Paraphraser
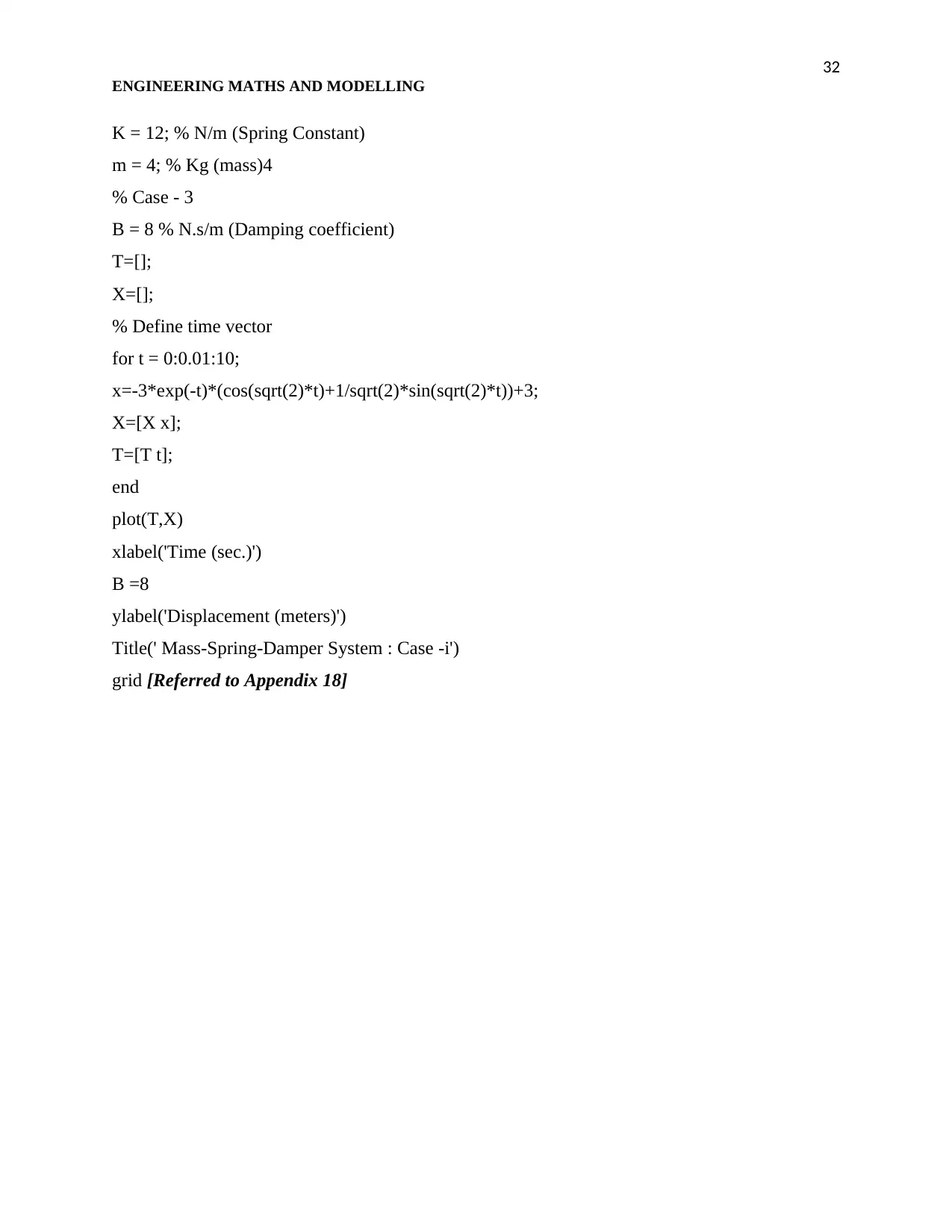
32
ENGINEERING MATHS AND MODELLING
K = 12; % N/m (Spring Constant)
m = 4; % Kg (mass)4
% Case - 3
B = 8 % N.s/m (Damping coefficient)
T=[];
X=[];
% Define time vector
for t = 0:0.01:10;
x=-3*exp(-t)*(cos(sqrt(2)*t)+1/sqrt(2)*sin(sqrt(2)*t))+3;
X=[X x];
T=[T t];
end
plot(T,X)
xlabel('Time (sec.)')
B =8
ylabel('Displacement (meters)')
Title(' Mass-Spring-Damper System : Case -i')
grid [Referred to Appendix 18]
ENGINEERING MATHS AND MODELLING
K = 12; % N/m (Spring Constant)
m = 4; % Kg (mass)4
% Case - 3
B = 8 % N.s/m (Damping coefficient)
T=[];
X=[];
% Define time vector
for t = 0:0.01:10;
x=-3*exp(-t)*(cos(sqrt(2)*t)+1/sqrt(2)*sin(sqrt(2)*t))+3;
X=[X x];
T=[T t];
end
plot(T,X)
xlabel('Time (sec.)')
B =8
ylabel('Displacement (meters)')
Title(' Mass-Spring-Damper System : Case -i')
grid [Referred to Appendix 18]
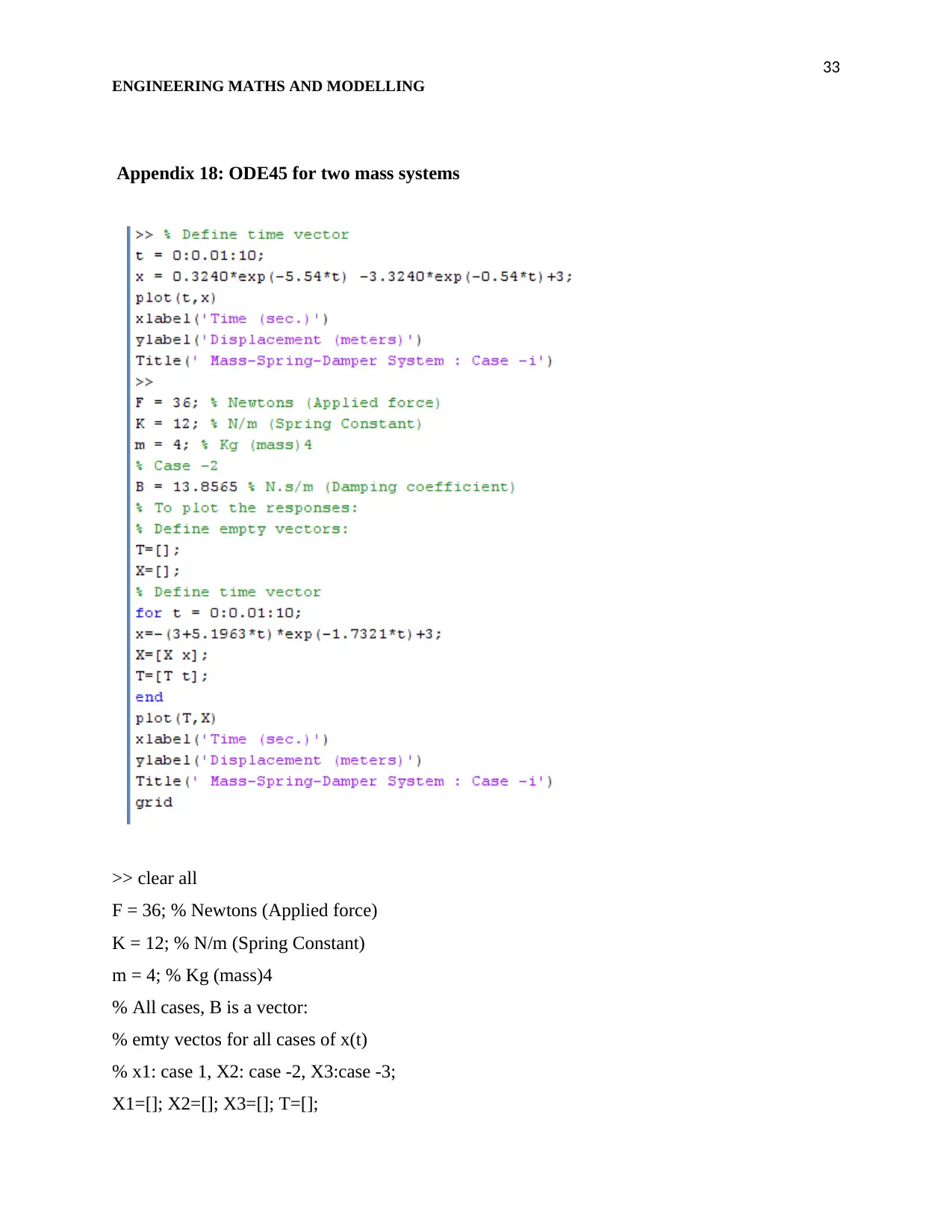
33
ENGINEERING MATHS AND MODELLING
Appendix 18: ODE45 for two mass systems
>> clear all
F = 36; % Newtons (Applied force)
K = 12; % N/m (Spring Constant)
m = 4; % Kg (mass)4
% All cases, B is a vector:
% emty vectos for all cases of x(t)
% x1: case 1, X2: case -2, X3:case -3;
X1=[]; X2=[]; X3=[]; T=[];
ENGINEERING MATHS AND MODELLING
Appendix 18: ODE45 for two mass systems
>> clear all
F = 36; % Newtons (Applied force)
K = 12; % N/m (Spring Constant)
m = 4; % Kg (mass)4
% All cases, B is a vector:
% emty vectos for all cases of x(t)
% x1: case 1, X2: case -2, X3:case -3;
X1=[]; X2=[]; X3=[]; T=[];
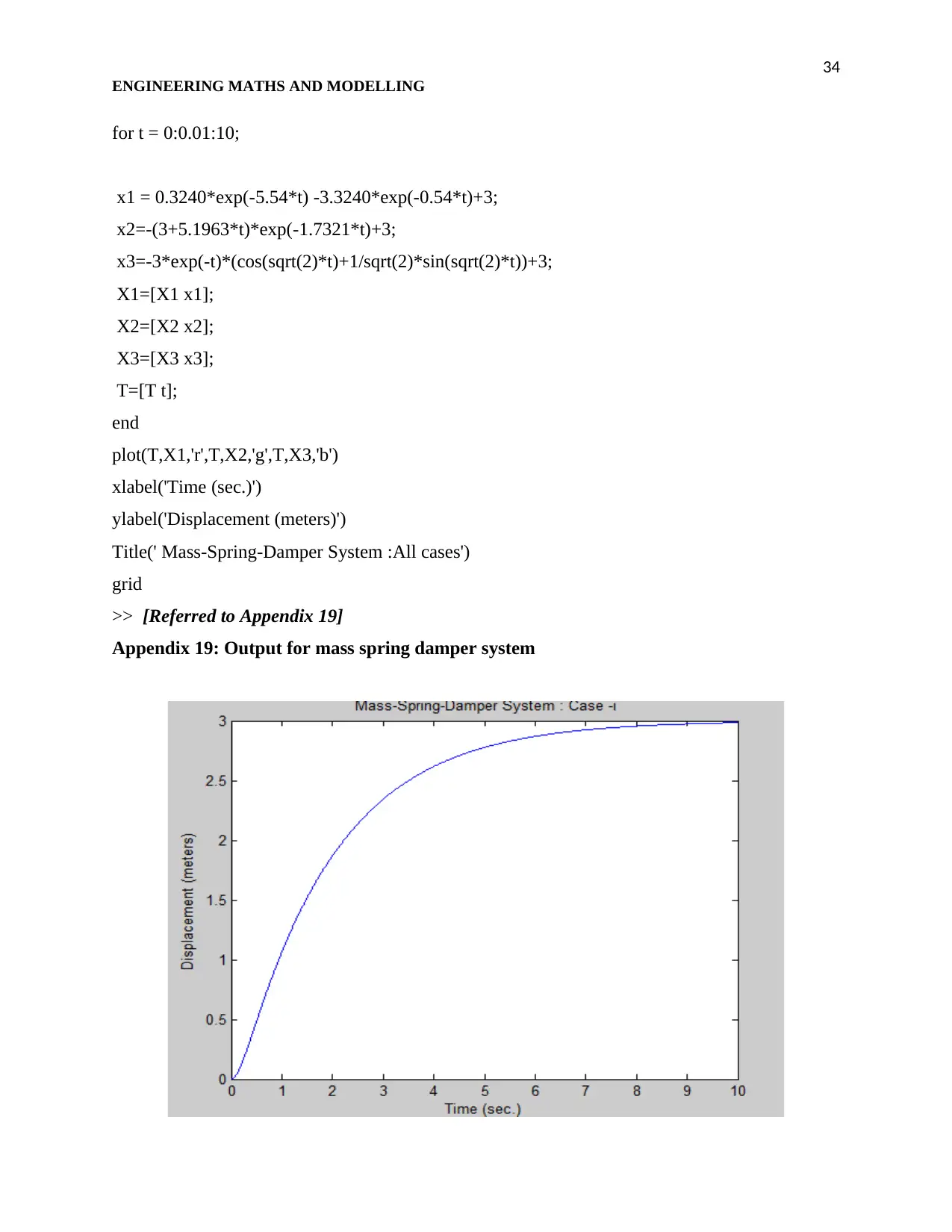
34
ENGINEERING MATHS AND MODELLING
for t = 0:0.01:10;
x1 = 0.3240*exp(-5.54*t) -3.3240*exp(-0.54*t)+3;
x2=-(3+5.1963*t)*exp(-1.7321*t)+3;
x3=-3*exp(-t)*(cos(sqrt(2)*t)+1/sqrt(2)*sin(sqrt(2)*t))+3;
X1=[X1 x1];
X2=[X2 x2];
X3=[X3 x3];
T=[T t];
end
plot(T,X1,'r',T,X2,'g',T,X3,'b')
xlabel('Time (sec.)')
ylabel('Displacement (meters)')
Title(' Mass-Spring-Damper System :All cases')
grid
>> [Referred to Appendix 19]
Appendix 19: Output for mass spring damper system
ENGINEERING MATHS AND MODELLING
for t = 0:0.01:10;
x1 = 0.3240*exp(-5.54*t) -3.3240*exp(-0.54*t)+3;
x2=-(3+5.1963*t)*exp(-1.7321*t)+3;
x3=-3*exp(-t)*(cos(sqrt(2)*t)+1/sqrt(2)*sin(sqrt(2)*t))+3;
X1=[X1 x1];
X2=[X2 x2];
X3=[X3 x3];
T=[T t];
end
plot(T,X1,'r',T,X2,'g',T,X3,'b')
xlabel('Time (sec.)')
ylabel('Displacement (meters)')
Title(' Mass-Spring-Damper System :All cases')
grid
>> [Referred to Appendix 19]
Appendix 19: Output for mass spring damper system
Secure Best Marks with AI Grader
Need help grading? Try our AI Grader for instant feedback on your assignments.
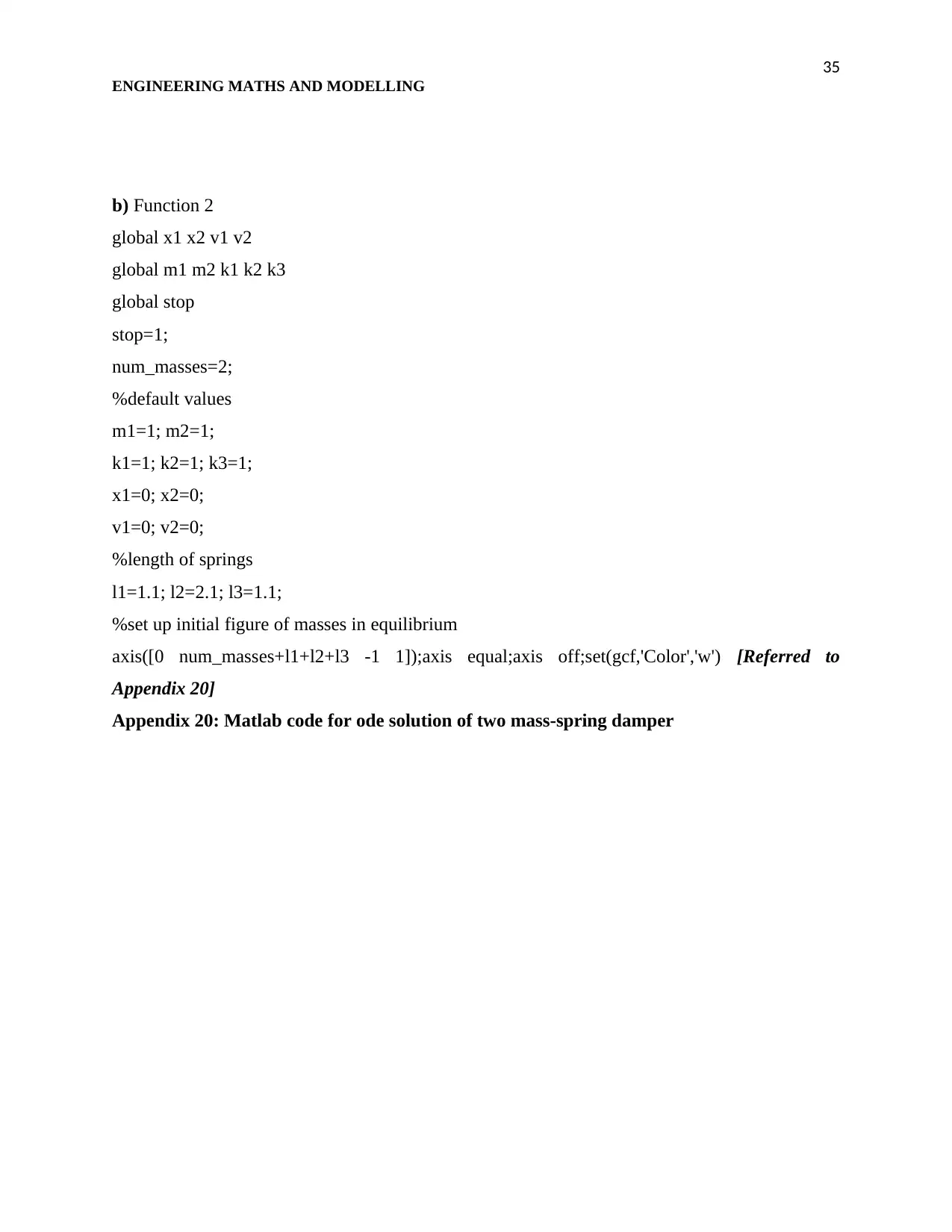
35
ENGINEERING MATHS AND MODELLING
b) Function 2
global x1 x2 v1 v2
global m1 m2 k1 k2 k3
global stop
stop=1;
num_masses=2;
%default values
m1=1; m2=1;
k1=1; k2=1; k3=1;
x1=0; x2=0;
v1=0; v2=0;
%length of springs
l1=1.1; l2=2.1; l3=1.1;
%set up initial figure of masses in equilibrium
axis([0 num_masses+l1+l2+l3 -1 1]);axis equal;axis off;set(gcf,'Color','w') [Referred to
Appendix 20]
Appendix 20: Matlab code for ode solution of two mass-spring damper
ENGINEERING MATHS AND MODELLING
b) Function 2
global x1 x2 v1 v2
global m1 m2 k1 k2 k3
global stop
stop=1;
num_masses=2;
%default values
m1=1; m2=1;
k1=1; k2=1; k3=1;
x1=0; x2=0;
v1=0; v2=0;
%length of springs
l1=1.1; l2=2.1; l3=1.1;
%set up initial figure of masses in equilibrium
axis([0 num_masses+l1+l2+l3 -1 1]);axis equal;axis off;set(gcf,'Color','w') [Referred to
Appendix 20]
Appendix 20: Matlab code for ode solution of two mass-spring damper
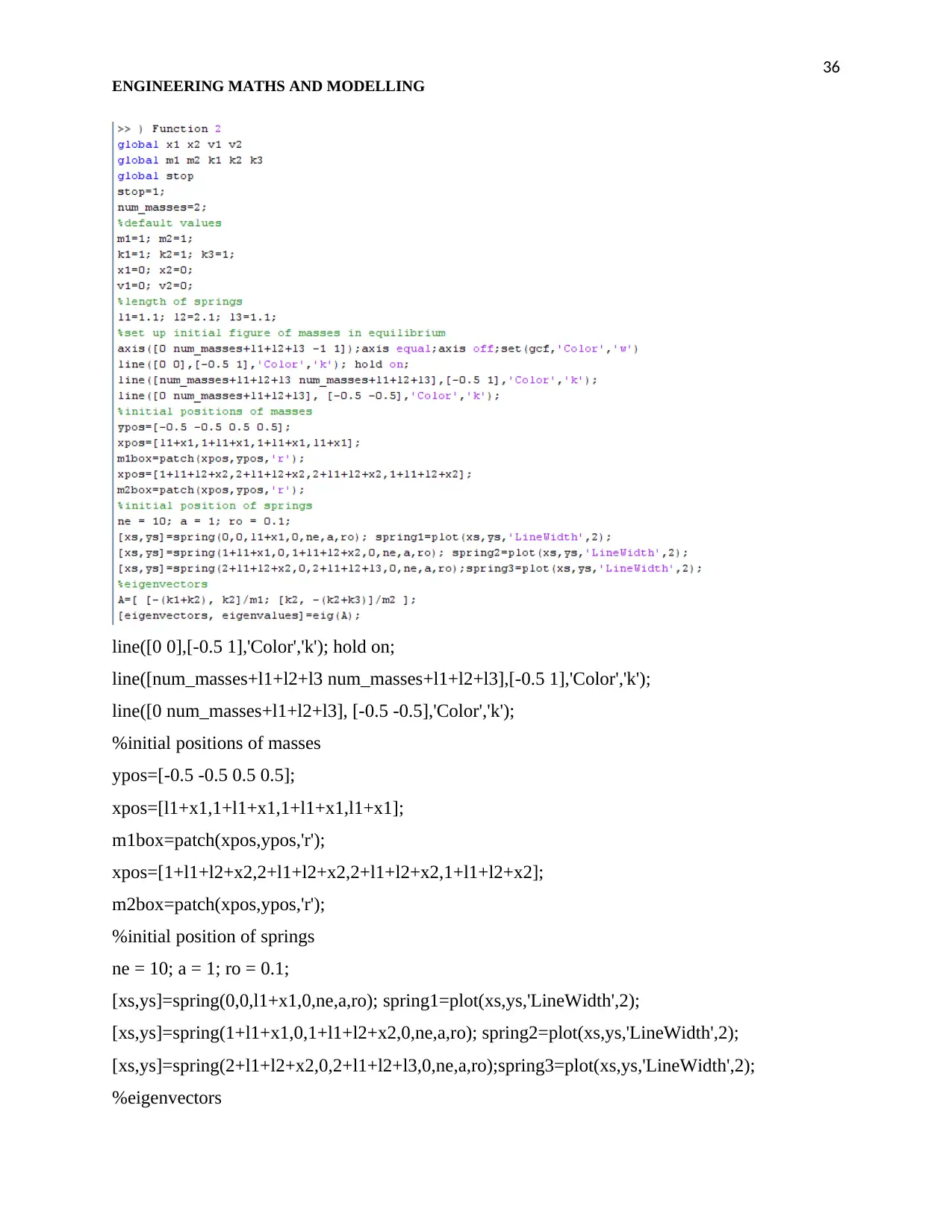
36
ENGINEERING MATHS AND MODELLING
line([0 0],[-0.5 1],'Color','k'); hold on;
line([num_masses+l1+l2+l3 num_masses+l1+l2+l3],[-0.5 1],'Color','k');
line([0 num_masses+l1+l2+l3], [-0.5 -0.5],'Color','k');
%initial positions of masses
ypos=[-0.5 -0.5 0.5 0.5];
xpos=[l1+x1,1+l1+x1,1+l1+x1,l1+x1];
m1box=patch(xpos,ypos,'r');
xpos=[1+l1+l2+x2,2+l1+l2+x2,2+l1+l2+x2,1+l1+l2+x2];
m2box=patch(xpos,ypos,'r');
%initial position of springs
ne = 10; a = 1; ro = 0.1;
[xs,ys]=spring(0,0,l1+x1,0,ne,a,ro); spring1=plot(xs,ys,'LineWidth',2);
[xs,ys]=spring(1+l1+x1,0,1+l1+l2+x2,0,ne,a,ro); spring2=plot(xs,ys,'LineWidth',2);
[xs,ys]=spring(2+l1+l2+x2,0,2+l1+l2+l3,0,ne,a,ro);spring3=plot(xs,ys,'LineWidth',2);
%eigenvectors
ENGINEERING MATHS AND MODELLING
line([0 0],[-0.5 1],'Color','k'); hold on;
line([num_masses+l1+l2+l3 num_masses+l1+l2+l3],[-0.5 1],'Color','k');
line([0 num_masses+l1+l2+l3], [-0.5 -0.5],'Color','k');
%initial positions of masses
ypos=[-0.5 -0.5 0.5 0.5];
xpos=[l1+x1,1+l1+x1,1+l1+x1,l1+x1];
m1box=patch(xpos,ypos,'r');
xpos=[1+l1+l2+x2,2+l1+l2+x2,2+l1+l2+x2,1+l1+l2+x2];
m2box=patch(xpos,ypos,'r');
%initial position of springs
ne = 10; a = 1; ro = 0.1;
[xs,ys]=spring(0,0,l1+x1,0,ne,a,ro); spring1=plot(xs,ys,'LineWidth',2);
[xs,ys]=spring(1+l1+x1,0,1+l1+l2+x2,0,ne,a,ro); spring2=plot(xs,ys,'LineWidth',2);
[xs,ys]=spring(2+l1+l2+x2,0,2+l1+l2+l3,0,ne,a,ro);spring3=plot(xs,ys,'LineWidth',2);
%eigenvectors
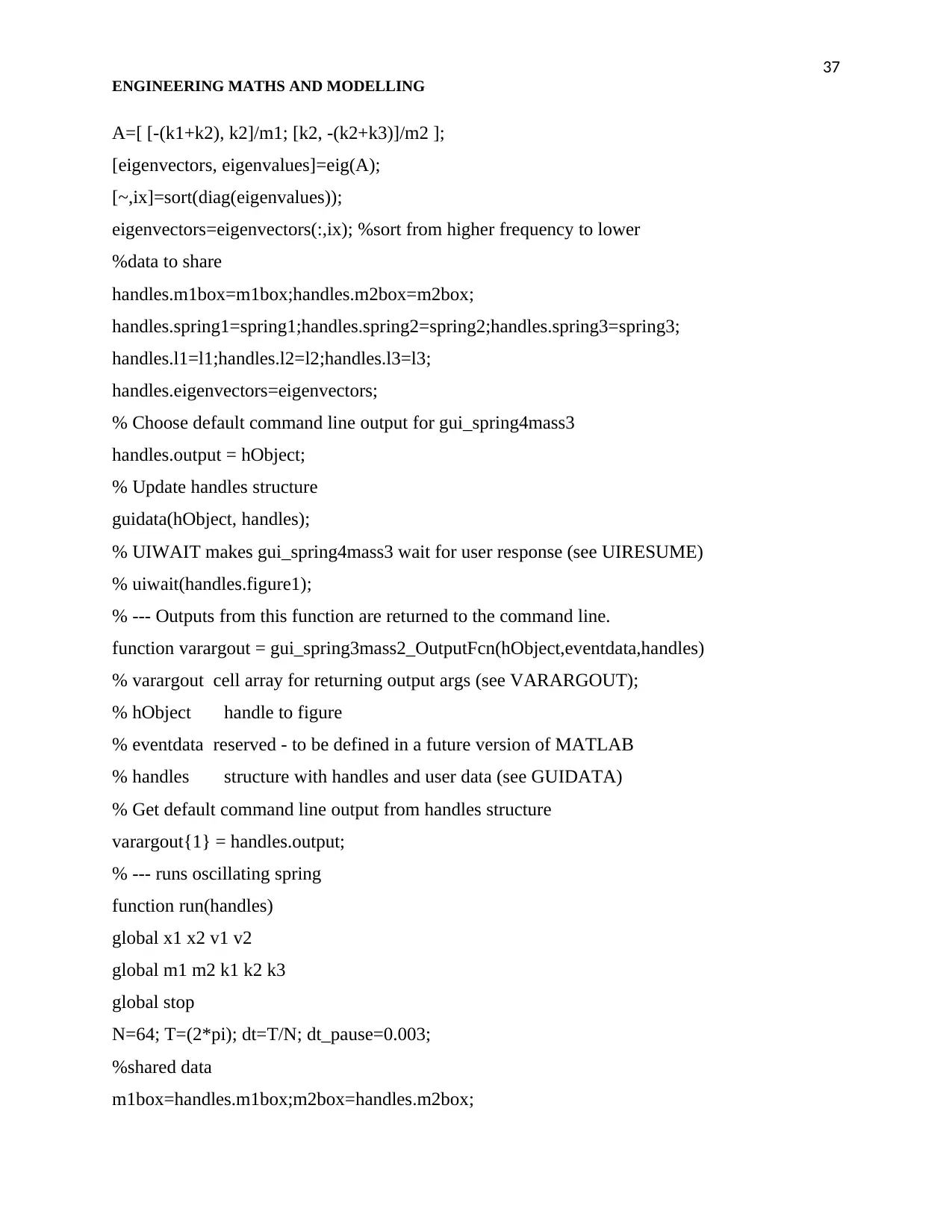
37
ENGINEERING MATHS AND MODELLING
A=[ [-(k1+k2), k2]/m1; [k2, -(k2+k3)]/m2 ];
[eigenvectors, eigenvalues]=eig(A);
[~,ix]=sort(diag(eigenvalues));
eigenvectors=eigenvectors(:,ix); %sort from higher frequency to lower
%data to share
handles.m1box=m1box;handles.m2box=m2box;
handles.spring1=spring1;handles.spring2=spring2;handles.spring3=spring3;
handles.l1=l1;handles.l2=l2;handles.l3=l3;
handles.eigenvectors=eigenvectors;
% Choose default command line output for gui_spring4mass3
handles.output = hObject;
% Update handles structure
guidata(hObject, handles);
% UIWAIT makes gui_spring4mass3 wait for user response (see UIRESUME)
% uiwait(handles.figure1);
% --- Outputs from this function are returned to the command line.
function varargout = gui_spring3mass2_OutputFcn(hObject,eventdata,handles)
% varargout cell array for returning output args (see VARARGOUT);
% hObject handle to figure
% eventdata reserved - to be defined in a future version of MATLAB
% handles structure with handles and user data (see GUIDATA)
% Get default command line output from handles structure
varargout{1} = handles.output;
% --- runs oscillating spring
function run(handles)
global x1 x2 v1 v2
global m1 m2 k1 k2 k3
global stop
N=64; T=(2*pi); dt=T/N; dt_pause=0.003;
%shared data
m1box=handles.m1box;m2box=handles.m2box;
ENGINEERING MATHS AND MODELLING
A=[ [-(k1+k2), k2]/m1; [k2, -(k2+k3)]/m2 ];
[eigenvectors, eigenvalues]=eig(A);
[~,ix]=sort(diag(eigenvalues));
eigenvectors=eigenvectors(:,ix); %sort from higher frequency to lower
%data to share
handles.m1box=m1box;handles.m2box=m2box;
handles.spring1=spring1;handles.spring2=spring2;handles.spring3=spring3;
handles.l1=l1;handles.l2=l2;handles.l3=l3;
handles.eigenvectors=eigenvectors;
% Choose default command line output for gui_spring4mass3
handles.output = hObject;
% Update handles structure
guidata(hObject, handles);
% UIWAIT makes gui_spring4mass3 wait for user response (see UIRESUME)
% uiwait(handles.figure1);
% --- Outputs from this function are returned to the command line.
function varargout = gui_spring3mass2_OutputFcn(hObject,eventdata,handles)
% varargout cell array for returning output args (see VARARGOUT);
% hObject handle to figure
% eventdata reserved - to be defined in a future version of MATLAB
% handles structure with handles and user data (see GUIDATA)
% Get default command line output from handles structure
varargout{1} = handles.output;
% --- runs oscillating spring
function run(handles)
global x1 x2 v1 v2
global m1 m2 k1 k2 k3
global stop
N=64; T=(2*pi); dt=T/N; dt_pause=0.003;
%shared data
m1box=handles.m1box;m2box=handles.m2box;
Paraphrase This Document
Need a fresh take? Get an instant paraphrase of this document with our AI Paraphraser
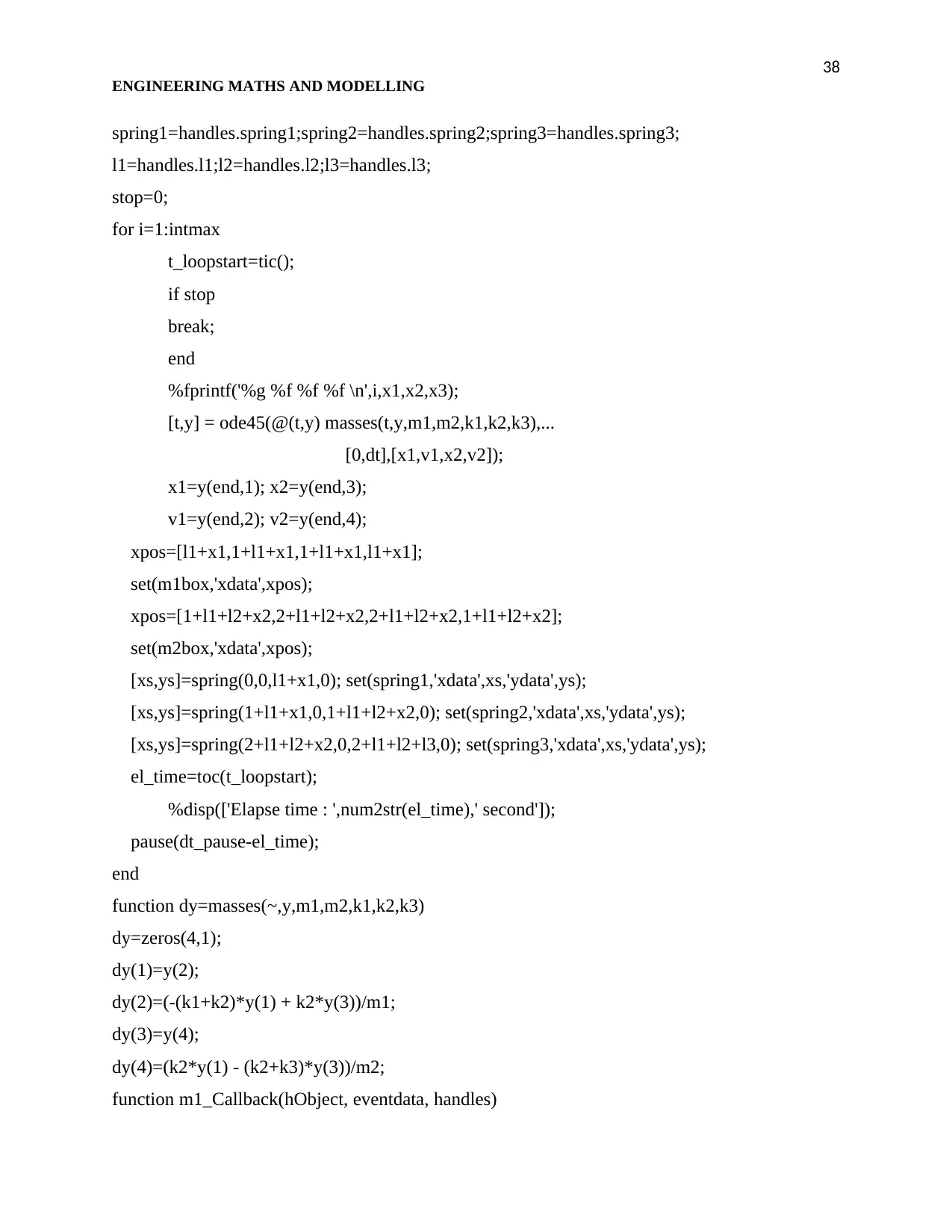
38
ENGINEERING MATHS AND MODELLING
spring1=handles.spring1;spring2=handles.spring2;spring3=handles.spring3;
l1=handles.l1;l2=handles.l2;l3=handles.l3;
stop=0;
for i=1:intmax
t_loopstart=tic();
if stop
break;
end
%fprintf('%g %f %f %f \n',i,x1,x2,x3);
[t,y] = ode45(@(t,y) masses(t,y,m1,m2,k1,k2,k3),...
[0,dt],[x1,v1,x2,v2]);
x1=y(end,1); x2=y(end,3);
v1=y(end,2); v2=y(end,4);
xpos=[l1+x1,1+l1+x1,1+l1+x1,l1+x1];
set(m1box,'xdata',xpos);
xpos=[1+l1+l2+x2,2+l1+l2+x2,2+l1+l2+x2,1+l1+l2+x2];
set(m2box,'xdata',xpos);
[xs,ys]=spring(0,0,l1+x1,0); set(spring1,'xdata',xs,'ydata',ys);
[xs,ys]=spring(1+l1+x1,0,1+l1+l2+x2,0); set(spring2,'xdata',xs,'ydata',ys);
[xs,ys]=spring(2+l1+l2+x2,0,2+l1+l2+l3,0); set(spring3,'xdata',xs,'ydata',ys);
el_time=toc(t_loopstart);
%disp(['Elapse time : ',num2str(el_time),' second']);
pause(dt_pause-el_time);
end
function dy=masses(~,y,m1,m2,k1,k2,k3)
dy=zeros(4,1);
dy(1)=y(2);
dy(2)=(-(k1+k2)*y(1) + k2*y(3))/m1;
dy(3)=y(4);
dy(4)=(k2*y(1) - (k2+k3)*y(3))/m2;
function m1_Callback(hObject, eventdata, handles)
ENGINEERING MATHS AND MODELLING
spring1=handles.spring1;spring2=handles.spring2;spring3=handles.spring3;
l1=handles.l1;l2=handles.l2;l3=handles.l3;
stop=0;
for i=1:intmax
t_loopstart=tic();
if stop
break;
end
%fprintf('%g %f %f %f \n',i,x1,x2,x3);
[t,y] = ode45(@(t,y) masses(t,y,m1,m2,k1,k2,k3),...
[0,dt],[x1,v1,x2,v2]);
x1=y(end,1); x2=y(end,3);
v1=y(end,2); v2=y(end,4);
xpos=[l1+x1,1+l1+x1,1+l1+x1,l1+x1];
set(m1box,'xdata',xpos);
xpos=[1+l1+l2+x2,2+l1+l2+x2,2+l1+l2+x2,1+l1+l2+x2];
set(m2box,'xdata',xpos);
[xs,ys]=spring(0,0,l1+x1,0); set(spring1,'xdata',xs,'ydata',ys);
[xs,ys]=spring(1+l1+x1,0,1+l1+l2+x2,0); set(spring2,'xdata',xs,'ydata',ys);
[xs,ys]=spring(2+l1+l2+x2,0,2+l1+l2+l3,0); set(spring3,'xdata',xs,'ydata',ys);
el_time=toc(t_loopstart);
%disp(['Elapse time : ',num2str(el_time),' second']);
pause(dt_pause-el_time);
end
function dy=masses(~,y,m1,m2,k1,k2,k3)
dy=zeros(4,1);
dy(1)=y(2);
dy(2)=(-(k1+k2)*y(1) + k2*y(3))/m1;
dy(3)=y(4);
dy(4)=(k2*y(1) - (k2+k3)*y(3))/m2;
function m1_Callback(hObject, eventdata, handles)
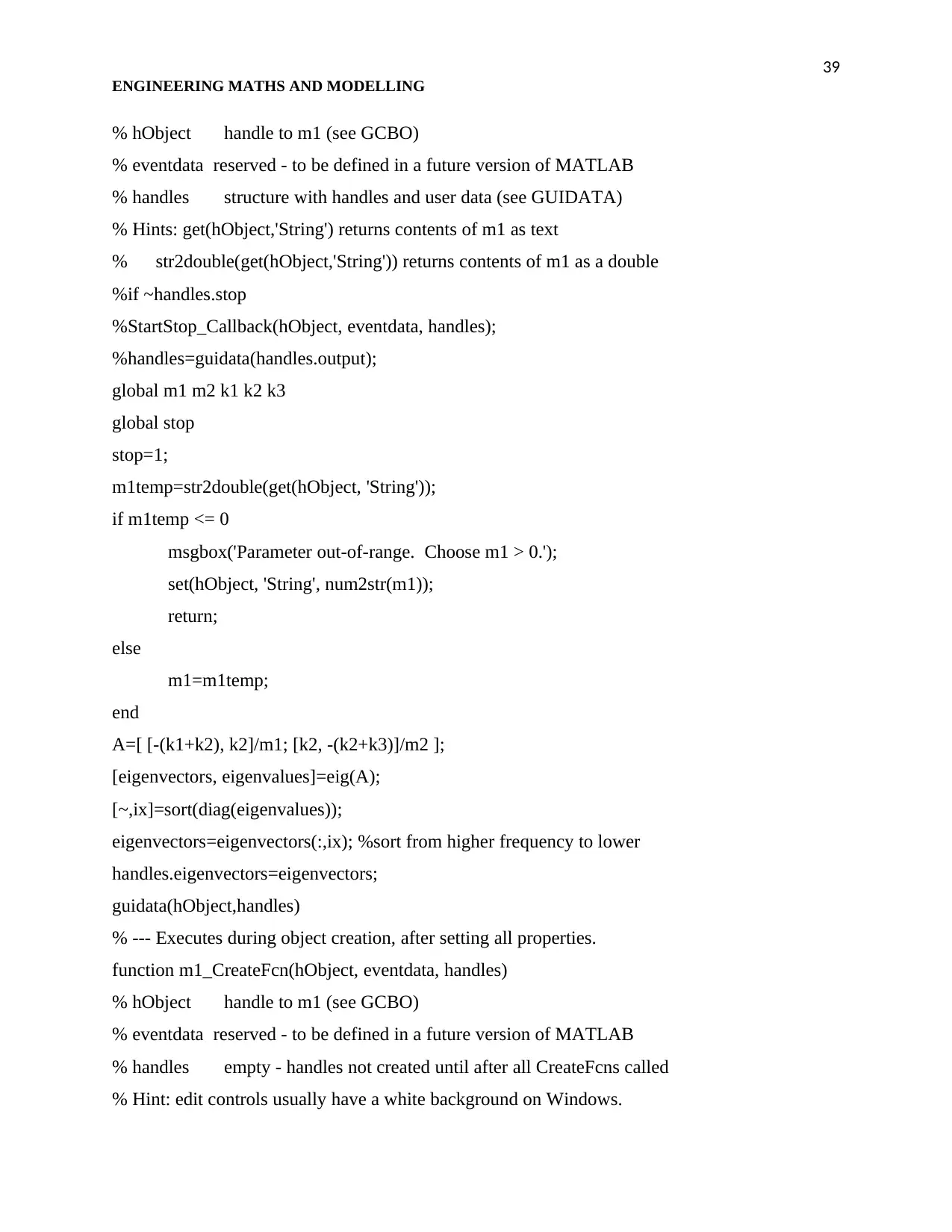
39
ENGINEERING MATHS AND MODELLING
% hObject handle to m1 (see GCBO)
% eventdata reserved - to be defined in a future version of MATLAB
% handles structure with handles and user data (see GUIDATA)
% Hints: get(hObject,'String') returns contents of m1 as text
% str2double(get(hObject,'String')) returns contents of m1 as a double
%if ~handles.stop
%StartStop_Callback(hObject, eventdata, handles);
%handles=guidata(handles.output);
global m1 m2 k1 k2 k3
global stop
stop=1;
m1temp=str2double(get(hObject, 'String'));
if m1temp <= 0
msgbox('Parameter out-of-range. Choose m1 > 0.');
set(hObject, 'String', num2str(m1));
return;
else
m1=m1temp;
end
A=[ [-(k1+k2), k2]/m1; [k2, -(k2+k3)]/m2 ];
[eigenvectors, eigenvalues]=eig(A);
[~,ix]=sort(diag(eigenvalues));
eigenvectors=eigenvectors(:,ix); %sort from higher frequency to lower
handles.eigenvectors=eigenvectors;
guidata(hObject,handles)
% --- Executes during object creation, after setting all properties.
function m1_CreateFcn(hObject, eventdata, handles)
% hObject handle to m1 (see GCBO)
% eventdata reserved - to be defined in a future version of MATLAB
% handles empty - handles not created until after all CreateFcns called
% Hint: edit controls usually have a white background on Windows.
ENGINEERING MATHS AND MODELLING
% hObject handle to m1 (see GCBO)
% eventdata reserved - to be defined in a future version of MATLAB
% handles structure with handles and user data (see GUIDATA)
% Hints: get(hObject,'String') returns contents of m1 as text
% str2double(get(hObject,'String')) returns contents of m1 as a double
%if ~handles.stop
%StartStop_Callback(hObject, eventdata, handles);
%handles=guidata(handles.output);
global m1 m2 k1 k2 k3
global stop
stop=1;
m1temp=str2double(get(hObject, 'String'));
if m1temp <= 0
msgbox('Parameter out-of-range. Choose m1 > 0.');
set(hObject, 'String', num2str(m1));
return;
else
m1=m1temp;
end
A=[ [-(k1+k2), k2]/m1; [k2, -(k2+k3)]/m2 ];
[eigenvectors, eigenvalues]=eig(A);
[~,ix]=sort(diag(eigenvalues));
eigenvectors=eigenvectors(:,ix); %sort from higher frequency to lower
handles.eigenvectors=eigenvectors;
guidata(hObject,handles)
% --- Executes during object creation, after setting all properties.
function m1_CreateFcn(hObject, eventdata, handles)
% hObject handle to m1 (see GCBO)
% eventdata reserved - to be defined in a future version of MATLAB
% handles empty - handles not created until after all CreateFcns called
% Hint: edit controls usually have a white background on Windows.
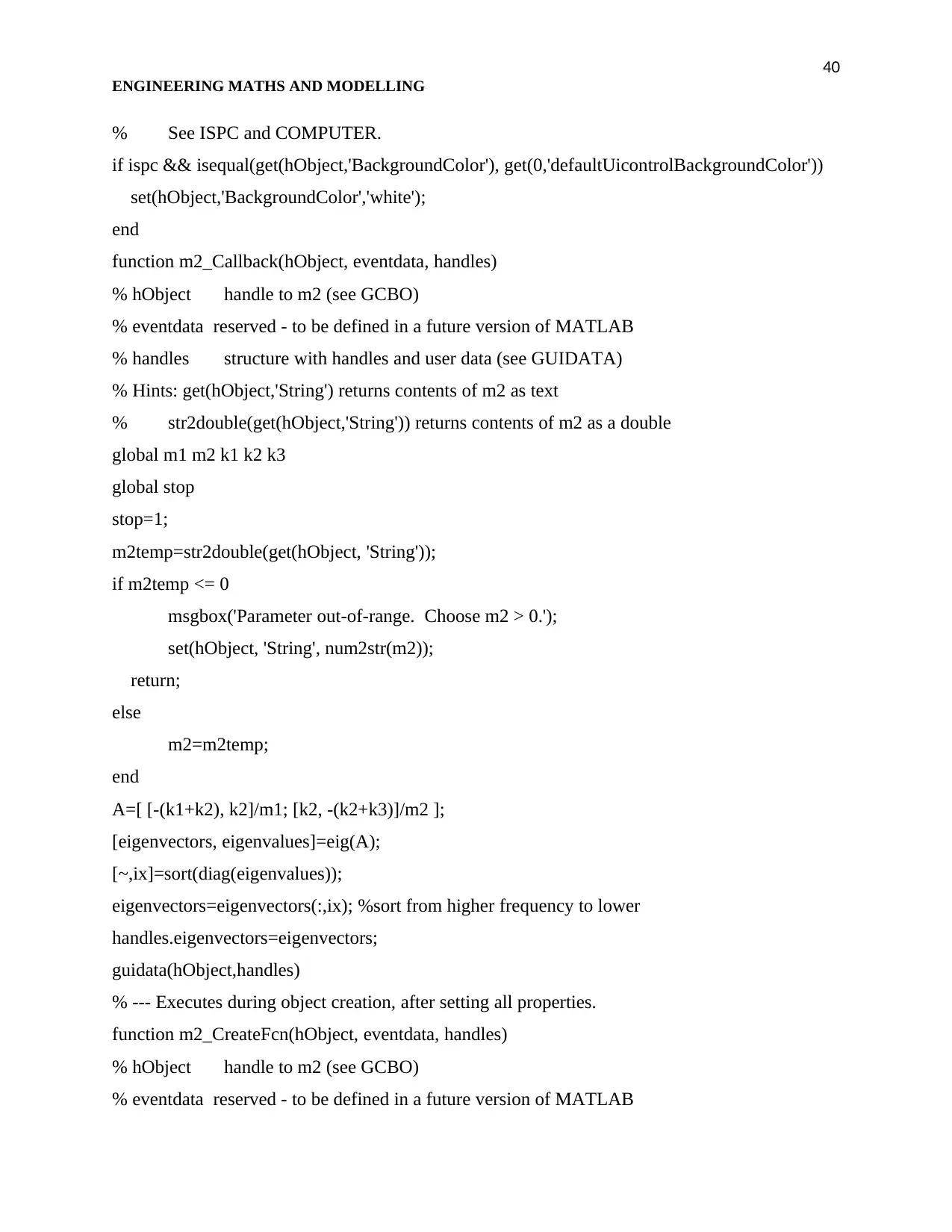
40
ENGINEERING MATHS AND MODELLING
% See ISPC and COMPUTER.
if ispc && isequal(get(hObject,'BackgroundColor'), get(0,'defaultUicontrolBackgroundColor'))
set(hObject,'BackgroundColor','white');
end
function m2_Callback(hObject, eventdata, handles)
% hObject handle to m2 (see GCBO)
% eventdata reserved - to be defined in a future version of MATLAB
% handles structure with handles and user data (see GUIDATA)
% Hints: get(hObject,'String') returns contents of m2 as text
% str2double(get(hObject,'String')) returns contents of m2 as a double
global m1 m2 k1 k2 k3
global stop
stop=1;
m2temp=str2double(get(hObject, 'String'));
if m2temp <= 0
msgbox('Parameter out-of-range. Choose m2 > 0.');
set(hObject, 'String', num2str(m2));
return;
else
m2=m2temp;
end
A=[ [-(k1+k2), k2]/m1; [k2, -(k2+k3)]/m2 ];
[eigenvectors, eigenvalues]=eig(A);
[~,ix]=sort(diag(eigenvalues));
eigenvectors=eigenvectors(:,ix); %sort from higher frequency to lower
handles.eigenvectors=eigenvectors;
guidata(hObject,handles)
% --- Executes during object creation, after setting all properties.
function m2_CreateFcn(hObject, eventdata, handles)
% hObject handle to m2 (see GCBO)
% eventdata reserved - to be defined in a future version of MATLAB
ENGINEERING MATHS AND MODELLING
% See ISPC and COMPUTER.
if ispc && isequal(get(hObject,'BackgroundColor'), get(0,'defaultUicontrolBackgroundColor'))
set(hObject,'BackgroundColor','white');
end
function m2_Callback(hObject, eventdata, handles)
% hObject handle to m2 (see GCBO)
% eventdata reserved - to be defined in a future version of MATLAB
% handles structure with handles and user data (see GUIDATA)
% Hints: get(hObject,'String') returns contents of m2 as text
% str2double(get(hObject,'String')) returns contents of m2 as a double
global m1 m2 k1 k2 k3
global stop
stop=1;
m2temp=str2double(get(hObject, 'String'));
if m2temp <= 0
msgbox('Parameter out-of-range. Choose m2 > 0.');
set(hObject, 'String', num2str(m2));
return;
else
m2=m2temp;
end
A=[ [-(k1+k2), k2]/m1; [k2, -(k2+k3)]/m2 ];
[eigenvectors, eigenvalues]=eig(A);
[~,ix]=sort(diag(eigenvalues));
eigenvectors=eigenvectors(:,ix); %sort from higher frequency to lower
handles.eigenvectors=eigenvectors;
guidata(hObject,handles)
% --- Executes during object creation, after setting all properties.
function m2_CreateFcn(hObject, eventdata, handles)
% hObject handle to m2 (see GCBO)
% eventdata reserved - to be defined in a future version of MATLAB
Secure Best Marks with AI Grader
Need help grading? Try our AI Grader for instant feedback on your assignments.
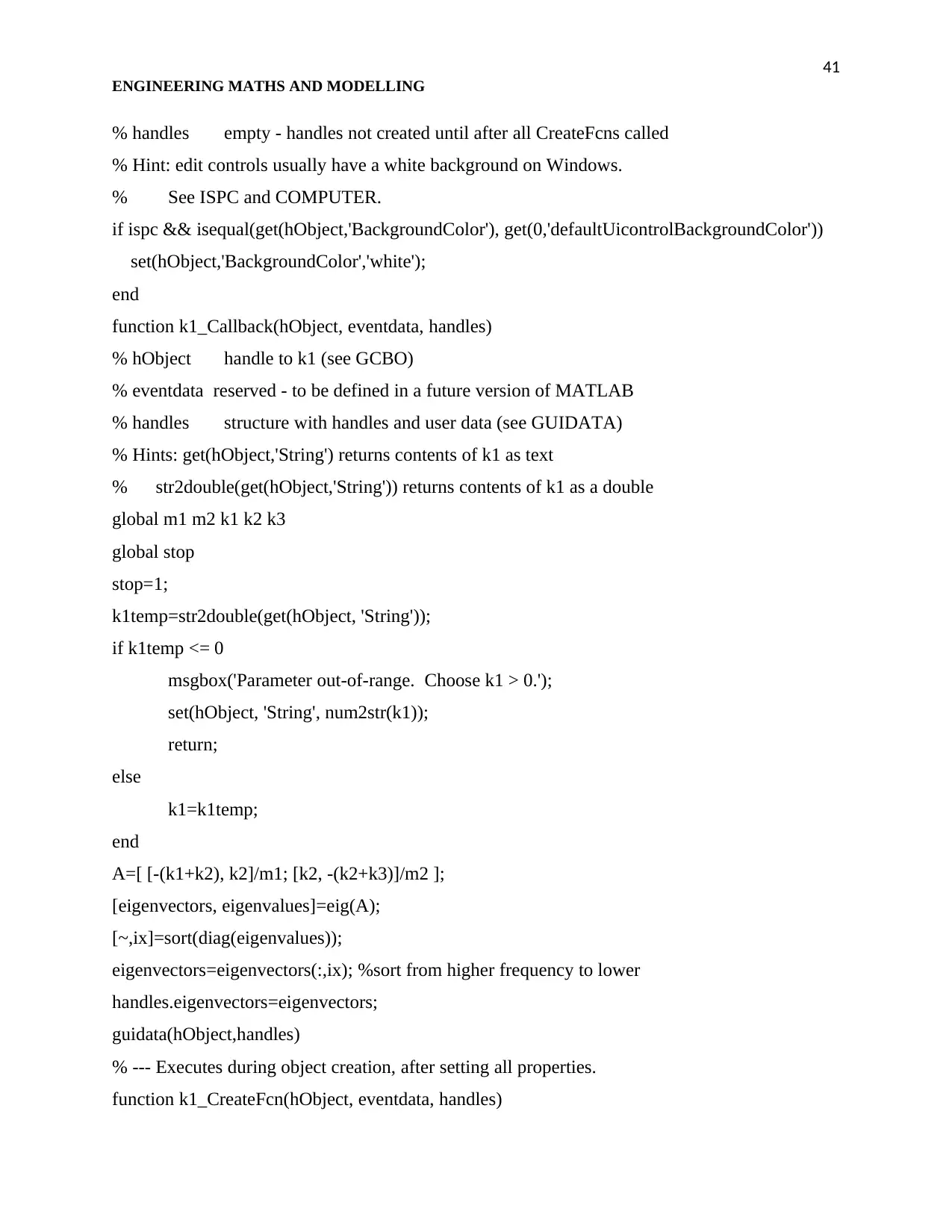
41
ENGINEERING MATHS AND MODELLING
% handles empty - handles not created until after all CreateFcns called
% Hint: edit controls usually have a white background on Windows.
% See ISPC and COMPUTER.
if ispc && isequal(get(hObject,'BackgroundColor'), get(0,'defaultUicontrolBackgroundColor'))
set(hObject,'BackgroundColor','white');
end
function k1_Callback(hObject, eventdata, handles)
% hObject handle to k1 (see GCBO)
% eventdata reserved - to be defined in a future version of MATLAB
% handles structure with handles and user data (see GUIDATA)
% Hints: get(hObject,'String') returns contents of k1 as text
% str2double(get(hObject,'String')) returns contents of k1 as a double
global m1 m2 k1 k2 k3
global stop
stop=1;
k1temp=str2double(get(hObject, 'String'));
if k1temp <= 0
msgbox('Parameter out-of-range. Choose k1 > 0.');
set(hObject, 'String', num2str(k1));
return;
else
k1=k1temp;
end
A=[ [-(k1+k2), k2]/m1; [k2, -(k2+k3)]/m2 ];
[eigenvectors, eigenvalues]=eig(A);
[~,ix]=sort(diag(eigenvalues));
eigenvectors=eigenvectors(:,ix); %sort from higher frequency to lower
handles.eigenvectors=eigenvectors;
guidata(hObject,handles)
% --- Executes during object creation, after setting all properties.
function k1_CreateFcn(hObject, eventdata, handles)
ENGINEERING MATHS AND MODELLING
% handles empty - handles not created until after all CreateFcns called
% Hint: edit controls usually have a white background on Windows.
% See ISPC and COMPUTER.
if ispc && isequal(get(hObject,'BackgroundColor'), get(0,'defaultUicontrolBackgroundColor'))
set(hObject,'BackgroundColor','white');
end
function k1_Callback(hObject, eventdata, handles)
% hObject handle to k1 (see GCBO)
% eventdata reserved - to be defined in a future version of MATLAB
% handles structure with handles and user data (see GUIDATA)
% Hints: get(hObject,'String') returns contents of k1 as text
% str2double(get(hObject,'String')) returns contents of k1 as a double
global m1 m2 k1 k2 k3
global stop
stop=1;
k1temp=str2double(get(hObject, 'String'));
if k1temp <= 0
msgbox('Parameter out-of-range. Choose k1 > 0.');
set(hObject, 'String', num2str(k1));
return;
else
k1=k1temp;
end
A=[ [-(k1+k2), k2]/m1; [k2, -(k2+k3)]/m2 ];
[eigenvectors, eigenvalues]=eig(A);
[~,ix]=sort(diag(eigenvalues));
eigenvectors=eigenvectors(:,ix); %sort from higher frequency to lower
handles.eigenvectors=eigenvectors;
guidata(hObject,handles)
% --- Executes during object creation, after setting all properties.
function k1_CreateFcn(hObject, eventdata, handles)
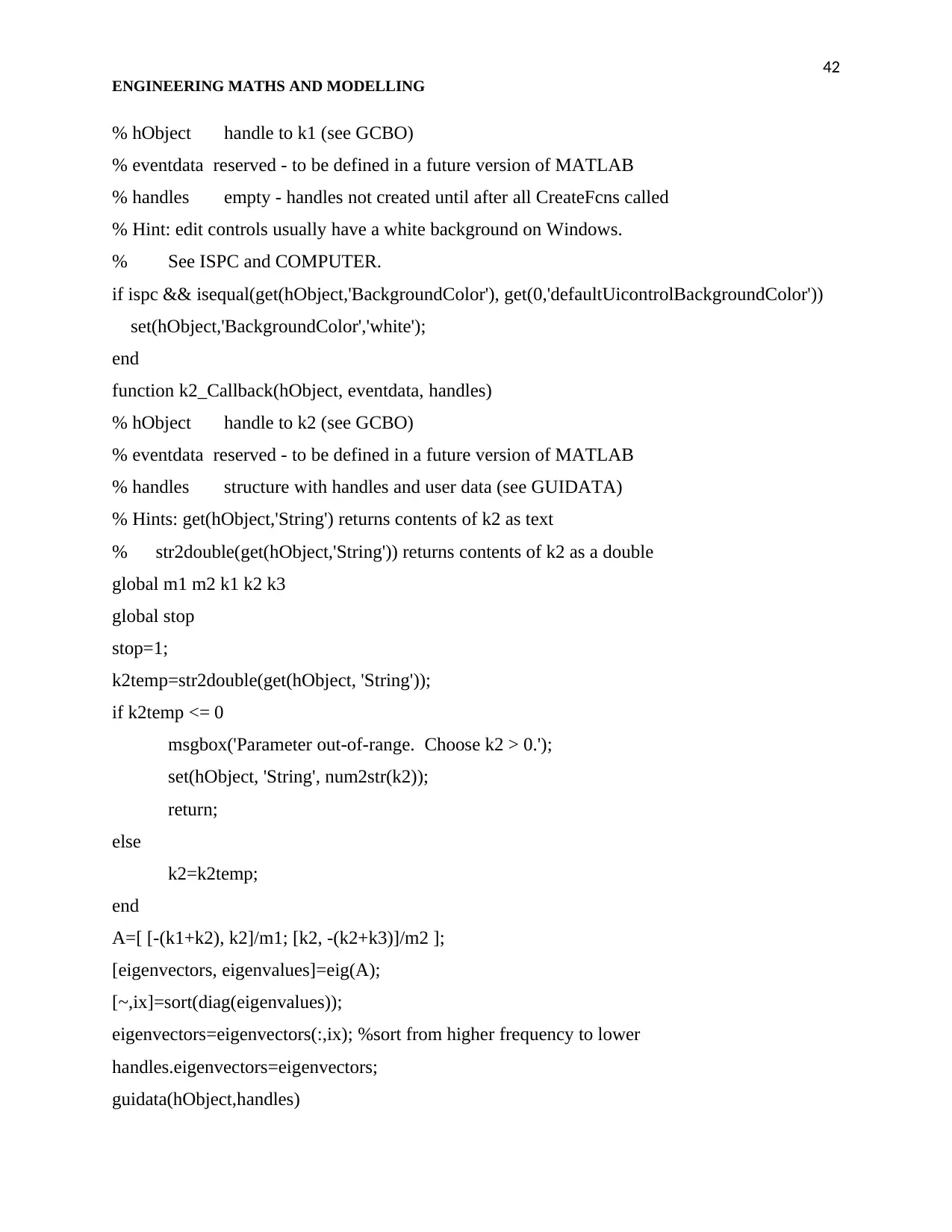
42
ENGINEERING MATHS AND MODELLING
% hObject handle to k1 (see GCBO)
% eventdata reserved - to be defined in a future version of MATLAB
% handles empty - handles not created until after all CreateFcns called
% Hint: edit controls usually have a white background on Windows.
% See ISPC and COMPUTER.
if ispc && isequal(get(hObject,'BackgroundColor'), get(0,'defaultUicontrolBackgroundColor'))
set(hObject,'BackgroundColor','white');
end
function k2_Callback(hObject, eventdata, handles)
% hObject handle to k2 (see GCBO)
% eventdata reserved - to be defined in a future version of MATLAB
% handles structure with handles and user data (see GUIDATA)
% Hints: get(hObject,'String') returns contents of k2 as text
% str2double(get(hObject,'String')) returns contents of k2 as a double
global m1 m2 k1 k2 k3
global stop
stop=1;
k2temp=str2double(get(hObject, 'String'));
if k2temp <= 0
msgbox('Parameter out-of-range. Choose k2 > 0.');
set(hObject, 'String', num2str(k2));
return;
else
k2=k2temp;
end
A=[ [-(k1+k2), k2]/m1; [k2, -(k2+k3)]/m2 ];
[eigenvectors, eigenvalues]=eig(A);
[~,ix]=sort(diag(eigenvalues));
eigenvectors=eigenvectors(:,ix); %sort from higher frequency to lower
handles.eigenvectors=eigenvectors;
guidata(hObject,handles)
ENGINEERING MATHS AND MODELLING
% hObject handle to k1 (see GCBO)
% eventdata reserved - to be defined in a future version of MATLAB
% handles empty - handles not created until after all CreateFcns called
% Hint: edit controls usually have a white background on Windows.
% See ISPC and COMPUTER.
if ispc && isequal(get(hObject,'BackgroundColor'), get(0,'defaultUicontrolBackgroundColor'))
set(hObject,'BackgroundColor','white');
end
function k2_Callback(hObject, eventdata, handles)
% hObject handle to k2 (see GCBO)
% eventdata reserved - to be defined in a future version of MATLAB
% handles structure with handles and user data (see GUIDATA)
% Hints: get(hObject,'String') returns contents of k2 as text
% str2double(get(hObject,'String')) returns contents of k2 as a double
global m1 m2 k1 k2 k3
global stop
stop=1;
k2temp=str2double(get(hObject, 'String'));
if k2temp <= 0
msgbox('Parameter out-of-range. Choose k2 > 0.');
set(hObject, 'String', num2str(k2));
return;
else
k2=k2temp;
end
A=[ [-(k1+k2), k2]/m1; [k2, -(k2+k3)]/m2 ];
[eigenvectors, eigenvalues]=eig(A);
[~,ix]=sort(diag(eigenvalues));
eigenvectors=eigenvectors(:,ix); %sort from higher frequency to lower
handles.eigenvectors=eigenvectors;
guidata(hObject,handles)
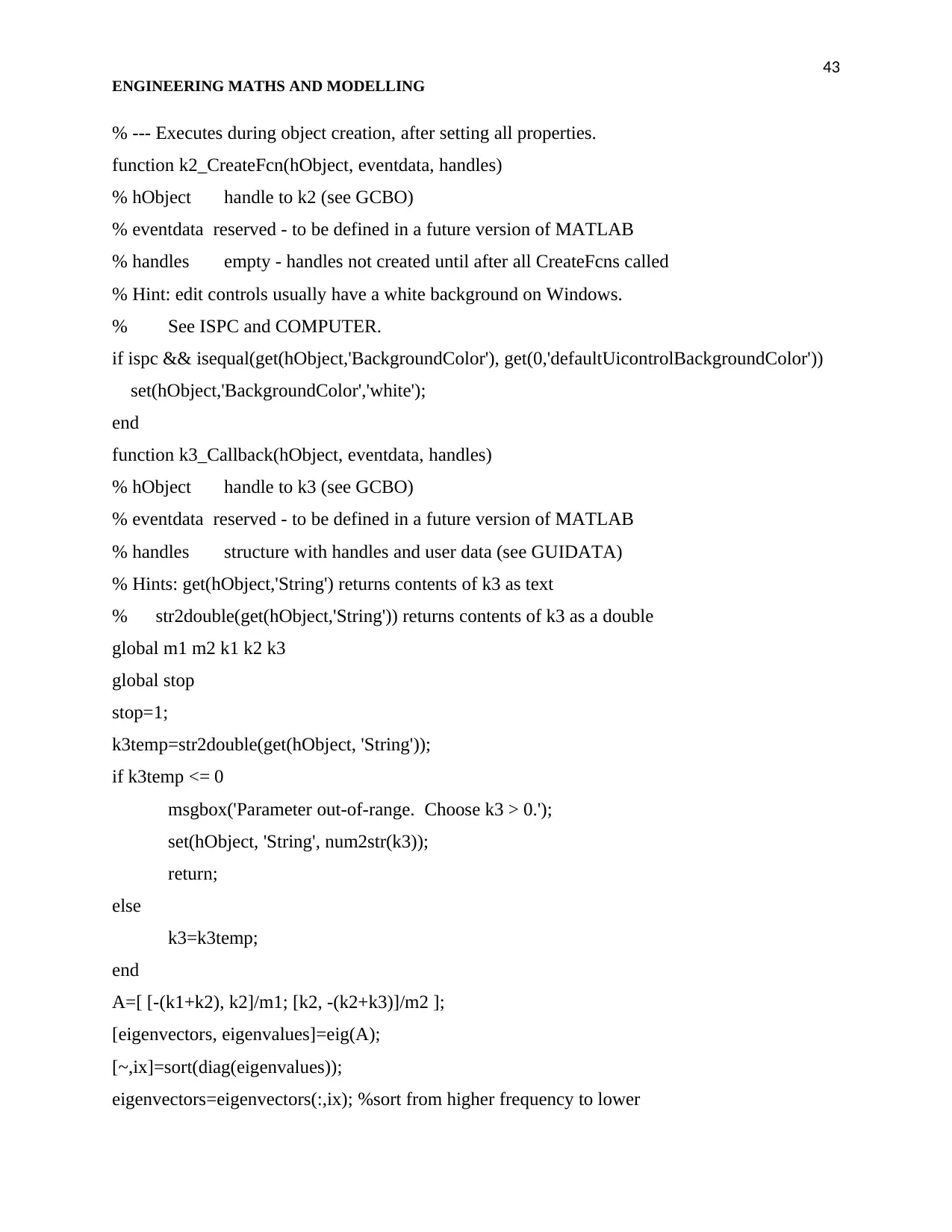
43
ENGINEERING MATHS AND MODELLING
% --- Executes during object creation, after setting all properties.
function k2_CreateFcn(hObject, eventdata, handles)
% hObject handle to k2 (see GCBO)
% eventdata reserved - to be defined in a future version of MATLAB
% handles empty - handles not created until after all CreateFcns called
% Hint: edit controls usually have a white background on Windows.
% See ISPC and COMPUTER.
if ispc && isequal(get(hObject,'BackgroundColor'), get(0,'defaultUicontrolBackgroundColor'))
set(hObject,'BackgroundColor','white');
end
function k3_Callback(hObject, eventdata, handles)
% hObject handle to k3 (see GCBO)
% eventdata reserved - to be defined in a future version of MATLAB
% handles structure with handles and user data (see GUIDATA)
% Hints: get(hObject,'String') returns contents of k3 as text
% str2double(get(hObject,'String')) returns contents of k3 as a double
global m1 m2 k1 k2 k3
global stop
stop=1;
k3temp=str2double(get(hObject, 'String'));
if k3temp <= 0
msgbox('Parameter out-of-range. Choose k3 > 0.');
set(hObject, 'String', num2str(k3));
return;
else
k3=k3temp;
end
A=[ [-(k1+k2), k2]/m1; [k2, -(k2+k3)]/m2 ];
[eigenvectors, eigenvalues]=eig(A);
[~,ix]=sort(diag(eigenvalues));
eigenvectors=eigenvectors(:,ix); %sort from higher frequency to lower
ENGINEERING MATHS AND MODELLING
% --- Executes during object creation, after setting all properties.
function k2_CreateFcn(hObject, eventdata, handles)
% hObject handle to k2 (see GCBO)
% eventdata reserved - to be defined in a future version of MATLAB
% handles empty - handles not created until after all CreateFcns called
% Hint: edit controls usually have a white background on Windows.
% See ISPC and COMPUTER.
if ispc && isequal(get(hObject,'BackgroundColor'), get(0,'defaultUicontrolBackgroundColor'))
set(hObject,'BackgroundColor','white');
end
function k3_Callback(hObject, eventdata, handles)
% hObject handle to k3 (see GCBO)
% eventdata reserved - to be defined in a future version of MATLAB
% handles structure with handles and user data (see GUIDATA)
% Hints: get(hObject,'String') returns contents of k3 as text
% str2double(get(hObject,'String')) returns contents of k3 as a double
global m1 m2 k1 k2 k3
global stop
stop=1;
k3temp=str2double(get(hObject, 'String'));
if k3temp <= 0
msgbox('Parameter out-of-range. Choose k3 > 0.');
set(hObject, 'String', num2str(k3));
return;
else
k3=k3temp;
end
A=[ [-(k1+k2), k2]/m1; [k2, -(k2+k3)]/m2 ];
[eigenvectors, eigenvalues]=eig(A);
[~,ix]=sort(diag(eigenvalues));
eigenvectors=eigenvectors(:,ix); %sort from higher frequency to lower
Paraphrase This Document
Need a fresh take? Get an instant paraphrase of this document with our AI Paraphraser
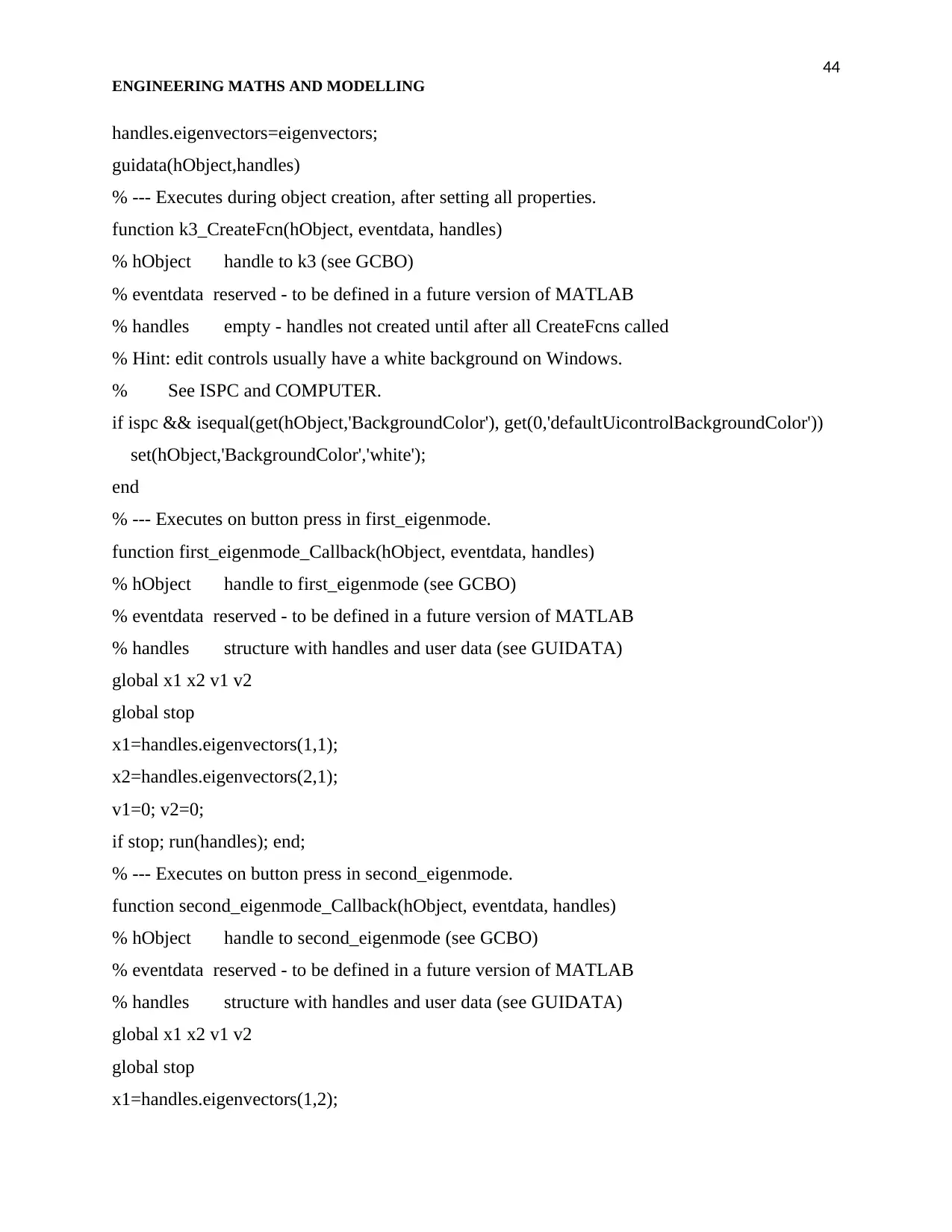
44
ENGINEERING MATHS AND MODELLING
handles.eigenvectors=eigenvectors;
guidata(hObject,handles)
% --- Executes during object creation, after setting all properties.
function k3_CreateFcn(hObject, eventdata, handles)
% hObject handle to k3 (see GCBO)
% eventdata reserved - to be defined in a future version of MATLAB
% handles empty - handles not created until after all CreateFcns called
% Hint: edit controls usually have a white background on Windows.
% See ISPC and COMPUTER.
if ispc && isequal(get(hObject,'BackgroundColor'), get(0,'defaultUicontrolBackgroundColor'))
set(hObject,'BackgroundColor','white');
end
% --- Executes on button press in first_eigenmode.
function first_eigenmode_Callback(hObject, eventdata, handles)
% hObject handle to first_eigenmode (see GCBO)
% eventdata reserved - to be defined in a future version of MATLAB
% handles structure with handles and user data (see GUIDATA)
global x1 x2 v1 v2
global stop
x1=handles.eigenvectors(1,1);
x2=handles.eigenvectors(2,1);
v1=0; v2=0;
if stop; run(handles); end;
% --- Executes on button press in second_eigenmode.
function second_eigenmode_Callback(hObject, eventdata, handles)
% hObject handle to second_eigenmode (see GCBO)
% eventdata reserved - to be defined in a future version of MATLAB
% handles structure with handles and user data (see GUIDATA)
global x1 x2 v1 v2
global stop
x1=handles.eigenvectors(1,2);
ENGINEERING MATHS AND MODELLING
handles.eigenvectors=eigenvectors;
guidata(hObject,handles)
% --- Executes during object creation, after setting all properties.
function k3_CreateFcn(hObject, eventdata, handles)
% hObject handle to k3 (see GCBO)
% eventdata reserved - to be defined in a future version of MATLAB
% handles empty - handles not created until after all CreateFcns called
% Hint: edit controls usually have a white background on Windows.
% See ISPC and COMPUTER.
if ispc && isequal(get(hObject,'BackgroundColor'), get(0,'defaultUicontrolBackgroundColor'))
set(hObject,'BackgroundColor','white');
end
% --- Executes on button press in first_eigenmode.
function first_eigenmode_Callback(hObject, eventdata, handles)
% hObject handle to first_eigenmode (see GCBO)
% eventdata reserved - to be defined in a future version of MATLAB
% handles structure with handles and user data (see GUIDATA)
global x1 x2 v1 v2
global stop
x1=handles.eigenvectors(1,1);
x2=handles.eigenvectors(2,1);
v1=0; v2=0;
if stop; run(handles); end;
% --- Executes on button press in second_eigenmode.
function second_eigenmode_Callback(hObject, eventdata, handles)
% hObject handle to second_eigenmode (see GCBO)
% eventdata reserved - to be defined in a future version of MATLAB
% handles structure with handles and user data (see GUIDATA)
global x1 x2 v1 v2
global stop
x1=handles.eigenvectors(1,2);
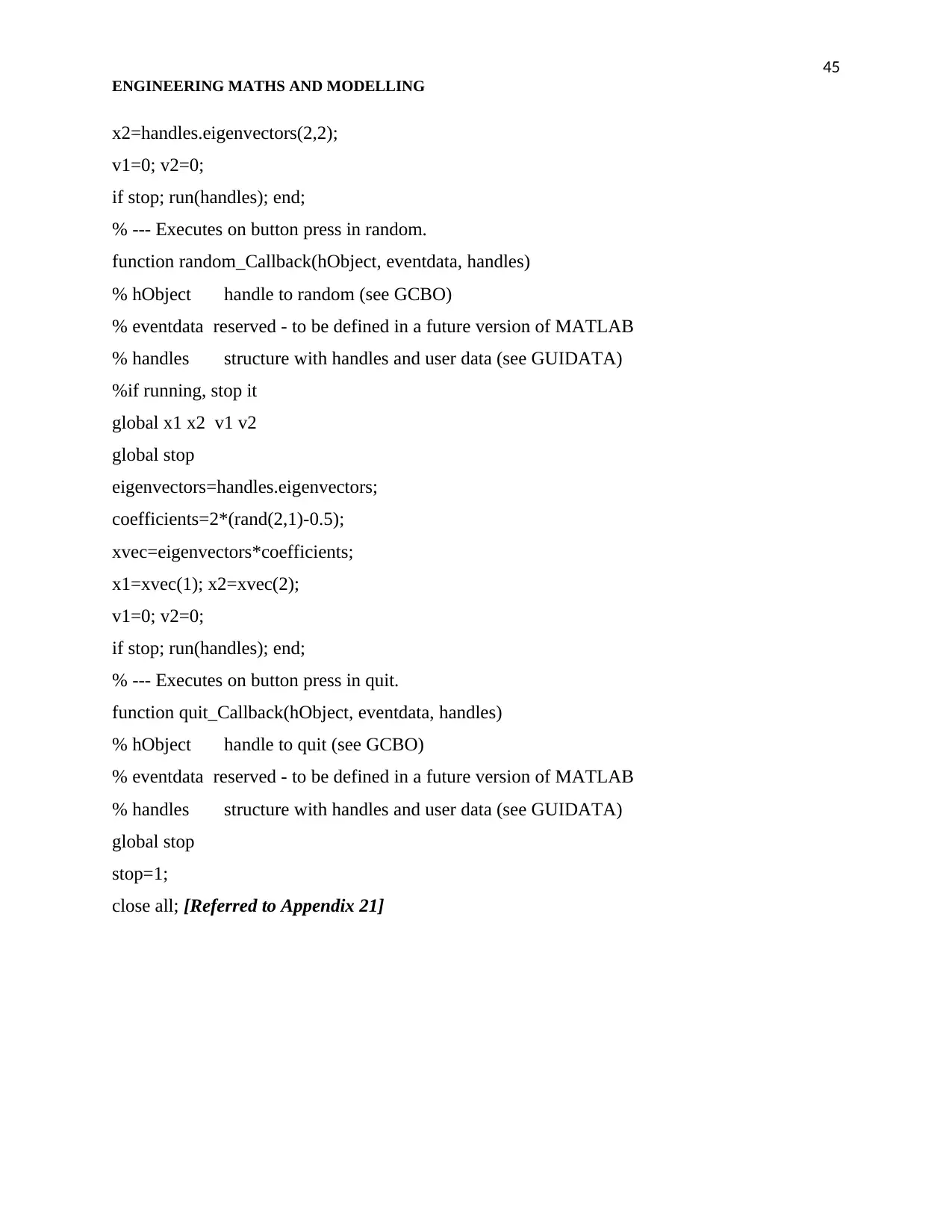
45
ENGINEERING MATHS AND MODELLING
x2=handles.eigenvectors(2,2);
v1=0; v2=0;
if stop; run(handles); end;
% --- Executes on button press in random.
function random_Callback(hObject, eventdata, handles)
% hObject handle to random (see GCBO)
% eventdata reserved - to be defined in a future version of MATLAB
% handles structure with handles and user data (see GUIDATA)
%if running, stop it
global x1 x2 v1 v2
global stop
eigenvectors=handles.eigenvectors;
coefficients=2*(rand(2,1)-0.5);
xvec=eigenvectors*coefficients;
x1=xvec(1); x2=xvec(2);
v1=0; v2=0;
if stop; run(handles); end;
% --- Executes on button press in quit.
function quit_Callback(hObject, eventdata, handles)
% hObject handle to quit (see GCBO)
% eventdata reserved - to be defined in a future version of MATLAB
% handles structure with handles and user data (see GUIDATA)
global stop
stop=1;
close all; [Referred to Appendix 21]
ENGINEERING MATHS AND MODELLING
x2=handles.eigenvectors(2,2);
v1=0; v2=0;
if stop; run(handles); end;
% --- Executes on button press in random.
function random_Callback(hObject, eventdata, handles)
% hObject handle to random (see GCBO)
% eventdata reserved - to be defined in a future version of MATLAB
% handles structure with handles and user data (see GUIDATA)
%if running, stop it
global x1 x2 v1 v2
global stop
eigenvectors=handles.eigenvectors;
coefficients=2*(rand(2,1)-0.5);
xvec=eigenvectors*coefficients;
x1=xvec(1); x2=xvec(2);
v1=0; v2=0;
if stop; run(handles); end;
% --- Executes on button press in quit.
function quit_Callback(hObject, eventdata, handles)
% hObject handle to quit (see GCBO)
% eventdata reserved - to be defined in a future version of MATLAB
% handles structure with handles and user data (see GUIDATA)
global stop
stop=1;
close all; [Referred to Appendix 21]

46
ENGINEERING MATHS AND MODELLING
Appendix 21: Mat lab output for ode solution of two mass-spring damper
c) Function 3
>> clear;
m = 1;
k = 1;
timef = 60;
n = 1000;
ts = timef/n;
v = zeros(1, n+1);
x = zeros(1, n+1);
ENGINEERING MATHS AND MODELLING
Appendix 21: Mat lab output for ode solution of two mass-spring damper
c) Function 3
>> clear;
m = 1;
k = 1;
timef = 60;
n = 1000;
ts = timef/n;
v = zeros(1, n+1);
x = zeros(1, n+1);
Secure Best Marks with AI Grader
Need help grading? Try our AI Grader for instant feedback on your assignments.
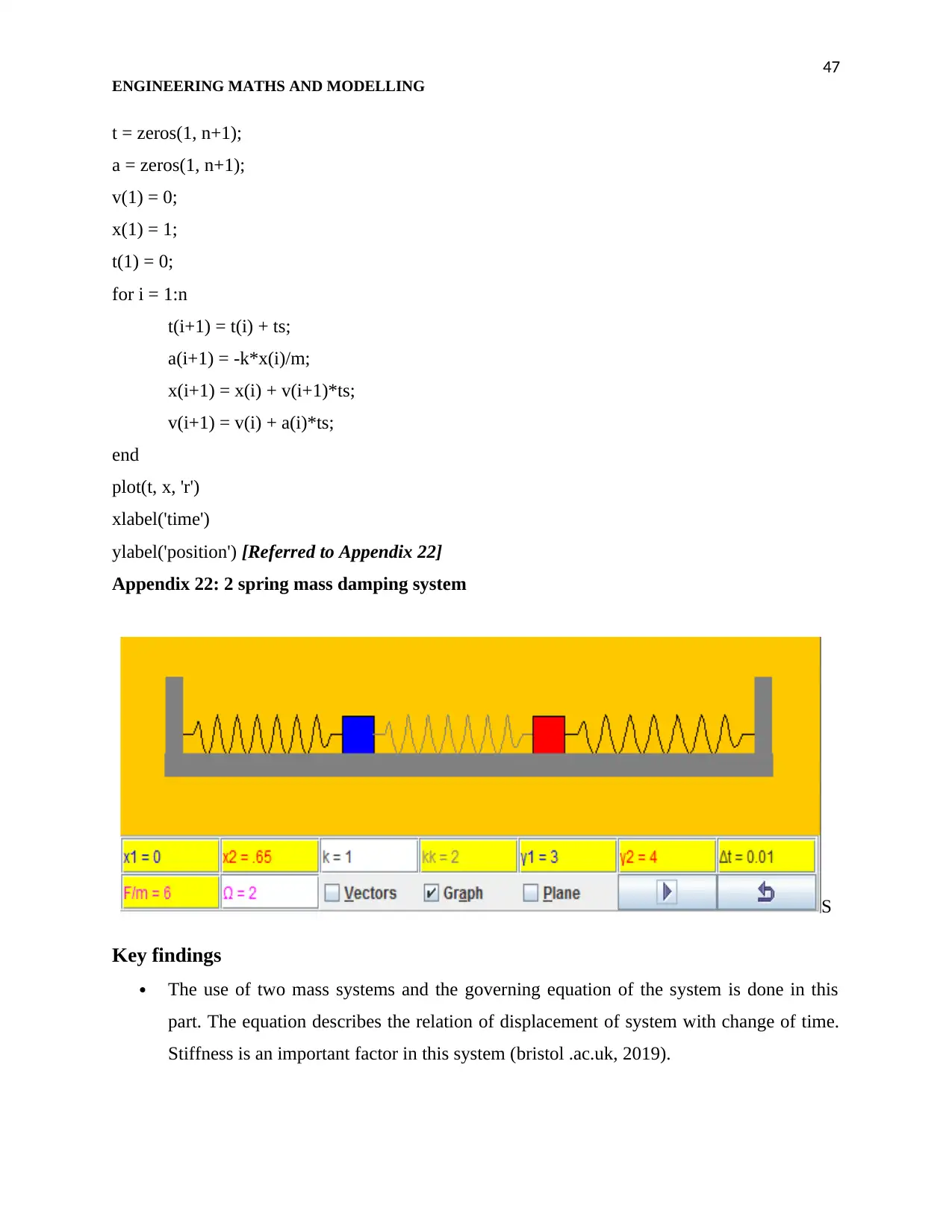
47
ENGINEERING MATHS AND MODELLING
t = zeros(1, n+1);
a = zeros(1, n+1);
v(1) = 0;
x(1) = 1;
t(1) = 0;
for i = 1:n
t(i+1) = t(i) + ts;
a(i+1) = -k*x(i)/m;
x(i+1) = x(i) + v(i+1)*ts;
v(i+1) = v(i) + a(i)*ts;
end
plot(t, x, 'r')
xlabel('time')
ylabel('position') [Referred to Appendix 22]
Appendix 22: 2 spring mass damping system
S
Key findings
The use of two mass systems and the governing equation of the system is done in this
part. The equation describes the relation of displacement of system with change of time.
Stiffness is an important factor in this system (bristol .ac.uk, 2019).
ENGINEERING MATHS AND MODELLING
t = zeros(1, n+1);
a = zeros(1, n+1);
v(1) = 0;
x(1) = 1;
t(1) = 0;
for i = 1:n
t(i+1) = t(i) + ts;
a(i+1) = -k*x(i)/m;
x(i+1) = x(i) + v(i+1)*ts;
v(i+1) = v(i) + a(i)*ts;
end
plot(t, x, 'r')
xlabel('time')
ylabel('position') [Referred to Appendix 22]
Appendix 22: 2 spring mass damping system
S
Key findings
The use of two mass systems and the governing equation of the system is done in this
part. The equation describes the relation of displacement of system with change of time.
Stiffness is an important factor in this system (bristol .ac.uk, 2019).
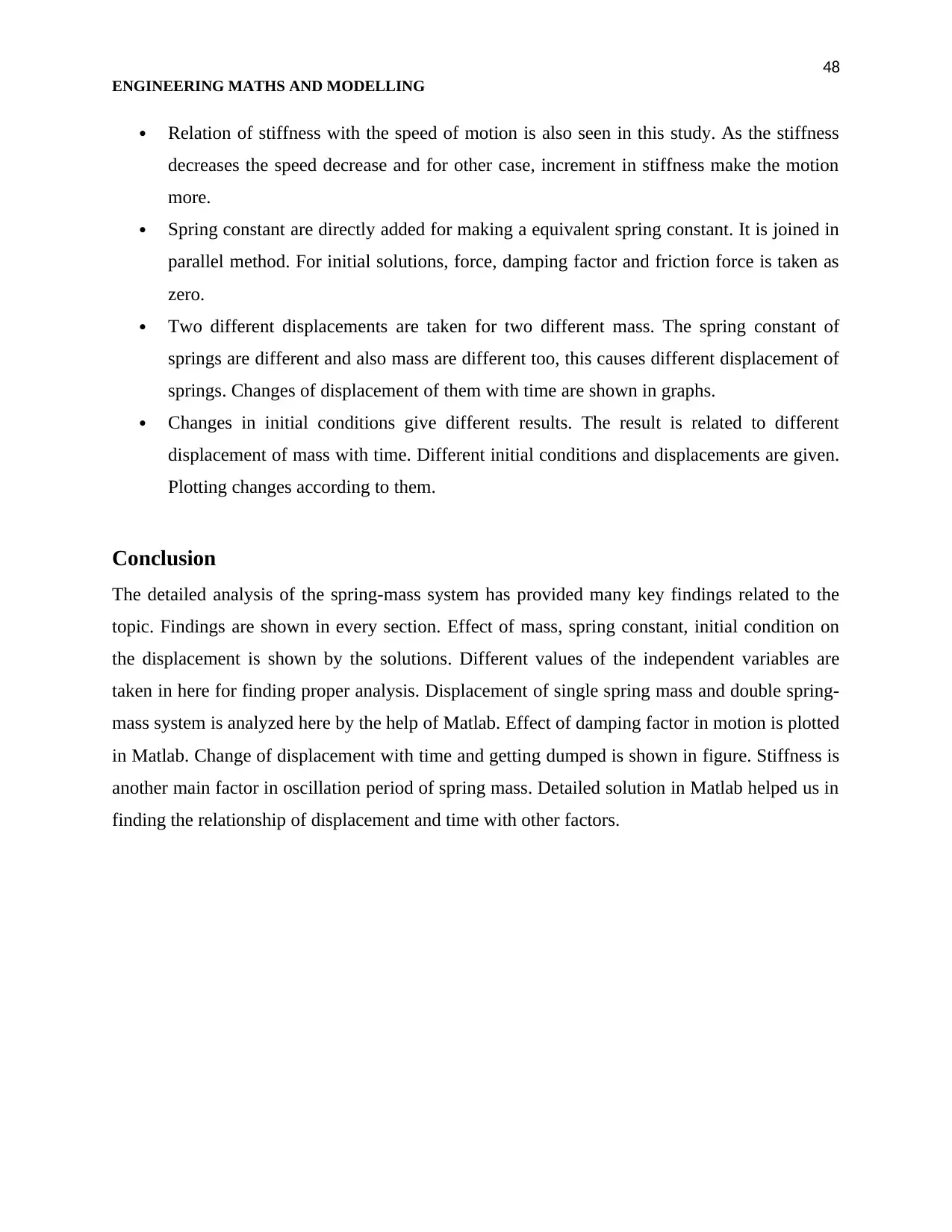
48
ENGINEERING MATHS AND MODELLING
Relation of stiffness with the speed of motion is also seen in this study. As the stiffness
decreases the speed decrease and for other case, increment in stiffness make the motion
more.
Spring constant are directly added for making a equivalent spring constant. It is joined in
parallel method. For initial solutions, force, damping factor and friction force is taken as
zero.
Two different displacements are taken for two different mass. The spring constant of
springs are different and also mass are different too, this causes different displacement of
springs. Changes of displacement of them with time are shown in graphs.
Changes in initial conditions give different results. The result is related to different
displacement of mass with time. Different initial conditions and displacements are given.
Plotting changes according to them.
Conclusion
The detailed analysis of the spring-mass system has provided many key findings related to the
topic. Findings are shown in every section. Effect of mass, spring constant, initial condition on
the displacement is shown by the solutions. Different values of the independent variables are
taken in here for finding proper analysis. Displacement of single spring mass and double spring-
mass system is analyzed here by the help of Matlab. Effect of damping factor in motion is plotted
in Matlab. Change of displacement with time and getting dumped is shown in figure. Stiffness is
another main factor in oscillation period of spring mass. Detailed solution in Matlab helped us in
finding the relationship of displacement and time with other factors.
ENGINEERING MATHS AND MODELLING
Relation of stiffness with the speed of motion is also seen in this study. As the stiffness
decreases the speed decrease and for other case, increment in stiffness make the motion
more.
Spring constant are directly added for making a equivalent spring constant. It is joined in
parallel method. For initial solutions, force, damping factor and friction force is taken as
zero.
Two different displacements are taken for two different mass. The spring constant of
springs are different and also mass are different too, this causes different displacement of
springs. Changes of displacement of them with time are shown in graphs.
Changes in initial conditions give different results. The result is related to different
displacement of mass with time. Different initial conditions and displacements are given.
Plotting changes according to them.
Conclusion
The detailed analysis of the spring-mass system has provided many key findings related to the
topic. Findings are shown in every section. Effect of mass, spring constant, initial condition on
the displacement is shown by the solutions. Different values of the independent variables are
taken in here for finding proper analysis. Displacement of single spring mass and double spring-
mass system is analyzed here by the help of Matlab. Effect of damping factor in motion is plotted
in Matlab. Change of displacement with time and getting dumped is shown in figure. Stiffness is
another main factor in oscillation period of spring mass. Detailed solution in Matlab helped us in
finding the relationship of displacement and time with other factors.
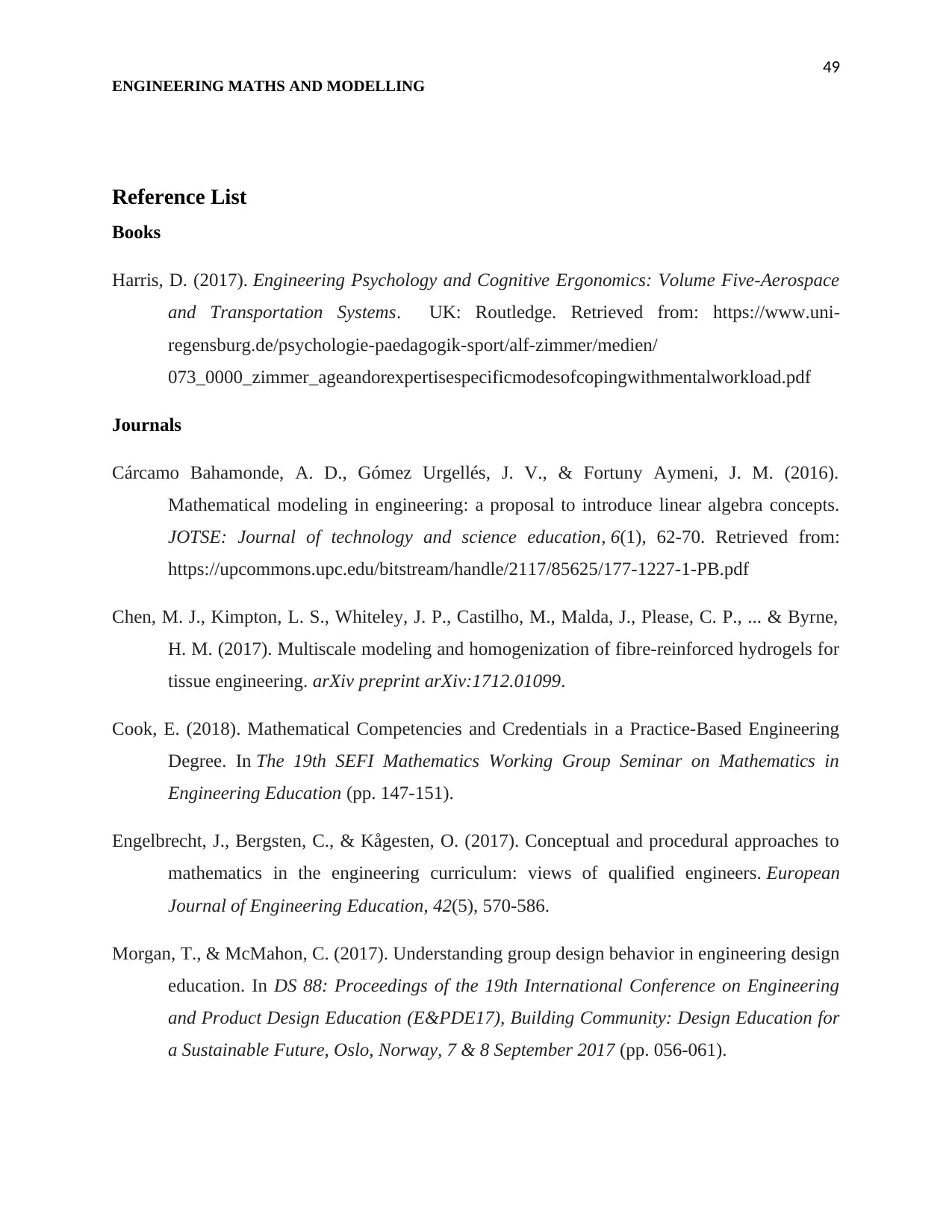
49
ENGINEERING MATHS AND MODELLING
Reference List
Books
Harris, D. (2017). Engineering Psychology and Cognitive Ergonomics: Volume Five-Aerospace
and Transportation Systems. UK: Routledge. Retrieved from: https://www.uni-
regensburg.de/psychologie-paedagogik-sport/alf-zimmer/medien/
073_0000_zimmer_ageandorexpertisespecificmodesofcopingwithmentalworkload.pdf
Journals
Cárcamo Bahamonde, A. D., Gómez Urgellés, J. V., & Fortuny Aymeni, J. M. (2016).
Mathematical modeling in engineering: a proposal to introduce linear algebra concepts.
JOTSE: Journal of technology and science education, 6(1), 62-70. Retrieved from:
https://upcommons.upc.edu/bitstream/handle/2117/85625/177-1227-1-PB.pdf
Chen, M. J., Kimpton, L. S., Whiteley, J. P., Castilho, M., Malda, J., Please, C. P., ... & Byrne,
H. M. (2017). Multiscale modeling and homogenization of fibre-reinforced hydrogels for
tissue engineering. arXiv preprint arXiv:1712.01099.
Cook, E. (2018). Mathematical Competencies and Credentials in a Practice-Based Engineering
Degree. In The 19th SEFI Mathematics Working Group Seminar on Mathematics in
Engineering Education (pp. 147-151).
Engelbrecht, J., Bergsten, C., & Kågesten, O. (2017). Conceptual and procedural approaches to
mathematics in the engineering curriculum: views of qualified engineers. European
Journal of Engineering Education, 42(5), 570-586.
Morgan, T., & McMahon, C. (2017). Understanding group design behavior in engineering design
education. In DS 88: Proceedings of the 19th International Conference on Engineering
and Product Design Education (E&PDE17), Building Community: Design Education for
a Sustainable Future, Oslo, Norway, 7 & 8 September 2017 (pp. 056-061).
ENGINEERING MATHS AND MODELLING
Reference List
Books
Harris, D. (2017). Engineering Psychology and Cognitive Ergonomics: Volume Five-Aerospace
and Transportation Systems. UK: Routledge. Retrieved from: https://www.uni-
regensburg.de/psychologie-paedagogik-sport/alf-zimmer/medien/
073_0000_zimmer_ageandorexpertisespecificmodesofcopingwithmentalworkload.pdf
Journals
Cárcamo Bahamonde, A. D., Gómez Urgellés, J. V., & Fortuny Aymeni, J. M. (2016).
Mathematical modeling in engineering: a proposal to introduce linear algebra concepts.
JOTSE: Journal of technology and science education, 6(1), 62-70. Retrieved from:
https://upcommons.upc.edu/bitstream/handle/2117/85625/177-1227-1-PB.pdf
Chen, M. J., Kimpton, L. S., Whiteley, J. P., Castilho, M., Malda, J., Please, C. P., ... & Byrne,
H. M. (2017). Multiscale modeling and homogenization of fibre-reinforced hydrogels for
tissue engineering. arXiv preprint arXiv:1712.01099.
Cook, E. (2018). Mathematical Competencies and Credentials in a Practice-Based Engineering
Degree. In The 19th SEFI Mathematics Working Group Seminar on Mathematics in
Engineering Education (pp. 147-151).
Engelbrecht, J., Bergsten, C., & Kågesten, O. (2017). Conceptual and procedural approaches to
mathematics in the engineering curriculum: views of qualified engineers. European
Journal of Engineering Education, 42(5), 570-586.
Morgan, T., & McMahon, C. (2017). Understanding group design behavior in engineering design
education. In DS 88: Proceedings of the 19th International Conference on Engineering
and Product Design Education (E&PDE17), Building Community: Design Education for
a Sustainable Future, Oslo, Norway, 7 & 8 September 2017 (pp. 056-061).
Paraphrase This Document
Need a fresh take? Get an instant paraphrase of this document with our AI Paraphraser
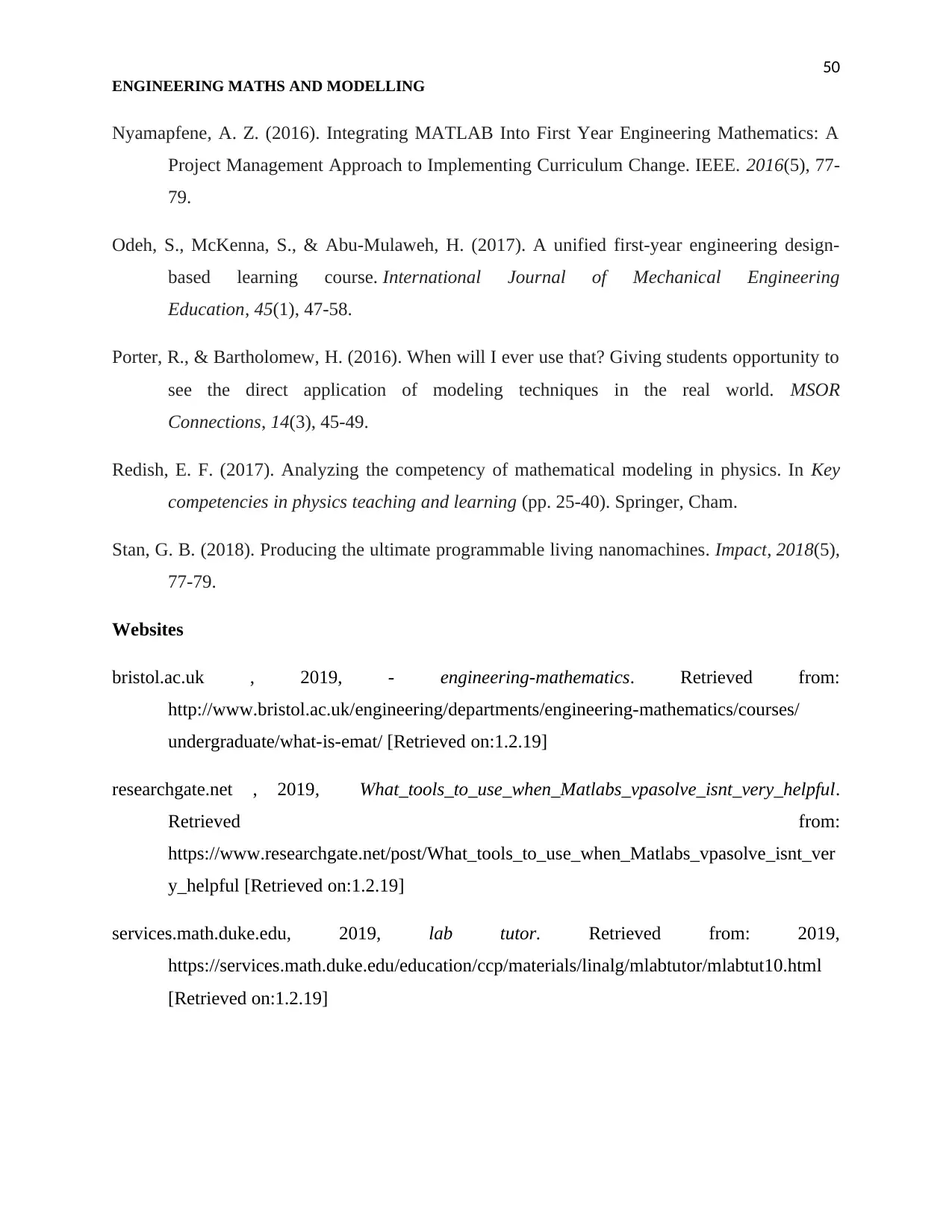
50
ENGINEERING MATHS AND MODELLING
Nyamapfene, A. Z. (2016). Integrating MATLAB Into First Year Engineering Mathematics: A
Project Management Approach to Implementing Curriculum Change. IEEE. 2016(5), 77-
79.
Odeh, S., McKenna, S., & Abu-Mulaweh, H. (2017). A unified first-year engineering design-
based learning course. International Journal of Mechanical Engineering
Education, 45(1), 47-58.
Porter, R., & Bartholomew, H. (2016). When will I ever use that? Giving students opportunity to
see the direct application of modeling techniques in the real world. MSOR
Connections, 14(3), 45-49.
Redish, E. F. (2017). Analyzing the competency of mathematical modeling in physics. In Key
competencies in physics teaching and learning (pp. 25-40). Springer, Cham.
Stan, G. B. (2018). Producing the ultimate programmable living nanomachines. Impact, 2018(5),
77-79.
Websites
bristol.ac.uk , 2019, - engineering-mathematics. Retrieved from:
http://www.bristol.ac.uk/engineering/departments/engineering-mathematics/courses/
undergraduate/what-is-emat/ [Retrieved on:1.2.19]
researchgate.net , 2019, What_tools_to_use_when_Matlabs_vpasolve_isnt_very_helpful.
Retrieved from:
https://www.researchgate.net/post/What_tools_to_use_when_Matlabs_vpasolve_isnt_ver
y_helpful [Retrieved on:1.2.19]
services.math.duke.edu, 2019, lab tutor. Retrieved from: 2019,
https://services.math.duke.edu/education/ccp/materials/linalg/mlabtutor/mlabtut10.html
[Retrieved on:1.2.19]
ENGINEERING MATHS AND MODELLING
Nyamapfene, A. Z. (2016). Integrating MATLAB Into First Year Engineering Mathematics: A
Project Management Approach to Implementing Curriculum Change. IEEE. 2016(5), 77-
79.
Odeh, S., McKenna, S., & Abu-Mulaweh, H. (2017). A unified first-year engineering design-
based learning course. International Journal of Mechanical Engineering
Education, 45(1), 47-58.
Porter, R., & Bartholomew, H. (2016). When will I ever use that? Giving students opportunity to
see the direct application of modeling techniques in the real world. MSOR
Connections, 14(3), 45-49.
Redish, E. F. (2017). Analyzing the competency of mathematical modeling in physics. In Key
competencies in physics teaching and learning (pp. 25-40). Springer, Cham.
Stan, G. B. (2018). Producing the ultimate programmable living nanomachines. Impact, 2018(5),
77-79.
Websites
bristol.ac.uk , 2019, - engineering-mathematics. Retrieved from:
http://www.bristol.ac.uk/engineering/departments/engineering-mathematics/courses/
undergraduate/what-is-emat/ [Retrieved on:1.2.19]
researchgate.net , 2019, What_tools_to_use_when_Matlabs_vpasolve_isnt_very_helpful.
Retrieved from:
https://www.researchgate.net/post/What_tools_to_use_when_Matlabs_vpasolve_isnt_ver
y_helpful [Retrieved on:1.2.19]
services.math.duke.edu, 2019, lab tutor. Retrieved from: 2019,
https://services.math.duke.edu/education/ccp/materials/linalg/mlabtutor/mlabtut10.html
[Retrieved on:1.2.19]
1 out of 50
Related Documents

Your All-in-One AI-Powered Toolkit for Academic Success.
+13062052269
info@desklib.com
Available 24*7 on WhatsApp / Email
Unlock your academic potential
© 2024 | Zucol Services PVT LTD | All rights reserved.