Equipment Downtime Analysis - Trend, Pareto Analysis and Ranking
VerifiedAdded on  2022/10/01
|11
|1464
|482
AI Summary
This report analyses the trend of downtime of 8 equipment monthly and quarterwise, Pareto analysis of downtime of machineries and ranking of equipment based on performance for the last 26 months. It also includes an analysis of downtime of equipment, ranking and finding the reason for downtime for critical machinery.
Contribute Materials
Your contribution can guide someone’s learning journey. Share your
documents today.
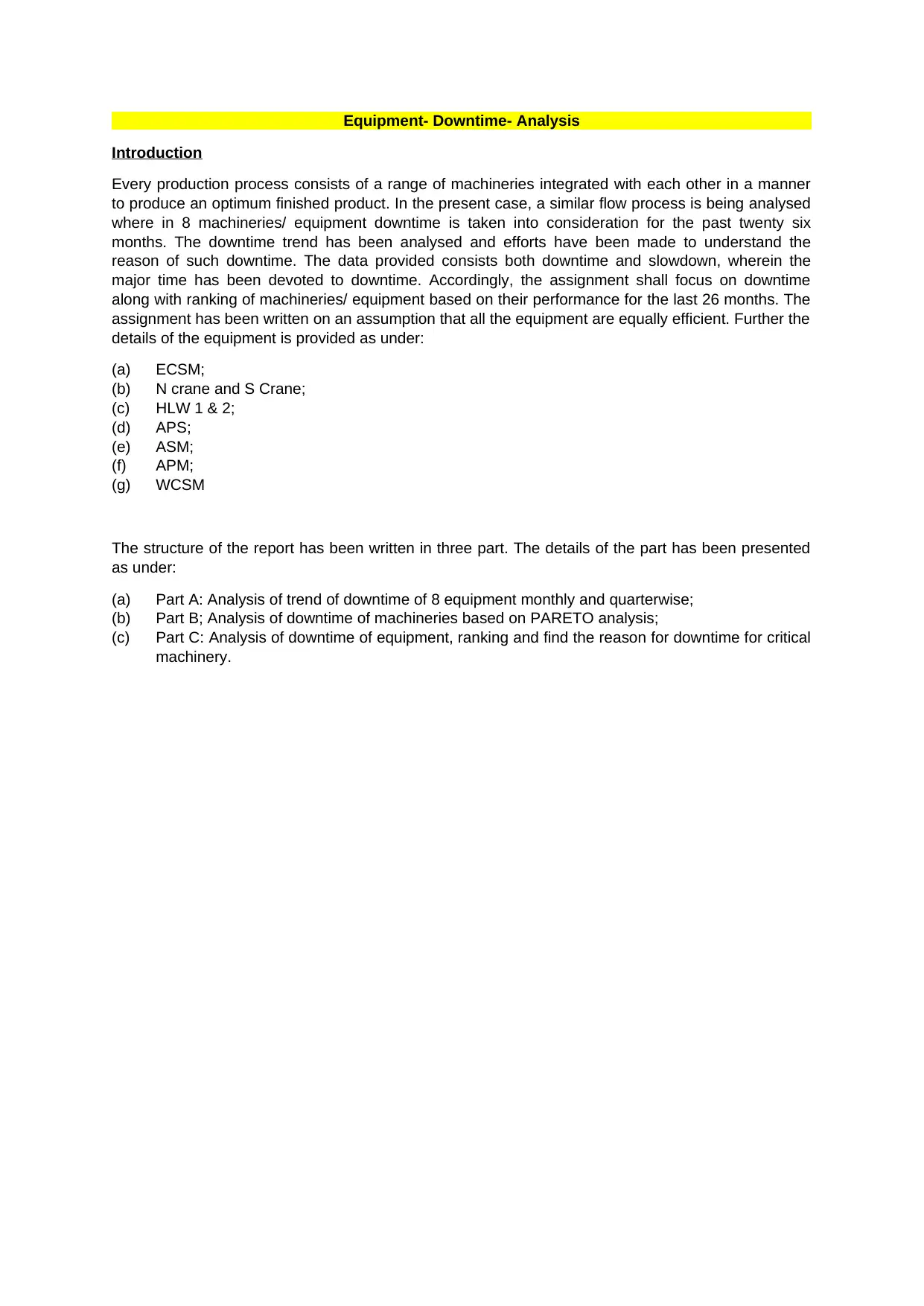
Equipment- Downtime- Analysis
Introduction
Every production process consists of a range of machineries integrated with each other in a manner
to produce an optimum finished product. In the present case, a similar flow process is being analysed
where in 8 machineries/ equipment downtime is taken into consideration for the past twenty six
months. The downtime trend has been analysed and efforts have been made to understand the
reason of such downtime. The data provided consists both downtime and slowdown, wherein the
major time has been devoted to downtime. Accordingly, the assignment shall focus on downtime
along with ranking of machineries/ equipment based on their performance for the last 26 months. The
assignment has been written on an assumption that all the equipment are equally efficient. Further the
details of the equipment is provided as under:
(a) ECSM;
(b) N crane and S Crane;
(c) HLW 1 & 2;
(d) APS;
(e) ASM;
(f) APM;
(g) WCSM
The structure of the report has been written in three part. The details of the part has been presented
as under:
(a) Part A: Analysis of trend of downtime of 8 equipment monthly and quarterwise;
(b) Part B; Analysis of downtime of machineries based on PARETO analysis;
(c) Part C: Analysis of downtime of equipment, ranking and find the reason for downtime for critical
machinery.
Introduction
Every production process consists of a range of machineries integrated with each other in a manner
to produce an optimum finished product. In the present case, a similar flow process is being analysed
where in 8 machineries/ equipment downtime is taken into consideration for the past twenty six
months. The downtime trend has been analysed and efforts have been made to understand the
reason of such downtime. The data provided consists both downtime and slowdown, wherein the
major time has been devoted to downtime. Accordingly, the assignment shall focus on downtime
along with ranking of machineries/ equipment based on their performance for the last 26 months. The
assignment has been written on an assumption that all the equipment are equally efficient. Further the
details of the equipment is provided as under:
(a) ECSM;
(b) N crane and S Crane;
(c) HLW 1 & 2;
(d) APS;
(e) ASM;
(f) APM;
(g) WCSM
The structure of the report has been written in three part. The details of the part has been presented
as under:
(a) Part A: Analysis of trend of downtime of 8 equipment monthly and quarterwise;
(b) Part B; Analysis of downtime of machineries based on PARETO analysis;
(c) Part C: Analysis of downtime of equipment, ranking and find the reason for downtime for critical
machinery.
Secure Best Marks with AI Grader
Need help grading? Try our AI Grader for instant feedback on your assignments.
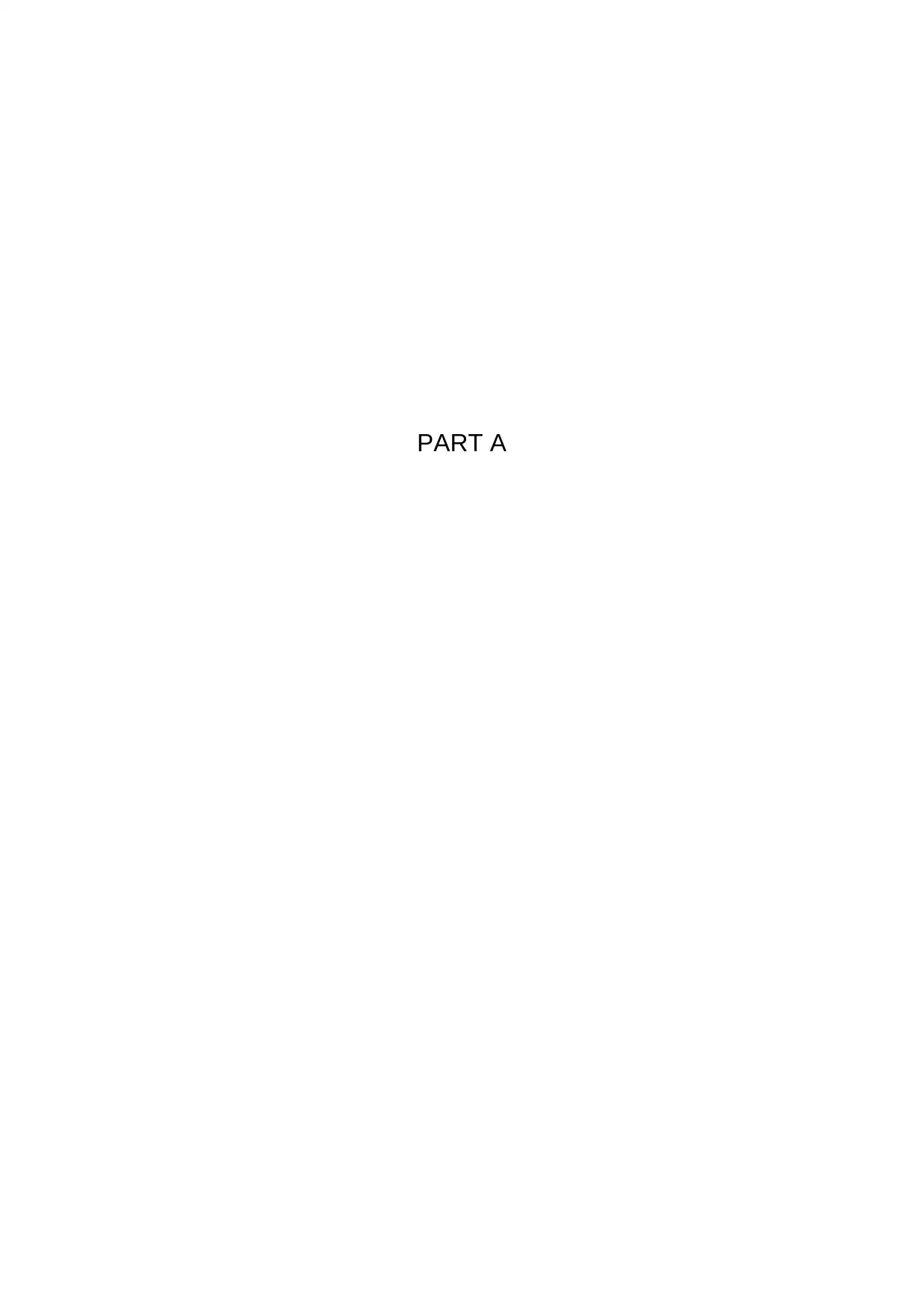
PART A
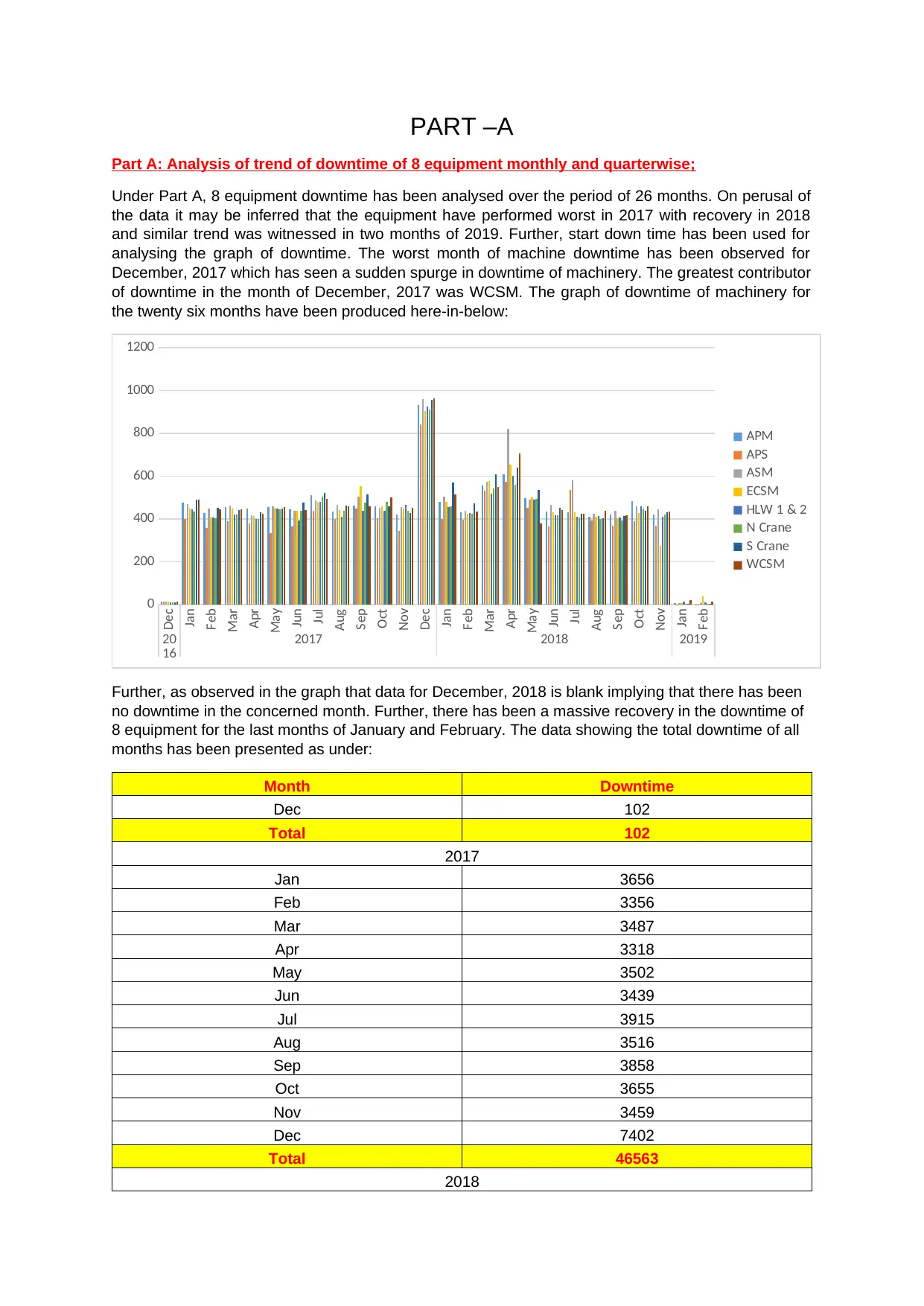
PART –A
Part A: Analysis of trend of downtime of 8 equipment monthly and quarterwise;
Under Part A, 8 equipment downtime has been analysed over the period of 26 months. On perusal of
the data it may be inferred that the equipment have performed worst in 2017 with recovery in 2018
and similar trend was witnessed in two months of 2019. Further, start down time has been used for
analysing the graph of downtime. The worst month of machine downtime has been observed for
December, 2017 which has seen a sudden spurge in downtime of machinery. The greatest contributor
of downtime in the month of December, 2017 was WCSM. The graph of downtime of machinery for
the twenty six months have been produced here-in-below:
Dec
Jan
Feb
Mar
Apr
May
Jun
Jul
Aug
Sep
Oct
Nov
Dec
Jan
Feb
Mar
Apr
May
Jun
Jul
Aug
Sep
Oct
Nov
Jan
Feb
20
16 2017 2018 2019
0
200
400
600
800
1000
1200
APM
APS
ASM
ECSM
HLW 1 & 2
N Crane
S Crane
WCSM
Further, as observed in the graph that data for December, 2018 is blank implying that there has been
no downtime in the concerned month. Further, there has been a massive recovery in the downtime of
8 equipment for the last months of January and February. The data showing the total downtime of all
months has been presented as under:
Month Downtime
Dec 102
Total 102
2017
Jan 3656
Feb 3356
Mar 3487
Apr 3318
May 3502
Jun 3439
Jul 3915
Aug 3516
Sep 3858
Oct 3655
Nov 3459
Dec 7402
Total 46563
2018
Part A: Analysis of trend of downtime of 8 equipment monthly and quarterwise;
Under Part A, 8 equipment downtime has been analysed over the period of 26 months. On perusal of
the data it may be inferred that the equipment have performed worst in 2017 with recovery in 2018
and similar trend was witnessed in two months of 2019. Further, start down time has been used for
analysing the graph of downtime. The worst month of machine downtime has been observed for
December, 2017 which has seen a sudden spurge in downtime of machinery. The greatest contributor
of downtime in the month of December, 2017 was WCSM. The graph of downtime of machinery for
the twenty six months have been produced here-in-below:
Dec
Jan
Feb
Mar
Apr
May
Jun
Jul
Aug
Sep
Oct
Nov
Dec
Jan
Feb
Mar
Apr
May
Jun
Jul
Aug
Sep
Oct
Nov
Jan
Feb
20
16 2017 2018 2019
0
200
400
600
800
1000
1200
APM
APS
ASM
ECSM
HLW 1 & 2
N Crane
S Crane
WCSM
Further, as observed in the graph that data for December, 2018 is blank implying that there has been
no downtime in the concerned month. Further, there has been a massive recovery in the downtime of
8 equipment for the last months of January and February. The data showing the total downtime of all
months has been presented as under:
Month Downtime
Dec 102
Total 102
2017
Jan 3656
Feb 3356
Mar 3487
Apr 3318
May 3502
Jun 3439
Jul 3915
Aug 3516
Sep 3858
Oct 3655
Nov 3459
Dec 7402
Total 46563
2018
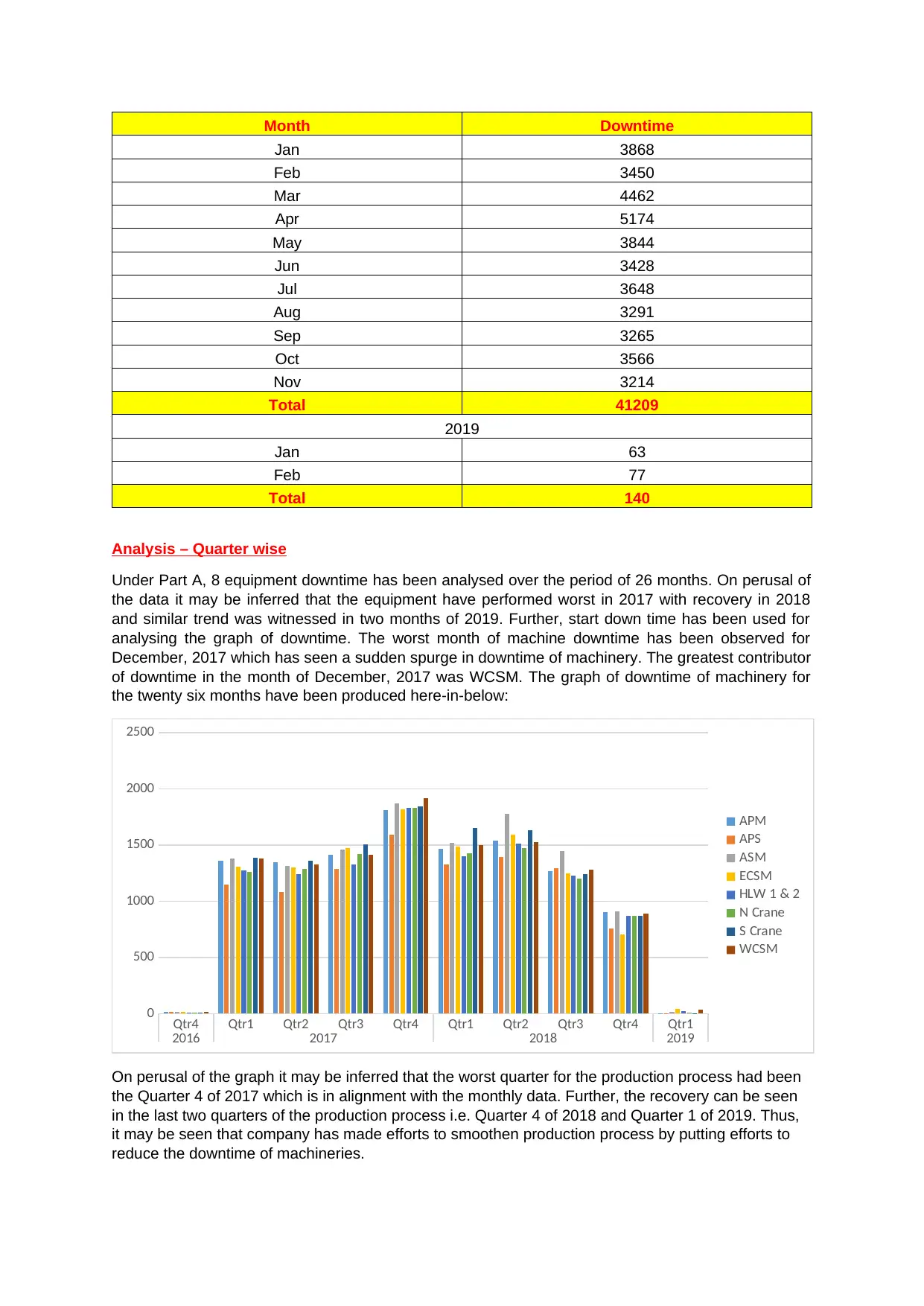
Month Downtime
Jan 3868
Feb 3450
Mar 4462
Apr 5174
May 3844
Jun 3428
Jul 3648
Aug 3291
Sep 3265
Oct 3566
Nov 3214
Total 41209
2019
Jan 63
Feb 77
Total 140
Analysis – Quarter wise
Under Part A, 8 equipment downtime has been analysed over the period of 26 months. On perusal of
the data it may be inferred that the equipment have performed worst in 2017 with recovery in 2018
and similar trend was witnessed in two months of 2019. Further, start down time has been used for
analysing the graph of downtime. The worst month of machine downtime has been observed for
December, 2017 which has seen a sudden spurge in downtime of machinery. The greatest contributor
of downtime in the month of December, 2017 was WCSM. The graph of downtime of machinery for
the twenty six months have been produced here-in-below:
Qtr4 Qtr1 Qtr2 Qtr3 Qtr4 Qtr1 Qtr2 Qtr3 Qtr4 Qtr1
2016 2017 2018 2019
0
500
1000
1500
2000
2500
APM
APS
ASM
ECSM
HLW 1 & 2
N Crane
S Crane
WCSM
On perusal of the graph it may be inferred that the worst quarter for the production process had been
the Quarter 4 of 2017 which is in alignment with the monthly data. Further, the recovery can be seen
in the last two quarters of the production process i.e. Quarter 4 of 2018 and Quarter 1 of 2019. Thus,
it may be seen that company has made efforts to smoothen production process by putting efforts to
reduce the downtime of machineries.
Jan 3868
Feb 3450
Mar 4462
Apr 5174
May 3844
Jun 3428
Jul 3648
Aug 3291
Sep 3265
Oct 3566
Nov 3214
Total 41209
2019
Jan 63
Feb 77
Total 140
Analysis – Quarter wise
Under Part A, 8 equipment downtime has been analysed over the period of 26 months. On perusal of
the data it may be inferred that the equipment have performed worst in 2017 with recovery in 2018
and similar trend was witnessed in two months of 2019. Further, start down time has been used for
analysing the graph of downtime. The worst month of machine downtime has been observed for
December, 2017 which has seen a sudden spurge in downtime of machinery. The greatest contributor
of downtime in the month of December, 2017 was WCSM. The graph of downtime of machinery for
the twenty six months have been produced here-in-below:
Qtr4 Qtr1 Qtr2 Qtr3 Qtr4 Qtr1 Qtr2 Qtr3 Qtr4 Qtr1
2016 2017 2018 2019
0
500
1000
1500
2000
2500
APM
APS
ASM
ECSM
HLW 1 & 2
N Crane
S Crane
WCSM
On perusal of the graph it may be inferred that the worst quarter for the production process had been
the Quarter 4 of 2017 which is in alignment with the monthly data. Further, the recovery can be seen
in the last two quarters of the production process i.e. Quarter 4 of 2018 and Quarter 1 of 2019. Thus,
it may be seen that company has made efforts to smoothen production process by putting efforts to
reduce the downtime of machineries.
Secure Best Marks with AI Grader
Need help grading? Try our AI Grader for instant feedback on your assignments.
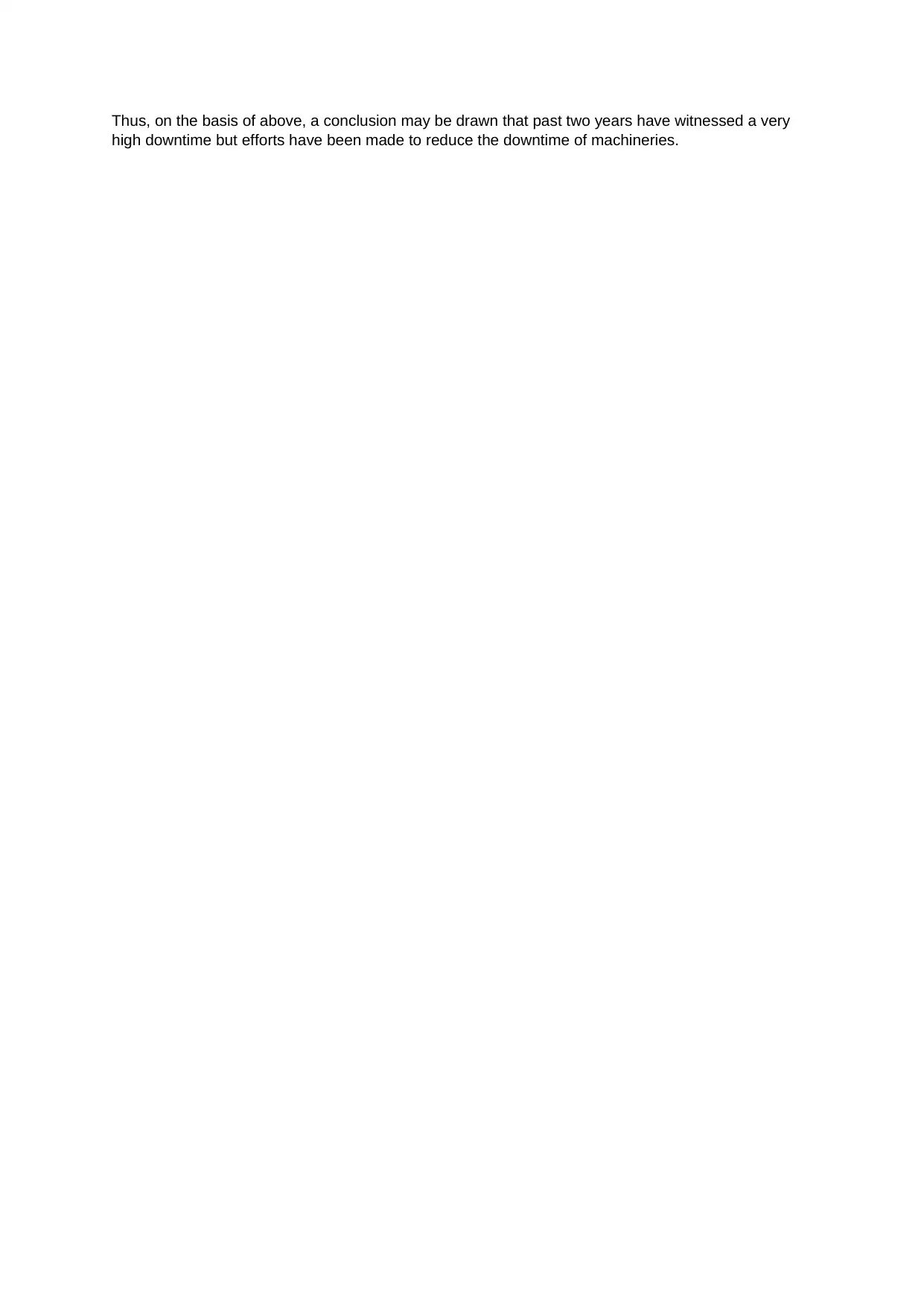
Thus, on the basis of above, a conclusion may be drawn that past two years have witnessed a very
high downtime but efforts have been made to reduce the downtime of machineries.
high downtime but efforts have been made to reduce the downtime of machineries.
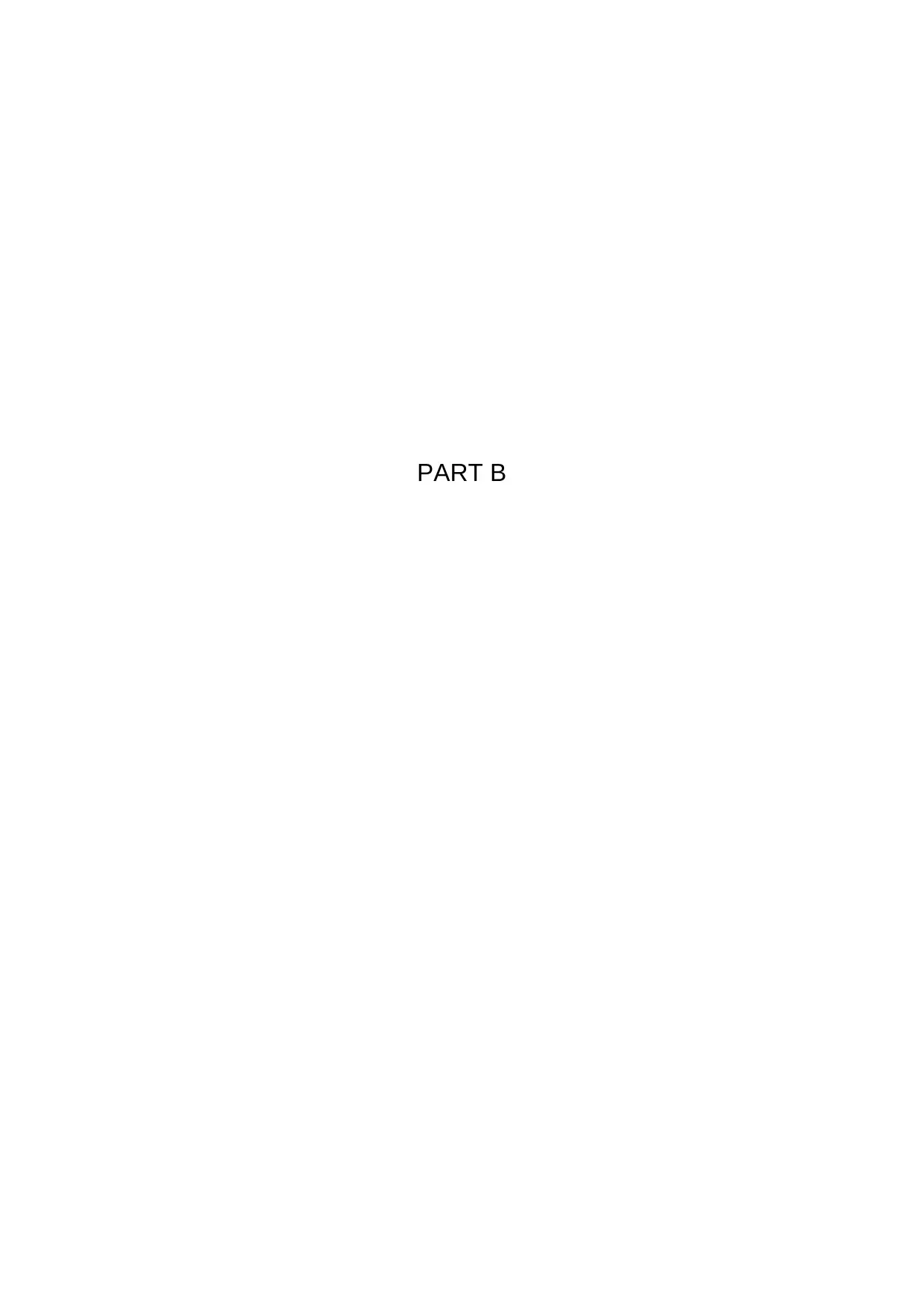
PART B
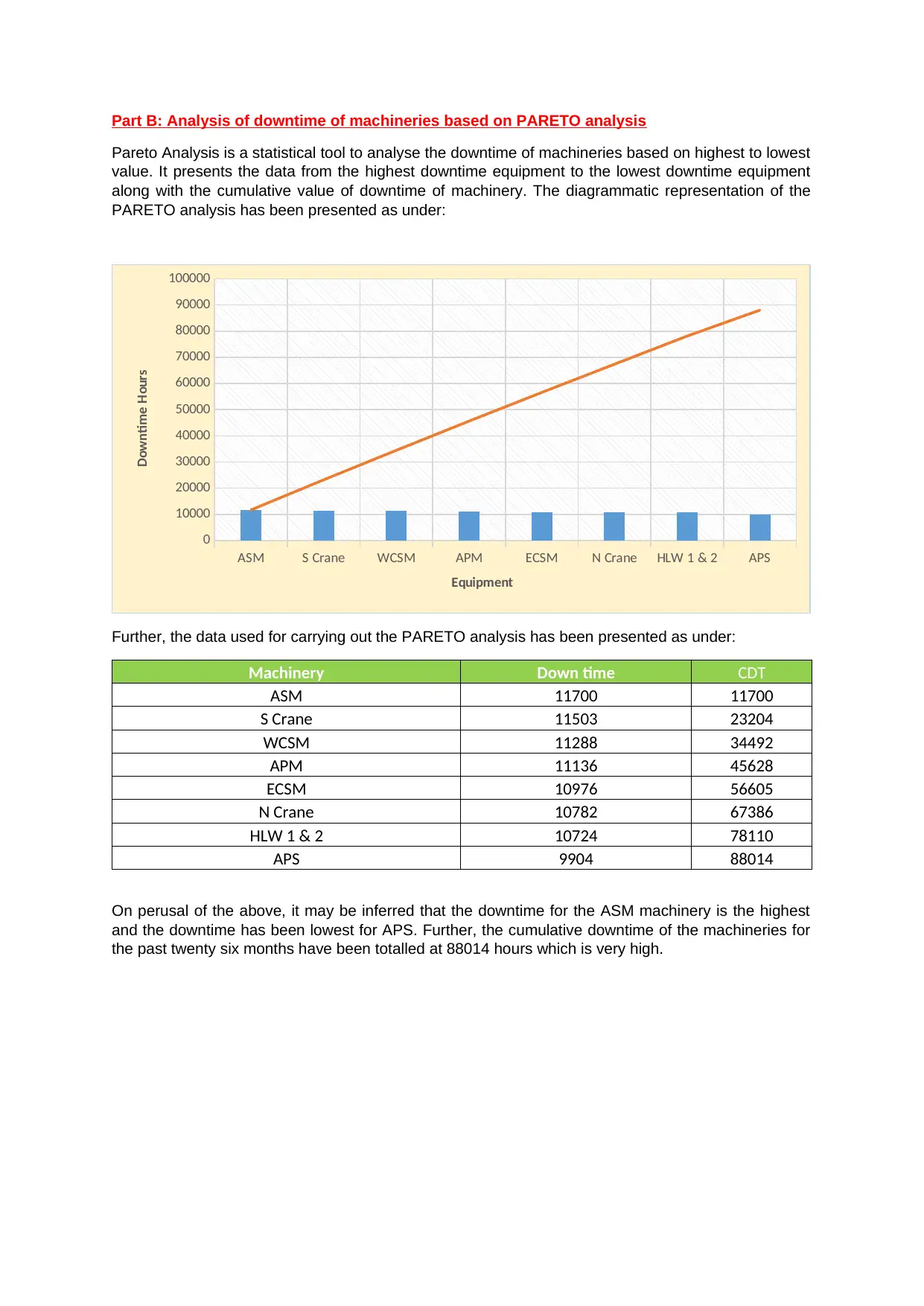
Part B: Analysis of downtime of machineries based on PARETO analysis
Pareto Analysis is a statistical tool to analyse the downtime of machineries based on highest to lowest
value. It presents the data from the highest downtime equipment to the lowest downtime equipment
along with the cumulative value of downtime of machinery. The diagrammatic representation of the
PARETO analysis has been presented as under:
ASM S Crane WCSM APM ECSM N Crane HLW 1 & 2 APS
0
10000
20000
30000
40000
50000
60000
70000
80000
90000
100000
Equipment
Downtime Hours
Further, the data used for carrying out the PARETO analysis has been presented as under:
Machinery Down time CDT
ASM 11700 11700
S Crane 11503 23204
WCSM 11288 34492
APM 11136 45628
ECSM 10976 56605
N Crane 10782 67386
HLW 1 & 2 10724 78110
APS 9904 88014
On perusal of the above, it may be inferred that the downtime for the ASM machinery is the highest
and the downtime has been lowest for APS. Further, the cumulative downtime of the machineries for
the past twenty six months have been totalled at 88014 hours which is very high.
Pareto Analysis is a statistical tool to analyse the downtime of machineries based on highest to lowest
value. It presents the data from the highest downtime equipment to the lowest downtime equipment
along with the cumulative value of downtime of machinery. The diagrammatic representation of the
PARETO analysis has been presented as under:
ASM S Crane WCSM APM ECSM N Crane HLW 1 & 2 APS
0
10000
20000
30000
40000
50000
60000
70000
80000
90000
100000
Equipment
Downtime Hours
Further, the data used for carrying out the PARETO analysis has been presented as under:
Machinery Down time CDT
ASM 11700 11700
S Crane 11503 23204
WCSM 11288 34492
APM 11136 45628
ECSM 10976 56605
N Crane 10782 67386
HLW 1 & 2 10724 78110
APS 9904 88014
On perusal of the above, it may be inferred that the downtime for the ASM machinery is the highest
and the downtime has been lowest for APS. Further, the cumulative downtime of the machineries for
the past twenty six months have been totalled at 88014 hours which is very high.
Paraphrase This Document
Need a fresh take? Get an instant paraphrase of this document with our AI Paraphraser
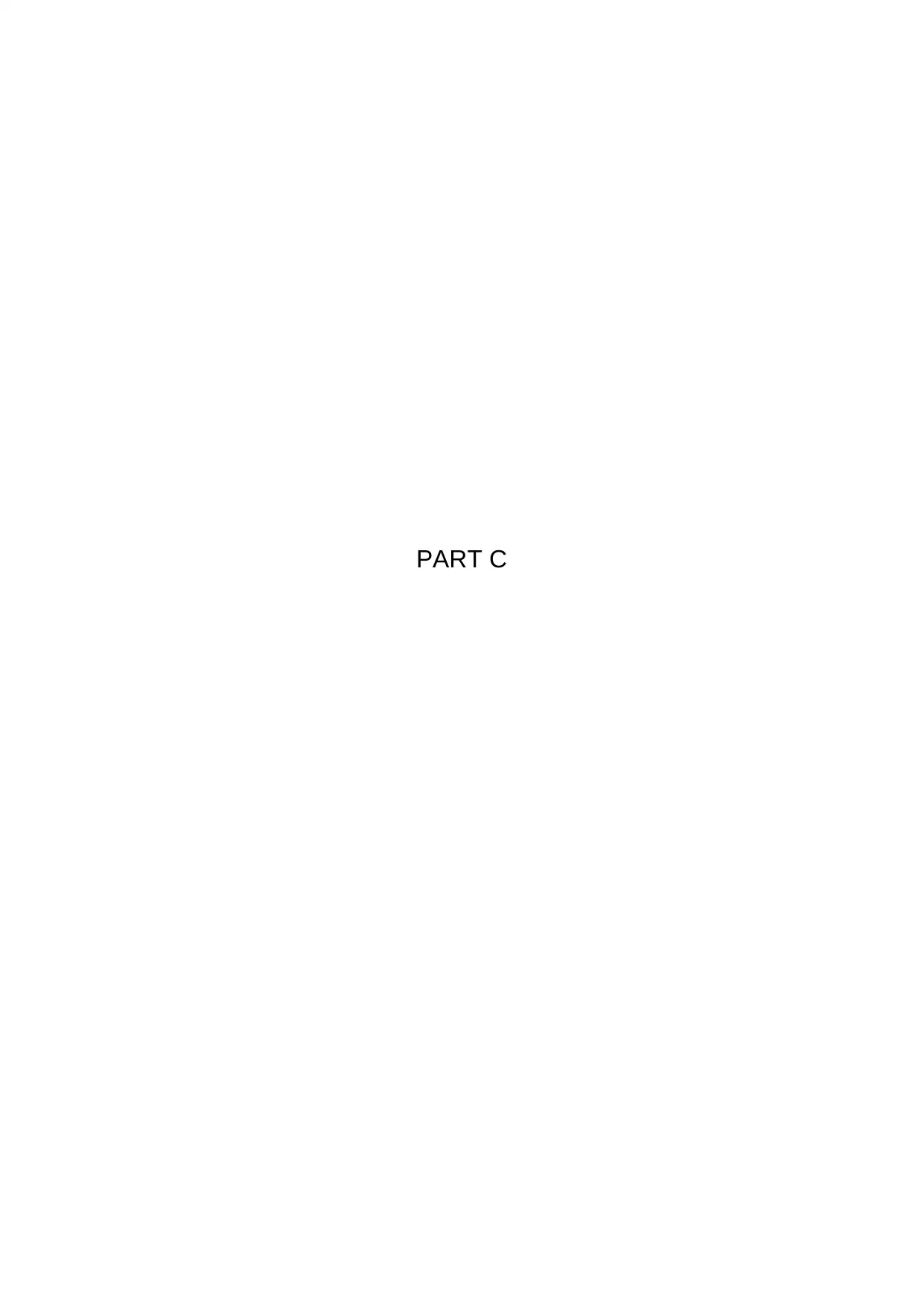
PART C
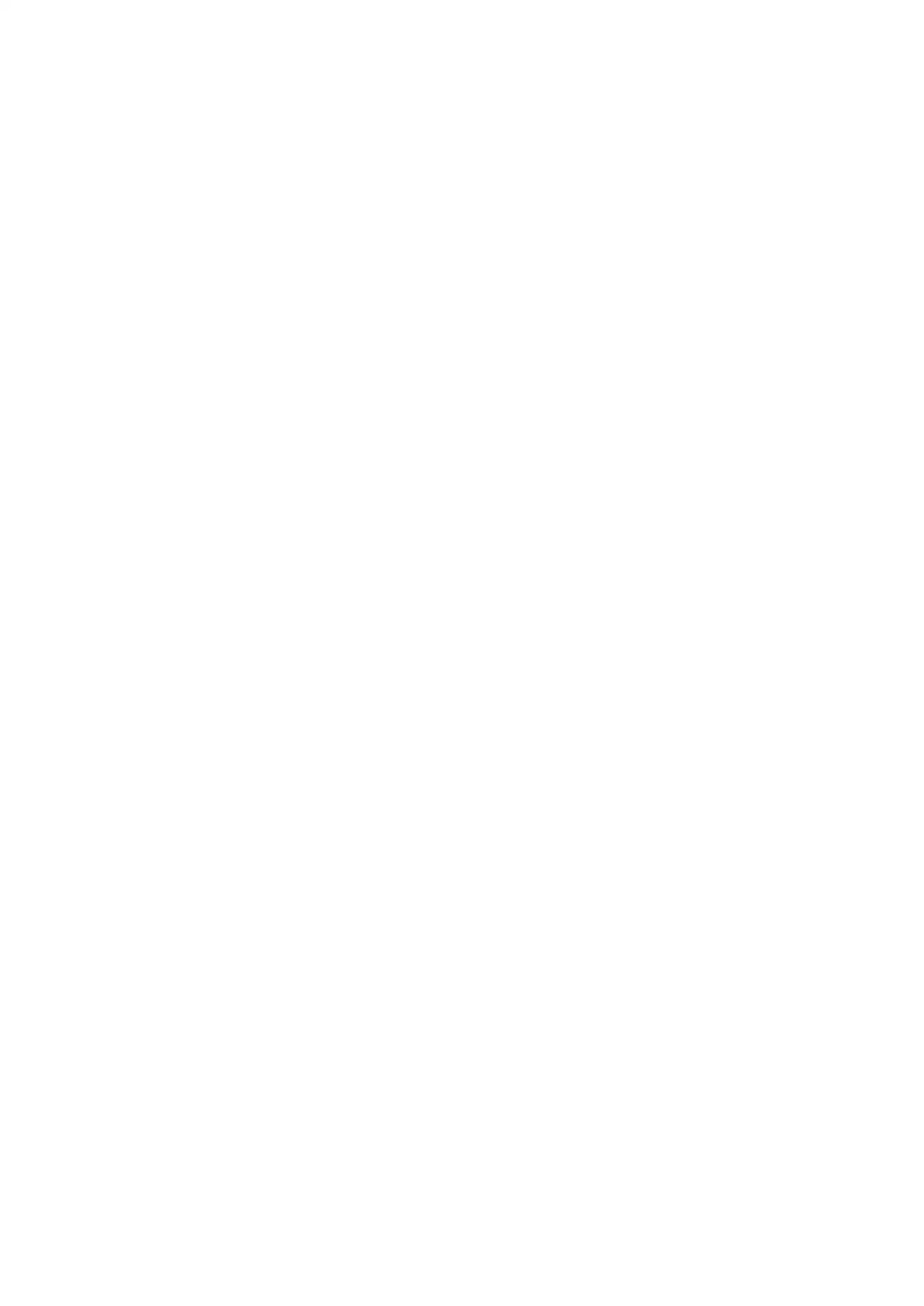
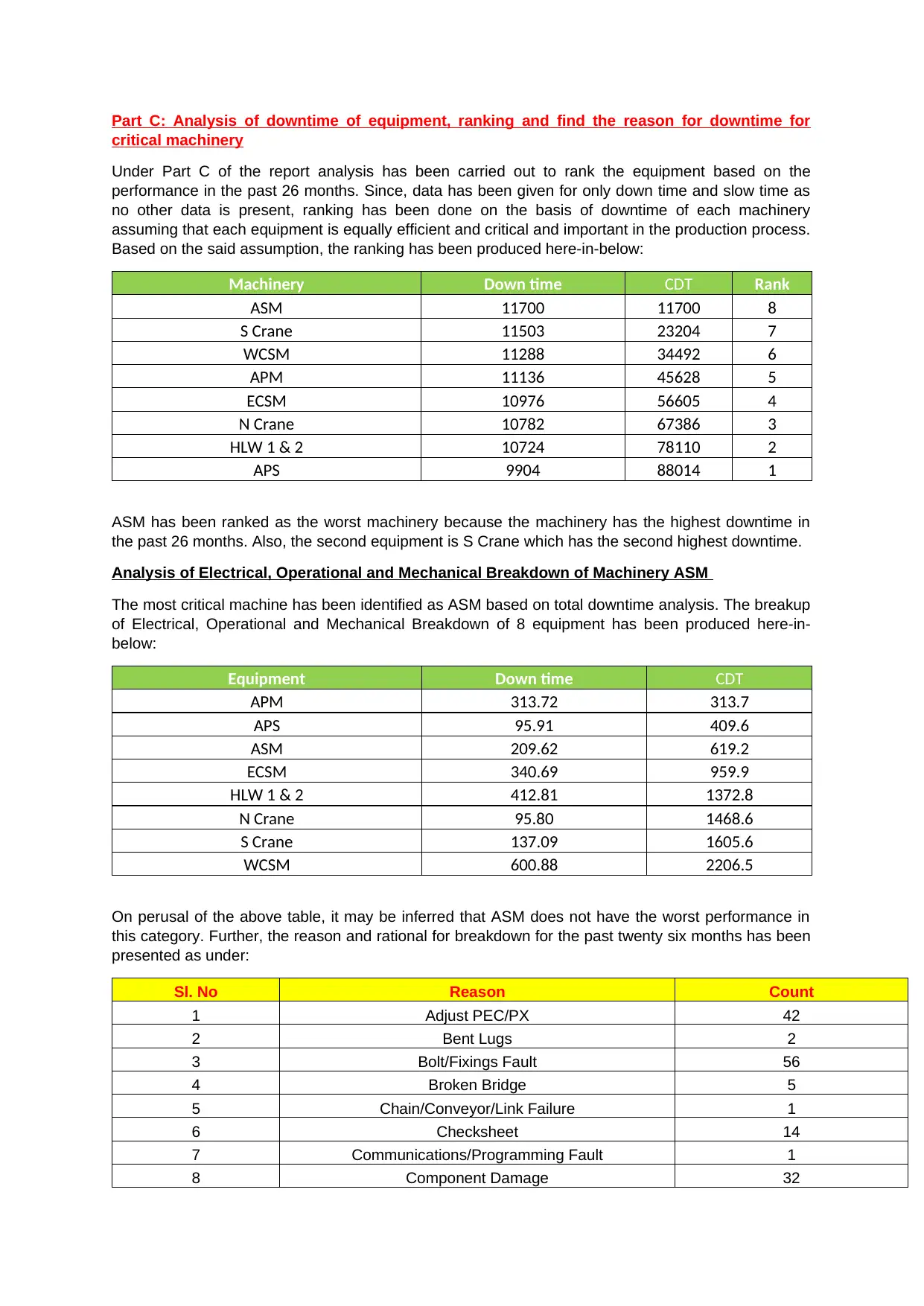
Part C: Analysis of downtime of equipment, ranking and find the reason for downtime for
critical machinery
Under Part C of the report analysis has been carried out to rank the equipment based on the
performance in the past 26 months. Since, data has been given for only down time and slow time as
no other data is present, ranking has been done on the basis of downtime of each machinery
assuming that each equipment is equally efficient and critical and important in the production process.
Based on the said assumption, the ranking has been produced here-in-below:
Machinery Down time CDT Rank
ASM 11700 11700 8
S Crane 11503 23204 7
WCSM 11288 34492 6
APM 11136 45628 5
ECSM 10976 56605 4
N Crane 10782 67386 3
HLW 1 & 2 10724 78110 2
APS 9904 88014 1
ASM has been ranked as the worst machinery because the machinery has the highest downtime in
the past 26 months. Also, the second equipment is S Crane which has the second highest downtime.
Analysis of Electrical, Operational and Mechanical Breakdown of Machinery ASM
The most critical machine has been identified as ASM based on total downtime analysis. The breakup
of Electrical, Operational and Mechanical Breakdown of 8 equipment has been produced here-in-
below:
Equipment Down time CDT
APM 313.72 313.7
APS 95.91 409.6
ASM 209.62 619.2
ECSM 340.69 959.9
HLW 1 & 2 412.81 1372.8
N Crane 95.80 1468.6
S Crane 137.09 1605.6
WCSM 600.88 2206.5
On perusal of the above table, it may be inferred that ASM does not have the worst performance in
this category. Further, the reason and rational for breakdown for the past twenty six months has been
presented as under:
Sl. No Reason Count
1 Adjust PEC/PX 42
2 Bent Lugs 2
3 Bolt/Fixings Fault 56
4 Broken Bridge 5
5 Chain/Conveyor/Link Failure 1
6 Checksheet 14
7 Communications/Programming Fault 1
8 Component Damage 32
critical machinery
Under Part C of the report analysis has been carried out to rank the equipment based on the
performance in the past 26 months. Since, data has been given for only down time and slow time as
no other data is present, ranking has been done on the basis of downtime of each machinery
assuming that each equipment is equally efficient and critical and important in the production process.
Based on the said assumption, the ranking has been produced here-in-below:
Machinery Down time CDT Rank
ASM 11700 11700 8
S Crane 11503 23204 7
WCSM 11288 34492 6
APM 11136 45628 5
ECSM 10976 56605 4
N Crane 10782 67386 3
HLW 1 & 2 10724 78110 2
APS 9904 88014 1
ASM has been ranked as the worst machinery because the machinery has the highest downtime in
the past 26 months. Also, the second equipment is S Crane which has the second highest downtime.
Analysis of Electrical, Operational and Mechanical Breakdown of Machinery ASM
The most critical machine has been identified as ASM based on total downtime analysis. The breakup
of Electrical, Operational and Mechanical Breakdown of 8 equipment has been produced here-in-
below:
Equipment Down time CDT
APM 313.72 313.7
APS 95.91 409.6
ASM 209.62 619.2
ECSM 340.69 959.9
HLW 1 & 2 412.81 1372.8
N Crane 95.80 1468.6
S Crane 137.09 1605.6
WCSM 600.88 2206.5
On perusal of the above table, it may be inferred that ASM does not have the worst performance in
this category. Further, the reason and rational for breakdown for the past twenty six months has been
presented as under:
Sl. No Reason Count
1 Adjust PEC/PX 42
2 Bent Lugs 2
3 Bolt/Fixings Fault 56
4 Broken Bridge 5
5 Chain/Conveyor/Link Failure 1
6 Checksheet 14
7 Communications/Programming Fault 1
8 Component Damage 32
Secure Best Marks with AI Grader
Need help grading? Try our AI Grader for instant feedback on your assignments.
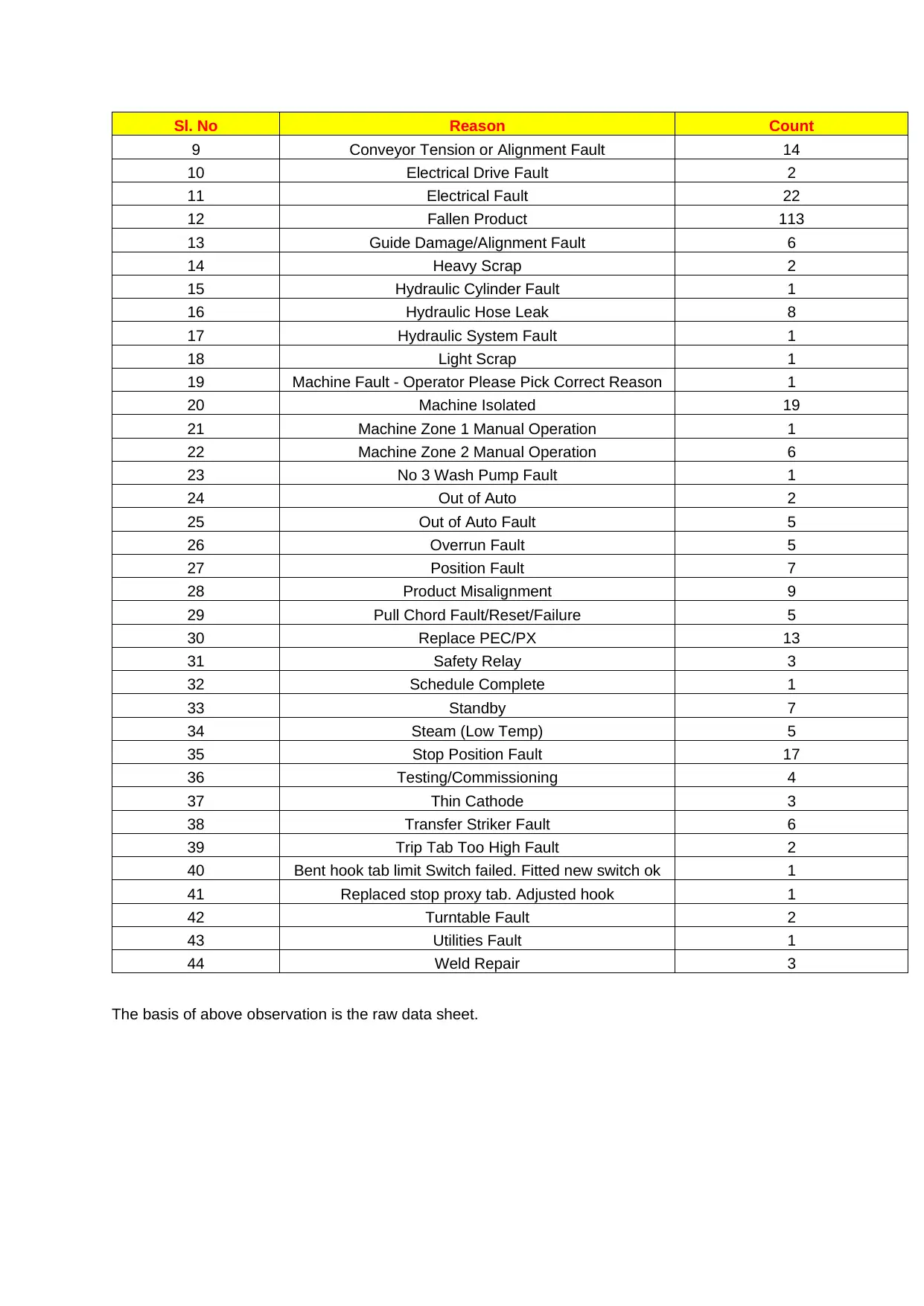
Sl. No Reason Count
9 Conveyor Tension or Alignment Fault 14
10 Electrical Drive Fault 2
11 Electrical Fault 22
12 Fallen Product 113
13 Guide Damage/Alignment Fault 6
14 Heavy Scrap 2
15 Hydraulic Cylinder Fault 1
16 Hydraulic Hose Leak 8
17 Hydraulic System Fault 1
18 Light Scrap 1
19 Machine Fault - Operator Please Pick Correct Reason 1
20 Machine Isolated 19
21 Machine Zone 1 Manual Operation 1
22 Machine Zone 2 Manual Operation 6
23 No 3 Wash Pump Fault 1
24 Out of Auto 2
25 Out of Auto Fault 5
26 Overrun Fault 5
27 Position Fault 7
28 Product Misalignment 9
29 Pull Chord Fault/Reset/Failure 5
30 Replace PEC/PX 13
31 Safety Relay 3
32 Schedule Complete 1
33 Standby 7
34 Steam (Low Temp) 5
35 Stop Position Fault 17
36 Testing/Commissioning 4
37 Thin Cathode 3
38 Transfer Striker Fault 6
39 Trip Tab Too High Fault 2
40 Bent hook tab limit Switch failed. Fitted new switch ok 1
41 Replaced stop proxy tab. Adjusted hook 1
42 Turntable Fault 2
43 Utilities Fault 1
44 Weld Repair 3
The basis of above observation is the raw data sheet.
9 Conveyor Tension or Alignment Fault 14
10 Electrical Drive Fault 2
11 Electrical Fault 22
12 Fallen Product 113
13 Guide Damage/Alignment Fault 6
14 Heavy Scrap 2
15 Hydraulic Cylinder Fault 1
16 Hydraulic Hose Leak 8
17 Hydraulic System Fault 1
18 Light Scrap 1
19 Machine Fault - Operator Please Pick Correct Reason 1
20 Machine Isolated 19
21 Machine Zone 1 Manual Operation 1
22 Machine Zone 2 Manual Operation 6
23 No 3 Wash Pump Fault 1
24 Out of Auto 2
25 Out of Auto Fault 5
26 Overrun Fault 5
27 Position Fault 7
28 Product Misalignment 9
29 Pull Chord Fault/Reset/Failure 5
30 Replace PEC/PX 13
31 Safety Relay 3
32 Schedule Complete 1
33 Standby 7
34 Steam (Low Temp) 5
35 Stop Position Fault 17
36 Testing/Commissioning 4
37 Thin Cathode 3
38 Transfer Striker Fault 6
39 Trip Tab Too High Fault 2
40 Bent hook tab limit Switch failed. Fitted new switch ok 1
41 Replaced stop proxy tab. Adjusted hook 1
42 Turntable Fault 2
43 Utilities Fault 1
44 Weld Repair 3
The basis of above observation is the raw data sheet.
1 out of 11
Related Documents
![[object Object]](/_next/image/?url=%2F_next%2Fstatic%2Fmedia%2Flogo.6d15ce61.png&w=640&q=75)
Your All-in-One AI-Powered Toolkit for Academic Success.
 +13062052269
info@desklib.com
Available 24*7 on WhatsApp / Email
Unlock your academic potential
© 2024  |  Zucol Services PVT LTD  |  All rights reserved.