Project Improvement Plan
VerifiedAdded on  2020/03/28
|12
|3604
|36
AI Summary
This assignment focuses on developing a comprehensive project improvement plan. It outlines key activities such as assessing the current situation, identifying causes of issues, setting objectives, determining timelines, strategizing improvements, implementing solutions, overcoming obstacles, communicating progress, monitoring effectiveness, making modifications, sustaining efforts, and executing the final plan.
Contribute Materials
Your contribution can guide someone’s learning journey. Share your
documents today.
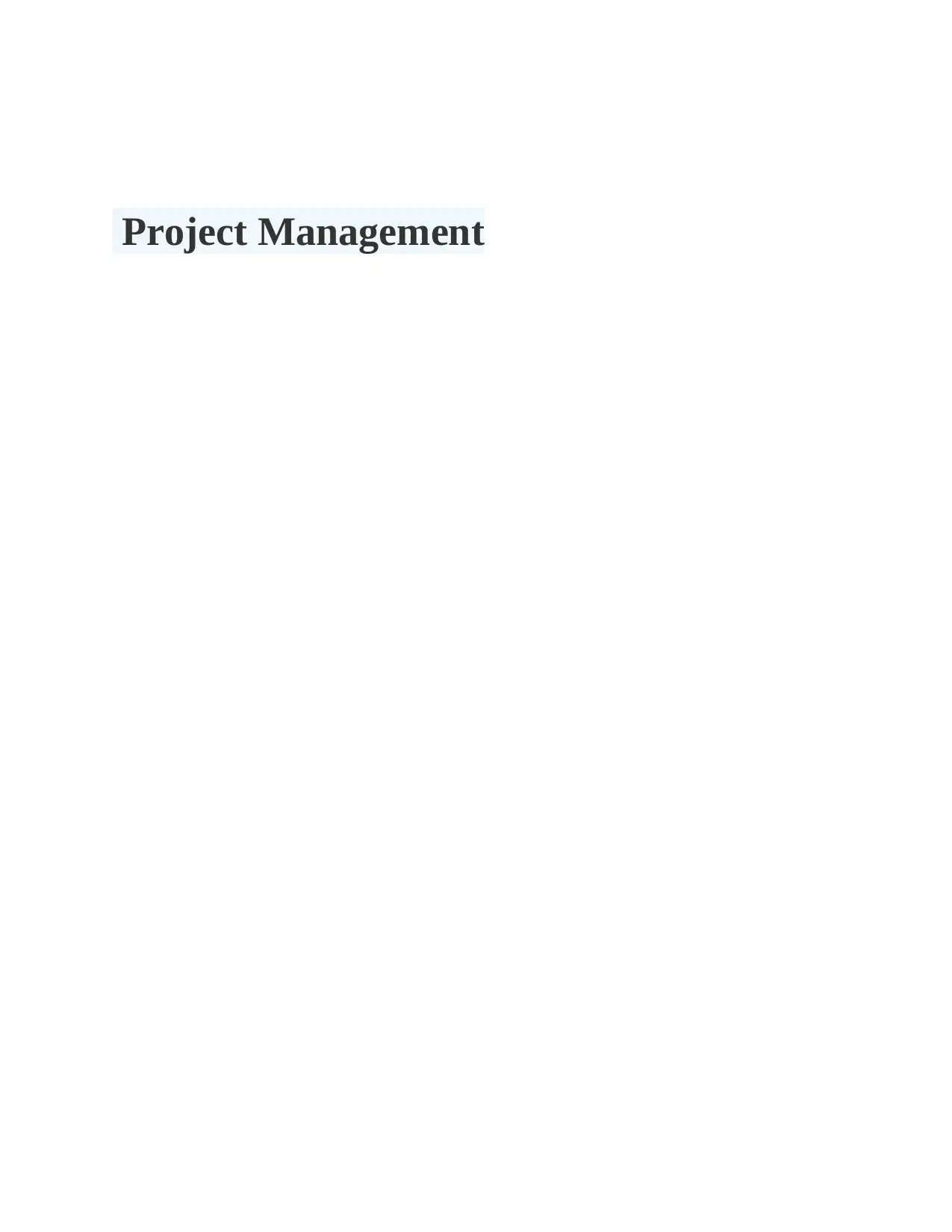
Project Management
Secure Best Marks with AI Grader
Need help grading? Try our AI Grader for instant feedback on your assignments.
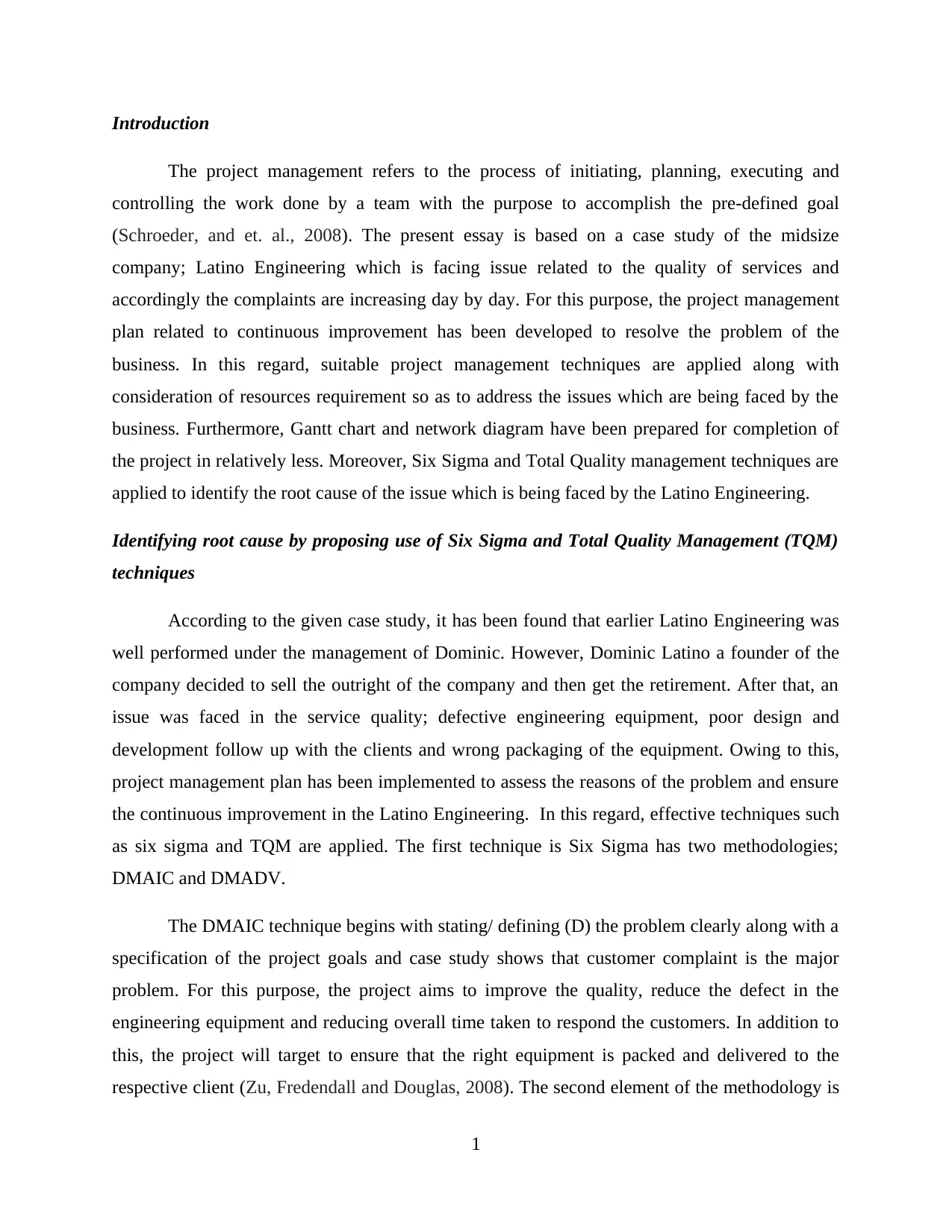
Introduction
The project management refers to the process of initiating, planning, executing and
controlling the work done by a team with the purpose to accomplish the pre-defined goal
(Schroeder, and et. al., 2008). The present essay is based on a case study of the midsize
company; Latino Engineering which is facing issue related to the quality of services and
accordingly the complaints are increasing day by day. For this purpose, the project management
plan related to continuous improvement has been developed to resolve the problem of the
business. In this regard, suitable project management techniques are applied along with
consideration of resources requirement so as to address the issues which are being faced by the
business. Furthermore, Gantt chart and network diagram have been prepared for completion of
the project in relatively less. Moreover, Six Sigma and Total Quality management techniques are
applied to identify the root cause of the issue which is being faced by the Latino Engineering.
Identifying root cause by proposing use of Six Sigma and Total Quality Management (TQM)
techniques
According to the given case study, it has been found that earlier Latino Engineering was
well performed under the management of Dominic. However, Dominic Latino a founder of the
company decided to sell the outright of the company and then get the retirement. After that, an
issue was faced in the service quality; defective engineering equipment, poor design and
development follow up with the clients and wrong packaging of the equipment. Owing to this,
project management plan has been implemented to assess the reasons of the problem and ensure
the continuous improvement in the Latino Engineering. In this regard, effective techniques such
as six sigma and TQM are applied. The first technique is Six Sigma has two methodologies;
DMAIC and DMADV.
The DMAIC technique begins with stating/ defining (D) the problem clearly along with a
specification of the project goals and case study shows that customer complaint is the major
problem. For this purpose, the project aims to improve the quality, reduce the defect in the
engineering equipment and reducing overall time taken to respond the customers. In addition to
this, the project will target to ensure that the right equipment is packed and delivered to the
respective client (Zu, Fredendall and Douglas, 2008). The second element of the methodology is
1
The project management refers to the process of initiating, planning, executing and
controlling the work done by a team with the purpose to accomplish the pre-defined goal
(Schroeder, and et. al., 2008). The present essay is based on a case study of the midsize
company; Latino Engineering which is facing issue related to the quality of services and
accordingly the complaints are increasing day by day. For this purpose, the project management
plan related to continuous improvement has been developed to resolve the problem of the
business. In this regard, suitable project management techniques are applied along with
consideration of resources requirement so as to address the issues which are being faced by the
business. Furthermore, Gantt chart and network diagram have been prepared for completion of
the project in relatively less. Moreover, Six Sigma and Total Quality management techniques are
applied to identify the root cause of the issue which is being faced by the Latino Engineering.
Identifying root cause by proposing use of Six Sigma and Total Quality Management (TQM)
techniques
According to the given case study, it has been found that earlier Latino Engineering was
well performed under the management of Dominic. However, Dominic Latino a founder of the
company decided to sell the outright of the company and then get the retirement. After that, an
issue was faced in the service quality; defective engineering equipment, poor design and
development follow up with the clients and wrong packaging of the equipment. Owing to this,
project management plan has been implemented to assess the reasons of the problem and ensure
the continuous improvement in the Latino Engineering. In this regard, effective techniques such
as six sigma and TQM are applied. The first technique is Six Sigma has two methodologies;
DMAIC and DMADV.
The DMAIC technique begins with stating/ defining (D) the problem clearly along with a
specification of the project goals and case study shows that customer complaint is the major
problem. For this purpose, the project aims to improve the quality, reduce the defect in the
engineering equipment and reducing overall time taken to respond the customers. In addition to
this, the project will target to ensure that the right equipment is packed and delivered to the
respective client (Zu, Fredendall and Douglas, 2008). The second element of the methodology is
1
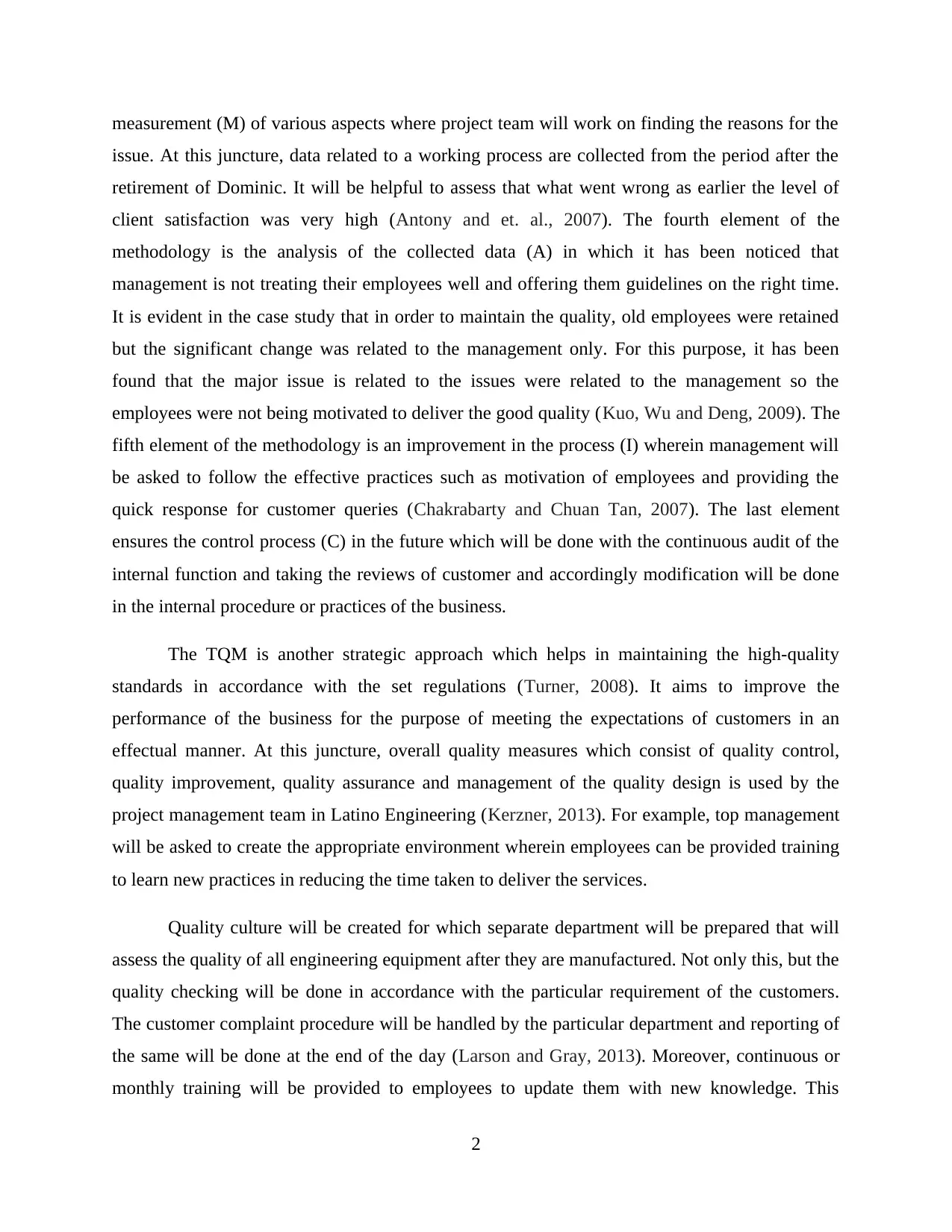
measurement (M) of various aspects where project team will work on finding the reasons for the
issue. At this juncture, data related to a working process are collected from the period after the
retirement of Dominic. It will be helpful to assess that what went wrong as earlier the level of
client satisfaction was very high (Antony and et. al., 2007). The fourth element of the
methodology is the analysis of the collected data (A) in which it has been noticed that
management is not treating their employees well and offering them guidelines on the right time.
It is evident in the case study that in order to maintain the quality, old employees were retained
but the significant change was related to the management only. For this purpose, it has been
found that the major issue is related to the issues were related to the management so the
employees were not being motivated to deliver the good quality (Kuo, Wu and Deng, 2009). The
fifth element of the methodology is an improvement in the process (I) wherein management will
be asked to follow the effective practices such as motivation of employees and providing the
quick response for customer queries (Chakrabarty and Chuan Tan, 2007). The last element
ensures the control process (C) in the future which will be done with the continuous audit of the
internal function and taking the reviews of customer and accordingly modification will be done
in the internal procedure or practices of the business.
The TQM is another strategic approach which helps in maintaining the high-quality
standards in accordance with the set regulations (Turner, 2008). It aims to improve the
performance of the business for the purpose of meeting the expectations of customers in an
effectual manner. At this juncture, overall quality measures which consist of quality control,
quality improvement, quality assurance and management of the quality design is used by the
project management team in Latino Engineering (Kerzner, 2013). For example, top management
will be asked to create the appropriate environment wherein employees can be provided training
to learn new practices in reducing the time taken to deliver the services.
Quality culture will be created for which separate department will be prepared that will
assess the quality of all engineering equipment after they are manufactured. Not only this, but the
quality checking will be done in accordance with the particular requirement of the customers.
The customer complaint procedure will be handled by the particular department and reporting of
the same will be done at the end of the day (Larson and Gray, 2013). Moreover, continuous or
monthly training will be provided to employees to update them with new knowledge. This
2
issue. At this juncture, data related to a working process are collected from the period after the
retirement of Dominic. It will be helpful to assess that what went wrong as earlier the level of
client satisfaction was very high (Antony and et. al., 2007). The fourth element of the
methodology is the analysis of the collected data (A) in which it has been noticed that
management is not treating their employees well and offering them guidelines on the right time.
It is evident in the case study that in order to maintain the quality, old employees were retained
but the significant change was related to the management only. For this purpose, it has been
found that the major issue is related to the issues were related to the management so the
employees were not being motivated to deliver the good quality (Kuo, Wu and Deng, 2009). The
fifth element of the methodology is an improvement in the process (I) wherein management will
be asked to follow the effective practices such as motivation of employees and providing the
quick response for customer queries (Chakrabarty and Chuan Tan, 2007). The last element
ensures the control process (C) in the future which will be done with the continuous audit of the
internal function and taking the reviews of customer and accordingly modification will be done
in the internal procedure or practices of the business.
The TQM is another strategic approach which helps in maintaining the high-quality
standards in accordance with the set regulations (Turner, 2008). It aims to improve the
performance of the business for the purpose of meeting the expectations of customers in an
effectual manner. At this juncture, overall quality measures which consist of quality control,
quality improvement, quality assurance and management of the quality design is used by the
project management team in Latino Engineering (Kerzner, 2013). For example, top management
will be asked to create the appropriate environment wherein employees can be provided training
to learn new practices in reducing the time taken to deliver the services.
Quality culture will be created for which separate department will be prepared that will
assess the quality of all engineering equipment after they are manufactured. Not only this, but the
quality checking will be done in accordance with the particular requirement of the customers.
The customer complaint procedure will be handled by the particular department and reporting of
the same will be done at the end of the day (Larson and Gray, 2013). Moreover, continuous or
monthly training will be provided to employees to update them with new knowledge. This
2
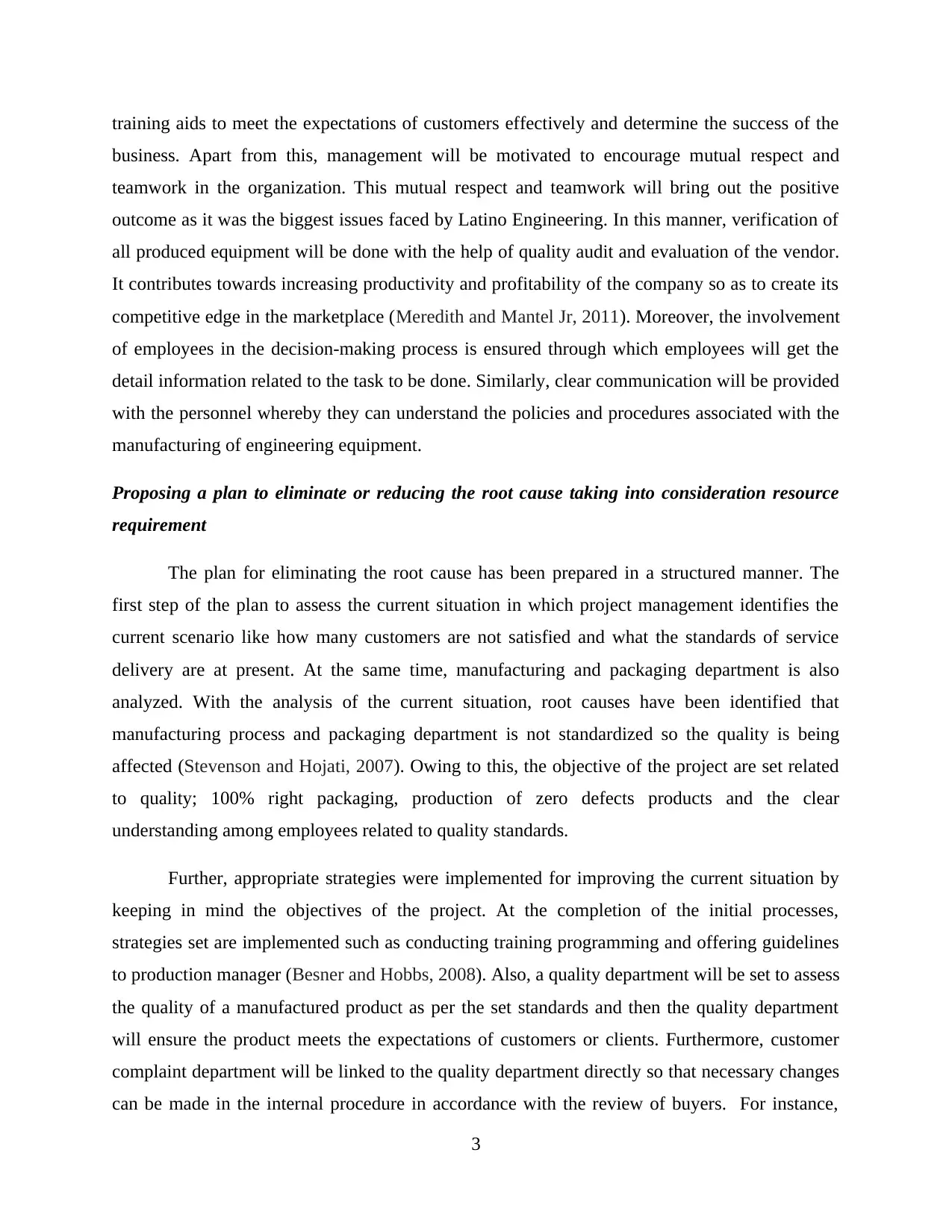
training aids to meet the expectations of customers effectively and determine the success of the
business. Apart from this, management will be motivated to encourage mutual respect and
teamwork in the organization. This mutual respect and teamwork will bring out the positive
outcome as it was the biggest issues faced by Latino Engineering. In this manner, verification of
all produced equipment will be done with the help of quality audit and evaluation of the vendor.
It contributes towards increasing productivity and profitability of the company so as to create its
competitive edge in the marketplace (Meredith and Mantel Jr, 2011). Moreover, the involvement
of employees in the decision-making process is ensured through which employees will get the
detail information related to the task to be done. Similarly, clear communication will be provided
with the personnel whereby they can understand the policies and procedures associated with the
manufacturing of engineering equipment.
Proposing a plan to eliminate or reducing the root cause taking into consideration resource
requirement
The plan for eliminating the root cause has been prepared in a structured manner. The
first step of the plan to assess the current situation in which project management identifies the
current scenario like how many customers are not satisfied and what the standards of service
delivery are at present. At the same time, manufacturing and packaging department is also
analyzed. With the analysis of the current situation, root causes have been identified that
manufacturing process and packaging department is not standardized so the quality is being
affected (Stevenson and Hojati, 2007). Owing to this, the objective of the project are set related
to quality; 100% right packaging, production of zero defects products and the clear
understanding among employees related to quality standards.
Further, appropriate strategies were implemented for improving the current situation by
keeping in mind the objectives of the project. At the completion of the initial processes,
strategies set are implemented such as conducting training programming and offering guidelines
to production manager (Besner and Hobbs, 2008). Also, a quality department will be set to assess
the quality of a manufactured product as per the set standards and then the quality department
will ensure the product meets the expectations of customers or clients. Furthermore, customer
complaint department will be linked to the quality department directly so that necessary changes
can be made in the internal procedure in accordance with the review of buyers. For instance,
3
business. Apart from this, management will be motivated to encourage mutual respect and
teamwork in the organization. This mutual respect and teamwork will bring out the positive
outcome as it was the biggest issues faced by Latino Engineering. In this manner, verification of
all produced equipment will be done with the help of quality audit and evaluation of the vendor.
It contributes towards increasing productivity and profitability of the company so as to create its
competitive edge in the marketplace (Meredith and Mantel Jr, 2011). Moreover, the involvement
of employees in the decision-making process is ensured through which employees will get the
detail information related to the task to be done. Similarly, clear communication will be provided
with the personnel whereby they can understand the policies and procedures associated with the
manufacturing of engineering equipment.
Proposing a plan to eliminate or reducing the root cause taking into consideration resource
requirement
The plan for eliminating the root cause has been prepared in a structured manner. The
first step of the plan to assess the current situation in which project management identifies the
current scenario like how many customers are not satisfied and what the standards of service
delivery are at present. At the same time, manufacturing and packaging department is also
analyzed. With the analysis of the current situation, root causes have been identified that
manufacturing process and packaging department is not standardized so the quality is being
affected (Stevenson and Hojati, 2007). Owing to this, the objective of the project are set related
to quality; 100% right packaging, production of zero defects products and the clear
understanding among employees related to quality standards.
Further, appropriate strategies were implemented for improving the current situation by
keeping in mind the objectives of the project. At the completion of the initial processes,
strategies set are implemented such as conducting training programming and offering guidelines
to production manager (Besner and Hobbs, 2008). Also, a quality department will be set to assess
the quality of a manufactured product as per the set standards and then the quality department
will ensure the product meets the expectations of customers or clients. Furthermore, customer
complaint department will be linked to the quality department directly so that necessary changes
can be made in the internal procedure in accordance with the review of buyers. For instance,
3
Secure Best Marks with AI Grader
Need help grading? Try our AI Grader for instant feedback on your assignments.
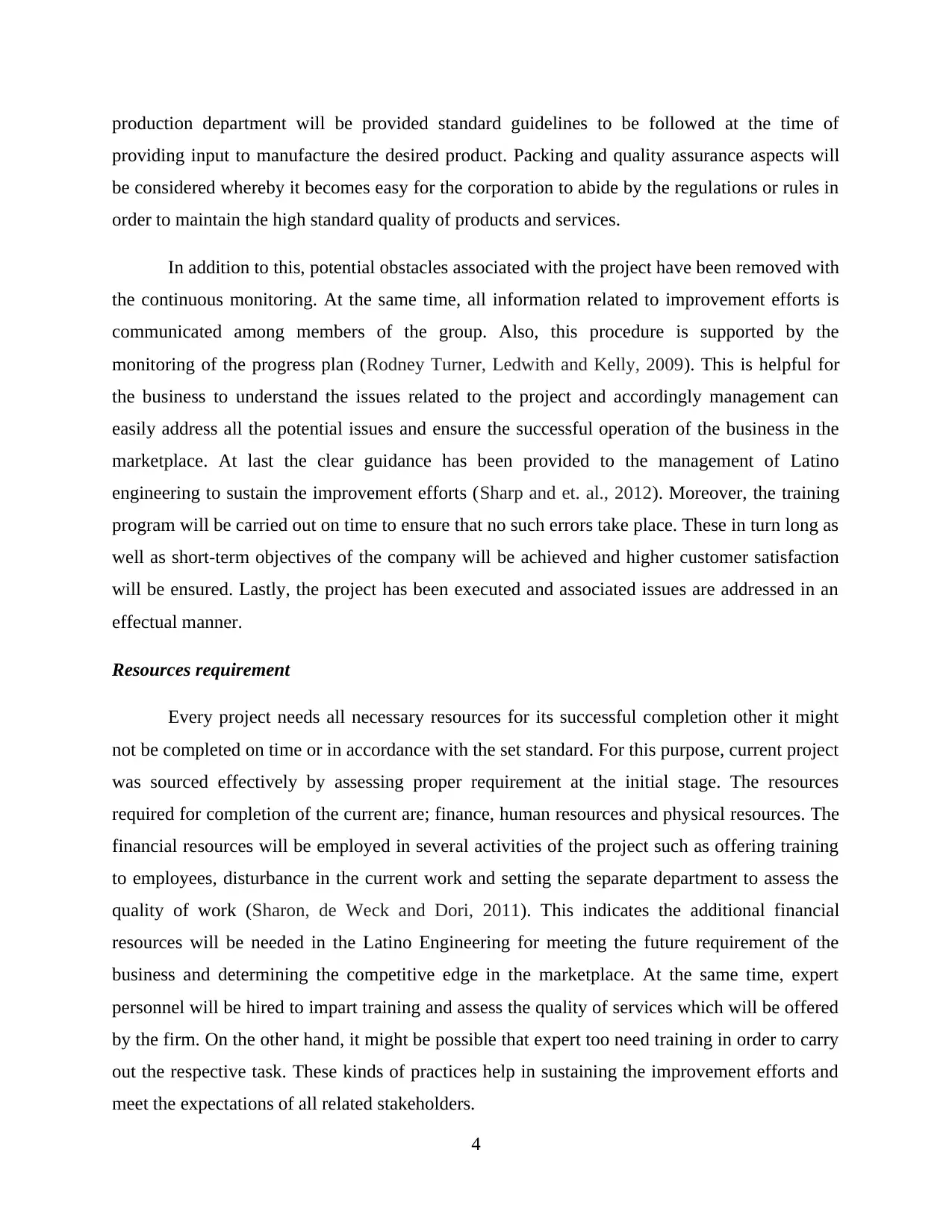
production department will be provided standard guidelines to be followed at the time of
providing input to manufacture the desired product. Packing and quality assurance aspects will
be considered whereby it becomes easy for the corporation to abide by the regulations or rules in
order to maintain the high standard quality of products and services.
In addition to this, potential obstacles associated with the project have been removed with
the continuous monitoring. At the same time, all information related to improvement efforts is
communicated among members of the group. Also, this procedure is supported by the
monitoring of the progress plan (Rodney Turner, Ledwith and Kelly, 2009). This is helpful for
the business to understand the issues related to the project and accordingly management can
easily address all the potential issues and ensure the successful operation of the business in the
marketplace. At last the clear guidance has been provided to the management of Latino
engineering to sustain the improvement efforts (Sharp and et. al., 2012). Moreover, the training
program will be carried out on time to ensure that no such errors take place. These in turn long as
well as short-term objectives of the company will be achieved and higher customer satisfaction
will be ensured. Lastly, the project has been executed and associated issues are addressed in an
effectual manner.
Resources requirement
Every project needs all necessary resources for its successful completion other it might
not be completed on time or in accordance with the set standard. For this purpose, current project
was sourced effectively by assessing proper requirement at the initial stage. The resources
required for completion of the current are; finance, human resources and physical resources. The
financial resources will be employed in several activities of the project such as offering training
to employees, disturbance in the current work and setting the separate department to assess the
quality of work (Sharon, de Weck and Dori, 2011). This indicates the additional financial
resources will be needed in the Latino Engineering for meeting the future requirement of the
business and determining the competitive edge in the marketplace. At the same time, expert
personnel will be hired to impart training and assess the quality of services which will be offered
by the firm. On the other hand, it might be possible that expert too need training in order to carry
out the respective task. These kinds of practices help in sustaining the improvement efforts and
meet the expectations of all related stakeholders.
4
providing input to manufacture the desired product. Packing and quality assurance aspects will
be considered whereby it becomes easy for the corporation to abide by the regulations or rules in
order to maintain the high standard quality of products and services.
In addition to this, potential obstacles associated with the project have been removed with
the continuous monitoring. At the same time, all information related to improvement efforts is
communicated among members of the group. Also, this procedure is supported by the
monitoring of the progress plan (Rodney Turner, Ledwith and Kelly, 2009). This is helpful for
the business to understand the issues related to the project and accordingly management can
easily address all the potential issues and ensure the successful operation of the business in the
marketplace. At last the clear guidance has been provided to the management of Latino
engineering to sustain the improvement efforts (Sharp and et. al., 2012). Moreover, the training
program will be carried out on time to ensure that no such errors take place. These in turn long as
well as short-term objectives of the company will be achieved and higher customer satisfaction
will be ensured. Lastly, the project has been executed and associated issues are addressed in an
effectual manner.
Resources requirement
Every project needs all necessary resources for its successful completion other it might
not be completed on time or in accordance with the set standard. For this purpose, current project
was sourced effectively by assessing proper requirement at the initial stage. The resources
required for completion of the current are; finance, human resources and physical resources. The
financial resources will be employed in several activities of the project such as offering training
to employees, disturbance in the current work and setting the separate department to assess the
quality of work (Sharon, de Weck and Dori, 2011). This indicates the additional financial
resources will be needed in the Latino Engineering for meeting the future requirement of the
business and determining the competitive edge in the marketplace. At the same time, expert
personnel will be hired to impart training and assess the quality of services which will be offered
by the firm. On the other hand, it might be possible that expert too need training in order to carry
out the respective task. These kinds of practices help in sustaining the improvement efforts and
meet the expectations of all related stakeholders.
4
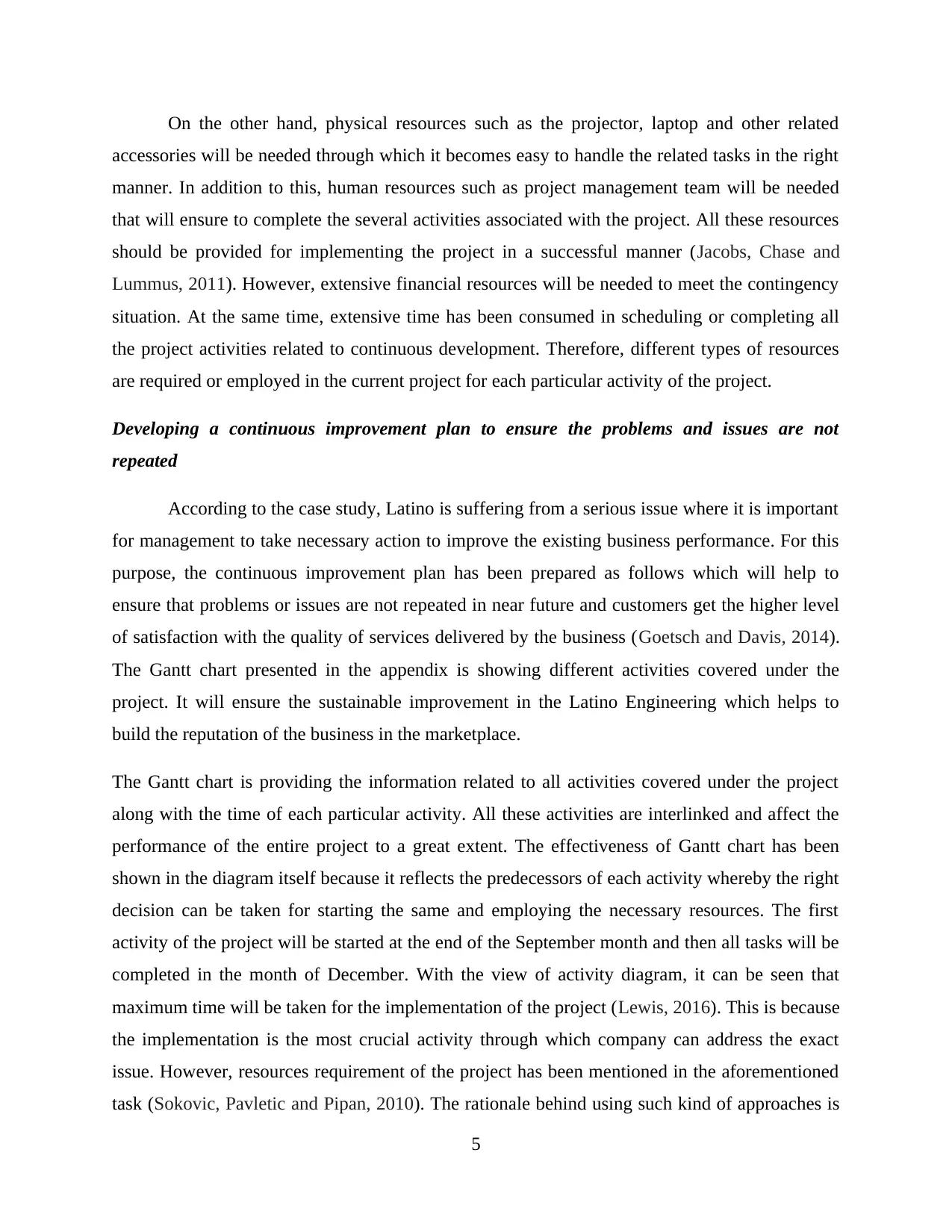
On the other hand, physical resources such as the projector, laptop and other related
accessories will be needed through which it becomes easy to handle the related tasks in the right
manner. In addition to this, human resources such as project management team will be needed
that will ensure to complete the several activities associated with the project. All these resources
should be provided for implementing the project in a successful manner (Jacobs, Chase and
Lummus, 2011). However, extensive financial resources will be needed to meet the contingency
situation. At the same time, extensive time has been consumed in scheduling or completing all
the project activities related to continuous development. Therefore, different types of resources
are required or employed in the current project for each particular activity of the project.
Developing a continuous improvement plan to ensure the problems and issues are not
repeated
According to the case study, Latino is suffering from a serious issue where it is important
for management to take necessary action to improve the existing business performance. For this
purpose, the continuous improvement plan has been prepared as follows which will help to
ensure that problems or issues are not repeated in near future and customers get the higher level
of satisfaction with the quality of services delivered by the business (Goetsch and Davis, 2014).
The Gantt chart presented in the appendix is showing different activities covered under the
project. It will ensure the sustainable improvement in the Latino Engineering which helps to
build the reputation of the business in the marketplace.
The Gantt chart is providing the information related to all activities covered under the project
along with the time of each particular activity. All these activities are interlinked and affect the
performance of the entire project to a great extent. The effectiveness of Gantt chart has been
shown in the diagram itself because it reflects the predecessors of each activity whereby the right
decision can be taken for starting the same and employing the necessary resources. The first
activity of the project will be started at the end of the September month and then all tasks will be
completed in the month of December. With the view of activity diagram, it can be seen that
maximum time will be taken for the implementation of the project (Lewis, 2016). This is because
the implementation is the most crucial activity through which company can address the exact
issue. However, resources requirement of the project has been mentioned in the aforementioned
task (Sokovic, Pavletic and Pipan, 2010). The rationale behind using such kind of approaches is
5
accessories will be needed through which it becomes easy to handle the related tasks in the right
manner. In addition to this, human resources such as project management team will be needed
that will ensure to complete the several activities associated with the project. All these resources
should be provided for implementing the project in a successful manner (Jacobs, Chase and
Lummus, 2011). However, extensive financial resources will be needed to meet the contingency
situation. At the same time, extensive time has been consumed in scheduling or completing all
the project activities related to continuous development. Therefore, different types of resources
are required or employed in the current project for each particular activity of the project.
Developing a continuous improvement plan to ensure the problems and issues are not
repeated
According to the case study, Latino is suffering from a serious issue where it is important
for management to take necessary action to improve the existing business performance. For this
purpose, the continuous improvement plan has been prepared as follows which will help to
ensure that problems or issues are not repeated in near future and customers get the higher level
of satisfaction with the quality of services delivered by the business (Goetsch and Davis, 2014).
The Gantt chart presented in the appendix is showing different activities covered under the
project. It will ensure the sustainable improvement in the Latino Engineering which helps to
build the reputation of the business in the marketplace.
The Gantt chart is providing the information related to all activities covered under the project
along with the time of each particular activity. All these activities are interlinked and affect the
performance of the entire project to a great extent. The effectiveness of Gantt chart has been
shown in the diagram itself because it reflects the predecessors of each activity whereby the right
decision can be taken for starting the same and employing the necessary resources. The first
activity of the project will be started at the end of the September month and then all tasks will be
completed in the month of December. With the view of activity diagram, it can be seen that
maximum time will be taken for the implementation of the project (Lewis, 2016). This is because
the implementation is the most crucial activity through which company can address the exact
issue. However, resources requirement of the project has been mentioned in the aforementioned
task (Sokovic, Pavletic and Pipan, 2010). The rationale behind using such kind of approaches is
5
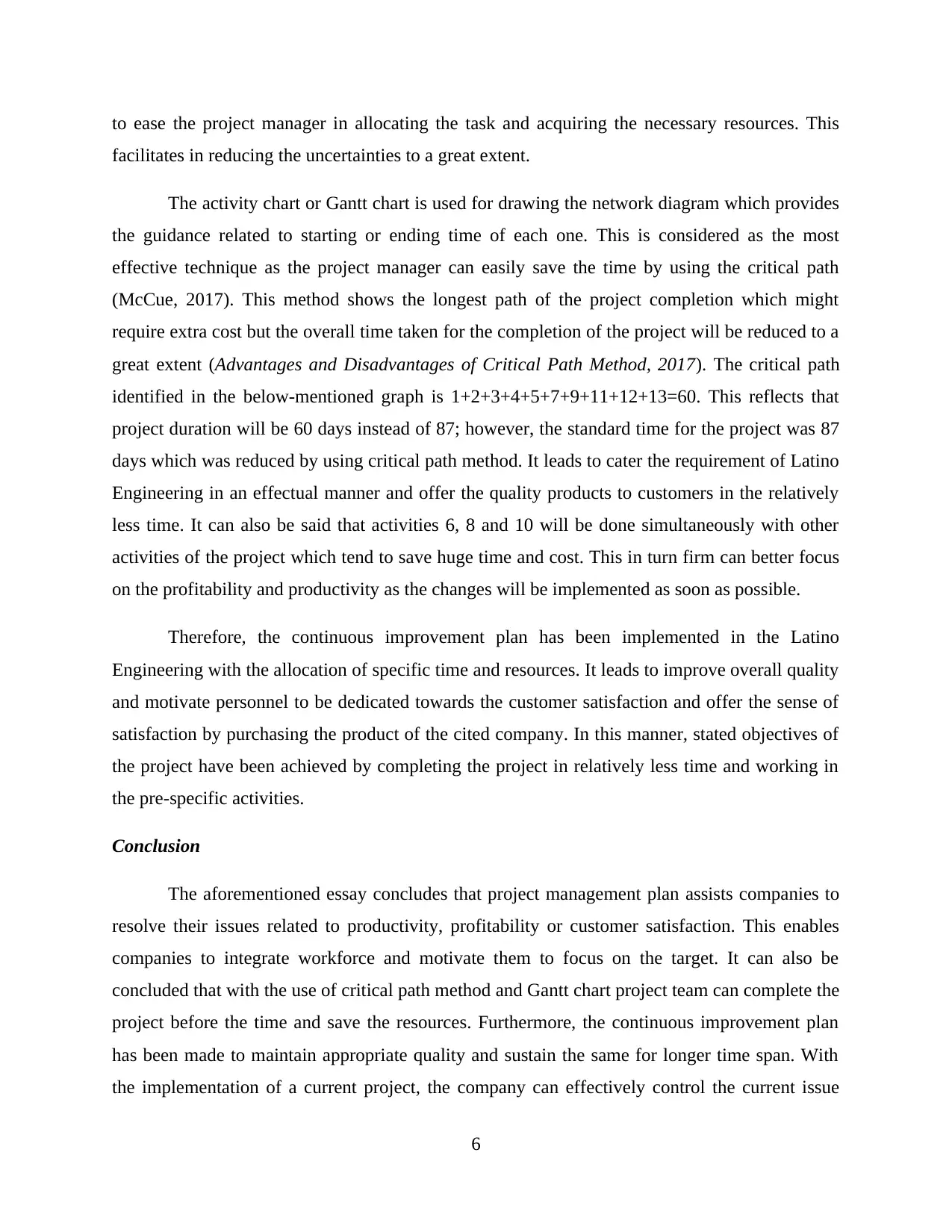
to ease the project manager in allocating the task and acquiring the necessary resources. This
facilitates in reducing the uncertainties to a great extent.
The activity chart or Gantt chart is used for drawing the network diagram which provides
the guidance related to starting or ending time of each one. This is considered as the most
effective technique as the project manager can easily save the time by using the critical path
(McCue, 2017). This method shows the longest path of the project completion which might
require extra cost but the overall time taken for the completion of the project will be reduced to a
great extent (Advantages and Disadvantages of Critical Path Method, 2017). The critical path
identified in the below-mentioned graph is 1+2+3+4+5+7+9+11+12+13=60. This reflects that
project duration will be 60 days instead of 87; however, the standard time for the project was 87
days which was reduced by using critical path method. It leads to cater the requirement of Latino
Engineering in an effectual manner and offer the quality products to customers in the relatively
less time. It can also be said that activities 6, 8 and 10 will be done simultaneously with other
activities of the project which tend to save huge time and cost. This in turn firm can better focus
on the profitability and productivity as the changes will be implemented as soon as possible.
Therefore, the continuous improvement plan has been implemented in the Latino
Engineering with the allocation of specific time and resources. It leads to improve overall quality
and motivate personnel to be dedicated towards the customer satisfaction and offer the sense of
satisfaction by purchasing the product of the cited company. In this manner, stated objectives of
the project have been achieved by completing the project in relatively less time and working in
the pre-specific activities.
Conclusion
The aforementioned essay concludes that project management plan assists companies to
resolve their issues related to productivity, profitability or customer satisfaction. This enables
companies to integrate workforce and motivate them to focus on the target. It can also be
concluded that with the use of critical path method and Gantt chart project team can complete the
project before the time and save the resources. Furthermore, the continuous improvement plan
has been made to maintain appropriate quality and sustain the same for longer time span. With
the implementation of a current project, the company can effectively control the current issue
6
facilitates in reducing the uncertainties to a great extent.
The activity chart or Gantt chart is used for drawing the network diagram which provides
the guidance related to starting or ending time of each one. This is considered as the most
effective technique as the project manager can easily save the time by using the critical path
(McCue, 2017). This method shows the longest path of the project completion which might
require extra cost but the overall time taken for the completion of the project will be reduced to a
great extent (Advantages and Disadvantages of Critical Path Method, 2017). The critical path
identified in the below-mentioned graph is 1+2+3+4+5+7+9+11+12+13=60. This reflects that
project duration will be 60 days instead of 87; however, the standard time for the project was 87
days which was reduced by using critical path method. It leads to cater the requirement of Latino
Engineering in an effectual manner and offer the quality products to customers in the relatively
less time. It can also be said that activities 6, 8 and 10 will be done simultaneously with other
activities of the project which tend to save huge time and cost. This in turn firm can better focus
on the profitability and productivity as the changes will be implemented as soon as possible.
Therefore, the continuous improvement plan has been implemented in the Latino
Engineering with the allocation of specific time and resources. It leads to improve overall quality
and motivate personnel to be dedicated towards the customer satisfaction and offer the sense of
satisfaction by purchasing the product of the cited company. In this manner, stated objectives of
the project have been achieved by completing the project in relatively less time and working in
the pre-specific activities.
Conclusion
The aforementioned essay concludes that project management plan assists companies to
resolve their issues related to productivity, profitability or customer satisfaction. This enables
companies to integrate workforce and motivate them to focus on the target. It can also be
concluded that with the use of critical path method and Gantt chart project team can complete the
project before the time and save the resources. Furthermore, the continuous improvement plan
has been made to maintain appropriate quality and sustain the same for longer time span. With
the implementation of a current project, the company can effectively control the current issue
6
Paraphrase This Document
Need a fresh take? Get an instant paraphrase of this document with our AI Paraphraser
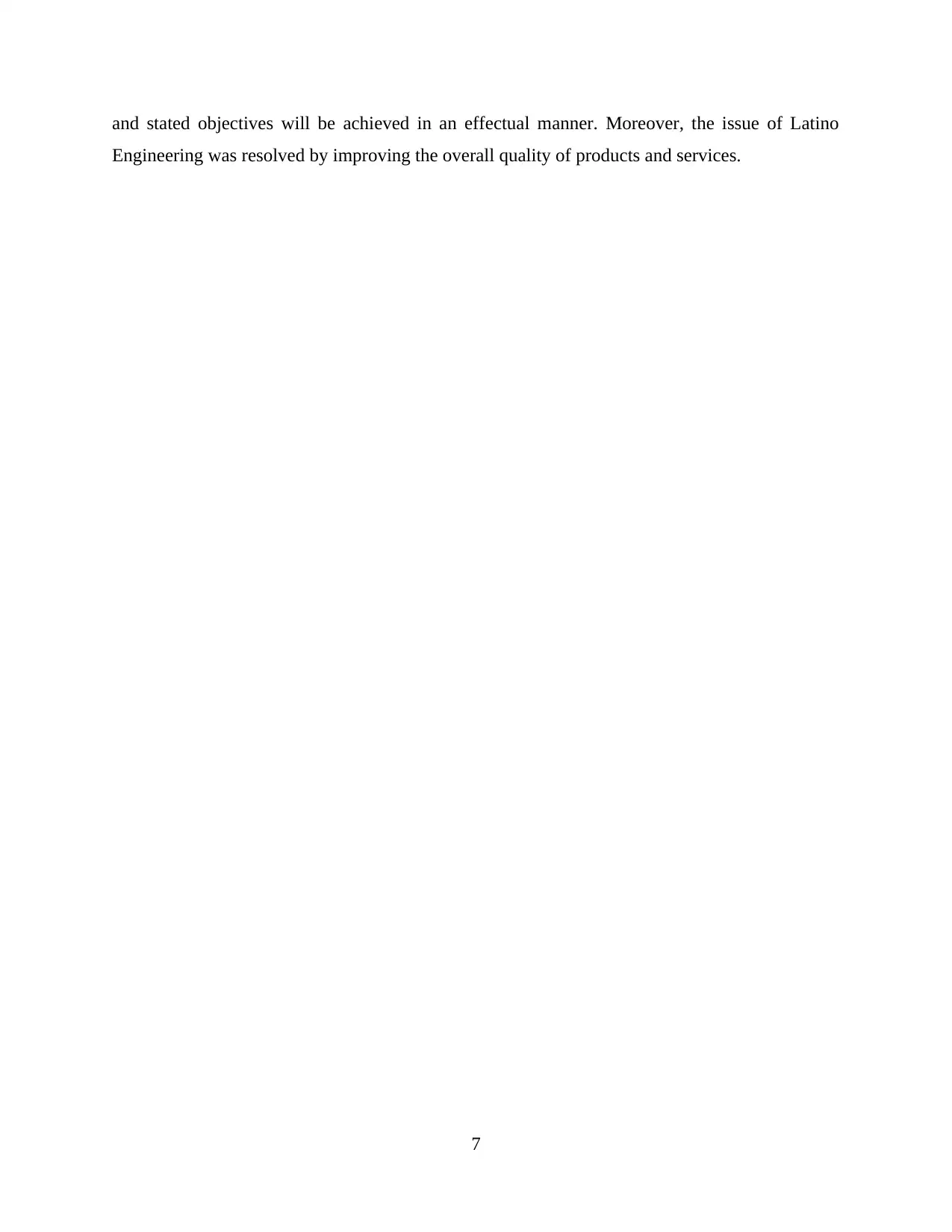
and stated objectives will be achieved in an effectual manner. Moreover, the issue of Latino
Engineering was resolved by improving the overall quality of products and services.
7
Engineering was resolved by improving the overall quality of products and services.
7
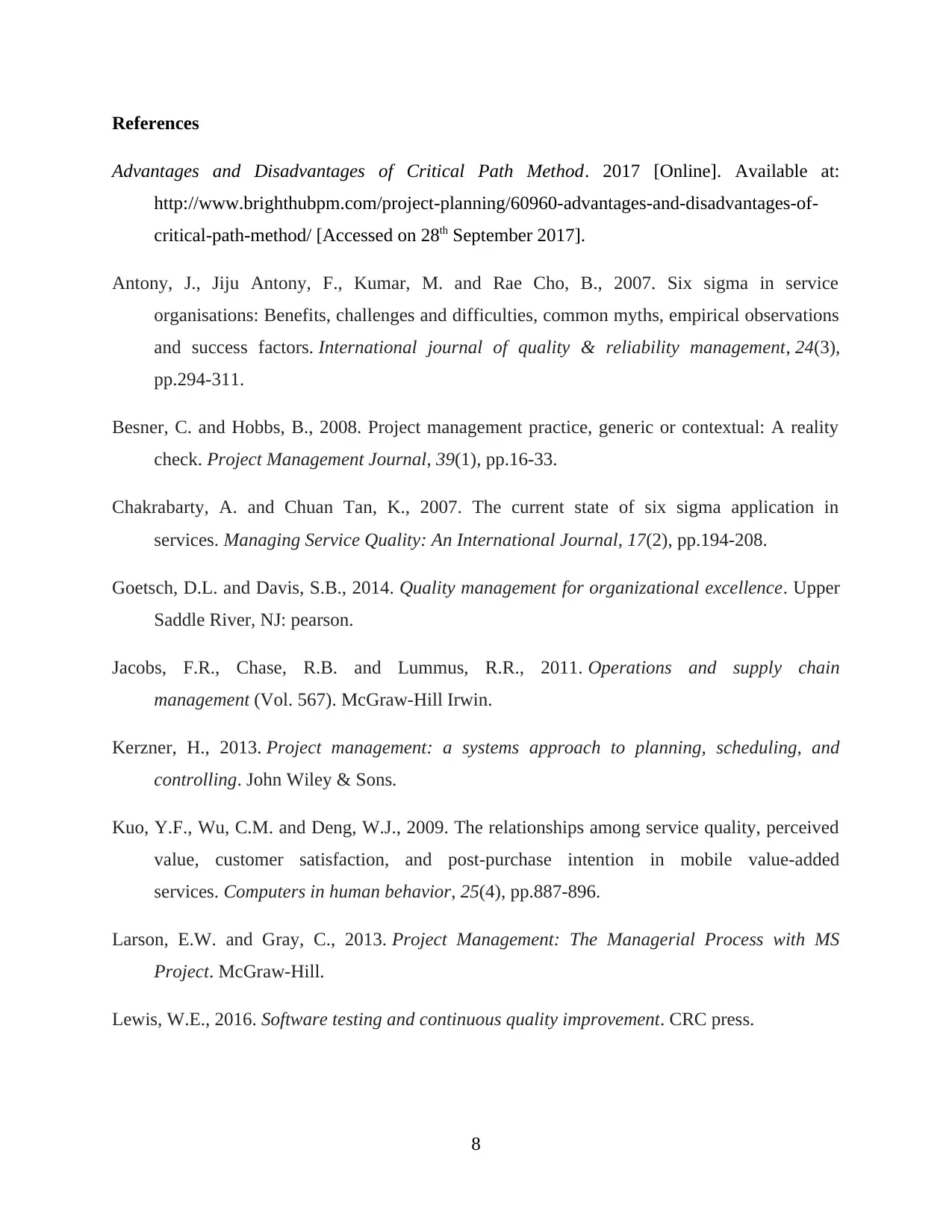
References
Advantages and Disadvantages of Critical Path Method. 2017 [Online]. Available at:
http://www.brighthubpm.com/project-planning/60960-advantages-and-disadvantages-of-
critical-path-method/ [Accessed on 28th September 2017].
Antony, J., Jiju Antony, F., Kumar, M. and Rae Cho, B., 2007. Six sigma in service
organisations: Benefits, challenges and difficulties, common myths, empirical observations
and success factors. International journal of quality & reliability management, 24(3),
pp.294-311.
Besner, C. and Hobbs, B., 2008. Project management practice, generic or contextual: A reality
check. Project Management Journal, 39(1), pp.16-33.
Chakrabarty, A. and Chuan Tan, K., 2007. The current state of six sigma application in
services. Managing Service Quality: An International Journal, 17(2), pp.194-208.
Goetsch, D.L. and Davis, S.B., 2014. Quality management for organizational excellence. Upper
Saddle River, NJ: pearson.
Jacobs, F.R., Chase, R.B. and Lummus, R.R., 2011. Operations and supply chain
management (Vol. 567). McGraw-Hill Irwin.
Kerzner, H., 2013. Project management: a systems approach to planning, scheduling, and
controlling. John Wiley & Sons.
Kuo, Y.F., Wu, C.M. and Deng, W.J., 2009. The relationships among service quality, perceived
value, customer satisfaction, and post-purchase intention in mobile value-added
services. Computers in human behavior, 25(4), pp.887-896.
Larson, E.W. and Gray, C., 2013. Project Management: The Managerial Process with MS
Project. McGraw-Hill.
Lewis, W.E., 2016. Software testing and continuous quality improvement. CRC press.
8
Advantages and Disadvantages of Critical Path Method. 2017 [Online]. Available at:
http://www.brighthubpm.com/project-planning/60960-advantages-and-disadvantages-of-
critical-path-method/ [Accessed on 28th September 2017].
Antony, J., Jiju Antony, F., Kumar, M. and Rae Cho, B., 2007. Six sigma in service
organisations: Benefits, challenges and difficulties, common myths, empirical observations
and success factors. International journal of quality & reliability management, 24(3),
pp.294-311.
Besner, C. and Hobbs, B., 2008. Project management practice, generic or contextual: A reality
check. Project Management Journal, 39(1), pp.16-33.
Chakrabarty, A. and Chuan Tan, K., 2007. The current state of six sigma application in
services. Managing Service Quality: An International Journal, 17(2), pp.194-208.
Goetsch, D.L. and Davis, S.B., 2014. Quality management for organizational excellence. Upper
Saddle River, NJ: pearson.
Jacobs, F.R., Chase, R.B. and Lummus, R.R., 2011. Operations and supply chain
management (Vol. 567). McGraw-Hill Irwin.
Kerzner, H., 2013. Project management: a systems approach to planning, scheduling, and
controlling. John Wiley & Sons.
Kuo, Y.F., Wu, C.M. and Deng, W.J., 2009. The relationships among service quality, perceived
value, customer satisfaction, and post-purchase intention in mobile value-added
services. Computers in human behavior, 25(4), pp.887-896.
Larson, E.W. and Gray, C., 2013. Project Management: The Managerial Process with MS
Project. McGraw-Hill.
Lewis, W.E., 2016. Software testing and continuous quality improvement. CRC press.
8

McCue, P. E., 2017. Risk Reduction with Effective Critical Path Method (CPM) Schedules.
[Online]. Available at: http://mdcsystems.com/risk-reduction-with-effective-critical-path-
method-cpm-schedules/ [Accessed on 28th September 2017].
Meredith, J.R. and Mantel Jr, S.J., 2011. Project management: a managerial approach. John
Wiley & Sons.
Rodney Turner, J., Ledwith, A. and Kelly, J., 2009. Project management in small to medium-
sized enterprises: A comparison between firms by size and industry. International Journal
of Managing Projects in Business, 2(2), pp.282-296.
Schroeder, R.G., Linderman, K., Liedtke, C. and Choo, A.S., 2008. Six Sigma: Definition and
underlying theory. Journal of operations Management, 26(4), pp.536-554.
Sharon, A., de Weck, O.L. and Dori, D., 2011. Project management vs. systems engineering
management: A practitioners' view on integrating the project and product domains. Systems
Engineering, 14(4), pp.427-440.
Sharp, N., Enzi, J., Fountoulakis, E., Lam, B. and Rabbior, M.C., 2012. International Business
Machines Coporation, System and method for displaying gantt charts with other project
management tools. U.S. Patent 8,245,153.
Sokovic, M., Pavletic, D. and Pipan, K.K., 2010. Quality improvement methodologies–PDCA
cycle, RADAR matrix, DMAIC and DFSS. Journal of Achievements in Materials and
Manufacturing Engineering, 43(1), pp.476-483.
Stevenson, W.J. and Hojati, M., 2007. Operations management(Vol. 8). Boston:
McGraw-Hill/Irwin.
Turner, J.R., 2008. Handbook of project-based management. McGraw-Hill Professional
Publishing.
Zu, X., Fredendall, L.D. and Douglas, T.J., 2008. The evolving theory of quality management:
the role of Six Sigma. Journal of operations Management, 26(5), pp.630-650.
9
[Online]. Available at: http://mdcsystems.com/risk-reduction-with-effective-critical-path-
method-cpm-schedules/ [Accessed on 28th September 2017].
Meredith, J.R. and Mantel Jr, S.J., 2011. Project management: a managerial approach. John
Wiley & Sons.
Rodney Turner, J., Ledwith, A. and Kelly, J., 2009. Project management in small to medium-
sized enterprises: A comparison between firms by size and industry. International Journal
of Managing Projects in Business, 2(2), pp.282-296.
Schroeder, R.G., Linderman, K., Liedtke, C. and Choo, A.S., 2008. Six Sigma: Definition and
underlying theory. Journal of operations Management, 26(4), pp.536-554.
Sharon, A., de Weck, O.L. and Dori, D., 2011. Project management vs. systems engineering
management: A practitioners' view on integrating the project and product domains. Systems
Engineering, 14(4), pp.427-440.
Sharp, N., Enzi, J., Fountoulakis, E., Lam, B. and Rabbior, M.C., 2012. International Business
Machines Coporation, System and method for displaying gantt charts with other project
management tools. U.S. Patent 8,245,153.
Sokovic, M., Pavletic, D. and Pipan, K.K., 2010. Quality improvement methodologies–PDCA
cycle, RADAR matrix, DMAIC and DFSS. Journal of Achievements in Materials and
Manufacturing Engineering, 43(1), pp.476-483.
Stevenson, W.J. and Hojati, M., 2007. Operations management(Vol. 8). Boston:
McGraw-Hill/Irwin.
Turner, J.R., 2008. Handbook of project-based management. McGraw-Hill Professional
Publishing.
Zu, X., Fredendall, L.D. and Douglas, T.J., 2008. The evolving theory of quality management:
the role of Six Sigma. Journal of operations Management, 26(5), pp.630-650.
9
Secure Best Marks with AI Grader
Need help grading? Try our AI Grader for instant feedback on your assignments.
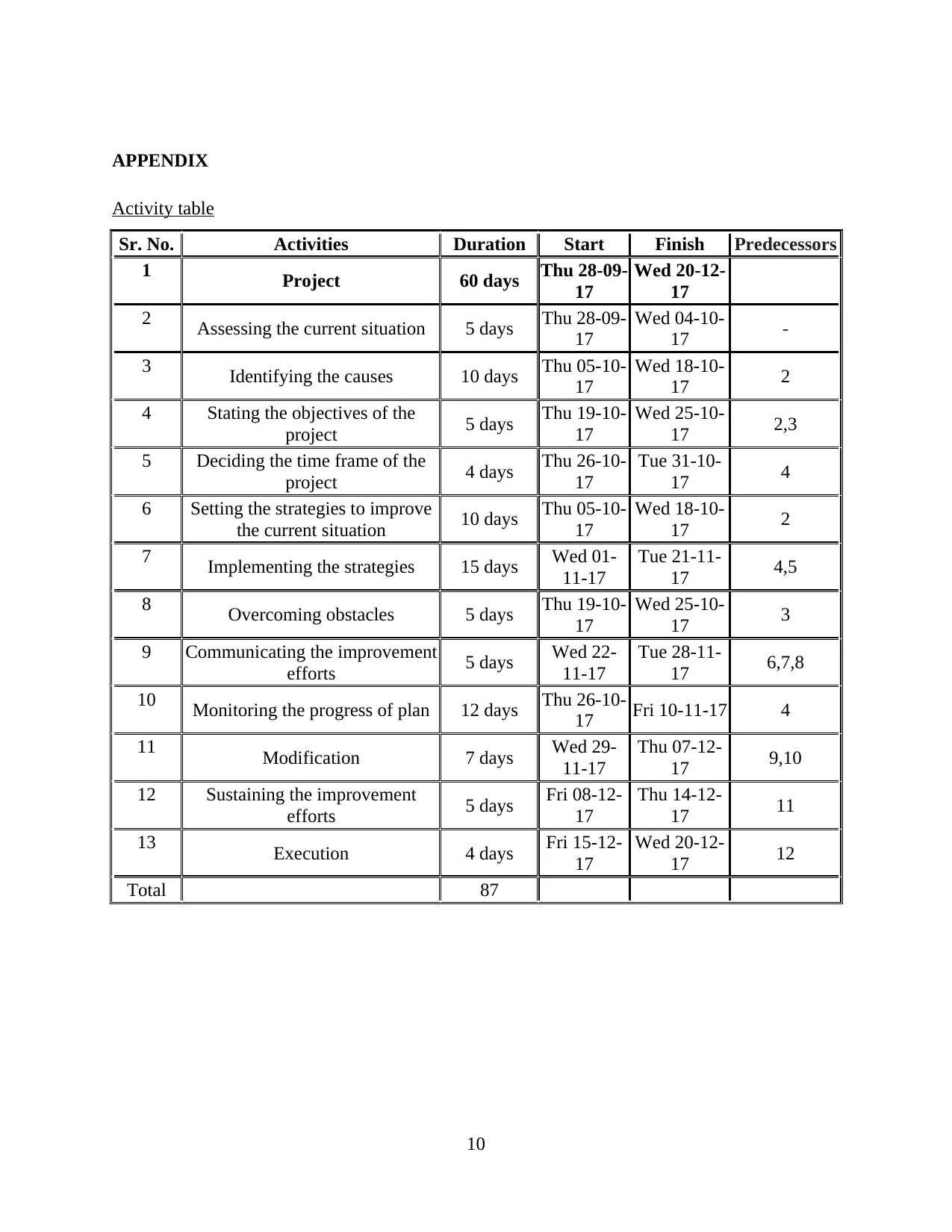
APPENDIX
Activity table
Sr. No. Activities Duration Start Finish Predecessors
1 Project 60 days Thu 28-09-
17
Wed 20-12-
17
2 Assessing the current situation 5 days Thu 28-09-
17
Wed 04-10-
17 -
3 Identifying the causes 10 days Thu 05-10-
17
Wed 18-10-
17 2
4 Stating the objectives of the
project 5 days Thu 19-10-
17
Wed 25-10-
17 2,3
5 Deciding the time frame of the
project 4 days Thu 26-10-
17
Tue 31-10-
17 4
6 Setting the strategies to improve
the current situation 10 days Thu 05-10-
17
Wed 18-10-
17 2
7 Implementing the strategies 15 days Wed 01-
11-17
Tue 21-11-
17 4,5
8 Overcoming obstacles 5 days Thu 19-10-
17
Wed 25-10-
17 3
9 Communicating the improvement
efforts 5 days Wed 22-
11-17
Tue 28-11-
17 6,7,8
10 Monitoring the progress of plan 12 days Thu 26-10-
17 Fri 10-11-17 4
11 Modification 7 days Wed 29-
11-17
Thu 07-12-
17 9,10
12 Sustaining the improvement
efforts 5 days Fri 08-12-
17
Thu 14-12-
17 11
13 Execution 4 days Fri 15-12-
17
Wed 20-12-
17 12
Total 87
10
Activity table
Sr. No. Activities Duration Start Finish Predecessors
1 Project 60 days Thu 28-09-
17
Wed 20-12-
17
2 Assessing the current situation 5 days Thu 28-09-
17
Wed 04-10-
17 -
3 Identifying the causes 10 days Thu 05-10-
17
Wed 18-10-
17 2
4 Stating the objectives of the
project 5 days Thu 19-10-
17
Wed 25-10-
17 2,3
5 Deciding the time frame of the
project 4 days Thu 26-10-
17
Tue 31-10-
17 4
6 Setting the strategies to improve
the current situation 10 days Thu 05-10-
17
Wed 18-10-
17 2
7 Implementing the strategies 15 days Wed 01-
11-17
Tue 21-11-
17 4,5
8 Overcoming obstacles 5 days Thu 19-10-
17
Wed 25-10-
17 3
9 Communicating the improvement
efforts 5 days Wed 22-
11-17
Tue 28-11-
17 6,7,8
10 Monitoring the progress of plan 12 days Thu 26-10-
17 Fri 10-11-17 4
11 Modification 7 days Wed 29-
11-17
Thu 07-12-
17 9,10
12 Sustaining the improvement
efforts 5 days Fri 08-12-
17
Thu 14-12-
17 11
13 Execution 4 days Fri 15-12-
17
Wed 20-12-
17 12
Total 87
10
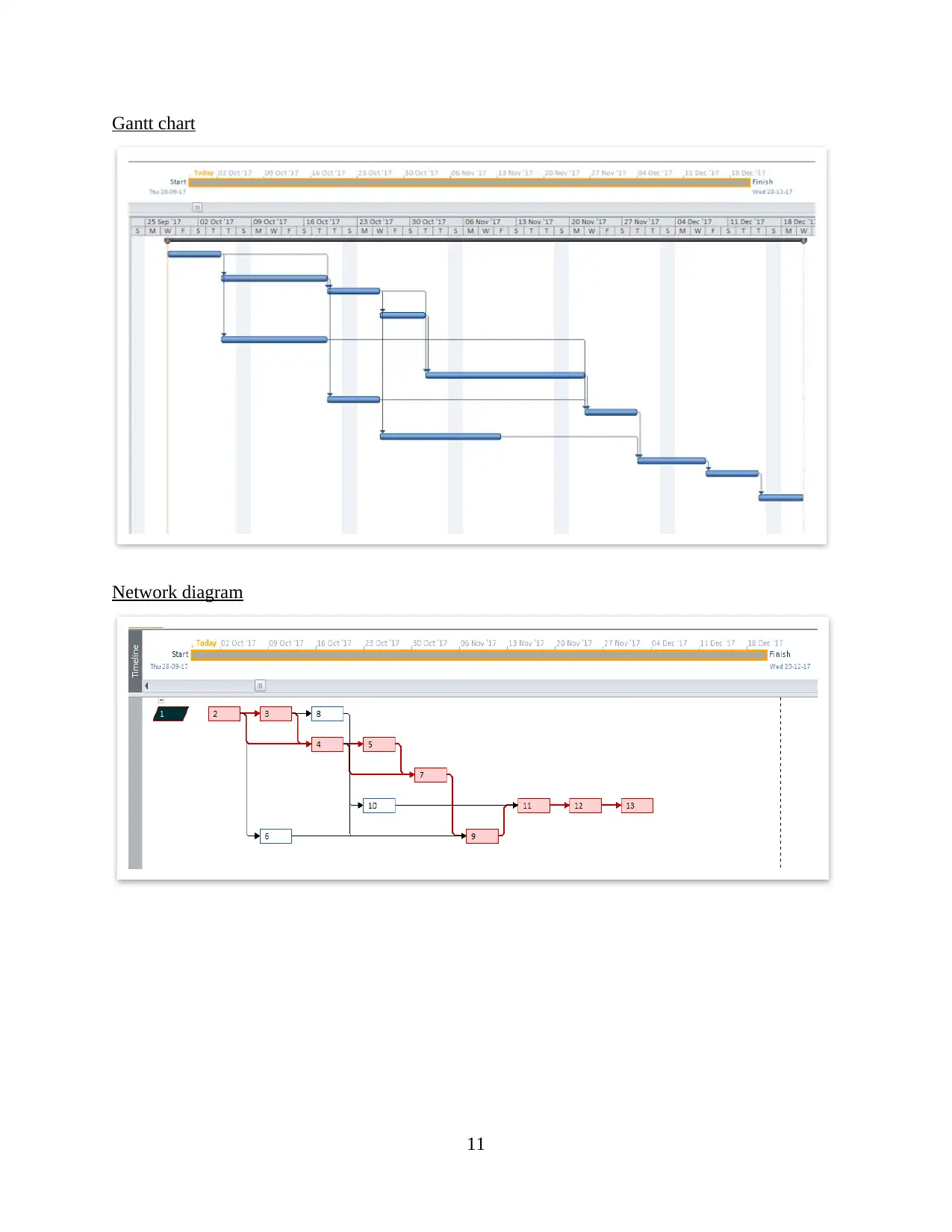
Gantt chart
Network diagram
11
Network diagram
11
1 out of 12
Related Documents
![[object Object]](/_next/image/?url=%2F_next%2Fstatic%2Fmedia%2Flogo.6d15ce61.png&w=640&q=75)
Your All-in-One AI-Powered Toolkit for Academic Success.
 +13062052269
info@desklib.com
Available 24*7 on WhatsApp / Email
Unlock your academic potential
© 2024  |  Zucol Services PVT LTD  |  All rights reserved.